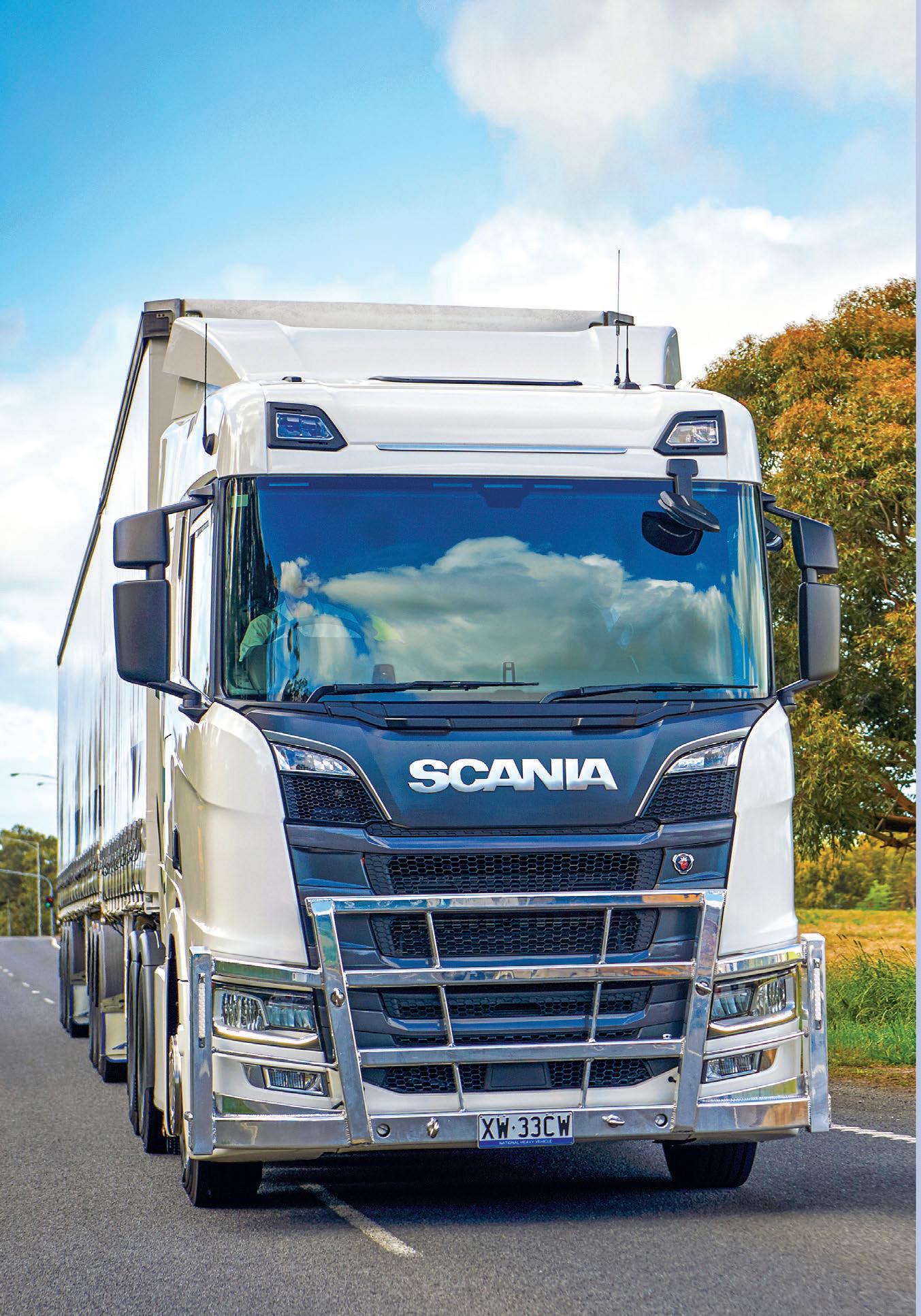
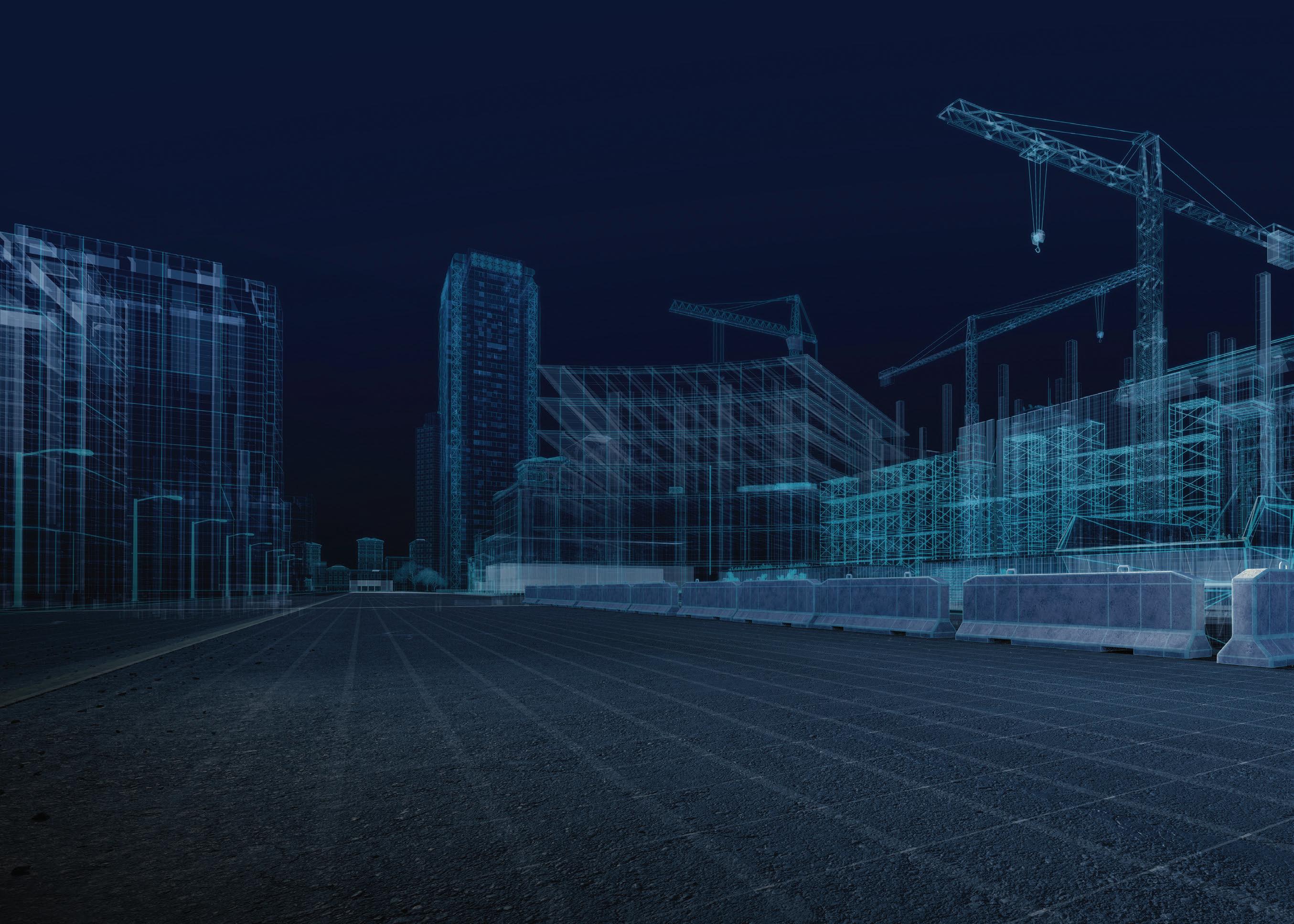
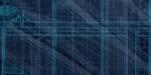
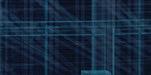
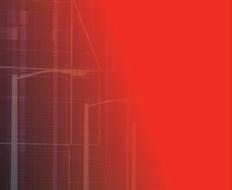
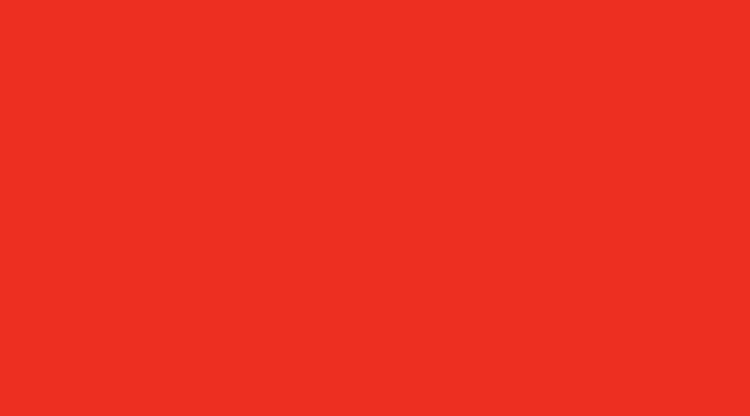

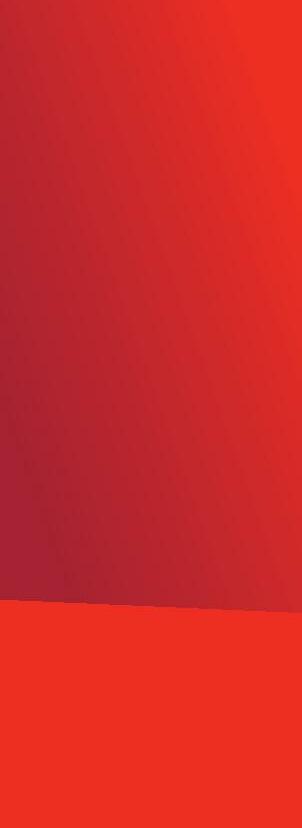


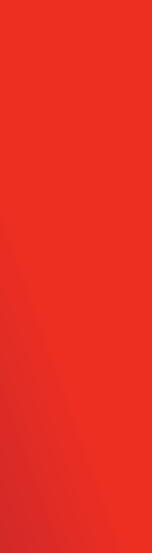
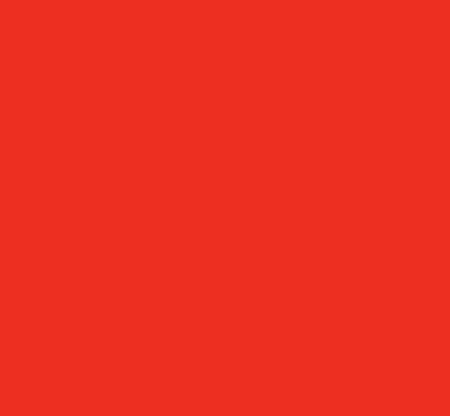
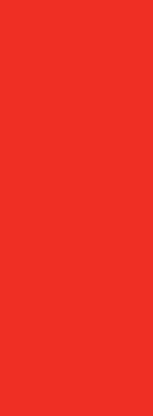

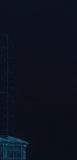
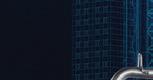
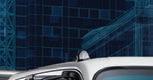
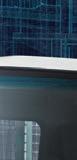
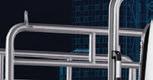
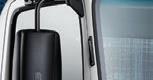

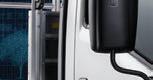
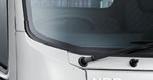
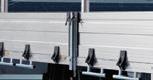
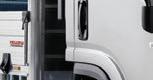
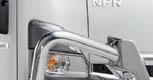

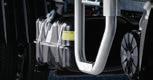
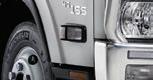
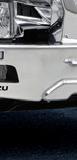
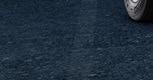
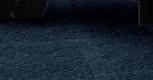

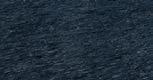

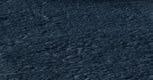
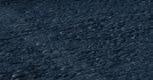
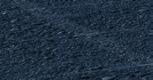
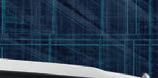
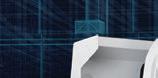

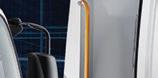
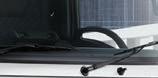
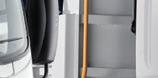
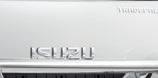

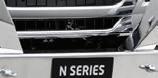
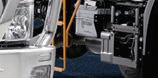

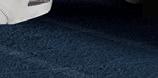

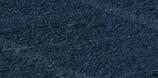

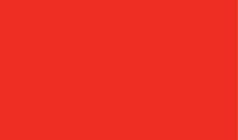

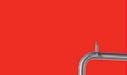
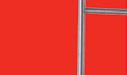
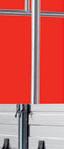
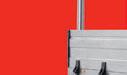
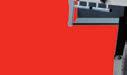
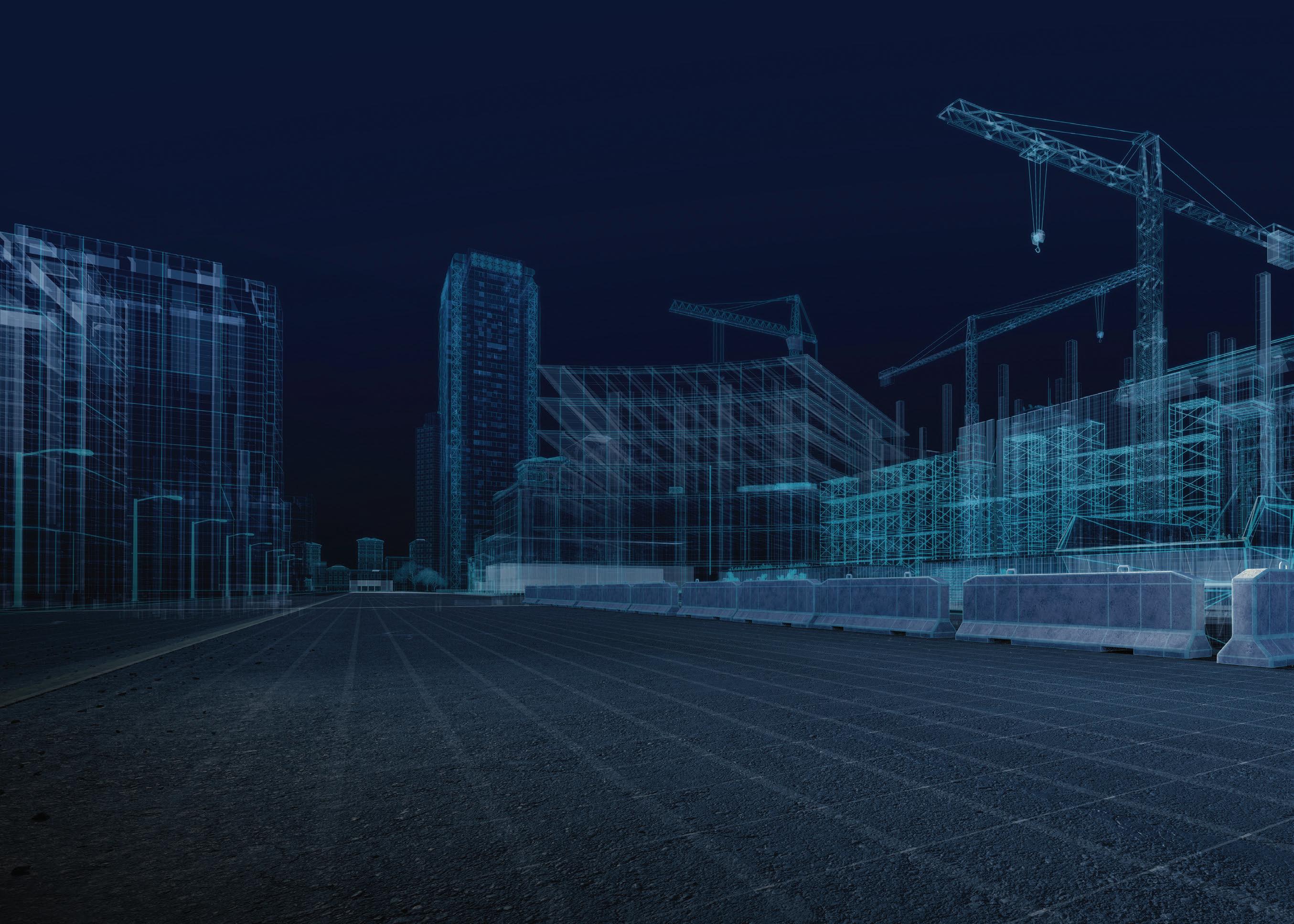
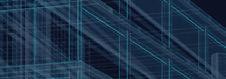
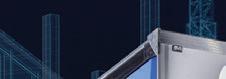
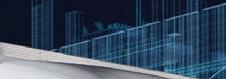
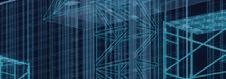
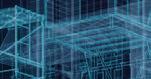

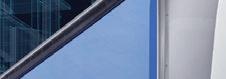
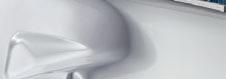

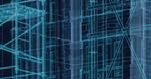
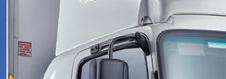

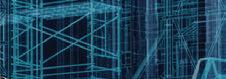
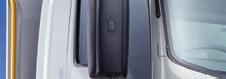
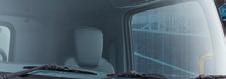
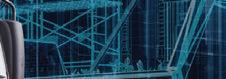
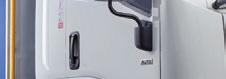
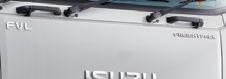
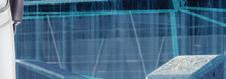
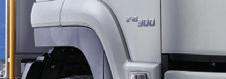
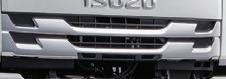
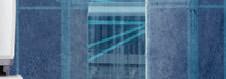
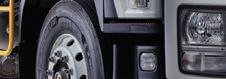
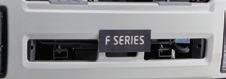
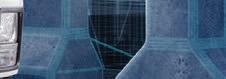

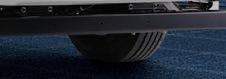
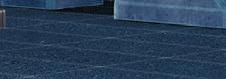

