
6 minute read
Custom-designed machinery
CUSTOM-DESIGNED MACHINERY, MADE FOR
AUSTRALIAN ROADS
MATTHEWS BROTHERS ENGINEERING’S CUSTOM-BUILT MACHINERY HAS SERVICED THE AUSTRALIAN ROADMAKING INDUSTRY FOR OVER A CENTURY. AS OWNER PAUL MATTHEWS TELLS ROADS & INFRASTRUCTURE, THE BUSINESS CONTINUES TO BE AN INNOVATOR IN THE MARKET.
As a third-generation family owner of Matthews Brothers Engineering (MBE), Paul Matthews is proud of his family’s legacy of producing affordable and durable road making machinery. This commitment was highlighted last year as the company celebrated its centenary.
Founded by Vic Bradley and Roy Matthews in 1921, MBE was a key supplier of bitumen spraying gear and bitumen kettles to the Victorian Country Roads Board during the peak road-building era in the early 20th century.
Over the years, the company has built a reputation for manufacturing affordable and highly customised roadmaking equipment, including bitumen sprayers, dog trailers, melting tanks, spreader boxes and multipurpose asphalt vehicles.
MBE’s bitumen sprayer units fit on existing truck chassis and are made to order as per the requirements of each client. The sprayers, which are manufactured in-house by MBE at its workshop in Altona North in Melbourne, feature an optional Guaranteed Target Application Rate, or G-TAR system, that helps operators achieve precision and consistency in bitumen application.
“Over the years, we have grown from making small trailer-mounted bitumen sprayers to manufacturing 14,000 litre, twin-bar bitumen spraying units with all the bells and whistles. Our products are known for their reliability and the fact they are specifically designed for Australian conditions,” says Matthews.
Today, MBE continues to grow its equipment offerings, with its bespoke bitumen tankers and spray sealing equipment forming the cornerstone of the company’s product range.
MBE designs a range of bitumen sprayers, including models with 4000, 6000, 10,000 and 14,000 litre tank sizes, all of which are built to comply with Australian Standards and the Transport of Dangerous Goods Act.
Matthews says feedback from clients have contributed to safety and efficiency improvements to the classic bitumen sprayer model.
“MBE has created a sprayer automation system called G-TAR. This is a computerised spraying control system with spraying tables built in and intuitive operation of the touchscreen allowing for simplified spray bar operation leading to less manual handling and achieving consistency of application rates,” he says.
“In 2001, MBE introduced OZIBAR, a premium spray bar system specifically built for Australia’s challenging and wide-ranging conditions. All of these improvements have resulted in a safer and more efficient equipment.”
Feedback from operators has also influenced many safety improvements, some of which were previously optional, to be installed as standard on the classic bitumen sprayer model. This includes provision for safety showers and a pressure shutdown system.
MORE THAN MEETS THE EYE Just like its bitumen sprayer, MBE offers a classic model for its range of dog trailers. Available in 14,000, 19,000, 20,000 and 25,000 litre tank sizes, the dog trailers also provide two, three or four axle configurations.
This allows operators to customise the trailer to suit their needs. Whether this be a simple mobile storage unit, or to power integrated bitumen pump agitators. All MBE dog trailers also feature air suspension and multi voltage anti-lock braking and electronic braking systems.
Matthews Brothers Engineering has been manufacturing affordable roadmaking equipment for over 100 years. Pictured: custom-made bitumen sprayer.
Matthews says that operators will notice similarities between the company’s bitumen sprayer and dog trailer models.
“Our piping and burner system design is duplicated on both the bitumen sprayer and the dog trailer, so operators can feel a sense of familiarity when operating either machine,” he says.
For a more versatile design, MBE also designs and manufactures multi-purpose asphalt vehicles (MPAV’s).
“All MPAVs are custom-built to each client’s specification. There is no ‘classic build’ here. MPAVs are essentially utility vehicles that go onsite with spraying crews and each company has their own template for what their crews need,” Matthews says.
These setups can support a range of attachments.
“They can be made up of small emulsion tanks with spray bars and include intermediate bulk containers, hose and reels, toilets, tool and equipment storage, generators and even small cranes,” Matthews says.
FOR INTRICATE APPLICATIONS MBE also designs machinery which is suitable for smaller repair jobs, such as bitumen melting tanks.
