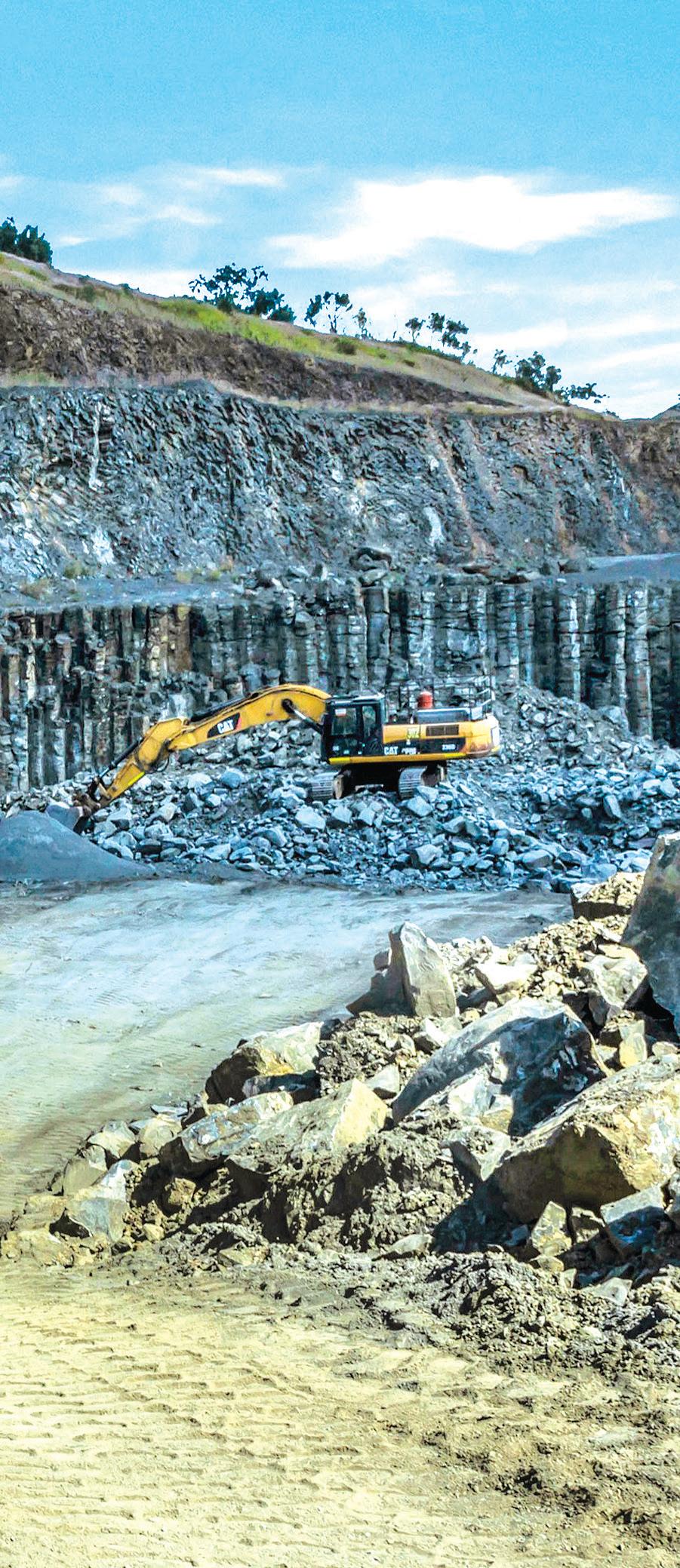

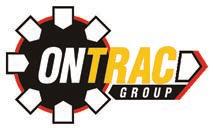
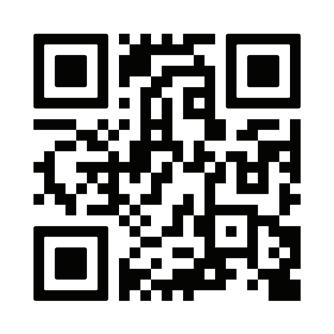
Komatsu’s Smart Quarry Site is an innovative fleet management solution designed to empower site and project management personnel with unparalleled production visualisation for quarry and major civil construction sites. With a simple glance, you gain access to real-time animated insights into every aspect of your production machines, as well as the material they are handling, extracting, shifting, or placing.
visit https://komatsuweb.link/smart-quarry-site
22 APTELLA’S NEW ERA
Aptella, formerly Position Partners, has revealed its new name and branding.
24 DOUBLE DELIGHT
Caterpillar has designed the 988 GC Wheel Loader to deliver production targets at a lower cost per hour through lower fuel and maintenance costs.
28 LIVING THE DREAM
Komatsu’s Live Your Dream grants aim to create positive change.
32 FANTASTIC 50
CJD Equipment celebrated its 50th year in February.
34 NEW HORIZONS
Walker Quarries commissioned its new wash plant from CDE in 2023.
36 PRICING AND QUOTATION
Steve Franklin looks at some new developments that could make a tangible difference to your bottom line.
40 ROCKING REGIONAL
Astec Industries has a strong reputation for hard rock crushing, which is on display at Regional Recycling.
46 PRECOAT PERFECTION
Precisionscreen’s range of precoat solutions enables operators to deliver high-quality precoat material.
48 OPTIMUM PROCESSES
Kleemann demonstrates how technical innovations and good planning guarantee efficient processes.
50 SUPERIOR IDLER EMERGES
Superior Industries has reworked the design of its conveyor idlers, incorporating an upgraded bearing seal.
Working in an office carries with it several hazards.
Poor lighting can lead to eye strain, water on the break room floor could create a nasty fall, and with so many electrical devices floating around there’s always the possibility of a shock.
These hazards, while plentiful, are relatively low risk. That means the possibility that harm might occur when exposed to them is unlikely (though still possible).
Out in a pit, the stakes are much higher. With so much heavy machinery moving about, it’s vital that operators and management eliminate the risks staff face. In fact, there is legislation in place to ensure this is done properly.
Management of risks requires an assessment of the risks and hazards at a site. Often, these risk assessments will involve looking at what could happen if someone is exposed to a hazard, and how likely it is to happen. Workers will likely know where these hazards are and can help find ways to mitigate them.
A hierarchy of control measures can help control risks and reduce exposure to hazards, with the highest level of protection and
reliability being to remove the risk entirely. On the other hand, the lowest amount of protection and reliability is relying entirely on personal protective equipment and administrative controls. This is because they rely on human behaviour and supervision.
Correctly assessing and managing risks on a quarry site can save lives, so it is vital for managers, supervisors, and key support personnel to ensure they have the skills required for the task.
The Institute of Quarrying Australia (IQA) understands how important it is to the industry, which is why the organisation provides high-quality educational courses to members and non-members.
Education is not just something that happens at the start of your career. It should occur all through out as you learn about new technologies and skills. Continued professional development is vital in the quarrying industry as it makes workplaces safer, more sustainable, and improves community and business outcomes.
William Arnott EditorCORRECTLY ASSESSING AND MANAGING RISKS ON A QUARRY SITE CAN SAVE LIVES, SO IT IS VITAL FOR MANAGERS, SUPERVISORS, AND KEY SUPPORT PERSONNEL TO ENSURE THEY HAVE THE SKILLS REQUIRED FOR THE TASK.
Published by:
379 Docklands Drive
Melbourne VIC 3008
T: 03 9690 8766
www.primecreativemedia.com.au
Chief Executive Officer
John Murphy
john.murphy@primecreative.com.au
Managing Editor
Paul Hayes paul.hayes@primecreative.com.au
Editor
William Arnott william.arnott@primecreative.com.au
Journalist
Adam Daunt adam.daunt@primecreative.com.au
Business Development Manager
Les Ilyefalvy les.ilyefalvy@primecreative.com.au
Client Success Co-ordinator
Janine Clements janine.clements@primecreative.com.au
Design Production Manager
Michelle Weston
michelle.weston@primecreative.com.au
Art Director
Blake Storey
Graphic Design
Michelle Weston
Subscriptions T: 03 9690 8766
subscriptions@primecreative.com.au
The Publisher reserves the right to alter or omit any article or advertisement submitted and requires indemnity from the advertisers and contributors against damages or liabilities that may arise from material published. © Copyright – No part of this publication may be reproduced, stored in a retrieval system or transmitted in any means electronic, mechanical, photocopying, recording or otherwise without the permission of the publisher.
It takes a different kind of brain behind the brawn. Fired up like a turbo diesel. Gears constantly churning. Hardwired beneath hard hats to solve problems, or avoid them altogether. With you and your crew at the helm, and Deere at your back. The workarounds, ideas and innovations that move earth, and your business, forward. Because that’s what it takes to win in the dirt. And that’s what it means to be Never Idle.
IQA Branches are the lifeblood of the IQA. The branches are how we as an organisation connect the extractive industry and support professional development of people in the industry.
The IQA has branches in every state and territory, with several sub-branches in New South Wales, Queensland, and Victoria. Branches bring our industry together and being involved is extremely rewarding, letting you grow your networks and share your ideas across the sector.
Operators, geologists, CEOs, directors, surveyors, engineers, production managers, site managers, laboratory staff, landscape architects, environmental specialists, sales staff, health and safety officers, and more are all branch members.
Being a member means enhanced networking opportunities at a local level.
I strongly recommend and encouraged all members keep their eyes open to all events as networking and developing connections is paramount to growing the industry. Branch events are held regularly across Australia and are open to both members and non-members.
Networking doesn’t end at those within the IQA. Giving back to communities and encouraging involvement from those outside to join in and spread the word is one of many ways in which we can encourage young people in the industry to become aware of the IQA and sign up so that we all can benefit.
The IQA will continue to offer opportunities, training, and recognition across all of Australia to provide much needed support to our industry and continue to grow our industry.
It also provides many benefits including access to the latest technical, environmental, and commercial industry developments. Members can also gain exclusive access to online resources such as webinars and fact sheets.
As always, a massive thanks to our branch members, our committee members and the broader IQA community, without your continued support and contributions the IQA would not be as it is today.
Duncan Harris PresidentInstitute of Quarrying Australia
I STRONGLY RECOMMEND AND ENCOURAGED ALL MEMBERS KEEP THEIR EYES OPEN TO ALL EVENTS AS NETWORKING AND DEVELOPING CONNECTIONS IS PARAMOUNT TO GROWING THE INDUSTRY.
The Institute of Quarrying Australia
Educating and connecting people engaged with the extractive and associated industries.
www.quarry.com.au
The IQA’s Strategic Plan 2023 to 2026 embodies the following vision, values and strategic priorities:
Vision:
Thriving communities supported by a sustainable industry
Operational Priorities:
• Deepen industry participation
• Sustainable revenue streams
• Highly capable team
• Technological innovation
• Effective engagement
• Great governance
Strategic Priorities:
• Support industry participants with compliance and regulation
• Build a diverse and skilled industry workforce
• Foster strong industry connectivity
IQA Contacts:
Phone: 02 9484 0577
Email: admin@quarry.com.au
Deputy President
Sarah Bellman
Company Secretary
Rod Lester
For all education, member and branch enquires please email: admin@quarry.com.au.
Holcim has revealed that Miljan Gutovic will take over as chief executive from Jan Jenisch in May.
The announcement comes as Jenisch has been tasked with leading the US listing of Holcim’s North American business. Jenisch will remain as chairman and stand for re-election at the annual general meeting in May.
“I am very pleased that the Board has appointed Miljan as the new CEO of Holcim. He is a highly qualified successor who has played an instrumental role in Holcim’s successful transformation to become the leader in innovative and sustainable building solutions,” Jenisch said.
“Miljan has strengthened our business with record profitability in
Europe, closing strategic transactions and building winning teams.”
Gutovic, who hails from Australia, has been on Holcim’s group executive committee since 2018, alongside previous roles as Head of the Region Middle East and Africa, followed by the Region Europe and Operational Excellence.
