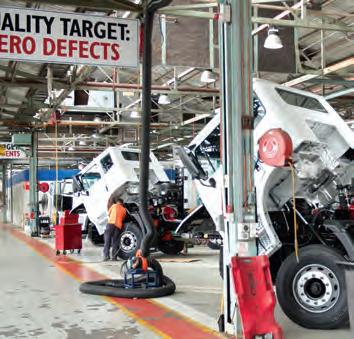
48 minute read
NEWS AND VIEWS
As part of a global transformation process, Iveco has announced the development of a Customisation & Innovation Centre (CIC) and this means Iveco truck full manufacturing in Australia is to end.
In announcing the development of the CIC, the company also advised it would move to fully import its Heavy Duty range from Iveco’s manufacturing facility in Madrid, Spain. This transition is anticipated to take place from the end of June 2022.
Iveco currently fully imports its Light Duty, Medium Duty, selected Heavy Duty, Minibus and Off-Road models. As an example, the first cab off the rank will probably be the new S-WAY model, which will arrive next year and launch in Australia according to the global launch plan.
Iveco states that the decision to fully import its Heavy Duty range will allow the operation in Australia to more closely align model year introduction timings with that of its parent company in Europe.
The fully imported dual control Acco model for the local waste market will be part of this new process arriving here as a built up truck and will be customised at the CIC to ensure its compatibility with the needs of the waste industry in Australia.
The arrival of the new S-WAY model for the Australian and New Zealand market will probably herald the end of full truck manufacturing at the Dandenong plant for Iveco. This will mark the end of a long history, dating back to 1952 of full truck manufacturing taking place at the Dandenong facility.
“Historically, our most unique value proposition has been our ability to customise and specialise vehicles for our market, leveraging the expertise of our local engineering team and the local facility,” said Michael May, Managing Director Iveco Australia and New Zealand. “By further enhancing this service, we believe there is considerable potential to provide additional value to existing and prospective customers, while growing the CIC’s capacity and scope of work.
“Given our brand’s long history of manufacturing in Australia, this next step towards customisation strengthens our ability to remain agile and responsive to demanding regional requirements. This move will also ensure that we are in a position to offer the market the very latest in Iveco performance, comfort and safety innovation, in the most timely fashion, and at the same time, capitalise on our design and validation engineering expertise and customisation capabilities.”
Iveco stated that it will continue to engage with its employees who may be impacted by this announcement, and will provide appropriate support to the involved workforce.
INTERNATIONAL TRUCK OF THE YEAR DOUBLE
DAF has achieved an International Truck of the Year double, scooping both the ‘Truck of the Year 2022’ gong and the ‘2022 Truck Innovation Award’. The prestigious award was handed over to Harry Wolters, President of DAF Trucks.
With a winning score of 150 votes, the Dutch long-haul heavy-duty truck range fought off the challenge posed by Iveco’s recently-launched T-Way construction series and Mercedes-Benz’s batteryelectric eActros (second generation).
Taking full advantage of the EU’s new mass and dimension regulations, DAF has created a truck range that dramatically improves aerodynamics, fuel efficiency, active and passive safety, and comfort for the driver.
During extended test drives in Spain and central Europe, the IToY jury members appreciated the excellent visibility provided by a large, curved windscreen, side windows with low beltlines and the kerb-view window. These features, along with the digital vision system that replaces the traditional rear mirrors and the new corner view camera, offer excellent all-around visibility, protecting vulnerable road users.
The IToY journalists also praised the performance of the new highly efficient powertrains, based on the Paccar MX-11 and MX-13 engines, coupled with TraXon automated gearbox, and the advanced features of predictive cruise control with extended Eco-roll functionalities.
“With the introduction of the New Generation, DAF has delivered a hightech heavy-duty truck range that sets a new benchmark in the truck industry,” said Gianenrico Griffini, International Truck of the Year Chairman. “In addition, it is future-oriented, as it also represents a complete platform for new generations of alternative drivelines”.
Read driving impressions of the winner of the 2022 Truck Innovation Award from PowerTorque’s European Correspondent, Will Shiers, on page 66 of this issue.

The announcement of re-opened applications for projects under the Heavy Vehicle Safety and Productivity Program and the Bridges Renewal Program will mean increased infrastructure spending to improve truck productivity.
NatRoad welcomed the Federal Government’s announcement of the $250 million committed to the Bridges Renewal Program (BRP) and the Heavy Vehicle Safety and Productivity Program (HVSPP) programs, saying it needed to be applied swiftly.
“Our roads and bridges are the arteries of our road freight system so continually renewing and upgrading them is essential in a country ruled by distance,” said Warren Clark, NatRoad CEO. “Time and time again, we’ve seen situations where one bridge with an inferior weight tolerance compared to others on a road freight route acts as a bottleneck on productivity.
“Funding an upgrade strategically can make the freight task so much more efficient. The better we can assess and classify road freight routes to reflect their capabilities and weaknesses, the easier it is to make them safer and more productive.”
David Smith, Australian Trucking Association Chair said the announcement would result in more rest areas and better road access for safer and more productive trucks.
“Truck drivers need rest areas so they can take safety breaks and meet their compliance obligations. But there just aren’t enough rest areas on the road system,” said David. “As far as the trucking industry is concerned, every new rest area on the roads is a win.
“The rest areas funded under the heavy vehicle safety program should be required to meet the Austroads rest area guidelines. Austroads developed these guidelines in consultation with the industry. They set out the facilities that drivers should be able to expect at rest areas as a basic right.
“It is also essential that bridge and productivity upgrades be matched by automatic access for the appropriate class of truck. When a bridge or road is upgraded under these programs, the local council should be required to add them to the defined network and not require trucking businesses to lodge expensive and time consuming permit applications.
“The Australian Government has every right to insist on this as a requirement – particularly since it is now going to fund up to 80 per cent of the cost of upgrade projects in rural and regional areas.”
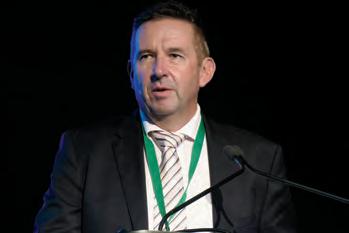
Warren Clark, NatRoad CEO.`
ELECTRIC TRUCK IS GOING INTO THE WOOLWORTHS FLEET
Linfox announced that its first refrigerated electric truck has gone into the Woolworths fleet delivering fresh produce to stores in metropolitan Melbourne.
The Volvo FL Electric will transport fresh produce daily from the Melbourne fresh food distribution centre operated by the Woolworths Group’s supply chain arm, Primary Connect.
Just one of two Volvo FL Electrics in Australia and 75 released globally, it is the only Volvo FL electric vehicle in Australia to be fitted with refrigeration. The jointly branded vehicle can deliver up to 8 pallets of produce to Woolworths supermarkets at a time.
The Electric FL utilises four batteries to achieve an energy capacity of 200 kWh, however, future iterations will feature a capacity of 265kWh, such is the pace of battery development. The electric driveline provides 425Nm of torque which is delivered to the rear wheels via a 2-speed I-shift automated transmission.
“From the products in our supermarkets to the trucks that deliver them, we know the changes we make to become more sustainable today will create a better tomorrow for generations to come,” said Chris Brooks, Acting Managing Director of Primary Connect and Chief Supply Chain Officer of Woolworths Group. “Linfox has been with us on our journey of electric vehicles since 2018 and we share a commitment to sustainability.
“We’re excited to deepen our investment in electric vehicles in partnership with Linfox, as we pave the way for a greener next-generation supply chain. We supply more than 1,000 supermarkets across the country, and the ongoing development of heavy electric trucks represents an opportunity for us to drive positive change on Australia’s roads.
“We will be watching the results of this trial closely with Linfox to understand how electric trucks can support our shift to a low carbon future in the years ahead.”
A charging station at the Melbourne Fresh DC will charge the battery while deliveries are unloaded. The EV can travel up to 200km before needing to be recharged and takes nine hours to fully recharge.

An announcement of structural changes at the top has confirmed Scania as the lead brand in the global Traton Group. As a result of the changes, Christian Levin takes on a changed role which merges his current role as President and CEO of Scania with the role as President and CEO of Traton.
Traton CEO Matthias Gründler and CFO Christian Schulz are leaving the company forthwith. As well as Christian Levin’s appointment, Annette Danielski, currently Head of Corporate Finance at Traton, will become the new CFO.
“I am honoured to take on the role as CEO of the Traton Group while continuing on as CEO of Scania,” said Christian Levin. “Looking ahead, focus will be on transforming business into new technology areas and geographies, whilst leveraging further synergies through modularisation and scalability.
“The evolution of the Traton Group continues and builds on the Traton strategy which the current management team established and which is now pushed into a different gear. The strategy includes a stronger focus on sustainability not the least through e-mobility, digitalisation and connectivity; continued integration of Navistar and growth in the North American market, as well as continued investments in China over the next few years. This change will comprise of several steps over time and by the end of the year a fuller plan will be presented.”
On this next step of the Traton journey, the strength, competence and business logic in each brand in the group, MAN, Navistar, Scania and Volkswagen Caminões e Ônibus, will continue to be leveraged.
“I see Christian Levin as a strong leader to execute on the next chapter for the group,” said Hans Dieter Pötsch, Chairman of the Traton Supervisory Board. “He has my full support to lead the journey towards stronger profitability and growth. Christian Levin and Annette Danielski will consequently implement the jointly developed new Traton strategy.”
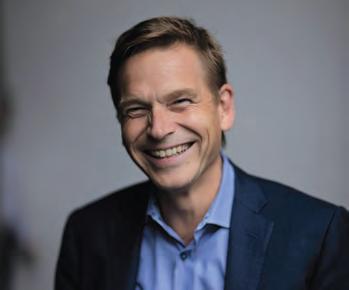
Christian Levin, Scania President and CEO.
FUTURE STRATEGY FOR INDUSTRY REGULATION
1. LEFT HAND PAGE

