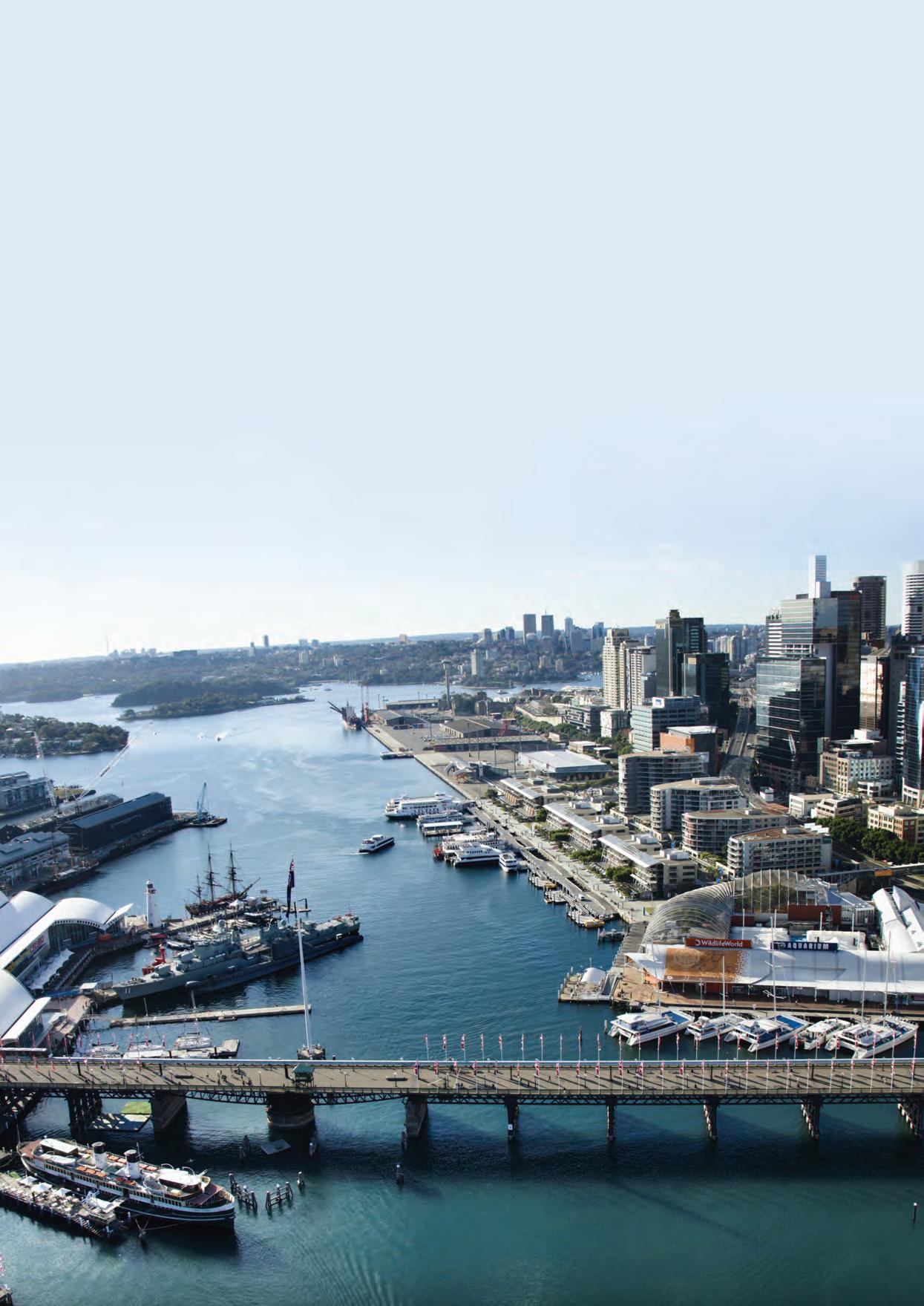
11 minute read
Warehouse innovation – looking back
WAREHOUSING INNOVATION – LOOKING BACK, LOOKING AHEAD
CBRE is this year’s sponsor of the MHD Warehouse Showcase. The real estate services group’s Christine Miller, Head of Supply Chain Advisory – Pacific, and Cameron Grier, Regional Director – Pacific, Industrial & Logistics Services, sat down for a discussion around the long view in warehouse innovation – explaining developments over the past couple of years, as well as what the future might have in store for the warehousing sector.