The University of Technology Sydney graduate, with degrees in civil engineering and a PhD in material sciences and engineering, said he was humbled by the opportunity.
“As a civil engineer who is passionate about the construction industry, Holcim is the best company to be part of. With decarbonization and advanced technologies transforming how we build, there has never been
John Fahey, Fellow of the IQA, has formally announced his retirement from BQC Quarries.
Fahey was a former chairperson of the North Queensland Branch.
He is considered a key figure of Queensland’s quarrying industry, especially in Northern Queensland, with his decades of experience and involvement at BQC Quarries.
In his announcement, Fahey said it has been an incredible journey to help build and grow BQC Quarries over the past 46 years.
“MILJAN HAS STRENGTHENED OUR BUSINESS WITH RECORD PROFITABILITY IN EUROPE, CLOSING STRATEGIC TRANSACTIONS AND BUILDING WINNING TEAMS.”
JANJENISCH
“I will cherish the memories we’ve created together and the relationships that have been built,” he wrote.
“While I may be stepping away from the day-to-day operations, my commitment to the success of BQC Quarries remains.
His son, Lawrie Fahey is also involved with the IQA and up until last year was the Chairperson of the NQLD Branch and is still on the branch committee.
“For the past five or so years the business has been in the very capable hands of my son, Lawrence Fahey, as Operations Manager,” Fahey wrote.
a more exciting time for our sector,” Gutovic said.
“I look forward to working with the Holcim teams around the world to advance our leadership.”
Holcim has announced its intent to list its North American business with a full capital market separation.
The company said the newly listed business will help drive long-term growth in the rapidly expanding North American market with a “pure-play” building solutions company.
According to Holcim, the listed North American business will be the leading pure-play building solutions company in the region, with an estimated EBITDA1 margin of more than 27 per cent for 2023. It estimates the North American business will execute an accelerated growth strategy to achieve more than USD $20 billion in net sales and more than USD $5 billion in EBIT with industry-leading margins by 2030.
“Holcim has reached a new level of financial performance and a superior earnings profile with industry-leading margins and a strong balance sheet,” Jenisch said.
“With a US listing, we will unleash its full potential to be the partner of choice for our customers in one of the world’s most attractive construction markets.
“This next step of growth and value creation is possible thanks to the outstanding leadership of our empowered teams around the world delivering record results year after year.”•
“Lawrence has a wealth of knowledge and experience and has shown great dedication and passion in ensuring the business continues to thrive and be successful.”
BQC Quarries farewelled the quarrying stalwart who officially departed in December last year.
“Everyone at BQC Quarries would like to congratulate John and wish him all the happiness in his retirement with his wife Elizabeth,” the company wrote in a statement.
“Congratulations John, you will be missed.” •
CRH Ventures has unveiled its latest move in the artificial intelligence space, which will further digital support for quarries.
CRH Ventures has partnered with SafeAI for the program which will take place at one of the former’s quarrying subsidiaries in North America. The test truck will be equipped with SafeAI’s technology and operated under supervision.
It will evaluate the feasibility and capabilities of SafeAI’s innovative technology for autonomous operations in quarrying.
“This pilot program with SafeAI aligns with our commitment to explore innovative solutions for more efficient and sustainable quarrying operations,” Head of CRH Ventures Eduardo Gomez said.
“We are excited to assess the potential of autonomous hauling technology in a controlled environment and the possibilities for future scaling.
“While this marks an important step in our exploration of autonomous hauling
solutions, it’s crucial to clarify that, at this stage, CRH Ventures is focusing on piloting the technology before finalising any strategic investments.”
The pilot program is designed to simulate quarry operations and will run for approximately one year. The success of the initiative will be evaluated based on predetermined Key Performance Indicators (KPIs) over various test scenarios, comparing autonomous performance against traditionally staffed operations.
“We’re excited to partner with CRH to advance its vision for sustainable, efficient quarry operations. Together, we can showcase the capacity for new technologies to create a safer, more productive future for the quarrying and construction industry,” SafeAI chief executive and founder Bibhrajit Halder said.
“Autonomous solutions have the potential to transform heavy industry; we work with forward-thinking companies to bring this potential to life.” •
Heidelberg Materials has revealed the EU Innovation Fund will turbocharge its plans for a fully decarbonised cement plant in Germany.
The fund, which is one of the world’s largest for low-carbon technology, will invest €191 million ($311m AUD) to develop the project at Heidelberg Material’s German Geseke cement plant.
The plant will produce carbon captured net-zero cement and clinker with the help of the funding which became active on January 1 following the successful grant agreement.
Chief sustainability officer and member of the managing board of Heidelberg Materials Dr Nicola Kimm
said the successful agreement was a major milestone.
“(It) demonstrates the relevance of GeZero for the decarbonisation of our sector, and the trust that European authorities place in our approach.”
“We just recently introduced our evoZero brand, the world’s first carbon captured net-zero cement on the market. The product will initially be offered through our Brevik CCS project in Norway. Once other capture projects such as GeZero start operations, these plants will also be able to deliver net-zero cement and clinker to customers, significantly speeding up the decarbonisation of our industry,” she said.
Deputy Prime Minister of the State of North Rhine-Westphalia Mona Neubaur said the project was a boost for the German region.
“About one third of the German cement production is located in North Rhine-Westphalia. We are therefore delighted that the first carbon-free cement plant in Geseke in the district of Soest is a flagship project for a sustainable and climate-neutral future in the cement industry,” she said.
“GeZero shows how climate protection through new technologies and processes can also be achieved in energy-intensive industries. The project represents a decisive step towards a future-proof cement production and the transition to a net-zero industry in North RhineWestphalia, Germany and beyond.”
The EU Innovation Fund focuses on flagship projects with European value added that can bring significant emission reductions. In response to its third call for large-scale projects, the European Commission had received 239 applications while 37 were selected for funding. Last year, Heidelberg Materials’ Bulgaria site was chosen by the fund.
“Together with our partners, we walk the talk and pave the way for CCUS in Germany,” Christian Knell, general manager for Germany of Heidelberg Materials, said. •
The National Heavy Vehicle Regulator (NHVR) has unveiled a new, interactive site for all the heavy vehicle access information across Australia.
The regulator has launched the National Network Map, which is a targeted initiative aimed at improving heavy vehicle operators’ efficiency and decision-making.
The digital offering brings together state-based maps in one location, which is believed to be a first for Australia.
The regulator said the focus has been on including the correct road ownership information, providing more comprehensive and accurate
data for road managers when making access decisions.
With the network map up and running, the NHVR will train operators to get the most from the platform. The training will allow operators to use the self-service tool to update heavy vehicle networks on the map and update gazetted and preapproved routes.
The National Network Map is available on the NHVR website or through an NHVR Portal account.
For more information, a recorded online seminar is available here, with further webinars planned across 2024. •
In enclosed transfer points, the accumulation of pressure can result in the build-up of dust.
This dust is problematic for conveyor componentry function, operational site cleanliness, as well as environmental and personnel health and safety. Kinder Australia’s DustScrape has been developed by engineers to effectively resolve and mitigate dust formation, transforming the way industries handle dust-related challenges.
DustScrape does this by incorporating a specialised filter cloth. This cloth captures fine dust particles produced during bulk material transfers. Its intelligent design allows for air permeability, accommodating the resulting overpressure. By reducing the pressure while containing the dust, DustScrape facilitates the settling of bulk material, ensuring a cleaner and more efficient conveyor system.
Key features and benefits:
1. Qualit y stainless steel: DustScrape is available in a stainless steel option, ensuring durability and resilience in various environmental conditions and material applications.
To submit new product and equipment releases, email: les.ilyefalvy@primecreative.com.au
2. Installation simplicity: Operators can integrate DustScrape into their existing conveyor systems.
3. Versatility in application: DustScrape is adaptable to conveyor belt widths of varying belt widths.
4. Maintenance free: DustScrape operates without direct contact and requires minimal maintenance.
5. Self- cleaning efficiency: The unique self-cleaning feature of DustScrape enhances its overall effectiveness and longevity.
6. Reduces Dust Up-Drift: DustScrape actively suppresses dust up-drift, for an efficient and reliable containment.
7. Compatibility with Extraction Systems: DustScrape may work together with dust extraction systems if required.
8. Synergy with AirScrape: When paired with AirScrape, the patented sidewall seal (not included) forms an exceptionally effective system that combats dust generation.
Kinder offers the option for customised solutions. Get in touch with Kinder’s field application specialists and engineers to discuss how DustScrape can benefit an operation at conveyorsolutions@kinder.com.au or 03 8587 9111.
In the ever-evolving landscape of heavy machinery, innovation is the key to unlocking new levels of efficiency and productivity. Tricon Equipment, a trusted name in the industry, runs us through the Terex MDS M515 heavy duty track trommel.
At the heart of the Terex MDS M515 lies its unparalleled performance capabilities. Designed with heavy-duty tasks in mind, this track trommel boasts a robust build and a powerful engine, ensuring seamless operation even in the most demanding environments. The machine’s high-capacity drum allows for the efficient screening of a variety of materials, from aggregates to mining and quarries, with precision and speed.
One of the standout features of the Terex MDS M515 is its track-mounted design, providing unmatched mobility on the job site. This not only enhances the machine’s manoeuvrability but also reduces setup time, allowing operators to transition between locations with ease. The track trommel’s ability to navigate challenging terrains ensures that it remains a versatile asset across different industries.
The Terex MDS M515 incorporates advanced screening technology, setting it apart from traditional trommels. The trommel’s drum features customizable screen configurations, enabling operators to adapt the machine to the specific requirements of their operation. Whether it’s fine screening or coarse screening, the Terex MDS M515 delivers consistent and reliable results.
Tricon Equipment understands the importance of user-friendly interfaces in maximizing efficiency. The Terex MDS M515 comes equipped with an intuitive control system, allowing operators to easily adjust settings, monitor performance, and troubleshoot issues on the go. This focus on user experience not only streamlines operations but also reduces downtime. In an era where environmental sustainability is paramount, the Terex MDS M515 stands out with its eco-friendly
design. The machine incorporates fuel-efficient technology, reducing both operational costs and carbon footprints. Additionally, the track trommel’s innovative dust suppression system ensures a cleaner and safer working environment, aligning with modern environmental standards.
Tricon Equipment’s commitment to providing top-tier machinery is evident in the Terex MDS M515 heavy duty track trommel. With a reputation for reliability and performance, Tricon continues to be a trusted partner for industries seeking cutting-edge solutions.
The Terex MDS M515 stands as a testament to the company’s dedication to pushing the boundaries of what’s possible in the field of material processing.
For more information call 1300 859 885 or visit triconequipment.com.au
ONTRAC and the XMOR®️ bucket had a significant year in 2023. Quarry looks at the reasons behind the product’s rise and what will come for the year ahead.
When ONTRAC launched the XMOR bucket into the Australian market a few years ago, some quarry operators were hesitant. It looked different from traditional excavator buckets.
SSAB’s Hardox®️ 500 Tuf and Strenx®️ Performance steel meant it was lighter and featured an inverted tub and unique
mechanical heel segments. Yet, the XMOR bucket grew in popularity again in 2023, and ONTRAC plans to expand its presence across Australia in 2024.
According to the company, word of mouth between the closely connected quarrying industry is talking about the benefits of the bucket.
ONTRAC product specialist Nick Espie said it was a sign that the XMOR bucket, with its unique design, is winning over the industry as it proves time and again, that there are ways to boost excavator productivity.
“When you enter the market with something different, it is always going to be met with a little bit of resistance,” he told Quarry.
“It does look different, so a lot of guys are put off by the look because it doesn’t look the same as what they’re currently using, and they thought it wasn’t going to do the same work.
“We’re trying to encourage people have a new way of thinking. When the customers see the numbers and what they can achieve, especially now that we’ve got real time data, that answers a lot of questions. We are getting a lot of positive feedback from customers who may have been sceptical but now wouldn’t go any other way but XMOR.”
