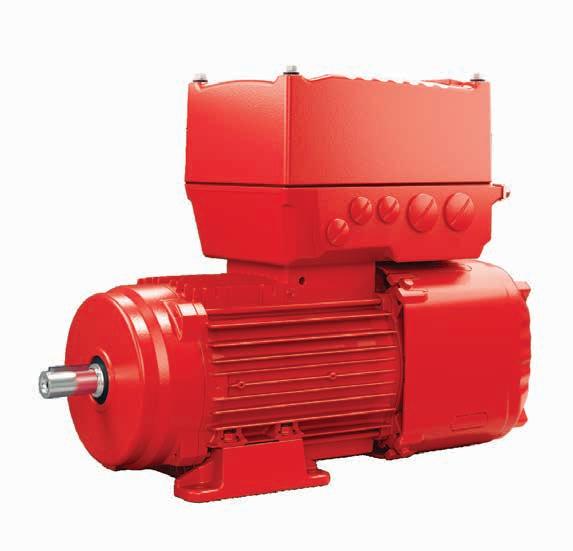
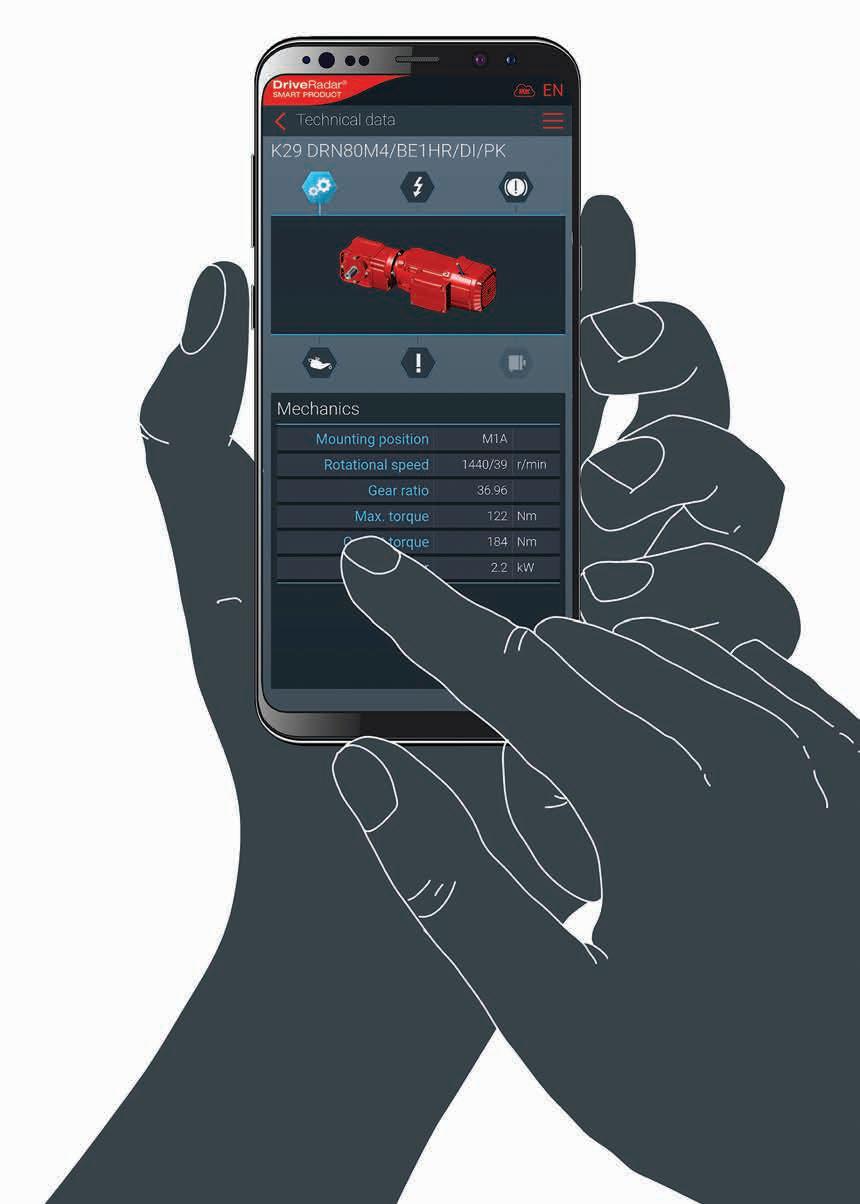
As industrial automation becomes more embedded into the integrity and profitability of many businesses in Australia, increasing system uptime, and reducing system downtime become the focal point.
This increased demand for end-to-end Asset Management Systems, Condition Monitoring and Smart Services, which are able to harness the power of device level data, providing live and historic conditions of powered drive systems.
Your Benefits:
• Early detection of potential faults/failures, mitigating undesired downtime and disruptions.
• Seamless access to complete Asset Identity and Device Manufacturing data.
• Data analysis, actionable service and inspection recommendations, actionable forecasting.
manmonthly.com.au twitter.com/Manmonthly facebook.com/Manmonthly linkedin.com/showcase/manufacturer’s-monthly/
CEO: John Murphy
Chief Operating Officer: Christine Clancy
Managing Editor: Syed Shah
Editor: Billy Friend billy.friend@primecreative.com.au
Journalist: Mignon D’Souza mignon.dsouza@primecreative.com.au
Production Coordinator: Michelle Weston michelle.weston@primecreative.com.au
Art Director: Blake Storey
Design: Kerry Pert, Tom Anderson, Louis Romero
Sales/Advertising: Danny Hernandez
Ph: 0431 330 232 danny.hernandez@primecreative.com.au
Subscriptions
Published 11 times a year
Subscriptions $140.00 per annum (inc GST)
Overseas prices apply
Ph: (03) 9690 8766
Copyright
Manufacturers’ Monthly is owned by Prime Creative Media and published by John Murphy. All material in Manufacturers’ Monthly is copyright and no part may be reproduced or copied in any form or by any means (graphic, electronic or mechanical including information and retrieval systems) without written permission of the publisher. The Editor welcomes contributions but reserves the right to accept or reject any material. While every effort has been made to ensure the accuracy of information, Prime Creative Media will not accept responsibility for errors or omissions or for any consequences arising from reliance on information published.
The opinions expressed in Manufacturers’ Monthly are not necessarily the opinions of, or endorsed by the publisher unless otherwise stated.
© Copyright Prime Creative Media, 2021
Articles
All articles submitted for publication become the property of the publisher. The Editor reserves the right to adjust any article to conform with the magazine format.
Head Office 379 Docklands Drive Docklands VIC 3008
P: +61 3 9690 8766 enquiries@primecreative.com.au www.primecreative.com.au
Sydney Office Suite 3.06, 1-9 Chandos Street
Saint Leonards NSW 2065, Australia
P: +61 2 9439 7227
In the April edition of Manufacturers’ Monthly, we celebrate businesses making a concerted innovation effort.
Valiant Space is one such example. Three young Queenslanders are making their mark by designing space rocket parts bound for orbit. The startup is the first to send locally-made components into orbit, onboard SpaceX.
Printed by: Manark Printing 28 Dingley Ave Dandenong VIC 3175 Ph: (03) 9794 8337
Elsewhere, we tell the story of Motion Control investing in a new assembly machine, making it the first local distributor to offer certified assembly of Bonfiglioli solutions. Read on to discover how the investment in the assembly machinery enables Motion to better service Bonfiglioli customers across South Australia
We delve into the latest edition of the Crafted with Capral series, in which two local Australian manufacturing success stories are celebrated. Quality aluminium has enabled Vawdrey to become the country’s leading manufacturer of quality semitrailers, while the same can be said for Louvreclad’s ability to design, engineer, supply and install louvre screens and bespoke façade solutions.
CAPS has launched an exciting new range of oil-free compressors. The allincumbent new range is allowing spaces like the pharmacutical and dental industries to maintain high air purity at all times.
Manufacturers’ Monthly is glad to partner with industry to tell the important stories – despite clear challenges, Australian manufacturing is in good hands.
Integrated solution with dryer, filtration and 250L air receiver.
Ideal for a wide range of applications which require oil-free air inluding medical, laboratory, food and bevergae processing or packaging applications.
Single Phase from 1.5 - 2.2kW
Three Phase from 3.7 - 7.5kW
CALL 1800 800 878 OR VISIT CAPS.COM.AU
HE landscape of Australian manufacturing has undergone significant changes over the years. While traditional manufacturing practices such as welding and fabricating continue to play a vital role in the industry, the advent of advanced manufacturing and new technologies has transformed the sector.
The rise of advanced manufacturing has allowed businesses to create products that are smarter, faster, and more efficient than ever before. Technologies in robotics, automation, and additive manufacturing have greatly enhanced production processes and helped reduce costs while improving quality, helping give Australian manufacturers a competitive edge in the global marketplace.
Despite these advancements, the importance of Australian made products remains as critical as ever. In a world where global supply chains are often disrupted and quality is increasingly important, Australian-made products offer a sense of reliability and quality assurance. On top of placing emphasis on quality, buying local of course not only supports the local economy but also helps to create jobs and build a more sustainable future.
As we move forward, it’s essential we invest in manufacturing and embrace the latest technologies and practices to stay competitive. At the same time, we must remain committed to preserving the art and science of practices like welding and fabricating that have long been the backbone of Australian manufacturing. By combining traditional practices with modern technologies, we can create a dynamic manufacturing ecosystem that is both innovative and sustainable. It’s time for businesses and policymakers alike to recognise the value of local manufacturing and invest in growing Australia’s manufacturing ecosystem for a brighter future.
Australia’s first ever National Battery Strategy is an encouraging sign of our government’s forward thinking. Minister for Industry and Science Ed Husic formally launched the campaign at a recent visit to Energy Renaissance, an Australian lithium-ion battery technology and manufacturing company, at Tomago in the New South Wales Hunter Valley.
Husic said the Strategy will be integral to help Australia transition to a decarbonised economy, hit ambitious emissions targets, foster Australian
innovation and support Australian industry.
He added domestic battery industries will be buoyed by Australian know-how and domestic access to minerals to help power the move to clean energy here and around the world.
“Our general approach should be one where if we mine it here, we should make it here,” Minister Husic said. “Large scale uptake and manufacture of batteries will be vital transitioning to net-zero. New battery capacity will help support grid scale capacity, power our homes, and electrify our transport sector.”
“We know there is huge demand for energy storage to support the widespread uptake of solar generation by households, business and industry. Global demand for existing and next-generation batteries is forecast to increase nine to 10-fold over the next decade.”
We are starting to see the fruits of the Government’s $15 billion National Reconstruction Fund for the manufacturing industry.
For example, a $3 million investment is set to build Australia’s manufacturing capability and create around 300 jobs at ANCA, establishing a precision
manufacturing cell at its Bayswater headquarters, using the grant delivered through the Modern Manufacturing Initiative.
Assistant Minister for Manufacturing
Tim Ayres said he was pleased to announce the grant, delivering this advanced manufacturing capability at a time when building sovereign capability has never been more important.
“Over the last decade, Australian exports have slipped down the global value chain as our exports have become less complex,” Assistant Minister Ayres said.
“This grant will enable ANCA to build a new designated precision manufacturing cell and continue enhancing Australia’s sovereign manufacturing capabilities.
“It will also create an estimated 157 highly skilled jobs during the project and about 330 jobs after five years.”
All in all, we are encouraged by the recent uptake in higher value orders and products in recent years. The global pandemic has highlighted the importance of self-sufficiency and local manufacturing, and it’s encouraging to see Australia taking proactive steps to build a stronger and more resilient manufacturing sector.
We have made significant strides in advanced manufacturing technologies, such as robotics, automation, and 3D printing, which are required for creating those high-value products. These technologies have the potential to drive innovation, increase productivity, and create new jobs in the manufacturing sector.
Of course, developing a strong local manufacturing sector is not without its challenges. The cost of production in Australia can be high compared to other countries, and there is a need for significant investment in skills training and technology to keep pace with global competition.
Overall, however, Australia’s focus on developing its local manufacturing capability and making higher value products is a positive step forward. By investing in the latest technologies and focusing on innovation, Australia can create a sustainable and competitive manufacturing sector that benefits both the economy and the country as a whole.
The modern plant needs more than condition monitoring to ensure assets are healthy and meeting production demands.
To
To support a successful predictive maintenance program you need realtime streaming analytics.
ifm’s moneo is an easy to use, self service software platform that simplifies the integration of Industry 4.0 concepts into existing systems.
The in-built DataScience Toolbox enables operators and engineers to leverage their knowledge of equipment with the benefits of AI-assisted predictive analytics and machine-learning techniques. This empowers businesses to identify and remedy anomalies before they become expensive, big problems.
Weld Australia has welcomed the Federal Government’s New Energy Apprenticeships program, and the updated Australian Apprenticeships Priority List. The financial support provided by the initiatives will be a drawcard for some businesses and apprentices. However, according to Weld Australia, much more must be done to tackle the nation’s deficient of skilled welders.
WELD Australia is calling for a radical three-pronged approach to overcome the nation’s skilled welder shortage that includes: an overhaul of welder training; a focus on STEM training in schools; and investment in TAFEs nationally.
There is no magic solution to Australia’s skills crisis. We need a radical approach. The same old approach that we’ve taken for years will not arm Australia with the skilled workers needed to deliver the record number of projects we’re seeing in industries like defence, renewables and infrastructure.
A veritable army of skilled workers, including welders, will be required to build and install the infrastructure needed
to achieve the Federal Government’s 43 per cent emissions reductions target by 2030 and net zero by 2050. Unless action is taken now, Australia will be at least 70,000 welders short by 2030.
It truly is the definition of insanity: doing the same thing over and over again, and expecting different results.
The Federal Government has committed to spending over $95 million to support 10,000 new apprenticeships under the New Energy Apprenticeships program, and another $1 billion on a 12-month Skills Agreement that promises to deliver 180,000 Fee-Free TAFE places to priority groups in 2023. While these initiatives will provide welcome financial incentives for both employers and their apprentices, this is just one small piece of the puzzle. These initiatives alone will not solve the skills crisis.
