SETTING THE SUSTAINABILITY STANDARD
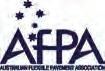
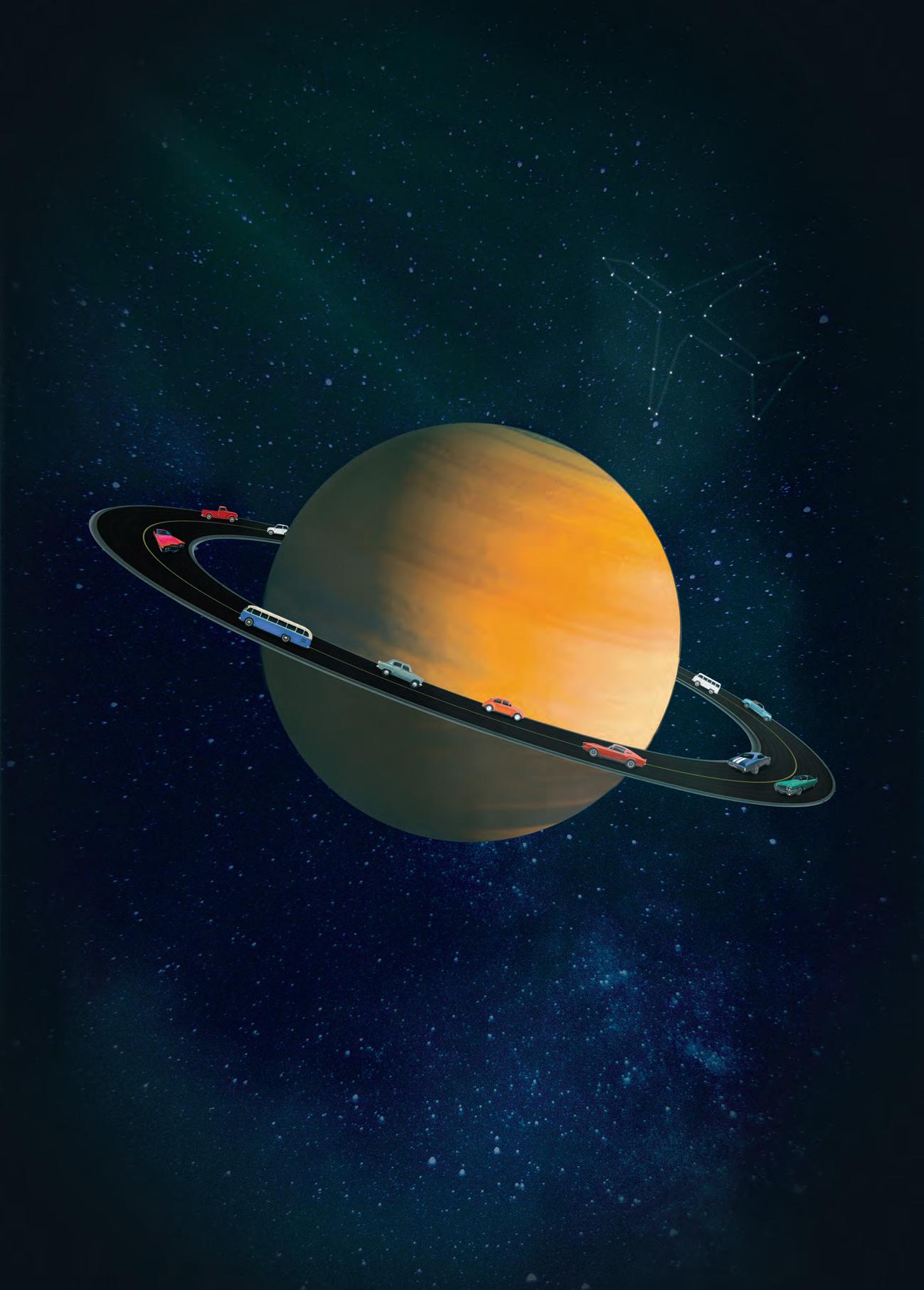
How the NTRO is shaping the future of sustainable infrastructure
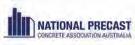
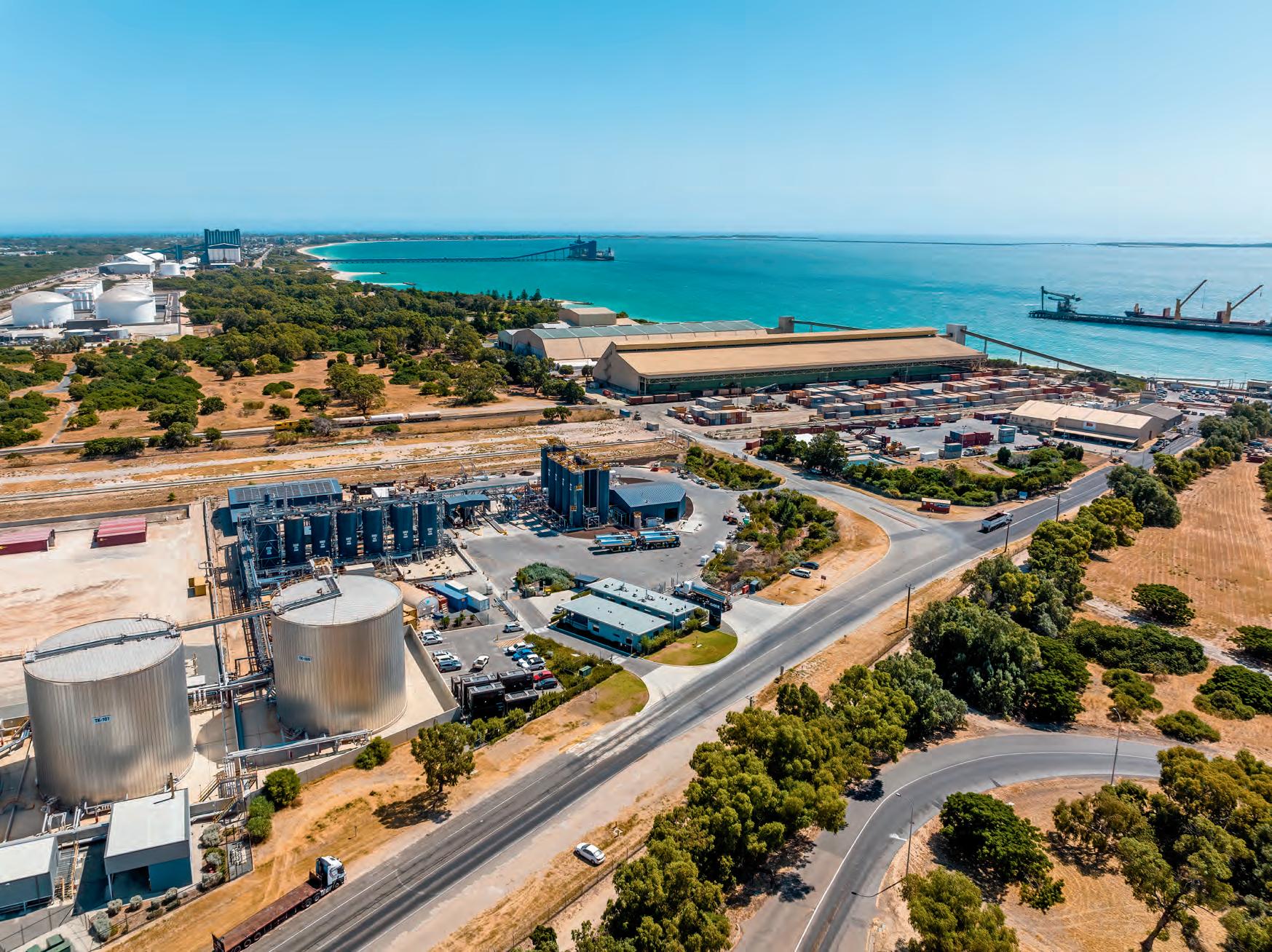
FORGING NEW PATHWAYS
The story behind the first female CEO in the geotechnical and civil construction material testing industry in Australia
How the NTRO is shaping the future of sustainable infrastructure
The story behind the first female CEO in the geotechnical and civil construction material testing industry in Australia
SAMI Bitumen Technologies has outlined the road that needs to be taken to heighten the quality of Australia’s road network
14 The choice of resilient pavement
How SAMI Bitumen Technologies’ is supporting the development of sustainable roads.
18 We asked the industry’s decisionmakers, ‘What are the challenges for greater use of recycled materials in roads and pavements?’
20 Revealing the Riverlink
Uncovering the sub-surface elements of one of New Zealand’s largest every infrastructure projects.
23 Forging new pathways
Dawn Watt’s story and how she’s helping to forge more pathways for women in the industry.
26 A crucial connection
Madison Express is eyeing the infrastructure sector as its next big venture.
29 Family first
Peter Knight reflects on the threegeneration long ownership of Flocon Engineering.
32 Setting the standard for sustainability
The organisation behind the guidelines and specifications for sustainable product development.
35 Recycled tyres for sustainable roads
A collaborative project has uncovered a new alternative for asphalt production.
38 Proof is in the pavement
A new asphalt additive has proven to deliver better performance, sustainability and lower costs.
40 Put to the test
Recent trials have put the PGXpand polymeric-additive to the test.
45 Aiding a global movement
Viva Energy is working to further develop alternative and sustainable fuels.
48 A sustainable and renewable cleaner
The Recosol 195 renewable plant-based performance fluid is being used in a variety of applications.
50 Navigating machinery claims
Tips and tricks to aid the insurance claim process for machinery coverages.
53 Packing a punch
How New Zealand’s first telescopic sprayer is making a splash in Australia.
56 Answering the call for transport solutions
A range of heavy haulage equipment has been designed to cater for the toughest conditions.
59 The all-round paver
Two generations of operators in a local asphalting business have been united in their use of Astec machinery.
62 The premium circle
More about John Deere’s ‘Premium Circle’ option and what it provides.
64 Energised by ZenergiZe
Inside CEA’s low emission and electric range of equipment.
66 Green electricity driving forward
How Komatsu machinery is helping to provide performance and environmental benefits.
68 Inside Construction Expo
Roads & Infrastructure provides a sneak-peek into this year’s Inside Construction Expo.
70 No-Dig Down Under 2023
What to expect from the highly anticipated No-Dig Down Under Conference.
72 Quantifying the circularity of materials
The importance of the Materiality Circularity Indicator in assessing the sustainability of different applications.
75 Managing risks
AfPA provides their insight into the dangers of Respirable Crystalline Silica and the preventative measures that can be taken.
77 A sustainable milestone
An overview of works on the Koo Wee Rup Bypass project.
78 Contracts in brief
Roads & Infrastructure provides an update on some of the contracts and tenders recently awarded or put to market across the infrastructure sector.
4 Editor’s letter
6 News
AS I DISCOVERED THROUGHOUT this edition of Roads & Infrastructure Magazine , sustainability is so much more than a buzzword for the construction and infrastructure sectors.
Driven by the Federal Government’s target to achieve net zero emissions by 2050, industry has been keen to play its role by incorporating environmentally friendly alternatives, such as low-emission technology and recycled materials.
As we learn in the September edition, companies employing sustainable techniques, material sourcing and manufacturing are benefitting from cheaper, efficient and socially responsible business practices.
For this month’s cover story, we speak with SAMI Bitumen Technologies to hear how the company is pushing to leave a sustainable legacy on the industry. SAMI CEO Sebastien Chatard speaks of the company’s efforts to influence a brighter future through community engagement, as well as looking at potential improvements within the business itself.
Viva Energy is similarly seeking to leave a positive impact on the environment for the betterment of future generations through its development of low-emission and alternative fuel sources such as hydrogen, electric and solar energy. We speak with a core member of the company’s ‘Carbon Solutions’ team that’s dedicated to the development of such technologies, to find out what’s on the horizon for sustainable fuel development.
The National Transport Research Organisation (NTRO) is playing a pivotal role in forging pathways for the use of sustainable products. Through the development of its performance guidelines, as well as collaboration with both private industry and government, the NTRO has helped to validate and specify the use of recycled materials like plastic, recycled glass, reclaimed asphalt pavement, concrete, crumb rubber and more.
In this month’s Roads Review column, we hear from some of the industry’s key decision makers on overcoming the challenges for greater use of recycled materials in roads and pavements.
Finally, we also provide previews of upcoming conferences in 2023, with plenty of opportunities on show for government and industry.
Happy reading!
COO
Christine Clancy christine.clancy@primecreative.com.au
GROUP MANAGING EDITOR
Sarah Baker sarah.baker@primecreative.com.au
MANAGING EDITOR
Mike Wheeler mike.wheeler@primecreative.com.au
EDITOR
Tom O’Keane tom.okeane@primecreative.com.au
JOURNALIST
Chris Edwards chris.edwards@primecreative.com.au
DESIGN PRODUCTION MANAGER
Michelle Weston michelle.weston@primecreative.com.au
ART DIRECTOR Blake Storey DESIGN
Bea Barthelson
BUSINESS DEVELOPMENT MANAGER
Brad Marshall brad.marshall@primecreative.com.au
CLIENT SUCCESS MANAGER
Salma Kennedy salma.kennedy@primecreative.com.au
HEAD OFFICE
Prime Creative Pty Ltd 379 Docklands Drive, Docklands VIC 3008 Australia p: +61 3 9690 8766 f: +61 3 9682 0044 enquiries@primecreative.com.au www.roadsonline.com.au
SUBSCRIPTIONS
+61 3 9690 8766 subscriptions@primecreative.com.au
Roads & Infrastructure Australia is available by subscription from the publisher. The rights of refusal are reserved by the publisher.
ARTICLES
All articles submitted for publication become the property of the publisher. The Editor reserves the right to adjust any article to conform with the magazine format.
COPYRIGHT
Tom
O’Keane Roads & Infrastructure MagazineRoads & Infrastructure Australia is owned and published by Prime Creative Media. All material in Roads & Infrastructure Australia is copyright and no part may be reproduced or copied in any form or by any means (graphic, electronic or mechanical including information and retrieval systems) without the written permission of the publisher. The Editor welcomes contributions but reserves the right to accept or reject any material. While every effort has been made to ensure the accuracy of information, Prime Creative Media will not accept responsibility for errors or omissions or for any consequences arising from reliance on information published. The opinions expressed in Roads & Infrastructure Australia are not necessarily the opinions of, or endorsed by the publisher unless otherwise stated.
Five new trams have arrived for the Gold Coast Light Rail Stage Three expansion in Queensland, as works progress on the $1.2 billion project.
The project is delivering a new 6.7-kilometre extension of the existing public transport network and will feature eight stations, the addition of the newly delivered trams, as well as dual track in the centre of the Gold Coast Highway.
The project will aim to reduce travel times, increase the efficiency of the network and increase accessibility. The upgrade will also help to increase capacity along the network.
The five new trams will feature enhanced accessibility elements, including double accessible spaces, braille signs, 20 priority seats on every tram and vertical handrails have been
shifted to create wider passageways for wheelchairs, prams, walkers and other mobility aids.
They will now undergo testing before being absorbed into the current operational fleet.
Major construction on the third stage of the project is progressing as
John Holland upgrade and relocate underground utilities. Track laying will commence in 2024, with these works expected to be completed in 2025. The project is being delivered by both the Queensland and Federal governments, as well as the City of Gold Coast.
Major construction works are now underway on the METRONET New Midland Station in Western Australia, which will replace the ageing station infrastructure with a modern facility.
The project will build a modern, three-platform station between Helena and Cale streets, bringing it closer to the heart of Midland’s town centre and improving connectivity to Midland Gate
Shopping Centre and Midland Health Campus. The new station will include a 12-stand bus interchange, a multi-storey car park with more than 800 parking bays, and secure bike parking.
Initial works will concentrate on building the car park, which has necessitated the closure of the western end of the station’s existing passenger car park. The car park on Railway Parade to the east of Helena Street will also close to facilitate construction of the new station.
The project is being delivered by the Midland Junction Alliance McConnell Dowell Constructors, Georgiou Group, Arcadis Australia Pacific and BG&E.
Once rail services are moved to the new station – expected to occur in early 2025 – the existing 55-year-old station will be decommissioned and demolished.
The $330 million New Midland Station project is jointly funded by the Federal and State governments.
In this game, there’s no substitute for experience. But finding expert Motor Grader operators can be tougher than the terrain they’ll be tackling. That’s why John Deere is the only player in Australia to be offering Motor Grader automation upgrades to all machines from 2019 onwards. Spec’d out with the latest tech including Machine-Damage Avoidance, Auto-Articulation, Auto-Pass, Auto-Shift Plus, and Blade Stow, less experienced operators can get to grips with the machine double quick, and takes the pressure off your more experienced hands. Take your operation to a whole new level. Check your serial number with your local dealer, today.
Heavy vehicles working on the first stage of the Mickleham Road Upgrade in Victoria will be the first in Australia to benefit from new safety technology.
The new MAX-SAFE technology has been installed in some heavy vehicles being used on the road project – with trials of the audible and flashing light alert system to help reduce the likelihood of injuries and deaths associated with heavy vehicle movements.
Automatic detection systems have been installed inside these heavy vehicles to alert the operator within the cabin that a vulnerable road user, such as a pedestrian, cyclist or scooter rider is in the vicinity – in particular during left-hand turning manoeuvres.
Powered by an artificial intelligence based smart camera, this Side View technology as part of the MAX-SAFE system is specialised in detecting specific vulnerable road users, and not other objects or obstructions.
Electronic flashing lights and alarms will initiate inside and outside the vehicle, providing the crews who are operating
The new technology aims to increase the safety of nearby bystanders to heavy vehicles. Image courtesy of the Victorian Government.
heavy vehicles and machinery the advanced warning they need to assist with avoiding an unexpected collision with a vulnerable road user. It also acts to alert those outside of the vehicle.
Without intervention, pedestrians, cyclists and scooter riders could be at a heightened risk of entering a heavy vehicle operator’s blind spot. Instead this system aims to negate this risk and maintain a form of visibility, especially during left hand turns.
The ground-breaking system trial is the result of collaboration between Major Road Projects Victoria, construction partner BMD and SGESCO-MAX, to find new ways to reduce the likelihood of safety incidents with members of the public during construction. Success of the
new technology will be closely monitored and evaluated.
The safety trial is part of Stage One of the Mickleham Road Upgrade, which is building extra lanes in each direction on Mickleham Road between Somerton Road and Dellamore Boulevard, along with new traffic lights, intersection upgrades, and better walking and cycling connections.
The Mickleham Road between Somerton Road and Dellamore Boulevard is used by more than 25,000 vehicles each day and is a key arterial route for Melbourne’s growing north-west.
The Victorian and Federal governments have invested $222 million for the Mickleham Road Upgrade. Stage One of the project is expected to be complete in mid-2025.
Early works are now underway on the first stage of the New Richmond Bridge project in New South Wales which forms part of a $500 million program for traffic improvements in the area.
Investigation works and the relocation of utilities have kicked off for the project, that aims improve safety, flood resilience and cater for future traffic growth.
