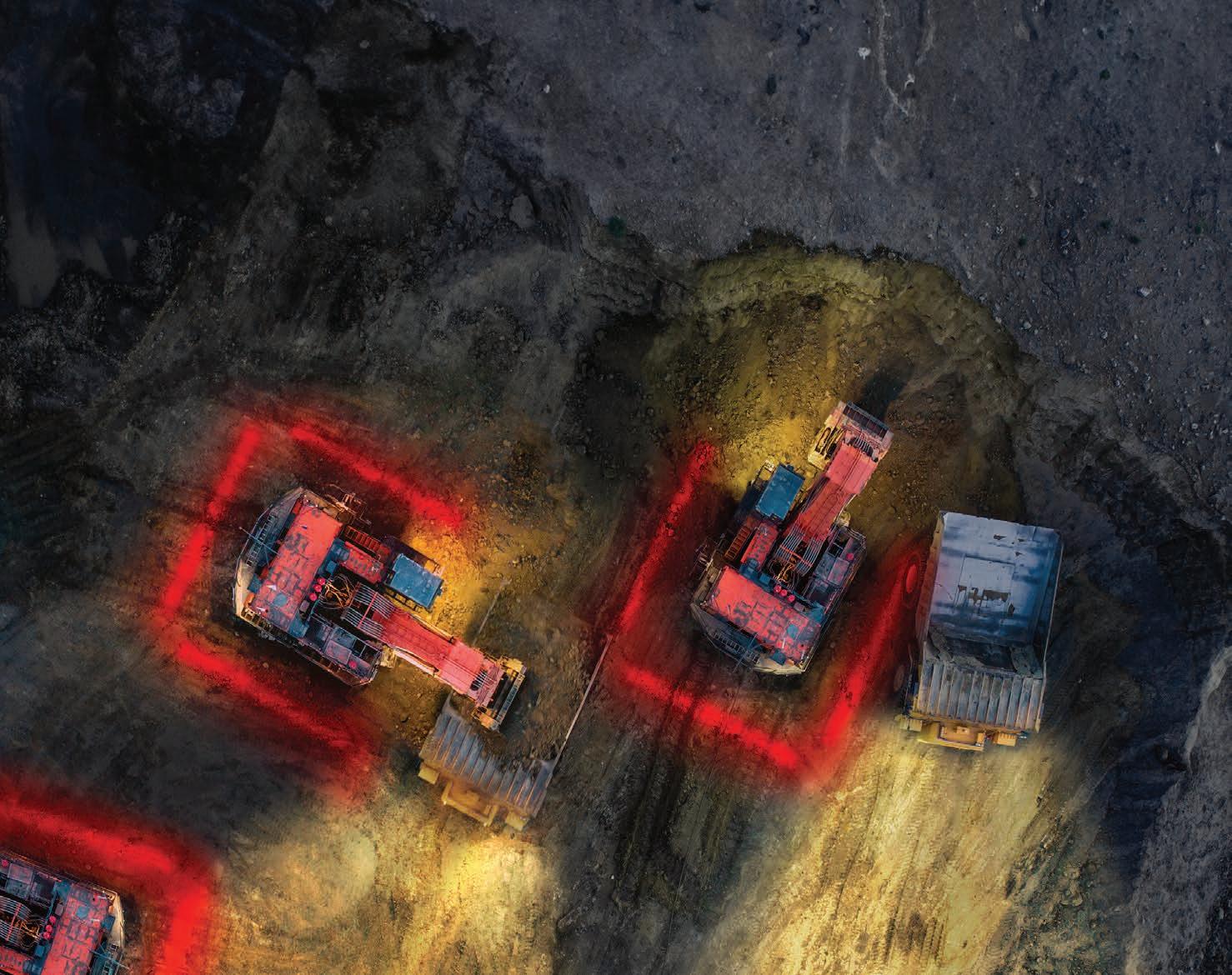
Keeping
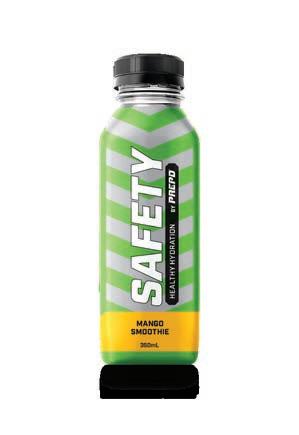

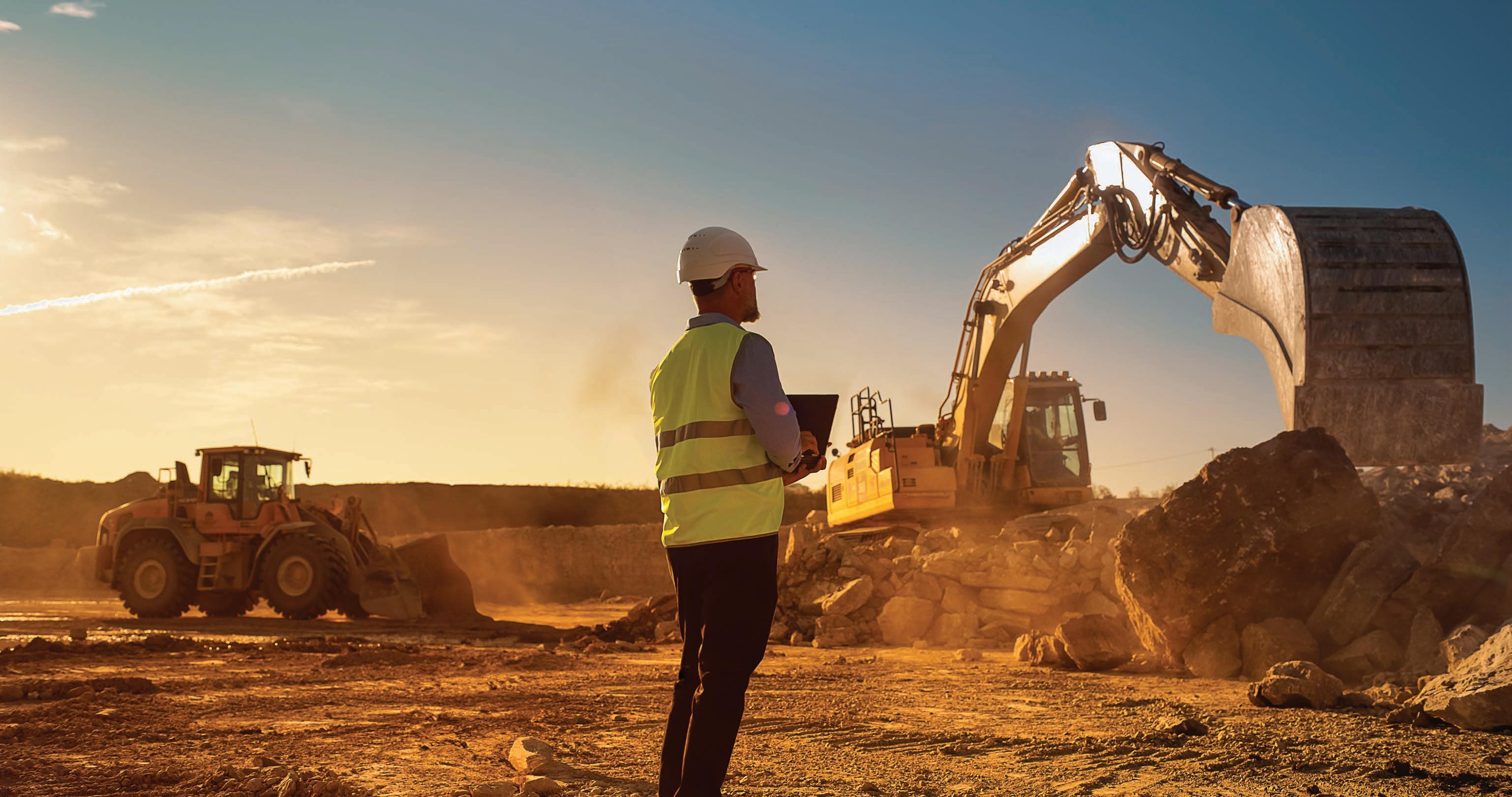
Keeping
Collision Avoidance System is able to detect objects in the collision risk area, evaluate the collision risk level and take interventional collision avoidance action. The system is able to alert the operator and, if required, can even take actions through the control system of the machine to prevent accidents by automatically slowing down the speed or braking the machine to a stand still.
Available for both loaders and trucks, CAS is your new best friend when it comes to risk reduction.
epiroc.com.au
There are few jobs where fatigue doesn’t affect a person’s performance (with sleep studies or drug trials possible exceptions). And there are even fewer jobs where the risks of fatigue can be more catastrophic than in the resources industry.
