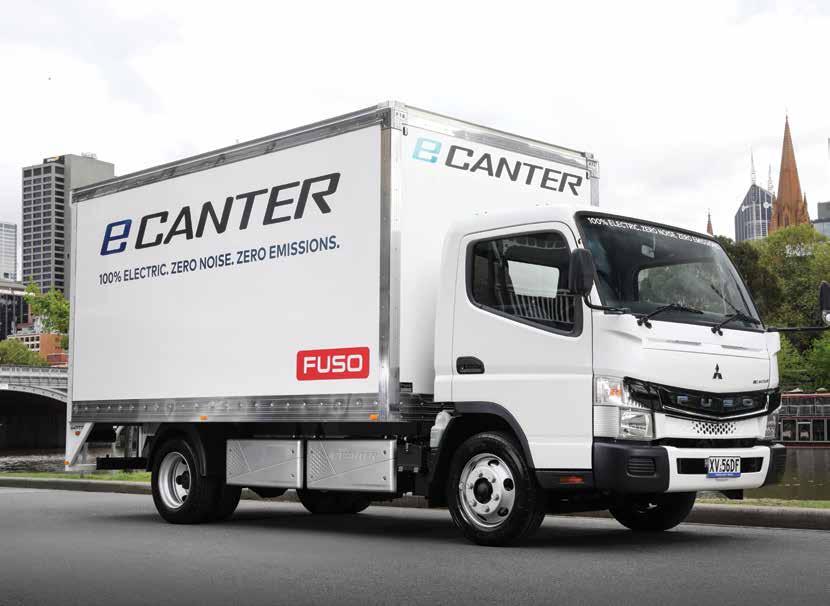
12 minute read
Final Mile
CE THE SOUNDS OF
even more electro-magnetic retardation and the effect is significantly better than what can be experienced in an equivalent sized diesel truck and from our brief experience we conclude that brake pads will outlast the rest of the truck as the brakes are only used when coming to a complete stop. Obviously without a conventional engine or transmission servicing costs will be low across the lifetime of the truck but will require technicians with expanded skill sets in order to be able to work safely with the high voltage power circuits.
Maximum power is delivered from zero rpm for stunning accleration.
Small electric motors provide the power to run the cooling pump and fans, the power steering, the air conditioning and the electro-hydraulic wheel brakes. Inside the wide cab (which seats three adults comfortably) with the audio system off the only perceptible noise at 60 km/h is a slight hum from the tyres on the pavement and the whir of the air conditioner’s ventilation fan. The eCanter will quietly (pun intended) gain the attention of potential operators, politicians and environmentalists and for the moment at least, it has the major
Liquid cooled lithium ion battery packs mounted on the outside of each of the chassis rails.
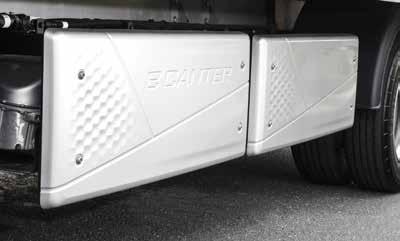
advantage of being a product totally developed by a global player such as Daimler, a fact not lost on local senior management. “The eCanter is not available in Australia just yet, but when it is, it will come with all the benefits of being backed by an established truck maker,” says Daniel Whitehead, president and CEO of Daimler Truck and Bus Australia Pacific. “That will include the assurance of parts, service support and warranty coverage provided by our national Fuso dealership network.”
