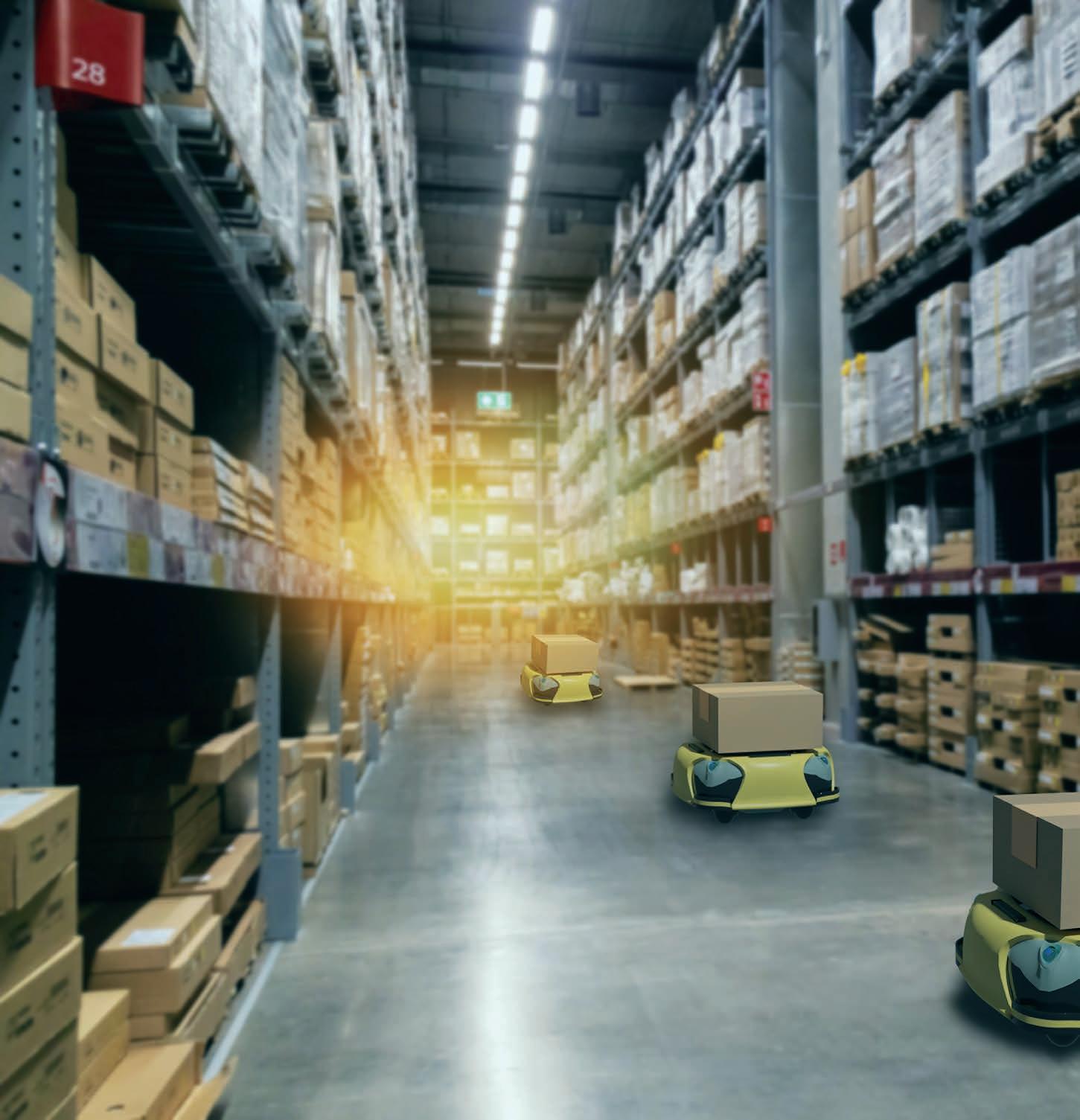
10 minute read
Industry Focus
Path to a collision-free autonomous robot
Manufacturers’ Monthly speaks with the University of South Australia STEM program director and mechatronics engineering lecturer, Dr Habib Habibullah, about a new path planning algorithm that his team have developed to make autonomous mobile robots safer and more efficient.
