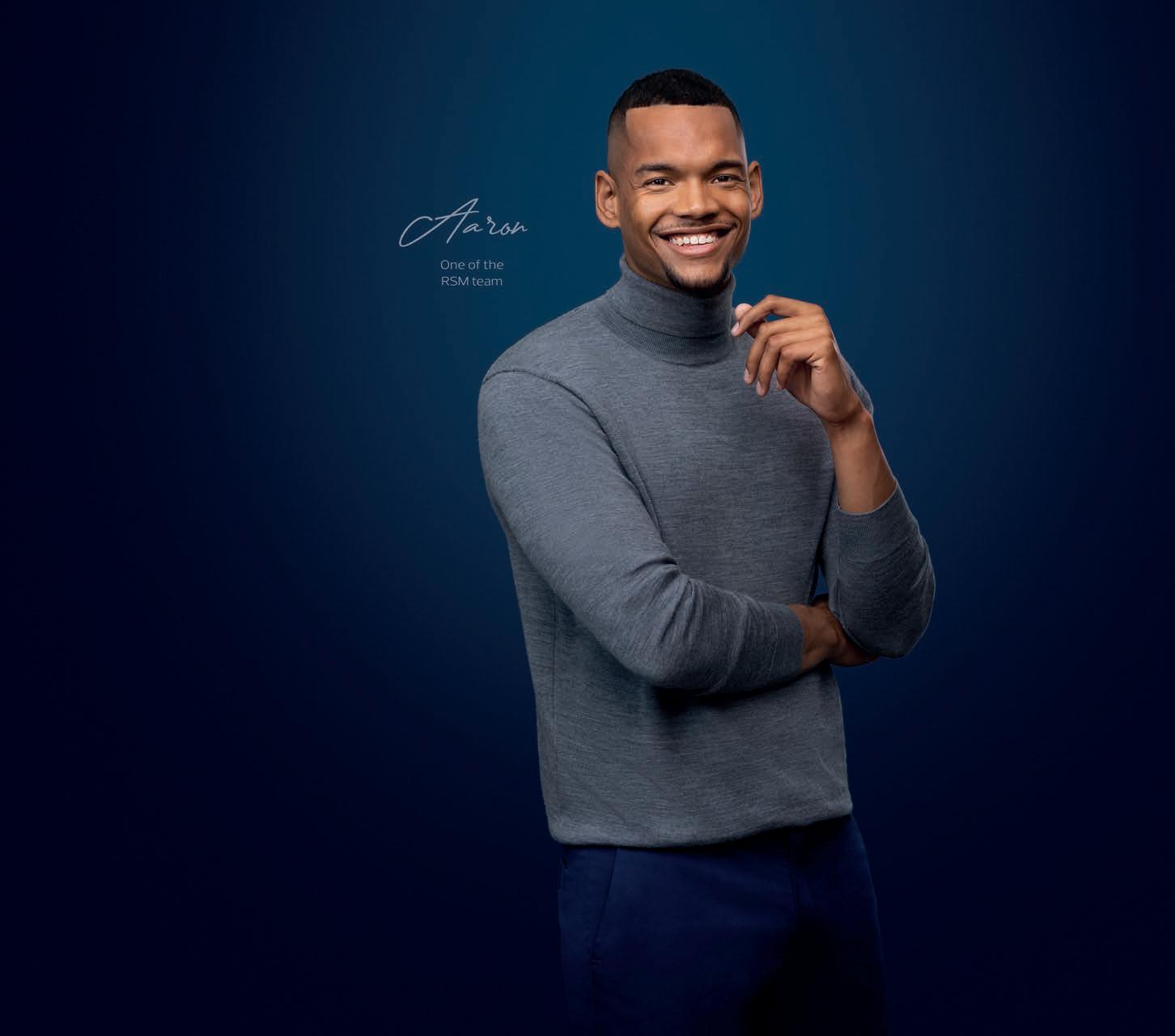
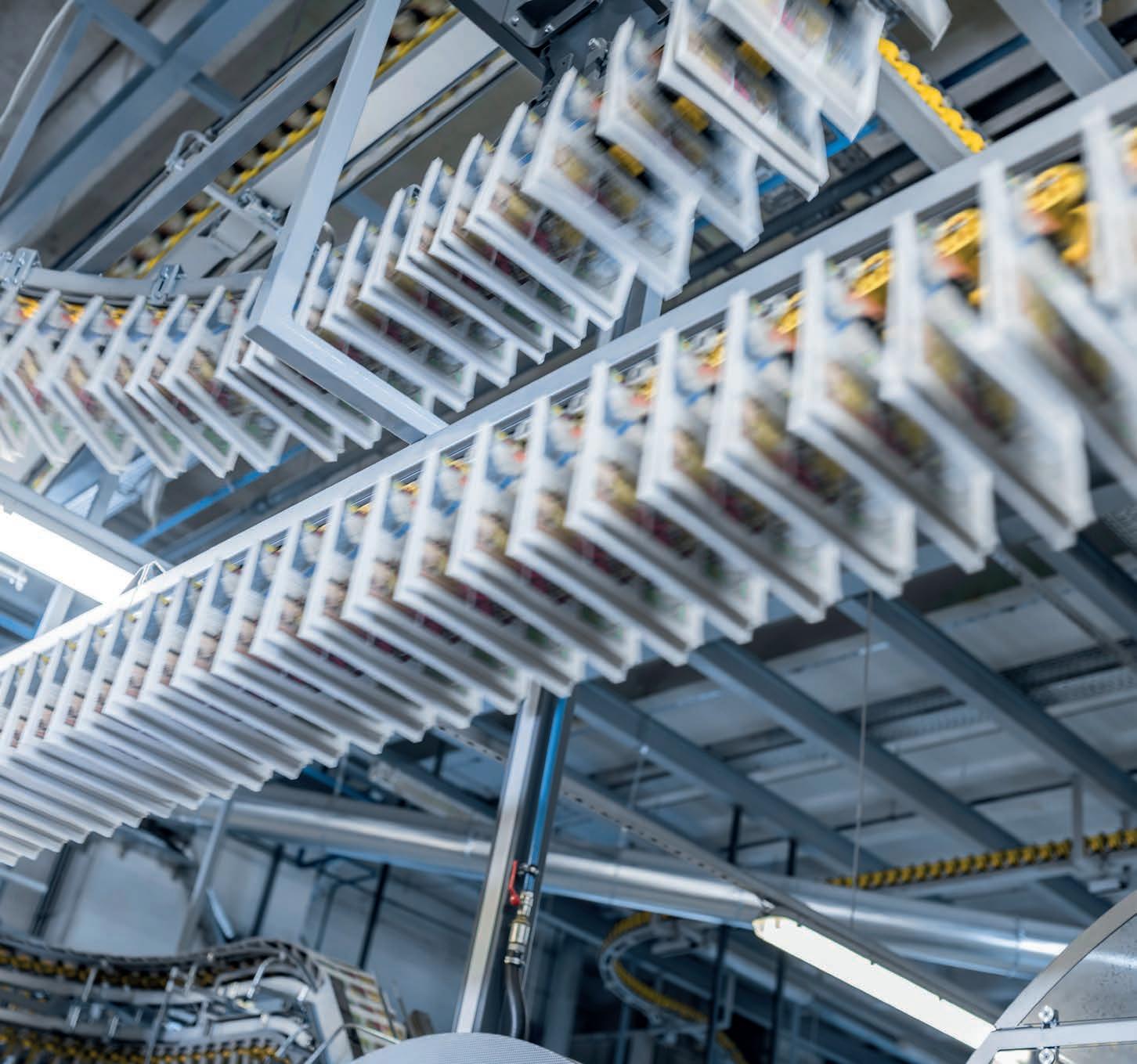
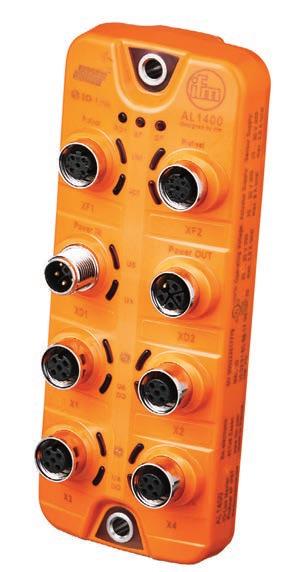
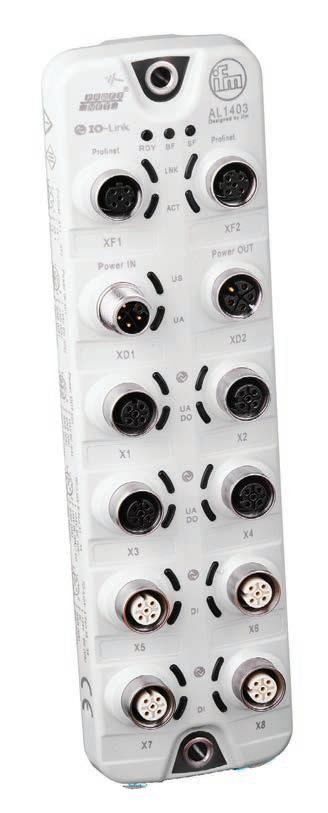
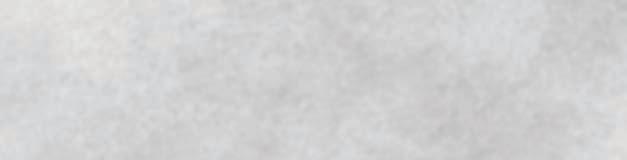

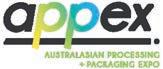
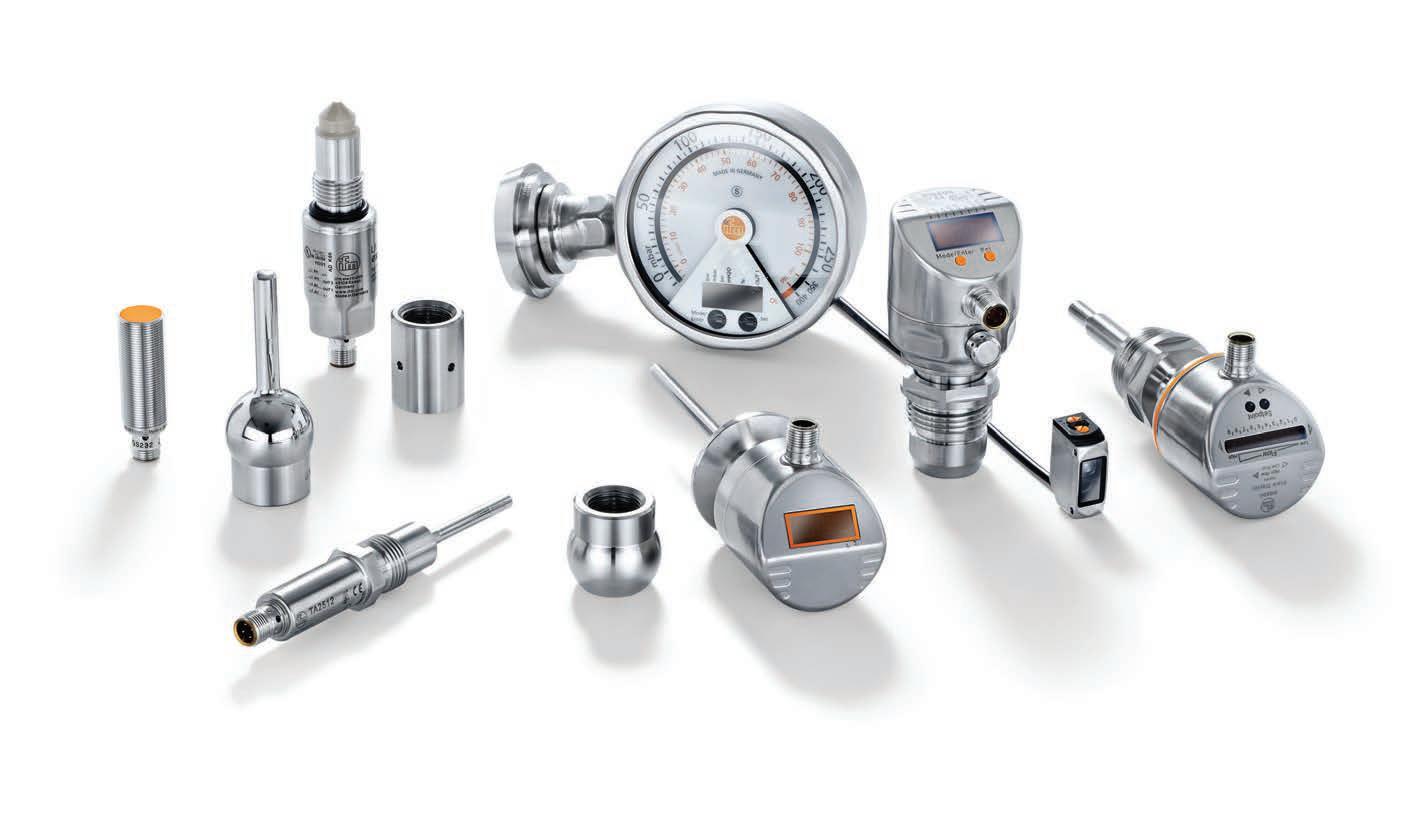
Are you ready to take your manufacturing facility to the next level of performance, quality, and efficiency?
With IO-Link, you can enjoy the benefits of digital communication and data access for your process instruments.
IO-Link is a simple, flexible, and cost-effective way to connect your sensors and actuators to your higher level controller.
Here are some of the advantages of IO-Link for your manfacturing facility:
Boost your product quality with reliable and accurate digital signals and predictive sensor information.
Save money by eliminating the need for analog input cards and shrinking your control cabinet size.
Increase your efficiency with bidirectional data exchange between your devices and your controller.
Improve your machine uptime by replacing faulty devices quickly and easily with the automatic device replacement feature of IO-Link enabled sensors.
Don’t miss this opportunity to upgrade your facility with IO-Link, the smart solution for Industry 4.0. Contact us today to find out more!
1300
sales.au@ifm.com www.ifm.com/au
R & I Instrument & Gear Co, with a history of 75 years, operates as a division within the Hardman Group of Companies, an Australian-owned enterprise of distinction. The group is renowned as a premier provider of precision machining and gear-cutting services throughout Australasia with a legacy dating back over 70 years.