The Federal Government appears to have given little thought to encouraging young people into an apprenticeship. It’s all well good offering fee-free TAFE places—so long as they are filled. This is why STEM training in schools must be a focus. We need to educate kids, and their parents, so that they understand all the opportunities a career in STEM can deliver.
STEM training in schools must be refocused to showcase the opportunities in trades and encourage women and other underrepresented groups into careers in STEM. Weld Australia has been working with the New South Wales Department of Education for the past three years on an Advanced Manufacturing School Outreach Program
for schools. This program relies upon the use of augmented reality welding simulators to give kids a real welding experience. Weld Australia proposes that this Program be rolled out nationally.
Despite the Federal Government announcing funding for 190,000 TAFE places nationally, there has been no additional funding allocated to TAFEs to enable the delivery of training for all these additional places. Governments must invest in TAFEs nationally so that apprentices receive the best training possible, ensuring that they are jobready and actually complete their apprenticeships.
National data reveals that just 54 per cent of trade apprentices who started in
2017 completed by the end of 2021, down from 57 per cent of those who started a year earlier. One in three drop out in their first year.
TAFE requires proper funding to invest in new technology and equipment that better reflects what is in use in industry. Not only will this better prepare graduates for the workplace, it will also keep them engaged and should see completion rates improve. TAFEs also require funding so that they can employ the best possible teachers—people who are passionate about the trade and understand the industry.
It is imperative that sufficient investment be made in the TAFE system to ensure that it is a world class technical teaching organisation capable of meeting Australia’s demand for skilled tradespeople. Weld Australia proposes that funding properly reflect the cost of infrastructure, equipment, time, and materials required to teach to internationally recognised Standards.
A welding apprenticeship currently takes three years to complete. This means that new welders will not be qualified until at least 2026 and, even then, will not be skilled or experienced. We simply won’t have the skilled welders required to build and instal the green energy infrastructure to meet the 2030 targets.
This is why Weld Australia proposes that the current welding apprenticeship is condensed into one year.
The existing Certificate III in Engineering (Fabrication) is a nominal 720 hours of face-to-face teaching at a TAFE interspersed with practical experience in the workplace via an apprenticeship. This is spread over three years. If this was condensed into one year, the existing training package would remain unchanged but would be taught in two 24-week blocks consisting of 14 weeks of face-to-face training, and 10 weeks of Structured On the Job Training (SOJT) in the workplace.
Once an apprenticeship is complete, competency will be assessed and the Certificate III qualification awarded. Graduates will then be required to qualify to ISO 9606, the internationally recognised standard for welding competency. The shorter course will be less daunting to school leavers and will encourage mature aged applicants.
Training will be more intensive and is therefore likely to be more efficient. The number of apprentices graduating should increase, and the skills of welders should increase dramatically.
Welder training courses also need to be overhauled. The TAFE welding course and curriculum has not been updated or revised since 1998. It is a wonder that new welders complete their training, based as it is on theory and textbooks which hardly relate to the work they hope to make into their career.
Welding is an exciting, innovative, and dynamic industry – but the training offered to aspiring welders is dry and static. As covered above, this situation is no way the fault of TAFEs, or of TAFE teachers; they are at the mercy of the government funding merry-go-round.
Weld Australia is already working to overcome this situation. We have designed and released advanced learning resources mapped to the national Metals and Engineering (MEM) the MEM training package. These new resources are completely online, allowing students to access learning at the time, place and pace that suits them best. Highly interactive
and featuring the latest technology, these learning resources keep kids engaged and enthusiastic.
These resources are already in use in several TAFEs in Western Australia, but need to be rolled out nationally.
The Federal Government recently added an extra 39 occupations to the Australian Apprenticeships Priority List. The list has grown to encompass 111 occupations, as Australia continues to struggle with skills shortages across a range of different sectors—particularly welding and fabrication.
Several occupations related to welding and fabrication were added to the Priority List, including Welder, Pressure Welder, Fitter, Metal Fabricator, Metal Machinist, Metal Casting Trades Worker, Sheetmetal Trades Worker, and Blacksmith. In fact, 11 per cent of the occupations included in the Priority List are now related to welding.
Occupations on the Priority List are eligible for financial support through the Australian Apprenticeships Incentive System. A wage subsidy of 10 per cent is provided to businesses in the first and
second year, and then it drops to 5 per cent in the third year. Up to $5,000 in direct payments is made to apprentices across two years.
The skills crisis is not unique to Australia; the US fabrication industry will face a shortage of 500,000 welders by 2030, and by 2050 Japan will need around 250,000 welders. This means that we cannot rely on skilled migrants to fill workforce vacancies, nor can we import wind towers and other green energy infrastructure—global capability is at capacity.
This global shortfall of welders is driving most developed nations to implement extraordinary measures to resolve it. Australia must follow suit. We need a practical, actionable plan that can be implemented now to overcome the welder skills shortage—a plan that delivers more than just financial support to employers.
We must take three key actions to overcome the nation’s skilled welder shortage: welder training courses must be overhauled; STEM training in schools must be a focus; and our governments must invest in TAFEs nationally.
IN 2020 Australia ranked 91st in the Harvard Economic Complexity Index (ECI). This Index brings into sharp focus Australia’s economic reliance on exporting largely raw materials and highlights the need to diversify our economy.
But we need to play to our strengths.
And while I know I’m preaching to the choir here in Manufacturer’s Monthly, I’d like to hone in on the role of emerging digital manufacturing technologies. Through my role as Future Digital Manufacturing Lead at Australia’s National Science Agency CSIRO, I know I’m not alone in seeing a ‘once in a generation’ opportunity before us in regard to emerging Future Industries.
The adoption of Industry 4.0 technologies such as high-performance computing, Artificial Intelligence (AI), machine learning, sensors and the Internet of Things (IoT), robotics and other advanced technologies, is accelerating around the globe. Additive manufacturing is a prime example of how CSIRO is applying these advanced technologies in areas such as 3D printing,
providing designers with immense opportunities to optimise parts for performance by removing the limitations imposed by traditional manufacturing methods.
CSIRO is forecasting the next wave of digital innovation is expected to generate $10–15 trillion globally, and current available technologies could contribute $140–250 billion to Australia’s GDP by 2025. Australian manufacturing is the industry where these technologies can generate economic growth and ongoing employment.
Advancing Australian manufacturing relies on a foundation of collaboration, insight, strategy, technology and delivery. And we all have a role.
The future for ambitious and competitive organisations is not business as usual. First adopters are moving beyond lowest cost economy of scale, differentiation and niche positioning and shifting gears toward cost leadership, value-chain leadership, design leadership and business model innovation (or servitisation).
There are now many varied ways of
seeing the world through a different industrial manufacturing lens. Let’s take a look at potential emerging technologies in more detail and reflect on how they can impact specific strategic positionings.
Imagine you’re a designer of complex devices in the chemical, aerospace or biotech industries. You use computational fluid dynamics to develop catalytic static mixers (CSMs) for bespoke flow chemistry systems.
You have some great tools already at your figure tips to optimise the CSM, but you’re unlikely to create the best possible solution for each and every application. But artificial intelligence (AI) can.
An AI enhanced design system could find an optimum, world-first solution. So far, this approach has been used successfully for robotic fruit grippers and catalytic direct air capture structures. I’d challenge you to think about how AI can shift the gears of your business and create new ways of working.
Figure: An AI for Design catalytic
structure. Source: CSIRO report Combining AI and CFD to design static mixers
Manufacturers producing collaborative robotics, also known as cobots, and designers of intelligent autonomous service robots are having a huge impact in sectors as diverse as mining, agriculture, space, rail, heavy engineering, health and aged care.
Technology is moving quickly in this space and companies are now using robotic solutions that are agile and deliberate in their movement and feature advanced computer imaging, real-time process analysis, AI decision making, and situational awareness and collision avoidance.
But they are limited by the strength of their current software, middleware and development team. Enter the CSIRO-led ROSella platform, which builds upon the global ROS2 initiative and provides up-todate reusable libraries and algorithms for robotics and sensor systems development. The team are also using the technology CSIRO designed to achieve equal second place in the DARPA subterranean mapping challenge.
ROS2 and ROSella promise to underpin code that can be quickly deployed and then reliably maintained long-term, through leveraging a large, growing and proven library of routines and tapping global ROS2 developments. It offers a standardised platform with long term technical support.
We’re all seeing how important it is to minimise our environmental footprint – for our environment, to save money in the long run and for our consumers. Many Australian manufacturers use legacy equipment and systems that are challenging and expensive to integrate into modern energy management and
enterprise resource planning systems.
CSIRO is aiming to help to optimise legacy equipment until new equipment can be bought. Our Embedded Intelligence Platform (EIP) takes static capital equipment, relocatable instrumentation, scattered
sub-assemblies and work-in-progress, hazardous materials, etc, and tags them with low-cost wireless, networkintegrated devices.
These devices can recognise and communicate with surrounding devices, can read legacy gauges and control panels,
communicate with wireless sensors, reliably pass data to a cloud platform and then use sophisticated rules to create useful actionable notifications and dashboards. In this context CSIRO’s EIP is a maturing IoT Platform-as-a-Service that can be used to create smart connected machines from older equipment and provide accurate, reliable and trusted manufacturing operational data.
Manufacturers and facility managers are coming to recognise the potential of digital twins – the ability to model, simulate, and visualise complex processes. Digital twin technology can assist to manage construction, to virtually simulate commissioning and operation while the hardware assembly is still in progress.
Additionally, it could monitor and optimise performance during service, to virtually test operational scenarios without risking the in-service production system, and finally, manage the end-oflife processes.
Future digital manufacturing – also
known as smart manufacturing, digital transformation, or Industry 4.0 – is not business as usual. It is the next step in the evolution of manufacturing and will feature a suite of new and emerging tools to once again transform our society. The world embraced steam, then electricity, then micro-electronics, and now Australian business can strive to keep step with global competitors and embrace new intelligent technology.
At CSIRO, we support Australian businesses through research and development and testbed environments. CSIRO’s Future Digital Manufacturing initiative brings together our domain experts and world leading innovations across physical and information sciences to support business aspirations. If you are an ambitious SME, or you deliver high-value manufactured solutions, or are seeking to target emerging future industries, then CSIRO is positioned to be a solution partner.
trusted partner
logistics
materials handling
of experience in developing specialised solutions, combined with our expertise in logistics and materials handling, makes Bonfiglioli your trusted partner.
SEMMA recently announced Honi Walker has taken the reigns as CEO following Vonda Fenwick’s retirement. Manufacturers’ Monthly catches up with the new CEO to find out the industry group’s agenda for 2023 and beyond.
SEMMA was born to be a voice for manufacturers in the South East Melbourne region. The peak industry association represents over 200 leading manufacturing companies as a professional association dedicated to promoting the interests of its members. With a commitment to advocating for good government policy and decision making, SEMMA strives to keep manufacturing viable in a local and global context. The charter of SEMMA is focused on influencing government policy in an apolitical manner, promoting members and regional capability locally and internationally, identifying business opportunities, stimulating manufacturing businesses, encouraging collaboration between members, and committing to corporate, environmental, and social responsibilities. The association also recognises the importance of manufacturing to the community at large and aims to help all members achieve high levels of success to ensure that the industry remains a powerhouse of
economic development for the region.
SEMMA is managed by an elected board of 10 voluntary manufacturing members, as well as representatives from education, research and development, global specialisation, and the City of Greater Dandenong Business Development. With its dedication to promoting the interests of its members and the manufacturing industry as a whole, SEMMA is a vital resource for manufacturers in the South East region of Melbourne.
After being part of the initial SEMMA Board, Vonda Fenwick became CEO in 2019. Fenwick helped to guide members through the adversities thrown up by a global pandemic, actually growing its membership base during the worst of the lockdowns. She recognised members were hurting financially and set up the SEMMA Buying Group to use the power of negotiating group pricing to benefit members. The on-going skills shortages prompted SEMMA to develop its own 4-week basic welding skills
course which saw the pilot programme successfully place more than 90 per cent of its ‘graduates’ with SEMMA members. Fenwick’s advocacy and representations to both State and Federal Governments meant that SEMMA ensured that the importance of manufacturing in Australia, the need for strong local content policy and the critical nature of SMEs in our supply chains were being heard at the highest levels.
Big shoes to fill. Luckily SEMMA has appointed Honi Walker as Fenwick’s successor, who is so excited about her mission to represent the interests of manufacturers and advocate on all issues impacting manufacturing in the local region. Walker’s passion was evident during a recent interview with Manufacturers’ Monthly
“Vonda has a stellar reputation with all our members, and we are excited to continue the great advocacy work to government for members and keep building our SEMMA membership,” she said. “SEMMA is primed to begin a
new phase of growth as we support our members to identify their capabilities enabling them to embrace new opportunities for manufacturing through innovation, technology, and industry networks.”
Over the last twenty years, Walker has dedicated her career to business development, strategic relationship building and communications as well as co-owning a local manufacturing business. These skills will be invaluable in building SEMMA’s new phase of membership growth and public awareness.
Walker’s communication roles in the manufacturing sector include tenures at PPG Industries Australia Pty Ltd, Thiess Pty Ltd and Monsanto Australia Pty Ltd. Experienced in Association management and culture, Walker also served as the Industry Development Manager/Executive Officer for APSAA (Asia Pacific Student Accommodation Association) and as the Public Affairs Manager for PACIA (Plastics and Chemical Industries Association).
Masters in Professional Communication, Walker has an outstanding history in education, also earning her Graduate Diploma of Public Relations from Deakin University and an Associate Diploma of Business from Holmesglen TAFE.
Melbourne’s South East is one of Australia’s most dynamic manufacturing regions, contributing to almost half of Victoria’s manufactured products. Australian local manufacturers are exactly that – local. They use local suppliers and create local jobs. SEMMA’s partnership with Australian Made two years ago looked to grow on this, and the push for local production is off to a strong start in 2023.
“The feedback we’ve got from our members is an uptake in higher value products being made locally,” she explained. “In the past, manufacturing has been ignored, not regarded as a ‘sexy’ industry like retail or hospitality, but we employ thousands of people and contribute billions to the local economy. We’ve been making essential productsthink housing, clothing, food and other fundamental items for hundreds of years for the domestic market and we are going to keep manufacturing essential products that enhance and enable our modern lives. We have so many innovators – who
aren’t afraid to invest their time and money to grow.”
