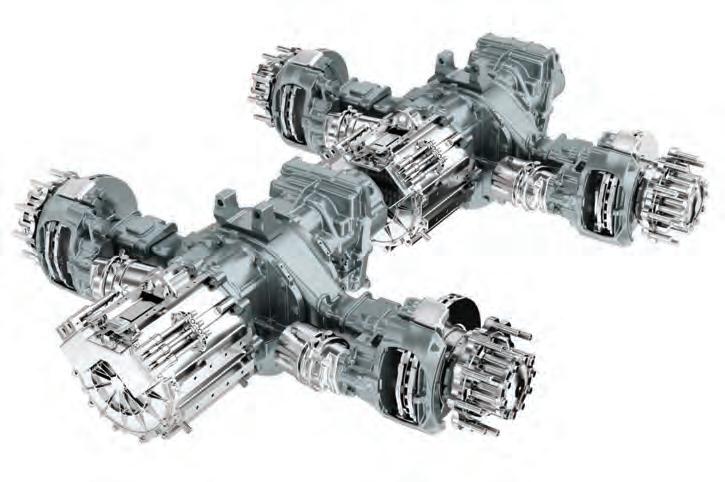
8 minute read
TRANSFERRING POWER FROM DIESEL TO ELECTRIC
TRANSFERRING POWER
FROM DIESEL TO ELECTRIC
The next decade is going to be about moving across to new drivelines, to be compatible with alternative power sources, and a large amount of energy is going to be needed in transferring power from diesel to electric.
The migration across from internal combustion engine (ICE) powered drivelines to those using electric power to drive the wheels is going to happen, whether the preferred power source is hydrogen fuel cells or battery electric, or something else. If technology like hydrogen internal combustion engines take hold they will be able to use adaptations of existing diesel power trains.
There are a lot of different aspects and layout options for an electric driveline and each one will have to be designed to suit a particular task. There may well not be one single solution for electrified trucks in Australia it may well be the case that a variety of systems and layouts will need to be employed.
In recent years Dana has been moving ahead in this space anticipating the growth in demand for electric drivelines. These may not just be in new trucks, operators may seek to repower existing trucks with an electric driveline, as the economic and environmental climate changes. The company has been developing and acquiring the technology to be a major player in this space.
As an indication of the growing interest in this area, Dana has recently opened the company’s largest facility of its kind in Europe in Åmål in Sweden to build electric motors for the vehicle industry, increasing, what it calls, ‘Dana’s ability to deliver clean-energy technologies and fully integrated e-Propulsion systems across all mobility markets.’
Of course, Australia is going to be lagging behind the developments in Europe, but we will be following more advanced countries down this route (Australia is a technology taker). This is a major transition of technologies and the process is going to take a long time as suppliers have to gear up and the industry needs to be aware of the novel technical challenges which will confront it.
AN ELECTRIC DRIVELINE At its simplest the electric driveline consists of some basic components. There is the battery which stores electrical energy, whether it comes from a charging station or an onboard hydrogen fuel cell is immaterial. A DC current goes from the battery to an AC/DC converter to produce an AC supply for the electric motor.
From this electric motor, mechanical power travels down a driveshaft to a transmission. The transmission then processes the original mechanical power and torque into the right kind of torque for the drive axle to propel the truck along the road.
The inclusion of a transmission is not necessarily the case, especially at the smaller end of the truck market. The electric trucks currently on sale in Australia, from SEA and Fuso, do not have a transmission, these are the simplest drivelines with a direct drive from electric motor to rear differential.
Another component supplier, Eaton is already developing transmissions where they are needed for the truck makers.
“We have got some smaller two and four speed transmissions that can go behind electric motors,” says Graeme Weston, Business Unit Manager at Eaton. “We are integrating with electric motors and that’s a growing part of our business. Talking to some of the electric vehicle makers, we are finding it is hard to get the spread of ratios, in order to get the right torque for launch, but you also run the electric motor at a sweet spot, at a higher rpm.
“Essentially you can downsize the motor, so you can get the torque multiplication for launch, with the advantage of going to a two-speed option, as opposed to a single speed, being that you can run a smaller electric motor. You can still get the torque, but then finely tune the other gear to get the most out of the rpm the motor runs at.”
This is why the two-speed transmission
The Dana_Zero-8_Tandem eAxle.
Simple Electric Vehicle Driveline
SERIES OF POWER CONVERSIONS
has been used quite often in electric trucks, one ratio generates enough torque to take off and the other ratio lets the electric motor run around its most efficient rpm.
NEW DRIVELINE OPTIONS The basic electric driveline layout will often mimic the diesel driveline, simply replacing one component with another. However, because this power can be transmitted as electrical energy and not just as mechanical energy, different options become available.
One option which was evident at the Brisbane Truck Show last year was the e-Axle. This uses an axle mounted component to handle several of the driveline tasks. The power comes from the battery, though the inverter to an axle mounted assembly which is electric motor, transmission and differential all in one piece.
This substantially reduces driveline complexity and reduces packaging requirements. The complete unit on the axe does not take up much more space than the current differentials in a traditional driveline.
