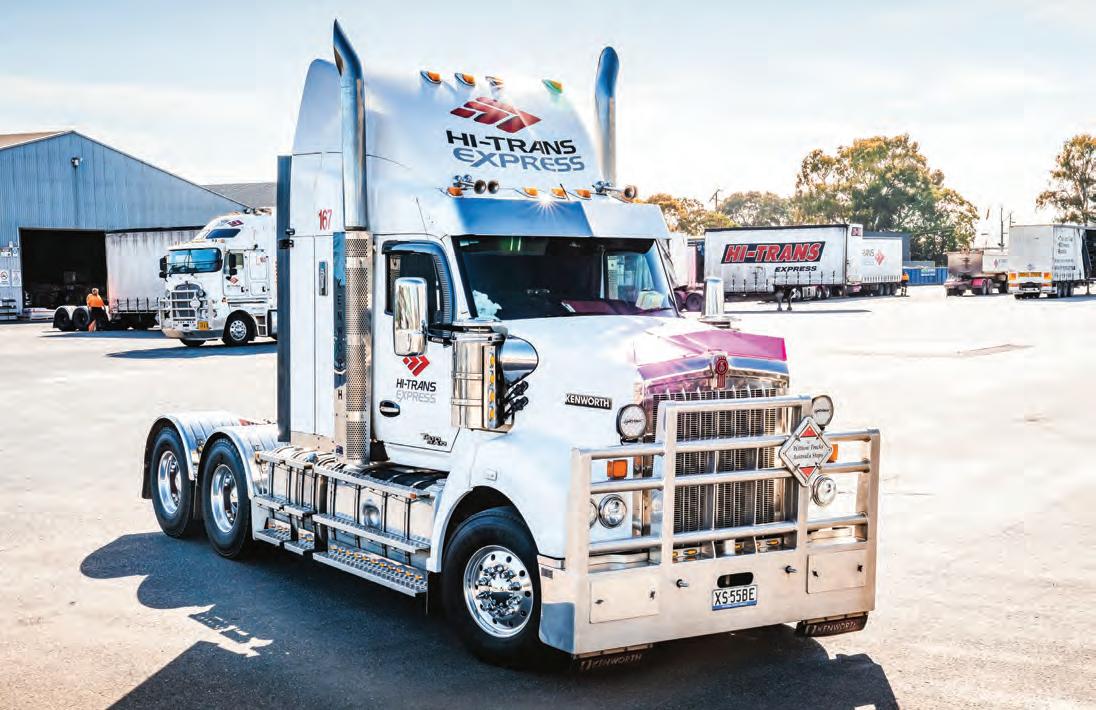
12 minute read
COVERING ALL OF THE BASES
management system every day.
“I am able to preplan all of the servicing of the vehicles a number of weeks before they are due, because I know what work they will be doing. Then I let the depots know when any unit is needed for servicing and they get sent to the appropriate service location.
“All of my preventative maintenance and everything else is in this system. I don’t really have to think of a thing, it’s simply a matter of getting the information in and updating it. It’s straightforward easy system to use and when we get our audits, I can pull all of the information out and make hard copies, if needed.”
ADAPTATION AND DEVELOPMENT Over the past 12 years Hi-Trans has adapted and developed the system to work precisely to help improve fleet performance. The Hi-Trans Express business model is all around depot to depot line-haul over long distances, where the most important factor is the reliability and consistency of the rolling stock day-in-day-out.
The Sydney to Adelaide trucks do around 400,000km per year, running a changeover regime, a pattern which is repeated between most of the capital cities in Australia.
There are over 40 trucks in the fleet as well as over 150 trailers. There are also lot of subbies involved in the operation hauling the trailers, as well. Monitoring of the trailers is an important part of the data collection, ensuring they are fit for purpose on each night run. Trailer maintenance is all done in-house by the operation.
“If you plan everything in advance, it’s so simple,” says Andy. “It’s not reactive maintenance, it’s all planned maintenance. We also do a lot of history reporting, with every repair having a job associated with it. The stock of spares is also allocated to each job and monitored to assess costs.
“Every tyre is monitored. If you put air in the tyre or torque them up, look at steer tyres and rotate them, everything goes into the system and is put against that asset.”