Three factors support the XMOR bucket’s emergence on the quarry scene: Increased productivity, durability, and support.
One of the factors behind the XMOR bucket’s growing popularity is its BHC variant, which provides a harder wearing option.
When most consider the XMOR bucket, they are likely considering the BHB version.
It features a lightweight, rounded design with SSAB’s Hardox 500 Tuf wear plate. ONTRAC Group takes a site-by-site approach when recommending an XMOR bucket for a particular site, however, the BHB is generally for moving overburden or bulk earthmoving to achieve higher productivity than traditional buckets.
The BHC type has the same components as its BHB counterpart, but is beefed up to deliver a more robust bucket for more abrasive environments. It still maintains a lightweight design, with the inverted tub and mechanical wear parts, to reduce weight and downtime, like the BHB model.
It has a flat cutting edge with a straight top beam, compared to the BHB’s curved appearance , with increased steel thickness to enhance the BHC’s wear and longevity.
“The extra wear and longevity are useful for applications like granite, higher material densities and abrasive environments,” Espie said.
“It manages to work in these environments while offering the increased durability and productivity of the XMOR bucket.
“The limited downtime and ease of maintenance are still due to the easily
interchangeable parts like the BHB, but in a beefed-up model.”
One quarry operator in Sydney’s south, considered a larger quarry by Australian standards, took on XMOR’s BHC bucket from ONTRAC.
The quarry runs two to three shifts daily, focusing on high-volume material being shifted in a hard rock, abrasive environment.
ONTRAC worked closely with the site to match the XMOR BHC bucket to their needs, and Espie said the operator had nothing but positive feedback since taking delivery.
“We’re receiving really positive feedback, the bucket is wearing very well, and holding up to the material.”
Overall, he said the feedback throughout 2023 on the XMOR buckets has been “they are wearing very well and much better than the traditional quarrying buckets they have used in the past.”
“The XMOR buckets are doing what we’ve described; customers are shaving one to two, sometimes, three passes off their truck loading, and that’s the efficiency that the XMOR is all about and fuel savings as well.”
Espie spends a lot of his time visiting quarry clients on the coalface. He has heard a common refrain in his travels: downtime costs money.
Quarries can ill-afford having their buckets out of action for lengthy periods when deadlines must be met amid strong demand for construction materials.
This is why ONTRAC houses a full range of wear parts for the XMOR bucket at its warehouse.
The XMOR’s design, compared to traditional buckets, means some of its wear parts are bolt on as opposed to being welded on.
This design feature enables faster maintenance, which ONTRAC says can be two to four hours instead of two days for welded parts.
“Downtime, particularly in a quarry, is money. So, we need to ensure that we’re quick and prompt with what we need to do,” he said.
“We can get wear packs and teeth out to our customers quickly, which is the advantage of being Australian-made and manufactured.
“We are in a good place to be able to respond quickly to any small issues that might have hampered customers’ operations.”
FUTURE VIEWS
ONTRAC does not plan to rest on its laurels. Instead, the company is working behind the scenes to ensure more quarries across the country reap the benefits of the XMOR bucket.
“It was a great year for ONTRAC, particularly for the XMOR product. We saw a big uptake in it, and the industry’s knowledge of it expanded quite a bit,” he said.
“We saw a greater uptake on it from the big OEM brands, and allowing customers to see how the XMOR could work with their machines was great.
“We believe the XMOR bucket can help quarries, and we want to work with the quarries and the OEMs to help them see how the XMOR could make them stand out.”
ONTRAC can work with quarries to deliver a complete productivity study that considers the quarry’s production, machinery,
environment and what similar sites have achieved. This information enables ONTRAC to suggest the best configuration of XMOR to help accomplish the quarry’s goals.
“Creating a win-win situation for us and the quarry is our ultimate goal; it’s the driving force behind what we do,” Espie said.
“We can go into a quarry and straight away see how an XMOR bucket would help them and provide a return on investment, sometimes within two months.”
Espie said the company would happily show any quarry operator what could be achieved by switching to the XMOR bucket.
“We’re always happy to sit down with an operator and show them in real-time what they could achieve with ONTRAC and the XMOR bucket,” he said.
“Any time is a good time to start talking to us about an XMOR bucket.”• For more information, visit ontracgroup.com.au.
The Warrnambool Community Garden is a treasure of the local community, yet up until 2015 it was an eyesore. Quarry explores the transformation of the space over the years.
The Council Quarry in Albert Park quarry had been many things to the Warrnambool community, but perhaps most commonly it was seen as an “eyesore”.
After its days as a productive sandstone quarry, it was never officially a rubbish dump, yet plenty of waste material and junk from road works could be found in it.
Blackberries and numerous other weeds had infested the site, and the uneven nature of the quarry made it unsafe to walk down.
The quarry has since become an amphitheatre filled with bird songs and Australian native plants and produce.
Quarry spoke to the Warrnambool Community Garden (WCG) team about the challenges and success of transforming the quarry into an award-winning garden space.
“Our 2016 consultations about repurposing the quarry sparked memories from
the community about working there or playing there as kids,” WCG convenor Rob Porter said.
“It showed that this area meant a lot to the local community.”
The initial discussions for a community garden adjacent to the quarry occurred in 2005 before a meeting established the Warrnambool Community Garden Inc. (WCG) the following year.
The meeting showed an appetite for the site to be transformed as 65 people attended the meeting, which established the WCG group, which still takes care of the space almost two decades later.
The WCG agreed with the Warrnambool City Council, who managed the land, to have only the bottom third. This is now the most
developed space, with individual garden plots, several community vegetable, herb and fruit tree areas, a children’s garden, hothouse, chook yard, community centre, garden shelter and more.
But perhaps it was their conviction in the ambitious transformation that by the second lease agreement, they had leased the entire site, including the quarry.
A key consideration at the time, which helped shape the quarry transformation, was the neighbouring water treatment plant. If a large discharge from the plant was required, it would be safer if there was no permanent infrastructure on the quarry floor.
The question of what to do with the quarry space was taken to the community as the WCG and council tried to establish the best use for the former sandstone site, which had seen better days.
Warrnambool has a proud quarrying history.
At one time, it was estimated that 12 quarries operated there. It is understood that the council operated the Albert Park quarry from the 1900s to the 1960s when it ceased production.
The quarry became a favourite site of Edmund Gill, a renowned Australian geologist.
Warrnambool resident and academic Dr John Sherwood told researcher and writer Kirsty Hawkes that Gill enjoyed the site “because it contained the most cemented and therefore oldest calcarenite in town,” which proved fruitful for his research.
More than two decades after Gill’s passing in 1986, the quarry was a ruin to a previous era in the Warrnambool.
“Some of the suggestions were fairly dramatic; one suggestion was just to fill the quarry in,” WCG committee member Geoff Rollinson said.
“Other suggestions were to do something like the Eden Project in the UK that placed a
glass dome over a disused quarry, which we costed at $10 million so too expensive.
“But the idea that it could be an amphitheatre seemed to resonate with people, so we set about putting the plans in place after a fairly exhaustive consultation process.”
The road ahead for the quarry was about as easy to navigate as its blackberryinfested surfaces.
Landscape architects were called in, geotechnical work was carried out, and a concept plan was drawn.
Contractor workers and community planting days coincided with turbocharging the quarry to its new use.
“Even as a concept plan, I was pretty impressed with the degree of technical work that had gone into developing it,” Porter said.
“It was a pretty amazing thing to witness.”
The Warrnambool Community Garden was helped by the support of local institutions, including council grant programs, Beyond Bank and Wannon Water, the region’s water authority.
The Victorian government’s “Pick My Project” grant program in 2018, which delivered $194,000 and Warrnambool City Council’s Small Infrastructure Fund in 2022, which contributed $150,000, paid for most of the groundwork.
Other small grants and philanthropic donations helped deliver the concept plans and other initial planning like geo technical work which helped leverage larger grants.
Their combined financial and other support helped pave the way for the quarry and the broader transformation of the gardens.
“They’ve always been supportive of the garden and its philosophy and what it is trying to do in the community,” Porter said.
The amphitheatre held its first event in late 2023, eight years after rehabilitation work began, with a rousing reception from the Warrnambool community.
Live in the Quarry, held on the lands of the Peek Whurrong and Maar Nations, saw live music and food stalls fill the grassed area of the quarry for its first event in years.
WCG deputy convenor and Warrnambool’s young citizen of the year 2024, Courtney Mathew, said the community event capped the quarry’s transformation.
“There was a real smorgasbord of people, from two-week-old babies to 90-year-olds, coming to enjoy the serenity of the gardens and the amphitheatre,” she said.
“We hope it becomes this space for a range of events and can activate the arts, music dance and education for the town.
“And hopefully, it contributes to making Warrnambool a nicer place to live.”
The site’s transformation into a garden and amphitheatre took a lot of work from a group of committed volunteers.
But their work was noted as the WCG scooped the Premier’s Sustainability Awards 2022 as the sustainable places and destinations category community winner. They were also finalists in the 2023 Banksia Awards and the 2023 Volunteering Victoria Awards.
“The award recognition probably coincides with the development of the quarry, not that the quarry is responsible for all of it, but it has helped,” Porter said.
“When you’ve become used to something, you stop being impressed by it, but to be the winner in that category of the Premier’s Awards was pretty exciting.”
The site continues to evolve, with the WCG planning to open a gully area at the top of the site furnished with boardwalks and paths. It will tell the story about water, conservation, and the environment in an
educational way for the community.
When asked to reflect on the journey of the WCG and old Warrnambool Quarry, Porter said sometimes he needed to remember just how far they had come.
“Those of us that have been coming through the gates a long time probably need to remind ourselves of this place’s impact,” he said. •
The New IMS-BP1200-48TB Track Blender, with four five-meter-long feed hoppers holding 12m3 each with separate feed hopper conveyors with attached belt scales and fully automate with a PLC control and recording system that can be operated with an iPad from a loader or site office. Powered by a Cat C7 Generator that can be connected to mains power, driving Nord Electric motors with variable speed and feed hooper stop/start sensors with remote. The genset can also drive a 24-meter radial conveyor. The BP1200-48TB can produce up to 1000 tonnes per hour.
IMS have added the new BP1200-48TB track electric twin power blender to its impressive collection of blenders and pugmills, the new BP1200-48TB has four separate feed hopper each five meters long holding 12m3 each. All feed hopper conveyors are fitted with belt scales and controlled by a PLC control and recording system that can be operated from an iPad or phone from its own Wi-Fi system from a loader or site office. A Cat C7 Generator powers the Nord electric motors all fitted with invertors offering variable speed to each feed hopper conveyor. The generator can be connected to mains power and could power an extra 24-meter radial stacker increasing the stockpile capacity.
A new IMS-PM1200-20TB Track Pugmill with twin 10m3 feed hoppers has just commissioned to Braeside Quarry on the New England Highway Warrick in Qld, the options the PM1200-20TB offered Braeside improved product management with the twin feed hoppers blending fines into roadbase to make spec or having two different products available ready for moisture control and CTB. The PLC control and recording system can be operated from an iPad in a loader managing all aspects of the operation including loading trucks and multiple trailers stopping when the required weight has been reached for each unit and recording the ID number of each load.
The BP1200-48TB can also work in conjunction with the IMS modular electric pugmill on skids producing up to 500 TPH of water or powder blended material and stockpiled with an IMS 24-meter radial conveyor with auto radial return.
IMS – PM1200-20TB Track Pugmill with two separate five-meter-long feed hoppers holding 10m3 each which can be extended to 12m3, the feed hoppers have the option of fitting vibrating hydraulic tipping grids. Both feed hoppers have front of hopper adjustable flow gates, variable speed, and belt scales with the option of being fully automated. There is the option of adding two powder hoppers and two liquids.
Aptella, formerly Position Partners, has revealed its new name and branding. The technology services company talks to Quarry about the change.
Aptella officially changed its name in January, with a roll-out occurring across its social media, branding, and equipment.
