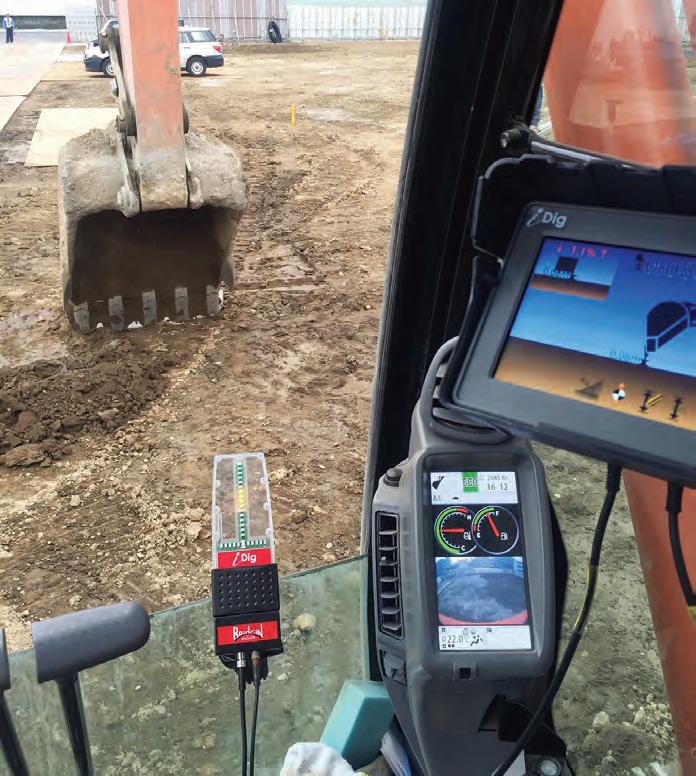
6 minute read
2D or 3D?
CONTRACTORS HAVE LONG SPECULATED ON THE DIFFERENCES BETWEEN 2D AND 3D EXCAVATOR MACHINE CONTROL, AND WHICH OPTION IS SUITED TO THEIR ROAD CONSTRUCTION SITE. POSITION PARTNERS SETTLES THE 2D/3D DEBATE WITH AN EXPLANATION.
Each machine control system comes with a range of benefits and these can be optimised to site specifications.
Strict excavation tolerances during site preparation on road construction projects keep the ground level and stable for the rest of the project.
Each site will have a unique set of tolerances that are crucial to avoiding any disruption to underground and surrounding infrastructure.
To achieve precise and swift site preparation work, excavator machine control systems are crucial to increasing productivity and accuracy.
When looking to invest in the best excavator control systems for road construction work, there are fundamental differences between 2D and 3D machine guidance systems.
When optimised, these systems can facilitate greater job productivity, accuracy and efficiency when clearing construction sites.
Each excavator control system aims to fulfil the same essential function: positioning relative to desired grade. However, the 2D and 3D methods use different technology to achieve these results and the choice between these systems is a common concern for road contractors.
Position Partners Construction Business Manager Josh Allan says the primary point of difference is how 2D and 3D variants use different technology to provide positioning assistance and guidance solutions.
“2D control systems commonly take advantage of both physical landmarks and laser technology as reference points throughout the excavation process. 3D control systems have the advantage of GPS or total station technology, which can digitally project site plans and generate realtime data to provide accurate positioning relative to a complex design,” Mr. Allan says.
Each machine control system comes with a range of benefits and these can be optimised according to site specifications and overarching project requirements.
“While 3D machine control gives access to greater functionality, with the option for advanced automated control, it is more expensive and depending on the project the cost may not be justified, especially for smaller development projects,” Mr. Allan adds.
A simple method to understand which guidance alternative is most suited to a project involves examining exactly how each works.
“You need to understand the technology and the variety of benefits which underpin
each system. This can help narrow the selection process and ultimately guide a decision,” Mr. Allan says.
2D MACHINE CONTROL SYSTEM Mr. Allan says the 2D machine control system is a common choice for Position Partners customers across a wide range of excavation projects.
The 2D system provides access to costeffective guidance methods and these focus on enhancing machine utility and maximising return on investment.
The technology takes advantage of physical landmarks, stakes or laser technology for reference during operation.
“This serves to provide or create accurate benchmarks that increase accuracy on excavation processes,” Mr. Allan says.
