
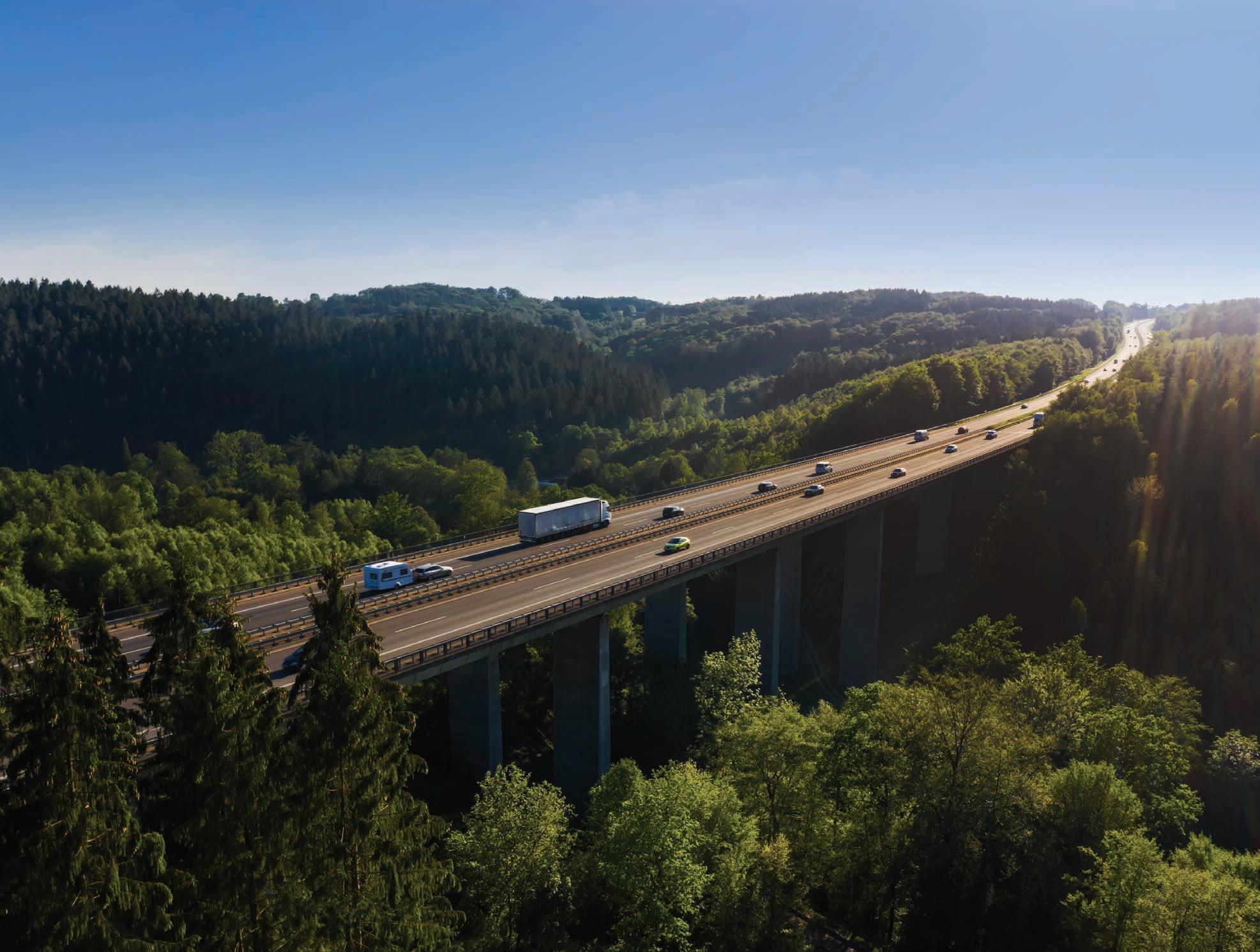
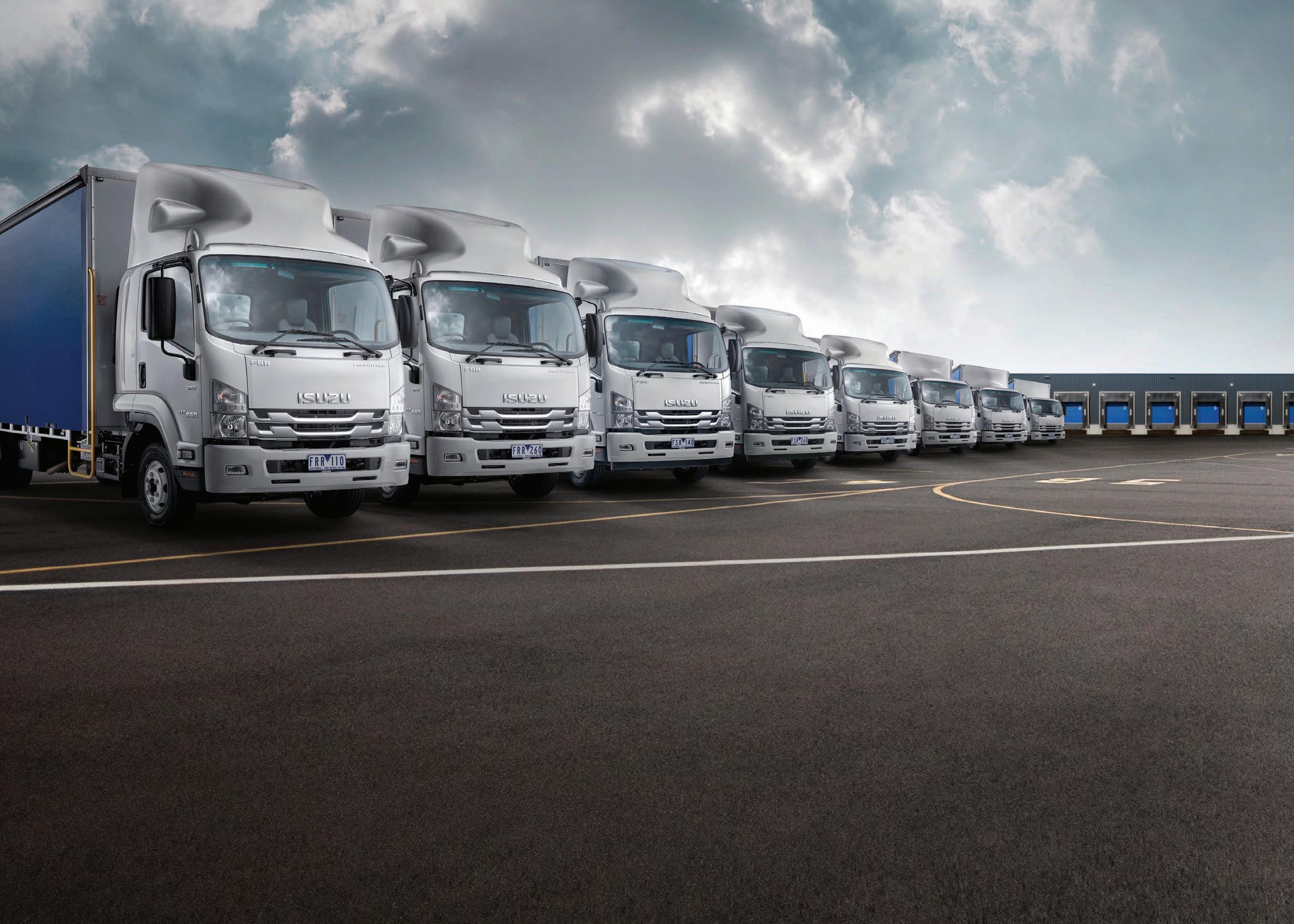
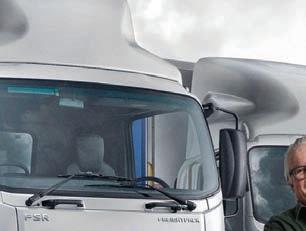



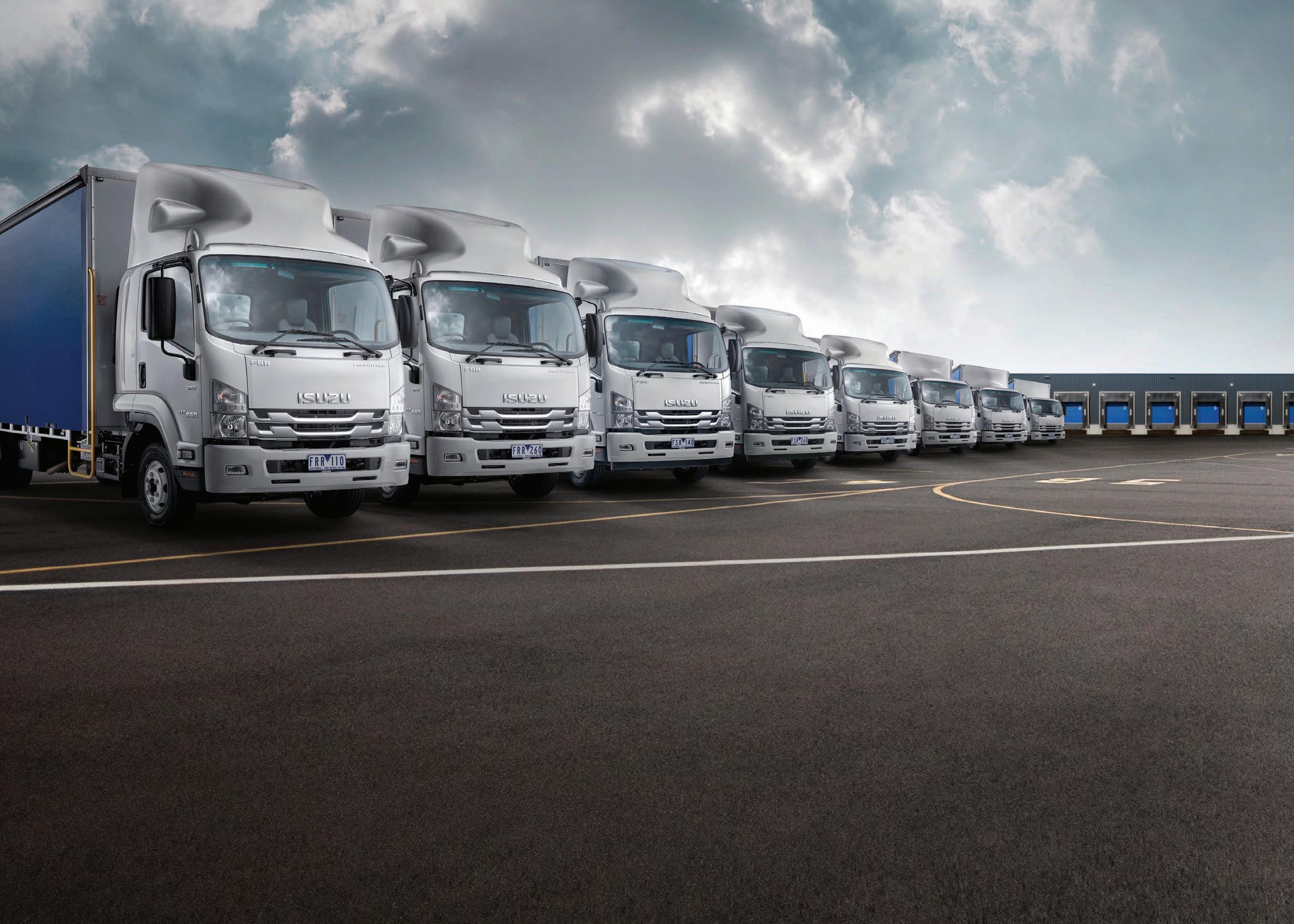
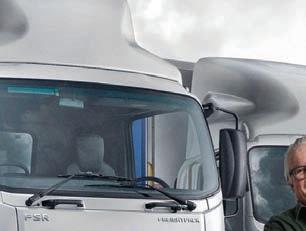
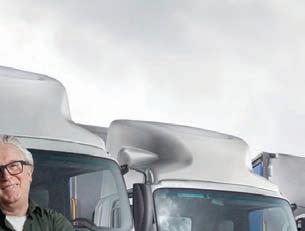


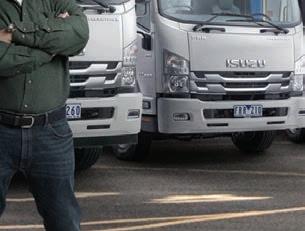





Australia’s leading truck magazine, Prime Mover, continues to invest more in its products and showcases a deep pool of editorial talent with a unique mix of experience and knowledge.
John has been the nation’s foremost authority in commercial road transport media for almost two decades and is the driving force behind Prime Creative Media becoming Australia’s biggest specialist B2B publishing and events company. Committed to servicing the transport and logistics industry, John continues to work tirelessly to represent it in a positive light and is widely considered a true champion for the growth of the Australian trucking and manufacturing industry.
Over the past two decades William has published widely on transport, logistics, politics, agriculture, cinema, music and sports
He has held senior positions in marketing and publicity for multinational businesses in the entertainment industry and is the author of two plays and a book on Australian film history. Like many based in Melbourne he is in a prolonged transition of either returning or leaving.
A seasoned transport industry professional, Peter has spent more than a decade in the media industry. Starting out as a heavy vehicle mechanic, he managed a fuel tanker fleet and held a range of senior marketing and management positions in the oil and chemicals industry before becoming a nationally acclaimed transport journalist.
Having recently completed his Bachelor of Media and Communication (Media Industries) degree at La Trobe University, Peter brings a fresh perspective to Prime Mover
Invaluable experience obtained during his time at upstart, La Trobe’s newsroom, has been supplemented by direct industry experience in a Council placement. Peter is looking forward to contributing to the magazine’s image as the leading publication for commercial road transport with his developed skills.
Handling placements for Prime Mover magazine, Ashley has a unique perspective on the world of truck building both domestically and internationally. Focused on delivering the best results for advertisers, Ashley works closely with the editorial team to ensure the best integration of brand messaging across both print and digital platforms.
ceo John Murphy john.murphy@primecreative.com.au
editor William Craske
william.craske@primecreative.com.au managing editor, Luke Applebee transport group luke.applebee@primecreative.com.au
senior feature Peter Shields writer peter.shields@primecreative.com.au
Ashley Blachford ashley.blachford@primecreative.com.au 0425 699 819
art director Blake Storey blake.storey@primecreative.com.au design Kerry Pert , Louis Romero, Tom Anderson journalist Peter White peter.white@primecreative.com.au
design production Michelle Weston manager michelle.weston@primecreative.com.au
client success Justine Nardone manager justine.nardone@primecreative.com.au head office 11-15 Buckhurst Street
South Melbourne VIC 3205
P: 03 9690 8766
F: 03 9682 0044 enquiries@primecreative.com.au
03 9690 8766 subscriptions@primecreative.com.au
Prime Mover magazine is available by subscription from the publisher.
The right of refusal is reserved by the publisher.
Annual rates: AUS $110.00 (inc GST).
For overseas subscriptions, airmail postage should be added to the subscription rate.
All articles submitted for publication become the property of the publisher. The Editor reserves the right to adjust any article to conform with the magazine format.
PRIME MOVER magazine is owned and published by Prime Creative Media. All material in PRIME MOVER magazine is copyright and no part may be reproduced or copied in any form or by any means (graphic, electronic or mechanical including information and retrieval systems) without written permission of the publisher. The Editor welcomes contributions but reserves the right to accept or reject any material.
While every effort has been made to ensure the accuracy of information Prime Creative Media will not accept responsibility for errors or omissions or for any consequences arising from reliance on information published. The opinions expressed in PRIME MOVER magazine are not necessarily the opinions of, or endorsed by the publisher unless otherwise stated.
“We can go straight into the port on our PBS permit which is a big change for us. Now we carry up to 130 export containers out of Tamworth each week and every one of those 40-footers was previously a single truck.”
anticipating some big things from its new Third
which has arrived on the Australian market.
customer service has been one of the key factors behind the success of Carey’s Freight Lines for the past
diverse range of operations, a strong relationship with Toll
a focus on customer service
Hillman’s Transport.
been key to the success of
trying times for road transport across many industry sectors, labour shortages are posing major challenges that are being dealt with differently.
inherent challenges of doing business in
freight industry
interfered with the continued growth being achieved
logistics
Wymap
West Logistics
took
of a new longwheelbase 6x4 UD Quon. In addition to being the first of five forthcoming units it also marks the first of its kind in Australia.
Editor
NASA claims the technology that helped humanity to set foot on the moon or at least to leave low level orbit way back in 1972, has been lost to us. As if the indispensable science, we’re coercively often asked to trust, was destroyed in the same fire that razed the Library of Alexandria. Even with half a century of technological advancement since the last official Apollo moon mission, no country, including the United States, has been able to replicate this feat. Are there no longer any astronauts and engineers with the proverbial ‘right stuff’? If not for great feats how else might we measure, even imprecisely, our civilisation in the form it momentarily subsists? Another theory, of course, persists. What if we never went to the moon? What if the space race was a giant public relations stunt for liberal democracy? These questions have grown more troubling as the years have gone past especially for those who get troubled turning their minds to such questions. Whatever the case the public appetite for major crewed space flight would seem to have shifted injudiciously. As the quest for feats of engineering greatness moves from the public arena to domains of private equity, the greatest scientific discoveries, once celebrated as international historical events,
move increasingly inwards, if the strange rites pursuant to CERN and its stakeholders, are the new industry benchmark.
In Osaka, where the next World Expo will take place in 2025, the theme of ‘Designing Future Society for Our Lives’ hardly smacks of adventure. It sounds, at least to suspicious ears, like more lockdown life only with virtual reality. During the first world fair held on the Champs-Élysées in 1855, Alexander Graham Bell’s telephone and Thomas Edison’s phonograph were unveiled. At the 1889 event, where the Eiffel Tower was conceived as the entrance arch, millions of visitors were amazed by Emile Berliner’s gramophone. Few decisive, absolutely, new inventions have been unearthed since that period according to historian Stanley G. Payne, who points out that the development of the computer and discovery of nuclear fission happened only a few years later. Nobody it seems told Duke Ellington. Stereo, generally regarded as an invention of 1985, along with the lithium-ion battery, looks to have been the brainchild of a sound engineer at RCA Victor more than half a century earlier. Two record collectors, called Lasker and Kay, when going over old recordings in 1981 found what, at first, they thought to be an alternate take of Ellington’s band recording a medley in 1932 — the same year the Waldorf Astoria was upstaging Uber Eats with room service. Upon closer inspection of the newly discovered recording, which was also designated its own session number (71837) it seemed almost identical to the original pressing only with one
jarring difference. The drums of Sonny Greer sounded more immediate, while the horn section was muted, acutely distant. It was almost as if they were listening to the same performance from two different perspectives. Could there have been another directional mic located on the other side of the bandstand? Years pass by. Eventually the two records are synchronised on separate channels of a stereo tape machine. It becomes apparent that RCA-Victor recording session 71836 and 71837 when put together make stereo. The conventional progressions of technology people have grown used to are suddenly thrown out: true stereo 20 years ahead of hi-fi. By the time of the discovery, Wellington was no longer around to reap what Plutarch called the “advantages of continuity”. Many others, however, have. NASA might take note. Without the willpower and the means of distribution genius, as Edison, Berliner, Ellington all verify, languishes in a realm of dream, the metaverse of desire. It’s here where the ideas of innovation don’t get realised. The digital sphere substitutes the eternal for the internal. Teenagers, of all ages, are fomenting strife right now battling Moors, Nazis, Pirates, South Central cops, in worlds of adventure that have already happened. Should boredom become a thing of the past the conditions conducive to greatness are likely to follow with it.
The new Hino 700 Series rewrites the rules in safety, emissions and connectivity. It’s our safest truck ever, with an enhanced Hino SmartSafe package including Pre-Collision System, Pedestrian Detection, Lane Departure Warning System and Driver Monitor. Designed to meet Euro 6 exhaust emission standards, it’s the cleanest Hino heavy-duty yet. With Hino-Connect on board as standard, benefit from superior business intel and support, it’s next-generation telematics delivered in real-time. The all-new 700 Series is the truck of the future, here today. Find out more at hino.com.au
Penske Australia and MAN Truck & Bus have revealed the new MAN truck generation in an exclusive event held in Brisbane. Long awaited, the MAN new truck generation is the first from the German OEM in two decades.
The TGL, TGM, TGS and TGX ranges have been attuned for an enhanced driver fit, greater efficiencies, economy features and optimised uptime.
An intuitive dash layout, multifunction steering wheel, advanced infotainment system, and SmartSelect navigator provide a user-friendly and ergonomically-optimal cabin environment.
Economical engines range from the 250hp D08 to the 640hp D38 Euro 6e engine, with various options in between.