The University of South Australia’s algorithm helps robots avoid incoming objects.
IndustryFocus
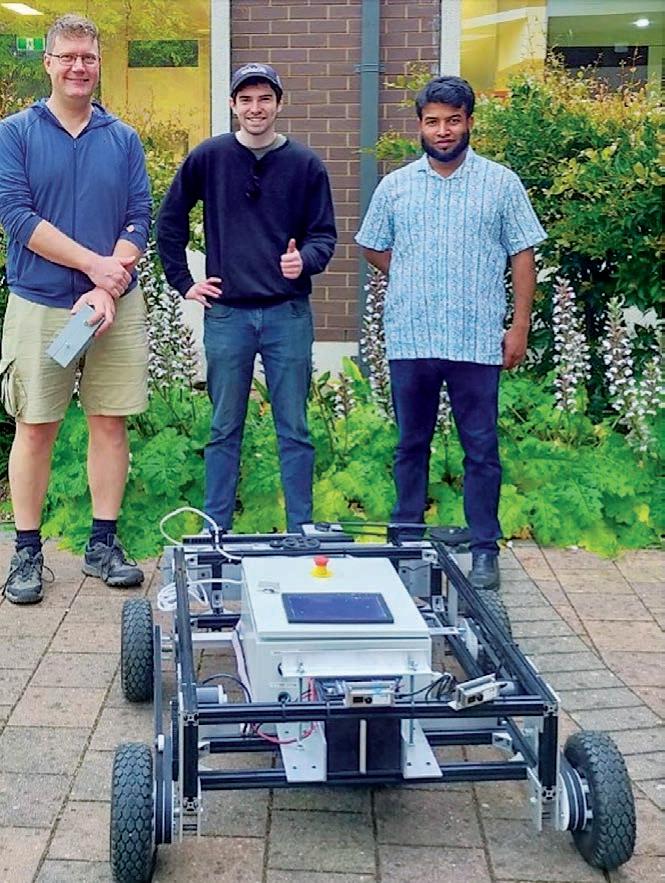
IN September 2021, the Australian team from CSIRO’s Data61 competed in the global DARPA Subterranean Challenge in the US – otherwise known as the “Robot Olympics” – and came second in the finals for pushing the boundaries in autonomous robotics. Six autonomous robots were placed in real-world scenarios and awarded points for correctly locating items, maintaining autonomy, and mapping the terrain. These robots would have used a path planning algorithm to navigate their way to victory.
According to ScienceDirect, path planning (or motion planning) is defined as a computational problem that finds a geometrical path from the vehicle’s current location to its goal location, while avoiding obstacles.
Advanced robotic systems such as those displayed in the Subterranean Challenge have been increasingly adopted in the manufacturing industry under the Industry 4.0 revolution, and have achieved great benefits. The Advanced Manufacturing Growth Centre’s Sector Competitiveness Plan 2017 stated that robotics and automated production processes enable “greater productivity, lower costs, improved workplace safety and higher production quality.”
One of the Plan’s priorities for improvement through research and development in this space begged the question: “How can robots better develop situational awareness to interact with workers and customers and in controlled environments?”
Investigating this question, a team led by Dr Habib Habibullah from the University of South Australia has created a path planning algorithm that addresses how autonomous mobile robotic systems can work in harmony with humans, both safely and effectively.
An in-house built weeding robot designed and developed at the University of South Australia by electrical and electronics engineering honours thesis students.
How the algorithm works
The concept behind the project was to design an autonomous robot with multiple objectives and uses, such as picking and placing objects based on an area tag or barcode in a warehouse setting. The robot would have the ability to operate where it may encounter dynamic obstacles such as human movement or other moving machines, like forklifts, as well as static obstacles in the environment, like shelves.
In the initial testing phase, the team achieved a high success rate in avoiding obstacles in a series of nine different simulations.
“It was not expected that it would reach the goal,” Habibullah said. “We restarted the scenario and implemented several other algorithms, but we only found a 50-60 per cent success rate. But in this special case, we succeeded in achieving obstacle avoidance at a higher rate, close to 100 per cent.”