This will be achieved by upgrading a 3.8 kilometre section between Londonderry Road and Blacktown Road. These upgrades will improve ‘the Driftway’, an approach road to the New Richmond Bridge that will help to redirect traffic from the Richmond town centre.
Preparations for Stage Two continue to progress, with the contract now awarded
for consultants to prepare the concept design and environmental assessments. Site investigations for Stage Two are now underway, with a concept design and environmental assessment expected to be on display in mid-2024.
Stages One and Two will upgrade four intersections, improve existing roads, construct a new road, as well as provide a dedicated active transport path between Richmond and North Richmond that will encourage bike use and exercise.
Introducing the first and only skid steer with a telescopic boom the JCB Teleskid; a truly unique, versatile skid steer with endless possibilities. Now you can lift higher, reach further, dig deeper.
Introducing the first and only skid steer with a telescopic boom the JCB Teleskid; a truly unique, versatile skid steer with endless possibilities. Now you can lift higher, reach further, dig deeper.
This revolutionary product is designed to suit all types of job sites meeting the need of multiple machines wrapped nicely into one. Combining the strength and safety of our single side boom with side door entry and extendable boom JCB has increased the versatility of the SSL-CTL world.
This revolutionary product is designed to suit all types of job sites meeting the need of multiple machines wrapped nicely into one. Combining the strength and safety of our single side boom with side door entry and extendable boom JCB has increased the versatility of the SSL-CTL world.
To find out more contact your local JCB CEA dealer today. Ph: 1300 522 232
To find out more contact your local JCB CEA dealer today. Ph: 1300 522 232
www.jcbcea.com.au
www.jcbcea.com.au
The longest green track in Australia is being used to provide a sustainable alternative for the first stage of the Parramatta Light Rail project in New South Wales.
Stage One of the Parramatta Light Rail will connect Westmead to Carlingford via the Parramatta CBD and Camellia with a two-way track spanning 12 kilometres, and is expected to open in 2024.
The green track features grass and vegetation, and has been applied between and along 930 metres of rail tracks, reducing concrete by 81 per cent compared to a standard concrete embedded track form.
Compared to a concrete-embedded track form, the green track absorbs heat reducing the air temperature in the area, minimises noise and glare,
Geotechnical drilling has commenced ahead of major construction later this year on the 15-kilometre M1 Pacific Motorway extension to Raymond Terrace in New South Wales.
Th extension of the M1 will aim to improve traffic flow and increase connectivity to support the growing region.
In December last year the Federal and New South Wales governments announced John Holland Gamuda Australia Joint Venture as the successful contractors for the southern contract, which is a 10-kilometre section that extends from Black Hill to Tomago.
Seymour Whyte Constructions were also announced as the successful contractors for the northern contract, which is a five-kilometre section that bypasses Heatherbrae.
This comes as works begin on the Hexham Straight Widening project that will transform a six-kilometre section from two lanes to three in each direction, improving traffic flow for the 50,000 motorists and freight vehicles who use this route daily.
filters stormwater, reduces flooding and encourages biodiversity.
The grass species chosen for planting in the green track was selected through a 12-month study and trials that compared grasses to the rate of growth, climate suitability, growth height and species’ lifespan, amongst other characteristics. Following the study, ‘Nara’ Zoysia was selected, a native species to Australia.
SAMI BITUMEN IS CEMENTING ITS PLACE AS AN INNOVATOR IN ROAD RESILIENCY AND SUSTAINABILITY ACCORDING TO DR. HAMIDREZA SAHEBAMANI –TECHNICAL SERVICES MANAGER.
nfrastructure Australia’s defines resilience as communities that “have the ability to resist, absorb, accommodate, recover, transform and thrive in a timely, effective manner in response to the effects of shocks and stresses to enable positive economic, social, environmental and governance outcomes.”
There are two terms in this definition to understand: shocks and stresses.
Shocks are sudden disasters like storms, floods, earthquakes, and fires that cause immediate damage.
Stresses are long-term issues, like aging infrastructure or rising sea levels, that gradually weaken systems over time. These shocks and stresses are happening more frequently and severely due to climate change.
According to Advisory Paper One by Infrastructure Australia in June 2022, the cost of natural disasters in Australia is expected to more than double by 2050. It will increase from around $18 billion per year to over $39 billion annually. These numbers show how much money natural disasters could cost in the future and highlight the need for measures to increase resilience.
Roads and airports are some of the most important pieces of infrastructure, especially during times of disaster. They play a vital role in connecting people and places, enabling essential assistance and support.
Resilient roads include various features across different aspects, including geometric design, elevation, location, and subgrade properties. Another crucial aspect is the road pavement which carries the traffic load.
The concept of resilient pavement has gotten significant attention and discussion
among industry professionals, owner agencies, and academics.
The majority of Australia’s heavy-duty pavements are constructed using asphalt, known for its strength, flexibility, durability, and rapid repair capabilities to withstand varying conditions and recover swiftly from unexpected events. Although the resilient features of asphalt pavements are inherent, they are often not viewed through the lens of resilience by typical pavement engineers and designers.
Examples of these resilient features include quick constructability for responding to disaster damage, component materials with climate adaptability, asset strengthening through stage construction, utilisation of sustainable technologies to increase haul distances and insitu recycling of reusable pavement materials, mixtures designed to store and infiltrate stormwater, mitigating flooding risks and the use of EME2 structural asphalt to future-proof pavements.
Traditional pavement design relies on historical climate data to anticipate local temperature ranges and precipitation patterns.
However, shifting climate trends, evolving rain events and the escalation of extreme weather occurrences challenge the validity of this approach.
It becomes evident that various pavement distresses are closely tied to climatic parameters when analysing the influence of temperature, precipitation, and sea-level rise on pavement performance and service life. Beyond pavement potholes, varied environmental conditions lead to an array of distresses including cracking, rutting, shoving, and corrugation – each governed by temperature variations. Similarly, subsurface moisture variations affect rutting, cracking, and load-bearing capacity, while precipitation fluctuations impact the pumping of fine materials which weakens the base.
Drought can also lead to shrinkage and significant deflections (ground subsidence) in certain types of soils. This phenomenon is currently quite prevalent in some countries, where the water table is receding, resulting in frequent reports of substantial sinkholes appearing.
On the contrary, long periods of drought
can lead to reduced pavement maintenance requirements due to less damage from moisture.
Significant future trends influencing pavement performance encompass temperature-related factors like elevated temperatures, increased extreme temperature events, heightened frequency and duration of extremes, and reduced freezing days.
Additionally, precipitation-induced impacts entail shifts in average annual precipitation –resulting in wetter winters and drier summers in some regions and vice versa in others –alongside intensified precipitation intensity. Furthermore, rising sea levels and associated phenomena like flooding, groundwater elevation, and saltwater intrusion contribute to the complexity.
Elevated average temperatures yield consequences such as enhanced rutting and shoving potential, necessitating rut-resistant asphalt mixtures through adjustments in bitumen grade, polymerisation, and aggregate structure. Likewise, addressing bitumen aging requires the adoption of age-resistant binders and increase utilisation of surface preservation techniques. Concurrent drought situations amplify the risk of subgrade shrinkage and exacerbate asphalt rutting and shoving during heat waves, underlining the need to revise historical binder grade selection criteria.
The effects of precipitation on pavement components are multifaceted.
Enhanced surface friction necessitates attention to texture, skid resistance, cross slope, and porous surface mixtures to mitigate water spray. Whereas expanded surface drainage requirements warrant increased capacity for ditches, culverts, and elevated pavement sections.
Here optimal subdrainage design, installation, and maintenance are imperative. Elevated precipitation jeopardises embankment stability, structural capacity reduction of unbound bases and subgrades during inundation highlights the need for in-depth understanding and mitigation strategies.
Moisture susceptibility mitigation measures for unbound base and subgrade materials are necessary and enhanced pavement drainage at the surface and subsurface levels requires implementation of various strategies.
SAMI offers a variety of products and solutions that play a significant role in enhancing the resilience of road pavements.
Hybrid modification of bitumen is a concept that involves incorporating two or more additives and polymers with different properties into the bitumen.
This is done to harness the beneficial properties of each component. SAMIfalt I-Brid is a high-performance hybrid-modified binder that exemplifies resilience in flexible pavement construction. It combines the advantages of both elastomeric and plastomeric modified binders.
The performance grading of this binder is PG88-28. This designation indicates its ability to withstand extreme temperatures, making it resilient to unexpected climatic shocks and stresses. SAMIfalt I-Brid can effectively endure thermal fluctuations that occur between day and night, as well as summer and winter conditions.
In addition, it exhibits a higher modulus than normal elastomer-modified binders, particularly at elevated temperatures. This characteristic alleviates concerns about
potential structural capacity issues in hot climatic conditions in the future.
The moisture sensitivity of this modified binder is lower compared to conventional elastomeric and plastomeric modified binders. This property renders it suitable for application in very wet conditions. SAMIfalt I-Brid also boasts superior rutting resistance and fatigue performance when compared to conventional plastomer and elastomermodified binders. Furthermore, it exhibits fuel-resistant properties.
Stabilising granular base courses is one of the solutions to enhance the resiliency of pavements. This process reduces the susceptibility of pavements to the effects of fluctuations in the water table. Additionally, it improves the impermeability of the pavement structure. Special emulsions, formulated by SAMI, are utilised for treating the base courses.
The stiffness modulus of this mixture is higher compared to other forms of treated bases, resulting in a reduced final pavement thickness. This reduction contributes to lowering greenhouse gas emissions, energy consumption, and the use of raw materials.
A recent study, which was presented at the second AustStab conference in August 2023, highlights that the utilisation of Emulsiontreated base (ETB) and foam-treated base (FTB) can lead to a substantial reduction in pavement thickness.
Specifically, in the case of very high-traffic roads, employing ETB has the potential to decrease pavement thickness by 43 per cent, while FTB can achieve a reduction of 36 per cent.
Moreover, adopting these treatments has a
positive environmental impact, as greenhouse gas (GHG) emissions are projected to decrease by 44.1 per cent for ETB and 31.0 per cent for FTB when compared to conventional designs that rely on granular base course.
Enhancing temperature susceptibility is a critical attribute for resilient pavement, as roadways must now endure more pronounced climatic shocks and stresses than ever before.
SAMIfalt Multigrade Plus is an unmodified multigrade bitumen that boasts a significant advancement in temperature susceptibility when compared to standard bitumen. This solution is accurately engineered to improve crack and rut-resistance, ensuring enhanced durability over time.
One of its standout advantages lies in its ability to exhibit heightened stiffness at operational temperatures and lower stiffness at low temperatures, coupled with remarkable resistance to stripping. These qualities have made SAMIfalt Multigrade Plus the preferred binder for the intricate project of Sydney Airport taxiway rehabilitation projects.
The improved cohesive properties inherent in SAMIfalt Multigrade Plus have also
rendered it exceptionally effective for runway rehabilitation endeavours, exemplified by its successful deployment at the HMAS Albatross military base in Nowra, New South Wales. Moreover, SAMIfalt Multigrade Plus has earned a reputation as the binder of choice for Brisbane City Council, which prioritises its utilisation for maintaining its expansive road network due to its cost and versatility.
Ensuring a proper seal on the base courses is essential to render the granular layers impermeable from surface water. This aspect becomes particularly critical in situations where the risk of damage arises due to water penetration into the granular layers.
SAMI offers a range of products to address this, such as the SAMIfloat, a polymermodified cationic high-float emulsion with a substantial residual binder content.
This emulsion is applied to create various types of seals, such as primerseal, graded seal, Otta seal, and spray seals. The gel-like structured thick binder covers the entire aggregate surface, even in dusty conditions, eliminating the need for pre-coating the aggregates. The high residual content of
the emulsion minimises the runoff while maintaining sufficient flexibility to prevent brittleness in cold conditions.
In addition to SAMIfloat, the SAMIflex E range offers polymer-modified bitumen emulsion. This emulsion contains SBS-modified binders as its base bitumen. Utilising these binders in spray sealing applications brings several advantages.
This approach reduces the negative environmental impact, as there is no longer a need for kerosene. Furthermore, it eliminates risks and hazards for users.
Making resilient pavement requires utilising the full capacity of the pavement layers, which rely on ensuring their unified integration. This integration is essential for treating the pavement layers as a unified, monolithic structure.
To achieve this, it is vital to have a reliable high-performance tack or bond coat. This type of bond coat ensures the secure attachment of all pavement layers, even under prolonged stress conditions.
SAMIbond 007 is a high-performance polymer-modified, trackless tack coat specifically designed to serve as a binding layer, effectively uniting all pavement layers. Notably, the bonding shear strength offered surpasses that of conventional tack coats. Furthermore, its trackless properties play a pivotal role in maintaining the proper placement of bitumen particles throughout the construction stage, which means preventing the pickup of bitumen because of sticking to the truck and paver tyres. With specialised products, SAMI offers solutions for making and preserving resilient pavements and plays a pivotal role in protecting the infrastructure against deterioration and enhancing sustainability. By offering versatile solutions that not only improve pavement performance but also contribute to reduced environmental dependency, SAMI helps shape the future of resilient transportation systems.
• A Pathway to Infrastructure Resilience –Advisory Paper 1, Infrastructure Australia, August 2021
• Resilience Principles, Infrastructure Australia, June 2022
• Resilient asphalt pavements, NAPA, October 2022
• Boosting pavement resilience, Public roads, FHWA-HRT-19-001,
For over 60 years we have only had one thing in mind: making measured values ever more precise. But we also never lost sight of the need for human values, too. By combining these it makes a remarkable radar level sensor possible. The best value there is: VEGAPULS 6X.
DR M. REZA HOSSEINI, SENIOR LECTURER, DEPUTY DIRECTOR, MEDIATED INTELLIGENCE IN DESIGN (MIND) RESEARCH LAB, SCHOOL OF ARCHITECTURE AND BUILT ENVIRONMENT, FACULTY OF SCIENCE ENGINEERING & BUILT ENVIRONMENT – DEAKIN UNIVERSITY
A significant obstacle to the broader adoption of secondary materials and products in the Australian construction industry is the absence of a quality assessment scheme that can determine the suitability of such items for design purposes while complying with building codes and standards. This lack of a system discourages designers and contractors from using secondary materials due to potential risks and liabilities. As a result, they tend to opt for virgin products where the risk is perceived to be lower. Therefore, the urgent need for a secondary material accreditation scheme is paramount to mitigate risks and encourage the use of such materials by designers and contractors.
ANNA D’ANGELO, EXECUTIVE DIRECTOR TECHNOLOGY & LEADERSHIP – THE AUSTRALIAN FLEXIBLE PAVEMENT ASSOCIATION
The situation may vary for each State in Australia, however one of the challenges is related to the availability of good quality and consistent supply of the recycled material and in some cases the lack of a developed supply chain. The other issue is related to the current definition of waste and its reuse, which in some states is subject to strict EPA regulations limiting the capacity to recycle materials. Additionally, some specifications may not allow or limit the amount of recycled materials and lastly, local asphalt plants configuration might not be able to include recycled materials and, although contractors could upgrade their facilities, this would require the need of market demand to justify the investment.
CAMERON
Ensuring that the recycled materials meet the required quality and performance standards for road construction can be a challenge. Variability in the composition and characteristics of recycled materials may affect the structural integrity and durability of the roads. The absence of standardised guidelines and specifications for using recycled materials in roads can hinder their widespread adoption. Establishing clear guidelines is essential to provide confidence to road builders and regulators about the suitability and safety of recycled materials. More research is needed to explore the performance of different types of recycled materials and their long-term behaviour under various traffic and environmental conditions. Despite these challenges, there is an increasing awareness of the benefits of recycling and sustainable construction practices. As technology and infrastructure continue to evolve, some of these challenges may be addressed, paving the way for greater use of recycled materials in roads and
Key challenges to the uptake of recycled materials in roads for designers include a low familiarity of available materials, negative perceptions or lack of awareness and a risk averse mindset. A further challenge is a lack of consistency across the country around regulations on the use of recycled products and in some cases, a lack of stable supply. To pave the way forward, recycled materials and circular resource practices must be integrated into engineering design practices. This requires collaboration between government agencies, designers, engineers, construction professionals, the recycling industry, and researchers to increase awareness and confidence in materials.
There’s an immense opportunity to create lasting value from resources, by utilising recycled materials in our built environment. Sustainability Victoria is partnering with councils to do this through its Buy Recycled Service. While the use of recycled materials in roads is widely adopted by Victorian councils, the sector can further strengthen markets by designing products for disassembly to be reused at end of life, boost local supply and provide further information on end-of-life recyclability, long-term performance, and lifecycle analysis. Additionally, standards that allow for a higher proportion for the use of recycled materials, supported by performance testing, provide a solid foundation to advocate for their use.
ecologiQ has seen great progress in the use of recycled materials in road and pavement construction, however it hasn’t been without its challenges. Barriers to the use of recycled or reused materials can be perceived or real. Some of the barriers we have come across include misconceptions about the quality of recycled products, inconsistent and lengthy approval processes and prescriptive technical standards that don’t allow for recycled products. The ecologiQ program has been instrumental in addressing these challenges by updating specifications, investing in research and educating industry on what is possible. But there is still more to be done and we need to work together.
If you or someone at your organisation is an industry leader and would like to be a part of this monthly column in 2023, please get in touch with Editor, Tom O’Keane: tom.okeane@primecreative.com.au
efore now, the infrastructure sector’s lack of knowledge regarding subsurface utilities was often a pain point.
Utility strikes have caused unforeseen delays and damage, so much so that typically 20 per cent of associated costs for infrastructure projects are set aside to cater for related issues with unforeseen subsurface conditions (per Reveal).
Sam Clive, Reveal’s Head of Delivery, says the company’s process helps to take the guesswork out of this potential headache.
“We do large-scale data conflation and investigations to create a three-dimensional model, which can be used right from the preliminary phase to the conceptual phase, so they can have the most accurate and complete information possible to design the project appropriately,” Clive says.
As experts in subsurface utility engineering, locating and surveying, Reveal utilises a variety
of technologies to uncover the truth when it comes to the subsurface.
“We used the same concept for the Riverlink project,” Clive says.
“We’ve done some of the largest utility mapping projects on the planet. So we were able to give them a methodology for a very large 3D model and we were able to do so in a three-to-four-month timeframe.”
Riverlink is a collaborative project between the Greater Wellington Regional Council, Hutt City Council, Waka Kotahi New Zealand Transport Agency, iwi mana whenua Taranaki Whānui ki te Upoko o te Ika (Taranaki Whānui), Ngāti Toa Rangatira (Ngāti Toa), and the AECOM-Fletcher alliance.
The project aims to increase flood resiliency, support urban growth and provide better transport solutions throughout the region of Lower Hutt (just northeast of Wellington) by delivering a holistic package. This includes infrastructure development and transport improvements on a large scale.
“We were engaged by the project funders in early 2023 to create what they referred to as a base utility model that they could hand over to the design engineering alliance prior to them starting their works on the project,” Clive says.
