Pumping LNG & CSG
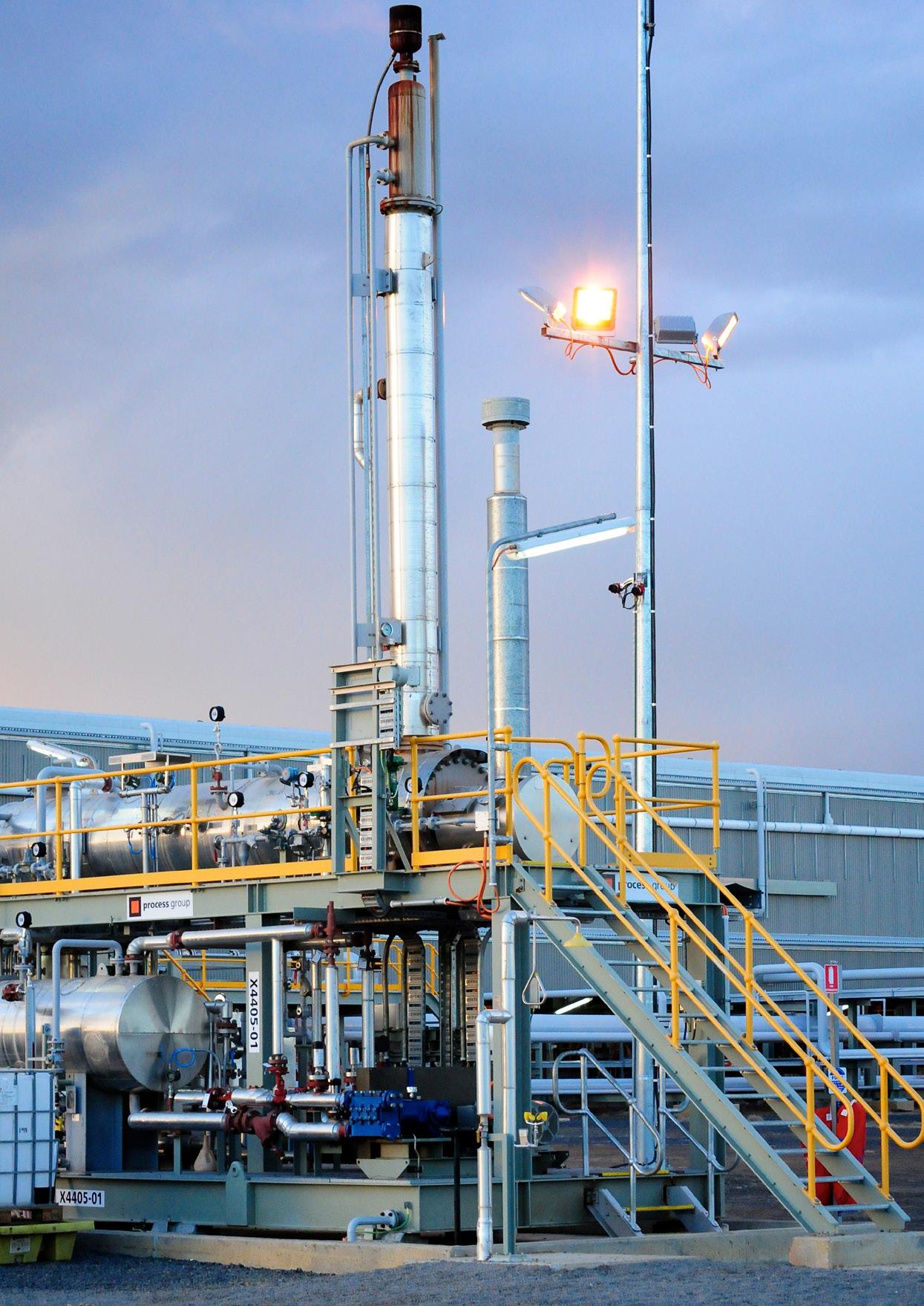
FEATURES:
• Industry training
• Understanding pump curves
• NSISP Project Manager interview
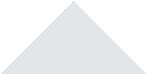
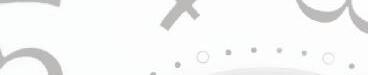

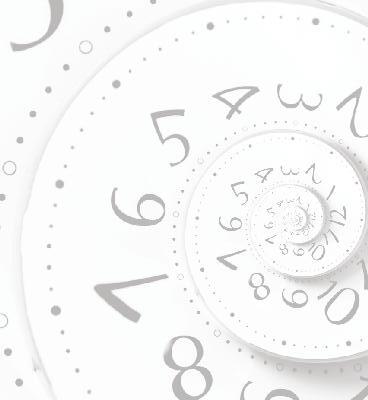

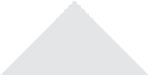


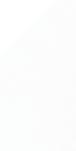
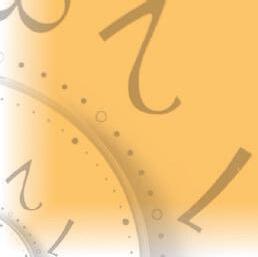
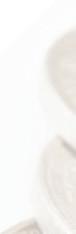


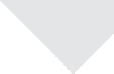
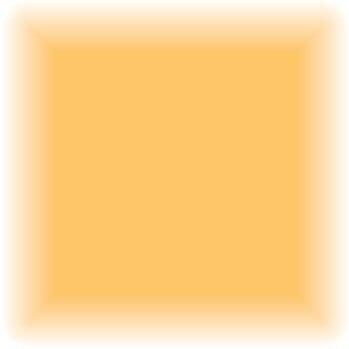





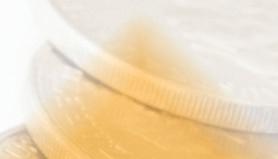





NSW - SYDNEY - Registered Office
Toshiba International Corporation Pty Ltd
2 Morton Street, Parramatta NSW 2150
Tel: +61 2 9768 6600 Fax: +61 2 9890 7546
NSW - NEWCASTLE
Toshiba International Corporation Pty Ltd
Unit 1, 18 Kinta Drive, Beresfield NSW 2322
Tel: +61 2 4966 8124 Fax: +61 2 4966 8147
QLD - BRISBANE
Toshiba International Corporation Pty Ltd
Unit 4, 20 Smallwood Place, Murarrie QLD 4172
Tel: +61 7 3902 7888 Fax: +61 7 3902 7878
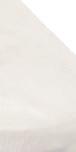


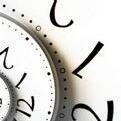

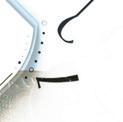


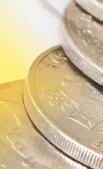


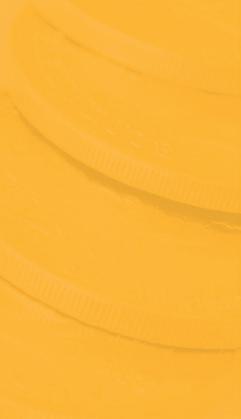




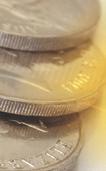
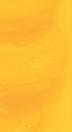

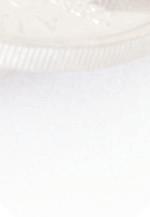

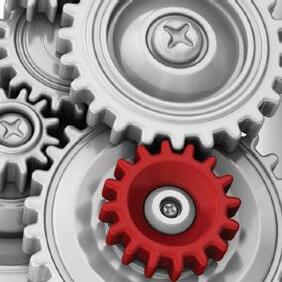



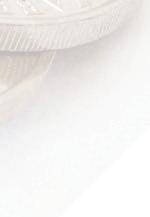




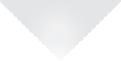
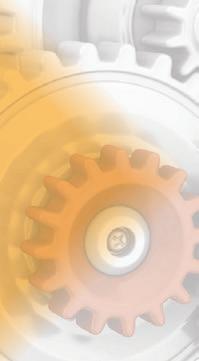
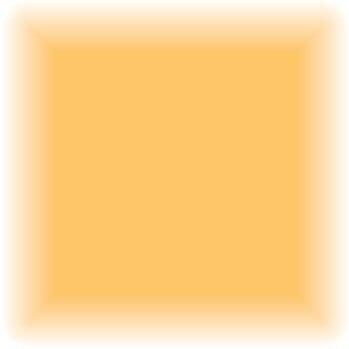



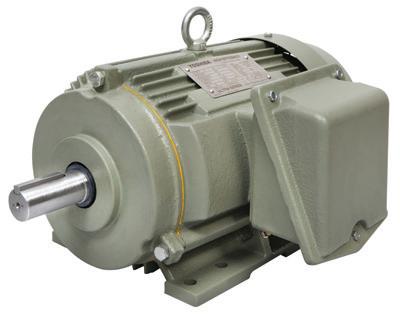
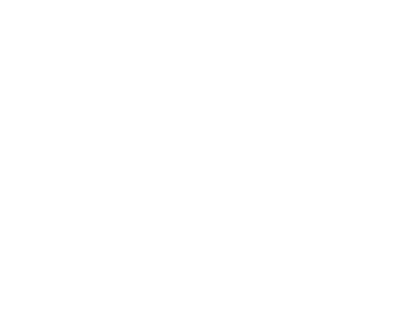
TOSHIBA INTERNATIONAL CORPORATION PTY LTD
QLD - MACKAY Toshiba International Corporation Pty Ltd
Floor, 41 Wood Street, Mackay, QLD 4740 Tel: +61 7 4953 4184 Fax: +61 7 4951 4203
VICTORIA Toshiba International Corporation Pty Ltd
Ferntree Gully Road, Mount Waverley, VIC 3149
Tel: +61 3 8541 7960 Fax: +61 3 8541 7970
WESTERN AUSTRALIA
International Corporation Pty Ltd
Anderson Place, Perth International Airport, WA 6105
+61 8 6272 5600 Fax: +61 8 6272 5601
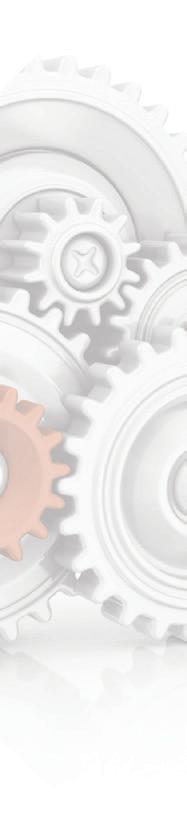



Pump Industry Australia Incorporated
Kevin Wilson – Secretary
PO Box 55, Stuarts Point NSW 2441 Australia
Ph/Fax: (02) 6569 0160 pumpsaustralia@bigpond.com
Ron Astall – President United Pumps Australia & Astech Consulting Services
John Inkster – Vice President Brown Brothers Engineers
Geoff Harvey - Councillor Davey Products Pty Ltd
John Link – Councillor Link Pumps
Martin O’Connor – Councillor KSB Australia
Alan Rowan – Councillor Life Member
Keith Sanders – Councillor Australian Industrial Marketing & Life Member
Two positions remain vacant, contact Kevin Wilson to nominate.
President’s welcome
Welcome to a new year, a new issue of pump industry and a new PIA Council from a new President.
At the November 2012 Annual General Meeting, our President Harry Katunar surprised us all by announcing that he was unable to renominate for the role. He has taken up a position with KSB as the new chief of their operations in Shanghai, China.
We are indebted to Harry for his excellent leadership and for his contribution to a very successful year for PIA. Shanghai’s gain is certainly our loss.
Congratulations Harry; all the best, and keep in touch with your friends in the sunburnt country . . . the land of droughts and flooding rains!
Brown Brothers Engineers’ John Inkster has moved into the Vice President’s role and KSB have kindly provided a replacement councillor in Martin O’Connor; however at the time of writing, two council vacancies remain which we are keen to fill. Please contact our secretary, Kevin Wilson if you can assist. Active involvement brings its own rewards. More on this later!
The excellent work of our executive officers continues:
1. Marketing & Media; Keith Sanders is the engine room of our marketing activities including our recent Melbourne pump exhibition the PIA newsletter and our market research & statistics.
2. Publications; Alan Rowan’s work on updating the PIA Pipe Friction and Technical Handbooks is ongoing with input from a number of our experienced members.
3. Standards; Ken Kugler’s influential work on the fire pump standard AS2941 has been of great value and our liaison with Sustainability Victoria and the E3 committee’s development of Minimum Energy Performance Standards (MEPS) is continuing.
PIA is a pump industry association, representing not only pump manufacturers, but dealers, importers, distributors, resellers, and suppliers of products and services to the pumping market place. Our membership includes some very large companies through to some very small single person enterprises. We have some big manufacturers of small pumps and some small manufacturers of big pumps. We have those with large distributor and dealer networks, while others deal directly with their end users. Our member’s markets include irrigation, water supply, waste & wastewater, power generation, petrochemical, oil & gas, general industry, domestic, and rural. This is a diverse association.
The challenge for any industry association is to fairly represent its membership. Sometimes we may find that the very diversity of our membership will produce a corresponding diversity of opinions on some issues.
The challenge for our members is to get involved. The vision for PIA is to play a leadership role and provide the pump industry with a voice in the market place, and where appropriate, to lobby policy makers on issues of importance. We cannot do this properly without active communication and involvement from our members. At all times you are encouraged to contact PIA with your ideas, comments and concerns through our national secretary, myself or any of the PIA Councillors. Get involved!
And yes, we have two council vacancies to fill. A role on the PIA council is a great way to be aware of and to influence PIA’s activities.
Interested? Contact Kevin Wilson and get involved.
Ron Astall President, Pump Industry Association& CSG pumpindustry
Pumping
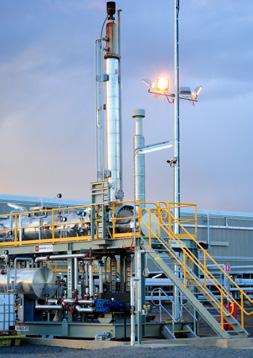
Cover
eventually form an integral part of one of the largest coal seam gas (CSG)
liquefied natural gas (LNG) projects in the country. The processing plant features 17 reciprocating and screw compressors (total 30,000 horsepower compression) delivering gas at 10 megapascals output pressure into the pipeline that feeds Origin’s Darling Downs Power Station and the Wallumbilla Gas Hub.
Photo: Chris Zipf.
Published by
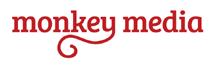
Monkey Media Enterprises
ABN: 36 426 734 954
GPO Box 93, Melbourne VIC 3001
P: (03) 9440 5721
F: (03) 8456 6720 monkeymedia.net.au info@monkeymedia.net.au pumpindustry.com.au magazine@pumpindustry.com.au
Design by Linda Tucker
Happy Places Design www.happyplaces.com.au
ISSN: 2201-0270
Editor’s welcome
The response to our first issue has been really amazing and I just want to start by thanking everyone who has supported this new project, whether through advertising or supplying articles, or subscribing, reading the magazine, checking it out online or just providing me with your feedback.
To start with, I’d like to share a few statistics;
• We printed 2,800 copies of Issue 1 and so far 2,359 have been sent out or given out
• The digital edition has been read 2,782 times
• The website has had 3,141 visitors who have accessed over 10,000 pages
• 182 new people have contacted us to sign up for a subscription since Issue 1 went out
• We’ve sent out six email newsletters, with an average open rate of just over 50% (the average for this type of thing is around 20%)
• We have published at least one new news story every day on the website
If you don’t currently get the email newsletter, you’re missing out. It’s free so head to www.pumpindustry.com.au now and sign up.
All these figures mean our magazine is getting out there and the readership is growing. I’ve also been very pleased with all the people who contacted me specifically with their feedback.
The future is looking bright for pump industry magazine, and as well as seeing four print editions of the magazine, there are lots of other big plans in the works for 2013.
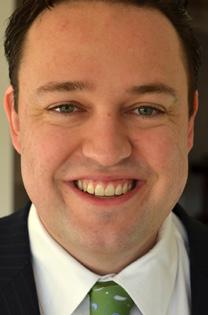
We are upgrading the digital edition to improve the experience for readers and provide more links and integration.
We are expanding the range of information available on the website to offer more exclusive only content, data and statistics.
And there are a few other plans in the works that I hope I can let you know about in the next edition.
I’ve indebted to a great many PIA Councillors and members for all their support in making this happen, but this issue I want to particularly thank outgoing President Harry Katunar for his enthusiastic support for this project, and wish him all the best in his new role.
Pumps are used in such a wide variety of applications, one challenge of publishing is always going to be covering the full range of industries and ensuring the magazine stays relevant to everyone. This issue we look at the critical role pumps play in Australia’s booming gas industry on both LNG and Coal Seam Gas projects.
A strong dialogue between pump suppliers, engineering consultants and end-users is essential to the successful functioning of the industry, and I hope this magazine helps facilitate that. To that end, we have the first in an ongoing series of interviews with people in industries using pumps.
I hope you enjoy this issue, and your feedback is always welcome at magazine@pumpindustry.com.au
Chris Bland Publisher and Editor
Acromet (Aust) Pty Ltd design and manufacture innovative solutions for a wide range of system applications.
• Customised Design
• Detailed Manufacturing
• Comprehensive Factory Testing
• Professional Installation
• Reliable Service
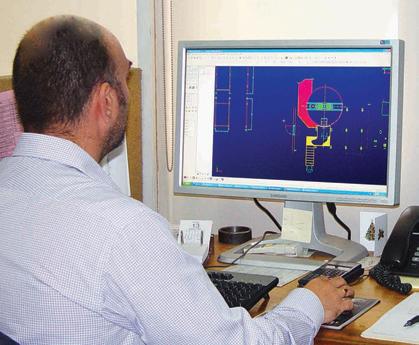
Acromet’s extensive experience and proven track record, delivers a cost e ective solution to meet the client’s operational demands.


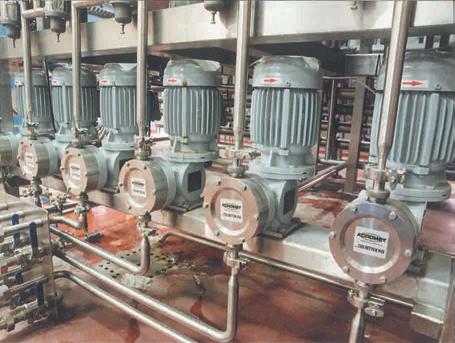
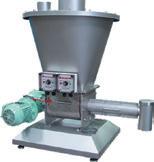
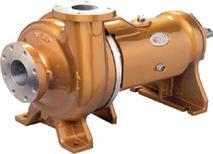
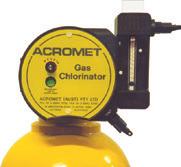

pumpindustry
Including contracts awarded, projects, standards and industry developments.
in review, plus a look at recent events and the technical handbooks
MAIN FEATURES
Pumping LNG
An in-depth look at the pumping technology used on LNG projects as well as an up-close look at the pumps used on Australia’s largest resource development, Gorgon.
Coal Seam Gas 30
As Australia Pacific LNG picks up the pace on one of Queensland’s leading resource development projects a variety of pumping and pressure applications are playing a critical role in extracting, managing, compressing and transporting coal seam gas (CSG).
33
Training
Keith Sanders reflects on this history of pump training in Australia with some recommendations for the future, as well as look at some the options available today through RTOs.
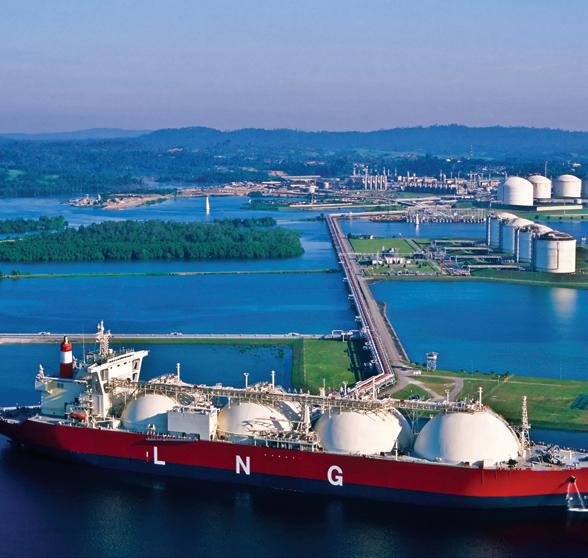
46
Valves: controlling fugitive emissions
Since valves are the number one source of leakage, those faced with reducing fugitive emissions need to look at the most challenging type: control valves. This article highlights some of these options for typical control valve features, characteristics and options.
PUMP PIONEERS
Antony Grage 52
In the ongoing Pump Pioneer series, we catch up with some of the legends of the industry to get their perspectives on pumps. This edition, we speak to Antony Grage, a life member of PIA.
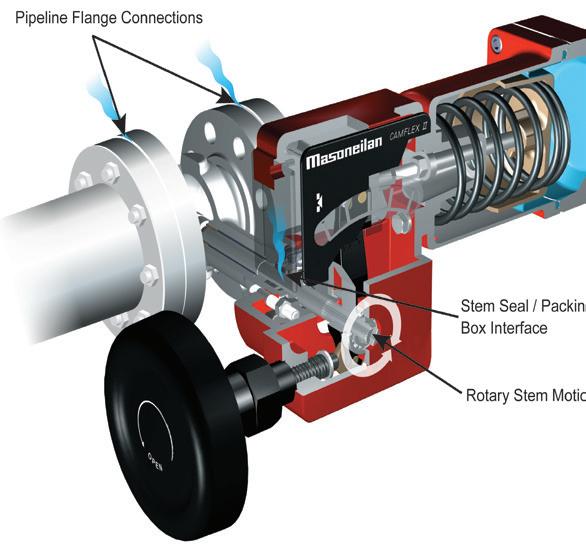
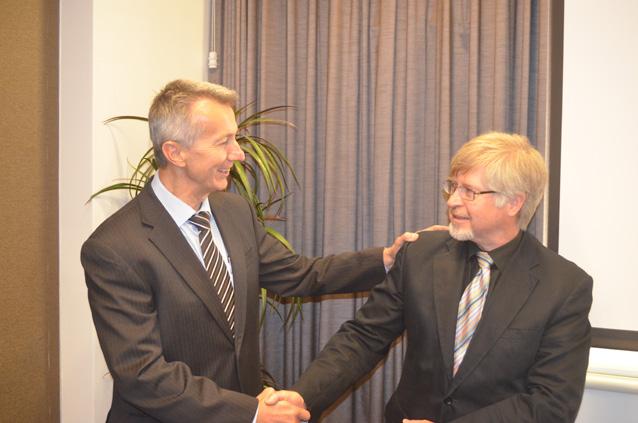

Top 7 tips for marketing your pump company
19
The range of marketing options available to companies in the pump industry continues to grow and change. Chris Bland attempts to de-mystify some of the options.
Balancing to a standard
Industrial balancing and vibration analysis on rotating machinery enables the early detection of faults before breakdown, and assists commercial and industrial facilities reduce their maintenance costs and unscheduled downtime.
A new benchmark for urban pump stations
42
The $403 million North South Interconnection System Project (NSISP) is one of SA Water’s biggest infrastructure projects, with the largest geographical footprint of any project undertaken in metropolitan Adelaide. Chris Bland recently interviewed Project Director, Gary Neave.
Pump up the Projects
38
Pump House Projects designed, constructed and commissioned the first and largest amended water treatment facility for CSG water in Australia reducing the environmental impacts of discharging saline water to the environment. This plant employed patented technology to efficiently manage the quality of discharged water to DERM/EPA standards.
Commissioning a new recycled water plant
Commissioning of the $94 million Northern Water
40
Plant – the Geelong region’s first Class A recycled water plant – has started. The new facility is essentially two treatment plants in one; an aerated biological nutrient removal plant, followed by an advanced water treatment plant incorporating membrane technology.
Understanding pump curves
50
Some pump curves look different. When a pump curve has a hump in it or a high point away from zero flow it is said to be “unstable”. A “stable” curve has maximum head at zero flow and a negative gradient (constantly falling) as flow increases.
54
Mechanical pumps are the second most common machine in the world (after the electric motor), so here are some of the most commonly used pumping terms and symbols.
SHOWCASE
Chemical handling made safe and easy and Versa-Matic Pumps launches mobile app
Funding announced for MurrayDarling Basin
Prime Minister Julia Gillard has pledged $1.77 billion over ten years from 2014, aimed at adding an additional 450GL of environmental water to the Murray Darling Basin.
Modelling released by the Murray-Darling Basin Authority showed that through a combination of relaxing capacity constraints and providing an additional 450GL of water above the 2750GL described in the plan, environmental outcomes for the basin can be improved.
Water efficiency is the answer
The Australian Water Association has released a new position paper on water efficiency to coincide with National Water Week.
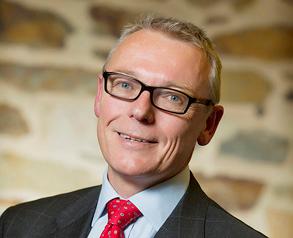
AWA CEO, Mr Tom Mollenkopf, said that it is important to remember that although we have had a recent abundance of rain on the east coast, our climate is variable and volatile.
“The Water Efficiency Position Paper highlights how paramount water efficiency is in how we use our most valuable resource. This is particularly so as climate change and population growth will mean that in future more will need to be done with less”, Mr Mollenkopf said.
The report considers the energy efficiency gains to be made through greater water efficiency, including efficient pumping, stating; ‘there is a direct link between water consumption and energy consumption. Energy consumption will likely rise as the population increases and as water sources that are more energy intensive are utilised (e.g. water sourced from remote locations requiring pumping and the use of lower quality water that requires energy intensive treatment including wastewater, stormwater and ocean water).
“On a network distribution scale, less energy is required to treat and pump water from the supply dam, groundwater source or recycling facility and on-site. Water distribution pump sizes can also be optimised to match demand levels better”
The paper makes that through saving water there is less need to pump as much water, heat as much water, as well as using energy to build new, and maintain existing, infrastructure.
Pentair & Tyco Flow Control merge Pentair has completed its merger with the Flow Control business of Tyco International Ltd. Pentair, Inc. and Flow Control have combined to create Pentair Ltd., an industrial growth company that is a global leader in water and fluid solutions, valves and controls, equipment protection and thermal management products.
The company now has 30,000 employees located in more than 30 countries, operates more than 100 manufacturing facilities and markets its products and services around the globe and the merger will impact all global operations including Australia.
Pump efficiency number one
A recent survey of pump design engineers at consulting and original equipment manufacturing companies by UK-based ADT has found that improving impeller designs for better efficiency was very important for the majority of the respondents. The ADT 2012 Pump Design Survey found:
• 84 of 90 respondents stated that improving impeller design for better efficiency is very important.
• 79 of 90 respondents stated that improvement to pump stage efficiency is very important.
• 65 of 90 respondents stated that improvement to pump stage cavitation performance is very important.
• Just 50 of 90 respondents stated that reduction in manufacturing costs was very important.
Slurry pump inventor awarded Dr Charles Warman inventor of the Warman Slurry Pump has been recognised for his contribution to the City of Kalgoorlie-Boulder with a plaque on the Kalgoorlie-Boulder Walk of Fame.
Dr Warman’s invention, The Warman Slurry pump, improved the efficiency of slurry pumps worldwide and have continued to be used in the mining industry for over 50 years.
Santos announces Australia’s first commercial shale gas
Santos recently marked a historic milestone for the Australian resources industry, announcing it has commenced commercial natural gas production from its Moomba-191 shale well in the Cooper Basin.
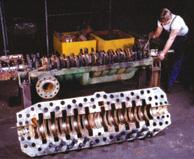
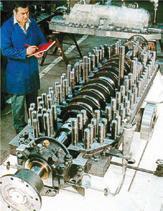
Hydraulic Institute releases new controlled volume metering for test standard
The Hydraulic Institute (HI) has released a new test standard for Controlled Volume Metering Pumps.
The ANSI/HI 7.6 Controlled-Volume Metering Pumps for Test standard is for the testing of positive displacement reciprocating controlled-volume metering pumps (see ANSI/HI 7.1-7.5 ControlledVolume Metering Pumps for Nomenclature, Definitions, Application, and Operation). Variations in test procedures may exist without violating the intent of this standard. Exceptions may be taken if agreed on by the parties involved without sacrificing the validity of the applicable parts of the standard.
The ANSI/HI 7.6 – 2012 standard provides uniform procedures for hydrodynamic controlled-volume pump performance testing and for recording of the test results of metering pumps. Vibration and acoustical testing methods are not included in this standard. Refer to ANSI/ HI 9.1–9.5 Pumps –General Guidelines for Types, Definitions, Application, Sound Measure-
ment and Decontamination, Section 9.4 Measurement of airborne sound, for acoustical testing procedures.
New code of compliance for sewage pump stations
The new Queensland code of environmental compliance for sewage pump stations—ERA 63(3) is now in effect.
The update was originally announced in August, with Minister for Environment and Heritage Protection Andrew Powell saying “Following extensive consultation with industry representatives, the Department of Environment and Heritage Protection (EHP) has developed a new code of environmental compliance for operators of sewage pumping stations which will save millions in application costs,” Mr Powell said.
“The new code allows operators of pumping stations with a capacity of greater than 40 kilolitres per hour to operate under set conditions, without having to apply for a development approval for an environmentally relevant activity (ERA).
“Industry estimates this will save between $20 to $30 million in application costs and will significantly reduce assessing and processing times for departmental staff who can then direct more time to the ongoing protection of Queensland’s environment.
“It is estimated that the new code will apply to over 1000 existing sewage pumping stations and 24 new stations expected to start construction in the next 12 months.”
New Sydney Water sewage pumping station code now available
The Sydney Water Edition 2012 of the Sewage Pumping Station Code of Australia, WSA 04—2005 Version 2.1, is now available for purchase from the Water Services Association of Australia (WSAA).
This edition includes the specific requirements of Sydney Water. It comes with a CD of the complete Sydney Water Code, including drawings. Updates to the Sydney Water edition are advised by Sydney Water through their asset creation management process.