The MAN Tipmatic gearbox shift system uses software to determine the optimum moving off and gearshift
strategy in all situations in conjunction with load and inclination detection, and is coupled with SmartShifting and the idle speed driving functionality.
A media drive day at the Mount Cotton test track saw key MAN and Penske Australia management in attendance including Randall Seymore, Executive Vice President, Global Commercial Vehicles & Power Systems, Craig Lee, Executive General Manager –On-Highway, Sergio Carboni, MAN Product Manager and Thomas Hemmerich, Head of Cluster MAN Australasia, who oversees 13 countries including Australia.
Speaking at the event, Lee, explained the significance of the new truck generation and pointed out that it had been built on 250 years of quality German engineering.
“MAN has proven their truck for the long haul all around the world.
Importantly MAN and Penske are commited to the long haul here in Australia. We are delighted to introduce the all-new MAN truck generation to our customers and the Australian market,” he said. “We’ve set about over the last number of years to build a strong foundation to support our customers. Customers can clearly see that the newly-developed trucks are a game-changer for the transport industry. We’re confident that the new MAN truck generation will redefine trucking.”
Efficiency is further improved through an enhanced overall aerodynamic package and the Turbo EVBec that produces 840hp of engine braking. Among its other selling points, the MAN TG3 boasts the longest bed in the class at over 2.1 metres long and is the first truck globally to have the SmartSelect control module in the cab.
Mercedes-Benz Trucks will begin a local evaluation program for the allelectric eActros in Australia and New Zealand. Early next year, four eActros trucks will get to work in Australia and one unit will hit the road in New Zealand, with additional units to follow. The eActros has just been launched in Europe.
Mercedes-Benz Trucks Australia Pacific Director, Andrew Assimo, said the local evaluation program for eActros was part of a drive towards CO2-neutral goods transport.
“We are excited to conduct this extensive testing program on the roads of Australia and New Zealand for the advanced and innovative all-electric eActros, a truck that represents an exciting new chapter for sustainable
road transport in our region,” he said. “Mercedes-Benz Trucks always makes sure the advanced technology we introduce locally is tailored for our unique conditions and meets the specific requirements of our customers with extensive local evaluation and it is no different with zero emission electric technology.” Daimler Truck is committed to advancing battery electric technology for trucks and buses but is also working on hydrogen fuel cell technology that is well suited to Australian requirements of longer distances at higher weights. While hydrogen fuel cell trucks are currently being tested they are still some years away from introduction. Battery electric Mercedes-Benz trucks are
already in production and out on the road with leading European fleets.
The focus of the eActros is for heavy-duty short radius distribution and development trucks have been working away in select fleets in Europe since 2018.
Assimo said Mercedes-Benz Trucks is excited to fulfil customer demand and bring the all-electric eActros to Australia and New Zealand.
“Our key customers are very passionate about advanced electric heavy vehicles and we are thrilled to begin the evaluation program that will ensure our electric Actros will succeed in our market,” he said.
No date has been formally confirmed for when the eActros will be made available in Australia.
WorkControl has introduced three new Mercedes-Benz Actros 2653s to its regional NSW operations. The vehicles will pull Etnyre Falcon triaxle walking floor trailers specified for asphalting work.
Founded in Forbes by Kevin and Colleen Gunn, the roadworks and traffic control business is now run by their sons Ben and Joe Gunn and operates across six locations throughout western New South Wales. It currently employs 300 people and has a fleet of 130 vehicles. WorkControl has expanded recently to
include roadwork services, prompting the purchase of the three Actros trucks that feature striking artwork celebrating the Wiradjuri heritage of the Gunn family. The advanced active safety features of the Actros proved a major selling point. Advanced Emergency Braking System (AEBS) including the latest generation Active Brake Assist 5, which can come to a complete stop for pedestrians as well as vehicles, helped sway Ben Gunn.
“Safety is at the very centre of everything we do at WorkControl,” said
Gunn. “Keeping workers safe is the very reason our business exists, so it is only natural that we choose trucks like the Actros with all their safety gear.”
The Actros models were provided by Daimler Trucks Huntingwood by salesman Mark McKenzie, in conjunction with Troy Azzopardi from Muscat Trailers, who delivered the Etnyre Falcon trailers.
The 2653 Actros features the muscular 13-litre six-cylinder Mercedes-Benz engine that generates 530hp and 2600Nm of torque.
In transport there’s no one size fits all. That’s why we have a wide range of sleeper cabs locally engineered to maximise the living quarters of your most important asset, your drivers. When it comes to comfort and well-being, size matters. kenworth.com.au
Notice 2022 is being touted as a win for some heavy vehicle operators in South Australia. Operators of eligible livestock carriers, AB-triples and Type 1 roadtrains – including non-modular and modular B-triples – in South Australia can now operate at increased mass limits on designated routes, it was announced recently.
The exemption applies to these heavy vehicle operators providing their vehicle has certified road-friendly suspension.
NHVR Chief Regulatory Policy and
Standards Officer Don Hogben said the new South Australian Class 3 Road friendly Suspension Mass Exemption Notice 2022 allows certain heavy vehicles and combinations fitted with certified road-friendly suspension to operate at masses equivalent to Higher Mass Limits, without needing to be enrolled in the Intelligent Access Program (IAP).
“The notice replaces the South Australia Class 3 (HML Application) Mass Exemption 2021, and includes beneficial changes to vehicle eligibility
and networks,” said Hogben. “This notice represents significant progress towards removing the need for multiple permits in South Australia,” he said. Australian Transport Association Chair David Smith welcomed the notice as a significant win for Class 3 operators in South Australia.
“This is an important step towards national harmonisation and improved productivity for heavy vehicle movements, and that’s good for the industry and the local economy,” he said in a statement.
T610SAR models with O’Phee B-double road transpec configurations. The Kenworths feature a Cummins X15 Euro V engine with 615hp and 1850 lb-ft of torque, each rated to 97 tonnes. The trucks will be carrying general freight along the East Coast between Cairns and Adelaide, along with cotton, wind and solar farms freight and power and infrastructure goods. In addition to the new vehicles, Jarratt is also welcoming four new truck drivers to the
times ahead for Jarratt Transport Solutions,” the company announced on social media.
Managing Director, Phil Jarratt, told Prime Mover he was excited by the prospect of the new additions to the fleet.
“I couldn’t be happier with them and I think they’re good enough that we’ll probably buy some more,” he said.
“We’re thrilled with them, we’ve been Kenworth clients for a long time. I bought
The O’Phee trailers were picked up from trailer builder, The Drake Group, the day following the arrival of the new Kenworths. Jarratt Transport Logistics specifies the Kenworths in the fleet, for the main part, with icepacks, microwaves, inverters, full digital onboard scales and Teletrac Navman telematics.
“The four new ones are now into the fold and their drivers are settling in,” added Jarratt. “‘Let the games begin’ was the catchphrase on Wednesday.”
source for transportation by 2030. The project would likely be located adjacent to Woodside’s proposed H2Perth project, a proposed domestic and export-scale hydrogen and ammonia production facility.
Hydrogen is proposed to be produced using a 2-megawatt electrolyser, powered by renewable energy sourced from the South West Interconnected System.
Production will be timed to occur during periods of excess solar in the grid and stored on-site.
Where needed, Woodside will also use Renewable Energy Certificates.
Western Australian transport company Centurion is set to buy and operate two hydrogen powered prime movers.
The move comes as it announced its partnership with Woodside Energy and BGC, a construction and housing specialist, that would also invest in hydrogen heavy vehicle technology. It was anticipated that BGC would purchase and operate between five to ten hydrogen fuel cell concrete agitator trucks.
The news follows an announcement that all three companies were set to advance plans for a proposed selfcontained hydrogen production, storage and refuelling station situated at the Rockingham Industry Zone. With support from the Western Australian Government, the project was proven successful in the Expressions of Interest stage of the Department of Jobs, Tourism, Science and Innovation’s $10 million Hydrogen Fuelled Transport Program. The Program aims to accelerate the uptake of hydrogen fuelled transport, build local skills and capability, and stimulate local hydrogen production in Western Australia. With
matched funding from Woodside, the proposal targets delivery of hydrogen fuel at a globally competitive price of $11 per kilo and subsidises a number of large hydrogen fuel cell electric vehicles. Centurion CEO, Justin Cardaci, said it was crucial for the company to support the development of transport sector related technology.
“Transport and logistics is an emissions intensive sector and it is incumbent on businesses like ours to actively participate in the energy transition and the journey towards a net-zero emissions future”, he said. “The investment by the WA Government and Woodside in hydrogen refuelling technology is a material step for companies like ours to accelerate the use of renewable fuel in the transport sector to transition its sustainability pathway.”
Named the Hydrogen Refueller @H2Perth, the project aims to supply low cost, renewable hydrogen fuel for local customers and stimulate and enable hydrogen demand in Western Australia where the State Government wants hydrogen to be a significant fuel
Initially, Woodside is targeting production of 235 kilograms per day of hydrogen at the Hydrogen Refueller @H2Perth, with the potential to scale up to a targeted 800 kilograms per day. Hydrogen Refueller @H2Perth will be available to industrial customers, as well as the public.
Woodside has signed conditional, non-binding offtake Memorandums of Understanding (MoU), stating its intention to supply hydrogen from Hydrogen Refueller @H2Perth to BGC and Centurion, both of which will invest in hydrogen fuel cell vehicles as a result. BGC CEO, Daniel Cooper said the initiative would be important to the future of mainstream hydrogen uptake in WA.
“BGC welcomes the opportunity to work with Woodside, Centurion and the State Government to progress the energy innovations needed to keep our industries powered into the future,” he said.
“We look forward to assessing the performance of these vehicles and sharing our learnings broadly to build the case for wider deployment.”
It is envisaged the grant will support BGC and Centurion with purchasing the vehicles to replace large diesel trucks currently in use.
Woodside also proposes to lease a small fleet of Hyundai Nexo vehicles which are to be refuelled at the facility.
Austroads is encouraging drivers, employers and trainers to have their say on proposed changes to heavy vehicle driver licensing in Australia. The changes are documented in a Consultation Regulator Impact Statement (C-RIS) which seeks feedback on proposed changes to the National Heavy Vehicle Driver Competency Framework NHVDCF).
At the request of transport ministers, Austroads has been undertaking an extensive program of work to review and improve the NHVDCF. Four key areas of change have been proposed in the review the first of which is the need to manage individual driver risk ensuring only drivers without serious driving offences are eligible to hold a heavy vehicle licence. Making competency requirements specific to each licence class based on strengthening skill and knowledge in addition to setting minimum
course length, and recognising the extra skill needed to drive the most complex vehicles.
Austroads also recommended that embedding behind-the-wheel experience requiring minimum behind-the-wheel time pre-licence and supervised driving sessions post-licence; and introducing experience-based progression options enabling those drivers who can demonstrate driving and work experience to progress to higher licence classes more rapidly.
The review, according to Austroads, aims to deliver a harmonised Australian license training and assessment framework that produces safe and competent heavy vehicle drivers, and reflects the current and future needs of heavy vehicle operators and the future freight task. Austroads Chief Executive, Geoff Allan, said that effective driver licensing is the answer to Australia’s demands.
Queensland-based Richers Transport has taken delivery of a new Mack truck – its 200th to date. With a history that stretches back nearly 90 years, Richers Transport started out with just one Model T Ford and last year took delivery of the first Mack Anthem to hit the road in Australia.
The 200th Mack truck also carries the Anthem badge.
“We choose to go with Mack for drivability, they’re great for the drivers, for fuel economy, and are equipped with a good safety package,” said Tom Richers, Richers Transport Operations Manager.
“They’re great from a maintenance perspective as well. The service and back-up we get from the dealer network is fantastic.”
Operationally, Richers Transport covers the entire Australian eastern seaboard from Cairns to Adelaide transporting groceries, particle board, alcohol, and general freight.
“We often talk about durability when we talk about Mack trucks,” said Tom
“With a growing freight task and changing vehicle fleet, Australia needs a lot of well-trained and capable heavy vehicle drivers,” he said. “Industry feedback, emerging research and evidence suggest we should prioritise strengthening driver competencies, skills assessment, and licensing policy.”
According to Allan, the proposed changes will help increase the number of heavy vehicle drivers to combat countrywide shortages.
“The driver shortage is a broader problem than licensing alone can fix,” he said.
“But the proposed changes have been developed so that there are faster ways to progress through heavy vehicle licence classes.
“Making the pathway to licences faster may help expand the pool of drivers, and the improved competency standards should make new drivers more jobready.”
Chapman, Vice President Mack Trucks Australia.
“However, durability of customer relationships such as the one forged between Mack and the Richers family over many decades is perhaps even more important.”
Productivity and efficiency are vital in a modern transport operation. According to Chapman an enduring partnership based on trust in both people and product, however, doesn’t just happen overnight — its built over many years.
“I’m very proud to mark this milestone event with the Richers family, it’s a testament to the strength of both brands, Richers transport and Mack trucks,” said Chapman.
The distinctive green and white Richers livery of the milestone Anthem is subtly complemented by custom stainless-steel work and signwriting.
The MP8 powered Mack Anthem also features a walk-through 36-inch sleeper cab, and an integrated Bendix Wingman
Fusion safety system as standard equipment.
Truck and logistics operator, Mainfreight, has announced its electric vehicle strategy in a new report released to the public. In the Mainfreight Sustainability Overview 2022, the company has summarised its current procurement strategy for lower emission commercial vehicles across several international regions including Australia where it maintains a growing presence.
In Australia, Mainfreight has eight new electric truck builds underway including two Hino 300 glider kits with SEA 85s and six Foton iBlues. Both variants have a similar range of approximately 200km and operating payloads between 2.5 tonne and 5-plus tonne.
Mainfreight confirmed it expects all eight units will be on the road by the end of the year predominantly serving major metro areas.
In New Zealand Mainfreight is now operating four Fuso eCanters in Auckland and Hamilton, with options for a further
ten also being considered. Mainfreight has also committed to operating its own battery swapping and charging infrastructure in Hamilton using energy generated from its own onsite solar installations.
According to Mainfreight, the E700 with battery swap will be installed as New Zealand’s first heavy intercity general freight model, operating between Auckland and Hamilton.
“Battery Swap electric vehicles offer an attractive solution to several of the drawbacks in hydrogen fuel cell electric vehicles and battery electric vehicles,” the company said in the report. “Specifically it takes advantage of battery electric lower operating costs but overcomes the range, charging time and payload restraints, by having smaller quick to charge batteries.
“This allows the use of Lithium Ferrous Phosphate batteries rather than lithiumion which are safer, more stable and
less environmentally harmful. We expect this vehicle will reduce our road freight emissions by over 100 tonnes of CO2-e per year.”
Low emission heavy vehicles, according to the report, are going to be critical in efforts to decarbonise road freight. “The rate of innovation and development in these technologies is exciting but still has some way to go before widespread adoption,” Mainfreight said. “Our current explorations focus on supplementing our fleet with battery electric vehicles and Battery Swap Electric Vehicles.”
Hydrogen fuel cell electric vehicles and hydrogen dual fuel vehicles do not currently feature in Mainfreight’s fleet mix but remain technologies of interest the company said.
Mainfreight has also procured a MAN e-TGM and DAF EV for the Dutch city of Tilburg which is among the first of the Netherlands cities to impose a ban on fossil fuel vehicles in major urban areas.
The new MAN generation redefines trucking in the modern age. Elevating driver fit, efficiency and economy, MAN optimises profitable working time.
To put it simply, when it comes to trucks, MAN is the only choice. MAN. Simply My Truck.
New Mack units have joined the Diamond Brothers fleet recently as it seeks to satisfy driver requirements and efficiency gains. The Adelaidebased operation has been providing its customers tailored transport solutions for nearly seven decades. With an early history in car carrying, the company has evolved to a dedicated interstate general carrier servicing all east coast capitals as well as Perth, Western Australia in predominantly B-double and B-triple applications.
As it looks to further boost customer service and operational efficiencies more Mack trucks have been introduced to the fleet in recent years to satisfy the expectations of not only the company itself but also the drivers as well. Kym McDermid, CEO Diamond Brothers Transport said the new generation of Mack trucks are continuing to impress with their efficiency and performance.
“With over 50 years of Mack being
made here in Australia we have the Anthem that is a new generation, not only does it look fantastic it does the job too,” he said.
McDermid was aware of the Mack brand from a young age, having been brought up knowing massive Macks were carrying Buntine roadtrains all over Australia.
Diamond Brothers now have two Mack Anthems working linehaul for the business with more on the way.
“We have better fuel economy with the Anthem, it’s really been exceptional on fuel economy,” he said. “Fuel efficiency is important for two reasons, one is obviously, the cost of fuel and you want to keep your costs down as much as you can. But it’s also about your carbon footprint as well. So that’s been good for us also.”
While the bottom line is important, a driver’s perspective is also just as vital. Long-term Diamond Brothers driver, Andy Price, is a fan of the Mack Anthem.
“I’ve been in the Anthem for over a year now. I find I’m actually less fatigued than I would if I was driving a more conventional truck,” he said. “With the 8-airbag system on the rear and the parabolic leaf spring suspension up the front, the ride in the Anthem is incredible. A lot of trucks would kick and buck like you were riding a horse but the Anthem is a lot smoother to drive.
“I’ve noticed it’s a lot friendlier truck, you’ve got the space. You don’t feel like you’re squashed — the Anthem seems to be just more driver friendly.”
As a linehaul driver Price spends more time on the road than he does in his own bed.
“The Anthem has got the comfort, it’s got a nice bedroom, nice comfortable seats and it’s got the space, it’s a good truck to be out on the road and away from home in,” he said. “I think the Anthem is going to be a gamechanger.”
Good design is a hallmark of DAF trucks, and with the latest model range our distinctive exterior styling means our trucks are instantly recognisable on the road. Not only that, our latest design features also contribute to excellent aerodynamics to enhance your bottom line.
Whether it’s moving freight across the nation, or going the last mile, DAF Trucks are Always Delivering.
Industry veteran, road transport pioneer and CRT Group boss Colin Rees has been awarded the prestigious Personality of the Year. Rees was recognised in front of peers at a packed Crown Palladium for the 32nd Australian Freight Industry Awards.
For over 60 years Rees and his family have developed a number of innovative transport businesses across bulk haulage, timber transport, taxi trucks and the Ettamogah Rail Hub.
Rees, who turned 75 the week prior, said the industry had been good to him after more than 50 years before acknowledging the support he received from his wife.
“You can’t do this without a good backstop. I’ve certainly had that in Val,” he said to cheers. “Transport can be pretty tough on relationships but through it all Val has been there supporting me doing the things that
need to be done to get you through,” he said.
ARTSA’s Rob Perkins was among those that he thanked.
“Everybody needs a good sidekick particularly in the transport industry to keep you focused and to be there when you need somebody to support you,” said Rees.
Following a three-year hiatus, nearly 700 people gathered to celebrate the achievements of transport operator and supplier companies and individuals across a range of categories.
Surpassing a record number of nominations lodged in 2020 – when the Awards were presented virtually –over 60 nominations were submitted this year from small, medium and large operators from all over Australia. Other winners include Cara Spencer from the Alex Fraser Group for the Female Leadership Award;
Claudia Jennings, Linfox, for the Young Achiever of the Year Award; SEA Electric for the Sustainable Environment Award; Knorr Bremse Australia, for the Application of Technology Award; Wettenhalls, for Best Practice Safety Award; and Qube Bulk, for the Investment in People Award.
“Every one of our winners and finalists should be proud of their accomplishments, and particularly that they were achieved during a time of great challenge and uncertainty in people’s professional and personal lives,” said VTA CEO Peter Anderson. “Their endurance, commitment and effort are reflective of every transport worker that has stood up and served our communities over the past three years, and it was terrific to recognise that in person at our awards presentation.”
The 11L Quon just got even better with its latest enhancements improving its already outstanding fuel efficiency and performance.
11-litre Quon’s new driveline features a cleaner, improved ‘GH11 Engine’ with increased horsepower and torque, and the legendary ESCOT 12-speed automated manual transmission is now even better with new software enhancements that have to be tried to be believed.
These upgraded features also help to reduce carbon emissions, with the added bonus of delivering an even smoother ride for comfortable driving with minimal fatigue.
For over 85 years, UD Trucks have delivered ultimate dependability. No wonder this is the truck Australia trusts.
To find out more, contact your UD Trucks dealer on 1300 BUY A UD or visit udtrucks.com/australia
A restored World War 2-era Blitz truck was recently handed over to the Royal Australian Air Force (RAAF) Amberley Aviation Heritage Centre. The truck, with the serial number 19012, was restored by the History and Heritage – Air Force’s Restoration Support Section (RSS).
Australia and its allies used Blitz trucks extensively during World War II in various roles including transporting troops and cargo. An estimated 800,000 Blitz trucks were manufactured in Canada by Ford, General Motors and Dodge, and shipped around the world to assist with the war effort.
