
16 minute read
Warehouse innovators showcase 2021
AMAZON ROBOTICS FULFILMENT CENTRE
Australia’s biggest warehouse will hold more than 20 million shoppable products on the back of the country’s e-commerce boom.
Amazon Australia’s mega robotics centre in the heart of Western Sydney will be the same size as Taronga Zoo, doubling the company’s footprint in Australia.
The ground floor will control the in and out movements, with conveyors to send inventory to levels two, three and four. The products are stored into four sided towers or ‘cubes’ with different sized letter box spaces for certain products. The drive units or ‘bots’ then slide underneath the cubes, picking them up and moving them to a specified location.
The fulfilment centre will have a total floor area of around 200,000 sqm across four levels – which Craig Fuller, Director of Operations Amazon Australia, says is equivalent to eight standard storeys.
The robotic technology will increase the building’s storage capacity by up to 50 per cent versus a traditional building design, creating more space for inventory for Australian sellers and enabling Amazon to increase selection for customers. They also help speed order processing time by moving shelves to employees, thereby reducing the time taken to store items for sale or pick them for new customer orders.
“The beauty of the technology is that all the spaces that you would normally require in a normal warehouse for aisle movement where forklifts or people move up and down aisles to pick products from the shelves, just disappear,” he says. “You don’t need it anymore because the robotic drives can move sideby-side and this can basically double the inventory footprint.”
Craig says once complete the centre could theoretically deliver products to 85 per cent of the population in 12 hours from its location in Western Sydney.
“When we receive the customer order the the inventory might be in multiple locations around the building,” Craig adds. “The order triggers movements among the drive units to move the different storage pods to a pick station where they present themselves in the right order so that we pick and then pack the product to be shipped out.”
Amazon has leveraged its international pedigree for the project, consulting with its teams around the world who have already developed
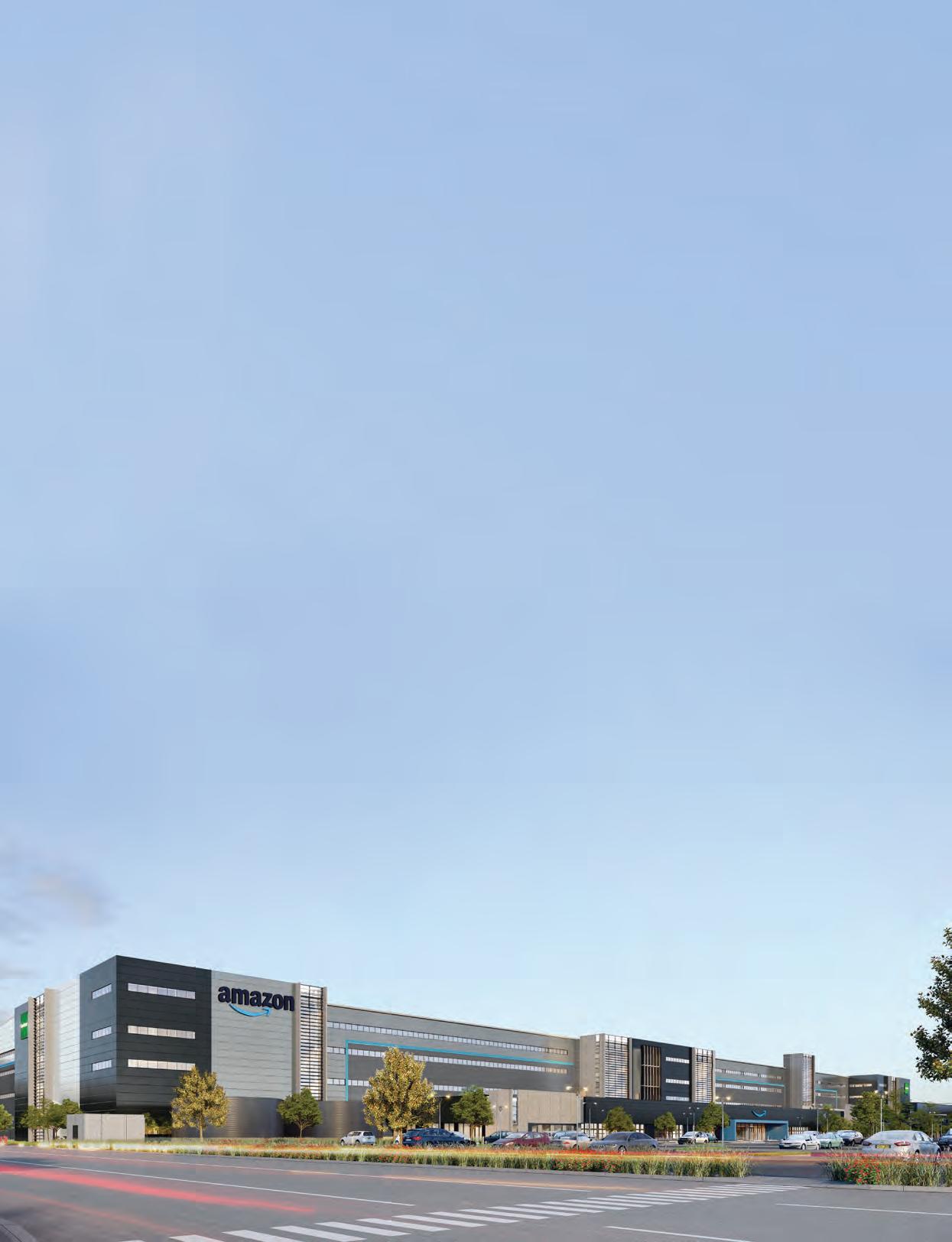
Craig Fuller, Director of Operations Amazon Australia, at Amazons first robotics fulfilment centre.