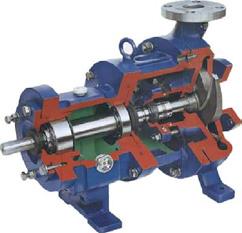
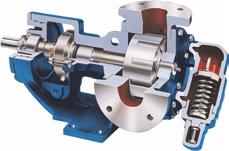
•
•
•
•
•
•

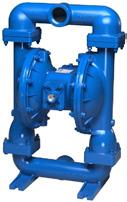
•
•
The standard is available from WSAA.
•
•
•
Gosford sewage pump station
Gosford City Council has awarded a tender worth $1 million for the refurbishment of Sewage Pump Stations KA1, FB3 and SD5 to Carey Constructions Pty Ltd.
The refurbishment is part of the extensive Sewage Pump Station Upgrade Program aimed at improving the reliability, capacity and performance of the region’s sewer network.
Golf Course pump station
Brimbank Council has awarded a contract to Planned Irrigation Projects for the Keilor Golf Course Pump Station.
The job requires the company to design, supply and install a pump station and filtration plant into an existing pump house structure.
The pump station will connect into the existing irrigation system for the Keilor Golf Course. Irrigation water will be extracted from an existing 7 ML storage dam.
Mackay Council water recycling
Mackay Regional Council has awarded a $25 million tender to Transfield SKM Joint Venture for the construction of a new water recycling facility in Sarina.
A separate tender totalling $3.5 million was recently awarded to G&MA Lemura Contracting for the construction of a major sewerage pump station and rising main in Sarina to pump the sewage to the new facility.
SCADA and Telemetry upgrade
Mackay Regional Council has awarded the tender to implement a new SCADA and Telemetry system at 78 sewage pump stations and 10 water reservoirs and pump stations to MPA Engineering Pty Ltd.
According to the council; “the current telemetry network in Mackay uses a ClearSCADA (Supervisory Control and Data) control system operating at Paget Depot, along with Rad-Tel RTUs (Remote Terminal Unit) at the numerous sewerage pumping stations (160) and water asset sites (25) within the Mackay networks.
“The next phase of the overall SCADA and telemetry upgrade project involves replacement of the existing obsolete 3000 and 5000 Series Rad-Tel RTUs along with their analogue radios with new RTUs and digital radios.
Dimboola to Nhill pipeline
Goulburn Murray Water has awarded contracts for the supply and construction of a transfer pump station and construction of the Dimboola to Nhill pipeline.
The contract for supply and construction of a transfer pump station in Dimboola has been awarded to CHS Group Australia with works expected to commence in January 2013.
The contract to construct a 38 km pipeline to supply drinking water from the Dimboola Water Treatment Plant to Nhill has been awarded to Mitchell Water Australia.
Wheatstone pump contracts
A range of new pump supply contracts have been awarded on Chevron’s Wheatstone Project as part of the Bechtel Onshore LNG Plant.
United Pumps Australia has been selected to supply API 610 pumps for the two LNG trains.
Flowserve has been selected to supply lean Solvent Charge API pumps while Sundyne has been selected to supply various centrifugal API pumps.
Curtis QCLNG maintenance
QGC Pty Limited has awarded a contract worth more than $80 million to Australian company Monadelphous Group Limited for maintenance of the Queensland Curtis LNG (QCLNG) liquefied natural gas plant.
The Gladstone arm of Monadelphous will support maintenance activities on Curtis Island including supply and operation of cranes, scaffolding, mechanical and electrical equipment.
This maintenance will help to ensure the safe and reliable operation of the LNG plant during operational preparations in 2013 and when LNG production starts in 2014.
QGC has also awarded a contract worth up to $80 million for the first stage of natural gas processing facilities in the Surat Basin for the Queensland Curtis LNG Project.
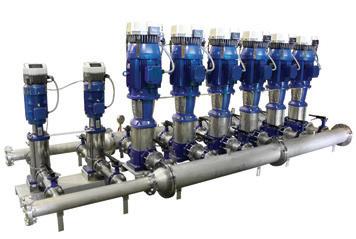
• Motor or wall mountable
• Fully programmable on site
• Software specifically designed for pump operation, control and protection
• High level hardware design
• More flexibility and cost savings
• Energy savings up to 70%
• Simple mounting “clip and work”
• Multi-pump capability up to 8 pumps
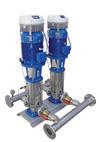
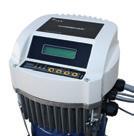


Forge gets EPC contract for Rio Tinto fuel infrastructure
Cimeco, a subsidiary of Forge Group, has been awarded a $70 million contract by Rio Tinto for the design and construction of Fuel Infrastructure at both the West Angelas and Brockman iron ore mines in Western Australia’s Pilbara region.
ABB gets automation contract for Grosvenor coal mine
Power and automation technology group
ABB has won an order worth US$38 million to design, engineer and supply an integrated automation and electrification system for Anglo American’s new Grosvenor coal mine in Queensland on the east coast of Australia.
ABB’s delivery includes ABB’s Unigear ZS1 switchgear and space saving water-cooled multi-drive equipment for a smaller substation footprint that will result in a lower capital cost for the project. The customized solution will also use ABB’s System 800xA automation system to integrate and control all processes and
power systems to enhance productivity. System 800xA is well-suited for composite mining projects that realize engineering and operational cost savings with the integration of plant-wide process control and electrical power systems.
Caval Ridge coal mine plant contracts awarded
Thiess has been awarded two new contracts for approximately $220 million with BHP Billiton Mitsubishi Alliance (BMA) for construction works on the Caval Ridge Mine Project in the Bowen Basin in Central Queensland.
The Thiess contracts are for the construction of a coal preparation plant (CPP), part of the coal handling and preparation plant (CHPP), for approximately $125 million and a rail loop and holding roads for approximately $95 million.
Monadelphous meanwhile was awarded the contract for the provision of civil, structural, mechanical, piping, and electrical and instrumentation works on the CPP.
Keep up-to-date with all the latest news
You can get all the latest news daily online at the pump industry website.
Sign up for the free newsletter so you don’t miss anything.
Get the latest contracts and tenders awarded at; pumpindustry.com.au/category/awarded/
See the latest open tenders at; pumpindustry.com.au/category/tenders/
Sign up for the free online news at; pumpindustry.com.au/subscribe/
Or just visit the home page and follow the menu options.
Got any news?
If you have any news, such as people movements, new staff, contracts awarded, projects completed etc, please submit to the editor at


New President caps off successful year for PIA
Ron Astall has been elected as the new President of Pump Industry Australia Inc (PIA), replacing outgoing President Harry Katunar.
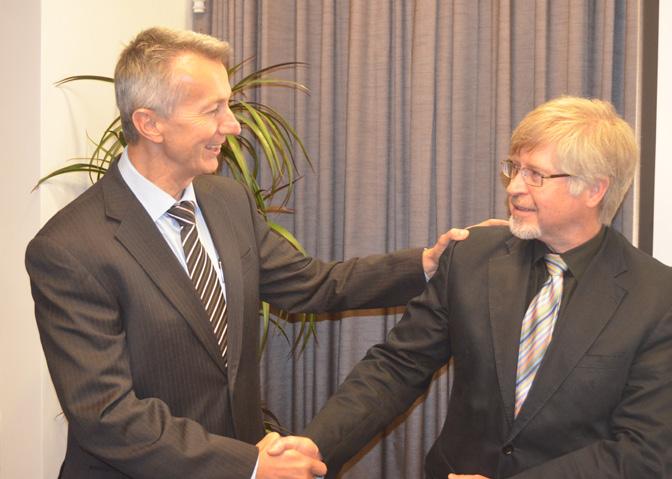
Previously serving as PIA Vice President, Ron was elected at the PIA AGM on November 22, which also saw the election of John Inkster as Vice President.
Both Ron and PIA Secretary Kevin Wilson paid tribute to outgoing President Harry Katunar, who is leaving the role as he will be soon taking up a position with KSB in Shanghai, China.
Kevin noted that it had been a very successful year for PIA under Harry’s leadership and wished him all the best.
The office bearer’s reports at the AGM all noted that the association was continuing to strengthen, with many successful events and publications in recent years contributing to that success.
The AGM was followed by the PIA Annual Dinner where members caught up in a relaxed atmosphere. See page 18 for photos.
Outgoing President’s Report
Dear Members,
2011/2012 has been another busy year for PIA. My thanks to all of you who have contributed towards our successful seminars and events during the year.
We have actively worked towards providing services and support to our existing members, as well as growing our
membership, with the addition of 12 new members over the past year. We welcome new members big and small on board and look forward always to feedback on how we can add value to your membership.
We have continued with our policy of taking regular general meetings to State Capital Cities and rural areas. Council mini meetings are also held more frequently with the use of teleconferencing. Our meeting schedule this year included:
• February 2012- Bankstown Gold Club, Sydney – Our thanks to White International.
• May 2012- Tocumwal Victoria– Our thanks to Batescrew.
• August 2012 – Brisbane Riverside Centre – Thanks to all members that attended.
• November 2012 – AGM and annual dinner at Melbourne University.
It’s exciting to see the successful launch of a world class magazine dedicated to our local industry. The Pump Industry Magazine, published by Chris Bland of Monkey Media has set a high standard with the first issue. I encourage members to support Chris in his new venture by advertising in future issues, and providing interesting stories on projects, products and people.
Keith Sanders’ regular PIA newsletters continue to keep members and the general public informed of our activities and our website still generates a large number of hits from all over the world.
We have increased profile of the Pump Industry by engaging in dialogue with Government Departments and other Industry Groups.
• Our March Industry breakfast held at Carlton Football Club featured The Hon. Richard Dalla Riva, Victorian Minister for Manufacturing.
• Our Victorian magical mystery bus tour in May took members & partners up through the heart of Victoria to the mighty Murray River, visiting Flowserve & Batescrew
• A second Breakfast meeting was held on 10 July in Nunawading when Brenda Pritchard - Regional Manager, Market Facilitation – S & E Metro (Higher Education and Skills Group) provided members with the latest information on training programs for Industry and Government support for training costs.
• The Brisbane Resources Seminar in August attracted over 60 participants who saw some excellent papers presented on new technology for the mining and oil & gas industries.
• The October Pump Industry Exhibition, held at the Whitehorse Centre in Melbourne attracted acceptable attendance from members and nonmembers over 2 days.
Thanks go to Keith Sanders, Ron Astall and the organising committee for arranging these successful events.
We have continued to work with other Associations and organisations to provide useful networking opportunities for members.
Other initiatives include:-
• Continued dialogue with BMPA
• Attending meetings with AMCA on the introduction on Building Industry Modelling.
• Maintaining our relationships with
Pump Selection Guide
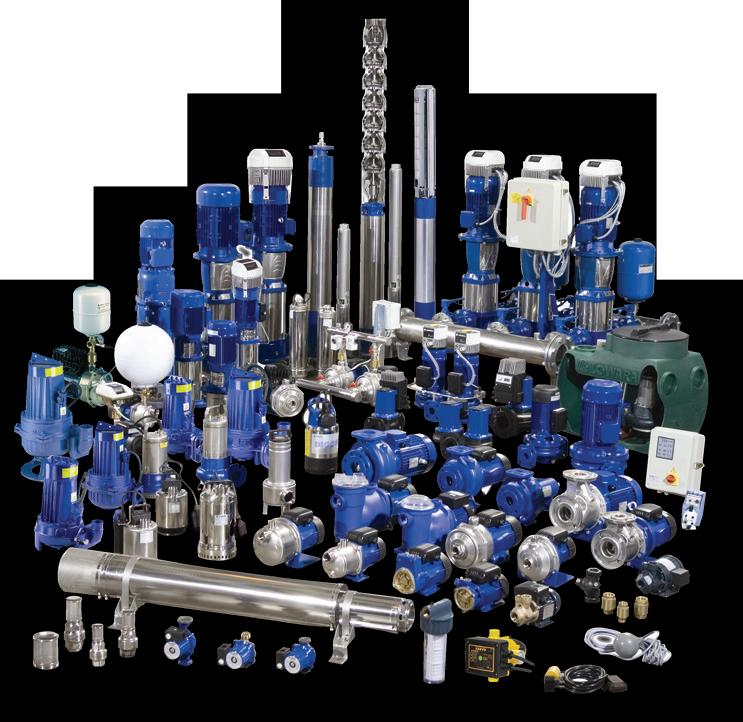

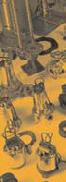
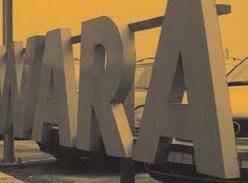
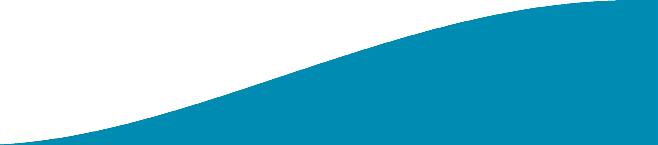
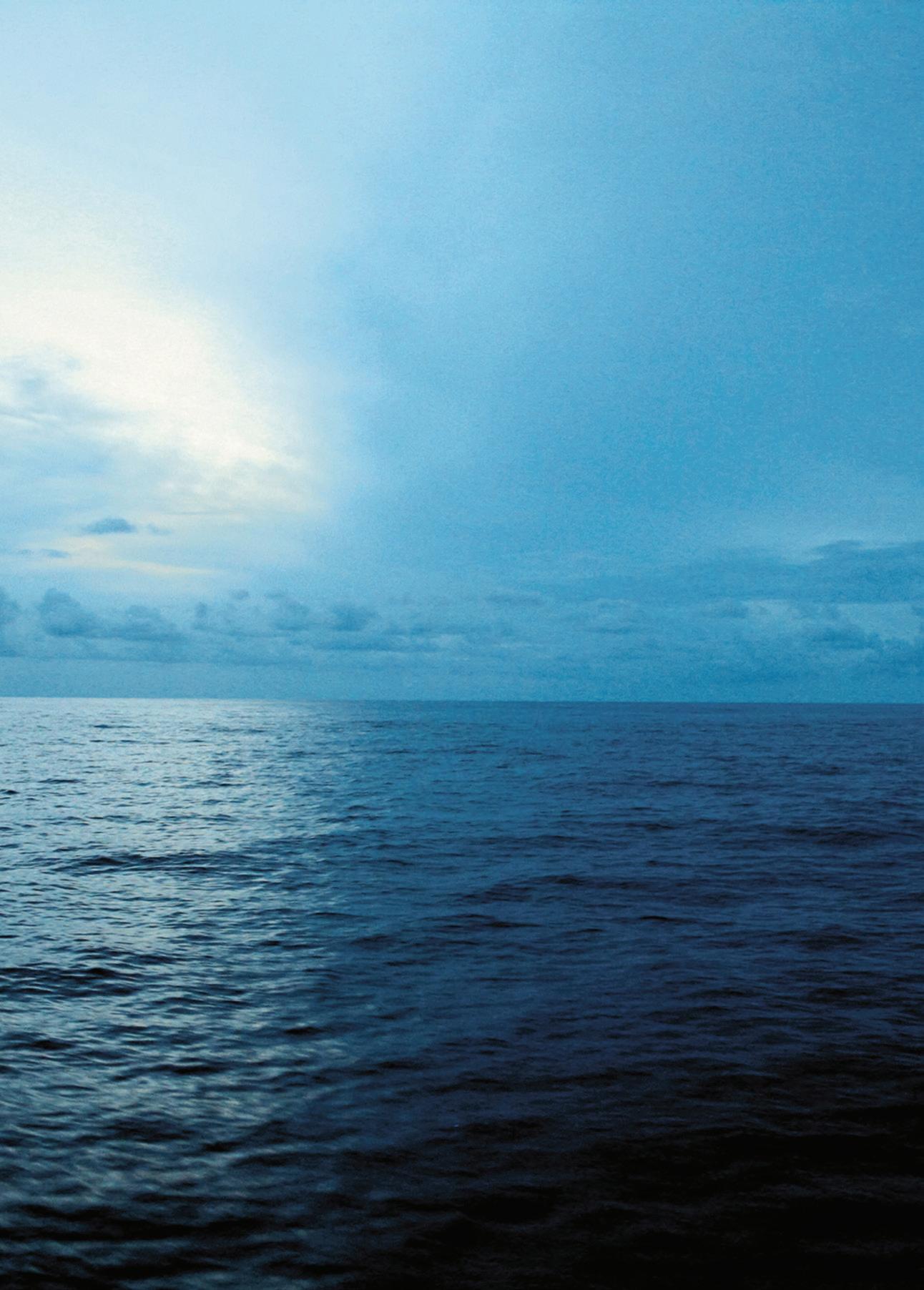
AIRAH, Engineers Australia & the Fan Industry.
• Working with AIG, ICN, Sustainability Victoria and the E3 Committee.
• Discussions with Irrigation Australia on proposed changes to legislation that may affect pumps servicing.
• We continue to play an active role in new developments and changes that may impact on our members.
• Our Standards sub-committee has been involved in discussions on a number of important issues.
• AS 2941 – Fire Pump Standard –The work done by Ken Kugler to draft amendments to this standard has now been approved and will be issued for public comment in early 2013.
• MEPS for Pumps – This project was initiated by Sustainability Victoria in 2009. Keith Sanders has maintained contact with the E3 Committee and Dept of Climate Change and Energy Efficiency to ensure PIA members opinions are taken into account.
Publications continue to be an important part of the Association revenue stream
and sales in 2011/2012 have been strong. We thank Alan Rowan and his team for his continued involvement in the updating and administration of both the Technical and Pipe Friction Handbooks. Work is almost complete on revised versions of both handbooks.
My special thanks go to our Secretary Kevin Wilson. Under his strong administration, and financial acumen, the PIA is well placed financially in fulfilling our obligations to our members. His support has certainly made my role as President relatively straight forward.
I was not able to stand for President again, due to business obligations. My time as a councillor, vice president & president has been most enjoyable.
Best wishes to my successor who will be supported by a strong experienced council, and an effective team of executive officers.
The PIA is well positioned to serve your interests for the next 12 months and beyond.
Yours sincerely
Harry Katunar Outgoing President - PIAMagazine deal
The AGM also saw Pump Industry Australia and Monkey Media ink a new deal for the ongoing publication of this magazine. The deal will ensure the two parties continue to co-operate to produce Pump Industry quarterly into the future, both in print and online.

Event Calendar
PIA Events
PIA General Meetings (subject to change)
12 February 2013 – Melbourne
14 May 2013 – Adelaide
13 August 2013 - Sydney
12 November 2013 (AGM)– Melbourne
Plus other seminars to be announced
For more information or to register for PIA events, visit pumps.asn.au or email pumpsaustralia@bigpond.com
Other Events
Australasian Oil & Gas (AOG)
Perth 20-22 February, 2013 www.aogexpo.com.au
WIOA NSW
Canberra April 10 -11, 2013 www.wioa.org.au
OzWater
Perth 7-9 May 2013 www.ozwater.org
Auspack Plus
Sydney 7 - 10 May 2013 www.auspackplus.com.au
National Manufacturing Week
Melbourne 7-10 May 2013 www.nationalmanufacturingweek.com.au
APPEA
Brisbane 26-29 May, 2013 www.appea.com.au
PACIA
Melbourne 4-6 June 2013 www.pacia.org.au/events/
WIOA Queensland
Gold Coast June 5-6, 2013 www.wioa.org.au
IPWEA
Darwin 11-15 August, 2013 www.ipwea.org.au


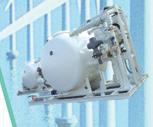
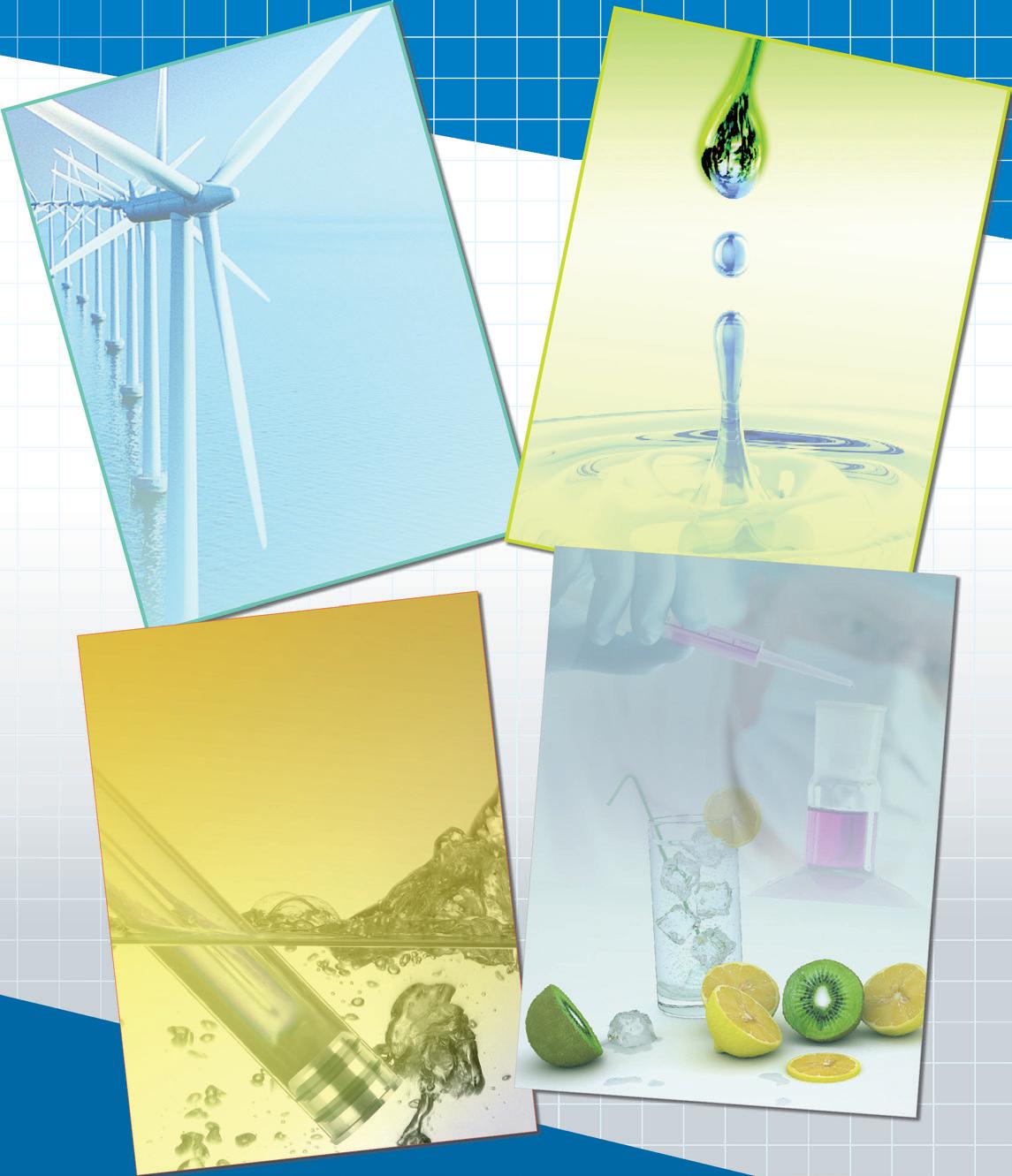

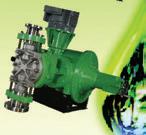
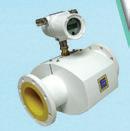
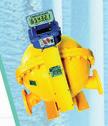
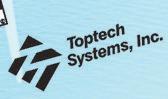
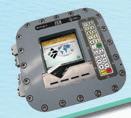




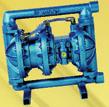
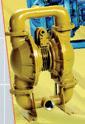
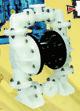

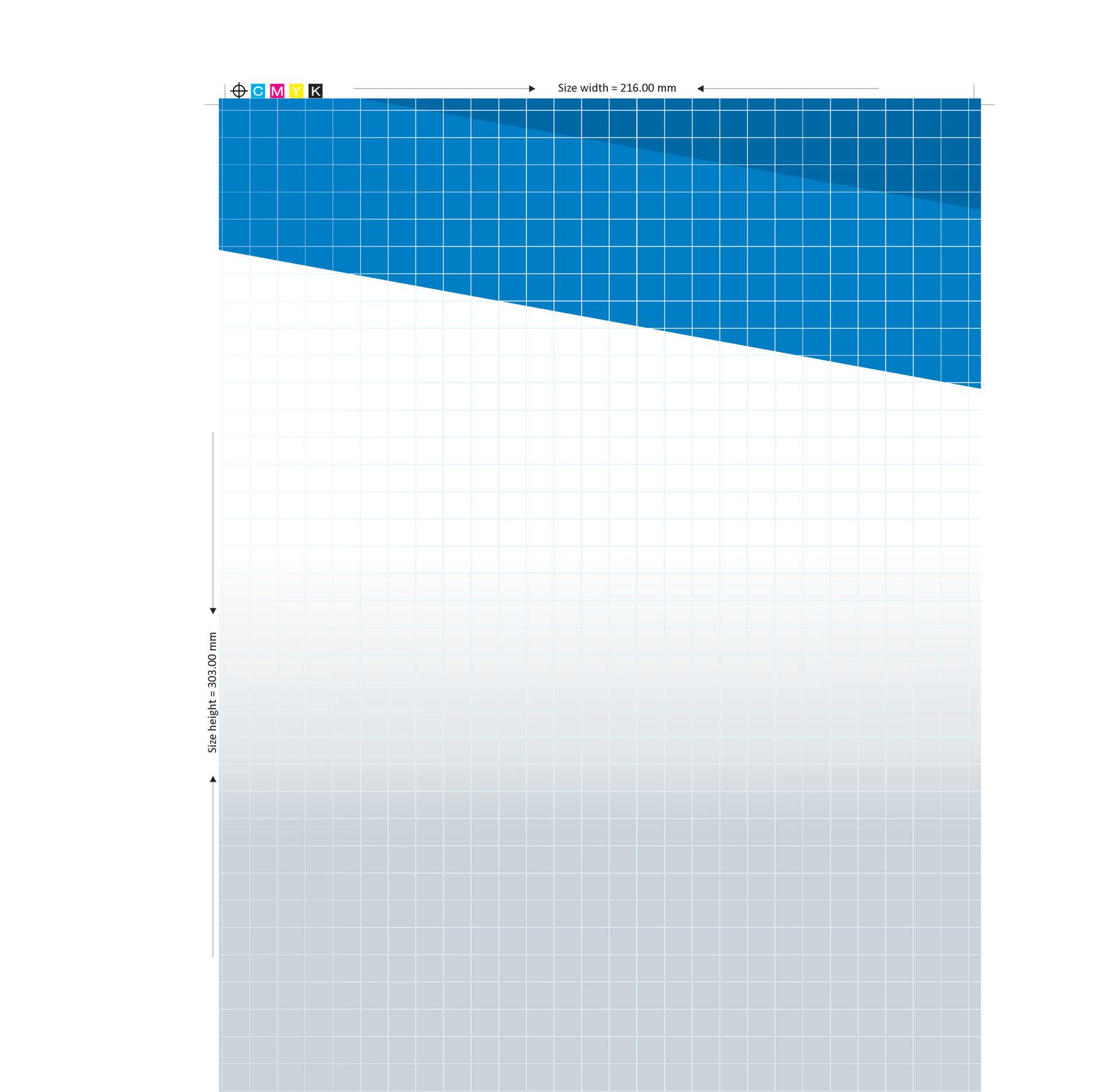
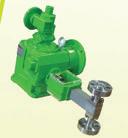
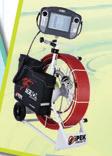
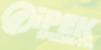

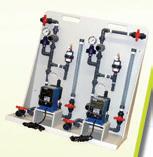
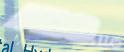




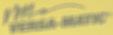
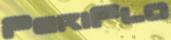
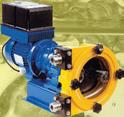
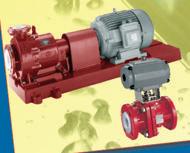
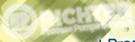
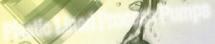
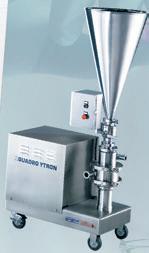

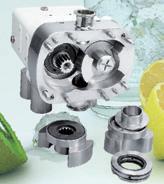
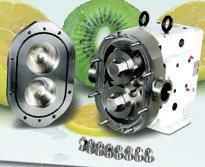
First pump expo in 14 years
Pump Industry Australia held its first exhibition since 1998 at the Whitehorse Centre, Nunawading, Victoria on 9 & 10 October 2012.
The Exhibition was conducted in a relaxed atmosphere and allowed some of Australia leading Pump Suppliers to share their expertise in applications and technologies that are leading edge.
Seminar
The general theme of the seminar program was “environmental protection and energy efficiency”, with pumps as the main focus of attention and delegates heard the following presentations;
Are you running your pumps too slowly?
-Ron Astall, Astech
ErP directive on MEPS for pumps in Europe-David Kerridge, Wilo Australia
MEPS for Pumps in Australia -Ian McNicol, Sustainability Victoria
Developments in small pumping systemsAshley White, Davey Water Products
Innovative vacuum pumping systemsDavid Hobson, Emtivac Engineering
VSD’s in pumping systems - Bou Spithoven, CAP Industries
Exhibition
The exhibition featured the following companies;
• Acromet
• Australian Industrial Marketing
• Brown Brothers Engineers
• CAP Industries
• Crusader Hose
• Davey Water Products
• Emtivac
• John Crane
• KSB Australia
• Link Pumps
• PIA & Monkey Media
• Pump Engineers Australia
• Sterling Pumps
• Stevco Seals & Pumps
• Welling & Crossley
• White International
• Wilo Australia and also featured a museum courtesy of John Link of Link Pumps and others.

