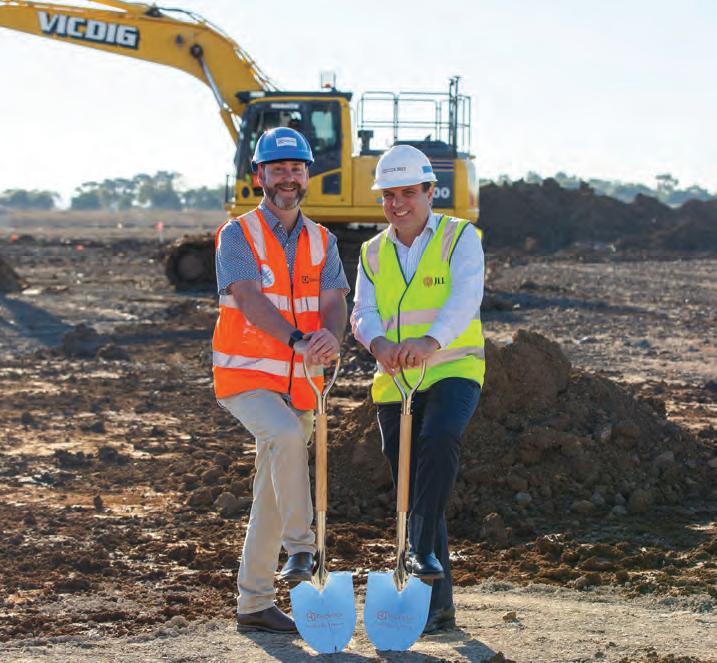
6 minute read
JLL’s sustainability key to
from MHD November 21
by Prime Group
SUSTAINABILITY KEY TO FUTURE-PROOFING WAREHOUSES
Reducing the environmental impact of warehouses is becoming more integral for many owners and occupiers. JLL and Dexus show MHD the benefits of prioritising warehouse sustainability through Electrolux’s new warehouse at Dexus’s industrial estate at Ravenhall, in Melbourne’s West.
After years of industrial real estate brokerage, JLL created a dedicated supply chain team in Australia in 2018. Bruce Myers was brought to the company in 2018 to spearhead the consulting service as Director of Supply Chain & Industrial, bringing years of experience in network strategy, inventory optimisation, warehouse design and facility master planning
Leveraging off its award-winning research division, JLL’s supply chain focus allows the company to zero in on warehouse processes which drive the key industrial decisions.
Allan Frydman, JLL Supply Chain & Logistics Principal Consultant, says individual and group expertise across transport, warehouse design, network design and inventory analysis allows JLL to tackle the full gamut of supply chain challenges.
“By sitting client-side to understand their operations we can make sure the warehouses are in the right position with the right number across the country,” he says.
JLL creates a more global network by using its expertise and resources in the APAC region for customers in the Australian market as required.
“Having supply chain experts across Australia, Singapore, India, China, Japan, Vietnam and Thailand gives us a really big global network – and the majority of our clients are interacting with Asia – so we’re able to bounce off that interaction,” Allan adds.
SUSTAINABILITY FOCUS
JLL’s sustainability sub-team works with both owners and occupiers to reduce the environmental impact of facilities and operations. Allan says the team, led by Loretta Brazukas, works early in the master planning process to identify sustainability pain points.
JLL has seen a huge push towards sustainability on behalf of clients – as the company aims to be carbon neutral itself by 2030 – Allan says sustainable features can provide significant cost savings for businesses’ real estate requirements.
“If you want to be renting this facility in five or 20 years you can’t just put four walls and a roof on without considering the environment,” he says. “Solar cells on your roof can reduce electricity bills by 10-15 per cent. A more efficient fleet with correctly located vehicles is the easiest saving. Reducing emissions per kilometre gives a sustainability benefit which directly translates to a proportionate cost benefit as well.”
This transport benefit is exemplified in Electrolux’s new warehouse, being developed by Dexus at their industrial estate at Ravenhall in Melbourne’s West.
Moving from the south of Melbourne will reduce Electrolux’s travel distance to the port and to customers – saving money on freight. The Ravenhall estate is
JLL and Electrolux have worked closely with Dexus in the construction of the new facility.
well connected to the Western freeway, which will provide a further cost and sustainability advantage to facilities closer to Melbourne’s CBD.