Following World War II, Australia continued to use Blitz trucks in its defence, forestry, agriculture, transportation and engineering industries. Wing Commander Kevin
Aviation Heritage Centre, said the vehicle was versatile.
“The Blitz truck saw service in all theatres and was used by all branches of the Australian military and allied Commonwealth forces,” said Wing Commander Kovic. “This particular truck was in RAAF service and was used as a recovery vehicle.”
The RSS team, led by Corporal Steve
Luyten, Max Farrell, Doug Eadie and Charlie Miles, painstakingly rebuilt the Blitz truck 19012 from the ground up over many years – including a period of intensive activity from 2020-22. The restoration included overhauling the truck’s engine, rebuilding its clutch and brake systems, re-wiring its electrical system, and manufacturing and fitting the half-doors and modified tray bed.
While Blitz truck 19012 was originally fitted with a crane, the restoration team manufactured and fitted a replica cargo tray.
“We at the Amberley Aviation Heritage Centre are extremely pleased with the great attention to detail in its refurbishment, as performed by our restoration volunteers and reservists,” said Wing Commander Kovic.
Freightliner Cascadias for the work it undertakes in and out of the Australian food bowl. The Goulburn Valley produces more than 25 per cent of Victoria’s food output, including vast amounts of fruit, vegetables, meat and milk, and much of it is exported. This huge demand is one of the reasons that Kreskas Bros Transport is the largest road carrier of shipping containers between the Port of Melbourne and regional Victoria. Kreskas Bros runs a mixed fleet of trucks that includes traditional cabovers, Mercedes-Benz Actros and some recently arrived Freightliner Cascadias. Its first experience with the Cascadia came
industry icon and longtime friend of the Kreskas Bros team, took on a central role in the Australian test program for the new Freightliner.
McCarroll evaluated a Cascadia test unit B-double five days a week for 18 months, storing it overnight at the Kreskas Bros yard. A Cascadia 126 in Kreskas Bros colours joined the fleet just months after the Cascadia was officially launched in Australia in late 2019 and soon impressed the team running as an A-double between Shepparton and Melbourne. One of the first things that stood out was the comfort of the advanced bonneted truck that has a spacious 48-inch
sleeper cap and the latest ergonomic interior design.
“Anyone who drives it will tell you how comfortable they are to drive,” said Kreskas Bros Transport Fleet Manager, Kevin Mutton. “Keeping our drivers comfortable is very important to us, they spend a lot of time in the truck, so that is a really big positive.”
Another standout early on was the excellent fuel consumption.
“It’s clear that this is a very efficient truck,” said Mutton. “After 290,000km we can say the Cascadia is clearly the most fuel efficient truck in our fleet.”
Kreskas Bros Transport General Manager, Adam Katsoutas, said the integrated active safety systems like the radar and camera-based Advanced Emergency Braking System (AEBS) that can automatically detect, and fully brake for, moving pedestrians in addition to vehicles are important.
“Safety is paramount for our team at Kreskas Bros Transport, so the kind of safety features in the Cascadias are very welcome,” he said. “This is a simple way that we can best protect our drivers and the wider community.”
Nine New Zealand companies involved in civil maintenance, traffic management and urban delivery recently introduced unique purpose-built Fuso eCanter trucks as part of two emission-reduction projects. The projects launched by Christchurch City Council and co-funded by the Energy Efficient Conservation Authority (EECA) are supported by Fuso New Zealand and commercial vehicle lease specialists TR Group, telematics experts EROAD and renewable electricity generator and EV charging specialists Mercury NZ. The Civil Construction and Maintenance Services Project involves Citycare Property, Fulton Hogan Ltd, HEB Construction Ltd, Higgins Contractors Ltd, and Isaac Construction Ltd, which all service Christchurch City Council contracts.
The Shopping District Battery Electric Truck Delivery Services Project involves Bidfood, Halls, PBT Transport Ltd and Toll New Zealand. These companies will deliver goods to the Papanui shopping district, with both Northlands and Northlink Shopping Centres involved, and to the Christchurch
Airport shopping district.
The Fuso eCanter electric trucks have been fitted with a variety of applicationspecific body types. These include chiller bodies for fresh food distribution, curtainsiders for express freight delivery, and a range of flat deck and utility configurations for civil infrastructure, maintenance work and traffic management.
Fuso New Zealand General Manager, Kevin Smith, highlighted the broad scope of body types as a positive demonstration of the versatility and adaptability of the all-electric 6T and 7.5T Fuso eCanter range.
“It has been Fuso New Zealand’s pleasure to work closely from day one with Christchurch City Council to formulate these two projects, and to collaborate with participating businesses
across a range of industries,” said Smith.
As the number one selling truck brand in New Zealand, Fuso provides a mature and highly accessible nationwide parts and service network 24 hours a day, seven days a week.
Christchurch City Council Resource Efficiency Manager Kevin Crutchley said the projects would provide invaluable learnings not only for the Council and participating business, but for other local councils and the wider transport and civil contracting industries, as well as others.
“We’re gathering practical learnings from the projects, so that truck operators can see how to best use battery electric truck technology for their operations,” said Crutchley. “It’s important to note that all equipment and plant use from these battery electric vehicles will have zero exhaust emissions. The projects
As Euro VI looms as the emission limit for new trucks, it’s time to identify the required technologies to have a 100 per cent carbon neutral product line-up by 2040.
As industry groups in Europe and the US debate when and how to move to Euro 7/ VII and equivalent vehicle emission limits, here in Australia it appears that we may soon have some certainty for the introduction of Euro VI limits for heavy vehicles, having had mandatory Euro V new vehicles on the road for more than 11 years so far. We expect that Euro VI compliant engines for all new trucks sold will be required by the second half of 2025. On the other hand, Euro 6 for light vehicles is potentially a little further away due to issues around petrol fuel quality sold in Australia.
As Australian vehicles progress slowly towards improved emissions standards, the question remains, what part does this country’s ageing truck fleet play in applying the handbrake to the important goal of cleaner air for the generations ahead? By way of some background on this issue, European emission standards were first introduced in 1992 to lower harmful exhaust emissions of new vehicles sold in the European Union (EU), the European Economic Area (Iceland, Liechtenstein and Norway) and the United Kingdom.
More than 80 per cent of the global car market has already adopted Euro 6 vehicle emission standards, including Europe, the United States, Canada,
Japan, Korea, China, India and Mexico. Under the current Australian regulations, all heavy vehicle models sold in Australia must comply with the Euro-V noxious emissions standards.
In 2015, the former government set up a Ministerial Forum on Vehicle Emissions to review whether Australia should adopt the Euro 6/VI standards. That is, Euro-6 for cars and other light vehicles, as well as Euro VI for heavy vehicles. In late 2020, the federal Department of Infrastructure, Transport, Regional Development and Communications released draft regulation impact statements (RIS) that estimated the costs and benefits of improving noxious emissions standards for light and heavy vehicles.
Adopting the next level of emission limit, the Euro 6, would reduce the emission limits for oxides of nitrogen (NOx) by up to 80 per cent and reduce emission limits for particulate matter by up to 66 per cent, according to the RIS. The RIS found adopting the stricter emission targets would generate significant benefits for government in the form of $6.7 billion in avoided health costs. But there would also be significant costs for vehicle makers.
“The analysis suggested that, if adopted, the introduction of Euro VI for heavy vehicles for all newly approved models manufactured from 1 July 2027 and for
all new heavy vehicles manufactured from 1 July 2028 would result in … increased capital costs to manufacturers of $985 million over the period to 2050,” the RIS said.
While my organisation, Isuzu Australia Limited, (IAL) wholeheartedly supports the move to cleaner vehicles, it’s counter-productive to suggest vehicle manufacturers alone should foot the entirety of this bill. Industry needs improved clarification on when new emission limits will be introduced. Everyone involved in the road transport industry needs time to plan and prepare for the stricter limits, which for some will mean a significant capital investment. The new Australian Federal Government, elected in May, has already signalled a strong commitment to reducing greenhouse gas emissions. On 16 June, Prime Minister Anthony Albanese said Australia’s new Paris Agreement commitment would be to reduce emissions by 43 per cent by 2030.
According to the Federal Government’s Green Vehicle Guide, emissions from
light passenger and commercial vehicles account for 61 per cent of greenhouse gas emissions produced in Australia. That means the transport industry, in lockstep with government, has a big part to play in Australia’s effort to reduce its emissions footprint.
IAL is strongly in favour of Australia’s transport fleet becoming cleaner and greener, which, with the current technological advances, also means safer. And that means getting older, unsafe trucks off the road and replacing them with low-emission vehicles. Isuzu believes the Federal Government could offer incentives to owners of pre-1996 trucks to upgrade to Euro V or higher compliant truck models. This could be in the form of an accelerated depreciation or investment allowance. To this end, there’s several different models that could work, but any allowance should work in concert with additions to the existing uniform capital allowance and to be fully effective, should also include a provision for the purchase of late model second hand trucks, too. The outcomes of this are as
straightforward as they are beneficial — vastly improved emissions standards, improved overall road safety and greater efficiencies, more uptime equating to economic gains through improved productivity.
IAL and its parent company Isuzu Motors Limited in Japan have committed to achieving net zero greenhouse gas emissions by 2050. This will be achieved in part by reducing energy use and actively introducing clean, renewable energy technologies. To make sure Isuzu meets its 2050 targets, the company has set some goals, including identifying the required technologies by 2025 to have a 100 per cent carbon neutral product line-up by 2040. By 2030, Isuzu also aims to have halved the level of the company’s 2013 carbon dioxide output.
Isuzu has a proud history both globally, and here in Australia, of working to transform road transport products for the better and to our collective benefit. As Euro VI looms for new trucks, it’s time to eat the emissions elephant one bite at a time, and from both ends.
Uncompromising customer service has been one of the key factors behind the success of Carey’s Freight Lines for the past 75 years.
Carey’s Freight Lines has been based in Tamworth for 75 years, a remarkable achievement in road freight operations which the company has celebrated by proudly specifying heritage liveries to its 2022 model Kenworths and Mercedes-Benz prime movers to reflect the longevity of the service Carey’s has provided to the local region. Harold Carey bought his first truck in 1947 after he returned to Tamworth
from the war. Harold carried timber and wheat on a four tonne Ford tabletop, before he progressed to a Chev Maple Leaf prime mover connected to a single axle trailer, a world away from the modern equipment the company utilises today.
Harold’s sons John and Michael (Mick) took over after Harold’s retirement in the early ‘80s with Mick looking after the workshop which at one point was a service agency for Mack trucks, and
John handling operations. The company is today run by the third generation of Carey’s with Mick’s son Darren as the General Manager and his brother Todd following in their father’s footsteps in maintenance. John’s son Rick, meanwhile, works in operations. Carey’s first Kenworth, a T600, was purchased in 1990. Kenworths with Cummins engines have been the mainstay of the fleet ever since due to reliability and longevity. The current
fleet of 74 prime movers remains predominately Kenworth with some Mercedes-Benz and Volvo models added over the past few years. The prime movers are complemented by a number of 14-pallet rigid Tautliners and fridge vans with tailgate loaders which are mostly Isuzu with the odd Fuso as well.
Carey’s is equipped with 210 trailers. The latest additions are from Vawdrey and Krueger and join a differing fleet of trailer brands containing the likes
of Maxicube, Freighter, Barker and FTE. Many of the Kenworths have been more recently assigned to local work having completed their time on long highway duties.
“We have a lot of local work involving low kilometre trips from the depot which is performed by 15 to 17 year-old Kenworth trucks with up to 2.5 million kilometres on them,” says Darren. “They can still do the job thanks to the support from our local Cummins people, and Kenworth through the local Brown and Hurley dealership. Most of the fleet is cabover because they are so flexible, yet we’ve always had a couple of bonneted trucks which can do single fridge van work and can also pull B-double skels. “With cabovers we can have plenty of space, so we don’t have to worry about squeezing in our 34-pallet fridge vans to fit in with the 26-metre maximum length.”
Carey’s recently took delivery of two Kenworth T410s with PACCAR MX
engines and transmissions intended for a specific single application.
Darren generally prefers automated transmissions but has also recently added three Kenworth T610s with manuals.
“Two were dealer stock trucks which we needed desperately last year and the other was the SAR which was a bit of a special build,” he recalls.
The operations of Carey’s are diverse. They include general freight, dry and refrigerated grocery distribution to supermarkets throughout northwest NSW, domestic and export meat from meat processing facilities in Tamworth, as well as building materials and steel.
Carey’s also is involved in the supply, transport and sale of bricks and tiles for which local deliveries to building sites are made using two drop deck trailers and Manitou all-terrain forklifts.
“Being diverse and not having all your eggs in one basket has been a successful strategy and is important to us,”
says Darren.
The transport company operates across three sites in Tamworth consisting of the freight distribution centre, a wellequipped maintenance facility, and a container handling yard. Carey’s also has a depot in Sydney. Meanwhile a new facility opened in Brisbane at the beginning of August this year.
As far as policy goes, each truck has its own dedicated driver, with the exception being a couple of specific runs where two drivers operate on a change-over system. The container trucks operate on the higher mass limits of 68 tonnes and four Kenworth A-double PBS combinations run between Tamworth and Port Botany, and to Brisbane’s Fisherman’s Island port facility.
Darren says the A-doubles have been a gamechanger.
“We can go straight into the port on
our PBS permit which is a big change for us. Now we carry 120 to 130 export containers out of Tamworth each week and every one of those 40-footers was previously a single truck,” he explains.
“That means we can get two 40 foot refrigerated containers on an A-double, and we are doing that seven days a week.”
The scope of operations may be diverse yet there is a clear realisation that doing what you know well is preferable to extreme expansion which can often prove chaotic.
“We don’t do any typical interstate work,” says Darren. “We basically concentrate on our operations to Tamworth and the northwest area of NSW out of Brisbane and Sydney. This means our trucks are home regularly for services, and the drivers can have more of a home life.”
Drivers regularly have their seven-hour breaks in their trucks but are always at home for 24- and 48-hour breaks.
The general consensus is that this does help to attract and retain drivers. It’s by no coincidence that Carey’s retains a number of drivers with over 20 years of service, while many more are either ten or 15-years in. The majority of drivers are Tamworth locals, but the nature of the Carey’s operations means drivers can be located anywhere between Sydney and Brisbane along the New England Highway. As with most other industries and transport particularly, there is the universal challenge of recruiting new people, especially young people.
“In Tamworth we are pretty lucky. We’ve got three abattoirs and a lot of other industry,” says Darren. “If you’re in Tamworth and you haven’t got a job you pretty much don’t much want one.
We have a lot of local work and this helps getting young guys a start in the industry. We will help them get their forklift licence, then progress to heavy rigid to semi-trailers. They can run around town and then do an occasional longer trip to get some experience and learn from the older drivers.”
Vehicle servicing is performed in-house in a fully-equipped six bay drivethrough workshop located within walking distance of the main depot. The workshop has a staff of 12 including a welder, a fibre-glasser and a designated trailer washer as well as the mechanics. Truck dealerships including Brown and Hurley and the local Cummins facility are located nearby.
“We do take a fair bit of work to the local Cummins branch,” says Todd Carey, who supervises the fleet’s maintenance operations “They do most of our engine work as we don’t do a lot of intense engine work here and any rebuilds go to Cummins.”
The majority of Carey’s late model Cummins engines are rated at 550hp and 2050 ft/lbs of torque.
“We have extended the oil drains on the Euro V engines out to the 60,000
kilometres as recommended by Cummins,” Todd explains. “They do a fine job. The older ones obviously are less but we haven’t got many of them left.”
Safety of the drivers and other road users is paramount at Carey’s. All available safety technologies are explored by the company. Every vehicle in the fleet is GPS tracked, fitted with multiple cameras, Seeing Machines and electronic work diaries, all of which are looked after by Teletrac Navman. These technologies allow the management team to stay on top of where drivers and vehicles are at any time for effective scheduling and fatigue management. Though the acceptance by drivers of new technologies has been a challenge in the past.
“It’s like all technology. When we first put GPS tracking in some drivers thought we were just spying on them. Forward facing cameras were far easier for them to accept but not the Seeing Machines,” recalls Darren. “Nobody wants to be told they’re not doing their job correctly, so we invited them all in and explained these aren’t a camera intended to watch them. We showed
some of them footage of themselves and they hadn’t realised how tired they looked. We are definitely getting better acceptance of them now.”
After a period of operating the paperbased work diary parallel to electronic work diaries, Carey’s are in the early stages of making the switch to electronic work diaries only. There is a genuine and obvious effort to stay abreast of the technological advances for safety which has been recognised by the Tamworth Business Chamber Awards, as well as SafeWork NSW who have nominated Carey’s for the workplace health and safety category in its annual awards. Darren Carey is proud of the opportunity the business has given not only his family, but so many Tamworth families as well.
“We have many second-generation drivers here. Ageing workforce is a challenge, so it is important to keep the family connection with our long-term staff,” he says. “I am proud of our trucks and our staff and the fact so many of them are proud to work here. It makes me happy to see so many of our trucks washed and polished and treated by the drivers as if they are their own.”
range of operations,
been
Before he became involved in transport Lloyd Hillman was a mechanic, and by all reports, a very good one. Lloyd performed a lot of turbo work including turbocharging Toyota Landcruisers back in the ‘80s which was before turbos became more common as standard equipment. Today Lloyd still loves his cars and the single truck operation he started when he hung up his spanners has grown to 42 prime movers and 100 trailers of varying configurations with the transport business now run by his sons Chris and Steve.
Hillman’s Transport operates express freight services which cover Western and Central Queensland including places such as Rockhampton, Chinchilla, Mackay, Gladstone, Longreach, Cloncurry and Mount Isa, as well as all mainland capital cities.
As the Hillman’s Transport operation has grown there are a number of different divisions within the business including linehaul operations out of the Toowoomba base to Darwin and Mount Isa which typically uses triple and quad roadtrains. Currently six prime movers with similar trailer combinations
a focus
customer service
operate from the Townsville base moving freight to places such as Cloncurry and Mount Isa.
The agricultural division predominantly involves picking up bales of cotton from the various gins around Dalby and transporting them using A-double combinations to the Port of Brisbane to be exported.
The grocery division has Hillman’s prime movers towing trailers to locations such as Armidale and Narrabri in New South Wales. This involves mainly refrigerated trailers and there are dry goods carried as well. Steve concedes
the mining division can be somewhat ad hoc in its fluctuating demands. At peak times up to 50 trailers are used to service mining and gas sites throughout the Serat and Cooper Basins, carrying general freight including generators, oil, and accommodation modules (“dongas”). Hillmans can also provide a dedicated ‘hot shot’ service for when more urgent deliveries are required, as well as OSOM wide load heavy haulage services.
“It was a lot bigger back in 2013-14 before a big mining slow down but it is coming back again now,” says Steve. “Mining just keeps rolling around and where one section goes quiet another becomes busy.”
The diversity of the Hillman’s operations has an influence on the equipment they purchase with an aim to specify prime movers so that they can be utilised throughout the entire fleet. A truck such as a 600 horsepower Volvo must be capable of deployment in situations that require hauling single trailers up to quad roadtrains on bitumen as well as unsealed roads.
All trucks are on service contracts through the manufacturers and are generally replaced at 1.2 million
kilometres. None are kept longer than five years, and the current average age is well under three years. Hillman’s Transport is an accredited member of TruckSafe as well as the National Heavy Vehicle Accreditation Scheme for Mass and Maintenance and Basic Fatigue Management. The company is also certified under the Coal Seam Gas Logistics Safety Code.
Volvo, Mack and Kenworth are the dominant brands in the Hillman’s fleet and a couple of DAF CF530 models have been recently added for grocery work. A total of 30 new Mack and Volvo trucks are on order for delivery in late 2022 and into 2023.
“We choose trucks for service, especially the service they give us if we break down in the bush,” says Steve. “We believe the
Volvo Group looks after us very well. In the past we’ve had other brands seeming to fight over who is responsible for what parts. At Volvo Group they manufacture the whole product, so I haven’t had that argument at all. We also look for reliability. We have trucks which go to 1.2million kilometres and we don’t have many trucks sitting on the side of the road because of breakdowns.”
All vehicles are managed using the MTData telematics system and the Volvo and Macks have the additional proprietary Volvo Dynafleet and Mack Telematics systems which are integral to the management of the servicing
arrangements.
“We run the Guardian systems as well,” says Steve of the Australian developed driver monitoring safety system. “With our drivers it’s about making sure the right people are in the right jobs and we have a strong base of drivers with many who have been here for 15 years. Some of the drivers didn’t like the Guardian system at first but we get them in and show them the footage where someone has had a nod off and I invite their wife and kids to come in and have a look too. It’s not about us spying on people, it’s about protecting lives – theirs’ and other road users. That’s the main thing. We can
always replace trucks and trailers, but we can’t replace a life, so to me they are worth their while.”