Hardman Group expanded through two additional acquisitions. Presently, it comprises three distinct business units - Hardman Bros, R & I Instrument & Gear Co, and Marks 4WD.
• We operate a Quality Management System that is able to support the manufacture of high precision machined components and gear cutting to leading Original Equipment Manufacturers (OEMs).
• Gear cutting and precision machining, shaping, milling and grinding, CNC machining, honing, broaching and wire cutting.
• Assembly and sub-assembly and production onsite with over 7,500m2 of floor space.
• Manufacture to print, maintenance, repair and overhaul capability.
• Work with customers from prototype, reverse engineering, to make to print production.
CEO: John Murphy
Chief Operating Officer: Christine Clancy
Managing Editor: Syed Shah
Journalist: Phillip Hazell phillip.hazell@primecreative.com.au
Production Coordinator: Michelle Weston michelle.weston@primecreative.com.au
Art Director: Blake Storey
Design: Cat Zappia
Sales/Advertising: Emily Gorgievska
Ph: 0432 083 392 emily.gorgievska@primecreative.com.au
Subscriptions
Published 11 times a year
Subscriptions $140.00 per annum (inc GST) Overseas prices apply Ph: (03) 9690 8766
Copyright Manufacturers’ Monthly is owned by Prime Creative Media and published by John Murphy. All material in Manufacturers’ Monthly is copyright and no part may be reproduced or copied in any form or by any means (graphic, electronic or mechanical including information and retrieval systems) without written permission of the publisher. The Editor welcomes contributions but reserves the right to accept or reject any material. While every effort has been made to ensure the accuracy of information, Prime Creative Media will not accept responsibility for errors or omissions or for any consequences arising from reliance on information published.
The opinions expressed in Manufacturers’ Monthly are not necessarily the opinions of, or endorsed by the publisher unless otherwise stated.
© Copyright Prime Creative Media, 2023
Articles All articles submitted for publication become the property of the publisher. The Editor reserves the right to adjust any article to conform with the magazine format.
Amiga Engineering recently took out the Manufacturer of the Year at the 2024 Endeavour Awards. In March’s Manufacturer Focus, we will dive into what has made the company a success including moving into the additive manufacturing space, whilst maintain its machining wing to meet the needs of Australian industry. Also in this issue, we check-in with Endeavour Awards nominee, SiteHive, and their environmental monitoring services. Then finally, we look at gear manufacturing from Hardman Bros, then Capral, a legacy manufacturer of aluminium products, and space suit design from Metakosmos.
In the dynamic landscape of Australian manufacturing, the unveiling of the Government’s $392.4 million Industry Growth Program marks a pivotal moment, heralding a new era of innovation, capability building, and strategic growth for the sector. This bold initiative, aimed at fostering the development of small to medium enterprises (SMEs) with groundbreaking ideas, is not just a financial investment in the industry but a commitment to the future of Australian manufacturing.
The Industry Growth Program, designed to fuel the ambitions of innovative SMEs, provides a comprehensive framework for not just conceptualising but actualising big ideas. The introduction of Industry Partner Organisation (IPO) grants, offering between $500,000 and $2 million over two years, is a testament to the government’s vision of nurturing a vibrant ecosystem where startups and scaleups can thrive. These grants are more than just financial aid; they represent a lifeline for businesses at the forefront of innovation, enabling them to access expert, sector-specific advice and specialised advisory services in priority areas for the National Reconstruction Fund (NRF).
The significance of these IPO grants cannot be overstated. They ensure that businesses with the potential to significantly impact Australia’s manufacturing landscape and contribute to our national capabilities are given every chance to succeed. By providing funding to eligible organisations, the program facilitates a nurturing environment where SMEs can access
industry connections, investment opportunities, specialised facilities, and support with IP creation. This approach not only accelerates the commercialisation of innovative ideas but also fosters a culture of growth and development within the sector.
The role of Industry Growth Advisers in this ecosystem is crucial. Appointed to offer advice and support, these advisers are the bridge between innovative SMEs and the broader industry objectives. Their expertise and guidance are invaluable assets for businesses looking to navigate the complexities of commercialisation and growth. With sector-specific know-how and a deep understanding of the challenges and opportunities within the industry, these advisers are poised to make a significant impact on the success of the program.
Minister for Industry and Science, Ed Husic, has aptly highlighted the transformative potential of the Industry Growth Program. By leveraging the sectorspecific expertise of industry organisations, the program ensures that SMEs are not just surviving but thriving in a competitive landscape. The emphasis on collaboration and support underscores the government’s commitment to not just sustaining but elevating Australia’s manufacturing capabilities. This initiative is a beacon of hope for an industry that is at a crossroads, facing challenges from global competition, technological advancements, and the pressing need for sustainable practices. The Australian Government’s strategic investments, including the $200 million grant to upgrade
Australia’s steel industry, reflect a broader vision of positioning Australia as a leader in clean, innovative, and sustainable manufacturing on the global stage.
The future of Australian manufacturing looks bright, with initiatives like the Industry Growth Program paving the way for a new chapter of growth and innovation. As we stand on the brink of this transformative era, the success of our manufacturing sector hinges on our ability to adapt, innovate, and collaborate. The Industry Growth Program is not just an investment in businesses but a vote of confidence in the ingenuity, resilience, and potential of Australian manufacturing.
As we look ahead, the challenge for industry stakeholders, policymakers, and businesses will be to harness the momentum generated by these initiatives. It is an opportunity to redefine what Australian manufacturing stands for, to build on our strengths, and to carve out a niche in the competitive global marketplace. The journey ahead is fraught with challenges, but with the right support, vision, and collaboration, the future of Australian manufacturing is not just promising – it’s exciting.
The Industry Growth Program is more than a policy measure; it’s a catalyst for change, a tool for empowerment, and a stepping stone towards a brighter, more innovative future for Australian manufacturing. Let us embrace this opportunity with open arms and work together to realise the full potential of our manufacturing sector, for today and for generations to come.
Choosing lower-carbon aluminium in your next project can reduce the embodied energy of your aluminium products by up to 75%* LocAl® Green (8kg CO2e/1kg AL) and LocAl® SuperGreen (4kg CO2e/1kg AL) are the responsible choice for a locally extruded, lower-carbon option in your next project.
FOR MORE INFORMATION VISIT: lowcarbonaluminium.com.au
* When compared with global average CO2e for primary aluminium production, Scope 1 and Scope 2 ex smelter.
POWERED BY
Australian businesses, communities, First Nations, and workers stand to benefit significantly from the energy transition – so long as our governments prioritise local content requirements in the drive to decarbonise our economy and transition to net zero. Local content legislation must specify that 60 per cent of all fabricated steel used in our renewable energy projects is manufactured in Australia by local welders.
The Federal Government’s Capacity Investment Scheme presents a critical opportunity to bolster local economic participation in the renewable energy transition. The Scheme, a federal initiative that complements state efforts, aims to expedite dispatchable renewable energy and storage, supporting the federal target of 82 per cent renewable energy by 2030.
The Scheme provides a national framework to encourage new investment in renewable capacity, such as wind and solar, as well as clean dispatchable capacity, such as battery storage.
When it was first announced in December 2022, the Federal Government estimated that the Scheme would drive approximately $10 billion worth of investment in renewables.
The Scheme’s expansion in November 2023 promises a substantial increase in clean energy investment.
The expansion will encompass a new revenue underwriting scheme that the Hon Chris Bowen, Minister for Climate Change and Energy, hopes will unlock $40 billion in private investment, adding
another 32 gigawatts of capacity on top of the 28 gigawatts of clean energy already in the National Electricity Market.
While the expansion of the Scheme and billions in private investment are obviously welcome, it is essential that local and First Nations content requirements are incorporated into Capacity Investment Scheme tenders. This will fortify domestic clean energy supply chains, boost investor confidence, and cultivate a skilled workforce for the energy transition, positioning Australia as a global renewable energy leader. Australian businesses have long advocated for specific, measurable local content requirements in government contracts.
Even the recent House of Representatives committee report into manufacturing in AustraliaSovereign, Smart, Sustainable recommended stated that: “All levels of government have potential to drive developments in advanced manufacturing by
targeted procurement of Australian products.”
The report continues, recommending that: “In partnership with the states and territories, the government should identify further steps it could take to increase locally manufactured content in renewable energy infrastructure and equipment installations, and other areas where governments are major customers.”
However, tangible examples of local content procurement policies are yet to materialise in Australia.
Globally, since 2008, more than 140 local content requirement programs have been employed in a variety of sectors from automotive to extractive industries . However, policymakers have focused heavily on wind and solar power in recent years to foster economic and technological development. Prominent cases where solar or wind energy local content requirement have been introduced include the US, India, China, Brazil, Indonesia, South Africa, and Turkey.
In the United States, the Inflation Reduction Act requires that all structural steel in new products is manufactured in the US. In addition, the minimum percentage of domestic content for manufactured products in solar, battery, and wind installations (including the labour costs required to make them) must be 40 per cent for projects on which construction starts by the end of 2024, 45 per cent for projects starting construction in 2025, 50 per cent in 2026 and 55 per cent thereafter.
In India, the government implemented the ‘Make in India’ initiative in July 2019. Under this program, solar cells and modules must be manufactured domestically, and wind projects must be comprised of 80 per cent local content. Another driver is the $5 billion scheme known as the PM Kusum program to develop decentralised, small-scale solar for agricultural consumers. The program components focused on solar water pumps mandate the use of domestically manufactured cells, modules, and balance-of-system parts.
In addition, India has a national certification program requiring that any manufacturer wanting to sell turbines in the country must have quality certification for its devices together with a local assembly unit and an operations and maintenance (O&M) team. This is done to ensure that only quality equipment is installed domestically.
The main competition for Australian wind tower manufacturers are overseas suppliers from Vietnam, China, and Indonesia. The issue is that the quality of imported wind towers is appalling. They do not adhere to Australian Standards. Local fabricators comply to internationally recognised Australian Standards and are certified
by the relevant Australian authority. In this way, Government and private clients can ensure the quality and safety of projects. Imported steelwork, which does not meet these requirements, is often of inferior quality and may not meet the Australian safety requirements.
These quality and safety issues will only be exacerbated by increased global demand in the race to net zero. The whole world is looking to transition to renewable energy. Countries like Scotland, New Zealand and Sweden are all investing in wind power. Not only will increased global demand likely reduce the quality of wind towers manufactured overseas, but it will also increase scarcity of supply. There are already global supply chain issues—imagine how these will be magnified.
Local manufacturers like Keppel Prince Engineering and Crisp Bros. & Hayward cannot win jobs on their doorstep when governments and multi-national companies place a premium on price over and above quality and safety.
The Federal Government must commit to building sovereign manufacturing capability for renewable energy projects by legislating local content policy. Local content legislation must specify that 60 per cent of all fabricated steel used in our renewable energy projects is manufactured in Australia by local welders. This local content legislation must be drafted in conjunction with industry to eliminate the loopholes that so often arise in these types of policies.
This will create a capacity mechanism that generates a clear, long-term signal for investment by private equity and local manufacturers. The Federal Government must also mandate that all wind towers are constructed, erected, and inspected according to Australian Standards.
Local welding and manufacturing companies will
then be assured of the security of sufficient orders to enable them to invest in the necessary workforce, plant, and equipment to deliver high quality, cost effective renewable energy assets. With long-term demand a reality, local manufacturers—like Oxycut who are world leaders in building wind tower anchors — will have the confidence to improve production efficiencies and global competitiveness.
Unless industry and governments come together now to formulate a plan of attack, when the time comes to manufacture the assets needed for our clean energy transition, there will be no fabrication facilities, no skilled workforce, and no regulatory frameworks in place. There will be no sovereign manufacturing capability. Specifying local welding companies in the Federal Government’s Capacity Investment Scheme tenders is imperative.
Building on the momentum of the 2023 National Manufacturing Summit, which focused on Renewable Energy: Challenges and Opportunities, the 2024 Summit embarks on an ambitious journey with its theme: Pathways to Success Making the Renewable Energy Revolution a Reality.
The 2024 Summit will delve into the practical aspects of manufacturing within the renewable energy sector, highlighting the essential components that will drive Australia’s transition to a sustainable future. It will be held at the Amora Hotel in Brisbane on 31 July and 1 August.
As we gear up for the 2024 Summit, we invite industry leaders, innovators, policy makers, and all stakeholders to join us in this pivotal event. Together, we can transform challenges into opportunities, setting a global benchmark in the renewable energy sector. Join us in shaping the future of manufacturing and renewable energy in Australia.
wiring system, being able to remotely configure and monitor, and obtaining more accurate data from the sensors.
In addition, one of IO-Link’s great advantages is the automated data backup of the sensor data that takes place in the background. Each sensor (device) sends its parameter sets automatically to the IO-Link master. There, they will be mirrored and stored as a backup. If a sensor needs to be replaced due to failure or damage, the data is exchanged automatically with the new device. This reduces machine downtime and the workload of the service and maintenance staff significantly.
All these benefits lead to reduced overall costs, increased process efficiency, and improved machine availability. IO-Link has already been widely used in several industries in Australia as below:
• Food and beverage: Monitoring product temperature, pressure, and fill levels for precise control and improved quality. Many of ifm’s food & beverage customers have mentioned that the solution allows for increased availability of data. This, in turn, opens for features like condition monitoring, optimised CIP solutions, and enhanced valve control.
• Packaging: Optimising filling lines, tracking product movement, and ensuring package integrity.
• Mining and resources: Remote sensor data for equipment health monitoring and improved safety.
• Water and Wastewater: Whether you are working with water at the source, using industrial or ultrapure water for the treatment and recovery of drinking water, the IO-Link solutions can bring many benefits from reducing the time required for wiring, being able to monitor your assets remotely and gathering quality data throughout the process, ensuring your brand image is protected. With more exciting technologies such as IO-Link safety and IO-Link wireless on the horizon, this is just the start of a megatrend. According to the report published by Allied Market Research, the global IO-
IO-Link masters act as gateways, connecting up to eight IO-Link devices.
Link market generated $6.10 billion in 2020 and it is projected to reach $74.08 billion by 2030. IO-Link is not just technology, it’s a mindset shift. It’s about embracing data-driven insights and empowering sensors to become active participants in the manufacturing process. The future of manufacturing lies not just in machines, but in the data, they generate and the intelligence they communicate.
With over 50 years of experience in industrial manufacturing, ifm is your reliable partner for the implementation of the smart factory.