A more radical approach again is the introduction of the e-Hub. In this case, the power from the battery will go through one inverter for each drive wheel. That AC output goes to a large assembly at the wheel hub, which includes an electric motor, a transmission and wheel hub.
Again, this design has a benefit in packaging. The only components attached to the chassis are batteries and inverters, the rest are mounted at the wheel itself. At this point the driveline looks completely different to the traditional layout.
As a way of comparing the two drivelines Dana look at the figures around an electric drive system, the Dana TM4 SUMO LD HV1200 electric motor up against a Cummins 6.7-litre truck engine. The diesel puts out 1152Nm (850 ft lb) of torque while the TM4 produces 1200Nm (850 ft lb). Power from the Cummins is 375hp (276kW) while the TM4 produces 272hp (200kW). The mass of that Cummins is 480 kg, while the inverter weighs 12kg and the motor 87kg, a total of 99kg. This is a substantial difference of 381kg.
The other components to compare are fuel tanks to batteries. This is more difficult to ascertain. We know how heavy a diesel tank to get the truck 500km will be and a matching battery may well be able to keep driveline mass in the same ballpark. However, battery technology is progressing very fast, and we know that a battery to get an electric truck 500km will be lighter next year than it is this year.
While the diesel flows from the tanks for the ICE, the battery array on a truck needs a battery management system to control charge. Fuel lines are replaced by the bright orange cabling we see prominently on electric trucks.
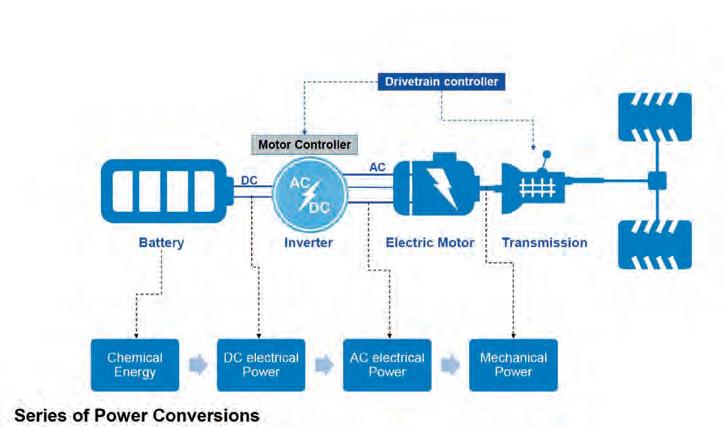
CENTRAL DIRECT DRIVE SYSTEM
The electric motor powers the driveshaft and axle to propel the vehicle.
E-MOTOR / INVERTER CENTRAL GEARED SYSTEM
The electric motor attaches to a gearbox which then powers the driveshaft and axle.
E-MOTOR / INVERTER
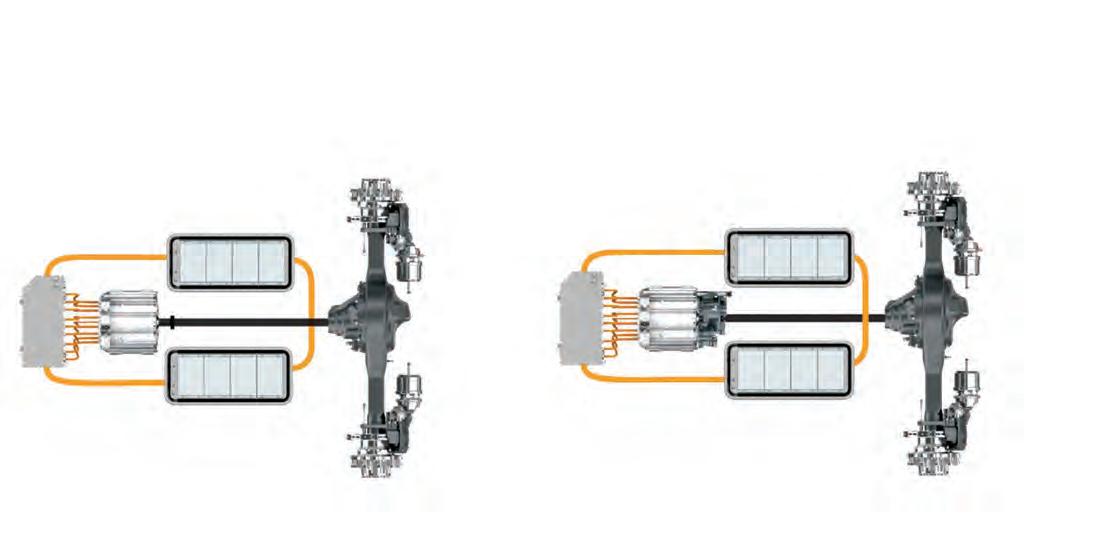
E-AXLE
The motor is engineered to fit within the gearbox or axle, further reducing driveline complexity. Available options: • Independent E-MOTOR • Rigid
BATTERY INVERTER E-HUB
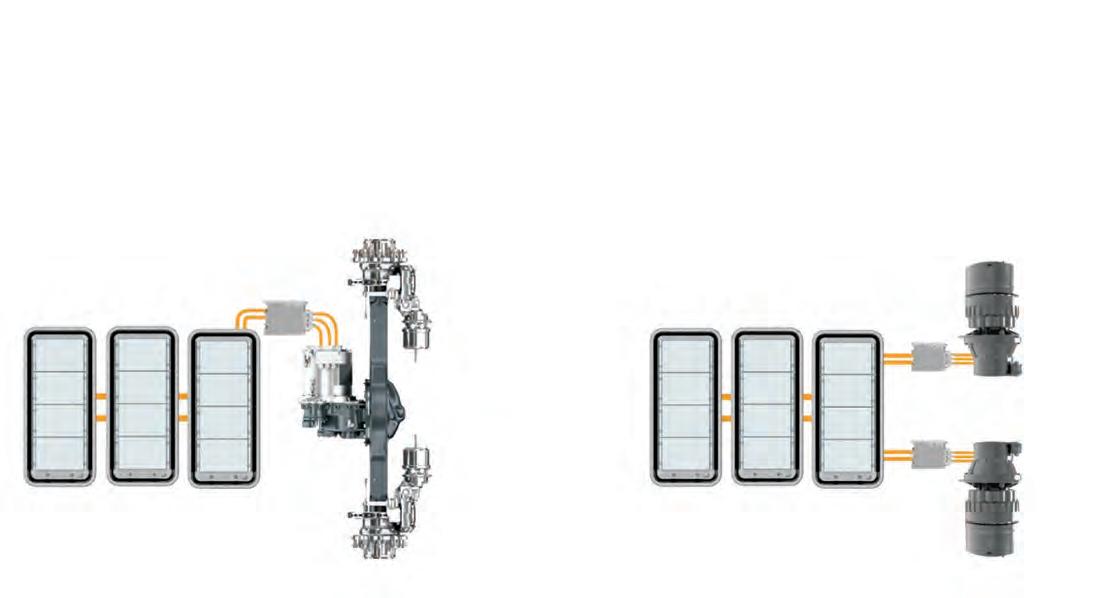
The motor is engineered to fit within the hub of the wheel, further reducing driveline complexity and packaging space.
BATTERY INVERTER
E-MOTOR
GEARBOX INVERTER
