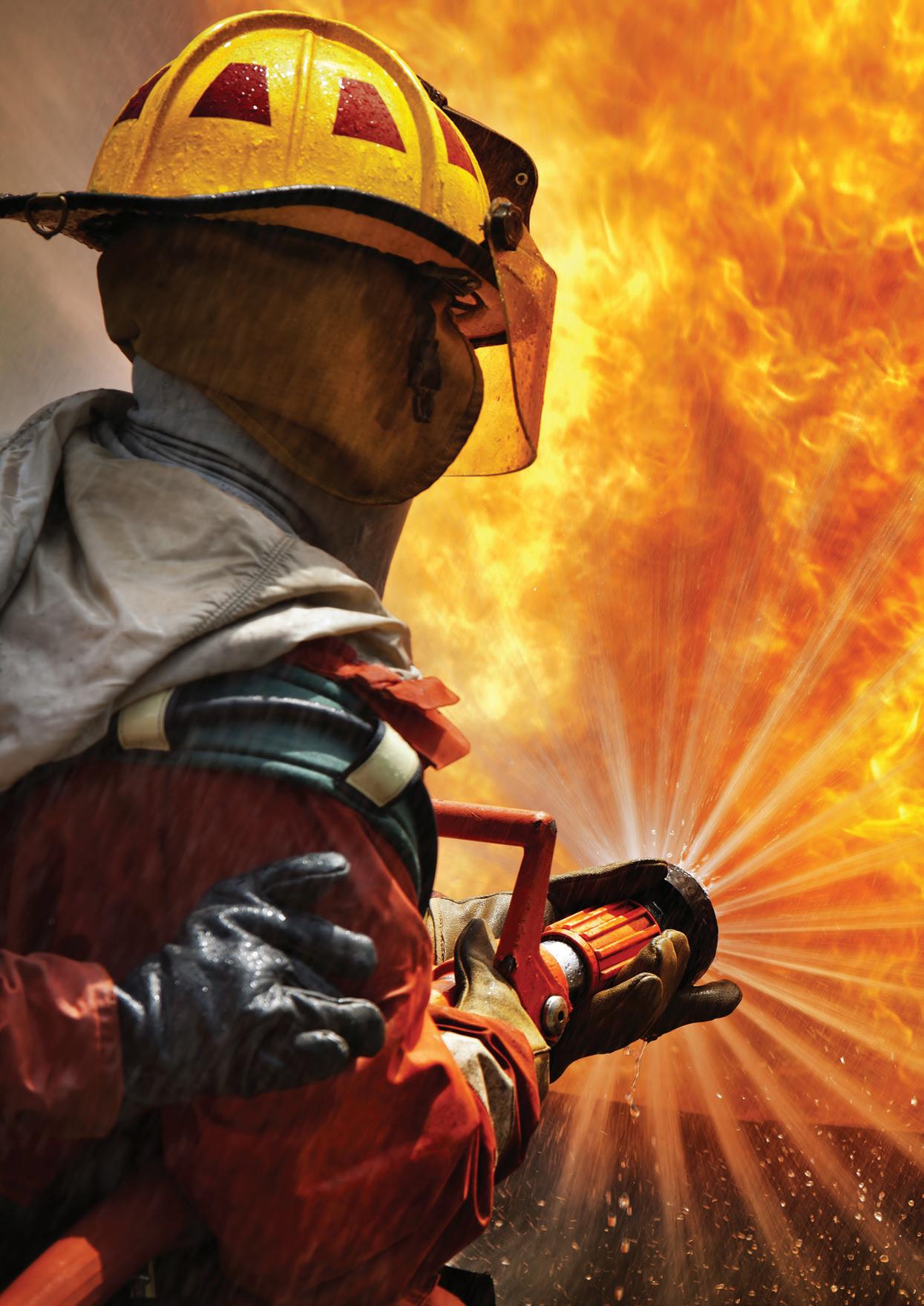
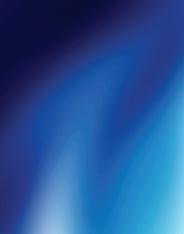
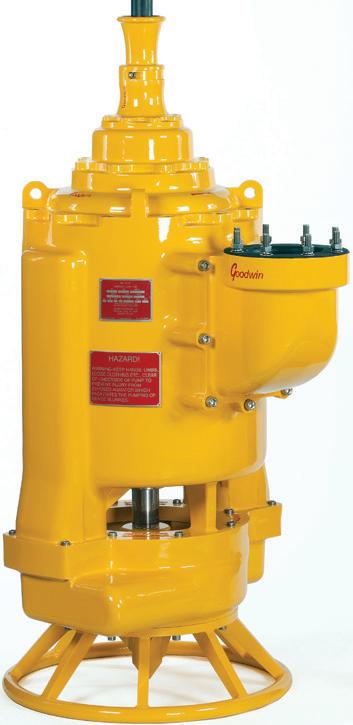
Submersible Slurry Pumps for the most demanding environments
September 2015 marks the first anniversary of Goodwin Submersible Pumps debut into the Australian market. Goodwin Submersible Pumps are recognised globally for their unrivalled heavy duty performance.
The Australian mining industry has been taken by storm by the Goodwin precision engineered slurry pump, outclassing the competition with its strength and endurance.
Initially located in Brisbane, the company have now expanded nationally and feature sales offices in Perth and Sydney. All of our technicians are fully trained to help and advise with commissioning and installation, as well provision of ancillary products to assist your pump needs.
The 100 and 200 Submersible Pump Range are available in the ANZE, NZE and HNZB variant, with full spares for servicing and maintenance. All pumps fully comply to Australian mining standards.
The technical expertise of Goodwin Submersible Pumps has been proven in the steel, power and mining industriespumps are now sold on five continents with centres of excellence in Europe, India, China, Brazil, South Africa and now Australia.
For further information & a Submersible Pump Trial... Call +61 (0)7 3205 7860
www.goodwinaustralia.com.au
Pump Industry Australia Incorporated
Kevin Wilson – Secretary PO Box 55, Stuarts Point NSW 2441 Australia
Ph/Fax: (02) 6569 0160 pumpsaustralia@bigpond.com
Ron Astall – President United Pumps Australia & Astech Consulting Services
John Inkster – Vice President Brown Brothers Engineers
Mike Bauer – Councillor Dynapumps
Frankie Camilleri – Councillor John Crane
David Alexander – Councillor KSB Australia
Alan Rowan – Councillor Life Member
Keith Sanders – Councillor Australian Industrial Marketing & Life Member
Ashley White – Councillor Davey Water Products
David Brooks – Councillor Flowserve Australia
Is government action necessary to generate industrial energy savings?
In some sectors, probably! The incentives for energy saving have never been better and yet the take up seems slow. Whether there are government incentive programs or not, I believe that the scope for energy saving in pumping systems is massive.
At United Pumps Australia, we recently performed a fairly simple upgrade to the hydraulics of some 250kW cooling water pumps, which could generate annual electric power savings of more than $250,000. This was the figure without any grants or incentives applied and the payback is obvious. In this instance, the customer did indeed have a governmentsponsored incentive program as well.
This example involved improved pump hydraulics and reconditioned running clearances. More typically, however, is the scenario where pumps are oversized and are throttled back – wasting considerable energy. It is estimated that the difference between best practice and the status quo could be in the range of $20,000 to $100,000 per annum in a typical high-rise office tower.
British Pump Manufacturer’s Association Executive Director Steve Schofield related a number of stories where annual paybacks of $20,000 to $50,000 had been identified – and were theoretically achievable though impeller trims or the use of variable speed drives – and yet, despite clear short-term payback, no action had been taken after twelve months and the report had been shelved.
It is my view that in general the pump industry is ahead of the game, with many suppliers and manufacturers actively promoting energy saving products and systems. But the specification writers, designers and worst of all, those responsible for implementation, seem to be lagging behind.
As massive consumers of energy the pump industry has an obligation to continue to foster awareness on this issue.
Should we be lobbying the legislators?
Ron Astall President, Pump Industry Australia3,318
Published by Monkey Media EnterprisesABN: 36 426 734 954
PO Box 3121
Ivanhoe North VIC 3079
P: (03) 9440 5721
F: (03) 8456 6720
monkeymedia.com.au
info@monkeymedia.com.au
pumpindustry.com.au
magazine@pumpindustry.com.au
Publisher and Editor: Chris Bland
Managing Editor: Laura Harvey
Marketing Director: Amanda Kennedy
Marketing Consultant: Aaron White
Marketing Consultant: Jordan Harbinson
Associate Editor: Michelle Goldsmith
Journalist: Emily Thomas
Creative Director: Sandy Noke
Designer: Alejandro Molano
ISSN: 2201-0270
In this issue of Pump Industry I’m thrilled to present our inaugural Industry Capability Guide, the key reference tool for all pump users in 2016.
We’ve designed the guide with you, the reader in mind. The guide features company entries, which outline the capabilities and services our entrants provide, and importantly, the guide also features indices which allow users to search by industry and product, to find the supplier that best caters to their needs.
The guide also has an online home –www.pumpindustry.com.au/directory/–which makes it even easier for users to search for the best product or service provider for them.
The Australian Pump Industry has evolved from the days of a small number of large manufacturers. This has been replaced with a much larger number of small to medium companies who often excel in their particular area or niche, and offer a range of very high-standard products and engineering expertise.
I hope that the guide, in both its print form and online, is a useful way to connect our readers and pump end-users everywhere with the products and services they need.
The Industry Capability Guide has been a labour of love to put together, but it’s a product I’ve wanted to create since I first started this journey of
This magazine is published by Monkey Media in cooperation with the Pump Industry
not necessarily the views of either the publisher or the PIA. Neither the
advertisers. All communication should be directed to the publisher.
The publisher welcomes contributions to the magazine. All contributions must
By providing content to the publisher, you authorise the
combined with other content in any of its publications and in any
publishing Pump Industry back in 2012. My thanks go out to all the companies that have been involved; and to those who have missed out, keep your eyes out later next year, when we will begin the production of the 2017 edition of the guide.
We have plenty of other features in this edition which I’m excited to share with you. We have continued our exploration of the theme of energy efficiency, providing you with an update on where the industry is at with this issue. While some may see energy efficiency as a challenge, the PIA is firmly advocating for the industry to view energy efficiency as an incredible business opportunity which we can all benefit from.
We also have an update on the latest fire protection standards; and we take a look at a new pumped storage hydro project which is in the planning stages and could provide a boost for the National Electricity Market.
This quarter also includes the PIA Annual General Meeting in November, and I look forward to catching up with many of you there. If you’re reading this magazine and are not yet a member of the PIA, please see the contact details on the previous page and join today.
Chris Bland Publisher and Editor Cover image highlights our feature on fire protection in this issue. Turn to page 36 to read more.ships first load of
has been made of the potential to improve the efficiency of pump systems globally. With more than 40 per cent of the world’s energy consumed by pumps, the potential to have a real and lasting impact on energy consumption is significant. Here, we take a look at what is being done around the country to educate pump manufacturers, suppliers and end users about the energy their pumps are consuming – and the steps they can take to make their systems more efficient.
for Xylem Oceania
for
Lev Nelik, or Dr Pump as he is also known, is an international pump industry stalwart with over 30 years of industry experience and over fifty publications about pumps to his name. In addition to his consulting work, he currently teaches pump training courses worldwide and publishes pump tips, advice and troubleshooting on his website. Much of his advice focuses on preventative maintenance methods to improve reliability, reduce energy consumption and optimise the operation of pump systems. In this article, we look at some of his top tips to ensure pump reliability.
Pump industry legend John Link shares his reflections on a life spent developing businesses, inventing equipment and mentoring colleagues in this latest edition in our ‘Pump Pioneers’ series.
Buyer’s guide: choosing the right
We’re still receiving entries in our ‘Pump up your selfie’ competition. Our favourite entry of the quarter came from Shakti Pumps, who snapped themselves reading their favourite magazine at their factory premises in India.
Pictured is Anshul Gupta, Shakti’s National Manager Australia, who was showing Atul A. Janawade, Shakti’s General Manager Exports, the company’s ad in the August 2015 edition.
At Pump Industry, we love our readers, and we love to see photos of you reading your favourite magazine. To encourage you all to share a photo of yourself reading Pump Industry at your workplace, we’re giving away a copy of the Australian Pump Technical Handbook for the best pump reader selfie.
We extended the deadline for entries to this competition, with a final cut-off of 30 November 2015. Entering your selfie is easy – just take a snap of yourself reading Pump Industry (or feel free to ask someone to take the
picture for you), then either send it to Managing Editor Laura Harvey or tweet it and tag @pumpmag with the hashtag #pumpupyourselfie.
The best picture, as judged by Pump Industry, will receive a copy of the
Our continuous exposure to a wide range of problems and Industrial applications across numerous markets, has ensured we have the know how to handle pump repairs of all sizes and complexities, including re-engineering, testing, laser alignment, condition monitoring.
