pumpindustry
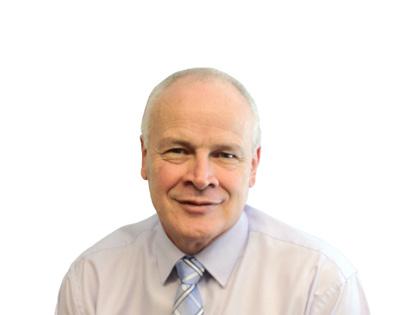
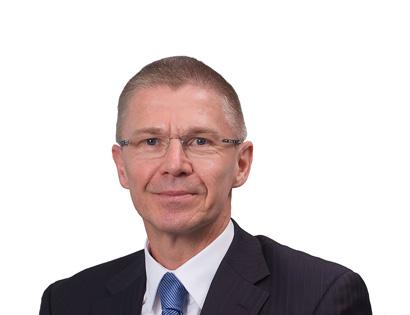

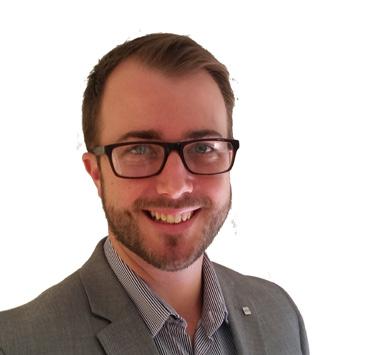
ALSO FEATURING:
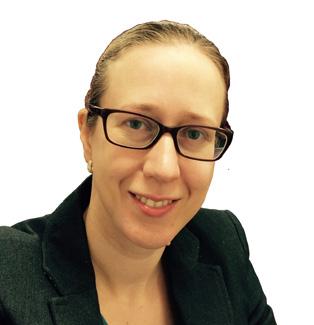
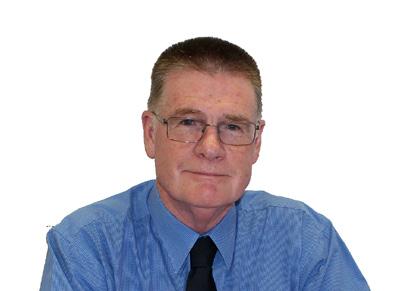
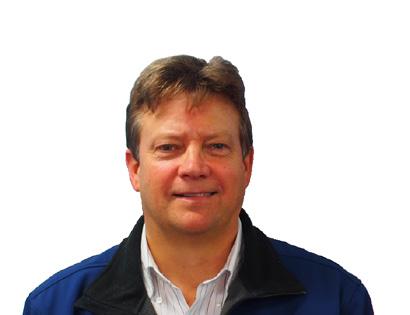
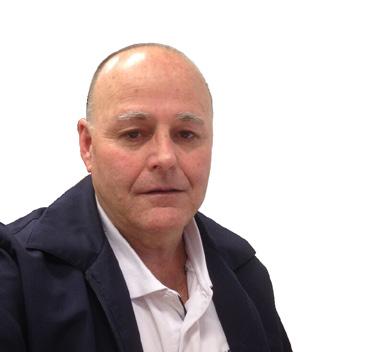
Franklin submersible pumps and motors are ideal in the most demanding applications and offer unmatched reliability.
Franklin motors provide a long and dependable working life. The motor shown here was still operating effectively after 53 years.
• 4’, 6”, 8”, 10”, 12”
• 0.37kw to 400kw
• 230, 415, 1000 volt
• 304, 316, 904L construction
Pump Industry Australia Incorporated
Kevin Wilson – Secretary PO Box 55, Stuarts Point NSW 2441 Australia
Ph/Fax: (02) 6569 0160 pumpsaustralia@bigpond.com
Ron Astall – President United Pumps Australia & Astech Consulting Services
John Inkster – Vice President Brown Brothers Engineers
Mike Bauer – Councillor Dynapumps
Frankie Camilleri – Councillor John Crane
David Alexander – Councillor KSB Australia
Alan Rowan – Councillor Life Member
Keith Sanders – Councillor Australian Industrial Marketing & Life Member
Ashley White – Councillor Davey Water Products
David Brooks – Councillor Flowserve Australia
Since the last issue we have run PIA meetings in Melbourne, Adelaide and in Brisbane. Attendances have been excellent and the feedback very positive. Aside from the technical presentations, we have been highlighting the ongoing development of the PIA Installation and Commissioning training program, as well as our ideas for cooperation with the Hydraulic Institute, which include Pump System Optimisation training, and PIA marketing various Hydraulic Institute publications. We will be making some further announcements on the latter very shortly.
We see these initiatives as exciting and challenging developments for PIA. Together with similar cooperation with BPMA, the common theme is education and energy efficiency.
Right now I do not believe that the Australian market has anywhere near the same driving force behind energy efficiency programs that we are seeing in Europe and the USA. In Europe there are compulsory energy audits on large organisations and in the USA there are also massive financial incentives for energy efficiency programs. In Australia there are some dollar for dollar incentive programs (particularly on lighting) but there does not appear to be a
systematic approach to energy saving in legislation, nor any general awareness of what incentives exist for industry.
At PIA we are continuing to push the energy saving barrow because we see this as a major role for the Australian pump industry and we are aiming to get ahead of the game; because we believe that the incentives that now exist in Europe and the USA will eventually trickle down to Australia. Pumps are massive energy consumers; in manufacturing, pumps can consume up to 70 per cent of installed electric motor capacity.
Aside from our planned training and expanded publication initiatives, we are happy to provide speakers on pumping related topics for seminars and for general training. We have already done this for the ARBS exhibition, AMCA and NEBB. If this is of interest to you or your organisation, feel free to contact us.
Ron Astall President, Pump Industry Australia3,318
ABN: 36 426 734 954
PO Box 3121
Ivanhoe North VIC 3079
P: (03) 9440 5721
F: (03) 8456 6720
monkeymedia.com.au
info@monkeymedia.com.au
pumpindustry.com.au magazine@pumpindustry.com.au
Publisher and Editor: Chris Bland
Managing Editor: Laura Harvey
Marketing Director: Amanda Kennedy
Marketing Consultant: Aaron White
Associate Editor: Michelle Goldsmith
Journalist: Emily Thomas
Creative Director: Sandy Noke
Designer: Alejandro Molano
ISSN: 2201-0270
Welcome to this latest edition of Pump Industry. We’re particularly excited to share this edition with you, as we’ve given the magazine a bit of a facelift. We hope the new look is clean, fresh and modern - and that our content lives up to the same standard!
In this issue we’ve taken the time to get to know some of the people and personalities that make the Australian pump industry tick; and to give our readers some insight into these personalities through a series of interviews. In an industry which is quite technical in terms of products and capabilities, it’s refreshing to get to know the people behind the pumps a little bit better, and gain some insight from these individuals about what they love about the industry - and importantly, where they think it is heading.
I’m also pleased to share our recent audit figures with our readers and supporters. For Pump Industry, the latest audit results bring good news, with our circulation increasing to 3,318 copies per issue - which represents growth of eight per cent over the previous 12 months. In a time when the audited circulation of many magazines is shrinking, these results show that people really like reading this magazine, particularly the end users of pumps across all industries.
In my role, I get to talk to pump companies every day, which provides
me with a good measure of the state of the industry. Like any industry, it’s always a bit of a mixed bag. Even at the best of times some companies are doing it tough, and even in the worst of times some companies will prosper.
There’s no doubt that in recent times, the pump industry has faced some of the toughest market conditions in some time. However in recent months I’ve seen continuing signs of improvement in the industry, and overall there’s a more positive vibe from the people I talk to. I hope this is a sign of better things to come.
I’ve previously mentioned that our review of the history of the PIA, which we published as a separate liftout in the November 2014 edition, had led us to discover the original Australian Pump Journal, which was published in the 1960s. I’m pleased to be able to share these original journals in a little more detail, with a feature on this publication from page 62. I’d like to thank the original Commercial Editor of The Australian Pump Journal, Bob Pullen, for sharing his magazine with us. As you’ll see, in the almost fifty years since it was first published, while some things have changed, many in the Australian pump industry have interestingly remained the same.
Chris Bland Publisher and EditorThis magazine is published by Monkey Media in cooperation with the Pump Industry Australia Inc. (PIA). The views contained herein are not necessarily the views of either the publisher or the PIA. Neither the publisher nor the PIA takes responsibility for any claims made by advertisers.
All communication should be directed to the publisher.
The publisher welcomes contributions to the magazine. All contributions must comply with the publisher’s editorial policy which follows. By providing content to the publisher, you authorise the publisher to reproduce that content either in its original form, or edited, or combined with other content in any of its publications and in any format at the publisher's discretion.
Cover image shows a collection of some of the key pump people in the Australian industry. Turn to page 18 to read more. Published by Monkey Media EnterprisesPump Industry magazine has taken a peek behind the scenes, gathering together some of the influencers within the industry to gain an insight into their careers in pumps. Here, we take a look beyond the technology and the issues and meet the personalities that make the pump industry Down Under tick.
We offer a comprehensive range of mechanical seals from simple pusher styles to single, double and split cartridges, and custom engineered sealing systems.
We supply seals for pumps, mixers & reactors and for duties including water, chemicals, hydrocarbons, pharmaceutical, sewerage, paper pulp and food & beverage. Contact us to discuss your sealing needs.
Our ‘Pump up your selfie’ initiative is continuing to draw entries from members of the pump industrysometimes in unusual and exotic locations.
One of the best entries we’ve received so far has come from Maurice Calderon, Marketing Manager for NOV, taken whilst travelling through the city of Muscat in Oman.
At Pump Industry, we love our readers, and we love to see photos of you reading Pump Industry. To encourage you all to share a photo of yourself reading your favourite magazine at your workplace, we’re giving away a copy of the Australian Pump Technical Handbook for the best pump reader selfie.
We’re still accepting entries for this competition, but entries close on August 31.
Entering your selfie is easy – just take a snap of yourself reading Pump Industry (or feel free to ask someone to take the picture for you), then either send it to Managing Editor Laura Harvey or tweet it and tag @pumpmag with the hashtag #pumpupyourselfie.
The best picture, as judged by Pump Industry, will receive a copy of the Australian Pump Technical Handbook, the Australian pump industry’s one stop guide to all things pumps, valued at $90.
So get creative and share your snaps with your colleagues and fellow readers today!
Inpro-Seal compound labyrinth bearing seals and air purged product seals. Manufactured in high quality bronze or stainless steel to suit your application.
The next PIA General Meeting will take place in Sydney on Tuesday 25 August 2015.
All members are encouraged to come along to this event and take advantage of the chance to catch up on the latest PIA activities, and to network and socialise with industry colleagues and friends.
The meeting will take place from 4.30pm to 6.30pm, with
complimentary refreshments to follow. Location is still to be confirmed but will be advised in future editions of the Pump Industry weekly enewsletter.
Members who are interested in attending should register their intention to attend the meeting with PIA Secretary Kevin Wilson via email at pumpsaustralia@bigpond.com.
The Dodge Vertical Gearmotor provides an alternative to common vertical pump drive technologies and offers significant benefits when compared to other systems.
The Vertical Gearmotor is built on a standard low pole count motor platform utilizing proven Dodge planetary gear technology. This results in a smaller, lighter, more cost-effective and highly efficient package.
www.abb.com/mechanicalpowertransmission
SA Regional Development Minister, Geoff Brock, has announced that Joyson Orchards at Lenswood is investing in a $4.5 million capital project to redevelop the Gumeracha vineyard within the Adelaide Hills.
“This project is bringing new life to an abandoned site, increasing the premium food and wine produced in the area and creating seven new full time equivalent jobs by 2018,” Mr Brock said.
“The critical step in this development is to secure sustainable and reliable access to water for the vineyards and orchards.
“A containment dam and pump will be installed for storing treated wastewater from the Gumeracha wastewater treatment plant, supplementing the existing water supply over the growing season which will allow for a further 10 hectares to be planted,” Mr Brock said.
Peter Oborn from Joyson Orchards said the project represented the opportunity for high quality South Australian produce to be grown sustainably using recycled water with a unique twist.
“Our aim with this project is to reinvigorate the existing vineyard infrastructure to create premium quality wine and integrate into the land a contemporary orchard reflecting industry leading growing techniques,” Mr Oborn said. “With our Torrens Valley Road frontage, it’s envisaged that a ‘pick your own’ orchard will complement the commercial orchard, offering a unique tourism attraction and showcase great Adelaide Hills produce.
“Our primary objective is to build a sustainable and resilient food production system to satisfy both local and international demand for high quality South Australian foods,” Mr Oborn said.
Joyson Orchards received the $200,000 grant through the enhanced $15 million a year Regional Development Fund to go towards the water infrastructure component of the project totalling $535,000.
The Fund drives economic growth and productivity by offering grants to boost investment in regional infrastructure and create jobs and new opportunities for regional South Australia.
Water Corporation is upgrading the wastewater pump station and associated pressure main at Bedingfield Way No.1 Pump Station in Australind, WA.
The existing pump station serves the Australind Sewerage District and is located approximately 150 metres west of the Brunswick River.
The project works will involve:
• Construction of about 406m of 250mm diameter below-ground pressure main and associated
• Recommissioning of about 81m of redundant water distribution main on the Paris Road Bridge, to be used as a pressure main
• Upgrade of the pump station capacity, including provision of a new odour filter pit and a new bypass arrangement.
These works are expected to proceed soon, and will take about 11 months to complete.
While works on and around the Paris Road Bridge will be appropriately timed to minimise inconvenience to pedestrians and motorists, some traffic delays can be expected.
The community will be advised of the timing and traffic management arrangements for the Paris Road Bridge works in due course.
Works have begun on upgrades to two sewage pumping stations at Blue Bay and Toowoon Bay (NSW), representing a $2.6million investment in the Shire’s water supply.
Almost all of the 148 sewage pumps in the Wyong City Council (NSW) region were affected by recent storms in the area.
Power outages during the storms
become inundated with water, putting strain on the overall system.
Residents were advised to stay out of the lakes for a few days but drinking water was not affected at all. No licence breaches occurred during the storm event.
Whilst resources were deflected to cope with the storm events, upgrades to the Mardi Dam Fire Trails and the
track to be completed by the end of the financial year.
Wyong Council Mayor Doug Eaton has said, “Our pump stations really did cope well under the extreme conditions of the recent storms – as our drinking water was not affected at all.
“We will continue to invest in our pumping stations and water supply network to ensure we can cope with
What is recirculation, and what are some of the end results of recirculation?
Recirculation is the reversal of part of the flow back through the pump impeller and occurs when the pump operates at a rate lower than best efficiency point. Recirculation can occur at both the suction and discharge of the impeller.
Recirculation warning signs include a random loud crackling noise with high intensity knocks.
What’s the result of recirculation?
Cavitation damage at:
• The underside of the impeller blades
• Guide vanes in pump suction connection (if fitted)
• Cutwater or diffuser vanes
• Vibration and mechanical damage such as bearing and seal failure.
As with cavitation due to low net positive suction head the overall potential impact is increased maintenance and downtime of the pump - which means greater costs.
Article courtesy of Kelair Pumps Australia – When Pump Knowledge Matters. For more information phone 1300 789 466 or visit www.kelairpumps.com.au.
Western Australian Water Minister, Mia Davies, has announced that $713million has been committed to Water Corporation projects across Western Australia, as part of the 2015-16 State Budget.
Residents in the Kimberley and Eyre regions (WA) will benefit from a $275million investment in regional water and wastewater projects.
Member for the Mining and Pastoral Region, Dave Grills, welcomed the announcement. “The State Government is making wise investments in water and wastewater infrastructure that will guarantee the long-term sustainability of our regional communities,” he said.
“This latest wave of investment announced in the 2015-16 State Budget will help to ensure regional communities from Broome to Esperance have access to quality and reliable water and wastewater services.”
In the Kimberley, the government will invest $7million to upgrade wastewater infrastructure in Derby. This will include construction of a new wastewater pump station on Sutherland Street, a 3km wastewater pressure main and gravity sewer. Work is expected to be completed in early 2016.
Broome residents will also benefit from the latest wave of investment, with work to continue on upgrading the town’s water supplies. A new water pipeline along Fairway Drive will be constructed, with $460,000 allocated to the project in 2015-16.
In Halls Creek, $2.3million will be invested on wastewater upgrades. The Halls Creek project will involve construction of 4.1km of wastewater pipeline.
This pipeline is in addition to a recent wastewater pump station upgrade and will cater for anticipated long-term population growth in the town.