In the past, modern manufacturing strategies have been geared towards supporting large companies. This is at odds with the fact that 95 per cent of employment in manufacturing in Australia is within SMEs.
“We need to recognise that the landscape is made up of family businesses and SMEs so the strategy should reflect and support that,” she said. “Contracts with onerous risk clauses which cascade down the supply chain can make it impossible for local manufacturers to participate.”
SEMMA advocates for both policy settings and the percentages in place to guarantee local content, and it appears that the current government is putting this forward which aligns with advocacy over recent years. Another part of SEMMA’s advocacy is to dispel the misconceptions about the manufacturing industry.
“Manufacturing in the 21st century is clean, modern, and safe and offers a career pathway for those who want it with secure and flexible employment for those who have busy family lives,” Walker enthused.
“Manufacturing is secure. There are
factory floor and move into management, sales, operations,” Walker explained. “There are opportunities for different cohorts – kids who don’t want to go to university, migrants or women re-entering the workforce, for example – to find secure, safe and progressive work. We need to attract more people and we are part of a wider campaign doing just that.”
According to Walker – we need to find the skilled, semi-skilled and low-no skill workers to fill a wide variety of jobs. SEMMA hopes to close any disconnects between universities and TAFEs in the skills required for industry by collaborating with education providers like Chisholm TAFE, Federation University and Swinburne University of Technology.
“Some members are investing in automation, including robots to perform essential tasks, - but this method is costly and not available to everyone” she noted.
“I think we need to be a lot more creative about what we do to start building those skills. You would be aware of the welding programme that SEMMA developed which was a huge success. It gave us great industry insight and we will continue collaborative initiatives to help members with the skilled labour challenge.”
Manufacturers are amazing at what they do, but marketing and
ambiguous world. SEMMA wants to support members in the brand recognition journey to help expand their suppliers and customers.
Since taking the reigns, Walker has been inspired by the passion which SEMMA’s members have for their businesses.
“Our members are so great at sharing their needs and connecting to different networks,” she said. “It’s exciting because it makes growth easier when you’re working collaboratively and collectively. And for SEMMA – now in our 20th year of operation – as the voice for manufacturing in the South East of Melbourne, we’ll continue to provide a valuable service to our membership by giving members what they need – advocacy, promoting their regional capabilities locally and internationally, connecting them through strategic collaborations – like our buying group – and identifying business opportunities that stimulate manufacturing businesses.”
SEMMA is currently having a membership drive. Sign up and get 10% off the General Membership fee and if a current member refers a new member (and they sign up) both receive 10% off the General Membership fee. (Applies to General Membership applicants only).
DURING my 20 years of supporting a breadth of sectors on our “golden soil”, I’ve been fortunate to witness firsthand the truly impressive ingenuity, resilience and attitude our diverse workforce demonstrates in the face of enormous challenges that have come and gone.
This Aussie Spirit has weathered recessions, pandemics, supply chain challenges and periods of rapid growth – always somehow finding a way to navigate through rough seas to calmer shores, leaving us more aware of what makes Australia one of the most admired countries on our planet.
In my experience however, we often need a compelling reason to be convinced to fundamentally change the way we’ve always done things – especially when we have so much of our pride invested in the path we’ve travelled and what we have to show for it.
Like many other developed countries, Australia has been forced to make a necessary transformation in its traditional segments primarily due to increased global competition and outsourcing to lower-cost countries, which has forced a shift towards higher-value manufacturing activities that require more sophisticated skills and technology.
Despite employment in our industry hovering around the 1 million mark since 2002 – we’ve increased our total value of production to $357.6 billion up from $212.3 billion, doubled our manufacturing exports to over $103.7 billion with China, the United States and Japan acting as our largest markets (source: ABS, adjusted for inflation) – yet only yielded modest uptakes in productivity (which I’ll return to later).
These times have been putting extreme demand on the likes of our primary industries and food manufacturing sector, for example, as we strive to provide the world a taste of Australian quality and our unique offerings, as much as it has our mining and processing sectors.
As inflation, costs and workforce stability challenges continue to rise (as I write this), the considerations boards
and owners need to contemplate for their organisations to not just survive but thrive over our next 20+ years are nothing short of massive and will challenge that ability to retain a positive attitude while our resilience is being tested.
As we all work to serve our sovereign demand, leveraging our national brand to carve our path into foreign markets, our manufacturing leaders, teams and entire support ecosystem (educators, peak bodies, governments) are going to be put to the test to produce what’s necessary in terms of human capability, processes and technology for us to achieve truly sustainable growth.
This is where our ingenuity is needed to uncover not just incremental competitive advantages in our traditional areas of operation, but accurately predict entire new opportunities and the right business models to create and capture the value that can be backed by investment and government support, such as the key priority areas of the $15 billion-dollar National Reconstruction Fund:
1. renewables and low emissions technologies
2. medical science
3. transport
4. value-add in the agriculture, forestry and fisheries sectors
5. value-add in resources
6. defence capability
7. enabling capabilities. (i.e. supporting your pathway to Manufacturing Excellence)
Many AME Australia Members like Sutton Tools, Magic Mobility, Faber Group and Note Printing Australia have found their pathway to sustainable growth though this ingenuity and by building on excellence principles.
They identify value creating opportunities for the market, deliver on (and beyond) customer expectations with minimal waste in their processes to drive down cost while engaging their teams with a people-centric leadership approach.
These impressive companies are underpinned by an ongoing purpose for their leaders to align their teams and to invest in people, process and technology
to effectively evolve the organisation, what exactly it produces and how it serves its customers to stay ahead in a world that’s not flat.
Along these cycles, key investment and supply partnerships have been instrumental in raising their productivity in efforts to be a low-cost solution provider (not low-value/quality) who again and again have served their niches, leveraged innovative technologies and continually improved to be better implementors of product/service into their designed value streams.
This includes reaching new markets, establishing larger and smarter operations, verticalising ownership and extending services more and more into pre and post sales to expand their margin opportunities across the lifecycle of their products. Even to the point where secondary markets benefit from last-gen models that have reliably stood the test of time (and abuse) available at exceptional value through lifecycle extension and refurbishment programs.
Participation in a circular economy and reducing waste to landfill is another opportunity our members have seized to reduce input costs and curb various supply constraints that have resulted in additional working capital for strategic investment in R&D, commercialisation, technologies and human capital development.
So, what qualities and approaches do all of these – and Australia’s other best manufacturers – share that helps them through a successful evolution and what can they do to build long-term resilience over the next 20, 50, 100 years?
Firstly, they follow a process of exploration – they must identify an unmet need either in an underserved market or further afield beyond the borders of their traditional areas of operation to arrive at an insight which they can validate and quantify.
This may come from observing the use of their current products, customer
behaviour and the environments they’re operating in. It may come from a previously unknown challenge or lack of solution in a region, social or sector context – this may particularly come from commercial pathways enabled by strategic free trade agreements.
But regardless of source, the insight will define where there’s an opportunity to remove a common problem faced across a repeatable situation where a new solution could eliminate the pain and creates a gain that a customer needs.
These solutions usually aren’t iterations like a rounder wheel, a better mousetrap or faster horses, they’re typically inventive evolutions that take a new form and meet the function that addresses the unmet need.
The solution may not be a single product SKU or service, it may be a replacement of an entire way of doing business or type of value a consumer receives – which is what innovation is at its core.
Ideation of these solutions will require collaboration with not only the users and your people, but also the likes of the CSIRO, specialist higher education institutions & their researchers, IP Australia, strategic supply partners or, most likely – all of the above.
The minimal viable product (MVP) you create, whether simulated digitally, prototyped from an additive manufacturing process or coded into a test environment, needs to be iteratively but rapidly tested against its required properties and manufacturability –presenting a lower risk proposition that will have a better chance of being backed by any number of potential investment mechanisms and stakeholders who expect that the solution delivers against target value providing solid return on investment.
The investment pathways and partners come in many shapes and sizes – funding may be a standalone internal proposition from the balance sheet, from shareholder capital or it may leverage debt. It might instead involve new avenues like project funding, crowdfunding or venture capital, and, if available, government awarded
grants or investment funds may beneficially support this new direction. If external, best of there is domain expertise that accompanies investment so that deeper engagement can be created that minimises a disconnection and misunderstanding of actual work being invested in.
How to bring it all together?
Treating your innovation implementation as a new venture that invites cross-functional subject matter experts and leadership from your existing operations to be the ‘start-up’ team can be a very effective method – the benefits being that you leverage trusted resources while retaining aspects of existing culture & values, while building new ways of working without the mistakes of the past. This is a strategy that allows the new product, service or model to be born without risking focus and ability within the current, provided that you’re prepared
to support emerging talent into the vacant roles you are creating.
If a joint venture, one effective approach is to have the team co-create their own commercialisation program ahead of implementing it in an agile and flow-based process to uphold timeline, quality and budget. This again requires the right crossfunctional mix of skills and experience, as well as facilitation to steer the team through Tuckman’s curve (Forming, Storming, Norming and Performing) through at least their first year.
Manufacturing Leaders who recognise the need to seek new ways to ensure their longer-term prosperity are strongly recommended to invest time in learning more about the typical startup-to-scale-up journey dos and don’ts
– regardless of past success in the sector you’re in now.
Plato said “our need will be the real creator” so if you’re seeking that compelling reason to change, perhaps consider what the Australian manufacturing landscape looked like 20, 50, 100 years ago and compare it to 20, 50, 100 years from now.
Standing still is not an option, standing out is.
With that in mind, ask yourself
what efforts you’re making today to gain the insights needed to correctly inform your innovation efforts to attract investment which enables you to address unmet market needs through your new solutions?
The Aussie Spirit of ingenuity and attitude just might be our key to building the future as Leaders of the 21st century. “Australians all let us rejoice For we are young and free We’ve golden soil and wealth for toil”
The 58-metre ADV Capricorn is the fourth of eight Evolved Cape-class Patrol Boats to be delivered by Austal Australia to the Royal Australian Navy.
The first three Evolved Cape-class Patrol Boats (ECCPBs), ADV Cape Otway, ADV Cape Peron and ADV Cape Naturaliste were delivered in March, August and November 2022, respectively.
The Evolved Capes feature new, larger amenities to accommodate up to 32 people, improved quality of life systems and advanced sustainment intelligence systems that further enhance the Royal Australian Navy’s ability to fight and win at sea.
The patrol boats will be utilised for a wide variety of constabulary and naval missions and play a critical role in Australia’s national security, as a highperforming, reliable and effective maritime asset.
Austal Limited’s chief executive officer, Paddy Gregg said the delivery of the fourth ECCPB highlighted Austal’s consistency in production and efficiencies at the Henderson shipyard.
“Austal has now delivered four Evolved Capes to the Royal Australian Navy since the contract was signed in May 2020 and we are launching a new vessel every three months, after around 12 months of construction.
“The fifth vessel, the future ADV Cape Woolamai, is alongside now and we have three more Evolved Capes at various stages of production, here in Henderson,” he said.
“With the continued support of our trusted supply chain partners from across Australia and around the world, the Austal shipbuilding team is well on track to deliver all eight Evolved Cape-class Patrol Boats to the Navy by mid-2024, on schedule.”
and we are proud to play an integral role in delivering naval assets for Australia,” Gregg added.
Austal Australia continues to employ approximately 400 people (directly) in Western Australia and is engaging more than 300 supply chain partners across Australia, to deliver the Evolved Cape-class Patrol Boat Project (SEA1445-1) for the Royal Australian Navy.
Boat fleets operated by the Australian Border Force, Royal Australian Navy and Pacific Island nations is provided by Austal Australia through dedicated service centres located in Henderson, Western Australia; Cairns, Queensland; and Darwin, Northern Territory.
Austal Australia is also contracted to deliver 22 Guardian-class Patrol Boats to Australia under the Pacific Patrol Boat
The Australian Industry Group (Ai Group) has been selected as the ongoing custodian of futuremap – a diagnostic platform developed by the IMCRC to help SMEs embrace digital transformation.
The Innovative Manufacturing Cooperative Research Centre (IMCRC), an independent, government-funded organisation with a fixed lifespan, closed its doors at the end of January.
However, the value of futuremap for Australian manufacturing saw IMCRC launch a search for a new long-term custodian late last year.
After a competitive process, IMCRC selected Ai Group – a leading peak national employer association with extensive reach into businesses across the economy – as the custodian of futuremap to guarantee the long-term success of the platform.
Ai Group’s chief executive Innes Willox says, “We are focussed on empowering industry success and supporting our members in lifting their international competitiveness. Custodianship of futuremap will expand Ai Group’s capability to help Australian industry to become more innovative, networked and adaptable.
IMCRC’s outgoing CEO and managing director David Chuter said, “Over the past four years, futuremap has helped over 1000 manufacturers transform their digital operations. Recent findings of an independent study conducted by Swinburne University of Technology has confirmed the effectiveness of the tool.
“Businesses participating in futuremap were found to be growing faster and innovating more than their closest peers, reporting an average increase of 15.5 per
cent in sales, 21.5 per cent in wages and 6.6 per cent in staff.
“The results demonstrate futuremap could and should continue to add value to Australia’s manufacturing ecosystem by helping SMEs innovate. We are incredibly pleased that, under Ai Group’s custodianship, this important tool can live on and continue to grow postIMCRC.”
The arrangement ensures that existing deployment partners – Swinburne University of Technology, University of Technology of Sydney and the Advanced Robotics Manufacturing (ARM) Hub –maintain non-exclusive licenses to deploy futuremap.
This also ensures the program will have a national delivery footprint and will continue to benefit a wide range of businesses across Australia.
The futuremap® offering has already begun to evolve, with the launch of a new net zero module designed to help businesses prepare for and embrace the transition to a low-carbon economy.
“After working with IMCRC since its inception, we recognised the benefits and ongoing potential of futuremap, especially for Australian SMEs,” Willox said.
“We are looking forward to integrating this invaluable program into our service offering, so we can expose businesses to transformative new processes, technologies and ways of working.
“By facilitating self-assessments and stimulating conversations, futuremap acts as a necessary catalyst to streamline current practices and encourage innovation, both of which are critical to business growth,” he concluded.
