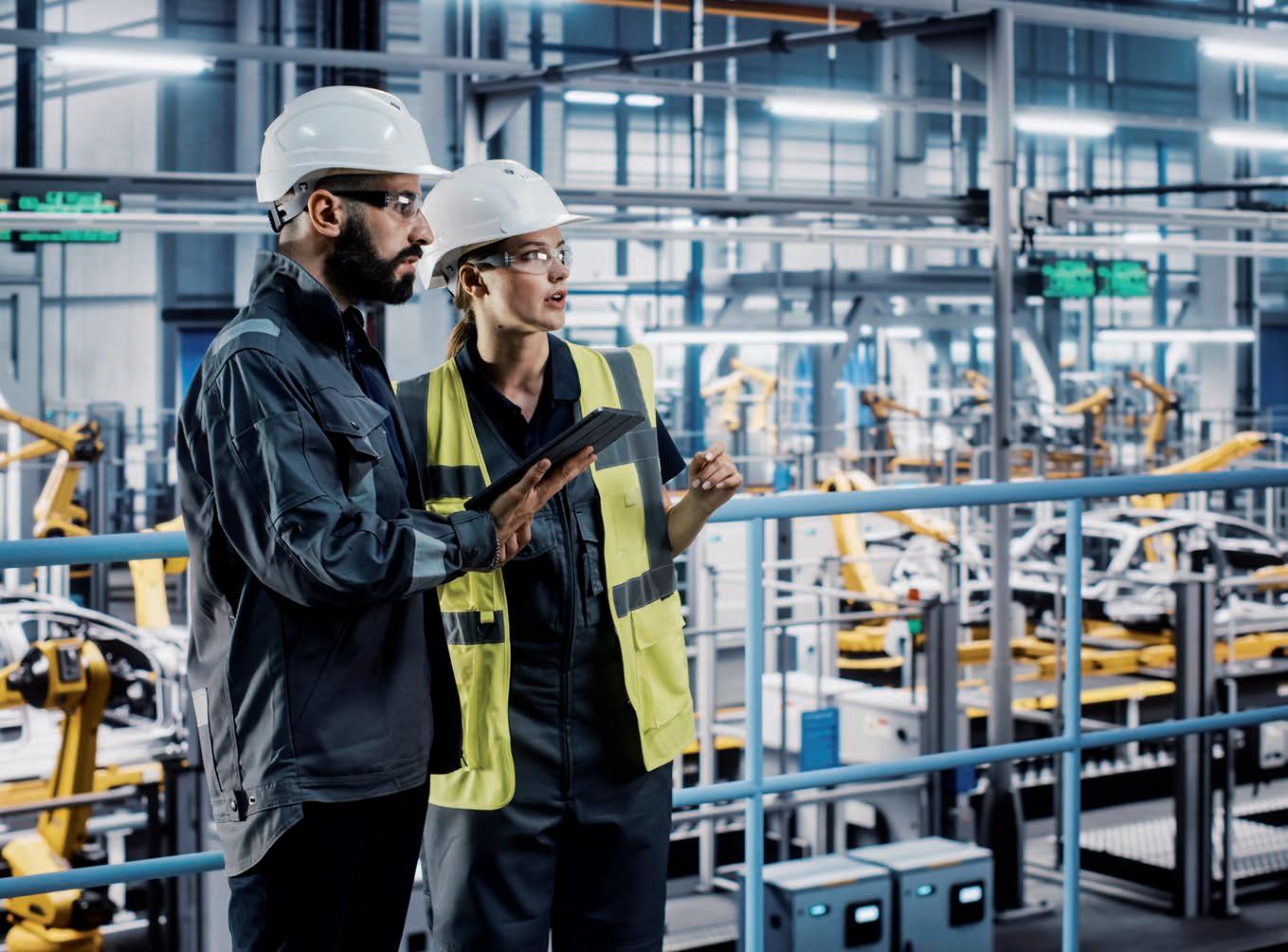
12 minute read
Comment
GEOFF CRITTENDEN – CEO, Weld Australia
Manufacturing for a sustainable future
THE war in Ukraine has changed the world.