Delivering truly borderless operations and increasing flexibility for safe operators is outlined in the National Heavy Vehicle Regulator’s future strategy for industry regulation, Strategic Directions 2021-2026.
The NHVR’s long term strategy talks about the regulator pursuing ambitious and relevant industry reform to the Heavy Vehicle National Law, currently under the spotlight.
It also emphasises a number of imperatives: • “Borderless operations are essential to the NHVR’s risk-based regulation approach, which targets those operators and supply chains that put safety on our roads at high risk. It also aims to create positive behavioural change through innovative regulatory approaches for the majority of operators who want to do the right thing. • “Heavy vehicle compliance is consistent, data led and risk based, with a focus on regulatory action towards operators and supply chain parties
MAKES COMPLETE COMMERCIAL SENSE
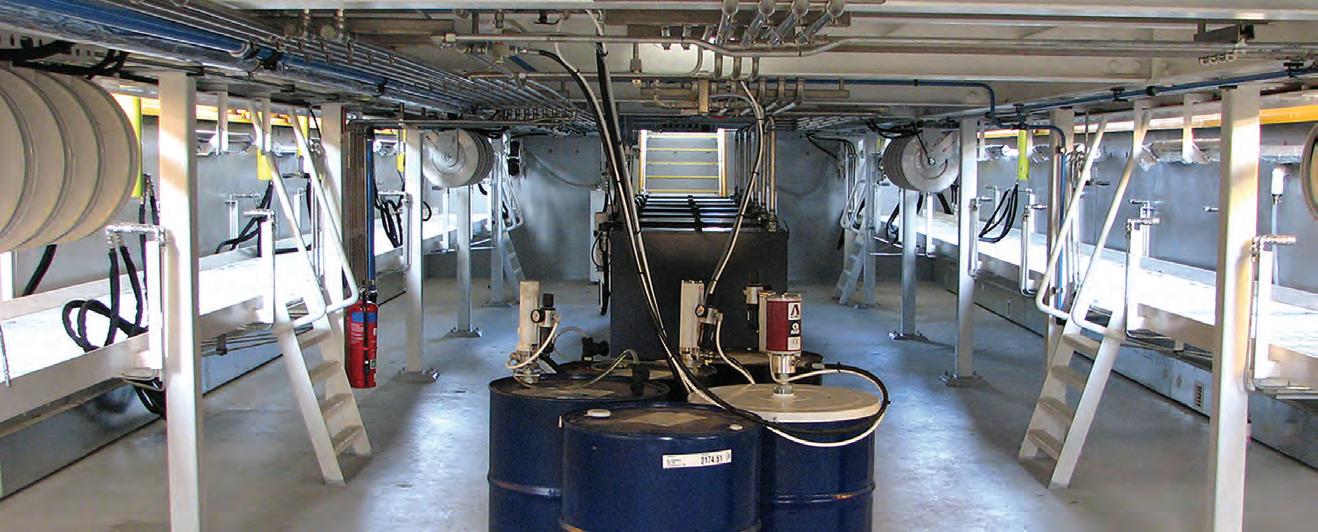
who pose the greatest safety risk to road users. • “Deliver an appropriate compliance response that includes education to ensure positive behavioural change. • “Focus on investigating primary duty offences and holding to account parties most responsible for the safety risk. • “Encourage broad industry uptake of safety management systems scalable to the size and complexity of a business.” • Duncan Gay, NHVR Chair says the regulator has learnt a lot over the last five years, like the importance of driver physical and mental wellbeing and its impacts on road safety, and increased its capability to share safety insights with industry to collectively pursue better outcomes. • “We are also going back to basics to develop a national understanding of freight infrastructure, ensuring
consistent assessments that open up productive networks which are critical to the success of our road transport task,” said Duncan. • “Transitioning operations from New
South Wales and Queensland will provide consistent regulation right across the eastern part of the country, ensuring industry experience and the same on-road interactions regardless of where people are working.”
THE NEW BIBLE FOR INSPECTORS
The latest release from the National Heavy Vehicle Regulator has come into force, the new edition of the National Heavy Vehicle Inspection Manual.
The NHVIM Version 3.0 is the reference point used when inspecting vehicles for NHVR officers. The manual provides authorised officers and industry with consistent criteria for heavy vehicle inspections.
The NHVIM was introduced by the NHVR) as part of its task to develop and introduce a single national approach to ensuring heavy vehicle roadworthiness. The NHVIM applies to all vehicles that have a gross vehicle mass over 4.5 tonnes.
The idea behind the NHVIM is to provide authorised officers (including safety compliance officers and police), approved vehicle examiners (AVEs) and other vehicle inspectors with a nationally consistent set of failure criteria to be applied when conducting a heavy vehicle inspection. It also provides vehicle operators with an easy to follow set of requirements to know when a vehicle is considered defective.
When using the NHVIM, the NHVR applies a number of basic principles, including the fact that equipment required by the Vehicle Standards or ADRs must be present and work properly: • Equipment that is essential for compulsory components to function, the safe operation of a vehicle, or the control of its emissions, must be kept in good condition. • Equipment that is not required by the
Vehicle Standards and has no direct effect on the vehicle’s safe operation or the control of its emissions does not have to function, as long as it does not interfere with compulsory equipment that is required. • Manufacturers’ recommendations relevant to the safety of particular vehicle parts or to the control of emissions must be considered. • Test methods or other conditions have not been specified except where they are necessary to determine whether criteria are met. • Examiners will utilise their qualifications and experience in vehicle repairs and maintenance and refer to any relevant information
regarding vehicle manufacturer’s specifications to ensure that the vehicle meets the requirements of the Vehicle Standards or ADRs. • Relevant ADRs are noted at the beginning of each section of the NHVIM. Some of the ADRs may have been repealed or updated since publication of the NHVIM, however, depending on the age of the vehicle being inspected, the ADR or aspects of the ADR may still be applicable. • All relevant documents should be consulted for a complete list of the 1. RIGHT HAND PAGE requirements.

Complete Workshop Fitouts
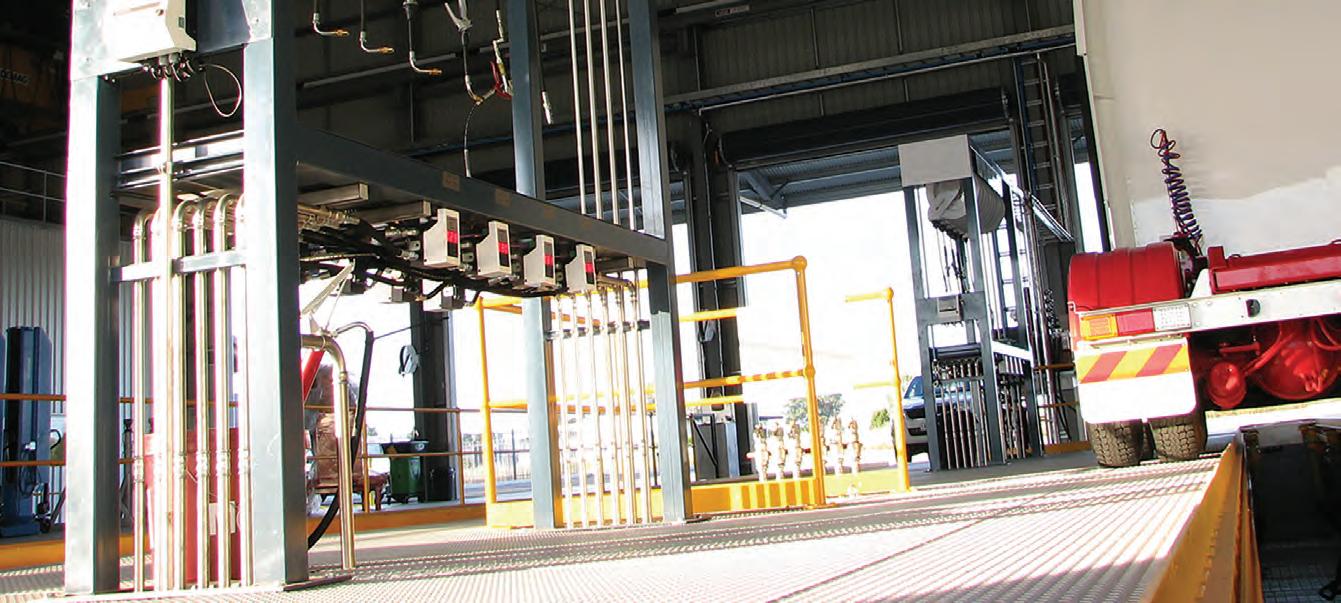
IMMEDIATE ACCESS TO RELEVANT PBS NETWORKS
A notice released by the National Heavy Vehicle Regulator will provide eligible Tier 1 Performance Based Standards (PBS) vehicles immediate access to relevant PBS networks across Australia to operate on approved networks without the need of a permit as soon as a Vehicle Approval is issued, although this may be at a restricted mass.
The new ‘National Class 2 Performance Based Standards (Tier 1) Authorisation Notice 2021 notice’ delivered by the NHVR will give eligible Performance Based Standards (PBS) vehicles immediate network access when they receive a vehicle approval with a Tier 1 bridge assessment.
South Australia’s Minister for Infrastructure and Transport Corey Wingard said all PBS vehicles must pass various safety and infrastructure standards, such as acceleration capability, turning space, pavement wear, and mass and dimension limits.
“Previously operators of these approved PBS combinations would have to apply for a permit after receiving their vehicle approval,” said the Minister. “This National Class 2 Performance Based Standards (Tier 1) Authorisation Notice 2021 eliminates the requirement of a permit application and allows operators automatic access to approved networks.
“This is another example of governments and the regulator reducing red tape and providing increased access for the heavy vehicle industry, which has continued to keep Australia moving during the pandemic.”
NHVR CEO Sal Petroccitto said the Notice establishes a platform to provide operators with guaranteed PBS access before they build their vehicle.
“Operators have told us that knowing they have immediate network access would be a big factor in deciding whether to invest in a PBS vehicle or expand their PBS fleet,” said Sal. “It will certainly encourage the take-up of these smarter, safer and more-productive PBS vehicles in the Australian heavy vehicle fleet.
“We will continue to build on this Notice by starting to roll out a higher productivity PBS notice later this year.”
The National Class 2 Performance Based Standards (Tier 1) Authorisation Notice 2021 applies in South Australia, the Australian Capital Territory, New South Wales, Tasmania and Victoria.
Each network, as shown in the Notice’s jurisdictional schedules, has a maximum mass cap and a specified length limit for eligible vehicles.
Operators must ensure they check their vehicle approvals against the conditions of this Notice.