REVEAL’S WORK ON NEW ZEALAND’S RIVERLINK PROJECT HAS VALIDATED THE IMPORTANCE OF AN INCREASED UNDERSTANDING OF UNDERGROUND UTILITIES FOR INFRASTRUCTURE PROJECTS. SAM CLIVE, REVEAL’S HEAD OF DELIVERY, TAKES ROADS & INFRASTRUCTURE INSIDE THIS VENTURE.An artists impression of the proposed infrastructure development of Lower Hutt, as part of the RiverLink project. Image courtesy of Te Awa Kairangi.
“They wanted the engineers and contractors, when they came on board, to have some form of a model that they could use to start works immediately.”
The proposed utility engineering works required accurate subsurface data; therefore, the first step was to collate information that had already been gathered by utility owners.
“This approach has been refined by Reveal, and not many other firms do it this way,” Clive says. “The way that we like to approach the first step is to compile all existing records in one place to look at what we have.
“We go through the process of extracting and transforming that information into a consistent database that digitises and georeferences all the PDF plans. From there we can go through a phase of verifying and correcting the data, because some of these records can be inaccurate, whether it be the wrong location or depth.”
Clive says the next step is known as ‘aerial picking’, a process of evaluating aerial imagery of objects such as chamber lids, cabinets, valve covers and more. This information is then overlayed with existing records to paint a more accurate picture.
The third phase of the process features the use of ground-penetrating radar. This
technology uses radar pulses to create an accurate image of subsurface utilities and “unknowns”.
This technology is towed behind a vehicle at night, thus minimising impacts on local businesses and the community – prerequisites that were outlined in the proposal phase.
“Minimising disruptions is really a key driver of what we do. People want to minimise the number of disruptions, which ultimately ties back to our service. Unknown subsurface utilities and consequently, utility strikes can create significant losses,” Clive says.
“With the technologies that we’re adopting as a firm, we try and be as non-invasive as possible. Rather than leaving permanent markings, we capture and digitise our records. That way we don’t have to do rework and that extends to our clients. They won’t need to do rework and create more disruptions for traffic in their projects for example.”
In order to also cater for both budget and time constraints, both Reveal and the project stakeholders went for a broad stroke approach. Instead of concentrating on a specific section, this model provided a wider overview for works on Te Awa Kairangi ki Tai.
“Using our software and the initial model that we created, the idea is that [Waka Kotahi] will be able to do more investigations over time and improve it as part of a risk-based approach,” Clive says.
“So instead of throwing every tool out for every square metre of the project, we can create a base model for the whole project. Then they can understand where the risk lies.”
for these changes to occur.”
Clive adds that the model used for this project can cater for infrastructure projects of varying scope and scale.
“It fits within whichever [project] phase that you’re in. Whatever budget you’ve got, or risk approach you take, there’s something for everyone,” Clive says.
He says the Riverlink is a “great example” of this collaborative process.
“It shows that they’re progressive. They’ve been incredibly supportive of our ability to test the status quo; to do something innovative. They’ve been willing to invest to solve what could potentially become an issue,” Clive says.
As one of Australia’s largest construction materials testing providers, we’ve been delivering testing services to the transport infrastructure, public utility, residential and commercial development, oil and gas, and mining industries for over 60 years.
We have an extensive network of permanent and site-specific testing facilities located across Australia, including in some of Australia’s most remote locations.
Dawn Watt is a trailblazer within an industry that is one of the single most male-dominated sectors nationally.
Presenting at the recent Women and Construction breakfast for the Queensland Major Contractors Association, Watt described her journey, as well as the defining moments that made her into the leader and woman that she is today.
In her position at Coffey Testing, Watt is aiming to ensure that meaningful
change can lead to more opportunities and greater diversity within construction.
Born in Canada, Watt grew up in a regional town of just 700 people. As she recalls, the example set by her mother played a large role in her foundational years.
“It meant learning how to change a tyre or changing the oil in my car. It also meant taking some responsibility for the household and my younger brother
whilst my mother pursued her career as a Chemical Engineering Technologist, working in oilfields in Texas and the Gulf of Mexico,” she says.
“I didn’t realise it then, but she would be my first female role model.”
Despite having an early passion for science, Watt’s first exposure to the industry came in 1996 when she began working as a Construction Materials Technician.
Even though she was one of the few women in concrete testing, Watt says
Coffey Testing has more than 60 years’ experience in aggregates and concrete testing.
she never considered herself to be different or in the minority. Instead, she rightfully saw herself as just another employee.
“I was one of the few females doing this work. However, I had never felt like being the only female made me different. I never considered myself a female tech. I just considered myself a tech,” she says.
Watt’s journey in Australia began in 2001, when she started working for what was then Coffey Geosciences. She says the differences between Australia’s and Canada’s Construction Materials Testing industries was glaring, particularly when it came to the culture and working environment.
“They didn’t know me, and I didn’t know them, but I was going to make sure that I advocated for myself. I proudly described my successes over the past eight years, letting them see my passion and knowledge of the
business and the construction industry,” she says.
“I boldly told them the way to increased profitability could only be done under my leadership. Unsolicited, I presented them with reports full of data to back up my claims.”
After arriving in Australia in 2001 Watt had already accumulated 15 years worth of experience when Coffey Testing was bought. Six months after that she was appointed the role of CEO, making her the first female CEO in the Geotechnical and Civil Construction Material Testing industry in Australia.
Three years later, in 2019 she also became an owner, following the company’s separation from Tetra Tech.
Watt now leads one of the nation’s largest construction materials testing services. The company has more than
60 years’ experience in aggregates and concrete testing, as well as 25 laboratories nationwide.
During this period Watt has overseen systematic change throughout the organisation to create a greater platform for female representation, even within her own team.
“As the owner and CEO of Coffey Testing, I have taken strides to improve gender diversity in my company. In 2003 I was the only female technician in the company,” she says.
“As of today, Coffey Testing has 40 female lab employees, six of whom are in positions of management across 12 labs, and of my senior leadership team, 40 per cent are women.”
But she isn’t done yet, with an exciting future ahead for the company and the industry.
“It’s an extremely important industry to the economic health of Australia and I am so proud to be a part of it,” she says.
She says that for fellow females who are aspiring to enter or advance careers in the construction sector, the first step it to say yes.
“I had been told by my mother when I was younger, don’t say no, give everything a try,” she says.
“Believe in yourself, challenge yourself, seek to teach yourself, and conquer your fears by saying yes.”
And for the wider industry, the benefits are clear, she says.
“Men and women naturally have different points of view and approaches to problem solving that come from different life experiences. This can lead to creativity and innovation, something that many construction companies are looking for to increase productivity and efficiency,” she says.
“Equality in the workplace will be achieved when more women start applying for roles in every sector of the Construction industry.
“Employers, colleagues, spouses, the industry, and academic institutions need to be supportive of women striving to be employed in these exciting roles.”
“AS OF TODAY, COFFEY TESTING HAS 40 FEMALE LAB EMPLOYEES, SIX OF WHOM ARE IN POSITIONS OF MANAGEMENT ACROSS 12 LABS, AND OF MY SENIOR LEADERSHIP TEAM, 40 PER CENT ARE WOMEN.”
THROUGH ITS PEOPLE FOCUSED APPROACH AND EMPHASIS ON QUALITY, MADISON EXPRESS HAS ELEVATED ITSELF AS ONE OF THE PREMIER PROVIDERS OF FIBRE AND TRAFFIC CABLING FOR INFRASTRUCTURE PROJECTS. CHIEF EXECUTIVE OFFICER STEVE MANNION EXPLAINS HOW.
Underground utilities are often an underthought or underappreciated aspect of road and infrastructure development. This includes electric, telecommunications and data cables.
For years, Madison Express’ name has been associated with commitment and quality. The Australian owned and operated business offers a variety of cable and connectivity solutions, with a range of products for communication and industrial applications.
Madison Express is now looking towards new horizons.
The company’s entry into the infrastructure space has been years in the making, but as CEO Steve Mannion explains, the firm is well equipped to push the envelope in fibre, instrumentation and traffic cabling.
“Roads and infrastructure are part of our strategy going forward. There’s obviously a lot of growth across the sector,” he says.
“What makes us different is that we’ve got an expert technical background. We have the ability to design and develop products to suit our customer’s needs. We’re also quick to respond, which means there’re more opportunities for us to provide a range of bespoke products to suit a wider range of applications.”
Despite its focus on the development and distribution of products suited to the cabling, networking, wireless, telecommunications and infrastructure sectors, Madison Express has always highlighted the importance of people. Not only in creating desirable outcomes for product development, but also helping to shape the future of infrastructure for generations to come.
“I absolutely love it when our engineers get to speak to the customer’s engineers. It’s transparent. It’s factual. It helps us to come to a solution that everyone understands,” he says.
“Then we see our cable go into a large infrastructure project. That’s a fantastic outcome and that’s what really excites me.”
This passion extends to the company’s
commitment to quality.
Mannion says close engagement with both government bodies and private industry has helped Madison Express to cater its products specifically for market, implementing feedback to improve its range over time.
“Over the years we’ve worked with lots of different organisations and project bodies, for example Transport for New South Wales for works on the Sydney Metro Project or large integrators for the Metro Trains project in Victoria,” he says.
“The business that we’re in is very much about forming strong relationships. It’s a two-way trust and trust is in our DNA.”
Another example is the company’s works on the Cross River Rail Project in Queensland. The project will consist of a new 10.2-kilometre rail line from Dutton Park to Bowen Hills, which includes 5.9
standards,” Mannion says.
“We were notified by the cable specifier and regulator that we were the only supplier to meet these standards. In the first stage we supplied 30 kilometres of cable, which will be used in Wooloongabba station. This is the first of six stages and form part of the underground station security infrastructure.
“We have already received our next order for this project.”
Through Madison Express’ own brand Garland, the manufacturer has provided both road and rail cables for infrastructure projects of varying scales.
These cables assist with vehicle detection, as well as multi-cored feeder cables to support multi-lane intersections to be wired more efficiently. The company can also build custom designs for special
changes for projects.
“For lots of these infrastructure projects, some requirements can be well-planned, but there can also be some last-minute changes that require urgency,” he says. “We have the ability to go and meet with our customers face to face to address their needs quickly.”
“We’re very transparent and proficient in providing that information.”
By tailoring these options to suit, Mannion adds that Madison Express is helping to set a standard for future fibre and traffic cabling applications.
“What often happens is that we design a cable to suit an application and that cable becomes a mainstream product going forward,” Mannion says.
This includes different colours and structures, as well as qualities for specific requirements, such as fire resistance. Each cable then enters a quality assurance and testing process that consists of both internal and external trials.
“I think the testament in our quality is that people seek us out. Our Garland brand has been going for over 45 years, and we spend a lot of time and effort to make sure that the cables we supply are of the highest quality to suit any given
“That
really easy to sleep
Madison Express is currently considering more opportunities across the infrastructure sector. Mannion says the company sees a “huge opportunity” in related infrastructure for both roads
“We’re heavily moving towards a complete solution, making sure that we can provide the customer with a complete end-to-end solution, where it makes
“These things take time and money, but the fact that we’re constantly looking at bringing in new products shows that we’re committed to our customers.”
“THREE CUSTOM SECURITY CABLESWERE DESIGNED BY OUR MEX STAFF TO SUIT CRITICAL AND STRINGENT DESIGN STANDARDS. IN SHORT, THE CABLES HAD TO MEET UP TO SEVEN DIFFERENT CONSTRUCTION AND PERFORMANCE STANDARDS.” Madison Express Chief Executive Officer Steve Mannion. Madison Express is targeting the infrastructure sector as a new opportunity for its high-quality fibre and traffic cabling solutions, such as its Garland Vehicle Detector Cable MC7052JFSTD.
FLOCON ENGINEERING’S HISTORY IS SURPASSED ONLY BY ITS DEDICATED FAMILYORIENTATED OWNERSHIP, WHICH NOW SPANS THREE GENERATIONS. FORMER EMPLOYEE PETER KNIGHT TAKES ROADS & INFRASTRUCTURE INSIDE THE BUSINESS’ EARLY DAYS.
The road equipment manufacturer has three generations worth of ‘Knight’s’ to show for it.
Now retired, former Company Director Peter Knight began his tenure at Flocon Engineering more than four decades ago. As a young mechanic making his way through the industry, Knight serviced trucks that came through what was then known as Flow Controlled Transport.
Peter, under his father and mother Jim and June Knight who started Flocon, and along with his brother Steve, contributed to the initial growth of the company. Peter Knight’s contributions were particularly impactful for the company’s success in expanding to Brisbane.
Relatively inexperienced in the sector, Peter Knight made his way across to Queensland. What was initially supposed to be a 12-month trip slowly turned
across the industry.
Knight’s stint in Queensland would endure for another seven years, turning into a self-sustaining expansion site for the company.
“Now we’ve got several depots in different states that just do servicing and spare parts. Nearly all of it used to be done out of Melbourne,” he says.
Flocon has been building and supplying its diverse range of road maintenance equipment to the market since Jim Knight started the business in the early 1970s. It was a family affair since day one, with Peter and Steve following in his footsteps – working and eventually succeeding him as heads of the company.
The first unit was manufactured in 1975, with the first asphalting patching unit being delivered to Moorabbin City Council in 1982.
This was a key milestone for the business, which would soon eye further expansion interstate, as well as the international markets.
A key step was establishing suitable infrastructure and skilled personnel to allow the business to design, develop and deliver its own products, through its own facilities.
“We used to work on 10 trucks at a time maximum. They’re now working on more than they ever have. There used to be ebbs and flows outside of busy periods, but now it’s constant,” he says.
“We do our works in-house now, instead of using sub-contractors.”
Knight says that while the technology and processes may have changed over time, the company and his family’s desire for quality has never dwindled.
“There’s a real passion in the family to support one another,” he says. “Sometimes you hear in other companies that the third generation usually says ‘bugger it’ [to joining the business]. The third generation has come in and they’re so passionate to
grow the company ever further.”
This generation consists of Peter Knight’s children Ryan and Melissa, as well as his niece Simone and nephew Rory, the current Director of Flocon Engineering.
Peter Knight says a passion “for the tools” is consistent across all three generations.
“I was a young man from a mechanical background, [Dad] learnt on the tools early on and Rory has a diesel mechanic background,” he says.
“For me, the whole business is for the family.”
So is the commitment to Flocon Engineering’s customers.
“Someone once told me that you can’t make money from friends, but when you spend your life doing this, you get to have great relationships with customers,” he says. “I’m still friends with a few of my long-time customers. All it took was time and dedication.”
Knight jokes that modern technology has altered the ability to establish meaningful relationships with customers.
similar principles. This is reflected in the company’s customer relations, as well as the development of its equipment.
“We’ve always built products for what the customer wants and needs, not just what we want,” he says. “We still do that, and I think that comes from being a family-owned business; everyone is connected to every single product.”
“[The team] is very personable, eager, professional and passionate. They’ve been given the reins and they know what they’re doing. I trust them.”
“Rory’s very personable. He’s a great listener and he has the freedom to try new ventures.”
One such venture was the company’s development of its new forwardmoving aggregate spreader. A machine that Knight says was years in the making.
Despite retiring a few years ago, Knight says he still remains in contact with the Flocon Engineering team on a consultation basis. Although he missed it at first, Knight says he knows that the company is in good hands.
With Reveal, you can eliminate subsurface risks, deliver infrastructure projects faster and minimise cost blow-outs and variations.
If you need to understand your underground, get in touch with the world’s leading subsurface experts.
ORGANISATION (NTRO) AND
ARRB HAVE HELPED TO INTRODUCE PRACTICAL, SUSTAINABLE ALTERNATIVES TO VIRGIN MATERIALS FOR MAJOR INFRASTRUCTURE COMPONENTS. NTRO TAKES US INSIDE THIS RESEARCH AND OUTLINE WHAT’S TO COME.
In 2020/21, Australia generated an estimated 75.8 million tonnes of waste, equivalent to 2.95 tonnes per person. The biennial 2022 National Waste Report found that Australia’s recycling rate remains stagnant at 60 per cent.
The National Transport Research Organisation (NTRO), previously known as the Australian Road Research Board (ARRB), has had a lasting impact on the development and use of sustainable materials throughout the roads and infrastructure sectors.
NTRO has validated the use of recycled materials like plastic, recycled glass, recycled concrete and brick, reclaimed asphalt pavement, concrete, crumb rubber, recycled solid organics and other recycled roads.
NTRO also works with all levels of government as well as industry, as part of its role to refine and update industry specifications for the use of recycled and sustainable materials.
As NTRO’s Sustainability and Materials Performance National Leader, Dr Clarissa Han oversees and advises the delivery of research and practical work into recycled or alternative materials. She says the NTRO plays an invaluable role in promoting the use of recycled materials.
“We’ve been researching sustainable options since we started. We are a thought leader in Australasia across the innovative material science space,” she says.
“The vision for sustainability and materials performance is to accelerate the transformation of Australia to a circular economy. Our focus has been on increasing the use of recycled and upcycled materials to support the sustainability and resilience of transport infrastructure.”
The resilience aspect also ties back to performance. In part due to NTRO’s research, many recycled materials can now perform as well as, if not better than their virgin material counterparts.
By using current sustainable materials, contractors and asset owners can help to increase the resiliency, durability and chance of road failure across Australia’s road network, while also helping to reduce the volume of material being sent to landfill.
An aspect where NTRO plays an integral part.
“We offer quite a wide spectrum of services, knowledge and solutions. We develop standards and specifications, which we constantly review. These provide solutions for developments such as noise
walls made out of recycled plastic, recycled plastic pipes and more,” Han says.
“We also have the national materials laboratory that’s national standard lab and NATA accredited. We do a whole spectrum of testing services for our aggregates, binders, asphalt.
“We offer the commercialisation pathway for emerging industry products to be applicable to the transport infrastructure sector. We also give supporting services like
a lifecycle evaluation, environmental impact assessments and legislation analysis.”
NTRO also undertakes a thorough approvals process to ensure that its specifications are both accurate and appropriate.
“For the development and publication of these specifications there’s quite a rigorous process to help the end user. It always goes through a review of both domestic and international best practice against existing specifications,” she says.
“There’s reflection, consultation and a couple of rounds of reviews.”
Dr Han says the persistence and hard work of NTRO has been a contributing factor in helping to influence the industry’s culture and perspective on recycled materials.
“Even a couple of years ago, there was this kind of conservative culture. But I’m impressed by the way people are learning and accommodating sustainability,” she says.
“More often than not in this sector you’ll find that community and industry move faster than government. Our role is really to connect the forefront of research with an understanding from key stakeholders.
“Their understanding of this knowledge is very important. That’s why we go through this testing, evaluation and trial process to help collect evidence and present it to them. That’s the most satisfying part of this whole process.”
One of NTRO’s key projects has been research into the re-use of plastic and its implementation into infrastructure components.
A report last year from NTRO provided insight into the potential for one of Australia’s most problematic waste streams. Per NTRO’s research, plastic can be used across a variety of applications for building both road and rail infrastructure.
