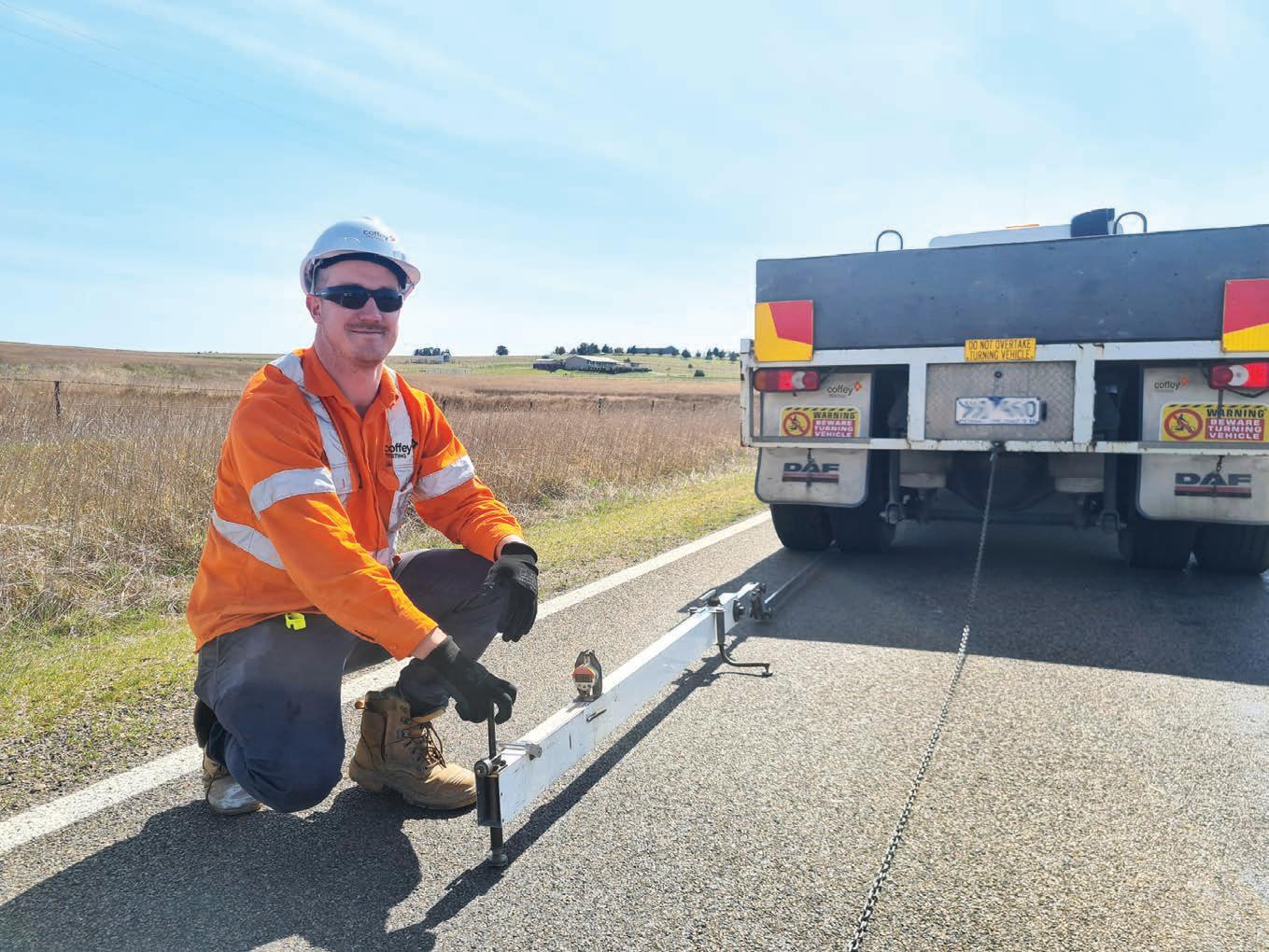
4 minute read
The secret to pavement longevity
THE SECRET
TO PAVEMENT LONGEVITY
IN THE PURSUIT FOR DURABLE PAVEMENTS THAT CONTRIBUTE TO BROADER SUSTAINABILITY, COFFEY TESTING SPECIALISTS CAMERON BIK AND RUSSELL BOOTH BELIEVE MATERIAL TESTING IS AN IMPORTANT, BUT UNDERESTIMATED, PIECE OF THE PUZZLE.
The adage ‘proper preparation prevents poor performance’ is certainly relevant to pavement construction, where future savings and, more importantly, safety of commuters, rely on satisfactory performance of pavements.