In Eyre, the government will invest $1.3million in 2015-16 to continue work on installing a new groundwater bore at the Butty Borefield, located about 20km
west of Esperance.
Mr Grills said the new bore was expected to increase water supply by almost 10 per cent, or 850,000 litres of water each day, and help improve the quality of the water supply in Esperance.
“The increased capacity of the borefields will help cater for Esperance’s growth over the next five years,” he said.
Esperance residents will also benefit
from a $3million investment in the Esperance 15B Infill Sewerage Project. The project will cover 123 residential lots and is part of the State Government’s $50million Infill Sewerage Program.
These projects will improve Water Corporation’s services, and ensure its customers have access to quality and reliable water and wastewater services.
If you’ve spent much time around water wells and other water pumping systems, you will probably have seen the devastating effect iron bacteria can have on a water supply system - and on your water source. What you may not know is that this costly problem can be easily avoided, simply by choosing the right components for your water supply system.
In a world of increased costs, we all search for ways to become more efficient in everything we do. When we see inefficiencies, we deal with them immediately and the result is savings and increased profitability. But what happens when we do not see inefficiencies? The cost of ignorance is immeasurable.
With a large percentage of the Australian population, livestock and industry presently dependent on groundwater, it is of interest for all of us to ensure the long-term sustainability of this most precious asset, water.
Pumping water from underground is a hidden operation. We cannot see the water, the pump or the drop pipe. We only see a surface tank or piping leading away from the well.
Given that most of the equipment in a groundwater pumping operation is completely hidden, it can be easy to miss some of the problems that can occur and decrease the efficiency of a water pumping system.
Buildup of iron bacteria is one such common problem. Iron bacteria can present in a number of ways, including a strong, unpleasant smell or taste, stained or coloured water, and a sticky slime, typically rust in colour.
In water wells or groundwater pumping systems, one of the biggest challenges associated with iron bacteria is that it can significantly reduce the yield of a system by clogging up its pipes and equipment.
The other main problem with iron bacteria is that once it’s present, it can be very difficult to get rid of it. Treatment options include physical removal of any rusting of equipment that has occurred; and chemical treatment of water supplies. Both of these are costly options, and if the level of iron bacteria is high, may not actually be entirely effective.
Like many things in life, prevention of the problem is easier than the cure. This means making sure that pumps and all other equipment relating to your water system are sterile when installed, and only using appropriately licensed contractors to carry out works on your system.
If you’re installing a new submersible bore pump and water well system, it is important to review the components that
The effects of iron bacteria can be dramatic.
make up your system to ensure they are not subject to the encrustation and blockage that iron bacteria causes. Encrustation and internal iron bacteria build up in the riser pipe leads to reduced flow rates and inefficient pumping. By choosing a flexible riser such as Flexibore Hose, there is no chance for iron bacteria build up inside the pipe, due to the swelling characteristics of the materials used. The polyurethane flexes and hence does not allow the iron bacteria to build up, thus keeping pumping costs down. This is not the case with rigid risers made of steel, fibreglass or polypipe.
The Flexibore Hose ensures simple and effective bore water retrieval, mine dewatering and municipal water supply. It’s a flexible yet resilient layflat hose that can be installed with great ease compared with rigid pipes.
Nicolas Huvelle, an experienced agronomist in the Warialda NSW region, had a problem with not only his submersible bore pump clogging up with iron bacteria, but his fibreglass riser pipe too.
Flows were reduced by 15 per cent due to clogging within the pump impellers. Mr Huvelle ran the numbers and realised that the iron bacteria blockage was costing him $115 per week due to the inefficiency of his blocked system.
After doing some research, Mr Huvelle came to the conclusion that the capital cost of replacing his riser pipe with Flexibore Hose would quickly pay for itself thanks to the regained efficiency his unblocked pipe would offer. Most
importantly, he wouldn’t have to worry about iron bacteria building up in the pipe again, as no iron bacteria could build up inside the riser. Another benefit was the fact that the pump could be easily lifted whenever the pump needed to be cleaned and the bore redeveloped.
Since installing the Flexibore Hose Mr Huvelle’s well efficiency has improved, resulting in lower running costs and less wastage of water and energy - all thanks to the choice of riser used.
Iron bacteria in a fibreglass riser.
For more information on how Flexibore Hose can help you to avoid iron bacteria in your water supply system, contact Crusader Hose Managing Director Francois Steverlynck on 03 9720 1100 or visit www.crusaderhose.com.au.
22 Industry Place Bayswater VIC 3153 Australia
Phone: +61 3 9720 1100
Email: sales@crusaderhose.com.au
www.crusaderhose.com.au
The Shakti story dates back to 1982 producing stainless steel submersible pumps, energy saving submersible motors, vertical multistage centrifugal pumps, pressure booster, selfpriming, end suction, open well and solar pumps. The company has grown phenomenally and has become one of the few pioneers in the world to produce 100 per cent stainless steel submersible pumps.
The company employs international best practice technology to manufacture its products. This technology includes cutting-edge Japanese and European machines, modern CNC machines and stamping machines.
Owing to its dedicated efforts in R&D and technological innovation, Shakti has emerged as a leading entity in the pump industry, catering to domestic as well as international markets with a notable reach of more than 100 countries. Today, Shakti is among the best brands in the world, thanks to state-ofthe-art technology and continuous innovation.
The main focus of the company is to manufacture quality products matching global benchmarks with higher energy efficiency, better durability, and which are easy to maintain. With its diverse product portfolio, Shakti is catering to the world’s water needs with steady growth year after year. Equipped with strong product verticals and international standards of technological excellence, Shakti Pumps has carved a niche amongst quality conscious users around the world.
An ISO 9001-2008 certified company, Shakti has a sprawling state-of-the-art manufacturing facility. Shakti manufactures diverse models of submersible pumps, motors and other application pumps for a wide range of applications. Over the years, Shakti has seen a steady growth trajectory and has become one of the leading pump manufacturers and exporters.
With its advanced assembly line system, the manufacturing facilities are equipped with highly efficient precisionequipment, specialised in rolling out intricately designed
and assembled superior quality products from the factories manned by skilled and talented manpower. A fully computerised testing division monitors the performance of every pump that is made, thus maintaining consistency in quality.
As the farming community forms a major chunk of its end users, Shakti Pumps offers comprehensive and reliable pumping solutions with superior quality and energy efficiency. The pumps are largely used for applications like drinking water supply, irrigation, industrial applications and processes, pressure boosting in high rise buildings and townships, rural/ urban community water supply schemes, waste and sewage water treatments and firefighting.
Shakti’s aim is to become the world’s leading pump manufacturer, attaining global benchmarks in pumping solutions. Its fully-fledged R&D division is dedicated to research and development of innovative products with new materials, applications and processes. With an urge to succeed, Shakti continually innovates and introduces new products and pumping solutions that satisfy the market needs. Quality is the key in all Shakti products. This compels the company to focus on construction and design with special care while selecting materials and production methods. Shakti uses advanced fabrication technology and produces most of the components in-house, ensuring higher standards of quality.
The excellence in quality coupled with energy efficiency is the key that differentiates Shakti Pumps from its competitors and helps it to maintain leadership in global pump industry.
Corrosion has always been a challenge for pump manufacturers, especially in brine, seawater, acid, chlorinated water and alkaline liquid circuits. The use of thermoplastics in pump construction is proving to be an innovative and effective solution and has quickly gained popularity in Europe.
The Nozbart Thermoplastic Pump range brings a cost-effective, corrosionfree and beautifully designed solution to the Australasian pumping market. Distributed by Action Aquatics, the new thermoplastic range provides smooth internal surfaces which reduce turbulence and noise, whilst being lightweight and almost silent during operation. The range of models is wide, covering duties as small as 2m³/hr to over 500m³/hr with a pump heads up to 32metres.
These thermoplastic pumps are ideal for aquaculture and marine circuits,
swimming pools, water parks, cooling tower circuits, milk and food grade pumping circuits, and large public aquariums.
After test-running Nozbart pumps for three years in Australia across a range of environments including seawater installations, aquariums, water parks and pools, Action Aquatics have recently launched these pumps at the Australian Water Association Conference in Adelaide with resounding success.
On first sight, these pumps have a modern new look about them. The volute and discharge are made up of a number of major components, each of which can be replaced in minutes. The modern design is incredibly lightweight and even the largest pumps within the range can be lifted by one person, doing away with the need for overhead cranes and special lifting devices. The brass and stainless nuts and bolts do not corrode
and even after years of use, come apart with ease. It also allows for quick installation and disassembly.
There are no metals in contact with the liquid pumped. The impeller is made from high strength reinforced thermoplastic and all other components are made from a unique thermoplastic.
The thermoplastic body absorbs sound, so much so that there have been a number of instances where pumps have been reported as having stopped, only to find that they are running normally, but silently. This means that where a decibel rating is part of a specification, these thermoplastic pumps could provide an answer.
There is no doubt that thermoplastic pumps will bring about radical changes to the pump industry, especially where corrosive liquids are being pumped.
The Sunraysia Modernisation Project (SMP) enhancement will see the project area extended to provide irrigators in the Red Cliffs district (VIC) with year-round access to irrigation water.
The project is a joint initiative between the Commonwealth and Victorian State governments and Lower Murray Water (LMW).
SMP Project Director, Mike Walsh said, “These works ensure that the Red Cliffs district receives maximum benefit from the $120million dollar SMP, the biggest upgrade of irrigation infrastructure in the history of the Sunraysia region.
“As we progressed through the SMP’s detailed design phase we identified opportunities where we could value-add, and the Red Cliffs Pipeline
System is the third enhancement we’ve been able to incorporate,” Mr Walsh said.
“The work at Red Cliffs will now extend the proposed pipeline by an additional 3.9km, from C re-lift pump station to Pillars Outfall,” he said.
“This means the area serviced by 365-day supply in the Red Cliffs district will increase by 905 hectares. In Red Cliffs 91.5 per cent of irrigation assessments will receive 365-day water supply, up from 71.5 per cent previously planned.”
Mr Walsh said a major benefit to the Red Cliffs community would include additional channel removals through urban areas.
“2.2 kilometres of channel through Red Cliffs will now be removed, including the channel running adjacent to the
nursing home. Three council channel bridges and several private bridges will also be removed,” he said.
Mr Walsh said the additional work would be achieved within the agreed budget, without any extra capital expenditure or funding and within existing project milestone dates.
The Red Cliffs announcement follows enhancements previously confirmed for the Merbein and Mildura districts.
“Our focus is to deliver 365-day water supply to as many irrigators as possible. Our aim is to deliver a flexible and practical plan to achieve the maximum possible benefit for irrigators and the community,” Mr Walsh said.
•
• Torque control, smooth start and stop modes to avoid water hammering
• Dedicated software for pump control systems
• Programmable timers with real time clock
• Early warnings and safety stops
• Optimized monitoring for energy saving
• Control of up to 7 pumps
• IP20/21 and IP54 rating
John Inkster is the CEO of Brown Brothers Engineers New Zealand, Brown Brothers Engineers Australia and Kelair Pumps Australia. Mr Inkster joined Brown Brothers Engineers in Christchurch, New Zealand in 1986 and moved to Australia in January 2000.
Prior to joining Brown Brothers Engineers, John worked for a firm of engineering consultants in Christchurch for 12 years and was involved in the design and construction of rural water supply schemes, and feasibility studies for large irrigation schemes.
During this time, John spent two years in Western Samoa as part of New Zealand’s bilateral aid agreement with the Western Samoan government, designing and constructing small village-based water supply schemes on the islands of Upolu and Savaii.
Brown Brothers Engineers was formed in 1908 and is one of New Zealand’s oldest pump companies. Brown Brothers Engineers and Kelair Pumps are part of the Mace Group
of Companies a third generation, family-owned engineering company headquartered in Christchurch, New Zealand.
Mr Inkster is mindful of the impact the economy is currently having on the Australian pump industry. “With the Australian economy facing strong head winds and below trend GDP, most businesses in the pump industry are finding business tough going and we are no exception. We need to be very mindful of costs and await the slow recovery of the economy and an improvement in business confidence.
“Until this happens we are going to see a continued period of consolidation, belt tightening and some further redundancies and lay-offs. There will be no risk taking. The global pump market is exposed to the same issues and I am seeing the same outcomes with the suppliers we are associated with.
“Globally the pump market is striving for better efficiencies and improved life cycle costs so we can expect to see competition driven by new and improved technologies.”
Building connections with colleagues and clients has been the most rewarding part of being involved in the pump industry in Australia. “When I first came to Australia in 2000, Brown Brothers Engineers was not well known, nor was I, so joining the PIA enabled me to meet others involved in the industry. In doing so, BBEA has become more well-known. We have been in Australia now 20 years and are an established player in the pump industry; our association and involvement with the PIA has played a significant role in exposing our name to the greater pumping fraternity.”
Steen Holm Jensen is Managing Director for Grundfos Pumps in Australia and is also the Chairman of the Board for Grundfos Pumps NZ. Mr Holm Jensen has over 30 years’ experience working with Grundfos, and has over this period been on the Board of Directors of more than 25 Grundfos companies, including companies in the United States. Mr Holm Jensen has extensive management experience and holds a tertiary degree in Economics from Aarhus University in Denmark, supplemented by various seminars and three stays at the IMD Business School in Lausanne, Switzerland.
While with Grundfos, Mr Holm Jensen has held positions within Information Technology and Finance. Prior to being appointed as Managing Director for Grundfos Pumps in 2001, Mr Holm Jensen held the position of Global
Segment Director for Wastewater with Grundfos Management A/S.
Outside of Grundfos, Mr Holm Jensen is also the Chairman of the Board of Directors of BKB Building Solutions and is the Honorary Danish Consul to South Australia, a position he has held since 2013.
Mr Holm Jensen believes that moving forward, the pump industry must constantly look at new ways to provide value to its customer base. He also believes that it is important to acknowledge some of the new trends currently emerging in the water industry. For Mr Holm Jensen, this includes the evolution of water and wastewater infrastructure, which will be looked more at as a business opportunity attracting stakeholders of all sizes.
“With its relative isolation and unique environmental challenges, the Australian market is well placed as the “first mover” on new business concepts,” said Mr Holm Jensen.
“In many industries, there is a drift towards status quo,” he added. “It is my strong belief that the survivors longer term will be the entities with the ability and courage to drive change.”
For Mr Holm Jensen, the people, the opportunities and the challenges are what he loves about the pump industry in Australia, fuelling his desire to continue the growth of Grundfos Down Under.
Garry Grant started his pump career in 1990 at Pacific Pumps, where he was the Product Manager for Gorman-Rupp pumps. In 2000 he made the move to Engineered Products Group as the General Product Manager of Pumps, Hydraulics, Transmission and Engines divisions. In 2008 he started Hydro Innovations, where the main focus of the business is the importation, application and distribution of Gorman-Rupp Pumps.
After 25 years in the industry, it’s the people and the challenges that keep Mr Grant excited. “I love the characters one meets in this industry, and I love the challenges,” he said. “I have had the pleasure of rubbing shoulders with operators, engineers, asset owners and folks in many positions in between. Everyone has a story to tell, axe to grind or (sometimes!) helpful advice to offer.
“In this industry each day presents new challenges. New products, competitors, customer expectationsfor me, they all help to make the industry interesting even after all these years.”
In the years to come, Mr Grant sees the next major challenges to be centred around the need to deliver more sustainable solutions to customers. “This includes providing not only energy efficient solutions, but efficiency in labour utilisation, efficiency in resources utilisation as well as delivering lower equipment life cycle costs,” he said.
“Also, as insurance premiums increase and safety regulations tighten (such as confined spaces), companies will need to deliver safer solutions to their customers’ pumping needs.”
Mr Grant also has a few predictions when it comes to the changes we are likely to see in the industry. “I think that safer and more innovative level control systems will become more demanded, particularly in the municipal wastewater sector,” said Mr Grant. “I also see the use of more sustainable wastewater wet well designs becoming increasingly sought after. These things have already started to appear in Europe, with customers being delivered safer solutions, combined with systems that use less of our natural resources, with lower civil costs and lower life cycle costs. And although the use of variable frequency drives has been increasing, I see their use on pumps increasing even further as sustained pumping efficiency is demanded by the market. I see pump manufacturers looking to design pumps that maintain efficiency, including sewage pump manufacturers who will be asked to maintain peak efficiencies even when pumping wastewater.”
