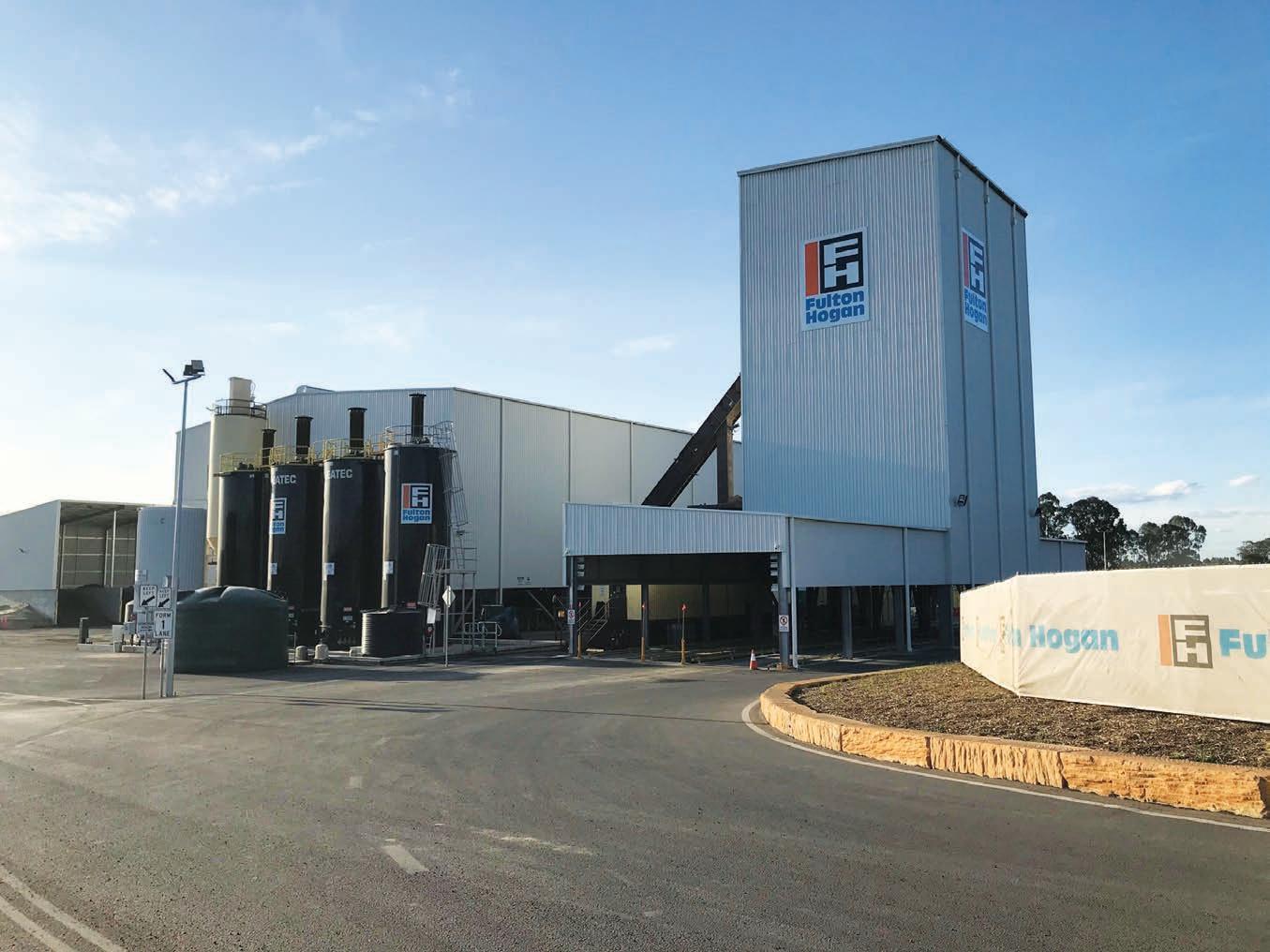
5 minute read
Behind Fulton Hogan’s ‘levelled’ asphalt production
VEGA’s level measurement sensors are installed at Fulton Hogan’s Eastern Creek asphalt plant in New South Wales.
