How Premier Cranes & Rigging’s contributions are supporting the delivery of Melbourne’s West Gate Tunnel Project
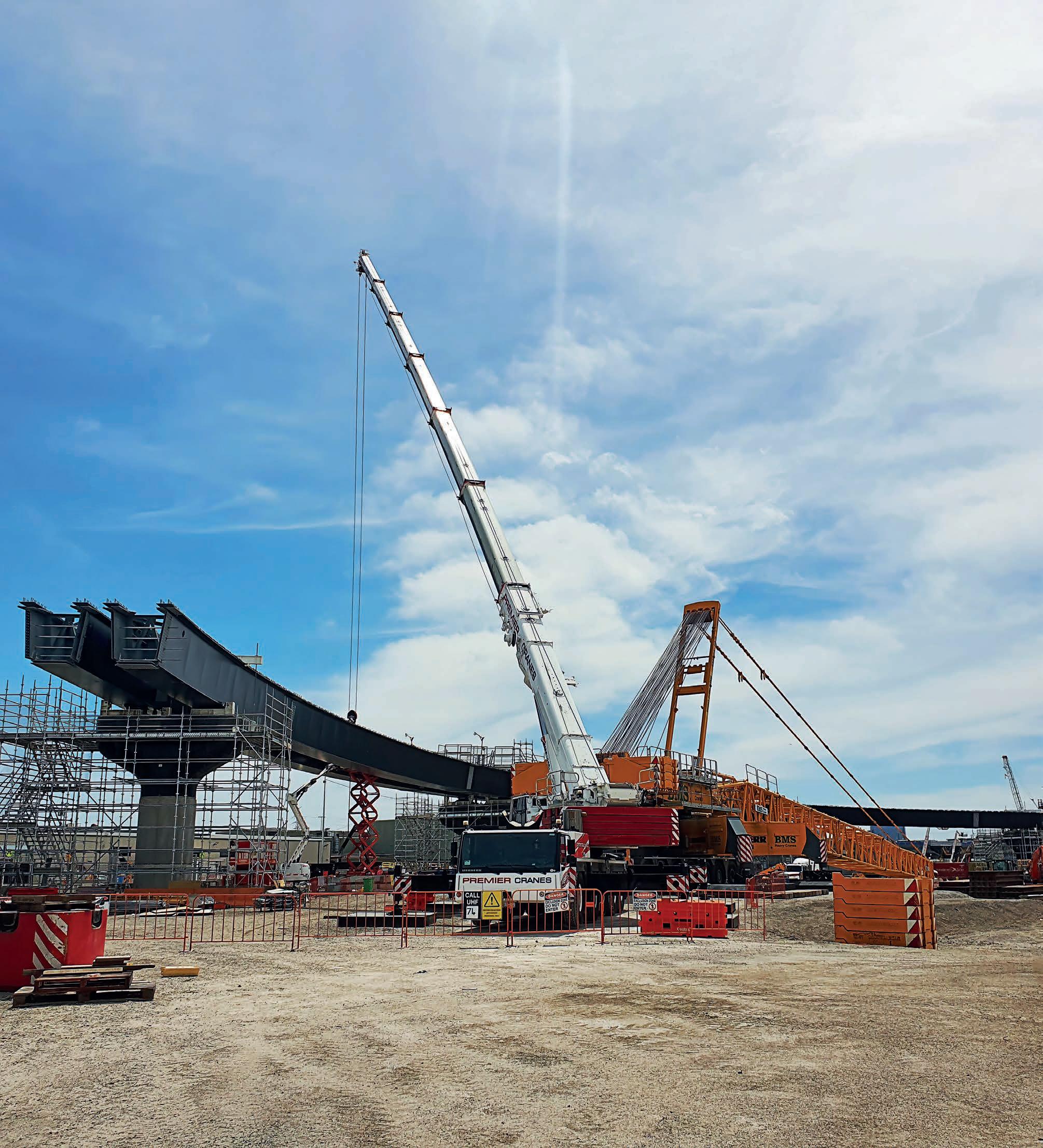
How Premier Cranes & Rigging’s contributions are supporting the delivery of Melbourne’s West Gate Tunnel Project
How one of Alex Fraser’s rising stars is representing a new generation of leaders in sustainable project delivery
THE TIME IS NOW
We ask leading decision makers how the industry is supporting diversity right across the sector
16 Once in a lifetime
Premier Cranes & Rigging is supporting the delivery of Victoria’s massive West Gate Tunnel Project.
20 This month, we asked the industry decision-makers, ‘What is the industry doing to encourage greater diversity across the sector?’
22 Kate’s story
The journey so far for Kate Lynch, who represents a new generation of leaders in sustainable project delivery at Alex Fraser.
26 Strength in perspective
Roads & Infrastructure hears from four women who are thriving in the civil infrastructure space with the support of their employer Rokon.
29 A critical step
The foundation and rise of Plan B Comms in Australia’s communication infrastructure sector.
32 The future of Flocon
Third-generation employee Rory Knight reflects on Flocon’s rich history in Australia’s road maintenance sector.
35 A call for digital unity
How technology solutions could evolve to better serve the data needs of the civil construction industry.
38 Patching a gap
&
A preview of the new Cat AP400 Asphalt Paver, and what its flexibility will offer the Australian market.
41 New era road planers
Evolution and innovation have guided FAE’s development of its new range of road planers.
44 Continuing growth
An overview of what has contributed to SANY’s substantial growth across its national dealer network.
46 A true utility machine
Popularity is growing towards Road Widener’s options for utility works in Australia and the United States.
48 The pick of the bunch
Francrane Managing Director Brenton Owst-Atkinson explains what the TIDD PC28 brings to the business.
51 Safety leaders
Roads & Infrastructure sits down with Matthew Bereni, newly appointed CEO of the Traffic Management Association of Australia (TMAA).
53 AfPA’s Federal Budget submission snapshot
An overview of the Australian Flexible Pavement Associations’ recent Federal Budget Submission for 2023-24.
55 Productivity gains
How Precasters with digitised QA are delivering productivity gains to the civil sector.
56 The Infrastructure Sustainability Council reflects on the year just past, through its 2022 Impact Report.
58 A summary of the contracts awarded for major infrastructure projects across Australia.
4 Editor’s note
6 News
14 People on the move
ACCORDING TO the Australian Constructors Association, women make up 12 per cent of Australia’s construction workforce. More companies in the roads and infrastructure sectors are embracing new methods to attract talented individuals from a diversified and wide employment pool.
But there’s clearly more work to be done, in order to bridge the gap in representation.
For the March edition, Roads & Infrastructure Magazine celebrates the work being done by inspirational figures across the sector to encourage and support diversity, in what remains to be a male-dominated industry.
Trailblazers, such as Alex Fraser Project Manager Kate Lynch, are helping to lead the way. Lynch’s contributions have been instrumental for the development and delivery of Alex Fraser’s new Asphalt Plant in Epping, Victoria. As Lynch tells Roads & Infrastructure Magazine , Alex Fraser’s career pathway programs have helped her and other graduates to get a head start in their careers.
Then there is Rokon, which has always supported the development and leadership of female leaders within its workplace, epitomised by its “we are many teams, but one family” ethos. In this edition, we showcase women whose commitment has helped the company to become one of Melbourne’s leading civil works contractors.
In this month’s Roads Review column, we hear from some of the industry’s top decision makers on how the industry is working to promote diversity.
The March cover story features an in-depth look into the West Gate Tunnel Project, one of Victoria’s largest infrastructure projects. Through the eyes of Premier Cranes & Rigging, we explore the challenges, achievements and future hopes for the project, which is set to improve Melbourne’s road infrastructure for generations to come.
Finally, in this edition, the Infrastructure Sustainability Council (ISC) reflects on the year just gone, as part of its release of the 2022 ISC Impact Report. The report paints a positive outlook for the industry as we head into 2023, with the industry introducing 30 Australian firsts when it comes to sustainable procurement, methods and material use. 2022 was also the largest year ever for the IS Council’s IS Rating Scheme, which helps to evaluate the sustainability and social achievements being made on major infrastructure projects across Australia and New Zealand.
Happy reading!
Tom O’Keane Roads & Infrastructure MagazineCOO
Christine Clancy christine.clancy@primecreative.com.au
GROUP MANAGING EDITOR
Sarah Baker sarah.baker@primecreative.com.au
MANAGING EDITOR
Mike Wheeler mike.wheeler@primecreative.com.au
EDITOR
Tom O’Keane tom.okeane@primecreative.com.au
JOURNALIST
Leon Cranswick leon.cranswick@primecreative.com.au
DESIGN PRODUCTION MANAGER
Michelle Weston michelle.weston@primecreative.com.au
ART DIRECTOR Blake Storey
DESIGN
Bea Barthelson
BUSINESS DEVELOPMENT MANAGER
Brad Marshall brad.marshall@primecreative.com.au
CLIENT SUCCESS MANAGER
Glenn Delaney glenn.delaney@primecreative.com.au
HEAD OFFICE
Prime Creative Pty Ltd 379 Docklands Drive, Docklands VIC 3008 Australia p: +61 3 9690 8766 f: +61 3 9682 0044 enquiries@primecreative.com.au www.roadsonline.com.au
SUBSCRIPTIONS +61 3 9690 8766 subscriptions@primecreative.com.au
Roads & Infrastructure Australia is available by subscription from the publisher. The rights of refusal are reserved by the publisher.
ARTICLES
All articles submitted for publication become the property of the publisher. The Editor reserves the right to adjust any article to conform with the magazine format.
COPYRIGHT
Roads & Infrastructure Australia is owned and published by Prime Creative Media. All material in Roads & Infrastructure Australia is copyright and no part may be reproduced or copied in any form or by any means (graphic, electronic or mechanical including information and retrieval systems) without the written permission of the publisher. The Editor welcomes contributions but reserves the right to accept or reject any material. While every effort has been made to ensure the accuracy of information, Prime Creative Media will not accept responsibility for errors or omissions or for any consequences arising from reliance on information published. The opinions expressed in Roads & Infrastructure Australia are not necessarily the opinions of, or endorsed by the publisher unless otherwise stated.
The Inland Rail project has reached an important milestone with the beginning of major construction works in Victoria, meaning construction is now underway in two of the three states.
The Australian Rail Track Corporation (ARTC) marked the occasion with a community event in Glenrowan, welcoming construction in Victoria after a thorough planning, engagement, and design process.
Connecting Melbourne and Brisbane via regional Victoria, New South Wales and Queensland, Inland Rail is Australia’s largest freight rail infrastructure project and will aim to better connect businesses, manufacturers, and producers to national and global markets, and create new opportunities for Australian industries and regional communities.
Victoria is expected to benefit significantly from Inland Rail with freight efficiencies and investment opportunities expected to boost the state’s potential output by $6 billion over the first 50 years of operation.
According to the ARTC, businesses in
Victoria are already benefiting from Inland Rail, with 58 contracts at a value of $269.1 million committed to Victorian businesses, as of December 2022, for services and supplies on the Victorian section of the project.
Inland Rail follows along the existing North East Rail Line that was upgraded in 2021. To enable double stacked trains ARTC must upgrade existing infrastructure at 12 sites across the state.
McConnell Dowell, the appointed
contractor on the first four projects at Seymour, Barnawartha North, Glenrowan, and Wangaratta, has commenced preliminary site works and will soon move into major construction.
The remaining projects are currently in the reference design stage.
Inland Rail has already completed the Parkes to Narromine section in New South Wales with major construction works also underway on the Narrabri to North Star section in the state.
The final connection has been made between the Sydney Metro City & Southwest with
Sydney Metro City & Southwest line to the Metro North West Line was constructed over two years, including the installation of tracks and all operational services in the 15.5-kilometre twin tunnels between Chatswood and Sydenham.
The final connection of the two metro railways was made with four sections of rail and almost a kilometre of copper overhead wires between Chatswood Station and the new Sydney Metro City & Southwest tunnels. Six teams and more than 200 workers worked around the clock over one weekend to make the final connection.
Sydney Metro is Australia’s biggest public transport project. By 2030, Sydney will have a network of four metro lines, 46 stations and 113 kilometres of new metro rail.
From 2024, passengers can travel from Tallawong in Sydney’s north, into the city in under 50 minutes, Castle Hill to Barangaroo in 33 minutes and Chatswood to Martin Place in 11 minutes on a fast and reliable metro service.
Testing on the new connection will commence later this year, ahead of passenger services starting through the Sydney CBD in 2024.
The Metro Tunnel Project has reached another milestone as workers begin installing platform screen doors in the five underground stations.
Platform screen doors are a hallmark of
world-class metro rail systems, such as those in London, Singapore, Hong Kong, and Paris. The Metro Tunnel doors will be the first in Victoria’s rail network.
Installation is underway at Parkville,
The Infrastructure Sustainability Council has awarded the Rookwood Weir Project in Queensland with an “excellent” rating, celebrating the project’s economic, social, and environmental performance.
The $367 million project of the new weir on the Fitzroy River near Rockhampton includes wider works to upgrade existing infrastructure to support the construction and operation of the new weir.
It’s expected to provide greater water security to help grow and diversify agriculture in the region. It will also support industrial growth in the Gladstone, Capricorn Coast and Rockhampton regions.
The project has been recognised for its innovative fishlock and turtle passage, both of which will help local river species safely navigate the weir with the flows of the Fitzroy River.
It has also achieved significant energy and carbon savings, with design elements reducing both the amount of cement required for construction and the volume of earth to be extracted.
Construction activities at Rookwood
Arden, and Anzac stations, and is set to begin shortly at State Library and Town Hall stations.