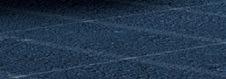
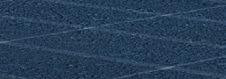
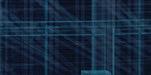
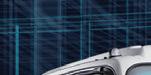


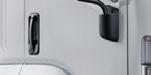
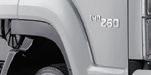
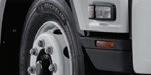
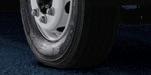

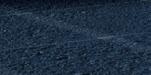
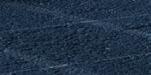

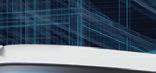
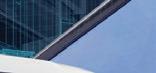
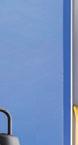
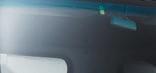

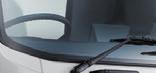
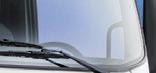
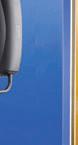
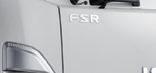
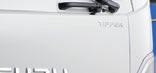


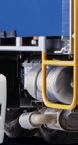
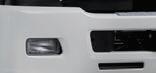
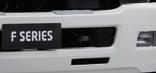


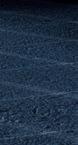
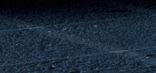
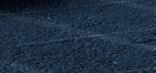
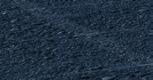

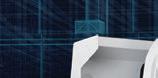
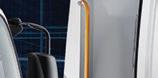
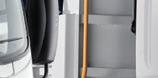