Industry and research will lead the most advanced future Energy Transition Hub of its kind in Australia at the Swinburne University’s Hawthorn campus in Melbourne.
Featuring some of the most advanced digital energy technology from Siemens and the technical, R&D and teaching expertise of Swinburne, the $5.2 million Hub aims to build a future energy grid laboratory accessible to students and industry.
When fully operational, the Hub will also offer researchers and industry the opportunity to work on solutions for greener, more efficient future energy systems using Siemens Xcelerator, a new open digital business platform and marketplace.
Deputy vice-chancellor, research, Professor Karen Hapgood, stated, “Australia’s ambitious carbon reduction targets need a multi-pronged approach by industry, research and government.
“The new Siemens Swinburne Energy
Transition Hub will be working on new technologies to improve energy efficiency, supply, integration, storage, transport and use, as well as how we can improve existing technologies and frameworks. We need change fast, and the SiemensSwinburne team will focus on taking ideas to market – where they can make the most impact as quickly as possible.”
The Hub will enable users to leverage digital twins of energy grids, map scenarios, research new findings, develop original and creative hypotheses, and test results. It will be home to a digital twin of Australia’s energy grid that commercial research teams can use to run simulations of new, innovative solutions and software.
In addition to R&D and commercialisation projects, the hub will deliver short courses for industry professionals. It will also give back to Swinburne students, with Siemens software and the company’s real-world industry experience integrated into
engineering technology courses.
Peter Halliday, CEO and Chairman, Siemens Australia and New Zealand, said, “Our relationship with Swinburne University of Technology is long-standing and we’re proud to extend it through the new Siemens Swinburne Energy Transition Hub.
“Collaboration between industry and academia is critical to driving better outcomes on key topics of national importance such as the energy transition. Digitalisation allows you to do more with less as technology assists you in identifying the opportunities for reducing energy consumption and emissions whilst acceleration the journey to net zero.”
In addition to microgrid and planning stations, the Hub will also feature Siemens’ microgrid management system (MGMS) and decentralised energy optimisation platform (DEOP) software.
The microgrid technologies include SICAM A8000 and SIPROTEC5 devices
for control and protection. The planning stations feature Siemens PSS® software which is used by over 70 per cent of utilities and independent system operators including AEMO and grid operators.
Jose Moreira, Country Business Unit head – Grid Software, Siemens Australia and New Zealand, added: “Tackling the speed and change in the energy landscape to create solutions that help achieve net zero requires a collaborative and cocreative approach. Siemens has a strong history of working with universities to empower the next generation of workforce on energy systems of the future.
“We’re proud to present the Siemens Swinburne Energy Transition Hub not just to students but to industry as well. The Hub features some of the latest and best technology used by organisations across the world and will hopefully spark new Australian innovations for future energy challenges.”
Deakin University’s expanded $20 million ManuFutures hub is now complete and working in partnership with 14 successful and emerging businesses to grow advanced manufacturing capability in regional Victoria and Australia.
The new-look ManuFutures building at Deakin’s Waurn Ponds campus has doubled in size to deliver an increased number of tenancy opportunities, new manufacturing incubator programs, training, and product engineering services.
The expansion was funded by the Victorian Government ($10 million) and Deakin University ($10 million) as part of the government’s $350 million Victorian Higher Education State Investment Fund (VHESIF) launched post-COVID.
Deakin Research Innovations regional manufacturing director Mark Curnow said the completion of ManuFutures2 puts Deakin University at the forefront of manufacturing innovation for entrepreneurs, start-ups and existing businesses.
“Our new ManuFutures2 building includes collaborative working spaces, further rental tenancy bays for manufacturing businesses, and an Innoveering Centre that includes product engineering and development capability, and opportunities for research collaboration and integration,” Curnow said.
“Four new manufacturing businesses have already moved into the new spaces as tenants, with room for two more. A total of 14 successful and emerging global manufacturing businesses now call Deakin’s ManuFutures home.”
Deakin University deputy vicechancellor research Professor Julie Owens said ManuFutures demonstrated Deakin’s leadership and success in real world research and commercialisation, in partnership with industry.
“Since opening in 2018, ManuFutures has a successful track record of helping entrepreneurs and start-ups take ideas from paper, to prototype, to emerging global businesses,” she said.
“ManuFutures has helped create more than $1 billion in company value, incubated more than 17 advanced manufacturing start-ups, helped companies establish export markets in more than 35 countries, hosted 500 student placements, and created more than 120 advanced manufacturing jobs.”
Victoria’s minister for training and skills, higher education, and agriculture, Gayle Tierney, said that the Victorian Government’s investment in ManuFutures as part of the Victorian Higher Education State Investment Fund is helping to strengthen innovation, training, and industry collaboration in regional Victoria.
Minister for Industry and Science Ed Husic formally launched consultations for Australia’s first National Battery Strategy to support the transition to clean energy.
Minister Husic said domestic battery industries will be buoyed by Australian know-how and domestic access to minerals to help power the move to clean energy here and around the world.
“Our general approach should be one where if we mine it here, we should make it here. Large-scale uptake and manufacture of batteries will be vital
transitioning to net zero. New battery capacity will help support grid-scale capacity, power our homes, and electrify our transport sector.”
“Australia has globally significant deposits of essential battery materials and strong local innovation and research capabilities. By drawing on these strengths, Australia can take its place in the profitable global battery supply chain,” Husic added.
Developing the Strategy will help Australia transition to a decarbonised economy, hit our ambitious emissions
targets, foster Australian innovation and support Australian industry, according to Husic.
The announcement was made during Husic’s visit to Energy Renaissance, an Australian lithium-ion battery technology and manufacturing company at Tomago in the New South Wales Hunter Valley.
Globally, Bloomberg New Energy Finance estimates that 387 gigawatts of new energy storage will be added by 2030, providing an excellent opportunity for Australian battery industries.
Bolstering Australia’s battery
manufacturing capability presents an opportunity to integrate and diversify global battery supply chains. A joined-up national approach to battery technology will also work to support Australia’s National Electric Vehicle Strategy.
“The National Battery Strategy will complement the development of Australia’s new Critical Minerals Strategy to articulate a clear pathway for integrated, end-to-end onshore battery minerals supply chains,” Husic said.
“Together, these will provide a clear plan to ensure Australia maximises its
economic potential in these fast growing and lucrative markets. The consultations around the Strategy are designed to find ways to get our country manufacturing Aussie batteries.”
“A coherent, national approach to the development and uptake of
emerging technologies won’t just deliver economic growth and jobs, but also help safeguard our national wellbeing,” Husic concluded.
The Federal Government will work closely with states and territories, and consult widely with industry,
community and experts to shape the strategy and help grow globally competitive domestic battery industries.
Engagement on the Strategy will help inform other elements under the Australian Made Battery Plan including creating a Battery Manufacturing
Rachel Barritt from Dovetail Electric Aviation, Swinburne University’s first Founder in Residence, will work with researchers to develop new aviation and aerospace ventures.
Barritt will work closely with the team from Swinburne’s Aerostructures Innovation Research Hub (AIR Hub), utilising the hub’s cutting-edge capabilities in intelligent manufacturing processes, advanced composite materials, advanced air operations, and sustainable fuels.
Alongside Dovetail Electric Aviation, they will bring to life the most innovative
and cutting-edge technologies to help shape the future of sustainable aviation.
The Founder In Residence initiative is designed to bring experienced entrepreneurs to Swinburne to supercharge commercialisation pathways, supported by Swinburne’s world-leading facilities, capabilities and research.
“As a Founder In Residence at Swinburne, I am excited to be working at the forefront of aerospace technology. This program represents the future of innovation,” Barritt said.
“Working with leading experts from
industry and academia, we will help translate cutting-edge research into sustainable, real-world solutions for the aviation industry.”
“We are thrilled to welcome Dovetail Electric Aviation and Rachael Barritt to Swinburne,” said Dr Werner van der Merwe, Swinburne’s vice president for innovation and enterprise.
“By connecting experienced entrepreneurs and leading researchers, we are accelerating the commercialisation of new technology to put Australia at the forefront of global innovation. Together,
Precinct, in partnership with the Queensland Government; establishing a Powering Australia Industry Growth Centre to support industry translation of research into local jobs and investment; and supporting 10,000 New Energy Apprenticeships.
we are paving the way for a sustainable future for air travel.”
Barritt is the first Swinburne Founder In Residence to be announced for 2023. The program will drive marketled venture creation across three of Swinburne’s flagship research areas – space and aerospace technology, innovative planet, and medical technology.
The program will create new ventures of mutual benefit to entrepreneurs and researchers, fast-tracking technological advancements and developing robust market-ready solutions.
In a first for the Avalon Innovation Awards, both the National and the SME Innovation Awards have been won by the same company – Melbourne-based 1MILLIKELVIN Pty Ltd.
1MILLIKELVIN was named winner of both the National Innovation Award and SME Innovation Award at the presentation ceremony, held as part of day one of the AVALON 2023 Australian International Airshow & Aerospace and Defence Exposition at Avalon Airport at Geelong, Victoria.
1MILLIKELVIN won both awards for its work developing a stress imaging camera system that provides a fullcolour representation of the stress on a mechanical structure under loads, such as the airframes of crewed and uncrewed aircraft and helicopters.
The panel of eight judges, led by former deputy chief defence scientist Dr Bill Schofield AM, agreed that 1MILLIKELVIN’s entry was a deserving winner for both awards.
The Young Innovator Award was presented to BAE Systems Australia Melbourne engineer, Callum Rohweder,
for his work on developing the core guidance, navigation and control algorithms at the heart of the Australiandeveloped Vehicle Management System (VMS) for the Boeing MQ-28A Ghost Bat uncrewed aerial vehicle.
This year, for the first time, the winners of the SME Innovation Award and Young Innovator Award were presented with a cheque for $50,000 each.
These monetary Awards, funded entirely by AMDA Foundation Limited, are meant to be life-changing, especially for the winner of the Young Innovator Award.
“A sum like $50,000 can lever as much again in grants and project funding to help a project across the so- called ‘valley of death’ and turn a smart idea into a proven reality,” said AMDA Foundation CEO Justin Giddings.
“It can help a young innovator undertake a Masters or a Ph.D, to study overseas or undertake an internship focussed on mastering a new technology.”
The awards are sponsored this year by Synergy Group, a team of thinkers, solvers and doers focussed on innovation and professional services.
The winners are:
AVALON 2023 National Innovation
Award: 1MILLIKELVIN Pty Limited (VIC)
AVALON 2023 Defence SME Innovation
Award ($15,000): 1MILLIKELVIN Pty Limited (VIC)
AVALON 2023 Young Innovator Award
($15,000): Mr Callum Rohweder, BAE Systems Australia Limited (VIC)
In addition, three award contenders won a High Commendation:
• AVALON 2023 National Innovation Award HIGH COMMENDATION: DMTC Limited (VIC)
AVALON 2023 SME Innovation Award
HIGH COMMENDATION: MicroTau Limited (NSW)
• AVALON 2023 Young Innovator Award
HIGH COMMENDATION: Mr Michael J Scott, RMIT University (VIC)
The Innovation Awards were created by AMDA Foundation Limited and presented for the first time ten years ago at the 2013 AVALON Australian International Airshow & Aerospace and Defence Exposition.
Since then, some $485,000-worth of SME and Young Innovator Awards have
been presented. This year, that total climbed to $585,000.
“Our Innovation Awards are designed to recognise and reward the innovativeness and achievements of innovative Australian companies and individuals. They’re still the only Awards of their kind and have become increasingly prestigious,” said Giddings.
“The quality of the entries received this year is a reflection of both the excellence and ambition of Australian companies serving the country’s defence market. “They also reflect the increasing attention paid by the industry to export opportunities: a number of the entries are already very active in overseas markets.”
All of the Avalon 2023 Innovation Award winners were presented with engraved glass trophies, designed and made by Wathaurong Glass & Arts, an indigenously owned and managed cooperative in Geelong.
“That the awards have been won by such high-quality candidates speaks for the growing depth and capability of Australia’s growing industry and defence innovation ecosystem,” Giddings added.
BAE Systems Australia has teamed with local industry to launch Australia’s first domestically designed, manufactured and armed VTOL (Vertical Take-Off and Landing) Uncrewed Air System (UAS).
The STRIX hybrid VTOL UAS is being developed by BAE Systems Australia and Perth-based Innovaero at the 2023 Avalon Airshow in Geelong, Victoria.
The collaboration brings together BAE Systems’ global expertise in autonomous platforms and its vehicle management system (VMS) technology with Innovaero’s knowledge of aeronautical product design and manufacture in the Australian market.
A hybrid, tandem wing, multi-domain and multi-role UAS capability, STRIX could be used for a variety of missions including air-to-ground strikes against
hostile targets and persistent intelligence, surveillance and reconnaissance (ISR). It could also act as a ‘loyal wingman’ for military helicopters.
Designed to carry up to a 160kg payload over 800km, STRIX will be capable of operating in high-risk environments. With a collapsed footprint of 2.6m x 4.5m, it could be easily transported in standard shipping.
Its VTOL capability means STRIX could be used without relying on an airfield. It could also be operated from a helicopter to expand the mission set and protect aircrew in high-threat environments.
BAE Systems has an extensive history of developing autonomous systems globally, including the Taranis and Mantis uncrewed autonomous demonstrator aircraft.
The STRIX VMS already guides platforms, including the M113 for the Australian Army’s autonomous systems program and MQ-28 Ghost Bat drone for the Royal Australian Air Force’s autonomy program.
STRIX will look to increase Australian sovereign capability by leveraging domestic expertise, such as Innovaero’s aircraft concept design and rapid prototyping. There will also be opportunities for wider Australian SMEs and academia to get involved in the development, delivery and flight test of the prototype.
STRIX will have the capacity to accommodate a range of munition types, including those currently in service with the Australian Defence Force. BAE Systems Australia will also
deliver a new low-cost precision guided munition, known as RAZER, which could be integrated onto the platform to complement STRIX‘s strike capability.
BAE Systems Australia chief executive officer, Ben Hudson, said, “STRIX leverages existing, proven technologies to provide an affordable and cost effective capability that is mission configurable and upgradable in response to emerging technologies or threats.