The toughened glass sliding doors will open and close in tandem with the fleet of Melbourne’s new High-Capacity Metro Trains – creating a barrier between the track and platforms to improve passengers’ safety by preventing people and objects from falling into the path of oncoming trains, and stopping trespassers entering the tunnels.
The new technology has been tested in a series of rigorous trials over several years, both in virtual development and at a test platform at the Pakenham East train depot.
There will be 60 doors installed at each station, making 300 in total – enough to stretch from Flinders Street Station to the Melbourne Cricket Ground.
The Metro Tunnel’s stations are also quickly taking shape, with the fit-out of lifts, escalators, security systems, CCTV, passenger information displays and emergency phones underway, as well as tracks being laid along the nine-kilometre twin tunnels.
Weir are on track to be completed in late 2023, which will be followed by a period of commissioning.
The project is being delivered by the Rookwood Alliance, which comprises Sunwater, construction partners ACCIONA, McCosker Contracting and design partner GHD.
The $367.2 million project is jointly funded by the Federal and the Queensland governments ($183.6 million each).
Introducing the first and only skid steer with a telescopic boom the JCB Teleskid; a truly unique, versatile skid steer with endless possibilities. Now you can lift higher, reach further, dig deeper.
This revolutionary product is designed to suit all types of job sites meeting the need of multiple machines wrapped nicely into one. Combining the strength and safety of our single side boom with side door entry and extendable boom JCB has increased the versatility of the SSL-CTL world.
To find out more contact your local JCB CEA dealer today. Ph: 1300 522 232 www.jcbcea.com.au
The latest round of the New South Wales Government’s electric vehicle (EV) fleet incentive is now open for applications, with up to $15 million available in funding.
The incentive aims to support the purchasing of battery or fuel cell electric vehicles.
The New South Wales Government is investing $105 million into the incentive program which aims to encourage organisations to accelerate their shift towards EVs, therefore also reducing their emissions.
It’s estimated that the average fleet driver in New South Wales can save around $3100 in annual running costs if they make the
switch to electric.
There will be multiple funding rounds until 2024. Funding allocated to eligible organisations will support the procurement
of approximately 2000 battery electric vehicles and 1800 smart chargers. Round three of the incentive is now open until Tuesday 23 May 2023.
The $124.5 million Port Wakefield Overpass and Highway Duplication projects are complete and have officially opened.
Recent long weekends and school holidays have seen traffic flowing smoothly through the town and on towards the Yorke Peninsula and the state’s north.
Completed works include two lanes in each direction through Port Wakefield, with allowance for safe U-turns; a new two-lane overpass for traffic travelling southbound from the Copper Coast Highway to Port Wakefield, and for traffic travelling along the Augusta Highway to the Copper Coast Highway; and the removal of hazardous turns at the intersection of the Port Wakefield, Copper Coast and Augusta highways.
The projects have also included improved pedestrian access and landscaping in the township of Port Wakefield, improved parking through the town to support local businesses, realignment of the Balaklava Road intersection, and new bridges over
the Wakefield River.
Port Wakefield Highway typically carries nearly 9000 vehicles per day, however this can almost double during holiday peak periods and on long weekends.
The project has been delivered by the Port Wakefield to Port Augusta
(PW2PA) Alliance, a consortium comprising CPB Contractors, Aurecon, and GHD, in conjunction with the South Australian Department for Infrastructure and Transport.
The project has been jointly funded by the Federal and South Australian governments on an 80:20 basis.
Transport for New South Wales has released the preferred option for upgrades to the Princes Highway at Jervis Bay Road to Hawken road, near the border with Victoria.
The Federal and NSW State governments have committed $500 million to this six-kilometre stretch of the Princes Highway, from Jervis Bay Road to Hawken Road, between Falls Creek and Tomerong.
The upgrades will boost the safety and efficiency of the connection. This will be achieved by reducing congestion, improving access to local roads and improving the resilience of the network.
The upgrade is set to feature a realignment of the existing highway and widening from two lanes to a four-lane divided highway with median separation, as well as a major intersection at Hawken Road.
The preferred option for the project features an s-type grade separated intersection (or overpass), as well as service roads to connect properties.
Transport for NSW is encouraging the community to provide feedback on the preferred option to help refine the design and prepare the Review of Environmental Factors (REF).
Feedback will be considered as part
of the REF assessment process. The REF and concept design are expected to be available for comment by early 2024.
The Western Australian Government has finalised a strategy to reconnect the Great Northern Highway at Fitzroy Crossing, which saw sections completely washed away in the recent one-in-100-year flood event.
Tropical Cyclone Ellie, which began in December 2022, crossed the Northern Territory coast over New Year, causing significant damage to the Fitzroy Crossing Bridge and sections of Great Northern Highway.
As a result, the Fitzroy Crossing Bridge
sustained significant damage and will need to be fully replaced.
Main Roads Western Australia will utilise a barge system to help construct a low-level floodway crossing, which will provide an alternative option while the full replacement of the Fitzroy Crossing Bridge is completed.
The barge system will initially be operated by tugs, with a cable system to be operationalised shortly after. It can be adapted when the river levels fall too low, using portable pontoons,
which would act as a temporary crossing. Construction of the alternative crossing is expected to take around four months to complete.
Planning for the new bridge across the Fitzroy River is well underway. The new bridge will need to be higher and longer, and will be dual-lane, rather than the current single-lane bridge. Main Roads WA will commence a fast-tracked procurement process to select a preferred contractor for this project.
The Committee of Sydney has appointed Eamon Waterford as its new Chief Executive Officer. The organisation acts as an urban policy think tank which aims to develop solutions for the city’s economy, infrastructure, planning, governance and more. Waterford joins the Committee from the NSW Department of Enterprise, Investment and Trade, whereas Chief Strategy Officer he leads cluster strategic planning for 5000 staff responsible for supporting NSW’s economy and communities. He was also previously Deputy CEO and Policy Director at the Committee for Sydney, working with both previous Chief Executives –Tim Williams and Gabriel Metcalf. As the Committee’s Policy Director, he delivered more than 40 reports, including the opportunity of a six-city megaregion unlocked through fast rail. Waterford will begin the role of CEO in late February. In the interim, Michael Rose will continue as Executive Chair and Ehssan Veiszadeh will remain as Interim CEO.
Image courtesy of the Australian Investment Council.
Downer has announced the appointment of Peter Tompkins Executive Director. This follows Downer’s previous announcement in December 2022 which appointed Tompkins the role of CEO and Managing Director of the Downer Group, following the retirement of Grant Fenn, which occurred on February 27. Fenn served as the CEO for 12 and a half years and said it was an honour to contribute to the company’s success. Peter Tompkins joined Downer in 2008 and was appointed Group General Counsel in 2011. After the acquisition of Spotless in 2017, he was appointed Project Director for the Royal Adelaide Hospital PPP and in 2018 was appointed CEO and Managing Director of Spotless Group Holdings Ltd (listed on the ASX) leading the integration of Spotless into Downer. In 2021, Peter was appointed Chief Operating Officer for the Group.
Image courtesy of the Downer Group.
The Traffic Management Association of Australia (TMAA) has appointed Matthew Bereni as its new Chief Executive Officer, effective immediately. Bereni has extensive industry and leadership experience in the public and private sectors in civil and transport engineering. Prior to joining TMAA, he held the role of National Director of Strategy and Innovation with the Australian Road Research Board (ARRB). His previous roles included Manager of National Harmonisation at the National Heavy Vehicle Regulator (NHVR), and Manager of Pricing and Economics at the National Transport Commission (NTC). The appointment – finalised by TMAA’s Board of Directors in December 2022 – sees Bereni take on the role from outgoing CEO Louise Van Ristell, who stepped down in November 2022. TMAA is the national peak body for Traffic Management. It represents the Traffic Management and Traffic Control industry throughout Australia.
Image courtesy of TMAA.
PREMIER CRANES & RIGGING IS DOING THE HEAVY LIFTING FOR ONE OF AUSTRALIA’S LARGEST INFRASTRUCTURE PROJECTS, THE WEST GATE TUNNEL.
Since its construction in April 1968, the West Gate Freeway has served as one of Melbourne’s busiest connections across the Yarra River.
With its innovative design, the freeway catered for Melbourne’s growing population for decades.
Moving more than 200,000 vehicles daily, the West Gate Freeway’s ability to provide an efficient traffic network into the heart of the city has declined. When at full capacity, incidents on the connection can at times bring the West Gate Freeway and Bridge to a standstill.
In order to ease congestion and increase the efficiency of Melbourne’s road network, the Victorian Government introduced plans to provide an alternative road connection, the beginning of what would become the West Gate Tunnel.
Local contractors, such as Melbourne’s Premier Cranes & Rigging, are assisting with the delivery
of crane lifts for sections of the project, such as the elevated connection above Footscray Road.
The elevated road will add an extra connection for motorists between the tunnels and CityLink, Dynon Road, Footscray Road and Wurundjeri Way.
This will also connect new bridges, which will be constructed over the Maribyrnong River, therefore granting motorists access to a second river crossing.
Premier Cranes & Rigging Director, Steve Warton, says Premier is well equipped to provide services for the delivery of infrastructure projects, due in part to the organisation’s systematic development and growth.
“We’ve not only grown our fleet, but we’ve grown our people, systems and our office base,” Warton says. “We’ve really structured our whole business to align ourselves with major projects like this.
“Our business culture is centred around the ethos that ‘our cranes complement our people’, not the other way around. This basically means
that our difference point is our people, the people who are on the ground getting the job done.”
This focus on delivering a result, which is “above and beyond” for the client, was one of the major factors for Premier Cranes & Rigging’s selection to support works on the project, across the West, East and Tunnel zones.
The ‘West, East and Tunnel’ project areas refer to works that form part of specific sections of the project.
As part of its works on the ‘Tunnel’ zone, Premier Cranes & Rigging provided both cranes and crews to complete the major lifts in both the North and South portals. This is also on top of significant general lifting, and barrier relocation works which Premier has completed previously on the project.
Now the company has shifted its focus to the ‘East’ zone, an exciting and new challenge for the crane hire provider.
These ‘East’ works, which include the steel rigging work of the elevated road at Footscray are a top priority, and now represent a major slice of Premier Cranes and Rigging’s contributions to the project.
The difficulty of the works on the elevated road should not be understated, as Warton explains.
“It’s really all systems go on the East portion of the works (which includes the elevated road) in 2023. For these works, they have brought in massive cranes from overseas companies to assist with the big lifts,” he says.
“While using our cranes, the project is also using our people to crew and rig these larger machines. It’s a partnered result, as opposed to just labour hire. Our leaders such as Brad Briggs, Cam Wakefield, Wayne Robinson, Chris Reid and Jay Thompson (along with the rest of the crew) have been integral to this.”
Included in this scope of works is the lifting of all major steel and required rigging, and temporary steel installations.
Warton says the majority of these lifts are 150+ tonne, rare for consistent lifts over a large section of works.
“It really is a once in a lifetime project,” Warton says. “These sections are filled with very unique builds which present a range of challenges. But our people and our cranes are up to the challenge.”
Before becoming Premier Cranes & Rigging’s Heavy Lift Superintendent, Travis Smith began as a Steel Rigger, before working his way through the ranks.
Smith’s knowledge of the crane industry,
as well as what’s required to support major infrastructure works, has boosted Premier’s stride towards increasing its participation in projects such as the West Gate Tunnel Project.
As he explains, filling the project authority and staff on site with confidence of performance and reliability is one of the first crucial steps to achieving a desirable outcome, no matter the size of the project.
“We want to give the best result all the time. Sometimes the best doesn’t just mean using the biggest crane, but the best solution for the job at hand,” he says.
Smith is one of many key contributors from the company who have supported the elevated section above Footscray Road, arguably the most technically demanding works within the ‘East’ section of the West Gate Tunnel.
The elevated section above Footscray Road has seen the use of the 400-, 250- and
200-tonne Liebherr cranes, with previous auxiliary works featuring the 250-, 220- and 200-tonne models also.
This site presented a variety of challenges, some of which Premier Cranes & Rigging are still persisting through today.
“Access around the portals, traffic and lifting the columns around all of work areas on the ground were just some of the problems we had to deal with initially,” Smith says. “Once we started with the launching gantry, our priority then shifted to getting around all of the concrete segments.”
The elevated road section is being constructed using a ‘span-by-span’ method, which sees the continuous construction of the road deck from the end to the beginning. Each concrete segment is then placed one after the other.
Supporting this construction requires precise lifts over sustained working hours, while also
incorporating limitations such as a restricted head height.
Smith says overcoming these challenges and more reflected Premier Cranes & Rigging’s strength in establishing and maintain meaningful relationships while going “above and beyond” for a construction partner.
“We were coming into a well-established system for completing these works and our goal was to provide excellent cranes and people, not to re-invent the wheel. Some of the site team have worked on this project for years, so we just assisted in delivering their system and plans,” he says.
“We like to be as transparent as we possibly can be, with everything that we do. That counts for our clients and our partners. We have an open book policy and that starts at the very top.”
As of early February, Premier Cranes & Rigging has spent more than 25,000 hours on site and has lifted more than 5,000 tonnes of steel. This includes lifts for 32 girders and in excess of 460,000 bolts in total.
And this only represents a fraction of the total works to be completed, with more works slated for the remainder of 2023 and beyond.
As part of its works on the West Gate Tunnel Project, Warton and the rest of the Premier Cranes & Rigging team knew they had to align its brand with a reliable crane manufacturer.
As Warton explains, Premier Cranes & Rigging decided to go with what he considers to be the “Rolls Royce” of the craning world. “We hold ourselves to a very high standard,” Warton says. “If we were going to hold ourselves to this standard, it was important that we had the cranes to back that up. And Liebherr cranes were the right choice.”