AMBITIONS DRIVING
In the interests of best serving fleet operators Australia-wide, global insurance company, Zurich, has aligned itself closely with road safety experts from the National Road Safety Partnership Program (NRSPP). The NRSPP helps Australian businesses to implement effective road safety strategies in the workplace and provides myriad resources, research papers and case studies for heavy transport operators online. “Avoiding crashes should be the first priority of every heavy transport operator as it can severely affect the future wellbeing of their greatest assets – the drivers. But crashes also temporarily halt their trucks from delivering, lower their revenue and profits, and can harm their reputation and customer contracts,” explains Mervyn Rea, Zurich’s Head of Risk Engineering. “The NRSPP is a valuable tool for improving work-related road safety awareness, particularly for those in the mid-market and SME segments of the transport industry who may not have a dedicated in-house resource for safety and risk management.” Earlier this year, the NRSPP released a discussion paper that outlined five key considerations for the successful implementation of telematics into an organisation. Those considerations according to NRSPP Discussion Paper: InVehicle Monitoring Systems (IVMS): Safety Through Good Practice Telematics included clearly defined goals; selecting technologies for now and future use; building employee acceptance; real-time monitoring and feedback; and management of feedback. Zurich’s partnership with NRSPP is just one example of their commitment to improving the safety and wellbeing of drivers in the transport industry. Their in-house Risk Engineers and underwriters also work closely with fleet operators to help them get the most out of their telematics systems from data optimisation to reporting. While it doesn’t prescribe to a particular provider, Zurich, according to Merv, simply guides its customers through the key features and benefits of a comprehensive telematics solution, in particular around the monitoring of key driver behaviour metrics such as acceleration, braking, cornering and speed. “Many heavy goods trucking fleets are utilising telematic systems for a variety of functions, including condition monitoring and maintenance, efficiency and utilisation, location and projected estimated time of arrival and driver safety,” Merv says. “Zurich’s risk engineering team can help their customers determine the best telematics solution. We also assist our customers to develop a driver coaching and continuous improvement program, using the telematics data as a trigger for improvement actions.” Safer drivers have also been proven to be more efficient with fuel consumption. Zurich’s Risk Engineers have found that a robust driver-monitoring and coaching program not only reduces crash frequency, but it also reduces maintenance and fuel costs by around 10 per cent on average. It doesn’t end with telematics. Zurich can also assist their customers to determine what other technologies can assist them to increase driver safety, and as a result reduce crashes, improving productivity and customer service along the way. Zurich have worked with their customers to manage and assess the outcomes of pilot programs using Seeing Machines technology to detect driver distraction or fatigue early, reducing the potential for a crash. “Zurich is committed to the transport and logistics industry,” says Craig Sandy, Zurich’s National Underwriting Manager for Motor. “Our expert underwriters, specialist heavy motor claims team and risk engineers work closely together to provide a tailored solution that best meets our customers’ needs.” WITH SPECIALIST UNDERWRITING AND CLAIMS EXPERTISE – BOLSTERED BY ITS RISK ENGINEERING AND COLLABORATION WITH NATIONAL ROAD SAFETY PARTNERSHIP PROGRAM – ZURICH SUPPORTS AUSTRALIAN TRANSPORT BUSINESSES 24/7. Zurich assists customers develop driver coaching.

MUCH MORE THAN TRUCK INSURANCE.
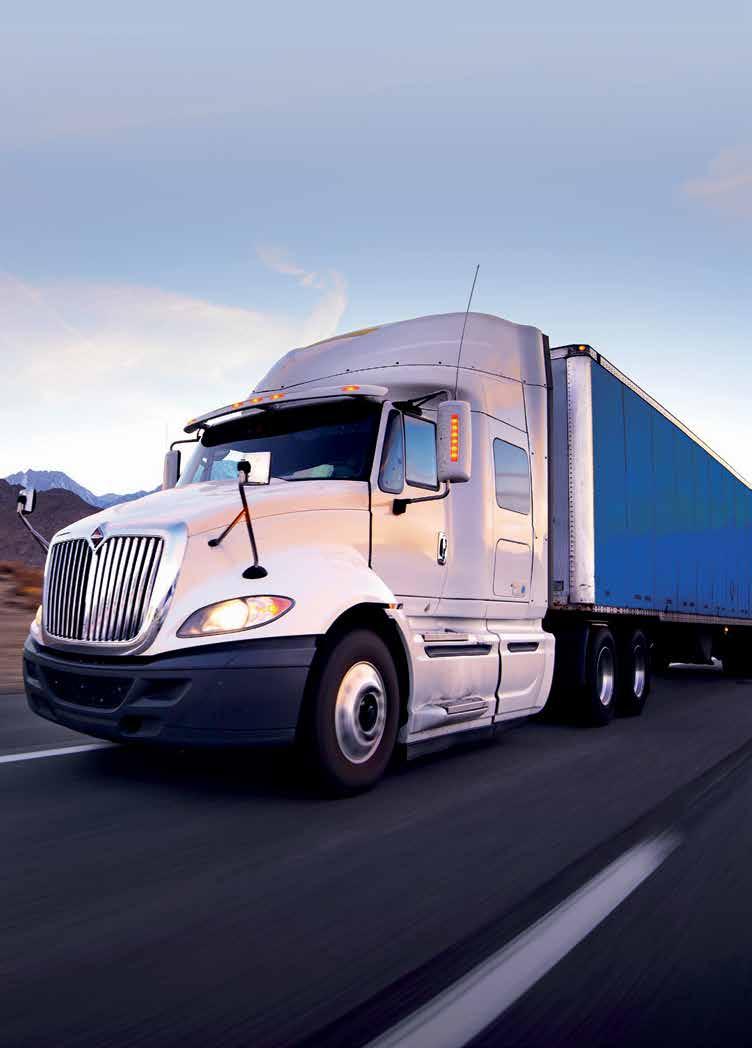
Zurich helps to improve workplace safety in the trucking industry through market-leading risk engineering solutions.