Principal Professional Dr James Grenfell’s work as part of the SMP team, as well as collaborative projects with the National Asset Centre of Excellence and the Western Australian Road Research and Innovation Program has helped to further investigate the potential of this material.
He says the first big milestone for the NTRO team was the involvement of state government departments and subsidiaries.
“We were looking at implementing recycled plastics into transport infrastructure in a safe and sustainable way,” he says.
“We have done quite a bit of work with Major Roads Project Victoria (MRPV), helping them to develop fit-for-purpose, performance specifications to be used in certain applications. That way if anyone can design a recycled plastic product that can meet the performance requirements, then there’s a clear pathway to these products being used.”
MRPV’s interactions with NTRO led to the development of a performance-based technical specification for noise walls implementing recycled plastics.
“The use of recycled plastic in transport infrastructure has expanded away from just asphalt and bitumen modification to ancillary devices like noise walls, safety barriers, pipes and more,” Grenfell says.
“You name any product; chances are we’ve looked into it to see what could be done in Australia from either a manufacturing or recycled plastics processing perspective. Then it’s also essential to understand what the potential barriers could be to implementation, such as a lack of specifications or a lack of knowledge.”
Dr Grenfell says the team at NTRO are always looking for ways to change specifications to encourage greater
recycled plastics from being used.
“DTP’s Chief Engineer wanted us from the outset to develop a specification with a view of it becoming an Australianwide specification, not just a Victorian specification,” he says.
Shortly after, Grenfell and his team received word that other state departments were interested in the newly formed specification.
“WE OFFER QUITE A WIDE SPECTRUM OF SERVICES, KNOWLEDGE AND SOLUTIONS. WE DEVELOP STANDARDS AND SPECIFICATIONS, WHICH WE CONSTANTLY REVIEW. THESE PROVIDE SOLUTIONS FOR DEVELOPMENTS SUCH AS NOISE WALLS MADE OUT OF RECYCLED PLASTIC, RECYCLED PLASTIC PIPES AND MORE.”
innovation, while accelerating the use of recycled materials.
“Sometimes products don’t fit within a certain specification, even though they meet the performance requirements. A lot of old specifications can be very prescriptive,” he says.
MRPV implemented noise wall structures containing recycled plastic content on the Mordialloc Freeway. These were a proprietary product, where industry had innovated to allow recycled materials to be used, whilst still meeting the desired requirements.
However, the newly implemented noise walls did not meet the current specifications, which were very prescriptive and did not allow recycled plastics to be used. MRPV had the desire to use the product more readily, but needed a specification to allow them to do so. NTRO was then engaged by MRPV to develop a performance-based specification
“Other road agencies that were working with plastics said that as long as there was a quality output, they would likely adopt [the specification] as well. It was a sign that our expertise was being recognised.”
This specification has now been approved and published on the Austroads website as ATS 4450 and is free to download.
Another example where NTRO is working in the recycled plastics space is assisting with the implementation of recycled plastic and composite rail sleepers in Australia. These are designed to replace regular timber and concrete sleepers. In the case of timber sleeper replacement there is the possibility to extend their lifecycle by three to four times.
NTRO’s journey is just beginning, with a variety of projects and developments already underway. This includes ongoing bids and investigations into new specifications and guidelines.
alternative to fine ground limestone in asphalt. It helps to reduce the reliance on mining natural resources and the carbon emissions associated with the extraction of virgin materials and the production of asphalt.
Over time, the availability of ground limestone and filler materials has depleted in cities like Melbourne due to the increased, long-term demand for its growth and infrastructure needs.
Therefore, the cost and cartage requirements to attain these limited, carbon-heavy, natural resources has increased.
By replacing fine ground limestone with rCB the carbon emissions of asphalt production can be significantly reduced.
Alex Fraser’s Asphalt GM Brendan Camilleri says the possibility of developing a new high-recycled product utilising a priority waste stream like tyres was an enticing prospect.
“Alex Fraser first began innovating with recycled materials derived from tyres in 2021. We retro fitted our Narangba asphalt plant to operate utilising tyre derived fuel oil – an alternative fuel supply made from end-of-life tyres in place of fossil fuels. That’s when we discovered that another end-of-life tyre byproduct could be used as a filler substitute in asphalt production,” he says.
“Alex Fraser’s Sustainability Charter drives our focus on innovating heavy construction materials to incorporate priority recycled content.”
According to Tyre Stewardship Australia (TSA), Australia generates around 459,000 tonnes of waste tyres annually. Thanks to the support of both government and private industry, as well as development by companies such as Alex Fraser, approximately 70 per cent of these waste tyres are recovered (per Tyre Stewardship Australia).
Alex Fraser’s expertise and eagerness to develop sustainable solutions for the betterment of the industry has led to the development of TyrePave rCB (Recovered Carbon Black), one of its newest innovations in tyre recycling.
The Pound Road West Upgrade was the first Victorian major project to trial the use of rCB, a recovered carbon product made from endof life tyres used as a carbon saving substitute for limestone needed to produce asphalt.
‘rCB’ has been engineered to be a sustainable
The ‘Recycled Tyres for Sustainable Roads’ project represents a collaboration between Alex Fraser, Seymour Whyte Constructors, Major Road Projects Victoria, ecologiQ, NTRO (National Transport Research Organisation), TSA and Entyr – the accumulation of many months of research, planning and innovation.
Camilleri says that Alex Fraser embraced the support of its industry partners.
“The Pound Road West trial is a great demonstration of what can be achieved in infrastructure sustainability when our industry’s innovators work together.”
“A key focus of the collaboration was ensuring alignment with the specifications and registration for the new asphalt mix.”
Camilleri says that without this registration, the mix would not be acceptable for use in the major road network.
As such, Alex Fraser and its partners completed thorough testing and trialling of the product against a set of key criteria.
This included material compliance, bitumen performance characteristics, stripping potential,
A COLLABORATIVE VENTURE HAS LED TO THE DEVELOPMENT OF AN ALTERNATIVE FOR ASPHALT PRODUCTION IN VICTORIAN ROADS. ROADS & INFRASTRUCTURE SPEAKS WITH ALEX FRASER, ECOLOGIQ AND ENTYR TO LEARN MORE.
as well as rutting and cracking resistance.
“In innovating infrastructure sustainability, our key driver is to ensure that our products are infinitely recyclable. Our roads are not rubbish tips,” Camilleri says.
Our recycled materials must meet the highest quality standards and be perpetually recyclable.”
As part of a TSA-funded research program, the NTRO and Entyr – an end-of-life tyre innovator – investigated the effects of adding one per cent of rCB (by mass) into an asphalt mix.
ecologiQ also played a key role in progressing the trial.
Alexis Davison, Executive Director Engineering and Program Services, Major Road Projects Victoria, says working with project teams early helps to maximise opportunities to integrate recycled materials into the design of road projects.
“ecologiQ started working with the Pound Road West Upgrade project team in 2021 during the planning for the project,” Davison says.
“As part of our role, we held a series of workshops with the team to identify opportunities to optimise the use of recycled and reused materials on the project. One of the opportunities identified was to conduct a trial of a new sustainable asphalt product.”
A 500-metre section of the Pound Road West Upgrade is the first Victorian road to be built with a high-recycled content ‘Green Roads’ asphalt mix containing rCB.
Wearing course works were completed at night to minimise disruption and to improve rideability, a shuttle buggy enabled longer, uninterrupted runs; achieving a superior pavement with minimal construction joints.
Alex Fraser completed the remaining asphalting works with its Green Roads Construction Materials products, containing up to 40 per cent recycled content.
It is estimated that using Green Roads Construction Materials on this project has helped reduce carbon emissions by 291 tonnes. Davison says such projects work to encourage innovation to accelerate greater acceptance of sustainable materials.
“The recent trial on the Pound Road West Upgrade is a great example of how government, projects and suppliers are collaborating to look at innovative ways to transform waste into a resource and work towards a greener infrastructure future,” she says.
“Following the successful trial, we are now looking to develop a new specification for this material to enable wider use.”
Camilleri believes the trial validates the use of rCB as a potential solution for the wider industry, for its performance and environmental benefits, but also long-term reductions in environmental impacts.
“We are pleased with the performance of the rCB used in place of naturally extracted fillers in the trial section of Pound Road West Upgrade,” Camilleri says.
Works on the upgrade were completed in June this year, ahead of schedule. The upgrade is expected to reduce congestion, improve traffic flow and safety for pedestrians and cyclists, while providing enhanced connections for the community.
Gary Foster, Entyr CEO says the company was delighted to provide technology and recycled products to the project.
“Using Entyr’s recovered carbon black and tyre-derived fuel oil in the creation of asphalt avoids the use of virgin resources and creates a superior asphalt proven in both laboratory tests and road use,” Foster says.
The end result for Pound Road West will be a measurable improvement in safety and sustainability.”
Camilleri says the collaborative nature of the project, as well as the successful trials are a standout example of creating positive change in infrastructure sustainability.
“By recycling tyres into asphalt we’re collectively combatting the global challenge of tyre waste. rCB has the potential to substitute 100 per cent of extracted fillers,” he says. “We are confident that this finished pavement will prove to be a durable and long-lasting road that provides exceptional ride-ability and improved sustainability outcomes.”
ON TOP OF PROVIDING SUSTAINABILITY BENEFITS, CLOSE THE LOOP’S TONERPLAS ASPHALT ADDITIVE HAS PROVEN TO DELIVER BETTER PERFORMANCE, LOWER CARBON FOOTPRINT AND LOWER WHOLE-OF-LIFE COSTS THAN STANDARD ASPHALT ROADS. ROADS & INFRASTRUCTURE LEARNS HOW.
different types of plastics and toner. It took quite a long time to try all of these different ingredients while also aiming to optimise performance. We tried a few different iterations.”
This led to the development of TonerPlas’ predecessor.
“We had a product called TonerPave that was really the precursor to all of this,” says Henderson. “It was quite reasonably successful, but the market was mostly unaware at the time about recycled toner, they didn’t realise that toner could be recycled.
“[Close the Loop] started with soft plastics from the REDCycle Group. They melted that with toner, and it produced some great results. We had our first trial for the Hume City Council where we put in down on the first road and that was a great success.”
Persistence was key for Henderson and Morriss as they eventually broke into the market.
“We managed to get into the Victorian State Government, which was aided by ecologiQ. They saw an opportunity and facilitated conversations with the Department of Transport to listen and work with us,” he says.
“We went through that process and [TonerPlas] eventually ended up going into the M80 and Monash Freeways. Those were the first two projects and it’s been in numerous since. So far around the country, we’ve laid about 420,000 tonnes of product.”
The TonerPlas additive has been designed to melt into a bituminous binder and the asphalt mix. This helps to enhance the performance properties of the asphalt, increasing the durability, water and rut-resistance while also providing a sustainable alternative.
Close the Loop’s founding ‘zero waste to landfill’ brand promise, and a healthy dose of determination, laid the groundwork for the creation of what would become an award-winning asphalt additive.
Staff from sustainable solution provider
Close the Loop deeply characterised waste toner powder and travelled the world looking for recycling solutions before one trip to the United States, where they learned the potential for waste printer toner, a material that contains a high-grade polymer, to improve the resilience and performance of asphalt.
After developing an initial product and proposal, Close the Loop went door knocking. This led to a fateful conversation with asphalt and road maintenance provider Downer.
Graham Henderson, Manager Pre-Contracts and Development – Downer Group, says the initial proposal was enticing, in part due to the aspirations and passion of Steve Morriss, the Founder of Close the Loop.
“From Downer’s perspective there was sort of a light bulb moment, I guess you could say. We knew this was something that we needed to get behind,” Henderson says.
Then began development and trials, testing the products applicability in a variety of binders, mix designs and conditions.
“Steve Morriss and his team worked closely with our research and development department. It’s been a long time in development. I’d say it took about 10 years to achieve,” he says.
“[Close the Loop] did a lot of work with
This is thanks to the recycled content, comprising toner from end of life print consumables such as toner cartridges, bottles and waste hoppers. Mixed post consumer soft plastic packaging waste and even recycled oil form part of Close the Loop’s patented formulation as well.
As Close the Loop Founder and Head of Circularity Steve Morriss recalls, the basis and foundation of TonerPlas’ success was centred on validating its quality and performance, instead of its obvious sustainability benefits.
Polymers have been used to improve the performance of the world’s best roads for over 50 years. TonerPlas is an extension of that knowledge, just using recycled polymers.
“The whole-of-life carbon footprint of the road is significantly reduced by the use of TonerPlas,” he says. “There’s also reduced whole of life costs, because you’ve got that
“In the case of TonerPlas, there can be misconceptions and prejudices. For some people, as soon as you mention recycled, they think back to a time when recycled meant poor quality. TonerPlas’ performance is backed by independent science and we are now working with experts to accelerate improved materials circularity as well.”
This quality was validated during Close the Loop and Downer’s works on the M80 Freeway project and hundreds of council roads before that.
“The M80 project used TonerPlas in a middle layer, a large volume of asphalt. We were able to save the Victorian State Government money as we were using a C320 binder, compared to a C600. TonerPlas performed better than the C600 binder, which is more expensive and more refined,” Morriss says.
“For TonerPlas to be part of a mix design approved by the Victorian Department of Transport and Planning with strong commitment to innovation and recycled content by CPB Contractors, was a significant milestone on this shared journey to low carbon asphalt.
“It proved there is only upside to using this product.”
Morriss reaffirms the importance of Downer’s contributions to the development and use of TonerPlas, saying the company opened new doors for the Close the Loop team.
“The partnership with Downer has been pivotal. Back in the day I was getting some mixed receptions and scepticism. I finally knocked on Downer’s door and the relationship really took off,” he says.
“They’re a top-tier asphalt company in this
has never been an asphalt company, but we’re manufacturers of additives. We didn’t have the equipment or personnel to test the asphalt itself. We were able to evaluate the performance characteristics and improvements in a multitude of different binders and under a range of conditions.
“Between us we’ve laid thousands of kilometres of roads across every state in the country. It’s an awesome relationship but does not exclude Close the Loop working with any contractor or asphalt company. Downer wants this technology to grow just as much as we do.”
Morriss is similarly appreciative of ecologiQ’s contributions, saying the collaboration is a great example of circularity in action.
“There’s no doubt that we wouldn’t be where we are today if it wasn’t for the foresight of the Victorian Government to create [ecologiQ]. They recognised that you can have product stewardship programs, but unless someone is facilitating use of the resultant recycled materials and breaking down barriers, it won’t succeed,” he says.
Alexis Davison, Executive Director Engineering and Program Services, Major Road Projects Victoria says ecologiQ is committed to the advancement of products that can utilise Victorian priority waste streams and work toward a circular economy.
“It’s been amazing to witness the growth in the use of recycled materials across major transport projects since the Recycled First Policy was introduced. It’s helped to drive market demand and encouraged suppliers to innovate,” Davison says.
“These projects have not only considered the environmental benefits when choosing to use recycled products, but have also looked at the performance, quality and whole-of-life costs of these products.”
Close the Loop is set to increase its manufacturing capacity for products such as TonerPlas, with proposals being finalised for the expansion of the company’s current infrastructure.
“The future for us is about thinking global but acting local, making and using TonerPlas with local waste and local jobs. We see a future where TonerPlas is used in all new asphalt roads in Australia,” Morriss says.
Close the Loop’s work in this space has also helped to increase awareness around the recyclability of print cartridges. The ‘Cartridges 4 Planet Ark’ program, co-created with Planet Ark, sees Close the Loop collect, recycle and recover these products and materials as part of its zero waste to landfill promise.
This initiative has collected and recycled over 56,000,000 cartridges since its creation 20 years ago. Close the Loop is now the largest collector and recycler of end of life imaging supplies in the world.
Morriss says the appetite for low carbon, high performing asphalt solutions is there. Now the challenge will be catering for the growing market demand.
“That’s happening at a rate we believe requires us to decentralise and ramp up our technology and manufacturing capabilities. The key now for the industry is going to be balancing the ability to manufacture with the growth in demand,” he says.
SRIPATH TECHNOLOGIES’ PGXPAND® POLYMERIC ADDITIVE HAS BEEN PUT TO THE TEST, WITH RECENT TRIALS EVALUATING ITS PERFORMANCE IN HOT SPRAY SEAL APPLICATIONS. ROADS & INFRASTRUCTURE LEARNS THE OUTCOMES OF THESE TRIALS, AS WELL AS THE IMPLICATIONS FOR THE ROAD CONSTRUCTION SECTOR.
The bitumen additive market has grown exponentially throughout the past 20 years.
Developments in technology, as well as a renewed focus on improving the sustainability and performance of pavements, has accelerated the procurement of additives that improve performance of bitumen and asphalt mixes.
One such product is Sripath Technologies’ PGXpand.
PGXpand is a bitumen-friendly polymeric-additive, specially designed to increase the performance attributes of bitumen and asphalt mixes, especially when it comes to the overall durability in paving applications.
Ravi Rajagopalan, General Manager,
Sripath Asia-Pac says the product has already been used across a variety of applications.
“In Australia, our customers are using PGXpand for hot asphalt mixes, hybrid PMBs, hot spray seal, and high stiffness applications,” Rajagopalan says.
Recent trials on the Melba Highway in Dixons Creek, Victoria, put PGXpand to the test.
Deepak Madan, the company’s Chief Marketing & Business Development Officer, says the trials evaluated the potential for the product to be used Australia-wide.
“PGXpand has been tested, vetted and used worldwide since 2016.
We have repeat customers in the USA, Canada, India, Australia, and the Middle East. Customers in New Zealand, South Africa, and Europe are in final stage of approval,” Madan says. These trials also aimed to evaluate the performance of PGXpand with crumb rubber in hot spray seal applications.
The trial, which was conducted in collaboration with the Victorian Department of Transport and Planning, was largely hailed as a success across a number of key criteria.
Conducted in March this year, this trial utilised a 500-metre stretch of road. The hot spray seal was used across two lanes on what is a frequently trafficked section, with up to 5000 vehicles using the connection daily.
A two coat 14/7 spray seal was specified for this road which consists of two through lanes and shoulders.
PGXpand plus crumb rubber was used in the first binder coat in the shoulder. This sprayed so well that the
PGXpand and crumb rubber was added to the binder for the seven millimetre binder coat over the full pavement width
Rajagopalan says the trial aimed to show how PGXpand could be used in Australian conditions while applying local methods.
“They blend it at around 180-200 degrees centigrade and then it’s ready to be sprayed. First they spray the modified bitumen on the road and add the first layer of aggregate. Then, they spray another layer of modified bitumen and lay a finer aggregate on top to create the second layer,” Rajagopalan says.
“Department of Transport and Planning was looking for improved performance. Therefore, they wanted to try PGXpand.”
Class 170 bitumen was combined with 18 parts crumb rubber. This “recipe” was used for the main lane trial as part of the first layer, as well as the full width of the road in the second layer. The second coat also featured one per cent PGXpand.
For the first layer on the road shoulder, the recipe differed slightly, this time with 10 parts crumb rubber and 0.8 per cent PGXpand.