To match the diversity of the company’s operations a wide selection of trailers is employed to suit individual job requirements including curtainsider B-doubles, 45-foot flat-tops with container pins, a 45-foot drop deck with hydraulic loading ramps, plus sideloaders and extendable 45-foot trailers capable of stretching to 71 feet lengths.
At the height of the COVID situation operations were maintained despite the almost continuous changing of rules relating to border crossings.
“We’d come to work in the morning and the rules would have changed about crossing the border by the afternoon and that was our biggest challenge,” says Steve.
“At times it was very hard to keep up but we all pulled together and got through it in the end but I’d be lying to say it wasn’t a challenge. But it’s funny what human beings can do when they have to do it and everyone is in the same boat.”
Steve acknowledges the entire staff rose to the occasion.
“It was a challenge we all had, and we all had to deal with it. If anything, it’s a testament to Australia that we came together and the shelves still had
something on them. Maybe not the full range of items but we still had food available. Everyone could still go shopping and fuel up their cars. I don’t know if that can be said for the rest of the world.”
The ongoing disruptions to the general supply chain continue to present some logistical challenges in relation to changes at short notice of shipping movements both in and out of port.
“In this world we now live in it seems to be short notice on everything and that can become a bit of a challenge when you only get a day or two notice when
unpredictability of it all is the hardest part at the moment.”
The second half of 2022 looks to be an exciting propsect for Hillman’s Transport as it moves into a new purpose-built facility located adjacent to the BP truck stop at Charlton on the Warrego Highway just out of Toowoomba.
“It’s a big deal for us with a lot more room than where we have been for the past almost 20 years,” says Steve. “We’ve just outgrown where we were.”
The new facility includes five acres of concrete hardstand and a drive through
The inherent challenges of doing business in the freight industry have not interfered with the continued growth being achieved by independent aviation logistics firm, Wymap Group.
Airside resource company,
Wymap Group, provides specialist services to the airfreight, airport and airline industries. The company has a presence, following its expansion into Perth earlier this year, at all major mainland airports in Australia. It also operates in Auckland, New Zealand. Wymap’s commercial fleet comprises approximately 100 vehicles including prime movers, specialised trailers, single and bogie axle rigid trucks, vans and utes. Primary operations hinge largely on moving aircraft unit loading devices (ULDs), a mechanism commonly used to restrain cargo for air transport. Wymap Group relies heavily on its roller fleet for this task.
The process, in short, involves use of a rollerbed system that can be installed onto trailer floors, flat beds and vans. Sometimes, depending on the nature of the work, chainbed trailers that run on three phase power will also be utilised to secure aircraft containers, aircraft pallets or a combination of both. Essentially considered aircraft pre-loading, ULD container build-up serves the purpose of grouping consignments at cargo warehouses to accelerate the loading and unloading of aircraft while serving to protect the contents that are loaded from loss and damages.
A Wymap Group truck is customarily required to back up to either an airfreight hoist or main deckloader where the ULDs, depending on whether it is an arrival or departure, then roll
onto or roll off the truck’s trailer. When dispatching the freight, the truck will travel to a customs bonded facility where the load gets broken down before it gets delivered for last mile. Wymap Group plays a role here, too, delivering on behalf of the customer in a semitrailer or Tautliner. The Tautliners are also deployed to cargo terminals where the freight is broken down internally and loaded by forklift akin to what is common practice at a distribution centre.
Wymap Group deals in the main part with network integrators like FedEx, a long-term partner, DHL Express & Global Forwarding and UPS, to name a few. They also have domestic partners in Australia Post and StarTrack.
“There’s a lot of parcel movements happening in that space,” says Wymap Group Managing Director Justin Bailey.
“But ultimately, it’s the traditional business of international air freight. Whatever comes in on an aircraft we’re going to be moving it.”
Wymap Group boasts major market share for air freight support in this country and has, of late, been riding a rising wave of activity. Demand for essential supplies and exploding e-commerce trade have, during this period, been felt industry wide. Just as container backlogs choked ports, air freight fast became an emergency go-to for freight forwarders when passenger airlines, confronted by drastically reduced flights caused by COVID measures, began carrying more freight to make up for the shortfall.
their versatility although price is a chief consideration, according to Justin, as mileage remains a lesser determinant in this line of work. Fuso have been brought in more recently for operations at airports while a new Mercedes-Benz Actros prime mover was introduced into the interstate linehaul segment of the business, a revenue stream Wymap Group is also looking to grow long-term. “Road feeder service has traditionally been dominated by Jets Transport and the likes of Skyroad Logistics, who have entered that segment more recently,” says Justin. “We see an opportunity in that space. Realistically, we feel that we can provide the same customer base with a different service experience. We are seeing it grow. We’ve just got to manage the growth and continue to deliver for our partners.”
Managing expectations in this new operational field will be partly conducted by external forces. The supply chain for one.
“To be honest, we don’t want to run too hard in that space just yet,” says Justin.
Established in 1981, Wymap Group now five decades on has had to draw upon every bit of experience, street smarts and internal wherewithal to adapt to the sudden extremes of a marketplace undergoing quicksilver changes.
According to Justin, freight, until recently, was coming into the country at unprecedented volumes in methods completely different to what the business was used to.
“There was a lot of chartered flights and a lot of PPE coming in. Rapid antigen tests. All of this type of product was arriving unabated, and it really kept us moving,” recalls Justin. “It was fortunate for us that freight volumes were very strong especially coming into Sydney. We were seeing a lot of that interstate transport happening.”
Any number of challenges brought on the industry over the last 18 months would have given serious pause to the most organised and professional of transport organisations. Managing the daily demands of staffing, equipment, fuel and customers before adding
never ending. There’s been a steep learning curve asked of everyone without warning, according to Justin, something he believes the industry should not lose sight of.
“We’ve all had to sit back and be prepared to learn again,” he says. “It doesn’t matter how much experience you’ve had, none of us have ever seen it before. My big cliché at the moment, especially in regard to lack of staff and challenges for finding drivers, is it’s all about coaching now, not managing.”
When it comes to staff management Justin suggests making employees better should be of primary concern in view of the myriad pressures they have had to cope with. Mental health, consequently, is taken very seriously internally at Wymap Group. Justin anticipates that mental health will be, for many other companies, a potential stumbling block if the approach is not right.
“We run a labour hire business at most of the federal airports with 400 hundred to as many as 600 hundred people out a day in that space,” he says. “So we’re
in an environment as hectic as this one has been its ability to retain talent.
Across both Australia and New Zealand Justin is proud that he has not let any drivers go.
“It was really important to us to keep the fleet running and the drivers working, outside of any behavioural issues of course,” he says. “That was first and foremost a priority for the business and myself.”
By keeping his UD trucks running on the highway, what’s more, at greater cost to the business as linehaul was not necessarily the traditional stomping ground of these vehicles, the drivers were in work. It proved an effective defence against the skilled labour scarcities of the last three years. The expansion into RFS (Road Feeder Service) partly came about from this decision.
When the rail line into Western Australia was damaged on 21 January, due to a once in a 200-year flooding event that adversely impacted multiple locations along a 300-kilometre stretch of track, Wymap supported some of their partners
present themselves.
“We were able to support Snap on Tools through that time and process. They’d been let down by one of their partners and we just made it happen,” says Justin.
“It was good for us. Though it wasn’t air freight, we were able to establish that we can do it. When we look to talk about those air freight opportunities in future we know we’ve done it before and created that experience internally so when we’re right to press the button and put into a schedule that we’ve had that experience behind us.”
The company has since established a branch manager in Perth following years of encouragement by various partners to commit a presence out west. Having ground management at the airport became the main step to redeploying mobile assets and other equipment.
“It’s no different to the way I look at Auckland. Did I really want to go there?
Probably not,” explains Justin. “But when the opportunity presented with the right contract frame we thought we’ll set it up and have a longer-term investment
sure it’s working well and then continue to invest in that part of the country.”
As it stands, Wymap Group will continue to attract interested partners who are eager to align with them at these newest locations. Part of the company planning strategy also involves ensuring adequate lines of stock of AdBlue, which Justin believes will became scarce again in the not-too-distant future.
“I think we managed the AdBlue situation quite well. We got on the front foot when shortages were happening and we were able to store enough but as you know it has a limited shelf life,” says Justin. “The fleet manager and general manager in the business did a really good job in making sure we planned ahead. Because we’re running around the clock, there’s certain times of day that we need these trucks fuelled up. We’re working with our partner in regards to that. It’s the old story you want to control what you can control so we’re doing the best that we can in that respect. These are absolutely challenging times.”
Vertex Allsands is, by extension of its owner’s family lineage, a thirdgeneration transport business operating around metropolitan Sydney and its surrounds.
The Menon family has been buying Mercedes-Benz branded trucks for the best part of 60 years. For Michael Menon who runs Vertex Allsands, an outfit that transports sand, soil, aggregate and other supplies for building, landscaping and infrastructure adjacent projects, the move to Daimler Trucks is more recent having added three new MercedesBenz commercial vehicles earlier in the year. Given the expansion underway of the business, which has been steadily
improving its footprint across the building supplies sector, Michael, put simply, needs trucks.
In semi-trailer and heavy rigid applications, the fleet has grown in recent months with the additions of a new Mercedes-Benz Aroc 8x4 and two Actros prime movers. All three trucks have been delivered in a low roof medium cab with Euro 6 compliant powertrains and the latest in safety technology including MirrorCam. The trucks are running at 57 tonnes under the Performance-Based Standards (PBS) mass
management scheme.
Although a little heavier than the American counterparts in the fleet, what the new Mercedes-Benz trucks lose in payload is more than balanced out by the savings in fuel they are delivering according to Michael.
“The offset front axle means our axle spacings under PBS need to be different,” he says. “Whatever you’re losing in payload though is gained back on the fuel side. A few of the bigger cartage companies have done their homework.
Companies like Hanson have also come to that conclusion. Giving up a tonne or a tonne and a half payload you do make up for it in fuel consumption and all the other consumables.”
The fleet, moving between quarries, often ventures well beyond the Sydney city limits often travelling over Mount Victoria en route to Hartley, up to Newcastle and around the Maroubra area with the occasional foray into Cowra. It’s not exactly short haul work but the distances travelled, on average, rarely exceed 900
kilometres a day. Kilometres covered have not been factored into the buyback scheme as the newest purchases are part of the Daimler Velocity dealer program.
“They look after us and take care of nearly everything,” says Michael. “These current trucks are not hot seated. The next round of units I will take on board will be set up to run 24 hours day and night. I’ll be increasing the kilometres and the service intervals on the next purchase.”
Michael, at current, finds himself having to make what he calls the best guestimate on mileage and hours of operation before the trucks are even built. Because of this, the next round, he explains, will be based on twice the driving time.
“It’s a funny thing now that I’m buying trucks.
You discuss the whole life of the truck at the beginning of it,” he says.
“You’re buying
them with the express purpose of giving them back.”
Vertex Allsands also moves gravel. organic soil, garden mix and mulch. If it’s loose, then they will likely pick it up. It stands to reason, under this model, that operations cater also to cartage work for concrete plants.
High tech quarry companies are, in recent times, keen to sign up for the services Vertex is providing. New work in the current climate of supply chain disruption is beholden until that time Michael can procure more trucks — a situation largely beyond his control. Having flatbed trailers, however, enables the fleet to perform contract cartage work involving the transportation of bits and pieces for non-traditional clientele. The semi-trailer, recently purchased, will pitch in for one of the brick companies that involves deliveries around Sydney. That’s another point of difference offered by Vertex. “We’re not exclusively doing our own stuff. We’re more open to different work, as long as the trucks are working,” says Michael. “That’s my main focus. Obviously, the big thing we do is sand. But I don’t care where the work is coming from.”
Building supplies applications prove unique in the commercial road transport industry given the requirement for a variety of vehicles operating in a smaller fleet.
The Mercedes-Benz Actros tipper features a factory fit power take off and rear stabiliser bar to suit the application. Its MercedesBenz OM 473 S6 engine produces up to 578 horsepower generating a torque output of 2800Nm into a 12-speed Powershift 3 automated transmission. The Actros 2646LS.3250 prime mover comes with a dual plate self-adjusting clutch. Both feature full disc brakes and the latest in EBS, ASR and ESP technology. Sydney’s sprawling traffic, especially during trading hours is notorious, and to help navigate this challenging environment the truck safety package offers Active Brake Assist 5, Lane Departure Warning, Proximity Control and Attention Assist. All three vehicles including the Aroc 8x4 feature MirrorCam for superior visibility. For the older drivers, used to older technology, it has taken some getting used to. “It means breaking the habit of looking out of the can rather than inside the cab,” says Michael. “Driver acceptance really depends on how old they are. The younger blokes have taken to it pretty easily.” MirrorCam compels more than just an enhanced view through its replacement of conventional door-mounted side mirrors. While the unobstructed view no doubt abets the tight manoeuvring operators are likely to come across in residential streets, construction sites and some
quarry entrances, indicator lines donating different references of distance on the display screen, can help drivers estimate oncoming traffic behind the vehicle and obstacles in low visibility conditions and terrain. The lowest line from the top of the screen is adjustable. This allows the driver to precisely mark the end of the trailer at ground level.
Mastering MirrorCam is, ultimately, more a matter of training than complexity. In coaching the older drivers through its utility and advantages, they are fast seeing how beneficial it is according to Michael. “Once you set up all your parameters it’s actually a very useful tool,” says Michael. The crash avoidance system is also proving to be a major advantage having come into a play a few times already with passenger vehicles in urban areas and on highways where the fleet might encounter wildlife straying from national parks and bushland areas.
“The Mercedes-Benz trucks really do stop on a dime like most of the European stuff does,” Michael observes. “Across the mountains and backwoods regions the crash avoidance system has certainly justified itself.”
That said, Michael notes that the system, like any adaptable tool, can be finetuned with experience so that it differentiates between debris and live moving objects.
“It’s important for our efficiencies not to have it jumping at shadows,” Michael says. “Again, it’s about knowing your parameters. The same goes for setting up the cameras for the mirrors and reversing. It’s all very useful once you familiarise yourself with its functions.”
Should a truck want for anything — coolant, tyre tread, fuel — pre-warnings allow for early awareness and intervention to make later dramas like breakdowns in traffic entirely avoidable. Life for the driver is stress-free in that sense.
“There’s no fear the truck is going to overheat sitting there on the freeway idling for an extended period,” says Michael. “It’s very handy when you’re doing 100 kilometres per hour. You can take your foot off the throttle and it will idle the engine and hold you there reducing fuel consumption. If you need to tap the
accelerator it’s as if it wasn’t even turned off. They’re very good on fuel.”
The coasting feature delivers extra savings across this concern, as Verdex is running the new trucks on PBS at maximum weight. The trucks don’t mind the stopstart nature of heavy traffic. Michael wonders, jokingly, if it’s possible the trucks are too smooth and quiet for his drivers.
“I don’t want them to get bored,” he says. “The comfort and ride are first class. It’s like you’re sitting in a floating lounge room.”
As an historical note, Vertex Allsands is a spinoff company whose origins go back to Michael’s grandfather, a World War II immigrant from Italy. He was driving trucks for a Port Kembla transport company when he was supposed to deliver a load of soil that the intended customer no longer wanted. Told he could do whatever he wanted with it he took it home to Bass Hill.
“One day somebody walked past and asked if they could have some and it snowballed from there,” recalls Michael. “He got his start in a way by luck. Then my father and his brothers continued the
business on at another location.”
That business is still going. When Michael started his own company it was slanted more towards building and landscape supplies, doing a similar thing, only a little bit differently. That has involved getting tech savvy, going paperless, by moving administration onto the cloud and diversifying its portfolio of customers to move beyond smaller builders. The business still caters to half-tonne orders for fixing up front yards but it also engages on large infrastructure projects, the type of which are burgeoning across Sydney of late.
“The crane and forklift work has exponentially increased given the nature of how Sydney is building at the moment,” explains Michael. “Cranes were a bit of a gimmick back in the ‘80s and ‘90s. Then it really took off in the 2000s. Sydney’s market became very much like the European and UK market where everything is delivered in bags. So we’ve embraced that.”
Vertex’s tippers are primarily used to feed its own yard where the materials are processed and distributed on flatbeds and
cranes. The main difference, of course, is the technology. The aim of which is to be far more responsive for operational requirements according to Michael.
“I’ve been around the industries and I’ve been able to learn from different places and different people,” he says. “I’ve been able to fold all that different information and experience into something that will hopefully keep growing into the future.”
The orange and blue livery of the newest vehicles are eye-catching as they are meant to be. Michael considers the vehicles moving billboards and when it comes to advertising, much more cost-effective. Business, for the moment, is at capacity with an industry running hot. There’s been competition creep in as customers, desperate to get product, are getting less fussy in how it’s delivered. According to Michael, the business is curbing its growth as it awaits new vehicles to come online.
“There’s no use taking the work if I can’t service the work,” he says. “At the moment we’re pushing what we’ve got to its limits, calling in subbies when we have to. We’re definitely looking to fold more into the fleet as we get busier.”
Mercedes-BenzWorking with many of the country’s largest telecom carriers such as Optus, Telstra and Axicom, HVAC is responsible for completing large volumes of structural steel upgrades throughout the telecommunications sector. By introducing Isuzu to its fleet, HVAC’s telecommunications division was able to increase its productivity, efficiency and value for money.
Heating, ventilation and air conditioning (HVAC) project managers are constantly monitoring all aspects of projects, from the delivery of raw materials to fabrication timelines and installation requirements. They understand all too well the impact of poor equipment performance and how it can affect project timelines and overall quality.
With head offices in Brisbane and Sydney, and operations nationwide, HVAC is an infrastructure service provider with a Telco division that provides design and construction services to Australian telecommunication companies. HVAC, as part of this service, offers a broad range of services for the design, construction, integration and maintenance of all telecommunication infrastructure. These services include constructing complete mobile base stations, tower and pole structural upgrades, site and electrical surveys, rooftop installations, helicopter installations and more.
One of HVAC’s major projects was the Wyong Hospital Redevelopment, which involved the construction of a new Clinical Services Building (CSB) in New South Wales, compromising a six storey CSB, Link Bridge, minor refurbishments to the existing building associated with the link bridge connection, formalisation of the existing east-west road connection to Louisiana Road and formalisation and upgrade of the car parking.
Over time HVAC expanded to offer custom solutions on a wide variety of engineering and fabrication needs. These have since been refined and adapted to Australian industry needs which has subsequently seen its services expanded across five main sectors, including specialised fabrication, mechanical services and air conditioning services, industrial ventilation, the fabrication of pipe fittings for large scale water infrastructure projects and telecommunications infrastructure.
The reliability of vehicle fleet in rough conditions is a key factor that prompted HVAC Telecommunications Project
Manager, Stephen Coates, to purchase an Isuzu NPS 75-155 4x4 Crew –HVAC’s first ever truck and a prototype model for the company.
“I’ve driven a few other truck brands in the past but when it came down to it, reliability was the main factor for us,” he says. “The professionalism Isuzu demonstrates was definitely a big drawcard, and Nicholas Greet at Brisbane Isuzu made the entire process of acquiring the NPS 4x4 truck very simple for us.”
The NPS 75-155 Crew features a GVM rating of 7,500 kg and a generous GCM of 11,000 kg, plus a 4,500 kg towing capacity with a standard 50 mm tow ball. Stephen’s 4x4 model also comes equipped with Isuzu’s 4HK1-TCN turbocharged diesel engine, offering 144kW of power at 2,600 rpm and 419 Nm of torque between 1,600 –2,600 rpm.
Stephen’s department is responsible of fabricating, supplying and installing structural steel on towers, poles and guyed masts across five states throughout Australia, along with the
installation of Greenfields sites – areas without an existing telecommunications structure in place.
“We have teams of field staff that have the capability to construct a small telco site on a city rooftop to a large, full-scale 120-metre guyed mast telco installation
in remote areas including the fabrication and supply of the steelwork for construction,” he says.
According to Stephen, HVAC’s biggest issue with finding suitable vehicles has been payload.
“We own 20 utes and trailers, but they
don’t really fit the purpose that we need them to,” he says. “We carry a lot of heavy steel that is often oddly shaped, so we really need payload and the room to carry these things safely.”
Two-seater utes, which Stephen is familiar with having used them in the past, obviously limits HVAC to carrying two people at a time to each site. The problem is that most of the time he needs to send more than two technicians to a job, so previously he has had to send two vehicles instead of one. However, the new NPS completely eliminates this problem.
“Our NPS 4x4 Crew can carry twice the payload as well as an additional five staff, so we eliminate the costs involved with sending an extra vehicle to site,” he says. “We save on fuel, wear and tear, servicing, you name it.”
Working from Northern Queensland down to South Australia and across the waters to Tasmania, HVAC’s vehicles are clocking up between 30,000 to 50,000 kilometres per year. On top of improving productivity and efficiency in Stephen’s operations, his brand-new
Isuzu also keeps a few extra dollars in his pocket.