JLL WORKING WITH ELECTROLUX
Electrolux’s looming lease expiries prompted discussions with JLL about the future of its warehouse operations in Victoria. From dedicated research to understanding Electrolux’s business, JLL created a comprehensive supply chain review, in-turn defining KPIs and benchmarking these indicators against industry.
Allan says this initial process actually instigated a change in belief for the home appliance distributor in identifying which warehouses were performing the best.
“Electrolux has five warehouses across Australia. We were able to identify which of those warehouses had the best operating processes and structures in place,” Allan says.
“Electrolux then took that on board as a project and has been working on standardising its processes across its five sites, which has delivered significant labour savings. We were able to do similar activities with their secondary freight network.”
Having been in the south of Melbourne for 20 years, the decision to uproot Electrolux’s loyal staff to the other side of town wasn’t taken lightly.
David Mair, Electrolux Acting Operations Director Australia New Zealand, says sustainability and a need to be closer to customers were at the core of this strategy.
“We looked at our environmental footprint within the Victorian market and saw moving west as an opportunity to invest in a more economically, sustainably rated building,” he says.
“It also brings us closer to ports and the airport and some of our key customers with distribution centres in Truganina.”
Once a thorough supply chain review indicated that moving to a new facility was Electrolux’s best option, JLL’s project delivery services team developed a detailed specification brief for the building. The brief considered operational constraints, operational requirements, supply chain requirements, and building requirements – and was taken to market to run a competitive tender process.
DECISION TIME
David says Dexus’s ability to understand the building brief separated it from the other shortlisted developers.
“We provided one of the most comprehensive briefs I’ve seen, which is a credit to JLL,” he says. “Dexus was one of the few developers that really understood our sustainability and production goals and presented back to us the type of land option that would help our business over the next 20 years.”
Set to move into the facility in late February, Electrolux has set a target of a 20 per cent uptake in productivity. David adds the company’s reduced carbon footprint in primary and secondary transport will lead to substantial cost savings.
“We are hoping this innovative 6 Star Green Star Design and As Built rated facility will help us reach our goal of being carbon neutral by 2025,” he says. “We’re so excited about the Ravenhall facility becoming Electrolux’s first 6 Star rated facility globally. Building design and implementation normally takes a couple of years – but to finish in basically twelve months is an amazing effort.”
The Green Building Council of Australia’s Green Star rating system is Australia’s largest holistic sustainability rating system for buildings and fit-outs.
Chris Mackenzie, Dexus Head of Industrial Development, says Electrolux jumped at the opportunity to move into a 6 Star Green Star Design and As Built rated facility – the top category reserved for world-leading sustainability innovation – at Dexus’s 130 hectare masterplanned estate in Ravenhall.
In order to be world-leading, developers have to execute the fundamentals first, Chris adds.
“The right orientation, location for office, and even roller doors: there’s a myriad of obvious yet smart ideas you should be embedding in your design that’s going to set you up really well for success in terms of picking up those next features,” he says.
“Green Star has evolved and is no longer just about the built form and is inclusive of the precinct. The beauty of estates, rather than singular sites, is you can establish smart road layouts and connectivity, which is a fantastic base for sustainable operations.”
Chris says by focusing on a company’s operational costs, the extra expense of lights, daylight sensors and solar starts to make sense for both big and small companies.
“Those simple initiatives can save businesses between two to five dollars per square metre on operational costs,” he says. “For Electrolux, we focused on lighting and power-lighting systems and putting a battery system in the main switchboard. There’s a 300 kilowatt system on the roof that strategically picks up all the sunlight.”
“The mechanical system has enough redundancy to Power Up and Power Down, depending on the heat demands for the day. A mechanical design feature should have a number of smaller systems that can control zones, meaning it’ll be off for much of the day.”
By providing future-proofing initiatives and solutions, Dexus hopes to be with its customers for more than just one lease renewal.
“Not only do we think about sustainability in an environmental context, we also have to consider sustainability in the sense of allowing the facility to expand within its own skin,” Chris says. “We don’t take the typical developer approach of selling and moving on. We want to build for the long-term.” ■