“STRIX could be ready for operational service as soon as 2026 and work is already underway on a STRIX prototype. We’re excited that this is the first UAS of its kind to be developed in Australia and look forward to working with partners across the country to deliver this capability to customers.”
The pharmaceutical company is expanding production capacity by 50 per cent at its Braeside facility in Melbourne as part of a $35 million project.
The company produces more than 150 dermatological skincare products for local and international markets, with its brands including QV, SunSense, Elucent and Aquim.
The project will add new cream and filling lines to Ego’s Braeside manufacturing facility and extend its distribution centre in Dandenong South, increasing capability and capacity to support local and fast-growing export markets.
Minister for industry and innovation and manufacturing sovereignty Ben Carroll announced the Victorian state government’s support of the expansion, which will create 90 new jobs.
“Ego Pharmaceuticals’ decision to expand its operations in Victoria demonstrates the strength of our nation-leading advanced manufacturing industry and highly skilled workers,” Caroll said.
“We’ll continue to back local manufacturers because it builds our capacity to make more things in Victoria and creates secure jobs.”
Ego Pharmaceuticals managing director Alan Oppenheim said, “Keeping our high-technology manufacturing in Australia has and always will be important to us. This grant will help us further in creating good jobs to support our local economy as we continue to grow and will enable Ego to transform more lives through the science of healthy skin across many nations.”
The company was founded 70 years ago by Gerald and Rae Oppenheim, who began creating skincare products out of their Elsternwick home. Ego Pharmaceuticals has since grown into a global brand with more than 730
Shipbuilding unions have called for the Federal Government to build conventional submarines in Australia to protect local manufacturing and defence capability.
A recent report released by the Australian Shipbuilding Federation of Unions (ASFU) calls for urgent political action to build at least four, and up to six conventional submarines commencing by 2026. This would create up to 2,500 secure jobs in Australia.
The report states this will fill a capability gap between when the Collins-
class submarines reach their end-of-life and the nuclear-powered vessels arrive in up to three decades, as part of the AUKUS arrangement.
The dumping of the French Naval Group deal has left the local shipbuilding industry in jeopardy and thousands of jobs at risk while we wait for the nuclearpowered vessels, according to the ASFU.
The report adds that seven in ten Australians say submarines should be built in Australia, even if they will cost more.
ASFU national convener Glenn Thompson said, “Building and maintaining
our submarine fleet has always mattered to Australians; our industry employs nearly 30,000 workers across the country. We can no longer afford a government that neglects local manufacturing.
“We’re calling for political action now to save critical manufacturing shipbuilding jobs. We need a government committed to supporting Aussie made.”
“Building up to six conventional submarines keeps our skilled shipbuilding workers on the job in communities like Osborne and Henderson, while growing our industry,” Thompson added.
employees in 15 countries, including around 400 employees in Victoria.
Ego Pharmaceuticals’ products are stocked in more than 20 countries and exports across Asia, the Middle East and the United Kingdom now make up half its business.
From sunscreen products to hand sanitiser and gentle skin lotions, Ego Pharmaceuticals has manufactured all its products in Victoria for 70 years.
Member for Mordialloc Tim Richardson said, “This support for Ego Pharmaceuticals will boost the local economy and create new job opportunities in the area.”
“A failure to do so would hand the economic benefits of building these submarines to another country and betray the shipbuilders in Australia who have fought to get the industry out the valley of death over recent years.
“Building them now will not only create secure jobs for up to 2,500 workers across Australia, ensuring we are positioned to build our future submarine fleet, but the spin off effect will also support jobs throughout the value chain, helping small and medium businesses to scale up production.”
Australian battery manufacturing company Li-S Energy will partner with ARC Research Hub on the $1.23 million project to develop solid-state lithium sulfur battery cells.
Li-S Energy will invest $450,000, with SafeREnergy and Deakin University contributing $360,000 and $417,617, respectively. T
he project will be led by Li-S Energy, and the resulting intellectual property will be solely owned by the company as a part of its battery technology IP Portfolio. This joint project aims to tackle these obstacles and bring solid-state technology closer to reality.
The rapidly evolving technology and growing demand for batteries make it crucial to explore complementary solutions that could advance Li-S batteries still further.
Solid-state batteries — which offer improved safety and performance — are seen as a promising solution for the electric vehicle industry, which requires
longer-range, faster charging, longerlasting, and safer batteries.
Despite the potential benefits, solidstate batteries have yet to enter mass manufacturing to enable broad market adoption due to challenges with capacity, heat, and stability.
This three-year research and development project highlights the importance of continued exploration and innovation in the battery industry.
By combining Li-S Energy’s lithium sulfur and lithium metal technologies with solid-state solutions, there is potential to deliver even higher performance and increased safety.
The partnership with SafeREnergy and Deakin University marks a significant step towards realising the potential of solid-state batteries and revolutionising the energy industry.
Li-S Energy CEO, Dr Lee Finniear said, “This exciting step into solidstate lithium sulfur batteries is a key progression of the work being
undertaken by our research and development team.
“Our lithium sulfur and lithium metal cells have been scaled up progressively over the last 12 months. Now the opportunity to integrate solid state technologies has the potential to add significant additional performance and safety advantages to our future
commercial cells.”
I would like to commend both the ARC Research Hub and Deakin University for their collaboration and significant contribution to this important project. I expect this to enable our battery technology to be even more attractive in its future commercial deployment,” Dr Finniear added.
Since 1962, All Metal Products has committed to quality in its light metal works. Billy Friend sits down with the company’s CEO to learn about the recent shift to higher value orders on the back of more interest in local manufacturing.
FOUNDED by two Dutch immigrants in 1962, All Metal Products (AMP) is an Australian manufacturer which has grown steadily from humble beginnings. Despite the challenges of economic downturns and global crises, the company’s founders remained committed to Australian manufacturing and continued to invest in their business and their people.
Today, AMP is a thriving enterprise with a 9000 square metre facility in Western Sydney. The company’s team operate a state-of-the-art engineering facility that delivers reliable, high-quality products for a range of industries. The business has built its reputation through an ability to effectively fabricate a range of tube, sheet and wire products from a variety of materials and complement this with its own in-house powder coating line.
From medical equipment to hospitality furnishings, retail displays,
and construction materials, AMP has the capability to manufacture just about anything made from metal.
CEO Grant Forsdick is a degreequalified mechanical engineer who holds an MBA, with over 20 years’ experience in manufacturing. He has brought his expertise to AMP in managing large scale organisational change through the implementation of lean thinking and world class manufacturing and services best practice concepts.
Forsdick explained how the company uses different skillsets during the early stages of projects.
“Depending on the customer’s level of expertise, we can work with them to bring their inquiry to life,” he said. “For example, when we were developing an ICU trolley for a hospital, we had ongoing engagement with the customer to understand their requirements, including the dimensions and functionality. From there, we quickly produced a CAD
design and a prototype in our in-house factory. Our team prides itself on their skills and experience, from estimating to production capabilities. We work with our customers to determine the most practical way to manufacture the product before we begin production. For products that require safety testing, such as those for the medical industry, we make prototypes that are tested in the field by clinicians and nurses to ensure they meet the functional requirements. For our standard products, we look for ways to make them more efficiently. Overall, our in-house design and prototyping phase allows us to create custom solutions that meet our customers’ unique requirements.”
AMP has accelerated its work with Australia’s medical industry, stemming from a surge in demand in the COVID-19 pandemic.
“There’s obviously been a resurgence in interest in Australian manufacturing,”
he said. “As a result, we are seeing a different profile of customer coming through which is very encouraging. We’re seeing an increase in the value of orders coming through.”
With overseas suppliers unable to meet the needs of Australian customers, AMP stepped up to fill the gap, producing essential medical products like sneeze screens, , medication trolleys, hand sanitiser stands, and even ICU transport trolleys. Despite the challenges of the pandemic, the company managed to keep all its staff employed and it continues to build on its team in Western Sydney.
All Metal Products has expertise in the medical space due to its experience dealing with very fine stainless steel welding and processes – recognising the high value and importance of quality in
this field – and take great care to ensure products are reliable and consistent. The company also specialise in specific designs and requirements, such as material handling equipment, that cater to customers who want more than just a flatpack container from China, for instance.
A current significant problem in intensive care units is that critical care patients are disconnected and reconnected to life support equipment for transport, while a fleet of mostly redundant and idle patient transport ventilators are maintained in the intensive care units. To solve this common challenge, AMP has designed and manufactured a specialist ICU tower to take risk out of the equation for ICU
patients requiring critical ventilation.
The ICU tower project came about as a collaboration between Prince of Wales Hospital and UNSW, as they were looking for a new workflow for ICU clinicians to enable life support and patient monitoring equipment to remain connected during transport.
The project was initiated by the industrial design team at the hospital, who engaged AMP for input.
“The focus was on reducing the risk of infection control and ensuring interoperability between the trolley and all the different bed designs,” Forsdick said. “Four product types have been manufactured and are currently being reviewed and tested. The company has had a great relationship with universities and hospitals, particularly in the medical space, where homegrown solutions tend to be the norm. It’s important to have qualified people on both sides to codesign high-level concepts and designs.”
The ICU Tower offers a new workflow for ICU clinicians and enables life support and patient monitoring equipment to remain connected to the patient during transport, removing the risk of errors that come with connecting vital patient lines and resulting in a much more efficient workflow. There are approximately 2200 ICU beds in Australian hospitals, and AMP sees opportunities to sell the ICU
tower into all these sites as well as the demonstrated international market.
“When we saw the need for a better ICU transport trolley at hospitals, we stepped in and offered a more effective and durable stainless-steel option. Galvanised steel is cheaper, but it’s important for us to understand our customer’s process to deliver the best product possible.”
In 2021, 25 ICU towers were introduced at the Prince of Wales Hospital and Prince of Wales Children’s Hospital, with 25 additional mechanical connections for alternative bed types rolled out to the hospitals in 2022. After an initial entry into the market, AMP wants to expand and strengthen its hospital relations within NSW Health and broader Australia so that the trolleys are available for every hospital with an ICU ward.
AMP continues to collaborate with UNSW and is currently co-designing a new linen trolley with NSW Health that requires stability and weight distribution to avoid toppling.
“Multiple mechanical connections have been designed and manufactured to suit different types of beds and different changes made to suit the trolley being transported across different types of flooring and flooring heights,” Forsdick added.
Sustainability has become an important issue in the business world in recent years, as consumers, investors, and regulators are increasingly demanding that companies take responsibility for their impact on the environment and society.
There are several ways in which manufacturers are taking sustainability measures. Some are investing in renewable energy sources, such as solar or wind power, to reduce their carbon footprint. Others are implementing programs to reduce waste and improve recycling, or using sustainable materials and practices in their manufacturing processes. Many companies are also implementing social responsibility initiatives, such as fair labour practices and community outreach programs.
There is a growing recognition among manufacturers that sustainability is not only good for the environment and society, but also good for business. Changing manufacturing processes with this in mind is easier said than done.
Under the expertise of Forsdick, AMP uses a six-step environmental impact plan to guide its decision making and behaviour:
1. Develop the sustainability Baseline and what we have ‘NOW’
2. Develop Environmental and Sustainability policies
3. Implement policies and reporting framework
4. Gain Internal Engagement
5. Supply Chain / Stake holder engagement and Communication
6. Monitor and Continual Improvement
Since reflecting on how AMP could develop more sustainable processes, the company separates recycling bins from scrap metal, uses recycled transport pallets, energy-efficient lighting and a 100 kilowatt solar panel system attached to the factory.
“We engage in time-saving and energy saving practices,” Forsdick said. “If we run a production cycle faster, we can have more time to shut down and save power. For example, the powder coating line isn’t run every day as we group orders together. We also decrease the number of machines that are needed to manufacture certain products if needed.”
AMP’s powder coating facility uses state of the art powder collection, automation and recycling technology,
minimising any pollution. This ensures all acids and solvents used are minimised in production. Furthermore, cooling water for its welding transformers is managed with an internal recycled water system to minimise water use.
“We work with start-ups, established small business, government departments and multinationals to deliver excellent products in a sustainable and timely manner - with a focus on sharing our experience, acting ethically and value adding in production.”
In his long career in manufacturing, Forsdick has focused on the education of management teams and the senior change management structure, in the principles of lean thinking as applicable to the particular industry. This process includes the introduction of the best practice of leading and managing the change process, the setting up of problem-solving structures and coaching senior management in the required changes in behaviour that are necessary to support a new lean organisation.
“We’ve embedded all of that thinking into our business in a staged manner,” he said. “The real focus has been teaching our staff what the eight categories of waste are. Waste isn’t just what you throw in the bin, it’s too much walking in the factory between processes or using equipment which takes longer than necessary.”
AMP has recently installed a new laser cutter and two new press brakes in its St Marys factory to bolster operations. Forsdick explained how AMP is transitioning the layout of its factory to be more efficient and keep up with demand.
“Bringing in the new equipment is part of our plan to improve the workflow through the factory,” he said. “We are moving from an old-style factory –where everybody’s got their little nooks and crannies – to a more open factory where you can monitor and see what’s happening. We’re at the early stages of introducing teamwork, where each production team gets together every day for a few minutes to chat about the day.
That’s all about transferring responsibility and accountability – I’m a great believer that problems in the brake press need to be solved by people in the brake press, not somebody in the office.”
Forsdick referred to the office as ‘the factory upstairs,’ where the business applies lean thinking principles to information flow to insure that ‘administrative processes’ facilitate the ‘flow of value’ through operations.
“Irrespective of which machines are running, the most important thing is that your bottleneck doesn’t stop,” he noted. “I like referring to lean thinking rather than Lean manufacturing because Lean Thinking is a broader concept. Lean is about waste elimination, or reduction across your business, not only in the factory. We work really hard on maximising throughput without overinvesting in capital equipment.
“The success in our improvements to date has been more about ‘thinking and doing’ differently, than a massive investment in capital equipment.”
Brisbane-based start-up Valiant Space has made history as the first Australian company to send locally made components into space. Manufacturers’ Monthly sits down with co-founder and CEO Andrew Uscinski to discuss the company’s growth and aspirations in the burgeoning Australian space industry.