With so many moving parts across a mining operation, not to mention all of the activity that’s involved with people and machinery coming and going to a site, even the slightest loss of concentration or focus can quickly snowball into a major incident.
Things like long hours, harsh conditions, repetitive activities, remote workplaces, and fly-in, fly-out work can make mine workers susceptible to fatigue, and the associated safety issues can be disastrous.
Cognitive and physical exhaustion is a significant risk in the mining industry, particularly
when fatigued workers operate high-risk machinery like heavy vehicles. Indeed, most fatiguerelated incidents on mines occur behind the wheel.
That’s why this issue of Safe to Work looks at some of the common risks associated with fatigue across a mine site and showcases some of the OEMs, innovations, and technologies that help workers manage fatigue, while keeping them energised, alert and out of harm’s way.
Moving away from the mine site, this edition of the magazine breaks down some important changes to workplace safety legislation in 2024. From the commencement of ‘Same job, same pay’ legislation to improved long service leave for casual coal miners to tighter sexual harassment regulations, there are many legal changes that employers and employees should be aware of.
We also look at Australia’s news multi-enterprise bargaining laws and how they may affect the local mining industry.
Elsewhere, we explore the safety risks that come with working from heights.
Working from heights is a common risk in the mining industry, presenting not only the risk of a fall but also a danger to people on the ground.
Though the risks seem apparent, they can be challenging to mitigate – with the consequences of failure severe – so it pays to be aware of potential issues across a mining operation.
Paul Hayes Managing EditorCOO CHRISTINE CLANCY
MANAGING EDITOR
PAUL HAYES
Tel: (03) 9690 8766
Email: paul.hayes@primecreative.com.a
ASSISTANT EDITOR
TIMOTHY BOND
Tel: (03) 9690 8766
Email: tim.bond@primecreative.com.au
JOURNALISTS
ALEXANDRA EASTWOOD
Tel: (03) 9690 8766
Email: alexandra.eastwood@primecreative.com.au
OLIVIA THOMSON
Tel: (03) 9690 8766
Email: olivia.thomson@primecreative.com.au
KELSIE TIBBEN
Tel: (03) 9690 8766
Email: kelsie.tibben@primecreative.com.au
CLIENT SUCCESS MANAGER
JANINE CLEMENTS
Tel: (02) 9439 7227
Email: janine.clements@primecreative.com.au
RESOURCES GROUP LEAD
JONATHAN DUCKETT
Mob: 0498 091 027
Email: jonathan.duckett@primecreative.com.au
BUSINESS DEVELOPMENT MANAGER
NATALIE HERBSTREIT
Mob: 0412 741 068
Email: natalie.herbstreit@primecreative.com.au
DESIGN PRODUCTION MANAGER
Michelle
A
8 Labour laws: What you need to know in 2024
Safe to Work looks at the nuts and bolts of important changes to workplace legislation in 2024.
10 Pulling back the covers on fatigue
Recent studies have placed a spotlight on the effects of fatigue at mine sites across the country.
14 PREPD for SAFETY
Likened to an internal hard hat, SAFETY by PREPD Hydration is becoming a staple in the fight against dehydration and fatigue in the mining industry.
20 A beacon of safety
HELLA’s newest work lamp for mining vehicles is helping reduce operator fatigue, eye strain and safety incidents.
32 Balancing maintenance costs
Martin Engineering examines the importance of cleaner monitoring and maintenance in conveyor safety.
38 Keeping workers safe at heights
Falls from height are a leading cause of injury in the mining industry, but how do these risks actually come about?
44 Across the Pacific
The PNG Industrial & Mining Resources Exhibition and Conference will debut under new ownership in 2024. Safe to Work highlights at what attendees can expect.
52 Game-changer in mill relining safety
Bradken’s MillSafe Solutions are keeping personnel safer during mill relining.
54 Keeping current with electrical safety
The current-limiting protector from CSE Uniserve is a proven solution to a complicated problem.
SAFETY by PREPD helps you:
• Have more energy in the morning
• Feel less fatigued in the second half of a shift
SAFETY by PREPD is a proven hydration enhancer, designed to make water work harder so your employees can work better, safer and smarter.
Coming to work dehydrated can cause a 4-5% loss in body fluid throughout the day3
Workers in a physical role require almost DOUBLE the hydration as an office-based employee¹
Being just 3% dehydrated can slow reaction time to the same extent as being over the legal blood alcohol limit¹
Dehydration can result in poor decision-making and poor cognitive performance¹
Being just 5% dehydrated can reduce productivity by up to 50%²
More than 50% of underground mine workers show signs of clinical dehydration at the end of a shift
Wearing protective clothing increases the speed of dehydration by up to 2.25L per hour3
Dehydration & heat exhaustion contribute to accidents/ fatalities. Costing the mining industry $4 Billion every year
• Get better sleep
SAFETY by PREPD provides the benefits you need for a long day at work:
• High dietary fibre content for satiety and prebiotic fibre for gut health.
• Vitamin B12 for improved concentration.
• Sustained hydration and energy from fibre.
• Promotes fat burning and appetite suppression
• Low in sugar, lactose-free, and gluten-free.
BACKED BY 20+ YEARS OF SCIENCE DEVELOPED BY YALE & FLINDERS UNIVERSITIES & TESTED BY OVER 3500 CUSTOMERS
SCAN THE QR CODE TO FIND OUT MORE:
Yancoal has been working hard to drive down health and safety incidents with holistic training programs. And those efforts are now paying off.
At the end of the December 2023 quarter, Yancoal reported a 12-month rolling total recordable injury frequency rate (TRIFR) of 5.3, well below the industry weighted average of 8.3.
For Yancoal, this is a significant reduction from its TRIFR of 8.1 in 2022 and 8.4 in 2021.
Results are thanks in part to the company’s ‘Safe Way Every Day’ training program, rolled out in 2022. The five-year program is designed to provide a consistent approach to health, safety and training management across all Yancoal operations, and to support the integration of a safety culture across the business.
“The initiatives and training provided involve simple concepts
and tools that our whole workforce can use to enhance personal safety, happiness, health and wellbeing, both on the job and in their personal lives,” Yancoal said.
Yancoal hopes the whole-ofbusiness approach will help progress safety culture across its operations.
On the mental health side of things, the company rolled out a
four of the program kicked off across the company in 2023, with modules to address topics like mental illness and suicide.
“The program intends to promote and support positive mental health management, encourage help-seeking behaviours amongst our workforce, change perceptions of mental health, and equip our people to better to support their teams, co-workers, family and friends,” Yancoal said.
At the 2023 Australian Mining Prospect Awards, Yancoal head of training and safety culture Craig Hagan was recognised as the Safety Advocate of the Year.
Hagan played a large part in ushering in Yancoal’s new safety and
“Craig has been working in highrisk industries for over 30 years, and he’s seen first-hand how critical it is to slow down and focus on what matters,” Yancoal said.
Following the rescue of a South Australian man who spent 24 hours trapped in a Coober Pedy opal mine at the start of the year, Safe to Work took a closer look at safety in one of Australia’s most iconic industries.
A 16-man rescue team comprised of State Emergency Service (SES), Country Fire Service and the local mine rescue squad members assembled at the Nine Mile opal field outside of Coober Pedy.
They worked for three hours to free the man from the 25m shaft, with SES rescue coordinator Vincent Scully describing the process as a “very complex technical rescue”.
A rescue squad member descended into the shaft to retrieve the man, with the other volunteers helping to haul the pair up.
The man sustained a broken leg and dislocated shoulder in the incident
and was also badly dehydrated. He was flown to Coober Pedy hospital for treatment.
Opal fields are typically dotted with vertical shafts that descend many metres underground where mining takes place.
Opal mining can often be considered more a matter of luck than geological mapping, so mining corporations tend to steer clear. This means in places such as Coober Pedy, opal mining is the business of individual prospectors – and as such is often conducted alone.
Extreme heat, falls from heights, working in confined spaces, and tunnel collapses are a few of the risks associated with opal mining.
After a string of serious injuries and two fatalities at the Lightning Ridge Minerals Claims District in New South Wales, the state Resources Regulator
published a video to increase safety awareness in opal mining.
The video includes an interview with a miner who was badly injured in a fall in an opal shaft and an interview with the partner of a miner who was fatally injured at Grawin in 2020.
“The video encourages opal miners to understand the importance of safety when accessing their mine using ladders, including the use of a fall arrest, such as a harness, to improve their safety,” then NSW Resources Regulator executive director Garvin Burns said.
“Many miners work alone without fully appreciating the risks of falls when working at height.
“We encourage the industry to visit the regulator’s website to access information, improve compliance and increase safe work practices.”