The bitumen in the tanker was maintained at a constant temperature of around 200 degrees Celsius. The final, polymer-modified bitumen was digested for 20 minutes and kept at a temperature of 180 to 185 degrees
Halligan was present at the Department of Transport and Planning trial of PGXpand. He says that apart from beneficial attributes in the softening point and viscosity, the visual performance of the product also stood out.
“I could see that we were getting better spray performance than our earliest sprays. When the PGXpand wasn’t being used I could see a bit of tram tracking,” he says. “When we sprayed with PGXpand, any evidence of tram tracking was gone.”
Halligan believes the results of the trial show the potential for PGXpand to be used nationwide.
“One of the biggest learnings from the trial is that the product can be applied anywhere in Australia where the product can be blended on site.”
Sripath Technologies’ PGXpand is an environmentally sustainable product, resulting in lower GHG gas emissions and lower energy consumption. It boosts the high temperature performance, the paving grade and the softening point. It also delivers excellent rutting resistance.
Kate Brough, Director Digital Marketing, says these are just some of the many products that make up the suite of Sripath Technologies’ sustainable products.
“Sripath strives to develop and market environmentally friendly products such
Celsius. Then finally, the spraying was done at a temperature between 175 to 180 degrees Celsius.
Steve Halligan, Director of Road Surfacing Solutions, says these trials can give the industry confidence that this product could be applied on more heavily trafficked sites.
“When I was initially presented with the results and I looked at the increase in the softening point and changes in viscosity, I just thought ‘no way’. I thought that wasn’t how [similar additives] normally behave,” he says.
“But I was wrong by a country mile.”
as PGXpand, NuMIXER, and ReLIXER. These versatile and sustainable additives help lower the carbon footprint, reduce greenhouse gas emissions, and decrease energy consumption,” Brough says.
Through international research and development, these products are well suited for use in Australian applications.
“It’s also exciting to have the unique properties of PGXpand to deliver solutions for Australian issues,” Brough says. “It’s even more gratifying for us that people are now beginning to accept the material and understand its virtues, while thinking about it within
“ONE OF THE BIGGEST LEARNINGS FROM THE TRIAL IS THAT THE PRODUCT CAN BE APPLIED ANYWHERE IN AUSTRALIA WHERE THE PRODUCT CAN BE BLENDED ON SITE.”
the context of what they have to deal with on a day-in, day-out basis.”
Rajagopalan witnessed the trial on behalf of Sripath. He says the support of Department of Transport and Planning was absolutely pivotal to the success of the trial.
“It was very satisfying to not only deliver the conceptual underpinnings of this trial, but also to have a customer run a trial that was nearly flawless,” he says.
RMIT (Royal Melbourne Institute of Technology) University was also a key supporter of both the development and the trials.
Filippo Giustozzi, Associate Professor – Civil and Infrastructure Engineering, says development on such a product was sparked through demand from both industry and government.
“Department of Transport and Planning aimed to improve the high temperature performance of their standard products in use, which is sprayed seal that only includes crumb rubber. Past applications of this product have highlighted issues of flushing and softening of the seal, especially during the summer season. Therefore, DTP VIC asked for a new product that
could modify the high temperature properties of their standard sprayed seal with crumb rubber but without compromising on the viscosity,” Giustozzi says.
“At the time RMIT University was currently conducting research activities on behalf of Sripath on a novel polymeric material – PGXpand –that has the ability to boost the high
between the aggregate and the binder was improved, hence suggesting greater durability of the sprayed seal compared to the standard DOT practice. The application in the field went smoothly and the operators did not have to adjust the sprayer and/or the spraying temperature after the addition of PGXpand.”
These benefits are also reflected in the versatility of the product. So much so, that operators don’t need to make any changes to their equipment and processes.
“Those small additions of the right polymer can significantly increase the service life of our sprayed seal roads. All without the need for new equipment or drastic operational changes,” Giustozzi says.
As part of the trial, PGXpand was successfully field blended into the bitumen along with the crumb rubber. Crews also found the PGXpand with PMB blend was easy to spray, as Rajagopalan explains.
“There were no issues, it went over very well and seamlessly,” he says.
“Professor Filippo looked at various percentages of crumb rubber and PGXpand and discovered during this investigative phase that PGXpand is actually able to enhance the adhesion of the binder to the rock.”
“I’m very optimistic and enthused as we can offer a hot spray option that
“SRIPATH STRIVES TO DEVELOP AND MARKET ENVIRONMENTALLY FRIENDLY PRODUCTS SUCH AS PGXPAND, NUMIXER, AND RELIXER. THESE VERSATILE AND SUSTAINABLE ADDITIVES HELP LOWER THE CARBON FOOTPRINT, REDUCE GREENHOUSE GAS EMISSIONS, AND DECREASE ENERGY CONSUMPTION.”
temperature performance without modifying the final viscosity of the binder.”
He says the performance of the product outweighed expectations.
“The product performed in the field exactly as it did in the laboratory at RMIT University during the experimentations. The high temperature performance was improved without compromising on the final viscosity of the binder, which remained unchanged after the addition of one per cent PGXpand,” Giustozzi says.
“We also found that the adhesion
can help to reduce temperatures and environmental impacts, while at the same time delivering a much higher performing roadway. It’s very exciting,” Rajagopalan says.
Following the success of the trials, Sripath Technologies is hoping to conduct further tests before seeing a wider rollout of products across Australia and New Zealand.
“We’re really excited, not just about the trial, but what it portends for us in various states. We’re now exploring New South Wales, Western Australia and Queensland,” Rajagopalan says.
Rodent attack is a major problem for optical fibre cables installed underground in unsealed or non-metallic conduits.
Garland’s new GLT-AZB series offers the protection needed for your next Fibre Optic installation. Designed in Australia, the GLT-AZB series has undergone and passed rigorous testing.
o For use in ducts or direct burial applications
o Non-metallic design suitable for use near power cables and in areas of high lightning strike rates
o Available from fibre counts of 6 up to 144
o C omplies w ith T MR Q ueensland r equirement
Garland has been manufacturing quality cables for over 45 years. We’re owned, made and distributed by Madison Express, so get in touch with our friendly team for bespoke solutions and quality cable, made to last.
Over the last 20+ years, we’ve listened to our customers’ feedback and continuously evolved our range of sprayers, meeting the specific and unique demands of the Australasian roading market.
From our highly manoeuvrable 4.5m telescopic urban sprayers right up to our 6.0m reseal sprayers we have the right sprayer for the job – all offering the ease of use and efficiency of our telescopic spray bar.
Find out today why operators across Australia and New Zealand are ditching fixed wing sprayers and demanding SRE’s range of telescopic bitumen sprayers.
www.specialisedroadingequipment.com
Email info@specialisedroadingequipment.com
Ph +64 7 848 1197
ince records began in 1880, the Earth’s temperature has risen every decade. The rate of warming has more than doubled since 1981 (NOAA Climate.gov).
And as of 2022, the global economy is consuming 70 per cent more virgin materials than the world can safely replenish (RECYCLING Magazine).
Global policies, such as the Paris Accord and Australia’s own commitment to reduce emissions by 2030 have created change.
Robert Cavicchiolo, Viva Energy – Carbon Solutions, says this journey is very much in its infancy.
Viva Energy is the Shell licensee in Australia
and one of the nation’s largest suppliers of fuels for a diverse range of sectors.
Cavicchiolo is a part of Viva Energy’s Carbon Solutions team, a department whose focus is to help customers decarbonise their operations through the development and distribution of low-carbon alternative fuels.
He says that despite the establishment of global and domestic policies, more is required to stem the impacts of global warming and climate change.
“Companies have made commitments such as being net zero by 2050 but have also set some interim targets to reach before 2030 or even earlier,” Cavicchiolo says.
“For our customers, their biggest generator of emissions can be the use of diesel, so we realised that we’ve got a responsibility to provide pathways for our customers to help them address that over time.”
It was this ethos that led Viva Energy to look internally and realise the potential for alternative and low-carbon fuels to reduce –and in some cases even eliminate – impacts on the environment.
“We realised that we were an important part of that journey and that we had to look at providing innovative solutions and products that allow businesses to utilise low carbon, or potentially zero-emissions technologies, in the marketplace,” Cavicchiolo says.
He adds that this push from industry led to the creation of the department that he is now part of.
“Particularly in the last four years, we’ve seen rapid change,” he says. “Which is why we set up a new team called Carbon Solutions, which is essentially there to address this issue and help our customers along their decarbonisation journey.”
One way that Viva Energy is helping its customers to reduce their environmental impact is the development of ‘opt-in’ carbon neutral products. These products are Climate Active certified and a voluntary option. Cavicchiolo says these products enable
he says. “You’re using carbon credits to offset those emissions associated with the combustion or utilisation of those fuel sources.
“Offsetting should be used after companies have investigated other ways to avoid, reduce or eliminate their carbon emissions. We realise that customers might want to start that journey straight away and that’s one of the easiest ways customers can start that process.”
Viva Energy’s Geelong Energy Hub forms part of this vision. The potential projects under this proposal include a gas terminal and a solar energy farm, as well as developing Australia’s first publicly accessible service station that offers electric vehicle recharging and hydrogen refuelling for heavy fuel cell electric vehicles.
The ‘New Energies Service Station’ will be located in close proximity to the Energy Hub.
Viva Energy also has plans in place to develop infrastructure to support the utilisation of used cooking oil, animal fats and components from plastic waste that would otherwise end up in landfill. These alternative feedstocks will be blended with crude oil to reduce the carbon intensity of fuel produced at the refinery.
Viva Energy has also set its own decarbonisation agenda with commitment to achieve net zero for Scope One and Two emissions across its retail, fuels and marketing departments (all non-refining parts of the
On top of developing infrastructure for sustainable fuels like hydrogen and electric, Viva Energy is also investing in bringing to market a range of drop-in fuels such as biodiesel.
These ‘FAME’-based biodiesel blends will likely form part of the company’s short- to medium-term vision for increased sustainability, Cavicchiolo says.
“That comes out of working collaboratively as a fuel company with OEMs and the end customer to learn what their requirements are. Then we can make sure that we are supplying these products to meet the market’s needs,” he says.
“We adopt the right product quality and the fuel management and have the programs and processes in place to ensure that they’re getting what they need. Products like renewable diesel or HVO (Hydrotreated Vegetable Oil) are now truly accepted by OEMs both locally and globally as an approved pathway to decarbonise their existing fleet and equipment.”
For asset and fleet owners who aren’t sure where to begin, Cavicchiolo says creating an understanding of your current carbon
zero-emissions products for the longer term,” he says. “It is also important for companies to liaise with their own customers to find out about their emission reduction or carbon footprint initiatives.
“People need to consider the macro environment to address customer and contractual commitments. You’ve really got to collaborate with your fuel suppliers to help understand the different options available.”
Cavicchiolo says the road ahead relies on commitment and action from both private and public industry to drive change.
“Companies will have to adapt, using technologies and solutions in the marketplace to remain relevant,” he says. “We see it as an opportunity, but it’s a really complex journey that we’re all going on. We are talking to a lot of our customers about how we can help them on with their decarbonisation plans and targets.
“Ultimately, we have an obligation, irrespective of your views on global warming. For me, personally, I’ve got an ambition to make sure that we’re able to leave a better environment for my children and future generations.”
“COMPANIES WILL HAVE TO ADAPT, USING TECHNOLOGIES AND SOLUTIONS IN THE MARKETPLACE TO REMAIN RELEVANT.”Viva Energy is developing adequate demand and infrastructure for the future of sustainable fuels.
RECOCHEM’S RECOSOL 195 IS THE NEWEST ADDITION TO ITS RENEWABLE PLANTBASED PERFORMANCE FLUIDS. YET THERE ARE SO MANY OTHER APPLICATIONS THAT MAJOR BITUMEN AND ASPHALT CONTRACTORS CAN BENEFIT FROM USING RECOSOL 195.
ecochem’s Recosol 195 is a diesel replacement for producing cold mix asphalt. It represents an evolution from Recosol 175 through Recosol 185 to Recosol 195. The Recosol 195 represents an improved, premium product for Australia’s road and infrastructure markets.
“Recosol 195 is a more refined product than Recosol 185. It is evident in the light colour of the fluid,” says James McAllister, Business Development Manager – Special Projects for Recochem.
This sustainable, biodegradable fluid can lubricate conveyors and slips within the asphalt plant. It can be used as a truck slip for asphalt vehicles. Recosol 195 can also assist in rejuvenating recycled asphalt pavement for blending purposes.
ALTERNATIVES TO RECOSOL 195 HAVE RISKS
Kerosene and diesel are commonly used to clean bitumen off plant and equipment. Kerosene is among the group of Class Three Flammable Liquids. Class Three Flammable Liquids are liquids, or mixtures of liquids, that have a closed cup flash point of less than 60.5°C. This is usually referred to as the Flash Point. This can include paints, lacquers, varnishes, and kerosene.
Australia. By contrast, Recosol 195 is not considered hazardous.
A measure of a fluid’s solvency is its Kauri-butanol (Kb) value, an international, standardised measure of solvent power for a hydrocarbon solvent. A higher Kb value represents a stronger solvent. Recosol 195 has a Kb value of 54, which is higher than kerosene (34) and diesel (32).
The table shows the risks associated
with using kerosene and diesel, including flammability, aspiration, and marine pollution. Recosol 195 does not have these risk pictograms, reflecting the importance Recochem has placed on workplace health and safety.
Recosol 195 does not have as strong an odour as other cleaners. It is much safer to work with due to its high flash point (170°C).
Diesel is a suspected carcinogen. Reducing the exposure of this fluid in cleaning operations within the operations must be a clear improvement in workplace health and safety.
“Operators have commented on the lack of fumes and odour whilst cleaning with Recosol 195, compared to diesel and kerosene,” says McAllister. “With the high solvency of Recosol 195, there is a performance improvement compared to conventional hydrocarbons.”
When it comes to cleaning operations within bitumen and asphalt plants, Recosol 195 has many applications. It can be considered for trucks and tankers, bitumen filters, general plant and equipment, flushing of bitumen discharge lines, and specific laboratory applications.
Recosol 195 can be enhanced as a cleaner by adding selective emulsifiers and co-solvents. This will enable the Recosol 195-based cleaner to be hosed off with water in an emulsion form if required.
Recosol 195 can extend d-limonene, a costly specialised solvent for the laboratory. It can also raise the flash point of a mixture of the two to reduce its flammability. The strong solvency of Recosol 195 can lower the cost of d-limonene when a blend is utilised.
“Products like Recosol 195, a nonVOC (Volatile Organic Compound), can support organisations’ push towards achieving improved sustainability outcomes,” James says.
Many companies talk about their employees’ and contractors’ safety as part of their mission statements. Using products like Recosol 195 is moving towards that continual improvement they are trying to achieve.
Recosol 195 provides benefits for both
the short-term and future generations.
“It has been enormously satisfying to Recochem over the past seven years to observe the commitment of the major organisations in the bitumen and asphalt industries,” says McAllister.
“We have seen more companies utilising the renewable Recosol range.
This benefits both the environment and the safety of their workforce. There is a further opportunity for continuous improvement in HS & E by replacing kerosene and diesel with Recosol 195 in plant cleaning applications.”
For more information, visit https://www.recochem.com/.
UAA has more than 30 years’ experience in providing expert consultation and managing claims for clients across Australia, New Zealand and Asia.
Using this experience, UAA is equipped to provide specialist product and claims knowledge.
One example of the company’s insurance package offerings is its Industrial Special Plant cover, comprising machinery such as cranes, pavers, earthmoving and construction equipment.
As National Claims Manager
Underwriting Agencies of Australia (UAA), Michelle Morrissey says it’s important to clarify that plant and machinery insurance is an accidentbased policy, not a maintenancebased policy.
“What the policy really tailors to under the industrial special plant policy is your cranes and earthmoving equipment, that’s where our expertise lies,” she says.
Morrissey adds one step that machinery operators and fleet managers can do to ensure that they’re maximising their coverage is to report and review.
“It’s important to look at your sums insured for each piece of equipment. Our clients set their own sums insured, one of the major downfalls that we’ve seen out of COVID-19 is that machines weren’t appropriately insured,” she says.
“It might be something that people actually miss. It’s really important to sit down and look at each piece of equipment that’s in your fleet to determine if you’ve got appropriate levels of insurance to safeguard you at the time of a loss, this includes financial losses that can be inevitable if key pieces of equipment are not in operation,” she says.
“There are a number of items that can be left off by mistake, such as your buckets and other attachments. Look at the actual sums insured and ask if you’re adequately covered. If some of these larger assets are taken out of operation due to an incident, would you have enough financial protection cover to
When incidents do occur, UAA’s claims team has the knowledge and experience with insurance solutions to lodge any claim.
“Upon receipt of your claim, our team will allocate it to an experienced claims consultant who will lodge the claim. In most cases, an independent assessor will be appointed to inspect the damages and will contact you within 48 hours to arrange the assessment of your machine,” Morrissey says.
“Once the assessment report is received, our claims consultant will make an informed decision regarding the indemnity available to you and the quantum of your claim. In general, claims result in either repairs or, if the cost of the damage exceeds the market value of the machine, the machine is treated as a total loss.
“ONE OF THE KEY TAKEAWAYS IS TO ACTUALLY LOOK AT YOUR LABOUR FORCE BEFORE THEY GO OUT ON A JOB, LOOK AT THE JOB ITSELF AND MAKE THEM AWARE OF THE RISKS.”Michelle Morrissey, National Claims Manager – Underwriting Agencies of Australia, says communication and transparency are essential for an effective mobile plant and equipment insurance claim.
“While each claim may vary in terms of the information required, the most important step is to promptly notify UAA of any potential claim. This notification should be made as soon as possible and is especially crucial for claims that may result in a loss of revenue.”
To assist in achieving a smooth claims experience, Morrissey says communication is key.
“To ensure a smooth and timely claims experience, it is essential to complete the claim form in its entirety,” she says. “This minimises the need for additional information and ultimately avoids delays in the assessment process.
“Providing an honest and detailed description of the incident enables UAA to promptly assess liability and determine the indemnity.
“Effective communication and cooperation between assessors, investigators, and insured individuals play a vital role in the smooth progression of claims.
“Assessors value the information provided on your machines and can provide valuable risk mitigation strategies
to benefit your business.”
On top of providing UAA is also using its expertise and impact to support businesses to further decrease associated risks.
One such example, Morrissey says, is UAA seeing an increased volume of incidents involving cranes and other large machinery used across the construction and infrastructure sectors.
She says this has led to a greater emphasis on operator training. Therefore reducing the risk of these incidents occurring.
“We’ve seen a dramatic increase in claims for cranes, the majority of the time it’s down to operator error,” she says. “We present the trends to the industry in an effort to increase awareness and reduce risks.”
Morrissey adds that lasting financial and skilled labour constraints have exasperated the issue.
“I think finding skilled labour is really hard in every industry at the moment, especially in the cranes and machinery
sphere,” she says.
