COMBI CB3000 The ForkliftMultidirectionalOriginal•IMPROVEWORKFLOWANDSAFETY•DESIGNEDTOCARRYPALLETISEDORLONGLOADS•INCREASEYOURSTORAGEBYUPTO50%combilift.com manmonthly.com.au MANAGEMENT >> TECHNOLOGY >> SOLUTIONS AUGUST 2022
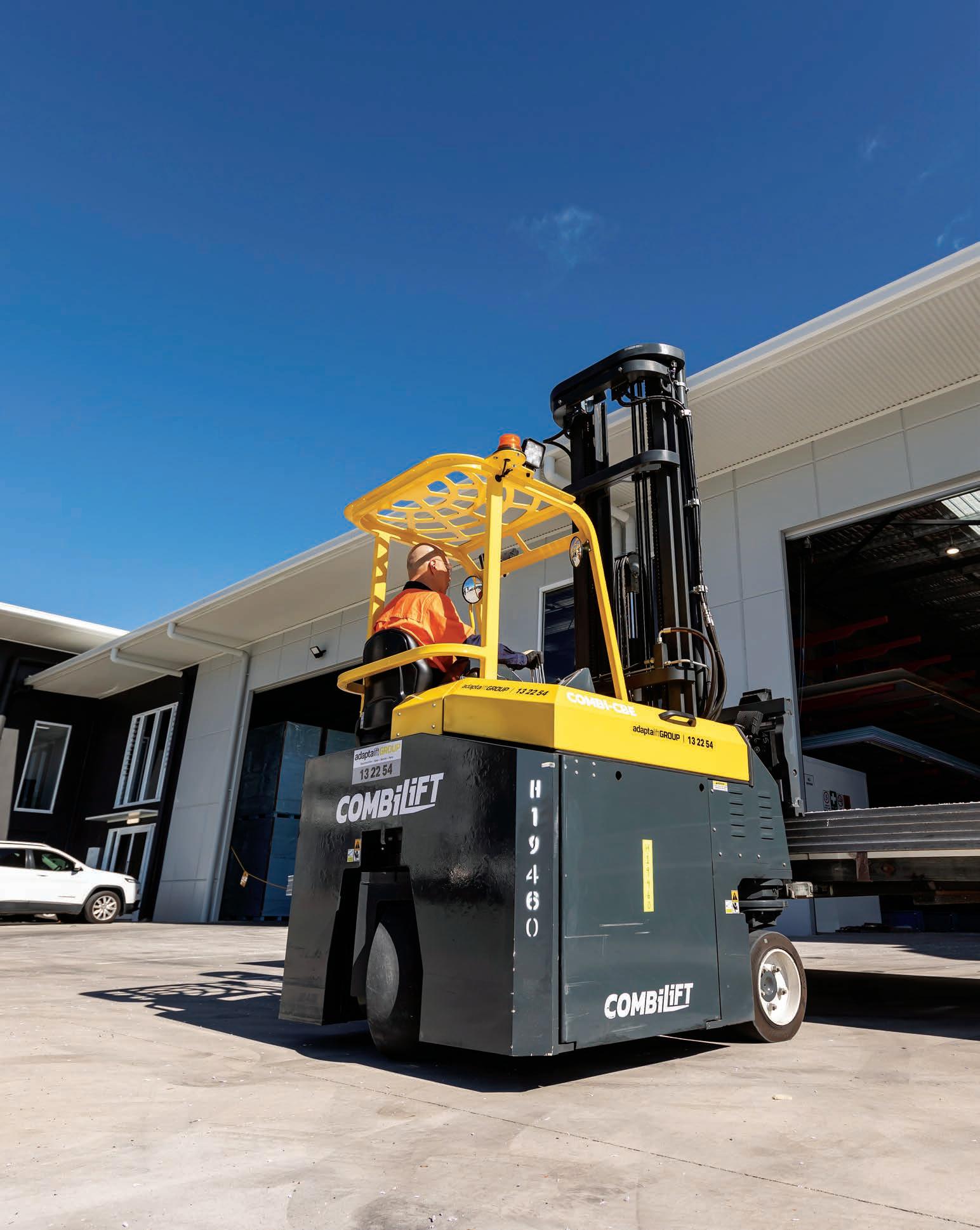
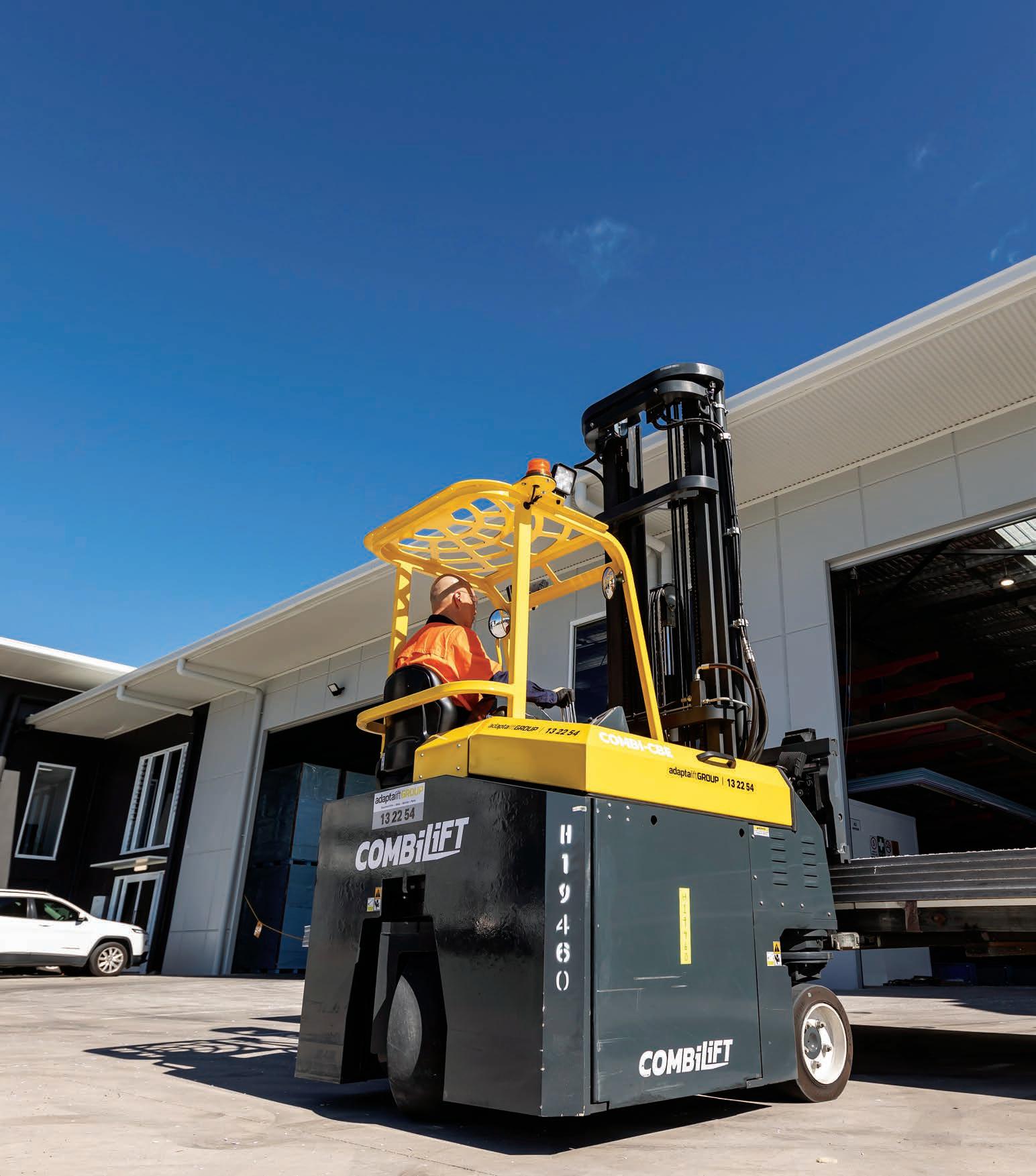
The Combi CB3000 multidirectional forklift allows operators to transport palletised loads, as well as long loads in sideways directions. Featuring four-way lever positioning of wheels, it offers the advantages of a counterbalanced vehicle, side loader, and very narrow aisle (VNA) truck all in one, compact unit. Intuitive and ergonomic controls, paired with load sensing steering, ensure ultimate safety during operation. The unit is highly customisable to suit specialised applications, with a wide range of engine technology, fork sizes, spreaders, tyres and attachments to choose from. Cabins can be half open, or fully enclosed with heating options also available. • LPG, DIESEL OR ELECTRIC MODELS • LIFT CAPACITY 3,000 KG • LIFT HEIGHT UP 4.04 M • PLATFORM LENGTH 1.15 MWithcombilift.comtheCombilift CB3000

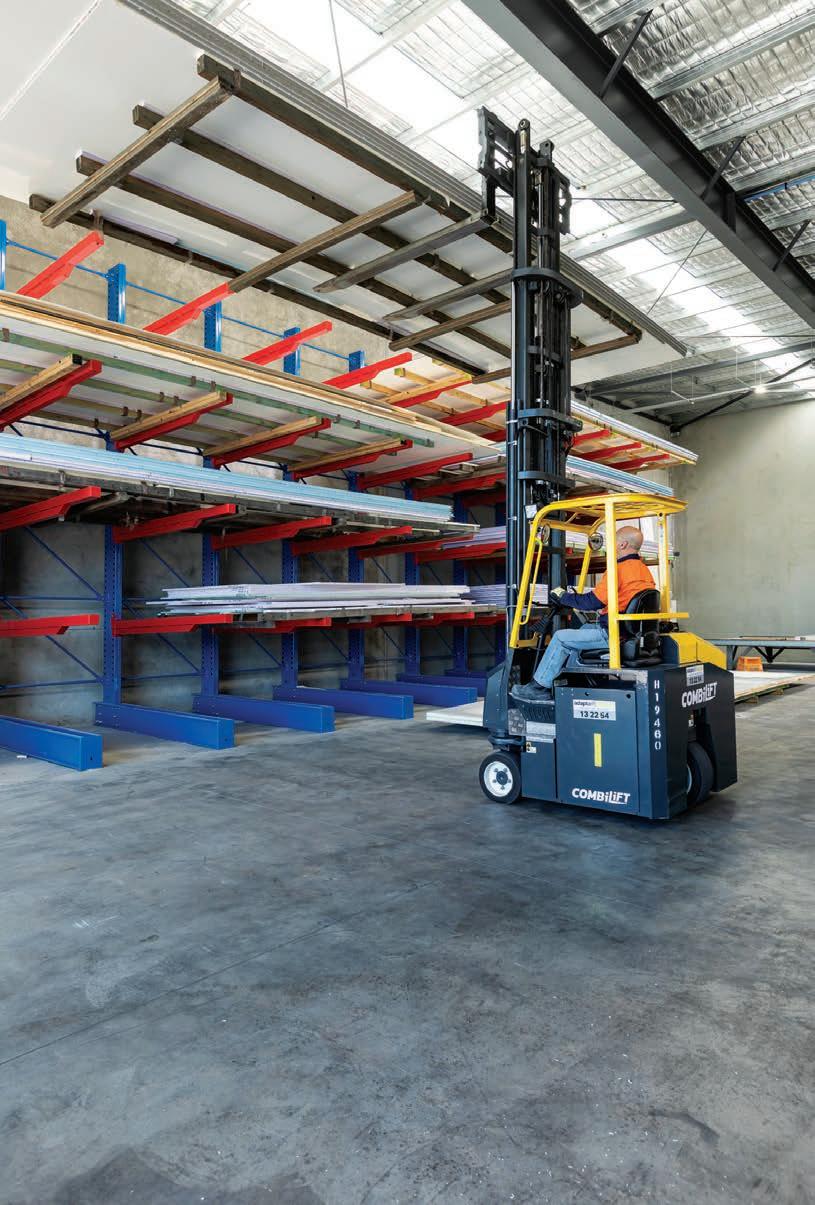
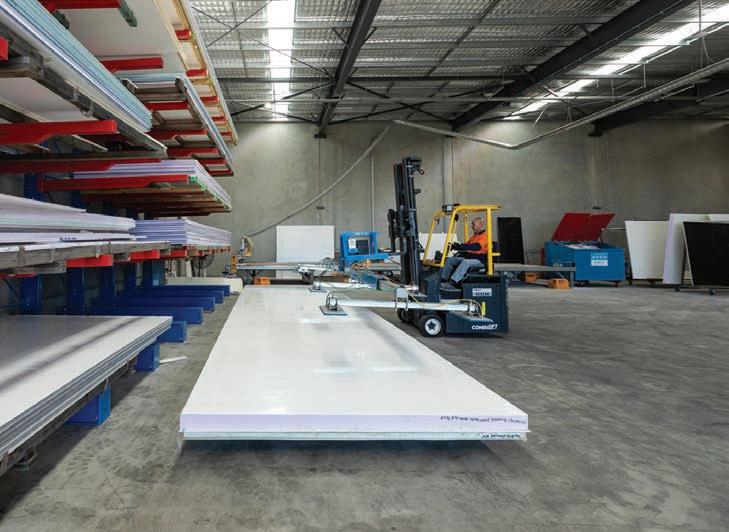
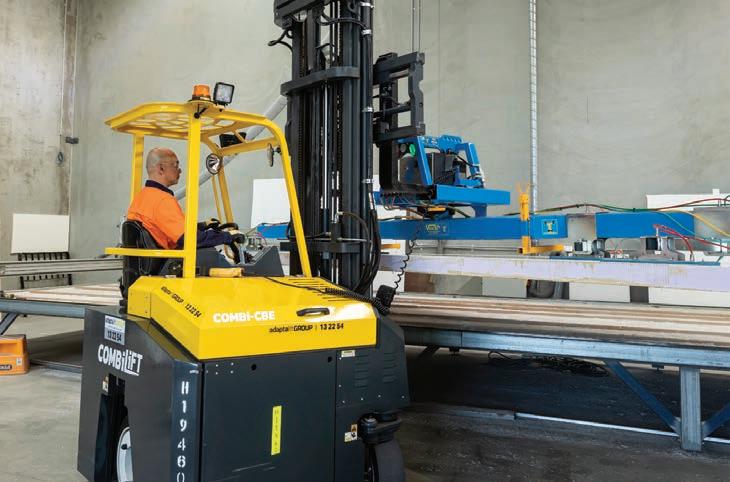
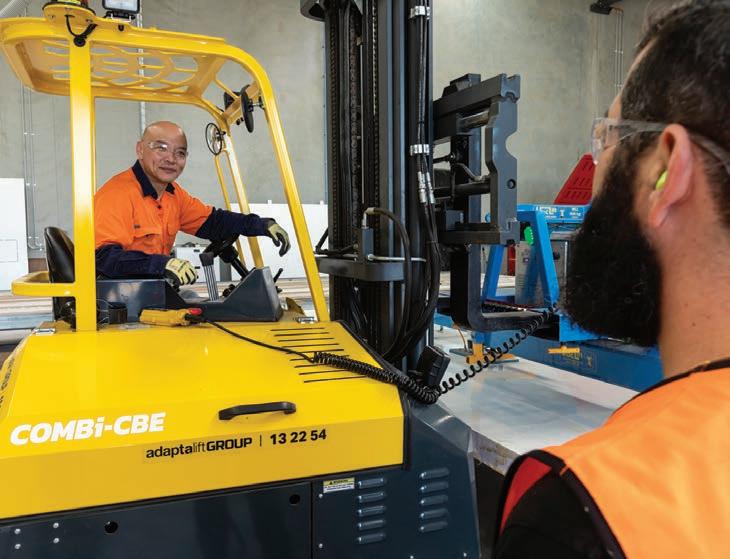
manmonthly.com.au MANAGEMENT >> TECHNOLOGY >> SOLUTIONS PP100007882ApprovedPostPrint >> INSIDE >> A special aluminium construction project 30 AUGUST 2022 ACHIEVING DIGITALISATION COOLON LED: The possibilities of additive manufacturing 46 Official Industry Partners The artform of metal rollforming 32
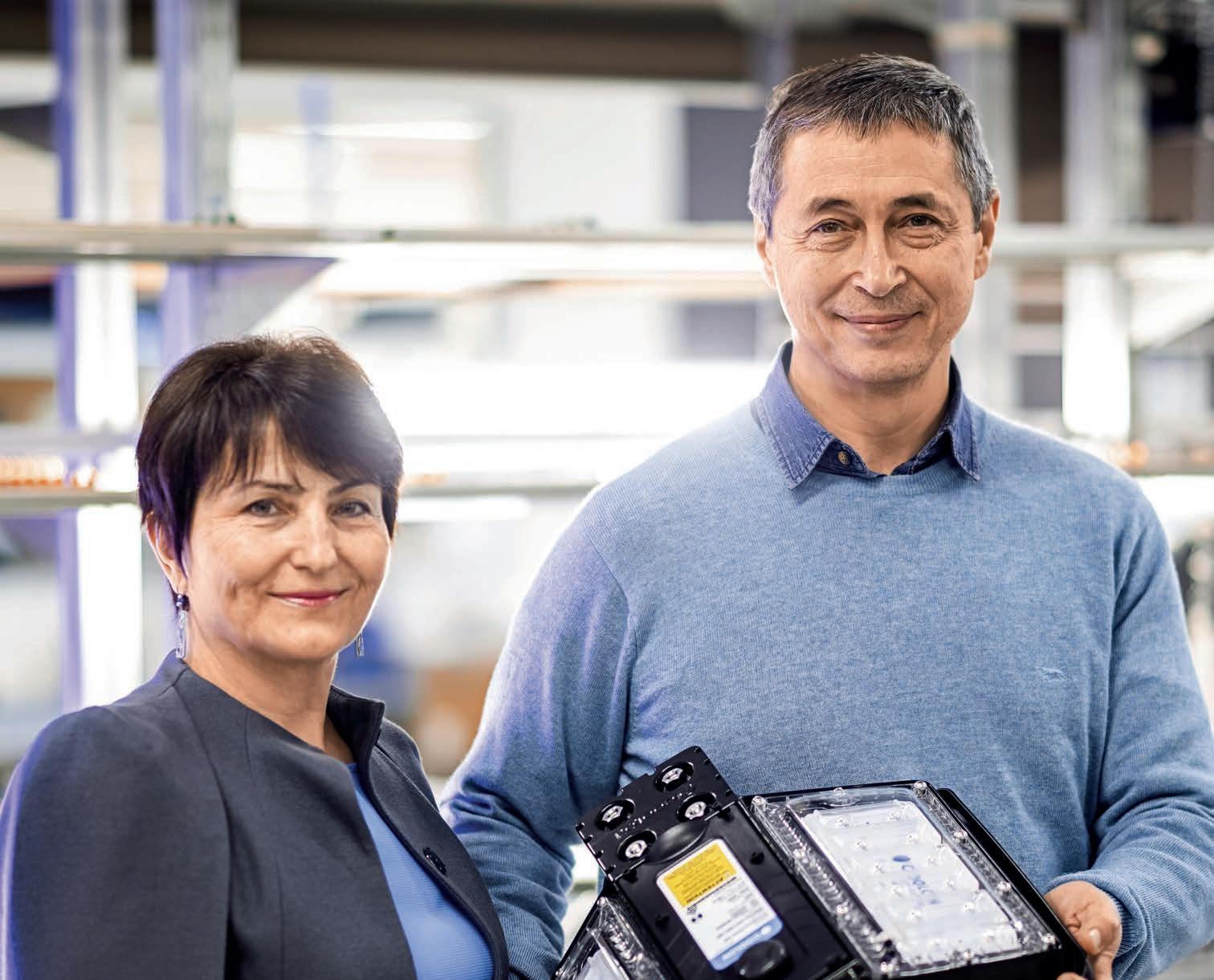
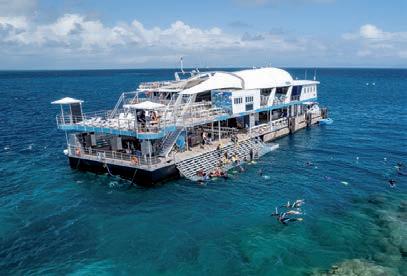
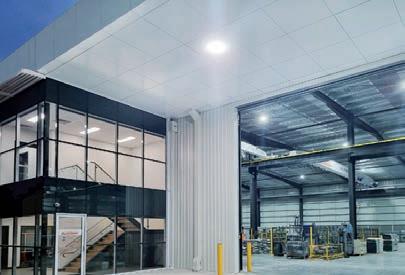
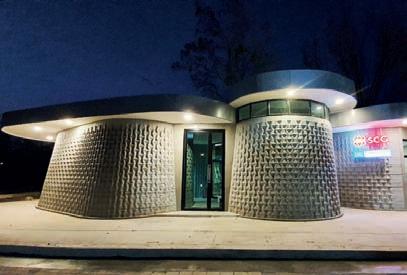
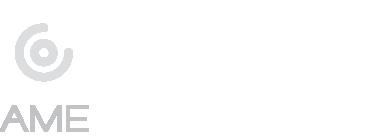
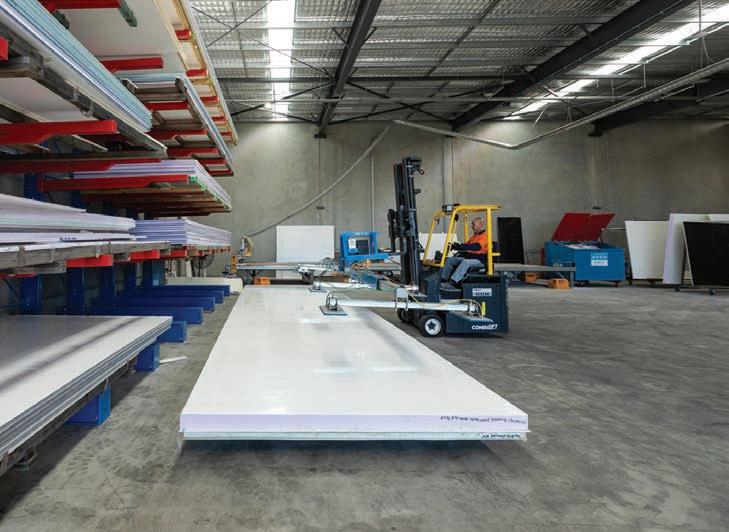
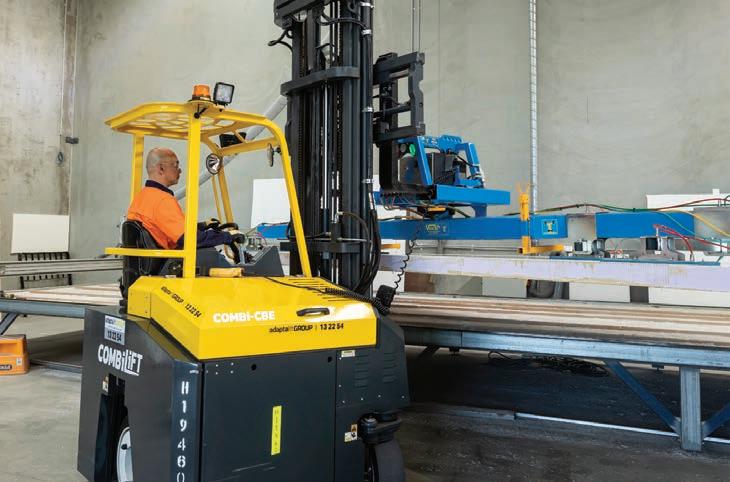
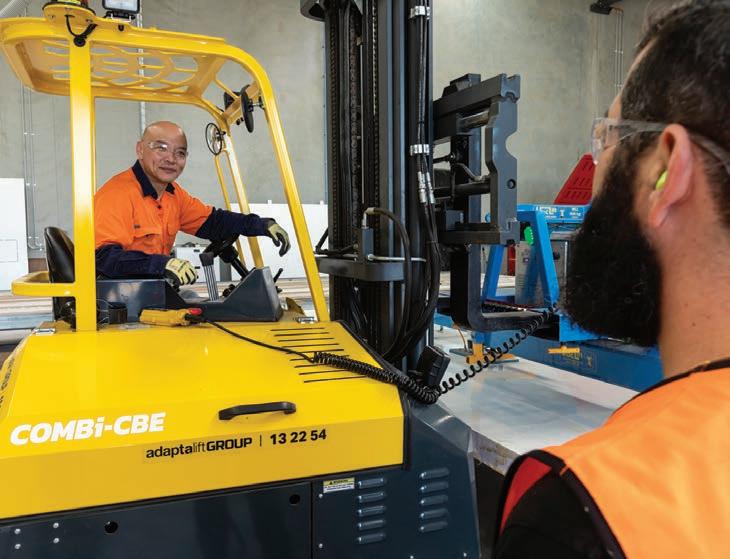
reject any material. While
for errors or omissions
on information published. The opinions
Art Director:
Publisher:MurphyChristine Clancy
part
© Copyright Prime Creative Media, 2021 Articles All articles submitted for publication become the property of the publisher. The Editor reserves the right to adjust any article to conform with the magazine format.
44Manufacturers’26
Monthly
4 AUGUST 2022 Manufacturers’ Monthly manmonthly.com.au For daily news visit manmonthly.com.au Inside
in
twitter.com/Manmonthlyfacebook.com/Manmonthlylinkedin.com/showcase/manufacturer’s-monthly/ manmonthly.com.au MANAGEMENT >> TECHNOLOGY >> SOLUTIONS >> INSIDE >> special aluminium construction project 30 ACHIEVING
46 Official
publisher.
Head Office 11-15 Buckhurst St South Melbourne VIC 3205 P: +61 3 9690 www.primecreative.com.auenquiries@primecreative.com.au8766 Sydney Office Suite 3.06, 1-9 Chandos Street Saint Leonards NSW 2065, Australia P: +61 2 9439 7227 Printed by: Manark Printing 28 Dingley Ave Dandenong VIC 3175 Ph: (03) 9794 8337 manmonthly.com.au DIGITILISATION COOLON LED: The possibilities of additive manufacturing Industry The artform of rollforming 32 Monthly Contents Behind the cover Digitisation is the ultimate goal of the rapidly evolving and seemingly limitless world of IoT. Each new technology brings game-changing value to the table and disrupts the industry. This edition’s cover story uncovers Coolon LED’s story, applying an expertise in system engineering in electronics to Australia’s industrial environments. Originally from Ukraine, company founders Svetlana and Alex Zatsepin explain how the idea of site digitisation is to link every piece of equipment, plant infrastructure and personnel together, forming a giant digital model that is fully transparent and can be used to accurately assess and predict operational disruptions in real-time. Coolon’s Brilliant Connected Lights represent disruptive innovation, but also provide a backbone for thousands of emerging IoT-dependent services and technologies. After a long journey, Coolon’s facility in Hallam has several assembly lines with modern automated component storage and test facilities. Speaking to Alex and Svetlana, it’s clear passion and knowledge combine as main drivers for Coolon’s success. Through the COVID-19 pandemic, the company didn’t stand still, instead leaning on research and development to bring innovative solutions to market. Exemplified by the stories in this edition of Manufacturers’ Monthly, even the most experienced manufacturers are looking for new ways to improve. In changing times with the constant improvement of manufacturing technology, standing still is the most dangerous course of action.
Partners
for
be reproduced or copied in any form or by any means (graphic, electronic or mechanical including information and retrieval systems) without written permission of
Production Coordinator:
Design:
and published by
Hernandez Ph: 0431 330 danny.hernandez@primecreative.com.au232 Subscriptions Published 11 times a year Subscriptions $140.00 per annum (inc GST) Overseas prices apply Ph: (03) 9690 8766 Copyright Manufacturers’ Monthly is owned by
All material in Manufacturers’ Monthly is copyright
of information,
6 Editor’s Note 8 1812CommentNews@MMManufacturer Focus 23 Australian Manufacturing Week 26 Materials Handling 28 Cold Spray Technology 30 Aluminium Construction 32 Metal Rollforming 35 Hoists & Chains 36 Electronic Components 38 Ventilation 40 Energy Chains 43 Metal Manufacturing 44 Welding 46 Additive Manufacturing 49 Events 52 Sustainability 54 What’s New 55 Last Word
Journalist:
CEO: John Group Managing Editor (Northern): Syed Shah Billy Friend billy.friend@primecreative.com.au Alexandra Cooper alexandra.cooper@primecreative.com.au Michelle Weston michelle.weston@primecreative.com.au Blake Storey Kerry Pert, Aisling McComiskey Danny Prime Creative Media John Murphy. and no may the The Editor welcomes but reserves the right to accept or every effort has been made to ensure the accuracy Prime Creative Media will not accept responsibility or any consequences arising from reliance expressed Manufacturers’ are not necessarily the of, or endorsed by the publisher unless otherwise stated.
Assistant Editor:
Sales/Advertising:
contributions
opinions

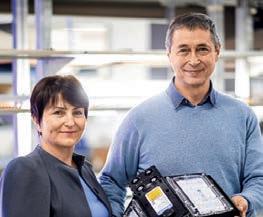



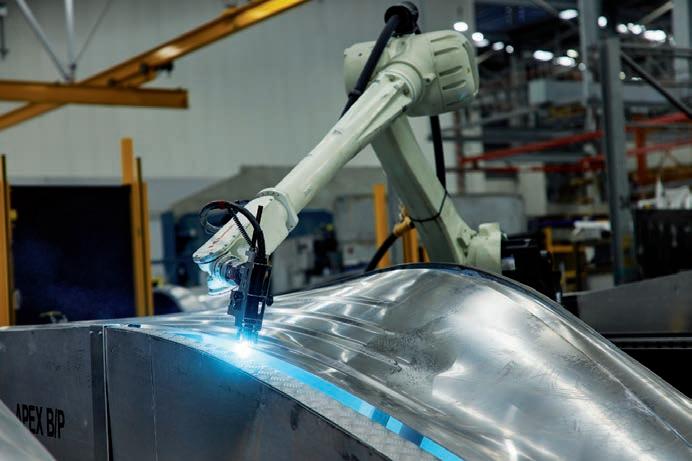
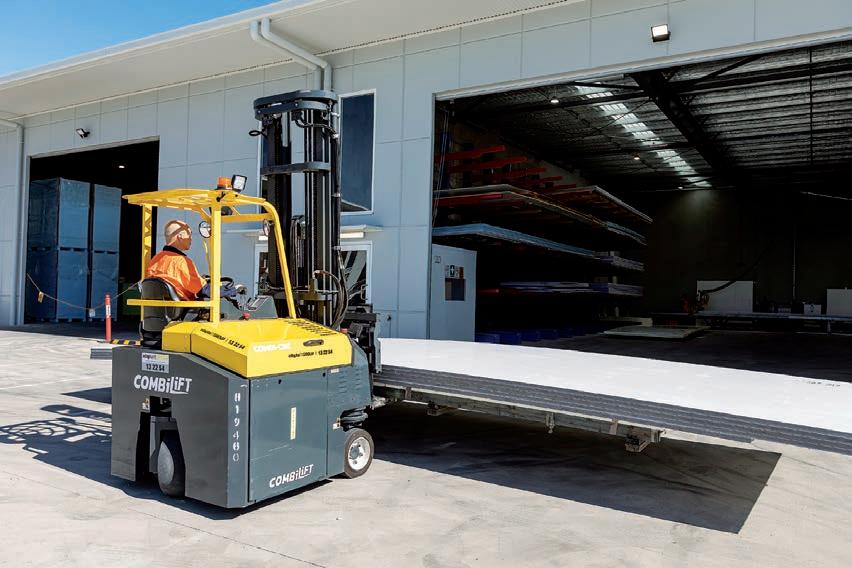
CANcapral.com.auYOU MACHINE ALUMINIUM TO MY CUSTOM REQUIREMENTS?
Capral prides itself on being able to deliver much more to our customers than the supply of materials. With our state-of-the-art machining equipment, we have the capability to supply semi-fabricated and finished rolled and extruded products. This can help you reduce your inventory, optimise your workspace and minimise manufacturing time, while reducing waste and improving efficiency. If you want Aluminium precision machined to your custom specifications, Capral can do.
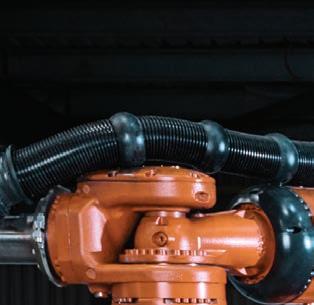

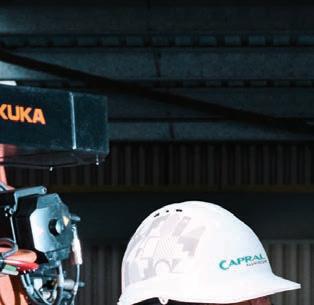
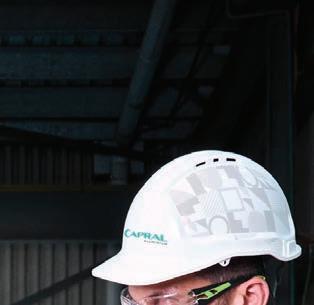
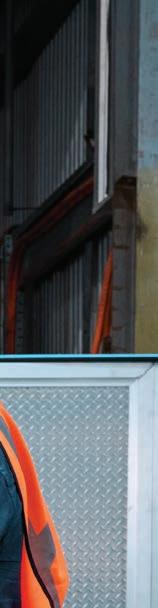
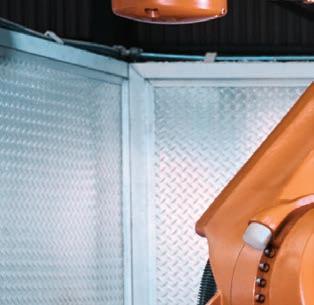
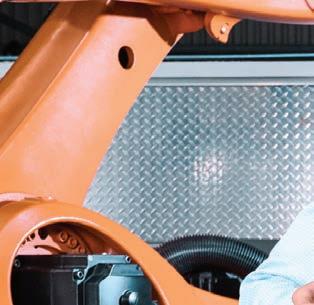
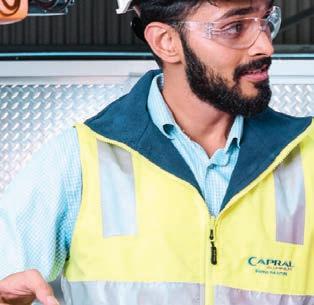

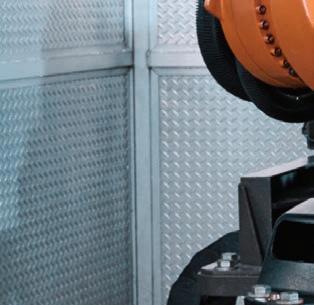
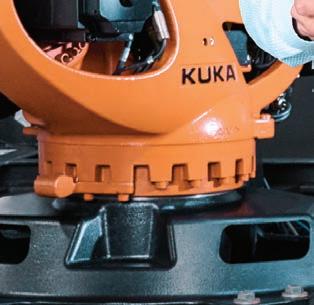
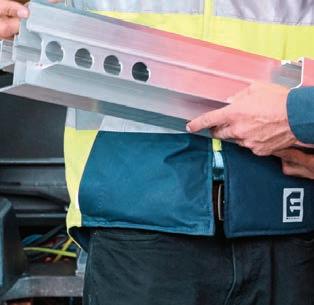
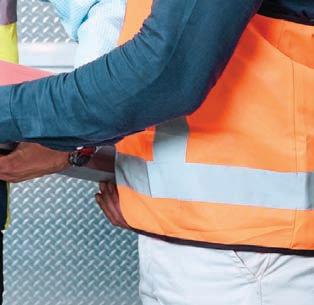
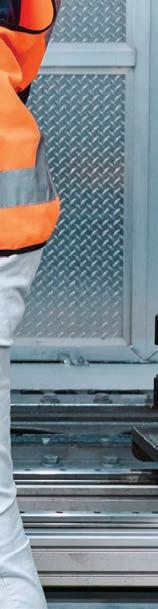
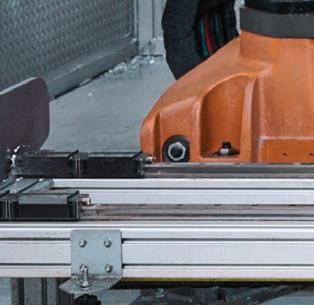
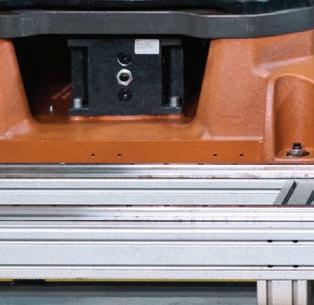
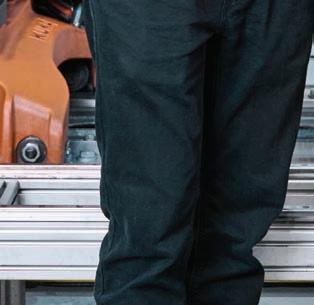
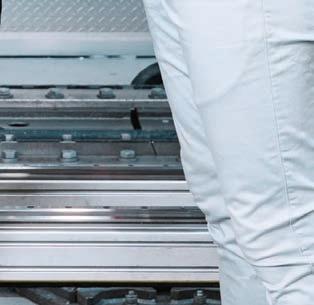
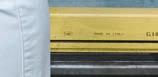
The August edition also discovers the grounds being made in the additive space. Earmarked as a big part of the future of manufacturing, many Australian companies are innovating on the world stage, exemplified by CNC Design’s projects through its Virtual Smart Factory Solution. Today, the IoT for the industrial sector – the Industrial Internet of Things (IIoT) or Industry 4.0, depending on the organisation you’re from – is highly developed, and the global market for it is large. Accenture’s report Winning with the Industrial Internet of Things already stated that the IIoT market will be more than $19.63 trillion by 2030. Our cover story shows how crucial Industry 4.0 is becoming across a variety of sectors. Coolon Brilliant Connected Lights ensure everything in an industrial environment is digitally connected, accounted for and reported on, enabling asset tracking services to locate equipment anywhere on site.
Turning technology into commercialisation IN Australia, while manufacturing reduced its greenhouse gas emissions significantly between 2008 and 2017, the industry still accounts for millions of tonnes of greenhouse gas emissions. The CSIRO found that Australian manufacturing sits in the equal second rung of carbon emitters, at 20.4 per cent. With energy price shocks now pressing in on business owners, along with interest rate rises, technology that can reduce costs are welcome. Such technology was showcased at this year’s Australian Manufacturing Week in Sydney, which was a terrific four days of celebrating industry leaders and innovators.Thisedition of Manufacturers’ Monthly reviews insightful conversations and presentations from the event, including Innovative Manufacturing CRC’s event and the Advanced Manufacturing Research Facility’s (AMRF) conference. Conversations we had with manufacturers on the trade floor had an undertone of positivity – the advancements being made in Australia are truly remarkable, but commercialisation remains a sticking point. Australia needs to improve its complexity of manufacturing to keep up with the rest of the world, supporting the great thinkers we have in this country. Prime Minister Anthony Albanese’s one billion dollar investment in advanced manufacturing will reportedly centre heavily across the energy sector. Qantas and Airbus are investing to establish a sustainable aviation fuel industry in Australia, which would help cut emissions by around 80 per cent compared with the fuels currently used.
government has invested over $800 million in scientific research.
6 AUGUST 2022 Manufacturers’ Monthly manmonthly.com.au
The New South Wales government is delivering the largest single investment in scientific research, innovation and technological development in the state’s history with a $832.7 million boost over four years. An investment in STEM programs will hopefully quell the skills challenge manufacturing has to overcome – teaching graduates and young people the skillsets required for the next era of advanced manufacturing. We must undoubtedly continue to bridge the “missing link” between universities who offer STEM courses and manufacturing companies who offer real-life work experience.
SYED SHAH – Managing Editor, Manufacturers’ Monthly Editor’s CommentTheNSW
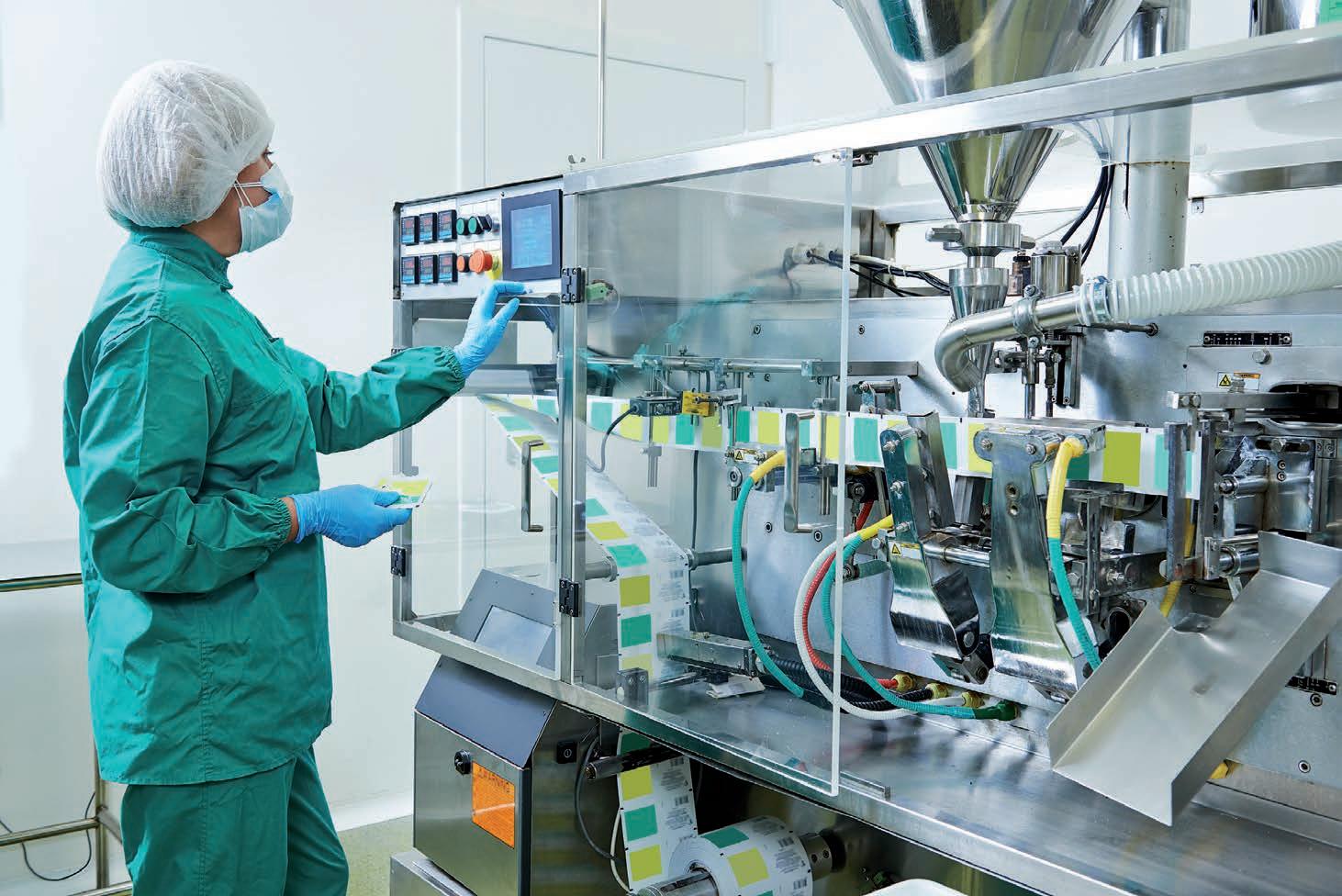
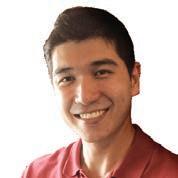

Taking low-pressure cold spray to the next level Titomic’s leading low-pressure cold spray systems make it easier, faster and more profitable to coat and repair temperature-sensitive materials like glass, ceramics and plastics. Unlock the limitless possibilities of cold spray technology for your factory floor – with less downtime, lower costs and no unwanted heat effects. info@titomic.com | titomic.com No need to pre-treat Spraywithinmetal10seconds competitiveCostRapidbuild-upcoating deformationsPrevent&stresses See what’s possible