SAFE TO WORK LOOKS AT THE NUTS AND BOLTS OF IMPORTANT CHANGES TO WORKPLACE LEGISLATION.
From the commencement of ‘Same job, same pay’ legislation to improved long service leave for casual coal miners to tighter sexual harassment regulations, there are many legal changes of which employers and employees should be aware with the new year now underway.
Changes to the Fair Work Act mean all workers in the black coal (thermal and metallurgical) mining industry, including casual workers, will receive the correct payment for long service leave.
“Casuals in the industry may work a compressed fortnightly roster – longer
hours in the first week and shorter hours in the second – but current weekly counting of these working hours reported by employers is denying casuals equality in their entitlements,” Federal Minister for Employment and Workplace Relations Tony Burke said.
Changes to the law will prevent casual workers from being disadvantaged compared to their fulltime counterparts.
Casual workers in the black coal mining industry will also benefit from an amendment that makes it clear long service leave must also include casual loading, ensuring workers do not take a pay cut when accessing their entitlement.
“Casuals in the black coal mining industry deserve fair treatment. They deserve the long service leave entitlements they earned,” Burke said.
The Closing Loopholes Amendment (‘Same job, same pay’) received Royal Assent in late 2023. This means the Fair Work Commission can now make orders requiring employers to pay labour hire workers the same rate as a host company’s direct employees doing the same job.
When making a regulated labour hire arrangement order (RLHA), the Fair Work Commission must consider a multi-factor test.
Putting it simply, in order to make an RLHA, the Commission must be
Under new laws, labour hire workers will be paid the same amount as a host company’s direct employees.
satisfied that the business in question will supply its employees to perform work for a host; that the work will not be for the provision of a service, rather than the supply of labour; and that it is fair and reasonable to make the RLHA.
If satisfied of all the above conditions, the Commission must make an RLHA order specifying the covered parties and the host employment agreement (for protected rate of pay), and the commencement of the contract.
These arrangement orders will commence from November 1.
Under another section of the Closing Loopholes Bill, wage theft may soon be criminalised at a federal level.
Employers who intentionally underpay employees could face harsh punishments, with the bill proposing fines of up to $1.5 million and a maximum of 10 years imprisonment for offending individuals. In the case
of a body corporate employer, these penalties are even harsher.
Unlike ‘Same job, same pay’, this amendment has yet to be passed by parliament. However, the Federal Government has indicated its intention to roll out this amendment by no later than January 1 2025.
The Respect at Work Act was introduced in December 2022 in the wake of the earlier ‘Respect at Work’ report, which set out a list of 55 recommendations to prevent sexual harassment in Australian workplaces.
Some of these recommendations have since been ratified into law under the Act. The most significant of these changes is that employers are now required to adopt proactive measures to prevent sexual harassment, sexbased discrimination and related victimisation in the workplace.
Under previous laws, employers could be held vicariously liable for this behaviour where they failed to make all reasonable steps to prevent the behaviour from occurring.
This is still the case; however, this is the first time the law has enforced a positive duty on employers. This means employers need to proactively take action to prevent unacceptable behaviour relating to sexual harassment in their workplace, regardless of whether a complaint has been made.
As part of the changes, the Australian Human Rights Commission (AHRC) has been empowered with the ability to enquire into, and report on, issues of systemic unlawful discrimination or suspected systemic unlawful discrimination. The AHRC can also issue non-compliant employers with recommendations and enforceable undertakings.
These AHRC powers commenced in December 2023, one year after the legislation, giving workplaces time to demonstrate compliance. This year, non-compliant workplaces can expect the AHRC to come knocking.
The final recommendation of the ‘Respect at Work’ report pertained to the risk of adverse costs associated with court cases. In a typical case, once a matter is settled, a court may order the losing party to pay the other sides’ costs – usually legal fees.
But matters of unlawful discrimination, including sexual harassment, are often between an employee and a company, representing a significant power and resources imbalance.
This imbalance alone can often be enough to dissuade a victim from coming forward.
The proposal suggests introducing cost protections, which already exist elsewhere in the Fair Work Act, to matters of unlawful discrimination.
The proposal has been drafted into a bill but has yet to be voted on by parliament. If ratified into law, it will mean the applicant (alleged victim) cannot be liable for costs unless one of the following apply:
• The applicant instituted proceedings vexatiously or without reasonable cause
• The applicant’s unreasonable act or omission caused the other party to incur the costs
• The other party is a respondent who was successful in the proceedings, the respondent does not have a significant power advantage over the applicant and the respondent does not have significant financial or other resources relative to the applicant
Similarly, the court must order the respondent (alleged perpetrator) to pay costs if the applicant is successful on one or more grounds, except where the applicant’s unreasonable act or omission caused the applicant to incur costs.
This year will see number of significant changes that will benefit the lives of workers across Australia. In an ever-changing regulatory environment, it’s essential to stay up to date.
Image:
RECENT
PLACED
Long shift work is a common practice in the mining industry, particularly in fly-in, fly-out (FIFO) arrangements, owing to the constant and often-remote nature of the work. While mine sites can run around the clock without issue, workers aren’t so lucky.
Fatigue can affect anybody, but on a mine site it tends to rear its head most when people jump behind the wheel of a vehicle. A 2023 study from the University of Queensland’s Sustainable Minerals Institute, ‘Fatigue Management in the Queensland
Mining Industry and its Relationship with Mental Health’, had a closer look at this relationship.
QUEENSLAND
The study found that 80 per cent of all fatigue-related incidents in Queensland mines since 2011 involved vehicles, with 85 per cent of these fatigue-related incidents occurring in heavy vehicles.
The report also identified heavyvehicle drivers on night shifts as most at risk of being involved in fatiguerelated incidents.
The data showed that workers were most likely to be involved in a fatiguerelated vehicle incident within the first three days of a seven-on, seven-off roster, as workers adapt to an altered sleeping schedule.
involving a vehicle, and 82 per cent of these occurring on a coal mine.
When working with enormous industrial equipment the margin for error is often small, making fatigue all the more dangerous.
The study found that fatigue-related incidents accounted for 2.5 per cent of all reported notifiable incidents across Queensland mines from 2011–22, with heavy-vehicle drivers to be most at risk, with ‘micro-sleep’ a common term in incident write-ups. It also found that over 80 per cent of incidents occurred at coal mines and, of these, 90 per cent occurred on surface operations.
The data from New South Wales mining operations told a similar story, with 95 per cent of fatigue incidents
Though the sample size was much smaller at only four-and-a-half years of data, results did show a drop in the number of incidents. This was further backed up by anecdotal comments by the NSW Resources Regulator, suggesting that eye camera technology in heavy vehicles had lowered numbers of fatigue incidents.
Though the numbers are relatively low, potentially serious incidents still happen. The NSW Resources Regulator investigated two fatiguerelated incidents that took place in August 2023.
The first involved a worker microsleeping behind the wheel on their 20th consecutive 12-hour shift, resulting in a crash. Fortunately, the worker escaped injury.
After investigating, the safety watchdog determined that control measures such as fatigue risk assessments were not being undertaken for workers who had
a combined work and travel time that exceeded the mine’s fatigue management plan.
The second incident, the nature of which was not disclosed, involved a mining electrician who was on his 10th consecutive 12.5-hour shift when he had an accident involving a vehicle.
The Sustainable Minerals Institute’s study looked at more than 5000 potentially serious incidents (where no injury occurred) which took place in WA between 2010 and 2020. It was determined that fatigue was a factor in 1.7 per cent of these incidents.
Similarly to Queensland and NSW, the vast majority occurred in heavy vehicles on surface mines. And 82 per cent of these vehicles involved in fatigue incidents hit something that caused the operator to wake up, with 61 per cent hitting a safety barrier.
These types of near misses are cause for alarm because they so clearly highlight the potential
danger of fatigue. While the number of incidents may be lower than anticipated, any one of these incidents could have involved an operator colliding with another vehicle or worker, or even driving off an embankment.
The study compared the mine incident data to road statistics.
According to studies cited in the report, fatigue plays a role in 10–20 per cent of all road crashes globally. In Queensland, fatigue contributes to 20–30 per cent of all deaths and serious injuries on the road, which is comparative to speeding and drink driving.
“It would be a mistake to assume from these results that operator fatigue is perfectly managed on (mine) sites,” the report stated.
“It appears that controls are in place to prevent or minimise the impacts of fatigue, particularly in single-vehicle collisions. Fatigued operators driving heavy vehicles that interact with other types of vehicles, pedestrians and
infrastructure in multiple scenarios remain a considerable risk. Evidence of the risk of fatigue is clearly shown in the results of the impact of fatigue in the transport industry.”
The study also notes that it is likely fatigue events are under-reported across the mining industry.