Having previously used the Liebherr
is aligned with Liebherr’s commitment to quality.
Andrew Esquilant, General Manager Mobile Crane and Crawler Cranes – Liebherr Australia, echoes Warton’s sentiment, saying both companies see eye-to-eye on a number of aspects.
“We’re very blessed to have relationships like this with Premier Cranes because we’ve got two things in common right from day one. One of those is that Premier Cranes is a family-orientated business,” he says.
Designed to satisfy heavy lift requirements, the LR1350/1 utilises a derrick boom and suspended ballast to perform lifts of up to 350 tonnes. The crane is also manoeuvrable and can be set-up with logistical ease, making it ideal for works on major infrastructure projects.
Esquilant says Liebherr cranes are well suited for works on the West Gate Tunnel Project, in part due to their robustness, as well as the support services offered to customers.
“Big infrastructure jobs mean there’s big money on the line, and the project needs to get delivered in a timely matter. It comes back to reliability and downtime,” he says.
Premier Cranes & Rigging’s ambition to work on larger projects has led to the much-anticipated purchase of not one but two of Liebherr’s largest all terrain mobile cranes.
Their first Liebherr LTM 1450-8.1 is a 450-tonne mobile crane, is now available for hire from Premier Cranes & Rigging’s site in Melbourne. This LTM 1450-8.1 features an 85-metre telescopic boom and despite its size, can travel on public roads to and from the job site.
Esquilant says the 450-tonne crane houses a manoeuvrable and compact design while offering a considerable lifting capability.
“It’s a very adaptable machine and it’s got great rideability. When you look at the boom, the length, strength and radius really stand out,” he says.
“For a company like Premier Cranes & Rigging, and where they are in terms of their development, I truly believe this machine will play a great next step for their business in taking on a greater volume of work and having more exposure to other industries as well.”
Premier Cranes & Rigging has also taken out an order for a second 450T which is due mid 2023, adding further depth to the company’s extensive crane range.
Warton says Liebherr cranes, as well as Premier Cranes & Rigging’s wider crane range, will back the company’s future ambitions, which includes increasing its participation in major infrastructure projects across the state.
“When you look ahead to the next 10 years, Victoria is a great place to be when you talk about major projects and large-scale construction,” Warton says.
“These larger cranes give us a ‘fuller capacity’. During procurement and planning, project delivery authorities can look at us and on paper we can now serve projects holistically. We’ve gotten a larger workforce and we now have the cranes to fully complement our crews.”
Puma binders with Cargill Anova™ Warm Mix Additive allows production of asphalt at temperatures up to 50 degree celcius lower than conventional hot mixed asphalt. It also minimises fume and odour emissions and improves working conditions for asphalt crews.
Mixing asphalt at a lower temperature results in the following approximated savings in cost and CO2 emissions per tonne of asphalt.
Assumptions: Diesel price $1.5 per litre / Natural gas price $20 per GJ / Diesel emission factor 70 kg CO2-eq/GJ
(Australian National Greenhouse Accounts Factors) / Natural gas emission factor 52 kg CO2-eq/GJ
(Australian National Greenhouse Accounts Factors)
Things are certainly changing and there seems to be a real desire to do better. At Fulton Hogan we’re doing a number of things to drive greater diversity, one of which is our partnership with Construction Industry Culture Taskforce for the five day working week trial at our Brunt Road Project. The initiative aims to provide more time for life, better wellbeing and greater diversity from reduced flexible working hours for individuals working on our project sites. We are also excited to be entering our fourth consecutive year of our partnership with the Richmond AFLW program as we continue to provide alternative career pathways for women into our industry.
The Australian Flexible Pavement Association (AfPA) firmly embraces and encourages diversity and inclusion – committed to inspire, support and engage our current and future workforce about our industry and associated opportunities for all people. It is from an extensive range of skills, expertise and experience that we will enrich the ideas and approaches to the delivery and maintenance our most valuable essential asset, our roads. AfPA is proactively creating the opportunities for conversations to understand the issues and barriers in our workforce to encourage greater diversity and inclusion. Hearing directly from stakeholders is informing a range of industry-specific initiatives and strategies both underway and planned – from targeted sessions and training, through to broader industry-wide events. The AfPA Industry D&I Roadmap is currently being finalised, as developed by and for our industry to encourage diversity and inclusion. We acknowledge that change of this scale takes time, and we are proud that our industry is openly sharing learnings and are a leading employment industry of choice that embraces all.
This is only my second year in the industry but in that time, I’ve noticed more and more women in operational roles. While there’s still a long way to go, I’m a good example of the kinds of opportunities that are opening up for women in the construction industry. I joined Alex Fraser in early 2022 as Workshop Administrator. At the start of 2023 I was supported to take on an apprenticeship in Metal Fabrication (Boilermaker). I’m really enjoying the challenge and feel very well supported by my male and
We’re seeing more meaningful employment opportunities opening up for people living with disability across the roads and infrastructure sector. These include direct employment through either contract labour assignments or ongoing assisted employment where work can be co-designed through a strengths-based approach to tailor roles to people’s abilities, with supports provided to the employee by organisations such as ours at no cost to the employer. We’re also seeing increased diversity in supply chains where social enterprises have the opportunity to compete and provide goods and services, such as our OC Eco T-Top Bollards, which creates further indirect employment for a greater diversity of people who may also be experiencing barriers to mainstream employment.
Addressing the historical lack of diversity across Victoria’s civil construction industry is a key business priority for Major Road Projects Victoria (MRPV). Through our innovative Program Delivery Approach (PDA), MRPV works closely with our construction partners to ensure public infrastructure expenditure is leveraged for greater social value and inclusion outcomes. Introduced in 2019, the PDA approach is a collaborative procurement model that aims to get the best value for money outcomes for our projects, including through facilitating increased employment opportunities for traditionally marginalised groups as well as sustainable business opportunities for social benefit suppliers across MRPV’s supply chain. Driven by state government policies, such as Victoria’s Social Procurement Framework, the PDA model has allowed MRPV to increase spend with social enterprises and Aboriginal businesses by over 600 per cent since 2019. These organisations are known to hire more diverse teams and to reinvest profits back into their local communities. MRPV is proud to play our part in creating a more sustainable and diverse civil construction industry and is committed to continuing that work with our PDA construction partners.
If you or someone at your organisation is an industry leader and would like to be a part of this monthly column in 2023, please get in touch with Editor, Tom O’Keane: tom.okeane@primecreative.com.au
Understanding the term sustainability and safety is the first step toward having a measurable impact. Where artificial intelligence turns data into insight, it empowers meaningful insights into sustainable practices.
Health & Safety
Analtyics to curb poor behaviour and improve on safety through coaching.
Sites of cultural significance
Tech to protect & promote sustainabile innovative projects.
Preserve natural ecosystems
Ensure the protection of the environment for the future generations.
Data to reduce carbon emissions to contribute toward Net Zero.
KATE LYNCH IS A SHINING EXAMPLE OF THE VALUE WOMEN BRING TO THE CONSTRUCTION INDUSTRY; AND REPRESENTS A NEW GENERATION OF LEADERS IN SUSTAINABLE PROJECT DELIVERY. ROADS & INFRASTRUCTURE SITS DOWN WITH THE ALEX FRASER PROJECT MANAGER TO LEARN MORE.
According to the Australian Constructors Association, only 12 per cent of Australia’s construction workforce is female.
Important initiatives, such as the Victorian Government’s ‘Women in Construction Strategy’, as well as the National Association of Women in Construction, are helping to provide platforms for female workers to excel throughout the construction sector.
While there’s much more work to do, organisations within the industry are
making progress in attracting more women into the industry and supporting them to maximise their professional growth and career potential.
One such organisation is sustainable construction material provider Alex Fraser.
Along with Hanson Australia, Alex Fraser made a commitment to increase female participation and to develop rewarding career pathways for all employees.
The companies’ Trainee Driver Program for Women is a thriving example of their
collective drive for diversity. Established in 2018, the program aims to increase female representation among truck drivers, enabling women with a standard motor vehicle licence to train and upgrade their license to drive heavy rigid vehicles, like concrete trucks and tippers.
It is programs like this along with Hanson’s Graduate Management Development Program, that are helping Alex Fraser to ‘kickstart’ careers for people of all backgrounds, cultures and genders.
Project Manager Kate Lynch, began her career as a graduate, setting her on course to become one of Alex Fraser’s rising stars. Lynch started with Alex Fraser in 2017, as a Management Trainee, and played a key role in the build of Alex Fraser’s state-of-the-art glass recycling plant in Laverton. She went on to complete her graduate program, taking on a range of challenging
roles in affiliated businesses along the east coast, before returning to Alex Fraser as a Project Manager in 2020.
Ready to take on her next big challenge, the timing could not have been better. Alex Fraser was in the planning stage for its next Green Roads Asphalt Plant, to be collocated onsite with its recycling facility in Epping, Victoria.
As Lynch explains, her initial attraction to the role was born out of a desire to achieve sustainability on a personal level, while being part of something that could make a positive impact.
“When I used to think about sustainability, I’d think about recycling on a small scale. Like recycling my paper, glass, and plastic waste at home, using public transport, and carrying a keep-cup for my coffee,” Lynch says.
“At Alex Fraser, sustainability is demonstrated in the huge number of tonnes it recycles and its commitment to reducing carbon emissions – that delivers big environmental returns. That’s what really drew me in; an opportunity to continue my sustainability focus and maximise outcomes, at home and at work.”
Based in Victoria and Queensland, Alex Fraser is one of Australia’s largest producers of recycled construction materials, having recovered and recycled more than 50
million tonnes of refuse concrete, brick and asphalt, and 5.4 billion bottles worth of kerbside glass waste.
Lynch quickly established herself as a key cog in the company’s project delivery machine. She says that Alex Fraser’s supportive work culture helped nurture a creative and productive environment, contributing to her growing success.
“When I look back at tangible examples of this support, there was all of the practical training, which prepared me to manage every element of my projects from workplace health and safety to the procurement process; from contract management to overseeing dozens of trades and contractors working on site,” she says.
Despite her short time in the industry, Lynch says she has seen positive progress made on diversity throughout the construction industry; which she hopes will only build much needed momentum.
“There are definitely more women around our sites. I’m based out at Epping, so I’ll often see some of the female truck drivers on site,” she says. “There’s far greater diversity in the industry now than even two years ago.”
“I think it’s important to look into how we can create pathways and how we can retain workers from diverse backgrounds. “How do we make the workplace more inclusive?
“It’s important to provide people with a clear vision of the career pathways and progression in place. You’ll see the flow on effect, which will hopefully lead to more women in leadership positions.”
Lynch says she’s also seen improvements in sustainable project procurement and delivery.
“The appetite for sustainable products has certainly grown. We can see it in the changes to policy around sustainable infrastructure at a government level; in the increasing demand from customers for greener products; and in the actions of industry leaders like Hanson who are increasing their focus on sustainable product development and supply,” she says.
“Many of the contractors who come and do work for us on our sites actually use our products, so, there’s a growing interest there too.”
Lynch credits Alex Fraser’s senior leaders like Brendan Camilleri, Albert Yung, and Peter Murphy for their support of her professional growth, and for encouraging her to take on
“AT ALEX FRASER, SUSTAINABILITY IS DEMONSTRATED IN THE HUGE NUMBER OF TONNES IT RECYCLES AND ITS COMMITMENT TO REDUCING CARBON EMISSIONS – THAT DELIVERS BIG ENVIRONMENTAL RETURNS.”Alex Fraser Project Manager Kate Lynch, pictured in front of the company’s new Epping Asphalt Plant. Kate Lynch completed her first major project as a graduate in 2018, which was Alex Fraser’s ‘Billion-Bottle’ glass recycling plant.
new challenges that became key steps along her career path.
Lynch says one of her biggest joys in her current role is having the opportunity to apply herself to challenging projects, as part of a multi-skilled and highly experienced team. She says the varied experience and backgrounds of the project management team ensures they bring a range of skills and perspectives to any new project.
“In terms of day-to-day work, it’s great to be able to bounce off ideas off with my team. We’re always looking at how things can be done differently, and we’re open to finding new ways to get things done, to improve efficiencies, reduce costs and increase sustainability,” she says.
Lynch is part of an accomplished projects team led by Senior Project Manager Akshay Kumar, and supported by Project Support Lead Eddie Rincon-Marquez, and Project Manager Jenny Dinh.
They are just some of key people behind the to the successful build of Alex Fraser’s newest world class asphalt plant in Melbourne’s north.
The new plant consists of a Benninghoven ECO 3000 240tph batch plant and has the capacity to produce more than 100,000 tonnes of Green Roads asphalt every year.
Lynch’s team was responsible for coordinating the year-long build from the ground up.
To provide a safe working environment for everyone on site, Lynch and her team conducted a daily work group meeting, or ‘toolbox’. This meeting informed up to 40 contractors every day, each working to their own deadlines in their designated work areas.
“We actively managed the traffic flow on the project, ensuring the many trucks delivering to the project could make it in and out of the site safely and efficiently.”
“One of the biggest challenges was coordinating the works across separate groups in what was quite a tight working area.”
“The plant components were shipped in from Germany, in 40-foot shipping containers. It took months for all parts to be delivered, and deliveries were sometimes unpredictable,” she says.
Melbourne’s weather was another impacting factor, with ongoing rain impacting deliverables towards the end of the project.
Lynch says having a clear project plan in place was absolutely essential.
“It was good to have a plan and timeline to work towards. It’s a good way to break down a huge project into manageable tasks, and keep everything and everyone on track,” she says.
“It was helpful asking myself “what do we need to prioritise?” and “how can we plan for next week?” I felt that the project was more manageable when I was on site talking to contractors and my colleagues.”