Over the course of the last month, the world has returned to a pre-1989 Cold War state—with the added threat of nuclear and chemical weapons.
How has this happened? Well, during the intervening 30-odd years since the end of the Cold War, many of the democratic nations of the world have settled into complacency on several fronts. This has invited the autocratic global states to try their luck—the war in Ukraine is just one result.
The sanctions placed on Russia by Western nations will have an enormous impact on their economy. Australia and the United States have prohibited the import of oil, refined petroleum products, natural gas, coal and other energy products from Russia. The United States, United Kingdom and European Union have introduced unprecedented financial penalties on Russia. Exporting goods to Russia—including cars, clothing, chemicals and art—has been banned. Russian imports are attracting taxes of 35 per cent, and the assets of Russia’s central bank have been frozen. Rightly so.
The impact of these measures is already being felt. The cost of basic products has skyrocketed, job losses are looming, and hundreds of international companies are pulling out of Russia. Even McDonald’s has closed their 800 restaurants in Russia.
Imagine if Australia was on the receiving end of such draconian sanctions.
It is not such a far-fetched proposition. China has already placed sanctions on Australian barley, wine, beef, seafood, cotton and coal.
China is our largest trading partner by far. According to figures from DFAT, China holds a 35.3 per cent share of Australia’s export market, accounting for $167.6 billion annually. Coming in second—by a long way—is Japan, with just 11.8 per cent of Australia’s export market. Given the huge proportion of Australia’s export market the country holds, imagine if China imposed harsher economic sanctions.
Imagine if China decided not
Australia must maintain a strong local manufacturing industry and manufacture value-added products domestically.
to accept our iron ore, or coal, or natural gas. Imagine if China refused to supply Australia with electronic chips and electrical equipment, machinery, furniture and textiles. Australia would be as vulnerable—possibly even more vulnerable—than Russia. This vulnerability stems from the demise of Australia’s manufacturing industry.
The demise of Australian manufacturing
During World War I, the Australian Government quickly realised that our economy was too reliant on imports; it was near impossible to source many products in wartime. As a result, Australia started to manufacture a range of products on-shore during the war, from aspirin right through to chlorine. Our steel industry also experienced enormous growth. BHP opened a new steelworks in Newcastle in 1915, which generated huge profits due to the unprecedented demand for steel to build ships, ammunition and artillery. Australia quickly matured from a rural economy into a substantial manufacturing power.
The 1920s marked the beginning of the car manufacturing boom in Australia. By 1929, 440,000 people were employed in manufacturing, approximately 18 per cent of the total population.
When World War II hit in 1939, Australian manufacturing was poised to play an even greater role than it had during World War I. With imports scarce, local demand was high. And, Australia also became an important supplier of manufactured goods to the United Kingdom and the United States. Australian manufacturing remained strong in the years immediately after World War II. Throughout the 1950s and 1960s, Australian manufacturing was responsible for approximately 28 per cent of the GDP, and 28 per cent of all employment.
Fast forward to today and, while manufacturing remains a vital part of the Australian economy, it is responsible for just 5 per cent of the GDP, and only 5.4 per cent of total employment.
Australia’s governments must come to realise that, without a strong local manufacturing industry, our economy is weakened substantially. Without sovereign manufacturing capability, Australia is vulnerable to coercion from more powerful economic states. In times of turmoil, we cannot presume to
rely on the generosity of our allies. After all, our allies will be focused on supplying their own citizens, industries and defence forces. We need only look to the recent global supply chain issues caused by the COVID-19 pandemic for confirmation of this fact.
