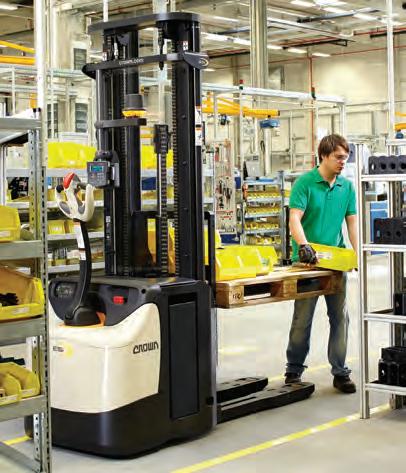
6 minute read
Combining automation and manual
from MHD November 21
by Prime Group
DREAM TEAM: HOW AUTOMATION AND MANUAL OPERATIONS CAN WORK TOGETHER
Crown Equipment explains the unique cost-effectiveness and flexibility of automated technologies that can be reconfigured for manual handling.
When it comes to supply chain automation, there are very few questions about whether this technology is a viable option. Numerous successful projects and applications across the industry have shown there can be benefits to incorporating certain types of automation into warehouses and distribution centres.
As supply chain managers begin to research automation solutions, they are often presented with case studies showing new, fully automated facilities that can sometimes make it feel like the technology is still somewhat out of reach. For many companies, building a new, completely automated facility may not be possible in the short term.
While technology is evolving quickly to make automation more practical for use in warehouse and distribution environments, the significant upfront investment and infrastructure requirements of an all-or-nothing approach typically involves long-term strategic planning and preparation.
So, if you’re one of the supply chain managers trying to determine which automation strategy and technologies are right for your operation, what should you do?
You can start by identifying the tasks and equipment that are ideal candidates for automation.
Next, prioritise those opportunities based on metrics that make sense for your business and begin with a project of a size and scope that fits your comfort level and business case.
Crown provides a materials handling solution specific to a business’s requirement, need, or circumstance.
STRATEGIC AND SCALABLE SOLUTIONS
Any effort to introduce automation to your facility should ideally be guided by a realistic plan with achievable expectations that can also be scalable based on success and growth. Develop a clear path for tangible return on investment (ROI) and determine a process and mechanism for building upon your success. This will help you strategically grow and evolve your automation efforts.
Given its prominent role in enabling product movement across the supply chain, the forklift provides an ideal starting point for a scalable automation initiative.
One approach to forklift automation that is gaining a lot of attention is ‘dual mode’ technology that enables both automated and manual operation.
Dual mode automation can be an ideal approach for companies that may not have a warehouse management system but would still like to realise the benefits provided by automation technology. Operations that do utilise a warehouse management system may contain a small percentage of exceptions that seem ill-suited for automation. Dual mode functionality can also help manage these exceptions without requiring a separate solution.
IMPLEMENTING DUAL MODE AUTOMATION
So, what is meant by ‘dual mode automation’?
Forklifts with dual mode automation technology can switch between manual and automated operations, depending on the needs of the facility. Dual mode automation enables warehouses to take an incremental approach to deploying automation solutions with minimal or no supporting systems or infrastructure.
The important thing to understand about dual mode technology is that it is based on automated equipment that can be operated manually – it is not a piece of manual equipment that has been engineered to operate autonomously. The equipment’s automation features are fully integrated into the vehicle as they typically are in a fully autonomous vehicle. The difference is that the dual mode technology allows the equipment to be used as any other manual equipment would be used when a particular application calls for it.
For instance, consider a tow tractor used to pull carts from point A to point B in a facility, with material being loaded and unloaded at each point. With a dual mode tow tractor, travel
between the two fixed points could be automated, freeing up an operator to focus on other tasks. Should the tow tractor encounter an obstacle in the set path – such as a pallet in an aisle – a typical trained forklift operator could quickly switch the vehicle into manual mode to navigate around the obstacle. It could then be returned to automated mode to continue to its destination, thus maintaining the flow of the system.
A dual mode system doesn’t require the specialised staff that may be required with a fully automated solution. In addition, one employee can often manage multiple dual mode vehicles, stepping in only when manual operation is needed.
This is just one example of a process that could be streamlined with dual mode automation. The possibilities will only increase as dual mode technology continues to evolve. And, by enabling a scalable approach, dual mode automation technology offers the flexibility companies need to evolve their automated processes at their own pace.
When implemented strategically and deliberately, establishing and expanding automated solutions within the facility can provide incremental benefits that prove the viability of the technology in your operation. As you explore options for dual mode technology, an experienced material handling partner can help determine how best to integrate the technology into your processes in a way that enables the benefits of the technology to be fully realised and ROI to be generated with each deployment.