With each repair job we implement a thorough inspection process and follow strong control and stringent acceptance criteria carried out by dedicated team dedicated to keeping your pump working at optimal performance.
Link Pumps has been servicing the needs of Australian Industry with pump hire solutions for over 50 years, and as such has built a reputation for being able to solve complex engineering problems and additionally undertake complex setups with complete reliability notwithstanding working to the exacting standards of environmental and occupational health and safety expected by that of our customers and regulatory authorities.
Australian Pump Technical Handbook, the Australian pump industry’s one stop guide to all things pumps, valued at $90.
So get creative and share your snaps with your colleagues and fellow readers today!
For all your Pump Hire and Repair needs you can’t go past Link Pumps, so call us now…. We perform, Anytime, Anywhere
The Hydraulic Institute has released the Reliability of Pumping Equipment Guidebook, which is now available for purchase online.
The guide provides insight on how to maintain the reliable operation of your pumping equipment.
Improving and maintaining the reliability of rotodynamic pumping equipment is essential for those with an interest in improving the cost, safety, and reliability of pumps and related equipment.
This guide provides reliability insights such as expected reliability levels, monitoring approaches, and methods of improvement. Information is also
included on how to identify satisfactory operation for different pump types, classes of service, and importance.
Maintenance and reliability professionals looking to benchmark and improve reliability and cost of ownership will benefit from the information contained in this guide.
This guide is available in the HI eStore in hardcopy or secure electronic PDF format. Head to estore.pumps.org to order your copy.
SEEPEX Smart Conveying Technology extends the life of your stator. Adjustment of the retaining segments takes just 2 minutes and restores 100% pump performance.
Tests have shown up to 3x stator life compared to conventional progressive cavity pump design Join the smart revolution and test our innovation “Smart Conveying Technology”.
SEEPEX Australia Pty. Ltd.
Tel +61.2.4355 4500
pvila@seepex.com
www.seepex.com
Esso Australia Resources, a subsidiary of ExxonMobil Australia, will soon embark upon a $400million project to replace a 187km pipeline to transport crude oil and condensate between its Longford and Long Island Point facilities in Victoria.
The pipeline will allow the continued safe delivery of crude oil and condensate and ensure that natural gas from offshore Gippsland operations continues to flow to Australian households and businesses.
The pipeline replacement has received full project funding from Esso Australia Resources and Gippsland Basin Joint Venture partner BHP Billiton. Each have a 50 per cent interest in the project, with Esso Australia Resources acting as the operator.
Pending regulatory approval, construction of the replacement pipeline is expected to begin in late 2015.
“With an approximate project
cost of $400million, the replacement pipeline represents another significant investment in the continuation of our Gippsland operations, which have provided crude oil, condensate, LPG and natural gas to the Australian market since operations began in 1969,” said Richard Owen, ExxonMobil Australia Chairman.
Mr Owen said it is anticipated that, at its peak, the project will generate approximately 500 jobs, as well as deliver additional indirect employment opportunities.
“Development of Gippsland’s oil and gas has historically brought the region significant long-term benefits, boosting economic growth and creating new jobs,” Owen said. “Our commitment to the continued safe, reliable supply of cost-effective energy is demonstrated through this key infrastructure investment and our continuous pursuit of opportunities to reduce cost and improve productivity.”
The PIA will be running the initial presentation of its new Pump Installation & Commissioning Training Program in Melbourne in October.
This one-day course will take place on Wednesday 28 October at Link Pumps in Williamstown. There are a maximum of ten places available, in order to ensure strong interaction between the trainers and participants.
The course will be run in two parts: a theoretical session, followed by a practical session in the Link Pumps test area, where a unit will be set up for commissioning.
The training program will be presented by PIA Executive Officers Alan Rowan and Ken Kugler. The cost of the course is $400 plus GST to PIA members and $500 plus GST for non-members. Attendees will be required to wear work clothes with heavy footwear for the practical session.
Ten places only - register early
Date:
Wednesday 28 October
Venue: Link Pumps
4 Ponting Street North Williamstown
VIC 3016
Time:
8:15am to 5pm Register your interest in attending with PIA Secretary Kevin Wilson at pumpsaustralia@bigpond. com.
Please note, applicants may be requested to demonstrate a working knowledge of pumps prior to their registration for this course, either
by previous experience or by past attendance at an approved pump technology training course.
• Ultra tough, portable pumps
• Pump coal, sand, sludge
• Mining slurry, drill cuttings
• Mud and slimes
• Up to 60m3/hour transfer
A recent upgrade to a sewage treatment plant highlights the long-term benefits investing at the capital stage can offer.
The Mornington Peninsula has long been a favorite holiday destination for residents of Melbourne. It has a permanent population of around 125,000, which can double during summer. The Boneo wastewater treatment plant serves most of the Peninsula and was upgraded by South East Water (SEW) to better handle the peak summer loads.
Due to higher than anticipated growth, SEW predicted that the plant would overload in the summer holiday period of 2015. SEW engaged UGL to design, construct, commission and maintain a major upgrade at the Boneo sewage treatment plant (STP).
Duplication of the plant was not practical as the existing plant could cope with the load for 11 months of the year, so the upgrade was tailored specifically to handle the summer peak loads. Capital expenditure had to be minimised and the solution had to be installed without disrupting the existing plant operation.
The first action was to increase the air capacity in the plant. There was an initial preference to duplicate the existing positive displacement blowers as it was straightforward and standardised spare parts and maintenance. However, UGL
performed a whole of life cycle cost calculation against HST compressors. The capital investment was higher, but the payback period was calculated at just over one year of operation. In addition to the energy savings, the maintenance requirements, noise levels and footprint of the HSTs were superior to the existing blowers.
The upgrade included two Sulzer HST turbocompressors. The HST20 is an integrated package. The turbocompressor is designed for ease of installation and operation, with an inlet silencer, an outlet silencer and a silenced blow-off valve incorporated into the cabinet. Complexity is reduced, along with the cost of installation. The new HST turbocompressors offer energy savings of approximately 33 per cent compared to the existing positive displacement blowers. Modifications to the system have subsequently been made so that the HSTs can supply the old diffuser system. This allows SEW to benefit from the efficiency gains of the new blowers when the plant is in normal operation.
The second phase was to install additional aeration equipment. Several options were analysed. The existing diffuser system functioned well, but
duplication of the system was not possible without taking the bioreactor offline and demolishing some concrete baffle walls. The solution was to install four submerged Sulzer OKI aerators, two in each bioreactor, to cater for the peak periods. The OKI units were ideal for this application as they can be installed, moved and removed for maintenance without taking the bioreactor offline.
Key customer benefits included:
• Reduced footprint, noise and maintenance costs. Nearly maintenance-free operation
• 33 per cent reduction in energy consumption compared to previous blowers, which is real direct LCC savings for SEW
• Magnetic bearing technology allows the HST to run alongside PD blowers
• Easy installation of the OKI units –no fixing to the floor is required.
For more information on our products and solutions for wastewater treatment, please visit sulzer.com.
Less than two months after its official opening, AGL’s $310million dollar Newcastle Gas Storage Facility (NGSF) at Tomago in New South Wales has shipped its first consignment of liquefied natural gas (LNG).
The shipment, 17 tonnes of LNG, has been supplied to a commercial processing facility in the Hunter region.
The NGSF is Australia’s largest LNG facility servicing the domestic market. LNG is produced by purifying and cooling natural gas to -161°C, the point where methane condenses to a liquid form. It is then pumped into the 63,000 cubic metre insulated storage tank.
AGL’s Executive General Manager Group Operations Doug Jackson said
initially there would be two to three LNG deliveries a week from the NGSF.
“Not only does the NGSF ensure gas supply security for peak usage periods or supply disruptions, but it can help meet the growing commercial LNG needs of Australian industry as it seeks lower carbon-emitting fuels in a costeffective manner,” Mr Jackson said.
“The use of LNG may offer significant cost savings over LPG or diesel. It produces 10-15 per cent less CO2 than LPG, and with significantly lower particulate emissions than coal or diesel, it represents an eco-friendly and costefficient fuel alternative for regional Australian businesses that are located off the gas network,” he said.
“The processing plant that converts pipeline natural gas to LNG is capable of processing up to 66,500 tonnes of LNG per year and storing 30,000 tonnes throughout the year. This makes AGL’s NGSF the largest LNG facility in Australia servicing the domestic market,” Mr. Jackson said.
The LNG is stored and vapourised at the customer’s premises, the pressure is regulated and its usage metered.
AGL offers a ‘turnkey’ service and converts burners, boilers, and other gas appliances on customer sites, and will assist customers meeting codes and compliance and certification requirements.
There are many companies which openly advertise the sale of spare parts for all progressive cavity pump brands. Usually their prices are considerably less than what is offered by the original equipment manufacturer (OEM).
Our progressive cavity pump expert is Peter Vila, Managing Director of SEEPEX Australia.
Peter has been involved with pumps for 35 years. He spent the first five years repairing them and the subsequent 30 years directly in technical sales, and for the past 15 years he has been predominately involved with SEEPEX progressive cavity pumps.
Non-original stator.
If you ask this question of any OEM, they will tell you that the use of original parts is absolutely crucial to pump performance and reliability. There are many reasons for this stance and following are some comments and a few examples of potential issues which may be faced by PC pump operators when not using genuine OEM parts.
When considering the purchase of a new pump, the lifetime cost of your equipment is obviously important. The high quality and precise fit of the main pumping elements, the rotor, stator and the joints determine the reliability, life and durability of the pump.
Non-original stator.
When replacing parts, matching the materials of construction to that of the initial build specification is vital to maintain good service life. By doing so, you ensure that the pump is returned to its quality, efficiency and performance. Using any other option brings with it the risk of premature failure, reduced performance and lower efficiencies.
Is it worth the risk? If you are thinking about using alternative parts for your PC pump, please consider the following examples of some failures and concerns that our customers have highlighted to us.
This is a new, unused stator as delivered, with very poor surface finish and quality. As a result, the customer can expect lower volumetric efficiency, reduced pressure handling capability, reduced pumping capacity and shorter rotor/stator life.
Poor fit (clamping) between rotor and stator.
Sometimes the fit can be too tight, resulting in issues such as the pump not starting, overload of stator and drive train, overload of the joints and increased power consumption. At other times, the fit can be too loose, which results in reduced pumping capacity, shorter service life and increased slip/backflow of the product, leading to increased wear.
Non-original joint sleeves typically have less material used in manufacture, thinner wall sections and the seal contact profiles are usually wrong. The sealing is weaker by design, resulting in the wear/failure of joint sleeve, loss of lubrication, product contamination of the joint, and premature wear/failure of universal joints.
Common issues include the supply of non-hardened coupling rod pins, coupling rod bushes with poor interference fit or incorrect positioning, restricted eccentric movement, or the wrong type of lubrication supplied and used. The end result is typically pins sheared due to an inability to cope with the high transfer torque, bushes rotating and shattering, and the overloading and overheating of lubricant which is transferred to individual components, ultimately resulting in complete joint failure.
All of these examples are from genuine field cases. Each had severe implications to process and incurred very high incidental costs.
So...is it really worth the risk? Listen to your OEM and only use original spare parts – quality pays for itself in the long run.
In July, Jim Athanas took over the role of Managing Director for Xylem Oceania. In this role, Jim will be responsible for driving revenue and market share expansion and will be based in Sydney.
Jim brings extensive commercial leadership expertise to Xylem.
He has more than 20 years of experience in a variety of water-related companies and has served in sales, marketing and general management positions with a heavy focus on driving business growth and profit organically and through acquisition. His previous positions include Managing Director for Nilfisk Australia, in addition to management positions at Ecolab and Nalco.
Most recently Jim served as the Managing Director - Pacific for Nilfisk
Australia, and previously at Ecolab as Vice President and General Manager, Pacific - Water Care Division.
Prior to Ecolab, he held several positions at Nalco, including an Asia Pacific assignment based in Singapore.
Jim holds an undergraduate degree in Chemical Engineering with Honours from the University of New South Wales, received his Master of Management from Macquarie Graduate School of Management and is a graduate from the Australian Institute of Company Directors (AICD).
•
•
•
• Torque control, smooth start and stop modes to avoid water hammering
• Dedicated software for pump control systems
• Programmable timers with real time clock
• Early warnings and safety stops
• Optimized monitoring for energy saving
• Control of up to 7 pumps
• IP20/21 and IP54 rating
A new and patented self-cleaning sump is now available in Australia through Hydro Innovations. Developed by Hydro-Plus of Belgium, in conjunction with Gorman-Rupp, the self-cleaning sump is said to address many of the issues confronting owners of sewage pump station assets.
