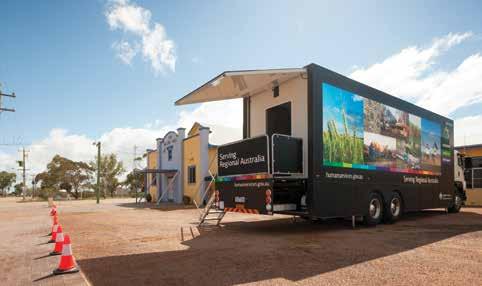
16 minute read
Here to Help
namely accommodating the number of customers in the vehicles with the maximum amount of service points. In addition to the onboard technology and resources, the builds encompass fuel range, fuel tanks and storage for the 200 litre tanks of water they carry, which all need to be stored under the chassis. With that weight distribution comes another consideration. Materials for the build are chosen for how they might affect fuel efficiency and travel range. As the Australian Government Mobile Service Centres are sometimes dispatched to rural locations, even crossing the Nullarbor once annually, having the widespread SG Fleet network of service providers at its disposal is a major drawcard. SG Fleet also offers vehicle tracking and a pool vehicle booking system. “In these rural communities, we often draw on SG Fleet’s network of service providers to get us on the road again if we have an issue around vehicle repairs or maintenance. SG Fleet is fantastic as they allow us to tap into that network. Even when they are not the actual provider, they’ll find someone who can get us on the road again should we have an issue.” More recently the Mobile Services Centre vehicles attended sites in New South Wales and Queensland where communities had been ravaged by bush fires. Safety is the first priority, according to Colin, particularly when it comes to delivering services in an area suffering from a natural disaster. “You need to be in the right place at the right time. That’s really front of mind. You might have flood waters rising or fires moving through the district. The challenges for us are that we really need to understand what the community’s needs are, determine we have the right service offer and make people aware of our visit,” he says. “Moving heavy vehicles on rural roads is a risky affair. We take that very seriously.” To mitigate those risks, the Department of Human Services achieved national TruckSafe accreditation to ensure it understands the issues around fatigue management, vehicle maintenance and driver training. “In all of those things, we adopt industry
The Mobile Service Centres are housed in purpose built Isuzu FX rigids.
best practice through our quality control,” Colin says. Recognising the risks of driving the heavy vehicles in areas stricken by natural disaster means a professional standard is required of the operation. Industry experience, Colin explains, is valued and professional drivers are recruited as part of the department’s safety strategy. “Then we underpin that with our driver training and our support programs. We invest in that. We make sure we have our drivers undertake advanced driver training, regularly,” he says, acknowledging support is also provided in skills testing. “All the drivers take great pride in the job because they know that they’re recognised as professionals and are trained and equipped to deliver to quality standards we have through our TruckSafe Accreditation and all the other courses we can do around fatigue management and chain of responsibility legislation.” A rotational system is in place for the three vehicle crews. Two crews are always on with one crew off. For every week off, two weeks are spent on the road so that the vehicles are kept on the move as much as possible. Having well-trained and well-equipped drivers helps to insure daily checks are completed and faults in reports are followed up so the vehicles, during handovers, are in great shape. Inspect365, SG Fleet’s fleet management tool, has enabled the Human Services Mobile Service team to automate its manual process of daily checking and
fault reporting. As it takes a driver through a sequence of checks in the morning, the faults are then logged and registered so they are prioritised. “The management information in Inspect365 underpins the integrity of our quality systems and our truck safe standards and that keeps us at industry best practice,” Colin says. “Working within the realms of government services, we still adopt those industry best practices around vehicle maintenance, driver training and fatigue management. Everything that’s involved in the chain of responsibility legislation is covered to mitigate all of those risks and that’s where we want to stay.” Colin came across from the Department of Agriculture in 2004. He’s been involved in managing rural programs and regional servicing strategy for much of his career. The new technology and management now available, he explains, helps identify risks and provides greater visibility as to where the vehicles are. It’s a big country after all. “We get reports on heavy braking and speed and it gives you a lot more helpful information to manage risks,” Colin says. “We’ve got access to people and information and support at the touch of phone. That’s really what it’s about. It’s about making problems go away. If there are issues we need to find solutions and that’s where SG Fleet comes in. From our point of view, we’ve really got to make sure that we’ve got these trucks working on the road and delivering what they need to do all the time.”