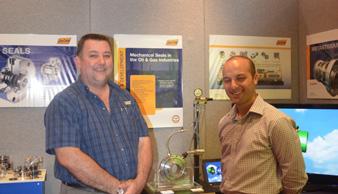
Best stand award
An award for best stand was presented by Geoff Harvey of Davey and Chris Bland of Monkey Media. The high standard of booths was noted by all and the winner was John Crane, with the judges noting the range of products displayed, overall presentation and attention from the booth staff.
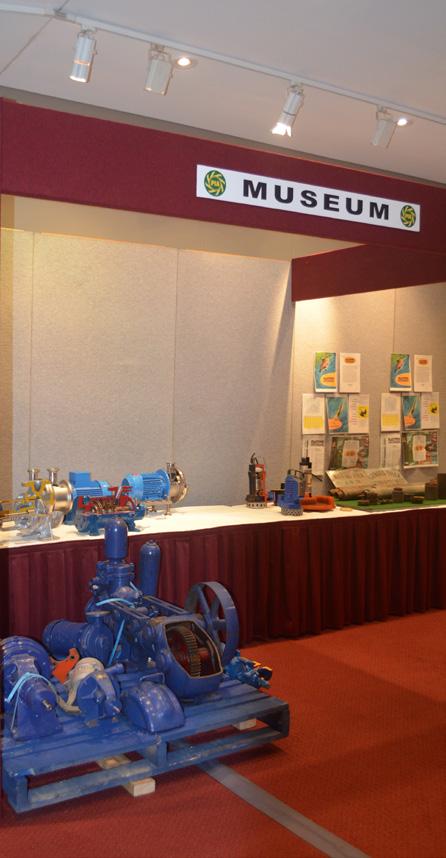


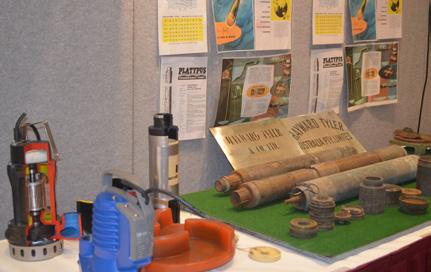
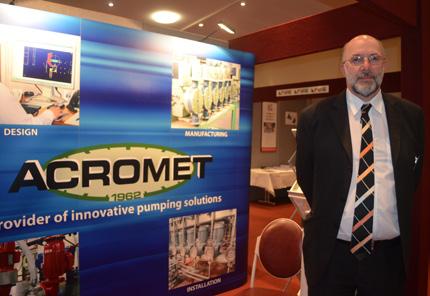

Join Pump Industry Australia
There are many worthwhile benefits you’ll receive from becoming a member of Pump Industry Australia Incorporated. Membership of the Association is available to the following types of persons or organisations:-
Member Qualifications
• Pump manufacturers.
• Pump importers
• Pump wholesalers
• Pump retailers
• Pump repairs & maintenance
• Pump consultants
• Pump training or education
• Suppliers to the pump industry
Membership Benefits
• Regular general meetings held at a members’ facilities provide the
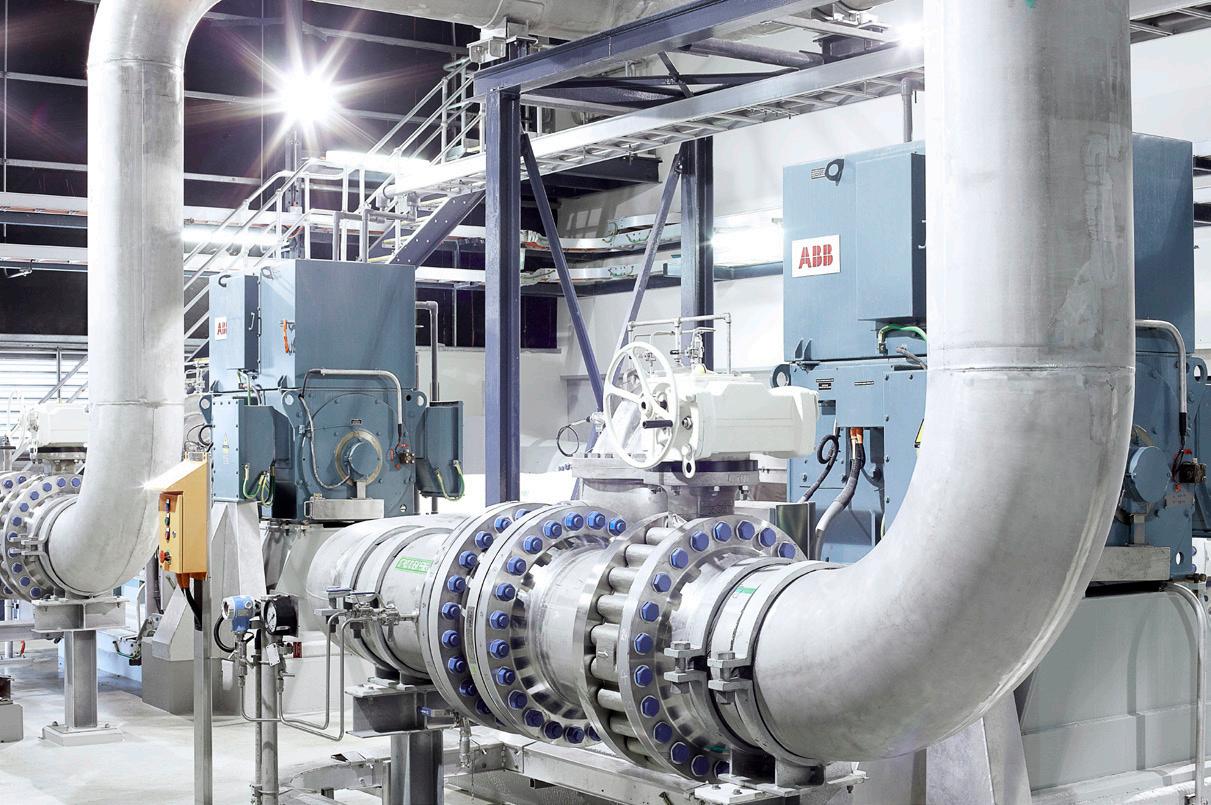
opportunity to see different aspects of the industry, and to formally discuss current market conditions and other issues.
• Occasional Technical Seminars with presentations by specialists on the latest technology in pumping equipment and systems.
• Informal networking within the association with customers, suppliers and competitors.
• Discounts off retail prices when purchasing PIA publications.
• Annual Dinner with partners and guests.
• Opportunity to lobby government on issues important to the Industry.
• Discussion groups on marketing, statistics and training.
Annual Membership Fees
• Private Member $80 + GST
• Company Member less than 10 employees $150 + GST
• Associate Member (for large companies who are not participating directly in the pump industry however do have a strong interest in the industry eg. a motor supplier $250 + GST
• Company member (10 to 25 employees) $300 + GST
• Company member (25 to 100 employees) $600 + GST
• Company member (over 100 employees) $1,200 + GST
Technical handbooks: a vital resource
Pump Industry Australia publishes two handbooks which are specifically designed for the Australian Pump Industry; the Australian Pump Technical Handbook and the Australian Pipe Friction Handbook. These publications are for those who work and are associated with the pump industry such as manufacturers, distributors, educators, designers, operators and users. Both of the books are easy to follow and can be readily understood with a basic knowledge of physics.
Pump Technical Handbook
The Pump Technical Handbook was produced to assist all pump users and those interested in learning about pumping in having technical knowledge of pumps and their operation including the overall pump system in which the pump works,
The Technical handbook covers a wide range of topics beginning with the definitions used when working with pumps. It is then followed by details of the classification of both centrifugal and positive displacement pumps.
Sections of the book comprehensively deal with the characteristics, selection and application of centrifugal pumps as well as sections covering the same for positive displacement and slurry pumps.
The book discusses, in detail, Pipe Systems together with a section on the calculation of system head which should be done in conjunction with the PIA Pipe Friction Handbook.
What are pumps made of? This is covered in the Pump Materials Section which discusses the materials pumps are constructed in and relates these materials to various Australian and International standards.
Intake design is critical to the correct and efficient operation of a pump system, so
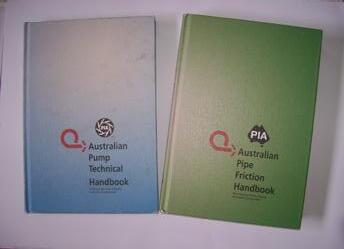
the Technical Handbook covers this topic. How are pumps tested, to what tolerances and what date can you expect from a pump test? The Pump Testing Section of the handbook covers this and more.
After covering the working of pumps and pump systems the last section tells the reader about the installation, commissioning and maintenance of pumps.
This brief outline of what is in the Pump Technical Handbook illustrates its comprehensiveness and how useful it is for those in the pump industry and associated with it.
Pump Friction Handbook
The Pipe Friction Handbook is designed to complement the Pump Technical Handbook in assisting pump system designers to calculate the friction in either proposed or existing pump systems.
The main feature of the Friction Handbook is almost 200 Pages of pipe friction tables including tables for viscous liquids and a chart on the friction loss through lay flat hose.
In general the friction tables are based on pipe, tube and hose which conform to an Australian Standard with the exception of ASTM Schedule 40 pipe which is in common use.
The friction tables cover the following commonly used pipes, tube and hose:
• Commercial Steel Pipe
• Large Fabricated Steel Pipe
• Medium & Heavy Duty Galvanised Steel Pipe
• Uncoated & Cement Lined Ductile Iron Pipe
• Copper Tube’
• Brass Tube
• Stainless Steel Tube
• Aluminium Irrigation Tube
• PVC Pipe
• Polyethylene Pipe
• Concrete Pipe
• Elastomeric Rubber Hose
In general for each type of pipe, tube and hose the tables cover all the sizes covered in the appropriate Australian Standard, in some case up to 1800mm N.B.
In addition to the tables the book gives the technical background to the calculation of the tables which will also allow the reader to calculate friction for pipes in materials and sizes not covered by the book.
After the friction tables there is a separate section which provides general information mostly in table form relating to the calculation of losses in a pump system including data to let the reader calculate among other things the friction loss in valves and pipe fittings and shows a sample friction loss calculation. As well data on valve and fitting losses there is data relating to gravity at selected sites, viscosity of liquids, losses through nozzles and many others.
This handbook covers all a reader needs to calculate friction losses in a pump system.
These two complementary books form the ideal tool for anyone working in or associated with the pump industry and provide an excellent learning tool for those embarking on a career in the pump industry.
The Australian Pump Technical and Pipe Friction Handbooks can be purchased from Pump Industry Australia Inc via the PIA website at www. pumps.asn.au

PIA Annual Dinner
PIA members caught up with colleagues and old friends at the Annual Dinner, held after the AGM, on November 22 at Graduate House at the University of Melbourne.
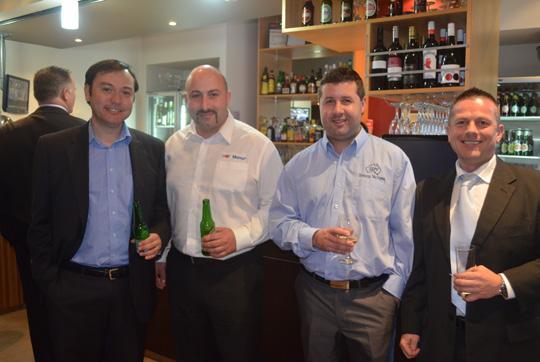
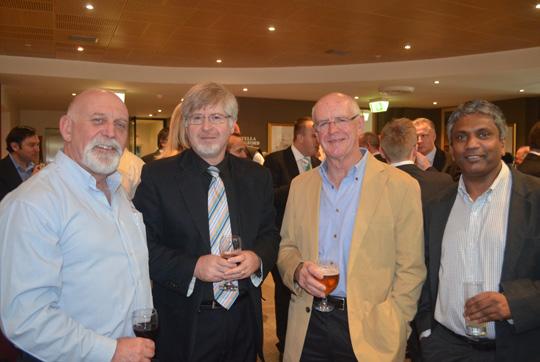

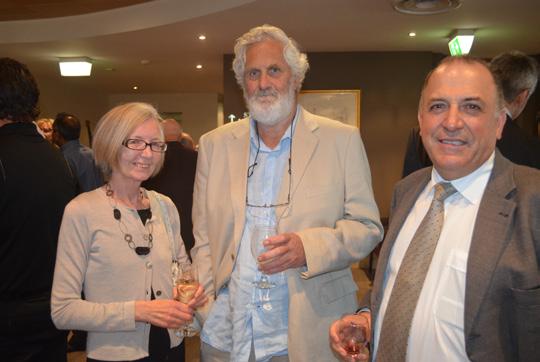

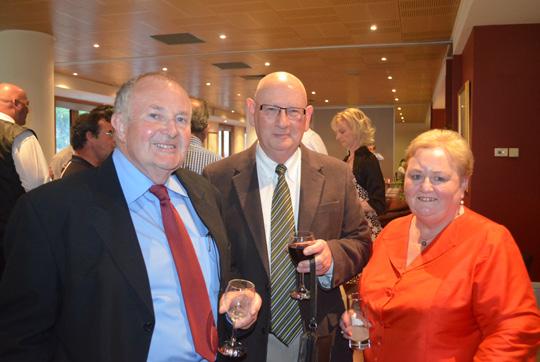
Top 7 marketing tips for 2013
For a long time, your marketing budget would be spent on print ads, events and brochures. Then came online, SEO, social media and now the options are far more complicated. With a decade’s experience in marketing for niche industrial companies, Chris Bland attempts to demystify some of the options.
1. Be clear about what you want
Whatever your marketing goals are, they are much better achieved if you know two things;
• Where you are now
• Where you want to be
You will get much more out of a marketing campaign if undertake some research to learn ;
• How your brand is viewed
• How you compare to your competitors
• What your customers want from you.
2. Know the value of print
The true value of print advertising has been made clearer as marketing has gone digital. Print publications remain valuable precisely because there is so much information online now, a quality print magazine is more rare treat and stands out. Industry journals in particular retain a strong prestige and capture people’s attention in much greater depth than fast-moving digital content. Readers recognise value in what they see in print and pay it much closer attention to it.
3. Know the purpose of online
This does not mean there is no benefit in online - far from it - you just need to know what you are getting. Online advertising can generate an instant and measureable response and this is how it is best used.
Most marketers have moved away from misleading terms like ‘hits’ and now talk about unique visitors and page impressions. But it’s also important to be wary of the many tricks websites use to bolster these numbers, from the relatively innocent such as multiple pages on short articles, to the more devious paying for low quality web traffic from overseas.
You don’t want to just drive traffic to your site, you want to make sure it’s quality traffic and one of the most important things an online campaign can do is capture qualified traffic and drive it to your own website.
You can also make use of lead generation techniques, such as offering free whitepapers in return for people’s contact details to ensure you are attracting qualified potential customers.
4. Let your website find you customers
Many companies now spend big on their own websites, and it should be professional and reflect your business, but make sure you ask these questions;
• What do your customers want from your website?
• How do you capture their details?
• How do you keep them coming back?
If you are using online advertising to drive traffic to your website, you also need to make sure the site is easy to navigate and you can convert them to the outcome you’re looking for.
5. SEO: content is king
Everyone talks about Search Engine Optimisation (SEO), but how many of them know what they’re talking about?
Like any new area, it attracts its fair share of charlatans selling easy solutions but in the end Google and other search engines will keep working to outwit them, because their only goal is to make sure the person searching actually finds what they want.
So how do you actually SEO your website then? While there are a few technical rules to make sure it is friendly to Google’s automated crawlers, the best way is to actually provide the content that your customers want and search for, and this way you will always stay in favour with the search engines.
This can be a challenge for many companies, especially if you’re an engineer not a publisher, but keeping your site up-to-date with fresh content, case studies, technical information, webinars etc will not only keep you top of the search results, but also present you as an expert in your field.
6. Get real about social media
The only thing that gets more hype than SEO is SMM, or social media marketing, and I’ve seen a few too many companies in the industrial and business-to-business (b2b) space spend up big to create a facebook page then get absolutely no return. Many social media channels work
best in consumer markets, as in the end you need to market where your customers are. But there are some good SMM options for b2b companies as well, particularly with LinkedIn, an online professional network, which is very useful for;
• Sales reps to identify and connect with prospects
• Sharing your company’s relevant and useful content (see tip 5) to potential customers via LinkedIn Groups
• Driving quality traffic to your own site
7. Use events effectively
I’ve seen too many companies shell out big bucks to be at an event, not to mention taking the time away from their usual day to day work, then waste the opportunity once there. A few tips to make sure you get the most out of an event;
• Ensure your booth is staffed at all times, by competent staff who know your products. A flashy booth might draw crowds but make sure you have something of substance to show them and talk to them about once you have their attention.
• Contact any clients or prospects in that area and invite them along, encourage them to visit your stand or better yet, buy them tickets to a social function
• Work with the event organisers to see how much you can find out about who is attending and what options there are to make contact beforehand. Many modern event planners can offer some great options to connect you with delegates, while staying on the right side of privacy laws.
• Plan time in your diary to follow up, then actually do it! You’ve put the effort in, don’t let months go by before you take action.
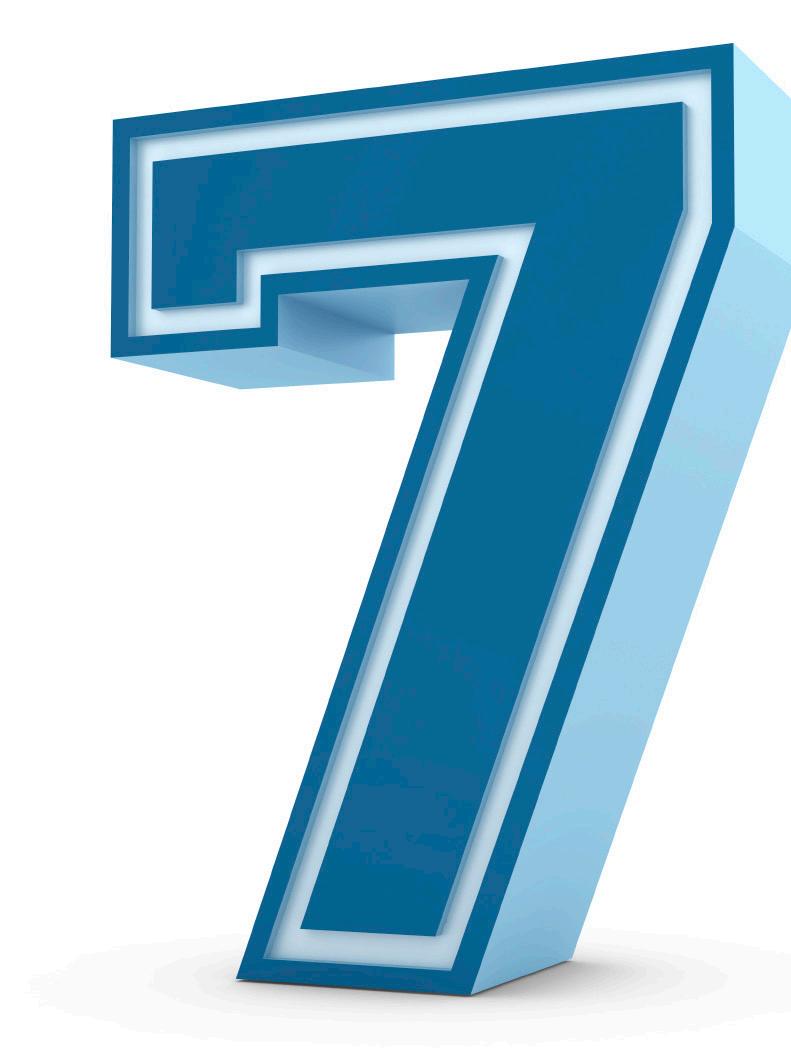
Asia Pacific to drive demand
Fuelled by the growth in China, India and other developing countries, the positive displacement (PD) pump market in Asia Pacific is expected to witness strong growth over the medium term. Water and wastewater, oil and gas, and the food and beverage sectors are expected to see robust demand growth for PD pumps.
Rapid industrialization and rising standards of living are driving the need for better sanitation, infrastructure and food delivery systems in the developing economies. This is expected to positively impact the growth of the total PD pumps market in this region.
Frost & Sullivan estimates that PD pump market revenues in Asia Pacific will grow at a compound annual growth rate (CAGR) of 14.0 percent; to rise from $2.31 billion in 2012 to $5.09 billion in 2018.
Drilling down further, the PD Pumps market in the combined market of Southeast Asia and Australia & New Zealand generated revenues totalling $650.8 million in 2012. This region is expected to grow at a lower CAGR than the total Asia Pacific market; at around 4.0 percent CAGR through to 2018.
Australia and New Zealand alone accounted for $146.3 million in PD pump market revenues for 2012 across all end-use sectors, growing at a CAGR of 2.3 percent over the period to 2018.
The high-growth markets in the region though, are elsewhere in Asia. China’s 12th 5-year plan calls for extensive energy savings measures, which should provide significant retrofit and service opportunities. Increasing demand from the chemical and oil and gas industries has been the prime driver for PD pumps demand in China. The oil and gas sector in Malaysia, Indonesia and Vietnam is expected to exhibit strong growth as the demand
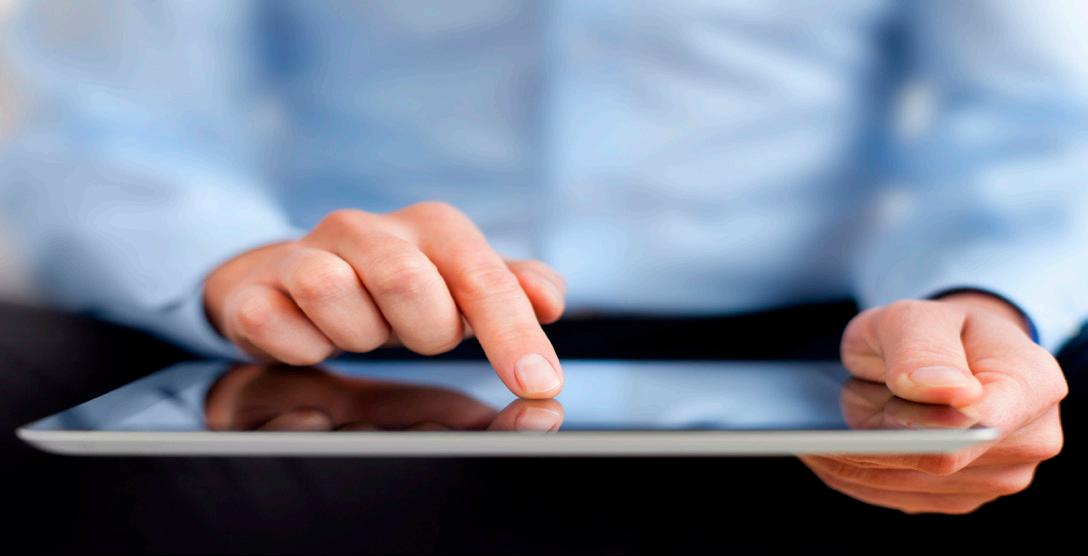
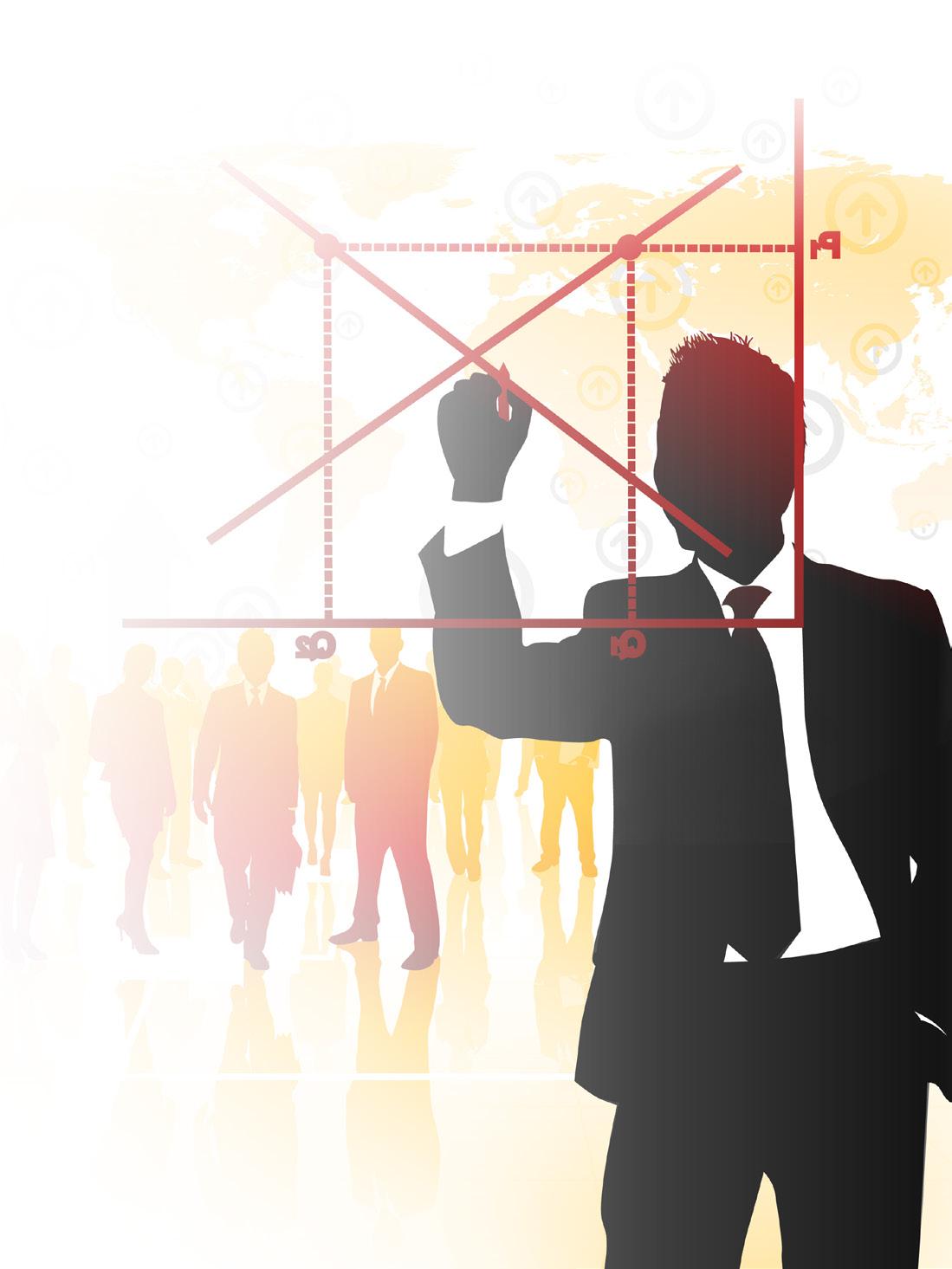
Read more online