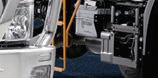
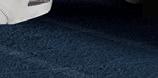
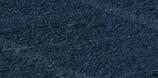
After over twenty years reporting on the ups and downs and ongoing issues of people working in the trucking industry, I have probably become somewhat jaded in my attitude to new initiatives and developments.
Working in the trucking industry, as I have for 45 years, is still a commitment to a working life which is very different to the ‘office hours only’ and benign workplaces many people think of as their working environment.
There are some extreme conditions, which definitely make being a truck driver a lifestyle choice, rather than a career choice. Most office workers don’t stop drinking at lunchtime on Sunday to make sure they can work legally on Monday morning, truckies do. A bank teller doesn’t get fined if they misspell a word on a docket about a financial transaction and not many factory workers cannot be sure at the start of any shift, whether or not they will make it home at the end of that shift.
All of those issues are part of that lifestyle choice, part and parcel of a job which, and don’t get me wrong, can be rewarding, but is not what the vast majority of the working population expect from their paid employment.
There are some compensating factors here. The need for a major personal commitment does mean that people in the industry have some skin in the game, they are also committed to the culture of the industry.
What this means is that there is a much tighter bond between people working in the industry, a common bond derived from the common commitment we make to be part of the industry and accept it ‘warts and all’. We all have made that commitment to put parts of our lives at risk to be part of the industry.
It is this very commitment, which others in the industry have also made, which makes the industry special, and makes us feel like we are part of a larger community bound together by the privations we have to undergo, but also the feeling that we are all in it together.
This collegiate culture we feel, especially when dealing with others from outside the industry, is what makes us stick with a job which is not good for our social life or our sleeping patterns.
The continuance of the somewhat strange culture within the trucking industry has sustained us so far, but the kind of commitment being demanded of people just to have a job in our industry is no longer attractive to the young people coming through who will replace us, as we drop off the perch.
So, what does getting better look like? Can our industry survive a transformation, which makes the trucking game more attractive to the generation coming through? Would any transformation destroy a strong culture which has seen the trucking industry through in the past, or would a new culture be just as efficient, without forcing people to compromise their personal life for a job which has few long term rewards?
Prime Creative Media Pty Ltd ABN 51 127 239 212
379 Docklands Drive, Docklands VIC 3008 Australia
Telephone: 03 9690 8766 Fax: 03 9682 0044
Email: enquiries@primecreative.com.au
Publisher and Managing Editor: John Murphy Editor: Tim Giles
Contributors: Paul Matthei
Correspondent: Will Shiers (UK)
Advertising Manager: Trevor Herkess: 0411 411 352, trevor.herkess@primecreative.com.au
Client Success Manager: Salma Kennedy, salma.kennedy@primecreative.com.au
Production Manager: Michelle Weston
Circulation & Subscriptions Manager: Bobby Yung
Designers: Blake Storey, Kerry Pert, Tom Anderson, Louis Romero
Official Media Partner:
REGISTERED BY Australia Post - ISSN 1445-1158
SUBSCRIPTION
03 9690 8766
subscriptions@primecreative.com.au
PowerTorque Magazine is available by subscription from the publisher. The right of refusal is reserved by the publisher.
Annual rates: AUS $60.00 (inc GST). For overseas subscriptions, airmail postage should be added to the subscription rate.
PowerTorque Magazine is owned and published by Prime Creative Media.
All material in PowerTorque Magazine is copyright and no part may be reproduced or copied in any form or by any means (graphic, electronic or mechanical including information and retrieval systems) without written permission of the publisher.
The Editor welcomes contributions but reserves the right to accept or reject any material.
While every effort has been made to ensure the accuracy of information, Prime Creative Media will not accept responsibility for errors or omissions or for any consequences arising from reliance on information published.
The opinions expressed in PowerTorque Magazine are not necessarily the opinions of, or endorsed by the publisher unless otherwise stated.
Engineered for Allison Transmission by Castrol, the technology and market leader for over 20 years.
Builds on the outstanding performance of the original TranSynd formula with enhancements that include: improved wear protection, extended anti-shudder durability and extended clutch-friction durability.
There was one overarching message coming out the display stands at the IAA Transportation exhibition in Hanover, and that was bye-bye diesel and hello electric.
What began as a simple truck test drive turned into a journey of discovery, this article is all about one truck, two stories and a new initiative. PowerTorque Editor, Tim Giles, gets out on the highway driving the latest revamped V8 from Scania.
No transport task is simple and hauling frames and trusses onto building sites has the effect of increasing the level of difficulty, for an operation in Geelong.
The new range from Western Star brings a set of wholesale changes to the overall design of the trucks available from the brand. PowerTorque drills down into the X Series details.
The team at Daimler Trucks took the opportunity at the IAA Transportation event to communicate their vision for drivetrains down the track. What ere the options for electric, hydrogen and diesel?
There is little doubt as to what would make life for rural carriers in New South Wales a little easier; it would be genuine state wide farm gate access.
It has been a long wait for the trucking industry, especially in rural areas, to get to a point where we can see daylight on the horizon, in the form of rational progress on on board mass.
PowerTorque sat down with Paul Ilmer, who leads Volvo’s electric truck program, to discuss the road ahead for electric trucks in Australia.
PowerTorque’s European Correspondent, Will Shiers gets behind the wheel new DAF XD, which was crowned International Truck of the Year 2023 to discover whether it really was a worthy winner.
The Australian Livestock and Rural Transporters Association (ALRTA), together with the National Heavy Vehicle Regulator (NHVR), is working on a livestock transport effluent management plan.
The two organisations are calling for public feedback on the draft Industry Code of Practice – Managing Effluent in the Livestock Supply Chain (the Effluent Code). Feedback should be provided by Friday November 4. The project is being funded by
the NHVR’s Heavy Vehicle Safety Initiative, supported by the Federal Government.
“The Effluent Code is a practical guide that assists livestock transporters and parties in the Chain of Responsibility (CoR) to comply with their primary duty and other obligations under the Heavy Vehicle National Law (HVNL) relevant to managing livestock effluent during road transport,”said Scott McDonald, ALRTA National President.
After an initial announcement back in 2012 and a lot of federal government inaction since then, at last the future of diesel engine emissions trucks has become clearer, as ten years later Euro 6 finally arrives.
The Minister for Infrastructure, Transport, Regional Development and Local Government, Catherine King, announced a new ADR 80/04 based on the Euro 6 requirements will be phased in for newly approved heavy vehicle models first supplied to Australia from November 1 2024 and for existing heavy vehicle models still being supplied to the Australian on or after November 1 2025.
The fine print of the final ADR 80/04 is still under consultation with stakeholders, but the final ADR will allow vehicles meeting equivalent US or Japanese standards to be deemed to meet the requirements of the ADR. There will also be new allowances for trucks meeting the new standard. According to the Catherine King statement the technology required to meet Euro 6 will increase the cost of supplying a new truck or bus to Australia by three to five per cent or $4,000-$6,000.
The Transport Women Australia Limited Driving the Difference scholarship winners have been announced for 2022, sponsored by Daimler Truck Australia Pacific. The awards are for women in the transport and logistics industry who want to advance their career within the industry or to enter our industry.
There were six very worthy candidates presented with their certificates at end of year functions in the city closest to them: the successful applicants are Ainsleigh Bilato of Adelaide, Brooke Tran of Perth, Ellen Tandy of Forbes, and Nichole Speers of Wollongong, both
Regional NSW, then Joana Feiteira and Sally-Ann Eather of Sydney.
All the candidates provided outstanding applications and courses that will assist them in advancing within our industry and contribute to the future of all women as leaders. Leadership skills and careers are enhanced by programmes such as these, and the opportunity that the scholarship provides, being awarded the Driving the Difference scholarship means that those successful applicants can undertake a course of study that might otherwise be out of their reach.
The National Heavy Vehicle Regulator (NHVR) says it will be introducing changes to the Performance Based Standards (PBS) scheme Vehicle Approval (VA) document to reduce issues around getting vehicle approval, but will PBS be easier to utilise?
This change will reduce issues around getting the basic approval for a vehicle, but will not address the main issue which has hamstrung the PBS process, getting access from the local road managers in certain areas.
“The PBS scheme allows heavy vehicle operators to use innovative and optimised vehicle designs – allowing freight to be moved in a safe way with fewer truck movements,” said Sal Petroccitto, NHVR CEO. “As the sector continues to address the challenges associated with COVID, including driver shortages and the growing freight task, it is critical we improve accessibility to these safer and more productive heavy vehicles.”
award will be presented at the Annual LBRCA Conference at Tamworth 10-11 March 2023.
“The young driver award recognises our top young drivers and showcases their commitment to safety and best practice,” said Wade. “We’re looking for young talented individuals who are making a difference in the road transport industry. The award winner must demonstrate a best practice approach to driving and safety and will be rewarded with a $5,000 study tour to the United States, New Zealand, or Western Australia.”
LBRCA President, Wade Lewis announced that the Livestock, Bulk and Rural Carriers Association is seeking nominations for young driver of the year for 2023. Nominations are open until 20 January 2023. The
PLUS: Anyone who qualifies for this LBRCA award is also eligible for entry into the Rural Transport Rising Stars Award, a collaboration between PowerTorque and the ALRTA. Scan QR Code to enter:
Adam Ritzinger has been appointed as the new Chief Technical Officer at the HVIA, bringing with him a wealth of knowledge as an experienced and accomplished mechanical engineer embedded in Australia’s heavy vehicle transport industry. He is a passionate trucking and transport enthusiast who understands trucks, the regulations they operate under, and the stakeholders that influence the transport industry at all levels.
Cummins and, Indian industrial giant, Tata Motors, have signed a Memorandum of Understanding (MoU) to collaborate on the design and development of low and zeroemission propulsion technology solutions for commercial vehicles in India, including hydrogen-powered internal combustion engines, fuel cells, and battery electric vehicle systems.
N Chandrasekaran, Executive Chairman, Tata Sons, and Tom Linebarger, Executive Chairman, Cummins signed the deal at Tata Sons Headquarters in Mumbai, India.
The Cummins B6.7H hydrogen engine with up to 290 hp (216 kW) output and 1200 Nm peak torque is an all-new engine platform. Performance is said to be compatible with current transmissions, drivelines, and cooling packages. The engine is derived from Cummins fuelagnostic platform offering the benefit of a common-base architecture and low-to-zero carbon fuel capability.
The Director of a NSW waste company has been ordered by the Parramatta court to comply with an Enforceable Undertaking (EU) voluntarily entered into with the National Heavy Vehicle Regulator (NHVR), following a breach of the EU conditions.
NHVR Acting Executive Director Statutory Compliance Belinda Hughes said the Director failed to undertake three safety initiatives within 12 months, as required under the EU.
“The court issued the Director
an order to comply with the EU conditions within 12 months, as well as a Conditional Release Order for a period of two years,” said Belinda. “If the Director doesn’t comply with the Court order, they may be prosecuted again and risk a more severe penalty.
“The NHVR offers EUs as an alternative to prosecution because they provide real safety benefits for the transport industry and the community. If a company, or person doesn’t comply with the conditions in an EU, the NHVR will hold them accountable.”
Victoria’s revised approach to allowing heavy vehicles leeway with curfews is a step in the right direction, has been welcomed by NatRoad. The Victorian Government has introduced a planning exemption as part of its return to COVID normal settings.
The exemption allows deliveries of essential goods to premises one hour before and one hour after times specified in any planning permit condition. This measure is being introduced for up to 24 months on a
trial basis with comment invited from industry and local government.
“This is a win for common sense and will help ensure supermarket shelves remain stocked and pharmacies have medicines they need,” says Warren Clark, NatRoad CEO. “It is a fact that supply lines remain under stress and that’s been exacerbated by the recent East Coast floods. It makes no sense for truck drivers to miss delivery cut-off times by a few minutes and have to wait until the following day.”
The 2022 Hino National Skills Champions have been crowned with Bevan Joseph from Sydney’s City Hino (Sales), Heath Bonney from Sydney’s Adtrans Hino (Parts) and John Dempsey from Mt Gambier’s Barry Maney Hino (Service) taking out the coveted titles.
After a COVID-enforced hiatus for two years, 18 of the best staff from the Hino Australia dealer
network competed against each other in the Hino National Skills Final, having completed a series of qualifying rounds.
Finalists in the Sales and Parts categories demonstrated their expertise through real-world roleplay scenarios and theory tests while the Service Technicians were tested on their diagnostic, analytical and technical skills in a series of hypothetical exercises.
NatRoad has told Austroads that it’s time to move heavy vehicle driver licensing in Australia to a national competency-based system. The call comes in a submission providing feedback on the Consultation Regulation Impact Statement outlining proposed changes to the National Heavy Vehicle Driver Competency Framework.
NatRoad wants Austroads to drop its proposal for post-licence behind-the-wheel supervised training and says its members have
also made it clear that they do not support a time-based heavy vehicle licensing system.
From 1 December 2022, Performance Based Standards (PBS) vehicles will be able to use a broader range of tyres, removing the restrictive and outdated tyre requirements that created unnecessary costs, and allow PBS operators to use any brand and model of tyre, as long as it meets relevant PBS Standards. https://www.nhvr. gov.au/road-access/performancebased-standards/pbs-review-project/ generic-tyre-approach
“At all levels of government, we have a responsibility to ensure the heavy vehicle industry can meet the country’s growing freight task,” said Sam Farraway, NSW Minister for Regional Transport and Roads. “PBS vehicles allow more goods to be delivered with fewer vehicles in a safe and sustainable manner, offering productivity improvements of 15 to 30 per cent compared to their prescriptive counterparts.
National Heavy Vehicle Regulator CEO Sal Petroccitto said the NHVR is committed to reforming the PBS scheme to break down barriers and make it easier for operators to get on with doing business.
Following a roadside intercept where a vehicle carrying metal, aluminium and car parts was found to be substantially over mass and incorrectly restrained, the National Heavy Vehicle Regulator (NHVR) followed the Chain of Responsibility (CoR) back to a consignor, issuing an Improvement Notice.
NHVR Investigators found the consignor had no procedures, training or induction materials in place for mass
Open for business, selling and servicing Fuso trucks and buses as well as providing service support and spare parts for Freightliner and Mercedes-Benz Trucks, is Daimler Trucks Dubbo. Located at 7L Boothenba Rd, Dubbo, the branch covers an area in the important Central West region of New South Wales.
The business is backed by Dubbo
local businessman Chris Gibson, who has drawn together a sizeable team led by General Manager, Damian Brewer.
“We are really excited that Chris and his team are committed to supporting Daimler Truck customers in the Central West region of New South Wales,” said Daniel Whitehead, Daimler Trucks Australia Pacific President and CEO.
or load restraint requirements.
“If you are not a transport operator but you engage the services of a transport operator, you must ensure the safety of that activity, it’s a shared responsibility,” said Belinda Hughes, NHVR Acting Executive Director Statutory Compliance. “This particular investigation demonstrates that the NHVR will investigate all parties in the chain to ensure they meet their obligations.”
Planned infrastructure spending in the future included a freight route spending boost in the budget to be announced on October 25.
The plan is reckoned to be delivering on $9.6 billion of election commitments for vital infrastructure projects across Australia.
The commitments funded in in the Budget include:
• $300 million f or Western Sydney Roads Package and $500 million for the High Speed Rail Authority
• $2.2 billion f or the Suburban Rail Link in Victoria
• $586.4 million of additional funding for a major upgrade of the Bruce Highway to widen a 13-kilometre stretch through Brisbane’s outer northern suburbs
• $1.5 billion f or upgrading important freight highways, sealing the Tanami, and upgrading Central Arnhem Road, as well as the Dukes, Stuart and Augusta highways in SA
• $540 million to upgrade Tasmania’s important road corridors, including the Bass Highway, the Tasman Highway and the East and West Tamar Highways
• $125 million funding to help build an electric bus network for Perth
A $4 million heavy vehicle safety grant program is open for submissions.
The National Heavy Vehicle Regulator (NHVR) has opened submissions for Round 8 of the Heavy Vehicle Safety Initiative (HVSI) to fund new projects to deliver a safer heavy vehicle industry.
Project submissions must address the themes of safer drivers, safer vehicles or safer road use by investing in driver or supply chain skills and training, vehicle
safety technologies and improvements, or heavy vehicle educational tools and resources.
Submissions close on 5pm AEST Monday 20 February 2023. For more information on the NHVR’s Heavy Vehicle Safety Initiative program, scan the QR Code.
After thousands of driver records were found destroyed in a chemical bath of weed killer, a former transport company director has been convicted and fined in a South Australian court, following a lengthy investigation by SA Police.
The former director pleaded guilty for failure to exercise due diligence in complying with a safety duty and was fined $14,000. A Prohibition Order, made under the HVNL, was imposed for a period of 12 months, excluding the director from engaging in any transport activities.
The company was also convicted of one count of failing to comply with its safety duty. The court indicated a fine of $120,000 but was reduced to $84,000 due to a guilty plea.
What began as a simple truck test drive turned into a journey of discovery, this article is all about one truck, two stories and a new initiative. PowerTorque Editor, Tim Giles , gets out on the highway driving the latest revamped V8 from Scania.
After some time in this game, it is not very often that PowerTorque is genuinely surprised by a truck test drive. The new vehicle on test is often a known quality, and one which has been previewed in the build up to its launch. However, Scania managed to spring a surprise on this test driver with an initiative we certainly didn’t see coming.
There is plenty to remark upon with the arrival of the latest version of the Scania V8 engine. This is the first upgrade of this engine since the launch of the New Truck Generation in Australia in 2018. It’s still a 16.4 litre 32 valve, twin internal cam V8, and the engine in question on this test is the 590hp version. Europe have a 530hp V8 which is not needed in Australia as the 13 litre does go to 560hp. The V8 also comes in at 660hp and 770hp.
In terms of technical changes to the V8, one aspect is the increase in the
compression ratio, plus new engine management, a new new turbocharger and new exhaust system. The new turbo is referred to as the ‘ball bearing’ turbo, which couples with a new manifold design enabling it to spool the turbo at quite low rpm.
Torque is produced at 3050Nm (2250ftlb), looking at the power and torque curves the crossover point between torque and power takes place at 1350rpm. At a lower rpm, torque sits at its maximum, while above 1350rpm, power makes the final step up from 560hp to 590hp. This is the kind of performance which makes life easier for the transmission. From 925rpm up to 1900rpm the driveline has either maximum power or maximum torque available.
Changes have been made to the SCR unit introducing twin dosing. The first dose is injected just after the turbocharger, where the exhaust gases are turbulent and very hot, improving
the mixing of gas and fluid. The second is further down the exhaust flow in a more traditional position. Even though there are two doses being added, Scania reckons the amount of adblue the SCR consumes has been reduced. The engine does not use EGR.
Out on the road the truck was hauling a B-double running at 62 tonnes GCM. The route did include several sections of the old Hume Highway heading north, including up and over ‘Pretty Sally’, a useful test of the pulling performance of the driveline. Setting off from traffic lights at the bottom of a climb shows just how smoothly and quietly the engine piles on the torque to get going while pulling up a grade.
This is the point at which the other new element in the driveline comes into play. This is also an all-new transmission. It is a first for Scania, an AMT with constant mesh gears as opposed to the synchro gearboxes the brand has preferred in the past.
Scania’s 16.4 litre 32 valve, twin internal cam V8.
It is quite normal in these pages to be test driving the first of something, but on this occasion, PowerTorque is test driving possibly the last V8 engine from Scania.
This new gearbox is a clean sheet design from the bottom up bringing Scania into line with the rest of the trucking world which has been using constant mesh AMTs for the last twenty years.
The Opticruise G33CM uses a completely brand new alloy housing which saves over 60kg in tare. The unit is a lot smaller then its predecessor, because it’s done away with synchros. Importantly the new AMT runs out to a wider set of ratios. From crawler up to direct drive, there’s a much bigger spread. The overdrive is not hugely different to the old AMT, but the changes are more centred around the lower box improving drivability at lower speeds.
This also gives buyers the opportunity to try different ratios,
meaning that many of the V8 trucks use a 1:3.07 ratio as a general diff option and not the 1:3.42 which has been standard in the past. There is also a 1:2.92 available which might suit operators looking for fuel savings and less concerned about drivability.
If you are asking why it has taken Scania so long to get to a constant mesh gearbox, the answer is likely to be along the lines of, if it’s not broken, don’t fix it. This is the good old fashioned Scania conservatism coming through, which we have seen before with the tardiness of the brand in getting rid of the clutch pedal.
The new AMT doesn’t have a separate reverse gear anymore. Instead, the box locks up the planetary gears at the back of the gearbox, which actually gives you the whole gearbox in reverse.
Drivers can access up to eight reverse gears. This means that when reversing this truck can actually start changing gears. This sort of functionality will be useful in some tasks, like those around road building and repair.
The new transmissions are used throughout the range, with the G25 for 7L, 9L and 13L up to 460hp, and then the G 33, which is for 500hp and above on the 13L, plus the 590hp and 660hp V8. There is not a constant mesh gearbox ready for 770hp engine, as yet. It will come, but they are still working on it.
There have been a couple of changes to the interior of the cabin. The electronic park brake is now standard. Because there is no longer a trailer brake hand-piece, there is a tug test button to test trailer brakes, when needed.
The truck in the test drive is a Scania R590 prime mover pulling a 62 tonne B-double set around country Victoria. Its performance has been excellent and it has smoothly pulled in the right places and cruised along in a relaxed manner in others.
No surprises there, the surprise is revealed when it turns out that the truck is running on 100 per cent biodiesel. Something which has been available for some time, but also something which did not catch on when it first appeared over 15 years ago in Australia.
Why would this technology which garnered very little interest back in the noughties, come back in the 2020s? There are several answers to this question, which go to the heart of the debate, here in Australia, about the road ahead for truck propulsion and climate change mitigation.
Biodiesel is a renewable, biodegradable fuel manufactured domestically from vegetable oils, animal fats, or recycled restaurant grease. It is often referred to as B100 or neat biodiesel in its pure, unblended form.
