Toyota Material Handling Australia and Coates on their renewed partnership COVER STORY TO STRENGTHSTRENGTHFROM project44 on how its visibility platform is up to the job OPEXKITTINGTRANSFORMSPROCESS How an educational resource provider boosted its output SEPTEMBER 2022 TACKLING OCEAN TRANSIT CHALLENGES
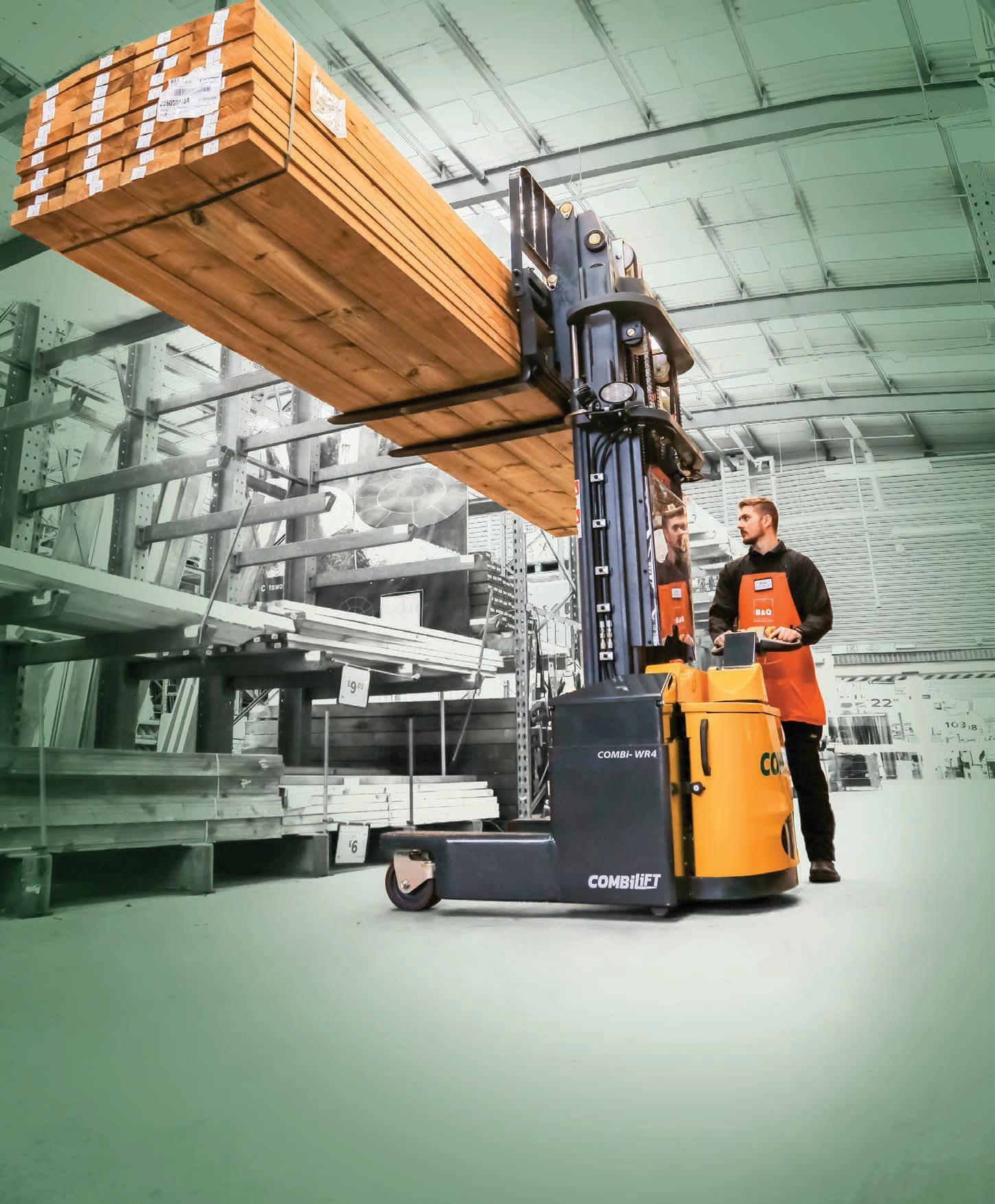
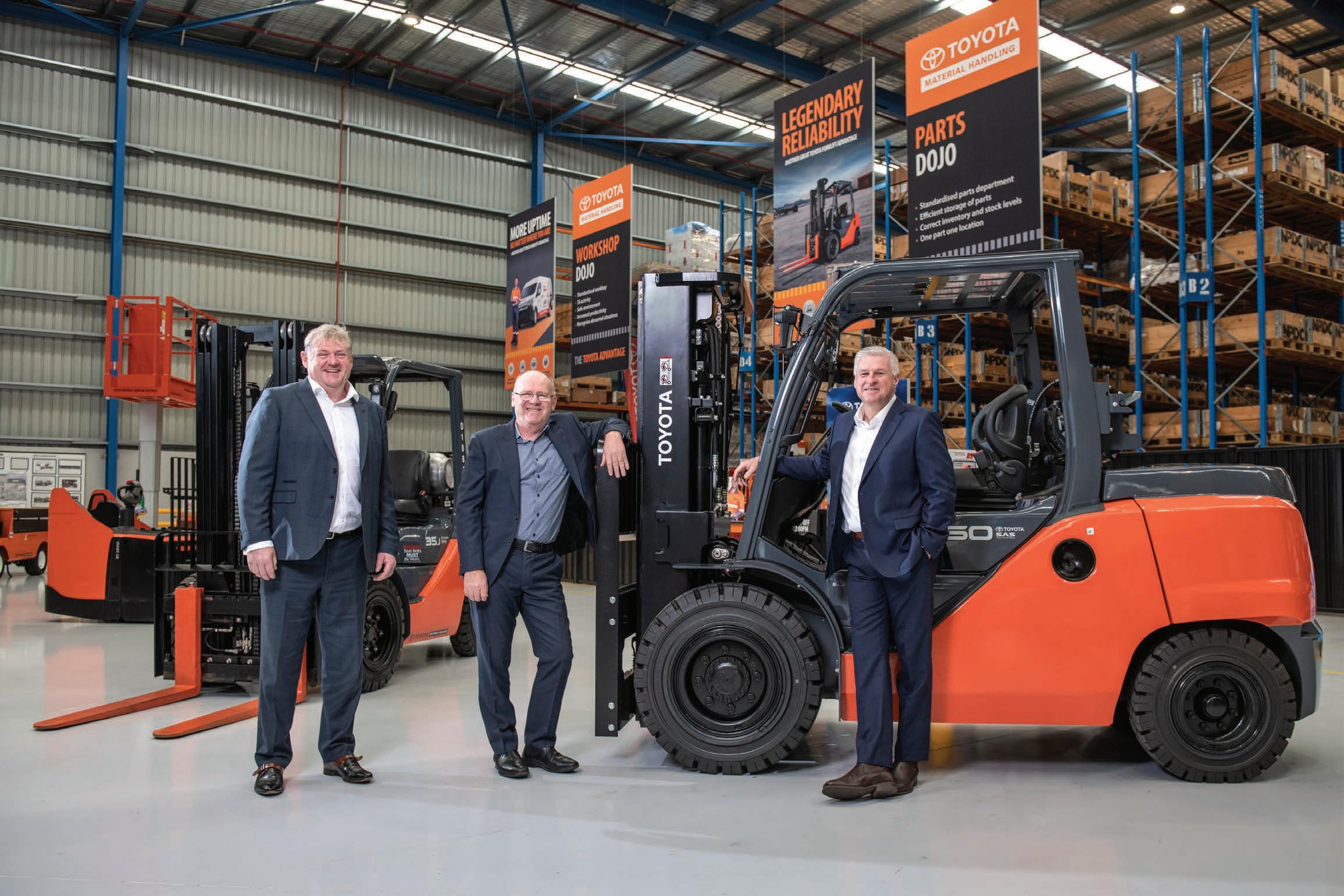
As a result of the increasing benefits of cobots in the DC environment, Körber has partnered with Locus Robotics, a leading provider of autonomous mobile robots (AMRs), including collaborative robots, to bring cutting-edge solutions to the Asia Pacific market.
koerber-supplychain.com
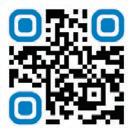
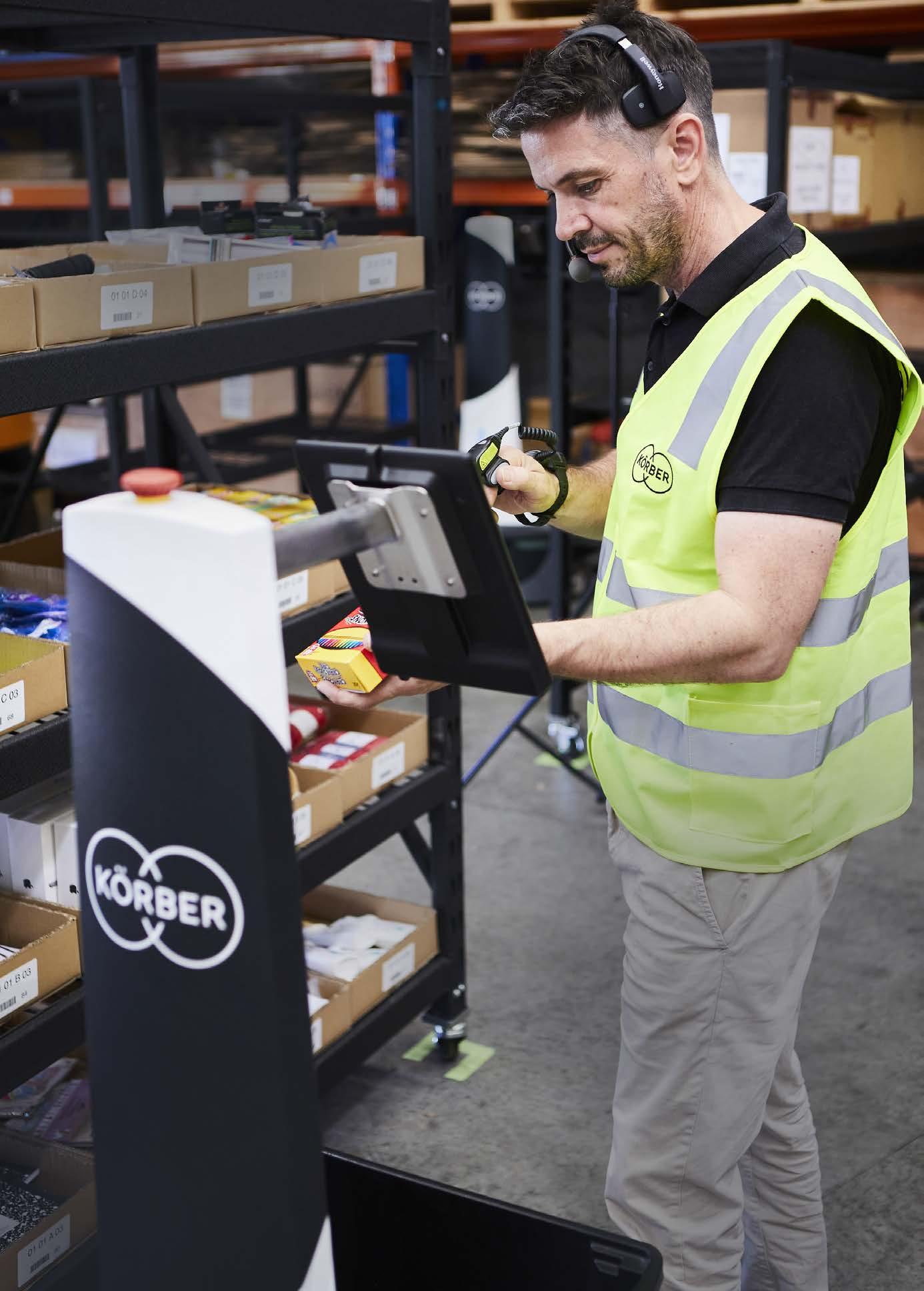
LocusrobotscollaborativeDiscoverwith
Watch the demo
Design Production Manager: Michelle Weston
While we’re living in a rapidly changing world where crises are common, fortunately, the industry is up to the task.
MHD
3yrs (18 issues) for $157.50 – Saving 30%
Graphic Designers: Louis Romero, Kerry Pert Client Success Manager: Janine Clements
THE TEAM
Contact: Beth beth.jarvis@primecreative.com.auJarvis
FOR ADVERTISING OPTIONS
SUBSCRIBE
ACKNOWLEDGEMENT
Telephone: (+61) 03 9690 8766 Website: www.primecreative.com.au
Art Director: Blake Storey
This September edition of MHD Supply Chain Solutions features insights into supply chain transformation, sustainable technologies, the importance of data, WMS, ocean visibility, and sundry other innovations in warehousing and distribution centres as well as supply chain more generally.
In this connection, ‘reliability’ is a keyword. And indeed, in our cover story for this issue, you’ll read how Coates and Toyota Material Handling Australia have built a partnership based on a shared commitment to trust, reliability, and a shared commitment to sustainability. Happy reading. See you next month.
1yr (6 issues) for $78.00
MHD SEPTEMBER 2022 | 3 MHD FROM THE EDITOR
Journalist: Joseph Misuraca
Edward Cranswick edward.cranswick@primecreative.com.auEditor
11-15 Buckhurst Street, South Melbourne VIC 3205
C
Managing Editor: Syed Shah
To subscribe and to view other overseas rates visit: www.mhdsupplychain.com.au or Email: subscriptions@primecreative.com.au
Chain MHD Supply
ON A ROLL
CEO: John Murphy
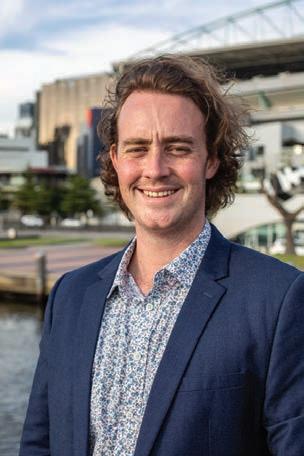
MHD Supply Chain Solutions is published by Prime Creative Media

Supply Chain Solutions
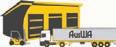
oming off MEGATRANS2022 the MHD team is as excited as ever to bring you the best knowledge of solutions across the supply chain and logistics space.
MHDCOPYRIGHTmagazine is owned by Prime Creative Media. All material in MHD is copyright and no part may be reproduced or copied in any form or by any means (graphic, electronic or mechanical including information and retrieval systems) without written permission of the publisher. The Editor welcomes contributions but reserves the right to accept or reject any material. While every effort has been made to ensure the accuracy of information Prime Creative Media will not accept responsibility for errors or omissions or for any consequences arising from reliance on information published. The opinions expressed in MHD are not necessarily the opinions of, or endorsed by the publisher unless otherwise stated.
Business Development Manager: Beth Jarvis
CONTACT
Australian Subscription Rates (inc GST)
2yrs (12 issues) for $120.00 – Saving 20%

MHD Supply Chain Solutions magazine is recognised by the Australian Supply Chain Institute, the Chartered Institute of Logistics and Transport Australia, the Supply Chain and Logistics Association of Australia and the Singapore Logistics and Supply Chain Management Society.
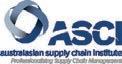
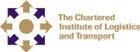
Inside this edition you’ll read about Vative’s work with the Supply Chain and Logistics Association of Australia (SCLAA) and Swinburne University to foster innovative thinking in supply chain. You’ll also read the latest about Biogone’s efforts in the biodegradable packaging space – giving a lift to ever more pressing issues of sustainability and environmentalism in warehousing.Aswe’reabout to head into the fourth quarter of 2022, it’s important to consider how businesses can better prepare for the frenzy of online sales during the festive season and gear up for what will likely be a busier and just as unpredictable New Year.
Chief Operating Officer: Christine Clancy
AllARTICLESarticles submitted for publication become the property of the publisher. The Editor reserves the right to adjust any article to conform with the magazine format.
Editor: Edward Cranswick


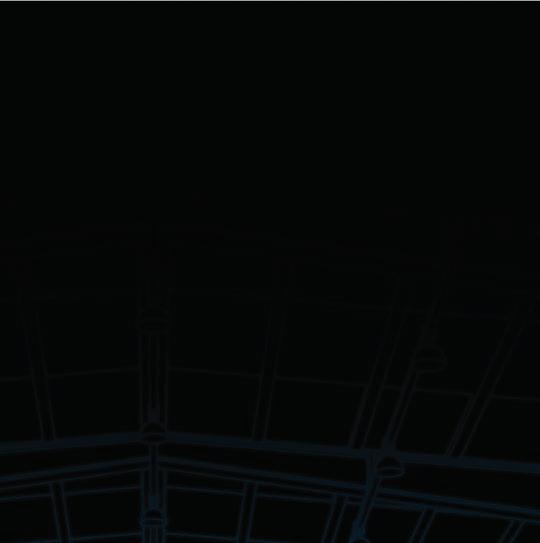
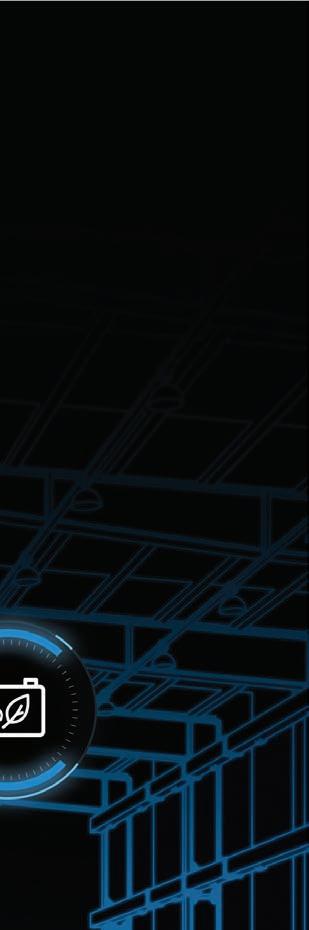
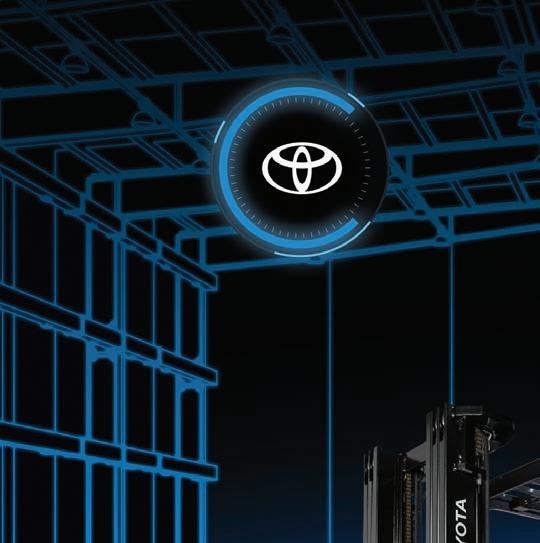
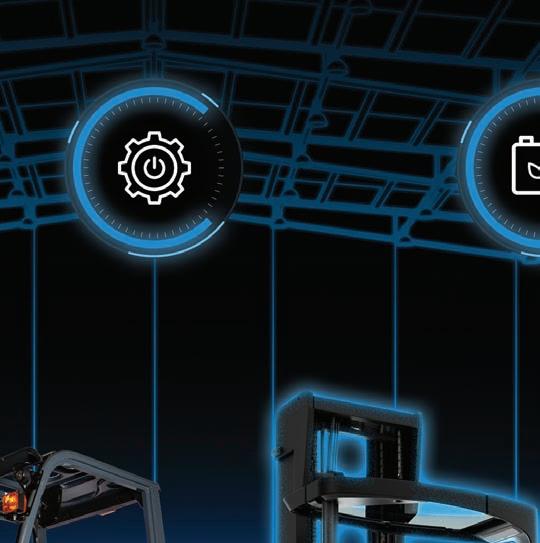
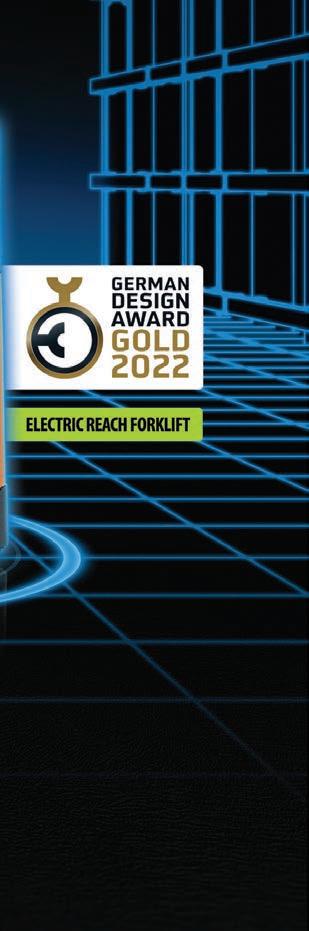
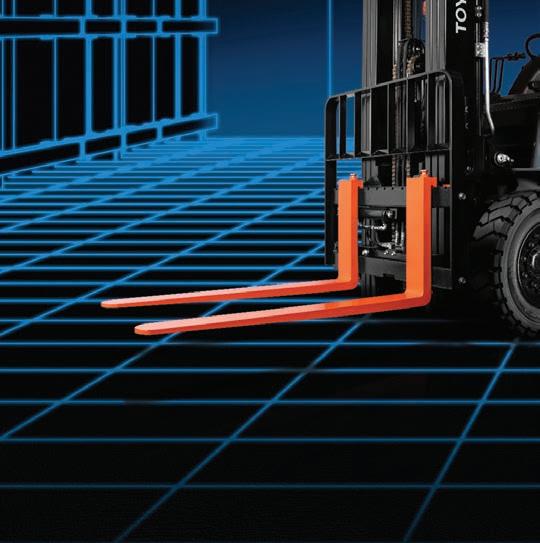

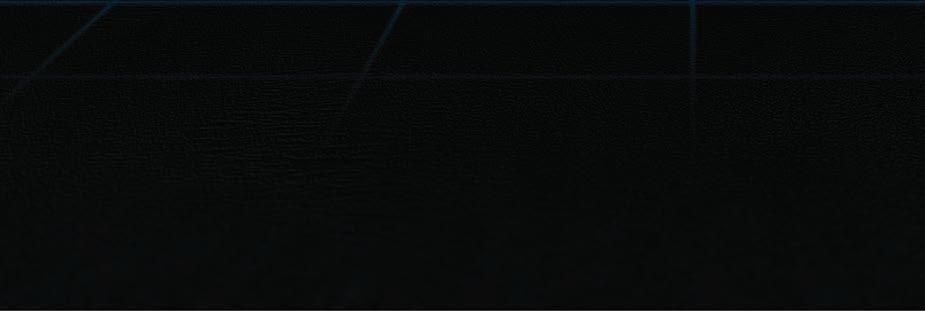
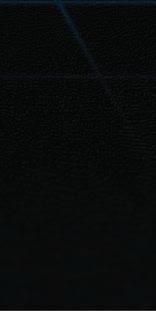
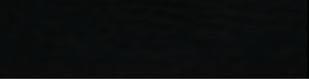
MHD SEPTEMBER 2022 | 5 COVER STORY 12 The Toyota-Coates Partnership SUPPLY CHAIN 17 Körber on same-day delivery 20 Dematic’s relationship with Tasty Fresh 26 Procore looks at supply chain challenges 34 project44 using visibility to tackle challenges 40 Argon & Co. on supply chain transformation 44 Vative on supply chain innovation 47 Vic Govt invests in rail infrastructure for port 48 Mercury Awards’ winners in supply chain MATERIALS HANDLING 31 Combilift plugging into greener power 23WAREHOUSING Opex using educational resources to transform kitting process 29 GPC on its new DC 37 Microlistics accelerating omnichannel retail success 43 Kardex on intralogistics solutions for 3PLs DEPARTMENTS AND REGULARS 06 Industry News 58 Colliers’ Property Focus 60 Prological’s Logical Outlook 62 RWTA’s Frank Vale Tech tour 64 SCLAA 65 Products 66 People on the Move Toyota Material Handling Australia and Coates on their renewed partnership COVER STORY FROM STRENGTH TO STRENGTH project44 on how its visibility platform is up to the job OPEXKITTINGTRANSFORMSPROCESS How an educational resource provider boosted its output SEPTEMBER 2022 TACKLING OCEAN TRANSIT CHALLENGES ON THE COVER Toyota Material Handling Australia and Coates on their renewed partnership and the values that undergird it SEPTEMBER 2022ISSUE #19 VOLUME 53 THIS ISSUE 34 12 COVER 43STORY
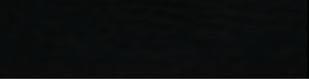
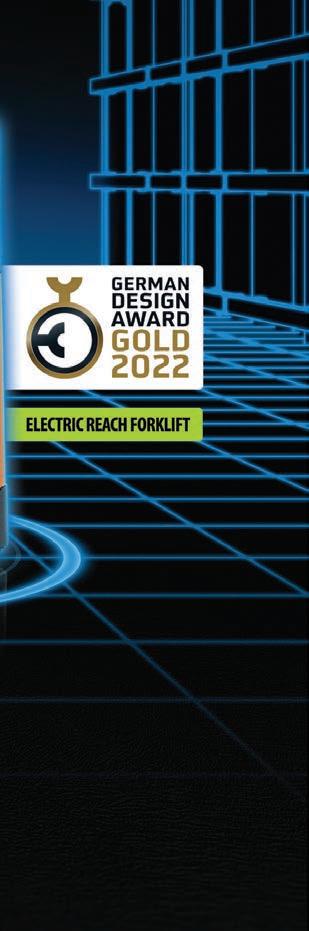
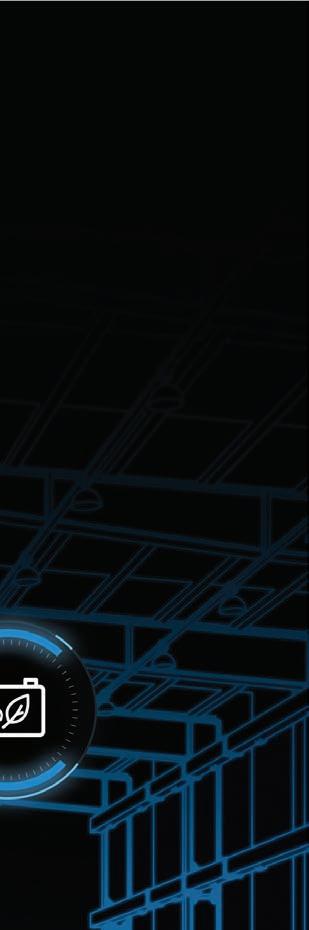
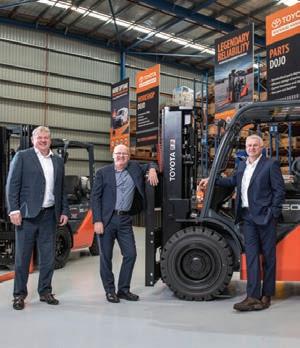
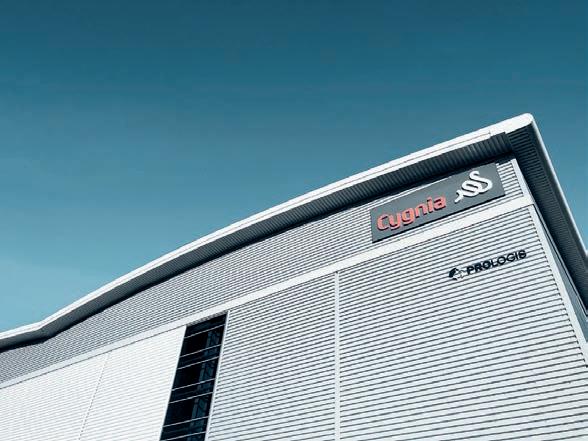
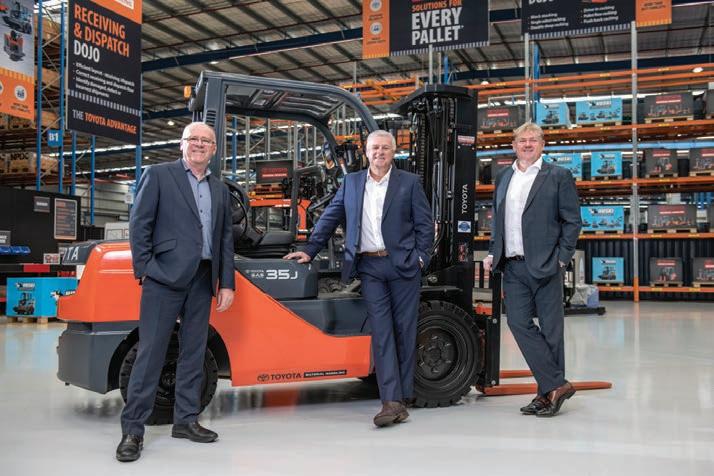
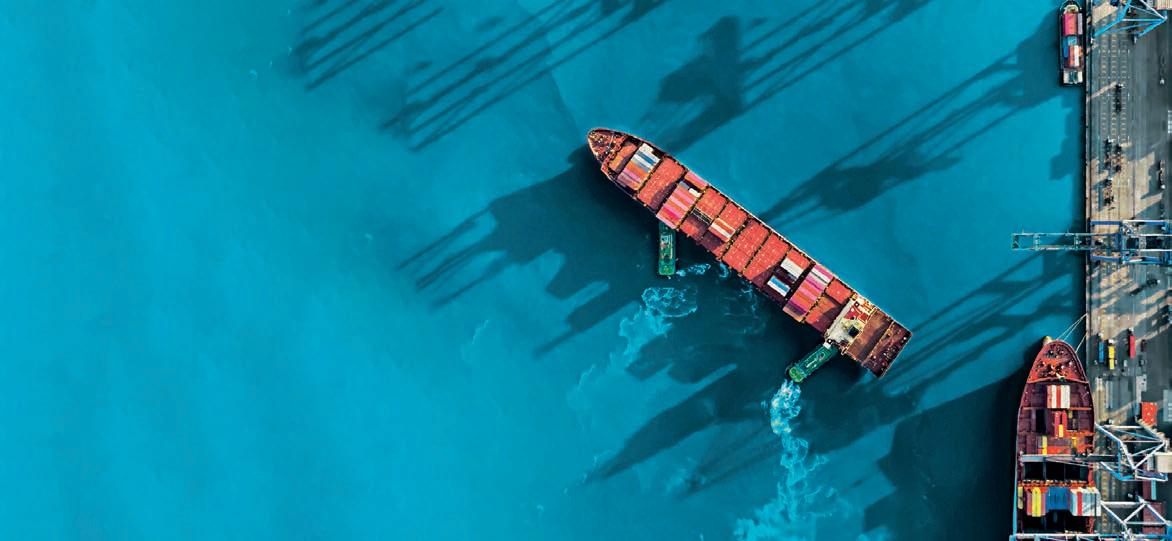
chain advantages. Unfortunately for Revlon, it missed the market transition, and with this the new opportunities, and has been suffering ever since.
Suddenly, brands like Revlon were seen as conservative, dated and out of touch. Then, with the continued rise of social media and blogging, celebrity brands began to emerge, leveraging existing fan-bases for exposure, and diverting traditional advertising spend into product innovation and supply
After a period of instability and supply chain challenges, Revlon has filed for Chapter 11 Bankruptcy in the United States. For the makeup company, the filing represents a final lifeline, as it attempts to rectify debt with creditors by borrowing more than $370 million.
In the 2010s, the narrative around beauty shifted dramatically – beauty became celebratory, more diverse, and more Insteadpersonalised.ofbeingtold of this season’s ‘must-haves’ by a beauty advisor in a department store, women began doing their own research online.
However, in an attempt to become omni-channel, Glossier spent big on aesthetically stunning bricks and mortar stores, contrasting designs of traditional beauty outlets, which would later ruin its supply chain.
Blogs, forums, and other digital communities emerged, where consumers would connect over their love of products, share beauty secrets, and seek advice from other ‘real women’, taking the power away from brands that struggled to dictate the narrative around ‘what beauty should be’.
A
Known as a trailblazer, Revlon was once the most radical company in its space.
Bankrupt beauty: Lessons from Revlon’s supply chain failures
For Revlon, some key mistakes in its supply chain have created a dominoeffect, costing the company many of its suppliers, customers, and creditors. Growing pressure from incumbent brands has heightened competition for materials, as those with healthy liquidity can pre-pay creditors and benefit from large orders and scaled economies.
THE DEMOCRATISATION OF BEAUTY
In the 1990s, the company’s ‘Colorstay’ range of makeup gained notoriety for its patented formula which promised to stay on all day: a new frontier in cosmetics.
WHAT WENT WRONG?
Under Chapter 11 Bankruptcy Protection, the company is able to continue trading while it attempts to correct crippling fractures in its supply chain, in a desperate move to retain some of its once sizeable, indeed, dominant market share.
cosmetics company to feature an African-American model, icon Naomi Sims, in its advertising. In the 1980s, its radical campaigns featured diverse, not-yet-famous, new models like Claudia Schiffer, Cindy Crawford, and Christy Turlington, who would later become synonymous with the highest of high-end fashion.
Glossier, best known for its billiondollar valuation, sprung on to the beauty scene in 2014, providing direct-to-consumer products aimed specifically at millennials.
New York-based beauty manufacturer
Supply chain failures are impacting almost every sector, made worse by the COVID-19 pandemic. Earlier this year, Australia Post struggled so much under the weight of online orders and increased numbers of isolating staff
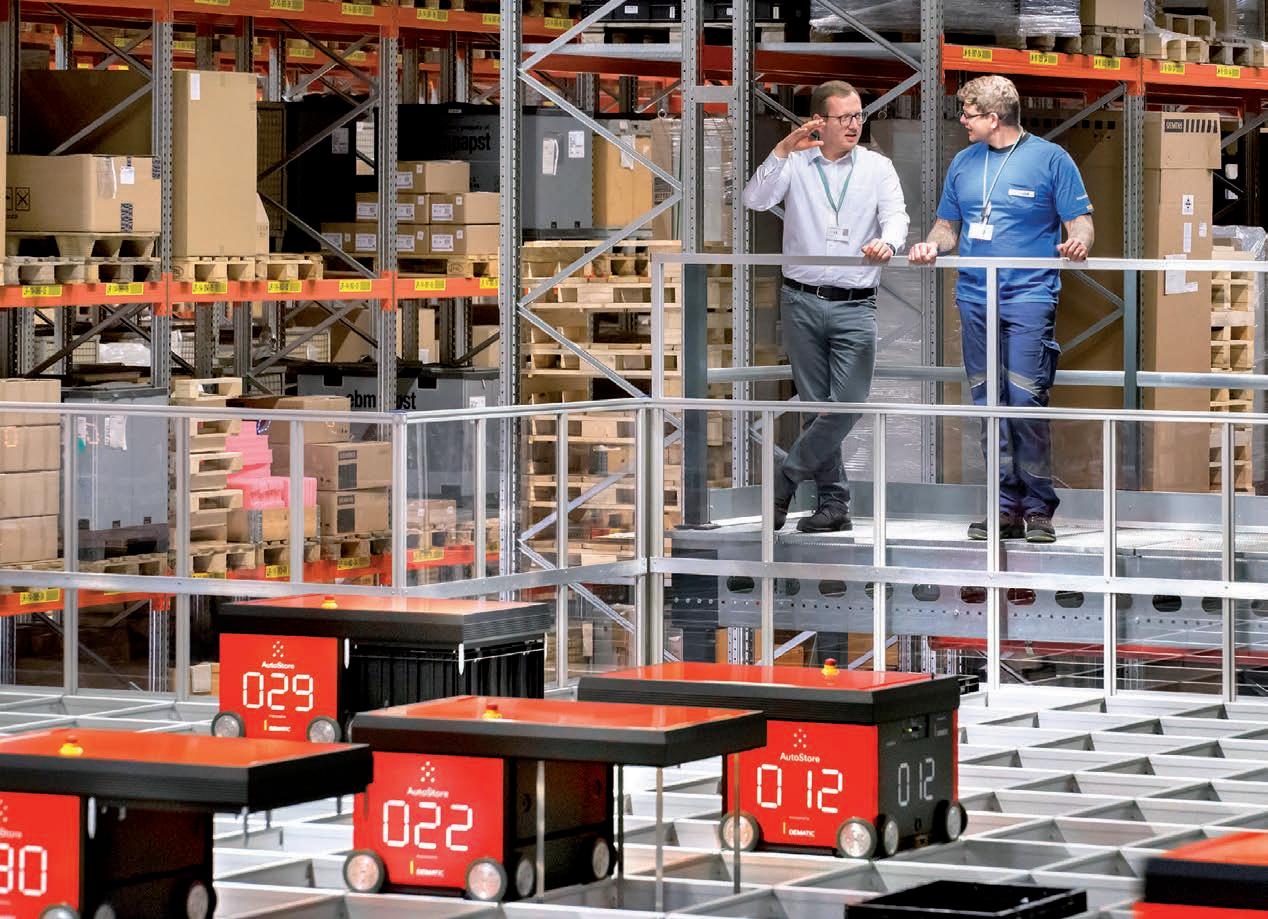
The brand’s low-maintenance, accessible and affordable ethos provided a lucrative antidote to the over-lined lips, perfectly angled eyebrows, and single brand loyalty that had been taken for granted by Revlon and other legacy brands since World War CapitalisingII. on the e-commerce preferences of millennial shoppers, it owned the conversation around accessible beauty.
For Revlon, cumulative debt has meant some of their raw material suppliers are no longer sending shipments, cutting production, and leaving the company only able to fulfil 70 per cent of orders, against an industry standard of around 95 per cent.
Its boycott of third-party retailers like Sephora and Ulta, as well as its failed international expansion saw the brand begin to fall almost as quickly as it rose. In 2020, Glossier closed its retail stores in the US, and in January 2022, it laid-off a third of its corporate team.
merican beauty corporation Revlon recently shocked the business world by filing for Chapter 11 Bankruptcy Protection in the US. Peter Jones, Managing Director and Founder at Prological Consulting talks through some of the marketing, supply chain and operational mistakes that led to the decline in market share for the 90-year-old beauty giant.
Also, labour shortages due to the COVID-19 pandemic have slowed manufacturing, resulting in late product shipments and fines from retailers, as well as mismanaged inventory and failed forecasting.
MHD NEWS & OPINION 6 | MHD SEPTEMBER 2022
In 1970, it was the first American
When business was booming, Revlon’s strategy was to expand sales through mass market department stores, as well as buying expensive advertising. Like other legacy brands, it invested in magazine editorials which drove shoppers into stores, where sales would be converted through personal selling and glossy displays. As a strategy, this worked well into the 2000s, but failed dismally thereafter.
EVEN THE MOST INNOVATIVE COMPANIES FALL PREY TO SUPPLY CHAIN DISASTERS
Its pastel packaging, crowdsourced products and disruptive campaigns solidified its position as the fastest growing beauty brand of all time.
A CAUTIONARY TALE FOR ALL SECTORS
4 times the storage capacity, 3 times the withperformancepickingAutoStore ™ Getting More With Less at Siemens info.anz@dematic.comDematic.com0294865555 Scan to watch the video!
With 34 AutoStore robots, five picking ports, and storing 45,000 segmented bins in an overall footprint of just 760 square metres, the AutoStore system holds four times more stock in the same space, and Siemens can now handle more orders, more accurately, in less time.
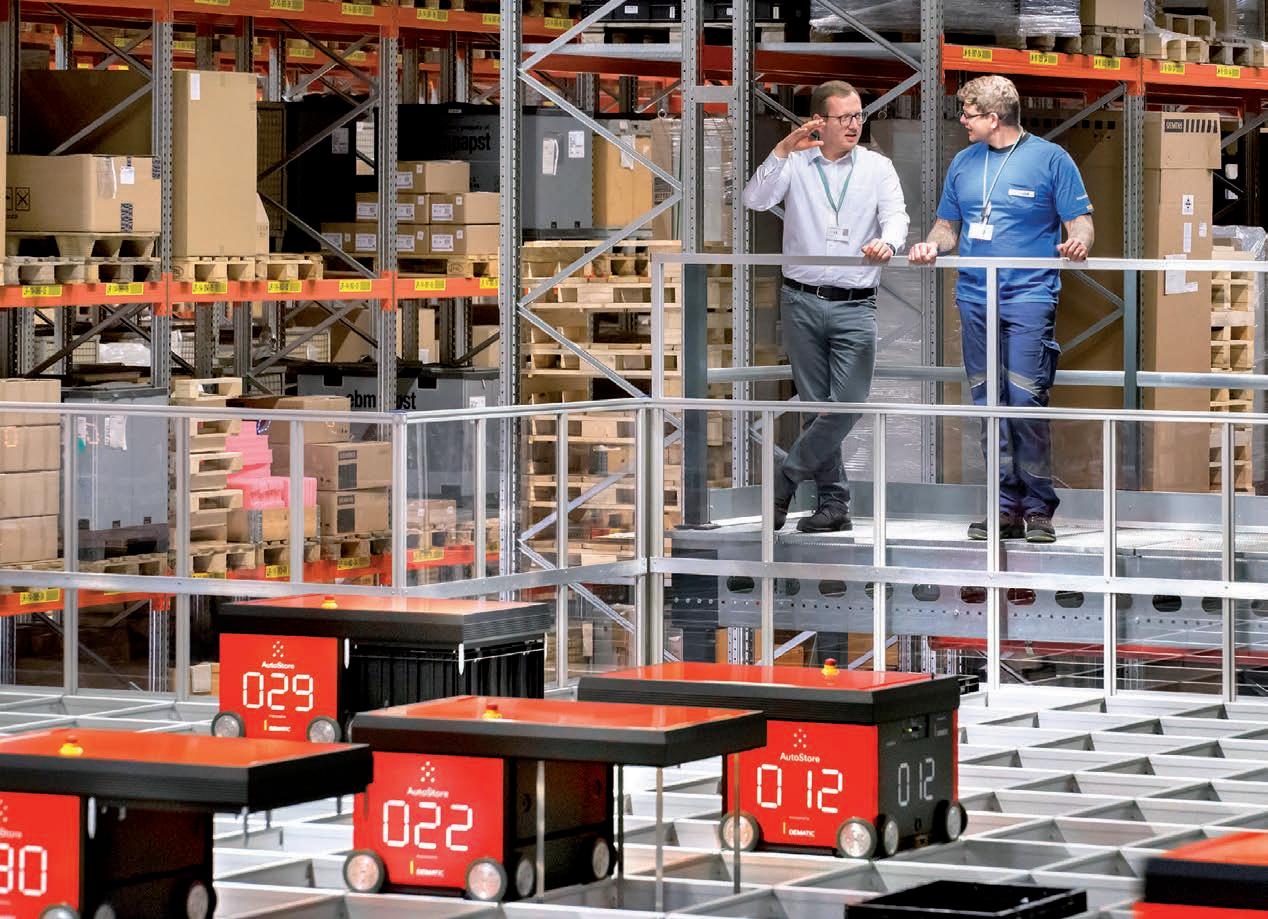
At its plant in Chemnitz, Germany, Siemens manufactures advanced electrical equipment as well as assemblies and devices for machine and plant manufacturers worldwide. To improve on its previous manual shelf storage system for small parts which had reached its capacity, Siemens switched to an AutoStore goods-to-person picking system from Dematic.
Scan the code below to learn more.

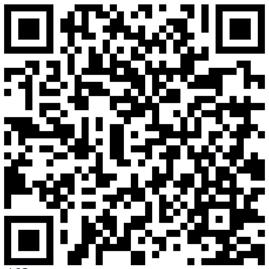
biosecurity delays are one of many causes of container detention fees that are costing importers $500 million every year. This is on top of surcharges, terminal access charges, and record high freight rates that are rapidly escalating supply chain costs and adding to inflationary pressures.
T
WHAT CAN BE DONE?
Biosecurity threats such as Foot and Mouth Disease (FMD), Japanese encephalitis, African Swine Fever among others will have devastating impacts on Australia’s agricultural industries, environment, health, and economy.
“We well and truly understand the need to protect against biosecurity risks and would be prepared to pay additional transactional fees on the proviso that this directly translates to commensurate improved and immediate trade facilitation measures.”
very few have truly mastered the ability to deliver these consistently at scale, which will separate the winners from the losers.
Paul Zalai, FTA Director says these biosecurity threats such as Foot and Mouth Disease (FMD), Japanese encephalitis, African Swine Fever among others will have devastating impacts on Australia’s agricultural industries, environment, health, and economy. He adds that the Department of Agriculture, Fisheries and Forestry use labour intensive processes with biosecurity officers physically assessing import documentation and selecting consignments on a set criterion for “Itinspection.isabroken and hopelessly outdated system unable to keep pace with increases and changing patterns of international trade – despite the best efforts of officers, the department cannot keep up and industry is paying the price,” Paul says.
a delay in returning empty containers yet insist they are returned within prescribed timeframes to add to their stockpile congesting our port precincts,” Paul says.
To apply the tale of Revlon to all sectors, while an all-day red lipstick may look bright and powerful, to be successful as a business now requires a lot more than it once did.
“Whilst document assessment processing times fluctuate, inspections and the issuing of import permits can take weeks to complete,” he adds.
He also says that if funds are the problem, then the government should talk to industry.
“Whilst applauding and supporting these initiatives, we urge the federal government to introduce immediate relief measures,” he adds.
he Freight and Trade Alliance (FTA), the peak industry body representing customs brokers, freight forwarders and importers says biosecurity threats and processing delays are adding costs and inflationary pressures to supply chains.
The Australian Retailers Association
predicts supply chain issues will continue, likely through to 2023 and beyond. Globally, we will see increasing pressure on pricing and margins, and only those who have a resilient and agile supply chain will survive.
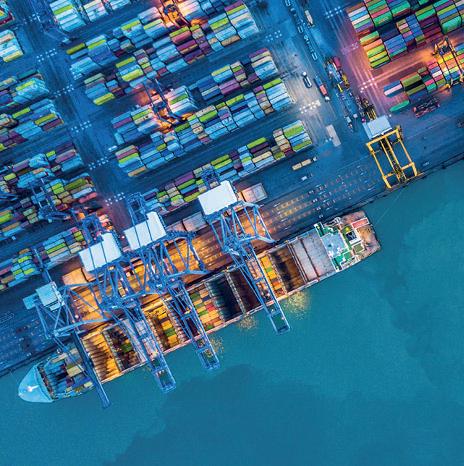
Biosecurity threats affecting supply chains
He has raised concerns that some of the new and emerging risks may take limited biosecurity resources away from business-as-usual trade facilitation Theactivities.FTAsays
“Thesecommerce.longer-term strategies have the potential to set a benchmark of global best practice in safeguarding against biosecurity risk whilst facilitating legitimate trade,” Paul says.
To design quickly and deliver great customer outcomes requires sophisticated adaptive analytics, automation, optimisation, and agility. Although many retailers are investing in personalised customer interactions,
It adds that the department is co-designing solutions with industry including examination of commercial practices to reduce the risk of introducing and
Peter Jones, Managing Director and Founder at Prological Consulting
According to the FTA, this is causing significant delays for importers to gain access to cargo, adding to storage costs and generating significant container detention fees administered by and payable to foreign-owned shipping “Shippinglines. lines don’t care why there is
that it stopped taking e-commerce collections twice in eight weeks. In June, the International Monetary Fund cited supply chain failures as a main factor in its downgrade for global economic growth for 2022 from 4.9 per cent to 4.4 per cent. For retail and distribution, supply chain issues are here to stay.
spreading contaminating pests and therefore minimise the associated regulatory consequences for Australian
8 | MHD SEPTEMBER 2022 MHD NEWS & OPINION
ImproveSafety. LowerCosts. Deliveringsolutions forcomplexlogisticsproblems. Contactustomoveforward. DiscoverhowBestrane’sFleetAssuranceandTelematics solutionscanimprovesafetyandefficiency,whilstreducing costs,withsolutionsthathelpyouto: bestrane.com.au 150AlbertRd SouthMelbourne3205 +61390011565 •Improvedriverandvehiclesafety •Improvedriverbehaviour •SimplifyCoRcompliance •Improvefleetvisibility Geotab™telematicsprovidetrackingand managementsolutionstomanageyourfleet. Designedas'plugnplaydevices'Geotabdelivers greaterefficiency,costcontrolandsafetyfromyour fleet,withpowerfulcloudsoftware,custom reportingandahostofhardwareand softwareintegrations.
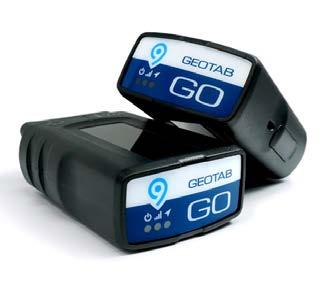
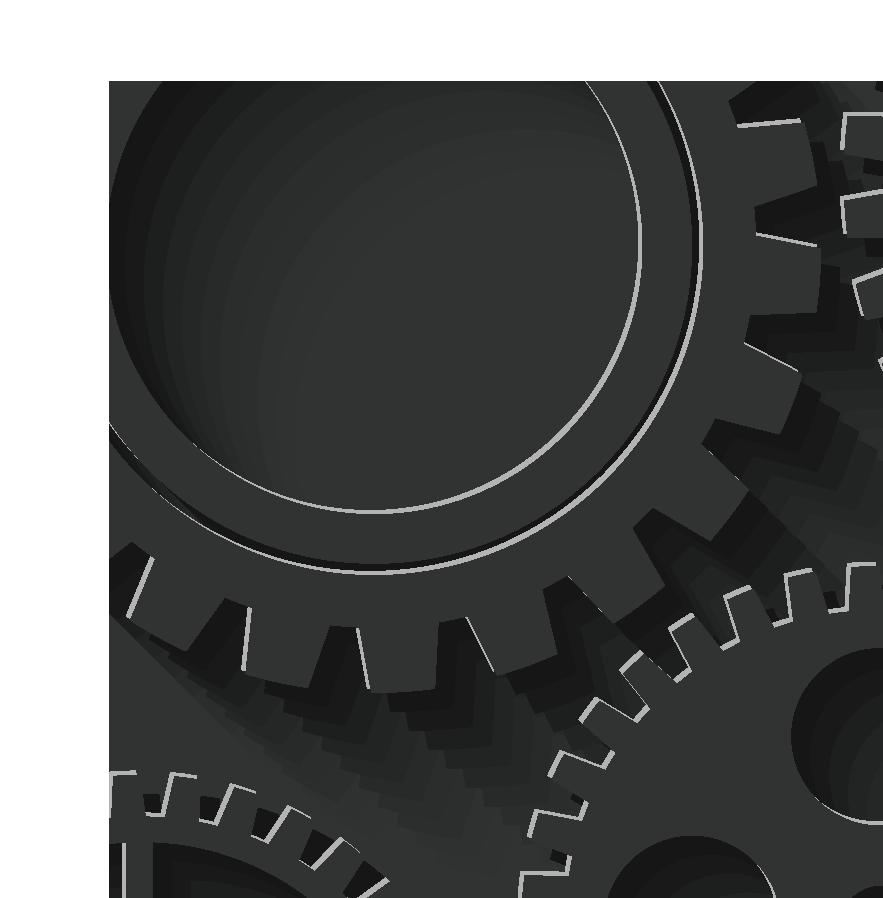
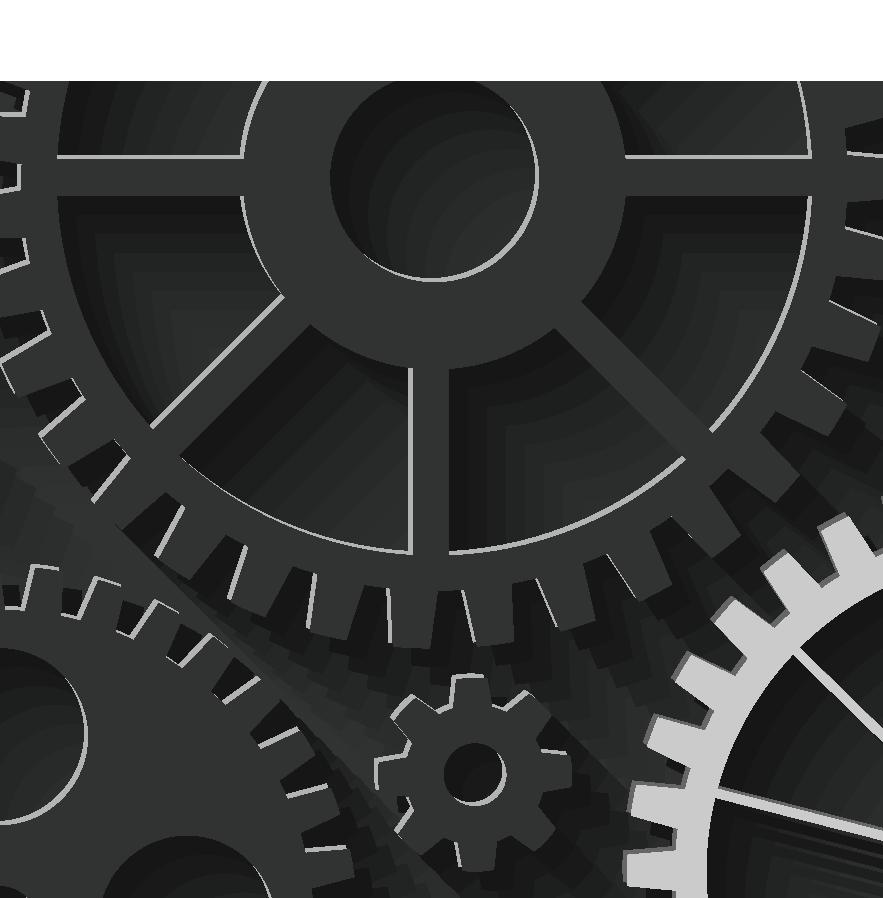
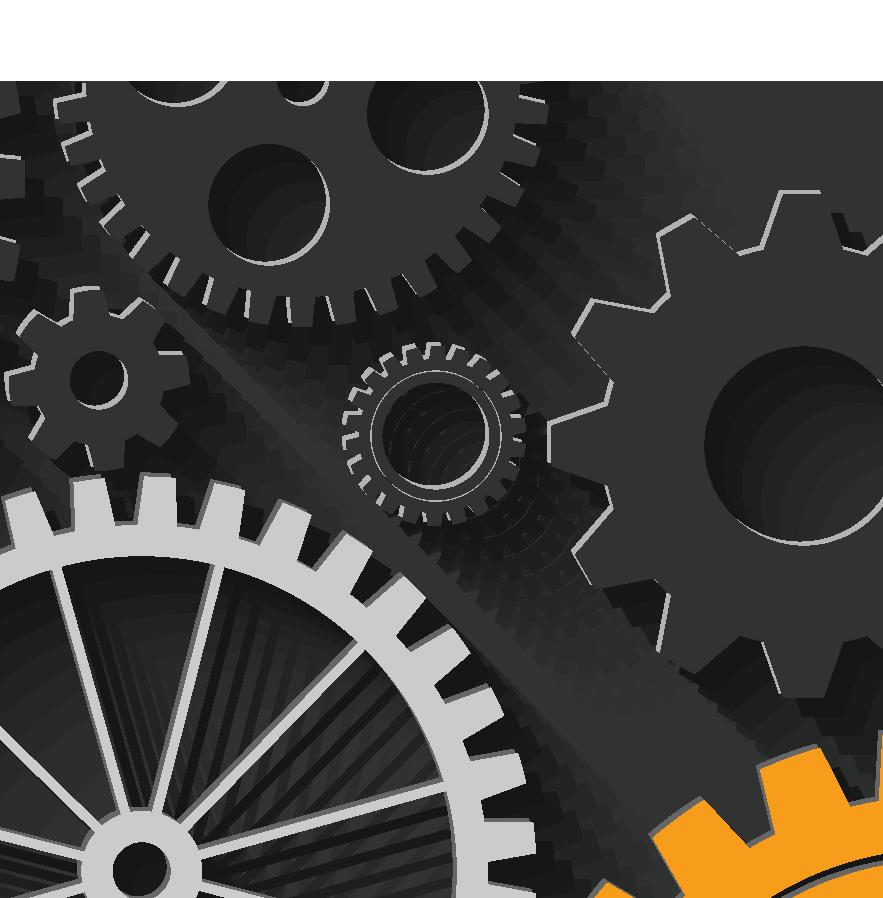