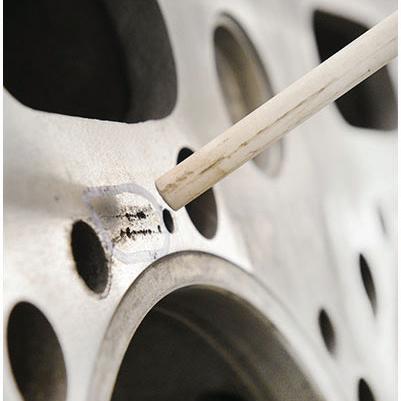
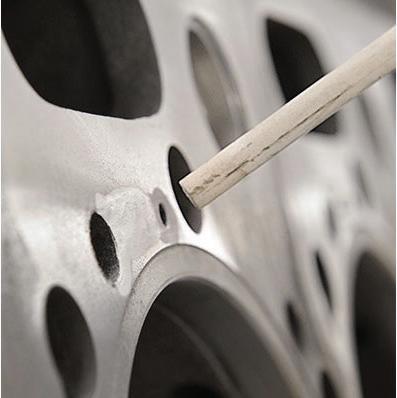
The problem is, in Australia, there are only two companies that manufacture wind towers: Keppel Price Engineering in Victoria, and Crisp Bros. & Hayward in Tasmania. By comparison, the wind market in the United States has grown substantially over the years into an increasingly complex supply chain. There are now more than 500 US manufacturing facilities specialising in wind components such as blades, towers, and generators, as well as assembly, across the country. Australia’s two local manufacturers price wind towers on a per project or a per section basis. This pricing model is required because they have a relatively small capacity (of less than eight sections per week), there are no long-term supply agreements with minimum demand requirements in place, there are design variations between OEMs, and the fluctuating exchange rate effects the cost of steel and shipping. All these factors impact the competitiveness of locally supplied wind towers. The main competition for Australian manufacturers are overseas suppliers from Vietnam, China and Indonesia. These suppliers operate large facilities with enormous capacity of up to 100 sections per week, have long-term supply contracts that facilitate improved production efficiencies and stability of supply, and some are exempt from import tariffs. Low cost labour, buying power and relative economies of scale are all in favour of imported product.
The transition to a clean energy future will require an enormous amount of additional generation and storage capacity. Wind power is the lowest cost form of large-scale renewable energy available to the market.
A Huge Opportunity for Local Manufacturers and Regional Areas Wind tower manufacturing offers a host of opportunities for local manufacturers. Fabrication facilities set up for onshore wind can transition to offshore wind with additional investment, increasing the lifespan and opportunities for the fabrication facility. Fabrication facilities designed for wind towers are multi-purpose—they can also be used to manufacture pumped hydro pipes, piling (for ports and bridges) and other large-scale heavy round manufacturing. Wind tower manufacturing requires a large numbers of employees. For example, a facility manufacturing eight wind tower sections per week could employ up to 120 full-time employees. Greater than 50 per cent of this workforce could be unskilled and trained on the job or via the TAFE training system. This means that there are training and employment opportunities for apprentices, trainees and Indigenous Australians. Wind tower manufacturing also generates demand for higher skilled roles (in areas such as engineers, quality assurance, and non-destructive testing), and a logistics network for movement of tower sections and raw materials into the facility.There are also downstream benefits for local suppliers of welding consumables, electrical components, safety equipment, painting consumables, internal components like platforms and handrails, hire equipment and facility maintenance.Importantly, wind tower manufacturing requires a large area, making it suitable for regional locations. As such, establishment of a wind tower manufacturing facility would generate immediate employment, economic and related benefits in regional communities. For the public, locally manufactured wind towers meet all Australian Standards across all components, from fabrication and electrical components, through to coatings. This means that both quality and public safety are assured.While our governments can wish, and hope, and make public pledges about Australia’s transition to renewable energy, we simply do not have the sovereign manufacturing capability to make this a reality. There is an answer though. Industry and Government Support To overcome the established overseas supply chains and generate investment into fabrication capability, local manufacturers need certainty of demand. This demand must stem from
Sovereign Manufacturing Capability is Essential for Australia’s Renewable Energy Future
Imported steelwork, which does not meet these requirements, is often of inferior quality and may not meet the Australian safetyTheserequirements.qualityand safety issues will only be exacerbated by increased global demand. The whole world is looking to transition to renewable energy. Countries like Scotland, New Zealand and Sweden are all investing in wind power. Not only will increased global demand likely reduce the quality of wind towers manufactured overseas, it will also increase scarcity of supply. There are already global supply chain issues— imagine how these will be magnified.
Practical and Political Uncertainty
The issue is that the quality of imported wind towers is appalling. They do not adhere to Australian Standards. Local fabricators comply to internationally recognised Australian Standards and are certified by the relevant Australian authority. In this way, Government and private clients can ensure the quality and safety of projects.
A USTRALIA is rapidly moving from carbon fuelled power generation to a renewable energy system. Renewable energy accounted for 32.5 per cent of Australia’s total electricity generation in 2021, an increase of almost 5 per cent compared to 2020. In the past five years, the proportion of Australia’s electricity that comes from renewables has almost doubled, increasing from 16.9 per cent in 2017 to 32.5 per cent in 2021. Last year’s renewables growth was led by small-scale solar, which added 3.3 GW of new capacity to record its fifth-straight record-breaking year. The large-scale sector also had a bumper year in 2021, adding 2,955 MW across 27 projects, which included Australia’s three largest solar farms and two of the country’s three largest wind farms. A further 68 large-scale projects were under construction or financially committed at the end of 2021, representing more than 9 GW of new capacity. However, the pipeline of new large-scale renewable energy projects slowed considerably in 2021, with the volume of new capacity committed falling from 3,001 MW in 2020 to 2,116 MW in 2021.At this rate, it is unlikely that Australia will achieve the more ambitious climate targets announced by Prime Minister Anthony Albanese in June 2022. Albanese pledged to cut carbon emissions by 43 per cent from 2005 levels by 2030, up from the previous government’s target of between 26 per cent and 28 per cent. The new target brings Australia more in line with other developed economies’ Paris climate accord commitments. For instance, Canada is aiming for a reduction of 40 per cent by 2030 from 2005 levels, while the United States has a target of up to 52 per cent. To put this into perspective, when Australia manufactured and erected the existing power grid, it took between 40 and 50 years. With Albanese pledging to cut carbon emissions by 43 per cent from 2005 levels by 2030, we have just eight years to manufacture and erect the assets required for the shift to renewables. It is an enormous project that must be completed in a very short space of time. It will necessitate the manufacture of thousands of wind towers and transmission towers, as well as thousands of kilometres of transmission lines. All this will require millions of tonnes of steel, and a highly skilled workforce. So then, with these more ambitious climate targets on the table, why is the renewable energy pipeline of work seemingly shrinking, when it should be expanding?Itisaresult of continued practical and political uncertainty for local manufacturers.
Local manufacturers like Keppel Prince Engineering and Crisp Bros. & Hayward cannot win jobs on their doorstep when governments and multinational companies place a premium on price over and above quality and safety.
8 AUGUST 2022 Manufacturers’ Monthly manmonthly.com.au GEOFF CRITTENDEN – CEO, Weld Australia Comment
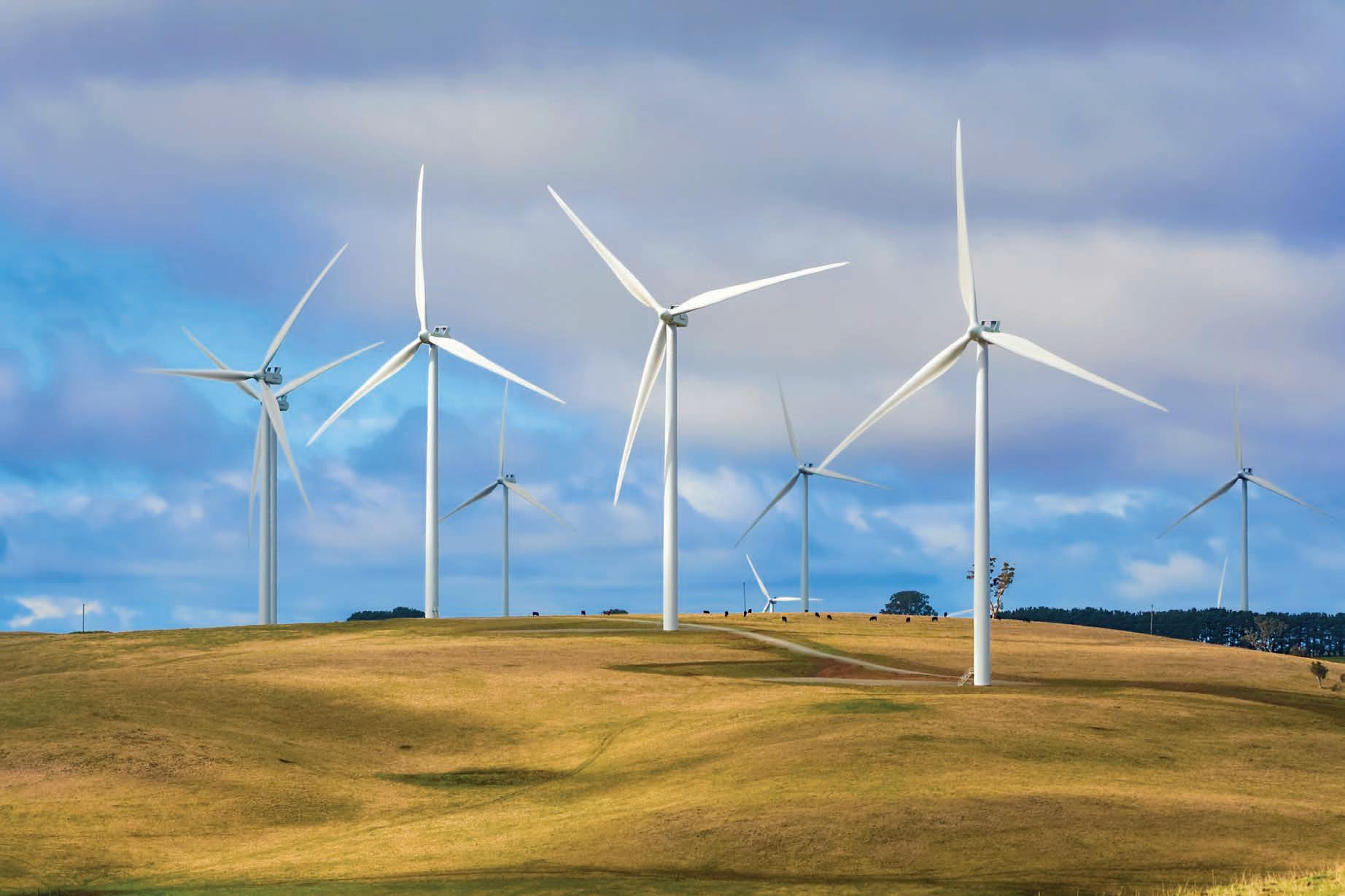
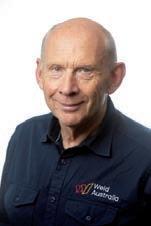
Demand for steel from the energy sector is likely to increase in the coming years.
Government must legislate local content policy. This will create a capacity mechanism that generates a clear, longterm signal for investment by private equity and local manufacturers. The Federal Government must also mandate that all wind towers are constructed, erected and inspected according to AustralianSecondly,Standards.withaclear commitment from government in place, Australia will need to invest in its steelmaking facilities. There are literally billions of tonnes of steel required. According to Australian Energy Market Operator’s (AEMO) 2022 Integrated System Plan, demand for steel from the electricity sector (NEM-wide) is likely to increase by approximately 50 per cent from 2021 to 2027. These demands equate to 8 per cent of Australia’s annual crude steel production, most of which is needed for wind turbine towers. Both the Whyalla and Port Kembla steelworks will need to be upgraded to
willing to investment the significant sums of money required—and with good reason.Next on the list: Australia will need to establish at least one, if not several, manufacturing hubs for wind towers, as well as transmission towers. Both industry and government will need to invest in these hubs significantly. Local manufacturers will need to invest in their own capacity and capability, from technology, plant and machinery through to employees.Lastly,wewill need welders. We will need to invest heavily in welder training, as well as welder recruitment and retention programs. Weld Australia is already liaising with key players in the manufacturing and energy industries. We are working with state governments across the country with a view to holding a series of roundtables to discuss the regulatory, logistics and engineering aspects required to fulfil training to devise a long-term plan. The Federal Government and state governments can wish their renewable energy policies into existence, but without a massive investment in fabrication and steelmaking facilities, and skills and training in each state, it will not be achievable.TheFederal Government must commit to building sovereign manufacturing capability for renewable energy—in the same way that it has for shipbuilding. It must mandate local content, as well as adherence to Australian Standards. Only with this commitment in place will industry have the confidence to invest. Unless industry and governments come together now to formulate a plan of attack, when the time comes to manufacture the assets needed for a clean energy transition, there will be no fabrication facilities, no skilled workforce, and no regulatory frameworks in place. There will be no sovereign manufacturing capability.
Renewable Energy Target (VRET) legislation has helped to support the domestic manufacturing industry. In addition, local content policy must be legislated. Given the huge scale of potential demand, local content need not be 100 per cent – VRET required 64 per cent local content and 93 per cent locally milled steel. With this local demand a reality, improved production efficiencies and stability of supply can improve competitiveness.WeldAustralia has been calling on the Federal Government for the last five years to mandate that all steelwork in Australia—both local and imported—is manufactured and erected according to Australian Standards. The Federal Government must act now to create a sovereign wind tower manufacturing industry, create jobs in regional areas and ensure public safety. Significant investment is also required.
manmonthly.com.au Manufacturers’ Monthly AUGUST 2022 9
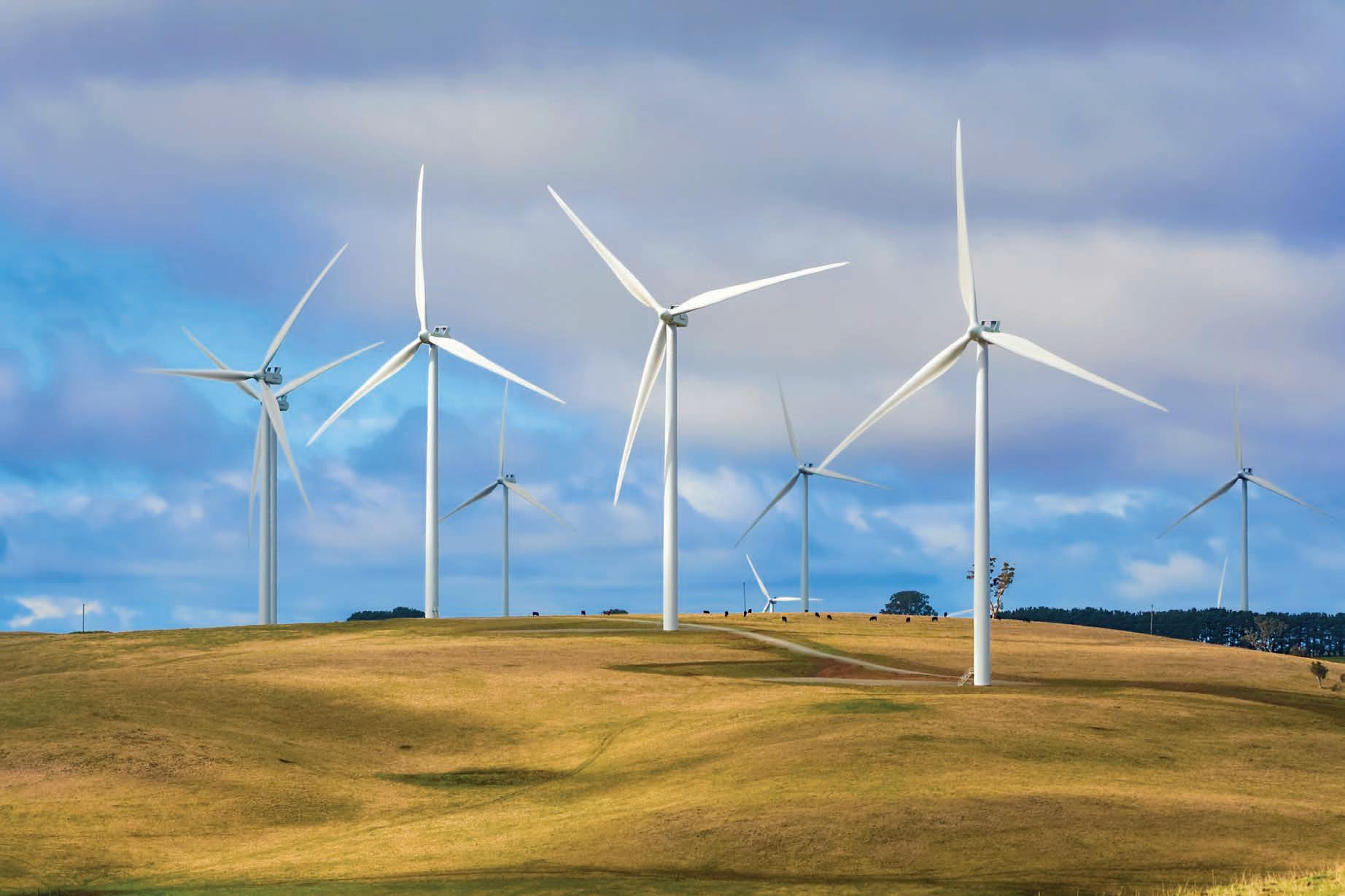
What does the new government need to do to improve local content in manufacturing?Australian
WITH a new government in charge, eyes are peeled on Anthony Albanese to see what proactive strategies Labor will implement to help Australian manufacturing. In June, the Prime Minister announced a billion-dollar investment as part of the country’s new advanced manufacturing strategy. Albanese said, “I want to use the power of government to bring back Aussie manufacturing. Because Australia should always be a country that makes things.” Targeted government support for local manufacturers may be key to helping Australia catch up to the pace of the global economy – Manufacturers’ Monthly posed the question to SEMMA CEO Vonda Fenwick.
Skills are key to securing local content – CEO,
10 AUGUST 2022 Manufacturers’ Monthly manmonthly.com.au VONDA FENWICK
SEMMA Comment
95 per cent of employment in manufacturing in Australia is within SMEs.
First of all, we were heartened by Anthony Albanese’s budget reply and his campaign announcements because they talked about their ‘Buy Australian Plan’. We have advocated strongly for quite some time – particularly in the last 12 months when we had the ear of both government and opposition MPs – on the importance of local content in government procurement. Mr. Albanese referred to the Australian government spending around 190 billion on government contracts at the federal level over the last three financial years, major economic lever available to drive the economic recovery. And when you are looking at those kinds of numbers, it is quite clear that if we can get a significant proportion of those contracts, it is going to benefit our manufacturers. They talked about actually locking in laws that would establish key elements of the Commonwealth procurement rules to fully support local industry accessing government purchasing opportunities. This is done at the Victorian level and the Local Jobs Commission has been quite active with improving the percentage of local content in our major infrastructure and rail projects – to see that happen at a federal level would be great. from the new Federal Government involved opening the door for more government work for small and medium businesses by decoding and simplifying procurement processes. One of the challenges we have found when talking to government about large contracts is that they are not often geared to deal with SMEs.We have always said that there needs to be recognition at government level that 95 per cent of employment in manufacturing in Australia is within SMEs. We understand the government cannot be all things to all people, but a little concern at the moment is they seem to be picking up on the same six Manufacturers’ Monthly speaks with South East Melbourne Manufacturers Alliance CEO Vonda Fenwick about the government’s approach to local content and the skills challenge facing Australian manufacturing.
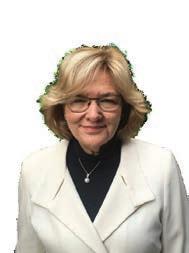
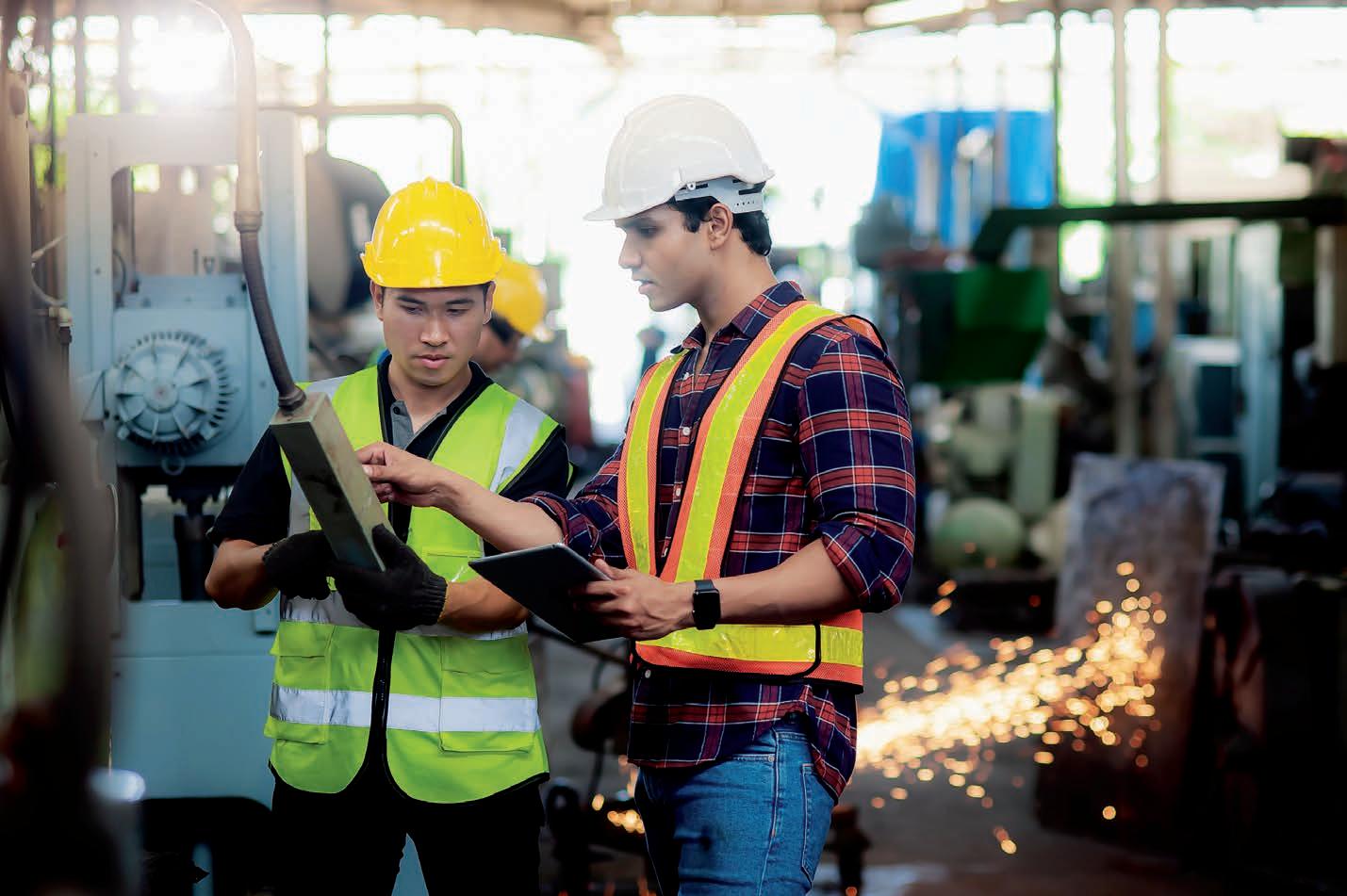
were focused on. You obviously have to have defence and medical equipment capabilities, and if the pandemic taught us anything, it’s that we need to be much more self-sufficient. Government is starting to look at the semiconductor space, because you cannot have smart defence equipment and you cannot have smart medical equipment or other smart high value products unless you have got semiconductors. It is a huge investment, but if we do not have at least some access to semiconductors, we have got a significant problem. We think the Southeast would be ideal for setting up that kind of process because the region is geologically stable with access to water as well as transport options and easy access to CSIRO facilities, the synchrotron and university precincts.
Skilled workers are crucial to supporting local manufacturing content.
In order to help grow SMEs, they will have to grow in size themselves. How can we help train and upskill more workers into different manufacturing roles?
There are several fronts on which we can tackle that. There is a big focus on creating jobs, but jobs are not the problem which needs fixing – we need to find the skilled workers to fill the jobs. Some of our members cannot afford to limp along for another few years or knock orders back due to a shortage of skilled labour , so they are investing in automation, including robots to perform essential tasks Once again, the government has talked about 465,000 fee-free TAFE places, but one of the challenges we find is that the need is there right now. Not just in our industry but across the board, but especially in manufacturing, the need for skilled workers happened yesterday rather than in three years when people exit with their trade and university qualifications. So, I think we have to be a lot more creative about what we do to start to get those skills. You would be aware of the welding programme that we have developed. We are about to do our fifth pilot course in our SEMMA Welding program next week, and I can tell you from our first few courses the model works a treat. We have been able to take unskilled people who never held a welding gun and in four weeks, they are heading out to a job with one of our SEMMA manufacturing members because they have developed that basic skill set. Critics will say it won’t replace a trade qualification: we agree and do not want it to replace a qualification – it creates a basic skillset. A number of people from the course have been offered apprenticeships with companies. You can provide someone who has done nothing more than low skill, insecure casual work for years, with a real career path in manufacturing. We also have a perception problem at the front end. One of the programs that I was involved with in the employment space through the Southern Metro Partnership, which is a Victorian government initiative, was looking at trying to attract people not just to manufacturing, but also to aged care and hospitality. They ran three information sessions, one for aged care, one for hospitality, and one for manufacturing. And they measured the level of interest of various age groups. In hospitality, 58 per cent of the 15 to 24 age group were interested in work in the hospitality sector . For aged care, the figure was around 30 per cent in the age group. In manufacturing, there was no one from the 15 to 24 group who said I’m interested in manufacturing, not one.
Some schools have some great initiatives in place to encourage students to consider careers in manufacturing. However, we have talked for years about needing a national initiative similar to the tourism advertising drives – something really visible in prime time television or on social media which is going to highlight how essential and wonderful manufacturing is. We are seeing more emphasis on STEM subjects, but we need something national which gets young people and their parents excited about manufacturing as a career.
manmonthly.com.au Manufacturers’ Monthly AUGUST 2022 11
When we had a look at the six preferred categories, it leaves out something like 70 different sectors within manufacturing, so I think the approach needs to be a little more flexible in terms of spending and investment. The problem with the distinct categories is if there is a limited amount to spend, we may end up filling a quota in a chosen category where it could be more cost effectively invested elsewhere. It seems to me that with policy at times, and certainly we have seen that with the modern manufacturing strategy, there has been a focus on gearing it towards large companies. There needs to be recognition that the manufacturing landscape and the supply chains are made up of small to medium enterprises and the legislation needs to reflect and support that. For example, we have seen contracts where onerous risk clauses had been cascaded so far down the supply chain that it was impossible for our local manufacturers to participate.Weneed to have both policy settings and the percentages in place to guarantee local content, and it appears that the current government is putting these forward which aligns with the advocacy we have been doing over recent years and have put to government members repeatedly in the last 12 to 18 months.
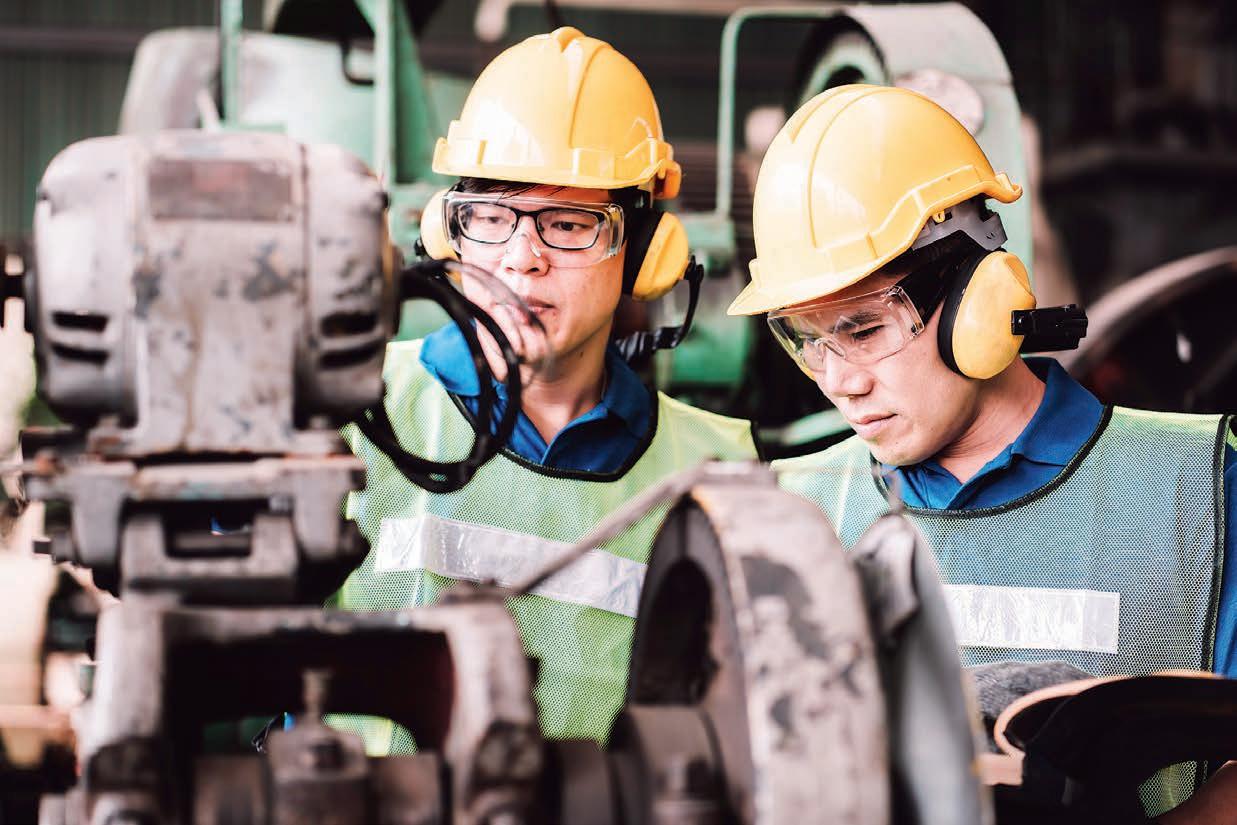
Composition, shape, and surface properties must be controlled closely to ensure a cell performs reliably over many years.Mines and petroleum minister “The McGowan government is committed to growing and diversifying Western Australia’s mining industry,” he added. “Western Australia isn’t just famous for having all the minerals you need to make a battery, we also have the capabilities to progress down the value chain and grow our battery manufacturing and downstream processing industries.”
The Cathode Precursor Production Pilot Plant is backed by 19 industry, research and Government participants, representing a major step in Australia’s journey to expand its presence throughout the global battery value chain. The first of its kind in Australia, the plant will establish the technology and capabilities for Australia to design and build cathode precursor manufacturing facilities on a commercial and industrial scale.The news comes after the Future Battery Industry CRC welcomes the announcement from the Queensland government to boost the state’s contribution to the energy storage revolution, with a $15 million investment in the National Battery Testing Centre (NBTC) in Brisbane. This facility will also be a first of its kind in Australia, backed by 36 industry and research participants. Cathode precursors are precisely engineered materials, the highest cost component of a cell, and a crucial element of the battery value chain. The FBICRC’s report — Future Charge — Building Australia’s Battery Industries — identified establishing an active materials manufacturing capability as an
12 AUGUST 2022 Manufacturers’ Monthly manmonthly.com.au News @MM
The project looks to capitalises on Australia’s strong position in mining and its emerging battery metal refining industry. Australia is building from its mining strength to develop diversified battery industries which generate greater value. The facility will link with other FBICRC flagship projects across Australia, including the National Battery Testing Centre at the Queensland University of Technology, battery materials research at the University of Technology Sydney, electrolyte research at Deakin University and battery anode research at the University of Melbourne. Shannon O’Rourke, CEO of the FBICRC said the launch of the Cathode Precursor Production Pilot Plant is the culmination of several years of hard work, collaboration and integration by industry-leading partners and academic institutions, to progress the current and future needs of industry. “We’re delighted to see this world class facility up and running,” O’Rourke said. “The incoming government has Plant will be a key enabler to build an Australian manufacturing capability.” Co-precipitation units used in the German facility will be used for the new plant in WA. The global battery market is expected to grow 9-10 times by 2030 and 40-fold by 2050. In a net-zero world, between now and 2050 over $23 trillion will be spent on batteries. Australia is well positioned to capture more of this value given it is the only country with leading resources of all raw materials required to make high performance batteries – Nickel, Cobalt, Manganese, Graphite and Lithium. Cathode precursor materials are further processed to create cathodes in the humble battery cell. The performance, durability, safety, and operating envelope of a cell are impacted by the properties of precursor materials.
A manufacturing technology fund could help hit renewable targets
FBICRC launches cathode precursor plant.
Jessica Farrell, asset president at Nickel West, said the launch of the Cathode Precursor Pilot Plant is a vital step towards developing a future growth industry in Western Australia. “The launch of this plant, made possible through the repurposing of equipment from our Nickel Sulphate Pilot Plant, will allow the FBICRC and the State Government to explore further options for a downstream battery materials manufacturing industry,” she noted. “This is another exciting step for BHP as a major supplier of nickel, a commodity highly sought after by car and battery manufacturers across the globe.”

Australian Rollforming Manufacturers Pty Ltd ABN 30 160 982 178 46A Brooks Drive Dandenong South VIC 3175 T +61 3 8769 7444 F +61 3 8768 7496 CONTACTwww.ausrollform.com.auinfo@ausrollform.com.auUS03 8769 7444
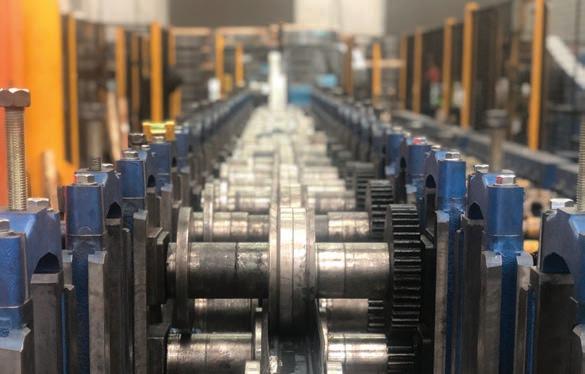
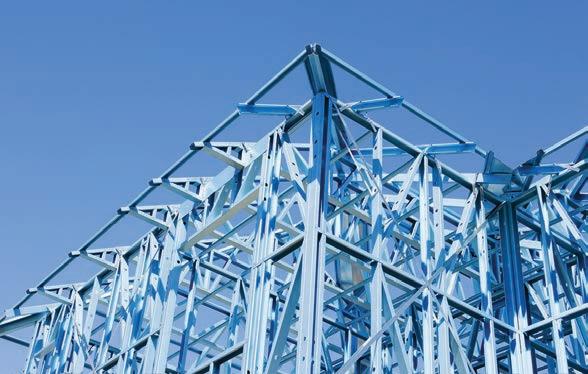
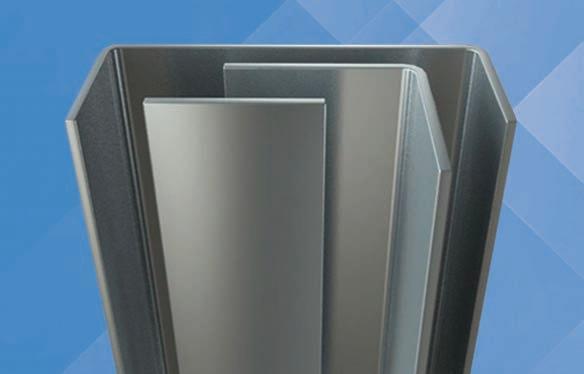
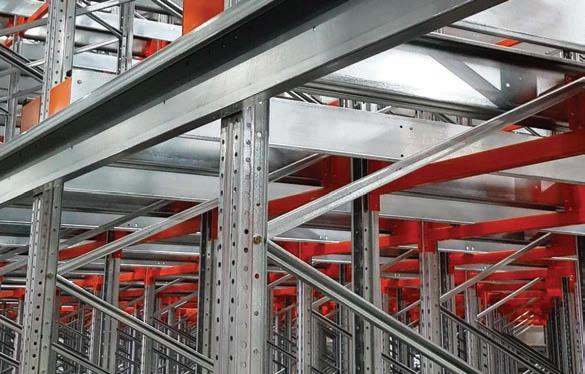
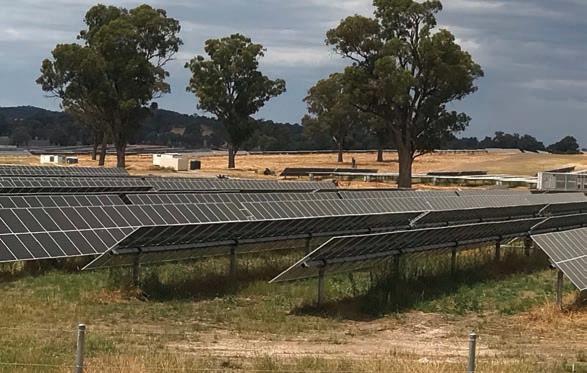
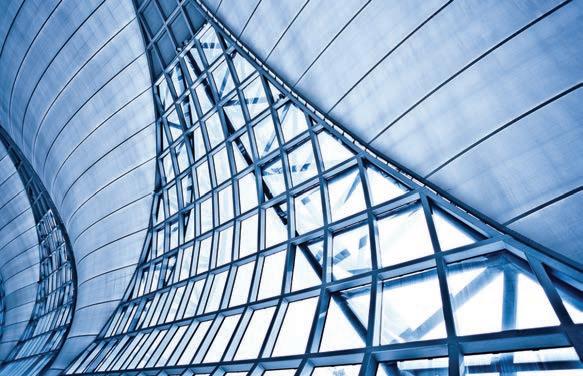
A joint investment from Airbus and Qantas will kickstart an Australian biofuels industry.
The new fleet will offer a significant reduction in fuel consumption and carbon emissions of up to 25 per cent from day one and are all already certified for operation using 50 per cent SAF. According to Joyce, the investment would accelerate the development of SAF in Australia, create jobs and reduce the nation’s dependence on imported fuels. “The use of SAF is increasing globally as governments and industry work together to find ways to decarbonise the aviation sector,” Joyce said. “With this investment, Qantas and Airbus are putting our money where our mouth is and betting on the innovation and ingenuity of Australian industry.”
The New South Wales government will deliver the single largest investment in scientific research, innovation and technological development in the state’s history, with a landmark $832.7 million boost over four years under the 2022-23 NSWMinisterBudget.for Science, Innovation and Technology, Alister Henskens, said the Budget would turbocharge NSW’s innovation ecosystem, creating jobs and new industries in line with the state government’s 20-Year Research & Development Roadmap. “The NSW Budget delivers unprecedented investment in research and development and commercialisation initiatives to create new jobs and drive growth in emerging industries and deliver long-lasting economic prosperity,” Henskens said. “The Budget will invest in innovation and commercialisation, attract international investment and help homegrown talent turbocharge their R&D work. This landmark investment is a game changer for NSW and demonstrates the NSW government’s commitment to turning local research into new industries and jobs for future generations.”
• $12.5 million for RNA R&D Initiatives ($119.1 million over 10 years) to accelerate the translation of RNA research into new products, services and jobs.
• $342.4 million over four years to boost support for the commercialisation of products, services and emerging digital technologies in fields that will grow the economy and providing targeted support to research institutions, startups, scale-ups and small- to-medium enterprise sectors in NSW $72.2 million in capital expenditure for the development of the RNA Pilot Manufacturing Facility
“We’re calling on other companies and producers to come forward with their biofuel projects. In many cases, this funding will be the difference between some of these projects getting off the ground.“The aviation industry also needs the right policy settings in place to ensure the cost of SAF comes down over time so that the cost of air travel doesn’t rise. We’ve had some encouraging discussions with the incoming Australian government given their strong focus on emissions reduction and look forward to that progressing.”Faurysaid that ensuring a sustainable future for the industry has become the priority for Airbus. “The increased use of sustainable aviation fuels will be a key driver to achieve net zero emissions by 2050. But we can’t do this without viable industrial systems to produce and commercialise these energy sources at affordable rates and near to key hubs around the world,” he said. “This is especially true for a country like Australia, which is geographically distant and highly reliant on aviation to remain connected both domestically and internationally.”
The Budget includes a $703.4 million investment to establish the Future Economy Fund, which will expand and accelerate R&D and commercialisation opportunities across the state, building on the work of the NSW government’s R&D ActionBudgetPlan.highlights for 2022-23 include: $252.4 million ($703.4 million over four years) for the Future Economy Fund NSW’s first dedicated fund to target the end-to-end stages of business growth – from R&D and commercialisation, through to industry growth, investment attraction and maturity. The fund will include investments of: • $142.0 million over four years to drive research, development and innovation growth in sectors where NSW has a natural competitive advantage, and advance collaboration with universities, CSIRO and the private sector
The Qantas Group and Airbus are investing up to $287 million to establish a sustainable aviation fuel (SAF) industry in Australia in a landmark agreement. The Australian Sustainable Aviation Fuel Partnership was signed by Qantas Group CEO, Alan Joyce and Airbus CEO, Guillaume Faury ahead of the IATA AGM. The lack of a local commercial-scale SAF industry has meant that Australia currently exports millions of tonnes of feedstock each year, such as canola and animal tallow, to be made into SAF in otherThecountries.QantasGroup, which has committed to using 10 per cent SAF in its overall fuel mix by 2030, is sourcing SAF overseas, including 15 per cent of its fuel use out of London and 20 million litres each year for flights from Los Angeles and San Francisco to Australia from 2025. Sustainable fuels cut greenhouse gas emissions by around 80 per cent compared to traditional kerosene and are the most significant tool airlines currently have to reduce their impact on the environment – particularly given they can be used in today’s engines with no modifications.TheQantas and Airbus partnership will provide funding for locally developed and produced SAF and feedstock initiatives. Projects will have to be commercially viable and meet a strict set of criteria around environmental sustainability. Airbus and Qantas agreed to work together on the sustainability initiative part of the airline’s recently announced orders. These include the A350-1000 to operate “Project Sunrise” non-stop flights from Australia to New York and London, and the selection of the A220 and A321XLR under the carrier’s “Project Winton” domestic fleet renewal, as well as lower emission aircraft for Jetstar.
“The agreement we are signing with Qantas today reflects the new level of partnership between our two companies and our firmly shared commitment to act as catalysts of change to ensure a bright future for our industry.”
The single largest R&D investment in NSW history
Airbus.credit:Image
14 AUGUST 2022 Manufacturers’ Monthly manmonthly.com.au News @MM
Qantas and Airbus to establish sustainable aviation fuel in Australia
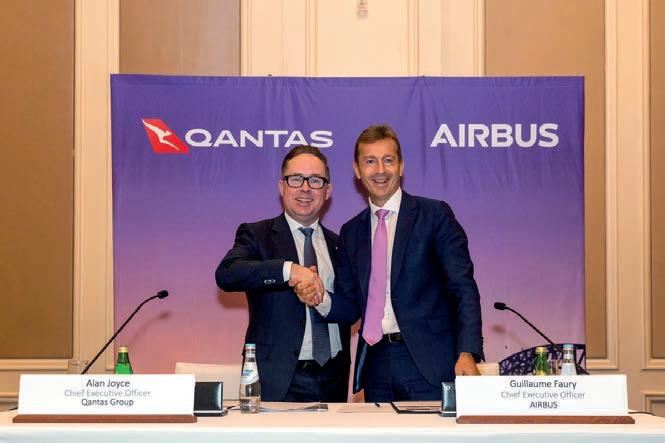
will help industry construct quantum models for new products.
The
Quantum technology breakthroughs in communications, sensing and computing boost this strategically important sector, which is estimated to deliver $4 billion in economic growth and 16,000 new jobs by 2040.”There are over 17 quantum related companies in Australia which have received combined funding and investment of over $400 million across the breadth of quantum technology types, hardware, software and consultancy capability in recent years. SQC is Australia’s world leading quantum company developing a siliconbased quantum computer. Professor Michelle Simmons is SQC’s founder who recently launched a $130 million Series A capital raising to fund the next phase of the computer’s development. quantum breakthrough that will fuel Australian breakthrough
manmonthly.com.au Manufacturers’ Monthly AUGUST 2022 15 News @MM Australian quantum computing company, Silicon Quantum Computing (SQC), has announced the world’s first integrated circuit manufactured at the atomic scale two years ahead of schedule. SQC is leading the world in developing silicon-based quantum computing by creating an integrated quantum processor that accurately models the quantum states of a small, organic polyacetylene molecule which will help create new materials.Ledby Professor Michelle Simmons, this scientific breakthrough will allow SQC to help industries construct quantum models for a range of new products such as pharmaceuticals, materials for batteries and catalysts. “SQC’s breakthrough in quantum computing is big news and a terrific reflection on the quality of local knowhow. It’s providing a clear pathway for new and emerging technologies to support our world class industries,” minister for Industry and Science Ed HusicThesaid.federal government has announced an investment of $1 billion in the form of a Critical Technology Fund, as part of the broader National Reconstruction Fund. This will help to support home-grown innovation and production in areas like engineering, data science, software development, AI, robotics and quantum. To ensure the continuous growth and supercharge the quantum computing industry, the government is also providing $4 million for up to 20 PhDs in quantum research to support universities establish national research and education partnerships.“Australia’s research capabilities lay the foundations to build a strong quantum industry both domestically and with our like-minded international partners.
industry The leading supplier of high quality components and products to industrial markets Flexible MeasuringCablesSystemsFlexibleConduits Chain ex Cables Energy Chains Cable Accessories Gear boxesBearings Linear ConnectorsSensorsUnits Australian owned & managed | 1300 65 75 64 | www.treotham.com.au | info@treotham.com.au CHECK OUT OUR NEW WEBSITE Safety Products The
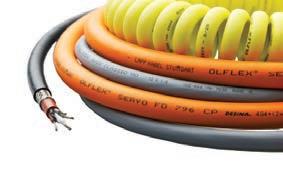
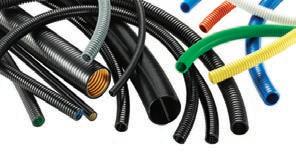
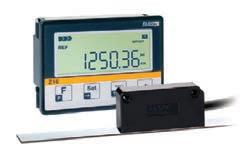
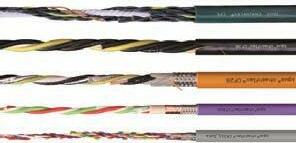
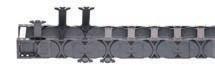
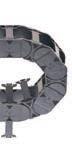
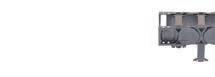

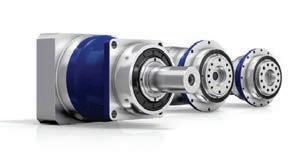
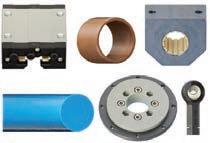
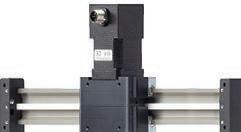