The solution
Australia must build its selfreliance. Instead of mining our natural resources and shipping them offshore, we need to be manufacturing value-added products here at home. In 2018, Australia surpassed Chile to become the largest producer of lithium by metric tonnes. And yet, Australia does not manufacture batteries. Instead, we ship most of our lithium to China as spodumene, where it is manufactured into batteries that Australian then imports back. We need to be manufacturing our own batteries locally. We need to encourage electronics companies to set up shop in Australia so we can manufacture circuit boards and electronics chips locally.
Similarly, Australia has one of the world’s largest supplies of iron ore. Again, we dig it up and ship it overseas, adding absolutely no value. Australia needs to be investing in the capacity and capability of its local steel industry. Australia is home to some of the world’s leading steel manufacturers, including BlueScope, InfraBuild and Bisalloy. Why not invest in their local operations to bolster our sovereign capability?
This is particularly important given that China announced in December 2021 that it is set to boost domestic iron ore production by 30 per cent, significantly ramp up
investments in overseas mines and strengthen scrap steel recycling under a plan designed to break their dependency on Australia’s most valuable commodity export.
A skills-led recovery
This manufacturing reinvigoration will rely on a skills-led recovery. And yet, Australia’s largest, oldest and most essential vocational education provider, TAFE, has had courses and budgets slashed over the last 10 years. According to the Australian Education Union, since coming to power, the Federal Coalition has cut $3 billion from vocational education funding, and overseen a 24.5 per cent decline in TAFE enrolments. These cuts to TAFE funding have had a severe impact on course and campus closures, attraction and retention of teaching staff and workload.
The result? TAFE graduates who are under-skilled, and an Australian industry that is faced with a severe skills shortage.
The federal government has also failed to implement the recommendations outlined in the Joyce Report, handed to them three years ago. Of the 71 recommendations, just one has been implemented.
Weld Australia is calling on the federal government to implement the ‘Early Actions’ recommendations of the Joyce Report without further delay. These include disbanding the existing infrastructure for developing training packages and qualifications and replace it with industry led Skills Organisations; strengthening quality assurance by introducing independent student assessment to international standards; introducing vocational pathways in schools as part of the STEM program; and establishing a National Skills Commission to generate skills demand forecasts and realistic pricing models.
With proper funding and a systematic overhaul as recommended in the Joyce Report, there is a brighter future for TAFE and skills development to help foster the reinvigoration of the manufacturing industry. We just need the Federal Government to make it happen.
A commitment from government
We have massive gaps in our industrial capacity and the Australian governments is not showing any signs of filling them. We need to manufacture our own batteries, electronics, plastics and composites. We need robust, cuttingedge aerospace, fabrication, and steelmaking industries. We need to add value to our natural resources.
There is a strategic imperative on the Australian government to realise that the world changed when Russia invaded Ukraine. As a result, Australia must reinvigorate its manufacturing industry. We cannot rely on our allies and trading partners to fill the gaps in our industrial capabilities. We must have a robust manufacturing industry to ensure a sustainable future.
Australian manufacturing needs strong leadership, the support of all levels of government, and investment in technology, education, and resources. It needs a commitment from government to foster the ingenuity of our inventors and engineers, as well as our manufacturers. Only then can Australian manufacturing return to its former prosperity and make a vital contribution to Australia’s economy, workforce, and future.
Comment
VONDA FENWICK – CEO, SEMMA
Training the next generation of welders
What happens when a hairdresser, a plasterer and a store person walk into a bar? They talk about welding, of course, because that is what they have in common after four weeks of SEMMA Welding Skills training. Each of these people, who had never held a welding gun in their lives, have been snapped up by eager SEMMA members to work in their manufacturing businesses on welding and other production tasks.
SEMMA is delighted to advise that we successfully ran our first of five pilot courses designed to prove our industry-led welding skills short course. The welding skills short course runs for 4 weeks and is intended to allow participants to develop a basic level of welding skills, sufficient to tackle many manufacturing welding tasks.
