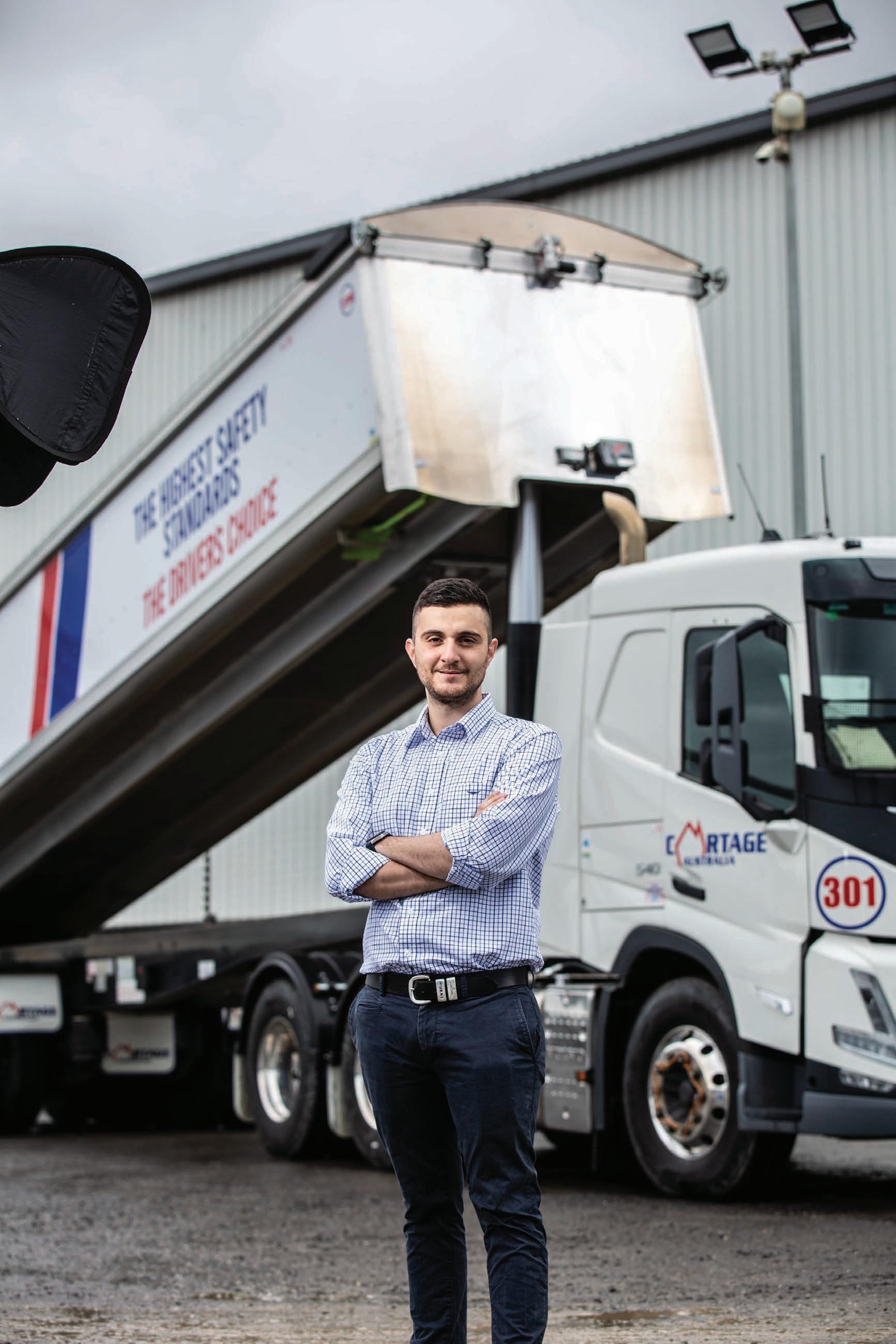
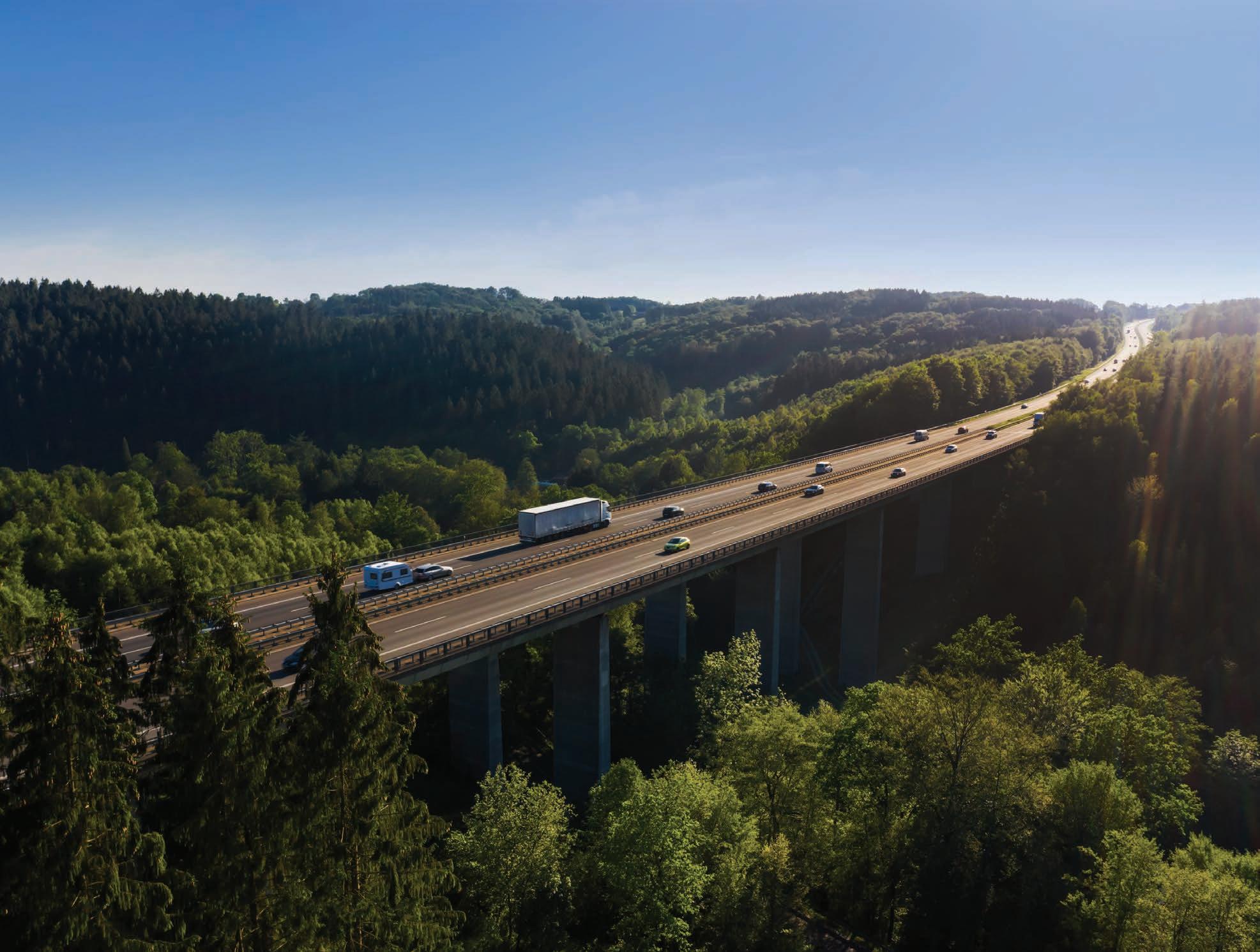
At Isuzu, we understand that when you trust your fleet to us, you’re trusting us with your most precious business asset… your reputation. And that’s a responsibility we don’t take lightly. So when your customers demand complete reliability, we won’t rest until we make sure you deliver. To find out more, visit isuzu.com.au/fleet
Visit twusuper.com.au/insurance
The most-tested Western Star ever, the all-new X-Series is seriously tough. Boasting our legendary Star durability, the X-Series features a powerful integrated driveline, advanced safety systems, and superior comfort - even in the most rugged of applications. But talk is cheap. Experience it for yourself.
John has been the nation’s foremost authority in commercial road transport media for almost two decades and is the driving force behind Prime Creative Media becoming Australia’s biggest specialist B2B publishing and events company. Committed to servicing the transport and logistics industry, John continues to work tirelessly to represent it in a positive light and is widely considered a true champion for the growth of the Australian trucking and manufacturing industry.
Over the past two decades William has published widely on transport, logistics, politics, agriculture, cinema, music and sports He has held senior positions in marketing and publicity for multinational businesses in the entertainment industry and is the author of two plays and a book on Australian film history. Like many based in Melbourne he is in a prolonged transition of either returning or leaving.
A seasoned transport industry professional, Peter has spent more than a decade in the media industry. Starting out as a heavy vehicle mechanic, he managed a fuel tanker fleet and held a range of senior marketing and management positions in the oil and chemicals industry before becoming a nationally acclaimed transport journalist.
Having recently completed his Bachelor of Media and Communication (Media Industries) degree at La Trobe University, Peter brings a fresh perspective to Prime Mover. Invaluable experience obtained during his time at upstart, La Trobe’s newsroom, has been supplemented by direct industry experience in a Council placement. Peter is looking forward to contributing to the magazine’s image as the leading publication for commercial road transport with his developed skills.
Australia’s leading truck magazine, Prime Mover, continues to invest more in its products and showcases a deep pool of editorial talent with a unique mix of experience and knowledge. www.primemovermag.com.au
Handling placements for Prime Mover magazine, Ashley has a unique perspective on the world of truck building both domestically and internationally. Focused on delivering the best results for advertisers, Ashley works closely with the editorial team to ensure the best integration of brand messaging across both print and digital platforms.
ceo John Murphy
john.murphy@primecreative.com.au editor William Craske william.craske@primecreative.com.au managing editor, Luke Applebee transport group luke.applebee@primecreative.com.au senior feature Peter Shields writer peter.shields@primecreative.com.au
business Ashley Blachford development ashley.blachford@primecreative.com.au manager 0425 699 819
art director Blake Storey blake.storey@primecreative.com.au design Kerry Pert , Louis Romero, Tom Anderson
journalists Peter White peter.white@primecreative.com.au
Anjali Behl anjali.behl@primecreative.com.au
design production Michelle Weston manager michelle.weston@primecreative.com.au
client success Justine Nardone manager justine.nardone@primecreative.com.au
head office 379 Docklands Drive, Docklands VIC 3008 enquiries@primecreative.com.au
03 9690 8766 subscriptions@primecreative.com.au
Prime Mover magazine is available by subscription from the publisher.
The right of refusal is reserved by the publisher.
Annual rates: AUS $110.00 (inc GST).
For overseas subscriptions, airmail postage should be added to the subscription rate.
All articles submitted for publication become the property of the publisher. The Editor reserves the right to adjust any article to conform with the magazine format.
PRIME MOVER magazine is owned and published by Prime Creative Media.
All material in PRIME MOVER magazine is copyright and no part may be reproduced or copied in any form or by any means (graphic, electronic or mechanical including information and retrieval systems) without written permission of the publisher.
The Editor welcomes contributions but reserves the right to accept or reject any material.
While every effort has been made to ensure the accuracy of information Prime Creative Media will not accept responsibility for errors or omissions or for any consequences arising from reliance on information published.
The opinions expressed in PRIME MOVER magazine are not necessarily the opinions of, or endorsed by the publisher unless otherwise stated.
in accordance with PAS 2060, see www.castrol.com/cneutral for more information.
The C02e emissions are calculated in accordance with the Greenhouse Gas Protocol’s Product Life Cycle Standard and includes life cycle emissions. The demonstration of carbon neutrality will be assured by an Independent Third-Party and certified to BSI’s PAS 2060 carbon neutral specification. See www.castrol.com/cneutral for more information.
“In recent times with COVID we’ve also had parts shortages, truck shortages and that’s required us to become a bit more creative when carrying more capacity to assist with those challenges.”
To combat the ongoing driver shortage, Cartage Australia has taken a different approach by introducing two new A-double sets to its fleet entirely composed of Performance-Based Standards vehicles.
PBS pioneer, Clenton’s Transport, has introduced the Hammar MegaReach to industry, a split-quad side loader that is fast delivering clear productivity gains in the container haulage operations of its Sydney-based business.
The ubiquitous wooden pallet was invented by Howard T. Hallowell almost 100 years ago in 1925. Pallets, to this day, remain an essential component of many modern freight operations including JATEC Transport.
50 The Birth of Cool EJS Logistics pushes its prime movers on punishing interstate linehaul. The Dana products incorporated on its latest Kenworth additions have made it an avowed enthusiast.
It became, not unexpectedly, the year in which Friedrich Hayek came back to haunt us. “When security is understood in too absolute a sense, the general striving for it,” he noted, “far from increasing the chances of freedom, becomes the gravest threat to it.”
In January, a $1.9 trillion infrastructure bill was passed in the US. Among its 2,702 pages was a proposed safety measure for cars built after 2026 removing operational control from the occupant via a vehicle kill switch mandated for automobile manufacturers that would “passively monitor the performance of a driver of a motor vehicle to accurately identify whether that driver may be impaired.”
The open system enables third parties to remotely access the data at any time according to an algorithm in which the driver has little to no control. It was, somewhat understandably, described as a “privacy disaster,” but not in the same sense of the one that gave the world Kim Kardashian. The agents behind this civil liberties obscenity don’t work in the entertainment industry.
Putting aside the wider implications on freedom of movement, one is left to
reflect on how the same technology might be used, for instance, on the Cadillacs found in the presidential motorcade? It’s a difficult concept to fathom just alone for reasons of national security - there’s that word again. When it comes to matters of digital integrity 2022 has taught us there are more than a few limitations that a mere four years are not bound to rectify. Highly ambitious roll outs in unconvincing timeframes are, as the Tesla Cybertruck keeps reminding us, nothing new. If you’re into cosplay and armoured personnel carriers, you’re probably a member of the World Economic Forum with an unhealthy obsession with James Cameron’s Aliens. What’s more, to judge by the 1.3 million others who have made a downpayment on the Cybertruck, you’re not alone. Just in time for Christmas – next year – the oft-delayed Tesla Cybertruck is set to complete its “final lap” as Elon Musk put it in an investor conference call last month. One can’t help but guess, like a kid in front of the bowl of jellybeans, as to the number of semiconductors that will go into its first phase of production. Spoiler alert: heaps. Toyota, it would appear, could well do with some. As of November, the leading car brand in the wake of widespread microchip shortages has been forced to ration ‘smart’ keys to its customers, meting out one per car in Japan with something similar on the cards for the North American market. Such is the deficiency in chip supply, the automaker has resorted to these provisional measures aimed at delivering cars to customers as quickly as possible. Up to 14 different models will be affected.
For leading-edge industries, where semiconductors are the single most important technology, the situation is delicately balanced. A modern dieselpowered prime mover can utilise up to 500 semiconductors, a tenth of what will go into an electric heavy vehicle.
As a nation, with some niche exceptions, Australia, according to a report from the Australian Strategic Policy Institute (ASPI) is almost entirely dependent on foreign-controlled microchip technology, making it increasingly vulnerable to global supply-chain shortages, shutdowns and disruptions. “Such occurrences have become all too common,” observe authors of the report Alex Capri and Professor Robert Clark, “either because of events such as the COVID-19 pandemic or because of other governments’ attempts to weaponise supply chains for geopolitical reasons.”
I would argue the former falls under the latter category, regardless. Policymakers, all the same, according to the ASPI report, “must treat semiconductors as a vital public good, almost on par with other basic necessities such as food and water supplies and reliable electricity — a reality that would become immediately apparent in a time of international crisis resulting from, for example, wars or natural disasters.”
Microchip manufacturing for the entire world is concentrated in East Asia. The main volume percentages are split between Taiwan (64), South Korea (16), and China (10). To conceive, develop and execute a national plan enabling us the capacity to build and compete in the semiconductor space the ASPI report outlines four overarching objectives. One of them is geared around leveraging our security partnerships and alliances like the Quadrilateral Security Dialogue, AUKUS and the Five Eyes network. It’s a bold plan to enmesh our industry in the global value chain. The mere mention of intelligence agencies, working as a cudgel against our sovereign vulnerabilities, however, doesn’t make me feel any more secure. You?
cabin options, including the largest cab on the Australian market, the 72” Stratosphere sleeper.
Featuring an integrated driveline and advanced safety package, the X-Series is underpinned by the legendary durability that customers expect from a Western Star according to Penske Australia.
“The new X-Series is lighter, safer, stronger, and more spacious than any Western Star before,” said Kurt Dein, Penske Australia, Head of Western Star Trucks. “Ingrained with the tough Western Star DNA for which we are renowned, the X-Series-specific cab is reinforced with steel for added strength ensuring customers can continue to depend on Western Star in the most challenging of applications – whether that is heavy haulage onhighway or heavy haulage off-road,” he said.
The local market has gotten its first glimpse of the brand-new Western Star Trucks X-Series including the 48X — an Australian-exclusive.
Last month, Penske Australia unveiled the new truck at customer and media events in Brisbane. Touted as the most tested Western Star ever, the X-Series has been designed from the ground up and comprises the 47X, 49X, and 48X, which is powered by the 450-525hp Detroit DD13 Gen 5 or 500-600 hp DD16 engine, and features a setforward front axle, with a bumper-toback-of-cab (BBC) measurement of 113.5 inches.
“We are thrilled to unveil the brandnew X-Series to our Australian customers,” said Craig Lee, Penske Australia Executive General Manager On-highway.
“Our team has worked closely with Daimler Trucks North America on the design of these three models, including the 48X which is a global exclusive, to deliver a product that is bespoke to our local needs,” he said. “We’re excited by what the X-Series means for Australian customers.
We have passionate Western Star enthusiasts who will want a 49X 6x4 with the 600 hp Detroit DD16, drum brakes, spring suspension, and an Eaton Fuller manual transmission – a space in which we are renowned – and we can deliver that.
For fleet operators after a 47X or 48X to haul B-doubles with Detroit’s DT12 transmission and all the advanced telematics that comes with that, Penske Australia, according to Lee, can deliver that too.
“The Detroit DD13 13-litre engine in the 47X and 48X also open up new markets for Western Star, such as local distribution or B-double intrastate,” he said.
The 47X has a short, sloped bonnet that yields payload flexibility, a setback front axle, and choice of power with the Cummins L9 or the Detroit DD13 Gen 5, either the Detroit DT12, Allison fully automatic, or Eaton Fuller manual transmission, and various sleeper options.
The 49X is powered by the 500-600 hp DD16, has up to 200+ tonnes GCM capability, and is available with multiple
“Inside the cab, premium noise and temperature insulation and triple door seals deliver a quiet and comfortable environment, and the multi-function steering wheel and primary instrument cluster result in a highly intuitive workspace.
“From the 36” mid and trench sleeper options to the market-leading 72” Stratosphere sleeper, the cabin options are unbeatable said Dein.
“The 72” Stratosphere is seriously spacious and includes a 65-litre fridge, generous storage solutions with microwave prep, and either a Murphystyle bed – with a foldaway dinette/ work table – or a double bunk option,” he said.
“With Active Brake Assist 5, lane departure warning, adaptive cruise control, side guard assist, tailgate warning, brake hold mode, an improved visibility package, and a RollTek driver’s seat with rollover restraint and a seat-mounted airbag, drivers and fleet operators can have complete peace of mind that their Western Star will protect their most important asset, the occupants.”
