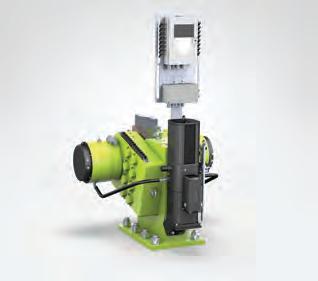
2 minute read
State-of-the-art monitoring for brakes in mines
State-of-the-art condition monitoring solutions for brakes in mines
BRAKE SYSTEMS ARE MADE UP OF A BASIC BRAKE WITH ADDITIONAL MODULES LIKE HYDRAULIC POWER, CONTROL AND MONITORING UNITS. DELLNER BUBENZER GIVES AN OVERVIEW OF THE STATE-OF-THE-ART SOLUTIONS THE COMPANY OFFERS TO MONITOR SUCH A SYSTEM.
Brakes in mining applications are of essential importance.
They are holding and stopping loads even under the worst conditions.
Typical applications are belt conveyors, ship-loaders, mine hoists, stackers, reclaimers, AG, SAG and ball mills as well as all kind of winches.
Modern industrial brakes are opening and closing, and many applications require “intelligent brakes” that can supply exactly the required brake torque depending on the load.
The demand for monitoring capabilities has grown with the increasing digitisation of the industry.
Basic functions like brake open/close, wear of linings and air gap are normally checked by limit (proximity) switches that are hardwired to the control system.
In case customers want to monitor additional brake parameters DELLNER BUBENZER is offering its VSR3 system (Visual Status Reading Third generation).
The sensor data is collected in one device and customers can read out relevant information on a display.
The VSR3 system can also visualise brake pad temperature, analogue stroke sensor and a wear sensor that is integrated in the lining carrier so that customers have all relevant information at a glance.
In addition, an alarm buzzer or light through a 10-amp dry contact alerts of possible over-range conditions at one or more sensors.
DELLNER BUBENZER mining worldwide sales director Arno Weil says this warning feature helps get important information about the brake early, so customers are able to act before it is too late.
If the environment is more complex or maybe unmanned, sensor data and parameter must be automatically transferred to the “brain” of the plant.
Communication is often realised via fieldbus protocols like PROFIBUS, a standard for fieldbus communication in automation technology, or PROFINET, an industry technical standard for data communication over industrial ethernet.
The DELLNER BUBENZER CMB3 (Computer Monitored Brake Third generation) monitoring unit provides the PROFIBUS and PROFINET feature.
Furthermore, the CMB3 measures the contact force of the brake.
Brake force data acquisition is based on strain gauges that are integrated in the force flow of the brake.
Contact force measurement is not only available for thruster disc brakes but also for huge hydraulically released, spring applied disc brakes with contact forces up to 510 kilonewtons (kN).
The CMB4 system is finally completing the DELLNER BUBENZER product range of monitoring units and is part of the smart hydraulic power unit series.
CMB4 checks parameters including oil temperature, oil level, pressure, moisture content and contamination of the oil.
The HPU sensors are connected to an electronic box that is hosting the required hardware and software.
A 4.3-inch TFT color display is also part of the setup. Information can be read out at site as well as by remote access.
The CMB3 measures the contact force of the brake.
The VSR3 system can also visualise brake pad temperature.