The first point to make here is that the performance of the truck using biodiesel was not noticeably different to the expected performance, if the truck had tanks full of diesel instead. This performance issue is important to keep in the back of the mind, when considering the other issues around the use of biodiesel.
There was no noticeable reduction in performance with the truck using B100 fuel, and the plus for the environmentally responsible trucking operator is that using biodiesel gives them an 80 per cent reduction in carbon emissions, in the operation of this B-double.
This is not a zero emissions solution,
but it is a way that the industry can start to make that transition away from fossil fuels and operate at low emission levels now, before the technology picture becomes clearer over the next decade or so. It can be seen as a bridging strategy across to genuine zero carbon operation.
The other strand to this option is the fact that if an operator decides to try this solution, secures a supply of B100 biodiesel and begins to operate a truck
like this, they are not locked-in. If the experiment is deemed as not an optimal solution, the truck can simply return to its original diet of mineral diesel and carry on its merry way with no negative consequences.
What this initiative does offer is a choice to operators and a way to begin the journey to a zero carbon trucking operation. One of the vital tools in any transition like this is full disclosure of potential issues and the supplier of the
You have to hand it to Scania for pulling off the big surprise of only telling us the full story about the truck on test, halfway though the R590 test drive.The truck is running on 100 per cent biodiesel.
truck explaining exactly how to get the best out of a truck running on B100.
“This is a here and now solution, so we can do, 320 hp and 280hp seven litre engines, plus 320 and 360hp nine litre, and 460 and 500hp 13 litre, and a 590hp V8 running with B100,” says Ben Nye, Director of Truck Sales at Scania Australia. “It’s here and now, literally out of the factory, it’s an $800 option. Or to do it locally, it costs roughly $1800, because you’ve got to change some o-rings in the fuel system to a different type to deal with biodiesel. Then there’s a software update, so it knows that it’s running on B100.
“It’s completely flex-fuel as well. So, for example, if we were on our way to Sydney and we were not going to get to our depot, we can put mineral diesel in the tank and it will run fine. You can run it on B100, full mineral diesel or a blend of both.”
One of the issues operators need to take into account is that swapping between different diesel does come with some issues. Whether or not the truck is running on B100 all of the time, it does have an effect on the
maintenance regime.
“There’s a negative to every positive,” says Ben. “So it does increase service intervals and does increase oil drains. We’re still establishing an exact maintenance schedule for our B100 trucks because we’re just getting back into it now. We did it a long time ago.
“Biodiesel does act almost like a degreaser. Therefore, as with any combustion engine, a little bit of fuel will get past the rings and into the oil. It means you do have to change the oil more often. But apart from that there’s being more stringent with the fuel filter changes. That’s really dependent on the quality of the fuel, as well. If you’re getting good quality fuel, you shouldn’t have fuel filter issues.”
Scania in Australia have signed memoranda of understanding with suppliers and their quality passes all of the Scania standards which have been set. So far, Just Biodiesel and Ecotech Biodiesel are on board, as well as biodiesel infrastructure suppliers Refuelling Solutions. The price of biodiesel is currently around $2.75/litre.
In terms of legislation there is no
current incentive for trucking operators to begin cutting down on carbon emissions.
“What we’re finding at the moment is that electrification has been our biggest biofuel seller, because the big fleets come to us wanting to make progress on electrification, then they realise that there are certain applications where electrification is not quite there yet,” says Ben. “They ask what they can do and biodiesel is definitely a solution. At the moment enquiry is extremely high.”
On Euro6 engines, those using biodiesel produce more NOx than those using diesel. This is taken care of through the SCR process, but the performance of the systems vary at different power ratings and not all engines can simply flip over to B100 and keep within the ADR 80/04 parameters. This is because some engine designs are closer to the edge of that NOx limitation than others.
Here in Australia, the incentive to move across to B100 will be for the operator sitting at the negotiating table with a big corporate client and being able to say, they can achieve an 80 per cent decrease in carbon emissions from transport now.
Those companies involved with the MOUs already set up can install pumps, tanks, within a transport depot, which will work for depot-to-depot operations. These companies also have some fuelling sites, but they are quite limited.
One of the issues for Scania is going to be the matter of explaining very carefully when it sells somebody a truck, that the quality of the biodiesel is a critical factor in the effectiveness of the solution.
Some of the older Scania trucks in Australia can be retrofitted to run on B100. However, some of them will require a DPF replacement, as the changeover from diesel to biodiesel can cause problems. Taking an older truck and converting it across to run on B100 also requires a series of short successive fuel filter changes, because the biodiesel actually cleans the fuel tanks. Once that process has flowed through the fuel filters, maintenance can return to the normal B100 schedule.
Getting its product from A to B is no easy task for MB Prefab Frames, based in Geelong, an operation which prefabricates and delivers roof trusses, wall frames and floor trusses for the building industry, predominantly residential.
“The building industry is, to say the least, an out-of-control environment,” says Darren Benn, MB PreFab Frame’s Fleet Manager in Geelong. “Material suppliers are a challenge at the moment. But with the team we’ve got, we have some stable, reliable sources for materials coming into us. Our relationships with our suppliers are absolutely paramount, especially timber, coming into the business, and we’re pretty fortunate to have some who keep up with the demand.
“The long-term relationships are what we work off, it’s absolutely paramount to our business. That shows in the fact that we are still open, we remained open during the pandemic, we were classified as an essential service as we were providing manufacturing to the building industry.
“We had a couple of close calls during the pandemic, the same as everyone. It is a bit of a roller coaster, but we managed to stay open and we’ve been able to supply our regular customers, which is what has been our main aim.”
The operation is part of the Big River Group, but prior to that it was a family-owned business, MB Prefab Framing. It was acquired by Big River Group in 2018, who have been in the industry for over 100 years, while MB Prefab Framing has been in business since 1977.
The operation has developed supplying roof trusses and wall frames
No transport task is simple and hauling frames and trusses onto building sites has the effect of increasing the level of difficulty, for an operation in Geelong.
PowerTorque Editor,Tim
Giles, pays a visit to its busy yard.Darren Benn, MB PreFab Frame’s Fleet Manager.
to the residential and general building industry in the Geelong greater region. Some work will go to Melbourne, but it is predominately around the Geelong and Surf Coast area, and along the Great Ocean Road.
“It’s crazy at the moment and we’re just trying to manage it, stay safe and supply our customers, that’s what we’re going to do,” says Darren. “The facility in Geelong is our main manufacturing site. We’re part of the Big River Group now, so we are one of 23 sites and this is, predominantly, our manufacturing site for roof trusses.”
The site gets its raw material delivered directly onto the site and the finished product is all going out as prefabricated roof trusses, wall frames and floor trusses.
“Once we have received packs of timber, we run it through our factory or we detail design it to the shape of whatever house is required,” says Darren. “We put it through our factory, where it gets assembled into the shape of wall frames or roof trusses. Then it is banded and bundled up into transportable packs. Then our drivers load them onto the truck and head out onto site.
“They’re all basically custom made, and every house is different. We’re like a more boutique type company. We seem to cater for the abnormal, higher end sort of stuff. No one else wants to manufacture some of the frames we do. We do build some normal sort of residential houses but a lot more at the bespoke end rather than the mass production end.
“Timing depends on the customer and the client. We’re dealing with builders and building sites so that is always a moving target. We try and build or design the frames, probably, about a week and a half to two weeks out. So when we actually manufacture we leave it out in our yard for, something like, three days is ideal.”
“Timetabling and scheduling manufacturing is fraught with issues, like rain, and problems like COVID and even the government authority’s team working from home when issuing permits.”
The total workforce on the Geelong site, including designers, office and people on the floor, is 64 people. Included in this total are four delivery drivers who run three Iveco prime movers and a Fuso tray truck. The fleet
is more than adequate for what the operation needs to ship.
The trucks do need specialist equipment like onboard cranes. The trucks are running over width most of the time and over length less often. One of the trailers is extendable to fit the longest loads. A transport coordinator handles the permits as and when required.
“We had a bit of trouble for a little while with permits,” says Darren. “But have got hold of one person issuing permits who is working well and we go through them all of the time. Once we get out of the local area and onto the Great Ocean Road it can be a problem, it’s a tourist road, we get caught there, frequently. If so we head inland and go through that way.”
Trailers include the extendable dropdeck, and another drop-deck with the rest being flat-tops. The fleet mainly use drop-decks for trusses. The smaller timber packs are laid out on the bottom deck and then the trusses can be laid out flat on top, over the full length of the trailer.
“Roof trusses are all triangular and there is an art in how these things get stacked onto a trailer,” says Darren.
The trailers don’t carry a lot of weight and are only occasionally over 10 tonnes. Therefore they all have tandem axles. The prime movers are sleeper cab with a crane on the back. The sleeper cabs are rarely used, although an occasional job as far away as Mildura brings them into play.
“It’s nice to have a bit of space and they’re a lot more comfortable,” says Darren. “We did take a look at the day cab and it was a little bit cheaper, but for what it was worth, we said we’re gonna stick with the sleeper. It does
work better with the crane, the sleeper cabin, because it does take weight back off the front axle.
“When it comes to finding drivers, we’re consistent. It’s always a challenge trying to find a crane truck operator, but the beauty about our operation, is we’re a Monday to Friday operation with the occasional Saturday morning. Because we delivered a building sites and those building sites generally start from 6.30 to four o’clock.
“That’s the beauty about our sort of industry, the drivers are not running
interstate and there is less pressure. While there is a bit of pressure, you know, these guys are good operators and they pull up on site and get builders who will say they need those trusses lifted up on here or there. It’s up to these guys to make sure that, number one, the builders are on site, because we won’t lift the trusses with a crane onto the top plate of a set of frames without a builder being on site. We’ve got to make sure the structure is stable in its own right.
“At the same time, we have to look out for overhead powerlines. We’re delivering to a lot of residential plots and we’re challenged all the time, especially with extensions in older residential areas. It’s okay when you go to a new area because there’s very little overhead powerlines or obstructions, other than tight streets.”
Delivering into built up residential, existing areas, there’s all sorts of things that can happen with power lines. The Logistics Production Coordinator has to be on top of these issues and doing all the homework prior to the trucks getting out on site.
The team will send people to take photos, if they’re not quite sure, they don’t want surprises. There is a check sheet that the builders go through and
“Once we have received packs of timber, we run it through our factory or we detail design it to the shape of whatever house is required.”The trucks do need specialist equipment like onboard cranes.
they tick it’s all OK, but when the truck arrives there can be issues around powerlines or access. If the crane can’t operate that means it’s going to be a hand unload of the product on site.
“We’ve got to have all the requirements when it comes to safety inductions,” says Darren. “We have a safe work method statement. The drivers go out and they assess the site to make sure that before they unload the crane or start unloading they make sure that the site is safe.
“The policy is that the drivers have to contact base if they don’t think it’s safe for them to get in there and do a job. We’ll deal with it from here, from a management level. It’s the drivers call, in the end, to make sure that the site is safe to unload. We will back them all the way, which is what you need to do. The last thing we want is some sort of injury or illness.”
The operation is willing to invest the time in training if it’s the right person with the right attitude. If they’re willing to learn, the company can give them another skill set. whether it’s a crane expert learning to drive a truck or a truck driver learning to drive a crane.
The prime movers in the fleet are all Iveco Stralis with a 455hp Cursor engine with the Eurotronic AMT. The trucks do get stuck on sites, and for the driver an initial walk through may not help them identify some of the soft spots on a site.
“There is growth, and potentially the workload is there, we’ve just got to make sure that we control any growth,”
says Darren. “Number one, with material that’s available to us within the building industry. We’re continually having our door knocked upon with potential new clients, given the current climate and status of building.
“There’s always growth potential here but you know, we’ve got to do it in a controlled way, and we have achieved that in the last couple of years.”
The frames being delivered are becoming more complex due to the fact that the industry is changing, with tools AutoCAD, and newer programs like Revit, which give designers a lot more flexibility with their design. This has
the effect of making frames a lot more difficult to build. Clients also want their own little unique stamp on the new house’s design.
“The people coming up with the new designs, don’t think about how to get them out to a site,” says Darren. “We do get challenged by the architects, designers, and when they come through here, it’s it’s up to us to make sure the structure is going to be fit for purpose and also for transportation. We have to ensure we can assemble them, put them together and they can be also be stacked safely to be actually transported.”
While no one can predict the future with absolute certainty, we’re confident it’ll be brighter with the new Scania Super. Our new powertrain has already gained a reputation for not only providing the smoothest drive on the road but also being the most fuel efficient in it’s class. Our new 13-litre platform, which now extends to 560hp, delivers a fuel saving of at least 8 %* allowing you to increase your fuel efficiency while also reducing greenhouse emissions.
But it doesn’t stop there. As with our new V8 engine family the Scania Super 13L engine can also run on B100 biodiesel**, further reducing your CO2 emissions by up to 80% with no adverse impact on engine performance.
So if you’re ready to meet the commercial and environmental challenges of today and tomorrow, you’re ready to meet the all new lean green Scania Super. Contact your nearest Scania Account Manager or go to www.scania.com.au to find out more.
*The new Scania Super powertrain, with the combustion engine as its centrepiece, will deliver a fuel saving of at least 8% compared to Scania’s current 13 l engine (DLU). The comparison is made for long distance operations.
**Applies to 13-litre 460hp & 500hp and 16-litre 590hp only.
The new range from Western Star brings a set of wholesale changes to the overall design of the trucks available from the brand. You’ve seen the big picture, now, PowerTorque drills down into the new trucks, getting down to X Series details.
Launching a new truck range for a brand like Western Star can be a tricky task. Any renewal has to balance the need to retain the traditional strengths of a good-looking dependable robust truck, with the requirements to include all of the latest technology, in terms of driveline, electronics and comfort.
This can be achieved by getting the small details right as well as the headline items. Here, PowerTorque looks at the fine detail put into the new trucks’ design and runs through the features drivers will notice.
FROM THE OUTSIDE LOOKING IN There are a number of changes in the X Series that are unique to the Western Star brand in the Australian market. The truck which emphasises this point the best is the 48X a truck, which doesn’t exist anywhere else in the world. The BBC configuration, with the DD16 engine and a raised cab is all unique to the 48X. Then there’s the 47X coming in an 8x4 configuration, another Australian only option.
When it comes to the 49X, it’s got the power hood, a larger bonnet with more internal volume than anything used in the US. The design includes a lot of features and improvements underneath which are needed for our higher temperatures and increased GCM which 49X will run at here in Australia,
plus coping with the rougher roads.
The model of the 49X on display at the launch was fitted with a King Bullbar, with posts designed to be as wide as possible. The bonnet has a bigger front end opening than on previous Western Star models, which already coped well in Aussie conditions. Western Star has actually increased its cooling capacity overall.
The trucks have now got LED headlights a standard with a polycarbonate lens cover, in a fully sealed assembly and with a rating of 4000 lumens, the maximum allowed by the ADR. Although, Western Star are confident of the capability of these lights, the example on show still had extra large driving lights added, because the road train customers will always specify them anyway, it’s true, you can never have too many lights.
The bonnet is now made from a moulded resin instead of the previous fibreglass design. This makes it more flexible, and is claimed to be more durable and impact resistant than the previous model. It’s also 46 to 49kg lighter than its predecessor. Mounting the air intakes inside the bonnet brings an additional 27 kilos of weight saving.
It’s now easier open up the bonnet with one hand, and it now automatically locks down. The bonnet is no longer chassis mounted, but on a dual coil over shock system, to take out chassis
vibration on the bonnet. The bonnet is a three piece meaning it will be possible to just replace one section instead of the whole thing.
The chassis design now has splayed frame rails at the front, and in conjunction with the larger bonnet, this enables Western Star to fit the radiator inside the chassis rails and keep it mounted high. Another plus is the fact that the chassis rails now come right through to the front of the truck, making it less prone to animal strike damage.
The new trucks also include a coated steel engine tunnel, making the engine noise inside the cab quieter. It also reduces any heat transfer up to the cab, the coated steel acts as a dampener for both heat and for noise.
The 49X is fitted with a 1600-squareinch-aluminium radiator, with improved capacity when compared to the copper brass unit used in the past. Aluminium improves cooling and larger tubes help dissipate heat. There are one inch longer fan blades and additional blades (now up to 11) and this all helps cooling capacity as well. Higher cab mounting on some models also helps improve air flow allowing hot air to escape out of the engine compartment.
The layout of components under the bonnet has been tweaked, making daily checks easier and more convenient. The splayed rails mean there’s more room around the engine, making it easier to service, for a technician. When it comes to a rebuild, it’s easier to get the engine in and out.
The under bonnet air filter interval of 12 months, or 160,000km comes from the fact that air cleaners that have been tested here in Australia and they’ve only been reaching 30 percent of the capacity of the filtration system.
The larger cabins now available have come from the Daimler (Freightliner) catalogue, but when fitted, to retain durability there are steel crossbeams fitted to maintain rigidity. These are exclusive to Western Star. Customers will expect the new models to match the previous models and live with all the offroad conditions, corrugated roads and perform in the worst of applications and stand up to the battering.
Overall, there is an eight per cent weight saving on the cab compared to the Constellation on the previous models.
Another change with the new 47X model is the availability of lower cabin heights, with what the US calls the ‘trench roof’. The name comes from the shape profile of the roof when looking from the rear. This roof design is 39mm lower than the standard day cab, with the sleeper option 30mm lower.
This change should help Western Star in those applications where cabin height is at a premium, in sectors like car carrying. With the top of the trench roof day cab 1903mm above top flange face of frame and 36-inch sleeper trench roof at 1912mm above top flange face of frame, Western Star are back in
Ergonomically, the soft touch dash works well with all of the controls at arm’s length.
a sector its cabs outgrew in the past.
The new X Series sees the arrival of the rectangular fuel tank solution as an option, round tanks are still available. With the four tanks on the 49X on show, the fuel capacity is just under 2,000 litres. The 48X can get up to 1500 litres fuel capacity. In fact, the design of the new range means there is a more flexible and customisable array of fuel tanks options.
The chassis rail uses high tensile 120 KSI steel single rail and Western Star have moved away from split conduit plastic wiring, to a fully wrapped concealed electrical loom, with bodybuilders able to run any wiring separately on the chassis. These new models have a full multiplex wiring system, making access to vehicle data available around the truck meaning controls are available as plug-and-play options in the cabin.
The standard chassis will be built with threaded bolts, but customers will have the option to go with huckbolts, if they prefer. One change on chassis design is for the bolts to be threaded though the rail with the bolt heads on the inside of the rails and the nuts on the outside. This is reckoned to improve maintenance outcomes and simplify some tasks around the chassis.
As a power plant, there’s the Detroit DD 16 engine, coupled with a choice of Allison auto, Eaton Roadranger and
the Detroit DT12 AMT (More on this in a subsequent article). The truck has a completely 12-volt system, as you would expect from a North American truck.
FROM THE INSIDE LOOKING OUT Climbing up into the new cabin the first thing you notice is the ’70 degree ingress’ which describes the way the aluminium steps are set back so that it’s
It’s now easier open up the bonnet with one hand, and it now automatically locks down.
not a vertical climb up into the cabin, it’s more like a set of stairs. This is corrosive proof aluminium and there’s checker plate around the exhaust box as well. There are five points of contact when you’re getting into the truck because there are the steps, an outside grab handle, one on the door and two grab handles inside the door.
There’s a cab isolation switch on the floor next the driver’s seat as standard, with the option of an added battery isolation switch as well. The seats are well specced Isri models.
Of course, it would not be a new modern truck without the full multifunction steering wheel, with which we are becoming more and more familiar.
Looking at the dash it is a well laid out, but a standard looking array. To the driver’s left, on the binnacle, there are dials, radio and aircon controls. One step to the right is the customisable area. This is where operators can put any sets of controls they want or leave it blank. This will be the home of the screen for the entertainment system which will follow later this year.
Below these two areas is a long set of multiple switches, plus the maxis and trailer brake. This is where the magic of multiplexing comes into its
own. All of these switches are plugand-play. Along the bottom is an array of hardwired 10-amp switches which can be pulled out and moved, they’re interchangeable. The operator can swap these around. When they clip out the blocks of switches, a driver can tailor the dash layout whichever way they want it.
The new X Series dash, directly in front of the driver, has a fully electronic screen and the driver can toggle through options on the screen to suit their tastes. This is where the driver will control the driver assistance system. They can set options like following distance with adaptive cruise control, plus there are a large number of vehicle settings and monitoring available on a system with which many would be familiar as
it appears elsewhere in the Daimler Trucks portfolio.
There is also a series of digital gauges, from turbo and temperature, diff temperatures. This is where all of the diagnostic information a driver needs will appear. In the same way as the multifunction steering wheel has become the norm, so have these information screens.
One of the parameters the driver can control is the amount of overspeed allowed, when in cruise control, before the engine brake kicks in. This can be set from one km/h up to over 20 km/h, but there is also a no limit option available.