The issues confronting asset owners include high capital costs, high energy consumption, and the cost of intervention when the likes of sediment, solids or fat build up, or for removing chokes from pumps. Operator safety is also an ever present issue with ever changing regulations.
The self-cleaning sump (SCS) concept has been developed to address these issues. The conventional 2-3m diameter cylindrical wet well is replaced by an inclined collector pipe from which self priming pump suction lines access the wastewater. Nothing electrical or mechanical is in the SCS. This system is used in conjunction with VFD controlled pumps and an air bubbler liquid level control system to reduce energy consumption over the conventional DOL or soft starting pump systems.
The philosophy behind the system is to keep solids (sediment, fat, rags, etc.) in suspension and moving, and to
take all issues associated with operator intervention (maintenance, blockage removal, etc.) to the surface where it is easier and safer for operators to address them.
Keeping the solid matter in suspension and removing it quickly does not allow time for fibres and rags to ball and mat together, or for sediment or fat to build up. This should reduce the incidence of pump blockage caused by balling rags and greatly reduce the need for vac truck intervention.
Because pumps are mounted on the surface, there is no need for operators to open wet well lids (exposing them to falls or drowning) or employ lifting devices (exposing them to heavy swinging weights and the associated dangers of working with cranes). This
makes any sort of intervention much easier and safer for operators. Blockage removal, clearance adjustments, oil inspection or changes, valve greasing or exercising can all be done safely by one operator working out of a standard vehicle, rather than a crane truck with an additional person or two.
The civil construction costs are also said to be much lower using this system because of the inexpensive HDPE collector pipe, which is much cheaper than a full concrete wet well/valve vault combination, and the smaller excavation footprint.
The generation of fresh ideas, the need for progress and the ongoing development of products has never been more important for manufacturers in the Australian pump industry. Here, we take a look at some of the benefits Australian manufacturers enjoy by continually focusing on a paradigm of innovation.
The global economy is changing. New technologies and smart companies lead. New industries and new sources of wealth are emerging. New skills are required for workers at all levels. Australians must decide whether we will be at the forefront of these changes or be left behind.
This is the current message from the Federal Government, which has adopted a strongly pro-innovation stance. There’s a particular emphasis on science, technology, engineering and mathematics (STEM), which as a group
have been defined as the building blocks for Australia’s future.
It has been estimated that more than half of today’s jobs will not be in existence by 2050 – these roles will be superseded, with service based jobs becoming increasingly obsolete. The jobs of the future will be knowledge based, geared towards solving the problems the global population will face, such as climate change.
The Federal Government promotes innovation in Australian businesses through its R&D Tax Incentive program, a targeted, generous and easy to
access entitlement program that helps businesses offset some of the costs of doing R&D.
The program aims to help more businesses do R&D and innovate. It is a broad-based entitlement program. This means that it is open to firms of all sizes in all sectors who are conducting eligible R&D.
Australian pump industry manufacturers can enjoy the benefits this grant program offers. One company which has done so is Crusader Hose, a manufacturer of flat lay hoses and
associated equipment.
The importance of innovation is well understood by Crusader Hose Managing Director, Francois Steverlynck. In its 30-year history, the company has consistently focused on customisation, and has invested in R&D to continually improve the products it brings to market.
“Over the years we’ve always invested in the continual development of our products, and as we celebrate our 30th anniversary this year, this has culminated in the opening of an Innovation Centre at our head office in Victoria.
“We’ve been able to open this new facility thanks in part to the generous support of the Federal Government through the R&D Tax Incentive program.
“At the new facility, we’ll be focusing on analysing hose developments in a laboratory type environment, using equipment such as tensile testers, microscopes and abrasion testers. These are all requirements from our client base to improve and develop our layflat hose characteristics.”
The new facility was opened earlier this year at an event attended by more than 100 people, including AusIndustry’s Assistant Program Manager for Business Services, Shirley Campbell, and State Government Member for Bayswater, The Honorable Heidi Victoria MP.
“The success of our company has really been built on the back of a culture of innovation,” said Mr Steverlynck. “As STEM disciplines become more and more important for
Australian businesses – especially for manufacturers in the pump industry – this will continue to be the case. The importance of listening to one’s customers, then acting on their needs, will apply more than ever.”
Businesses in the pump industry have a choice. We can’t afford to be complacent in the years ahead - the global market is at a critical stage in its development, and we are now facing a reality where companies must innovate or be left behind, particularly due to the competition from our competitors in the Asian region.
But if we keep on innovating now, keeping abreast of worldwide standards, an exciting and successful future can be obtained.
The R&D Tax Incentive provides a targeted tax offset to encourage more companies to engage in research and development. It has two core components: a 45 per cent refundable tax offset for eligible entities with a turnover of less than $20 million per annum, provided they are not controlled by income tax exempt entities; and a non-refundable 40 per cent tax offset for all other eligible entities.
Unused non-refundable offset amounts may be able to be carried forward to future income years. For more information go to www.business.gov.au.
Lower Murray Water (LMW) is running a new awareness campaign to get customers to think about what they are putting down their household drains and toilets that can block the area’s sewer systems.
The campaign aims to educate customers about how the things that go down their sink, toilet and household drain has a big impact on our environment, our treatment plants and the cost of treating the wastewater.
LMW attends on average 85 sewer blockages each year, costing up to $1000 per blockage.
Replacement of pumps due to irreparable damage from blockages can cost up to $50,000 per pump.
LMW has over 630km of sewer pipes which supply wastewater treatment
plants, which process more than 15million litres of wastewater every day, that’s the equivalent of 15 Olympic swimming pools of wastewater every day.
Over the years LMW has accumulated a mass of false teeth, mobile phones, wallets, toys and cameras at its treatment plants.
Other items flushed include nappies, wipes, sunglasses, soft toys, children’s teddies, pet gold fish, jewellery, underwear, tennis and golf balls and pens/pencils.
These items cause damage to filter and pump systems and push the prices up for customers.
LMW Managing Director Phil Endley said “Customers may think small insignificant items like personal wipes
may be okay to flush, but when mixed with household fats and food scraps they can become a real problem and can cause obstructions in the sewerage system.
“This can be a time-consuming and costly exercise for both LMW to resolve and, depending on the location of the blockage, for the customer as well.
“Customers can avoid unnecessary calls to plumbers, protect their pipe work and assist LMW to protect the environment by following some simple steps,” Mr Endley said.
“By far in recent years the biggest maintenance issue LMW has faced is the introduction of the ‘flushable wipe’. However, just because the wipe can be flushed doesn’t mean it should,” he added.
Tsurumi has finished the design, prototyping, and laboratory-based testing of its 1000V submersible dewatering pumps - and now the pumps are set to hit live mine environments in Australia.
Australian Pump Industries, Tsurumi’s distributor, are working with key mine operators on a program that will offer 11kW through to 110kW 1000V dewatering pumps for field testing.
“The plan is to introduce Tsurumi LH high head pumps. They offer real advantages over current design, and significant price and cost benefits,” said Australian Pump’s John Kofron. “Tsurumi are famous for their advanced design and heavy duty construction. They have the capacity to build over 1.5 million pumps a year!”
The 1000V series was specifically designed to withstand the punishing conditions found in mining sites. The three-phase pumps have flows of up to 6,500 lpm and maximum head of up to 200m.
Tsurumi’s KTV and three phase LH series high head pumps are already well established in Australian mine and quarry applications. They have been selected by consultants and specified by pump engineers in projects including Gina Reinhardt’s Roy Hill mine.
“The pumps are loaded with features designed to give mine operators the lowest possible total cost of ownership,” said Mr Kofron. “Many of these are quite unique to Tsurumi and are in line with their philosophy of no-compromise design.”
The motors feature inbuilt thermal protection that cuts power on overcurrent or extended dry run conditions. The self-reset activates once the motor has cooled, allowing the pump to automatically restart.
Like all Tsurumi submersible pumps, the 1000V series includes exclusive features that maximise the uptime of the pump. They include an anti-wicking cable entry that prevents water from entering the motor if the power lead is damaged or nicked.
A double silicon carbide seal is standard on all models. Both seal surfaces are submerged in an oil chamber, away from the pumped liquid. This ensures lubrication and protects against ingress of foreign materials.
The mechanical seal design features a patented Tsurumi oil lifter that increases seal longevity. The lifter ensures both the upper and lower seals are lubricated and cooled, even if the oil level in the chamber is low, or if the pump is operating out of level.
“These features virtually knock out the biggest failure points on any
submersible pump,” said Kofron. “Better products, lower initial and operating costs, and Tsurumi’s dedication to ‘total quality’ makes this product perfect for a mining industry looking for cost reduction.”
The new 1000V series of Tsurumi dewatering pumps are going live in mining sites around Australia as part of the field test program.
Further information on Tsurumi’s 1000V series of dewatering pumps is available on the Australian Pump Industries website, www.aussiepumps.com.au, and from Australian Pump Industries distributors throughout Australia.
HYDROVAR®, the modern variable speed pump drive taking pumping to a new level of flexibility and efficiency.
• Motor or wall mountable
• Fully programmable on site
• Software specifically designed for pump operation, control and protection
• High level hardware design
• More flexibility and cost savings
• Energy savings up to 70%
• Simple mounting “clip and work”
• Multi-pump capability up to 8 pumps
Call us today for a Hydrovar® technical brochure to see how we can deliver your pumping solutions.
Ph: 1300 4 BBENG www.brownbros.com.au
The Shakti story dates back to 1982, when the company began producing stainless steel submersible pumps, energy saving submersible motors, vertical multistage centrifugal pumps, pressure booster, self-priming, end suction, open well and solar pumps.
In recent years the company has grown phenomenally and has become one of the few pioneers in the world to produce 100 per cent stainless steel submersible pumps.
The company employs international best practice technology to manufacture its products. This technology includes cutting edge Japanese and European machines, modern CNC machines and stamping machines.
Owing to its dedicated efforts in R&D and technological innovation, Shakti has emerged as a leading entity in the pump industry, catering to domestic as well as international markets, with a notable reach of more than 100 countries. Today, Shakti is among the best brands in the world, thanks to state of the art technology and continuous innovation.
Shakti Pumps provides a range of solutions in many areas with its array of world class, cost and energy-efficient pumps.
Domestic
Shakti domestic pumps are ideal for homes to maintain water pressure in taps and for general applications like watering gardens and supplying fountains.
Agriculture
Shakti Pumps easily meet varied agricultural needs, be it drip irrigation, agricultural sprinkler systems or in the watering of fields.
Industrial
Shakti Pumps are used in industries for a variety of purposes that include cutting and grinding, fire-fighting, managing sewage, heating and cooling of systems and much more.
Commercial building sector
Shakti pumps is a major force in commercial buildings including hotels, corporate offices, shopping centres
and other buildings where heavy pressure and boosting is required. The company supplies pumps with the latest digital technology for cooling, heating, wastewater management and more.
Solar
A channel partner for the Ministry of New & Renewable Energy (MNRE), Shakti Pumps has a range of solar pumps between 0.75 to 75kW that are simple and easy to operate, offering 40 per cent more discharge than other ordinary pumps.
Sewage & drainage
From draining flooded water from various areas like basements, car parks and empty cesspools, to managing sewage in a water treatment plant, Shakti Pumps are widely used in the domestic and industrial sectors as well as many others.
For more information about Shakti Pumps, visit www.shaktipumps.com.
In the oil, gas and process industries, it is anecdotally believed that up to 70 per cent of installed electric motor capacity is for pumping.
Much has been made of the potential to improve the efficiency of pump systems globally. With more than 40 per cent of the world’s energy consumed by pumps, the potential to have a real and lasting impact on energy consumption is significant. Here, we take a look at what is being done around the country to educate pump manufacturers, suppliers and end users about the energy their pumps are consuming - and the steps they can take to make their systems more efficient.
Energy efficiency, and how we can make our pumps and pump systems more efficient, has been a core focus for Pump Industry Australia (PIA) for more than 12 months now.
Last November, British Pump Manufacturer’s Association Executive Director Steve Schofield travelled to Australia and provided a range of insights into the energy efficiency programs currently in place in Europe and the US. During his visit his
presentations provided food for thought and serious inspiration for both the PIA and the companies who attended his seminars.
Since Steve’s visit, PIA has been working with various sustainability bodies around the country (including the NSW Office of Environment & Heritage, and Sustainability Victoria, among others) on a range of initiatives, designed to inspire and motivate the industry to take charge of what is, essentially, an incredible opportunity for the Australian pump industry. Armed with the knowledge that pumps contribute so significantly to global energy use, the opportunity is in our hands to build efficiency into our pumps and pump sets - providing customers with massive increases in efficiency and serious reductions in costs.
“This topic has been at the forefront of PIA activities and will remain so,” said PIA President Ron Astall. “It is my view that in general the pump industry is ahead of the game, with many suppliers and manufacturers actively promoting energy saving products and systems,” said Ron. “However, the specification writers and designers seem to be lagging behind.