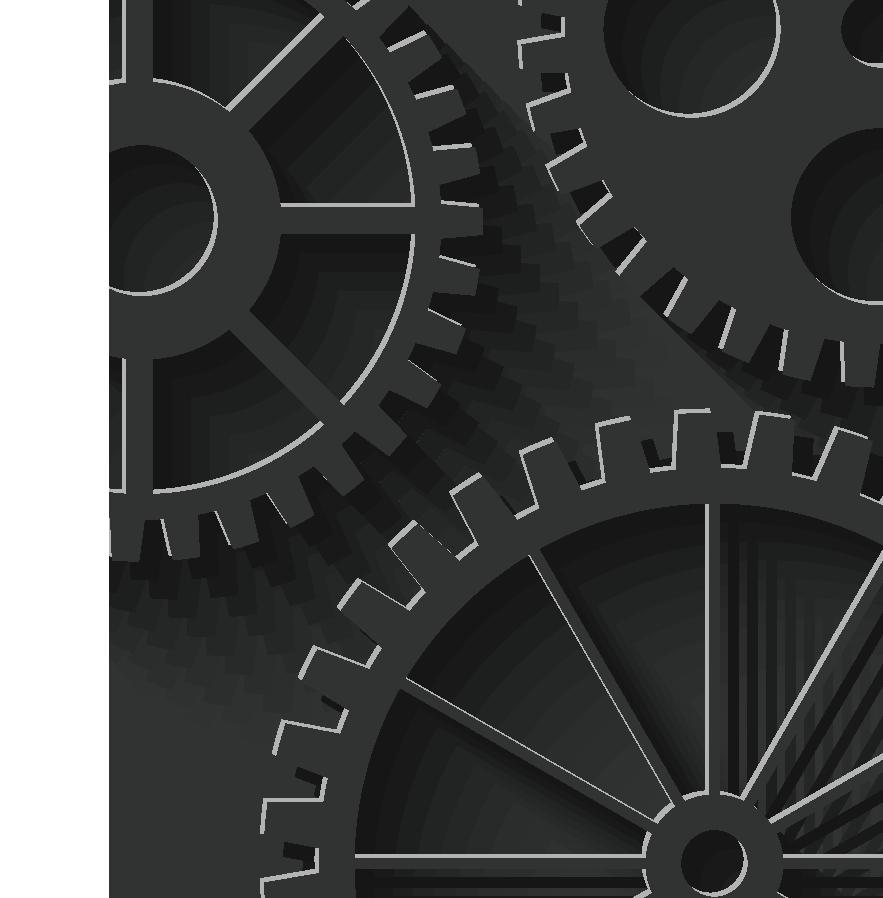
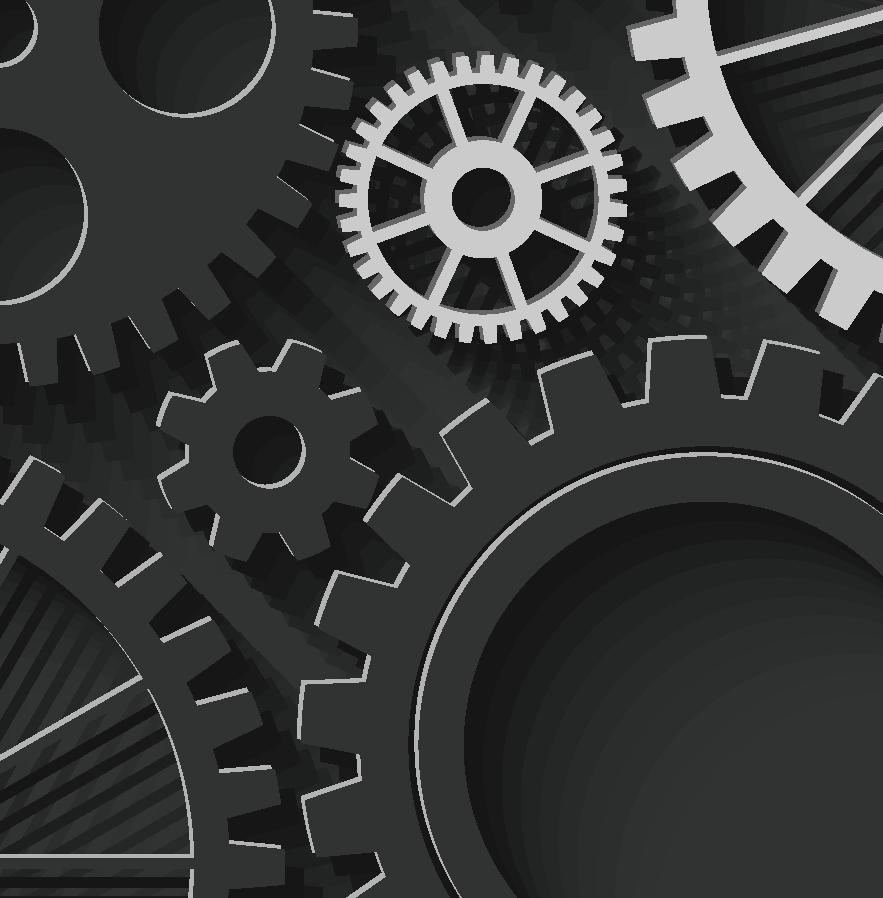
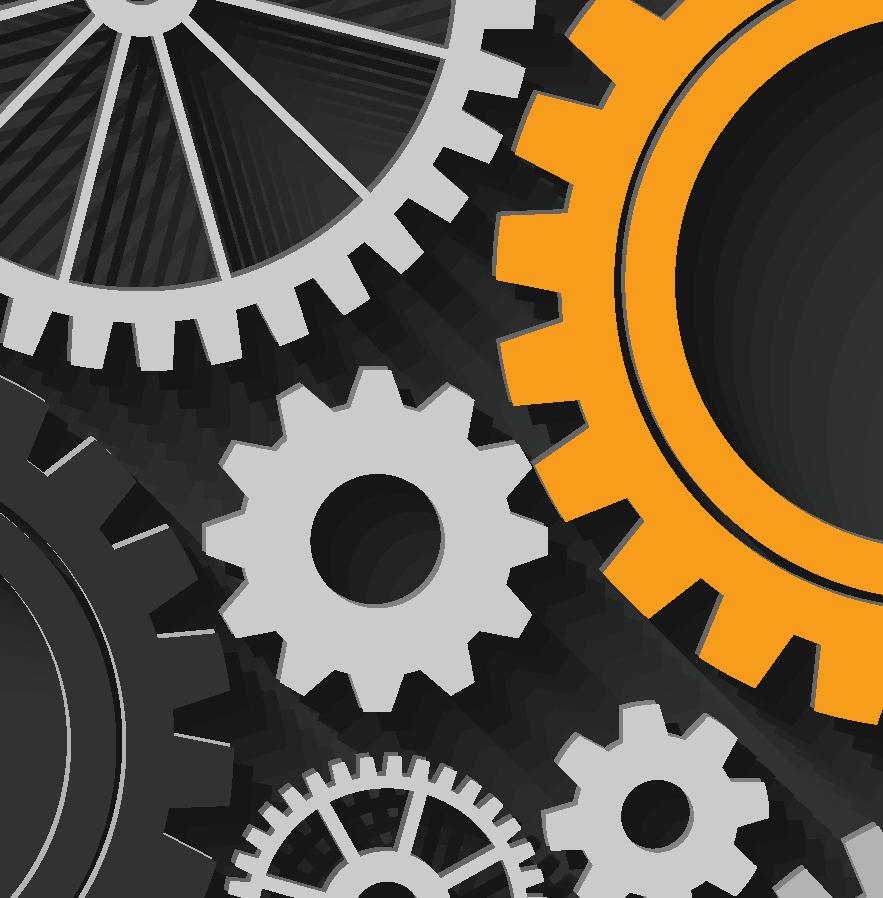
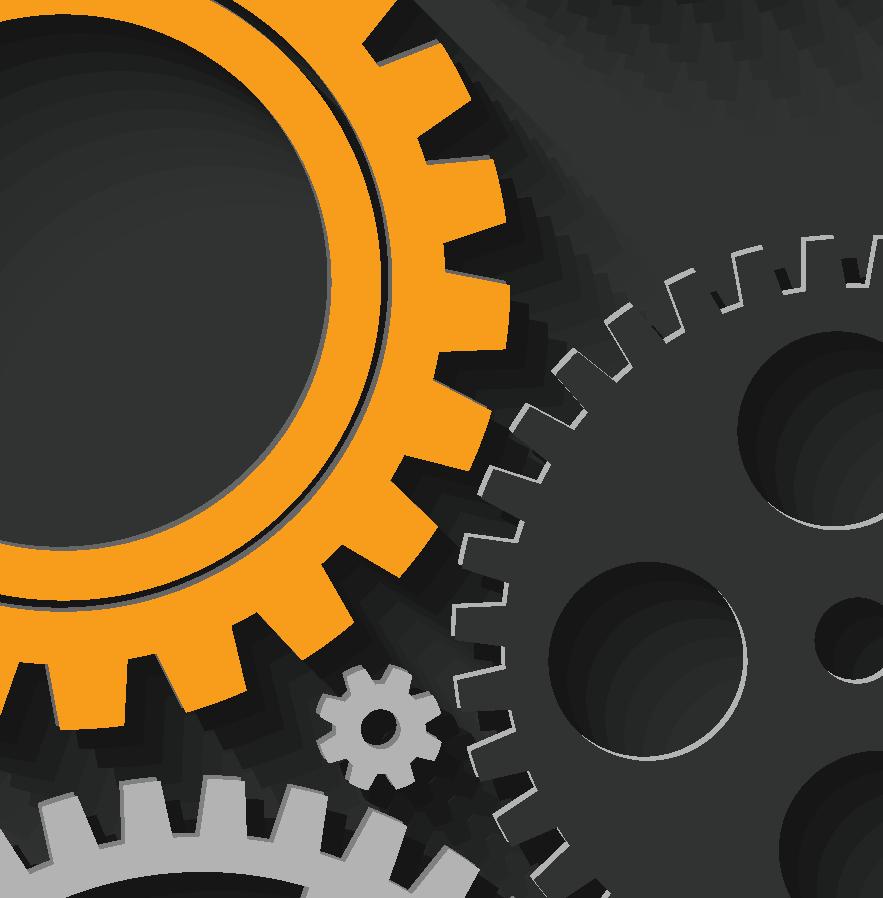
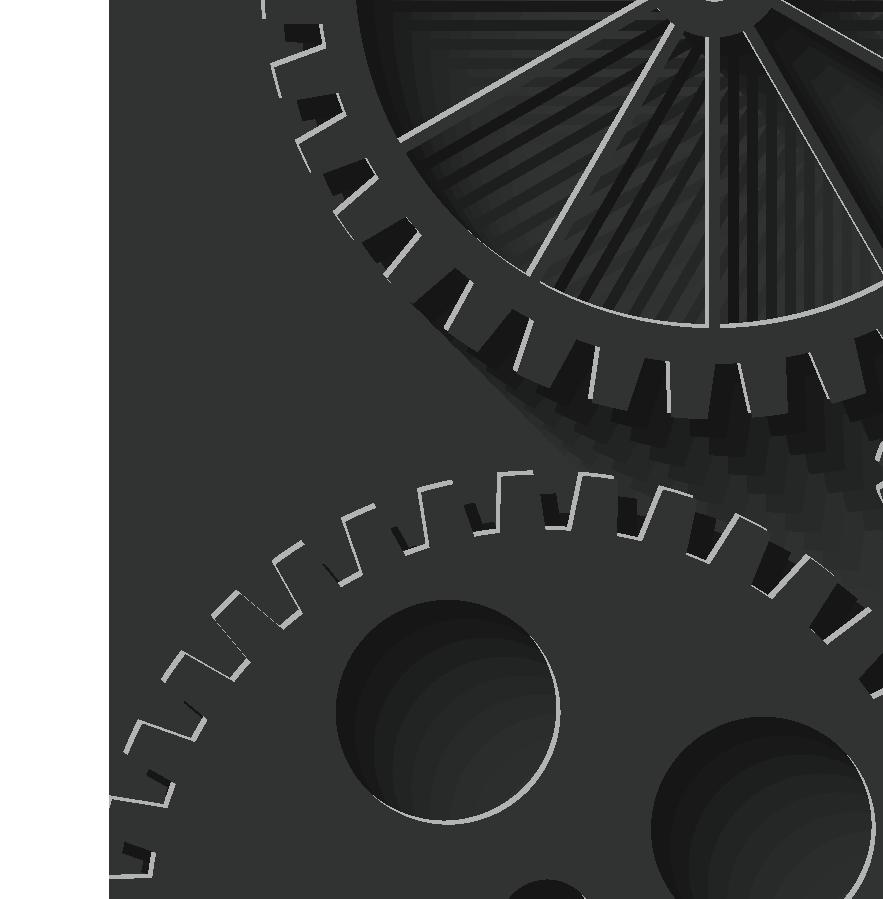
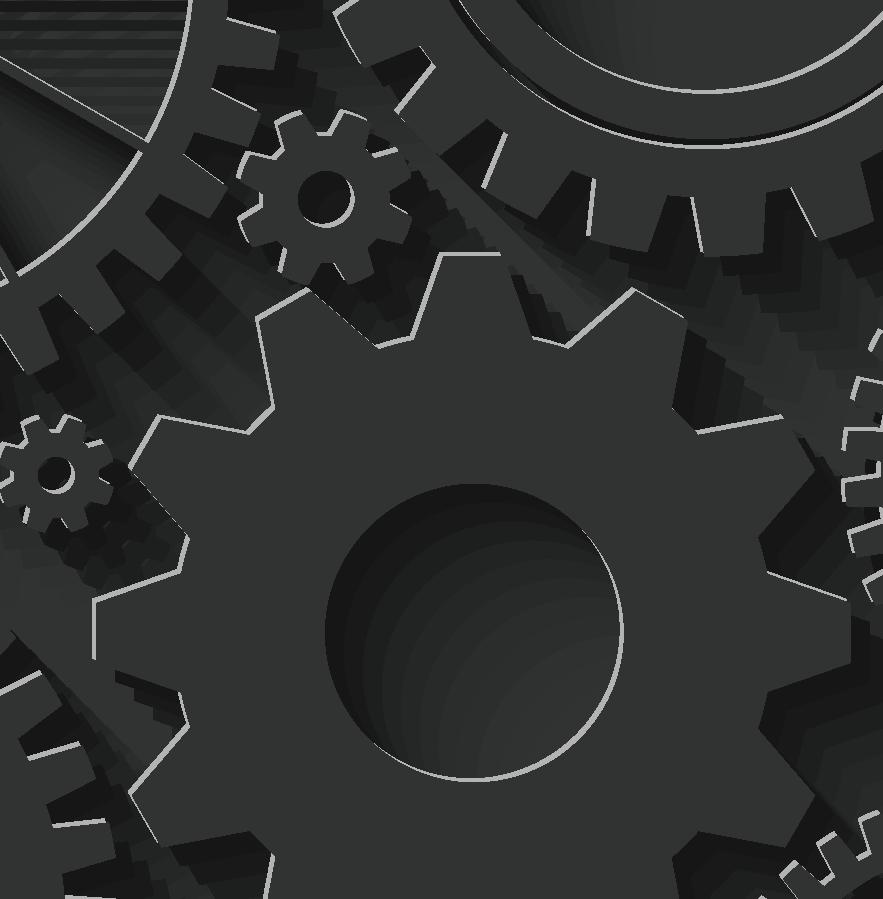
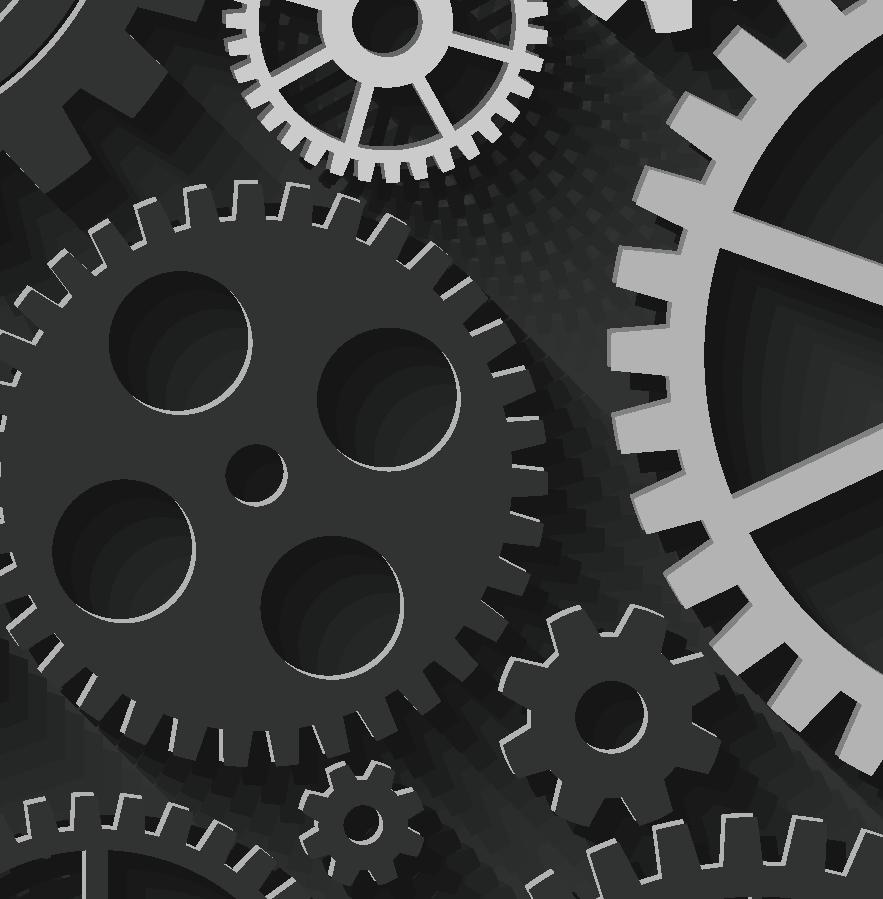
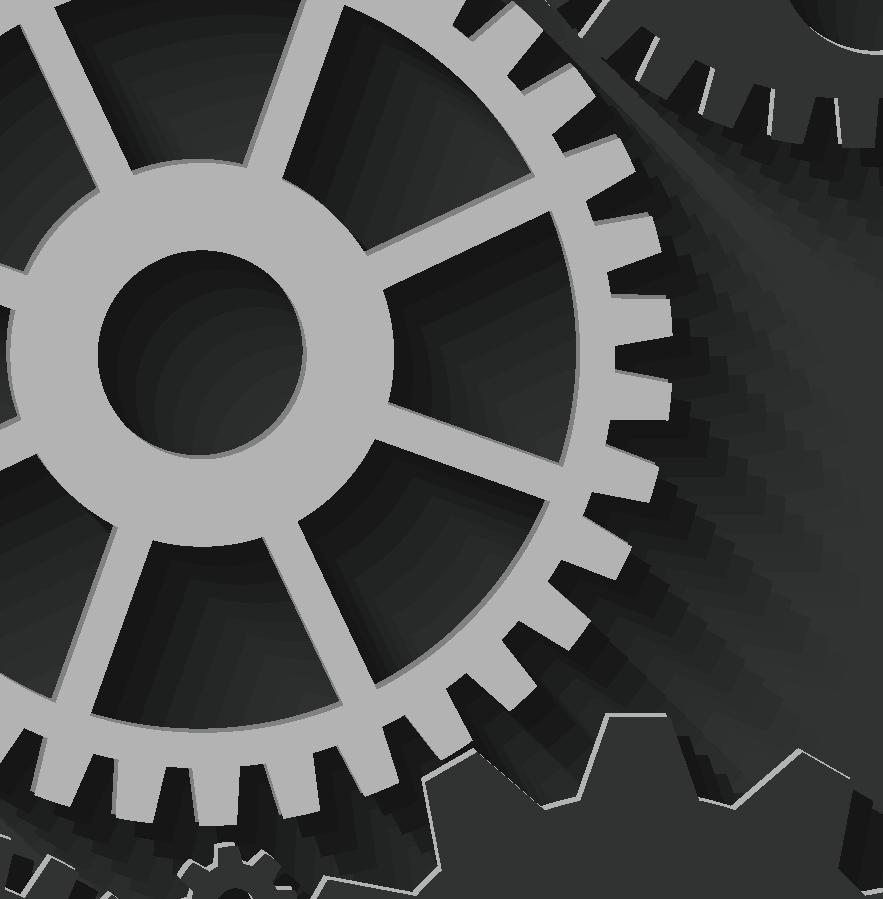
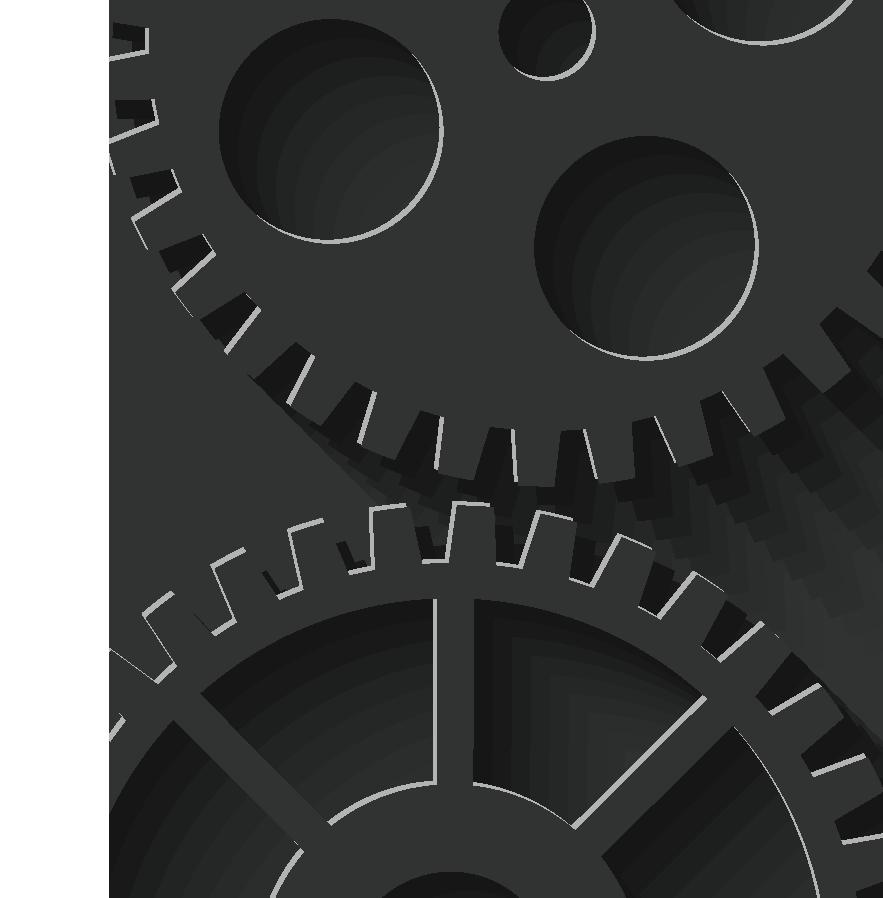
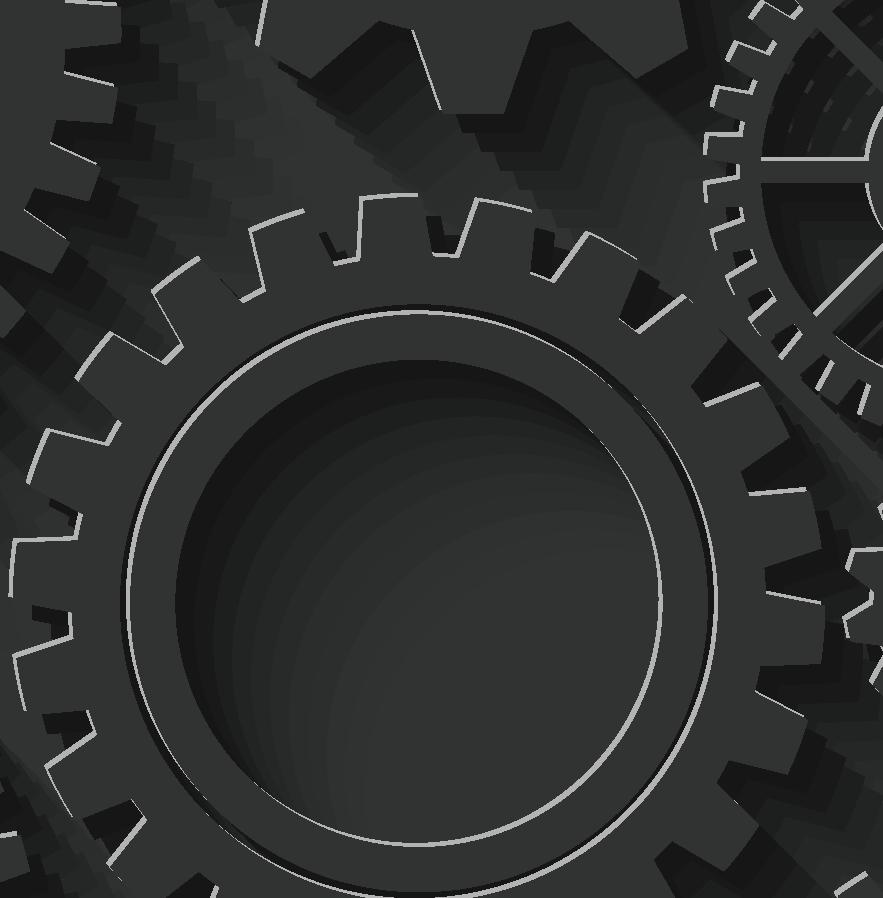

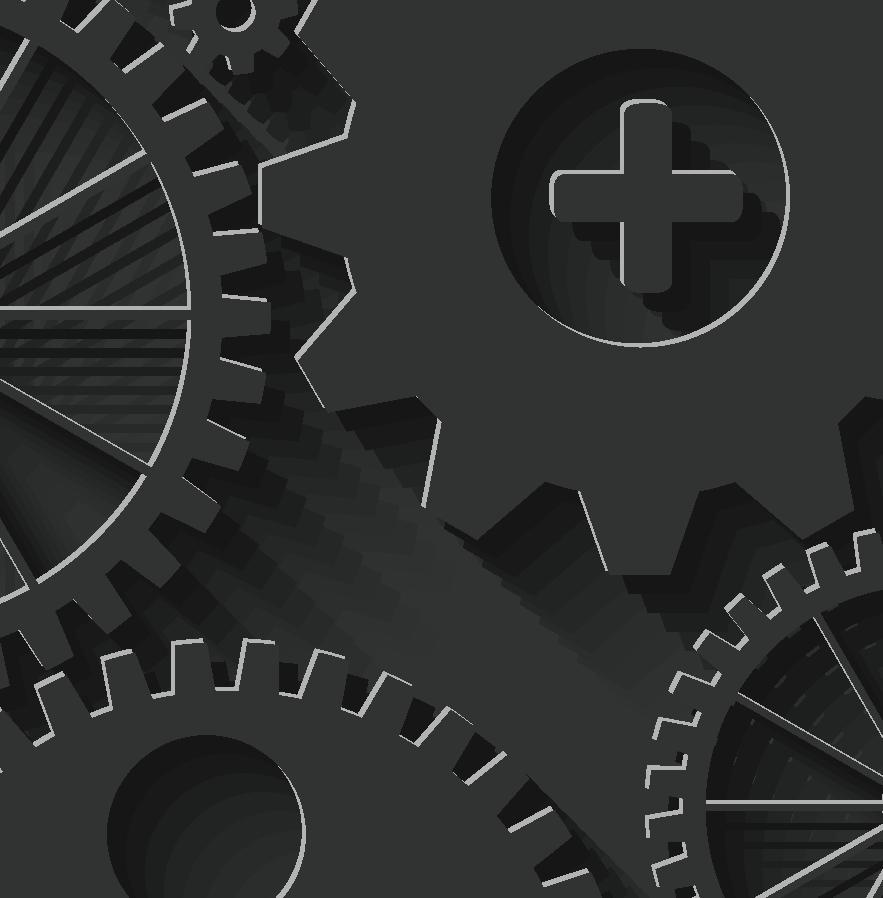
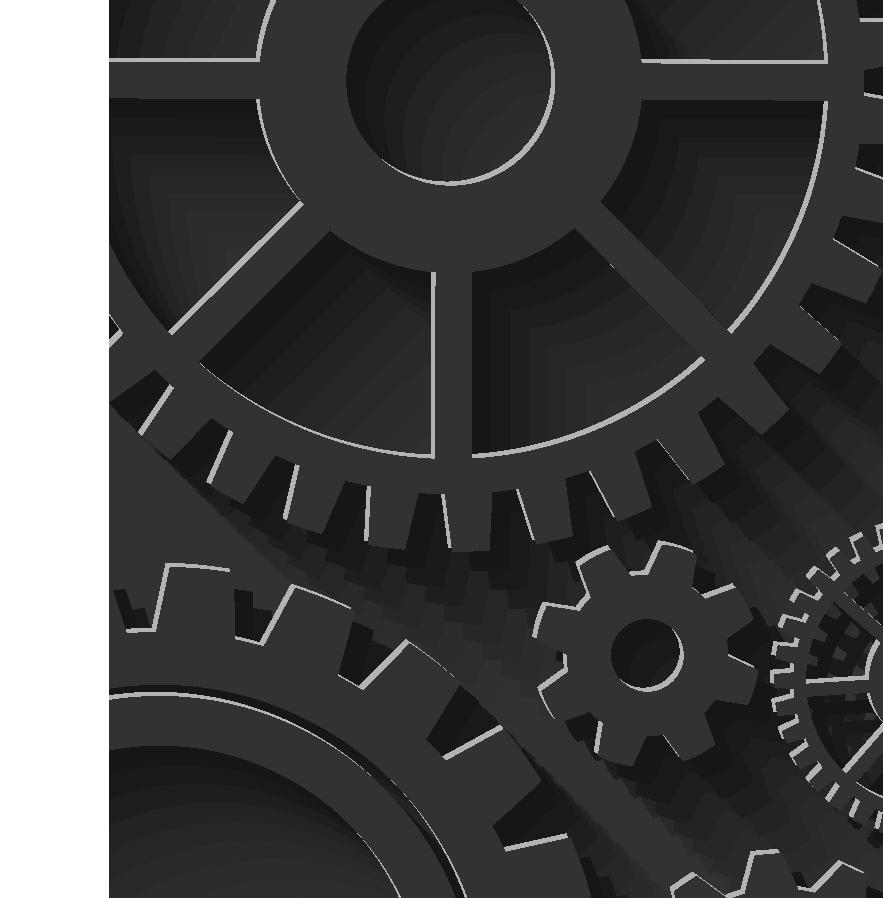
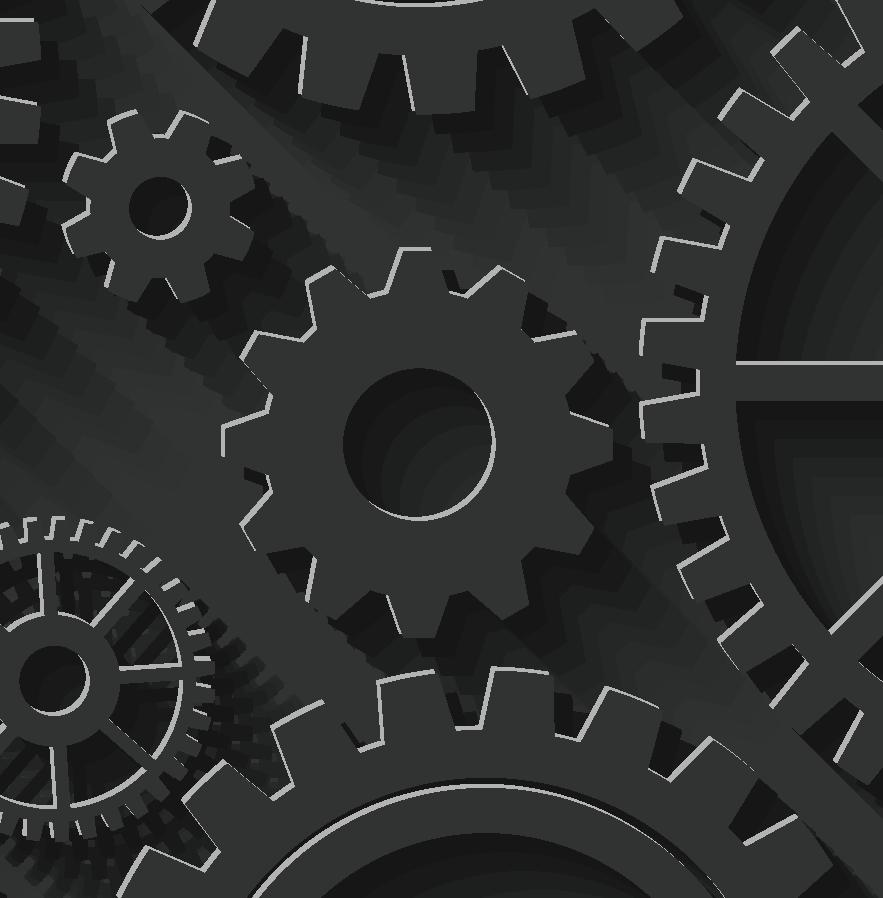
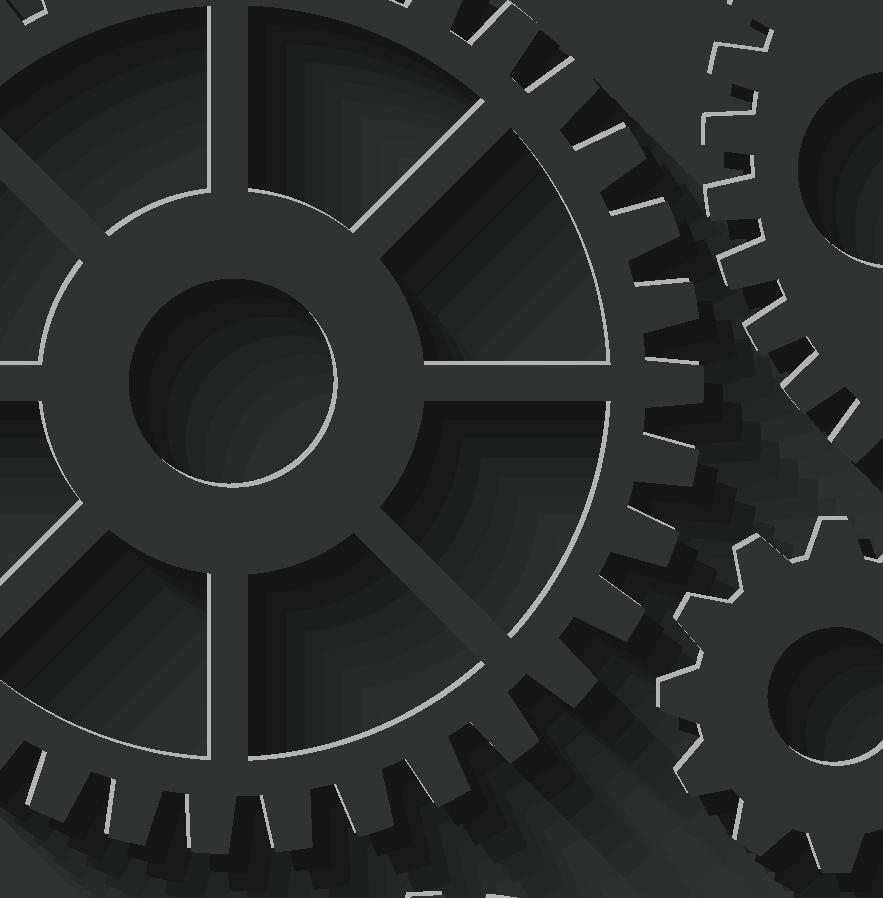
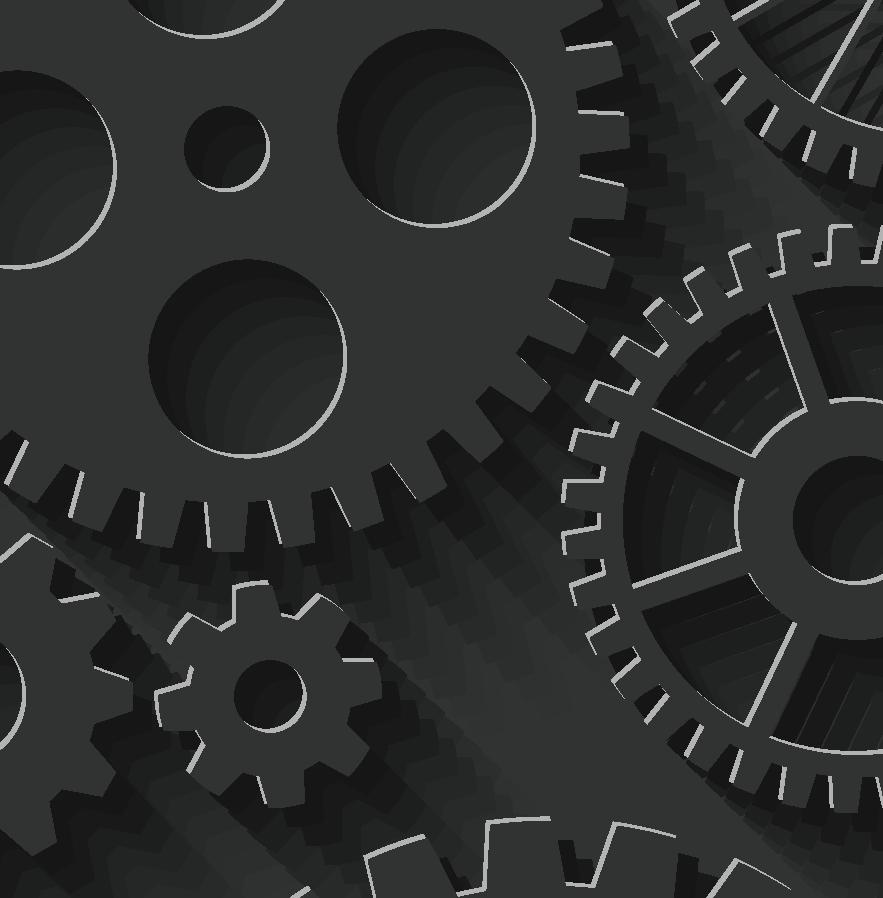
Visitors will see the company’s technology in action, meet the people who help pick, pack and ship orders around Australia, and get to see the millions of products stored in the fulfilment centres.

MHD NEWS & OPINION MHD SEPTEMBER 2022 | 11
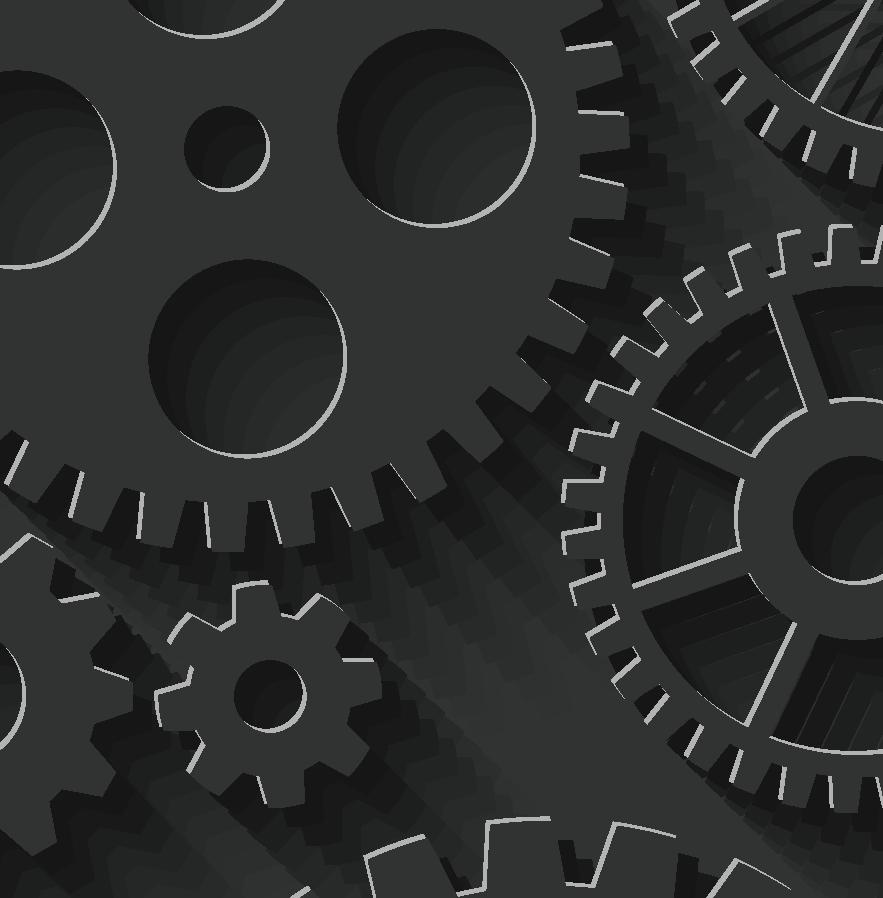
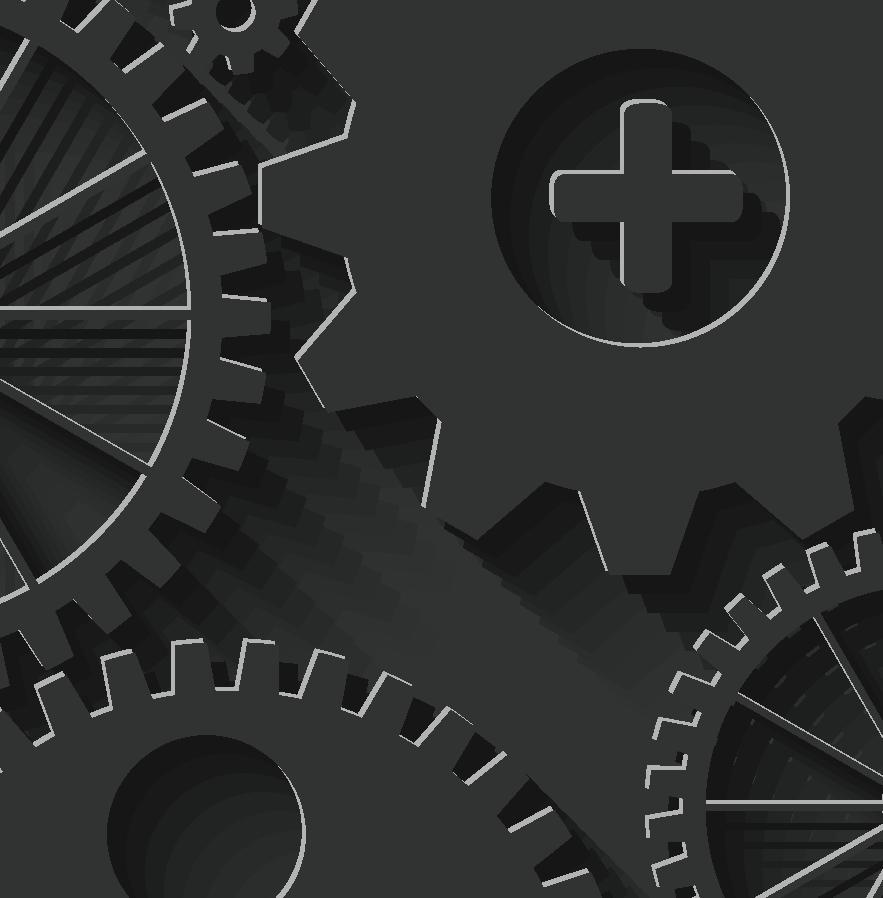
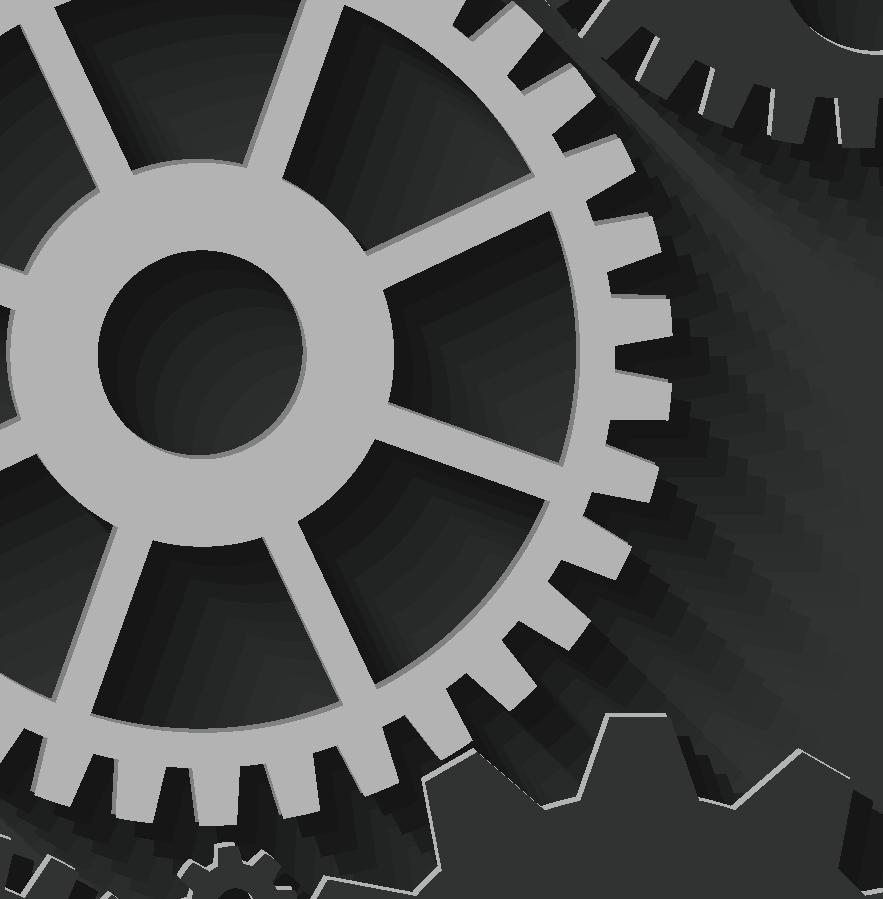
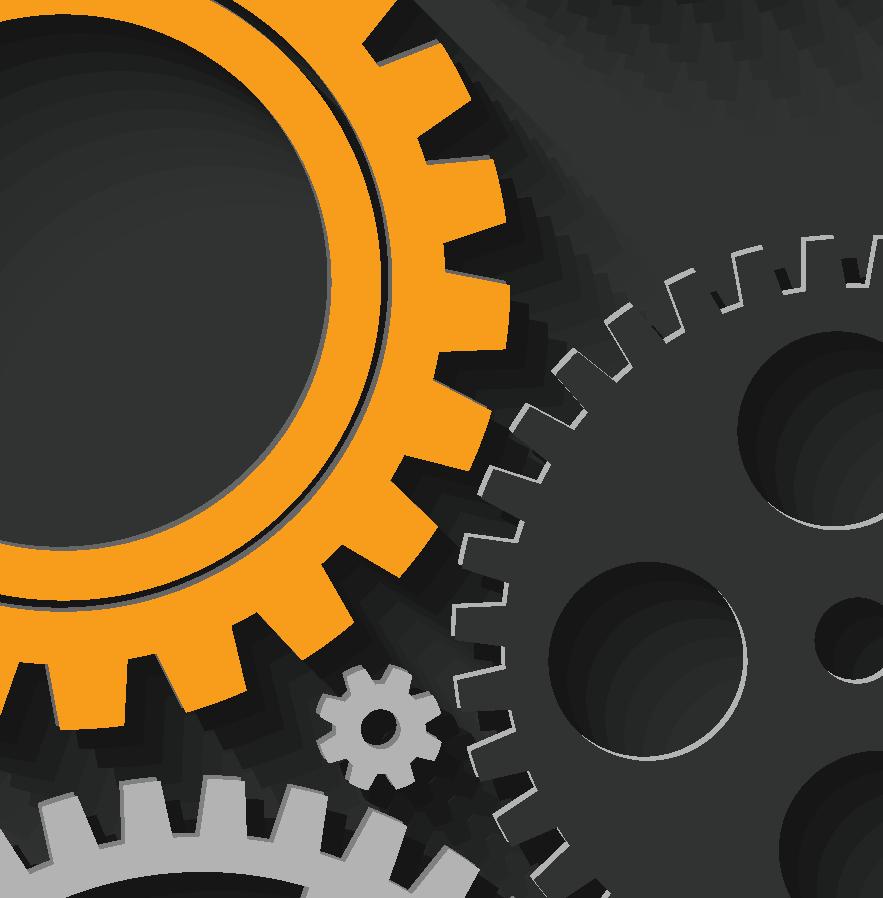

