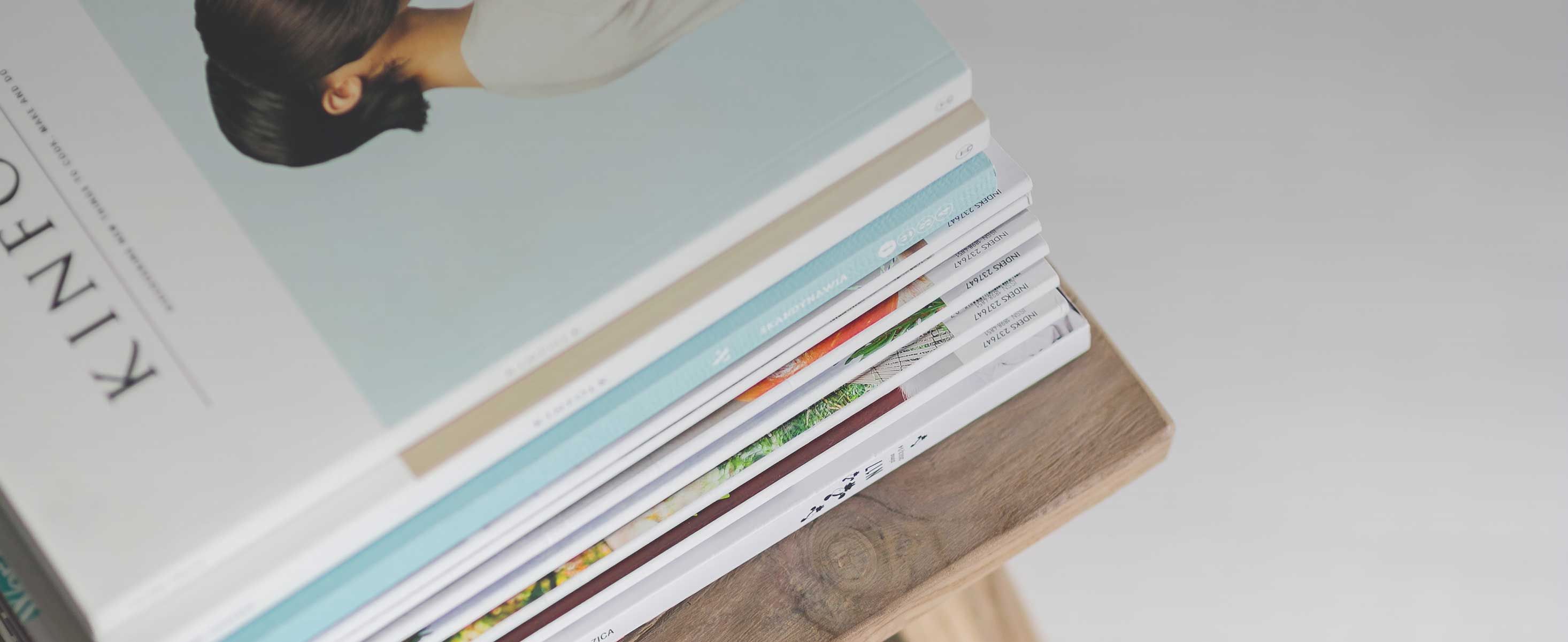
2 minute read
Editor’s Note
Comment
SYED SHAH – Managing Editor, Manufacturers’ Monthly
Investing in local manufacturing beyond COVID-19
AT the end of 2020, the federal government announced its $1.5 billion Modern Manufacturing Strategy. A vital part of Australia’s response to the COVID-19 crisis, the strategy was introduced to help Australian manufacturers scaleup, improve competitiveness and build more resilient supply chains.
Australia has long depended on international trade and imports, but adversity from the pandemic has pivoted into money-making and job opportunities. Manufacturing is critical to safeguard Australia’s economic future and the success of other industries that tie into it.
By no means are we at the end of the line with COVID disruptions, but things are looking to be on the up. We have perhaps said this before, but little victories like the removal of mask mandates at workplaces and relaxation of work from home rules form as a little light peeking out of the end of the tunnel.
Then, just when the world looks like it is about to emerge from COVID hell, harrowing images have gone across the world of Russia’s invasion of Ukraine, putting into perspective how lucky some of us are. The world seems to be fighting crisis after crisis in recent years, some impacting Australian manufacturing more than others, but the investment in Australian-made products remains front of mind for industry leaders and government. Sentiment is growing that an investment needs to be made separate to our response to COVID-19, rather for the country’s future landscape.
Aluminium prices are heading towards record highs, following financial sanctions on Russia for invading Ukraine. In this edition, Capral Australia talks about how local manufacturers are benefiting from the reduced presence of imported aluminium products, spurring on increased demand for locally fabricated aluminium products.
The global aluminium supply disruption will surely only increase demand for local manufacturing, with prices of the metal hitting a record of $3,525 a tonne on the London Metal Exchange in the past month.
Rusal is the world’s biggest aluminium producer outside China, accounting for around 6 per cent of global supplies, estimated to be 70 million tonnes this year.
Russia supplies the world with around 10 per cent of global nickel, which is used to make batteries for electric vehicles, but shipping lines halting traffic to and from Russia could disrupt supply to global customers. According to the Cooperative Research Centre, the national batteries industry could generate more than $7bn annually by 2030. In a pre-budget submission to the federal government, the Future Battery Industries Cooperative Research Centre (FBICRC) said that a potential 34,700 jobs could be created within the next 10 years.
CSIRO writes about a development opportunity for the whole battery value chain from mining of battery minerals to processing, battery active materials and eventually cell manufacture. One hundred per cent of Australia’s lithium-ion batteries currently imported from overseas, but with the global market projected to be worth $242bn by 2026, industry experts are working to change this.
Also in this edition, we look at innovation on the global scale. International expert Chikashi Kimura from Air Liquide explains how industrial gases can reduce the carbon footprint of industrial processes, but there is no one future-proof solution. His team is conducting extensive research around the world into different glass melting technologies, including the potential upside of hydrogen as an efficient route to decarbonisation.