“We were spending a lot of money on transport,” he says. “Along with the added payload, our new Isuzu truck is also a way for us to reduce our whole-of-life costs. Once we have more trucks in our fleet such as the NPS replacing our current utes, we expect this to reduce even further.”
HVAC supervisors customarily drive the new Isuzu. Equipment that was previously scattered in the ute trailer has been easily fit into the NPS’s fabricated toolbox according to Stephen.
“We’ve also set up the truck with a fridge and other bits and pieces inside the cab to make it more comfortable for our drivers,”he says. “The truck has been really good.”
Stephen found Brisbane Isuzu and the body builder, Mini Body, a pleasure to work with during the process in bringing
HVAC’s prototype truck to life.
“Nicholas Greet at Brisbane Isuzu has been really super to work with,” he says. “He was always there to answer any and all questions, and when I wanted something else, he was more than happy to get it done. Mini Body also
The NPS fabricated toolbox neatly fits equipment scattered across the utes..
did an excellent job on the toolboxes and tray – the whole process was a bit
Gus Belanszky.
Utilising an intuitive and easy to use interface, the HinoConnect advanced telematics system provides access to key performance data on the vehicle.
Only a little more than a decade ago the term “telematics” usually failed to pass spellcheck on most computers. In the intervening time, the telematics industry has grown exponentially and now is an essential component in fleet management. Using sophisticated on-board computerisation and a web-based software platform, HinoConnect collects, transmits and analyses a wide range of vehicle information which can influence performance efficiency, safety and vehicle utilisation. Built and designed in Australia by Directed Electronics in Melbourne, Hino-Connect was the first Australian developed telematics system to enable direct
communication with the driver through the truck’s multimedia unit. Initially standard equipment in the Hino 700 Series, the availability of Hino-Connect has been expanded across the 500 Series Standard Cab, Wide Cab, and 4x4 models. A modified version of Hino-Connect featuring the business intelligence elements became available as an accessory on Hino 300 Series light-duty trucks in early 2022.
Hino-Connect is much more than a basic mapping and tracking tool and even goes well beyond simply combining truck and GPS data. The system incorporates a suite of business analysis tools designed to assist in managing fleet vehicles while they are on the go. The Hino-Connect
system is the next generation of business telematics with real-time performance data tracking, remote diagnosis of vehicle faults 24/7 and includes access to the dedicated Hino-Connect call centre for specialist support. Hino-Connect also proactively monitors service scheduling so that operators can plan ahead and minimise down time and operational disruptions. Built from the ground up in Australia, including the local manufacture of the Hino-Connect telematics hardware, the program is customised around the unique dataset available from Hino vehicles in combination with the capabilities of the multimedia unit fitted to the cab’s dashboard. In the event of a fault being detected, in addition to the remote diagnosis of the specific fault, a recommended course of action is delivered to the driver via the multimedia unit screen. In the unlikely event of a severe vehicle fault in addition to the alert and suggested remedy being delivered through the multimedia unit, information pertaining to the fault situation is also sent to the customer and a Hino-Connect Specialist via email. An additional unique element of Hino-Connect is the casemanagement provided by the Sydneybased team of Hino-Connect Specialists who support the customer, driver and dealer and monitor the progress of any repair necessary to get the truck back on the road quickly.
“At Hino, we are committed to placing our customers at the centre of our operations, by providing them with experienced specialists in our head office call centre in Sydney and, with Hino-Connect, we
provide a complete support solution that minimises their downtime,” says Gus Belanszky, General Manager - Service and Customer Support for Hino Australia. With Hino-Connect, fleet and business managers can use an online portal and a smartphone mobile app to access data and real-time insights into their fleet including live vehicle performance data such as fuel usage, the cause and effect of driving performance, as well as safety alerts. Other features include live GPS tracking and detailed trip reports as well as useful tools such as ‘movement without ignition’ alerts and geo-fencing which provides instantaneous vehicle location and fleet security and also ensures operators are notified if a vehicle leaves a designated area. Another feature Hino-Connect offers its users is an API (Application Programming Interface) data feed, which is rFMS compatible. For those of us not familiar with this type of technical jargon, this feature allows multi-branded fleets to plug the data from the Hino-Connect module straight into their own third party fleet management systems, providing customers with full visibility of their entire fleet, not just the Hinos. Using the real-time data combined with historical insights, Hino-Connect will automatically analyse the cause and effect of driver performance, safety behaviour, and vehicle utilisation using simple dashboards available in the portal. Hino-Connect also gathers live vehicle performance data to provide full operational visibility to business managers including brake application count, gear change numbers and even the amount
optimum RPM band. Hino-Connect uses its Driver Score Reporting to monitor key indicators like harsh braking or acceleration, over revving or speeding, to identify poor performance that can then be addressed through coaching to enhance driving techniques The parameters used can be modified to ignore instances such as minor over-revving of the engine when the engine brake is activated. HinoConnect can also identify the drivers who are achieving the most effective operation of their vehicles.
“Hino-Connect is a natural evolution of the decade-long partnership between Hino Australia and Directed Electronics, which has been made possible by the high level of support provided by the team at Hino Motors Ltd in Japan,” says Gus. “Directed Electronics has built the hardware and firmware to suit the current market and their high level of expertise and capability allows us to deliver the right ‘plug and play’ solution for the Australian market and provides flexibility to adapt the system
Business managers can also track current fuel usage of individual trucks and use the forecasting tool to estimate future fuel costs.”
The live GPS tracking and detailed trip reports allow fleets to update their customers with accurate delivery times while also identifying inefficient routes. Automated email notifications provide full visibility of the Hino trucks’ Active Safety Systems including any Pre-Collision System activation alerts to provide another level of fleet safety. Hino-Connect also proactively monitors maintenance reminders so customers can schedule ahead and liaise with their service dealers in order to minimise downtime.
“At Hino, we are committed to leveraging our detailed knowledge and understanding of our trucks, our dealer network and our customers to developing and delivering impactful digital solutions,” says Gus. “While others can claim business intelligence, we believe Hino-Connect truly delivers this for our customers.“
Great customer service, strong relationships, strategically located Parts Distribution Centres and sophisticated managed dealer inventory systems are some elements that keeps PACCAR Parts and TRP dealers at the front of their field, but ultimately, it all goes towards the goal of having the right parts available at the right time to keep trucking operators mobile.
important thing to our customers. It’s what brings them in the door and it’s what brings people back again. Having the right range of parts means people know they’ll be able to complete their repairs and get their trucks back on the road the same day,” says Rod. “That’s important because when the wheels aren’t turning, they aren’t making any money. Everything PACCAR Parts do with its plan, inventory and ordering system is all geared around availability. Not just the next day availability but on the same day as when the customer needs it.
The phrase “it’s the economy, stupid,” was first coined by James Carville, a strategist for Bill Clinton during the 1992 US presidential campaign and is often referenced during political debates to hone-in on what really matters to voters. There’s an obvious parallel in the trucking world, where keeping heavy vehicles on the road is essential for the success of any operation. “Availability, availability, availability. We live and die by our ability to keep the big trucks on the road,” says Jack
Greig, WA State Parts Manager for the CJD Group, when asked what is most important to his customers.
“We’re a mining state and we’re very dependent on iron ore and so forth, which means big trucks earning big money, so availability (of parts) means everything to us.”
It’s a view supported by Rod Leake, Parts Manager at Mildura Truck Centre, who says PACCAR’s reliable and fast parts service is vital to keeping his customers mobile, and happy.
“Availability of parts is the most
“Customers come in the door and need the parts and we have them on the shelf and can complete the order today, not order them in for tomorrow or maybe the next day. We set the bar high because that’s what our customers expect, especially in the trucking industry where the vehicles are so big and expensive – they need to go, they can’t be sitting around.”
Joel Bray, Parts Manager at Wagga Wagga’s Inland Truck Centres agrees that the PACCAR Parts range and accessibility is one of the most important ways the company supports its customers.
“For most locations around Australia, PACCAR Parts offer an overnight service for the odd part that is not stocked. MDI (Managed Dealer Inventory) planned inventory helps to limit stock outs and to ensure we have the part on the shelf for that breakdown in the middle of the night — that untimely fan belt that lets go in the middle of harvest or that radiator hose that blows in the heat of summer with a load of cattle on board,” says Joel. “Planned inventory ensures we have the right part on the shelf 97 per cent of the time. PACCAR dealers are also fully factory trained, so our parts, sales and service technicians are always up to date with latest technology to ensure we can support our customers as efficiently and professionally as we can.”
Matt Neilson, Truck Parts Manager for Mount Gambier’s Barry Maney Group says the way PACCAR dealers work with their service departments is another way they ensure customer satisfaction.
“We pre-pick parts for our future work, to be certain that the right parts are supplied when the vehicle arrives for service or repair. By constantly reviewing the demand side of things, as well as updating the parts inventory as new makes and models arrive, we’re also ready for any unexpected jobs that might arrive,” says Matt. “Because truck and trailer combinations can be made up of many different configurations, detailed analysis of our customers’ vehicles helps us identify the type or brands of parts we need to have in our inventory.”
Over at Kenworth DAF Melbourne, in Melbourne’s western suburbs, Parts Sales Manager Peter Mammarella says the focus his operation puts on the service department is key to building successful customer relations. “We’ve got a dedicated team of parts interpreters set up to service primarily the workshop, and we have a team of three people to look after their needs,” he says. “One of the other things we’re trying to do is better plan our
availability to support the interpreters’ requirements. What we’re trying to get to, is a level of forward planning where, if they know we have a vehicle coming in that may need something left-of-centre, they give us notification ahead of time and we can ensure that we have that stock here to support that requirement.”
It’s another example of how PACCAR Parts and TRP dealers work with their local market to ensure their needs are met, something Rebecca Patton, Parts Manager at TRP in Emerald, QLD, also puts plenty of focus on.
“We work very hard on building open and trusting relationships with our customers through promotions, customer visits, information evenings and ongoing communication,” she explains. “This means we are in constant communication with our customers to ensure we’re stocking what they need to keep them up and running.”
Whether it’s the old school boots-onthe-ground approach of parts reps spending time out in the field getting to know their customers’ needs, the sophisticated algorithms that underpin PACCAR’s MDI system to ensure the right breadth of stock is always on hand, or strategically located PDCs (parts distribution centre) to shorten delivery lead times, owners and operators can be sure that PACCAR and TRP Parts dealers are committed to doing everything they possibly can to keep big wheels turning. PACCAR and TRP Parts’ extensive nationwide dealership network is staffed by friendly and expert industry specialists who can supply parts promptly from the front of a truck to the back of a trailer, so customers need look no further for their specialist truck and trailer maintenance requirements, or for industry-leading parts at competitive prices.
Find your nearest PACCAR Parts dealer or TRP® store at paccarparts.com.au/find-a-dealer or scan the QR code.
ohn West Logistics, not unlike any good business predisposed to innovation, goes after things with a singular vision. Working up and down the Australian eastern seaboard as well as New Zealand, the company runs a large fleet of vehicles that encompasses curtainsiders, rigids and B-doubles. Crane mounted trucks are, for the most part, the dominant application identifiable in its vehicle range. Though the business began mainly in dangerous goods storage and distribution back in 2000, the company’s eponymous managing director, whose background and expertise were in warehousing and contract logistics, always knew that’s where the business was likely headed. John West sold the name, DGL, and the dangerous goods arm of the business back in 2018 and has maintained and grown the contract logistics revenue stream ever since. Its latest additions to the fleet attest to a decisive and ongoing commitment to its customers. One of these is leading building manufacturer and supplier Stramit, for whom it has maintained an alliance for nearly 20 years. On this account no two loads are the same. The product carried by John West Logistics varies in widths and lengths, some of it up to nine metres long. Such variation has required a build to accommodate the task of transporting anything from reobar, mesh, roofing, guttering or flashing while incorporating the presence of a truck mounted crane. Once settled it was clear a longer wheelbase and new drive axle configuration were priorities. Another brand in Australia offered something similar but for John, whose fleet consists in the majority of the three brands associated with the
Volvo Group — UD, Mack and Volvo — looking elsewhere was never going to be long-term solution.
“We don’t own a spanner in our business,” says John. “All of our fleet is maintained by either Volvo Group under contract maintenance and service agreements or other suppliers depending on where our fleet is.”
All roads, as they say, lead to Rome or rather, as the case might be, Ageo,
Japan. John first began lobbying UD Trucks Australia for the truck build modification around three years ago. Talks soon advanced to the point UD head office in Japan got involved, with all three parties determined to make the new customised design happen.
“We’re really happy with the way they look after us and we’re happy with the performance of the UD Quon,” John says. “That’s why we kept talking to
pushing Japan. Hence, we’ve got the first ones now which is great.”
The new 6x4 UD Quons are fitted with a double decker tray. This helps with appropriately fitting the smaller building materials underneath while the larger building products are carried on top where it is craned and unloaded. Cranes are customarily supplied by either Palfinger or Hiab.
“We had to get the chassis’ a lot longer and we needed the bogie drive aspect as we’re going into building sites,” John explains. “That also allows us to get the right balance of weight spread over the axles given we put the cranes on the rear as well.”
The five new Quons have already been allocated to different drivers. For John the UD brand has always been synonymous with Japanese reliability — a major factor in any of his equipment purchasing decisions. The Volvo Group influence, however, has taken the trucks to a whole
social, civic and fiscal responsibility.
“The great thing about UD now are all the safety protocols that are in the truck,” he says. “They’re brilliant. That Volvo influence has had a huge impact on making the driver and environment around him even safer now and helped shape the transition where UD, over the years, have gone from being basically a very reliable Japanese truck to a very safe and reliable truck through the Volvo partnership.”
The new Quons feature safety systems based on advanced technology including Traffic Eye braking and Driver Alert.
Of his fleet of around 300 vehicles, 70 per cent of which are trucks in crane mounted applications, there are approximately 80 UD units. They are also proving very economical when it comes to fuel usage.
Getting the application right for the job is sometimes only half the battle. Offering his drivers top of the range
another factor.
“Our biggest issue like everyone in our industry is we have a severe shortage of skilled drivers,” John says. “With the shortage of drivers out there they’re not going to come and drive an old truck when someone can drive a new truck. You’ve also got to make sure that they have the skills that you need to do it along with the right specc’d truck.”
Even so, the new drivers often don’t have the skill set required of them which means further training. John West Logistics, for this reason, always buddy them up with an experienced operator so they can learn from them.
“With our internal apprentice program, we can bring a person on board and with zero experience and they will have a medium rigid truck licence with all the skills that they need in 13-14 weeks, to go solo “ John says. “If they’ve been doing it for some time and they’ve got all the tickets then that’s fine. But
we find that most of them come to us without the training required to operate a crane or deliver building products so it can vary between a week to four weeks depending on the person before they can go solo.”
Five new UD Quons have been purchased for the Stramit contract.
Stramit have input into the John West Logistics vehicle procurement spec to further improve the efficiency and the productivity of the freight movements while being mindful of how best to look after the product when it is being
transported and delivered onsite.
“We’re always looking at ways to improve what we do,” he says. “Especially in consultation with the customer.”
The new trucks delivered to John West Logistics have been, uncharacteristically by industry standards, wrapped in the Stramit livery. And there’s a very good reason for this according to John.
“Nearly all of our trucks are all branded in our customers colours and livery. We advertise them,” he says. “They’re the ones that make us the money. They’re the ones that we advertise. Not that we’re not proud of our name. But our view is that we should be advertising our customer. The more work they get the more work we get.”
It’s this continual willingness to go the extra mile for its customers that has helped make John West Logistics an esteemed transport business for those who are privileged enough to partner with it.
Despite interest in alternative fuel and vehicle technologies, at least in the short-term, many options are still a few years away from going mainstream in Australia. It’s one reason why many road transport companies and freight carriers are still cautious in their future commitments.
Prime Mover: Thanks for catching up with us Rob. It’s an interesting time for transport operators on their pathway to a lower carbon future. Why is Viva Energy looking at lower carbon options?
Rob Cavicchiolo: Companies like Viva Energy recognise that they have a really critical role to play in the energy transition underway. We still need to keep safely and reliably supplying the fuels that our customers need for the technology and the businesses they have today, but we also need to be working with our them and other stakeholders on the energy and technologies that will be needed for a lower carbon future. In my role, I talk to a wide range of industries including the transport sector and their own customers about how they are going to reduce their carbon footprint. These include large and multi-national corporates who have a keen focus on decarbonising their operations. These companies are all asking similar questions about what low carbon options are available over the short to longer timeframes and how can we can help them reduce their greenhouse gas emissions. The need to decarbonise is being raised as a critical topic at senior executive levels of management, by company boards, investors, shareholders, private equity, and
owners of private companies, all who are very keen to understand what is required to contribute to a lower carbon future and as a result, we are seeing emission reduction targets being set. For example, a majority of companies, like Viva Energy, are aiming to be net zero by 2050.
RC: What we are also now seeing is those 2050-emission reduction targets being progressively brought forward. Companies are revising their emission strategies and implementing 2030 targets, with aims to achieve 20 to 30 per cent lower emissions compared to their established carbon emissions baseline. In talking to our customers, they are saying that they expect to achieve emission reductions of five to ten per cent by 2025-2026 and this is starting to drive a change in the marketplace.
Companies also have a responsibility around their own ESG (environmental social governance) policies to drive this low carbon agenda across their business and to demonstrate to their own customers and end consumers, how they are going to decarbonise their operations. Consumers want change and they want to see action starting now, and they expect companies to help deliver that change, to reduce their impact on climate change and their own carbon footprint.
So with that background, a company like Viva Energy which has decades of experience in energy supply and has deep relationships with our customers, it makes absolute sense for us to be looking at options we can provide our customers today while we work on the fuels and
technologies of the future.
PM: So what does this mean for transport operators?
RC: For commercial fleets and trucking businesses, there are new pressures emerging to reduce their carbon footprint and we are starting to see this flow into procurement and new business activities. At Viva Energy, we are seeing it happen with customer tenders that we are bidding on. While traditionally tenders with the transport industry have focused primarily on providing the cheapest fuel price’ to enable them to offer the cheapest freight rates, in the last eight to 12 months, we are seeing customers not only wanting a price for our traditional fuels but also the price for low carbon options, which can help them achieve their decarbonisation goals. We expect this to continue to be a growing focus over the next few years. We believe that transport operators have started to see or will start to see shortly the same pressures to decarbonise their operations from their existing clients or for new business they are trying to win. To address this, we have developed low carbon options for transport operators to utilise to help them decarbonise. What is going to be interesting to see is which transport operators will adopt a low carbon pathway early in their strategy and how this might be used as a differentiator from their competitors. It’s really going to be fascinating to see it play out.
PM: What can transport operators do now to help lower their emissions?
RC: As mentioned earlier consumer sentiment is changing. There was a strong
focus from voters in the recent federal election to address climate change and Australia’s contribution to reducing emissions. Companies are also acting on this consumer sentiment. Many companies are looking to accelerate how they meet their own emissions targets and looking to their suppliers to help them decarbonise their operations. If you’re a transport company who is carrier of a customer’s goods, your scope 1 emissions contribute to their customer’s scope 3 emissions. So taking action now will start their journey to reducing the carbon footprint of their operations. There will also be a need to start to adopt low carbon technologies that are available as drop-in solutions to existing equipment and existing infrastructure that they have in place. There are a number of pathways that are available now and in the medium-term before EVs and hydrogen solutions become more readily available. One example of a short-term low carbon pathway is biodiesel because it is a drop-in solution that can be used now in existing engine technologies. You don’t necessarily have to change your fleet or fuel infrastructure. We’re also seeing B5 blends (5 per cent bio/ 9 per cent diesel) which is fast becoming a minimum requirement for use in certain industries such as the construction and infrastructure sector. Bio blends up to B20 are also starting to be requested from our customer base.
in a reduction of up to 90 per cent C02 emissions compared to diesel. Another option available now is to use offsets to help achieve carbon neutrality from the use of diesel fuel. Viva Energy is looking to offer a Climate Active certified carbon neutral diesel in the near future to provide another short-term pathway to help our customers decarbonise.