thriving community right here in my neighbourhood,” Joshua Dawe, tour guide at Amazon’s Sydney robotics fulfilment centre, says.
“At Amazon, our promise is all about providing great value and fast delivery for our customers,” Mindy EspidioGarcia, Director of Operations at Amazon Australia, says.
now a part of everyday life, this is the perfect opportunity for customers to join us for an hour to see what happens after they place their order.”
It adds that each tour will give Aussies a chance to get behind the scenes at all three sites to see how their online shopping cart gets to their doorstep.
It also notes the onsite tour hosts will facilitate Q&As with attendees to help them understand how the company’s operations come to life.
“We’ve hired talented employees from right across the country and invested in the systems and technology to support them,” she adds. “With online shopping
Amazon Australia launching live interactive tours
mazon Australia says as of Monday August 15, Australians can join free live virtual tours of its Sydney, Melbourne, and Brisbane fulfilment centres with tours on offer four days weekly.
“I can’t wait to show people the heart of our operations as well as the people and technology such as our robotic drives, which help move the inventory around the site,” he adds. “It’s not every day you get to see robots in Amazonaction!” Australia says the free tours will run for one hour at 10:30am on Monday and Thursday, and 1:30 pm on Tuesday and Friday.
Amazon Australia notes three expert onsite tour guides will lead the virtual tours in the three major Australian cities. Visitors will see the company’s technology in action, meet the people who help pick, pack and ship orders around Australia, and get to see the millions of products stored in the fulfilment Additionally,centres.there will be opportunities for visitors to ask the tour guides “Iquestions.grewup in Kemps Creek and it’s been exciting to watch this robotics fulfilment centre grow into a
“A cheap price doesn’t always represent a good deal,” Steve notes. “Without a national support network, with the human and backup resources available when you need them, equipment hire companies can be left stranded – and that will negatively affect them in terms of customer perception.”Stevesays that with TMHA, Coates has for a decade been able to rely on a network of support, which is in turn a boon to its equipment hiring customers.“WithTMHA, Coates procures a tier-one product matched by an equally impressive quality of service,” he says. “They can ring us up in Darwin, Cairns, Western Australia, and we’ll always be front and centre. There’s no spot on the Australian map where we’ll be forced to say, ‘Sorry, we can’t help you out’.
Peter Davis, Executive General Manager –Asset Services at Coates (left) and Steve Takacs, President & CEO at Toyota Material Handling Australia.
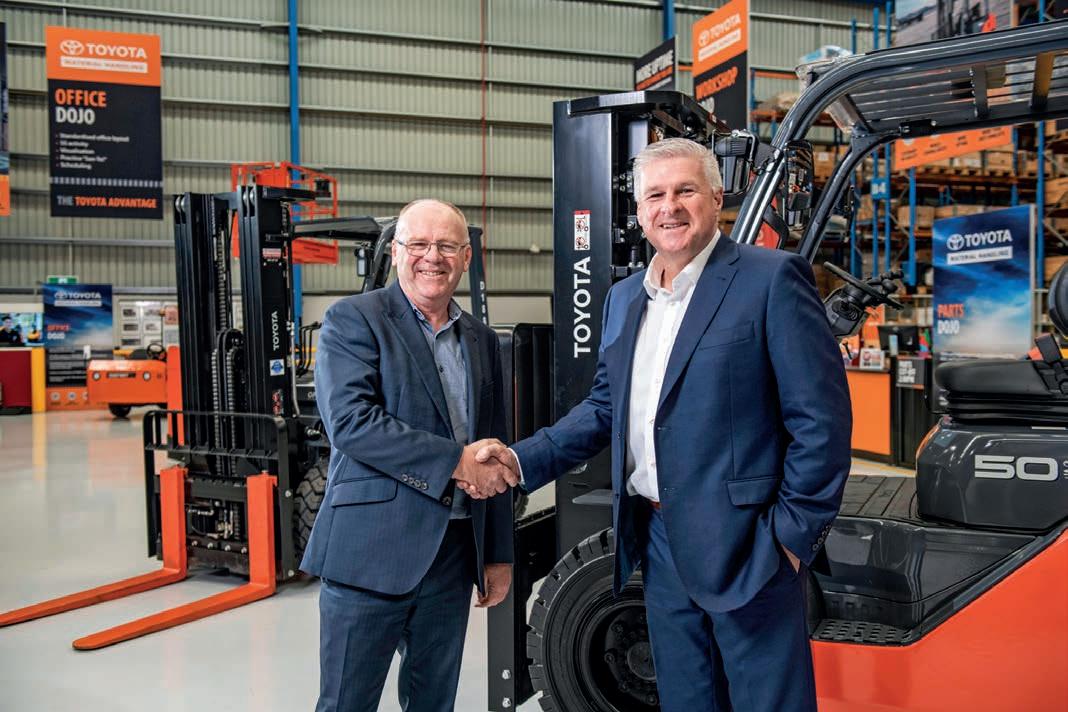
As Australia’s largest and most esteemed equipment hire provider, Coates puts a premium on delivering quality, reliability, and support for its equipment-hire customers. Before partnering with TMHA, Coates had struggled to find a primary supplier with sufficient national coverage to service and support the company in meeting customer
12 | MHD SEPTEMBER 2022 MHD COVER STORY
FROMTO STRENGTHSTRENGTH
S
“This breadth, availability, and quality of service is something we
teve Takacs, President & CEO at Toyota Material Handling Australia (TMHA), describes TMHA’s partnership with Coates as a multi-tiered relationship that has grown in stature and importance with every year. After more than ten years working together, the two companies recently renewed their working agreement – with Coates making a clear commitment to TMHA as its industrial forklift manufacturer of choice in updating Coates’ for-hire fleet.“The confidence in both the
The nation’s largest and most diverse equipment rental company, Coates, has renewed and expanded its procurement of Toyota Material Handling Australia (Toyota) forklifts as its majority brand. MHD explores the past, present, and future of their partnership – and how its success is built on a foundation of shared values and aspirations.
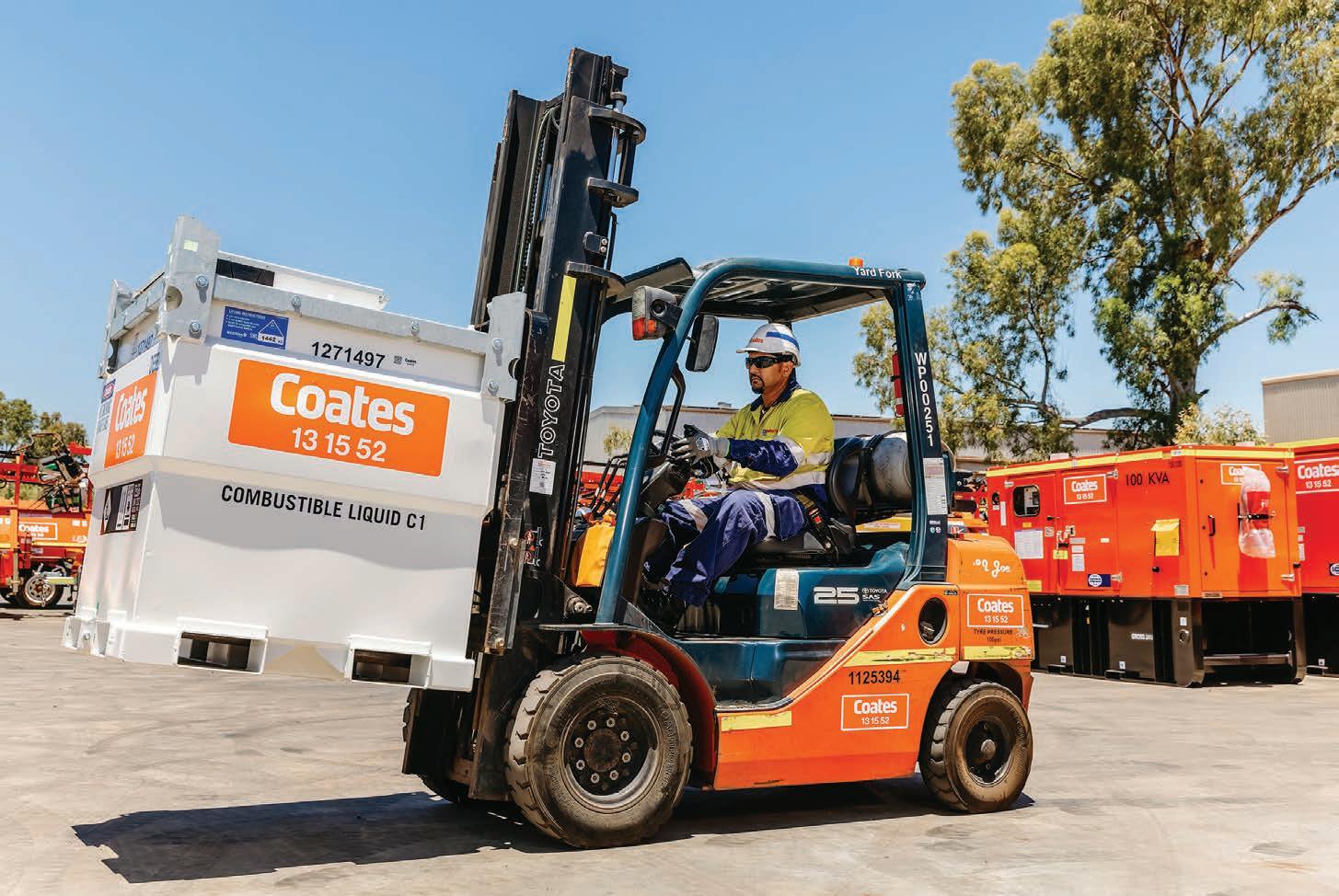
products and the organisation has made it seamless and easy for Coates to renew with us and probably renew for the next three to five years as well,” Steve says. “It’s a layered partnership, because aside from the executive management at TMHA, there are multiple touch points for Coates throughout the organisation and in every TMHA branch, sales, and service locations. There are branches in our network across the country proximal to every Coates branch. That’s a real advantage to our relationship, because if they have a
problem with a piece of our equipment – or need an issue resolved quickly –Coates can just pick up the phone and we’ll action a solution immediately.”
THE RELATIONSHIPTMHA-COATES
“
“Coates also has its own registered training organisation that includes safety training, including for forklifts. Our goal is to match the best in safety training with the best in forklift safety features.”
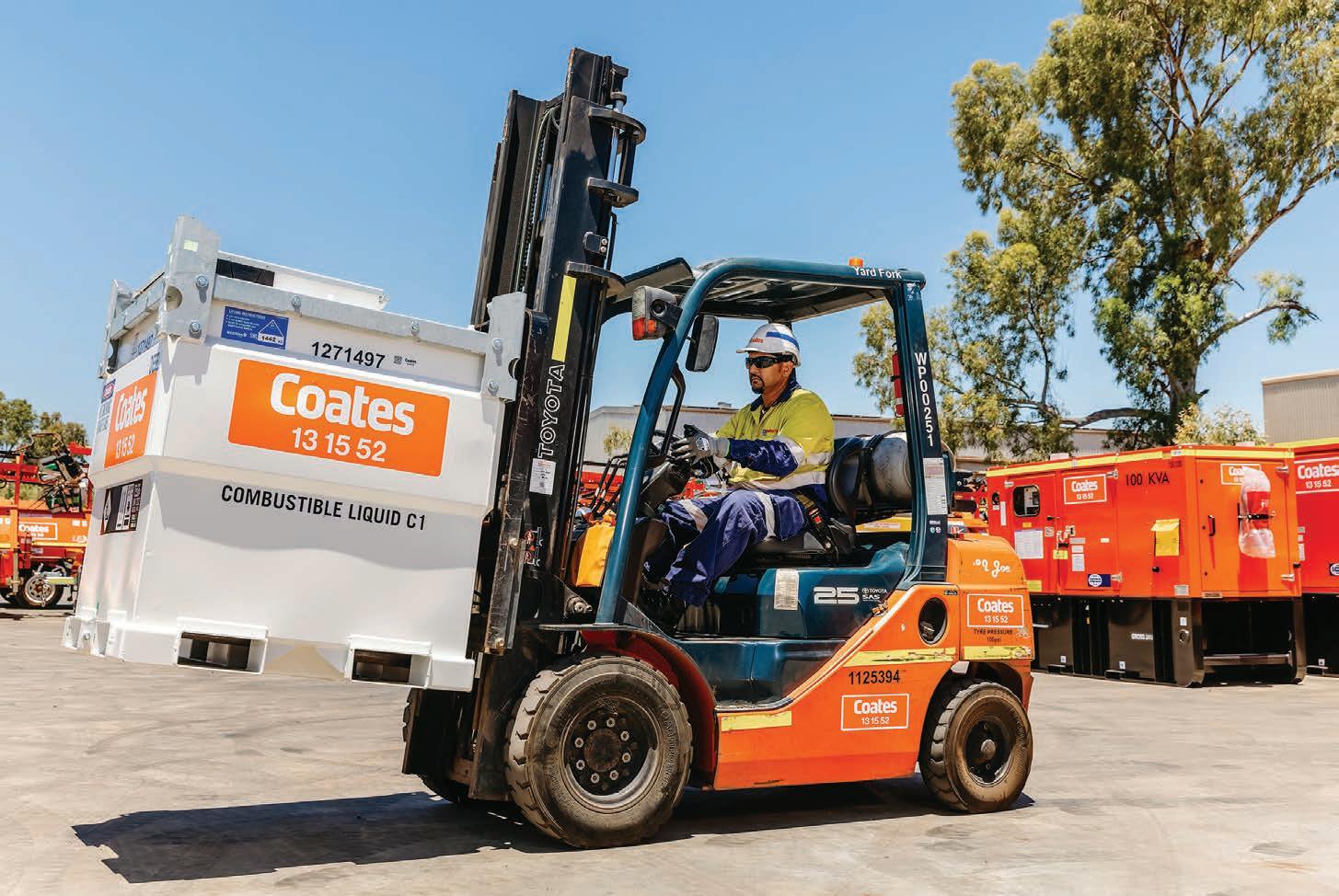
Forklifts are typically a 10-year investment, so for Coates, procuring a reliable and effective product for its re-hire service is paramount.
“We are seeing increasing expectations from our customers that the equipment we hire out to them meets their safety standards,” he adds. “Toyota’s safety innovations such as active stability control
The new deal represents a substantial capital expenditure for Coates and exemplifies the trust it has in TMHA’s products and accompanying services.
This isn’t just a one-way street ... TMHA is thrilled to have the own.alignedandreliability,commitmentbecausepartneropportunityongoingtowithCoates,theirtoservice,excellenceiswithour ”
MHD SEPTEMBER 2022 | 13 MHD COVER STORY
As a re-hirer of equipment, Coates has over many years dealt with multiple forklift companies that offered varying gradations of equipment reliability, work levels, health and safety features, and contractor entry issues.Naturally, over the course of their
Cameronaccessibility.”Paxton,Vice President and COO at TMHA, adds that Coates’ preference for TMHA equipment also results from TMHA’s strong record on safety criteria. “Coates is the market leader in equipment hire, and they know material handling equipment inside and out, so it’s a real compliment that they view TMHA products as those that best meet the performance and safety criteria of their customers.”
Coates. They have a major reputation to sustain, because they are hiring TMHA forklifts to their own customers who in turn expect and rely on that dependability and service
Steve elaborates: “With a forklift being a heavily regulated piece of industrial equipment – heavily regulated from a safety and compliance point of view –Coates have taken comfort in the fact that Toyota will be supplying those services in line with the law and making sure that we stay on top of all the necessary points to keep their equipment safe.”
AN EVOLVING PARTNERSHIP
“The level of commitment speaks volumes about both parties,” Steve says. “This isn’t just a one-way street, either. TMHA is thrilled to have the ongoing opportunity to partner with Coates, because their commitment to reliability, service, and excellence is aligned with our own.
Peter Davis, Executive General Manager – Asset Services at Coates, underscores the importance of safety for Coates’ operation. “Safety is something we take very seriously for our employees and our customers, and we ensure all products that we hire out and work on meet stringent safety standards.
“We know that they will get the best of our equipment into the right hands and support their own customers with TMHA equipment every step of the way. We wouldn’t agree to provide equipment to a re-hire company that didn’t share our commitment to excellence. And Coates is an indispensable partner in that sense. So, we’re thrilled that they have renewed and expanded their relationship with TMHA.”
and operator restraints are a big advantage for us. It helps with compliance.
Peter Davis says that although the relationship with TMHA extends back more than two decades in total, the increasing shift towards preferring TMHA equipment resulted from Coates’ adopting ever more refined and exacting procurement methodologies.“We’vealways known Toyotas to be good, solid products – that’s why we’ve had them in our fleet for so long. But over the years we’ve become more stringent in how we procure our equipment,” Peter says. “It’s important for us to be in front of the technology and safety curves, because for us a forklift is typically a 10-year investment.”Butinaddition to superior technological and safety features, Peter notes that TMHA comes out ahead of the competition in terms of a lower total cost of ownership.
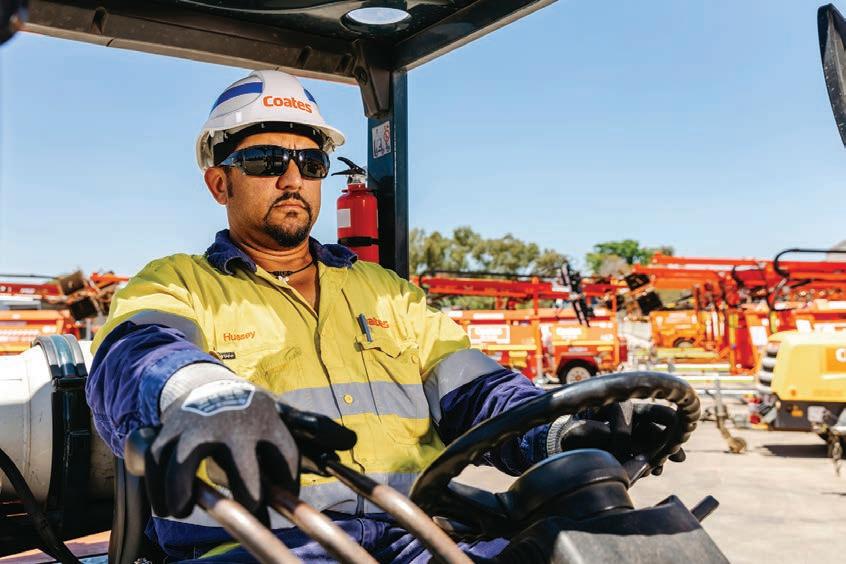
money throughout its life. In that case, any upfront savings are lost, and it can hurt your bottom line very quickly.“Forus, it’s about minimising maintenance and labour costs all the way through, because those can be higher than the original purchase price. And it’s not just how the equipment is serviced – that is actually relatively minor compared with the number of inspections we
“Our model is typically short-term hire, so we inspect the equipment every time it comes back from a customer, before it goes back out again. That happens more frequently than servicing and because of that it must be efficient. So, the machines must be designed to access and check easily, and Toyota forklifts tick that box.”Peter adds that Coates primarily rents Toyota forklifts out to customers
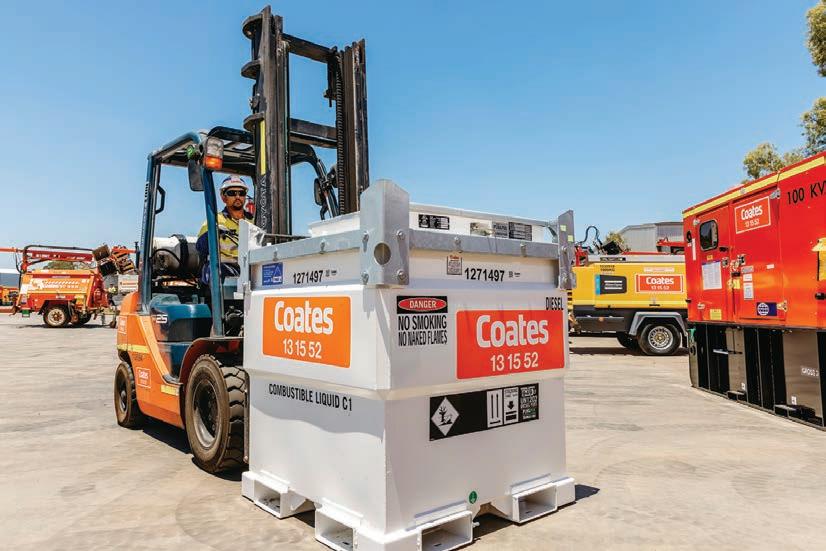
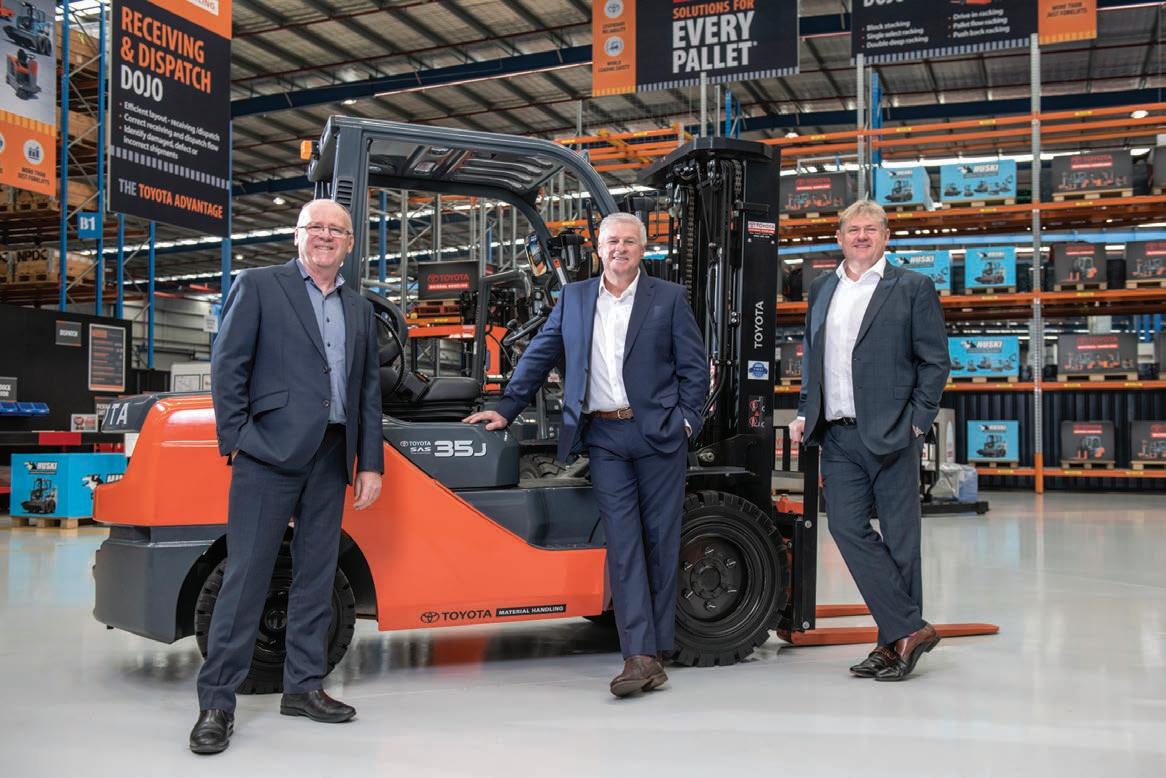
“A large part of what we do is ensuring the total cost of ownership over the life of an asset is as low as possible,” he says. “We of course need to get the best price we can based on the quantity of our order, but that can easily be undone if we buy inferior
14 | MHD SEPTEMBER 2022 MHD COVER STORY
decade-long partnership, Coates has come to see TMHA as standing out from the pack.
Coates’ preference for TMHA equipment is in no small measure due to the latter’s strong record on safety criteria.
Shared values and strong commitments – from customer service to sustainability objectives – underpin the TMHA-Coates partnership.
For Cameron, TMHA’s and Coates’ complementary sustainability objectives show how in-sync the two companies are. Two independent titans of industry with shared values – and an ethos that puts people first.
• Eliminate CO2 emissions from suppliers and dealers;
NEW DEAL, NEW POSSIBILITIES
equipment must be up to the task.
As Steve Takacs puts it, one of Coates’ goals was to streamline and centralise its rehire arrangement with TMHA.
This year, Coates launched its
“
•globally:Reduce CO2 emissions from new vehicles by 90 per cent (2010 baseline);
• Conserve water and protect water resources;
■ MHD SEPTEMBER 2022 | 15 MHD COVER STORY
There can be no doubt that TMHA – and Toyota as a whole – does share Coates’ commitment to sustainability.
Greener Choices range of products and solutions, as part of its ongoing commitment to reducing its own and its customers’ environmental impact.
“We have our own target of achieving net-zero emissions by 2040, and it’s important that we work with suppliers and customers who have the same aspirations as us when it comes to sustainability.”
SUSTAINABILITY SUPERSTARS
In 2015 Toyota announced the ‘Toyota Environmental Challenge 2050’ – setting challenges for all Toyota subsidiaries
Predicated on the circular economy model, Coates Greener Choices is among the five pillars that Coates has detailed in its Sustainability Strategy. “Coates is a natural participant in the circular economy because our hire and solutions business model is inherently circular,” Peter says.
• Eliminate CO2 emissions from operations;
• Support a recycling-based society; and Conserve biodiversity, protect species, and restore habitats.
“We primarily supply to the construction and mining industries, where equipment gets a hard life compared to, say, a warehouse. So, it’s paramount that our forklifts are tough and last the distance. That’s why quality, durability and reliability are so important to us. The Toyota product is market-leading in that regard, which makes it great for our total cost of ownership.”
Thirty years ago, Toyota made a bold commitment to preserving the environment with its 1992 Earth Charter. Since then, Toyota has repeatedly upped its ambitions on this front, and across all its subsidiaries.
TMHA is meeting and exceeding its ambitious objectives. Indeed, for its own operations the Toyota Industries Corporation set as its target a reduction of 26 per cent of emissions (from fiscal year 2012 baseline) by 2021. Toyota’s European factories – which manufacture some of TMHA’s equipment – well exceeded that goal, achieving a reduction of 31 per cent.
“Put simply, it’s two market leaders joining together here with the shared aim of supplying satisfaction and reliability to our end customers, at the same time as we uphold our social and environmental responsibilities.”
It’s a vote confidenceofin us [TMHA], that they [Coates] recognise that we are a specialised material handling company and trust us to deliver the quality of service which has long been a calling card of Coates. ”
TMHA will assist in remedial maintenance and servicing on the Coates fleet.
“We’re now working through the final details such that Coates can contact us, and we will be a primary supplier for rehired equipment,” he says. “By supplying through us, that means that they get our service and invoicing with all the benefits that come with that.”
The deal also included a significant number of trade-ins, with Coates trading equipment directly to TMHA. The forklift specialists will also assist in remedial maintenance and servicing on the Coates fleet.“That was a great feather in our cap considering that Coates has their own service crew across the country,” Steve says. “It’s a vote of confidence in us, that they do recognise that we are a specialised material handling company and trust us to deliver the quality of service which has long been a calling card of Coates.”
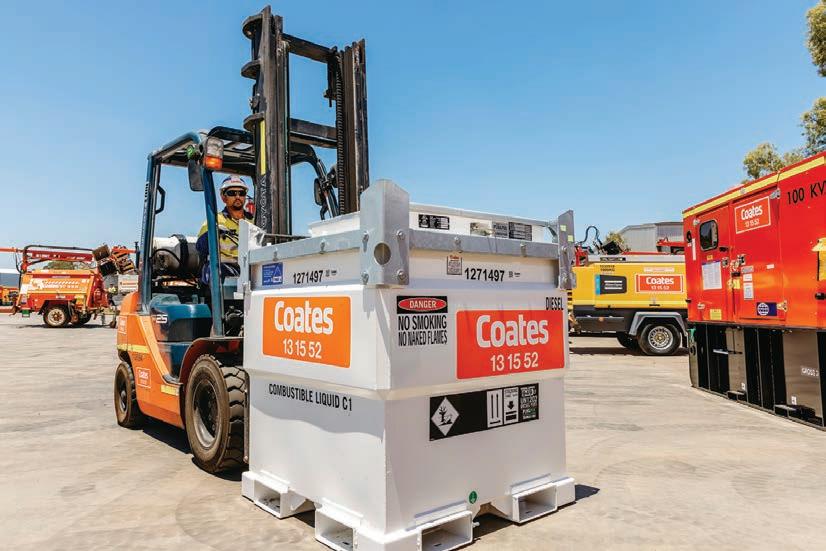
Start your searchIndustrial Solutions 2022 Accelerating success. Outlines indicative only 0418 799 792 Dan Dwan 0402 026 825 Anthony White * Approx. colliers.com.au/p-AUS66017662 Huge power, cranes & heavy duty hardstand 6,350m²* corner83,380m²*onsite 44 Witmack Road, Wellcamp, QLD Industrial For Lease | Available Immediately Landmark Manufacturing and Distribution Facility For Lease Outlines indicative only 0431 156 990 Richard Wilkinson 0401 693 450 Jonathan Mercuri * Approx. colliers.com.au/p-AUS66017709 Largesupplypower Total building area: 4,632m²* 1/1834 Dandenong Road, Clayton, VIC Industrial For Lease Prominent Office Warehouse with Power For Lease Artist’s impression 0410 532 022 Steve Smith 0401 145 028 Paul Tierney * Approx.colliers.com.au/p-AUS66017262 Highclearance13.7m* 6,886m²* respectively7,485m²*& Wingfield Industrial Estate, 2 Francis Road, Wingfield, SA Industrial For Pre-Lease 2 Brand New Office & ForWarehousesLease



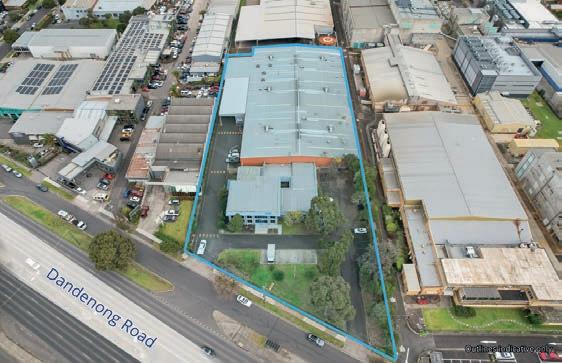

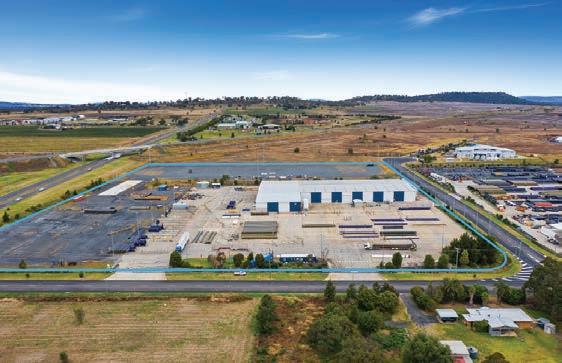



As large e-commerce and brickand-mortar retailers strive to implement similar models, increasing the availability of same-day delivery services inevitably causes an expectation by consumers that they will be able to purchase most goods with a same-day fulfilment promise. Although same-day delivery is yet
WHY HASN’T SAME DAY DELIVERY HAPPENEDALREADYINAUSTRALIA?
Until recently Australian customers
With the rapid uptick in e-commerce, demand for same-day delivery to customers is heating up.
THE DEMAND SAME-DAY-DELIVERYFOR IN AUSTRALIA IS GROWING
During the pandemic, consumers were required to order essentials, medication, and fresh food – all preferably without leaving their homes.Thisdramatic shift in consumer behaviour accelerated the nation’s interest and expectations for a good online shopping experience.
n the past three years, Australia Post has delivered more than 900 million parcels. In a country with a population of 25 million people – that’s a rapid rise in market penetration for online retail.
WILL BECOMEDELIVERYSAME-DAYEVERAREALITYIN AUSTRALIA?
As a result, leading online retailers such as Amazon, Catch and The Iconic have stepped up to the challenge and have been offering same-day delivery. Usually only available for orders placed before a certain cut-off time in
MHD SUPPLY CHAIN MHD SEPTEMBER 2022 | 17
easily accessible areas such as inner Melbourne and Sydney, is it a sign of things to come?
Last month, the nation’s parcel provider Australia Post revealed that in the past financial year, a record 9.3 million Aussie households shopped online. Breaking all previous records set, online purchases grew almost 12 per cent compared with the previous financial year.
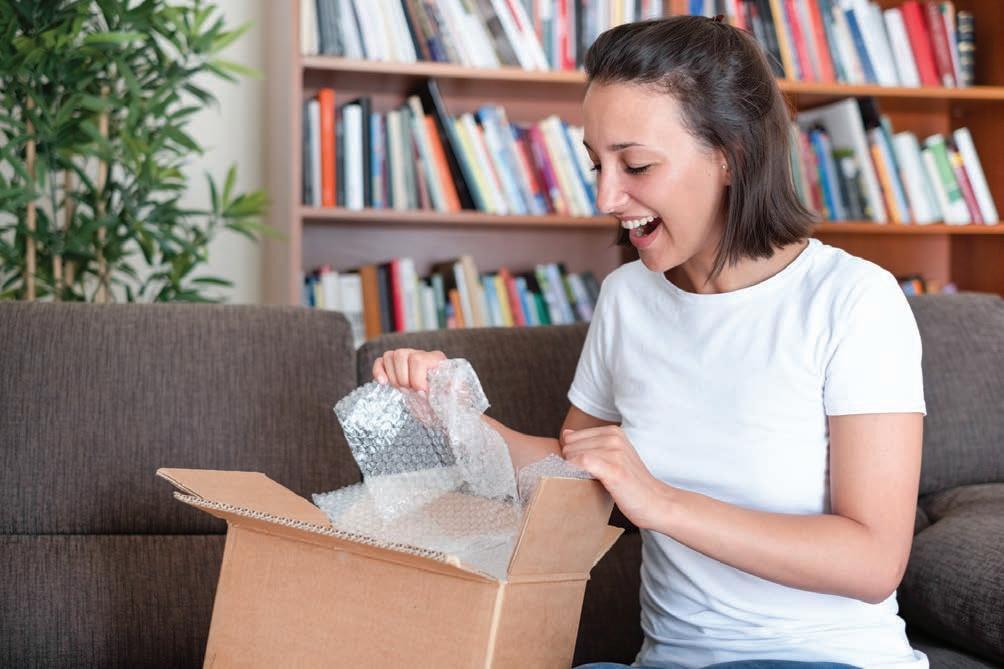
I
While some global cities have started to see same-day delivery from major retailers and e-commerce leaders, we discuss the unique supply chain challenges that have made it difficult to introduce in Australia.
to become a key driver for companies in Australia, the implementation of Click and Collect/Deliver services during the pandemic makes same-day delivery the next natural step – but how realistic is it and what is holding Australia back?
Australia’s dramatic shift to online shopping is showing no signs of slowing down, putting increased pressure on retailers to provide fast, convenient and reliable delivery. As a result, the rush is on to win the same-day delivery race – but is it realistic in Australia?
Investing in these advanced technologies can help businesses differentiate themselves in the drive to offer same-day delivery in more markets.
didn’t expect retailers to offer same-day delivery; they were happy to wait a couple extra days to get their order. With COVID-19 and the pandemic shifting consumer expectations rapidly, businesses have suddenly had to adapt and switch from the previously acceptable three-to-four day delivery
HOW CAN BUSINESSES UPDATE THEIR PROCESSES TO MAKE SAME-DAY DELIVERY A REALITY?
Although same-day delivery is yet to become a key driver for companies in Australia, the implementation of Click and Collect/Deliver services during the pandemic makes same-day delivery the next natural step.
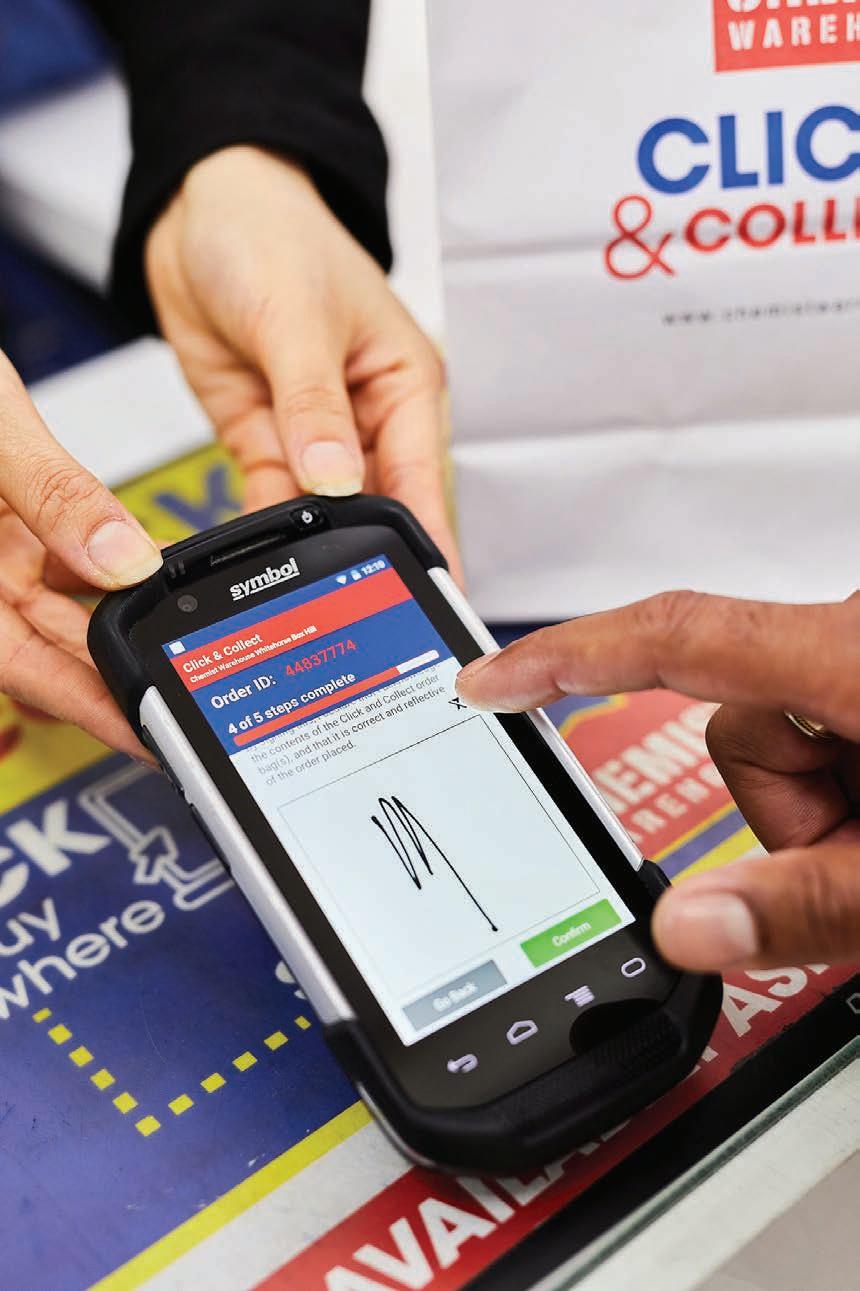
To learn more about how our solutions can help make same-day delivery a reality for your business, contact Körber today.
“ The deliverytoadvancedavailabletechnologyisnowenoughmakesame-dayareality. ”
There's a lot of options for businesses to make same-day delivery a reality. Warehouse technology, like autonomous mobile robots (AMRs), can significantly increase the speed of picking and packing in warehouses, getting packages out the door faster. Decentralising supply chains and the use of advanced technology to obtain more accurate delivery information can help businesses make faster deliveries and have better interactions with consumers.
A combination of the right last-mile logistics operation and strategically placed warehouses will allow businesses to reach their customers much quicker. As availability and normalisation of same-day delivery increases, it’s set to become a key strategy in meeting evolving consumer expectations.
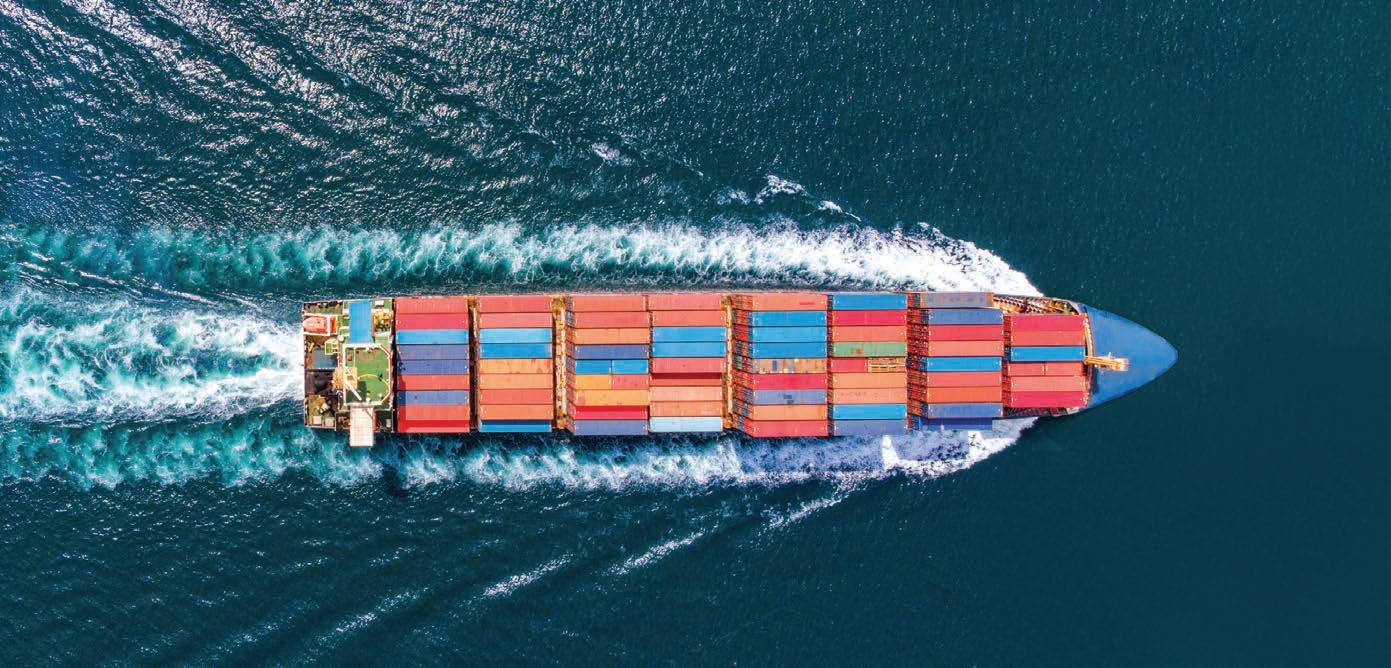
Drones for same-day delivery are also on the table and are already being tested by Project Wing (a Google-owned company) in flat, urban landscapes in Australia – such as Canberra and Logan.
its population live, and where orders come from. The vast size of the country means transport has a long way to travel, and by companies offering same-day delivery to certain customers, others who are more rural may miss out.
HOW CAN KÖRBER HELP MAKE SAME-DAY DELIVERY A REALITY?
Previously,standards.thecomplex geographical nature of Australia deterred businesses from implementing same-day delivery. Australia faces unique challenges in terms of where
The good news is the technology available is now advanced enough to make same-day delivery a reality, at least on the eastern seaboard where 80 per cent of the nation’s population is located.
To make same-day delivery a reality, retailers need to know how quickly they can pick, pack, and ship out an order as soon as it comes Körberin.is well-prepared to support retailers and make same-day delivery a reality, with multiple software solutions, various automation, and workflow enablement technologies as well as standout micro-fulfilment strategies.
■ MHD SUPPLY CHAIN 18 | MHD SEPTEMBER 2022
Port Intel delivers global, accurate, real-time intelligence on port and vessel activity so supply chain professionals can plan proactively, respond to exceptions, and meet customer expectations.
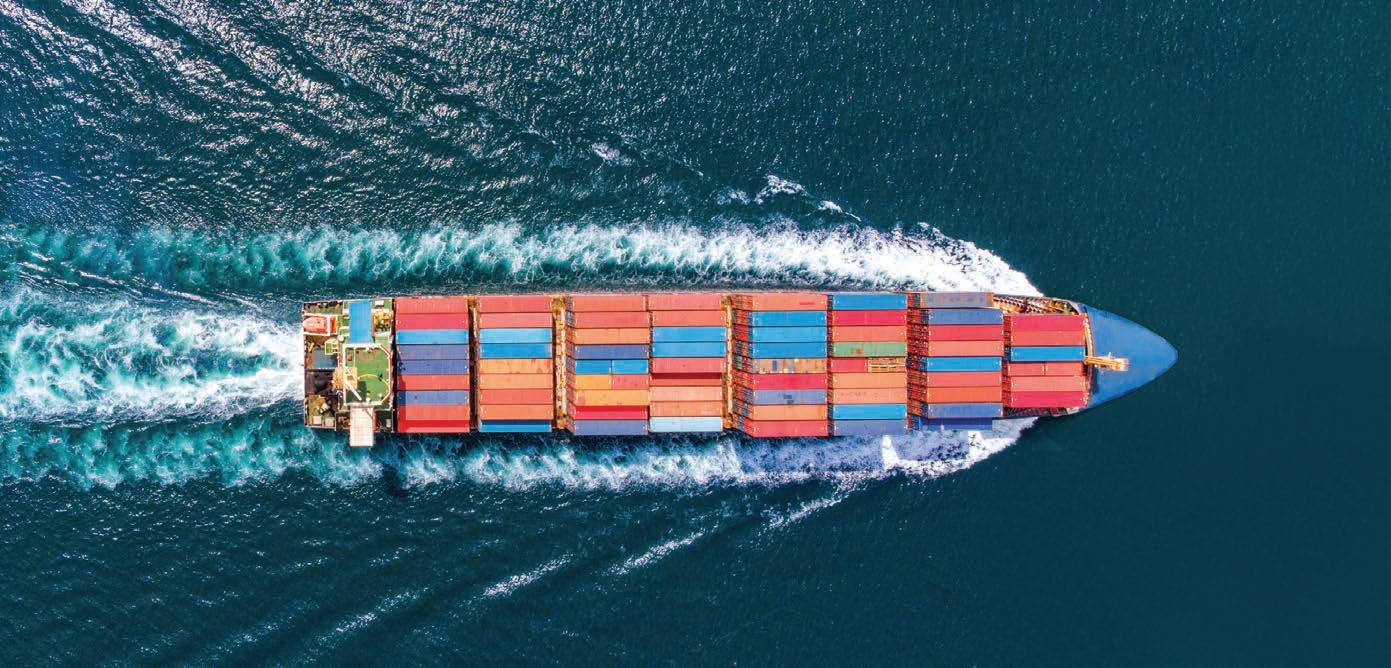
Use actionable intelligence to overcome port delays and mitigate the impact of maritime disruptions.
Access Real-Time Intelligence
project44.com info@project44.com
Global Coverage with Precision
project44 covers all international ports and has 20-meter precision to 11,800 berths.
Agile Decision Making
Manage Global Disruptions with Real-Time Port Intel
Get timely details on port activity around the world. Identify growing congestion and assess shipping volatility.
Under the Voice system the Tasty Fresh team member is advised which
A key focus of the project was to be able to provide data back to Tasty Fresh Food Co for inventory and reporting purposes. A Honeywell Dematic Real
The strong collaboration between the project team members meant the Voice project was delivered seamlessly on time and within Budget.
asty Fresh Foods Co is an Australian business success story – a company that originated from humble beginnings more than four decades ago. Today Tasty Fresh delivers fresh and hot food, snacks, and drinks right to the door of workplaces daily in Melbourne, Perth, Sydney, Newcastle, and Queensland.
“The Voice solution was deployed at each Tasty Fresh depot,” Deane says. “The two primary Voice workflows that were implemented were pick to trolley and van loading.”
TASTY
“Tasty Fresh Food Co is a national business that started back in 1979,” Colin Lear, Founding Director at Tasty Fresh Food Co, explains. “We have six outlets across four states and service around 35,000 customers per day from around 153 vans. We produce around 60,000 units per day from our facilities and we handle around a 100,000 units per“Ourday.service is provided every business day of the year and we have over 500 employees around Australia that make that happen.”
“Today, many small and medium businesses still use manual methods to carry out the majority of tasks within the supply chain, as well as scanners and other technologies, which are not centrally connected, not to mention extremely time consuming,” Rob Deane, Southern Regional Sales Manager at Dematic, says.
Tasty Fresh approached Dematic to move from a manual way of tracing stock with paper and tablets to a more automated and centralised solution for its supply chain, which would deliver much higher efficiency, productivity, and“Tastyaccuracy.Fresh’s stock taking processes previously involved each individual Van Sales Manager doing a stock take on each individual SKU on our vans,” Adam Van Bergen, National Operations Manager at Tasty Fresh Food Co, explains. “With so many people counting so many SKUs, accurately managing stock was a real challenge.”
FINDING THE RIGHT SOLUTION FOR TASTY FRESH
“My favourite part of the Voice technology is the traceability, the ease of use, and the support we get from Honeywell and Dematic,” Van Bergen says. “I definitely recommend Voice to any business that wanted to look at it.”
T
Voice technology can also scale to suit changing business requirements, while empowering management with greater control, flexibility, and visibility over the supply chain.
HOW VOICE FOROPERATIONALIMPROVESEFFICIENCYTASTYFRESH
For Dematic, the first step in finding the right supply chain solution for Tasty Fresh Food Co was going on site and learning about the business. It was crucial that a clear understanding of the business’ current processes and the key outcomes they were seeking to achieve was“Wedeveloped.wereinstantly impressed that Dematic wanted to understand our operations, and that they came through our facility multiple times,” Van Bergen adds. “Dematic understanding and not just telling us what we wanted to hear was a big reason why we chose to partner with them.”
Time Logistics Voice on Android solution was selected as the best system to meet the needs of Tasty Fresh.
TRANSFORMSFRESHPICKING,STOCKTAKEANDSUPPLYCHAIN
quicker and more accurately.”
“As customer expectations continue to rise, product delivery becomes increasingly demanding, and supply chains are under more pressure than ever before to pick and pack products
Honeywell Voice is a seamless, paperless, and hands-free, eyes up solution. Using the solution, workers are guided through a workflow using a mobile device and voice headset, with inputs from voice and scanning automatically sent back to Tasty Fresh Food Co’s central supply chain system. This includes data gathered through anything from order-picking to replenishment and stocktake.
Dematic explains to MHD how it’s helped Tasty Fresh Foods Co, an Australian food and beverage business, automate and centralise its stock by providing it with the Honeywell Dematic Real Time Logistics Voice on Android solution.
MHD SUPPLY CHAIN 20 | MHD SEPTEMBER 2022
AUTOMATING TASTY FRESH FOOD CO’S SUPPLY CHAIN
– Improved supply chain efficiencies, productivity, and accuracy flow on to benefit the end customers.“Every change we make in our business, it's always about how will this affect the customer? The move to Voice is giving us a better opportunity to satisfy our customer by picking the correct product,” Lear says. An additional benefit of the Voice system for Tasty Fresh Food Co, has been the ability to re-deploy staff to more productive tasks.
Due to the success of the Voice solution rollout at Tasty Fresh Food Co, the company is looking to roll out many more applications - from confectionary picking and production picking right through to its fleet of food vans and all other areas of the business.
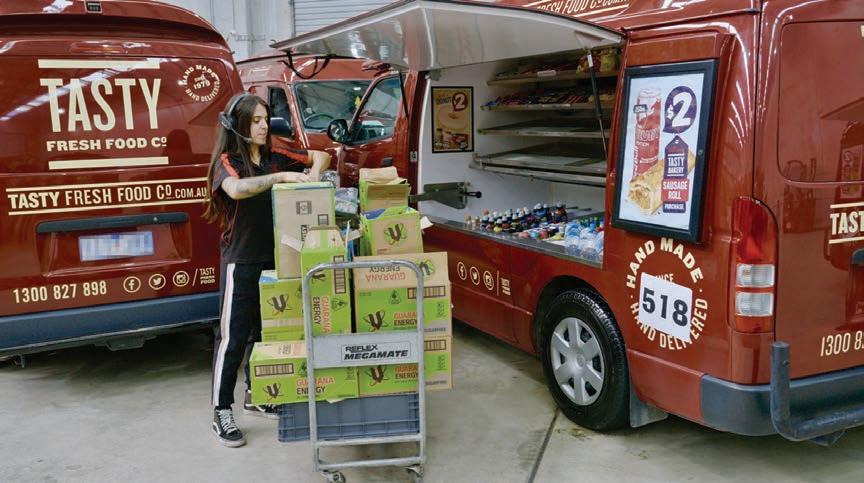
“The Voice system tells us what to load inside the vans, and also it tells the system how many we are loading,” Aline, Brisbane Warehouse Manager at Tasty Fresh Food Co, says. “This means that at the same time that we are loading, we are also doing the stock take. It’s a great system which gives us the flexibility to make sure that our stock is right by generating reports to check our sales match with the stock being loaded in the vans.”
• Increased productivity – Voice technology delivers up to a 35 per cent productivity improvement from legacy systems, through allowing workers’ hands to always be free to pick products and complete all warehouse tasks.“Voice has improved productivity across the business,” Van Bergen says. “Instead of having 157 people stocktaking, we now only have 20-25. “We're saving between five and 10 minutes a day per van sales manager. That might not sound like a big deal, but five to 10 minutes across 170 employees a day is quite a cost saving.”
USAGE ACROSS NEW BUSINESS AREAS
food or drink product SKUs and quantities are to be loaded onto each trolley. When completed, they proceed to van loading. The team member is then instructed – per van ID – which SKUs and associated quantities are to be replenished into each van in SKU sequence.Product shorts, overfills and audit are all tracked simultaneously, saving workers the time spent having to go back and forth doing these tasks separately. This helps Tasty Fresh to check expected stock from point-ofsale deductions versus physical van replenishment, all through the one Voice technology process.
MHD
SUPPLY CHAIN MHD SEPTEMBER 2022 | 21
• Enhanced customer service
satisfaction.“It's great to have our hands-free, with no paper,” Mirella, Brisbane Warehouse, Tasty Fresh Food Co, says. “Instead, I'm able to use my hands to do the job quicker. It's also safer because I don't have to be holding the paper while handling the food and drink products.”
Tasty Fresh approached Dematic to move from a manual way of tracing stock with paper and tablets to a more automated and centralised solution for its supply chain, which would deliver much higher efficiency, productivity, and accuracy.
Some of the key benefits that the Voice solution has provided to Tasty Fresh are all about management of inventory and providing traceability of that inventory.
• Empowering management – Voice technology offers management greater visibility, control, and flexibility over supply chain operations.“The Voice technology makes my job a lot easier because I'm able to easily trace where stock's going, what stock's doing. Before, I would have to sift through hours of data just to find what I needed,” Van Bergen says.
• Integrated bundle solution – Voice solutions are a simple bundle offering including hardware, headset, the application, and licencing for an easy purchase, deployment, and support guideline.
• Enhanced employee satisfaction and safety – Heightened worker productivity with voice guidance makes the employees’ roles more intuitive and focused, resulting in less errors and better worker
THE IMPACT OF VOICE FOR TASTY FRESH
• Improved accuracy – With eyes always focused on the job, workers can quickly find, pick and pack the right products, reducing errors by up to 50 per cent. Additionally, automated stocktake has also reduced not only time, but also errors through manual counting.
EXPANDING VOICE
“It's been a terrific partnership with Dematic. That's why we want to look to take it as far as we can in our business where everything that's handled and picked, Voice and the Dematic system will take care of it for us,” Lear says. ■
arise Honeywell and Dematic fix it within 24 hours.”
• Ease of worker training – The Voice solution is extremely easy and intuitive to train workers on, particularly when used on the Android platform which is familiar to most people. “The training for the Voice system is exceptionally easy. We're able to train new staff up within half an hour,” Van Bergen adds. “And the feedback from staff is that it’s great, that it’s easy to use, and any problems that
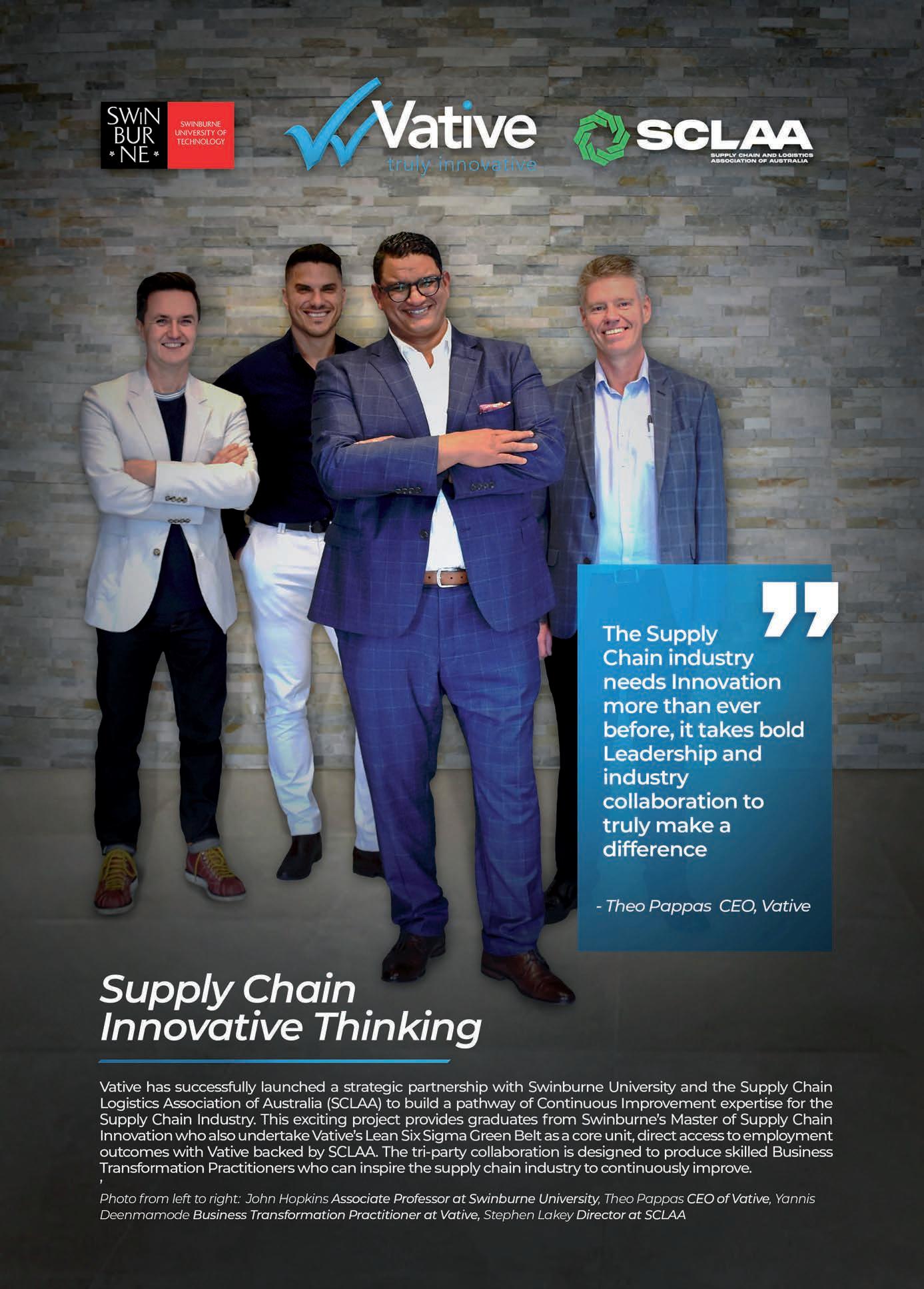
THE SOLUTION
MHD SEPTEMBER 2022 | 23 MHD WAREHOUSING
Kookaburra worked closely with OPEX® integrator partner, Dexion® Liverpool, to find a better solution for its order fulfillment process and implemented the OPEX Sure Sort® automated sorting system in October 2020.

