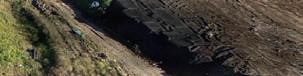
9 minute read
Soil treatment: Leaving no trace behind
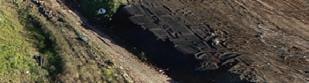
The SUEZ-Ventia soil processing facility is located within the Taylors Road Landfi ll in Melbourne’s south-east.

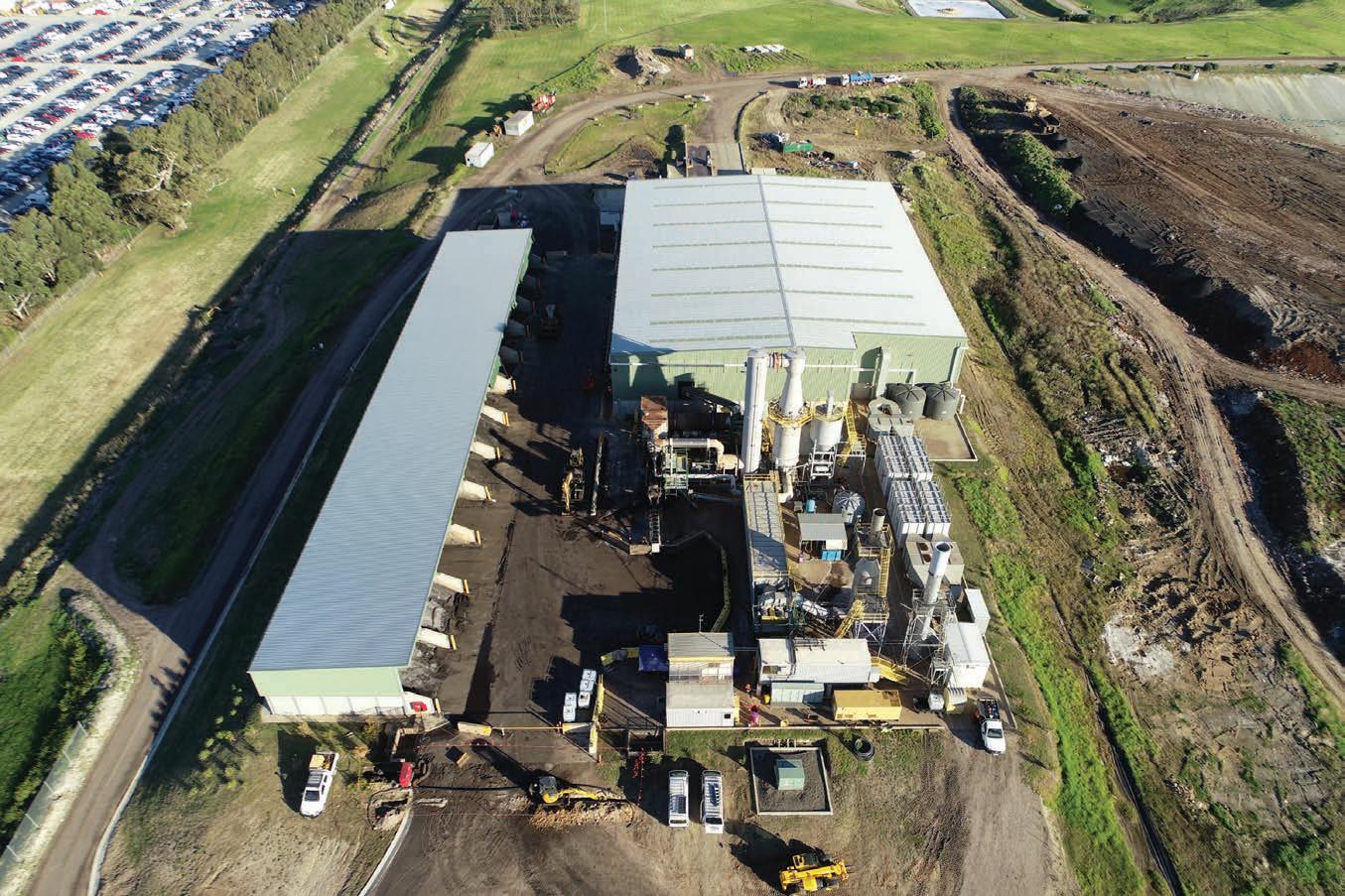
THE SUEZ-VENTIA CONTAMINATED SOIL PROCESSING FACILITY IN MELBOURNE’S SOUTHEAST FACILITATES ZERO-RESIDUE TREATMENT OF CONTAMINATED SOILS. ROADS & INFRASTRUCTURE INVESTIGATES THE SUSTAINABLE SOIL MANAGEMENT OPTIONS THE SITE OFFERS TO THE CONSTRUCTION INDUSTRY.