Peter Vila’s career in the pump industry spans more than 35 years. His first five years in the industry were spent servicing and repairing pumps, with the following five spent in pump sales. Over the next 25 years Mr Vila worked in a range of management roles with several prominent pump companies, and since 2012 he has been the Managing Director of SEEPEX Australia, a progressive cavity pump manufacturer with headquarters in Germany and branches worldwide.
Mr Vila has been keenly following the changes in the industry in recent years, and has noticed a shift from a focus on being ‘green’ to being ‘smart’.
“A few years back, the buzz word in industry was green, but that seems to have been replaced recently with a new word, smart. Technology is racing ahead at an incredible rate and for all companies the challenge is to ensure we are not caught standing still as future generations embrace continued technological progress. The pump manufacturers which previously incorporated something green into their product lines must now do likewise with smart technology. Bottom line is remaining connected to one’s markets and listening to their needs,” said Mr Vila.
“At the moment, competition in Australia between global pump manufacturers seems to be at an all time high, certainly in my lifetime. Many overseas manufacturers have been facing challenges for some time on their
home turf, and have therefore searched for other opportunities, ultimately seeing Australia as a land of opportunity.
“The result is that we now have more international pump manufacturers with a direct presence in Australia than ever before. From a buyer’s perspective that’s probably a great thing, but for the pump manufacturers, there is the challenge of survival within this congested and highly competitive market. As mentioned previously, smart technology is now a major consideration and it’s only a matter of time before this starts being specified and requested as mandatory, rather than optional. Manufacturers who embrace this technology, incorporate it into their designs and remain firmly connected to their market/s will stand a far greater chance of survival. What happens in Australia won’t be unique to our land, as the world continues to become a smaller place, with events on the other side of the globe often feeling like they’re just next door.”
For Mr Vila, it’s the people and the variety that come with the pump industry that he loves.
“The pump industry is a tight-knit group and over the years you come across the same faces, sometimes not seeing someone for over a decade, then suddenly this young guy you remember is now an old timer standing in front of you, which brings the realisation of how long we’ve been playing this game.
“There’s not too many jobs which take you to the variety of places attended by those in the pump industry. Water and sewage treatment plants, mine sites, mineral processing plants, food and beverage processing plants, pharmaceutical manufacturers, refineries and fuel terminals, chemical processing plants, paper mills, sugar mills, power stations, large ships - they all need pumps. Each visit gives an opportunity to meet new people and learn new processes, all experiences provided by the pump industry and for which I will be forever grateful.”
Mark Goddard
Managing Director, Sulzer Pumps
Mark Goddard started his career in the aero industry, qualifying as an aircraft technician before moving into the pump industry in South Africa in the 1980s with Stewarts and Lloyds. Mr Goddard then moved to Allis-Chalmers as Product Manager, then was offered the role of General Manager for Morris Pumps (Goulds), where he spent a number of years servicing the mining sector. After a stint in the pulp and paper industry, Mr Goddard made the move to Australia with Sulzer Pumps, where he was responsible for the growth and development of the mining segment for Sulzer in Australia and the South Pacific Islands.
Mr Goddard worked his way up from Sales Manager for Mining, then took on the role of National Sales Manager responsible for mining and pulp and paper. In the last three years Mr Goddard has had the role of Managing Director and Legal Entity Head.
“It has been an incredible journey, challenging but fun. I am fortunate to have been supported by a very competent, dedicated and focused team that has made huge difference. Over the last twelve years the business landscape has changed significantly, the mining boom has come and gone, the influx of cheap imported pumps, the decline in the industrial sector.
“The current market conditions are very volatile and companies need to be agile and dynamic, and able to adapt and change direction very quickly.
One needs to constantly monitor trends and needs of the market and then be able to manipulate resources to meet these new requirements.
“On the manufacturing side this downward trend will continue, and we will still have to compete with low cost imported products flooding and diluting the market. End users are concerned about efficiency and quality, pricing is a major driver, based on their budget constraints. Globally the trends are similar, but they are more aware of life cycle costings, efficiency and maximising up time of their equipment.”
For Mr Goddard, it’s the fact that there’s never a dull moment that forms the appeal of the pump industry. “Putting it simply, there is never a dull moment when one is involved in the pump industry, it is dynamic, every day brings different situations and challenges. The last few years have been exciting and with the change in the business landscape of late the next few years are going to challenging but very exciting.”
David began his career in the pump industry over ten years ago and is the current Managing Director of Wilo Australia, a full subsidiary of the German group Wilo SE. Mr Kerridge was involved with the foundation of Wilo in the Australian pump market and has since progressed through the company in key positions to now lead the Australian subsidiary. With key interests in marketing and management, Mr Kerridge was voted in 2013 as one of the Top 30 Young Managers Under 30 in Australia by the Australian Institute of Management. The ultimate driver for Mr Kerridge is to steer a company with a strong culture at its heart that focuses on delivering best in class products, services and experiences.
For Mr Kerridge, there’s much to like about being a part of the Australian pump industry. “The pump industry offers large possibilities in a relatively
stable career environment for the right person,” he said. “The Australian industry is well known for long-term personal relationships formed in people’s networks. The constant challenge of meeting and exceeding customer expectations is what drives me and my team.”
Mr Kerridge believes that companies in the pump industry need to adapt to meet current market conditions. “Wilo is going beyond pumps. We’ve identified that providing solutions rather than products is what the market is now demanding of manufacturers,” he said. “We are looking to combine energysaving products with smart system solutions to assist our customers tackle the global megatrend of energy shortage.”
According to Mr Kerridge, energy efficiency is the key change taking place in the industry at the moment. “Following on from the trend in Europe, I think such a developed and mature country like Australia will move towards energy efficiency and technological advanced products. The payback periods on these investments are getting shorter and shorter and I firmly believe this will be the largest growth area in the coming years.”
Julie Truss has been involved in the mining industry and with slurry pump systems for over 12 years. After completing a Bachelor of Engineering (Chemical) from University of Adelaide with first class Honours, Julie spent four years as an Area Manager for Weir Warman (now Weir Minerals Australia), supporting mine sites across South Australia and the Northern Territory. Julie was then promoted to Territory Manager for SA/NT/Vic/Tas, and completed an MBA from University of Adelaide in 2010, where she won the prize ‘The Head of School’s List of Top MBA Graduates’.
In 2011 Julie became Weir’s Product Manager, Slurry Pumps. In this role she remains passionate about understanding individual site needs situations and delivering real benefits through practical, reliable pumping solutions.
“At Weir Minerals, we need to continually focus on creating products and processes that really maximise profits for our customers,” said Ms Truss.
“This includes focusing on equipment design as well as materials technology - creating products that not only deliver the best throughput, but last between
“We need to think outside the box - how can we create better solutions for our customers? Understanding how pumps fit in the system is critical...by combining technology with industry leading processing equipment products, we can provide complete plant solutions.”
scheduled maintenance periods. We look at continuous improvement for our existing pump models, and pioneer developments to create the pumps of the future. We have the centrifugal slurry pump Global Design Centre of Origin right here in Australia - where our engineers are working every day on developing Warman pumps to meet our customers’ needs. We need to keep listening and working with our customers to provide them with the solutions they are looking for.
“We also need to think outside the box - how can we create better solutions for our customers? Understanding how pumps fit in the system is critical - Warman pumps are, and have long been, a trusted brand in the industry, but by combining this technology with the industry leading processing equipment products that Weir Minerals offers, we can provide complete plant solutions. By maximising efficiency and throughput at every stage of the process we ensure that all equipment works together to give the most reliable, optimised slurry transportation system.”
Ms Truss is expecting big changes for the industry in the near future, particularly in light of the current state of play in the mining industry. “As grades decline, for example iron ore, customers will continue to focus on maximising throughput with the greatest efficiency possible,” said Ms Truss. “They will continue to ask for more reliability and longer wear life from their existing slurry equipment. Capex available for new equipment is becoming more scarce,
so aligning with customers to optimise their existing pumps and systems will be very important. Thankfully, this is nothing new for us, as the product development team for Warman pumps has been doing it for decades, and Weir Minerals is dedicated to continuing this business model.
“Globally there will be similar trends towards efficiencies, although some countries are bound to see a greater volume of capital spending than Australia.”
For Ms Truss, being involved with Warman pumps for over 12 years has been a really enjoyable ride. “I have met some amazing, talented, passionate and extremely knowledgeable people in my time,” said Ms Truss. “Collaborating with customers has meant I have been involved in solving numerous problems, saving much downtime, reducing spend and adding value to their businesses. There aren’t many industries/jobs where you get that combination of passionate people coming together, willing to try new ideas and make improvements.
“I have enjoyed seeing pumps leaving the factory looking pristine, but probably more so seeing Warman pumps on a mine site where they have been tirelessly pumping slurry around since before I was born. My favourite nostalgia moment was visiting a site only to find that the Warman pump I was there to look at was actually pump #391 built by the Warman Equipment Company in Kalgoorlie back in the 1940s - it even had the original nameplate!”
John Weaver began his career as an apprentice motor mechanic at the original MMBW – the Melbourne & Metropolitan Board of Works. After a number of years and having moved through several roles within the organisation, Mr Weaver took up his first appointment with the German based safety company Draeger as a sales representative. Over the next 14 years with Draeger, Mr Weaver progressed through a number of senior sales and marketing roles. Mr Weaver then made the move to Davey Water Products, where again he moved through a number of senior sales and marketing roles over thirteen years, embracing a diverse range of pump products for rural, household, fire-fighting, industrial and swimming pool applications.
Two and half years ago, Mr Weaver joined Xylem Water Systems as General Manager – Oceania, with the brief to significantly expand applications for the diverse pumping products available under a range of market leading brand names. Internationally recognised brands such as Lowara, Vogel, Bell & Gossett and Gould’s Water Technology head up a stable of world leading products being promoted into this region of the world.
Mr Weaver believes that the companies that will succeed in the years to come are those that are continually reviewing the way they do business and reacting to changes in the market. “Whether they are cost changes,
technology changes or demand changes, it is important to continually look at what you are doing and how you are doing it,” he said. “During the millennium drought it was easy to gain pump sales as the market was driving sales and demand was high. As conditions change (weather, economic or technology) it is important to accept the change quickly and to keep moving forward to capitalise or adapt to the new market conditions. The market today is different to the market of two years ago and the market today will be different to the market in two years’ time.
“Companies have to accept the prevailing conditions in which we operate and adjust their strategic approach to those conditions. Past
successes guide us but keeping a close eye on prevailing and potential future conditions provides future success in changing markets.”
Mr Weaver has identified new performance standards and energy efficiency regulations as driving pump technology towards new and improved products. “In a world where energy conservation is paramount in society, it is incumbent upon product manufacturers to develop products that deliver savings in operational costs as well as offering opportunities to enhance their environmental footprint,” he said. “The new pump efficiency requirements introduced into Europe earlier this year will create a flow on effect into this part of the world. By default more efficient products will flow
into our region and will create a demand or expectation from users to be able to utilise these efficiency gains in their day to day operations.”
For Mr Weaver it is the variety the pump industry offers that is fulfilling to him. “The pump industry in Australia offers so many varied areas in which to operate. For Xylem, our success is found in decades of technology and innovation in the water industry. Being involved with a company that has strong values of respect, responsibility, integrity and creativity with our long standing customer relationships is exciting and rewarding.
“The challenge of providing distinctive water solutions to our customers in Australia makes going to work each day an enjoyable challenge.”
It is often the simplest ideas which create the best outcomes – and so it was with Sydney Water’s Andrzej Krawiec and Martin Byrnes’ simple modification of sewage pump operating protocols, which is now saving Sydney Water around $6million in operational costs each year.
The idea was seeded in 2011 following a safety incident that occurred during the manual cleaning of a sewer pump station wet well.
Andrzej Krawiec, Service Delivery Officer at Sydney Water said “The safety incident triggered me to think that there must be a better way? Why do we continue to clean wet wells in this manual and dangerous way? Surely we can come up with some way to automate this process?”
Mr Krawiec sought the guidance of Martin Byrnes, SCADA Configuration & Test Engineer at Sydney Water and together they created an innovative solution to the problem which reaped far greater benefits than they initially imagined.
At sewage pump stations, grease, fat and other material such as wet wipes combine on the well surface over time and can form a significant crust. Heavy silt builds up on the well floor. Combined, these factors cause significant odour and many operational and maintenance problems, such as:
• Level sensors and instruments become blocked and malfunction
• Pumping equipment can fail and pump impellers can be damaged
• Pumps are choked by this material and floating material causes odour build up.
Traditionally maintenance crews were needed to regularly clean the wet well at sewage pump stations manually using suction hoses.
Issues with this manual cleaning process, known as flushing, include:
• High labour costs
• Safety risks and confined space entry
• Isolation of the sewage pump stations
• Pump chokes
• Ineffective cleaning
• Excessive potable water usage.
As materials become consolidated over time they choke pumps, which to remedy, requires the expensive process of lifting the pump out of the well to clean and restore the pump to operation, involving crane hire and multiple people on site.
Each sewage pump station required on average five to six manual flushes per year, plus two de-siltings per year,
with each manual clean requiring flow isolation of the system. The combined cost of manual cleaning was around $2million per year for Sydney Water.
The innovation
“I thought that if we could just get the material to go through the pumps one small piece at a time, rather than allowing it to consolidate, then we would have much less of a choking problem,” said Mr Krawiec.
The traditional setup for operating levels and pump cut-in and cut-out, ensures the well surface stays above the pump body and definitely above the pump intake. The well surface is not disturbed during the pump down which causes crusting on the surface and silt build up on the well floor.
Mr Krawiec and Mr Byrnes developed a simple and automated ‘Auto Flushing’ process which created self-cleaning of
wet wells on submersible sewage pump stations.
The process involved automatically pumping the wet well down to very low level so that it draws the floating material into the pump intake and removes it on a daily basis. Also the bottom silt gets swept up by the turbulence and is drawn into the pump intake.
Sydney Water uses its SCADA system IICATS to control level changes which can be time scheduled for any time of day or night. The process is undertaken at peak inflow times for additional turbulence which creates more effective cleaning. For some particularly problematic sites this Auto Flush period is repeated in the evening peak, or more often if necessary to keep the well clean.
In cases of heavy crusting, a manual clean may be necessary prior to commencing Auto Flush. In other cases where level instruments are so encrusted
with fat, a manual clean and re-calibration is necessary to get an accurate reading at low levels so that Auto Flush can be effectively implemented. In both situations manual cleaning was not required after Auto Flush was implemented.
Sydney Water initially ran the Auto Flush concept as a trial of 18 sites, for which the worst sewer pump stations were chosen. Some of these trial sites had experienced persistent odour complaints and were ideal candidates to determine if the Auto Flush process would be effective.
The trial results in reducing monthly overall operating costs for the 18 trial sites were outstanding, with significant reductions in cleaning costs, breakdown costs, corrective maintenance, preventative maintenance costs and any general costs. Once initially implemented, most other costs gradually
declined because of less instrument failures, less pump chokes and less pump breakdowns.
The trial was so successful that Sydney Water rolled out the protocol to 485 sewage pumping stations.
Since undertaking the trial, Sydney Water has experienced a number of benefits.
• Across the whole system Sydney Water is trending toward an annual operating cost saving of $6 million or better
• Fully automated cleaning (flushing and dredging)
• Manual cleaning costs eliminated or reduced
• Potable water saved by not doing manual flushing
• Safety risk from manual cleaning removed
• Corrected other sewage pumping station faults during implementation
• Reduced odour complaints
• No capital outlay for equipment or construction.
Wider operational benefits include:
• Maintenance costs reduced by around 75 per cent
• Breakdown costs reduced by 66 per cent
• Reduced level sensor failures
• Reduced pump breakdowns and chokes
• Reduced occurrence of false suction safety alarms
• Improved Sewage Treatment Plant (STP) operation
• Increased processing of Bio-solids at STP
• Cleaner rising mains – less pigging
• Potential reduced chemical dosing for odour
• Improved pump performance.
The success of the Auto Flush protocol has created a culture where the wider group of Sydney Water engineers is now looking for other ways
to innovate to improve operations. The success also provides proof that on-the-ground operational staff are often best served to understand problems and to find relevant solutions.
Successful innovation doesn’t always require new technology – the more effective utilisation of existing technology can create outstanding improvements.
Gary Hurley, Sydney Water’s Networks Manager said “Sydney Water is proud to have innovative people such as Andrzej and Martin working to improve the way we do our work.
