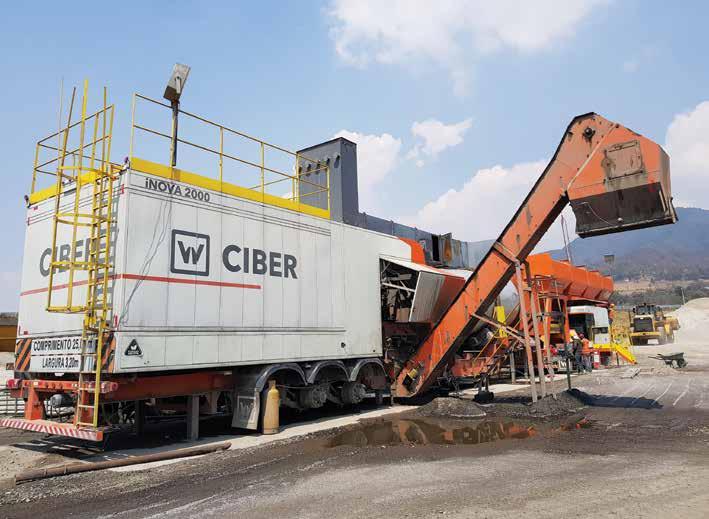
4 minute read
Mobile plant
MOBILE PLANT FOR MAJOR PROJECTS
CIBER’S INOVA 2000 WAS THE MOBILE ASPHALT PLANT OF CHOICE FOR THE CONSTRUCTION OF IMPORTANT HIGHWAYS IN MEXICO’S FOREMOST ECONOMIC REGION.
Currently, Mexico is among the 10 largest car producers and five largest exporters in the world. It is projected the country will produce six million vehicles by 2022 with more than half to be exported.
Many of the main car manufacturers for several automobile brands are located in the central region of the country, just 67 kilometres from the nation’s capital. Due to the industrial and economic importance of the region, one of the main highways, the Toluca-Naucalpan highway, has been under construction since 2014.
The works for the project included the construction of the A4 highway with two lanes in each direction for a total length of 39 kilometres, budgeted at $398 million. The road has a capacity of 30,000 vehicles daily and connects five municipalities.
It brings social and economic advantages to the region channelling vehicles from the northern and western region of the Valley of Mexico to the city of Toluca. Vehicles from these places currently travel on the
The iNOVA 2000 speeds up production time.
Chamapa-Lecheria Highway, which operates with low traffic volume during peak hours.
The Toluca-Naucalpan highway has been affectionately dubbed the “Green Road” because of the benefits it is expected to bring to surrounding areas in terms of environmental sustainability.
Mezcla Asfáltica de Alta Calidad (MAAC) has been carrying out the works for the project. Founded in 1999, the company represent the benchmark in production of asphalt material within the quality standards and specifications required by the Federal Communications and Transport Department and the international entities of the sector.
To aid the construction of the highway, MAAC chose to partner with Ciber, an established asphalt plant manufacturer. MAAC decided to use Ciber’s iNOVA 2000 mobile asphalt plant.
The iNOVA 2000 provides versatility for the large production volume required by the project. It has a production range from 100 to 200 tonnes per hour, which makes it a good fit for a project such as the highway.
“The iNOVA 2000 is an automated plant, which speeds up production time, reducing execution times and the duration of work, ensuring fuel efficiency,” General Director of MACC, Alberto Luthe says.
The continuous mobile asphalt plant features four feeder bins with individual weighing capability. It has new aggregate drying technology that ensures maximum thermal efficiency for low fuel consumption.
The plant has a Ciber Total Air burner to give a constant burning, and an external mixer to ensure quality of the asphalt mixes. Customers are also able to use Reclaimed Asphalt Pavement up to 15 per cent depending on its configuration.
The iNOVA 2000 also has a new command centre, with a diagnosis and remote monitoring system to give control of production.
The machine can be used on a range of projects from small to large job sites where daily production is a requirement. Ciber also offer a range of similar mobile asphalt plants to suit any project or site.
The plant used on this particular project was the first to be manufactured in the series and is available in three continents.
Ciber had carried out more than two years of testing before bringing the product to market in order to guarantee its performance and the equipment’s functionalities.
Mr. Luthe says the mobile installation of iNOVA 2000 facilitates the use of the equipment for jobs carried out by the company.
“The flexibility of the equipment and the
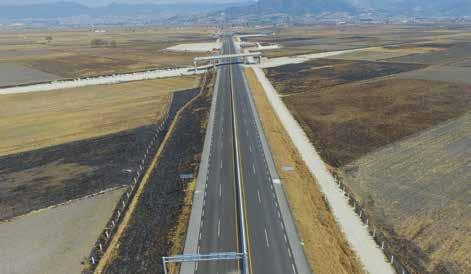
Ciber carried out more than two years of testing before bringing the product to market.

ability to adapt to the evolutionary needs and stages of the project, as well as ease of use and transfer speed make it easy to complete the works,” he says.
The new technologies featured in the iNOVA 2000 ensure the productivity of the mobile asphalt plant, regardless of input materials and what the project involves. It also helps to ensure clients meet quality requirements that are in line with the parameters specified for the project.
Ciber, a member company of the Wirtgen Group, offers a complete line of equipment for building, maintaining, and repairing pavements.
Focussing on application technologies, the company invests in research and development, constantly qualifying equipment produced and always keeping in mind the demands and needs of its customers.
The iNOVA 2000 adds high technology to the customer’s requirements, offering new devices capable of reducing impact on the environment, such as the new aggregate drying technology, enhancing the experience for the people who work with the machine, whether it be operators, or the people living close to the building sites.
The company is always available to help solve any concerns clients may have for a range of issues – from customer services or support, to spare parts or training.
“The efficient operation of our equipment ensures a fast and simple logistic cycle for the provision of material, saving time for customers and carriers alike. These advantages put us in a position to accomplish the main goals we have as a company,” says Mr. Luthe.