With almost 100 years of quality solutions and trusted services, Smedley’s is the largest and only national PBS provider with experience across all areas of the transport industry.
Did you know you could be carrying between 30% and 60% extra payload than what you are now?
At Smedley’s Engineers, we help you optimise payload profit on your entire fleet. Our goal is to take the process of navigating PBS off your hands so you can get on with what you do best. We partner with clients to provide essential advice relating to engineering compliance, optimising payload and any expansion of your fleet as your business grows.
We also assist with the ongoing management of PBS compliance and access across your fleet.
Building material company, Hanson, has created a concrete agitator specifically designed for the most extreme underground conditions.
The Mack Metroliners, three in total, operate at the Fosterville Gold Mine, an all-underground mine that runs 24 x 7, 28 kilometres northeast of Bendigo in Victoria. To prevent the mine shafts collapsing, the miners spray highdensity, rapid-drying shotcrete onto the walls and ceiling.
Hanson’s Concrete Plant Manager, Matthew Bray was charged with solving the problem of getting the concrete down into the mine.
“It’s a harsh, incredibly dusty environment that often turns to mud and slurry the moment it is exposed to water from the water carts or mining machines,” said Bray. “The temperature down the bottom can get up to 50 degrees centigrade. Truck filters clog up quickly which compound into a vast array of truck faults.”
Hanson installed all heavy-duty fittings on the Mack Metroliners, including extra layers of paint and rust-proofing, large custom external trays and a single conveyor guard over the drive wheels with additional bracing to handle the bumpy and steep conditions.
The single guard gives Hanson more room to change the tyres out, according to Bray, as they go through about ten
tyres a month.
“The single guard allows us to mount larger external trays on top, which hold the chutes and some custom wheel chocks we’ve had manufactured,” he explained. “When the floor is underwater conventional chocks can float away, and if we’re on an extreme gradient they can slip. Having these handy around the truck gives us a bit of reassurance and prevents the truck sliding.”
Bray and his team worked closely with Mack’s engineers to customise all aspects of the Metroliners, using an agile development process that saw them making changes on the fly as new truck data came to hand from the mine. A part of this process involves keeping the trucks slow enough to stay in control. The track is a steep and narrow tunnel that reaches a 7-to-1 gradient in places.
“Slowing the truck down enough on the descent is a major safety issue, especially when the roads are wet,” said Bray. “If the driver sits on the air-brakes all the way down the compressor can’t keep up and you risk running out of air and not being able to stop. Besides the obvious potential damage caused to the truck, sliding into the tunnel wall could also cause large safety and structural concerns, so this was a large challenge we worked with Mack to engineer out.”
To get around this problem, Hanson imposed a speed limiter of 30 km/h on the engine, installed a transmission retarder to reduce the need for braking, and lowered the diff ratio so the retarder cuts in earlier than usual at low speeds.
“Ideally, we want the drivers to be able to get down there without using the brakes much at all,” explained Bray.
In this regard the retarder is crucial as it functions as the control mechanism on the descent, especially when roads are slippery, which is often.
“The drivers are super-excited about it, they’ve had the experience of hubs overheating from riding the brakes and the seals blowing, and we’re confident this approach will solve that.”
In the confined space of the tunnels there’s very little room to traverse, so Hanson went with a single-steer model Metroliner and added a four-way camera system so the driver can see all around the vehicle.
Rollover protection was added on the top in case Hanson had to modify it. It’s been fully-enclosed with all the bolts removed along the top to make it smooth.
“We wouldn’t be popular if we ripped the air ventilator bags along the roof of the tunnel,” joked Bray.
Designing and engineering trucks locally in Australia gives Mack the flexibility to create fully customised trucks for unique tasks.
“Pushing the boundaries to drive application excellence is a very strong pillar of the brand and something we’re very proud of,” said Tom Chapman, Mack Trucks Vice President. “Partnering with Hanson to trailblaze safety and technology advances for the Fosterville Gold Mine project is a great example of this. It’s a real testament to what can be achieved with a strong business partnership where there is a commitment to mutual progress and success.”
The three new Metroliners are expected to enter service before year’s end and will run continuously 24 x 7.
Team Global Express has officially unveiled its new brand and logo at an event in Brisbane.
The rollout of the new brand has been 12 months in the making as the company updated its branding across its fleet, uniforms buildings, digital assets and signage.
In August Toll Global Express announced it was changing its name and brand identity to Team Global Express. According to a statement issued by the company, ‘Team Global Express’ reflects the passion, commitment, and integrity of its people who it identified as being the most integral part of the business.
The Team Global Express brand is “committed to the highest level of customer service and performance,” according to Michael Jothy, Director of Commercial Finance. “Backed by an unrivalled network, delivering to more places than any other transport provider, Team Global Express builds unique, innovative and tailored
solutions across road, rail, air and sea providing transport, logistics and business solutions to customers throughout Australia and New Zealand,” he said.
The distinct olive and lime green scheme reflects, along with the brand, its heritage, culture, and commitment to deliver trusted and reliable services for its customers.
“Today is a proud day for me as Chair of Global Express, as we unveil the company’s new name – Team Global Express,” said Adrian Loader, Founding member of Allegro Funds and Chairman of the TGE Board of Directors. “The culture of collaboration and teamwork at Team Global Express is one of the most unique and special I have experienced in my career. It’s why this new name resonates with me and the wider group so much — as we are a true team dedicated to each other and our customers.
“We like to say we ‘bleed green’ to define our commitment – because we
really are here for each other and our customers.
“Almost a year ago, we embarked on a journey to transform this business and despite a challenging operating environment, I am proud to say Team Global Express has returned to growth. We [have] recorded a first half FY23 revenue growth of 20 per cent compared to the prior period.
“While there is much more hard work ahead – today I am pausing to celebrate the successes we have had to date and again thank our amazing people for helping us achieve all that we have.”
In September Team Global Express signed a $250 million loan facility with the Commonwealth Bank of Australia (CBA). As part of an agreement to refinance its business, the funding will underpin Global Express’ business transformation and provide additional liquidity to support further investment into the business and fund its growth plans.
Emissions standard, Euro VI, will be phased in over 12 months from 1 November 2024 for new trucks and buses according to the Federal Government. By introducing tighter noxious emissions standards it is the Federal Government’s aim to save lives, prevent toxic air pollution and provide environmental and economic benefits for communities.
The Australian Government’s Bureau of Infrastructure and Transport Research Economics estimates introducing Euro VI will save the Australian community $6.4 billion over 25 years from fewer premature deaths and chronic illnesses.
Australian based truck manufacturers and importers have been calling for the introduction of Euro VI standards for years. These standards are already in place in the European
Union and United Kingdom, and equivalent standards also apply in most developed countries, including the United States and Japan. China and India have also recently adopted equivalent standards.
Introducing Euro VI will mean manufacturers must add the advanced safety and fuel-saving technologies to Australian models that other countries already have. This will help improve safety outcomes, and contribute to our emissions reduction targets.
The National Heavy Vehicle Regulator and National Transport Commission are working with state and territory governments to make changes to ensure operators purchasing cleaner and safer trucks maintain productivity when the new standards become mandatory.
Further improvements to fuel quality
could help support introduction of tighter standards for light vehicles, known as Euro 6d. The Government is considering how best to improve fuel quality and enable all new light vehicles sold in Australia to meet Euro 6d standards.
“Australia has been lagging in our vehicle noxious emissions standards for years now, and this move will help bring our vehicle market into the 21st century – and into line with overseas vehicle markets,” said Infrastructure, Transport, Regional Development and Local Government Minister, Catherine King. Climate Change and Energy Minister, Chris Bowen, said the Government had hit the ground running in cleaning up transport pollution by reducing the amount of sulphur in petrol and now introducing tighter noxious emissions standards.
> Australia to tighten new truck emission regulations
ACFS Port Logistics has taken delivery of a new Mercedes-Benz Actros — its 50th from the brand. The largest privately-owned container logistics operator in Australia, which runs 15 warehouses around the country, received the Mercedes-Benz Trucks model at its Port of Brisbane facility.
AFCS Port Logistics Fleet and Compliance Manager, Alan Guest, was there to receive the keys from Daimler Trucks Gold Coast’s Brock McGarity.
ACFS Port Logistics, which moves 1.2 million TEU (Twenty Foot Equivalent Units) every year, has another 50 Actros units on order from Daimler Trucks Gold Coast.
Safety sits at the top of the ACFS list of priorities, while efficiency is also prominent. Guest was instantly impressed when he trialed an Actros in 2019, with both the standard safety features and inherent fuel efficiency of its Euro VI engines standing out.
ACFS operates a mix of 530hp 13-litre
“The Actros delivered significant fuel savings over the truck it replaced and it continues to deliver fuel numbers that are absolutely brilliant,” said Guest.
In order to cut emissions and fuel use even further, Guest has always enabled the Actros models to switch off their engines after three minutes of idling. It is a measure that saves a vast amount of fuel and emissions over the whole fleet. As for safety, the Actros comes with safety systems including the fifth generation radar/camera Advanced Emergency Braking System (AEBS) called Active Brake Assist, which can now automatically perform full emergency braking for vehicles and pedestrians.
All Actros models also come standard with Lane Departure Warning System (LDWS) and Attention Assist (AA). ACFS adds its own task-specific safety items on top of the suite of standard safety features including five cameras
as fitting its trailers with all the latest features including electronic aids. “Safety is critical for ACFS,” said Guest. “The level of standard safety in the Actros is welcome because we want to do everything that we can to maintain the safety and wellbeing of our people and those they interact with.”
The cabin, which features two large high-resolution tablet screens and a modern ergonomic layout, has been well-received by drivers, as has the performance of the Mercedes-Benz Trucks engines and the 12-speed AMT transmission.
“The comfort and the features are just sensational and the drivers just love them,” continued Guest.
The 50th Actros is one of two trucks that ACFS operates as an A-double, which is able to carry 80 pallets to leading supermarkets from the Port of Brisbane. ACFS is also looking at a range of other higher productivity combinations including a trial of AB-
For more than 120 years, Shell has been supporting Australia’s truck drivers with high quality fuels.
We’ve come a long way since 1901. Today we offer a wide range of driver amenities, a national network of strategically located truck-friendly Shell service stations, and a price discount every time you refuel with Shell Card. And that’s just for starters.
Talk to us about Shell’s Australian Truck Network, and how we can help drive your road transport business towards a better future.
shell.com.au/trucknetwork
with the handover of two special vehicles to key customers.
The keys to a 50-year branded Volvo FH700XXL were handed over to Scott and Regina Harvey at the event while Nathan Stephens of Ipswich based JR Stephens also took delivery of a 50year themed Mack Anthem.
Volvo Trucks International Senior Vice President, Per Erik Lindstrom was also present at the anniversary event. “We talk about the Volvo family, and you as customers are part of that family,” he said. “I am super proud to be here to help celebrate 50 years of building trucks here, this country is very important to Volvo Group, and we are here to stay.”
Martin Merrick, Volvo Group Australia President and CEO echoed the sentiment. “While this is a celebration of our success and longevity in one of the toughest trucking markets on the planet, this is also a celebration of customer success,” he said.
“Without long term customers like SRH and JR Stephens we wouldn’t be able to mark this occasion,” continued Merrick. “Our customers challenge us to go on the journey with them. As they
“These companies are just a small part of the colourful tapestry of characters and stories that make up the Australian transport industry yet their contribution to our society and our economy is invaluable.”
Gary Bone, Vice President Volvo Trucks Australia, also spoke at the event.
“It’s when you dig into the history of these customers and their partnership that you reflect on the journey that they’ve taken over the years,” he said.
“Scott and Regina Harvey started SRH milk haulage back in 1996 with a single Volvo at Hexham NSW. Move on 26 years, over half the time that Volvo has been building trucks in Australia, they’re now in three states with over 60 trucks utilising both the Mack and Volvo brands.”
SRH Milk Haulage Managing Director, Scott Harvey called his 26 years in transport an adventure.
“But I’ve thoroughly enjoyed it all the way through,” he said. “For me it’s the people and the relationships that make it work. The backup and support, especially when you’re on milk 24/ 7, has always been there for SRH without a doubt.”
thoughts during the handover.
“We’ve actually been building trucks in Australia for 59 years now, and this year marks 20 years of Mack trucks being built at our Wacol plant,” he said. “And JR Stephens have been here from the beginning, they have been with us on the journey for the entire time.”
JR Chapman is also a logistics supplier to the VGA factory, further testament to the relationship according to Chapman.
“Over 50 years we’ve built a relationship with Volvo Group, it’s definitely the people that make the business,” reflected Nathan Stephens, JR Stephens, General Manager. “From the salespeople to the workshops to engineering, we really appreciate the rapport that we’ve been able to build over the years.”
Volvo Group Australia’s Wacol, Queensland manufacturing plant was established in June 1972. Since that time more than 70,000 Volvo and Mack trucks have been produced at the site. Production of battery electric trucks is also expected to commence at the Wacol plant by 2025.
The National Heavy Vehicle Regulator (NHVR) will be introducing changes to the Performance-Based Standards (PBS) scheme Vehicle Approval (VA) document. In a move to reduce administrative burden for industry and provide a better customer experience, NHVR CEO Sal Petroccitto said the changes would remove some of the unnecessary complexity in getting a PBS vehicle approved.
“The PBS scheme allows heavy vehicle operators to use innovative and optimised vehicle designs – allowing freight to be moved in a safe way with fewer truck movements,” said Petroccitto. “As the sector continues to address the challenges associated with COVID, including driver shortages and the growing freight task, it is critical we improve accessibility to these safer and more productive heavy vehicles.”
The aim for the NHVR is to permit safer,
transfer of PBS vehicle applications when a vehicle is sold and removing duplication, which will reduce the size of a vehicle application by 30 per cent,” said Petroccitto. “These changes are just the latest improvements in a suite of initiatives we will be delivering over the next year to reform and modernise the PBS scheme.”
The changes to PBS VAs will be introduced from 14 November 2022, following industry stakeholder consultation earlier this year. The first change includes removing the operator’s name from the PBS VA. This means that the VA will become an authorisation to the vehicles listed on the VA, regardless of who owns or operates them, eliminating the need for a VA transfer when vehicles are sold. Also, subcontractors will be able to use the VA without having to transfer it into their name.
Access permits will also be unaffected by these changes according to the NHVR statement.
In the second change, the NHVR will be replacing the specification tables with a simpler table.
Specification tables contain key vehicle parameters, including dimensions, components and Vehicle Identification Numbers (VINs). The new table will only contain key vehicle information, such as VINs, vehicle make and model. This will eliminate duplicated information and reduce the workload for PBS certifiers.
Heavy Vehicle Industry Australia CEO Todd Hacking has welcomed the changes.
“HVIA welcomes this red-tape reduction initiative of the NHVR, and, on behalf of our members, we look forward to simpler, quicker PBS assessments as a result,” he said. “The more efficient
The Cascadia represents a new era for Freightliner. Engineered and built to Daimler Truck’s world-leading manufacturing standards with unprecedented levels of research, development and real-world testing, this is a Freightliner like none before it. With superior comfort, fewer maintenance intervals, better fuel efficiency and improved ride quality,* the Cascadia is a truck you can rely on for optimal performance day in day out, in any application or condition.
*Compared to previous Freightliner models.
The Victorian Transport Association (VTA) is advocating for a heavy vehicle licensing regime that prioritises training over experience. This is in response to Austroads’ National Heavy Vehicle Driver Competency Framework Consultation RIS (Regulation Impact Statement), where the VTA reiterated industry concerns that the current licensing system does not produce the safety standards or skill levels that meets community and industry expectations.
The VTA submission advocates for focused training at the front end of the licensing process, with adequate time to ensure candidates are well trained before being engaged as a professional driver.
It also reaffirmed VTA’s support for young people to be trained at an early age as a heavy vehicle driver, putting it at odds with Austroads and its Consultation RIS.
VTA CEO, Peter Anderson, said that under the current time-based graduated system, an aspiring driver can only attain the entry level heavy vehicle license at the earliest age of 19
after holding a car license for a year.
“It then takes another year to graduate to the next level and a further year still before a license can be granted for all heavy vehicles on Australian roads,” he said. “This has led to a situation where the necessary skills and competencies are being learned on-the-job rather than prior to taking the job.
“This is one of the basic deficiencies with the current licensing system, whose focus is on assessment rather than effective heavy vehicle driver training.”
In its submission, the VTA expressed concern that heavy vehicle licensing is not sufficiently focused on risk, presenting safety challenges for all road users. According to Anderson, heavy vehicle crashes are serious because of their size and weight, regardless of who is at fault.
“It is the skill, knowledge and training of the driver that maintains a safe outcome for all road users,” he said. “However, while the current system satisfies the criteria of our institutionalised licensing system, it is not recognised by industry as being able to produce competent,
Isuzu Australia Limited has welcomed the team at Double R Trucks after its recent acquisition of the former Peel Valley Tamworth Isuzu dealership.
Beginning as an equipment repairs provider, Double R Trucks delivered on and off-site maintenance solutions to industry and equipment owners before branching out into new equipment sales. Commenting on the change of ownership, IAL Chief of Sales and Aftersales, Ben Lasry, welcomed Double R to the Isuzu Trucks family.
“We’re really pleased to have Double R Trucks on board representing the country’s top truck brand in northern New South Wales,” he said.
“The team at Double R have an excellent read on the market in and around Tamworth, and we’re excited to see what
safe, low risk drivers.”
The submission was also critical of statutory authorities’ inability to provide license applicants with the skills, knowledge and training required to ensure they can drive a heavy vehicle in a safe manner.
“Given licensing services are consumed by those wanting to enter the road transport industry, heavy vehicle licensing should also adequately prepare applicants by ensuring that they receive adequate Behind the Wheel training in driving environments they are likely to be exposed to on a daily basis,” Anderson said.
As a result, the VTA rejected Austroads’ proposal for lack of practical time behind the wheel.
“The proposed six to ten hours behind the wheel training for rigid license holders is totally insufficient and does not provide adequate time to effectively cover the 130 plus areas and competencies required to produce a safe, low risk heavy vehicle driver,” Anderson said. “This is a major limitation and deficiency of the Austroads proposal.”
the future holds.
“After spending time with the team in recent months, I can say with great confidence that truck customers in regional New South Wales are in the safest of hands with Double R.”
This is the first Isuzu truck dealership acquisition for Double R, which Managing Director, Rusty Russell, said is a momentous achievement for the whole team.
“The excitement and the nervous energy have been bubbling through the Double R team at Tamworth to take on Isuzu Trucks and everything’s set to deliver outstanding results,” he said. “Any business that can stand by a reputation of 50 years of trading trucks in Australia is a business that Double R Trucks looks forward to learning from and working with.”
The NSW Liberal and Nationals Government will invest $50 million to help regional and rural councils fix the increasing number of potholes brought on by this year’s extreme wet weather.
Minister for Regional Transport and Roads Sam Farraway said under the new Fixing Local Roads Pothole Repair Round, councils can apply for funding to help them address their highest priority pothole repairs.
“NSW has had more than its fair share of natural disasters and extreme weather and it’s promising to see that more than 135,000 potholes have been repaired on State roads in regional NSW since February,”
said Farraway. “However, plenty more potholes still require attention, particularly on council-managed roads, which is why our Government is putting more money on the table for councils to repair potholes on the roads regional communities use every day.”
