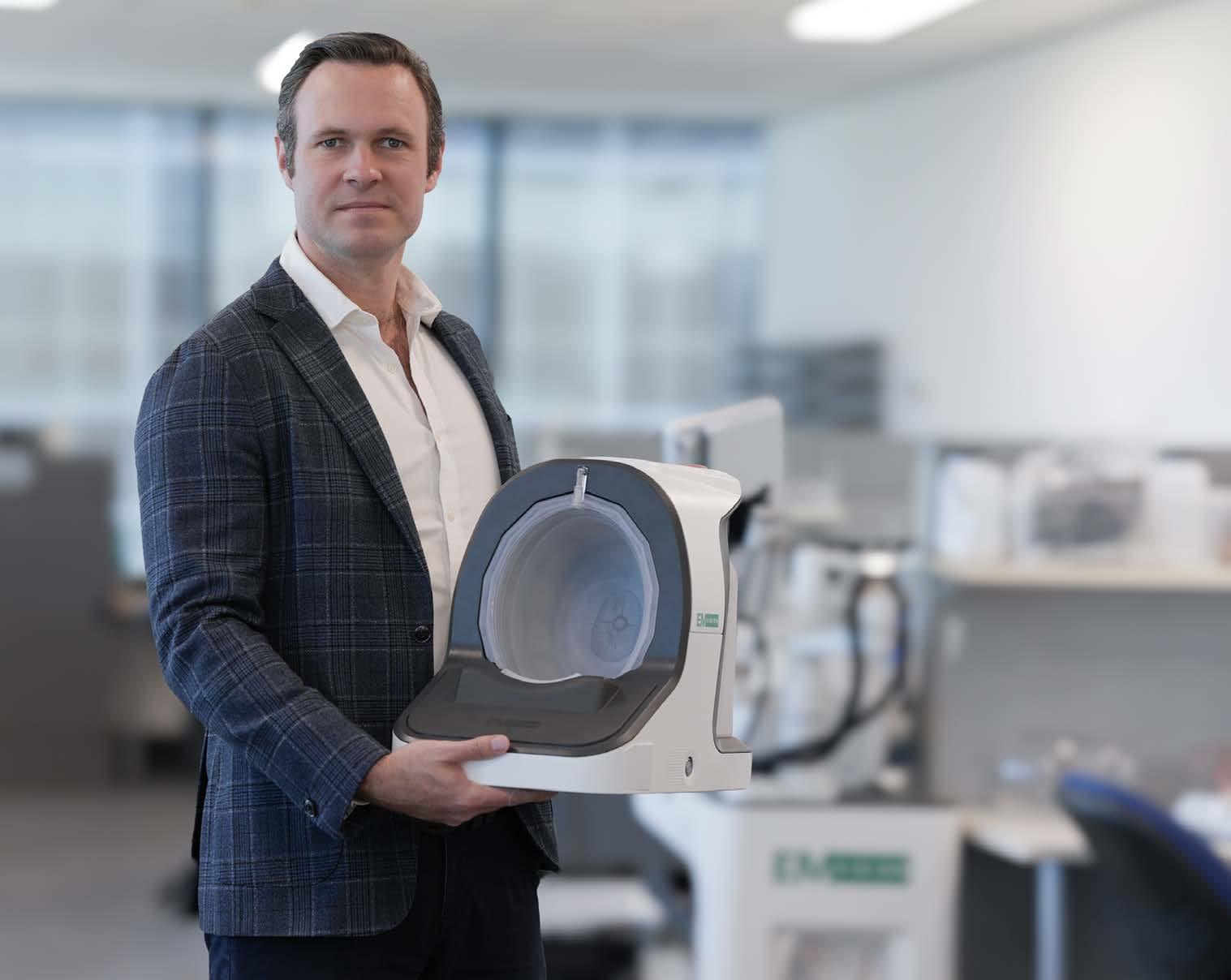

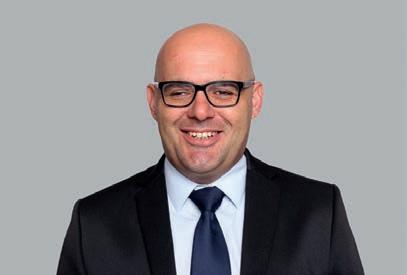

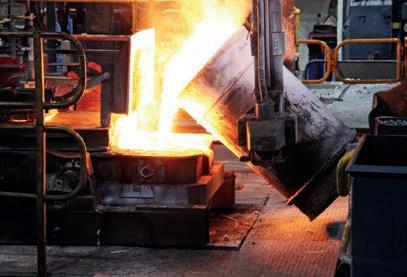
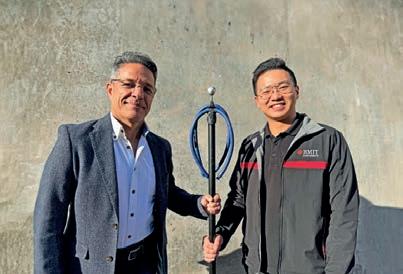
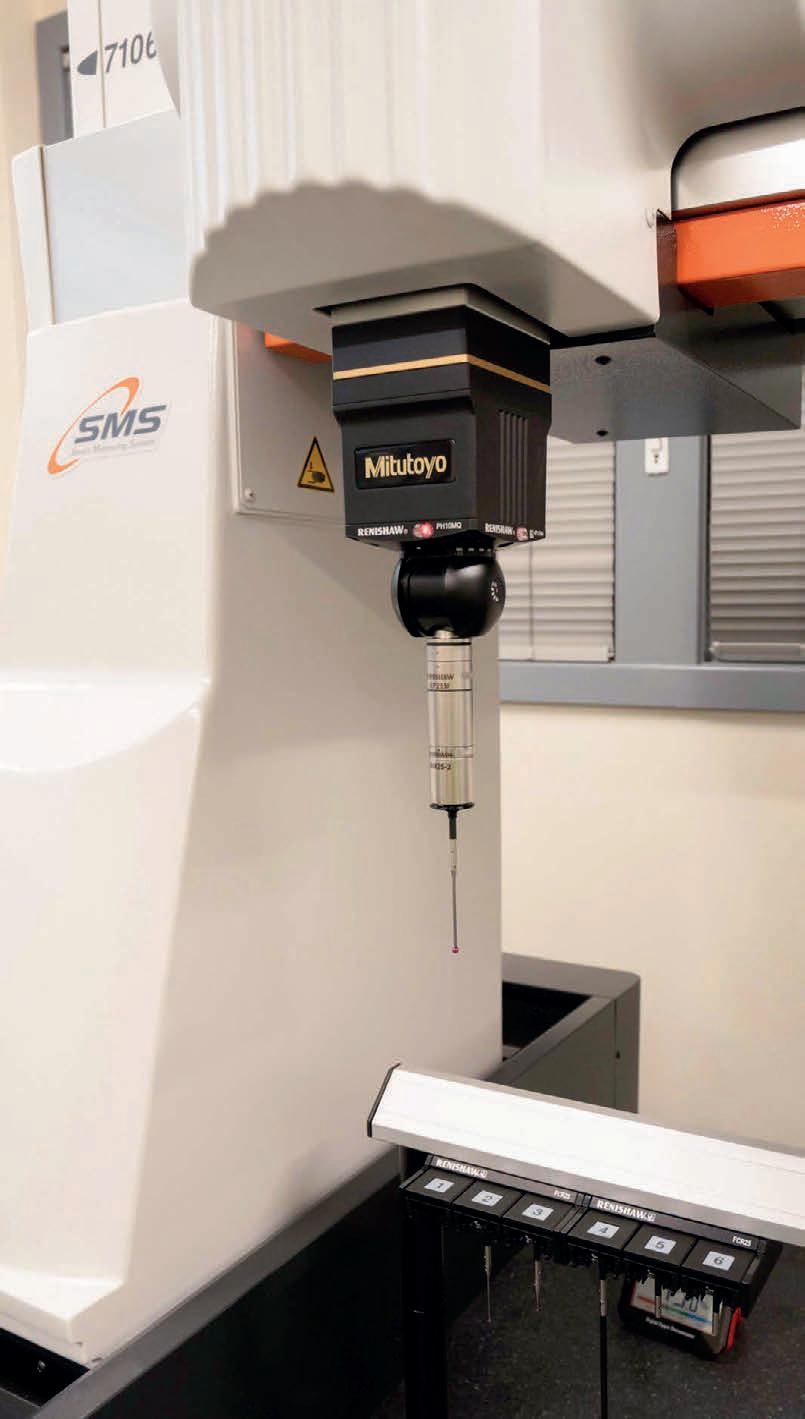
Over the past year, Lightforce Group has cemented its status as a premier designer, innovator, and manufacturer of military and law enforcement solutions, showcasing our dedication to South Australia’s manufacturing goals.
Join us at the 2024 LandForces International Land Defence Exposition! Visit Site A069 to discover our groundbreaking solutions and engage in impactful discussions.
CEO: John Murphy
Chief Operating Officer: Christine Clancy
Managing Editor: Mike Wheeler
Assistant Editor: Phillip Hazell phillip.hazell@primecreative.com.au
Journalist: Jack Lloyd jack.lloyd@primecreative.com.au
Production Coordinator: Michelle Weston michelle.weston@primecreative.com.au
Head of Design: Blake Storey
Design: Cat Zappia
Sales/Advertising: Emily Gorgievska Ph: 0432 083 392 emily.gorgievska@primecreative.com.au
Subscriptions
Published 11 times a year
Subscriptions $140.00 per annum (inc GST)
Overseas prices apply
Ph: (03) 9690 8766
Copyright Manufacturers’ Monthly is owned by Prime Creative Media and published by John Murphy. All material in Manufacturers’ Monthly is copyright and no part may be reproduced or copied in any form or by any means (graphic, electronic or mechanical including information and retrieval systems) without written permission of the publisher. The Editor welcomes contributions but reserves the right to accept or reject any material. While every effort has been made to ensure the accuracy of information, Prime Creative Media will not accept responsibility for errors or omissions or for any consequences arising from reliance on information published.
The opinions expressed in Manufacturers’ Monthly are not necessarily the opinions of, or endorsed by the publisher unless otherwise stated.
© Copyright Prime Creative Media, 2024
Articles
All articles submitted for publication become the property of the publisher. The Editor reserves the right to adjust any article to conform with the magazine format.
Head Office
379 Docklands Drive
Docklands VIC 3008 P: +61 3 9690 8766
enquiries@primecreative.com.au www.primecreative.com.au
Sydney Office Suite 11.01, 201 Miller St, North Sydney, NSW 2060
Printed by: The Precision Group 83-89 Freight Drive. Somerton Vic 3062
Ph: (03) 9794 8337 manmonthly.com.au
Welcome to the September edition of Manufacturers’ Monthly. In this issue’s Manufacturer Focus, EMVision creates portable brain scanners for rapid stroke diagnosis, aiming to improve speed and accuracy in diverse settings. Learn more about the company’s inception and journey towards commercialising their product. Later in this edition, we speak with representatives from the Australian Foundry Institute who have raised concerns about issues facing the industry. Finally, in this month’s Engineering Focus, we speak with RMIT engineers, who are developing a modified speargun for cost-effective seabed soil testing. Happy reading!
Dear Readers,
As we step into the September edition of Manufacturers’ Monthly, it’s an opportune moment to reflect on the evolving landscape of Australian manufacturing and the exciting developments shaping our industry.
This month, our coverage highlights the strides being made in defence, sustainability, and local manufacturing – each contributing to the growth and innovation of our sector.
In the defence sector, the Federal Government’s commitment to bolstering Australia’s maritime capabilities continues with the ongoing development of the medium landing craft.
This $2 billion project, with vessels designed by Birdon and built by Austal, is a cornerstone of our defence strategy. It represents not only an investment in national security but also a substantial boost to our shipbuilding industry, promising to sustain jobs and stimulate economic activity well into the future.
As these vessels prepare to enter service, they
will enhance our operational flexibility and support regional humanitarian missions, reinforcing Australia’s role as a key player in maritime defence.
On the sustainability front, RMIT University’s groundbreaking work in low-carbon concrete is setting new benchmarks for the construction industry.
The innovative concrete, which reduces cement usage and increases the recycling of coal ash, is a major step forward in addressing environmental impacts.
By cutting CO2 emissions and offering long-term durability, this advancement not only supports Australia’s climate goals but also paves the way for more sustainable building practices globally. The integration of such technologies is crucial as we head towards a greener future in construction.
Then there is Victoria’s manufacturing sector, which is receiving a boost from the Made in Victoria – Manufacturing Growth Programme. This initiative, aimed at enhancing
competitiveness and driving innovation, is supporting nine SMEs with grants to upgrade technologies and improve productivity.
This investment highlights the state’s commitment to fostering growth and creating highly skilled jobs.
As these businesses advance, they will contribute to a more robust and dynamic local manufacturing ecosystem.
Lastly, the effort to save Silver Fleece, an iconic Australian knitting mill, reflects the resilience and dedication inherent in our industry.
Spearheaded by the Australian Fashion Council and Sunset Lover, this initiative aims to preserve a legacy of Australian craftsmanship while addressing rising demand for sustainable products.
The revival of Silver Fleece not only safeguards local jobs but also champions the value of supporting Australian-made goods.
These stories encapsulate the spirit of progress and innovation that defines our industry.