“One of the key takeaways is to actually look at your labour force before they go out on a job, look at the job itself and make them aware of the risks.”
She says presenting the risks increases awareness and may assist in reducing the likelihood of a major incident occurring.
Morrissey says UAA can answer specific questions around the application and process used for machinery and plant insurance claims.
“When it comes to managing claims for mobile plant and machinery, our highly specialised team at UAA Claims has extensive experience,” she says.
“Our focus at UAA is to ensure a smooth, timely, and positive claims experience, and we encourage our customers to reach out to us as soon as an incident occurs.
“By working together and providing the necessary information promptly, we can expedite the assessment and claims settlement, getting you back to productivity swiftly.”
To answer the growing demand of our customers for safe, sustainable solutions, Recochem have launched a range of renewable fluids. These readily biodegradable products are highly refined.
Recosol 195 can replace diesel in Cold Mix Asphalt, be used as a slip agent on asphalt trucks and plant conveyors, and can be utilised to assist the rejuvenation of RAP for blending in asphalt grades.
More recently Recosol 195 has proven to be a more effective cleaner of bitumen than conventional diesel and kerosene in the areas of plant and equipment, filters, discharge lines, sprayers and, in certain laboratory applications, in Bitumen and Asphalt plants. Using Recosol 195 in these instances will provide a safer working environment for the operators due to its high flash point, low odour and non hazardous classification according to Safe Work Australia.
Recosol 195 is also being evaluated as an alternative to diesel in the pre-coating of aggregates for spray seal operations.
spark for the development of the 4.5 metre Telescopic Sprayer concept. He says that the machine can provide financial benefits for businesses of all sizes, particularly those of a
“This machine can help the smaller guys to really establish themselves and get their foot
“It’s really been noticeable because we’re selling the machine to people who are having their first experience of purchasing a brandnew sprayer. Most of them are coming off using second hand machinery.
“Some can’t justify cashing out on an 8x4 chassis and six metre telescopic bar, so they want something that’s got the bells and whistles at a lower price point for them. And this is a great way to be able to get the upside of a smaller and more manoeuvrable package.”
One of the biggest benefits of the smaller 4.5 metre unit is its increased manoeuvrability.
Wansbrough adds that the machine is well suited for works in metropolitan areas, offering an increased ability to work in confined spaces compared to conventional sprayers.
“It’s well suited for smaller maintenance works in urban environments. You have that versatility with a telescopic bar around intersections, roundabouts, and other places that can be quite confined,” he says.
“We designed the sprayer to allow the right (drivers) side to wing extend up to 1.8m from the side of the truck, which is unique to a telescopic sprayer of this size. This allows you to reduce the number of taper runs around driveways, roundabouts and more. That’s really where the versatility comes in.”
Chris Kaelin, SRE Technical Manager, says the unit also caters for newer and inexperienced operators due to its simplified design.
“For larger sprayers you have to understand a bit about computers to learn how to use them. Obviously, there’s some efficiency gains in controls being automated, but you need to have a higher level of operator,” he says.
“Whereas the 4.5 metre replaces some touch screen functionality with toggles, switches and rotary knobs that are easy for most people to understand. Some of the feedback that we’ve gotten is that modern machinery has too
ROADING EQUIPMENT’S NEW DOWNSCALED TELESCOPIC
DESIGN IS HELPING TO PROVE THAT THE BEST THINGS DO COME IN SMALL PACKAGES.Specialised Roading Equipment’s patented Telescopic Sprayer.
many touchscreens.”
“Some operators say that it’s nice to have large switches that you can feel and identify while you’re spraying or backing up to do your next run.”
This is thanks for the SRE TECH-Lite control system, an in-cab control platform fitted with clearly labelled controls. This includes automated pump speed with adjusting for spray width, as well as an engine speed display.
Operators can also alter the spray modes from within the cabin, such as normal, fixed wing, wheel track, tack coat and taper. Wansbrough says simplifying these controls has also helped both large and smaller
businesses to attract operators of varying experience, in what is a competitive market.
“A lot of businesses have told us that it’s really hard to find well trained operators; that it’s getting harder to find this talent when they’re all competing with each other,” he says.
“The beauty of the 4.5 metre is that the simplicity means that you can widen the field in terms of recruiting staff. A lot more people are capable of operating this machine, while still maintaining high productivity.”
Fleet managers and owners can also review the spray run information, providing insights into run number, sprayed litres per run and average hot rate. This information
can be stored and transferred via a USB, with USB supported ports included on the operating system.
Both Wansbrough and Kaelin have spent considerable time in Australia during their times at SRE, talking with industry and servicing equipment.
It’s evident that the development of the 4.5 metre Telescopic Sprayer is a beneficiary of these experiences and previous learnings. One such example is ensuring that the machine is compatible with the use of crumb rubber and emulsion materials, products that are seeing a spike in usage across Australia and New Zealand.
“The key is to cater for different product types. In New Zealand it’s more focused around emulsions, whereas Australia is more geared towards crumb rubber. There’s distinct differences between the pumping and filtration systems, so in New Zealand we usually run a suction filter,” Kaelin says.
“But in Australia with the crumb rubber you need to have a larger displacement pump with a pressure filter to maintain constant flow.”
SRE already has orders for 4.5 metre Telescopic Sprayers in Australia, including clients who are already using the company’s six metre model.
Kaelin says that both models can complement each other well when used in tandem.
“Customers have talked about using the six-metre model for their main spray runs and using the 4.5 metre for their smaller works, such as segments of intersections, driveways and other nooks and crannies,” he says.
“Even on its own, you can still do quite a large reseal, you can still spray at the same throughput compared to the larger sprayers, albeit in a slightly narrow spray run.”
Wansbrough says the 4.5 metre Telescopic Sprayer option is well suited to Australian conditions and applications.
“The [4.5 metre Telescopic Sprayer] is a really great foot in the door, even for smaller operators who aim to grow into large civil providers over time. A lot of operators are looking to replace their old pieces of kit and the options are pretty limited for them,” he says.
“They often have to get a second-hand machine to replace the second-hand machine they just had. We can actually give them a brand-new machine that they’ll get 15-20 years of life out of, all for a similar price [than older machinery].”
Tidd Ross Todd (TRT) has specialised in the development and distribution of both cranes and crane trailers for more than five decades.
Throughout this time, the company has experienced rapid expansion. One of the company’s biggest milestones was its expansion to Australia from its home in New Zealand.
As Jeremy Carden, Trailer Sales – TRT recalls, this expansion started from humble beginnings.
“My family, including my father Bruce Carden who is the Managing Director of TRT, lived over in Brisbane for around two and a half years to push the product,” he says.
“Back then we had just a PO Box and an email address, but we still managed to push a lot of trailers into Queensland and then in a broader sense, into the whole eastern seaboard. A lot of our Castor Steer House trailers started turning up throughout NSW and Victoria.”
In 2016, TRT purchased a site in Queensland, which is now its Australian branch, with a lot of OEM products from New Zealand and overseas going through Brisbane. This site is also responsible for the distribution of Manitowoc, Grove, Kobelco Cranes and TRT’s very own TIDD Pick and Carry Crane, the only production line motor vehicle being manufactured over in New Zealand.
TRT offers an extensive lineup of trailers, including platforms, rows of eight, axle wideners, deck wideners, quads, dolly’s, house trailers, forklift trailers, crane trailers, and construction tippers.
Renowned for its commitment to innovation and engineering excellence, TRT’s solutions are engineered to maximise the productivity of assets, ensuring they operate at their fullest potential day after day.
This includes TRT’s Patented ESS trailers. “They’re tailored to our customers. We don’t just do general flat decks or general freight. We’re in the specialised market in terms of our house trailers, platform trailers and other specialised gear,” Carden says.
This ethos has forged a reputation for TRT as being high-quality and highly engineered products for the road transport and
construction industries across Australia, New Zealand and the Asia-Pacific.
One example of TRT’s innovation is the safety features and capabilities of its equipment. Despite the size of each unit, TRT has worked to ensure that fleet managers can maximise the safety of their operators.
“What we’ve tried to do is differentiate ourselves when it comes to our range of trailers. For the safety aspect we’re using double-acting suspension in all of our hydraulic loaders. This is a much more stable and safer system for tire changes, site manoeuvring, loading and unloading.” Carden says.
“Its all about peace of mind for the owner and operators. Over the years there have been several tragic deaths in the industry caused by single-acting ramps falling on people. Doubleacting cylinders are the only way to go.”
Carden adds that another point of difference for TRT is the load carrying capabilities of its crane trailers.
“The crane trailers are probably our highest selling products. They’re very specialised in the way that we construct them. They’re incredibly lightweight,” he says.
“In some aspects they’re the hardest working trailer that we manufacture.”
Jeremy adds that this is due to the trailers capacity to carry a payload that is up to eight times its own tare weight, designed efficiently to stow, secure and transport crane components on-site.
“The ‘taxi crane’ market is highly competitive,
and our range of crane trailers give our customers a big advantage,” Carden says.
Since 2009 TRT has supplied Borger Cranes and Rigging with a diverse range of crane support trailers and hundreds of crane outrigger pads.
Borger Crane Hire and Rigging Services has been in the business since 1980, providing a safe economical crane hiring and rigging service throughout the Sydney metropolitan area and have now expanded operations throughout Queensland and over into South Australia.
Its service extends from local builders and general taxi-crane hire, to working closely with John Holland Group on major infrastructure projects. Borger Cranes Transport Manager, Rob Beukers says the concept of purpose-built trailers is what initially attracted Borger Cranes to TRT’s products and services.
“The ability to customise designs specific to our needs for each of our Cranes is ideal in our industry,” he says.
In total, Borger Cranes have over 80 purpose built manufactured TRT trailers including equipment trailers, CW slab/Wing weight slab trailers and B-doubles.
There are also another 15 trailers on order over the next eight months.
“What differentiates TRT’s Trailers from other machinery is the quality of their equipment along with their ability to custom build designs specific to our requirements,” Beukers says.
“Our TRT Trailers have been purpose-built
TIDD ROSS TODD HAS DEVELOPED ITS RANGE OF TRANSPORT SOLUTIONS OVER MULTIPLE DECADES. JEREMY CARDEN, TRAILER SALES, EXPLAINS WHAT SETS THESE PRODUCTS APART FROM THE REST.TRT’s trailers have been used to move major infrastructure components.
to support our extensive fleet of cranes. The trailers are built specifically for the counterweights on each of our cranes. Similarly, the pads are also used on each one of our cranes. Both the trailers and the pads have both performed exceptionally well.
“The products we have received from TRT have always been of superior quality and have always met our requirements. The support from their staff has always been willing and helpful, adding to the quality experience.”
Another key area of strength for TRT has been the company’s success in the heavy haulage space. The company’s established Electronic Steering System (ESS) represents the enterprises’ progress in further pushing the envelope.
“This is not a new concept; it’s proven technology that has been used in the construction and design of mobile and allterrain cranes and Self-Propelled Modular Transporters since the 1990s,” says Carden.
The system offers redundancies and backups for each of its key features. The trailer’s computer system aims to detect the offset angle created as the truck turns either left or right.
These angle changes are picked up by encoders, simple mechanical cogs connected to the slew ring mounted to the trailers skid plate.
These signals are sent to transducers which are housed within the steering ram of each axle leg. The signal tells the transducer where the hydraulic cylinder needs to displace the oil to achieve the correct angle demanded by the truck. This happens simultaneously, resulting in near-perfect steering geometry as the truck completes on-site manoeuvring.
“Some people look at it and think ‘from a steering systems perspective it’s not going to be any good with our harsh conditions’. But that’s a misconception because the product is still 95 per cent mechanical. It’s
TRT’s heavy haulage products are designed to withstand tough applications.
simply communication and signals. It’s a really effective system,” Carden says.
This system enables operators to have flexibility and actively shift the trailers pivot point from the comfort of the truck cab, allowing them to manoeuvre the machine around corners and obstructions with ease.
Each system is programmed according to the size and specifications of each trailer. Once the operator has calibrated the load, the system then sends a signal to each axle, assisting with the movement of the trailer.
Beyond reducing risks, operators can also reduce tyre scrub while also increasing the efficiency of the trailer movements.
“I’d say that we’re still at the top end in the technology side of things,” Carden says.
Carden says the designs of TRT’s heavyhaulage trailers, as well as the wider product range, are supported by the company’s experienced design team.
“We have nine designers that are permanently employed up in the design office. They’re not a revenue gathering resource, they’re a service provider. In that office alone there’s over 150 years of experience.”
Jeremy adds that even despite on-going shipping and freight issues, TRT is still well equipped to support its customers due to its network of support staff.
“Our warehouse in Brisbane has continuously
expanded, growing in size over time. They’re keeping a lot more stock on the shelves these days,” he says. “We have our product support agents in each state who are on top of things when it comes to our range of products.”
TRT can also bring in specialised and rare parts from its warehouses in Australia or New Zealand.
“We believe in giving our customers the best,” Carden says.
One such customer that has received products and support from TRT is Holz Heavy Haulage based in New South Wales.
Director of the Australian heavy haulage specialist Maree Holz says the company’s initial interest in TRT equipment was sparked after seeing the quality, design, suspension, and pivot bearings of TRT’s designs.
“TRT products and equipment are a clear stand out for us and our heavy haulage business. Their products are of high quality, are reliable and allow us to manoeuvre with ease Australia-wide,” Holz says.
“We transport earth moving equipment daily, using TRT trailers without complications. All trailers have performed well leaving us nothing but satisfied with TRT’s products.”
Holz Heavy Haulage now has two TRT 2x8 dollies, two 5x8 floats, three 3x8 floats, one 4x4 steerable deck widener and have recently ordered two more, with an expected delivery for next year. Holz says the commitment of TRT to its customers stands out, particularly for a family orientated organisation such as Holz Heavy Haulage.
“Being a small family run business ourselves, we love their reliability, service and their passion for their family-based business. We have always found TRT to be very accommodating and we have loved working alongside this company since 2011,” she says.
“They are very approachable and any minor issues have always been quickly resolved without any fuss. We can’t thank them enough for their customer service and providing such high-quality products.”
For a family-owned enterprise like K-P Asphalting, it’s imperative to operate only the best equipment.
Backed by more than six decades of experience, K-P Asphalting has delivered a variety of works across its home state of Tasmania, as well as from its expansion site in Queensland.
Founder and owner, Steve Pregnell, says one thing has remained constant in the company’s growth – the use of Astec machinery.
Pregnell says he’s seen it all, with works across airports, freeways, subdivisions and more. Through all that, he says no other piece of equipment has stood up to the task like the Carlson CP-130 asphalt paver.
“We actually bought the first CP-130 in the country,” Pregnell says. “In 50 years, I’ve used a lot of pavers and I’ve never come across a better one than this
particular machine.
“It’s a small machine but it handles the bigger jobs with ease. It’s extremely versatile.”
Despite its economical size and being ranked as a commercial size paver, the CP-130 has the capability of a smaller highway class paver. This is due, in part, to the CP-130 paver having a highhorsepower Cummins QSF 3.8 Tier III engine, that delivers not only excellent power and torque but lower exhaust emissions as well.
For Pregnell, capital costs are also a significant factor.
“The CP-130 performs like larger machines which do have a higher investment cost and additional routine maintenance expense compared to the Carlson paver,” he says.
The advantages don’t end there.
THE ASTEC CP-130 PAVER HAS BECOME THE MACHINE OF CHOICE FOR TWO GENERATIONS OF THE K-P ASPHALTING’S BUSINESS. ROADS & INFRASTRUCTURE LEARNS WHY.K-P Asphalting’s crews using Astec machinery’s Carlson CP-130 paver.
The CP-130 paver is of a smaller scale, but fully capable of contributing to larger projects.
According to Pregnell, the CP-130’s lower height has opened the door for works that were previously unmanageable with larger paving equipment.
“It means we can do underground car parks for example. Now we don’t need to worry about the restricted ride height,” he says.
“In Tasmania, we also work a lot on hills. With this tracked machine there’s no problems whatsoever in moving up and over hilly sites. If I was to compare it to an excavator, I would have to say it was a 10-tonne excavator built with 20-tonne components.
“It’s the little man doing the big man’s show.”
Garry van den Beld, National Account Manager – Mobile Asphalt says the CP-130 is ideal as an ‘overlap’ machine, capable of working across a variety of project types and sizes.
“That’s where this paver really comes into its own; it’s a small machine that can work in confined spaces, but does the job on larger projects as well,” he says.
Van den Beld says another key feature of the CP-130 is its “class-leading” screed design. The EZCSS screed has a paving width of 2.38 metres to 4.4 metres, and a maximum paving width of 5.0 metres with optional boxes which is unique in this class paver.
“The screed design is very versatile in today’s world as contactors’ demands have changed. It retracts down to ensure the paver is only 2.5 meters wide for transporting purposes from jobsite to jobsite,” he says.
The EZCSS screed also includes adjustable slide blocks, spring-loaded heated end gates and can be fitted as an option with grade and slope automation, all of which contributes to a high-quality matt finish.
Van den Beld says another benefit of the CP-130 is the exclusive horizontal sliding damper doors, which add versatility and flexibility to any paving job. The doors can be adjusted for different material requirements and paving widths.
He adds that the paver’s unmatched control system helps to consistently distribute material effortlessly for a superior finish.
“The damper door design is different
platform was designed for maximum operator comfort.
“It’s a dual control system with precise movement joysticks, making this paver very easy to use. The switches on the operator stations are user-friendly with very easy to read large screens that provide readouts electronically,” he says.
Despite being located in Tasmania, Pregnell says he’s always been well supported by Astec.
“Because we’re in a different state, and being on an island, we could be a bit handicapped as far as access to parts and components. But Astec have been there when we’ve needed them and they’ve done a good job,” he says.
Steve Pregnell’s initial impression of the machine was so positive that K-P Asphalting’s expansion site in Queensland has also recently taken delivery of a new CP-130 paver.
Son, Kirk Pregnell, runs the Queensland business and says his father could not have recommended the Astec CP-130 more highly.
Located near the Gold Coast, the Queensland site services an area of more than 400 square kilometres, and has well-established relationships with local councils, state government departments and private industry.
As Kirk Pregnell explains, the expansion
“IT’S A DUAL CONTROL SYSTEM WITH PRECISE MOVEMENT JOYSTICKS, MAKES THIS PAVER VERY EASY TO USE. THE SWITCHES ON THE OPERATOR STATIONS ARE USER-FRIENDLY WITH VERY EASY TO READ LARGE SCREENS THAT PROVIDE READOUTS ELECTRONICALLY.”
to any other machine out there,” he says. “With our CP paver range, you can use minimal asphalt while maintaining a consistent level.”
Pregnell says the damper door system really surprised him.
“There are only three or four components to them and they’re probably the best flow control system I’ve ever come across. They’re built into the back-end of the machine, so you can easily see the head of material and control the amount of material needed for the situation to get the desired rideability on the road,” he says.
Van den Beld says the operator
of the business, as well as the purchase of the CP-130, has helped to diversify the company’s services.