“The Auto Flush innovation has the potential to be implemented by the water industry across the globe.”
Sydney Water is happy to help other organisations to realise the benefits that this great innovation can deliver. For more information, contact Gary Hurley at gary.hurley@sydneywater. com.au to discuss how this may be implemented in your company.
A single dissolved air floatation (DAF) pump has the potential to replace the entire air bubble system on DAF plants, according to pump supplier, Hydro Innovations.
Their Edur® multiphase pumps draw in air through a snorkel in the suction line, shear the air, then feed it into the DAF plant, producing a discharge stream into the tank that is saturated with 30 to 50 micron air bubbles.
Conventional DAF systems normally consist of a wastewater tank, compressor, air saturation vessel, and effluent pump. The effluent pump draws effluent from the tank and pumps it into the air separation vessel. A compressor pumps air into this same vessel. The air/water mixture is ‘saturated’ under pressure, then released back into the wastewater tank at atmospheric pressure where tiny bubbles form and adhere to the suspended matter (fats, oils and other small wastewater particles). The bubbles, with their attached suspended matter, float to the surface of the tank, where floatables can be skimmed off the surface.
By using Edur multiphase pumps, which can produce their own microbubbles, asset owners can do away with the compressor, the air saturation vessel and any control and/or ancillary components for these items. The reduction of these system components and the simplification of the system design results in lower investment costs and higher operational reliability.
The Edur multiphase DAF pump is also an efficient alternative. Now, one pump can replace the conventional pump, air saturation tank, and the compressor. Energy costs, as well as maintenance costs, of running the compressor are eliminated.
Edur multiphase pumps can deliver flows from 1L/s for smaller DAF plants to 15L/s for larger DAF plants, and produce pressures to 12 bar. A variety of materials and seal arrangements enable Edur pumps to operate in a very wide range of applications. Available materials include ductile iron, ‘gunmetal’ bronze, stainless steel and super duplex. Mechanical seals are available as balanced, double and tandem.
For more information on these pumps email info@ hydroinnovations.com.au or call on (02) 9898 1800.
Australian Pump Industries, Australian distributors for Tsurumi Pump products, is bringing an exciting range of wastewater treatment pump products to the market.
Tsurumi’s reputation in Australia is largely based on their expertise in dewatering pumps. However, what many don’t realise is the company is also a major manufacturer of a complete range of wastewater treatment equipment.
The company manufactures advanced design bar screens, a huge range of specialty sewage pumps that include cutter, grinder and vortex pumps, and compact submersible aerators. At Tsurumi’s huge plant in Kyoto, the company develops and comprehensively tests new concepts in wastewater treatment before putting them on the market.
The company’s range now dominates large sections of Southeast Asia, with large programs running in Thailand, Cambodia, Vietnam and more recently Myanmar.
Pump products include Tsurumi’s VANCS series, where both single and three phase pumps made of stainless steel and FRP resin are able to handle compressible solids. These pumps feature large passage vortex impellers. The VANCS range, available in discharge ports from 40 to 80mm, are available with optional sliding guide rails for permanent installation.
Tsurumi developed a unique auto duplexing system that does away with expensive control panels. The simple dual pump system can be set by using an automatic and alternating pump, no complicated external control panel is required. The installer simply connects power to their pump. By adjusting the float levels the pumps can be set to run alternatively. If extra capacity is required both pumps will automatically work together. The alternating model has
three floats that can be identified with a suffix W in the model name.
These pumps are available in the same output range as the automatic pumps, allowing the complete priming and secondary operating system to be installed.
The VANCS series have flow rates of up to 950L/m and heads of as high as 26 metres. A VANCS Tsurumi pump was recently discovered in a permanent installation in Tasmania where it had been running continuously for 87,000 hours!
Tsurumi’s sewage pump range includes a range of vortex pumps in both 2 and 4 pole configuration. The 4 pole pumps can interchange with Flygt and Grundfos, making replacement installation easy. The pumps range in flows of up to 2,600L/m with maximum solids handling of up to 100mm.
Low cost, efficient aeration systems using submersible aerators, pumps and mixing equipment, are simple to install and easy to maintain.
A similar product range, the Tsurumi B Series is a channel impeller style available in an extensive range right up to 800mm port size. These heavy duty pumps will interchange with other brands and designed for sewage, wastewater and effluent draining. Guide rail kits are available for all models.
C series cutter series pumps that incorporate a channel impeller with a cutter mechanism are also proving popular in Australia. A centred tungsten carbide alloy tip is braised onto the impeller vane and rotates against the serrated edge of the suction cover. This mechanism cuts fibrous matter that flows into the pump with ease.
Grinder pumps are also availableTsurumi’s MG Series, with a grinding mechanism in the suction port that chops incoming solids into small pieces. This enables the pump to handle sewage via a small diameter pipe without the fear of clogging.
Both the MG and C Series pumps are interchangeable with Flygt.
The big B Series pumps are available with flows of over 100 cubic metres per minute and are installed in some of Japan’s biggest sewage installations.
Tsurumi’s TRN Series aerators are self-aspirating submersible aerating devices.
A built in special semi-open impeller, made from cast 410 stainless steel, draws in air which is mixed with the liquid and discharged at high pressure. This innovative design leads to highly efficient aeration.
Easy and low cost installation makes these reliable aerators great cost cutters for sewage and waste water system designers. The range extends right up to 40 kW versions capable of handling air flow rates of up to 528 cubic metres per hour. Starting method is DOL for the smaller models but Star Delta for the models between 12 and 40 kW.
These submersible aerators can be installed in tanks, pits or sumps and are available with maximum water depths of 6 metres. Aerators can be supplied with stand or draught tube for special applications.
The adoption of a Tsurumi aerator with an optional stand or draught tube could be the solution in a number of applications where the aerator is to be installed in existing tank, and is not possible to alter the depth of the tank. Two or more aerators may be installed in the tank to work together depending on the size.
The oxygen transfer rate is the speed the oxygen in the air dissolves into liquid. It can be a guide when a biological treatment is being designed. The oxygen transfer rate is not the one that is directly measured but is given from a calculation taking various factors such as DO concentration, ambient temperature and water temperature. The oxygen transfer rate may vary by up to approximately 10 per cent.
Tsurumi’s biggest aerator, the 150 TRN440, has an oxygen transfer rate of 28.9kg O2 per hour.
“Australian Pump Industries has produced a wastewater treatment guide that focuses on Tsurumi’s excellent wastewater treatment equipment. Tsurumi is the only company we know of that will offer a three year warranty on submersible sewage pumps and aeration equipment,” said Product Manager, Craig Bridgement.
The products are backed by the company and are already used in a wide range of applications in Australia in the non-government sector. Tsurumi plan on sending a team of engineers to Australia to investigate public works and to identify applications for their wastewater equipment in the coming months. Watch this space!
The Pentair/Tyco Flow merger has expanded the range of product that is available to Pentair Flow & Filtration Solutions in Australia and New Zealand, allowing the best available product to be offered to our valued customers.
This is reflected in the updated range of Everflow line shaft turbines and submersible borehole pumps now available. The main feature of the additional models is an increase in operating efficiencies, due to the use of 316 stainless steel investment cast impellers, providing an excellent surface finish, resulting in higher operating efficiencies.
Depending on the flow and head required, many duties can be achieved with a reduced number of stages, which reduces the capital cost of the installation.
The improved performance can also allow the use of a size smaller driver, which provides a further saving in capital cost, as well as an ongoing savings in operating cost. In the case of electric motor drives, there may also be savings in the power supply and the switchgear required.
The new Everflow models are available in standard construction with cast iron bowls, 316 stainless steel investment cast impellers and 431 stainless steel shaft, and fit directly on the standard Everflow column and shaft, and use the Everflow discharge head, and drives. Alternative materials of construction are available for those applications that require a higher level of corrosive resistance. Pentair will continue to support the Everflow models that have been replaced with spare parts.
Pentair are proud to continue to offer our customers the best solution for their pumping applications, from residential, agricultural and HVAC to municipal, industrial and mining.
Xylem has been working with water and sewerage services provider Unitywater in Queensland to significantly reduce energy consumption and eliminate blockages at a number of Unitywater’s wastewater pump stations.
Unitywater is one of Australia’s largest water services providers, servicing over 16 per cent of Queensland’s population with 17 wastewater treatment plants and 778 sewage pumping stations.
Xylem and Unitywater piloted the revolutionary Flygt Experior wastewater pumping solution at the Bli Bli sewage pump station near Maroochydore. This initial trial resulted in a 57 per cent reduction in energy consumption compared to the original pumping equipment. After an additional six similar trials at other Unitywater wastewater pumping stations throughout Queensland, Flygt Experior has provided substantial reductions in energy use and pump blockages. Unitywater is currently evaluating where to install the wastewater pumping system to improve operational reliability across their wastewater pumping network.
Unitywater Executive Manager for Infrastructure Services Glen Babington said, “The equipment at this trial site resulted
in significantly fewer blockages and service call-outs, helping to reduce its running and maintenance costs. Such savings have the potential to help us keep cost as low as possible for our customers.”
Xylem’s Flygt Experior solution is specifically designed for wastewater pumping, combining N-hydraulics, premium efficiency motors and intelligent controls to deliver reliable, clog-free and efficient wastewater pumping.
Terry Gralton, Market Manager, Municipal Pumping Oceania for Xylem, said, “At Xylem we work to develop innovative solutions to support the smarter use of water – Flygt Experior is a great example of that. The system is installed in pump stations across the globe and it has proven time and time again to significantly reduce energy use and minimise blockages. We are delighted that Xylem’s system will support the delivery of an efficient wastewater service for communities in Queensland.”
Electrical signature analysis is a powerful tool when diagnosing motor issues in poorly performing pumps. Here, Howard W Penrose presents a case study example, highlighting the performance of two pumps and the insights electrical signature analysis is able to provide into their performance.
While sometimes referred to as motor current signature analysis (MCSA), which involves the collection of motor current data only, electrical signature analysis (ESA) utilises both voltage and current data, including values, phase impedance, power harmonics, and other information that can provide a solid look at the condition of both electrical and mechanical components upstream and downstream from the electric motor. This means that ESA will provide you information on the health of your electrical system, motor, driven equipment and even further into the process off of a single set of data. Pump systems can be easily evaluated, including cavitation, flow, impeller, and even seal issues, whether the motor and pump are directly coupled, the impeller is mounted on the motor shaft, or even in those unusual belted applications. While a little more complex, ESA is effective in inverter applications, regardless of whether the variable frequency drive (VFD) output is pulse width modulated (PWM) or multi-step.
In this article we will use the example of two 30 horsepower lightly loaded submersible pumps. The abilities of ESA technology stretch across all pump sizes and voltages. The machines tested were two 30 horsepower, 1,800 RPM, 60 Hz, 460 Vac, 39 Amp pumps, one in distress and one in good condition, tested unloaded. They each have 44 rotor bars and 36 stator slots. When performing ESA, this information is vital for accurate analysis and, when possible, knowledge of the number of vanes in the impeller. The applied
technology is an ALL-TEST Pro® II ESA data collector.
A few basic points on ESA/MCSA
Current fast fourier transform (FFT) spectra of amplitude versus frequency are a direct result of variations in the magnetic field, as the rotor moves within the air gap of the motor both torsionally and radially. As shaft material is ‘elastic’ and bearings have clearances, as vibration from the motor can cause the rotor to move side to side within that air gap. As most issues in a rotating machine are repetitive, such as unbalance, there are distinct frequencies that exist on top of the current sine wave. The results in an evaluation are based upon an amplitude modulated (AM) signal which has, by definition, sidebands as opposed to vibration signatures, which have single peaks for specific signatures.
The signals are processed in pretty much the same way as vibration analysis spectrum, as well as a variety of power quality and waveforms, including shaft torque. The result is an FFT signature pattern that can be analysed for anomalies that have a mathematical relationship, in most instances, and recognised patterns for which the reasons are still being explored. In the application of pattern recognition it is not unusual to find a multiple of a running speed signature, then start looking throughout supplied information and drawings to determine what that multiple represents. For instance, a result of ‘47’ might relate to rotor bars in the motor, or some other issue within the system.
In vibration, the noise that results from cavitation, a raised noise floor based upon a great many peaks, can often hide other important signatures. ESA has a similar signature, however, cavitation tends to occur in very tight bands around related impeller signatures. Most other signatures of interest remain visible to the analyst including the running speed. The impeller signature has been found to reside as two peaks around 5Hz and 15Hz in virtually all pump applications.
As noted in Figure 1, there is a raised noise floor about the impeller signature which allows the analyst to determine the running speed of the motor. Once the analyst has the running speed and has access to information on other components any potential problem can be identified.
The reason for the raised noise floor is that cavitation relates directly to the significant energy that occurs as gases in the fluid being pumped come into contact with surfaces such as the impeller and collapse, putting off significant energy. This represents enough energy to remove small amounts of material from these
components as well as damage seal surfaces. As these ‘explosions’ are random, they result in a very random vibration pattern that are related to the impeller. As noted in Figure 1, the raised noise floor is occurring on either side of the line frequency peak at about 5Hz.
When taking data and a known good machine is available, it provides the ability to compare it to other machines. In this case, the two unloaded 30 horsepower submersibles are readily compared in order to contrast a good and bad machine. In Figure 2, the complete low frequency spectra can be analysed to evaluate conditions related to the motor shaft and impeller.
In Figure 2, the top spectra is the RMS current of the pump in question, the middle spectra represents the frequencies immediately surrounding the line frequency, which is the highest peak, and the bottom spectra is the demodulated low frequency spectra. The RMS current represented here indicates that the machine is running smoothly without too many variations
and is turned off at the end of the analysis. The peak to the far left and noise to the far right in the +/- 45-55Hz range on either side of the 60Hz line frequency, which would be +/- 35-45Hz in a 50Hz environment, is a seal frequency. An existing peak in this range normally means some seal wear, in a mechanical seal. If these peak continue to rise, it normally indicates failing seal surfaces. The remainder are all under -65dB from the peak current, indicating
no other issues.
The three red vertical lines in Figure 3 relate to the running speed times, the number of rotor bars and then line frequency sidebands around that point. This is directly related to static eccentricity. As noted, the lines do not fall across these peaks and, instead, these peaks relate to line frequency harmonics as multiples of the applied 60 Hz.
Figure 4 relates to the torque ripple at running speed of which there will be some level in most applications. In this case, the torque line is nearly flat with little variation, meaning that the motor is running relatively smooth. The small amount that exists comes from a variety of conditions from fluid flow to power harmonics.
Contrast a pump with major issues
A second pump is operating suspiciously and requires a comparison. Like the good pump, it is operating lightly loaded. Unusual vibration and noise are detected.
When comparing Figure 5 to Figure 2, it is immediately apparent that there are significant differences. There are a series of peaks surrounding the line frequency peak and the RMS current is very choppy. By comparing the seal signatures between the two figures, it can be seen
that a seal issue may occur soon and the high peak close to 5Hz, which has a raised noise floor in the middle spectra, means that something is going on around the impeller. The harmonics that are seen that are direct sidebands of this frequency often indicate some kind of impact or rubbing.
In the case of the second pump compared to the first pump, Figure 6 shows definite static eccentricity, which means the motor rotor is running to one side of the stator. In fact, the situation is a little more serious as shown in Figure 7,
which indicates running speed sidebands around these peaks and dynamic eccentricity, or orbiting of the rotor within the air gap.
While rather low, it is still present which may indicate a bent shaft or some other condition that is causing the rotor to operate off centre.
Figure 8 is the torque ripple at running speed which is surprisingly low. This can help the analyst come to the conclusion that something is happening at the impeller that is causing some level of rub and is either the result of a bent shaft,
indicated by the dynamic eccentricity, or that the rubbing impeller is causing the dynamic and static eccentricity, such as if it were loose or crooked on the shaft. In either case, there is justification for removing the pump from service.
In the examples relating to the good and bad submersible pumps, the bad pump could be identified with or without the data from the good pump. However, a direct comparison between the two, or even if we were comparing a pump to itself over time, would indicate the severity of the issue. One of the key advantages to the use of ESA is that the load on the machine does not matter. The analyst is only required to compare the amplitude of existing peaks directly to peak current and voltage.
ESA is a very powerful tool with a single reading taken from a motor control center or disconnect being able to supply data from incoming power to driven load. While it is not a replacement for vibration analysis, it becomes a valuable tool in improving troubleshooting and trending times significantly and, when used along with other technologies, allows a rapid response to potential problems within a facility. Just this fact alone will often cost justify the addition of ESA to a maintenance or reliability staff’s arsenal.