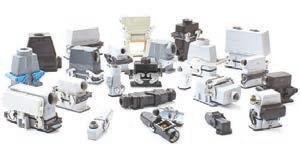
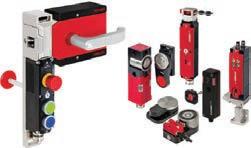
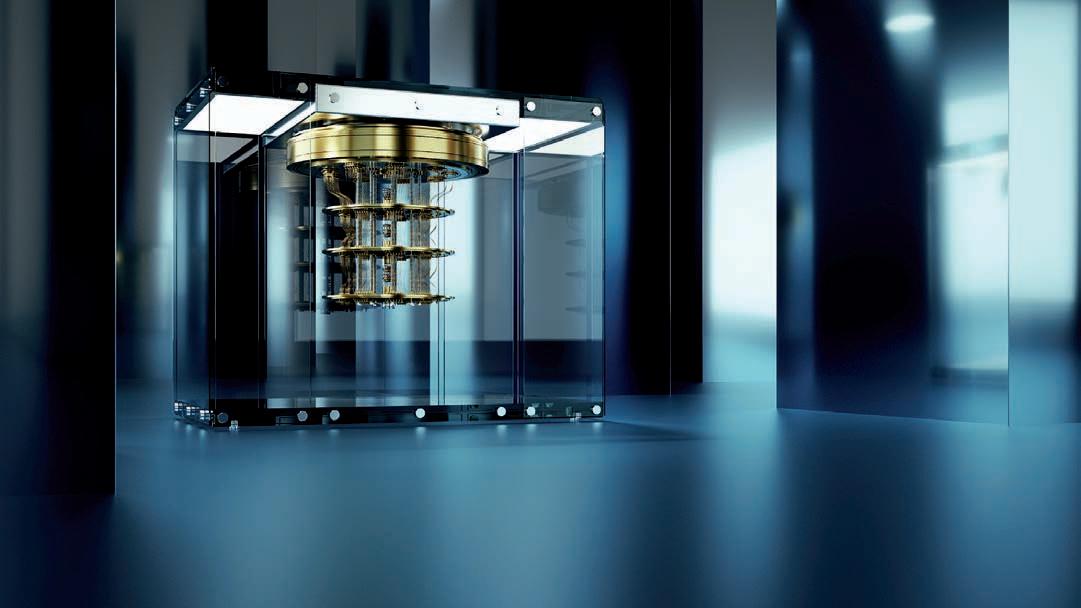
• Dr Julie Wheway – gemaker; Sally-Ann Williams – Cicada JInnovations;anMason–chief executive Women;
The Australian Academy of Technology and Engineering (ATSE) has appointed 16 STEM champions from industry and academia to lead an Advisory Group for the $41.2 million Elevate: Boosting Women in STEM program. Funded by the federal government, the program will award up to 500 undergraduate and postgraduate scholarships over seven years to women in science, technology, engineering and mathematics. ATSE has partnered with government, industry, and the higher education and research sectors.
• Dr Morley Muse – Women in STEMM Australia;
ATSE is a Learned Academy of independent experts helping Australians understand and use technology to solve complex problems. This news comes after a recent ATSE report stated that Australia must capitalise on its renewable technology advantage and invest in rapid deployment to decarbonise energy systems.
• Beata Khaidurova – FB Rice; Scarlet Kong – DMTC;
New Advisory Group elevates women in STEM
16 AUGUST 2022 Manufacturers’ Monthly manmonthly.com.au News @MM
• Kylie Walker – CEO, ATSE; and Dr Marguerite Evans-Galea – director, STEM Careers Strategy, ATSE.
• Professor Sumeet Walia – Science & Technology Australia;
ATSE.credit:Image
The Elevate Advisory Group will be co-chaired by non-executive director, engineering leader and former president of the World Federation of Engineering Organisations (WFEO), Dr Marlene Kanga, and Dr Adi Patterson – an international leader in nuclear science and technology, and a champion of change.TheAdvisory Group will champion the program, secure sector wide partnerships, and guide strategy and implementation of the program. “I am proud to lead this incredible project which we hope will shift the dial in the level of participation of women in STEM. This is vitally important to secure Australia’s future as a technologically advanced nation,” Kanga said. “The Advisory Group comprises 16 of Australia’s most experienced STEM ambassadors who will collectively transform our assumptions about who can work in STEM.” “The Advisory Group will champion diversity and inclusion, and help shape an immersive program for scholarship recipients, exposing them to inclusive leaders, programs, networks and organisations, that nurture and support their professional development and futureATSEcareers.”CEOKylie Walker said the support for Elevate from across the STEM community and sectors has been humbling.“There is genuine excitement for this program, and its potential to transform the standing of women in STEM careers,” Walker“Elevatesaid.must be designed with partners across the very broad range of Australian sectors that rely on a highly skilled STEM workforce; we’re designing the program to meet Australia’s skills demand by supporting diverse women to pursue tertiary education and careers in STEM, and by propelling them into leadership.According to Walker, the Elevate program is built around three pillars: education and impact, skills building, and“Theleadership.first,Education and Impact, will support scholars to become Australia’s future leaders in STEM research and commercialisation. Second, Skills Building, puts the focus on professional development, mentoring and exposure to the innovation pipeline,” she said. “Third – Leadership – will accelerate women’s career trajectories into senior leadership and support them as mentors, board directors, and influencers, stimulating more womenled decision-making throughout the STEMTheecosystem.”federalgovernment’s Women in STEM Ambassador, Professor Lisa Harvey-Smith, has also joined the Advisory Group. “The power of this Advisory Group is the broad range of expertise of its members and their profound interest in the issues faced by women in STEM,” Harvey-Smith said. “Their collective vision and focus on solutions will drive real change in STEM disciplines.”
• Dr Frazer Thorpe – Cooperative Research Australia;
• Dr Udani Reets – Women in Leadership Development (WILD); Luke Sheehy – the Australian Technology Network of Universities (ATN);
STEM champions have been appointed to lead an Advisory Group for the Elevate program.
The Elevate Advisory Group also includes representatives from program partners and includes: Dr Marlene Kanga and Dr Adi Paterson – co-chairs; Professor Lisa Harvey-Smith –Women in STEM Ambassador; Shanan Gillies – Department of Industry, Science, Energy and Resources;
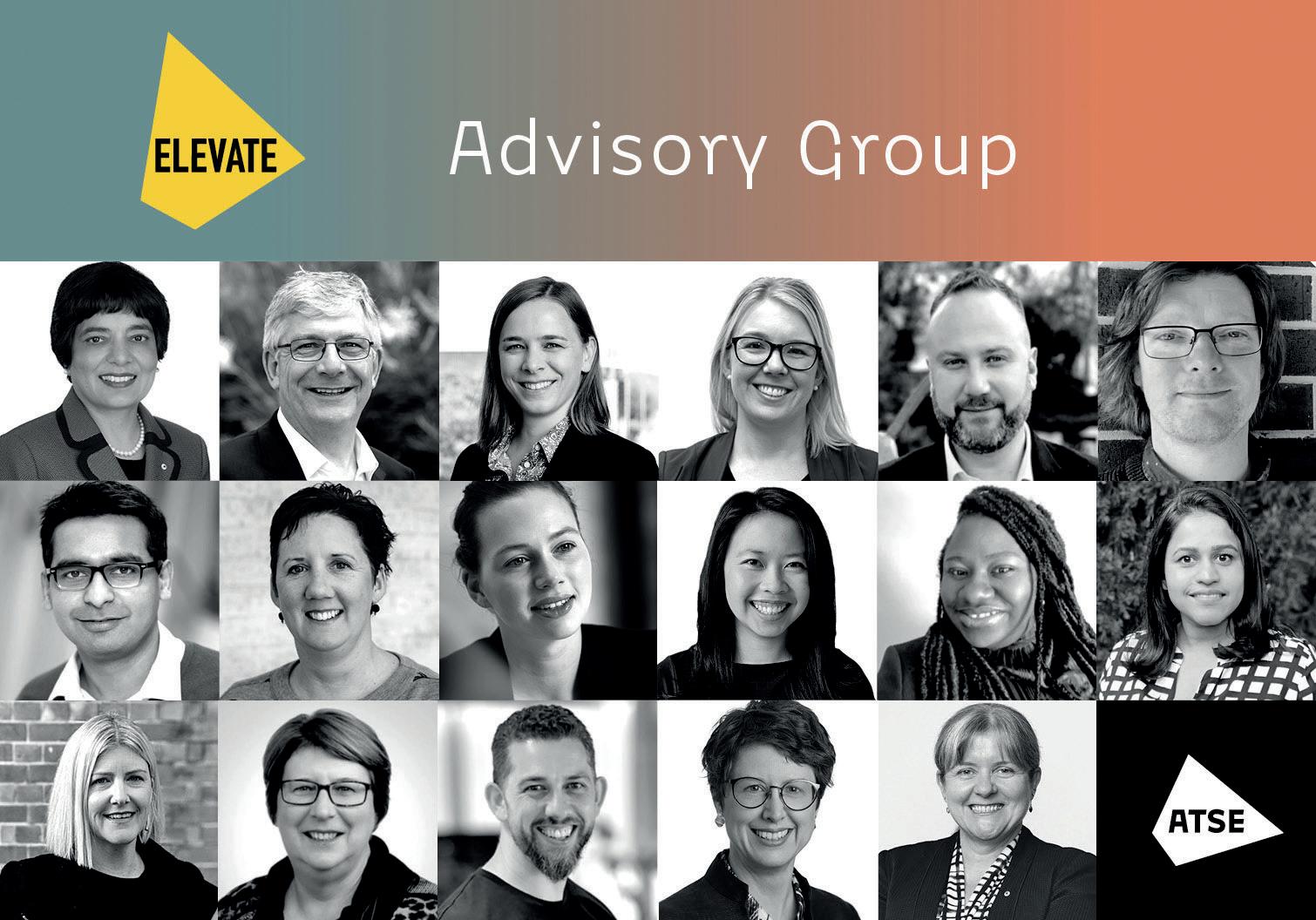
Act now to secure your company’s place at
manmonthly.com.au Manufacturers’ Monthly AUGUST 2022 17 News @MM
A new solution for stem cell manufacturing
UTS biomedical engineer, Professor Majid Warkiani, led the translational research, in collaboration with Regeneus – an Australian biotechnology company that develops stem cell therapies to treat inflammatory conditions and pain. “Our cutting-edge technology, which uses 3D printing and microfluidics to integrate a number of production steps into one device can help make stem cell therapies more widely available to patients at a lower cost,” Warkiani said. “While this world-first system is currently at the prototype stage, we are working closely with biotechnology companies to commercialise the technology. Importantly, it is a closed system with no human intervention, which is necessary for current good manufacturingMicrofluidicspractices.”istheprecise control of fluid at microscopic levels, which can be used to manipulate cells and particles. Advances in 3D printing have allowed for the direct construction of microfluidic equipment, and thus rapid prototyping and building of integrated systems. The new system was developed to process mesenchymal stem cells, a type of adult stem cell that can divide and differentiate into multiple tissue cells including bone, cartilage, muscle, fat and connective tissue.
Researchers from the University of Technology Sydney (UTS) and industry partner, Regeneus, have developed a unique 3D printed system for harvesting stem cells from bioreactors. This heralds the potential to produce high quality stem cells at a wide scale in Australia, at a lower cost. Stem cells offer great promise in treating many diseases and injuries, from arthritis and diabetes to cancer, because of their ability to replace damaged cells. But the current technology used to harvest stem cells is labour intensive, time consuming and expensive.
Mesenchymal stem cells are initially extracted from human bone marrow, fat tissue or blood. They are then transferred to a bioreactor in the lab and combined with microcarriers to allow the cells to proliferate.Thenew system combines four micromixers, one spiral microfluidic separator and one microfluidic concentrator to detach and separate the mesenchymal stem cells from microcarriers and concentrate them for downstream processing. Warkiani said other bioprocessing industrial challenges can also be addressed using the same technology and workflow. This would help to reduce costs and increase the quality of life-saving products.
Through REACH, Deakin University will help create scalable pathways for renewable technologies. Australia’s Southern Hemisphere.
own international industry event, the most comprehensive aviation, aerospace and defence exposition in the
PREVIOUSHIGHLIGHTSEVENT l 38,952 Trade Visitor Attendances l 698 Participating Companies l 41 International Air Chiefs and Representatives l 161 Official Delegations WWW.AIRSHOW.COM.AU
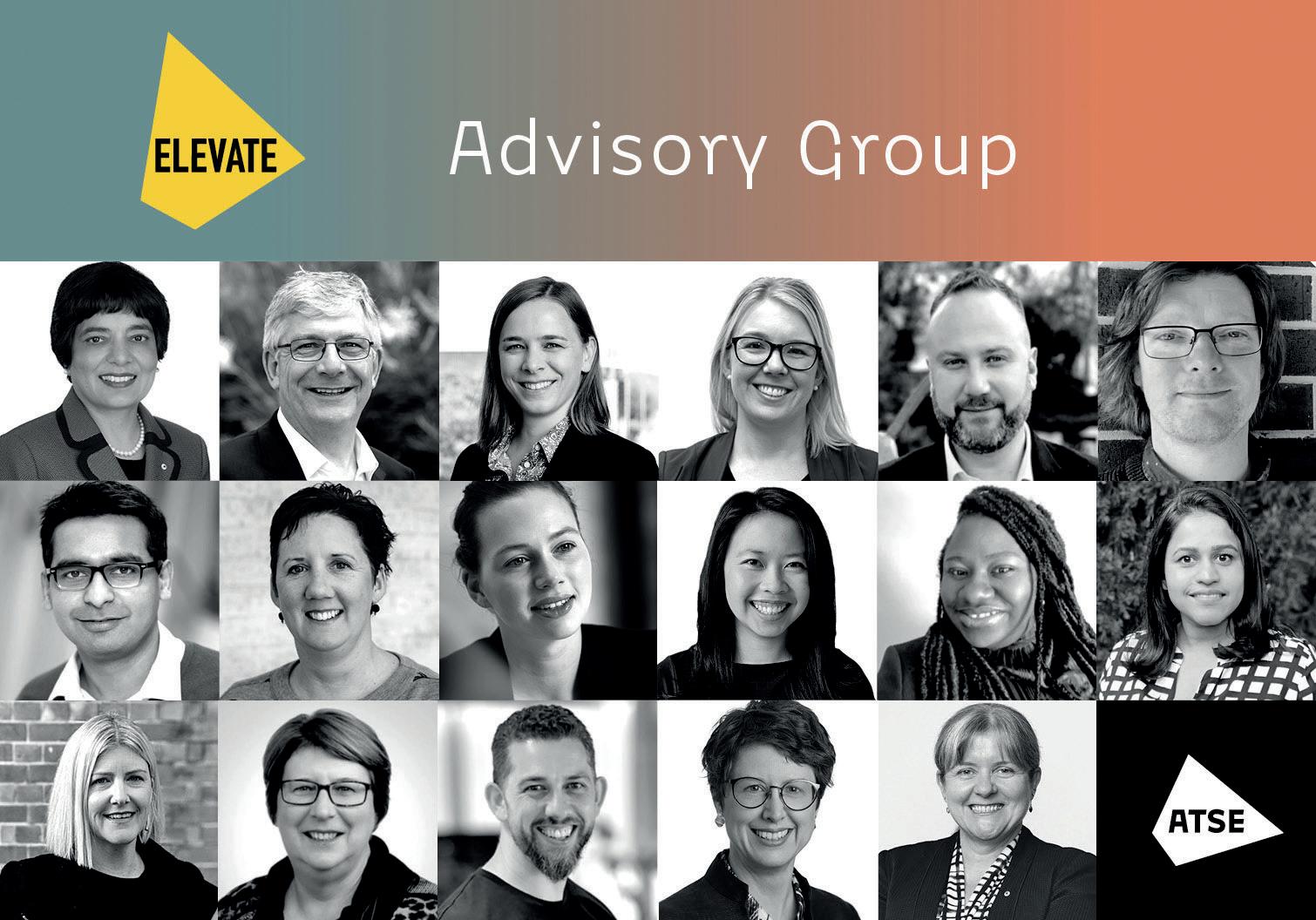
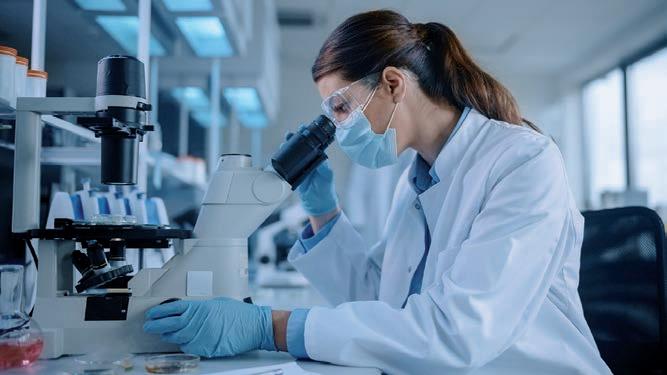
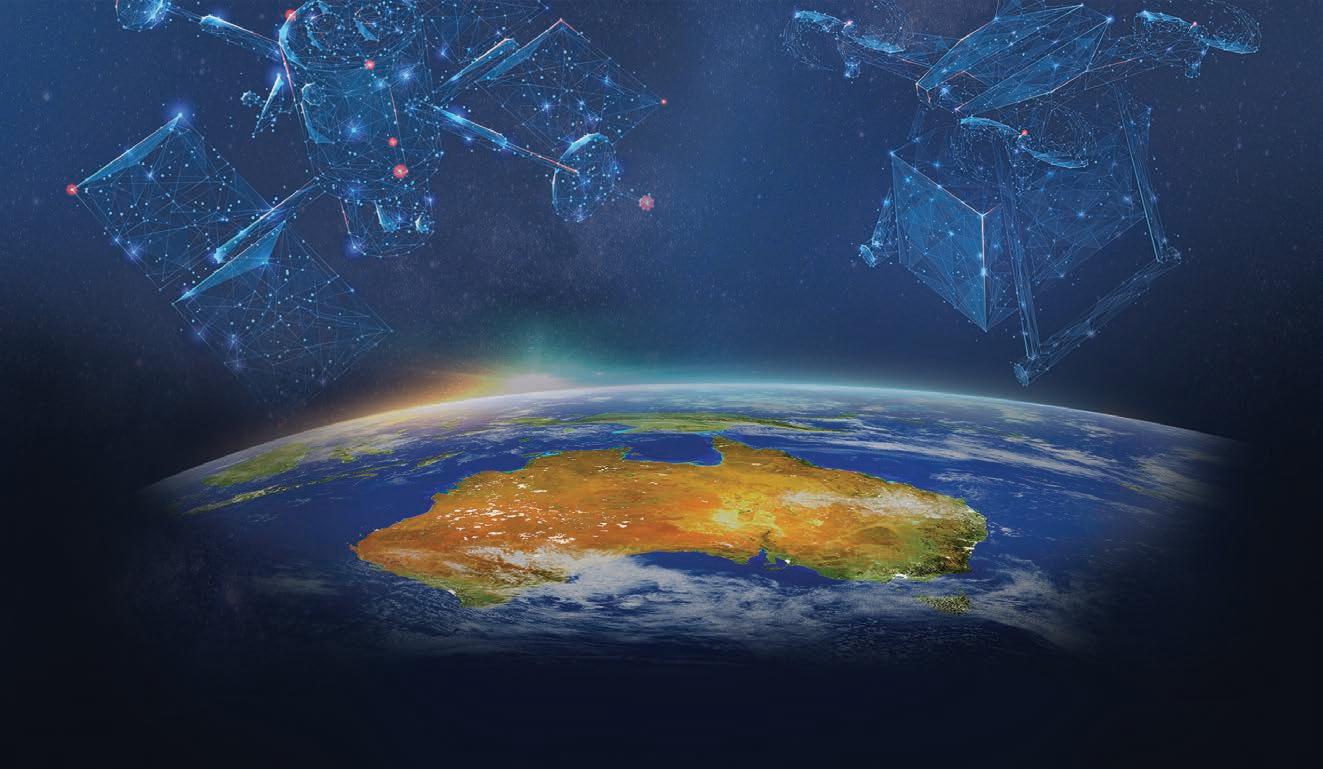
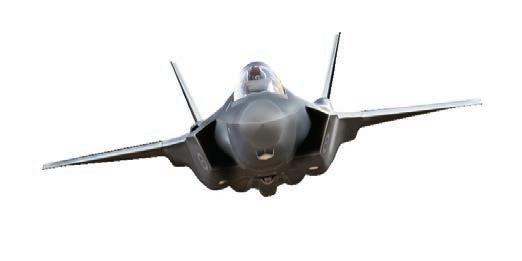
Alex was first involved in electronics in 1972 in Ukraine, working with ham radios and morse code radio communication. From then, he developed a passion for technology and electronics which carried over to his life in Australia. The pair quickly worked out a winning formula for their own business, with Alex’s design intelligence and Svetlana’s propensity for maintaining quality in manufacturing. Coolon LED Lighting was created in 2001 from FLC Microdesign, a contract manufacturing business. When Svetlana founded FLC Microdesign in 1993, she quickly established herself as a reliable high-quality manufacturer due to an extreme attention to detail and an indepth knowledge of underlying processes and electronic components. Her previous experience working in research and development for a semiconductor firm in Ukraine and a qualification of System Engineering in Electronics contributed to this initial success. The business was centred around the programming of leased semi-automated assembly equipment and perfecting the quality of printed circuit boards (PCBs) by experimenting with different brands of soldering alloys and fluxes. Obsessed with manufacturing quality, Svetlana consulted with clients on how better to design PCBs in line with Design for Manufacturing (DFM) guidelines. Throughout the early years, Svetlana was personally involved in assembly, while also looking after accounting, purchasing, testing, quality control and the setup of defined processes within the company. She redesigned the production floor layout to increase the throughput of manufacturing processes and created assembly manuals to allow the staff without formal qualifications to avoid errors in the assemblies of the most complex PCBs. Her attitude to quality
18 AUGUST 2022 Manufacturers’ Monthly manmonthly.com.au Manufacturer Focus
WHEN Svetlana first met her husband Alex at university, his love for electronics immediately struck her. “It was contagious for him and it became contagious for me,” she said. “He really understood electronics on a deep level and he wanted to share the enjoyment of knowledge with me. He took real pleasure in finding things out.”
Coolon’s technology offers a backbone for asset tracking service providers to roll out services with high accuracy and low latency.
The journey to lighting innovation
Coolon LED Lighting has invested heavily in research and development to provide the most impactful industrial lighting products to the Australian market. Billy Friend sits down with founders Alex and Svetlana Zatsepin about the ethos of the company and its continued expansion mission.
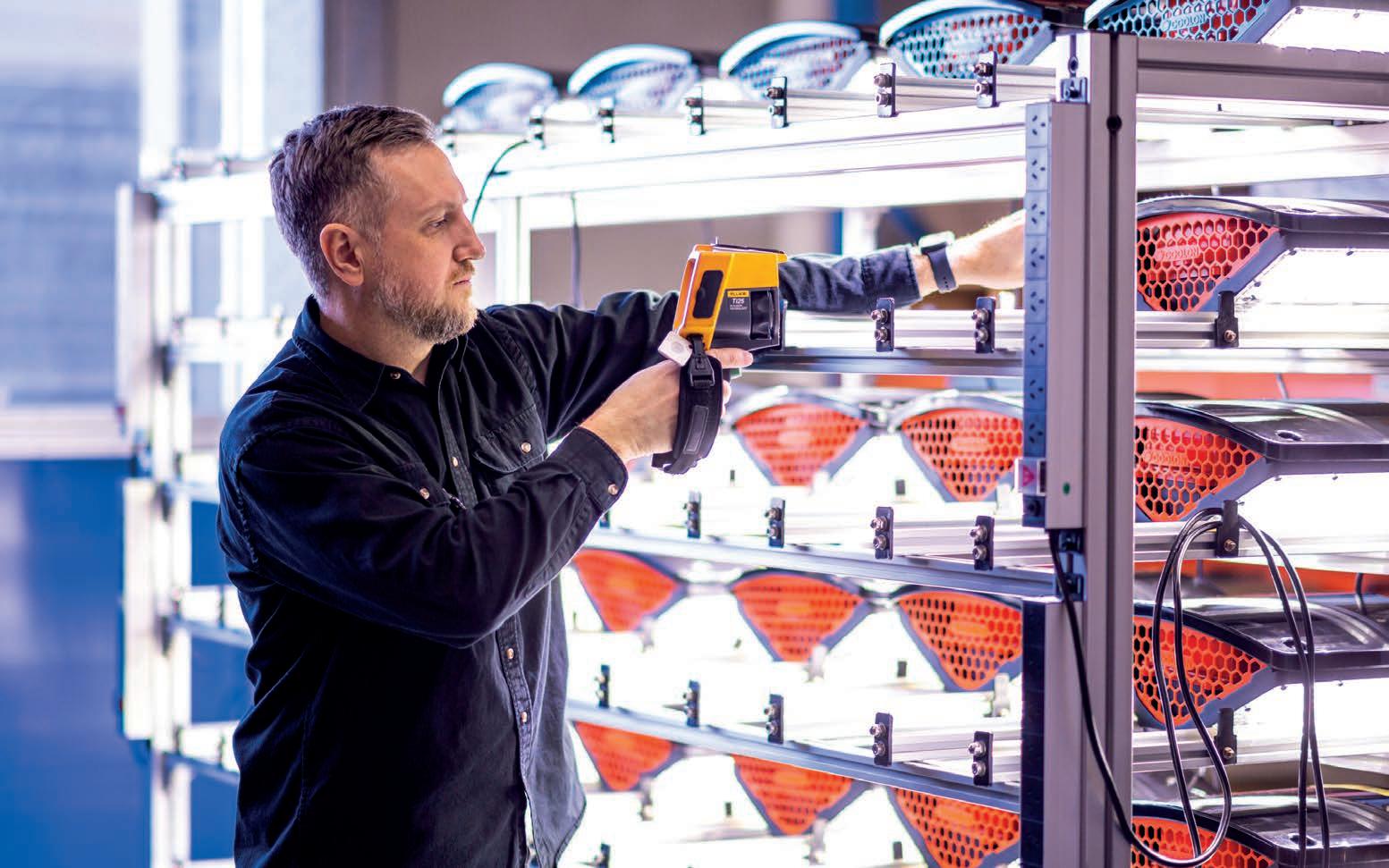
The facility in Hallam has several robotic assembly lines linked with modern automated component storage and test facilities, using the highest quality equipment. All products are produced within a system of full traceability and undergo multi-stage computerised testing to eliminate the probability of early failures. All assemblies are performed inhouse and shipped across Australia as well as exported “Manufacturingoverseas.in-house and keeping Focus Alex and Svetlana Zatsepin’s shared passion for electronics has reaped rewards for the business.
Three years later, Alex left a secure job at Bosch to join the business full-time, providing design services in addition to contract manufacturing. This was a turning point in Coolon’s history. A breakthrough invention by Japanese scientist Shuji Nakamura sparked the inspiration for Coolon’s LED lighting. Nakamura, with two other engineers, invented highly efficient blue LED in Japan in “With1993.blue LEDs you can create white light by mixing red and green or by adding phosphor,” Alex explained. “For traditional light bulb manufacturers, switching to LEDs was a major step, while for us LED was just an electronic component with new amazing properties making it suitable for lighting.”
Coolon’s lights come fitted with smart wireless mesh networking nodes inside.
manmonthly.com.au Manufacturers’ Monthly AUGUST 2022 19 Manufacturer
was, and remains, the cornerstone of the business – a systematic approach to manufacturing and operations continues to serve as an engine of the company’s evolution.“Inthe early days it was really difficult to start a successful business without having savings behind us,” she said. “We didn’t have the luxury of choosing which projects we would take on, so most assemblies requested by clients were very labour intensive. However, we had sufficient patience and perseverance together with confidence in our knowledge. Our customers felt confident with us, which kept us busy, but their rising cost pressures were put onto our shoulders. When we finally decided to design and make our own products, I felt we were making a strategic decision that would truly set us on a path to success.”
Coolon is a pioneer of Industrial LED lighting in Australia. The company was one of the first to provide a custom solution for the architectural market using its expertise working with semiconductor devices, and experience in the use of microprocessors and embedded software.
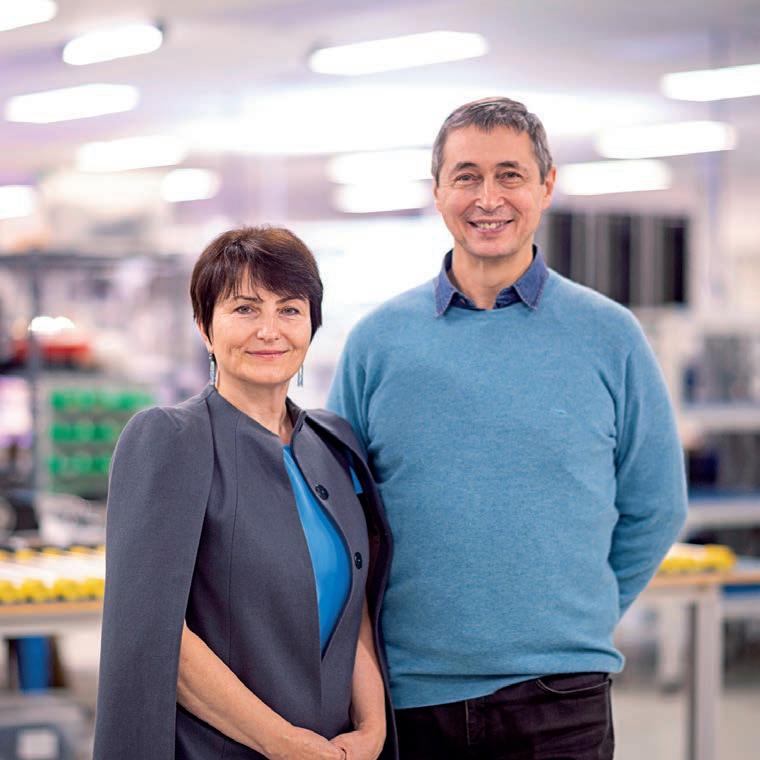
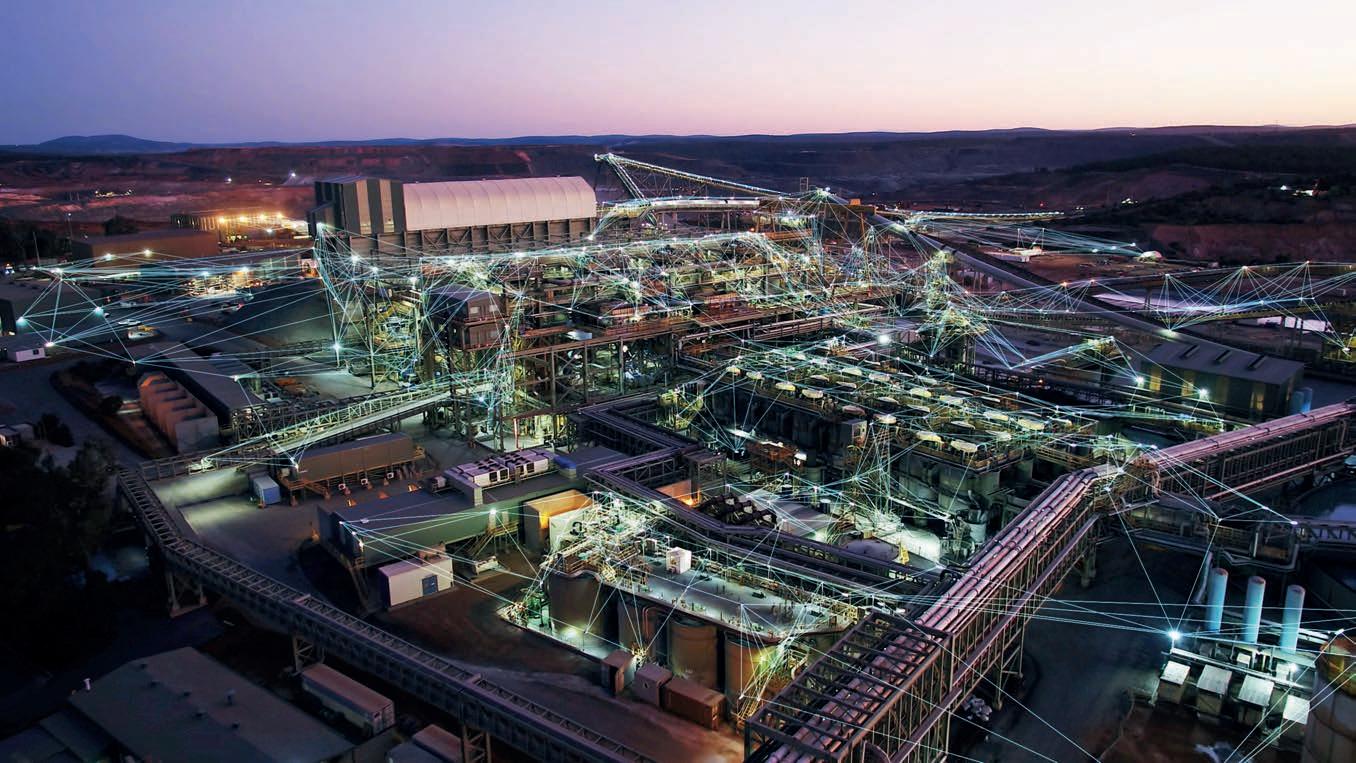
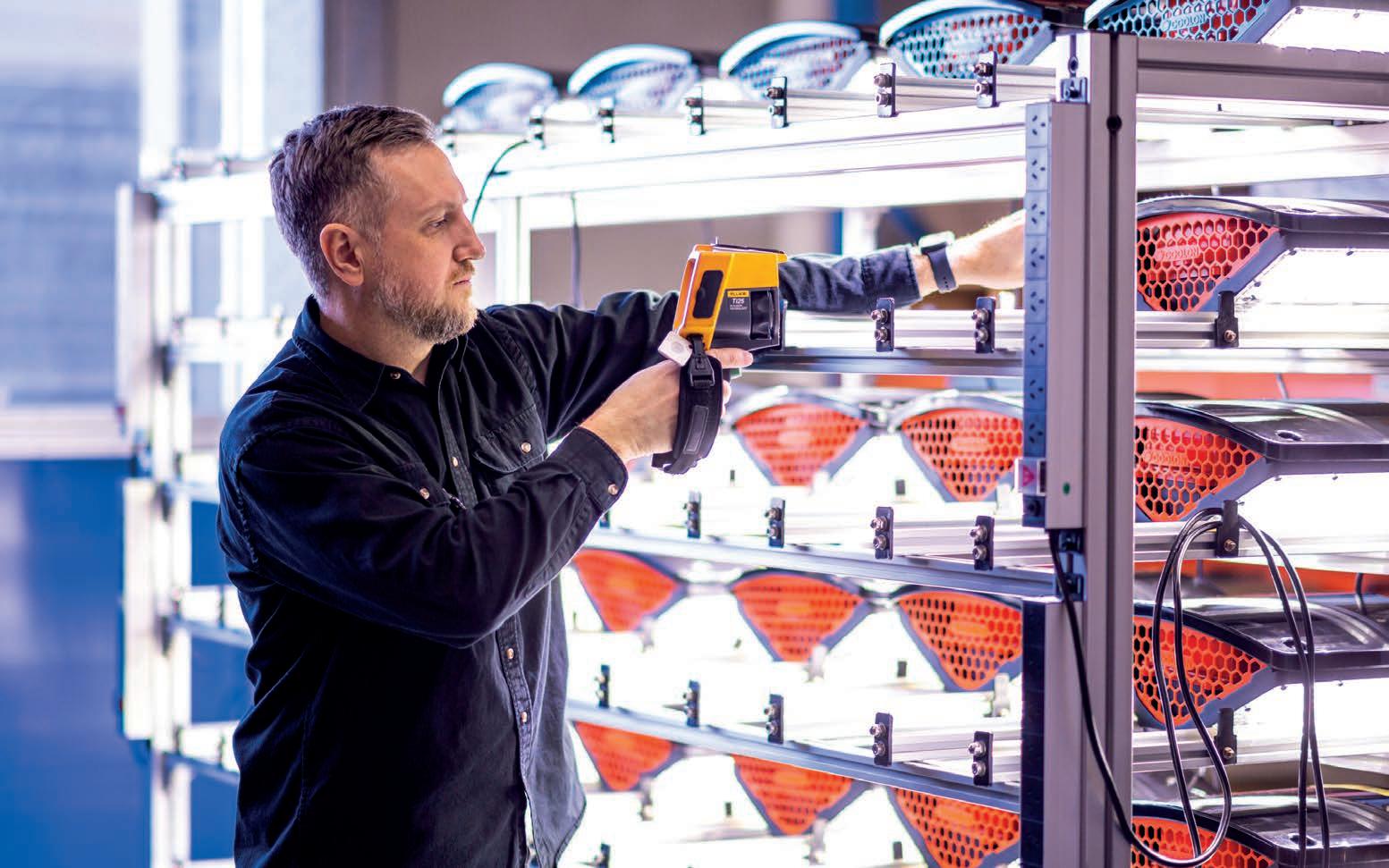
20 AUGUST 2022 Manufacturers’ Monthly manmonthly.com.au Manufacturer
Focus Research and development is crucial to Coolon’s ability to provide unique solutions.
“This approach to product development continues to this day, and, together with our attitude to quality, is a key factor to Coolon’s success,” Svetlana added. “Coolon has always put the interests of the client first.”
The Brilliant Connected Lights range is at the soft launch stage, after significant investment in research and development over three years. The project earned year’s Endeavour Awards, including Manufacturer of the Year. Digitisation is the ultimate goal of the rapidly evolving and sometimes seemingly limitless world of Internet of Things (IoT). With this in mind, Coolon LED Lighting puts smart networking nodes inside the industry’s best, most robust lights, enabling digitisation in any mining, industrial, manufacturing, chemical, defence, food and beverage, commercial or other industry facilities. Alex explained the digitalisation of industrial processing plants remains challenging due to the complex and often hazardous“Runningenvironment.cablesandsetting up Wi-Fi coverage is costly and disruptive to operations,” he said. “Radio signal propagation is often unpredictable due to the presence of massive steel and concrete infrastructures, as well as prevalence of electromagnetic noise from various types of equipment. Coolon’s lights now come fitted with smart wireless mesh networking nodes inside. Laying cables is not an option. The new technology acts almost like a network of satellites which can achieve a variety of things that traditionally were not done before.
“Our presentation and subsequent demonstrations of the first high power LED floodlight prototype at Whaleback BHP were very well received,” he said. “The trip back was full of ideas brainstorming and excitement from the realisation of how much difference our solutions could create for mine operators.”Subsequent launch of tooling and preparation for serial production coincided with the 2008 GFC. Strong demand for iron ore allowed mines to continue producing this soon-to-be in high demand commodity. It was the right time to introduce Coolon’s new, highly reliable luminaires, which saved maintenance time for mine operators, freeing up resources to look after equipment involved in the main tasks of digging and processing the iron ore. Thereafter, Coolon identified that many other luminaires on mine sites were often failing, as they were made using traditional, existing technologies.
Coolon Brilliant Connected Lights From its humble beginnings, Coolon has its sights set on continual expansion.
“Alex, together with our BDM Andrew Orkin, left for Newman, armed with probably the highest power LED luminaire prototype in the world at that time. They wanted to learn BHP’s problem first-hand and demonstrate to site management what a well-made LED luminaire was capable of. It was Coolon’s first visit to a mine site in search of new knowledge and market opportunities for our own products.” could develop something to make mining operations safer and more environmentally friendly by reducing maintenance costs and improving lighting conditions for personnel.
outsourcing, is extremely important for high quality,” Alex said. “We can identify any problems before the final assembly. Failures are extremely rare, and the most important thing is that nothing is dispatched until it is 100 per cent checked, tested and ready for the client.”
LED Lighting for mining Svetlana recalls, “In 2008 Coolon received an enquiry from BHP Mt Whaleback asking for a solution that would reduce the environmental impact and maintenance costs of lighting fixtures. BHP mentioned that the site contains between 10,000 and 15,000 light fittings and costs associated with maintenance, repair and replacement were ‘extensive’.
DLK and DLK2, changed not only the frequency of servicing luminaires, but the nature of the electricians’ workload, as they were previously engaged in routinely changing bulbs and luminaires along endless conveyor lines. Instead of putting a light designed for commercial purposes into an industrial mining environment, Coolon’s approach was to design the luminaire specifically for the harsh conditions of mining operations, by visiting the mine site in person, engaging directly with the users, and learning about operating electrical, mechanical and thermal conditions.

Luminaires are naturally positioned to provide the best wireless mesh network coverage, by being mounted in elevated positions, constantly powered, located throughout the site, routinely inspected and essential to any facility.”
Visual emergency status propagation Emergency status alerts such as lightning proximity or evacuation can be propagated through the lighting network in realtime across the site with built-in colour changing visual warning indicators. In case of an emergency, the warning indicator will switch to a pre-defined flashing colour pattern, alerting the personnel of a specific emergency status and making sure no one is caught unaware. Every light can also act as an emergency light Every single light is equipped with a battery, providing the power backup for both lighting and networking functions, ensuring a safe and smooth evacuation process in case of a power outage. Superior illumination uniformity and a reduction in shadowing also enhance hazard perception and visibility, maximising the safety and smoothness of the evacuation process.
The skills shortage facing Australian manufacturing is real. Many small-tomedium sized businesses are struggling to find the right workers, which is forcing the hand of decision makers to turn to more automation. Coolon seems to have countered the challenge by creating an environment where people want to stay, while also attracting high performing staff.
Svetlana has an eye for quality that holds the team to the highest standard, but counterbalances this by facilitating the creation of a ‘family’ atmosphere on the factory“Henryfloor.Ford once said, ‘Quality means doing it right when no one is looking.’ These words directly apply to Coolon crew and constitute the base for a quality culture,” she noted. “We have a dedicated screen showing projects as they are being completed with products made by our crew. We’ve found this has a great impact on employees in seeing the results of all their hard work in the form of the final product. “We have many people who’ve worked here for more than a decade, some more than two. We know everyone well, we’ve been through a lot together, we wrote company history together, and we all share a passion for Australian manufacturing. We share a goal to keep innovating and to be the best we can be. I value all our people, I’m proud of them, and I really mean it when I say our people are our best asset.” Coolon’s products were in high demand during the pandemic, with staff understanding the importance of maintaining a continuous supply of products to Australia’s core industries “There was a lot of fear in the market, uncertainty, and businesses were facing closures and laying off staff,” Svetlana said. “Coolon was prepared to sustain the income of the entire crew for up to a year in the worse-case scenario. In the end the situation changed, and we innovated and are facing excellent prospects. This was all due to the hard work and dedication of our team.”
This innovative technology holds many advantages, including improving the safety of the mining and industrial sectors. For instance: Personnel locating Coolon lights make it possible to instantly account for everyone on site, locating missing workers and sending help directly to those in need in case of an accident. The mesh network enables real-time visibility into areas without the need for GPS, mobile or CB radio coverage, ensuring the safety of all site personnel, even in the most secluded areas of the facility.
Coolon smart lights nodes enable “plug-and-play” capability, offering immediate and effortless digitisation for mining and industrial sites, regardless of the size or complexity of the infrastructure. Once installed, the lights can automatically create a wireless mesh network that covers the whole site, solving connectivity challenges: one node only needs to service a limited area around itself and pass the data onto its neighbour for retransmission.
Alex explained Coolon Brilliant Connected Lights do not only represent disruptive innovation but provide a backbone for thousands of emerging IoTdependent services and technologies. “We spend a lot of time and most of our money on research and development,” he said. “And we will continue to update our product range with new technology. It’s about the technology revolutionising what people do from day-to-day.”
A rigorous testing process ensures Coolon’s products are customised and efficient for customers.
A family environment
manmonthly.com.au Manufacturers’ Monthly AUGUST 2022 21 Manufacturer Focus
This mesh network serves as a platform to enable multiple industrial applications and IoT services. For instance, it offers the ideal backbone for asset tracking; gaining real-time sitewide visibility enables site management to instantly locate any tagged item anywhere on site, including indoors and underground, with relative precision, maximising asset utilisation efficiency and“Aproductivity.rangeofinexpensive, batterypowered sensors enable real-time condition monitoring of many critical machines around the site,” Alex added. “This helps maintenance engineers find early warning signs of potential malfunctions, allowing them to schedule preventative maintenance, and eliminate unexpected, costly downtime. The equipment is constantly monitored and reported on, immediately alerting the operators of any deviations and anomalies, allowing maintenance to be scheduled before a malfunction occurs and preventing any accidents.”
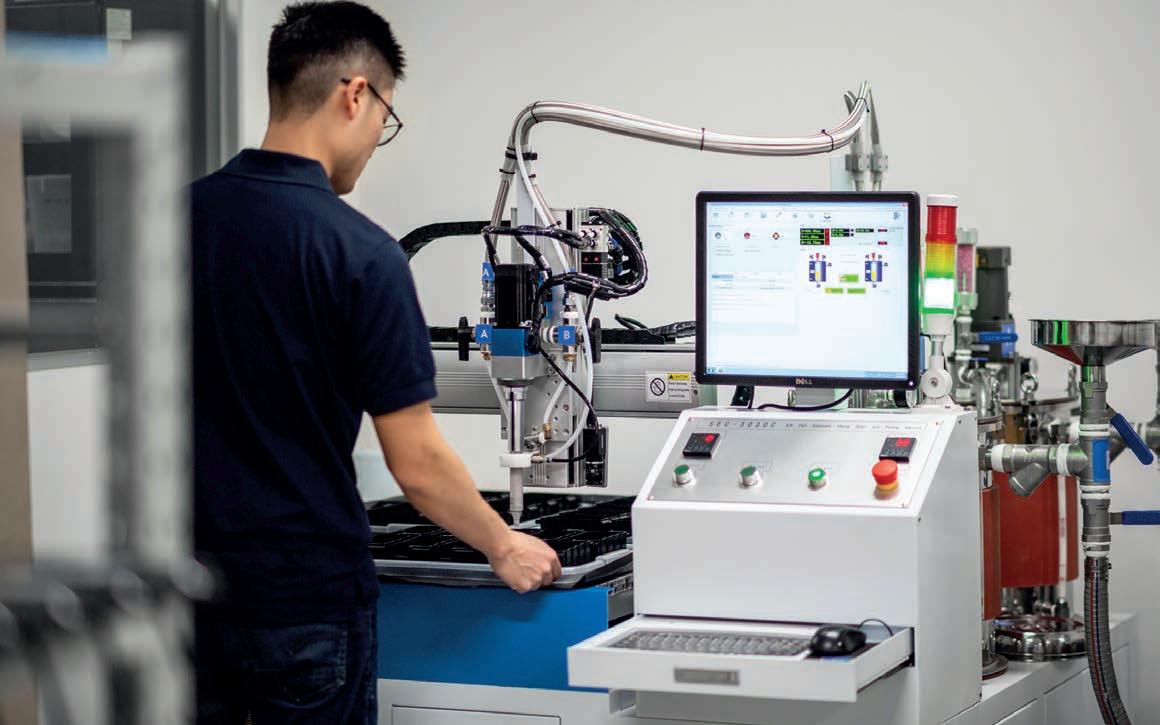
Your single source product, processing and service solutions solutionsandQualityprovidersteelaluminium As one of Australia’s leading national steel and aluminium distributor and solutions providers, BlueScope Distribution has the product range, processing capability, and technical expertise to deliver your requirements for either bulk steel or aluminium, semi or fully processed componentry through to fully project managed material solutions. For more information bluescopedistribution.com.auvisit or call us on 13 72 82 Steel. Knowhow.Aluminium. ™ BlueScope Distribution® is a registered trademark of BlueScope Steel Limited. © BlueScope Steel Limited March 2022 ABN 16 000 011 058. All rights reserved. Perth Esperance PortlandAdelaideBallaratHobartAlburySydneyMelbourneLauncestonNewcastleBrisbaneGladstoneTownsvilleMt Isa
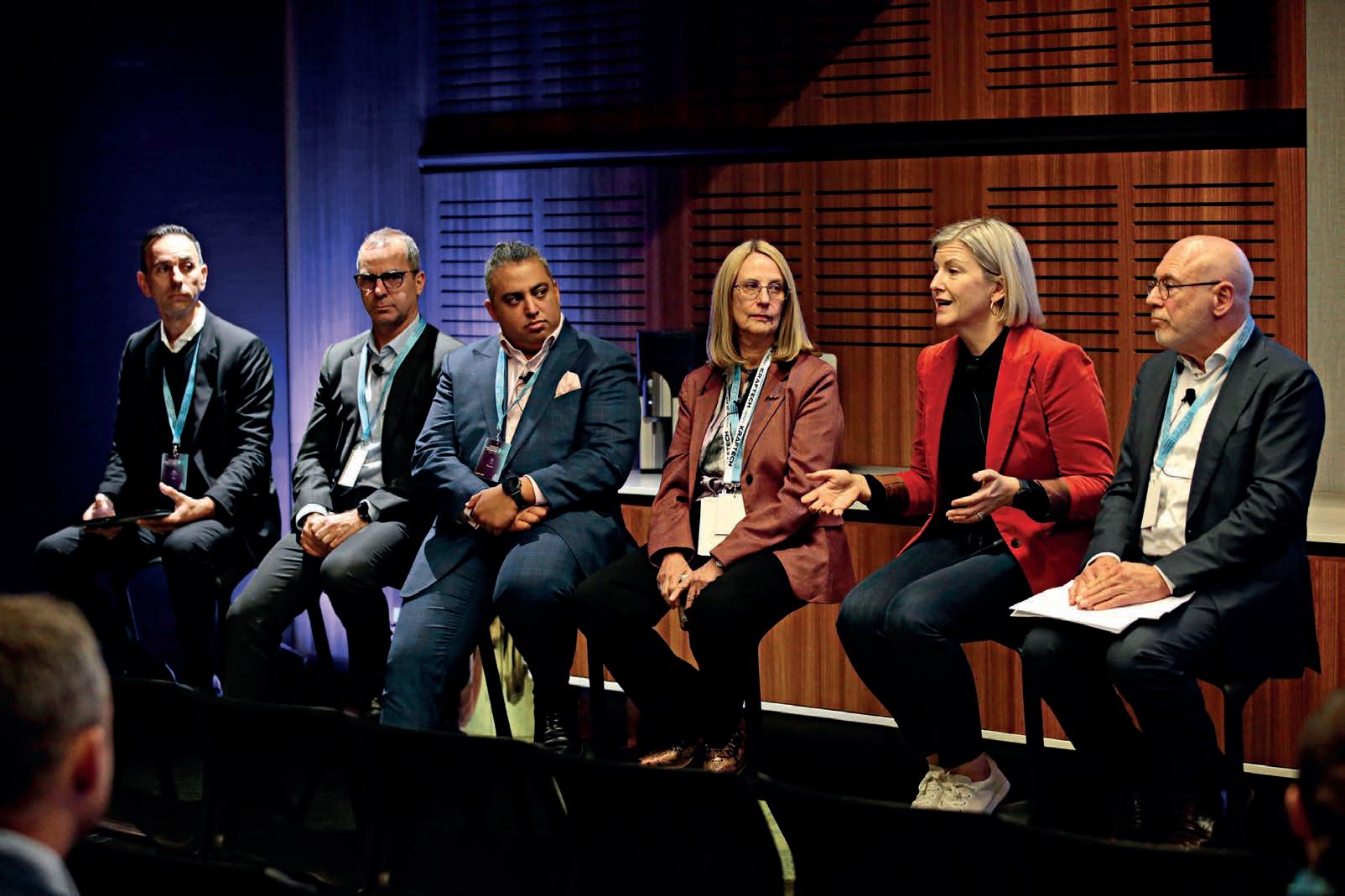
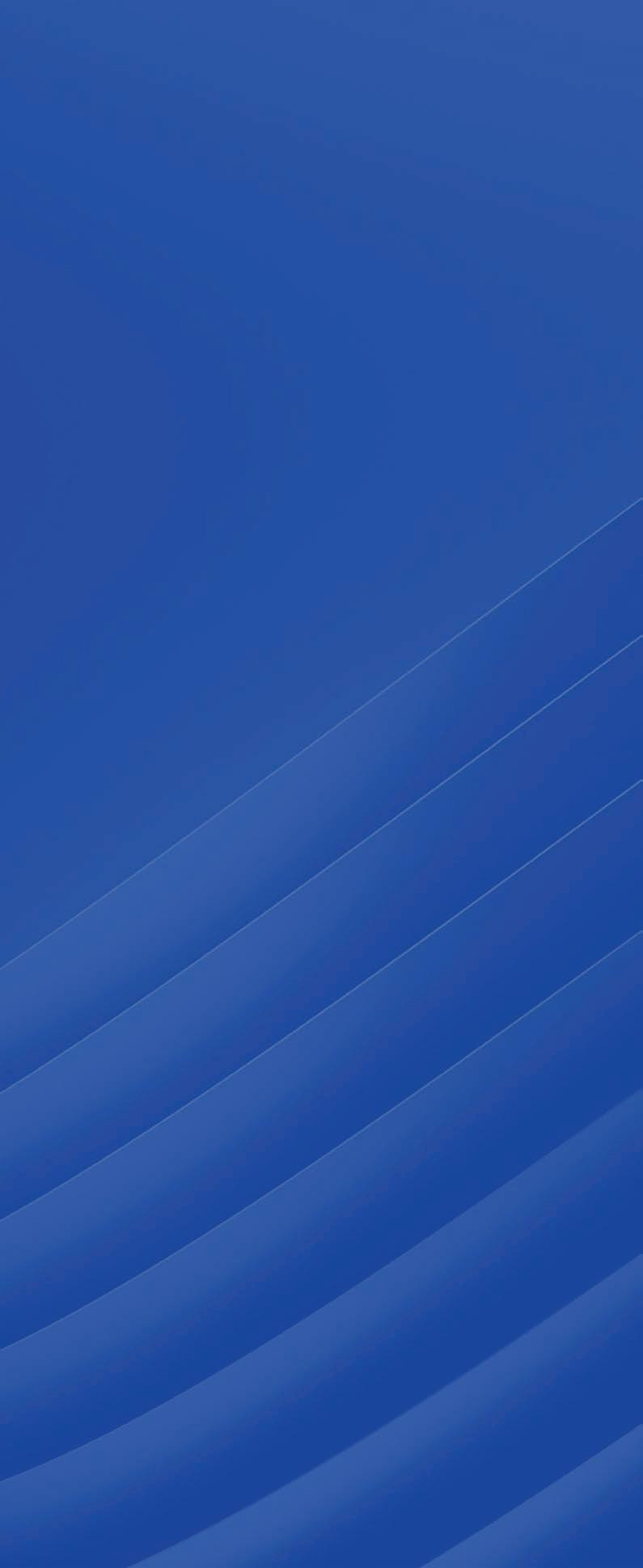
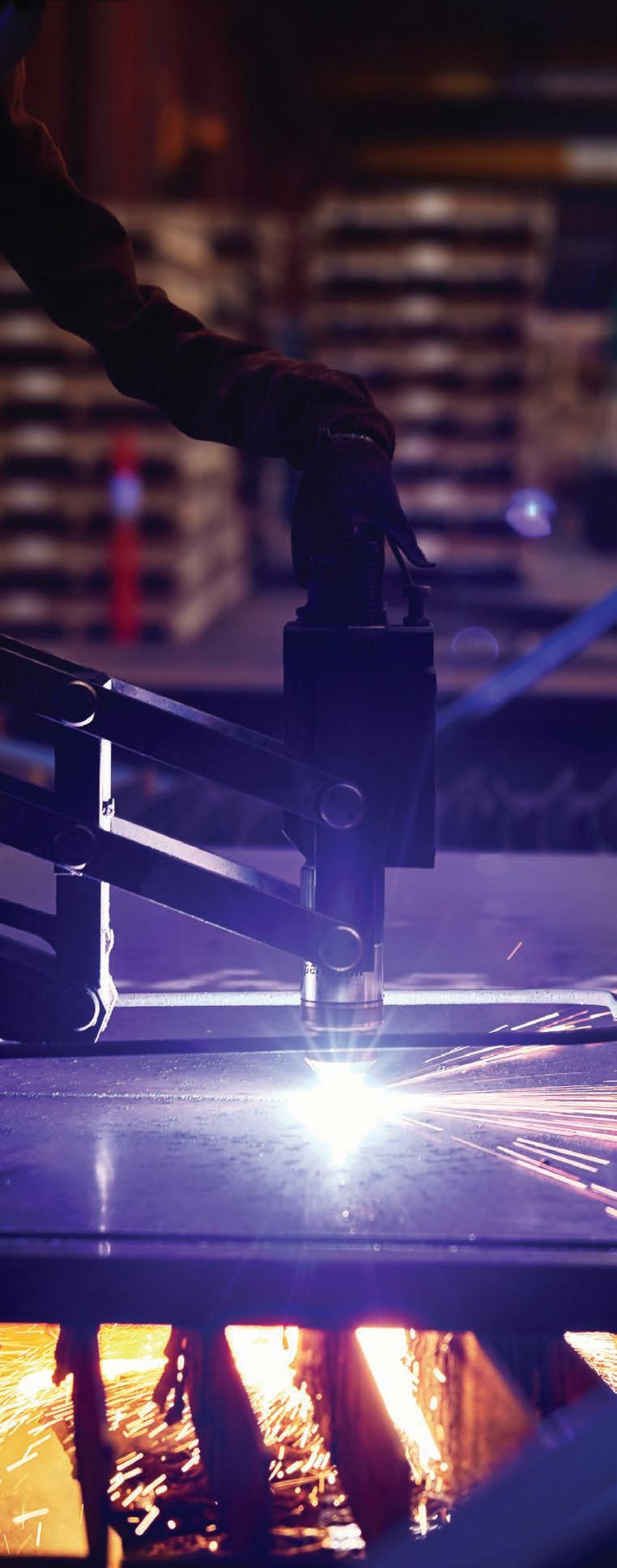
AMW showcases exciting times for Australian manufacturing
manmonthly.com.au Manufacturers’ Monthly AUGUST 2022 Events23
Currently, Australia ranks 86th, between Paraguay and Uzbekistan. Australia is known as the lucky country, but it can become the smart country through the application of advanced manufacturing technologies.
Godeau discussed how Australia needs to be better, not cheaper, by adding value and making more complex products, to grow its manufacturing future. Sarah Sharp, GM technical and engineering for Thales’s Integrated
Harvard University’s Economic Complexity Index (ECI) ranks a country’s ability to manufacture and export diverse and complex products and components.
The New South Wales Government is building an Australian-first, shared-use advanced manufacturing research facility in the heart of Western Sydney. At the doorstep of the new Western Sydney International Airport, the Advanced Manufacturing Research Facility (AMRF) will be a hub of collaboration and innovation supporting the growth of future-facing industries. On day two of AMW, a raft of key speakers gathered for the AMRF’s manufacturing technology conference, sharing their expertise and advice for the continued mission to move Australian manufacturing forward. The conference provided opportunity for industry to engage with advanced manufacturing technology providers, hear from the AMRF team about new business opportunities and engage with other manufacturing businesses. Organised by the AMRF team from the Western Parkland City Authority (WPCA), the conference was a hit for those who attended.KellyGodeau, AMGC’s director of corporate affairs, addressed the crowd about capability and complexity in Australian manufacturing. A key message from her presentation was, “It’s not what you make, it’s how you make it.”
David Camerlengo, Maurice Ben-Mayor, Dr Jehan Kanga, Sylvia Tulloch, Sally-Ann Williams and Professor Roy Green at the IMCRC conference.
The Australian Manufacturing Week was a week of celebrating and highlighting the full spectrum of industry. Billy Friend attended the event and spoke to industry leaders about emerging trends and highlights from the conferences and trade floor.
THERE was a buzz of activity on all four days of the Australian Manufacturing Week in Sydney’s International Convention Centre. 170 exhibitors across a myriad of sectors presented their latest technology and services to 6099 attendees from every state across Australia and all around the world. In fact, over 200 attendees came from across our shores, with 1649 of them being CEOS, general managers or owners. As the country emerges from the impacts of the global pandemic, business bodies and governments have been reevaluating processes, introducing fresh ideas to boost sovereign capability and reduce overreliance on imports. AMW supported this new trend by showcasing technologies and processes across six key product zones: Machine Tools, Additive Manufacturing, Robotics and Automation, Weld Solutions, Manufacturing Solutions as well and a separate Australian Manufacturing PavilionTheevent covered every aspect of manufacturing technology, from the largest machine tools, down to the smallest precision cutting tools, as well as state-of-the-art support systems, software and accessories, and the many other services that are essential to manufacturing enterprise. As mentioned, COVID has had a debilitating effect on workforces of the world over the last two or so years. This has affected workforces, logistics and shipping of stock, well, everywhere. You wouldn’t know it, with so many positive conversations and outlooks to keep improving the state of Australian manufacturing. Make the Future
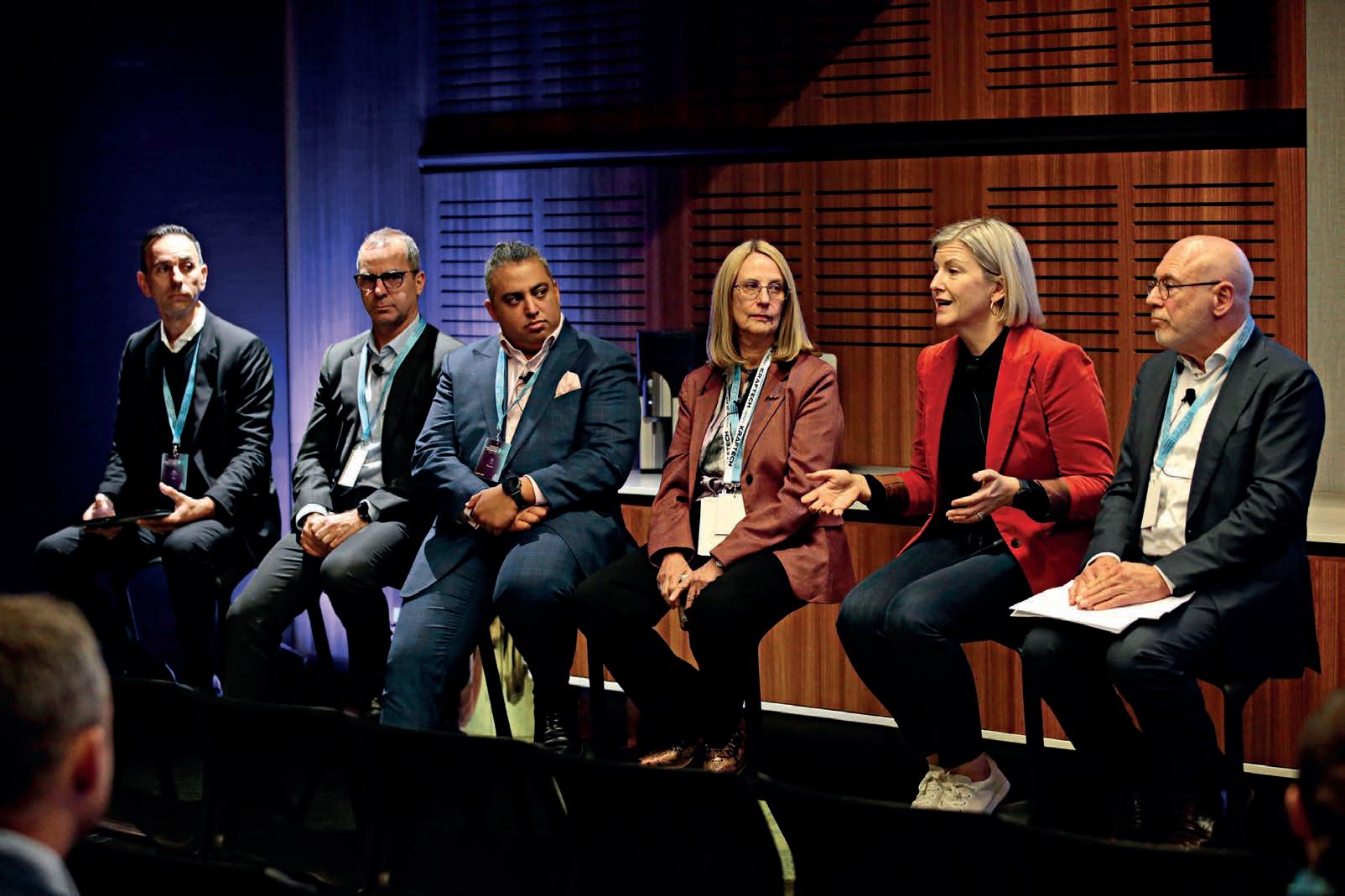
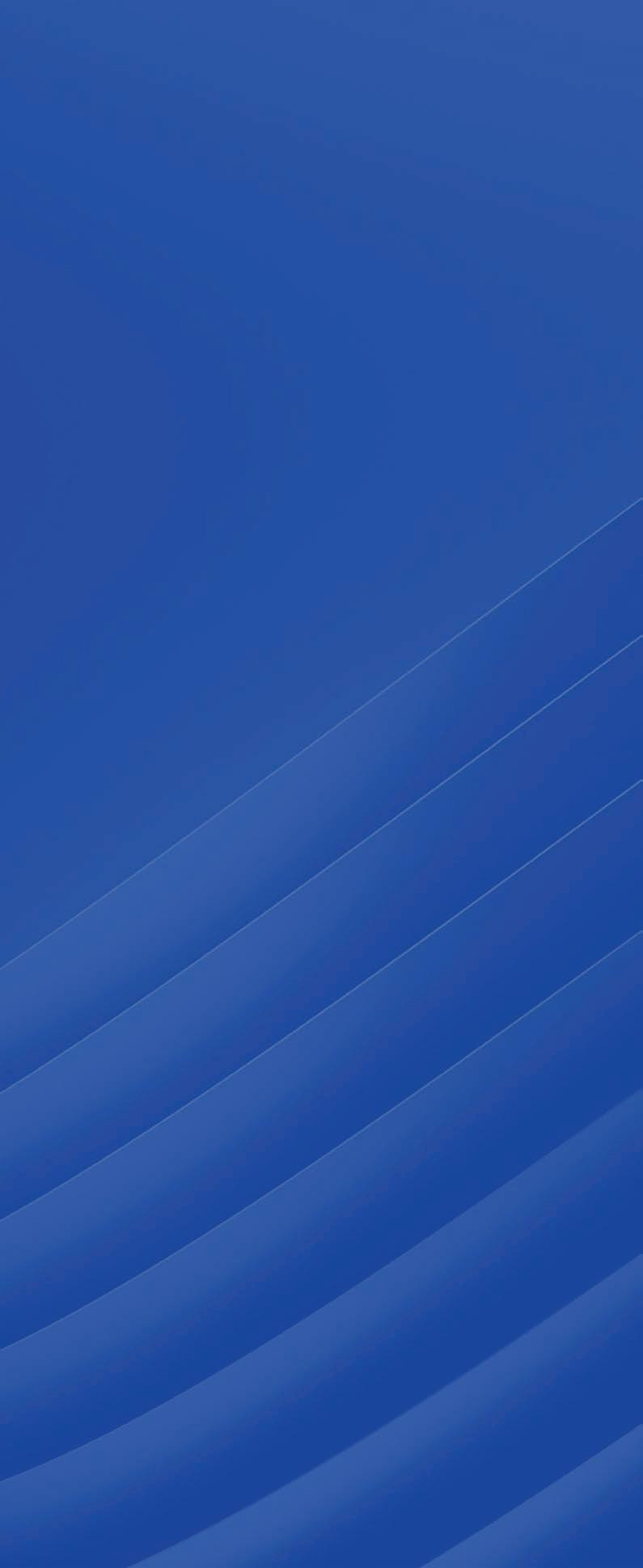
Weapons and Sensors business line, spoke about Thales introducing a range of advanced manufacturing technologies to its everyday practices in its facilities industry.“Weare really keen to engage with this project,” she said. “It will help fill a gap between research and industry. Being “There’s so many new technologies coming out at the moment which are able to help us increase our efficiency and increase capacity, which helps us respond systems, everything requires new manufacturing capability technologies. We really need these centres of expertise to translate for these technologies because we’re doing things we’ve never done before – the manufacturing processes need to keep up with new advancements and“Thalesresearch.”works across a number of domains – space, aerospace, transport, communications – working heavily on innovation and disruptive products. We’re working closely with universities and small to medium enterprises as really strong partners for us in our innovation. No one can do everything, so working together gives us that opportunity to speed up development, to get these technologies into actual products a lot quicker.”Peter Mackey, executive director, skills and industry capability at the Western Parkland City Authority sat down with Manufacturers’ Monthly to explain the new education and training model (NETM)– a $37.4 million New South Wales-funded pilot program to deliver 100 microcredentials over the next four years. “We’re trying to build a skills density that’s going to enable the people of Western Sydney to realise and get some
24 AUGUST 2022 Manufacturers’ Monthly manmonthly.com.au EventsTheAdvancedManufacturingResearchFacilitywillhelpsolidifyadvancedmanufacturingasaprioritysector.
Over 6,000 people attended this year’s AMW.
AMWcredit:Image
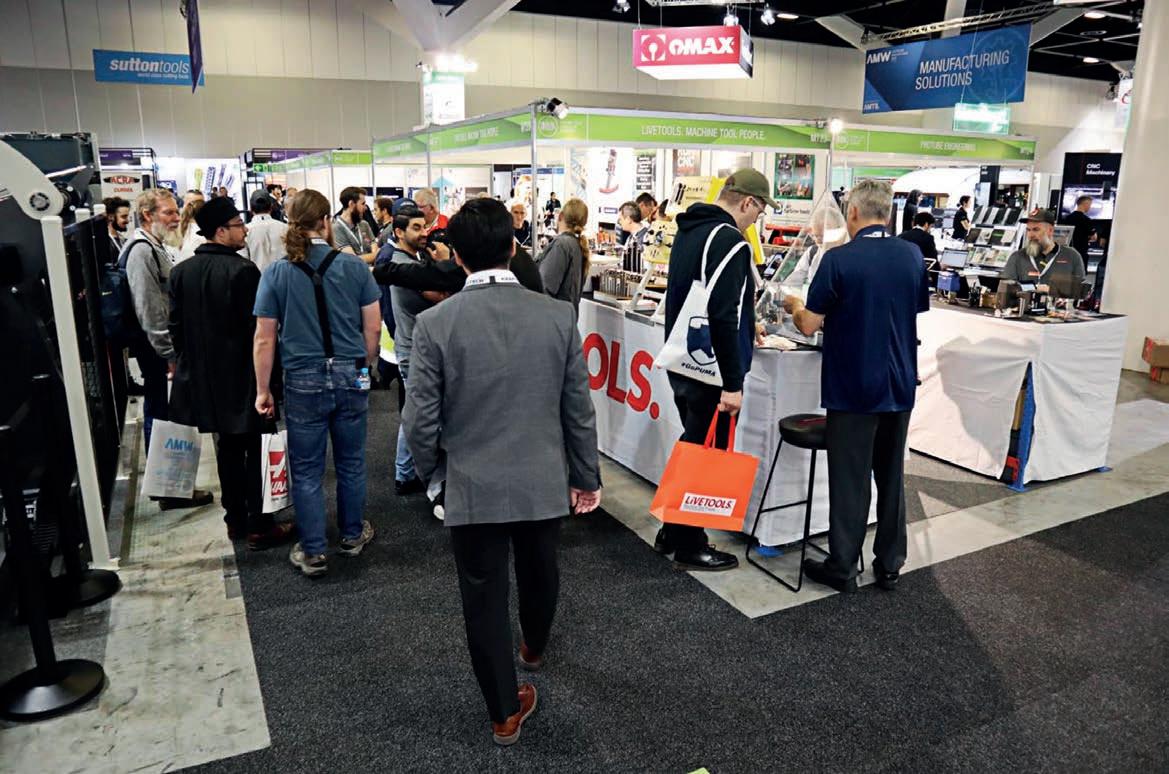