For smaller projects, this system provides essential information to reduce downtime across core jobs such as flatwork prep, foundation work and trenching initiatives.
“2D excavation systems are distributed for a lower up-front cost with a range of tangible benefits that are proven to enhance productivity, accuracy and efficiency,” Mr. Allan says.
He says some of the benefits of the 2D system include improved safety, cost savings and maximised machine utility. Minimal training time is needed due to the simplicity of the system and it achieves accurate grade and excavation work.
Optimisation for mass excavation, slope control and real-time depth and distance reporting are some of the other ways the system achieves accuracy on excavation jobs.
3D GPS MACHINE CONTROL SYSTEM Increased location accuracy and new technical components are among the reasons contractors choose 3D systems. Though more expensive than its 2D counterpart, 3D features are well suited to larger sites where multiple machines are working simultaneously to a complex design.
The 3D machine control system uses advanced technologies including multiple machine sensors and the use of either GNSS or optical total stations to deliver real-time data to the operator..
“The 3D machine control system often entices customers as on most major projects 3D has become the standard that’s required to win work,” Mr. Allan says. 3D systems position digital site plans in front of the machine operator, providing exact grade location and eliminating the need to manually set stakes or stringlines.
“These systems are used across larger and more complex projects that prioritise leading productivity, accuracy and downtime reduction. When using the 3D system, operators gain access to exact machine locations and site specifications which overall, produces leading results,” Mr. Allan says.
He adds that despite the greater functionality of 3D systems, the investment may not be worth it for some. 3D control systems cost more due to extra system components and enhanced functionality, which require data model preparation and more complex training.
“When dealing with large or long-term projects, 3D machine control provides more tangible benefits and often leads to a greater return on investment,” Mr. Allan says.
He says major advantages of the 3D machine control system include live depth, distance and grade data, increased accuracy and precise locating. It enables elevation reference and site optimisation to ensure the settings suit different job requirements.
The 3D control also aims to reduce downtime and fuel wastage.
THE DECISION Mr. Allan says to best facilitate project results, there must be an understanding of both site and budget requirements.
Each control system can then be optimised for individual project needs, based on a project’s specifications.
Mr. Allan says there are three common factors that help dictate whether to purchase a 2D or 3D excavator control system.
The first factor he notes is price. Mr. Allan says 2D systems are notably more cost-effective, however, provide limited functionality and less flexibility than their 3D counterparts. The cost is a result of increased componentry, which when adhering to a budget, may not be a viable option.
Choosing a brand of machine control that is forwards and backwards compatible is vital to ensure contractors aren’t “locked in” to a single system, Mr. Allan adds. This way contractors can start with a 2D system and build on it, upgrading to 3D if they need to by hiring additional components without the capital outlay of a 3D system straight up.
Time is the second factor. When analysing time restrictions, both staff training and manual labour should be taken into consideration.
“3D control systems have many advantages. As long as you’re getting the right system for the work you’re doing, the time you invest at the outset to learn the system will pay off quickly with the reduction in manual labour, rework and material waste,” Mr. Allan says.
The third factor is functionality, and Mr. Allan says this is possibly the most important element when deciding which machine control system is optimal.
“3D GPS systems offer significantly more features as machine positioning and grade specifications are tracked exactly. When looking to just measure excavation depth and distance, 2D variants may be suitable for the project. However, if the project calls for advanced technology to integrate with site plans, 3D systems will be required.”
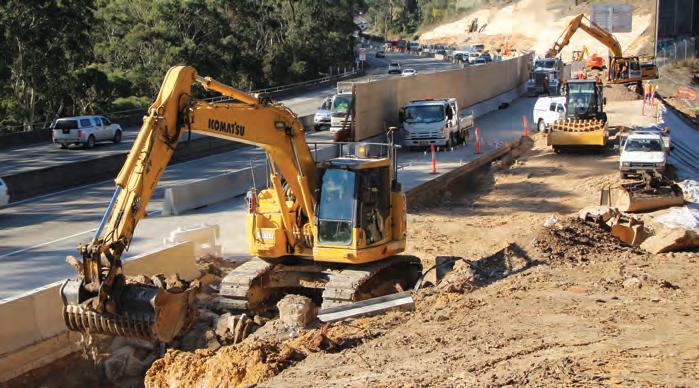
3D GPS systems offer significantly more features as machine posiitoning and grade specifications are tracked exactly.