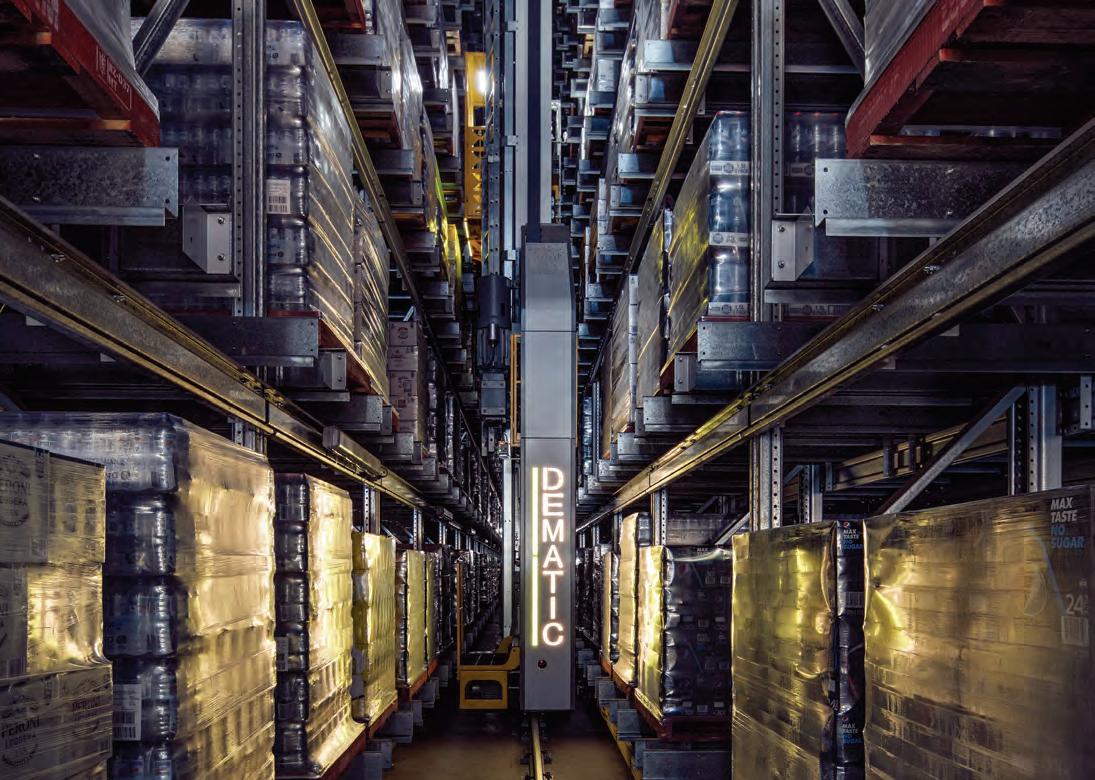
8 minute read
Dematic unlocking
UNLOCKING DISTRIBUTION OPTIMISATION
Distribution is a dynamic and always changing area of supply chain. Pas Tomasiello, Dematic Senior Regional Director explores some of the most efficient automated solutions for optimising supply chains after a year of progress and innovation for many Australian businesses.
Asahi’s ASRS has more than 31,500 pallet storage positions.
According to Pas Tomasiello, Dematic Senior Regional Director, businesses are under pressure from customer and market demand for competitive pricing, shorter lead times, products delivered anywhere, in full, on time, and in the case of retail customers, in a store friendly format.
“For online orders, customers want up-to-date information on stock availability, and status of their orders,” he says. “On top of it all, businesses continue to contend with increasing labour and land costs and pressures from increased regulation and safety requirements, and ongoing uncertainties relating to the pandemic. Whether your business is feeling the pressures of a changing market and customer landscape or is looking to adopt leaner processes to address operational speeds and costs, the importance of optimising supply chains and distribution has never been as high as it is now.”
While no one solution fits all businesses, the level of technology and automation isn’t just dependent on scale. Rather, there are many interconnected factors at work.
Pas Tomasiello, Dematic Senior Regional Director.
250 PER CENT PRODUCTIVITY BOOST FOR ASAHI BEVERAGES
When Asahi Beverages consolidated their multiple Brisbane sites into one DC, the company decided to upgrade to an automated warehouse solution, as they previously had a very labourintensive system in place. Asahi implemented an ASRS 13 levels high, 34 bays deep, with six cranes servicing channels six pallet positions deep on either side, accessed by satellite carts. With over 31,500 pallet storage positions, the system provides excellent storage density and a greatly reduced storage footprint. The system eliminates most of the manual handling of pallets, reducing errors and product damage, creating efficiencies and a high productivity boost of 250 per cent, and increasing safety for Asahi’s employees.