Aptella chief executive Martin Nix said the name encapsulated the brand’s growth since it was formed by five state-based distributors in 2008.
“The Position Partners name and brand has served us well,” he said.
“Sentiment from our employees and customers was that the time was right for a fresh new identity to better represent the experiences people can expect from us as their vital technology provider.”
Aptella has over 350 employees operating in six countries, advising clients on automated positioning technology solutions in several industries, including quarrying.
Nix said the change came about in response to feedback from Aptella’s customers and employees to reflect its international presence.
“We wanted a name that was short, easy to say, and memorable in all countries we do business in. As a company operating across six countries, we also needed a global .com presence online,” he said.
“Whilst the name and branding are changing, the core aspects of our business and what people love about us remain as strong as ever.”
While the Aptella carries a new name into 2024, it will still deliver the same breadth of services to the quarrying sector.
Aptella’s quarrying services, which are carried out across Australia, NZ, and Indonesia, include weighing and calibration technology.
The company has a team of scale verifiers who are certified by the National Measurement Institute (NMI), Australia’s leading measurement body.
Aptella’s team of verifiers can go across Australia, New Zealand and Southeast
have all the equipment required to conduct weighing calibration at the quarry site,” he said.
“There is no need to borrow equipment or anything, we have trucks in all the main regions of Australia to do the test masses for the calibrations.
“We can do any brand of loader scale or excavator scale and weighbridges, batch plants or laboratory bench scales and flow metres; we can do it all for calibrations.”
The introduction of the National Heavy Vehicle Regulator’s Chain of Responsibility legislation has made easy access to information even more critical.
The legislation means everyone who works with heavy vehicles can be held responsible for breaches of road laws and may be legally liable if they have control over the transport – not just the driver or operator of the heavy vehicle.
“Weighbridges won’t let trucks out,
which must be certified.”
Aptella, with its longstanding experience in the weighing calibration space, can help quarries find the best solutions for their needs.
“We work with the operator so we can quote accordingly and put a plan in to look after all their sites and all the scales on those sites for a set period, whether that’s one year or sometimes up to five years,” he said.
“We recommend getting a weighbridge calibration conducted yearly, although some higher-volume operations may want to do it every six months.
“It also gives them confidence that 50-tonne is 50-tonne so they can become more efficient and have confidence in their product.” •
For more information, visit aptella.com
Insights into how to reduce your CO 2 footprint
Volvo develops equipment to meet strict emission standards
Volvo strives to lead innovation for a cleaner, smarter and connected world
Optimise how you work with Volvo Co-Pilot, your partner in the cab. The high-resolution 10” touch screen provides access to a range of Assist applications, designed to boost productivity, accuracy and efficiency.
Harnessing the full power of machine data and site analysis through connected technologies is one of the first steps towards a more sustainable quarry site.
Volvo have initiatives to reduce their carbon footprint across product life cycles
Sustainability is central to Volvo’s commitment, spanning manufacturing to disposal
Caterpillar has designed the 988 GC Wheel Loader to deliver production targets at a lower cost per hour through lower fuel and maintenance costs.
When the Caterpillar team was designing the Cat® 988 GC Wheel Loader, they knew it needed to achieve two main factors for quarry operators. It needed to move more material at a lower cost per hour.
The two factors, in combination, would enable quarries to achieve a faster return on investment and help quarries meet increased material demand.
The 988 GC Wheel Loader entered the market with features to reduce maintenance and fuel consumption and increase operator comfort to meet the needs of modern quarries.
According to its internal data, the 988 GC Wheel Loader can deliver five per cent less fuel consumption and up to 15 per cent lower maintenance costs than the Cat 988K while remaining within six per cent of the 988K in truck loading applications.
The 988 GC Wheel Loader is designed as an optimised 45-tonne (50-ton) truck match loader with reliability and efficiency at its foundations. The 988 GC’s cooling package offers higher heat rejection with an
on-demand fan strategy and two available fan speed settings for standard and highambient-temperature configurations.
Caterpillar has powered the 988 GC Wheel Loader with a Cat C15 engine. The engine offers configurations to emit equivalent to EU Stage IIIA / U.S. EPA Tier 3 or meet EU Stage V / U.S. EPA Tier 4 Final emissions standards. The engine is a vital part of the wheel loader, achieving more production at lower fuel costs, which is around five per cent better than other comparable Cat machines.
A comfortable operator is a productive operator, and Caterpillar knows operator comfort, which can withstand the rigours of a quarry site, is critical.
The heart of operator comfort on the 988 GC Wheel Loader is the Steering and Integrated Control (STIC™) steering. The feature, partnered with a Cat Comfort Series III seat and its seat-mounted implement pod, has been shown to achieve 47 per cent quieter operation, according to Caterpillar’s internal data. Further to that, machine vibration feedback to the operator is reduced
using cab isolation mounts and seat air suspension, and an optional air-cooled and heated seat is available for increased operator comfort.
Product Link™ offers wireless access to essential operating data for valuable insight into how the machine is operating. Standard rear Cat vision enables visibility behind the 988 GC, allowing the operator to work safely and confidently.
The 988 GC can be equipped with Cat Detect technology that enhances awareness of the environment around operating equipment, which, according to the company, improves the safety of workers and assets.
Cat also offers optional technology platforms to help make an operator’s life easier. These include real-time data displays like the optional Cat Payload, which provides on-the-go weighing for materials hauled and loaded. The optional Advanced Productivity subscription provides comprehensive, actionable information to help manage and improve operational productivity and profitability.
The reduced maintenance was at the forefront of the 988 GC Wheel Loader’s design, which features durable structures to handle harsh conditions.
loader platform, a common Caterpillar feature. Its full box-section rear frame can resist torsional shock and twisting forces. Its forefront has been redesigned to withstand larger loads and features a new lift arm design. Ground-level or platform access to grouped service points delivers convenient servicing.
Access doors are on both sides of the engine compartment and provide easy access to necessary daily service checks. Centralised ground-level grease points and sight gauges simplify daily greasing and oil-level checks for major machine systems.
According to the company, its onboard diagnostics alerts the operator of machine
Tracked Jaw Crushers GT125, FT2650 & FT3055
Tracked Scalpers GT206 & GT165
issues so that problems can be resolved before failure.
The features have been proven by Caterpillar’s internal tests to increase machine uptime and reduce maintenance costs by up to 15 per cent compared to the previous 988K model.•
For more information, visit cat.com.au
CRUSHING & SCREENING POWER IN STOCK. AUSTRALIA NOW!
Tracked
FT200 & FT300
Tracked Incline Screen GT205S
High Frequency Screen GT2612V
U p t o 300 t onne s p e r ho ur
CAT p o w e r ed Engine
Ca p able of handling r ock s up t o 600 mm
U p t o 500 t onne s p e r ho ur
CAT p o w e r ed Engine
Ca p able of handling r ock s up t o 800 mm
T : 1300 859 885
www.tr icone qu i p men t. com . a u
Komatsu’s Live Your Dream grants aim to create positive change within communities. Quarry explores how they are helping Australian communities.
Nearly a decade ago, Komatsu launched a program that transformed the lives of people and communities across Australia, New Zealand, and New Caledonia.
In the time since, Komatsu employees have used the Live Your Dream grants to fund programs that impact childhood cancer, premature babies, drought–stricken farmers and disadvantaged youth, among other causes.
Quarry investigated the latest announcements within Komatsu’s lifechanging program and how it benefits the lives of their employees and the communities around them.
Stacey Renata works as an apprentice plant mechanic at Komatsu’s Welshpool branch in Western Australia. Renata’s mother is Monica Morunga, the founder and chief executive of not-for-profit Feed It Forward, which supports families and people who struggle to access food.
Having witnessed many families going without what others take for granted, Renata knew she wanted to help.
“Participating in the Komatsu Live Your
shine a light on the collective power of a community and how that can bring about positive change,” she said.
“I collaborated with over 500 Feed it Forward volunteers, local businesses, schools and community groups to collect nonperishable food items and raise awareness about the challenges of food insecurity.”
The $10,000 grant launched a food drive, which secured 250 tonnes of food, while the awareness campaign reached 20,000 individuals and over 100 businesses.
She said it was a fantastic initiative that went beyond her expectations for what could be achieved.
Julie Aplin and her family lived every family’s worst nightmare when her son, Scotty, was diagnosed with a grade three brain tumour.
The diagnosis began a journey that involved two brain surgeries, radiation therapy and 12 months of chemotherapy in a tough time for her family.
“To watch not only our son but so many other children go through such a horrendous course of treatment was heartbreaking,” she said.
and leaves survivors with severe life-long impacts. On average, two kids are diagnosed with brain cancer every month in WA.”
Nowadays, Scott is living well posttreatment, but Julie always wanted to give back to those who helped in her most challenging time.
With her $10,000 grant from Komatsu, she devised a fundraiser for childhood brain cancer. Julie hopes businesses will get involved and nominate their bosses to ‘walk the plank’ to raise money for cancer treatments for youth this year.
“Dr Nick Gottardo and his huge team from The Pirate Ship Foundation work tirelessly to save so many kids, so I wanted to find a way I could give back,” she said.
“Thank you so much to Komatsu for supporting this cause that is so close to my and my family’s hearts. It’s great to see the prize being put towards research that is so badly needed.”
Zonta House has played a crucial role in providing essential services for families in domestic violence situations.
Its annual 16 Days in WA invites the WA community to play a part in encouraging change to stop violence against women. The campaign takes place from 25 November, the International Day for the Elimination of Violence Against Women, to 10 December, Human Rights Day.
Komatsu’s employees decided to help support Zonta House’s programs with a $10,000 grant. Zonta House’s Communications and Engagement Officer, Ella Kent, said the funds will go to support the charity to provide safe, essential support to women experiencing family and domestic violence.
“Generous donations such as this Live Your Dream from Komatsu will provide muchneeded funding for our programs, which are reliant on donations,” she said.
“We are incredibly thankful and excited for this support, and it will definitely make a big difference and a positive change in our community.”
Mick Bartlett has seen the impact of poor mental health on regional communities.
Last year, Bartlett and his local community witnessed four suicides, which heavily impacted the locals.
Bartlett, a service supervisor at Komatsu’s Tom Price branch in WA, set out to change it with the help of the Komatsu program
“So many of these towns in remote WA are isolated, with little to no support for issues like men’s mental health, which is often overlooked,” he said.
“Being based out at Tom Price, it’s an issue I see day after day, and one I knew I wanted to
tackle and see what I could do to support.
“It’s heartbreaking and impacts each and every one of us in some way.”
He used the $10,000 grant to support the Regional Men’s Health Awareness, a not-forprofit that raises awareness about men’s wellbeing in remote WA.
The not-for-profit will use the funding to help support education programs and initiatives like the Pilbara Bruthas Poker Run, which Bartlett does, which raises mental health awareness with poker tournaments.
“Organisations like the Regional Men’s Health Initiative help us to connect with each other and show that there is support out there for people
that are doing it tough. Sometimes it’s just a conversation that can set us on the right path,” Bartlett said.
“We start in Paraburdoo, then head to Onslow, Karratha, Port Hedland, Tom Price & back to Paraburdoo for the final prize giving. There is free camping along the journey with daily prizes, and we encourage anyone to come and join us.
“Our motto is ‘It’s not just about the ride, it’s about the journey’ – and with thanks to Komatsu and the Live your Dream program, we can help spread the word and support further in these communities that need it the most.” •
For more information, visit komatsu.com.au
Quarry learns how and why Duggans Quarry in Tasmania replaced one of the most vital pieces of equipment on site.
Harry Duggan started up the Duggan business in 1927 when he purchased his first truck and built a road. The business grew along with his family when he formed a partnership with five of his seven sons, diversifying into farming, transport, and concreting.
In the late 1970s, concrete aggregates needed to be purchased from quarries in Hobart and shipped over to Cradoc over the narrow and windy Huon Road. To overcome this, it extended its existing quarry to include the production of concrete aggregates.