We work closely with customers to optimise business processes and driver behaviour. This helps to reduce claims, keeping your trucks on the road.
ASK YOUR BROKER ABOUT ZURICH TODAY.
ZURICH INSURANCE. FOR THOSE WHO TRULY LOVE THEIR BUSINESS.
THE FIX I S IN
EVERY MINUTE YOUR TRUCK IS OFF THE ROAD IS A MINUTE IT’S NOT MAKING MONEY. THAT CAN SPELL TROUBLE FOR ANY BUSINESS. NTI HAS HEAVILY INVESTED AND CONTINUES TO INVEST IN ITS OWN ‘ACCIDENT ASSIST’ AND ‘PREMIUM REPAIRER’ NATIONAL NETWORKS.
The immediate response to an accident often sets the tone for all the actions that follow. NTI has its own locally dedicated call centre solution and an incident response team which has access to its National Heavy Vehicle Towing and Recovery network. It consists of 35 tow operators with 376 heavy units. “We’ve got long-term tow partners who know how to influence what happens, control costs and clean up a job,” says Richard Gibson, NTI Manager – Repairer Network and Technical. “Some of them have been partners since 2002, so there’s a lot of trust and a lot of confidence.” Participation in the program involves partners undergoing internal training, regular reviews and adopting agreed standards to ensure quality and consistency so that partners can reduce costs and turnaround times all while remaining fully compliant with safety and regulatory standards. When an incident occurs and Accident Assist is notified, NTI will immediately dispatch, from its national towing network, a representative and/or the necessary resources to scene, where they will either manage the scene or
The national network of Premium Repairers can start all NTI jobs the moment they arrive at the repairer.
assist emergency services where able. While this is unfolding it is crucial to recover and transport the vehicle to a place of repair and attend to its load. At the same time other processes are at play with the call centre communicating with drivers, their families and businesses so they are all kept in the loop. The national network of Premium Repairers, according to Richard, have the advantage of starting all NTI jobs the moment they roll through the door of the repairer. The ability to start a job straight away reduces time off road by days and sometimes weeks. “We’ve seen cases where two trucks are involved in an accident, and our Premium Repairers get their truck repaired and back on the road before the other vehicle has even been assessed,” he says. “It’s an unreal advantage.” That’s not to say that the work is rushed or substandard – far from it. NTI has worked with its repair partners to create a set of standards to make sure both sides are clear on what is needed, and both sides can deliver the highest level of standards available to industry with a focus on professionalism and safe truck repairs.
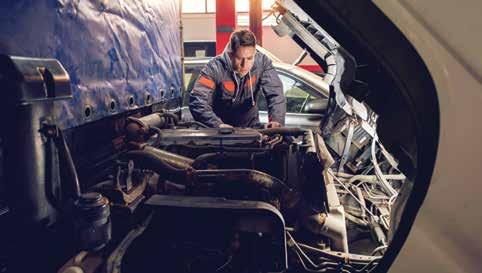
NTI’s own Repair Managers really focus on the repair process and relationship with its repair network to make sure the claims experience is class leading. NTI and its Premium Repairer network constantly review the requirements to complete a heavy vehicle repairs. Processes, equipment and trade personnel are always improving to provide the ultimate service to the client. On average, repairs are completed six days faster than other insurers can manage. This helps protect the insured businesses from undue disruption and loss of earnings. Whether it’s fuel, milk or livestock, cleanups can be costly when trucks have an accident and spill the load. NTI’s Accident Assist program also provides its own Incident Response Team. In these situations, NTI can provide clarity and comfort to both the insured and business that remediation of the incident scene is under control. The team works with its localised network service providers with good local knowledge to get the best possible results. “They’re special guys with that exceptional drive to get the job done. They know what government experts – EPA, police, fire, ambulance, local, state and federal governments – require and they know how to comply, so they’re not adding cost or complexity to the process,” Richard says. To pass the best experience onto the customer in a time of need, NTI is focused on running a reliable, efficient and highly trusted tow and repairer network. It’s an approach, according to Richard, that pays dividends, helping NTI make accurate and timely decisions on repairs and write-offs. “It’s all about protecting your livelihood,” Richard says. “The best thing we can do for our customers is get them back on the road, with a fully repaired vehicle, as efficiently and as little inconvenience as possible.”