“There are significant energy saving opportunities to be had with pumps and pumping systems. For example in the oil, gas and process industries, it is anecdotally believed that up to 70 per cent of installed electric motor capacity is for pumping. How true this is across all areas is difficult to gauge but it is clear that pumps are big consumers of energy.”
According to Ron, energy saving opportunities can be divided into equipment issues (pumps, drivers, controls) and process issues.
To some extent there has been a move to address pumping equipment efficiency already through Mandatory Energy Performance Standards (MEPS) on electric motors. The PIA assisted with a proposed MEPS scheme for pumps through the Victorian Department of Sustainability and the Environment. A draft proposal was issued, but this has been put on hold for the moment; largely due to the fact that MEPS for centrifugal pumps is a very complex issue.
Pump efficiency varies inherently with pump size, with the rated performance conditions and by the application; such as solids handling, sewage, clean liquid, high viscosity etc. Efficiency mandates for positive displacement pumps are
even more complex and at the moment MEPS for positive displacement pumps have yet to be developed.
Pump designs are relatively mature and it is not considered that massive efficiency improvements are feasible for individual types of pumps. Possible improvements of up to 4-5 per cent may be feasible where a particular manufacturer’s products are not yet state of the art. In the US, the Department of Energy is currently working on a labelling scheme for certain categories of mass produced centrifugal pumps; similar to the star rating we see on domestic appliances in Australia.
One area where larger gains could be made is by ensuring that inherently more efficient pump types
are selected. In other words, making sure that operating speeds and pump configurations are ideal for the best pump selection. In this area, we believe that the difference between poor practice and best practice could reap potential improvements of between 30-50 per cent. This is primarily an educational issue and PIA has been very active here, providing speakers at technical conferences and by assisting other trade associations with training. We believe that there is definitely scope for the development of pump selection and best practice guidelines in this area.
This relates to the design of the whole processing system. There is no benefit in having an efficient and well
Globally, pumps have a crucial role to play in reducing energy consumption.
selected pump if the design and control of the system into which the pump is installed is very poor.
An obvious example is where pumps are oversized and need to be wastefully throttled to maintain system control. Systems with undersized piping components that create excessive internal friction losses are another example.
This is an area that could be successfully addressed through pumping system audits and best practice guidelines. It’s worth noting that in order for regular system audits to become commonplace within industry, some sort of government intervention –in the form of regulation and regulatory requirements – will likely be required.
Where to now?
The next steps for the PIA – and indeed the industry more broadly – in the energy efficiency journey were discussed at the recent PIA General Meeting, held in Sydney on August 25.
Rebecca Williamson from the NSW Office of Environment & Heritage (OEH) attended the meeting and spoke to members about OEH’s plans for the energy efficiency landscape. The cornerstone of this is the NSW Energy Efficiency Action Plan, which sets out the steps the state needs to take to improve efficiency, with a clear goal of achieving annual energy savings of 16,000 gigawatt hours by 2020.
Ms Williamson is part of the Energy Efficient Business Team, which works to both strengthen the energy efficiency market and unlock energy productivity opportunities within business and
industry. Ms Williamson’s team has a clear focus on the role priority sectors – such as manufacturing, commercial buildings, water treatment, aquatic centres and irrigators – can play in these energy savings. The team recognise that pumps cut across all of these sectors, and valuing the impact the pump industry could have in contributing to business action on energy efficiency, established a relationship with the PIA. Together, OEH and the PIA are focused on tackling energy efficiency in a few ways:
• Providing subsidised energy audits to businesses in OEH’s priority sectors, whereby eligible businesses can be subsidised for up to 50 per cent of the cost of an audit that will identify the business’ big energy savings opportunities
• Develop and deliver energy efficiency training to overcome key barriers such as understanding energy management, tools to develop a business case and how to optimise equipment and processes
• Encouraging NSW businesses and the pump industry to access the NSW Energy Savings Scheme, which creates upfront financial incentives for organisations to invest in energy savings projects.
For Ms Williamson, the focus is really on the benefits members of the pump industry can enjoy by being proactive about energy efficiency.
“We find that many businesses tend to see their energy costs as fixed, and it’s just not the case. Energy costs can be variable and are influenced by three things, the type of equipment
chosen, how that equipment is used, and when that equipment is used,” said Ms Williamson. “There’s nothing fluffy about understanding where energy is being used, and actively working towards reducing it. At the end of the day it’s about business improvement, reducing operating costs and ultimately making your business more competitive,” said Ms Williamson.
Ms Williamson issued members with a challenge to get involved in the drive towards improved energy efficiency, speaking with passion and enthusiasm on how industry associations such as the PIA could work together with the office to develop and publish best practice guidelines and training initiatives on energy efficiency.
“We want to work with the industry to better understand the challenges that are being faced, and we want to work with you in partnership to help NSW businesses realise many of the benefits energy efficiency can provide,” she said.
According to Ron, Rebecca was an excellent spokesperson and her presentation created a great deal of interest. “With members from a wide range of pumping applications including domestic, irrigation, water supply, drainage, through to heavy industrial pumping, we have available a significant group of experienced and knowledgeable people,” he said.
“It’s early days, but we are committed to continuing to explore the ways that the PIA can be involved in promoting the benefits of energy efficient design, and to encourage our members to be proactive in this space,” concluded Ron.
SIGNIFICANT SAVINGS ON YOUR ELECTRICITY BILL AND CO2 EMISSION MAY ONLY BE A FEW STEPS AWAY...
Realise the hidden savings in your pumps with a FREE Grundfos Energy Check. By a simple inspection of your pump installation, we can calculate potential savings and recommend high performing, energy efficient solutions. A free report is included with every Grundfos Energy Check detailing your current pump installation and operation costs and the potential savings you can achieve.
1. ONSITE INSPECTION
3-4 hour inspection of your pump installation. The inspection requires no down time to your system.
2. ENERGY CHECK REPORT
Current installation and operating costs, along with potential savings are detailed in a FREE energy check report.
3. REALISE SAVINGS
Realise potential savings energy efficient Grundfos pumps can offer.
For more information or to book a Grundfos Energy Check, please contact our Energy Optimisation Coordinator on (03) 9544 3655
FINANCIAL BENEFITS
• Typically 30-50 % reductions in energy costs
• Short pay-back time (1-5 years)
• Reduced risk related to increasing energy prices
• Reduced operating and maintenance costs
OPERATIONAL BENEFITS
• Reliable operation
• Low failure rates
• Reduced down-time
• Reduced repair costs
• Complete overview of pump installations
ENVIRONMENTAL BENEFITS
• Typically 30% reduction of CO2 emissions
• Green corporate image
• Pump life-cycle analysis and documentation
• Compliance with energy regulation
When we start the pump selection process for a particular application, one of our major concerns is efficiency. If several different models of similar quality meet our conditions we will usually select the one with the highest efficiency. After all, higher efficiency reduces the cost of electrical power. There are times, however, when efficiency can take a back seat to the true, overall cost of operation.
Solids handling pumps used in municipal and industrial applications are a good example. Large sewage pumps can use mixed flow or radial flow impellers with little concern of plugging or clogging due to the inherent size of the flow passages. As discharge and vane size decrease, however, the potential for clogging increases.
In the early 1900s a new impeller design was developed by A.B. Wood of the New Orleans Sewage and Water board. Known as the ‘non-clog’ impeller, it consisted of two vanes with blunt leading edges that allowed the passage of larger solids and reduced the opportunity for stringy material to accumulate at the vane entry. Today, most solids handling pumps, with discharges smaller than 10”, utilise some variation of this design.
Those of us familiar with these pumps know that there is no such thing as a non-clog pump – ‘seldom clog’ is probably a better terminology. But, as discharge size decreases to 4” or smaller, ‘often clog’ can become the description of choice.
Now, some 3” and 4” pumps can pass a full 3” spherical solid, but some applications cannot accommodate the higher flows they produce and high concentrations of stringy material can still cause problems. If a small non-clog performs well in an application it is probably the best choice but, if plugging is a continual problem, you may want to consider an alternative.
The vortex pump, also known as a recessed impeller pump, is usually considered to be a member of the centrifugal family. This is not entirely accurate, but since there is no such thing as centrifugal force, it probably doesn’t matter anyway. It is, however, a dynamic pump as it imparts energy
continuously to the fluid it is pumping.
Unlike the typical centrifugal pump, its pumping action is a two stage process. The impeller, which is located outside the flow area of the volute, produces a primary vortex or swirling action in the water that resides in and around its vanes. This vortex creates a secondary vortex in the volute that produces flow. Figure 1 illustrates this process.
The pumping action of the vortex pump offers several significant advantages. Since the impeller is recessed, it has little contact with the majority of the pumpage. Even when solids do contact the impeller, they do not have to traverse the vanes so the potential for erosion is greatly reduced. In addition to reduced wear, its recessed position also allows the passage of larger solids and stringy materials that might otherwise plug a true centrifugal pump. Almost any solid that can enter the suction will exit the volute and stringy materials pass through without entanglement. Still another advantage is a reduction in the radial forces that act upon its impeller. Because of this reduction, many vortex pumps can operate at very low flows or even shut off for extended periods without damage.
Unfortunately, that two-step pumping process also has a disadvantage – a much lower hydraulic efficiency. This trade off tends to be acceptable in many industrial markets but, unfortunately, it will often eliminate the vortex pump from consideration by some specifying engineers in the municipal arena.
Figure 2 compares a 4” vortex pump with a 4” non-clog. Both are rated to pass 3” spherical solids and reach their peak efficiency at the design point (450 gpm @ 46’). At this point the non-clog requires about 7.4 horsepower (efficiency = 70 per cent) while the vortex pump requires about 10.7 horsepower (efficiency = 48 per cent). Obviously, this almost 45 per cent increase in horsepower could have a rather large impact on long term electrical costs, but will this increase always make the non-clog the better choice? Lets take a look at a actual municipal example.
A small municipality in the western US installed a duplex lift station, with alternating 4” non-clogs, to service a retail complex. The complex consists of retail shops, a supermarket/department store, and several restaurants. The station has an average of six to seven starts per day and the run time for each cycle is approximately five minutes. In addition to normal human and food wastes, disposable diapers, feminine products, and high fibre paper towels are also a daily occurrence. This waste mix resulted in partially plugged pumps that had to be pulled for cleaning every seven to ten days. Late last summer, the non-clogs were replaced with 4” vortex pumps that produced similar head capacity characteristics. Since start up of the new pumps, no plugging has occurred.
Although the vortex pumps consume
Three times longer life for pump components significantly lowers production costs.
High fluid velocity means wear, erosion and corrosion at high impact points like pump impellers, valve seats and stems, and bends and elbows in pipe work systems. A worn component means inefficiency and delays. We work with both pump OEMs and end-users to produce cost-efficient long-wearing solutions to high wear components. Our unique surface engineering technologies - developed to increase resistance to wear and corrosion – optimise component and system performance so they work better, last longer and cost you less.
Production equipment and components surfaceengineered by Laserbond® will operate in-situ for longer and perform more efficiently. An extended operating life increases the cycle time for regular maintenance and decreases maintenance costs.
Pump impellors, pump shafts, housings and seal areas are returned to original specification with laser cladding and machining. LaserBond® surface engineering improves and maintains operating efficiency, improves the overall process, and cuts production loss.
Find out more at laserbond.com.au/fluid_handling
approximately 38 per cent more horsepower than the non-clogs they replaced, the total power consumed is still relatively small since the pumps run no more than 35 minutes per day (213 hours per year). On the other hand, cleaning of the original non-clogs (over and above normal maintenance) required an average of 12 hours per month (144 hours per year). The replacement resulted in labor cost savings that far outweighed the additional electrical cost and, most importantly, made the pump station completely reliable.
There are times when we have to look beyond efficiency and its effect on electrical consumption, especially if operational hours are low. In the example above, and many more like it, overall cost and reliability can be far more important considerations.
Joe Evans accidentally entered the pump industry in 1986, and has been trapped there ever since! He is passionate about the sharing of knowledge within the industry. To read more of his insights into the world of pumping, head to www.pumped101.com.
An innovative new pumped storage project is being developed in Queensland, with the potential to generate significant power for the National Electricity Market.
The Kidston Pumped Storage Project is located in northern Queensland on the site of the historical Kidston Gold Mine. Genex Power purchased the disused mine from Barrick Gold and is now proposing to use the old mine site to establish a power generation project.
Situated some 270km north-west of Townsville, near the township of Georgetown, the project is deceptively simple in its design. The Kidston site currently features two large adjacent pits, which will act as the upper and lower reservoirs for the Pumped Storage
Project. Given the significant potential water head differential that the pits offer, and the vast quantity of water the pits can hold, the Kidston scheme has been designed to deliver up to 330MW of rapid response, flexible peaking power into the National Electricity Market.