Amiga Engineering has long been a beacon in the Australian manufacturing landscape for diversifying and meeting the needs of wider industry and remaining relevant. It is beginning to reap the rewards of this commitment.
Amiga Engineering is an Australian based manufacturing company known for its innovation and advancements in the industry.
Starting as a small business in 1988, Amiga has grown into a leading manufacturer in the country, providing advanced manufacturing services to a range of industries. Amiga has made significant investments in additive manufacturing, which has enabled it to create complex geometries and intricate designs with great precision.
This transition has allowed the organisation to bring its manufacturing expertise into this exciting new space.
The company has also established Australia’s first metal powder atomising machine, allowing them to produce high-quality metal powders that are essential for its advanced manufacturing processes.
Despite its humble beginnings, Amiga’s commitment to innovation and excellence has enabled it to become a leading player in the manufacturing industry. With its cuttingedge technologies and focus on customer satisfaction, Amiga continues to provide advanced manufacturing solutions to a range of industries, both in Australia and internationally.
The challenges Amiga Engineering faced back in the mid 2000’s was one many manufacturers have had to contend with.
Founder and director Michael Bourchier explained how the company diversified operations to remain relevant in the Australian manufacturing landscape.
“We identified the additive space as one we could move into, we could bring our skills to that field and be one of the first in Australia to capitalise on this technology,” he said.
“We invested strongly in additive equipment; we made the conscious decision to go for the top end of this technology and it has paid off.”
It took some time to find the space in the market that Amiga wanted to operate in but they have found the niche that suits them.
“The medical industry would approach us, but that would be for one-off components that were never going to be profitable for us,” Bourchier said.
“We knew we had pulled the trigger at the right time going into this space, other companies had gone five or six years before us and struggled but the appetite was there in Australia.
“You look at it now, Europe was six years ahead and the US was four or so, and now everything that is going up on SpaceX, Blue Origin and other programs is 3D printed, Australia is starting to become like that,” he said.
By investing in this technology when it did, Amiga ensured that as the appetite grew in Australia, it was ready to service that need.
As the oil and gas industry is slowly departing Australia, Bourchier felt the time was right to make the transition into additive.
“It seemed to work as soon as we got into it, whilst a lot of it started small, we have been slowly making the right connections,” Bourchier said.
“We began working with the right designers and people who were thinking outside of the square and instead of going overseas they began to approach us.
“Working closely with universities has been key to our success, taking the research component into the real world has been imperative,” he explained. We also had Andre (from the Additive Manufacturing Precinct at RMIT) join us and build the foundation of our Metal additive manufacturing lab with me from the start.
Amiga Engineering is currently operating at around 30 per cent capacity, ensuring it is prepared to meet the needs of Australia’s additive manufacturing industry.
Amiga Engineering has several machines to meet its additive manufacturing needs, as some of them can run for several days working on a single project. It has the largest service bureau in Australia for metal and polymer additive manufacturing.
The company is currently operating 3D systems branded machines and has begun incorporating ways of closing the loop of materials to manufacturing into its process as Bourchier explained.
“The powder comes out of the machine and into the sieve where it is recycled which minimises our losses to around 3 per cent,” Bourchier detailed.
“Some of our newer 3D systems machines have this recycling component built in which is helping us to minimise manual handling of the powder.” This type of forward thinking and technology integration has been key to Amiga Engineering’s success. The company has been working with Inconel, titanium, stainless steel, and now exclusive Tungsten and Scalmalloy; and is beginning to ramp up its titanium usage for ballistic titanium protection. Amiga’s newest arrival of its 4th 3D Systems metal printer (5th metal printer overall) will be focussed on ballistic titanium armour, full time; providing a new capability globally for shaped ballistic protection
“Scalmalloy is about to become one of our go-to materials, it is what industries such as Space and Aerospace can benefit from,” Bourchier said. Raindance Systems has been Australia’s first to implement Amiga’s exclusive certified metal printing capability of Scalmalloy.
For the team at Amiga Engineering, it is about building trust within the industry that the company can meet the requirements of a range of sectors.
“When people come to us, they can trust that we will customise a solution for them, being a machining company and an additive manufacturer, we can deduce what is required,” Bourchier explained.
“Some manufacturers will try to 3D print everything but if we identify cost savings utilising machining it is an integration of solutions, we will recommend that.”
Amiga Engineering have been working closely with a range of Australian start-ups including companies
like Hypersonix Launch Systems, and it has begun working with major international players, which poses new challenges.
“It does not matter what environment you are working in where there is engineering involved, third party validation is required,” Bourchier said.
“Working with organisations requiring specific standards (such as NASA), they will usually ask you to provide test bars to be validated, once you have that validation, they will give you the space and freedom to do more work.”
For the team at Amiga, they have identified learning from each and every job to ensure development continually occurs.
“For us it is basically like we are engineering each and every time we put something together, we will look at the component and understand what could be done and subtle improvements that can be made,” Bourchier explained.
“By ensuring we have continual development, it allows us to remain competitive, particularly when going up against international companies.”
Bourchier told the Manufacturers’ Monthly team a project Amiga had worked on in which they had provided an item that was a consumable that needed to be replaced every couple of weeks. Six months later when Amiga reached out to see if they needed more, they were informed the product was far stronger and had not needed to be replaced, showing the strength of the metal 3D printing
process (Laser powder bed fusion technology) coupled with the strong design processes.
Whilst Amiga Engineering made the shift to additive manufacturing, it never forgot its roots in the machining industry, fabrication and its gearbox division.
“The company began its life producing pipe flanges, fittings and special components for companies like Woodside, Worley Parsons and Esso and their gas lines,” Bourchier said.
“Unfortunately for us they decided they wanted to source these components from overseas.”
The company manufactures the only Australian made brand of industrial gearboxes, general fabrication and industrial maintenance all in a bespoke nature to suit the needs of clients.
The industrial gearboxes which are the Genat and Wood branded gearheads are known for longevity and durability, ideally suited to the Australian market.
Keeping these skills in house has not only allowed the company to remain relevant in these spaces, it complements its modern manufacturing processes.
As Bourchier explained, additive manufacturing will never 100 per cent complete a component so it will always require an extra step to be utilised.
“3D metal printed requirements will always need extra machining on tight tolerance areas, and that
is where our expertise really comes in. With a fully versatile CNC machine shop that works with our metal 3D capabilities under one roof is unique,” he said.
“We will ensure the components are printed to the highest quality and then machine them to the exact specifications the clients require.”
Bourchier explained that the company is looking to bring the right people into the company to ensure prolonged success.
“We do occasionally get some throughput when people enter the manufacturing industry and realise it isn’t for them,” he said.
“A lot of the people coming out of university have not had the opportunity for hands on learning, so when they come on board with us it is about giving them that experience and getting them to a point where they can work independently and for realworld applications.
“We are beginning to look at ways we can train newcomers, the AM space has so much information it definitely has the potential to burn people out, so we need to ensure we manage that effectively,” Bourchier said.
A challenge facing Amiga Engineering currently as an SME, is finding skilled tradespersons. This is why Amiga have made the commitment and are investing in a minimum of 3 apprentice fitter and
turners to help build back this skill set.
“We are aiming to keep talent long term, keeping them on sensitive but exciting projects using a range of technologies that is not available anywhere else under one roof, and then having them understand the sensitivity of their work,” he said.
Whilst attending Amiga Engineering, the Manufacturers’ Monthly team got to meet some of the young apprentices who have come on board at Amiga.
“The apprentices have been great, they have come in and really utilised their knowledge and skills and been keen to learn,” Bourchier said.
“If we could continue getting people like this in the door we would be very happy.”
During covid much of Australia began to face crippling supply chain issues, with much of the supply coming from offshore, many Australian companies could not meet their needs, as Bourchier explained.
“We definitely saw a pickup of work during covid, emergency works for oil and gas companies was something that really came to the fore, they knew we still had the capabilities so they turned to us” he said.
“As they came to us, they realised we have these
capabilities locally still, and that work has lightly continued since then.
“We are currently doing some maintenance work for Esso which is great for us, just keeps the work diversified and not too many eggs in one basket,” Bourchier explained.
When investing in additive manufacturing, Bourchier and the team made the conscious decision to not leave behind the work that had treated them so well.
By doing so they ensured an ability to meet the needs of Australia when the time came. As many companies begin to look back to Australia for products, Amiga is primed to address these needs head on.
Winning the manufacturer of the year at the Endeavour Awards for Amiga Engineering was truly a culmination of years of hard work for Bourchier, his wife Cecily Bourchier and daughter Dee Bourchier. He spoke about what it means for the company.
“We have been privileged to work with some really exciting companies like Hypersonix Launch Systems and Raindance Systems (first company in Australia to utilise the benefits of Amiga’s Scalmalloy metal 3D printing capabilities) since we moved into this space,” he said.
“It has allowed us to not only survive but thrive since we adjusted our direction, making this change was so critical.”
“We honestly didn’t even know we were up for the award,” Bourchier laughed.
“Some impressive manufacturers were in attendance at the event and to go up against them we were proud to take home the award.
“It is nice to be recognised for the work we do and to celebrate alongside some of our closest partners such as Hypersonix Launch Systems.
“Awards like these are so important to celebrate the manufacturing industry and we were honoured to take home the main award,” he said.
Bourchier acknowledged that the success of the company was not simply down to him but it was a true team effort for the growth and success of Amiga engineering.
“I wanted to take the time to thank my wife who has been along for the entire journey supporting me all the way and being a critical cog in our success,” he said.
“My daughter Dee has been an immense help in really bringing our company into the 21st century, updating our website and improving our marketing strategy.
“The broader team has been critical to our success and without them the company would not exist.”
Ivan Power has been appointed as the chief executive officer (CEO) of the National Reconstruction Fund Corporation (NRFC).
Power has over 25 years’ experience in global investment and holds considerable experience working with early-stage companies and social ventures.
He spent over 20 years at Macquarie Group in Sydney and London and is also a board member of Generation Australia and former board member of Lifesavers with Pride and The Westmead Institute for medical research.
Power has also worked with several governments and agencies, and gained experience creating productive links between
government, business, and non-government organisations.
Minister for finance, Katy Gallagher stated, “We welcome the appointment of Mr Ivan Power as the CEO of the NRFC to help manage the $15 billion National Reconstruction Fund.
“Mr Power brings 25 years of experience to the NRFC and will help deliver a future made here in Australia.
“The NRF is getting on with the job of rebuilding Australian manufacturing and creating jobs.”
Power was appointed CEO by the independent NRFC Board, which makes decisions to provide finance to Australian-based investments in
seven priority areas of the Australian economy.
The Government’s $15 billion National Reconstruction Fund Corporation was established late last year and is the biggest investment in growing Australia’s manufacturing capacity in living memory.
Appointment of Power as NRFC CEO is another major milestone for the NRFC which will enable them to deliver on this important Government initiative.
Minister for industry and science, Ed Husic said, “The NRF Board has made an outstanding choice in Ivan Power as the inaugural National Reconstruction Fund Corporation CEO, and I congratulate him on his appointment.”
Nearly
According to the Deloitte Access Economics’ Business Outlook report, Victoria will lead all states in economic growth over the next five years.
Treasurer Tim Pallas said the report showed the Victorian Government’s strategy for sustainable, job-creating growth was working.
The report forecast Victoria’s growth in gross state product in 2023-24 will be 2.5 per cent, outpacing all states and territories, and Victorian economic growth will lead all states over the five years to 2027-28 at an average annual rate of 2.3 per cent.
The forecasts follow recent Australian Bureau of Statistics figures showing Victoria’s
economic growth has outpaced New South Wales, Queensland, Western Australia and Tasmania over the past two years.
Victoria’s strong economy has enabled record job creation and employment levels are just shy of the all-time high achieved late last year – 3.68 million in total.
Almost 530,000 Victorian jobs have been created since September 2020 when the pandemic economic shock was at its height – the best performance of all the states. The labour force participation rate at 67.4 per cent is around a record high, which shows workers have confidence in getting a job.
Pallas stated, “Our economic strategy is growing
jobs, keeping local communities strong and encouraging businesses to invest and expand their workforces.
“Victorians are confident about the future and reports like this show that confidence is well placed.”
The Deloitte Access Economics report forecasts household consumption to grow by 1.3 per cent in 2024 in Victoria, outpacing the national forecast of 1.1 per cent.
Victoria’s services exports are estimated to have lifted by almost 50 per cent last year, led by the rapid return of international students to Victoria’s higher education sector and supported by a rebound in international tourism.
The Federal Government is investing up to $70 million to develop the Townsville Region Hydrogen Hub in north Queensland, creating regional jobs and supporting Australia’s future as a renewable energy powerhouse.
The project delivers on the Government’s election commitment to establish a hydrogen hub in North Queensland.
It will create at least 200 direct job opportunities for local electricians, plumbers, fitters and concreters during construction, as well ongoing jobs in technical and engineering roles.
Prime Minister Anthony Albanese stated, “The global shift to clean energy and decarbonised economies is a huge economic opportunity for
North Queensland. We are determined to grasp this opportunity and are investing half a billion dollars into regional hydrogen hubs all around Australia.”
The initial stage of the hub will produce 800 tonnes of green hydrogen per year, enough to fuel over 40 heavy vehicles a year. It will ramp up to around 3,000 tonnes for domestic supply, and ultimately in excess of 150,000 tonnes for export.
The hub, led by Edify Energy, will produce green hydrogen for use by local industry and in zeroemissions transport. It will also deliver a 17.6 MW domestic production facility with integrated renewable energy generation and battery storage.
Edify and its partners – including Siemens
Energy, Queensland TAFE, James Cook University and Townsville Enterprise Limited – will work with industry bodies to provide education and training to ensure Townsville’s workforce is skilled and ready to develop and sustain the region’s hydrogen industry.
Construction will begin next year and be complete in 2026, with initial commercial operations scheduled to start in 2027.
The project has over $137 million of combined investment. The Commonwealth’s contribution is up to $70 million, including $20.7 million from the Australian Renewable Energy Agency. The remaining funding is being sourced from industry and the German Government.
In a historic move, Banana Shire Council and AUKUS Forum have signed a landmark partnership, marking the first-ever membership agreement between a Local Government body and AUKUS Forum.
The collaboration is set to spotlight Queensland’s regional manufacturing and industrial capabilities on the global stage, reaching AUKUS partners across the country, in the United States and United Kingdom, to drive innovation, investment, and economic growth in the region.
