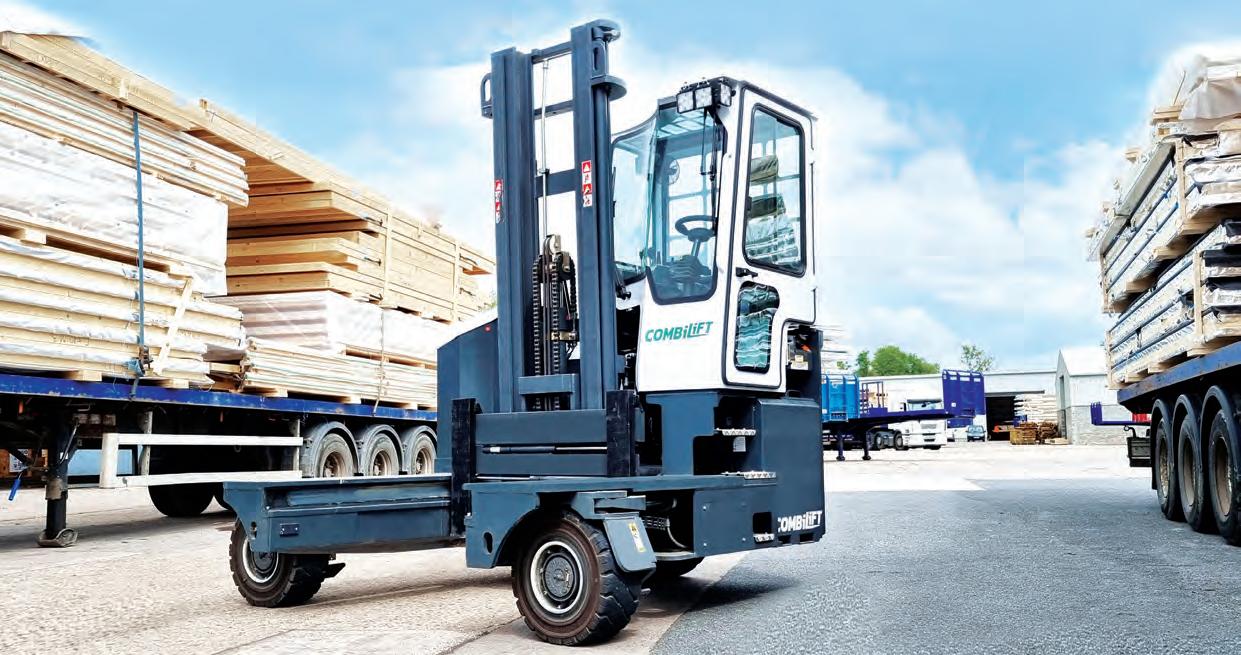
4 minute read
Capitalising on warehouse space
from MHD November 21
by Prime Group
CAPITALISING ON WAREHOUSE SPACE WITH SUSTAINABLE EQUIPMENT
Upon the launch of Combilift’s newest electric forklift, MHD talks to CEO and Co-Founder Martin McVicar about how investing in sustainability is helping businesses make the most out of warehouse operations.
The Combi-XLE is Combilift’s latest addition to its fleet of electric forklifts.
Irish materials handling specialist Combilift has officially launched its latest product, the Combi-XLE, as a further addition to its range of electric models. Combilift CEO and Co-Founder Martin McVicar says the product is in line with a growing demand for electric powered equipment.
“The vehicle allows clients to optimise their warehouse space,” Martin says. “Maximising the warehouse footprint is key to reducing carbon emissions for any business. The multidirectional forklift with up to five-tonne lift capacity, combines emission-free operation with powerful performance for a wide range of industries and applications.”
The original engine powered XL C-Series model was developed to address the requirements of tough working environments such as those in the timber, concrete and steel sectors. The new Combi-XLE incorporates the same key design features as its earlier counterpart such as high ground clearance, large cushioned front and rear tires and a spacious cab, allowing smooth operation on semi rough terrain whilst offering a high level of driver comfort.
With sustainability ever higher on the agenda, Combilift further helps its customers achieve their environmental goals with its versatile “3 forklifts in 1” models, which work inside and out, reducing fleet size and thereby their carbon footprint.