MASSIVE ORDER FOR SEA OF OVER 1,000 TRUCKS
Australian electric truck maker, SEA Electric, has taken a significant step forward in the USA, with a massive order for SEA of over 1,000 trucks. The oder is for SEA Hino M5 EVs and is the single largest order in the company’s history.
The new truck are to be delivered to GATR EV and will feature the patented SEA-Drive Power System, a system which is adaptable to most OEM truck glider chassis platforms.
Now headquartered in Los Angeles, SEA Electric has been making waves in the North American market over the past 18 months, establishing a nationwide network of technology partners, plus collaborations with leading OEMs.
The SEA M5 EV model features an SEADrive 120a Power System, and is specified for truck platforms with a GVM of 6000kgs to over 8,000kg. The package features a 1500Nm electric motor, in combination with a 138 kWh battery pack.
“This deal is the culmination of years of research, development and growth, and proves that SEA Electric is on track to be number one when it comes to electrifying fleets across the world,” said Mike Menyhart, SEA Electric President, Americas and Chief Strategy Officer. “The market is looking for a proven EV solution, and with SEA Electric, we bring that to the industry technology which has been verified with millions of miles of real-world use.
“Furthermore, this announcement reaffirms our commitment to continue our rapid expansion within the North American market, and sets the scene for an exciting 2022.”
For SEA Electric, the milestone far exceeds the previous benchmark order for the company.
“This is our first four-digit order, and it comes in a non-incentive state, which proves that commercial EV solutions can expand in areas with no incentives, while all corners of the market are seeking premium EV solutions,” said Nick Casas, SEA Electric Vice President of Sales and Marketing. “GATR should be congratulated for being at the forefront of EV supply and being capable of servicing the needs of large fleets immediately.
“GATR has a partnership with Merchants Fleet, which will benefit the end-user, who will not only be able to access an electric solution straight away, but will be able to transact with one of the most respected leasing companies in the USA.”
Merchants Fleet has committed more than $2.65 billion toward having 50 per cent of its mobility fleet electric by 2025 and 50 per cent of its clients’ fleet electric by 2030. The company has also launched an innovativeAdopt EV program,designed to help guidebusinesses through each step of the fleet electrification process, from assessing needs, to purchasing the right vehicles,to charging options and infrastructure support.
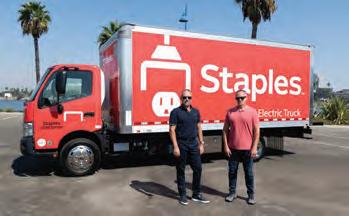
B-DOUBLE TRAILER SET COMMEMORATING TRUCK DRIVERS
Sarena Nolan, Darren Nolan, Daphne Nolan, Flea Nolan and Sandy Nolan in front of the new b-double fridge van set commemorating the Lights on The Hill memorial.
Nolan’s Interstate Transport and Volvo Group Australia revealed a B-double trailer set commemorating truck drivers in the lead up to the Lights On The Hill memorial event. The B-double set is designed with artwork paying tribute to those who have lost their lives in transport accidents.
Sponsored by Volvo Commercial Vehicles Australia the new refrigerated units acknowledge the ‘Lights On The Hill’ memorial in Gatton and the sacrifices made by drivers and their families while keeping the wheels of the Australian industry turning.
Located an hour west of Brisbane’s CBD, the Gatton Memorial in the heart of the Lockyer Valley, is updated each year
and is marked with a two-day convoy featuring drivers and vehicles from the local area’s transport companies. As a pillar of the Gatton community for over half a century, the Nolan family is intrinsically linked with The Lights on the Hill Memorial, participating every year and offering support in numerous ways. As the Memorial has grown, so too has the Nolans’ involvement. “It’s important to be with the drivers and wives who have lost loved ones and friends in the industry,” said Flea (Adrian) Nolan, Director Nolan’s Interstate Transport. “To be involved is a particular passion of mine and it is great to see the event and the recognition it gets grow every year.” The sponsorship by VCV Australia includes supporting the design and branding of the trailers, which in this Power Torque Ad 3-Final2.pdf 3 26-Jul-21 3:26:04 PM case features a mural of the memorial wall in Lake Apex Park.

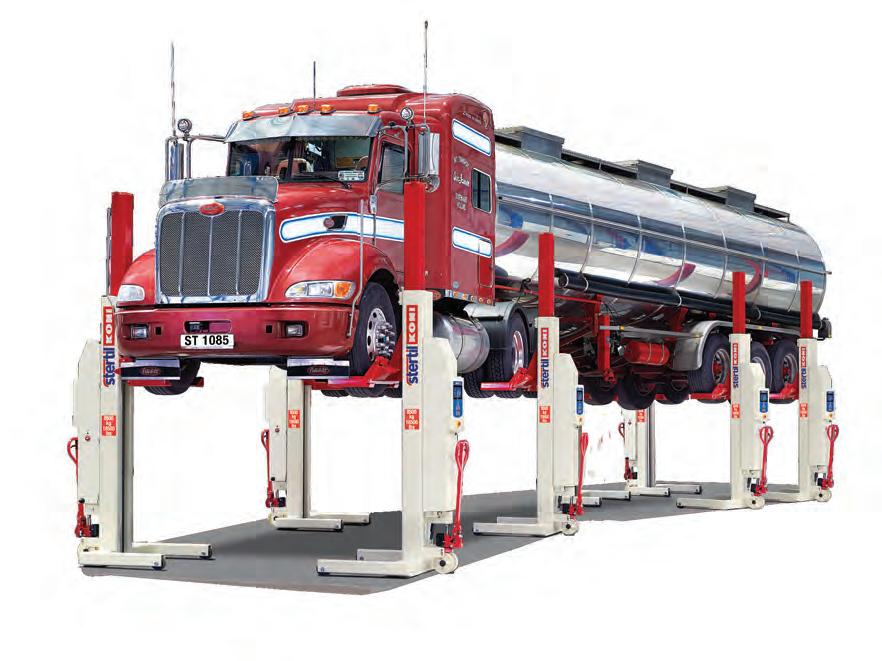



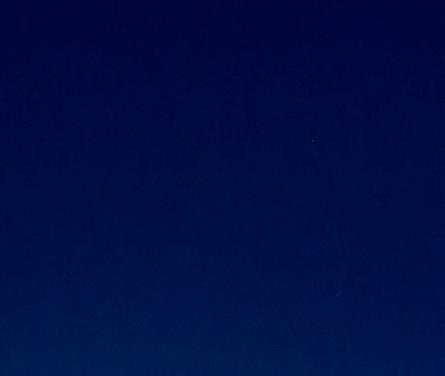
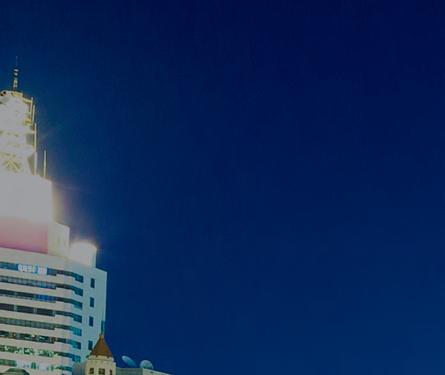

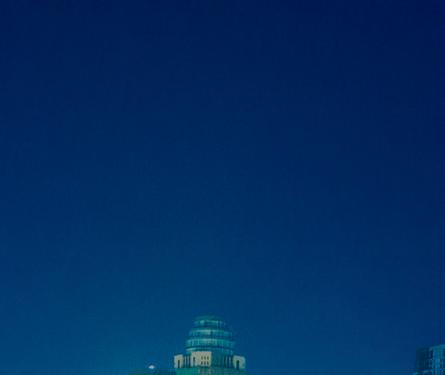
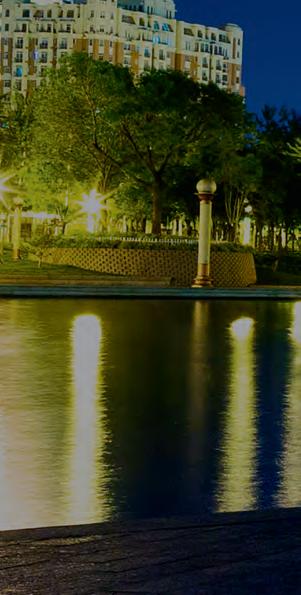
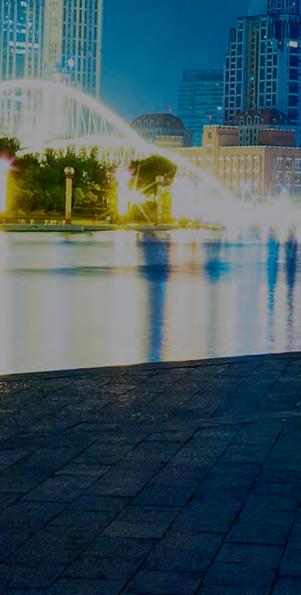

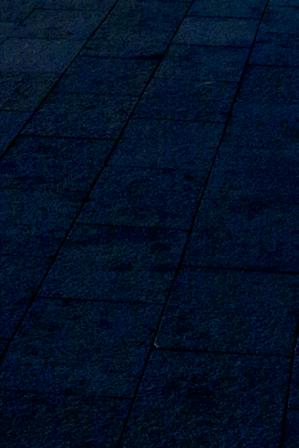
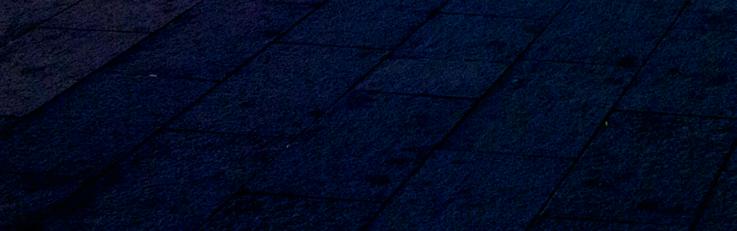
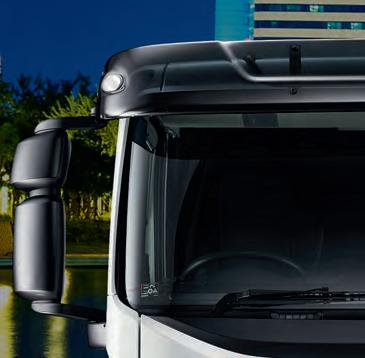
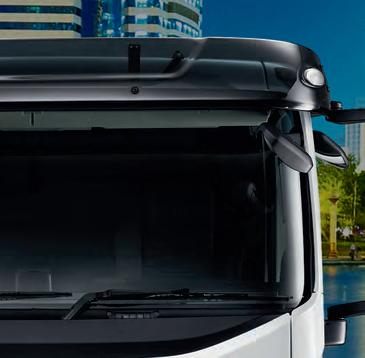
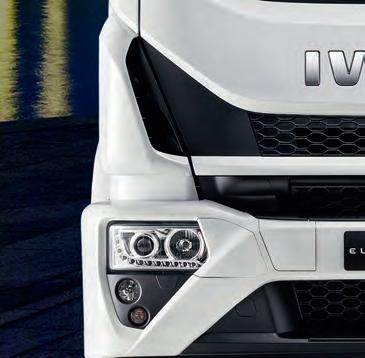
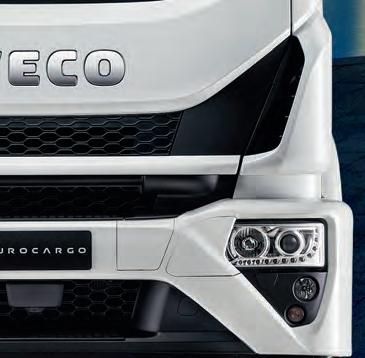