Howard W Penrose, Ph.D., CMRP is the president of MotorDoc LLC, the Executive Secretary of the Society for Maintenance and Reliability Professionals (SMRP) and the Institute of Electrical and Electronics Engineers (IEEE) Dielectrics and Electrical Insulation Society (DEIS) Web-Editorin-Chief and Power Engineering Society Materials Subcommittee Webmaster. He has over 30 years experience in the electric motor and related machinery industry, starting with the US Navy through to machine repair, design, hybrid vehicle design and electric machinery system forensics. He has won numerous awards for consulting, training and publishing including his books Electrical Motor Diagnostics: 2nd Edition and Physical Asset Management for the Executive. MotorDoc LLC is an SMRP Tier 1 Approved Provider of Electrical Motor Diagnostics and Motor Management training programs. Howard can be contacted by email at hpenrose@motordoc.com or through his website, www.motordoc.com.
As part of their continuous commitment to introduce into the market the best and most recent industrial innovations, Regal Australia are pleased to introduce a new range of AC variable speed drives: Marathon Drives.
The Marathon Drives series offers a range of different types and models of AC drives, carefully selected and created to suit customers needs and market requirements, at the best value whilst complying to all modern technologies.
The Marathon Drive platform is available in 5 models:
• MD100C: Compact drive to fit anywhere when size is a major problem in small panel arrangements
• MD100G: General purpose drive for a broad range of applications in the industry
• MD100P: Special pump/flow
drive with add on features and requirements in this specific industry
• MD100H: HVAC&R drive addressing all building automation specs with unique features when cost matters
• MDHP: High performance drive comes with all that you need in high performance, high precision automation systems and PM motor control.
The Marathon Drive range is currently
available from as low as 0.1kW and up to 450kW as standard. Higher power is also available upon request.
Marathon Drives are designed to operate the motor using the lowest possible energy consumption and highest energy efficient performance to meet all energy efficient levels and standards. They also meet all required industry approvals: CE, C-Tick, and UL.
Marathon Drives are the smart way to go with great performance and easy motor control for a competitive price.
Selecting the right coupling provides significant savings on pump operating costs, while also increasing pump life cycles – two good reasons to take a close look at KTR pump components, distributed exclusively in Australia and New Zealand through Deanquip.
KTR couplings meet the special requirements of the pump industry, in particular API 610, 671 and 685 and certification ATEX 95.
Certificates for the oil and gas industry
Signed, sealed and delivered – KTR’s strict quality standards are officially approved by a string of certifications. The oil and gas sector applies extremely strict standards to any company joining its select group of suppliers. Certifications for major oil companies can only be obtained after years of preparation. That’s why KTR is particularly proud of being a certified partner to Saudi Aramco, Petroleum Development Oman, Saipem and Shell.
ATEX explosion protection
In line with European Directive 94/9/EC, known as ATEX 95, KTR has arranged for key products in its overall range to undergo inspection by an independent institute to assess their suitability for use in explosion-prone areas.
Perfect power transmission for all media
KTR offers an extensive product range of flexible torsionally stiff couplings, with or without a spacer, both for universal applications and particularly difficult ambient conditions.
For pumps: the torsionally flexible jaw coupling ROTEX®; the short, axial plug-in, torsionally flexible, failsafe jaw coupling POLY-NORM®; and the non-failsafe POLY coupling, as well as the torsionally rigid, backlash-free steel lamina couplings RADEX®-N and RIGIFLEX®-N. The double cardanic design was developed particularly for pump drives. It corresponds to API 610 or 671 and accepts temperatures between -30°C and 280°C thanks to its all-steel design. For a non-contact torque transmission in pumps for aggressive and toxic media, the permanent magnetic coupling MINEX® is used. DATAFLEX® has proven its worth as an accurate measuring device
for development and quality assurance.
For mobile compressors: the highly flexible flange coupling BoWexELASTIC® or DATAFLEX®.
For stationary compressors: ROTEX®, RADEX®-N, RIGIFLEX®-N, BoWex-ELASTIC® or DATAFLEX®.
For vacuum pumps: ROTEX® and ROTEX® FNN with fan, in addition to BoWex®, POLY-NORM®, MINEX® or DATAFLEX®.
In addition to its extensive standard range of products, KTR develops thousands of customised solutions every year for use on every kind of pump, either for fluid or gaseous media, on vacuum pumps and compressors.
The KTR industry brochure for pumps and compressors outlines the full range of power transmission solutions for all media types and is available for download at www.deanquip.com.
In the downstream oil, gas and petrochemical industries, reliability and operating cost are two of the major consideration factors when dealing with plant equipment. Stuart Morrison, Aftermarket Technical Services Manager at ClydeUnion Pumps, an SPX Brand, discusses how aftermarket pump refurbishment services improve reliability and save the industry time and money.
As plants age, process conditions often change as well. Output requirements can diminish and pumps, which were originally designed for optimum performance, become oversized providing too much head and too much flow. Pumps that are not matched to current process conditions are inefficient and become less reliable. They increase operating costs, often using up to 30-50 per cent more energy than a correctly matched pump and, while they are working outside of their optimum flow range, are more susceptible to maintenance problems.
Although adjustments can be made to system controls by throttling the pump to try to compensate for the equipment/ process mismatch, this doesn’t efficiently decrease the energy requirements of the pump. For long-term process changes such practice can be costly and has been shown to greatly increase maintenance problems. In such cases, greater benefit can be seen by correcting the mismatch through de-staging or re-rating the pump to more accurately reflect the up-to-date needs of the application. Taking this approach reduces operational costs and increases pump reliability.
Refurbishing a pump when it is no longer operating near its optimum efficiency flow can have more advantages than saving energy and increasing operational reliability. Older units are typically constructed from 316 stainless steel, which has now been surpassed by the super duplex grades that offer greater resistance to corrosion in seawater applications – a feature that is important in the oil, gas and petrochemical industries.
Furthermore, the latest revisions of specifications such as API 610, the standard for centrifugal pumps adopted by the petroleum industry, reflect modern day industry knowledge and best practice to improve pump performance and reliability. Pump upgrades carried out during a repair or refurbishment to meet required process conditions can also bring it up to date with the latest standards, incorporating features such as a back pullout design for faster and easier maintenance.
A competitor’s OH2 end suction pump was proving increasingly unreliable and performance had deteriorated over time due to wash-out in the volute areas of the casing. When a need arose to repair the pump casing, the customer decided to incorporate a new latest edition API 610 back pull-out bearing assembly and new mechanical seals.
Repairs to volute tips, suction and discharge flange faces were also carried out. A new bill of material was generated for future spare parts and the pump has operated reliably since its installation. The total cost of repair and upgrade to a new back pull-out was around £19,000 and completed in three weeks –offering a 25 per cent saving on the estimated cost of a new installation with an expected 26-week lead time.
New upgraded pump parts are designed and engineered to order, enabling any existing issues to be designed out. Examples where this is done are wide and varied and include areas such as incorporating the redesign of bearing housings to remove issues where the bearings are running hot. Other overhauls of old pumps have included removing the gland packing and putting in modern mechanical seals for greater reliability.
On one particular project new process conditions for gas oil pumping required the re-rating of two pumps (duty and standby) that were suffering from cavitation problems. This was resolved by increasing the impeller diameter to handle the new flow and adding a custom designed inducer to avoid cavitation by optimising the net positive suction head (NPSH). The resulting pumps provided increased capacity, increased mean time between outages (MTBO) and reduced maintenance because of the removal of cavitation issues.
Another project saw the upgrade of a competitor’s 4-inch barrel pump on a refinery, which was experiencing regular shaft breakages. Inspection identified an outdated design of thrust bearing. This bearing design has three pads mounted on two conical washers on its inactive side. These washers tend to rub against each other and lock up, preventing the thrust pads from moving with the thrust collar. This results in the collar moving back and forth on the shaft, which, in turn,
bends the shaft forwards and backwards until it fails.
Simple form and fit replacement of the thrust bearing with a ‘JHJ’ type (which uses six pads on the inactive side) reduced wear, the risk of the washers locking and likelihood of shaft breakage. The upgrade of this pump also included replacement of the stack up rotor and upgrade of the internals from cast iron to cast steel parts to reduce corrosion. The changes were invisible to the rest of the installation and pump reliability was greatly improved.
When a pump is de-staged or re-rated rather than replaced, the impact on the existing installation is minimal. Surrounding equipment such as the driver, baseplate and lubrication system along with connecting pipework can remain undisturbed. The installation time is significantly quicker than installing a new system and minimises system downtime and cost.
Old pump assets may also experience obsolescence issues, perhaps because the original equipment manufacturer (OEM) is no longer in business and spare parts are unavailable. OEM companies offering refurbishment options for pumps can also often supply a re-engineered customised spares service utilising 3D scanning of existing components to produce new parts. Added value can be obtained from this work by using the more modern, corrosion resistant materials available even on a part-by-part basis.
Parts within a design that are proving unreliable can undergo further investigation with full laboratory metallurgical failure mode analysis. This can assist in understanding complex reliability problems and provide information to enable engineers to improve designs resulting in increased efficiency, increased part strength, reduced stresses and overall better reliability.
As with a new installation, changes to application requirements for a pump should be looked at in terms of the total life cycle cost. A pump running inefficiently can have a huge impact on the energy bill associated with it. Over its lifetime the cost of energy may be as much as 90 per cent of the total ownership cost of a pump. Although the initial investment of de-staging or re-rating a pump is a consideration, the cost of energy over its remaining lifetime will far outweigh the initial outlay for change if the pump is operating outside of its optimised flow range.
Keeping up to date with the latest best practices, materials available and changing application requirements can save time and money. As well as reduced energy costs, there is the consideration of unplanned system downtime and ongoing maintenance costs – along with the issues of having fewer skilled onsite personnel to handle equipment with high maintenance needs.
A wide variety of challenges are faced by different installations across the oil, gas and petrochemical industries but careful design and engineering can solve existing problems, dramatically improve pump efficiency and increase reliability without the need and costs associated with a complete replacement installation. Limited on-site resources and budgets make aftermarket pump engineering a profitable choice, which can add real value to an operation.
there’s no better time than process uptime
SPX products deliver the power you need for quality processing performance and greater productivity. And when it comes to keeping your SPX equipment running like new, choosing genuine OEM parts delivers total peace of mind.
SPX aftermarket services offer:
• Local, stocking distributor partners
• Optimized performance of your equipment
utilizing genuine OEM parts
• In stock parts and fast deliveries (Quick Ship)
• Preventative maintenance, inspection and repair services by factory trained technicians
When quality, dependability, service and performance matters -
Contact SPX for all your high quality OEM Spare Parts, Email: ft.aus.cs@spx.com,
Tel: 03 9589 9222 or visit www.spx.com.au
Dealing with by-products in the food industry is a challenge virtually all manufacturers face. A number of companies are discovering the benefits of using pump systems to process and remove waste from high care operation areas.
Most food factories produce by-products, particularly if their business is that of primary processing, converting raw materials into finished products. Processors need to remove waste by-products from their production areas as efficiently and hygienically as possible, incurring the lowest cost and maximising any potential revenue to be gained.
Traditionally there have been different removal methods used, such as:
• SEEPEX open hopper pumps and waste removal systems
• Manual removal using tote bins
• Blown air systems and vacuum systems
• Flumes using water as a transport medium.
Many processors use combinations of these, often determined by plant layout, previous experience and regulatory demands. With the exception of the SEEPEX pump systems however, they all incur high running costs in the form of manual labour, energy use or water treatment.
SEEPEX systems all incorporate a progressive cavity pump, capable of pumping both high and low viscosity products, with and without solids. For most applications a patented design pump which can chop and pump food waste with up to 40 per cent ds, without added water is used. The open hopper BTM range pump has an auger feed into fixed and rotating knives which can chop most products.
The design means that any discarded products, defective raw materials, trimmings and rejects (including overrun), can be handled in a single system, enabling pre-treatment and source segregation of waste and by-products, even when they vary greatly in solids contents and viscosity. There are now more biogas plants in operation,
This SEEPEX BTM pump has helped a fresh food company to remove salad waste from high care areas.
many of which need food waste to produce energy and the SEEPEX pump produces an ideal feedstock for biogas operations: a liquid slurry that contains no contamination.
The pumps can handle whole cabbages and wet coleslaw, whole raw potatoes and mashed potatoes, whole chickens and chicken trimmings, all in a single multipurpose unit. Efficient and hygienic removal from high care and low risk areas is ensured, providing food processors with the least cost removal together with highest residual value of by-products as demonstrated by the following case studies.
A fresh food company wanted to remove tote bin traffic from high care to low risk areas, due to the subsequent return of the tote bins proving a hygiene issue. The volume of waste from vegetable preparation was high, and in comparison to the weight, transport costs for removal were high. The factory
was expanding to fulfill increased demand for ready prepared vegetables and SEEPEX installed a hygienic BTM open hopper pump to chop and remove the waste directly from preparation areas.
This company now has a low volume by-product removed directly from production areas without the need for manual movement of tote bins.
Other fruit processors have installed SEEPEX pumps with auger feeds into vertically mounted grinders to handle difficult waste from stone fruits such as mango and peaches. The use of these removes all waste from processing areas, producing a slurry which is then sent to biogas plants for energy generation.
Chicken processors have to segregate those birds which are dead on arrival at processing plants, together with any diseased birds found by subsequent inspection. Regulations typically require that these have to be
A SEEPEX BTM open hopper pump, showing detail of rotating and fixed knives.
cut and dyed before segregation for rendering or other further processing before disposal. The SEEPEX BTM pump takes whole chickens and then chops them with the addition of dye before pumping them in an enclosed system to the disposal area. This gives customers complete confidence with demonstrated compliance.
SEEPEX have provided a different system for one poultry plant, to enable entrails to be chopped into a suitable pet food raw material. This uses an auger feed to a vertical macerator followed by a pump. The entrails are removed directly from the main processing area
SEEPEX pump, macerator and auger combination for processing poultry by-products.
as slurry, which is then frozen for pet food use.
Another food company had problems with mixed consistency food waste which was too liquid for solid waste and not liquid enough for tanker transport. SEEPEX installed a BTM open hopper
pump with an additional macerator to ensure smooth slurry was produced from the mixed ready meal waste. This high energy value waste is now transported in road tankers to a nearby biogas plant, saving the food company considerable transport and waste disposal costs.
SEEPEX pumps and systems provide a flexible means of removing waste and by-products from food and beverage processing areas without the use of excess energy or added water. For more information, or to request a free site survey to establish if we can help you, please contact SEEPEX Australia on 02 4355 4500 or
SEEPEX Smart Conveying Technology extends the life of your stator. Adjustment of the retaining segments takes just 2 minutes and restores 100% pump performance.
Tests have shown up to 3x stator life compared to conventional progressive cavity pump design Join the smart revolution and test our innovation “Smart Conveying Technology”.
SEEPEX Australia Pty. Ltd. Tel +61.2.4355 4500 pvila@seepex.com www.seepex.com
Manufacturers in the food industry are learning that eccentric disc pumps provide the perfect solution to commonly faced problems such as product wastage and high maintenance costs.
The food processing industry has traditionally used lobe and piston pumps, and in most situations they offer good sanitary qualities and are flexible across multiple products. However, the technology has its limitations, which were accepted by the food manufacturers as something inevitable.
High maintenance costs, low accuracy, poor volumetric consistency and significant product loss are burdens of the manufacturing industry. These problems are caused by constant rebuilds, leaking seals and product left at the bottom of the tanks and in the pipes – all these facts should lead savvy managers to look for the alternatives.
The most efficient solution is an eccentric disc pump, operating on the eccentric movement principle – the disc placed inside a pump cylinder rotates, creating two distinct pumping chambers. This produces a regular flow rate with low pulsations, low cavitation, and limited slip or shear even when handling the most delicate products, such as whole strawberries in syrup.
The manufacturer of the eccentric disc pump, Mouvex, says there are ten key advantages of its pump technology over competing technologies:
• Self-priming
• Effective line-stripping
• High volumetric consistency against varying pressure
• High volumetric consistency against viscosity changes
• High volumetric consistency against wear
• No mechanical seals
• No pulsation
• Dry-run capable
• Totally hygienic (CIP, 3A, EHEDG approved)
• Low shear.