CITY MORE THAN MOTOR
DETROIT TODAY MEANS MORE THAN MAKING ENGINES. THE COMPANY HAS DEVELOPED AN EXTENSIVE RANGE OF MODERN COMPONENTS ENGINEERED AND MANUFACTURED AT ITS OWN PREMISES. PRIME MOVER RECENTLY WALKED DOWN THE PRODUCTION LINE AND CAME AWAY RATHER IMPRESSED.
At the 3.2 million square foot facility in the city of its namesake, Detroit, Michigan, the Detroit company manufacturers major powertrain components including the range of Detroit Diesel engines as well as driveline components including the DT12 automated manual transmission and Detroit rear and front axles. Initially owned and operated by General Motors the plant commenced production in 1938 and has been building truck engines since 1955. The facility has undergone several multi-million dollar upgrades since the beginning of the 21st century and the organisation was rebranded as Detroit in 2011 as it had become more than just an engine manufacturer. Production of the first of the DD platforms began in 2008 with the DD15 and the facility currently produces the DD13, DD15 and DD16 heavy duty units and the DD5 and DD8 light duty engines. Since it began operations more than eighty years ago Detroit has produced more than five million engines including one million during the past 20 years. The current annual production
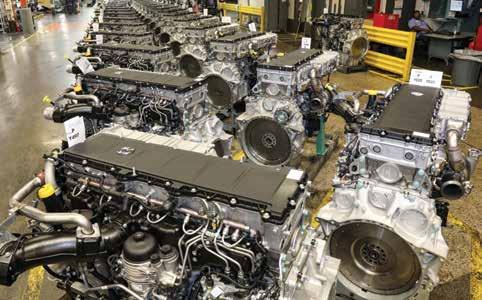
amounts to 110,000 heavy duty engines, 10,000 medium duty engines and 45,000 transmissions. Detroit was purchased by Daimler in 2000 and has since been a key factor in the global developments and manufacture of Daimler’s major driveline components. Product engineering and testing are under the same roof, as is the Detroit national customer call centre, creating a situation which streamlines the process from product inception all the way to aftermarket support. All displacements of the Detroit engines have similar designs and construction which incorporates wet cylinder liners, cast engine blocks and one piece cylinder heads. Extensive webbing on the Detroit blocks is used for strength as well as reduction in noise and vibration. Raw engine block and cylinder head castings are produced in South Africa and are then machined at the Detroit facility. Improvements in design are such that only 35 pounds of material needs to be removed from a DD15 block compared with the 150 pounds that used to be machined off a block for a Series 60 engine. It takes around four hours for an engine to be processed down the line, and each is subjected to rigorous inspections at five ‘quality gates’ as more components are
added. Torque tools are used extensively, not just on bearing and head bolts and every bolt and nut associated with the fuel rails is double checked. The aim is for each shift to produce 163 units. Every engine is hot run tested on one of the 42 Dynometer prior to being shipped. At the Daimler truck plant in Charlotte North Carolina the engines are retested after installation into Freightliner and Western Star trucks to ensure there are no issues and to confirm power and torque ratings. An increasing range of components are being manufactured ‘in-house’ to ensure quality and maximise production efficiencies. Turbochargers used to be either the number one or two components subject of warranty claims. After two years of development the turbos began being produced at the plant in 2015 using a Daimler design identical to the Mannheim units used on Daimler truck engines in Europe. Around 85,000 complete turbos are manufactured each year at the Detroit plant and rotor components are also exported to be used by Mannheim. The turbo shafts have a tolerance of just six microns and bar codes and data matrix stamps ensure the aerospace-like quality which has resulted in drastic reductions in any turbo problems associated with Detroit engines. Turbocharger testing involves shaft speeds of up to 405,000 rpm. The use of the proprietary asymmetric turbo reduces weight and complexity plus delivers improved performance with sustainable reliability. Behind the products are the people who make them and there is a palpable evidence of pride on the shop floor. The turbo division is a great example where there are nine employees dedicated to producing the turbos and all are qualified for each other’s roles. Despite its massive size the overall facility shows a commitment to energy efficiency and environmental stewardship. Since 2008, the factory’s energy consumption has decreased by 48 per cent, while at the same time production has increased significantly. LED lighting is used extensively, and the facility-wide recycling
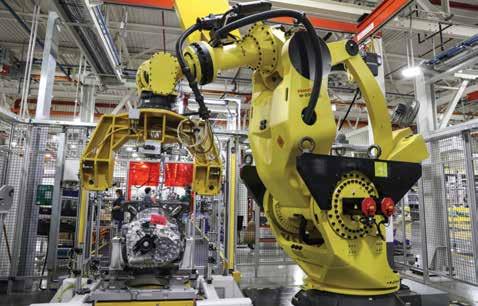
program involves recycling or reusing items such as component packaging. The most recent developments of Detroit engines such as the DD13 have focused on delivering a long flat torque curve to provide the driveability and fuel efficiency associated with engine down-speeding. This has resulted in the DD13’s ability to deliver 90 per cent of its peak torque in just 1.5 seconds whereas in the same time a competitor’s engine will only be at 50 per cent. Factors contributing to this improved performance include the use of the non-waste gated turbo and low inertia camshafts. As an adjunct to the power, the engine’s retardation braking capabilities have been enhanced with the improved ‘Jake’ engine brake which is integrated into the camshafts rather than sitting on top of the rocker arms. This design change provides three stages of engine braking and is much