Steve Duggan, managing director and thirdgeneration family member, told Quarry that the site is the southernmost hard rock quarry in Australia.
“Our quarry plays an important role and supports our three other divisions – premix concrete, precast concrete manufacturing,
“Many major road projects, built by both state government departments, local governments, and private contractors, depend on the materials supplied from the quarry.
“We also export our precast all over Tasmania and even into Antarctica for construction projects there.”
The site’s secondary cone crusher is an integral part of the business. Almost everything in the quarry business flows through it, whether it ends up as concrete, road base or sold to the public.
The company had established a five-year program to upgrade its fixed crushing plant, replacing technology that had been serving since the 90s.
Duggan wanted to see the new crusher increase the site’s crushing capacity and efficacy, modernise the plant, and renew it for the next step of the quarry’s operations.
He said the family business had a long history of using Terex Jaques equipment, so they installed a Terex Cedarapids Model TGS220 Cone Module.
The TGS cone crusher is ideal for large feed secondary applications and can accept a 65 to 80 per cent larger feed in size compared with other cones in the same power rating. The steep-angled head design accounts for an increased throughput capacity and the ability to sustain an on/off feed.
Its consistent feed-in opening, through the full wear life of the liners, results in no reduction in maximum feed size and limited fluctuation in output gradings. Duggan said Terex Jaques’ vast range of equipment means
the company could pick the right fit for the job, and it benefits from ongoing technical support.
“The crusher was able to be upsized to fit the current demand and capacity of our plant,” he said.
“Terex Jaques supplied the crusher and support structure in containerized modular form so that we could install it ourselves. We built a new feed bin, screen mount, and conveyor system around it while the existing plant was working.
“It was a simple swap between the old crusher and the new one, with minimal downtime.”
The TGS Series cones come with advanced automation cone controls as standard. This provides the Duggan team with all the information they need to know, including wear rate and crushing settings.
The quarry can then use this information to plan shutdowns for maintenance, all the while being supported by Terex’s Victorianbased team.
Duggan said the crusher is simple to maintain, and its serviceability has been exceptional.
“We support our business with our own maintenance department. They’ve changed out some of the wear parts and found it very easy to do,” he said.
“We’re planning to grow for the quarry’s crushing capabilities, and Terex has been great to work with.” •
For more information, visit terexmps.com
Meet the XD Series of heavy excavators – designed to tackle the toughest challenges. From Australia’s best-selling heavy excavator brand, the SK380XD and SK500XD represent the pinnacle of Kobelco’s legendary reliability, fuel efficiency and productivity.
Featuring a rugged machine body, and reinforced boom, arm and undercarriage to conquer the most punishing of worksites around the world, these machines deliver the lowest total cost of ownership in class. XD Series. Built for power. Built for reliability. Built to last.
During February 2024, CJD Equipment, a proud WA privately owned organisation, celebrated its 50th year in operation in February.
Fembodied and, along with Rafferty and Jowett, steered the business through a huge growth phase of the company. This included spearheading a rapid national expansion program following the appointment of the business as the national distributor for Volvo Construction Equipment.
rom humble beginnings at the Guildford location, with 28 willing staff on board who shared the vision of founders Ron Rafferty and Rob Jowett, CJD Equipment’s legacy began. Five decades later, with nearly 600 dedicated staff members across 23 national locations, the legacy of the CJD Equipment continues.
Rafferty and Jowett first met as part of the sales team of Chamberlain Industries, a Welshpool-based organisation specialising in tractors and farm equipment. In 1974, a wonderful yet daunting opportunity arose to become the West Australian dealer for the Chamberlain John Deere construction equipment product. The pair were off and running; armed with a desire to succeed, a mantra that “we will make it happen,” and always to be customer-centric and invest in staff to be the best they could be.
Today, business revolves around people and products. That is why CJD Equipment believes it is important to have not only the best people but also to represent quality, world-class products. The company operates on the national stage and represents brands in both the construction equipment and the transport industries.
CJD Equipment is the national dealer for both Volvo Construction Equipment and SDLG Construction Equipment. In the trucking space, CJD is the West Australian, Northern Territory and Tasmanian dealers for both Kenworth and DAF trucks and the Isuzu dealer for the Northern Territory.
Rafferty has always said, “relationships are the backbone of any business”, and this mantra proves true for CJD Equipment. Relationships with customers are pivotal, and that is why CJD Equipment has always had a “can do” attitude when it comes to servicing its customers.
The same is true when it comes to suppliers.
The entire CJD Equipment team has pride in the duration of partnerships with its supplier base, with a 40-year partnership with Paccar and over a 32-year relationship with the Volvo Construction Equipment product. The length of these relationships means the company can talk the talk and walk the walk when it comes to sales, service and support of the products it represents.
Jowett said that CJD Equipment is only as good as the sum of its people.
“It is the people involved in the business, their passion, enthusiasm, and commitment that has led to CJD Equipment’s long-term success,” he said.
Jowett said he took pride in the fact that CJD Equipment has second and third-generation families employed at the company.
Alan Barnett joined the CJD family in a commercial and marketing role in 2001. It was only a short period of time until Barnett progressed his way to becoming CJD Equipment’s managing director as well as part of the business ownership structure. Barnett shared all of the values that CJD
“We are a growing business, we will always want to be a growing business and at our core we are a sales business,” Barnett said.
“In order to keep growing, we must keep selling and for this to happen we must deliver the best products, the best customer experiences and the best quality back up and support possible to each and every one of our customers, all of the time.”
CJD Equipment has always identified the saying “big enough to trust, small enough to care” as key to its success. This small statement has been at the heart of the business and has contributed in no small part to CJD Equipment’s ability to grow into a strong national business over a long period of time while maintaining its founder’s mentality and family values.
“I’m incredibly proud of the 50-year milestone that we will be celebrating, and I look forward to watching the business continue to go from strength to strength in the many years to come,” Barnett said.•
MID NORTH COAST
MID NORTH COAST SOUTH KEMPSEY, NSW SOUTH KEMPSEY, NSW
The owners are highly motivated to pass this opportunity onto enthusiastic energy driven individuals or companies who can make this opportunity a further success.
Take advantage of the natural resources the site has available and capitalise on the Major Local and Regional construction and infrastructure projects with an estimated value over $1 billion.
Experienced quarry manager Wayne Chapman said that the business has seen record production rates and uptime since installing the new CDE wash plant at their Wallerawang Quarry, west of the Blue Mountains in New South Wales.
The easing of production bottlenecks and the new plant’s flexibility in its configuration has allowed Walker Quarries to develop new products, such as its new Thermal Resistivity (TR) Sand, which it is now producing at a consistently high grade.
Chapman said that the TR Sand is quartz-based, well-graded sand and offers an extremely low thermal resistivity rating of approximately 0.63Km/W, at 97 per cent compaction of MDD and 0.04 per cent moisture.
The TR Sand is used for underground power cable installation. It is a qualityassured, industry-leading, engineered backfill
Chapman said the test results from NATAbased laboratories are available upon request and provide technical analysis and support of the product.
“Reliable supply is key for all areas of the construction materials industry,” he said.
“We know that current and future clients always leave our site confident that we will be able to deliver the tonnes that we promise, safely and at a very high quality”.
Walker Quarries initially met CDE, a wet processing solutions specialist, in 2019 at the German trade exhibition Bauma.
The quarry had consulted with many suppliers from around the world before ultimately choosing CDE, with its 30-year experience in washing, dedicated local project management, and aftersales support teams acting as catalysts for the deal.
“We’re delighted with the success of the entire project, from the initial discussions,
operation and we really look forward to seeing where this partnership can take us.”
Through its team of professionals, CDE has assisted Walker Quarries in the design, construction and commissioning phases of the wash plant project. The result is a firstclass wash plant that is highly sustainable through its approach to water recycling and fines filtration.
Both companies have worked in partnership to develop new sand products for the industry whilst supporting the need for renewable energy installations that have low-impact environmental solutions.
Walker Quarries will host an open day on April 11, where prospective customers can view the newly developed product. A tour of the CDE plant will also take place. •
For more information, visit cdegroup.com or email sales@walkerquarries.com.au’
WOMEN IN INDUSTRY NOMINATIONS ARE NOW OPEN. Now is your chance to nominate an industry leader who you believe is advocating for positive change and deserves to be recognised.
PROUDLY PRESENTED BY
MHDThurs 20 June, 2024
The Women in Industry Awards recognise outstanding women leaders from across Australia’s industrials sector.
Maintaining an effective handle on the sales process, quotation and pricing is critical to any quarry business. Steve Franklin, founder of Eltirus, looks at some new developments that could make a tangible difference to your bottom line.
Any size company can be effective in sales. However, very small sales teams are generally more effective than larger teams because the future revenue of the company directly depends on the actions of a few people.
In smaller teams, the tendency is for everyone to work together in the same location, and they have the advantage of
understanding the end-to-end sales processes (for example from quote to cash) and being involved in that process on a daily basis.
Spreadsheets are often the preferred tool for these type of smaller businesses as they are cheap, flexible and can support almost any business process like price or cost analysis, forecasting, sales pipeline review and even producing quotes. The
limitation however is that as more and more people are involved, the opportunities for errors and omissions grow and they become increasingly more unwieldy.
Larger teams require more advanced management, more rapid information sharing and sales process standardization across the team members. Cloud-based applications are perfect for the instant processing of large amounts of data and their ability to share it across a geographically dispersed team and with other connected applications. It is simply much quicker, more consistent, more secure, and more reliable because it drives the process standard for all users.
While many larger companies have a Customer Relationship Management (CRM) system, standard CRM packages are generally not industry specific and can be difficult to adapt to the construction materials industry. Configure, Price, Quote (CPQ) solutions such as Price Bee are specifically designed for our industry and focus on ensuring that the functionality that is important to industry sales professionals us easy to use and what’s not relevant is left out.
Whether a small or large team, it is vital that the responsible salespeople are aware of the sales strategy and understand how their day-to-day quoting contribute to that overall picture.
With every quote they make they should know if it is good or bad for pricing and more importantly, consistent. Once this level of understanding is established, a more analytical approach to pricing can be taken, informed by strategy, and driven by information from the market.
There are a range of different methodologies that can be used to unlock additional profitability, including pricing selfassessment and diagnostic and customer attractiveness matrix.
Which one is applicable is dependent on the level of pricing maturity of the company.
For aggregates, there are generally two methodologies that gel with almost everyone.
For smaller clients, pricing is a good way to go forward. When we talk about a small client (depending on the market), we are generally talking about a client buying some 500 - 5,000 tons per year. Work needs to be done to get a sense of what the different size groups of customers the business has as a first step. Sales teams easily buy into the concept of price differentiators between larger and smaller clients as well as the need to have more discipline around price setting and quoting.
Those are small and easy wins from revenue increase perspective, but they serve as a basis of further pricing transformation.
Customer attractiveness matrix is a customer benchmark approach which is codeveloped with the client. The Price Bee team design six to nine sales and pricing indicators and use a scoring methodology to calculate how good each customer is for the business.
Compared to the first approach, this one is harder to build (and to explain) but can be quite eye opening for key account managers.
Once you have a good pricing methodology in place, effective quotation is vital.
From a sales process perspective, quotation plays a critical role. A quote is a key touch point with the customer and provides a written proof of price, validity, and relevant conditions.
It’s also a highly time-consuming part of salespeople’s job. According to the Price Bee 2021 study, “Salespeople spend up to 60 per cent of their time on quotation and order fulfillment activities.”
A quote tends to reflect the company’s order-fulfillment process because sales can only quote what can be processed by their point-of-sales, dispatch and (if relevant) ERP systems. This is probably a reason many
smaller players choose to quote using paper and/or emailing Microsoft Word or Excel documents. They feel in control and get so used to the simplicity and ad-hoc adjustments this approach enables that transitioning to another approach is very difficult without a major change of viewpoint, systems, and methodology.