for oil increases and these countries have abundant natural reserves. In India, power generation, oil and gas, and water and wastewater industries are expected to provide good long term growth opportunities. Also, the use of Reverse Osmosis systems is increasing in Asia, and these systems are more likely to use PD pumps than other desalination systems. Perhaps, the one downside in the region has been the sluggish market in Japan that continues to be impacted by the 2011 tsunami natural disaster and the resulting nuclear catastrophe.
In terms of type of pumps, reciprocating pumps appear to show the most volatile growth in the Asia Pacific market, with rotary pumps the most stable. Peristaltic pumps have benefited from expansion in the food and beverage and agriculture markets in this region.
Despite the forecast for strong growth in the region, the PD pump industry faces significant challenges that can hamper market expansion.
Profitability concerns
Sharp increases in the prices of raw materials and energy have followed economic recovery. This has increased the difficulty amongst PD pump manufacturers to transfer their input costs to end users. The price of PD pumps is expected to remain stable in the short term and this is expected to hurt profitability for PD pump manufacturers.
Innovation a luxury
Major end users constantly aim to upgrade existing technologies with innovative solutions that provide increased energy efficiency, quality, reliability, and performance, with lower operating costs. PD pump manufacturers are therefore, challenged to develop and introduce new products at regular intervals to meet dynamic customer requirements. However, due to economic uncertainty, major PD pump manufacturers have reduced R&D spending; thus hampering their ability to release new products and technologies to the market.
The threat of substitutes
PD pumps are used for high-pressure, low flow-rate applications, and centrifugal pumps are used for high flow-rate applications. For medium flow-rate applications that do not require high pressure,
either a centrifugal pump or a PD pump can be used. As centrifugal pumps have a simple design, easy maintenance, and competitive prices, end users prefer using them for medium flow-rate applications. Moreover, within the PD pumps market, different types of pumps can be used for the same application. For example, gear pumps, lobe pumps, and peristaltic pumps can be used for the same food and beverage application. End users are often reluctant to switch to a different type of pump because they are not familiar or comfortable with certain pumps. Manufacturers would need to invest in raising customer awareness about the relative merits and demerits of alternative products and solutions being offered in the market.
Skilled workforce shortage
The industry is experiencing a shortage of skilled technical personnel, which challenges both manufacturers and end users. Manufacturers have been faced with the need to develop pumps with simpler designs that are easy to assemble. Moreover, as end users face a shortage of maintenance personnel, they require intelligent pumps and asset management solutions to improve equipment uptime and reduce maintenance costs. These improvements will likely require manufacturers to develop intelligent pumps and other solutions to gain a competitive advantage in the market.
In other markets
Europe’s sovereign debt crisis continues to hamper growth amongst end-users as they remain wary about investing in new equipment under the current economic situation. While Western Europe is hampered by the Eurozone crisis, Eastern Europe is expected to offer growth potential; driven by the developing economies such as Poland, Hungary and Czech Republic.
North America, while being the most affected by the economic recession, witnessed a strong recovery in 2010 and 2011. End-user industries such as food and beverage, oil and gas and water and wastewater are expected to spur increasing demand for PD pumps. Though negatively affected by political instability in the short term, the Middle East and African markets are expected to experience robust demand growth for PD pumps.
This article was authored by Ivan Fernandez, Industry Director, Australia & New Zealand Industrial Practice. For media queries or more information please contact djeremiah@frost.com.
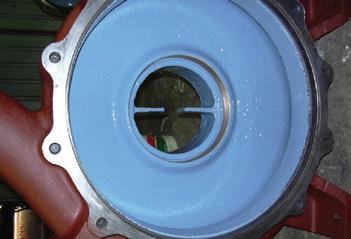
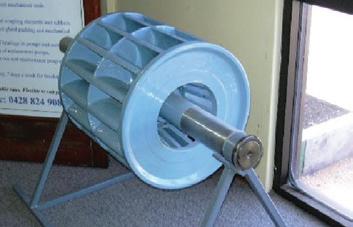
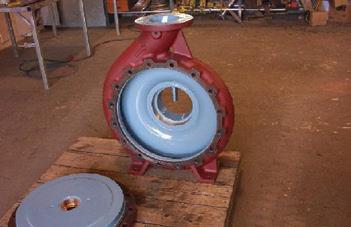
Pump services in the LNG industry
By David A. Coyle and Vinod Patel, Kellogg Brown and Root, Inc, Houston, TexasThe process of turning gas into LNG, storing it and loading it onto an LNG tanker requires many pump applications. In this arena, achieving low cost per tonne of LNG and high reliability makes the product attractive, and improving economy of scale with larger plants and equipment continues to enhance the odds of winning. It is this reality that is driving the technology forward. At the same time, the entire industry is based on converting a gas that has to be compressed for transport into a liquid that can be pumped; pumps will continue to play an indispensable role. With a good understanding of the basic LNG chain and the forces driving innovation, the pump manufacturers and rotating equipment engineers will be able to anticipate and respond to industry demands in a manner that provides high value for their customers.
The LNG chain
The LNG chain starts with gas production, usually from offshore wells though some plants receive gas from onshore sources. The gas produced can be from a gas field (non-associated gas) or may be produced along with oil (associated gas). The distinction between associated and non-associated gas is important because associated gas must have LPG components (i.e. propane and butane) extracted to meet heating value specifications of the LNG product.
The produced gas enters the LNG liquefaction facility and goes through several steps of treating before being liquefied. The LNG leaving the liquefaction plant must be stored until a ship arrives to transport the product.
For a facility making 8 MMTPA a 140,000 m3 ship will arrive every three days. The ships are powered by steam engines and typically travel at 19 knots, thus a round trip voyage of 5,000 miles takes between
nine and ten days of travel plus at least a day of turnaround at each end for a total duration of 12 days. The time it takes to load a ship once the loading pumps are started is about 12-14 hours.
The LNG liquefaction facility
The liquefaction facility is the greatest contributor to the LNG price at the receiving end, with the possible exception of shipping depending on distance to market. LNG plants produce LNG and condensate (natural gasoline) products, and in some cases LPG (propane and butane).
The major pump services in the liquefaction unit are:
• Amine circulation
• Reflux for scrub column and fractionation towers
• LNG product pumps
• Seawater pumps (if seawater cooled)
• Hot oil pumps
Liquefaction process
See the block flow diagram in Figure 1. The first step in the process is removal of acid gases such as CO2 and H2S. CO2 would freeze at cryogenic process temperatures and H2S must be removed to meet the LNG product specifications. Typical specifications for acid gas removal are 50 ppm for CO2, 4 ppm for H2S, and total sulphur content less than 25 ppm. An amine solvent process is most common for acid gas removal. The process has an absorber tower where “lean” solvent contacts the natural gas and absorbs acid gas components, thus becoming “rich” solvent. The rich solvent leaves the bottom of the absorber and regenerates with a drop in pressure and heating in the stripper tower. The regenerated solvent is now “lean” again and cooled and pumped up to the absorber pressure.
The amine solvent pumps are often the largest pumps in the plant, especially when the natural gas contains a high

amount of CO2 (10-15 mol% CO2 is considered high though some natural gas reserves have even more). The solvent can be MEA, DEA, MDEA, Sulfinol, DGA or others, but the current trend is towards activated MDEA based solvents.
The amine pumping service is often split into two parts: a low head pump working at high temperature followed by a high head pump operating at near-ambient temperature. Using the low head booster pump at the high temperature avoids problems with cavitation within the pump which would be present if the high head pumping were done at high temperature. The amine circulation rate depends on the amount of acid gas but a train making 5 MMTPA of LNG with a natural gas feed containing 15% CO2 can have a circulation rate over 2000 m3/hr handled with 3 x 50% pumps.
The gas leaving the acid gas removal unit is saturated with water from the amine solvent, and a dehydration unit removes the water. The dehydration unit consists of multiple mol sieve beds and regeneration equipment. Typically two mol sieve beds run in adsorption mode while a third bed regenerates. Hot, dry natural gas flowing through the bed accomplishes the regeneration. After regeneration, cool natural gas cools the bed and then the bed cycles into adsorption mode while one of the other beds cycles to regeneration.
The treated and dry gas now enters the liquefaction unit which chills and liquefies the gas in a refrigeration process. Figure 2 is a drawing of the Air Products and Chemicals, Inc. (APCI) process which makes about 85% of the world’s LNG production. A multiple stage propane refrigeration system first chills the gas through a series of heat exchangers down to about -30 C. The natural gas drops out liquids at this temperature, and the scrub column removes these heavy liquids (especially benzene and other aromatics) which would otherwise freeze in the main cryogenic heat exchanger. The reflux pumps for the scrub column operate at about -30 to -50 C, and in the fractionation unit the de-ethanizer reflux

pumps also operate at about -30 C. The flow rates of these pumps depend to a large extent on the natural gas composition. For a 5 MMTPA train handling associated gas the scrub column reflux flow can be in the 350-400 m3/hr range, though a plant processing non-associated gas usually has a smaller scrub

• 4” 0.5kw to 7.5kw
• 6” 7.5kw to 45kw
• 8” 30kw to 93kw
• 10” 75kw to 150kw
• 12” 93kw to 300kw
• 14” to 30 “ up to 2500kw
column reflux pump. The scrub column reflux pump size depends to a great extent on the aromatics present, but in some cases where the natural gas contains little ethane and propane, recovering refrigerant components can be the main factor that determines reflux pump size.
The natural gas leaves the scrub column overhead drum and enters the main cryogenic heat exchanger (MCHE) where it is cooled down to about -160 C at which temperature the natural gas is a liquid at atmospheric pressure. The stream exits the MCHE and becomes the LNG product after running down to storage. The refrigerant for the MCHE is a mixture of mostly methane and ethane which can be made up from the natural gas feed.
Sterling Submersible Motors.
Engineered and proven in the toughest conditions

2 pole, 4 pole, 6 pole and 8 pole 415v, 1000v, 3300v, 6600v and 11000v.
All motors are wet stator re-windable.
Materials of construction include: Cast Iron, 304ss, 316ss, Duplex 2205, Super Duplex 2507, CuNi 90 10, NiAl Bronze, Zeron 100.
Sterling Pumps is an ISO9001 certified company.
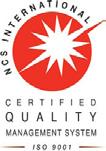
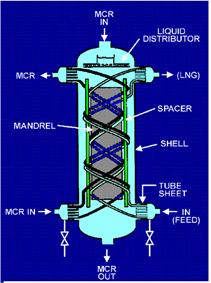
The LNG product pump has a special design for cryogenic service and is mounted inside a container. The container, flooded with LNG during operation, also contains the motor. The suction of the pump is at the bottom of the container and the LNG discharge flows through the motor thus providing cooling for the motor. There are no cryogenic rotating seals with this arrangement; the only seal needed is for the electrical connection box, and the box is always purged with nitrogen to prevent natural gas leakage through the conduit.
Several variations exist for the liquefaction process including nitrogen removal options on the back end of the plant (LNG typically has a maximum nitrogen specification of 1%), and processes licensed by other companies besides APCI. Such processes include Phillips Optimized Cascade, Axens Liquefin, Black & Veatch Pritchard Single MR, and Linde Mixed Fluid Cascade among others. The differences in licensed processes are small with respect to thermodynamics and cost. The real key in selecting a liquefaction process is equipment selection and meeting the plant capacity goals.
Equipment selections include MCHE type and compressor driver. The APCI process uses a spiral wound type heat exchanger shown above. Other licensed processes use plate fin heat exchangers. The plate fin exchangers tend to cost less than spiral wound but are more susceptible to leaks caused by thermal stress, and maintenance can be difficult if the plate fins are installed in a “cold box” insulation system where the exchangers are placed in a sheet metal box filled with perlite. Getting to the exchangers is difficult because the insulation is similar to a white dust. The spiral wound exchanger can be maintained by access to the tube sheets by manhole or hand hole. The plant owner makes the choice of exchanger type based on these trade-offs in addition to their own operating experiences.
Compressor drivers in the past were
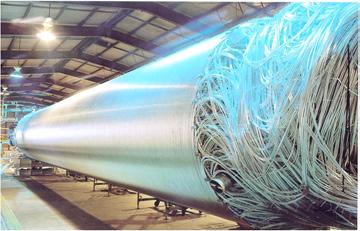
typically steam turbines but the trend today is almost universal use of gas turbines. The steam system costs more, adds equipment to the project, and takes more plot space; KBR expects the trend to continue.
One other critical decision for the liquefaction plant is the cooling medium. Fresh water is not available at most liquefaction sites and the usual choice is between once through seawater and air cooling.
The seawater pumps are very large in a baseload LNG plant and the pumps are mounted vertically in a seawater intake basin. The flow rates of these pumps are commonly in the 15,000-18000 m3/ hr range. In some plants the seawater removes heat from a fresh water loop, instead of the more common oncethrough cooling where the seawater goes directly through heat exchangers and then discharges back to the sea. The fresh water loop circulation rate is similar to the seawater rate, but the liquefaction unit exchangers exchange heat with fresh water. The advantage of using the extra cooling loop is higher reliability and lower cost materials in the liquefaction unit. The disadvantages are extra cost and equipment for the fresh water loop and a higher heat sink temperature for the process (which makes the process slightly less efficient).
The liquefaction process, in spite of being cryogenic, still requires some heating services. Examples are the amine stripper reboiler and fractionation reboilers. However, most gas turbine driven LNG plants do not have heat recovery steam generation (HRSG) and in such cases hot oil is a common heat medium. The hot oil is circulated between the heat source and process services with hot oil pumps. In some cases steam is used as a heating medium and in such cases condensate pumps and boiler feed water pumps replace the hot oil pump services. This substitution commonly takes place when there are enough sulfur compounds
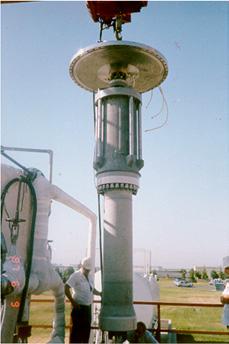
in the gas to make sulfur recovery in a Claus unit necessary; the Claus unit generates low pressure steam which is available for process heating services.
Cryogenic liquid expanders
One other service in liquefaction related to pumps is the cryogenic liquid expander. The liquid expander is like a pump running in reverse; the fluid enters at high pressure and exits at lower pressure, and shaft power is generated instead of being consumed. The drop in pressure is controlled with a back-pressure valve to prevent the discharge from flashing into two phases.
LNG storage
There are three common types of LNG storage, known as “single containment”, “double containment” and “full containment.” In all cases there is secondary containment in the event of a spill, and the differences between the types is mostly in the method of secondary containment. The single containment storage has a 9% Nickel self-supporting inner tank and a carbon steel outer wall. There is perlite insulation between the two tanks. In the event of an inner tank leak, the outer wall fails because carbon steel is not capable of holding cryogenic materials. In this case secondary containment is provided by a dike surrounding the tank.
The double containment tank has a posttensioned concrete outer wall capable of holding cryogenic materials, and no dike is needed because the outer wall provides the secondary containment. However the cold vapors contacting the roof may cause the roof to fail, thus the containment is not “full containment” because vapors may be released in the event of an inner tank leak.
The full containment tank is similar to double containment except that the roof is made of materials which can handle cryogenic temperatures and if the inner
tank leaks all liquids and vapors are still contained within the outer wall and roof.
The main advantage of the single containment tank is the low cost relative to the other storage types. The main disadvantage is that the impoundment basin requires more land and then providing enough distance between the dike and the plant fence to protect the public from heat and vapor dispersion requires even more land.
The LNG loading pumps are similar to the LNG product pumps in that they are submersed in the LNG, but instead of a separate container the pumps are inside pump columns that extend to the tank roof, as shown in above left. The key design feature of this pumping system is that it is possible to pull the pump for maintenance while continuing to operate the storage tank. There is a foot valve at the bottom of the column that prevents LNG from entering the column when the pump is pulled. The operators purge the column with nitrogen and then remove the pump from the top of the column.
In-tank pump process objectives
The LNG loading pump capacities are usually based on filling a ship in twelve hours. The liquefaction plant typically has multiple storage tanks, and 2 to 4 pumps per tank. It is common to have a total of eight pumps running during loading, each with a capacity in the 12002000 m3/hr range and 150-160 metres of head. In many plants there is also a smaller pump in each tank in addition to the loading pumps. The purpose of this smaller pump is to recirculate LNG in the loading lines when no ship is present. The loading lines are large diameter (2436”) and must be kept cold between ship loadings because cooling them down is a long procedure.
LNG shipping
LNG terminal layout and site selection are typically based on the following ship parametres:
• 130,000 to 135,000 m3 capacity, having an overall length of up to 310 m, width of 46 m, and fully loaded draft of 11.6 m. The net delivery
unloading rate into the receiving terminal is approximately 10,000 m3/ hr. There are smaller ships (down to less than 60,000 m3), but the industry trend is towards larger ship sizes with designs on the drawing board for up to 250,000 m3.
• 15 metres minimum water depth
The LNG ships have two different types of pumps. These are the large cargo pumps for transferring LNG, and the small spray pumps which provide LNG for the spray ring that helps keep the entire storage container in a cool state. The storage on the ship is usually one of two types, either self-supporting aluminum spheres or stainless steel membrane compartments supported by the ship hull. There are either 4 or 5 spheres or compartments, and each contains two cargo pumps and one spray pump. The cargo pumps usually have a capacity of 1200-1400 m3/hr and the spray pumps have a capacity of 40-50 m3/hr.
Chemical Metering and Transfer Equipment from ProMinent® for process and water treatment in the Mining, Oil and Gas Industry
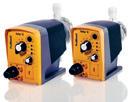
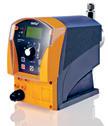
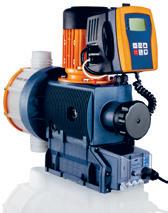
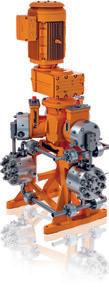
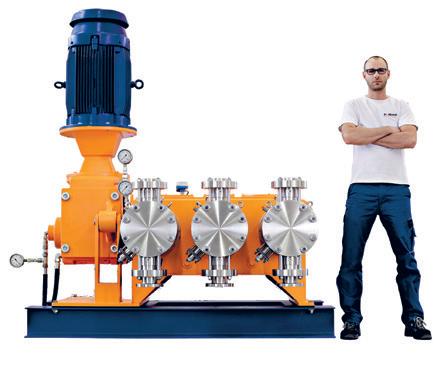

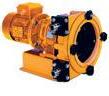
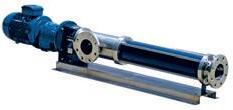
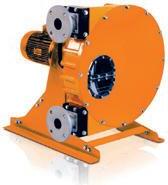
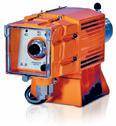

Pump operations on an
LNG plant
Raw gas feed
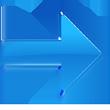
MEG back to wellhead to be injected for re-use
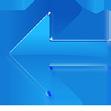
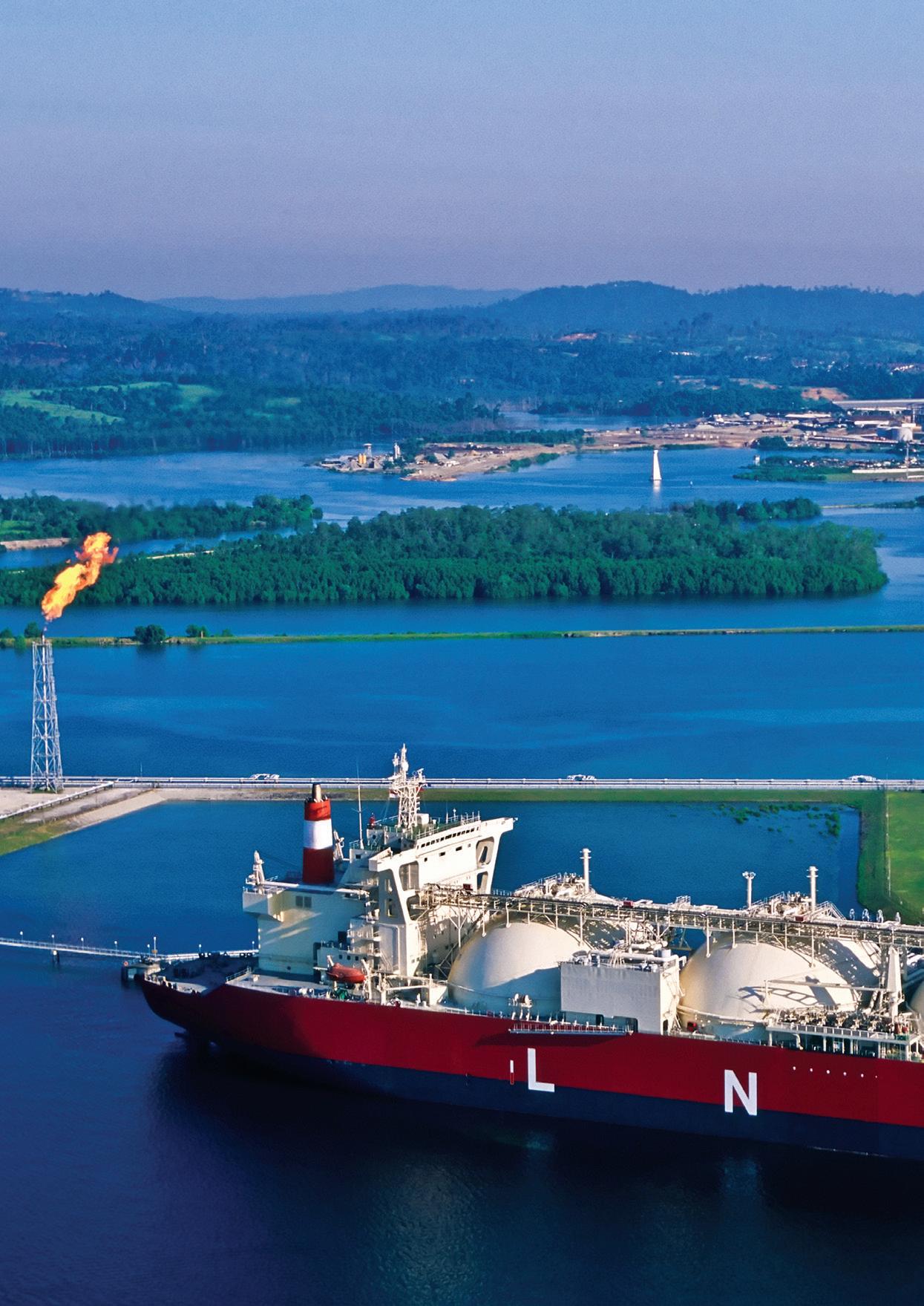
Separated gas
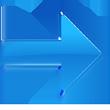
Separation of gas and liquids
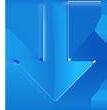
MEG
MEG Pumps
Usually involves centrifugal pumps for recycling the separated MEG and Reciprocating pumps to reinject MEG at the wellhead
AGRU (Acid Gas Removal Unit)
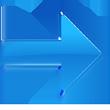
Dehydration Slug Catcher
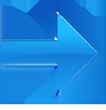
Mercury removal/ scrub column
Solvent Pumps
Often the largest pumps in the plant, these can be split into two parts. A low head pump working at high temperature and a high head pump working at nearambient temperature.
Lean booster pump
Capacity (m3/hr): 500-1800
Head (metres): 80-120
Fluid: Amine or potassium carbonate solution
Lean charge pump
Capacity (m3/hr): 500-1800
Head (metres): 600-750
Fluid: as above
Scrub column reflex pumps
Operate at about -30 to -50 C. The flow rate can vary greatly depending on the natural gas composition.
Capacity (m3/hr):150-400
Head (metres): 90-100
Fluid: Hydrocarbon
Spray pumps
Keeps storage container cool
Capacity (m3/hr): 40-50
This shows a typical LNG process based on a 5 MMTPA train LNG plant Plant (Mono Ethylene Glycol)Heating pumps
Some elements of the plant, such as the amine stripper reboiler, still require heating. Some plants use a hot oil system while others use hot water
Capacity (m3/hr): 1500-2000
Head (metres): 120-140
Fluid: Hot oil or hot water
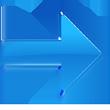
Liquefaction unit/main cryogenic heat exchanger
Product pumps
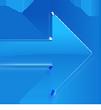
Specially designed for cryogenic service and mounted, with the motor, inside a container which is flooded with LNG during operation. The suction of the pump is at the bottom of the container and the LNG discharge flows through and cools the motor.
Capacity (m3/hr): 1300-1400
Head (metres): 80-110
Fluid: Hydrocarbon
Operating temperature: -160 C
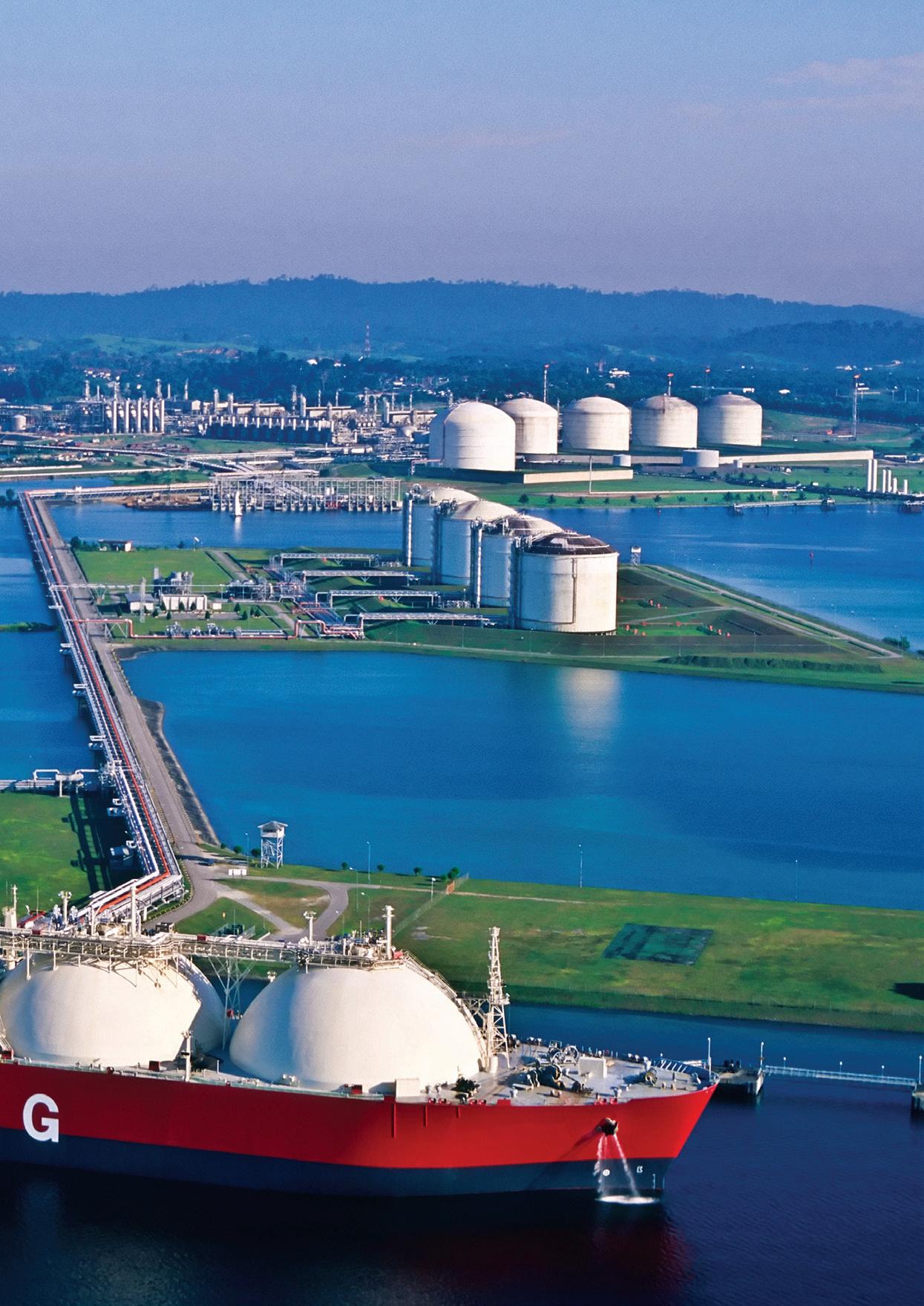
Endflash, cryogenic liquid expanders
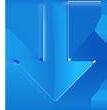
Storage tanks
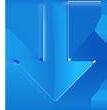
Loading pumps
Usually based on filling a ship in 12 hours, with 2-4 pumps per tank
Capacity (m3/hr): 1200-2000
Head (metres): 150-160
Fluid: Hydrocarbon
Cargo pumps
Transfer the LNG onto the ship
Capacity (m3/hr): 1200-1400
Water pumps
Many plants are seawater cooled, while others use fresh water. These very large pumps are mounted vertically in a seawater intake basin.
Capacity (m3/hr): 15,000-18,000
Head (metres): 50-60
Fluid: Seawater or fresh water
To LNG receiving terminal
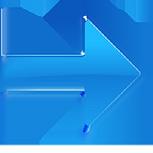
More than 1000 pumps make Gorgon go
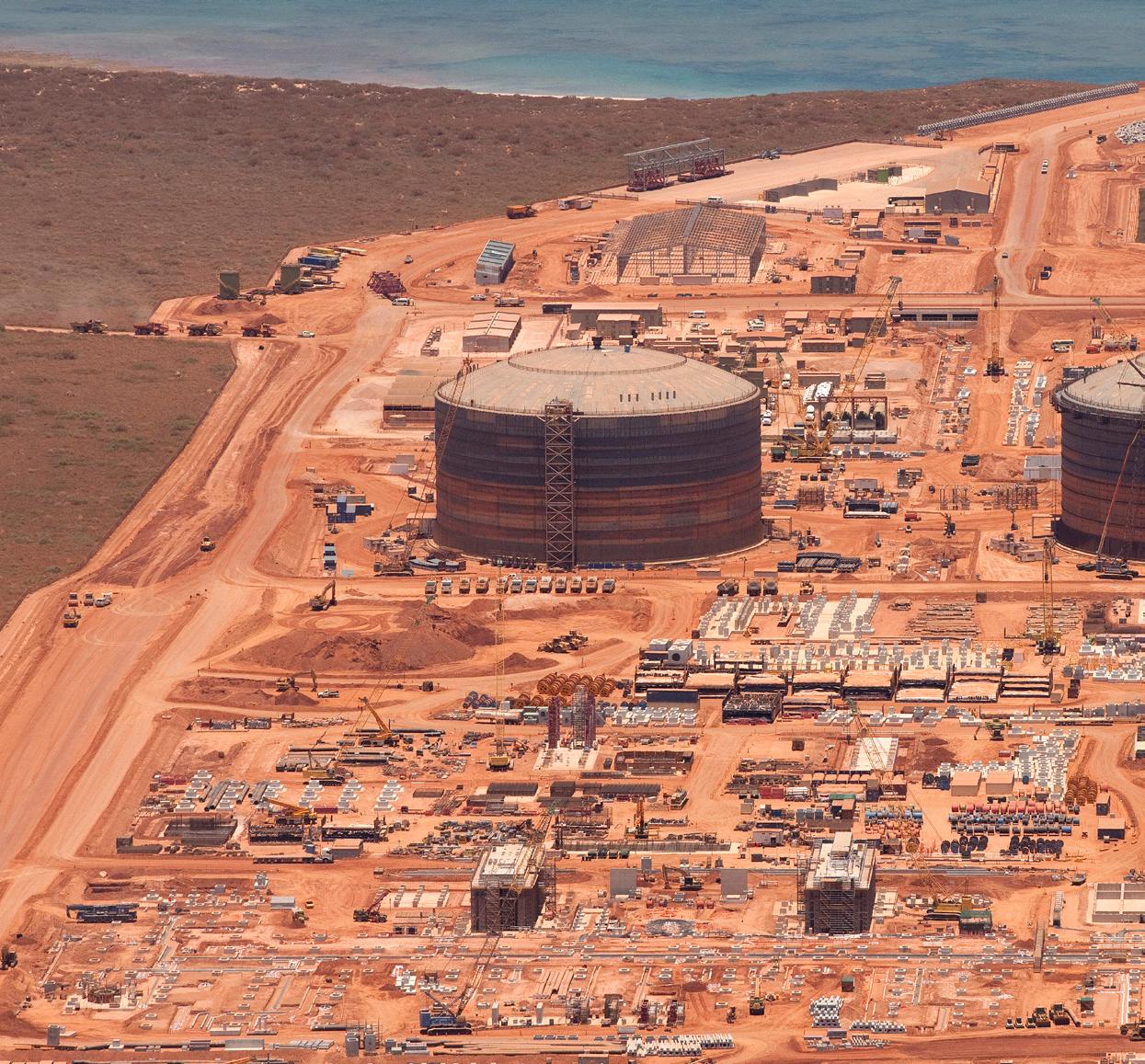
TGorgon is largest single resource natural gas project in Australia’s history. It includes the construction of a 15 million tonne per annum (MMTPA) Liquefied Natural Gas plant on Barrow Island and a domestic gas plant with the capacity to provide 300 TJ per day to supply gas to Western Australia. Underpinning the operation at every turn, is over 1,000 pumps.
he project will develop the Gorgon and Jansz/Io gas fields, located within the Greater Gorgon area, about 130 kilometres off the north-west coast of Western Australia. The resource contains about 40 trillion cubic feet of natural gas. The Gorgon Project is located on Barrow Island around 60 kilometres off the north west coast of WA. First LNG production is scheduled for 2014.
Upstream
The Gorgon Upstream Joint Venture is an unincorporated joint venture between Technip and JP Kenny to provide Engineering, Procurement and Construction Management (EPCM) services for all upstream facilities necessary to produce gas from the gas fields via subsea infrastructure and subsea and onshore pipelines back to the shorebased LNG plant on Barrow Island.
The field development plans centre on the use of subsea completions at the Gorgon and Jansz-Io fields and tied-back to the onshore LNG plant via a system of pipelines and control umbilicals. These subsea production centres feed the LNG plant on Barrow Island via independent 30 inch multiphase flowlines
The upstream development includes the following works for the Gorgon field
• 2 production centres in the initial development, Manifold 1 (provision for up to 6 subsea wells initially) and Manifold 2 (provision for up to 4 subsea wells).
• 65 km of 30 inch Corrosion Resistant Alloy (CRA) clad export pipeline to shore.
• 12 km onshore line to LNG plant.
• 65 km parallel umbilical, mono-
ethylene glycol (MEG) and service pipelines.
• 6 km infield flowlines between Manifold 1 and Manifold 2.
• Additional manifolds will follow throughout the field life to maintain production levels.
as well as similar works for the development of the Jansz-Io Field.
Downstream
Chevron Australia and its joint venture participants have contracted the Kellogg Joint Venture - Gorgon (KJVG) to design the LNG plant, the domestic gas plant and related infrastructure, to procure all the necessary equipment and materials, and to manage the contractors and subcontractors during project construction and commissioning.
The downstream development includes
• 3 x 5 million tonnes per annum LNG processing trains
• 2 x 180,000 m3 LNG Storage tanks
• 4 x 38,000 m3 Condensate Tanks
• 300 TJ/day Domestic Gas processing plant
• 5 x 118 MW gas–turbine power generation units
• 8.4 km CO2 pipeline to injection well sites
• 2.1 km long Materials Offloading Facility (MOF) & Causeway
• 2.1 km long LNG Jetty, with two loading berths
• Operations & maintenance buildings
• Operations Accommodations
• Construction Accommodations Pumps
The project will install approximately 1039 pumps with a wide range of duties including water, chemicals, and hydrocarbons, lube oils. A range of types including centrifugal, high speed centrifugal, positive displacement, and cryogenic and sizes ranging up to 3.3MW.
Recycle gas hydrocarbon return pumps
Controlled volume pump
Supplier: Lewa Herbert OTT GMBH
Cryogenic pumps
Includes scrub column reflex pumps, LNG rundown pumps, transfer pumps and loading pumps
Supplier: Nikkiso Company Limited
Firewater pumps
Fresh water and sea water
Supplier: SPP Pumps Ltd
High speed centrifugal pumps (AP1610 OH6)
Includes LPG, Ethane, Propane and Butane reinjection pumps
Supplier: Sundyne
MEG injection pumps
Well Head Injection Pump - Gorgon and Jansz - Reciprocating
Supplier: Peroni Pompe SPA
Positive displacement rotary pumps
Supplier: Netzsch Pumps
Vertically suspended pumps (AP1610 VS)
Includes Centrifugal MEG Sump Pumps and Amine Sump Hydrocarbon Pumps . Rotary oil water sump pumps and Stormwater Holding Pond Pumps
Supplier: Flowserve
Sulzer Pumps
One of the largest pump suppliers on the project was Sulzer, we had the opportunity to ask them about their work
Sulzer Pumps was selected to supply more than 150 pumps to the Gorgon project. Engineered amine pumps, used for CO2 scrubbing, were supplied from Leeds, United Kingdom and most of the API process pumps were packaged and tested in our facility in Germany using pumps supplied from our customer approved India and Mexico plants. The ISO/ANSI utilities pumps were supplied from Finland and United States and packaged in Perth; fulfilling local content of the Australian Industry Participation requirements. Project Management and Packaging were carried out by the local team of Sulzer Pumps in Australia.
Sulzer Pumps had been appointed as the sole supplier for API pumps to the project, which involved management of the entire project, from the complexities of multiple Engineering, Procurement and Construction companies (EPCs), evolving specifications and international supply chain.
The on-site delivery dates for the modules were imperative to project success and our team had worked closely with the customer’s procurement and project management team to expedite the required materials to site and maintained the overall project schedule.
Due to the Class 1 Nature Reserve on Barrow Island, special packaging of the pumpsets was required, for example:
• Equipment had to be completely cleaned of dust, pollen, seeds and insects and all holes plugged.
• New H3 treated and certified Pine
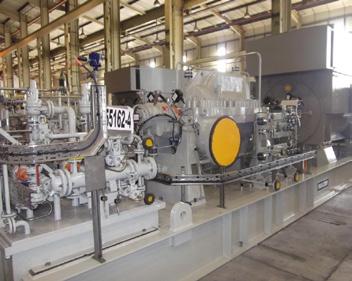
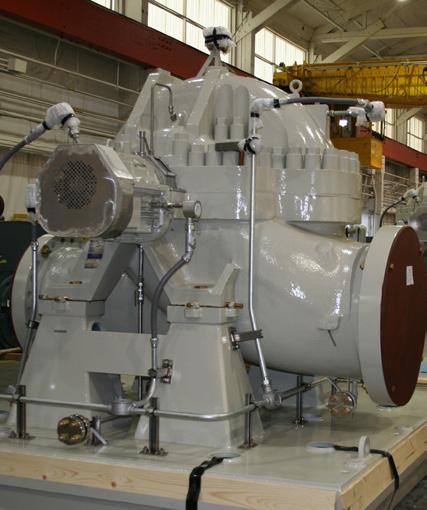
Timber export cases with close fitting panels and removable side and top with plastic sheet lining to prevent ingress of foreign particles.
• Insecticide and fumigation for quarantine and specially cleaned shipping containers.
Types of pumps supplied from 20092012 are 10 units of BB1, 13 units of BB2, 13 units of BB3, 4 units of BB4, 24 units of OH1 and 92 units of OH2.
Sulzer Pumps provided local customer support services that will contribute to the start-up and commissioning, including operator training of the customer’s personnel. We continue to provide services to the customer for the commissioning and start-up phase of the project with the establishment of Inventory Management of Critical Equipment and Spare Parts. With this process in place, we are well positioned to support the customer in the next expansion phase of the project and future successful operation.