Sydney-based Genex Power has been working to get the project off the ground for a number of years already; and with its listing on the ASX in July 2015, is starting to achieve some critical milestones in the timeline towards the commencement of construction.
Since listing, Genex Power has a market capitalisation of $29million (as of September 2015) and $10million in working capital. The company is now moving forward with a detailed feasibility study and is beginning the process of securing the approvals required to move ahead with the construction of the ambitious project.
“The project offers a large-scale, low-cost and flexible solution to Queensland’s growing peaking power requirements,” said Genex Power Executive Director Simon Kidston.
“It is expected that the project will be
“Large-scale storage projects provide stability in supply to the grid which will become even more important because of the intermittent generation issues which come with renewable energy.”
well positioned to take advantage of the combined effects of an oversupply of base load generation capacity; and escalating peak power prices being driven by increasing generation costs, thanks to rising gas prices due to the export of LNG from Gladstone.”
According to Mr Kidston, as renewable power gains momentum in Queensland, especially the prevalence of rooftop solar, the need for energy storage and energy management will play a far more important role in the electricity network.
“Large-scale storage projects provide stability in supply to the grid which will become even more important because of the intermittent generation issues which come with renewable energy,” he added.
How will it work?
A concrete-lined pressure tunnel will connect the upper reservoir to the underground generation powerhouse. A concrete-lined tailrace tunnel will, in turn, connect the powerhouse to the lower reservoir. A shaft from the surface will connect the underground infrastructure to a surface power control room, which will be connected to a transformer station located on an existing pit bench.
During peak power demand periods, water will be released from the upper to the lower reservoir, passing through 3x110MW reversible pump/generators acting in generation mode. During off-peak periods, water will be pumped back from the lower to the upper reservoir with the pump/ generators acting in pumping mode.
Initial modelling indicates a change in water level of approximately 8m in the upper reservoir and 44m in the lower reservoir during a full generation
Local Manufacture and Local Support from a company that designs and manufactures in Australia
COMPREHENSIVE PUMP TESTING UP TO 1.2MW
• Engineered submersible motors 4” to 24”
• Fabricated stainless steel submersible pumps and motors
• Vertical turbine pumps 6” to 90”
ENGINEERED SUBMERSIBLE PUMPS AND MOTORS
• De watering pumps
• Submersible Sewage pumps
HORIZONTAL
cycle, with an average water head of approximately 190m over the course of the cycle.
The Kidston generation site benefits from extensive existing onsite infrastructure and materials, mitigating the need for significant capital
expenditure normally associated with building a large-scale pumped storage hydroelectric generation scheme. This includes:
• An upper reservoir (Wises Pit)
• A lower reservoir (Eldridge Pit)
• Significant volumes of good quality
water currently in pit
• An onsite power distribution substation
• An existing 132kV transmission line connecting the site to Powerlink’s Ross substation near Townsville
• The existing 20,600ML Copperfield
Dam located approximately 18km from the site
• A water pipeline from the Copperfield Dam directly to the Kidston site
• Existing water rights to draw up to 4,650ML of water annually from the Copperfield Dam
• Significant quantities of onsite building materials required for the civil construction process
• Onsite accommodation and catering facilities, roads, fencing, diesel storage facilities, electricity and water.
The Kidston scheme will be a closed loop system, which will involve the transfer of water from the upper reservoir to the lower reservoir. This will ensure minimal environmental impact during operation, on what is already a disturbed historical mining site.
The path to construction
Genex recently completed a pre-feasibility analysis which shows the Kidston Project to be economically and technically viable. The Kidston Project benefits from the presence of significant existing in-situ infrastructure such as existing reservoirs, a water source, powerlines and immediate site access. The presence of these attributes is expected to mitigate a significant portion of the capital costs that would normally be associated with the building of a large-scale pumped storage hydroelectric scheme.
The pre-feasibility analysis estimates a capital cost of $282million with construction scheduled to commence in the first quarter of 2017, subject to having the necessary approvals in place. Following a two-year construction period, first generation is planned for 2019.
A tender for the pump turbines to be used on the project will be issued in the second half of 2016.
According to Mr Kidston, in evaluating the tenders, Genex Power will prioritise cyclical efficiency and the ability of the turbines to efficiently cope with changing water head, as these are the critical drivers for the financial model that the project has been built on.
Once complete, Genex Power expects the Kidston Pumped Storage Project to be operational for fifty years.
For more information about the Kidston Pumped Storage Project, visit the Genex Power website at www.genexpower.com.au.
there’s no better time than process uptime
SPX products deliver the power you need for quality processing performance and greater productivity. And when it comes to keeping your SPX equipment running like new, choosing genuine OEM parts delivers total peace of mind.
SPX aftermarket services offer:
• Local, stocking distributor partners
• Optimized performance of your equipment
utilizing genuine OEM parts
• In stock parts and fast deliveries (Quick Ship)
• Preventative maintenance, inspection and repair services by factory trained technicians
When quality, dependability, service and performance matters -
Contact SPX for all your high quality OEM Spare Parts, Email: ft.aus.cs@spx.com, Tel: 03 9589 9222 or visit www.spx.com.au
When CS Energy needed to quickly refurbish a cooling water pump at the Callide Power Station in Queensland, they knew Hydro Australia was the company best equipped for the task ahead.
CS Energy’s Callide Power Station is located near Biloela, 120km south-west of Gladstone, Queensland. Victorian-based Hydro Australia was successful in winning the tender to repair and refurbish one of the power station’s cooling water pumps during an April 2015 outage. Hydro Australia had successfully carried out the same work during previous outages in 2013 and 2014. Refurbishing a split case water pump is a relatively straightforward exercise, however this project had a number of challenges to be managed.
First up, the pump is large, with 1,400mm diameter flanges, axially split case, 3.5m x 3.5m x 3m high, and weighing in at near to 24,000kg, it requires a low loader to transport. Also, due to the oversize dimensions of the pump, the transportation can only be carried out during daylight hours. This means three days’ travel each way between Biloela and Morwell.
Due to time constraints with the unit overhaul program, the pump was required to be in and out of Hydro Australia’s workshop in 13 days. Any later and the unit’s return to service would be delayed, something that neither CS Energy or Hydro Australia wanted to happen.
The refurbishment had a fairly typical work scope. Grit blast and coat the casing, upgrade the bearing housing
to accommodate new labyrinth seal designs, new components consisting of bearings, shaft sleeves, throat bushes, mechanical seals and casing wear rings, balance the rotor and assemble.
Knowing the job details well in advance made the process easier. Hydro Australia were able to purchase in all the components required, and raw materials were pre-machined for components including the throat bushes, case wear rings and shaft sleeves. The decision was made early to have a dedicated project manager walk the job through from the start, a decision that proved very worthwhile when the timeframe kept dropping.
On top of the time delay in getting the pump removed, a few other obstacles arose once the pump was stripped and assessed. Firstly, the casing required line boring past the erosion/corrosion damaged areas under the case wear rings. This was accompanied with new oversized
stainless steel wear rings in excess of 1,100mm in diameter. The next issue was the impeller – a missing/broken suction vane in the impeller eye, 17 cracks in the impeller, with many cracked through, and severe cavitation on all suction vanes.
After careful consideration and formalising the weld procedures and repair methods, the impeller repairs were successfully carried out by Harvest Engineering in Melbourne. Once the impeller was repaired and inspected, work started on the rotor with dressing of the weld repaired areas, skimming the wear rings and rotor balancing. Consecutively the casing was blasted, line bored, inspected and coated internally in preparation.
After only eleven days, the pump was completed and ready for the long trip home, two days ahead of schedule. In such a short time the pump was rebuilt to a high standard and will provide reliable service for the power station.
Since 1969, Hydro has built its worldwide pump service organization by bringing a high level of engineering expertise and quality service to the pump aftermarket. Hydro Australia works with our customers to evaluate and understand the root causes of pump degradation or failure and to provide unbiased engineering analysis, quality workmanship and responsive field service for improved plant operation.
Certified Service Centre
Hydro Australia has always been committed to Quality and Occupational Health & Safety. Hydro Australia holds the AS:NZS ISO 9001:2008 certificate in addition to the AS:NZS 4801 and AHSAS 18001 certificates.
Turnkey, Field Service and 24/7 Emergency Response
Hydro Australia’s Field Service team has extensive knowledge of pumps from most major manufacturers and provides turnkey service, installation / start-up supervision, field machining, vibration analysis, laser alignment, pump system troubleshooting and emergency field response 24 hours a day, 7 days a week.
Pump Parts
When you require a part and are facing a long lead time, Hydro Australia can meet your needs in a reduced time frame through our reverse engineering, patternless casting and integrated manufacturing processes. Hydro's engineers review and evaluate all parts to offer important upgrades and apply new technologies that will reduce wear and improve reliability.
Pump Testing - Managing Risk
Ensure your pump will perform as required. Hydro’s 5000HP Performance Test Lab, located in the United States, is compliant to API610 and Hydraulic Institute standards and can test horizontal, vertical, and submersible pumps.
Training
Hydro teaches practical solutions and troubleshooting techniques for common pump problems and offers specialized hands-on training programs. View upcoming courses online at www.hydroinc.com.
Call Hydro Australia at (03) 51650 390 with your pump service inquiries or contact Ross Bertolimobile: (0418) 581190 email: ross@hydroaustralia.com.au.
Norm Winn has been working in the fire protection industry for over fifty years. Being an Officer with the Country Fire Authority, and more recently as a consultant to the fire protection industry, there’s not much about fire protection pumps that he doesn’t know. We spoke to Mr Winn about his experience in the industry and gained his insights and thoughts as an end user specifying pumps for clients today.
Mr Winn worked for the Country Fire Authority as the Officer in charge of Training, Fire Protection and other departments for over 30 years. Following the Ash Wednesday bushfires he was appointed to the Premier’s Bushfire Reconstruction Task Force; and over the course of his career he has presented papers in the UK, USA, Canada and Australia.
In the past 24 years, Mr Winn has been running a consulting business, specialising in building audits, emergency response, training and fire protection. He has been a member of the Fire Protection Association, Australia since 1963. Some years ago Mr Winn was honoured with a Life Membership of the Association. Mr Winn also chairs the Australian Standards Committee FP 17 AS 3745 – Planning for Emergencies in Facilities.
Between all of these roles, Mr Winn has seen a plethora of pumps for fire appliances and system installations develop and evolve over the years.
According to Mr Winn, there are several key factors he takes into account when specifying pumps for fire protection – the size of the driver and the capacity of the driver.
“The main requirement is of course to have sufficient capacity to drive and sustain a centrifugal pump and enable a fairly hefty output, whether on a fire appliance or a sprinkler/hydrant system,” said Mr Winn. “Because a lot of the fire appliances were located in fairly reasonable sized townships, that in itself created another add-on to enable us to go across to compression ignition drivers on tankers and variable split pump systems on major appliances, providing either volume or high pressure. Fixed pump installations for sprinkler/hydrant installations have greater demands depending on the risk the installation is protecting.”
The biggest change Mr Winn has seen over his years in the industry is the increase in size of pump sets required to optimise demand for the output design.
“The increase in the size of the pump set today is due to the development of both industrial complexes, hazardous materials installations, high rise buildings and storage facilities. Smaller pump sets required to protect assets such as aged care structures and small hospitals within our communities are the biggest changes I’ve seen in recent years,” he said.
“Maintenance and testing requirements are another major part of ensuring the pumpset installation is ready to respond reliably when required to quell a developing fire.
“Today, the firefighter requires a higher pressure to operate some of the specialist equipment, and there is the requirement to be producing fairly large litreage per second or high pressure for mist/fog demands.
“Generally, to operate satisfactorily the pump sets have to be well above 700kpa.”
According to Mr Winn, the process of specifying a pump system has become increasingly challenging.
“These days I’m having great difficulty with specifying an appropriate pump set because the pump provider buys
an engine, and buys a pump. Then they build that onto a bed, which you’re well aware of. But the major issue is being able to confirm that the driver meets Australian Standards or FM approval for installations. A lot of the drivers being brought in from overseas just don’t meet that requirement.”
Of course working in fire protection, another critical requirement is that pumps and pump sets can go from stop to maximum output within ten seconds.
“Of course that’s a high demand requirement,” said Mr Winn. “Adding to those demands, obviously the system needs temperature control, particularly in the diverse climate ranges experienced on our continent. The pump design criteria, types of jacking pumps to be used to maintain pressures and fuel systems have all altered dramatically in the last decade or so.
“For me, the pump itself has to be reliable and its maintenance is absolutely critical. Maintenance is probably one of the main issues that I’m confronted with on a regular basis. Conforming with relative Sections of AS 1851 Routine servicing of fire protection equipment is both critical and a major cost to the community.