Alex Fraser’s latest Asphalt Plant is collocated with its northern recycling facility, creating the company’s second Sustainable Supply Hub. Only minutes for the Hume Highway, the hub is ideally placed to recover demolition materials from the inner city for recycling and to supply recycled products to major projects and new developments in the northern growth corridor.
Lynch says Alex Fraser’s investment into new sustainable production facilities at Epping complements the company’s established network of facilities surrounding metro Melbourne, which are supplying the construction industry with great volumes of recycled construction material needed to build greener roads and infrastructure.
“My next project is about to take off just a few hundred metres away from the new asphalt plant on the same site. I’ll be leading the build of a rock crushing plant which will play a critical role in supplying the asphalt plant with the raw, recycled materials needed to produce Green Roads asphalt,” she says.
“It’s exciting to play a little part in bringing the circular economy to life.”
Alex Fraser’s Epping Asphalt Plant is in the final stages of commissioning and is already supplying sustainable materials for the Sunbury Road Upgrade for Major Road Projects Victorian and Winslow Infrastructure.
Lynch says the completion of the Epping Asphalt Plant has been her greatest accomplishment during her time at Alex Fraser. While she is humble in sharing her achievements, her ambition is palpable. It’s clear that this young professional has her sights set on completing her next challenge and expanding her reach into strategic planning for project development.
“I’m excited about jumping into the next project on the recycling side of the business,” Lynch says.
“In the long term I think I’d like to be more involved in the strategic side, supporting the business to look into further opportunities for growth and diversification, and being part of the earlier planning process behind these types of projects.”
We want to help shape the future of Victoria’s infrastructure one lift at a time. Because you and your team deserve lifting solutions you can trust, not problems!
Our cranes compliment our people, not the other way around. Our people are guided by Premier’s #TeamLifting culture where we collaborate and empower each other to reach new heights of success. Premier invests heavily in the teams professional development which translates to a stronger level of commitment and engagement towards our clients projects.
With a diverse fleet of compatible cranes and transport vehicles, strategically acquired to set up Premier Cranes to scale, combined with our elaborate operational structure we have consistently demonstrated excellence in major projects.
Premier offers start-to-finish lifting solutions from project initiation to safe & efficient execution that protects your reputation. Our services include crane & labour hire as well as specialist rigging for structural installations, occupation works, project-logistics, night works, traffic control & more!
Meanwhile, we use clever engineering to develop practical lift plans, site surveys & lift studies. Backed by 13 years of industry expertise, we have undertaken a range of bridge / road / rail infrastructure projects, as well as civil and industrial works.
Our promise? To deliver transparently assured results on each job!
Ready to get started on your next project? Call (03) 9311 1499 today
Or scan the QR code to use our industry-first crane calculator to find out the right crane size for your next lift.
PLUS - Bonus instant price estimate form feature.
*Calculated on a minimum requirement basis
Rokon is one of Victoria’s largest civil contractors, but its growth has never come at the expense of family values.
It’s an approach that Managing Director Jim Thomas says has been key to the company’s success over the past 24 years – one strengthened by a diverse team and the breadth of life experience and expertise that brings.
“Our core values guide us in creating a workplace environment that values and respects all employees and supports their growth and development,” Thomas says.
“These values drive our commitment to foster a diverse and inclusive workplace where all employees’ unique perspectives and experiences are valued, which is to the benefit of both the company and the industry.”
“We believe in continuously striving towards a brighter future for all, where everyone feels valued and respected.”
Executive Director Steve Traicevski says a diverse workforce is crucial to the ongoing growth and strength of the infrastructure and construction sector.
“Diversity of experiences and ideas leads to better decision-making, increased innovation, and a more engaged and satisfied workforce,” he says.
“The industry has made some progress in increasing diversity, particularly in terms of increasing women’s representation –however, there’s still work to be done. Rokon is committed to promoting diversity and inclusion throughout our business, including in recruitment, training, professional development, and leadership opportunities.
Thomas says Rokon’s message to women considering a career in construction is simply to seize the opportunities that exist.
“This field is changing and offering increasing opportunities for women,” he says. “And at Rokon, we are dedicated to fostering a supportive and inclusive workplace where everyone can reach their full potential.”
While for some it may still evoke images of steel-cap boots, high-vis gear, and yellow machinery, the modern civil construction sector presents opportunities for a wide range of people from all walks of life.
In search of change, Elizabeth Prestipino pivoted from a 20-year career in retail management to a Plant Operator role at Rokon.
“I was drawn to the civil construction industry because of my love for the outdoors and a willingness to try something new,” she says. “Additionally, I have always been told that I have strong driving skills, so I decided to give civil construction a go – and I love it.”
Site Safety Coordinator Claire Bourdon had always had an interest in construction, but had originally not considered it as a potential career path.
“My journey began through a friend, who introduced me to the industry, and I fell in love with it,” she says. “From then on, I continued
to build my skills and knowledge, eventually making it my full-time profession.”
Others, such as Graduate Engineer Maryam Khan and Project Manager Eva Nardo, came to the sector from the engineering side.
“My career in the civil construction industry was driven by my desire to make a positive impact on society,” Khan says. “As well as to experience a sense of accomplishment from working on projects that require hard work and dedication.”
Nardo’s career was a natural progression of her interests and studies.
“I was always fascinated by the process of designing, building, and maintaining infrastructure that are essential for the functioning of society,” she says. “I wanted to be a part of the team that brings projects to life and makes a positive impact on the community.
“After completing my university education in civil engineering, I was eager to apply
my knowledge and skills in the field. I was particularly interested in working on the contractor side, where I could be involved in the practical aspects of construction and make a hands-on contribution.”
All four women agree that Rokon’s strong foundation of values has been central to their experience.
“Rokon has been incredibly supportive, fostering a family-oriented and supportive work environment with opportunities for training and career growth,” Khan says. “The company values diversity and equality, treating everyone with respect and valuing their ideas.”
Prestipino adds that positive values and culture have been a great support, particularly early on in her career.
“Rokon is committed to the well-being and safety of its employees, which was especially important for me as a new member of the industry,” she says. “Everyone is supportive, encouraging, and helpful, which makes it a fantastic place to work.”
Nardo, in her three years with the company, has also made the most of Rokon’s focus on professional development.
“This supportive culture has been a great source of motivation for me in my role as Project Engineer,” she says. “I was able to work with a team of talented and supportive individuals who encouraged me to continuously develop my skills and grow in my role.
“Over time, I was able to progress from Project Engineer to Project Manager, and I attribute my success to the support I’ve received from my colleagues and the company’s management team.”
Nardo says there’s been a noticeable change in the industry’s attitude towards diversity in recent years, and has seen this reflected in an increase in female engineers and other diverse professionals entering the industry.
“It’s a positive step forward in breaking down the stereotypes and biases that have traditionally held women back from pursuing careers in the industry,” she says.
Bourdon says Rokon is proud to be at the forefront of this change.
“The industry has been making significant progress in its attitude towards diversity, particularly when it comes to women,” she says. “The whole industry is starting to recognise the value that women bring to the workplace, and the importance of promoting a more diverse and inclusive work environment.”
Khan acknowledges that things are trending in the right direction, but there is still a long way to go.
“While the industry’s attitude towards diversity has seen some improvement in recent years, it’s still a male dominated industry,” she says. “Positive changes are being made, but it’s a gradual process.”
Despite this, Nardo says that for women considering a career in construction, there is no reason to be hesitant.
“The industry is actively seeking diversity and is open to new perspectives and ideas,” she says. “Women bring unique skills and perspectives to the table and are an important part of building a more inclusive and balanced workplace.
“With the right education and training, women can make a valuable contribution to the industry and have a successful and rewarding career.”
For Bourdon, Rokon is just the right place for women to both start and progress their careers in civil infrastructure at all levels, from labouring to Senior Management.
“The company has shown its commitment to promoting diversity and inclusion in the workplace – particularly with regard to increasing women’s representation in the industry,” she says. “It’s a very supportive environment where women can thrive and succeed.”
“My advice is to maintain a positive attitude,” adds Prestipino. “Don’t be afraid to try new things and don’t feel inferior to your male colleagues.
“If you have a passion for being outdoors and trying new things, the sky is the limit.”
Thomas says Rokon aims to engage the best talent available for any job in the business, regardless of gender.
“We are proud to have many talented women on our team who excel in various roles in the field and office,” he says. “In addition, our company is always open to expanding our team and welcoming individuals from diverse backgrounds.”
PLAN
It goes without saying that telecommunications have become a central component to modern society. For personal use, business, health and more, telecommunications have transformed access to everyday services.
Telecommunications has also long been an essential component to consider during infrastructure project development and delivery.
This includes considerations such as the location, requirements and installation of suitable telecommunications infrastructure that could be used for generations to come.
These concerns can often be daunting for project managers, whose role necessitates juggling multiple balls to ensure an efficient and timely project delivery.
But there are services and support available to take the guess work out of overhead and underground telecommunication works.
Jim Bozikis is the General Manager of Plan B Comms, a privately owned company whose expertise provides a variety of communication services.
Plan B Comms forms part of the wider Plan B Group, which is made up of two other subsidiaries (Plan B Services and Plan B Auditing). Founded in 2004, Plan B Group is now one of Australia’s largest electrical consultancies in Australia.
He says the introduction of Australia’s National Broadband Network (NBN) in 2012 provided the “perfect opportunity” to introduce a dedicated provider of communication services for residential, commercial and industrial development markets, which had nothing at the time.
“Communication infrastructure is basically installed in the same trench as electrical. We thought ‘this gives us an opportunity
to possibly work with communications’, as we were often designing it as part of our electrical infrastructure,” he says.
“When we were designing electrical infrastructure and we started to also offer communication design. We could coordinate both services from the same office, where an electrical and communications designer could work together, to ensure that both designs worked seamlessly.
“When the NBN came in, we saw it as an opportunity to create a business that was purely suited for tackling communications. So, we created a communication consultancy called Plan B Comms.”
Plan B Comms provides a number of services for the residential, commercial and
industrial developments.
From telecommunication infrastructure relocations, to administration, feasibility modelling and design and construction, Bozikis says his team prides itself on providing a comprehensive service. For multidisciplinary projects, Plan B Comms can work with other Plan B Group subsidiaries to satisfy the needs of clients on almost any project.
For example, Plan B Comms and Plan B Services can deliver the electrical and communication installations required on a project, using effective and efficient coordination.
Plan B Comms and Plan B Services also communicate directly with civil consultants and the relevant authorities
B COMMS HAS GONE FROM WORKING ON MINOR PROJECTS,
SUPPORTING SOME OF VICTORIA’S LARGEST DEVELOPMENTS. GENERAL MANAGER JIM BOZIKIS DISCUSSES THE COMPANY’S ORIGINS AND PROVIDES AN INSIGHT INTO HOW THE COMPANY CONTINUES TO INNOVATE.Plan B Comms is experienced in delivering communication services for major infrastructure and residential developments.
on the developer’s behalf, again boosting coordination and efficiency.
“I think the reason why our clients are the biggest developers in Australia is because we have a sense of ownership with our projects. We give confidence to a client that we understand the timeframes and what’s required,” Bozikis says.
“This has helped us to strengthen our relationships with our clients, some of whom have worked with us for more than 10 years, as well as some of Australia’s largest telecommunication companies.”
Plan B Comms is currently contributing to residential and commercial developments across Victoria, with several projects around Melbourne.
A number of these works also coincide with on-going upgrades to Melbourne’s Road infrastructure.
“Around the site where the roads will be constructed, we’ll often work with multiple carriers at once. Instead of the developer having to contact each carrier individually, they come to us,” Bozikis says.
“We can discuss options, coordinate multiple carriers at once, and then design
their infrastructure and ensure that it’s built simultaneously. We can utilise the existing relationships that we have with these established telecommunication providers.”
Plan B Comms recently contributed to works on a road upgrade in Armstrong Creek. The client was preparing to complete a road upgrade across two separate stages as part of their construction program.
After conducting a feasibility assessment, Plan B Comms suggested that the client complete the works as one large project, to streamline construction.
This ended up saving the client over $500,000, while also reducing construction timeframes significantly.
“What could’ve been a 12-month long project was completed in around six months,” says Harrison Kelly, Business Delivery Manager for Plan B Comms.
“The client was able to continue on with their construction without having a large amount of downtime, which is obviously very valuable.”
Plan B Comms is currently preparing for their next major relocation project, the Gunns Gully Interchange. This will be a $100 million project along the Hume Freeway.
“We will be involved in the early works
stage, relocating a significant amount of NBN and Telstra assets to allow an overpass, entry and exit ramps to be constructed on the Hume Freeway,” Kelly says.
And as it did with the NBN, Plan B Comms is actively looking for new innovations and technology to embrace as part of its communication services.
As Bozikis explains, the company often looks internally and externally for new ways to support its clientele and staff.
“It’s an exciting space to be working in and it’s very dynamic. We’re no longer just working on developments, which has helped us to balance and diversify our portfolio,” he says.
“I THINK THE REASON WHY OUR CLIENTS ARE THE BIGGEST DEVELOPERS IN AUSTRALIA IS BECAUSE WE HAVE A SENSE OF OWNERSHIP WITH OUR PROJECTS. WE GIVE CONFIDENCE TO A CLIENT THAT WE UNDERSTAND THE TIMEFRAMES AND WHAT’S REQUIRED.”Plan B Comms General Manager Jim Bozikis. The Plan B Comms team features individuals with diverse working backgrounds.
FLOCON ENGINEERING HAS A RICH HISTORY IN AUSTRALIA’S ROAD MAINTENANCE SECTOR. DIRECTOR AND THIRD GENERATION EMPLOYEE, RORY KNIGHT, REFLECTS ON THE PAST AND OPENS UP ON THE COMPANY’S FUTURE.