Titomic Kinetic Fusion® provides rapid, no-heat metal repairs and cost-effective titanium manufacturing for defence applications. This technology is enabling new manufacturing capabilities, including the ability to fuse different metals without heat, manufacture titanium without size restraints, and much more.
TKF1000
Create large, strong multi-metal parts
MULTI-METAL, SINGLE-PIECE PARTS
BALLISTICS SHIELDING
TOOLING
STRUCTURES
D523/D623
For versatile in-field battle damage repairs
METAL DEPOSITION
Across Australia, and in particular the building and construction industry, the need to boost productivity is more critical than ever.
Nationally, labour productivity growth has been slowing since the mid-2000s.
According to Treasury reports, the decade to 2020 experienced the slowest productivity growth in 60 years, falling to a yearly average of 1.2 per cent. By comparison, the late 1980s to early 2000s saw a labour productivity growth rate of around 3 per cent.
While this downward trend is roughly in line with the average OECD labour productivity growth rate of 1.4 per cent, Australia has dropped from number 20 to 41 globally in terms of workplace productivity. The slowdown in productivity growth has concerning implications for our economic growth, real wages, and overall living standards, which are key to prosperity.
The construction industry ranks among the
lowest in terms of productivity performance: even an increase to the national average would deliver billions of dollars to the economy. What’s more, Australia’s state and federal governments have a pipeline of infrastructure, housing, and energy projects that are not achievable with our current productivity performance. Solving the productivity problem is paramount to their success.
Labour productivity is a major contributor to economic efficiency and rising living standards. Over the past 30 years, labour productivity has accounted for around 70 per cent of the growth in Australia’s living standards, as measured by real gross national income (GNI) per person. For living standards to improve, we need sustained labour
productivity growth – defined as the ratio of output to labour input.
In the construction sector, lack of productivity gains is one of the greatest challenges to project completion, resulting in only 50 per cent of project owners meeting delivery deadlines. Poor productivity is placing increased pressure on businesses that are already feeling the squeeze of rapidly escalating labour and supply chain costs, high inflation, and long wait times for equipment and materials. Improved productivity performance is crucial to delivering on the Federal Government’s pipeline of $120 billion infrastructure spend and $800 billion of investment in renewable projects by 2050.
On a broader level, Australia’s capacity to navigate economic challenges and capitalise
on opportunities hinges on having dynamic, productive, and innovative businesses. Weak productivity hampers the economy: in fact, the past 30 years of slow productivity growth has equalled approximately $47 billion in lost opportunity.
A driving factor behind the productivity slowdown is a decline in business dynamism. This has slowed the rate of technological adoption and innovation and inhibited resource allocation to more productive companies. As a result, there are a growing number of zombie firms – businesses that are unprofitable but remain in the market, sometimes with government support. At the same time, increased market concentration has led to reduced competition and higher price markups.
Recent years have also seen large structural changes in the economy, with shifts towards the services sector, which typically has slower growth according to traditional productivity metrics. The ongoing impacts of COVID-19 on productivity remain uncertain, as working-from-home models could enhance productivity in some sectors while worsening pre-existing challenges for productivity growth in others.
According to the Federal Government’s projections, the current productivity growth rate of 1.2 per cent will erode relative living standards— with GNI per person forecast at $32,000 lower than an LP rate of 1.5 per cent. However, we are unlikely to see an increase in Australia’s LP rate without additional government policy drivers aimed at addressing barriers to business dynamism, driving technological transformation, and incentivising businesses to improve productivity performance.
In the construction industry, while the number of workers has increased in the past decade, output per worker has reduced. On average, people are working two hours less per year with 25.4 per cent lower output – calculated as construction work completed divided by the number of workers. For example, worker output in 2023 was $180,100, compared with $196,800 in 2018. With demand for skilled workers continuing to outpace the available supply, greater productivity is key to raising worker output.
In the welding industry, productivity is equally imperative to driving innovation and growth. Welding businesses that maximise efficiencies and optimise operations benefit directly from cost savings and better use of resources. Labour, equipment, and materials can be more effectively allocated to minimise waste and energy consumption. Productivity gains lead to faster project completion times – enabling companies
to exceed client expectations and ensure repeat business.
Our recent member survey revealed that twothirds of Australian welding businesses rate the productivity of their staff as good or excellent. However, more than 42 per cent of welders are spending eight hours or less on site every day, and one-quarter spend less than two hours of their shift doing actual welding. The factors most likely to impact on the productivity of welding staff are materials handling and staff shortages.
A clear pathway to productivity is through technology. When companies are focused on improving their processes, they naturally innovate – implementing the latest technologies in a bid to streamline operations. However, Australian companies generally lag their global competitors in digital adoption and unfortunately the welding sector is no exception. Uptake of advanced welding technology remains relatively slow, and this lack of tech adoption is impeding our ability to navigate the current challenges facing the industry.
Most welding businesses are still not leveraging robots or collaborative robots, known as cobots. These are robotic arms equipped with sensors so they can safely work alongside humans, unlike traditional industrial robots, which are a potential hazard to human workers. They are designed to take on mundane and repetitive tasks, freeing up workers to take on high-value tasks.
By leveraging the benefits of cobot welding, businesses can increase their productivity and reduce labour costs, while improving the quality of their welds. Given that the major barriers to productivity are materials handling and a lack of skilled staff, there is an opportunity for welding businesses to harness the capabilities of advanced welding technologies to overcome these issues.
To address the productivity challenge in Australia’s welding and fabrication industry, Weld Australia is seeking grant funding for a productivity-based training scheme. Under the program, fabrication companies would be supported to conduct their own staff training at little to no cost – with Weld Australia providing advanced learning resources, training for the instructor, and accreditation for the training facility. We would also quickly certify production welders according to ISO 9606 or AS/ NZS ISO 1554–so that businesses don’t have to wait three or more years for a Certificate III or IV trained welder.
Weld Australia is also undertaking research into welder productivity, which is defined by the number of arc-on-time per welder per shift. In Australia, our member reports show that the average arc-on-time is around two hours – compared with approximately fi ve hours per welder per day in countries like the United States and Germany, which have similar Workplace Health and Safety Standards.
Our research will investigate the reasons behind this marked difference in productivity, with the objective of identifying potential solutions such as using robots and cobots, and trades assistants for tasks such as griding, set up and cleaning.
These two projects could help raise the welding capacity of the Australian industry by enabling us to match international productivity standards. If you would like to be involved in Weld Australia’s Productivity Improvement Projects, please contact Cornelis Van Niekerk (business manager, Weld Australia) via c.vanniekerk@weldaustralia. com.au or 0409 609 031.
The Federal Government has accelerated the $2 billion build of 18 medium landing craft for the Army’s new littoral fleet which is set to be designed by Birdon and built by Austal.
The first of the vessels will be built at the Henderson Shipyard in Western Australia and is expected to be delivered in 2026.
“This pipeline of work will result in opportunities for the Australian defence industry and support
a highly skilled shipbuilding workforce for years to come,” said minister for Defence Industry, the Hon Pat Conroy MP.
These vessels are an essential component of Army’s transformation and optimisation for littoral manoeuvre.
They are set to support a strategy of denial, which includes deploying and sustaining modernised land forces with long-range land and
The Federal Government has awarded Thales Australia with a $45 million contract to build an additional 15 Bushmaster Protected Mobility Vehicles.
The company will build the Bushmaster vehicles in Bendigo, supporting hundreds of jobs in the local economy and more jobs across the supply chain in Victoria.
The additional 15 Bushmasters will facilitate command and control of Army’s High Mobility Artillery Rocket System long-range fires regiment.
Minister for Defence Industry, the Hon Pat Conroy MP, said the investment is another step toward a future made in Australia.
“I am delighted to be back in Bendigo to announce a further $45 million investment in the region, with the production of an additional 15 Bushmaster protected mobility vehicles,” said Conroy.
This supports the Federal Government’s $1.6 billion investment to accelerate the delivery of the first land-based long range fire capability for the Australian Defence Force.
maritime strike capabilities across our region.
The Landing Craft Medium can transport up to 90 tonnes, equivalent to one main battle tank, or one infantry fighting vehicle and two Bushmasters.
These landing craft will be supported by Amphibious Vehicle Logistics, which can navigate over beaches and through waterways.
“These new vessels will enable the ADF to deploy and sustain land forces to beaches, rivers and ports in Australia and across our region, enhance our ability to work with regional military partners, and support communities across the Indo-Pacific with humanitarian and disaster relief operations,” said Conroy.
The local build of the medium landing craft is in addition to up to eight heavy landing craft, which will also be built by Austal at Henderson.
The $2 billion project is expected to create 1,100 direct jobs and more than 2,000 indirect jobs.
This project is a part of the Federal Government’s investment of $7 billion towards littoral manoeuvre vessels.
Bushmasters are currently in use in nine countries and are renowned for their high level of protection and mobility for troops.
Notably, it has seen service in Ukraine through
medical evacuation, command and control, and fire support roles.
This contract will continue Bendigo’s more than 20-year history of producing these vehicles.
At the launch of the GSEM Jobs and Skills Roadmap, Federal Skills minister, Brendan O’Connor, said that the Greater Southeast Melbourne region is the key to a future made in Australia.
The roadmap was launched at Parliament House in Canberra and will help O’Connor assist regions right across the country.
“It will help inform me about how other regions of Australia can take the best approach to ensuring that we have successful economies, good jobs,
and of course, ultimately, a successful nation,” said O’Connor.
“Planning for skills needs is critical at a time when the economy and labour market are rapidly changing.”
O’Connor described GSEM as critical to Australia’s manufacturing sector and invited the region to continue to engage closely with Jobs and Skills Australia and the national Jobs and Skills Councils.
The minister said that the region and the federal
government understand the need for greater collaboration to address workforce requirements.
“We understand the importance of improving equity, inclusive growth, and reducing disadvantage in our VET (Vocational Education and Training) sector.”
O’Connor also invited GSEM to engage with the government to help ensure better analysis of the labour market and to better understand trends in local economies.
One of the world’s largest manufacturers of 4WD accessories, ARB, has opened a new $25 million global headquarters and Research and Development Engineering Centre in Kilsyth, VIC.
The Victorian Government supported the expansion, as the facility has the potential to foster local jobs, investment, and innovation in the automotive sector.
The 5,100 square metre Centre is adjacent to
ARB’s new state-of-the-art showroom, where the company continues to manufacture 4WD equipment.
Bringing ARB’s HQ, R&D centre, showroom, and manufacturing facility together at Kilsyth is creating up to 70 new local jobs for Melbourne’s east. Established in Melbourne in 1975, ARB has grown into a company with an export network that extends across more than 100 countries.
The Kilsyth hub is now home to 600 staff, including 85 engineers, with the company’s employee numbers growing to over 2,000 across Australia and internationally.
Victoria’s $33.5 billion manufacturing industry is a driving force of Victoria’s economy. The sector is made up of over 23,000 businesses, supporting more than 260,000 jobs, and exporting goods worth $23.9 billion.
Almost $2 million from the Australian Renewable Energy Agency (ARENA) will support 10 businesses to undertake feasibility studies to deploy energy efficiency and renewable energy initiatives.
It will help Brown Family Wine Group’s vineyard electrify their operations, O’Connor Beef deploy new technology that captures biogas during wastewater processing, and Real Pet Food Co better manage heat from manufacturing processes and reuse it.
The funding will help hard to abate businesses across manufacturing, wine, meat, and water, in making every Watt count.
Assistant minister for Climate Change and Energy, Jenny McAllister, said this funding is an example of how ARENA is partnering with Australian industry.
“With ARENA’s expertise, these grants will not only help businesses scope and pioneer clean energy innovation but demonstrate the technology to help Australian industries decarbonise and become more competitive,” said McAllister.
The projects supported with the new grants include:
• $399,503 to investigate renewable energy initiatives and a covered anaerobic lagoon to treat wastewater at the G&K O’Connor meat processing facility in Pakenham, Victoria.
• $250,400 to develop a heat energy recovery system at Real Pet Food Co’s manufacturing sites
in Queensland and New South Wales.
• $244,677 to improve energy efficiency and examine electrification options at Quantem in Port Botany, West Melbourne and Brisbane.
• $242,924 to modernise refrigeration infrastructure at the George Weston Food small-goods facility in Castlemaine, Victoria.
• $205,000 for site-wide energy efficiency and electrification projects at the Beston Global Food Company dairy factory in Jervois, South Australia.
• $149,850 to develop a decarbonisation roadmap at three of Unilever’s hygiene and food manufacturing sites across New South Wales and Victoria.
• $147,800 to examine options to harness energy from waste through biomass processing at the Bindaree Beef meat processing facility in Inverell, New South Wales.
• $117,515 to optimise energy efficiency across the Grampians Wimmera Mallee Water pipeline in Western Victoria.
• $116,397 to identify low emissions and energy efficient technologies at the Brown Family Wine Group winery in Milawa, Victoria.
• $110,000 to investigate a geothermal heating system to provide process heat at the Paper Australia barramundi farm in Latrobe Valley, Victoria.
For over three decades, we have played a vital role in the design and manufacture of defence equipment in Australia.
From selecting the best design and validation software to deployment and configuration, consulting on simulation and data management, we ensure the design and engineering teams in defence are proficient and ready to use these tools from the outset. Tailored training programs elevate the skills of personnel, ensuring teams are adept with the latest technologies and methodologies. This holistic approach enhances their capability to develop cutting-edge solutions and maintain a competitive advantage.
