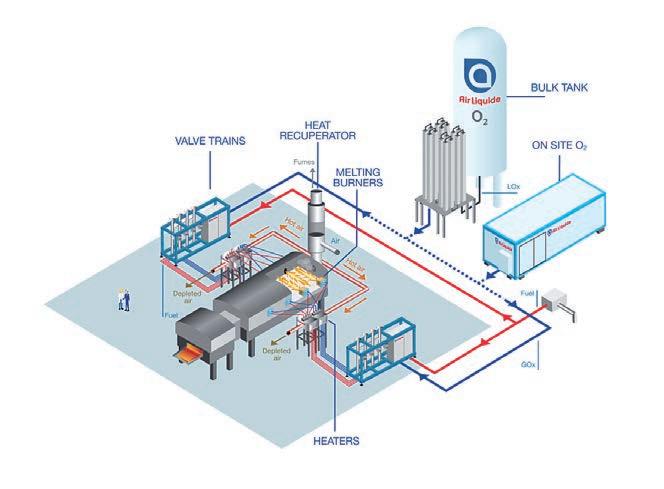
7 minute read
Energy Management
The future of combustion energy in glass melting
Manufacturers’ Monthly talks to Air Liquide’s international oxygen combustion expert about how its heat recovery packaged solution decreases the environmental impact of glass melting – and the potential upside of hydrogen as an efficient route to decarbonisation for melting technologies of the future.
AUSTRALIA consumes about 1.36 million tonnes of glass packaging per year: wine and beer bottles, glass jars and containers.
In Western Europe, the average person consumes 18 kilograms every year.
The manufacturing processes of products like glass contributes to more greenhouse gas emissions than the chemical and metal industries. Front of mind for forward-thinking companies is reducing this impact – and industry has started taking steps to revolutionise the future of glass melting.
Chikashi Kimura, NEAPac international expert (combustion) for Air Liquide, said industrial gases can reduce the carbon footprint of industrial processes, but there is no one future-proof solution.
“Several options might emerge, alone or combined, with the electrical melter: co-firing with Biogas or Hydrogen, heat recovery and ultimately Carbon Capture Use and Storage (CCUS),” he said. “All these energies can be combined with oxy-combustion technology for better effectiveness.”
Having been with Air Liquide for more than 15 years, Kimura noted customers are prioritising low carbon materials in order to be selected for major contracts.
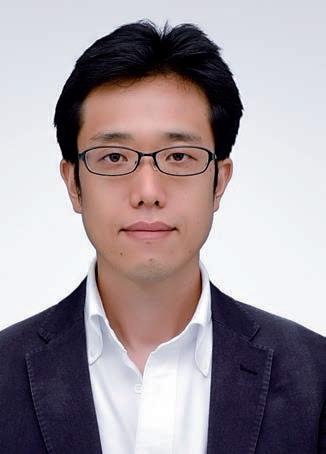
Heat Oxy-Combustion
Air Liquide’s Heat Oxy-Combustion technology has become renowned in the glass industry, and its effectiveness has only improved since it was recognised with the innovation award at the 2015 Paris Climate Conference. Leveraging off the experience of a brain like Kimura, the company continues to make strides in the research space for glass melting.
“The main principle of heat oxycombustion is to recover a substantial portion of the heat lost through flue gases by indirectly preheating fuel and oxygen,” he said. “That heat extracted from the combustion fumes is used to heat oxygen and fuel, thereby improving oxy-combustion performance by at last 10 per cent and even more with new upcoming developments. Compared to air combustion, this technology provides up to 50 per cent energy savings and up to 50 per cent CO2 emission reduction (excluding emissions generated for oxygen production).”
To develop this patented technology, safe and reliable equipment with specific material is designed and fully integrated with glass-melting furnaces. The equipment is made of special materials suited for very hot reactants.