The contract signing on Wednesday signifies a groundbreaking commitment, with Banana Shire Council’s Mayor, Cr Nev Ferrier emphasising the substantial benefits this partnership holds, including job creation, investment attraction, economic growth and diversification.
“We are at the beginning of a new chapter of innovation and economic growth for our community and the Banana Shire is well placed to make the most out of this new partnership. Local small, medium and large industries within the Shire are set to benefit from this partnership with the aim of attracting investment and creating more skilled jobs within our region.”
AUKUS Forum founder, Michael Sharpe, commended the Council’s initiative, saying
BAE Systems successfully tested its Armoured Multi-Purpose Vehicle Counter-Unmanned Aircraft System prototype during a recent live fire demonstration.
As part of a collaborative effort with Moog, these positive results exemplify opportunities for future capability growth within the purpose-built modular framework of the AMPV platform.
In various realistic battlefield scenarios at the Big Sandy range in Kingman, Arizona, the AMPV C-UAS prototype demonstrated the ability to accurately detect, track, identify, and defeat or disable stationary and moving aerial and ground targets. The exercise displayed the turret engaging with ground targets and utilising a slew-to-cue capability to target both stationary and moving small drones with 30mm proximity rounds.
“From the earliest combat capability concept stage of the AMPV program, we intentionally designed a modular and flexible configuration to provide an adaptable and ready-for-growth platform for the warfighter,” said Bill Sheehy, BAE Systems AMPV program director.
The versatile prototype, which was showcased at the Association of the United States Army
Annual Meeting & Exposition in October, was designed with the same proven chassis as the existing variants in the family of vehicles, but also possesses the key enhancements of BAE Systems’ External Mission Equipment Package top plate.
ExMEP demonstrates real options for rapid integration of future technologies and capabilities onto the AMPV. The integration of the
it aligned seamlessly with the Forum’s mission to leverage the AUKUS agreement and the opportunities it brings.
“This partnership will facilitate regional companies, particularly Small and Medium Enterprises (SMEs), in tapping into adjacent markets and empower local businesses by connecting them with international players hungry for Australian collaboration.”
Banana Shire Council’s decision to partner with AUKUS Forum stems from a strategic agenda to attract contracts, diversify into the defence space, and position the region as a first mover in this exclusive collaboration. The Council’s foresight in choosing AUKUS Forum as the ideal partner underscores its commitment to fostering economic growth and innovation.
As part of this collaboration, an upcoming event in the region alongside Banana Shire Council is scheduled in July 2024, which aims to foster connection and collaboration across industries and provide a platform for local businesses to explore new opportunities.
adapting at a swift pace.
The ExMEP on the AMPV C-UAS prototype is configured with the Moog Reconfigurable Integratedweapons Platform turret.
The AMPV program was awarded a full-rate production contract for five different variants in 2023 and is actively fielding the FoV to Armoured Brigade Combat Team units.
As the underpinning of the future for the Army
The Queensland Government manufacturing grant has helped Rockhampton herbicide manufacturer, Cirrus Ag expand and create 5 new jobs and attract interstate customers.
Assistant Minister Bruce Saunders visited the Kawana work site of the Made in Queensland Round 3 recipient.
With the almost $1 million grant, Cirrus Ag have been able to purchase, install, commission and operate a leading-edge granule manufacturing plant including advanced software control systems.
Saunders is encouraging other manufacturers to apply for support through Queensland Government grant programs, “Cirrus Ag is a brilliant example of
how well a business can grow after receiving the right support at the right time. Our investments in these programs have created and supported more than 7000 jobs across Queensland. I encourage all Queensland manufacturers to seek out these business-bolstering grants.”
The Miles Government’s Manufacturing Energy Efficiency Grant program is available to help manufacturers reduce their energy usage and cut energy costs, by providing direct support to manufacturing businesses.
Eligible manufacturers can apply for matched grant funding of between $5,000 and $25,000 to buy equipment or introduce processes that will
reduce energy consumption and carbon emissions.
Businesses across Queensland are also benefitting from the $28.5 million Manufacturing Hubs Grants Program as part of the invaluable support provided through the more than $60 million investment in the six manufacturing hubs in Cairns, Townsville, Mackay, Rockhampton, Gladstone and the Gold Coast.
This grant supports development of businesses’ advanced manufacturing capabilities like technology adoption, skills and training and business development.
Round 3 is open until 30 June 2024 or until all funding is allocated.
Six projects have received a total of nearly $900,000 in funding for the seventh round of the Defence Innovation Partnership’s Collaborative Research Fund (CRF) in South Australia.
Supporting genuine collaboration across government, the university sector and industry, the CRF is a catalyst for defence-relevant research, development and innovation.
Defence South Australia’s acting chief executive, Reg Carruthers, said the calibre of applications is continuing to increase each round.
“The applications received were of an incredibly high quality, and from across a variety of themes, which is demonstrative of the depth of research and industry expertise in South Australia,” said Carruthers.
“It is encouraging to see such close collaboration between South Australian researchers with Defence Science and Technology Group (DSTG) involvement across all projects.
“The projects chosen focus on Defence priorities, so we are investing in research activities that address a specific need aimed at improving capability for our Defence Forces.”
Associate professor Ling Yin from the University of Adelaide’s School of Electrical and Mechanical Engineering said their project aims to strengthen Defence’s sovereign manufacturing capability and assist in the production of reliable 3D-printed metal structures for extreme environments.
“It is critical for Australia to develop and produce high-tech value-added metal products
that deliver value for money and assist in the development of cross-cutting technologies,” said Yin.
“This project will also provide excellent training opportunities for young engineers, scientists and students, who represent the future of Australia’s professional work force in high tech industries.
“The CRF process enables collaboration across our project partners—Flinders University, DSTG and AML3D—with each partner bringing a high level of expertise to the table.”
Including this latest round, the CRF has now funded 35 projects and approximately $5 million from state government, with additional funding leveraged from Commonwealth, industry and university contributions.
Engineers in Australia have developed a small ammonia gas sensor that could enable safer hydrogen storage and specialised medical diagnostic devices.
The simple yet effective proof-of-concept sensor described in top academic journal Advanced Functional Materials is the result of collaboration by researchers at RMIT University, the University of Melbourne and the ARC Centre of Excellence for
Exposure to high levels of ammonia can lead to chronic lung conditions and irreversible organ damage.
An estimated 235 million metric tonnes of ammonia are produced globally, but with ammonia being touted as one of the best ways to store hydrogen for clean fuel, we may be seeing a lot more of it.
New 3D-printable material could enable cheaper manufacturing processes for OLED televisions, smartphones, light fixtures, and wearable devices
A research team led by Lawrence Berkeley National Laboratory (Berkeley Lab) has developed “supramolecular ink”, a new technology for use in OLED (organic light-emitting diode) displays or other electronic devices. Made of inexpensive, earth-abundant elements.
Supramolecular ink could enable more affordable and environmentally sustainable flat-panel screens and electronic devices.
Principal investigator and a faculty senior scientist in Berkeley Lab’s Materials Sciences Division and professor of chemistry and materials science and engineering at UC Berkeley, Peidong Yang, stated, “By replacing precious metals with Earth-abundant materials, our supramolecular ink technology could be a game changer for the OLED display industry. What’s even more exciting is that the technology could also extend its reach to organic printable films for the fabrication of wearable devices as well as luminescent art and sculpture.”
If you have a relatively new smartphone or flat panel TV, there’s a good chance it features an OLED screen. OLEDs are rapidly expanding in the display market because they are lighter, thinner, use less energy, and have better picture quality than other flat-panel technologies.
OLEDs contain tiny organic molecules that emit light directly, eliminating the need for the extra backlight layer that is found in a liquid crystal display (LCD). However, OLEDs can include rare,
Reliable and sensitive ammonia detection will be essential to quickly spot potentially dangerous leaks of ammonia gas during transportation of hydrogen, to ensure safe operation.
But while human exposure to ammonia can be harmful, the gas is also found in human breath and can serve as a vital biomarker for diagnosis of many diseases such as kidney and liver-related disorders.
Given that the team’s sensor can measure tiny amounts of ammonia, it could be engineered to detect the gas on people’s breath to alert doctors to health disorders.
Senior lead researcher Dr Nitu Syed said the sensor featured atomically thin transparent tin dioxide that can easily track ammonia at much smaller levels than similar technologies.
The presence of ammonia in the air changes the electrical resistance of the tin oxide film in the sensor: the higher the level of ammonia, the greater the change in the resistance of the device.
The team conducted experiments with their sensor in a specially designed chamber to test its ability to detect ammonia gas at various concentrations (5 – 500 parts per million) under different conditions, including temperature. They also tested the device’s selectivity of ammonia against other gases, including carbon dioxide and methane.
expensive metals like iridium.
The Berkeley Lab team recently discovered how the new material could potentially adopt a cheaper fabrication process for electronic displays.
The new material consists of powders containing hafnium (Hf) and zirconium (Zr) that can be mixed in solution at low temperatures – from room temperature up to around 80 degrees Celsius – to form a semiconductor ink.
A plan to streamline the approvals process for new renewable energy projects has been unveiled by the Tasmanian Government which will ensure Tasmania continues to be the renewable energy powerhouse of the nation.
Minister for energy and renewables, Nick Duigan, said in a new move to secure the ongoing expansion of the sector, a dedicated approvals pathway will assist the continuing rollout of major renewable energy projects.
“I’m very pleased to be progressing the new Renewable Energy Approvals Pathway – also known
as REAP,” said Duigan.
“The Renewable Energy Approval Pathway (REAP) will provide a pathway for projects, such as wind farms and transmission lines, through the Major Projects Assessment Process.
“We already have significant renewable energy projects in the pipeline, and the new approvals pathway will ensure we continue to build that resource.”
The dedicated major renewable energy projects approvals pathway is the result of the Government’s Renewable Energy Coordination Framework.
Duigan said that the Government is now developing a separate supporting initiative for statutory recognition of the Reserve Activity Assessment (RAA) process, including required assessment timeframes.
“Major Projects provides a more contemporary assessment process that is designed to align with community expectations of project assessment,” said Duigan.
“Opportunity for public involvement will continue to be provided through consultation and exhibition processes as well as public hearings.”
The Australian Government’s $200m grant to upgrade Australia’s steel industry is a crucial early step to realising Australia’s potential as a global green steel powerhouse, according to the Australian Workers’ Union.
The federal government has announced the first round of the Powering the Regions Fund (PRF) will provide funding to BlueScope Steel Limited and Liberty Steel Australia.
Bluescope will use $136.8m to upgrade of its No. 6 Blast Furnace at the Port Kembla Steelworks.
LIBERTY has also been awarded $63.2m towards the purchase and commission of a low carbon electric arc furnace to replace its blast furnace at
the Whyalla Steelworks.
AWU national secretary Paul Farrow said, “The AWU has long argued that Australia is ideally placed to become a global green steel powerhouse of the 21st century, but to realise that exciting future we need strategic investment today. Thankfully that’s what we’re finally seeing through the government’s Powering the Regions Fund.”
“The decision to fund projects at BlueScope Steel Limited and Liberty Steel Australia is a testament to our nation’s readiness to embrace a clean steel future.”
“This transition is more than just an
environmental imperative; it’s an economic opportunity for Australia to become a leader in clean steel in Asia and globally.”
“The projects at BlueScope and LIBERTY will not only reduce emissions but also create hundreds of jobs, ensuring a vibrant future for the steel industry in our regions,” Farrow continued.
“We tend to hear a lot of doom and gloom about manufacturing in Australia, but the fact is the future looks extremely bright if we seize our opportunities.”
“This investment demonstrates the will of the government to help drive Australia’s growth into a clean steel future.”
Origin Energy (Origin) has approved construction of a large-scale battery at the Mortlake Power Station in south-west Victoria, committing to an investment of approximately $400 million.
The Mortlake Power Station battery will have a capacity of 300 MW, and is expected to deliver output of up to 650 MWh, helping to firm variable renewables supply and maintain reliable power for customers.
Origin CEO Frank Calabria said, “The Mortlake battery is another significant step in our ambition to lead the energy transition through cleaner energy and customer solutions.
“I am pleased to announce that contracts have
been signed with global energy storage systems supplier Fluence and site preparation and civil works are expected to commence over coming months.
“Origin’s strategy is to accelerate renewable energy and storage in our portfolio and we expect large-scale batteries and other storage technologies to play a vital role in Australia’s energy transition.
The announcement follows our decision last year to approve Origin’s first large-scale battery at Eraring, which is currently under construction.
“With the proliferation of wind and solar farms, particularly in Victoria’s South West Renewable
Energy Zone, the Mortlake battery will help keep the grid stable and support more renewable energy coming into the system as the market continues to decarbonise,” said Calabria.
Mortlake Power Station is the largest gas-fired power station in Victoria with a generation capacity of 566 MW. The peaking power station is powered by gas from the Otway Basin.
The project has been awarded conditional grant support from the Australian Renewable Energy Agency (ARENA) as part of its Large Scale Battery Storage Funding Round.
The battery is expected to be commissioned late in 2026.
With the expansion of the Capacity Investment Scheme, Weld Australia is calling on the federal and state governments to legislate local content procurement policies. These policies must state that stipulate that 60 per cent of all fabricated steel used in renewable energy projects is manufactured in Australia by local welders.
The Federal Government’s Capacity Investment Scheme presents an opportunity to bolster local economic participation in the renewable energy transition.
When it was first announced in December 2022, the Federal Government estimated that the Scheme would drive approximately $10 billion worth of investment in renewables. The Scheme
was expanded in November 2023, with the aim of unlocking $40 billion in private investment, which would add another 32 GW of capacity to the National Electricity Market.
CEO of Weld Australia, Geoff Crittenden, stated, “The Federal Government must commit to building sovereign manufacturing capability for renewable energy projects by legislating local content policy. Local content legislation must specify that 60 per cent of all fabricated steel used in our renewable energy projects is manufactured in Australia by local welders.”
Local welding and manufacturing companies will then be assured of the security of sufficient orders to enable them to invest in the necessary workforce,
plant and equipment to deliver high quality, cost effective renewable energy assets. With longterm demand a reality, local manufacturers—like Oxycut, Keppel Prince Engineering and Crisp Bros. & Hayward —will have the confidence to improve production efficiencies and global competitiveness. Unless industry and governments come together now to formulate a plan of attack, when the time comes to manufacture the assets needed for our clean energy transition, there will be no fabrication facilities, no skilled workforce, and no regulatory frameworks in place. There will be no sovereign manufacturing capability. Specifying local welding companies in the Federal Government’s Capacity Investment Scheme tenders is imperative.