Beyond tangible incidents, the study also noted a number of gaps in the industry’s approach to fatigue. One of these is a lack of monitoring of the long-term health effects of fatigue, such as insomnia and obstructive sleep apnoea.
Another risk is the failure to properly consider mental health outcomes of fatigue. Data in this area is limited, but research shows that shift workers with sleep disorders in mining were reported to have higher levels of psychological distress, fatigue and depression. Women and young people are among the most susceptible.
From a business perspective, a Caterpillar Global Mining study showed that shovel operators worked roughly 3.2 per cent slower in terms of
dig rates when affected by fatigue, with haul truck drivers similarly showing a 3.3 per cent slower spot time. That means more fuel burned and slower production.
In spite of their apparent low incidence, the study shows that where fatigue-related accidents do occur, they carry serious risk.
And while people will always need sleep, the mining industry has made strides in developing technology to protect operators from the effects of fatigue.
Glencore was recently recognised by the NSW Minerals Council for its Operator Awareness System, which monitors vehicle drivers for signs of tiredness, triggering alarm and vibration systems when the operators’ eyes close.
In a more recent development, wearable monitoring technologies also present a possible real-time defence against fatigue.
There are many such technologies emerging on the market, as more miners begin to acknowledge and address the threat of fatigue.
The
• Intelligent work lamp with smart features enabling easy adjustment to different weather, driving and lighting conditions
• Ensure the highest possible visibility in a range of environments including dust, snow, rain or fog
• Available in six different illumination variants and amber or green colour change options
• Fast and easy installation
• For the toughest industries in the world
Dimming
Helps reduce output during the day or to reduce glare at night
Memory
Stores the different settings into 3 available memories
Anti-theft protection
Once activated the lamp won‘t work on any other vehicle (unless has SMART setup)
Colour temperature change
Reduces eye strain and fatigue by adjusting to daylight conditions
Contact info.au@hella.com or ph.: 1800 061 729 for more information.
Colour change
Assists in poor visibility (snow, fog, dust) to create safe operating environments
Lifetime management
Notifies the operator if the lamp is near end of life, helping to reduce downtime
LIKENED TO AN INTERNAL HARD HAT, SAFETY BY PREPD HYDRATION IS BECOMING A STAPLE IN THE FIGHT AGAINST DEHYDRATION AND FATIGUE IN THE MINING INDUSTRY.
The opening months of 2024 were marked by heatwaves that scorched their way across Australia.
Parts of Perth hit 45 °C, smashing multi-year records. Birdsville in centralwest Queensland recorded its hottest ever January day at 49.4 °C, and many other regions in Western Australia, like Marble Bar and Paraburdoo, pushed similarly sweltering numbers.
Working in that kind of heat can of course take a significant toll.
When the body’s core temperature exceeds 37°C, it reacts by increasing the blood flow to the skin, producing sweat that cools the body when it evaporates. That means workers in the heat will quickly lose fluids through sweat and become dehydrated.
Dehydration has been shown to increase fatigue, and impair physical performance, reaction time and decision-making, the consequences of which are potentially severe and even fatal in a mining environment.
Though strides have been made in safety technologies that protect workers from their environment, a worker’s individual health is just as critical to the equation. That is to say that when it comes to safety, there’s no replacement for proper hydration.
This is a fact that PREPD Hydration chief executive officer Andrew Perry knows only too well.
“The science shows us that 70 per cent of miners arrive at work already in a dehydrated state,” he told Safe to Work.
“In an industry like mining, people are losing approximately a litre of fluid an hour. Say you’re a 100kg person, it’ll take you roughly three hours to become three per cent dehydrated.
“At that level, your reaction time and decision-making are impaired to the same extent as being over the legal blood alcohol limit. You wouldn’t let workers have two or three alcoholic beverages at lunch before jumping back behind the wheel of a haul truck, but that’s the equivalent of what’s happening with dehydration.”
This is the problem that SAFETY by PREPD was created to solve.
Built on 20 years of research, SAFETY is a hydration drink with a package of health benefits, but the main one is that it helps the body optimally absorb fluids.
A fruit-based smoothie with a thick, silky texture, SAFETY is currently available in two flavours: mango and strawberry. It’s already being rolled out at mine sites across Australia, including with some of the biggest names in the industry.
But to understand the drink, it’s important to understand the science behind it.
“In the 1990s the World Health Organization asked for help in dealing with a massive issue in India and Bangladesh, where millions of children were dying annually, caused by dehydration from rotavirus and cholera,” Perry said.
“Gastroenterologists at Flinders University in Adelaide and Yale University in the US found that if you put a certain fibre into an oral rehydration solution, the body’s ability to absorb fluids increased significantly.
“They were able to use that science in India and Bangladesh to save millions of lives.”
PREPD Hydration is a spin-out of Flinders University’s commercial arm. Having refined the same science that was once used to save millions of lives,
intestine, which is what needs to happen to keep you hydrated – it’s as simple as that,” Perry said.
“SAFETY by PREPD Hydration contains a patented fibre that resists being broken down in the stomach. This means it reaches the small intestine, promoting optimal fluid absorption and pushing water molecules into the bloodstream.”
Unlike sugary drinks, which can’t properly be absorbed by the body and merely pass through it, SAFETY
has a low sugar content that makes it optimal for fluid absorption.
In addition to hydration, SAFETY promotes gut health – a major driver in the body’s immune system.
“The magic really happens when the drink reaches the large intestine,” Perry said.
“There it produces short-chain fatty acids which, on top of being good for gut health, signal to the brain that there’s fluid in the large intestine, which the body can then absorb into the bloodstream again.
“So not only are we optimally absorbing the fluids that we’re normally drinking through the small intestine, but we’ve also opened up a 5L reserve in our large intestine that we bring back into our bloodstream.
“That’s where the real science sits.”
For Perry, PREPD Hydration is a perfect fit for the mining industry.
“Dehydration and heat exhaustion contribute to accidents which cost the mining industry roughly $4 billion every year,” he said.
“Miners are also required to wear heavy PPE [personal protective equipment], which can actually
increase the rate of dehydration to up to 2.25L per hour.
“SAFETY allows workers to stay better hydrated, and if we’re better hydrated, we’re healthier individuals, we cognitively perform better, and we’re safer.”
From an operational standpoint, Perry said that being just five per cent dehydrated can reduce productivity by up to 50 per cent. Add in the disruptions to operations that can occur after an incident, and mine sites have plenty of reason to keep their workforce hydrated and alert with PREPD.
“When they’re not out in the heat, miners are usually in air-conditioned dongas, workstations, airplanes or vehicles,” Perry said. “That means they’re always in an environment where they’re susceptible to infection.
“By promoting gut health – which contributes to around 70 per cent of the immune system – SAFETY can help with that.”
PREPD conducted a case study of the effects of SAFETY on workers maintaining a railway line at an iron ore hub in the Pilbara.
“The feedback was that the workers using it had more energy in the morning,” Perry said. “They felt better in the second half of the shift in terms of their ability to physically do their job.
“They also reported sleeping better at night; hydration and sleep go hand-in-hand.”
SAFETY by PREPD Hydration is promoting optimal hydration, protecting mine workers against heat and fatigue.
“We have had people tell us that they used SAFETY during their steam shutdown, which is usually physically and mentally demanding,” Perry said.
“They found having SAFETY each morning and night set them up for their day and they honestly felt the difference in their energy levels and mental clarity.
KAL TIRE’S NEW TAILORED PRE-TASK STRETCHING PROGRAM SHOWS THAT THE COMPANY PUTS JUST AS MUCH CARE INTO ITS OWN TEAM AS IT DOES ITS CUSTOMERS.
The rapid development of technology is making workplace safety better than ever. But with machines shouldering much of the heavy lifting when it comes to safety, it can be easy to overlook what workers can do. That’s why Kal Tire, a tyre management and supply partner to the mining industry, is rolling out a physiotherapist-designed stretching program to keep its workers safe.
The Kal Tire team supports the Australian mining industry with the changing out of tyres and wheels as required. Tyre management is also a big part of the business, with Kal Tire helping its customers achieve their tyre goals, whether that be optimising vehicle performance or maximising tyre life.
With permanent boots on the
mobile drive-in, drive-out support as required to many more, Kal Tire understands how rigorous tyre maintenance can be.
“As a tyre service provider to customers all across Australia, our technicians are required to change tyres on many different types and sizes of vehicles. That means we use a lot of heavy equipment,” Kal Tire managing director for Australia Miles Rigney told Safe to Work. “In some cases, our teams are squatting for a length of time. As some of these tyres we work on can be 4m in diameter, you can imagine that there’s a lot of reaching involved in the job.