It was this monitoring which brought
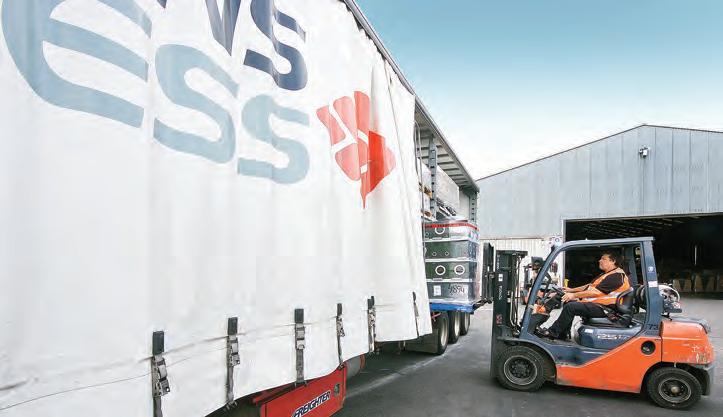


Andy’s attention to the efficiencies of the recently introduced Bridgestone M866, with the new drive tyre exceeding mileage expectations across the line-haul operations. Hi-Trans Express recorded 364,688km from a set, with another set of M866 tyres involved in the trials also projected to have a life of 360,000km and beyond.
The net result of Hi-Trans Express’ experience with M866 is an average of five to ten per cent improvement over its predecessor, the M766.
“These are the best tyres we’ve ever run. I’ve only got positive things to say since we started running them,” says Andy. “The M766 was a very good tyre overall, but we’ve never seen results like we have from the M866.”
Hi-Trans Express was one of ten Bridgestone customers to conduct extensive real-world testing of the M866, contributing around 1.2 million km of data to the development including direct comparisons with the predecessor model and the competitor’s product. The trial was conducted on the Adelaide to Sydney return run and Adelaide to Emmdale return runs.
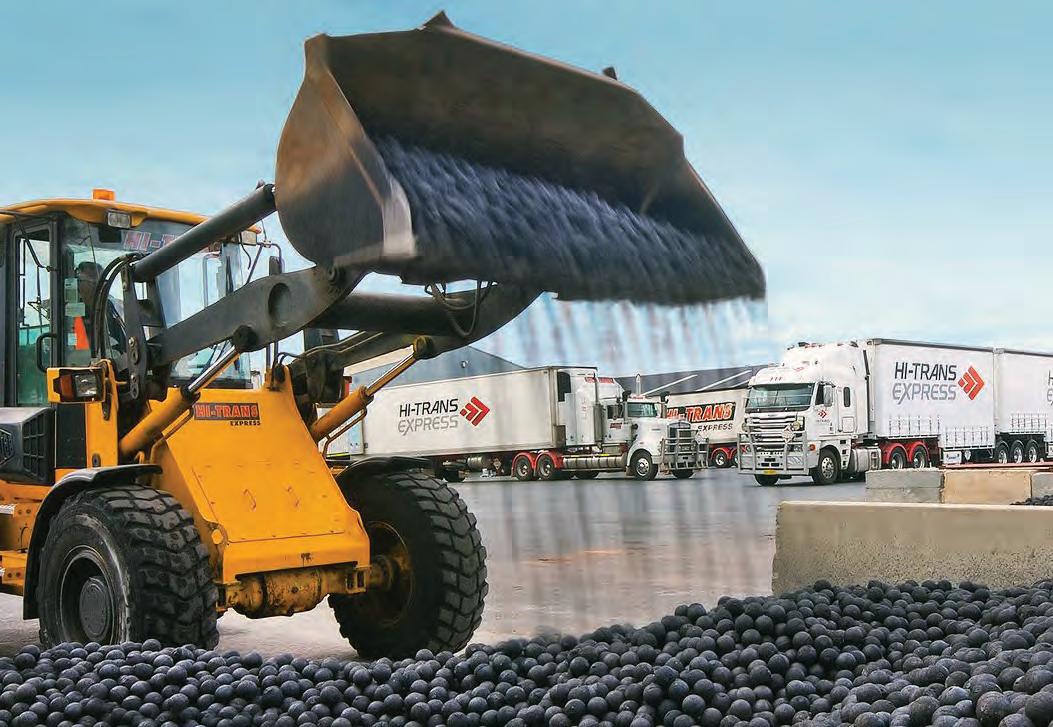
LOOKING FOR EFFICIENCIES A fleet like Hi-Trans Express is always going to be looking for efficiencies, but is also committed to operating a carbon neutral line-haul fleet by 2025 and is actively investigating ways to reduce its environmental footprint with operational efficiencies, such as those achieved with these new drive tyres.