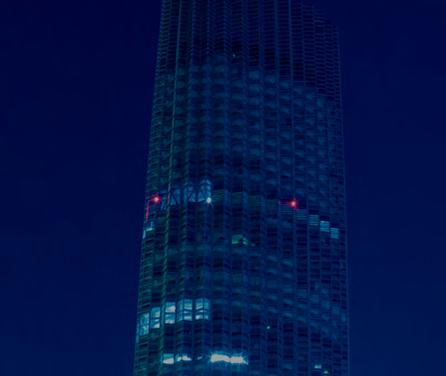

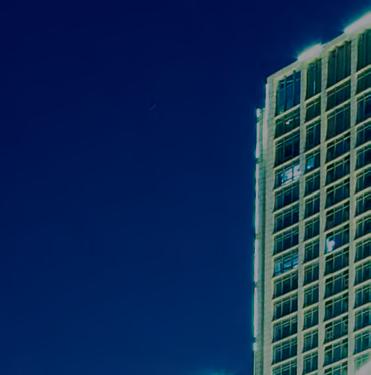
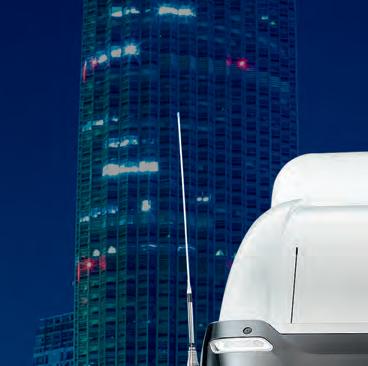
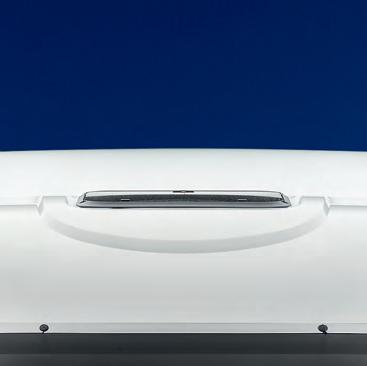
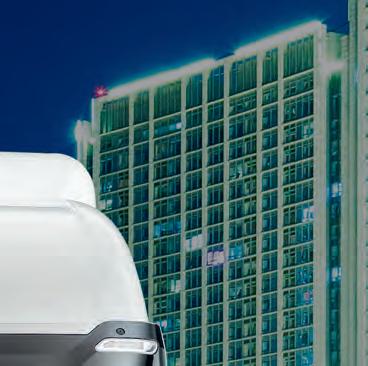


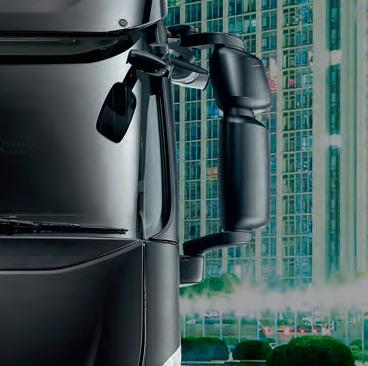
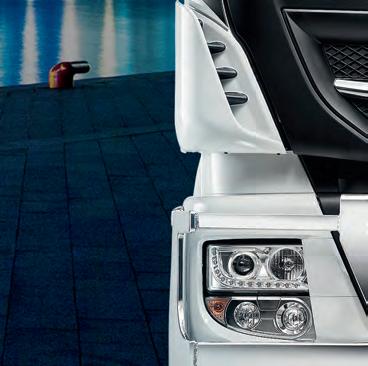
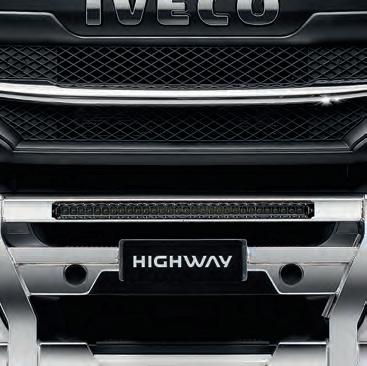

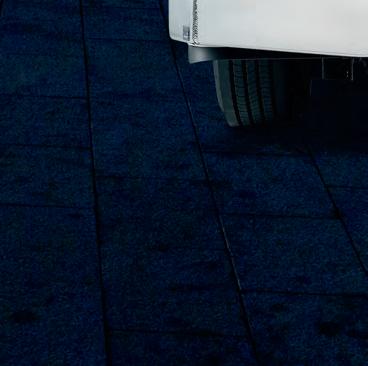
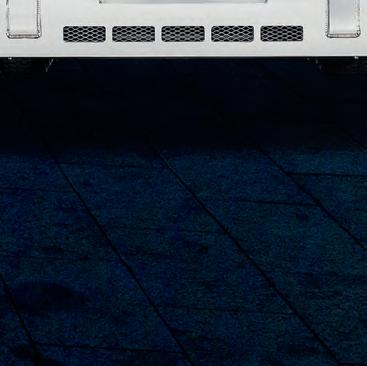
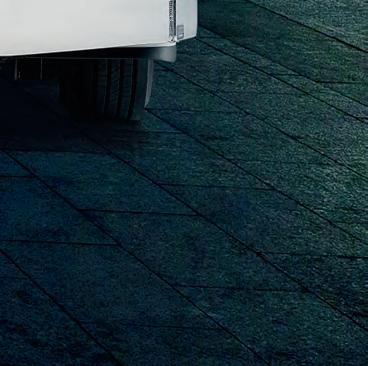