In an analysis conducted by Additive Manufacturing Research, the market study titled “Additive Manufacturing in the Energy Sector: Market Analysis & Forecast“ reveals significant opportunities and potential for 3D printing in the Energy sector, and compelling insights into the transformative role of AM within it.
The latest report forecasts a market activity of $2.6 billion in 2023, with anticipated growth to $17 billion by 2032, highlighting the increasing adoption of additive manufacturing technologies in the energy sector.
The comprehensive study sheds light on the rapid evolution and potential impact of additive manufacturing technologies on the oil & gas, nuclear and renewable energy landscapes.
The study’s findings hold significant implications for energy providers, technology providers, investors and policymakers, indicating the need for proactive measures to harness the full potential of additive manufacturing in addressing the ever-evolving energy landscape.
As the world confronts a move towards decarbonisation and in an era defined by escalating and evolving geopolitical concerns, the integration of additive manufacturing is poised to make its mark on the way oil and gas, nuclear, and renewable entities conceptualise, develop, and deploy and maintain critical assets and equipment, whilst simultaneously pushing innovation of next-generation energy sources using advanced production technologies.
“Additive Manufacturing in the Energy Sector” highlights current trends, opportunities, challenges, and the outlook of AM, with the technology maturing to the point of providing on-demand manufacturing, reducing downtime, and enhancing operational efficiency through advanced part design.
It also addresses challenges such as material limitations, regulatory compliance, and the need for industry-specific certifications and standards, all of which are already being addressed. Additionally, the report includes a market forecast, highlighting the significant growth potential of AM in the energy sector, segmented by technology, material, and application.
Electro Optic Systems Holdings (EOS) announced that it has secured a contract to supply Slinger counter-drone systems valued at approximately A$15m, to Diehl Defence in Germany.
EOS announced that its Defence Systems business has secured a contract to supply its world-leading Slinger counter-drone system to Diehl Defence in Germany. The systems will be integrated by Diehl
Defence onto a lightweight 4×4 platform, providing a defensive capability to protect critical assets from drone attacks.
Dr Andreas Schwer, chief executive officer for EOS, said, “The contract with Diehl Defence represents yet another key milestone in the global success story of our Slinger counter-drone system, launched in early 2023.”
Minister for resources and northern Australia Madeleine King will visit Japan and the Republic of Korea (ROK) this week to promote investment in Australian resources projects and reinforce Australia’s role as an export partner.
Minister King will use the trip to meet Japan’s newly-appointed minister of economy, trade and industry, Ken Saito, and to meet ROK’s newlyappointed minister of trade, industry and energy, Duk-geun Ahn.
Minister King will also meet executives from major industries and utilities in Japan and ROK, including major buyers of Australian resources and large investors in Australia’s resources and energy sector.
“Japan and the ROK have been long-standing supporters of Australia’s resources and energy sector, and Australia has a rock solid commitment to continue to support the future resources and energy needs of both Japan and ROK,” said King.
Japan and ROK are Australia’s second and third largest export markets for resources and energy respectively. Both countries also provide major foreign investments that support thousands of jobs in Australian resources and offshore gas projects.
Australian resources and energy exports to Japan,
The contract includes the provision of systems, spares, training and related services and is valued at EUR 9m (approximately A$15m). The systems are expected to be delivered in 2024, in accordance with agreed milestones and other customary terms.
The contract is subject to export approval by the Australian government. In performing this contract, EOS will draw upon a support network and supply chain consisting of over one hundred suppliers located across Australia, and others internationally.
The EOS Slinger counter-drone system was developed to track and engage moving drones at a range of more than 800 metres, depending on the weapon configuration used. It can incorporate unique ammunition making it suitable for built up environments, and includes a radar system, a range of weapon configurations and EOS’ proprietary stabilisation and pointing technology.
Slinger was designed and developed in Australia specifically for export markets, with a focus on addressing contemporary and emerging threats based on lessons learned in recent conflicts.
EOS proprietary stabilisation and pointing technology was developed over thirty years to provide world-leading accuracy, which is critical for effective counter-drone applications.
including LNG, iron ore and coal, were worth $99 billion in 2022-23, while total Japanese investment in Australia was worth $259 billion.
Resources and energy exports to ROK, including iron ore, LNG and coal, was worth $47.5 billion in 2022, and ROK investment in Australia was worth $28.1 billion.
Australia and Japan are partners in the Japan-
Australia Critical Minerals Partnership, which affirms a shared commitment to stable critical minerals supply.
Australia and ROK have a Memorandum of Understanding on Cooperation in Critical Minerals Supply Chains which will deliver the shared ambition to develop robust and commercially viable critical minerals supply chains.
The Federal Government claims to have secured hundreds of highly skilled jobs while driving innovation in Australia’s local defence industry with the allocation of an additional $399 million for the ongoing development of the MQ-28A Ghost Bat.
The MQ-28A Ghost Bat, known as a Collaborative Combat Aircraft (CCA), is being developed in cooperation with Boeing Defence Australia. It is the first military combat aircraft to be designed, engineered, and manufactured in Australia in more than 50 years.
An entirely new technology, it is designed to act as a loyal wingman which will be able to protect and support our military assets and pilots and undertake a wide range of activities across large distances, including performing combat roles.
The Government is now moving forward with the next stage of the program, including delivery of three Block 2 aircraft which have an enhanced design and improved capabilities. This funding
boost will enable a focus on developing sensor and mission payloads, an integrated combat system and autonomous systems.
Minister for defence industry, Pat Conroy, said, “this is the first military aircraft to be designed, engineered and manufactured in Australia in more than 50 years and underscores the depth of innovation and expertise in our defence industry.”
“More than 200 Australian companies have already contributed to the MQ-28A program, including more than 50 small and medium enterprises within the supply chain. This project demonstrates that with the appropriate support from government, Australia’s defence industry can continue to be a world leader and a key source of jobs.”
“The prosperity and security of our nation and will always be a top priority for the Albanese Government. That’s why giving our Air Force the critical capabilities it needs to protect Australians,
and their interests, is paramount.”
The additional funding announced today also secures over 350 jobs across Australia and will ensure ongoing work for over 200 suppliers, supporting the local defence industry and further contributing to well-paid employment opportunities for Australians.
The further development of MQ-28A Ghost Bat comes after the Government agreed with a Defence Strategic Review recommendation that options be developed for collaboration and technology sharing with the United States. In line with the Government’s response, Defence signed a CCA development project arrangement with the United States on 30 March 2023.
More than 70 per cent of the MQ-28A Ghost Bat delivery program is being directed towards Australian industry content, delivering substantial benefits to local companies and their highly skilled workforces.
The Queensland Train Manufacturing Program’s (QTMP) facility near Maryborough will be built with steel supplied by a Beenleigh company through a $40 million contract that will create new jobs and apprenticeship opportunities.
Beenleigh Steel Fabrications has been awarded the government contract to supply and install 2400 tonnes of structural steel for the buildings that will make up the QTMP train manufacturing facility at Torbanlea, near Maryborough.
The industry leader was awarded the contract following a competitive tender process due to demonstrated capability and capacity, its stateof -the-art fabrication workshop at Berrinba and commitment to local and indigenous employment. Buildings being constructed by Beenleigh Steel Fabrications at Torbanlea include the train manufacturing facility, administrative building, a gatehouse and pump house.
Beenleigh Steel Fabrications director Anthony Stoeckert said, “Beenleigh Steel Fabrications is delighted to team with Downer and John Holland in bringing back train manufacturing to Queensland through the QTMP.
“We have long been associated with large projects in Queensland. This one is particularly special however, as it will enhance the manufacturing capacity of the state through its long-term development of the skills and infrastructure that is needed to keep up with the projected growth of industry in Queensland.”
The contract is expected to create six new jobs, and the hiring of 10 apprentices and four trainees. The new jobs will bolster Beenleigh Steel Fabrication’s 80 strong Queensland workforce.
Minister for regional development and manufacturing, Glenn Butcher stated, “We know our Queensland manufacturers are some of the best in the world, so it’s fantastic to be part of the Miles Labor Government that’s bringing train manufacturing back to local workshops.
“More than 360 jobs will be supported during construction of the facility overall, with another 380-plus long-term manufacturing jobs supported to build the QTMP trains when manufacturing begins.”
Construction of the train manufacturing facility buildings is scheduled to start mid-2024 and is
planned for completion in early 2025.
Beenleigh Steel Fabrications has a 44-year involvement in Queensland’s construction landscape with multiple large projects including Suncorp Stadium, the Gabba and Cross River Rail.
The company’s new Berrinba workshop was built with support from the Queensland Government’s $175 million Jobs and Regional Growth Fund.
Deputy premier, treasurer, minister for trade and investment and state member for Woodridge, Cameron Dick said, “Queensland has a great manufacturing history which is why it was important to bring train manufacturing back to the Sunshine State.
“Beenleigh Steel Fabrications, based in the Woodridge electorate, is one of these great Queensland manufacturing success stories, a story that will continue for years to come.
“The new jobs at Beenleigh Steel are part of 360 needed to build the Queensland Train Manufacturing Program facility and more than 380 required to manufacture the trains.”
Electromechanical
RSM’s ‘Securing Australia’s Manufacturing Industry’ report explores the evolving landscape of the Australian manufacturing sector, transitioning from traditional industries into a more digitalised and automated industry, with insights from leaders and experienced business specialists. Manufacturers’ Monthly reports.
RSM Australia is a professional services firm that specialises in offering expert corporate financial and advisory accounting services. With a distinctive one-firm national structure and a global network of member firms, RSM prioritises a client-focused culture, aiming to cultivate strong collaborative partnerships.
RSM functions as a trusted advisor for manufacturing businesses seeking to commercialise new products and expand into global markets.
With a focus on trust and strategic insights, RSM is dedicated to helping manufacturers navigate the complexities of their industry, fostering growth and ensuring success in an ever-evolving global marketplace.
RSM has recently released the ‘Securing Australia’s Manufacturing Industry’ report, which aims to provide a comprehensive update on the current state of the sector.
In the face of ongoing challenges and changes, this report offers an in-depth analysis of the industry’s dynamics, highlighting key trends, concerns, and potential strategies for the future.
Jessica Olivier, the National Leader, Manufacturing and Partner in the R&D Tax Services Division in Sydney, said the report aims to “provide a comprehensive update of the manufacturing landscape across Australia for all of our clients.
“The report touches on Australia’s current manufacturing capabilities and all the obstacles that we’re seeing in front of mind for our manufacturing clients. Obstacles like digital transformation, artificial intelligence, additive manufacturing, and cybersecurity.”
RSM’s report explains that Australia’s manufacturing sector is primarily dominated by several key industries, such as food and beverages, machinery and equipment, petroleum, coal and chemicals, and metal products collectively constituting to around 80 per cent of the total industry, as per the Reserve Bank.
This marks a significant shift from the 1990s, where metal products, textiles, clothing and footwear, and machinery and equipment had a more substantial presence, while non-metallic
mineral products, wood and paper products, and food, beverages, and tobacco were less prominent.
Since the onset of COVID-19, there has been a noticeable emphasis on industrial manufacturing in high-value sectors like health, defence, and energy.
However, the manufacturing landscape in Australia is largely shaped by small businesses, with nearly 95 per cent of firms employing 20 or fewer people.
Obstacles persist due to Australia’s remote geography, contributing to transport costs that are 20-25 per cent higher than the global average.
Notably, labour costs in Australia are high compared to other markets, with nominal manufacturing labour costs rising approximately 80 per cent in Australian dollar terms from 1997 to 2012, averaging 4 per cent per year.
This has posed a challenge to maintaining international competitiveness, as productivity gains have not kept pace with increasing domestic labour costs and a stronger Australian dollar.
The relatively high labour costs indicate a comparative disadvantage in producing homogenous, labour-intensive goods.
Automation is reshaping traditional practices by minimising manual labour and elevating overall efficiency.
Despite efforts to offset rising labour costs with productivity gains, Australia’s manufacturing sector faced a loss of competitiveness against other economies until 2012. This high labour cost scenario indicates a disadvantage in producing uniform, labour-intensive goods domestically.
Experts highlight the possibility of elevating manufacturing to a high-value, high-tech sector, leveraging a skilled workforce and continuous investments in research and development, alongside incentives and co-investments.
A 2022 report from an Australian Parliamentary Committee on the manufacturing industry emphasised the imperative for Australia to adapt its industry to stay competitive.
Manufacturers can adapt by embracing the technological revolution.
The manufacturing sector in Australia is becoming increasingly influenced by technological advancement, with automation, artificial intelligence, additive manufacturing (3D printing), and the Internet of Things (IoT) standing out as key drivers of progress.
“We’re seeing a huge amount of robotics and automation software development in my day-today work for R&D Tax and Government Incentives, as well as through RSM’s Environmental, Social and Corporate Governance, Cyber and Digital practices,” said Olivier.
Simultaneously, 3D printing is revolutionising manufacturing processes, offering precision, waste reduction, and accelerated prototyping.
This technology ultimately enables manufacturers to produce intricate and tailored components with precise accuracy, utilising materials such as plastics, polymers, and metals.
By layering these materials to construct objects layer by layer, 3D printing has markedly decreased waste, lowered material costs, and streamlined the prototyping and production processes, contributing to increased efficiency in manufacturing.
However, despite the potential advantages these technologies bring, there is a prevailing concern that Australian manufacturers may not be adequately investing in these advanced processes.
“The onset of technological advancement is somewhat removing the need for labour, but it also brings its obstacles in terms of cyber risks,” explained Olivier.
The Advanced Manufacturing Growth Centre
emphasises the need for manufacturers to focus on improving specific metrics to propel growth and enhance competitiveness in the global market.
In response to the evolving manufacturing landscape, RSM’s report offers five practical recommendations for manufacturers seeking to adapt.
RSM suggests boosting funding and government contracts for advanced manufacturing to enhance
Australia’s global competitiveness.
While the $15 billion National Reconstruction Fund is noteworthy, it falls short compared to much larger allocations in the US and European countries.
RSM proposes concentrating grant allocations by offering larger amounts to a select few companies, ensuring a more substantial and impactful contribution to the industry.