“Everything is measured and monitored,” says Andy. “We can have a fairly stable cost base for the business with the products we know. We can look at history reports and look at different parameters and compare them in our system. We can then put a cost against those kilometres and work out our CPK on each route.
“Every run is a bit different and by analysing them we know the run to Sydney from Adelaide is not going to cost as much as the run up to Broken Hill, where the road conditions are worse and the truck is pulling a road train.”
All of this monitoring will also effect how the service life of a piece of equipment may

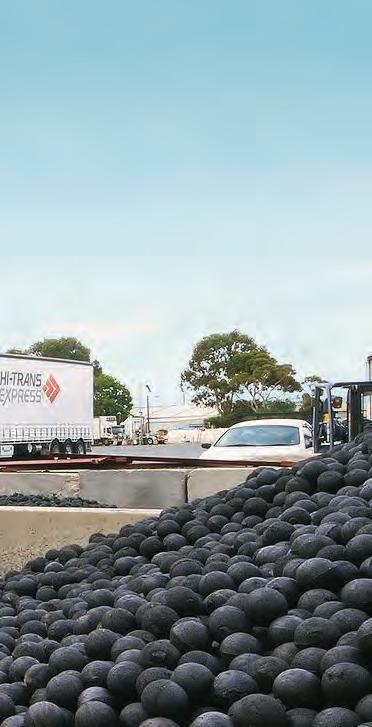
vary depending upon performance and longevity. It’s not only performance on the road, it is also how the vehicle is purchased. Different agreements lead to different service lives.
The fleet includes mainly Kenworth and Mercedes Benz trucks. While the Benz trucks are on a long term maintenance contract, the Kenworths are purchased and serviced. As a result the Benz will remain in the fleet until the end of its contract, usually 1,000,000km, and will then be moved on.
The Kenworth is a different proposition and, as a result, normally remains in the fleet much longer. The decision in this instance uses the long term data collected to estimate when the truck will start costing more to maintain and needs to be moved on.
Operations like the Hi-Trans Express fleet are those at the cutting edge of the search for improved productivity. High mileage line-haul creates a lot of wear and tear on a truck and dramatically accelerates the ageing process, when compared to many operations in the trucking industry.
Monitoring costs at all levels is vital just to stay competitive, in a very competitive market. Systems like those employed by Hi-Trans keep pushing the envelope on what is achievable with smart planning and equipment selection, something which is becoming a higher priority across the trucking industry.
TM

COMMERCIAL VEHICLE DISC BRAKE PADS

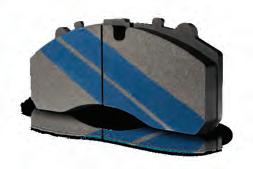

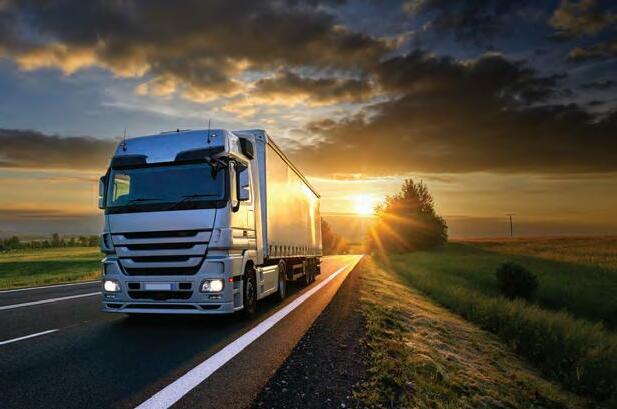
To combat the extreme pressures that heavy duty vehicles such as Cement Agitators, Garbage Compactors or City Route buses are exposed to, Bendix has created Bendix Protrans™HD. Protrans™HD has a heavy-duty formulation designed to cope with high temperatures found in constant braking and full GVM loading which requires a higher performance brake pad.