IT’S NO ACCIDENT NTI AND SEEING MACHINES HAVE JOINED FORCES.
Great things happen when two industry leaders work together. That’s why National Transport Insurance and Seeing Machines have formed an exclusive partnering arrangement: to use data to drive change. Together, they offer an intelligent driver monitoring system with the power to reduce driver risk in your business, while also providing exclusive insurance benefits to maximise your return on investment. To find out how you can benefit, visit nationaltransportinsurance.com.au or talk to your Insurance Professional.

DRIVE INTO THE FUTURE MEGATRANS.COM.AU
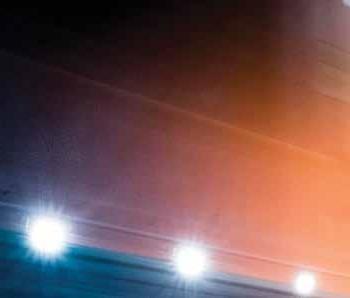
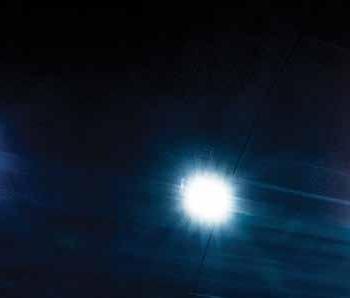

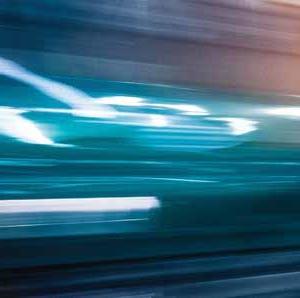
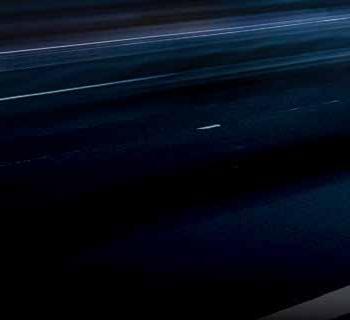
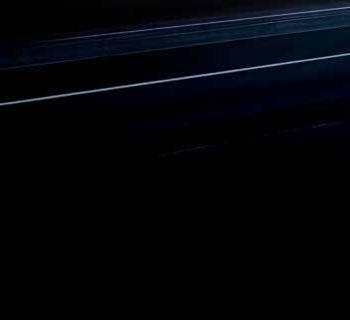



SUPPORTING SPONSORS

CONFERENCE SPONSORS
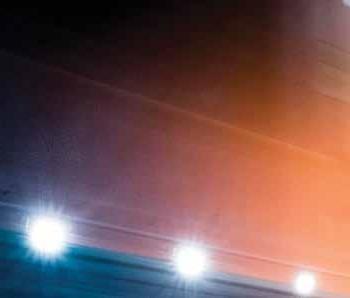
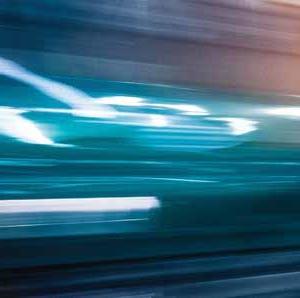
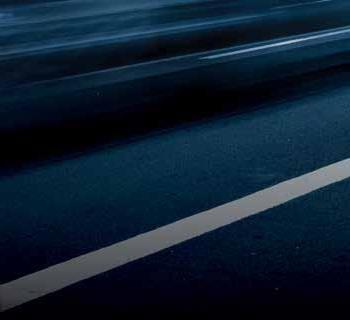

ASSOCIATION PARTNERS

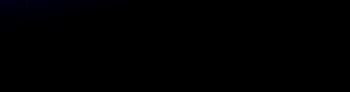
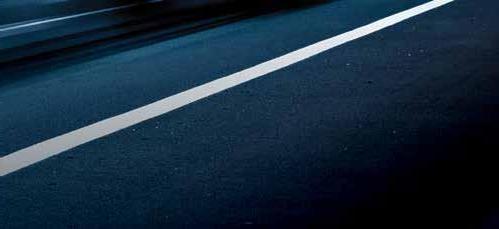
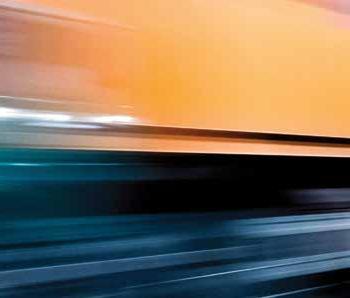
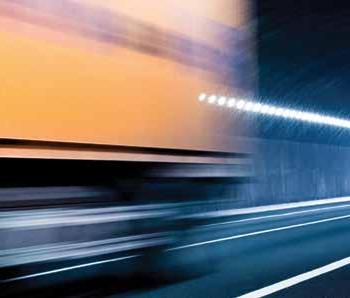
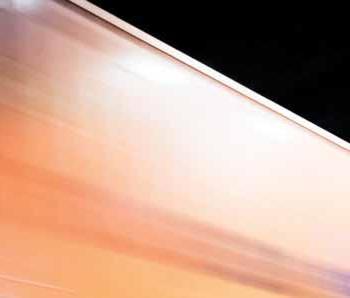
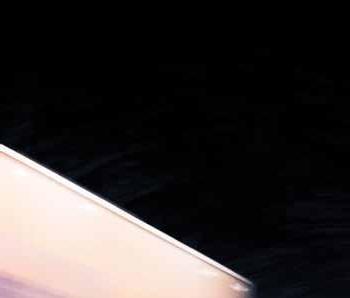
1ST - 3RD APRIL 2020 MELBOURNE CONVENTION & EXHIBITION CENTRE
OBSE SSED SAFETY
ADAM RITZINGER IS WELL REGARDED IN THE HEAVY VEHICLE INDUSTRY FOR HIS CONTINUAL FOCUS ON SAFETY ACROSS RESEARCH, CONSULTING, PRODUCT DESIGN AND ENGINEERING MANAGEMENT. HE HAS WORKED AT THE AUSTRALIAN ROAD RESEARCH BOARD, THE GERMAN FEDERAL HIGHWAY RESEARCH AGENCY, ADVANTIA TRANSPORT CONSULTING AND EQUIPMENT MANUFACTURER SAF-HOLLAND. ADAM IS NOW THE HEAVY VEHICLE ACCREDITATION SYSTEMS MANAGER AT TOLL, WORKING WITHIN TOLL’S ROAD TRANSPORT SAFETY AND COMPLIANCE UNIT.