The major advantage of eccentric disc pumps for the food processing industry is their ability to reduce operational costs via their product recovery capability. Here are some examples:
A manufacturer of cookies was losing ca. 50kg of white chocolate coating per week, and was forced to clean the pump several times per month. They changed
the lobe pump to an eccentric disc pump, which resulted in trouble-free 24/7 operation for over two years (and counting).
Due to poor volumetric consistency of an external circumferential piston pump, a sauce manufacturer was rejecting 15-20 per cent of the pouches not meeting the pre-determined weight. Changing to Mouvex allowed the manufacturer to save on time and money and significantly reduce product losses.
Yogurt manufacturers were losing more than $100,000 in product per line per year. An eccentric disc Mouvex pump helped the manufacturer recover over 70 per cent of the product and significantly improved their bottom line.
Australian manufacturers also value Mouvex pumps and use them for pumping chocolate, glucose, galactooligosaccharides (GOS), yoghurt, cream and sauces. If you seek to improve your bottom line and achieve considerable product recovery, talk to us about this fantastic invention – the eccentric disc pump.
Imbalances within a network do not often result in positive outcomes. Unsurprisingly the same applies to rotating machinery, pumps and fans, where vibration caused by imbalance can become a significant engineering problem. For over 20 years, Precision Balancing has been helping its clients overcome these problems, enabling them to quickly get their machinery back online.
If the centre of mass within a rotating device does not coincide with the centre of rotation, the mass centre axis will be different to its running centre axis. Vibration will then result, gradually causing damage to bearings, followed by malfunction or breakdown of the machine.
When it comes to longevity and lifeexpectancy of a pump, fan or rotating machine, it is therefore crucial to ensure balance within the system.
Vibration is primarily the result of imbalance created by minor imperfections within the rotating component, or non-symmetrical elements commonly found in newly machined parts. It is then the centrifugal force due to the unbalance which causes the device to vibrate.
Precision Balancing uses industrial
balancing and vibration analysis on rotating machinery, enabling early detection of faults before breakdown. Mass distribution of a product is checked and adjusted in order to ensure that the forces on the bearings are created equal. As the mass centre line approaches the true axis, weight is either removed or added to the unit so as to make the two centres coincide. Such analysis also helps facilities to greatly reduce maintenance costs.
The wide capabilities of Precision Balancing mean that the company can balance a vast range of items both within their workshop or on-site. No object is too large or too delicate for their expertise, with specialisations covering objects as diverse as drums, automotive equipment, centrifuges and couplings.
Apart from improving overall safety of your pumps, fans or rotating machinery,
balancing your equipment lengthens the service life of the product. This aids in reducing the chances of downtime or machine failure. Performance of equipment is also enhanced, which naturally saves on time and money. Bearing load is reduced and so too is noise, resulting in a more highly efficient, quiet and reliable machine.
Proudly Australian owned
Precision Balancing is an Australian owned and operated company based in Melbourne Australia, offering in-house and on site dynamic balancing and vibration analysis services since 1989. Precision Balancing is owned and operated by qualified Mechanical Engineers who are members of the Australian Institution of Engineers. As a team, Precision Balancing has years of experience in Mechanical Engineering and Industrial Balancing, as well as other related industries that require this specialised range of services.
Unbalance is one of the most common causes of high vibration in machines. If vibration analysis shows that the largest component in the spectra is at 1X (i.e. at the frequency corresponding to rotation speed), then unbalance is a likely cause. Balancing is therefore a regular maintenance activity in many workplaces. Ray Beebe explains a method that has been successfully used on rotors large and small, with the only instrumentation required for balancing being the stopwatch feature of a mobile phone.
It is assumed that the severity of vibration has been assessed as unacceptable according to sources based on wide experience, such as the relevant part of AS 2625.4-2003 (or ISO 10816) Mechanical vibration – Evaluation of machine vibration by measurements on non-rotating parts.
Even if a machine’s vibration meets such criteria, it may be causing annoying vibration of adjacent parts.
Looseness is another of the most common causes of vibration and a check of foundation tightness is usually recommended before proceeding to balancing.
If suitable facilities are not available, this expedient method is suggested. It has been used successfully for short rotors such as pump impellers. I do not know the source of the method, but I learned it in my first job at a power station in the 1960s. The equation used is derived from the theory of the compound pendulum.
Higher than desired 1X vibration was evident on a ten-stage boiler feed pump of the ring-section design (where each stage’s impeller is assembled in turn with its matching stationary section). At the time, the available balancing machine could only hold the total assembly, requiring all the impellers to be assembled on the shaft. Balance mass
corrections could be made only on each of the end impellers: not the ideal when unbalance was likely to be distributed along the rotor line.
A better result would be obtained by balancing each impeller individually. We clamped a pair of parallel ways set to be horizontal to the bed of a milling machine. A mandrel was made to suit the impellers so that each in turn could oscillate freely on the parallel ways.
The impellers should be inspected to
ensure that the discharge areas around the impeller periphery are even within about 1 per cent. On another design of multi-stage boiler feed pump, high 1X vibration was eventually found to be caused by the use of replacement non-OEM impellers that had outlet widths varying up to 10 per cent. The resultant fluid pulse gave similar vibration symptoms to that of mechanical unbalance – but the impellers had been balanced individually mechanically .
The process for each impeller in turn was:
• Numbers were marked around the impeller, evenly spaced. Use the vanes as a guide.
• A swing mass was chosen (e.g. a pot magnet, or a clamp for non-magnetic impellers) to fasten on the impeller, to give a to-and-fro oscillation time of about 20 seconds. (This gives some allowance for reaction time in operating the stopwatch feature of your mobile phone).
• With the swing mass fixed to the impeller at Position 1, the impeller is set so that the swing mass was at one horizontal position and stationary.
• The impeller is released and let swing freely under its own inertia –it was not be pushed in any way.
• The time was recorded for a to-and-fro oscillation from the horizontal position. The left part of Figure 1 illustrates the process.
• The impeller is turned so that the swing mass was at the horizontal position on the other side, and repeat.
• The mean time of swing was calculated for this position, and plotted on a graph of time against position as shown in Figure 1. With position numbers evenly spaced, one position appears twice - at the start and the end of the position axis.
• The swing mass was moved to Position 2, etc. and the process repeated for all the marked points.
• The graphed points are connected with a smooth sine wave shape, and the maximum and minimum times of swing read off: T and t.
• The size of balance mass required is found from:
Balance mass = swing mass X
• The balance correction was made by removing mass from the rotor from the position of minimum swing. This was achieved using an end cutter on an adjacent milling machine. A table was calculated and drawn up giving the depth of
cut required corresponding to the mass and cutter diameter. The position was marked clearly on the impeller, and it was passed to the machinist who cut the required mass from the back shroud.
• Note that if the correction mass is at a different radius to that of the swing mass, then calculate the mass size to achieve the same moment (i.e. mass × radius).
• The result was verified by repeating the swing test for three spaced points.
The method gave satisfactory results. At the time, arguably, the impeller-by-impeller method gave a more satisfactory result.
This method has also been used in place on overhung fans up to 2m diameter and also on smaller fans with two bearings that are nearer to what are considered ‘long’ rotors. The rotor must be in rolling element bearings, and not be affected by crosswinds.
For field balancing of fans, the usual safety precautions for opening any
Figure 1. To-and-fro oscillation from the horizontal position (left) and the mean time of swing plotted on a graph (right)
An impeller where this method was used. The reddish colour is due to the magnetite layer that is established throughout the steam/water cycle.
machine must of course be taken to isolate mechanically and electrically so that process gases are excluded and the machine cannot be switched on while the work is in progress.
For fans, the balance adjustment will usually be attaching a mass, rather than removing metal. The mass is fixed on the impeller at position of maximum swing time. The fixing must of course be sufficiently strong not to allow the mass to fly off at operating speed. If welded, allow for the mass of the weld.
Following 28 years in power generation in Australia and the UK, where he worked in condition monitoring development and application of pumps, steam turbines, heat exchangers, boilers and associated machines, Ray joined Monash University in 1992 and was a Senior Lecturer and Coordinator of the postgraduate online distance learning courses in maintenance management and reliability engineering from 1996 until retiring in 2010. He continues teaching his subject of condition monitoring.
Ray has written three books and over 80 papers for conferences, and many have appeared in journals worldwide. Ray’s consulting activity has served over 35 customers in Australia and overseas. Ray is a Fellow of the Institution of Engineers, Australia, A Chartered Professional Engineer (retired) and a Lifetime Member of the Asset Management Council.
The Roy Hill project is a 55 million tonne per annum iron ore mining, rail and port project being developed in Western Australia’s Pilbara region. Dewatering for the project is a significant and complex operation which has required careful consideration.
Situated approximately 115km north of Newman, Roy Hill is a world-class, low phosphorus, Marra Mamba iron ore deposit located in the Pilbara – one of the world’s premier iron ore provinces – and the only independent iron ore project with West Australian majority ownership.
The project will consist of a:
• Conventional open pit, bulk mining operation from multiple production benches
• 55 million tonne per annum (Mtpa) wet processing plant
• 344km single line, heavy haul railway
• Purpose built, dedicated two berth iron ore port facility at Port Hedland, capable of receiving, stockpiling, screening and exporting 55Mtpa (wet) of direct shipped iron ore as lump and fines.
The Roy Hill project has a defined mineralisation of more than 2.3bt of +50
per cent Fe iron ore of which 1.2bt is +55 per cent Fe, enough to sustain a mine life of more than 20 years.
The Roy Hill Mine has an initial mine life of 17 years, with a likely extension beyond that of 12 years. Roy Hill is an owner operator, conventional open pit, drill and blast, truck and excavator bulk mining operation.
Over the 17 year life of the project, 4,909Mt of material will be moved. This equates to an average yearly mining
rate of 272Mtpa (dry), to produce approximately 68Mtpa (wet) of run of mine (ROM) ore feed for the processing plant. This makes Roy Hill one of the largest mining operations in the Pilbara.
The Roy Hill Mine has an average strip ratio of just under four tonnes of waste and low grade mineralisation to each tonne of ore. A quasi strip mining approach is utilised where the bulk of the overburden and waste is dumped back into the previously mined out pit voids. This process helps minimise haulage distances for waste rock, as well as the footprint of mining activities.
Waste dumps are progressively rehabilitated over the life of the mine, to ensure that mined areas are rehabilitated to their natural state as quickly as possible.
Multiple pits are in production at any one time, with each pit being broad and relatively shallow in nature, with the deepest pit prescribed in the life of mine plan being less than 110 metres in height.
ROM pads and crusher stations are located in close proximity to each pit with the crushed ore then conveyed to the processing plant. Three crushing stations are in operation at any one time, which provides operational flexibility. Large ROM stockpiles ensure suitable material is available for the processing plant at all times.
A detailed dewatering strategy and water management plan has been developed. This ensures dry mining can occur and the necessary water is available for the processing plant.
Roy Hill’s principal iron ore operations based in the Pilbara region of Western Australia. The operation comprises a complex integrated system of seven inland mining operations.
Easternwell’s General Manager, Sheldon Burt, said “We are pleased
Ore which will provide us with the opportunity to build on the excellent work we have completed to date in the Pilbara, allow us to invest further in our equipment and to continue the development our people.”
Roy Hill Iron Ore has recently undertaken a Drilling Services Agreement with Transfield Services subsidiary Easternwell.
The agreement is for the supply of dual rotary drilling services as part of the dewatering drilling programs, which includes the drilling and installation of production and monitoring bores at
ANDRITZ Ritz is breaking new ground in the field of mine dewatering, drawing on 140 years of experience with the manufacturing of pumps in the waterworks and mining fields.
Diverse mine operators all around the globe trust in the submersible motor pumps made by ANDRITZ Ritz, which are installed into well shafts and operate there in a fully maintenance-free manner. Their unique long service lifetime and performance profiles are made possible by ANDRITZ Ritz’s patented doublesuction heavy duty mining (HDM) design.
However, in recent years, many mine operators and pump experts have increasingly approached ANDRITZ with requests for conventional dry-mounted high-pressure pumps.
In order to arrive at a solution, engineers and development experts at ANDRITZ, mine operators and their pump advisors participated in a workshop in 2014. Given that the installation of submersible motor pumps might not be possible in convoluted mines, due to the spatial conditions, there was an incentive to rethink and break new ground in order to adapt the robust and proven performance characteristics of the double-suction HDM pumps to a dry-mounted pump solution.
The aforementioned double-suction HDM technology was used as the development’s starting point, as it had already distinguished itself due to its high service lifetime and general durability in the past decades. This is due to the design that is entirely free of any axial thrust effects, thereby reducing wear and stress on components to a minimum, which is, in turn, reflected by the significantly increased service lifetime and lower operating costs, for example with regard to the required maintenance intervals.
Industries
• Dewatering
• Food & Beverage
• Agriculture
• Oil & Gas
• Waste Transport
• Chemical Products
• Industrial Hose
• Hose Assemblies
• Hose Management
• Hose Fittings
• Valves & Accessories
• Pipe Fittings
• New LDH couplings shoulder victaulic style to suit hose
With conventional HDM technology for submersible motor pumps, the pump unit is directly suspended into the body of water that is supposed to be pumped out. However, the objective of this particular pump construction was to develop a solution that could be dry-mounted while still offering the same pump characteristics, such as the long service life and lack of axial thrust effects.
This new development was to be used in all those mining areas where the proven HDM technology is considered unusable. The engineers therefore faced the challenge of adapting this proven “wet technology” to a dry working environment.
Due to the fact that a new highpressure pump was just being developed for the water market in parallel to this new technological ‘quantum leap’, it was possible to equip the dry pump with hydraulic systems of the newest generation. These allow for efficiency rates of up to 85 per cent, in accordance with the latest state-ofthe-art technology.
ANDRITZ Ritz is also able to offer additional benefits and advantages in the form of some special features for the new pump, which provide the operators with significant operating benefits and, thereby also reducing costs.
This includes bearings for the newlydeveloped pump generation. Until now, the pumps had to be extensively dismantled in order to conduct any maintenance on the bearings – and then, of course, be reassembled again afterwards. A modular replaceable bearing now substitutes the conventionally used slide bearings. This bearing offers the advantage of being replaceable without having to dismantle the entire unit. The new technology saves a considerable amount of time and thereby costs for mine operators.
Likewise, the engineers developed a new method for the simple horizontal installation and removal of pumps due to the prevailing low shaft heights, which can be used without requiring any
• Zero Axial Thrust – reducing maintenance costs.
• Andritz HPM series brings in the highest efficiency possible.
• Various bearing options.
• Easy Maintenance - No special tools required. Shaft seal by adjustable gland packing. Other seal options available.
• All important components are protected by wear parts
special tools or auxiliary means and thus were, once again, capable of satisfying the requirements of mine operators and their pump advisors.
These are pumps for experts - made by experts. Or ‘taken from practice for use in practice’, as the new high pressure mining pumps precisely satisfy the wishes and requirements expressed by the mine operators with regard to their efficiencies, performance ranges, the part standardisation strategy as well as ease of maintenance thanks to their simplified assembly and disassembly.
And, of course, every unit is inspected and checked at the in-house test bed not only for its general condition, but particularly the bearings and seals, as well as for its efficiency, performance and service life, regardless of its size and the planned area of application. This way, every mine operator receives a unit that is tailored precisely to his needs and requirements.
• Heads up to 1300m
• Pressures up to 160 Bar
• Power up to 5000 kW
Global pump giant Sulzer has turned to AllightSykes to spearhead its future growth in dewatering pumps across Australia and New Zealand.
The distribution deal adds Sulzer’s market-leading submersible dewatering drainage and sludge pump lineup to the Sykes auto-prime dewatering range and opens up exciting new opportunities for the partnership in the competitive dewatering sector.
From its global headquarters in Switzerland, Sulzer has specialised in devising and delivering pumping solutions for over 180 years. The group serves clients around the world through a network of over 150 production and service sites and with its 15,000 employees generates annual sales in excess of $4billion.
Since May 2015, AllightSykes has had the rights to distribute Sulzer’s extensive range of dewatering pumps to the mining, construction, rental and general industries.
AllightSykes Pump Business Unit Manager Darren Coles said “As a business, securing the right partners is as essential as providing the ultimate equipment solutions. The Sulzer
submersible dewatering pumps are a perfect fit as a companion product for the Sykes auto-prime range.”
AllightSykes Pump Product Manager Chris O’Brien said “Sulzer submersible dewatering pumps boast cutting edge technology that provides end-users great value for money.