HEAVY HINO HAULING
What we expect from a heavy duty truck is changing fast, and truck makers need to keep up with the times. Hino has come up with a model which is precisely tailored to this decade’s Australian heavy market preferences.
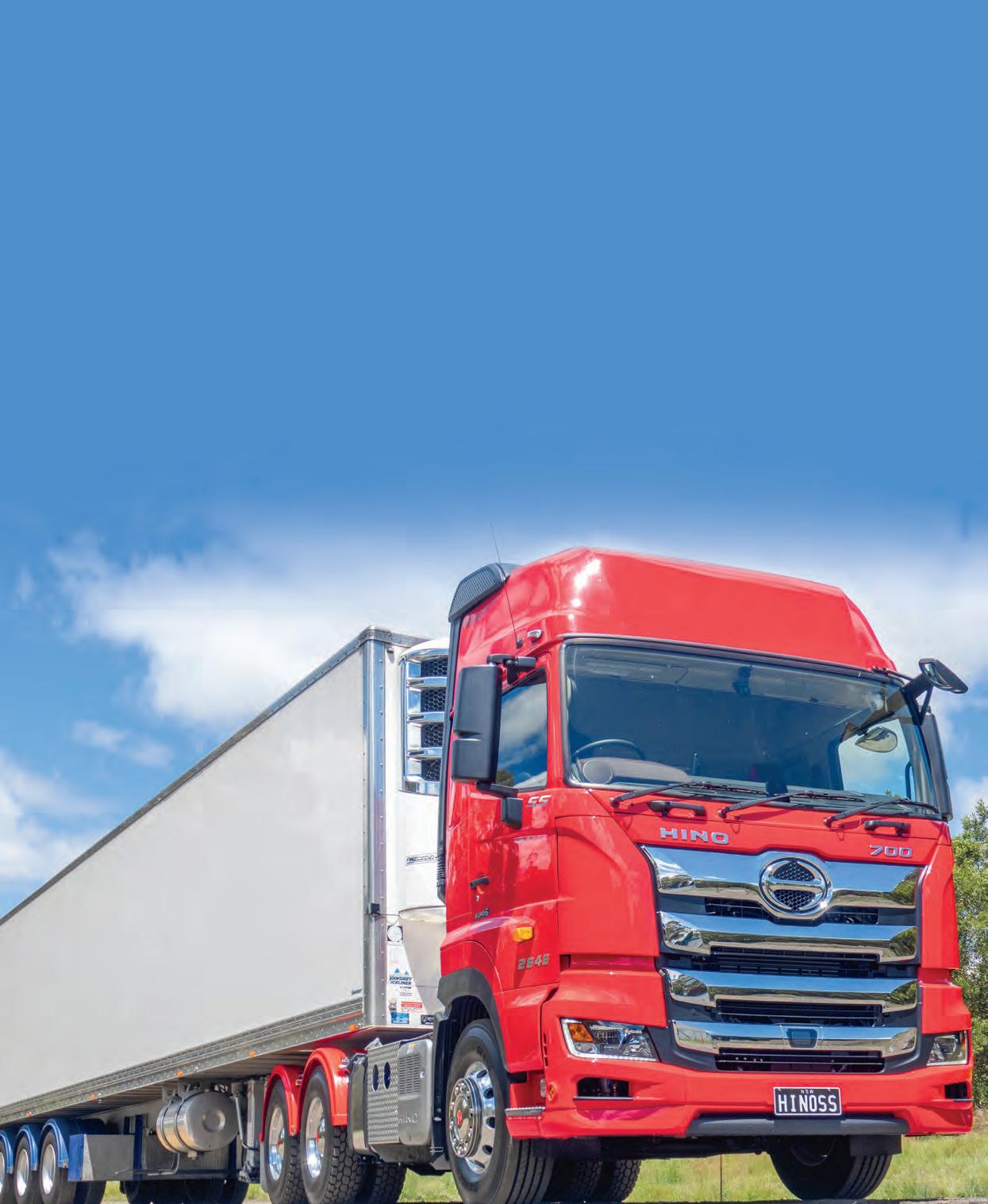
Traditionally, the Japanese truck makers have been well behind both the North American and European truck makers in the heavy duty market. However, over the past ten years the Japanese truck makers have made inroads into different sectors of the heavy duty market. The specifications on offer have moved slowly but steadily towards those on offer from elsewhere.
Now, Hino have come up with an all-new 700 Series range, which has extended the overall range and now includes all of the state-of-the-art electronic sophistication you can throw a stick at. Apart from a full safety suite, there is now a new engine available, at nine litres, and a much improved transmission, a genuine 8x4, plus a refresh of the overall look and feel of the 700 Series.
PowerTorque took two examples of the new Hino models out on the road to get some perspective on the new models and to test their mettle. We took the nine litre around Brisbane and up the Toowoomba Range, then tested the 13-litre hauling a fully loaded semi up the gruelling climb of Cunningham’s Gap.
THE HINO 8X4 It has been a long time coming, but the Australian truck market now has a Hino 8x4 with a load sharing suspension, which will enable the model to maximise mass potential on our roads. This was PowerTorque’s first time in a twin steer Hino and a chance to see how well this model will perform in Aussie conditions.
The Hino organisation has a long tradition of building right hand drive 8x4 models, not only for Japan, but also for the truck market in the UK and Ireland, which has a requirement for 8x4 tippers capable of handling rough quarry conditions and a 32 tonne GVM, with an axle maximum capacity of 8.55 tonnes.
The truck on test was the FY3036 8x4, with the Hino A09C-VN engine rated at 360hp (265kW) with 1569Nm (1157 ft lb) of torque on tap. This engine drives through the Allison 4440 auto six-speed transmission. The grunt from the engine, alongside the capabilities of the torque converter in the Allison makes this truck a solid performer.
This is exactly how the truck felt getting out on the road. The combination of enough power and torque, with such a responsive truck, delivers for the driver. Of course, smooth ratio changes are a given and having enough under the right foot at the right time is also a given with an engine of this power and torque.
The relationship between the engine and the transmission is excellent with both knowing and anticipating what the other is doing. This is a finely tuned relationship and the smooth communication makes life easy for the driver.
The hooklift truck is running at over 1700rpm at 100 km/h, as one would expect, with short diffs on a vocational truck. When getting into the climb up the grade on the old Toowoomba range the speed drops away quickly, as it does with any loaded truck. The Allison keeps the torque pouring on to maintain speed in what is a steep climb.
Using cruise control set at 100km/h from the foot of the grade, the Hino, and the Allison transmission, don’t miss a beat and pull on up and over the crest at a very respectable speed creeping back up to over 40km/h after capitalising on any reduction in the grade.
This truck is fitted with a hooklift and loaded close to maximum GVM and runs well, the driver is relaxed and does not have to work hard to keep the momentum going.
There are now two engine braking options, available via a dashboard switch. One lets the driver pull the steering column stalk backwards and increase engine braking manually and the other switch position enables the driver to access all of the braking options via the foot pedal.
In this second option, if the driver simply press the brake gently, the exhaust brake activates, press more strongly and the inbuilt retarder will activate, if fitted, and then if you need more braking, a further push activates the service brake. This is the kind of braking control we have only seen in European trucks in the past.
Toggling between the two modes can be a trial-and -error process and the driver can choose whatever mode they prefer. I tended to prefer the non-sync mode by the end of the drive, but it’s simply a personal preference.
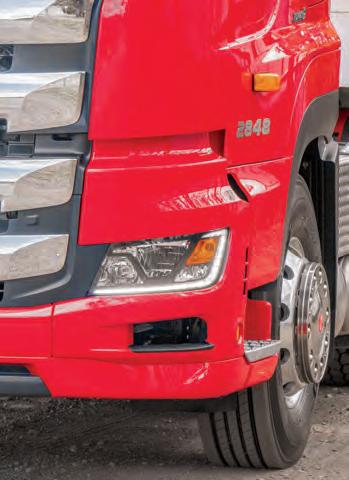
TRUCK FEATURES With the gear selection part of the driving task taken care of, it is possible for the driver to work through all of the features which are available on these new 700s. The FY model is aimed at the vocational end of the market, although it may also serve well as an urban distribution truck. As a result it does not have all of the sophisticated electronics, and does not need them.
Of course all of the safety devices
“A SOLID PERFORMER IS EXACTLY HOW THIS TRUCK FELT GETTING OUT ON THE ROAD. THE COMBINATION OF ENOUGH POWER AND TORQUE WITH SUCH A RESPONSIVE TRUCK DELIVERS FOR THE DRIVER. OF COURSE, SMOOTH RATIO CHANGES ARE A GIVEN AND HAVING ENOUGH UNDER THE RIGHT FOOT AT THE RIGHT TIME IS ALSO A GIVEN WITH AN ENGINE OF THIS POWER AND TORQUE.”
A refresh of the overall look and feel of the 700 Series.
This truck is fitted with a hooklift and loaded close to maximum GVM.
are available and many of them will automatically turn on when the truck is started. This means, if the driver is one of those people who wants to turn all of the automatic systems off, they are going to have to studiously turn them off quite a few times each day. The truck records these instances and that kind of behaviour may lead to the driver getting involved in some ‘counselling’.
The camera mounted on the nearside A-pillar is part of the optional monitoring Hino can offer as part of the package. There is also a function on the Hino Connect system which allows the driver to have video calls direct to HQ if and when required. On one of the drives, I connected to Barry Noble, from Hino Product & Engineering Support, remotely from the cabin to run through the intricacies of some of the connectivity and electronic systems.
The entertainment system screen on the 700 is now the same as the one we have seen released on the 300 and 500 Series models in the past couple of years. The information screen in front of the driver has improved greatly, as Hino transitions across to the latest technology. There is a commonality of both functions and controls across the Hino range from light duty up to these heavy models.
Functions like cruise control and following distance for the Adaptive Cruise Control are on the steering wheel. This seems to be the home for these kinds of controls in all of the latest trucks coming onto the scene.
The interior designers of the cabin have come up with some neat ideas, but there still isn’t a drinks holder big enough for a large water bottle or flask. However, the triangular tray on the top of the central binnacle has enough room for all of the odds and ends a
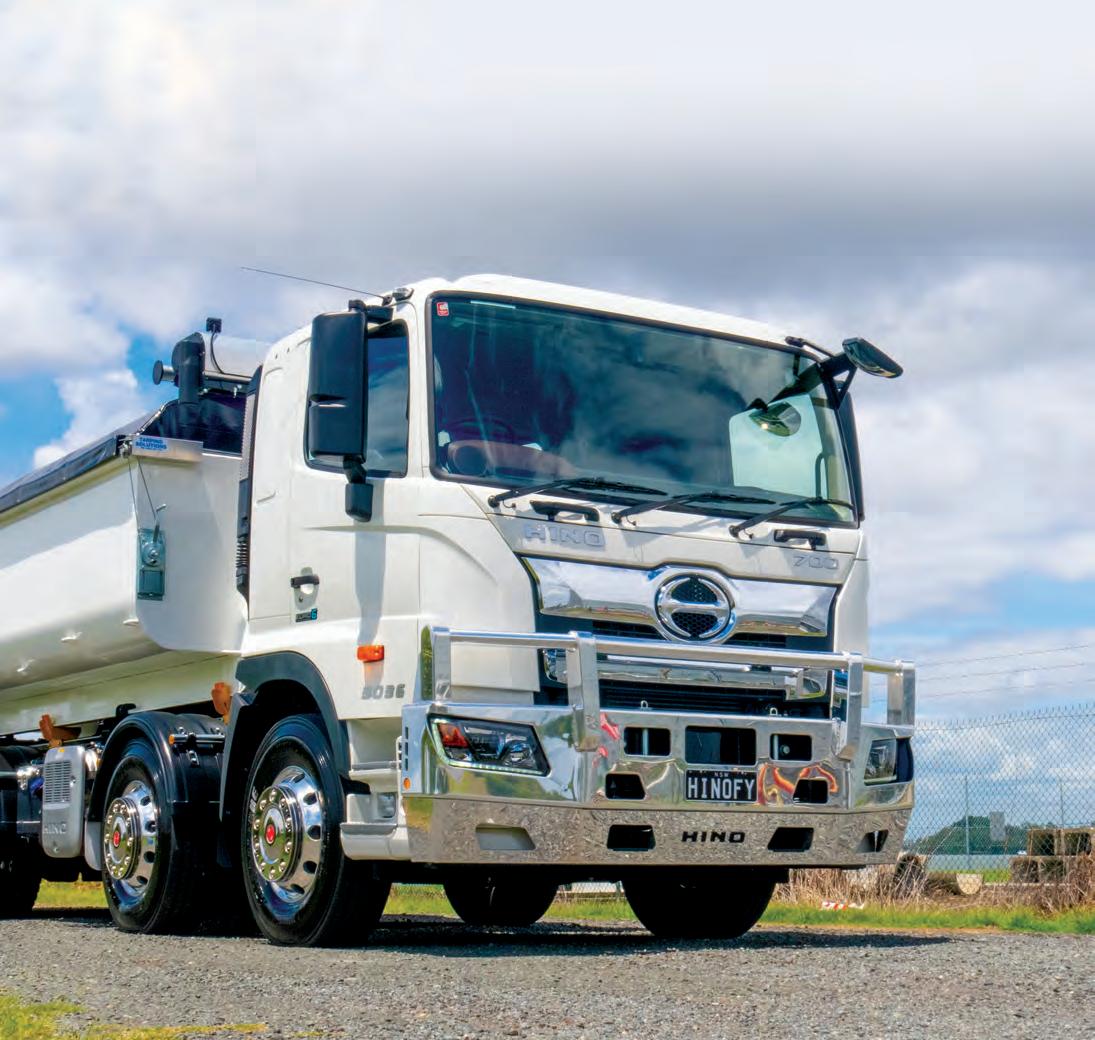
driver needs to keep close at hand.
This tray also includes an additional slot along the nearest edge which is deep enough to drop a mobile phone into. On this drive it was possible to keep my phone, my sunglasses and my EWD visible in the slot as I drove along.
From the driver’s point of view, most controls are simple and close at hand. The left-hand button on the left-hand side of the steering wheel controls the multiinformation display in the middle of the dashboard, directly in front of the driver. Left and right buttons scroll through the information a driver can use for a pre-trip routine. The right-hand side buttons on the wheel are those for the cruise control.
THE PRIME MOVER Climbing up into the cabin of the larger prime mover, the SS 2848, is a different proposition to the FY model. The 700 cabin with the 13 litre engine sits 120mm higher than the model fitted with the nine litre. They are both 700 Series models but they really do look and feel different.
The SS model with the ZF Traxon AMT has an extra control stalk to the left of the
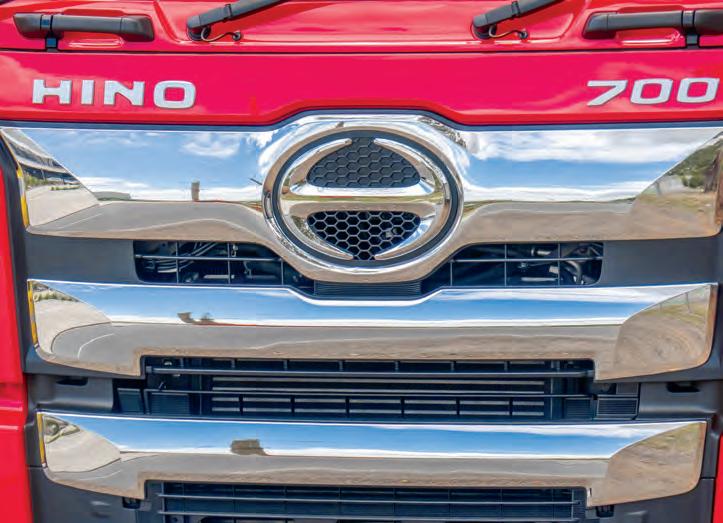
The Australian truck market now has a Hino 8x4 with a load sharing suspension.
steering column. The dial on the dash can be twisted when stationary from neutral to drive to slow manoeuvring drive to reverse to slow manoeuvring reverse. However, the stalk is used when actually out on the road. This has a paddle to go up and down a gear and the button to toggle from auto into manual and back.
Taking off, the 16-speed AMT really comes into its own. This is a proactive gearbox which wants to work and wants to get going. The last twenty years of the ZF AMT have seen it progress from a smart functioning idea to an extremely smart mature technology. The difference is the quality of the data the controlling computer is receiving from systems all over the truck to ensure it makes the right decision in a nanosecond, when required.
The AMT has three modes, eco, standard and power. When the truck was under load in power mode, the Traxon would not make an up-change until hitting over 1800rpm and rarely let the revs drop into the green band.
The competition between all of the major transmission designers has been hot and the resulting product has been forged by the need for each iteration of each box to get one small step ahead of the competition. The result is a choice of highly sophisticated AMTs from just about every truck brand.
For retardation the stalk on the steering column has four stages, with the engine brake increasing in two steps and then the Intarder adding a further two steps of really effective retardation. The combination of the Intarder and the Traxon AMT means it is possible to wash off all of the speed going into an intersection or a parking bay by simply pulling on full retardation and allowing the combination of the two to bring the speed back to a point were a small application of the service brakes is all that is needed to bring the combination to a halt.
A ZF Intarder on the 13-litre engine at relatively high masses has proved to be very effective part of the driveline and will considerably improve brake life.
On the larger SS prime mover with the ZF box, Hino have finally got the message and moved the transmission controllers to the dashboard, leaving enough space for the driver to be able to comfortably climb into the middle of the cabin.
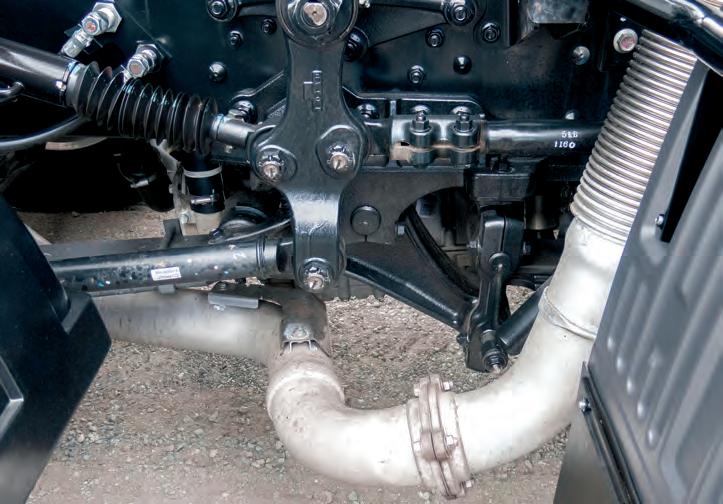
The truck on test was the FY3036 8x4, with the Hino A09C-VN engine.
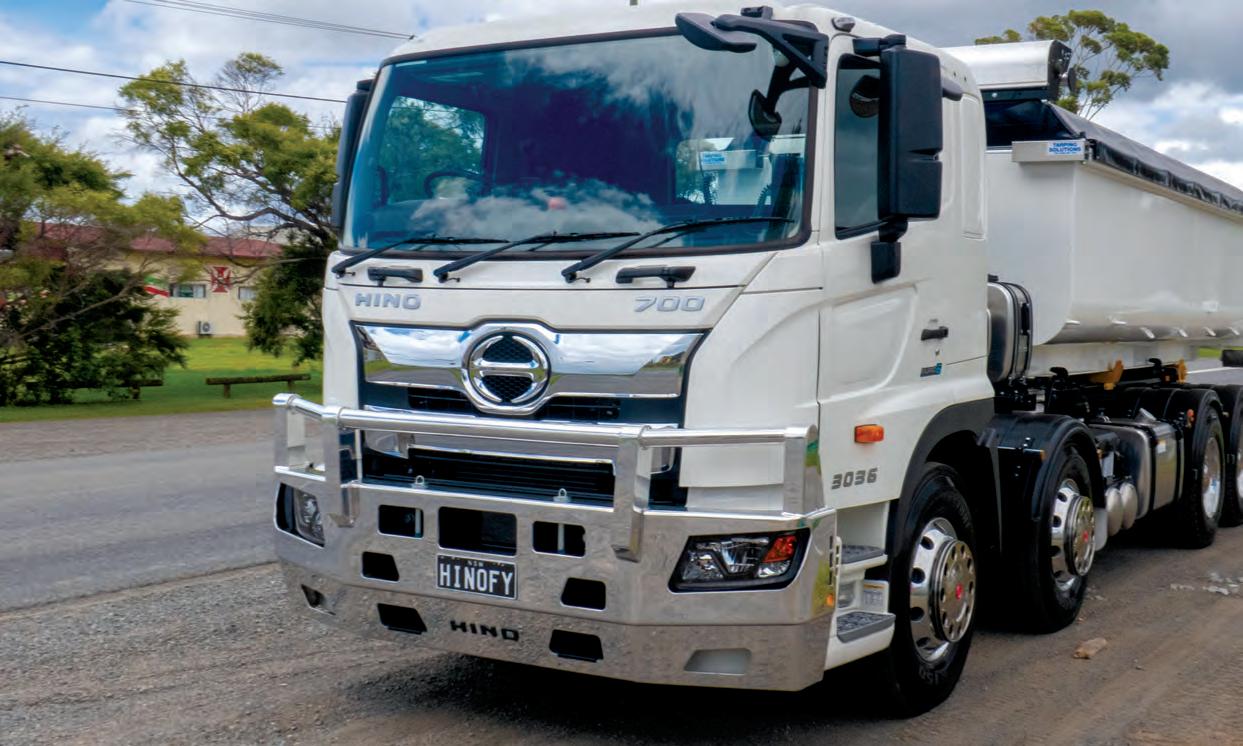
At 480hp this engine has enough to handle single trailer work and runs at 1500rpm at 100km/h easily, holding on well out in undulating countryside. Surprisingly, the green band on the tachometer is marked from 800 to 1400rpm, suggesting running at highway speed is just outside of its most economical zone. A taller diff would get the revs down into the green band at 100km/h, but may compromise performance elsewhere, where it is needed.
Power was the right mode setting as the semi approached the foot of the Cunninghams Gap grade. Once the truck got into the climb, the Traxon worked to make sure the engine was close to 1400rpm, clearly the home of the best torque from this engine.
When into the meat of the grade the truck was comfortable at 35km/h in 11th gear at 1400rpm and it could grind the climb out, despite the changes in grade. At other times, it will allow the revs to drop well below 1300 and then take a single gear to get back to 1500rpm as it grinds up the grade.
The smartness of the AMT becomes clear when the transmission makes surprising choices which turn out to be the right ones. Sometimes it will hold a gear until the revs get over 2000, and then at other times it will grab two gears and drop it down below 1450 rpm while climbing hard. All of these moves proved to be correct, the power and torque available were more than capable of handling the task set by the transmission.
This tray also includes an additional slot along the nearest edge which is deep enough to drop a mobile phone into.
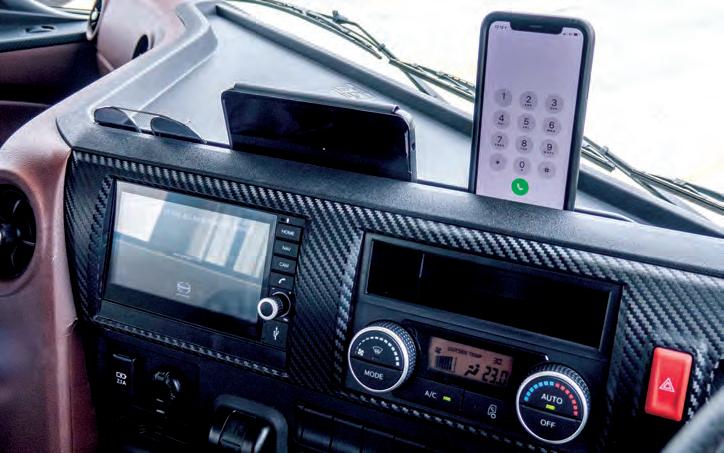
This is a Hino 13-litre engine rated at 480hp and we can’t expect it to fly up this ascent pulling a fully loaded semi. There is something about the quality of the torque an engine produces and Japanese engines rarely really impress, but it does do a commendable job, it seems to be well within its comfort zone all of the way up the Gap.
The return descent of the Gap saw the new Intarder now fitted on the Hino 700 prime movers come into its own. Dropping the AMT into manual, selecting 12th gear and pulling the lever to full retardation gives the driver a smooth descent with no need to apply the brakes and no worries about over speeding. Speed can be simply controlled by changing up and down manually.
Moving up into 13th and 14th gear the Intarder continued to hold the truck back easily. This is a top highway prime mover level of retardation, available on a Japanese prime mover, a surprise.
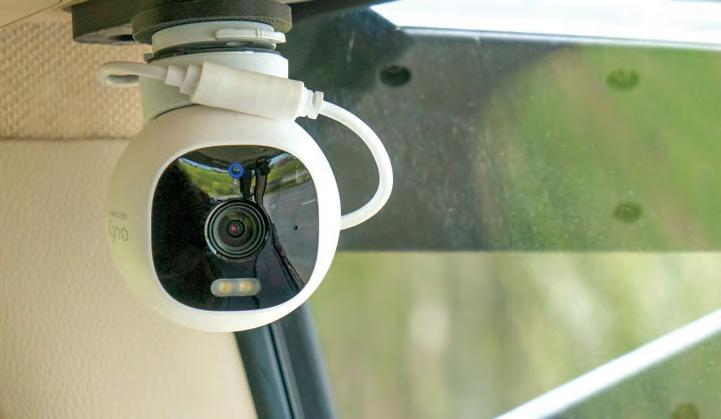
The camera mounted on the nearside A-pillar is part of the optional monitoring Hino can offer as part of the package.
THE CONCLUSION Like everything Hino come up with in terms of design this is a functional truck, but, despite that functionality, the interior looks and feels comfortable and sufficiently modern. Sophisticated no, effective yes.
The nine-litre engine is an innovation, and a good one for Hino. It provides them with a model which fits into many operator preferences around the lighter end of the truck market over 16 tonnes GVM. This does not have the feel of a truck design shoe-horned into an application, it performs like a truck designed specifically for these kinds of vocational tasks.
When it comes to the prime movers, the 700 has come a long way from the first models brought into Australia nearly twenty years ago. This has the look and feel of a sophisticated prime mover and all of the systems available as standard on the truck stand as testament to the radical development path Hino have been on.
Limitations like a small choice of wheelbases may well be a disadvantage, but if that is its only drawback, other factors may well get the new 700 over line in many cases.