PM: Your roles over the years have always pointed strongly towards road safety in the heavy vehicle industry. Why does this sector interest you? AR: I was fascinated by machines at a young age and always knew that I would pursue an engineering career. Road safety is another topic that I’m very passionate about. Over the years I’ve been incredibly fortunate to have been able to apply my engineering expertise to deliver positive road safety outcomes through research, policy, and product design, which is an incredibly fulfilling space to work in. When given the opportunity to work in Toll’s Road Transport Safety and Compliance Unit, I was excited not only because Toll is the largest supplier of transport and logistics services in the Asia-Pacific region, but also because Toll’s approach to safety is perfectly aligned with my own. At Toll, we believe everyone has the right to return home safely and we are working towards creating a workplace free of incidents and injuries. Toll developed an HSE strategy which is called ‘Safety Obsessed’, a concept that underpins everything that Toll does.

PM: What are some of the ‘Safety Obsessed’ initiatives? AR: The key focus areas are developing a safety-first mindset, the introduction of a new Toll Reporting and Compliance system (TRAC), and investment in safety technologies in our fleet. The first area is really about fostering the ‘safety obsessed’ culture in our employees. We are engaging all staff across Toll, encouraging them to speak up, reach out and actively care for each other, and are supporting this by running hundreds of face-to-face ‘Incident and Injury Free’ workshops in every location Toll operates. The TRAC system has been rolled-out to over 25,000 staff, and will enable greater integration between HSE technology, culture and management, leading to enhanced HSE practices globally. But given my technical background, I have a specific interest in the fleet safety technologies. Toll is investing $1.6 Billion in its fleet, and, as a result, all new Toll vehicles are fitted with telematics, and all new linehaul, remote area and dangerous goods vehicles are equipped with Driver State Sensing (DSS) technology to manage fatigue risk.
PM: How has safety technology become part of Toll’s vehicle specifications? AR: Toll’s current standard spec is the