“In the US, the federal government has allocated $75 billion to local manufacturing support, and we’re seeing, which we should replicate here, that they have given priority to their local American businesses in relation to manufacturing contracts,”
said Olivier.
“It would be good if we could see more money going into the NRF, because it’s a fraction of what other countries have.”
“It would also be beneficial to see government contracts to be given priority to local businesses rather than overseas businesses.”
Moreover, RSM recommends directing the NRF towards critical industries where Australia holds a competitive edge.
This includes areas like space manufacturing, advanced and additive manufacturing, defence,
“According to Gilmour Space, the capacity for them to be doing satellite imagery, technology and artificial intelligence services globally is enormous and the ability is here, it’s just whether it’s supported,” said Olivier.
Olivier explains that the NRF must also emphasise transparency in both funding allocation and sector priorities to address the existing challenge of unclear visibility regarding where this funding will
“There’s a growing concern that manufacturers’ don’t know where the funding from the NRF is being directed,” said Olivier.
“When the board for the NRF published its Investment Mandate in November, it wasn’t clarified how that $15 billion in total is going to be
RSM advises maintaining international agreements to integrate Australian manufacturing into global
This can be achieved by exploring the possibility of an Australia-centric supply chain criteria for significant projects, along with mandates favouring predominantly Australian-owned companies to promote local business support.
Similar practices are already implemented by some trading partners like the US and EU, prioritising their local manufacturers and potentially creating an uneven competitive landscape for
Finally, RSM recommends the restoration of immediate tax write-offs for assets used by Australian manufacturing businesses to facilitate the acquisition of new capital equipment and
The upgrading of production processes and equipment not only aids in decarbonisation but also promotes increased productivity, use of greener technologies and the adoption of advanced manufacturing techniques.
Capral Limited, with a legacy spanning an impressive 88 years, epitomises endurance and adaptability in the everevolving landscape of Australian aluminium manufacturing. Manufacturers’ Monthly reports.
Dating back to its establishment in 1936, Capral has been an integral part of the country’s industrial fabric. A recent transformative phase, marked by a strategic investment program, underscores the company’s commitment to fortifying its manufacturing capabilities and aligning with emerging trends in extruded aluminium products.
Guiding this transition is CEO Tony Dragicevich, whose leadership extends beyond immediate operational considerations to envision Capral’s role in navigating the profound changes anticipated with the wave of decarbonisation.
This forward-looking perspective aims not only at enhancing the company’s competitive edge but also at contributing to the broader goal of reducing Australia’s reliance on imported aluminium.
The infrastructure underpinning Capral’s operations is nothing short of extensive. With six manufacturing plants strategically distributed, eight extrusion presses, and a well-established distribution network with over 20 sites across Australia, the company boasts a substantial presence.
This, coupled with a workforce exceeding 1000 employees, positions Capral as a significant player in the aluminium manufacturing and distribution sector.
The strategic moves made by Capral in recent years go beyond mere expansions or efficiency drives; they reflect a nuanced understanding of market dynamics.
The acquisition of the GJames extrusion plant and
the meticulous upgrade of the Penrith extrusion press exemplify the company’s commitment to evolving its manufacturing capabilities.
These endeavours, notably, have not only enhanced operational efficiency but have introduced critical services, such as powder coating, showcasing Capral’s adaptability to changing market needs.
“These and other strategic initiatives are positioning Capral for its next growth phase,” said Dragicevich.
“The investments enable Capral to be more innovative and agile, work closer with our customers, and expand into new markets. We are responding to our customers’ needs for more sophisticated and sustainable aluminium products.”
Integral to Capral’s evolving narrative is its commitment to sustainability. The company, cognisant of the increasing importance of environmental considerations, has positioned itself as a participant in the broader environmental discourse.
The introduction of LocAL, a certified lower-carbon primary aluminium option, underscores Capral’s commitment to providing sustainable solutions.
Ambitious targets, including achieving netzero emissions by 2050, and certifications like the Aluminium Stewardship Initiative (ASI) Performance and Chain of Custody Standards, reflect the company’s commitment to environmental stewardship.
“We want to develop a stronger circular economy for aluminium in Australia and move away from the
current practice where nearly all aluminium is sent overseas for remelting,” said Dragicevich.
Ensuring sustainable manufacturing Sustainability, for Capral, is a guiding philosophy that permeates various facets of its operations.
The year 2020 saw the formation of a National Sustainability Committee, indicative of a structured approach to sustainability goals.
In late 2022, Capral introduced LocAL into Australia, providing a certified lower-carbon primary aluminium option across its locally manufactured extruded aluminium products.
The two variants, LocAL Green and LocAL Super Green, offer environmentally conscious alternatives, with the latter boasting carbon emissions significantly lower than the average for primary aluminium, positioning it as one of the lowest-carbon aluminium options globally.
Capral’s sustainability commitment extends beyond primary production to include recycling initiatives.
The goal is to cultivate a stronger circular economy for aluminium in Australia, moving away from the prevalent practice of shipping almost all aluminium overseas for remelting.
Tony Dragicevich emphasises, “Over the next five years, I am certain Capral will be viewed as having the strongest green credentials in our market, and as a sustainability leader in the global aluminium industry.”
“We have a deep commitment to reducing carbon
heightened significance in the context of global supply-chain risks.
The disruptions experienced globally, particularly during the COVID-19 pandemic, have led to a reassessment of the vulnerabilities associated with extensive global supply chains.
The rising sovereign risk and the growing trend of ‘reshoring’ are indicative of a paradigm shift, with companies seeking to bring larger parts of their supply chain back to their home countries.
Aluminium imports to Australia, a crucial aspect of the industry’s dynamics, have seen a noticeable shift.
Dragicevich observes, “After COVID-19, there has been greater interest in using locally manufactured extruded aluminium. Customers recognise there is far greater supply-chain risk and longer lead times with imports. It doesn’t take much to go wrong with global aluminium supply for local firms to be left high and dry.”
Capral’s emphasis on local manufacturing is not merely a response to market dynamics but a proactive stance in addressing supply-chain vulnerabilities.
The company’s unique position as the only independent national manufacturer of extruded aluminium provides a level of autonomy that aligns with the growing sentiments of ‘reshoring’ and mitigating risks associated with extended supply chains.
Tony Dragicevich, recognising the importance of local manufacturing, joined the Board of the Australian Aluminium Council, a peak body representing the local aluminium industry.
advocating for fair trade, and actively contributing to industry discussions and policy advocacy.
“We’re doing things in extruded aluminium that haven’t been possible before in Australia. It’s an exciting time for Capral as we lead local innovation and sustainability in aluminium manufacturing,” notes Dragicevich.
Capral’s advocacy for fair trade aligns with its broader commitment to the protection and growth of the Australian aluminium industry.
The company’s efforts contribute to maintaining a level playing field for Australian manufacturers and ensuring fair competition in the global market.
The expanded local capabilities of Capral, coupled with its advocacy for fair trade, serve not only as a response to recent disruptions but also as a strategic positioning in a changing global landscape.
The emphasis on reducing supply-chain risk and supporting Australian manufacturers aligns with broader economic trends and considerations of national resilience.
As a responsible corporate entity, Capral has embraced the principles of Environmental, Social, and Governance (ESG) in its operations.
The company’s commitment to reducing carbon emissions and promoting sustainability aligns with the broader global shift toward more responsible and ethical business practices.
Capral’s engagement with the Aluminium Stewardship Initiative, its establishment of a National Sustainability Committee, and the incorporation
The company’s focus on the social aspect of ESG is evident in its workforce of over 1000 employees.
Capral’s operations, spanning multiple manufacturing plants and distribution sites, contribute significantly to local employment.
The commitment to sustainability, including initiatives for recycling and remelting aluminium locally, not only aligns with environmental goals but also supports the social aspect of responsible business practices.
As the company navigates through the challenges of a rapidly changing global landscape, its commitment to reducing environmental impact, supporting local manufacturing, and advocating for fair trade emerges as a blueprint for responsible and resilient business practices.
Capral’s story is not just a chapter in the history of Australian manufacturing but a testament to the possibilities when a company aligns its growth with environmental stewardship, social responsibility, and a commitment to the well-being of the industry and the nation.
“Capral’s investment means it can support more Australian manufacturers with comprehensive aluminium extrusion, distribution and supply,” said Dragicevich.
“Capral has world-class finishing, machining, and fabricating technology; access to the lowest-carbon aluminium; and a unique national footprint.
“We’re doing things in extruded aluminium that haven’t been possible before in Australia. It’s an exciting time for Capral as we lead local innovation and sustainability in aluminium manufacturing.”
was a stand-out finalist for the 2023 Awards. Manufacturers’ Monthly reports.
The Outstanding Start-Up Award, proudly sponsored by BlueRock, recognises an Australian manufacturing start-up that has introduced a new product to market, filling a market gap.
A finalist for the Outstanding Start-Up Award, SiteHive, has been innovating the environmental management space over the last five years.
The company provides businesses with real-time environmental monitoring devices and software.
Designed and manufactured in Australia, its products transform how construction and other industrial sites manage the impact of environmental aspects such as noise, dust and vibration.
Manufacturers’ Monthly spoke to SiteHive’s co-founder, Ben Cooper-Woolley, to find out more about the future of SiteHive, and the environmental and manufacturing advantages of the Australian company.
Cooper-Woolley said the Endeavour Awards nomination highlighted the strength of the local industry and reflected what it means to share ideas, skills, knowledge, and experience.
Cooper-Woolley stated that the Endeavour Awards were “an opportunity to showcase and promote local manufacturing and for companies to connect and support each other on the journey as well.”
“It is important for us to get involved and engaged, and play our small part in the industry overallanything we can do to support and promote the industry.”
SiteHive’s products are a modern take on traditional ways of monitoring noise and dust pollution, and vibration impacts, for industrial work sites. SiteHive
has produced the latest technological advancements for effective and accurate environmental management.
SiteHive Hexanodes are a family of environmental monitoring devices that enable the measurement and management of noise, dust, and vibration.
Cooper-Woolley says that the key components for creating an efficient product are to ensure it is proactive, accessible, and easy to use.
“Unlike with traditional devices, we calibrate SiteHive Hexanodes, and we maintain them. You just plug your SiteHive Hexanode in, and they do all the work and monitoring for you,” Cooper-Woolley explained.
“As well as data on noise, dust and vibration levels, they also capture a lot of additional contextual information. For example, we provide directional noise and dust data: we know where noise is coming from by using multiple MEMS microphones, and we map it out.”
“We can also trigger image capture in different directions, and record audio. For the latter, we classify it using AI.”
The SiteHive Hexanodes can distinguish noises that are exclusively related to the work that is being done.
“For instance, if there is a bird sitting out of the frame of view causing noise, you can’t always see that it’s what’s making the noise. Recording audio provides a unique opportunity for recognising patterns in what is happening and determining the cause of noise,” said Cooper-Woolley.
Each SiteHive device is significantly lighter and smaller than traditional devices, making them easier to use and move in the field.
Cooper-Woolley describes the SiteHive Hexanode
devices as, “compact, and very mobile in a busy environment.”
The innovative SiteHive Hexanode products include three devices each managing and monitoring a different environmental issue: noise, dust and vibration. Plus one device that manages both noise and dust at the same time..
As outlined by Cooper-Woolley, a significant appeal of the modern technology that SiteHive provides is the real-time software that allows people to proactively manage noise, dust, vibration, and water quality so that their effects are minimised - and thereby protect work teams, communities, and the environment.
Cooper-Woolley said this was a major advantage on worksites.
“In my previous work, we were paying consultants hundreds of dollars to tell us what happened based on information from a month ago. But now these devices can capture images, monitor data and relay information in real-time. So people can make decisions and take action in the moment,” he explained.
SiteHive celebrates innovation, and the emerging field of AI has been embraced in their products. Cooper-Woolley explained how the use of AI is advancing SIteHive’s technology and providing new opportunities.
“We’ve developed an AI-based audio classifier that has been trained very heavily on sounds of the built environment, including things that aren’t construction noise like bird sounds, motorbikes, sirens, background traffic - that sort of thing. SiteHive Enviro
software uses this to classify and identify all the individual noises, so people can see immediately what’s construction noise, and what has nothing to do with the construction project.”
SiteHive’s environmental focus
SiteHive has grown quickly. Since being founded as a start-up in 2019, it has developed into a successful organisation working with industryleading clients in infrastructure development, construction, and the extractive industries.
Cooper-Woolley credits his previous engineering, environmental science, and technology background as a solid foundation for implementing change in the environmental management industry.
“We’re confident we have the right product for the market. We are being used actively on over 200 sites across Australia and New Zealand, and now it’s about how we scale up our manufacturing and supply.”
Cooper-Woolley highlighted the importance of environmental management in an economy that is shifting towards higher environmental sustainability.
SiteHive enables proactive environmental management that keeps teams and communities safe, builds stakeholder trust, and minimises environmental impact.
“Community scrutiny is on the rise,” CooperWoolley said. “I think a catalyst for this was the bush fires a few years ago. After that, people started taking a real interest in their own personal air quality and the impact on their own health. We
are now seeing that interest transfer into the urban environment, post the bushfires and COVID.”
In response to the rise in environmental sustainability, SiteHive has seen a new demographic of potential users.
“We’re seeing contractors, in particular, but also property developers and owners being more socially conscious,” said Cooper-Woolley.
“The environment and the Environmental Social Governance Agenda has really come to the forefront; and organisations are taking their corporate social responsibility seriously. SiteHive provides tools and technologies that allow people to be proactive about understanding and managing their environmental impact.”
SiteHive has identified the industries that use their products the most, with construction work, operational ports and mines being their major clients. However, as Cooper-Woolley explains, there is a lot of room for growth.
“The potential opportunities for this type of product expand way beyond infrastructure and construction, and into mining, ports, operational facilities, waste facilities, saw mills and even domestic situations,” he said.
“I think as urban density only increases, the opportunities for these types of products are only going to increase as well.”
SiteHive’s products are manufactured exclusively in New South Wales. Their electronics supplier is
based in Hornsby (CNS Precision Assembly); the housings are made by an engineering company in Botany (Deepdish Engineering); and the assembly and testing are completed at the SiteHive headquarters in Surry Hills.
Cooper-Woolley sees the local nature of this as an advantage to his business, stating, “a key element of us working with [the supplier] is because we get to do it locally, and we get to learn on the journey.
“We get to iterate a lot faster as well. We have been able to do small batches, and faster iteration, which in product innovation and development has been critical.”