Rory Knight is proud of his family’s heritage. More than 40 years ago, his grandfather, Jim Knight, founded Flocon Engineering in his backyard. It was the beginning of what is now a fourth-generation family owned and operated business.
The first unit manufactured under the Flocon Engineering name was delivered to Moorabbin City Council in 1982. In the years following, the company grew, increasing its portfolio of road maintenance machinery, as well as staff numbers.
Jim Knight’s sons, Peter and Steve (Rory’s father), would eventually succeed him as the leaders of the company, during a period which saw growth for Flocon Engineering both nationally and internationally.
Now the next generation of Knight’s is ready to make its mark.
Director Rory Knight says the company’s past has laid the foundation for the enterprise’s future.
“From my grandparent’s backyard, and since the delivery of the first unit, things have really taken off and boomed,” Knight says.
“We now have multiple representatives
across a number of states nationally. We’ve also serviced the needs of the international market for some years now in New Zealand, Samoa, China, United Kingdom and the Philippines.”
Flocon Engineering manufactures a range of road maintenance equipment out of its headquarters in Melbourne, including aggregate spreaders, road patching and repair units, cement or lime spreading units, bitumen emulsion sealing units, forward moving spreaders and more.
Its road maintenance equipment has been manufactured and developed to handle hot mix, cold mix or premix asphalts, cement lime, aggregates and bitumen emulsions soils.
Each of Flocon Engineering’s products are backed by more than 40 years in research and development, including close consultation with industry stakeholders to improve the performance and safety of each machine.
Flocon Engineering also used a hire fleet for 20 years, providing a platform for research, evolution and improvements to its products.
This includes field testing with Federal, state and local road authorities. Rory Knight says the result is safe, comfortable and easy-to-use equipment.
“One of our biggest strengths is our experience. We’ve learnt a lot from our time in the industry,” he says.
“We also get very positive feedback from our customers on the simplicity and ease-of-use which our units provide for the operator. We also manufacture and develop our equipment in-house, meaning our customers can have a onestop-shop for purchasing, repairs, and general enquiries.”
Flocon Engineering has never been afraid of adapting and embracing new technologies, according to Knight.
The company’s newest innovation reflects its commitment to pushing the boundaries of technology in the road maintenance sector.
As Knight explains, the technology will open new doors for the company and operators alike.
“We started development and planning for a new internal system for our machines in 2019. We worked closely with one of our main suppliers to move away from the old switch system. We wanted to streamline
the controls and make it easier for ourselves and the operator,” he says.
Using a new system from the supplier, Flocon Engineering has implemented its own program to deliver an intuitive operating platform.
Via an LCD touch screen, operators can control all operations of the machine from within the vehicle cabin. The rear button control pads are remote controlled.
Knight says the system provides the full picture for operators on the performance and operational status of their equipment.
“The system can give you information on hydraulic pressures, mechanical faults, operational hours, temperatures, oils and more,” he says. “If an operator was using an attachment or was spraying on our old system, they’d have to manually select which options they wanted to use. Now, with this system, our customers can select these options just by swiping their finger.”
“It simplifies everyday operations and fault detection for the user.”
Knight acknowledges that the introduction of new technology can cause hesitance among customers. But he says the biggest priority during development
was to deliver a simple and easy to understand system, which could be used by operators of all ages.
“It’s as simple as selecting the options that you need. It’s not daunting to look at, with screens and buttons staring back at you,” he says. “We can also spend some time with the operator to familiarise them with the system, to make sure that they can make the most of it.”
The product also underwent testing in the field. Knight says the findings from these trials were “really pleasing”.
“Our first unit was trialled in 2020 by a local operator in their spray sealer. We received fantastic feedback; those guys absolutely loved it,” he says. “Some of our larger clients are now requesting for the units to be installed into their trucks.”
Knight says the next step for the system will be remote logging, a feature which Flocon Engineering is developing with a technology provider.
“This will allow our maintenance team to rectify machinery issues remotely, making it simple to send across spare parts or whatever the customer requires,” he says.
“THESYSTEM CAN GIVE YOU INFORMATION ON HYDRAULIC PRESSURES, MECHANICAL FAULTS, OPERATIONAL HOURS, TEMPERATURES, OILS AND MORE.” Flocon Director Rory Knight.
In any industry circle, ‘sustainability’ is a familiar term. But it’s one with an extremely broad – and growing – range of interpretations.
James French, Application Specialist at Teletrac Navman, says you’ll get a different answer to ‘what is sustainability?’ depending on who you ask and when.
“Everybody talks about the environmental component, but there’s a lot more to it than that,” he says.
“Sustainability is also about community, education, health and safety, knowledge sharing, and more. And technology fits in with all these components.”
A big part of French’s job is helping customers in the construction, infrastructure, and transport sectors harness data to optimise the operation of their businesses – both for today, and the future.
In this industry context, French says it helps to interpret and address sustainability more holistically – incorporating smart, environmentally, economically, and socially conscious practices.
“This helps businesses grow sustainably, foster a fulfilling work environment to maximise employee retention, and ultimately deliver projects that will support future generations,” he says.
This also means digging deeper – going beyond investment in zero-emissions vehicles and equipment, planting trees, and building with recycled materials.
As valuable as these elements are, French says, they are pieces of a broader sustainability puzzle.
In Australia and New Zealand, the Infrastructure Sustainability Council’s IS Rating Scheme for infrastructure projects
considers a broad range of economic and social factors – not just environmental ones.
“Knowledge sharing and education on construction methods and technology is also an important part of sustainability,” French says. “Sharing information with another company for the purposes of education and the betterment of the industry can be factored into sustainability ratings.”
Sustainability also extends to the makeup of the workforce, particularly in an industry that has traditionally been considered male-dominated, and intertwined with certain stereotypes.
French says investing in and prioritising the culture of a business, as well as thinking laterally about how it’s put together, can pay dividends.
“If you’re trying to run a business where
everybody agrees with everybody, it just becomes an echo chamber,” he says.
French says bringing together a team with a diversity of experiences, with different ideas, and who are comfortable voicing them, can only help set up a business for sustained success.
“You don’t want 11 football managers running your football team – they’ll all have the same kinds of answers to any problem,” he says.
“But if you bring in the perspective of psychologists and fitness trainers for example – people who will question things that don’t make sense – then that’s building something more sustainable.”
With the skilled labour shortage facing Australia, retaining staff has never been more critical.
In the transport industry, technology also has a big role to play in both supporting and empowering employees to do their best work – while also prioritising safety and wellbeing.
French says the use of telematics platforms such as Teletrac Navman’s TN360 can provide a range of benefits to drivers, including fatigue management, data-driven coaching, and simplified reports.
The same data is also valuable for fleet managers trying to optimise fuel burn, and even manage the impact of a project on the community.
“TN360 can bring that data in from multiple subcontractors on a single job – which makes it easy to see where everything’s coming and going,” French says.
“As well as giving you the confidence that subcontractors are managing fatigue and maintenance properly, there’s also an audit trail that can be followed when it comes to chain of responsibility.”
GPS data and geofences can also be leveraged to track wear and tear on roads,
as well as to avoid areas of environmental or cultural significance.
“This can help if you’re dealing with community objections, for example,” French says. “You’re able to demonstrate that all your trucks are tracked, and you can quickly and easily retrieve that data.
“If you take an infrastructure project in the middle of the city, it’s going to have a range of impacts – from the people who live in the area, the traffic, and the local businesses. The addition of technology such as TN360 can help mitigate risk across the spectrum.”
While capturing large volumes of data is a relatively simple matter, it is only made valuable with the ability to interpret it effectively.
“The data itself is of no great interest to us a company,” French says. “But the integrity of the data, and the ability to present it in a usable format is what’s important.”
French says it helps that the Teletrac
Navman team pools expertise from across industries, including construction, transport, and heavy machinery – it’s not all software engineers. This industry knowledge helps the team make real-world sense of large banks of collected data – and make it easily available to even the most techaverse customer.
“It’s these insights that can have a real impact on the overall sustainability of a business, whether it’s improving workflows, health and safety, or profitability,” French says.
Data accumulated over periods of months or years can also prove valuable when a contractor is bidding on future projects.
“One of the big benefits of the use of technology is the ability to aggregate both live and historical data to produce a comprehensive history of a project,” French says.
“It’s about painting that bigger picture –not just in economic terms, but the impact a project is having on the environment, the community, and the people driving the trucks.”
“TN360 CAN BRING THAT DATA IN FROM MULTIPLE SUBCONTRACTORS ON A SINGLE JOB – WHICH MAKES IT EASY TO SEE WHERE EVERYTHING’S COMING AND GOING.”TN360 can incorporate data from multiple subcontractors on a single job. Teletrac Navman offers practical insights into collected data.
The Cat® AP400 Asphalt Paver has been designed to fill a hole – not just down the road, but in the Caterpillar® paver line up as well.
According to Chris Harkness of Caterpillar, the upcoming 13.6-tonne paver fits nicely in the Caterpillar Asphalt Paver offering, which previously jumped from the 8-tonne AP300 to the 16-tonne AP500F.
“With the AP400, we think we’ve got something that’s going to round out our product line really nicely,” he says.
Harkness is Industry Territory Manager for paving products for Australia. Prior to joining Caterpillar, he spent 20 years with New South Wales Cat dealership Westrac – so he knows a thing or two about what Australian customers are looking for in an asphalt paver.
“The AP400 covers a lot of bases,”
Harkness says. “It’s identical in width to our larger 500 and 600 range pavers, but it’s a bit lighter and a bit shorter, which makes it easier to move around – great if you’re transporting multiple machines.”
He says the AP400 offers a simplified control system compared to previous models.
“It has a single console rather than a dual console. We also offer two options for grade control – either the full Cat Grade Control system, or the entry-level Basic Grade Control. So, it caters to people looking for value, but if you want to spec it up a little bit more, that can be done as well,” Harkness says.
The AP400 can be tailored to suit a contractor’s needs and budget – and
Harkness expects it will hit the “sweet spot” for a range of customers.
“It’s great for car parks, driveways, and patch work,” he says. “But it’s a very flexible machine. You can also put extensions on it and take it out to six metres for those larger jobs.”
The AP400 will also become the entry-point in the Cat paver range for front-mounted extension screeds, which Harkness says have been increasing in popularity in Australia.
“I’d say 75 per cent of the larger pavers sold here today have front-mounted extension screeds, so I think having that option – the SE47 FM – on this lighter, smaller paver will make it a popular choice,” he says.
“But we’ll also offer the rear-mounted extension SE47 VT Tamper Bar Screed,
which is very popular in Europe and New Zealand, as well as the SE47 V which is a rear-mount extension vibratory only screed, without the tampers.
“The AP400 is all about flexibility. Whatever your paving style we’ve got all those options covered.”
Caterpillar will also offer either a steel or rubber tracked version, the AP455, for customers who prefer tracks to wheels.
Harkness says the AP400 offers a compelling combination of user comfort and safety features to help contractors get the job done safely and efficiently, whatever the conditions.
Depending on the needs of the contractor and their working conditions, the paver can be accessorised with an optional ventilation system, canopy, windshield, and umbrellas on either the tractor or screed.
“Because it’s a lower paver, you’ve got great visibility of the whole job site too,” Harkness says. “You’ve got great capacity for communication, as it’s a relatively quiet machine – so you won’t be losing your voice after a day’s work.”
The AP400 also features easy viewing touchscreen displays with adjustable brightness to suit all lighting conditions –even direct sunlight.
Simplified controls, customisable shortcut keys, as well as the option to automate processes such as the feed system, can all be combined, meaning operators can focus on the task at hand.
“Operating a paver is quite specialised,
compared to an excavator, for example,” Harkness says. “But anybody’s who’s been around asphalt for a while will find the AP400 intuitive to operate.
“If you’re new to paving, there’ll obviously be a learning curve there – but the controls are all positioned in a way that makes sense. It’s not a complicated system.”
For communication beyond the job site, the as-standard Product Link Elite telematics system offers real-time data on fuel burn, idle time, and location to help operators maximise efficiency.
“This also provides remote access to fault codes,” Harkness says. “If a technician is going out to inspect a potential fault, this can help speed up the process by communicating what sort of tools and parts they might need to bring. Which helps get you back to work faster.”
Harkness says the support of the Caterpillar dealer network can offer added peace-of-mind – particularly for smaller businesses without the benefit of their own workshops.
The Cat AP400 is expected to start reaching Australian shores in the second half of 2023.
“IT’S A VERY FLEXIBLE MACHINE. YOU CAN ALSO PUT EXTENSIONS ON IT AND TAKE IT OUT TO SIX METRES FOR THOSE LARGER JOBS.”The AP400 features a simplified, single-console control system. The AP400 fills a gap in the Caterpillar asphalt paver range. A range of options and accessories means the AP400 can be tailored according to needs and budget.
For over 60 years we have only had one thing in mind: making measured values ever more precise. But we also never lost sight of the need for human values, too. By combining these it makes a remarkable radar level sensor possible. The best value there is: VEGAPULS 6X.
FAE has enhanced its construction portfolio with an important new addition. The line of hydraulic driven heads has been expanded with a new category: road planers for skid steer loaders and compact track loaders. The line-up consists in three products: the RPL/SSL, RPM/SSL and RWM/SSL.
The key difference between these products is the rotor, which is available in a traditional cylindrical design for the RPL/ SSL and the RPM/SSL and a disc-shaped design for the RWM/SSL. This small change represents a revolution, offering customers a wide choice of solutions that meet the widest range of needs and applications.
