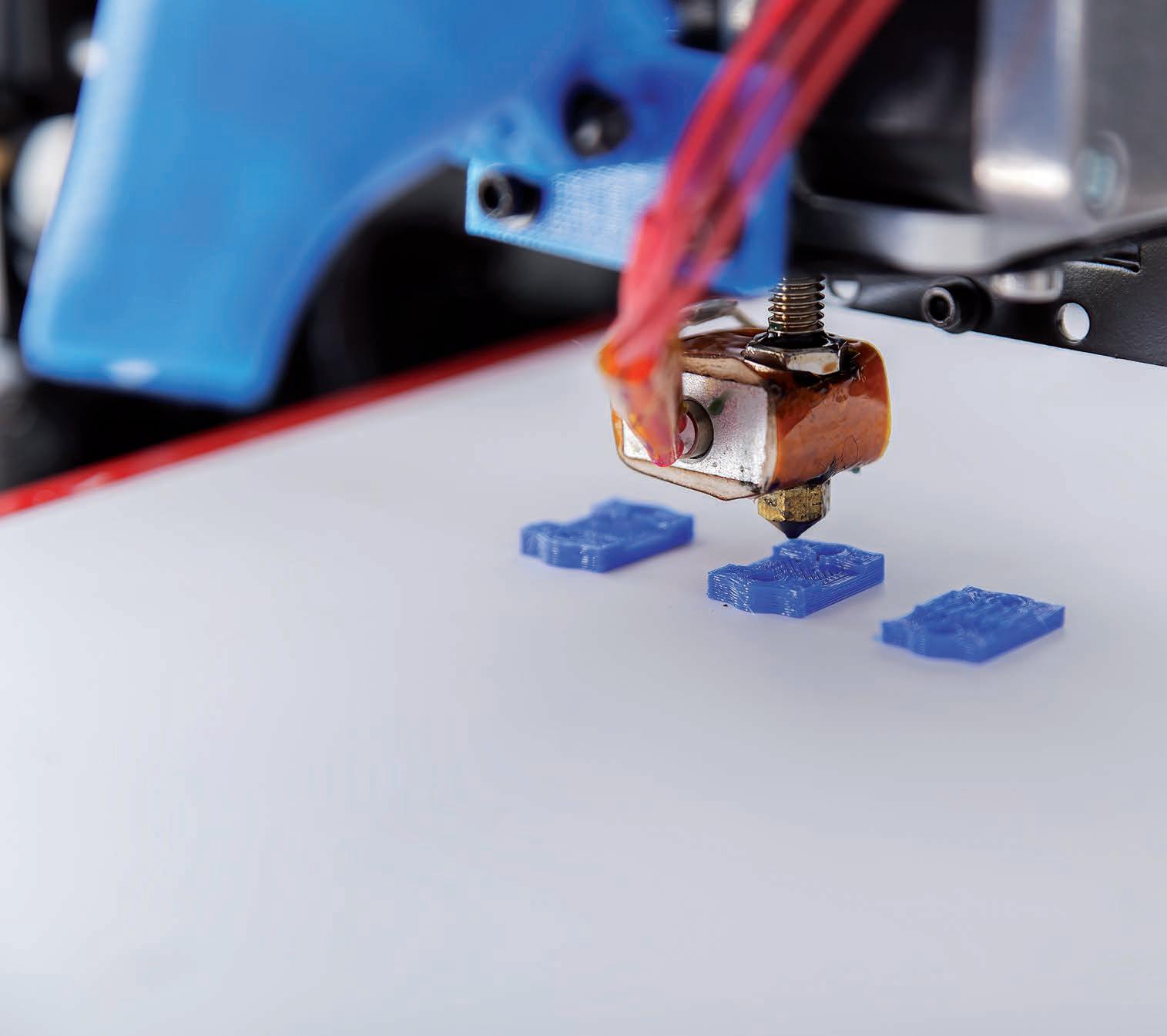
6 minute read
Industry Focus
Engineering Focus
Researchers from UNSW have discovered a process to create a self-healing 3D printed plastic.
Self-healing 3D printed plastic components
A team of University of New South Wales researchers, led by Professor Cyrille Boyer from the School of Chemical Engineering, discusses a novel treatment used in 3D printing that allows the material to repair itself with Manufacturers’ Monthly.
AS additive manufacturing becomes an increasingly widespread process for various applications, what happens if a 3D printed component is damaged? How much would it cost to fix or replace, and how much downtime would it require? How much waste would it incur?
According to a Macromolecules article, “Living Free-Radical Polymerization by Reversible Addition−Fragmentation Chain Transfer: The RAFT Process,” reversible addition fragmentation chain transfer (RAFT) – a form of living radical polymerisation – was discovered by the CSIRO in 1998. The CSIRO had studied linear growing systems and how to make polymer chains that incorporated a “living” group on the end.
“It’s a very versatile technique that they developed, and I think it’s used in a lot of industrial applications as well, just because you can make very well controlled polymer chains and you can have very different chemical compositions and polymer chain topology,” UNSW School of Chemical Engineering researcher, Dr Nathaniel Corrigan said.
Since then, several RAFT agents have been found. One class of them are known as trithiocarbonates.
In a recent study led by a team at the UNSW School of Chemical Engineering, Professor Cyrille Boyer and his associates including Corrigan and PhD student Michael Zhang, found that trithiocarbonate can be used as a special additive in the liquid resin used as a material for additive manufacturing.
By using this particular additive, the nanoscopic network of elements can be rearranged within 3D printed plastic that has become damaged. This fuses the broken pieces together, in response to light.