similar robotics facilities, and adapting the design to reflect local nuances. For example, the Australian site uses an adapted dock layout and design to reflect the typical vehicles used in Australia. The local team also considered ways to future proof the building in light of the pandemic, widening major thoroughfares and larger breakrooms to better enable social distancing.
“There’s lots of learnings we’ve taken from Italian and UK teams who built a similar centre a couple of years ago,” he says. “We’ve got the systems in place to capture those learnings so that the playbook we run with is being built from experience.”
Despite timelines being impacted by the challenges facing Western Sydney during the pandemic, construction and fit out of the facility is nearing completion and it is set to be operational in the first quarter of next year. ■
The fulfilment centre will have a total floor area of around 200,000 square metres.
Australia Post’s Brisbane Parcel facility can process 700,000 parcels per day.
BRISBANE PARCEL FACILITY, REDBANK

Australia Post’s Brisbane Parcel facility in Redbank opened its doors in late 2019, and not only is it the organisation’s largest parcel processing facility, it’s the largest in the southern hemisphere. The size of eight football fields and featuring both large and small parcels automation, the facility is capable of processing up to 700,000 parcels per day. With the incredible growth in e-commerce brought about by the global pandemic, the Brisbane Parcel Facility has been instrumental in enabling Australia Post to continue delivering for customers, with almost 200 million parcels processed at the site since it opened. Over the last two years, a number of improvements have been made to further boost capacity and increase efficiency, which has resulted We know our customers want their parcels delivered as quickly as possible which is why sites like our Brisbane Parcel facility are so important for Australia Post. ”
in a 20 per cent improvement in processing throughput.
To further increase capacity across its network, and as part of a three-year $1 billion dollar network investment plan, Australia Post has introduced new facilities in Sunshine West (VIC), Adelaide (SA) and Botany (NSW) over the last 12 months. An additional four processing facilities are also underway in Perth (WA), Bayswater (VIC), Western Sydney (NSW) and Tullamarine (VIC) and all due to go-live by mid-2022.
Rod Barnes, Australia Post Executive General Manager Deliveries says these investments are part of Australia Post’s ongoing efforts keep up with the ever-increasing demand for e-commerce and deliver for the 9.2 million Australia households that are now buying online.
“We know our customers want their parcels delivered as quickly as possible which is why sites like our Brisbane Parcel facility are so important for Australia Post,” Rod says.
“Australia’s habits have changed, and online will continue to be a critical shopping channel post-COVID so the additional capacity these new sites provide will be critical in enabling us to continue delivering for our customers right across the country.” ■
CEVA’S SUSTAINABLE WAREHOUSING
For assessing the performance of its facilities in Australia and New Zealand, CEVA Logistics uses the Green Building Council of Australia Green Star rating tool, a standard that focuses on several main criteria, including reducing the impact of climate change, enhancing health and quality of life, restoring and protecting biodiversity and ecosystems, driving resilient outcomes for buildings, fit outs, and communities, and finally, contributing to market transformation and a sustainable economy.
Four CEVA facilities currently possess a six-star rating, indicating world-class leadership, with four other facilities receiving five stars, signifying countrylevel excellence. Across Australia and New Zealand, the sustainability efforts of CEVA Logistics are estimated to reduce annual emissions by 4300 tonnes of CO2 equivalent.