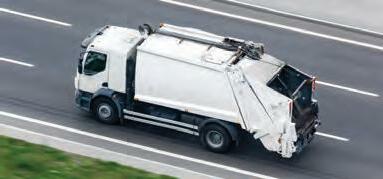
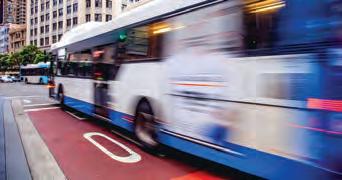
MATERIAL REFERENCE APPLICATION
Protrans™HD Super Heavy Duty – Severe duty applications, Refuse Compactors, Concrete Agitators, Route bus applications. Frequent braking environments, heavy traffic, steep gradients. Long wear life at high brake temperature. Strong resistance to fade at very high temperatures. FE 500°C
FRICTION CLASSIFICATION MAXIMUM CONTINUOUS WORKING TEMPERATURE
COMBATING DRIVER FATIGUE WITH TELEMATICS
Get a better understanding of driver fatigue and how to use technology to manage it.
The (U.S.) National Safety Council (NSC) found that driving after more than 20 hours without sleep is the same as driving with a blood alcohol concentration of 0.08 per cent, more than the legal limit. Based on this fact alone, it’s more important than ever for fleet managers to monitor and combat dangerous driving habits like driving while fatigued.
WHAT IS DRIVER FATIGUE? Driver fatigue is often seen as an underestimated danger of being on the road. Drivers often face long trips and inconsistent driving schedules, leading to situations where they potentially find themselves driving while tired and drowsy.
Technology can play a key role in reducing the number of fatigue-related collisions among fleet drivers. For example, vehicle features and ADAS solutions, including drowsiness and lane departure alerts are prime examples of technology that can detect common drowsy driving habits and notify drivers to stay in their lane or take a rest.
COMMON DRIVER FATIGUE SYMPTOMS Fleet and business safety managers can increase safety by encouraging their drivers to spot key driver fatigue symptoms and stay off the roads when they feel tired or drowsy. To help get a better idea of behaviours to look out for, here is a quick list of the signs of fatigued driving from
The National Institute for Occupational Safety and Health (NIOSH): • Being awake for a long period of time • Lack of sufficient sleep over a several day period • Long durations of inaction or monotonous work • Sleep disorders • Medications that include drowsiness as a side effect
As well, the following symptoms may also be noticeable in fatigued drivers: • Falling asleep at the wheel • Slow reaction times to changing road
conditions, obstructions, traffic or even pedestrians • Poor decision making • Lane drifting • Tunnel vision • Microsleeps (brief moments of sleep lasting anywhere up to 30 seconds) • Lack of memory about recently driven miles
DRIVER FATIGUE STATISTICS According to the Australian Automobile Association (AAA), the peak organisation for Australia’s motoring clubs such as NRMA and RACQ, as much as 30 percent of all car crashes in Australia are due to fatigue. The National Road Safety Strategy states that “fatigue is four times more likely to contribute to impairment than drugs or alcohol.”
With that in mind, note that there is often difficulty in generating these estimations as it is hard to prove fatigue as the sole cause of collisions. Unlike a breathalyser test, there are no tests that can be administered to prove impairment due to fatigue and police currently do not include a regulated fatigue assessment in investigation practices.
Driver fatigue also poses an increasing threat for companies who rely on their drivers to be safe and alert. According to the Sleep Health Foundation and Deloitte Access Economics, inadequate sleep cost the economy $1.9 billion in 2016-17, or $252 per person.
DRIVER FATIGUE MANAGEMENT It is the responsibility of both fleet organisations and their drivers to maintain the safety of their drivers and encourage best practices behind the wheel. This is why Geotab offers fleet dashboard camera integrations that offer added benefits for fleet management, including:
Recording and saving collision footage and filing proper evidence if any collisions result in a lawsuit.
Identifying impaired or distracted driving, not only in instances of fatigue, but also eating, drinking, smoking, or being on the phone.
A live view of drivers’ routes that can be triggered by events like speeding or harsh braking, allowing for quicker reactions by fleet managers to potentially dangerous situations.