Pumps at the heart of
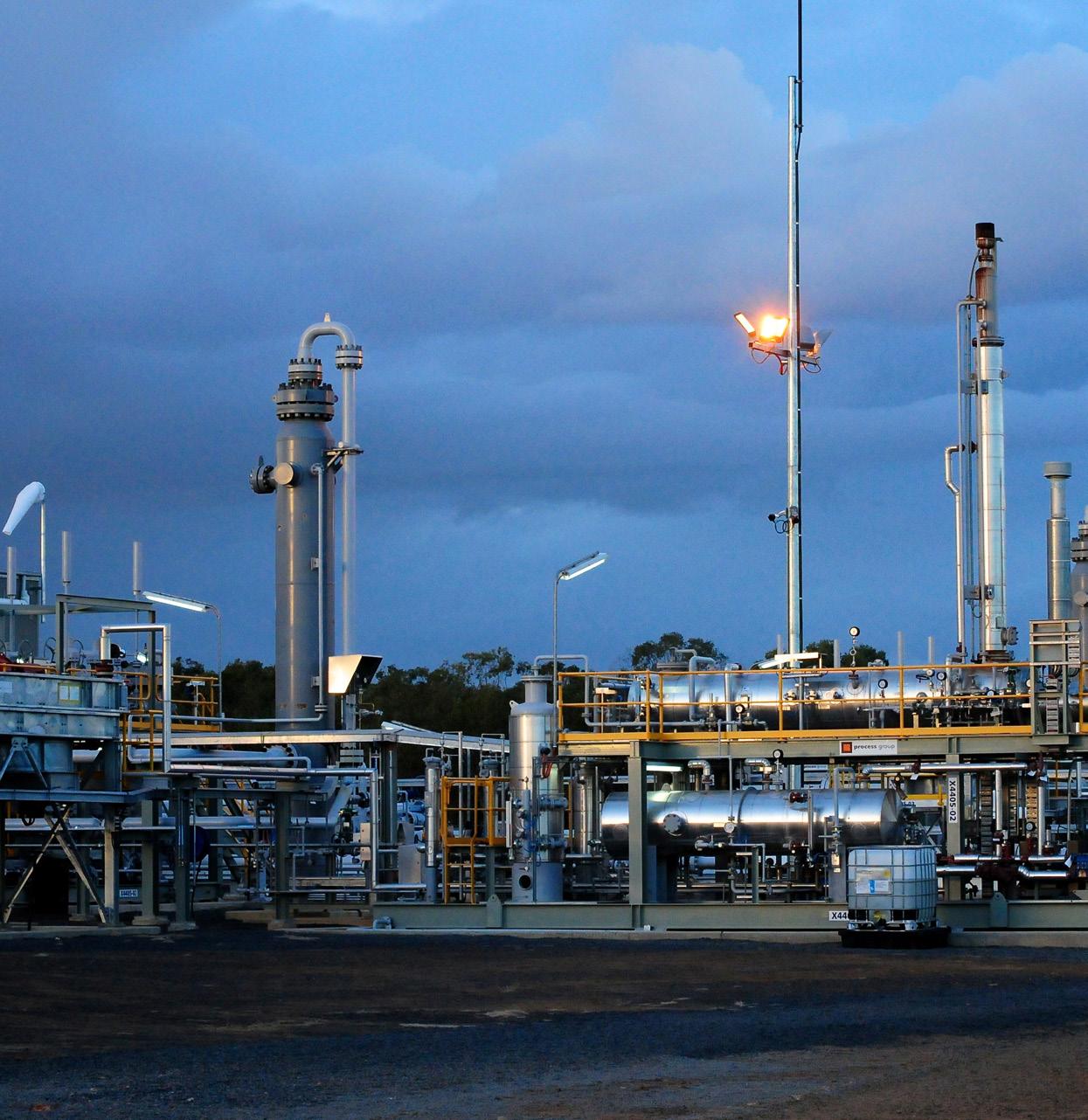
As Australia Pacific LNG picks up the pace on one of Queensland’s leading resource development projects a variety of pumping and pressure applications are playing a critical role in extracting, managing, compressing and transporting coal seam gas (CSG).
Australia Pacific LNG
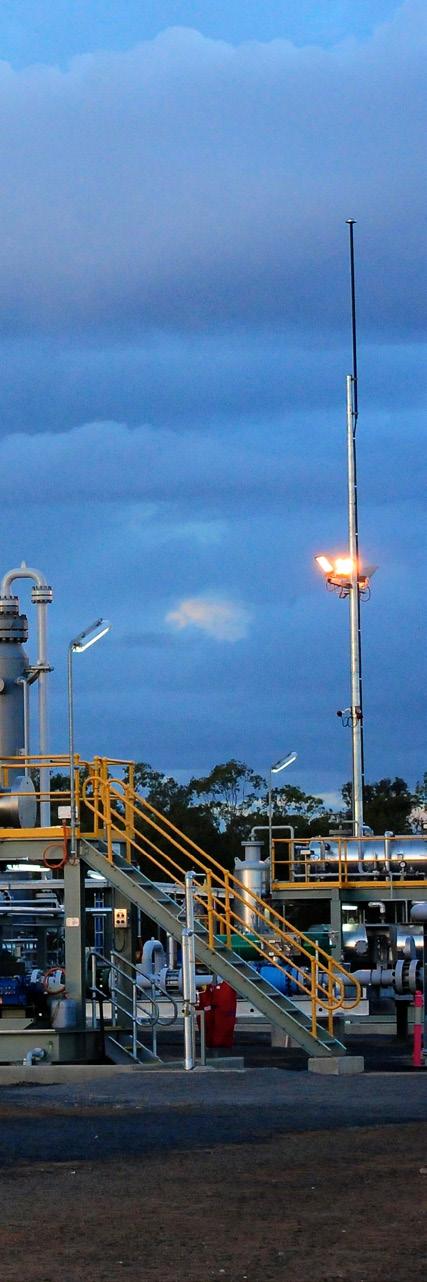
Australia Pacific LNG is the leading CSG producer in Australia. A joint venture between Origin, ConocoPhillips and Sinopec, Australia Pacific LNG is currently undertaking a major CSG to liquefied natural gas (LNG) project that will supply natural gas to both the domestic and international markets.
The $23 billion Australia Pacific LNG Project involves significant capital investment through to 2020 through the creation of a new, long-term gas processing and export industry in Queensland.
The construction phase of the Project will create 6,000 direct jobs, and a further 1,000 operational jobs, and brings opportunities to increase local skills and expenditure in regional economies.
The Project consists of three key parts:
• further development of Australia Pacific LNG’s gas fields in south-west and central Queensland;
• construction of a 530 kilometre gas transmission pipeline from the gas fields to Curtis Island off the coast of Gladstone; and
• an LNG facility on Curtis Island, with two gas production trains processing up to 9 million tonnes per annum.
The gas field development activities are located in the Surat Basin and the Bowen Basin regions of south west and central Queensland. Australia Pacific LNG’s CSG permits cover approximately 36,000 square kilometres in these regions, which are also home to cattle grazing and other farming activities.
Origin is responsible for drilling and gas field development, building on more than 15 years’ experience in developing CSG in south west and central Queensland.
Gas field development will occur over four years and include up to seven gas processing facilities and two new water treatment facilities.
Origin has engaged specialist contrac-
tor MCJV Australia to construct the high pressure main gas transmission pipeline, which will be 42 inches in diameter and traverse 530 kilometres between the gas fields and Curtis Island.
The pipeline project involves construction of gas and water gathering pipelines in the gas fields, and a channel crossing from the mainland to the LNG facility on Curtis Island.
Construction and operation of the LNG facility on Curtis Island, including LNG production trains, storage tanks, loading facility and wharf, is being managed by ConocoPhillips.
The state of the art LNG facility will use ConocoPhillips’ Optimized Cascade Process LNG technology, and features two LNG trains each with a capacity of 4.5 million tonnes per annum.
ConocoPhillips awarded EPC construction work to Bechtel – which has international experience in LNG facility construction. Bechtel will construct the LNG facility on Curtis Island while ConocoPhillips will operate the facility once construction is complete.
How coal seam gas is produced
CSG is a naturally occurring gas, mostly methane, found in the coal measures deep underground. These coal measures are geological layers that consist predominantly of impermeable mudstone and siltstone that have thin seams of coal running through them.
These coal seams are discrete and not continuous over large distances; they generally form only 10 per cent of the total thickness of the coal measures. Small amounts of gas collect in the many gaps, called cleats, within the coal deposits.
The gas is bonded to the coal and held in place by water pressure. CSG is extracted by removing some of the water and reducing the pressure holding the gas to the coal, allowing the gas to flow into the gas well.
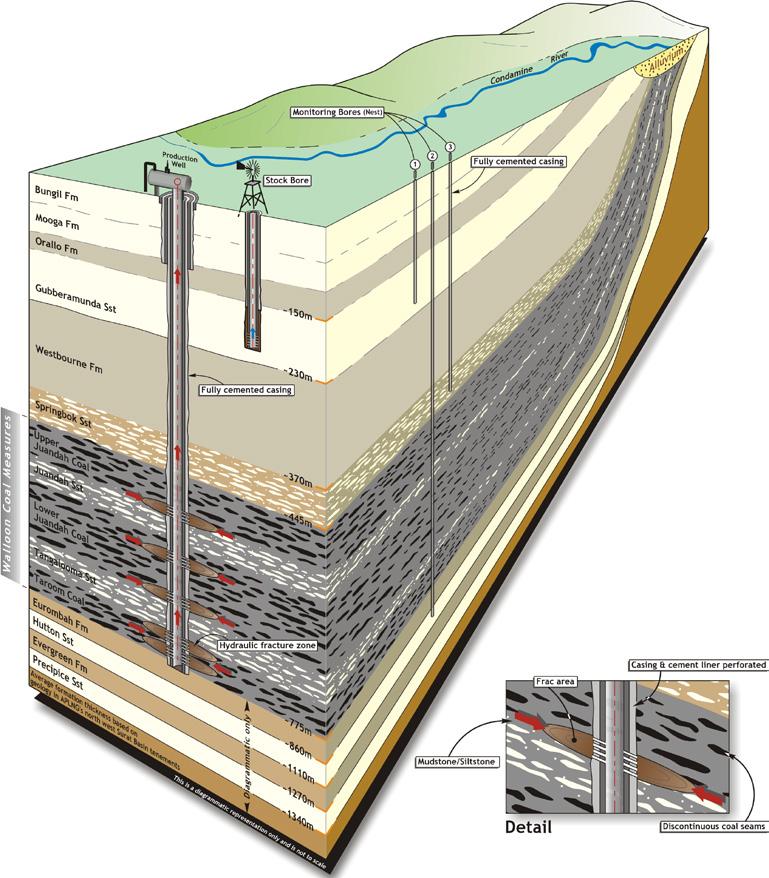
Both the gas and associated water are extracted via the CSG well. On the surface they are separated and pumped to relevant treatment facilities via separate pipelines.
Australia Pacific LNG pumps its associated water to a water treatment facility where it is treated via reverse osmosis to remove any dissolved salts and impurities. The water is treated to better than World Health Organization standards, and is then suitable for beneficial use.
CSG is pumped to a gas processing facility. At the facility the gas is further dehydrated and any remaining water removed. Once completely dry the gas is compressed and then transported via high pressure pipeline to domestic and commercial customers such as power plants.
Pumping applications
In upstream gas and water production activities, there are two primary pumping and pressure applications – extracting water and gas from the wells, and then compressing the gas to sales gas pressure for transport via high pressure pipelines.
At the individual well heads water is extracted using progressive cavity pumping systems. Extraction of water reduces pressure in the coal seams being targeted, allowing the gas to flow to surface inside a steel well casing.
Progressive cavity pumps are lowered inside the well casing on steel tubing to a depth of around 800 to 1000 metres - depending on the location of the coal seams - and driven by a rotating steel shaft connected to the surface.
The progressive cavity pumping shaft is rotated by either a hydraulic power unit
driven by a six-cylinder gas-fired engine, or electrically using a 30 kilowatt gasfired “microturbine” and variable frequency drive combination.
As the pump rotor spins, water is forced up inside the steel tubing, and gas released from the coal seams flows to surface between the well casing and tubing as a result of the lowering of water levels and pressure.
The extracted gas and water are separated at the well head and sent via separate low pressure (around 350kPa) gathering pipeline systems to centralised water treatment and gas processing facilities.
At the water treatment facility the water is treated via reverse osmosis to very high standards.
At the gas processing facility the gas is compressed to high pressure using a multi-stage reciprocating gas compressor.
The compressor increases gas pressure from around 350kPa to over 10MPa. Each reciprocating compressor is powered by a 12-cylinder gas-fired engine outputting around 4,000 horsepower. The gas is also dehydrated before the gas is transported via high pressure gas pipeline.
In some fields, the gas is initially compressed using a centrifugal screw compressor to raise the pressure from 350kPa to around 1400kPa, which then feeds the inlet of a multi-stage reciprocating gas compressor.
At this pressure the gas can enter sales gas pipelines for distribution to customers. The Project’s new 42 inch, 530km pipeline now under construction will connect Australia Pacific LNG’s gas processing plants with the new LNG facility on Curtis Island near Gladstone.
CSG will be pumped to the LNG facility where it will be chilled to -161 degrees Celsius and transformed into its liquid state. This liquefied gas is then ready to be safely transported to international markets.
About the Australia Pacific LNG joint venture partners
Australia Pacific LNG is a joint venture comprising Origin, ConocoPhillips, and Sinopec.
Origin is Australia’s largest integrated energy company, is listed in the S&P/ASX 20 and has diverse operations spanning gas exploration and production, power generation and energy retailing to 4.4 million customers in Australia.
ConocoPhillips is an integrated energy company with global operations and a market capitalisation of around US$96 billion. It has over 40 years’ experience in LNG and 25 years’ experience in CSG.
Sinopec is Australia Pacific LNG’s foundation customer, with LNG off-take agreements for 7.6 million tonnes per annum over a 20 year period providing essential stability and reliability of energy supply. Sinopec is China’s largest petroleum products supplier and second largest crude oil and natural gas producer with a market capitalisation of around US$96 billion.
A history of pump training
By Keith Sanders, PIA Life MemberWhen Chris Bland asked me to write an article for Pump Industry, I had no problem accepting the task, because I have had more the 55 years involvement in the process from an engineer’s perspective; firstly as a student, then as an employer and finally as a trainer.
Under the post war Labour Government in UK, there was a significant emphasis on education to replace what was effectively a “lost generation” of people, who should have taken up the jobs in manufacturing, commerce and social services. As a result, my involvement in serious education & training began in 1958, when I was encouraged to stay on in the Sixth Form for 2 additional years schooling and prepare myself for a University education in Mechanical Engineering.
What followed was a 5 year Graduate apprenticeship with Hawker Siddeley Group in UK and a career in the manufacturing sector, largely with rotating equipment manufacturers of printing press drives, conveyors, overhead cranes and, finally, pumping equipment.
Today, I am still involved in this field. I run a small consultancy business, which has a clear focus on the transfer of knowledge to young people entering the pump industry or enhancing the appreciation of the technology behind the equipment with operational and service personnel of pump users.
While the Pump Industry may not be a major manufacturing activity in Australia these days, it still has to cater for increasing demand for sophisticated pumping solutions and the market is clearly growing based on PIA market research. The challenge the Industry faces is to provide ongoing expertise to the many thousands of users of pumping equipment in all aspects of our modern society. Supply and servicing such equipment at world competitive levels remains a major strategic issue for Manufacturers, Distributors and Service providers. How can this expertise be transferred to the next generation?
Company training
When I came to Australia in 1981, the Australian Pump Industry was represent-
ed by the Australian Pump Manufacturers Association (APMA) and nearly all the major pump manufacturing companies had a representative on the Council. APMA was instrumental in publishing the first edition of the Technical Handbook, to provide a basic training tool with generic information about a wide range of pump types and pumping applications. This was quickly adopted as a “must have” in one’s personal library. However, at that time, most of the companies ran in-house training programs which were designed to develop the next generation of talent to fill key role in the business. These were programs that combine both “on the job” and “off the job” education and training to develop the skill levels necessary to secure the future of the business moving forward.
Most of these companies had professional Human Resources Departments, whose role was to prepared development plans for individuals based on their
education level, their aptitudes and the career ambitions. It was not a “one size fits all” approach and managers were encouraged to communicate with staff on a regular basis so that any investment in education and training had a concrete payback for the business. Personal development plans were mutually agreed and provided clear career path opportunities for those prepared to make the effort to improve their knowledge and skill levels.
Southern Cross was famous in the Industry for its training program for young engineers, which consisted of spending a period in the plant in Toowoomba to understand what the company made, how it was made, how it was used by customers and how it needed to be serviced. There were modules covering all the major products that Southern Cross supplied in the Australian market. Sadly this program is no longer available in the form that existed through to the 1990’s when mergers and takeovers changed
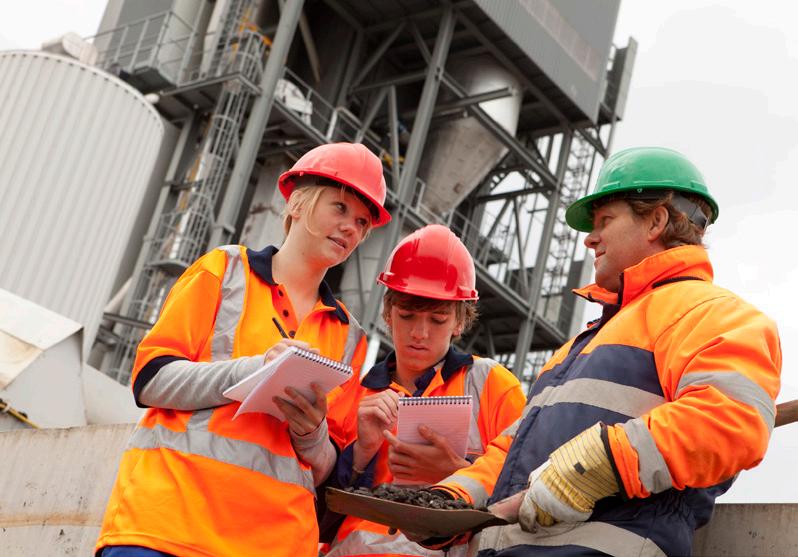
the previous management style of the business owned by the Griffith family. PIA personalities like Andrew Black, Geoff Sheedy and Bou Spithoven were inducted through this program. The company also supported me personally when I took up a distance learning program to complete an MBA at Deakin University. I will be forever grateful for that support.
Ajax Pumps, as part of the Macpherson’s Group, also ran a Cadet program from the Factory in Tottenham. Some of the senior members of PIA Council and Executive participated in the program. Harry Katunar and Ken Kugler immediately spring to mind.
These are only two examples, but this was typical of the “win-win” approach to education and training accepted by most of the major companies in Australia.
Apprenticeships
One of the significant features of this period of Australian Industry was the strong connection between these major engineering firms and the Institutes of Learning. Whether we are talking about Universities, Institutes of Technology or TAFE colleges, there were educational programs designed to support the needs of Industry for well educated and well trained staff, such that recruitment opportunities were easily filled and career development for individuals was assured. It might be argued that this was modelled on the UK experience of the 1960’s. There were educational and training programs and apprenticeships to cater for every level of worker that needed to be accommodated within the system.
Craft apprentices – these were usually blue collar workers who would undertake trade skills development by working
along-side qualified tradesmen. Their trade educational needs were catered for by outside Institutions of Learning by attending day release or evening classes at Technical Colleges for Trade certification.
Technical Apprenticeships – were for white collar workers who could be involved in drafting and design roles, works engineering or installation supervision, sales positions etc. Again, their educational requirements were met by outside Technical Colleges at Ordinary or Higher Certification levels that are required to meet the technical challenges of their intended role in the business.
Graduate Apprenticeships – were for white collar workers who were seen to have management potential and who could occupy future leadership roles in the business. The educational needs of such personnel were met by Universities or Institutes of Technology, offering degrees or diplomas in various disciplines such as Engineering or Sciences.
As a result, Australia developed a reputation for being a reliable supplier of pumping equipment, manufactured and tested in Australia to very high engineering standards. I spent 5 years in S. E. Asia from 1977 to 1981 working for Kelly & Lewis Pumps and, during that time, Australian companies were held in very high regard for the quality and reliability of their pumping equipment. Distributors would fight to acquire an Australian Agency for pumps, since this was a product vital to the development of S E Asian nations as they struggled to provide basic services of housing, water and power for their communities.
The changing scene
Significant market rationalisation has
occurred over the past 25 years and the scene in 2012 is significantly different. Most of those traditional Australian pump manufacturers have either been acquired by foreign investors or gone out of business. Imported products have increased significantly. While demand for pumping equipment continues to trend upwards, manufacturing in Australia has become less competitive due partly to the reduction in tariffs and other forms of protection, partly due to economies of scale in overseas factories and partly due to the high Australian dollar.
Not much can be done to arrest these trends in the short term. However, in my view, the most significant threat is the loss of skills within the Pump Industry and the ability of local businesses to offer world class solutions for the complex range of pump applications needed in the Australian market. We need to ask ourselves some serious questions about the future career prospects for young engineers who may wish to consider entering the business and allow them to reach their full potential as engineers or executives.
In this respect, I am conscious of a lack of human resources to meet the current demand for competent staff. As a trainer, I am often asked “Can you recommend anyone for this vacancy?” This demonstrates there is a need for more qualified people in the employment market.
In addition, it is evident that Australia has well developed education resource in Universities, Institutes of Technology and TAFE Institutions.
However, there seems to be an apparent disconnect between Industry, Institutes of Learning and the current crop of students passing through the system. What
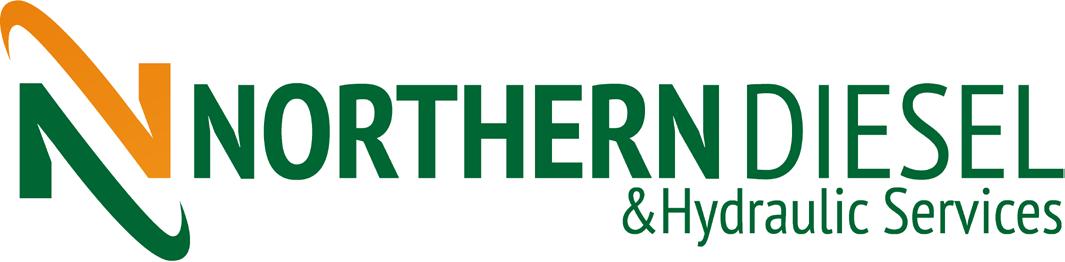
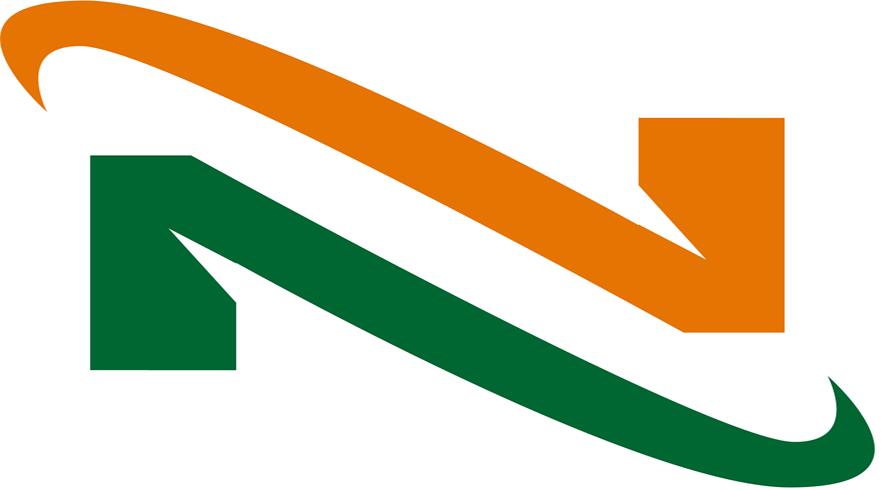
do we need to do to make a career in pumps “sexy”?
• PIA has had a mixed experience in working with educators in the recent past. Some years ago, PIA funded a Pump Test laboratory at Caulfield. Within a couple of years this facility was closed down due to a lack of demand.
• More recently PIA worked with TAFE at Moorrabin to develop a comprehensive pump training course. This was partly funded by PIA, in an effort to get something up and running. Again, the program was dropped shortly afterwards due to lack of interest.
• Efforts to invite University and TAFE students to PIA seminars at no charge have not been taken up. Clearly, the current crop of students does not see the Pump Industry as an attractive career path.
With a low unemployment level in Australia, it seems that people can pick and choose the career that will provide them with the best work/life balance. Employment opportunities in the Resources sector are skewing the segmentation of jobs in the short term, but most of us realise that Australia will require other sectors of the economy to pick up, once the boom
subsides. This will include manufacturing and by extension, the pump industry. The Government seems determined to prop up the motor industry with huge subsidies, yet pumps do not capture the imagination as readily as that glossy Holden in the Executive car park.
Some solutions?
What is needed is a “Master plan” with inputs from all stakeholders, addressing the challenges that lay ahead. The resources are basically there and it just requires a properly coordinated effort to bring them together.
• Australia need pumps;
• Pumps need servicing;
• People provide services;
We need to raise the profile of the Industry to a level which will encourage young engineers to join our ranks. This can be done by developing genuinely attractive career paths for them and publishing the benefits of making such a commitment. Ad hoc training programs to meet immediate short term objectives often do not get the intended longer term outcomes.
Why not a PIA award for the best performing graduate in Hydraulic Engineering?
Why not a PIA stand at end of year career Expos for new Graduates?
Why not integrated work experience for
Optimize process performance without compromising energy efficiency.
under- graduates to get a taste of the charms of the centrifugal pump?
In addition, we must develop links with senior course designers to ensure that the significance of pumping equipment in modern society is reflected in the course content and that the material is practical and relevant to present applications. Who needs Archimedes?
Finally, we need to get Government to find some new funding initiatives for both product innovation (R&D) and education & training. All too often, funding is linked to very prescriptive program designs and does not appear to encourage specialist training in particular areas of expertise. Bottom line is that State & Federal Governments are just too hard to deal with on many occasions.
Meanwhile, the “old-timers” of the Industry lament that there are few opportunities to pass on the knowledge that once made pumps an important part of the Australian manufacturing scene. In my opinion, this provides a real opportunity for PIA and the larger multi-national pump suppliers to draw up a coordinated program for the future. We want our industry to thrive, not just survive and this means we have to take the lead role in generating solutions.
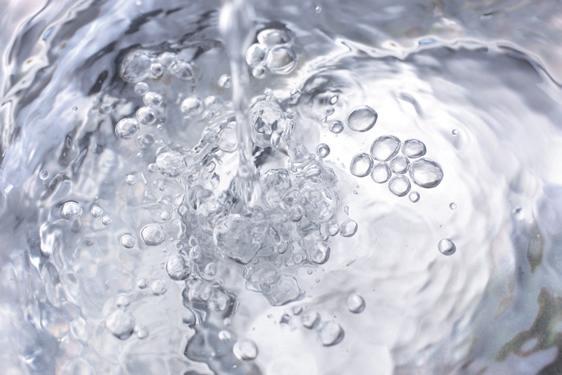
Water and wastewater utilities are facing many challenges from managing leakage and pressure, optimizing pump performance, improving potable water quality, reducing energy consumption and CO 2 emissions to lowering maintenance costs. ABB’s drives, motors and PLCs are designed to help motor-driven applications such as pumps, fans, compressors and conveyors, tackle these, and other, challenges. To discover how to improve your utility’s energy efficiency and productivity, visit www.abb.com/water
Help at hand for training
While most business owners recognise that the return on investment in staff training can be significant, many are held back by not knowing where to start, how to find the right training provider for their needs, or by concerns about the cost, or of productivity suffering during training. If this sounds like you, a chat with Market Facilitation Manager Suzanne Wells is a good place to start. Suzanne was recently appointed to the Eastern Metropolitan Region, which incorporates a good part of the pump industry in Victoria.
Suzanne attended a recent breakfast meeting for the pump industry and says she was pleased at the level of interest in staff training.
“The pump industry encompasses so many different skills areas and it was great to see the general recognition of the value of training in your industry. The Victorian training system has been through a number of significant changes in recent times, so I encourage business owners and employers to get in contact and find out exactly what’s out there,” Suzanne says.
Funded by the Victorian Government through the Higher Education and Skills Group, Victoria’s Market Facilitation Managers can help employers with a range of skills training issues including getting a skills audit to determine their training needs, finding the right training provider and finding out about eligibility for government-subsidised training.
Also available is ‘Training and your business’, a handy toolkit for employers
considering training. This introduction to the Victorian training system has helpful information including a checklist for comparing training providers, steps to getting the best training for your business, how Recognition of Prior Learning works and case studies of businesses with successful training programs (see Wilson Transformer Company’s story, below).
The Victorian Skills Gateway, a major new skills and training website scheduled to launch in early December, will also be a significant resource for employers.
The website - at www.education.vic.gov. au/victorianskillsgateway - has a dedicated employers section with information to make it easier to shop around for a training provider and to get the training that your business needs. There are tools to help you determine whether your employees may be eligible for a government-subsidised training place under the Victorian Training Guarantee, and to understand the value of apprenticeships and traineeships.