This available funding will be enough to help every regional council across the state to carry out emergency repairs and in turn fix roughly more than 420,000 potholes on their roads.
“This additional support will help ease the pressure local councils are facing and boost the resources they can draw upon to repair their most damaged roads to improve safety and
Amendments to the Road Traffic Vehicles Regulations 2014 have been made as part of the Western Australian Government’s ongoing tow truck industry reform. These have introduced consumer protections for vulnerable road users involved in an accident, along with updating technical standards and inspection requirements for tow trucks. From 7 November 2022, WA tow truck drivers will be required to declare the maximum fees that will be charged for the towing, salvage, and storage of a vehicle before the vehicle is towed. The maximum fee must be displayed on the written statement a tow truck driver provides to the person authorising the tow. The amendments also prohibit the charging of any additional fees other than for the towing, salvage, or storage of a vehicle from the scene of an accident.
Drivers are reminded that they have the right to refuse a tow from the scene of an accident if the maximum fees to be charged have not been disclosed on the tow truck driver’s statement, or if they are asked to sign a statement that has not been completed in full by the tow
truck driver.
Tow truck technical standards have also been brought up to date to reflect current industry practices and contemporary vehicle standards.
As of November 2022, tow trucks will be required to meet these updated technical standards before a vehicle licence can be granted. To allow the industry time to ensure that currently licensed tow trucks can meet the updated technical standards, the requirement for tow trucks to be inspected annually will not commence until 7 November 2023. After this date, all tow trucks will require an inspection before a licence can be renewed, and annually thereafter. The State Government is now in the process of developing a second tranche of tow truck industry reforms, which will further strengthen protections for consumers.
Western Australia Transport Minister
Rita Saffioti said progress had been made by the State Government on its commitment to reform the WA tow truck industry and better protect drivers involved in a crash.
“The requirement to include maximum fees for the towing, salvage, and
reduce wear and tear on vehicles,” said Farraway.
The new funding builds on the $500 million invested by the NSW Government through the Fixing Local Roads program to help regional councils repair, maintain and seal local roads across the state.
Funding under the Fixing Local Roads Pothole Repair Round is available to 95 regional councils and authorities to help repair potholes on regional and local roads. Work must be completed by 1 January 2024.
Applications for funding are open for two weeks from today with funding announced in November so councils can begin work as soon as possible.
storage of a vehicle in the tow truck driver’s statement intends to provide price transparency for road users, while the State Government works on further reforms to the industry,” she said. “Drivers have the ability to refuse a tow from the scene of an accident if the tow truck driver has not declared the maximum fees to tow and store the vehicle, and should not sign a tow truck driver’s statement authorising the towing of the vehicle if it has not been completed and provided to the driver.
“Amendments to technical tow truck standards will bring them up to date with contemporary industry practices to improve safety and roadworthiness.”
A tow truck attends an incident on a Perth freeway.
> WA tow truck drivers required to declare maximum fees
The addition of the new Isuzu F Series has helped bolster sales in 2022.
Isuzu Australia Limited (IAL) has bettered the all-time truck sales record with two months remaining in the calendar year it has announced.
That same record was attained by the brand just last year. Despite economic and supply chain disruptions, Isuzu Trucks enjoyed a record-breaking year in 2021, setting a new high watermark of 10,175 truck deliveries at the end of December.
That trend has continued unabated with Isuzu’s internal sales figures indicating that the 10,175-mark had been surpassed as of mid-October 2022, producing yet another all-time sales record for the nation’s number one truck brand.
Isuzu Trucks finished September 2022 with 9,642 sales year-to-date, a 32 per cent increase in volume on this time last year. The brand has also improved market share over the same time in 2021, according to official Truck Industry Council market figures, with 29.9 per cent of all trucks sold bearing the famous Isuzu badge.
Isuzu share for the same time in 2021 stood at 24 per cent.
The Japanese truckmaker continues its dominance of the light-duty segment at the end of September, with 5,492 units sold to consolidate 46.5 per cent share year-to-date, and sales volume increase of 30 per cent. This is close to 1,300
competitive segments in the market. Isuzu have again built share and volume here, with sales some 28 per cent above 2021 figures and share increasing from 39.5 per cent.
At the heavy end, Isuzu continues to stand firm in third spot at the close of September, with 1,485 units sold for 14 per cent share, and sales volume growth of over 50 per cent.
Isuzu’s 4,500 kg Gross Vehicle Mass (GVM) light-duty models, including the NLR, NLS, NNR, NPR and NPS variants continue to play a major role in the company’s enduring success.
“As an indicator of how well these models are being received by Australian businesses, we can see that in the month of September 2021, Isuzu delivered 310 units,” said Les Spaltman, IAL Head of Sales.
“Compare that to the same time this year and we’ve delivered 572 trucks,” he said in a statement.
Isuzu’s newly updated 6x2 and 6x4 F Series range, including FVM & FVL, FVZ and FVY variants, continue to perform well with Australian workers according to the company.
“We’ve worked hard to ensure that these models are continuing to tick
Spaltman. “We’ve raised the bar when it comes to safety, comfort and user experience across our medium and heavy-duty range, so it’s great to see consistent sales performance in this model group across the last 12 months.”
Spaltman said the unprecedented achievement was tribute to the fierce loyalty of Isuzu customers and the hard work of the Isuzu dealer network. “We’re extremely proud of this unprecedented result and it really is testament to our thousands of customers out there that have ridden the bumps with us and stuck by the brand through some challenging times,” he said. “I can’t let a milestone like this go by without a huge thank you to our amazing Isuzu dealer network, whose hard work and commitment to customer service has made this record-breaking run a reality for the second year in a row.
“These achievements don’t just happen by themselves and there’s a huge amount of work that goes on behind the scenes to get product into the country, get it processed and then out into our dealerships. For that, I extend a big thanks to the team at IAL.”
Queensland-based cold carrier, JD Refrigerated Transport, has appointed a Cold Storage General Manager. Steve Johnstone was officially announced as the latest member of the JD Refrigerated Transport team in October. Described as a passionate, solutiondriven logistics professional, Johnstone has over 30 years of experience in the cold storage and refrigerated transport industry and a reputation for building strong customer relationships with local, national, and multi-national clients. For the past 15 years, he has dedicated himself to growing a private family-owned cold storage facility with in excess of 25,000 pallet spaces.
As a qualified refrigeration and air conditioning technician, Johnstone has developed his understanding of mechanical and compliance requirements for refrigeration transportation and cold storage operations.
The National Heavy Vehicle Regulator (NHVR) has appointed Patrick Conlon to its board. The former South Australian Minister for Transport brings a wealth of experience with his appointment. Conlon represented the Electoral district of Elder in the South Australian House of Assembly as a member of the Labor Party from 1997 to 2014. He was Minister for Transport, Minister for Infrastructure, and Minister for Energy, as well as the Leader of Government Business in the Lower House.
Deputy Chairperson Julie Russell and fellow board member Catherine Scott have been re-appointed for a second term.
The NHVR is governed by a skillsbased board, which plays a key role under the Heavy Vehicle National Law (HVNL) to ensure the NHVR functions in an effective and efficient way and is accountable to responsible ministers. Responsible ministers from Queensland, the Australian Capital Territory, New
JD Refrigerated Transport Director, Joe Joseph said Johnstone’s values and passion for refrigerated logistics couldn’t be a better fit for the company.
“As the JD Transport business continues to grow, one of my most important roles is to ensure we are attracting and retaining the very best people,” he told Prime Mover. “Equally important is that these people embody the customer centric values our business was built around. I am very excited to have Steve join the business,” said Joseph.
Joseph noted Johnstone had an exceptional focus for servicing customer requirements regardless of the complexities involved.
“His knowledge and expertise in the transport and cold storage sector is well known but his strong work ethic, collaborative style and genuine desire to see people succeed and customers prosper makes him the perfect addition
to the JD Leadership Team,” said Joseph.
Johnstone told Prime Mover he was excited to be joining JD Refrigerated Transport.
“Having been involved in cold storage and distribution for over 25 years, I see the opportunities and challenges presented to staff, customers, and suppliers in the ever-changing growth of supply chain,” he said. “My hands on approach to servicing customer requirements whilst managing our people aligns strongly with what JD Transport has been built on,” said Johnstone. “JD Transport’s vision of building exceptional relationships with their customers to supply compliant on time logistics solutions is what has attracted me to the business. I look forward to contributing to the continued growth of the business as we strive to implement logistic solutions to food processors and manufacturers.”
South Wales, South Australia, Tasmania, Victoria, and the Australian Government have voting authority at the Infrastructure and Transport Minister’s Meeting to make board member recommendations.
Ministers have unanimously agreed on Conlon’s appointment, which fills the vacant position created after the resignation of Ken Lay in June.
Under the HVNL, the Queensland Minister (as host jurisdiction) is responsible for appointing NHVR board members upon the unanimous recommendation of responsible ministers, including appointment of the chairperson and deputy chairperson.
A staggered approach to board appointments began in October 2018 to ensure continuity of knowledge and a smooth transition for new membership.
Duncan Gay will continue on as NHVR Board Chairperson until October 2024, as will board member Robin Stewart-Crompton. Board members are appointed for a period of three years.
Federal Minister for Infrastructure, Transport, Regional Development and Local Government Catherine King said Conlon had a distinguished career in the South Australian Government, having held a number of ministerial portfolios. “During his ten years as transport minister he was a strong advocate for national consistency in heavy vehicle regulation and worked together with then Federal Transport Minister Anthony Albanese to advance that agenda,” she said. “Mr Conlon also has extensive experience in board advisory roles and has recently provided strategic advice to a range of clients in the transport, energy, infrastructure and property industries.
“I congratulate Mr Conlon, as well as Ms Russell and Ms Scott for their re-appointments, and look forward to working with them and the NHVR as we continue to drive a safe, efficient and productive heavy vehicle industry. I also thank Mr Lay for his service.”
> NHVR appoints board members
The eActros 300 has successfully crossed the Arlberg Pass in Austria, Mercedes-Benz Trucks recently announced. Covering a total distance of 111 kilometres, sometimes at an elevation of more than 1,800 metres, the electric truck was fully loaded to 40 tonnes by engineers as part of a series of tests in Tyrol.
A special focus was put on energy recovery through recuperation, which can be used extensively in the alpine topography of the region. During recuperation, energy gained while braking is returned to the eActros’ batteries and is then made available to the drive unit.
In this way, the electric tractor unit was able to recover a total of around 180 kWh of energy. At the end of a demanding tour that involved moving through Bludenz, Stuben, St. Anton and
Lech, about 40 per cent of the energy recovered was still available for use. The electric semi-trailer tractor is based on the same technology as the eActros 300/400. Three battery packs, each with an installed battery capacity of 112 kW, enable a range of up to 220 kilometres on a single battery charge.
“The tractor unit version of the eActros 300 expands the application options of the eActros for heavy-duty distribution transport,” said Stina Fagerman, Mercedes-Benz Trucks Head of Sales, Marketing and Services.
“The intensive tests in Austria have shown our electric truck can reliably fulfil its tasks, even in a particularly challenging topography with extreme uphill and downhill grades.”
In total, the electric semi-trailer climbed 2,300 meters in altitude during the test – the maximum grade was at 13 per cent. On the way to the test area, the truck’s batteries were only charged at public charging stations.
Series production launch of the eActros 300 semi-trailer tractor is planned for the second half of 2023.
It recently appeared at the IAA Transportation event in Hanover.
After five years of delays the Tesla Semi is set to enter the market. Tesla CEO Elon Musk confirmed that the allelectric class 8 truck would commence production with PepsiCo receiving the first deliveries 1 December.
A Megacharger station was installed at PepsiCo’s Modesto facility last year leading to speculation that it would be the first company to take delivery of the new electric truck.
The much-hyped truck, first unveiled in 2017, has undergone myriad disruptions, including recent delays in the wake of global microchip and componentry shortages that have limited production capability of the lithium-ion 4680 battery cell.
In September Tesla had revised its application for Giga Texas with room for a 500,000 square foot expansion of the automaker’s electric vehicle production factory located outside of Austin, where it plans to move to higher volume production of the Semi and Cybertruck, its battery-powered pickup. Musk, on Twitter, said the Semi “had
a 500-mile range and was super fun to drive.” Tesla has yet to confirm the battery capacity of the truck which has a reported gross Combination Weight of 37,195 kilograms fully loaded and a range, in Australian terms, of 800 kilometres. A version with a smaller battery pack and a range of 480 kms will
be made available later.
During the Q3 2022 earnings call, Musk noted the aim for Tesla was to produce 50,000 units annually in 2024 in North America. Tesla, if it were to achieve this feat, would become the second largest manufacturer of Class 8 trucks in the US, behind only Freightliner.
Detroit’s DD16 delivers all the power you need.
With up to 600 horsepower and 2,050 lb-ft of torque, the big bore workhorse provides efficient and dependable power and performance without compromise. Detroit’s advanced technology also means GHG17 requirements are met through innovative fuel efficiency resulting in lower emissions.
This power, performance and efficiency prowess is backed by our industry-leading warranty and extended coverage packages that ensures the highest level of support for our customers.
Combined with superior fuel economy and the absence of a midlife change out, the DD16 delivers an enviably low total cost of ownership and maximum uptime.
This is all backed by our well-established and extensive national service and support network which, together with our highly skilled factory-trained technicians, means you can count on getting the right advice when you need it.
With Detroit, there’s no compromise.
Frank Sandy, CEO of TWUSUPER has been with the fund since 2005. His previous roles have involved managing both finance and human resources. Frank is a CPA and has a Degree in Business Studies in accounting as well as a wealth of experience in finance and superannuation.
Insurance is one of those grudging bills that we pay – home & contents, car, health, boat. It can be a long list. It’s a topic we often don’t think about, unless of course we need to make a claim. Then we pull out the paperwork or look online with fingers crossed. Insurance included with super, such as Total and Permanent Disablement (TPD) Cover and Death Cover (sometimes ironically called Life Cover), is paid for from superannuation contributions. Being cover purchased and tailored in bulk, this brings with it significant cost and cover benefits. But there is a huge issue for people working in transport not covered by their super funds insurance policies — but I’ll get to that. Recent research we conducted of TWUSUPER members indicated less than half of respondents did not know they have insurance included with their super. The younger the age bracket, the less the knowledge. Also concerning was that only 18 per cent had some idea that not all super funds even cover transport jobs, which is disturbing, but unfortunately not surprising. Occupations commonly excluded by insurance offerings within super but which TWUSUPER does provide coverage for (and has members employed in) often include: truck drivers, mechanics, loaders, warehouse personnel, aircraft refuellers, armoured car drivers, bus and coach drivers, cartage contractors, couriers, dangerous goods drivers, flight attendants and pilots. Many superannuation and general insurance options that might be
available to transport workers outside of their TWUSUPER accounts may also be restrictive in the events and types of claims covered. Adequate insurance cover is important for family security and peace of mind, with a large proportion of Australians gaining life, TPD, and income protection cover through their superannuation at a cheaper rate due to the scale benefits that group insurance arrangements can provide. TWUSUPER, with the support of its insurer, understands that due to the risk profile of the industry, many of its members would not be able to obtain equivalent insurance cover outside TWUSUPER, at an affordable cost. With this in mind, TWUSUPER does not have occupation exclusions or loadings. We also ‘switch on’ default insurance for people from 18 years of age (subject to eligibility requirements), compared to many funds that do so at 25. Our rationale is based on claims history, where young people do have accidents and need protection. This means no member of TWUSUPER will have an application for additional insurance or a claim declined because of their occupation. Unfortunately, under the ‘stapling’ changes contained in the Your Future, Your Super legislative package passed in 2021, employees new to transport are likely to be stapled to a super fund that cannot provide the same protection as TWUSUPER. Often the insurance that transport workers are able to access via their accounts with TWUSUPER is the only insurance
More and more people in transport are finding out the hard way, that the insurance included with their super isn’t suitable for their job. Are your people at risk?
available to them, as many key transport industry occupations are what is termed by insurance companies as ‘excluded occupations’ which renders those workers uninsurable. In the road transport sector alone, a study by Monash University (based on compensation claims over a 12-year period) found that truck drivers are 13 times more likely to die at work than any other profession while the long hours, social isolation, time pressure and physical nature of work add to the risk. These issues are demonstrated in the Fund’s claims statistics for the year to 30 June 2021 where TWUSUPER’s top five TPD claims were categorised as follows:
• Musculoskeletal
• Mental health
• Spinal injuries
• Cancer
• Heart conditions
Many people already working in transport have policies that are not fit-for-purpose.
Musculoskeletal issues account for over 50 per cent of the TPD claims and would be caused from a wide range of issues attributable to injuries occurring from getting in and out of heavy vehicles, spine injuries, and others that are related to the nature of work in transport. Many of these health issues tend to manifest later in life and will mean that many people have to retire before they are eligible for benefits such as the aged pension. So what are we doing about this issue?
The simple fact is all policies should cover transport jobs but they don’t due to legislation introduced in 2019. To help shape better policy, we have submitted a paper to a Treasury’s review of 2021’s Your Future, Your Super changes. Our submission outlines the issues for people in transport and focuses on the impacts of ‘stapling’ on workers occupations deemed ‘hazardous’ for insurance purposes.
Stapling of super is where a person’s super follows them from job-to-job, which means a person can enter the transport industry with insurance not designed for their occupation. Indeed, many people already working in the industry would be in policies that are not fit-for-purpose. We have been running a national digital insurance campaign advising people who work in transport and logistics to check their cover. This is an industry issue and I have been encouraged by businesses that are taking a proactive approach to their people, letting them know they should check with their super fund.
If you have read this thought-piece and would like to know more – we would like to help, either you as an individual, or for people at your business. Simply drop me an email at ceo@twusuper.com.au.
To combat the ongoing driver shortage, Cartage Australia has taken a different approach by introducing two new A-double sets to its fleet entirely composed of Performance-Based Standards vehicles.
Quarry product transport specialist, Cartage Australia, runs over 110 rigid tippers and dogs across its 24-hour operations in Victoria. The vehicles in the fleet can, in the main, be identified by a truck, usually a Volvo, pulling a dog trailer en route to or departing from one of its two depots. These can be found in Truganina out west, and Devon Meadows in the southeast, where the brand is a frequent presence on the South Gippsland Highway.
The six-axle truck and dog configuration typifies a predominant specification across the fleet although it also runs five- and four-axles. With virtually every unit approved under the PerformanceBased Standards (PBS) scheme, Cartage Australia has, since the inception of PBS in 2007, when Co-Founder and Company Director Ray Cauchi
participated in the pilot program, forged a reputation as a reliable and everimproving organisation.
Fleet procurement is overseen by Ray’s son, Manager Jake Cauchi. The decision to add two high productivity A-double combinations last year, according to Jake, was prompted, in part, by the current climate of challenges being felt right across the industry.
“There’s always been a driver shortage,” he says. “It’s been an issue in our industry for as long as I’ve been in it which is now ten years. My father has been in it since 1978. It’s a problem that hasn’t gone away.”
Carrying extra capacity becomes a must when supplementary drivers are increasingly hard to find and demand for product continues to increase.
In keeping with this, the A-doubles serve to reduce gaps in personnel and supply that have plagued even the most
adventurous, resourceful and innovativeminded businesses.
“In recent times with COVID we’ve also had parts shortages, truck shortages and that’s required us to become a bit more creative when carrying more capacity to assist with those challenges,” explains Jake. “Traffic on the roads, for one example, is only going to get worse. It becomes much harder to move product under these conditions.”