The University of South Australia’s algorithm combines several common avoidance algorithms together, including Dynamic Window Approach (DWA) and an improved Follow the Gap Method (IFGM). According to Habibullah, the algorithm works by taking the dimensions of the robot and potential obstacles into account and calculating the distance between them. Using this data, it makes an arbitrary judgement on the potential speed of the oncoming obstacle.
“If a human obstacle is walking at one or two metres per second, we considered that the speed for the robot needs to be a little bit faster than the human’s movement,” Habibullah said. “When the obstacle’s speed increased, the algorithm was efficient in determining the distance between the obstacles and the robot itself, and also the relative velocity of the obstacle and the robot. And counting that towards hitting the goal, how much time it will have before colliding with the obstacle. If it calculates that it’s going to collide with the obstacle, then the robot will
Industry Focus
A TurtleBot project completed by a group of undergraduate students.
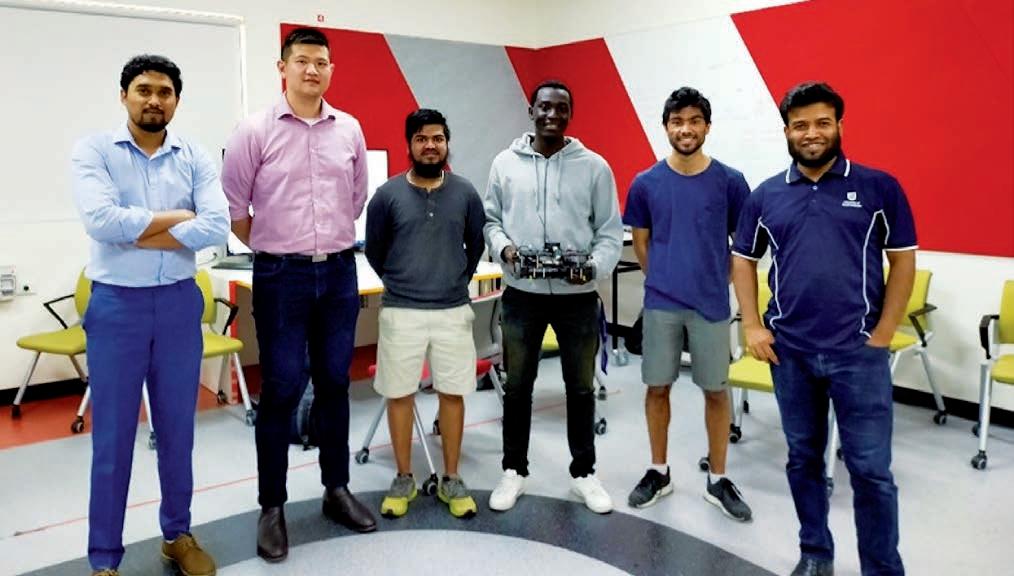
slow down at a speed that will let the obstacle pass and then the robot will continue on.”
In an instance where the obstacle is in line with the approaching robot and the robot cannot safely pass in time, the algorithm predicts a separate trajectory to reach its end goal.
TurtleBot test
Upon confirming that the algorithm functioned at different levels of speed, Habibullah and his team transferred their tests to the Resource Lab, using a TurtleBot as a prototype. A TurtleBot is an entrylevel mobile robotics platform which can run Simultaneous Localisation and Mapping (SLAM) algorithms to build a map. It is controlled remotely from a laptop or smart phone.
“We used other mini robots as moving obstacles so that when the TurtleBot moves autonomously, the algorithm imported into its brain will readily apply and calculate parameters and uncertainties, the velocity and distance of obstacles and how to travel from the starting position to the goal position,” Habibullah said.
This allowed the team to optimise the algorithm within the TurtleBot system and publish the results in a report, “Local path planning for autonomous mobile robots by integrating modified dynamic-window approach and improved follow the gap method,” in the Journal of Field Robotics in December 2021.
“This has huge potential with respect to applications in the manufacturing industry,” Habibullah said. “From that point of view, if a robotic arm needs to be manoeuvred along the production line or support a different line of operation, we can adapt an autonomous mobile robot to do that. So, we can reduce the set-up time and initial capital investment and also get a better return on that investment.”