“Injuries can occur when a team member is not properly prepared for these manual handling tasks.”
With the risks of the job in mind, Kal Tire engaged a physiotherapist to help develop its dedicated stretching program based on the kind of movements required of a tyre technician during maintenance.
“While there have been other stretching programs that some of our customers have implemented for their employees – which our team members have joined in on – we now have our own customised program,” Kal Tire health and safety manager Paul Coverdale told Safe to Work
“It comes from the experience of a trained physiotherapist and was developed by looking at the all the lifts, twists and turns our technicians perform during typical tyre maintenance activity.
“This way, if a task requires a certain type of lift, a technician can use the program to see the best type of exercise or stretch to prepare their body.”
The program comprises of over 50 exercises, some of which can be done in a worker’s room while others can be done on the workshop floor. The range
gives workers the ability to vary the program to match their work for the day, while also keeping things interesting.
Rigney and Coverdale, both of whom have past experience on the workshop floor, said they were excited to start rolling out the program across Kal Tire’s Australian operations.
“I think what ‘good’ looks like is a reduction in the risk of sprains and strains for our team,” Rigney said.
“They can put in a little bit of time before the task to get their muscles properly warmed up so that they don’t feel sore afterwards.
“That would be a great outcome.”
Easing some of the physical challenges associated with tyre maintenance will also help make the role more accessible.
“With the labour shortage in the Australian market at the moment, a typical tyre service technician today might look very different to how they looked 20 years ago,” Rigney said.
“They could also be relatively new to the mining industry, and we’ve got more female representation in our organisation than ever before.
“So we’re doing everything that we can – not just to strive for best practice in safety, but also to help ensure that as new people enter our industry we’re doing everything we possibly can to keep them free from harm.”
In addition to the new stretching program, Kal Tire employs a safety management system to report incident and close-call data to all parts of its operations, right up the chain to the leadership of the company. This data comes from employees, resources regulators, and even incidents that occur at unaffiliated mine sites.
In other words, Kal Tire has its finger on the pulse when it comes to best practice in safety.
“There would be nothing worse than having to learn the same lesson twice.” Rigney said.
From autonomous haul cycles to proximity detection, the mining industry has taken strides in automating mining machinery to keep workers out of the line of fire.
But what about the safety of the men and women who maintain those machines?
Nivek Industries has been asking that question since 2008.
The Lift Assist 40 (LA40) is just one of the many ways the Australianowned business is making the lives of workers safer and easier.
weight while the operator guides it into place.”
The LA40 is a lift assist arm designed to take the weight of tooling up to 40kg.
“The arm can take the weight of rattle guns, impact drivers and torque tooling, reducing the risk of fatigue and musculoskeletal injuries for anyone working with heavy tools,”
“Not only does this allow for precise work but it reduces vibrations and manual handling for workers.”
Six points of articulation provide the arm with a full 360° circle of movement, with the swivel boss providing the ability to rotate tooling. Combining this with the
The LA40 mounting plate has been designed to allow operators to easily design a fixed attachment point, or it can be mounted to Nivek’s Tracked Elevation Device (TED). Nivek is also currently developing a mobile stand, which the company is hoping to have ready in the coming months.
The LA40 can be fitted with custom attachments to handle different kinds of tooling, such as the hydraulic torque wrench tool.
“The hydraulic torque wrench tool allows operators to position the tool in place and stand back during operation, therefore eliminating the risk of finger crush and/or oil injection injuries,” Cant said. “The ability for the arm to hold the tool in place greatly reduces workers suffering from fatigue, as they no longer need to hold these heavy tools during operation.
“It was created to stop people from holding these heavy hydraulic tools, particularly above their shoulders.”
Thanks to the success of the LA40, Nivek is on the cusp of releasing the LA80, an actuated arm with an 80kg lift capacity.
“The LA80 is designed to lift heavy components into place like heavy tooling, truck brake callipers, wheel
cleats, pumps – those annoying 40 or 50kg components that workers often have to lift with chains and slings into awkward positions,” Cant said.
“Since the arm is electronically controlled, there’s no bounce in the arm, which allows for stable and precise alignment of components.”
Nivek is working with a company to use an LA80 to install super-nuts on the underside of a crusher.
“That particular LA80 will be mounted onto a fixed structure and is to be used to hold and manoeuvre the 30kg super-nuts into position during install and removal.” Cant said.
“Ordinarily, a worker would have to lift and hold these 40kg nuts in place overhead while another person tightens them up. The LA80 makes this a oneman job, holding the nuts in place while a worker safely secures them.
“That way they don’t have to risk an injury while lifting these heavy components.”
In addition to reducing the risk of physical injury, the LA40 and LA80 significantly ease the physically stress of an employee’s work. This helps to limit fatigue, allowing people to work more efficiently and safely, while also promoting a more positive working environment.
As machines get bigger and better, their maintenance requirements will evolve along with them. Fortunately, Nivek Industries has its finger on the pulse, engineering best-practice safety solutions for maintenance in the mining industry.
HELLA’S LATEST WORK LAMP FOR MINING VEHICLES IS HELPING REDUCE OPERATOR FATIGUE, EYE STRAIN AND SAFETY INCIDENTS.
Proper lighting is essential to mining operations that run at all hours of the day and night. But to the woe of many, its importance is matched by its complexity.
According to Safe Work New South Wales, poor lighting can lead to eye strain, headaches, fatigue, musculoskeletal issues from straining to see, psychological issues, and increased risk of injury from slips, trips and falls, particularly around machinery.
At the other end of the spectrum, excessive lighting and glare can similarly cause eye strain, vision damage, discomfort and fatigue.
While the risks are many, good lighting can bring a whole slew of benefits to a workplace. Proper lighting improves safety, minimises
fatigue, allows employees to work more efficiently, enables precise and accurate work, and provides a more comfortable work environment.
And when it comes to mining, workers are never more at risk than when operating around heavy machinery, so getting lighting right in that space is critical.
That’s where HELLA, a lighting solutions provider for mining vehicles, comes in.
HELLA is a supplier of lighting and electronics, including premium-quality work lamps for heavy industries. The company’s latest product to hit the market, the RokLUME 280N SMART, is ideal for vehicles in surface and underground mining.
The RokLUME 280N SMART is a work lamp that can change colour to maximise visibility depending on
the environment it operates in. The lamp comes in three variants: white to green lighting, white to amber lighting, and white lighting only.
While white light is most commonly found on a work site, in many circumstances it can actually hinder an operator. Green and amber lighting, on the other hand, are both better suited to dust, snow, and fog, making them ideal supplements to white lights.
“Mine sites operate in a range of weather conditions like dust, rain and fog,” HELLA product manager Jigar Patel told Safe to Work
“White light is easily reflected in these conditions, making it very difficult for the operator of a mobile asset to see what they are doing. This also creates glare, which causes eye strain and fatigue.
Images: Hella
“But RokLUME’s amber and green lighting can penetrate those harsh conditions, significantly improving visibility for an operator.”
On the safety side, the RokLUME 280N SMART makes mining vehicles more visible to workers and other vehicles, reducing the risk of a collision. And by reducing glare with green or amber light, eye strain – a significant cause of fatigue – is reduced for workers. This is particularly relevant to mobile plant operators, who account for the vast majority of fatigue-related accidents on mine sites in Australia.
“The colour temperature of the lamp can also be changed between warm and cold lighting,” Patel said.
“It has a range of 3000K [Kelvins] to 6800K, meaning the lights can be adjusted to best suit the time of day.
“This is another feature that optimises visibility and minimises eye strain for operators.”
The lamp, which pumps out up to 3500 lumens, can also be adjusted for brightness.
“Some mine sites require work lamps to be on 24 hours a day, so making sure they run efficiently can benefit a company in many ways,” Patel said.
“Because brightness can be adjusted on the RokLUME 280N SMART, the lamp can run in low-power mode through the day.
“That means less strain on the lamp, reduced power usage, and reduced carbon emissions.”
All of these features can be adjusted with ease with inside the vehicle using either the HELLA control panel or the machine’s native dashboard, depending on how the RokLUME 280N SMART is installed. Settings can be saved using the system’s memory function.
The process of installing the RokLUME 280N SMART is low impact. The control unit sends signals to the
lamps via existing cables, so all of the machine’s original wiring is preserved.
The RokLUME 280N SMART also features zero-glare capability, which ensures that light does not blind oncoming drivers. A sharp horizontal cut-off serves to direct the light onto the ground in front of the vehicle instead of towards oncoming vehicle operators.
HELLA is giving its mining industry customers more control over their lighting than ever before. The RokLUME 280N SMART’s adjustable features are helping operations run more efficiently, reducing operator fatigue and – most important of all –keeping workers safe.