The issue of land contamination and the risks it poses to safe and effi cient handling of infrastructure projects has been brought to the spotlight recently, particularly with the development of two events last year.
First was the high-profi le case of Melbourne’s West Gate Tunnel project, where disputes over how to manage the project’s waste, some of which was contaminated with potential carcinogens called per- and polyfl uoroalkyl substances (PFAS), delayed the project’s expected delivery by at least two years and led to nearly $2 billion in cost blow-outs.
While in this case, after much consideration for the environmental impacts, a decision was reached to dispose nearly three million tonnes of contaminated rock and soil from the project in a landfi ll facility, there has been growing support within the industry for re-use and recycle of contaminated soil as a more sustainable option.
Moreover, new environmental legislation from the Victorian Environment Protection Authority (EPA) has signifi cantly shifted the regime of risk associated with soil containing asbestos, PFAS and other chemicals on major property and infrastructure projects.
Amendments to the Environment Protection Act (2017) that came into effect on 1 July 2021 have replaced the old system that governed liability for polluted soil and given the Victorian EPA new powers to enforce compliance across the sector.
As a result, landholders, property developers, contractors, sub-contractors and third parties can be held to signifi cantly higher levels of accountability for actions that are harmful to the environment or community, with their liability now even extending for decades beyond their direct involvement with the project.
The above two scenarios help explain the critical importance of having sustainable options available for re-use and recycle of contaminated soil, to make sure the remediated soil can be safely and effi ciently returned to the environment without
creating more pollution in the process.
This is exactly what SUEZ, a global leader in the waste and resource recovery industry, and Ventia, a company with 20+ years of soil remediation expertise, have set out to do at their EarthSure Soil Processing Facility in Melbourne.
EARTHSURE SOIL PROCESSING FACILITY Located within an industrial zone in the outer south-east Melbourne suburb of Dandenong South, the SUEZ-Ventia EarthSure facility is a soil remediation plant capable of treating both organic and inorganic contaminated soils with zero residues.
While the SUEZ Taylors Road Landfill Smart Cell has been an important public resource for Victoria’s waste needs for over two decades, the decision to co-locate a soil treatment plant within the hub came in 2015, when the Victorian Government identified the landfill as a compatible site for resource recovery.
In 2017, construction of the EarthSure plant commenced, which uses direct thermal desorption treatment and stabilisation technologies to treat a range of contaminated soil to minimise its environmental impact and create the potential for re-use.
In 2019 and after fulfilling a series of stringent compliance measures from the EPA, the EarthSure facility received the EPA’s seal of approval to treat categories A, B and C soils – which include almost all categories of contaminated soils that require treatment before disposal.
Since then, the plant has been involved in diverting waste from landfill on several infrastructure projects, including Metro Tunnel and the West Gate Tunnel in Victoria, Central Station in Sydney and complex gas remediation projects in Wollongong, Fitzroy and Highett. These projects alone have diverted over 40,000 tonnes from landfill.
The completed facility has the capacity to process up to 100,000 tonnes of contaminated soil each year. This includes soil contaminated with coal, crude oils and gasworks wastes; petrol, diesels and hydraulic oil; pesticides and carcinogens found in transformer oils and old appliances like refrigerators.
The Taylors Road Landfill is the only facility in Victoria that can receive soils or waste that have been stabilised or chemically immobilised. Heavy metals can only be treated via the method of immobilisation used by EarthSure, making EarthSure’s position within the Taylors Road Landfill boundary an added advantage. It’s also further reassurance for customers that their material will be in the right place post treatment.
Treated soil from the plant can be returned to the source site or reused elsewhere. In the absence of demand, all treated products can also be sent to the Taylors Road Smart Cell, where clean fill is beneficially reused as top-dressing to cover layers of compacted solid waste.
HOW IT WORKS So how does the thermal desorption process work and how does it ensure a zeroresidue soil remediation outcome?