Peter Mackey addressing the crowd about the new education and training model for advanced manufacturing.
The NETM is not only place-focused, but it’s also very much sector focused. We’re looking at sectors like advanced manufacturing, aerospace and defence, freight and logistics, agribusiness, because all those businesses will proliferate once the airport comes online.
The Innovative Manufacturing CRC is an independent, for-impact cooperative research centre. The CRC has supported more than 70 industry-led research collaborations, of which 80 percent have been with SMEs. At AMW, the IMCRC hosted an industry network which function which offered a fresh perspective on innovation. The presentations explored how breakthrough ideas can be turned into real-world solutions. Organisational psychologist Dr Amantha Imber and a panel of industry experts shared how they are fostering innovation within their own organisations and what is required for Australia’s innovation ecosystem to flourish.Industry experts who spoke on the night included Sally-Ann Williams, CEO of CICADA Innovations, Sylvia Tulloch, Lava Blue chair, Dr Jehan Kanga, CEO and founder of Rux Energy, Maurice Ben-
“We’re very conscious that CRC exists for a fixed period of time and we’re designed to solve a problem and to capitalise significant investment,” he said. “We granted our last project back in November last year, so our job now is to make sure that the projects we’ve invested in over multiple years really push for outstanding commercial outcomes and real-world impacts. “And so the purpose of today was firstly to bring people back together after a long period apart – I think we’ve heard the power of getting people together. We’ve heard that innovation is about people, it’s about culture. But also to encourage people to accelerate their journey, not to sit back on their haunches because of one successful project and wonder what’s next. Today was about driving some inspiration, driving some more ambition, and creating the power of partnerships and collaboration so that we can rebuild and reinvent our manufacturing sector.”
The conference pitched Bradfield City Centre as Australia’s first 22nd Century City. It aims to be a globally competitive centre for advanced manufacturing and the best location in the Indo-Pacific for industry to research, develop and commercialise innovative products and processes.
Innovative acceleratedmanufacturing
NEPEAN Engineering Innovation is an engineering service provider and a trusted supply chain partner of Defence primes.“We employ 130 People in advanced manufacturing only 20 minutes away from this new facility,” he said. “We feel that we can get stronger and grow our business and our capability by being a partner and collaborator with AMRF. It’s just changing the momentum of manufacturing, particularly advanced manufacturing.”“Theabilityto have the new assets or new technology so close to us that we can train our young people and get them involved in events management and manufacturing at an early stage is so exciting. I keep coming back to the momentum and excitement in the industry – I haven’t seen it in 25 years, it’s such a great time to be in manufacturing.”
of these highly skilled, high paid jobs that are close to home,” he said. “The second reason where we are doing NETM is to try and build skills intensity that is going to keep the confidence for all of the major firms we are trying to get to invest into the aerotropolis because what we know one of the barriers they have a moment is a lack of confidence that we have that skill density.”NETM is a four-year pilot funded by the state government to rapidly upskill 3000 people in the existing boundaries of Western Parkland City. Very specific targeted training interventions in the form of micro credentials – short, sharp, 40 hours of content that an existing worker can do while they’re working – will look to deliver a significant amount of content, but not take so much time that an employer is worried about being taken offline.“The NETM is not only place-focused, but it’s also very much sector focused. We’re looking at sectors like advanced manufacturing, aerospace and defence, freight and logistics, agribusiness, because all those businesses will proliferate once the airport comes online. The other target for us is graduates who are about to enter the workforce because employers tell us there’s often a gap between what you get from an engineering degree and what’s expected when you start your first day at work.”Peter Buckley, general manager of NEPEAN Engineering & Innovation, told Manufacturers’ Monthly there is a buzz of excitement about the AMRF project.
Mayor, Stryker South Pacific president and David Camerlengo, global sector lead manufacturing and technology at Austrade.DavidChuter, CEO and managing director of IMCRC, caught up with Manufacturers’ Monthly at the event.
manmonthly.com.au Manufacturers’ Monthly AUGUST 2022 Events25
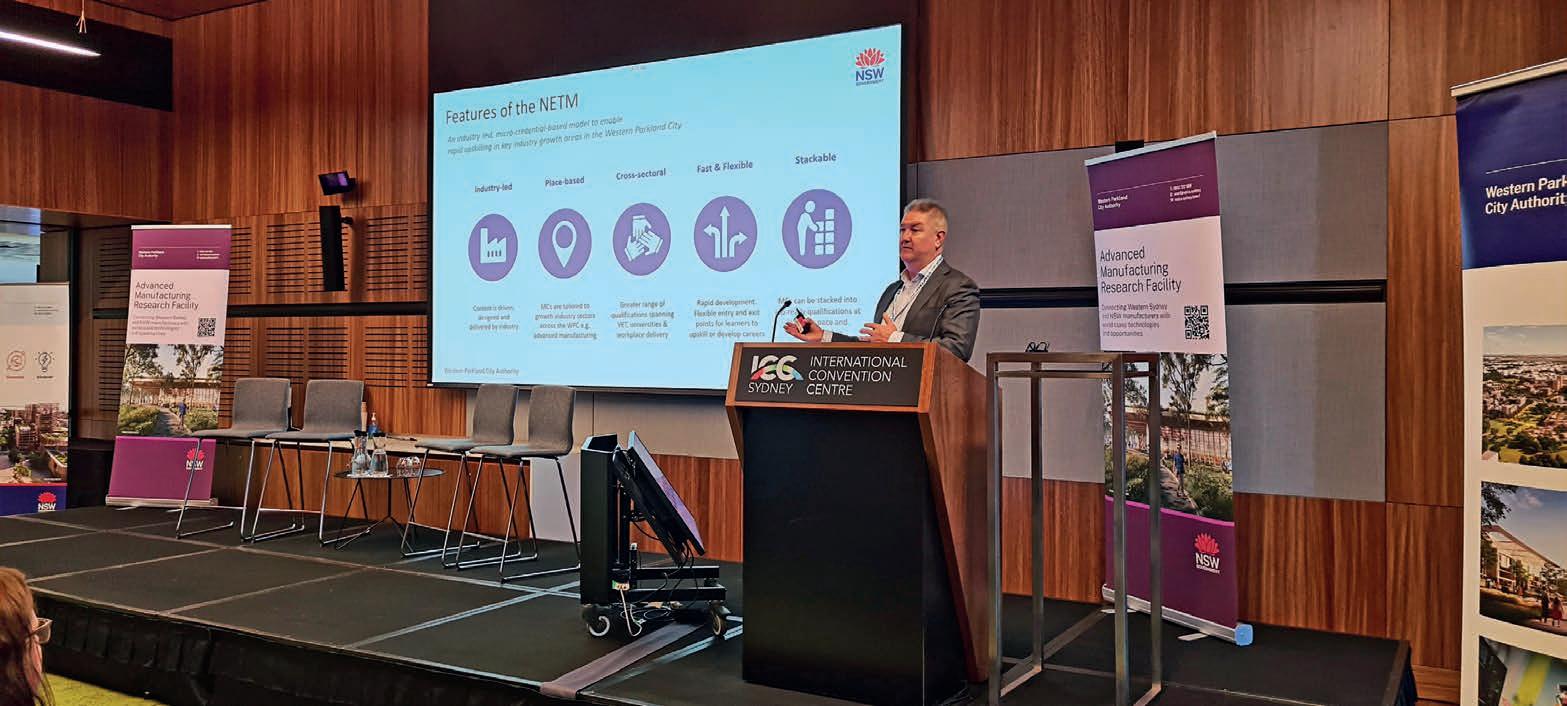
Queensland composite panel supplier Link Composites uses Combilift forklifts to provide a safer, space-saving material handling process at its new factory on the Sunshine Coast.
The company uses high quality, lightweight, efficient composite materials to manufacture panel systems. recently a hot melt continuous panel lamination line. Robinson explained Link Composites also provide cutting services, with three CNC routers in house for all the profile cutting for windows, door cutouts or the overall shape of whatever unit customers are building. “What we’re trying to do is encourage a transition of current build methods to new products – composite products using advanced materials,” he said. “We’ve got core materials here which are 100 per cent recycled so the environmental impact of residential construction can be reduced. All that aside, it’s just a far quicker method of building. I think a step forward for the construction industry is to go to a panel system, and to educate existing trades people in the use of customers they can meet current demand by significantly reducing their build times.”Link Composites utilises Combilift’s multi directional counterbalance forklift, the CB3000, to save space and create a more efficient material handling environment. The first Combilift unit was purchased for the previous facility in Nambour, where the factory space was designed around the capabilities of the forklift. Much of the floor was taken up by six vacuum tables, which laminated large format sandwich panels. “The Combilift is key not only for its material handling capability, but for that multi directional function,” Robinson explained. “Our panels can be up to 15 metres in length, so the long loading Combilift’s CB forklift was introduced in 2006, where the company identified a market for customers that needed to use a regular forklift for handling palletised loads, but also the ability to drive sideways when handling long loads. Regular forklifts are designed for handling palletised loads, so the different design gives the vehicle an ability to travel sideward. Given the success of the Combilift at Link Composite’s previous facility, it continues to play a crucial part in the next phase of its composite panel manufacturing.“We’vejustgone through a heavy transition from our previous manufacturing processes,” Robinson said. “We had to run two shifts on the six vacuum tables just to keep up with
The CB3000 handles the composite panels.
Stepping into modern manufacturing with Combilift
Handling
26 AUGUST 2022 Manufacturers’ Monthly manmonthly.com.au Material
LINK Composites is one of Australia’s leading advanced composite materials and systems suppliers. With experience working in the composites industry in Victoria, managing director William Robinson started the business in 2018 after identifying a gap in the market for a volume supplier of fibreglass sandwich panels and despite clear challenges from the pandemic, has not looked back. “We’re investing in design – we all have that front of mind,” he said. “We have a big focus on research and development which helps with product diversity and innovative designs.”