SOLUTION STRATEGIES FOR SUCCESS
Pas says while solutions are tailored to an organisation’s specific supply chain and broader operational requirements, there are several key technologies that can be implemented either as stand-alone or integrated solutions to drive improved customer service, productivity, capacity and operational agility benefits through improved processes, human factors, and optimisation of inventory. According to Pas, some of the biggest improvements for Australian supply chains have come from the implementation of the following solutions: • Software Best-of-breed supply chain software elevates and optimises applications with Industry 4.0,
IoT (Internet of Things) and AI capabilities, to ensure a seamless, optimised interface between operators and data. This enables optimal flow of goods and information through supply chain and warehousing operations, while allowing businesses to maximise system performance, responsiveness, and agility, and empowering them to better meet customer demands. • RF & Voice Many manual operations can be improved by adding a smart overlay of data-enabling devices that bring instructions from the warehouse software to the shop floor in real time, boosting accuracy and real time inventory management. Some technologies also help optimise human processes, such as Voice technology, which allows operators to work hands- and eyes-free. • Automated Guided Vehicles (AGVs)
AGVs are used in a variety of industries to transport and store all kinds of products and materials and are a safe and secure way to increase process efficiency and improve business profitability; all without human intervention. AGVs automatically, transport, put away and retrieve from storage and transfer goods between processes. • Automated Storage and Retrieval Systems (ASRS) Whether it’s large unit load systems for pallets and bulky goods, or Multishuttle systems handling totes and cartons, Automated storage systems are the ideal solution for maximising storage capacity and density. They secure product, eliminate damage, and increase productivity and accuracy. Automatically receiving, putting away and retrieving your stock means storage is fast, efficient, cost effective and very reliable. With no labour requirements, ASRS also provide significant productivity, inventory visibility, and OH&S benefits. • Goods-to-Person (GTP) One of the most significant developments for distribution logistics success is a solution where travel is eliminated altogether. In a GTP system, the products required to fulfil orders are retrieved from a Multishuttle system and delivered to ergonomically optimised high-rate pick stations precisely when they are needed,
maximising picker productivity, efficiency, accuracy, and safety. • AutoStore An all-in-one storage buffer and order fulfilment solution,
AutoStore offers the highest-density automation storage solution for small items. An AutoStore system reduces space requirements to as little as 25 per cent, while at the same time providing a highly efficient order fulfilment operation built around the
GTP principle. With a flexible design,
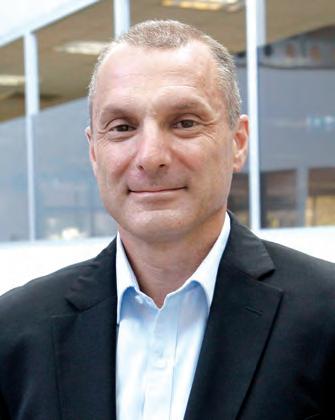
For online orders, customers want up-todate information on stock availability, and status of their orders. On top of it all, businesses continue to contend with increasing labour and land costs and pressures from increased regulation and safety requirements, and ongoing uncertainties relating to the pandemic.
VOICE HELPS AMERICOLD KEEP ITS COOL
For Americold to meet the increasing demand for cold storage and transportation services within Australia, the company’s management recognised the need to constantly improve standards, practices and technology. The company replaced its paper-based picking with an advanced Voice picking system, allowing operators to work more efficiently and hands-free, providing increased accuracy and productivity, as well as facilitating a real-time, two-way data flow between pickers and the WMS. Plus, without the need to work with paper lists or key information into devices, operators can now keep their gloves on – a definite plus for a chilled environment.
For online orders, customers want up-to-date information on stock availability, and status of their orders. On top of it all, businesses continue to contend with increasing labour and land costs and pressures from increased regulation and safety requirements, and ongoing uncertainties relating to the pandemic.