As part of the CMA CGM Group, CEVA Logistics commits to the protection of the environment. The CMA CGM Group aims at becoming carbon-neutral by 2050. CEVA helps its customers make the best decisions when planning their logistics and freight transport operations to reduce environmental impact as they balance the business and timing needs of their supply chain processes and shipments. ”
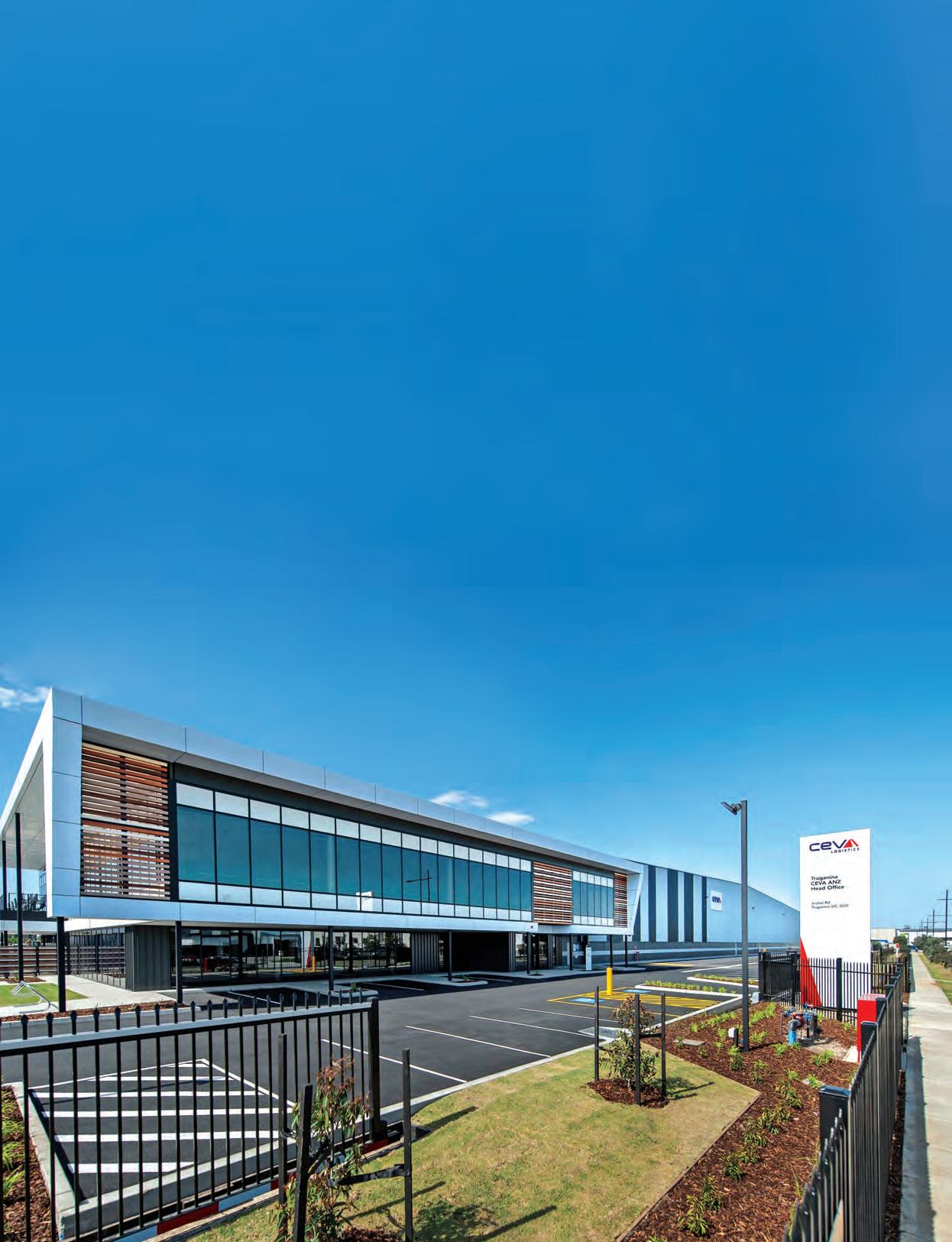
CEVA helps its customers make the best decisions when planning their logistics and freight transport operations to reduce environmental impact as they balance the business and timing needs of their supply chain processes and shipments. CEVA believes estimating carbon footprint and planning accordingly is the first step towards a more sustainable supply chain, and the company offers customers an eco-calculator on its website and through its MyCEVA digital booking platform to estimate the logistics carbon footprint of a shipment via ocean, air or ground.
The company also regularly assesses its environmental footprint to look for areas to further improve its environmental sustainability and support of local communities. The teams in local facilities around the world are committed to sustainable development and reducing waste at CEVA locations.
CEVA’s presence in Australia and New Zealand highlights these commitments. The company manages programs in waste control, energy and water conservation, operational improvement and knowledge sharing to enhance the sustainability of its activities and to positively contribute to the local communities around its facilities. From solar panels, automatic lighting and AC systems to efficient truck routing to eliminating plastic and foam cups to repairing and reusing damaged pallets, the company takes a holistic approach to its operations. ■
CEVA’s site at Truganina is one of the biggest warehouses in the southern hemisphere and home to many of CEVA’s largest clients in Australia.
Saul Resnick, CEO, DHL Supply Chain, Australia and New Zealand.