Fuel and lubrication are to machinery what machinery is to the mining industry: utterly critical. Without them, the wheels stop turning.
But fuel and lubrication are challenging areas to manage. Inconsistent maintenance, improper equipment and human error are just a few of the many factors that can lead to spills, leaks and contamination. And in an environment like a hot Australian mine site, the associated accidents can be catastrophic.
When the stakes are so high, it’s important to have an expert like JSG Industrial Systems in your corner.
These hazards are most commonly seen in areas where fuels and lubricants are stored or transferred, such as fuelling stations, storage tank areas and maintenance workshops.
“They are also common around heavy machinery and vehicles, including excavators, trucks and conveyors,” JSG told Safe to Work.
According to JSG, improper handling during transfer between storage tanks to machinery is one of the most common causes of spill and leak incidents. Equipment failure is another common cause, with the degradation of hoses, pipes, tanks and seals leading to such incidents.
Fuel and lubricant can also escape due to poor storage practices, and when tanks are unsuitable for the contained substance, overfilled, not correctly maintained, or corrode in harsh environments.
There is also a significant human element to fuel and lubrication management, with worker fatigue exacerbating the risks of leaks and spills.
“Fatigue impairs a worker’s alertness and situational awareness,” JSG said. “In a mining environment, where constant vigilance is required to monitor fuel lines, tanks and equipment, reduced awareness can lead to missing early signs of leaks or spills.
“Handling fuel requires precise physical coordination, especially when connecting and disconnecting hoses or operating valves and pumps. Fatigue can diminish these motor skills, leading to mistakes that cause spills.
“In the event of a minor spill or leak, quick reaction is key to containment. Fatigue slows reaction times, potentially turning small issues into larger incidents.”
Given fuel is often highly flammable, spills and leaks pose a significant fire and explosion risk. Direct exposure to these substances through skin contact or inhalation can also be a health hazard for workers. Slippery surfaces caused by spills also create a slip hazard.
Spills and leaks can also contaminate the environment, damage equipment and disrupt operations.
In mining operations, lubricants are crucial for the smooth and efficient operation of machinery. However, these lubricants can become contaminated, which can in turn have detrimental effects on equipment.
“Given the nature of mining operations, dust and dirt are prevalent contaminants,” JSG said.
“They can cause abrasion and wear on moving parts, reducing the lifespan of equipment and increasing maintenance costs.”
Water, metal particles, fuel and other fluids like coolants are also common contaminants on a mine site. These contaminants can cause wear and tear, increased maintenance
minimising the risk of drips when the nozzle is removed from a tank.
Flomax fuel nozzles can also reduce harmful vapour emissions by sealing the tank during refuelling. This not only helps in preventing spills but also minimises the release of volatile substances into the environment.
“These nozzles are compatible with various sizes of fuel tanks, which translates to efficient fuelling and spill prevention across diverse applications,” JSG said.
need to pressurise the fuel tank or use
splashing or overfilling is reduced leading to a safer and cleaner refuelling environment” JSG said.
“In pressurised systems, there’s always a risk of over-pressurising the tank, which can lead to spills, leaks or even ruptures.”
These systems are also equipped with an automatic shutoff mechanism that can detect when the tank is full, preventing overfilling and further enhancing safety and reducing waste.
Spectrum oil containers are designed with a wide base and low centre of gravity for maximum stability.
“These containers have easyto-operate spouts and contoured surfaces that work together to reduce the risk of accidental spills during transport and pouring,” JSG said.
“The ergonomic design can also minimise strain on the workers, reducing the risk of spills caused by physical fatigue or awkward handling.”
Spectrum containers can be equipped with a variety of lids ideal for controlled and precise pouring, rapid pouring of oils and breather vents that easily twist to provide hands-free control. These features reduce the risk of lubricant contamination and spills during filling and lubricant dispensing.
But perhaps the most unique feature of Spectrum is its colourcoding system. The nozzle and breather vent of Spectrum oil containers come in up to 100 different colour combinations.
“Implementing a colour-coding system helps in easily identifying
reducing the chances of using the wrong product and the subsequent mishandling that might lead to spills,” JSG said.
“Using different containers for different lubricants not only prevents spills but also reduces the risk of cross-contamination between different types of lubricants, which can be harmful to machinery.
“Along with colour-coding, clear labelling on containers can provide essential information like the type of lubricant, handling instructions, and safety precautions, further reducing the likelihood of errors that could lead to spills.”
JSG stocks a broad range of heavyduty hose reels to strengthen a mine site’s fuel-management system.
“Reels are a practical and effective tool for reducing spills and leaks in mining, contributing to better hose maintenance, enhanced safety, and operational efficiency,” JSG said.
Utilising a hose reel means hoses are better protected from kinks and twists, as well as environmental wear from ultra-violet exposure, extreme temperatures, and abrasive surfaces.
JSG reels feature controlled retraction mechanisms, helping to ensure hoses are retracted slowly and smoothly. This prevents the hose from snapping back, which can cause wear or damage.
“When hoses are stored on reels it can help to maintain the integrity of connection points, which are common sites for leaks,” JSG said.
“And when hoses are neatly stored on reels, it’s easier to inspect and perform maintenance on them, ensuring any potential issues are identified and addressed promptly.”
There are many challenges associated with managing fuel and lubrication on a mine site, with mishandling having steep consequences for workers, operations and the environment. Luckily, JSG Industrial Systems is hard at work keeping Australian mine sites free from dangerous leaks and spills.
SAFETY MATE OFFER THEIR ‘BLACK DOG’ GLOVES TO SUPPORT THE WORK OF BLACK DOG INSTITUTE.
Mental health is becoming widely acknowledged as an important component in business stability, workforce and even productivity. 20% of Australians will experience symptoms of mental illness each year. The Black Dog Institute does important work in this space.
Now available with QR code on vending wrapper that provides quick access to tools and resources to help boost better mental health.
3030V
P2 pre-formed cup shaped respirator with industry leading industry face fit testing results
Lightweight, cup shaped respirator
Four point headstrap adjustment
CONTINUOUS LOOP HEAD STRAP
FULL FOAM FACE SEAL
Preformed nosebridge removes the need for regular adjustment
PREFORMED NOSEBRIDGE
SAME PROTECTION, NOW SUSTAINABLE
Safety Mate’s latest innovation is the new NXG GreenTekTM environmentally conscious range of gloves which are manufactured using up to 50% recycled yarn. Every pair of GreenTekTM gloves repurposes one to two plastic bottles.
SCAN FOR
TM
SCAN FOR MORE INFO AND TRIAL SAMPLES
FEATURES
+ Touchscreen compatible
C-5135
+ Using recycled plastic content = 1 plastic bottle per pair
+ Heavy Duty cut level D glove
Gloves that help the environment without compromising performance Working together to reduce plastic waste
SCAN FOR MORE INFO AND TRIAL SAMPLES
In an industry heavily governed by protocol, policies and procedures, the standard has been set to adopt in-vehicle monitoring or safety management systems to protect workers. However, these solutions may offer limited capabilities and can neglect to address issues of risk and risk exposure.
The importance of workforce safety means organisations need technology support that seeks to prevent incidents before they happen. The right solutions mean companies can reduce potential injuries, manage incidents and eliminate fatalities.
This is where Optix, a safety management solutions company that has established itself in transport and logistics industries over the past 25 years, can support a business.
Through product development and emerging technologies such as machine vision and artificial intelligence, Optix is bringing its range to the mining sector to provide solutions that align with industrystandard safety goals.
“The mining industry will benefit greatly from the solutions we provide because we’re passionate about saving lives and preventing catastrophic outcomes,” Optix chief commercial officer Craig Forbes told Safe to Work.
“We’re a solutions–capability business that prioritises duty to the customer rather than just the sale of the goods. We listen to our clients, look at what they can manage and how we can provide value to their business.”
While there are many safety initiatives on mine sites that focus on productivity and sustainability, Optix has found that the health and wellbeing of the workforce can be overlooked in areas such as transport and equipment, and general vehicle operations.
Optix fills this gap through its integrated technology combined with managed safety programs that provide the mining industry with insights and data into its operations.
In addition to its safety solutions and capabilities, Optix’s mantra, ‘Safely home’, aligns with
its mission to deliver proactive road safety education.
“There are three big factors in what we do with our solution capabilities: driver safety, data-driven insights, and coaching and education,” Optix senior fleet safety consultant Michael Giess told Safe to Work
“A lot of businesses focus on reacting to a fatigue event. Our solutions are preventive in nature, and our coaching and education is designed to ensure drivers are equipped to address the signs of fatigue, protecting the driver and other road users and neighbouring pedestrians.”
In preventing safety incidents, Giess said many mining operations are only looking at fatigue management, which means they’re trying to ensure someone doesn’t get drowsy or fall asleep.