You can add to our initial 3 trainees, a young man who did some welding during a training exercise with the Scouts and enjoyed it. After ‘graduating’ from our course he was given a one-day work trial with one of our SEMMA members and was subsequently given an offer of employment. This young man was very quiet, and the employer admitted that if he had come for an interview, without having been referred from the program, the company would probably not have employed him. What we have developed is a Win-Win-Win; our manufacturers get skilled employees, the trainee gets a job with a pay packet, and the government no longer provides financial support to a person who initially had limited employment prospects.
One participant, a VCE qualified student who had not had any longterm employment, had worked previously in stores and other casual work. He developed good welding skills during the 4-week course (one of three participants described as ‘naturals’) and went on to join a SEMMA member and has been offered an apprenticeship by the company.
Back in early 2021 in a Manufacturers’ Monthly opinion piece we advised that we had struggled to get funding for our industry-led pilot program. We subsequently successfully secured a contract with the Department of Education Skills and Employment, Local Jobs Program to pay for equipment and training. SEMMA member Hilton Manufacturing in Bangholme Road in South Dandenong very generously provided us with both formal classroom training space and also much needed production floor space for the set up of our training welding bays. This has enabled us to give participants the feel of working in a production space while learning.
A very valuable component of the training has been incorporating a welding simulator into the program. We have a very experienced welding engineer who runs prospective students through an exercise on the simulator. This has the benefit of allowing participants to get a feel for wearing a welding helmet and doing a test weld in a safe, fun way while getting a baseline ‘score’ for their attempt. There is a strong, positive correlation between performance with the simulator and subsequent performance with the actual physical MIG welding performed in the welding bays.
Purchase of a welding simulator enabled our contract trainers from Chisholm TAFE to provide feedback to trainees not only on their simulated work pieces but also to reinforce areas for improvement with their ‘on the job’ performance. The simulator can demonstrate the impact on the quality of the weld if the operator uses the wrong speed or angle while welding.