DHL SUPPLY CHAIN
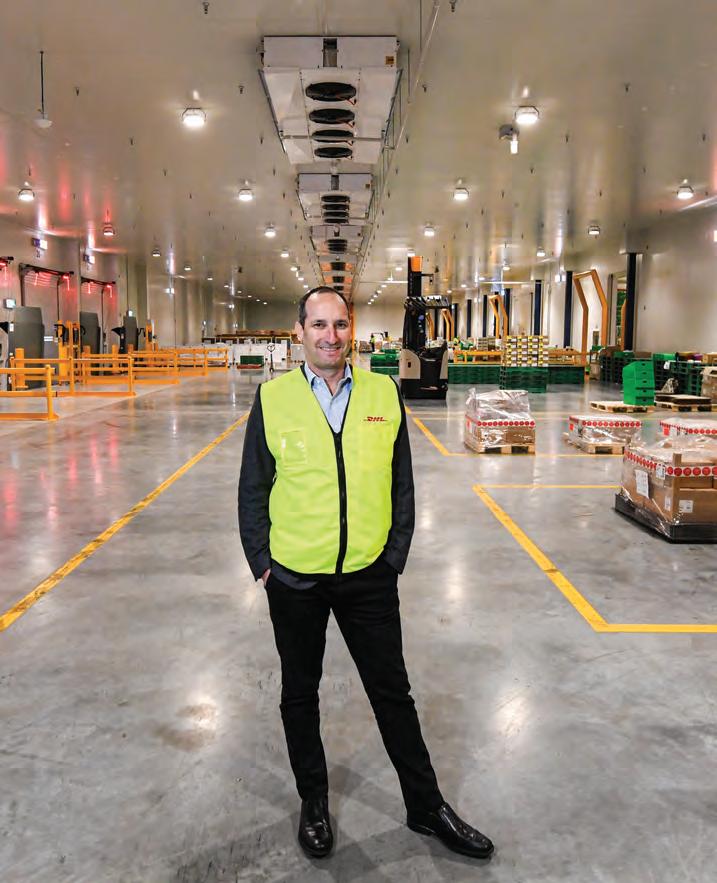
DHL Supply Chain has launched a number of new healthcare-grade warehouses in Australia and New Zealand over the past year, with a combined total floor space of more than 75,000 sqm. Featuring DHL’s leading cold-chain facilities, which store pharmaceutical products at between 2-8 degrees Celsius, the warehouses also support the storage and management of medical devices, vaccines, animal health, diagnostics, and consumer health products. The additional capacity also enabled DHL to efficiently manage the storage and distribution of COVID-19 vaccines in both nations. Flexible operations are a key part of ensuring supply chains stay resilient, especially when it comes to critical cargo like healthcare products. While some healthcare products must be stored between 2-8 degrees, some require 8-25 degree Celsius temperatures. Others require extreme cold temperatures to maintain their integrity – this is why DHL Supply Chain augmented its cold chain capabilities with 12 specially designed freezers capable of storing vaccine products at below -70 degrees Celsius. But storing products in a freezer is only one link in the cold chain. In order to safely and efficiently transport healthcare products around the country, DHL Supply Chain also launched 60 new, purpose-built temperature-controlled trucks that feature an Australian-made dual The Life Sciences and Healthcare industry is one of the most heavily regulated industries. DHL has seen growing interest for our industry-leading cold storage facilities which in turn, drives better outcomes for the storage and distribution of healthcare products. Increasingly, we have also seen a growing appetite for local distribution centres to be an ongoing part of global supply chains. ”
temperature cab solution with 2 -8°C and 15-25°C temperature ranges, to ensure label claim compliance (delivery as per the temperature instructions on the packaging of the product) as prescribed by the manufacturer. This solution is a first for the Australian market and ensures healthcare manufacturers can stay ahead of evolving compliance regulations. DHL has also invested in a new multi-million-dollar transport management system and national control tower, to support more efficient consignment planning and offer customers greater visibility of their deliveries. To best manage the distribution of cold-chain products, DHL Supply Chain has proprietary packaging solutions which are designed specifically for pharmaceutical products to ensure health supplies are delivered in the perfect condition. This includes Woolchill, a FSANZ Food Safe certified natural cooling system made from sheep wool, which maintains chilled products for up to 50 hours, removing the need for refrigerated vehicles and plastic or polystyrene packaging. ■
Dematic’s GTP solution delivers items directly to pick stations.
SIGMA HEALTHCARE
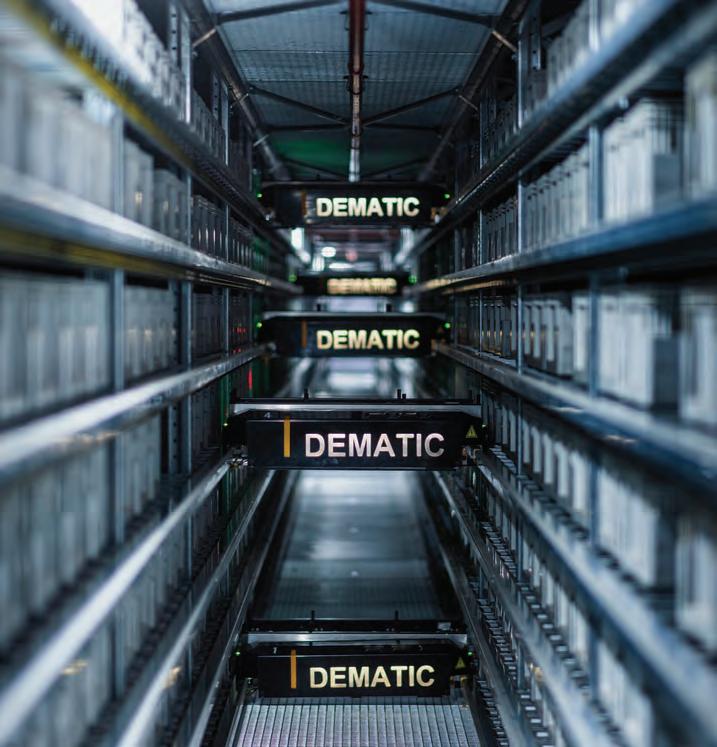
Sigma Healthcare has one of the largest pharmacy networks in Australia, distributing to both community and hospital pharmacies nationwide. At its new distribution centres (DCs) in Perth and Brisbane, Sigma implemented innovative automation solutions for order fulfilment.