quieter in operation. Lifetime servicing is enhanced by the location of most key maintenance components above chassis rail for direct access which results in less service time and improved heat dissipation. The larger capacity of the sump helps extend oil drain intervals as does the maintenance free crankcase breather which is a closed system and returns oil to sump. The DT12 automated transmission has been a success story for Detroit with 45,000 being produced at the facility annually. The DT12 has well-recognised capabilities and its contributions to efficiencies begins in the basic architecture that utilises an alloy case and two gear shafts instead of three to significantly reduce weight. Rear axles are another area where Detroit has pursued efficiencies which complement the down-speeding of the engines, and final drive ratios of 2.0:1 or 1.9:1 are becoming the norm, with even lower numerical ratios currently being assessed and likely to enter production soon. The Detroit steer axles may not be as complex as engines or transmissions, yet they are a vital component of modern trucks. The Detroit front axles feature Torrington bearings to handle the thrust forces and to provide a long life of smooth steering. For decades the terms ‘Detroit Diesel’ or ‘GM’ were commonly associated with the supercharged two stroke engines which the company produced for under GM’s ownership. The modern ‘Detroits’ continue to derive some of their heritage from those venerable green painted icons that were a mainstay of truck and bus engines for decades. The North American manufacturer’s and Daimler’s inputs, since 2000, today deliver a range of modern major driveline components that are able to operate seamlessly together regardless of the brand of vehicle they are fitted to.
BLAST FROM THE PAST
The sheer magnitude and geography of Australia has made communication and information sharing essential to building the country. Reliable radio access has been vital in farming, freight movements, emergency services and infrastructure. Of course, over the last six decades none of that has changed even while GME has continued to evolve along with radio communications. Founded by engineer Edward Dunn in 1959, Standard Components, based out of Sydney’s northwest, originally specialised in TV tuner reconditioning before branching out into other aspects of TV services. By 1964, as television became the dominant medium in the country, it had expanded its range of Kingray products. Its primary product at the time was the Masthead Amplifier, an analogue unit that accepted signals from separate UHF and VHF antennas, or UHF/VHF combination antennas, and output the amplified signal down a single cable. It was popular in remote areas where it facilitated a higherquality TV signal. In 1972 Dunn partnered with close friend Phil Dulhunty, and formed Greenwich Marine Electronics, now known as GME. This signalled a new direction for the company which had started to branch out into the communications industry as a distributor of 27MHz Marine Radios. GME entered into the 27MHz CB market in the late ‘70s when it debuted its first radio model, the GX275. A new decade brought with it a range of new designs which the company had, as it diversified its revenue streams, commenced manufacturing inhouse. In the Bicentennial year, 1988, Standard Communications, by way of realising it had to compete internationally, recognised it needed to streamline, and wherever possible, automate its production practices, installing surface mount technology machinery. As part of this technological transition the company incorporated a comprehensive Total Quality Management program. Since then the company’s CB Radios have gone through an evolution afforded by new communications technology and innovation. Selective Calling is now standard in the CB Radio market following the launch of the TX4000, which GME introduced to market in the early ‘90s. GME has since unveiled the TX4500, one of its flagship products and a portfolio of super compact units popular with truck drivers across the heavy vehicle industry and 4WD enthusiasts alike. GME over the years has expanded and opened a new purpose-built headquarters in Winston Hills in 2013. The facility houses all aspects of its current business including manufacturing and engineering capabilities, warehousing and marketing. At present GME employs over 200 Staff to ensure its commitment to Australian design and manufacturing is ongoing. More recently GME released the first connected UHF CB Radio Platform, the XRS Connect in 2016. Compatible with smart devices via Bluetooth, the range of radios enable the user to personalise the settings of the XRS, use the dedicated smartphone apps, XRS Location Services and XRS Connect and download firmware updates to access new features. GME recently confirmed it was committed to releasing a minimum of one new upgrade for XRS every year. This will ensure, according to the company, that its users will always have access to the latest technology available. Dedicated customer focus such as this has long been an integral part of the company ethos and brand. The legacy of founder Edward ‘Ted’ Dunn, who passed in 2001, lives on through the family ownership and the many active long serving staff who worked alongside him. A LEADER IN THE FAST-CHANGING COMMUNICATION TECHNOLOGY SECTOR, GME IS CELEBRATING 60 YEARS AS A 100 PER CENT AUSTRALIAN-OWNED FAMILY BUSINESS. GME’s Winston Hills facililty.