The high voltage cables have to meet ISO6469 (hence the orange colour), so truck manufacturers have to ensure the correct shielding, insulation and keep outside the maximum bending radius rules when routing the supply. These requirement do add substantial cost to the electric truck’s power system. Layouts using e-Hubs and e-Axles can reduce that cost, as much of the cabling is already enclosed.
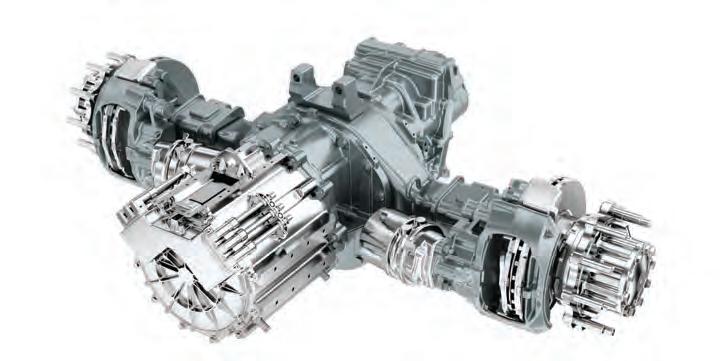
POWERING THE PERIPHERALS The basic principles explained above only make the wheels turn and get the truck moving. There are many more systems needed on a truck to keep it safe and cool. These will have to change and new systems will need to be added to the componentry on a truck.
The ICE uses an engine control unit to control the engine to provide the torque requested by driver inputs. Those driver inputs to the motor control unit simply get the same torque from the electric motor. While the ICE needs an alternator to power the accessories on the truck, the electric truck’s converts voltage from the 400plus volt power battery to a typical 12- or 24-volt circuit.
Where the steering pump is powered mechanically by the ICE, the steering pump on an electric vehicle uses a small electric motor. The ICE’s mechanically driven air conditioning compressor is replaced by an electric compressor on the electric truck.
When it comes to the truck’s air compressor, the mechanical power on the ICE is replaced by an electric induction motor. Both power systems need cooling and a water pump. For the ICE it is again driven by the engine, while an inverter produces AC for an electric pump.
Surprisingly both types of truck need a run-of-the-mill 12 or 24 volt battery. On the ICE it is for cranking the engine, electronic controllers and accessories, but on the electric truck it is only needed for the electronic controllers and accessories.
Where the ICE truck needs a heavy and expensive after-treatment system to meet exhaust emissions rules, the electric truck produces zero emissions. However, on the flip side the electric truck does need a dedicated charging system, a power distribution unit, a brake resistor to enable regenerative braking when the battery is fully charged and an inverter for accessories needing an AC supply.
As it turns out, it is not as simple as ripping out the old diesel engine and slotting in an electric motor. However, this is the way we are going to have to think about trucks and their drivelines in the future.