“The competitiveness of the pharmaceuticals industry today is very high. Pharmacies are constantly pushing Sigma as their sole distributor for increased service levels, which were just not achievable at previous operation rates,” says Paul Brown, National Operations Manager, Logistics for Sigma. “By initiating a more innovative approach to fulfilment, we can make the most of our DCs with advanced automation ensuring the highest efficiency”.
The overarching goal was to modernise its new DCs with the latest in automated picking technology. Sigma selected a Goods-to-Person (GTP) Picking Solution from Dematic, to provide enhanced speed, productivity, and accuracy rates through the reduction of manual put away, replenishment, and picking processes.
The GTP solution delivers items directly to ergonomically optimised pick stations – eliminating the need for operators to manually locate and retrieve items by travelling across the DC floor. The solution enhances operator performance by combining high-density, secure storage with the rapid rates and accuracy of the pick stations.
The solution also provides a safer workspace for all DC staff, meeting all regulations for Work Health and Safety, OH&S, Guide to Good Distribution Practice (GDP) for Medicinal Products, and the government health regulations around COVID-19.
The DCs efficiently handle current The competitiveness of the pharmaceuticals industry today is very high. Pharmacies are constantly pushing Sigma as their sole distributor for increased service levels, which were just not achievable at previous operation rates. By initiating a more innovative approach to fulfilment, we can make the most of our DCs with advanced automation ensuring the highest efficiency. ”
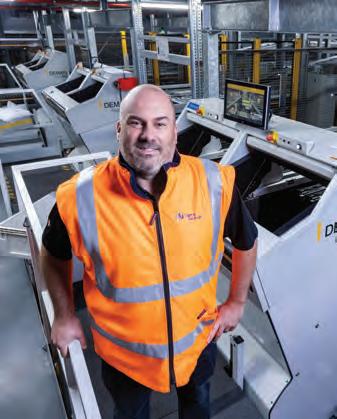
Paul Brown, National Operations Manager, Logistics for Sigma.
order volumes and the increased number of SKUs, with room to accommodate future volume growths. Accuracy has improved markedly, and product damage has been reduced.
“The modular and scalable solution provides us with the flexibility to optimise current operations and to expand as our business grows,” says Paul. “Likewise, the ability to manage logistics costs and forecast budgets has been a significant benefit to Sigma.” ■
CAVPOWER GROWING FOR THE FUTURE
Cavpower’s Service Operations Centre in South Australia is helping the official Caterpillar dealer service customers in the mining, construction, energy and transportation sectors. Partnering with Ahrens, Cavpower was able to see this $20 million facility brought to life, with Ahrens’ work allowing Cavpower to more efficiently distribute, maintain and repair Caterpillar equipment such as new and used machines, work tools and power systems. Drawing on a complete range of in-house capabilities and their own structural steel fabrication, Ahrens worked alongside Cavpower to deliver a variety of works that spanned across two levels. Ahrens’ work on the specialised workshop for Cavpower comprised of 26 bays which are fitted with Drawing on a complete range of in-house capabilities and their own structural steel fabrication, Ahrens worked alongside Cavpower to deliver a variety of works that spanned across two levels. ”
heavy duty overhead cranes, ranging from 12.5 to 25 tonne in capacity for large off-highway Caterpillar trucks and dozers. Catering for Cavpower’s bespoke design requests, Ahrens also completed an additional mezzanine fit-out to house a first-rate training facility for the client’s apprenticeship and upskilling programs, training technicians entering the industry and developing new skills for future technologies. In order to aid in the relocation of key components of the Cavpower business from Enfield to the new headquarters in Gepps Cross, Ahrens have been developing multiple facilities on the site over several years and have completed over 1000 sqm worth of work. This includes construction of Cavpower’s world-class Component Rebuild Centre and its recent extension providing a stand-out laboratory, store room, open plan office, meeting rooms and all associated modern amenities. Cavpower’s partnership with Ahrens has ensured their ‘world class standard’ is met, safeguarding their facilities for both current and future generations. ■
Cavpower’s specialised workshop is comprised of 26 bays.