LION BEER AUSTRALIA’S FUTURE-PROOFED SUPPLY CHAIN
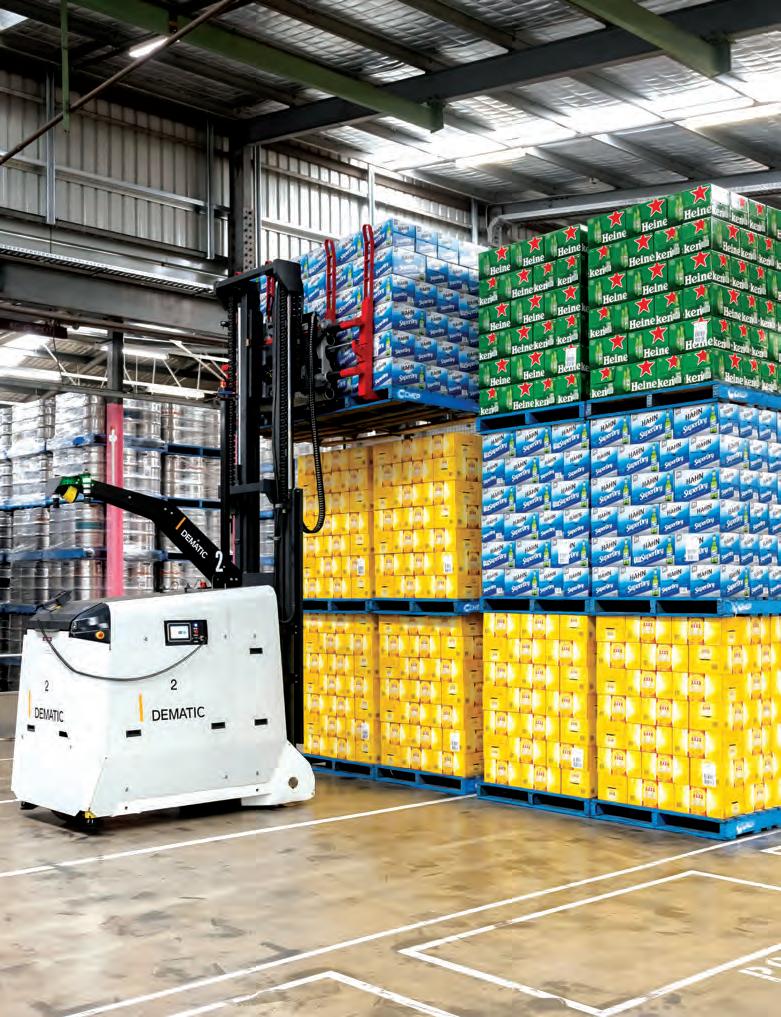
Following significant growth in its product range, Lion initiated a re-structure of its supply chain and internal fulfilment operations to future-proof its manufacturing and supply chain operations to maintain competitiveness and resilience. Lion invested in fleet of seven AGVs to streamline its end-of-line operations, eliminating bottlenecks and delivering a predictable logistics operations. The use of AGVs has vastly reduced wastage and errors and has improved the overall safety for operators at the facility.
it can fit into a wide variety of building environments and being modular and scalable, can be readily expanded as required. • Sortation By combining orders for several customers into batches, pickers can increase efficiency by picking multiple orders at once. Once picked, batch-picked goods can be automatically sorted back to individual order requirements by smart sortation systems designed for the diverse product handling and throughput requirements of warehousing and distribution centres. • Robotic Picking Advances in machine learning software, product storage, buffering, sequencing, vision
A Dematic AGV in action at Lion Beer’s Tooheys Brewery.
recognition systems, and high-speed articulated robots with versatile product gripping tools, have driven the development of fully automated robotic picking systems capable of handling a diverse range of products.
Robotic picking eliminates the need for picking labour, provides high and predictable throughput, superior accuracy with 24/7 operations, delivering increased system reliability and resilience. • Automated Mixed Case Order Fulfilment solutions Dramatically reducing picking labour and rapidly building high-density, storeready mixed-case pallets and cages, these automated palletising
AUTOSTORE FULFILMENT SYSTEM FOR C.E. PATTBERG
C.E. Pattberg is a gift and decoration ribbon manufacturer. At its German facility, C.E.’s products were previously stored in a 6000 square metre warehouse with manual order picking, with significant labour costs and high error rates. C.E. invested in an AutoStore system, reducing the majority article storage space to 170 square metres. The solution has significantly increased the productivity of order processing and reduced labour costs, as well as virtually eliminating costly picking errors, with flexible expansion options for future business growth.
An AutoStore system reduces space requirements to as little as 25 per cent.