Even though SiteHive has grown exponentially over the last five years, Cooper-Woolley and his cofounder are always looking for ways to develop and improve. He shared some upcoming and exciting new developments for the future of SiteHive.
“We are focussing on building our team on the goto-market side. So we’ve got a real focus on that in the next two, three years,” said Cooper-Woolley.
“This will enable us to broaden our client base within the construction industry, as we will be able to service and supply a lot more of the mid-range and smaller projects now.”
“We do a lot of major infrastructure projects, but we think there’s big opportunity and potential with smaller builders like education precincts, campuses, hospitals, and all the way down to residential buildings too.”
With around 145 years of combined history, Hardman Bros and its subsidiary R&I Instrument and Gear Co. are looking to the future to improve their specialised capabilities. Manufacturers’ Monthly reports.
Over the course of the last seven decades, the Victoria-based and family-owned manufacturers, Hardman Bros and R&I Instrument and Gear Co, have been gearing up to enhance their manufacturing capabilities.
This collaborative effort has not only withstood the test of time but has also resulted in the establishment of one of the most diverse workshops in Australia.
The combined legacy of 145 years reflects a shared commitment to innovation and excellence, culminating in a powerhouse of manufacturing expertise.
Their success can be accredited to several robust investments in collaboration, new equipment, and a forward-looking approach to embracing new technologies.
Their ongoing capital expenditure (capex) program is a strategic move aimed at not only enhancing their current manufacturing capabilities, but also expanding into new markets and cultivating a broader customer base.
“As part of our growth strategy, there’s a real capex programme in place now to underpin the growth of the businesses, and find new customers,” said Andrew Rowell, general manager at R&I Instrument & Gear Co.
The collaboration between Hardman Bros and R&I Instrument and Gear Co has resulted in a unique
synergy, offering a diverse range of manufacturing capabilities.
Their specialised, and in some instances rare machinery, reflects years of dedicated investment and commitment to their craft.
“Gear cutting is a niche of both Hardman Brothers and R&I,” said Rowell.
“R&I can cut down to an extremely small diameter, gears that would go into a wristwatch for example, and Hardman Brothers can cut gears up to 1.6 metres in diameter.”
Looking ahead, their capex project is a pivotal component of their growth strategy. It seeks to elevate current capabilities while embracing advancements in artificial intelligence (AI) and automation, positioning the companies at the forefront of innovation in gear manufacturing.
As they upgrade capabilities, every facet of the process is scrutinised for its potential impact, ensuring a seamless integration of legacy machines with cutting-edge technologies.
“Moving forward, as our capability upgrade project rolls out, we will be aligning further with a much higher capability to our customers expanding our service offering, consolidating what we already manufacture, and provide an add on at the same time,” explained business development manager for R&I and Hardman Group, Steven Ullness.
“The plan is to rapidly leverage that expansion
within both businesses.”
This evaluation, coupled with a focus on innovation and growth, positions Hardman Bros and R&I Instrument and Gear Co as would-be trailblazers in the manufacturing industry, ready to leave a lasting imprint on its evolution.
Situated within 10 km of Dandenong, Victoria’s manufacturing hub, R&I’s manufacturing facility co-located with Hardman Bros stands out for its diverse capabilities.
Spanning almost 7,500 square metres of floor space on a five-acre site, the hub offers a range of in-house computerised numerical control (CNC) services.
The facility’s expertise includes gear cutting and CNC gear grinding with dimensions reaching 800 mm x 650 mm width.
Other services encompass 5-axis simultaneous milling, CNC surface grinding, CNC slotting, cylindrical grinding, precision honing, and horizontal & vertical broaching, including FROMAG keyway slotting up to 800 mm.
“Over the last five to seven years, we have invested heavily into five axis CNC machining,” said Rowell. “We’re in the process of ensuring that we can meet current demands and make demands as we grow and expand our presence.”
In the realm of metrology and inspection, the facility also employs advanced tools like MicroVu and Optical comparators for vision inspection.
The Brown & Sharp coordinate measuring machine (CMM) with NIKON software and RENISHAW PH20 probe ensures precise measurements within an envelope of 900 x 1500 x 800 mm.
Not only do these companies boast great shared manufacturing capabilities, but their collaboration enables them to provide unique services.
“With around 140 machines used for gear cutting, and machining supporting our existing and potential customer base, we can either lead with our current capability, or promote with the fact that we’re a world class manufacturing facility in our own right,” said Ullness.
The incorporation of technology, advanced machining, and fabrication capabilities from both Hardman Brothers and R&I operates in tandem, allowing both companies to produce individual components and assemblies into larger systems. Ultimately, this enables the companies to
As part of our growth strategy, there’s a real capex programme in place now to underpin the growth of the businesses, and find new customers.
”
manufacture advanced components, but also assist their clients with the fabrication and assembly process.
“We’re able to provide complex components, individually, and we also have the ability to provide full blown complex assemblies as well,” said Ullness.
The two companies boast expansive capabilities, and currently operate across various industries, producing specified products tailored to distinct requirements.
Noteworthy is their facility in Victoria, the companies have distinguished themselves as one of the sole specialists in fine pitch gear manufacturing in Australia.
“At the moment, we have specific strategies around aerospace, defence, medtech, foodtech and support to mining rail and energy sectors” said Hardman Group chief executive officer, Simon Bell.
“Regarding the manufacturing industry as a whole, we are very focused on our existing clients and our future Customer acquisition strategies.”
Maintaining AS9100D accreditation, essential for aviation, space, and defence applications, the Hardman Group facility operates as a reliable partner, offering end-to-end solutions and collaborating on R&D projects from prototype to production.
Holding the AS9100D certification since 2016, with a recent reissue in September 2023, underscores the company’s dedication to meeting high standards in aerospace and defence manufacturing.
“We have a differentiation within our AS9100D certification, we are registered for assembly of electro-mechanical power transmission products including related repair, overhaul and provisions of spares which further enhances our services,” said Ullness.
The Hardman Group has obtained ISO9001 accreditation in the 1990’s, which emphasises a comprehensive approach to quality management.
In adherence to defence industry protocols, R&I complies with Defence Industry Security Programs (DISP) Entry Level requirements, emphasising a commitment to robust security measures.
Actively participating in industry networks, R&I is affiliated with associations such as AMTIL, ODIS, AIDN, Australian Defence Alliance, and Victorian Defence Alliance in Aerospace, Land Systems, and Maritime.
The company also engages with industry platforms like ICN (Industry Capability Network) and BENCHON to foster collaboration and connectivity within the manufacturing ecosystem.
With a history of enduring partnerships, R&I has served as a trusted partner for key aerospace and defence customers, including BAE Systems Australia, EOS Defence Systems, Trakka Corp Pty
Ltd, and AVT Australia (formerly UAV Vision), with partnerships spanning from 7 to over 25 years.
The Hardman Group also sources machinery from leading suppliers like DMG Mori Seiki, Hermle AG, and STAR Micronics.
Contributing to workforce development initiatives, The Hardman Group collaborates with Chisholm Institute, particularly through the Local Jobs Program and Training.
These partnerships secure these companies as stalwarts in the industry, uniquely equipped with a century and a half of cumulative knowledge.
As they set their sights on the future, the collaboration between Hardman Bros and R&I Instrument and Gear Co. underscores a commitment to enhancing and expanding their specialised manufacturing capabilities.
Thurs
WOMEN IN INDUSTRY NOMINATIONS ARE NOW OPEN. Now is your chance to nominate an industry leader who you believe is advocating for positive change and deserves to be recognised.
PROUDLY PRESENTED BY MHD
The Women in Industry Awards recognise outstanding women leaders from across Australia’s industrials sector.
The start-up currently partners with the Australian Postgraduate Research Intern (APR.Intern) Network, enlisting the expertise of Australian PhD students for the research and development of spacesuit components and technologies.
Recently, Metakosmos was selected for the Seed Program by the NSW Space Research Network, which is renowned for its role in identifying and nurturing early-stage space technology startups displaying significant potential for growth and innovation.
As part of the New South Wales Space Research Network (SRN) Seed program, the University of Technology Sydney (UTS) has secured a grant to engage in a collaborative venture with Metakosmos.
The goal of the venture is to address the customisation of spacesuits for diverse body shapes and sizes using exclusive digital optimisation techniques.
geometry processing mesh parametrisation and digital fabrication will be path breaking for this collaboration.”
Since the mid-to-late-20th century, spacesuit manufacturing was naturally a highly specialised process involving the creation of protective garments designed for astronauts set for space exploration. In the process of spacesuit manufacturing, engineers and designers meticulously crafted detailed designs to ensure the safety of astronauts exploring space.
These blueprints were tailored to meet the specific demands of each mission, incorporating considerations for ergonomics and essential safety features.
These suits protected astronauts against the vacuum of space, regulated extreme temperatures,
stand as remarkable engineering achievements, they were not without shortcomings.
Metakosmos, however, is on a mission to build upon these historic efforts and bring about improvements in spacesuit manufacturing using digital optimisation.
“We have a collaboration going on, where the professor at UTS would bring in their expertise, or specialisation into the workflow that we’re working on. So, this is essentially digitally optimising the fit of the spacesuit designs that we have created,” said Rambhatla.
So that would help us translate these designs to hosted body shapes and sizes, because traditionally, suits have been made in a certain specification in size, they wouldn’t fit all the astronauts well. So, this is a step in that direction to ensure you have a fit, which essentially sits well on the astronaut’s body.”
Rambhatla explained that their digital optimisation
is a unique approach. Therefore, he believes that their designs will be a “game-changer” within the space industry.
“What is usually shown is the suit aesthetics. Agencies press releases generally do not dive deep into suit sizes for different body-shapes. Designing the first spacesuits used for various body shapes and sizes for mass-level consumption will be the gamechanger.”
Metakosmos’ algorithm enables the company to manufacture spacesuits beyond the confines of the basic small, medium to large-size categories.
Metakosmos is developing a customised platform, called the Unified Receptive Production System (URPS), which is a complete solution, designed to advance the traditional spacesuit manufacturing process and to produce suits at scale. It’s an integrated platform for product lifecycle management and manufacturing execution system.
“Our unique system can accommodate the UTS algorithm. This algorithm goes beyond the modern standard size models (small, medium, and large), to account for the compression and the fit of an individual,” said Rambhatla.
So, the digital optimisation process would ensure that a 3D scan of the form of the body is available as digital files in our platform, to the specified size and fit, this assists in streamlining the manufacturing
process and for iterative design.”
Ensuring that the astronaut has a perfectly fitted spacesuit is essential for several reasons.
As pressure increases within the suit, it becomes crucial to maintain a specific pressure level for the well-being of the occupant along with internal thermal management and joint mobility.
When exposed to the extreme conditions of space, the suit structure may expand, which can limit mobility. Therefore, the occupant must be capable of regulating the mobility of their joints within the suit structure.
“It has been incredibly hard to design suits and to manage all of those variables in the past. That meant, once the suit is pressurised, the dimensions of how the suit sits on top of the user may change, which can shift everything inside it,” explained Rambhatla.
“That would lead to a lot of issues related to mobility, and increased joint torques, as well. So, the suit must be pressurised enough to be able to achieve a minimal movement that you could do very easily here on Earth. All of these things add to the complexity of the architecture of the suit.”
Throughout their endeavour to improve spacesuit design, the Metakosmos team encountered several challenges – addressing the costs of the
manufacturing process remains a major challenge.
The cost of manufacturing a spacesuit can vary widely depending on the type of spacesuit and its intended use. However, it is generally considered to be an expensive process.
Extravehicular activity or EVA suits require an array of features like mobility joints, life support systems, thermal control, communication systems, and shielding from micrometeoroids, all of which add to the total cost.
They also require specialised components to manufacture, which can of course become expensive to source.
After the manufacturing process, spacesuits must undergo rigorous testing and certification processes to ensure they meet safety standards.
Each phase of spacesuit manufacturing often requires agencies to outsource skillsets or materials from multiple different industries.
Accordingly, combined with other budget considerations of space travel, the number of astronauts being trained per year is limited.
Currently, The National Aeronautics and Space Administration (NASA) has only employed 360 astronaut candidates.
“The agencies are often restricted in the number of people that they can take into these programmes because the training infrastructure and costs of suits
What we’re trying to do now is build an internal production platform to make mass production much easier later in the future.
“ ”
are high.,” said Rambhatla.
“We believe if you could reduce these costs, there’d be an opportunity for more people to be onboarded into these programmes to get trained,” explained Rambhatla.
Metakosmos is now aiming to make the process of spacesuit manufacturing more economical by housing multiple skillsets under one roof.
“Traditionally, spacesuit manufacturing has been a very expensive process, because manufacturers would often have to bring skillsets from different industries, it’s largely been in the domain of defence,” Rambhatla said.
“You’ve got some processes that are done through computers, some processes by hand and those operations are managed by multiple suppliers as well. So, it’s been a bit of a complicated process, and it still runs that way.
“What we’re trying to do now is build an internal production platform that makes it very easy to mass produce these things in the future.”
Currently, the testing process is widely dispersed because the suits are not manufactured for commercial use. As a result, there is no standardised method for conducting tests.
Throughout their testing process, the Metakosmos team refers to NASA’s safety standards for their spacesuit design.
Over the past five decades, NASA has dedicated considerable time to ensuring spacesuit safety, and they have since shared this acquired knowledge with the global community.
Ideally, this wealth of information would be integrated into a process akin to an ISO standard for the aerospace and defence industry, ensuring a high-quality management process that is universally attainable.
“We are making a plan to have our suits tested to the highest standards for extreme environments, radiation temperatures and chemical exposure,” Rambhatla said.
Many of the fabrics used in spacesuit manufacturing must also possess ballistic resistance to safeguard against rapid-moving objects such as small micro-meteorites.
“There’s a host of testing standards that have been defined by NASA, in the 60s and 70s, which are
still evolving, to ensure that all these things are captured well enough,” explained Rambhatla.”
“We are designing an internal production platform, that has the entire engineering process digitally mapped. This makes it easier to source materials from other industries that meet the standards and requirements.”
The Metakosmos team is looking to commercially license their digital optimisation platform for research purposes – Rambhatla said that potential partners from India and the Middle East have already expressed interest.
“We have had collaborations on research projects with CSIRO and academia, on focus areas such as biomechanics, biomarkers, and human performance in extreme conditions. We have had discussions with potential partners in Australia, USA, India, and the Middle East on the deployment of the suit platform.”