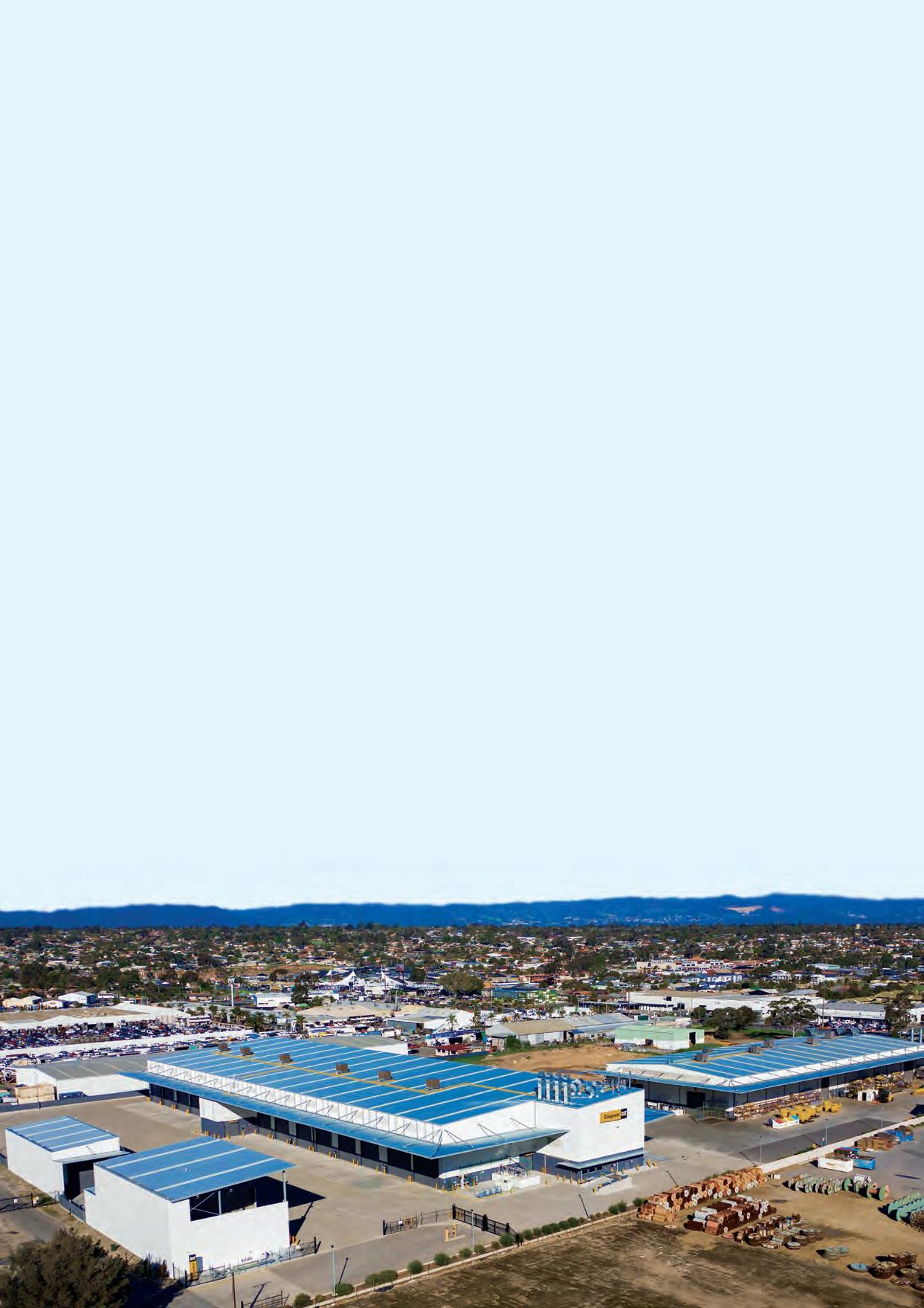
JAYCAR’S HIGH BAY FACILITY
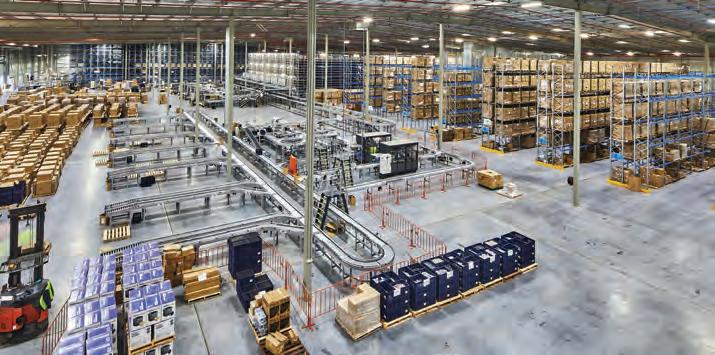
Frasers Property Industrial successfully completed its first high bay facility for Jaycar at Eastern Creek Business Park in Western Sydney on March 20, 2020. The $80m facility, including automation fit-out, features 21,688 sqm of floorspace and a soaring 25.5m dedicated high bay section that is capable of a 20,000 pallet capacity. The technical design is leading the way in industrial innovation in Australia and was constructed as the first of its kind in NSW by Frasers Property Industrial.