“Dad knows what he’s talking about, so I didn’t hesitate to go for the CP-130 paver,” he says.
With that recommendation and his own earlier experience in Tasmania with the machine, Kirk Pregnell says he’s ready to hit the ground running with the new paver.
“We’ve got plenty of work coming up – small and large jobs – government contracts, subdivisions, driveways and more. And the CP-130 will handle them all,” he says.
“It ticks all the boxes.”
Unlike a standard circle, which necessitates maintenance and wear insert replacements, the ‘Premium Circle’ is a game-changer. It boasts a completely sealed bearing system, eliminating the need for shoes, wear inserts, and jack screws.
This revolutionary design can only be found on John Deere machines and aligns perfectly with the cutting-edge John Deere SmartGrade mastless GPS system, further enhancing performance.
On a standard circle, the circle is more exposed by design leading to wear over time over the course of the machine’s operation. Wear inserts inside a standard circle require adjustments to keep a good tight circle for accuracy and to prevent damage to the circle before eventually,
needing to be replaced. Customers could spend valuable hours in the workshop replacing or shimming the wear inserts as opposed to being on the job, leading to increased downtime over the lifetime of the machine.
In comparison, in the Premium Circle option, there are no shoes, no wear inserts or jack screws exposed with the system completely sealed with the wear inserts being replaced with a sealed bearing. The pinion and circle teeth are also completely sealed from dirt and debris to minimise wear. John Deere’s design was focused on completely sealing, rather than simply covering the circle pinion drive that can still attract and hold debris.
The option has also been designed to create a more simplified maintenance
process. One of the main differences is the larger gearbox which has increased the oil change intervals to 4000 hours. The bearing circle has five easy access grease points on the bearings circle, four on the table and one on the pinion. The recommended service intervals on these grease points are every 500 hours.
The Premium Circle presents a host of advantages that surpass conventional motor grader circles. Most notably, it offers an increase of up to 15 per cent in circle speed and up to 40 per cent in circle torque compared to the standard option. By eliminating the need for timeconsuming maintenance and providing enhanced speed and torque, the Premium
IT’S BEEN NEARLY THREE YEARS SINCE JOHN DEERE LAUNCHED ITS FACTORYINSTALLED PREMIUM CIRCLE OPTION FOR ALL JOHN DEERE G-SERIES, GP-SERIES AND SMARTGRADETM MOTOR GRADERS. ROADS & INFRASTRUCTURE LEARNS MORE ABOUT THE OPTION AND WHAT IT OFFERS THE INDUSTRY.John Deere’s premium circle option in action.
The Premium Circle option helps to provide greater efficiency, as well as reduced maintenance costs.
“CUSTOMERS USING GRADE CONTROL SYSTEMS WILL NOTICE THEY NO LONGER HAVE TO COMPENSATE FOR WEAR IN THE CIRCLE OR STOP THE MACHINE TO ADJUST FOR LOOSENESS OF THE CIRCLE WHEN USING THE PREMIUM CIRCLE OPTION.”
Circle significantly boosts productivity and reduces downtime for contractors and government sectors alike.
John Deere has also focused on simplifying the service requirements with the Premium Circle. The larger gearbox on the Premium Circle contributes to its durability, while also extending the service interval for the circle drive system from 2000 to 4000 hours.
Additionally, the Premium Circle features five grease points on the bearing circle, providing easy access for maintenance. With four grease CRCs on the top of the table and one on the pinion, technicians can efficiently lubricate these points every 500 hours during routine service intervals.
The Premium Circle offers substantial value to both contractors and government sectors. With its enhanced performance, streamlined serviceability, and increased
productivity, the Premium Circle enables contractors to complete grading tasks with unparalleled precision and efficiency.
Mark Johnson, the Motor Grader Product Consultant for John Deere says the company’s innovative breakthrough helps to reduce long term costs associated with operation.
“Customers using grade control systems will notice they no longer have to compensate for wear in the circle or stop the machine to adjust for looseness of the circle when using the option,” he says.
He says its especially impactful when coupled with the innovative John Deere SmartGrade system.
“The same grader can now be used from initial site clearing to final grade without stopping to install masts or downing the machine to adjust for looseness in the circle,” he says.
Government entities can benefit from the reduced maintenance requirements and
improved operational capabilities, allowing for optimal utilisation of resources and timely completion of infrastructure projects.
Motor graders continue to play a pivotal role in construction and infrastructure development, and John Deere’s commitment to innovation and customer satisfaction shines through in this “ground-breaking” feature.
“The take rate of the Premium Circle is high, and the customer feedback has been that all of their future graders will have it,” Johnson says.
He says the efficiency and lower maintenance it provides makes it a nobrainer for businesses.
“Deere is still the only manufacturer who offers this industry exclusive, and it’s available right now on every grader model we make for the Australian market,” he says.
The Premium Circle’s sealed bearing system, increased speed and torque, and simplified service requirements exemplify the manufacturer’s dedication to pushing the boundaries of motor grader technology. With the Premium Circle, the future of grading has never been more precise, efficient, and productive.
To find out more, visit www.deere.com/en/ campaigns/smartgrade-motor-graders/
The new ZenergiZe range from Atlas CEA takes modular energy storage to a new level. Developed with sustainability in mind, it helps operators dramatically reduce fuel consumption and CO2 emissions. It also delivers optimal performance with zero noise and virtually no maintenance.
Leveraging the benefits of high-density lithium-ion batteries, the ZenergiZe units are compact and light compared to traditional alternatives. They can provide over 12 hours of power with a single charge.
They are ideally suited for noisesensitive environments, such as event or metropolitan construction sites, telecoms, or rental applications, or to resolve low-load problems. They are also suitable for sites where diesel emissions are an issue.
The ZenergiZe range perfectly fits with applications that require a continuous and demanding flow of electrical power energy. It is ideal for properly sized cranes and other electric motors.
The ZenergiZe can also be used for events celebrated in noise-sensitive locations and other stationary applications such as hospitals or recharging points for electric cars.
The ZenergiZe can be synchronised with other energy storage systems, which allows the machine to become the storage of all the energy sources connected to a microgrid.
Hutchinson Builders are currently operating several ZenergiZe units. Wade McGrath is a Site Manager for Hutchinson Builders and has been in the
industry for decades.
“I started as a ‘chippy’ and have worked my way up the ladder,” he says. “I progressed to foreman and eventually to site manager. I suppose it was a goal of mine — I wanted to climb the ladder.”
McGrath has been with Hutchinson Builders for just over a year. His influences and knowledge stem from his time at companies such as Evans Built, BADGE Construction and Evans Harch.
“When I joined Hutchinson Builders, I worked with a full site team, a safety officer and site foremen. It’s a big improvement over when I was managing multiple roles. I’ve got a fantastic work environment now,” McGrath says.
McGrath believes there is an increased focus on sustainability in the construction and infrastructure industries. This has arisen from the government’s desire for contractors to focus on their environmental aspects.
“We’re going away from petrol and diesel vehicles while shifting towards electric vehicles across society,” he says.
“We are also seeing this trend in the building industry as we always want a smaller environmental impact. Using the battery setup from Atlas CEA has been a
WITH GOVERNMENT CONTRACTS INCLUDING CLAUSES AROUND SUSTAINABILITY, NEW TECHNOLOGY TO POWER SITES WHILE REDUCING EMISSIONS OFFERS OPPORTUNITIES FOR THE SMART INFRASTRUCTURE MANAGER.The ZenergiZe can be combined with solar panels to enhance the ESG goals of the project.
massive tick. Government contracts are increasingly looking at the sustainability side of things, and I wouldn’t be surprised if it becomes a requirement.”
Hutchinson Builders hired a ZenergiZe ZBP 45, which runs with a JCB G60 generator. McGrath believes the company has the right solution for its needs.
“It always comes down to the job size,” he says. “Atlas CEA does have bigger units, such as the ZBC100-500, but we didn’t have that much demand for power. While we were drawing a big load, the actual demand was not as high. That’s because we don’t have a tower crane or multiple work fronts connecting
to multiple sheds.”
McGrath found that the ZenergiZe could support their electricity needs along with their generator. With the restrictions on generator usage at night, they could operate at all hours off the back of their silent ZenergiZe. It also meant that any emergency lighting could run off the ZenergiZe battery.
Not only is ZenergiZe providing the power that Hutchinson Builders need, but it’s also helping them to save on operating costs.
“We’ve worked out that we are saving about 500 litres a week of diesel,”
McGrath says. “That’s if we work the generator 24 hours a day, seven days a week. While it’s still early days, we believe we are saving about $4000 or so a month. Those funds have allowed us to invest in other energysaving projects.”
This includes investing in solar panels. The increased possibilities of solarpowered facilities with energy inverters could provide construction sites with power to operate at all times.
“These inverters are taking in the energy from the sun and saving it for us. The industry appears to be working towards creating sheds with solar panels installed on the roof. We will be able to connect all the sheds together as a central input into the ZenergiZe,” McGrath says.
The future could be a solar farm that fits inside a sea container. With four to six solar panels, it is possible to develop enough power to run the site from solar energy, along with the ZenergiZe on stand-by. Such a development could support the likely government regulations around sustainable power.
“We already have to do hours’ worth of upskill training,” McGrath says. “I can see a similar requirement around energy efficiency and the size of our carbon footprint in the future for contracts over a certain size. We are already ahead of the game in that regard.”
For more information, visit https://www.atlascea.com.au/
Komatsu is strongly committed to environmental best practices, with a continuous focus on reducing its environmental impacts and carbon footprint.
In its mid-term management plan, Komatsu made a steadfast commitment to minimise its environmental impact through various initiatives.
The company is aiming to achieve a 50 per cent reduction in CO2 emissions from both the use of its products and the production of its equipment by 2030, compared to 2010. Additionally, the company set a challenging target of attaining carbon neutrality by 2050.
To support its customers’ carbon neutrality goals, Komatsu has been providing an array of products, services, and solutions that reduce environmental impacts, including hybrid hydraulic excavators, electric mini excavators, and advanced electric models.
Komatsu has been exploring cutting-edge technologies to power its construction equipment to further its commitment to carbon neutrality. One such technology is the hydrogen fuel cell system.
By partnering with Toyota, Komatsu adopted a hydrogen fuel cell system
and hydrogen tank for its medium-sized hydraulic excavator.
Komatsu has developed a concept machine for a medium-sized hydraulic excavator that combines a hydrogen fuel cell and Komatsu-developed key components to achieve carbon neutrality at workplaces of construction equipment. By advancing the Proof of Concept (PoC) tests it started in May 2023, Komatsu will accelerate its efforts to commence commercial production of mediumsized and large construction equipment powered by hydrogen fuel cells.
Combined with Komatsu’s comprehensive control technology and
critical components, this approach aims to achieve zero exhaust emissions, substantial noise reduction, and decreased vibrations while delivering the same powerful performance and operability as traditional engine-driven excavators.
Komatsu is also working towards zero exhaust emissions and significantly reducing noise and vibration. Its excavators will deliver the same powerful digging performance and high operability as engine-driven excavators.
Medium-sized and large construction equipment requires a power source with higher energy density than small construction equipment, leading to electrification with batteries.
Hydrogen has a higher energy density and can be refuelled faster than recharging batteries. As such, Komatsu has been advancing its research and development efforts as a promising electrification choice for medium-sized and large models.
To contribute to realising a hydrogen society and carbon neutrality, Komatsu will continue its efforts toward the commercial production of mediumsized and large construction machinery equipped with hydrogen fuel cells by conducting PoC tests of this new concept machine.
The WA Electric Concept Wheel Loader further exemplifies Komatsu’s dedication to sustainability. As a fully electric and remote-controlled machine, this loader eliminates emissions and reduces its carbon footprint significantly.
Equipped with a 22 kW onboard charger, the loader can operate seamlessly and efficiently with minimal downtime. Integrating linear electric actuators for critical functions adds to its efficiency and eco-friendliness.
This is because the electric actuators reduce energy consumption and maintenance requirements.
With a chassis based on the Komatsu WA70 wheel loader, the WA Electric wheel loader concept machine was developed in partnership with Moog Inc. Utilising an intelligent electrification system; this wheel loader features an electric traction motor, lift, tilt and steering cylinders, power electronics, system control computer, battery and battery management system.
A nother addition to Komatsu’s ecofriendly fleet is the three tonne Electric Concept Mini Excavator. It is driven by seven electric motors, powered by a lithium-ion battery, and operated through a simple remote control via wireless LAN. This mini excavator demonstrates impressive power and efficiency while producing zero emissions. By eliminating hydraulic equipment from its design, maintenance becomes virtually non-existent, further reducing environmental impact and operating costs. The remote control offers a new workstyle of operating it without boarding it, reducing the operator’s fatigue and improving workplace productivity.
Thanks to electrification and remote control, this machine should be stress-free for the operator, as it’s easy to operate in confined sites.
Komatsu’s strides in electrification have already yielded impressive results. The company has sold over 1300 electric drive trucks in Australia and over 380 electric mining excavators globally, with demand continuously increasing.
The success of electric-driven models like the PC210E all-electric hydraulic excavator and the electric mini excavator PC01E-1 showcases the company’s dedication to sustainable equipment solutions. The future arrival of these products in Australia provides more opportunities for companies to leverage their sustainability outcomes.
ROADS & INFRASTRUCTURE PROVIDES A SNEAK-PEEK INTO THIS YEAR’S INSIDE CONSTRUCTION EXPO.
An event dedicated to major commercial and civil projects in the Australian construction industry, Inside Construction Expo is being held from 20 to 21 September 2023 at the Melbourne Convention and Exhibition Centre.
With a robust conference program featuring top-level speakers, a world-class exhibition showcasing the latest equipment and technology, and the Inside Construction Foundation Awards celebrating talented industry individuals and businesses, Inside Construction Expo 2023 is a mustattend event.
Set to connect constructors with OEMs, sub-contractors, and operators, Show Director Lauren Winterbottom says the event is positioned to foster the successful delivery of projects in the pipeline.
“Inside Construction Expo was created to fill the gap in events targeted at major commercial and civil projects,” she says.
In the 2022-23 Federal Budget, the Government increased its 10-year infrastructure investment pipeline to a record $120 billion. The 2022-23 Victorian Budget outlines $85.3 billion in general government spending on infrastructure over the next four years.
Many projects are planned nationwide over the next decade, but considerable industry challenges remain.
Inside Construction Expo 2023 will provide a platform to canvass solutions to the
issues hampering the commercial and civil construction sectors.
With multiple stages across the event focusing on Health, Safety and Wellbeing; Training, Education and Careers; Digital Transformation and Connectivity; and Construction Productivity, there will be a wealth of industry information and solutions.
“Throughout the conference, attendees can expect to hear from executive-level representatives from Australia’s major constructors and suppliers, alongside research and education bodies and government figures,” Winterbottom says. “The exhibition show floor will display the latest construction machinery and equipment.”
Inside Construction Expo is backed by support from several valued organisations and media partners. Without this support, Winterbottom says, the event would not be possible.
“We’re pleased to partner with industry associations and peak bodies to bring Inside Construction Expo to life,” she said. “Specialist in assembly and fastening materials, Wurth Australia has come on board as a supporting sponsor for the Expo.”
“We are thrilled to be part of the 2023 Inside Construction Expo, which promises to be a game-changer for the industry. This event will provide an unparalleled opportunity for us to showcase our latest products and innovations, as well as to connect with fellow professionals and
share insights and expertise,” says Serge Oppedisano, CEO of Wurth Australia.
Winterbottom also pointed to intelligent positioning solutions provider Position Partners and manufacturer Komatsu as proud conference sponsors.
In the lead-up to the event, over 19 industry-leading publications continue to cover the latest in Expo news extensively.
“We have seen their coverage reach more than 80,000 decision-makers across multiple sectors,” a spokesperson says.
“We’re excited to connect with delegates at Inside Construction in Melbourne this year. Events are experiencing a resurgence post-lockdown, and nothing beats inperson conversations, especially when it
“THROUGHOUT THE CONFERENCE, ATTENDEES CAN EXPECT TO HEAR FROM EXECUTIVE-LEVEL REPRESENTATIVES FROM AUSTRALIA’S MAJOR CONSTRUCTORS AND SUPPLIERS, ALONGSIDE RESEARCH AND EDUCATION BODIES AND GOVERNMENT FIGURES,”
comes to showcasing new technology,” says Gina Velde, Marketing and Communications Executive Manager of Position Partners.
As part of this year’s Inside Construction Expo, the Foundation Awards will be held on 20 September 2023 to celebrate the individuals, businesses, and projects championing transformation in the construction industry.
With a focus on showcasing the initiatives that seek to promote core standards around safety, diversity and environmental sustainability throughout major and local projects, the Foundation Awards will be a premier event on the construction industry calendar.
PLAN YOUR ATTENDANCE
Whether you’re a project manager, superintendent or an engineer, all
professionals in the field of construction are invited to attend Inside Construction Expo 2023. Registration is free for both the exhibition and the conference. You’re welcome to come and go as you please and curate a conference experience that suits you.
As the construction industry continues to face ongoing challenges, from skills shortages and lack of digitisation to poor productivity and inadequate safety management – this year’s Inside Construction Expo will encourage transformation and a brighter future for the sector.
For more information, visit www.insideconstructionexpo.com.au
technology sector.
Lauren Winterbottom, No-Dig Down Under Show Director says the conference will allow stakeholders to connect directly with decision makers.
“As always, the event will also focus on new technologies and products that will help make the industry more efficient, safer, and provide more benefits for both those within the industry, and the broader community,” Winterbottom says.
Organised in partnership with the Australian Society for Trenchless Technology (ASTT), No-Dig Down Under features a large-scale exhibition,
Directional Drilling (HDD), the largest HDD component completed in a single pipeline in Australia.
Also covered is works on the North East Link project. Micro-tunnelling works, adjacent to the southern portal of the North East Link, are contributing to the relocation of the Yarra East Main Sewer, as part of early works on the project. The presentation will cover the problems faced, the solutions found and the scope of further works on the project.
Councils and the like will also be able to have key takeaways from a presentation focusing on the Narangba Sewer Transport System in Queensland. The
“The industry is focused on communicating the benefits of trenchless technology – for the environment with less disruptions to wildlife, for the community with less disruption to roads and other infrastructure while making repairs or installations, and for the financial bottom line with lower costs to complete major projects,” she says.
These are just some of the many presentations in store for attendees at this years No-Dig Down Under Conference.
For more information, visit: https://www.nodigdownunder.com/
Roads
A CIRCULAR ECONOMY USES SYSTEMS THINKING TO DESIGN OUT WASTE AND POLLUTION, KEEP PRODUCTS AND MATERIALS IN USE AND REGENERATE NATURAL SYSTEMS. IT IS ALSO A MECHANISM TO DRIVE DECARBONISATION.
Circularity has become a market trend on the journey to address climate change. And now, some manufacturers have started to act on the need for a quantifiable way to measure and demonstrate progress in circularity.
There are a variety of mechanisms being deployed to advance more circular practices and decarbonisation.