The second Australian-built Parramatta River Class ferry, named John Nutt, has sailed towards the sails of the Opera House.
John Nutt completed her maiden landing at the Man O’War steps following a successful three-day voyage across Bass Strait.
The ferry is the second of seven new Northern
Beaches designed vessels being built by Hobartbased shipbuilder Richardson Devine Marine.
The first vessel in the fleet, Frances Bodkin, has been in service since April.
A team of 60 people is working to build the remaining fi ve, which are expected to progressively enter passenger service over the
The Federal Government will invest more than $100 million to boost the ADF’s arsenal of drones, ensuring Australian military personnel are provided with cutting-edge lethal and non-lethal capabilities.
As a part of this $100 million investment, the Government announced the acquisition of two small uncrewed aerial systems (SUAS), the Quantum-Systems Vector 2-in-1 and the Sypaq Systems CorvoX.
These systems will bolster the ADF’s ability to carry out surveillance and reconnaissance and augment the ADF’s existing stock of drones.
The systems have capabilities across land and littoral operations and can support the Australian Army and Royal Australian Air Force in confined areas, including small marine craft, and urban environments.
Both systems can be deployed as a complement to crewed systems.
Minister for Defence Industry, the Hon Pat Conroy MP, said Defence’s partnership with these two companies shows how the Federal government is investing in capabilities the ADF needs to keep Australians safe.
“The delivery of these uncrewed aerial systems in 2025, within a year of project approval, is a significant demonstration of Defence and industry’s strong partnership, and intent to
course of the next 18 months.
Member for Parramatta, Donna Davis, said these ferries are intended to meet the growing population across the Sydney Olympic Park precinct.
“These new ferries, and the more frequent timetable on the popular F3 route, are a big win for anyone catching the ferry to work, school, or events around Sydney,” said Davis.
“The population right across the Sydney Olympic Park precinct is growing, and we need more public transport services to meet demand.”
The Australian-made fleet is set to be more reliable and comfortable than prior models, with upgraded safety systems, greater accessibility, and sleeker design.
The seven new vessels will replace the RiverCat and SuperCat vessels, which will be retired after 30 years of service.
The John Nutt vessel will now be handed over to operator Transdev for final checks to ensure she’s in ship-shape before the first passengers board in July.
enhance the speed at which we introduce capabilities in support of current and future Defence requirements,” said Conroy.
The partnership with both Quantum Systems and Sypaq Systems is expected to create at least 30 highly skilled jobs in Brisbane and Melbourne.
The two new SUAS will be delivered in 2025 as Defence continues expediting the acquisition of new drones while continuing to trial low-cost,
expendable uncrewed and autonomous systems.
This approach will add to the more than 20 drone systems already acquired including models that have been in service for more than a decade and platforms with multiple payload options.
The Federal Government is investing more than $10 billion on drones, including at least $4.3 billion on uncrewed aerial systems and $690 million on uncrewed tactical systems for the Army.
Austal Limited have entered a Memorandum of Understanding (MOU) with Civmec Limited to form a Joint Venture (JV) that will submit a proposal to the Commonwealth of Australia to support the LAND8710 Phase 2, Landing Craft Heavy (LC-H) project.
The LAND8710 Phase 2 (LC-H) is a proposal that has the potential to deliver enhanced transport and littoral manoeuvre capability to the Australian Army and thus enable greater reach over the Indo-pacific region.
The JV is planning to contract directly to the Commonwealth to undertake shipbuilding tasks for the LC-H project within the assembly hall at Civmec’s Henderson facility.
CEO of Austal, Paddy Gregg, said the company is excited by what the partnership could mean for sovereign shipbuilding, especially in WA.
“It would provide the Commonwealth with immediate access to a larger pool of skilled shipbuilding workers that can transition across multiple projects via a ‘consolidated Henderson’ model,” said Gregg.
“It will allow the Commonwealth to continue to leverage Austal’s naval shipbuilding experience and track record of delivery for the Commonwealth, including the upcoming Landing Craft-Heavy program.”
Civmec’s executive chairman, Jim Fitzgerald, said the JV will be an important step in ensuring the continuation of shipbuilding at Henderson.
“By combining Civmec’s Henderson shipbuilding facilities, which include the largest heavy engineering facility of its kind in Australia, our systems, steel manufacturing expertise and 4,000 strong labour force, together with Austal’s naval shipbuilding experience and long track record of
delivery, the JV would be very well placed to deliver efficient Continuous Naval Shipbuilding in Western Australia to Defence,” said Fitzgerald.
The MOU will see both Austal and Civmec developing the structure, delivery process and detailed scope of the JV.
This will help in preparation to submit tenders to the Commonwealth for LAND8710 Phase 2 (LC-H).
The iconic South Australian knitting mill, Silver Fleece, has been saved by the sustainable fashion company Sunset Lover, who has officially secured all its assets.
Co-founders of Sunset Lover, Dean and Melanie Flintoft, were behind announced the acquisition, which was made possible by a successful 48-hour capital raising media campaign.
The quick and successful capital raise not only signals a strong comeback for Silver Fleece but also paves the way for new business partnerships and strategic growth opportunities.
Sunset Lover will now work alongside existing clients like Cricket Australia and private and public schools nationwide, something the Flintoft’s can’t wait for.
“We get the ‘keys’ today and will immediately reassure all existing customers of our renewed operations, well-capitalised status, and continued commitment to excellence, whilst concurrently building a new portfolio of clients to further strengthen our position and get the mill operating at 100 per cent capacity,” said the Flintofts.
Silver Fleece is a renowned Australian brand with a remarkable 73-year history that is dedicated to producing high-quality, locally made products with a focus on sustainability and ethical practices.
The Flintofts said that moving forward it will also offer Australian yarn and a full ethical traceable
production process for all clients.
“Our ethos is to manufacture exceptional, proudly Australian-made products. With our industry experience and commitment to sustainable fashion moving forward, and the overwhelming response to our capital raising campaign - we are confident that we can revitalise Silver Fleece and make our investors happy because Australians do care about where ‘their clothing’ is made,” said the Flintofts.
The pair also announced the upcoming Sunset Lover Resort 2024/25 collection will launch the first capsule under this innovative collaboration with Silver Fleece, representing a significant milestone in the brand’s journey towards innovation and excellence.
“This is a dream partnership for Sunset Lover because Silver Fleece 100 per cent aligns with sustainable Australian made fashion. It will showcase the blend of craftsmanship and sustainability that this knitting mill can produce. We can’t wait to bring other Australian companies into the fold that care about Australian manufactured garments like we are,” they said.
Luxury fashion brands, corporates, government, healthcare, sporting clubs and schools are on the immediate client hit list with Silver Fleece being one of the few options left for Australian made knitwear.
Silver Fleece is equipped with state-of-the-art Shima Seiki Japanese knitting machines, known in
the industry as the best in the world.
Over the coming months the new owners will introduce a brand new Shima Seiki Wholegarment knitting machine to improve the capabilities and efficiency of the factory.
This will help to further leverage the recent fundraising campaign which undeniably demonstrated Australians’ passion for sovereign manufacturing.
“The iconic Australian-owned mill that honours the beautiful Australian artisan craft of knitting wool has been preserved and we would like to offer our heartfelt thanks to everyone, including people like the CEO of the Australian Fashion Council, Jaana Quaintance-James who believes in this craft like we do - we won’t let you down!” said the Flintofts.
Silver Fleece, which was established in 1951 and has a rich lineage of Australian craftsmanship, will resume ‘business’ today under the new management.
The 20 skilled staff and technicians whose jobs have been saved are primarily women and include younger employees eager to learn and preserve the artisan craft.
The Adelaide-based knitting mill entered administration last month, with a general meeting on 26 June 2024 resolving that the company be wound up.
Pfizer Australia has announced a major upgrade to its facility in Melbourne to make it one of the most advanced pharmaceutical production facilities in Australia’s fight against antimicrobial resistance (AMR).
Pfizer has invested AU$150 million to offer advanced pharmaceutical production facilities in Australia for new antimicrobial treatments aiming to help address rising levels of antimicrobial resistance, considered one of the biggest threats to global health.
Pfizer Australia & New Zealand managing director, Anne Harris, said the company is thrilled with reaching this milestone.
“We are thrilled to reach this important milestone in our investment to support the development and delivery of new antimicrobials at our Melbourne site, and to be investing in Australia’s advanced manufacturing capabilities,” said Harris.
The Hon Natalie Hutchins MP, Victorian minister for Jobs and Industry, visited the site to mark the milestone installation of key technology known as lyophilisers.
AMR has been described as ‘the silent pandemic’ and is considered by the World Health Organization to be a top 10 area of public health concern.
AMR makes infections harder to treat, increasing the risk of disease spread, severe illness and death, with annual deaths from AMR predicted to rise to 10 million by 2050.
Without intervention, it is estimated that by the same year, 10,000 Australians will die each year from drug-resistant infections.
“A key strategic pillar of Pfizer’s product innovation work is our effort to help slow the spread of antimicrobial resistance, one of the biggest global health threats of our time. We are also pleased to be providing 500 advanced manufacturing jobs at our Melbourne site,” said Harris.
Investment in the Melbourne site has included the construction of a new separate facility that hosts two newly installed freeze-drying machines known as lyophilisers, which are used in the antimicrobial manufacturing process.
The site has also been selected for a trial of Artificial Intelligence (AI) technology designed to
work and be operational by mid-2025, with commercial manufacture commencing in 2026. Medicines currently manufactured at the Melbourne site – which include those for treatment of cancer as well as antimicrobials, anaesthetics, antiinflammatory and other medicines – are exported to
Sydney-based MedTech manufacturer, EMVision, creates portable brain scanners for rapid stroke diagnosis, aiming to accelerate diagnostic speed and accuracy in both rural and urban settings.
EMVision Medical Devices are developing portable, light-weight brain scanners designed to rapidly diagnose strokes and other time-sensitive medical emergencies.
The technology aims to reduce the inequality between rural and metropolitan stroke outcomes by bringing advanced neurodiagnostic capabilities directly to patients through lightweight, affordable neuroimaging devices.
Based in Macquarie Park, Sydney, the company manufactures emu, an in-hospital bedside scanner designed to improve the speed and accuracy of brain imaging.
Scott Kirkland, CEO of EMVision explained that the emu scanner can quickly and easily be brought to the patient’s bedside instead of moving a criticallyill or unstable stroke patient to a CT Machine or MRI.
“Our emu scanner offers advanced neurodiagnostic capabilities, perfect for rural emergency departments and wards,” he said.
“In settings where traditional tools like CT and MRI may be inaccessible and specialised operators are scarce, this capability is invaluable.
“Given the critical time sensitivity of stroke diagnosis, emu allows nurses to perform scans, with expert guidance via telehealth opening the door to earlier triage, transfer and treatment decisions — potentially making the difference between a life of disability and a full recovery.”
In addition to the bedside scanner, EMVision recently unveiled its First Responder prototype, a portable scanner, weighing about 10 kilograms.
“It’s designed for pre-hospital deployment, making it suitable for use by paramedics, emergency physicians in both road and air ambulance services,” said Kirkland.
EMVision was founded in 2017, originally spun out from the University of Queensland, where cofounders, Scott Kirkland and Ryan Laws, acquired the original patent portfolio from research led by Professor Stuart Crozier, EMVision’s Chief Scientific Officer, and Professor Amin Abbosh.
“The University of Queensland had prototypes for three different types of scanners: a torso scanner for assessing liver fat and scarring (fibrosis), a skin scanner for assessing and diagnosing potential melanomas, and a brain scanner for identifying
potential bleeds or blockages in the brain,” said Kirkland.
“Our preliminary research led us to focus on the brain-scanner technology, due to the significant global health and economic burden of stroke.
“One in four adults will experience a stroke in their lifetime, and many of those result in some form of permanent disability.”
Now, with 36 staff members in NSW and Queensland, EMVision intends to lessen the burden of time sensitive emergencies that impact patients and their families.
In stroke care, the “golden hour” refers to the critical window immediately following stroke onset, during which, prompt medical treatment can improve patient outcomes.
“Bringing neurodiagnostic technology to the patient, rather than transporting the patient to a CT or MRI, can save crucial time,” said Kirkland.
“Approximately two million brain cells die every minute during a stroke. Faster diagnosis and treatment can lead to better outcomes. Every minute saved through accelerated treatment matters.”
The engineering
The emu bedside unit is a trolley-mounted system with an articulated arm connected to a helmet, which fits over the patient’s head.
The unit features Integrated antennas that surround the head and capture data from the scan.
The unit can be operated by medical staff with minimal training, enabling timely assessments of suspected stroke and stroke subtypes.
By utilising electromagnetic sensing and imaging technology, the device transmits low-energy radio waves from the ring of antennas.
As these waves pass through tissues, they create distinctive signatures indicative of healthy brain or brain pathology.
It is changes in the dielectric properties of brain tissue that provide these critical insights, and inform if a stroke is present or not, and if a stroke is present, whether it is a bleed (hemorrhagic stroke) or blockage (Ischaemic stroke).
The First Responder unit has a lighter miniaturised design and expanded antenna coverage, allowing complete cranial vault coverage in a single scan.
“One antenna emits a radio frequency signal, while the remaining antennas listen for the signal as it transmits, reflects, and scatters,” explained Kirkland.