Striving for efficiency
To make the University of South Australia’s path planning algorithm more efficient than others on the market, Habibullah and his team used a sensor fusion approach. In this approach, data is extracted from multiple sources to form a single, highly accurate model of the robot’s surrounding environment. This helps the robot validate how it should act.
“We modified the algorithm so that we can validate this data in more than one source, so that it is definite and reliable,” Habibullah said. “When working in a collaborative workspace with humans and machines, there is a high level of safety that we have to ensure so that no major accident occurs. We came up with a solid, reliable calculation process that will support safe travelling.”
For example, a driverless vehicle currently on the market can track its location and the distance between itself and the vehicle in front of it using data from its GPS device, LIDAR sensors and camera. However, a driverless vehicle that relies solely on GPS data will lose its location as it travels through a tunnel. Without the correct data coordinates, this could lead to an accident.
“By combining three different sources of sensor data, we can produce a better, more resilient map that will guide the vehicle, achieve better reliability and reduce the probability of committing an accident,” Habibullah said. “These are the considerations that we put in place to develop this algorithm, and our resource team are currently working on that to investigate any shortcomings it may have.”
Applying the algorithm in industry
Habibullah has ambitions to help companies that are on the digitalisation route and are seeking to use autonomous mobile robots in human-machine collaborative workspaces, such as a manufacturing facility. To achieve this, the parameters of the algorithm need to be adjusted to become a fit-forpurpose model before it is ready for deployment.
This was the case with a recent project in which two of Habibullah’s undergraduate students designed and developed a weeding robot for vineyards.
“I had a client last year that works in the Riverland area, a threehour drive from Adelaide. He was looking to semi-automate or fully automate a device so that it can autonomously work in the orchard for weeding, spraying and crop monitoring,” he said. “It will move along the row, take images from different plants and then process the images live to see the condition of the trees or crops. From that, it can predict where it should spray and then directly take action. At the moment, we’re working to implement that as the first outdoor application of this algorithm for agricultural robotics.”
Recently, another four students at the University of South Australia worked to implement the algorithm into temperature sensor technology for SensorTec. In this instance, these temperature sensors were used in farms to determine the pH levels and
IndustryFocus
moisture levels at different depths of the soil.
“In doing this, we were working to automate the production line,” Habibullah said. “But we found some difficulties in doing that. The robotic arm, supplied by Omron, had a 1.3m reach but the length of the moisture sensor probe itself was only 120cm. This meant that the robot was not able to reach up and move it from one tray to another tray.
“In that case, we recommended coming up with a mobile station for the robotic arm so that it can travel to the tray, or it can pick up and then take the probe to the testing station and then put it in either the faulty tray or success tray.”
The path planning algorithm can also be applied to rugged mobile vehicles used in the mining or welding industries.
“We had an email from a client who has a business in mining,” Habibullah said. “They are looking to perform welding tasks at different spots. They want a mobile vehicle so that it can move to that particular point, with pre-set coordinates for the location of where it has to weld. Then the robot can move from station to station.”
The University of South Australia’s algorithm, used in conjunction with the robots within the Robotic and Automation Laboratory, could help to spark further change in the way that robotics is used in the manufacturing industry. An example of this is a potential application for car manufacturing.
“I have a plan in the near future to automate our robotic and automation station and make a prototype for other manufacturing systems. For example, in car manufacturing or other manufacturing systems where a different, more complex reach may be needed for the robot; meaning it has to travel to do that particular job,” Habibullah said. “For car manufacturing, even within the car body itself, the robotic arm would have to move from the bottom to the top side, to the inside and so on. In that case, if we implement this kind of algorithm and find the safe distance between the nearest possible obstacles, we could make it a safer environment and produce a greater surface finish. We’re planning to enhance our capability to showcase this to our clients, both nationally and internationally.”
Skills of the future
As Habibullah moves forward to identify new challenges and address them in order to attain the technology readiness level that is necessary for the new path planning algorithm, he is also preparing the next generation of skilled workers required to maintain the technology in the future.