It took approximately three months from the date of purchase for the Sure Sort system to be fully installed, allowing Kookaburra to get up and running quickly.
Founded by a teacher in 1989, Kookaburra is an entirely Australianowned and operated family business based in New South Wales, handling everything from customer orders to distribution. In addition to office and stationery, Kookaburra provides arts and crafts, learning aids, robotics and STEM, sports, and interactive solutions to its customers.
During the COVID-19 pandemic, they received more orders than usual, due to increased online buying. Kookaburra’s picking and sorting process was completely manual, only allowing them to complete around 285 to 300 packs per day. Each unique student pack ranged in size, with some packs having anywhere from 30 to 44 pieces. To improve customer service and order accuracy, Kookaburra wanted to reduce the time required to fulfil orders while using less labour.
ookaburra Educational Resources, one of Australia’s largest wholesale education suppliers, primarily provides office and stationery supplies to schools as well as government offices across the country.
THE CHALLENGE
A unique solution from OPEX and Dexion Liverpool enabled Kookaburra Educational Resources to increase its output by 60 per cent. Find out how they did it.
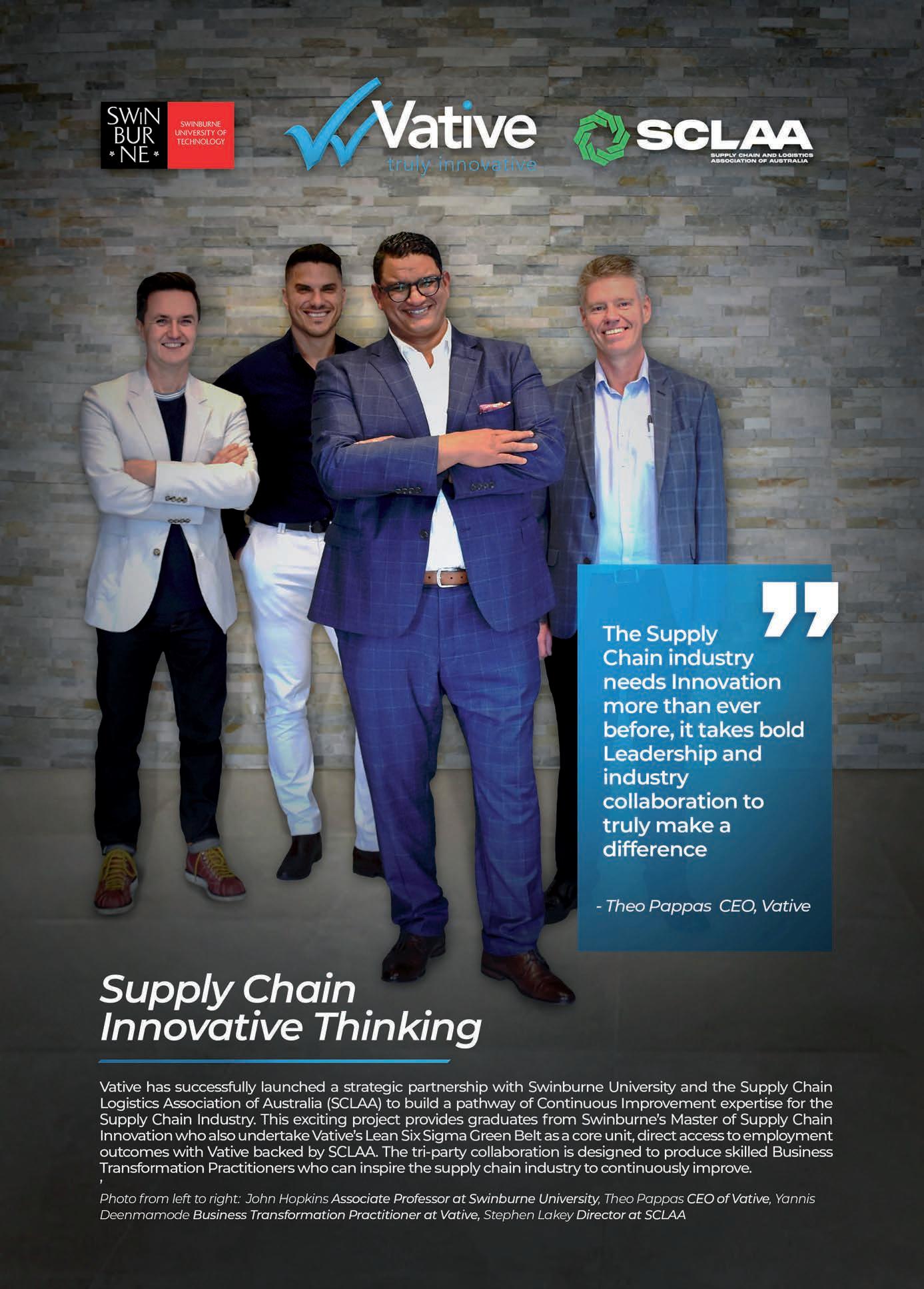
KITTING PROCESSEDUCATIONALKOOKABURRARESOURCESTRANSFORMS
Implementing the Sure Sort system allowed Kookaburra to reduce its reliance on labour, requiring only 21 of the original 60 employees that worked during the dayshift, a 65 per cent reduction in labour. They also were able to eliminate their night shift.
The OPEX Sure Sort system allowed Kookaburra to boost productivity while saving on labour costs.
When paired with software solutions from Dexion Liverpool, the Sure Sort system allowed Kookaburra to blindsort their small items without barcodes, improving the flow of their pick cycle in the distribution centre. Innoware, Dexion Liverpool’s preferred Warehouse Control System (WCS), ensures efficient product flow across the Sure Sort, conveyor system, label applicators, and check weigh system deployed at Kookaburra.
increased Kookaburra’s output per day, while achieving sorting rates of 2400 items per hour. Deploying the Sure Sort also resulted in Kookaburra picking significantly larger batches of orders – enhancing their picking efficiencies – which resulted in an overall costreduction of over 45 per cent per order.
One of the primary services Kookaburra provides is building unique custom kits and supply packs for students, with items picked by individual schools, parents, and students.
Automating their sorting process
It used to be the case that during peak seasons, when students were going back to school, Kookaburra required 60 employees to keep up with demand.
K
“OPEX Sure Sort is an innovative order consolidation solution that not only enhances the sorting efficiency across multiple product profiles but also indirectly improves the picking efficiency in the warehouse,” he says. “OPEX Sure Sort provides customers with an efficient, high speed sorting solution that occupies a very small warehouse footprint while consuming very little electricity.”
www.nord.com
Khurshed Mirza, Director of Business Development, APAC at OPEX summarises why Sure Sort is so effective.
THE FUTURE
With the success of the Sure Sort system in their wholesale business, Kookaburra is looking to expand into other opportunities within its DC.
NORD Drivesystems (AU) Pty Ltd I Fon +61 3 9394 0500 info@nord.com.au I
Version reduction through system solution
COMPATIBILITY.FORALL-ROUNDERSALL-AROUND
24 | MHD SEPTEMBER 2022
Innovative, compatible, future-proof: DuoDrive, IE5+ and NORDAC ON. “
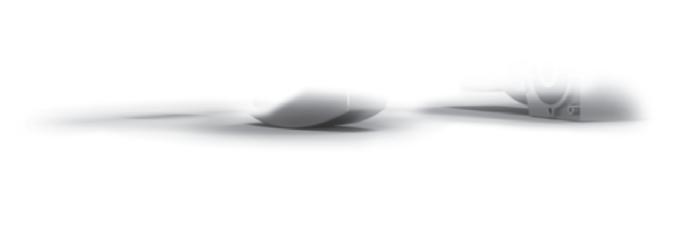
Now that the solution from OPEX and Dexion Liverpool is in place, Kookaburra is able to grow its business and improve both its upstream and downstream processes without the constraint of time-consuming, manual processes.
■
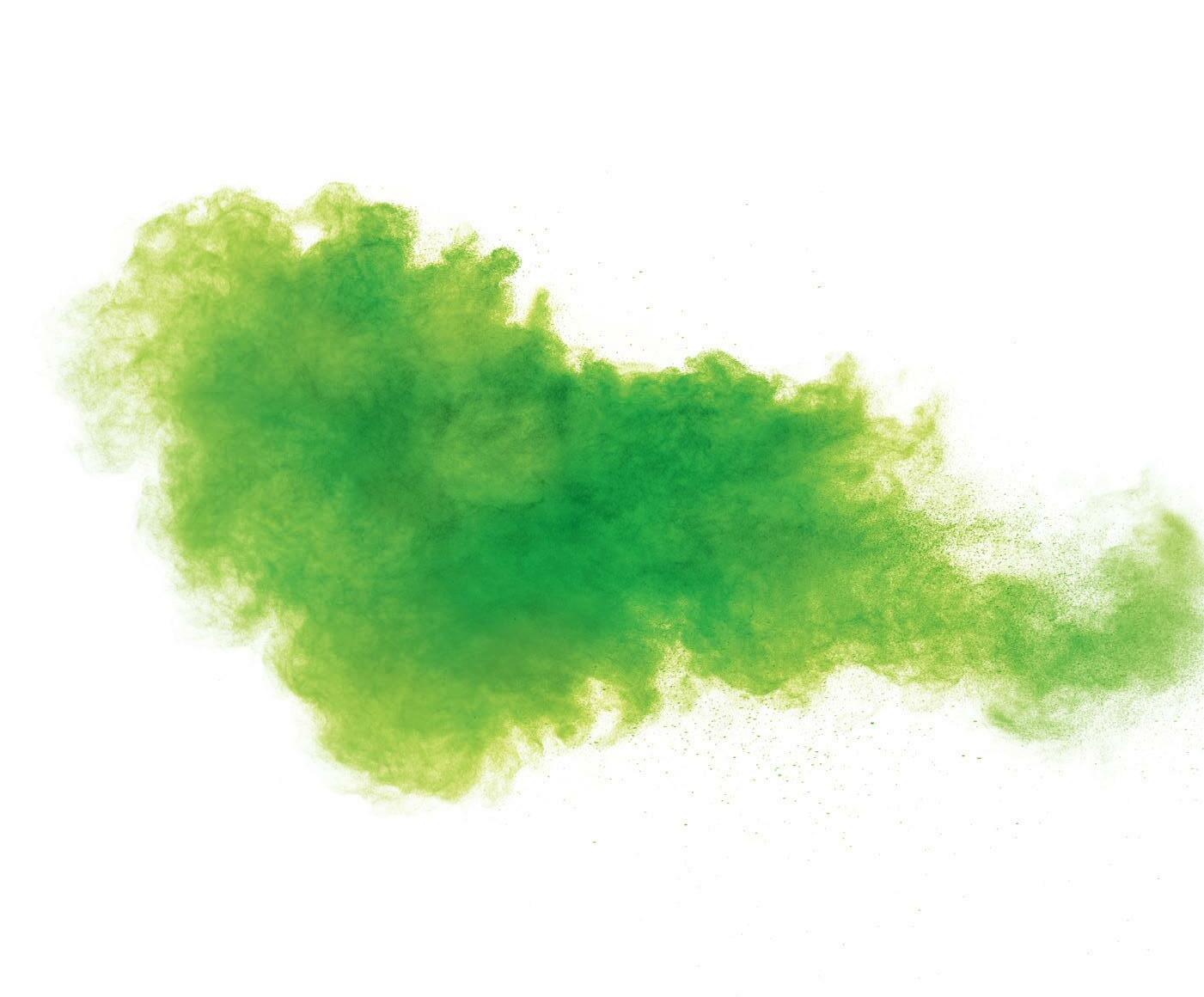
Extremely high system efficiency
Compact and hygienic design allows for ultimate application diversity
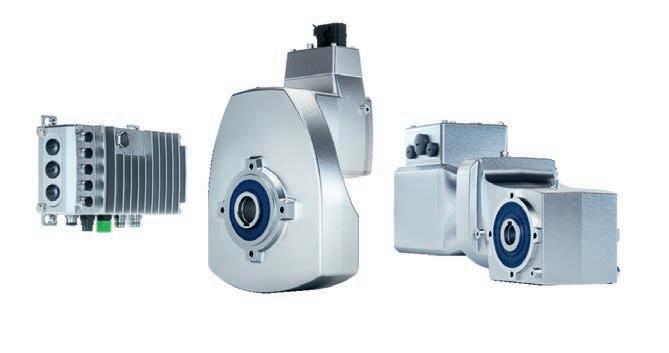
Optimised installation space
OPEX Sure Sort is an innovative order consolidation solution that not only enhances the sorting efficiency across productmultipleprofiles but also warehouse.efficiencyimprovesindirectlythepickingintheOPEX
” MHD WAREHOUSING
Sure Sort provides customers with an efficient, high speed sorting solution that occupies a very small electricity.consumingfootprintwarehousewhileverylittle
No two logistics problems are alike. Neither are their answers. Each requires a point of view. A new angle. look for solution, by data and insights. gain a deep understanding of your business, part of your commercial real estate strategy, you can realise
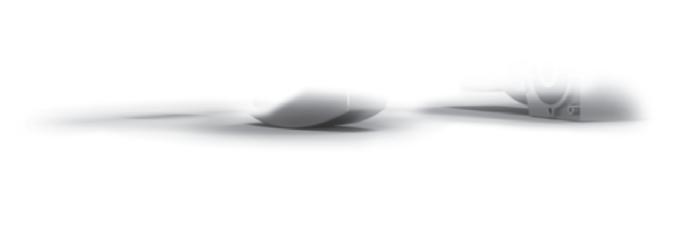
Together, we’ll
guided
so
We’ll
“ Xxxxx ”
an integrated
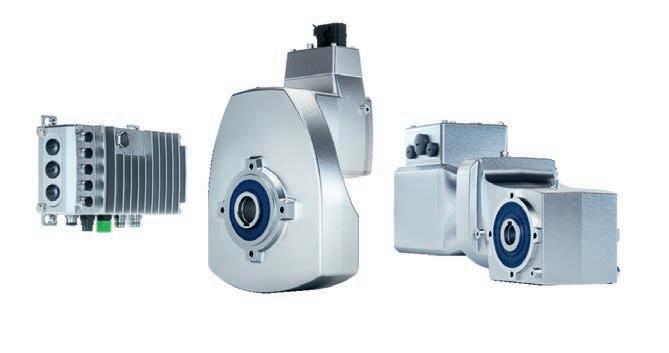
and consider every
Solutions from all sides.
anything. cbre.com.au
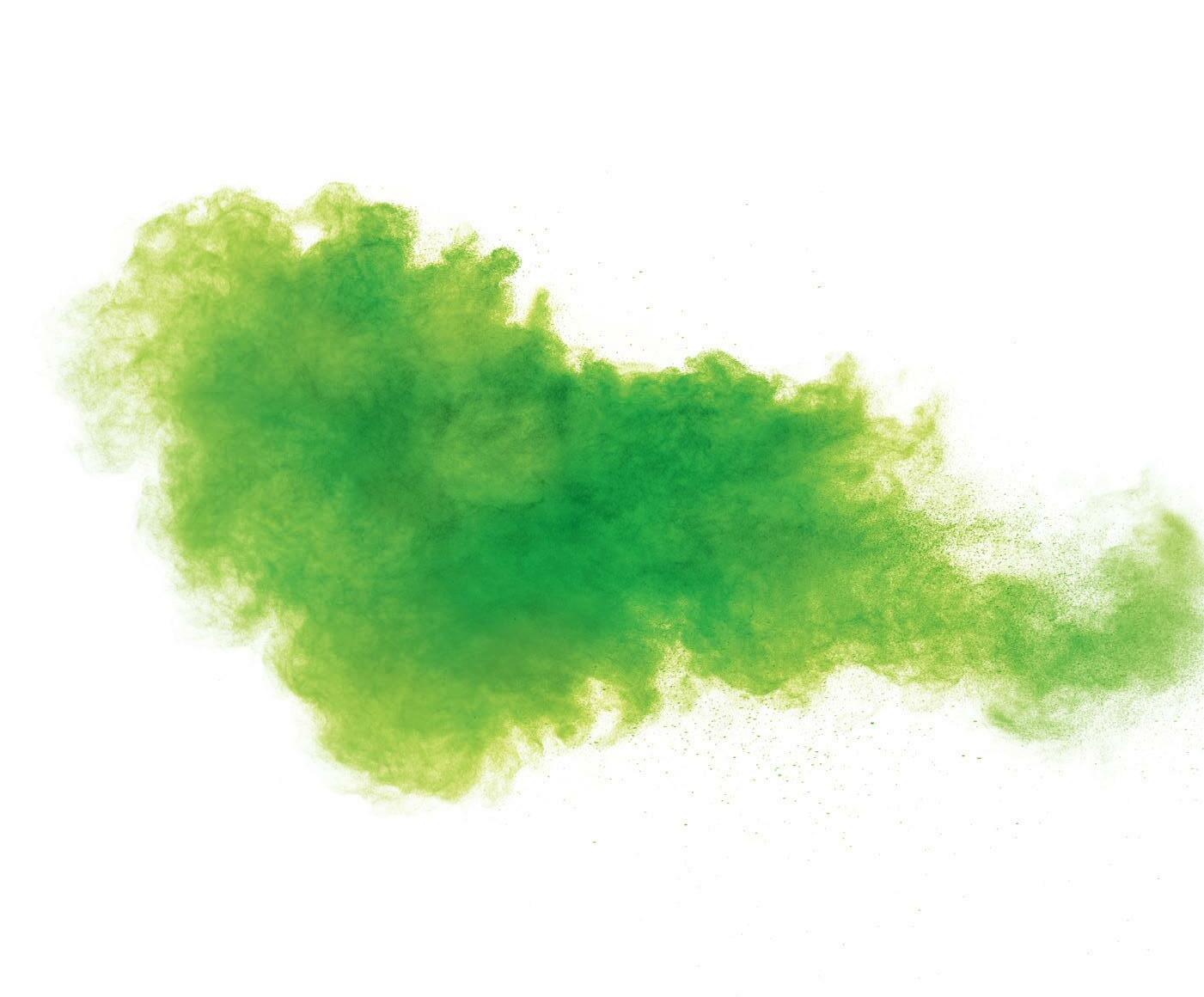
Scan the QR code to find out more.
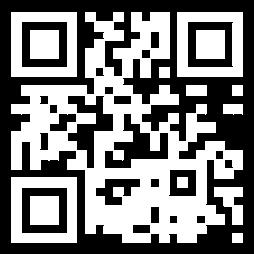
26 | MHD SEPTEMBER 2022 MHD SUPPLY CHAIN
With limited resources and labour available to deliver projects, delays are becoming even more costly and frequent, causing a knock-on effect throughout the industry. Timelines often blow out when people aren’t honest with each other about their commitments,
and transparency between different parties will help teams maximise labour availability, leading to increased trust, retention, and stronger partnerships.
FACING UP THE CHALLENGETO
Alongside tightening up design and procurement, there is also an increased focus on sustainability, and these work hand in hand. Using data to forecast materials required and scrutinising material orders up front is one way to reduce waste and rework, lowering the environmental impact of construction projects. Sustainable objectives can therefore drive the dual outcomes of not
In addition to stronger collaboration, project owners can use digital tools to track workforce availability, maximise existing resources and communicate more efficiently and effectively about when they will be required on a project.
The way in which contracts are written and negotiated is also being reviewed through this inflationary period. Previously, it was common that design and construct contracts were handed over to contractors with design being 70 per cent complete. There are now scenarios where contractors are not taking on work unless design is greater than 90 per cent complete.
A
Will Twomey, Director of APAC Solutions Consulting, Procore, discusses the primary challenges facing supply chain in APAC today, and strategies
Will Twomey, Director of APAC Solutions Consulting, Procore.
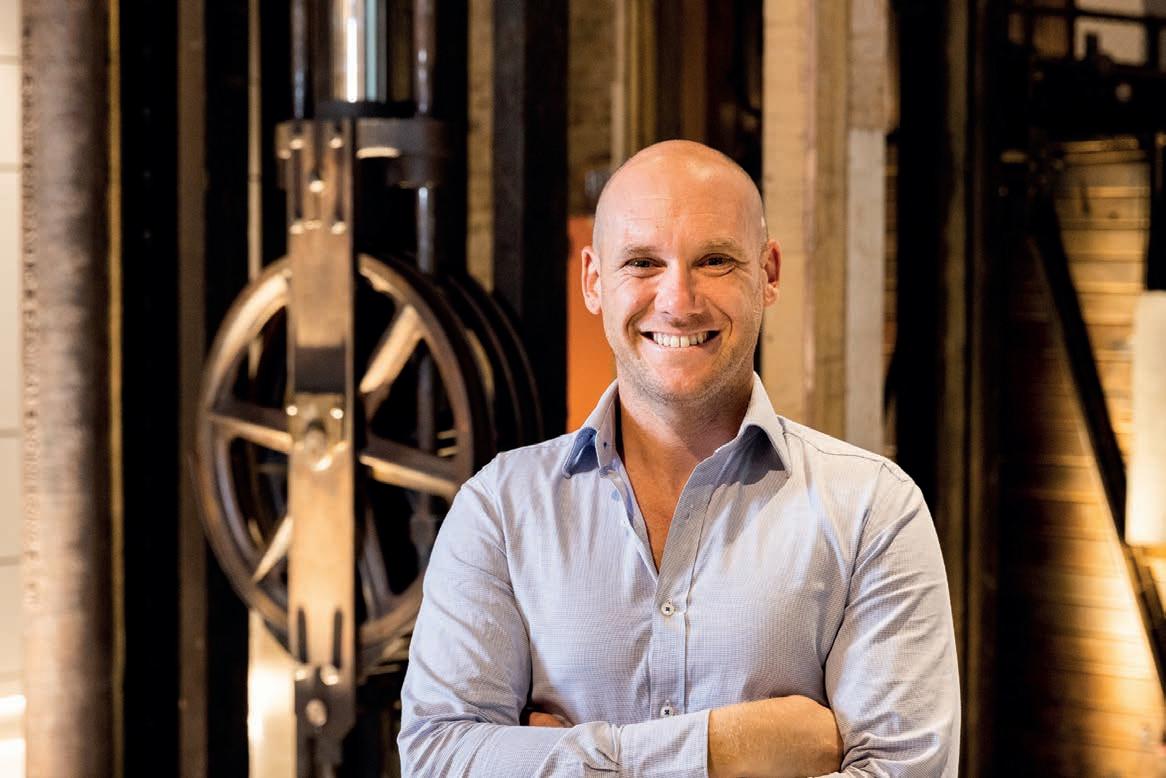
Rising costs of materials and equipment is the biggest concern for the Australian construction industry in 2022, according to 63 per cent of respondents in Procore’s How We Build Now report.
WHAT IS THE INDUSTRY DOING TO MANAGE RISING MATERIAL COSTS?
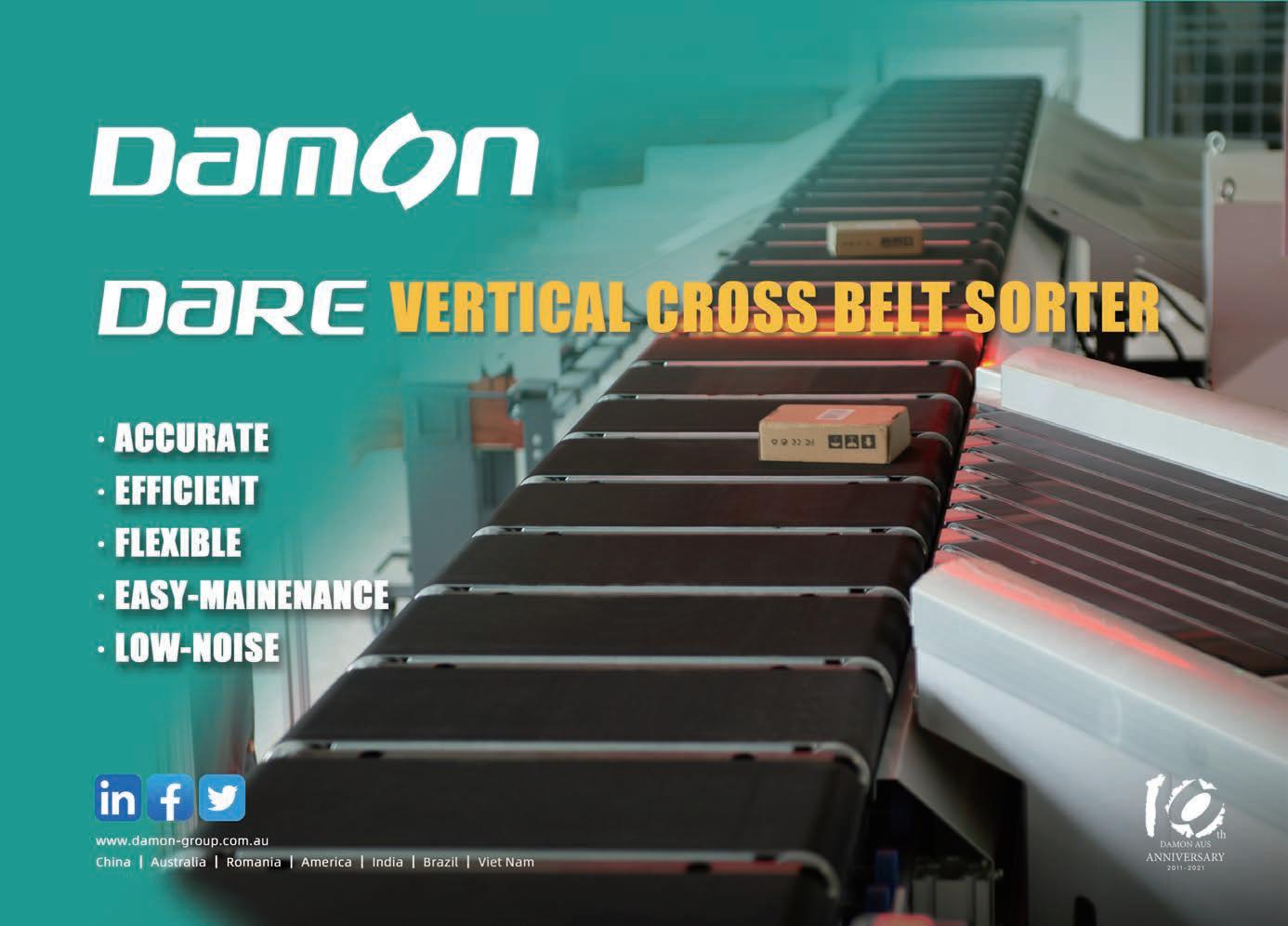
To help manage the impact of this, we are seeing a greater emphasis on and investment in the design phase
believe the industry is suffering from a ‘brain drain’, and it is hard to compete with other industries for good employees. Indeed, hiring and retaining skilled staff was identified as the second greatest challenge for the year ahead in Procore’s recent How We Build Now 2022 benchmark report. Nevertheless, 85 per cent of Australian respondents remained confident about the next 12 months ahead. For the construction industry to succeed and maintain this confidence, greater collaboration is required between everyone working on the construction of a project, including the developer, designer, contractors, and specialty trades.
increased collaboration during this phase,
design is as complete as possible prior to it being passed over for construction.
With so much data now at our fingertips, it has never been easier for businesses to maintain visibility across complex development projects. Following the example of data centre developers, other construction business can analyse their data and use the learnings to make smarter business decisions, manage challenges and delays, or optimise future projects.
MHD SUPPLY CHAIN
There needs to be greater discipline introduced across the construction industry, as we are running out of alternatives to streamline processes. The only viable option to reduce risk and ensure time and cost overruns are minimised, is to drive efficiencies, improve quality assurance and greater visibility, all of which can be achieved through the digitalisation of processes. ■
WHAT ARE BUSINESSES DOING TO CENTRES?ANDBUILDINGS,SUCHVISIBILITYMAINTAINONPROJECTSASINDUSTRIALWAREHOUSES,DISTRIBUTION
I have come across many companies who, through a period of relative price stability in materials and labour, have a strong history of delivering projects “by look and feel”. With pricing on an inconsistent upward trend, and labour
shortages causing delays, the “look and feel” model has become fraught with risk.
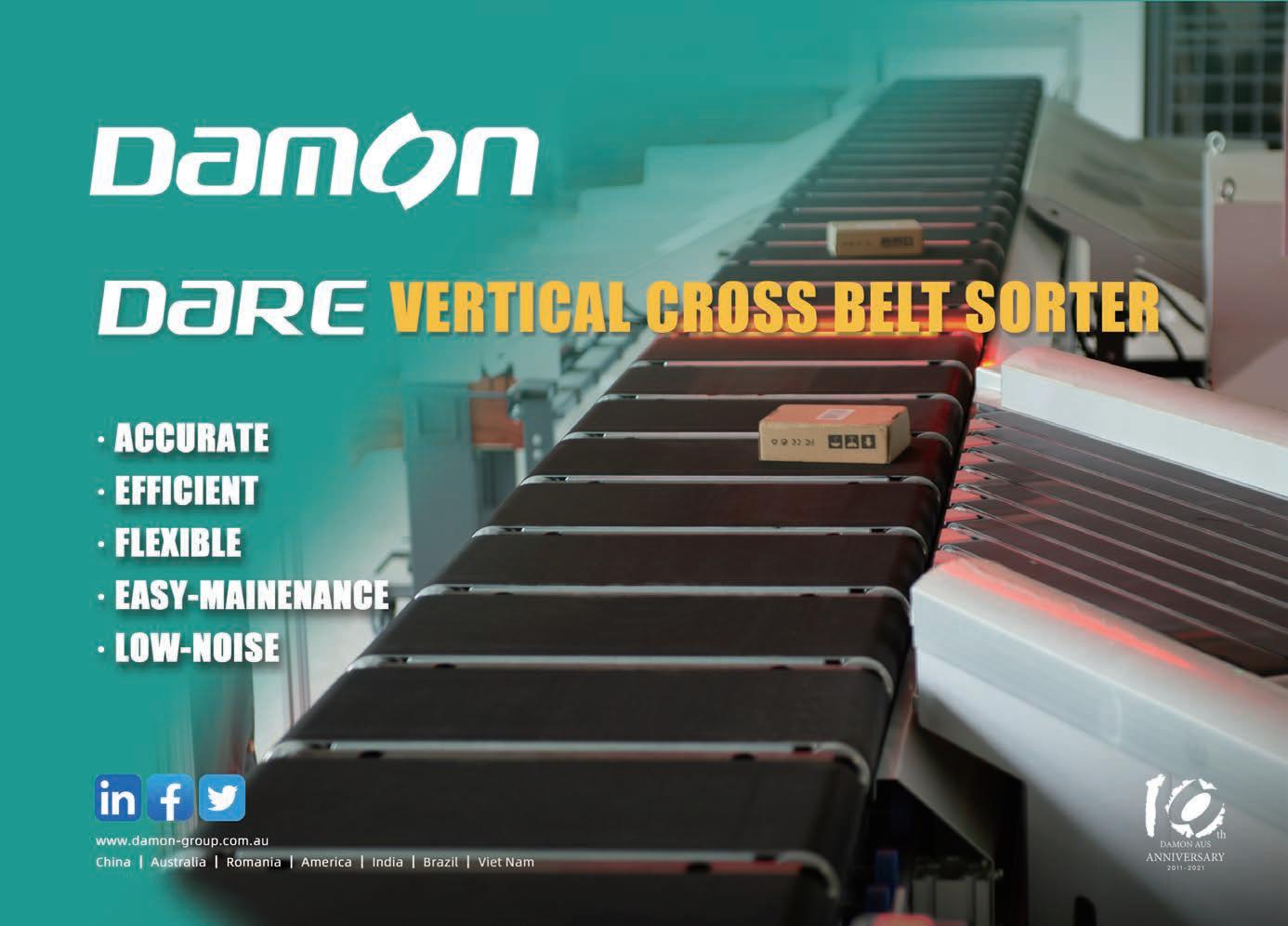
HOW CAN BUSINESSES UTILISE THEIR RESOURCES EFFICIENTLY SO THEY CAN STAY WITHIN BUDGET?
One way that companies are getting greater visibility across their industrial and warehousing projects is to share learnings with sub-verticals within the construction industry. With increased activity in the data centre space, we are seeing developers leverage their advanced knowledge of technology, including the utilisation of data-driven insights across their portfolio. This allows them to not only immediately capture and report on the reality of what is happening onsite, but to use analytics and predictive intelligence to better plan their future works.
For example, Vantage Data Centers
Alongside better collaboration, using a technology platform to provide real time visibility into business operations is critical to companies utilising their resources more efficiently. Technology and data can be used to track project progress, timelines, performance, and costs in real time, allowing project managers to review and adapt as needed.
With margins for error contracting significantly in recent years, particularly due to material and labour shortages, project owners and managers can’t afford to wing it anymore.
has established a holistic view of business data to assess project health across their global portfolio to make better decisions in real-time, as well as analyse and learn from historical data to make future improvements.
only reducing waste but also managing the cost of materials.
business.TransformingtheLeadingway.
argonandco.com
Argon & Co is a global management consultancy that specialises in operations strategy and transformation. With expertise spanning the supply chain, procurement, finance and shared
services, we work together with clients to transform their businesses and generate real change. Our people are engaging to work with and trusted by clients to get the job done.
GPC NEW DC “BEST IN CLASS”
■ MHD WAREHOUSING
he Genuine Parts Company (GPC) new distribution facility will afford the company a host of advantages including faster product movement and order retrievals – which is a boon for its customers.JonLongbottom, Chief Supply Chain Officer at Genuine Parts Company, says the new distribution centre will speed up the company’s retrieval times eight-fold.
“We had to adjust our ways of working considerably but we did not deviate from our commitment or timeline,” Jon says.
“The building itself in many respects was the easy part.”
“This facility and the technology being introduced provides the most advanced logistics operation for our sector within the ANZ market and provides flexibility to adapt as the market grows.”
commissioning early 2024.”
“LOGOS is our development partner and FDC is building the facility. As referenced, SSI Schaefer has been selected as our Automation provider for our both our Melbourne and Auckland DC’s.”
Other areas of heavy focus at the new
“Our new Distribution Centres have been designed with a strong emphasis on team member wellbeing and fulfilment as well as environmental sustainability.”
Genuine Parts Company has a new distribution centre.

TMX Global, experts in property, building and automation, partnered with GPC on the project, along with the extensive tender process including conducting a comprehensive property search to ensure the GPC found the best development partner in the right location and for its business requirements.
“We recognised the growing demand in Australia and the fragmented nature of our supply chain network that had evolved over time and hence the need to consolidate and optimise our supply chain infrastructure,” Jon says.
“The global automation tender ultimately led us to the decision to partner with Schaefer,” says Jon.
The design process of the new distribution centre was informed by extensive customer feedback, particularly with respect to technology and the delivery units used to service each channel.“Wealso stayed close to our store network as we progressed through detailed design to ensure that we understood existing pain points and opportunities to be addressed,” says Jon.
“The impact of COVID in early 2020 caused us to reassess all of our investments and major projects across the business – but we recognised this as key to our long-term strategy.”
This new distribution centre, along with another in Auckland, New Zealand, makes up a significant capital investment for GPC, which meant considerable time was spent planning the projects.
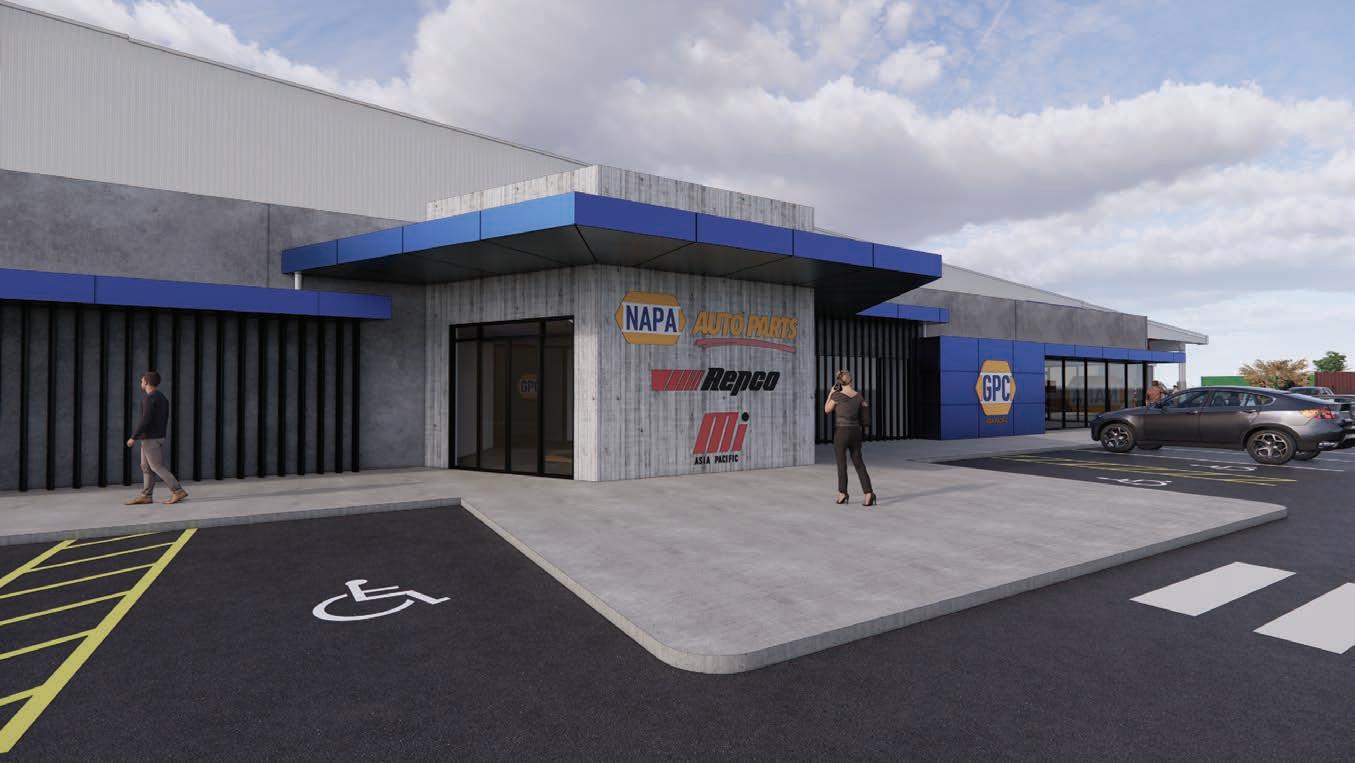
MHD learns about GPC’s new warehouse, and how it underpins its distribution strategy for the future.
MHD SEPTEMBER 2022 | 29
T
“Customers in the automotive and industrial sectors require immediate service to get their vehicles, equipment and machinery back operational and on the road and keep the wheels of industry turning,” Jon says.
“The building is under construction in partnership with both Logos and FDC and installation of the automation will commence around April 2023 with
The unforeseen impacts on the project meant that GPC had to pivot quickly.
distribution centre were optimising presentation of stock to its branch network, improving visibility of stock movement through our supply chain, streamlining invoicing and paperwork, and working closely with the supplier network.“Allwith the overall purpose of making our business as user-friendly as possible for our customers,” says Jon.
Jon says the new distribution centre is a critical part of the GPC’s long-term future in “ItAustralia.alsorepresents the second of our greenfield distribution centres that is currently under construction – with the Auckland DC just completed building and the first of our Industrial business units moving in at the time of this interview,” he“Weadds.are constantly assessing the right sizing of our overall distribution infrastructure portfolio to ensure all our Automotive and Industrial customers needs are best served at all times, and these two new facilities will go a long way to making this happen.
LOGOS is GPC’s development partner, and FDC is building the facility.
With flexible terms to assist your growth, discover a pipeline of new developments in key logistics corridors with excellent connectivity, proximity to main freight modes, capital cities and employee catchments.
Find your space to thrive. Enquire today at stockland.com.au/logistics or scan the QR code.
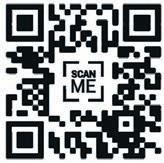
stockland.com.au/logistics
Discover a space that evolves with your business
At Stockland, we offer a diverse portfolio of properties of varying size and design specifications that can be modified as your business evolves.
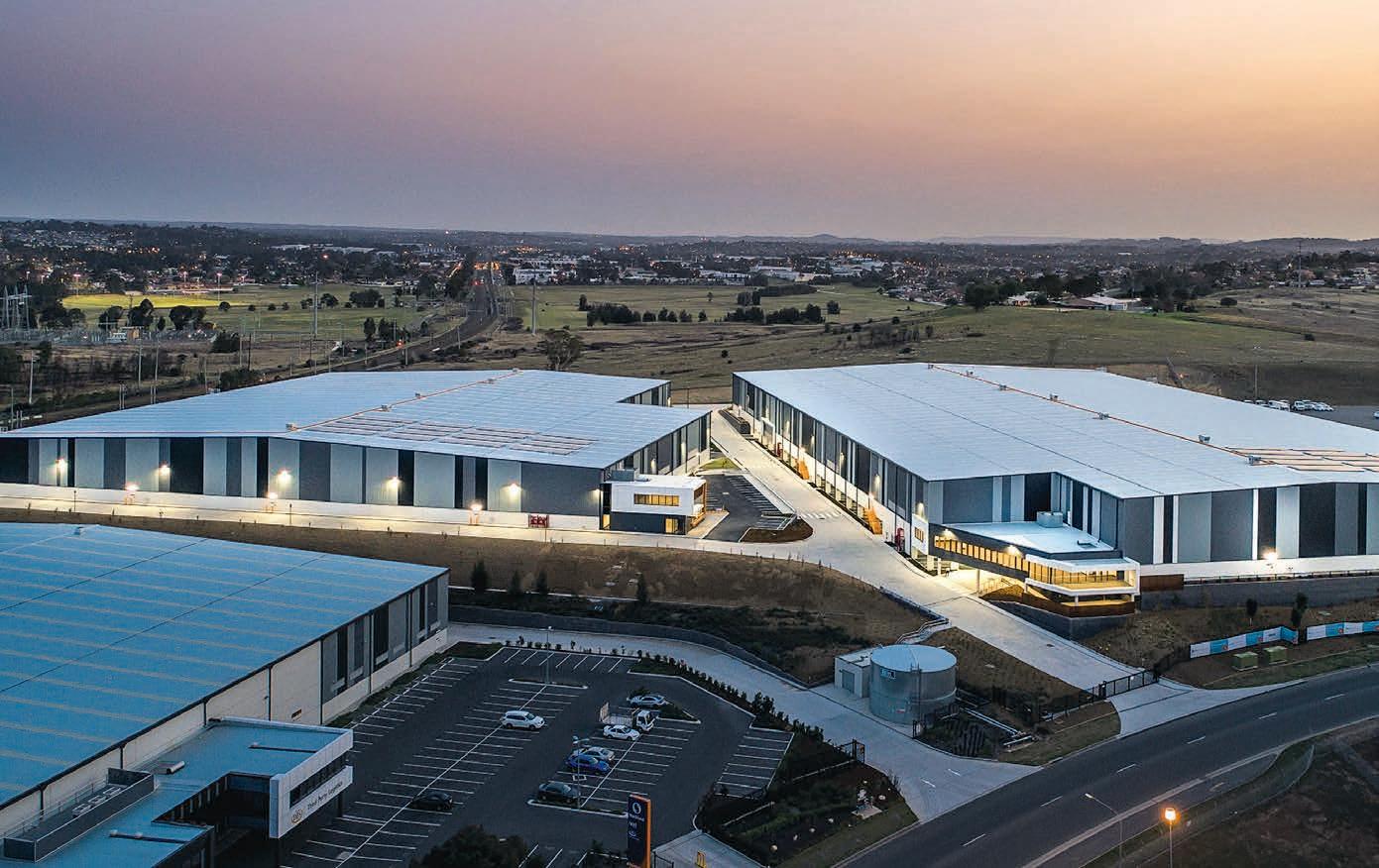
WIDE-RANGING BENEFITS
When Combilift was established in 1998, the world was quite a different place. In that year, Google was incorporated as a private company in California and only 9 per cent of households had access to the internet. And in the world of industrial vehicles, diesel power was the default choice for the majority, as it was considered to offer the best performance in demanding working conditions.Timeshave of course changed, and the growing demand for electric powered vehicles and equipment has been fuelled by shifting public attitudes towards pollution and more stringent legislation. This has put pressure on manufacturers and companies in a wide variety of industry sectors to “clean up their act” and to focus more on sustainability. The latter is all about taking a longterm look at how you operate, and this will often involve investment in new technology.Switching to an electric fleet from diesel is now a much more attractive option than it once was, and this is down to improved battery performance and technology, which enables ever increasing lift capacities, longer run times and much longer intervals between charging. The latest generation of electric trucks are also versatile and can work indoors and out, which can reduce the overall number of forklifts required and consequently the carbon footprint – as well as operational costs and outlay for insurance, maintenance and so on. So what is good for the planet can also be good for your business.
Switching to electric power is not only good for the environment but also for your workforce, your neighbours and your balance sheet – says materials handling
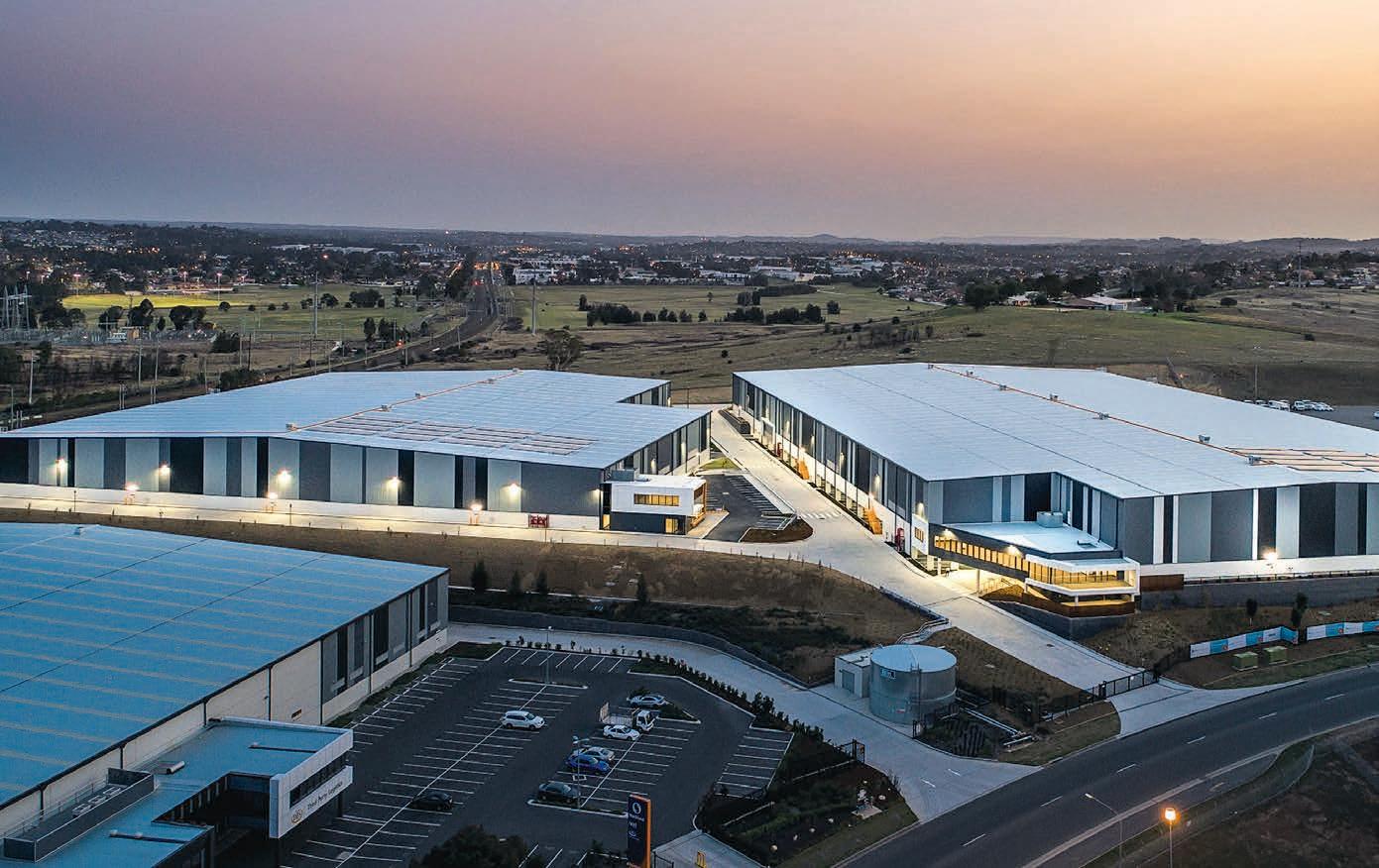

MHD MATERIALS HANDLING MHD SEPTEMBER 2022 | 31
PLUGGING IN TO GREENER POWER
Talking of finances: the initial cost of an electric truck may be somewhat
The Combi-FSE in action.
MHD MATERIALS HANDLING 32 | MHD SEPTEMBER 2022
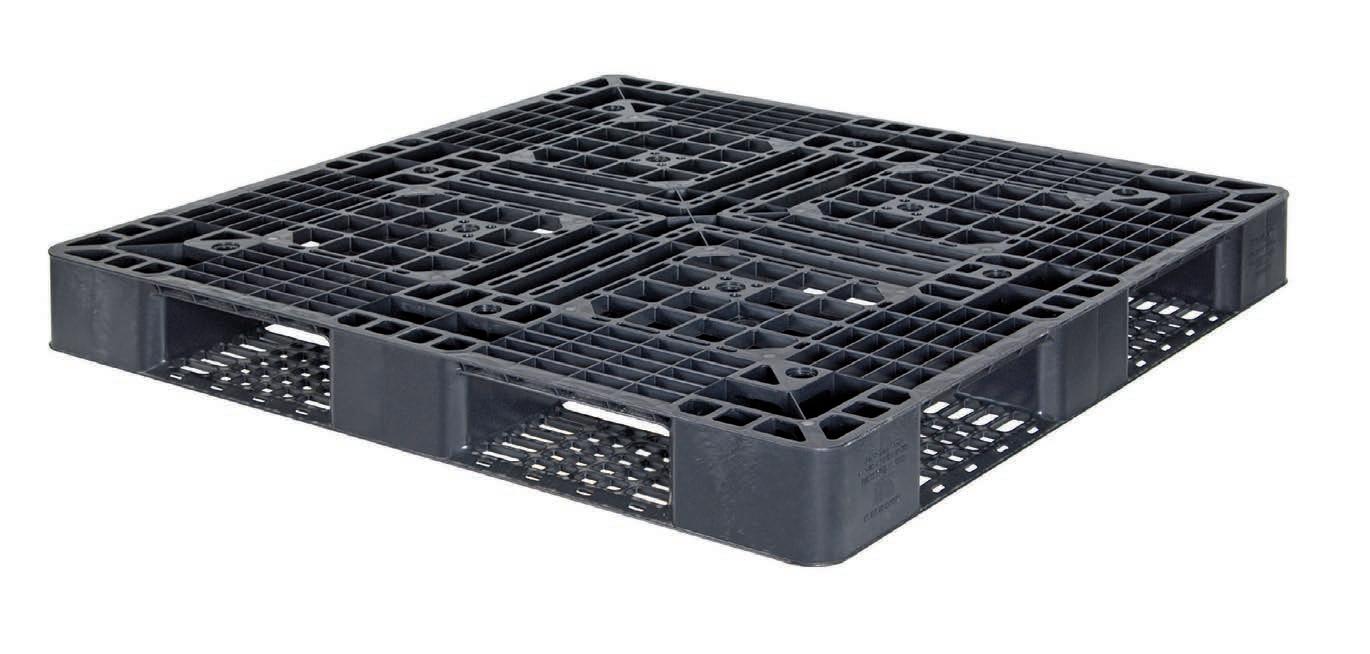

NEW MODELS
Martin McVicar comments: “We introduced our first four-wheel sideloader around 10 years ago, after initial requests from companies in the timber sector, and it has since become pretty much a standard solution for those who run intensive schedules which clock up many operational hours. The advancements in battery technology since then means that it was a natural progression to develop this electric model, which will help customers to drastically reduce their carbon footprint.”
CEO and Co-Founder Martin McVicar: “We made our first electric C-Series over 18 years ago, and we are supporting our customers in their aims for more sustainable operation by expanding our range of electric powered products. In the last year alone we added four new electric models to our portfolio, and more than 60 per cent of the trucks that come off the production lines in Monaghan are now electric. As more and more of our customers are opting for electric power it is obvious that they are as committed to sustainability and a circular economy as we are.”
“ The latest model, which premiered at various trade shows in mid-2022, is the Combi-FSE – a four wheeled, two sideloaderdirectionalwith 5000 or 6000 kilogram lift capacity. ”
Sussex based English Woodlands Timber (EWT) supplies boards, cladding and a wide range of species such as oak, elm, ash and sweet chestnut to the bespoke joinery sectors. It switched to Combilift’s handling solutions from counterbalance trucks and now operates two C4000E trucks together with two two-tonne capacity Combi-WR4 multidirectional pedestrian stacker trucks. These have been instrumental in enabling the company to maximise storage space without needing to expand facilities and to keep pace with the recent 50 per cent growth in business. Equally important, however, is the fact that they are electric, according to Director Ian Mcnally. “Sustainability is a byword at the EWT woodyard, with solar panels on roofs and charging stations for those who drive electric vehicles. Chippings are used for biomass and other material is recycled into bedding for horses for example. Nothing goes to waste and it’s electric power wherever possible here, so Combilifts were therefore the machines of choice, as they are emission free and are also very quiet compared to diesel machines, which is much appreciated by all on site.”■
10 sites in London and numerous others across the south of England and the home counties. David Harvey, Group Transport Manager says: “As a lot of our branches are in residential or urban areas, our electric trucks have enabled us to keep noise levels to a minimum for our neighbours – and of course for the drivers and visitors on site.” At James Latham, quiet operation has also been beneficial as many depots work 24 hour shifts to maximise delivery capacity, so good neighbourly relations can be maintained in spite of these anti-social hours.Combilift’s
www.combilift.com
rear axle to be controlled individually, with the speed of each wheel governed by the steer angle of the front wheels to provide improved steering control for the operator, better truck turning radius and reduced tyre wear. This new technology, when combined with regenerative braking (which recaptures the truck’s kinetic energy during deceleration and can be used to recharge the batteries to extend battery life), makes for Combilift’s most advanced steering system on its four wheeled trucks to date. The generous glazing of the cab, particularly the roof to floor windscreen, allows the operator to have an excellent field of vison of the load, the machine, and the surroundings, guaranteeing the best operator visibility of any comparable truck.
The latest model, which premiered at various trade shows in mid-2022, is the Combi-FSE – a four wheeled, two directional sideloader with 5000 or 6000 kilogram lift capacity. The patented traction system plays a major part in ensuring optimum performance in all weather conditions. Sensors in the front steering axle linked to the innovative Electronic Traction Control system enable the two independent 15kW drive motors on the
The new models recently developed by Combilift are eminently suited to the requirements of the timber sector. The Combi-XLE multidirectional forklift, which was launched in 2021, has a 5000 kilograms lift capacity, combining emission-free operation with powerful performance. It benefits from the same features as its original IC counterpart: high ground clearance, large cushioned front and rear tyres and a spacious cab, allowing smooth operation on semi rough terrain while offering a high level of driver comfort. It incorporates up-to-the-minute technology such as patented all-wheel traction that reduces tyre wear and load swing and enhances braking. Also included is a newly developed, patented Eco-Steer System which provides a smaller turning radius and improved user experience.
ALL ELECTRIC FLEET FOR ENGLISH WOODLAND TIMBER
Lower cost PLASTIC EXPORT PALLETS Faster EnvironmentallyISPM-15HygienicschedulesReliabledeliverysupplychoiceCompliant sustainable op�on 02 9672 8588 info@plasticpallet.com.au www.plasticpallet.com.au Ozkor Pty Ltd, 3/44 Bessemer Street, Blacktown, NSW 2148 Now made in Australia
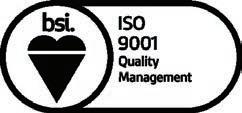
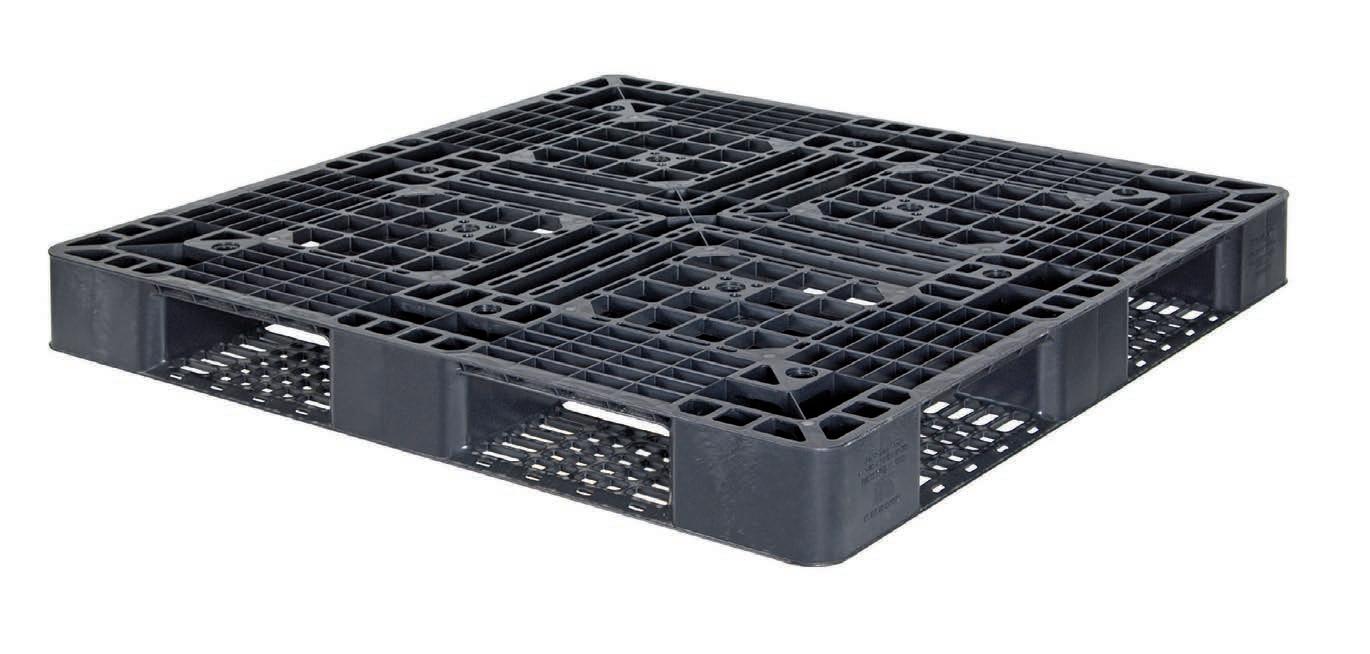
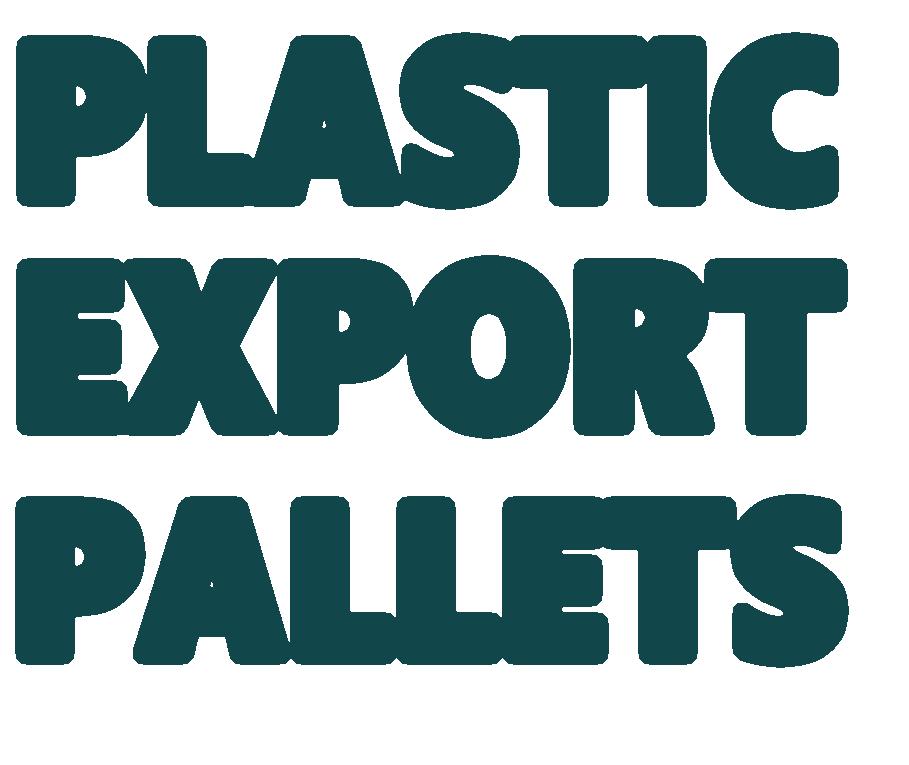