Road planers are machines that can scarify and cut road surfaces, gradually removing the asphalt or concrete layer, partially or fully. This can be done for small or medium jobs on surfaces of various sizes.
The new FAE road planer models scrape and cut pavement using a special round-bit teeth set in a rotor, with a specific layout designed by FAE, to increase performance and reduce vibrations.
The RPL/SSL and RPM/SSL models are used in road surface maintenance work. Other possible uses are preparing an area to restore the road surface, making it possible
to lay a new layer of asphalt or concrete, or preparing an area for excavation work. In this last scenario, the resulting material can be recovered, if necessary, and used to refill the excavated area.
The RWM/SSL model, equipped with disc rotor, is primarily used for excavations with a limited width and for laying conduits for electrical lines, water, gas and fiber optic cables.
The RPL/SSL is available in three working widths, 45, 60, and 75 centimetres (18, 24, 30 inches), while the RPM/SSL comes in a working width of 60 centimetres (24 inches). The working depth of these models can
EVOLUTION AND INNOVATION ARE THE VALUES GUIDING FAE TO INVEST IN CONTINUOUS RESEARCH AND DEVELOPMENT, WHILE EMBRACING NEW TECHNOLOGIES.FAE has developed a new range of road planers designed for skid steer applications.
be adjusted independently for the right skid and left skid through two hydraulic cylinders. Two depth indicators, clearly visible from the skid steers’ cab let the operator monitor this parameter. Being able to independently adjust the skids makes it possible to achieve a perfectly flat surface or a sloping surface, useful for promoting rainwater drainage, and therefore reducing road surface erosion and deterioration. Depending on the requirements and use, it’s possible to work down to 170 millimetres (seven inches) deep for the RPL/SSL and down to 250 millimetres (10 inches) deep for the RPM/SSL.
With the RWM/SSL, it’s possible to work with the disc rotor down to 500 millimetres (20 inches) deep. The working depth is adjusted hydraulically. During excavation, the worked surface is eroded and the material is brought to the surface. The debris, appropriately redirected, mainly comes out from the sides of the RWM/SSL and, when necessary, from a third discharge hole near the attachment frame which, using an appropriate redirection plate, makes it possible to intercept and redirect any material that enters in the internal chamber.
The rotor has a disc with excavation segments screwed on. According to the thickness of the mounted segments, it’s possible to execute excavations with different widths: 80 millimetres/three inches (standard), 100 millimetres/four inches and 120 millimetres/five inches (options). Removable segments on the cutting disc grants the operator access to variation in the excavation width, applying
the appropriate segments without having to replace the entire disc.
It is important to note that, for all of these new models, the working depth is kept constant regardless of the milling plan: the right skid and left skid automatically align to the road surface, making it extremely simple for the operator to use these machines. The skids are also equipped with interchangeable Hardox anti-wear plates for outstanding strength and durability.
The hydraulic side shift functionality is standard, enabling FAE road planers to shift a total 560 millimetres (22 inches) to the right. This function has been specially developed
and designed for pavement milling or excavation almost right up against a wall (on the right side).
The models RPL/SSL and RPM/SSL feature a mechanical floating tilt system with shockabsorber. The maximum angle of lateral tilt is ±8°, which can be controlled with a special indicator positioned centrally in the upper part of the machine, making it easy for the operator to see from the cab.
Other key features and functions of the new FAE road planers include electrical and hydraulic connections for the leading skid steer loaders and compact track loaders available on the market, as well as a pressure gauge to control the working pressure.
The hydraulic valves, hoses and system components are also fully integrated, protected, and easy to access for maintenance
When it comes to working, a cutting indicator placed on the side of both skids shows the teeth’s point of contact with the road surface, based on the working depth (for RPL and RPM). Each machine can also be equipped with a WSS Basic Water Spray System.
WHAT DOES THE FUTURE HOLD?
FAE’s will expand this new line of road planers with other models distinguished by skid steer power, and working width and depth, according to market demand.
“BEING ABLE TO INDEPENDENTLY ADJUST THE SKIDS MAKES IT POSSIBLE TO ACHIEVE A PERFECTLY FLAT SURFACE OR A SLOPING SURFACE, USEFUL FOR PROMOTING RAINWATER DRAINAGE, AND THEREFORE REDUCING ROAD SURFACE EROSION AND DETERIORATION.”
LEADING FROM THE FRONT, TRT CONTINUES TO ENHANCE THE OVERALL OPERATOR EXPERIENCE AND PERFORMANCE WITH THE NEW TIDD PC28-2.
A more powerful front suspension improves lift capacity by up to 17%. New steps in the load chart improve lift control. Faster software processing gives even greater control response and the re-engineered ROPs cab has lower ambient road noise.* Designed and manufactured by TRT, TIDD Crane offers a better experience and investment for the life of your crane.
SANY IS SEEING SUBSTANTIAL GROWTH ACROSS ITS DEALER NETWORK. ROADS & INFRASTRUCTURE HEARS FROM SANY AUSTRALIA’S DIRECTOR AND GENERAL MANAGER, NITIN KHANNA, TO LEARN WHAT HAS CONTRIBUTED TO THE COMPANY’S SUCCESS DOMESTICALLY.
The SANY brand continues to build momentum globally, as the quality and reliability of its machinery is recognised and sought after.
The Annual Forbes 2000 List recently ranked SANY as the second largest heavy equipment manufacturer in the world. Additionally, sales of more than 98,000 excavators globally helped SANY to become the global leader for excavator sales in 2020.
In Australia, SANY has created a strong dealer network through partnerships with reputable and experienced businesses, whose core purpose is to understand their customers’ needs.
Nitin Khanna, Director and General Manager for SANY Australia Oceania, says this network continues to be the prime driver for business across Australasia.
“Dealerships are the backbone of our business model in Australia. With our strong dealer network and their deeprooted market and customer knowledge base, we aim to be the market leaders in
excavator sales within the next five years,” Khanna says.
Growth is a common theme across the dealer network for sales, fleet range and dealership locations.
According to Khanna, the New South Wales and Queensland markets are witnessing strong activity in the infrastructure works sector combined with Australia’s housing boom.
The demand for excavators across the range has kept the team at YELLO Equipment – an authorised dealer of SANY Australia – busy with requests for mini and small excavators for small commercial and farming applications through to larger machines for civil projects, quarrying and waste.
As the authorised SANY dealer in NSW and QLD, YELLO Equipment is also looking at expanding with sub-dealer locations across both states to meet demand and provide localised service.
Khanna says the Western Australian market is also seeing growth in local construction and equipment needs. New dealerships have also opened in Western Australia with the appointment of Brooks Equipment as an authorised SANY dealer to expand the coverage in the state.
With more than 40 years’ experience in earthmoving machinery, Brooks Equipment provides eight additional SANY dealership branches across Western Australia and a thorough understanding of the needs of this market.
Brooks Equipment recently delivered several 50-tonne excavators such as SANY models SY500H excavators fitted with features such as auto grease, fire suppression and Top Con 3D GPS to meet the requirements of the market. Brooks Equipment also customised a SY215C with a long reach boom, demonstrating its commitment to providing unique solutions.
RONCO (another authorised SANY dealership) which also services the Western Australian region, continues to invest in the employment of staff and training to support the growing demands of the construction industry.
“The future of the construction business in Australia is bright and SANY wishes to play a significant role in shaping that future along with its dealers and customers,” Khanna says.
SANY’s Victorian dealer, Vertu Equipment, has also recently grown its sales and service network across regional Victoria and Dandenong.
South Australia dealer, Adelaide Heavy Machinery, has also seen growth and interest in SANY machines. With the
opening of its showroom in Adelaide, the team is excited and ready to embark on further expansion into other regional areas later in the year.
Outside of construction applications, SANY excavators are also carving out a niche for themselves in the forestry industry. SANY dealer Randalls Equipment has seen an increases in sales of specially designed elevated cabin models like the SY245.
The recent arrival of the SANY SY870H has been much anticipated nationally. According to Khanna, feedback from the SANY dealer network has been positive, as this machine places itself as a top contender in the high-performance civil machinery category.
Powered by an engine, the SY870H is easy to transport, can be street ready with bolton rubber pad option, comes with minimal tail swing, and delivers reliable performance.
Khanna says this growth nationally, combined with the dedication of its authorised dealers, is helping to cement SANY’s stature as one of Australia’s leading machinery providers.
“SANY’s vision of being a sustained market leader in Australia cannot be realised without the commitment and customer centric approach of our dealers. We are all aligned to a single important goal of providing the best in class after sales support for all our customers in Australia,” he says.
The Oxford English Dictionary defines versatility as “the ability to adapt or be adapted to many different functions or activities”.
But what does versatility mean to a road and utility equipment manufacturer such as Road Widener?
For Todd Dohnal, Road Widener Business Development MGR, versatility is no longer a buzzword. Instead, it’s a requirement.
“We’ve placed a focus on ensuring that our machines are more versatile and can be used in more applications, not just rolling,” he says.
Renowned in the United States for its design and production of material placement and compaction equipment for road and utility construction applications, Road Widener’s presence in Australia
continues to grow.
Founded in 2007, the company now services the equipment required for road widening, shoulder repairs & remediation, curb backfilling and asphalt/ aggregate placement.
Now Road Widener is now eyeing further expansion, this time with a focus on specific projects in the public works sector.
“Instead of rebuilding, we’ve opened ourselves up to different sectors, both [in the United States] and Australia. One of these applications are utility works.”
Initially used solely in road construction and remediation, Road Widener’s FH-R material placement attachments are symbolic of the company’s commitment to versatility—
especially with the increase in popularity of the attachments in utility applications such as trench backfilling.
These attachments are available in both single and dual material discharge configurations, can function with standard or high-flow hydraulics and can work with virtually any brand of host machinery. This includes loaders, skid steers, compact track loaders, wheel loaders and road graders.
The FH-R along with a host machine is also towable on any common width trailer, with no transport permits required.
“These machines can be transported around on a much smaller scale than other machinery on the market, which translates to reduced costs and more profits,” Dohnal says.
In fact, it was the versatility of these attachments which enabled Road Widener to explore options across the utility works sector in the first place, as Dohnal explains.
“We discovered opportunities across a wider range of applications when we attended some public works sector shows in the [United] States,” he says. “These cover works such as underground utility gas lines, fiber optics and more.”
“When contractors remove the trench for these works, our units are well suited to reload this material back to where they need it. It’s a very easy method of backfilling.”
Road Widener’s Offset Vibratory Roller attachment is also well suited for utility works, thanks to its ability to complete compaction works below grade.
On top of having three drum sizes and widths in widths ranging from 61 to 121.9 centimetres, the Offset Vibratory Roller attachment is ideal for trench works thanks to its reach of 76 centimetres below mounting point.
Operators can benefit from the same advantages while using either the material placement or roller attachments, particularly when it comes to safety and costs.
According to Road Widener, the FH-R and Offset Vibratory Rollers all require
90 per cent less maintenance than selfpropelled machines.
Contractors can also increase the safety of their operation for the user and nearby workers.
For the FH-R, this is thanks to the remotecontrol operation of the attachment. When it comes to the Offset Vibratory Roller, in addition to remote-control operation, the attachment utilises an offset arm to eliminate the risks of rollover, for works on unstable ground. This is because the attachment allows the operator in the host machine to remain on flat ground while compacting, rather than operating on slopes where risk of rollover is high as traditional self-propelled machines require.
“While versatility is a big focus of ours, so is safety, particularly in Australia. Our products can take more personnel out of harm’s way, thanks to the remote-control features on the FH-R and offset vibratory roller,” Dohnal says.
The FH-R and Offset Vibratory Rollers have also undergone a rigorous testing process, to ensure reliability and quality.
“Australia’s conditions are unique and at times can be brutal. Some companies even use Australia as a test centre for their machinery,” he says. “Our products are proven in Australian conditions.”
John Zuber, Chief Instruction Officer at Ultimate Internet Access Inc is one of many beneficiaries of Road Widener equipment.
While using the FH-R as part of the company’s utility works, Zuber says he’s been impressed with both the simplicity, userfriendliness and reliability of the attachment.
“After demoing the FH-R material placement attachment for a day, we were impressed with the results and decided to purchase one. Since then, I have continued to be happy with the ways the FH-R has boosted efficiency as we install one-gigabyte fiber for high-speed internet,” he says.
“The FH-R allows us to place asphalt exactly where we need it, eliminating a lot of shovelling and hand work. Less shovelling means less manual labour required which allowed us to double the production time with half the crew. We expect it to continue to be a tremendous asset to our operation.”
Matt McDonald, Project Supervisor at Cox Construction, says the vibratory roller attachment
“The offset vibratory roller has been
a game changer for our company. Not only does it improve safety, but it also offers increased efficiency. We do a lot of resurfacing roads, and these projects often involve very narrow shoulders with dangerously steep drop offs into the ditch,” McDonald says.
“Ride-on rollers put the operator at risk of tipping and injury. The OVR attaches to the skid steer already in our fleet allowing our crew to drive on the level road with the offset roller compacting on the shoulder. The risk of rollover and injury to my operator is eliminated and I’m seeing improvements in efficiency.”
Dohnal says Road Widener is looking at future opportunities to develop its products further, which will form part of the company’s placement at 2023 Conexpo-Con/Agg in Las Vegas.
“We have a meeting every few months to discuss ideas and possible improvements,” he says.
“The idea is to make our products more versatile for more applications such as utility works. That’s something that we’re testing and looking at for the future and we’re hoping to develop some interesting ideas.”
Western Sydney’s Francrane has been providing crane hire, lift and shift, and transport solutions Sydney-wide for more than 30 years.
Managing Director Brenton OwstAtkinson started the business in 1989, and has steadily developed its reputation as a trusted and versatile operation.