together a new manufacturing facility which is capable of producing higher volumes of product and the Combilift forklift is entrenched into those design plans.”Tosupport expansion plans and continued R&D investment, Link Composites recently moved into a new, modern premises on the Sunshine Coast, custom-designed to support a new project.“Our new method of manufacturing fibreglass sandwich panels is using a hot melt adhesive,” Robinson explained. “Over the last 12 to 18 months, we’ve been designing a continuous semi-automated production line for that purpose. That whole project has been tied into a full relocation of the business over into the Coolum industrial estate. Our production line is capable of producing panel continuously at up to 6 lineal metres per minute.”After an intense year and a half of design and research, the project is fully commissioned and operating. Link Composite’s team of managers, engineers and skilled operators all understand the core of the business is design, which prompts more innovation to push the envelope on traditional manufacturing methods.“Isatdown with our automation engineer and designer to draw up this production line,” Robinson said. “Once that was drawn up, we designed the entire site we are currently operating at, mapping out factory layout, inventory storage right down to production flow. By simulating workflow, we could implement lean workflow processes in place before we even had the keys to the building.” Pallet racking was built from the floor to ceiling in height, so Link Composite needed the Combilift unit to lift up to 7.5 metres. This capability has resulted in three more bays worth of storage for inventory. The production line is 30 metres in length and is a continual process down to the end of the line where it shifts to move the composite panels onto a pallet. Once the pallet is loaded, the CB3000 picks up a pallet of panels and uses its manoeuvrability to traverse long loads out of the factory door into a neighbouring CNC shop. “When you look at material handling I think it’s important to think of your operators,” he noted. “With the Combilift there’s next to zero actual physical lengths of steel, timber or aluminium is an inherently dangerous process for operators. Not only do the right materials handling safety procedures help avoid serious injury, they also protect the product and reduce warehouse damage. A standard counterbalance forklift has been commonly used in these applications for years, but more companies are utilising a more manoeuvrable solution to safely move longer loads. Combilift is ahead of the pack and is helping companies like Link Composites facilitate an increase in output by providing that added layer of staff welfare and safety.
Robinson explained that the CB3000 is used in conjunction with a custom vacuum lifter for handling the composite panels. “We use an attachment with vacuum pads on it that can pick up a panel and load it onto our CNC machine,” he said. “Again, it’s not our operators having to do this process. We rely on the Combilift and vacuum lifter as a duo to handle the workflow through the CNCs.”
Moving into the ‘virtual space’ is working for Link Composites: embracing the simulation of processes and Industry 4.0 to improve output continues to be a focus for Robinson going forward. “The automation we are adopting is helped by the Combilift at the site being something we don’t ever need to worry about. The CB3000 does the heavy lifting for us.”
manmonthly.com.au Manufacturers’ Monthly AUGUST 2022 27 Material Handling
Light Composite uses quality composite materials to manufacture panel systems.
The CB300 can lift more than four metres.
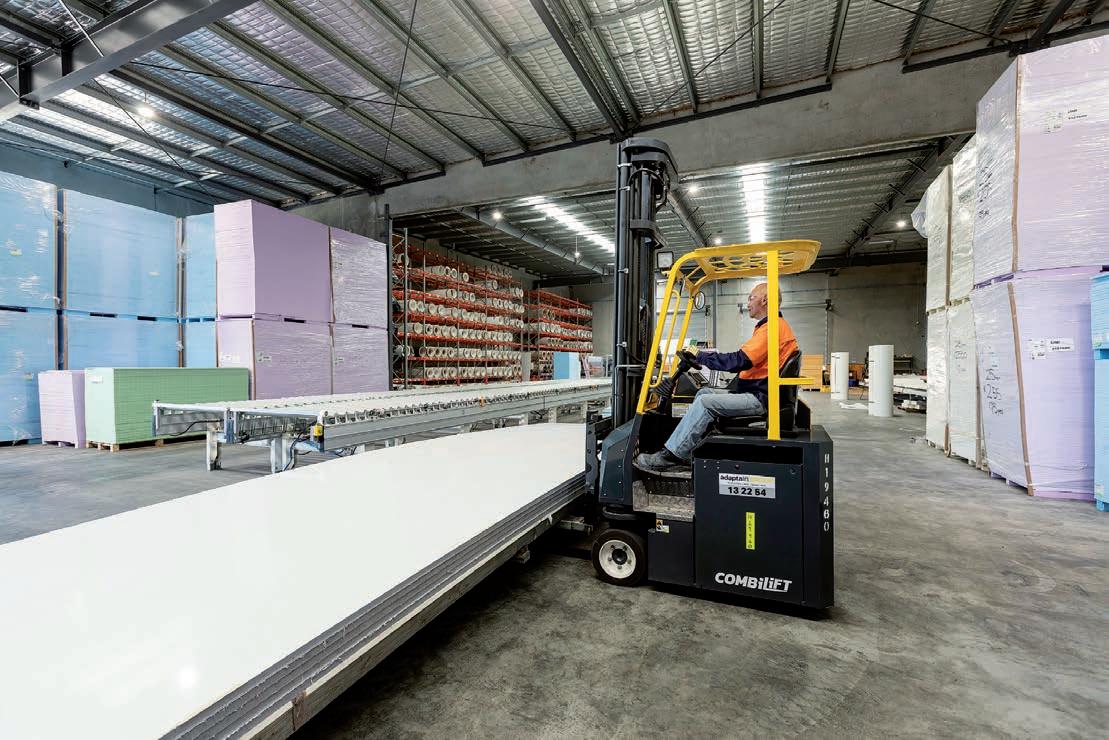
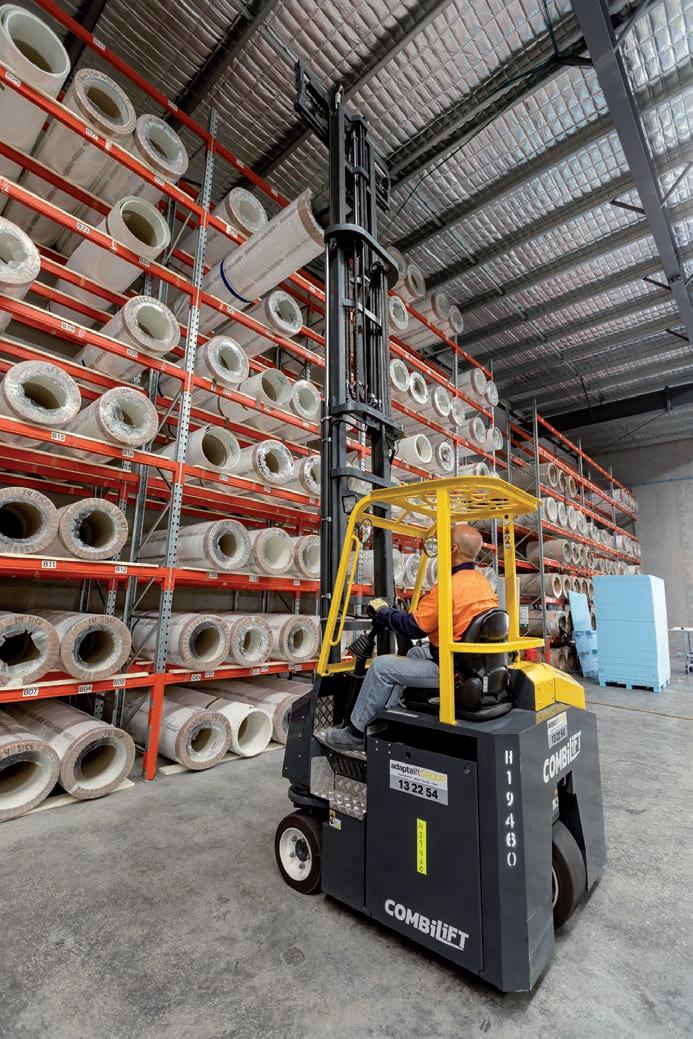
Australian company, using its patented cold spray technology known as Titomic Kinetic Fusion. The business exists to not just provide equipment to manufacturers, but to allow industrial users across different sectors innovate their own processes. The cold spray technology is making ground in different sectors including aerospace, defence, shipbuilding, oil and gas and mining. Cold spray is a process typically used in the remanufacturing of engine components and restoration of various equipment and surfaces. The system is comprised of a hand-held spray gun, two powder feeders and a touch screen controller in an IP50 case. Using metal powder, compressed air, and singlephase power, it can repair damaged components to original conditions in only a fewTitomicminutes.Kinetic Fusion utilises the supersonic particle deposition of metal powders to create industrial-scale parts. To build upon this, Titomic acquired a Netherlands-based cold spray technology company, Dycomet – now Titomic Europe - at the end of last year, which has a portfolio of portable cold spray solutions, materials and the provision of servicing, spare parts, and consumables for its systems.“Titomic provides a complementary advanced manufacturing ability,” Koeck said. “Spraying metal on metal can achieve and deliver certain services which are innovative for more traditional manufacturing.”“Ourfirststream of revenue is like many other companies – we are selling our machinery and service equipment, but that doesn’t differentiate us from many other manufacturing or 3D-printing companies, but Titomic has evolved beyond a 3D-printing company. What we are doing is engaging with manufacturing companies, where we provide a complementary technology which adds value to the manufacturing process, thereby creating a joint venture together. The Joint Ventures solidify Titomic’s technology as commercially competitive and demonstrates the strength and success of our go-tomarket strategy. It is one of Titomic’s key commercial focuses for accelerating growth within key markets, including defence and aerospace.” Koeck explained that Titomic doesn’t want to be a disrupter for manufacturers –instead the technology can be an extremely valuable tool in their tool box. The company has joined experienced businesses to not displace, but to improve processes which have already been refined over a number of years. By understanding these companies’ strengths, Titomic is able to bring the technology faster to market by leveraging off existing expertise and customer relationships that have been in place for years.“I’m prudent enough to say that we can’t understand all these industries as well as some existing players in certain industries,” he said. “We can bring technology into an actual manufacturing process faster than if we would do it on our own at half the cost. We are building our own relationships with defence and aerospace manufacturers, but these joint ventures are the most efficient way right now for us to bring this outstanding technology to the people who will benefit fromGlobalit.” challenges facing manufacturers don’t seem to be easing, which is opening the door for Titomic to partner with more manufacturers. Disrupted supply chains and geopolitical situations are leading to longer lead times for parts and raw elements, costing companies time and money.
An integral part of Titomic’s business model is what Koeck refers to as ‘the kitchen.’ The kitchen (Titomic’s innovation centre) refers to Titomic’s manufacturing operations in Melbourne, where the company operates its own machinery. When a new trend emerges in a particular industry or the cold spray experts identify a use case for a specific application, the thought must be validated by results and data. “When there is an idea, we have to validate it in the kitchen,” Koeck explained. “We conduct hundreds of small tests to optimise a process, going back and forth. The consequence of this could lead to another joint venture going forward. Usually in any kind of joint venture you have to consider the technical path and the commercial path – these two elements have to be intertwined. It’s easy to get overexcited about what we can do in-house if it’s not a good value proposition for businesses.”
Manufacturers’ Monthly sits down with Titomic managing director Herbert Koeck to learn about the company’s future plans – and how it continues to harness cold spray technology as a valuable tool to enter joint ventures with different Tmanufacturers.ITOMICisanemerging
Herbert Koeck, Titomic managing director.
Titomic’s partnership with Nèos International in the UK is an example of carving out a solution to supply issues, after the pair signed an agreement to create an advanced joint-manufacturing facility in Halesowen, England. The world’s first large scale additive manufacturing facility will manufacture and sell Invar36 faceplates and additively manufactured metal product solutions for customers in the United Kingdom and Europe for the aerospace, space, defence, automotive, and nuclear industries.
A world first facility Titomic recently signed a comprehensive Joint Venture agreement to establish the world’s first hybrid cold spray, flowforming manufacturing facility with Repkon Machine and Tool Industry and Trade Inc. In December 2021, the experienced manufacturer of weapons barrels became a strategic investor in Titomic through a $2.5 million investment. Koeck noted the successful progression to a Joint Venture with Repkon validates Titomic’s commercial approach and believe in the technology.
“The Titomic-Repkon Joint Venture has opened the door to a world-first high volume hybrid cold spray manufacturing facility. This was only possible by bringing Titomic’s TKF process and Repkon’s patented flowforming process together to produce high-performance components for weapons barrels,” he said. To establish the facility, Titomic expects to sell two TKF Systems to the Titomic-Repkon Joint Venture, with the TKF Systems providing one of the two core processes in the manufacturing of barrels for the defence sector. This
will 28 AUGUST 2022 Manufacturers’ Monthly manmonthly.com.au Cold Spray Technology
Partnering for success
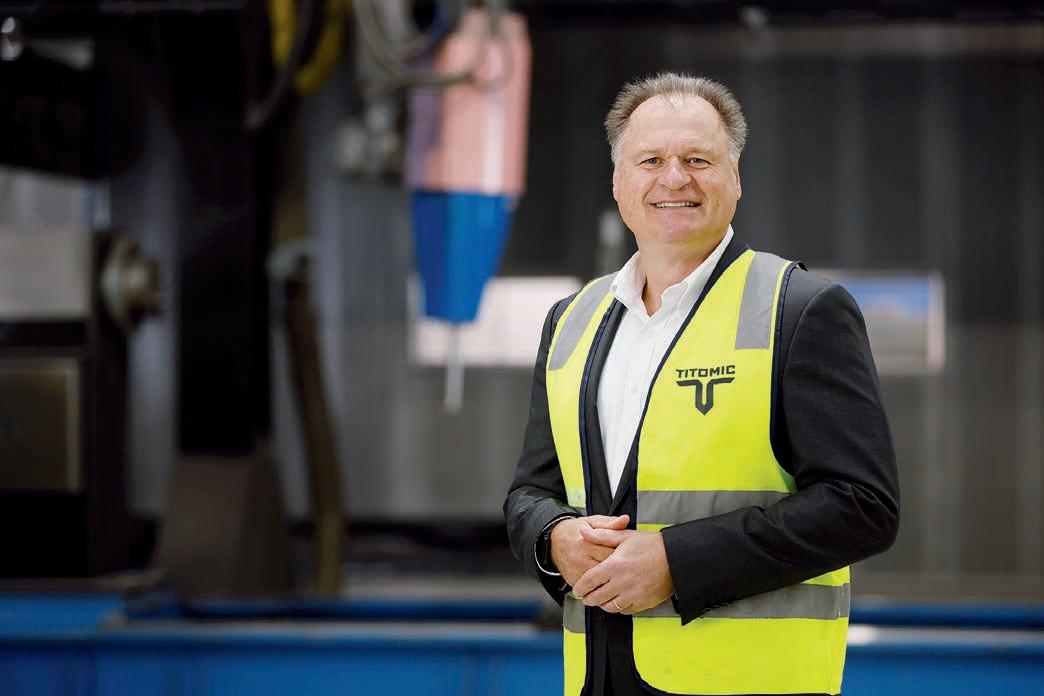
The Titomic-Repkon Joint Venture’s facility, located in Turkey, will leverage both Titomic’s TKF and Repkon’s flowforming technologies, introducing new capabilities to barrel manufacturing within the defence sector including reduced lead times, diverse and unique material compositions and capabilities, reduced weight, and improved performance.“Thejointventure shows that Titomic’s cold spray process enables metal additive manufacturing in a high-volume commercial manufacturing environment, for a technically critical end application,” Koeck added. “With its ability to utilise the combination of two innovative processes in barrel manufacturing, the facility will lead the production of next-generation barrels with tailored performance characteristics for specific applications and missions. It opens up a world of many design features for barrel manufacturing which were not previously possible.”
Ibrahim Kulekci, CEO of Repkon, said the working relationship is a step forward
Titomic’s cold
manmonthly.com.au Manufacturers’ Monthly AUGUST 2022 29 Cold Spray Technology BOC Shielding Gases A welding optimisation tool. To find out more about how BOC’s shielding gases can help optimise your welding, contact us on 131 262 or visit www.boc.com.au. Scan the QR code to watch our video featuring our state-of-the-art Applications Technology Centre and BOC shielding gases. BOC Limited 95 000 029 729 | 10 Julius Avenue, North Ryde NSW 2113 Australia. BOC is a trading name of BOC Limited. © BOC Limited 2022 | MP22-0506 | VS | 0622 MP22-0506 Man Monthly HP advert_shielding_gases.indd 1 6/29/2022 3:11:02 PM
spray technology is being used to improve manufacturing processes.
include a TKF 1000 and a bespoke TKF 3250R, as well as consumables (powder).
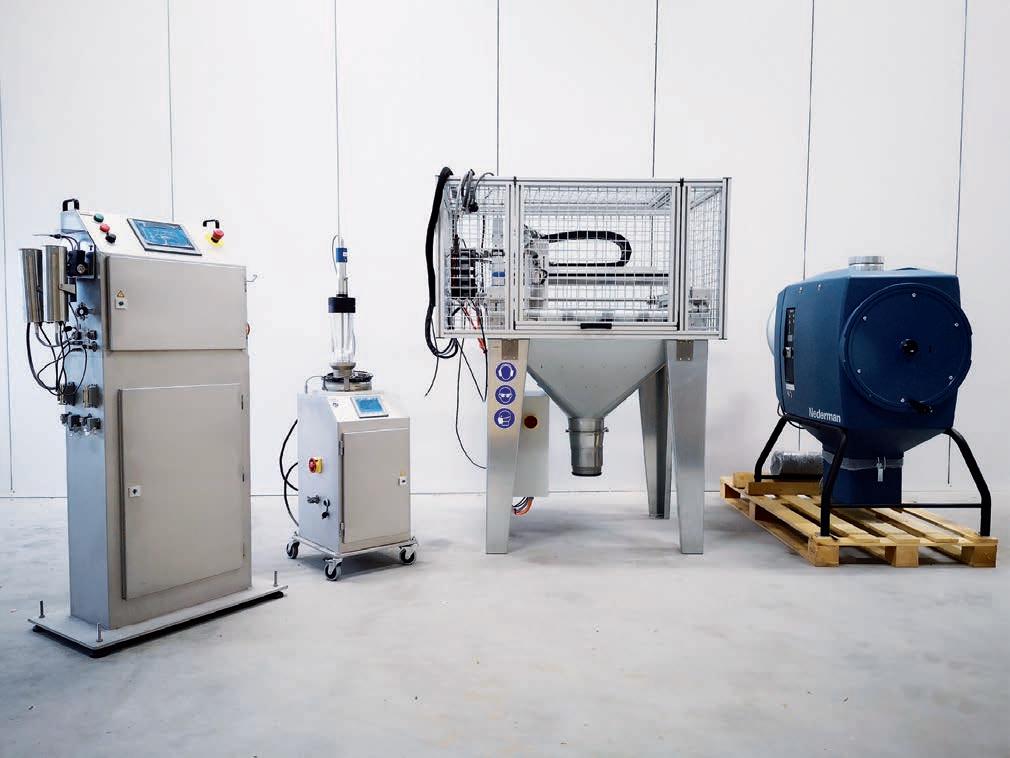
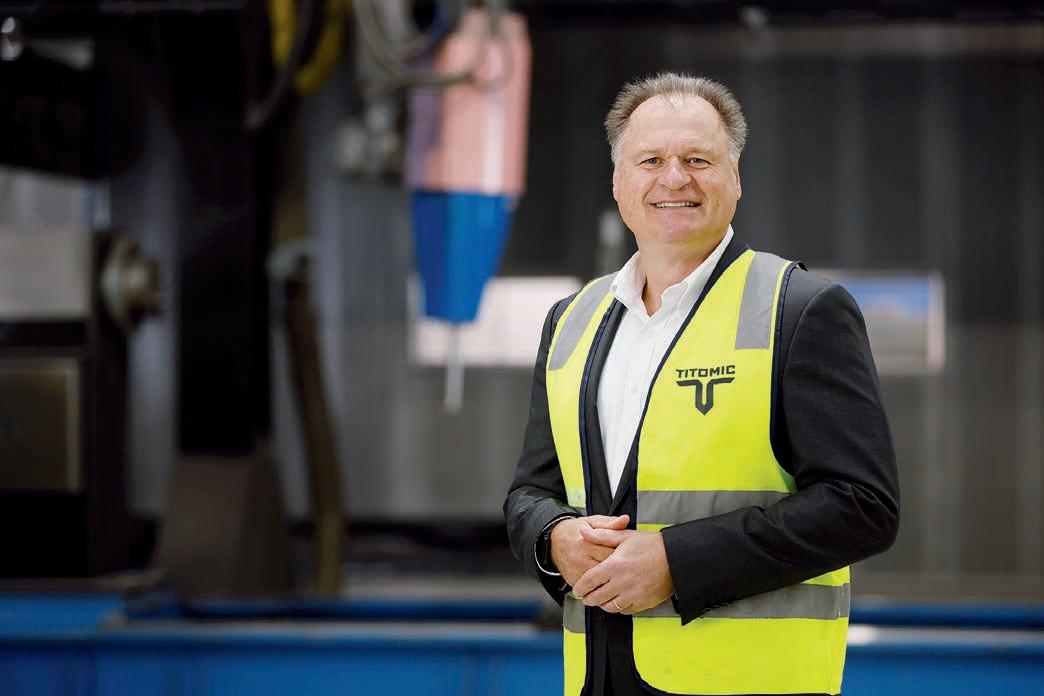
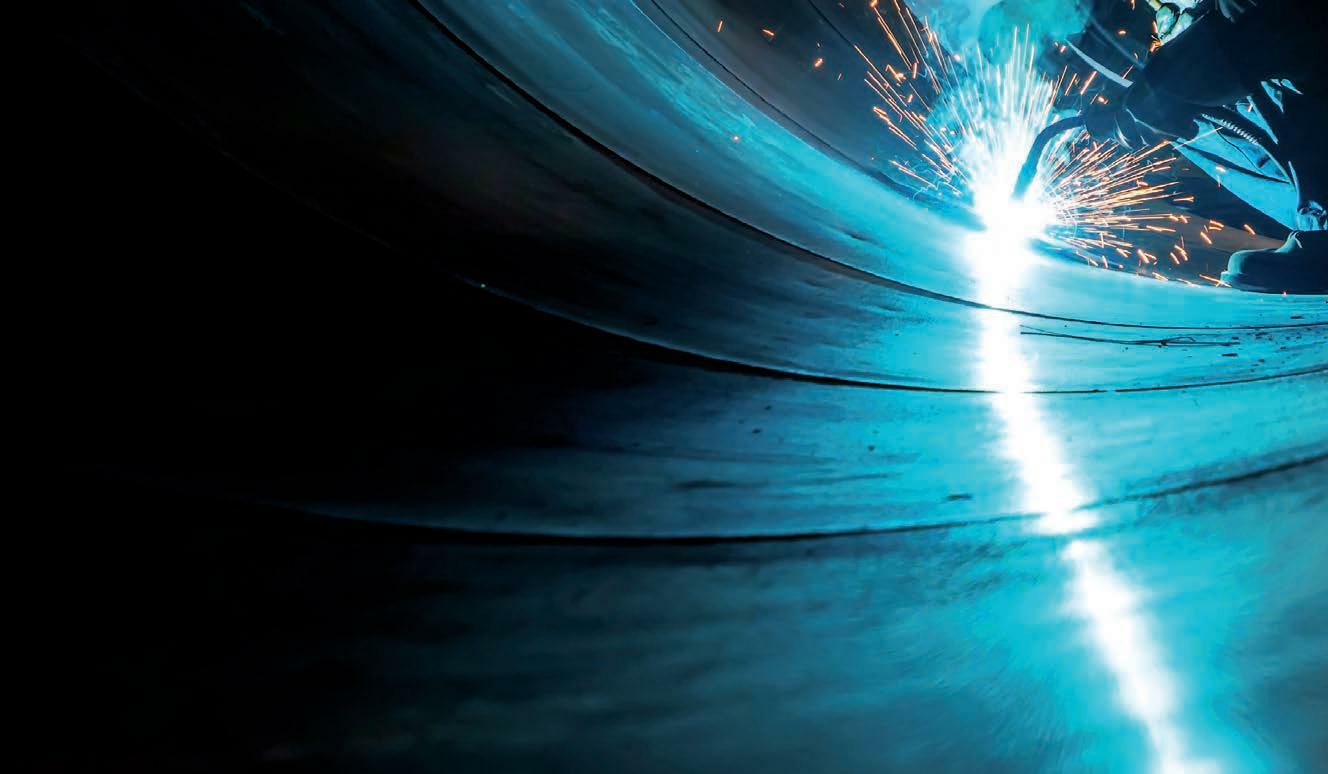
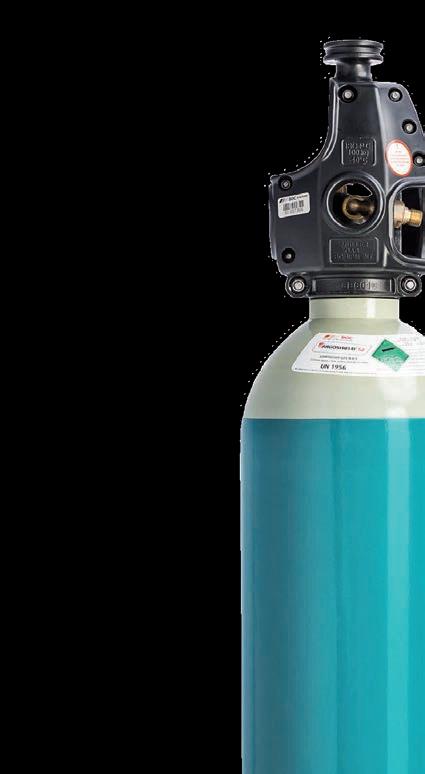
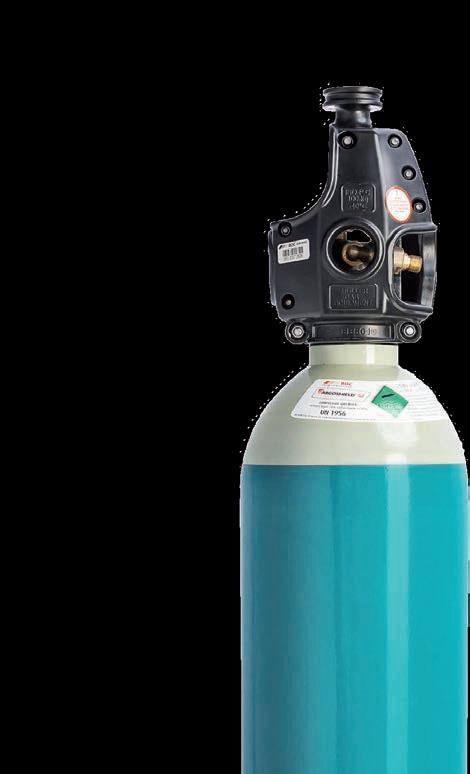
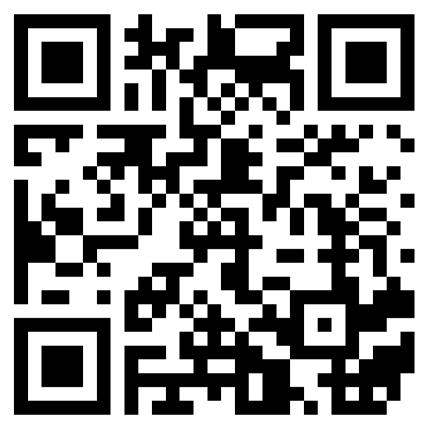
“As this 250-tonne structure is built to survive 30 years on the reef, it needs to endure cyclones and extreme weather.
The Reef Magic Pontoon is over 45 metres long.
Marine Survey requirements called for the aluminium plate to have ‘DNV’ test certificates.”Capralsupplied English Engineering with the certification required for all aluminium used on the build as nothing less would be accepted by the Marine Surveyors and the ‘Australian Maritime Safety“CapralAuthority’.iscurrently the only DNV certified manufacturer of aluminium extrusion in Australia. The business also has the largest stocked range of DNV certified plate, sheet and extrusion in the country. Having access to DNV certified material locally is so important for the Australian marine sector,” she said.Manufactured in Cairns, the worldleading vessel is a genuine one-off, according to Plath.
Leading adventure and leisure tourism company, Experience Co., recently put the finishing touches to one of Australia’s most ambitious construction projects – the state-of-theart Reef Magic Pontoon. Serving as an extensive research and tourism base for the Great Barrier Reef, the structure was designed and manufactured by English Engineering with extensive use of Capral materials.Thepontoon is a staggering 45.6 metres long and 12 metres wide, with two continuous decks of around 1000 sqms in area and an underwater observatory on the third deck with floor to ceiling windows. The project required a year of planning, plus a full year of construction. Tourism co-exists with a comprehensive scientific focus, with a lab and accommodation onboard to cater for marine biologists staying on the pontoon to study the reef in detail. The world-class research and education headquarters symbolises Experience Co’s commitment to sustainability, culture, and biology. The large interactive underwater observatory doubles as a classroom, with views of underwater life, commentary from marine biologists, and a dedicated laboratory facilitating partnerships with world-leading researchers. The laboratory contains everything required to teach visitors about the reef, including examples of starfish and other underwater sea Environmentally,life. the pontoon has been designed with sustainable principles. With three wind generators and 16 solar panels generating 48kW of power, the massive structure creates all the energy required to carry out its vital workSusancontinuously.Plath,marketing and development manager at English Engineering, outlined some crucial features – explaining how the Reef Magic pontoon does a brilliant job of facilitating tourism.“Itenables everybody to access the wonders of the Great Barrier Reef, even without a boat or snorkelling equipment,” she said. “With disabled entry and scuba facilities, it’s basically a one-stop shop for visiting the reef. The underwater observatory allows people to observe the reef without swimming, and there’s lifesaver towers for those wishing to swim.”Plath explained the Reef Magic Pontoon uses Capral 5083 marine-grade structural aluminium for plates and 6082 marine-grade structural aluminium for extrusions.“Capral’s local representative, Bill Lonergan, put in a great effort throughout the entire project,” she added. “Capral worked closely with the marine engineers to work out which materials were ideal to use in each specific area, giving us the best possible result.
Manufacturers’ Monthly sits down with English Engineering about a ground-breaking aluminium construction project in one of Australia’s most iconic locations.
30 AUGUST 2022 Manufacturers’ Monthly manmonthly.com.au Aluminium
Construction
Exploring the reef’s wonders
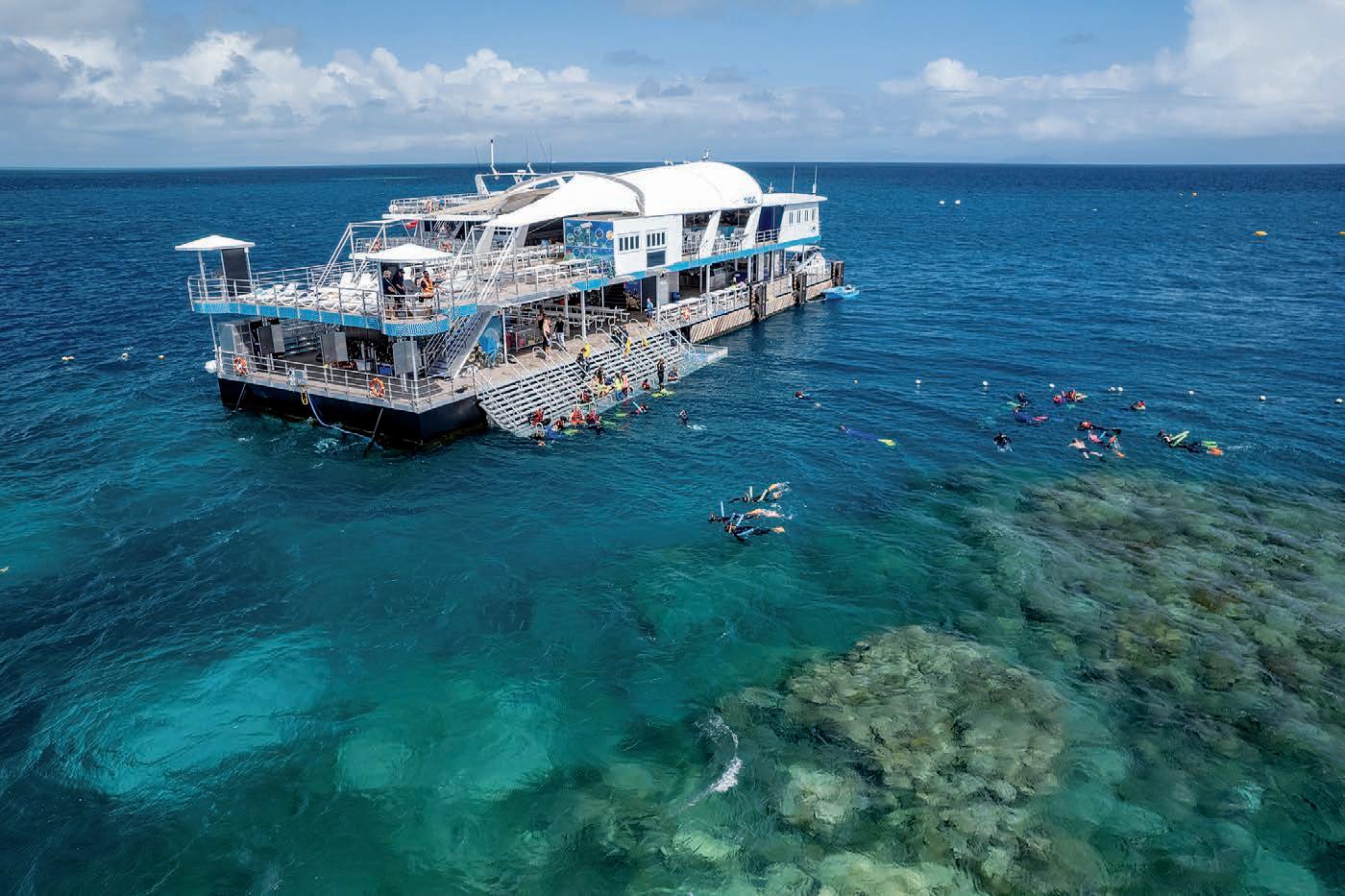
“There are only about ten similar pontoons in the world, with seven or eight currently off the Queensland coast. Everything had to be custom-made. It was designed for the client’s specific needs (including wind loads), making it invaluable to have a supplier like Capral working closely with the engineers,” she explained. “Many components were used innovatively, such as the Capral ‘Quiklock’ screen system with powder-coated white pearl finish, usually used in fencing and screens, in the massive 45m x 10m ceiling, turned horizontally. The scale was daunting at first, but we nutted things out with their assistance.”
The remote location at Moore Reef –about 45 kms and 90 minutes from Cairns - is a spectacular location to experience the “Oncereef. there, you can scuba, snorkel, or even helmet dive, and for those wishing to stay dry there is touring in glass-bottomed boats and semi-submersibles,” Plath said. “There’s even a special metre-high child’s pool for children learning to swim, separated, and protected from the reef, with Capral aluminium.”
The structure’s central 15 metre diving platform makes it safe for passengers to enter and exit the reef. There’s also a dive entry area for certified divers and helmet diving“Thistours.innovative new platform features a series of substantial ‘grandstand’ like platforms running down the side of the structure,” she noted. “Instead of a rectangular platform, visitors now walk down the substantial stairs (30 lineal metres in area) and straight into the water. Seeing a cavalcade of people visiting the reef from the pontoon is extraordinary. “Fish usually welcome visitors into the world of the reef. People can get up close with the Mori Wrasse, locally known as ‘Wally’. It’s almost like the reef dwellers are proudly welcoming you into their home, showing off its beauty and wonder, I’ve even been escorted around the reef by what seemed like a hundred little yellowThere’sfusiliers!”capacity for 250 people on the Reef Magic pontoon, with the layout designed to make the reef easily accessible to all.“The mammoth process of creating the pontoon has all been worth it,” Plath noted. “After 14 months of exertion, we all love her and we’re extremely proud of the end result.” 0413 606
manmonthly.com.au Manufacturers’ Monthly AUGUST 2022 31 Aluminium Construction Call us now for a quote and 10% discount on your order Ron Parker -
456 E:www.bollardsdirect.net.auinfo@bollardsdirect.net.au Australian Made Bollards. Manufactured to the highest quality to protect what’s valuable to you. • Bollards designed to protect your Business, Property and Assets. • Stop Unauthorised access • Preventing vehicles smashing into your premises, protecting Staff and Assets • Suits all types of applications Protecting What’s Valuable To You The pontoon uses Capral 5083 marine-grade structural aluminium for plates.
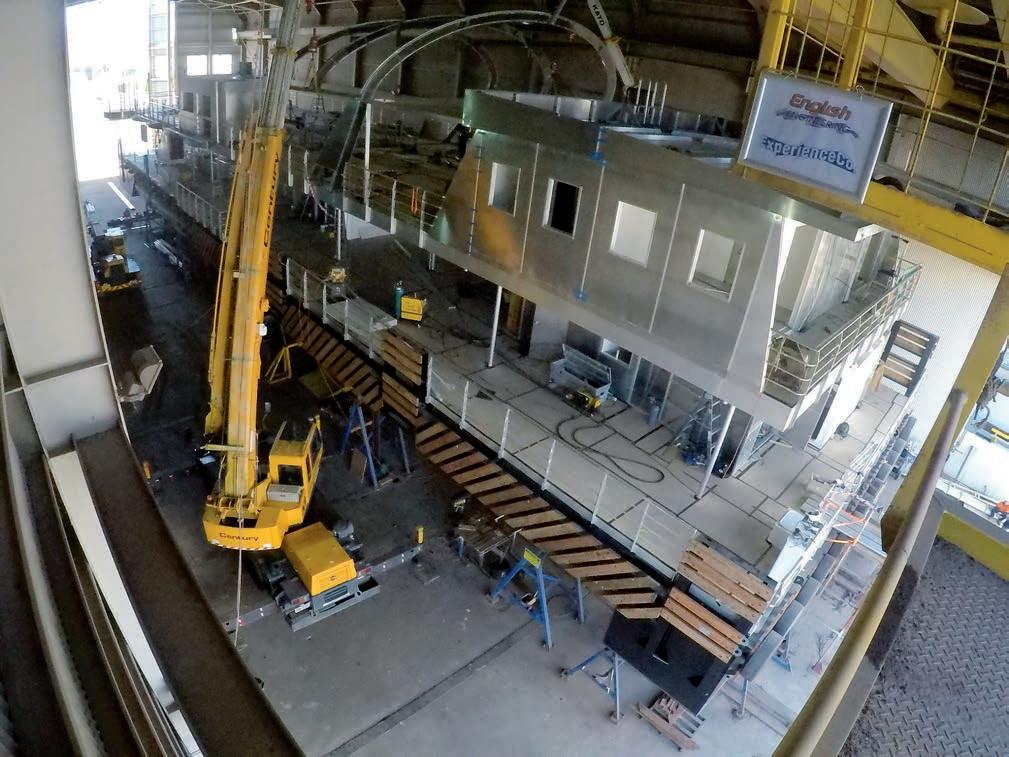
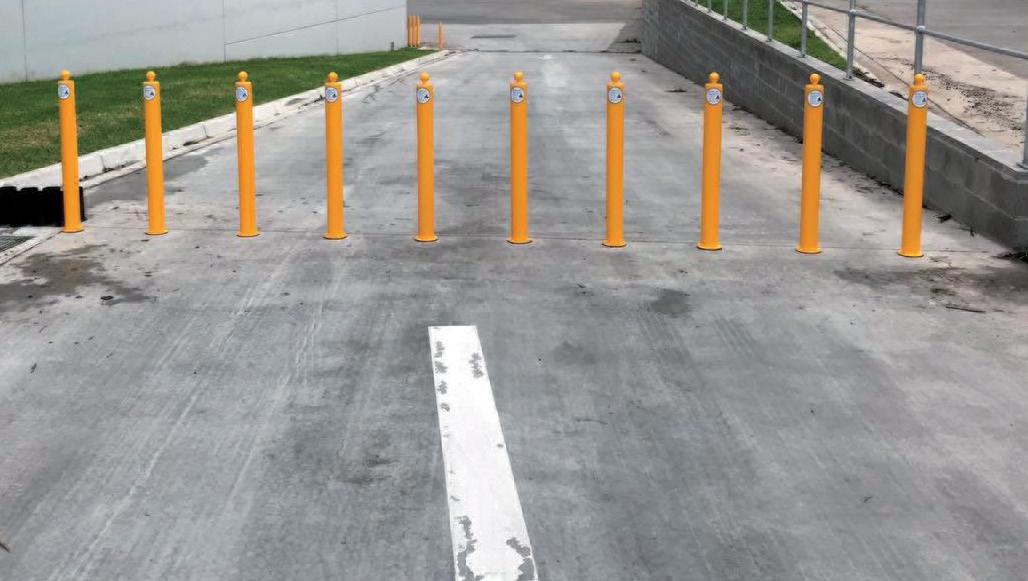
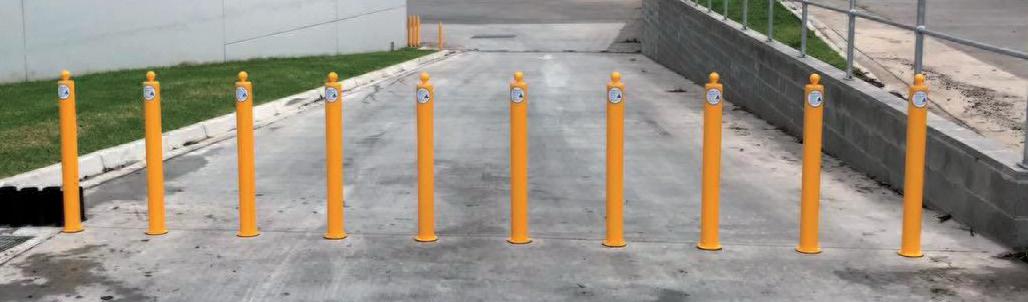
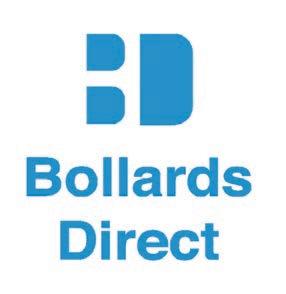
Metal
32 AUGUST 2022 Manufacturers’ Monthly manmonthly.com.au
Rollforming – A unique metal forming process Metal rollforming is a continuous bending operation where a strip of metal is passed through consecutive sets of rolls, each performing an incremental part of the bend until the cross-section profile is obtained. ARM is adept at working with a wide range of materials including
ARM has consolidated its warehouse and manufacturing facility into one space.
corrosion resistance because the zinc has 3 per cent magnesium content and 3.5 per cent aluminium. The magnesium creates a stable and durable layer across the ARMsurface.”produces a range of DuraGal® angles, lintels, flats and channels, all rollformed from high strength grade steel with a highly corrosion resistant zinc coating.
Rollforming
“The first special section rollformer was bought into Australia in the 40s,” Wolfkamp said. “I started my career fresh out of university with Fisher & Paykel, who had 120-metre-long production lines. Somewhere amongst the punches, the folders and guillotines was a rollformer for the edges. The company didn’t have much experience in rollforming, but had many experienced toolmakers for folding and punching, so they thought to give the rollforming to the new guy.” Initially, ARM lived off projects as special profile manufacturers. Now, the DuraGal® brand is ARM’s bread and butter, occupying around two thirds of operations with special sections being the other integral component. “We are now competitive on price with imports from China and Vietnam while said. “There’s uncertainty with Chinese products – long lead times, huge prices on shipping for imports and rising prices has led to more focus on local manufacturing. The challenges are felt around the world too, especially with steel mills around Europe being disrupted by the RussiaUkraine conflict.”
DuraGal® Profiles Kylie deMole, national manager, explained that as a manufacturer of DuraGal®, ARM produces profiles for unlimited length with consistency, closer and tighter tolerances, high volume, high-speed preparations and a superior surface finish. “With a prepared surface finish, DuraGal® Profiles are supplied ready to use, removing a need for priming or shot blasting after fabrication,” she
Tground at Australian Rollforming Manufacturers’ (ARM) new facility in Dandenong South. The manufacturing capability and efficiency immediately catches the eye, so it was no surprise to learn that ARM rollform, shape, drill, punch and cut more than a million metres of metal every year. The work is managed by highly knowledgeable engineers, with experience working across thousands of custom profiles, converting sketches and drawings into superior design results. History is etched into the ethos of ARM, evidenced by a filing cabinet at its manufacturing facility storing the original tooling and drawings from the company’s beginnings in 1941. Henry Wolfkamp has been in the rollforming industry for 44 years, acquiring expertise which enables
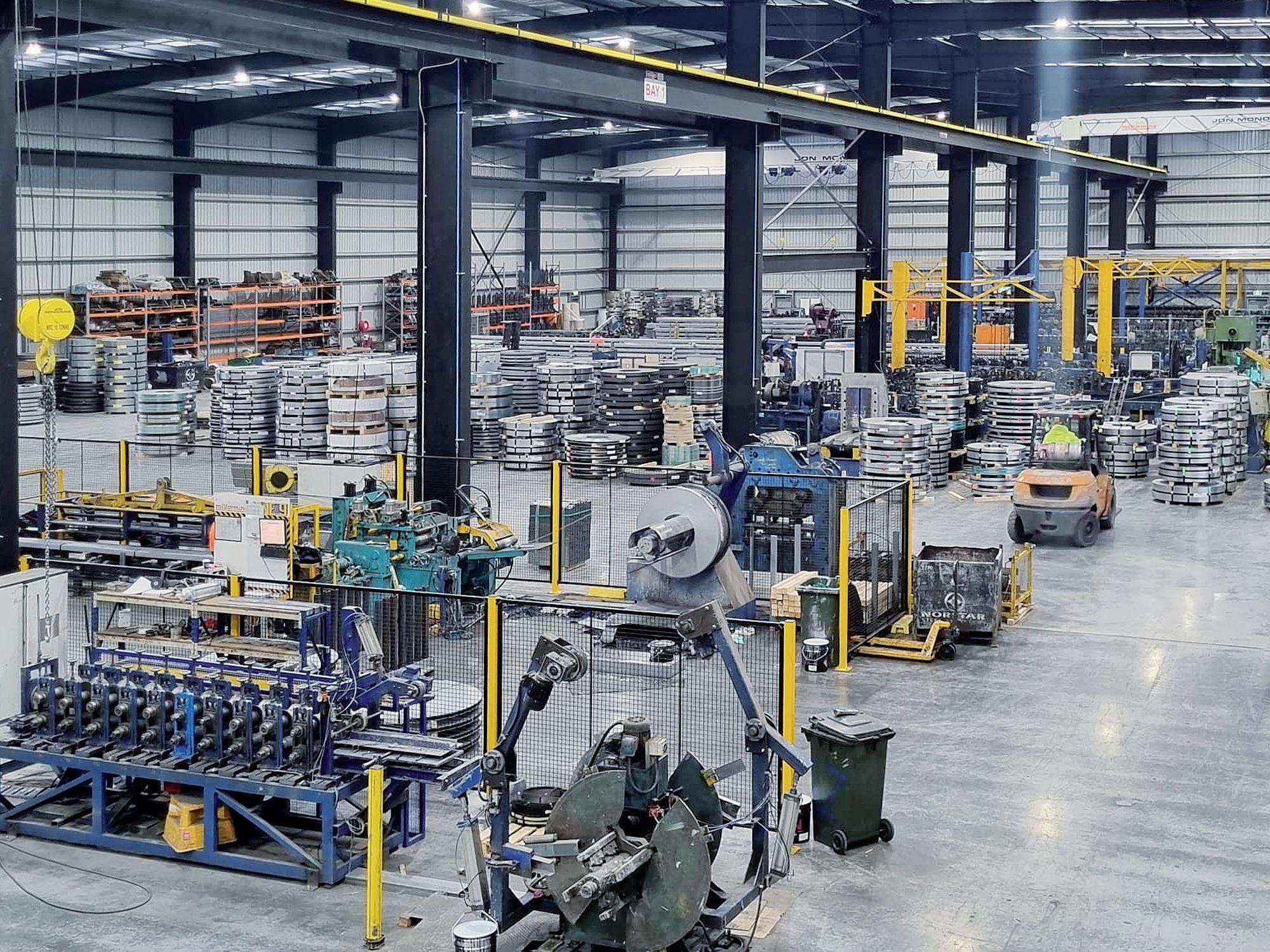
A custom-designed facility
stainless steel, titanium for a special case, aluminum, copper, mild steel and all types of coated coil. Wolfkamp explained rollforming as a design process, in which exact formulas don’t yet exist for. “Punching a hole, bending a piece of steel – there are formulas for that,” he said. “Rollforming is a three-dimensional process and the maths isn’t around for it. Therefore you rely more on people’s experience. To do this job, you have to have a creative skillset.” Finding enough people with such a skillset to problem solve is a huge challenge for the special sections sector. Many of the country’s skilled engineers have swapped over to computer programming or IT-related jobs, leaving a gap to be filled. “I think we’re going to struggle for another decade. Manufacturing used to be just over 30 per cent of Australia’s GDP. It’s now under six per cent. To bring all this work back onshore to increase that figure, businesses have to double in size.” To compensate for this challenge, ARM is investing in improving technology to automate more of the rollforming procedure. With Deakin University’s Institute of Frontier Materials, ARM’s rollforming research and development team is hoping to advance available technology.
“The computer power is improving, it’s not quite a production tool yet and is mainly still in the lab,” Wolfkamp explained. “You have to analyse the material, so that your process becomes more predictable and then you have to have a stable supply of that material. Improving the technology will lead to even more Deakin’sproduction.”latestFinite Element Analysis complex’s innovative cladding on the building’s façade.
manmonthly.com.au Manufacturers’ Monthly AUGUST 2022 33 Metal RollformingSpecificationsandtolerancescanbemetbyARMin-house.
The new building is only adding to one of ARM’s big competitive advantage: its ability to rollform up to ten millimetres of thick steel. Powered by advanced software, ARM is able to quickly respond to customer needs by undertaking all tooling work in-house. “We’re always taking on new projects,” Wolfkamp added. “We are remaking a train part which is being used for the structural beams which run on top of the trains for the Perth Metronet project. It’s made out of a very high tensile stainless steel which hasn’t been on the market very long, so the current rollformer supplier overseas just can’t do it. It’s about understanding how a certain material behaves and knowing its characteristics. Years of knowledge helps.” That knowledge translates to a tremendous diversity of products ARM provide, including collector plates, noise bridge deck, sheet piling, trench sheeting,
Australian Rollforming Manufacturers’ new facility in Dandenong South.
In December last year, ARM consolidated its warehouse and manufacturing facility into one larger, 6000 sqm space. It was a factory custom-designed for ARM, with thoughts of expanding in mind. In fact, the design included purposefully another 3000 square metres of floor space.“It’s a lot easier to ramp up productivity now because we are all on the same page,” he said. “We aren’t so fragmented, so the bread and butter of the business works like clockwork. We’ve realigned our tool room workshop into a more streamlined process, so we can get the tools assembled and into the machine more efficiently. The emphasis was on changing the way the machines were loaded and set up so there was no overhead crane-jam anymore.”
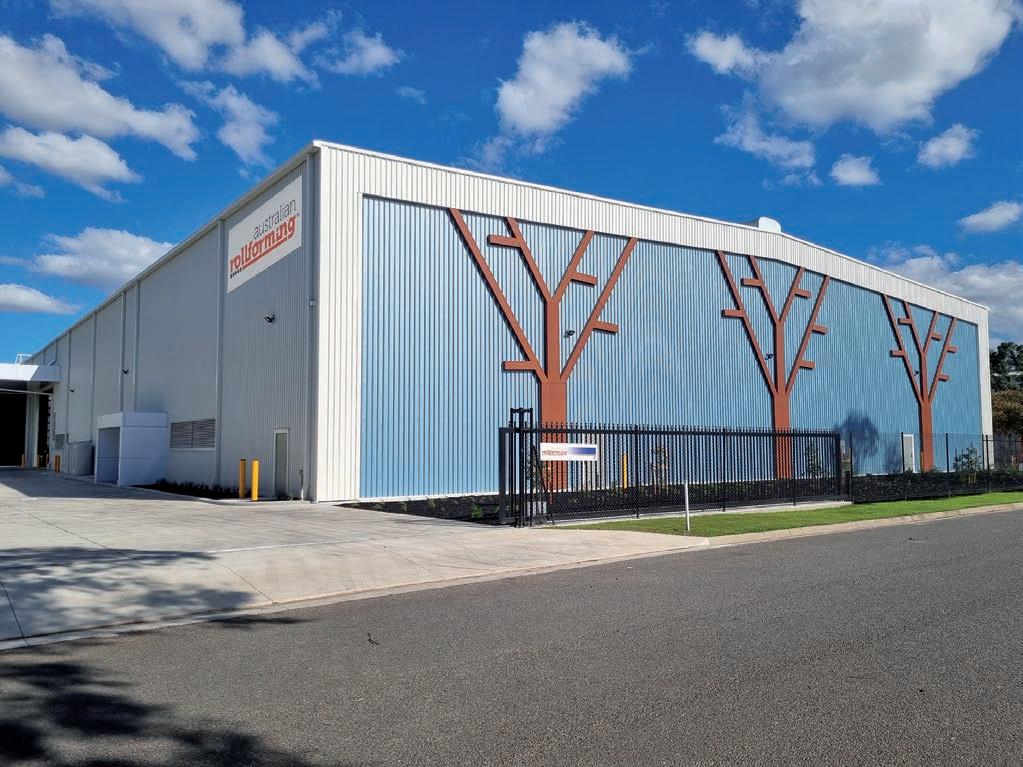
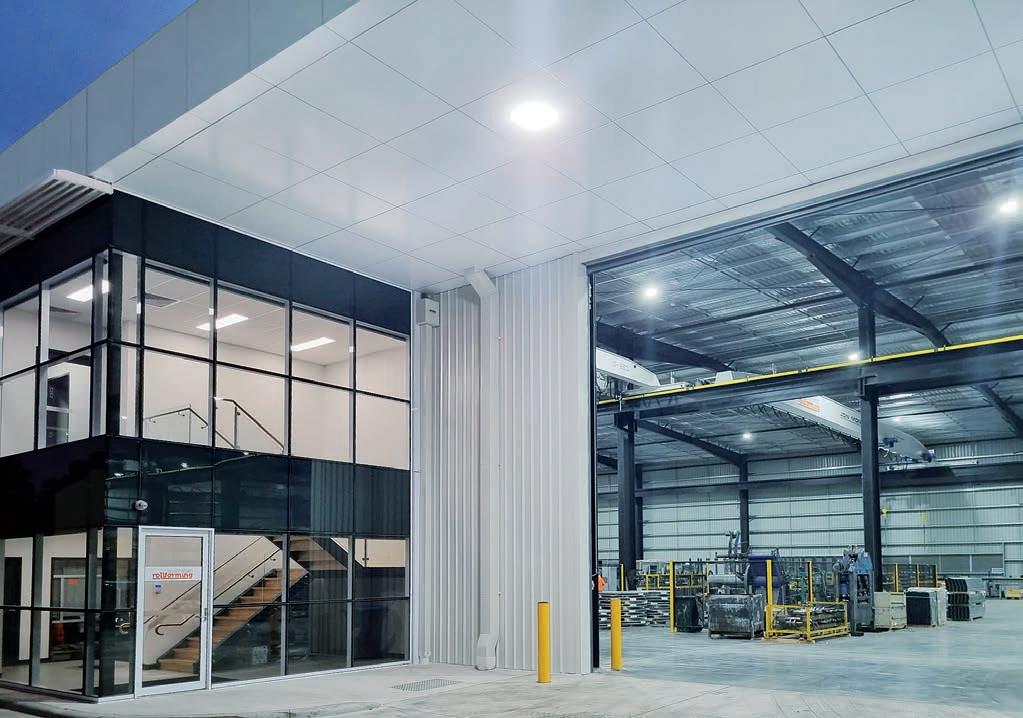
3D Printers for Additive Manufacturing of Large Parts. Big Area Addative Manufacturing Large Scale 3D Printing + 5 Axis Machining Melbourne 2/137-145 Rooks Road Nunawading VIC 3131 +61 3 9417 john_croft@cncdesign.com.au2820 Sydney 22/457 Victoria Street, Wetherill Park, 2564 T +61 2 9737 825 Brisbane 7/65 Business Street Yatala, QLD 4207 T +61 7 3343 8811 +61 (0)414 747 636 +61 (03) 9417 john_croft@cncdesign.com.au2820virtualsmartfactory.com MARKETS & INDUSTRIES Construction Aerospace Mining Defence Entertainment Education ManufacturingVehicle Boat Building VSF Composite For production of large thermoplastic parts and moulds. Scan for video and further information VSF Concrete For printing on-site or off-site.prefabrication Scan for video and further information VSF Wax Digital Manufacture of recyclable moulds for production. Scan for video and further information Robotic Gantry 3D Printers Virtual Smart Factory® (VSF) is a unique and versatile solution for Additive Manufacturing of large parts for Construction, Aerospace, Mining, Defence and other manufacturing industries. VSF gantry-based systems are the 3D printers constructed in the southern hemisphere and can combine Additive and 5-axis machining in a single machine.



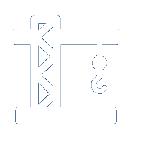

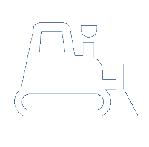
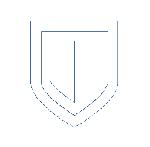

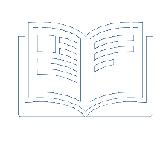

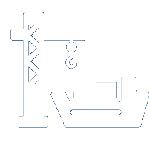
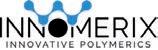
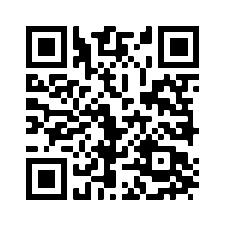
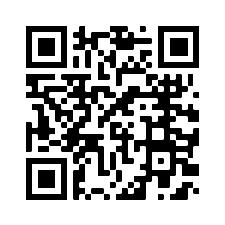
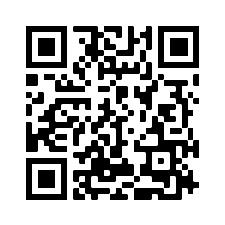
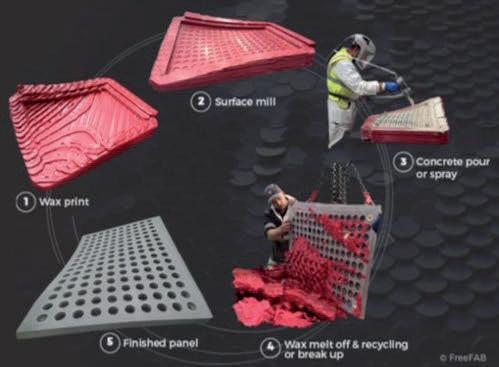

“From an end-user point of view, that quality and durability is what they want,” he said. “End users should be specifying KITO because they know their cost of ownership or runtime costs will be much lower compared to others. When you increase productivity and reduce ongoing repair costs it makes a difference in the long run. Generally speaking, our spare parts are priced lower because of the durability of the hoist.”RY series wire-rope hoists are designed and developed in-house in Japan. A hugely experienced team of engineers and designers have developed the technology to feature an original variable frequency control system, pull-rotor motor braking and aluminum casing, for a safe and more functional product. The hoist has been well received globally and is starting to build momentum in the Australian market. “KITO has been a leader for developing the inverter control for their hoisting for a number of years,” Morgan hoist,inverterchaindevelopedthemoved“They’veexplained.basicallyacrosstechnologyonthehoistwiththetothewiregettingthe full benefits and utilise how to use the technology at its greatest capacity.”
The inverter control is a dual speed variable frequency (VFD), which controls both hoist and trolley for optimum speed adjustability as well as lifting and lowering accuracy. VFD incorporates an easily accessible condition monitoring system via an hour meter and operation counter. This means users can plan their preventive maintenance based around the exact hours of operation and the exact operations the hoist has done.
“The condition monitoring features enable the end user to actually plan any major servicing of the hoist,” he said. “Major inspections are usually scheduled for every ten years, but can be prolonged because you can base it on actual usage rather than time. Customers can plan oil replacements and some of the inspections on gearings based on usage – most people don’t use the cranes as much as they’re designed for.”
The best solution to heavy load challenges KITO PWB’s new RY Series Wire Rope Hoists are designed for safety, reliability and performance.
The KITO RY Wire Rope Hoists are produced to comply with the Australian Standard AS 1418. 12 hoist models can manage different kinds of heavy loads –
• Electronic overload limiter – detects overload instantaneously and shuts off the lifting circuit. Electric thermal motor protection – detects overheating and stops the operation to protect the motor. External upper/lower limit switches –enabling you to set the desired range of operation easily.
• Upper emergency paddle limit – set in accordance with the Australian Standard AS 1418 to ensure optimum safety. Ease of maintenance
manmonthly.com.au Manufacturers’ Monthly AUGUST 2022 35 Hoists & Chains
Manufacturers’ Monthly finds out why end users should be asking crane service providers for the best available hoist in the market. KITO has a global reputation for manufacturing hoists and cranes. With 85 years of hoist manufacturing experience, the company has been able to refine its chain hoists, lever hoists, wire rope hoists and cranes to achieve a certain level of durability and quality.According to Glenn Morgan, national hoist specialist, the RY Series Wire Rope Hoists will be popular in the hoist replacement market, largely in part to its ability to extend the life cycle of the equipment. The level of durability is its calling card, which can conflict with crane provider’s interests, to the detriment of the end user. In some instances, crane service providers have strayed from KITO products, because of the superior durability. Minimal service is required for KITO’s equipment across a long period of time, losing opportunities for providers to make more money off repairs.
Cost of ownership is lower with KITO products.
• Easily accessible condition monitoring via Hour Meter & Operation Counter – users can plan their preventive maintenance based on the exact hours of operation and the exact operations the hoist has done. High-performance motor brakes – the robust motor brakes are maintenancefree for operation up to 1 million starts. This means no re-adjustments necessary and virtually eliminates motor brake downtime.
• Low-load high speed function – the hoist can operate at 1.5 times the rated speed when carrying a load less than 25 per cent of the rated capacity, which means quicker process time thus efficiency gained. Dual speed VFD control on both hoist and trolley – for optimum speed adjustability as well as lifting and lowering accuracy. It is the only WRH in the market offering this feature as standard. High level of safety
Minimal service is required for KITO’s equipment across a long period of time.
The five-tonne hoist can make lifts of 7.6 to 10.2 metres, while the 10-tonne can lift heights of 9 to 12 metres. Benefits for end users Increase in productivity