Archival Garcia, Vice President and General Manager for ANZ and SEA at project44, discusses how the company’s unique visibility platform is suited to tackling the ocean transit challenges of today’s complex global supply chain.
wrong in monumental ways. Errors like incorrect timestamps, out-of-sequence timestamps, incorrect transit types, and incorrect milestones – just to name a few – make it impossible to derive an accurate understanding of shipment whereabouts and ETAs, so those customers can efficiently manage their operations and inventory.”Therefore, Archival notes, in ocean transit – when every logistics decision depends on some sort of information –nothing is more critical than mastering theButdata.what is the difference between mere access to and use of data, and quality data?
“Unfortunately, these sources can be difficult to understand without the right technology,” Archival says. “More importantly, they’re dogged by inaccuracies – in fact, experts estimate some of this data is incorrect 15 per cent to 40 per cent of the time.
Currently, Archival says, “in ocean transportation, disruptions are the new normal”. Part of the reason for this sad state of affairs is the reliance upon static sources for information regarding ocean shipments: (1) The ocean carrier’s website; (2) Standardised shipment milestones (via the industry’s pseudo-standard EDI method); and (3) Geolocation of vessels (based upon data from the satellite-enabled AIS).
“Things have forever changed,” Archival says. “First, consumer giants like Amazon made immediacy and accurate ETAs table stakes. Then, this rare sequence of major macroeconomic events related to COVID exposed just how fragile ocean transport reallyConsumersis.”
“The tricky part is that not all journeys are created equal,” Archival says. “In the past, the majority of the time, shipments were on time, and often exceptions only result in a slight delay. But today, far more often than we’d like, there are big exceptions that cause massive issues, such as lockdowns, strikes, asset and resource constraints and it is these shipments that cause a flow-on effect that adversely impacts cost, reliability, and customer experience.
confined to their homes during the pandemic triggered an unexpected surge in import demand, causing major bottlenecks, capacity crunches, and rate increases. Furthermore, busy ports became global supply chain traffic jams, with overwhelmed terminal operations forcing vessels to wait offshore for days before they could unload their freight.“While you’ll never eliminate ocean transit delays altogether, these events made it clear you need to significantly improve the way you manage uncertainty in ocean shipping,” says Archival. “But,” he asks, “how can you do things like proactively adjust lead times for your customers if you can’t predict when shipments will arrive at port or their final destinations?”Hesaysthat while many ocean visibility
He says that data issues quality should be evaluated in four primary ways:
34 | MHD SEPTEMBER 2022 MHD SUPPLY CHAIN
1. Completeness – the data is not
USING VISIBILITY TO TACKLE OCEAN TRANSIT CHALLENGES
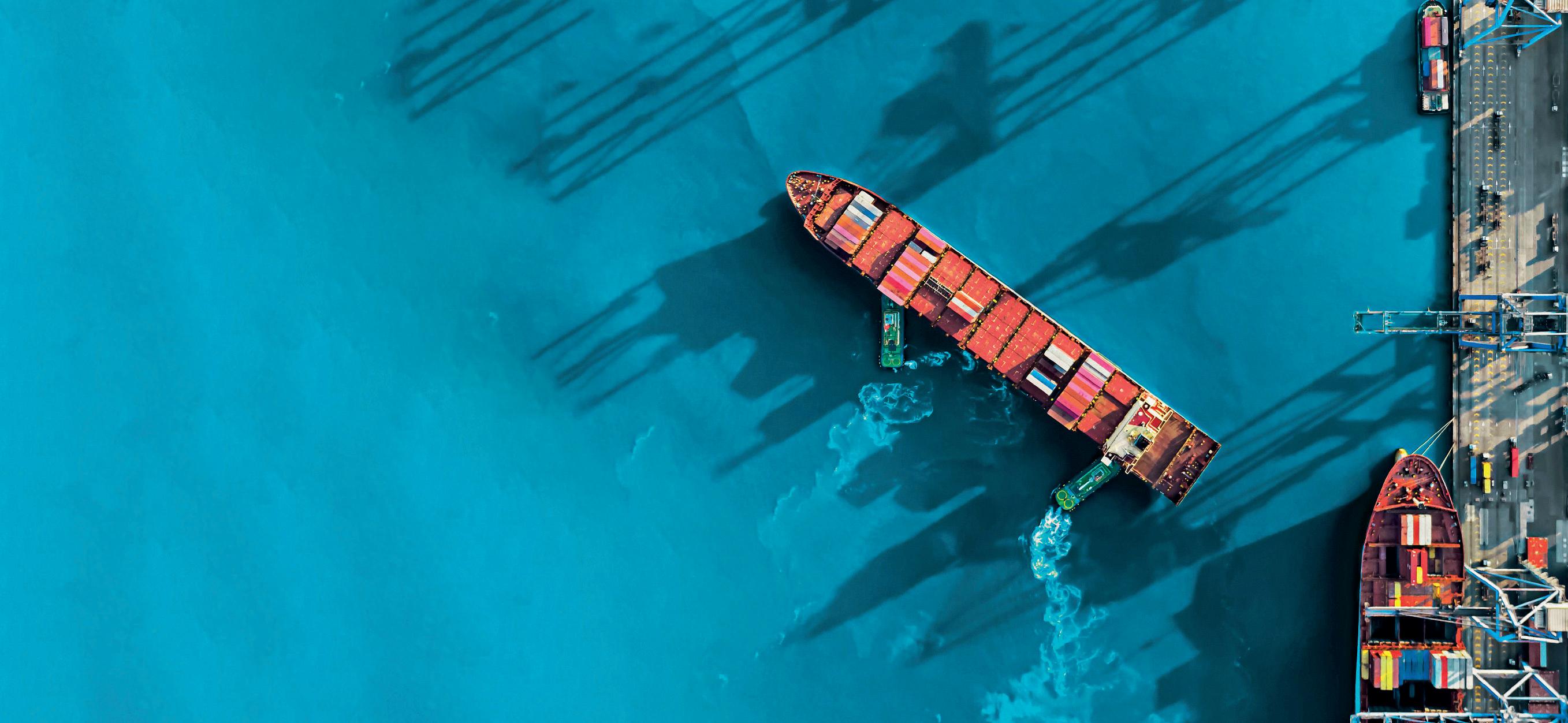
HIDDEN CHALLENGES IN OCEAN TRANSIT
Archival says that data quality issues such as these often prevent executives from making properly informed decisions, resulting in poor customer experiences.
navigate delays and disruption.
4. Fidelity – the data is low fidelity and milestones lack context.
• Increase personnel productivity –by giving employees high-quality, trusted, order-level data, so they can spend much less time manipulating spreadsheets and much more time solving customer problems;
• Shrink excessive logistics costs –
• Improve customer service – by giving agents more transparency and ready access to highly accurate visibility data, so they can more quickly answer customer questions;
3. Latency – the data is not on time; and
Low quality data can create big problems for ocean transit, Archival says.
• Make transport planning and procurement more agile – with realtime data, dynamically generated transit-times and analytics that ensure optimal freight procurement, lead-time accuracy and delay avoidance; Manage inventory levels properly – by giving foresight from upstream raw material manufacturing inputs to predicted warehouse and store-shelf arrival times; and
2. Accuracy – the data is not accurate;
Archival says that by checking vendor’s ability to address the above, you can sort out the best ocean visibility vendors from the rest. “In this climate of serious ocean transit challenges, we encourage those in need of the best in ocean visibility solutions to get in touch with project44.”
“While carrier-developed booking platforms solved the data access problem in the late 1990s and early 2000s, they did little to solve the data quality issue,” he says. “Legacy visibility vendors haven’t been able to solve it either, due to software architectures that have become antiquated and incapable of handling modern demands for agility.”
complete;
Archival says that before now, it was impossible to achieve the efficient, cost-effective, reliable, and sustainable global ocean visibility needed to
■ MHD SEPTEMBER 2022 | 35 MHD SUPPLY CHAIN
Today’s ocean transit challenges are ever more complex, so a true ocean visibility solution is integral to effective supply chain operations.
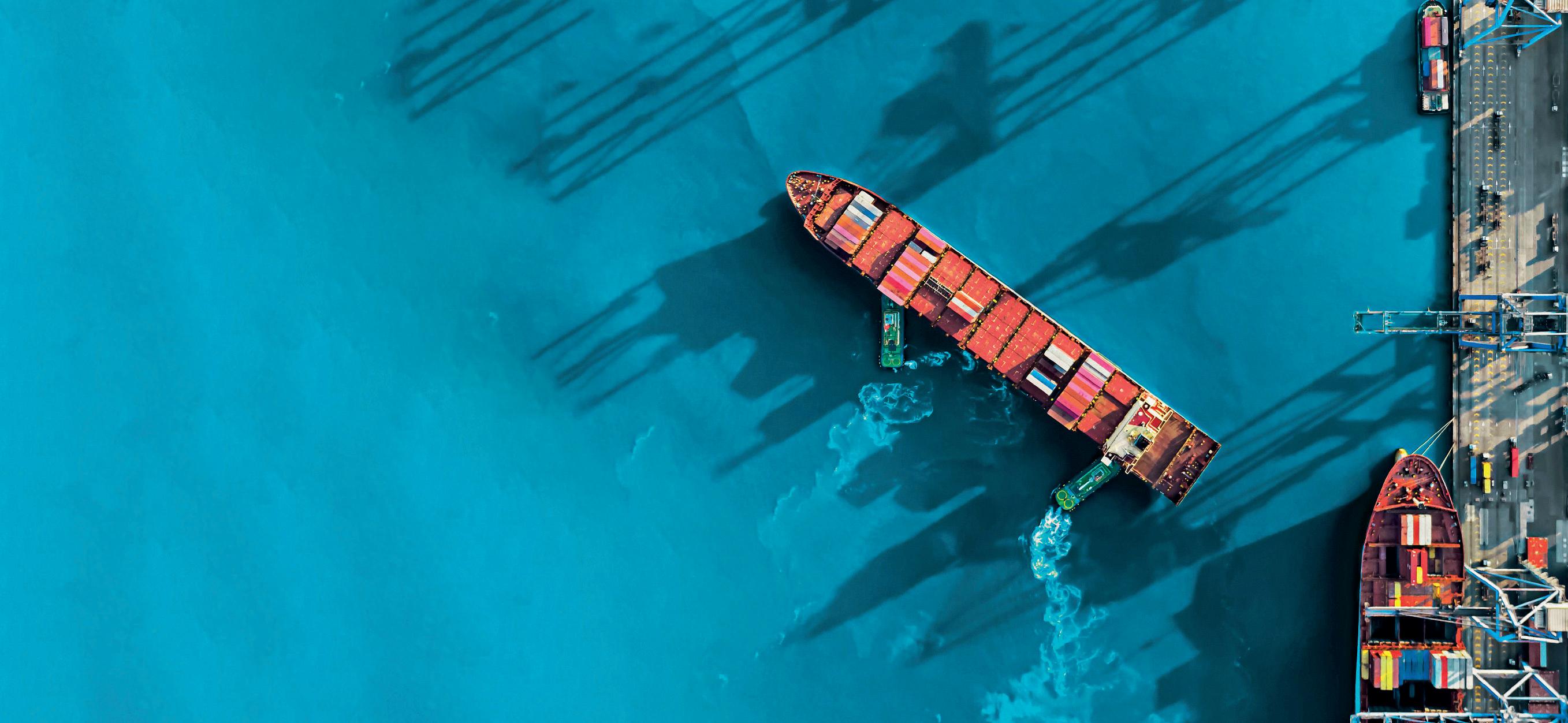
“Due to low-quality data, shippers and 3PLs have poor ocean visibility –particularly for complex, international journeys with multiple interchange points such as trans-shipment ports, ocean-torail interchanges, and transload centres,” he“Owingnotes. to diminished visibility, frontline logistics professionals have to manage shipment exceptions in a reactive manner; logistics costs are significantly higher than they need to be; and sales teams and customer service agents can’t give customers accurate information about shipments.“International logistics planners struggle to improve on-time delivery because they can’t determine which transport mode, carrier and lane are the best ones to utilise; and manufacturing teams can’t adjust production and distribution to offset lengthened lead times.”
• Make in transit inventory allocatable for more streamlined omni-channel
With the application of machine learning, a whole new set of advanced ocean visibility tools have emerged, tools which project44 is utilising to deliver on a big“Ourgoal.goal, with our advanced visibility platform, is to eradicate once and for all ocean transit’s persistent data quality issues, so you can finally have the high quality data, shipping intelligence, accurate ETAs, and proactive exception management your business demands –and your customers deserve,” Archival says.Not all new ocean visibility solutions are created equal, he adds. While many might claim amazing results on ETAs and predictions, only true ocean visibility solutions – such as project44’s – will enable supply chains to do the following:
WHY YOU NEED TRUE OCEAN VISIBILITY
3 transportation emissions – with shipment-level measurements of ocean emissions that enable teams to take more proactive action to reduce these emissions.
by greatly reducing the number of unnecessary expedites;
• Become proactive about exception management – with accurate data, ETAs and alerts that keep teams focused on the shipments that matter most;
Reducefulfilmentscope
As Australia’s leading long load and narrow aisle specialists, we create efficient, space-saving solutions for the handling of long, bulky and difficult loads with our range of German-built Multidirectional Sideloaders and Order Pickers. Handling pallets and need to increase warehouse capacity or condense your storage area? Not a problem! Bendi Articulated Forklifts are designed to give you up to 50% more storage or floor space; and they work outdoors too!

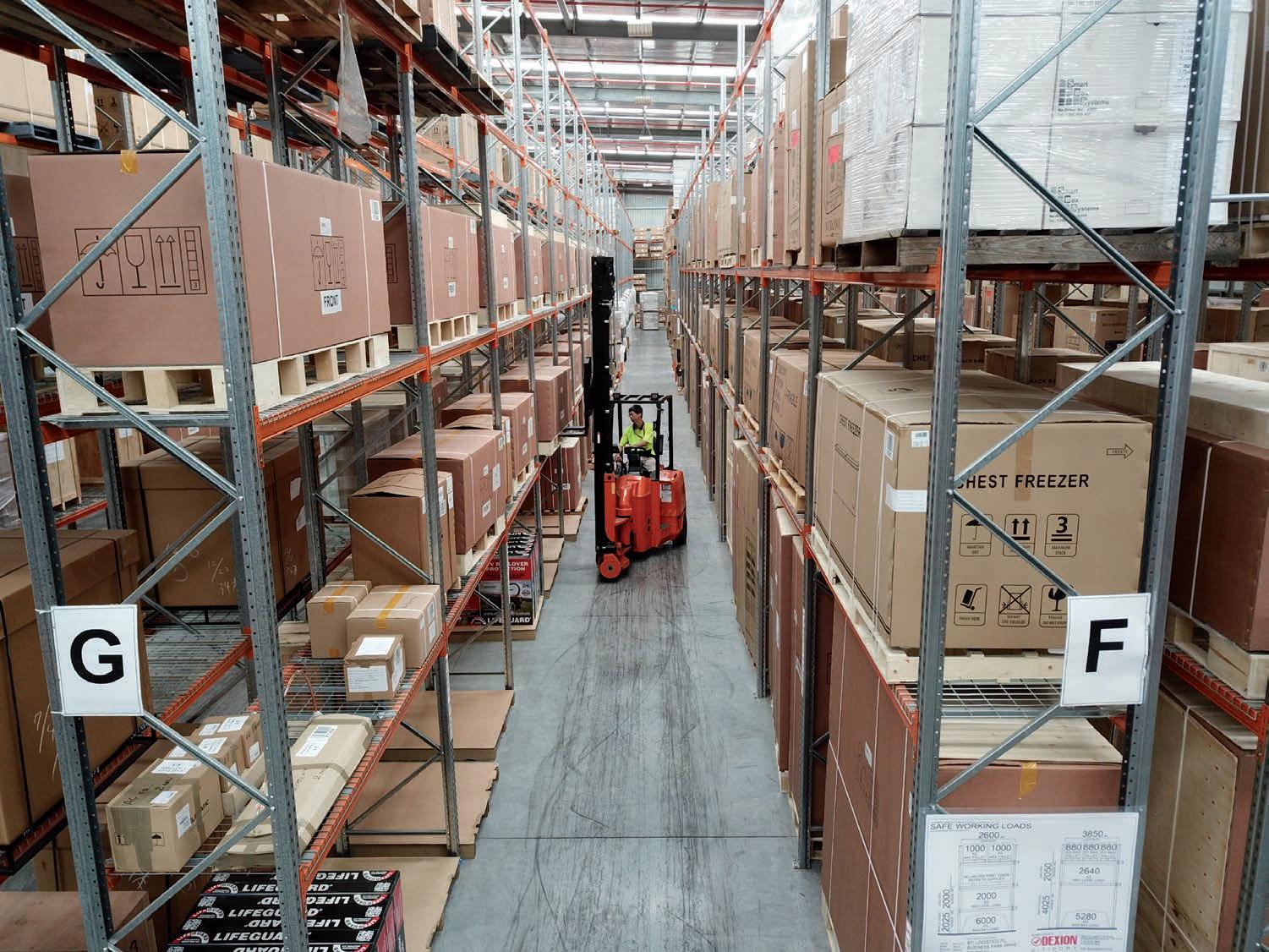
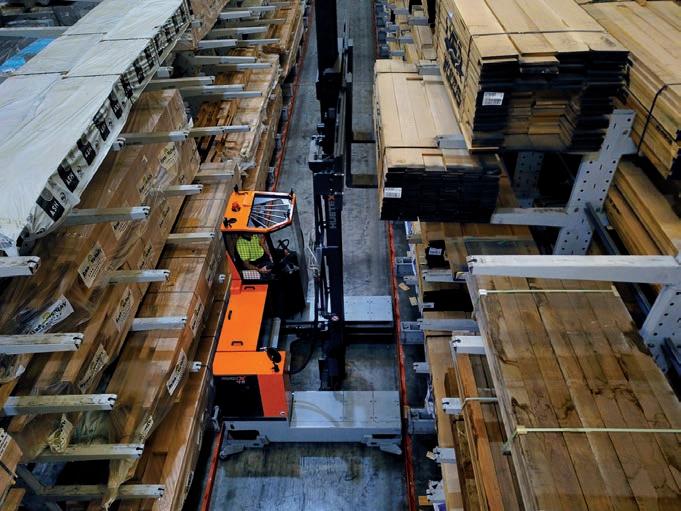
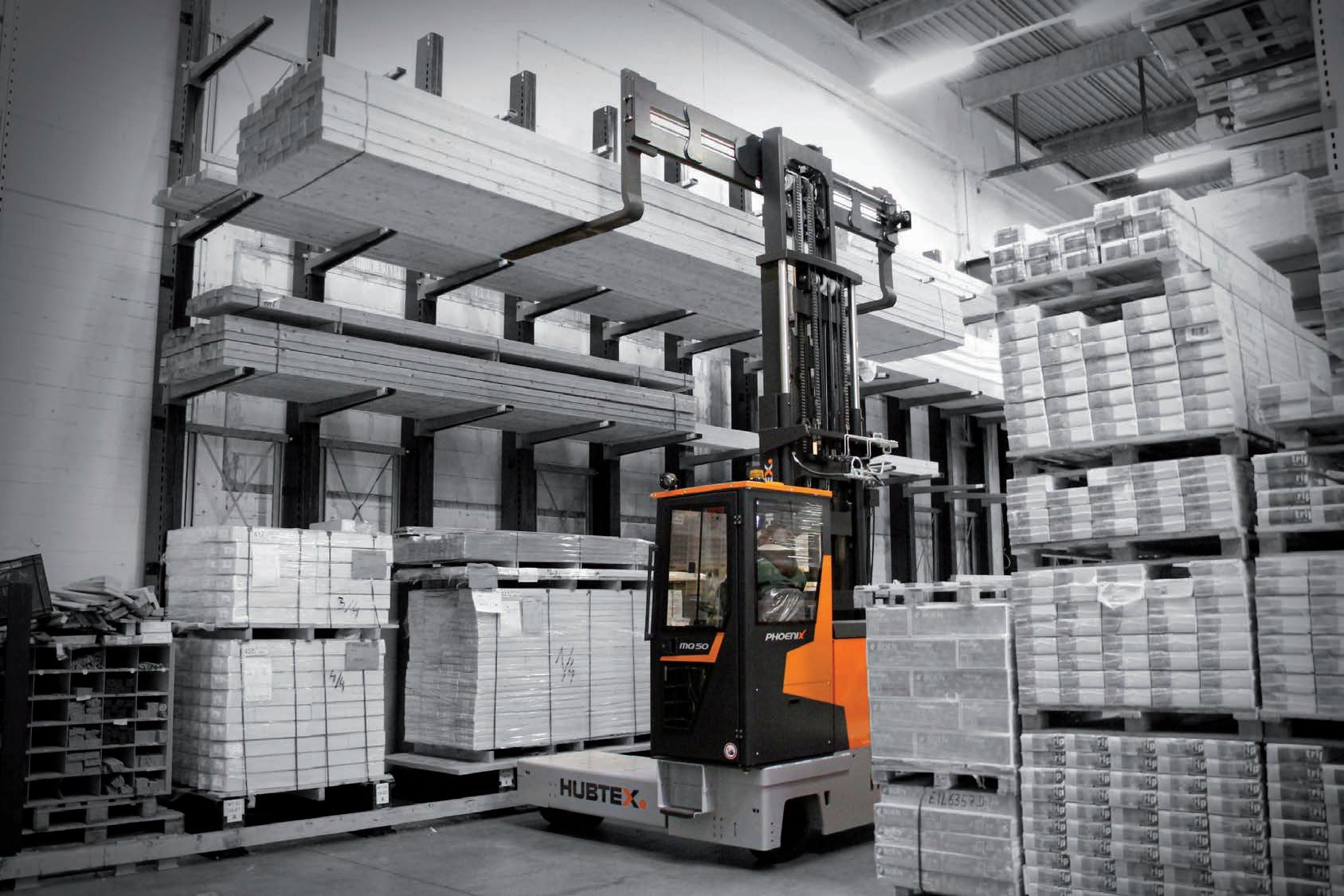
NEW STOCK AVAILABLE FOR IMMEDIATE DELIVERY!ElectricMultidirectionalSideloaders ForkliftsArticulatedBendi 1300 365 621 info@hubtex.com.au www.hubtex.com.au WE THECREATEUNIQUE. There could be another option, call our space-saving experts today on 1300 365 621. THINKING OF EXTENDING OR RELOCATING?EXTENDEDUNTIL 30TH JUNE 2023

The transition to B2C sales can be daunting for businesses who are comfortable operating within the B2B environment. Microlistics employs a ‘warehouse-in-a-warehouse’ concept with customers to help maximise the impact of technology investments without
are being forced to embrace the e-commerce supply chain as 3PLs are displacing traditional B2B movement to survive or expand their own
“ The operationstoconceptin-a-warehousewarehouse-allowsyouappendontoyourtohandle the e-commerce side of things ”
“We say continue the bulk of your business in your main warehouse with your new three million dollar project. Microlistics has the same, if not better functionality than an e-commerce fulfilment platform – the ‘mini’ warehouse is able to communicate with the main warehouse to fulfil individual item orders and maintain stock-on-hand.”Thisstrategyhelps businesses move away from pushing inventory out the door only in bulk – it is ideal for brick-and-mortar retail distribution centres and stores looking to better support omnichannel fulfillment, brands looking to sell direct-to-consumers and better
“You can buy almost anything you want at any store, and you will find a parking space outside that building that says, ‘Store Pickup’, whether it be a pharmacy or a retailer – it doesn’t
Martin Hespeler of Microlistics talks to MHD about the concept of a ‘warehousein-a-warehouse’ as a hybrid strategy for modern distribution – and how companies can achieve order driven fulfilment in the age of e-commerce.
compared to the larger cartons and pallets within B2B operations. However, the cost and the transition can be a tough pill to swallow,” he says. “The warehouse-in-a-warehouse concept allows you to append into your operations to handle the e-commerce side of things.”
A warehouse-in-a-warehouse strategy entails having a dedicated area of an existing warehouse for e-commerce fulfilment. This allows a particular business to ease into an e-commerce journey without the time and money required to completely re-engineer its entire operation. Martin explains why the approach is suitable to so many companies needing to adjust to a change in order type.
MHD SEPTEMBER 2022 | 37 MHD WAREHOUSING
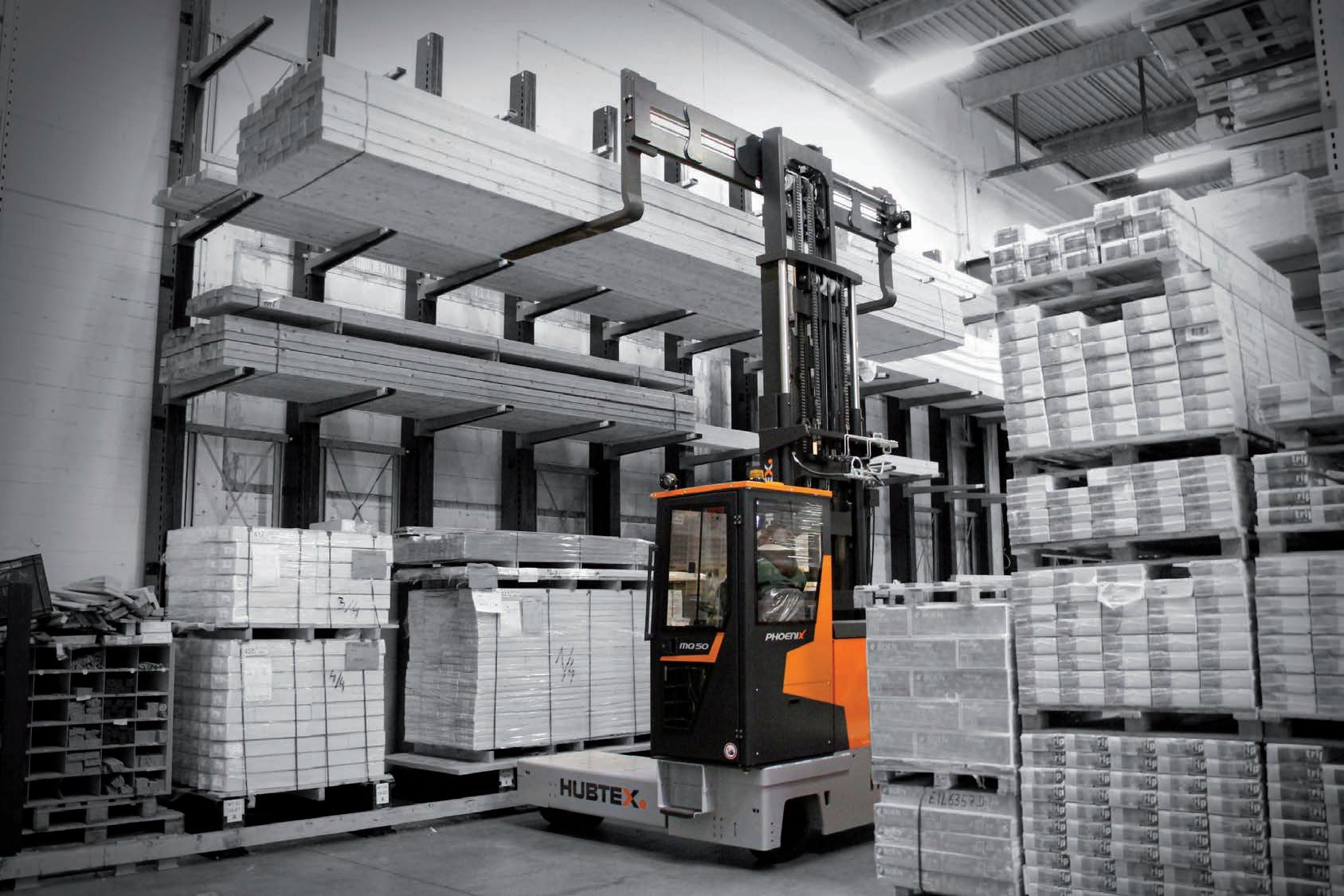
“A legacy WMS does allow a business to pivot to handle the higher volume, smaller orders
“When a company gets to the back end of a new warehouse implementation project, they might have spent say three million dollars to receive goods, store goods, fulfil store orders, send bulk pallets out to other distribution centres within their network,” he says.
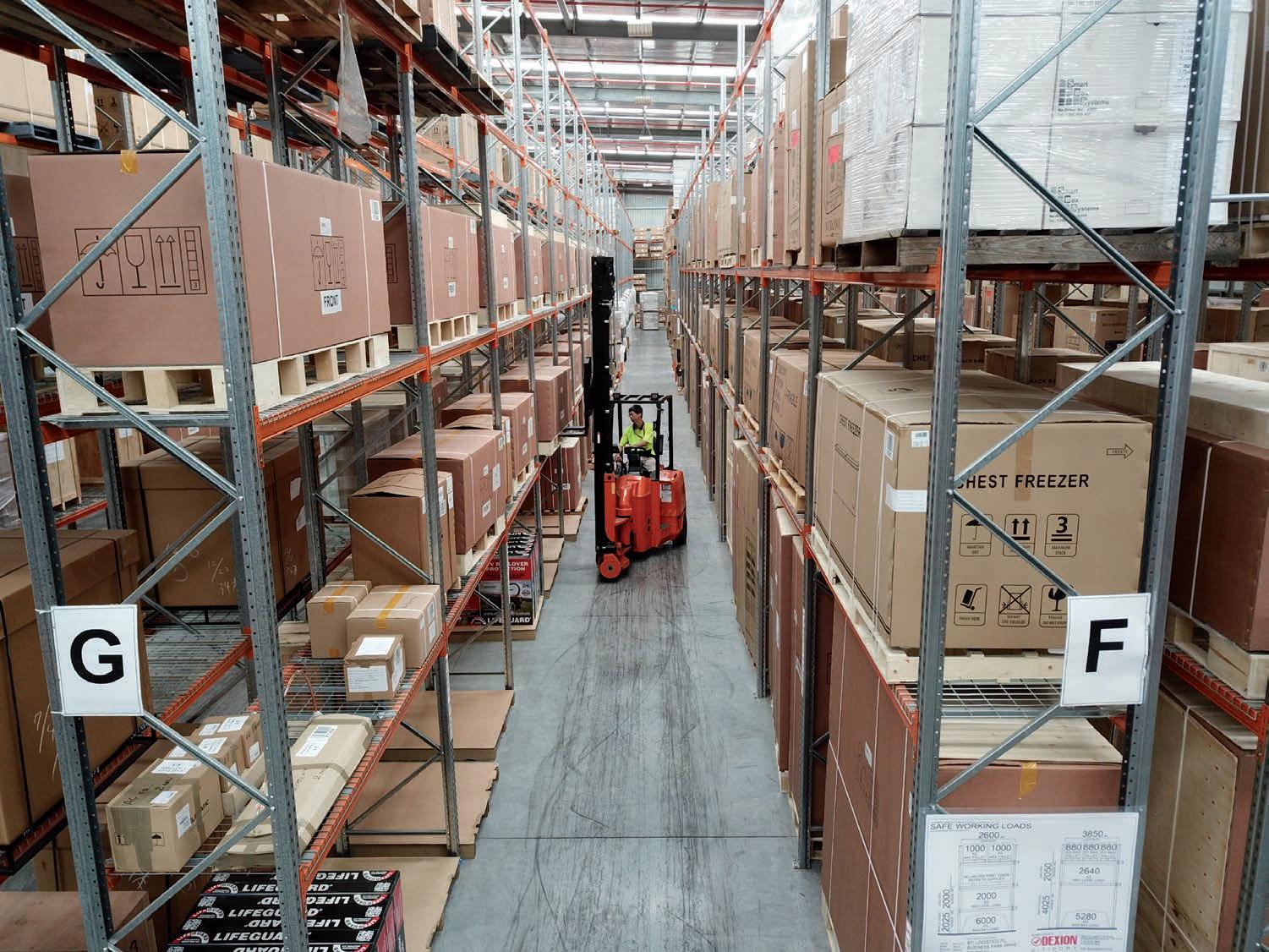
“Ordering online is pick-pack-parcel at the warehouse level. You’ve got the buy online pickup at the store, which involves them taking orders and doing a last-mile delivery in those stores. They’ll also do online pickup at store, so you have kerbside pickup. This has been happening in the US since the COVID-19
“Suddenly you’re an e-commerce business where you shift to getting thousands of lineitem orders for single piece items every day. You built the warehouse to handle massive supply chain movement of product, but now you’re dealing with a pick a piece and ship it model because there’s more margin in it.
RETAIL SUCCESSOMNICHANNELACCELERATING
organisations develop and scale.”
Navigate complex warehouse challenges
If a customer has an existing legacy system which they don’t want to discard, the Microlistics Retail/eComm solution can be extremely beneficial in fasttracking towards e-commerce efficiency.
support downstream customers and 3PLs who want to move beyond the B2B supply chain and add e-commerce fulfilment to their service offering.
A strategywarehouse-in-a-warehouseentailshavingadedicatedareaofanexistingwarehousefore-commercefulfilment.
Microlistics Cloud is a fully managed service with the company providing all aspects of deployment, including maintenance and optimisation so there’s no need for the customer to have its own internal IT capacity or supporting infrastructure.Itofferscloud hosting, incident management, continuous deployment, monitoring and alerts, backup and restore, security, and administration. ■
The reason businesses need this option is because retail has different styles, sizes and colours – an added layer of complexity not necessarily found in wholesale bulk operations. Warehouses are
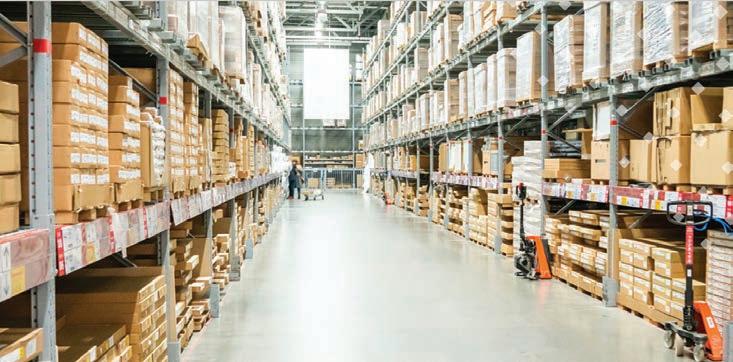
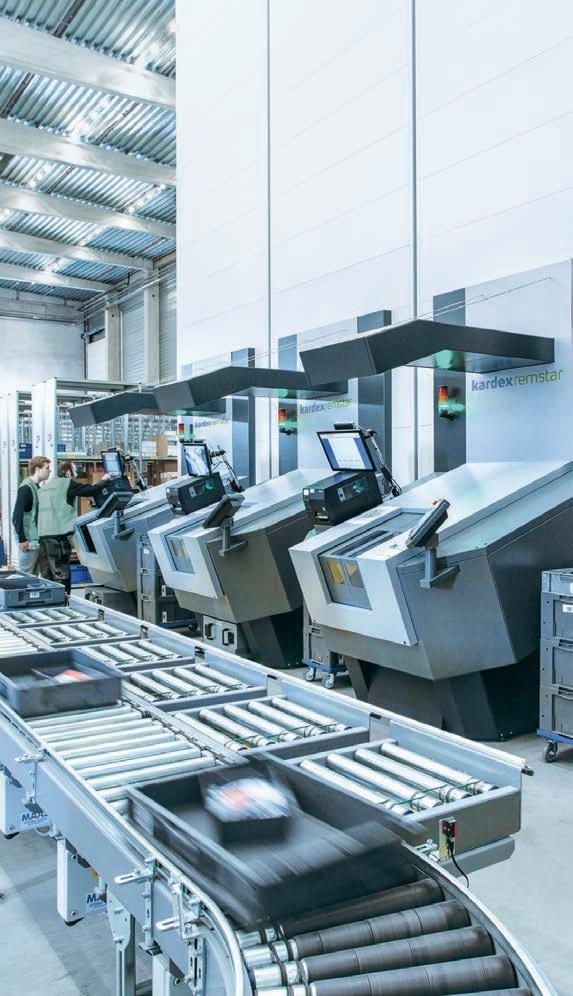
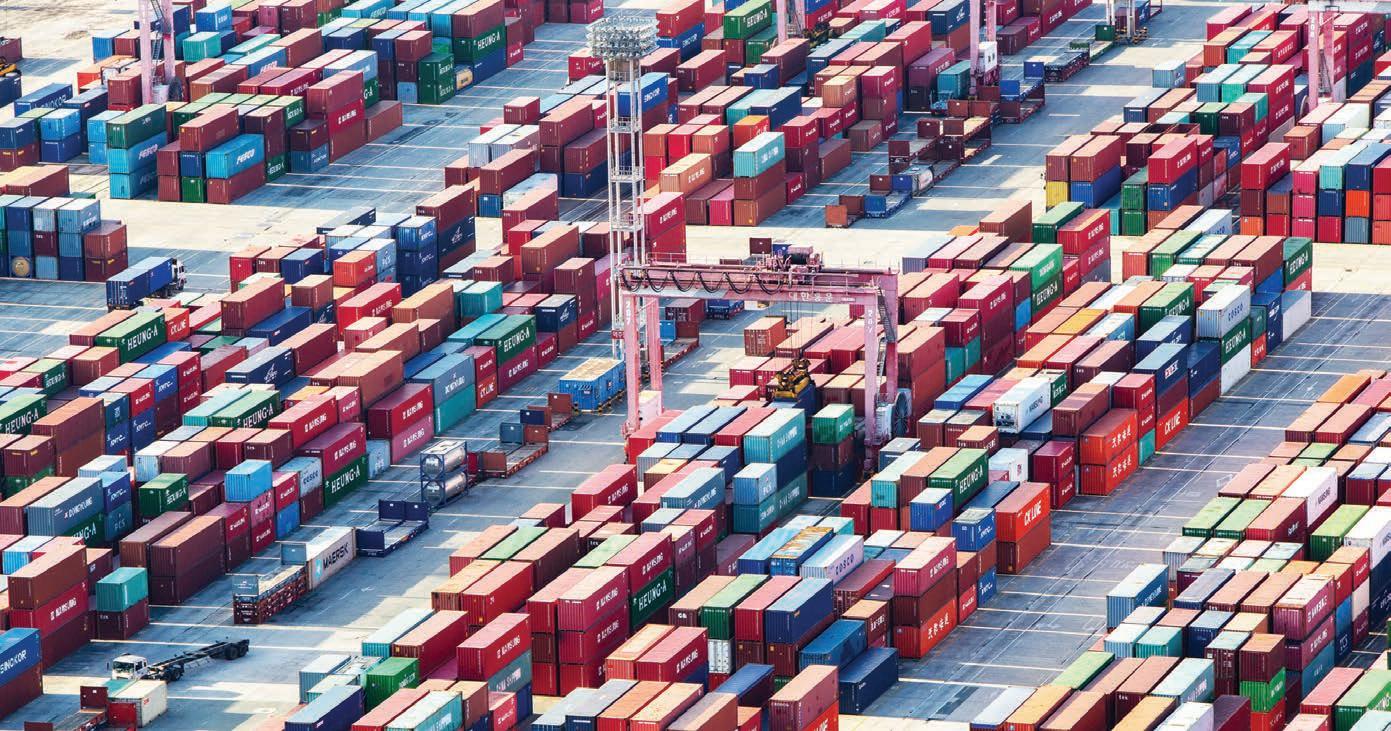
Automation for 3PL Warehouses
Increased
performancepickingby200% Flexible and scalable solution Reduced footprint by 80% ergonomicaccessibleTransparent,and
Customer benefits
The Microlistics Web Portal was recently redesigned and rebuilt from the ground up to accommodate the needs of warehouse operators, providing a seamless online view of logistics operations to customers, suppliers, retail outlets and distribution teams.Theportal makes it easier for third parties – retail stores or the customers of a 3PL – to track what’s going on in terms of inventory management and movement.
“Old legacy systems often run a business quite well, but you can guess what they don’t do well – e-commerce,” he says. “This is where Microlistics comes in to help the 3PLs run their e-commerce to help not only the big players but smaller
“You drop in the Microlistics WMS for a few hundred thousand instead of one or two million and you’re up and running in two or three months instead of six or 12 months,” he says. “If the customer sees Microlistics handling their big constraint – which is their e-commerce fulflilment –then they can use the WMS to run the full facility if they want. We’re just showing them a quick, convenient, relatively inexpensive path to be operational to do a very high margin business for them.”
also at the mercy of sales-driven demand, requiring flexibility to absorb sudden and substantial increases in demand while keeping a relatively flat cost-to-serve. In a world where customers are looking for instant purchase gratification, prompt order fulfilment and swift shopping – real time visibility on orders, inventory and deliveries is critical.
MHD WAREHOUSING kardex.com
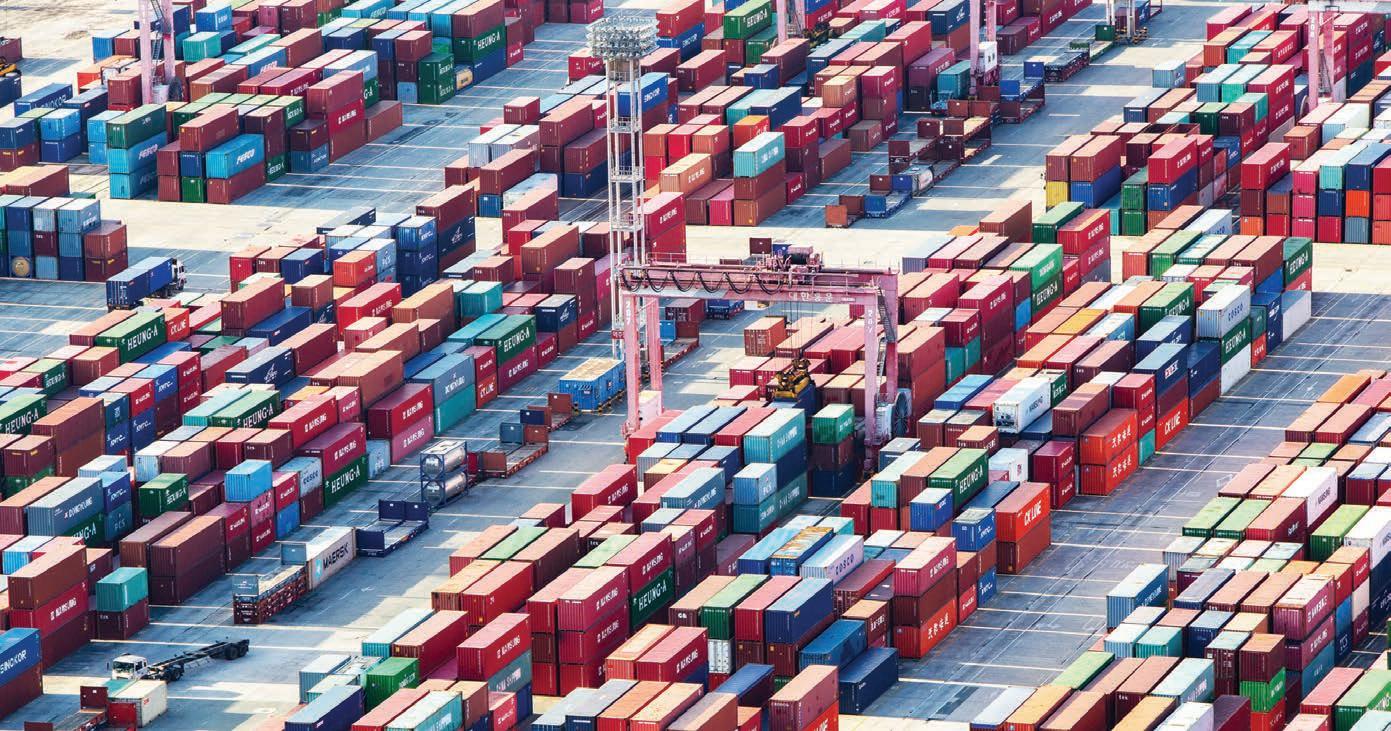
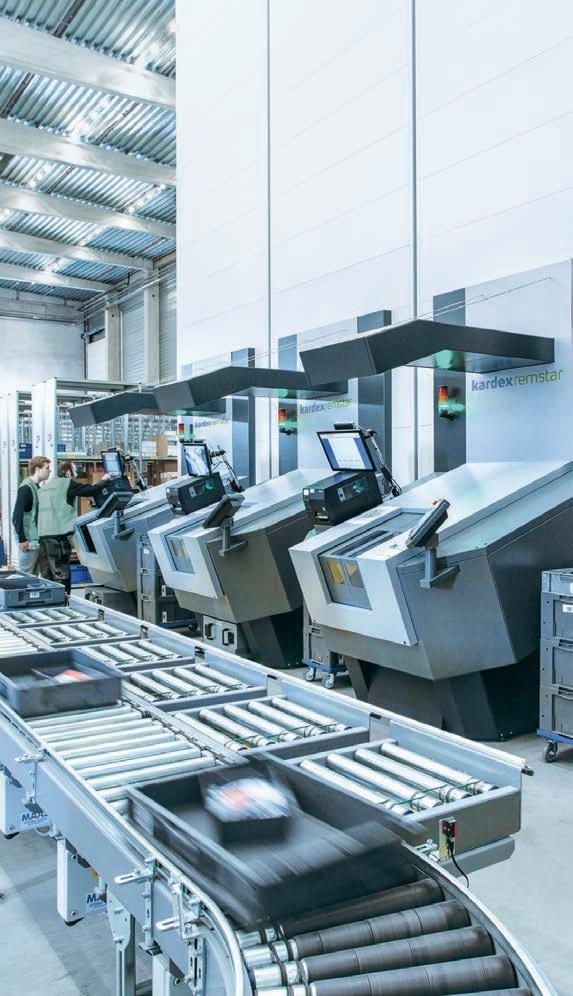
Supply chain transformation involves everything from services to the business customers to raw materials to automation and optimising the end-to-end supply chain via workers andPaulsystems.Eastwood, Managing Partner at Argon & Co. founded Pollen Consulting six years ago. Since then, the consulting firm’s team has grown to a team of more than 70, delivering several large and complicated supply chain transformation. It recently merged with Argon & Co. in January this year. He elaborates on what supply chain transformation entails in 2022.
“Businesses that think smart and differently about their supply chains can leverage a significantly more efficient model, which gives them the competitiveness to win in the market
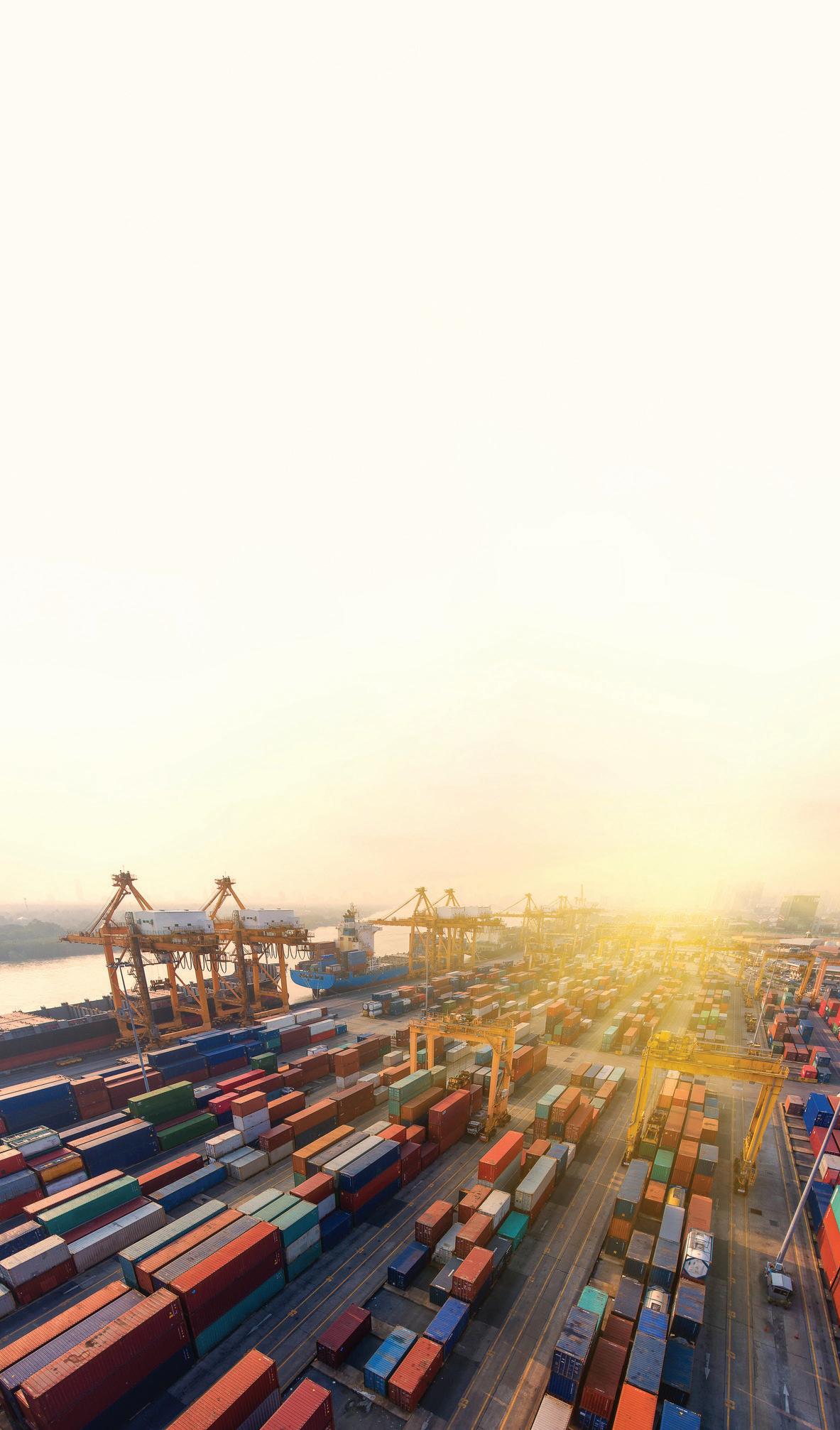
ROLE OF SUPPLY CHAINS
The right time for the right quantity is more important to the customer. Businesses should optimise each part of the supply chain based on what the end customer wants.
or even end-customers, Paul explains. Supply chain business units have become integral to overall business success, and people are at the heart of it.
“It’s not about charging more for the service, but potentially gaining more customers because they return to the business for that service,” Paul says.
they’re playing in,” Paul says. “Whether that’s in the ability to deliver ready meals to people’s homes, or to deliver products to other businesses in a more effective way.”Clever businesses not only hold stock and inventory to service a customer and ensure it’s available ‘just-in-case’, but also know cost advantage in supply chain involves understanding the customers’ needs, and the best way to service them, by employing a lean efficient model – in other words, incorporating a ‘just-intime’ element as well.
Paul Eastwood, Managing Partner at Argon & Co. explains to MHD why supply chain transformation will be the key enabler to a company’s future strategy, and how it encompasses more than simply costs incurred, omni-channel services, or warehouses and distribution centres.
Historically, businesses have looked at their supply chain units and seen them only as costs to be incurred, whereas today there’s a significant move to supply chain as more people-focused, whether that be business customers,
40 | MHD SEPTEMBER 2022 MHD SUPPLY CHAIN
Reliability and predictability are more
TRANSFORMATIONSUPPLYHARNESSINGCHAIN
Businesses can rethink their supply chain physically by investing in automation and optimising the end-to-end supply chain via physical assets.
The ability to deliver on time at the right time means businesses can optimise their own supply chains if they know they have a good partner supplying to them. “You want to be able to deliver your product within four hours these days – if it’s a service the customer’s willing to pay for,” he Supplysays.chains are going to become a competitive advantage for businesses because the customer wants a premium service at the same time as complexity in supply chain is growing – with omnichannel services and numerous global constraints, challenges, and pressures.
By understanding what the customer wants, notes Paul, a business can ascertain what the value is to the customer.
“By doing the smart things with people and systems for supply chain transformation, you can have a major impact on the cost involved to physically initiate change in your business,” he explains. “The world is rapidly changing, so when looking at supply chain transformation, it’s imperative that you assess what you currently have in designing the future state.
He says this isn’t all necessarily within a business’s control because it might be servicing through a retailer to the endconsumer, but it’s paramount that the business understands the entire supply chain lifecycle and remembers that what the customer wants drives the supply chain.Businesses can rethink their supply chain physically by investing in automation and optimising the end-toend supply chain via physical assets, notes Paul. However, it’s more important to do so through systems and people.
“The retail experience now comes through many channels,” Paul says. “As businesses are evolving their own strategies internally as to how they grow their commercial customer base, they look to increase their sales through different channels.“Akeyenabler to that needs to be supply chain because it enables a service delivery for the customer that is different from“Forcompetitors.example,if I order an orange juice from an online shop and I want it in 30 minutes, I might not need a variety of brands of orange juice to choose from. I only need to know that I can get the orange juice in 30 minutes.”
He says this means that an online grocer doesn’t always require a wide selection of product brands available. Instead, it’ll only need a sub portfolio that can be delivered quickly – because the shopper is shopping for an occasion, not a product.
“If the customer knows what time the product they’ve ordered is going to arrive – that’s more important to them than it arriving in four hours’ time,” he says. “The question is: are they willing to pay for that service, or are they just willing to give you the volume or make the purchase with you because of your service?
“Supply chain transformation is looking from the very beginning of where your materials come from, e.g., the raw ingredients, or it could be where you source your materials, through to the endcustomer, what they want, when and how it gets to them.”
right controls of your processes through the system, then you’ve got people not doing transactional activity, but doing the smart thinking,” he adds. “You can then optimise the physical network.”
When a business has a safety net of six weeks’ worth of stock coverage to make sure it can service its customers – a just-in-case capability – utilising smart systems and predictive capabilities and knowing that its inbound supply chain can deliver what it says it can deliver, it can reduce that safety net to two weeks, he notes.
“People have got to match their supply chain transformation with the knowns and the unknowns that are going to exist in the future so they can build their future state in more bite-sized chunks. The process should be more iterative and responsive because the surrounding supply chain context is so fluid.
■ MHD SEPTEMBER 2022 | 41 MHD SUPPLY CHAIN
“Supply chain transformation is not warehouses and sheds,” he says. “This is where people are getting confused with the phrase in the industry. I hear the term ‘supply chain transformation’ when people are simply building a new warehouse or distribution centre – but that’s only part of the process.
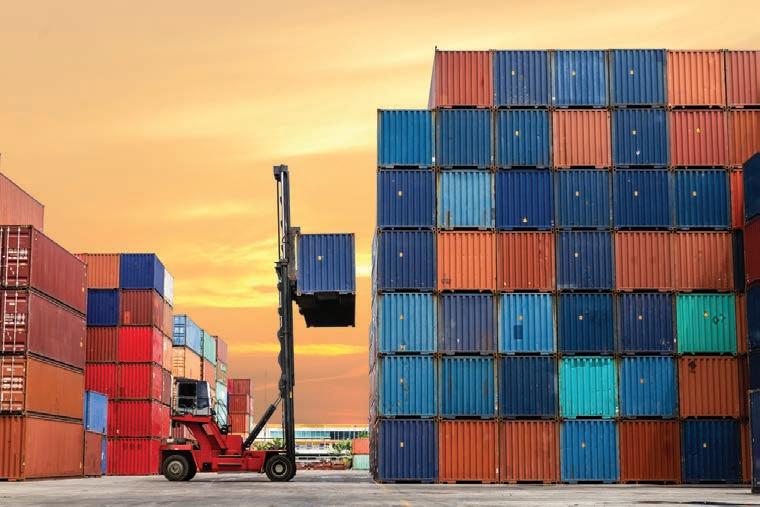
“There’s some smart thinking that people need to do to connect retail and supply chains together,” Paul concludes. “And Argon & Co. are here to help them every step of the way.”
Businesses should optimise each part of the supply chain based on what the end customer wants.
NEED FOR SPEED
“It can be very expensive to service direct-to-customer models. The customer asks, ‘If I order the product now, will I get it today, and do I know what time it’ll be delivered?’ It’s not just about designing for speed; it’s about designing for consistency in what the customer wants and expects.”
“If you’ve got the right systems, the right analytics, the right data, and the
Nowadays, businesses can provide their customers with an online experience along with the traditional retail experience.
“This drives a different supply chain and inventory policy when servicing the
Paul says a customer might want a product from JB Hi-Fi and the delivery service – knowing what time it’ll be delivered – is what matters to them because they want to ensure they’re home to receive it. Knowing the precise time of arrival is more important than getting it in four hours and having to sit around waiting for it to arrive at a non-specified time within that four-hour window.
important than sheer speed, he notes.
customer,” he explains. “It’s all about designing your supply chain to service your customers’ needs.”
OPTIMISING VIA A PHYSICAL NETWORK
Companies need to think a lot more about how their supply chain delivers their customer experience, and that’s where supply chain transformation comes in because they’ve got to consider their business strategy to unlock it through supply chain transformation, notes Paul.
The impact this makes on the physical footprint requirement is huge. We are seeing too many businesses sinking millions of dollars into oversized warehousing because they did not invest in smart systems and start with end-toend supply chain transformation first.
MEET THE SOLUTION TO YOUR LABOUR CHALLENGES Maximise your warehouse space and manage peaks in demand without relying on additional labour—trust OPEX® for the latest in scalable, flexible warehouse automation technology. LEARN MORE AT WAREHOUSEAUTOMATION.COM
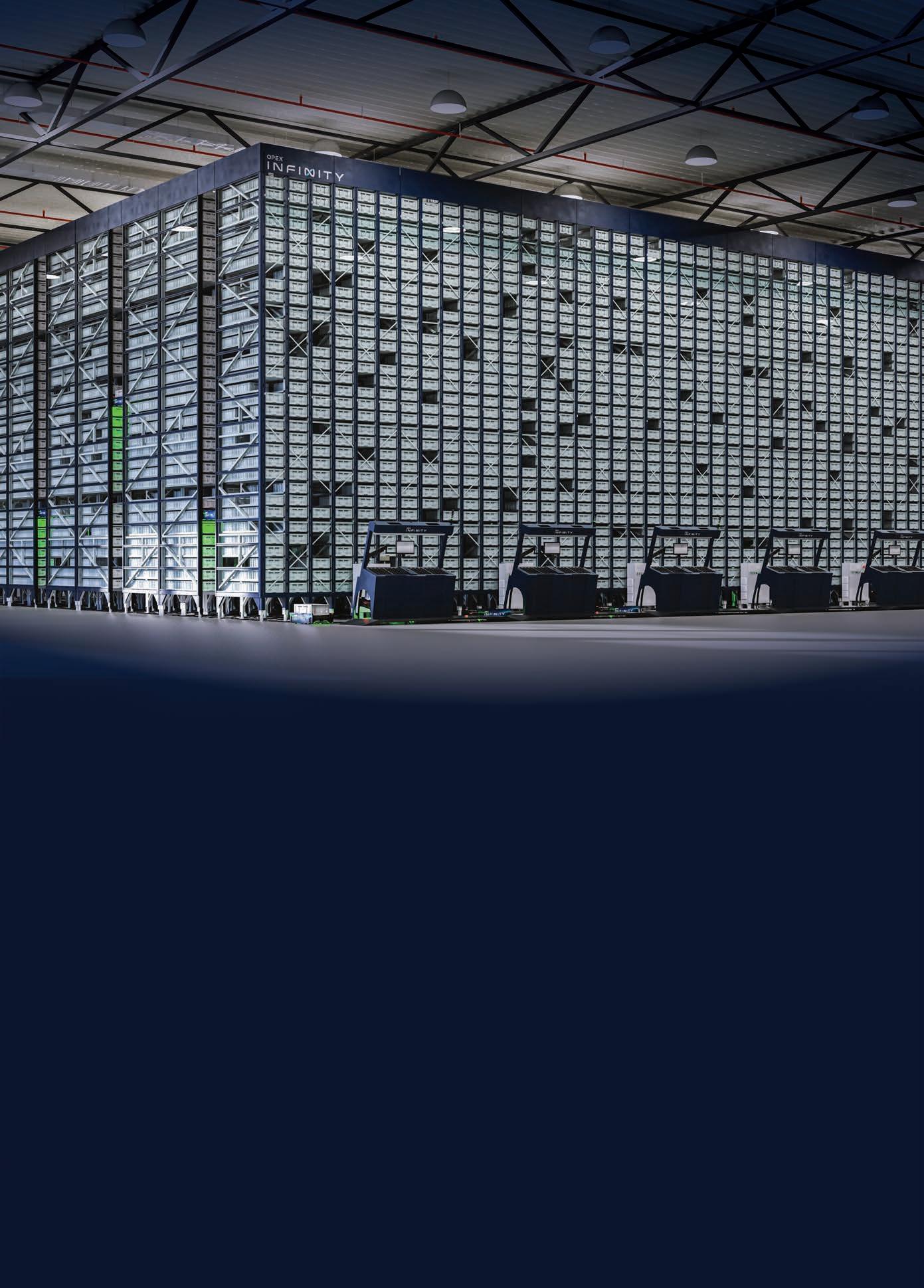
State-of-the-art automated order fulfilment and order consolidation solutions are the answer. To pick, pack and ship orders efficiently, many warehouse and distribution centers leverage a zone picking strategy. Automated order consolidation before shipping or packing is critical to efficiently utilise space, labour, and capital investments.
As more businesses turn to 3PLs, they will
WHY AUTOMATE?
Based on decades of hands-on experience partnering with warehouses worldwide, Kardex understands how to use automation to strengthen warehouse intralogistics and help companies deliver innovative and unrivalled intralogistics. Kardex’s modular solutions provide fast fulfilment and enable flawless material flow.
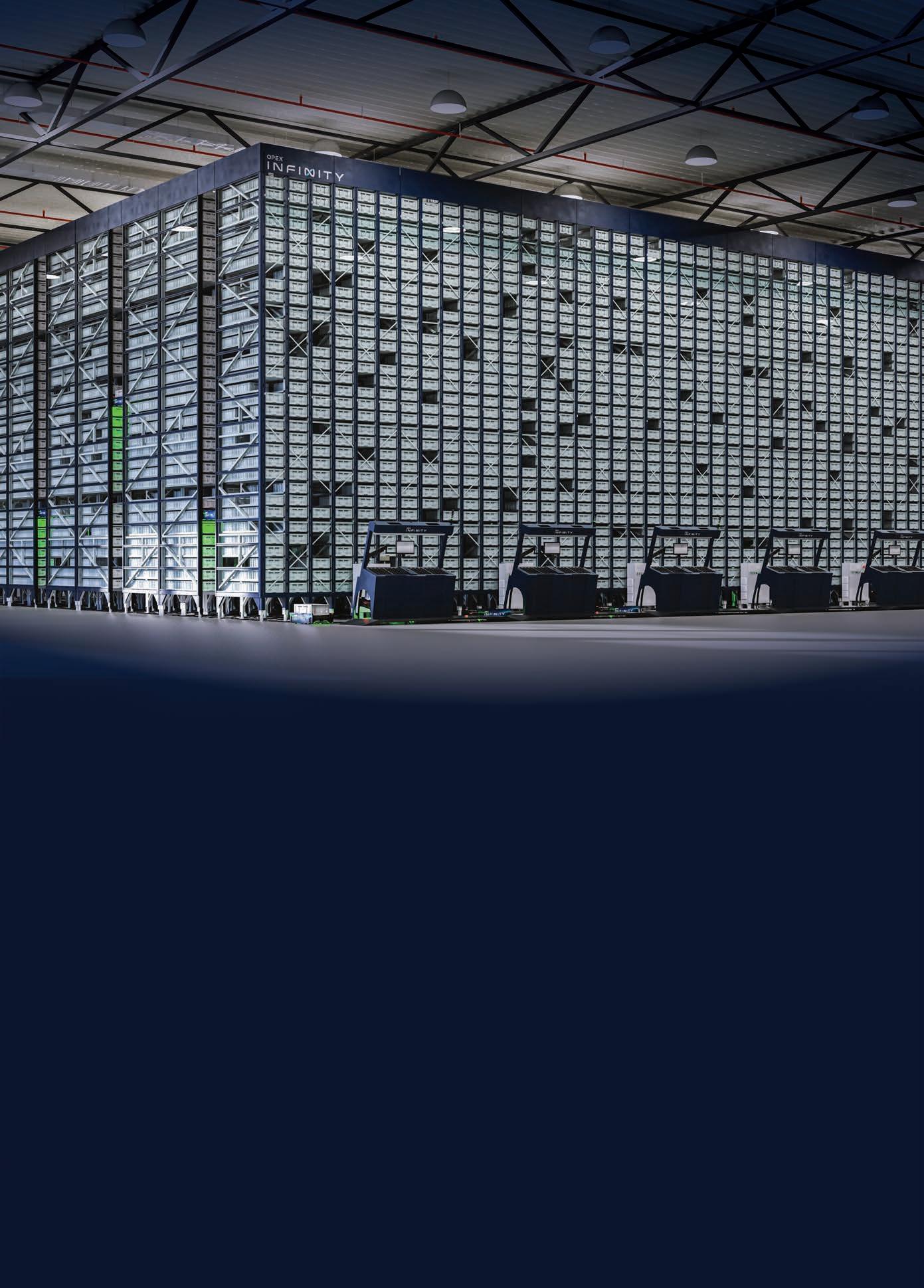
MANAGING CURRENT AND FUTURE GROWTH
Withahead?increasing e-commerce sales, customers’ expectations and behaviours continue to change – next day or even same-day delivery is now the standard. The challenge is how to manage increasing order volumes and escalate order fulfilment to the next level.
EFFICIENT KARDEXCONSOLIDATIONORDERWITHCOMPACTBUFFER
into the existing in-house system. The solution freed up more than a third of Cygnia’s warehouse space, reduced travel time, increased efficiencies and delivered unforeseen savings in time and accessibility. Future, scalable units are planned as growth projections come to fruition.
Kardex addresses how 3PLs manage the continuously changing demands of customer portfolios in their warehouse operations – and some of the solutions it
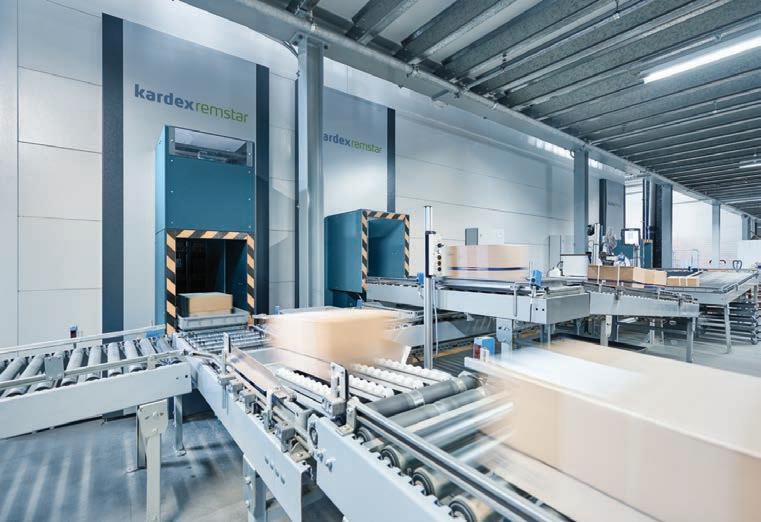
MHD SEPTEMBER 2022 | 43 MHD WAREHOUSING
hird-party logistics (3PL) providers face a unique intralogistics challenge: how to manage frequently changing customer portfolios without re-organising the warehouse every few years? When servicing several customers simultaneously, it is critical that every section of the warehouse can manage a wide range of goods and easily adapt as customers themselves and their individual needs change.
T
Cygnia, based in England, is the digital and e-fulfilment sector of Wincanton, providing logistics solutions to a wide range of retail sectors, including omnichannel. Cygnia needed to expand its storage capacity and find a way to efficiently increase stock throughput for current business demands as well as future demands. Kardex created a tailored solution that included installing six 9.8metre high Kardex Megamat 650 units and a Kardex Colour Pick System – all seamlessly managed by a warehouse
need the proper tools to support and retain customers. Automation is no longer an option, but a must. Kardex offers various order fulfilment and picking strategies including the Kardex Colour Pick System and Kardex Frame Pick System. These easily add or reduce labour, speed up order picking, minimise errors, reduce walking, provide ergonomic working conditions and optimise space and storage volume. The Kardex Compact Buffer is suitable for small parts and used for order fulfilment or as a consolidation buffer to increase productivity, save space, support packaging and alleviate bottlenecks.
SOLUTIONSINTRALOGISTICSFOR3PLs
SMART INTRALOGISTICS
Hella Distribution GmbH is a logistics service provider with long-standing experience in the automotive industry. From its headquarters in Germany, the company ships 2000 orders daily to customers worldwide. Hella Distribution selected Kardex to implement an efficient and ergonomic order consolidation process. With the task of transitioning the manual processes of loading cartons onto pallets and storing them until needed into an automated solution, Kardex installed a six-meter high Kardex Compact Buffer with three access openings and conveyor technology. This serves as a consolidation buffer and pre-sorts items waiting to be shipped.
Hella Distribution selected Kardex to implement an efficient and ergonomic order consolidation process
■
Adding to these traditional challenges comes further pressure from COVID-19, delivery demands and labour shortages. As supply chains move from linear to more complex networks, how can a 3PL stay a step
One major mistake some companies make, he notes, is attempting to control factors that are beyond anyone’s control.
“The world is only getting more
By way of illustration John points to COVID-induced labour shortages, shipping disruptions, rising inflation, high fuel prices, geopolitical tensions in the Pacific, trade wars, and renewed hostilities in “AndEurope.while we are hopefully closing
“I talk with businesses every day that are hurting because of the issues John mentioned,” Theo says. He adds that every business also faces challenges and pain-points unique to them.
In a supply chain sector perpetually in flux, fortune favours the bold.
But toughness isn’t about gritting your teeth, digging in your heels, and trying to weather the storm as it heads towards you. Grit is the ability to survive, thrive, and adapt to changing environments.
Theo Pappas, CEO of Vative, an expert in business transformation who assesses and devises solutions utilising a range of methodologies, strategies, and tools – as well as a knack for creative thinking – is a bold man whose passion is to inspire boldness in others.
“Most people in supply chain, if they’ve been in the industry for a while, tend to continue doing what they’ve always done,” Theo says. “But with new challenges facing supply chain every day,
adages again spring suddenly to life, and in the current global supply chain climate, one such saying is more relevant than ever: ‘When the going gets tough, the tough get going’.
tough years, new public health threats are waiting in tow,” he says. “We’re seeing a resurgence of foot and mouth disease and monkeypox.“Asidefrom the health ramifications, these new threats will impact food prices in this country – and that’s no small thing. On top of inflation, further spikes to food prices impact everyone. Individuals and organisations will be paying more, with knock-on effects on purchasing power and wage pressures.”
In facing down global supply chain challenges, our greatest weapon may well be the ability to think outside the box. Vative’s Theo Pappas, Kyle Rogers of SCLAA, and Swinburne University’s John Hopkins, sat down with MHD to explore the new
John Hopkins, Kyle Rogers, and Theo Pappas are working together to develop innovative supply chain mindsets among a new generation of workers.
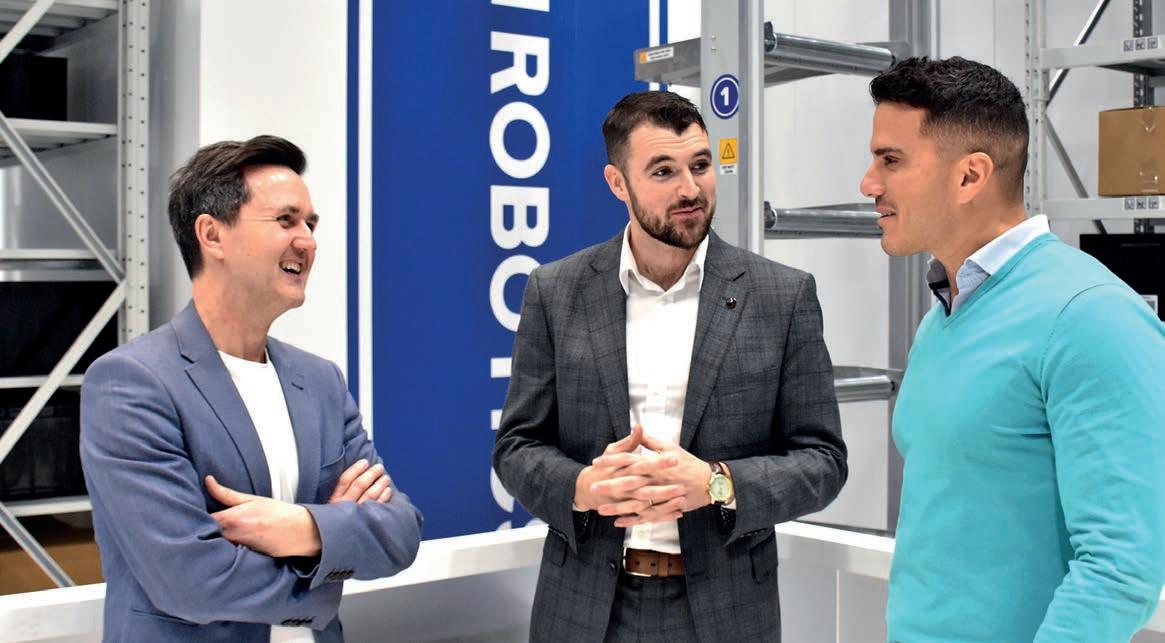
backwards.“Whatwe do at Vative is work with companies to change their culture, help them challenge the status quo, and get them to think differently.”
The challenges facing global and Australian supply chains are too numerous to enumerate here, but John Hopkins, Associate Professor, Supply Chain Management, at Swinburne University of Technology – with whom Theo and Vative have a longstanding, established partnership – offers a no-nonsense summary: “We’ve always had challenges – but we probably have more challenges facing us now than we’ve ever encountered historically.”
BRAVE NEW WORLD, BOLD NEW STRATEGIES
T
44 | MHD SEPTEMBER 2022 MHD SUPPLY CHAIN
SUPPLYINNOVATIONCHAIN
Theo and the Vative team specialise in training and coaching teams in workplace culture, innovation, and process improvement – improving productivity, job satisfaction, and worker retention.
It is, says Kyle, the triumph of ‘co-optetition’ over competition.
“My advice is congruent with what we’re focusing on in our own business,” Theo says. “The great resignation is real, the low unemployment rate is a flow-on effect from tighter immigration restrictions across the globe, and this is creating greater demand for labour – skilled and unskilled – that is exerting pressure across all industries. Overwhelmingly, people do not leave workplaces simply for more income; people typically resign due to toxic cultures, high stress environments, and unresourceful leaders. Focusing on Leadership development, training, and coaching teams on process improvement and innovation will create a performing culture that is too attractive to leave. That is the key message.”
A business affiliate of Theo and sometime collaborator through SCLAA – of which Vative is a national partner – Kyle and uTenant (‘The Warehousing Matchmaker’) have pioneered new ways of working that seek to leverage the strengths of partners that in an earlier era might have been competitors.
works to the benefit of both. Through sharing of information, cross-pollination of ideas – and an understanding that robust, independent tenant- and landlord-representation can effect positive results for both sides rather than either/or – uTenant and JLL are disrupting the industrial property and supply chain space with consistently innovative and positive results.
“Vative is very fortunate to have partnered with Swinburne over many years and to deliver that continuous improvement mindset by delivering a core unit – Lean Six Sigma Green Belt – as part of the Master of Supply Chain Innovation course,” Theo says. “And we’re delighted to strengthen this partnership through a strategic collaborative effort together with SCLAA to create and promote our Graduate Program – as a funnel to bring Supply Chain innovative thinking back in to “We’reindustry.now working on expanding this collaboration to attract international talent at a time where there are major resource constraints in the country.
The first equation emphasises price as the sum of costs plus profits, whereas the second equation emphasises profits as price minus costs. By emphasising profit as the end goal – and underlining that costs are to be subtracted from price in reaching that goal – it refocuses businesses’ attention to how they can achieve more lean, efficient, and productive operations. Oftentimes, businesses regard costs as ‘fixed’ or ‘static’. This equation emphasises the agency businesses exercise over their own cost-reduction processes.
Theo illustrates this point by recalling a recent discussion with a client who was battling to meet customer demands due to the scarcity of skilled labour.
“Cost-cutting doesn’t have to be a zero-sum game where one side loses
Theo notes that many supply chain companies remain beholden to an antiquated notion of “profit” – to a way of conceptualising how prices, costs, and profits relate to one another in the simplest business formula.
One approach Vative deploys is to train and coach leadership skills across all levels of management, and furthermore to inculcate a servant-leadership mindset. “Servant-based leadership breeds humility,” Theo says. “People perform at their best and without fear in such contexts, and productivity increases are achieved without strain or pressure.
INNOVATION AND DISRUPTION IN ACTION
In this vein, uTenant – which represents tenants – formed a strategic partnership with JLL, which represents landlords.Without compromising the integrity of either company’s commitment to their own clients’ interests, uTenant and JLL have forged an independent strategy that
“Vative’s business model is predicated on holistic deployment. We engage with the supply chain industry in a top-downbottom-up approach. We know that to optimise a business, you need to work with the leadership, ensure they’re aligned with a common vision, and understand the guiding values and behaviours to get there. By the same token, it’s equally imperative to engage those workers on the front line – those on the operational floor – and get them to understand and identify waste and opportunities for improvement.
TO THE FUTURE AND BEYOND Vative, SCLAA, and Swinburne all recognise the importance of fostering innovative supply chain thinking in the next generation of professionals. And that’s why Theo, Kyle, and John are proud to work in tandem towards a positive future for the whole supply chain industry.
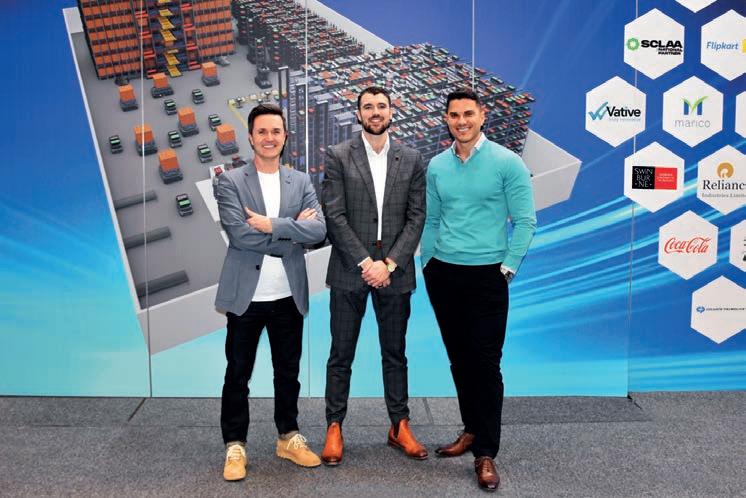
“Traditionally, businesses rely on a simple – but misguided – formula for setting their prices: price equals cost plus profit [Price = Cost + Profit],” Theo explains. “A better way of formulating the equation is the following: price minus cost equals profit [Price – Cost = Profit].”
■ MHD SEPTEMBER 2022 | 45 MHD SUPPLY CHAIN
“This is an exciting project that unites three powerhouse organisations that are passionate about contributing to the Supply Chain community’s continuous improvement.
at another side’s expense,” he says. “Supply chain companies can not only save on costs with careful strategy, but actually reap rewards across various other workplace metrics.”
Vative plays an integral role in facilitating innovative thinking in supply chain.
complex with greater volatility and ambiguity, so we at Vative are advising our customers to focus on what they can control, not what they can’t.”
Kyle Rogers, Co-Founder of uTenant and an Independent Director of SCLAA, knows whereof he speaks when it comes to innovative supply chain thinking.
“Co-opetition, in brief, is collaboration with your competitors,” Kyle says. “Take Amazon Web Services. Its third largest global customer is Netflix, but Netflix is a competitor of Amazon Prime. As Theo has touched on in a different context, innovative thinking requires abandoning zero-sum competition in favour of win-win co-opetition.”
At GPC, the leading AU & NZ automotive business, we are investing in state-of-the-art supply chain solutions to house our iconic brands such as Repco, AMX, Rare Spares and NAPA. Leading the industry requires leading technology, that’s why we’re building a brand-new Distribution Centre. Featuring cutting edge technology and operations, the development will back a growing product range, advancing the store network and supporting Australian motorists into the future.
gpcasiapac.com
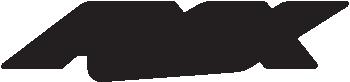
• 39,000 square metres of warehouse space • State-of-the-art technology • Faster, more accurate service for customers • Improved distribution efficiencies • Employment opportunities • 5 Star Green Star Communities rating DRIVING INNOVATIVEAN FUTURE
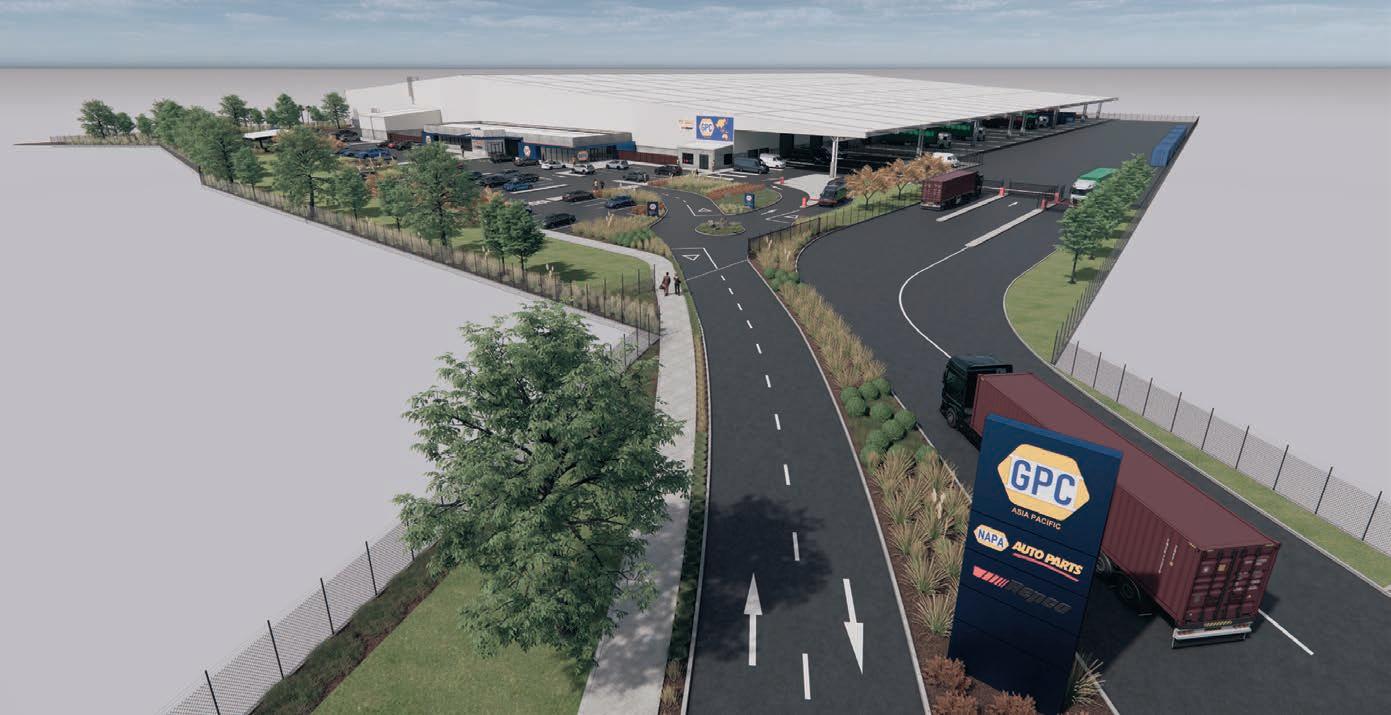
The Victorian government has partnered with the private sector to develop the network. Operators of terminals located at Altona, Somerton and Dandenong South have been selected to build the new rail sidings and connections needed for the efficient operation of the network.
Victoria’s freight volumes are expected to grow to around 900 million tonnes annually by 2050, up from around 400 million currently. The new intermodal precincts will perform a key role in handling this forecast increase in the state’s freight volumes.
Improving rail access to the Port of Melbourne was a legislated condition of the port lease negotiated between the Victorian government and the port’s new owners in 2016.
amenity issues for nearby residential areas
■
• Conflicts with competing land uses
The proposed network promises an efficient and cost-effective alternative to road transport, as well as catering for empty containers and potentially
• Reduce truck movements through Melbourne’s inner west
• Complement other improvements to the north-south intermodal rail supply chain with matching capacity and service level improvements
PORT OF INFRASTRUCTUREINVESTSMELBOURNEINRAIL
The Port Rail Shuttle Network will be key to the Victorian government’s plans to deliver importers and exporters new efficiencies in their supply chains by moving more freight onto rail.
interstate freight.
In the longer term, the development of new intermodal freight precincts will:
The co-location of warehousing, distribution centres and other associated functions with the new precincts, combined with initiatives like the Inland Rail, are aimed at boosting rail’s share of the interstate freight task.
The state’s interstate rail freight task is handled mostly within the Dynon freight precinct. Dynon has a number of limitations that preclude a significant increase in capacity. They include:
• Rail connections that preclude double stacking of containers on trains
• Road connections that generate
• Enhance national productivity by lowering the door-to-door cost of freight for interstate movements
The Victorian government is planning for a new intermodal freight precinct at Truganina in Melbourne’s west. The role of the new precinct will be primarily to handle interstate freight, but also the import and export container trade. The Victorian government will also protect land for a new freight precinct in Melbourne’s outer north for development in the longer term.
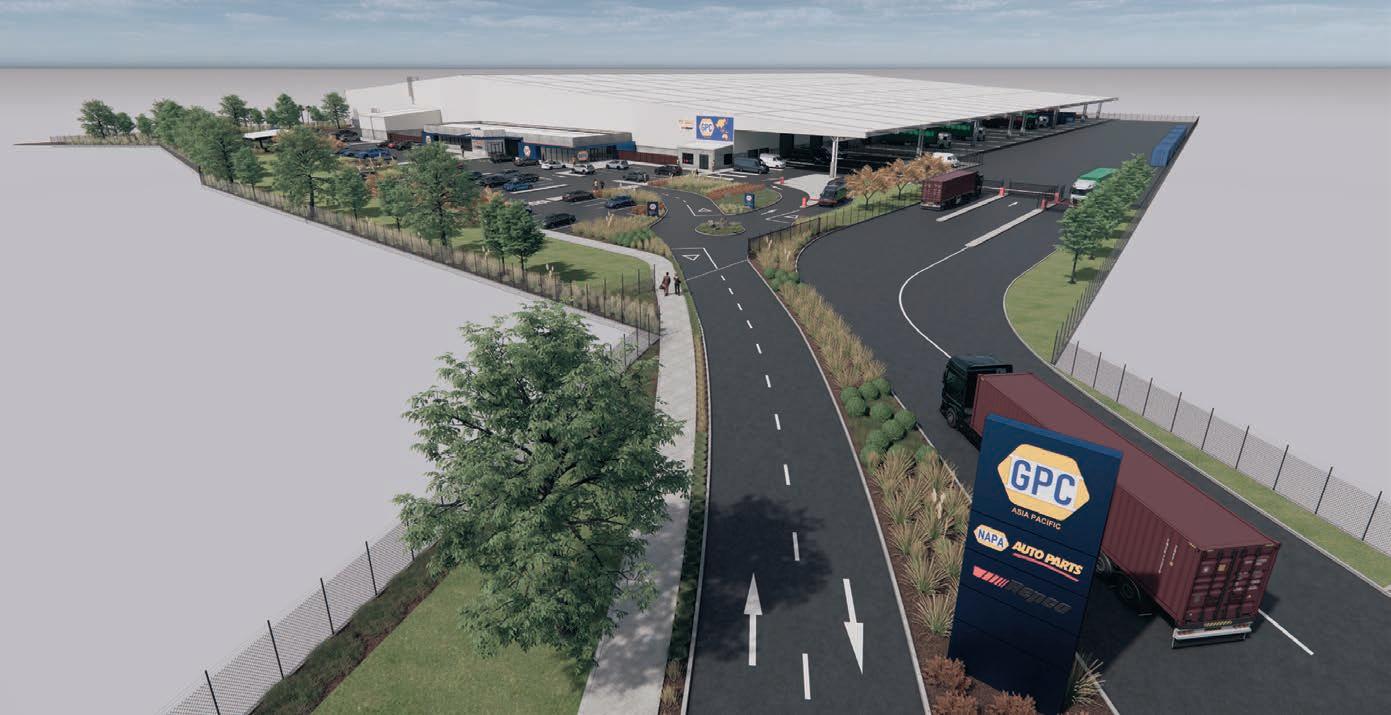
• Improve rail access for port-related freight by removing many non-port freight movements from the Dynon precinct.
The Port Rail Transformation Project will make rail transport more competitive, cut the high cost of the last mile and reduce truck congestion at the port gate. It will boost rail’s share of the port’s transport task, which currently sees fewer than 10 per cent of containers handled by rail.It will also form a crucial part of the Victorian government’s plans for a shorthaul rail network connecting freight hubs in Melbourne’s north and west to the port.
• Create opportunities for urban renewal in the North Dynon area
T
The proposed Port Rail Shuttle Network will establish terminals in the city’s west, north and south-east, where import containers are railed prior to delivery by road to their final destinations.
• Lack of space to store and handle containers
Rail is also seen as critical to the Port of Melbourne’s future success as container throughput triples by 2050.
• A track layout that limits the efficient handling of longer trains.
• Significantly improve the capacity of interstate freight transport in the north-south and east-west national corridors
he investment will deliver new sidings and rail connections to Swanson Dock – home to two of Victoria’s three stevedores.
Victoria will also be seeking additional interstate rail capacity to capitalise on the benefits being delivered by the Inland Rail Project.
The Pacific National container train at West Footscray.
MHD SEPTEMBER 2022 | 47 MHD MEGATRANS
Rail has been underutilised in Melbourne for short-haul freight operations, with the entire metropolitan freight task currently undertaken by road transport. 87 per cent of import containers handled by the port travel to a destination less than 50 kilometres distant.
The Victorian state government tells MHD why exporters will be the big winners from Port of Melbourne’s investment in new rail infrastructure.
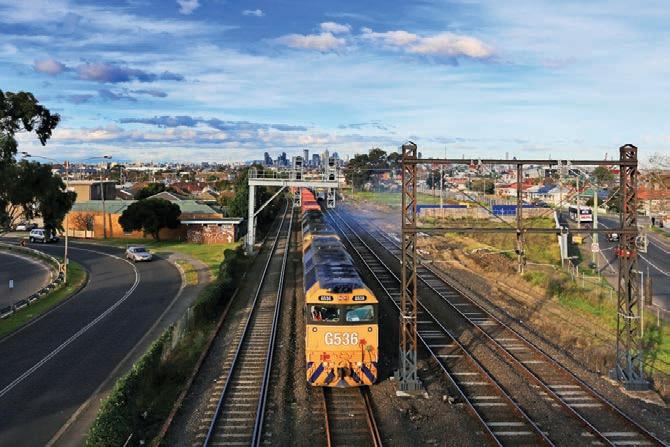
The following winners were:
MHD MERCURY AWARDS 48 | MHD SEPTEMBER 2022
(The Award was accepted on behalf of Complexica by judges of the Awards and the editorial team of MHD.)
use of AI-enabled automation and optimisation, with the potential to unlock further value through “global optimisation” (i.e. whole-of-supply chain optimised decision-making).
Finalists were assessed on how their technology has improved logistics and materials handling efficiency and cost-saving, as well as how it has improved either the environment, production outputs or safety.
AWARDS 2022MERCURY
• FinalistsComplexicawere assessed on what the company has done to disrupt the supply chain industry, as well as the capability to introduce their project to the wider Complexicaindustry.won for developing Supply Chain Optimisation & Planning Environment (SCOPE) that can optimise the end-to-end wine supply chain. Complexica then partnered with the global winemaker Pernod Ricard to unlock the value within its operational silos through the
Swisslog’s CarryStar fully automated order fulfilment system won the Best Technology Application Award. The system combines Automatic Guided Vehicles (AGVs), KUKA Star Robots and the latest Swisslog SynQ software
Media personality Nicky Buckley hosted the ceremony where workers and companies in the supply chain, logistics and materials handling industries were recognised for their outstanding achievements.
Swisslog Australia – CarryStar Fully Automated Order Fulfilment System
Mercury and Bulk Handling Awards 2022.
Swisslog Australia won the Best Technology Application of the Year Award.
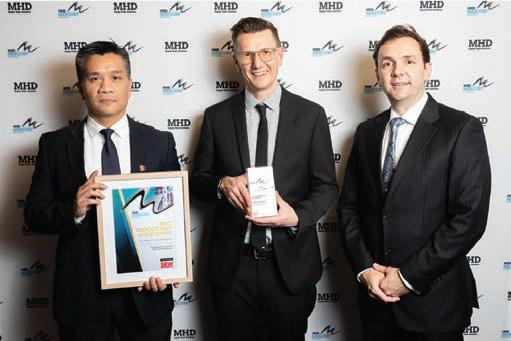
n Thursday August 25, Prime Creative Media’s Mercury and Bulk Handling Awards Gala dinner took place at the Arts Centre in Melbourne as part of the biannual MEGATRANS event.
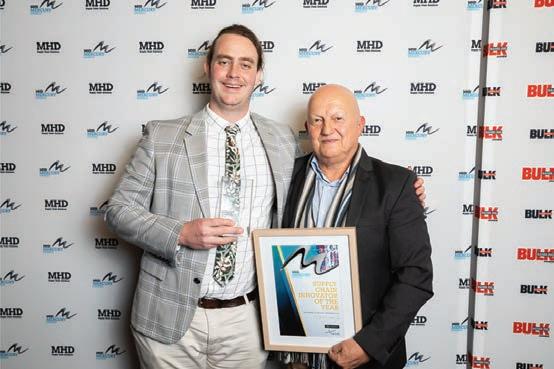