The intention of our SEMMA Welding Skills Short Course pilot programme is to: 1. Enable participants to develop a basic level of MIG welding skills sufficient to be able to work in a production environment. 2. Demonstrate that the four-week course can produce ‘job ready’ production welders. 3. Provide successful ‘graduates’ from the programme with a job with our
SEMMA members.
We would like to see our SEMMA industry-led model adopted more broadly to provide a constant supply of skilled employees to our manufacturers, desperate for employees with basic welding skills.
When SEMMA first proposed this skills course, there was confusion in the broader manufacturing/ engineering training community that this was somehow meant to be used in place of full trades training. This is not the case, and we are hopeful that some
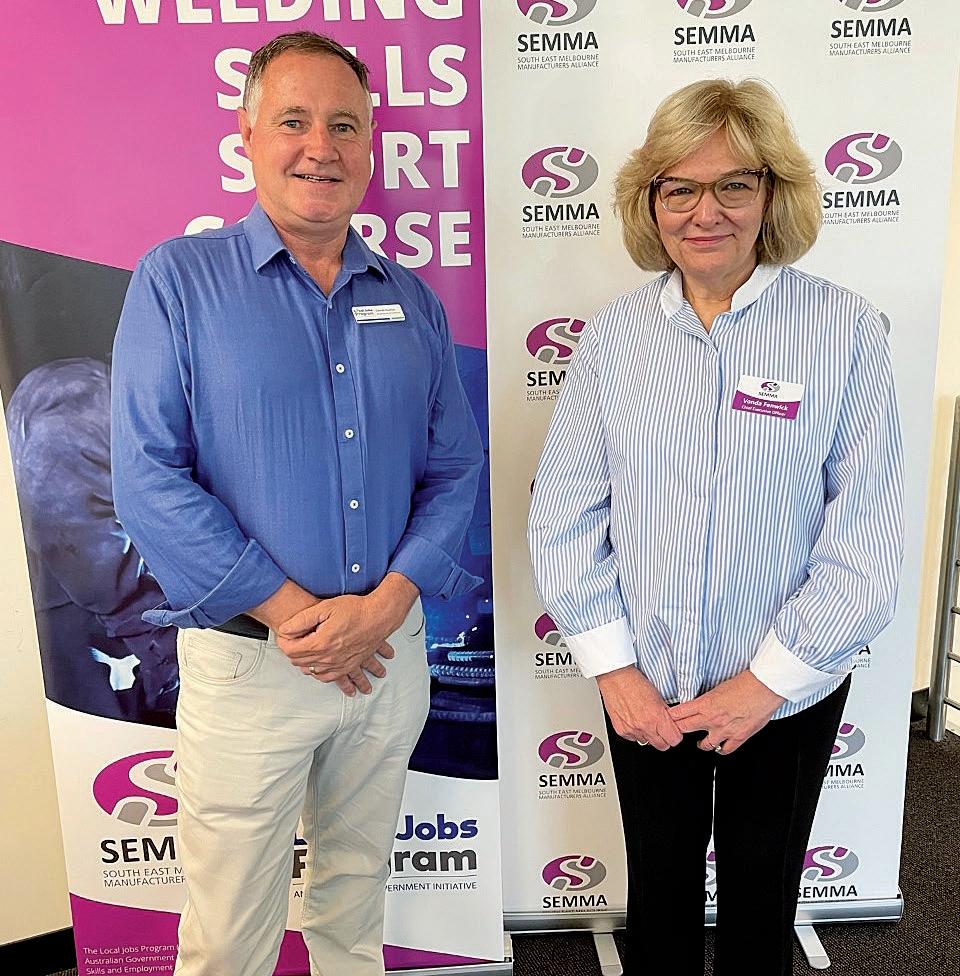
SEMMA ran the first of five pilot courses designed to prove its welding skills short course.
Skilled welders remain vital for local manufacturing.
of our graduates will go on to pursue further study in the art of welding, whether that is through other short courses such as welding to a particular standard or through an apprenticeship. The course was planned to fill an immediate need, recognising the dire shortage of people with welding skills.
One voice of dissent claimed, “Oh yeah – great idea … and we’ll let them weld submarines and aircraft.” Clearly the intention with our course is that we train in basic skills, have people who successfully complete the short course go to employers who recognise the need to support the new employee and provide further training as needed. It would be wonderful in a few years if some of our trainees go on to do more training and become specialised, highly skilled welders. Commonsense dictates that 4 weeks, even for someone with natural ability and good hand-eye co-ordination, will not see them welding safety-critical equipment.
A key feature of our course is the “speed dating” event held in week three, where our trainees meet prospective employers in an informal lunch meeting. Employers who have taken part in the speed-dating are very enthusiastic and have subsequently employed a number of the trainees.
Peter Angelico, MD of the Abeck Group, is very happy with his new employee who is producing jig welded parts, freeing up a higher skilled welder to complete more critical work. Peter commented the skills course is “designed to fill an immediate need which enables us to maintain our customer’s confidence” that we can deliver in full and on-time. He went on to say, “there are plenty of full-time positions in manufacturing, we need to bring people in at the bottom end with micro credential courses such as this that are specifically designed to suit what our customers need”.