BUSINESS BASED ON LOYALTY AND CONSISTENCY
It’s rather rare to find an operator who has stuck steadfastly with a single brand of truck for more than half a century. Yet that is exactly what Paul Matthei discovers when conversing with Ross Hardy and his son Laeton, who along with other family members own and operate bulk transporter Hardy’s Haulage.
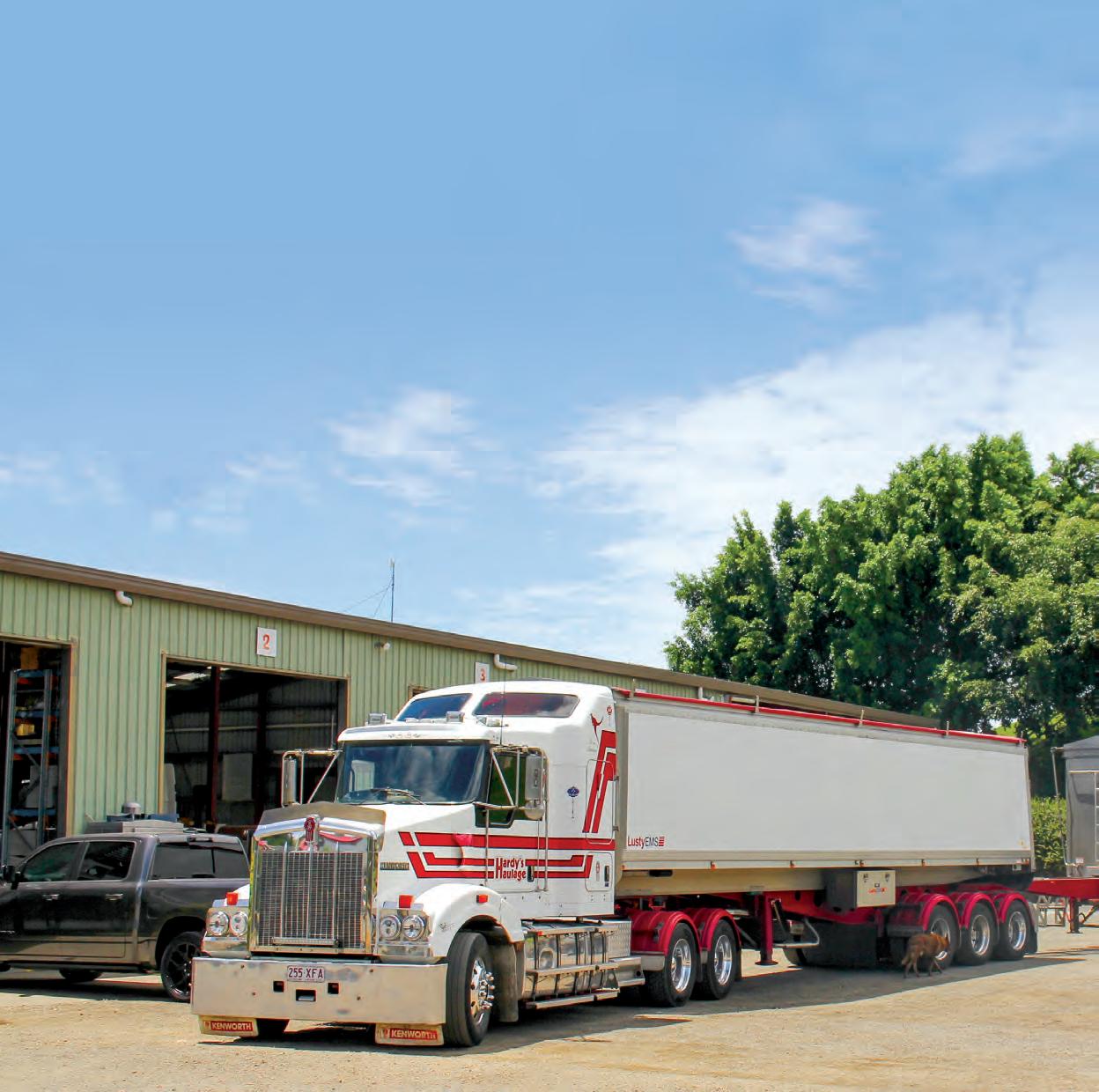
Located at Cudgera Creek near the small town of Pottsville, nestled among the glorious green hills in the coastal fringe of New South Wales’ Far North Coast, the Hardy family has owned property long enough to have a road named after them.
In fact, Ross, who was born in May 1946, is the fourth generation bearing the Hardy name to live and base a business there. In long bygone times the property was farmed and ran cattle and in the earlier half of last century Ross’s Grandfather and Father established a butcher shop in Pottsville.
Ross started working part-time at the tender age of 12 doing slaughtering and butcher shop work for the family business and then left school at the earliest opportunity working on the farms before going on to pursue a career in road transport.
In the early 1960s he started working for two local carriers, firstly as a mechanic in the workshop and also driving after hours. Eventually he gave up working as a mechanic and went full time driving.
He purchased his first truck in 1970, a fully imported Kenworth K125 cab-over built at the company’s Seattle plant in the USA and bought through Kenworth Trucks at Coffs Harbour for $25,000. The branch was then managed by long-term employee Alan Stead, who went on to become a lifelong friend of the Hardys.
This was the year prior to Kenworth’s parent company Paccar commissioning its Australian manufacturing facility at Bayswater in Victoria, and from 1972 onwards every prime mover Ross has purchased was built at that factory.
Ross was as proud as punch of his first Kenworth and used it to haul mineral sand from various locations along the east coast back to the processing plant at Kingscliff. During the early 1970s, in between plant shifts, he was also a tow operator for Trial Bay Haulage and Frigmobile and did flat top work carting timber to Brisbane.
Talking with Ross, one gets the impression he quietly wishes he was still in possession of his first truck.
“The original K125 was a good, basic, well-engineered and very reliable truck which formed the foundation of our business; perhaps the saddest day in my career was the day we sold it, to a subcontractor, after 18 years of faithful service,” says Ross.
It certainly laid the foundations for an all-Kenworth fleet that continues with gusto today, and with absolutely no signs of changing course anytime soon.
Moving on, he says those early days were all about making your own luck through long hours and doing as many loads as possible.
By 1977 the Hardy fleet had grown to six trucks and then nine in 1982, before the State Government closed some mineral sand mining leases in NSW. This impacted the viability of the business dramatically, so the company redirected its core operations to carrying industrial bulk products which soon became the mainstay of the business.
During the 1980s, Hardy’s Haulage had a mixed trailer fleet comprised of convertibles, flat tops and tankers to carry dry bulk, general and corrosive goods. By the 1990s the company was firmly focussed on long-distance dry bulk haulage which to this day remains 100 per cent of the business.
In the early ‘90s when the Road Transport Federation, (later the Australian Trucking Association), was formed, Hardy’s Haulage was one of the inaugural Team200 (now TruckSafe) members and has remained member No. 25 since then.
In addition, Hardy’s was selected by the NSW Road Transport Association to develop the roadworthiness section for TruckSafe through RTA consultant Justine McGuire.
Today, the trailer fleet consists of Lusty-EMS and Graham Lusty Trailers 25m Stag B-doubles and tri-axle single tippers operating throughout the mainland eastern states from Melbourne in the south as far north as Townsville in Queensland, with the main depot at Pottsville now augmented by subsidiary branches at Warwick and Yatala.
KENWORTH CONNECTION In 2022, Hardy’s Haulage operates 29 prime movers, mostly Cummins powered Kenworths of various models and ages, along with 58 tipping trailers.
Ross maintains that his early workshop experience with the Kenworth product convinced him that regular servicing, from day one, is the key to reliability, and that the Kenworth marque is second to none in terms of its rebuildability.
“We’ve been with Kenworth the whole way through, that’s virtually all we’ve ever had, Kenworths powered by Cummins engines,” says Ross.
Ross goes on to say that in his view the brand has come a long way over the last 20 years in terms of improved comfort for the drivers. Furthermore, he contends that this was a necessary progression to ensure his company could retain good drivers, particularly older ones who might have otherwise curtailed their careers with Hardy’s at an earlier date.
“In former times, Kenworths were always touted as a work truck first and foremost and most people just accepted the fact that they weren’t the most comfortable or driver orientated truck,” explains Ross. “That was fine to a point but as we progressed through the ‘90s and into the new millennium, the comfort difference between Kenworth and its competitors was becoming stark and we were having problems recruiting staff because the trucks weren’t as appealing from a driver’s perspective.
“I think it took Kenworth quite a while to recognise that it wasn’t only the reliability factor that mattered, the trucks needed to be just as good for the drivers as they were for the owners.”
According to Ross, particularly with the new T610 models Hardy’s has invested in, Kenworth has clearly achieved this goal and the company plans to keep buying them knowing the legendary Kenworth reliability is now matched with comfort and safety levels comparable with other heavy-duty prime movers.
“In our view the T610 represents a huge step forward for the brand and overall is a far more acceptable truck than the Kenworths of yesteryear in terms of driver comfort and convenience,” says Ross.
Ross Hardy and his son Laeton.
CONSISTENCY IS KEY As the conversation progresses, Ross mentions that the company has always trod the middle ground when choosing its prime movers, neither going for the top end of town or the poverty pack.
“We’ve always had the attitude that payload pays us all so having a truck that’s one to two tonnes heavier than necessary for the job is not all that beneficial,” says Ross. “And if you buy a bigger flashier truck then nobody wants to drive the lesser ones.”
Yet looking at Hardy’s wellpresented fleet it’s easy to appreciate that Ross and Laeton are all for having nice looking trucks.
For instance, the company’s latest T610 Kenworths have down-swept exhaust pipes rather than shiny chrome stacks, which provide a clean, modern look with the operational benefit of improved fuel efficiency through better aerodynamics.
“Our drivers, with the workshop’s permission, can add some items such as a light or two to make the truck their own, but we don’t go overboard with buying gear that won’t earn us any more money and can actually end up costing us money through extra maintenance and tare weight,” says Ross.
For the Hardy boys, running a successful transport company is all about staying ahead of the economic wave and they firmly believe the key to longevity is finding a niche market and sticking with it.
On the other hand, they lament the fact that finding sufficient suitable staff members is an uphill battle and significantly hampers the growth of the business.
“We could have twice the trucks here, if we could find more suitable staff,” says Ross. “And that’s not just us, we know everyone in the transport industry is crying out for competent staff.”
That said, Ross concedes Hardy’s is fortunate to have a high percentage of dedicated staff members who understand their roles without needing to be educated on a daily basis.
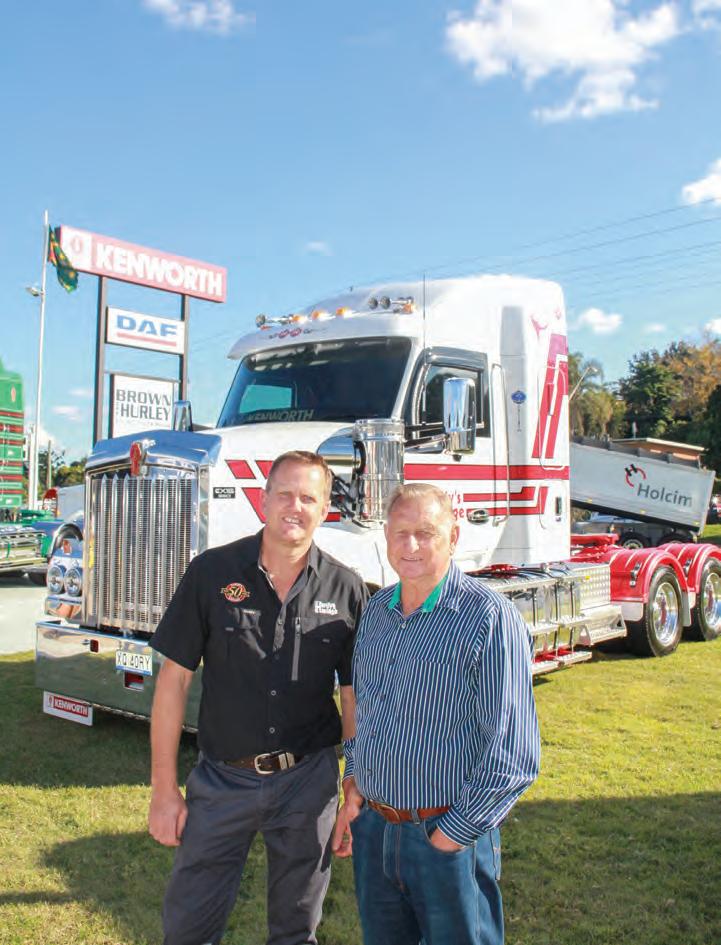
PASSING THE BATON Ross is now 75 and remains actively involved in the business on a parttime basis. Ross was inducted into the Road Transport Hall of Fame at Alice Springs in 2012.
While he and his wife Elaine are still owners of the business under a family trust structure, their son, Laeton, is now running the show with the help of his wife Kim, who is Office Manager, and Nigel Bailey who is Operations Manager at the Warwick depot.
Ross says being married to the right girl, he and Elaine were married in 1966, has played a big part in the success of the business.
“Elaine’s efforts are 50 per cent of this business because she reared our children and looked after the home environment while I was out doing all the loads for all those years,” he says with obvious pride and gratitude towards his ‘better half’.
Born in 1973, Laeton Hardy has grown up with the business, completing a heavy vehicle/diesel mechanical apprenticeship in the workshop and then going on to become workshop manager. His attention to detail and dedication to the role earned him the Australian Trucking Association’s
The latest diagnostic equipment and training the company’s mechanics in how to use this equipment has been a priority in recent years.