All of this is a big step forward for Western Star, arriving along with the X Series, taking the brand out of the older, more basic world of the past into
a pragmatic future, where electronics and software work alongside the metal of the analogue world. Access to the technology is right in front of the driver’s eyes.
Ergonomically, the soft touch dash works well with all of the controls at arm’s length. The driver position is much improved with everything at hand. The environment is also quieter and more relaxed for the driver, with engine noise reduced and comfort levels improved.
All round visibility has improved with a windscreen which is slightly larger. Western Star reckon the visibility is a 30 per cent improvement on the previous models. The single windscreen also includes the camera for the safety systems and a rain sensor, in the middle at the top.
Programmable switches are quite a revelation for the brand. The requirement to fit different control boxes in the cabin for items like tippers and tarps can be avoided as the wiring for the controls can be programmed into the existing switch options. This makes life easier for maintenance, but also tidies up the cabin interior
It is possible to program a switch for many functions which operators require. One example quoted, is the need by some tipper operators to be able to keep the prime mover brakes on but release them on the trailer to make tipping easier. It is possible to program this in with any number of preconditions, e.g. the driver is in their seat, the engine is running, the flashing beacons are on, the driver’s door is closed and to sound the horn twice.
When this has been programmed on the technician’s computer, it can be allocated to a truck or trucks. When the truck comes in for a service and a laptop is plugged into the diagnostics, it will download that function into the specified switch. This opens up whole load of safety functionality possibilities for operators.
In the past, this could only be done by a specialist fitting complex control systems and hardwiring added onto the existing wiring loom. It also enables Western Star to keep bodybuilders out of the multiplexed wiring system, but still get the functionality needed for
individual operators.
This is the kind of customisability which truck buyers will be looking for in the future as the systems in and around the trucks they buy, become more complicated and sophisticated.
A large information screen as the window into a new infotainment system is in the pipeline coming in 2023. This screen can be simply used as an entertainment system and will be able to use Apple CarPlay and Android
Play, providing a platform for countless apps. However, if required the screen may also display some different difital gauges, which the driver may need.
The new X Series models are also fitted with the Detroit Connect telematics system with five years of access to the system coming bundled with every new truck purchase. The full details of this offering and the power of the system will be explained as part of a subsequent article on the Detroit contribution to the new trucks, in terms of engine, transmission and telematics. This story is slated for the March issue of PowerTorque.
Walking around inside the 72-inch cabin, the options available look able to match or surpass the fit and finish offered by the competition. Clearly this is the top of the range option and only available to truck buyers where BBC dimension is not a major issue for the operator.
The large bunk with a 40-inch coil sprung mattress can be folded back out of the way and a section of the bed base lifts up to become a table with a seat either side. There is also room for plenty of cupboard space, TVs and microwaves. This cabin is available as either a mid roof or Stratosphere high roof option.
Shell Card is the culmination of all we’ve learned about Australia’s truck drivers since we first started working together in 1901.
It’s your passport to our Australian Truck Network, giving you access to discounted fuel, a wide range of driver amenities, a national network of strategically located Shell service stations, and a whole lot more.
Talk to us about Shell’s Australian Truck Network, and how Shell Card can help drive your road transport business towards a better future.
shell.com.au/trucknetwork
Despite the fact that the new alt-power technologies dominated the event, IAA also witnessed the presentation of the International Truck of the Year being awarded to DAF, for the Paccar brand's XD model, designed to handle urban distribution and short haul tasks.
Here the IToY is handed over by Gianenrico Griffini, International Truck of the Year Chairman, to Harald Seidel, President of DAF Trucks. This is the second year in a row that the DAF brand has landed this prestigious trophy
The Dutch truck manufacturer's distribution series fought off tough challenges from Scania's new Super long-haul driveline range and Mercedes-Benz's heavy-duty Actros, equipped with the third-generation OM 471 engine.
The seismic shift in truck manufacturing which many have been talking about in recent years made itself very visible at the IAA Transportation exhibition held in Hanover, Germany. It wasn’t just about electric trucks, there were plenty of hydrogen drivelines on the displays, but not many diesels.
The were many stands at the event which were allelectric and not one truck stand which was only displaying diesel models. The smaller ancillary stands were also dominated by exhibitors who were also in the alt-power space, with electric chargers, hydrogen fuel cells, hydrogen tanks, battery technology et al.
The usual selection of European-based manufacturers were joined by a substantial presence from Chinese electric truck makers who were displaying substantial altpower truck ranges in Germany, alongside the growing number of independent electric truck start-ups popping up around Europe.
Of course, the truck count at the exhibition doesn’t mean we are all going to be buying electric and hydrogen trucks next week, but it does illustrate a step-change in the way trucks are designed and built is with us, and there are going to be plenty of new technologies moving into the road transport space, firstly in Europe and the US, but increasingly, here in Australia.
Here’s a selection of the exhibits on display:
The winning truck range dramatically improves direct visibility (a key factor for distribution vehicles), internal cab space, aerodynamics, fuel efficiency, active and passive safety, and driver comfort. Read about our first road test of the new model on page 62.
There was one overarching message coming out the display stands at the IAA Transportation exhibition in Hanover, and that was bye-bye diesel and hello electric.
The
With a winning score of 112 votes, Mercedes-Benz
(BEV)
The IToY journalists praised the advanced characteristics of the eActros LongHaul, which employs fast-charging longservice life lithium-iron phosphate cell technology (LFP), and the speed of Mercedes-Benz Trucks' R&D process. Indeed, announced for the first time in 2020, the eActros LongHaul is already undergoing intensive testing, is already on public roads this year, and near-production prototypes will go to customers for real-world use testing in 2023.
Cummins seemed to have a solution on display for every eventuality. The company has two-bob each-way on whatever alt-power driveline becomes popular in the trucking industry.
On display was this agnostic internal combustion engine platform which has a different cylinder head for hydrogen, biodiesel and biogas. If you aren't keen on a combustion engine, but would like to use hydrogen, then Cummins had a fuel cell option on display.
The Quantron brand out of Germany displayed a range of trucks which can be powered by hydrogen fuel cell or battery-electric. The company has developed its fuel cell together with Ballard Power Systems.
Although originally developed in the US, the Nikola hydrogen fuel cell truck brand is now working with Iveco as a partner. The new trucks are being built at the former Stralis plant in Ülm in Germany, for the European market, based on the Iveco S-Way model.
Tevva is an electric truck brand from the UK, which was test driven and featured in the May 2022 issue of PowerTorque magazine. BYD is a serious player from China, which showed a substantial range of electric trucks at the IAA. DongFeng displayed a light duty range of electric trucks.
All of these electric trucks need to be charged. The makers of the various charging systems on the market had a major presence, as the need for this kind of infrastructure ramps up. Brands on display included, Siemens, TruckCharge, Eaton, EKO Energetyka.
On the Mercedes Benz GenH2 truck, the fuel cell lives where the engine normally sits, the liquid hydrogen tanks replace the diesel tanks and there is plenty of ancillary equipment involved in the system, which fills this space to the rear of the cab.
This IAA event saw all of the big brands go electric, to a greater or lesser extent. The new Fuso eCanter was on display, Volvo's stand was all-electric, including this smart FM prime mover and MAN had this heavier prime mover, with a high claimed range on its stand.
The Scania low diesel consumption candidate is the new Super driveline, in a distinctive red and white livery and test driven in PowerTorque in the March 2022 issue.
As the world of trucks heads into an era where technologies are going to start changing fast, the trucking exhibition at IAA Transportation in Hannover, Germany, last year was an opportunity to get a deep dive into Daimler Trucks’ technology strategy globally and how the company’s three brands want to shape the future of sustainable transportation.
PowerTorque spoke with Dr Andreas Gorbach, Daimler Trucks CEO – Truck Technology, about how the next decade or so is going to play out in terms of driveline technology.
“We have to look at where we
come from, more than 120 years of diesel,” said Andreas. “That’s really remarkable right? This technology is everywhere, from the cities of Austin, São Paulo, to mining in Indonesia, to construction sites in China, and long haul trucks in Europe. All these different transportation tasks, the different market requirements, and different legislations. We always answer these different questions with the same technology, diesel, because it creates the most value for shareholders, customers and for society.
“It was a robust, cheap technology, available everywhere. Looking backwards, that’s really remarkable, one size fits all. Then we added
electronics, we call it the decades of sophistication, where we added intelligence to the truck, step by step. We brought in functions, and we added more and more intelligence to the truck.
“Both pillars, diesel and electronic architecture are the foundation of our success today. The best functionalities, be it driver assist, brake assist, predictive intelligence, plus best in class powertrain. That’s the foundation of our business and also the cash generator for what we do in the future.
“Now the two big changes are decarbonisation and CO2 at the tailpipe is something which needs to end to if we want to comply with the Paris Accord, and we are committed to the Paris Accord. So we cannot continue with diesel.”
If Daimler Trucks is going to meet the requirements of the Paris Agreement, it’s got a hard target to meet. There are going to be a series of stages to get from here to there. PowerTorque asked whether Daimler had quantified those stages and decided when it will reach the each technological goal, then move on to the next one and the next one.
There may, or may not, be a breakthrough in battery technology but is there a particular point or a particularly year as a final deadline?
“We basically are now, step by step, electrifying our portfolio by 2025/26,” said Andreas. “We will have all relevant trucks, for every niche application. We will have all relevant trucks electrified and then we have hydrogen. We do believe that the limiting factor in speed and volume of truck development will not be the product portfolio anymore.
“The dominating factor for the speed of the transition across to zero emissions trucks will be infrastructure, plus, the question around total cost of ownership for our customers. It
The team at Daimler Trucks took the opportunity at the IAA Transportation event to communicate their vision for drivetrains down the track. What are the options for electric, hydrogen and diesel?
very much depends on the price of electricity, the price of hydrogen, and the price of diesel. A couple of years back people were looking at us saying you have to get started. That was the rationale for the CO2 regulations which came into place.
“Now the industry, not only Daimler Trucks, but the truck industry will not be the limiting factor anymore. From a product side everybody will be there. We will have the flexibility to develop at the same pace as the infrastructure or the total cost of ownership case for the customers. I am honestly rather scared that the speed on the infrastructure side is not fast enough to comply with the Paris Accord.
“That will put us in a very difficult situation at the dealership level in the future, they want to sell a truck the battery electric truck or hydrogen truck and the customer says I can’t buy it, because there’s no infrastructure. Then the dealer has to tell the customer they cannot sell them the diesel truck, because they cannot pay the fine. It’s too high. That could be an awkward situation. We want to be so flexible that we will never be the bottleneck for deployment of the technology.”
There’s going to be declining volume for diesel over time. Large truck makers are going to be partnering with others on diesel technology as well. Sharing platforms across brands.
“On the medium duty side we have already disinvested completely in our own proprietary driveline product and gone with Cummins,” said Andreas. “Cummins is the last man standing. It’s a question of who sells the last diesel engine on this planet and it will probably be Cummins.
“We needed consolidation on the medium duty side, it’s not viable as our volume is too low. Also the speed of decarbonisation is higher on the medium duty side when compared with heavy duty. In heavy duty we have, what I’d say, is the best product and we still have enough scale to make it worthwhile for us. This is why we will still invest, but we will also partner here.”
On this topic Andreas confirmed that we can expect an announcement, sometime this year, on a major collaboration project between Daimler and one of the other global truck and engine makers for future heavy duty diesel engines.
“We have still have to invest in heavy duty diesel,” said Andreas. “As the volume does go down over time, and the regulators are also working on
new regulations, so we invest in battery electric trucks and in hydrogen electric trucks. This can only be done with partners. We are doing it with Volvo on the ‘Cellcentric’ fuel cell development and there are more partnerships to come.
“This is most likely to be the biggest challenge this industry has ever seen, also the biggest opportunity, but this challenge, we can only solve it together and we will do it with other value partners, other OEMs and other tier one manufacturers. We need to keep the volumes high for our suppliers. We need consolidation in the diesel engine industry.
“Frankly speaking, we don’t know when we will finally eliminate diesel engines from our product range, but we are shooting for the year 2039, for the main markets. But we cannot answer the question because the decarbonisation speed is not only dependent on our product portfolio, it will, in the end, be determined by infrastructure and energy prices.
“If there’s still one drop of oil below the surface of this planet and worth more than 40 megajoules per litre, and the agreement between the states in the Paris Accord becomes unstable, then some countries will continue with diesel. Then we could consciously decide not to sell to those countries, but then some other OEM will sell to them.
“WE DON’T KNOW WHEN WE WILL FINALLY ELIMINATE DIESEL ENGINES FROM OUR PRODUCT RANGE, BUT WE ARE SHOOTING FOR THE YEAR 2039, FOR THE MAIN MARKETS.”
We are not expecting transportation to go away.
“We need really strong collaboration amongst the states that signed the Paris Accord and they all need to invest in infrastructure and provide cheap green energy. This is the solution. This is why it’s so difficult to ask when do you sell the last diesel? It’s a fragile system on this planet at the moment. Who has the power and the political willingness to really go down that path and continuously invest in green energy?”
“What is technology for us in a truck?” said Andreas. “Technology for us is always a key lever to create value for our customers, for our shareholders and at the end also for society. This is how we innovate, how we engineer, how we purchase, how we produce and how we sell. This is how we tick, technology is a key, technology always creates value.
“There are two attitudes that are the most relevant, one is long term differentiation and the other is commonality. Long term differentiation asks, which technology in front of the
customer makes a difference in all the markets, for all brands now, for five years and 10 years? Commonality this is basically the role we play to engineer and deploy global platforms. These two attributes describe our key technology, the best needs to differentiate
everywhere, and we need to roll it out to create scale, scaling to profit.
“Now what are the most relevant technologies to meet these needs? How do we reduce climate change, is it with diesel, battery electric or fuel cell? Intelligence comes from everything related to electronics and software. These are the two main differentiators for our customers moving forward.
In terms of digitalisation, we need to transform the truck into a programmable device, and this hardware based architecture with decentralised intelligence, will not carry us forward.”
The process of dealing with climate change creates disruptive changes. On the propulsion side, Daimler will focus on diesel in the transition, while pushing two zero emission technologies, battery electric, and hydrogen-based propulsion.
In terms of intelligence, the truck maker is moving forward to what it calls software-based architecture. This is more centralised electronic hardware with more computing power, where all the of the separate units speak the same language, use the same operating system and data can be flashed across applications, and integrate the truck in the control systems of truck customers.
The interest in electric truck is going through the roof at the moment. Customers ask their transport suppliers what their zero carbon plans look like and this request passes down the chain. At the same time, there are few electric trucks on the road, for now. Truck manufacturers who have an electric option in their line up are flooded with enquiries. Truck makers without an electric option are being asked when they will have one.
“We’re in this interesting situation, where we’re out of the introduction phase,” says Paul Ilmer, Vice President Emerging Technology Business Development at Volvo. “We’ve integrated the trucks and they are just a part of our portfolio. It’s no different than a diesel truck, the salesman orders the vehicle and they follow the same process, talk to the same people. The trucks are fitted up, the body is prepared.
“We’re doing a lot around deliveries, but then at the same time, we’re doing a lot around the preparing for the heavy
duty range in 2023. Regulations are still an issue and we’re doing as much as we can through the Truck Industry Council, the Australian Trucking Association and the Electric Vehicle Council, to try and raise awareness that it is the only thing holding us back, there is nothing else.
“The regulations are the primary one, and when we talk to the government, to
those in charge of the programs, most of the time, they’re looking for something else. This is it, everything else is in place, and we’re saying all you need to do is to have a sensible front axle mass limit for these trucks. You cannot make them lighter because a battery cell is a battery cell and you need so many of them to travel 300 or 400 kilometres.”
The truck manufacturers also need to get involved in the electric infrastructure as well, to aid customers in getting the right supply of electricity in the right locations to make their freight task work.
“We’ve established a lot of partners and use, for example, Jet Charge, ABB, Kempower and Siemens,” says Paul. “We’ve got a lot of partners we bring in to help support with electric infrastructure and the ecosystem of electric mobility. We commission them to do the site audits. A customer will have so much energy available, now, but wants to use so much more in the future. Is there room for a 100kW DC charging or 50kW or 22kW AC charger?
“At the moment, I reckon 50 per cent of our time now is spent on the truck, and 50 per cent of the time is on
the charging. Customers really need good, trusted advice, they need good chargers that have aftermarket support. If a customer can’t supply energy to the truck, it’s a useless situation for them. A lot of our work has been finding really good partners to work with, and then, if there is a challenging aftermarket, they’ll provide the same support to the charger that we will for the truck.”
“When we have discussions with customers, we can do range simulations, even prior to them even thinking about electric,” says Paul. “To help a customer make a decision whether electric is for them now or later, they can do it virtually, which takes all the risk away.
“We can plug in charge points, we can add the diminishing nature of the load, the consumption of a tail lift, for example. When their trucks are in service that allows us to monitor the vehicles, as well, and try and work out things like, we’ve had some trucks coming back with 50 per cent charge in them. Then we’re saying to the customers, they can still do another 120km with this thing. It has been helping the customers, when the vehicles are in service, to get the most out of them.”
Practical experience with the trucks on Australian roads for Volvo, indicates the electric trucks are four to five times cheaper to run, especially if you factor
in current fuel prices. In terms of initial outlay Volvo are quoting electric trucks as being around two and a half times more expensive than the equivalent diesel model.
“The cost case for electric trucks is quite compelling now, we started doing these calculations on $1.50 per litre for diesel,” says Paul. “Now, it’s a very different story. Then, of course, if the government decides to throw in some support, as part of the National Electric Vehicle strategy, we will be run off our feet.
“Even now, with the demand that we’re getting, there’s this pragmatic view that the technology is just being launched and it’s not going to be the same price as a diesel. So the cost doesn’t come into it a lot, it’s more around the carbon abatement and the opportunity to move towards zero.”
It is now possible to mount an economic case in a business to transfer over to EV and achieve a cost saving overall. Add into this, the number of operators with large depots which can put solar on the roof.
The whole idea of fleets of electric trucks and the development of an electric truck ecosystem is dependent on well informed transport operators and truck makers who understand what electric truck customers want.
“Corporately, we talk about a total solution, it’s how to get from current state to future state, from the electric truck perspective, from the charging perspective, from a driver training perspective. It’s really starting at the basics, like range, payload, then moving into things like overnight charging versus opportunity charging.
“Sometimes it’s a bit of a consortium, bringing in the customer, ourselves, the charging supplier, the charger, the charger commissioner. It’s very different, customer by customer. But the basic starting point at the moment is, what is an electric truck?
“We try to understand the business, you kind of need to understand, what the customer does today, what does the customer want to do tomorrow. In some cases, we have to say, ‘electric isn’t for you yet, it might be in five years time’. We have to be quite upfront, otherwise, we create a situation for the customer and for ourselves. For a cement mixer, for example, we say, ‘No, it’s not yet, it’s
probably a couple of years time.”
The Volvo team may suggest electric is applicable elsewhere in the customer’s business. Perhaps a support truck might make sense for the customer, to get them started, to get into the rhythm of electric transport, for the fleet managers to get used to it and allow the drivers to experience it.
It can be an education process to begin with, a toe in the water. It can also be a process of understanding the solution. They can work out whether they should buy the truck outright or over an operating lease, there’s a number of different avenues, they can go down with electric.
“It does mirror, the same approach as a diesel truck, quite often,” says Paul. “There are times when a customer wants the body, the truck, and the charger, and we then have an almost pick and pay approach depending on the customer’s needs. There are times when a customer has a charger, so we don’t have to worry about that. We have to be ready for various options and we have to be fairly agile around
how this approach may work for customer A versus customer B.
“From a safety perspective, we made sure that the dealerships are trained in 600V systems and how to do that safely. We’re rolling that out now. We can manage the resource workload, where the first trucks are going, we focus on those dealers first. The dealers are so engaged in this, the salespeople love it, it’s a different technology.
“It’s interesting, and it’s kind of exciting and they love to be on the cutting edge of this stuff. Some of our work involves getting them involved with charging suppliers. Part of the requirement to be an EV certified dealer is you have to have a charger on site.”
Trucking is looking at the current electric offering and asking about what a battery electric truck is going to look like in the foreseeable future is there going to be stability in the product range?
“With the medium duty EV, we’ve gone through a couple of iterations, when it comes to batteries, and I think with the heavy duty arrangement we’ll have in 2023, I think that’ll be stable for probably seven or eight years,” says Paul. “From an investment perspective, you have to be able to pay back the investment. You don’t want to be changing every three years because, then all of a sudden, on these projects, your rate of return and the payback period becomes too short.