Operating 24/7 from its facility in Mt Druitt, Francrane services any customer requiring machinery lifted, transported, stored, or relocated – either interstate or overseas.
The family-owned business is powered by a team with more than 100 years’ collective experience in the crane and transport industries, as well as an extensive partner network with the ability to offer cranes of any size to customers across Australia.
Owst-Atkinson says Francrane takes pride in its “we do what others don’t” mentality.
“We don’t shy away from helping anyone and never have,” he says.
“Like our team, our fleet is versatile, and we work closely with our clients to provide them with the best available service – which hopefully ensures they continue to use our services, enabling continued investment in the fleet.
“This in turn ensures our fleet remains contemporary, and with all assets fully utilised.”
Francrane recently took delivery of a new TIDD PC28 pick and carry – the second TIDD to be supplied to the company by TRT Australia through its New South Wales dealer, The Baden
“We have been very impressed with the performance of the TIDD that we already have in the fleet,” Owst-Atkinson says.
“It’s a solid machine, made to a high specification in New Zealand and it has proven itself with us at Francrane. It has performed well, and it also travels on the road well and suits our type of work. We can’t fault it,” he says.
The TIDD PC28 features a range of improved operational features designed to boost efficiency and comfort, whether on construction sites or on the road. With an increased 28-tonne lift capacity, greater manoeuvrability, and a small footprint, the crane is designed to thrive in tight work areas.
The TIDD PC28 also offers a suite of safety features designed in consultation with the industry, including Dynamic
combine to make the TIDD PC28 a perfect addition to the Francrane fleet.
“Our team likes the TIDD because it does exactly what they ask it to do – this seems to be the most common response from all our operators,” he says.
“With the addition of the new TIDD PC28, we now have five pick and carries in the fleet with lifting capacities ranging from 10 to 28 tonnes. We also operate two crane trucks, plus a range of forklifts with jib with capacities ranging from three to 12 tonnes. These are supported by semis with a range of trailers.”
To keep day-to-day operations running smoothly, Owst-Atkinson says it’s critical that the support of Francrane’s suppliers mirrors the level of support that he aims to provide his own customers.
“The Baden Davis Crane Connection is our local dealer, and they are there for anything we require. They are very customer-focused and willing to help if we are every in a bind,” OwstAtkinson says.
“The back-up support from both The Baden Davis Crane Connection and TRT has been fantastic.”
LMI (load moment indication) with a deadlock switch inside the cabin and an LMI bridging switch outside, as well as improved visibility thanks to wide view top glass and optimised mirror placement.
The crane also features Slew Safe, a TRT-developed safety innovation exclusive to TIDD pick and carry cranes.
Slew Safe is designed to help operators to keep loads within the chart, minimising the risk of overloads or rollovers. With audible and visual alarms, LMI warnings, and power steering restriction, this allows operators to pick and carry with peace of mind.
Slew Safe comes standard on all new TIDD PC28-2 cranes, and can be retrofitted to all existing PC28s and PC25s.
The TIDD PC28 has also been designed for the operator, offering improved comfort and reduced fatigue, especially during long hours. The ergonomically designed forward-mounted ROPS cabin features a double-door configuration, ducted air conditioning, 150-kilogramrated air suspension seats, and threepoint safety belts.
Owst-Atkinson says these features
TIDD PC28’ssafety features were designed in consultation with industry.
“OUR TEAM LIKES THE TIDD BECAUSE IT DOES EXACTLY WHAT THEY ASK IT TO DO – THIS SEEMS TO BE THE MOST COMMON RESPONSE FROM ALL OUR OPERATORS.”
WOMEN IN INDUSTRY NOMINATIONS ARE NOW OPEN. Now is your chance to nominate an industry leader who you believe is advocating for positive change and deserves to be recognised.
WOMENININDUSTRY.COM.AU
THURS
8 JUNE 2023
The Women in Industry Awards recognise outstanding women leaders from across Australia’s industrials sector.
PLEASE TELL US A LITTLE ABOUT YOURSELF, AND WHAT’S LED TO THIS LATEST CHAPTER IN YOUR CAREER. The first thing people usually notice about me is my French accent. For years I was self-conscious about it and have tried my hardest to get rid of it! More recently though I have embraced that I actually have this in common with millions of migrants who work hard to build a prosperous life in Australia.
I have taken the advice of wiser and more experienced colleagues and friends to accept my heritage as part of who I am. Now, hearing my young kids speak with a twisted Australian-French accent always puts a smile on my face.
I moved from Paris to Melbourne in 2009 where I spent six years with the National Transport Commission (NTC). Here I led major transport policy reforms using the experience I gained in Europe. It was during my time working for the European Commission and the Organisation for Economic Co-operation and Development (OECD) that I formed a strong interest in creating policy and regulatory consistency to the benefit of all road users. This led me to the newly formed role of Manager of National Harmonisation with the National Heavy Vehicle Regulator (NHVR) in Brisbane which my family and I now call home.
While at the NHVR, I worked with all levels of government to create and implement nationally consistent transport regulations for our heavy vehicle industry. While Australia has fewer states than the European Union, it remains challenging to unpack and simplify decades of statebased regulations.
My next role was with the Australian Road Research Board (ARRB) where I led the Queensland team. Here I worked closely with our main client, the Department of Transport and Main Roads in Queensland, under our joint R&D program, the National Asset Centre of Excellence (NACOE). As the National Director of Strategy and Innovation, one of my main goals was
passionate about.
TMAA is the peak body for the Traffic Management Industry in Australia. Our members are safety professionals with firsthand experience in what works and what does not work when it comes to keeping all road users safe.
I am proud to say that TMAA channels the collective intelligence and experience of its members to advise government on current and future regulatory changes. In
return, this allows us to keep our members informed about the latest relevant updates or changes to our industry, whether it be domestic initiatives or international best practices and innovation.
We also love celebrating our most talented members through our yearly conference and the Traffic Controller of the Year National Award. Our industry can be undervalued or unappreciated at times and one of TMAA’s primary goals is to change this perception and give traffic management and traffic controllers the
WHAT HAVE YOU LEARNED IN YOUR FIRST FEW WEEKS AS TMAA CEO?
Before starting with TMAA, I did some ‘light’ reading over the Christmas break and familiarised myself with the ten parts of the Austroads Guide to Temporary Traffic
As a lifelong learner, I was also keen to gain practical experience in the industry, thus also putting myself through the Traffic Controller and the Traffic Management Implementation courses in my first two
I had the opportunity to spend 20 hours on the road alongside a crew of experienced traffic control workers. Quite frankly, this placement was akin to being thrust into The Apprentice, as I definitely felt out-of-my comfort zone holding the Stop/Slow bat managing traffic on the Gold Coast.
It was an eye-opening experience that gave me a true appreciation for the hard work and dedication that goes into keeping Australians safe on our roads, and just how hard a traffic controller’s job can be.
HOW IS TMAA ADAPTING TO CHANGES IN THE INDUSTRIES IT SERVES?
We are witnessing some fantastic changes in the road and infrastructure sectors, many driven by the latest innovation and technological improvements. While technology can be a source of driver
F AUSTRALIAMatthew Bereni, TMAA CEO.
distraction, it can also be a wonderful source of safety gains by reducing the level of risk on road work sites. However, even portable traffic lights need to be installed on site so we will never be able to completely remove the risk factor from the road work equation.
Data published in January 2023 by the Federal Government [www.bitre.gov.au] shows that during the 12 months ending December 2022, there were 1187 road deaths – an increase of 5.1 per cent from the 12-month period ending December 2021.
In this context, TMAA’s vision to foster a safe and zero-harm traffic management industry across Australia could not be more relevant. Traffic Controllers are the first people that road users meet on roadwork sites. As such, our members have become ambassadors for road safety on worksites. This is an evolution that TMAA has fully embraced and is promoting within our industry. We’ll continue working with the road sector to ensure that Traffic Controllers are seen as a priority and lead safety champions on all road construction sites.
Like many other sectors of the transport industry, Traffic Management is going through a phase of national consolidation and harmonisation driven by Austroads, the collective of the Australian and New Zealand transport agencies, representing all levels of government.
With more Australians moving interstate, TMAA fully appreciates the national harmonisation effort. With our members’ support and guidance, we provide some qualified and evidence-based advice to the
National Harmonisation Working Group to progress the National Harmonisation agenda rapidly as we believe it will deliver some much-needed safety and productivity benefits to Australia and our workforce.
Having worked with government and industry, I am aware that there is much more that unites us rather than divides us. Anyone serious about our industry knows that the safety of all road users is a non-negotiable priority and I want to lean on this shared goal to make TMAA the focal point for road safety improvements and innovation in Australia. There is a lot more for us to achieve under the National Road Safety Strategy 2021-30. TMAA and its members want to actively take part in the Coalition of the Willing aimed at reducing our worsening road toll.
On a more personal level, I have always enjoyed the role of facilitator and enabler. I get a real kick out of helping others, removing red tape, and improving the status quo. I am sure that the TMAA CEO role will give me plenty to work on and improve, in partnership with all our industry and government stakeholders.
We are witnessing some incredible changes in our industry at all levels. Sustainability is a very strong focus, and is actually one of the key topics of our national conference held in March on the Gold Coast. It is a change that TMAA fully embraces, like the majority of our partners.
For instance, did you know that hybrid and fully electric Truck Mounted Attenuators (TMA) are available for sale
in Australia? Many of our members even recycle or buy recycled plastic traffic barriers, cones and bollards. And of course, traffic management businesses enjoy cost savings thanks to the use of solar panels and LEDs on their equipment.
Another very exciting change is the latest development in connected and automated vehicles. In Queensland, the Department of Transport and Main Roads has established the Cooperative and Automated Vehicle Initiative (CAVI) to help prepare for the arrival of new vehicle technologies with safety, mobility, and environmental benefits on Queensland roads.
One of this technology’s key benefits is informing drivers about what is ahead of them before they can see it. This could naturally include road workers.
As Vehicle to Infrastructure (V2I) communication will become the norm, there will be a day when vehicles will automatically slow down when approaching road work sites. In the meantime, new generations of autonomous vehicles are trained to read and understand changing road working conditions, but with mixed success so far.
It will be important for our industry to be consulted to ensure that technological changes do not put road workers at risk.
Reflecting on my recent experience managing traffic on the road, I have realised that traffic management is as much about keeping road workers safe as it is about keeping all road users safe.
So please, stay safe on the road and be kind to our traffic controller professionals who work so hard to keep us out of harm’s way day and night.
Across all aspects of our day-today lives, roads bring us together, facilitating all functions of our social fabric and economic activities.
The ongoing viability, level of service and safety is entirely dependent on the significant contributions of all levels of government to new projects and maintenance of the existing network, and equally a skilled competent workforce to deliver on these commitments.
In the Australian Flexible Pavement Association’s (AfPA) recent submission to the Federal Government’s Pre-Budget 2023-24 submission process, AfPA has stated and made calls for more sustainable, longer-term pipelines of investment, with a focus on fixing it first.
The report states “This means not just fixing problems retroactively but ensuring that roads stay well-maintained, making them more resilient to catastrophic weather events. Government allocating more spending for longer periods of time to road maintenance will ensure communities are safely and reliably connected and can drive transport productivity. Whilst we commend the continual spending into new capital projects, we recommend elevating spending, especially within regional and rural areas, as doing so would have significant safety and economic benefits.”
Sperling says AfPA commends the Federal Government on the ambitious and ongoing infrastructure investment, which has served to connect communities, support jobs and helped push the industry’s performance to record levels. The road and bridge construction industry heavily depends on ongoing public funding and urgently requires a commitment to existing infrastructure maintenance and renewal.
Lise Sperling has recently been appointed AfPA Head of Federal Advocacy and Government Relations focused on advocacy efforts with the Federal Government and oversight of government advocacy campaigns in partnership with State Executives.
AfPA’s key recommendations to the Federal Government’s pre-budget submission process seek to address the deteriorating condition
of Australia’s roads (especially regional and rural systems) and call for longer-term funding commitments and better fiscal coordination to ensure the best outcomes for Australian communities and value for money.
Sperling says currently, much of the spending is decided year by year which often leaves industry struggling to plan, resource and meet the increasing demands to support urban, regional and remote areas.
As a part of this submission, AfPA has identified another key issue that is impacting many sectors and industries nationally, stating that “Australia must take the opportunity to invest in a more skilled workforce, one which is capable of applying ‘band-aid’ fixes to urgent road issues as well as longer-term pipelines of maintenance funding. Both streams will require skilled workers who are ready to respond nimbly to road damage and capable of thinking innovatively and sustainably for longer-term road benefits.”
disproportionately affected by road maintenance backlogs and damage.
That the Federal Government works toward addressing the high proportion of sealed roads and unsealed roads that are in poor condition, function and capacity and close to reaching the end of their useful life. AfPA is also hoping that the Federal Government can focus on sustainable pipelines of road maintenance and innovative repair methods to protect Australia’s assets against weather instability.
AfPA is also calling for the Federal Government to ensure collaboration and communication between all levels of government and industry remain the foundation under which all infrastructure investment is built and establish of better pathways via Immigration Laws to access lower skilled visa entry for labourers interested in working in Australia.
Calls have also been made for the Federal Government to develop a skilled workforce
She says that recent events, including ongoing weather instability and the COVID-19 Pandemic, have exposed major shortfalls within our industry – specifically, the availability of trained and skilled workers.
According to AfPA, this shortage inhibits the ability to sustain key infrastructure: “The challenge for our industry, however, is that the work we are completing is not just new projects but often urgent repairs on damaged roads that save lives. The inability of skilled labour to be brought to Australia from overseas has exacerbated this issue even further, resulting in delayed work and unfulfilled critical repairs.”