“Not complying with maintenance requirements can result in, at times, catastrophic outcomes, endangering life and property. With pumps, it’s not just about design and meeting output capacity, it’s also a matter of regular, ongoing maintenance.”
One particular area of technology that has evolved and grabbed Mr Winn’s attention is in the area of pump set impellers and casings.
“The pump set impeller and its casings are probably one of the important things,” said Mr Winn. “Obviously it’s the impeller that provides the output and the ability to produce the water delivery that’s required. But it’s the pump casing, I find, that’s one of the most interesting parts of it, the technologies that are being developed now to achieve high output.
“In days gone by, we used to get away with large volume pumps. But now we find that it’s not just volume, it’s high pressure that in itself has resulted in
demands for changes to occur. The majority of design change comes from overseas due to higher population bases. That is not to say that there are many skillful, innovative people in Australia who lead the world in pump design.
“We’ve got some pretty smart people in Australia, but because of our lack of manufacturing capability, we’ve lost a lot. As an example, Thompsons Pumps have a wonderful history, their pumps were always simple and very good. Some of the technology that they’ve developed, such as lightweight pump casings, are a really great innovation. To date, I haven’t had or heard of any failings.”
efficiency and solar
Energy efficiency is a subject that most in the pump industry are starting to factor into their products, but for Mr Winn, when specifying pumps for the fire protection industry, it’s almost impossible to specify pumps that are both energy efficient and capable of achieving the outputs the industry requires.
“It’s difficult because we need significant power for output, so that in itself means we’re going to use a lot of fuel, be it electrical or hydrocarbon.”
“Really there’s not a lot that we can do to conserve energy while retaining the outputs that are required. What I’m really looking forward to in the very near future, is the day that we’re able to run fire pump sets from solar energy. From the electrical point of view, that would be great.”
On that note, Mr Winn doesn’t believe it will be too long before we start to see some solar applications for the pumps that are used in fire protection.
“I don’t think it’s too far away. I’m a solar panel user from way back, I’m a believer in it and Australia is one of the sunniest continents on earth – but we don’t maximise use.
“But the new accumulators and battery systems that are being developed – that is really exciting stuff, and I think that opens the doors for some innovation, to create worthwhile electrical storage capacity so that we’ve got reliability, as well as meeting electrical driver output.”
This development is critical if solar pumps are to be used in fire protection, because, as Mr Winn points out, we have as many, if not more, fires outside of daylight hours.
When specifying pumps, Mr Winn says that while we’re largely tied to the relative Australian standards or other accepted standards – FM Approvals, he does place careful consideration on the high standard of reliable maintenance performance demanded of a maintenance provider.
“The critical issue is to ensure that the maintenance providers really understand the unit that they’re maintaining. A lot of people just think that it’s about the pump; but it’s drivers, it’s housing, it’s the environment it operates within, appreciating at times, the quite warm or very cold temperatures that they operate under.
“Maintenance is critical – but it’s just as essential to have a competent maintenance provider. That’s a real issue.”
When it comes to managing maintenance, for Mr Winn, it all comes
back to training of the provider at the coal face.
Mr Winn has considerable experience with the Fire Protection Association, which provides training courses which enable the passing of knowledge between industry veterans and the new players making their way through the ranks.
“We lose a lot when long standing industry members retire. It’s sad; but it’s a fact of life. And it’s not just the pump industry or the fire industry, it’s across the board in the community.
“The best thing that we can do is capture the knowledge and skills before our experts retire and make sure it’s passed through to the next generation. Sometimes it’s the little things, the anecdotes and on-the-job learningthey’re the facts that need to be included in our training courses.”
Mr Winn believes that the future of the pump industry will largely be influenced by the new and greater demands made for innovative pump design in the fire industry – both fire services and the community at large – commercial, industrial, high rise
We offer a comprehensive range of mechanical seals from simple pusher styles to single, double and split cartridges, and custom engineered sealing systems.
We supply seals for pumps, mixers & reactors and for duties including water, chemicals, hydrocarbons, pharmaceutical, sewerage, paper pulp and food & beverage. Contact us to discuss your sealing needs.
[apartment / office], hazardous materials and shipping all require specific needs – our challenge in the pump industry is to both forecast and meet our nation’s changing needs.
“I’m of the opinion that with the development of technologies, whether that’s impeller development, actual usage of pump sets or new types of metals with greater tolerances, automation is going to have a major effect.
“We can’t lose site of the fact that we have to be innovative to provide for our future industry and community safety, because a lot of people don’t realise that pumps are what drive our sewerage and water systems, which we can’t live without. But also pumps protect lives and property.
“We’ll have to build on not only the technologies, but longevity into the pump sets.
“It’s an exciting time for the industry, in the next decade or so, as to how we can design and develop pumps that will last for the next 30 to 40 years – the general building life expectancy or ever increasing variations required by fire services to protect fire firefighters and the community they serve.”
Ken Kugler reviews the new marking requirement for fire pumps, explaining the rationale behind it and outlining why it is necessary.
There has been a new inclusion to the ‘marking’ requirements of firewater pumpsets. Under AS2941 2013 cl.3.13.2, marking of the pumpset identification plate now requires the additional item maximum test flow to be added.
But why is it necessary? Does everyone really need this information? The pumpset plate already includes duty flow, duty pressure, duty speed and maximum power required. From my point of view it has been included to protect the pump and its drivers (i.e. the electric motor or diesel engine), during testing, from incorrect operation or rather from operation outside the pump and driver’s design range.
From a practical point of view, maximum test flow is obviously only recognised when the system includes a flow measuring device and the pump is discharging through the flow test line. Flow measuring devices, generally an Annubar, are only installed when the pumpset system is being tested, say during initial system commissioning and/or the AS1831 maintenance requirements for an annual performance test. At other times, for example during routine monthly tests, the pump is generally being operated without a flow measuring device, so how would the operator know whether the maximum pump flow is exceeded? As fire pumps
are (in the main) centrifugal pumps, and as a discharge pressure gauge is permanently installed, then perhaps the AS2941 requirement should read “minimum discharge pressure equating to maximum test flow”. Suction conditions need to be considered to determine this value.
To be clear, the only time the maximum test flow of a fire pump may be expected to be exceeded is when the fire pump flow measurement pipeline is utilised to test the pump’s operation. (Routine monthly testing may only include pump discharge through the circulation relief valve which is only a relatively low flow.) All the fire suppression requirements are included in the system designed by the fire engineer and these should all be less than the maximum flow as defined in the Standards.
Let’s take the example of a fire pump installed in the basement of a high-rise building. To keep the maths simple, this pump draws water from a suitable storage tank, and has a duty head (pressure) of 1,000kPa at a duty flow of 1,000L/min. In accordance with the Standard, the pump secondary duty would thus be a maximum flow of 1,300L/min at a minimum head of 800kPa. (As per AS2941 cl.3.1, at 130 per cent duty flow, head should be greater than 80 per cent of duty head.)
Now let’s look at the flow test pipe system installed. It takes water directly from the pump, after the non-return valve, the water then passes via a tee through the flow test isolating valve, the flow measuring device (most likely an Annubar), then through the flow control valve and via an as-short-as-possible return pipe and a minimum number of bends back to the storage tank.
With the isolating and flow control valves both fully open, the pipe friction losses are extremely small. In fact, in this example the pipe calculated friction loss is about 6m at 1,300L/min. The discharge pressure could drop below 60kPa, 6 per cent of the designed duty pressure and the flow rate may exceed 2,000L/min(200 per cent of duty flow).
Unfortunately, the site test procedure is often:
1. Check shut valve pressure
2. Check duty pressure at duty flow
3. Check operation at maximum flow (i.e. fully open the flow control valve is often the request).
The installed pump was never designed for operation at such low pressure. Firstly, the pump itself will probably be cavitating in the extreme, and more importantly perhaps, absorbing an extremely high level of power. This will be obvious from a diesel engine labouring and dropping
in speed. An electric motor may be drawing an excessive amount of current, even to the level of causing failure of the electrics.
Why do we need the new marking?
Most modern centrifugal pumps utilised for Australian fire installations are selected from commercially available ranges of pumps. (Unlike the American fire pump market where a pump is pre-tested to specific requirements, approved and listed by a government approved agency for a fire pump installation.) The commercially available pumps have been designed by engineers endeavouring to extract the maximum flow from a particular suction and discharge size. This has tended to make the pump characteristic QH curve much flatter – generally a good point for the fire engineer as shut valve pressures are much lower. However, a consequence is that the power curve continues to rise as the flow increases, it does not plateau out. The pump’s limitation becomes the NPSH available or simply the amount of suction head or suction pressure on the pump. If our example above was drawing water directly from a town main then excessive power absorption would be much more pronounced.
AS2941 – 2013 specifies that the driver power should exceed the
System resistance curve at Duty
System resistance curve at maximum flow
System resistance curve of test pipe with control valve fully open
System resistance curve of test pipe with control valve fully open
Pump operates at the intersection of the pump curve and the system resistance curve. This example leaves a question as to what maybe the actual maximum test flow.
maximum absorbed pump power for flows between zero and 130 per cent of duty by a minimum factor of x1.15. This is quite generous but is simply not
always sufficient if the pump is operated beyond the 130 per cent of duty flow. Hence the requirement to indicate a maximum test flow.
Possibly, but when it comes to compact inline grinders, the case for twin shaft over single shaft is not necessarily as clear cut.
The essential difference is that twin shaft grinders create the shearing action by interlacing the cutter blades on each shaft, whereas a single shaft achieves this by rotating its blades through a fixed element in the housing. In either case, these cutter elements introduce an obstruction to the flow which then results in a pressure drop across the grinder unit. That pressure drop, although small, is typically two to three times greater in a twin shaft grinder.
Most, if not all, inline grinders are motor driven; if the power fails and the motor stops, then the only flow possible is that which can pass through the available open space. In a twin shaft unit this is very restricted, leading to the system backing up rapidly, whereas the single shaft grinders have a large open centre design as a functional necessity and allow a much greater degree of bypass.
A consequence of this open centre requirement is that the rotating blade element will have a significantly larger outside diameter than the twin shaft cutters. This increases both the peripheral tip speed and the shearing energy they generate, leading to a more efficient cutting action and a lower risk of jamming.
As with most things, the fewer number of parts involved, the lower the risk of breakdown. Servicing is simpler and maintenance time and spares costs
are reduced. Typically a single shaft grinder can contain up to 30 per cent less parts than an equivalent capacity twin shaft.
Conhur is the distributor for Sydex’s range of Defender inline or channel grinders, which feature all of these advantages:
• Single shaft design, high strength double bearing support
• Low head loss, high bypass capability
• European built, CE marked
• Excellent reduction, output size just 4-5mm
• Readily available
• Quiet, 70 dba
The Defender range offers an appropriate compact inline grinder for any 4, 6, 8” pipelines, preserving the upstream functions whilst protecting the downstream activities.
When used in conjunction with the solids handling capability of the Sydex positive displacement pumps, this creates a formidable combination of process capability and exceptional service life.
If your problems need cutting down to size, Conhur can help!
Maintaining effective flow through small bore pipes over longer distances or high lift is notoriously difficult when dealing with fluid with a high level of solids or suspended materials. By ensuring the input to the pump is reduced to small particles, the risk of blockage, backflow premature wear and pump damage are all but eliminated. This self-priming positive displacement macerator pump is capable of significant suction lift, making it ideal for many difficult applications. The hardened stainless steel cutter of the integral macerator unit cuts and shreds the solids into small particles before entering the pumping element. This efficiently macerated waste is then easily transferred to the final destination without risk of blockages or failure. Ideal for domestic or small commercial premises where main sewerage or drainage is not available or where gravity feed is insufficient, the Eliminator can be an attractive and very cost effective solution.
Sydex is a modern, global manufacturer of progressing pumps, grinders and macerators. Sydex and Conhur provide extensive expertise and knowledge throughout the World, enabling us to become totally focused on our customers needs from manufacturing through to delivery, documentation, installation and after-sales support.
Offices in VIC, NSW and Qld servicing
Australia wide
Australia Ph: 1800-422615
NZ Phone: (09) 2787109
sales@conhur.com
By industry: waste water, water treatment, biogas, general industry, food and drink, oil & gas, marine
Pump range: horizontal and positive displacement cavity pumps, macerator pumps, hopper feed progressing cavity pumps, barrel pumps
Grinders and macerators: grinders and macerators for solids handling and pump protection in sewage, waste water and industrial processes.
Shaftless Screw Conveyors for the efficient transportation of de-watered sludges from centrifuges and belt-presses
Lev Nelik, or Dr Pump as he is also known, is an international pump industry stalwart with over 30 years of industry experience and over fifty publications about pumps to his name. In addition to his consulting work, he currently teaches pump training courses worldwide and publishes pump tips, advice and troubleshooting on his website. Much of his advice focuses on preventative maintenance methods to improve reliability, reduce energy consumption and optimise the operation of pump systems. In this article, we look at some of his top tips to ensure pump reliability.