When down time is your enemy
Burt added that Injectronics can also recommend alternative parts that can be retrospectively installed. There are of course components that are specific to brand, but there are many key electrical items that could be replaced with better quality by Injectronics. “It gives some peace of mind that I’m making a good business decision,” he said. As a manufacturing line manager, business owner or service agent –Injectronics is a local alternative to costly replacement parts – offering a 24-48 hour inspection and advice turn around, with dedicated resources for industrial repair applications.
To stay informed with solutions on offer, visit industrial.injectronics.com.au or call the team on 1300 646 948. inspection and advice turn around results in timely feedback for customers.
36 AUGUST 2022 Manufacturers’ Monthly manmonthly.com.au Electronic Components 24-48 hour
Injectronics speaks to Manufacturers’ Monthly about its dedication to providing electronic and mechatronic repair services to a variety of manufacturing markets. Manufacturing in Australia has a long history and has grown efficiently with the use of electronic assisted production lines. While we have some of the latest manufacturing technology, thanks to both local and international suppliers, we are also a country that maintains and continues to service existing equipment. It is not uncommon for some of our production lines to be utilising 10-ormore-year old technology. For business owners and service agents, this creates a challenge when faults develop. Replacement parts are commonly no longer available, if they are in stock the parts are typically from European manufactures and take time to dispatch to Australia, but often the price is prohibitive and this is all with the question – will the new part even fix the problem?Theservice and repair sector of the automotive industry faced this exact challenge from the late 80s, as motor vehicles moved from a mechanically controlled system to electronic control modules. This issue had a solution - Injectronics. Part of the IM Group, Injectronics is a leading supplier of quality new and remanufactured automotive electronic components, as well as the preferred repairer of electronic and mechatronic parts. The business is a repairer of electronics used for industrial applications, including but not limited to:
• Control IndustrialModulesControl Panels Human Machine Interfaces (HMI)
• Programmable Logic Controls (PLC) Variable Frequency Drivers (VFD) For production line managers, business owners and service and repair agents, Injectronics presents an attractive option when it comes to making a decision to repair, replace, or upgrade. With a team of electrical and electronics engineers able to interrogate and provide advice on many electrical devices in a 24-48 hour window, Injectronics provides feedback that could mean the difference between ordering a new part, repairing the existing, or uncovering that the part in question has no fault at all. James Burt, general manager of Uneek4X4 Australia and Barden Fabrication, experienced this exact scenario when a control module on a plasma cutting line began to fault intermittently.Serviceagents initially advised a wear and tear component required replacement; at $11,000 the part was installed only to find the same issue persisting. Production had been offline for one week at this stage. Round two on the diagnosis pointed to a control module needing replacement, presenting a three week wait and purchase price in excess of $15,000 with the advice this may not resolve the issue. Down time is the enemy of any production line and facing a backlog in production, impacts on customer orders and company revenue, Burt was forced to make a Awaredecision.oftheservice Injectronics offer, Burt delivered the control module for inspection.Theengineers quickly identified the faulty unit on the circuit board, while also identifying a potential root cause of the fault. A power output device was arcing against wiring on the PCB and causing external contactors to fail and throw fault codes.After some discussion and further testing with the service agents, the repaired control module and new contactors were installed returning the line to operation. In hindsight, Burt believes the service Injectronics provided was the difference between a 2-week offline window and potentially over a month. “For factory managers and business owners this service gives us options,” he said. “Service agents can’t keep parts on the shelf and can only offer a replacement service. It can feel like we are throwing parts at problems. Injectronics gave me the option to quickly gain additional data assisting in my decision. This is highly valuable.”
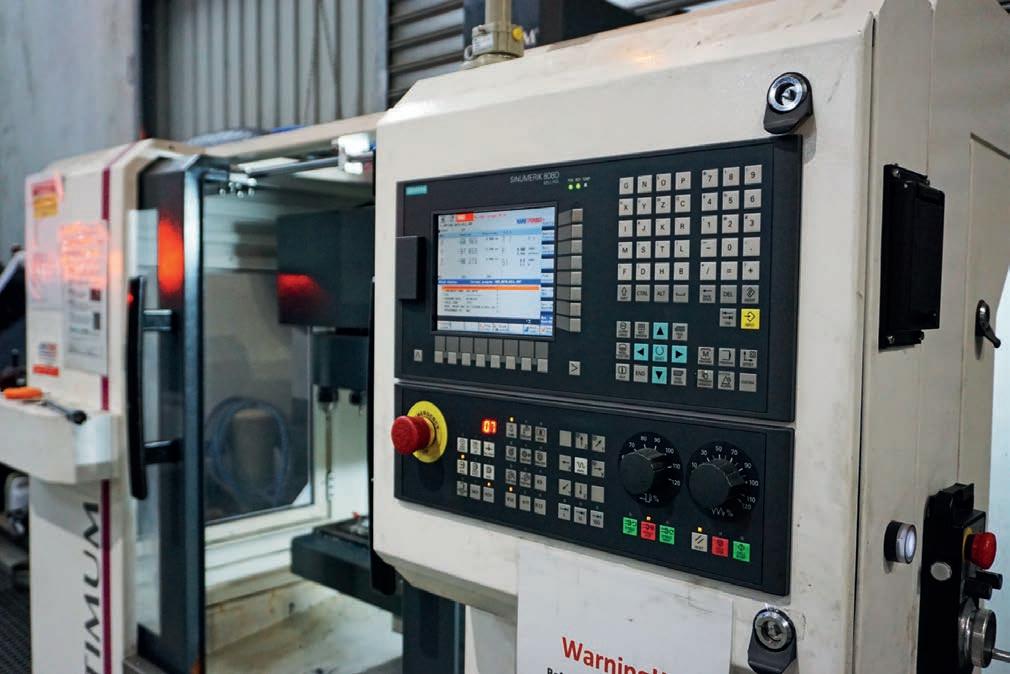
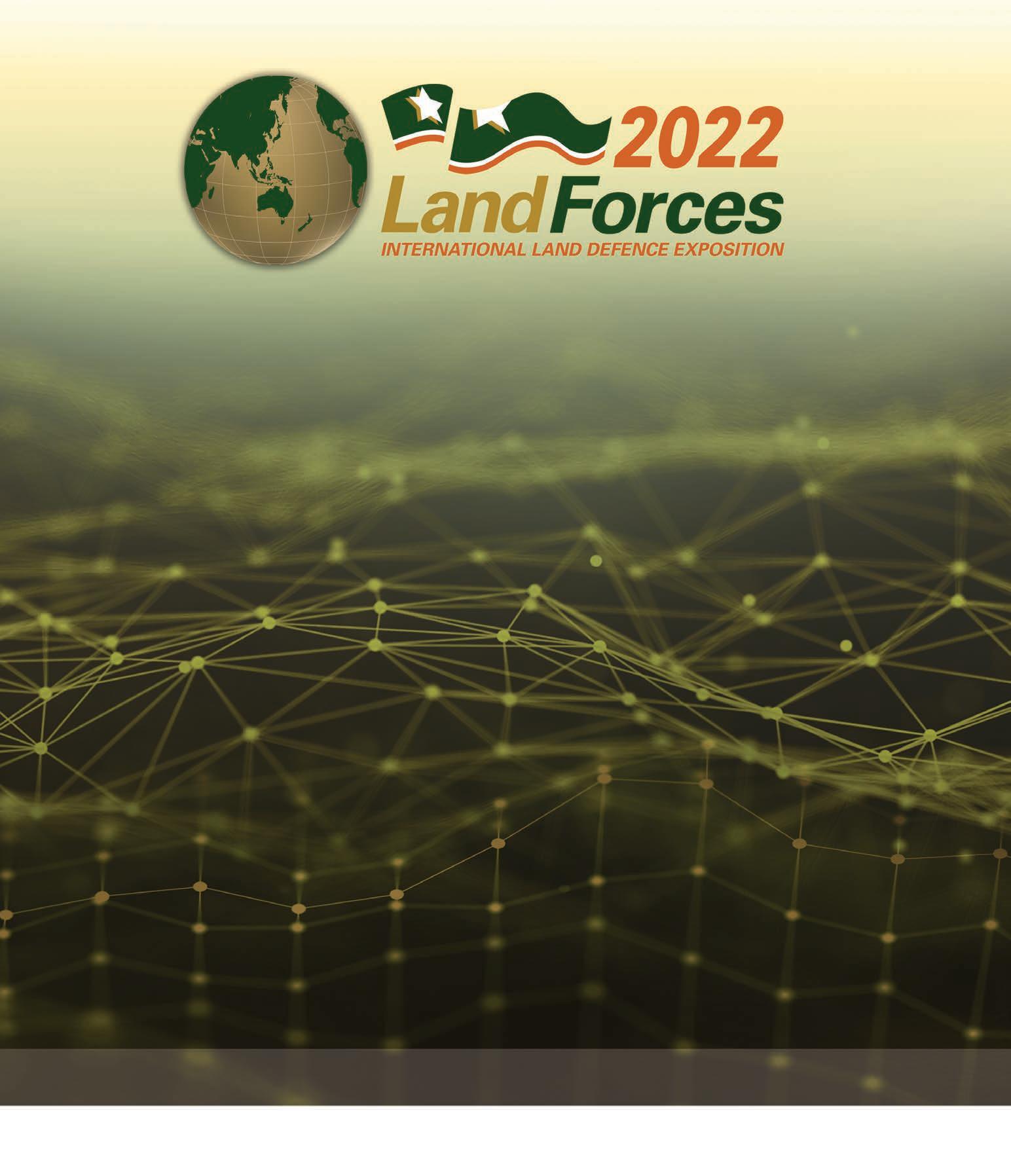
Network and connect with key military, industry and government decision makers at the premier land forces exposition for Australia and the Indo Pacific region. LAND FORCES will highlight defence capability and equipment, as the Australian Army undergoes the most substantial period of recapitalisation and optimisation since the Second World War. l Defence, government and industry conferences, briefings and symposia l International defence, government, industry and academic delegations l Comprehensive industry exhibition (718 participating companies in 2021) Don’t miss this opportunity to network and connect with key thought leaders through this established, world-class exposition. 4 - 6 OCTOBER 2022 BRISBANE CONVENTION & EXHIBITION CENTRE AUSTRALIA PLATFORMS - EQUIPMENT - SUPPORT - TECHNOLOGIES landforces.com.au For further information contact the LAND FORCES Sales Team: T : + 61 (0) 3 5282 0500 E : expo@amda.com.au SUPPORTED BY Queensland Government is the Host Sponsor of Land Forces 2022
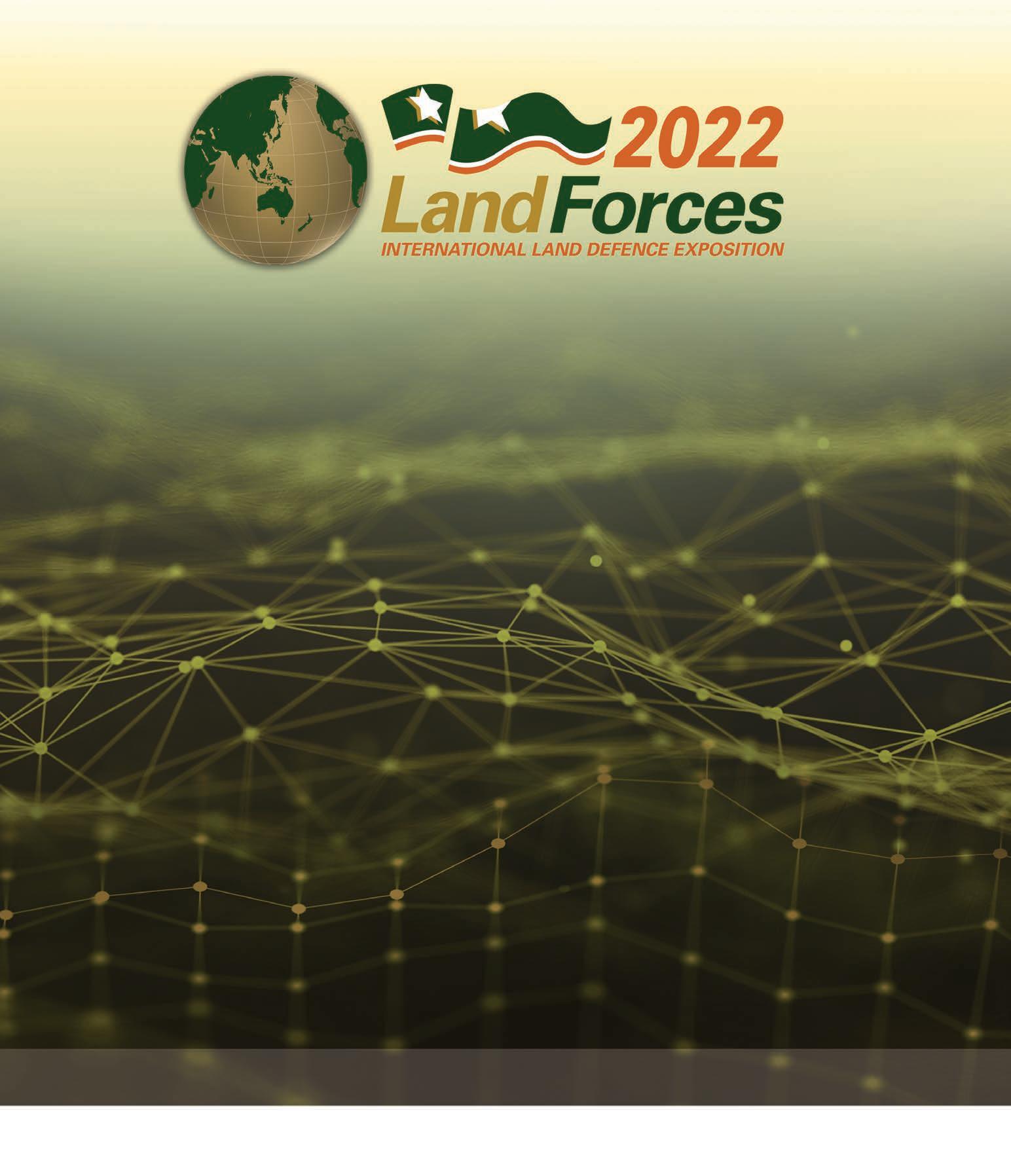
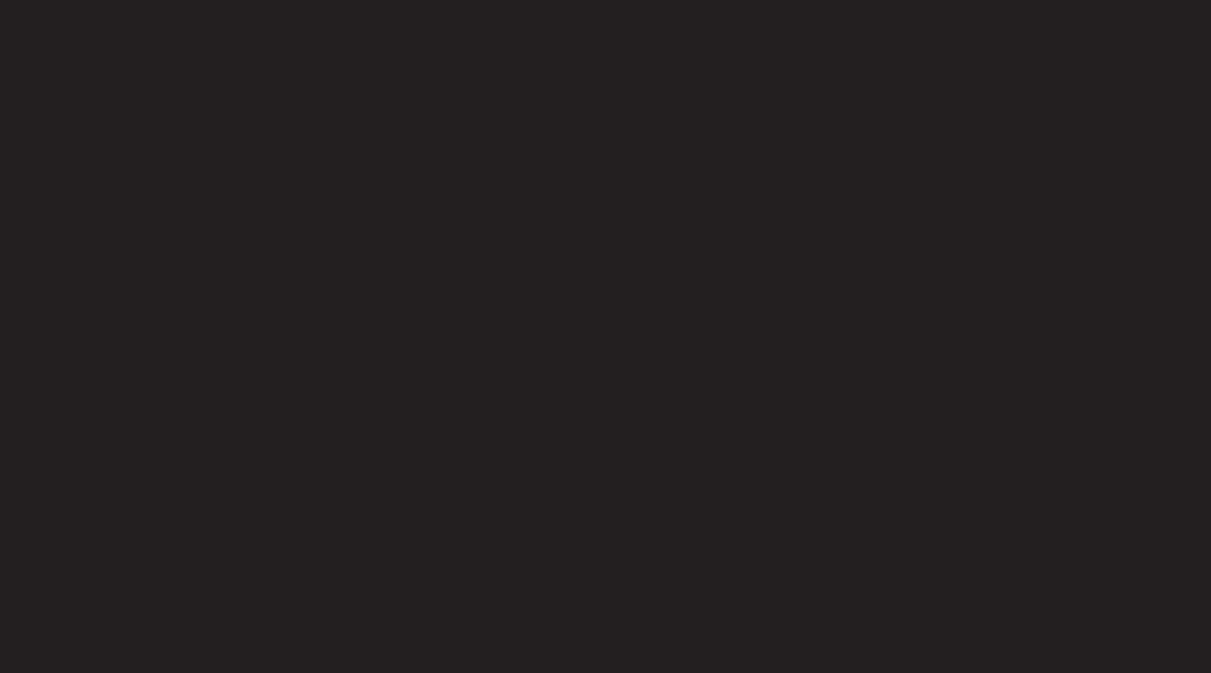
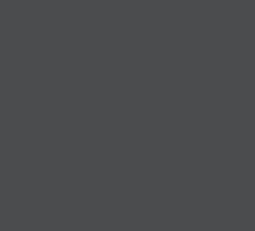
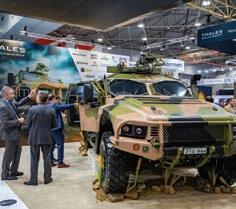
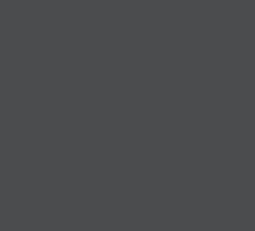
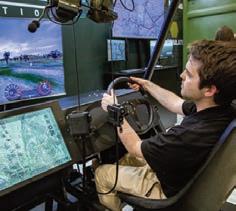
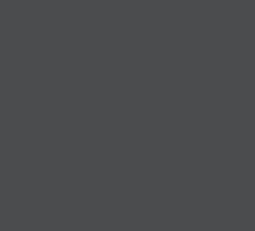
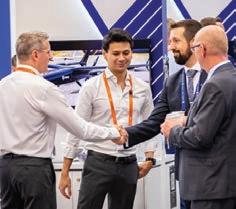
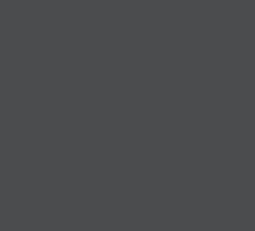
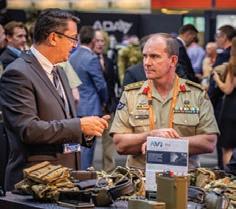
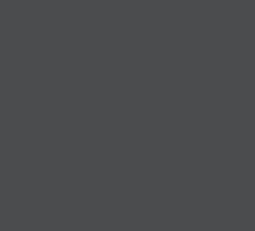
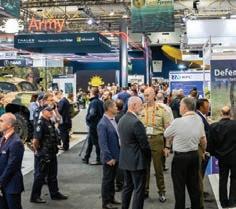
38 AUGUST 2022 Manufacturers’ Monthly manmonthly.com.au VentilationCorrectlysizingadustcollectormachineisimperative.
Nordfab’s recent acquisition of EziDuct, an Australian company specialising in dust collection and fume extraction equipment, has positioned the company well in bringing its solutions to the local market.
Renovators Paradise Renovators Paradise, which supplies recycled building materials in Keysborough in Victoria, were impressed with the eCono 15000 they had seen employed at Bucci’s Cabinets nearby and contacted Nordfab. “They said, ‘That’s exactly what we’re after, come and help us out,’” Inifer said. “I went and had a look at what machinery they had. The client had proposed different layouts to start with and had a new moulder coming in. I put the dust collector at the back of their building and revamped the layout for them, making it around half the price.”
A ducting success story
speaks with Nordfab branch manager David Inifer about why installing the A S the world’s ductingmanufacturerlargestofclamp-togetherfordustcollectionand process ventilation, Nordfab’s presence in the Asia Pacific region has given Australian manufacturers access to industrial ventilation that is locally made. According to Nordfab branch manager David Inifer, there are huge advantages to this.“One big advantage for customers is we build our own dust collectors, so there’s a great advantage if something goes wrong as customers can easily get spare parts,” he said.
After the dust collector was installed in December 2021, Renovators Paradise received the moulding machine in early 2022 and Nordfab was able to complete the ducting to create the best solution for the company’s needs. “The moulding machine had six inputs of varying sizes, so we had to wait until they got the machine so we could work out the final part of the ducting and size that correctly,” Inifer said. Inifer, who has been with Ezi-Duct for over five years, has a background in compressors and pneumatics and has been
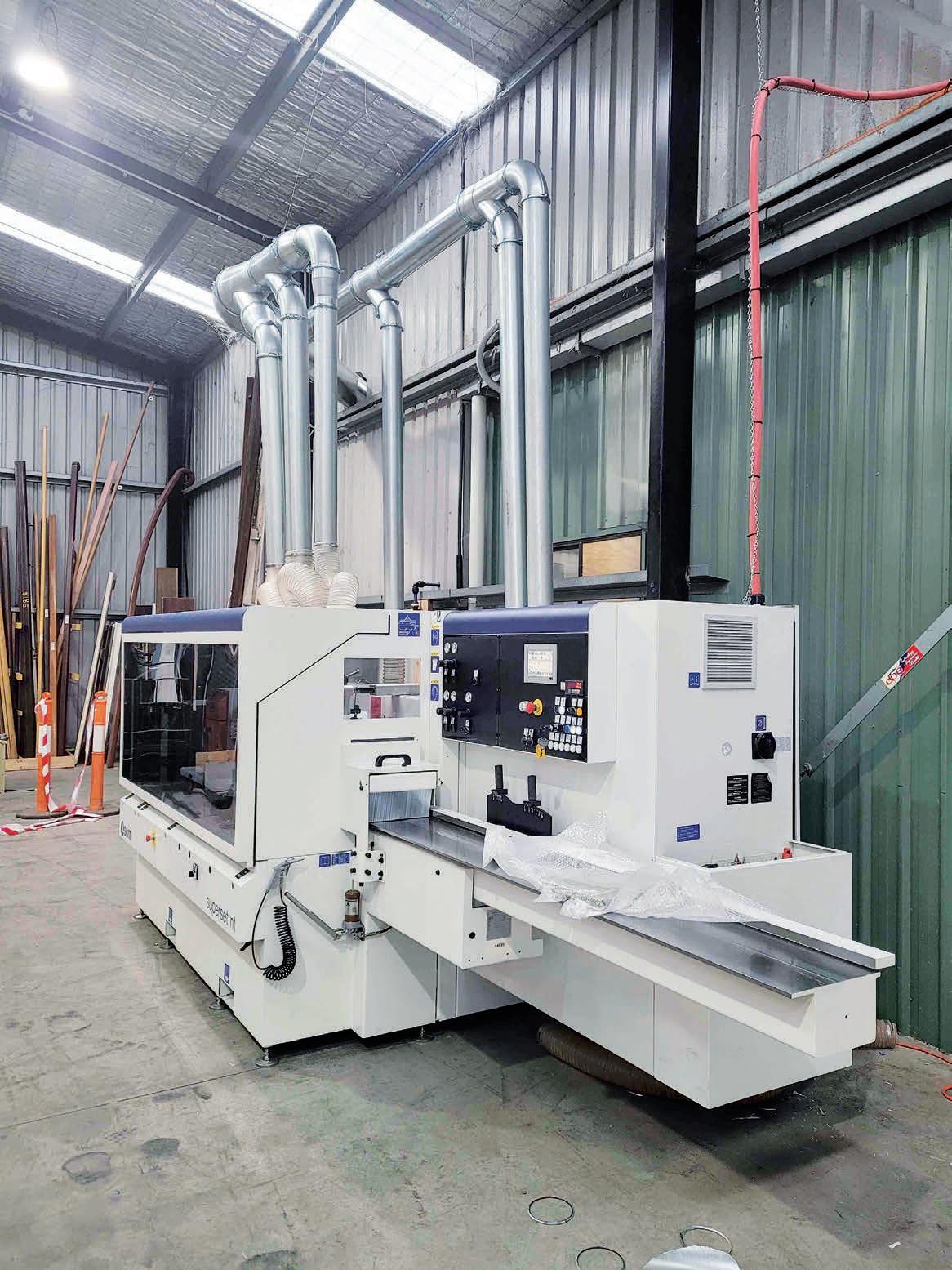
manmonthly.com.au Manufacturers’ Monthly AUGUST 2022
According to Safe Work Australia, breathing in dusts, gases, fumes and vapours can damage the lungs and potentially lead to conditions like asthma, lung cancer and hard metal pneumoconiosis. Manufacturing workers could be exposed to a range of hazardous material, including: orne flour dusts from mixing ingredients in food manufacturing; dusts created from wood and textile weldingmanufacturing;fumesfrom metal and machinery manufacturing, and chemical vapours in rubber and chemical manufacturing. This means that installing the right ventilation in the manufacturing industry is of the utmost importance, to ensure the health and safety of employees.
“It also has options for dust collection in the way that you can put either eight bags underneath, or you can put it over the top of three cubic metre bins, or over the top of two wheelie bins,” Inifer said.
Although powerful, the eCono 15000 is not an oversized machine, ensuring it can fit into many workshop spaces. And there are a great many options that customers can add on.
A dust collector that is the incorrect size for the site can be detrimental to a company’s ducting system, which can have a major impact on occupational health and safety.Inifer explained, “the biggest thing that can go wrong is to incorrectly size a dust collector machine. While ducting can always be changed and fixed up, it’s very hard to swap over the size of a machine because its capabilities are only a particular flow of “I’veair.”been to some sites where a competitor has installed a ducting system
Ventilation39
Ascertaining air flow When Nordfab takes on a project, its team conducts a site visit to evaluate the machines on-site and the dust outlet size of each machine. This ascertains the air flow rate that is required for the machines, determining the size of the dust collector needed.“Every machine has a dust outlet where you hook on a piece of ducting and take it away for dust extraction,” Inifer said. “We have a chart that we work by, which gives you a certain flow rate depending on what the dust outlet size is on the machine. “For example, for a 100mm dust outlet on the machine the required flow rate is 565 cubic metres an hour. So, if you have five machines with 100mm outlets, that gives you a total of around about 2800 cubic metres an hour, which is what your dust collecting machine should be capable of at a minimum.”
Nordfab’s range of eCono Dust Collectors meet Australia’s strict OHS and clear air environmental regulations. Made with corrosion resistant and robust galvanised steel, they are fitted with high quality snap lock, quick fit, no leakage filter bags that are manufactured from polyester anti-static needle felt. These whenTheoperating.eConoDust Collectors come in a variety of sizes, from the smaller eCono 1500 to the powerful eCono 15000, which uses a 18.5 kW industrial fan. “The eCono 15000 is probably the largest machine in their smaller range of dust collectors,” Inifer said. “It’s an optimum size for a standard cabinet maker or kitchen maker workshop. The standard machines they would have in those sorts of workshops would be a CNC, panel saw and edgebander. The 15000 would give them great suction and they have the option to incorporate extra connections, like a vacuum wand or a floor sweep.”
The range of dust collectors have been in circulation for around 20 years
Why is ducting important for manufacturers?
Industrial quality centrifugal fans produce a greater air volume at a greater pressure for less energy. The eCono 15000 is for workshops with medium sized dust loads.
responsible for the installation of around 120 systems in his time at the company.
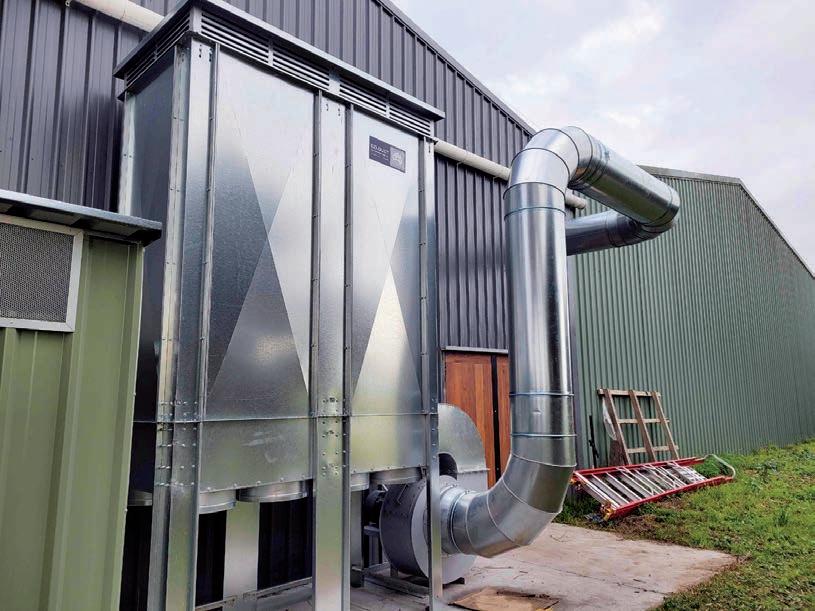
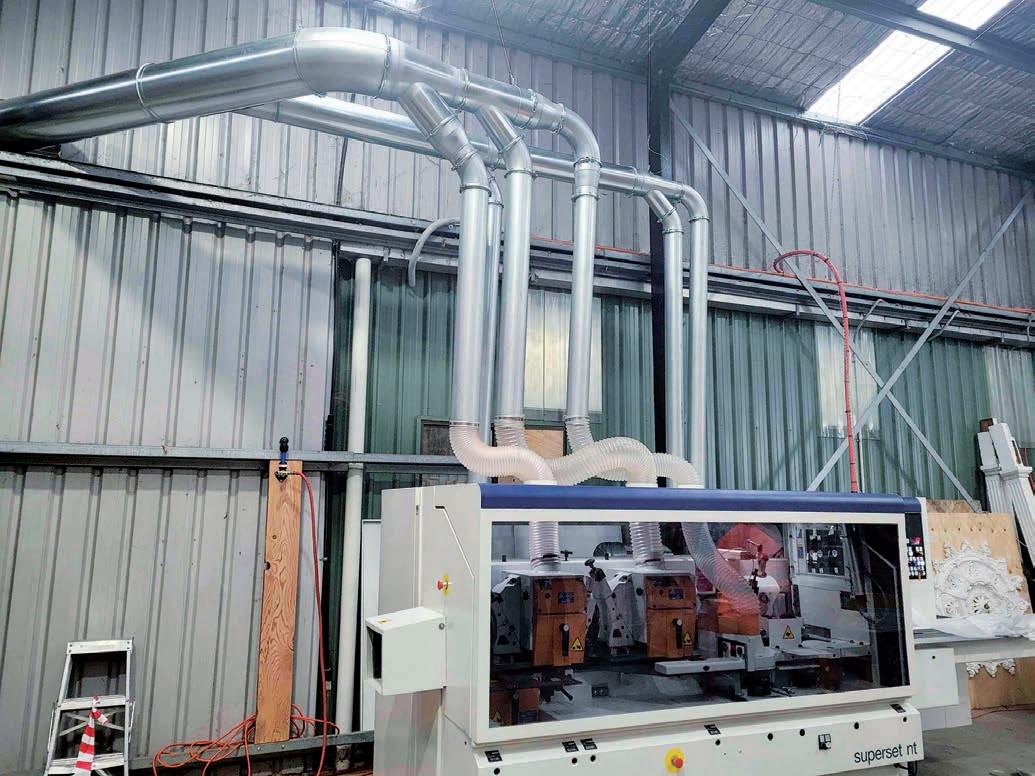

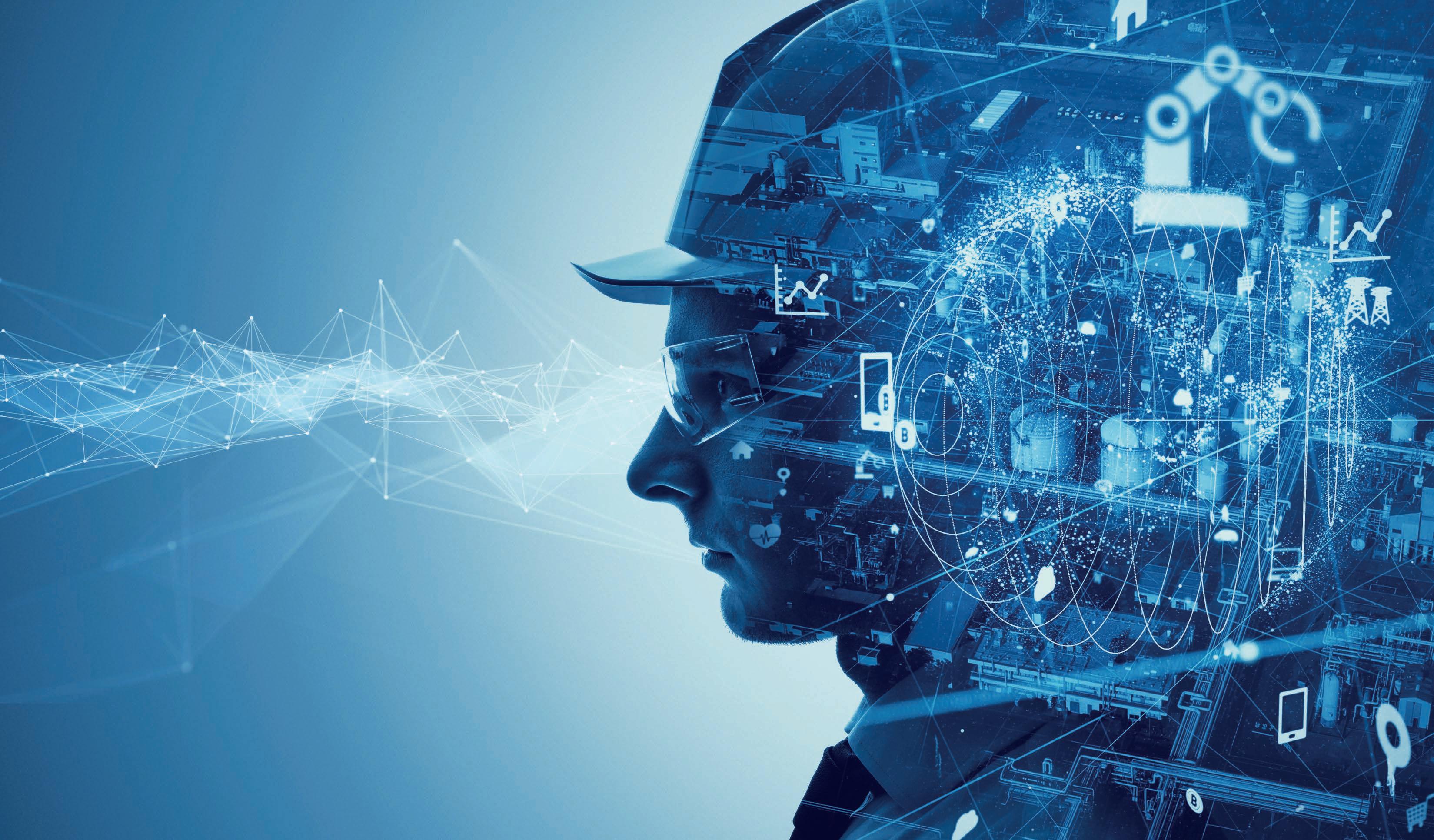
NOW ON SALE
IN PARTNERSHIP WITH AUSTRALIA’S LEADING MANUFACTURING AWARDS

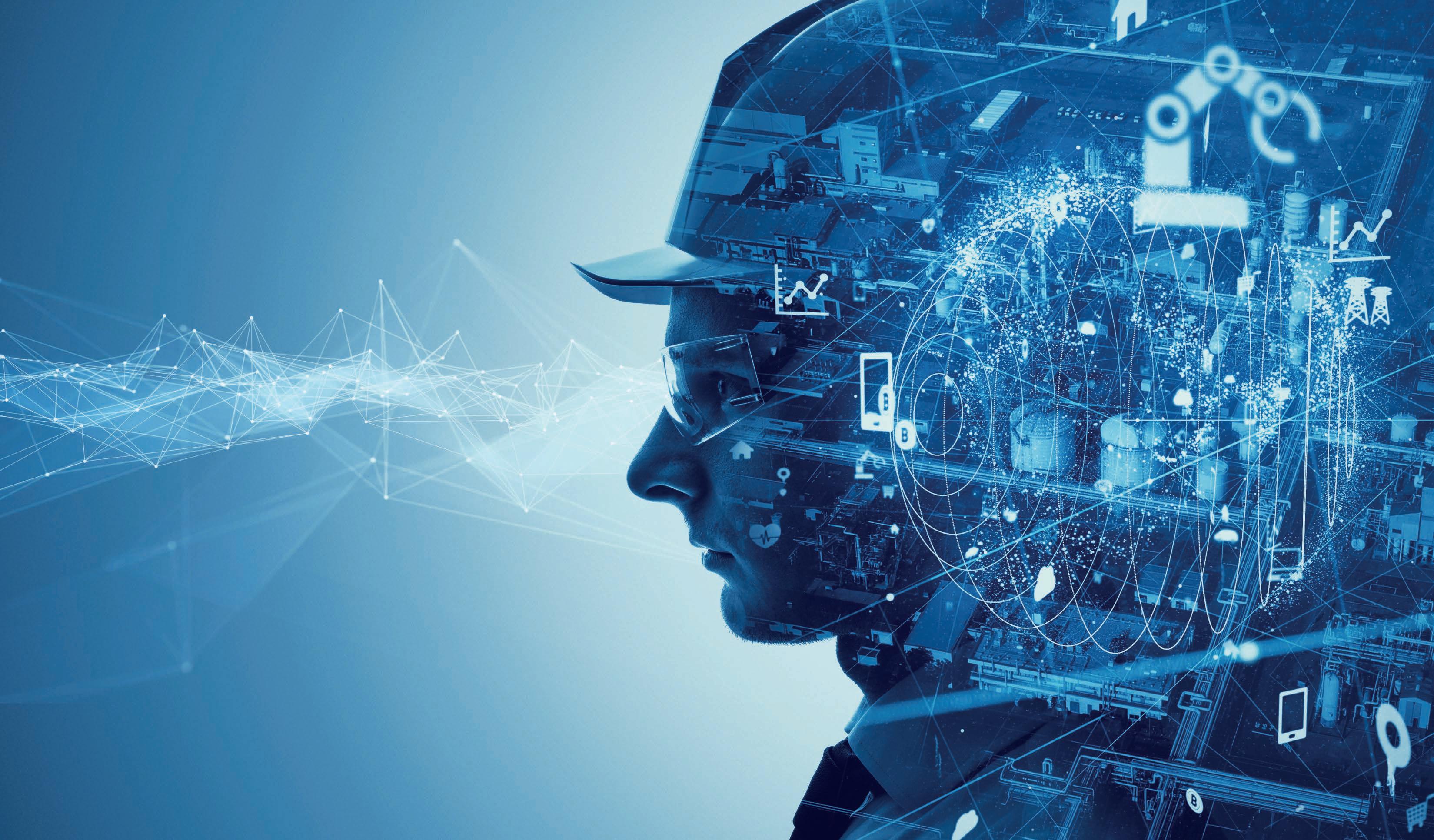
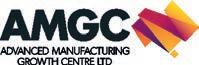
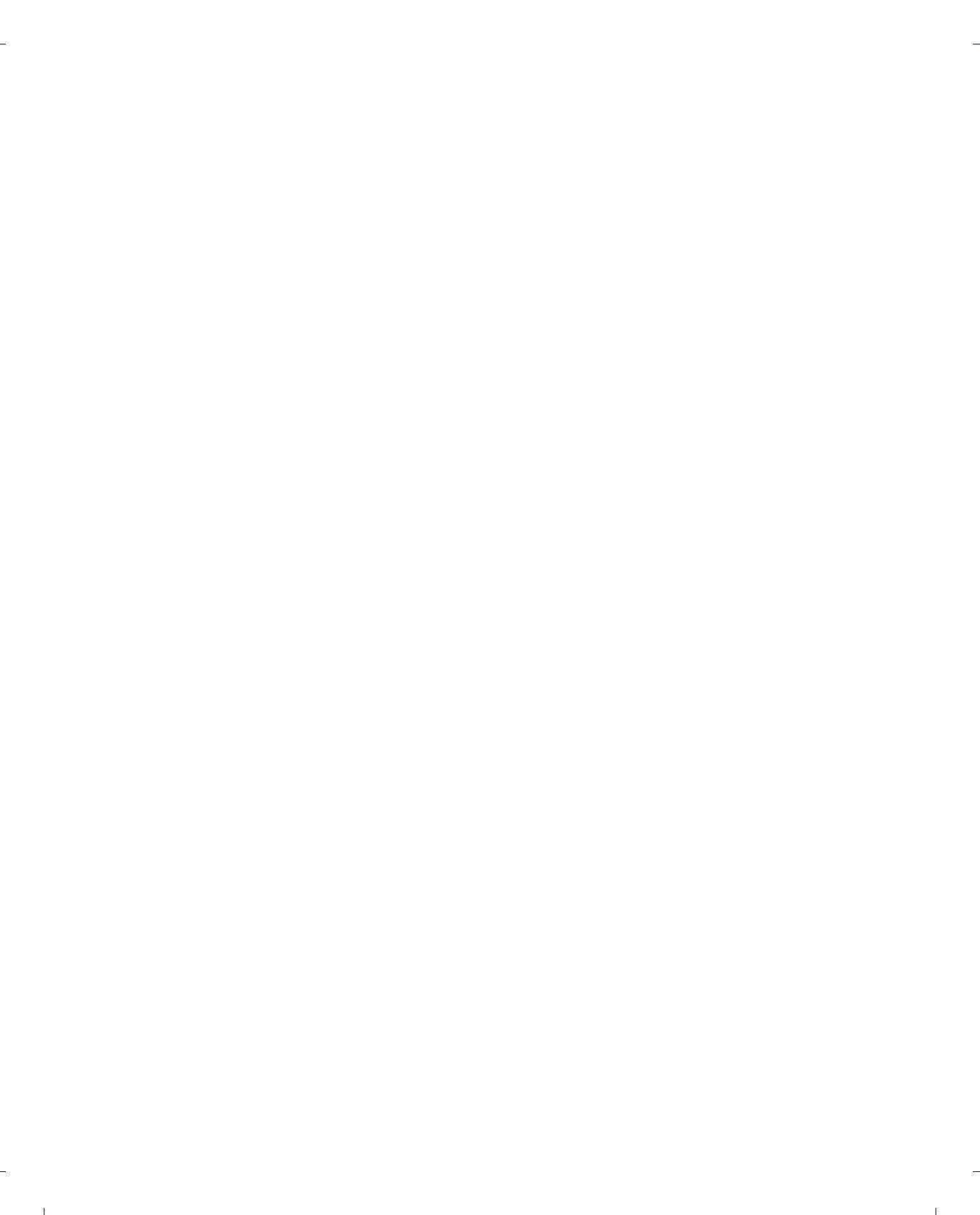
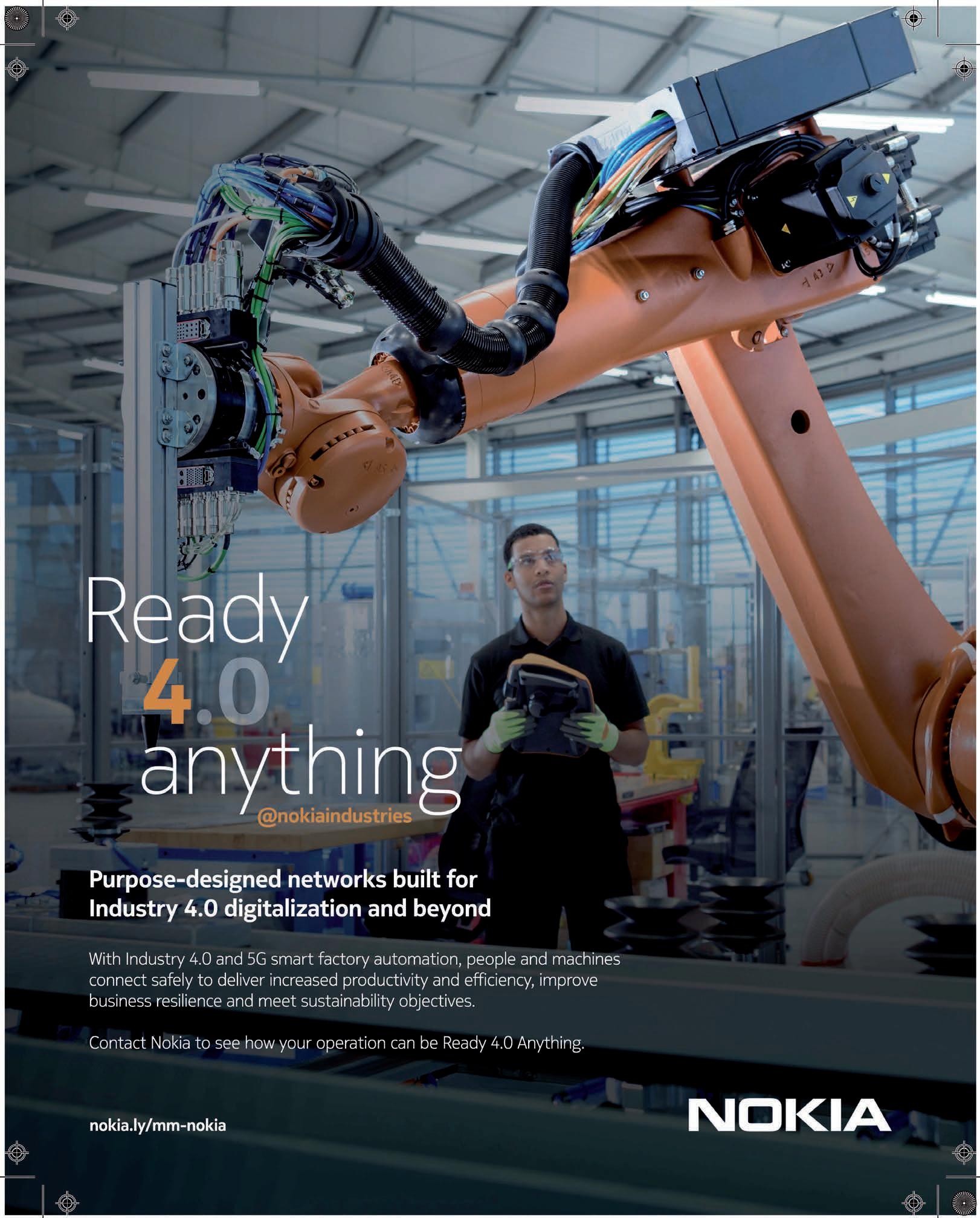
BlueScope Distribution is changing the way customers perceive the brand.
W HILE BlueScope Distribution has been a long-term player in both the steel and aluminium sectors for many years, most customers’ awareness of the brand is as a steel distributor, processor and solutions provider. However, this perception is changing.BlueScope Distribution’s range of aluminium sheet, plate, coil and treadplate, as well as standard and customer exclusive extruded products, is regularly expanding. Innovation within the business is well entrenched, with continued focus on improving the products, processing and solutions offered to customers in the steel and aluminiumBlueScopespace.Distribution is not just all about products, it also adds value by offering aluminium processing services to its customers.Thecompany’s capabilities include flat plate and sheet profiling by CNC router cutting, slitting of coil, shearing custom lengths, guillotining, CNC drill, tap and etching. This provides efficiencies for customers because they receive processed products that are fit for purpose, which reduces handling and fabrication required on arrival. Furthermore, customers can free up time and reduce costs, enabling them to invest in other development opportunities within their business. Other solutions from BlueScope Distribution include project management capabilities, end to end supply chain solutions, consignment stock, as well as innovative ways of supplying pre-cut components in kit form. “Our kitting solutions enable us to supply customers with finished, precut components which they focus on assembling into their own end user products,” BlueScope Distribution national aluminium manager Brad White said. These kitting solutions have been particularly popular with BlueScope Distribution’s marine customers and are also available for the transport, defence, mining, leisure and agricultural industries.
For more information about BlueScope Distribution’s aluminium services, visit bluescopedistribution.com.au/aluminium-www.suppliers.
The BlueScope Distribution range of products is assessed on an ongoing basis and is regularly adjusted to ensure the company is keeping up with the latest global trends, innovations and customer requirements.Withmetropolitan locations in all state capital cities as well as regional locations totalling 16 sites, BlueScope Distribution is well placed to deliver its range of aluminium products right across Australia.“Ourexpanded processing capabilities will ensure that we continue to provide our clients with a reliable, highquality service, while also offering the convenience of a single point of contact for all of their aluminium and steel requirements,” White said. For added peace of mind, BlueScope Distribution’s range of aluminium products comply with Australian Standards in accordance with AS/NZS 1866:1997 and AS/NZS 1734:1997, as well as other industry specific standards like ASTM, AAMA, IS and EN.
BlueScope Distribution’s range of aluminium products comply with Australian Standards.
Primarily known as a steel distributor, BlueScope Distribution is expanding its capabilities through an extended product range, paired with aluminium processing services.
manmonthly.com.au Manufacturers’ Monthly AUGUST 2022 43
White said that the business also makes the effort to learn about a customer’s business from front to back supply“Havingsolutions.strong industry knowledge and a focus on listening to customer needs are other factors in which BlueScope Distribution is different to most,” he said. “We take the time to learn what clients require so that we can offer them a complete solution complementing product, service and value. If a customer needs seven or eight different aluminium products, we’re committed to providing the full suite of products, not just the basic readily available ones, but the more complex ones to source.” Also, to provide more efficient access to BlueScope Distribution’s processing solutions, the company now offers coil shearing services from its facility in Westall in Melbourne. The additional processing is highlighted by the ability to shear coils into cut sheets of up to 4mm in gauge, 900mm to 1,500mm wide at sheet lengths of up to 6 metres long. BlueScope Distribution is able to offer its customers an extensive product range comprising of three, five, six and seven thousand series aluminium alloys with numerous temper variants, each with different characteristics to suit specific or generic applications like corrosionresistance, strength levels, wear resistance and suitability for hot and cold treatments. A number of finishes are also available including mill finish, mill bright, mill enhanced, polished, and linished.
Metal Manufacturing
The company has also recently become a “distribution member” of the Australian Aluminium Council, the country’s peak association representing the aluminium industry. BlueScope Distribution’s involvement with the Council will enable its teams to stay informed on the latest industry information and trends, providing customers with up-to-date details related to the aluminium products they use and standards maintained and upheld.
Processing capabilitiesDistribution’sBlueScopealuminium
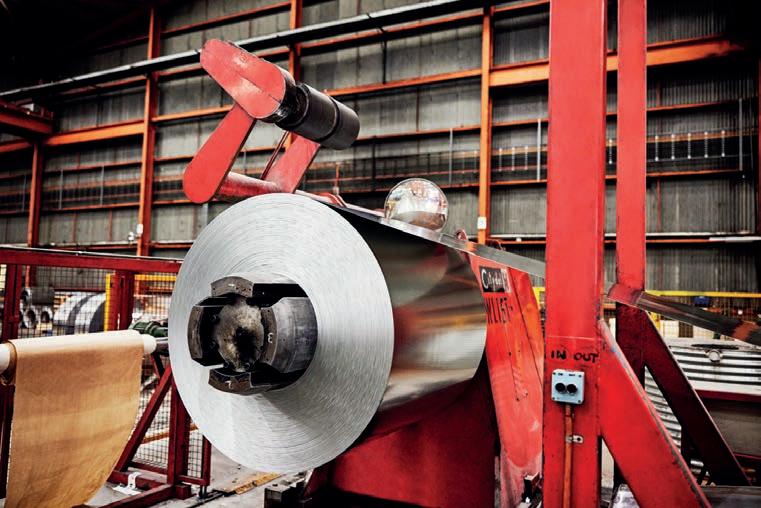
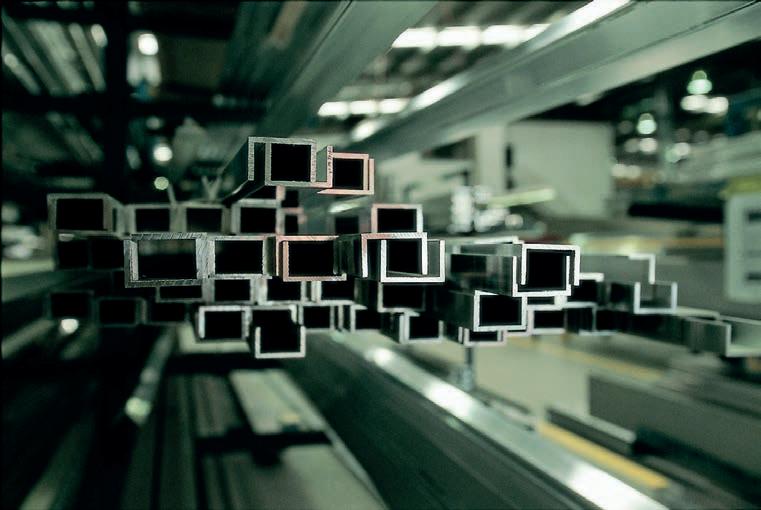
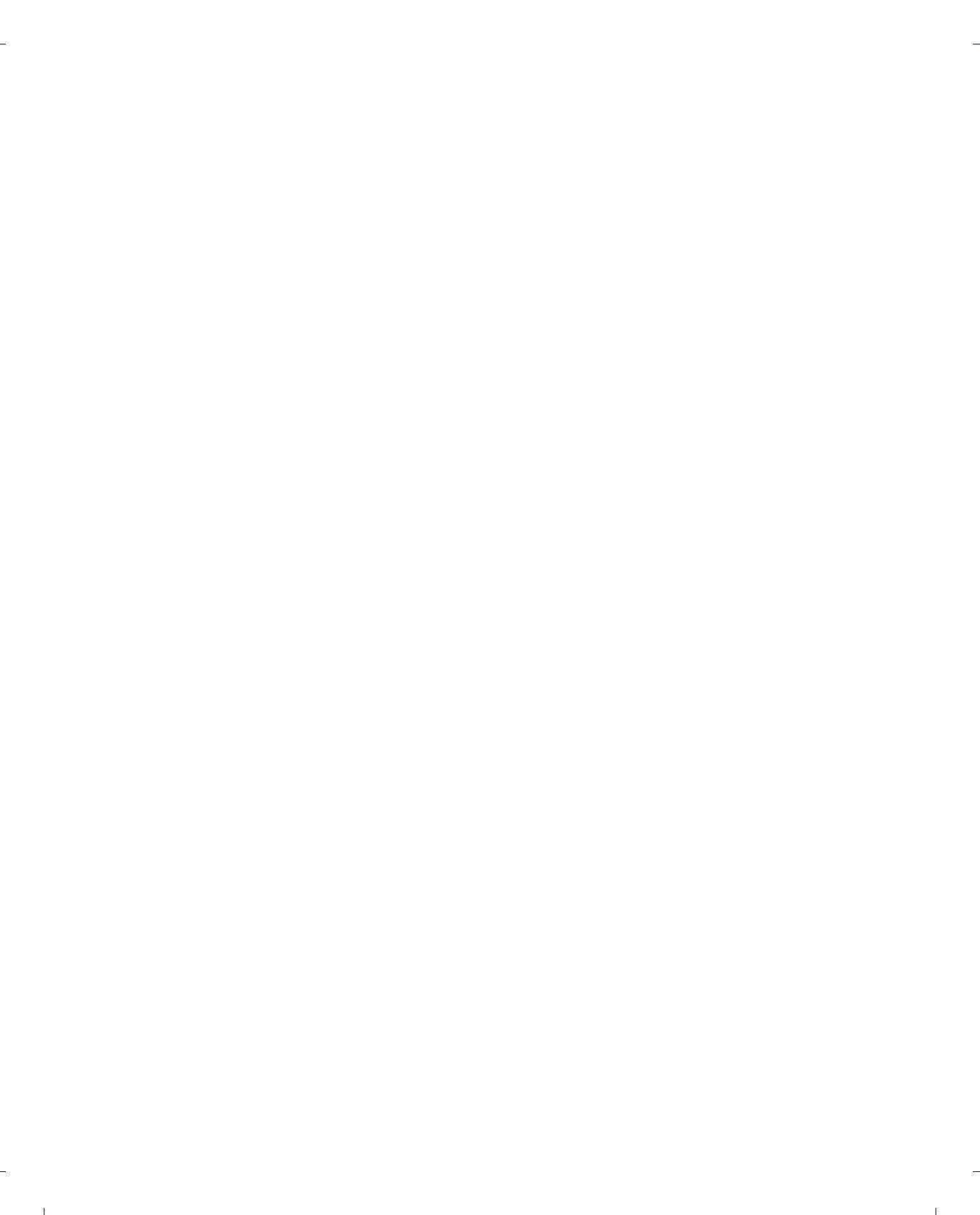
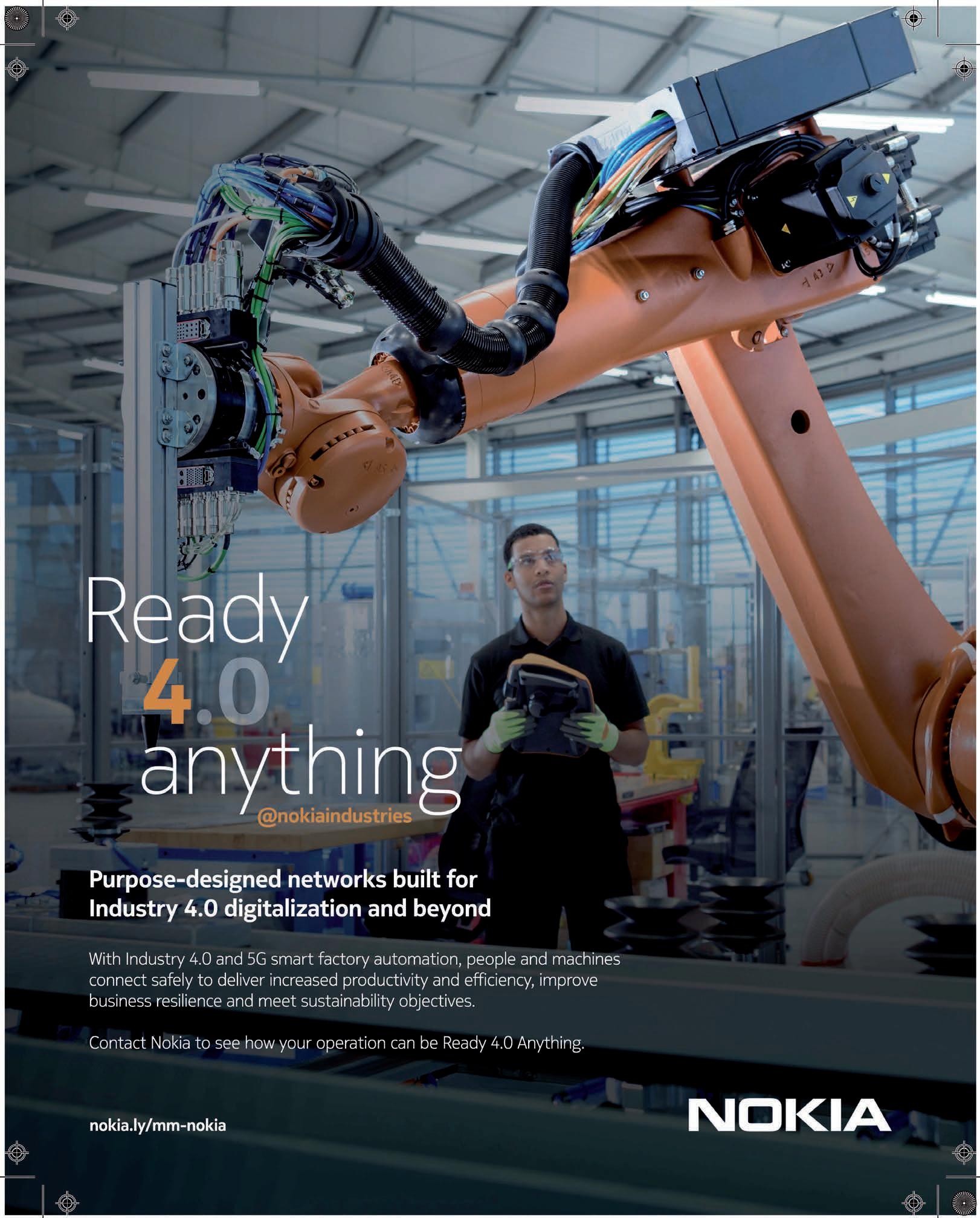
TELWATER – which designs and manufactures Australian aluminium boat brands including Quintrex, Stacer, Savage and Yellowfin Plate – is comprised of a team of expert welders and painters, research and development technicians and many more who are committed to high quality workmanship. Having opened its doors on the Gold Coast in 1988, the iconic boat building company has become synonymous with innovative design, advanced technology and a range of boat models.Delivering a high-quality product in an efficient, safe way is key to Telwater’s success. So, to maintain its reputation as a leading Australian manufacturer, Telwater invests in new solutions to improve efficiency, safety and reliability across its substantial manufacturing operations.
Better welding yields better boats
In manufacturing multiple boats per day often to tight deadlines, the team at Telwater relies heavily on welding equipment and gases to deliver high quality aluminium welds. “If we don’t have a good end product, there are lots of warranty claims which can be extremely time-consuming for our customers and employees. That is why we continually invest in the latest welding equipment and processes,” Telwater welding supervisor Robert Potts said.“The benefits of changing welding processes and investing in new equipment are significant and shouldn’t be understated. We use welding equipment to manufacture every part of the boat so having efficient, reliable and updated technology is crucial.” After a review of the market, Telwater started using BOC’s liquid argon in 2013 to support its welding. BOC’s Air Separation Unit, located within an hour As part of this, BOC offered the Telwater team training on the MIG and TIG projectors which were set up on site at Telwater. The training worked through identifying welding defects and setting of parameters, which helped the Telwater team better understand how to set up their welding machines and maximise productivity.Afterworking with BOC for just over one year, Telwater switched to BOC for its welding wire. “We use a great deal of welding wire per boat so it’s really important we use a wire that is reliable and high quality. That’s why we switched to BOC’s premium aluminium wire,” Potts said. With 65 welders on site every day, Telwater’s welding machines became dated with low reliability. Given the success of the gas mixtures and aluminium wire, Telwater decided to work with BOC to review their welding machines. Welding solutions In 2016, Telwater commenced a welding trial. After a couple of weeks of testing, the Telwater team knew that to keep up with demand while consistently delivering a high-quality product, they needed to make the jump.
44 AUGUST 2022 Manufacturers’ Monthly manmonthly.com.au WeldingTelwar’sstrongrelationshipwithBOChascontributedtobetterweldingprocesses.
Welding equipment upgrades from BOC has seen the iconic Australian boat manufacturer, Telwater, deliver quality results and improve on training.
Through BOC, Telwater can deliver highquality products safely and efficiently.
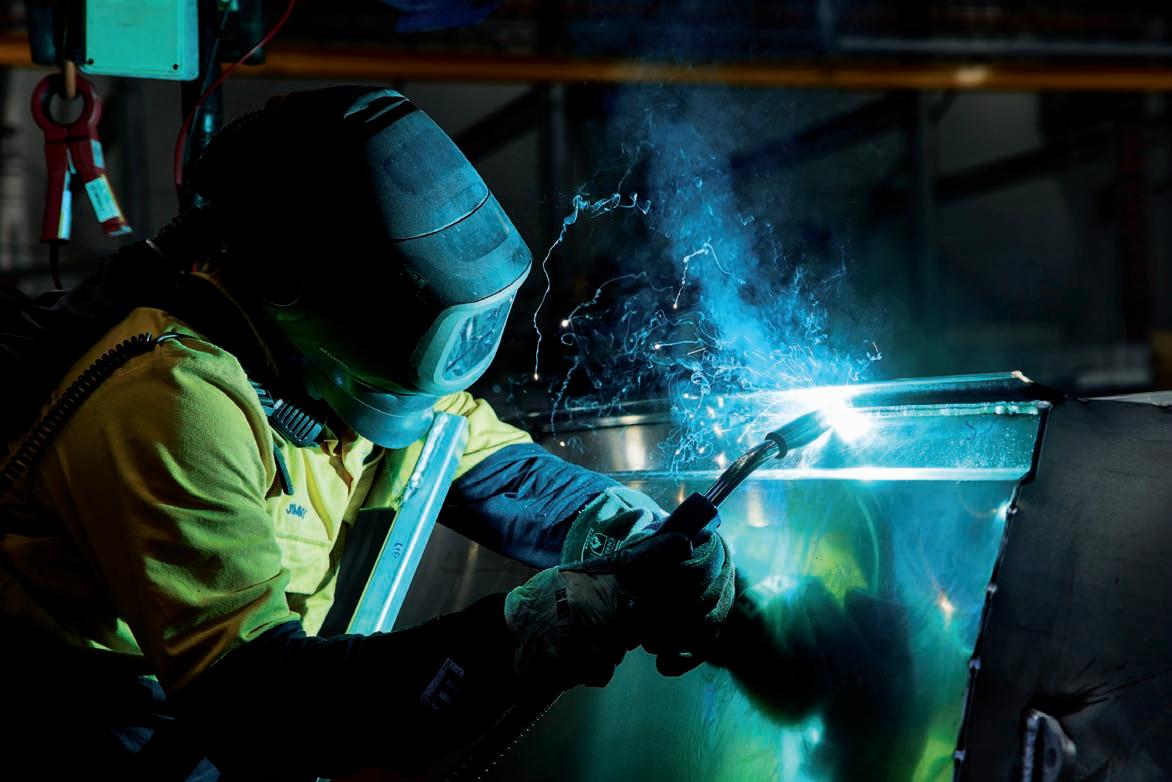
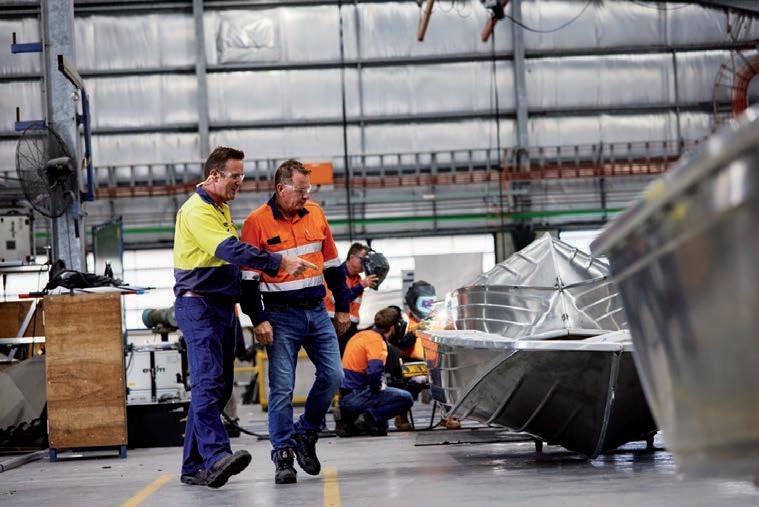
has delivered 74 EWM PICOMIG 355 Pulse Multiprocess welders and 11 EWM TETRIX 300 AC/DC TIG machines. Ideal for busy workshops involving heavy industrial work, the EWM Tetrix 300 ACDC is designed with EWM patented processes for faster results. The Picomig 355 D3 Pulse is ideal for tough environments and boat building. Telwater’s success Collectively, the welding wire, argon shielding gas and EWM machines led to an overall better weld quality for Telwater’s boats resulting in less rework. The EWM Tetrix 300 ACDC allowed Telwater to be more flexible and specific when it came to its designs, as the machine allows the user flexibility in joining different aluminium plates together.ThePicomig 355 is a four-in-one multi-process welder that offers MIG/ MAG pulse. Its reliable pulse welding feature produces superior results when working with stainless steel and aluminium.“Theweld quality is better, there is less spatter, it’s less time-consuming and we are using less consumables and wire. It’s a win-win for us,” Potts said. The portable and easy-to-use equipment has become an integral part of Telwater’s growing training program. Both machines allow the user to program welding tasks to save time when working on repetitive tasks. This feature is important when an inexperienced welder is learning the basics. “What also stood out to us the most was its useability. Since using EWM, we have been able to train more efficiently and more often. It has become key in our training processes,” Potts said. “We currently have five trainers, and we train in groups of between five and 10. EWM equipment has made it a lot easier for us to develop and improve our training program, something which helped us stand out from other boat manufacturers.”
According to Potts, the manufacturer has trialled various products over the years, but always return to BOC. “The end-result was always of a high quality, and it used less energy than other equipment we tested which saves us money on power bills,” he said. “Whenever we have needed something, BOC has always been really good to deal with and would send out a representative within 24 hours. For us, working with BOC means you don’t have to worry.”BOCand Telwater are continuing to work together on quality and productivity improvements, including trialling new shielding gas mixtures that can reduce costs by up to 20 per cent.
manmonthly.com.au Manufacturers’ Monthly AUGUST 2022 Welding45Nordfab’s CLEAN MOVEMENTAIR Join us in creating a safer, cleaner, more sustainable work environment. We are the leading supplier of high-quality dust and fume extraction products. High performance products Team of experienced engineers Over 20 year’s experience Part of Nordfab Ducting globally Local knowledge and support Friendly staff Quick turnaround contact@nordfab.com 1800 673 828 nordfab.com For Telwater, having efficient, reliable and updated technology is crucial.