Some companies attempt to build an in-house quoting system but even with the
best intentions, they often end up with an IT roadmap that prioritises the weighbridge/ dispatch system remaining unchanged, resulting in a system more aligned with order fulfillment processes and missing key elements like haulage cost calculation, quote life cycle management or, even worse, completely ignoring critical customer information that is not relevant to order taking or invoicing.
The above-mentioned examples are at two ends of the spectrum. The first, though highly flexible is generally dependent on the people who created it and has no long-term future; the second will survive much longer, but is inflexible, makes data analysis difficult and ultimately, will not appeal to a younger generation of salespeople.
This said, there are some smart businesses that just get quoting right, either as a result of forward-looking sales management, robust processes, software and offline models or more sustainably, through putting in place a dedicated, purpose built, end-to-end CPQ system.
From a broader pricing strategy perspective quoting could appear less critical because not all sales are quoted, and some smaller producers actually don’t quote at all.
However, once a company reaches greater sales volumes and pricing maturity, the need for consistent pricing is vital to meeting strategic targets and monitor performance.
For example, if target prices are defined using margin objectives, an effective quoting tool would allow for a real time analysis of all quotes and a clear view of how each salesperson, customer, site, or product are doing with regards to the desired target price and any quoted target price variance.
Although the interpretation of quoted prices can be highly contextual, it is still a great way to gather real time market feedback in relation to the company’s pricing strategy. While many sales professionals rely on won and lost reports to assess performance, this is generally a lagging indicator and tells us very little about the effectiveness of the pricing strategy. Having a good understanding of sales teams’ pricing behaviour provides realtime feedback regarding the pricing strategy and an indication of market position.
Quotes can also be used to help improve pricing strategy by capturing information about discounts given to customers. One of the challenges of pricing is to correctly determine what the acceptable discounts levels should be, generally by volume grouping. Analysing the discount ranges of quoted products is a great way to identify
fair discount levels for customer groups all the while getting a clear picture whether a desired discount policy is working or not.
To effectively put in place price rises and manage margin, a company needs more than just a vision or a presentation. It needs the data to about the market and its position in it to make informed decisions about pricing, discount levels and approach. An effective, industry specific CPQ system ensures that management have the data they need for analysis and correction and the sales team have the tools to simplify their job of quoting and closing work.
It is truly impressive how much sales teams can achieve with a good pricing strategy, effective tools, and good implementation. When you put in place simple companywide methodologies like cost plus pricing or consistent discounting based on customer size, the results are almost immediate.
The key is to realise that it is not the just the methodology that delivers the revenue increase, but the team. So, in choosing methodologies and software, it is important not to over complicate things and to provide the training and support a sales team needs to transition to next level pricing. •
Eltirus is a Price Bee partner. For more information, email steve.franklin@eltirus.com’
“THE BENEFITS OF THE
AND OUTPUTS ARE ALREADY EVIDENT IN OUR OPERATION, AND WE REALLY LOOK FORWARD TO SEEING WHERE THIS PARTNERSHIP CAN TAKE US.”
WAYNE CHAPMAN, QUARRY MANAGER
WALKER QUARRIES
Astec Industries’ strong reputation for hard rock crushing is on display at Regional Recycling in Victoria.
Dick Lewis knew there was a future in recycled rock, he just needed a system which could turn unwanted stone into a sellable product.
Lewis began the family-operated Regional Recycling in 2002, back when a lot of demolition waste and unwanted rock like farm stone would find its way to landfill.
With a few decades of experience under his belt, Lewis established his company to work across crushing, demolition, civil engineering, and site remediation with the aim of creating zero waste.
In the crushing arm of the business, especially working with paddock rock, Lewis partnered with Astec Industries.
“Paddock rock requires a good jaw crusher because you are putting the best and the biggest rock through the crusher all the time,” Astec Industries’ Adam Gordon, business line manager for material solutions at Astec Industries said.
“You’re crushing 80 per cent or more of this big paddock rock, and it has no stress points like the usual quarry rock.
“You can hear it in the machine from 500 or 600 metres away. It’s quite a tough challenge.”
Astec supplied Lewis with the FT2650 mobile jaw crusher, which has a 66cm x 127cm feed opening that can handle production rates up to 500 tonnes per hour. The compression from the crusher’s increased stroke can help operators achieve more relief, faster throughput, and up to 25 per cent more capacity.
“Whereas our hydraulic relief feature allows pressure to be relieved in the crusher, so the operator can hit reset and start again.”
When equipment breaks down the cost of lost productivity, unscheduled maintenance, and equipment hire adds up.
It’s not uncommon for crushing equipment to have to process generally uncrushable material such as drill pieces or steel.
This can become an issue in a normal crusher as the foreign material can cause the machine to seize up or become damaged. But not the Astec FT2650. This heavy-duty, high-capacity crusher features an optional hydraulic tramp iron relief system that eliminates the issue.
The system, comprising two hydraulic rams, assists with controlling torsion forces at the toggle and protects the FT2650 from tramp iron overload. This hydraulic relief feature enables the jaw crusher to open up when overloaded with the energy being released instead of stressing the jaw or main frame.
“In a traditional crusher, a steel piece, which is stronger than the crusher, would cause enormous stress to the machine. You’ll bend a shaft or, next time it happens, it’ll break in half,” Gordon said.
Depending on the operator’s volume, these costs can range from a few thousand to a few hundred thousand dollars. Which is why, Gordon said, the Astec FT2650’s optional hydraulic relief feature has become increasingly important. The hydraulic circuit enables the operator to cycle material in the jaw crusher and break it up without the need for someone to manually clear out the rock.
“With the FT2650, when an uncrushable comes through, it is not a problem. Dick Lewis can just hit relieve, open up the crusher and there’s no stress on the frame,” Gordon said.
“It also means someone doesn’t have to manually open the jaw crusher. They can stay safely outside the machine, and the rock is broken up without anyone being exposed to danger.”
Gordon said he was impressed with how the Regional Recyling business has grown.
“If I go back 10 to15 years ago, recycled product had a bad name, it was considered inferior. Today, it’s certified by VicRoads and you have everything from recycled brick to asphalt to concrete,” he said. “Recycling is now an industry worth hundreds of millions of dollars, and Dick was one of the first people to see its potential.”
Through its mobile crushing and screening range, including the FT2650 mobile jaw crusher, Astec is helping quarry operators recycle materials and create value-added products – which is a win for customers and for the environment .•
For more information, visit astecindustries.com
At the IQA, we are committed to providing educational training and workshops held both onsite and online.
Explore a snapshot of what’s coming up in 2024.
Effective Leadership for Senior Managers
Leadership for Senior Managers involves a complex and multifaceted set of skills and responsibilities. Senior Managers often occupy executive or leadership roles within an organisation, play a crucial role in shaping the direction, fostering organisational culture, and ensuring the achievement of strategic goals.
This workshop has been designed to develop the leadership capability of senior managers to a consistent standard, resulting in a high performing culture that delivers consistent results. In this course, you’ll learn how to effectively influence people at work to build a constructive culture.
Whether you’re a seasoned executive looking to refine your leadership approach, or a rising senior manager preparing for increased responsibilities, this workshop provides a platform for continuous growth and improvement in leadership.
This workshop will be delivered online on Wednesday 3 April 2024.
IQA education programs may be claimable as CPD under the NSW Maintenance of Competence and QLD Practising Certificate schemes.
Quarry Materials Production & Quality Management
Introduction to Safety & Health Management Systems
Verification of Competency (VoC)
Quarry Roads & Onsite Vehicle Safety NSW
14
“Good content presented to a wide range of experienced participants in a way all could understand.”
— Workshop Participant
Quarry learns how a Victorian sand quarry has improved its cycle times by purchasing a Kobelco SK500XD excavator.
Sand can be a major nuisance. It can be coarse, rough, and get everywhere. It is also a vital part of construction materials such as cement and concrete.
In Victoria, the Regional Group digs for sand at its Grantville site. Sean Murphy, Regional Group’s operations manager, told Quarry there is a layer of clay overburden at various depths on top of yellow deposits of fine to medium sand.
“Conditions during winter make the site muddy, so we work during the summer months,” he said.
“Down in the pit, it is free draining, but you’re dealing with abrasive sand on the tracks.”
The site had previously used three excavators, but they were getting long in the tooth and had some repair and maintenance issues.
The quarry was also looking to improve its cycle time. With three excavators, it took around 12 minutes to move material from the bit to the bin. With a bigger machine, the site could cut this down significantly.
As part of the replacement, the Regional Group purchased Kobelco’s SK500XD. The excavator has been specifically designed for extreme durability, allowing it to operate in some of the harshest quarrying conditions around the world.
Weighing in at 52,200 kilograms, the machine is one of the heaviest in its class and comes with substantial reinforcements to all key stress and wear areas.
Chris Wolf, Kobelco Australia’s general manager of marketing and direct sales, said the key factors behind the Regional Group’s purchase of the machine are its reliability, resale factor and fuel efficiency.
“The SK500XD goes above and beyond –it’s been purpose-built with a robust machine body with an extreme-duty boom and arm. That provides additional strength from a mechanical engineering perspective than a standard heavy-duty design,” he said.
“The boom and arm have internal and external reinforcement to take it to another level. These machines are being used to rip
rocks and break stone day in, day out, for up to 25,000 hours in some of the toughest markets of the world like India, China and Southeast Asia.”
The SK500XD also features a quadruple track guide frame, which provides reliability in harsh and rocky underfoot conditions, while reinforced heavy-duty 600mm triple grouser shoes make it manoeuvrable across rough terrain.
The durability of the track links has also increased. At the same time, the idler frame has received substantial double reinforcement plating inside and out, resulting in improved undercarriage reliability while preventing premature wear of this key structure.
A heavy-duty, steel-bolted underbody guard protects vital machine components and provides additional weight for greater stability. The Regional Group has had the machine since December.
“It’s quite a smooth machine to utilise. It’s also very stable. Even at full bucket extension,
“It has a good breakout force to deal with our clay. The team has said the track frames are a good design, as they don’t retain much dirt around the tracks, so there’s no material caking around our idlers and rollers.
“They’ve also said it’s comfortable to spend a full shift in – they don’t feel tired or sore after a full day’s work.”
Kobelco designed the cabin with a front window that provides a wide, unobstructed view for greater visibility. It is also pressurised, providing a quiet and airtight work environment free from dust.
A heated and air-cushioned suspension seat provides protection from vibration, while an automatic climate control system vents air towards the operator’s neck and back. An LCD multi-display screen shows the
well as an integrated rear-view camera.
Murphy said he was impressed with the machine’s fuel efficiency.
“Compared to a 45-tonne machine, we’ve improved fuel efficiency by around 10 litres per hour,” he said.
The SK500XD is designed to deliver an average fuel consumption of under 30L per hour in typical Australian heavy digging conditions. Its new boom-to-arm regeneration system more efficiently controls hydraulic fluid flow and delivers a significant reduction of in-line resistance and pressure loss. As the need for fluid to be forced from the pump is reduced, less engine and hydraulic workload means higher fuel savings.
Three work modes allow the operator to select the best mode for the job at hand—
company, the Maas Group, are connected with lifetime subscriptions to the telematics system.
“They can track and schedule downtime and maintenance using one simple platform from its head office in Dubbo,” he said.
“The response to the XD range from the quarry industry has been awesome. Since we launched this machine, it’s been a number-one seller across several states in the country.
“Our quarry customers have seen what the product has to offer them, and it’s opened a few eyes. They can tell you’re getting a reliable, fuel-efficient performance leader.” •
For more information, visit kobelco.com.au
• Production of quality iron ore/mineral/sand sand from deposits featuring impurities
• Consistent material quality via automatic process control
• Low energy requirement and low wear
• Processing of grain sizes up to 4 mm
• Generates autogenous heavy slurry for the separation of light materials
• Various build sizes with diameters of up to 7 m
• Can handle up to 2,000 m3/h of feed material and 800 t/h of solids in one unit
• Hydraulically controlled discharge devices
• 3-stage process without moving parts
Machynlleth was a quiet market town in Wales until volunteers transformed its abandoned slate quarry into Europe’s leading showroom for sustainable living.