“An AI model then analyses these interactions to assess the relative dielectric values of the tissue being imaged.”
Kirkland noted that the process is swift, with their emu device averaging a completed scan time of about fi ve minutes in clinical studies.
Commercial pathway
EMVision has recently completed enrollment for a larger multi-site study involving hundreds of patients at Liverpool Hospital, Royal Melbourne Hospital, and Princess Alexandra Hospital, using the production equivalent emu device.
“We have reported very encouraging interim findings and are meeting our study objectives,” said Kirkland.
EMVision has also collaborated with the Australian Stroke Alliance, which is leading advancements in golden hour stroke care, including with their mobile stroke unit program in Melbourne.
“A mobile stroke unit (MSU) is a multimillion-dollar truck, equipped with a CT scanner and specialist team, that are deployed to treat suspected stroke patients at the scene, ideally within the critical first hour, to achieve excellent outcomes.
“We work closely with the Australian Stroke Alliance to ensure our solutions are clinically useful, can be suitable for broad use and to support our local rollout strategy.”
Kirkland explained that EMVision has already received interest from local and global prospective end users.
“The clinical enthusiasm for this technology is very strong so far, as it offers the potential for early stroke diagnosis in a point-of-care manner otherwise not widely available,” Kirkland added.
“We exhibited at the Radiological Society of North America conference in Chicago last November, one of the largest global imaging conferences.
“Our technology stands out because it is unique in its field, particularly compared to CT and MRI machines, which at their lightest, weigh around 500 kilograms.”
The company plans to enter key international markets, focusing initially on the United States, where they are pursuing FDA approval, as well as Australia and thereafter parts of Asia and Europe.
“Our bedside device will follow the FDA’s de novo pathway in the United States, signifying it as the first of its kind product,” said Kirkland.
“Under this pathway we run studies to demonstrate its safety and efficacy from first principles.
“Once emu is approved, it will serve as the
predicate device for our new First- Responder model, accelerating its path to market.”
The first generation of the technology, the emu bedside iteration, is anticipated to hit the market next year and will be targeted for use in rural and regional emergency departments alongside ICUs and stroke wards in city centres.
The second generation, first responder system, has yet to have a confirmed release date but is expected to be available shortly after the emu device.
The EMVision supply chain EMVisions plans to retain manufacturing locally and has established a pilot production line at Macquarie Park.
Under the current configuration, it is capable of building, testing, and releasing up to three of its emu devices per week.
“There are several reasons why we’re not pursuing markets with cheaper labour for manufacturing our product,” explained Kirkland.
“First, as a medical device, it requires the highest possible quality standards, and Australia has an excellent reputation in that regard.
“We believe there is a significant opportunity to continue to produce the device here and export it globally.”
While manufacturing locally, EMVision sources components from global and local suppliers.
The next steps
As EMVision Medical Devices pushes forward with its innovative brain scanning technology, the potential for transforming stroke diagnosis and treatment is immense.
By focusing on both its portable and bedside solutions, the company is poised to address critical gaps in rapid, accurate stroke assessment, whether in metropolitan hospitals or rural clinics.
In July, Lightforce Group announced the supply of 120 advanced, customisable night vision and thermal imaging systems to the ADF’s Dismounted Combat Program, along with ‘train-the-trainer’ instruction.
This development is just another in a series of contract wins for the Adelaide headquartered global business after it announced its intentions in 2017 to formally enter the defence manufacturing market.
The story of the Lightforce Group is an interesting and inspiring one. After three decades building arguably the best rifle scopes and lighting systems for militaries and hunters all around the world, the Lightforce Group brought together four of its
leading brands, Nightforce Optics, Horus, Gunforce and Lightforce Australia, to create its defence manufacturing arm, Force Ordnance. This story begins much further back in the early 1980s in the South Australian country town of Cleve when the company was founded by local dentist Dr Ray Dennis.
After searching the retail market for a high quality and robust spotlight for to eliminate feral pests and finding nothing suitable, Ray decided to build one himself…and the rest, as they say, is history. Being
a man of vision and foresight, Dr. Dennis recognised the potential demand for the lightweight, portable and handheld spotlight which lay before him. Enter Lightforce. It was a system powerful enough to use for professional purposes yet priced within the grasp of the enthusiast and sportsman. Ray soon produced his first commercially manufactured lighting system. Based on original designs, his lighting systems found such favour among professionals and sporting enthusiasts alike that production was increased,
and improvements incorporated. This brought greater diversity to the range, ensuring the growing success and popularity of the brand. Fast forward a couple of decades, and whether it’s in the frozen Arctic tundra to the scorching heat of the Australian Outback, Lightforce’s products are trusted on all seven continents. Lightforce Group now exports to more than 50 countries and has manufacturing facilities in Adelaide, South Australia, and in Idaho in the USA. A large proportion of Lightforce Group’s production is exported worldwide to major markets in Europe, Scandinavia, Africa, Southeast Asia and North America.
Lightforce’s first foray into the formal defence manufacturing sector came in 2021 when it announced Force Ordnance as a “systems integrator’’ and developer of the QTD1 Long Range Rifle - a completely Australian designed and manufactured sniper rifle including patented technology which allows users to switch out barrels in seconds without compromising accuracy.
At the company’s Hindmarsh facility products are designed, built and tested, with ex-special forces and law enforcement staff - including expert long range precision shooters - on board to guide the design process. Its weapons manufacturing credentials reside substantially in Ace Precision Rifle Systems (APRS) which has been building premium rifles in Adelaide for the past 15 years. Using the
finest components machined to exact tolerances, APRS produces the highest quality precision rifles and offers a full gunsmithing service.
In 2022, Lightforce Group grew its presence and influence in the local and international defence and law enforcement sectors with a series of wins that saw its world-renowned automotive and hunting lights being applied to illuminate the fields of battle and shine a light on crime. Locally, the Australian Defence Force’s trial of Australian Expedition Vehicles included Lightforce’s infrared and white light combination HTX2 lights, signalling the company’s first local win. Other clients included the Australian Customs & Border Protection which fitted their 41-foot MMI Interceptor boats with Lightforce ML240mm lights, as well as a number of state police agency vehicles that have been fitted with infrared Striker lights.
Internationally, Lightforce partnered with the armed forces of the Philippines for the provision of driving lights on military vehicles whilst in the US, several defence and police bodies are still shining a brighter light on suspects thanks to the Adelaidebased manufacturer. These include the Maryland Police, the US Marshall Service and the Georgia State Patrol who are all using Lightforce white and Infrared lights on their respective patrol and SWAT vehicles.
In perhaps its most significant defence contract
win to date, Lightforce Group was selected in 2023 to provide 400 of its world-leading Nightforce precision rifle scopes to the ADF as part of the Sniper Systems component of Land 159 Lethality Systems Project (LAND 159) Tranche 1. The development has paved the way for Nightforce’s MIL-SPEC ATACR 7-35x56F1 scope to bring ADF sniper capability up to Five Eyes nation standards through Force Ordnance. Nightforce Optics are now the chosen optical instrument for superior weapon systems throughout the Five Eyes Special Operations communities, with multiple contracts won in New Zealand, United States, Canada and the United Kingdom. Typical deployments of this optic will include support to patrols, operations, surveillance and other specified tasks as well as Anti-Materiel Sniper Capability (AMSC) for the purposes of providing precision fire against enemy materiel (such as vehicles and equipment) at ranges of up to 2500m in day and night conditions. The ADF is expected to take delivery of the scopes later this year and there are further exciting announcements expected in the not-too-distance future.
Australia’s recommitment to sovereign defence manufacturing capability has well and truly begun and is being driven by businesses like Lightforce Group that are putting home-grown innovation and manufacturing excellence back into the hands of service men and women.
The Australian Metal Casting Industry - a significant sector within Australia’s broader manufacturing landscape.
Castings are a fundamental foundation for all major industries in Australia. Every one of us is rarely more than 5 meters from a metal casting. You don’t buy metal castings in a supermarket but you do need them to build roads and buildings, to irrigate, to mine and process our mineral deposits, to manufacture wind turbines and solar panels, to sow and harvest crops, for all forms of transport, to sterilise medical instruments and to support our Defence industry.
The Australian metal casting industry directly employs 2000+ with annual sales of approximately $1.0 billion. Our businesses are largely small to medium size enterprises producing bespoke products in the low to medium volume market. Our point of difference is technical excellence, quality and reliability.
Amiga Engineering leads the charge in defence innovation with its Metal 3D Printed Ballistic Titanium Armour, surpassing the rigorous MIL-DTL-46077G V50 standards.
Amiga Engineering, an Australian leader in advanced manufacturing, is redefining defence protection with its revolutionary Metal 3D Printed Ballistic Titanium Armour. This innovation allows for the creation of complex and groundbreaking armour designs that are unattainable with traditional manufacturing methods. By leveraging advanced 3D printing technologies, Amiga’s armour surpasses MIL-DTL46077G V50 standards, delivering unparalleled durability, corrosion resistance, and lightweight adaptability.
The custom-shaped solutions provided by this 3D printed titanium armour are ideal for vehicles, protective gear, and critical component shielding, all without compromising structural integrity or design. This cutting-edge technology enhances operational efficiency and delivers superior ballistic performance, offering a decisive edge in modern military applications.
While Amiga’s ballistic titanium armour stands at the forefront of defence innovation, the company also distinguishes itself as the only firm in Australia certified to metal 3D print in Scalmalloy—a material prized for its high strength-to-weight ratio, particularly in aerospace applications. Additionally, Amiga is the sole Australian provider of metal 3D printing in Tungsten, a material essential for leading hot edges in hypersonic vehicles and for meeting heavy weight requirements in various industries.
Metal 3D Printed Titanium Ballistic Armour’s exceptional properties make it increasingly favoured in protective applications. Applications include providing vital protection in aircraft cockpits, safeguarding essential systems with lightweight, corrosion-resistant materials. Beyond aviation, titanium ballistic armour’s durability and resistance to corrosion make it an ideal choice for maritime use, including ballistic hatch covers that secure access points on marine vessels.
Amiga Engineering’s 3D printed titanium armour, offering advanced protection.
Amiga Engineering is also advancing personal protection with the development of body armour plates specifically designed for different shapes,
utilising the precision and versatility of additive manufacturing. Their 3D printed armour plates have been rigorously tested and proven to exceed military specifications by up to 40 m/s, maintaining superior performance with an areal density at 15 mm thickness—less than 5/8 inch.
Amiga’s armour has successfully stopped high-
Amiga’s advanced custom armour, engineered to stop high-calibre rounds, delivers superior protection through tailored, formed designs.
calibre rounds, including 39 API BX, M80 7.62 x 51, and 5.56 SS 109, with its 15 mm thick plates. The company has also developed a vehicle grill capable of withstanding these rounds, underscoring its commitment to robust defence technology. Future
projects include integrating composite layers to reduce weight and exploring the development of bulletproof alternators and other critical vehicle components for both civilian and defence applications.
Amiga Engineering’s innovations will be prominently displayed in the Innovation Precinct at Land Forces 2024, offering a unique opportunity for industry stakeholders to engage with the latest advancements in defence technology.
BlueScope Distribution is your single source provider of steel and aluminium products, processing and solutions.
With a national network of branches, including our National Product, Processing & Solutions Hub, our team can provide customers with world-class plate processing capability, optimised supply chain solutions with diversified transport options, and a dedicated project management team to help deliver projects on time and to specification.
• Complex processing and component manufacture
• End-to-end management of complex steel processing and supply
• Customer specific product in kit form ready for assembly
• Domestic supply and processing of steel for complex and significant projects
In high-tech industries, where high-mix, low-volume production intersects with complex products and rapid technological advancements, achieving precision in inventory management can pose a challenge.
Recognising the role of robust inventory management in overcoming these challenges, Raider Targetry, a force in military training solutions, unveiled an advancement in efficiency through the integration of Fishbowl Inventory, a software solution for inventory management.
Raider Targetry’s CEO & CTO Mick Fielding, alongside Executive Director Cody Webster, envisioned the company’s global potential since its inception.
Fielding emphasised the strategic importance of establishing a solid foundation for products and services to support the company’s growth trajectory, stating,
“When we were looking at building the business, we knew that we needed an inventory management system that would support us today, but also into the growth that we would expect in the future” he said.
“Accurate and efficient tracking of inventory movement from inception to its final consumption point is crucial for effective control and decision-
making processes within a business, ” said Simon Jupe, Fishbowl APAC managing director.
“Investing in a system that enables both signature tracking and inventory tracking facilitates swift resolution in cases where physical transactions diverge from the system records.”
Tim Kelly, Digital Systems Manager at Raider Targetry, expressed the transformative impact of Fishbowl
“Fishbowl’s been game-changing for us in terms of having that single source of truth that everybody can refer to, to understand the status of any particular work order at any point in time,” he said
“Fishbowl’s also been fantastic in terms of helping us to save costs, in particular the labour cost of trying to coordinate all of these different production and work orders.
“The main thing though, that Fishbowl’s really helped us with in terms of productivity is the ease of integration into the engineering software that we’re using.
“Implementing a new inventory management
system is often a big commitment for any organisation. Thankfully, the Fishbowl support team is fantastic, and they’ve made it really, easy for us to configure Fishbowl in a way that’s suitable for our organisation.”