There are a number of reasonably straightforward but highly effective things you can do to ensure efficient and reliable pump operation and realise substantial savings in the long term. Whether you’re new to the industry or just need a refresher after years working with pumps, these four tips are worth keeping in mind.
By making sure pumps operate as efficiently as possible, we can make substantial energy savings and reduce running costs. While we often take pump efficiency for granted, many pumps actually operate inefficiently. Where a pump operates on its headcapacity curve, with regard to Best Efficiency Point flow (BEP), has a very significant impact on the pump energy consumption.
Many plant pumps no longer operate at BEP, for various reasons including changes in plant operation or wear on internal components.
But what is the best solution?
Replacing an existing pump with one sized for the proper flow may work, but is often very expensive. Changing piping, if possible, is often even more costly.
A much more economical, expedient, and practical solution is to modify the internal hydraulics, by fitting the existing casing with a new impeller, specifically designed for the new required flow.
Tip 2: make sure your operators receive regular, hands-on training
For staff working on pumps to complete their jobs as effectively as possible they need to know pumps, not just theoretically, but on a practical,
hands-on level. Pumps on the plant floor often don’t look exactly like those in a text book.
Even long-time staff may need training to keep on top of the latest technical advances in the field.
The hands-on experience of taking a pump apart, touching and feeling its internals, coupled with basic pump theory often achieves the best results.
It’s also a good idea to train staff from different areas of the company, rather than just maintenance. This helps operators and engineers better understand the consequences of their actions, such as pump flow control, energy consumption and reliability issues, which are not normally apparent sitting at the control room.
Tip 3: select a specialty material to help improve the efficiency and reliability of a multistage pump
When designing a multistage pump system, the materials used for various components can have dramatic impacts on the reliability and efficiency of the systems in the long term.
For instance, a huge variety of different materials can be used for pump bushings, including metals (bronze, hardened steels), hard coatings (which can be applied by many methods – fused deposition (cold or hot methods), laser treatment, nitriding, carburising, etc.), non-metals (thermoplastics, thermosets, composites), ceramics. All of them have benefits and shortcomings, such as resistance to temperature, thermal or mechanical shock, machinability, galling resistance, dimensional stability, swelling, chemical resistance, abrasive resistance and, of course, cost.
It is important to do your research and match the material used to the pump system application and the fluid being pumped. Desktop research alone may not be enough, it is worth talking to a range of interested parties in the field (such as material manufacturers, pump suppliers, and end users) and collecting feedback on their experiences.
Tip 4: check the fits and clearances of centrifugal pumps and drives
I recommend creating a robust schedule of preventative maintenance checks to keep centrifugal pumps and drives operating efficiently and to prevent faults before they occur.
These tasks can be divided by those that need to be checked daily (e.g. flushing pumps, checking for leaks, noisy cavitation, discolouration and temperature), monthly (e.g. refilling oil in bearing reservoirs, cleaning oiler bulbs, cleaning, replacing guards), six monthly (e.g. service standby pumps, apply rust preventative coating), yearly (e.g. inspect disc coupling for signs of wear and cracks, check coupling alignment, check axial float) and seasonally.
The exact schedule for your equipment will depend on factors such as your pump system, application and the nature of the substance being pumped.
Pump efficiency and reliability are too important to neglect until something is obviously wrong and should be in the minds of all those working with pumps. More articles about pumps and their maintenance can be found on Dr Pump’s website www.pumpingmachinery.com.
Dr Nelik has 30 years of experience with pumps and pumping equipment. He is a Registered Professional Engineer, has a Ph.D. in Mechanical Engineering and a Masters in Manufacturing Systems and is the author of articles, chapters and books about pumps. He is a President of Pumping Machinery, specialising in pump consulting, training, and equipment troubleshooting. His experience in engineering, manufacturing, sales, field and management includes: Ingersoll-Rand (Engineering), Goulds Pumps (Technology), Roper Pump (Vice President of Engineering, and Repair/Overhaul) and Liquiflo Equipment (South-East Regional Sales Manager, and later a President). Dr Nelik is a Full Member of the ASME, and a Certified APICS. He teaches pump training courses and consults in the US and worldwide.
Regular readers of Pump Industry will be familiar with Ron Astall’s popular series of articles on understanding pump curves. After a brief hiatus, Ron is back to explain how to select for unusual running speeds.
This article describes how we can use standard centrifugal pump catalogue curves to select for other running speeds. For example you may have a low head application and suspect that an 8 pole operating speed may suit – but the catalogue that you have only shows 2 pole and 4 pole speeds, and there is no range chart for 8 pole speed either.
Most centrifugal pumps are driven by simple, rugged and reliable squirrel cage induction electric motors, which run at essentially a constant speed. Their speed depends on the number of poles in the motor and the electric supply frequency; usually 50Hz or perhaps 60Hz as in the Americas and some parts of Asia.
For electric motors we are stuck with the typical fixed speed options as shown below:
Available motor speeds Pump Running Speed - RPM (assuming typical 20 RPM slip)
Affinity Laws
As discussed in a previous article on variable speed, the performance of a centrifugal pump at different speeds can be predicted by the Affinity Laws as per Figure 1.
We can use these Affinity Laws in reverse to modify our flow and head to suit the speed of the available performance curves and range charts. Sound confusing? Not really. Let’s work through an example.
Let’s say we need to select a pump for a flow and head of 80L/s at 10m. For such a low head, it is likely that a low running speed will be involved. If we look at the 4 pole (1,470rpm) range charts (Figure 2) we can see that there is no pump selection matching this flow and head at 1,450 rpm.
It is logical to predict that if we were to run the pumps in the range chart at an even lower speed, say at 8 pole (730rpm), there ought to be a selection available. So let’s assume that there is available a hypothetical pump running at 730rpm that would suit our duty of 80L/s at 10m head.
We will now calculate what would happen if we were to speed this hypothetical pump up to 4 pole (1,480rpm) using the Affinity Laws. Going from 8 pole to 4 pole is theoretically doubling the speed, so we will ignore differences in motor slip and assume a 2x speed change. From the Affinity Laws, doubling the speed will double the flow. The head will increase by the speed change squared (22 = x 4). See Figure 3.
What we have done is calculate what an imaginary 8 pole speed pump selected for our duty of 80L/s at 10m would produce if operated at 4 pole speed. Now we can go back to the 4 pole range chart to see if this ‘speeded up’ duty corresponds to an actual pump. See Figure 4.
Sure enough – yes it does; we have a selection for a 250 x 250 – 400 pump. This tells us that this pump will do the duty we want when slowed down to 8 pole speed.
From the range chart we can now go to the actual pump curve at 4 pole speed and confirm the selection. We can mark the equivalent 4 pole operating point on this curve and then use the Affinity Laws to estimate the efficiency, power consumption and NPSHR for 8 pole (730rpm) operation. See Figure 5.
In this example the actual running speed will be half of the curve speed so from the Affinity Laws, the estimated power at 8 pole speed will be one eighth of the 4 pole curve. NPSHR theoretically follows the same Affinity Laws as for head and is thus estimated at a quarter of that of the 4 pole curve.
I have chosen the particular example of selecting a pump for a 8 pole running speed, but the principle is universal. Using the Affinity Laws, you can ‘adjust’ any proposed pump duty to allow initial selection from available standard range charts and curves. Other examples include selection for engine drives or using 50Hz curves to select for 60Hz service. A few more examples are shown in the table below:
Be careful!
Using the Affinity Laws in this way is great for the initial selection process, but these laws assume that pump efficiency does not change with speed. Efficiency correction factors may apply and the NPSHR prediction may not always be that accurate.
The pump manufacturer should ultimately be consulted to confirm pump performance at the final running speed and to confirm the impeller diameter.
When selecting pumps for a speed higher than the published curve, it is critical that the pump design be checked as being suitable for the higher power and pressure ratings that will result.
The above is a useful tool that allows us to select centrifugal pumps using available range charts and curves when published curves are not available at the intended running speed. However, care must to be taken to confirm actual performance and suitability once the initial selection has been made.
• For use in Irrigation systems, Dairy, Food-Processing and other Industrial Applications.
• Market Leading Range of Automatic Cleaning Technologies – including Vacuum, Brush, and Hydro-Jet.
• Hydraulic Turbine Compatible Filters Available – No Electricity Required.
• Epoxy Coated Steel, 304 Stainless Steel, 316 Stainless Steel, Duplex, and Titanium models available.
• Patented Inlet Design creates a rapid circular motion of water – causing a hydro-cyclone affect and turbulent cross-flow current over the filter surface.
• Substantially Increased Filter Service Intervals.
• Superior Flow Consistency.
• Flush-Valve for Fast and Efficient Filter Element Maintenance.
FOR FREE BROCHURES, ADVICE, OR NEAREST DEALER PLEASE CALL: 1300 134 812 EMAIL: solutions@winnowgroup.com
Since their introduction to the market over six decades ago, air operated double diaphragm pumps (AODD) have found uses in a number of applications across a wide range of industries ranging from the oil and gas sector to food processing and everything in between.
AODD pumps are at the forefront of pump technology and design. Key characteristics including their versatility, intrinsically safe design, flexibility/discharge rate and easyto-use nature have ensured they retain their competitive edge over alternative pumping methods in 2015 and helped to cement their position as ‘the pump of choice’ for many.
Reliable pump selection is essential in maximising a company’s profits. However, with so many different brands on the market today offering varying levels of customisation, it can be difficult to know which AODD pump is suited to a specific application.
David Rozee, Managing Director of Tri-Ark Pumps, shares his advice on the things to consider when choosing a diaphragm pump.
Purchasing a diaphragm pump from a reputable brand is strongly advised for a number of reasons. Investing in a more
Investing in a more established brand not only guarantees you a quality product, but it also ensures you have a support network, should you require spare parts or repairs in the future.
established brand not only guarantees you a quality product, but it also ensures you have a support network, should you require spare parts or repairs in the future.
Cheaper alternatives may seem tempting from the onset but often contain an inferior air motor technology, which could cause freezing, stalling and poor energy efficiency. The reliability of these pumps is questionable and
the cost associated with fixing them can be substantial. In some instances, the pump will need to be replaced altogether.
It is important to think of the impact this would have on your business in terms of increased downtime and additional labour costs, which can quickly erode bottom-line profits. This can prove catastrophic for any business.
There is no ‘one size fits all’ solution in the pump industry. A high level of customisation means that AODD pumps can be used to pump fluids as diverse as water, harsh chemicals and even naphtha. This ensures that the buyer is not trapped into purchasing an unnecessarily expensive model of pump for their desired application. For example, while a stainless steel solution could be used to pump petrol and diesel effectively, an aluminium construction would work just as well and cost the user four times less.
There are many materials of construction available for the pump body, diaphragms and check valves, which are dependent on the type and composition of a fluid and its desired application. Acetal, polypropylene, modified PTFE, Kynar, aluminium and stainless steel are just some of the materials used in the manufacture of diaphragm pumps.
Desired flow rate and potential pressure conditions will determine the size of the pump required for a particular application. AODD pump sizes range
Desired flow rate and potential pressure conditions will determine the size of the pump required for a particular application.
from ¼” to 4”, giving flow rates between 19lpm and 1,100lpm.
Standard units for AODD pumps are 1:1 ratio pumps, where users can expect pressures reaching up to 8 bar and these account for 99 per cent of AODD pump sales; the other 1 per cent is where a high pressure option is used where a user has 8 bar of air and is looking for a higher output, 2:1 and 3:1 ratio pump units are available with the only sacrifice being a lower pump flow output.
Some industries, such as the pharmaceutical sectors, require diaphragm pumps to be certified and comply with international safety guidelines. The food and beverage sector
is another industry where diaphragm pumps must follow strict regulations in order to be used in hygienic applications such as pumping beer, milk, strawberries and even peanut butter.
Other applications specify that diaphragm pumps are ATEX certified for use where the immediate environment is considered explosive. Since diaphragm pumps are driven by air, in as much as there is no risk of a short circuit or liquid penetrating through the wiring, there is an argument that static build up could be an issue. ATEX certification leaves users rest assured and this built-in safety advantage is an appealing USP for AODD pumps.
Pump industry legend John Link shares his reflections on a life spent developing businesses, inventing equipment and mentoring colleagues in this latest edition of our ‘Pump Pioneers’ series.
After a short time as a time and motion engineer, I started my first business in 1959 - a crop spraying business. I purchased a Govan Industry nylon roller pump, which led to stabilising sand dunes on the Mornington Peninsula, comparing bitumen emulsion with synthetic rubber to allow the seeds to grow through and stop the sand blowing away.