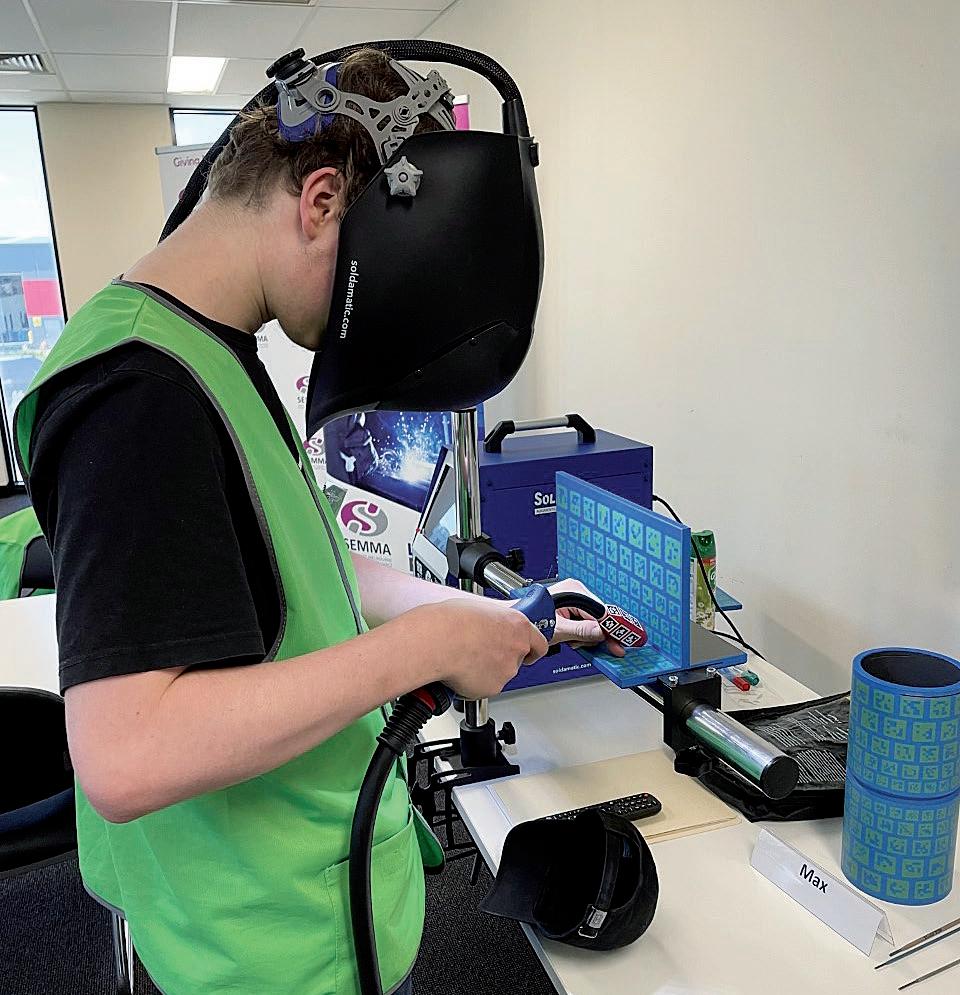
If you would like to learn more about the SEMMA welding course, please