The software’s capabilities extend to meeting regulatory requirements and ensuring compliance by providing accurate records, traceability, and comprehensive reporting features.
Kelly highlighted Fishbowl’s ability to digitally track and trace, serialisation, and manage complete bills of materials, ensuring the delivery of clean and clear, real-time information to the Defence Force.
“In the future, we’ve got an extensive amount of automated purchase order and production order planning coming into play,” he said.
“We’ve got additional integration through the full depth of our bills of materials, and we’re tracking alot of custom fields like NATO stock numbers and those kinds of things too.”
“Fishbowl in particular has a number of features which support what we do. Fishbowl gives us a single source of truth for everything we do within the business, especially when it comes to production, but also supporting our R&D activities,” said Raider Targetry’s Fielding.
“As high complexity, low-volume businesses grow or evolve, Fishbowl software can scale to help our clients meet their changing needs. This flexibility can be essential, especially for companies dealing with diverse and evolving product lines,” said Jupe.
“As a company developing high-tech solutions, we need high-tech business processes that support what we do, and especially those that scale with the business as we expand globally.
“The technology we’re developing has fast iteration cycles. They’re technically complex systems, and we need products that support the business that work in the same manner.
“Fishbowl was a natural fit for us and very much complementary to the tech stack we’d already brought on board. Now that we’ve partnered with Fishbowl, we’re really excited to see where the future will take us, and we have full confidence that we’ve got the right partners in place to get there.”
Raider Targetry’s strategic integration of Fishbowl Inventory represents a paradigm shift in inventory management, reinforcing its commitment to operational excellence, innovation, and global growth.
RSM Australia, an audit and tax consulting firm, has appointed Louis Quintal as the new head of manufacturing.
RSM Australia has appointed Louis Quintal as the new Head of Manufacturing, succeeding Jessica Olivier.
“I’m thrilled to step into this role and drive our manufacturing sector strategy forward,” said Quintal.
“My goal is to expand our capabilities and address the evolving needs and challenges of the sector.”
Olivier, with almost a decade of experience at RSM, has now moved on to become a national executive at the company. Quintal aims to expand RSM’s manufacturing service capabilities.
“Jessica and I are currently managing a handover and transition for projects. Jessica is wrapping up the projects she started, and over the coming months, we will gradually transition other relationships,” he said.
“This includes the one we are working on now, as well as two or three other key relationships.
“It won’t be a hard cutoff; instead, Jessica and I will work together over the next six months to ensure a smooth transfer of knowledge and expertise.”
Speaking on her departure from the role, Olivier said: “For me, the National Executive role is the next step in my career and in a firm where I want to be part of its long-term future.”
“It is also a way for me to lead by example and support others in our firm to follow a similar career path, should they so want.
“I am also excited to work as part of our National Executive to implement our 2030 Strategy, part of which includes servicing our clients with our ability to offer deep industry expertise and client-focused solutions.”
As Olivier transitions out of her role, RSM is ensuring continuity in their projects and client relationships.
“Louis Quintal, Ross Dixon and I have already worked together on the Manufacturing Strategy for FY25 and beyond, and in line with RSM Australia’s 2030 strategic priorities more broadly,” she said.
“In addition, I will continue in my role as R&D Partner and will also remain on RSM’s National Manufacturing committee and as a strong advocate for this sector.”
With a career spanning over 20 years, Quintal began at the RSM South African office, where he spent 18 years before transitioning to the Australian market for the past two and a half years.
Throughout his career, Quintal’s primary focus
has been on the manufacturing sector. In Africa, which has a low-cost base and significant production activity, he built his expertise and clientele in this field.
Once in Australia, he continued to concentrate on the manufacturing sector, further developing his career and client relationships.
This focus on manufacturing has been a cornerstone of his approach, which aligns with RSM’s broader strategy.
“The first step for us at RSM has been building our capabilities and expertise across various multidiscipline service offerings within the manufacturing sector,” said Quintal.
“Our newest areas include the digital space, cybersecurity, ESG, and CFO advisory services.”
Now that RSM have a suite of offerings, its focus is on marketing and branding these services within the industry.
As mentioned in their mission statement, RSM is committed to aiding Australian manufacturing businesses by serving as trusted advisors and providing tailored solutions to boost capability and success in a post-pandemic landscape.
It supports a range of manufacturers, from small firms launching new products to large global entities optimising their operations.
Leveraging its industry expertise and personalised
approach, RSM helps companies with their compliance requirements, cut costs, enhance efficiency, and drive profitability.
“We want to showcase a lot of case studies demonstrating how we’ve helped clients in the manufacturing sector through different stages of their business lifecycle,” said Quintal.
“This includes helping sole practitioners grow into SMEs and supporting them as they continue to expand.”
For example, Prinova, a manufacturer of ingredients and premixes for the food, beverage, and nutrition sectors, established a subsidiary in Australia in 2019 to meet rising demand in the APAC region.
To support this expansion, Prinova engaged RSM to assist with local Australian compliance and payroll, given the absence of a dedicated finance team.
RSM provided services, including advisory on entity establishment, Xero implementation, taxation related to imports and mergers, transfer pricing, and compliance with local regulations.
Quintal explained that RSM wants to effectively partner with clients to drive change and growth.
“Our key objective is to highlight our capabilities and how we can partner with clients to lead change. We aim to be the service advisor of choice, providing proactive and integrated support to our clients as they evolve,” he said.
Having established a strong foundation in manufacturing through his experience in both South Africa and Australia, Quintal’s understanding of the industry has now led him to recognise and address the current challenges faced by Australian manufacturers.
Quintal’s impression of Australian manufacturing
Reflecting on the past two and a half years, Quintal has found the Australian manufacturing market to be challenging relative to the previous markets he served.
The high labour costs in Australia set it apart from the global market and increased cost of energy leading to higher input costs.
Additionally, property rentals rates compared to other countries are higher, making it more costly to manufacture products in Australia compared to regions like APAC.
Further challenges to the sector include geopolitical matters, increased complexity in the regulatory environment, a lack of incentive to make new investments by government in the sector.
Quintal identifies the key challenges for the manufacturing sector as including the adoption of automation and robotics.
Traditionally, the sector relied on labour-intensive machinery, but modern automation presents both challenges and opportunities, says Quintal.
“The sector needs to focus on achieving efficiencies and producing high-quality products at a lower cost through advanced automation and robotics,” he said.
In addition to addressing labour shortages, Quintal
points out that another challenge is complying with Environmental, Social, and Governance (ESG) requirements.
“Manufacturing processes naturally involve carbon emissions, making it crucial for the sector to adapt to these compliance standards. This is a pressing issue not only in Australia but globally,” he said.
“However, despite all these challenges, I believe that Australian manufacturing, overall, offers highquality products comparative to global competition.
“The higher cost base results in a product quality that often exceeds expectations, which is a key differentiator.”
Quintal has also observed several key trends within the Australian manufacturing industry, namely, automation and improving operational efficiency.
He explained that automation could eventually become a solution to many of the challenges facing the industry and see less of Australian products been sent offshore for processing to only be imported back for consumption.
“The manufacturing sector is broad, encompassing 141 sub-sectors,” said Quintal.
“Food and beverage automation is evolving, while other sectors, such as submarine manufacturing, face unique challenges.”
“The faster automation technology advances, the quicker industries can adapt.”
Quintal said that the challenges of labour charges and cost of living are difficult to address, primarily due to supply and demand in the Australian market.
“The best solution is to embrace and adopt automation, robotics and tools to improve efficiencies and profitability margins,” he said.
“In my view, this is a key factor for the sector at this point.”
While addressing these industry challenges, Quintal is also looking towards the future of manufacturing and RSM’s role within the sector.
He envisions manufacturing becoming one of the leading sectors in RSM business and is focused on transforming RSM’s role in the industry.
Quintal also wants RSM to be recognised as the provider of choice, particularly in terms of service, understanding the client business and instilling change.
“We need to embrace change and build strong partnerships. Personally, I am a hands-on type of person, and I enjoy seeing things evolve,” he said.
“I am passionate about innovation and take pleasure in seeing people grow and benefit from these advancements.”
To achieve this vision, Quintal explained that RSM will be focusing on increasing its presence in industry-specific sectors by partnering with key organisations and sponsoring events.
“For example, we have partnerships with Manufacturers’ Monthly and Robotics Australia,” he said.
“Our goal is to engage with sector-focused bodies and enhance our branding through these sponsorships.
“Our ultimate mission is to not only adapt to changes within the industry but to drive and instil them, positioning RSM as the partner of choice for the manufacturing sector.”
Industry leaders call for strategic government intervention to prioritise local scrap consumption and rejuvenate manufacturing capabilities amidst global competition.
Metal Casting Industry leaders and the Australian Foundry Institute are calling on the government to recognise the challenges facing the metal casting sector in Australia.
The Australian metal casting industry differentiates itself on the global markets with its high-quality product, technical know-how, and the strong partnerships the metal casting businesses form with their customers.
Australian metal casters export ferrous and nonferrous castings to Europe, Asia, North and South America and Africa.
The cast metal industry in Australia heavily relies on recycled materials, primarily sourced from locally produced metal scrap as a feed material, but faces strong competition from international markets like China.
As Keiran Slattery, managing director at Hayes
for both sovereign capability and the wider Australian economy.
“The future of Australia’s metal casting industry hinges on Government action. Without it, we risk losing not just our economic edge but our national security capabilities in the event of crisis,” he said.
Slattery further warned that without federal support, the Australian metal casting industry could lose the ability to recycle domestically generated scrap metal locally. Australian industry can take advantage of the stored energy in scrap to recycle at home but now struggles to compete against global rivals for our scrap resources.
“It is time for the Government to take our calls seriously and create more sovereign capability for our Australian foundries before it is too late,” he said.
Metal casting is a manufacturing process where molten metal is poured into a cavity to form parts and components.
This method allows casters to produce complex and detailed shapes that are difficult to achieve with other techniques.
By using various metals and casting methods, casters can ensure that the final products meet all specified design requirements including integrity, strength and durability.
Non-ferrous metals include aluminium, copper, lead, nickel, zinc, and tin, each of which are valued for their specific metallurgical & mechanical properties.
Whereas ferrous metals are metals that contain iron as their principal element. Iron and steel continue to be vital for the global economy.
Crucially, the metal casting industry supports
Australia’s sovereign capability by ensuring a resilient supply chain for the Australian Defence Force (ADF) and all of the major industries in Australia.
The Australian Foundry Institute (AFI) plays a vital role in representing and advancing the interests of this sector, focusing on enhancing national industrial capabilities, particularly in defence manufacturing.
With more than 100 foundries and die-casting plants across the country, employing thousands of skilled workers, the industry generates around $1 billion for the Australian economy annually.
Essentially, metal casting is key to producing highquality parts efficiently and economically.
“It’s crucial to keep this industry thriving in Australia. While we might import cars or taps, the real concern arises when we face supply disruptions from other countries,” said Slattery.
“The COVID-19 pandemic highlighted this vulnerability, and with current geopolitical uncertainties, the risk of such disruptions remains.
“Maintaining a robust domestic metal casting industry ensures we have the capability to produce essential components when global supply chains falter.”
Additionally, the AFI has raised concerns over the cost of utility prices, which are in turn impacting the production cost in foundries.
Brett Lawrence, AFI national president and
general manager of Australia’s largest iron foundry Intercast & Forge, said: “Utility prices across the Nation with the exception of Western Australia, both from a gas and electricity perspective, have certainly increased substantially.”
“Energy supply is a fundamental building block for manufacturing in particular, and Australia has lost the competitive advantage that local lower energy costs once enabled.”
The non-ferrous metal casting industry relies heavily on metal scrap to create ingots, as opposed to raw materials.
The reason for this is that using scrap reduces the overall cost of feed materials compared to using primary metals, which can be more expensive to extract and process.
Additionally, recycling both ferrous and nonferrous scrap helps conserve natural resources and reduces environmental impact by minimising mining and refining activities by utilising the “stored energy” contained in scrap metal.
“When primary aluminium is produced in a smelter, it requires a significant amount of electrical power to convert alumina powder into solid aluminium forms,” said Slattery.
“However, once aluminium is in its solid state, recycling it only requires about 10 per cent of the original energy cost.
“This makes scrap aluminium highly valuable, especially to overseas markets like China, which imports scrap from around the world.”
As Slattery continued to explain, global competitors such as Japan, Korea and China have benefited from purchasing non-ferrous scrap, as the energy costs have already been incurred during the initial production phase thus avoiding the need to generate that extra energy themselves.
Many Countries have been utilising non-ferrous scrap metal for decades, but now as their demand for non-ferrous scrap increases, Australian metal casters are left with the ‘scraps’.
“China initially lacked primary smelters due to power shortages, so they began importing scrap metal from Australia Europe and America decades ago,” said Slattery.
“Over time, China has substantially increased its domestic electric power generation thus enabling it to build more primary aluminium smelters than any other country, yet they continue to purchase Australian scrap.
“Australia with its abundance of bauxite deposits and competitive mining and refining activities, once produced 10 per cent of the world’s primary aluminium, about 2.5 million tonnes yearly. Now, production has dropped due to high energy costs, even as global demand has risen.”
The pandemic lead to a disruption in global supply chains that forced casting buyers to reconsider
their purchasing strategies. The subsequent scramble to onshore was offset by the rising input costs for those feed materials that had to be imported together with rising energy costs.