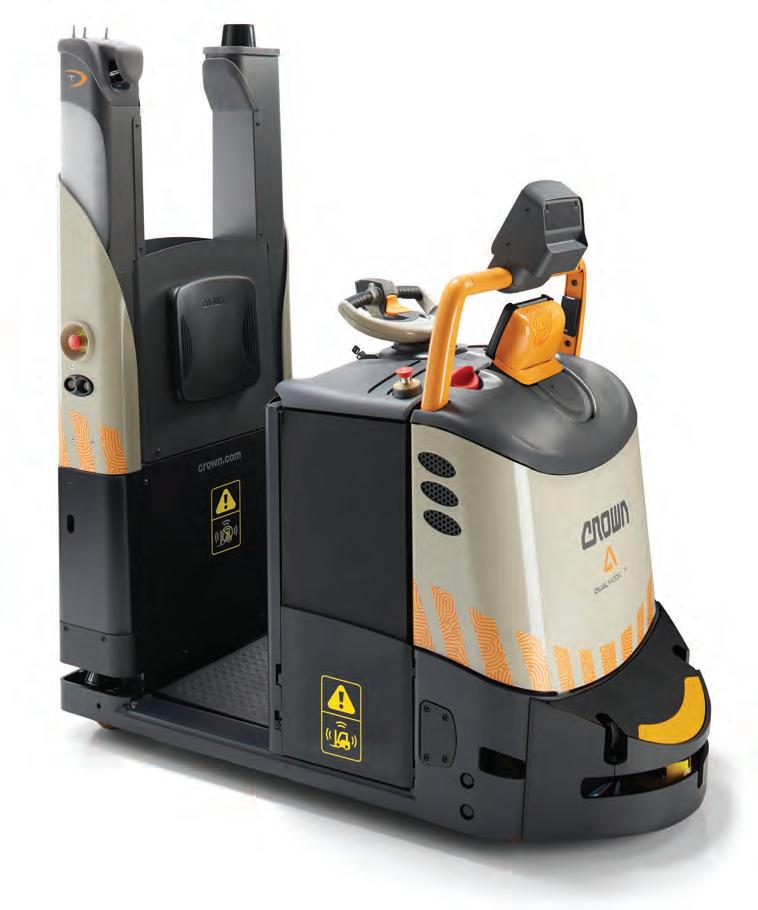
CROWN’S AUTOMATED DUALMODE T TOW TRACTOR
In many material handling applications, horizontal travel accounts for the majority of product movement. Today’s modern material handling operations have been optimised in many ways with equipment and processes designed to move product over these long distances without human intervention in warehousing, manufacturing and other process-oriented applications.
These automation improvements can help reduce the expense associated with the internal movement of materials. However, non-conveyable items, those that cannot be transported on conveyor systems due to their unique size, shape or bulk, can still require some form of manually controlled transport.
Because non-conveyables require human intervention to facilitate their travel, many companies are considering how automation might be applied to this process. Though automation typically works best in applications with repetitive functions in predictable environments, flexibility is the name of the game in non-conveyable transport.
Crown’s automated DualMode T tow tractor can provide a flexible alternative to manual transport of non-conveyable items in dynamic environments, without costly investment in significant warehouse infrastructure. A series of carts towed by the automated tow tractor can be loaded by a worker, who then enters the stop locations into the vehicle’s interface. The vehicle then traverses the facility – depending on the environment – using a natural feature navigation system, which can be deployed with little or no supporting infrastructure.
If the DualMode T tow tractor encounters an obstruction, it slows to a stop and alerts other workers that is path is blocked. When the path is cleared, the vehicle automatically resumes travel to its destination. When it reaches a programmed stop location that already has a vehicle parked for unloading, it will either stage behind that vehicle or use an established passing lane to continue to its final destination. When the mission is complete, the vehicle automatically returns to the next available loading location.
In select cases where the operations do not provide a clear path for the DualMode T tow tractor, the vehicle stops and notifies workers that action or attention is required. Since the vehicles feature dual modes of operation – automated and manual – any trained operator can manually move the vehicle and its cargo to its specified course and resume automated operation.
RESULTS
Automated vehicles such as the DualMode T tow tractor, equipped with natural feature navigation systems, can deliver non-conveyable items quickly, efficiently and safely to their destination – without the need for manual operation. Such systems can be easily reconfigured as transport needs evolve, without the complex infrastructure issues association with the reconfiguration of traditional conveyor systems. ■