BEHIND FULTON HOGAN’S
VEGA’S RANGE OF NON-CONTACT RADAR LEVEL TRANSMITTERS AND PRESSURE TRANSMITTERS HAVE SPELLED SAFETY AND RELIABILITY FOR FULTON HOGAN’S ASPHALT PLANTS IN AUSTRALIA. MARK WHEATLEY, THE TECHNICAL MANAGER-PRODUCTION AT FULTON HOGAN INFRASTRUCTURE SERVICES IN NEW SOUTH WALES, EXPLAINS WHY.
As Technical Manager-Production for infrastructure construction company Fulton Hogan, Mark Wheatley oversees asphalt production processes across a number of Fulton Hogan plants in New South Wales.
A common element in these plants, apart from the usual hubbub of asphalt production, is the presence of little, yellow-coloured sensors hidden in the – often difficult to access – nooks and crannies of the plant, sending real-time level measurement data to the control and monitoring systems.
These sensors, supplied by VEGA Australia, make sure the level of liquid and solid materials that make up the asphalt mix are reliably measured at any given time, so there’s no overfill or over-draw from the tanks.
With all the complexity and magnitude of an asphalt production plant, it’s easy to overlook the critical role the humble level transmitter plays in ensuring the plant’s reliability, Wheatley observes.
“You may not think a lot about the bitumen road pavement that you drive on, or the bitumen tarmac at airports, but these can be tricky products to manufacture and store. We deal with elevated temperatures in our tanks, fuming product, the existence of potentially flammable gases, and we handle not only liquid materials but also solids such as lime and dust,” he tells Roads & Infrastructure.
“We have different bitumen manufacturing plants which, for various reasons, have different approaches to tank level measurement. Some plants were constructed to measure liquid level via pressure instruments at the bottom of the tank, and some have top-mounted level instruments. We also have tanks of various shapes and sizes. I have found VEGA has the instruments to meet all our level requirements,” he adds.
NON-CONTACT LEVEL MEASUREMENT In recent years, advancements in non-contact level measurement with radar technology have made it easier to configure devices that are difficult to reach or located in harsh environments. VEGA, as a sensor manufacturer for high demand industries like mining and transport, has been a frontrunner in this space.
While conventional pressure gauges used for level indication were common in the
past, Michael Summersby, Area Manager, VEGA Australia, says many asphalt plants have upgraded to non-contact radar level measurement devices from VEGA.
“In many production facilities there are measuring points that are extremely difficult to reach and often located in dangerous places. Climbing into bunded areas or to top of tanks in bad weather with equipment, such as a tablet and adapters, can be a very difficult and dangerous task. Having the reliability of remote access to instrument setups and functions via Bluetooth has real benefits for plant operations,” says Summersby.
“Non-contact level measurement with radar is characterised by especially high measurement accuracy. The sensor sends microwave signals towards the medium from above. The surface of the medium reflects the signals back in the direction of the sensor. Using the received microwave signals, the sensor determines the distance to the product surface and calculates the level from it,” he adds.
For Fulton Hogan, VEGA’s non-contact radar level transmitters play key functions: they protect the tanks from overfilling, they ensure the heating coils in bitumen tanks remain covered, and they also help keep track of material availability.
“Our initial level requirement was for overfill protection,” says Wheatley. “By reliably and accurately measuring the level in our tanks, these instruments can interface with our safety interlock systems so we can avoid overfill and ensure heating coils in the tanks remain covered. The instruments also give us a backup to ensure we have adequate raw materials to meet customer orders and the required tank space to manage raw material deliveries.” EASE OF MAINTENANCE As a bonus, Wheatley says VEGA’s noncontact level transmitters are easy to setup and maintain.
“We have noticed that the lens-type radar level transmitters require little maintenance. They have been reliable, and upon checking, the face of the radar seems to remain unaffected by the atmosphere inside the tank,” he says.
“Our electrical contractor likes to familiarise himself with the instruments, because he has to incorporate them into a system which may not only include stop/ start interlocks and status indicating lights but may also include a remote level display for the plant operators or a display at the tanker loading area,” he adds.
As Summersby explains, VEGA Australia’s area managers often provide a familiarity training to electrical contractors onsite following an initial visit and offer consultation for product selection. This training is often enough for the contractors to set up and maintain the transmitters themselves. Support is also readily available from VEGA’s service department if the customer prefers.
“Our service department, of course, get involved if the installation is a bit tricky, or if the plant would like them to do the commissioning. We also have service contracts with some plants to carry out periodic audits of their VEGA instruments,” he explains.