Cameron Grier, Regional Director – Pacific, Industrial and Logistics Services at CBRE.

Even had Australia not been afflicted by the COVID-19 pandemic, we would still be experiencing a shift to e-commerce – and therefore an accompanying transformation in how warehouses operate – says Christine Miller, Head of Supply Chain Advisory – Pacific, at CBRE.
“The underlying trend was already there with regard to consumption patterns,” Christine says. “Back in 2018 and 2019 I was doing work with CBRE and the Property Council of Australia – identifying patterns and planning around them. The pandemic just accelerated that trend and created a sudden surge that no one was truly prepared for.”
With consumers increasingly desiring multiple channels to browse, sample, purchase, and receive products, this has resulted in far greater complexity for warehouse operations.
“If you look at warehouses in a historical perspective, even as recently as five years ago they would predominantly have been dealing with full pallets and full cases of product,” she says. “Now warehouses need to access individual items in a case, which introduces much more variation into the process. There is an increased need for space in warehouses, as well as new technologies that can adequately deal with items as opposed to cases and pallets.”
Prior to the pandemic, Christine says, the conversation around e-commerce was more relaxed insofar as it was construed in terms of how retailers would adjust to meet customer demands and manage costs. When COVID-19 hit, the conversation shifted Rather than just having one large warehouse, many operations are decentralising to have a lot of smaller warehouses spread out – which not only is useful for more agile last mile fulfilment, but also disperses the risk associated with having all your inventory in one location. ”
from a focus on optimisation to a focus on necessity.
“To take technology as an example, the question that used to be asked was, ‘If I automate my warehouse, how much can I save on footprint? How small can I go?’, whereas now no one asks that question anymore,” she explains. “Now what we’re talking about is how automation can increase throughput so that companies can achieve more volume within the same footprint. The emphasis on automation, last mile, operational complexity – all those drivers were already in place. With the onset of the pandemic, they just suddenly became imperative to address.”
Cameron Grier, Regional Director – Pacific, Industrial & Logistics Services at CBRE, adds that in fact the “footprint” perspective for most companies has flipped on its head.
“If anything, what we’ve noticed this year is that companies are wanting to increase their footprints, to accommodate increased inventory capacity that can be ready in the event of supply chain disruption,” Cameron says. “What we’re also observing is the desire for multiple warehouse locations as well. So, rather than just having one large warehouse, many operations are decentralising to have a lot of smaller warehouses spread out – which not only is useful for more agile last mile fulfilment, but also disperses the risk associated with having all your inventory in one location. When COVID hit, groups sharpened their focus on contingency-type warehouses – and that remains an ongoing focus.”
Cameron notes that Christine has previously observed – from her perspective as an expert in supply chain – that in terms of total supply chain costs, the real estate component accounts for only five per cent.
“This supports what I have seen this year with an increased appetite for more warehousing space,” he says. “With the real estate component being a relatively small proportion of overall supply chain costs, I’ve seen groups willing to commit on more speculative basis – just to ensure they have the space so they can sell their stock. I’ve never seen leasing demand like this in 20 years.”
THE AUTOMATION FACTOR
Christine says that recent innovations in automation have presented fresh and more broadly available opportunities for warehouses.
“Until relatively recently, automation was
Christine Miller, Head of Supply Chain Advisory – Pacific at CBRE.
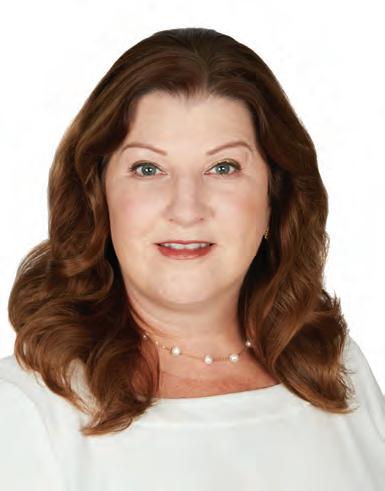
often considered only in terms of major, full scale automated operations,” she says. “These kinds of heavy, steel based, large capital expenditure solutions require such a scale of volume that it was only ever going to apply to a small segment of the market.”