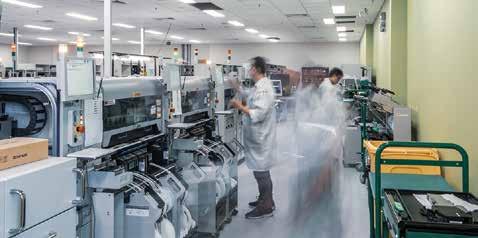
KEEPING UP APPEARANCES
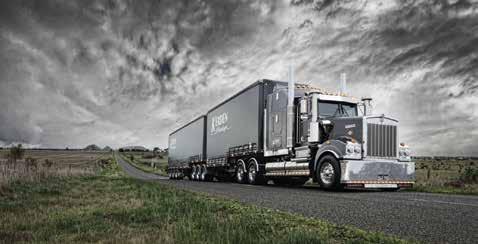
It’s not just its ability to tackle specialist tasks with no-fuss efficiency that has helped Kerden Haulage carv out an impressive reputation over the past 27 years. From the very first truck – a second-hand 1986 International S-Line – which Dennis and Kerry Radburn used to establish the business back in 1992, there has been a steady focus on projecting a smart, professional and eye-catching appearance. It’s a strategy that continues to pay dividends, according to Kerry. “We are very proud of our fleet and we get a lot of work out of the appearance of our trucks. Turn up with a tatty looking piece of machinery and that customer is not going to be too enthusiastic about giving you more work. When we turn up at a customer’s place, they often tell us how good the trucks look,” she says. Based in Nowra, on the NSW south coast, Kerden Haulage is still very much a family business, with Dennis and Kerry’s son, Damien, having joined to help run the growing company. After cutting its teeth in a variety of state-based work, such as supporting the construction of venues for the 2000 Sydney Olympic Games, Kerden Haulage has spread its wings along the east coast and across the country. Today, it’s engaged in a wide variety of work, including over-dimensional haulage for Qantas, storage and distribution for Todae Solar, express freight for DHL and haulage of precast concrete components for BCP Precast. It’s all about meeting the customer’s needs says Kerry. A lot of what it does is specialised work. As they cart products for Cromford Pipe Holdings, a poly pipe manufacturer, the company uses extendable trailers, drop-deck extendable trailers and crane trailers specifically to help transport their products. Kerden Haulage’s fleet has grown to 45 trucks, mainly made up of Kenworths, and most are finished in the company livery, consisting of gunmetal grey and contrasting white. With increasing vehicle numbers, however, came a growing issue with fleet presentation. While the liveries of different trucks often looked fine in isolation, when they were parked next to each other, noticeable differences became obvious and, in some cases, paint jobs were not to the company’s high standards. According to Tony Naughton, PPG NSW Commercial Transport Manager, PPG was approached by Kerden Haulage to reduce the varied colours and appearance of their fleet. “They take a lot of pride in their fleet and they wanted continuity of colour and finish because the look of their trucks reflects back on their business,” he says. “The service we were able to offer is called PPG FleetSpec. It’s a free service where we worked directly with them to precisely match their fleet colours and then prepare a PPG FleetSpec handbook dedicated to Kerden Haulage.” Inside the handbook are all the fleet’s colour codes and colour samples, the products and detailed processes to be used to paint the various substrates the vehicles are made from (steel, fibreglass, aluminium, etc), along with detailed views of the company’s livery and how it’s applied to different types of vehicles in the fleet. Copies of the PPG FleetSpec handbook get distributed to each Kerden Haulage depot, as well as the PPG FleetPool network of independent Commercial Transport repairers and refinishers. When a Kerden Haulage vehicle goes to any PPG FleetPool shop or PPG user around the country, they have everything needed to achieve the same colour and consistency of finish. “The Kerden Haulage colours are all listed on our PPG PaintManager XI software system so it’s simple for a user to look up the precise formulations,” says Tony. “In the same way, local trailer or truck manufacturers using PPG, such as Volvo, Mack, Kenworth and Iveco, can also access those colour formulations. Importantly, they get the uniformity of colour and finish that shows off their organisation in the very best light.” APPEARANCE IS CRUCIAL AT KERDEN HAULAGE AND REMAINS A KEY FACTOR FOR WHY IT PARTNERS WITH PAINTS, COATINGS AND SPECIALITY MATERIALS SUPPLIER, PPG, TO ENSURE A CONSISTENT, HIGH QUALITY FINISH ACROSS THE ENTIRE FLEET. PPG PaintManager lists the precise paint formulations.