Melbourne Arts Centre, where finalists from 2020 and 2021 competed for top prizes in supply chain’s night of nights.
Complexica won the Supply Chain Innovator of the Year Award.
BEST BYAPPLICATIONTECHNOLOGY(SPONSOREDSEW-EURODRIVE
O
(SPONSORED BY NHVR)
SUPPLY INNOVATORCHAINOF THE YEAR
The end-state vision for Pernod Ricard Winemakers is to use enabling technologies for process automation, predictive modelling and planning and scheduling optimisation, to provide “whole of supply chain” visibility and decision-making and realise business benefits in each operational silo.
FREIGHT (SPONSOREDSOLUTIONTRANSPORTOFTHEYEARBYVICTORIANGOVERNMENTDEPARTMENTOFTRANSPORT)
Finalists were assessed on the practicality of their solution, as well as how it improves efficiency, spacesaving or Schneidercost-saving.Electricwon the Best Storage Solution Award for its SMART Distribution Centre. By utilising Schneider Electric’s own EcoStruxure platform, they have implemented their own solutions, transforming a Sydney
This Contribution to Industry Award recognises an outstanding contribution to the supply chain and logistics industry.
This year’s winner was Meaghan Siemensma, Senior Implementation Manager at Bestrane Group. ■
IFC Global Logistics won the Freight Transport Solution of the Year Award.
Finalists were assessed on how well the solution enhances efficiency, traceability, cost-saving, or sustainability.Inlogistics, efficient distribution time is critical. IFC’s advanced International Direct-to- Store model – which won the Freight Transport Solution of the Year Award – enables customers to place bulk purchase orders with vendors in advance. The opportunity to build up inventory levels from a centralised international distribution centre represents goods being readily available for demand fulfilment with complete accuracy. Challenges that are associated with production lead time disruptions is now mitigated, as goods can be immediately delivered by the vendor in advance of the shipment window required date. This provides enhanced benefits to business operations as managing production lead times becomes better controlled which allows for enhanced promotion and sales planning, and easier on-demand ordering fulfilment through electronic data interchange.
warehouse into a SMART distribution centre. EcoStruxure is Schneider Electric’s single, open IoT enabled system which empowers innovation at every level across connected products, edge control and apps, analytics and services. The SMART DC program helps analyse data and discover meaningful insights, enabling action by closing the loop with customers through real-time information and business decisions for positive outcomes – connecting everything from the ‘shop floor to the top floor’. The digitisation of the SMART DC allows Schneider Electric to drive endto-end efficiencies.
MHD MERCURY AWARDS
Meaghan Siemensma
INITIATIVESUSTAINABILITYAWARD
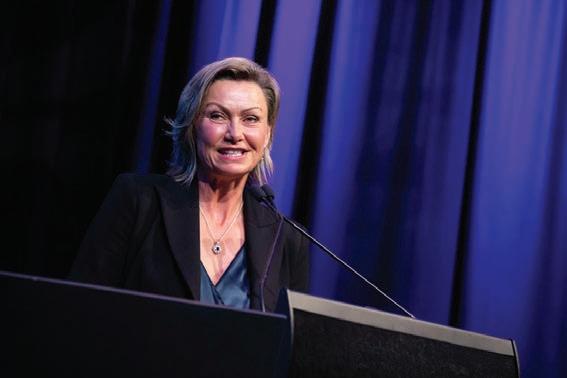
for optimum efficiency, flexibility, reliability and sustainability. The scalable and modular CarryStar fully automated solution is suitable for small, mid-size and large layer and stack picking operations. With minimal fixed infrastructure required and the ability to grow as a business expands its operations, CarryStar is ideally suited to retail, FMCG and pharmaceutical companies looking for a cost-effective, hygienic and efficient warehouse automation solution.
Schneider Electric – SMART Distribution Centre
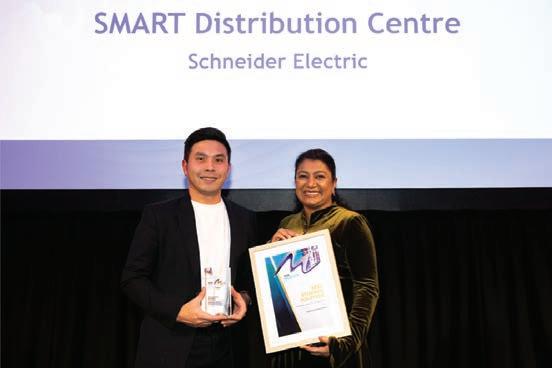
Gaprie Ltd won the Sustainability Initiative Award for its P.C. Nets. Australia uses an estimated 52,000 tonnes of shrinkwrap per year. P.C. Nets are flexible, reusable pallet netting. They simply slip down over the product on a full pallet and fasten. They can be reused multiple times, eliminating the need for plastic wraps. The nets also allow for product visibility, easy traceability with a QR code and are suitable for all stages of the pallet life cycle. Available at a low cost with rapid return on investment, P.C. Nets are suitable for a vast array of industries.
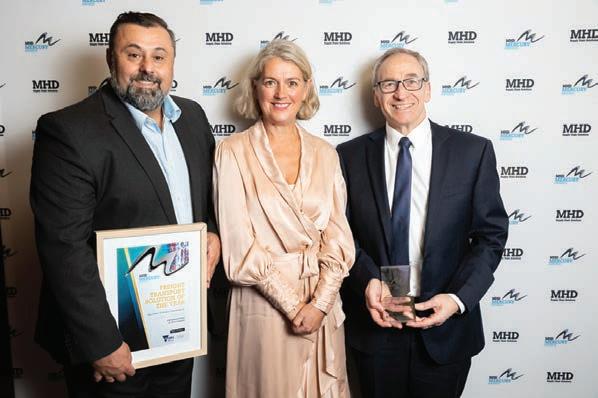
Gaprie Ltd – P.C. Nets
Direct to Store Program
Host Nicky Buckley announces the Gaprie Ltd at the winner of the Sustainability Initiative Award.
practicality of the program, as well as its difference to other projects available to the industry.
Schneider Electric won the Best Storage Solution of the Year Award.
MHD SEPTEMBER 2022 | 49
BEST STORAGE SOLUTION
Finalists were assessed on the
• IFC Global Logistics – International
CONTRIBUTION TO INDUSTRY (PRESENTEDAWARDBYSCLAA)
Meaghan Siemensma of Bestrane Group won the Contribution to Industry Award (here pictured with Stephen Lakey, Director at SCLAA).
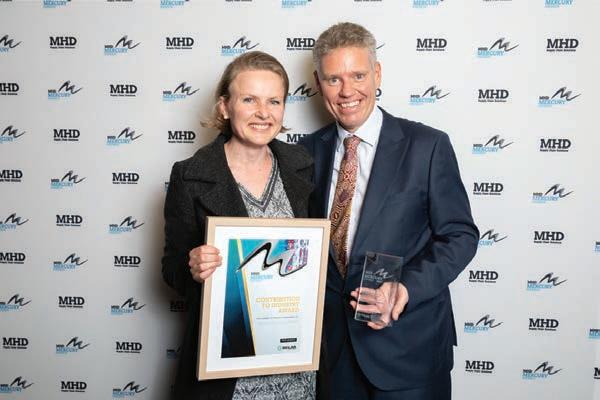
Filter water
faster The C85 Non Stop Cleaning is a state-of-the-art battery powered ride on floor scrubber that is eco-friendly and innovative. With an onboard filtering system that allows water used for scrubbing floors to be recycled, considerably reducing your water consumption. This machine features two different types of brush heads to optimise the clean on any floor surface. NSC Water Recycling System 2021COMAC©Copyright12/21AD302534COD.-equipamiento.aly/odiseñoalvinculadasestán scrubber dryer equipped with Non Stop Cleaning Premium system, not only reduces the unproductive loading and unloading times of the solution all, it saves up to 80% of water and 90% of chemical. This is an high economical advantage, that minimizes the environmental impact of floor operations without affecting the result. To save up to (1): WATER WASTEWATERPITCHEMICAL-80%-90%STOPTIME-85%-85% 3h a day, 5 days, with medium dirt grade, in Eco Mode. The advantages of NSC 80% less water usage 2021COMAC©Copyright-12/21AD302534COD.equipamiento.aly/odiseñoalvinculadasestánnoyreferencia,simpledeson Comac C85 scrubber dryer equipped with Non Stop Cleaning Premium system, not only reduces the unproductive loading and unloading times of the solution but, above all, it saves up to 80% of water and 90% of chemical. This is an high economical advantage, that minimizes the environmental impact of floor cleaning operations without affecting the result. To save up to (1): WATER WASTEWATERPITCHEMICAL-80%-90%STOPTIME-85%-85% (1) use 3h a day, 5 days, with medium dirt grade, in Eco Mode. TECHNICAL DESCRIPTION C85 NSC BaseC85 BS NSC BaseC85 B NSC PremiumCS85 BS NSC Premium Tank capacity l/gal 300/79,2 300/79,2 300/79,2 300/79,2 Working width mm/inch 850/33,4 850/33,4 850/33,4 850/33,4 Squeegee width mm/inch 1105/43,5 1105/43,5 1105/43,5 1105/43,5 Moving scrubbing brush head mm/inch 150/5,9 150/5,9 The advantages of NSC 90% less chemicals usage 2021COMAC©Copyright12/21AD-302534COD.equipamiento.aly/odiseñoalvinculadasestánnoyreferencia,simpledesonutilizadasimágenesLasequipamiento. Comac C85 scrubber dryer equipped with Non Stop Cleaning Premium system, not only reduces the unproductive loading and unloading times of the solution but, above all, it saves up to 80% of water and 90% of chemical. This is an high economical advantage, that minimizes the environmental impact of floor cleaning operations without affecting the result. To save up to (1): WATER WASTEWATERPITCHEMICAL-80%-90%STOPTIME-85%-85% (1) use 3h a day, 5 days, with medium dirt grade, in Eco Mode. TECHNICAL DESCRIPTION C85 NSC BaseC85 BS NSC BaseC85 B NSC PremiumCS85 BS NSC Premium Tank capacity l/gal 300/79,2 300/79,2 300/79,2 300/79,2 Working width mm/inch 850/33,4 850/33,4 850/33,4 850/33,4 Squeegee width mm/inch 1105/43,5 1105/43,5 1105/43,5 1105/43,5 Moving scrubbing brush head mm/inch 150/5,9 150/5,9 Working width with side brush mm/inch 1000/39.3 1000/39.3 Working capacity up to sq.m/h/sqft/h 6800/73194.596800/73194.596800/73194.596800/73194.59 Autonomy h 4 4 4 4 Disc brush (n.) mm/inch (2) 430/17 (2) 430/17 Cylindircal brushes (n.) mm/inch (2) 210x856 (2) 8,2x33,7 (2) 210x856 (2) 8,2x33,7 Brush pressure Kg/lbs 150/330,7 50/110,2 150/330,7 50/110,2 The advantages of NSC 85% less downtime Comac C85 scrubber dryer equipped with Non Stop Cleaning Premium system, not only reduces the unproductive loading and unloading times but, above all, it saves up to 80% of water and 90% of chemical. This is an high economical advantage, that minimizes the environmental cleaning operations without affecting the result. To save up to (1): WATER WASTEWATERPITCHEMICAL-80%-90%STOPTIME-85%-85% (1) use 3h a day, 5 days, with medium dirt grade, in Eco Mode. TECHNICAL DESCRIPTION C85 NSC BaseC85 BS NSC BaseC85 B NSC PremiumCS85 Tank capacity l/gal 300/79,2 300/79,2 300/79,2 Working width mm/inch 850/33,4 850/33,4 850/33,4 Squeegee width mm/inch 1105/43,5 1105/43,5 1105/43,5 Moving scrubbing brush head mm/inch 150/5,9 150/5,9 Working width with side brush mm/inch 1000/39.3 Working capacity up to sq.m/h/sqft/h 6800/73194.596800/73194.596800/73194.596800/73194.59 Autonomy h 4 4 4 Disc brush (n.) mm/inch (2) 430/17 (2) 430/17 Cylindircal brushes (n.) mm/inch (2) 210x856 (2) 8,2x33,7 Brush pressure Kg/lbs 150/330,7 50/110,2 150/330,7 Brush motor V/W (2) 36/750 AC(2) 36/750 AC(2) 36/750 AC(2) Brush revolution rpm 180 550 180 Vacuum motor V/W (2) 36/650 (2) 36/650 (2) 36/650 The advantages of NSC 85% less waste water 1800 314 commercial@godfreys.com.au580
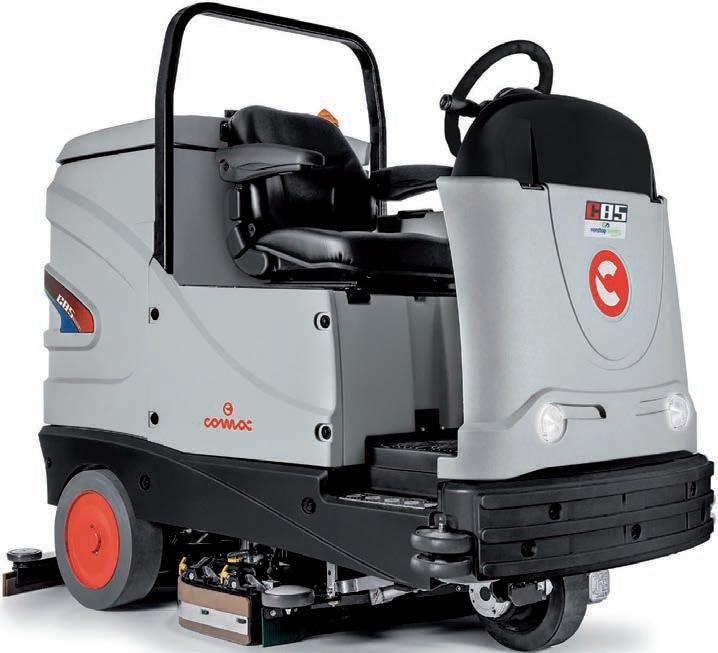