In order to address these issues, AfPA has made the following recommendations.
That the Federal Government continues to support and nurture rural and regional communities which continue to be
at home by providing access to secondary and tertiary funded (or other) programs to incite interest in roads construction at the grassroots level.
And lastly, AfPA is hoping that the Federal Government can assist its organisation and the broader industry with building recognised training programs for school leavers or young job seekers, and maintain current enterprise agreement schemes negotiated with partner sector unions to reduce further inflationary pressures and support the efficient delivery of Australia’s roads.
AfPA welcomed the opportunity to make a submission for the Federal Budget, saying it’s committed to working with all levels of Government towards building a stronger infrastructure future to support the current and future needs of the nation.
“THIS MEANS NOT JUST FIXING PROBLEMS RETROACTIVELY BUT ENSURING THAT ROADS STAY WELL-MAINTAINED, MAKING THEM MORE RESILIENT TO CATASTROPHIC WEATHER EVENTS.”
While civil construction has been used as a post-COVID economic stimulus, labour productivity in the sector has made few gains. While other industries have made improvements, civil construction has been left behind and waste is at an all-time high.
A 2014 Productivity Commission enquiry into Public Infrastructure Costs exposed three possible measures for the broader construction industry to reduce waste and each is equally applicable to civil construction. The first was better procurement and project management skills. The second was improved supply chain integration and importantly. The third possible measure was using technology to enhance project outcomes.
Regarding the first two, precast concrete offers immediate benefits.
Precast has long been recognised as way to deliver productivity benefits. Manufactured in purpose-built factories, it has all the benefits associated with offsite manufacture, such as improved quality, safer working conditions, less cluttered and safer sites, faster construction and cost savings.
Supply chains are improved with teams working together to benefit projects. Head contractors and major subcontractors – like Master Precasters – creatively problem solve to address and overcome engineering, logistic and programming challenges.
As builders examine precaster manufacturing methods, they are increasingly finding that technology is being utilised to improve quality management, which has benefits for both the precaster and the head contractor.
Master Precaster Hudson Civil has engaged digital software company CONQA to introduce transparency into their quality systems to improve internal productivity while its clients are realising the benefits of digitising.
Located in Launceston, Tasmania, the Master
Precaster has been manufacturing precast infrastructure elements for civil, mining, building development and rural projects for over 20 years and has become one of the leaders in major precast products and innovative design.
National Precast CEO Sarah Bachmann says that before going digital, the company already had a robust quality management system.
“That is one aspect of the comprehensive Master Precaster audit,” Bachmann says.
“Hudson’s quality system ensures that engineering design intent is achieved. There’s a particular focus around reinforcing requirements and Australian standards, to reduce risk across the board and to maximise production efficiency.”
Hudson Engineering Officer Michael Ross reports that Hudson has recently transitioned its system from a traditional paper-based system to a digital system.
He says that being guided by CONQA made the process simple.
“Our paper-based system worked well and we had minimal quality issues, but going digital has taken it to another level,” Ross says. “Paper had its limitations. There were always the challenges of documents being misplaced or damaged, and they were difficult to consolidate.
“This is easy for our guys to use, but more importantly, it brings everything out into the open. It gives our clients access to the documentation and processes we are happy to share, and that would have otherwise taken hours to compile. Our clients are happy as they are kept informed of progress and gives them confidence, we are on top of everything.”
Bachmann says that the current demands on civil construction head contractors and major suppliers – combined with labour shortages – mean that the Association’s members and other construction
stakeholders need to be as efficient as possible.
“More than ever, all stakeholders need to be addressing productivity and making more use of offsite manufactured products. Also critical is investing in upskilling workers, better time management and improved practices. Robust quality control systems are essential and need to be transparent across the board, from the developer down, and that requirement logically flows on to precast manufacturers. Accountability and transparency are key,” she says.
“Using precast manufactured by audited Master Precasters – especially those who have invested in digitised QA - is reaping rewards, and manufacturers and clients are wrapped with the results.”
THE INFRASTRUCTURE SUSTAINABILITY COUNCIL’S 2022 IMPACT REPORT HAS REFLECTED ON THE INDUSTRY’S PERFORMANCE, WHEN IT COMES TO SUSTAINABLE MATERIAL USE, PROCUREMENT, AND INNOVATION. ROADS & INFRASTRUCTURE SITS DOWN WITH CEO AINSLEY SIMPSON TO LEARN MORE.
The year 2022 can be regarded as one of the biggest years ever for the Infrastructure Sustainability Council (ISCouncil).
It marked the 10-year anniversary of the IS Rating Scheme, a system that is enabling change, while also promoting the sustainability of major and minor infrastructure projects.
As then Federal Infrastructure Minister and current Prime Minister, Anthony Albanese, told the ISCouncil, since its formation in 2012, the scheme has created a shift towards infrastructure benefitting the environment, economy and society’s cultural and social needs across Australia and New Zealand.
“Throughout history we have celebrated infrastructure as the material evidence of human progress. Whether it is aqueducts and bridges, roads and railways, undersea cables and skyscrapers, we find a source of wonder,” he says.
“Today, in projects across the country the Scheme is working to educate and inspire industry to design and construct sustainable infrastructure with expertise, experience, and optimism.”
This, and more, was recently reflected on, following the release of the ISCouncil’s 2022 Impact Report.
Ainsley Simpson, Chief Executive Officer of the ISCouncil says 2022 was a year of further
growth for the organisation and the industry.
“The sheer number of projects that are coming up across different asset types and areas across Australia and New Zealand is a sign of the growing commitment to sustainability” she says.
“One thing that has really stood out in 2022 is how much the industry wants to collaborate. The appetite for knowledge sharing is just phenomenal.”
The 2022 Impact Report acts as a tool for the ISCouncil to review its actions throughout the previous financial year, while also highlighting examples of innovation and sustainable outcomes in projects.
Beyond displaying the momentum being made towards sustainability across the infrastructure sector, the Report also evaluated the ISCouncil’s performance against four strategic goals.
These consist of leadership (encouraging best practice through sustainability), thriving industry (supporting collaboration and innovation throughout the sector), market transformation (advocating for change and transition) and healthy organisation (ensure the ISCouncil is driven by purpose, inclusivity and quality outcomes).
These goals have been formed “to deliver
on the organisations purpose, to ensure all infrastructure delivers social, cultural, environmental and economic benefits.”
This strategic plan is reviewed annually and will shape the actions and vision of the ISCouncil until 2025.
The year provided a host of highlights for the strategic plan. Forty-seven projects were certified under the IS Rating Scheme, while the ISCouncil saw growth in its online audience, as well as an increase in the number of employees (31 and 34 per cent respectfully).
also achieved. Around 6.4 million tonnes of resources were diverted from landfill, while 96 per cent of waste related to project delivery was diverted from landfill.
“The rise in focus on sustainability, along with growth in the infrastructure pipeline means we’ll see increase demand of driving and measuring outcomes using the IS Rating Scheme,” Simpson says.
“One of the good news stories was that across the projects certified over the last five years, we saw savings of more than 55 per cent for energy-related greenhouse gas emissions across asset life cycles.’’
Apart from the 10-year anniversary of the IS Rating Scheme, 2022 also saw the introduction of the ISCouncil’s inaugural
brings emerging and existing leaders together to discuss their ambitions and goals, as well as what they believe could be changed for the better.
Simpson hails the first cohort as a success and is looking forward to the program’s growth and expansion in the future.
“The ‘Rise’ program was launched at our March conference, and we had 19 mentees and 19 mentors, with the first program oversubscribed. It’s been designed to make sure that both mentees and mentors have something to gain. It’s showcasing real connection and purpose-led leadership,” she says.
As part of its commitment to support market transformation, the ISCouncil rewards innovation through the IS Rating Scheme, with participants able to collect an additional 10 points (contributing to a project’s overall rating) for using innovative technologies or methods during project design, delivery and operations.
Simpson says 2022 demonstrated a renewed effort and desire for alternative products and processes.
“What stood out to me is the jump in innovations from last year to this year,” Simpson says.
Reflected within an innovation snapshot in the 2022 Impacts Report, the industry introduced 41 new innovations on the regional level, 30 firsts at the national level
and four world firsts.
“It really highlights the industry’s appetite for delivering new ways of doings things, by making a change and making a mark in the industry. The industry has passionate people that are always looking for the next solution and a better way of doing things,” Simpson says.
Such innovations were prevalent on projects such as the second stage of the Monash Freeway Upgrade in Victoria, where the first use of Hydro Demolition Water Recycling in Australia enabled the project team to reuse 100 per cent of the water used for hydro demolitions.
The M1 Pacific Motorway Upgrade (Burleigh to Palm Beach) in Queensland also saw the use of an invertebrate sensitive road design. Structures such as culverts were designed to reduce the impact on local flora and fauna, such as a fish passage to preserve local habitats.
Simpson is enthusiastic for the future, with expectations that 2023 will be an even larger year for the ISCouncil and all beneficiaries of infrastructure sustainability.
“As the clock ticks closer to 2030 and the need to deliver on our collective carbon reduction commitments, we very much welcome the opportunity to collaborate across the sector to ensure all infrastructure is delivering environmental, social, economic and cultural benefits,” she says.
CIMIC Group subsidiary UGL has been appointed by Neoen to install the highvoltage infrastructure to connect a Tesla-supplied Battery Energy Storage System at Neoen’s Western Downs Green Power Hub, about 250 kilometres west of Brisbane. Following construction, the battery – which will also be installed by UGL – will work alongside Neoen’s Western Downs solar farm at the same site and allow stored energy to be transmitted into the electricity network from the Australian summer of 2024-25. UGL is a specialist in the design, construction and operation of renewables assets, having previously completed the construction of 11 solar farms, and the installation of three largescale batteries.
A d esign and construction contract has been awarded to ADCO Constructions for works on the Pimpama Station, the first of three stations which will be delivered as part of the Cross River Rail project in Queensland. The Pimpama Station will house five accessible car parks, throughlifts on each platform, a 40-bike lock-up enclosure and a pedestrian overpass. Early works and site establishment on the station are already underway, including construction of the station access road, drainage works and connecting infrastructure. Transport and Main Roads
Minister Mark Bailey said the South East Queensland-based contractor would start major works on the new station in early
2023. Progress is also being made on the Merrimac and Hope Island stations, the other two stations which will be developed as part of the Cross River Rail.
Contract awarded for Coxs River Road upgrade
E rtech has been awarded the contract for works on a new interchange at Coxs Rivers Road in Little Hartley, which forms part of the $2.5 billion upgrade towards the East and West sections of the Great Western Highway Upgrade in New South Wales. The new interchange is included in the design to upgrade the Great Western Highway to four lanes between Coxs River Road and the Hartley Cemetery. The project will be the first phase of work carried out in the Little Hartley to Lithgow section of the Great Western Highway upgrade between Katoomba and Lithgow. This section is about 2.4 kilometres long and will provide two lanes in each direction to allow traffic to flow smoothly between the Central West and Sydney. The new interchange will ensure motorists can safely travel over the new highway, and work will also include realigning parts of the existing highway to create a local service road, and upgrades to the intersections with Browns Gap Road and Baaners Lane. Early work at Coxs River Road began in September last year, with relocation of overhead powerlines and underground communication assets underway in preparation for the major construction work. The New South Wales and Federal governments have committed more than $2.5 billion towards the East and West
sections of the Great Western Highway Upgrade, between Katoomba and Blackheath, and between Little Hartley and Lithgow.
Contract awarded for introduction of Australian-first rail tech
H yundai Movex has been awarded a contract to design, supply and install 150 mechanical gap fillers, a first-of-itskind technology in Australia, at stations which will form part of the Sydney Metro City & Southwest project. The new technology will be installed at stations between Marrickville and Bankstown, on the Bankstown line. The new mechanical gap filler technology works automatically, extending quickly from the platform to the train before the platform screen doors open, allowing safe and easy access for all customers. The gap fillers have been developed specifically with the curved platforms of the T3 Bankstown line in mind and were selected based on their performance, reliability and safety. The contract also includes the delivery of 360 platform screen doors for installation at eight stations on the Bankstown line. The specialty doors will be installed at all Sydney Metro stations and are designed to keep people and objects like prams safe from the gaps between trains and platforms and allow trains to get in and out of stations much faster. Hyundai Movex will deliver the mechanical gap fillers and platform screen doors this year.
Built to withstand a variety of conditions the Atlas Copco range of lighting towers are robust and offer unrivalled efficiencies ensuring they are both reliable and can operate for an extensive period of time.
• Fuel efficient, ensuring longer running hours
• Specially designed directional optics offering incredible light distribution
• LED HiLight towers achieve up to 6.000 square-metres of light coverage with an average level of 20 luxes
• A life expectancy of more than 50.000 hours
• Aluminium casting, providing heavy duty protection
DYNAPACS SIXTH GENERATION SMALL ASPHALT ROLLERS - READY TO ROLL
Dynapac’s sixth generation CC1300VI and CC1400VI small asphalt rollers are designed and built to meet the construction industries ever evolving and tough conditions. The new design has resulted in a robust, comfortable and modern machine that still achieves the market leading compaction results that Dynapac is renowned for.
The new generation has a unique cross mounted engine providing exceptional access to engine and hydraulic components. This new engine concept and the slideable operators seat combine to increase visibility to drum edges and the greater worksite. High vibration frequency, offsetability of the drum, high efficiency eccentrics and options such as edge press devices and chip spreaders all improve compaction efficiency and versatility.
FROM TOP TO BOTTOM, WE SUPPLY THE BEST CONSULTATION AND TECHNOLOGY TO BUILD YOUR AUSTRALIAN ROADS.
STRAIGHT UP.