VALIANT Space was founded by three university students –Andrew Uscinski, Michael Douw and Benjamin Dodd – after they identified a gap in the market for space propulsion options that used non-toxic propellants. The team of three are mechanical and aerospace engineers who met at the University of Queensland and started the company in 2020 while they were still students.
“We were grouped together as a team in university around 2017, and we all wanted to influence the growing space industry in Australia,” Uscinski said.
That same year, at the International Astronautical Congress in Adelaide, the Australian government announced the launch of the country’s first national space agency – the Australian Space Agency (ASA).
“At the time of founding, there were no in-space chemical propulsion providers in Australia,” Uscinski said. “There are companies like Gilmore Space Technologies who are focusing on the launch segment, but what we are really focusing on is the inspace segment where collision avoidance, orbit maintenance, and deorbiting are really big factors. That capability had not existed in Australia yet.”
In 2020, the young entrepreneurs participated in the University of Queensland’s ilab Accelerator program, during which they were awarded $20,000 and received mentorship to grow their start-up. At the time, the team was building a tech demonstrator – a 1.5 kilonewton, moderately sized, rocket engine.
“That’s when we came up with the idea for the thruster with non-toxic propellants, which is our flagship product. The idea was brought on by a combination of a detailed market assessment that we conducted during the program, and the technology we were building over that time as a team,” Uscinski explained.
“We identified that the small propulsion system market or the small satellite market would be booming over the next decade. And with our skill set in propulsion, we were well positioned to do something meaningful in that space.”
Valiant Space manufactures a chemical thruster that provides the main propulsion system for the satellite and allows fast-acting orbit raising and
collision avoidance manoeuvres.
Existing thrusters used carcinogenic and difficult-to-handle chemicals that were expensive due to development costs.
“Traditional thrusters of our size and capability in the space industry have used hydrazine and other nasty chemicals, like dinitrogen tetroxide. These are chosen because they’re hypergolic propellants, which means that upon touching each other, they will spontaneously ignite; therefore, you don’t need an ignition source,” Uscinski said.
“On a handling front and hazards front, it’s incredibly dangerous – you have to ensure absolute leak tightness on all your systems, and you can’t have any cross contamination of propellants.”
Additionally, the people on the ground needed to be fully suited up in expensive Self-Contained Atmospheric Protection Ensemble (SCAPE) suits.
In contrast, Valiant Space’s thruster uses non-toxic nitrous oxide and propane – similar to what would be used in a barbecue but slightly more pure – which gives a comparable performance to the toxic options but without the need for high-cost handling infrastructure.
“In terms of the relative risk level, the amount of PPE required to handle these propellants is drastically reduced. And the overall process is simplified without the need for complex respirators or anything at all to be able to handle them,” Uscinski added.
The next challenge for Valiant was successfully launching the innovative product into space. This was realised when an integral part of Valiant Space’s thruster was sent into orbit with Elon Musk’s spacecraft company SpaceX, onboard Skykraft’s rideshare service from the Kennedy Space Center in the United States.
The journey to launching into space for Valiant was accelerated by securing $750,000 in funding from the Australian Government’s Moon to Mars Initiative supply chain grant, administered by the ASA. This grant will help them in getting flight validation on their product, building the supply chain, and upscaling their propulsion technologies to domestic and international customers.
The team previously won a Moon to Mars Initiative demonstrator feasibility grant in 2021, to accelerate the growth and development of their non-toxic thruster technology.
“The first ASA grant in 2021 helped us prototype and test our product, which has been instrumental in gaining market traction and momentum,” Uscinski said.
“As part of that grant, we worked with a Canberra-based project partner, Skykraft, an Australian aerospace and
satellite services company. Their Skyride rideshare program offers spare space on their satellites to be used as an experimental payload space.
“The coaxial solenoid valves, which we’ve developed and designed in-house and now manufacture in-house, are a critical component of our thrusters. They’re one of the only moving parts of the thruster and control the propellant flow and allow combustion to happen.”
Uscinski emphasised the importance of avoiding any leaks from the valve during the launch process and while in space. The valves are undergoing the first major testing after being sent into orbit onboard SpaceX from the Kennedy Space Center.
“We put together a box containing the valve and a couple of instruments that we could use to measure the performance of the valve. And we’re currently waiting for the Skykraft team to do some testing
to validate that performance. But it’s up there now and it’s likely to be around the next month or so when we’ll get some of that data back,” said Uscinski.
Once the valve proves it can survive a violent launch, 6-G gravitational force, extreme vibrations, and a wide range of temperatures on its journey into space, Valiant Space’s full thruster will be launched on a subsequent orbital mission in mid-2023.
“We’re happy to have secured our first customer already for our product, and additional propulsion systems and hardware, and a big next milestone for us is the launch of our thruster and our full propulsion system that we’re working with this customer,” Uscinski explained the next steps for the company. “We’ve got integration of the propulsion system happening right now in our facilities with the customer’s spacecraft.”
The support from the Queensland Government’s Advanced Robotics for Manufacturing (ARM) Hub has been crucial to the company’s success, according to Uscinski.
ARM Hub is funded by the Queensland Government, the Queensland University of Technology (QUT), the Commonwealth Scientific and Industrial Research Organisation (CSIRO), the Urban Arts Project and the Innovation Manufacturing CRC.
“We were one of the first ARM Hub tenants in November 2020,” Uscinski said. “ARM Hub offered us flexibility in leasing, which is fantastic for start-ups, and they have such a large warehouse that has allowed us to expand out as needed. The staff at ARM Hub have helped enormously by identifying funding opportunities and helping us write our first successful
Moon to Mars grant. They’ve also helped us gain exposure to a variety of people, including potential investors and ministers and MPs.”
Valiant Space has since moved out of the ARM Hub and is operating from its own facility.
“Mid-last year, we realised we had some really big CNC machines and we realised we had outgrown the space that we had there. ARM Hub has been quite supportive and excited about seeing us transition to the next step of growing our company,” he added.
Valiant Space is focusing on building Australia’s in-space propulsion capability, which has been traditionally procured from overseas. Valiant Space’s thrusters are 3D-printed and almost entirely
Australian made, which is an attractive value proposition to Australian and global companies.
The International Traffic in Arms Regulations (ITAR) is the United States regulation that controls the manufacture, sale, and distribution of defence and space-related articles and services as defined in the United States Munitions List (USML).
“Companies do not want to deal with the challenges and logistics of ITAR regulations of components from the United States as it can be very frustrating,” said Uscinski.
“The problem with ITAR is that it’s quite pervasive in terms of what it covers. And it’s also incredibly strict and difficult to get approval, if at all, to use parts which have any potential dual use. If you get your valves from a vendor in the US, you’re highly likely to be subject to ITAR
restrictions on your products, because those valves fall under that dual-use list. This is because valves can be used easily in either space applications or in missile or weapon systems applications.”
Uscinski added another of the challenges for new businesses in the space industry in Australia is the lack of base knowledge.
“This is because a lot of technology that start-ups in Australia have heritage overseas. Valiant Space has faced that on the propulsion front where we’ve done extensive testing on fluid properties, on flow rates, arc sizing and other aspects. In the long run, this has meant that we’ve got a very good understanding of the technology that we’ve developed,” he said.
“While Australia has grown in that homegrown knowledge base, it can sometimes be daunting when starting out to think that a comparable company or a
comparable team in the US is able to easily rely on prior experience and knowledge that exists pervasively throughout universities and other areas.”
Uscinski said that the accessibility to space is greater than at any other time in history when discussing opportunities in the sector.
“There are so many facets to space exploration and commercialisation, within all engineering and related nonengineering disciplines. Space is just ripe for collaboration and that shared mission towards common goals. And that’s not something that you see in many other industries, because everyone knows how hard it is to develop space technology. It is surreal to be able to literally look up and see hardware crossing the sky that we know we’ve put up there.”
Uscinski pointed out the opportunities for Australia’s space industry in the
homegrown push for missions locally – for Australian government-led or Australian commercially-led missions. The sector has seen tremendous growth of local companies like Skykraft, Fleet Space Technologies, Gilmore Space Technologies, Black Sky Aerospace, Hypersonix Launch Systems, and of course, Valiant Space.
“We are looking forward to when Australia itself and its ecosystem has matured because we’d love to be able to sell to domestic companies,” he said. “Right now, our sales pipeline is mostly in the international market, where there are bigger market opportunities, but you’re also facing competition within those areas. We’re keen on being able to see an Australian presence in the sector – we’re an Aussie company and we want to support Australian industry.”
IN many industrial applications, maintaining high air purity is critical to avoid product contamination or damage. While many manufacturers use oil-lubricated compressors, they require additional air treatment downstream to remove oil and moisture. An alternative approach is to use oil-free compressors, which can minimise the risk of oil contamination.
Although oil-free compressors come with a higher initial capital cost, they offer long-term benefits and risk mitigation, making them a smart investment for certain businesses. For instance, oil-free compressors are needed to reduce the contamination risk for food and beverage manufacturers. The pharmaceutical industry is highly regulated, while clean air is critical when dealing with toxic chemicals to avoid accidents or process disruption. Product quality is another consideration – expensive electronics
must not come into contact with oily or wet compressed air and fabrics in the textile industry can’t be stained or damaged with oil.
William Chan, CAPS product manager – with 25 years experience in the air compressor industry – explained how the market has changed over the years.
“From the user’s point of view, when I first joined this industry no one cared about energy because it was so cheap. In the last few years, energy prices have skyrocketed causing people to look at the bottom line more. Having compressors as energy efficient as possible helps the end user,” he said.
“From the OEM or distributor point of view, we need to bring products which are not only price competitive, but technologically advanced at the same time.”
CAPS has represented the AL Series of oil-free scroll air compressors for many years. The ‘scroll’ technology refers to
two spiral shaped members form crescent shaped gas pockets. One member remains stationary (fixed scroll), while the second orbits relative to the fixed scroll. This causes air to be drawn in and forced into the centre of the scroll, creating higher air pressure. The compressed air is then discharged through the outlet port at the centre.
These compressors are a fixed box unit, whereas the new range is all incumbent,
with the dryer, storage tank and compressor all in one.
“Instead of a single box, it is all integrated making it simpler for the client,” he said. “The new CAPS “single” scroll compressor range (CS series) is a tank mounted design with refrigerated dryer.”
The new compressor range includes:
• 1.5 & 2.2kW in 240V/1P/50Hz design
3.7 / 5.5 / 7.5kW in 415V/3p/50Hz design 250L tank mounted with oversized refrigerated dryer / filtration onboard. Oversized aftercooler suitable for 40°C ambient operation
Being a family-owned private business, CAPS isn’t restrained to working with set manufacturers, meaning it can use multiple OEMs and partner with renowned brands like Ingersoll Rand.
“We are not tied with a particular OEM so we can provide the correct solution relative to the client’s interests,” Chan explained. “We represent different compressor brands, meaning we can mix and match for certain applications, rather than being limited to one brand. This is usually in the best interest of the end user.”
Delivering a compressed air system, especially for the manufacturing segment, involves a specifically design system unique to every application. This is why CAPS Australia’s complete
solution provide system design via its in-house engineers, is built in Australian ISO9001 accredited manufacturing facility and commissions a custom-built system, perfectly matched to individual requirements.
CAPS Australia has 42 years of experience as an Australian owned business designing and supplying bespoke compressed air systems customised for each customer’s specific requirement.
“We can provide a complete end-toend solution including design, supply and installation of a custom, purposebuilt solution for each of our customer’s individual requirements,” he said. “Customers can access product managers who have years of expertise and specialise in certain products. We do site visits and interact directly with the customer, which some OEMs can’t provide because they are overseas. We operate in the same time zone and can be with the customer through the entire process, offering suggestions and advice.”
CAPS’ in-house ISO 9001 accredited engineering, manufacturing and testing
facility in Perth also provides an added layer of assurance.
“Our inhouse testing facility can test equipment up to 315 kilowatts, which is a unique service,” he said. “A customer can come to the facility and witness
test a certain product.”
With a huge inventory of spare parts and over 60 service technicians covering the whole of Australia, CAPS makes sure to be positioned to support its equipment for their entire lifetime.
“We have a branch in every state around the country, most recently opening a new branch in Tasmania,” he noted. “We can tailor make the parts to the client’s needs and then support them accordingly.”
ADELAIDE-BASED power transmission specialist, Motion Control, has invested in a Bonfiglioli assembly machine, sourced from the company’s headquarters in Italy. The acquisition makes Motion Control the only local distributor (besides Bonfiglioli itself) certified and accredited to carry out complete assembly of Bonfiglioli solutions.
Bonfiglioli is a worldwide designer, manufacturer, and distributor of a complete range of gearmotors, drive systems, planetary gearboxes and inverters, which satisfy the most challenging and demanding needs in industrial automation, mobile machinery and renewable energy. The Group serves more industries and applications than any other drive manufacturer and is a market leader in many sectors; our three business units - Discrete Manufacturing & Process Industries, Mechatronic & Motion Systems and Mobility & Wind Industriesembody all the expertise and experience acquired over the years in the respective industries. Established in 1956, Bonfiglioli
production facilities, a network of 550 distributors and about 3.770 employees.
“Our investment in the assembly machinery enables us to better service Bonfiglioli customers across South Australia,” explained Claude Masiero, general manager, Motion Control.
Among the benefits now extended to Bonfiglioli customers in the region is faster turnaround on deliveries and support.
“Previously we had to source products from Sydney and this meant clients waited for a week at least,” Masiero said. “Now we can offer the same day turnaround on delivery and don’t charge extra for it”.
The company also offers 24/7 support service (including breakdowns) and the supply of spares and repair services, as well as local building of planetaries.
“With the geographical area of South Australia being as large as it is, servicing the market remotely from Victoria was very difficult. Having a distributor like Motion Control, with assembly capability that can react to market requirement very
Vries, Bonfiglioli Regional Manager for South Australia. “The South Australian market, including the Victoria and Tasmania regions, has always been an important part of our business, making up 20 per cent of total sales. In spite of various challenges experienced in the last year, the opportunities for market growth are positive.”