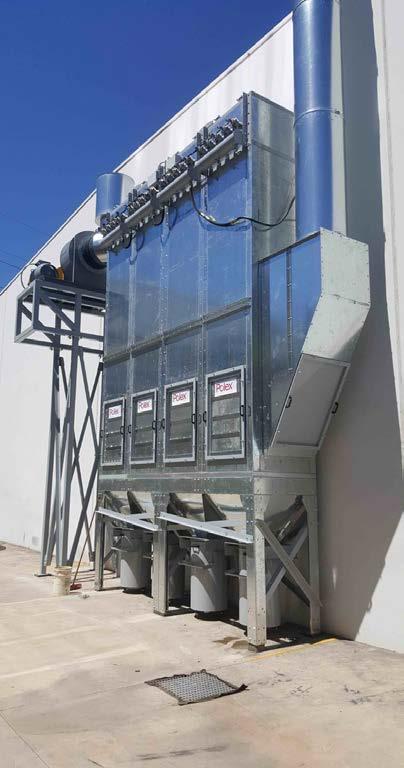
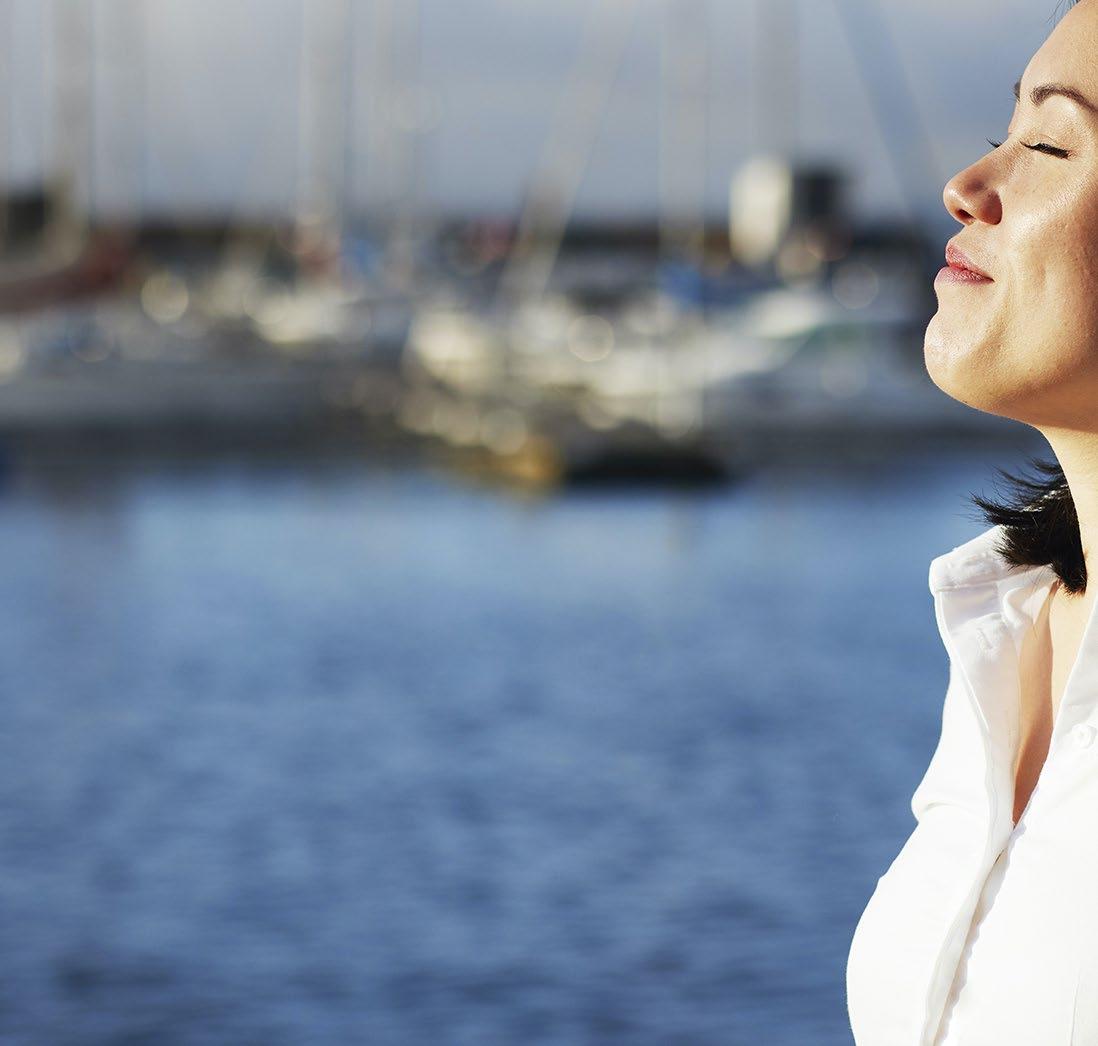
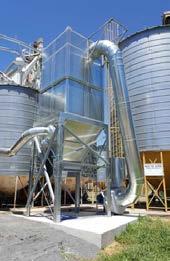
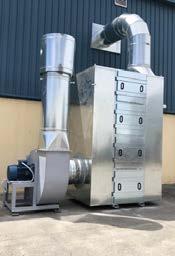
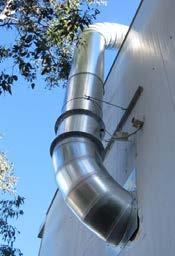
3D printing with limitless design
Manufacturers’ Monthly speaks with CNC Design about its additive manufacturing capabilities of large parts for different manufacturing sectors.
Almost three decades later, Croft continues to develop the craft through his work at CNC Design, a motion control solutions expert company specialising in VSF and CNC machines. Founded by managing director Bruce Rowley, CNC Design began as a CNC retrofit company, specifically around machine tools. Bringing something new to the Australian market, the company became the distributor in Australia and South East Asia for Siemens machine tool products, which remains an integral part of the business.TheVSF gantry-based systems are among the largest 3D printers in the world and can combine additive and 5-axis machining in a single machine. CNC Design started the research and development project for these machines in 2017, prompted by the requirements of a specific wax printing project in the UK. “It was seen by CNC Design as an emerging technology and an emerging market,” Croft explained. “There were a lot of players for small printers for plastics and metals, so we decided to move into larger-scale printing, beginning with wax and then developing the printer technology for concrete and thermoplastics.”Today,VSFcan print large components made of concrete as well as thermoplastic composites. An example of CNC Design’s 3D printers capability is in aerospace applications including the manufacture of vacuum molds using high-temperature thermoplastics (PEEK) combined with carbon fibre, considerably reducing tooling costs.
A research and development centre 3D printed in Thailand using CNC Design’s VSF onsite printer.
John Croft, development manager additive technologies for CNC Design, remembers his first encounter with additive manufacturing in 1991. Watching the FDM machine print a plastic part at Swinburne University of Technology, he immediately remarked, “Do you realise this is the future of manufacturing?” He recalled saying the technology wouldn’t be restricted to just polymers.
Additive Manufacturing 46 AUGUST 2022 Manufacturers’ Monthly manmonthly.com.au
VSF Composite VSF Composite uses a screw driven extrusion based system that can print with a wide range of thermoplastics including ABS, PC, HDPE, PEEK and composites reinforced with Carbon Fibre or Glass Fibre. CNC Design is supplying a composite printer to Queensland manufacturer Zone RV in what will be the largest 3D printing system in the Southern Hemisphere. The 22 by 5 by 1.6 metre will begin machining up the molds for the Coolum Beach based company’s range of off-road caravans that combine lightweight composite bodies with classleading“They’recomponents.usingthe large extruder system which has a capacity to extrude up to 200 kilos per hour,” Croft remarks. “Because of the weight, it will be a two-beam gantry system so the machining system is on a separate beam. It is capable of both 3D printing and machining.”TheLarge Area Gantry system is able to combine five-axis milling and three-axis printing in a single machine. Three-axis 3D printing is performed using a CNC Design Model 60-150 print head, featuring a vacuum pellet drying and conveying system, enabling printing rates of up 200 kg an hour with the larger extruder unit. CNC Designs extruder units start from 19kg per hour, with the next unit extruding up to 40kg per hour. The system also has the flexibility of five-axis machining, orbital sanding and spraying, with a tool rack and print head unit built in.
CNC Design has more recently extended into manufacturingadditivethrough Virtual Smart Factory® (VSF), a solution for 3D manufacturing of large parts for different industries such as construction, aerospace, marine and mining. It is a fit for many industries that are producing very large components.
“The FDM printer had a 250-cube build area, which was huge at the time,” Croft said. “A lot of industry weren’t ready for the capabilities of the machine and said it was too expensive. Companies held the belief it was still somewhat of a black art and wouldn’t take off, but now additive manufacturing is a multi-billiondollar industry. Industry is starting to gather momentum around what additive can do in the manufacturing process, but Australia is still 10 to 15 years behind much of the world.”
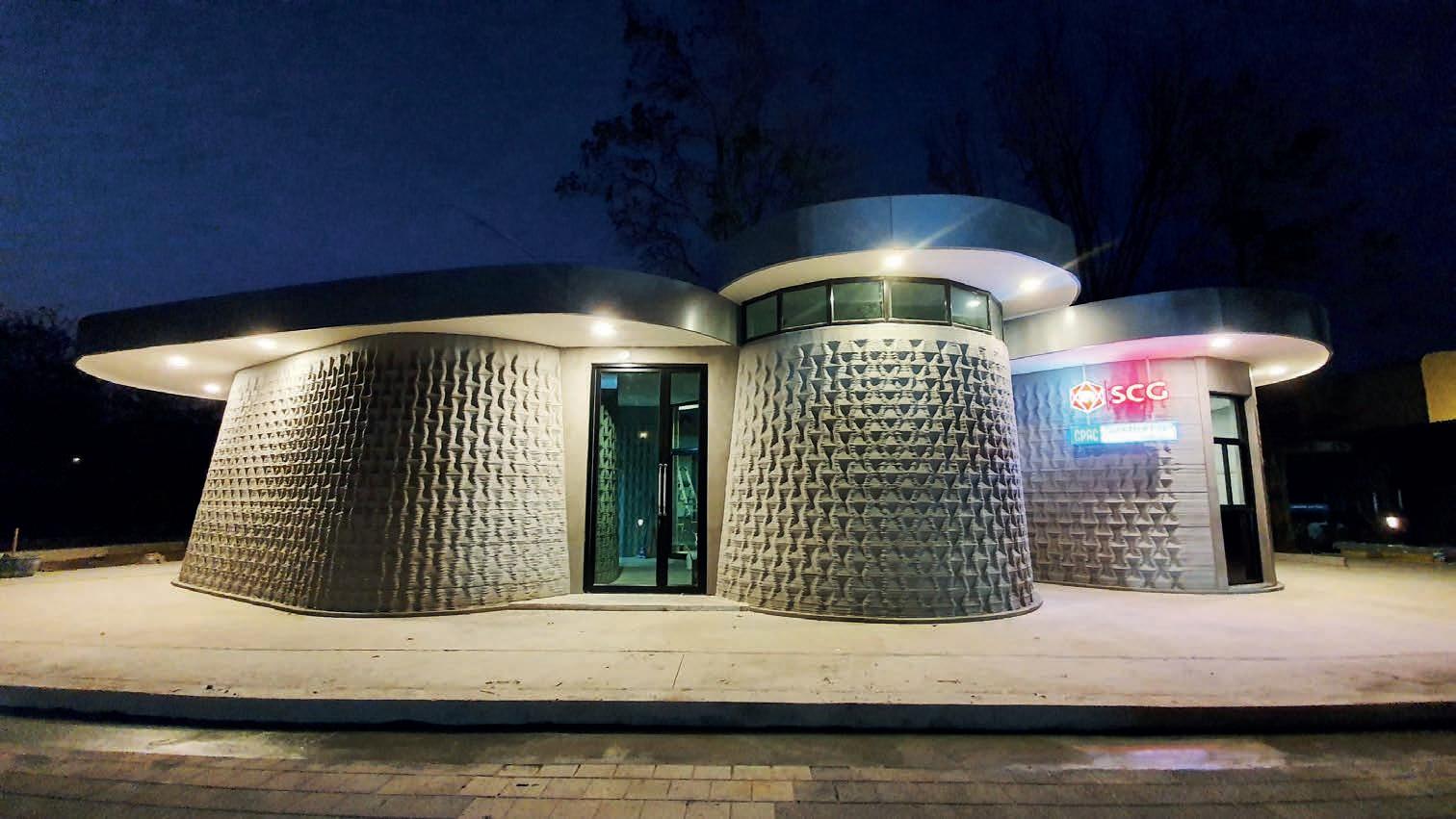
manmonthly.com.au Manufacturers’ Monthly AUGUST 2022 47 Additive Manufacturing
Virtual Smart Factory® composite 3D printer.
“The beauty of the flexible VSF design is they can be unlimited and we want to tap into new forms and design with different clients,” he said. “We will look into intricate designs where our VSF technology will play a major role.” CNC Design engineers and supplies the Virtual Smart Factory® (VSF) printer and the thermoplastic printing materials here in Australia. The company continues to field interest for this thermoplastic technology, and Croft expects the CNC Design’s main growth area to be in this field in the short term.
“The other major factor that is holding back the growth of the additive manufacturing (AM) industry is the skills as we need to concentrate on education to increase these skill sets enabling the growth of both AM and our manufacturing industry,” he said.
Virtual Smart Factory® (VSF) Range “Thermoplastic will take prior position and next will be the concrete,” Croft building practices. One of our biggest challenges globally is the waste caused by construction – 83 per cent of the world’s waste comes through construction also 27 per cent of Co2 emissions. More sustainable building is a big plus for the future.”
With continued growth in sight for CNC Design, Croft explained that customer education is crucial moving forward.“Weare trying to raise awareness in AM to Australian Industry,” he said. “This technology is actually happening and is available with full support and service happening here in Australia.”
VSF Concrete Concrete printing has been growing globally over the past decade and CNC continues to flourish in this area. Two recent customers utilised the VSF Concrete printers as high performance gantry systems, ideal for additive manufacture of prefabricated building modules and architectural parts. One being Siam Cement Group (SCG) – one of the largest cement companies in Southeast Asia. In late 2020, SCG 3D printed a 102 sqm research and development centre in Thailand using CNC Design’s VSF onsite printer. The printer is designed to be easily relocatable while retaining high speed and precision for printing, which allowed SCG to print an intricate textured wall surface. Using conventional methods would have required complex moulds and formwork to make this design.
CNC Design is supplying the largest composite printer to Queensland manufacturer Zone RV.
“The construction of the wall took around two days with five operators, which saved time and labour. The actual printing took two days to print with an accuracy better than five millimetres,” CroftCNCsaid.Design furthered these kinds of services in Southeast Asia when more recently its second customer – Singapore’s Housing Development Board (HDB) –approached the company after precast production processes were causing time delays and requiring more workers. The VSF solution was applied to machining, handling, and additive manufacturing, not only for concrete but also for wax, foam, and high-temperature plastics. As a result, Singapore HDB was able to 3D print unique concrete elements up to 9m long, 3.5m wide, and 3.8m tall.
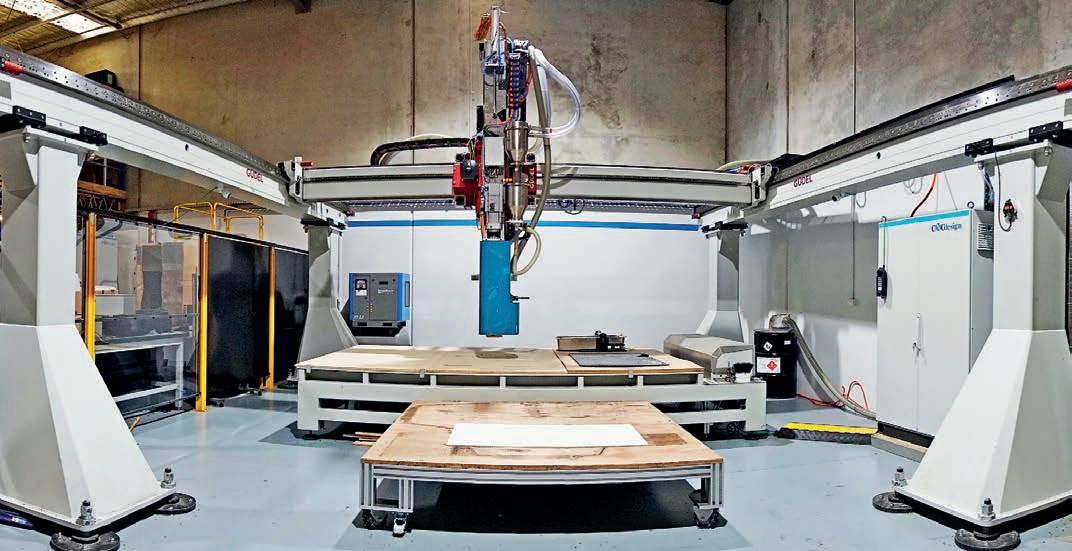
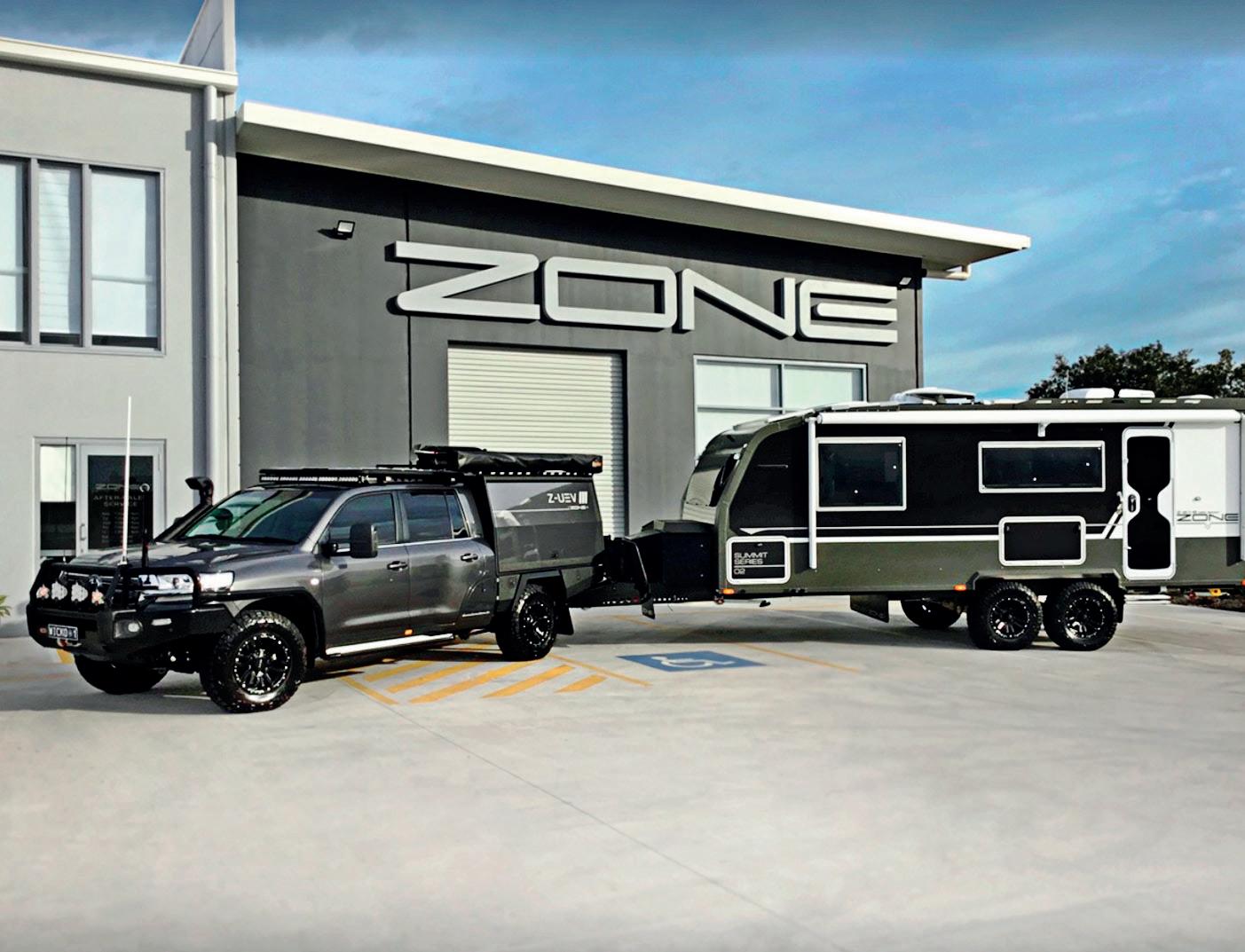
PROMPT ANALYSIS & REPAIR SERVICE INJECTRONICS INDUSTRIAL OFFER A UNIQUE SERVICE TO BUSINESS OWNERS, MANUFACTURING LINE MANAGERS AND SERVICE REPAIR AGENTS ALIKE. WITH A TEAM OF LECTRICAL AND ELECTRONICS ENGINEERS, INJECTRONICS INDUSTRIAL CAN OFFER A FAULT ANALYSIS AND REPAIR SERVICE FOR MANY APPLICATIONS INCLUDING DIFFICULT TO SOURCE AND OBSOLETE ITEMS. INJECTRONICS INDUSTRIAL PRESENTS A NEW, TIME SENSITIVE AND COST AFFECTIVE OPTION WHEN IT COMES TO MAKING A DECISION ON YOUR INDUSTRIAL REPAIR. • HMI (Human Machine Interface) • VFD (Variable Frequency Drive) • Servo Drive • Servo Valves • Spindle Drives • Stepper Drives • PLC • Timer and Counters • Power Supplies • HV Generator • Industrial Computer • Motherboards • CNC Boards • Industrial Control Panels • Preventative Maintenance The range of repairs available include, but are not limited to: 1300 646ELECTRONIC?ANYTHING948.com.auindustrial.
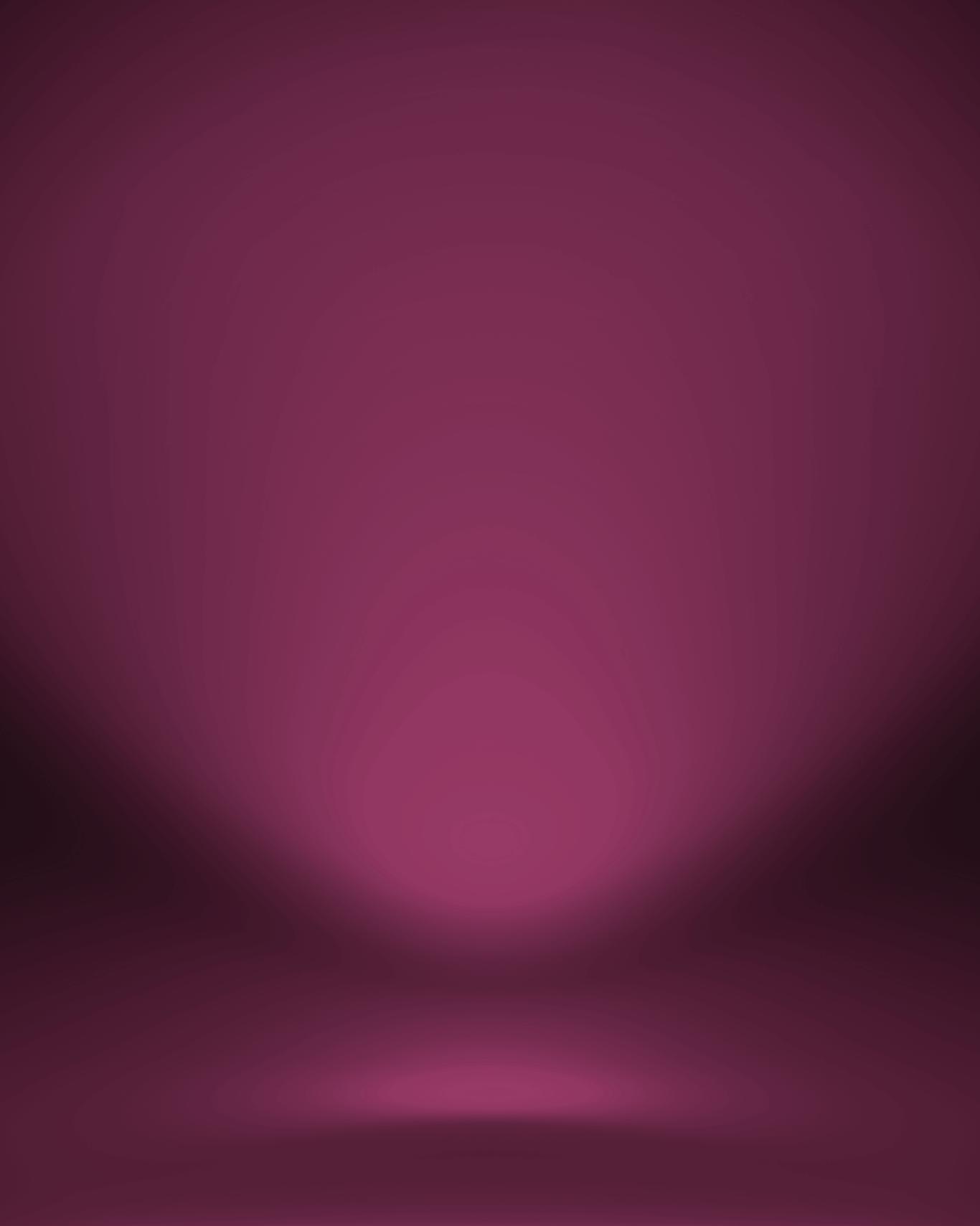
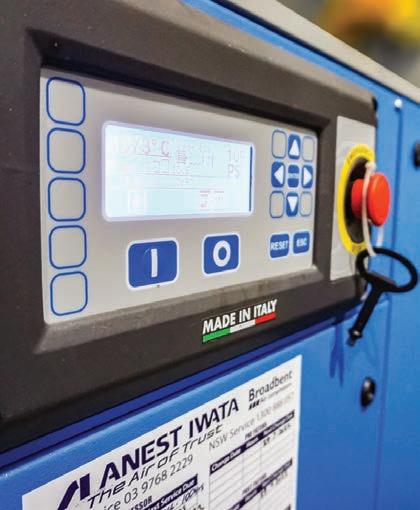
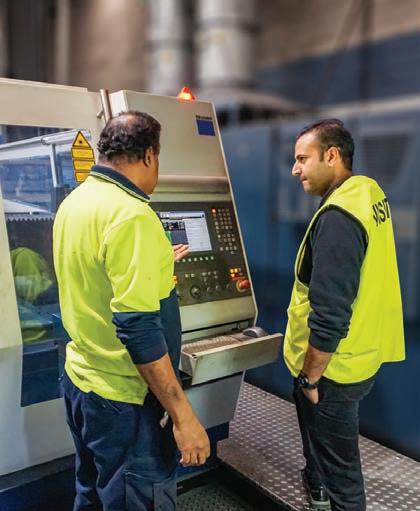
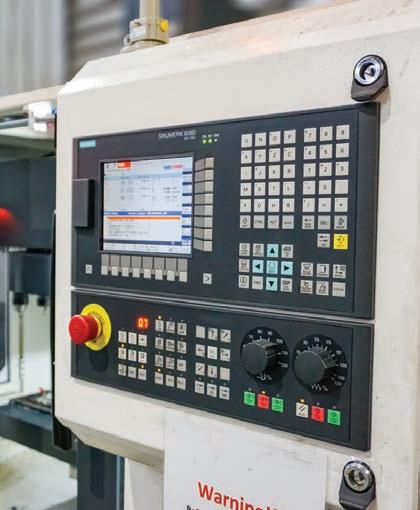

WITH the original industry exhibition floor plan overflowing, Land Forces organisers announced the release of an additional 2000 sqm of exhibition space early in July to meet continuing demand. Even with that extra space in the mix, 93 per cent of available space is now spoken for.Two months out from the event the Land Forces 2022 industry presence is already larger than that of Land Forces 2021, which attracted 718 participating exhibitor companies and 12,766 attendances from industry, government and defence over its three days in June lastLandyear. Forces is a long-established platform for engagement between defence, government, industry and academia. It combines a three-day conference program, a major industry exhibition and formal networking and business to business systems, offering a two-way flow of information around and between Defence and the industry that provides and sustains its capability. For Army and Defence, the event offers a stage from which to inform industry on issues and capability needs, paint a picture of the future battlefield and communicate priorities. It is also a rare informal opportunity for Army and the Defence Capability Acquisition and Sustainment Group (CASG) to see what is new and innovative in industry, simply by walking the exhibition halls or receiving an industry briefing. For industry, Land Forces is an opportunity to be noticed, to highlight capability and innovation, whether the end customer is Army, a prime contractor or an SME. It is where the normally invisible decision makers are often to be seen presenting at a conference or walking the exhibition floor, giving the opportunity to hear the important news straight from the source, or have a direct meeting or discussion. And the critical mass of engaged industry players is its own source of opportunity.
The Land Forces International Land Defence Exposition, set for 4-6 October at the Brisbane Convention and Exhibition Centre, is on track to become the largest defence industry event ever held in Australia.
“Land Forces brings the Australian and together like no other event in the region,” said Justin Giddings, CEO of Land Forces organiser AMDA Foundation. “The sheer concentration of defence, industry, government and academia creates opportunity. This is where the acquisition programs are side by side with their defence customers and with universities, potential suppliers, government agencies and export customers and partners. It offers every participant the potential to go home with new ideas, new insights and new relationships that may materially enhance the outlook for their organisation.”
The Land Forces conference program offers a mix of strategic program information, networking functions and “how to” sessions. At Land Forces 2022 Milspec Manufacturing will reprise its “Power Solutions for Vehicles and Field Applications”, while the Office of Defence Industry Support (ODIS) will detail how this “one stop shop” government agency can lead individual companies through the maze of Defence engagement, assistance and
“AreDefenceincludingconferencesSovereignaQueenslandIndustry,andwillTechnologyopportunities.corporationMicrosoftillustrateissuesofInteroperabilityCollaborationAcrossDefenceandTAFEQueenslandandtheGovernmentwillpresentSkillsBasedApproachtoBuildingaWorkforce.IndustryassociationstoowillpresentandsymposiaatLandForces,theAustralianIndustryandNetwork’s(AIDN)wellregardedYouDefenceReady?”symposiumand manmonthly.com.au Manufacturers’ Monthly AUGUST 2022 Events49
An additional 2,000 square metres of exhibition space has been added to the event. The Land Forces conference program has a variety of information sessions.
Land Forces set for massive event
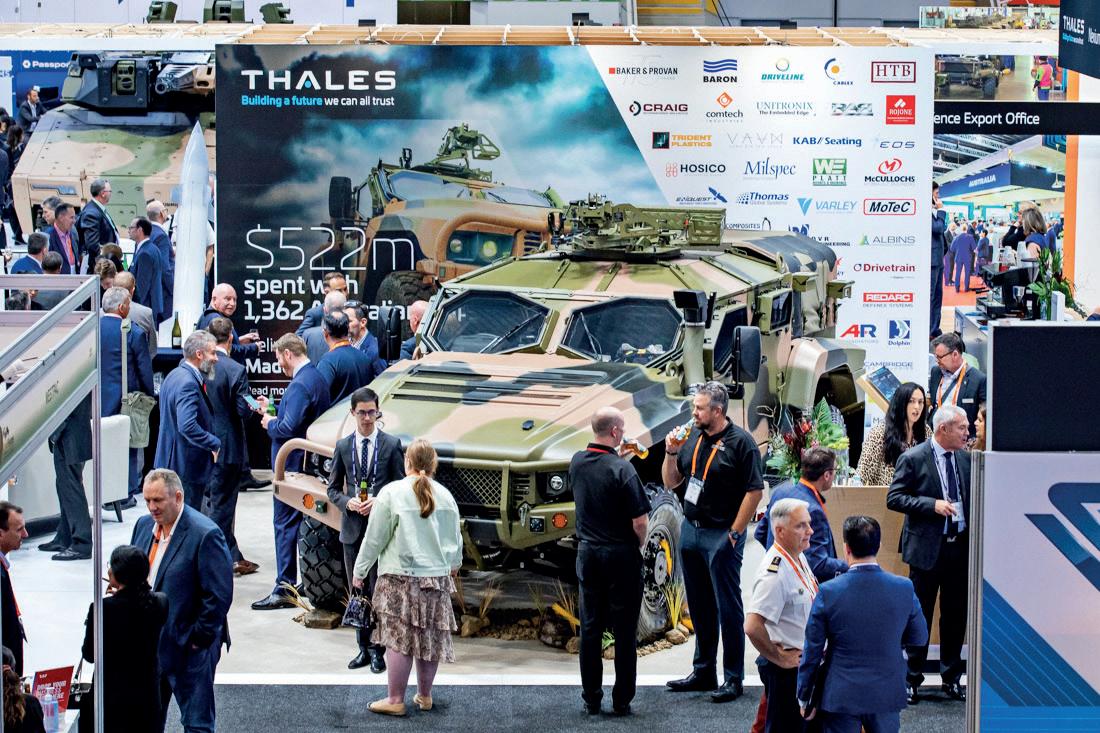

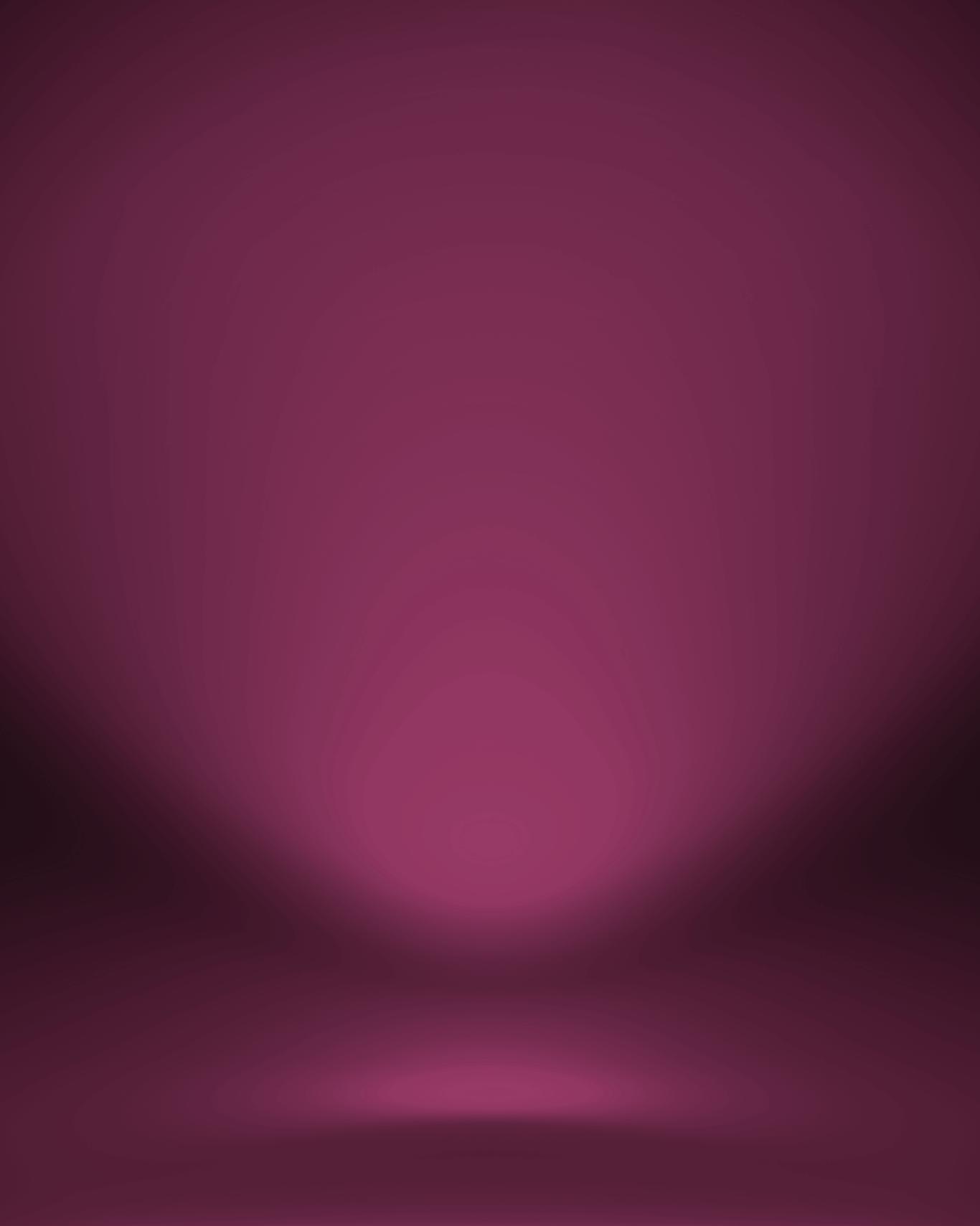

Simulation is becoming a critical element in training at every level and in every discipline, from medical assistance to strategic logistics, vehicle operation and weapons training. But creation of effective simulation depends on a clear picture of operational and training needs and desired outcomes.
• andProgrskilling.
Government agencies, think tanks, private companies, universities and research foundations will all combine for this year’s event.
Australia and overseas across a range of sectors, including defence and aerospace, and raised $40 million in additional funds to back industry,” said Tim Kelly, business development and lead engineer for ARM Hub.“The Hub and its network of experts are combining cross-cutting skills in data analytics, the Internet of Things, augmented and virtual reality, additive manufacturing and advanced materials.”
The Land Forces 2022 International Land Defence Brisbane Convention and Exhibition Centre. For more information go to www.landforces.com.au
• A prestigious innovation a program.
Land Forces is first and foremost a platform for engagement and promotion. For exhibitors, this extends to formal business to business and business to government mechanisms, communications channels and networking opportunities, including:
Systems (AAUS) Land Forces Conference. Every Land Forces introduces something new, and for 2022 the additions include the inaugural Australian Training, Simulation and Education ConferenceSimulation(AusTsec).isbecoming a critical element in training at every level and in every discipline, from medical assistance to strategic logistics, vehicle operation and weapons training. But creation of effective simulation depends on a clear picture of operational and training needs and desired outcomes. AusTsec will explore how training needs inform development of simulation technology and systems, and will detail recent innovations in capability and application. Leading industry experts in training and simulation will join defence and other NGO international workforces to address the multi-national audience. Land Forces 2022 will also introduce the Land Forces Hub, a new initiative designed to provide a platform for speakers to present their vision, insights and solutions to the questions posed by the land defence community, alongside the official conference program. The Hub offers 40-minute speaking slots, open to industry, academic and government representatives from both Australia and overseas. Interested speakers are invited to submit their the land defence domain, from industry briefings to supply chain opportunities, land defence program updates and academic findings. On the industry exhibition floor, expect to find the major players, companies such as Hanwha and Rheinmetall, CEA Technologies, NIOA and Thales. Land Forces will also host a sizeable overseas contingent. The USA Partnership pavilion, organised by Kallman Worldwide, is reaching capacity with 98 per cent of the exhibition space sold, and participation approaching preCovid levels. The pavilion will include leading international defence companies Northrop Grumman, Lockheed Martin andButL3Harris.alongside the prime contractors, expect to find the start-ups, the SMEs why no one ever thought of it before, and the companies providing the kind of specialist expertise that can often make the difference between hit and miss in the marketplace. And that’s across the board, from intelligence satellites to protective gloves, research and services. Land Forces is a melting pot of government agencies, think tanks, private companies, universities and research foundations. Many, such as research agency ARM Hub, both gain and share expertise across multiple sectors. Set to exhibit at Land Forces 2022, the Brisbane-based Advanced Robotics for Manufacturing Hub (ARM Hub) is helping Australian industry develop and adopt Artificial Intelligence (AI) and robotic technologies to build sovereign manufacturing capability.
• Formal business to business and business to government networking Austrprograms;alian and international defence, industry, government and scientific delegations, with formal delegation access programs; Small business and export development programs;
EventsMonthly
50 AUGUST 2022 Manufacturers’
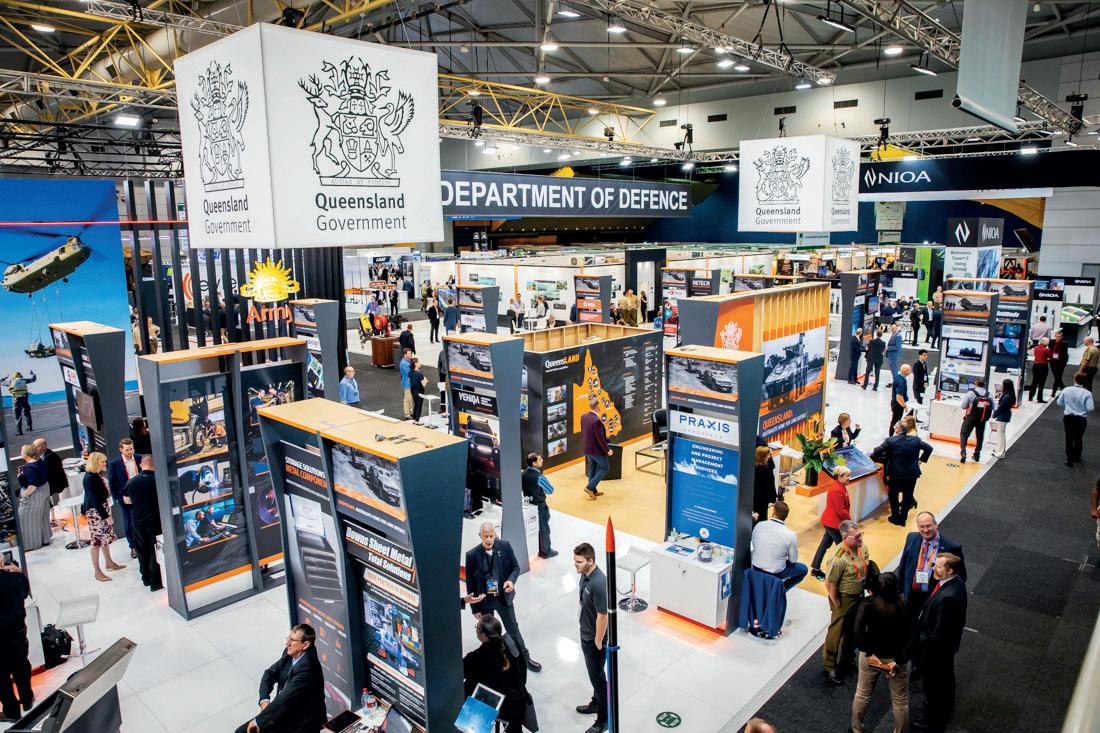