“We’ve discovered many organisations, including mining operations, aren’t educated on the behaviours and early signs of fatigue,” Giess said.
“Fatigue is a buzzword; however, we’re specifically looking at driver behaviour and safety, and what’s happening with the driver inside the vehicle. When we look at driver behaviour, we are also assessing fatigue, general distraction, if the driver is on their phone, and if they’re being attentive to what’s ahead and around them.
“When we work hand-in-hand with our clients to look at all aspects of their operations, we can then align our capabilities with their business.
“By combining the latest safety systems to identify risks and empower people with the knowledge and resources, mining companies can achieve impressive results that improve safety.”
A Komatsu technology brand, MST Global specialises in harsh industrial technology solutions, empowering customers to unearth safety and productivity improvements. We believe that, without the right technology solution for a mine’s unique situation, there is only partial components delivering partial results. Our disruptive digital vision for hardware and software embraces next-generation technologies and challenges paradigms to provide customers with value, now and into the future.
mstglobal.com
Between long shifts and constant stimuli, working on a mine site can take its toll. Even the most capable miner can fall victim to fatigue.
Operators may already have ways of monitoring alertness, but traditional methods like surveys and eye-tracking cameras can often take too long or are too unreliable to be as effective as needed.
Bodytrak offers an alternative on which workers can rely.
An in-ear wearable device capable of monitoring individual physiological responses, Bodytrak sends instant alerts to workers and supervisors when there’s a risk of fatigue.
According to Bodytrak’s senior physiologist James Davis, actionable real-time data that enables early intervention is the key to preventing incidents and even fatalities due to fatigue.
“Bodytrak’s ability to continuously monitor physiological responses,
such as heart rate variability [HRV], offers valuable insights into worker fatigue levels, enabling supervisors to intervene promptly when signs of fatigue are detected,” Davis told Safe to Work. “This proactive approach helps mitigate the risk of accidents and injuries caused by fatigue-related errors, ultimately enhancing workplace safety and reducing downtime.”
HRV is the measure of variance in time between consecutive heartbeats. It indicates the
“Bodytrak’s ability to continuously monitor physiological responses, such as heart rate variability, offers valuable insights into worker fatigue levels, enabling supervisors to intervene promptly when signs of fatigue are detected.”
function of the autonomic nervous system, which controls involuntary physiological processes.
Low HRV means the autonomic nervous system is not functioning efficiently, and the body may be fatigued or under significant stress.
“Through our in-ear wearable device, we are constantly monitoring HRV to determine a fatigue score,” Davis said. “If the user exceeds preset thresholds – meaning they’re at risk – they will receive an audio alert via their earpiece and their supervisor will receive an alerts via the Bodytrak dashboard and/or SMS, email and WhatsApp, so they’re aware action needs to be taken before a serious incident occurs.”
With fatigue scores based on each individual’s data, nothing is subjective or left to chance.
In 2023, the NSW Resources Regulator investigated incidents where fatigue was an influencing factor. This included a worker on his 20th consecutive 12-hour shift who was involved in a light vehicle rollover on a mine site, prompting warnings about the dangers of fatigue.
“Bodytrak’s data analytics capabilities allow Australian mining operations to identify patterns and trends related to fatigue incidents, enabling them to optimise work schedules and allocate resources accordingly,” Davis said.
“The insights from Bodytrak can inform targeted training programs to educate workers on recognising and managing fatigue, fostering a culture of safety and responsibility within the mining workforce.”
Where mine sites typically have multiple unintegrated monitoring devices, Bodytrak is a one-stop-shop solution tracking fatigue, heat stress, falls, lone working, and noise induced hearing loss.
The user’s geolocation at any given time is also instantly accessible when support is required, as are geofencing capabilities that control and restrict access to hazardous areas.
The Bodytrak solution consists of an earpiece and a communications pack smaller than a standard smartphone, suitable in even the most challenging environments.
“When the accurate and reliable data is captured it can be invaluable,” Davis said. “The ability to capture insights into users’ physiological responses in real-time can ensure mine sites take a proactive approach to health and safety.”
Fatigue can affect anyone. This is especially true for those working in the mining sector, where hours are often 24–7 and the work intensity is often high, with longer daily work hours and extended sequences of shifts, particularly night shift.
To combat this potential danger, Ethos Health developed FatigueTech, which allows workplaces to automate their fatigue risk management system
with a view of minimising the chance of related incidents.
The team at Ethos Health is now gearing up to release FatigueTech 2.0, providing an extra boost to workplaces looking to better manage risks.
“FatigueTech 2.0 brings a whole range of improvements to existing features, and some new features as well,” Ethos Health chief executive officer Dr Trent Watson told Safe to Work.
Watson outlined the ways FatigueTech 2.0 makes it easier for workplaces to meet health and safety obligations and to help workers with fatigue management.
“The app supports the implementation and monitoring of a fatigue risk management system,” he said. “The app also has a platform that will support and engage individuals to learn more about fatigue risk and strategies to manage it.”
FatigueTech 2.0 can plug into a workplace’s time and attendance system to notify a worker and their supervisor if someone has worked beyond their work hour guidelines. At this point, the employee will be prompted to do a fatigue check on the app.
“Another element of the app is that supervisors can see if an employee is at high risk of experiencing fatigue that day,” Watson said.
“It gives them the opportunity to go and check in with that employee
FatigueTech 2.0 also features a journey management plan to ensure any employees travelling to and from the site are safe before, during and after their travel.
“We’ve also added a scheduling function,” Watson said. “So if a site needs two extra people to do an overtime shift, the app will recalculate the working hours of whoever puts their hand up for the shift, ensuring that the working hours are kept within guidelines.”
The main goal for FatigueTech 2.0 is to provide the data, transparency and knowledge that is crucial when it comes to fatigue management.
“The app has an interface for scheduled work hours so it makes it easy for supervisors to go in and see, at a glance, who they can roster on and who has already exceeded their working hours,” Watson said.
“We know fatigue is one of the key health risks in mining. Given it’s a 24–7 workplace, it’s important that these things are managed well.”
To support the app, Ethos Health has also released its online Knowledge Centre. The site provides information on fatigue and its associated risks.
“Those wanting to learn more about their own personal risks can actually do a survey online and it will show them what their risk factors are,” Watson said.
“For people with more complex needs, there’s the virtual subjectmatter expert who they can sit down with and receive referrals for additional support if needed.”
For Ethos Health, it all comes down to ensuring the right information is in the right people’s hands to prevent an incident from occurring.
“Responsibility, transparency, support and shared action are four of the most important elements in health
and safety,” Watson said. “Without transparency, there’s no one taking responsibility and it’s unlikely that will lead to shared action.
“Everyone wants to do well at work – they don’t want to be perceived as not being up to a task –but there shouldn’t be any shame in feeling fatigued.
“Everyone, no matter their life or circumstances, experiences fatigue at some point. The key is getting people to understand their personal needs and giving them the support to manage them.
“A big part of managing fatigue is having safeguards within the workplace, so by virtue of getting the data from the app, mines are getting guidance on how they can better cater for the various needs of their workforce. While FatigueTech 2.0 can help manage fatigue when it becomes a problem, it is also about stopping that problem from starting.”
Move over ordinary tracked carriers, there’s a new name in town and it’s ready to rumble.
BOB isn’t your average carrier; it’s a versatile powerhouse designed to conquer any job site, terrain, or task you throw its way.
nivekindustries.com.au
Smart Attachments:
With an AUX port, the operator can control moveable smart attachments via the remote control for that added versatility
All Terrain:
With its low profile and track drive system, the BOB will traverse all types of terrain
1.5t lifting capacity: Effortlessly handle loads up to 1.5 tons
It’s no secret that Australian mining operations often face demanding environments, especially at night.
That’s why it’s crucial for heavy equipment operators to have the ability to monitor their surroundings and withstand challenging conditions. This is something US-based LED lighting solutions manufacturer J.W. Speaker understands all too well.
The company bases its lighting designs on lux as opposed to lumens. Lumens refers to the static brightness of the light itself, whereas lux refers to how bright a room or area is.
“You need good-quality colour and a high colouring rendering index. The higher the percentage, the truer the colour is,” J.W. Speaker Asia Pacific sales director Robert Johnstone told
Safe to Work. “You can have high lumens, but the lumen rating never changes at a distance; lumens is how bright it is to the eye, whereas lux does change. That’s why mine sites and port authorities use lux, as it shows how bright the ground is and needs to be for safety condition.
“If the ground is too bright or not bright enough, it’s not safe to work under.”
Coloured light from LEDs can be designed into a stripe, image or pattern to create a keep-out zone or illuminate a highly visible unsafe section to pedestrians or workers near work zones or dangerous areas.