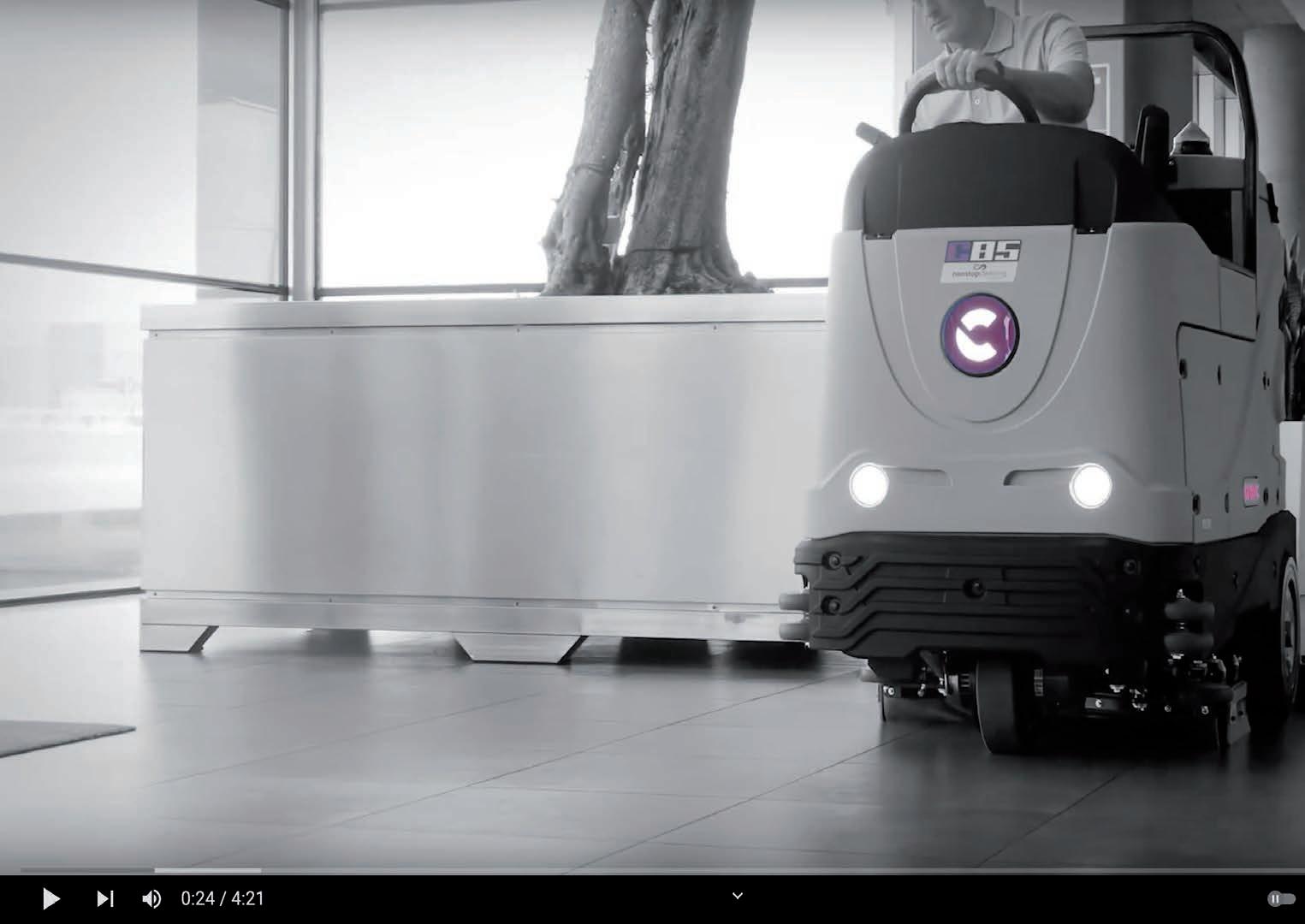
“There needs to be collection and recycling points and somebody who can re-manufacture it.
The British and some European countries are taxing virgin plastics. Ross estimates this to be a 20 per cent tax or 200-pound tax per ton in the UK but says the tax doesn’t apply to recycled plastics. The purpose is to
He says businesses could recycle a high percentage of their plastic waste with the right infrastructure in place. However, they’re still using threemillion-plus tons of plastic a year, which is going into landfills.
The 2025 targets – as Ross points out – aren’t law but are common goals companies should aspire to achieve.
Headifen founded Biogone 10 years ago. During that time, they have developed products that are recyclable and biodegradable –with an organic additive to help them biodegrade quickly when disposed of into a modern landfill. Now, the duo’s focus is on the 2025 National Packaging Targets (NPT).
John Mancarella and Ross
“A lot of companies are going to try and meet the targets, and other companies are doing half-hearted attempts,” Ross adds. “If you look at the current results so far, they’re going to miss those targets by 50 per cent. It’s probably going to get worse as we get closer to 2025. That’s why it’s imperative, in my view, to step up our game.”
John Mancarella and Ross Headifen, co-founders of Biogone, are encouraging Australian businesses to meet the 2025 National Packaging Targets by not buying or using virgin plastic products.
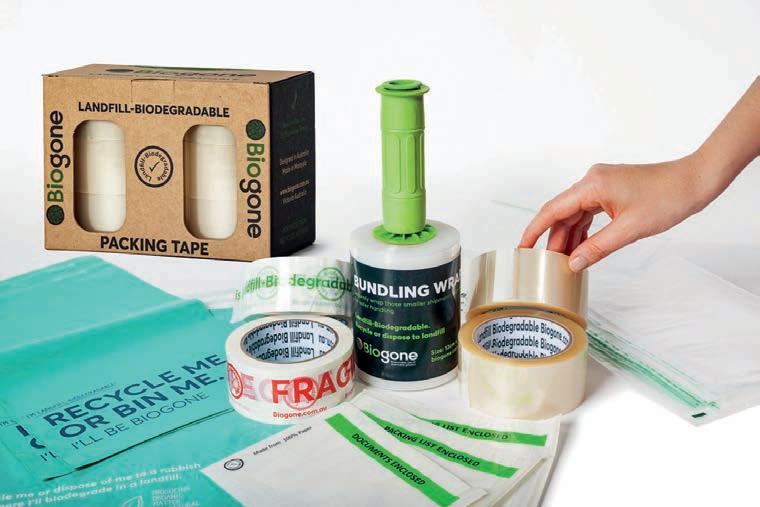
MEETING 2025 NATIONALTARGETSPACKAGING
products biodegrade in landfills within a few years instead of hundreds of years.
Biogone’s products biodegrade in landfills within years instead of hundreds of years. While John notes the preference is for the user to recycle, the accelerated biodegradation of Biogone products mean they won’t clog landfills indefinitely should they end up there.
“We’re only recycling 15 to 16
MHD SUPPLY CHAIN MHD SEPTEMBER 2022 | 512021COMAC©Copyright-12/21-AD-302534COD.equipamiento.aly/odiseñoalvinculadasestánnoyreferencia,simpledesonutilizadasimágenesLasequipamiento.dey/o times of the solution environmental impact of floor PremiumCS85 BS NSC Premium 6800/73194.596800/73194.596800/73194.596800/73194.591000/39.31105/43,5300/79,2850/33,44(2)210x856(2)8,2x33,750/110,2AC(2)36/750AC550(2)36/650
TARGETS AND CHALLENGES
The Biogone co-founders believe the debate will be ongoing. “A massive amount of infrastructure needs to be put in place to bring the plastic back from the end-user,” Ross says.
“Each user is going to have to sort their plastic out to a very high level. It’s not going to be one or two bins on the shop floor; it’s going to be a bin for plastic bags then different bins for otherDifferentitems.”types of plastics will need to be separated into LDPE or polypropylene or whatever other alternative plastics are used, notes John.
“The chances of getting the average consumer or warehouse person to do this is very slim,” Ross explains. “It's going to take a massive data collection program and a lot of infrastructure to get the spec and then that makes it very expensive. So why is an industry going to pay a lot more for recycled material if they can get virgin plastic knowing that the quality is high and keep making theirThisproducts?”isanother barrier he says industry needs to overcome.
INCREASING RECYCLING AND REDUCING WASTE
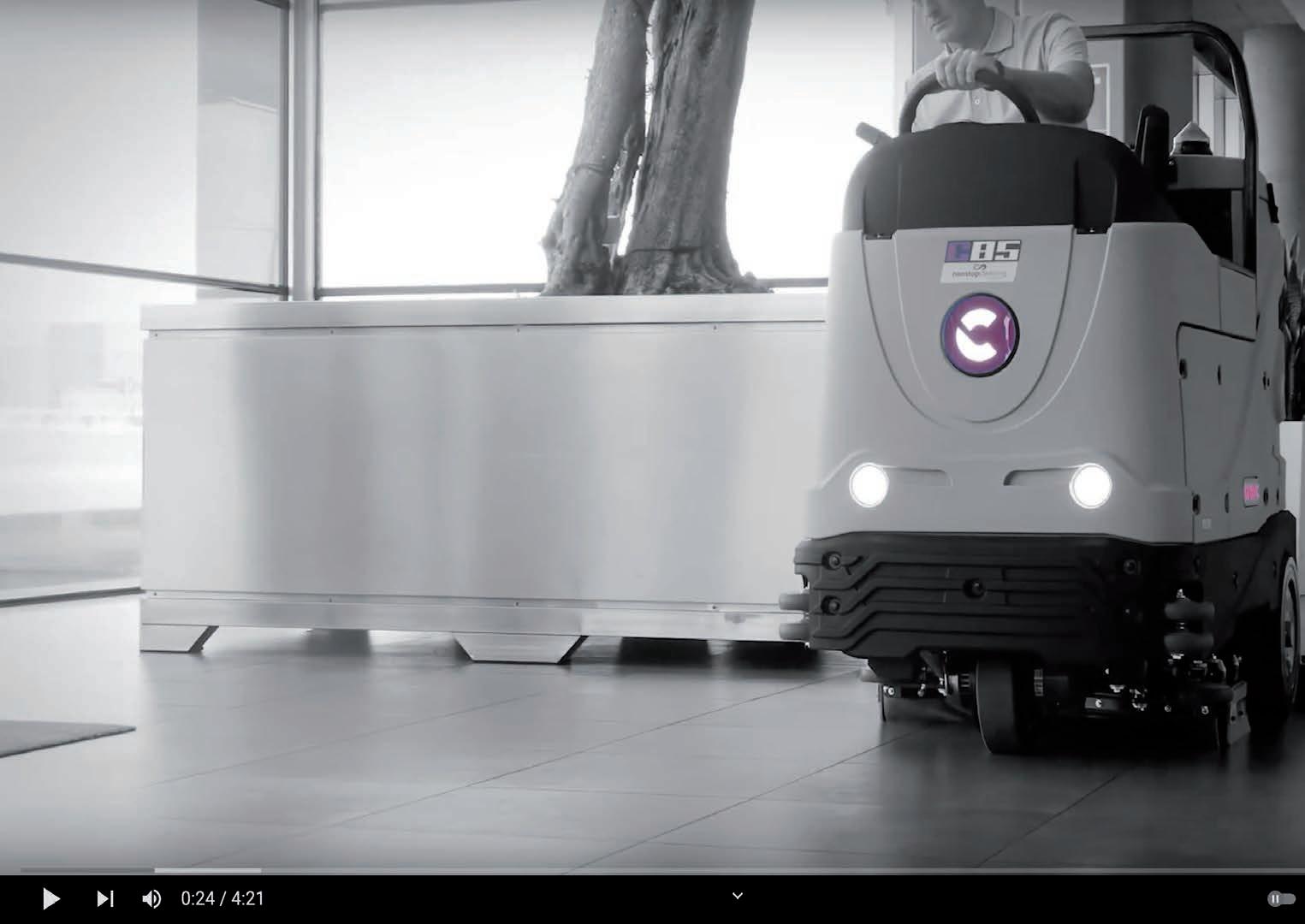
per cent,” Ross explains. “We went backwards last year, and the other 80-odd per cent of plastic going forward, is still going to need to be managed in some way for many years.”
Biogone’s
The two goals require changes from industry, government, and consumers. Ross and John say meeting the goals will be substantial and extremely expensive. Thus, the question is: who’s going to foot the bill?
With plastic waste, there’s no easy answer.
John and Ross say they chose this technology to develop Biogone’s products because it means they’re recyclable, and their embodied energy can be reclaimed at the landfill.
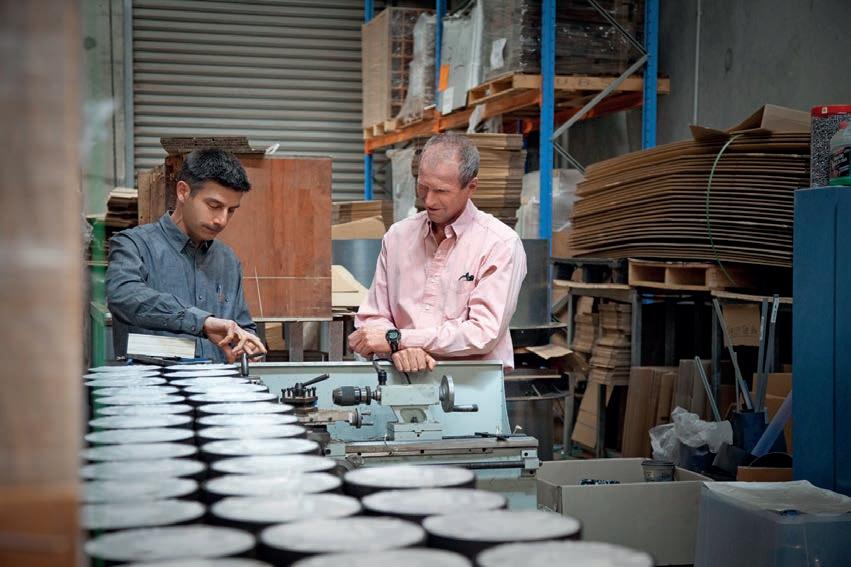
incentivise businesses to use recycled content instead.
■ MHD SUPPLY CHAIN 52 | MHD SEPTEMBER 2022
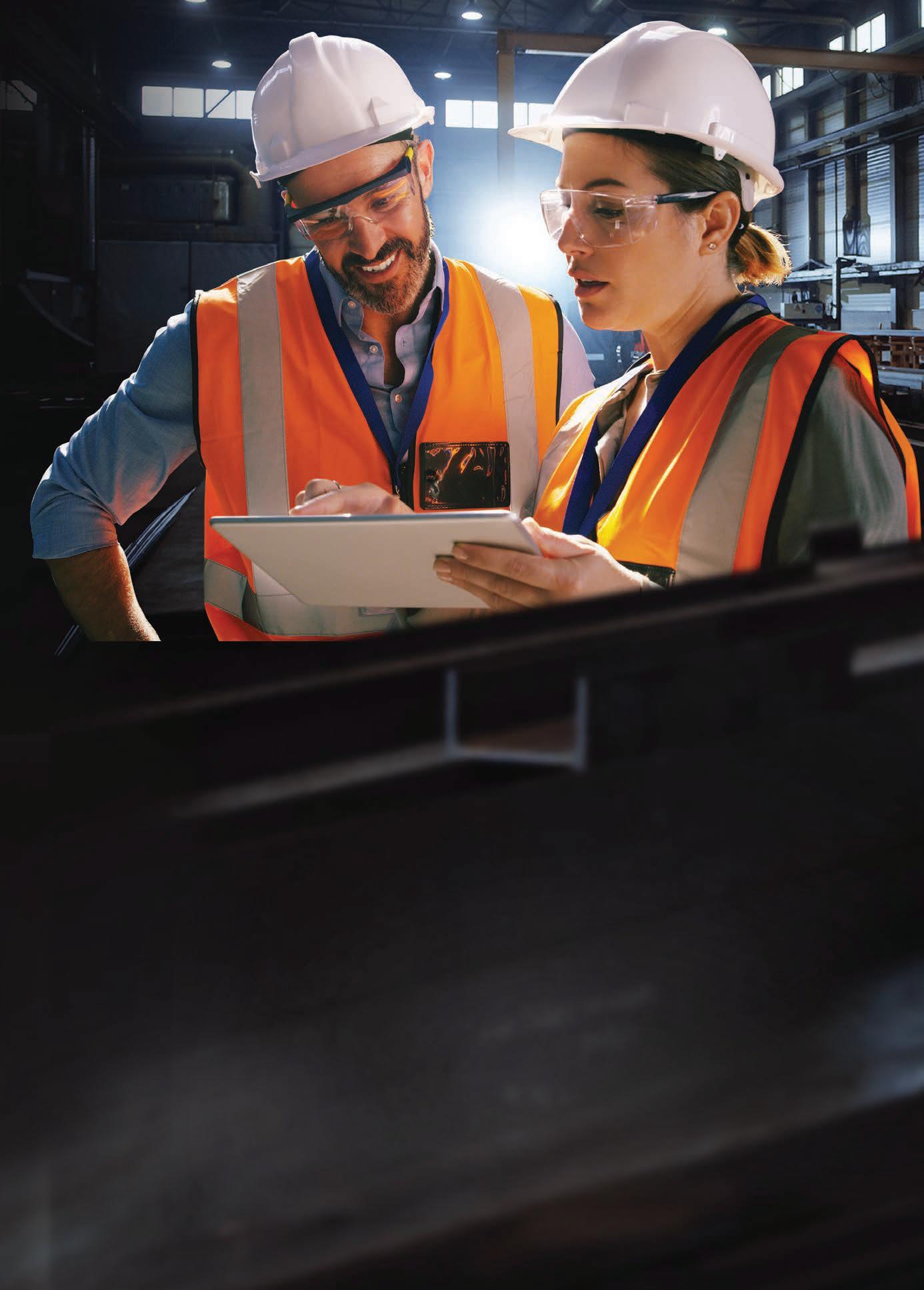
long will it take for Australia to meet these targets? Can we still recycle these problematic plastic products in years and decades to come?
PACKAGING AND SHIPPING
BIOGONE’S GOALS
The disposable facilities are not available for the general consumer and there’s no collection infrastructure for it to get to such a facility. Hence, it’s more than likely going to end up in a landfill where it won’t biodegrade.
It’s not recyclable, so it must be disposed. Home compostable is a modification to make it biodegrade at cooler temperatures. It requires the addition of a high-percentfossil-derived product to allow it to biodegrade at ambient conditions. The material has a short shelf life of nine to 11 months, making it tight to consider bulk stocking it in a warehouse.
Recycling involves recreating or repurposing a plastic product. John and Ross say it’s important that plastic is recycled like an aluminium can is recycled.“Thepurpose of recycling is that we don't have to import more virgin plastic to make a product. In theory, we could stop importing virgin plastic and just use material we have in the country now,” Ross explains. Hiding plastic waste in roads or concrete isn’t recycling as it doesn't stop the continued use of yet more virgin plastic material to produce the original plastic products – it’s not a circular path.
Businesses could recycle a high percentage of their plastic waste, but they’re still using three-millionplus tonnes of plastic a year and are depositing it landfills.into
“Because plastic is a molecular structure, not an atomic structure like a metal – unlimited recycling can't happen – unless you take it right back to its original constituents with some of these advanced recycling processes, which are still in the very early stages of proof of
“Technicallyconcept.it can be achieved, but the economics are still questionable. If you want to try those technologies, then you're going to have to pre-sort the plastic waste to a very high level, which adds another layer of complexity and expense to it.”
Commercial Compostable material requires a high temperature of 60 degrees Celsius, lots of active aeration and active moisture.
“In Australia, we are not big plastic producers,” Ross says. “We make three million tons worth of plastic products. Where’s the waste going to go? The government’s going to have to intervene, the producers are going to have to play a role in getting it back for recycling, and the consumers are going to have to be incentivised to return the product to a facility. Plus, they need to be deterred from buying cheaper virgin short life plastic products.”
Ross adds that some sources indicate virgin plastic is around a dollar a pound on the international market – which is roughly two dollars a kilogram – but recycled plastic is five-to-eight dollars a kilogram.“Askingindustry to start paying three times for their raw materials – that won’t go down well,” notes Ross. “Maybe the government can give businesses more incentive to use recycled,” John suggests.
“It makes more sense to target the people who are making the problem products to start with,” he says regarding whether the government should tax manufacturers of unsustainable products.
The questions he asks are what does the 2025 NPT real timeline mean? How
“The infrastructure that’s required includes facilitating high recycling rates,” John says. “Infrastructure is also needed to help recyclers get the product back – because the average business doesn’t have this ability.”
The first choice is for it to be recycled and if that doesn’t happen, it’ll go to a landfill where it’ll biodegrade, and the product’s energy can be utilised.
It’s still not recyclable and is perpetuating the liner economy, not a circular one.
As the product biodegrades, the gases it releases can be turned into green power, notes John.
The virgin tax the UK has is what Ross says is more appealing to the businesses using higher cost recycled plastics, a model which can perhaps be copied in Australia.
Biogone provides its products nationally and to New Zealand. John says there’s no difference in quality or shelf life when Biogone’s products are compared to a similar conventional product.
“It’s a better option because it’s recyclable, and if it’s not recycled, then it will biodegrade in a landfill – this is why it’s the best option as a commercial or warehouse product,” he adds.
“It can be stored in the same way that you have conventional plastic. It can be used in the same way as the same strength and functionality.”
“We try to educate people about the shortfalls of conventional plastic,” Ross adds. “It’s up to us to convince business by business to use our products.
procore.com StartsConstructionSmarterwithProcore Get real-time project visibility, and improved accountability across all stakeholders with Procore LEARN MORE ⟶
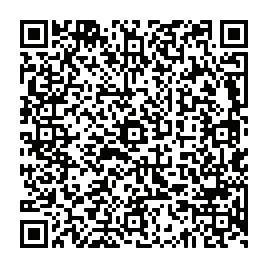
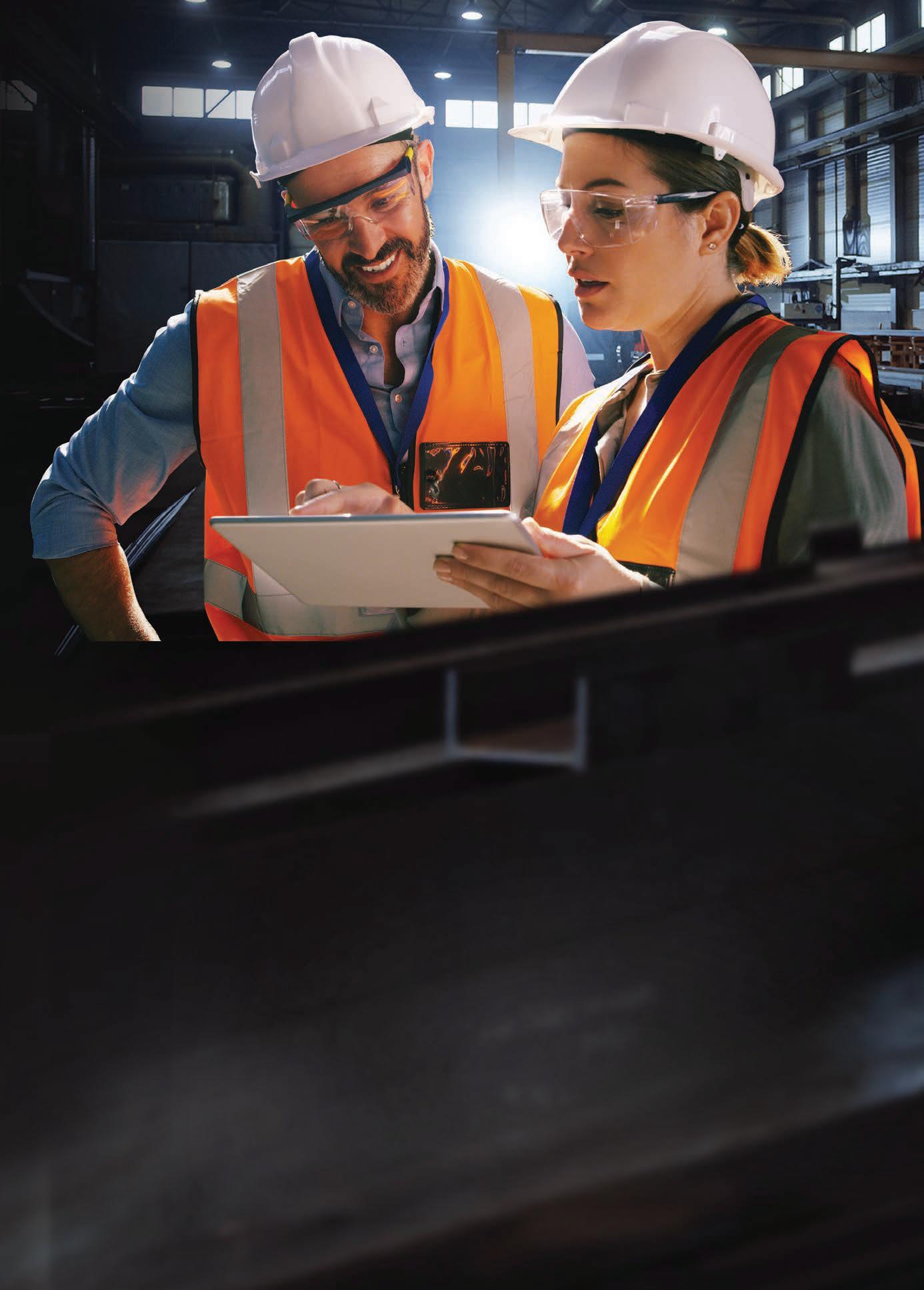
KEEPINGSPACESCOMMERCIALCLEAN
Godfreys has nine Service and Repair centres across the ANZ region, and its extensive distribution network covers Melbourne, Perth, Brisbane,Auckland.and

IMPORTANCE OF EDUCATION
O
doors in June of this year, but it’s now offering tours for clients and customers along with training and educational experiences.
Godfreys has been operating for more than 90 years and besides its logo being associated with its retail operations and offer of vacuums for domestic use, the company also trades via wholesale and online channels, including e-commerce, service and repairs, and distribution.
It provides its specialist commercial floorcare solutions for key segments via its direct sales channels. These are suited not only to industrial spaces such as logistics, warehousing, and manufacturing but to retail, aged and healthcare, and accommodation.
“Our showroom serves two different purposes,” Daniel Pisaniello, General Manager Commercial and Industrial
Daniel Pisaniello, General Manager Commercial and Industrial Division at Godfreys unveiled the cleaning company’s new Altona-based showroom on Wednesday August 10. MHD attended the industry event and spoke to him about Godfreys’ foray into the commercial sector with its range of cleaning products for industrial spaces.
MHD WAREHOUSING 54 | MHD SEPTEMBER 2022
One of Godfreys’ main brands called Comac is based in Italy where it manufactures floor scrubbers and sweepers.
n Wednesday August 10, Godfreys, the iconic Australian distributor of domestic and commercial floorcare and cleaning products for the Australia and New Zealand (ANZ) region, unveiled its Melbourne-based, new Commercial Office and Showroom dedicated to its Commercial division. The centre initially opened its
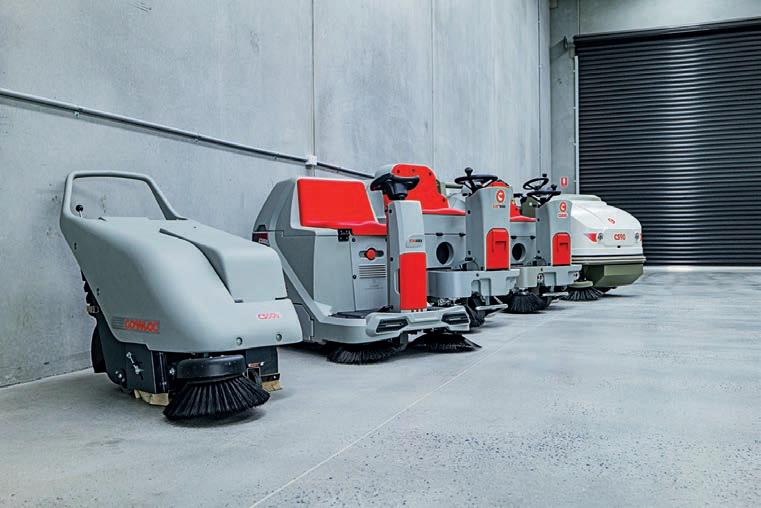
By doing this, users of the Godfreys’ cleaning products in the commercial and industrial spaces can avoid having to replace their equipment when they change warehouse or distribution centre or hire new operators who clean these
“Our floor scrubbers ensure that the floor is dry so we can reduce any liabilities with regards to wet floors where people can have accidents by walking and slipping.”
“Instead of filling up with water and emptying out dirty water every day, it only needs to be done weekly. The filtration system also stops a lot of those nasty particles going into our stormwater drains and it helps maintain a high level of cleanliness.”
Godfreys has several exclusive brands like Comac, Pullman, and Rosemor. It also has a range of unique cleaning products: backpack vacuums, canister vacuums, escalator cleaning machines, floor scrubbers, floor sweepers, stick vacuums, travelator cleaning machines, and wet and dry vacuums.

One of Godfreys’ main brands, Comac, is based in Italy where it manufactures floor scrubbers and sweepers, which Daniel says provide
great efficiencies and come in a variety of “Thesizes.Comac range is reliable and they’re great quality products, so the customer knows that they’re purchasing equipment that is built to do what they require on-site,” he adds.“Whether it’s a very dirty site, a dusty site, daytime cleaning, or nighttime cleaning, the machines cater for those different scopes of requirements because if cleaning is required during the day – the machines have an eco-mode – which reduces the machine’s noise level, so it doesn’t create any disturbances.
Godfreys looks at the market to see what gaps need to be filled. Training and education are a core focus. Indeed, it’s one of the fundamental pillars in the company’s structure and is part of its go-to-market strategy; it offers this in-house and on-site.
GODFREYS’ PRODUCT RANGE
Division, Godfreys, says. “One, it’s a showroom and training centre for our staff. Two, it’s so we can continuously educate our customers about our products. It helps us lift our brand up because it’s not about selling a product, it’s about the whole package: product with sales support and repairs, which is very important to us.”
“Wefacilities.offercertain packages within our pricing that incorporate a maintenance program. This way the customer is getting a two-in-one package so we can support them after they’ve purchased the machine.”
Godfreys has nine Service and Repair centres across the ANZ region, and its extensive distribution network covers Melbourne, Perth, Brisbane, and Auckland.Distribution is facilitated through
These are just some of the solutions Godfreys offers its commercial clients.
“We encourage everyone to come visit our new showroom in Altona, so we can walk you through not only the showroom itself – but the best cleaning solution for your business.”
■ MHD WAREHOUSING MHD SEPTEMBER 2022 | 55
“If we don’t educate our customers and give them the full support, it can result in short-term business,” Daniel explains. “We want longterm business, which involves our customers returning for their second or third After-salespurchase.”support and educating customers on maintaining the equipment they buy is important because it ensures that the products remain functional for a long time and this helps reduce costs as well as downtime, notes Daniel.
Godfreys has several exclusive brands like Comac, Pullman, and Rosemor.
multiple warehousing retail outlets, providing door-to-door supply. Godfreys Commercial and Industrial Sales provide freight services for all interstate and country deliveries with a 10,000-pallet warehouse as its head office.“One of the unique products within our range is a large ride-on scrubber that would traditionally be used in a warehouse or logistics environment,” Daniel explains. “This product contains a special filtration system where it recycles the water for five days so it not only provides efficiencies for the operator, but it also reduces the amount of chemical and water that the operator will need to use.
Use Biogone for packing and shipping products to help meet the 2025 National Packaging Targets
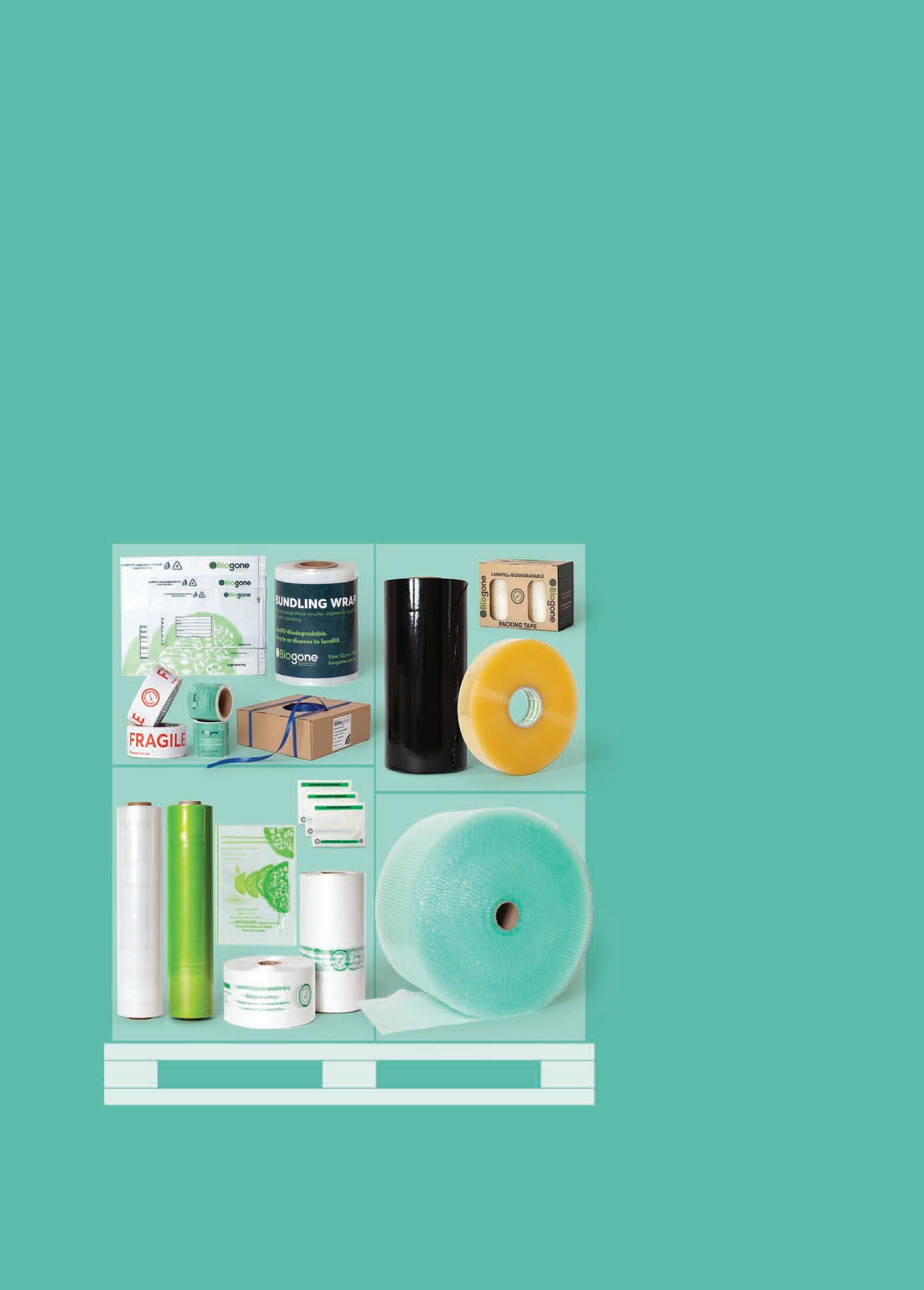
Another differentiator of HUBTEX Australia is its strong service philosophy, which has been present from day one –and has grown with the company, with offices in Sydney, Brisbane, Melbourne, Adelaide and Perth. Illustrating its high customer retention, HUBTEX’s very first customers are still with them today, Bruce says.
For the future of HUBTEX, Bruce expresses a desire to branch out further into New Zealand and Asia.
“It’s a huge market that’s undersupplied at the moment in terms of multi directional sideloaders, and we think that this could be a good regional headquarters that we could run the Asian operations from.”
While big players in the materials handling space primarily specialise in handling pallets, Bruce says the HUBTEX point of difference lies in handling
W
“The niche was to offer a machine that was a safer alternative to the way people were working with long products,” HUBTEX Australia CEO Bruce Peatman says.
Founded in 1995 and based in Riverstone in NSW, the original company Parry Forklifts changed name to HUBTEX Australia in 2000, and changed ownership in 2020. HUBTEX Australia initially specialised in textiles machinery and expanded to include machinery for other materials like timber, steel, and plastic. During 2020 ownership transition, founder Bill Parry passed over the reins to Bruce, while remaining in a managerial capacity, ensuring that the best of the Hubtex Australia traditions continue under the new owner.
hen it comes to operating forklifts within narrow aisles in the material handling industry, an issue that many have faced is being able to carry long load products safely. HUBTEX Australia is in a unique position to address this challenge.
HUBTEX Australia has carved out a niche as specialists in compatiblenarrow-aisleforklifts.
“It’s something we’re proud of, and we never rest in trying to keep it going and improve it,” he says. “We want to keep growing, providing a good service to our
“A company who we’ve dealt with for quite a few years have experienced phenomenal growth and they have a real need to automate at some point. But in the meantime, they need to store more product, and they’re looking at their storage density and how to improve it,” Bruce“They’veexplains.worked out that per square metre, they can double their storage space by using our equipment – high bay racking, narrow aisles, and store the product with that. That will create 100 per cent more storage capacity.”
HUBTEX Australia CEO, Bruce Peatman, takes MHD Supply Chain through the company’s upward trajectory navigating its customers’ narrow aisle needs and providing long load solutions for bulky goods.
In a climate where industrial vacancy rates are tight, HUBTEX Australia is particularly able to service growing companies that need to access more space in their warehouses.
customers so that when it comes down to buying new equipment, we’re the first port of call.”
“We’re not competing with other forklift companies – we serve a niche market for someone who wants to maximise their storage capacity. Everything is based around that narrow aisle philosophy.”
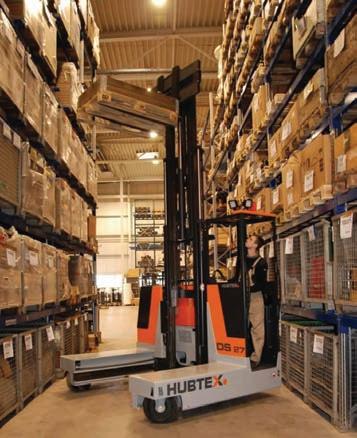
long products in a narrow space –and maximising storage capacity for its customers.
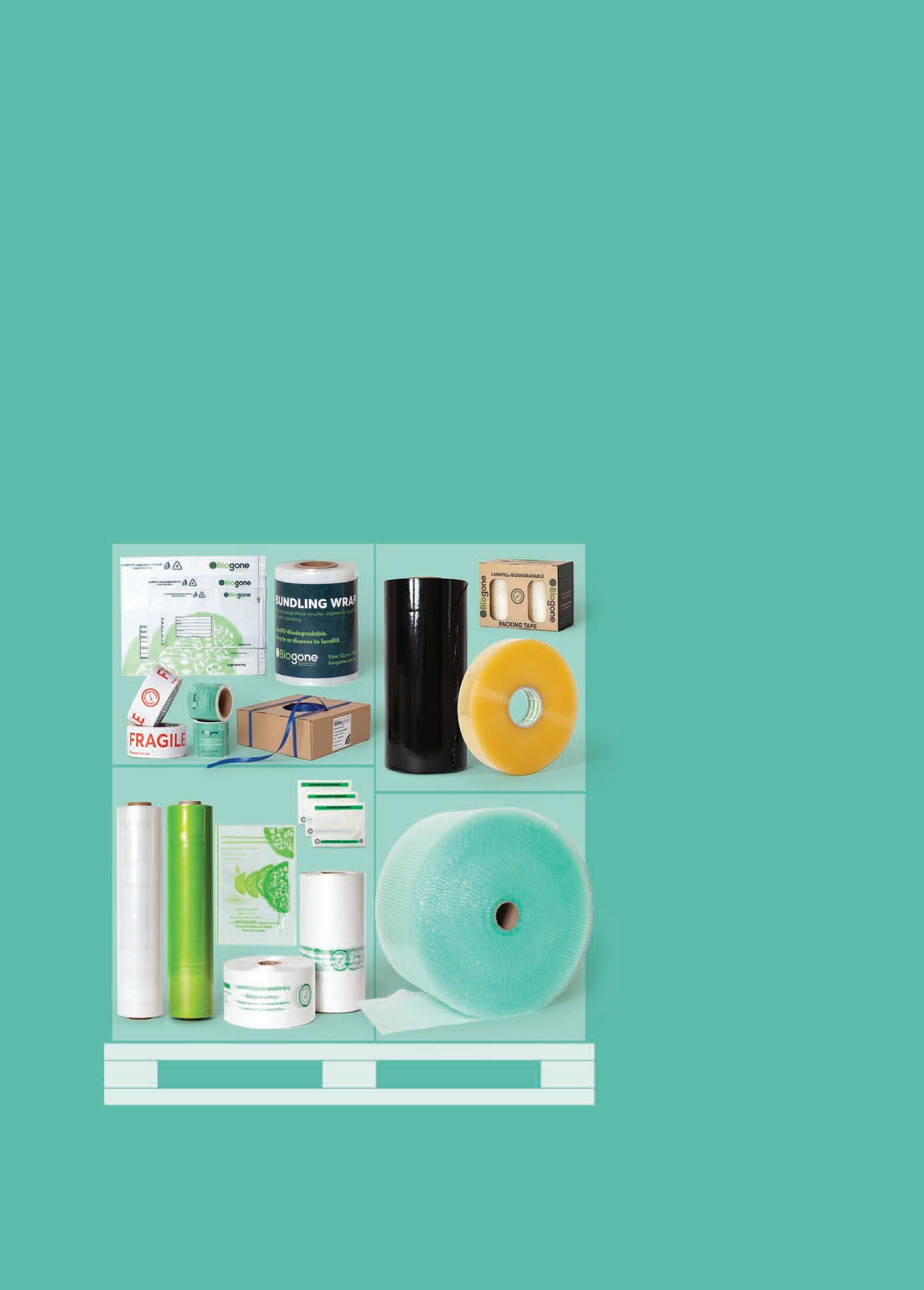
With a vast amount of parts in stock around the country, HUBTEX aims to provide its customers with easy access to after sales support regardless of their location.“We’ve always carried a lot more spare parts than other dealers and we carry them as close to the machines as we possibly can,” Bruce says.
“For example, we have the Bendi forklift, which is great for handling pallets in very narrow aisles,” Bruce says. “When you’re talking narrow aisles and space saving, that’s where we come in.
“Our machines can drive in all directions. We can unload a pack of timber off a truck, drive through a normal roller door into a factory, and store that pack of timber in racks in a guided aisle. If you’re handling long products in narrow aisles, that’s the machinery that we provide.”
HUBTEX also ramped up its new Hubtex and Bendi equipment stock to deliver anywhere quickly during the pandemic.
HUBTEX is a leading supplier of multidirectional forklifts and side loader fork trucks for handling long loads in narrow aisles. As an authorised distributer of global brands such as HUBTEX, Bendi, Drexel, Bulmor, Systraplan and Hoppecke, the material handling industry has benefited from its tailor-made solutions for more than 25 years.
■
A HUB FOR LOAD SOLUTIONSLONG
“New Zealand is a market that we already service, but we would love to be positioned there in our own right. Also, we have Asia on our doorsteps and there’s every possibility that we can service Asia from our base in Australia,” he says.
MHD SEPTEMBER 2022 | 57 MHD MATERIAL HANDLING
platform and brand that will help to accelerate your career in the commercial property sector in WA.”
“I look forward to leveraging my relationships and insights to unlock industrial investment and development opportunities for Colliers’ valued clients across the Perth market,” Catherine says. “I saw Colliers as a leader within the commercial real estate industry and I wanted to learn from the best.”
olliers is a name that is synonymous with sales, leasing, industrial property, and exceptional service. In January this year, it opened its new operations in Perth, Western Australia (WA) under its national business.
COLLIERS CEMENTING ITSELF IN WA
Hammond, Director, and Catherine van der Walt, Executive, both working alongside Hayden servicing WA’s Industrial market. Together they work on industrial sales and leasing, project and pre-commitment leasing, and back and speculative development.
Yields have remained steady in Q2 2022 and reflect the higher spread to the East Coast, which to date has provided somewhat of a buffer to rising funding costs.
Colliers has expanded its operations in Western Australia (WA) with its new Perth-based division, St Georges Terrace office, and growing team. Hayden Dick, Senior Executive Industrial, gave MHD insights into the investment management company’s role in Australia’s largest state, its approach to serving its clients, as well as its projects, investment opportunities, and plans for the mining capital.
Sam Hammond, Director Industrial at Colliers.
“We are thrilled to have Sam join the team,” Richard says. “He is a highly regarded market leader and plays an integral role in the growth of our Industrial and Logistics business in WA. Colliers provides an opportunity to work for a leading global property services organisation that has a market leading national
58 | MHD SEPTEMBER 2022
In Capital Market Sales, they work closely with their interstate counterparts such as Gavin Bishop, Managing Director Industrial and Sean Thomson, Head of Industrial Capital Markets, as well as other operatives across the national Colliers located in Melbourne, Brisbane, and Adelaide.
SERVING CLIENTS
Hayden Dick, Senior Executive Industrial at Colliers was promoted from Executive Industrial Sales and Leasing to his current role at the start of the year, in which he focuses on selling and leasing industrial assets in Australia’s largest state.
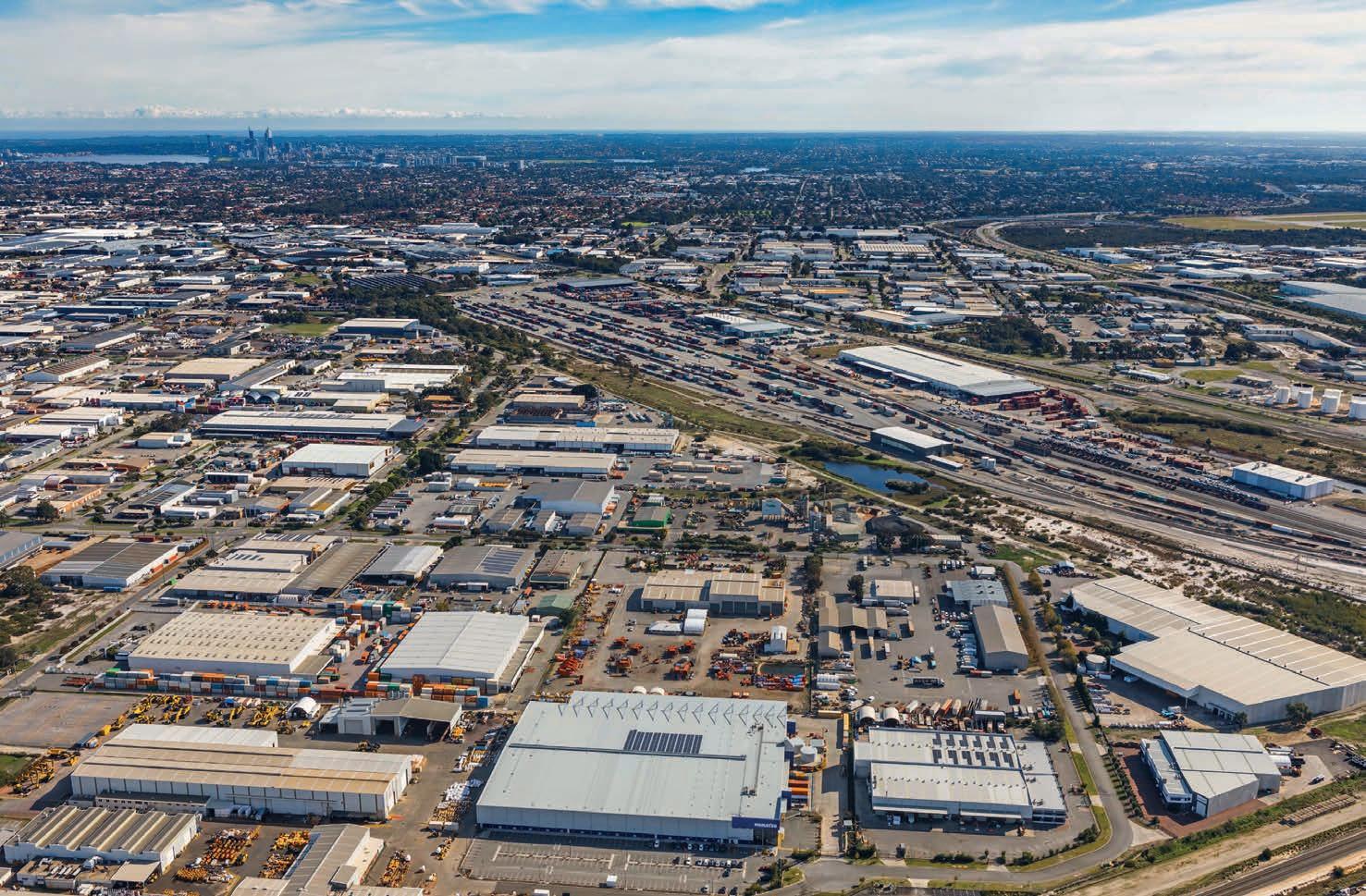
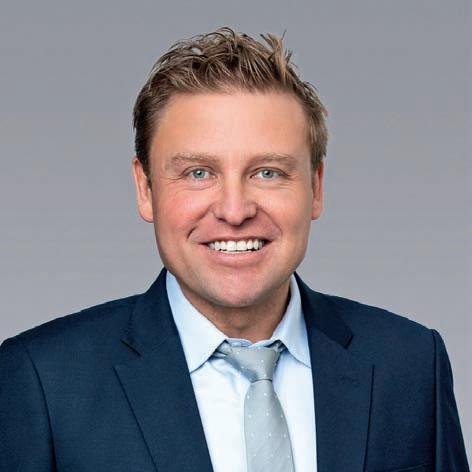
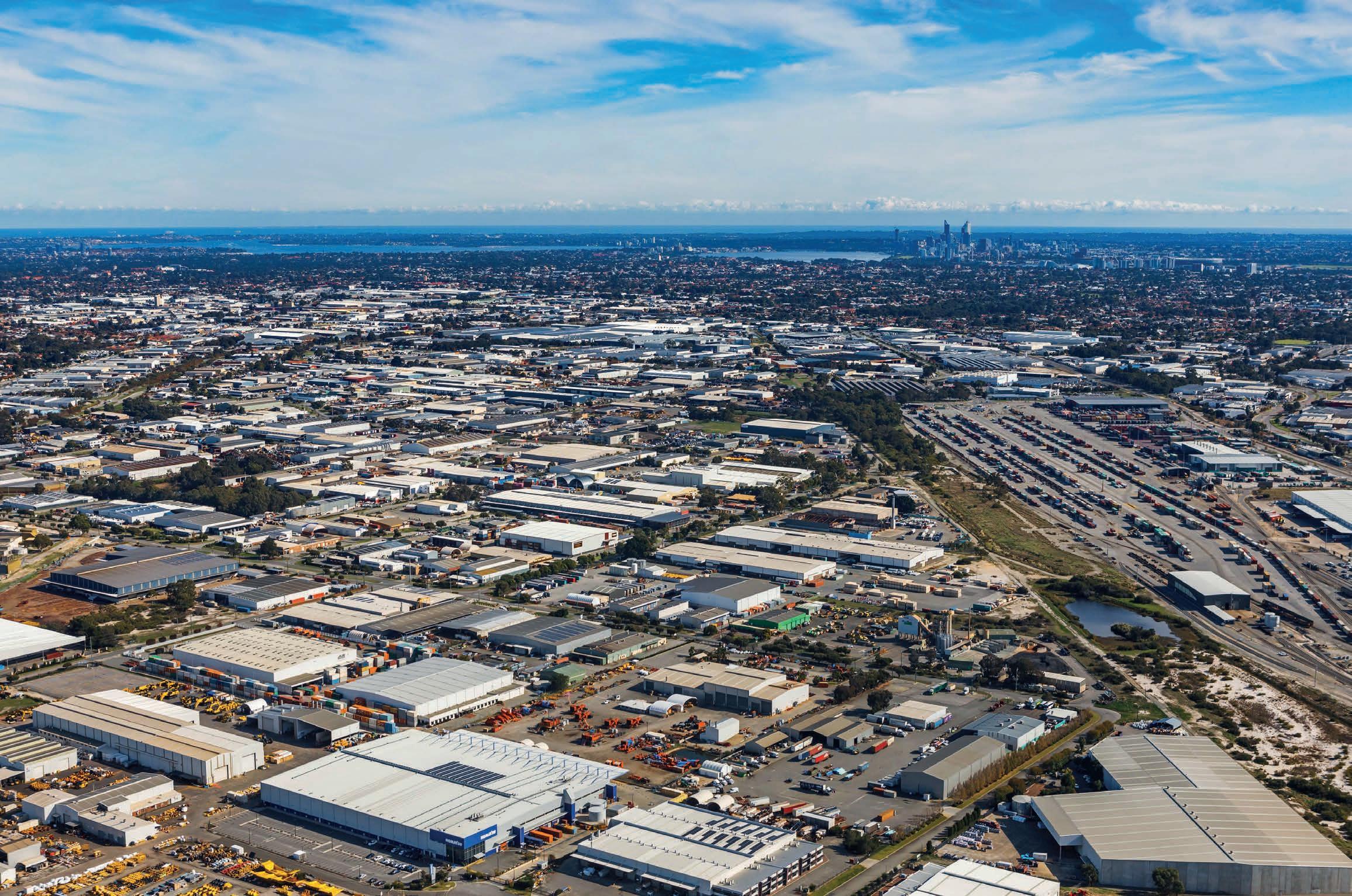
Expanding its operations in Industrial, Colliers appointed 15-year expert, Sam
As someone who has worked at Colliers for the past three years and completed a double major in Property and Finance as part of his Bachelor of Commerce degree, Hayden understands how to professionally service and add
Hayden says the collaboration between office locations nationally and internationally is second to none, sharing key insights and learnings for Colliers’ clients to use to their advantage.
Since opening its new companyowned operation on January 1, 2022, the Colliers team has expanded to include local market leaders across capital markets, sales, leasing, valuations, facilities management, research, and real estate management services.“Wehave been very pleased with the number of high-quality operators expressing interest in joining the Colliers owned operation in Perth as it provides a market leading platform to accelerate their success in the industry,” Richard Cash, Colliers State Chief Executive for WA, says.
COLLIERSFOOTPRINTEXPANDINGINWA
MHD PROPERTY FOCUS
C
FUTURE OF COLLIERS IN WA
He also says it’s important that there’s frequent communication and alignment during campaigns, so clients are kept well-informed that Colliers’ agents are representing their needs.
Colliers, on behalf of its national client, The Lester Group, has recently launched a pre-lease state-of-theart transport and logistics facility at 111-121 McDowell Street in the centre of Welshpool, one of Perth’s premier industrial locations.
The site provides great flexibility and can accommodate developments ranging from 10,000 sqm to 20,000 sqm.Colliers has been engaged by Australia’s largest listed pureplay industrial fund, Centuria Industrial REIT (ASX: CIP), to provide leasing services for its speculative development within the prime Perth industrial precinct of Canning Vale.
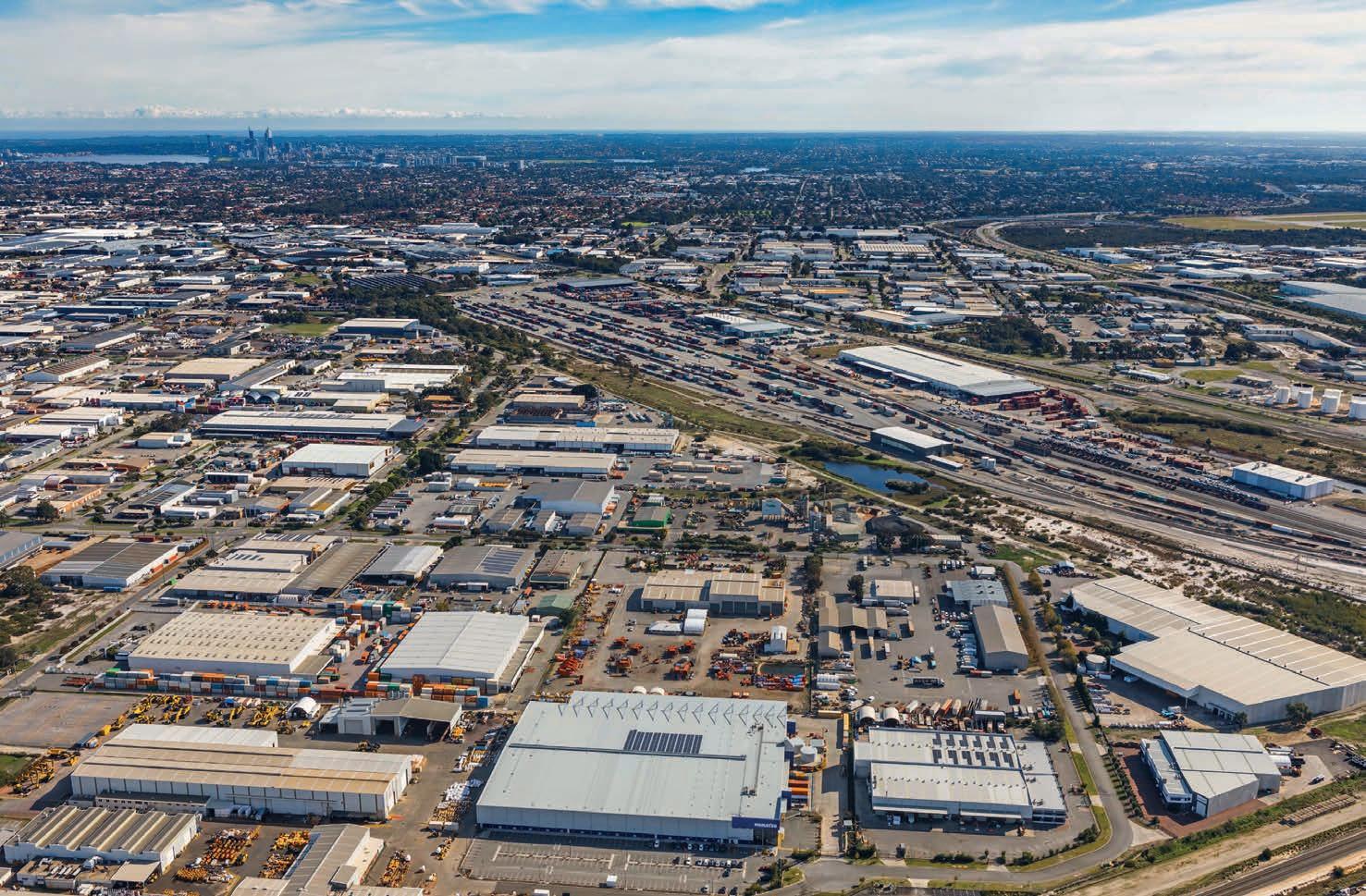
Hayden further adds that “Colliers provides us with an elevated platform to support our continued growth and ensure we continue to maximise the potential of the business to accelerate
value to a client’s portfolio.
OPPORTUNITIESINVESTMENT IN WA
MHD SEPTEMBER 2022 | 59
BROUGHT TO YOU BY
“Over the next few months, we will continue to expand our service offering to the WA market and make further high-calibre appointments from industry professionals in WA and further afield,” Richard says.
Yields have remained steady in Q2 2022 and reflect the higher spread to the East Coast, which to date has provided somewhat of a buffer to rising funding costs. Prime yields currently average 4.93 per cent while secondary is higher at 5.79 per cent.
Hayden Dick, Senior Executive Industrial at Colliers.
“With vacancy rates the tightest nationally, this rare opportunity to occupy a large-scale facility in a supply constrained market is a prime example of a product being created to meet market demand at the right time,” Hayden says.
Colliers’ WA team has recently been appointed on several significant projects, notes Hayden.
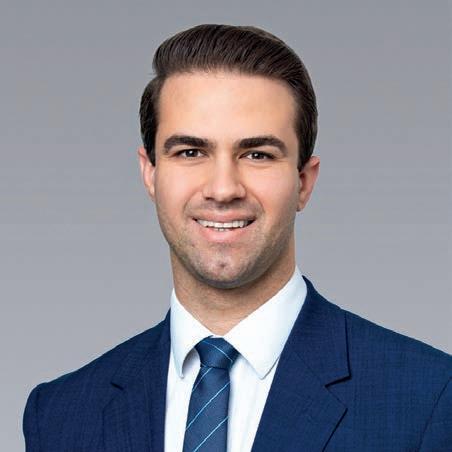
“I think the biggest part is knowing the market inside-out and making sure that you’re on top of the recent trends, especially here in Perth where the market is changing so frequently,” Hayden explains. “It’s important to have relevant and up-to-date data to make informed decisions for our clients’ properties to achieve the ultimate outcome.”
Catherine van der Walt, Industrial Executive at Colliers.
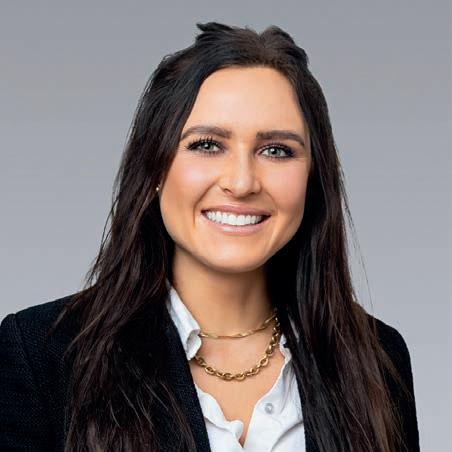
Investment volumes for industrial and logistics assets in Perth were at their highest level on record during 2021.
Investment volumes for industrial and logistics assets in Perth were at their highest level on record during 2021 with approximately $1.9 billion trading, up from $170 million in 2020. Almost $130 million was transacted up until Q2 2022.
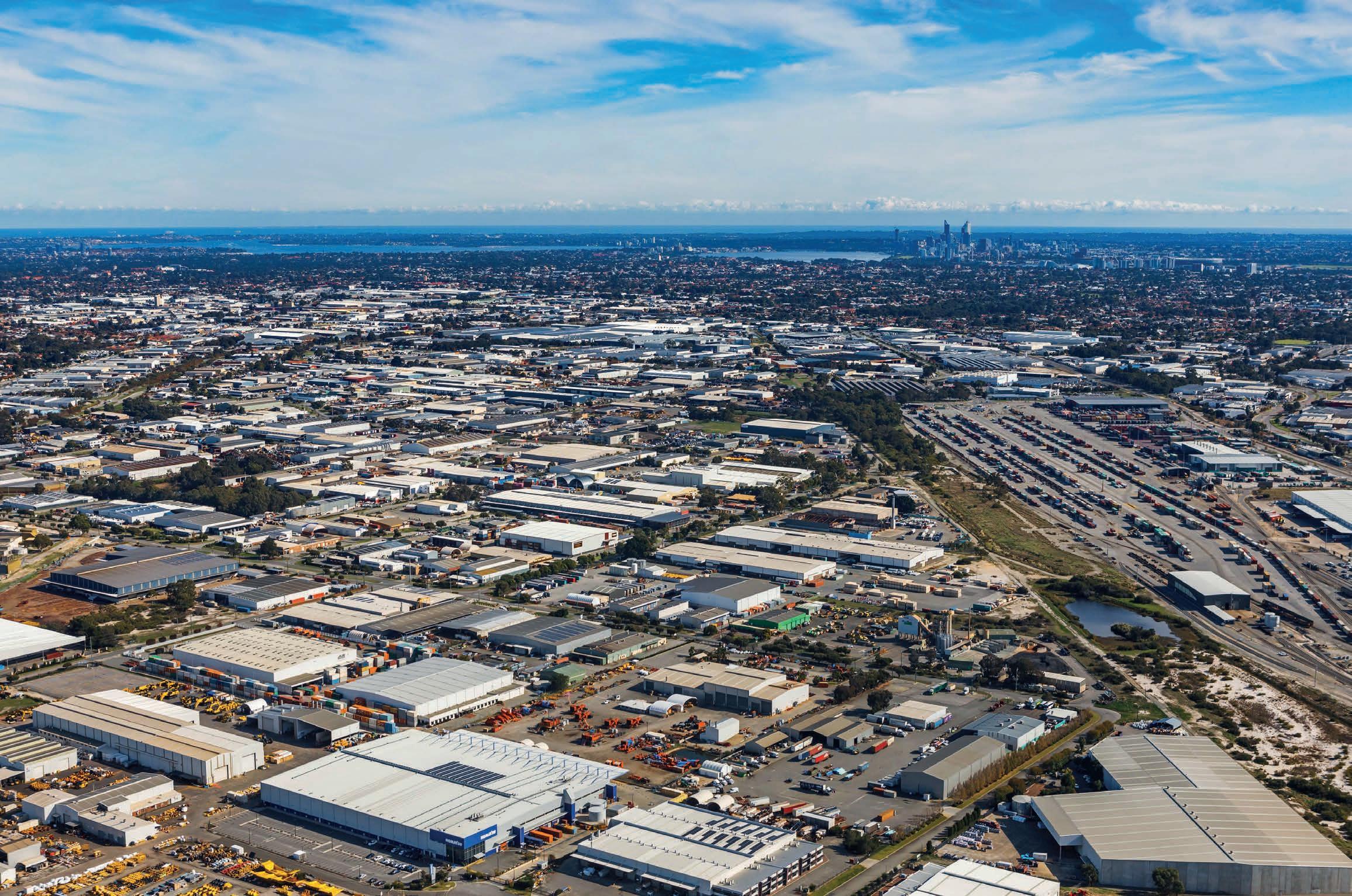
COLLIERS’ PROJECTS
Institutional interest for industrial assets in Perth has grown substantially, particularly over the past 12 months with many perceiving the market to offer value and upside when compared to the East Coast. However, large portions of the core industrial market are controlled by a number of high-net-worth individuals who continue to expand portfolios as opposed to divesting, which has
With practical completion expected in June 2023, this rare opportunity with premium exposure to Bannister Road will deliver approximately 12,300 sqm of modern sustainable industrial product with a 5-star Green Star target rating.
From working with Australia and New Zealand’s largest retailers and logistics companies, the Prological team share their innovative approach for developing Greenfield sites, and how this new way of thinking could save businesses in excess of $60 million in the case of a large development.
“Moving on from this, in our new white paper, ‘Rethinking warehouse design: Integrating innovation, from concept to delivery’, we discuss the pressures of the industrial property market, as well as the limitations of traditional approaches to site development.“Throughour recent research, we have discovered that the traditional way of planning and developing a Greenfield site is no longer fit for purpose – and mistakes in this process are currently costing organisations millions of dollars.”
With this fresh way of thinking, Prological
AUSTRALIA’S INDUSTRIAL PROPERTY MARKET: AN OUTLOOK
FLIPPING GREENFIELD DESIGN ON ITS HEAD
“It has been widely reported that Australia’s industrial property landscape is reaching record heights when it comes to rent costs (high), vacancy rates (low) and land availability (scarce),” says Peter Jones of Prological Consulting.
“ Through our recent research, we have discovered that the Greenfieldandwaytraditionalofplanningdevelopingasiteis no longer fit for purpose –currently costingin thisand mistakesprocessare organisations millions of dollars.
NEW WAYS OF BUILDING A GREENFIELD SITE
By 2026, the total value of investment-grade industrial property in Australia is set to surpass the office sector, by which time the Australian industrial and logistics industry is forecast to reach $424 billion. Occupier rates have also reached record highs, as have rent rates for both primary and secondary grade assets as the market struggles to cater for the growth in e-commerce as well as lack of available space. This combination of factors means traditional approaches to site development are no longer feasible: the way in which facilities are designed, built and operated must now change.
Until now, the most common process for site development began with estimating the footprint of the facility, choosing an adequate size site, and then fitting the warehouse with machinery and equipment. However, with the rapid pace of innovation, scarcity of available land and the proliferation of agile automation, this approach is no longer feasible. Today, traditional warehouse layouts are no longer fit for purpose, rents are too high and engineering is introduced too late in the development process.
Here’s a preview of Prological’s exciting new white paper, which can be explored in full by following the link at the bottom of the article.
“In Prological’s recently published white paper ‘Five processes to improve before you invest in automation’, we explored these challenges and offered several steps for organisations to complete before embarking on any automation journey.
” 60 | MHD SEPTEMBER 2022
Prological Consulting has released a new whitepaper on the changes in the industrial property landscape, its future-focused solution to site development, and how innovation is saving retail customers millions of dollars. Here’s a preview.
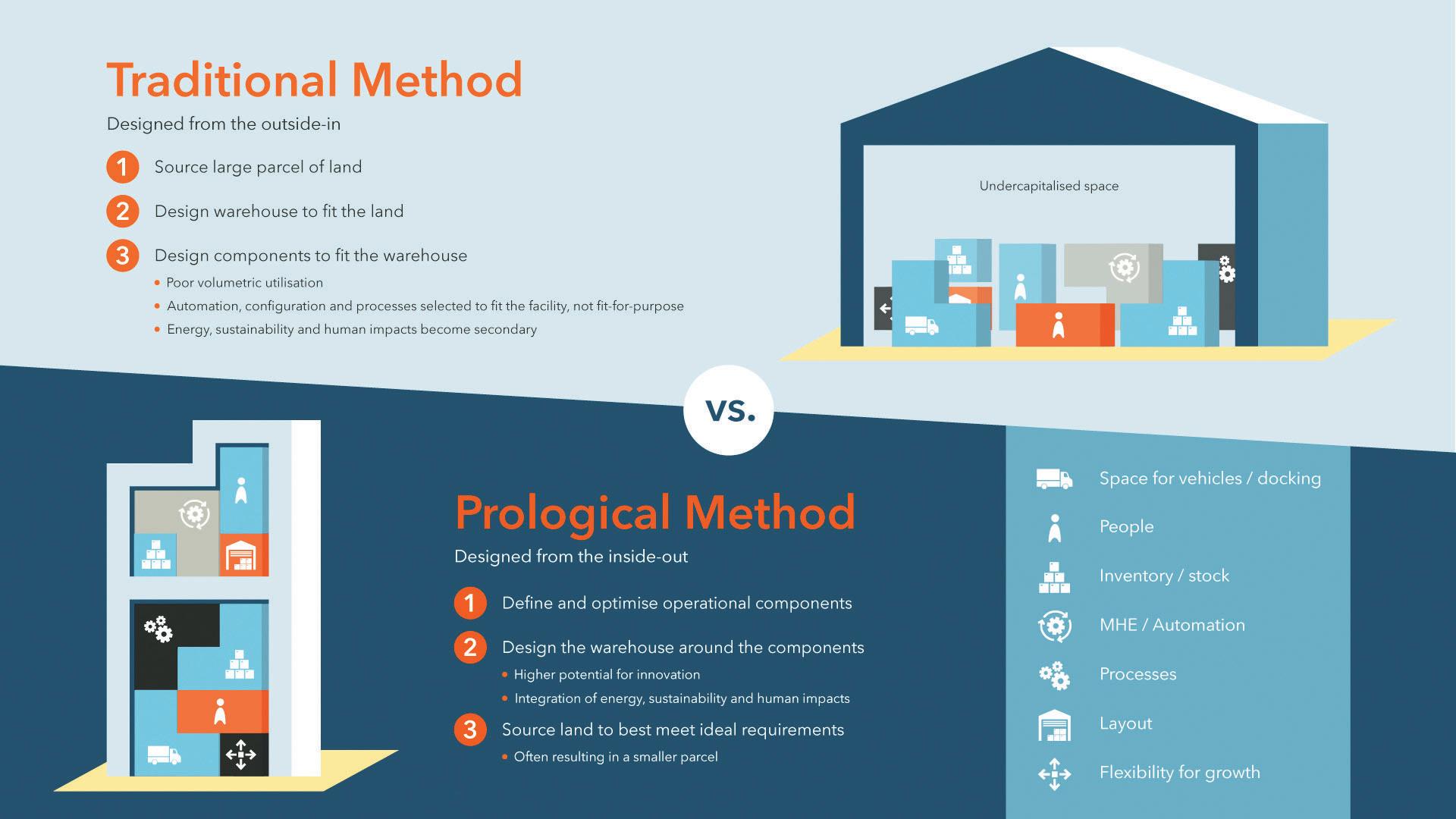
Pent up demand from consumers for online retail, and the continued unreliability of global shipping has pushed many businesses to expand into new facilities to meet rising demands.Recentdata from CBRE declared Australia’s industrial property market is the tightest in the world, with vacancy rates tumbling to 0.8 per cent in July 2022.
For the team at Prolological, the opportunity to innovate was clear. What if the fit-out design was done before the land was acquired? What if automation was considered early on, to optimize supply chains and reduce the size of warehouse space required? What would it mean to build vertically, not just horizontally? For Prological customers, these critical questions resulted in projected savings for customers that will in some instances be millions of dollars per annum.
3. Improving customer experience with faster, more accurate delivery times
4. Attracting, retaining and optimising staff through human centred design
Peter Jones, Founder and Managing Director of Prological.
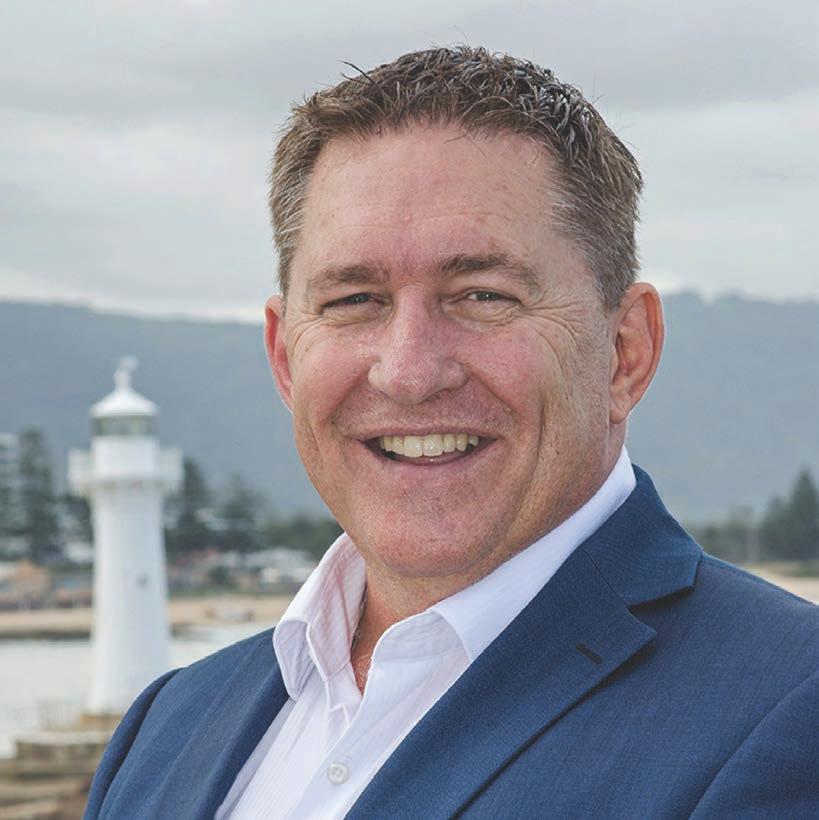
MHD SEPTEMBER 2022 | 61
Furthermore, its practical recommendations show where to begin and what to consider, based on Prological’s proven expertise in this evolving field. ■
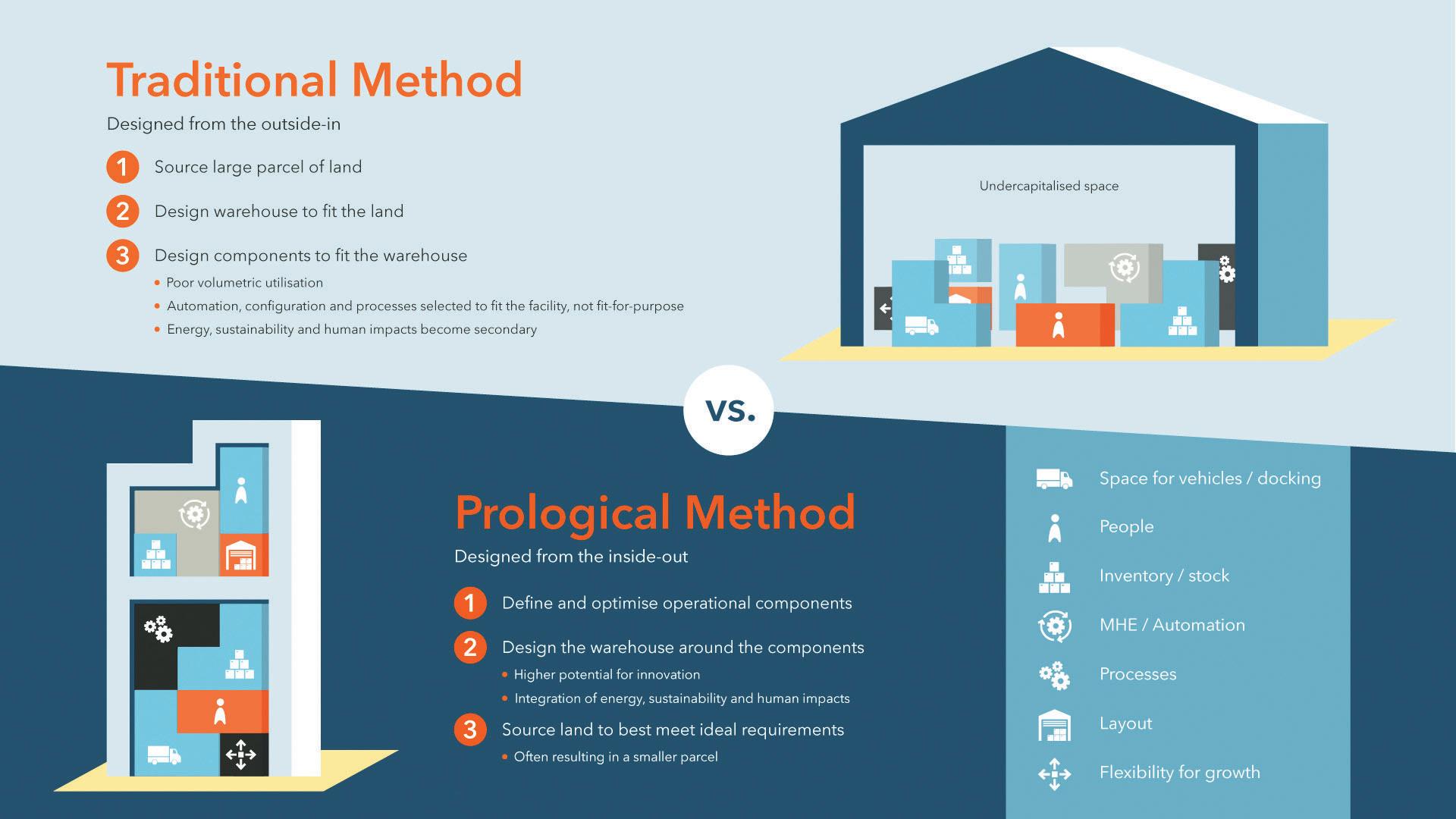
have uncovered a number of lucrative benefits for their customers and for the industry as a whole, including:
5. Becoming known for innovation from shareholders, staff and customers alike
2. Increased sustainability through warehouse positioning, thermal efficiency, reducing heat footprint and leveraging natural sunlight
The whitepaper examines how a commitment to innovation from the outset can produce significant benefits for customers who are faced with increasing market pressures.
To read Prological’s new white paper in full, use the QR code.
1. Reduced travel time through optimising production and work zones from the outset
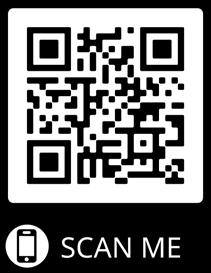
E
The Frank Vale Award has been awarded annually since 1993. This award is to acknowledge driven, emerging leaders within the industry. They must be 35 years of age or younger, have worked in the cold chain industry for a minimum of three years and have demonstrated to their employers that they have the potential to become future leaders; to
arlier this month, the Refrigerated Warehousing and Transport Association (RWTA), in conjunction with Swisslog and ASKIN Performance Panels, launched the inaugural 'RWTA Frank Vale Tech Tour'. This tour gathered Frank Vale Award participants, emerging leaders in the Australian Cold Chain to attend multiple automated sites in Sydney. Not without difficulty, this was an exercise in patience as COVID affected many attempts to proceed over the last two years.This opportunity was to encourage these cold chain future leaders to meet one another, network, and experience first-hand the future of their careers in automation.Companies visited included the likes of Blum Group, Linfox, BevChain and Coles. Experiencing the use of how automation can improve the working processes of warehouse and maximising the output of the existing labour force to promote safety and productivity was
MHD learns about the inaugural RWTA Frank Vale Tech tour, conducted in conjunction with Swisslog and ASKIN Performance Panels.
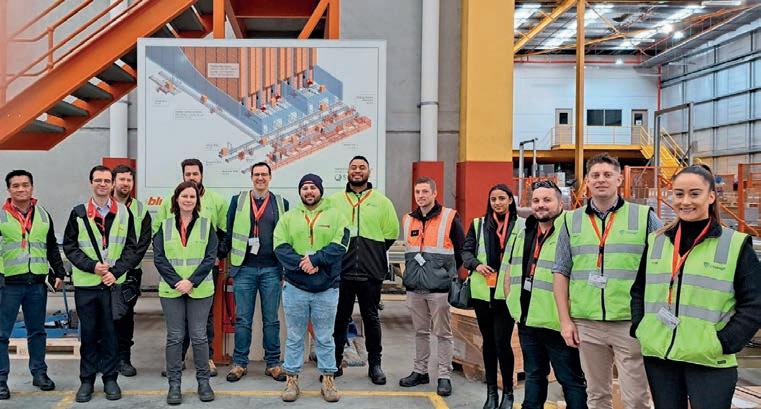
incredible for all who attended.
THE RWTA FRANK VALE TECH TOUR
Companies visited included the likes of Blum Group, Linfox, BevChain and Coles.
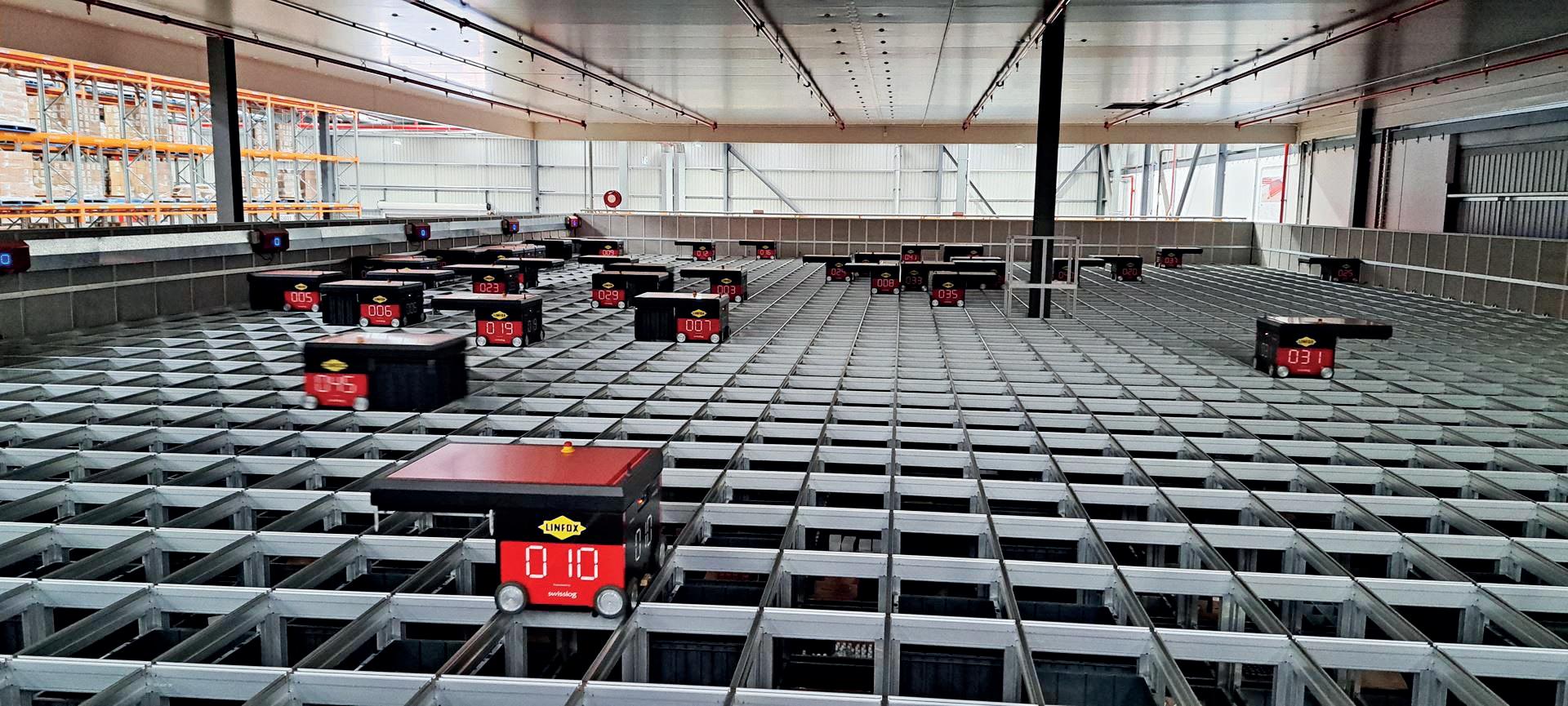
MHD RWTA 62 | MHD SEPTEMBER 2022
make a positive contribution to the development of the Australian Cold ChainStateIndustry.Finalists and their partners travel as special guests of the RWTA to attend the Annual RWTA Conference and Exhibition, with all travel, conference registration, accommodation and meal expenses of the State Finalists, and their partners, being met by the RWTA.
To read more about the Award, visit www. rwta.com.au/frank-vale-award
Attending the RWTA Conference and Exhibition provides State Finalists with an outstanding opportunity to broaden their knowledge and understanding of the Australian Cold Chain Industry, along with the opportunity to meet many of the key players.
MHD RWTA MHD SEPTEMBER 2022 | 63
The tour was a fantastic opportunity to see automation in a variety of sites. It was beneficial having existingintegratedhowtechnologyinsightpresentSwisslogtoprovideintotheanditmightbeintoouroperations.
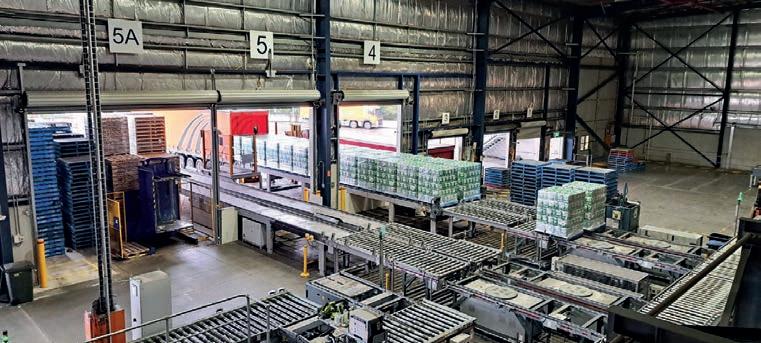
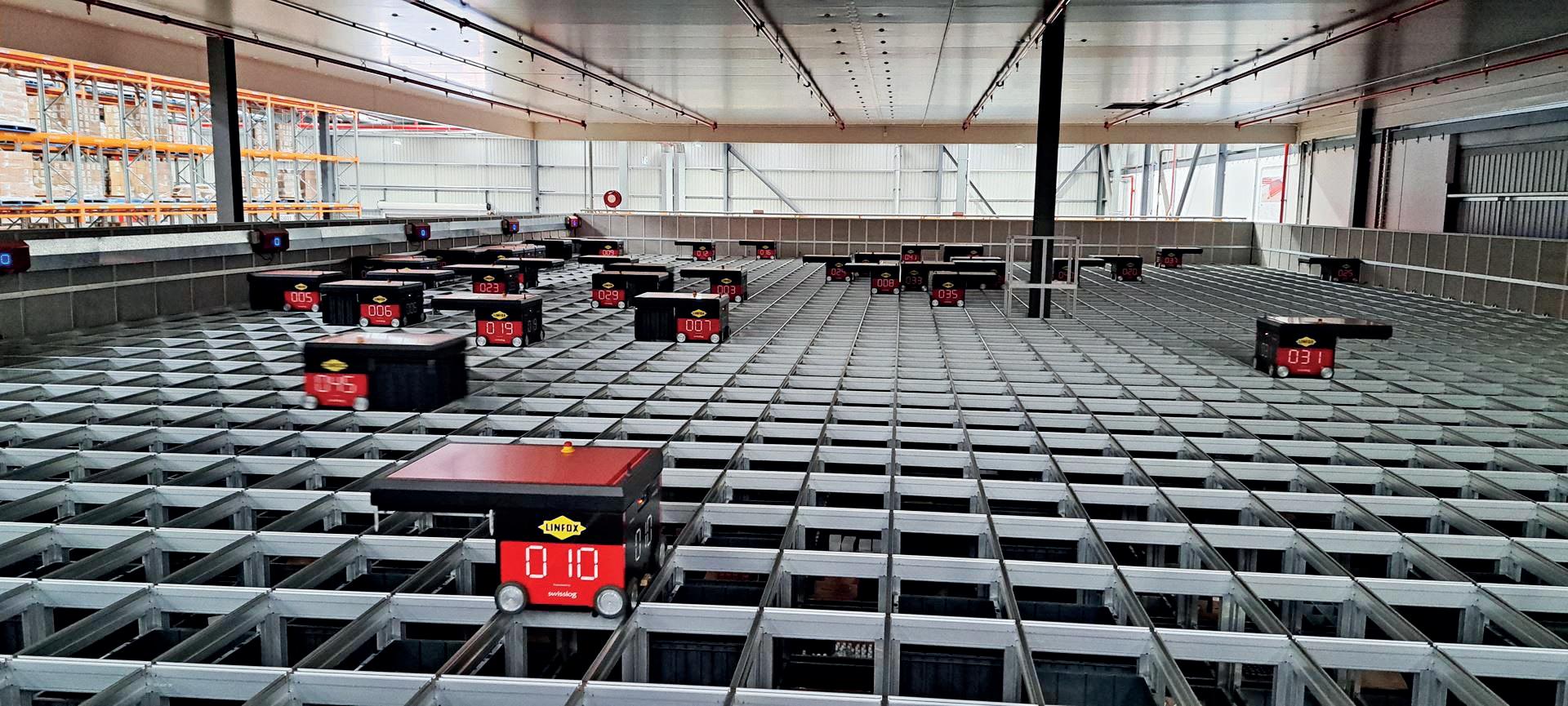
“ Thank you for hosting a fantastic day that insightfulwasand a great opportunity to catch up with the Frank participants.Vale
This prestigious award, now in its 28th year, provides a unique opportunity for employers to acknowledge the contributions and talents of outstanding young professionals, our future leaders of the Australian Cold Chain. Participation in the Frank Vale Award is a truly rewarding experience for all involved. Previous candidates speak of the great sense of personal pride they experienced, upon learning that
Demi Hiriaki, Frank Vale Award Winner 2019
This prestigious award, now in its 28th year, provides a unique opportunity for employers to acknowledge the contributions and talents of outstanding young professionals.
”
their employer had nominated them for this acclaimed Industry Award. They also speak of the personal and professional growth that accompanies theTheexperience.National Award Winner is flown to the United States of America to compete on an international stage annually. ■
”
Liam Neilly, Frank Vale Award Winner 2021
“
The Frank Vale Tech Tour in action.
The RWTA would like to acknowledge Swisslog for organising its automation partners to create an unforgettable day and to ASKIN Performance Panels for the sponsorship and the continued support of the RWTA Frank Vale Award.
Intelligence (BI) Award, ASCL Start-Up Award, ASCL Training, Education & Development Award, ASCL Future Leaders Award, ASCL International Supply Chain Award, ASCL Automation, Robotics or Emerging Technology Award, ASCL Environmental Excellence Award, ASCL Industry Excellence
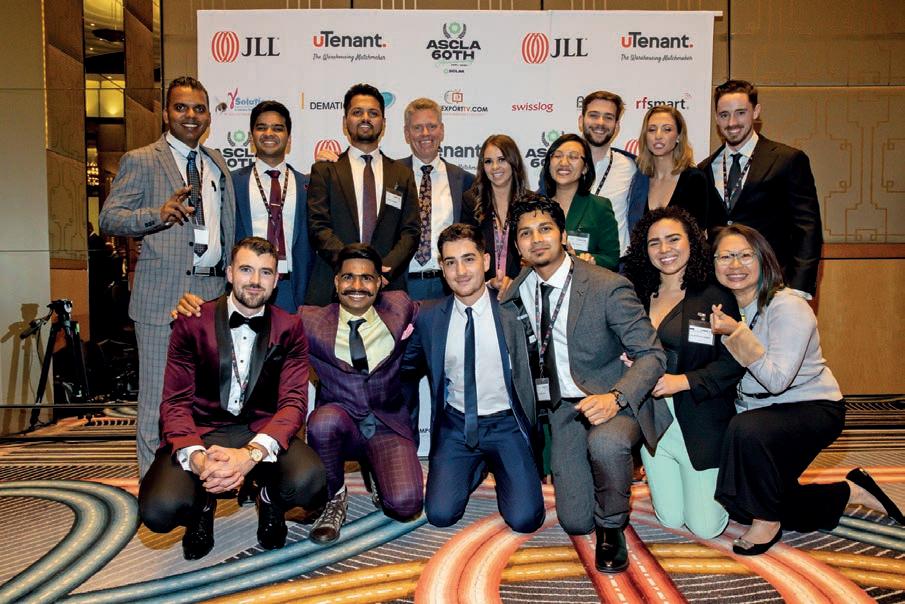
Winners announced at the ASCL Awards Gala Dinner on November 4,
Submissions close on September 23, 2022.Finalist/Shortlist announced on October 3, 2022.
he Supply Chain and Logistics Association of Australia (SCLAA) is calling for submissions to the Australian Supply Chain and Logistics Awards (ASCLA) with the closing date fast approaching. The award categories include ASCL Supply Chain Management Award, ASCL Big Data, IT & Business