CASE STUDY: Training enhances skills and capacity at Wilson Transformer Company
Investment in training, new facilities and equipment has paid off for Wilson Transformer Company, which has increased its market share, boosted productivity and quadrupled its production capacity in less than seven years.
Through long-term partnerships with several registered training organisations (RTOs), the Wodonga-based manufacturer of power and distribution transformers has enhanced the skills and flexibility of its workforce, and expanded its market share from 25 to 45 per cent.
Training Coordinator Julie Campbell said the company started to focus on training back in 2004 when it engaged private RTO Educational Living to conduct a skills audit of its workforce and align knowledge gaps with competency-based training.
“As a regional manufacturing business with staff working three shifts over 24 hours, one of the things we were looking for was high quality training that could be delivered onsite outside normal working hours.”
Melbourne-based Educational Living developed a tailored solution for the company, where the majority of training is now delivered onsite by three locallybased trainer/assessors across three shifts.
Staff are upskilling in qualifications including Mechanical Fitting, Fabrication and Electrical apprenticeships and the Certificate III in Engineering – Mechanical Trade (Production). Since 2006, 160 staff have completed Certificate III, IV or Diploma-level training.
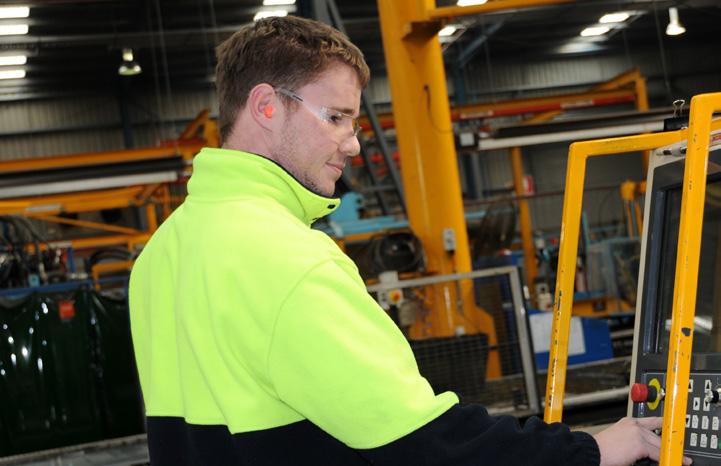
Wilson Transformer Company also has successful ongoing partnerships with Wodonga & Riverina TAFE and the National Industrial Skills Training Centre for onsite delivery of Certificate III in Warehousing and Distribution.
Recently the company invested more than $15 million in new facilities, including a dedicated training centre, where more than 80% of staff are involved in formal training at any given time. “Our employees now work across a number of areas and disciplines, which is a huge benefit in terms of production flexibility and keeping labour costs down,” Ms Campbell said.
Along with improvements to factory layout and associated training, she said the company had seen a significant return on its investment, with a high employee
retention rate, increased productivity and reductions in rework and waste.
“We’ve actually reduced our manufacturing cycle from 14 days to less than 2 days, while also increasing safety awareness and reducing our WorkCover premiums by 37 per cent since 2004.”
Director of Educational Living, Edward Stone said, “Wilson Transformer Company is a model for other businesses on how training can be used to help achieve production targets as well as support employees. The by-product is an enhanced regional workforce that is able to work in national and international markets.”
For more information about the training, contact Suzanne Wells on (03) 9938 0165 or at wells.suzanne.s@ edumail.vic.gov.au

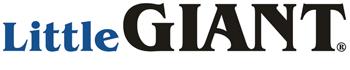
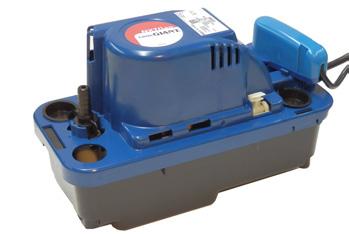

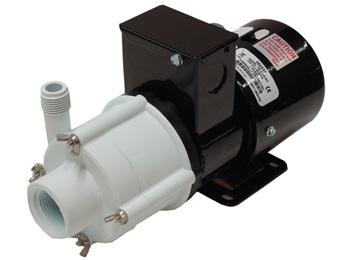
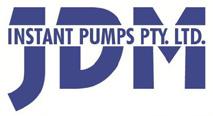
Pump up the projects
By Christine PitcherPump House Projects designed, constructed and commissioned the first and largest amended water treatment facility for CSG water in Australia reducing the environmental impacts of discharging saline water to the environment. This plant employed patented technology to efficiently manage the quality of discharged water to DERM/EPA standards.
The Pump House started business in 1987 and quickly grew to become the largest pump and irrigation specialist in South East Queensland
In 2006, the company was asked to develop a water treatment system for a major coal seam gas company.
It took two years of hard work, countless hours of design and dozens of meetings before The Pump House secured its first contract in September 2008.
The production of Coal Seam Gas, produces large volumes of waste water. Beneficial use of CSG produced water to irrigate trees is an innovative Pump House Projects approach that addresses the twin problems of CSG waste water salinity and volume.
The system takes produced water from the gas extraction process and treats it to irrigation standard suitable for use on forestry timber and leucaena plantations.
A strategic alliance was formed between Pump House Projects (the industrial arm of The Pump House) and Tree Crop Technologies to work on the first project. Tree Crop Technologies and Pump House Projects combined expertise includes tree and fodder crop water chemistry, site and land assessment, soil science, crop and plantation design and establishment, irrigation design and construction, ongoing asset management and environmental monitoring.
Tree Crop Technology researched the benefits of CSG managed water irrigated plantations and discovered that the trees survive as CSG water flow declines and eventually stops altogether. The plantations are established as a long term commercial crop for either timber harvesting or carbon sequestration. The average carbon sequestered by the plantations over multiple harvesting cycles is available to offset emissions from other areas of customer operations.
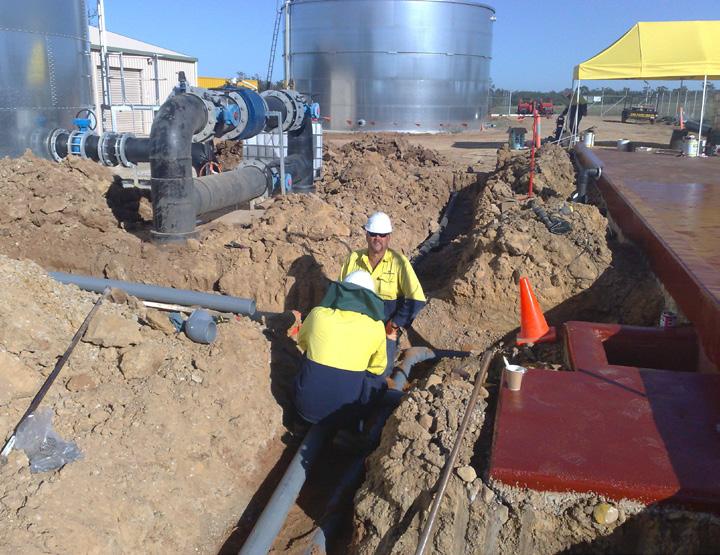
Other benefits of using CSG water include:
• Scalable with the capacity to handle large and variable volumes of water
• Can be safely established close to the gas fields to reduce infrastructure costs
• Environmentally sustainable
• Highly cost-effective relative to other water management options
• Adaptive irrigation management balances environmental considerations such as plant health and soil integrity against variable CSG water flows and changing weather conditions
• Creates a carbon sink to reduce emission intensity
After several large scale applications of CSG water onto irrigated crops now completed, Pump House Projects can now offer this alternative to more capital intensive solutions such as Reverse Osmosis and the environmentally-compromised evaporation option.
The future for Pump House Projects
Pump House Projects is heavily involved in the design and construction of pump stations for municipal, construction and mining.
The company specialises in delivering turn-key water treatment projects and has successfully completed over 3000 water projects across a wide variety of corporate, government and private sectors.
Due to the expanding coal seam gas market Pump House Projects is constructing a purpose-built showroom and workshop in Chinchilla. It is the centre of the coal seam gas market and the company expects to be trading by early 2013.
Pump House Projects Head Office is based in Nambour. Peter Chadband, the Managing Director is a respected leader in the Pumping and Irrigation industry.
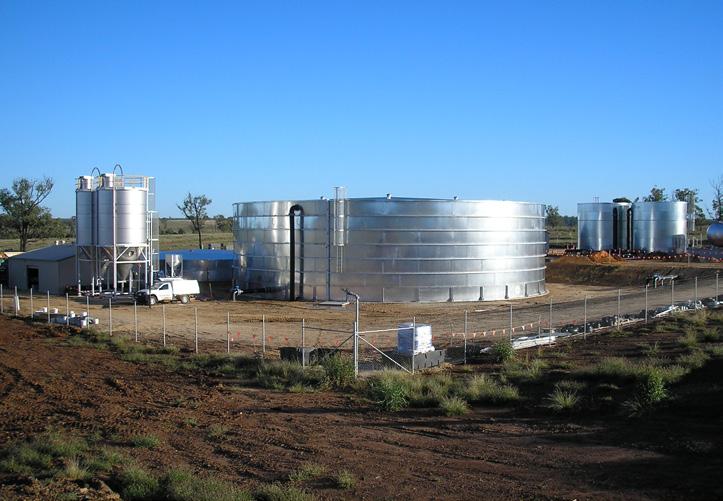

PROJECTS
From Mining to Agricultural , Commercial & Industrial projects , Pump House Projects offers the whole package.
• Design
• Fabrication
• Installation & Commissioning
– Turnkey solutions for any project involving water.
From treatment, transfer, storage, irrigation and filtration, Pump House Projects offers the complete water solution.
Case study: Demountable Coal Seam Gas (CSG) Water Treatment Plants
With their ongoing development of CSG wells, a CSG producer required multiple treatment plants that could be integrated with existing operations and deployed into site specific areas
Solution
Pump House Projects developed two demountable water treatment plants processing CSG water for two geographically separate locations
Scope
Pump House Projects provided a full turnkey project solution, including design, fabrication and site installation. Pump House Projects provided all aspects of project management and technical support for integrating with existing operations
Project Size
Treating 2.1ML/day per plant; Project Value $5 million
Timing
7 months duration – delivered Feb 2011
Result
The two demountable CSG water plants were factory tested at Pump House Projects’ fabrication facilities in Nambour Queensland then successfully installed on site.
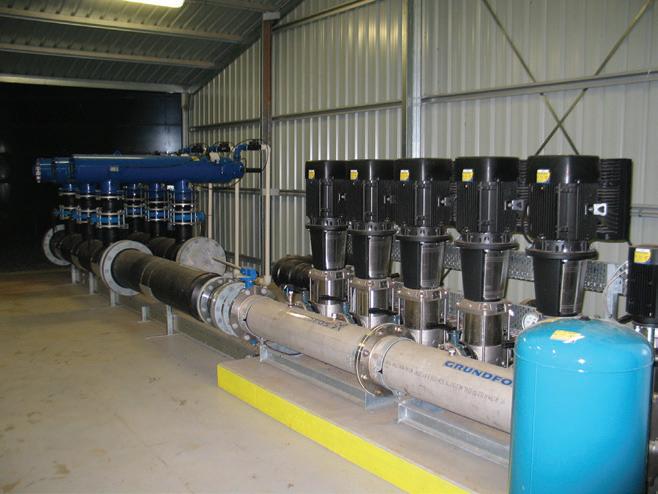
Commissioning a new recycled water plant
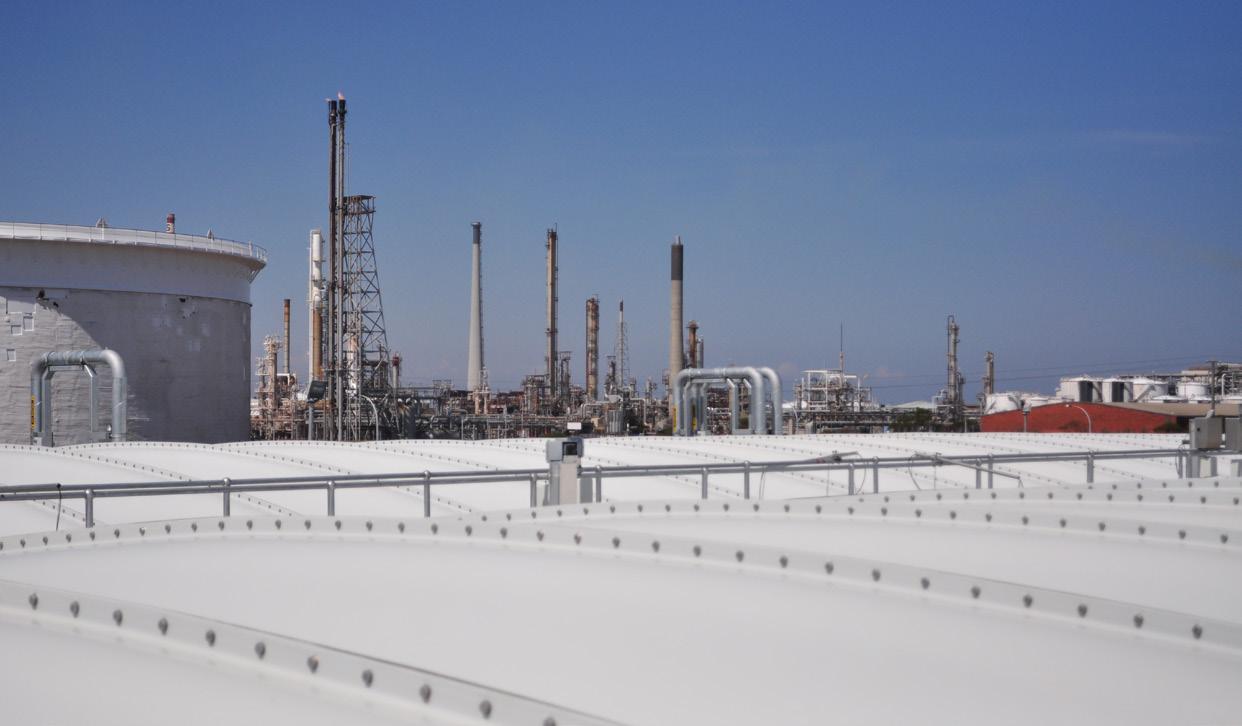
CCommissioning of the $94 million Northern Water Plant – the Geelong region’s first Class A recycled water plant – has started. The new facility is essentially two treatment plants in one; an aerated biological nutrient removal plant, followed by an advanced water treatment plant incorporating membrane technology. The plant is serviced by two new sewerage wet well pump stations integrated into the existing network.
ommissioning commenced in August, 2012 and the facility will be fully operational by February, 2013.
The plant will treat sewage and trade waste from Geelong’s northern suburbs and produce Class A recycled water for Shell Geelong Refinery. Recycled water will also be available for public use.
When fully operational, the facility will save about 2,000 million litres of drinking water a year, or 5 per cent of Geelong’s current consumption.
The Northern Water Plant is unique in Australia in that it combines several functions into one facility, including:
• domestic and industrial wastewater treatment
• Refinery waste water influent
• advanced treatment to generate the highest class of recycled water
• supply to industry
• supply to the community (for irrigation). There are several other advanced water treatment plants in Australia. However, the Northern Water Plant is the only facility that generates the highest class of recycled water from influent containing such a high proportion of industrial wastewater.
The Australian Government has contributed $20 million toward the cost, the Victorian Government $9.2 million, Shell $47.5 million and Barwon Water $17.5 million.
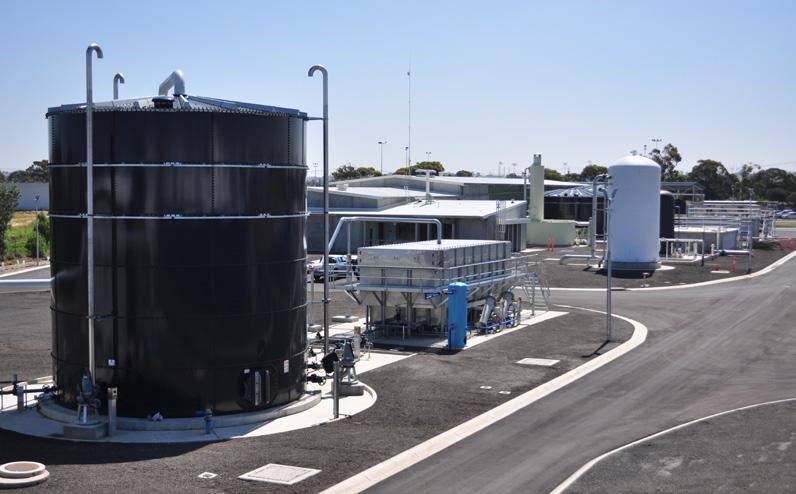
John Holland was awarded the construction contract in early 2011. Up to 150 new jobs were created during construction, with a workforce of 100 on-site at the peak of the works.
Background
In 2003, Barwon Water launched a major investigation into managing the increasing sewage flows from northern Geelong. The investigation assessed three options:
• duplicating the trunk sewer network to transport more sewage to the Black Rock Water Reclamation Plant at Connewarre
• transferring sewage from northern Geelong to the Werribee Treatment Plant
• the Northern Water Plant strategy. Shell Geelong Refinery, the region’s largest potable water user, was investigating ways to improve the quality of its wastewater and introduce recycled water for reuse. This included developing a strategy to reduce the amount of water being used.
One option considered was a recycled water pipeline connecting the refinery to the Black Rock Water Reclamation Plant, located 40 kilometres to the south. However, this was considered too expensive and unsustainable.
The options assessment identified that a joint project was the preferred outcome based on economic, social and environmental benefits. The joint project would
treat both trade waste from the refinery and domestic sewage from the northern suburbs while generating recycled water for Shell.
Importantly for Barwon Water, the plant would also relieve wet weather capacity issues in the system. The Northern Water Plant concept was a natural fit to meet the infrastructure needs of both organisations.
How the plant will work
The Northern Water Plant has the capacity to treat up to 7.5 million litres of domestic sewage and refinery wastewater a day. It is also capable of treating up to 20.7 million litres of wet weather flow a day though the continuously aerated biological nutrient removal plant. The biological plant includes clarifiers sized for wet weather with on-site sludge thickening.
Treated water will supply the ultrafiltration/reverse osmosis plant that will generate five million litres a day of medium and low salinity Class A recycled water. Treated wet weather flow will be temporarily stored on-site.
The high concentration of refinery wastewater presented a risk to conventional membrane designs. A pilot plant mimicking the biological and membrane trains was operated in 2010, which confirmed the design could meet the performance requirements. Importantly, excessive fouling from hard-to-treat compounds in Shell’s trade waste was not observed. The results of the pilot meant the design was a viable option in terms of capital and operating costs.
Due to the site’s proximity to nearby residents and businesses, the plant includes coverage and odour treatment from the
inlet works, biological tanks and solid handling processes.
The plant will be fully automated and staffed by three operators during normal business hours.
Communications and process information is exchanged with the refinery’s control system. If a fault or alarm is raised at the plant, the operators will receive immediate notification. As a fall back, the normal water supply and wastewater options will continue to be available to the refinery.
Pumps
The facility includes more than 70 pumps across the plant with a value of close to $1 million. Pumps are used to deliver sewage, transfer process water across the plant, throughout the advanced membrane plant , transfer sludge and deliver recycled water to Shell and other customers.
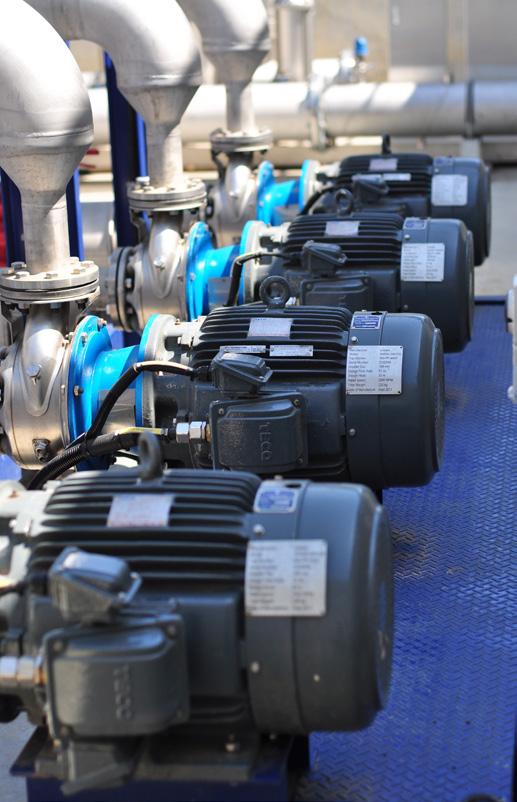
Pump sizes range from 1L/s to 70L/s. Types of pumps include centrifugal pumps, rotary lobe pumps, and diaphragm pumps. Due to such a wide variety of pumps, several suppliers were engaged to meet the needs of the design