But now, Christine says, recent innovations in automation are available to the “middle ground” of the market – automated solutions that can be more easily incorporated into existing premises.
“These types of automation don’t necessarily require a bespoke custombuild,” she says. “Only very large companies can afford steel based ASRS [Automated Storage and Retrieval] systems, with high bay capacity and reinforced floors to carry X amount of weight. But with AMRs [Autonomous Mobile Robots] – these are fantastic for e-commerce and can be flexibly deployed in existing warehouses at a much lower capex, which means it appeals to a broader range of the market. Management is more attracted to making those kinds of investments, as there isn’t such a huge capex hurdle to actually get it across the board or management level.”
Cameron agrees, noting that the prohibitive costs for ASRS style automation has often meant that – even in cases where companies wanted it – the majority of landlords don’t really have an appetite to fund it.
Cameron notes automation is still far from a majority consideration for most warehousing and logistics operations. “I’d ballpark that roughly 20 per cent of inquiries I’m working with include automation as part of the conversation. So, The question that used to be asked was, ‘If I automate my warehouse, how much can I save on footprint? How small can I go?’, whereas no one asks that question anymore. Now what we’re talking about is how automation can increase throughput so that companies can achieve more volume within the same footprint. ”
it’s still quite low in the overall scheme of things, but this will change.”
SUSTAINABLE DEVELOPMENTS
“Another big change I’ve registered in the past year or two has been the emphasis placed on solar power in warehouses – as part of an overall sustainability strategy,” says Cameron.
For a long time prior, he says, when a commercial negotiation was taking place, considerations around solar would often come in only at the end – more or less as a “box-ticking exercise”.
“The difference today,” Cameron says, “is that especially with major international companies – solar is right at the forefront of the conversation and an important commercial item rather than just a social one.”
He says that this trend has become particularly pronounced in the past 12 months, as companies embrace net-zero targets – an ambition that is widely shared at the international level among corporations and governments.
“I recently ran a property procurement process for a global occupier and the developer they ended up partnering with for their new fulfilment centre had a better solar solution than other short-listed competitors – which was a major factor in their decision.”
MHD asked Cameron whether this push towards solar and sustainability was primarily attributable to government pressures, PR considerations, or simply a shift towards greater cost effectiveness in solar technology. He says he couldn’t be 100 per cent sure – although it’s his impression that it’s coming from the top down – from senior management and investors – as well as expectations from the end-customers.
“I agree with Cam in that I think it’s coming from the investment community,” Christine says. “Whether there’s a groundswell from participants in super funds, or from senior management – I think at the investor level, ESG [Environmental Social Governance] is now really important. And that extends to ‘sustainability’ broadly construed. I’ve seen warehouses and offices where there is bicycle parking for employees, where there are basketball courts, where there are open spaces between warehouses. These in addition to solar, rainwater catchment and all these other more obvious sustainability developments people are doing. I think there is a major push to make sure workers find warehouses
or offices to be places they really want to work in; companies are taking increasing pride in that notion.”
Cameron adds that there is a clear customer demand component to sustainability considerations, too.
“I know that one of the major 3PLs has found that, when they’re pitching work to potential customers, those customers are asking these questions relating to sustainability capabilities and policies,” he says. “So, it’s become part of the opening pitch to customers – they’ve got a vested interest to make sure what they’re doing is sustainable.”
WAREHOUSING AND INNOVATION IN 2022 AND BEYOND
In the November issue of MHD Christine discussed the new developments occurring around converting shopping centre locations to hybrid retail-distribution locations to flexibly accommodate last-mile fulfilment.
Looking ahead into 2022 and the next five years, what are some other potential innovations that CBRE sees approaching across the horizon?