By installing dash cams, companies are prioritising fleet and driver safety while gaining an extra layer of visibility into their on-road operations. Geotab offers a number of dash cam options, safety reports, and many other safety solutions in the Geotab Marketplace that can be integrated with the MyGeotab platform. This can make it easier to manage all fleet cameras from one cloudbased dashboard.
In addition, Geotab offers Marketplace solutions for ADAS and cameras.
CONCLUSION With the help of technology such as dash cams and Geotab Drive, there is hope that many fatigue-related incidents can be avoided. For fleet managers, setting up policies and adopting technology that works to prevent driver fatigue is a great place to start. Working with drivers to monitor their health and wellness is another way to help lower fatigue-related incidents, keeping them alert, responsive and safe.
SCAN THE QR CODE TO FIND OUT MORE ABOUT GEOTAB
CREATING A SAFE, EFFICIENT WORKFORCE THROUGH DATA
Making changes to your operations to streamline practices and cut down on unnecessary costs is difficult at the best of times, let alone in the middle of a global pandemic. But the secret lies in making the most of your fleet’s data.
In fact, a PwC survey found that datadriven organisations were three times as likely to achieve major improvements in their decision-making capabilities.
Here’s how correctly gathering and analysing your fleet’s data and transform operations while ensuring the safety of everyone involved.
REDUCED COSTS Thanks to the data being collected from sensors and AI-powered devices, managers can gather a comprehensive understanding of the real costs behind completing certain tasks, how much fuel is used, how many team members are required, and the number of hours needed can all be viewed in real-time.
Managing trucks and other large assets can be complex, but with data collected via telematics, you can understand the condition of each vehicle without needing to physically inspect them. Potential issues can be addressed immediately, while ensuring that each asset is serviced when needed. With all these insights at your fingertips, you can use this data to cut down on unnecessary costs and improve efficiencies to make more money.
A COMPREHENSIVE VIEW No matter how much experience you have, being behind the wheel can be unpredictable. If you’re involved in a collision, it’s vital you have all the equipment you need to protect you, not just in terms of safety, but to back up your story and preventing falsified claims.
A smart, multi-camera solution installed around your truck keeps drivers safe from potential legal and compliance dramas. They capture a complete 360-degree view of the driver cabin, as well as finer details like license plates.
If an incident is caused by another road user, the business can refer back to the HD footage to determine who is at fault. Not only does this help from a legal standpoint, but by exonerating drivers of any guilt, multi-camera solutions help to protect drivers’ mental wellbeing.
ENHANCED DRIVER SAFETY When drivers are spending long periods of time on the road, away from family and friends, it’s vital that managers are aware of their staff’s health and wellbeing on the job.
EWDs enable drivers to self-manage their fatigue through automated in-cabin alerts, notifying them when it’s time for a break. Designed to keep you compliant with Chain of Responsibility (CoR)
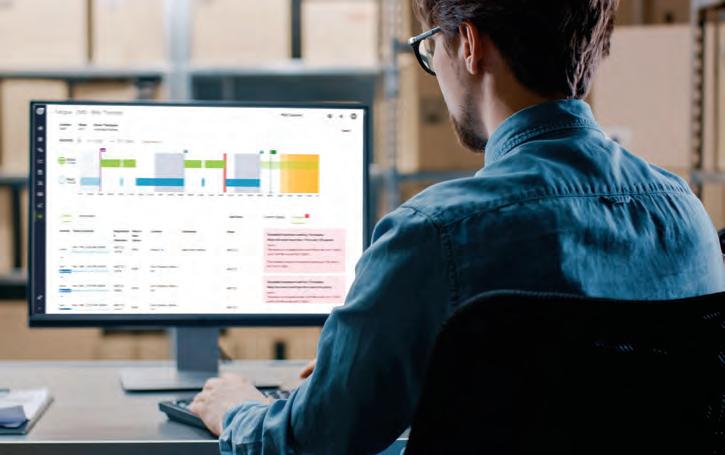
requirements, EWDs help drivers stay safe and give managers peace of mind that their team is doing the right thing.
EWDs provide back offices with second-by-second data, allowing them to better schedule jobs based on their real-time working hours. This ensures that all drivers are safely able to manage their fatigue levels from the get-go, while also ensuring that deadlines can be effectively met.
For fleets that can turn big data into actionable insights, you can expect to see increased productivity, reduced downtime and decreased admin costs, all while keeping your team safe and secure.