Casting Buyers that sourced Australian made product now prefer local suppliers for the security and certainty of a more reliable supply chain.
However, with input costs soaring, profit margins are squeezed resulting in a challenging financial environment.
Slattery and other industry leaders are calling for the Government to recognise the metal casting industry and consider measures to revitalise it.
“We aim to stabilise and potentially grow the metal casting industry with the right support and understanding from the government,” said Amber Maxwell, president of the Australian Foundry Institute, Victoria division.
“We’re not seeking a handout but rather recognition and support of our industry’s expertise, capabilities and critical contribution to our daily lives.
“If our contributions in metal casting aren’t acknowledged and leveraged, there’s a risk that our metal casting businesses could be lost.”
The leaders are ultimately calling for strategic
measures to, boost domestic manufacturing capabilities, enhance sovereign capability and support local scrap consumption
They believe that achieving these goals depends on government intervention and the introduction of incentives to attract the next generation of Australian workers into the industry.
“The ‘Made in Australia’ campaign is a great initiative, but its success hinges on genuine commitment at all levels,” said Maxwell.
“For it to make a real impact, it needs to be supported and understood from the grassroots up.”
This sentiment is affirmed by Lawrence.
“We need to return to grassroots and start discussing the value of manufacturing with students in schools,” he said.
“Victoria has been running a program for a few years now, introducing casting concepts through the ‘Foundry in a Box’ initiative at some high schools. This program provides students with a “hands on” manufacturing experience whilst at the same time engaging them in conversations about pathways and opportunities for what a career in the manufacturing industry offers”
“We’re working to expand this program into other states, as there is significant demand. It’s also important to educate career advisors, as many currently do not understand the opportunities
within the metal casting or manufacturing industry” explained Maxwell
Slattery also explained that there’s potential for innovation within the industry, as the CSIRO previously invested resources into researching alloys.
“Australia was once a leader in metal research, with significant contributions at both state and federal levels,” he said.
“Institutions like the CSIRO conducted extensive research in Victoria, and had facilities such as the CAST in Queensland, receiving funding from both the government and industry.
“Unfortunately, many of these research capabilities have dwindled.”
Previously, major companies invested in alloy research, but those centres are no longer operational.
Slattery said that there’s a need to focus more on developing new materials and improving existing ones.
“Big companies like Rio Tinto had centres focused on alloy development, such as the Research Centre in Melbourne,” he said.
“However, these facilities no longer exist. There is a pressing need to reinvest in research in Australia, particularly in developing new alloys, such as scandium-enhanced aluminium.”
Scandium is a rare metal that, when added to alloys like aluminium, can improve their performance. A small amount of scandium makes these alloys much stronger and more durable, while also making them lighter.
“There are many opportunities to improve alloys in this way. For the Australian casting industry, it’s crucial to highlight our capabilities and capacities to ensure we remain competitive,” says Maxwell.
Lawrence said that the Australian Government should prioritise local suppliers to preserve critical skills and industries.
“From a government perspective, purchasing policies—both federal and state—should prioritise Australian manufacturers to ensure we retain essential skills,” he said.
“Unlike Europe or the US, where foundries can be mothballed and later reactivated, Australian foundries often face permanent closure.
“I believe state governments need to recognise that our market is unique and may require different considerations compared to other markets they are benchmarking against.”
Ultimately, the Australian metal casting industry stands at a critical juncture, facing both challenges and opportunities.
With global competition intensifying and domestic resources under pressure, there
is a pressing need for strategic government intervention to ensure the sector’s survival and growth.
By prioritising local scrap consumption, investing in research and development, and fostering educational initiatives, Australia can strengthen its metal casting industry and secure its role in the global market.
The essence of what the industry is attempting to
communicate is the ingenuity of foundries to work with customers to develop complex and costeffective functional solutions for their needs.
As an industry we are a key recycler of metal scrap utilising our engineering & metallurgical expertise to repurpose scrap into functional castings with the mechanical properties required by virtually every market segment of our economy.
Mick Fielding CEO/CTO, Raider Targetry
Titomic recently detailed its advanced defence solutions, including additive manufacturing for high-performance parts and cold spray technology for in-field repairs.
Titomic’s cold spray technology facilitates rapid repairs of industrial equipment across various sectors within manufacturing.
Cold spray technology is a specialised additive manufacturing process where metal particles are sprayed onto a surface at high velocity to create coatings or repair surfaces.
To leverage the full potential of cold spray technology, Titomic has been focused on commercialising it within crucial sectors such as defence and aerospace.
Its goal is to transition the proven capabilities of cold spray from research labs to real-world industrial applications.
For years, Titomic has collaborated with research organisations, including the CSIRO, ANSTO, and universities, to enhance cold spray technology and expand its uses.
It is also working with various partners to establish and meet high industry standards for cold spray applications, especially in sectors with stringent process controls.
Dr. Arthur Gavrin, Vice President of Advanced Materials at Triton Systems, offers an in-depth perspective on the commercial impact of cold spray technology.
“Cold spray is an additive process versus a subtractive process, which translates to less material wastage and more efficient use of resources,” he said.
Titomic primarily provides products within two categories: large additive manufacturing machines and smaller machines often used for coating and repair applications.
Coating, in this context, refers to applying metal onto an existing metal geometry. One of Titomic’s
flagship products, is the D523 Standard & Custom Cold Spray system.
The D523 is a low-pressure cold spray system designed for versatile applications, including corrosion repair, bearing seat restoration, pattern restoration, hermetic sealing, and the addition of conductive layers.
The spray can be applied across a range of materials such as metals, glass, ceramics, and plastics.
The spray itself involves injecting powdered metal into a high-speed air stream and accelerating it to supersonic speeds.
Upon impact with the surface, the metal powder solidifies without melting, making the process both easy to use and safe for environments like oil rigs and operational areas.
Recently, Titomic sold 10 of its D523 systems to
the Royal Dutch Army, with nine of these systems being sent to Ukraine for vehicle maintenance.
“The Dutch Army reached out because they wanted to contribute positively to the efforts in Ukraine,” said Dominic Parsonson, head of sales and marketing, Titomic.
“They recognised that our cold spray technology could significantly aid in rapid infield repairs with a simple process that doesn’t require highly trained engineers.”
Typically, if a piece of equipment used in the field requires repairs, it would have to be brought back to a base for welding and other traditional techniques.
However, the goal for Titomic is to enable its clients to bring repair capabilities closer to the front lines.
“Our technology offers significant benefits, particularly with our smaller machines used for coating and repair applications,” said Parsonson.
“Originally focused on automotive remanufacturing and the oil and gas industry, our tech has adapted to meet evolving needs.
“Recently, due to geopolitical shifts, there’s been a push to maintain and repair existing equipment more rapidly and closer to the front lines.”
Not only with the cold spray repair parts, but it can also provide ballistic protection after the repair process has been completed.
“The technology is being developed to enhance ballistic protection for armoured vehicles by focusing on reducing their weight while still providing robust defence capabilities,” said Parsonson.
“This scalable technology, which can be used for both small and large components, has been tested against various ballistic threats and shown to be effective.
“It addresses the logistical challenge of balancing armour weight with operational mobility, particularly in battlefield conditions.”
Titomic’s D523 system, weighing 40 kilograms, can be easily transported and adapted for defence applications.
“Last year, we participated in a logistics exercise with the European Defence Agency, where various nations tested their technologies to address realworld problems,” said Parsonson.
“We discovered numerous opportunities to use our technology for repairing armoured vehicles,
tracked vehicles, and logistics vehicles.”
These systems are not only easy to transport and deploy but also highly intuitive, making them simple to use.
As Parsonson explained, someone with only 30 minutes of training can operate the D523.
“In areas like Ukraine, it’s essential that equipment isn’t just impressive but also practical and easy to use,” he said.
“Users simply match the colour-coded metal powder with the correct hopper, press the corresponding button, and within 15 seconds, they’re ready to start repairing metal equipment.
“In Ukraine, the war is fought with a mix of equipment, ranging from brand new systems from Germany to older gear from the 1960s and 70s.
“Maintenance of this diverse and ageing equipment needs to be done quickly, costeffectively, and often by personnel with minimal training.”
In defence applications, cold spraying is useful in various contexts.
When equipment suffers superficial damage, cold spraying provides quick solutions, minimising the need for maintenance and ensuring rapid repairs.
“Imagine a scenario where a bullet hole penetrates the top of an engine block. While this damage isn’t catastrophic enough to destroy the entire engine, it does render it non-functional due to oil leakage and the risk of overheating,” said Parsonson.
“Ordinarily, you would remove the damaged
part and replace it with a new one. However, in a forward operating environment, a replacement part might not be available.
“In such cases, a repair unit with a welder might be present. Unfortunately, welding cast iron or cast aluminium can lead to further damage, such as cracking or warping.”
Its benefits extend beyond saving time and convenience. Depending on what you’re using it for, the D523 can also save you money, as it only requires a cold work permit to operate.
Parsonson explained that when dealing with an oil rig or a mining facility, obtaining a red-hot work permit – which is required when working with exposed flame or sparks, such as with a welder –can be a challenge.
This process often necessitates shutting down the facility, leading to more costs.
In contrast, cold work permits are much easier to obtain and implement relative to red-hot working environments.
“The risks of getting it wrong are enormous for your operators, infrastructure, and personnel,” said Parsonson.
Central Innovation delivers cutting-edge design software, training, and consulting, enhancing efficiency and innovation, with a focus on defence capabilities.
Central Innovation is a leading provider of design technology solutions, training, and consulting services for professionals in manufacturing, architecture, engineering, and construction.
Specialising in powerful software like SOLIDWORKS and Archicad, they help businesses enhance design efficiency and manage complex projects seamlessly.
“Innovation is in our DNA, and we are constantly looking for ways in which we can support our customers better,” said Shannon Reshno, chief operating officer, Central Innovation.
“Be it consulting on the best product fit, using technologies correctly, getting or improving the skillset of their existing people, or any issues they are stuck with, we’re their one shop solution.”
Supporting Australia’s defence and strategic security
In recent years, investment in defence capabilities has become increasingly recognised.
As defence sectors grapple with funding fluctuations, the need for innovation and resource efficiency is critical.
Central Innovation plays a vital role in the design and manufacture of defence equipment in Australia.
Although much of this work remains unadvertised due to confidentiality, Central Innovation proudly supports the organisations that protect Australia’s freedom and sovereignty.
Seamless design, prototyping, and testing
Central Innovation provides comprehensive support throughout the entire design process for defence organisations.
From selecting the best design and validation software to deployment and configuration, they ensure defence teams are proficient and ready to use these tools from the outset.
This minimises learning curve frustrations
and maximises efficiency. Central Innovation’s advanced tools enable defence organisations to drive innovation through precise and efficient design processes.
Tailored training programs elevate the skills of personnel, ensuring teams are adept with the latest technologies and methodologies.
This holistic approach enhances their capability to develop cutting-edge solutions and maintain a competitive advantage.
“The key Central Innovation values that define our approach to business and how we do business are being performance driven, customer centric and innovative attitude,” said Reshno.
“We follow these tenets in our daily operations to ensure we truly become their trusted partner in their growth journey.
“Our team consists of very experienced and skilled professionals, with both academic and industry experience and the strong desire to help our customers succeed.”
Central Innovation’s offerings include software solutions that streamline design processes, simulation (design validation) and data management, making them more efficient and productive.
This includes products like MaXXlink, #task and Ci Tools that help improve efficiency and productivity as well as leading design and collaboration solutions like SOLIDWORKS, 3DEXPERIENCE, Driveworks, Archicad, BIMx and Solibri.
Apart from their suite of software solutions, Central Innovation also provides consulting services to help choose and implement the right software solutions as well as in areas of design validation and data.
They emphasise training and consulting, providing specialised courses to upskill teams and ensure businesses maximise their software tools.
Their consulting services are tailored to specific business needs, helping organisations implement best practices and optimise their design workflows.
Central Innovation’s Product Data Management
(PDM) services are focused on installing, configuring, and optimising systems that manage product data throughout its lifecycle.
These services include setting up standard or advanced PDM systems, customising workflows, ensuring compliance with quality standards, and maintaining PDM configurations on cloud platforms.
The goal is to streamline data management, improve workflow efficiency, and ensure data integrity.
Engineering Design and Validation services involve analysing and validating engineering designs through simulation tools.
This includes performing Finite Element Analysis (FEA) and Computational Fluid Dynamics (CFD) to test and optimise CAD models and providing training for using cloud-based simulation platforms.
The aim is to ensure designs are robust, functional, and optimised before production.
Design and Process Automation services focus on implementing and customising tools that automate design and manufacturing processes.
These services enhance productivity by automating repetitive tasks and customising solutions to fit evolving business requirements.
At its core, Central Innovation is dedicated to fostering innovation. By providing top-tier technology solutions and expert guidance, they help businesses navigate the complexities of modern design and engineering.
Their mission is to support companies in achieving excellence, driving innovation, and staying competitive in a rapidly evolving industry landscape.
“With the advent of industry 4.0, companies are constantly striving to improve products, customer service, time to market, operations, a way that is better than their competitors,” Reshno.
“Being competitive is no longer a choice, but a necessity, so companies are becoming innovative in terms of product, process and customer experience improvement.
“Though our suite of solutions, we help our customers to bring to life their vision of this innovation.”