These include national and state policies, incentivised procurement, frameworks and indicators like MCI (Material Circularity Indicator), circular materials and methodology.
Circular economy practices and materials deliver a number of business benefits beyond supporting decarbonisation targets. Minimising waste and allowing for increased resource management provides cost savings and retains the value of the raw material itself.
Circularity reduces the burden of virgin materials and supports the value proposition of the entire supply chain, reducing the risk to suppliers and consumers. There is also a reputation benefit as the focus on sustainability increases across the industry and nation.
In 2022, the Infrastructure Sustainability Council formed a three-year partnership with the Department of Climate Change, Energy, Environment and Water (DCCEEW) to enable circular economy outcomes in the infrastructure sector. The result has been the “Contributing to a Circular Economy” Innovation Challenge. The Challenge is open to all projects undertaking a Design/As Built or Operations IS Rating.
In support of DCCEEW’s National Waste Policy Action Plan, projects are rewarded for the increased use of recycled content, for
the responsible management of resource outputs, and for incorporating a material or product with a Material Circularity Indicator (MCI).
The Materiality Circularity Indicator (MCI) provides a way of measuring the circular outcomes of a material, making it an important decision-making tool for transitioning from ‘linear’ to ‘circular’ models at an organisational and economy-wide level.
Developed by the Ellen MacArthur Foundation and Granta Designs as part of their ‘Circular Indicators Project’, the MCI measures how restorative the material flows of a product or material are, creating a numeric value for its circularity.
In simple terms, the MCI measures the amount of recycled material used in the
manufacture of a product and how much of that product can be recycled at the end of its life.
This measure not only allows for comparisons between products but also builds awareness and understanding within the supply chain. While progress has been made in this area, there is still much to learn as the industry continues to evolve.
Conducted in conjunction with developing (or revising) an Environmental Product Declaration (EPD), the MCI process utilises much of the same data as the EPD, making the data collection process sizable, yet not significantly different from that required for an EPD. An MCI can also be incorporated into an LCA or can be assessed in a standalone study.
Including the MCI results in the EPD process ensured a critical review for the verification, which added credibility and robustness to the MCI results.
To calculate an MCI, the following inputs are considered: the amount of virgin and recycled materials and reused components used in the production process; the amount and fate of any waste generated during the production process.
Sustainably sourced biological materials are also considered.
Further inputs include the length of the product’s use phase and intensity of use in comparison to an industry average product of similar type; the amount of material going into landfill (or energy recovery) at end-oflife versus the amount collected for recycling and which components are collected for reuse; and the efficiency of the recycling processes used to produce recycled input and to recycle materials after use.
The result is a circularity value number between zero and one, with one indicating a product that has fully restorative flow. A higher value indicates better circularity properties for the material.
It is challenging to determine whether reporting MCI results will drive business demand, as more companies need to undertake the process to measure the
circularity of their products and enable a comparison between products. Monitoring will determine how demand and supply is affected.
The opportunity to drive and adopt greater resource efficiency in infrastructure is that it brings metrics to the conversation and quantifies the outcomes.
It shifts from just evaluating projects on the basis of recycled content, to a more rounded metric that better describes
tools will play an important role in this sustainable trajectory.
According to the Infrastructure Sustainability Council, InfraBuild is amongst the first to obtain an MCI for its steel products. InfraBuild understands the importance of having a quantifiable measure to constantly evaluate its products’ improvement.
Currently, InfraBuild’s Merchant Bar
circularity across the full product life cycle. However, the MCI is only one supportive tool in transitioning to a circular economy. Developing and implementing policies and frameworks will accelerate the process, along with mechanisms to incentivise the market.
These efforts can create an environment that supports and rewards the transition to circularity, leading to more widespread adoption of circular practices and tools like MCI. An infrastructure future which embraces circularity is in sight, which is integrated into the widely adopted IS Rating Scheme and MCI and other
products have achieved an MCI of 0.824, while its Reinforcing Bar scored 0.696, and Reinforcing Mesh scored 0.571. InfraBuild is committed to further improving these values over time as they strive to enhance their products’ sustainability.
The Infrastructure Sustainability Council CEO Ainsley Simpson says she welcomes such innovation across the industry to accelerate the transition to a circular economy.
“It is only through driving innovation that we will see industry transformation. Pursuing an MCI has demonstrated InfraBuild’s ongoing leadership and commitment to progress,” she says.
“IT IS ONLY THROUGH DRIVING INNOVATION THAT WE WILL SEE INDUSTRY TRANSFORMATION. PURSUING AN MCI HAS DEMONSTRATED INFRABUILD’S ONGOING LEADERSHIP AND COMMITMENT TO PROGRESS.”The Infrastructure Sustainability Council recognises and rewards the adoption of the circular economy through the IS Rating scheme. Photo: Sydney Metro.
THE AUSTRALIAN FLEXIBLE PAVEMENT ASSOCIATION SHEDS SOME LIGHT ON THE GROWING RISK OF RESPIRABLE CRYSTALLINE SILICA.
Nationally there has been growing action by regulators around the mitigation and management of exposure to Respirable Crystalline Silica (RCS) in industrial settings and work sites as awareness of the risks also increases.
While it is arguable that the operations of AfPA industry members do not generate significant risk of exposure to dust, the State Government’s across the country are taking a precautionary principle on the matter.
In Queensland, the state’s new RCS dust Code of Practice 2022 is targeted at managing exposure in construction and manufacturing of construction elements. This commenced on 1 May 2023.
Workplace Health and Safety
Queensland Inspectors have since then been undertaking on-site reviews of all industrial activities, applicable to all construction work, as well as the manufacturing of materials such as bricks, blocks, tiles, mortar and concrete.
The Queensland code outlines how
duty holders can meet the requirements of Queensland’s work health and safety legislation, including eliminating or minimising exposure to RCS at work.
This can be done by using tried and tested dust control methods that prevent silica dust from being generated or being released into the air. These include water suppression and ontool dust extraction; using appropriate respirable protective equipment to safeguard at-risk workers and using exposure data from air monitoring to check dust controls are effective.
Operators can also provide health monitoring to at-risk workers, with clearly defined triggers for testing based on level of risk; and consulting with workers, as well as training, education, instruction and supervision of workers.
Crystalline silica is a naturally occurring mineral found in various rocks, sands,
clays, and construction materials such as concrete, mortar, bricks, and pavers. When these materials are worked on, RCS dust is generated.
Road construction activities like cutting, sawing, milling, grinding, drilling, and crushing can release RCS particles into the air.
These particles are so small that they can penetrate deep into the lungs, causing severe health issues.
Chronic Silicosis, Accelerated Silicosis, and Acute Silicosis are the three main forms of lung diseases associated with RCS exposure. Symptoms include shortness of breath, severe cough, and weakness. It is crucial to understand that symptoms may not appear for many years, underscoring the need for proactive RCS control measures.
The Workplace Exposure Standard (WES) for RCS is set at 0.05 milligrams per cubic meter (mg/m3). Compliance with the
WES requires personal monitoring within the breathing zone of workers. Various stakeholders have specific duties to ensure the health and safety of workers.
The Person Conducting a Business or Undertaking (PCBU) or person/ employer is responsible for implementing control measures, maintaining their effectiveness, and conducting air monitoring and health monitoring programs.
Management and supervisors must identify RCS hazards, provide relevant training, and ensure the provision and maintenance of Personal Protective Equipment (PPE).
Workers are responsible for following procedures, minimising risks, reporting incidents or near misses, and wearing appropriate PPE.
Managing RCS risks in road construction involves a comprehensive risk assessment. This includes identifying substances and materials likely to contain RCS, processes or activities that generate RCS, workers exposed to RCS, existing control measures, and ongoing monitoring.
Mobile plant and equipment, such as profilers, mechanical broom attachments, and blower vacuums, have been identified as high-risk sources
Personal monitoring is essential to ensure compliance with the WES for RCS and assess the effectiveness of control measures. Monitoring should be conducted by competent professionals following relevant standards. Health monitoring should be provided to workers if there is a significant risk to their health due to RCS exposure.
This may include pre-employment/ exit medical examinations, regular health monitoring, and respiratory health questionnaires.
Workers should receive comprehensive education and training regarding RCS hazards, potential sources of exposure, associated health risks, implemented control measures, proper use and maintenance of PPE, and the importance of dust monitoring programs. Induction and refresher training programs should be conducted to ensure workers are wellinformed and actively engaged in RCS risk mitigation.
In the end with RCS, it is about effectively managing the risks associated. RCS in road construction requires a comprehensive understanding of the hazards, rigorous risk assessment, and implementation of control measures.
“WORKERS SHOULD RECEIVE COMPREHENSIVE EDUCATION AND TRAINING REGARDING RCS HAZARDS, POTENTIAL SOURCES OF EXPOSURE, ASSOCIATED HEALTH RISKS, IMPLEMENTED CONTROL MEASURES, PROPER USE AND MAINTENANCE OF PPE, AND THE IMPORTANCE OF DUST MONITORING PROGRAMS.”
of RCS generation. To control risks, the Hierarchy of Controls should be followed. Elimination or substitution of materials and tasks involving RCS is the most effective control strategy.
Engineering controls, such as using dust capture and suppression systems, are also crucial. Administrative controls, like providing information, instruction, and training, play a vital role in raising awareness among workers. PPE, including respiratory protective equipment, is a last resort when other controls are not sufficient.
Stakeholders, including the PCBU, management, supervisors, and workers, have distinct responsibilities in ensuring a safe working environment.
By following the guidelines provided in the document “Managing Respirable Crystalline Silica in Road Construction,” stakeholders can minimise RCS exposure, protect worker health, and promote a culture of safety. Proactive risk management and continuous worker education are key to mitigating RCS risks and ensuring the well-being of those in the road construction industry.
To assist in managing the risk of RCS exposure and to meet regulatory responsibilities, AfPA has made the following resources available in the online National Health and Safety:
Managing respirable Crystalline Silica
Dust in road construction – This procedure outlines measures to prevent and manage the risks associated with RCS dust exposure in road construction, including maintenance (eg asphalt laying and spray sealing). An overview is provided of the risk management process of RCS dust, describing Work Health and Safety (WHS) obligations and other relevant information relating to the implementation of control measures for RCS.
Risk assessment for exposure to Respirable Crystalline Silica in road construction – This risk assessment helps identify and evaluate potential hazards associated with exposure to RCS dust during road construction tasks. This risk assessment also describes and recommends a list of control measures to eliminate or minimise hazards associated with RCS exposure in road construction.
RCS Procedure – Training Slides 2023 – This set of training slides has been developed to assist members in communicating the principle of managing and mitigating RCS risks identified in the RCS Risk Assessment and Procedures.
Many thanks are given to those who assisted across Australia with the compilation of these national resources for AfPA members and in particular the University of Queensland (Dr Kelly Johnstone and Homare Atkinson), Pioneer North Queensland Fulton Hogan and Downer.
Fulton Hogan was a recipient of the AfPA 2023 Queensland Safety Initiative Award in July 2023 for their involvement leading in the RCS Dust Management Research Project.
As a state winner in Queensland this initiative will now go through to the national awards.
For more information on the three RCS resource documents AfPA members can visit: AfPA Health and Safety.
oo Wee Rup is a small town located in the Shire of Cardinia, about 60 kilometres southeast of Melbourne. The town has experienced significant population growth over the years, leading to increased traffic flow through its narrow roads, particularly during peak periods. This traffic congestion has not only affected local residents but also impacted the movement of freight and goods through the region.
To address these issues, the Victorian Government and VicRoads embarked on the construction of a $66 million bypass road that would divert traffic away from the town centre. A new 3.4-kilometre two-lane arterial road link between Healesville-Koo Wee Rup Road and the South Gippsland Highway will provide a safer and more efficient route for commuters and freight transport.
The Koo Wee Rup Bypass project has set the scene for sustainable road infrastructure construction, using sleepers that reduce environmental impact while ensuring longlasting durability.
1053 purpose built concrete sleepers manufactured by National Precast Precaster Sunset Sleepers have taken sleeper sustainability innovation to the next level. The company set out to pioneer a greener approach and turned to glass fibre reinforced polymer (GFRP) as a replacement for traditional steel reinforcement.
According to National Precast CEO Sarah Bachmann, GFRP as reinforcement offers several advantages, including high strength-to-weight ratio, corrosion resistance and longevity.
As well, the company has used a lower carbon concrete mix to manufacture the sleepers, to further reduce the carbon footprint. The mix incorporates recycled and waste raw materials. A 50MPa mix was selected to deliver enhanced durability.
PROJECT: Koo Wee Rup Bypass
CLIENT: VicRoads
HEAD CONTRACTOR: Lend Lease Engineering
PRECASTER: Sunset Sleepers
“By reducing the reliance on steel in the sleepers and using a high strength, lower carbon mix, carbon emissions have been significantly reduced. The sleepers will last more than a lifetime,” Bachmann says.
Bachmann believes that these innovations, combined with the inherent benefits of offsite precast concrete manufacturing, make these sleepers an environmentally friendly choice.
The sustainability and environmental benefits of using factory-made precast concrete elements are well known. Manufactured in a controlled environment, there is minimal waste, and any waste is recycled. Local employment is supported and workers enjoy a controlled, safe environment.
Meticulous quality control measures were implemented throughout the entire manufacturing process to deliver impressive results.
Every concrete delivery underwent thorough testing to confirm the correct slump and strength. A comprehensive inspection and test plan (ITP) was engaged with regular inspections and
tests conducted to verify quality.
The sleepers were cast after a suitable curing period and left wrapped in plastic for a minimum of seven days, promoting proper hydration and strength development.
All manufacturing processes and materials adhered to regulatory requirements and met the project’s stringent specified longevity and performance criteria.
Sunset Sleepers’ commitment to innovation and quality has set a new precedent for road infrastructure construction in Australia. With an expected lifespan of 100 years, these sleepers offer remarkable durability that can withstand the demands of heavy traffic and adverse weather conditions, which will contribute to reducing maintenance costs and environmental impact.
Their success paves the way for wider adoption of sustainable construction practices and materials, inspiring other infrastructure projects to prioritise longevity and sustainability.
Contract finalised for Norwest Metro Station works
Sydney Metro has awarded a contract for development works on the Norwest Metro Station site. Mulpha has won the contract which will see the delivery of up to 52,000 square metres of new commercial office space, short-term accommodation, and retail opportunities. This will include the development of three multi-level tower forms stretching from 13 to 21 storeys above two mixed-use podiums. The new buildings will benefit from access to the Norwest Metro Station, which will be located adjacent to the site. The Norwest Metro Station will form part of the Sydney Metro, the largest public transport project in Australia. This will include the construction of 31 new stations and a 66-kilometre metro line by 2024. Sydney Metro, together with signalling and infrastructure upgrades across the existing Sydney rail network, will increase the capacity of train services entering the Sydney CBD – from about 120 an hour today to up to 200 services. When Sydney Metro is extended into the central business district in 2024, metro rail will run from Sydney’s North West region under Sydney Harbour, through new underground stations in the CBD. Sydney Metro and Landcom – the NSW Government’s land and property development organisation – will work closely with Mulpha to ensure the site development meets all planning requirements.
Contract awarded for $120M Major Road Interchange
Acciona has been awarded a contract to design and build the Majors Road Interchange Project in South Australia.
The $120 million project will involve the construction of new on and off ramps to provide commuters in the southern suburbs further access to the Southern Expressway. This will improve access to community and recreational sporting facilities from the Southern Expressway. This is expected to benefit more than 13,000 motorists who travel on Majors Road daily. The project will also benefit the 74,000 vehicles using the Southern Expressway between Darlington and the Reynella Interchange each day. Major construction on the Majors Road Interchange Project is expected to begin in the last quarter of 2023 and final project completion is expected at the end of 2025. Both of the South Australian and Federal governments have committed $60 million each to the project.
UGL awarded Western Downs Battery project works
CIMIC’s UGL has been awarded a contract for works on the expansion of the Western Downs Battery project in Queensland. As industrial sized energy storage system, the battery will provide grid stability by dispatching stored energy to the grid during peak times of demand. The work, to be delivered by UGL and Tesla, will increase the Western Downs Battery installed capacity to 270 MW/ 540 MWh. The expanded battery is located alongside Neoen’s 460 MWp Western Downs solar farm and will enable stored energy to be transmitted into the electricity network from the Australian summer of 2024/2025. These works follow UGL’s announcement in January that it had been appointed to install Tesla
Megapack 2XL units and the high voltage infrastructure to connect them to Neoen’s Western Downs Green Power Hub, around 250 kilometres west of Brisbane.
Preferred bidder announced for Geelong centre
Plenary Conventions has been appointed to lead the project and will soon start on what will be one of the biggest developments in regional Victoria. The Victorian Government is investing more than $260 million into the project as part of the Geelong City Deal, with additional contributions of $30 million from the Australian Government and $3 million from the City of Greater Geelong. The Plenary Conventions consortium will transform the 1.6-hectare waterfront car parking site into a new precinct. The consortium comprises the Plenary Group as sponsor and investor, Built as builder, Woods Bagot as architect, BGIS as services contractor and Quintessential Equity as developer. It will include the construction of the purpose-built convention and exhibition space, incorporating a 1000 seat venue, two large exhibition spaces, meeting rooms, conference facilities and flexible event spaces. Preliminary works on the site are underway and construction is set to begin shortly, with the convention centre and hotel expected to be finished in 2026. The precinct development is the centrepiece of the Geelong City Deal – a more than $500 million commitment between the Australian and Victorian governments and the City of Greater Geelong.
Built to withstand a variety of conditions the Atlas Copco range of lighting towers are robust and offer unrivalled efficiencies ensuring they are both reliable and can operate for an extensive period of time.
• Fuel efficient, ensuring longer running hours
• Specially designed directional optics offering incredible light distribution
• LED HiLight towers achieve up to 6.000 square-metres of light coverage with an average level of 20 luxes
• A life expectancy of more than 50.000 hours
• Aluminium casting, providing heavy duty protection
DYNAPACS SIXTH GENERATION SMALL ASPHALT ROLLERS - READY TO ROLL
Dynapac’s sixth generation CC1300VI and CC1400VI small asphalt rollers are designed and built to meet the construction industries ever evolving and tough conditions. The new design has resulted in a robust, comfortable and modern machine that still achieves the market leading compaction results that Dynapac is renowned for.
The new generation has a unique cross mounted engine providing exceptional access to engine and hydraulic components. This new engine concept and the slideable operators seat combine to increase visibility to drum edges and the greater worksite. High vibration frequency, offsetability of the drum, high efficiency eccentrics and options such as edge press devices and chip spreaders all improve compaction efficiency and versatility.
The SAMIfalt I-Brid “Universal” Binder has officially entered the space-age. After two years of NASA-level testing, SAMI Bitumen Technologies is proud to introduce their latest innovation: the Samifalt I-Brid “Universal” Binder. Made for roads that carry heavy loads, this revolutionary new binder is highly resistant to even the most extreme temperatures—making it ideal for airports and highways (no matter where they are in the universe).