As a business, Cartage Australia sought to overcome the twofold challenge of rising demand and skills shortages by increasing productivity on a per combination basis. In essence it was a bimodal approach according to Jake.
“In one instance we help the community having taken trucks off the road and replacing them with A-doubles,” he says. “It also assists us in carrying that extra capacity to support all our customers.”
Working in close collaboration with
Smedley’s Engineers, Jake and Ray met with VicRoads to consider the best options. It resulted, initially, in a half dozen different A-double designs for the purposes of moving quarry material. Topping out at 68.5 tonnes GCM previously on the route in question, Cartage Australia determined that through the new high productivity vehicles an increase of 85.5 tonnes GCM could be achieved. An A-double tipper was soon agreed upon.
“Smedleys assisted in helping Cartage Australia go through several designs to identify the safest combination and making it as driver friendly as possible,” recalls Jake. “With Smedley’s we mapped out the level access 2a and 2b using the NHVR map and worked out every single route that we can currently get to the concrete plants that we have available.”
In collaboration with Ian Mond at VicRoads, Smedley’s helped guide
how the A-double combination would ultimately work best across the available network. Design assessments evaluated tare weights and payloads at once to narrow down the asset that would conform to the easiest swept path. After a series of long deliberations with Ian and Smedley’s, Cartage Australia devised an A-double combination it is confident will be used in future as a template across the tipper industry.
The next step, once access was confirmed in principle, was ordering the specialised equipment. Orders were placed with Hercules, who build all of Cartage Australia’s trailers and CMV Truck & Bus, who supply the majority of the fleet’s commercial vehicles. On this occasion it was a Euro 5 540hp Volvo FM with low sleeper cab — the driver rest option upgraded by the added bunk.
“We’re Volvo born and bred. CMV Truck & Bus have got to be the best service
department in Australia in our opinion,” says Jake. “They bend over backwards for us day and night to make sure everything is serviced and up to scratch. We’ve got Volvo gold contract maintenance on every asset.”
Enhanced visibility is a must when accessing quarries and concrete plants on the larger combination. The Volvo FM door line is low and the window surfaces, by design, are generous.
Every trailer also has a scheduled fourweek service.
Hercules offers a standard safety spec fitted across all trailers. These feature Wabco ABS/EBS systems on SAF-Holland Intradisc axles with patented Integral disc brake designs.
Cartage Australia maintains their own mechanics and workshop for minor breakdowns. Workshop Manager Danial Cauchi and Maintenance Manager Paul Charalambous work closely together to
ensure all assets are serviced correctly.
For Cartage Australia preventative maintenance is applied as part of an overarching objective in which it’s not enough to only have the safest vehicles but vehicles with the highest safety standards.
It’s one thing to get the design and build right, but an A-double needs route access. As one of the most critical steps in the process it can take time.
The 29-metre A-double design was developed according to the Victorian High Performance Freight Vehicle
western suburbs on the network. Getting A-double access to Werribee, however, was incumbent on receiving Forsythe Road approval which proved a hurdle initially.
“This involved collaboration with the Department of Transport in assessing the Forsyth Road bridge which took some time however DOT greatly assisted us,” says Jake
Access to both onramps and offramps can be a challenge under the current road management modelling. Returning from quarries via the Western Ring Road
combination (MC) licence, the different moving points on the trailers require some extra attention for new operators. Additional roads will need to be opened up also to encourage companies involved in major haulage operations.
“The Westgate Tunnel is the next major arterial route which will get us into Dynon road,” says Jake. “Once they do that than we can look at feeding a lot of the city area for higher capacities and then we’d look at getting more combinations.”
A-doubles, in a post-COVID world, are
and six-axle dog, Cartage Australia gets a payload of close to 48.5 tonnes total whereas the A-double improves it to 60-tonnes. The extra capacity has resulted in a net gain of just under 12 tonnes per trip for the A-double. Multiplied by the amount of trips it completes in a week, the A-double represents an enormous jump in productivity.
Smedley’s Engineers Managing Director, Robert Smedley notes that these units are only effective if access is granted at a reasonable mass.
trailer start to jack knife on the drawbar a buzzer sounds an alarm. The tippers are also equipped with tilt sensors. If the ground underneath the asset is uneven the body won’t go up for it to be able to tip. The PTO disengages. “That’s just the original Cartage spec that we affix to all of our vehicles,” says Jake. “From inception Directors, Wayne Vella and Ray Cauchi, made the decision that every truck and trailer bought will include every extra optional safety feature on top of the standard features. Everything Volvo can give us we have to make it the safest truck on the road.” Drive Support Systems on the new Volvos include Forward Collision Warning with Emergency Brake, Adaptive High Beam, Lane Keeping Assist, Passenger Corner Camera, Downhill Cruise Control, Stretch Brake, Electronic Stability Control, Driver Alert Support, Distance Alert and Adaptive
Also Included in Cartage Australia’s spec list are Artificial Intelligence cameras which identify distractions, dangerous driving, and mobile phone use. These are managed by Caleb and Jed Vella who run the operational office in Devon Meadows. They receive alerts concerning any unsafe behaviour so the company can educate and retrain heavy vehicle operators in any areas needed.
The system in place is very beneficial, according to Jake, as it helps the team address any distracted or unsafe driving before an incident occurs, rather than finding out after it’s too late.
“You’ve got a driver who is going to spend 12-13 hours in a truck and trailer, we want to make sure that they’ve got the best and safest truck possible,” says Jake. “That’s what we pride
The trucks are driver friendly across the whole operation for Cartage Australia. Manual tarps are long gone. To open and close tarps, and to tip off the body is now just the push of a button away. “There’s no getting out to roll back tarps or to close tailgates,” says Jake. “It’s really become a driver’s luxury truck. The manual labour component of it is
long gone”
The two Volvo FMs, paired on the A-double combinations, incidentally, came off a ship Volvo imported overseas with an estimated 500 trucks on it.
“It was one of the first times in history that they’ve done that to keep up with the demand,” says Jake. “We got both the A- and B-trailer in a matter of four weeks. Hercules have got a constant build slot with us.”
Given the critical timeline in place, delivery, however, was not the major focus of obstacles on the project.
Cartage Australia collaborate with Smedley’s Engineers and work with the Department of Transport to ensure final mile destinations with bridge assessments are approved before combinations are even operational. That said there are always improvements that can be done to improve the PBS process according to Jackson who cites the digitisation of certain process that the NHVR is currently working on to the streamlining of bridge assessments as positive steps that are being undertaken.
“With various odd requests appearing more often to fulfil customer needs these days anything that can be streamlined is a welcome opportunity,” he says.
“Internally we are working on things, externally the NHVR and the various road managers are also working away to try get everyone on the road sooner.”
The NHVR has always provided welcome technical assistance from those early, pioneering days when, Ray Cauchi, was working closely with Les Bruzsa, NHVR Chief Engineer, on the PBS pilot program, to the A-doubles of today. In terms of its size, the Cartage Australia PBS fleet comfortably sits inside the top 10 for units in the country. Smedley’s Engineers according to Jake, have been phenomenal for support and expertise from the outset of the latest project.
“Jackson Heil and Robert Smedley answer their phone calls and attend meetings no matter the time,” he says.
“When you have a question, they are there for you. When you need help, they are there, it doesn’t matter the time, they understand the urgency.”
PBS pioneer, Clenton’s Transport, has introduced the Hammar MegaReach to industry, a split-quad side loader that is fast delivering clear productivity gains in the container haulage operations of its Sydney-based business.
When it comes to Performance-Based Standards (PBS) vehicles, the short history of Clenton’s Transport, dating back to 2015, compares favourably to almost anybody. At the outset of the heavy vehicle PBS scheme, the business has been right at the forefront adopting high productivity combinations. Being the first carrier in Sydney to receive full route approval with unconditional
road access for 85 tonne GCM 30-metre A-doubles direct from Port Botany to its yard has paved the way, subsequently, for it to show great leadership in container transport innovation. This year, having sought a different solution for moving heavy and super heavy containers, Clenton’s Transport pushed the envelope again, by introducing a new Hammar MegaReach, the first of its kind in Australia.
Level 2 access restrictions currently
curtail the movement of the A-double sets it runs. Operationally, the imperative was to find a vehicle capable, under law, of traversing both Level 1 and Level 2 networks as part of the PBS network in Sydney. Achieving the same payload capacity as an A-double set, however, would be impossible. The necessity, consequently, was for the vehicle to accommodate a substantial increase in mass over a prescriptive semitrailer.
“Obviously, PBS through A-doubles are a great vehicle for high productivity
gains to run from wharf to the yard, but we needed to be able to take it one step further,” says Managing Director Jason Clenton. “We really needed to facilitate the access to be able to deliver direct to our clients from the wharf.”
As Jason was aware of several clients avidly looking for a carrier who could fulfil this request, he didn’t waste any time in putting the business forward as a preferred carrier that specialises in heavy containers direct from the wharf to the client. The only way to achieve this, however, was to enter into discussions
with Hammar. As the position and height of the goods inside of containers is not always accurately known, it presents a challenge in achieving the higher payload height required by Clenton’s Transport. A standard side loader, for instance, is not going to be suitable when moving imported concrete blocks on road.
A range of options, as is par for the course, were considered during the initial design phase.
“There was a consideration as to whether we used super singles or if it would not be a split quad at all and just be four axles,” says Jason. “What the experts tell us through the technology that they use to gain the maximum load height and, to be as safe as possible on our roads, is we needed to go with a split quad design over a 48-foot chassis instead of the standard 45 foot.”
That first conversation took place over two years ago. The high productivity solution that eventually would materialise was 12 months itself in planning.
“It was a mutual decision with Hammar to engage Smedley’s Engineers as the preferred engineering certifier to help us achieve the maximum load height and the distribution of weight across the axles,” recalls Jason. “There is overhang on each end and that helps us to have flexibility with being able to move the cranes on the chassis forward or back to help with the weight distribution across those axles. So you can actually move it all the way back and take the weight off your drive axle and put it over your quad which was a crazy advance in technology for us to be able to move the container onto the actual chassis.”
Technically, the configuration is a tandem-tandem split quad semitrailer, with each of the tandem axle groups on the trailer equipped with a steerable axle, to pass the PBS pavement horizontal loading and swept path requirements. Gross combination mass under a Tier 1 bridge formula is 55.1 tonnes on the PBS Level 2
network and 50.5 tonnes on the Level 1 network. Based on the manufacturers estimated tare weights this would afford approximately 34 tonnes in payload according to Smedley’s PBS Assessor Nathan Wiblin.
“The suspension models used for the trailers were some of the most important aspects of the build, as the payload height was critical on this vehicle,” he says. “It was pertinent that the suspension was able to display high roll performance.”
A secondary, but no less, crucial consideration to provide a reasonable factor of safety, was to ensure there was an ability to position the cranes and container/s on the trailer body to allow for correct weight distribution and therefore compliant axle weights. Knowing the maximum amount of weight possible on a crane was one
An extendable top arm offers six metres reach lifting up to 15 tonnes.
container than that’s no good. I would not have bought the machine,” he says. “But we were able to get full load height in the container which hasn’t been achieved before.”
Equipped with an extendable top arm, the Hammar MegaReach, has six metres reach lifting up to 15 tonnes. The top arm can extend up to 1.7 metres. Just as Clenton’s Transport already possessed a double stack solo side loader, it was important that the fleet had a second option on the ground. But instead of being able to stack containers two high next to the vehicle, the Hammar MegaReach can actually stack two high in the next row, across. Standard legs common on 195 side loaders are not able to achieve this feat. “We went for the overreach leg which gave us the flexibility that we can actually have a vehicle parked next to our vehicle and put the legs across and
the only restrictions determined by tyre size. In order to get the maximum amount of weight on the vehicle a polished alloy wheel was chosen as it was much lighter than what would have customarily been considered. These were supplied by Armoury Wheels, a loyal client of Clenton’s.
The project, as a result, would be classified under non-pre-advised vehicle design and require approval by the NHVR PBS panel. Fully operational since August, the split quad semi side loader has since it debuted in the fleet, increased network access when compared to a standard PBS quad semi. Moreover,it can also handle transporting 45-foot containers.
“This vehicle is able to cart significantly higher weight containers giving a hefty increase in tonnage per trip/km,” says Nathan. “It also has the ability to place the containers on the deck to achieve
collaborative project involved a 30-metre A-double set — two retractables skels joined by a dolly. It was an exciting project, according to Jason, realised in conjunction with MaxiTrans.
“It was important that we could use our current Vehicle Approval (VA) which would mean we have to have the axle positions in the same positions but the design would be slightly different because the trailers wouldn’t be fixed skels,” Jason explains. “The project was to take our old design, use that vehicle approval, develop or adjust a design plan that would fit into that spec and make it a 30 metre retractable A-double. They’re unique because they don’t just have the retractable rear ends on them. They look different from behind because they’re fitted with Ringfeder couplings and long vehicle signs which you don’t normally see on the back of retractables.”
With the support of more than 30 stores and depots, Lindsay Transport services customers across a wide realm that encompasses food processing, food services, fresh produce, agriculture and horticulture. More commonly, the business is regarded as an integrated transport, logistics and rural supply company, comprising three distinct business units, Transport, Rural and Fresh Logistics. As an essential service provider, Lindsay Transport helps to grow and move
an increasingly valuable commodity: food.
The founding business, Lindsay Brothers, which commenced operations in March 1953, thrived as a carrier of fruit and vegetables, loading up the trains at Coffs Harbour to supply the markets in Sydney. In time, it diversified its freight task to include timber and fuel and by the 1970s it expanded its transport portfolio to include state-of-the-art refrigerated trucks and trailers.
Its leaders, as the business grew, were committed to continuous improvement at
all levels.
In 1983 a small rural supply company in the Bundaberg region called P&H Rural opened its doors and would become the foundation of Lindsay Rural. Two decades of growth ensued.
By 2001 Lindsay Australia Limited listed on the Australian Securities Exchange, incorporating both the Lindsay Transport business and the Lindsay Rural business formerly known as P&H Rural supplies. The Brisbane markets welcomed the launch of Lindsay Fresh Logistics in 2014
The perks of diversifying and delivering innovative solutions has made PBS something of an ingrained mechanism at the major fleets across the country.
Lindsay Transport is one of them.
which offered industry a range of services including unloading, cross docking, storage, ripening, fumigation, sterilisation, quarantine and inspection-related services for produce export.
Today, the Transport division of the business, alongside Rural, provides complementary products and services along the supply chain that cover the key needs of its customers throughout the production lifecycle.
To appreciate the scope of its operations across Australia it is worth noting that
Lindsay Australia’s FY22 revenue of $553.1 million was 27.1 per cent above the prior year’s record despite extraordinary weather and COVID-19 disruptions. The Transport division benefitted from rail expansion, strong demand for its services and network investment in prior years. It is well positioned amid industry consolidation occurring, as a result of labour shortages, cost pressures, generational changes and increasing compliance.
Strong demand for the group’s services is expected to continue throughout the 2023
financial year and plans are already in motion regarding investments into the road fleet to deliver an increase in operational capacity to meet service demands. In its quest to improve safety and achieve gains in productivity and efficiency, Lindsay Australia has engaged the PerformanceBased Standards (PBS) specialists at Smedley’s Engineers for various consulting services in recent years. Nick Lindsay, Fleet Quality and Efficiency Manager at Lindsay Australia, says these services have been predominantly focused on assistance with
PBS vehicle approval design, inspection and permit applications.
“Smedley’s provides detailed technical expertise assisting our organisation in complex vehicle design and access applications,” he says. “The process of obtaining access approva equipment, for instance, has become easier with the help of consulting service providers such as Smedley’s. However, it remains an expensive and complicated experience which is enough to intimidate most operators. Smedley’s, though, has a strong understanding of operators’ requirements and a vast network of engineering knowledge to support this.”
Nick says productivity gains and fleet efficiencies can be achieved if an organisation is flexible enough to comply with robust regulatory conditions.
“The challenge is designing fleet composition around the purpose-built equipment and access restrictions,” he says. “Lindsay Australia looks to PBS to enhance its versatility and customer reach but, more importantly, to overcome the skills shortage currently challenging the logistics industry. The supply chain must find better ways to
number of vehicles on the road. This allows
process such as the 20m truck and dog gazette which is finding support within the industry. Some combinations that previously required PBS approvals to operate will now be able to run under a notice according to Smedley’s Engineers PBS Assessor Nathan Wiblin, although additional requirements under the notice are required and can be costly.
“The vehicle must still operate at the weights calculated on the tier 1 bridge formula and there are additional conditions required under the notice, but not under PBS, such as full contour conspicuity tape and a cumbersome access process. Many truck and dog operators and manufacturers have said they will stick with PBS due to these requirements,” he says. “But tyres are non-specific, which means operators aren’t stuck with a fixed list of tyres that must be fitted to remain compliant.”
This has removed a point of conjecture
there is room for improvement in the route access application process, an objective industry continues to strive towards.
“It is somewhat complex and difficult to understand,” Nick says. “The experience tends to create some confusion leading to frustration. Despite these regulatory hiccups, Lindsay Transport will continue to leverage technology and vehicle safety developments to drive better industry outcomes and improve overall road safety.”
More than a few recent developments have resulted in improvements to the PBS
uptake over the years.Currently, Lindsay Australia has five PBS combinations on the road of which four are 26-pallet semitrailer combinations and one A-double high productivity vehicle along with an additional three configurations in the
are expected to facilitate upwards of 30 additional combinations once approval is sought.
“Lindsay Transport has 12 sets of 42-pallet quad-quad B-double sets in production,” Nick says. “This will increase cubic capacity
Queensland to South Australia to Victoria. Once this equipment has commenced its work, there is a further commitment for 20 more sets throughout 2023-24.”
As for observations with PBS trends, Nick points to an increasing variety in vehicle configurations which may be attributed to operators and customers collaborating to establish dedicated freight lanes that facilitate compliance with PBS requirements. With that in mind, ultimately, it is safety and compliance that is at the heart of Lindsay Australia’s organisational values and decision making “Given our industry’s recent challenges throughout COVID, any productivity improvement that can result in a reduction in costs will be welcomed and implemented whenever possible,” Nick says. “PBS strongly appeals to Lindsay Transport due to its tendency to combine these elements which will undoubtedly figure in future
“The process of obtaining access approval for PBS equipment, for instance, has become easier with the help of consulting service providers such as Smedley’s. However, it remains an expensive and complicated experience which is enough to intimidate most operators. Smedley’s, though, has a strong understanding of operators’ requirements and a vast network of engineering knowledge to support this.”DAF CF480 with the new 26-pallet semi.
tests that leverage the latest vehicle measurement technology to give accurate measurements of how much road space these vehicles take up.
Iwant to emphasise the positive Performance-Based Standards (PBS) developments of 2022. Expanded High Productivity Networks, particularly A-doubles in NSW and more Reference Vehicles like AB-triples and B-triples in Victoria. Greater acceptance of semi-trailers with multiple axle groups, like spread quad and split tri-axles, which promise to take the emphasis off truck and dogs and finally deliver broad productivity gains for semi-trailers — the work horse of the Australian fleet.