“I think beyond the shopping centre and distribution hybrid model, Australia is going to get better at defining mixed use more generally,” Christine says. “Previously, mixed use has been defined really only in terms of retail and residential. I think we will get more flexible in terms of adding a logistics component into mixed use properties.”
She is sceptical about the potential
Driverless trucks operating between major warehousing hubs could be utilised sooner than many expect.
of some warehouse-distribution possibilities while optimistic about the near-term viability of others.
“For instance, I don’t think drones are going to take off like everyone thought they would, two years ago,” Christine says. “I know that there are some pilot programs out there, but I personally don’t think drones are the answer. On the other hand, I actually think that autonomous trucks could have a real impact on warehousing sooner than some might suspect. The possibility of autonomous trucks doing pickups and drop-offs between major warehouse or distribution hubs is an exciting possibility. I know that Walmart in the United States has been running trials with autonomous trucks operating within a closed loop, doing deliveries from warehouse to store. We’ll need to figure out precisely what that looks like in an Australian context, but there is a real opportunity there – with interesting implications from automation, sustainability, and safety perspectives.”
While noting that predicting the future is an often-fraught business, she is quietly optimistic about the potential for autonomous trucks in Australia within a five-year time horizon.
“I don’t think we’re going to see autonomous trucks doing deliveries into Sydney’s CBD,” she says. “But what I could see is trucks being despatched from Adelaide out to Perth. There’s no reason those kinds of long, straight hauls – from hub to hub, occupying that middle part of the distribution process – couldn’t be done with an automated truck without a driver.”
From Cameron’s vantage point as an expert in industrial and logistics property, he thinks that there will be some notable multi-level warehouse developments in the coming years.
“This isn’t an Australian innovation, as we have significant experience with multi-level warehousing and logistics properties in APAC more broadly,” he notes. “But in the case of Sydney – where land pricing has gone up 30 per cent on average, just this year alone – the scales have tilted to the point where multi-level is more viable for developers. We expect there to be two to three multi-level developments that could be built within the next two years in Sydney. It’s too early to accurately predict the timeline for multilevel in Melbourne. But certainly, with Sydney, I think we’ll see some genuine multi-level warehousing of the sort that we’ve already seen in more population-dense Asia.
The need for multi-level warehousing may become more imperative, given Cameron’s view of vacancy rates, increasing land costs, rental growth and oncoming developable land supply in the next few years.
“The market is extremely tight right now, and it’s my view that it will continue getting tighter for the next couple of years on the east coast,” he says. “Vacancy is currently sitting at around 1.5 per cent nationally and just to keep up with the growth in e-commerce alone, we’ll need 35 per cent more supply every year than we’ve had historically over the last ten years. While we don’t have a shortage of zoned industrial land in our country, because of the infrastructure required for servicing it – and the longer lead times being experienced in planning approvals – we will see demand outstrip supply in the near term.
“Therefore, it’s incumbent on occupiers to really be planning a lot further ahead than they’re used to, in order to secure their supply chains. As Christine has pointed out, across supply chain in Australia there has been a relatively sudden realisation around how important your warehouse is to your operations.” ■
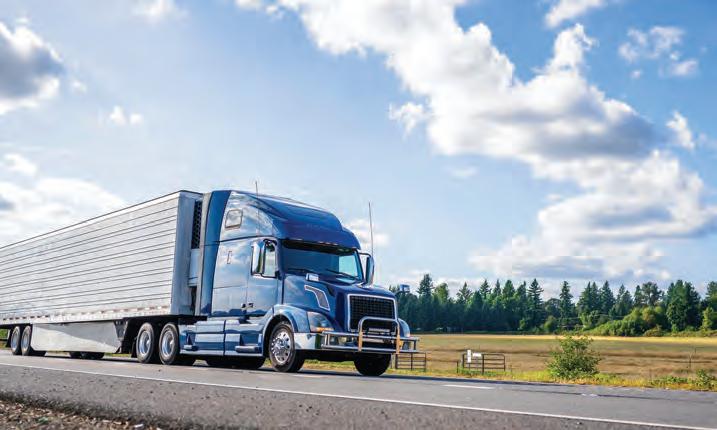