The remediation process starts by storing the contaminated waste material in a pre-treatment building on site where the material is tested, categorised and screened prior to treatment.
A powerful Emissions Control System (ECS) ensures the air in the pre-treatment building is constantly ventilated via an induced draft fan which draws the air through a series of particulate filters and beds of granulated activated carbon to purify the air. A continuous Emissions Monitor on the ECS ensures the treated air does not contain any dust particles or organic compounds.
Soil requiring treatment is loaded into a soil hopper. From the hopper, the soil is transferred through a series of conveyor belts, including a weigh conveyor to
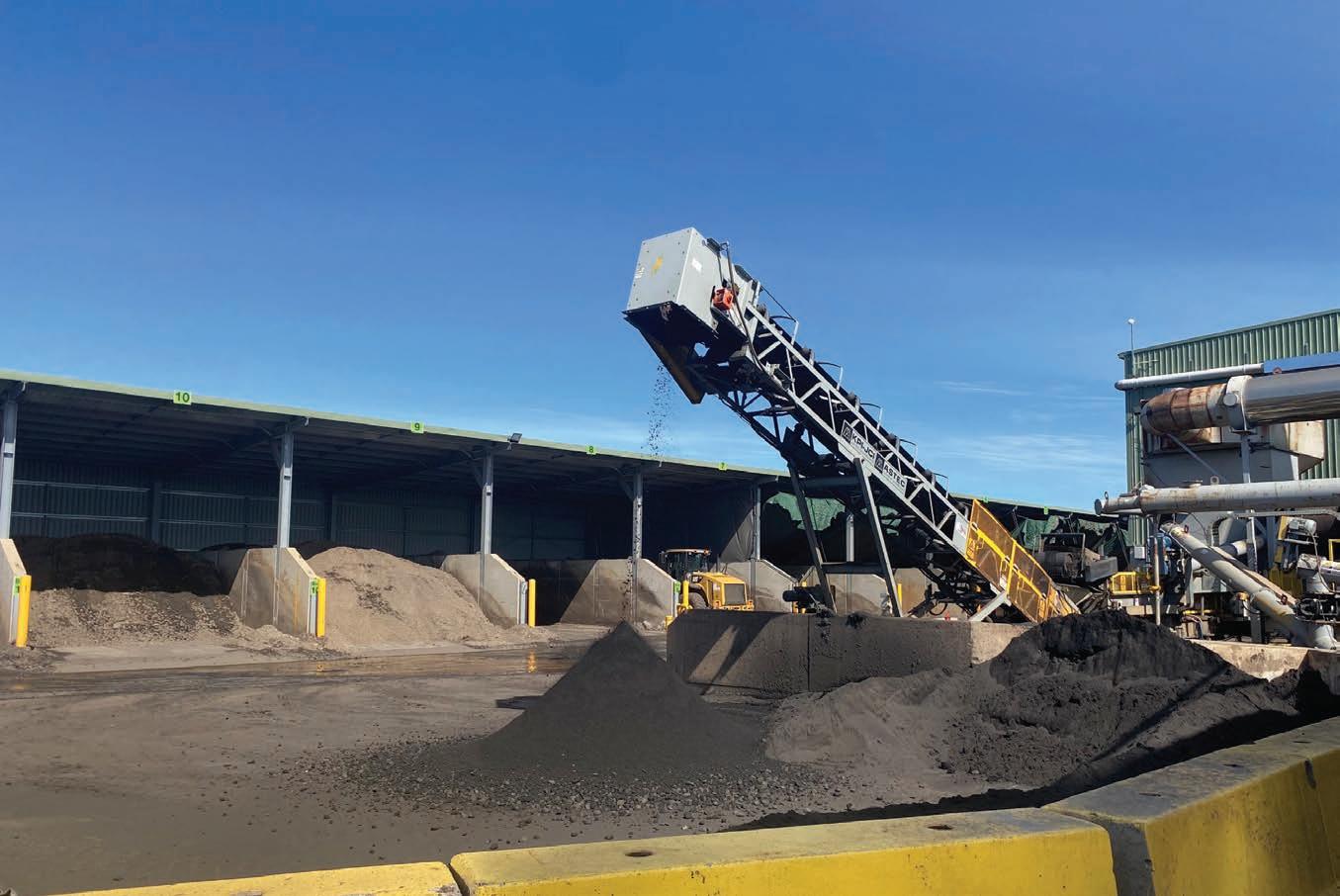
The EarthSure facility can process up to 100,000 tonnes of contaminated soil each year.
monitor throughput and a magnet conveyor which removes ferrous materials, prior to being directed into the direct thermal desorption system. Here, the soil is heated up to 550 degrees Celsius, which cleans the soil by liberating contaminants from it into the gas stream.