Craig Ros-eneder Award in 2014.
According to Ross, Laeton’s willingness to embrace the business and move it forward are among several key reasons why it continues to flourish today.
“Laeton came into the business at exactly the right time,” Ross explains. “Having done his apprenticeship after he left school then continuing to grow his knowledge, he’s become a whizz with electronics which modern trucks have in abundance, he has the means to optimise the potential of the fleet.”
Taking up the conversation, Laeton says investing in the latest diagnostic equipment and training the company’s mechanics in how to use this equipment has been a priority in recent years.
“They have all been trained to use Cummins, Eaton and WABCO EBS software and they use this during every service so that they stay up to date with the various systems,” Laeton says. “The WABCO EBS training was done by Shane Pendergast from Air Brake Services in Sydney. He came up to us and did the training in our workshop.”
Laeton explains that since then the company has retrofitted EBS to most of its older trailers so that a high standard in braking and stability of the vehicles is maintained across the board.
“The technology is relatively inexpensive and if it saves a driver from just one rollover it’s paid for itself many times over,” Laeton says, adding that it also helps the company in other ways such as the elimination of flat-spotted tyres.
According to Laeton, the EBS systems are checked during every A Service and a printout detailing any fault codes is generated so that the mechanics can see exactly what needs to be repaired and after the problem is fixed the fault code is cleared.
Hardy’s workshop is also equipped with a brake tester which is utilised at every A Service to ensure optimum
Hardy’s workshop is also equipped with a brake tester which is utilised at every A Service.
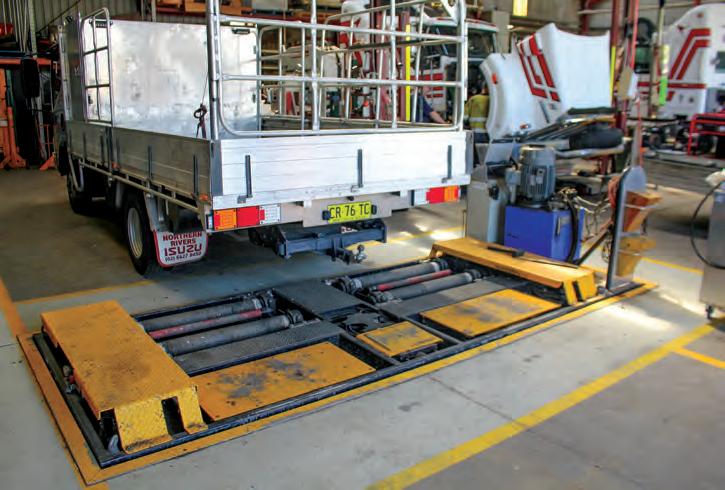
braking performance across all axles of each combination.
“It’s been a great investment, if a driver has a braking or steering issue the first thing we do is put the vehicle over the brake tester,” says Laeton. “That way any issues are highlighted straight away.”
He adds that sometimes it’s as simple as a dob of grease or a coating of dust in the brake drum causing ineffective braking, things that can’t be seen from the outside.
One of the products Hardy’s carries is bulk raw sugar from the various northern NSW sugar mills and Laeton says the dust from the sugar is a constant source of issues because it tends to coat the inside of the brake drums when the trailers are being unloaded over a pit.
“The dust gets into the drums and afterwards if there’s a slight amount of moisture it gets really sticky like toffee and is really hard to remove,” says Laeton. “It also degrades the tarps and eats into the paintwork on the trucks. Where you would normally get five years’ life out of a tarp, with sugar haulage you get three years, at best.”
Showing me through the well-equipped workshop, Laeton explains that the company does everything except engine, gearbox and diff rebuilds.
“We pull them out and replace them with a new or reconditioned unit so we can get the truck back on the road as soon as possible,” he says.
The company also has a well-stocked parts department and receives parts deliveries from Brown and Hurley at Kyogle twice a week.
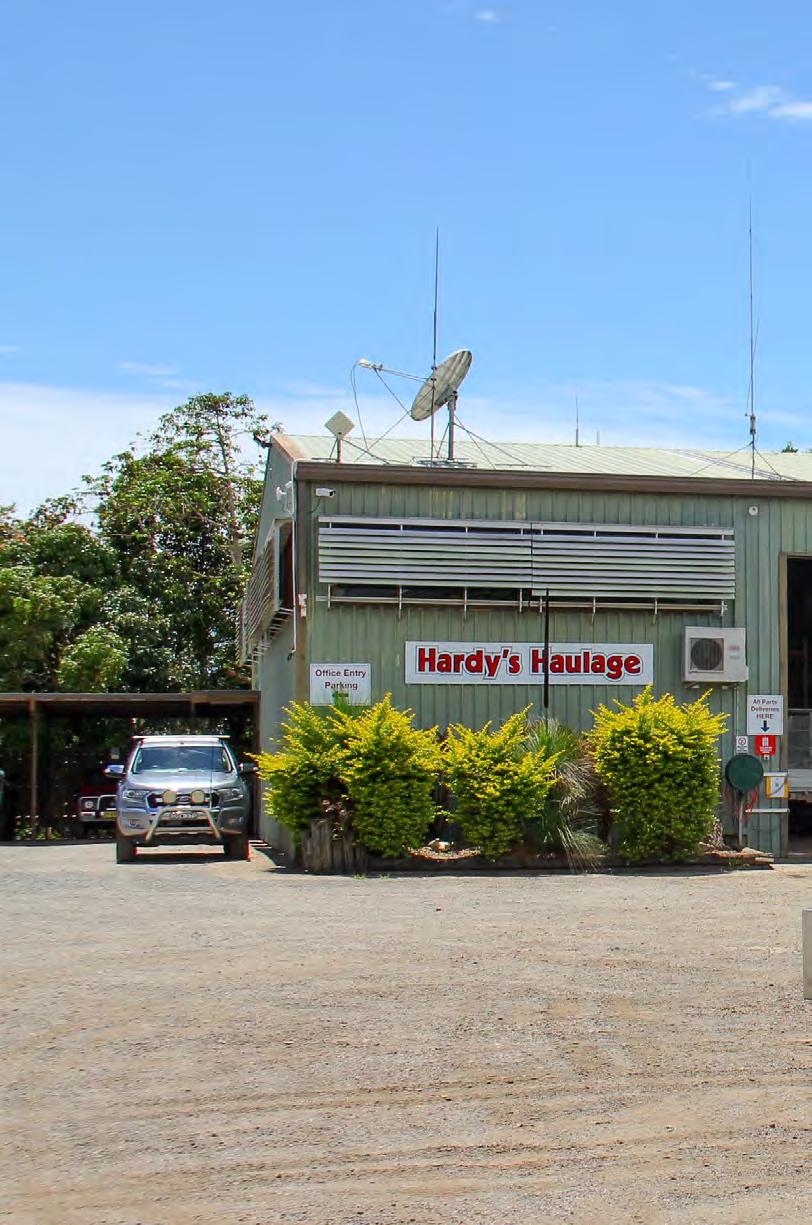
PARTS COMMONALITY Laeton says the company benefits greatly in terms of lower parts inventory from running single brands of equipment including Kenworth trucks and Hendrickson trailer suspensions.
“While the Kenworth models do change around a bit, at the end of the day they are still very close in specification which is helpful,” says Laeton. “With our trailers we run Hendrickson suspension throughout which means that we only have to stock the one type of S-cam, slack adjuster, brake lining and drum, which simplifies things enormously.”
Laeton relates that the ‘oneproduct rule’ the company strives to maintain occasionally needs to be altered for various reasons.
“We’ve had a great run from Cummins engines but for some of our single trailer work we’ve found the Paccar MX-13 engine fills the bill, so we are now running some of them and they are performing very well for us,” says Laeton. “They are rated at 510hp and are a lighter engine than the Cummins X15 which makes them ideal for our single trailer prime movers.”
Another commonality within the fleet is that all of the prime movers are B-double rated so that, if necessary, the single trailer units can also haul B-doubles.
Just like his Dad, Laeton is very much hands-on with the operational side of the business and can often be found at the workshop on weekends tinkering with or washing trucks.
“It helps to have a practical knowledge of the trucks when you’re spec’ing them so that you know you’re getting exactly what you need,” says Laeton, adding that the drivers are also invited to put for-ward ideas about how to improve aspects of the trucks from their own practical experience.
He provides the example of installing access doors in the front of each tipper to enable safe and easy access for the drivers to sweep out after unloading.
“We now have every new trailer built
“In our view the T610 represents a huge step forward for the brand and overall is a far more acceptable truck than the Kenworths of yesteryear in terms of driver comfort and convenience.”
with an access door and have gone through and retrofitted this feature to the entire fleet,” says Laeton.