“I think this is a period of stability. I think it gives the market confidence that they won’t have a different truck that can replace the truck they’ve got now. I think we’ve done so much R&D, like our partnership with Samsung, for example, on the batteries, it puts us in a position where we have quite a mature platform now.”
Volvo does have an e-axle in development, which was on show at the IAA in 2022, and this should flow through into the Volvo product around 2025.
Across Australia, many rural transport businesses are desperately short of workers. Drivers are top of the list, but we need more forkies, schedulers, diesel mechanics, fitters, electricians, welders, yard hands and just about everything else. But with every sector of the economy booming, where are these workers going to come from?
We have a real problem in Australia right now. After three years of ‘on again, off again’ COVID lockdowns our economy has rebounded in style. In the September Quarter 2021, our GDP decreased by 1.8 per cent. A lot of Australian businesses and workers felt that hit, with the Australian Government shoring things with Job Keeper and Job Seeker payments. Other governments at all levels provided different forms of relief and stimulus. The Reserve Bank of Australia (RBA) did its bit by reducing interest rates to near zero.
By 2022 there was a lot of cheap money floating around the economy accompanied by a lot of pent-up demand. We all know what happened next. Boom. GDP rocketed back to 3.9 per cent. Unemployment fell from 7 per cent to 3.4 per cent. And inflation jumped from -0.3 per cent to 7.3 per cent.
The RBA has since rushed to put the brakes on, jacking up interest rates on seven successive occasions. It’s fair to say we’ve over-cooked the COVID response and it will be a while before the kitchen cools down.
These are big national and global issues. Yet, the ALRTA is leading the way in dealing with the skills challenge.
Firstly, we have the immediate problem of sourcing job-ready workers. Incredibly, the Australian Government does not consider truck drivers to be skilled workers – so we are working to change that. We have already been successful in lobbying the National
Skills Commission to add truck drivers to Australia’s Priority Migration Skilled Occupations List.
This is a necessary first step to opening up new visa pathways allowing businesses to engage job-ready migrants. The next step will be to change the Australian and New Zealand Standard Classification of Occupations to elevate truck drivers from skill level 4 to skill level 3. Attaining recognition of skill level 3 would grant automatic access to important visa classes.
Secondly, ALRTA has supported the establishment of a new two-year driver apprenticeship based on certificate III in driving operations. This landmark qualification is now available in Tasmania and Queensland, with all other states and territories actively progressing the concept. A recognised national qualification will give credence to our argument that truck driving is indeed a skilled occupation, while also creating an attractive career pathway for young people who are considering entering the road transport industry.
Most parents want their children to get a recognised trade or other form of qualification so they always have something to fall back on. The truck driver apprenticeship has a status similar to that of trades like plumbing, electrical and mechanical. Parents and young people can now proudly pursue a truck driver apprenticeship knowing that a recognised qualification will be acquired, not just a job.
Thirdly, ALRTA has recently responded to a paper exploring possible changes to the National Heavy Vehicle Driver Competency Framework. The framework has not been adopted consistently across Australian jurisdictions and in many ways is not fitfor-purpose in a modern, safety-oriented world. The central beneficial change under consideration is a new competency-
based pathway for progressing through the various licence categories.
Currently, applicants obtain a lower-level heavy vehicle licence (e.g. medium rigid) and must then wait a minimum mandatory period (usually 12 months) before becoming eligible to apply for the next level. Under this system, it is not necessary to complete any actual driving time, while those who do rapidly build up significant skills are held back from progressing until the mandatory period is served.
A competency-based licensing pathway would reward good drivers. It could deliver better drivers, sooner. Exactly what we need right now.
Outside of the regulatory system, there are also positive ways to make our jobs more attractive. For example: schedules can get drivers back to family and friends more often; technology can help people feel less isolated; we can reduce workplace safety risks; we can stand behind staff who raise safety or cultural issues of concern; we can create rewarding career pathways; we can recognise excellence on the job; and we can celebrate diversity with a more open and inclusive workplace.
Fundamentally, we must stand proud, acknowledging the essential service that road transport provides for the rest of the Australian economy. We must demand a regulatory system that recognises our skills and professionalism. And most importantly, we must foster a workplace culture that job seekers want to be part of.
The Australian Livestock and Rural Transporters Association is concerned about the skills shortages affecting the industry.
The national and state road network is slowly opening up to higher productivity vehicles, but on sticking point has always been the last mile. This is true in the cities, but much more prevalent in rural areas. That last leg of the route, to farm gate, is often on local government roads, which are poorly maintained, at best.
In a move to improve access and to get more data on real world road use in these areas, Transport for NSW has developed a program to offer higher productivity vehicles farm gate access in return for anonymous data about truck movements in these areas.
The plan is to use this data set to be able to inform road maintenance plans. The ultimate goal would be for every vehicle to contribute information on how the network is used, to a point where it informs those assessing the need for funding that comes from the state government and federal government, to contribute towards
any road repair and upgrade.
If they see a trend that vehicles are traveling a large distance to get around a structure that can’t support access, then the data should be able to feed back into a bridge replacement programs to make it a priority structure to be replaced.
The need is to spend the very limited dollars available at the places that make the biggest difference as soon as possible. That that kind of thinking takes away the issue of state roads versus local roads, it may be that local roads are where you identify the biggest issues to be, It’s highly likely that authorities will find a lot of issues on local roads with this sort of data. This data will become useful, but only if vehicles are enrolled in the telematics application.
Scott Greenow, Director Operations Freight Regional and Outer Metropolitan at Transport for NSW talked at the LBRCA Conference about the concept behind the agency’s Farm Gate Access Network concept, which has been
though a pilot process in the state.
“A really fantastic piece of work, we’re quite proud of this, it was an opportunity that was derived from the LBRCA,” said Scott. “They also said, ‘if we’re honest, we already do it’. It’s just so hard to get compliant access, and to apply for permits, that we do it without them. The good thing is that this lines up with our ethos about access in New South Wales, we’re after safer, more productive, more sustainable access. So we don’t want you to go across a state bridge that can’t sustain it. You don’t want to go through a bridge, you don’t want to be responsible for making a breach that ruins it for the rest of that community.
“After these discussions, we turned to the state’s councils. Surprisingly, they said they were after safer, more productive or sustainable access. It occurred to me that this can’t be that difficult. If everybody wants the same thing, there has to be a solution to it. That’s when we realised that we don’t know enough about the network to be able to do assessments fast enough to provide the access that you guys need.”
The Transport for NSW team understood that the state’s road network has a genuine ability to sustain this access, because trucks are already going there. The fact they are being used is evidence of the route’s capacity. They also know that some bridges can’t sustain access.
The councils were asked how they would feel if they could see where everybody goes, when they’re on their networks? The answer came back that if the data was supplied, the councils could come up with approval. If real data about what was travelling where could be provided to road managers, they
There is little doubt as to what would make life for rural carriers in New South Wales a little easier; it would be genuine state wide farm gate access. A discussion at the Livestock and Bulk Carriers Association saw strong views on both sides of the argument.
would reduce restrictions.
“Is there a way that we can collect data from industry?” is the question Scott took to Transport Certification Australia. “Where I cannot see who owns the truck, or have any opportunity to identify who was driving it or where they were at a particular date or time. That’s where they introduced us to things like Road Infrastructure Manager (RIM), the Telematics Monitoring Application (TMA), and these were applications outside of IAP.
“That was where the magic really started to happen. With the LBRCA, with the service providers, with industry leaders in fitting telematics, and enrolling their telematics into RIM, what we were able to do was then provide information that road managers need to be able to say yes, to access. Also, the information, they need to be able to make smarter decisions on maintenance
on their road network and investment in that network.
“We had the ability for industry which were enrolled in these telematics to be able to access all the roads in those participating councils, without having to worry about the time it can take for the access assessment, etc. It was a fairly phenomenal piece of work to get to that point.”
The pilot started with six councils that put their hand up and said they’d like to be part of the scheme. In the first 12 months they would allow anyone that’s enrolled in RIM and meets the Livestock Loading Scheme or the Grain Harvest Management rules appropriate access in
their shires.
The local authorities would allow specified trucks, B-double, A-double etc on all roads in their area, apart from selected bridges that they identified, selected residential areas and some intersections that for road safety reasons they preferred trucks to avoid.
“All of a sudden, that changes the dynamic, for anyone that wants to operate in that area, you know where you can go,” said Scott. “If there’s a breach that blocks the ability to get there on your preferred route, you can use whatever other available local road network to get to that location, and continue to do the tasks that they already
“QUITEScott Greenow, Director Operations Freight Regional and Outer Metropolitan at Transport for NSW. Richard Jane, Director of Engineering at Forbes Shire Council.
do in those most productive vehicles.
“This is no longer a pilot and it has converted over to a permanent scheme within New South Wales, which I think is fantastic. I can’t emphasise enough, both of the New South Wales local government associations support this. The Australian Local Government Association have asked me to come along and talk to the other local government services agencies across the country to advocate for this approach across the country.
“This is a fantastic opportunity to be able to get broader access with relatively minimal steps at this point in time. I think the challenge that most councils still have is, that the more vehicles that are in role then the more appetite, they have to allow more access. It’s always a bit of a chicken and egg situation and the operators will enrol their vehicles when there’s networks to use, and the councils saying they’ll open more networks when there’s more vehicles enrolled in the scheme.”
There are currently 135 vehicles enrolled, made up of 71 unique vehicles that may work in different combinations. These come from 34 different operators. The scheme has opened up 10,000km of road, where all operators to do is to be enrolled in a telematics application that only hands over de-identified aggregated data to the authorities.
The road managers don’t know who is where, at any point in time. Instead they know how many times vehicles are going down a particular road, what sort of service it needs to provide, and what
maintenance investment will be needed.
In contrast to the good news on the agenda from Scott, Richard Jane, Director of Engineering at Forbes Shire Council was not backward in coming forward in expressing a strongly contrary position on this freer access regime.
“The process that we currently have in place ensures that we do a proper assessment using the Transport for NSW Restricted Access Vehicle Assessment Guidelines,” said Richard. “Any responsible engineers should do that before they open up to any restricted access vehicles. Quite frankly, I think it’s irresponsible, if they just create a blanket approval for any particular over-mass vehicle. Keeping that in mind, I am a huge fan of the people who run PBS Type 2 vehicles, and opening up the networks to B-doubles, which is essentially PBS Type 2B, I think this is the first aiming point that we should have.
“Forbes has got road train access on some of the roads. Anyone who’s been in the Livestock Exchange, would know that we’ve got ‘everything you can think of’ access from the Newell Highway into the exchange, including B-triples, and A-double road trains. That was assessed.
“Access for trucks has to be approached in a risk management fashion. I’m not completely against it, but I would insist, in the area I’m responsible for, that each individual A-double be assessed. That’s not what you wanted to hear.”
Richard points out his shire has got a lot of very narrow roads, and gravel
roads, and a road train or B-triple on those roads is problematic. He insists there are too many risks and he, as an engineer personally, won’t be signing off on anything unless it’s properly assessed.
In reply to the recalcitrant engineer, Scott Greenow pointed out that the operators admit they are already running on those roads and want to be open about the situation and the changes are not about opening up new tasks. It’s more about ratifying the movements that happen and get an opportunity to have visibility on that.
“This is an interim solution in an imperfect world to be able to get safer, more productive, more sustainable access for these combinations now,” said Scott. “As we move forward, we will identify and assess structures on our strategic routes to get a better understanding of the network. We need to be in a place where we have automatic assessments on vehicles, so a decision is made instantaneously.
“It doesn’t matter what combination you have, it doesn’t matter what your axle spacings are. Whatever your network is, whatever the route, the road network in New South Wales, plus state and local roads can accommodate, then that will be the network that’s provided to you. So what we’re aiming for is travel completely under notice, there should be no reason, that I can see that we would have permits in the future for Class 2 or Class 3 vehicles.”
2022 has been a catch-up year for many in the industry, in 2021, the only major event where people could meet up was in the small window between lock downs that allowed the Brisbane Truck Show to go ahead. This year has seen a full program of events and the chance renew old acquaintances
and build new ones.
The NatRoad Conference held on the Gold Coast is one of the larger trucking industry events and it saw the election of a new NatRoad Chairman, Paul Fellows. The new Chair, and his wife, Jenny, run a small bulk transport business out of Deniliquin in New South Wales.
“As I introduce myself I would like to briefly outline my priorities in taking on this challenging role,” said Paul. “We know through industry research and first-hand experience that declining profit margins are threatening the future of many road transport businesses across the nation. The increasing costs of fuel,
The effect of the Covid pandemic was to almost eliminate the face to face and person to person contact, unless it was absolutely necessary, but the trucking industry runs on personal relations between players in the industry.
tolls and wages, experiencing driver shortages, and an ageing workforce, plus the challenging complexity of compliance, cumbersome regulations are putting undue stress on many operators.
“Running a business, and particularly a small business is hard enough. It’s hard to even make small profits year after year. What we’re basically looking for answers, but it’s important to ask the right kind of questions so you are armed with the best information.
“As part of this, NatRoad is adopting a leadership position, by commissioning economic research through members to better understand these factors. This project will benchmark member businesses across the industry, in a way that has not been seen to date. It will give them an idea of how their businesses are really traveling in comparison to the rest of the industry. So they can make better business decisions and to help them tackle issues that are vital to the viability of the business.”
This new data will also be useful for NatRoad when talking to the government and help it to portray what’s really going on at an operator level. The association believes this groundbreaking research will add real value to what it can provide and build on that foundation.
“We are an association of people who employ themselves or relatively small numbers of people,” said Paul. “While it’s fair to say that we have not always seen eye to eye with governments from the left of the political spectrum, we also took strong issue with the last coalition government when it decided to strip away the fuel tax credit for six months. That was a knee jerk and uninformed decision and we worked really hard to get it overturned.
“I like to think that NatRoad has been apolitical to a degree. We’re looking to establish a really good meaningful dialogue with the Labor government. We’re not always going to agree, and I think that’s healthy. We need to be objective and constructive, we’ve all got the same aim, and that is to work together and to make the industry a better place.
When we see something contrary to our members interests, we will call it out. If we see a pragmatic solution to a problem, we will suggest it.
“COVID was a great example of how adaptable the transport industry is. A great example of how much
the general community relied on us to get food on the shelves at the supermarket, and how adaptable we are that we’re able to keep society going when it’s on its knees.
“Heavy vehicles are a major player in emissions reduction, and there are
“WE KNOW THROUGH INDUSTRY RESEARCH AND FIRST-HAND EXPERIENCE THAT DECLINING PROFIT MARGINS ARE THREATENING THE FUTURE OF MANY ROAD TRANSPORT BUSINESSES ACROSS THE NATION.”
significant environmental, social and commercial advantages to achieving net zero. But we all need to deal with the realities of operating road freight and the investment involved by 1000s of businesses. Change is coming but it won’t happen overnight, and without price signals and significant policy change from government.”
Labor Senator, Glenn Sterle, spoke at the conference. He represents Western Australia in the Senate and is also the Chair of the Senate Rural, Regional Affairs and Transport Legislation Committee. He was a long distance truck driver, founding his own business operating road trains in regional Australia before being elected Senator for Western Australia in 2014.
“Who would have thought 40 years ago that a TWU delegate and a long distance, road train operator, and then the organiser for the Transport Workers Union would be invited to a NatRoad conference?” said Glenn. “If Warren Clark, NatRoad CEO, hadn’t have reached out to us, those stupid, old ridiculous wars would have carried on, which does nothing for anyone in this industry. We agree on
so much more, than what we disagree on.
“Now is a golden opportunity to go forward together. I’m a firm believer, from my trucking days, there are five bits of glass to look through in my prime mover on the left-hand side and on the right-hand side I had a tiny little thing called a West Coast mirror, that was for looking behind, but the most important thing was that huge glass on the front, looking forward, and that’s where we’ve got to go. Let’s go together and let’s do things for this great industry while we can.”
Passing on to those attending the NatRoad Conference, Glenn Sterle shared the message from Assistant Minister for Transport and Infrastructure, Carol Brown, outlining the current government position, which includes a dataenriched approach to help keep freight moving, forecast demand, identify current and future critical infrastructure needs. It has committed to $16.5 million to establish the National Freight Data Hub to better collect and use data for industry, insight and innovation. It has already been used in some areas, including long haul route planning, and identifying rest stops for truck drivers.
There was also an Infrastructure and Transport Ministers Meeting held its August and September and transport ministers agreed on a package of reforms to the Heavy Vehicle National Law. Brown reckons we will see a new system to automate approvals for heavy vehicle access. There is also an ambitious goal to remove the need for 90 per cent of permits on freight routes over the next five years.
Glenn also passed on the news that the National Transport Commission has been tasked to prepare an impact statement for reforms and took this opportunity to thank NatRoad for its participation in representing Australia’s trucking industry. Glenn asserted that the association has a vital role to play in the success of these reforms.
The Infrastructure and Transport Ministers meeting asked Ken Kanofski to undertake stakeholder consultation on the Heavy Vehicle National Law (HVNL), after the proposed reforms were roundly rejected by the trucking industry. He was tasked with finding a way through the process, which would enable some form of consensus to prevail.
“I think HVNL reform is an important issue, which is why I agreed to look at it,” said Ken. “I was asked to have a look at, what are, the systemic barriers to reform and what do we do to get the HVNL reform going. In August of 2022, I took a raft of recommendations to Infrastructure and Transport Ministers, I’m happy to say they adopted all of them. I made it pretty clear to them, that those were an end point and not a start point.
“I managed to get a whole range of people in a lot of rooms and effectively negotiate what was an already compromised position and the big fear I had was the Ministry saying, ‘that’s all very nice, but we’d like that and then can we go on and have these other things’, and restart the negotiation cycle again. I was pretty blunt, with ministers about the risks in doing that and thankfully they took that on board.
“To say the reason for my
engagement was simply a degree of frustration, I think would be an understatement, with the way the work has been progressing. I say that without the criticism of the National Transport Commission. It is a very complex thing to do, and to lay blame at the feet of one particular agency, doesn’t serve us very well.”
In September, the Ministers agreed to set governance arrangements and an implementation plan. This means there is hope of a framework that allows us to get a new HVNL. Kanofski had spoken to 80 people from across government and industry, including all the main stake holders in a range of meetings. Ken says this process has proved the importance of getting all of the parties in a room together, discussing issues openly and honestly.
“There was an enormous amount of goodwill and great contributions from the industry,” said Ken. “One of the things I said to those groups is that government officials are naturally reluctant to talk about things in forums, where they don’t have an imprimatur from their minister. I get that more than most people, but of course, you’ve got to be able to talk about things.
“So what I asked the people in
those rooms to do was, if we read about what Victoria said, today, in the newspaper tomorrow, then this whole thing’s gonna just blow up. So I’m going to trust that we’re all going to deal in good faith, we’re not going to quote each other and we’re just going to get on with it. And that’s what happened. One of my other natural
inclinations is if you treat people like adults, they behave like adults. Hopefully, we can maintain that sort of will going forward.
“Seven overarching themes came out. A two-tier fatigue system, a prescriptive system and a more flexible system built around safety management systems and medical screening, reforms to access and PBS decision making, more accountability for road managers to improve productivity. Some people say road managers should be cut out completely, well you can’t. They own the roads and they take the risk of the roads, they are their responsibility.”
“SOME PEOPLE SAY ROAD MANAGERS SHOULD BE CUT OUT COMPLETELY, WELL YOU CAN’T. THEY OWN THE ROADS AND THEY TAKE THE RISK OF THE ROADS, THEY ARE THEIR RESPONSIBILITY.”
There is a glimmer of light and some real signs that the interstate differences which maximise difficulty and minimise the effectiveness of Smart OBM systems are going to be reduced over time. Many in the industry will be hoping these first signs of progress on the onboard mass (OBM) front may be the precursor of progress in other areas where interstate regulation incompatibility creates inefficiencies.
There has been a long gestation period and many, many interstate meetings, but finally Queensland has made an announcement, at the same time as an announcement which has come out from New South Wales. These two events indicate that most of Australia will, finally, have a national approach around OBM.
Smart OBM will be available across the Eastern Seaboard. The jurisdictions requiring it as a regulatory requirement will be Tasmania, Victoria, New South Wales and Queensland, all with a common approach. There are also moves to take this idea national, if possible..