Thanks to spread axle groups, prime mover semi-trailers may finally get the same weights and access as truck and dogs, 50.5 tonnes PBS Level 1 and up to 57.5 tonnes PBS Level 2. Semi-trailers are inherently more stable and safer than truck and dogs and operate across more industry sectors so should have a greater productivity impact. The National Heavy
Vehicle Regulator (NHVR) has been working on developing new standards which will help facilitate these vehicles and it promises to herald in an exciting new phase of PBS opportunities.
Industry is also discovering new ways to leverage the current scheme and take advantage of PBS to implement novel vehicle designs. For example, wider vehicles with technologies to improve workplace safety can get general access without a permit through PBS, and rigid trucks previously constrained by rear overhang.
Tiger Spider has been working with the Concrete Pump Association of Australia (CPAA) on improving concrete pump road safety and a key part of the work is reviewing PBS low speed turning requirements applied to large rigid concrete pump trucks. We’ve completed an extensive review of international standards and technologies and field
The work is partly funded through the NHVR Heavy Vehicle Safety Initiative (HVSI). We propose an alternative Low Speed Swept Path (LSSP) performance standard for concrete pump trucks. However, there is no reason this standard cannot be applied to all PBS combinations. It would be particularly useful for rigid trucks and buses which currently don’t benefit much from PBS. Manoeuvrability and road space demand can be improved without impacting productivity and vehicle length. By allowing more Tail Swing (TS), hence rear overhang, whilst reducing LSSP and Frontal Swing (FS) front axle weight can be reduced, and better weight distribution achieved on long rigid trucks. This change compliments the revised Pavement Horizontal Loading Standard (PHLS) work that the NHVR has been progressing and the generic tyre approach.
The implementation of generic tyres has taken longer than expected but the NHVR has had to work through many contentious technical and policy issues. The new system will incentivise tyres with higher load ratings. This doesn’t guarantee better cornering performance, but it may reduce tyre failure risk.
The most recent update from the NHVR removes certain truck and quad dogs from PBS. The NHVR released the
notice in late September, which came as a surprise to many since consultation was limited. It has disappointed some, as many operators have combinations that fail to meet the requirements of the notice. Despite having all their equipment inspected and certified to pass PBS, they are now competing with operators of conventional truck and quad dogs who believe they have a green light to operate at 57.5 tonnes without restriction.
Manufacturers are getting pressure to change designs, reduce prices and explain why their truck and dog still needs PBS. Assessors and Certifiers are wondering why they’ve had to ensure all applications have ‘Is’ dotted and ‘Ts’ crossed and measurements millimetre perfect, but now it’s fine for operators and enforcement officers to assess themselves without any technical training or assurance processes. It is critical that the NHVR achieve internal consistency with PBS reforms and doesn’t undermine the hard-fought gains and trust built with road managers. PBS has always been a long game, the short answer from road managers is always no. It has taken years of steady operation, consistency and a track record of success to win
over the naysayers within industry and government. There is no free lunch — the pursuit of ever greater efficiency brings complexity. We mustn’t throw in the towel when it gets a little tricky and return to 20th century policies. We need to embrace the data challenge, put appropriate quality and verification systems in place and lift the laggards up to industry best practice.
The NHVR claims that all truck and dogs that comply with the new notice are PBS compliant. The generic tyre policy, when implemented, will do the same. Unfortunately, in the aftermath
of an accident this may not hold true, and the onus is now on operators to show they comply with the notice. An operator cannot argue reasonable steps as easily without an independently certified PBS approval in place.
I’ve recently been involved in several meetings with operators and their customers about heavy vehicle accidents. Chain of responsibly demands answers. Invariably ex-post analysis of non-PBS vehicles confirms that accident risks may have been reduced if the vehicles complied with all PBS standards. PBS compliance up front can avoid costly modifications down the line if freight customers demand actions before allowing fleets back on the road.
The future looks bright for PBS. There is competition amongst road managers and regulators to put automated systems in place to finally solve the bridge assessment problem. State road managers are feeding off each other and agreeing on high productivity vehicle access frameworks and networks. The NHVR is slowly, but surely, improving the reform and putting the building blocks in place for PBS 2.0. Hopefully it can deliver both better processing efficiency and more flexible standards that will facilitate even more innovative vehicle design and ever greater productivity, safety and sustainability.
SThe ubiquitous wooden pallet was invented by Howard T. Hallowell almost 100 years ago in 1925. Pallets, to this day, remain an essential component of many modern freight operations.
The catchy name for JATEC Transport is an acronym of the first names of the Barlow family, parents Jane and Troy, and adult children Ethan, Aaron and Caitlin, the latter two now working in the family enterprise. It’s not quite the typical family transport company story, although, and similar to so many, Troy started out with a single truck in 2003.
The business strarted with deliveries to fast food outlet chains. It was a couple of years on from this that Troy commenced doing deliveries for a friend who had a small pallet manufacturing business.
Prior to its decision to concentrate on servicing the pallet industry, the JATEC fleet peaked in size at 25 trucks. Fast forward to the present day and the specialised pallet transport operation handles more than one million pallets each month for around 400 clients. Troy acquired his first Volvo truck in 2009. Volvo FMs were trialled, as were FH models powered by 540 horsepower engines before the ideal specification for the application was settled upon and the prime mover fleet currently consists of 12 Volvo FH models, all rated at 500 horsepower. The trucks normally average 80-90,000 kilometres per year and are replaced at around 500,000 kilometres. “Resale is not a problem and I’ve never traded a truck in,” says Troy. “I usually have a number of people wanting to buy them directly off us.”
Depending upon the type of pallet, a semi loaded with pallets weighs between 19 and 22 tonnes, so weight is not a major compliance issue, but overall height can be. Each trailer can carry 480
empty pallets and in order to be under the maximum legal height of 4.3 metres, low profile tyres are used on the trucks and trailers. The trailers are custom built by Vawdrey with low profile goose necks to accommodate the height of the loads. The latest Volvo FH to join the fleet is an exception and runs a medium height chassis and 11R size tyres to achieve the same loaded height as the others. The standard profile tyres are less expensive than the low profile 305/70s and are more readily available.
The Volvos are all on a contract maintenance program and serviced by the Volvo dealership at Prestons.
“When I first started we maintained the trucks ourselves as per Volvo’s specifications,” says Troy. “I worked out after the first five years it was $60,000 dearer for each unit for us to service them ourselves rather than Volvo.”
Troy travelled to Sweden with a Volvo study tour and remembers well one of the seminars hosted by fuel efficiency and Volvo Dynafleet telematics guru Carl Johan Almqvist who impressed upon the operators present that Volvo was spending millions in technology trying to save them just one per cent of fuel.
“They said the key to the business is driver training and that planted the seed,” recalls Troy. “As soon as I got back we put into action training the drivers how to use the trucks most efficiently.”
In addition to coaching from the local Volvo experts, Troy set up a weekly driver fuel challenge to incentivise the drivers to put their newfound knowledge into practice.
“When we first started it was for the best score each week, so often the same driver won every week and some of the others were losing interest,” says Troy. “So we changed it to any driver scoring a rating of over 95 on the Dynafleet scale receives a $50 fuel card. If they can get 95 or better that’s a fuel saving for the business of up to $480 per week so everyone is a winner.”
New drivers are usually found via referrals from existing drivers as well as Facebook and JATEC Transport has a strong and positive presence on the social media platform. The modern and well-maintained equipment is also an attraction to potential employees, as is the family-centric atmosphere of the workplace.
“It’s not just our industry, everybody’s looking for staff,” says Troy. “Yet I’d rather park a truck up than put some inexperienced operator in it. You just can’t afford to, it’s as simple as that.” New drivers are supported while they learn the intricacies of their roles and the clients.
“Once they’ve had a bit of time to find their feet, we’ll spend time to show them how to more effectively drive the truck,” says Troy. “For this we get great support from Ray Abella at Volvo. We meet with Ray to go over utilisation reports every
six to eight weeks. If a truck for some reason isn’t performing as well as it should he’s the first to say, ‘Hey mate, have a look at this. Have you changed drivers?’”
It might be a family, but it’s also a business. From the time when siblings Aaron and Caitlin Barlow indicated they wanted to get on board with the family business they haven’t felt their surname was sufficient to entitle them to a job. Prior to joining JATEC, Aaron completed his diesel mechanic apprenticeship at Volvo Trucks and was recognised for his talent and application. Caitlin went to university, while working full time at supply chain specialists including Bevchain and Metcash, and achieved a distinction when she graduated with her Bachelor of Commerce majoring in Entrepreneurship.
“I think the way we have done it is useful,” says Caitlin. “Coming from a corporate position I gave myself an induction plan when I started here, with the first week out with the drivers starting at 2.00am every day to see how they do it. Then a week in accounts and payroll. I did this so I know if I make any changes moving forward it’s not going to have a flow-on effect and disrupt anything else. That way I’m not making decisions without understanding
how it all works and the implications of change.”
Caitlin’s and Aaron’s considered approach has not only earned the respect of their parents, but the other JATEC employees as well. Caitlin initiated the company’s first anonymous ‘engagement survey’ in early 2022 and was delighted to learn that 98 per cent of drivers were proud to work with JATEC Transport.
“The overwhelming majority of staff and management participated,” Caitlin says. “Our metric was in the 90s and smashed industry standards.”
The team at JATEC is always receptive to new technologies. Two Volvo FH prime movers with the innovative Dual Clutch transmissions have been a part of the fleet for a while but it has been found that in this application there were no real savings or advantages
with the fuel efficiency much the same as from the conventional Volvo I-Shift transmissions. “We’ve got to think outside the box if we want to be better tomorrow than we are today,” says Troy.
The team is excited about the introduction of a paperless ‘sign on glass’ system which provides time and date stamping of truck movements, photographic evidence of each truck
as it is loaded and unloaded and the ability to provide vital information to clients in real time. JATEC Transport, moreover, is imbued with great community spirit and supports local sporting teams and the Kids with Cancer Foundation. Jane and Caitlin are both active members of Transport Women Australia Limited (TWAL) and attend school events to promote careers in the transport industry.
Founded in 2017 by Ed Slade, EJS Logistics is a specialty interstate transport company based out of Yatala in Queensland. Prior to this Ed worked for many years at Wadley’s Interstate Transport Service in New South Wales in an operational and management role. As a diesel mechanic by trade, Ed’s work life for more than 30 years has been vocational. His latest transport outfit revolves, at present, around eight trucks, all of them Kenworth prime movers, running mostly along the east coast of Australia. Six of which are powered by Cummins. The fleet services three main channels. It transports oil products; and it moves building materials like aluminium
extrusions and pavers; in addition to staging equipment for exhibition work for the events industry. Three of these trucks have been committed to a Sydney to Brisbane schedule. A permanent subcontractor runs to Melbourne twice a week while another does the whole eastern seaboard including Adelaide when required. One additional vehicle operates daily on tasks for Cameron Logistics. From the outset, the plan was for Ed to eventually transition to a role behind the scenes where his wife, Joanne, runs the administrative side of the business. For the moment, however, he adds more value being out on the road as a driver often handling special requests from
customers that might involve trips to Perth including work that falls outside the usual operational parameters. “It allows me to do the work that I want to do. There’s a couple of customers I handle myself who have been with us from the start,” he says. “Being on the highway helps in the sense of knowing what goes on. You can’t have the wool pulled over your eyes.”
The first new truck in the business, A Kenworth T909, was purchased last year followed more recently by another — a Kenworth W900SAR Legend. The latter has been spec’d differently to the rest of the fleet to allow it to pull roadtrains on specialty assignments in Western Australia, something Ed wants to do
more of in the future. Rated to 140 tonnes with a Euro 5 600hp Cummins X15, it features a Dana Spicer D2000F single steer axle, SPL 250 service free driveline and D46-170 tandem drive. Following some issues Ed had experienced with a competitor’s product, the Dana cooling package piqued his interest when a friend, who works in the industry, recommended it.
“At first, I went to Dana out of spite. My front diff was running nearly at 100 degrees Celsius. It was burning oil,” he recalls. “So, at 140,000 kilometres, the oil was cooked in it. It absolutely smelled like it had been burnt.”
Ed’s friend, who also operates heavy vehicles, had recently compared differentials himself within the marketplace and noted the improvement the Dana product offered. This wasn’t lost on Ed.
The Kenworth W900SAR Legend features a Dana front axle rated to 9.1
tonne along with the Dana driveline on non greasable units. In view of the operational context of the vehicle, the extra capacity on the steer isn’t necessary. It was more about ensuring integrity of the bearings explains Ed.
“Even on a heavier application you will rarely go nine tonnes on the steer axle,” he says. “It’s more about having bigger bearings on the front for less wear and to avoid, when running it deep on a mileage count, a bearing failure. It’s one of my pet peeves.”
The work asked of this vehicle is a mixture of light and heavy. Rated for a higher capacity even though it might not be utilised in that specification as much, the SAR is running on taller diff ratios in accordance with the advice Ed received from Cummins. A 2200 Series Eaton 18-speed double overdrive gear box on 4.3:1 differential ratios has helped to cut down AdBlue consumption to an average of 2 per cent. Another of the EJS
Logistics Kenworths operating at 4.1:1 uses an estimated 4 per cent AdBlue on average. Every little bit of savings helps reduce costs and improve efficiencies.
“I’m finding the trucks at 4:3s are pulling better on the hills by half a gear to a gear under weight sometimes,” says Ed. “The Legend is delivering 2.1km/litre before factoring in AdBlue costs.”
Over January this year, across the seven bonneted prime movers he had running, the EJS Logistics fuel bill was nearly $70,000. His fuel bill last month on eight trucks was closer to $180K. The cost of fuel has escalated to a point that any gain he can make through the drivetrain is critical.
The Legend has been the on the road just over six months. Even after clocking over 100,000 kilometres Ed can already determine the improvement in metrics.
“The Dana cooling package with oil pump is a lot better,” says Ed. “I’ve noticed the temperature on my front diff is anywhere around eight or nine degrees cooler than my previous diff in a similar application even though I’ve been running, if anything, a bit heavier.”
The SPL250 service free driveline eliminates the need to grease the driveline during the lifetime of the product. For smaller fleets, who can’t afford downtime as vehicles undergo repairs, it remains a strong selling point. Having been a big fan of the original Kenworth SAR, Ed was also looking to do something in tribute to his father who had owned three of them during his lifetime. When the opportunity to purchase the Legend no.45 released by Kenworth came up, Ed was moved to
“That was the year he was born in 1945,” he says. “If I couldn’t get number 45, I wouldn’t have bought one. I would have purchased another T909.”
One measure to counter overheads and the excessive amounts of AdBlue required of the new engines, is to undertake complete rebuilds of the powertrain just as Ed as done so before. Not long ago he commissioned one
on an older 2013 Kenworth T409SAR running in the fleet. A brand-new Cummins X15 engine has gone into that truck and been paired with a brand-new gearbox and clutch with a warranty of 1 million kilometres. The motor swap took place at Inland Truck Centre where Ed relies on Workshop Manager Luke McFall, a trusted friend. It’s now updated for the latest emissions compliance and back on the highway, delivering an excellent 2.3km/litre. Ed, where possible, will rebuild trucks. His first truck has 3.5 million kilometres on the dash and is still going strong. “You can always pull them off the road, rebuild them and they’re like a new truck again,” he says of the Kenworth, with its esteemed reputation for longevity in Australia. “Sometimes they have better fuel economy than the newest addition.”
In his line of work bonneted trucks necessitate an overlength consideration that brings with it the odd managerial vexation like when drivers forget to slide the turntable up which runs the risk of a fine. The next new truck slated for delivery in 2024 will be one of the last Kenworth K200s with a spec nearly identical to the new W900SAR Legend. The K200 truck has been built purposely for one of Ed’s drivers who he has known for nearly 30 years. It will feature the same 2200 series gearbox, Dana driveline and Cummins engine. “It’s not going to be a cheap truck to spec,” says Ed. “Neither was the latest W900 but I’m a firm believer that you do what you need to do in order to get the right driver of the truck. That’s what I’m doing.”
For the moment he’s reserving judgement on the new Kenworth K220 as he prefers the old-style wiring harness. Aesthetically, he takes a dim view, mostly because it evokes an image he just can’t shake.
“To me it looks like an old Arnott’s bicky barrel truck that came out in the late ‘70s,” he says. “But that’s subjective. That’s just me. Everyone else is different.
Some people don’t like the new SAR Legend. I do.”
Ed acknowledges the work his broker, Eric Van Gemeren, who is based in Adelaide at Chase Finance, has done in helping fund the fleet and procure or divest, as the case might be, assets.
(To date he has also sold two trucks). A colleague recommended Eric’s services over three years ago and the relationship has never been stronger.
“He’s got his finger on the pulse of the industry. He sees all the updates that come through SARTA, such as changes to the fuel excise, and he flicks it all on,” says Ed. “He’s proactive in what he does and has helped me build my business to no end.”
The latest trucks have been ordered from the Brown and Hurley Yatala dealership through Phil Salter, who Ed met through his wife as they both trained at the same gym at Beenleigh. Phil was always overly polite in their meetings.
“I told him if you’re buttering me up to
buy a new truck it’s not likely going to work,” Ed says. “Then I realised that was who he is. He’s generally interested in you and things in general.”
Then one day Ed walked into his office. Phil couldn’t help but stifle a giggle. “He said, you’re going to buy one aren’t you?” recalls Ed. “That was in the second half of 2020 after having known him for a couple of years.”
He’s now up to three trucks ordered from Phil. For the moment, both new trucks are exceeding expectations. The Kenworth W900 SAR Legend with the Dana package is far surpassing what Ed has had previously.
“I’m running nowhere near as hot and I am not having the same problem with the oil as I was in the previous truck I had bought,” he says. “That’s one of the biggest improvements I’ve focused on so far in that respect. Long-term, as far as longevity goes, we’ll see how it performs. All up, I’m finding the Dana solution superior so far.”
Available in six models, the new Isuzu Freightpack offers a choice of 10-pallet, 12-pallet or 14-pallet curtainside body configurations. To enhance its all-around
it with features to make it a must-have for fleets that are looking to expand their operational output.
Part of Isuzu’s Ready-to-Work range, the Freightpack features a comprehensive
and built to specification. Australia first laid its eyes on the new Freightpack at the 2019 Brisbane Truck Show where it was officially previewed to the transport industry. Ever since then the range
Australian fleets including the wellrespected Wallace International.
Wallace International has been providing Custom Brokering and International Freight Forwarding solutions within Australia and across the world for the last 40 years. Its international journey began in 1981 when Bob Wallace and his business partner decided to leave their jobs in multinational companies, after realising the need for a more personalised service where customers were treated based on their unique needs.
In so doing, Wallace International does not involve third parties in any of its processes. It remains one of the reasons the company has made itself known reputationally for the better among transport industry insiders. Overseeing all parts of the supply chain, it also offers 24-hour notice delivery and same day pick-up and delivery, solidifying its operational integrity.
“All of our operations are done under the one roof and is handled by our staff from start to finish,” says Warehouse and Transport Manager, Brad Greaves.
“Whether it’s from Sydney airport straight to the client, or direct from overseas all the way to the final destination. It sounds pretty simple, but there’s not that many people out there that do it. To fine tune and service our clientele fully, that’s the way we need to go.”
Isuzu has been the predominant brand for Wallace International for over 20 years, with its value for money and reputation for reliability key factors in
the relationship. Due to these benefits, Wallace recently added a FVL 240-300 Freightpack to its fleet of Isuzus.
“We’re expanding as a business again, and it was an advance in the footprint to increase our business with the help and support of Isuzu trucks to do our delivery,” Brad says. “We’re based in Brisbane in a new premises which we moved into at the beginning of this year.