Engineers from RMIT University are developing a technique to help underwater technicians by using a modified speargun to efficiently and cheaply test seabed soil.
RMIT University researchers, Professor Majid Nazem and Junlin Rong, have showcased an innovative method for testing soil, potentially streamlining the process for major infrastructure projects.
Specifically, these soil tests are designed to provide critical information to engineers prior to building offshore infrastructure such as windfarms and pipelines.
“These structures require geotechnical information. For instance, an example is the soil friction angle, which reflects how the soil behaves under a large amount of loading. This information helps engineers design structures,” said Rong.
“To obtain this information, the conventional method involves deploying a drilling rig to the site, drilling to determine the soil’s strength, and then
converting those measurements to determine the soil friction angles.
“These soil parameters are crucial. What we are doing now is trying to replace some of these tests, which usually require a significant number of tests to gather all the necessary information. This is where we play a role, substituting conventional testing methods.”
Conventionally, the typical method for testing seabed soil involves winching or dropping lightweight or heavy-duty probes – known as penetrometers – from the deck of a support vessel.
However, using these probes comes with a set of challenges in certain contexts.
For wind farm projects in shallower waters, lightweight probes can struggle to penetrate the seabed, while heavy-duty probes, which are
effective, can cost up to $200,000 per day.
Nazem and Rong’s method, using a modified speargun, utilises probes attached to a speargun bolt.
“The speargun is designed for challenging underwater environments, making it an ideal inspiration for a geotechnical engineering test device,” said Rong.
“Its mechanism allows for efficient penetration of topsoil, providing easy soil investigation.
“By adapting the speargun’s mechanisms, we can deliver considerable penetration forces, enabling faster geotechnical surveys.”
The RMIT researchers have tested this method by testing different probe tips in a water tank filled with various sand mixtures.
They used an array of sensors and high-speed
cameras to capture the results.
According to Rong, the results have demonstrated the device’s potential in field applications.
“In laboratory environments, the device showed considerably greater penetration potential compared to free-falling probes on soil,” he said.
“Notably, in high-density sandy material, the
penetration depth was twice that of previously reported values achieved by freely falling probes.
“This breakthrough technique has the potential to revolutionise site investigations for wind farm projects, offering significant time and cost savings while outperforming the embedment achieved by other dynamic penetrometers.”
Rong believes that conventional testing methods, like cone penetration, will remain as the more popular choice.
However, Rong hopes that their device could eventually provide an alternative method for testing, which could subsequently reduce the number of expensive tests needed.
Majid Nazem said the device was now ready for field trials,
“Now that our experiments have demonstrated the device’s ability to achieve considerable embedment depth in dense sand,” he said.
“We are keen to conduct field trials and collaborate with our potential industrial partners to further test its performance for offshore geotechnical engineering applications.”
Currently, the team is comprised of a project lead or director, Professor Nazem, who coordinates these efforts, while the laboratory partner, Rong, assists with design, planning, and conducting the tests.
Together, they analyse the data and draw conclusions based on their findings.
In addition to their internal team, they collaborate with other institutions such as the University of Melbourne, which helps with design and implementation through its expertise.
“We also work closely with manufacturing and application teams at RMIT, who help us build and test our devices,” said Rong.
“Additionally, the technical staff in RMIT’s heavy structural lab provides valuable support.
“This project is a team effort, and the credit goes to everyone involved, not just me or the project lead.”
The engineers will soon be setting the level for their field tests, expecting their speargun probe to penetrate the seabed to a depth of two to fi ve meters based on their laboratory tests.
However, in their Melbourne-based laboratory, they only used about 25 per cent of the energy of the spearguns due to safety limitations associated with firing the gun indoors.
“We haven’t conducted field tests yet. If we can apply 100 per cent of the energy in the field, we can test further and clarify our assumptions or hypotheses,” said Rong.
“Compared to conventional methods, we need to validate our data, which we are also doing in the lab, but field tests will provide more critical information.”
Field tests will also determine how viable the speargun is when deployed from a support vessel. Rong remains confident based on their preliminary data.
“There are more research questions we need to investigate to determine if this method fits the boats through this kind of testing,” he said.
“However, based on our laboratory test results, we are confident that these methods can provide a viable alternative to current test technologies.”
Rong also hopes to gain support from industry partners, who can then assist the engineers in developing a design for an enhanced shooting mechanism.
“Currently, in the laboratory, we are developing these models as prototypes. In the next stage, if we find suitable collaborators, we aim to further optimise the design and build a deployment rig or shooting mechanism,” he said.
“This could involve either using a remotely controlled vehicle from the seabed or shooting directly from support vessels or smaller ships.”
ROVs, or Remotely Operated Vehicles, are unmanned, remotely controlled submarines used for various underwater tasks.
They’re often used in industries like oil and gas, marine research, and deep-sea exploration.
Rong explained that a similar mechanism to their
speargun probe could soon be mounted onto an ROV.
“The remote-controlled vehicles currently used in the industry are typically employed for deepwater construction, where they monitor projects at depths of up to about 1,000 meters,” said Rong.
“These vehicles can carry equipment and allow for remote and safe operation of tests.
“If we were to use a boat for shooting, we would need to assess whether it is feasible to reach the seabed and penetrate the ground effectively from that distance.”
The engineers are pursuing different avenues to obtain partnerships with industry.
“We are participating in a field research conference where we are presenting our technologies and introducing them to the market,” said Rong.
“Currently, we haven’t received much feedback
from the industry. However, our goal is to showcase our technologies, generate interest, and explore potential collaborations for future developments.”
Their ultimate goal is to partner with a manufacturer who could enable the engineers to scale-up their device.
“Next, we can scale-up to conduct a full-scale test of this particular design,” said Rong.
“We plan to scale-up and gain a deeper understanding of how the larger equipment will perform.”
Rong expressed excitement about the prospect of obtaining an industry collaborator who can bring their technology to the next stage.
“If there are any potential collaborators or future funders interested, we are eager to engage in bringing these innovative solutions to the geotechnical field,” he said.
“We have everything ready and are prepared to move forward at any time.”
July’s Indian Ocean Defence & Security (IODS) event 2024 concluded with a deeper insight into the strategic significance and practical challenges of the AUKUS and Quad partnerships, drawing record attendance from industry and government officials.
Held at the Perth Convention and Exhibition Centre from 24-26 July, the Indian Ocean Defence & Security event was held over three-days. It attracted more than 4800 attendances from 25 nations. It had 112 government, industry and academic delegations from 15 countries and 110 participating exhibitor companies under the theme of Where AUKUS Meets The Quad.
The two-day conference program highlighted both the AUKUS defence partnership between Australia, the United Kingdom and the United States, best known for its Pillar 1 goal of acquiring nuclearpowered submarines for the Royal Australian Navy, and the Quad diplomatic partnership, which encourages closer cooperation between Australia, the United States, Japan and India on economic and technology collaboration across the region.
Western Australia’s Department of Jobs, Tourism, Science and Innovation and its defence arm, Defence West, partnered with Australian not-for-profit AMDA Foundation to deliver the event.
Professor Gordon Flake, founding CEO of the Perth USAsia Centre, which curated the conference program, opened the event with an acknowledgement of its strategic importance.
“This conference today brings together speakers, participants and exhibitors from almost every significant country in the Indo Pacific,” he said. “We
have here the greatest concentration of chiefs of navy ever in Western Australia. We have our acting Prime Minister and 10 other current, shadow or former ministers from the federal government. We’ve got a remarkable representation from our WA state government.
“We also have a strong representation from the diplomatic corps, scholars and business leaders and, perhaps most importantly, a delegation of about a
thousand strong who have registered for the next two days and shown their interest of our community and our broader community in the Indian Ocean Defence and Security Conference.”
IODS 2024 covered a raft of issues for both the AUKUS and Quad partnerships, including Indian Ocean political and trade stability, international naval cooperation, as well as the AUKUS submarine program and its implications for industry and national security.
The event featured the first Australian gathering of the chiefs of navy of all three AUKUS partners, Australia, the United Kingdom and the United States, plus the naval chiefs of Japan and Singapore.
“It is an important time to be having these conversations,” said Australian Chief of Navy, Vice Admiral Mark Hammond, at the opening of a special Chiefs of Navy panel session on day one.
“It is great to see the national literacy with maritime security affairs slowly increasing. We need to talk about maritime security issues. We also need to talk about events at sea that have shaped the history of this nation and will shape the future security environment for this nation.”
Event highlights included a panel session on implications of the AUKUS agreement for industry, an address from Acting Prime Minister and Minister for Defence, the Hon Richard Marles, and a spirited panel session featuring perspectives from four
former Australian Defence Ministers, which produced incisive debate with a touch of humour.
Elsewhere in the program, Australian innovators were honoured with a total of $120,000 in Indian Ocean Defence & Security Innovation Awards. This included Robert Dane of Ocius Technology for the Bluebottle Uncrewed Surface Vessel, Brennan Mills of Edith Cowan University for the ParaVerse parachute training simulator (who also received a specialist Collaboration Innovation Award) and Ayden McCann of the University of Western Australia for the Teranet-3 mobile high-speed laser communications system.
The Chair of the judging panel, Michele Clement, Director of the Western Australian Defence Science Centre, said the judges were impressed by the innovative nature and the depth and breadth of the ideas presented.
“We saw evidence of a really strong Australian innovation ecosystem that is taking ideas and turning them into a capability that would support our national security, not only for defence, but also in the broader civil sense as well,” she said.
The event also featured a day three Careers and Skills program, which saw more than 400 students exploring career and workpath options across the IODS 2024 exhibition floor, with presentations from the Australian Submarine Agency, Royal Australian Navy, Australian Federal Police and industry.
With the success of the 2024 event, Western Australian Minister for Defence Industry, the Hon. Paul Papalia, closed the conference with an announcement that it will become a biennial event, returning in 2026.
Backplane Systems Technology has announced the launch of the VECOWIVX-1000.
The VECOW IVX-1000 is an in-vehicle computing workstation designed to meet the demanding needs of the mining industry.
Powered by Intel Core i9/i7/i5/i3 processors from the 14th generation, this workstationgrade platform integrates the Intel R680E PCH, supporting CPUs with a maximum TDP of 65W. To enhance AI capabilities and computing productivity, the IVX-1000 optionally supports advanced NVIDIA Quadro MXM graphics.
Engineered for the harsh conditions of mining environments, the IVX-1000 features a fanless design, ensuring dust resistance and compliance with EN50155:2017 standards. Its robust 16V to 160V DC power input, with 4kV DC isolation and up to 500V surge protection, ensures stable operation even in fluctuating power conditions. The workstation also includes software ignition power control and optional UPS support for uninterrupted performance.
The IVX-1000 excels in connectivity, essential for mining operations. It boasts 8 independent 2.5GigE LAN ports, including 4 with IEEE 802.3at PoE+, along with an additional GigE LAN port. This ensures reliable communication and data transfer, crucial for real-time monitoring and
control in mining operations. Multiple wireless configurations, including 5G, WiFi, 4G, and LTE, provide versatile communication options for remote mining sites.
Security and network reliability are paramount in mining applications. The IVX-1000 supports Intel vPro, TCC, TimeSensitive Networking (TSN), and TPM 2.0, addressing these critical requirements. For AI-driven tasks, the workstation features Intel Deep Learning Boost and the Intel Distribution of OpenVINO toolkit. The optional VHub AIoT Solution Service further augments its AI capabilities, facilitating advanced edge AI applications.
• 16V to 160V DC Power Input with 4kV DC Isolation, up to 500V Surge Protection, Software Ignition Power Control, optional UPS supported.
• Fanless design for railway in-vehicle applications, fully compliant with EN50155 : 2017.
With its rugged reliability, high-performance computing, and versatile connectivity, the VECOW IVX-1000 is the ideal solution for enhancing productivity and safety in mining operations.
Key features:
• Workstation-grade Platform : Intel Core i9/i7/i5/i3 Processor (14th gen, codename : RPL-S Refresh/ RPL-S/ADL-S) running with Intel R680E PCH supports max 65W TDP CPU.
• Optional supports outstanding AI computing productivity by advanced and compact NVIDIA Quadro MXM graphics.
• 8 Independent 2.5GigE LAN M12 X-coded with 4 IEEE 802.3at PoE+, 1 2.5GigE LAN, 1 GigE LAN, 4 Isolated COM.
• 2 Front-access 2.5-inch SSD/HDD Tray, multiple 5G/WiFi/4G/3G/LTE/GPRS/UMTS..
• Supports Intel vPro, TCC, Time-Sensitive Networking (TSN), and TPM 2.0.
• Optional VHub AIoT Solution Service supports OpenVINO based AI accelerator and advanced Edge AI applications.
Company: Backplane Systems Technology Phone: (02) 9457 6400
Website: www.backplane.com.au/
ICP Electronics Australia is proud to introduce ICP DAS iSN-104-E. The ICP DAS iSN-104-E is a 4-channel Liquid Leak Detection Module designed for efficient and intelligent liquid leak detection. This Ethernet version device offers a low-cost solution for real-time monitoring and alarm control without needing additional conversion modules. The iSN104-E is ideal for critical locations like computer room base stations, warehouses, libraries, museums, and industrial sites. It also suits applications such as air handling equipment, refrigeration units, liquid containers, and pump tanks.