This is then followed by treatment of the contaminant in the gas stream at up to 1100 degrees Celsius. The high gas treatment temperatures destroy all organic contaminants by converting them into simple and harmless substances comprising primarily H2O, CO2 and acid gases such as HCl, which are neutralised to form common salt (NaCl).
The final product is an inert soil devoid of harmful contaminants.
Other treatment technology at the facility includes the stabilisation of inorganics such as lead and arsenic by the application of special additives to bind or immobilise the contaminants of concern to prevent their migration.
“It’s like a blank canvas. You can add the required additives to the treated soil and use it in agriculture or as topsoil, but you can also use it in landfills and project sites as alternates to raw materials like sand,” explains Tai Truong, Facility Manager at EarthSure.
The thermal desorption system is a state-of-the-art PLC controlled plant that is equipped with numerous safety interlocks to ensure the soil is cleaned without creating any risk of harm to personnel, environment or equipment.
The stringent discharge limits set by the EPA require the plant to continually monitor pre- and post-contaminant levels at the site. Ongoing testing of the discharge stacks remains highly regulated by the EPA, with discharge limits having to meet strict European Union guidelines.
“To give you an example, the limit set by the EPA for volatile organic compounds (VOCs) discharged from the plant is 0.83 grams per day, which is far less than the daily VOC discharge permitted from car exhausts,” says Truong.
Apart from the time required for routine maintenance, the EarthSure facility is capable of processing 15 tonnes of soil per hour, 24 hours a day, seven days a week. The plant is fitted with a rigorous system of controls and real-time monitoring including sophisticated alarms that help ensure full compliance throughout its operation.
A SUSTAINABLE SOLUTION Mark Globan, SUEZ’s Infrastructure Manager for Victoria, says both SUEZ and Ventia are proud of their contribution to delivering a safe, environmentally friendly and sustainable soil remediation solution.
“Our client base extends to local and federal government departments. We also work with contractors and developers involved in excavation and subdivision work on commercial and residential projects. In the past, we have also successfully treated material impacted by PFAS, which
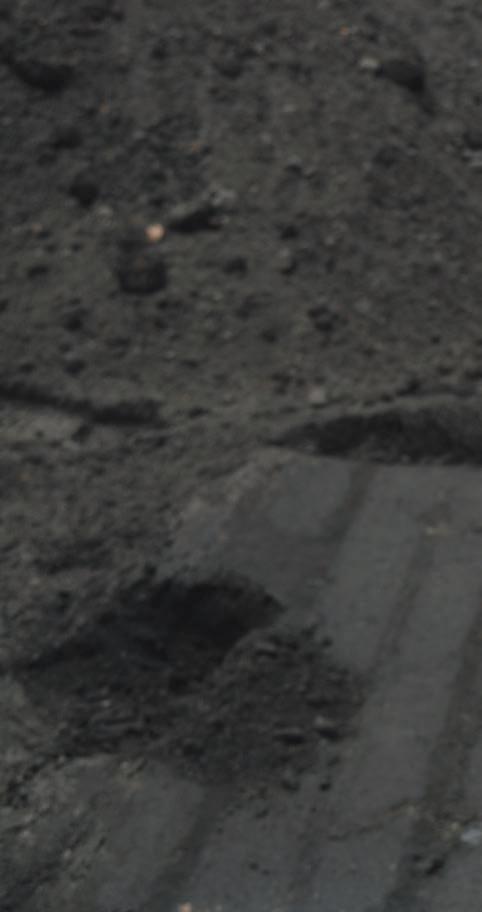