“We’ve been focused on updating the fleet to keep up with our expanded business.
I’m very happy with the new Freightpack and I have been for quite some time.”
Brad’s Freightpack runs a six-cylinder
turbocharged engine producing 221kW at 2,400 rpm and 981Nm of torque from 1,450 rpm. It has a Gross Vehicle Mass (GVM) of 24,000 kg.
Transmission-wise, the FVL comes in an Allison six-speed HD4430 automatic gearbox, but for those who prefer to shift their own gears, an Automated Manual
Transmission (AMT) option is also available for what the OEM describes as ‘smooth, car-like drivability’.
Isuzu’s Satellite Navigation is fitted as standard in this model, which is integrated within the multimedia unit. The system displays a range of helpful
information on a 6.2-inch display, such as points of interest and Isuzu truck dealer locations, road safety alerts, speed limits and traffic signals, and route selection based on entered information such as vehicle weight and dimensions.
Wallace’s Freightpack also comes with Isuzu’s Advanced Driver Assistance Systems (ADAS), which has been developed to help keep all road users safe. A stereo camera integrated into the dash provides data to some of Isuzu’s key safety features, including Advanced Emergency Braking (AEB), Lane Departure Warning (LDW), Distance Warning System (DWS), and Traffic Movement Warning (TMW).
Brad says the Freightpack truck is an updated model of Wallace’s previous Isuzu, which was a favourite amongst operators.
“It’s what we’ve always used,” he says. “I’ve been here for 26 years now and
when I came into it, they only had one eight-pallet truck. Since then, we’ve expanded into four 14-palleters as well as using them in our Sydney and Perth operations. They perform really well.”
However, the 240-300 didn’t arrive alone.
Brad explains that his two older Isuzu trucks nearing 20 years old needed to be replaced, so he picked up a twin-steer FYJ 300-350 as well. The FYJ is known for its ability to carry extra weight as well, which has been very helpful given the fleet’s demands.
“A lot of the pallets we carry are anywhere between 1,000 to 1,100 kg, and obviously a 14-pallet doesn’t take 14-tonnes, but with these new twin-steers, it makes a huge difference,” he says. “It saves double handling and sending two trucks instead of one. Moving forward, I think that truck will be well and truly used and we will probably expand into another one sooner or later as well.”
The older models have since been traded in for the new Isuzu vehicles, though Brad notes that despite their age they were still performing above expectations having just under a million kilometres on them. While Isuzu continued to impress by meeting operational needs, Wallace International has no reason to shop elsewhere in the market.
“Our body truck fleet is primarily Isuzus, apart from one,” Brad says. “They’re just great. I’ve been asked plenty of times why I use Isuzu, and that’s the reason why –reliability. You turn up every day, and it goes. There’s no major drama with it. “We’ve had a lot of manuals over the years, I’ve had other people with other brands that have had gearbox issues and interior issues, but ours just keep going on with regular servicing. Our trucks get serviced every 10,000 kms, no matter what. The reliability is unmatched, you just can’t go past it.”
DB Schenker traces its foundation back 150 years to 1872 when Gottfried Schenker started Schenker & Co in Vienna, Austria and offered the first consolidated rail shipments from Paris to Vienna.
The 2022 version of the organisation’s metrics are mind boggling with 72,200 employees in 2,100 locations across 130 countries. DB Schenker is acknowledged in Europe as the number one in land transport with 100 million land transport shipments per year, which translates to one every three seconds. There are 430 land transportation branches across Europe and DB Schenker is also a global leader in contract logistics with more than eight million square metres of warehouse space across 60 countries.
DB Schenker is focusing on participating in the green supply chains of the future and as an important step in its commitment to be net carbon neutral by 2040, DB Schenker has been an early adopter of Battery Electric Vehicle (BEV) technology and has already completed more than 1.5 million kilometres with electric powered vehicles in its European land transport network.
Since 2017 DB Schenker has been a pioneering customer of the Fuso eCanter and has continued to cooperate with the manufacturer in the development of practical zero emission commercial vehicles. Feedback from DB Schenker has been taken into account during the development of the second generation eCanter, particularly, in relation to operating range limitations being affected by time spent in traffic, the
topography of the area where the trucks are used, as well as battery drain caused by repeated operation of the tail gate lifters which are fitted to many.
The second-generation Fuso eCanter appears to have successfully addressed these concerns with its three modular batteries and eAxle technology providing additional range. The second-generation vehicles are now being confidently scheduled to perform shifts covering more than 100 kilometres. DB Schenker is currently operating the largest fleet of Fuso eCanters in Europe and is scaling up its efforts significantly to shift its urban collect and delivery fleet completely over to electric vehicles by 2030. This will require a major roll out of charging infrastructure throughout the various depots.
“The drivers are not getting nervous
DB Schenker is the largest provider of land transport in Europe and is an early adopter of electromobility commercial vehicles.
towards the end of their shift,” says Hendrik Nonnenmacher who is the manager of the DB Schenker branch in Frankfurt which has been the location for trials using Fuso eCanters. Frankfurt city is a classic dense urban area where a 100-kilometre operating range between recharges is fine except for the risk of getting caught up in traffic on it many narrow streets.
DB Schenker is not immune from the shortage of skilled drivers. In recent times this challenge has increased as many male drivers were based in Ukraine and have left the transport
industry to fight in the conflict with Russia. Drivers capable of handling larger trucks that often tow trailers, are in particular low supply so there is a move towards lighter trucks in the 7.5-tonne and 12-tonne categories, which still leaves the challenge of providing operators for the larger combinations.
“It’s difficult to get drivers, especially good drivers and we have begun targeting entry level younger drivers using eMobility as a recruiting argument,” says Hendrik. “They like the concept of driving an eTruck, and
even diesel drivers enjoy the eTrucks because they are much more quiet and comfortable.”
Incentives designed to attract and retain experienced drivers have gone as far as providing a company car in lieu of additional salary.
DB Schenker makes very good use of its innovative ‘swap bodies’ which are similar in dimension to 20foot containers and can be left at a customer’s premises to be loaded or unloaded while the truck can move on to perform other operations. No lifting equipment such as a crane or
sideloader is required as the swap body is able to stand on its own fold down legs. Lowering the truck’s airbag rear suspension drops the truck chassis away from the swap body so that the truck can drive clear and go on to the next pick up. Re-attaching the swap body is a simple reversal of the procedure with the suspension set in the lowered position for the truck to slide back underneath the body, and then raise itself again using the suspension’s airbags. The swap body is attached to the truck chassis using container lock devices. Recently joining the Frankfurt fleet are
a number of Mercedes-Benz eActros 300 models which have, as their drive unit, a rigid rear eAxle with two integrated electric motors and two-speed transmission. The eAxle driveline can provide a continuous output of 330 kW and a peak output of 400 kW. DB Schenker will soon be adding some prime mover versions of the eActros which were on display at the IAA Transportation show in Hanover. Practical zero emission electric vehicles are a key element in DB Schenker’s enthusiastic pursuit of sustainability and its commitment to be free of fossil fuels by 2040. The organisation already has more than 170 eVans, eTrucks and cargo eBikes similar to those being used by Australia Post. Being a good corporate citizen extends beyond environmental pursuits and DB Schenker has within
its social and governance policies a target of a 50 per cent female workforce globally by 2030. An additional 1,500 electric vehicles of various categories are currently on order, demonstrating not only DB Schenker’s serious commitment but also the recent and rapid level of maturity reached by electric vehicles as practical alternatives to those powered by traditional internal combustion engines. “DB Schenker is looking to join forces with shippers and freight forwarders to advance CO2-free land transport further,” says Jochen Thewes, CEO of Schenker AG. “We are making advanced investments in green supply chains despite high costs to protect our climate. Our appeal is to customers: The offer is there, now the demand and willingness to pay for clean transport must also pick up.”
Emerald Carrying Company amasses some 450,000 kilometres a year on fuel-haul B-doubles working tripleshifts. Cummins supports it every inch of the way.
The words are prominent on the door of the Kenworth – PRIDE, CARE, RESPECT, EXCELLENCE – and in a nutshell they embody what Emerald Carrying Co (ECC) is all about. The strong culture at ECC is palpable: Pride in everything is everything. It shows in the presentation of the immaculately maintained equipment.
This year the Queensland fleet will haul around three billion litres of fuel to mines, fuel depots and service stations. ECC operates depots in Brisbane, Rockhampton, Gladstone, Mackay, Townsville, Cairns and Emerald, the small Central Queensland town where the business was first established in 1965 by Bill Haylock who started out with a 4-tonne Austin carting off the
rail. With more than 145 prime movers and 350 types of trailing equipment, the long haul specialist in general freight and fuel deliveries is now into its third generation as a family business. Progress, across the last five decades, has been steady. Team effort, employee loyalty and business integrity have been guiding principles behind an operation that today runs top tier equipment on high utilisation schedules as part of the premium service it provides its customers.
In fact, high utilisation is a trademark of the fleet with some of ECC’s fuelhaul B-doubles clocking 450,000 kilometres a year on triple-shift work. Kenworth prime movers powered by Cummins engines dominate the ECC fleet which operates, by and large, in
sweltering conditions working in the Bowen Basin and on outback linehaul as far north as Darwin. Because of this ECC has forged, over the years, rocksteady relationships with its suppliers. Here an old axiom holds true: loyalty received is deserving of loyalty in return. Pursiant to this, an alliance with Cummins dates back to the 1980s. More recently, ECC put into service a set of B-double tankers promoting the Cummins brand – in particular the Euro 6 X15 with the accompanying message, ‘We’re ready when you are’.
“Cummins is the best engine brand on the market in terms of reliability and aftersales support,” says ECC fleet manager Matt Haylock. “We run our trucks into some extremely remote
areas across Queensland, the Northern Territory and New South Wales so reliability is crucial.”
When a Kenworth has done around 1.2 million kilometres, ECC rebuilds the engine or replaces it with a brand new one depending on how quickly the kilometres have been accumulated. The X15 is commonplace in the fleet. Earlier in the year ECC saw the first Euro 6 X15 engines enter service.
The latest innovation at ECC is the ‘Super Triple’, a PBS-certified combination that operates on the 900 km trip between Townsville and Mt Isa, hauling 130,000 litres of fuel – a gain of up to 22,000 litres compared with the capacity of a standard roadtrain triple.
The Super Triple, with 600 Cummins
X15 horses in harness, features a tridrive Kenworth T909 pulling Tieman quad-axle trailers and tri-axle dollies,
maintenance of the trucks. They are generally washed after every shift. Perhaps this is personified no better than the impeccable Kenworth K200 in the accompanying photos, which, at a guess, looks to be 12 months old with a few hundred thousand kilometres on the clock. It is, in fact, a 2016 model with over one million kilometres under the X15 rocker cover.
ECC runs a stringent maintenance regime which underpins the company’s fleet reliability and safety commitments.
“We have very few breakdowns – perhaps one a month, if that,” confirms ECC maintenance manager Chris Chalmers. “We’re proud of that considering the size of the fleet.” In addition to its current facilities across
Queensland and the Northern Territory, ECC under the banner of Monaro Fuel Haulage, which it acquired in 2016, also has a major presence down the eastern seaboard with depots in Sydney, Melbourne and Adelaide. At the time of the acquisition, the Monaro fleet totalled six trucks; today close to 40 trucks operate in the Monaro blue livery. “Our B-double prime movers are brought in for checks every 12,500 km which is generally a week to ten days while our engine oil change intervals are 50,000 km for the B-doubles and 25,000 km for the roadtrains,” Chris points out. “We look at fuel burn every service to check engine load factors and that our servicing intervals are where they should be.”
Accurate forecasting, according to Chris, is the key to the ECC maintenance system. “Each week we get an automated report detailing which trucks are due in for servicing,” he says. “We have five workshops and 30 mechanics including nine apprentices.”
In 2020 ECC relocated to larger premises in Lytton that allowed it to incorporate its Lytton Bulk Fuel team, Oil Logistics team, Head Office team and Brisbane General Freight team. With the busiest depots facilitating upwards of 70 B-double fuel loads a day, on an average of 51,000 litres per load, the company, as a vital cog across industries instrumental to the economy, must be a dependable force like its partners in Cummins and Kenworth.
Following the market launch of the eActros 300 and 400 production models in 2021, Mercedes-Benz Trucks continues to push ahead with the introduction of further batteryelectric models with a production prime mover version expected in 2023 to join the rigid models already available including the eEconic refuse vehicle range. Additionally, the battery-electric eActros LongHaul prime mover was unveiled at the IAA Transportation show in Hanover as a ‘design theme’ of the series-production vehicle planned to be available in at least the European market some time in 2024. On a single battery charge the eActros LongHaul will have a range of around 500 kilometres which will make it suitable for many European applications and even some in Australia. The e-truck will enable high-performance “megawatt” charging which can take the battery charge from 20 per cent to 80 per cent in just 30 minutes. The move towards electric prime movers and rigid/trailer applications is also likely to be accelerated with the use of electrified trailers that can significantly increase the driving range of electric trucks. Technology company Trailer Dynamics has developed an “eTrailer” in conjunction with trailer manufacturer Krone. At the core of the concept is an e-axle used in the trailer with its own batteries, which contributes additional motive power. Depending on the battery capacity of the eTrailer, ranges of more than 800 kilometres on one battery charge are expected to be possible when used with the series-production version of the eActros LongHaul. Meanwhile, as we wait for the production LongHaul, the current eActros 300 is now available with an electric power take-off solution to enable the drive for hydraulic
The Mercedes-Benz all-electric eActros is already proving to be a practical contender in the European market.
pumps in applications such as hook loaders and tippers.
The opportunity to drive the eActros 300 on the streets of Hanover is too good to pass up. Even the head of Daimler Trucks Martin Daum enthusiastically avails himself to a quick steer, along with the assembled global truck media and select customers.
The Mercedes Benz eActros 300 is driven by an electric drive axle with two integrated electric motors and a twospeed transmission. The two motors are mounted centrally on the rear axle and generate a continuous output of 330 kW (440hp in the old money) and a peak output of 400 kW (536hp). The direct torque delivery of the electric motors in conjunction with the two-speed transmission provides some impressive acceleration. Three battery packs are installed on the test truck, each with an installed capacity of 112 kW and provide a driving range of up to 220 kilometres. The electric motors are liquid cooled as are the batteries. The cooling is a function of Mercedes-Benz’s thermal management system which enhances component reliability and prolongs battery life. The batteries consist of either three (eActros 300) or four battery packs (eActros 400). With four battery packs, the eActros 400 has a range of up to 400 kilometres. Mercedes-Benz has committed to lithiumion phosphate cell technology (LFP) for its batteries to deliver more usable energy and a longer service life.
Getting behind the wheel of an electric vehicle encourages the driver to actively scan the road and traffic ahead, in order to temper the need for harsh braking or acceleration. This ultimately results in less drain on the batteries, along with the
opportunity to recuperate some electrical charge as the truck decelerates.
As expected, once out of the Daimler Trucks’ hall of the Hanover exhibition centre, the eActros is whisper quiet, with the only discernible noise identified as the electric-driven air compressor and the air conditioner fan. In terms of alternative power for commercial vehicles, Europe is already far ahead of Australia in its progress and expectations. Due to its quiet operation, the eActros safety equipment includes an external Acoustic Vehicle Alerting System in accordance with European legal requirements. The cab interior of the eActros is much the same as the familiar one found on local diesel-powered models of the Actros, other than the centre screen on the dash showing an animated driveline which displays the changes between Power and Recharge modes, as well as predicted remaining operational range. The eActros is equipped with the same electronic parking brake as the diesel models and most other controls are essentially the same.
Three power modes are available and are selected by a button on the end of right-hand steering column stalk: Range, Economy and Power Plus Boost. To initiate the latter after it has been selected, the driver operates a detent switch by pressing the accelerator pedal all the way to the floor which produces a surprising increase in the rate of acceleration. The boost effect is likened to a lesser version of the Drag Reduction System (DSS) used by Formula 1 cars to enable driver-initiated passing. Predictably, over-enthusiastic use is an additional drain on the battery capacity and reduces the available range, but we are repeatedly tempted to put the pedal to the metal especially when leaving some sporty
looking European sedans in our wake at traffic lights.
Instead of an engine or exhaust braking system usually found on diesel engine trucks, the eActros is equipped with an electric retarder which provides braking assistance by reversing the polarities of the electric motors and switching them to alternator mode. There are three levels of braking power selected via the column stalk operating wand which can be left in position to suit the current gross weight and road conditions. Leaving the retarder in standby assists in making the most of every opportunity to recharge the batteries, even if only for seconds at a time. In the full retard position the eActros decelerates as if the service brakes have been applied and we temper the effect by switching back to the intermediate level to enable a smoother drive while on city streets. The eActros features the fifth-generation Active Brake Assist with pedestrian detection as well as a “turning assistant” which uses the second-generation MirrorCam display screens mounted to the inside of the A pillars. The exterior mounting arms for the MirrorCam are now much shorter than the originals which should significantly decrease the
chance of damage caused by impacting branches, building structures or other vehicles.
Other applications of the eActros displayed at IAA Transportation 2022 included a hook loader and a skip loader equipped with the all-in-one solution eWorX system which has been developed by ZF. The aim is to efficiently electrify PTOs for operating hydraulic work equipment such as skip loaders, hook loaders, cranes or lifting platforms. The advantages of CO2-neutrality and greatly-reduced noise generation will appeal to applications intended for inner city and residential situations.
The batteries of the eActros provides the ZF system with electrical energy via a DC interface. In turn, the eWorX electric motor drives the hydraulic pump for the hook loader or skip loader. A mechanical connection to the axle mounted traction motors is therefore not necessary and the system is also suitable for applications such as powering refrigeration units.
In its quest to become more than a vehicle manufacturer, Mercedes-Benz Trucks is offering customers a holistic transport solution consisting of vehicle technology, consulting, charging infrastructure and
Paul Fellows has been involved in the road transport industry since 1981. This has given him a strong focus on safety, compliance and professionalism. With his wife Jenny, he owns and operates a bulk transport and grain storage business based in Deniliquin in New South Wales. He is also Deputy Mayor on his local council.
Prime Mover: What are some of the issues being faced by a member organisation such as NatRoad?
Paul Fellows: There are a number, including the viability of the industry, the reform of the Heavy Vehicle National Law, the Road User Charge, and how we address a carbon-free future.
PM: What are your thoughts on the Road User Charge (RUC)?
PF: The current RUC is flawed. We are responsible for paying for the maintenance of the roads but there is no transparency where the money is actually going. We’ve had three wet years of above average rainfall and the effect of that rainfall on the roads. Basically, the transport industry will be paying for the effect of climate change for these last three years. And that’s not fair. If climate change is going to see huge changes in weather, why are we the ones who are going to be paying for it?
PM: What can be done to address the industry’s universal driver shortage?
PF: One aspect is diversity. Only four per cent of truck drivers are women. The problem is we can’t attract women to the industry where we’ve got roadside rest stops with no or poor facilities. If
PM: You still drive the occasional trip yourself?
PF: I might do the occasional pre-load and meet up with the driver which increases utilisation of the asset and the driver gets two or three days off at home. I also do the odd Brisbane trip and driving to Brisbane is good because it enables me to see first-hand what our members are experiencing on the road.
PM: Does that help you suggest some of the agenda for the association?