RC: The first step is really to understand the scope 1 and 2 emissions — how much are they emitting from their operations and capturing this data to provide a carbon account baseline. We’ve been working both internally and with our customers to understand what their carbon emission profiles look like. For fleets who have not started the journey it’s critical that they establish this as without establishing a baseline, they really have no starting point to measure against. Transport operators are already implementing fantastic initiatives, which are reducing their carbon footprint such as using Performance-Based Standard (PBS) vehicles. These vehicles can not only provide operational and financial benefits but also CO2 emission reductions. Many transport operators are becoming more efficient with their freight and route planning, which provides another opportunity for them to realise
RC: Diesel is still going to be around for a considerable time yet but over the next decade there will be increasing pressure on all industry including transport operators to decarbonise. While we have some great future technologies coming, they are not going to provide the silver bullet in the short term with regards to how transport operators can lower their carbon footprint. And from a fuel supplier perspective, we will need to continue to work with our customers on their decarbonisation journey, providing options for low carbon pathways, while battery electric and hydrogen fuel cell vehicles become more available in scale and at a price that is commercially attractive. We are taking some important first steps to support a hydrogen future for our customers. With support from ARENA and the Victorian Government, we are in the process of developing a hydrogen refuelling service station in Geelong which will be the first commercial scale, publicly accessible hydrogen refuelling site in the country. Local transport partners will operate at least 15 zeroemission, hydrogen-powered heavy vehicles from the refuelling station once it opens in late 2023. Our hope is that this will provide the blueprint for a future network of sites along the busy east coast freight routes.
There is no doubt that, like the rest of the economy, transport operators will need to address the decarbonisation challenge. Whether they are looking to re-sign existing business or positioning their company for new growth opportunities, the market is looking for a step change when it comes to reducing the carbon footprint of operations. This is why Viva Energy created our Carbon Solutions business — to help our customers with their decarbonisation journey. The good news is that we have ready-made solutions that can be used now without a big change to an operators existing business. What is exciting, especially in my role, is how we are already seeing a change with requests for biodiesel, HVO and carbon neutral products becoming more common. I am looking forward to seeing how this plays out over the next three to five years.
In recent years MAN has built upon its fulfilment of the Rheinmetall contract to supply over 2,500 protected and unprotected medium and heavy military-spec vehicles to the Australian Defence Forces, and now MAN and the Penske Australia team have adopted a four key pillars approach to the implementation of its Third Generation of trucks to the commercial transport sector.
Initially, the MAN product must be “driver fit” with a high level of safety and comfort incorporating well advanced ergonomics. The aim is to assist in addressing the shortage of drivers by offering the best truck from a driver’s perspective. Secondly, the economy and efficiency of the new range must provide a positive impact on the vehicles’ total costs of ownership.
“Big trucks with bling and chrome are still a big part of the culture, but total costs of ownership are becoming more important,” says Randall Seymore, Executive Vice President, Global Commercial Vehicles and Power Systems at Penske Automotive Group and a 25 year veteran with the Penske organisation. This demand for the most economic overall cost of a truck over its effective lifetime is high on the agenda for an increasing number of fleet and
individual operators and is considered a major factor in the shift to European trucks such as the latest MAN.
The third plank in the Penske platform is the provision of optimised uptime which is a benefit to Penske truck customers and their freight clients alike by providing reliable and time effective freight deliveries.
The final factor is having a strong partnership between the factory, the distributor and the dealer network.
“MAN and Penske are committed to the long haul”, says Penske Australia’s General Manager of On-highway Craig Lee. “We’ve set about the last few years building a strong foundation to support our customers.”
In arriving at the four-pillar approach, Penske Australia surveyed 300 local customers in order to determine what was important to them in their choice of a heavy vehicle brands, and subsequently translating those findings into the Third Generation of MAN trucks. The four main pillars could be aspirational to probably every brand in the country, and at the launch it very quickly becomes evident that Penske Australia is serious in its stated aim of doubling MAN’s local market share. The ‘four pillars’ mantra is repeatedly referred to by various executives present at the
launch and, more than that, they seem to have the plan, and just as importantly, the trucks, capable of bringing a doubling of market share to fruition.
This Third Generation MAN is the first new major development of the MAN heavy duty range in two decades and includes 12 million working hours and more than four million kilometres of testing.
The Third Generation MAN range was launched in Spain in 2020 and that particular event was hampered by a severe winter storm which saw many flights containing executives, customers and media cancelled. Despite that initial setback, and the subsequent massive disruptions due to COVID, the new MAN TGX was awarded the prestigious
“International Truck of the Year 2021” (ITOY) which is decided by a jury of 24 trade journalists representing some of the most respected European specialist truck publications. Factors considered for the award included driving comfort, working and living conditions, safety, fuel efficiency, connectivity, innovative services, and operator control.
International awards notwithstanding, for this MAN to achieve Penske’s aims in Australia it has to suit Australian conditions, and from our brief exposure to a selection of models at the launch, it does that, and more.
Externally the cabs have been treated to some subtle changes designed to improve aerodynamics, a major contributor to long haul fuel efficiency. Access to the cab is enabled by 89 degree opening doors and a series of vertical steps which feature aggressive non-slip treads.
The mirrors are a new design with the glass area still much the same as previously with the revised design and location providing a gap between the mirror body and the ‘A’ pillar which opens up the usual blind spot to provide better vision when entering roundabouts and intersections. The passenger mirror has swing out function for reversing which increases vision on the ‘blind’ side. Operated via a button on the mirror control panel on the driver’s door, the mirror returns automatically
to its previously adjusted position after 60 seconds.
A handy innovation in the ‘why didn’t I think of that before?’ category is the ‘Easy Control’ switch panel located on the lower inside surface of the driver’s door which is accessed from ground level without having to climb back into the cab. It can remotely initiate engine starting, the operation of hazard lights, and can be programmable for the operation of other functions such as power take offs.
MAN claim 167,000 hours went into the cab design which incorporates a new grille and the subtle aero and cooling considerations are carefully blended into the overall aesthetics of the cab.
Aerodynamic fairings are designed to keep wet road spray off the sides of the cab including the mirrors. The aero enhancements and added insulation also contribute to the very low level of wind flow noise able to be heard within the cab.
Unique to MAN is the safety cell cab which in a frontal collision allows the cab to move rearward up to 750mm in order to absorb the energy while leaving the doors operational.
New for the Third Generation is a slightly curved dash layout which still permits easy cross-cab access to the passenger door.
The optional full digital instrument panel is combined with intelligent switch gear to provide an intuitive set of monitors and controls which improves the driver’s connection with the truck. An analogue
style dash is also offered.
Yet another outwardly simple but very effective innovation is the Smart Select control module for the 12.3-inch screen of the navigation system. This helps the driver toggle through the various menus with one hand rather than hunting and pecking on a touch screen.
The driver’s seat is a Recaro, a brand well respected in passenger and sports cars as well as commercial vehicles. An appreciative feature for long haul drivers is an optional passenger seat which can convert to a swinging armchair as well as a table.
In line with the commitment to provide a comfortable living and working environment the sleeping accommodation is quite luxurious and has a slat bunk base and the mattress in the TGX models is a category leading 2.1 metres long. A large 41-litre fridge is located below the bunk and is easily accessed from both seats and the bunk itself, and there are more storage options than can be found in many furniture stores. LED lighting is fitted to most storage lockers.
The engine line-up offered across the new range moves between the 8.0-litre 250hp DO8 to the 15-litre D38 which provides up to 640hp. The range topping TGX is available in three cab heights and choice of the 13.0-litre engine rated at 540hp or 580hp, or the 15.0-litre D38 engine rated at 640hp, all backed by ZF 12-speed Tiptronic automated manual transmissions
which have refined ‘smart’ shifting features and Efficient Roll which disengages the driveline allowing the truck to save fuel by allowing the truck to coast when appropriate with the engine merely idling. Reliability is underlined with a new electrical architecture with two main chassis wiring harnesses supporting the myriad of electronic systems ranging from engine control to braking and safety.
MAN’s “Brakematic” system incorporates electronic management to co-ordinate the functions of the EBS service brakes and the engine brake with priority activation of continuous brake before the service brake.
The engine and exhaust brake system on the D38 engine can provide up to a massive 840hp of driveline retardation. Since 2012 MAN has been engaged in the audits by the German Technical Inspection Agency (TUV) which examine the reliability of its vehicles and have resulted to improvements in components such as clutches, alternators and filters.
The engines feature extended oil drain intervals, another contributor to that allimportant total cost of ownership.
In addition to traditional linehaul, MAN customers can be expected to take advantage of the new range’s low tare weights in applications such as tipper and dog and container movements.
The nationwide dealer network and a comprehensive 24/7 roadside assistance program are supported by several levels of repair and maintenance contracts and warranties of up to one million kilometres or five years on some models, plus there is the support available from Penske Hiring and Leasing.
After a brief yet intensive experience at the controls of several examples of the Third Generation MANs, we can understand the confidence and enthusiasm of the Penske and MAN executives.
“We are expressly confident in the performance and delivery of the product,” says Craig Lee. “There have been exceptional results in Europe and we are confident we will be able to give our customers a product that will give them economical, reliable and effective transport solutions.”
No one is doubting him.
Under Performance-Based Standards heavy vehicle productivity has been transformed in Australia. In December Prime Mover will publish its annual PBS Special Report in conjunction with the National HeavyVehicle Regulator with data insights and the latest developments on the scheme. In the new era of high productivity freight vehicles (HPFVs) commercial road transport operators, OEMs and industry players are increasingly looking to PBS to reap the benefits of newfound discoveries in engineering and performance.As the efficiency gains of PBS-approved vehicles is becoming more well-known and recognised, access on major freight routes is fast becoming the norm for these often, impressive feats of engineering. Prime Mover offers an opportunity for businesses to present their products and solutions in this unique space.
In trying times for road transport across many industry sectors, labour shortages are posing major challenges that are being dealt with differently.
Arecent survey of young people in the United States found that one in four members of Generation Z plan on becoming social media influencers. Nearly 16 per cent of those surveyed said they were prepared to pay to become one. Last year the American Trucking Association reported a shortage of 80,000 truck drivers, an all-time high that is anticipated to blow out to 160,000 by 2030. Taken together these statistics shed some light on a very real rupture that has taken place between the service economy and the entertainment economy and the heightened generational incompatibilities deepening the separation of a digital existence from the physical world. While there is never going to be enough careers to go around in the social media influencer category and more than enough holes to fill in the truck driver column, the gap is instructive of a mindset, however, fantastical, that won’t be narrowed by manpower until other realities, socioeconomic for one, hit home. In Australia, skilled labour shortages are no less pronounced and the challenge of attracting younger workers to a rapidly ageing commercial road transport workforce never greater. Road transport companies in Australia are facing unprecedented skilled worker shortages especially in the heavy vehicle operator and technician fields.
The Victorian Transport Association (VTA), which has been running a driver training program for three and a half years funded by the State Government, makes no pretense to indulging the grave
demographic challenges that face the industry.
“Unless we can train young people to come into our industry, we’ll always be short on truck drivers,” says Peter Anderson, VTA CEO. “The issue we have is that we could be far more attractive as an industry if we were able to go to young people and talk to them about building a career.”
The driver training program the VTA currently superintends puts people behind the wheel for eight days — being taught under instruction of how to drive a truck properly as Anderson, who continues to be a vocal advocate for greater heavy vehicle driver training, describes it. Victoria, he points out, at present has around 170,000 professional heavy vehicle drivers.
“We have a licensing system that puts over 18,000 a year through the licensing program,” he says. “There are no training programs, it’s a licensing program. And yet, we’re still three to five thousand truck drivers short in Victoria and it’s been like this for years.”
To date, the VTA has delivered over 200 heavy vehicle drivers to the industry.
“What the VTA is calling for, as is most of the industry, is for heavy vehicle drivers to be trained, and to be trained at 18 years of age,” he says.
But there’s also crucial optics involved, Anderson acknowledges, to achieving this.
“Who wants to come to an industry when you think you have to be either halfway in jail or halfway to being a drug addict to be part of the industry, because that’s the mentality that’s out there,” he says. “We keep reinforcing that because we don’t
train people to drive trucks properly.”
National bulk carrier, McColls Transport, is headquartered in Victoria’s second biggest city Geelong. Given its vast fleet requires a large driver and technician pool it’s also feeling the pinch of skilled labour shortages.
“Mechanics and drivers have been hard to find. Everyone is experiencing something similar across the industry,” says Peter Shearer, McColls Fleet General Manager. “We’ve been trying to introduce some younger drivers into the business. It’s more difficult for us these days having moved away from general freight.”
A time-honoured model from yesteryear was to start yard hands on forklifts and transition them onto a rigid truck ahead of eventually working their way up to a semitrailer and heavier.
As McColl’s is primarily a tanker fleet these days there’s not as many rigids for its new staffers to access for intermediate training and experience before stepping up to prime movers. In light of this, the company has devised an interesting workaround that is, on a smaller scale, proving effective. Across a couple of its depots, namely Dennington and the new site at Warrnambool, the newer staff members start out on the truck washbays before they are introduced to a single trailer licence. Before long they build up enough experience and technical knowhow to pilot a B-double.
“Similarly with our depot in Nowra we have a couple of guys there who preload tanks for the drivers,” says Peter. “We’ve been using that as a way of introducing
them to the business and a system to help them upgrade their licences.”
The onus is on drivers, ultimately, having a multi-combination licence says Peter, a former driver himself. “In preference, 30 per cent of our fleet is still singles and the majority of the fleet is B-doubles,” he says. “Getting that MC licence is very important to us. It’s getting hard for the young guys to get a start. Everyone wants them with experience. A lot of young guys aren’t interested in transport which is a shame. I’m not sure how we fix that one. A lot of young guys don’t want to be away from the comforts of home. So that’s a difficult one that the industry is facing.”
Keeping drivers, in such a tough market, is of equal importance. To combat the driver retention challenge, McColls has taken to rewarding experienced operators with new trucks. Recently, one of its longest-serving drivers, who was contemplating retirement, has agreed to stay on having been given a new MAN TGX for the next few years. Across Sydney, major infrastructure projects, like the new airport, are in abundance. Orbiting these projects is yet smaller but no less prioritised and fast multiplying commercial and housing developments. For Vertex Allsands this activity will keep its revenue turning over into the future despite the issue of it finding fully qualified truck drivers.
According to Michael Menon, Vertex Allsands Managing Director, the business is having to pay well over the going rate for more drivers which adds to inflationary costs for the business and the marketplace. “In some way we’re fuelling the problem paying double to drivers for the same work they did just three years ago,” he explains. “Not to go too macroeconomic but that’s certainly part of the problem.” Human Resources, as Michael views it, is a major component of operations in this current climate. Keeping the house in order is no longer the moveable feast it once was in commercial road transport. “You’ve got to be pretty good to keep who you’ve already got,” Michael says. “That means having a pretty good setup to keep everyone happy especially your best drivers.”
Networking in an industry reliant on so
truck drivers in an enviable short time frame. One of the new employees is the son of a former driver, incidentally the longest serving driver in the company’s history. Another of the new additions is the colleague of one of the company’s original driving team, who shared with him knowledge that the business was adding several new Kenworth T610SARs.
“The other two called in one day by phone having just passed some of our trucks,” recalls Managing Director Phil Jarratt. “We’d just ordered the vehicles so I said ‘yes’ and that’s how they came on board.”
Good fortune like a good reputation, doesn’t go astray. Neither does first class vehicles when it comes to landing top tier talent. According to Phil the fleet was never in a position where it didn’t have a driver ready for the arrival of the new trucks.
“We had drivers in place far enough in advance for when the trucks were delivered,” he says. “It was a period of a couple of months to get them together.”
Whether it’s by chance or by good management or a mix of the two, Phil understands adding four new drivers at once is the exception rather than the rule. “Everybody’s experiencing driver shortages, there’s no secret about that,” he says.
Across the industry everyone is trying to do the best that they can with the resources and limited time they have been afforded.
“There’s no golden answer or silver bullet solution,” he says. “Everyone’s looking for staff across all industries, not just in transport.”
As the industry ages at a rate more than 2.2 times faster than all other industries, a steep cliff, replacing the learning curve politicians like to acknowledge, swiftly approaches. Online employment advertiser Seek listed more than 21,000 jobs for truck drivers as recently as July. Peter Anderson wonders if these prominent vacancies amount to more than just a shortage of labour.
“Is there too many jobs? The transport and logistics industry reacts to demand and demand has undoubtedly gone up,” he says. “[It’s] basic economics, supply and demand. The more people come into Victoria, the more demand there becomes, the more drivers we need. It’s a neverending circle, we’ve always needed more drivers, we’ve always needed experienced workers. The sad part about it now is that we’re just inherently short and we can’t see any light at the end of the tunnel.”
South East Queensland Hauliers, whose
tagline is, “innovate for tomorrow” just might see a faint glimmer. They are taking a slightly different approach to the problem. SEQH Deputy Managing Director, Nathan Craner, admits it’s near impossible to find an immediate fix for these staffing challenges. The question he and his colleagues are asking is this: how can they take feasible action today so that it will impact the business positively in the future? Theirs is a different strategy that in abnegating the compromises so far arisen from short-term pressures looks well beyond the horizon.
“For the training side of things we are cognisant about innovating and not just for now but for the future,” he says. “There’s plenty of problems and plenty of challenges in every industry. We’re looking at the challenges that come our way and looking to solve them even if it means taking a long-term approach.”
Much discussion, not always with practical application, surrounds the endeavour to attract females to the industry at the minute. When the opportunity arises, Nathan says SEQH is always seeking to talk to any female who has an interest in joining the business even offering part time and casual positions to better accommodate child-minding and school
runs.
“In the early hours of the morning or late at night if they’re driving a truck, only if it’s for four hours, that might only be a shortterm Band-Aid but you can potentially match people together and fill a truck for a 12 or 24 hour period,” he says. “Though long-term, when those kids grow up and the household is more self-sufficient, you have potentially got a full-time available worker. You might get a part-time solution for tomorrow but in ten years’ time or 15-years’ time you’ve got someone who you have given some skills and experience and a career pathway to that will payoff down the track.”
Australia’s top peak food industry bodies have calculated the food supply chain is short at least 172,000 workers from paddock to plate. This massive labour shortage will have significant long-term impacts on price and the availability of food for the consumer unless solutions are found quickly.
CEO of Independent Food Distributors Australia, Richard Forbes acknowledges the dire predicament the industry finds itself in.
“The ability to transport food is becoming harder by the day due the significant shortages of truck drivers across the country,” he says. “Coupled with that is an ongoing lack of skilled and unskilled workers in food warehouses to help pack and store food products and drive forklifts to unload trucks from suppliers and load them for food retail outlets. Recruiting and maintaining staff is almost impossible.” The post-farmgate meat supply chain is already under-resourced to process the number of livestock forecast to be produced in Australia in 2022. Forecasts for 2023-2025, according to Australian Meat Industry Council CEO, Patrick Hutchinson, can be anything between a 15-35 per cent increase in livestock numbers.
“This will obviously be catastrophic for Australian farmers if the volume of livestock is far greater than the meat processing industry can process, and the wider supply chain has the ability to manage,” he says.
In New South Wales agricultural workers
are being offered fee-free heavy truck driver training and licencing courses under a $15 million program sponsored currently by the state government. The additional training can be undertaken by anyone who presently works in the plant-growing agricultural industry sectors including grains, fibre, rice, viticulture, horticulture and agrifutures industries. AgSkilled launched the program to upskill NSW’s plant-growing agricultural workforce as measure to help it meet future challenges. The program, according to AgSkilled co-ordinator Claudia Vicary, has been an imperative part of strengthening the workforce across the NSW’s plant growing agricultural industries since its inception in 2017 and has generated opportunities to upskill workers and those seeking to build careers in the industry.
“Having staff on hand that can properly operate a heavy truck is integral to most farming enterprises, especially considering farmers have felt the pinch of workforce shortages over the last few years,” says Claudia. “AgSkilled aims to deliver training that makes things easier on farm and we want to help growers make their businesses more dynamic and efficient through investing in their people.”
The truck driving and licensing course has been particularly popular for people on farm, who are busily preparing for the winter grains harvest and ensuring their staff have the capabilities and expertise to safely operate heavy trucks during this time. The truck driver training and licencing courses are being run by Required Australian Industry Skills Education (RAISE) Training and Ironbark Training and will include competency-based assessment and licencing skillsets for heavy rigid (HR), heavy combination (HC) and multi-combination (MC) licenses. The course ensures participants have the skills and knowledge required to drive a heavy vehicle safely, including maintaining systematic and efficient control of all vehicle functions; coupling and uncoupling trailers; monitoring traffic and road conditions; managing vehicle condition; and performance and dealing with hazardous conditions.
Claudia notes that these courses will be
scheduled with participants based on demand. “Courses will include online theoretical training and be completed with one-to-one delivery of the practical components, there would be a limit of two participants from each company per financial year with eligibility restricted to those working on-farm,” she says. AgSkilled is supported by the Grains Research and Development Corporation (GRDC) and other industry partners such as Cotton Australia, Horticulture Innovation, NSW Wine Association and Agrifutures. Productivity was high across NSW and seasonal conditions have growers excited for the winter harvest and summer cropping prospects according to GRDC Senior Regional Manager – North, Gillian Meppem.