both nationally and internationally. The largest units are two 680kW high pressure supply pumps located within the reverse osmosis system.
The detailed design team spent considerable time on pump design and selection to meet the challenges of the project. A high proportion of variable speed drive pumps were selected to meet process demands. For example, product water pumps need to deliver flow to the refinery between 35L/s to 70L/s. Xylem’s (previously ITT) multi-stage booster pumps were selected for this application.
A key challenge for Barwon Water was how to best transfer sewage from two separate catchments to the plant. Two existing pump stations were expanded with a second wet well. The new wells will deliver average dry weather flow (ADWF) and wet weather flow up to a combined rate of 205L/s. The new stations were connected to the old wet wells to manage flow above 205 L/s along the old rising mains which will remain in place.
To avoid septicity in the old rising mains (which will be largely unused), the system includes a scour pump to drain fluids back to new pump wells after use.
A new benchmark for urban pump stations
The $403 million North South Interconnection System Project (NSISP) is one of SA Water’s biggest infrastructure projects, with the largest geographical footprint of any project undertaken in metropolitan Adelaide. Chris Bland recently interviewed Project Director, Gary Neave.
Gary, a graduate from the University of Adelaide with a Bachelor of Engineering (Civil), is on full time secondment to SA Water from Parson Brinckerhoff where he is a Major Projects Executive. He was selected based on successful completion of the role of Deputy Project manager/Infrastructure Manager on the $420 million Jacinth Ambrosia Mineral Sands mine site project for Iluka Resources. Of particular relevance was his knowledge of program delivery across the entire project life cycle and experience the structure and development of integrated project teams for in-house
delivery and risk management. He has a background in successful project delivery across most disciplines in both the public and private sector including a period as General Manager of a small to medium civil engineering construction company.
He was recently awarded AIPM National Project Director of the Year 2012, for his role in leading the NSISP.
Project scope
I asked Gary to outline the scope of the project; “The purpose of the project is to interconnect the traditionally gravity fed water distribution zones in metropolitan
Adelaide, ensuring flexibility of water supply and improving the ability to manage the broader network more efficiently.
“To undertake interconnection the project was made up of a number of elements, including the construction of four major transfer pipelines, with installation in main arterial roads and suburban backstreets, totalling 32 kilometres in length. Other works include the construction of three new pump stations in the residential suburbs of Wattle Park, Clapham and Gilberton and five new valve stations in Seacliff Park, Springfield, Wattle Park,
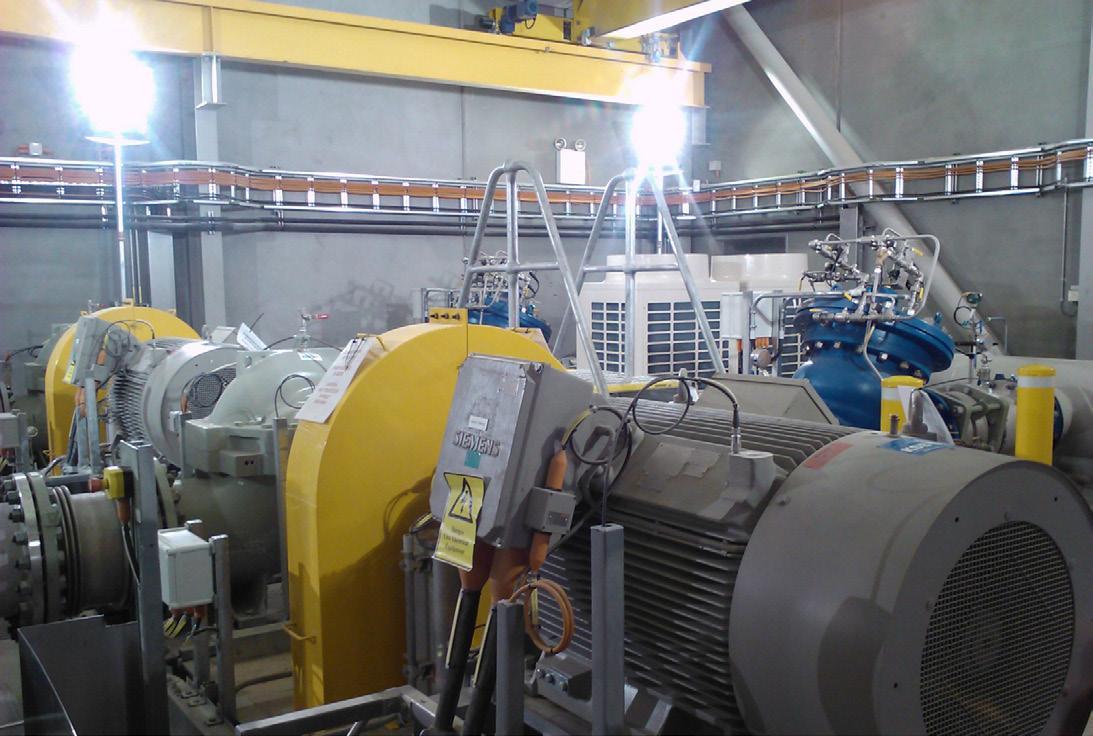
Gulfview Heights and Hope Valley. There are other installations and smaller upgrades at over 120 sites throughout the metropolitan area to integrate this new infrastructure into the existing distribution network. Given the nature and scale of the project there has been requirement for engagement with local communities to understand their views, educate the design process, and communicate effectively to manage project impacts.
Why is the project necessary?
“Water is South Australia’s most precious resource. It is critical to South Australia’s future prosperity as it underpins growth in the population and the economy. Through the Governments Water for Good strategy, a significant commitment to invest in a suite of water security measures was made, to improve and enhance the Adelaide’s water supply network. Innovative, long-term solutions had to be found to deliver the flexibility and reliability of water supply that is essential to meeting existing and future demand, while also ensuring water security during events such as prolonged drought.
“Prior to the NSISP Adelaide’s water supply network primarily operated as two separate systems – north and south. Each had its own water storage facilities and is separately augmented by pipelines from the River Murray. What does this mean? In simple terms, it means the majority of homes and businesses in the metropolitan area have had access to just one water supply source.
“This $403 million NSISP interconnects the drinking water distribution systems in metropolitan Adelaide, including providing access for the northern distribution zone to the new Adelaide desalination plant. This project has delivered flexibility and reliability of supply, enabling the majority of Adelaide to access more than one source of drinking water. Interconnection provides the foundation for resolving our water security challenges for the future and provides support for future growth in the city.”
What has been the greatest engineering challenge on the project?
“The level of architecture and landscape architecture employed on this project is unusual, however NSISP marks a shifting of the benchmark for infrastructure delivery and the level of community engagement to deliver new infrastructure in residential areas. Working collaboratively with the community provided a number of challenges especially when designing the new above-ground infrastructure.
Although, input from the community helped NSISP to design a building that was appropriate for the local area, it also challenged the project team to deliver buildings that had a minimised footprint and height, and to provide a high level of acoustic attenuation to reduce potential noise from the new infrastructure.
“One element of this project was delivery of the new Clapham Pump Station, the largest SA Water facility of its kind in urban Adelaide. This was a challenge to deliver as we not only had to incorporate the community input but also deliver the building and state-of-the-art operational and control technology from the ground up in the same time it takes to build an average sized house. To the casual observer this pump station building may appear large, but in reality it is small for the role it performs and the capability it contains. It is home to five one-megawatt high-voltage pumps capable of transferring up to 100 million litres of water per day (or the equivalent of 40 Olympic size swimming pools) from the Happy Valley clear water storage to the northern suburbs via Wattle Park.”
Pump Stations
Three pump stations were being built as part of the project, I asked Gary to provide some details on these;
“The Pump Stations symbolise a shifting of the benchmark for infrastructure development in urban areas. As mentioned previously, the high level of architectural amenity, the use of natural building materials and colours, the landscaping and the technology housed within the buildings have come together as a result of the collective efforts of the community, councils, our locally-based contractors and SA Water.
“We have also set noise and sound targets for all the new pump stations that are well below industry practice. We have configured our equipment and applied technology to enable us to reduce building heights and sizes to suit their urban locations. The landscaping yet to be completed will further enhance site amenity and streetscape appeal.
“Some challenges faced by the pump station designers were;
• The building footprint, which required a number of arrangement drawings and final selection included using a mix of left and right handed pumps
• The noise criteria at the boundary of the site from pumps, pump motor cooling and pump control equipment
cooling. Electronic equipment was cooled by refrigerative systems dissipating heat into the pump hall. The pump hall was cooled by evaporative cooling using high efficiency noise attenuators on both inlet and outlets.
• The range of duties for the pumps which are required to transfer as well as supplying the network through common pipes.. Extensive modelling of the range of duties in conjunction with the control system designers confirmed the range of required duties specified.
• Surge management (including the size limits) which resulted in the selection of flywheels rather than pressure vessels. The flywheels require a much smaller footprint than pressure vessels. Pressure vessels would be required on both inlet and outlet of pumps.
• Preventing the use by vendors of mixed bearings for pumps and motors, potentially resulting in high maintenance and assembly issues”
What monitoring equipment are you using?
“Bearing temperature of the Motor, Flywheel & Pump will be monitored by the bearing temperature sensors.
Motor Winding Temperature will be monitored by 9 no. temperature sensors (3 per each phase).
Temperature sensors and pressure transmitters installed on the u/s and d/s of pump casing enables the P22 instrument to be connected to monitor pump efficiency.
Tachometer on the shaft to monitor the speed of the pump.
Fast Tachometer will be provided to monitor pump performance during transitions. Accelerometer will be installed to monitor the vibration.
Gilberton – IFM vibration monitors are installed.”
What were the most important factors in pump selection?
“The selection of pumps was based the need for a low operational and capital cost which can best be provided by single stage, double inlet, centrifugal pumps operating at industry standard speeds using a VSD. The minimum pump capacity was achieved by integrating the pump selection with network tank filling criteria. For larger pump motors the use of higher voltage motors minimises space through smaller equipment sizes and better cable routes.
How important is energy efficiency and how does it factor into decisions?
“Although energy efficiency is important there are a number of vendors that can supply drives and pumps of high efficiency over the required range of duties. The energy efficiency of the pipework associated with the pumps was also assessed for each pump vendor. The energy efficiency of the operating regime plays a more significant role in overall energy use and this will be managed through the new central control centre. “
How important are the maintenance and repair schedule and costs in
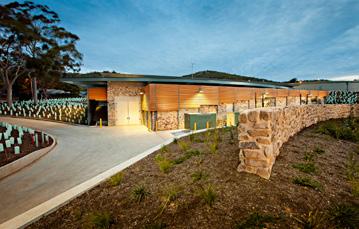
Clapham Pumping Station
• Clapham pumping station is designed to pump approximately 1750l/s from Clapham to Wattle Park.
• Clapham Pump station consists of 5 no’s of Horizontal, split case, centrifugal pumps (KSB Omega 250-800 A SC G F) each with capacity of 406 l/s at 191m head each powered by 1122 kW, 3.3 kV motor operated by VSD.
• Each pump is fitted with flywheel of weight 2737 kg providing inertia of 510 kgm² for surge mitigation.
• Each pump is automatically controlled by their local PLC or manually controlled via the HMI panel. A separate System Wide Control (SWC) PLC will provide control signals to each pump’s PLC and the critical control links, SCADANet and the other local PLCs on the site.
• Operating philosophy: When inlet valves from 2 different tanks (Beaumont, Burnside & Stonyfell) call for water, the pump starts. While in operation it maintains a pressure of 232m AHD at Stonyfell by the pressure feedback signal from pressure transmitters in the Wattle Park PSV station.
Volume: 150 Ml/day (1700l/s x 24 hrs)
project planning - is there an appropriate balance between this and up-front capital?
“The selected pumps use proven low maintenance components including rolling contact bearings and mechanical shaft seals. The small cost penalty for mechanical seals was considered insignificant. The motor bearings use high temperature grease rather than a relatively higher cost and maintenance oil cooling system for bearings. The use of flywheels eliminates the need for costly routine internal inspection of pressure vessels.”
How important is sourcing equipment locally, and ongoing
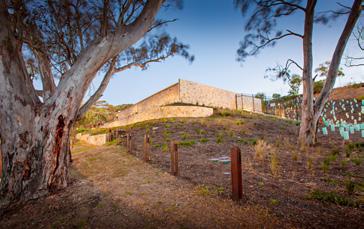
Wattle Park Pumping Station
• Wattle Park pumping station is designed to pump approximately 1250l/s from Wattle Park to Terminal Storage.
• Wattle Park Pump station consists of 3 no’s of Horizontal, split case, centrifugal pumps (KSB Omega 300-560 B SC G F) each with capacity of 416 l/s at 61m head each powered by 350 kW, 400 V motor operated by VSD.
• Each pump is fitted with flywheel of weight 1711 kg providing inertia of 197 kgm² for surge mitigation.
• Each pump is automatically controlled by their local PLC or manually controlled via the HMI panel. A separate System Wide Control (SWC) PLC will provide control signals to each pump’s PLC and the critical control links, SCADANet and the other local PLCs on the site.
• Operating philosophy When 2 inlet valves of tanks (Auldana, Rostrevor or Woodforde) call for water, the pump starts. While in operation it maintains a pressure of 232m AHD at Rostrevor by the pressure feedback signal from pressure transmitters in the Terminal Storage PSV station.
Volume: 110 Ml/day (1250l/s x 24hrs)
after-sales service?
“A well developed local support structure is vital given the critical nature of the infrastructure.”
When will the project be complete?
“The NSISP will be delivered on time and on budget with operational handover occurring in December 2012. Some minor works such as system integration will occur throughout 2013.”
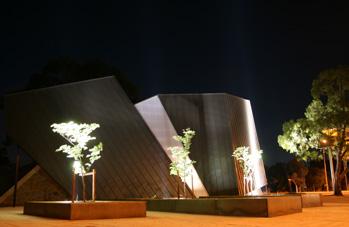
Gilberton Pumping Station
• Gilberton pumping station is designed to pump approximately 650l/s from Gilberton to Hope Valley 103 tank & supply zone.
• Gilberton Pump station consists of 2 no’s of Horizontal, split case, centrifugal pumps (KSB Omega 300435 B SC G F ) each with capacity of 325 l/s at 45m head each powered by 250 kW, 400 V motor operated by VSD.
• Each pump is fitted with flywheel of weight 1027 kg providing inertia of 95 kgm² for surge mitigation.
• Each pump is automatically controlled by their local PLC or manually controlled via the HMI panel. A separate System Wide Control (SWC) PLC will provide control signals to each pump’s PLC and the critical control links, SCADANet and the other local PLCs on the site.
• Operating philosophy: Based on the Hope Valley 103 tank levels the pump will on and off. The pump gets the start permission when the Clapham tank level is above 35% tank level and the pressure in the pump suction is above 95m AHD. Once on, the pump ramps up to the maximum speed to discharge the desired flow of 650l/s. When operating, it ramps up and down to maintain the suction pressure above 90m AHD. If unable to maintain the suction pressure and the pressure reaches 85m AHD the pump is switched off.
Volume: 55 Ml/day (625l/s x 24 hrs)
Balancing to a standard
Industrial balancing and vibration analysis on rotating machinery enables the early detection of faults before breakdown, and assists commercial and industrial facilities reduce their maintenance costs and unscheduled downtime. Industrial balancing is the procedure where the mass distribution of a product, be it a pump, roller, impeller or the like, is accurately measured and suitably adjusted.
Whether industrial balancing a pump impeller, fan or drive shaft; small or large, the process should be completed to a recognised international standard. This ensures balance quality and data consistency to ensure the item is correctly balanced within specified tolerances. The International Standards Organization (ISO) publishes several standards which are the global benchmark for industrial balancing.
The main one of these standards is ISO 1940-1:2003 Mechanical vibration -- Balance quality requirements for rotors in a constant (rigid) state. Part 1: Specification and verification of balance tolerances. This standard gives specifications for rotors in a constant (rigid) state according to their machinery type and maximum service speed. These recommendations are based on worldwide experience.
This standard also specifies Balance Tolerances, the necessary number of correction planes, and methods for verifying the residual unbalance. The standard is also intended to facilitate the relationship between the manufacturer and user of rotating machines, by stating acceptance criteria for the verification of residual unbalance.
The ISO standards contain detailed methods of calculating different static and couple unbalance tolerances that are dependent on the ratio of the part’s diameter to its length. The ISO standard also specifies a Balance Quality Grade. This is a term used to define the limits of residual unbalance. It represents the product of the eccentricity (in millimetres) times the operating frequency (in Hertz). The standard has issued guidelines with regard to a number of different kinds of devices. A balance quality grade of G6.3 is appropriate to most pump impellers. A tighter tolerance of G2.5 may be specified in some cases.
Precision Balancing has been offering in house and on site dynamic balancing and vibration analysis services since 1989 and have the equipment, skills and experience to satisfy your industrial balancing requirements. Precision Balancing strictly adhere to the requirements of the relevant ISO standard, and all jobs are tracked through our system and are issued with a certificate of compliance.
For more information on industrial balancing services and standards visit www.precisionbalancing.com.au
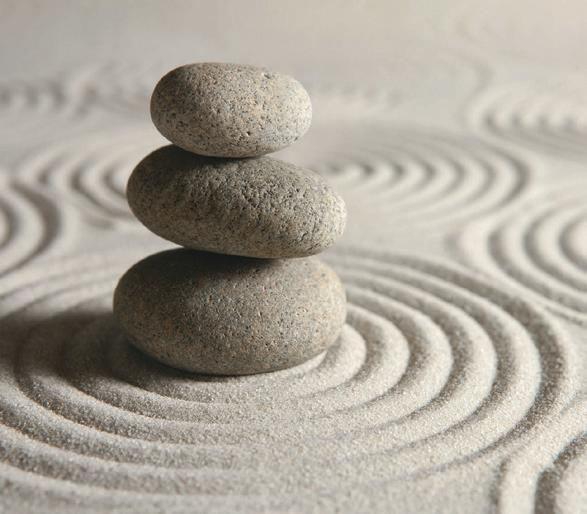
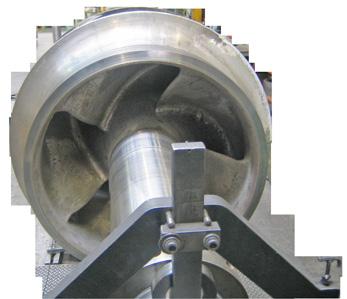
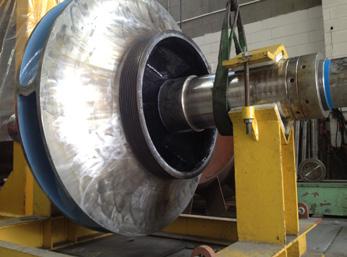
Controlling and monitoring control valve fugitive emissions
By Stephen M. Wing and Bradley K. SmithSince valves are the number one source of leakage, those faced with reducing fugitive emissions need to look at the most challenging type: control valves. This article highlights some of these options for typical control valve features, characteristics and options.
Process plant managers have a host of good reasons to minimize fugitive emissions from their facilities and reduce the amount of process fluid released into the atmosphere and surrounding environment. Those reasons include keeping employees and neighbours safe, lessening the facility’s environmental impact, complying with increasingly stringent air-quality regulations, optimizing the plant’s energy consumption and maximizing plant operating efficiency.
Industrial valves are a leading source of leakage from typical process plants. In fact, studies of refineries have shown that valves and relief valves account for about 75% of fugitive emissions.
Because of this reality, monitoring, controlling and reducing valve leakage can make a significant impact on overall plant fugitive emissions. Of particular concern are control valves, which pose a greater challenge than other industrial valves because of their typical operating mode and potential leak paths. There are, however, techniques, technologies and strategies that plant owners and managers can implement to better manage fugitive emissions from the control valves in their facilities.
Control valve leak paths
Standard control valve designs include a number of potential external leak paths. For example:
Globe-style Control Valves
Figure 1 shows a cross-section of a typical globe valve or linear operating valve, with the key potential leakage locations highlighted. The process fluid is contained within the valve body, which is a pressure vessel designed in compliance
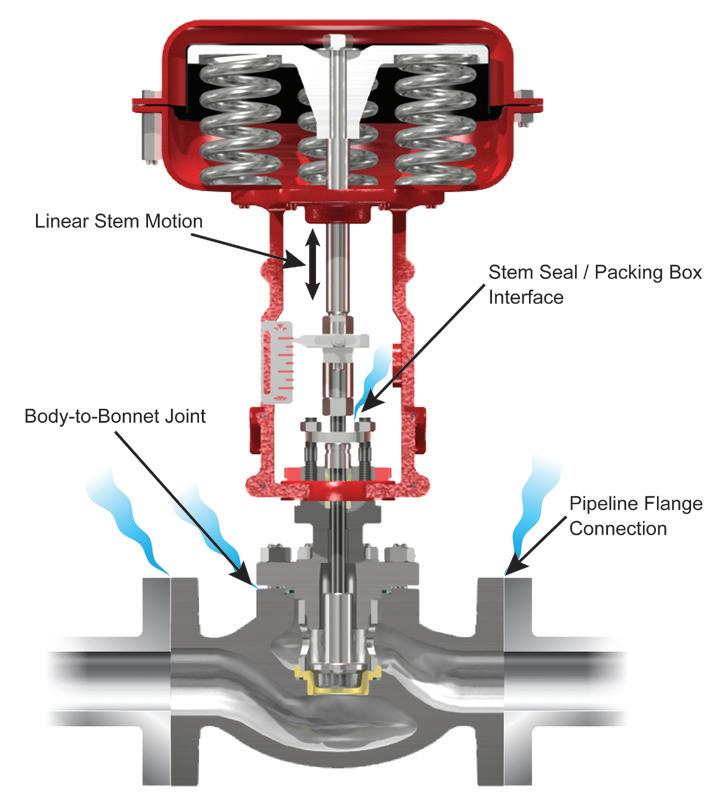
with standard pressure vessel codes, such as American Society of Mechanical Engineers (ASME), Deutsches Institut für Normung e.V. (DIN; in English, the German Institute for Standardization) or Japanese Industrial Standards (JIS). There are several static joints or locations
interfacing with the valve body where external leakage is possible, including the pipeline-flange connections and the valve-body-to-bonnet joint. Leakage at these joints is uncommon because of the static nature of these joints and the fact they are typically sealed with gaskets
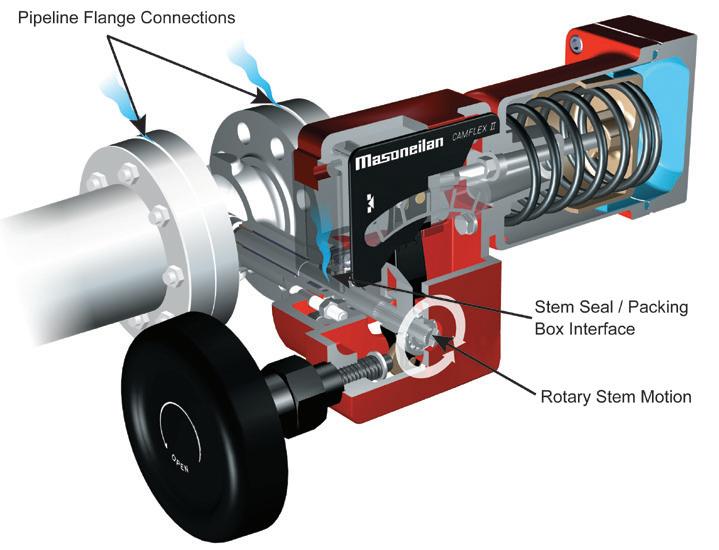
and then bolted together. Leakage is still possible, however, so these joints should be monitored.
The primary valve leak path is the stemseal interface, which is typically sealed using packing installed within the valve bonnet. This is a dynamic interface, as the stem moves up and down through the packing box area during operation.
Control valves are typically applied in continuously throttling services to maintain a specific set point or operating range for different process variables, such as pressure, temperature and flow rate. As a result, the valve packing wears over time, allowing more leakage across this interface. In addition, thermal expansion and contraction caused by the process fluid and ambient temperature changes can further increase the leakage rate. Thus, the packing must be periodically tightened or fitted with some kind of mechanical compensation, such as “live loading” the packing with springs to maintain the seal integrity and control leakage to the atmosphere.
Another key contributor to packing wear in globe-style control valves—and, thus, another source of potential fugitive emissions—is the presence of foreign particles or debris in the surrounding atmosphere. Since the globe valve strokes in a linear motion, the valve stem moves up through the packing area as the valve opens and then moves back down into the packing area as the valve closes. As the valve cycles from open to close, a portion of the stem is exposed to the environment, creating an opportunity for particles to
attach to the stem surface and potentially impact the packing wear rate and sealing capabilities. These particles also can increase the operating friction, which reduces the overall responsiveness and controllability of the valve.
Rotary-style Control Valves
Figure 2 shows a cross-section of a typical rotary-style or rotating-motion-design control valve. As with globe-style valves, the pipe-flange connections and the stem seal area are potential paths for process fluid to leak into the environment. However, many rotary-style control valves have an integrated body and bonnet, eliminating that location as a potential leak path.
A key advantage of rotary-style control valves in managing fugitive emissions
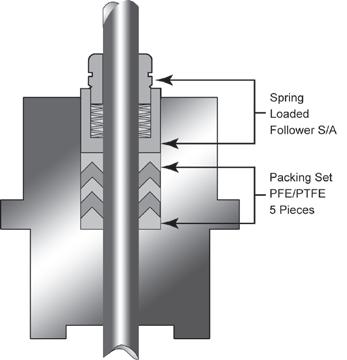
is the rotating motion of the valve stem as the valve is opened and closed. The stem stays within the stem seal or packing area, minimizing the possibility of introducing foreign particles or debris into the sealing interfaces. As a result, these valves are typically more effective in reducing the possibility of fugitive emissions leakage, and normally deliver greater reliability and operating efficiency from this perspective.
Drive towards lower emissions
A variety of factors, including government-driven regulatory requirements and the expansion of Environmental, Health and Safety (EHS) programs, have caused end users to place greater emphasis on reducing fugitive emissions. Regulatory standards were developed to control and lower fugitive emissions beginning in the 1960s, including the Clean Air Act in the United States and the TA-Luft requirements in Germany. Originally designed to meet regional or national environmental regulations and objectives, these sets of standards define specific test mediums, allowable leakage rates, test cycles and test methods.
The standards required industrial equipment suppliers, such as valve manufacturers, to evaluate, test and implement different sealing and packing designs to meet the specified fugitive emissions levels. The typical control valve in use at that time could emit anywhere from two to ten times the acceptable levels stated in these regulations, depending on the valve design, packing type and material, and operating conditions. To meet the new standards, control valve manufacturers developed low-emissions packing designs, including live-loaded constructions for globe-style valves and simple o-ring seals for rotary-type valves (Figure 3).

In 2006, the more stringent ISO 15848-1 was introduced as a low-emissions standard specifically for industrial valves. That standard includes various classifications and emissions levels for the potential leak paths described above. Specific to fugitive emissions, ISO 15848-1 sets maximum allowable emissions levels, testing procedures and type-testing criteria. Type-testing certification implies that compliance to the standard is based on the qualification test results for that type of stem seal or packing. The majority of the standards fall within this category as illustrated in Figure 4, which is a comparison of the most widely applied standards today—ISO 15848-1, ISO 15848-2, TA-Luft and ANSI/FCI 91-1—with respect to various test parameters and requirements. The one key exception to the testing requirements is ISO 15848-2, which also requires production testing to verify compliance.
Many end users are still trying to comprehend how the ISO standard applies to them and how to best implement its provisions into their facilities. At the same time, end users who already adopted the ISO standards are moving up the allowable leakage chain and implementing technologies that meet Class B, or even Class A, leakage rates, which compares to the Class C rates they may have previously reached for similar applications.
Several factors are driving this increased investment in reducing fugitive emissions. One is that regulatory fines for ex-
ceeding emissions limits have increased dramatically. But also, many end users are enhancing their EHS programs to protect the health and safety of employees, neighbours and the environment. Fugitive emissions reduction is often an important part of that enhancement.
Balancing control and low emissions
To improve plant operating efficiencies, many end users have implemented new process designs that operate at hotter fluid temperatures, higher pressures and larger flow capacities. Bigger, higher-pressure-class valves are required for these designs, creating new challenges for control valve suppliers as they balance two opposing objectives—minimizing friction and reducing fugitive emissions.
Control performance is directly related to the amount of friction created within a control valve assembly by the dynamic interfaces, including the valve stem and the stem seal or packing interface. Key factors that determine the amount of friction include the frictional coefficients of the mating parts, the dynamic surface conditions (including the impact of any foreign debris) and dynamic operating clearances dictated by overall alignment and the thermal expansion and contraction of the various components.
Teflon-based packing designs are attractive choices because they typically operate at lower friction and require less adjustment to maintain leakage rates. In higher-temperature applications, howev -
er, graphite or a similar material must be used, resulting in significantly increased friction and the need for more frequent adjustments.
However, there are ways to compensate for wider temperature and pressure swings while maintaining the dynamic clearances required for effective control and for meeting low emissions requirements. These include live loading the packing box, applying zero leakage designs such as bellows seals or creating a redundant sealing construction. These types of stem-sealing systems also minimize the need for manual adjustments—a key consideration in light of the leaner maintenance staffing found in today’s plants.
Specifying low-emissions technologies
The following are key factors that should be considered when specifying technologies to manage fugitive emissions:
• Local Conditions and Process Fluids: The location of a facility can play a significant role in determining the potential for harmful fugitive emissions and, therefore, the appropriate strategies for managing them. For example, the gas produced in places such as Iraq, Azerbaijan and the Caspian Sea contains much higher levels of potentially harmful impurities, thus operations there require more stringent emissions control standards.
• Equipment Accessibility: Valves
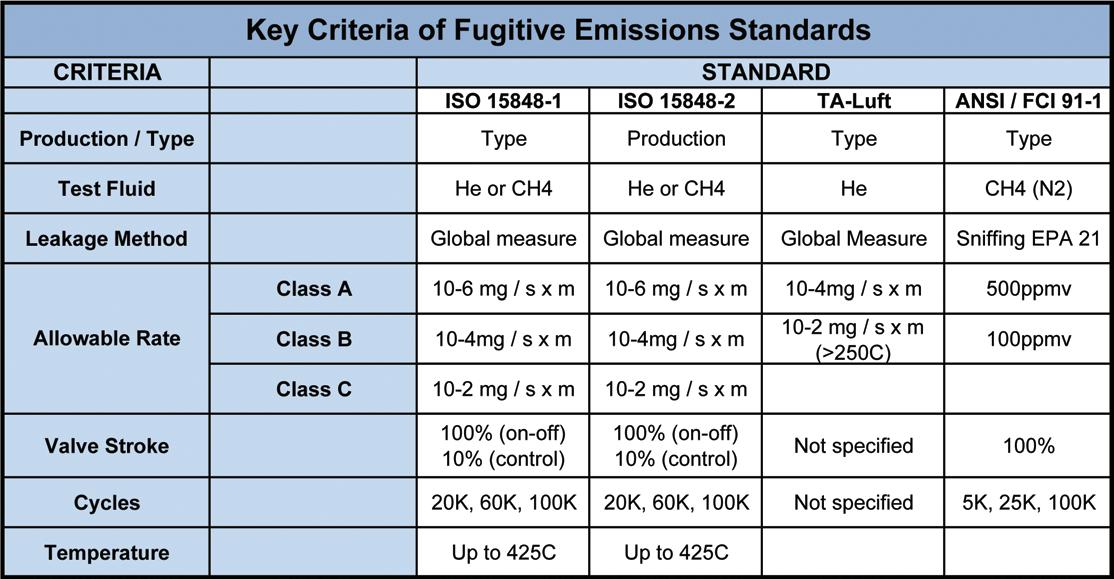
installed in remote locations or hardto-access areas will be more difficult to monitor and adjust, thus use of self-compensating stem sealing systems should be carefully evaluated.
• Interchangeability and Field Upgrade: Another key consideration in selecting low-emissions solutions is the interchangeability with the supplier’s standard packing or stem sealing options. Field upgrades may be required in existing plants to meet the latest regulatory requirements. Because of this, minimizing the amount of changes and rework is of high importance for ease of implementation.
Monitoring fugitive emissions
Implementing methods of adjusting the packing tightness to compensate for changes in operating conditions can minimize leakage, though some level of fugitive emissions will still exist. Zeroleakage designs, such as a bellows seal, should be used when a process involves extremely harmful or potentially lethal process fluids. But implementing these solutions throughout an entire plant would be extremely cost-prohibitive. To balance safety and economic realities, plant personnel should employ the best low-emissions sealing solution possible
and support it with an effective emissions monitoring system.
When most plant mangers hear the term “emissions monitoring,” they think of a manual process in which a portable analyser is used to take periodic measurements around all installed equipment. This is a time-consuming process, and with smaller teams of in-house maintenance personnel available, completing the tests frequently enough to meet regulatory requirements can be challenging.
The monitoring process can be automated, however, using a concept similar to the diagnostics capabilities offered by digital valve positioners. A series of sensors can be mounted on the valve assembly, which monitors fugitive emissions from the various leak paths and communicates the data directly to the digital positioner. The fugitive emissions limits or param-
STEPHEN M.
© 2012 Valve

