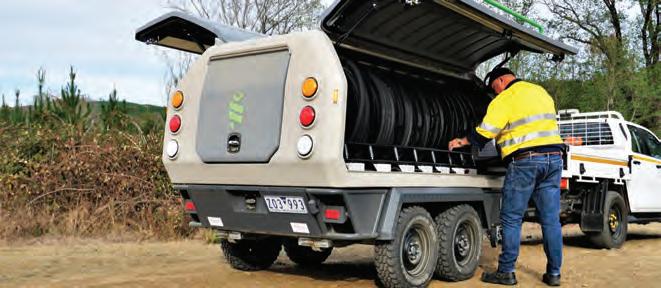
5 minute read
Increasing hydraulic uptime for the mining industry
WITH A LONG HISTORY SPANNING THREE GENERATIONS, BOA HYDRAULICS HAS TRANSFORMED AND EVOLVED TO BECOME ONE OF THE FASTEST GROWING HYDRAULIC COMPANIES, PROVIDING A TURN-KEY HYDRAULIC HOSE REPAIR AND MAINTENANCE SOLUTION TO THOSE WORKING AROUND HEAVY MACHINERY.
Maintenance is an important part of working with machinery, particularly in the mining and resources industry.
When a hydraulic hose bursts onsite, the compounding expenses to a mining operation is extreme, not just in terms of fixing the broken part, but the cost of machine downtime can be severe, especially when it is a frontline machine.
On-site maintenance is the most practical solution and enables a company to minimise downtime, through using existing clients already on-site working on their machinery to add hydraulic hose repairs to their service. This allows diesel fitters to drastically reduce downtime for their clients, becoming the one-stop-shop for their machinery.
BOA Hydraulics has spent many years listening to its customers and from this have developed an onsite mobile hydraulic hose repair solution that eliminates hydraulic downtime and dramatically increases productivity and profitability.
BOA Hydraulics chief executive officer and co-founder Simon Boakes says the aim of the company is to serve its customers and to be recognised in the hydraulics market for giving businesses back their control and autonomy.
“The problem we are trying to solve at BOA is that 37 per cent of unscheduled downtime for a hydraulic machine is due to hydraulic hose failure in the mining sector,” Boakes says. “This is nearly every second time a machine is down it is due to a hydraulic hose failure.
“The downtime isn’t just the time for the machine to be fixed, it’s the waiting time for the hydraulic hose technician to get to site, or a heavy diesel fitter to travel literally hours to get a replacement hose from town.” Boakes says there is a large amount of associated costs with downtime when a hydraulic hose breaks.
There is both the labour cost for the mining company and for the heavy diesel fitter who doesn’t get paid to travel into town to get a hose made.
“There is also the cost of the machine. A frontline machine costs thousands an hour if stopped and the line-up of machines reliant on the frontline machine also stop, causing a large accumulation of costs - and the crazy thing is it isn’t fully recognised,” Boakes says.
As part of its commitment to making the lives of its customers easier, BOA Hydraulics produced the BOApod Hydraulic Hose Repair unit, which is an integral part of the BOA Onsite Hydraulic Hose Solution. This all-weather, allterrain mobile unit enables the user to assemble hydraulic hoses following the same principles used in original manufacturing facilities, out there in the field. Another key pillar that makes up the BOA Solution is the BOAhub – an innovative inventory management and reordering app. Tightly integrated with the BOApod, the BOAhub’s scanto-reorder function makes inventory ordering a breeze onsite.
Boakes says the company works with its customers to make sure they get the best support and assistance available.
“We train and BOA-certify our customers, and we offer re-training at any time,” Boakes says. “We provide sales support, marketing support including customerbranded brochures, business cards, cab
BOA Hydraulics produced the BOApod Hydraulic Hose Repair unit.
stickers, and marketing advice, and we also offer technical product support. Access to quality hose and matched fittings with cost-plus pricing completes the full 360-degree solution for fitters in the mining industry.
“We believe it isn’t complicated to make a hydraulic hose with the right tools and skills.
“Our people, training and support is critical to the success of our solution.
“As a family-owned business, with three generations, we believe in win-win situations.”
Boakes says the customer feedback the company has received, especially regarding the downtime saved for their labour force, has been overwhelming.
Dan Davis from Madd Industries says he was onsite during a scheduled major blast, but when they were evacuating the pit in preparation, one of the frontline drill rigs blew a hose so they weren’t able to move it. Previously they would have had to cancel the blast because they couldn’t go ahead with a multimillion dollar machine right in the pit.
However, thanks to BOA Hydraulics, Davis was able to efficiently carry out a hose replacement and allow the machine to be moved. “It is the ease of the one-stop shop,” Davis says.
“We can be out on a job and we have the all the equipment, tooling, hosing and parts to do it immediately.
“There is no need to wait on a hose guy to turn up, allowing us to get the machine back up and running for the customer as quick as possible. “
Davis says with the previous methods of hose replacement, he would have a fitter and operator standing around waiting for a hose, which isn’t a good look for his company.
“It just eliminates machine and labour downtime,” Davis says.
“Labour downtime isn’t something tracked like machine downtime, but people are beginning to realise it is a big issue we need to eliminate.
“Being the one-stop-shop, it means just one phone call to get the job done.”
Boakes believes there is a better way to do things and encourages businesses working with heavy machinery to challenge themselves on the way they repair and maintain their hydraulic hoses.
“The hydraulic hose is the vein of hydraulic machine, yet they are largely poorly managed and the cause of this is an accumulation of costs to the mining industry,” Boakes says.