As an experienced pavement specialist, Cameron Bik, Coffey Testing’s General Manager for New South Wales and the Australian Capital Territory, has seen his share of pavements failing prematurely, where adequate investigation and testing could be a game-changer.
“Once a section of pavement is laid, it’s a very costly exercise to make any variations or improvements if design factors were assumed incorrectly in the first place. It’s also highly inconvenient to divert the traffic for a do-over if the original pavement fails prematurely. For these reasons, the best way to ensure durable pavements is to test the parameters correctly from the get-go,” he says.
As one of Australia’s industry leaders for material testing, Coffey Testing’s expert teams are often involved in pavement investigation, stabilisation trial mix design and conformance testing, deflection monitoring, material quality and conformance testing and compaction testing across all scales of pavement projects, from remote rural backroads to major distributors.
Coffey Testing’s network of NATA accredited base laboratories and associated annex laboratories assist clients to gain an in-depth understanding of ground conditions and soil composition for their projects, which enables them with better planning and construction, as well as mitigating potential risks.
“Soil investigations are very much reliant on skills and experience. There are, of course, guidelines as to how many samples are required to be taken. But, if you don’t send experienced people to the site, you might miss a defect or get samples that are not homogeneous or cannot be interpreted correctly, so it does not yield the desired results,” says Bik.
Bik says through his years of experience, he has come to ascertain that the secret to pavement longevity is thorough testing.
“The more we know about a pavement prior to construction, the better the risks
Coffey Testing’s Senior Technician Jordan Buttini conducting Benkelman Beam Deflection Monitoring on a remote road in New South Wales.
are controlled. By increasing the amount of investigation and associated laboratory testing, we reduce the risks of missing key areas and materials within the pavement, which may come to fore at the time of construction, or worse, six weeks after the road is finished,” he says.
“By undertaking testing, not only can we test a vast array of properties within the pavement’s materials, but we can also undertake investigation and trials to ensure the material properties meet the design option. This is critical because if these properties aren’t met, the pavement will fail prematurely.”
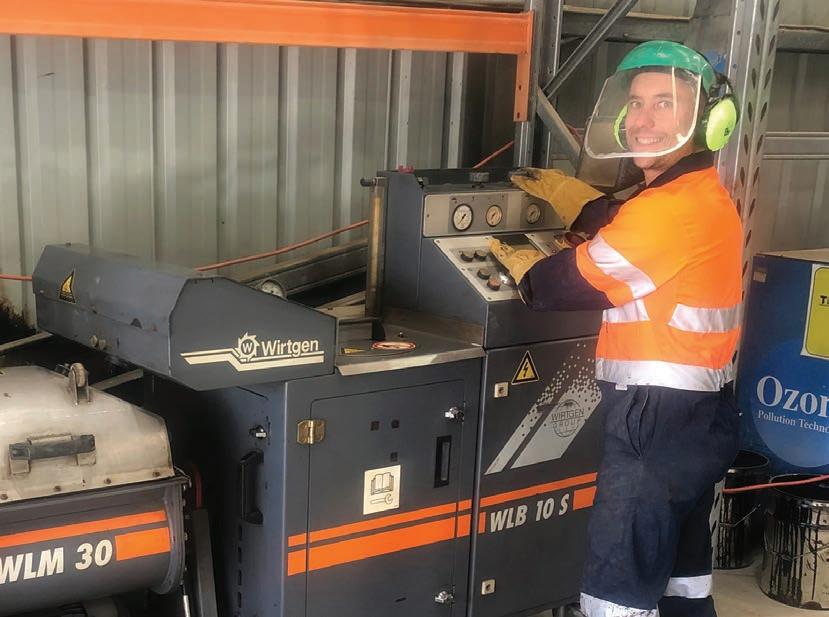
TESTING FOR ROAD REHABILITATION Apart from pavement construction projects, there’s one more area where material testing becomes critical to sustainability and longevity of pavements, and that is in pavement rehabilitation projects.
As Russell Booth, Coffey Testing’s Sydney Laboratory Manager observes, initiatives from local councils to rehabilitate existing pavements and re-use the material are on the rise across every state. Particularly, he says, use of foamed bitumen technique has been gaining more popularity.
“In-situ stabilisation design, particularly foamed bitumen is being used more. Pavement design software is now allowing for these to be modelled more easily in the latest version due to the versatility, reduced impacts to the environment, reduction in waste and time savings on completing projects which benefit the community,” he says.
“The design guidelines around these pavements are becoming more relevant on a local government area (LGA) level, meaning their yearly budgets are stretching further. There has also been a strong emphasis around recycled materials in terms of recycled crushed concretes for roadbases, selected material zones (SMZs) and crushed glass for drainage materials,” he adds.