“Much of the worldwide success of Sulzer’s submersibles stems from their ‘intelligence’ – a range of features that make them ideally suited for rental, tunneling, construction, mining, and general industry applications.”
Mark Goddard, Head of Sales, Sulzer Pumps (ANZ) said “We are delighted to have AllightSykes as our distributor for our submersible dewatering product range. Our range complements their products, it’s a great fit.”
When two of the world’s bestregarded pump brands Sulzer and Sykes unite behind a common goal to drive efficiencies and improve construction and mining project safety and productivity, the market response
will surely be positive. This partnership will be a force to be reckoned with in the dewatering space and both brands have a lot to look forward to.
Global pump giant Sulzer has turned to AllightSykes to spearhead its future growth of their submersible dewatering pumps across Australia and New Zealand
When large quantities of water are required for a pumping station or process, it is invariably drawn from the ocean, a lake, a river or a stream, and there is always the question of filtration - how do we deal with the debris drawn into the pumping station?
The answer is two-fold: there should be primary filtration, which should remove the larger and more intrusive debris, and then a secondary system which filters the flow sufficiently to allow free passage through the plant. Some plant items require further, finer filtration.
Both power station and raw water intakes for pumping stations or hydro-electric plants have to deal with debris floating in the flow. Recent television footage of inland floods indicates the type of overwhelming debris that can be carried along by inland floodwaters.
A typical seaboard power station may draw in over 100 m3/s of seawater for cooling water. Any floating debris in the intake will eventually be drawn into the power station inlet canal. The intake primary protection would be a trash rack, typically a screen with bars of 100mm by 10mm arranged at a 100mm spacing. Such a trash rack would very often be vertical, and sometimes they are installed in tandem, one behind the other, to ensure that any accumulations falling during the removal or cleaning process are caught by the second screen.
Trash racks used with raking machines are usually sloped, with dimensions suited to the rake. Some rakes are fitted with guides either side of the rack to guide the rake carefully to enable complete cleaning, although others may not use guides.
The trash racks, or primary screening, would remove logs, clumps of weed, sea grasses, driftwood, large fish, tree branches, seasonal weeds such as cabbage type weeds and filamentous algae (stringy weed), jellyfish and similar.
Some trash racks may be cleaned manually by divers, and others by mechanical rakes hired in for the occasion. Others may have a purpose-built raking machine. Trash racks need to be cleaned regularly to remove pressure losses caused by the build-up of debris. The frequency of cleaning depends entirely upon what is collected, which may change from day to day or seasonally.
For both seaboard and river intakes it is important that the downstream pumps and valves are able to withstand the entry of some debris which can fall from the trash rack, without suffering undue damage. Large axial flow pumps, especially those with open or semi-open impellers, may be able to pass large items of debris such as hard hats, large fish or floating tree branches. Most pumps cannot pass large debris, although pumps can be designed using single channel impellers to pass items up to 100mm, or may be fitted with vortex impellers which can pass large items, but at the expense of pump efficiency.
An important aspect of intakes is that the approach velocity has been found in practice to be approximately 0.3m/s through the trash racks. This enables a swimmer or rower to move away from the intake.
The velocity of 0.3m/s also applies to the protection of fish. It has been found that fish are still able to swim away from
intakes so long as the velocity does not exceed a nominal amount, and 0.3m/s has been taken as a good guide found from practice. With higher velocities, excessive fish kills can be found in the downstream plant.
Fish protection is today a major part of pumping station design. It would be wrong, in the writer’s opinion, to call fish or jellyfish debris or industrial waste, although such terms are common. The marine life is simply in its natural habitat. Some authorities require that anything taken from the water is deemed to be industrial waste, which needs to be disposed of. This emphasises the need to allow marine life to pass through the plant as innocuously as possible. There is a growing trend to provide fish ladders, to enable fish to swim around hydraulic structures, without having to negotiate their way around pumping plant and filters.
Although seawater systems are not so affected by floods and flood-borne debris, they have different problems such as blockage by migrating shoals of fish and jellyfish.
In Europe shoals of migrating sprats have been known to close down the cooling water systems of nuclear power stations. These shoals can be up to 10km long. Such occurrences are not uncommon, but are usually associated
with strong tidal currents, spring tides and gale-force onshore winds, i.e. unusually strong weather conditions.
In Australia, one power station was almost closed by shoals of jellyfish, again associated with strong inshorebound wind conditions. In New South Wales, some intakes have been inundated by small creatures called bryozoans. These creatures, also known as ‘moss animals’ are in themselves small (less than 1mm), but can adhere together to form complete blockages of filter meshes, or entire pipelines.
The best way around such problems is to be forewarned, so that protective measures can be put in place.
Another example is seasonal weed. In some places weed growing throughout the winter period can release itself in the spring, and inundate trash racks. Once the problem is realised, preventative methods can be put in place, such as the use of divers to clean the system, or the use of temporary nets to contain the weed. The alternative may be a plant
outage, with all the associated costs. Where drum screens have become blocked by stringy weed, or bryozoans and similar marine life, it has been found that a change from thin perforated plate to a thicker plastic mesh of 15mm thickness, can prevent the marine life from getting a foothold. This may, however, cause a higher headloss across the screen.
After the trash racks comes what could be called secondary screening. These screens would likely be made from wire mesh or perforated plates, and would take out all debris greater than approximately 10mm. One can see the need to remove the debris in stages. A filter with 10mm holes would be completely overwhelmed by tree branches or clumps of weed, and would soon cease to function properly.
The amount and degree of filtration required by any process will depend entirely upon the need in the
• For use in Irrigation systems, Dairy, Food-Processing and other Industrial Applications.
• Market Leading Range of Automatic Cleaning Technologies – including Vacuum, Brush, and Hydro-Jet.
• Hydraulic Turbine Compatible Filters Available – No Electricity Required.
• Epoxy Coated Steel, 304 Stainless Steel, 316 Stainless Steel, Duplex, and Titanium models available.
downstream plant. For example, if cooling flow has to pass through a heat exchanger with 25mm diameter tubes, then the flow needs to be filtered down to 25mm as a minimum, but in reality it requires to be filtered down to approximately 10mm as all debris is not round or in convenient shapes to suit the filter.
In the category of secondary screens are drum screens, travelling screens and pressure filters. Drum screens have been used on the seaboard intake on most seawater cooled power stations built on the east coast of Australia in the past 30 years. These designs have been aided by the small tidal variations on the eastern coast, as drum screens must still be able to operate at the lowest tide level, and this can lead to very large diameter, and more expensive, drum screens if the tidal variation is large.
Drum screens are very slow moving rotating screens, although they usually have two speeds. The double entry type allows the water to maintain its
• Patented Inlet Design creates a rapid circular motion of water – causing a hydro-cyclone affect and turbulent cross-flow current over the filter surface.
• Substantially Increased Filter Service Intervals.
• Superior Flow Consistency.
• Flush-Valve for Fast and Efficient Filter Element Maintenance.
symmetrical direction to provide good inlet conditions for the pump.
Travelling screens are similar to drum screens in that they need to cater for the lowest tidal levels. They are usually large structures, but more compact than drum screens. Today’s versions of these screens are made of better materials and are considerably more reliable than those of 20 years ago. Many travelling screens installed in Australia are of the vertical flow-through (or straightthrough) type, and have the potential for debris carry-over to the clean side, which then can enter the pumps.
A better design of travelling screen is to use the dual-flow or central-flow type, and with these arrangements the debris is not carried over.
In both drum and travelling screens, the water to be pumped passes through the screen, but the debris is caught in the buckets, and is then removed by the spray systems. The spray system will have its own filter and pump, and these should be regularly checked for correct functioning. It is important to have clear nozzles and fully functional sprays to avoid debris carry-over if the screens are of the flow-through type.
The installation of both drum and travelling screens are not always favourable to the inlet flow conditions to the pumps, and an allowance of additional space along with flow straightening vanes may be required to provide suitable inlet conditions for the pumps.
The care and protection of fish and other marine life is paramount. For example, on screens, plastic lining is sometimes placed on steel structures to avoid tearing the fish, and sluices are specially designed to accommodate fish,
Local Manufacture and Local Support from a company that designs and manufactures in Australia
• Engineered submersible motors 4” to 24”
• Fabricated stainless steel submersible pumps and motors
• Vertical turbine pumps 6” to 90”
ENGINEERED SUBMERSIBLE PUMPS AND MOTORS
• De watering pumps
• Submersible Sewage pumps
HORIZONTAL
avoiding sharp changes in direction.
Slow moving drum and travelling screens with low water velocities give fish the chance to swim away intact, and additional features such as rounded corners on concrete edges help the fish to negotiate plant items and bends, and swim through the plant to the outlet.
The alternative to using drum or travelling screens is to use pressure filters on the downstream side of the pumps, although this leaves the pumps relatively unprotected. Pressure filters can be designed suitable for seawater applications, and can be positioned independently of the tidal level. Pressure filters will incur a higher pressure loss which will increase the required pumping power. Drum screens and travelling screens, however, have low pressure losses but considerably higher associated civil costs, and when choosing which plant type to use, the civil, power usage and capital costs need to be evaluated. Pressure filters have higher velocities both on the filter face and in the backwash line, and may cause higher fish mortality.
However, such filters are very successful when installed immediately prior to condensers or heat exchangers, where they will remove mature mussels, which may otherwise block the heat exchanger or cause impingement attack to the tubes. There are a number of successful installations in NSW.
Mussels can and do cause problems in any seawater systems. Hundreds of thousands of microscopic mussel larvae enter into seawater intakes every day. They will then settle on any surface where they can gain a foothold, and will begin to grow. They may then adhere to the walls of pipework, valves and in particular the condenser waterbox, and then grow to full size. There is evidence that mussels do not attach themselves so readily where the surfaces are smooth, or the velocity is greater than 2.5m/s.
Where they do attach, the layers will build up, and in slow moving inlet conduits may grow to be 200mm thick. During an outage, due to the lack of flow and nutrients, many of these mussels will die and fall into the conduit.
Upon re-commissioning, they will be swept into the heat exchangers or other processes, and can completely block the inlet tube plate.
Pressure filters installed immediately before such heat exchangers or condensers will remove these mussels. This type of filter has been used in these situations at NSW seawater cooled power stations with great success, and by avoiding outages are very cost-effective.
Other methods of controlling mussel growth are by subjecting them to higher temperatures (thermal shock) or by chlorination. Experience in NSW and overseas with chlorination is that intermittent chlorination, even at a level which bleaches the mussel shell, will not remove them, although may stunt their growth. However, continuous chlorination at lower levels is usually more successful. Thermal shock has been used at several NSW power stations with considerable success, and the conduits remain very clean.
The position of the filters or screens is all-important, and an example is as follows: a prominent building in Sydney used seawater for cooling the air conditioning, and the seawater was filtered down to 2mm in a filter. The system had in place a plate heat exchanger with 5mm clearances. On the face of it, the design was right. However, after the filter, and before the heat exchanger, was a header, which provided a good environment for mussels to grow. The heat exchanger kept blocking and required outages for cleaning. The problem was not with the filter, but with the mussels growing in the header. These mussels would decay during the outage and fall to the bottom of the header, and then inundate the heat exchanger
during start-up. In this instance, a bypass line would have been useful to allow the debris to be flushed through the system and bypass the heat exchanger.
A word of caution is needed here, as it is also not environmentally acceptable to flush into an outlet any decaying or decomposing matter. The example however, indicates that to remove mussels, the filter should be as close as possible to the plant it is protecting.
Suction screens are another way to filter water entering a pumping station. These screens can be placed at the pump suction and filter the flow using perforated plate or perforated plastic sheets, and would remove the need for trash racks. When the differential pressure becomes too high, the screens can be backwashed by a high pressure air discharge. The design assumes that there is some flow along the river or seashore, to allow the debris to flow away from the screens. In addition, such screens would require some safety features in place to avoid an air discharge which affects the use of the river by others, or by causing undue noise.
Filtration of pumping stations is usually required at three levels: primary, secondary and in some cases tertiary devices. Filtration of seaboard and river intakes has significant technical difficulties, and also requires the primary consideration of marine life, and how the facility will affect that life. The question that should be asked is “Is the plant designed to keep debris away from the pump intakes, rather than to protect fish and marine life?”
Hopefully, both should be achieved.
John McAndrew is the owner of Efficient Pumping, a consultancy which provides design of cooling water systems, pumping systems and process plant for power stations, pumping stations and associated works such as pipework, filters and auxiliary systems. John has over 30 years experience in the design and contract management of hydraulic works such as pumps, valves, pipelines and pumping stations, and almost all of his career has been spent designing, contract managing, and consulting in this area.
Winnow Duraline Series Filters have taken efficient filtration to a new level with a specially developed series of filters for agricultural and industrial filtration.
Winnow™ Duraline Series Filters have a rugged stainless steel constructed filter that incorporates Winnow’s new ‘twin brush’ filter cleaning system.
‘Twin brush’ filter cleaning systems create a faster and more efficient filter cleaning process, requiring less mechanical rotations to clean the filter – therefore reducing the time it takes to carry out a cleaning process –saving water usage during cleaning, and reducing wear and tear on the brushes.
Winnow Duraline Series Filters are available in three configurations to suit a variety of installations, including flanged
or threaded connections ranging from 2 to 14 inches. Custom connections and configurations are also available to suit the client’s application.
14 inch models can take flow rates just under one megalitre per hour, providing a very cost effective solution in many high volume applications.
Winnow Duraline Series Filters are available in both automatic and
semi-automatic versions – making them an ideal filter solution to prevent nozzle and emitter blockages in centre pivot and lateral move irrigation systems, drip and micro-spray irrigation, wastewater and water reuse applications.
For a free brochure or quote, contact the Winnow Group on 1300 134 812, email solutions@winnowgroup.com or visit www.winnowgroup.com.
Regular contributor Heinz P. Bloch discusses the range of dual mechanical seals on the market and takes us through the advantages and disadvantages of various models available.
Dual mechanical seals are now widely accepted by pump users in many industries. In certain applications, they are the only choice suitable for safe and reliable containment. In other services, dual seals might be considered optional. Still, all major seal manufacturers can point out regulatory guidelines for using dual seals and assist in assessing their economics.
Safe and reliable fluid containment usually leads to pump maintenance cost avoidance in instances where the use of dual seals is mandatory. However, such benefits also accrue where using such seals is discretionary. Figures 1 and 2 are two of many different dual seal styles available today.
As pump users then consider dual seals, they may often note differences in the proposed method of heat removal from both pairs of seals. It’s in the nature of business that seal vendors are inclined to feature and favour their own design. Needless to say, not all vendors offer reliability and energy-optimised configurations. How the barrier fluid is
pumped around deserves to be studied. Some pumping ring styles in dual mechanical seals are based on a straight vane or paddle-type configuration (Figure 1). However, not much liquid is being moved and the head-flow performance of other pumping ring styles often exceeds that of straight vane designs. Test results shown in Figure 4 confirm that helical screws and, in particular, tapered bi-directional rings (Figures 2 and 3)
achieve better head-flow performance. Aside from that, straight-vane or paddle-type pumping rings will function only in the plane where the ports and the straight vanes (paddles) are located. Therefore, tangential porting will be required and even then, in many instances, little or no liquid is made to flow continually over the seal faces.
While helical pumping screws are more efficient than vane/paddle styles, high-efficiency helical screws rely
100mm (4 “) Seal with API 682 Radial Clearance-Head-Flow Characteristics for Various Circulation Devices on Water at 3600 rpm
Figure 4. In this test the head-flow characteristics of a bi-directional ‘tapered vane’ pumping ring are advantageous (blue line) compared to screw thread (purple line) and parallel slot (green line) pumping devices used with older sealing technology.
on a dimensionally close clearance gap between screw periphery and housing bore. This close clearance gap is thought to be a liability in situations where shaft deflection or concentricity issues exist. Designs with a close gap are not in harmony with one of the stipulation of the 2002 edition of API Standard 682. In 2002, API 682 recognised a minimum radial gap clearance of 1.5mm (0.060”).
Since that time, some mechanical seal designs gained pumping screw efficiency with a reduced clearance gap between screw periphery and housing bore. This generated a completely different concern; reduced clearances increase rubbing contact risk between close-clearance pumping screws and the surrounding stationary parts.
Only the bi-directional tapered pumping device (Figures 2 and 3) incorporates large clearances - low rubbing risk - and has excellent overall performance. The different head-flow characteristics in the comparison tests of Figure 4 are of interest also. Bi-directional tapered vane pumping rings incorporate the best of all approaches. They certainly deserve to be considered for reliability-focused installations.