“In seasons where high productivity is expected it follows that there will be increased pressure on harvest logistics, it’s important to ensure that the on-farm workforce can confidently and safely
operate a truck during key busy periods such as harvest and sowing,” she says. “I strongly encourage all growers to look at their businesses and staffing and assess how they could take advantage of this great opportunity to upskill their workforce and increase their productivity.”
The road transport industry has for many decades struggled to attract and retain the heavy vehicle drivers of the future, and this will only continue in the absence of reform to heavy vehicle licencing and training according to Peter Anderson.
“There’s a lot of positives with driving a truck, but at the moment the negatives are outweighing those positives,” he says.
“We’re not able to actually entice, draw and encourage people to come into our industry and join us because the system won’t let those people come at a time upon which they’re most likely to understand and learn – when they’re 18.”
For a system in desperate need of new ideas, the clock is ticking and it’s well past
midnight. Part of the process of reform will mean, according to Peter, helping people train so that they can see the value and worth in becoming a truck driver.
“Imagine an 18-year-old earning $80,000 a year living at home,” he proposes. “Don’t worry about Mum and Dad buying you an old $2,000 car, you’ll be able to buy your brand-new car, and the one you want. While all your mates are still at uni, and when they come out of uni at 22-23 years of age, they’ll be lucky to be earning $60,000 to $70,000 a year. You’ll have four or five years on them. You’ll have a deposit on a house while they’re still struggling with how they will do their internship. Then you can go on from there in the industry, you don’t have to stay as a truck driver.”
That’s a career trajectory that many in Generation Z can one day only dream of. It might also be true that to become a social media influencer a truck driver is not the worst place to start.
With a reputation for quality and high standards, Shell’s safety culture has helped to shape a 30year career.
From the first oil refinery to fuelling the first commercial QANTAS flight, Shell has a proud history of innovation to support Australian industry. It was that reputation for quality and high standards that first drew Darren Evans, Viva Energy Logistics Contract Lead to the company. It’s rare these days to see someone clock up three decades with the same employer. This year Darren celebrates 32 years with a business that has been operating in Australia for more than 120 - firstly as Shell and now as Viva Energy. From hands-on driving and maintenance to transport analysis, planning and contracts, Darren has seen the transport business from all sides.
“It was considered the place you wanted to work, the top of the tree for a driving job. I was getting promoted in another job, and I gave Shell one last phone call before I committed somewhere else,” recalls Darren. “I was straight off five years of driving stock crates, and a bit of a country bumpkin in Sydney.”
Since getting his start as driver, Darren has worked to the same high standards across transport analysis, planning, operations and contract management. The high standards on the job lived up to Darren’s expectations of safety and process.
“I’d come from an operation where I did all my own maintenance, so from a driver’s perspective, it was brilliant,” he says. “The role with Shell was in a highly regulated, well equipped environment with safety standards. It was like a breath of fresh air.”
Impressed by the Shell approach, Darren was keen to learn more in the fuel space. When Shell shifted away from owning its own fleet, Darren moved from driver to supervisor before he settled into operations based in Townsville.
“Townsville was great for learning all the different aspects of the industry,” he says.
“I worked in tank farm operations, ship to shore, you name it.”
The safety culture at Shell which has now transferred across to Viva Energy where
Darren works, and the community that grows around it, is a big part of what has kept Darren still learning across new roles.
“Safety is hammered into you from the start. It becomes part of your thinking in everything you do. Community builds around us, looking out for each other, doing our jobs to a high standard, so that everyone stays on course and goes home safely,” he says. “The company ethics and ethos align with mine. The commitment to safety, commitment to people and the desire to do the right thing are all part of it.”
Darren says people with an aptitude for workplace health and safety policies and processes are well suited to the safety culture of companies like Shell and Viva Energy.
“We don’t do shortcuts,” he says. “It’s not worth the risk to break the rules in this business. The consequences are pretty significant if you get it wrong.”
Even through the immense technological changes of the past 120 years, some
things don’t change — Shell still aims to proudly lead industry standards according to Darren. Although he says working to Shell’s standards can be a challenging change for new suppliers.
“The standards we set and the expectations we have can be a significant culture shock. Ultimately, many improve their businesses by meeting the standards we insist on,” he says. “We still lead the pack with standards. We’re part of a forum working to standardise carrier processes across industry.”
With great experience across business areas and also driving commercial vehicles, Darren plays an advocacy role for drivers. Experience in the driver’s seat helps inform decisions that prioritise health and safety.
“It can be difficult to teach people, if you haven’t done it. It’s a tough, specialised gig. You need an appreciation for what you’re asking from a driver to do if the job involves 1000km running on dirt,” he says. “We can’t automate the entire industry, it’s not like backing onto a dock and machine loading. Between process and policy, we need to take care of the people making this all work.”
One of the initiatives is no-fault incident investigation which helps to focus on the bigger picture of where an incident or error fits into the supply chain.
“It can be quick in the industry to point the finger at the individual at the end, the driver,” he says. “But what else is going on? It’s taking that blame game away to understand the cause of the issue.”
Staff like Darren, who boast such long histories, have spent their careers with the industry and see how important relationships are with suppliers and within the workplace. He recognises the challenges of bringing the right people in, training them to the right standards, and keeping them in the industry.
“When you get the right people together, operating with the same ethics, it’s a great group of people to work with,” he says. that “People trust Shell brand. From the strong network of servos across the country to the quality fuels and lubricants. Because they’ve been around a long time, they have earned a good reputation,” says Darren. “It’s that simple. People value the longevity of a brand and the quality of the products they sell.”
What’s different on the road?
A lot has changed in 120 years — and even in 30 years.
Get there faster
It takes a few hours to deliver fuel from Sydney to Canberra — in the 1940s it took 2 days.
More on board
Shell used to deliver a few thousand litres, now one truck delivers 70,000L.
Drivers can access bigger, high flow pumps to refuel faster.
More services, parking, meals, showers and facilities to cater for the driver experience.
Darren started out paying his fuel bill via cheque at the end of month, to digital payments on Shell Card.
Over 167,000 hours of design work alone have gone into the new MAN TG3 series truck. Sergio Carboni, who has been with Penske Australia for nearly six years, is in the driver’s seat, so to speak, to talk about the new range and what it will mean for the German brand locally.
Prime Mover: Are you excited about the MAN Truck Generation 3?
Sergio Carboni: I am honestly excited in anticipation of taking this brand to market in Australia. I think the product has always been very good, maybe even understated, and now we are in a great space with the launch of the new MAN truck generation to the Australian market. The level of engagement with the factory is unprecedented. We’ve identified opportunities here in Australia, and with the strong commitment from Penske Australia, we will take this brand to the next level.
PM: The MAN brand has a strong support package to offer. Is that part of the strategy or is it something that has evolved?
SC: The way we are going to market is with the overall package, both from a retail perspective and also from a fleet perspective. We identified a few years ago some of the gaps in the support side of our offering. For instance, the requirement for items such as 24-hour roadside assistance. We worked with NTI Truck Assist and looked at how to take the risk away from our customers and how best to support that. We also examined our warranty requirements
based on variations in applications as to whether we should be covering kilometres or hours. We’ve now got that flexibility depending upon the application. In mining, hours are important for customers, in on-highway kilometres and years are important. Hence the on-highway five year one million kilometres driveline warranty on our 13-litre and 15-litre TGX models is up there with the very best. We have great repair and maintenance packages as well. We haven’t compromised on the integrity or the safety of the truck, but we’ve looked at how we can create an overall package which is exceptionally good. Anybody can buy market share if they want to, but if you haven’t got the support mechanisms then it’s only a short-term solution. PM: Are the specifications with this new range right for Australia?
SC: I think the beauty about the MAN range is we’ve got medium duty, heavy duty and we’ve also got the market leading off-highway/all-wheel drive product. When you look at that spread I don’t think there are many OEMs with that range of product. So for us it’s about identifying our strengths and playing on them, such as with our all-wheel drive models. We’re also looking at our on-highway 13-litre and 15-litre trucks and growing that side of the business as well. We have looked at specific applications such as ‘wharf spec’ trucks for container work. We work with our dealers and our sales specialists to create a product with which we can go head-to-head with some of the major players in ‘wharf spec’ with key specifications such as a 360/440hp spread, the right size fuel tanks and a package of safety features and creature comforts. We looked at some of our construction market areas as well, such as tipper and dog applications, concrete pumps, cranes, and how we take advantage of the MAN’s low tare weight and translate it into that application.
PM: What’s next for MAN in Australia?
SC: Next is the all-wheel drive range including 4x4, 6x6, 8x8, and 8x4. We are looking at local availability in the third quarter next year to continue our market leading position in that category.
PM: Is the Australian market large enough to support such a wide range of off highway/all-wheel drives?
SC: It absolutely is. We would typically do between 130-150 units per year. We ‘own’ the Pilbara due to most of the
large miners, drill rigs, and exploration operators using MAN trucks. Our 4x4 models are also strong with the essential services who are managing the electrical wiring, such as Downer and SA Power. Essential services businesses love the MAN product because it’s engineered as an all-wheel drive product and not something on-highway that’s been cut and shut. The MAN all-wheel drive product is a stand-alone engineering solution and therefore it’s made for it, whether it’s the electronic architecture, or the PTOs or some of the specific requirements that are needed for an application. From a tare weight point of view, it’s very light as well so they can fit a lot of equipment on it. From an engineering aspect the MAN is highly regarded in this space.
PM: Are you comfortable with what
you’ve got as Medium Duty and Heavy Duty offerings for on-highway applications?
SC: We are constantly looking at where we can supplement some of our core business with some of these niche markets which we can also work in. We also feel there is so much opportunity in our 6x4 trucks that we haven’t tapped into yet and we are really keen to make that change to the dial. We’ve got an ability to order a variety of wheelbases directly from the factory. For example, we are a major player in the agricultural spreader market so we’ve got a 3.9 metre or a 4.5 metre wheelbase available, in both manual and automated transmission.
PM: Is supply a challenge?
SC: It’s been really difficult across the whole industry and other industries as
well. Fortunately, they’re back on full speed ahead now and we’ve got trucks built in Germany ready to go on boats. Some are already on their way, and we should see a good quantity arrive during the last quarter of 2022 and we’ve secured our build slots for 2023 and potentially for the first quarter of 2024 as well. A lot of it is already sold, and a lot of it is dealer stock so we’ve got a good combination of both. It’s good that Australia is one of the focus countries for MAN and therefore we get some sort of priority. It’s reassuring to hear that from MAN. So we are going to be hitting the ground running in the fourth quarter of this year. The investment continues into our own dealers, and our private dealers are also investing heavily in items such as training.
Marrying into a trucking family,
Tipping
about trucks and the transport industry. Yet, she still
It began in the 1930s. Her husband’s great grandparents were timber millers and log carters in the central western region of New South Wales.
Their children Richard and Judy — Sally Tipping’s in-laws — eventually branched out on their own and established a trucking operation in 1980.
The family then secured a long-term contract that spanned over 40 years involving, in the main, the delivery of concrete products to many of the new roads being manufactured throughout NSW.
Since joining the company in 1990, Tippings Transport and its dedicated industry have been a key part of Sally’s life. While the business continued to thrive throughout the decades, the recent events of COVID saw major changes sweep through the business’ operations.
“We’ve had a huge change in our business over the last two years,” she says. “We lost 95 per cent of our work since COVID hit, so we were kind of staring down a barrel of not knowing which direction to go. We had to quickly sell quite a bit of gear off and decide what direction we were going to take, but we’ve found a little niche going from Sydney to Dubbo with freight and also still doing deliveries out in the western area.”
Slowly recovering from the worldwide pandemic, Sally and Grant have been focused on bringing the current incorporated company to all new heights, while guiding it through the third generation of the family.
“We’ve found a really good group within
our industry, and we’re very positive for what the future holds,” she says. “One of our sons has just joined us in the workforce and we’re looking forward to our other son joining us in the near future, and that will catapult us into the next generation.”
Sally has made a lot of contributions to the transport industry, and three years ago she decided to do something truly remarkable. In September 2019, she started a Facebook page dedicated to raising public perception of truck drivers, ‘Wave to a Truckie’. The page currently has more than 43,000 followers, and it consists of endless positive posts aiming to increase awareness of the trucking industry.
“That all started a few years ago when I could see how people reacted to our industry, and I felt that we really needed to promote our industry,” she says. “I think sometimes we are talking about what’s wrong with the industry, but we don’t talk about what’s right with it and what we’re really good at.”
According to Sally, the industry deserves praise for what it achieves.
“Especially through the COVID situation, I felt that a lot of my drivers weren’t being given the respect that they needed at distribution centres or loading centres, and I think that if we start promoting our industry there will be positive effects on all different levels,” she explains. “Whether it’s through just road safety, whether it’s getting new people in our industry, and it also helps with communication between regulators as well.”
The reputations of truck drivers as a group have been damaged through misinterpretation by the media according to Sally. She believes that companies are continuing to blame truck drivers for accidents without knowing the full story, which then sends a subliminal message towards the general public that trucks shouldn’t be on the road. By creating the ‘Wave to a Truckie’ page, Sally has given the public access to knowing the day-today lives of truck drivers.
“It’s really just trying to acknowledge that truck drivers are humans and that they do struggle like everybody else in day-to-day
life,” she says. “If you see a truck driver, you don’t really know what they’re dealing with behind the wheel and what they’ve put up with to get to where they are. I think that just trying to acknowledge what drivers do day-to-day goes a long way to respecting them as well. The page is very positive, it’s really just a motivational page and it has been an incredibly rewarding thing.”
In the past truck drivers have been portrayed as these big, burly guys notes Sally.
“But that’s not the case anymore. They’re professional drivers and they need to be treated like professional people as well,” she says. “I think that goes into recruiting more people into workforce.”
Although the page has only been running for a few years, Sally has received a lot of positive feedback from truck drivers around the country and from followers in our community.
“I’ve had so many great messages and things like that,” she says. “I got a message the other day and someone said, ‘I really needed this today’. That’s all that was said, but you think obviously people are reading things and I think they’re grateful that people understand what they go through daily.”
Earlier this year Orange City and the
Cabonne Shire Council in NSW launched the ‘Tired? Power Nap Now’ campaign, which was aimed at educating drivers about early warning signs of fatigue while boosting awareness of power naps and their ability to prevent a tragedy. Sally is a high supporter of the message and its values, and has taken part by sponsoring it on one of Tippings’ trucks which allowed her to pay it forward to a fellow operator.
“On one of our trucks we are sponsoring the power nap campaign, and I got some feedback on the weekend where a driver said, ‘Oh my God, I needed to see this because it really saved my life,’” she says. “I got that message on Monday morning and I think that sort of stuff is really great in the industry.”
Sally has been recognised for her contributions to the transport industry, by recently receiving the 2022 Road Freight NSW Transport Woman of the Year and 2022 NRFA Terrie Bradley Memorial Award.
By creating a sticker with a local artist to display on Tippings Transport’s fleet, the initiative known as Wave to a Truckie came to exist. Together with the Facebook page which has now also carried over to Instagram, Sally and Grant continue to change Australia’s and the world’s reputation of truck drivers.
Toyota has confirmed an extensive development program in Australia for the Tundra pick-up. The move, speculated upon for many years, now demonstrates its intention for local development which should pave the way for experts to re-engineer Tundra in a right hand drive (RHD) format and evaluate the vehicle against Australia’s severe local conditions and tough customer use.
Toyota has partnered with Walkinshaw Automotive Group, for its extensive experience in this type of work, to develop and build Tundra RHD vehicles for Australia. Toyota’s focus on ensuring delivery of its hallmark quality, durability and reliability attributes is expected to result in one of the most thorough development projects undertaken for a vehicle program of this type in Australia. After significant development in-house, prototype testing on public roads will begin in September 2022.
Starting from Q4 next year, Toyota will
deploy approximately 300 of its cars all around Australia, as part of the final stage of the RHD re-engineering program. These vehicles will not be for sale but will involve monitoring under real world usage conditions in Australia. The program is expected to set a new benchmark in Australia for the re-engineering of a full-sized pick-up truck from LHD to RHD. It will include the adoption of key components from Toyota’s comprehensive global parts catalogue, including the steering column and rack, accelerator, brake pedals and shift lever from the LandCruiser 300 platform.
The vehicles will be equipped with a new inline hybrid system featuring a twin-turbo 3.5-litre petrol V6 – the most advanced and fuel-efficient powertrain available on this model.
While this is exciting news for Toyota and Tundra fans alike – an Australian RHD Tundra faces further checkpoints in Toyota’s global approval process
before its retail introduction can be confirmed.
Toyota Australia Vice President Sales, Marketing and Franchise Operations Sean Hanley said the local company and its dealers were eagerly anticipating being part of this unique program.
“This a dedicated re-engineering program, led by Toyota Australia and made possible by our global partners and is closely supported by our parent company and Toyota North America.
It will utilise OE levels of design, development, testing and componentry rooted in Toyota’s deep commitment to quality, durability and reliability,” he said.
“This project shows just how serious we are at Toyota about quality, and a RHD Tundra will not be available for sale in Australia, until we are totally satisfied.
“We are really excited to get such a significant project to this stage and look forward to seeing development prototypes on our roads and test tracks in the weeks and months ahead.”
space for big things
the longest loading length in its category: up to 4.15m best in class driving range available to order now
The SL Warrior is the latest Navara family member in the local market.
Nissan has unveiled the newest member of its locally developed ute family, the Nissan Navara SL Warrior by Premcar.
A product of Nissan and Premcar’s lauded partnership, the Navara SL Warrior is based on the popular SL 4WD dual cab, and unlocks a new entry point to the Warrior family for Australian ute buyers. Priced at MSRP $58,000 (manual) or MSRP $60,500 (auto) the SL Warrior joins the PRO-4X Warrior in Nissan’s made-for-Australia ute program, with new adventure-ready equipment, increased off-road capability and suspension tuned in Australia for Australian conditions.
“We’re thrilled with the response to the Premcar Warrior program to date, and we want as many people to experience these made-for-Australia products as possible,” says Nissan Australia Managing Director Adam Paterson. “With the new Navara SL Warrior by Premcar, a new and more accessible entry point to the Warrior family has been developed, but one that’s no less comfortable on the road, and no less capable off it. The SL Warrior will add to Australian Navara sales, rather than
subtract from it, with Nissan Australia securing additional units to meet demand. It is further proof of how highly the Warrior program is regarded.”
Developed with Nissan’s local engineering partner Premcar in the firm’s state-of-theart Victorian facility, the Navara SL Warrior has benefitted from the same exhaustive testing, tuning and localization program as the PRO-4X Warrior.
A hallmark of the Warrior program is to broaden the Navara’s capability, rather than simply shift it to off-road applications. Every change or addition made to the SL Warrior has been tuned and tested in all driving scenarios to ensure capability doesn’t come at the expense of on-road comfort. Nissan provide a comprehensive five-year, unlimited-kilometre warranty covering all Nissan and Premcar parts. New additions include, but are not restricted to, a winch-compatible hooped bullbar with integrated LED lightbar, “Navara” branded under-body black bash plate, 275/ 70/R17 Cooper Discoverer
All Terrain AT3 tyres with increased
tread depth, and an off-road focused tread pattern, suspension lift (+40mm) increasing ground clearance from 220m to 260mm and towbar.
The SL Warrior now boasts a 100kg GVM upgrade with 3500kg braked towing capacity as well as comprehensive suspension tuning with new springs, dampers and jounce bumpers. Front and rear damping has been revised for better compliance, sound isolation and reduced float when towing or carrying a load. The five-year factory warranty applies to all manufacturer components, while Premcar matches Nissan warranty on all Warrior enhancements.
The Navara SL Warrior also acts as a further shot in the arm of Victoria’s booming automotive manufacturing industry, with Premcar’s Warrior program — already home to more than 35 engineering and manufacturing experts — in the midst of a recruitment drive as it adds production shifts to meet expected demand.
The Navara SL Warrior is now available in Nissan showrooms.
National courier, Australia Post, has signed a new deal with the Federal Australian Government. The Pacific Postal Development Partnership is reported to strengthen postal services in the Pacific which involves a joint declaration with the Universal Postal Union (UPU) and Asian-Pacific Postal Union (APPU).
Announced in Bangkok on the sidelines of the 13th APPU Congress, the partnership is expected to improve the efficiency and security of postal services between Australia and Pacific island countries, benefiting consumers and businesses, including the estimated 200,000 people living in Australia with Pacific Island heritage.
To support the three-year partnership, the Government has provided Australia Post with a $450,000 contribution to target improvements to postal systems, processes, technology and training in the region.
This funding will be supplemented by Australia Post’s expertise and in-kind support, including equipment that can help meet the needs of Pacific postal operators.
The signing of this landmark joint declaration brings Australia closer together with key multilateral institutions in the postal sector.
The declaration will enable a coordinated approach to regional postal development, supporting Pacific island countries to continue to modernise their postal services, capture emerging opportunities and new markets, and showcase the value of the region’s postal sector globally.