eters for the specific plant or application can be compared by the positioner, which can then communicate any status reports or warnings back to the control system. As with any diagnostics tool, the accuracy of the sensors is critical, as is the ability of the positioner to convert the data collected into clear and easily understood actions for the plant operator.
For many solid reasons, fugitive emissions currently are under a bright spotlight. Since valves are a primary source of those emissions, it only makes sense to begin emissions management and control efforts with this part of the facility. Thankfully, today’s monitoring technologies, stem sealing techniques, packing designs and other advances can be powerful tools in assisting plant operators in meeting these challenges moving forward.
Understanding pump curves #2: stable & unstable curves
By Ron Astall, United Pumps AustraliaSome pump curves look different. When a pump curve has a hump in it or a high point away from zero flow it is said to be “unstable”. A “stable” curve has maximum head at zero flow and a negative gradient (constantly falling) as flow increases. A stable curve is sometimes known as a “CFC” or Constantly Falling Curve.
The term “unstable” sounds a bit scary. Should we be afraid of a pump with an unstable curve?
The answer is sometimes but certainly not always. There are indeed situations where a stable curve is mandatory and for this reason, manufacturers now rarely offer an unstable curve in their published catalogue, but in most pumping systems, an unstable pump curve will work just as well, and may even be better where a flatter pump curve can assist in circumstances where it may be desirable to maintain pressures over a range of flows.
Some pump types such as those with low flow high head radial vane impellers have inherently unstable curves. The real question is whether a pump will operate in a stable fashion in a particular system.
To answer this question, we need to understand how pumps interact with their systems by understanding the concept of the system curve.
See examples of stable and unstable curves below.
The System Curve
Consider the process involved in establishing the operating differential head of the system and the pump.
The differential head or system head is the energy required to move the liquid through the system. The pump provides this motive energy or head - but the system characteristics determine the differential head at the point of operation.
There are three components to the differential head :
Static Head Difference
• the difference in levels between the starting point and the finishing point of the system.
Pressure Head Difference
• the difference in static pressure between the starting point and the finishing point of the system.
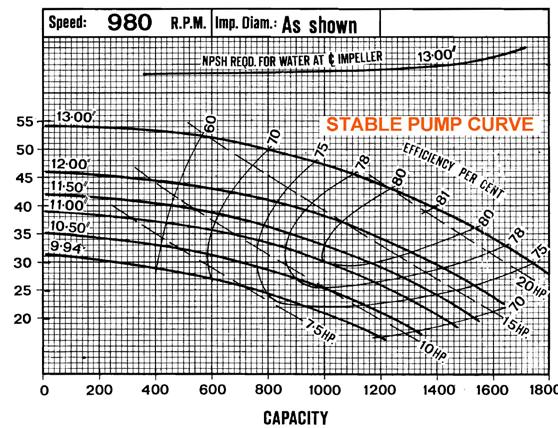
Frictional Resistance
• the head due to the resistance to flow as the liquid moves through the system.
Of the three components, only the frictional resistance changes with flowrate. It is realised that system levels and pressures may in fact change at different flowrates due to vessel capacity, but for the purpose of system analysis these are not considered to be dynamic changes that are inherently linked to flowrate (as is friction).
If there was no pipe friction, the pump differential head would be simple to calculate and would be constant regardless of flow. The system resistance as seen by the pump would just be the sum of the difference in levels and the pressure difference (expressed in terms of head). This is the minimum head which the pump must develop to hold station (prevent back flow) at zero flow. As flow
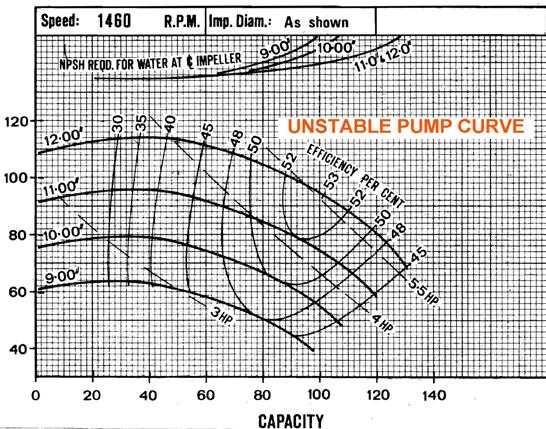
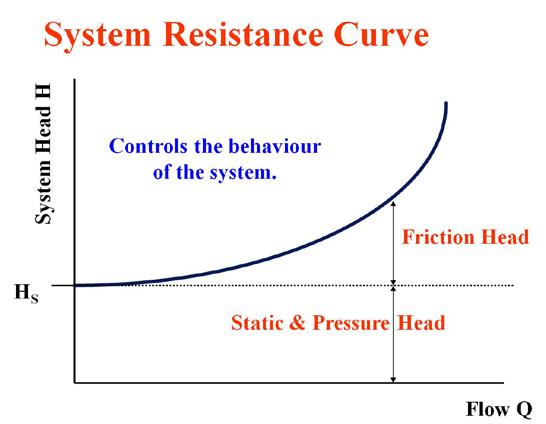

increases through the system, the frictional resistance must be added to give the total system resistance.
It is a valuable exercise to construct a curve showing the increase in total system resistance against system flowrate. This curve is called the SYSTEM RESISTANCE CURVE (above) and it is this curve that controls the flowrate of the pumpnot the other way around.
This System Resistance Curve shows the head required by the system to move the liquid through at a given flowrate. A pump will operate where it’s performance
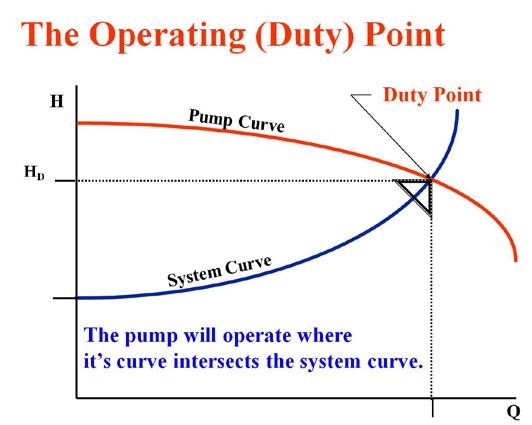
curve intersects the System Resistance Curve (above right) as shown by the dotted lines.
Actual on site performance will be given by the intersection of the pump curve with the actual System Curve.
System Stability
Let us look again at examples of “stable’ and “unstable” pump curves.
Overlaying the System Curve on the pump curve will show us where the pump will be operating.
If there is only one possible operating point then the pump and system combination will be stable.
Steep System Curve
When a system consists of mostly frictional resistance, it is termed a steep system curve.

A more detailed analysis of pumps operating in parallel will be covered in another discussion; however it is worth noting that unstable pump curves operating in parallel with other pumps can lead to system instability due to unequal sharing of the load.
Flat System Curve
When a system consists of mostly Static Head or Static Pressure difference, it is termed a flat system curve.
So what are the lessons here?
• For single pump operation in a system with mostly frictional resistance (steep) there is no disadvantage associated with an unstable pump curve. The majority of pumping systems would fall into this category.
• If you do not understand or do not know the shape of your system curve (steep or flat) then the safest option is to choose a pump with a stable curve.
• Stable pump curves are also recommended when operating two or more pumps in parallel.
Most important of all; understand your system.
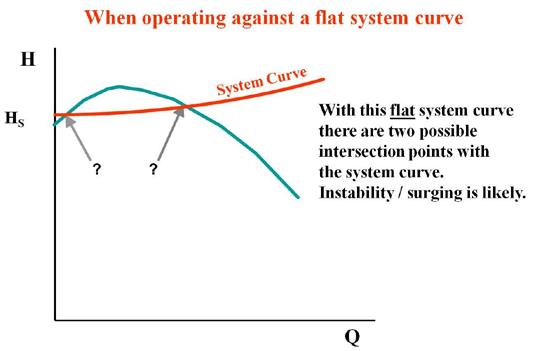
Antony Grage
In the ongoing Pump Pioneer series, Chris Bland catches up with some of the legends of the industry to get their perspectives on pumps. This edition, we speak to Antony Grage, a life member of PIA. In 1986, having left his first employer (after 23 years) in the road transport equipment industry, looking for a job with an Australian manufacturer, Antony joined Thompsons-Byron Jackson as Sales & Marketing Manager shortly before its amalgamation with Kelly & Lewis, which formed Thompsons, Kelly & Lewis. Antony
Antony stopped working at 68, and now at 72 has recently got a parttime job helping a small industrial company with the international marketing of their emergency flashing beacons. “Nothing to do with pumps, but still sold by the kilo. However, I enjoy going to some of the PIA meetings and to the annual dinner.”
I asked Antony how he first got started in the industry; “having worked for a company importing and distributing industrial equipment, my only criterion for a new job was to work for an Australian manufacturer of industrial machines; I believed that,


even in heavy industry, machines could be sold by value per kilogram so the type of machine didn’t really matter.
“I joined Thompsons-Byron Jackson in 1986 as Sales & Marketing Manager shortly before its amalgamation with Kelly & Lewis, which formed Thompsons, Kelly & Lewis (generally known as TKL). I knew a bit about hydraulic power transmission and the job I got happened to be with centrifugal pumps, and that turned out to be an unexpected bonus.
“Whilst only working for the one pump company, it really became a series of changing organisations as Thompsons took over Kelly & Lewis and then Ingersoll Rand Pumps. Also, after many years of working with our minority owner Dresser Pump Industries, which itself became Dresser Rand and then Flowserve Pump Division, TKL was eventually acquired by Flowserve so you might say I worked for at least four pump companies over 22 years.
What do you like about the pump industry?
“There are many things that I found fascinating about the pump industry. I like the touch of mystery attached to the technology of centrifugal pumps, and the manufacturing processes required for their complicated shapes. I was intrigued that so much energy could be transformed by such a relatively small machine, compared with the size of its driver. I particularly enjoyed working with customers on their wide range of applications: from irrigation schemes, to high-energy power station and oil refinery
pumps, and the rugged mineral processing machines. Site visits took me all over the world, and negotiating contracts to achieve the best solution was always an exciting challenge.”
What is your most memorable moment from your career?
“Two episodes stand out – you could hardly call them moments, as they evolved over quite long periods. One was winning and supplying a contract with Kvaerner Engineering of Norway for the majority of the pumps on the Woodside “Endeavour” offshore production and off-loading vessel. This is memorable because it was the largest order the company had ever won, and it taught us to work with an international contractor on a complicated job involving sophisticated metallurgy. Our contract management took a step increase in capability, which was of great benefit in administering future contracts. The other is being instrumental in the acquisition of a partly-developed range of slurry pumps, and then being involved in developing the complete range and marketing it to mining operators in Australia, and eventually in overseas mining regions from South America to Russia to Africa. The attraction of slurry pumps is in the speed with which they wear the wet-end components, ensuring a continuing stream of replacement parts. We saw that the world slurry pump market was dominated by the Australian manufacturer Warman, and we decided that there was an opportunity in being an alternative supplier to the market leader.”
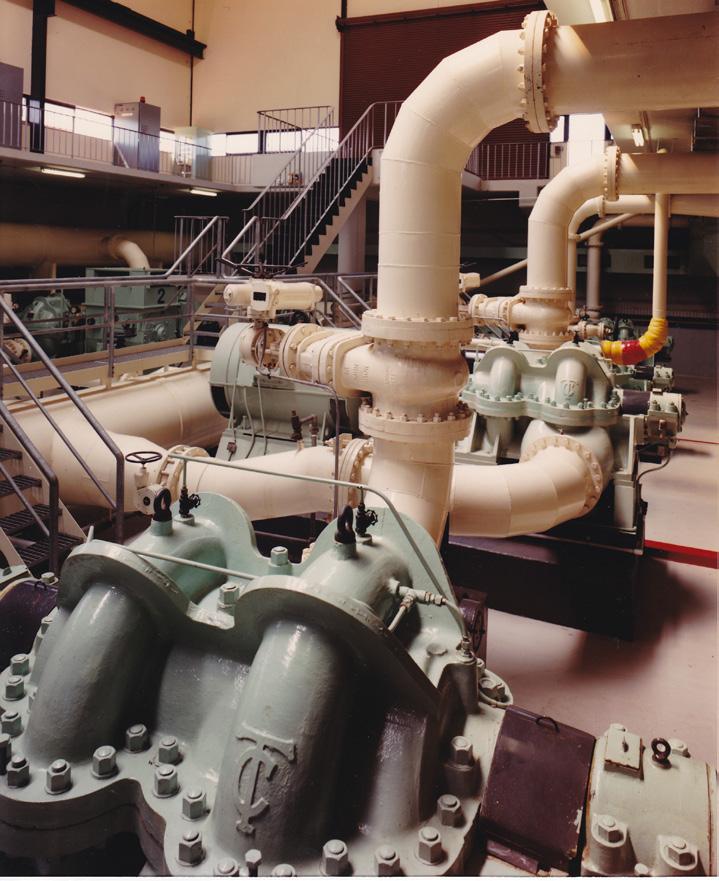
Did you have a mentor during your time in the industry?
“Bill O’Hehir was the managing director when I joined TKL in 1986, and he was already planning to retire in 1971; my office was next to his, and for all of those five years he taught me the intricacies of management - to change the things you could change, to accept those that you couldn’t, and to bet only on the things you knew were certain. He was an exemplary mentor.
“We had an excellent management team at TKL, remarkable for the mutual respect each of us had for the others’ various functions, for the way we worked to achieve an outcome once a decision had been taken, and for the humour that came out in every meeting. The faces didn’t change very often during my time: Bill Coulter took over from Bill O’Hehir as managing director, Les Shearer took over from Coulter as manufacturing manager, Chris Vickers took over from Malcolm McGibbon as engineering manager, and George Milford was finance manager for longer than I was sales manager. “We’ve all retired now, but most of us still
meet for lunch every few months. I also enjoyed being involved with PIA (and its predecessor APMA) as it gave one such a good insight into what was happening in the industry, and we had a lot of laughs at those meetings, too.”
How has the industry changed during your time in it?
“Every industry evolves in such a time span. The significant changes, in my opinion, have been: firstly, the elimination of Australian import tariffs, leading Australian manufacturers to be more competitive in an open market; secondly, the corporatisation of government departments responsible for water and wastewater treatment, and for power generation, which changed a long-established customer base with very focussed government engineers to one with more broadly-experienced contractors ; thirdly, the introduction of variable-speed AC pump drivers, which gave great flexibility in pump operation; and fourthly, the global amalgamations of long-established pump manufacturers, which brought Australian manufacturers into closer contact with foreign systems and products.”
What are the most significant developments you have witnessed in the industry?
“The use of computer-controlled machine tools for manufacturing, and computeraided design and drafting for engineering. What didn’t change much is the basic technology of centrifugal pumps which from their very start, well over a century ago, have been high energydensity machines. The changes in pump design were mainly in achieving greater hydraulic efficiency, and better mechanical reliability.”
What are the greatest challenges facing the pump industry? What does the future hold for pumps?
“Pumps are the second most common rotating machine after electric motors, so the future need for pumps is assured. The challenges facing companies in the industry are to move with the changes occurring in global sourcing, and to anticipate the changing needs of our customers. In other words, the challenge is to continually try to do better what we have always been doing.”
What advice would you give young people in the pump industry?
“Understand the Affinity Laws and the other rules governing pump selection, and listen to what your customer says he (or increasingly, thank heavens, she) needs rather than try to sell him what you’ve got on the shelf. In fact, listening to the customer’s needs invariably makes the difference in winning a contract at the best (and I don’t mean lowest) price. It’s a vital sales technique that can be taught, and is an essential part of sales training.”
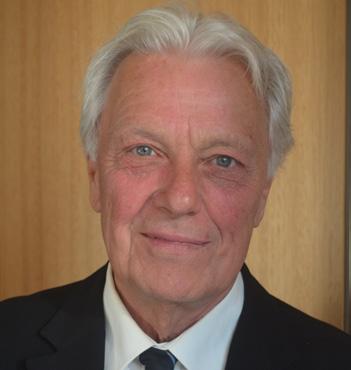
In his spare time, Antony looks after his grandchildren, goes sailing and indulges his interest in aviation history. He is also restoring an old car, “and my wife and I travel together every year, and go out for coffee together every morning.”
pump school

Most commonly used pumping terms and symbols
Brown Brothers Engineers Australia Pty Ltd, www.brownbros.com.au.
Mechanical pumps are the second most common machine in the world (after the electric motor), so here are some of the most commonly used pumping terms and symbols.
TERMS SYMBOL UNIT
Flowrate Q L/s
Head H m
Pressure P kPa
NPSH Available NPSHA m
NPSH Required NPSHR m
Velocity V m/s
Density ρ kg/m³
Gravitational Acceleration g m/s²
Efficiency η -
Rotational Speed N r/min
Area A m²
Absolute Viscosity μ mPa.s
Kinematic Viscosity v mm²/s
Specific Gravity S.G. -
Total Dynamic Head HZ m
Friction Head Hf m
Static Suction Head Hs m
Static Discharge Head Hd m
Atmosphere Pressure Head Ha m
Velocity Head Hv m
Total Static Head Hst m
Vapour Pressure Head Hvap m
Reynolds Number R -
Friction Factor f -
Length of Pipe L m
Internal
Pipe Diameter d mm
Absolute Roughness e mm
Resistance Coefficient K -
Total Suction Head Hss m
Total Discharge Head Hds m
Chemical handling made safe and easy
For the past 50 years Acromet has built an industry-wide reputation for its outstanding skill in handling difficult, aggressive chemicals in all forms.
The company’s range of magnetically-driven sealless process pumps easily meet the demands of complex chemical handling applications across a range of industries.
The pumps cover a wide range of liquid end designs from Sliding vane, Regenerative Turbine and specially lined Centrifugal Pumps to suit a wide range of applications and performance criteria.
Acromet’s sealless pumps cover a wide range of designs, from specially lined centrifugal pumps to sliding vane and regenerative turbine pumps, to suit a wide range of applications and performance criteria.
The company’s heavy duty sealless centrifugal pumps with permanent magnet drive system meet the requirements of API.685, ISO2858, DIN24256 and Atmosphere Explosives ATEX standards.
The majority of Acromet’s sealless pump ranges are of the traditional back pull out design, where the pump’s internals can easily be inspected and parts replaced without disconnecting system pipe work. When required, the pumps can be easily maintained with one of the company’s “quick change” impeller and inner magnet cartridge kits.
Acromet’s pump designs range in capacity from between 1 and 3500 cubic metres per hour, with discharge heads up to 140m.
Different pump styles are designed to operate in temperatures ranging from minus 120ºC to as high as 350ºC.
The pumps are available in a wide range of engineered plastic materials including ethylenetetrafluoroethylene (ETFE), paraformaldehyde (PFA) and polyvinylidenedifluoride (PDVF)
Acromet’s horizontal and vertical centrifugal pumps they are also available in CF8M, hastelloy C276, incoloy 825, duplex stainless, titanium, with other materials available upon request.
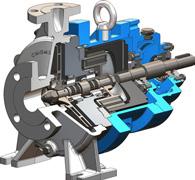
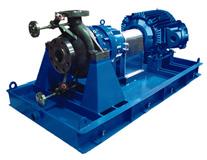
Versa-Matic Pumps launches mobile app
Versa-Matic, a leading brand in the world of Air Operated Double-Diaphragm (AODD) pumps, recently launched a unique mobile application specifically designed to support Air Operated Double Diaphragm (AODD) pumps. The new mobile application from Versa-Matic will help AODD pump owners quickly and easily find the tools needed to support pumps installed in the field, as well as pumps currently being built and shipped.
The Versa-Matic mobile app empowers users to quickly locate information related to a specific pump using My Pump Details through quick bar scanning or via a manual entry.
Additional features include the ability to instantly review Chemical Compatibility using the interactive guide, conveniently flip through the latest full line catalogs, watch helpful service and repair training videos and more. “We are excited to introduce this revolutionary tool to our end-users. Customer service is our top priority and the new mobile application takes service to the next level,” says Mathew Harris , Regional Manager. “For our global audience, the ability to use the mobile app any time of the day or night is a definite advantage to doing business with Versa-Matic. We will continue to develop this mobile app by adding more features over the next few months. ”
For more information on the mobile application, visit www.versamatic.com/mobileapps.asp. While on the site be sure
to flip through the new full line product catalog and view the helpful service and repair videos.
About Versa-Matic
The Versa-Matic brand is manufactured at the Warren Rupp, Inc. facility in Mansfield, Ohio. Versa-Matic AODD pumps provide high quality and the best value for your pumping needs. These dimensionally interchangeable products are the first choice for pump replacement upgrades. Versa-Matic pumps are available in a variety of plastic and metal materials such as polypropylene, acetal, aluminum and stainless steel. Sizes range from 1/4” to 3” and specialty features, including clamped design, bolted design, split manifold, side discharge and numerous others are also available. Products are supported nationally by TDA Pumps our factory-authorized Australian distributor.
For more information contact mharris2@ idexcorp.com ph- (02 4574 0448) or visit www.idexfmt-asia.com.
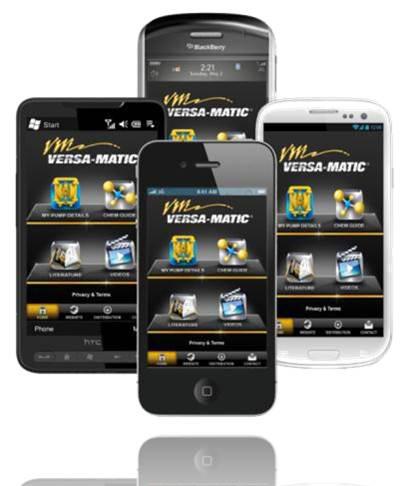
Editorial schedule
May 2013
Main feature
Reliability
Industry Focus
Water
HVAC
Plastics, rubber, chemicals
Pump Products
Seal-less pumps
August 2013
Main feature
Imports & exports
Industry Focus
Mining Food
Wastewater
Coal Seam Gas
November 2013
Main feature
Energy efficiency
Industry Focus
Power generation
Fire protection
Irrigation
Pump Products
Repair & maintenance
February 2014
Main feature
State of the industry
Industry Focus
Oil & Gas
LNG
Manufacturing & heavy industry
Pump Products
Vacuum pumps
Deadline: 22 March, 2013
Related Products: Seals Connectors
Couplings & seals
Bearings
Mechanical seals/support systems
Elastomeric seals/gaskets/packing
Wear rings
Deadline: 14 June, 2013
Related Products:
Motors and drives
Gears
Cylinders & actuators
Compressors
Fans
Pump Products
Balancing
Deadline: 6 September, 2013
Instrumentation, control & monitoring
Pressure, temperature and level gauges and sensors
Vibration instrumentation and analysis sensors
Flow meters, control panels
alignment tools
Condition monitoring sensors
Deadline: 29 November, 2013
Related Products
Valves
Manifolds
Pipes and piping systems
Filtration systems
Lubricant & lubrication systems
Coatings
Custom casting
Acromet
ANRO Engineering
Brown Brothers Engineers
Haskel
Idex Fluid & Metering
JDM Instant Pumps
Kelair Pumps Australia
Milton Roy
Northern Diesel & Hydraulic
PIA Membership
Precision Balancing
Prominent Fluid Controls
Pump Affinity
Pump Industry advertising
Pump Industry subscriptions
Sterling Pumps
Teco Australia
The Pump House
Toshiba International Corporation
United Pumps Australia
Xylem Water Solutions Xylem Water Systems
Missed out this time?
Didn’t manage to get an ad into this issue and wish you had?
Don’t worry, as the next edition is just around the corner
Contact Chris Bland now to book in now for the next edition to ensure you don’t miss out again
magazine@pumpindustry.com.au
(03) 9440 5721 Never
Go to www.pumpindustry.com.au and hit subscribe to ensure you keep receiving Australia’s best new trade magazine.
Hit

•
•
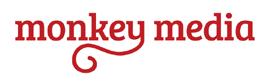
In the tradition of groundbreaking innovations comes…
Flygt E xperior™
Welcome to a new era in wastewater pumping. Where engineering excellence and a pioneering spirit combine with an unmatched understanding of your needs. The result is Flygt Experior, a uniquely holistic experience that combines state-of-the-art hydraulics, motors, and controls.
Today, Flygt Experior combines N-technology hydraulics and its adaptive functionality, premium efficiency motors and SmartRun – the all-new intelligent control. Flygt Experior comes from years of listening to you and applying our knowledge and expertise, to develop the most reliable and energy-efficient wastewater pumping. It is therefore the ultimate in our commitment to you.
Flygt Experior™. Inspired by you. Engineered by us.
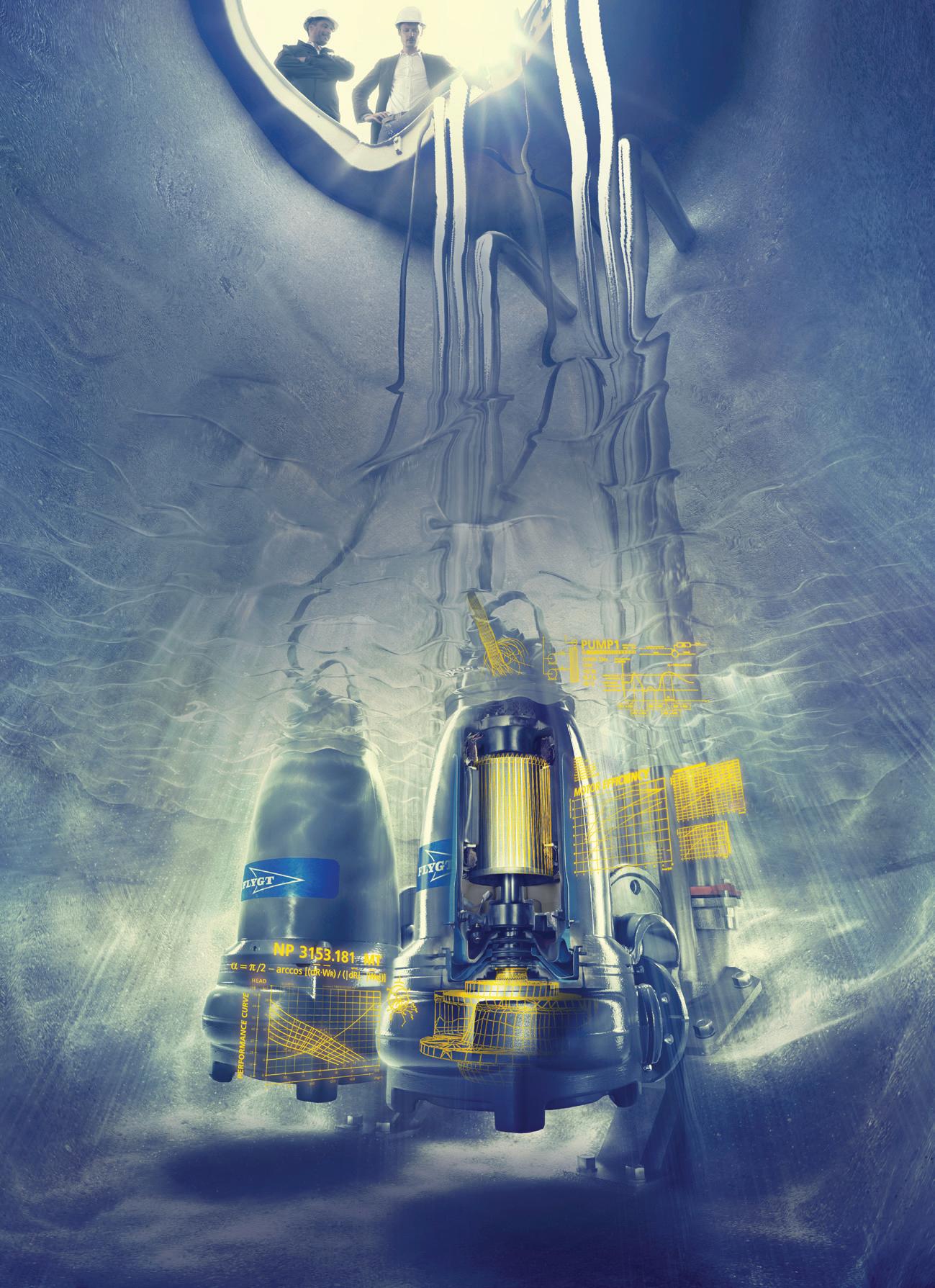