Motion Control has been supplying complete power transmission products to a wide range of industries (from food and beverage, to packaging, winery, automotive and mining) throughout South Australia, since 1993. The company provides solutions ranging from motor gearboxes to complete drive systems. Its large stockholding and extensive service offering has made it a valuable partner to Bonfiglioli.
“We have found that the diversity of Bonfiglioli’s range of solutions makes it well-suited for use across industries, and in applications of all types. Customers could use one brand all the way through their plant and this simplifies
maintenance,” commented Masiero.
The seamless and efficient collaboration between Motion Control and Bonfiglioli was demonstrated in a recent project completed for a steel plant located in South Australia. Motion Control was commissioned to upgrade a ball mill drive system and it recommended the installation of 2HD boxes, from Bonfiglioli’s range.
“Bonfiglioli assembled these gearboxes in Sydney, where they were tested and laser aligned. Bonfiglioli also carried out the commissioning on site. The customer will be able to secure spare parts and service from Motion Control,” elaborated Masiero.
“We have very good relationships with our partner OEMs. The good rapport we have established with these companies demonstrates the longevity of our relationships, and that we’ve seen each other through the good and bad times. Through our experience, we always work out the best solutions for customers. Our investment in the new Bonfiglioli assembly machine now enables us to put together products and solutions in no time”.
Motion Control has invested in a new assembly machine, making it the first local distributor to offer certified assembly of Bonfiglioli solutions.
20-21
Sept 2023
EXHIBITION SPACE NOW ON SALE
Inside Construction Expo will deliver
Targeted messaging in over 19 industry-leading publications that reach more than 80,000 decision makers across multiple sectors
Digital communications to 28,000+ engaged readers
Premium networking opportunity with industry leaders at the Foundation Awards gala dinner
insideconstructionexpo.com.au
Melbourne Convention and Exhibition CentreNearly 50 years ago, Mick Vawdrey started building truck bodies. Today, Vawdrey Australia is the country’s leading manufacturer of quality semi-trailers and original equipment, putting thousands of new semi-trailers on the road each year.
VAWDREY Australia designs and manufactures in Australia at its Dandenong facility in Melbourne’s south eastern logistics hub, custom-making equipment for Australian operating conditions. With customers including Australia Post, StarTrack, Freight Lines Group, and Mainfreight (NZ), the business produces everything from parts to curtains and signwriting and has repair and service workshops in Queensland and New South Wales.
Mick believes that an unwavering focus on quality and Australian manufacturing has paid off over the years.
“Everything is about quality. Everything we buy, we buy the best. If we can buy it Australian, we will. Everybody knows that our product’s better than our opposition’s, and it’s got to be.”
He revealed that another key to their success is change.
“If you can keep ahead of everybody else, you are better off. We have geared ourselves around change, which is the company’s biggest asset,” Mick said.
The company’s appetite for change has paid dividends when faced with competition.
“Others have tried to buy me out quite a few years ago, but I wasn’t for sale,” he added. “Then they said they’d squeeze us out and beat us on price and everything else. We decided the best way to stay ahead was to strengthen our engineering. That was the only way we could keep ahead of them, and it worked.”
Vawdrey’s list of advances includes the Wingliner, a futuristic semi-trailer with a folding side door, the automatic mezzanine desk system, and an automatic, buckle-less truck curtain. The firm also brought the performancebased standards framework to the general and refrigerated freight markets, helping Australia’s road transport community strengthen its position as the world’s most advanced.
Every time Vawdrey salespeople go and look at jobs, the Vawdrey team looks at how to improve trailer use and design and build it more easily.
This commitment to quality and innovation drives growth, with the business opening extra lines this year to meet demand.
For many of the 60-plus Vawdrey
team members, Vawdrey was their first job, and they have stayed.
“I am proud of our team: many have been with us since they were kids. We are a team, and we instill that in everybody. We look after the product, which looks after the customer, so they come back,” Mick said.
Australian-made is so critical to Mick that “Proudly Australian by Vawdrey” appears on every semi-trailer they produce.
“Australian-made means everything to me. If we can use Australian, we do. I don’t care if it’s a little dearer. We’re proud to be Aussie-made and supplied.”
Quality Australian aluminium is an integral part of Vawdrey products; every semi-trailer roof is aluminium, and extrusions for dry and refrigerated freight.
“Aluminium is light, strong and doesn’t deteriorate. It fits our purpose –it flexes, so it works with everything. It’s ideal on the roofs of the trailers; it just moves,” Mick noted.
Vawdrey Australia chooses to work with Capral and has done for more than 20 years.
“We buy the best. That’s why we use Capral aluminium. Capral’s quality is second to none, it’s cost-effective, and we have a good working relationship.”
Capral’s ability to customise extrusions and deliver on time is critical for the Vawdrey business. Capral also adds value to many of the products supplied to Vawdrey, including predrilling extrusions, saving many hours on the production line.
“We depend on Capral as much as our own blokes,” Mick emphasises. “If you have a good working relationship, it helps with everything.”
He reminisces that everything was made in Australia when he was a lot younger.
“We made our own cars, our own trucks. We made Australia. Semi-trailers are about the only thing on the road made in Australia, which is sad. Let’s hope it changes.”
SPECIALISING in the design, engineering, supply and installation of louvre screens and bespoke façade solutions, Louvreclad services the commercial, public, education, government and multi-residential sectors.
The firm’s remarkable building exteriors use innovative architectural louvre solutions to help achieve comfortable, healthy, safe and energyefficient working and living environments.
The Queensland-based business is widely recognised for setting new benchmarks for effective and sustainable façade and louvre designs and solutions for the Australian construction industry.
Founded and run by the Wright family, Louvreclad has headquarters in Ipswich and project teams in Victoria and New South Wales. The business designs, engineers and fabricates everything in-house; its products are 100 per cent Australian-made.
“Aluminium is an ideal match for louvre and façade manufacture,” said Louvreclad design consultant Uddhava Sharplin.
“It’s one of the most sustainable building materials and is incredibly corrosion resistant. We can often design out a support structure specified in steel and replace it with aluminium. It has great strength if designed and engineered properly.”
easier to work with than steel: “you can extrude, laser cut, and perforate it. You can’t do that with steel.”
Louvreclad has created solutions for significant construction projects, including Canberra’s Landmark Constitution Place, The Standard Apartments and the Gabba in Brisbane, and Sound Stage 6 in Melbourne’s Docklands. What sets Louvreclad apart is its capacity to engage from early project design and develop bespoke solutions.
“We have an amazing team of designers, engineers and façade specialists who understand how to integrate louvres and screens onto buildings. We often work with project architects from the early design stage and provide engineering advice to ensure projects run smoothly.”
The team draws on an extensive library of exclusive and standard aluminium extrusions to design and engineer bespoke solutions to meet design intent and requirements for airflow, wind pressure, rain protection, solar shading and connections.
For Constitution Place, the Louvreclad team needed to meet unique wind and rain defence requirements and kept returning to the drawing board to develop, test and refine a solution.
Series® 145, which delivered Class B 98 per cent effective rain defence and Class 1 aerodynamics. Louvreclad’s highperformance black vertical louvres were integrated and articulated the building as two stacked volumes.
Louvreclad’s design and engineering, sales, estimation, and fabrication teams work closely and share satisfaction in the firm’s achievements. A digital display on the fabrication floor showcases projects completed with Louvreclad’s ingenuity.
Capral has been Louvreclad’s supply partner for more than 20 years; the two businesses are neighbours, providing extra convenience to deliveries and collaboration on extrusion developments.
we need to create something new, it’s easy
team, and they quickly let us know if our designs will work and advise on lead times. It works very well for our business,” Sharplin said.
Adeline Wright from Louvreclad’s procurement team confirms the strength of the partnership and the importance of Capral’s support.
“We require a very high quality of aluminium because our products are used on building facades. Capral packages our extrusions very carefully in stillages to avoid any damage.”
She recently toured the Capral plant and was able to see the extrusion process and visit the die workshop to see how Louvreclad’s extrusions were created from design to final product.
Adeline underlines the fact that with Capral’s aluminium being manufactured locally, means quicker turnarounds and fewer project hold-ups for Louvreclad customers.
“When covid disrupted global supply chains, we were very grateful to entirely source and make in Australia,” Adeline says.
Like everyone on the Louvreclad team, Adeline takes great delight in walking or driving past one of their projects.
“It’s incredible to know that we played our part in creating these extraordinary buildings.”
Louvreclad has been helping leading architects, builders, and developers create some of Australia’s most iconic buildings and precincts for over three decades.
Chicago Pneumatic recently introduced its new 16 bar compressor for the laser cutting industry. Manufacturers’ Monthly finds out how the new cut through technology is helping businesses cut through the competition.
LASER cutting is one of the most efficient and precise thermal cutting methods. However, achieving perfect cuts requires the right combination of factors, including the power of the laser cutting machine, the type of auxiliary gas used, and the pressure and flow rate of that gas. Air compressors play a critical role in delivering high-quality auxiliary gas, making it essential to choose the right compressor for your laser cutting
Chicago Pneumatic has been in the compressor business for decades and has recently introduced a new product specifically designed to meet the demanding requirements of the laser cutting industry. This compressor has an outlet pressure of 16 bar, making it the perfect choice for those who require high cutting speeds and thickness.
The compressor also features dew point-controlled dry air, which ensures that the compressed air is free of any
filtration further purifies the air, removing any oil and dust particles. In addition, an activated carbon filter provides clean oil-less air, ensuring that the laser heads last longer and require less maintenance.
One of the major advantages of using Chicago Pneumatic’s compressor for laser cutting is the quality of the compressed air. With less water and oil in the air, the compressor ensures that the protective mirror of the laser cutting head stays clean, allowing for the transmission of the laser beam to remain focused. This, in turn, reduces the risk of incomplete cuts and wasted products, which can result from
In addition to high-quality compressed air, the Chicago Pneumatic compressor also offers a stable free air delivery. This ensures that the surface of the material being cut remains smooth, like a mirror, without any unevenness
With the development of laser cutting machines, the pressure requirement of the air compressor has also increased. The Chicago Pneumatic compressor is capable of delivering the high-pressure air required for modern laser cutting machines, making it an ideal choice for any business looking to improve cutting quality and efficiency.
In conclusion, choosing the right compressor is essential for achieving high-quality laser cuts. With its 16 bar outlet pressure, dew point-controlled
Chicago Pneumatic is a market leading manufacturer and distributor of compressed air products such as screw compressors, piston compressors and air treatment. When you are in need of an industrial or professional air compressor system, Chicago Pneumatic is sure to have the right solution.
We have used our years of experience to design compressors that are efficient and reliable. Our products are tailored to suit your needs.
Our people start every single day with a passion to research, develop, manufacture and deliver new products that are meant to meet your needs not only today, but tomorrow as well. All this has come together because we have consistently practiced our brand promise — People. Passion.
Performance.
So why wait? Call today and speak to one of our friendly specialists on 1300 555 284 or visit www.cpcompressors. com.au for more information.
dry air, and high-efficiency coalescence filtration, Chicago Pneumatic’s compressor offers an ideal solution for the laser cutting industry. The compressor provides high-quality compressed air, which helps to ensure the longevity of the laser heads and improves cutting efficiency. With the Chicago Pneumatic compressor, businesses can rest assured that they are getting a reliable and efficient compressor that will meet their needs for years to come.
Quality machine tools are vital in the manufacturing process of mechanical parts, including forming, cutting and joining of other tools.
In June 2022 – we will showcase businesses who supply the “work machines” which make the manufacturing industry tick. The edition is an opportunity for business to demonstrate the extent of their services in the machine tools space.
In every edition of Manufacturers’ Monthly, we’re proud to work with our commercial partners on content that helps connect you with your future customers.
Booking deadline: 27 April 2023
To book contact DANNY HERNANDEZ now danny.hernandez@primecreative.com.au | 0431 330 232
WOMEN IN INDUSTRY NOMINATIONS ARE NOW OPEN. Now is your chance to nominate an industry leader who you believe is advocating for positive change and deserves to be recognised.
WOMENININDUSTRY.COM.AU
THURS 8 JUNE 2023
The Women in Industry Awards recognise outstanding women leaders from across Australia’s industrials sector.
HE modern mine needs more than condition monitoring to ensure assets are healthy and meet production demands. To protect, you need to predict.
In the past, businesses have relied on data science experts to analyse equipment data and provide insights. Now, manufacturers can access these insights quickly and cost-effectively through the power of artificial intelligence, set up with an easy, self-service tool.
Technology and Artificial Intelligence (AI) has evolved to a point where we can obtain tangible results of how it can help the manufacturing industry identify inefficiencies and reduce waste. Freddie
Coertze, National IoT Business Manager at ifm, said there has been a big shift in the industry and business are turning toward “self-service” tools to make it easy to deploy models and gain insights to make more informed, data-driven decisions.
“To gain this level of insight, it often requires skills from a data scientist to build and code these models,” he explained.
“With a ‘self-service’ approach, it makes it very easy to harvest the data from a complex system, putting the power back into the hands of the business so they can achieve better productivity at their plant.”
The moneo platform is a self-service tool that enables successful predictive maintenance programs through the help of AI Methods.
Many software applications have unexpected cost blowouts once purchased, however, ifm’s moneo is basically “ready to use” right from the start. Continuous evaluation of process data provides the basis on which sustainable and successful business decisions can be made. And in order to obtain such data from the manufacturing floor, reliable connection of sensors to IT infrastructure is essential.
ifm’s moneo consists of a basic software as well as applications, for example, for condition monitoring or for IO-Link sensor parameter setting. As powerful as the software is in its full range, thanks to its modular design, it is only ever as big as the customer requires.
An important strategy for ifm is making it clear to businesses that it is best to start small and ‘grow as you know’.
“The simplicity and ease of use of the ifm moneo software means that you can set up an application dashboard in a matter of minutes and anyone can do it.,” he added.
“But if you take the same solution with another brand of software, you only get the core and have to develop software applications and pay for a software engineer to develop these types of solutions.”
With its modular structure, moneo consists of basic software plus
applications – for example, condition monitoring – making it possible to put together a tailor-made software package that suits unique business requirements.
Adoption of technologies such as moneo is not a matter of people not knowing what they’re doing – it’s a matter of managing that internal business case, Coertze explained.