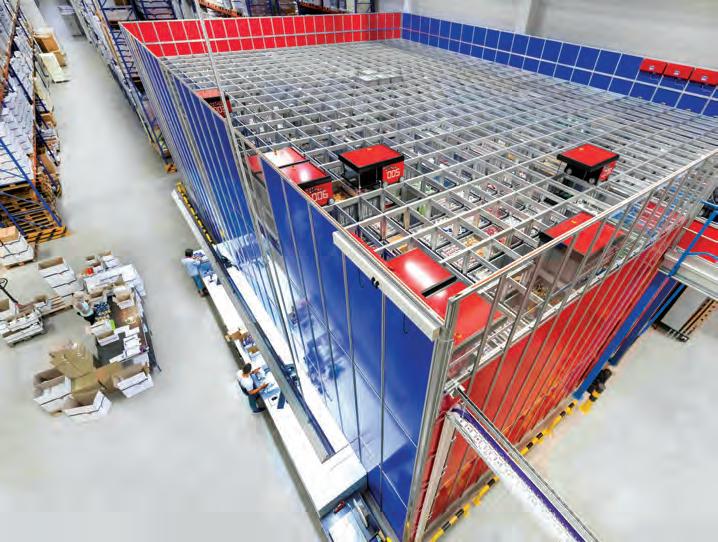
options handle a wide variety of products. They are highly accurate and compact to provide very high capacity and throughput levels in a reduced land footprint. Intelligent software manages the entire operation, including building pallets that match store planograms and account for crushability and product mixing restrictions. Pas believes knowing which strategies to apply where and when to get the best out of your business is the key, and there is no one-size-fits-all solution – every supply chain is different; hence the solutions and strategies are unique. “Addressing distribution challenges involves gathering information and using its insights to assess multiple strategies to compare how they would apply to a particular operation,” he says. “Working with a provider that focuses on a consultative approach allows for the establishment of the solution requirements, identification of potential growth parameters for the future, and the extensive data analysis required to properly focus on optimising your processes, human activities, and inventory.” ■
DRIVING INNOVATION AT BOLLORÉ LOGISTICS
Bolloré Logistics is a global leader in international transport and logistics as well as a Tier 1 partner to some of the world’s renowned brands. Their new Singapore Blue Hub facility is the largest and most advanced facility in Asia, designed for omnichannel distribution to cater for fast growth in e-Commerce. The main solutions are a GTP system, however to further drive innovation, Bolloré Logistics and Dematic introduced robotic piece picking into the operations. This technology will allow Bolloré to install goods-to-robot cells which can operate 24/7 without the need for pickers. The robotic picking cell was first installed in Bolloré’s innovation centre, to allow testing with actual products before being integrated into the operational system.
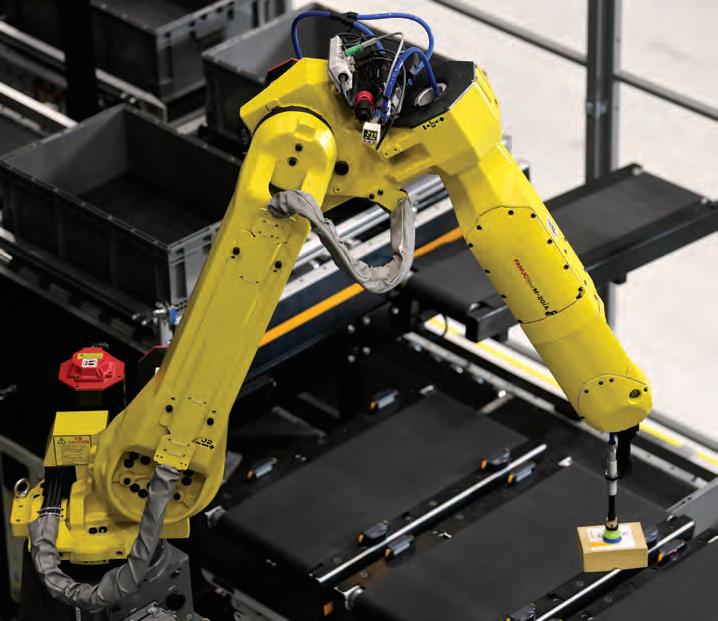
Robotic piece picking has been introduced to Bolloré Logistics new Singapore Blue Hub facility.
SORTATION IS THE PERFECT FIT FOR KATHMANDU
Kathmandu established one of Australia’s first purpose-designed omni-channel DCs in Melbourne, distributing across its Australian retail network, and to online customers globally. For Kathmandu’s business, a batch-pick sortation solution was the best fit, providing the high fulfilment responsiveness - critical given the success of its strong promotional model. Under the previous manual pick solution, if Kathmandu wanted to increase output by 50 per cent, it had to have 50 per cent more people in the facility. With the batch-pick sortation system, the business can scale up output without a linear increase in labour, Items for orders are picked in batches and fed onto a crossbelt sorter, which allocates the picked items to individual stores or to the e-Commerce packing area. An order can be picked, processed, packed and fed to despatch inside 20 minutes of the order being made available for picking.