“With a well-thought-out hydraulic hose repair solution, the savings can be drastic.
“With a mobile, on-site solution, we are giving those servicing heavy machinery back control and autonomy when it comes to hydraulic hose repairs.”
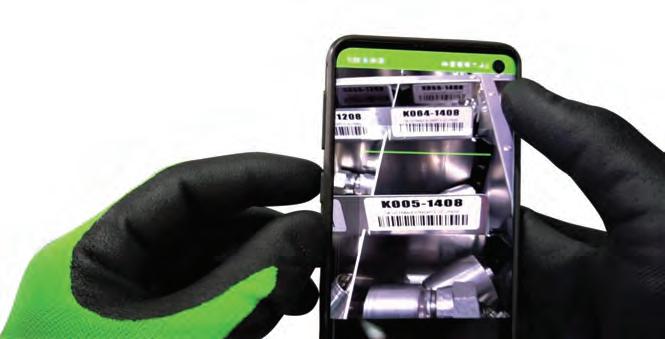
The BOAhub’s scan-to-reorder function makes inventory ordering a breeze onsite.
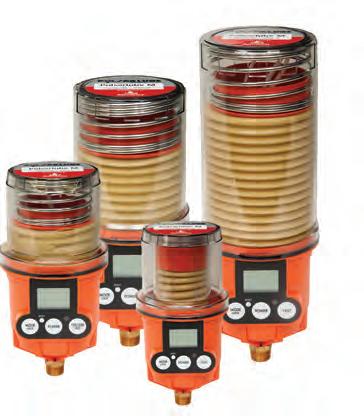
THINK EQUIPMENT SAFETY?
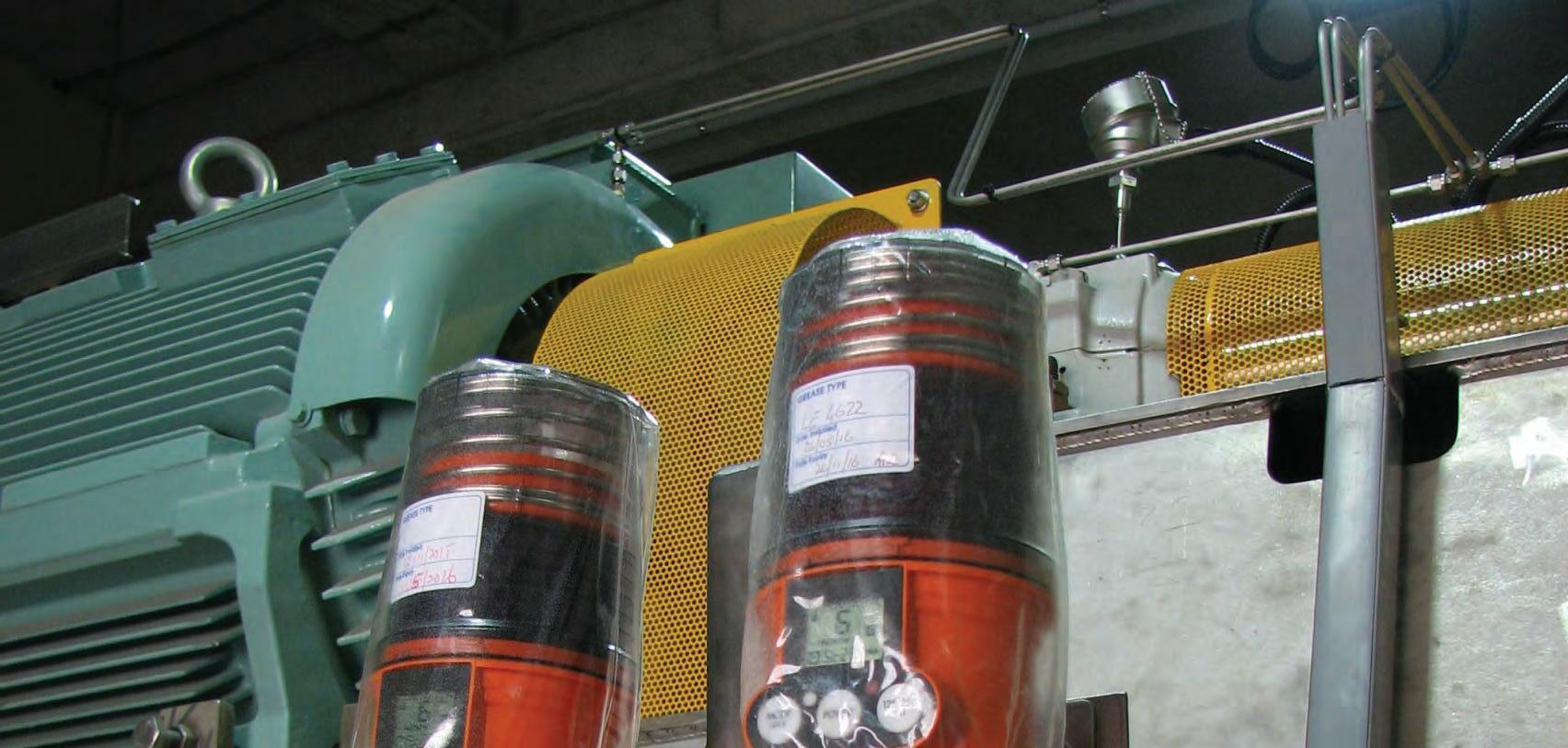