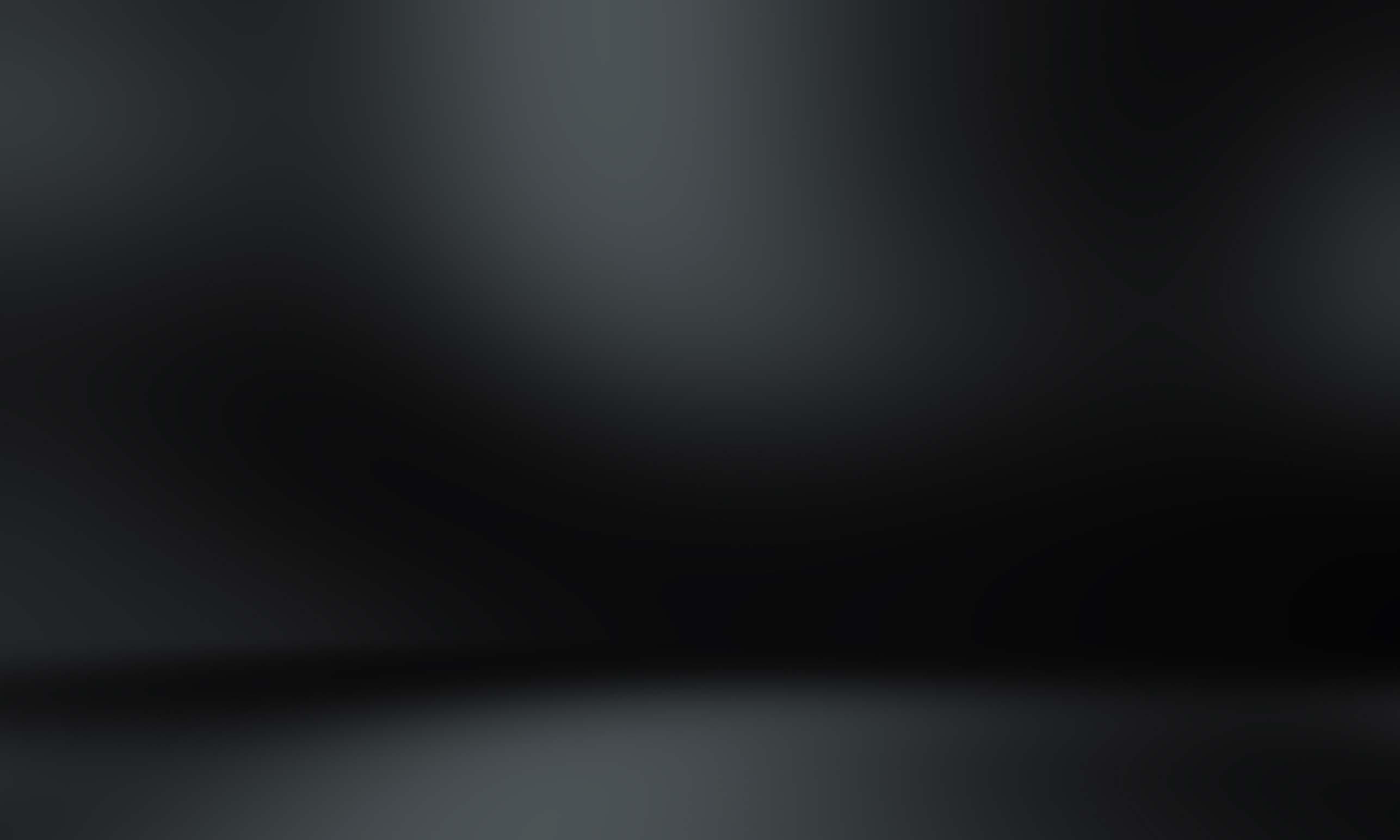
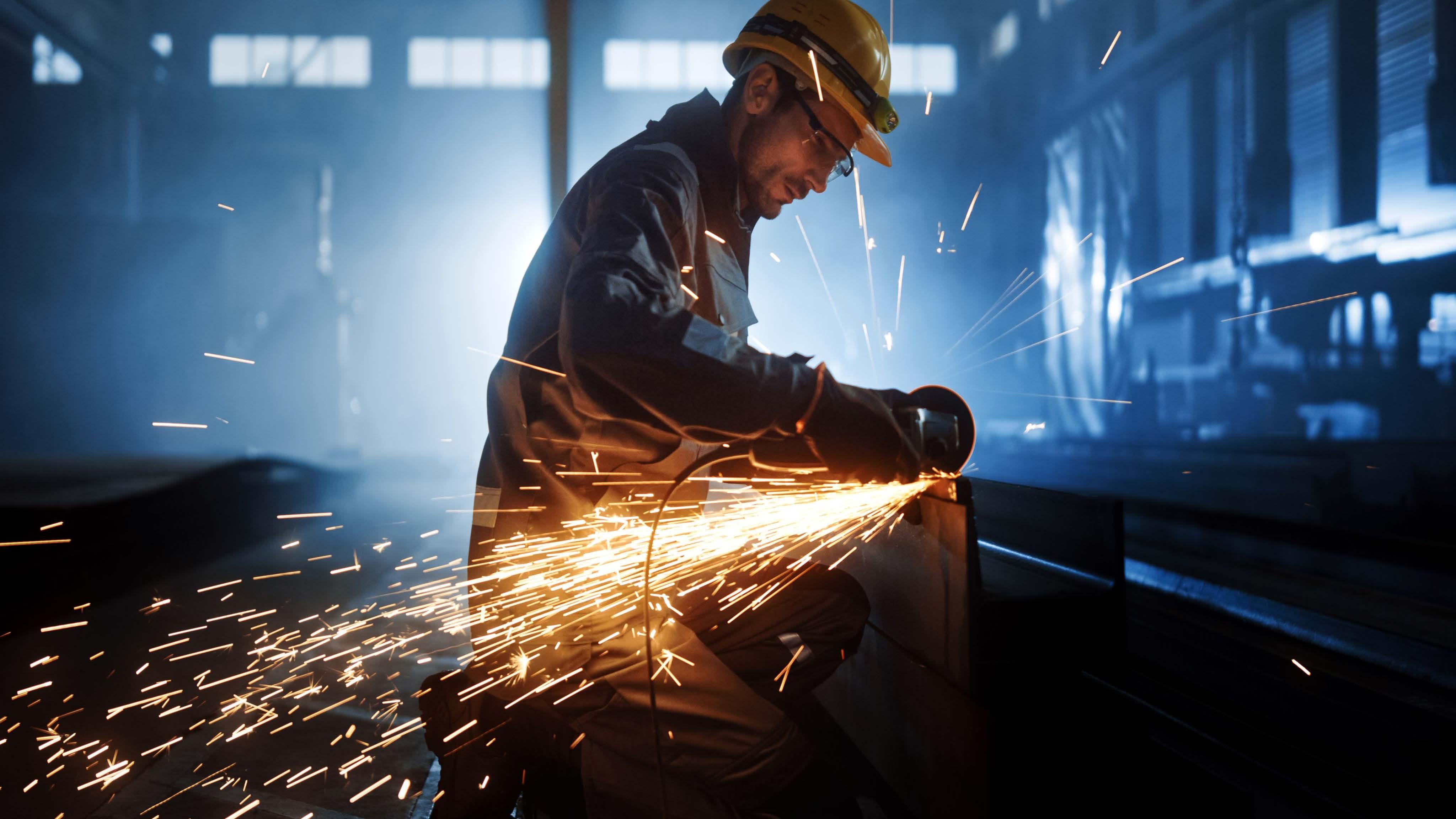
SHOWCASEFABRICATORS 2022 BOOKING DEADLINE: August 24 There are many different fabrication processes in manufacturing that depend on the initial material and the desired end product. In October 2022, Manufacturers’ Monthly is providing an opportunity for every fabricator to list their services. The showcase gives businesses the chance to state the service they offer and to demonstrate the extent of their services to the industries they serve. Our saegment is for Australian businesses who offer fabrication services to showcase their capabilities to the market. To participate, please scan the QR code or contact: 0431danny.hernandez@primecreative.com.au330232


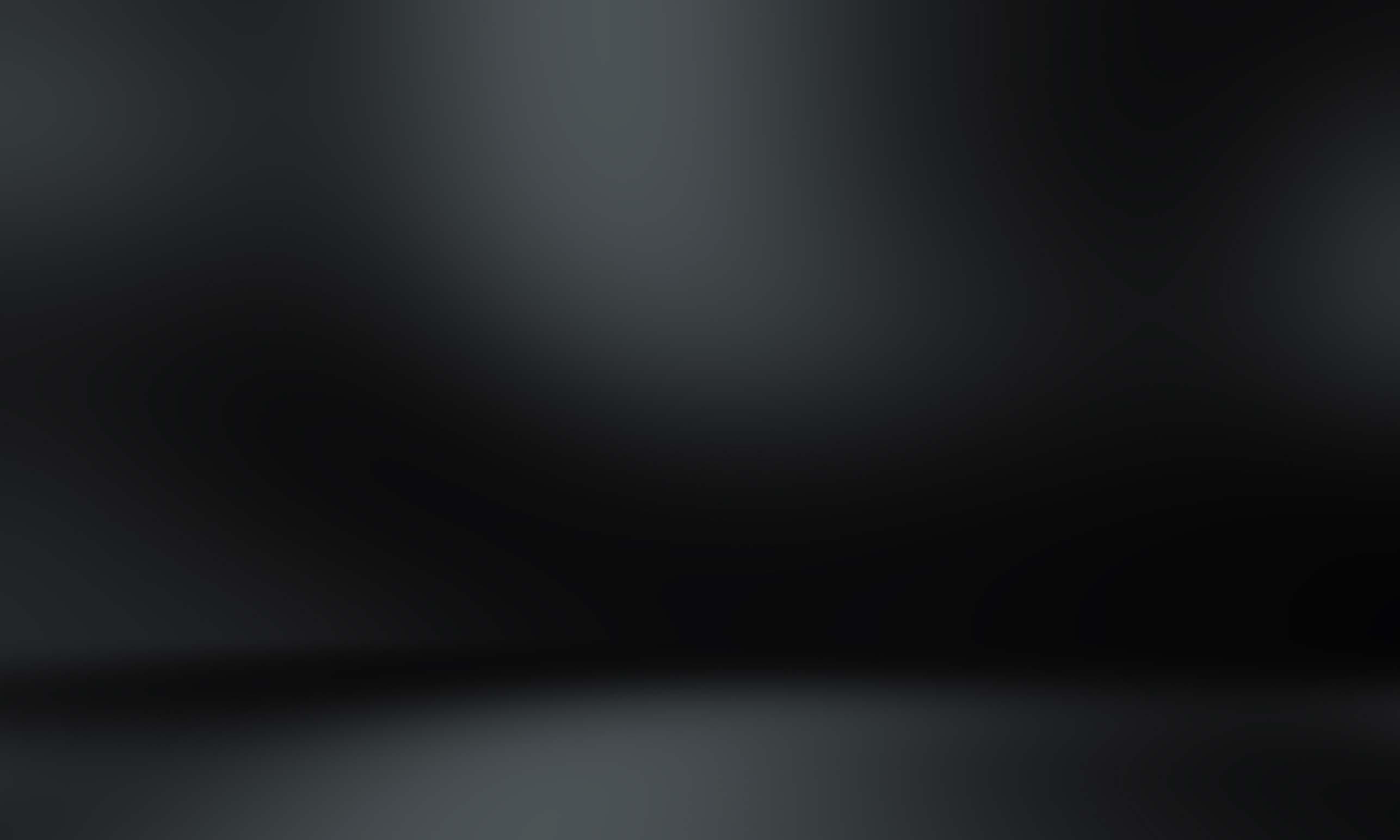
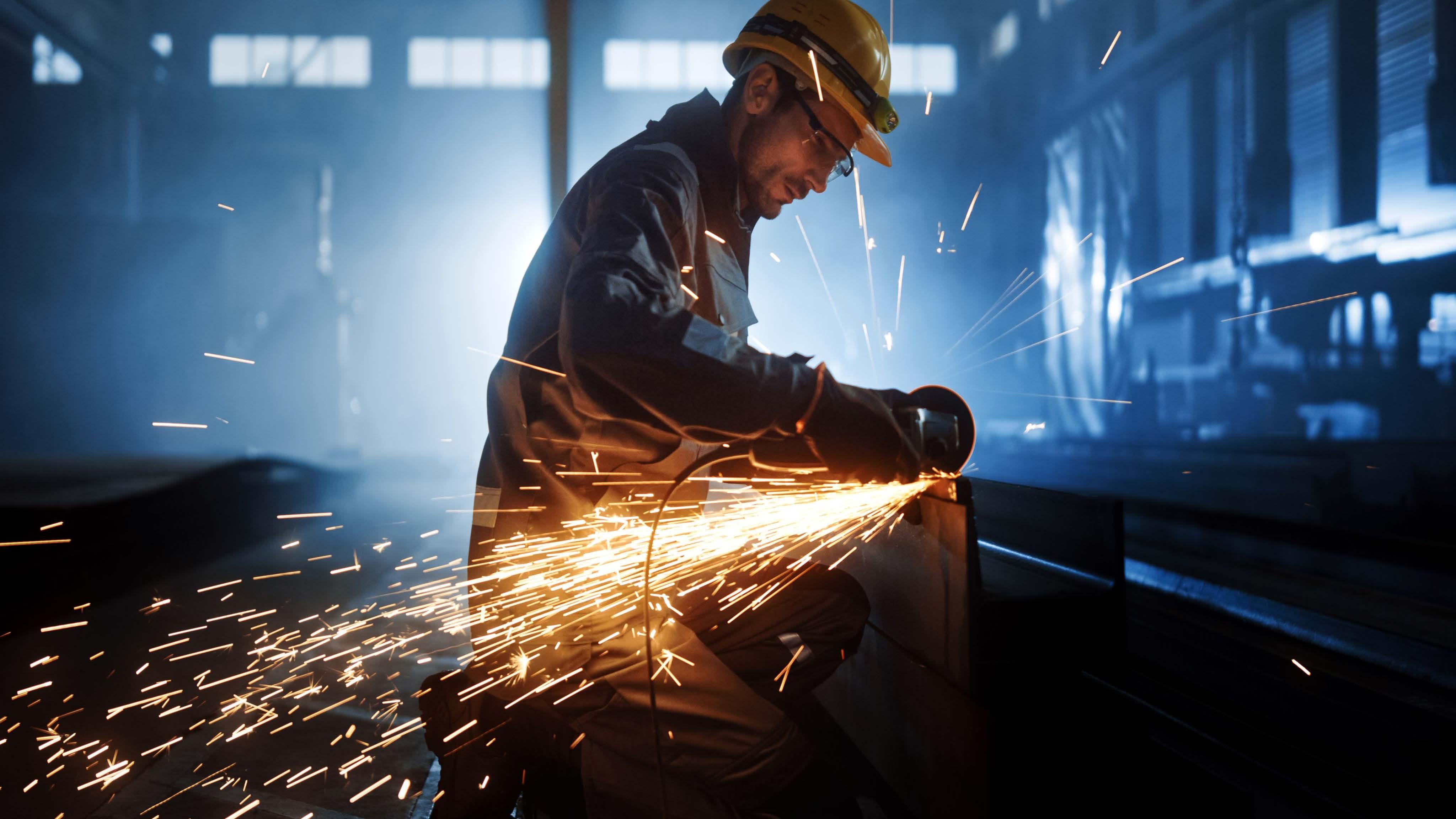
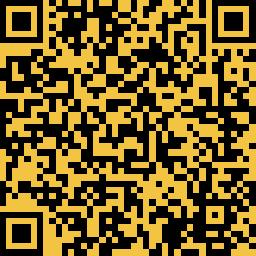
Sowing the seeds of sustainability Representatives from Motion Australia explain how it is facilitating sustainability best practice for businesses in their need to continuously update equipment and processes as they chase the goal of net zero emissions.
actionFAOSustainabilitydatahighlightsaneedforsustainableinfarmingandfoodproduction.
values are purposeful when it comes to environmentally responsible processes and products,” he said. And yet, Stefanec emphasises that sustainable agriculture is certainly not any single well-defined goal for anyone. In fact, the definition of sustainability has evolved over the past several decades to become less of a guideline for businesses and more of a set of mandated actions, he explained. “Across industries, this will require businesses to continuously update their equipment and processes to align with ever-changing best practices in sustainability,” Stefanec said. “This is why in the current industrial climate it is so important that solutions providers like Motion Australia bring to the table a strong working knowledge and host of technical capabilities in the area of sustainability. This will help our group of businesses and our customers’ businesses work better toward the goal of net zero emissions.”
“A few of the ways we hope to achieve this is by putting sustainability targets into practice across our own business,” he continued. “We can do this by implementing greener energy in our warehouses and improving our outputs in terms of waste across our supply chains. “We also want to work with our customers, partners, and suppliers to encourage greener processes and products that use fewer natural resources, improve energy efficiency, reduce waste, and eliminate eco toxic chemicals from production as much as possible.”
“This opens the door for a lot of conversations with both our suppliers and customers about how to reduce their carbon footprint,” Stefanec said. “But it also means that we have access to a much broader range of relevant skills and expertise across our network.”
52 AUGUST 2022 Manufacturers’ Monthly manmonthly.com.au
A significant endeavour, considering Motion Australia is responsible for distributing more than 600,000 unique products from more than 2,300 suppliers from around the world. This is particularly significant with the recent consolidation of all of Motion Australia’s iconic brands under one masthead, which includes a national network of more than 110 branches consisting of CBC, BSC, Hardy Spicer, AIP, CRAM, Seal Innovations, SpecFast, Walterscheid, Sealing Solutions, and Webster BSC locations.
THE future of food production rests on a more sustainable approach to agriculture that gives equal weight to environmental, social, and economic concerns, without compromising the finite supply of natural resources on the planet.Currently, approximately half of the world’s habitable land consists of farmland, while an ever-increasing need for animal-based products, fruits, and vegetables is expected to see demands exceed more than 60 per cent of current production levels by 2050 to a projected world population of 9.3 billion people –according to estimates compiled by the Food and Agriculture Organisation (FAO). The need for sustainable action in farming and food production is evidenced by this data, Motion Australia national business development manager for the Food and Beverage sector, Leon Stefanec said.“It has never been more critical for businesses to demonstrate that their
Motion Australia national product manager, Steve Keown notes that there has been a growing interest over the last decade in products that contain biodegradable and natural materials.
As a wholly owned industrial solutions provider with unmatched coverage of products and services within the Australian market, the scope of Motion Australia’s sustainability transition will be vast across their businesses.
“Suppliers who manufacture products such as lubricants, oils, cleaners, and degreasers are well-positioned to address environmental concerns,” he said. “These
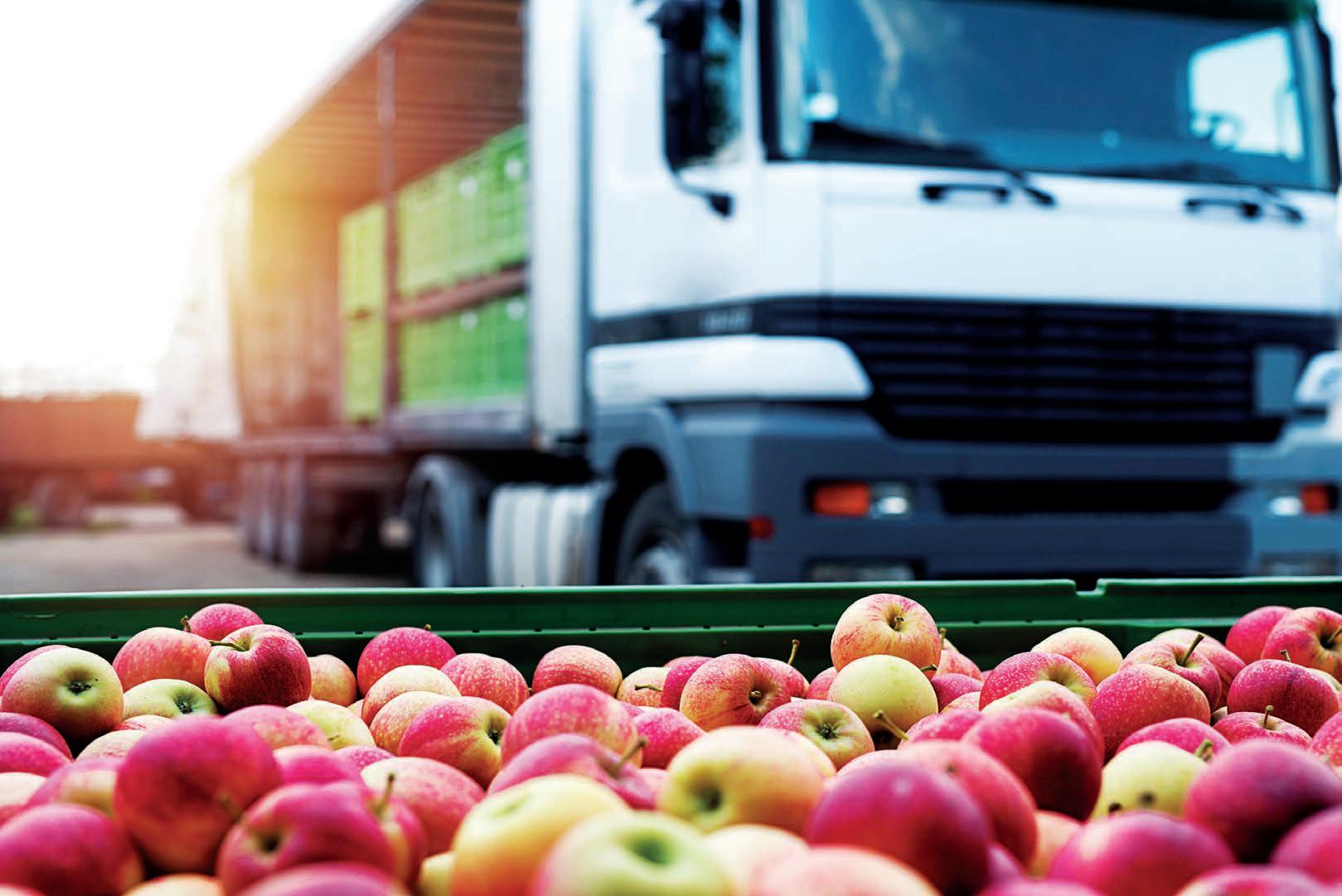
manmonthly.com.au Manufacturers’ Monthly AUGUST 2022 Sustainability53PREMIUM
types of products play an important role in the performance, reliability, and overall efficiency of parts and machinery on any operation, and customers who opt for environmentally accredited products can more readily meet their environmental targets by ensuring the products they are using are responsibly sourced.
When it comes to more sustainable solutions, Keown said that the agriculture industry has made a lot of progress, but it is still a long road ahead to achieve net-zero.“Customers in the agriculture and food and beverage sector have only recently started to overcome a few of the most common misconceptions about sustainability,” he said. “The most common being that it costs more to operate sustainably in the short-term. At Motion Australia, we are trying to promote more awareness about the longterm benefits of investing in sustainably sooner rather than later. To reach environmental targets we all have to pay it forward by investing a little more up front, to ultimately see greater returns in the future.” QUALITY HOISTING SYSTEM Electric Chain Hoists Duty Electric Chain Hoists High Demand Wire Rope Hoists
Viva Energy Australia has a mandate they call “Goal Zero” included in their Statement of Commitment to Health, Safety, Security, and the Environment that commits the business to monitoring performance and procedures on all operations through rigorous environmental assessments and the implementation of greener technologies.
From the Viva Energy portfolio of products, Shell Dobatex – which includes the Aqua Degreaser, Gold, and Platinum – is an organic, water-based cleaning range specifically developed for use on industrial applications that meets the Australian standard for Biodegradability, compliant with AS 4351.2. “The Dobatex products are a range of completely organic and non-toxic range of degreasers that can be used for cleaning equipment without degrading polished or metal surfaces,” Keown explained. “They are some of the most premium biodegradable products on the market right now.”
We also want to work with our customers, partners, and suppliers to encourage greener processes and products that use fewer natural resources, improve energy efficiency, reduce waste, and eliminate eco toxic chemicals from production as much as possible.
Heavy
“Quite a few of key suppliers and strategic partners have made commitments toward achieving net zero by 2050 by developing new ranges of products that are formulated from raw natural and biodegradable ingredients,” Keown said. “These same suppliers have also been taking steps to make their production and manufacturing facilities more sustainable by converting to renewable energy, using recycled materials, and introducing more sustainable packaging.”
In addition to this, Keown notes that Shell’s Naturelle range includes several environmentally acceptable lubricants (EALs) and biodegradable hydraulic fluids.“In the event of a leak or accidental spillage on site where there is the risk of groundwater contamination or impact on the local ecology, products such as the Shell Naturelle Fluid HF-E are advanced biobased solutions that are classified under the EU Ecolabel for Lubricants as non-toxic to bacteria, algae, freshwater, and marine invertebrates,” he said. “This is good if a customer has a piece of hydraulic equipment that is operating in a sensitive environment that requires operations to have low ecotoxicity.”
Production
One example of this, according to Keown, is Viva Energy, the exclusive macro distributor for the world leading energy company Shell in Australia.
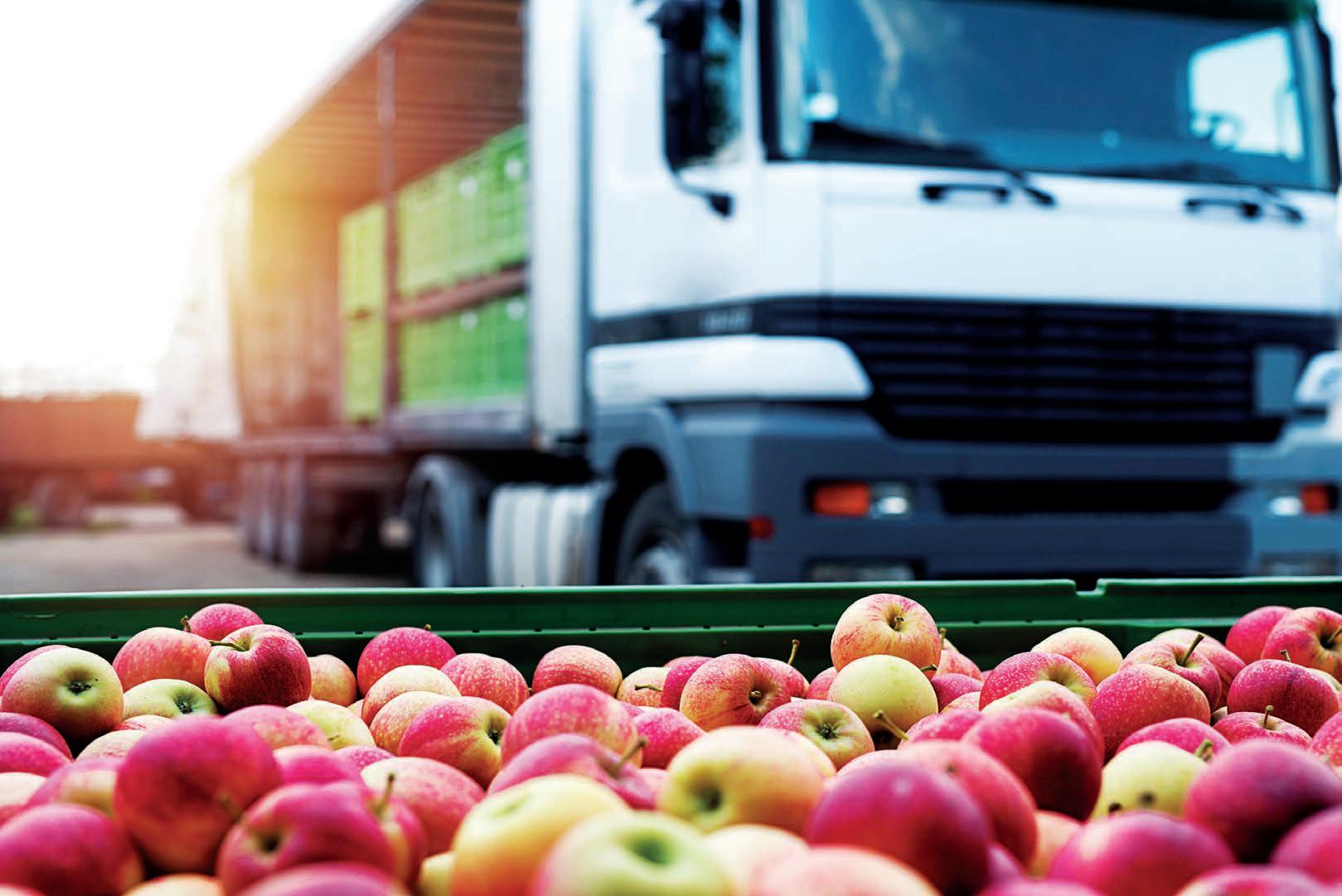
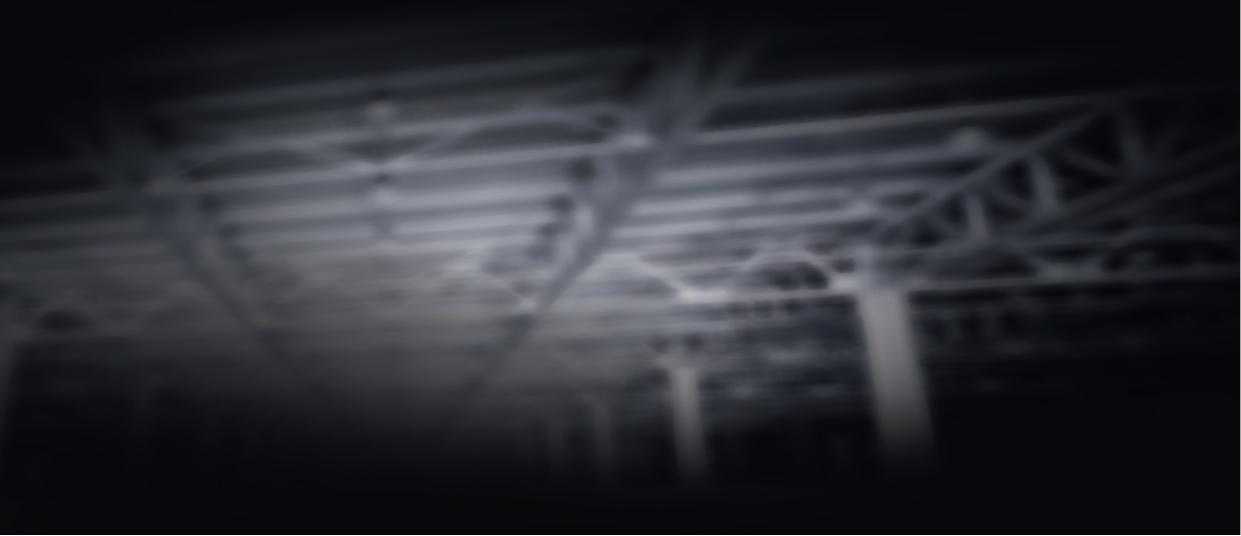

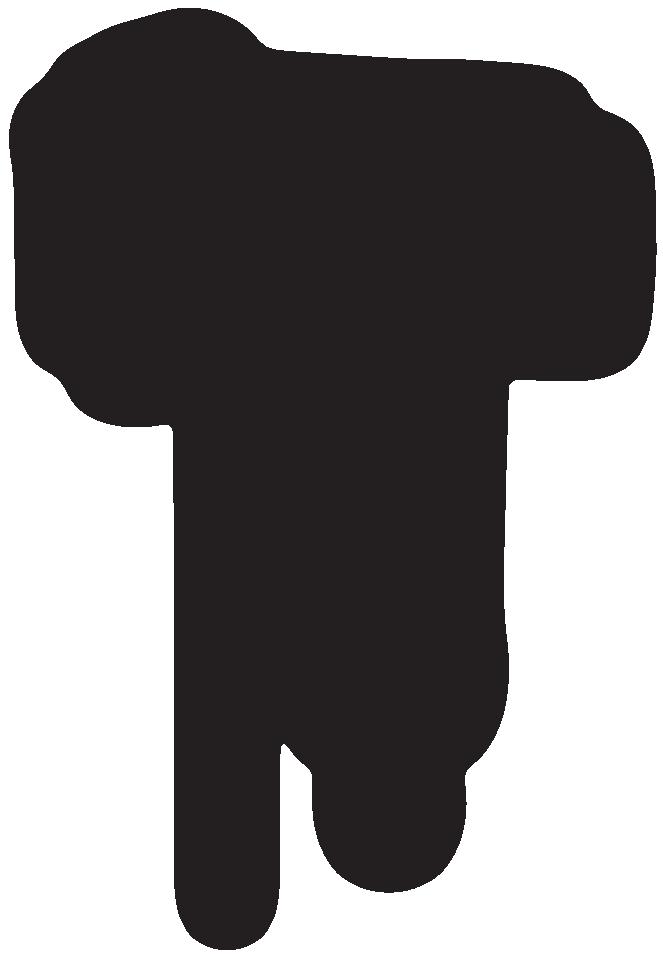

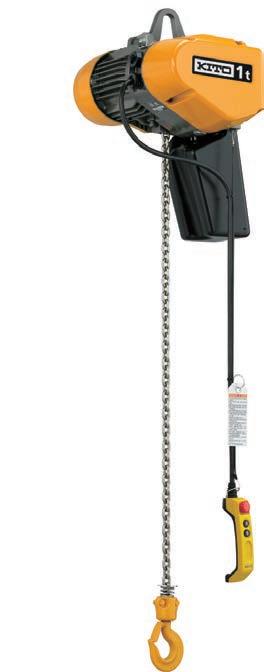
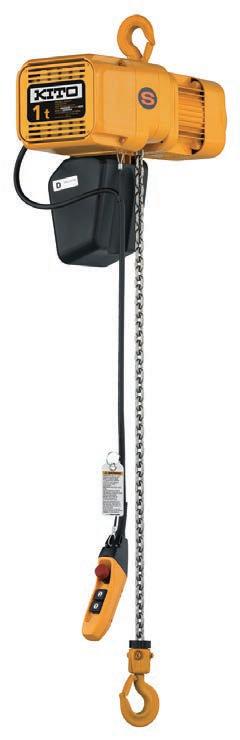

3D model visualises the installation space and movements of the linear robot The next step: configuring the linear robot. Sliders are available here, which can be used to set the stroke lengths of the X, Y and Z axes with millimetre precision. A dynamic 3D model of the linear robot, which can be rotated in all directions, visualises the settings in real time. “We have added a new function at this point,” Mühlens said. “With one click, it is now possible to also display the installation space of the linear robot. We use coloured areas for this. This gives users a visual impression of how much space their automation solution takesAdvancedup.” users can also export the 3D model as a STEP file and process it further in any CAD program. With the online configurator, it is even possible to define robot movements –by entering a few parameters and without programming knowledge.
As a well established brand, Bollards Direct is one of the largest “Australian Made” suppliers of key-lock bollards and permanent ram/secure bollards in the country. After being acquired by the experienced G&G Engineering last year, the company manufactures its bollards in Melton, Victoria, which are channelled through G&G’s distributors in every state.
With the help of the game engine Unity, motion plastics specialist igus has given its online configurator for low-cost linear robots a facelift, making its operation even more efficient.
54 AUGUST 2022 Manufacturers’ Monthly Brought to you by What’sNew
Now, users can configure an individual linear robot ready for connection faster and easier – in just five minutes. With the help of the online tools, any automation solution can be programmed and tested directly in the selected working area and also load CAD data and a suitable drawing. Even small and medium-sized companies can immerse themselves without a barrier in the world of automation – without the know-how of specialists and CADIncreasesoftware.efficiency, reduce errors and lower costs: many companies are recognising the benefits of process automation. But choosing the right robot can be time-consuming – and time is money. Last year, igus developed an online configurator to make it easier getting started with automation. With just a few clicks, customers can easily configure ready-to-connect low-cost linear robots based on sliding drylin linear guides. Linear robots are available without control system, and with control system and software. “Since the launch of the configurator, we received a lot of positive feedback on the gamification approach and intuitive usability,” igus head of the Automation Technology and Robotics division Alexander Mühlens said. “Nevertheless, we asked ourselves: ‘Can we continue to improve operation with this feedback?’ The answer was a resounding yes. As a result, we have further optimised the configurator and added new functions.”
“With this function, we follow the motto ‘Test before invest’. Thanks to the moving 3D model, operators gain a feeling for robot movements and cycle times,” Mühlens said. After online programming, the file can be displayed in virtual reality via an app or loaded into the real robot control system.
Options: Bollard Sleeve, Cap & Storage Holder are available as Spare Parts;
• Can powder coat special colours; • Can weld on attachments; and
Australian-made bollards by Bollards Direct
Company: Bollards Direct Phone: 0413 606 456 Website: www.bollardsdirect.net.au
For the new design of the configurator, the igus developers used Unity – a platform used in the development of games for PC and game consoles. Operation of the configurator is correspondingly intuitive. And it works as follows: in the first step, the user selects the kinematics, i.e. a line, flat or room linear robot. The view is reminiscent of a selection menu from a computer game, which players use to select racing cars, for example. With these standard configurations, the right robot can be quickly selected under clear conditions. For the first time, it is now possible to compile and enquire about a special linear robot. Whether ice cream maker, measurement system or palletising robot: many applications need to meet special safety regulations, for example, be splash-proof or work in very small installation spaces. The online configurator allows users to request a special linear robot that meets the specific requirements of their individual application.
• Can custom manufacture to your requirements.
Company: Treotham Automation Phone: 1300 657 564 Website: www.treotham.com.au igus linear robots – as easy as playing PlayStation
• 2 keys supplied per bollard.
Configure individual robots — even easier thanks to the gaming platform
BD90STD 90mm Diameter – 4mm Wall 930mm Height Weight: 9.8 kg The BD90STD is designed for RESIDENTIAL USE to protect Garages, Driveways, Carports and similar areas. Double locking cam system with internal mechanism; Galvanised steel tube; • Stainless steel internal components to prevent corrosion to all locking and moving parts; Can be keyed alike;
• Standard colours are Yellow or Black; Round handle which is gentle on the hands; and
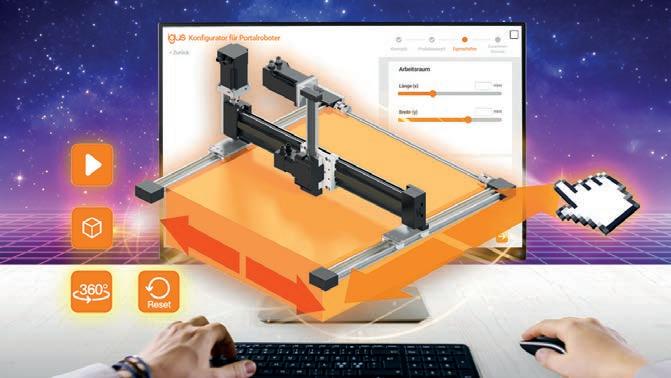

manmonthly.com.au Manufacturers’ Monthly AUGUST 2022 55
MEGAN LILLY – Executive Director – Centre for Education & Training, Ai
Digital transformation presents an incredible opportunity to grow and reshape our economy for the better, but the secret to unlocking this potential lies with people, not machines.
THERE’S no shortage of big economic challenges right now, but, looking on the bright side, there’s also a few opportunities. All around us, digital technologies are quietly providing the means to improve, optimise, expand and transform businesses of all sizes. This might seem like a lot of little opportunities, but taken together, these add up to one big opportunity for the nation – and the key to unlocking it is people. Digital transformation presents obvious benefits – productivity gains through automation and optimisation, the ability to reach potentially limitless markets and develop new business models.However, beyond that, digital technologies can be harnessed to change work for the better, with opportunities to improve flexibility, counter the tyranny of distance and improve diversity and inclusion.Butitall depends on how we, as a nation, navigate this transformation – our policy response is as important as the transformation itself. In a newly released report, Ai Group’s Centre for Education and Training has set out the scale of the digital transformation opportunity (and challenge) before us. The report makes it clear that, if we want to get this right, we have some work to do. Digital transformation is not about ordering some hardware and unloading it from a container ship at the dock. If only it was that simple. It’s actually about the capability and vision of the people who create, develop, service, and utilise digital technology and tools – without whom, technology is nothing. This is where Australia needs to focus. Over the next decade, it is expected that current skill shortages will blow out to 700,000 as the rapid development in technology drives demand for a digitally literate and technically skilled Australian workforce.
Group The Last Word
This can be a story of immense opportunity and growth, and, if we manage it correctly, higher skilled and better paid jobs, with more flexibility for moreButAustralians.weneedto ensure no one is left behind, as the inevitable disruption and displacement also means we risk a growing divide between the digital capability ‘haves’ and ‘have nots’. Successfully navigating digital transformation matters, to us all. As a nation, it’s critical to sustaining our productivity and global competitiveness. For enterprises, large and small, it’s life and death, as no business will escape the tide of digital transformation that is coming for them, whether they like it or not.It also matters to us all as individuals, as if we fail to develop the skills and capabilities required to realise the benefits of technology, and ensure they are shared, we’re in danger of going backwards in terms of the things that really matter. The sustained prosperity, and equity, for which Australia is worldrenowned.Butthe key is, Australian businesses need the leadership, capability, and skills to seize the moment. For that to happen, we need policy vision and leadership. See, all about people. And when it’s all about people, it’s all about education and training. We need to raise the level of digital literacy right across the board. We also need to make the tertiary education and training system fit for purpose in a fast-changing digital world. This means a system that enables lifelong learning and re-skilling, incorporates much more work-integrated learning, and acknowledges the importance of ‘human’ capabilities like collaboration and communication.There’salsono point seeking migrants with yesterday’s skills, so our migration program needs to be informed by timely, accurate data on changing skills needs. While we’re at it, we need policies in place to encourage investment at the firm level – not just in technology but also in the skills and capabilities that go with it. We need our current workforce, and the next generation, to be confident and skilled in the use of technology, and capable of reskilling and relearning as required.Wedon’t have the luxury of time to analyse and calmly prepare for a far off ‘a digital future’. There’s a sense of urgency, as we navigate all this in real time. This really is flying the plane and rebuilding it at the same time. The digital ‘wave’ is washing over all our workplaces, right now, and we all need to embrace it, learn to ride it, and help and teach others who are falling short.Our policy response needs to ensure Australian businesses can realise the potential of digital technologies – because Australian workers are skilled and ready to take them there. Access the full report www.aigroup.com.au/news/reports-policy-papers/here:
Digital transformation is more about people than technology
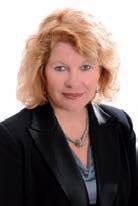
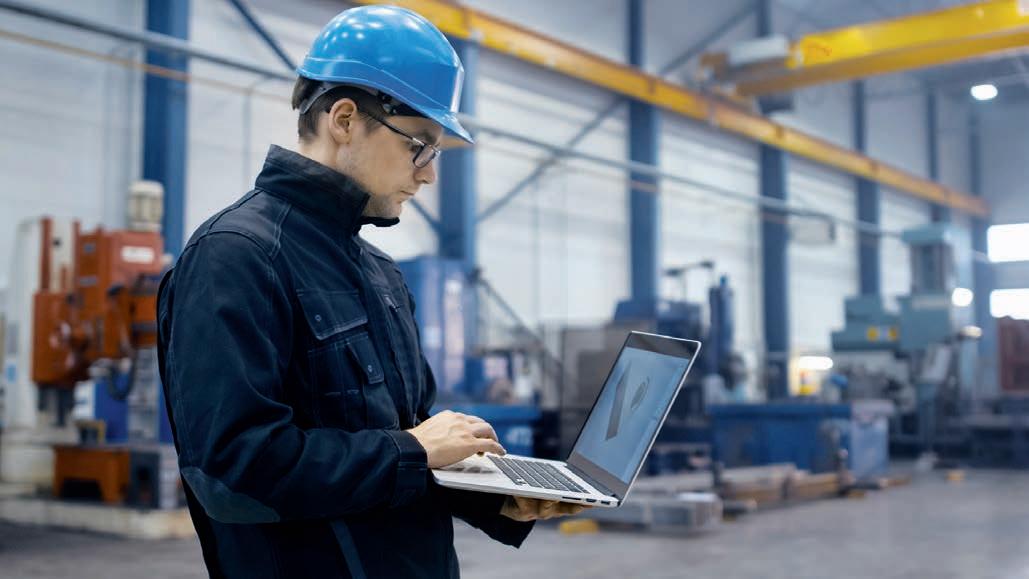
The Optimizer 4.0 can control and monitor up to 60 devices across 3 different compressed air networks but not every system needs such complex central controllers. Our Equalizer 4.0 and Equalizer Pro are perfectly suited to reduce wasted energy and minimise maintenance needs for simpler compressed air systems of between 2 and 8 machines. Now that we have minimised the electrical energy being used by your compressed air equipment, let’s see what wasted energy we can recover in step 8. Compressing air generates a lot of heat. In fact, over 90% of the electrical energy used by a compressor is converted into heat during the compression process. Why let your energy vanish into thin air? Using energy recovery systems is the single best thing you can do to reduce your energy consumption. Atlas Copco energy recovery systems can recover wasted energy from your air or water-cooled compressors and use it in your process, to pre heat boiler feed, for space heating or hot water storage for
it
Smart central controllers like our Optimizer 4.0 can accommodate different sized compressors with different technologies and control types to maximise energy efficiency and reduce your carbon footprint.
. Your
Now
do
Scan the
In the seventh step to greener products, we look at central control, with two or more machines working together. In such systems, even the most efficient machines can not reach their full potential without a central controller.
solution
Getcleaning.thecomplete with Atlas Copco’s team of experts on 1800 023 469 productionmoregreenerguide10-steptoaandefficient Wouldn’t be great if there was a way to make compressed air systems more efficient whilst saving money and the environment at the same time? The bad news is that there isn’t one way to do that. The great news is that there are 10 ways! QR code on steps through to 6. let’s a deep 8!
1
below! 1. Application 2. Storage Distribution& 3. Air Quality 4. Air Volume 5. TechnologyCore 6. EquipmentControl 7.ControlSystem 8. Maintenance9.RecoveryEnergySystem 10. MonitoringSystem Scan to download the FREE 10-stepguide In past issues of Manufacturers’ Monthly, we focused
dive of steps 7 and
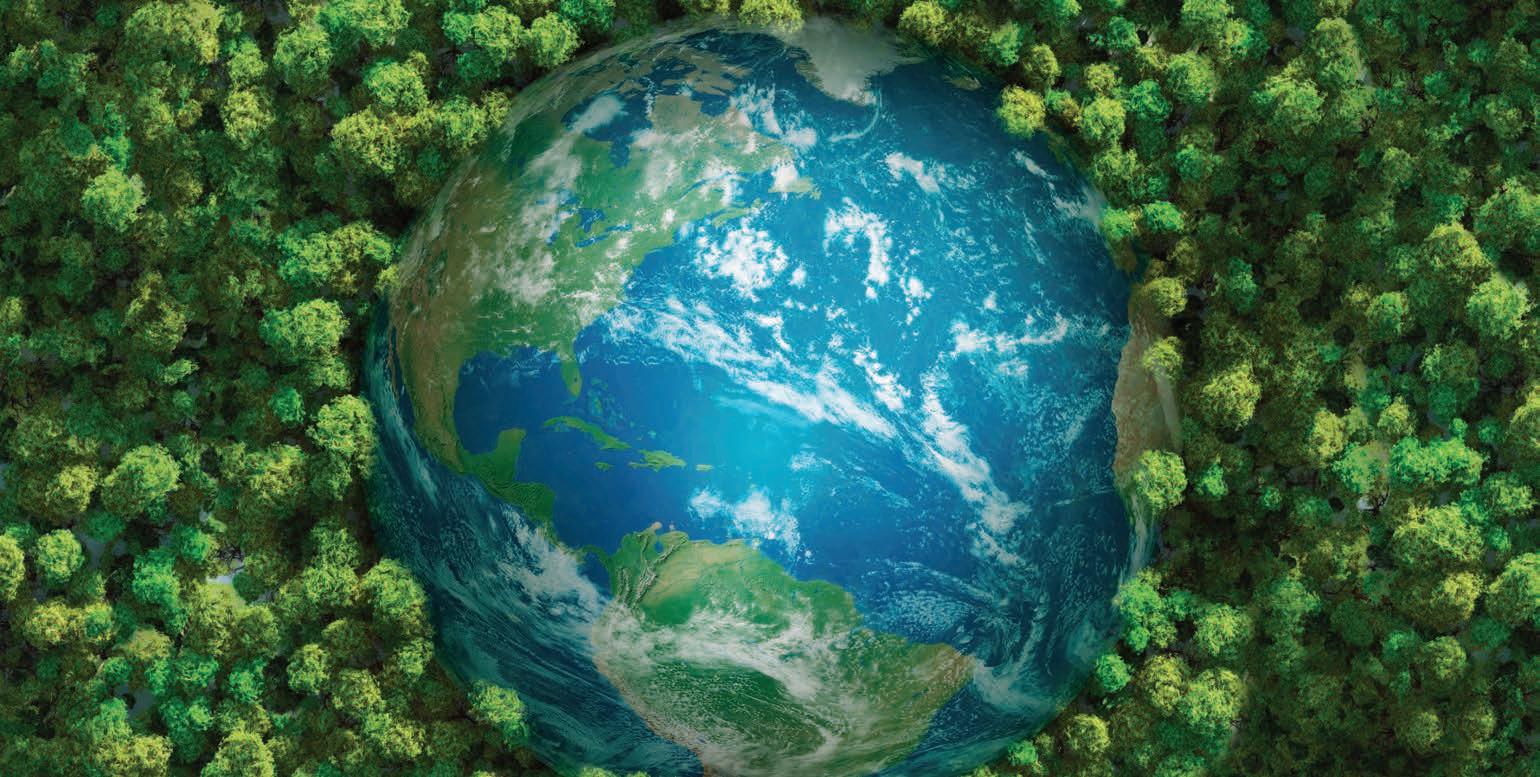
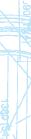
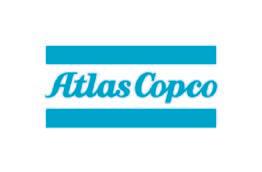

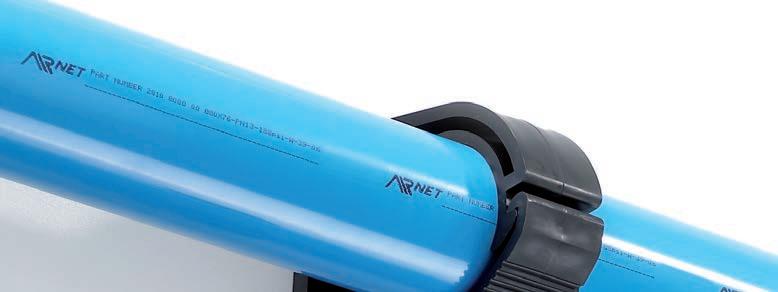
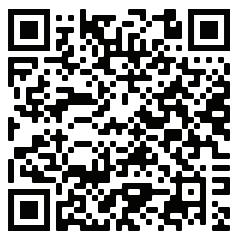
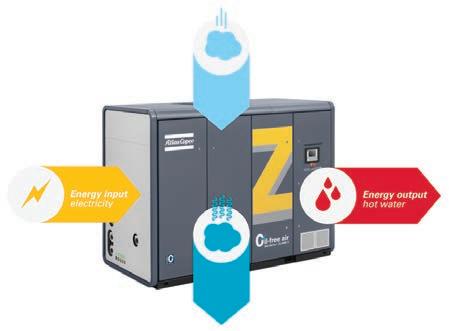