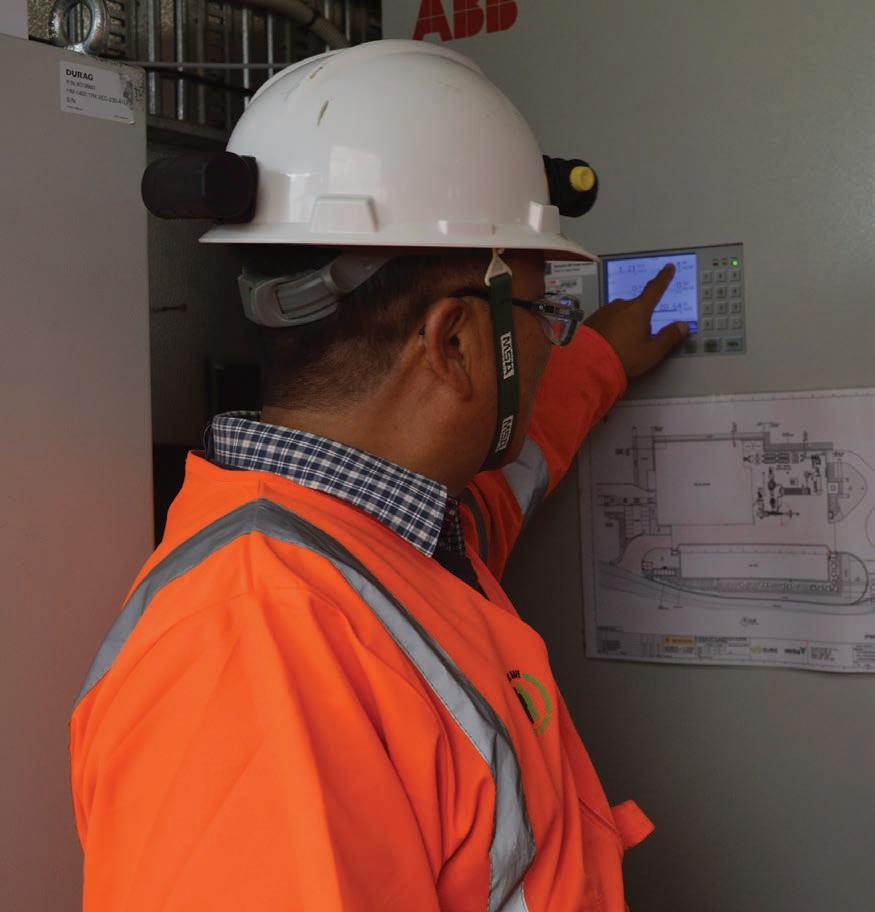
The thermal desorption system is a state-ofthe-art PLC controlled plant, equipped with numerous safety interlocks. Treated soil from the plant can be used in landfills, or returned to environment after further treatment.
we received from the state and federal government clients,” he says.
“Our treatment process has enabled these projects to meet sustainability targets and completely eliminate risk of future legacy liabilities by destroying the contaminants. We view our ability to offer our clients a disposal solution that prevents costly legacy issues down the track as a big differentiator that sets us apart.”
As awareness grows around PFAS contamination in the environment, Globan says thermal treatment would be the only viable option available to deal with future risks.
“PFAS is a group or family of persistent organic pollutants that is recognised as potentially very toxic and is arguably the most difficult to destroy or break down. While the awareness of the dangers associated with PFAS is relatively new, its ubiquity and enduring use as firefighting foam is well documented. Moreover, PFAS’ ability to migrate to far reaching areas has been demonstrated, its recalcitrance is acknowledged by scientists and its carcinogenic properties and general harm to all life is also now being recognised throughout the world,” says Globan.
“With continued development, more PFAS will be found. When temporary storage of PFAS containing water and PFAS impacted soil is no longer an option, pressure will mount to find a solution to the problem. Thermal treatment is the only technology available in the market to destroy the PFAS contaminants reliably and safely and remove all risk of leaving a potentially costly legacy behind.”
Beyond leaving a good legacy behind, finite landfill spaces would also require project owners to consider re-using waste from their projects, particularly when the cost of carrying the waste to a landfill area renders it unfeasible, Globan observes.
“With finite landfill space available, we need to help prolong these assets and divert the waste that can be reintegrated back into the economy. Our treatment process removes organic contaminants to well below the clean fill thresholds. What would otherwise be landfill then becomes available for use in infrastructure projects for a variety of purposes such as a road base, a structural fill or trench backfill in lieu of valuable virgin material commodities and natural resources such as sand and crushed rock.”