The declaration will be signed by Australia’s Ambassador to Thailand, Dr Angela Macdonald PSM, Australia Post’s General Manager for International Services, Michael Cope, the DirectorGeneral of the UPU, Masahiko Metoki, and the Secretary General of the APPU, Lin Hongliang.
Postal services in the Pacific are some of the most under-developed as measured by the UPU’s Postal Development Index. This impacts businesses and consumers through slower average delivery times, disruption and delays.
With the ongoing digitisation of the global economy, further investments will boost the ability of Pacific island countries to capture new market opportunities and meet consumer expectations to deliver secure, timely and efficient postal services.
The Government and Australia Post
individual needs. The first activities are expected to commence by the end of 2022.
Minister for International Development and the Pacific, Pat Conroy, said postal services across the Pacific have an important role to play as the region recovers from the economic impacts of COVID-19.
“Australia is committed to multilateral cooperation to uphold the international rules based order and address global challenges – and the postal sector is no exception,” he said. “This new Pacific partnership underscores our commitment.”
Paul Graham, Australia Post CEO and Managing Director, is proud to work with postal partners across the Pacific to provide expertise and tailored solutions to enable the provision of mail and parcel services for all.
“As part of this, we will meet with them to tailor our assistance to their specific needs – whether that be sharing our knowledge and expertise to the supply of equipment and technology,” he said. “Australia Post is particularly well placed to help these nations both respond to the challenges and take advantage of
AnThe Australian Road Research Board is a key player in road surface data collection and analysis services. Through its fleet of survey vehicles, ARRB goes far beyond just scratching the surface of road conditioning – it provides clients with detailed road surface analysis and data both above and below the road.
The Australian Road Research Board (ARRB) works with road agencies, all levels of government and companies in the road and transport industry. Its Infrastructure Measurement (IM) division has been measuring Australia’s and New Zealand’s Road infrastructure for over 35 years, giving its clients trusted insights that help them make smart spending decisions. Executive Director of ARRB’s IM division, Jeff Doyle, says their mission is to improve Australia’s roads by providing data on road conditions and assets.
“We add real value by helping our clients all over Australia and New Zealand better manage and maintain those assets so they can make confident spending decisions that make their
roads better and safer,” he says. “We’ve got a team of trusted experts that collect infrastructure data and report it back to our clients, so that they can make better economic, community, safety and maintenance decisions.” The IM division plays a significant role in the management of road assets by Local, State and Federal Governments. In Jeff’s words, he sees the team as the clients’ gateway to ARRB’s other groups, whether it be in asset management, safety, mobility futures or sustainability and material performance.
“It’s IM being an entrée to the other divisions within ARRB, who will then talk to the client about that data and do a lot of different things,” he says. “If we can collect the data, package it in the right way and give it back to our
Jeff Doyle.
clients, it helps answer a whole host of questions.”
ARRB has five Network Survey Vehicles (NSVs) in its fleet – a Mercedes Crafter and Sprinter, a Volkswagen Transporter and two Toyota Prado models – which can work on almost any piece of
One of ARRB’s five survey vehicles in the fleet.
road network.
“Our fleet of different vehicles do different things to assess roads,” Jeff says. “The way I look at it is: if our clients don’t measure it, they can’t manage it. So, the fleet monitors and measures clients’ assets so they can then manage and maintain them.”
The NSVs have the capability to assess multiple pavement conditions, which provides significant benefits to all road authorities.
“It’s a fully-integrated mobile data collection system that measures multiple pavement condition parameters, such as roughness, rutting, texture and cracking,” he says. “It also collects digital video imagery, and each NSV has at least five cameras that identify pavement surface defects and locate and monitor the condition of roadside assets. This information can be used to perform road safety audits safely in the office, as opposed to doing it on the road.”
These vehicles also measure road geometry and use GPS to spatially locate all the data they collect.
Jeff classes the NSVs as the workhorses of his fleet, providing not only local councils with the information but state road authorities as well – and all it takes is just one pass.
“Providing the information and data to our clients takes the guesswork out of making those better decisions from an economic and safety standpoint,” he says. “This is all done in a single pass. As a result, the NSVs predominantly come into play on larger road networks.”
ARRB’s largest survey projects involve two specific IM platforms. The first is their NSVs, which are equipped with Automatic Crack Detection (ACD) systems that locate and assess pavement cracking. The second is their Intelligent Pavement Assessment Vehicle (iPAVe), which combines Traffic Speed Deflectometer (TSD) technology with ARRB’s Hawkeye platform. ARRB says the iPAVe is unique for its ability to collect deflection data as well as all other pavement condition data. The multi-laser profilers (LP) used in
ARRB’s NSVs are extremely accurate.
As Jeff explains, since first use back in the ‘90s, LPs have had around 30 years of evolution and development to reach today’s high-precision quality levels. “NSVs were single-task vehicles for a number of years, but then the technology evolved, and we were able to incorporate the Traffic Speed Deflectometer as well,” he says. “That’s where our iPAVe came from.”
According to ARRB, the iPAVe is changing the way local government authorities and road agencies are managing their road assets. By providing pavement strength testing in a single pass along a road, the vehicle provides an accurate, cost-effective way of measuring the quality of road surface and sub-surface.
“The iPAVe then became our onestop-shop because it can assess
the condition of the road above and below the surface,” Jeff says. “It came into the market in 2014 and is now predominantly working for the state road authorities on their larger roads. We’re currently doing that in Queensland and we’re about to move into New South Wales. We’ve got these going around Australia and New Zealand, all year round.”
So, what’s next for ARRB? Jeff says the company is looking to expand its services to the broader transport industry.
“We’re now transforming ARRB into the National Transport Research Organisation. Not only are we looking at roads, but we’re looking at rail, ports and airports as well,” he says. “We’re taking the business from what was predominantly a roads business into a transport research organisation.”
About a decade ago Lindsay Fox called for all heavy trucks to have a ‘black box’ installed.
The idea was that if the truck was involved in a serious incident, there would be a record of the recent truck operating data and maybe vision of the driver to see what condition he or she was in. The idea had a lot of merit. Lindsay’s assumption was that someone would look at the crash data and learn from it.
Every two years National Transport Insurance publishes a detailed analysis of its large loss truck insurance claims. The analysis is actually done by National Transport Accident Research Centre (NTARC), which is funded by NTI. The
report provides great insight into the safety performance of the heavy vehicle fleet, as represented by the sample of trucks that NTI insures. There were 852 incidents that were assessed for the 2020 insurance year. About one in 400 trucks insured by NTI can be expected to have a large-loss claim per year. The classification of causes of the 2020 NTI large-loss crashes are shown in Figure 1. The majority of the incidents resulted from errors made by the heavy-vehicle driver. NTARC recently issued a collaborative report with the National Heavy Vehicle Regulator (NHVR) about the correlation between roadworthiness problems and the likelihood of having a large claim incident. NTARC is an important investigative body that is doing excellent work to inform the heavy vehicle road logistics sector about safety performance. But it is not enough.
The Bureau of Infrastructure and Transport Research Economics (BITRE) publishes a frequent report about road trauma involving heavy vehicles. In the 2020 calendar year a total of 177 people were killed in crashes involving heavy vehicles. Of this number 31 (17.5 per cent) were occupants of the heavy vehicle
cabin. For reference, the total number of road deaths in 2020 on public roads was 1,100. Therefore, the heavy-vehicleinvolved road trauma is about 17 per cent of Australia’s road trauma. The trends over the past two years – see Figure 2 – show a significant increase in road deaths involving rigid trucks and static performance for other heavy vehicles. Note that the BITRE data does not include work-place trauma. The NTI/NTARC reports do not identify the proportion of large-loss incidents that involve a fatality or serious injury. Furthermore, there is no tie-up with the BITRE report, at least not in the public domain.
The trends that are in evident in Figure 2 are gradually improving when the scale of the freight task is considered. According to NTI the number of trucks has increased by about 50 per cent since 2003. The freight tonne-kilometres has increased 55 per cent. Despite this, the level of road trauma has decreased, until recently. So, maybe we can just wait for roads to improve, trucks to get safer and drivers to get better. Sorry, I disagree.
Australia has a National Road Strategy and states and territories have strategies that are informed by the National Strategy. The National Strategy is developed by The Federal Office of Road Safety. The latest Strategy document concerns the period 2021-2030. It notes that there were a significant number of work-related deaths that were not the result of collisions. Thirty-one per cent of work-related fatalities were the result of falling from vehicles or being injured while loading vehicles. Therefore, a significant level of logistics-industry trauma does not appear in the road-safety trauma reports. The box shows an excerpt from the Strategy that concerns heavy-vehicle safety. The Strategy is necessary and appropriate. But it is still not enough because detailed proposals need to be developed and justified. All the reports and strategies I have identified in this article have merit and are important. I think we could do better. I
propose that a Heavy Vehicle Safety Office be established within AustRoads that reports to State and Territory transport ministers. This office should obtain reports about specific incidents involving heavy vehicles from insurance companies, from emergency services agencies (Police, EPAs) and from state Work Safety Regulators. Incidents might be defined as large-losses for insurers or serious roadside or workplace injuries. This Office should publish reports that classify and explain the causes of the incidents involving heavy vehicles and consider changes that could improve performance. It would work co-operatively with the Federal Office of Road Safety to fill in the details of the National Strategy needed to get heavy vehicle safety to the next level. Remember the adage that you can’t control what you can’t understand. The Heavy Vehicle Safety Office can be
paid for from heavy vehicle registration charges. It would soon pay for itself via a reduction in the number of safety incidents. It should report to transport ministers through existing regulatory structures. The Heavy Vehicle Safety Office would have access to registration data and could also obtain specific information from vehicle suppliers to determine what technologies were on specific vehicles. The Office would not conduct site investigations and it would not be called into legal disputes because it would not publish details about specific incidents. The Heavy Vehicle Safety Office would also be charged, for example, with monitoring the adoption of safety technologies on the road safety of heavy vehicles. The Federal Strategy makes no explicit reference to Autonomous Emergency Braking or Lane Departure Warning technologies. The case for
promoting these technologies probably exists in the crash data. The Office could also develop proposals for improved work practices by operators and driver accreditation levels. It could consider the details of a Safe Systems approach to workplace safety and try to explain what this means for industry. For example, an urgent need exists to improve the career structure, training and status of heavy vehicle drivers, who are the most important element in industry safety performance. Many of the improvements that are needed are outside the Federal Government’s domain for road safety. The Heavy Vehicle Safety Office could provide the leadership needed for our industry to significantly improve safety performance.
Dr Peter Hart, ARTSA-I Life Member
Road Trauma
- Regulate for and promote heavy vehicle safety technologies
- Strengthen national heavy vehicle operational regulation
- Provide community and novice driver education about sharing the roads safely with heavy vehicles
- Promote and reduce bar riers for the uptake of safe new heavy vehicles
- Protect all road user s from conflicts with construction vehicles through state/territory government construction contract requirements such as requiring inclusion of safety technologies
- Consider the scope for Safe System investigations of fatal and seriousinjury heavy vehicle crashes
- Suppor t fatigue management through investment in heavy vehicle rest stops
- See str ategy for OH&S items
In my column this month I am going to discuss the current global supply chain realty and the associated challenges that this continues to present for truck manufacturers. It is not news that new truck sales are strong. 2021 saw 41,404 new heavy vehicle sales, just 225 trucks short of an all-time record set in 2018. Sales are at similar levels this year with customer order intake not abating. A record in truck sales for 2022 looms. These sales are the result of strong consumer demand before, during and after the initial COVID outbreak, helped, in no small way, by Federal Government incentives to keep our economy from collapsing in the wake of pandemic. But there is a problem. Australian truck manufacturers, importers and distributors equally, are experiencing significant challenges within their supply chains both at the primary supply and secondary manufacturing stages. Due to the continuing disruption to global supply chains, truck suppliers face long lead times in delivering new truck orders.
To give perspective to the supply chain problems being faced by truck OEMs, we are all aware of the well-publicised worldwide shortage of microprocessors, however shortages are far more broad reaching, including availability of internal and external finishing trim materials; resin shortages for components such as, sleeper cabs, roofs
and bonnets; shortages in bullbars, fifth wheels, fuel tanks, exhaust pipes and mufflers, alloy wheels, mudguards, general metal components, and fluids for production; shipping constraints, skyrocketing shipping costs, shipping transit times now 100 days, up from 40 days; and my favourite, last year if you wanted your truck painted blue, good luck, no blue pigment could be sourced, worldwide.
In summary, all elements of truck building and delivery are in peak demand and under stress. These challenges are real, change daily and are set to get worse. They are today’s known problems. OEMs do not know the supply chain problems they will encounter over the next 12 months. They only know they will be difficult to predict. At best we can only manage — we cannot solve them.
With the reopening of economies creating strong demand in a post-COVID world, supply chain problems have obviously forced companies to rethink their corporate strategy. ‘Just in time’ has been the manufacturing sector’s mantra for some five decades but now has been found wanting in a COVID impacted world. Not unsurprisingly, management is now factoring into the equation of inventory management, the element of risk as opposed to the previously singular focus upon costs. Companies are now transitioning to a ‘just in case’ model of inventory management. Just in case, is a set of words that sounds like a warning. Just in case of what, was my first thought, going straight to a scenario
I do not want to think about. Risk, always a factor in business, has taken on a renewed management emphasis and is now the prime determinant for building enduring organisational capability. The pandemic has been the tipping point.
Countries are finding now that their supply chains are not as robust as they thought, in many cases, these chains have failed. Add to this, geopolitical tensions arising from a resurgent China, the world’s production plant and warehouse, as well as the war in Ukraine, our industry, the road freight sector, should heed the notice we have been given by the pandemic and assess our role in an increasingly troubled world. Resilience needs to be built into the Australian freight sector, ‘just in case’. COVID and the supply chain disruptions have established this as an urgent need. During COVID, Government established a National Coordination Mechanism to ensure the capabilities of federal, state and territory governments as well as the private sector, were brought to bear to address the crises. This happened after COVID hit.
A similar mechanism is perhaps needed now before a future event, as a different approach to address the strategic problems the world is presenting to Australia. The mechanism would for starters:
• Prioritise the security and efficiency of the national road network throughout Australia for freight distribution. The network must be resilient and have the capacity to respond to disruptions to safeguard domestic capability.
• Ensure diesel and diesel exhaust fluid security.
• Build a strategic workforce.
• Have bipartisan support.
I call upon Government to support and facilitate this action now, ‘just in case’
Tony McMullan CEO, Truck Industry CouncilThe VTA was thrilled to recently host an Alternative Fuels Summit to tackle the important challenge of how our industry can start the important transition away from traditional fossil fuels. The road freight industry is dependent upon diesel fuel to provide the services that all of the population in Australia needs. Our trucks need fuel to operate. We need consistency of supply, predictable costs and a return on effort and investment. Our sources of energy are changing, and the nature of fuel will look very different in the not-sodistant-future.
Changes to Earth’s climate driven by increased carbon emissions are already having widespread effects on the environment. The effects of global climate change have been slow and gradual, but consistent. But as these effects accelerate their impact, they have become more noticeable and more measurable. Global climate change is not a future problem. It is something that is being dealt with now. Stopping or repairing the effects of mankind on this earth is a goal that is a long way off. What we do today will have a significant effect on the generations that will come after us.
As our actions and attitudes towards slowing the effects of climate change also start to accelerate, it becomes apparent that the challenges of change become more confronting. We would all like the climate problems fixed, but to what
level of disruption in our day-to-day life?
We don’t all want to become Climate Warriors, but we do want to face our responsibilities.
Reducing our industry’s dependence on carbon-based fuels is one of those responsibilities. Acknowledging that we can reduce the negative effect of carbon emissions from the burning of diesel is an early step. But it is a very difficult step. We have become dependent upon the ease of process in maintaining this energy source and methods of operation, business measurement and levels of service expectations rest firmly in the steady supply of diesel. We focus on its cost, think rarely about supply disruptions and have not been supplied with any relevant alternative.
As I said to delegates at the Summit: why should I worry about climate change?
The answer is simple — change is coming and coming very quickly. Change can be difficult. Difficult to understand, difficult to foresee and difficult to adapt to. Understanding what we can do in our industry and our businesses is a vital first step in acknowledging any change.
The Alternative Fuels Summit was planned from a perspective of zero understanding. Knowing that the movement to reduce emissions is growing, all road transport operators should now be planning and estimating what level of action and commitment they will need to take to meet their future responsibilities.
It is very confronting. How will I operate without diesel? How will I meet my current or future capital commitments? What will it cost my business to change? Will my customers be willing to pay
more for the same service?
The Alternative Fuels Summit provided direction and confidence for operators to be able to understand what the future will look like. Our expert presenters took delegates on a journey. Why change our energy source? What fuels will be available in the future? What can the government do? What will transition look like? What products are available now?
It was terrific to hear about the exciting developments from fuel companies like Viva Energy who are leading the transport industry in transitioning to alternative fuels like hydrogen, that right now is being deployed to power heavy vehicles.
Viva is doing terrific work in making hydrogen available to freight operators with its charging hub in Geelong well on its way to becoming operational and able to fuel hydrogen buses, and heavy, waste and recovery vehicles. And of course, equipment providers like Volvo, Daimler, Hyzon and SEA Electric are already manufacturing vehicles that can tap into electric and hydrogen fuelling technology.
With the recent change of government and the subsequent legislation of a lower emissions reduction target of 43 per cent (based on 2005 emissions), the industry’s acceleration towards alternative fuels will rapidly increase. Operators that start to plan for the transition early will benefit from earlyadoption to the equipment, fuels, and technology of the not-too-distant future.
Peter Anderson CEO, VTAbuses operating in Melbourne were built prior to 2003, with a similar number of pre-2003 trucks and buses currently being used on Sydney roads. The 2003 date is significant given it marks when Australian Design Rule ADR 80/03 came into effect, essentially harmonising our exhaust emission standards with the then benchmark of Euro III. The Grattan Institute unrealistically called for pre-Euro III commercial vehicles to be banned by 2025, a situation for which almost the entire annual market for new trucks of just over 28,000 units would be required to address only the needs of our two biggest cities, without taking into account the additional vehicles required elsewhere and to handle the ever-increasing freight task. Various industry bodies responded by calling for more incentives to upgrade the national fleet, and also to encourage the take up of effective electric commercial vehicles.
The total sales of 3,426 new trucks during August was 12.8 per cent more than the previous month of July, and 16 per cent more than during August 2021. The year-to-date accrual at the end of August of 24,857 new cab-chassis and prime movers was 2,950 more than for the same period of 2021, showing an overall growth of 13.5 per cent. This is despite the widely acknowledged component and labour shortages being experienced by most OEMs which has created extended delivery lead times stretching, in many cases, well into 2024. The local market is yet to gauge the effects of Hino’s decision to suspend imports and deliveries to dealers while the investigation into the company’s “misbehaviours” in relation to emission testing is being finalised in Japan. As the perennial number two in terms of unit volumes in Australia, the overall impact has the possibility of becoming quite significant, although local Hino executives remain confident that the situation will be swiftly resolved.
The Light Duty category achieved sales of 1,432 new units during August, a growth of 17.3 per cent over August 2021, and the YTD total of 10,326 units is 11.1 per cent above the same time last year.
Medium Duty trucks accounted for 669 units in August, 4.7 per cent more (+30 trucks) then in August 2021, with the YTD of 5,223 representing a 10.9 per cent (+513 units) growth over the first eight months of 2021.
The juggernaut that is the Australia Heavy Duty truck market continues to push along at an astounding rate with 1,325 new units for the month, 21.2 per cent more than in August 2021 (+21.2 per cent). The YTD accrual reached 9,308 at the end of August which was 17.7 per cent more than at the same time last
year (+1,404 units).
The Federal Government’s much-hyped Job Summit at the end of August provided two key outcomes which should have a positive impact on the labour resources for vehicle manufacture, drivers and technicians. The increase in the migration program in 2022-23 from 160,000 to 195,000, and changes to the aged pension means test and the amount that pensioners can earn without affecting their payments, should encourage additional mature drivers to work a shift or two each week to supplement their retirement incomes.
ISUZU
FUSO
MERCEDES-BENZ
IVECO
TRUCKS
SCANIA
FIAT
FREIGHTLINER
RENAULT
WESTERN STAR
DENNIS EAGLE
ELECTRIC
CHASSIS/PRIME
VANS
43133.0%
31365.0%
191112.2%
141236.4%
909 -21.8%
857 -3.1%
758 67.3%
694 -7.7%
499 32.0%
387 2.1%
321 -11.6%
319 32.9%
260 28.1%
231 100.1%
182 20.5%
172 -28.6%
59 145.8%
40 -69.0%
30 -65.5%
-90.0%
1343-25.1%
955 23.4%
447 -44.1%
310 -67.0%
256 18.5%
139 -54.9%
3450-28.6%