“This is a rapidly changing technological platform – and whether it’s the manufacturing industry or the transport industry, including all robotic applications from warehouse problems to driverless vehicles, it’s a rapidly changing publish or perish campaign,” he said. “We oversee that when these technologies become available to the masses in the near future, we are running out of the skilled people needed in Australia. We need to have the back-up and support for a driverless vehicle or for an autonomous manufacturing system, but we don’t have the capacity of those skilled people in Australia. So, we are targeting and developing our courses at the University of South Australia and related linear programs, so that we can produce the skilled students to take those challenges on in the future.”
In terms of producing and manufacturing technological solutions such as the path planning algorithm in Australia, and effectively integrating them into diverse robotic applications, Habibullah said it is paramount that we need to work hard to produce the skilled capabilities needed sooner rather than later.
Experience the Power of Red
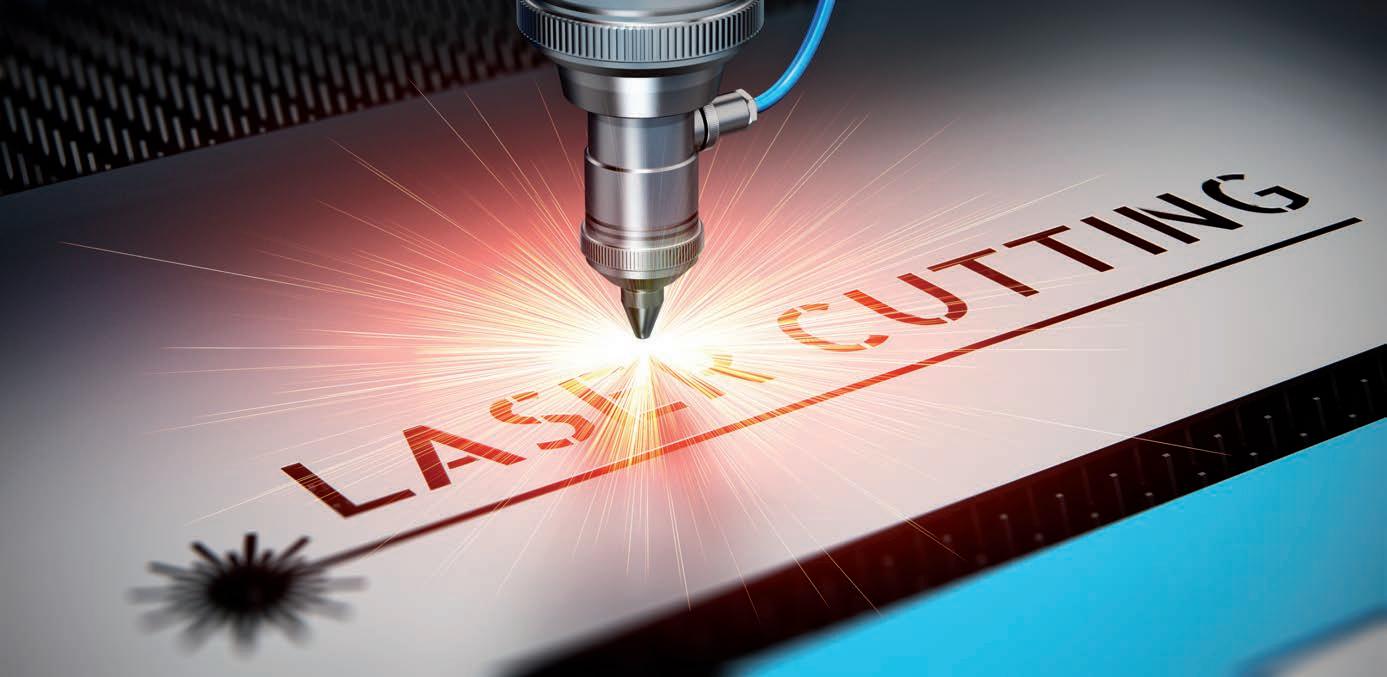
www.cpcompressors.com.au 1300 555 284 YouTube-LinkedIn-Facebook
Our brand NEW cut through technology so you can cut through the competition!
Features:
4 models (11-22kw) 16 bar Cutting speed and thickness
Complete Package: Compressor, 400L tank, Air Dryer, Pre/Post & Activated Carbon Filters