In recent years, operators looking to improve productivity have been hamstrung by the requirements in states like Queensland, which were incompatible with those in other states. New South Wales was also slow on its uptake of Smart OBM.
The position the states have come to is described by Gavin Hill, General Manager at Transport Certification Australia (TCA) as, “the
highest common denominator”.
“There are some grandfathering arrangements, for those already operating in Queensland with old systems, they will be able to continue to operate in Queensland,” says Gavin. “The important thing is, for any new vehicle that are getting fitted with OBM for the first time, you only need to have one system that’s recognised across all jurisdictions.”
This recognition issue has been a major aspect of the problems cross border operators have been dealing with in the last few years. Victoria would be telling an operator to get one kind of OBM, but they couldn’t use that in Queensland, because they didn’t recognise it. Transport operators trying to do the right thing were getting caught up in the middle of an argument between states.
Operators will now be faced with one Smart OBM system, one which is recognised across all jurisdictions on the Eastern Seaboard. Operators only need one kind of system to meet whatever the requirements are in whichever state they are travelling.
There will still be differences in the allowances and combinations in those different states, but at least the monitoring of those combinations will be recognised everywhere.
“When and where Smart OBM systems are required for use, it’s still a jurisdictional question,” says Gavin. “We are trying to harmonise that as much as we can, but just because you’ve got high productivity freight
vehicles operating in Victoria, with Smart OBM as a requirement, doesn’t automatically mean that those same vehicles with Smart OBM, in that combination, will have right of access to other jurisdictions.”
These changes are making it so that a smart OBM system is usable within any jurisdictions on the East Coast. It is a smarter solution to part of the interstate problem. The actual rules will continue to vary from state to state but the way an operator demonstrates compliance will be accepted across the Eastern Seaboard.
This leaves the trucking industry still having to find ways of working around jurisdictional inconsistency and decisions by road managers, but this is a sign of progress for the operator with trucks constantly crossing state borders. It’s one less thing to have to worry about.
“We might need to leave jurisdictional differences for another day,” says Gavin. “Wherever they require OBM, they’ll be asking for the same system, essentially. We’ve got other jurisdictions like Western Australia, looking at what they can do with Smart OBM, as well. Currently, the East Coast are the only jurisdictions using Smart OBM, but that will grow over time.”
Up until this point, New South Wales hadn’t bothered requiring Smart
It has been a long wait for the trucking industry, especially in rural areas, to get to a point where we can see daylight on the horizon, in the form of rational progress on onboard mass. Up until now, the fragmented state-by-state and sector-by-sector differences have caused many to put onboard mass systems into the ‘too hard’ basket.
OBM, now they’re extending the concept well beyond the very small number of vehicles (around 300) that had a Smart OBM requirement in NSW. Like Queensland, New South Wales will grandfather those existing vehicles, if an operator has got a system fitted today, but any new vehicle that comes in where OBM is a requirement, it will need Smart OBM. These new rules came into effect as of December 1 2022 in both New South Wales and Queensland.
As the inclusion of Smart OBM works its way through, Queensland will be moving away from the Intelligent Access Program over the next 18 months in a transition period. During this period, Class 2 vehicles, that is, B-doubles, A-doubles, B-triples, AB-triples and rigids with two dog trailers, will need to move across to Telematics Monitoring Applications (TMAs).
Any truck fitted with an existing IAP system will meet the TMA requirements, and be able to continue operating. Any new equipment brought in to handle the freight task will only have to meet the TMA requirements, rather than the
old IAP ones. These changes should have the effect of reducing cost pressures on trucking operators in these freight tasks.
Those operators who have got IAP system fitted already will benefit from having a reduced monthly subscription, by moving across to TMA. The new system will not require non-compliance reports which the IAP generates. TMA doesn’t generate non-compliance reports. This means service providers can reduce the costs that they incur by being able to tune down the functions in the system, and should be able to pass on those cost savings to customers.
There will still be IAP requirements for certain tasks in New South Wales, but the state introduced the option for transport operators of staying in the IAP or moving to TMA, a couple of years ago. Not many transport operators had taken up that option, because Queensland, at the time, did not recognise TMA, until the end of 2022. This may be a tipping point, because even if operators didn’t regularly operate across the Queensland border, many just wanted the option,
just in case. The cheaper, easier TMA alternative will do the job.
The effect of these changes is that IAP will be reserved only for the highest risk vehicles, large special purpose vehicles, mobile cranes etc. The go-to solution for many higher productivity vehicles will no longer be IAP, but TMA.
This reform has been a long time coming, but as the changes become clear and work their way through, it should make life a little easier for those who have to work as close to GCM as possible, to earn a crust.
Going forward, now that the states have come to an agreement and are using the same basic methods to demonstrate compliance, the next stage should involve scheme harmonisation. This is likely to involve another long drawn out process of negotiations between state jurisdictions with entrenched positions on the efficacy of their own individual schemes.
These changes, and the move away from IAP towards TMA, as this easier cheaper route to higher productivity becomes more viable, does mean a lot more data will be coming into the states. The hope is that the states will actually use this data rationally and get a better understanding of what their infrastructure can cope with. This may aid smarter route classification.
Local governments will have access to the aggregated and de identified reports generated by the TMA system, getting a clearer picture of truck activities on their local roads, by vehicle category. The TCA reports it is seeing tremendous growth in the number of local government users accessing its system for that purpose.
well into the summer.
My own travels took me through south-western New South Wales recently where the going was tough for anyone on four wheels, let alone 18. It was puzzling to see a media report in which people raising concerns that interstate truck drivers who had been forced a long way off their normal freight routes were pushing through back roads at excessive speeds.
Anyone who knows this industry will be aware that safety is paramount. All but a handful of operators drive to the conditions, religiously. They share the road because doing so is professional. Without getting into a contest, statistics show that most serious collisions between heavy vehicles and light are the fault of the motorist, not the truckie. So let’s not get worked up on either side.
average truck speeds were well down during the flood disruption. National operations manager Ben Fenna said all GTS drivers were acting professionally as they navigated lengthy detours.
There’s a simple fact at play here: You can’t move loads on smaller roads safely and efficiently as you can on well established freight routes. Road freight operators and primary producers do share common ground in that they’re all at the mercy of natural disasters that are pushing up costs across the board.
We were in the run-up to the Festive Season at the time of writing, but for many operators, this would be as tough a Christmas as the ones that were COVID-disrupted. The reason isn’t inconsistent border rules or swathes of red tape this time, but relentless floodwaters and the damaged roads they’re leaving behind.
Potholes big enough to swallow a small car…heavily eroded road shoulders…unexpected detours… stretches of road under repair. It’s all par for the course as 2022 neared its end. The extent of damage runs into the hundreds of millions of dollars and disruptions could stretch
It is true that interstate truck drivers are being forced to travel hundreds of extra kilometres across Australia due to highway closures. That costs extra time and money. The alternative, of course, is essential freight sitting in warehouses for interminable lengths of time.
I fully understand the frustrations of farmers moving stock on lesstrafficked rural routes having their work disrupted by unforeseen volumes of road freight. But it’s by necessity not choice - and those flood closures won’t last forever.
The complaints in the media story were countered by one of NatRoad’s members, GTS Freight Management in Mildura, pointing out that their
Poor harvests drive up the price of primary products exponentially. Farmers are often unable to pass on those costs at the farm gate because of long-term contracts with big supermarkets. Likewise, not every road freight operator can pass on costs to big customers although, thankfully, recent law changes may make unfairly restrictive contracts with big companies a thing of the past.
The pandemic made it clear to everyday people that road freight is an essential service and if trucks stop moving, so does Australia. It also underlined that we “were all in this together”. It’s worth a thought next time a truck driver and a farmer pass and nod to each other on a back road this summer.
For many in industry, 2022 was another very challenging year. While COVID19 border restrictions lifted, the industry still faced unique pressures and challenges including supply chain issues, increasing fuel costs, driver shortages and impacts of flood events not to mention supply issues around new vehicles and accessing spare parts.
But, as always, the industry was able to navigate these challenges and keep trucks moving safely.
We were proud to support these efforts and work with industry and regulatory partners to find practical solutions while still delivering on our commitment to pursue a modern regulatory strategy that is focused on informing, educating, and enforcing.
Our safety and compliance officers had open conversations with drivers about safety practices and to help establish positive and long-lasting safety behaviours. We continued to work closely with policing agencies to build stronger relationships and ensure consistency in the way compliance and enforcement activities are undertaken.
This approach was supported by moving a step forward towards national consistency with the successful transition of heavy vehicle services from Transport for New South Wales to the NHVR in August this year. Only five months in but already I’m seeing, as I hope you are, the first signs of the benefits of a single national regulator and our industry interactions becoming more consistent.
We also ramped up our focus on key decision makers under Chain of Responsibility which we know is key
to driving improved safety cultures and a key area industry has been advocating. This saw an increase in primary duties prosecutions over the year. 27 Executives, off road parties, operators and other parties in the chain were before the court for primary duty matters.
But prosecutions aren’t our key driver, we value working with businesses to improve their own operations, which is why, where appropriate, we will use alternatives to prosecution for industry. This year we accepted 15 Enforceable Undertakings
and close to 30 court imposed Supervisory Intervention Orders (SIOs), as well as a number of improvement notices. Rather than issuing a fine, these tools enable companies to invest in improving safety practices or developing safety tools that will benefit the entire industry and other road users.
As our roads became busy again, we made a dedicated investment to improve awareness of the broader community on improving their interactions with trucks. Our young driver initiative ‘Don’t #uck with
As 2022 comes to a close, Sal Petroccitto, National Heavy Vehicle CEO, turns his attention to the year ahead, it’s important to reflect on what we have achieved, and opportunities for 2023 to help ensure a safe, efficient and productive heavy vehicle industry that serves the needs of Australia.
a truck’ drove home an important safety message to our L and P platers in a purposely provocative way. We continued our ‘we need space campaign’ and partnered with Queensland Police Service to launch the ‘Sharing our Roads with Oversize Loads’ campaign.
After two years of virtual meetings and cancelled physical events, one of the major highlights of the year, for me, was the ability to reconnect with many of you in person. This interaction is something I truly enjoy and value as it gives me the opportunity to hear first-hand your concerns, issues or even just the opportunity to have a chat. There were robust discussions and information sharing at numerous conferences throughout the year and while I know there is still a lot of work to do, overall, I am confident that by working together we are starting to make a meaningful and positive difference. We have appreciated your honest feedback during the year, and I look forward to continuing to engage with you in the new year.
For those of you who have met me, you will know my passion for improving the way we deliver our services to you. We have spent a lot of time internally to continue to improve our approaches and I’m really pleased to see that we were recognised for these efforts and being named the 2022 Service Champion for the Customer Service Organisation of the Year – Government/Not for Profit category at the CSIA Australian Service Excellence Awards. This achievement is at the core of our values, to provide a consistent, accountable and transparent customer experience.
I look forward to continuing to work together in 2023, as we strive to keep delivering a safe and highly efficient road freight transport sector. Next year we will continue our journey to finalise the transition of heavy vehicles services from the states to the NHVR, which will go a long way to delivering a consistent and efficient regulatory service across the country.
We recently released a Performance Based Standards (PBS) 2.0 Discussion
Paper seeking industry involvement to shape the future of the scheme so we can get these safer and more productive vehicles on our road networks sooner. Our key priorities are focused on expanding access, moving mature combinations into the ‘as-of-right’ fleet and reducing end-toend approval times. We are holding a series of webinars early in the new year to ensure industry has a chance to provide input.
Continued improvements to the NHVR Portal, being the single-entry point for industry, government and road managers to manage access and other heavy vehicle regulatory services will see the release of the first national network map. This will save time and effort by removing the need for industry to access multiple state-based maps to plan and manage journeys and will start to provide dedicated heavy vehicle routing options.
Our commitment to improving the management of fatigue and helping drivers rest when they are tired and drive when they are fit will be a priority. We are focused on breaking down the barriers to help operators get into Advanced Fatigue Management (AFM). New resources and tools will be made available, including preapproved AFM work and rest examples and a new streamlined online AFM application process.
There are a lot of exciting and innovative projects in the pipeline over the next twelve months, and I look forward to continuing to work closely with everyone across the heavy vehicle industry and supply chain to ensure safe, more productive and efficient 2023.
I want to personally thank industry for your contributions in 2022 and well done – it is truly a remarkable effort.
I hope you and your families have a happy and safe festive season and I look forward to seeing you in the new year.
SCAN THE QR CODE FOR MORE INFORMATION FROM NHVR
Ask the question “what is the solution to the skills shortage facing the transport industry?” and see how many different answers you get. Some will be brilliant, some will be good and some will be...interesting. However, there is no single magic bullet.
Industry has a range of ideas and things in operation as we try to work together to address the skills shortage. We need to paint a clear and united picture of what we are trying to do and how it all hangs together.
Most initiatives address three issues:
1) How do we attract people to the industry?
2) How do we train people?
3) How do we retain people?
With shortages across the whole economy, we need to recognise that we are competing against every other sector for people. Great work is being done by industry, with programs that engage school leavers, migrants, refugees, young mums and mature age women, defence veterans, Indigenous people, disability groups and early release prisoners.
Let’s look at some different roles and how the industry is trying to fill these positions.
Warehousing is one of the fastest growing segments in transport and logistics as global supply chains adapt to the new reality. The South Australian Road Transport Association is pushing to have 16-year-olds drive forklifts. The Western Roads Federation and others have forklift training embedded in their
Heavy Vehicle Driver course.
•
Most member associations have a driver training solution. Both the Victorian Transport Association and the Western Roads Federation have training programs based on teaching skills and competencies prior to being employed. The Queensland Trucking Association has a program providing enhanced training and experience to those drivers who have licenses but are not employed in the industry. Other Transport Associations have variations. Further adding to the mix is an Austroads paper on the future of Heavy Vehicle Driver Licensing and the recent announcement of a Driver Apprenticeship.
• International Drivers
There has been concern regarding international drivers and questions about whether they should take part in a training program before they can operate. Furthermore, it should be noted that barriers to bringing in international drivers exist because the size of the driver shortage cannot be accurately quantified nor the impact on the Australian economy.
Some States report skills shortages in operational or non-driving jobs.
The Australian Furniture Removers Association run skills training for its members. The Queensland Trucking Association has micro-credentialing courses that up-skill members in transport business management. The Western Roads Federation is working with TAFE on a joint industry course for operations staff.
• Adapting to the Future
People in road transport industry management generally rise to
management levels based on hard won experience rather than formal education. This has served the industry well because change has been relatively incremental. However, are we prepared to take advantage of potential fundamental changes in technology, social obligations and supply chains that are on the road ahead? Would industry-specific formal education help?
National research shows up to 24 per cent of people are considering leaving the industry. With Australian Industry Standards estimates 20,000 people left the transport industry during COVID. It’s a loss we can’t afford. Again, good work is being done around things like mental health and rest areas but what else should we be doing?
How do we tap into the knowledge of our experienced people so they can pass it on to the next generation? Industry is doing good work on advocating to allow recently retired drivers to come back as driver mentors without losing part of their pension.
The various approaches taken by the member associations can build a holistic transport industry workforce strategy. We have a clear and cohesive picture to present to the government that sets out what we want and how it can be achieved. By working together, we can make real progress.
Cam Dumesny, CEO Western Roads Federation is asking how to solve the skills shortage facing the transport industry.
In September
It’s safe to say that nobody will ever make the perfect truck, but I reckon the new DAF XD is as close as anyone has got so far. But then the Dutch truck manufacturer has had plenty of time to get the design right, after all the first incarnation of the CF which it replaces was introduced in 1992.
Although the CF was of course heavily revised over the last three decades, the basic cab shell remained unchanged, and was beginning to show its age. Perhaps its biggest drawback was visibility, which seriously lagged behind some of the more modern competition.
This became particularly apparent in London, where it performs poorly in the Direct Vision Standard (DVS). The scheme, which is designed to protect vulnerable road users, measures how
much a driver can see through their cab windows. Out of a maximum of five, the CF scores a zero-star rating!
As it happens, DAF’s decision to eke out the CF for as long as possible paid off, because biding its time allowed it to take advantage of ground-breaking European truck design legislation.
In September 2020 the European Commission introduced long-awaited changes, relaxing the length limit of new trucks. Just about anything is permitted, so long as it complies with existing turning circle requirements.
DAF was first out of the box, putting these new mass and dimensions rules to good use with the launch of the XF, XG and XG+ in 2021. While the XG and XG+ both received additional space at the back of the cab for the driver, equally significant was what happened
at the front. All three models received a curved front end, elongated by 160mm compared with the previous XF. While it protrudes at the centre, it tapers outwards, resulting in a curved effect, allowing air to move more freely around the front of the truck, thus improving fuel economy.
DAF has applied exactly the same logic to the new XD, which receives an identical front end. It boosts aerodynamics by 19 per cent, which accounts for 6 per cent of the claimed 10 per cent fuel economy improvement over the CF.
Continuing with the exterior, I’m pleased to report that because the XD shares the same basic cab as its larger siblings, it also gets their generously proportioned side lockers. There are three different cabs on offer (Day,
Sleeper and Sleeper High), and all three are 2.5m wide, compared with the previous 2.3m CF.
Access to this truck couldn’t be simpler, thanks to two large steps (or three in the case of some trucks with greater ground clearance), which are nicely staggered, in a staircase-like manner. Inside is a pleasant surprise, especially to drivers used to the CF.
It gets a near identical interior to the new XF, including the same smart, functional and modern dashboard, with its 300mm configurable digital display, and secondary infotainment screen. The fit and finish is of the same high quality too, and it’s here that it’s blatantly clear that DAF really has raised its game. There are so many nice little touches, like the dashboard’s pull-out table.
All three cabs feel considerably more spacious than their predecessors, thanks mainly to an impressively low 320mm engine tunnel. I particularly like the Day Cab, which has an additional 150mm
behind the driver’s seat. This allows for the fitting of an optional full-size fridge. The bunks in both sleeper cabs are longer than in the CF, thanks to this being a full width truck.
From the driver’s point of view, it’s incredibly easy to get comfortable. Having more space to play with has allowed DAF to improve seat travel, so now even the tallest of drivers should have adequate leg room. What’s more, the steering wheel is now fully adjustable, and can be moved completely out of the way when not in use.
The multifunction steering wheel, which is again out of the larger trucks, has all the speed-related buttons grouped on the left, with audio on the right. This set-up is fast becoming an industry standard.
At a press event near the Spanish city of Barcelona, I had the opportunity to drive a variety of XDs, ranging from a ridiculously quick 449hp 19.5-tonne
skip-loader, to a 40-tonne semi with the same power rating. But the one I spend the most time in is an XD 410 FT 4x2 Sleeper Cab prime mover coupled to a tri-axle tipping trailer.
Sat in the driver’s seat, it immediately strikes me just how simple this truck is to drive. I instantly know where everything is, due to the logical positioning. Virtually all of the controls are at my fingertips, and those that aren’t are on easy-to-locate dash-mounted buttons. I don’t need to scroll through menus to get started. In other words, a driver can be thrown the keys to one of these, and they’d instantly know what everything does. Of course, like with any modern truck it’s advisable to read the manual to get the best out of it, but it’s not imperative.
Without doubt, this truck’s strongest point is its visibility, which really is outstanding. And I certainly appreciate it while navigating a Spanish town during the morning rush hour, with narrow
XD
streets, pedestrians glued to their phones, and motorists who seemingly don’t know what the flashing orange lights on the sides of their cars are for.
There’s a very simple way of improving a vehicle’s visibility, and that’s to replace metal with glass. This is something DAF’s designers have embraced, from the massive front windscreen, to the low beltline. There’s also a Vision Door, with a window located in the lower section of the passenger door. But needless to say, it’s pretty much pointless if you have a co-driver’s legs in the passenger footwell.
Full marks for the dashboard, which has a slightly smaller flat area than the one in the XF/XG. This allows it to slope downwards towards the windscreen, meaning you see beneath the windscreen wipers.
Then there’s DAF’s optional Digital Vision System. Two cameras located on the sides of the roof project rear view images to a pair of screens mounted on the A-pillars. The one on the nearside is 380mm high (the same as MercedesBenz’s MirrorCam), but the driver’s one is smaller (310mm). Not only is it less intrusive, but being smaller means there’s virtually no blind spot.
Gone are the days of moving your