The crop spraying and weed control business specialised in irrigation, channel weed control and submerged aquatics. My most notable jobs were injecting chemicals into Albert Park Lake in Melbourne and Lake Burley Griffin in Canberra which were so clogged boats could not travel. I made my own VW and Tiger Moth powered swamp boats to inject the chemicals. However, I sold the business in 1965 after reading Rachel Carson’s book Silent Spring, which opened my eyes to the environmental impact of spraying chemicals such as DDT. I left that industry using high pressures of 1000psi, so I could get very small droplets when spraying irrigation channels up to 100m wide of cane grass on large properties in NSW.
I then started specialising in pumps – I think I was about the first person to set up a pump company whilst never having worked for an established pump company. My four years at Caulfield Technical School (now Monash University) gave me only four hours of theory in pumps. Most of what I knew at the time was from the practical use of pumps when crop spraying.
In 1980, together with Rick Begg, I designed an underwater sand blasting system called the ‘Link Blaster’. This was a system for detecting cracks in the legs of oil rigs in the North Sea and Bass Strait. The system operated at (then) world record depths of 300 metres. A patent was taken out for this invention which had Det Norse Veritas approval and the rights were sold to an English pump firm. The ‘Link Blaster’ has since been superseded by ultra high pressure 40,000 technology.
My first big job in Australia was in 1982 when Chorley Engineering in the UK wanted help to test the North Rankin A gas pipe line in the Pilbara. This required an enormous investment at the time and my customer helped me in financing some of the equipment with
an advance of $80,000. This allowed me to purchase the diesels in advance of being awarded the contract – otherwise the time constraints could not be met. We used eleven Rolls Royce Diesel Engines (for which we were the Victorian distributors). At the end of the job, I utilised the large multi-stage pumps to bury a pipeline for McDermott in a swamp in Indonesia.
In 1986 we pioneered 40,000 psi water-jet cutting and cut un-machinable materials for BHP and CSIRO, and helped to cross section the spent uranium glass encapsulation system at Lucas Heights.
In 1987 I started an offshore fire fighting company based in Singapore with a large number of 700hp transportable fire pump sets that were mounted on work boats. These were sent to Tunisia, the Horn of Africa, Bulgaria, Burma, China, Borneo, Vietnam and many other places. This business ran until the Asian oil crisis when the sets were returned to Melbourne. My wife (of 40 years now) Annie and I even went to Bulgaria to fix some unusual problems (not of our own making).
In 1994 I won a worldwide tender to supply all the pumping equipment to test very large oil storage tanks at Port McCullah in Yemen. This required a shipload of equipment and included the camp workshop and generating equipment. The work was done near the Queen of Sheeba Road and subsequently at the wellhead, where 140 new Toyota cars, with a value of $US1.3 million, were hijacked at gunpoint from the main contractor. It was fascinating to be in an area mentioned 2,000 years ago in the Bible. MIG fighter jets were at the airport covered in dust. Once we had to supply our own hydraulic fittings to get the BOAC plane back to Dubai. I was impressed with the use of ‘grey tape’ on the inside fuselage doors to seal them. Once we waited in the airport for tyres to be flown from America so we could get off the ground.
In the early 1990s we were contracted to clean up the Coode Island chemical spill and pump the residues to the main sewer via a long 12” pipeline supplied by us and to work under flameproof conditions. Brendon Hare of Gardiner Bros was very helpful at the time and reminded me to take charge and lead, when at that time, there were no organised emergency provisions in place.
Also in the early 1990s we provided the equipment, manpower and piping to bypass the main sewer in Elizabeth Street Kensington when it collapsed the roadway into a four double decker bus-sized hole, which threatened to collapse the nearby three-storey brick factories. This job took up to 35 employees and about two years to complete – working 24 hour days.
Our next big job was to make a large expensive rock fracturing system for one of the big gold mines. It took nine months to design, build and test the 10,000psi, 600Kw, 1,000 volt system with all the associated electronics to control the growth of crack in the ‘cave mining’ system, which continuously drops the roof a meter at a time from 1km underground. Later we built a second unit.
More recently we were ‘first in’ at the Yallourn Power Station when the mine was flooded. 5,000hp and 3km of 13 bar hose was installed and six months later, after operating 24 hours a day, we were second last out. Resource Equipment got the difficult job of bypassing the entire river around the mine.
As the flood developed and the water rose, there was 27km of layflat hose in use and that was just in our section of the mine. In the end it seemed as if every large transportable pump in Australia was on site. The Yallourn management did a magnificent job in coordinating this job, which was like having to pump out Port Phillip Bay with The Heads still open.
Rick Begg was my first real friend in the pump business and we brought ourselves up by the bootstraps, solving differences of opinion by going to the workshop and testing our theories.
John Shanassy was my General Manager for many years and did a wonderful job. My business by then got too big for either my ability or wish to control it, so I sold the sales business to John and it became Pump Power. John’s son Michael now runs the business whilst John has retired. I found that a smaller business was more profitable than a large one and much more fun – 35 employees were a handful.
Roger Withers is another real friend and we have been doing business together for over 40 years. His company Regent Pumps is an outstanding pump company, known for fantastic service.
Alan Rowan made his mark at Link Pumps for five years with his explosive temper and extensive knowledge, gained during his Scottish days as an apprentice, where he was brought up from the factory floor to working at Ingersol Rand and Kelair amongst others.
Eric Wells was the first of my mentors and used to tell customers “you don’t need a pump - you need a boy with a bucket”. This led to a philosophy of doing root cause analysis and giving customers what they really needed and not just what they wanted. The business at this time was much smaller and we did everything from designing breast pumps to repairing embalming pumps. We provided a ‘womb to tomb’ service in pumps.
Kelly & Lewis, as a company, provided a lot of advice and I used to phone them regularly for answers to my practical problems, and I absorbed the theory. And the first pump I sold was a Southern Cross, to pump edible oil to a company in South Melbourne.
Geoff Smidt went with me in the early days to our first tropical location in PNG, where we had to design and supply helicopter transportable diesel pump sets to do a 26 foot suction lift (when the river went down) and pump water deep into a sago swamp to supply a drill rig. The locals were interesting and they
could screw right hand nuts onto left hand threads.
Geoff has a photographic mind and memorised the complete Melbourne tram system timetable and knew which intersection a tram could turn in all four directions. He was known for his enthusiasm for all things ‘Fybroc’ when we were the distributors.
Keith Sanders is a long time friend and has been a great asset to the Pump Industry Association, where he shook it into life and can always be relied on to be controversial and negative. He is best known for suggesting during a speech at an industry dinner that it was all a load of codswallop (which was probably true).
Ron Astall, the President of the Pump Industry Association, is one of the many pump people whose company I enjoy. He is a fun person and there is no one better to spend time with enjoying chilli crab in Singapore and absorbing his great depth of knowledge. Ron stands out as being a wonderful competitor in exhibiting at least the same depth of knowledge as myself on an extremely wide range of pumps. I like giving him a good Dorothy Dixer at his many good lectures.
Howard Mendel was my Senior Engineer for many years. We learned a lot about filtration when we worked on the Yemen job with its many problems of pumping sea water overloaded with plankton (which we weren’t expecting).
This job came about indirectly through squash and having to travel the world. Howard remains a close and good friend. I helped him start his own business about five years before he retired from Link Pumps.
Over the years I have carried my squash racquet to many jobs around the world and have made lasting friendships through being able to play squash. In June this year I came 17th in the 75-80 age bracket of the World Masters Squash Tournament.
It was through squash friends in Singapore that I started up the fire fighting company mentioned above. I also play Royal Tennis which has enabled me to make lots of friends.
My first difficult job came after a competition match in my early days in J grade, when I beat Dr Tom Penman. He mentioned two problems and I was able to supply four diesel pumps to convert carbon monoxide to carbon dioxide in the water gas reaction. These four diesel pumps ran 24 hours a day, seven days a week for ten years on hire, and I cut my teeth on running diesels and developed my love affair with them. I have a family of Fords, Cummins, Detroits and Rolls Royces.
I always under-stressed the diesels and in return achieved very long life and
remarkable reliability. Nowadays, it is usual, because of current competition, to offer engines with just enough horsepower to be acceptable, but without longevity, as we move further into the throwaway age.
Squash gave me entry into working offshore in Bombay, using high pressure pumps to clean the oil rig legs; plus a branch in Sharjah, Dubai, leading to pipeline burial work in the Red Sea in South Arabia.
I made a lifetime study of pumps and never passed one without finding what it was and how it worked.
In the pump industry today, I believe that there are too many suppliers and not enough projects or manufacturers. Overseas competitors are commoditising many things and what used to be custom-built pumps are now pumps in a box from Bunnings and others. As an industry, we are continuing to slide into a slump and our political leaders give no sign of understanding that small business is doing it hard.
The behaviour in Parliament is repellent and useless. To be fair, it is near impossible to turn an economy around, but it would be nice if they tried instead of concentrating on staying in power or winning the next election!
It would also be great if, as an
industry, we can pull together to help each other in the difficult time ahead.
Since 1994 Link Pumps has been located on four acres in Williamstown, backing on to an old migrant hostel where my collection of more than 500 pumps reside and are used in the hire fleet or sold as required. Only Resource Equipment in Perth has more pumps than Link Pumps. We have a full mechanic shop and test facilities for up to 24 pumps and can generate 700Kw of power.
I have always been very passionate about my customers, employees and business. Currently I have eleven employees, who I consider to be friends, and I run Link Pumps as a family business with pleasant customers who appreciate the informal friendliness of our service.
Tom, a welder, has been with me for 35 years, Bernadette for about 25 years and many others for up to 20 years, and they all form part of a wonderful team. Carlos has been the brains on the engineering side of Link Pumps for the last ten years. Our excellent repairers Russell, Tarik and Tony head up the pump repair section.
I have prided myself on always having high ethical standards, a caring attitude and always trying to give the best I can, taking an interest in others. My attitude
“I have always been very passionate about my customers, employees and business. Currently I have eleven employees, who I consider to be friends, and I run Link Pumps as a family business with pleasant customers who appreciate the informal friendliness of our service.”
is to help my competitors, particularly on the hire side, and we support them with the things they can’t do easily and congratulate them on the things they do well. I especially make a point of being friends with the fellow travellers in the pump business.
Making money has never been my goal and I have never had a plan nor a budget. Profit is the result of running an ethical business and has never been an objective for me. It is enough that we have risen to the opportunities as they presented themselves.
Link Pumps is called upon to solve the very difficult problems and has often been referred to as ‘the trouble shooters’ or ‘the company of last resort’.
At nearly 80, I still have the passion for pumps and people, but the business will soon need a new owner. Are there any pump enthusiasts out there who would like to have a lifestyle business near Williamstown Beach? We overlook a marine park with views of the Bay.
Enquire within!
Pump users are sometimes confronted with the problem of applying an existing centrifugal pump to viscous liquids. Published pump performance curves are normally based on liquids with a viscosity of one centistoke (cSt). When this viscosity is increased, the performance of centrifugal pumps is affected in the following ways:
1. A marked increase in power consumption
2. Reduction in head
3. Reduction in capacity.
The resulting impact of viscosity can be:
• An undersized pump which will not produce the desired flow and/or head; and
• Overloading of the electric motor.
Managing Director - MCM Consultants Pty Ltd; Predictive Maintenance & Condition Monitoring Expert; Sessional Lecturer – Federation University Australia RAy BEEBE
Technical Director – Martec Asset Solutions; Condition Monitoring and Diagnostics Specialist
Technical Director - All Areas Inspections; Senior Examiner of Boiler Inspectors; NATA Technical Assessor & Standards Australia Committee Member
This conference will be highly practical and offer delegates the opportunity to gain access to the most up-to-date information on the design, installation, commissioning, operation, maintenance, troubleshooting and management of two key interconnected and often challenging components – boilers and pumps.
• Condition Monitoring of Boilers and Heat Exchangers
• Operating Multiples Pumps or Boilers in Tandem
• Emission Levels of a Multifuel-Fired CFB Boiler in Australia
• Cracking in Water Tube Boilers
• Sealless Pumps – Advantages on High Temperature Fluids
• Boiler Water Treatment – Options, Selection and Monitoring Tools
• Online Acoustic Monitoring of Power Boilers
• Boiler Operation for Heat Recovery
• Recent Developments in Pulse Reflectometry for Tube Inspection
• Are your Pumping Applications a Waste of Energy?
• New Innovations in Burner Ignition - Plasma
• Practical Steam Accumulator Installations
• Reduce Energy used by your Pumps
• Harmonised Plant Regulations in the Australian States - Latest Developments
• Energy from Low Calorific Fuels
For more information or to register contact IDC Technologies: 1300 138 522 • conferences@idc-online.com • www.idc-online.com
We would like to offer readers of Pump Industry Magazine a 10% discount off the conference registration fee. Contact IDC Technologies to receive your discount: conferences@idc-online.com. Register early to avoid disappointment.
27 November, 2015