Key features include water leakage and cable break detection with an audible alarm, a mute button to silence the alarm, and fi ve LED indicators to display power and alarm status. The module supports liquid leak detection cables and extended cables up to 500 meters, with adjustable sensitivity for precise
detection. It is compatible with Modbus TCP/UDP and MQTT protocols, facilitating seamless integration with various monitoring systems for remote alarm and device control.
The iSN-104-E offers redundant power inputs, including PoE and DC input, ensuring reliable operation. Certified with CE, UKCA, FCC, RoHS, and WEEE, it guarantees high standards of safety and environmental compliance.
The iSN-104-E can be integrated into existing HMI or SCADA systems, enhancing maintenance in distributed control systems. Applications extend to water pipe leak monitoring in buildings, fire pipes, sewage pipes, and domestic water systems, promoting water conservation and safety. It can send out signals and alarms, and integrate with WISE IoT Edge Controllers or TPD/VPD Touch HMIs, further connecting with mobile apps or community systems.
Key features:
• 4-ch Liquid Leak Detection
• Water Leakage and cable break detection triggers and audible alarm
• A mute button to silence the audible alarm
• Five LED indicators to display the status of the power and the alarm
• Liquid Leak Detection Cable and Extended Cable can be up to 500 meters
• Sensitivity adjustable detection
• Supports Modbus TCP/UDP, MQTT
• Includes Redundant Power Inputs: PoE and DC Input
Company: ICP Electronics Australia Phone: (02) 9457 6011
Website: icp-australia.com.au
INNES WILLOX, CHIEF EXECUTIVE, AUSTRALIAN
We are trade reliant. One in four Australian jobs relies directly or indirectly on trade, whether in goods or services. In turbulent times, the changing shape of the world around us matters enormously to how we develop our future prosperity.
Within our immediate region, there are rapidly shifting sands that have huge economic consequences for a country that relies on trade. Geopolitics is now more consequential to global trade than at any time in our history.
When we emerged from our COVID restrictions, one of the big themes was that we had to develop economic resilience and, in some areas, self-
reliance. That was driven by a realisation that global trade could be distorted by events beyond our control.
We were cut off from China and then trade flows between the United States and China dominated, driving up shipping costs, rendering containers and pallets scarce and leading to product scarcity or hoarding. This feast or famine was coupled with increases in protectionism around the globe to defend or prop up ailing or deemed vital industries. All of this has driven the inflation contagion we still suffer from.
The government response was a sensible one – the encouragement of a “China-plus one”
strategy to try to shift our economy from what was an unhealthy over-reliance on one market or one source. Despite best efforts, it hasn’t really worked. Our reliance on China is virtually as strong as ever. Why is that? There are two reasons. One is that despite the recent trade troubles, China for many is still seen as cheap, reliable and known.
The regional alternatives are not straightforward either for businesses under cost and time pressure. Making new contacts, building relationships, developing supply lines all takes time.
But this is where geopolitics becomes important. Consider where our economy would be if China, having developed stockpiles and alternative
sources of the raw materials provided by Australia, decides at the end of the decade to turn off the trade tap. After years of trade wars with a renewed Trump administration, fighting tariffs with tariffs, Australia ends up as collateral damage in a global trade war.
That would be devastating to our prosperity. So would a conflict for Taiwan – a kinetic conflict would be devastating, a prolonged economic conflict resulting from a blockade or similar would be debilitating. Xi Jinping has made it clear he wants a military option for Taiwan to be ready for 2027 whether it is used or not.
There is also real risk of a South China Sea conflict over territorial disputes. We see China and the Philippines and others locked in conflict on the high seas which risks, either by accident or design, quickly escalating. There have been three near miss incidents between Australian and Chinese forces in recent months.
Despite all this, for now, even though there is a real understanding of the fragility of global trade, business has by and large gone back to what they know.
Why? Look at the region around us from a geopolitical sense.
Indonesia is soon to install a new president, who is friendly to the west, and who will visit China as his first international stop.
Singapore is about to change leadership so relationships at a political level will need to be reinvigorated.
Vietnam had been for some time amid a power struggle, and it recently intensified.
India now has a minority government with the instability that creates.
Bangladesh is currently the scene of intense rioting.
Burma could collapse at any moment which of course has regional implications. I could go on. Of course, none of this is impossible to navigate and is being navigated, but for business that craves certainty and stability to foster investment you can see the reasons for hesitancy or withdrawal.
The global trading system, meanwhile, is falling short. The World Trade Organisation has in recent years been stripped of funds and moral support, particularly by the United States. Despite best efforts, confidence in it as a disputes resolver and a confidence builder is diminishing.
Protectionism is on the rise and it seems there isn’t the political will to stop it. By October 2023, 11.8 per cent of G20 imports were affected by import restrictions implemented by G20 economies since the Global Financial Crisis in 2009. That is, in dollar terms, USD 2.287 billion worth of trade.
Since the pandemic, the Ukraine war and the rise of global food insecurity, we have only seen the rise of export restrictions.
The trade governance landscape is changing before our eyes. We are seeing the development of trade clubs and plurilateral grouping based on interests, geography or commodities like critical minerals. Interests are diverging and the role of global institutions are diminishing.
The next area to watch is the trade response to specific issues like climate change. We are seeing the rise of initiatives like carbon pricing in trade witnessed by European plans for a Carbon Border Adjustment Mechanism, which will undoubtedly
engender a response from other economies if and when implemented.
And finally, we are seeing the influence of technology on trade where traditional regulatory frameworks are struggling to keep pace. We’re seeing the digital transformation of trade through Industry 4.0, the Internet of Things and of course the rapid rise of artificial intelligence (AI).
AI can work for business in three ways –automation, adaptation and augmentation.
Australian businesses are taking a cautious approach – we are reported to be among the most wary economies in the OECD – and in Ai Group’s skills survey released earlier this year, 41 per cent of businesses said they had no engagement with AI because of barriers such as a lack of leadership knowledge, a lack of implementation skills and insufficient understanding of the opportunities.
But despite this, there is optimism with over 75 per cent of businesses reporting this year will be spent trying to lift leadership understanding and capability in AI.
Why is this important in a trade sense? Because AI will undoubtedly very quickly reshape how we relate and trade.
Of course, the bias of regulators will be to regulate. How fast, and how far they regulate will be key.
It is often said the United States innovates and Europe regulates. Where Australia sits on that spectrum will be a key to our future trading success.
And for a country where one in four jobs is trade reliant, keeping trade flows open and moving quickly to take advantage of new opportunities will be vital to our long-term economic prosperity.
Geopolitical tensions and trade disruptions challenge Australia’s reliance on China; diversification remains crucial for stability.
BRENT CLARK, CEO, AUSTRALIAN
As we remain in complex geopolitical circumstances, circumstances that many believe we have not seen the likes of since the 1930s, the need for a robust, sovereign and indigenous industrial base has become a mandatory requirement to achieve a high level of national strategic resilience.
The ongoing illegal invasion of Ukraine, the worsening situation in both the Gaza and elsewhere in the middle east combined with an ever-increasing forceful presence of China and the ever-present issues surrounding North Korea and negative influence of Iran all combine to place us all in a precarious position.
As the Western nations and allies work together to try and resolve these issues in a peaceful manner, the simple reality remains that the world is not a safe place, and tensions will not simply dissipate overnight.
Our global supply chains are heavily stressed, and in many cases, still have not recovered post the COVID pandemic, in some areas, whilst not at a breaking point, they are struggling to maintain the ability to meet the supply demand.
If our strategic circumstances were to further
diminish or worse still, the world was to enter a more encompassing conflict there would be the real possibility that the global supply chains would not cope.
Combined with these circumstances the current Australian Government has undertaken a significant pivot of what the ADF will be doing into the future. Nuclear Submarines whilst the largest single investment Australia will make are not the only aspect of what Government is striving to achieve.
The AUKUS arrangement will define Australia and Australia’s direction in a way not seen before. What is clear is that we are seeing a fundamental shift for Australia’s Defence Industry. Some businesses may find that unless they adapt or diversify, they may not be part of the Defence Industrial ecosystem into the future.
Whist the development of this concept is of huge
significance, it is vital that Australia’s indigenous defence industrial base is nurtured and invested in.
Australia must be a contributor to the world’s global supply chain, Australia as a country cannot simply be a drain or be seen as an export opportunity for multinational companies.
Australia has a sophisticated industrial base covering a broad range of sectors, mining and agriculture, rail, infrastructure, medical and manufacturing. An often-overlooked category is that of Defence Industry.
The Defence industrial sector comprises hundreds of companies, ranging from the large multinational defence primes to the small micro businesses provide boutique services.
All of these entities form the defence industrial ecosystem, and all of these enterprises contribute to the overall strength of the country.
Without strong oversight and investment by the Australian Government we run the risk that we miss the opportunity to this net contributor.
There are many arguments as to why the effort must be made to develop our indigenous sovereign capability. Clearly there is an economic benefit to Australia, there is of course the return on investment argument for the Australian taxpayer, however, the need for national resilience and the ability to resupply and provide maintenance for the ADF must now be considered strategic requirements.
Without a broad base manufacturing industry, Australia would struggle in times of global conflict and increased demands on a supply chain to ensure that the ADF is able to maintain the ability to contribute to a either a broad coalition of forces or indeed operating as an independent entity.
The need to include the Australian Industrial base into both global supply and production calculations is a fundamentally important element of any response the Western Allies may choose to undertake.
If Australian Industry is not incorporated into the planning for all Defence activities, we will simply place the fortunes of Australia into the hands of foreign governments and foreign multinational
companies. Who will in a conflict environment be fully engaged in the re-supply of their own defence forces, leaving Australia to sit in a queue waiting to be resupplied.
The benefits of secondary manufacturing capabilities cannot be overstated. Australia has the capability and competence to undertake these activities. For example, if we were to establish Australia as a secondary manufacture of ballistic missiles we could actively assist in the resupply of expended munitions, this would give an alliance a significant advantage.
Australia is a first world country a country with cutting edge technology and industry, and yet Australia is the only first world country without an Australian owned Prime Contractor in the Defence space. Our other industrial sectors do have such companies, the question must be asked why not in the Defence sector?
This is not to say that the foreign owned multinational companies do not have a significant role to play in the defence of Australia, they are an important component of the defence ecosystem.
What they shouldn’t be is the driving force in that ecosystem.
For Australia to simply hand over the responsibility of the defence industrial base to overseas countries
and therefore overseas governments is a position that we as a nation should reject.
The need for a sovereign industrial base is a fundamental pillar for the defence, security and therefore safety of the nation.
The ability to transfer the required intellectual property, technical information, technical knowledge and technical know-how needs to be a fundamental requirement to transition capability to Australia.
By upskilling both Australia’s industrial base and workforce then Australia becomes a vital link in the overall Western Alliance.
The simple solution is to state that the foreign owned companies are Australian because they employ Australians and have a presence in-country. However, this is a naive approach, the need for Australian owned or controlled companies, must be the standard we demand for our security.
The ability for the Australian Government, in times of conflict, to be able to in effect nationalise an Australian Industry base to achieve an outcome that is in the best interests of Australia becomes a key component in the self defence of the nation.
A strong, modern manufacturing base equally becomes a mandatory element in the defence of Australia.
Weld Australia’s Welding Excellence Awards are one of the most prestigious events on the welding industry calendar. The Awards promote high standards of craftsmanship, quality and professionalism.
The 2024 Welding Excellence Awards are a fantastic opportunity for welders, fabricators and educators across Australia to showcase their people and operations. Winners will be awarded in each state for each of the award categories below.
The Company of the Year Award recognises superior performance across a range of business metrics. There are three sub-categories: Fabrication Company, Supplier, and Indigenous Company of the Year.
This Award recognises professionals who are making a valuable contribution to the Australian welding and fabrication industry. The individual should demonstrate a high level of skill, knowledge or craftsmanship. There are three sub-categories: Welding Coordinator, Welding Supervisor, and Welding Inspector.
The Project of the Year Award recognises excellence in welding and fabrication projects, with a focus on exceptional craftsmanship, a commitment programs or initiatives.
This Award recognises tradespeople who are making a valuable contribution to the welding and fabrication industry. The individual should demonstrate a high level of skill and have professional development plans in place. There are three sub-categories: Young Trades Person, Young Indigenous Trades Person, and Trades Person.
The Training and Education Award recognises the outstanding achievements of a STEM or VET provider or program. Entrants may include secondary education and tertiary education providers. Criteria include delivery of quality, innovative training programs, involvement with industry, recruitment
• Queensland & Northern Territory: Wednesday 9 October at Waters Edge, 39 Hercules Street, Hamilton
• New South Wales & ACT: Wednesday 24 October at Kirribilli Club, 11 Harbourview Crescent, Lavender Bay
• Victoria & Tasmania: Wednesday 6 November at Crowne Plaza Melbourne, 1-5 Spencer Street, Docklands
• Western Australia: Thursday 21 November at Burswood on Swan, 1 Camfield Drive, Burswood
• South Australia: Thursday 28 November at Kooyonga Golf Club, May Terrace, Adelaide
weldaustralia.com.au/2024-welding-excellenceawards/
Unlock exclusive insights into the top manufacturers in Australia and around the globe.
Scan the QR code to secure your copy of the IBIS Top 100 list in the October edition of Manufacturers’ Monthly! For additional listing and visibility opportunities, contact: Emily Gorgievska | Business Development Manager, Manufactures’ Monthly emily.gorgievska@primecreative.com.au | 0432083392