Martin says a hallmark of Combilift products is the ability to increase storage
capacity without expanding the size of a facility, resulting in lower energy usage and associated costs such as heating, lighting and maintenance, which is of significant benefit to the environment and the workforce.
“The demand for warehouse space is at a premium across the developed world and acquiring skilled labour can pose a major challenge in Australia,” Martin adds. “Our drive comes from allowing customers to do more with their existing facility.”
Electric power also alleviates noise pollution and carbon emissions, which can impact on the health and well-being of people as well as wildlife. Drivers, employees and visitors on site appreciate the quiet operation, as do neighboring residents and businesses, particularly in urban areas.
Dave Clement, Production Director at Roger Bullivant Limited says the company has enjoyed a smooth transition to an electric fleet of Combilift vehicles.
Part of the Soletanche Freyssinet Group, Roger Bullivant Limited manufactures precast concrete elements for installation in engineered foundation systems.
“At our South Derbyshire precast factory, we use 5 multidirectional Combi-XLE trucks to transport product from the factory to storage and then to load-out for distribution nationwide,” Dave says. “As we had already been using Combi units for years, the product decision was straightforward, and from a driver perspective, the operation remains essentially unchanged. The reasons to move to electric were twofold: to eliminate exhaust particulates in the factory and as part of our Group environmental plan to minimize our carbon footprint. So, an improvement to the environment in more ways than one.”
The Combi-XLE incorporates up-tothe-minute technology such as the patented all-wheel traction that reduces tire wear, load swing and enhances braking. A newly developed, patented Eco-Steer System provides a smaller turning radius and improved user experience. Since Electric powered trucks do not have traditional combustion engines, or hydraulic transmissions, there is no longer any need to check and top up engine fluids or lubricants, We made our first electric C-Series over 18 years ago, and now over 60 per cent of the trucks we manufacture are electric, with availability in almost all models across our range. As more and more of our customers are opting for electric power it is obvious that they are as committed to sustainability and a circular economy as we are. ”
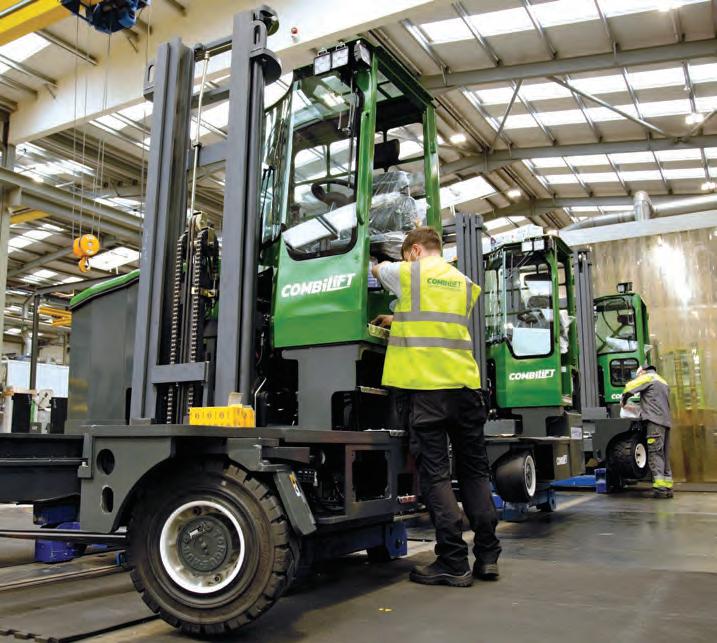
resulting in longer intervals between services, ultimately saving costs. The use of toughened, eco-friendly waterbased paint also dramatically reduces the amount of Volatile Organic Compounds (VOCs) during build.
“The technology we have incorporated into the Combi-XLE means that its performance is equally on a par with diesel or LPG powered forklifts when it comes to handling very bulky and heavy loads, whilst of course offering a greener operation,” Martin McVicar says. “We made our first electric C-Series over 18 years ago, and now over 60 per cent of the trucks we manufacture are electric, with availability in almost all models across our range. As more and more of our customers are opting for electric power it is obvious that they are as committed to sustainability and a circular economy as we are.”
At Combilift’s own manufacturing facility, features such as daylighting technology - LED lights with individual PIR sensors, solar panel energy and rainwater harvesting are all aimed at conserving natural resources and decreasing energy consumption. 92 per cent of all components used in the truck assembly are 100% recyclable and the company is also on track to save over 473 tonnes of CO2 by using carbon neutral wood chip instead of gas for heating within the factory.