head forwards and backwards to improve your view on the approach to junctions and roundabouts. In my opinion the screen clarity is classleading, and I find it to be perfectly good both in bright sunlight and in dark tunnels. Just like MirrorCam, the screens have lines on them, indicating the back of the trailer, and distances of 25m and 50m. It sounds like a gimmick, but it’s certainly useful to help gauge distances when you aren’t yet used to the system.
Model: DAF XD 410 FT 4X2
Cab type: Sleeper Cab
Engine: MX-11 10.8-litre
Max power: 408hp at 1,600rpm
Max torque: 2,150Nm at 9001,125rpm (multi-torque)
Gearbox: ZF TraXon 12-speed
Total vehicle weight (as tested): 36 tonnes
This said, I don’t have an issue with DAF’s conventional mirrors. Although large, they have a useful gap between the main and wide-angle sections. And because the wide-angle mirror is mounted on the lower half, you look downwards through this gap (towards the road) rather than upwards (towards the sky), which makes it that much more useful.
But, without a doubt, the biggest breakthrough in terms of enhanced visibility comes from Corner View. It consists of a camera located just beneath the windscreen on the front nearside edge of the truck, and a secondary screen on the nearside A-pillar, and does away with the physical mirrors which are normally located above the passenger door window and the windscreen. It not only gives a 270-degree view down the side of the truck, but unlike the mirrors it replaces, is directly in the driver’s line of sight. In the UK, DAF has made it standard on all XDs.
Thanks to a combination of all these features, an adult can walk around the sides and front of an XD cab without disappearing from the driver’s view. In
this respect it’s a game-changer, and explains why the truck gets a 4-star DVS rating.
The XD is only available with the 10.8-litre MX-11 engine, with ratings of 299hp, 341hp, 367hp, 408hp and 449hp. All have multi-torque (new for 299hp and 341hp), which means additional torque in top gear, allowing the truck to maintain speed for slightly longer on the hills. The XD uses the same ZF TraXon 12-speed gearbox as its predecessor, and there is no longer a manual option. I encounter some relatively steep motorway inclines on my test drive, and the engine has to work hard to maintain speed at 36 tonnes. But overall I am pleased with its performance, helped by revised gearbox software, which gives slightly quicker gear changes.
This said, operators running at top weights, or in hilly terrain, would be best off with a 13-litre MX-13. But seeing as it physically can’t fit under the XD cab, they’ll need an XF instead. With this in mind, DAF recently launched the XF with a Day Cab and low-roof Sleeper Cab, for vocational applications where a Sleeper High Cab is not necessary.
The ride is excellent in this truck, which has a steel front and rear air suspension, and tackles rough road surfaces with the utmost composure. I was already a big fan of the new generation DAF range’s handling, and this smaller, lower cab, only enhances drivability further.
The truck goes downhill better too, thanks to an improved engine brake. Its performance has been enhanced by up to 20 per cent, and working with the adaptive cruise control, certainly keeps my speed in check.
This year will mark 28 years of market leadership for DAF in the UK, where it has a 30 per cent-plus market share. By launching a near-perfect range of distribution trucks, it can only enhance this position.
I’ve been racking my brains, trying to think of just one negative thing to tell you, and have finally thought of it. For the time being Australia is stuck with the CF!
As a correspondent for several road transport magazines in Australia and New Zealand over many decades, high profile US trucking writer Steve Sturgess was a constant source of detailed and often ground-breaking reports on the North American trucking industry. Veteran Truck Commentator, Steve Brooks, recalls the passing of a friend and valued colleague.
his association and camaraderie with a couple of Australian and New Zealand editors made Steve Sturgess an ideal ally and valuable correspondent.
He genuinely liked Australia and New Zealand and often expressed considerable regard for the character and initiative of trucking in our part of the world.
Always cheerful and thoughtful, Steve passed away recently from a progressive illness and his long contribution to Australian and New Zealand trucking media will be sorely missed.
He was, above all, a good bloke.
As the person who took over from Steve Brooks as a magazine editor, resulting in having Steve Sturgess, as a US Correspondent passed on to me, I can only repeat Steve’s sentiments.
Steve Sturgess was certainly one of a kind. The old adage ‘they don’t make ‘em like that anymore’ would, in many ways, be a fitting epitaph for the man whose smiling presence and quickwitted conversation hid a deep and determined approach to uncovering the latest developments in North American trucking hardware and performance.
From the highest offices of massive fleets to the executive corridors of some of the world’s best known truck and component brands, and possessing a deft hand at the wheel of any truck, Steve’s ability to deliver accurate and authoritative reports on the people and products of the North American road transport industry had few peers.
Born in England and discovering early a passion for automotive pursuits,
it was his eventual move to the US where Steve forged the platform for a long and auspicious career in truck reporting.
He became, without question, one of the best known and most experienced writers on happenings within the North American trucking scene. With a naturally enquiring mind and inherent understanding of sometimes complex engineering developments,
He had an in-depth command of exactly what was going on in the North American trucking world and he could not disguise his love of all things truck and trucking. His commentary was always interesting and insightful.
On a personal level he was always a joy to work with. He had a great sense of fun and a dry wit, he never took himself too seriously and had a businesslike manner, when required.
The last couple of years had been hard for Steve, his health issues meant he couldn’t alway deliver a story for PowerTorque, but he did his best, hiding out in an RV somewhere in Colorado during the worst of the wave of Covid across the US. He will be sorely missed by the PowerTorqueteam.
“HE BECAME, WITHOUT QUESTION, ONE OF THE BEST KNOWN AND MOST EXPERIENCED WRITERS ON HAPPENINGS WITHIN THE NORTH AMERICAN TRUCKING SCENE.”
Ride Height adjustment on vehicle systems, either truck or trailer, is a critical part of vehicle suspension performance. The impact of incorrect ride height adjustment can be profound and results in instability and poor ride, as well as degradation of other vehicle system components.
On trailers with a split group suspension, the ride height of the steer axle also needs to be considered because any deviation from designed ride height will change the caster. Incorrect caster may then cause driveability and tyre wear issues.
Excessive right height can contribute to the following system deficiencies and failures:
• Poor vehicle stability and balance.
• Incor rect load share leading to improper brake balance and wheel end loading.
• Shock absorber catastrophic failure through over extension.
• Vehicle shimmy and tyre wear. This is because an increase in ride height can change caster in steering and steerable suspensions.
• Air spring failure through separation at the bead plate.
• Excessive driveline vibration through substantial change to pinion angles, which can lead to:
o Damaged universal joints
o Transmission output bearing degradation
o Differential pinion bearing degradation
o Pinion seal failure
Insufficient ride height setting can contribute to the following system deficiencies and failures:
• Incor rect load share leading to improper brake balance and wheel end loading.
• Vehicle harsh ride as the suspension is riding on or close to the air spring bump stops.
• Catastrophic failure of air spring.
• Catastrophic failure of shock absorbers if the suspension hits a fully compressed shock absorber.
• Vehicle shimmy and tyre wear due to changes in caster.
• Fatigue failure of shock absorber fasteners and mounts.
• Fatigue cracks of chassis frame and cross members.
Ride Height is normally measured from the centre of the axle to the underside of the frame. Vehicle manufacturers may advise of other supplementary methods to measure
ride height such as measuring shock absorber length or air spring height. Unless otherwise specified, all ride heights should be measured on the axle attached to the height control valve. On trailers with a split axle group, ride height should be an average of the single axle and the rest of the axle group to take into account any frame slope variations.
• Set trailer kingpin mounting plate height to specification before beginning.
• Ensure there is at least 90 psi (620 kPa) pressure available to the Height Control Valve.
• To ensure accurate adjustments, first lower suspension and then allow it to rise to set ride height.
• Allow sufficient time for the Height Control Valve to operate, as most have a built-in delay of around 10 seconds.
Paul Robinson has extensive experience in the mechanical field, having spent 30 years working for Caterpillar dealers in Australia and Africa.
He started as an apprentice Diesel Fitter at Cat dealer Barloworld Equipment in Botswana and then Leading Hand at Debswana Orapa Mine, Botswana.
Paul spent 11 years with Victorian/ Tasmanian Cat dealer William Adams as Field Service Manager/ Co-ordinator and Service Team Leader, and then Hastings Deering in Brisbane. Before moving across to The Drake Group in 2022, as head of the Service and Repair division in Queensland.
“It was something out of the ordinary, something I’d never done before and when I first saw Drake’s workshop it really got my creative juices flowing as I could see there was potential for me to use my previous experience to make it even better than it already was,” says Paul.
“Cat dealers are very particular about how their workshops are run and laid out to ensure the smooth and efficient flow of work and I saw this as an ideal opportunity to integrate those processes into the Drake service and repair operation.”
Some of the changes Paul has overseen include a new scheduling system which ensures every job is accurately tracked from start to finish, thus enabling customers to be fully informed about the progress of the work on their equipment.
“Another change has been to closely monitor the spend on each job to ensure that our budget is met and that customers are informed about the progression of their job,” says Paul. “Part of this involves the rebuilding of major components like hydraulic suspension and steering rams which are then put
into stock ready for when they are needed.
Paul explains that the workshop also stocks its own fast-moving new parts, such as brake linings, drums and other wear parts that are used regularly.
“One of the first things I did was to organise several new storage areas outside the workshop fitted with racking to house all the spare parts and also hydraulic hose manufacturing machinery which used to be in the workshop area,” says Paul.
“This has given us more space in the six-bay workshop and generally made the operation more efficient as everything is now kept in order and ready for use. Having the right stock on hand is critical to our operations due to a lot of our work being minor repairs that are turned around in one or two days.”
A full refurb can take up to two or three months or even longer for the larger steerable heavy haulage trailers with multiple rows of axles.
Drake’s Wacol facility has 16 fulltime employees, including admin,
boilermakers, trailer fitters, two apprentices, three tradesperson’s assistant (TA) a parts interpreter and a parts picker, who together manage everything from minor services through to complete overhauls, which may involve renewing entire steering/ suspension and braking systems after the chassis and body of the trailer has been sandblasted and repainted. The outcome is a trailer that rolls out of the factory in ‘as new’ condition.
A value-added aspect of the operation that has the potential to significantly speed up the repair process is a service-exchange program recently implemented which entails the stocking of commonly replaced components that have been refurbished and are therefore ready to be fitted to trailers.
Streamlining of The Drake Group’s Service and Repair division has been a critical step in enabling Paul and his team to keep abreast of the demand for trailer servicing, repairs and refurbishments in the Australian transport scene.
The Drake Group’s Service and Repair division has been given an overhaul in the interests of improving efficiencies to cater for increasing customer demand. As Paul Matthei discovers, key to the changes is the appointment of Paul Robinson as Branch Manager.Paul is quick to add that it’s imperative to adopt a steadyas-she-goes approach when implementing changes and that staff need time to appreciate the benefits of such changes.
They are the red and blue nylon lines that are the conduits for compressed air to pass from the prime mover to the trailer to respectively release the maxis and operate the trailer service brakes. But how on earth did the term Susie Coil originate?
Scouring a UK-based website for lorry drivers called TruckNetUK reveals a plausible explanation posted by Frankydobo in 2019. Now Franky is adamant that the correct spelling is Susie Coil, rather than Suzi Coil and that the term is essentially an acronym for SUSpended Insulated Electrical lead.
‘In the late ‘50s and early ‘60s the first coiled lead from truck to trailer was the electrical lead,’ Franky writes. ‘The air lines at that stage were still long, straight hoses with Palm Type couplings that often got snagged, or worse, when turning. Us Poms didn’t seem to go for the pogo stick affair the Yanks used to keep the lines held up.’
Franky explains that the early coiled electrical leads were thick and rubber coated with small coils and were heavy compared to the later ones.
‘So that is your original Susie, and I can only assume the industry adopted the same generic name for the coiled Poly Nylon air lines that replaced the problematic long air lines used previously,’ he writes, adding the salient points that the new suspended coiled air lines were not entirely immune from snagging or getting dirty.
Franky ends his post on a humorous note, writing, ‘… Hope this sheds some light but please don’t put a Z in Susie; it’s like saying ‘I’ve had a Cheeze sandwich’ and that’s not right is it!’
As Franky rightly points out, modern Susie Coils are not immune from snagging on the trailer corners if the trailer is jack-knifed when backing or turning sharp corners. When
this happens, as the combination is straightened the Susies can be stretched beyond their capacity to recoil which often means they will need replacing. The remedy here is to ensure there are no sharp edges or hooks on the trailer front that will cause snagging of the Susies.
Some Susies incorporate a length of stainless-steel coil on the outside which helps support the nylon tube where it mounts to the prime mover. While this should generally enhance the lifespan, care needs to be taken when the truck’s batteries are in the same proximity.
I’ve had the unfortunate experience of ruining a perfectly good Susie when trying to jump start a prime mover. The Susies were draped over the metal battery box and as I connected the
positive jumper lead clip it touched the stainless-steel coil which was earthed through contact with the battery box. Within an instant I caught the whiff of burning plastic and the Susie was fried and anything but airtight.
Another good practice is to cable tie both Susies and the electrical lead together at each coil along the entire length. This ensures they all stretch as a single unit during turns and means there is less likelihood of snagging. A side benefit is that it helps to keep the Susies looking neat and presentable.
Finally, when travelling bobtail, the Susie couplings need to be securely located to ensure they don’t fall down beside the chassis rails and risk being dragged along the road or wrapped around the tailshaft.
Have you ever wondered how Susie Coils got their name? Paul Matthei has, and he delves into this while also providing some tips on how to look after them and maximise their lifespan.
automatically, while the truck is driving.
This reduces labour costs, decreases component wear and tear and allows the truck to continue earning.
Advances in engine technology are permitting longer and longer service intervals which can translate into lower costs and greater productivity if a ALS automatic greasing system is installed.
Consider this…
Do you want to increase your equipment’s productivity and efficiency?• Need to save on maintenance costs, parts and down time? Working 24/7 and have no time for greasing? Introducing the Alemlube Automatic Lubrication System (ALS).
The best time to grease your vehicle is during operation - Small quantities of grease are measured and distributed to each point many times per day ensuring hard working components are always perfectly lubricated and damaging contamination is kept out.
Manual lubrication is eliminated, no more time wasted on servicing grease points.
Grease points can’t be missed. Difficult or hard to reach points can’t be missed out and are kept perfectly greased regardless of servicing schedules.
The working life of fifth wheels, compensators and ball races are also greatly improved.
Peace of mind - Your initial investment in the ALS will protect your capital investment, providing trouble free operation and creating the perfect working environment for all components for the life of your vehicle.
Breaking down the ALS:
The Alemlube ALS pump station is made of the latest engineering polymer materials making it lighter, stronger and more durable for the harshest operating conditions and exposure to the elements.
The integrated system controller has every feature for control and
monitoring built in.
Alemlube engineers the right volume of lubricant to each grease point and the precision machined progressive dividers ensure that each point receives the correct amount of grease.
Every component in the Alemlube system is designed for an industry best pressure of 280Bar (4,200psi).
Protects your investment and lets you know if any grease point won’t accept grease.
Of course the Alemlube ALS uses NLGI#2 grease, as recommended by every manufacturer of vehicles and machinery. You can choose the best grease for your operation, including greases with up to 5 per cent Moly (molybdenum disulphide).
With very high operating pressure and the ability to have up to three pump outlets, the Alemlube ALS has the ability to reliably service almost any application from a 4x2 truck to a garbage truck to a heavy haulage trailer.
Road transport today is extremely competitive with trucks commonly travelling 6,000km to 7,000km per week or more. The ALS grease system greases key components every hour,
The ALS system greases key steering, suspension and brake components every hour allowing the truck to stay on the road working and eliminating the need to come into the workshop between scheduled services.
Benefits are higher productivity and better reliability.
Another key benefit is the ALS system using #2 grease. Thicker #2 grease creates a barrier around pins and bushes preventing the entry of water and other contaminants, keeping critical components clean and contamination free means longer life – up to two or three times longer than when greased by hand or with liquid grease systems.
The ALS automatic greasing system allows important maintenance work to be done while the machine is working.
Additionally, working in such harsh conditions, contamination is a major problem and bearings block and pins fail quickly if contamination entry is not controlled.
By supplying fresh #2 grade grease to the bearings every half hour or hour, a protective barrier around all the pins is maintained to stop soil, dust and water getting in and eventually causing failures.
Contact Alemlube in your state or territory to benefit from the Alemlube ALS.
When considering the trucking industry, it’s helpful to remember the Slim Dusty song ‘Looking Forward, Looking Back’. The trucking industry has certainly come a long way, but there is still a long way to go. Australian Trucking Association Chief Engineer, Bob Woodward tells us more.
This will be my last PowerTorque column for the ATA. Over the many years I’ve been with the organisation, I’ve seen some remarkable people who give their all to the industry.
For example, the 25th winner of the prestigious Craig Roseneder Award, Jason Button from CHS Broadbent has a deep commitment to safety and has implemented a system which has significantly reduced the downtime for a fleet of vehicles.
A shout out too to Greg Brown from MaxiPARTS who is the winner of the 2022 Castrol Vecton Industry Achievement Award. Greg is an industry veteran, who has been with MaxiPARTS for more than 30 years. He’s an active member of ATA’s Industry Technical Council (ITC) and plays a lead role with the ATAITC rigid drawbar Converter Dolly project.
Over the years, there has been progress, there have been some issues that have been addressed like roller brake testing and non-compliant brake actuators.
However, there are many other issues that haven’t been fixed, including:
· Access
· Australian design rules
· PBS – safety standards reviews
· HPFVs
· Modular combinations
· Rest areas
One of the big advocates for change has been the ATA’s Industry Technical Council (ITC) which has been operating for 29 years.
The ITC was born out of a trip to
the US-TMC by former ATA Chairs and industry stalwarts Bruce McIver, Denis Robertson and along with the then Road Transport Federation (now ATA) CEO, Andrew Higginson.
Recently after seven years as ITC chairman, Kel Baxter handed the reins to Dennis Roohan (AJM Transport).
Kel Baxter has had a long involvement with the ITC, providing vehicle combinations for ATA-ITC demonstration days, including the first BAB Quad permit for the demo day at Narrandera in 2009 and Dubbo in 2010, and more recently an AB-triple at Albury-Wodonga.
Dennis and Deputy Chair, Lyndon Watson, will continue to lead the ITC in its technical goals.
It’s people like Jason and Greg who keep the industry ticking over and we owe them a great debt.
As I sign off, I want to say how proud I am to be a part of this incredibly rewarding profession. I can definitely recommend a career in trucking because there’s a role for everyone. I look forward to seeing the industry blasting through the obstacles and going from strength to strength.
Of all the Australian farm produce that depends on refrigeration and speed to get to market in good condition, some members of the berry family are prime candidates to demonstrate the golden rule of food transport, get the transport right, or better still, fit for purpose.
Specific transport rules covering pulp temperature, highest freezing point and maximum storage life apply to all farm produce, and will be listed in detail in a forthcoming Cold Food Code Produce Specifications schedule being finalised by the AFCCC and will be shared with the industry some time in 2023.
But to demonstrate the critical importance of reliable and smart refrigeration during transport, I have chosen products with the shortest shelf life, raspberries, blackberries and boysenberries.
Farmers and their agents have a maximum of three days to get their boysenberries and blackberries off the farm, transport them between zero and three degrees to market, and get them onto the supermarket shelves in an attractive condition.
If ever a transport needed to be fit for purpose, the berries demand it. For starters, the truck or trailer being used has to have a well made body, with a compliant K value in the order of .65 or less. K value is a value of the amount of thermal conductivity of heat, in watts, that is transferred into a truck or trailer body through leakage or failure of construction materials. The lower the K value, the higher will be the thermal efficiency of the unit.
Having found a transport fit for purpose, the next imperative is that the transport must be fitted with an intelligent refrigeration system, one that is capable of maintaining a temperature
of zero to three degrees over a whole day of travelling if necessary to reach the market. Refrigeration systems that have intelligent firmware settings in their controllers, capable of managing the temperature control between supply air and return air have been perfected by the major suppliers, Carrier Transicold and Thermo King.
Transport companies that aren’t prepared to invest in such technology can never carry berries at the right temperature, so a farmer’s choice of transport to market could mean the difference between a profit and a total loss. The temperature control is so critical that if it dropped below zero, they would freeze, ruining the load. The Cold Food Code will spell out that the highest freezing point for boysenberries and blackberries is -0.7 degrees Celsius, with a storage life of two to three days. The highest freezing point for raspberries is -1 degree Celsius.
All businesses involved in the handling and distribution of perishable food products from the farm to the consumer have an important role in ensuring that product quality and food safety standards are maintained.
The transport element of the cold chain accounts for a significant proportion of the shelf life of many perishable products such as fruit and vegetables. Product quality can quickly deteriorate during transport if inappropriate conditions and practices are used.
Food loss and waste due to inadequate cold chain practices has detrimental economic and environmental consequences.
For a carrier to provide the industry with the best service, fresh produce must be properly prepared before transport. This involves correct package selection and pre-cooling to the desired
transit temperature prior to loading. Refrigerated vehicles and containers are designed to maintain temperature during the period of transport, not to cool the product.
However, there is evidence that a significant amount of food is rejected at the point of unloading, mainly due to products not meeting temperature specifications set by receivers, with other reasons being:
· product damage
· missing a time slot
· product that is spoiled or over-ripe
· incorrect consignment paperwork.
The condition of food when it reaches the market is paramount, writes Mark Mitchell, Chairman of the Australian Food Cold Chain Council (AFCCC), he contends all cold food transport must be fit for purpose.
ALL
MUST BE FIT FOR PURPOSE