The facility also features a specialised low bay tote area for assembly and trade pick-up, 33m wide super awning structure and 1000sqm mezzanine office. The mammoth warehouse doubles the height of a standard Australian warehouse and has successfully streamlined Jaycar’s supply-chain systems and improved the company’s productivity. Highly automated, specialised engineering by Frasers Property Industrial was required to ensure the slab could withstand 29 tonnes from the automated pallet storage and retrieval system area. Fire engineering considerations were another design triumph, with sprinklers built into the high bay racking.
Proven high bay success has sparked a trend in the industrial development industry, where more facilities will be built to reach new heights as land scarcity increases. Frasers Property Industrial received more inquiry for
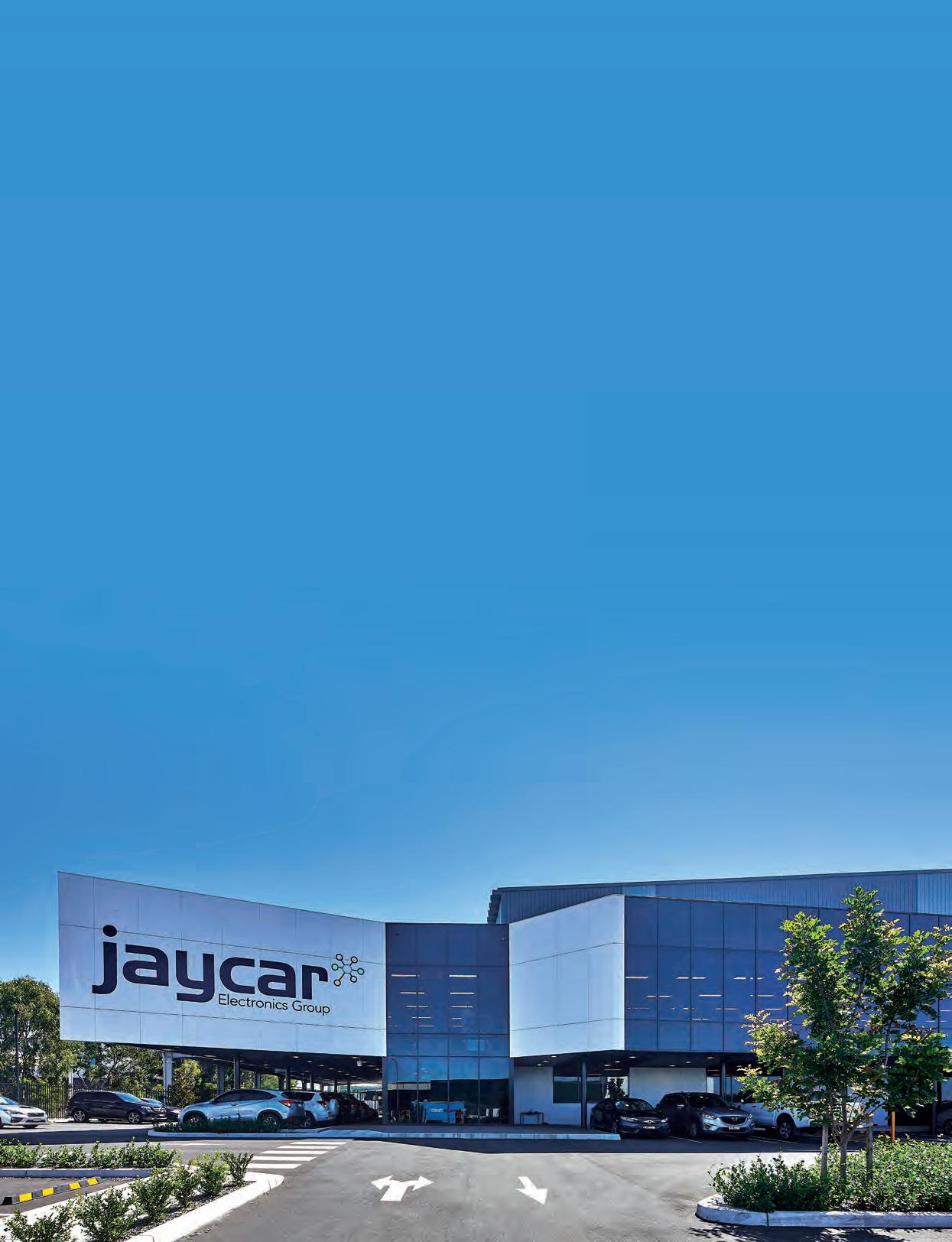
Jaycar’s facility has 21,688 sqm of floorspace.