contact us at info@semma.com.au
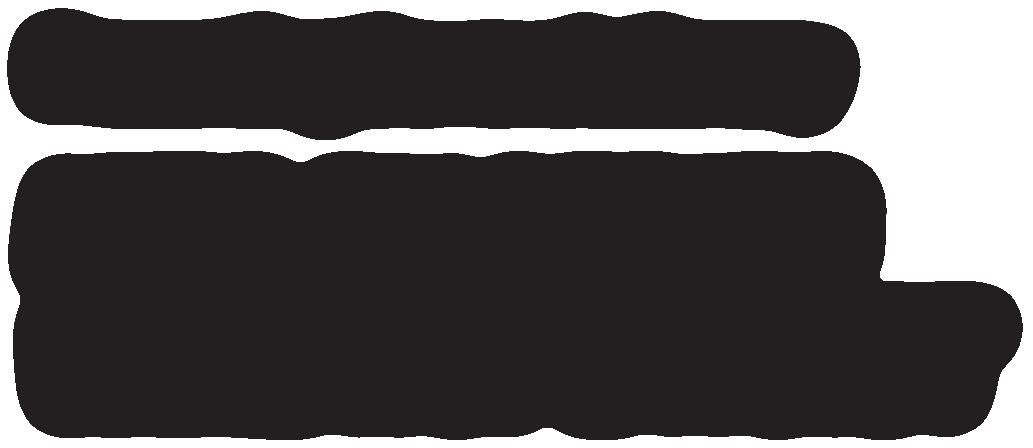

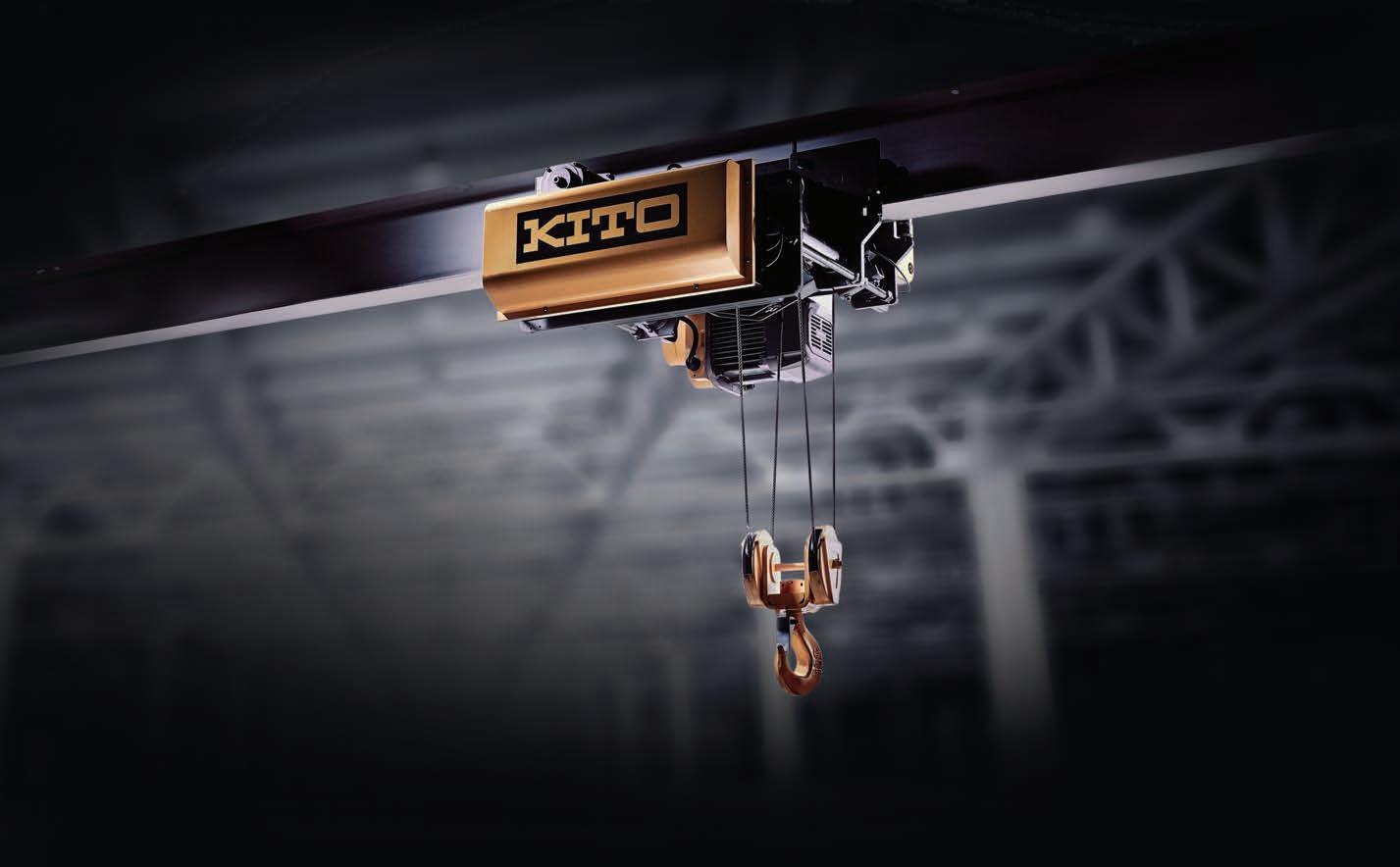