Melting-Heat oxy-combustion consists of:
• Oxygen supply: Liquid Oxygen storage (LOx) or low pressure gaseous state (FLOXALTMFloxal
Oxygen). This is a competitive on-site production offer which provides the required quantity of oxygen according to all your needs. • Glass melting patented technologies
Heat exchangers
A unique and patented combination of HEAT RECUPERATOR and HEATERS: • the HEAT RECUPERATOR recovers heat from hot fumes to air; • the HEATERS transfer heat from air to fuel and oxygen.
Patented burners
All burners are made of specific materials to comply with high temperature: • GLASS MELTING BURNER-FC-
HEATOX is a patented nonwater-cooled oxy-fuel burner for technical and containers glasstype applications. • GLASS MELTING BURNER-SUN-
HEATOX is a patented non-watercooled oxy-fuel burner for large furnaces, such as those that use float glass-type production.
Chikashi Kimura is an international expert, leading Air Liquide’s Oxy combustion team in Japan for the NEAPac cluster.
Real-world applications
In a project funded by the European Commission to help industry reduce its environmental footprint, Air Liquide’s Heat Oxy-Combustion is being used at a factory in Bulgaria for the Şişecam group. In just one example of the innovation’s real-world capability, a pilot-scale industrial furnace was set up for tableware glass that uses only hot oxygen and natural gas to reduce energy consumption and CO2 emission for standard industry furnaces.
The project focused on validating the technology on tableware glass ahead of its potential transfer to small and medium sized furnaces regardless of the sector.
Under the system, natural gas and oxygen consumption is reduced by preheating the reactants (natural gas and oxygen) up to 550°C with waste heat from furnaces. This system entailed installing a heat-ox burner that is dedicated to work with preheated reactants. The operation was then optimised, improving efficiency by 10 per cent compared to air furnaces. The technology was
Energy Management
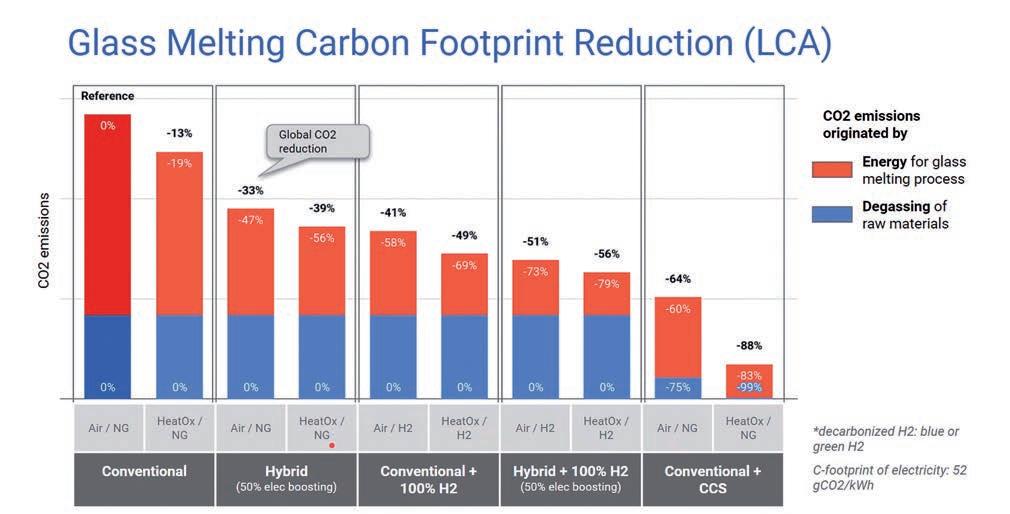
The reduction in carbon shown in different glass melting processes.
shown to reduce emissions of CO2 by 23 per cent and NOx by 90 per cent.
As project partner, Air Liquid conducted the detailed analysis necessary for the validation of the pilot furnace and its environmental results. The validation of the technology hopes to encourage glass producers to invest in it.
Hydrogen as a new source of energy
Kimura said because heat oxycombustion is already established, it will become more prevalent in the next 10 to 15 years. After 2035, however, the expert sees hydrogencombustion as an efficient technique, which is why Air Liquide continues to work with institutes around the world to develop more fundamental research to apply in the industrial field.