The bitumen melting tanks are available in 500 and 2000 litre variants. They are both self-contained and skid mounted, with the subframe of the product allowing it to be used with a third-party machine, such as a truck or a trailer.
As Matthews explains, the bitumen melting tank is complementary to MBE’s wider machinery range, which is suited for larger projects.
“It’s designed to allow clients to undertake small sealing repairs which don’t require a full spraying unit. They can be transported easily to site on the back of a flat bed,” he says.
MBE’s innovations for affordable and convenient roadmaking equipment do not stop there. The company has also designed a product which removes a serious headache for contractors and operators alike.
MBE’s rear spreader box units come in two varieties. One is ‘fixed’ and allows for a 2.7-metre spreader width. The other is an innovative ‘winged’ design which is 2.5- metres wide for transit purpose, but pneumatically extends to 2.9 metres during operation.
Matthews says the winged model was designed to address an issue many operators struggle with.
“The fixed width spreader box unit is often wider than the back end of the tipper truck they are installed on. As such, companies need to apply for oversize permits for travel and use,” he says.
“With the winged version of our spreader box, the body of the spreader box has the same width as the back end of the tipper truck. The winged sections only expand when in operation. Therefore, no oversize permits are required.”
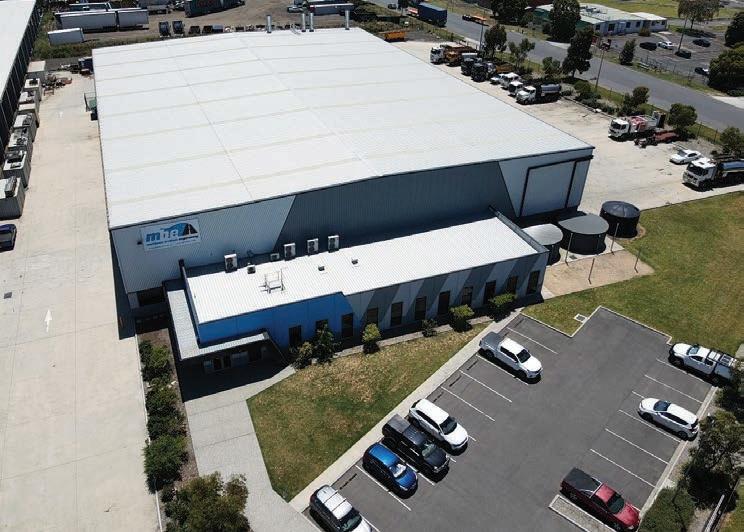
VERSATILE SUPPORT Matthews adds that customers receive fit-for-purpose machines from MBE, thanks to the manufacturer’s ability to customise equipment.
“For example, while we recommend the use of Scania’s Chassis range for our sprayer units, our team has also successfully built our sprayers on Mercedes Benz, MAN, Volvo, Hino and Izusu chassis,” he says.
For additional versatility, Matthews says MBE’s products can be used along machinery from other providers.
“The advantage of buying all equipment from MBE is we become a one-stop-shop for technical support and servicing,” he says.
“Many of our components are manufactured in-house, which assist us in avoiding supply chain issues. We can supply our clients with replacement bitumen pumps, plug cock valves, wedge gate valves and spray bar valves. We also have the capacity to make bespoke parts to order. Many of our spare parts are interchangeable between models.”
With a strong legacy to follow, Matthews says the company will keep on innovating and enhancing its product portfolio.
“We are always looking at areas to expand and develop ideas for our clients. MBE doesn’t offer a set product with no variations. Every unit that leaves our production workshop is different to the units before it and units after it. Our clients are provided with quotes that include an extensive list of optional extras and chassis options to build the perfect unit for their specific needs.”
Paul Matthews is the third-generation owner of Matthews Brothers Engineering. MBE’s equipment is manufactured at the company’s workshop in Altona North in Melbourne.

FOR FURTHER INFORMATION, CONTACT THE TEAM AT MATTHEWS BROTHERS ENGINEERING: Paul Matthews – Technical Director (paul@matthewsbrothers.com.au) Sally Rolfe – Sales and Operations (sally@matthewsbrothers.com.au) Richard Bailey – Design and Product Development (richard@matthewsbrothers.com.au) Simon Hunt – Production Manager & Technical Support (production@matthewsbrothers.com.au) Ronak Bhatt – Spare Parts Sales (sales@matthewsbrothers.com.au)