PF: I am aware through industry research and first-hand experience that our declining profit margins are strangling the future for many road transport businesses across the nation. The increasing cost of fuel, tyres, and wages, combined with driver shortages and an ageing work force, plus the complex challenge of compliance and cumbersome regulations, have seen significant stress put on many operators. Running a business, particularly a small business, is hard enough if you only make small profits year-after-year. Basically, we are looking for answers, but it’s also important when you ask a question that you’re armed with information. In light of this, NatRoad is adopting a leadership position by commissioning economic research for our members to better understand these factors. This project will benchmark different businesses across the industry and will enable members to have an idea of how their business is really travelling in comparison with the rest of the industry, so they can make better business decisions to help them tackle issues that are vital to the viability of their business. This will also be a valuable tool in presenting figures to government to portray what is really going on at an operator’s level. NatRoad has always been a trusted voice for
its members in providing advice on business issues and we believe this groundbreaking research will add real value to what we can provide and build on that foundation.
PM: Will this have an effect on NatRoad’s role as an industry association dealing with governments?
PF: NatRoad is apolitical and works with all sides of politics. We are essentially representative of the small business transport sector, and we are an association of people who employ themselves or relatively small numbers of people. While it’s fair to say we have not always seen eye to eye with governments of the left of the political spectrum, we also had some strong issues with the last government when they decided to strip away the fuel tax credit for six months. I’m not certain if it was a knee-jerk or uninformed decision, but we worked really hard to get it overturned.
We are establishing a really good dialogue with the Labor government and although we’re not always going to agree, I think that’s healthy. We need to be objective and constructive. Basically, we’ve all got the same aim which is to work together and make the industry
a better place. When we see something contrary to our members’ interests, we will call it out. If we see a pragmatic solution to a problem, we will suggest it. We are committed to working with the Albanese government. The reality is that COVID provided a great example of how adaptable the transport industry is and how much the general community relied on us to get food on shelves of supermarkets and how adaptable we are and we were able to keep our society fulfilled with its needs.
PM: How is the industry preparing for net zero emissions?
PF: Heavy Vehicles are a major player in emissions reduction and there are significant environmental, social and commercial advantages to achieve net zero. But we all need to deal with the realities of road freight and the investment involved by thousands of businesses. Change is coming, but
Last year marked the 40th anniversary of City Hino’s operations, making it one of the longest established truck dealerships in Australia. Award-winning Hino Salesman, Bevan Joseph, has been selling vehicles at the New South Wales dealership from its earliest beginnings.
Bevan Joseph’s journey began in the marine sector, selling boats. Having, from a young age, an interest in machinery, he particularly enjoyed selling large cruisers. The early 1980s recession gave him the incentive to join an industry which would provide a solid career in sales. It was his uncle who approached him with an opportunity that eventually would determine the trajectory of an entire career.
Working for the Suttons Motor Group at the time, an organisation which owns various franchises such as City Hino, Bevan’s uncle offered him an interview for a job that would see him leave the marine industry and enter the world of trucks.
Bevan was soon selling Bedfords, Holden cars and Leyland trucks. After a brief sojourn, he returned to the dealership which had then switched over to a Hino dealership. And, here he would remain as one of its most decorated salespeople though the roles have changed over the years.
“I’ve been doing fleet, government and a little bit of management, but mainly retail selling and small business customers,” he says. “I’ve also held a position of training
In 1986 he was the first person to sell a Hino FF Turbo and later a Dutro 2, as well as the 35,000th Hino FS from the Ranger series, which is still running today with almost 1.5 million kilometres on the dash.
Bevan has enjoyed selling tipper trucks throughout the years starting with the Super Dolphin. Vehicles from the 700 series remain a particular favourite due to their capabilities in tipper applications. “I’ve been the number one salesman in Australia twice in my career and I’ve participated in our skills contest and came second and third, which is a highly recognised thing within the Hino group,” he says. “I’m pretty much the oldest salesman here now.”
That also makes him a walking encyclopedia when it comes to Hino product.
Given its long-term presence in the transport industry, the dealership has been an integral part of the Hino history in Australia for over 55 years. It also makes City Hino one of the longest established truck dealerships in Australia – something Bevan and the team are very proud of. City Hino has won the Sales Excellence Award on several occasions and has been a top parts and service ranking dealership within the country. Thanks to Bevan, it has also been honoured with the Salesman of the Year twice. In fact, the entire sales team has constantly been in the Top Hino
Sales Guild during its six year history. Along with these accomplishments, it has been involved directly or indirectly in many landmarks for the brand as well. Back in 1981, the City Hino’s sales team sold one of the last of the Hino LB 560 models produced. It eventually became the F generation of Hino trucks. Three years later in 1984, City Hino was one of the first dealerships to retail a FS Super Dolphin. With the introduction of a new management team, City Hino packed up and moved to its new and current home at Arndell Park in 2017. Although it left 35 years of memories behind at its Guildford location, the team saw sales jump by 300 units per year, bringing it to its new benchmark.
“As far as the new building goes, we refurbished the whole dealership,” Bevan explains. “There’s been a lot of investment in service and spare parts, in the sales office and in trainees.”
According to Bevan, the dealership is performing to expectations and is wellpositioned in the market.
“We’ve got a good team here, it’s basically, in recent years, doubled in size,” he says. City Hino is selling on average around 600 trucks a year. That, according to Bevan, is exceptional. Having that many sales, he acknowledges, requires strong support, with the finance department recognised for the ongoing assistance it provides to help
with sales . Both the spare parts and service department has also grown.
The service department has also been recognised by its peers for its work by achieving several accolades within its field.
The sales staff now includes seven salesmen plus support staff, with the dealership team, as it currently stands, employing 85 staff members.
To celebrate its 40th anniversary, City Hino hosted the Hino Roadshow Open Day on 18 August 2022. Separate to this, City Hino held a special event. All staff, many customers and suppliers were all in attendance.
“We’ve taken pride in providing customers with a large range of new and quality used trucks,” notes Bevan.
Among its many accomplishments and accolades, what matters most to the team at City Hino, ultimately is its customers. Currently, one of the challenges Bevan faces is selling trucks when delivery times have been protracted by external market forces.
“We’ve never had to do that before, given we’ve always had trucks in stock but at the moment we’ve got nothing,” he says.
As part of the Suttons family group, there’s a continual focus on enhancing customer service.
“We want to be the number one dealer and we are the number one dealer in Sydney,” he says. “Hino’s decade of dominance is here.”
New research reveals one in two Australians use sales events to stock up on Christmas gifts.
Consumer habits regarding the October to Christmas peak period for parcel volumes is undergoing a seismic change according to parcel delivery specialist CouriersPlease. The company now expects its largest spike in volumes to take place in the second half of November following the Black FridayCyber Monday sales.
These changes in the buying habits of consumers have been reflected in a new survey that suggests events like midseason sales are increasingly being used for end-of-year gift giving.
The findings were derived from a survey of an independent panel of 1007 Australian online shoppers, commissioned by the courier company. According to survey results, 52 per cent of respondents use sales events to do their Christmas shopping, with the highest proportion among under-50s (65 per cent of all under-50s) and women (56 per cent of all women).
Last year, Australians spent $8 billion during the Black Friday-Cyber Monday sales period, a significant increase on previous years suggesting it continues to be the shopping event Aussies gravitate towards to snap up a bargain. This was backed by the survey results,
Boxing Day is no longer the biggest sales event on the calendar according to a new survey..
which found the largest proportion of consumers (26 per cent) shop at the Black Friday sales. A relatively high proportion of respondents also revealed they spend big during seasonal sales events.
Specifically, an equal 19 per cent said they spend the most during end-ofseason and end-of-financial year sales, and 7 per cent spend the most at midseason sales.
Just 17 per cent said they spend the most at Boxing Day sales – traditionally the biggest sales event of the year. CouriersPlease also asked respondents which sales event offers the deepest discounts.
Black Friday topped the list, with 30 per cent saying the event offers the best bang for their buck. One fifth (21 per cent) of respondents think the best discounts can be found at the Boxing Day sales, while 18 per cent stand by EOFY sales, and 14 per cent believe end-of-season sales get them the best discounts.
“An increasing number of savvy retailers are recognising that Black Friday is the sales event of the year, motivating many to start their sales event earlier and end
events that offer the deepest discounts.” August this year marked the 18th consecutive month of steady growth in household spending, with significant increases occurring across discretionary goods such as clothing and footwear.
Australians, however, may be prepared to continue spending strongly this Black Friday sales period, even in a climate of high inflation and increasing interest rates.
Despite cost-of-living pressures, consumer spending, Thame pointed out, is on the rise.
“While retailers have been preparing for a spike in Black Friday orders, it could be a good idea to roll out different offers in the lead-up to the event or start the event early to create an even flow of customers and keep up with orders,” he said.
To combat any potential customer issues, Thame said retailers should partner with a parcel delivery provider that has a Black Friday sales strategy and a strong track record of efficient, on-time deliveries.
“CouriersPlease, for instance, has planned for the event months in advance, onboarding additional
in Melbourne is expected to see RAM Trucks Australia continue its leadership in the full-size pick-up truck category. In September the brand sold 604 units, an increase of 45 per cent on 2021 year-todate, with the total number of RAMs sold to customers since production began now at 17,115 (before October ’22).
To celebrate this milestone, Bob Graczyk, Head of RAM International, visited Melbourne recently to see the significantly expanded production facility which now boasts three dedicated production lines running 24-hours per day.
“Australia is a super important market for us outside of North America, and the growth that we’ve seen here over the last few years has been phenomenal,” said Grazyk. “With the expansion of our plant this growth will continue. It’s incredible what the team has done at RAM Trucks Australia, Ateco Group and MMF. Outside of the US, we sell more full-size pick-up trucks than Ford and GM combined, and Australia representing a market
“It’s a dedicated group here that love RAM and it comes through in everything they do in Australia, so we are super proud of having more than 17,000 people out there driving our trucks.”
With the Melbourne Manufacturing Facility (MMF) of Ram Trucks Australia having expanded its size and capacity recently, the new 16,025m2 site now has two dedicated lines for its RAM 1500 Express Crew and Warlock models in the original DS variant and 1500 Laramie and 1500 Limited in the recently launched DT model range. A separate line is dedicated for heavy duty models. All lines are capable of producing up to 20,000 vehicles per year. MMF currently produces 10,000 vehicles per annum.
With 641 employees, RAM Trucks Australia is now considered the biggest vehicle manufacturer in Australia. In terms of total right-hand drive RAM trucks produced for the Australian and New Zealand markets at the end of September 2022, 18,019 vehicles have been remanufactured at MMF.
With 361 new parts on the DS, 402 on the there are significant local supply chain benefits of this fast-growing vehicle segment according to Ateco Group, the brand’s local distributor.
RAM Trucks Australia is the world’s only RAM-authorised manufacturer of righthand drive RAM trucks.
The relationship with RAM Trucks in the USA dates back to 2013. All RAM Trucks Australia vehicles are internationalspec vehicles, uniquely coded for the Australian market and the local build process.
“I was in our Sterling Heights, US, plant a few weeks ago and yesterday I got into a right-hand drive RAM TRX for the first time – the truck that is coming off the line here in Australia is as good as what’s coming out of our main plant,” said Graczyk. “We’re 1000 per cent supportive of the remanufacturing process here –we work very closely with the team and provide whatever they need in terms support, CAD data etc – and have full confidence in the team here to protect our brand, and to protect our truck.”
A BevChain operator using a fullyelectric Fuso eCanter to deliver beer kegs to Sydney suburbs daily has applauded the quick, quiet and efficient performance of the vehicle. Each day, Lance Valentine completes three to four loops out from BevChain’s Lidcombe base, delivering Tooheys kegs to pubs within a 40km radius.
Depending on traffic conditions and route, total mileage for Valentine’s daily deliveries could be up to 150 kilometres. However, Valentine said that after his first run, the battery still has decent range thanks to its regenerative braking.
“I tend to look ahead and see what I can do to harvest energy with the
regenerative braking, like lifting off to charge going down a hill or using the regenerative braking to pull up rather than use the brakes,” he said. “With the fast charger, I easily top it up in a very short time and that gives me enough to get out and back without having to worry about range.”
The eCanter has a power output of 135kW and 390Nm of torque, which can be delivered the moment the accelerator pedal is pressed. It also uses six liquid-cooled lithium-ion batteries mounted in the frame that store 82.8kW/h of electricity and feed a permanent magnet synchronous motor.
“It is smoother, more comfortable and there is hardly any noise,” Valentine
said. “It is also really easy to drive. Beyond the fact it is producing zero emissions, the quiet operation is also really important.”
The eCanter features a full suite of active safety features, including an Advanced Emergency Braking System (AEBS), which uses a radar to detect potential collisions and brake hard even in the event where the driver fails to do so. This system can even automatically begin braking if it detects moving pedestrians, which is especially important in urban areas. Other safety features include a Lane Departure Warning System, Electronic Stability Control, Hill Start Assist, a reversing camera and driver and passenger airbags.
Reducing fuel costs remains one of the final frontiers in which transport operators can still find those crucial extra gains. Stricter emission regulations, unpredictable fuel prices, advanced engine systems and growing competition continue to challenge the global commercial transportation industry. The Australian market itself poses a unique set of driving conditions for road transport fleets. Do you have a product specifically formulated for a variety of engine applications across heavy and light trucks? Can your product offering help prolong the life of equipment and help operators get the most out of the drivetrain? Be part of Prime Mover’s product showcase in February as we offer a platform in which to present your lubricants and oils to a market hungry to find that ultimate edge over the competition.
One Renault Master wasn’t enough for Team Tank Logistics to carry out its expanding operations, so it has returned to Renault several times to add more high-quality vans to its fleet.
Team Tank Logistics (TTL) is a specialised courier service based in Bendigo, Victoria. Trading since 2013, it is predominantly focused on providing specialised services through the transportation of a large variety of products varying from white goods and furniture to light freight solutions and contract pallet loads.
“We do everything and anything, really,” says TTL Director, Daniel Rowell. “We are a specialised courier service that offers high quality and affordable delivery services direct to the customer’s door
by appointment only.”
TTL was originally run as a one-manoperation by Daniel until he made the decision to expand. So, he purchased another van from Renault and hired another staff member. Since then, the company has expanded even further and has added two new Trafics to its fleet. Both Trafics have a long wheelbase, providing extra length to transport furniture and other large items in TTL’s daily operations.
“We regularly deliver for a play equipment company out of Melbourne and a number of other corporate customers that require delivery of items three metres long, so the longer wheelbase means we don’t have to take a larger van to do these things, we can run down in the Trafic and get the job done,” Daniel says. The bulkhead in particular was a specific requirement for the team as TTL often stacks parcels to the roof, allowing it to further utilise the entire cargo area. The current model Trafic also comes with a 7.0-inch infotainment system with Apple CarPlay and Android Auto, which is another one of TTL’s favourite features. “Being in a delivery industry, the way that Apple CarPlay syncs is great,” Daniel says. “We use it to route all our deliveries, and it puts them in the most efficient order. Once one delivery is completed, we can then see which one is next. It’s just really helpful and it streamlines our day. I can also communicate with my staff, whether it’s by email or just message.”
Before switching to the Trafic, Daniel had been using Renault’s Master models. However, he explains that he was looking for something smaller and easier to get around town.
“We needed a bit of length in the van, but we didn’t really need a bigger van, and the Trafic offered all of that in one,” he says. “We use the Trafics more locally where we’re doing multiple stops, in and out of town. They’re great for parking and we do scoot up to Melbourne a fair bit in them as well, so they’re really fuel efficient. They’re comfortable to drive.”
Economy is a major factor for TTL. It is currently running four vans, and with the
price of fuel at present, it is essential that the vans deliver every penny worth. As a result, Daniel says the team can get 1,000 kilometres done on highway conditions within a full tank.
“Renault’s economy side of things is definitely a bonus,” he says. “I could probably get even more out of it if I use the economy button, but I don’t. That, in itself, demonstrates the Trafic’s efficiency.”
Daniel found his first Master to be very reliable. The complete experience from purchasing the vehicle to receiving it proved to be exceptional. This initial impression is what convinced him to consider another option from Renault. “We found it easier to deal with, and being based in Bendigo, there wasn’t any issue with doing the deal over the phone with the dealer in Melbourne,” he says. “The reliability was the main thing that attracted us, and the price point was just right.”
TTL is also utilising a Trafic Crew van which Daniel has found is contributing to no end across many aspects of his daily life. Being a small business, the team is constantly working around family commitments and other requirements. The Trafic Crew allows Daniel to drop off his younger kids at day care and then go straight to a job and unload a pallet.
“As a small business and having younger kids, the flexibility of being able to do both things at the same time was a real bonus with the Trafic Crew,” he says. Another bonus Daniel finds very effective is the fact that the vans can be serviced every 30,000 kilometres, as opposed to every 10,000 kilometres. Overall, the whole experience of dealing with Renault has been nothing short of convenient for Daniel and the team at TTL, who are certain they will be completing even more orders in the near future.
“The reliability of them has been really good, we haven’t had any major issues,” he says. “We’ve had around seven or eight vans over the years, and it’s just been fantastic. I’ll definitely be buying a couple more in the nottoo-distant future.”
Hino is pursuing a renewed focus on its proven hybrid technology and the Hino 300 Series Hybrid may be the ideal light commercial vehicle for our time.
Just as fuel prices are at an all-time high with little or no relief in sight, and the investment into battery electric vehicles (BEV) and their associated infrastructures and limitations making that category an area for larger organisations for the time being, Hino’s Hybrid makes a lot of sense during this transitional period. The Hino 300 Series has been around for quite as few years and is currently the only light-duty hybrid electricdiesel truck available in Australia. More than 650 Hino Hybrids are currently operating around the nation. The Hino Hybrid can be categorised as embracing mature technology with associated reliability, fuel savings and
emission reductions. Hino’s parent company, the Toyota Group, is widely acknowledged as a world leader in hybrid technology and chances are the last time you rode in a taxi it was a Hybrid Camry. The updated Hino Hybrid was launched in 2020 and incorporates changes to the hybrid system aimed at improving fuel efficiency and reducing emissions. The Hybrid uses a parallel electric diesel design and a Toyota Group nickel metal hydride battery, which has been used in over 15 million hybrid vehicles worldwide.
Applications for the Hybrids are varied and range from dry van and refrigerated delivery trucks through to city and regional council vocational applications such as rear loader waste, parks and
garden service, and tippers.
When Hino launched the current version of 300 Series Hybrid models in 2020, it was anticipated that they could reduce a customer’s operational costs by up to 20 per cent, which also directly minimises the impact on the environment with an equal reduction in CO2 emissions.
“Recently, we have undertaken further real-world customer trials involving a 300 Series 616 Hybrid operating in a refrigerated delivery application which resulted in a 22 per cent improvement in fuel efficiency compared to the conventional diesel engine model,” says Richard Emery Hino’s Vice PresidentBrand and Franchise Development in Australia.
A major contributor to the improvement in fuel consumption is the reduction of idle time, which was around 50 per cent in Hino’s trials. This is managed by the Hybrid’s engine stop/start system and is a potential saving of up to 5.1 tonnes of CO2 emissions and over $4,000 per annum in fuel savings per truck.
“The current market conditions combined with our customers’ strong focus on reducing their CO2 footprint has seen us take record orders from new and existing Hybrid customers such as councils, and fleet customers like Altus Traffic,” says Richard. “A 300 Series Hybrid currently has a lower operational CO2 output and environmental impact than a battery electric truck plugged into the Australian grid.”