Gerard Morgan-Grenville’s arrival in the Welsh township in Machynlleth was unremarkable, yet his impact on the town, its disused slate quarry and alternative technology was telling.
In 1973, Machynlleth’s slate quarry was filled with mud and sludge after being abandoned and its slate production exhausted.
It was an unimaginative site, yet with Morgan-Grenville’s eye, he saw an opportunity to display sustainable living in action. In his memoir Breaking Free, released in 2002, he wrote about seeing his “social world as rather superficial” without any “willingness to do much more than talk” about the environment and humanity’s impact upon it.
The site, later named the Centre for Alternative Technology (CAT), would
encourage a self-reliant lifestyle through a range of practices to help the public reduce their impact on the environment.
Today, CAT stands as one of the shining examples of sustainable living in Europe, which transformed the township around it. Five decades ago, Morgan-Grenville had a vision but a small issue.
“There were just three difficulties; I had no staff, no place to put it and no funds,” he wrote in the memoir.
“(People heard) something was happening in a disused slate quarry in central Wales, volunteers started to arrive, unannounced, without tools, without skills and, mostly, without a penny to their name.”
These volunteers helped build an off-grid community and unique alternatives to fossil fuels. They helped design the water-balanced cart, believed to be one of the world’s
steepest railways, which still operates today.
The volunteers turned the slate quarry, with its crumbling buildings, into a living demonstration of sustainable living. It sounded nice in theory, but the reality involved a system where waste from people, animals and crops is recycled using composting toilets and reed beds.
Companies and businesses provided products to be displayed in action, while wind turbines, solar panels and spray-on insulation were prominent on the site.
In the 1980s, CAT transitioned to its current iteration as a study centre and tourism attraction for the public, schools, and researchers. Today, it teaches residential classes and houses a graduate school for master’s and doctorate research in environmental sciences and architecture, among others.
“Studying at CAT is not like studying at any other university. CAT has been a home, a family, and the greatest experience I have undertaken up to this moment in time,” Tiziana Di Ronco, CAT graduate, said.
The old stone buildings, left over from the site’s slate quarry past, gave way to new, innovative buildings that have garnered award-winning recognition.
Famed architect Walter Segal has a selfmade home on site, among other buildings using experimental construction materials.
The site’s WISE building, which houses the Wales Institute for Sustainable Education, was built from timber, earth, and hemp, including hempcrete.
The WISE building claimed the Regional Architecture Award from the Royal Institute of British Architects Award and the Outstanding Earthen Architecture in Europe Award in 2011.
Morgan-Grenville passed away in 2009, but CAT was left as his legacy to the region. In 2009, the centre had a staff of 150 and attracted 65,000 visitors across the year.
CAT’s impact on the township of Machynlleth, known by locals as Mach, is increasingly evident.
The Machynlleth Town Council made headlines in 2019 by becoming one of the first town councils in Wales to declare a climate emergency. It has invoked an action plan to become 100 per cent net-carbon neutral by 2050 after unanimously voting
The centre has played a role in the Machynlleth’s development. for the proposal after being presented with a petition signed by a quarter of the town’s population.
More than 2000 people have studied at CAT through postgraduate learning, while CAT’s staff have advised policymakers at United Nations climate talks.
Last year, the CAT postgraduate school celebrated its largest-ever cohort.
It has closed for day visitors but remains open for students, educational group visits, events, and courses with plans to redevelop the site, including a new visitor centre.
“The closure of the current visitor centre to day visitors will, however, allow CAT to focus on strengthening economically viable
aspects of its operations,” CAT’s co-chief executives Kinsman and Paul Booth said.
“(This will) help us deliver on our mission to create and share practical solutions to tackle the climate and nature emergency.”
The educational charity celebrated its 50-year milestone in the past year.
“CAT is much more than what goes on at our site in Mid Wales. We are a diverse and widespread community of people from all walks of life who share a vision of a safer, more sustainable world and are motivated to make it a reality,” CAT said in a statement.
And it all began with a vision and an abandoned slate quarry.•
Precisionscreen’s extensive range of precoat solutions enables operators to deliver high-quality precoat material anywhere in Australia.
NPrecisionscreen emerged onto the scene with screening plants built upon towable axles, enabling operators to go from quarry to quarry.
The success of these portable plants led to operators seeking the same mobility for other applications, especially pre-coating.
“There are very few units available that are Australian-designed and manufactured or even imported for this type of machinery,” Precisionscreen’s chief operating officer Jonny McMurtry said.
“Our ability to manufacture to Australian standards and expectations is seen as a big plus, especially with the 3000 and 6500 models being fully designed and manufactured in Brisbane.”
Over time, Precisionscreen has built and updated its Precoater range to suit the needs of the modern Australian quarry.
Before mobile precoating, all materials for the road-laying sector were made at quarries and shipped out to locations. It was time-consuming and costly for businesses working on tight deadlines with larger distances between job sites.
Images:
chute. This enables the Precoater 3000 to deliver a throughput of more than 120 tonnes an hour.
The larger Precoater 6500 has a 6500-litre tank, a ten-by-five-twin-deck screen box, and a discharge height of more than four metres. Equipped with 14 precoat nozzles, the Precoater 6500 can achieve a greater throughput than the 3000, which is over 150 tonnes per hour.
The machines can be made to customer specifications, including additional filters or modified spraying systems. Precisionscreen’s precoaters can use anything from a rubber or diesel-based product to an emulsion precoat blend.
The Brisbane-based company has worked with its electronic hardware supplier IFM to add electronic controls instead of the previous hydraulic lever controls. McMurtry said these changes made the Precoater 3000 and 6500 more friendly for operators.
precoating, other regions like the Northern Territory and Western Australia prefer using mobile Precoater machines for precoating at the required location.
“I would estimate that 90 to 95 per cent of our mobile precoating units are in WA and the Northern Territory because the units suit regional or site-specific precoating,” McMurtry said.
“We see a lot of repeat customers or customers with more than one mobile Precoater units simply because of the reliability, and they can confidently send them across the state.
“Our machines have enabled them to meet the state-wide precoating needs.”
The Precoater 3000 and Precoater 6500 can be towed to road-laying or between quarries for quick and effective precoating.
The Precoater 3000 features an eightby-four-foot screen box with a 3000-litre tank and a tail conveyor with a discharge point of over four metres. The smaller of Precisionscreen’s mobile precoaters has 12 individually controlled precoat spray nozzles across three bars attached to the tumbler
Both precoaters enable the operator to start and stop material flow remotely, while the Precoater 3000 or Precoater 6500’s CAT engines have a shut-down protection system to ensure safety.
“If an operator can confidently operate the machine from the cabin of their loader, it makes it easier and safer for them, especially in remote areas,” McMurtry said.
“They’re both incredibly useful machines for their size, especially with their mobility and durability.
“They can show up on site, screen off any oversized material or dust to enable and ensure material is suitably coated and offer the best precoated road chip without carting the material thousands of miles.”
Precisionscreen also offers the Scorpion Precoater for those looking for a quarrybased precoating solutions.
Like the Precoater 3000 and 6500, Precisionscreen’s Scorpion Precoater 804 can remove oversized material and dust from a precoat material but within a quarry setting.
The machine combines Precisionscreen’s Scorpion Reclaimer with its eight-byfour screen box, a CAT 2.2 powerpack, an onboard precoat chute, and it’s
Australian-designed and manufactured hydraulic system.
The Scorpion Precoater 804 can transport and precoat clean aggregate from the plant using its adapted Precisionscreen’s SM450 (10m) stacker/conveyor.
“Whether it is our precoater conveyors or a full turn-key solution of our Scorpion precoater, we do offer quarry-based precoat solutions,” McMurtry said.
“It’s a quick and effective way of quickly removing oversized particles and dust and adding a precoat mix onto your screened aggregate.
“We can adapt our precoater solutions to suit your needs.”
McMurtry said the machines offered applications in a highly mobile format.
“If there are any urgent or non-urgent requirements for support for your machines,
customers can reach out to our Brisbane headquarters and receive technical support,” he said.
“The simplicity of the machines and the aftersales support, especially as the precoaters are fully designed and manufactured in Brisbane, makes them ideal for Australian conditions.” •
For
Kleemann demonstrates how technical innovations and good planning guarantee efficient processes that use less material and fuel.
When it comes to sustainability, there are four key areas that manufacturer Kleemann counts on intelligent technology, trouble-free processes, good tuning, and consultancy.
Ben Lefroy, Wirtgen Australia’s national sales manager for Australia and New Zealand - Kleemann, said quarries have a great opportunity to create solutions with Kleemann.
“Kleemann has been manufacturing in the diesel and electric technology for the mobile crushing and screening industry for more than 40 years, which gives them a great foundation to help quarries,” he told Quarry.
“Kleemann has been using technology and electrical equipment to help quarries in various areas, including reducing fuel usage and cutting emissions.”
Kleemann has several processes to achieve optimisation, including precise regulating
instruments such as its continuous feed system (CFS).
The CFS ensures that the feed material at the crushers is always conveyed with maximum efficiency through the machines. The fill level of the crushing chamber is monitored continuously, and the feed is adapted to the process. This optimised process ensures that material wear is as low as possible and fuel consumption is reduced – both can be critical sustainable goals for quarries.
However, Lefroy said having an efficient, trouble-free process was just as crucial.
“The CFS is an example of how the complete process can be optimised by intelligent technology. Technical innovations, however, are only building blocks.
“Good planning of a plant train is just as important, if not more. Technical innovations can only fully demonstrate their strengths when all components closely mesh with one another.”
Keeping machines tuned to reach their optimum levels is vital for them to work effectively. Kleemann believes selecting the crushing plants with the matching crushing tools is decisive, and the screening
machines, equipped with the ideal screening media, must be well-tuned to the process.
Stockpile conveyors that offer a capacity that matches the complete plant must be provided, and consideration of the capacity of the loading device belongs to the overall process.
If machines are set accordingly, the power consumption can be reduced often.
Kleemann can help quarries optimise their process this way, which also achieves reduced wear.
Lefroy said this is also important because if components wear quickly, new components must be produced with a high material and energy input.
“Avoidance of unnecessary wear, therefore, not only helps save money but also reduces CO₂ emissions considerably,” he said.
Kleemann relies on comprehensive consultation with the customers to ensure the solutions help optimise the quarry’s goals.
Kleemann’s application advisers plan all processes in advance. In the case of extensive processes, a flow chart (AggFlow) is prepared to simulate the material flow in detail.
The consultation covers technical solutions and information on how processes can be better organised. Lefroy said the custom-fit engineering of a plant train requires good planning software and a lot of experience and instinct.
Kleemann, therefore, relies on technical solutions and support from experienced application technicians.
“Wirtgen Australia has dedicated team members across Australia and New Zealand that can assist quarries with optimising their sustainability,” he said.
“We’ve also invested heavily in our apprentice intake to ensure that our customers have access to skilled personnel in the medium and long term.
“We also regularly upskill our technicians with dedicated product training to ensure our customers can access the best help when needed.”•
For more information, visit wirtgen-group.com/australia
One key factor has always stood out to Riley Arndt as he approaches ten years at Superior Industries. The strategic accounts manager admires how Superior always puts the customer first.
“Everyone has a culture around their company, but what makes us special is the emphasis we put on the customer and our interest in trying to improve our products for their operation,” he said.
“This focus creates a great feedback channel, and I think it gives us a uniqueness that connects us with the customers and the industry; I enjoy that.”
This customer-centric approach led to Superior redesigning its conveyor idlers. In 2020, the company unveiled a series of
Superior Industries has reworked the design of its conveyor idlers, incorporating an upgraded bearing seal and weld procedure.
upgraded bearing seals to help its conveyor idlers withstand the different elements its customers were facing.