“Key studies we are conducting are showing a lot of potential options for the future,” he said. “There’s no single way in order to reach carbonneutral. The best solutions to grow and better our customers will change from country-to-country, so we are researching the best options for particular environments.”
One such study, based on the LCA (life cycle analysis) approach, was recently conducted by Air Liquide to assess the overall impact of the different decarbonisation strategies for glass melting.
A typical medium-size regenerative furnace operating with air and natural gas was chosen as the baseline scenario. Several technical improvements were then considered, like the replacement of the air with pure oxygen, the switching from natural gas to hydrogen and the addition of up to 50 per cent electrical boosting. The implementation of a Carbon Capture and Sequestration (CCS) unit was also considered to reduce the CO2 released in the atmosphere.
“Several options were compared for hydrogen production: Steam Methane Reforming (SMR), with or without a CCS unit downstream, or water electrolysis,” Kimura said. “As revealed by the study, the carbon intensity of the electricity has a strong impact on the overall emissions level. A sensitivity analysis was conducted on this parameter to better represent the variety of cases, from geographical areas with a high carbon footprint in the electricity mix to much lower levels like decarbonised electricity obtained from offshore wind.”
The most effective solution to reduce the overall CO2 emissions consists in installing a CCS unit directly at the exit of the glass furnace. This solution allows a reduction in both the CO2 coming from the combustion flue gases and the CO2 released by the degassing of the raw materials, leading to an overall 64 per cent reduction of CO2 emissions compared to the baseline scenario. Combined with a HeatOx, this figure can be further increased up to 88 per cent.
Kimura noted CCS can not be implemented everywhere and requires important infrastructure with significant costs.
“When focusing on the CO2 emissions due to the combustion part, different options without CCS were compared,” he said. “The first one consists in replacing 50 per cent of the input energy by decarbonized electricity (hybrid furnace). Considering the French CO2 emissions factor for the electricity (52g CO2 /kWh), 56 per cent of the CO2 emissions due to glass melting can be avoided with this hybrid furnace. The decarbonization of electricity leads to higher reductions, up to 62 per cent with offshore wind (15g CO2 /kWh) and 64 per cent with the theoretical 0g CO2 /kWh CO2 emissions factor.”
According to Kimura, a higher reduction of the carbon footprint can be reached by replacing natural gas by decarbonised hydrogen with air combustion (up to 88 per cent CO2 reduction with offshore wind electricity). This option can be further improved by the combination of reactants preheating with oxycombustion, leading to up to 92 per cent CO2 reduction.
“Finally, the best approach appears to be the H2-hybrid furnace,” he said. “This is obtained by combining 50 per cent electrical boosting with 50 per cent decarbonized H2 with heat oxycombustion. The approach leads to 94 per cent CO2 reduction for the combustion part (assuming offshore wind electricity).”
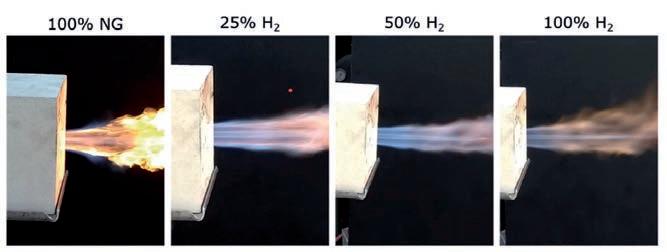
Undoubtedly – as the world continues on the path to a lowcarbon economy – demand for low-carbon glass will amplify with the development of new furnace generations and technologies. Air Liquide has already identified the hybrid melting tank (electrical melter + oxy-firing, possibly combined with HeatOx) as an efficient glass container production solution. Kimura concluded that technologies for a low carbon industry exist today and will continue to be competitive. “The benefits in terms of CO2 emissions reduction are highly dependent on several factors like the CO2 emitted during electricity production and cullet ratio,” he said. “Solutions needs to be assessed for each individual site and specificities. Heat oxy-combustion is particularly relevant when used with hydrogen but also for CCS purposes.”