COMBINATIONS FOR COURSES Speaking about trailer combinations, Laeton says the company is sticking with single trailer and B-double combinations because they suit the agricultural-based markets which the company serves.
“A lot of farmers really struggled during the lengthy drought that we’ve recently experienced,” says Laeton. “Because of this they often want smaller loads which is where our single trailers with a 27-tonne payload really come into their own.
“We have chosen not to go down the A-double road at this stage because there are simply too many permits needed operating between Melbourne and Townsville.”
For the foreseeable future Laeton says `the plan is to stick to the established formula that has been developed over many years, relying on proven products like Kenworth, Cummins, Lusty-EMS and Hendrickson.
“We’ve moved into the T610 and T410 Kenworths now and the drivers really appreciate the wider, more spacious cab,” says Laeton. “The T610 in particular is a really good prime mover for us.”
Keeping tare weight down is another priority and for this reason Laeton says the company only uses CentriFuse drums, low profile tyres and Alcoa alloy rims on its vehicles.
“We aim for the optimum balance between light tare and durability to ensure our payload capacity is as high as possible without compromising on longevity of the equipment,” says Laeton.
At the end of the day, it’s all about keeping the business sustainable and viable in order to best serve the loyal customers who rely on Hardy’s Haulage to deliver the goods all year round.