In addition to direct operational savings the Hino Hybrid brings with it a reduction in maintenance costs as the electric motor replaces the diesel engine’s starter motor and alternator, while the regenerative braking recharges the batteries and extends the lives of braking components such as disc rotors and pads.
Hybrid models are available across the Hino 300 Series range from the 616 Standard and Wide Cab car-licenced models through to the 716 Wide Cab and the 916 Wide Cab, which has a maximum Gross Vehicle Mass (GVM) of 8.5 tonnes.
The updated hybrid system uses a lightweight Power Control Unit (PCU) which weighs only 85kgs and incorporates the battery, inverter, Engine Control Unit (ECU) and DC-DC Converter.
The hybrid system operates by continuously seeking to supplement the diesel power delivery with electric power into the driveline, and the truck is constantly transitioning between diesel engine drive only; a combination of both electric motor and diesel engine drive; and can also utilise electric drive only during certain low load take-off situations. Our test unit has approximately two tonnes of weight on the back, so most start offs are
automatically programmed to use third gear and the diesel engine.
The Hino N04C-WR four cylinder common-rail injected turbo-diesel engine produces 150hp (110kW) and 470Nm of torque which is delivered in combination with the electric motor from a very low 1000rpm. The AC electric motor is rated at 35kW and 470Nm of torque. With maximum torque available at low rpm, fuel use from the 100-litre diesel tank is minimised. The electric drive motor is directly coupled to the automated manual six-speed transmission.
The six gears and the wide ratio spread enable the engine to spend longer in its most efficient rpm, resulting in maximum driving efficiencies, and the directly coupled electric drive motor results in smooth gearshifts and take-offs. The additional torque from the electric motor allows for earlier shift points than are at first expected. When the hybrid system is delivering drive from both the diesel engine and the electric motor, the power delivery is balanced by the hybrid ECU. The driver can over-ride the gear selection if necessary, but to maximise efficiency it’s best left to the vehicle to determine its up and down shift points, even if they occasionally seem a little early and slow to the uninitiated. The ECU’s remit is to maximise efficiency, so we are not ones to argue with its decisions.
The 4.1: rear axle ratio means the engine is revving at 2,050rpm at 100 km/hr. A fundamental key of the Hino Hybrid is that it doesn’t require external charging as the batteries are charged through the capture of kinetic energy via the regenerative braking system. The process also acts as an effective auxiliary brake and slows the vehicle as the electricity is transferred and stored in the battery to be used on the next take off and/or acceleration.
The Hino 300 Series Hybrid was the first and currently the only Japanesemanufactured light-duty truck in Australia to meet Euro VI exhaust emissions standards. This is achieved by using a combination of Exhaust Gas
Recirculation (EGR) and Hino Diesel Particulate Active Reduction Filter (DPR) system, combined with the Hino Selective Catalytic Reduction (SCR) system.
As in all Hino 300 Series 4x2 models, the Hybrid models features Hino SmartSafe, Hino’s comprehensive safety package with advanced driverassist technologies which provides an active focus in protecting the life of drivers, passengers and other road users.
Hino SmartSafe includes a Pre-Collision System (PCS) with Autonomous Emergency Braking (AEB), Pedestrian Detection (PD) and Lane Departure Warning System (LDWS).
This is in addition to Vehicle Stability Control (VSC), reverse camera, dual SRS airbags, four-wheel disc brakes, UN ECE R-29 cab strength certified and Easy Start to prevent rolling back on hill starts.
From a driver’s perspective there is little difference between an equivalent conventional diesel model and the Hybrid. We get the same drivers’ suspension seat on inclined seat rails, steering wheel controls for vehicle information and cruise control, a 4.2-inch touch screen and a smart multimedia unit with Wi-Fi connectivity. A version of Hino-Connect, featuring the business intelligence elements, is also available as an accessory for 300 Series customers.
A major advantage of the Hybrid is that customers can improve their fuel efficiency immediately, and it only requires diesel fuel, so there are no special refuelling or operating restrictions — operation is the same as a conventional diesel truck, albeit with reduced operating costs.
The Hino Hybrid is also an ideal solution for customers immediately wanting to reduce their fleet’s CO 2 levels. It also represents a valid stepping stone for many fleets on the road to net zero emissions and provides a real window of opportunity for Hino customers, particularly during the next three to five years.
The Performance-Based Standards Scheme (PBS for short) is having a noticeable influence on the development of the heavy vehicle fleet in Australia. ARTSA Data tracks the number and type of PBS vehicles. The bottom line is that about 18 per cent of new high productivity combinations (roatrains, truck + dog, B-doubles) are involved in PBS applications. The Performance-Based Standard Scheme was conceived by the National (Road) Transport Commission (NRTC, now the NTC) starting in the late1990s and accepted by Australian transport ministers as a national project in 2007. It was integrated into the National Heavy-Vehicle Law in 2014. In the interim PBS vehicles operated under state permits. The idea was to find a path for innovative vehicle designs that had improved productivity and met important safety standards. Compliance with safety standards is critical because transport ministers wanted reassurance that these vehicles would be safe. The context was that heavy vehicles were not popular in metropolitan Australia. On the other hand, improved road transport productivity is an imperative to reduce costs, emissions and staff shortages.
The development of the PBS safety standards took many years. In February 2002 the NRTC and the NZ Land Transport Safety Authority jointly hosted a seminar intended to develop the PBS technical standards. I remember attending the demonstration day held at Mangalore Airport, Victoria at which some lane-change tests were demonstrated
for different vehicle types. At this time the standards were being developed and explained to industry and regulators. The technical standards document that exists on the NHVR website had its origins in July 2007. I was involved in the development of the PBS standard Directional Stability Under Braking. Like all PBS standards, a performance level is specified. This particular standard also has a ‘deemed to comply’ path because advanced braking technology can be assumed to deliver the performance level. The best technical standards have a performance standard to facilitate innovation and a deemed-to-comply path to simplify compliance.
Over time, technologies or designs become known solutions and should be included into
regulations that can ‘normalise’ innovation. Figure 3 shows that tip-truck and tip-trailer combinations make up about 50 per cent of PBS approved vehicle types. Four- and fiveaxle dog trailer combinations can now travel under notice and have been taken out of PBS. Single semi-trailer combinations make up about 15 per cent of PBS applications. Most of these are 20 metres long. PBS can be a conduit for regulation reform because it provides regulators with comfort that the change will be safe.
The Australian PBS scheme has four roadaccess levels: Level 1 – General Access; Level 2 – 26m B-double network; Level 3 – 36.5 Type I roadtrain network; and Level 4 – 53.5 Type II roadtrain network. Level 2 has a sublevel 2A that is for volume and not mass-limited loads.
The following types of PBS combinations are eligible to access the pre-advised design approval process:
• Level 1, 3- or 4-axle truck and 3- or 4-axle dog combinations up to 20m long and 50.5t GCM.
• Level 2, 3- or 4-axle truck and 3- or 4-axle dog combinations up to 20m long and 62t GCM.
• Level 1, prime mover and tri- or quad-axle group semitrailer combinations up to 20m long and 50.5t GCM.
• Level 1, B-doubles fitted with
tandem or tri-axle groups up to 20m long and 505.t GCM.
• Level 2, B-doubles fitted with tandem or tri-axle groups up to 26m long and 68.5t GCM.
• Level 2, A-doubles with single, tandem or tri-axle semitrailers and tandem or tri-axle dollies up to 30m long and 85t GCM.
• Level 3, A-doubles up to 36.5m long and 95.5t GCM.
• Level 2, 3- or 4-axle truck and 5- or 6-axle dog combinations to 26m long and 73t GCM.
The great majority of the approvals are for Level 1 and Level 2 access, which is potentially applicable to the metropolitan main road network. See vehicle types at the various levels here: https://www.nhvr.gov.au/files/2018100923-pbs-vehicle-configurations.pdf
The assessment of route suitability for a PBS application is a substantial task. AustRoads and the Australian Road Research Board did important work to assist road owners to understand PBS and to make permit assessments. Most jurisdictions now have route-level maps on their websites.
The Australian PBS scheme is of international significance. PBS schemes exist in Canada (where the idea started), Scandinavia, New Zealand and South Africa. There are long
combinations running between some countries in Europe that take account of PBS standards. Each of these schemes has developed safety standards and procedures according to local requirements. There is also a local PBS scheme in Western Australia, which does not operate within the NHVR framework. There are significant political challenges to deliver longer vehicles on shared roads in most countries. Notably, the USA has no scheme to liberalise its road-transport logistics sector. The Australian PBS scheme has delivered productivity and safety improvements (one transport company holds 291 vehicle combination approvals). It has also been a spur for local heavy-vehicle innovation and manufacture.
In 2018 the NTC conducted a review in the PBS scheme and suggested some streamlining. One outcome was a greater concentration on pre-approved designs that can be adopted with minimal new simulation required. In a significant reform, the vehicle combinations listed in Table 2 can be approved based on previous approvals, which avoids the need for simulations. Access permits are still required. The following graphs developed by ARTSA Data in conjunction with the NHVR PBS Administration give a snapshot of the achievements of the scheme up to the end of 2021. It does not include approvals in the WA PBS scheme. Figure 4 suggests that the growth in PBS approvals is following an approximate linear path with a growth of 150 pa. In 2021 this amounted to a growth rate of ~ 7 per cent. Figure 5 estimates that the PBS productivity improvements equate to a total of 2.74 billion kilometres not travelled by non-PBS vehicles. The productivity improvements have been achieved with an overall reduction in road crashes of PBS vehicles compared to the conventional fleet of about 60 per cent. The PBS scheme is a success, and it shows how regulatory reform can deliver a win-win for all stakeholders.
Dr Peter Hart, ARTSA-I Life MemberFor those with a long memory, back in late 2015, the then Abbott coalition government announced, with much fanfare, “a whole of government approach” to the introduction of new vehicle emission standards. For heavy vehicles, that was to be ADR80/04, Euro VI and equivalent alternative standards from Japan and the USA. A year later, in late 2016, a draft Regulation Impact Statement (RIS) was released that outlined the health benefits of moving to cleaner vehicles in Australia. Unfortunately, nothing eventuated from that process. The Truck Industry Council (TIC) and its members, continued to lobby government for heavy vehicle noxious emission reform, something that would benefit the health of all Australians. Finally in October 2020, the federal Department of Infrastructure, Transport, Regional Development and Communications released a revised RIS for public information and comment, restarting the process for the adoption of better exhaust emission standards. In my December 2020 Prime Mover column, I called on the Australian Government to act on the recommendations in the RIS and implement ADR80/04. As I explained in that column, the Australian Federal Government has a mandate to align with international regulations wherever practical. This is part of an overarching global harmonisation strategy that is aimed at enabling
trade to be accomplished between our country and international markets, while reducing the time, effort and expense of developing Australian specific laws and rules. This is a two-way street, allowing products from Australia to be exported more efficiently and allowing us to import goods that have been developed to international regulations, rather than to Australian specific laws. The end result is the ability for our exporters to play on the world stage and more choice here for Australian consumers. I also pointed out in that 2020 piece, the environmental, health and safety benefits that would be gained from the implementation of ADR80/04.
The very compelling case detailed in that 2020 ADR80/04 RIS was supported by financial analysis by Bureau of Infrastructure and Transport Research Economics in Canberra, showing that there would be a direct benefit, to the health and wellbeing of the Australian community, of $6,672 million by 2050 if ADR80/04 was adopted by the mid2020s. The majority of health benefits will accrue in metropolitan areas, where the number of people and average level of exposure to noxious emissions from road vehicles is greater. This would have an indirect benefit to governments by reducing pressure on the public health system. Yet even with these findings, the coalition government chose not to act on the Department’s RIS recommendations and cleaner engine emission regulations were not introduced.
Roll on May 2022. A new Labor government was elected and in just five short months, they did what the previous coalition government did not do in their nine years of office. In mid-October 2022 Transport Minister, the Honourable
Catherine King, announced that the Albanese government would mandate ADR80/04, with implementation starting in 2024. This announcement was welcomed by TIC and its members. The benefits for Australia and our population, do not stop with the cleaner air health outcomes, the implementation of ADR80/04 will bring a reduction in new truck CO 2 emissions of approximately five per cent over current ageing regulations. This will be the first of many steps that truck and engine manufacturers, as well as their customers, in the road freight industry will take on our transition to a net zero emission future. These CO2 reductions also amount to operator fuel savings that will be had with new, cleaner engine technologies. Most importantly, Australia would see the introduction of the latest truck safety technologies from leading global markets. Safety systems that are largely unavailable on our current regulation ADR80/03 trucks, with these models being tied to electrical and systems architecture that is over a decade old now.
In 2015 the Truck Industry Council strongly supported the introduction of Euro VI and alternative emission standards from Japan and the USA, for Australia. That TIC position did not waiver over the ensuing seven years. TIC and our members continued to call upon our Federal Government to introduce ADR80/04 and finally that persistence has brought change for the good. This regulatory announcement has been a long time coming.
Tony McMullan CEO, Truck Industry CouncilThe Review of the Inland Rail announced in October by federal Transport Minister Catherine King is a fantastic and much-needed opportunity for a reset on an infrastructure project that can transform how freight is moved on Australia’s eastern seaboard, for the betterment of every mode of transport. When the project was announced, its managers adopted a truly intermodal perspective to its delivery of infrastructure, that by its nature, would involve significant interactions between road and rail freight.
It was a perspective that recognised the project’s capacity to deliver supply chain improvements that would benefit all Australians by providing greater efficiencies for transport operators and the customers and consumers they service. Regrettably, project managers have taken on an adversarial position towards modal value and positioning in recent years, with a narrative that suggests that somehow rail transport is better than road transport, and that the benefit of Inland Rail is its capacity to take trucks off the roads. This went against the original spirit of the project, which was its potential to create productivity improvements through greater choice of transport modes. The project was never created to have an adverse impact on one modality over another, but rather to continue our industry’s push towards greater intermodal connectivity.
Without a doubt, there will be an inevitable modal shift as the project is completed. But the very concept of taking heavy vehicles off the roads is a misnomer, considering the reality of our industry that ships, planes and trains carry freight, but only trucks deliver. The intermodal integration of transport modes is what drives supply chain efficiency, greater reduction of carbon emissions and provides consistency in process, and therein lies the real value and potential of Inland Rail. Ships will still carry freight in and out of Australia, and road freight operators will still be needed to carry that freight to the trains and ultimately onto its final destination. The terminals in the middle of these freight exchanges will need to be able to manage the types and volume of goods the Inland Rail business case predicts to be truly efficient and viable. Yet six years into the project we still have not decided where the Victorian terminal will be located.
The Western Industrial Freight Terminal (WIFT) and the Beveridge Industrial Freight Terminal (BIFT) are currently fighting for recognition, funding and a green light to start building. From a road freight integration perspective, it would seem the best intermodal connectivity will be through the development of the WIFT, whose positioning, connectivity and efficiency would ensure who that supply chain serves will get the best value with the least disruption. Putting the intermodal connectivity aside and referring back to the original business case, the Review presents an opportunity
to revisit key considerations that have been overlooked. For example, the current advertising of the project trumpets a 24hour transit time between Brisbane and Melbourne that will see thousands of tonnes of freight move from road to rail line haul.
Given the parlous state of Australia’s passenger airline industry, a 24-hour rail service will see a surge of enquiries from would-be passengers. Who wouldn’t want to board a non-stop train and travel in comfort through some of the world’s most spectacular countryside, whilst having the capacity to work and rest, and wake refreshed the next morning in Brisbane or Melbourne? Yet the business case makes no reference to revenues that may be gained on a service of this kind, and the project managers have not responded to its question being asked. Other details such as track allocation which, in the rail world, is a big issue, has been omitted from discussion.
The VTA will play a constructive role in the Review as it consults stakeholders on a project that has great potential to transform our national supply chain and create growth amongst all the transport modes. As we approach the end of another year, I’d like to thank Prime Mover readers for their strong interest in, and passion for, our great industry. The VTA wishes you a safe and happy Christmas, and I look forward to engaging with you on these pages in 2023.
Peter Anderson CEO, VTAduring October, 66 more than for the same month last year (+5.0 per cent) and the year-to-date accrual of 11,966 shows an increase of 1,549 units (+14.9 per cent). The rate of almost 1,000 new Heavy Duty trucks per month would possibly have been eclipsed if not for the previously mentioned component supply and labour issues.
Oct-22 % Change YOY
ISUZU 1190 31.0%
HINO 360 -1.1%
FUSO 430 4.1%
commercial vehicles sold in Australia to comply with the Euro VI standard. The new standards will be phased in over 12 months from 1 November 2024.
“These new standards will improve air quality and health outcomes and bring safer and more efficiency trucks into Australia,” said Infrastructure Minister Catherine King. Meantime, the local industry is seeking clarification on some aspects of the previous government’s instant asset tax write-off scheme which was brought in as a part of a broader financial package constructed to stimulate the COVID-affected economy. The current cut-off date of 30 June, 2023 puts extreme pressure on OEMs and body builders already dealing with component and labour shortages and many have order books indicating deliveries well into 2025.
The Labor government has produced its first budget in almost a decade with underlying factors such as inflation expected to peak at 7.75 per cent towards the end of 2022, and GDP growth expected to fall from 3.25 per cent down to 1.5 per cent during 2023 which is getting alarming close to recession territory. The unemployment rate is forecast to rise to 4.5 per cent by mid-2024.
Infrastructure spending will decrease over the next four years but will continue to be relatively high with $120 billion of spending expected over the next ten years. There will be 480,000 fee-free TAFE places over four years to address key skills shortages and an ambitious project to build 1,000,000 “affordable” homes. The infrastructure spend includes $1.5 billion allocated to the Freight Highway Upgrade Program which will include sealing the Tanami Track and upgrade several other significant freight routes in SA and NT, $1 billion for the Outback Way and, importantly, $80 million for Heavy Vehicle Rest Areas.
The year-on-year growth rate of the Australian truck market has slowed slightly according to statistics compiled by the Truck Industry Council, with a growth of 12.1 per cent during October which was down from September’s 13.1 per cent and August’s 13.5 per cent. The highest growth rate achieved so far during 2022 has been 14.7 per cent in March. Unit sales during October were 3,359, taking the year-to-date total to 31,647. The Heavy Duty sector delivered 1,379 new units
KENWORTH 282 6.5%
VOLVO 284 41.6%
MERCEDES-BENZ 122 -23.7%
IVECO 101 -2.9%
UD TRUCKS 123 64.1%
SCANIA 106 -6.0%
MACK 62 33.5%
DAF 79 0.0%
FIAT 70 -13.1%
FREIGHTLINER 37 19.9%
RENAULT 39 82.0%
MAN 7 -9.9%
HYUNDAI 22 16.7%
WESTERN STAR 11 -38.8%
VOLKSWAGEN 6 166.7%
DENNIS EAGLE 23 -35.3%
FORD 2 -71.3%
SEA ELECTRIC 3 N/A
INTERNATIONAL 0 -91.3%
CAB CHASSIS/PRIME 3359 12.1%
M-B VANS 133 -26.0%
RENAULT VANS 41 13.1%
VOLKSWAGEN VANS 153 -21.9%
IVECO VANS 70 4.1%
FORD VANS 7 -68.5%
FIAT VANS 36 -57.1%
VANS 440 -26.7%
TOTAL 3799 5.3%