Four years on, it has partnered those changes with a new-designed idler. The new design eliminates a common pain for customers by removing an exposed weld, which can cause premature roll failure.
Arndt said he believed customers would be impressed by the new idler entering the market in March.
“Through feedback from the industry and our customers, we’ve seen an opportunity to improve on what we have,” he said.
“We think we’ve created the next generation of idlers.”
Idlers can be overlooked in a conveyor set-up, especially when the focus is on the material being shifted rather than how it gets there. However, the malfunction of just one idler can cause delays to material delivery or damaged belting, which is expensive to replace.
One of the main reasons for idler malfunction is pinch points. The exposed weld, usually between the end of the stand and the outside of the roll, can snag foreign material and cause the roll to seize up. Other designs have lip at the end of the roll, which also is a well-known catch point.
It results in downtime and lost production and adds expenses to businesses already
dealing with rising costs in other areas.
Arndt said the new design of the Superior Industries’ conveyor idler changes that.
“That exposed weld has been a potential pain point for customers, and we’ve taken the weld and put it where it can no longer be a point of attack for foreign materials,” he said.
“The weld itself is fully contained and cannot be damaged by the belt; it should give customers peace of mind that their belting, which can be very expensive, is safe.
The design of the product enables the end disc to sit flush on the idler roll. Traditionally, many rolls feature an inset weld, where rocks and material can catch and seize the rollers.
The foreign material can damage the seal and the idler and create more resistance to the idler, which slows down throughput and increases energy. Superior’s new design prevents material from being trapped between the roll and idler frame, a time and money saver for quarries.
“It’s essential to keep your roll spinning freely and prevent any damage or pinch points,” Arndt said.
The new idler rolls will be available at all Superior Industries’ dealers, including Tricon Equipment in Australia.
Arndt said the key to Superior’s quality standards was the idler had to work in all environments, from high-tonnage mining and quarrying to humid and arid markets.
“The markets these idlers are going into will be tough and abrasive, but through the years
of testing that we’ve done, the idler itself has been better than the competition,” Arndt said.
“The longer that idler and roll can run, the more you’ll be able to use your maintenance time elsewhere.”
Superior launched four specialty seals to help its customers tailor their conveyor set-ups. The seals, alongside the company’s regular seal, came about after a customer contacted Superior Industries with a problem.
The customer’s tunnel, which housed a conveyor, would not stop flooding. This caused the belt to be underwater for a significant time.
The team at Superior went to work and returned with four seals. The SpinGuard Wet Seal is for high moisture environments with frequent washdowns and dredging; the SpinGuard Dry Seal is designed for environments with high dust concentration; and the Spin Guard Eco Seal is best for
lower power consumption on long-distance, overland conveyors.
The SpinGuard Titanium Seal is considered Superior’s top-draw seal.
It is a combination of wet and dry seals for a premium design meant to significantly extend idler bearing life.
“It offers protection against any moisture or dust and fines which could penetrate the seal and cause them to fail quickly,” Arndt said. “Some people call those applications extreme, but I see cases of moisture and dust effecting traditional idler performance at most quarries I visit.”
“The four types are built to help each operation have their choice to suit their situation best because not every conveyor is the same and not every application is the same. Our approach allows them to be application specific.”
Operators in the past may have replaced the entire idler, but as the industry tries to keep
downtime to a minimum, many are replacing or retrofitting rolls during maintenance hours.
Arndt said the new idler technology could be retrofitted to existing Superior idler frames and most other brand frames as well.
“If you have a current idler of Superiors, these will easily be implemented into those frames. And with our manufacturing, we can retrofit or make custom rolls to fit other frames just as fast as we make our own,” he said.
“This ensures you can get the new technology without investing more into a new idler set-up.”
Arndt believes it boils down to one thing when asked what his favourite part of the new idler technology is.
“We’ve been able to make this innovation by really listening to the voice of the customer,” he said.
“When you pair the newly designed roll with the seal technology, we launched in 2020, it’s effectively a super roll.” •
For more information, visit superior-ind.com
After more than 11 years in the role, Rod Lester retired as IQA company secretary in December.
Rod was the IQA’s first paid company secretary and over his tenure put in place a robust governance structure. Rod guided the organisation through a number of changes, including to becoming a streamlined governance structure suited to today’s business world.
As an experienced company director in his own right, Rod became a mentor to generations of IQA directors, many of whom were often in their first directors’ role.
In addition to his company secretary role, Rod took on a number of one-off projects on behalf the IQA’s directors. These projects included the coordination of the recruitment of two IQA chief executive officers (CEOs) and the resolution of a complex legal action against the IQA.
As a company secretary with a high attention to detail, Rod was able to reel off some interesting statistics in his farewell note to staff and directors. He worked with six IQA presidents, three CEO and 34 directors, while attending 12 annual general meetings, 86 board meetings, and nine conferences.
For my part, I was honoured to take over as the IQA company secretary in December after a comprehensive handover from Rod. I am excited to back in the extractive industry after
10 years as the general manager – finance for Boral in Victoria and Tasmania, and four years as head of finance for Downer Asphalt.
I am deeply indebted to Rod for the strong corporate governance structures and culture he has left in place as his legacy to the IQA.
The IQA held a farewell dinner for Rod in Melbourne and, as a mark of respect, all of the Australian-based past IQA presidents from Rod’s tenure travelled to the event at their own expense.
The IQA thanks Rod for his years of dedicated service and wishes him all the best for a long, healthy and fulfilling retirement. – David Cowie, IQA company secretary
The Tasmanian branch had a successful weekend in Swansea, Triabunna and Orford on November 25–26. This year our group numbered 29, and we once again had our international visitors Wayne and Vicki Scott attend from New Zealand.
I would like to thank our bus sponsors: Stopford Drilling and Forze Explosives. I’d also like to offer a shout out to those that helped with historical and geological details around Orford quarry: Admiral Ron Bugg, AKA ‘Buggie’, and the great team at Glamorgan Spring Bay Historical Society, Noel Stanley and Malcom Ward.
Friday night was the warm-up at the Waterloo Restaurant and the Swansea RSL. We arrived the next morning at Elphinstone
Engineering in Triabunna. Elphinstone started out as a chainsaw repair business and since 1976 has morphed into an engineering business manufacturing high-end logging, pole, semi and B-double trailers, including on board truck scales.
Graeme Elphinstone and his wife Sylvia met us on arrival and Graeme gave us a presentation on his business history and achievements, including three 1200km trips onto the Antarctic plateau driving the tractors towing a sled he built. Graeme and Sylvia put on morning tea before showing us around the manufacturing facility. I know a lot of members found the two multi tool/axis CNC machines especially interesting.
From there we went to Orford quarry, one of two on the sandstone cliffs between Shelley and Spring beaches. The quarry was opened around 1864 by Thomas Glaister, who had moved from the Ventenat quarry on South Bruny Island. The sandstone was used for local buildings and was transported to Hobart for the early buildings in the state capital.
The sandstone was described as an excellent building material cut “in the steep seaward cliffs” from “the great freestone quarries”. The cut stone in the form of “huge blocks” was shipped on trading ketches to Melbourne where, among others purposes, it was used to build the Melbourne Town Hall, Post Office and law courts. The quarry is now a protected tourist site and has been invaded by the endemic Oyster Bay pine.
NSW
NSW
NSW
Unfortunately, the rain on the day of our visit mean the access path into the quarry was deemed too slippery to attempt, so we viewed the quarry from the top bench.
After lunch we visited Tasman Sea Salt in Little Swanport, where we were met by geologist Chris Manson. Chris and Alice Laing started the business in 2013.
Our next visit was to Mayfield Estate Winery in Great Oyster Bay. The Dunbabin family has run sheep on their farm since 1969, growing super fine wools for the high-end Italian suit market. The last stop for the tech tour was at the Glamorgan
Spring Bay Heritage centre back in Swansea.
Our hosts Malcolm and Noel Stanley generously opened up all of their old records, papers and other information to share with us. The heritage centre also offers extensive mining and farming history of the area.
We had nowhere near enough time to take it all in and I know some members will go back to view more.
Dinner that night was in Swansea at Saltshaker Restaurant.
A great night was had by all – so much so that we have agreed to do another tech weekend in 2024.
The Burgess Shale is one of the world’s most famous fossil sites embedded at the heart of the Canadian Rockies. More than 100 years since its discovery, it is still delivering interesting finds.
Canada may be known for its unerring politeness, Ryan Reynolds, and ice hockey, but it’s the world-famous Burgess Shale that draws plaudits from paleontologists.
Found in the Canadian Rockies, the Burgess Shale has been one of the most consistent sites for fossil discoveries since it was discovered more than a century ago.
Dr Charles Doolittle Walcott did a lot for the Burgess Shale; in fact, he discovered it. The shale derives its name from Mount Burgess and the Burgess Pass in Yoho National Park, where Walcott and a rotating cast of his family members spent time around 1909. The site of the initial find is known as Walcott Peak, one of two areas named after the American.
Walcott took his second wife Helena until 1910 and then his third wife Mary until 1925 and then one of his four children until 1918, according to records.
Today, the Burgess Shale is considered to house one of the world’s first complex marine ecosystems, which houses soft-bodied animals and algae within the rock layers. The fossil finds date back 508 million years.
Initially, Walcott didn’t know any of that, but he did grasp that the fossil deposits within the shale layers were “very interesting” in his journals and new to science.
From the initial fossil discoveries in 1909, Walcott and his team established a small quarry, named after Walcott, where blocks of shale were slid down the mountain and transported by horse to camp for further examination and shipped to Washington.
Walcott developed a reputation for being incredibly committed to his research in the Burgess Shale and area surrounding the quarry which bared his name. Helena died in a train crash on July 11, 1911, yet Walcott returned to the Burgess Shale by August for research.
After almost a decade, Walcott seemed to fear that his activities had exhausted the fossil deposits.
He wrote in one report, published in 1918, that “this practically exhausts a quarry which has given the finest and largest series of Middle Cambrian fossils yet discovered and the finest invertebrate fossils yet found in any formation in any country.”
Walcott passed away in 1927 and his discoveries seemed to be regarded as novelty finds by an enthusiast rather than a major contribution to academia and were hidden in storage.
That all changed when Albert Simonetta and Laura Delle Cave stumbled upon Walcott’s findings and published several papers re-examining the discoveries. Walcott was also the subject of Stephen Jay Gould’s book Wonderful Life, which changed the negative stigma around his research.
In death, Walcott’s legacy of finding one of the world’s richest fossil deposits was rewarded by the National Academy of Sciences, where he was president for six years, awarding a medal in his honour every five years.
Ellis L. Yochelson, in his memoir of Walcott, summarised the man as an “excellent scientist” in his own right, yet “curiously … virtually unknown as the important historical figure” and researcher in America.
Long-time friend and collaborator Whitman Cross said Walcott’s achievements were “quite remarkable” given his rise in academia despite having no college education.
Walcott’s impact, with his quarry and peak, changed the course of palaeontology and Canada’s Rockies. •
InSitu Real Estate is a boutique agency providing real estate services to the extractive industry, mining, concrete & asphalt, waste & resource management, industrial and infrastructure markets.
Our experienced team provide complete real estate transactional services across the country, priding ourselves on our deep industry knowledge and an understanding of our clients needs.
InSitu Real Estate provides a full range of real estate services including sales, leasing and royalty negotiation, transactional management and occupier advisory.
If you’d like to chat further about how InSitu Real Estate can assist you with your requirements, or to discuss our current offerings, reach out today.
Todd Clark
Director
Licensee in Charge
+61 (0) 424 165 077
todd@insiturealestate.com
Suite 303, 17 Wurrook Circuit
www.insiturealestate.com
Caringbah, NSW 2229 InSitu
linkedin.com/company/insitu-real-estate