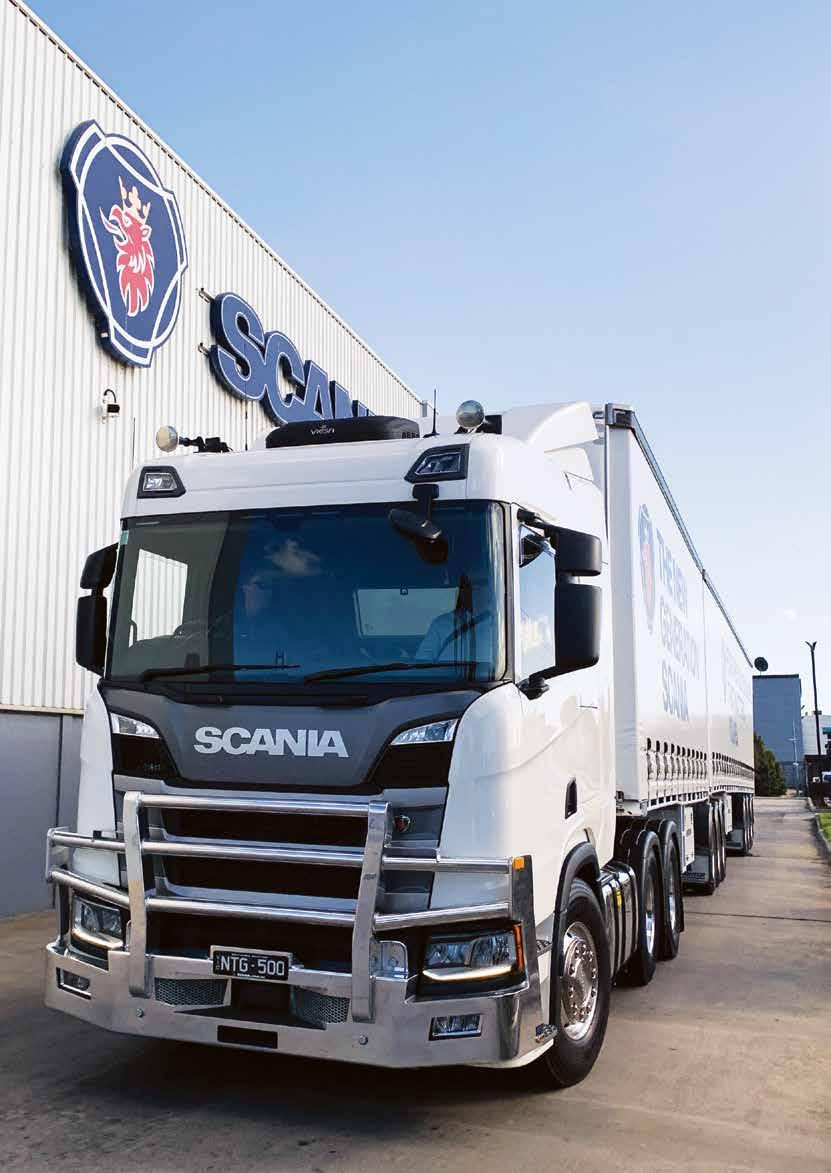