With the amendments to the Environment Protection Act placing greater responsibility on organisations and individuals with regards to soil contamination, Globan says a pro-active approach to environmental management on projects has never been more critical.
“Today, more than ever, Australians are being asked to take responsibility for their waste and we are seeing an increased focus on a ‘recycled first’ approach across major government infrastructure projects. With EarthSure, we are offering businesses an affordable and safe option today, to eliminate legacy concerns for tomorrow.”
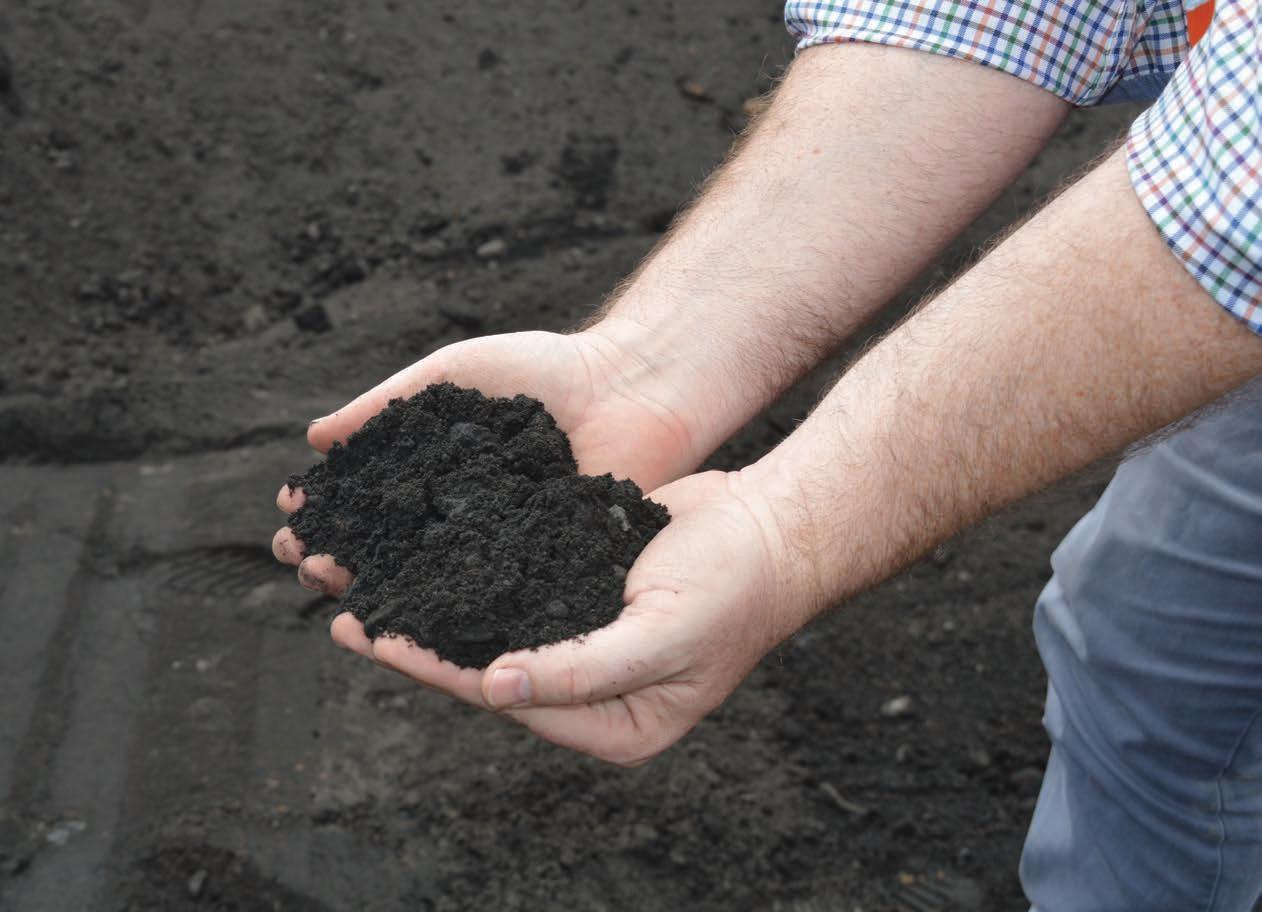