VEGA TOOLS Using the VEGA Tools application, plant operators and technicians can not only measure tank levels precisely in real time, but also adjust the parameters and set up the sensor remotely. All of VEGA’s different programmable sensors can be managed with the same app, allowing sensors to be parametrised wirelessly via PC, laptop, tablet or a mobile phone.
The VEGA Tools app can also be used to for demonstration/familiarisation purposes, even before the instruments are purchased. The simulation function allows plant operators and electricians to check that their system operation and logic is correct, as part of the commissioning process.
With certain tanks in asphalt plants containing hazardous and flammable materials, Summersby says VEGA’s area managers are also familiar with instrument certification, allowing them to offer the type of sensors that meet the customers’ certification requirements, such as intrinsic safety or SIL (safety integrity level).
“Depending on the nature of the product being measured, asphalt plants may or may not require radar sensors with additional certification and VEGA can accommodate so clients purchase sensors with these options only where necessary. This ensures clients get full value out of their purchase” he explains.
Back to Fulton Hogan, Wheatley says, using VEGA transmitters has ensured reliable and accurate level measurement across the company’s asphalt plants.
“I have to say, the non-contact radar level transmitters we use from VEGA have come a long way over the years. The instruments we have installed measure the level of different products very reliably, while being suitably certified for hazardous area installations. Our electrical contractor is impressed with how easy it is to set up and maintain the instruments, so it’s a win-win scenario for all of us.”
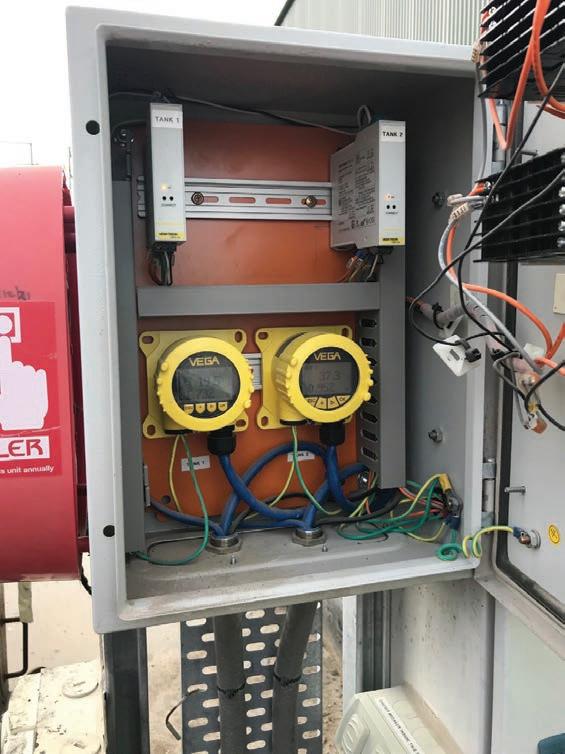
Using VEGA’s non-contact radar level transmitters (left) and remote level displays (right), operators can take level measurements for difficult-to-reach measuring points.
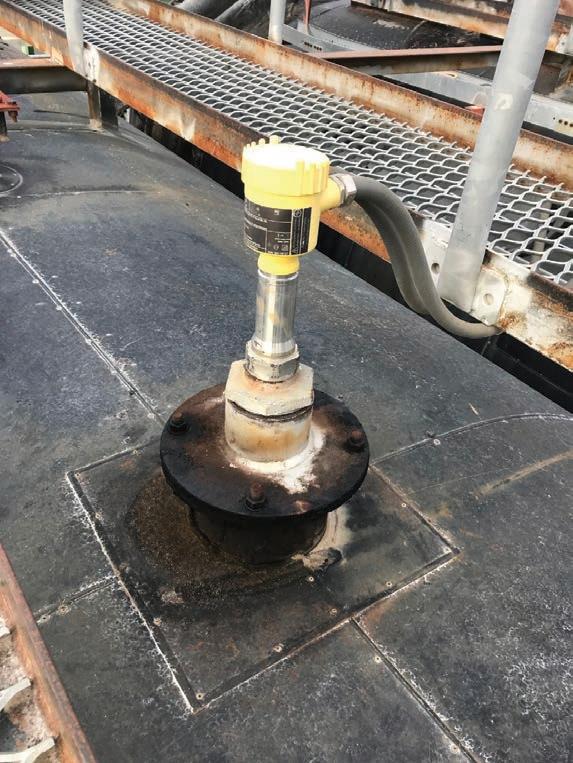