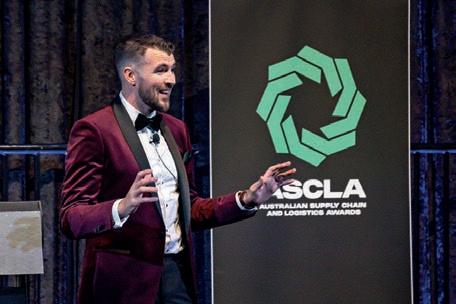
Sue Tomic, Board Chair of the SCLAA, giving her speech at ASCLA.
MHD SCLAA 64 | MHD SEPTEMBER 2022
Award, and ASCL Judges’ Choice Award.
T
Overview of the 60th annual ASCL Awards in March 2022.
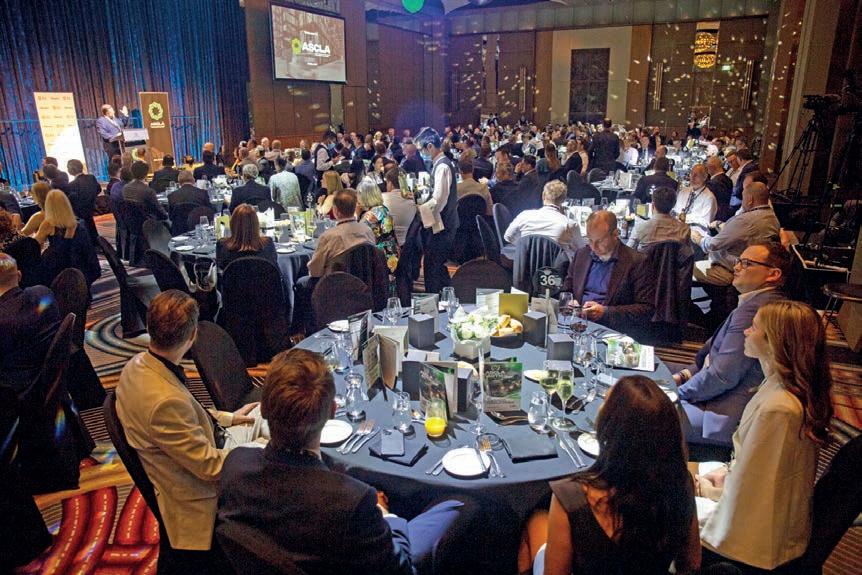
SCLAA CALLING FOR ASCLA SUBMISSIONS
Kyle Rogers, co-founder of uTenant and Independent Director of the SCLAA speaking at the ASCLA.
Members of the SCLAA board at the March 2022 ASCLA.
Winners of the ASCL Awards.
The Supply Chain and Logistics Association of Australia (SCLAA) will hold the Australian Supply Chain and Logistics Awards (ASCLA).
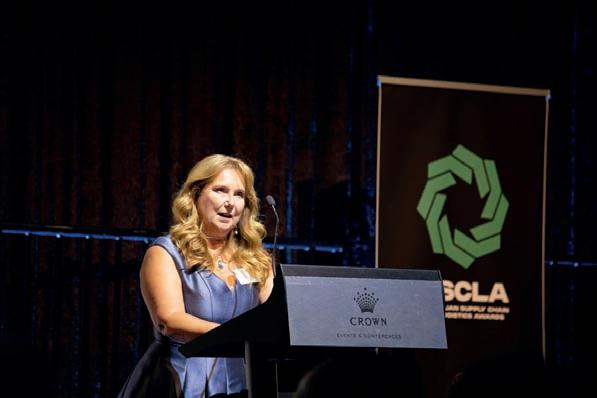
O2I – MULTICODE READER
For more information visit www.ifm.com/au/en
MHD PRODUCT SHOWCASE MHD SEPTEMBER 2022 | 65
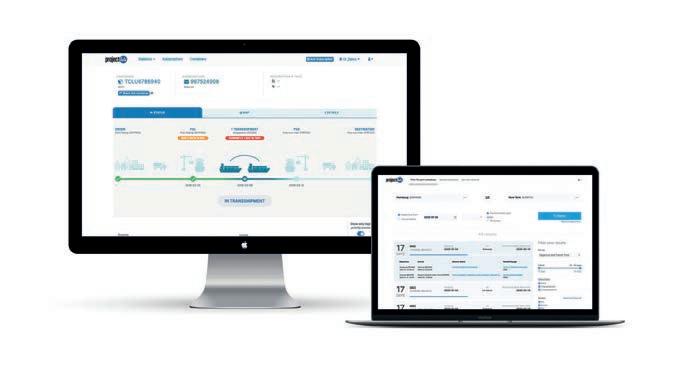
PROJECT44 OCEAN VISIBILITY
For more information visit www.project44.com
For more information visit www.combilift.com/combi-mr4
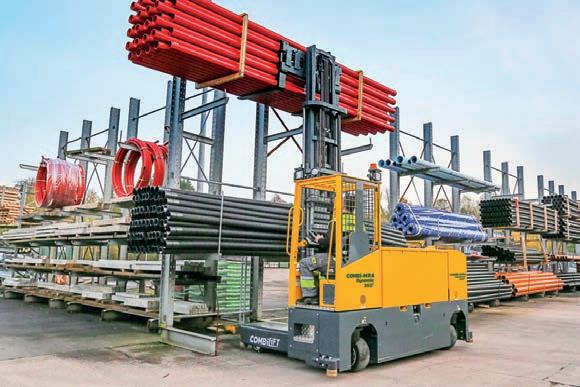
Poor ocean visibility puts a strain on global supply chains, logistics costs, and customer service. At the root of the issue is low-quality data that hinders personnel productivity, streamlined operations, and proactive exception management. Today, more than ever shippers and 3PLs need global ocean visibility with the data quality, intelligence, ETAs, and proactive exception management that ensures efficient, cost-effective, reliable, and sustainable global transportation. project44’s Ocean Visibility solutions is here to help, with a suite of solutions that uses first-in-class data and analytics to improve personnel productivity, allow for proactive exception management, reduce logistics costs, improve customer service, and empower users for agile transport planning and procurement.
DYNAMIC 360° ™ STEERING
Since Combilift launched its first C4000 model in 1998, multidirectional capability has been one of the major hallmarks of the company’s wide range of handling solutions. 24 years and thousands of R&D hours later, its latest product takes multidirectional capability to the next level. The Combi-MR4 is a 4-wheel electric powered multidirectional reach-truck, which incorporates Combilift’s new Dynamic 360° ™ steering, which provides rotation on each wheel, enabling seamless directional change of the truck while on the move. The system allows this extremely agile forklift to work in forward, sideward and crab steer mode, guaranteeing swift operation and excellent manoeuvrability. Hence the full name of the new model: the Combi-MR4 Dynamic 360.
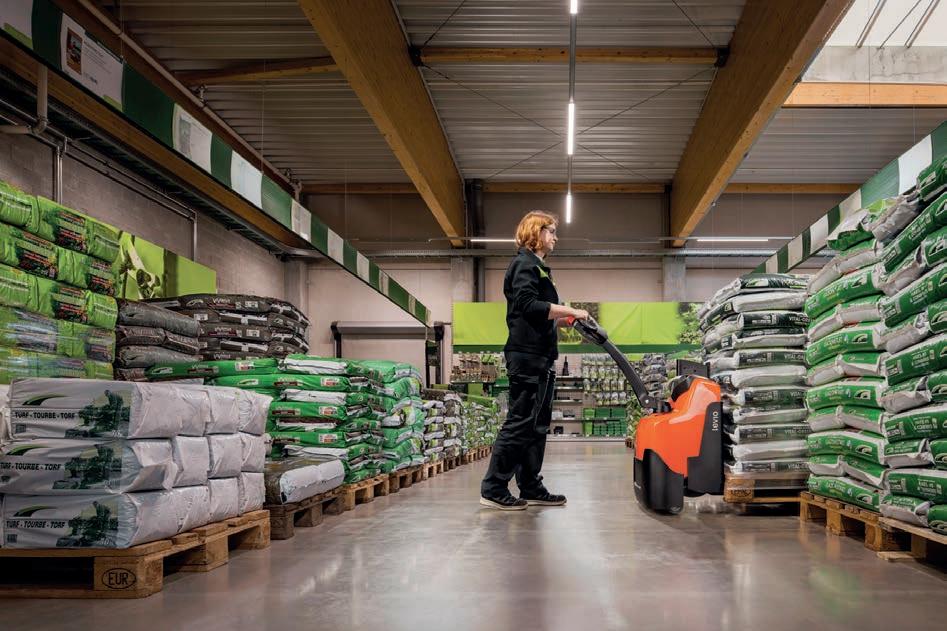
The Toyota Levio LWI160 Electric Pallet Jack features a lithium-ion battery, meaning it can be charged whenever there is downtime, unlike traditional lead acid batteries which require an eight-hour charge. The LWI160 is Toyota’s first pallet mover solely designed around the modular lithium-ion battery concept – allowing for a smaller, lighter, and more energy efficient unit. Its compact nature helps the LWI160 gain better access in tight areas. In some circumstances it may be the only option
TOYOTA LEVIO LWI160 ELECTRIC PALLET JACK
ifm’s O2I500 multicode reader is simple to use like a sensor, and reliably detects 1D and 2D codes. It delivers reliable reading results even in extremely difficult conditions, reading up to four different codes in milliseconds, which ensures efficient, and high-quality production. Thanks to the one-button teach function and the viewfinder, it makes the product immediately ready for use, saving time and costs. In addition to this, the O2I500 can be configured via an app or using the award-winning Vision Assistant software. The device has an exchangeable ifm memory stick, which can be used to save or load complete configurations of the multicode reader. This simplifies device replacement and the set-up of several units for the same application. The integrated optional illumination with polarisation filter, ensures sufficient contrasts to reliably detect codes even in the case of shiny surfaces such as metal. The ifm O2I500 multicode reader combines robustness, compelling design, and intuitive handling.
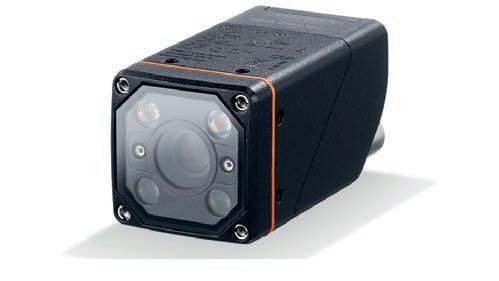
Dimitie joins project44 with over 20 years of experience helping large Australian and international businesses harness the power of technology to enhance efficiency and productivity, reduce costs and deliver better customer experiences. Her previous roles span a range of industries, including time at Australia Post and Dematic.
Do you have career news to share? Edward Cranswick at Edward.Cranswick@primecreative.com.au to be featured.
A monthly wrap up of the latest appointments in the supply chain, materials handling and logistics industry.

PEOPLE ON THE MOVE
MHD
DIMITIE GUBBINS JOINS PROJECT 44
UCS company dereOida has recently appointed Katie Walacavage as its Manager for Operations. Following previous roles at Fuzzy LogX and Vanderlande, Katie is looking forward to continuing her journey in the automation and warehousing space.
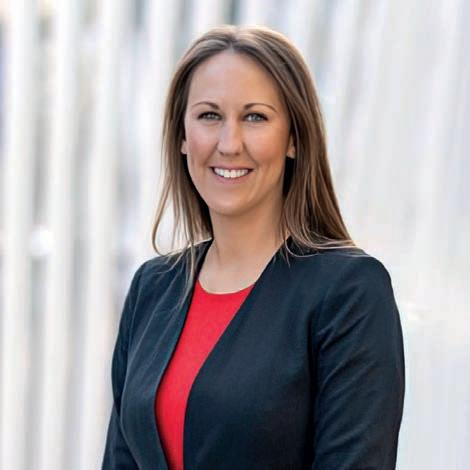
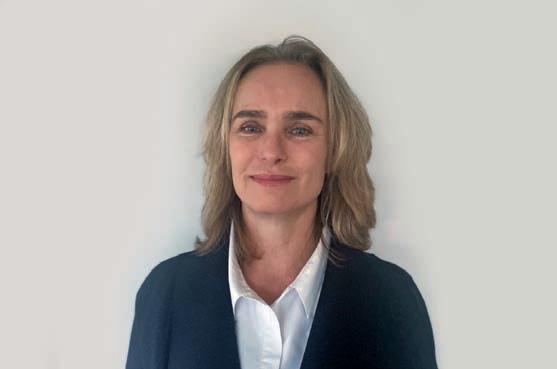
SONNY CHADHA JOINS PROJECT44
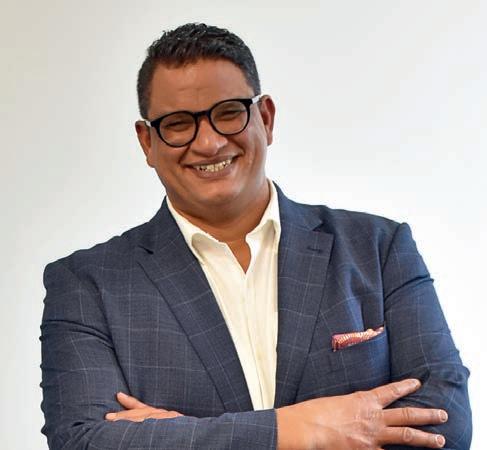
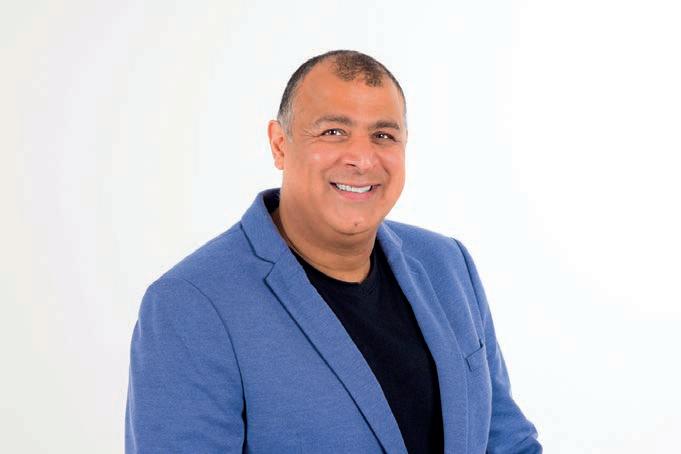
Dimitie is passionate about finding ways to optimise supply chains and is excited to introduce project44’s advanced visibility platform to Australian businesses
MHD SEPTEMBER 2022 | 66
DEREOIDA APPOINTS KATIE WALACAVAGE

VATIVE’S NEW TRANSFORMATIONBUSINESSPRACTITIONER
Yannis recently joined Vative, fulfilling the role of a Business Transformation Practitioner. Based in Vative’s Melbourne headquarters, Yannis is an energetic and passionate supply chain professional with experience across Logistics, Warehousing, Procurement, and Inventory Management coupled together with a Master of Supply Chain Innovation from Swinburne University and a Lean Six Sigma Green Belt, Yannis provides Vative’s clients hands-on capability in driving operational excellence.
In addition to his role at GS1 Australia, Michiel has taken on the role of T&L Sector Manager for the global GS1 Scan4Transport Centre of Excellence and co-chairs the Global and Australia/New Zealand Scan4Transport Work Groups. Prior to joining GS1 Australia in 2011, he held various business development and transformation roles within ICT and Retail businesses.
Sonny brings to project44 over 20 years of international achievements from London, Singapore, and Sydney. Having worked for leading carriers DHL and UPS, he understands the complexities, bottlenecks, and pain points of customers as their freight moves through the various modes. More recently, Sonny has moved into technology solutions to help drive efficiencies and improve customer experiences. He is very much focused on delivering tangible value for customers.
PEOPLE ON THE MOVE
SCAN4TRANSPORT CENTRE OF EXCELLENCE
Peaked your Interest?
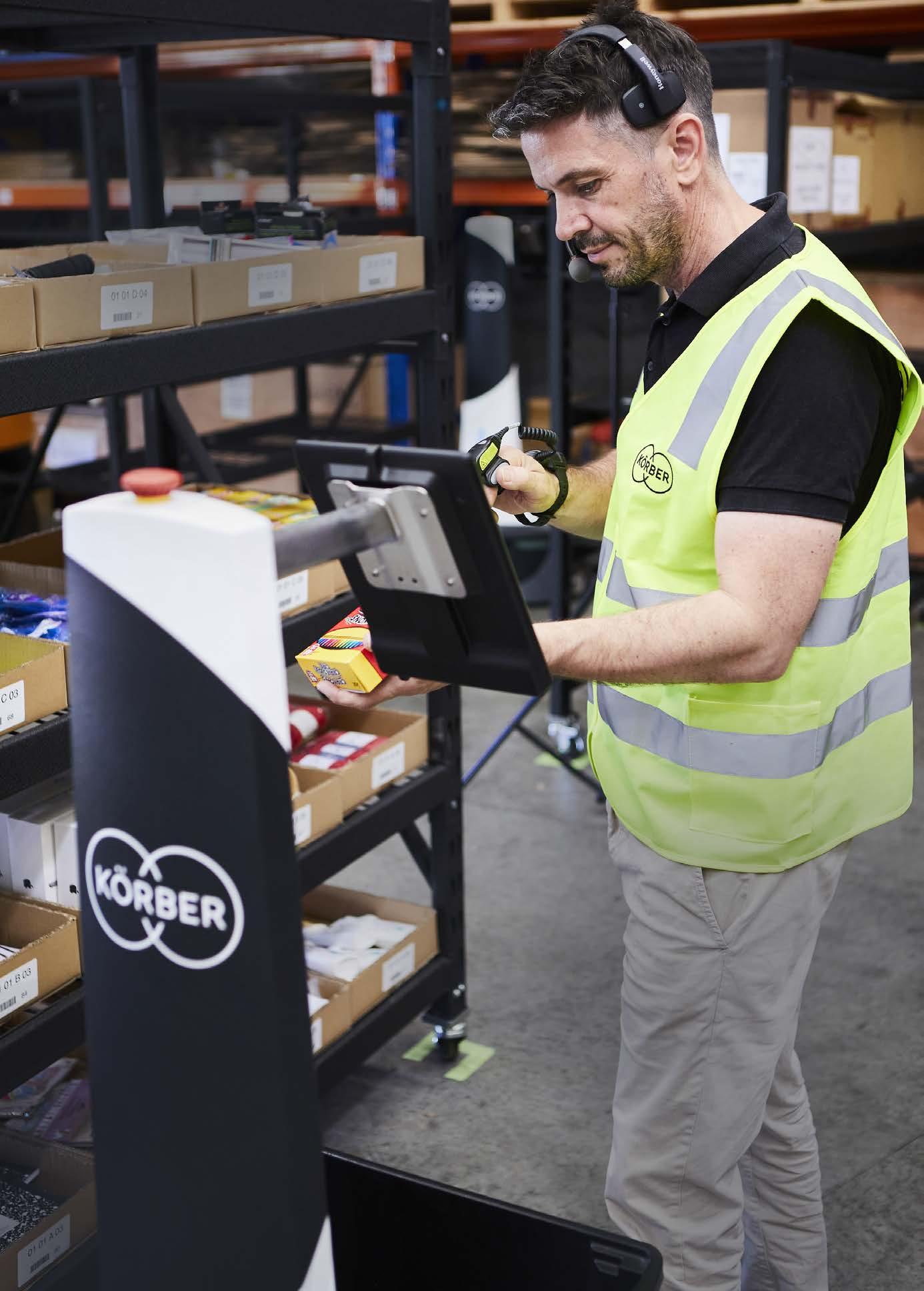
Enhance the Safety, Capacity and Efficiency of your Storage Facility
Storage Efficiency
Contact us to find out how Combilift can help you unlock every inch of your storage space and enhance the performance and safety of your operations.
• Safer Product Handling • Optimise Production Space • Improve Storage Capacity • Increase Productivity & Output • Enhance Profits • Improve Sustainability combilift.com
Combilift’s range of electric forklifts, pedestrian trucks and straddle carriers combine powerful performance, emission free operation and a host of up to the minute technologies to offer the most efficient way to handle long loads up to 12 tonne.
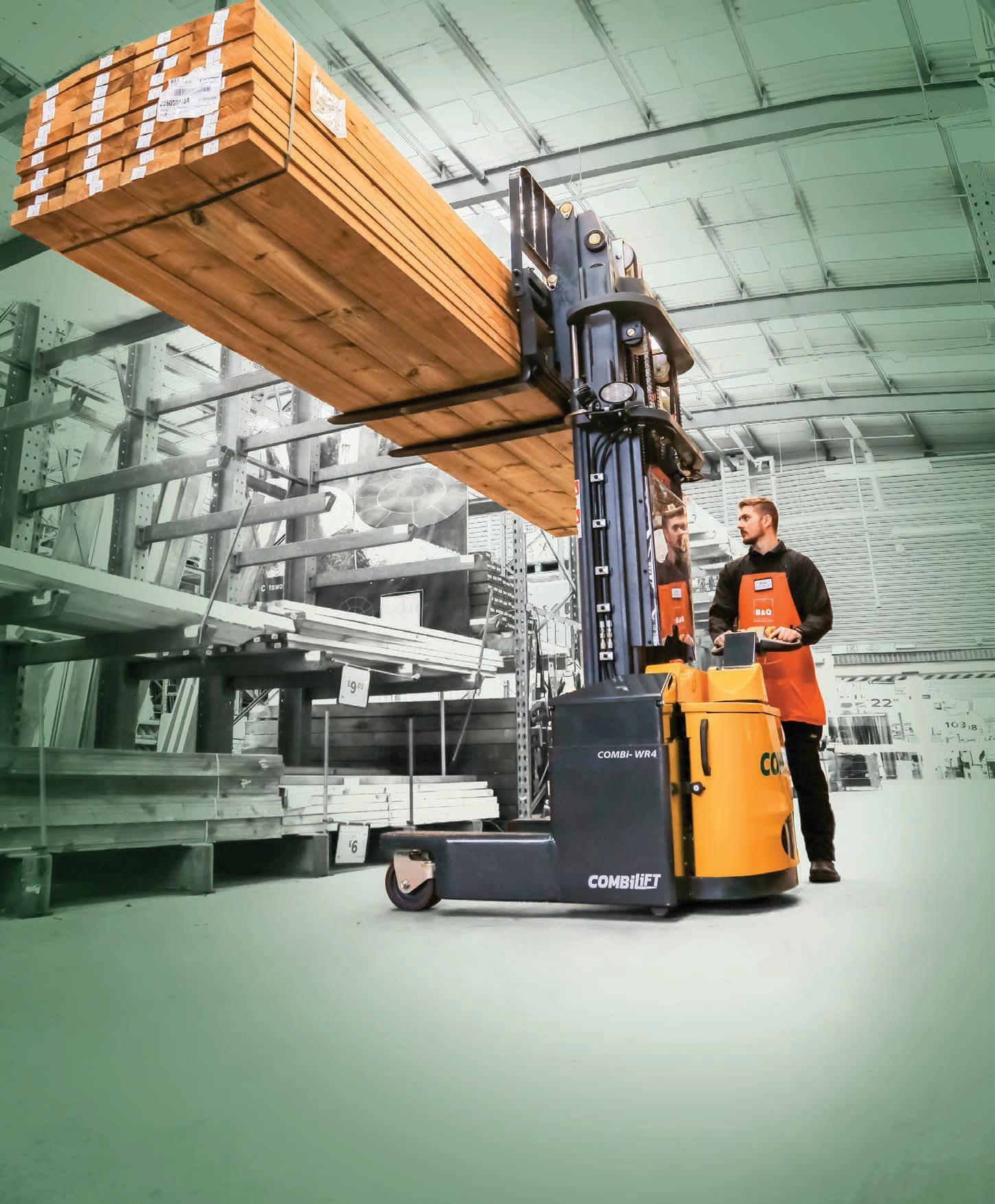
Safety
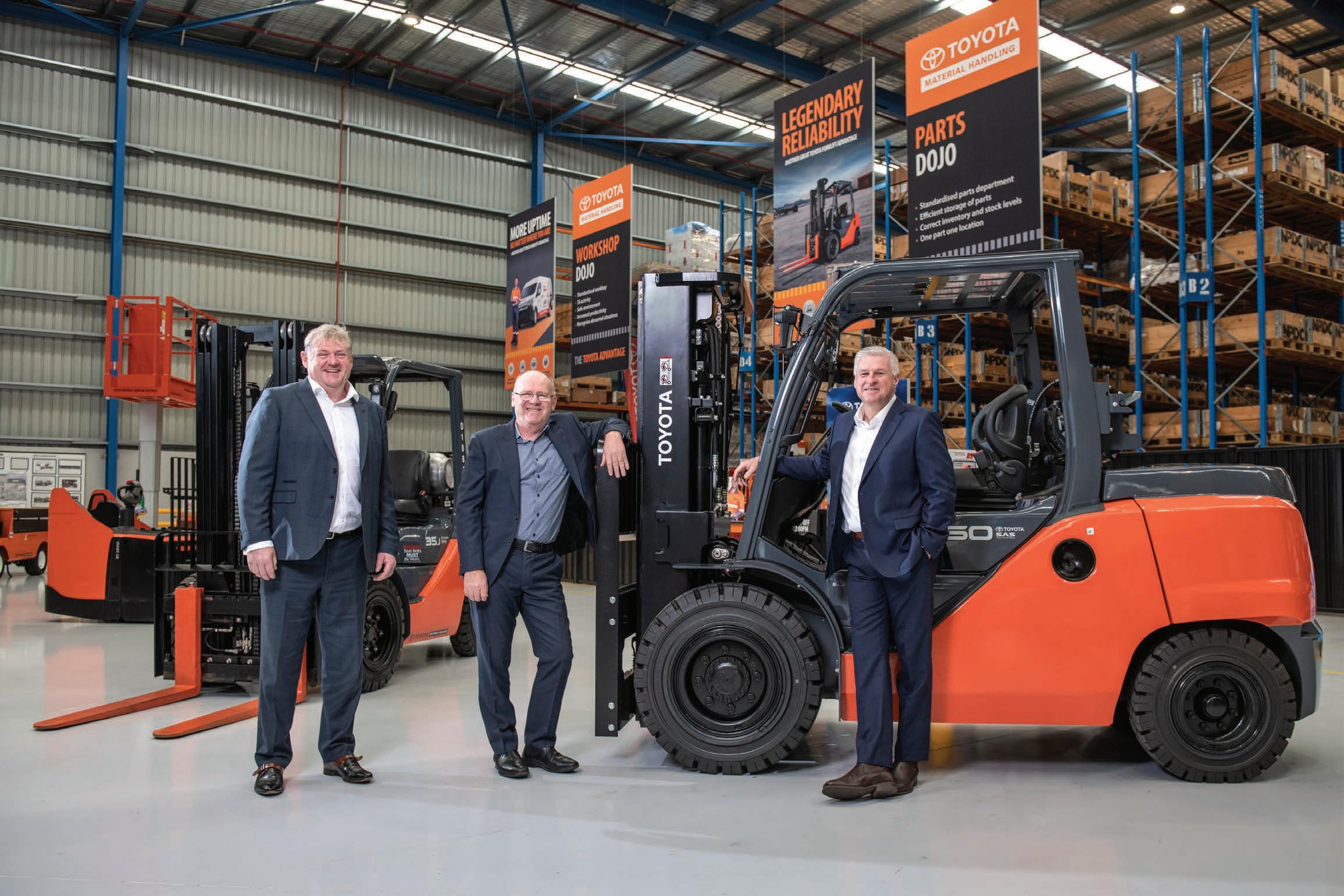