“The material can grow again, as it responds to light,” Boyer said. “We decided to exploit this ability to repair the 3D printed object.”
Grow and repair
With trithiocarbonate as a living group, it allowed the polymer chains to grow, according to Corrigan. “We’ve implemented trithiocarbonate because the chains are living, and when the material is broken you can regrow the
chains,” he said. “That regrowth of the chains and the regrowth of the polymer network enables the two 3D printed fragments to re-heal together.”
The UNSW team’s research was the first instance where a RAFT agent was used in 3D printed components. The initial aim was to reduce plastic waste for the long term in industrial applications, as broken plastic parts would not need to be discarded or recycled; they
could simply be repaired.
“If a component fails, you can repair the material without having to throw it away,” Corrigan said. “There is an obvious environmental
We’ve implemented trithiocarbonate because the chains are living, and when the material is broken you can regrow the chains,” he said. “That regrowth of the chains and the regrowth of the polymer network enables the two 3D-printed fragments to re-heal together.
Engineering Focus
benefit because you’re not having to re-synthesise a brand-new material every time it gets broken. We are increasing the lifespan of these materials.”
By using trithiocarbonate as an additive in the liquid resin that makes up the 3D printed plastic material, it plays a role both as a transfer agent as the network reforms and as an inhibitor, activated under radiation to allow the material to be modified.
“In this project, the RAFT agent can not only help to form a homogenous network, but also they can be reactivated under a UV light to start a secondary polymerisation and facilitate the self-healing process,” Zhang said. “Put simply, if we use this additive in a network of 3D objects and we shine a light on it, it can be reactivated into an active species, which then allows it to bring the broken parts together. That creates the self-healing process.”
A better method
While other processes of repairing 3D printed plastic components do exist, they rely on a more complicated method that takes longer and requires the component to be treated in a high temperature environment. Not only is the UNSW method simple and quick, it can also be achieved at room temperature by using a standard LED light.
“Other processes to heal the samples mainly rely on thermal chemical reactions and typically, it takes around 24 hours or maybe longer as well as a multi-heating cycle to heal the sample,” Zhang said. “And even then, it’s at a really high temperature – at around 100oC.
“When compared with our system, we don’t have to do that. We just put the samples in place and shine a light on it – and that’s it. On top of that, with a high concentration of the special powder in resin formulation the fractured materials can fully recover its strength within 30 minutes to one hour, so it’s much faster.”
Another benefit of adding the RAFT agent to the liquid resin is that the final 3D printed component would not have to be removed from the end-use device it is embedded into in order to conduct repairs.
“In our process, because it’s based on light, there’s the potential to be able to use it in situ and for the plastic component to be healed in place,” Corrigan said. “So, even for something as simple as a ring, if you take it out of the device it’s going to be a nightmare to get it back in. Whereas if you’re using light, you can do it in place and you can really spatially direct where you want the healing to occur and potentially also treat it through other objects or components, depending on how thick they are.”
Boyer agreed: “It’s easier if you can just repair the damage, as you don’t have to change the entire component.”
According to Corrigan, while other materials proved to be quite strong, they lacked functionality and once printed, they were not able to be repaired after a certain point.
“We found that first and foremost, the materials had to have that material strength – we needed our materials to be comparable to other 3D printed materials,” he said. “But the goal was to reduce that plastic waste by introducing another functionality, which was selfhealing. The materials are still rigid, they’re structurally sound, but we also added that other functionality – the self-healing capability.”
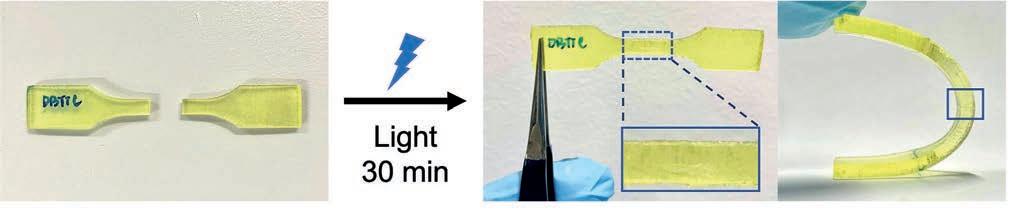
The future of 3D printing
The new technology has the potential to be utilised in a range of applications, wherever advanced 3D printed materials can be used in hightech specialised components such as wearable electronics and sensors.
“As we know, there are 3D printing techniques that are widely used in many different fields such as aerospace and electrical engineering,” Zhang said. “I think
A dumbbell-shaped sample in the self-healing process.
A 3D printed violin self-healing under light irradiation at room temperature for 60 minutes.
A 200g weightlifting test on a 3D printed hook, before and after the self-healing process.


this process could help to give the materials a longer lifespan, while also reducing the cost and resources waste. Anywhere where 3D plastic parts can be found, this technology can be of great use. It could even be used in dentistry, to make dental implants.”
To commercialise the new process, the UNSW research team believes further development is still required to make the 3D printed material more efficient.
“I think this process does require further development,” Zhang said. “We would like to actually make the materials stronger, but we also definitely want to ensure our materials have various properties, like the ability to make stretchy materials while still keeping it as strong as possible.”
Once commercialised, a selfhealing plastic material would reduce the amount of plastic waste and minimise costly repairs in terms of the funds and time spent.
“In terms of the commercial licencing, I think this process will definitely help to reduce plastic waste if all 3D printed materials are able to self-repair,” Zhang said.
The UNSW research team’s discovery has been published in the scientific journal, Angewandte Chemie International Edition.