Booth says Coffey Testing has a strong presence in this area as well. Currently, Coffey Testing is the only private testing laboratory network in Australia equipped with the specialised WLB10S Foaming Trial Machine for foamed bitumen modulus testing.
“Coffey Testing is a member of
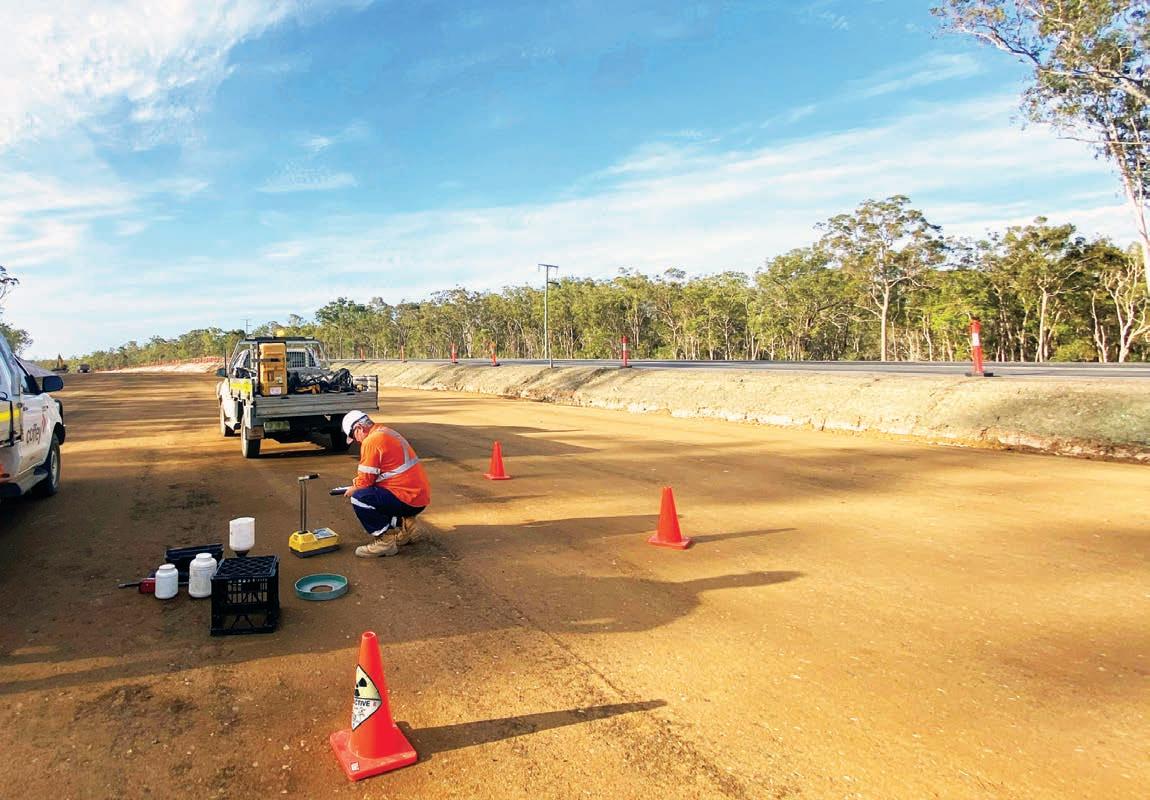
Coffey Testing’s Senior Technician David Doran performing the set up of a density bias for pavement materials in accordance with TMR methods.
Coffey Testing’s Pavement Manager, Mitchell Taylor, conducting foamed bitumen modulus trials on the WLB10S foam bitumen testing machine. AustStab – Australia’s pavement recycling and stabilisation association. We have members within the AustStab Technical Working Group, who are constantly discussing innovations, improving guidelines, and troubleshooting industry issues,” he explains.
“We have also moved into the trial mix design for foamed bitumen pavements. Our team can trial various percentages of binders and secondary binders to ensure the appropriate design modulus is met.”
These trials, Bik explains, can lead to significant cost savings on rehabilitation projects.
“For example, we might do a trial mix with a certain percentage of bitumen, and it might be overdosed. We can then do another test and reduce that bitumen content by, say, one per cent,” he says.
“Now, bitumen in a rehabilitation project counts for roughly about 30 per cent of the cost. So, if we can reduce that bitumen content by any small percentage, there’s huge savings to be made for the contractor. We then do more testing during construction to prove that the stabilised road section did meet the required strength.”
Given the benefits of conducting thorough material testing and trials, both for construction of fresh pavements and rehabilitation of existing ones, Bik’s message to contractors and asset owners is to not be afraid of ordering additional tests.
“Lack of investigation and testing is like crossing a busy highway with your eyes closed. You might make it to the other side, but why take the risk?”