Frasers Property Industrial received more inquiry for pioneering high bay designs in the past three years than it did in the past 20 years, partly due to the proven cost efficiencies of the Jaycar facility. ”
pioneering high bay designs in the past three years than it did in the past 20 years, partly due to the proven cost efficiencies of the Jaycar facility.
Jaycar will save significant supply chain costs in the first year alone due to improved operational efficiencies owing to the design. High bay construction requires significant design input from the project engineering group and delivery team, with engineers, project managers and construction workers navigating structural steel, roof cladding and wall cladding requirements at more than 20m high. Significant analysis of what sequence trade work should be performed in was undertaken. ■
The warehouse doubles the height of a normal facility.
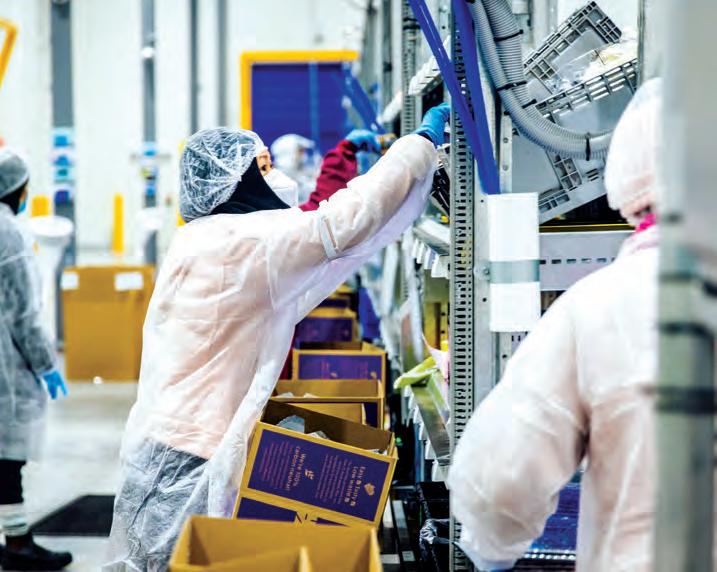
Meal kit delivery company Marley Spoon began production in a new fulfilment centre in Sydney’s Wetherill Park in July 2021. The meal kit company’s brands – Marley Spoon and Dinnerly – grew substantially throughout 2020 as the COVID-19 pandemic accelerated the demand for reliable food delivery services. In the 14,200sqm purpose-built, temperature-controlled fulfilment centre, Marley Spoon associates pick and pack fresh, dry and chilled ingredients and recipe cards for customers to cook at home into delicious meals. The nearly 250 Sydney staff working across production, sourcing, supply chain and people operations will now be based out of a facility that accommodates the growing demand of the meal kit business and allow for further innovations to improve the customer experience. The facility features multiple cool rooms for repacking ingredients and storage, as well as an oversized cool room where staff members pack boxes on conveyor belts using a unique, selfdeveloped packing system. In a highly competitive, consumer
The facility is Marley Spoon’s most environmentally friendly fulfilment centre.
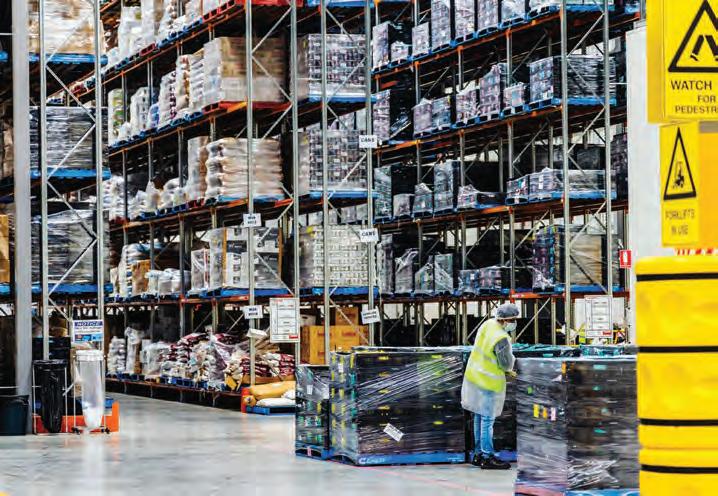
driven industry, offering flexibility and choice have been at the heart of the meal kit company’s brands, so the purpose-built facility will allow further automation and efficiency, while also allowing the company to expand its offering to customers, including launching a brand new pet food business, bezzie. The new facility is Marley Spoon’s greenest and most environmentally friendly production facility in the
Almost 250 staff work to pick and pack products.
In a highly competitive, consumer driven industry, offering flexibility and choice have been at the heart of the meal kit company’s brands, so the purpose-built facility will allow further automation and efficiency, while also allowing the company to expand its offering to customers, including launching a brand new pet food business, bezzie. ”
world. To achieve this, the company is preparing for a 5-Star (“Australian Excellence”) Green Star certification on the base building. Green Star is Australia’s only national, voluntary rating system for buildings and communities. With this in mind, the Wetherill Park facility has been outfitted with state of the art LED lights and motion sensors, 500kw solar PV systems, and rainwater harvesting systems. ■