“ifm wants to assist with that journey, and that’s why we’ve invested to help with our Consultancy Services. We help customers build a budget and a scope to help them sell it internally.”
The tool acts as middleware, which is a key enabler for a business on their digitisation journey, according to Coertze.
“With the rise of software platforms, it is important that software platforms are interoperable. Whether it is to collect data from existing systems, or sending data or notifications north bound to overarching platforms like SCADA. moneo edge
ifm’s Moneo solution combines operating and information technology to bring the power back into the engineer’s hands.
Manufacturers’ Monthly investigates why a ‘sensor to action’ approach is fundamental to proactively protect equipment.
connect has the ability to easily collect and push data to other systems,” he said.
“The aim is to create integrated solutions for IIOT that facilitate the vertical connection of the production level with the management level and the horizontal digitisation of all business processes.”
The traditional approach of identifying equipment problems by responding to alerts based on static thresholds comes with many trade-offs that can lead to compliance, economic and resource loss. ifm’s DataScience Toolbox aims to break these trade-offs by empowering operators and engineers to improve the remaining useful life of their equipment and at the same time avoid unplanned downtime and assist compliance.
“Anomaly detection by dynamic process monitoring lies at the core of ifm’s DataScience Toolbox with the primary
of the moneo industrial IoT software platform, simplifies the integration of Industry 4.0 concepts into your existing
identify anomalies and remedy minor equipment problems before they become expensive, big ones.
With moneo, the power can be put back into the engineer’s hands, by providing sophisticated insights with respect to different sets of variables, without requiring the expertise of a pure data science person. The purpose of the tool is to monitor the critical process value (target variable) with regard to the production quality or the plant condition (e.g. temperature, flow, vibration, current consumption) on an ongoing basis.
AI (assisted predictive maintenance) methods use a mathematical model based on historical data for a permanent target/ actual comparison between measured and predicted target values. This data enables the automatic and early detection of anomalies in a critical process value.
“The data science toolbox makes it easy for the engineer to start identifying problems,” Coertze said. “It’s easy to onboard devices themselves. Whether its temperature, pressure, flow, vibration, whatever the customer wants to monitor about the machines condition – they pull it into a five-step wizard that will do all those things in the background, meaning they don’t even need to know anything about databases or data science.”
Put simply, going alone requires access to data scientists, in-house project structure, manual data acquisition processing process and an extended project duration of at least three months. In comparison, ifm’s DataScience Toolbox
automated data preparation and AI training and scalability within the ifm moneo System.
The soft IoT tool helps engineers optimise manufacturing processes through early warnings and alarms.
“It really resonates with industry because they are used to always having to consult with IT, but now the engineer can take back the power and do what they do best – trying to predict problems and fix things.”
The adoption of IoT products and services has gained serious momentum over the last ten years in Australia. ifm now offers consulting to Australian businesses to help them fully profit from their foray into IoT, which was built out of a need in the market, said Coertze.
“We really saw there are a lot of constraints an engineer will go through on this journey – where to start, what software tools to choose, how to design and understand the whole system,” he said. “ifm understands the common problems across all kinds of industry. This is more a unique service we do on-on-one for the customer.”
After seeing other IoT technologies fail to solve business problems, ifm is also offering its expertise and working with universities, to help students entering the industry.
“We want to help people with their step into digital transformation,” he added. “Anyone can have the technology, but you always need to translate innovation into return on investment and gains in productivity.”
ICP Electronics Australia recently introduced the ICP DAS’s ECAT-2094DS. The ECAT-2094DS stepper motor controller is a two-phase bipolar stepper driver that is affordable. The ECAT-2094DS can manage up to four stepper motors at once. It allows for a maximum motor coil current of 3.3A/ phase and a motor voltage range of 9 to 29V DC. Software selections can be made for each motor’s maximum running coil current, micro-step resolution, and other motion parameters.
The ECAT-2094DS device can be directly connected to two-phase bipolar stepper motors. The gadget has a stepper motor open loop operation built in. The EtherCAT master and the application programme must configure the device. A distinct driver IC controls each stepper motor independently. The four driver ICs operate separately from one another and are not coordinated. The torque and position of the motor are automatically controlled by the driver. The acceleration and deceleration distance is automatically determined by an inbuilt ramp generator. In velocity mode, the controller accelerates the motor to the goal velocity while in position mode, it drives the motor to the desired position. Real-time adjustments are possible for all motion parameters.
There are four integrated incremental encoder ports on the ECAT-2094DS. The input signal from the external
The Australian Trellis Door Co. (ATDC) has installed its Double Diamond doors as a crowd control barrier at Woolworths Town Hall near Sydney.
These barriers screen off the escalators preventing public access afterhours to the Big W section of the business which is on the top floor of the building. The Double Diamond product was selected by the Big W construction team as it is much more difficult to gain a foothold and climb over this door.
These crowd control barriers are portable, retractable, relocatable and lockable.
For further information and other safety features on the Double Diamond crowd control barrier, visit the ATDC website.
incremental encoders is counted by four 32-bit highfrequency encoder counters. The encoder can be utilised, for instance, for homing and consistency checks.. To provide precise and slick motor movements, a high resolution of up to 256 micro steps per full step is supported.
Three digital input channels are offered by each motor: a left and right hardware limit switch, as well as a home switch. The three digital inputs can be utilised for home position search, and the hardware limit switch will halt the motor when it is activated. Three different power sources must be supplied to the device. a 24V DC control supply and two motor supplies. One power source is shared by two motors.
Company: The Australian Trellis Door Co.
Phone: 1800 657 435
Website: www.trellisdoors.com.au/productcommercial-security/ barriers-and-cafe-barriers
The most recent model in the popular Nuvo-8108GC series is a tough-edge AI platform created specifically for NVIDIA® RTX A6000 and RTX A4500 Ampere GPU cards. In order to advance GPU-accelerated edge AI applications like autonomous driving, vision inspection, and intelligent video analytics, the GPUs provide enormous computing power and long product life.
It features a solid basis for constructing a potent AI edge computing platform, powered by an Intel® Xeon® E or 9th/ 8th-Gen CoreTM (up to 8-core/ 16-thread) CPU with workstation-grade Intel® C246 chipset to support up to 128 GB ECC or non-ECC DDR4 memory. It incorporates a sophisticated thermal dissipation architecture to maximise GPU performance in hot settings.
A special mounting bracket for RTX A6000/ A4500 is also included with the Nuvo-8108GC-QD to keep the GPU card securely fastened in the PCIe slot. It guarantees rock-solid functioning under extreme shock and vibration situations, along with Neousys’ unique damping brackets*.
With the addition of the RTX A6000/ A4500 to Neousys’ GPU computer lineup, an edge AI platform with up to 309.7 TFLOPS tensor performance and 38.7 TFLOPS FP32 performance is realised. Edge AI computing now has access to unmatched lifespan, computational power, adaptability, and reliability thanks to Nuvo-8108GCcombination QDs of proven power design, guaranteed thermal efficiency, and better mechanical robustness.
Key Features:
• Supports NVIDIA® RTX A6000/ A4500 GPU cards
Supports Intel® Xeon® E or 9th/ 8th-Gen Core™ i7/ i5 LGA1151 CPU
• Up to 128GB ECC/ non-ECC DDR4 2133 (4x SODIMM)
One x16 (8-lanes), one x8 (4-lanes), Gen3 PCIe slots for add-on cards
• Dedicated GPU card bracket
8~48V wide-range DC input with built-in ignition power control
Patented thermal design for -25°C to 60°C rugged operation*
• Patented damping brackets* to withstand 3 Grms vibration
Interworld Electronics is excited to introduce the HELIO-9C series of rugged industrial all-inone HMI Panel PCs from Aplex Technology. The HELIO-9C series features a powerful Intel Tiger Lake 11th generation energy efficient Core i3/i5 processor with up to 64Gb of DDR4 RAM. It comes in a range of sizes from 10.1” – 21.5” TFT-LCD and has an IP66 certified front bezel.
The HELIO-9C series has a new modern design, with ultra-narrow frame, slim profile, and new fast mounting kit. It is constructed using an aluminium die-cast and fanless design, making it rugged, while still maintaining good heat dissipation. It has the ability to operate continuously for long periods of time under wide temperature ranges of 0°C~50°C or optional -20°C~60°C. This updated design provides a modern stylish look, decreases system weight, and also improves water and dust protection by eliminating the need for mounting holes on the chassis. It also offers 24/7 reliability, makes it easy to clean, reduces maintenance cost, and provides a long-lasting rugged enclosure.
The projected capacitive touch screen with multi-touch support, and anti-scratch surface helps to improve usability, while also providing the screen with tough protection. Optional auto dimming, 1,000nits high brightness, and optical bonding & AR coating, makes the HELIO-9C series perfect for a range of applications, no matter the environment or weather. With such a wide range of display options, choosing the best screen size, resolution, and brightness for your application is easy.
The HELIO-9C series offers a wide range of optional expansions to suit your needs including, Power over Ethernet (PoE), 5G, Wi-Fi 6, CAN bus, as well as additional Serial, LAN or USB ports that can be added. The HELIO-9C series also offers the optional smart battery backup feature, providing an emergency backup power source to protect data and the system from unexpected power outages.
The HELIO-9C series can be panel or VESA mounted, allowing the system to be
Company: Neousys Technology
Phone: +886-2- 2223-6182
Website: www.neousys-tech.com/en/
ergonomically positioned for operator convenience. The new fast mounting kit provides rapid positioning, with special fasteners that only require two screws to assemble, remove or install. Furthermore, with the special modular design and functionality of the box PC at the back of the HELIO series, it can easily be interchanged between the different panel sizes of the HELIO series, allowing for further flexibility.
“Iwouldn’t start from here” may be the punchline to an old Irish joke but it still best describes the policy dilemma the Federal Government faces in 2023.
The Government’s central ambitions, repeated many times, are sensible and vital. They are to engineer sustainable increases in real wages; promote economic and social opportunities for a wider cross-section of Australians; lift Australia’s productivity performance; and set the country on a low-cost yet convincing path to net zero emissions.
Even if we were starting from the best of positions, achieving these goals would not be easy.
A first step is to be honest about the scale of the challenges involved in meeting these goals.
Since the global financial crisis, Australia has experienced relatively low real wages growth. The same is true of average business incomes outside the mining sector.
It is widely agreed that this is not confined to Australia and that the stepdown in productivity growth across developed economies is at the heart of the slower rates of improvement in real wages. Low incomes growth is not something
that can be fixed with a wave of a magic wand, or by legislation, or by decisions of the Fair Work Commission. In the absence of improved productivity, any attempt to improve living standards simply by lifting wage rates, will be thwarted by higher inflation, fewer jobs, or both.
The truth is that raising the pace of productivity improvement is not easy. Collectively, for the best part of two decades, we have not been willing to take the often difficult decisions to achieve the uplift necessary for a larger increase in real incomes.
But the challenge now is even greater than it has been over the past two decades.
Not only are we now seeking to recover from the recent fall in real incomes and engineer a step-up in the pace of future real incomes growth, we also want to broaden economic and social opportunities and we want to transform our economy by putting it on a path to net zero carbon emissions.
That means a significant recasting of large areas of economic activity: stopping things; doing new things; and doing things in different ways.
The net zero challenge goes well beyond the energy sector: it covers whole
The net zero challenge goes well beyond the energy sector: it covers whole swathes of upstream manufacturing, agriculture, mining and our transport systems.
swathes of upstream manufacturing, agriculture, mining and our transport systems. And it requires an overhaul of our commercial and residential buildings.
Put simply, the net zero path we are embarking on is enormous. Taking the net zero journey while also channelling additional resources into higher real household incomes turns the enormous into the gigantic.
And, like the lost Irish traveller, we are not at the best starting point from which to begin this journey.
With its initial workplace relations changes and critically the setback to enterprise bargaining due to the broad extension of multi-employer bargaining and the hair-trigger on industrial arbitration, the Government has positioned itself well and truly behind the eight ball on the productivity agenda.
Compounding this is the threat of overreach inherent in the mandatory code of conduct for gas producers and the ongoing and as-yet-unspecified ‘reasonable’ price interventions in the gas and perhaps other industries. These uncertainties are not helpful to securing private sector investment and innovation.
All that said, we are where we are, and the disadvantageous place from which we embark on the journey is no reason to give up on widely shared objectives.
On the contrary, as 2023 gets underway, it means there is more urgency in setting a clear direction and at least taking the initial steps to get productivity moving across both private and public sectors.
Here are five steps that will help recover the lost ground.
The Government and the Parliament must be ready to fix the glaring and the as-yet-hidden problems with the Secure Jobs legislation that was rushed through
the Parliament in December.
In the design and implementation of the next tranche of workplace relations changes flagged for this year, the Government must ensure employers have an enhanced ability to lift workplace productivity and meet the flexible requirements of their employees and the circumstances of their businesses. Simply adding constraints, regulation and centralised decision-making will not cut it.
The Government needs to act quickly to clarify that its ambitions in the energy industry are limited to an ‘emergency’ response and demonstrate this in the design and implementation of its code of conduct.
The Federal Budget and the Employment White Paper need to put credible cross-federation grunt on the promising but as yet bare bones of the skills agenda. Nothing is as central to achieving ongoing productivity improvements. It is also the main means by which we can meet the ambition of extending opportunities much more broadly across the Australian community.
And as the fifth step, an early and constructive commitment to a program of measures informed by the Productivity Commission’s upcoming five-yearly report on Australia’s productivity performance will be essential. All indications are that there will be a rich selection to consider in this year’s report. And with the Commission’s earlier Shifting the Dial report still largely untouched, there will be no lack of directions from which the Government can draw.
Making sure these milestones are on its 2023 roadmap will go a long way to correcting for the Irish starting point the Government has created for itself.
need
Choosing lower-carbon aluminium in your next project can reduce the embodied energy of your aluminium products by up to 75%* LocAl® Green (8kg CO2e/1kg AL) and LocAl® SuperGreen (4kg CO2e/1kg AL) are the responsible choice for a locally extruded, lower-carbon option in your next project.
FOR MORE INFORMATION VISIT: lowcarbonaluminium.com.au
When compared with global average CO2e for primary aluminium production,
POWERED BY