Our new GHSVSD+ Vacuum Pump is like no other vacuum pump, ever. It’s what we put inside that changes
Want to learn more? contact
Freecall 1800 023 469
Tony Sgro has had a long and varied career in the Australian pump industry, although he has remained loyal to two great pump companies - Ingersoll Rand and Kelair - throughout his career. To mark his retirement just last month, we caught up with Tony to reflect on his years as a pioneer of the Australian pump industry.
When did you first get into the pump industry?
My first job was as an Internal Sales Engineer at the Ingersoll Rand (I-R), Sydney office starting on 6 January 1971. This job provided me with my first involvement with pumps and it was primarily with centrifugal pumps.
By training, I am a Chemical Engineer. During two stints of vacation training in my university years, it became clear to me that I was going to make a poor engineer. I started looking for jobs in the Sales and Marketing area and this ended with Bruce Ellis offering me the job at I-R. I-R’s product spread was very broad and I was trained and worked in pumps, stationary air compressors, air tools and gas compressors. I began specialisation in pumps in 1977 when I moved to the Pump Division in I-R’s Melbourne Head Office.
What do you like about the pump industry?
Pumps have been my primary involvement and I know pumps better than anything else. I especially enjoy the sales environment however my involvement with pumps has also allowed me utilise some of my engineering training. Any journey of 44 years would be meaningless if it were not for the people encountered along the way. I have made friends through my involvement with pumps and I am very good friends with people I met on my first visit to Ingersoll Rand Melbourne in January 1971. This is what I have liked most about my involvement with pumps.
What other companies have you worked for during your time in pumps?
I worked with Ingersoll Rand for nearly nine years beginning as an applications engineer. I progressed to a couple of different external sales roles then moved to Head Office with a regional responsibility and my final year was working with Ingersoll Rand International located in Jakarta in 1978. My father’s passing in 1978 forced an early return to Sydney and after a couple of months I joined Kelair starting on 1 February 1979. I have worked only for I-R and Kelair.
How has the industry changed during your time in it?
Changes such as the demise of our processing industries and of pump manufacturing in Australia have been mentioned
by previous interviewees.
The changes that I find difficult are of a more general nature rather than specifically pump industry related. The increase in sometimes draconian Terms and Conditions are now commonplace in business. These T&Cs are too often used as a tool for both imposing unfair directives and for boosting profits. It has made business sometimes confrontational and unpleasant. The final result is poorer for all concerned.
The level of pump knowledge in our client base is not what it used to be. In the 1970s, some clients had pump knowledge far greater than the pump company representatives. Selling value was understood and more readily accepted. This lack of knowledge leads to decisions often based on price rather than technical aspects. This also leads to a poorer result for all concerned.
I regret the diminishing of loyalty. By loyalty, I mean loyalty between employer and employee and also between customer and supplier. Whilst relationships in business are still and always will be important, they are more difficult to establish on a long term basis because people no longer remain in jobs for long periods of time.
Did you have a mentor at any time in the industry?
Both in my personal and professional life, I have learned from many people with whom I have crossed paths. I am sure there are lessons that I should have heeded and did not.
Yet, there are two people who have had a significant influence in my life in pumps. Peter Snow who I worked with
in my early years at I-R taught me most of what I know about centrifugal pump theory. I was a bit of a knowledge sponge and Peter was prepared to spend the time with a young, green engineer.
Bill Smith, the founder of Kelair, was a major influence in my education in sales and business. This started at I-R when Bill was my boss for a couple of years and progressed through the 25 years we had together at Kelair. They were both great teachers and I am indebted to them both.
Tell me about some of the other personalities in the industry that you have worked with?
Bruce Ellis, who moved on to be Managing Director of Mono Australia, gave me my first job. In my early years, I most likely gave Bruce many reasons to regret that decision but I do thank him for checking me out with the receptionist at I-R. Bruce was
not aware I had already charmed the lady. Bill Smith started in the pump game in either 1963 or 1964. That is over 50 years ago and I worked with Bill for over 33 years. Bill was both a dynamic and enigmatic personality. I also worked with another fiery Scotsman, Alan Rowan, in 1977 at I-R. His volcanic temper eruptions, usually followed by flying 5kg pump manuals, were legendary. However a short five minute walk would calm him down and he would return as if nothing had happened. I was fortunate to start work in the early 1970s when companies were hiring young people. Two good guys who started in pumps at about the same time as me and are still in the business with the Brown Brothers/Kelair group are Mal Eyre and Warren Smith. Quite a number who have worked at Kelair over the years are still in the pump game. These are people like Bob Exon who runs KSB in New Zealand, John Wilkins at ITT Blakers and Chris Wansbury at Brown Brothers, along with many others.
HYDROVAR®, the modern variable speed pump drive taking pumping to a new level of flexibility and efficiency.
• Motor or wall mountable
• Fully programmable on site
• Software specifically designed for pump operation, control and protection
• High level hardware design
• More flexibility and cost savings
• Energy savings up to 70%
• Simple mounting “clip and work”
• Multi-pump capability up to 8 pumps
Ph: 1300 4 BBENG www.brownbros.com.au
What are the most significant developments you have witnessed in the industry?
The major change is the almost total disappearance of Australian pump manufacture and the associated rise in overseas suppliers. This has developed over the last 40 years or so. Companies such as Grundfos and KSB were represented by local companies prior to establishing their own presence in Australia. Pump start-up companies generally representing overseas suppliers began to proliferate in the 1970s. This has led to a fragmented pump supply industry in Australia with just about every manufacturer of pumps in the world represented in some way in this country. This is how Kelair started.
A further development is that some companies now source products from all around the world. We see this particularly with EPC companies. Other EPC companies issue enquiries from overseas offices. We have also seen an increase in ‘global contracts’ and ‘preferred supplier agreements’ established between major manufacturers and customers. This presents problems in selling for smaller companies like Kelair.
Although not limited to pumps, another development is buyouts and mergers of companies. You may wake up one morning and have a different master than the day before. This is particularly significant to companies who represent overseas manufacturers as it could very well mean a loss of a major distributorship.
Are you still involved in the industry today?
I retired from Kelair and the pump game in July 2015.
What advice would you give young people in the pump industry?
Grasp those with knowledge and soak out as much of it from them as you can by being inquisitive. Do not expect that knowledge will be handed to you on a plate. Ensure you allocate time during your day to teach yourself. If you do not have knowledge, you are likely to be superficial in what you talk about.
I like reading quotations and one that sticks with me is: ‘Don’t look back; you are not going that way’.
What are the greatest challenges facing the pump industry? What does the future hold for pumps?
I believe the industry’s greatest challenge is attracting, training and retaining people. Engineering sales is not a ‘trendy’ vocation and our industry is not known for being the best paying in the world. Many accept a job in the pump industry as a stepping stone to a future position elsewhere. Today’s employee has grown up in an environment where changing jobs to get ahead is seen as not only acceptable but even as a necessity. They are very mobile in their professional lives. Attaining an acceptable level of pump knowledge takes many years and requires both application and a desire to learn on the part of the employee. I believe
that for this reason, pump companies no longer train and leave it to others hoping to pick up trained staff later in life.
My hope is that future is good for the pump industry. The pump industry will not disappear. The need for pumps will still exist. The one thing we can be sure of is that change will happen; yet I have no idea how change will impact on our industry.
What do you like to do in your spare time?
Kelair has been my hobby for 36 years and I have not given much time to anything else. My long suffering wife, Denise, and my daughters Gemma and Lauren would attest to that. I am an avid if poor golfer and have involved myself
extensively on the Board of my golf club over the last ten or so years. I have been fortunate in having the opportunity to do a lot of business travelling during my time at Kelair. I have also travelled with the family on a number of occasions and I enjoy this very much. I hope my golf handicap improves and the opportunity to travel increases now that I am retired. I have always wanted to learn to play a musical instrument and I intend to take up the guitar in my retirement as well.
Continuing our coverage of the Australian pump industry, in this issue we take a look back at the publication that first provided Australian pumpers with their regular fix of the best in local and international pump news.
The potential export market open to the Australian Pump Industry was particularly promising during the late 1960s. Countries such as Malaysia, Thailand, Taiwan and the Philippines had solid markets for pumps and mining purposes.
By delving into the past, we appear to have struck gold. We thought we were the first pump magazine to start from humble beginnings in Victoria, but it turns out our path had actually been trod 50 years earlier.
The Australian Pump Journal was the brainchild of Commercial Editor, Robert ‘Bob’ Pullen and Technical Editor, F. Muscroft. Their idea was to bring the industry a useful, relevant and helpful mix of news, information and technical
“Let’s face it. Looking at our curves the right way will help you more than those in the picture above. The Australian Pump Journal is offering to this month’s readers a friction loss graph wall chart in colour which will do more than just beautify the office wall.”
- The Australian Pump Journal Vol. 1 No. 3
Mono Pumps Australia congratulates The Australian Pump Journal for its service to the Pump Industry.
“The journal is more than just a magazine, it has in-depth topics such as theoretical impeller design and a review of the Snowy Mountains Authority. For readers who use pumping equipment in their everyday life, the journal will provide technical information to assist in solving pumping problems.”
- The Australian Pump Journal Vol. 1 No. 1
The Kelly and Lewis story Kelly & Lewis has an extremely long and proud history in the Australian pump industry, which has been documented in this magazine - but was first documented in The Australian Pump Journal
founders of The Australian Pump Journal, Robert Pullen and F.
The PIA’s Australian Pump Technical Handbook is a cornerstone text for the Australian pump industry and, in our opinion, a must have for anyone who deals with pumps on a regular basis. In this ongoing series, we feature abridged chapters from the classic book to showcase the various areas covered and to reacquaint readers with the technical aspects of pumps. In this issue, we explore the defining characteristics of centrifugal pumps.
As covered in the previous edition, Let’s get classy (Pump Industry, Issue 10, May 2015), a centrifugal pump is a rotodynamic pump in which a shaft-mounted impeller rotates within the pump casing, thus accelerating the pumped fluid radially outward. Therefore, the two main components of a centrifugal pump are:
• The rotating element, consisting of an impeller on a shaft.
• The stationary casing.
These components can come in a range of different types and centrifugal pumps come in various different configurations, depending on the requirements of the application for which the pump is required.
The impeller’s rotary motion imparts energy to the pumped liquid in the form of velocity, some of which is then converted to pressure within the impeller passages.
The different types of impellers used include:
Radial flow impellers
The liquid enters the impeller axially and discharges radially, changing the direction of the flow 90°. These impellers can be single suction (where the fluid enters the impeller from one side) or double suction (where fluid enters from both sides).
Axial flow impellers
The liquid both enters and discharges from the impeller axially (i.e. the flow does not change direction). Single suction only.
Mixed flow impellers
The liquid enters the impeller axially and discharges in both radial and axial directions. Can be single or double suction.
These are basically axial flow impellers with extended vanes. They act as an in-line booster for the main impeller when suction conditions are poor.
The conversion of velocity head to pressure head in the pump casing either occurs via a volute casing or by a stationary diffuser.
Volute casings
These are the most common type of casing. The cross sectional area of the volute increases from the cutwater (which directs the liquid to the discharge) to the inner end of the discharge cone, resulting in a near constant average water velocity. Most of the conversion from velocity head to pressure head occurs in the discharge cone.
Volute casings are available in both single and double volute designs. In
some situations, especially when the pump is operating at reduced flows, uneven pressure distribution around the impeller can cause undesirable radial loading on the shaft. A double volute design reduces this.
A diffuser fits inside the pump casing and directs the flow smoothly into the discharge pipe (or to the next impeller in the case of a multi-stage pump). The diffusers multiple vanes form radially diverging water passages around the periphery of the impeller and recover much of the total head.
A diffuser’s vanes can be radial or axial. Radial vanes are used for most applications. However, axial vanes may be used in cases where the outside diameter of the casing must be reduced or the clearance between the impeller and the diffuser vanes must be increased (e.g. to reduce vane tip erosion in very high speed pumps.
Shaft and bearings
The shaft transmits the driving torque to the impeller. With the support of bearings, the shaft also locates the impeller within the casing.
Single stage overhung impeller pumps usually operate in the stiff shaft mode (with no shaft bending) below the first shaft critical speed (the lowest natural resonant frequency of vibration of the pump rotor).
Multistage pumps often operate in the flexible shaft mode, above the first critical speed. In these pumps the hydrodynamic support and damping afforded by the clearances usually guarantees satisfactory ‘wet’ operation.
The combined unbalanced forces within a pump that act on the impeller and shaft end in the axial direction are known as axial thrust.
Contributors to axial thrust include suction pressure and ‘hydraulically imbalanced’ impellers (caused by an unopposed build up of pressure at the impeller back shroud). In smaller pumps where the suction diameter is similar to the shaft diameter the impact of this pressure is usually minimal. However in larger and/or higher head pumps axial thrust can be much greater and steps must often be taken to combat it.
The most common way to combat axial thrust involves the use of a ‘hydraulically balanced’ impeller with a back ring and balance holes, which reduces the pressure at the rear of the impeller by allowing leakage through to the suction side. Another method is to employ impeller rear (pump out) vanes.
Multistage pumps may have opposed impellers to balance axial thrust or may use a balancing device such as a balance disc or balance drum.
Single stage pump with double inlet impeller
While a pump of this type should theoretically be in complete axial
balance, slight casting differences can cause slight differences in the flow pattern of each impeller entry (eye), resulting in residual axial thrust. A ball bearing of the combined radial/thrust type is used to take this thrust.
Single stage overhung impeller
This impeller design involves a wear ring on the back impeller that simulates an additional ‘eye’ at the rear of the impeller. Near complete axial balance is achieved via ‘balance holes’ in the back shroud, which allow leakage to the suction side.
An unbalanced load towards the driver, caused by suction pressure acting on the shaft area through the stuffing box, may generate some residual axial thrust. However, this is usually small and can be taken by fitting a thrust bearing.
Multistage horizontal pump with balance disc
In this case, the unbalanced axial thrust is approximately equal to the pump differential pressure acting on the annular area of the impeller back shroud. The balance disc rotates with the shaft and automatically adjusts the gap so that the pressure in the inner balance chamber opposes the axial thrust of the impellers.
Multistage pump with balance drum
The area of the balance drum is similar to the impeller unbalanced area but slightly undersize to ensure a residual unbalanced load to keep the shaft in tension. The axial load is taken by a thrust bearing. The thrust bearing can be of the ball type but a tilting pad thrust bearing may be used for high speed or high thrust load applications.
When a single volute pump is operated at best efficiency flow rate the velocities, and therefore pressures, acting on the impeller are uniform around the volute. When the pump is operated at a flow rate other than best efficiency point (BEP) the pressures are no longer uniform, resulting in radial thrust.
The magnitude of radial thrust is determined by the total head, impeller diameter and impeller width. High head pumps with large impeller diameters will experience higher radial thrust. If pumps of this type are frequently operated below BEP, bearing life may be reduced and large shaft deflections may eventually result in shaft failure.
There are a number of options to combat radial thrust in this situation. One option is the use of an oversized shaft with larger bearings. However, this can substantially increase the cost of the pump.
Another solution for high head applications is to use a double volute casing. This divides the flow into two almost equal streams through the use of two cutwaters 180° apart. Although the volute pressure inequalities remain, the two opposing radial forces almost cancel each other out, significantly reducing radial thrust. Diffuser type casings also virtually eliminate radial thrust in a similar way. Further information and detailed diagrams and schematics can be found in the Australian Pump Technical Handbook, available from the PIA website (pumps.asn.au/publications).
the next edition of Pump Industry we will explore the concept of specific speed.
THE PUMP INDUSTRY CAPABILITY GUIDE 2016 WILL BE THE KEY REFERENCE BIBLE FOR ALL PUMP USERS IN 2016.
Included as a printed insert with the November 2015 edition, further copies will be distributed separately throughout 2016. The guide will also be available online in a fully-searchable format as part of the high traffic pumpindustry.com.au website.
This publication is a must for any pump or related companies that want to showcase their capabilities and make sure that pump users and specifiers can find their information when they’re ready to buy.
• Maximum energy saving due to EC motor, High Efficiency Drive and highly efficient pump hydraulics
•Long service life and high operating reliability due to corrosion-resistant stainless steel and integrated dry-running detection
•Simple operation and transparency about the operating status thanks to red-button technology and Smart Control
•BUS interface for intelligent incorporation into building management systems