“We’re looking at licencing models, so we can give our partners access to our design files. Once they have the files, they can quickly put a solution together. Our partners can locally source raw materials and then assemble their suit,” he said.
“Users may soon be fitted with Metakosmos suits for testing and training purposes, such as parabolic flights, underwater or defence activities. We are aiming for mass testing adoption across several terrestrial use cases.”
From theory to practical implementation, the tripartite AUKUS agreement between Australia, the United Kingdom and the United States is coming closer to cutting metal, or at least soil, for new nuclear-powered conventionally armed submarines.
And as milestones move closer, organisations with potential involvement are committing to the early preparation required to ensure they are in the right place at the right time, and New Zealand is asking questions about how it may join the team, or at least share in the technology and industry opportunities.
In November the South Australian and Australian Governments signed a land swap agreement, with South Australia giving up federal defence-owned land around the city of Adelaide for 60 hectares at the Osborne submarine construction site, for a construction yard and a training academy.
In December the US Congress passed the 2024 National Defense Authorization Act (NDAA), which officially rubber stamped the sale of three Virginia Class submarines to Australia, including two inservice submarines and one off the production line.
The same bill authorised maintenance of US submarines by Australians in Australia and the training of Australians in US shipyards, included a national exemption from US export control licensing requirements and added Australia and the United Kingdom to Title III of the US Defense Production act.
“The US Congress has provided unprecedented support to Australia in passing the National Defense Authorization Act which will see the transfer of submarines and streamlined export control provisions, symbolising the strength of our Alliance, and our shared commitment to the AUKUS partnership,” said Deputy Prime Minister and Minister for Defence, Richard Marles, at the time.
“We are on the precipice of historic reform that will transform our ability to effectively deter, innovate, and operate together.”
There are still pundits suggesting AUKUS is destined to be canned by a future Australian government or binned immediately if Donald Trump becomes the next US president, although Steve Bannon, Trump’s 2016 campaign manager, has recently dismissed such speculation.
But state and federal governments and industry seem committed to the pathway, in both the submarine related Pillar 1 of AUKUS and the diverse technologies for Pillar 2.
With workforce development expected to be a speed hump for production of the submarines in Australia, the Australian Government announced in November that it would fund 4001 additional
university places, to the tune of $128 million, across 16 Australian universities offering a total of 38 STEMrelated courses. This project is particularly aiming to attract more students to train in engineering, mathematics, chemistry, and physics.
Bisalloy Steel has also announced it is an early contractor for AUKUS, entering a contract with the fledgling Australian Submarine Agency for the steel to be used on the SSN AUKUS design, with its 4500test qualification cycle expected to be completed in the first half of 2025.
Other advances have been flagged with the AUKUS badge, including the Trusted Operation of Robotic Vehicles in a Contested Environment (TORVICE) trial, a combined US, UK and Australian exercise testing how autonomous ground vehicles might react when under attack from electronic warfare weapons.
And the Royal Australian Navy has also begun ramping up its move to become a nuclear-powered force. Earlier this year the RAN announced that three officers had graduated from the U.S. Nuclear Power Training Unit (NPTU) program in Charleston, South Carolina.
Lieutenant Commanders Heydon and Klyne and Lieutenant Hall are the first cadre of Royal
Australian Navy personnel to complete one of the U.S. Department of Defense’s most rigorous and demanding training pipelines.
“I was really looking forward to putting the concepts and theories we learned at power school into operation at the prototype training,” said Klyne.
“Operating a nuclear reactor was thrilling, humbling, and allowed us get that hands-on experience we need to safely operate the Royal Australian Navy’s future SSNs.”
With continuous activity in industry, government and defence on AUKUS, the Western Australian Government has staked its claim as a major venue for a national event unpacking how the AUKUS pact will influence Australia’s Indian Ocean strategy, diplomacy, and industry. And it has a point, with Western Australia likely to be one of the first places where the AUKUS program becomes visible.
Over the next decade, the Australian Government will invest up to $8 billion to expand the HMAS Stirling naval base which will house the AUKUS submarines on the west coast, creating around 3,000 direct jobs.
Western Australia is also set to receive more frequent port visits by United States nuclearpowered submarines, with the United Kingdom to follow from 2026. This will further strengthen Australia’s experience with SSNs in Western Australia.
As early as 2027, HMAS Stirling will host the rotational presence of UK and US nuclear-powered submarines. This initiative, known as ‘Submarine Rotational Force-West’ (SRF-West), will develop Australia’s ability to operate, maintain and safely steward our future SSNs by deploying our Navy personnel on visiting UK and US boats where they will gain at-sea experience with naval nuclear propulsion.
From the early 2030s HMAS Stirling will house Australia’s first sovereign SSN capability, the US Virginia class submarines.
With so much happening in industry, government and defence, the Western Australian Government has flagged its Indian Ocean Defence & Security 2024 (IODS 2024) conference and exhibition, at the Perth Convention and Exhibition Centre, as the place
to chart progress and discern what may come next.
The event will unpack the real-world issues and impacts of the tripartite Australia, United Kingdom, and United States AUKUS agreement and the fournation “Quad” dialogue between Australia, the US, Japan and India.
The event has already confirmed speakers including:
• Royal Australian Navy Chief of Navy, Vice Admiral Mark Hammond, AO, RAN;
• Admiral Sir Ben Key KCB CBE ADC, United Kingdom First Sea Lord and Chief of Naval Staff;
• Dr. Kurt Campbell, Deputy Assistant to the President of the United States and Coordinator for Indo-Pacific Affairs on the US National Security Council;
• Amb. Sujan R. Chinoy, Director General of the Manohar Parrikar Institute for Defence Studies and Analyses (MP-IDSA) in New Delhi.
The event’s 2024 theme, Where AUKUS Meets The Quad, will explore two of Australia’s premier international diplomatic partnerships and the challenges and opportunities they present for international engagement.
Interworld Electronics is excited to introduce the AUHMI-9C series of rugged industrial all-in-one HMI Panel PCs from APLEX Technology. The AUHMI-9C series features a powerful Intel Tiger Lake 11th generation energy efficient Core i3/i5 processor with up to 64Gb of DDR4 RAM. It comes in a range of sizes from 10.1” – 21.5” TFT-LCD and has an IP66 certified front bezel.
The AUHMI-9C series has a new modern design, with ultra-narrow frame, slim profile, and new fast mounting kit. It is constructed using an aluminium die-cast and fanless design, making it rugged, while still maintaining good heat dissipation. It has the ability to operate continuously for long periods of time under wide temperature ranges of 0°C~50°C or optional -20°C~60°C. The updated design offers 24/7 reliability, makes it easy to clean, reduces maintenance cost, and provides a long-lasting rugged enclosure. The projected capacitive touch screen with multi-touch support, and anti-scratch surface
helps to improve usability, while also providing the screen with tough protection. Optional auto dimming, 1,000nits high brightness, and optical bonding & AR coating, makes the AUHMI-9C series perfect for a range of applications, no matter the environment or weather.
The AUHMI-9C series comes standard with 1 x DP/HDMI graphics output allowing users to connect an additional screen, audio line out, 1 x GbE and 1 x 2.5GbE LAN ports, 4 x USB3, and 2 x series ports. It also features a mini-PCIe slot and an M.2 expansion slot allowing for a wide range of optional expansion to suit your needs including, Power over Ethernet (PoE), 5G, Wi-Fi 6, CAN bus, as well as additional Serial, LAN or USB ports that can be added. The AUHMI-9C series also offers the optional smart battery backup feature, and supports Windows 10 & 11.
For more information contact Interworld Electronics.
Company: Interworld Electronics
Phone: 03 9593 7555 Website: www.ieci.com.au
For efficient production, it should be possible to seamlessly integrate safety concepts into machine concepts. That is why the configurable safe small controller PNOZmulti 2 from Pilz supports the open communication system EtherCAT in combination with the safe protocol Safety-over-EtherCAT FSoE (= FailSafe over EtherCAT). As a result, PNOZmulti 2 enables the transfer of both control and safetyrelated information, thereby achieving efficiency in production. So PNOZmulti 2 now offers flexible, economic expansion options when connecting safetyrelated plant structures.
Company: Pilz Australia
Phone: 1300 723 334
Website: www.pilz.com.au
From Version 11.3 of the software tool PNOZmulti Configurator, the safe small controller PNOZmulti 2 can easily be configured as FSoE Master, FSoE Slave and EtherCAT-Slave. Up to four Master-Master and up to 60 Master-Slave connections are possible with the EtherCAT FSoE communication module, in conjunction with the base unit PNOZ m B1. This way it is simple to implement and expand flexible plant structures with a “one-cable solution” at fieldbus level. As a result, the certified safety system not only provides a high degree of safety but also efficiency for plant and machinery.
With PNOZmulti 2 as FSoE Master, it is easy to implement safety-related networking with the safe radar sensor PSENradar from Pilz and safe drive technology PMC (Pilz Motion Control) – both with FSoE functionality. The “one-cable solution” is also used here to incorporate FSoE-capable actuators and sensors flexibly into the network. As FSoE Master, PNOZmulti 2 combines monitoring of all of an application’s safety functions in one device – from E-STOP and safety gate to light curtains – and establishes connections to safe Slaves in the network. This minimises the wiring effort and saves costs. Comprehensive diagnostic options also ensure minimal downtimes, making production economical.
The protocol Safety-over-EtherCAT (FSoE) was defined to implement safe data transfer for EtherCAT. FSoE enables the transfer of safety and non-safety-related information in the EtherCAT communication system. As a result, in accordance with IEC 61508, FSoE is suitable for safety applications up to SIL 3.
AGRICULTURE FARMING EDUCATION WASTE MANAGEMENT RESOURCE MANAGEMENT CONSERVATION MANUFACTURING RESOURCES
ENERGY HEALTH & SAFETY INFRASTRUCTURE ENGINEERING MINING CONSTRUCTION
QUARRYING AGRICULTURE FARMING EDUCATION
WASTE MANAGEMENT RESOURCE MANAGEMENT CONSERVATION MANUFACTURING RESOURCES
ENERGY HEALTH & SAFETY INFRASTRUCTURE ENGINEERING MINING CONSTRUCTION
QUARRYING AGRICULTURE FARMING EDUCATION
WASTE MANAGEMENT RESOURCE MANAGEMENT
CONSERVATION MANUFACTURING RESOURCES
ENERGY HEALTH & SAFETY INFRASTRUCTURE ENGINEERING MINING CONSTRUCTION
QUARRYING AGRICULTURE FARMING EDUCATION
WASTE MANAGEMENT RESOURCE MANAGEMENT
SEARCH FOR TOP INDUSTRY TALENT THROUGH OUR JOBS BOARD.
CONNECT WITH ALIGNED CANDIDATES.
BOOST YOUR CHANCES OF FINDING SKILLED APPLICANTS.
SCAN TO CREATE AN ACCOUNT TODAY AND DISCOVER YOUR PERFECT MATCH!
Australian chief executives are looking to the year ahead more anxious and uncertain about the national economy than they have felt for more than a decade.
Despite the concern, businesses overall feel optimistic about their own ability to navigate the challenges ahead but are clear on what must be done to assist them.
If the mood could be summed up in one sentence it is this: Improving productivity is the key for industry success in an uncertain, supplyconstrained and slowing economy.
Since 2012, Ai Group has annually surveyed CEOs and leaders from across Australian industry. This year, the survey of 320 Ai Group members from across the manufacturing, construction, technology and supply chain and industrial
services fields, shows they believe we are entering an economic period similar to the stagflation of the 1970s with persistent inflation, rising unemployment and weak consumer demand.
Industry expects to, at best, work through mediocre business conditions this year. The economic momentum driven by government support and pent-up consumer demand that lifted us out of the COVID period is clearly over. The clouds of economic slowdown and conditions akin to a recession linger for some key sectors of the economy.
Forty per cent of industry leaders expect
conditions to worsen this year, while 27 per cent hope for better times – the biggest differential in the annual survey since the mining boom.
The key worries from industry leaders for 2024 are heightened uncertainty driven by our geopolitical environment; ongoing supply side constraints, especially inflation and labour shortages; and weak demand, driven largely by households tightening their belts as their disposable income shrinks.
Locally, there is a big increase in industry ranking among their top issues of concern the Federal Government’s current industrial
relations measures and further proposals. The fear of increased workplace rigidity at a time our economy needs more dynamism is real.
The business response to all of this is to pivot from growth objectives to strategies focusing on improving productivity, with investments and workforce plans being refocused on doing more with less in an increasingly tough climate.
The investment response will be to focus on business improvements and staff training. This will be coupled with an effort to reduce costs as much as possible by cutting out inefficiencies.
This focus on productivity enhancing measures ranks far ahead of expected funding of capital expenditure and research and development.
One key take out is that, given labour and skills shortages, businesses expect to significantly increase their investments in technology to drive productivity improvements.
This will affect employment and skills needs in the years ahead.
A big reason for the technology pivot is that 87 per cent of employers expect to face staff
shortages this year. We simply don’t have enough people with the skills we need. To counteract that, the response will be the investment in technology to reduce the need for labour while investing more in staff training and rewarding staff who produce more.
The productivity focus is both necessary and welcome given Australia’s anaemic productivity performance over the past decade or more.
Overlaying our domestic situation are the growing global uncertainties that are again threatening the resilience of global supply chains.
Ninety per cent of businesses see this uncertainty as negatively impacting their business prospects.
Conflicts and blockages of key supply routes to Australia, combined with our own difficulties facing our ports, are rekindling concerns that supply-chain pressures will keep inflation higher for longer this year and next.
Seventy-eight per cent believe this uncertainty will drive up their input prices this year. However, only 57 per cent expect to increase their sales
prices in response as they work to contain costs to offset the impact. This is telling us that industry will make every effort to contain the impacts on their customers and will drive efficiency and direct investment at containing costs.
So, what can be done to help mitigate this uncertain environment?
Governments create the circumstances for business to thrive or not. They can help by focusing on delivering productivity-enhancing support around skills and training, reducing costs in areas such as payroll tax and WorkCover premiums, supporting technology investments through incentives and write-offs, putting real downward pressure on energy costs, lightening the regulatory burden, reducing barriers to employment and paying their bills on time.
The reality is that when you are in choppy waters, you batten down the hatches to ride it out. That’s what a lot of Australian businesses will be doing this year, hoping to prepare for brighter and different times ahead.