“We made a conscious decision early this year to invest in carrying more raw materials to deal with supply chain challenges,” Martin adds. “At the back of our facility, we’ve added 4000 square metres of paved area for storage of raw materials particularly steel and heavy raw materials.” ■
Electric powered trucks don’t require topping up engine fluids or lubricants.
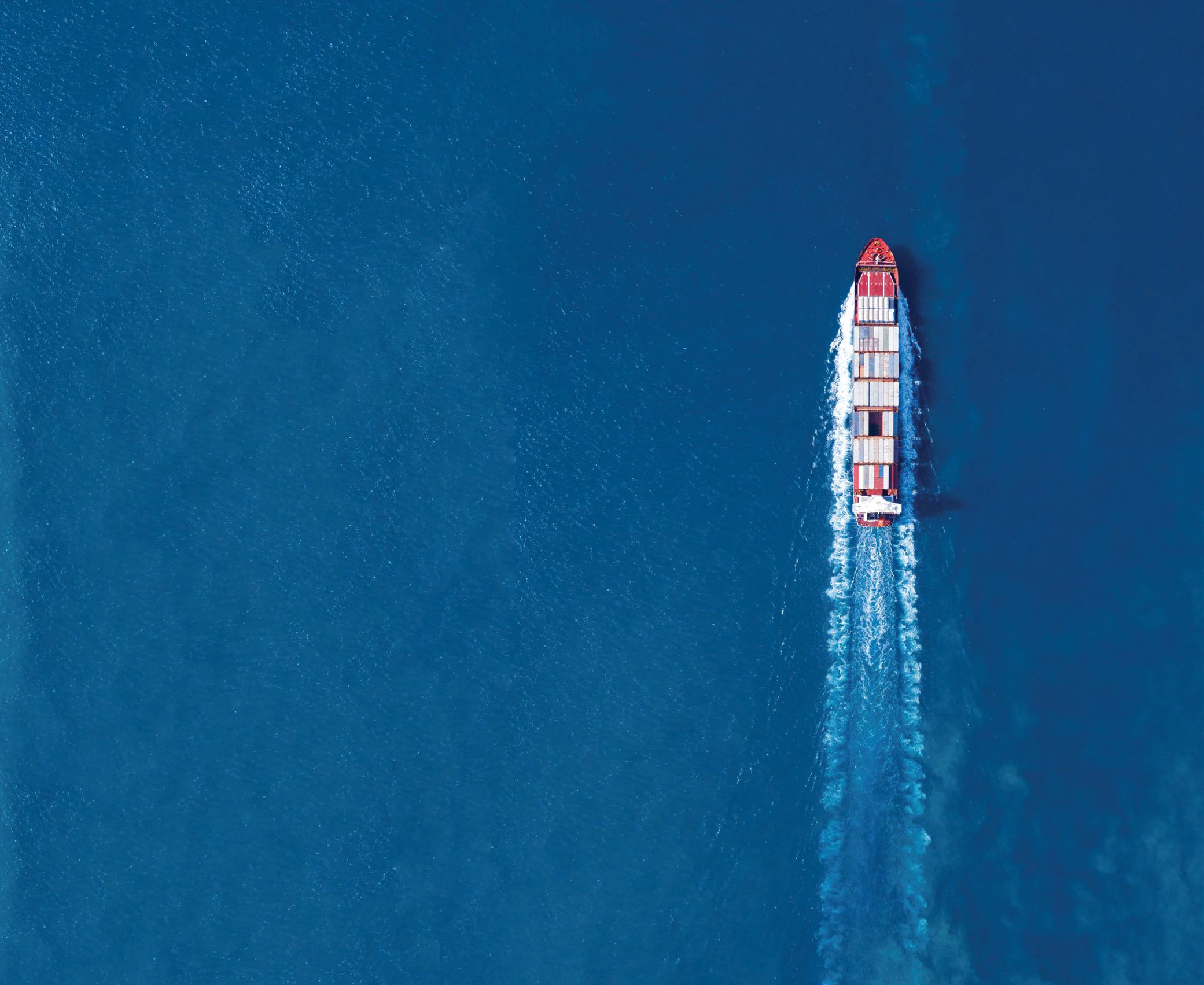