Advanced optics and robust designs are at the forefront of J.W. Speaker’s rugged work lamp portfolio,
which helps keep critical mining conditions safe for workers.
All work lights and headlights manufactured by J.W. Speaker operate at 5000–5500 kelvins (K), a good range for eye clarity and visibility, helping to reduce fatigue.
“Anything above 5000–5500K leaves a glare where there’s too much blue in the light,” Johnstone said.
“When HID (high-intensity discharge) lights first came out, halogen bulbs sat at 2800K, which was a warm and yellow-looking white. Then it increased to 4200K, which is a nice white colour.
“What’s happened now is we’re jumping up to 6000K-plus, and that’s too much blue; your eyes get tired and suddenly fatigue sets in. J.W.
Speaker designs between 5000–5500K because it’s a good working colour temperature.”
J.W. Speaker has a portfolio of LED options for the mining market, with the Model 527 as its flagship.
Model 527 is designed to provide a new level of safety by projecting a large keep-out zone of light onto the ground to alert pedestrians and vehicles to stay out of potentially hazardous work areas, such as the swinging path of a shovel or dragline.
Another option in the portfolio is the Model 529, which is a big LED stripe warning and safety light that identifies dangerous areas on a mining site. This powerful lights allows for the number of fitted lamps to be reduced from a standard six for a large shovel down to three.
“An Australian client of ours had a few accidents with some dozers,” Johnstone said.
“They couldn’t see at night-time, even with the flashing lights, so they went with Model 529 because it shines a long red line on the ground
Keep-out
so they can be seen by people in larger equipment.
“This increased their safety, reduced downtime and helped to avoid major accidents.”
The Model 793 serves as a new kind of keep-out safety light for trucks, utility vehicles or forklifts.
“If you’re working at heights on a scissor lift or lamp post at night, you can add a red or blue light around it,” Johnstone said. “It’s static and acts as a visual zone for the person walking underneath it.”
J.W. Speaker’s portfolio also features the Compact Work Light Family range, which comprises Models 792, 892 and 893, designed to replace larger lamps, but with the same output.
Each new model has been manufactured to endure rigorous stability requirements and resistance to surrounding elements while producing powerful flood or trap light patterns to illuminate dark work sites so production can continue, and workers are kept safe.
“(The new models are) very compact and bright,” Johnstone said.
“These models are best suited for haul trucks or smaller excavators. With port authorities or cranes, we offer larger lights. Now these other vehicles can have a smaller light at half the weight and price.”
Johnstone said J.W. Speaker listens to the end user when developing its products.
“A client of ours wanted a light on the ground to warn people with the big excavator. They also discussed how the work lights in front of their haul trucks glared onto the drivers,” he said. “In response, we developed the world’s first anti-glare headlight for a dump truck and red zone for larger shovels.
“J.W. Speaker is the leading manufacturer of rugged work lamps that can withstand the harshest environments.
“We understand the conditions these lamps have to perform under, as well as what it takes to keep the workers safe.”
If a conveyor belt is not sufficiently cleaned, fugitive dust and material get into machinery and rolling components, raising the potential for fires.
Clearing carryback from inadequate belt cleaning can increase the chances of workers making incidental contact with a moving belt, and that is one of the main causes of conveyor belt injuries, according to WorkSafe Australia.
The need for conveyor belt cleaning is well established. Excessive fugitive material can reduce component and belt life by as much as 30 per cent, while a multiple belt cleaner system contributes less than five per cent to overall belt wear, delivering a significant benefit.
For operators who have “tried them all” and can’t find a cleaner that works, it could be that the problem isn’t the equipment, but the maintenance.
It may sound elementary, but there is a great deal of knowledge and skill required to tune a beltcleaning system to work under varying material, environmental and belt cover conditions while still operating safely, effectively and economically.
Some manufacturers provide factory-trained direct service personnel and replacement parts, delivering expert maintenance for optimum performance and component life.
The number and style of belt cleaners depends on balancing many factors, the first of which is the level of cleaning. Applications like coal mining or power generation cannot tolerate much carryback because of the potential for accumulation to be the fuel in a fire.
Once the level of cleaning is established, the next task is determining the type and number of cleaners required to do the job. The trend in belt cleaning, regardless of application, is to plan for two or more cleaners per discharge (primary, secondary, tertiary).
In addition to better cleaning from multiple cleaners, there is a redundancy factor that can provide a longer service interval window. Then the tensioner and the best blade for the application are selected.
A trained service technician is aware of hazards involved with maintaining belt cleaners.
Having a trained provider who focuses on safety while being more productive than in-house maintenance can be a significant benefit given the importance of keeping shutdown times to a minimum.
There are specialised systems for servicing belt cleaners where the belt runs 24 hours a day and cannot be shut down, but virtually all other cleaner maintenance must be performed following lockout, tagout, blockout and testout (LO/TO/ BO/TO) procedures.
One primary cleaner design requires no tensioning and virtually no maintenance after initial installation. It features a matrix of tungsten carbide scrapers installed diagonally to form a three-dimensional curve around the head pulley and typically delivers up to four times the service life of urethane cleaners.
Safe inspection, tensioner adjustment and blade replacement are keys to conveyor efficiency.
lower, while the blade wear, belt wear and power consumption are higher.
phenomena and know how and when to adjust each style of cleaner.
Several researchers, including from the US Bureau of Mines, have established there are ‘sweet spots’ for cleaning pressures for different styles of belt cleaners. Outside of these ranges, the cleaning performance is
Reputable manufacturers design their cleaners and tensioners to achieve optimum cleaning performance versus blade wear. It may seem counterintuitive, but if the cleaner isn’t doing a good job more cleaning pressure can actually make the problem worse. Maintenance personnel must understand these
Some sophisticated users optimise their cleaning performance versus blade replacement costs by testing different blade materials at different cleaning pressures and changing blade materials and cleaning pressures for different seasons or run-of-mine (ROM) conditions.
maintenance as part of a managed service relationship.
Their monitoring systems can track component wear and update the service technician and/or operations personnel via Wi-Fi or a mobile phone on upcoming service needs.
details in their reports. Because they see so many different applications, these technicians can often alert on problems that maintenance personnel don’t see or have become accustomed to ignoring.
With factory-direct managed service, the responsibility for maintenance falls on the manufacturer, allowing the staff to focus on other priorities.
Reputable manufacturers design their cleaners and tensioners to achieve optimum cleaning performance versus blade wear. It may seem counterintuitive, but if the cleaner isn’t doing a good job, more cleaning pressure can actually make the problem worse.
There are some new systems that can even adjust belt cleaner tension automatically. The technology will also send an alert through a mobile app in the event of upset conditions.
Factory-trained service technicians provide an added set of eyes on the conveyors, travelling to and from the equipment to be serviced and logging
When calculating the return on investment for professionally installing and maintaining belt cleaners, the analysis should be done over the life of the belt cleaner assembly using a net present value calculation. Other benefits that can be
factored in include the savings from avoiding injury, increased equipment availability, improved equipment life, and reductions in citations and fines.
In addition, facility managers often find that the cash flow values are surprisingly large over the life of the equipment and service relationship.
Belt cleaner maintenance can be time-consuming and pull labour from other essential tasks, so it’s especially important to choose a supplier with trained and experienced service technicians who know the equipment and safety procedures and can respond quickly to customer needs.
Automated monitoring equipment mitigates some of the issues with blade wear and provides data and alerts when blades need servicing. This can help reduce labour costs and improve safety as a result of to fewer inspections and proactive maintenance.
Considering a managed service program can make safety and productivity sense and improve profitability with additional positive cash flow.
IT’S A NEW ERA FOR FIFO
It’s no surprise that a poor sleep can have dire consequences on a mine site, but that’s the potential reality for thousands of Australia’s miners contending with the fly-in, fly-out (FIFO) lifestyle.
‘FIFO Insider’,a new survey from the Creating Communities consultancy team, found traditional travel and accommodation arrangements are leaving workers wanting.
“Australia’s FIFO workforce powers much of the nation’s wealth,” Creating Communities managing director Donna Shepherd said.
“Ensuring this workforce is safe, engaged and enjoying their time in villages is crucial to the health of their families, communities and the nation’s economy.”
The survey found the cramped conditions of traditional FIFO accommodation, which usually consists of a ‘donga’ – a transportable building providing accommodation for one person – was significantly impacting mental health of workers and affecting sleep.
Adding shift work into the mix of uncomfortable accommodation and being away from home can leave workers and operators vulnerable to more than just a bad night’s sleep.
A CQUniversity study conducted in August 2023 found that FIFO workers who get better sleep are safer and more productive while on-site.
“Until now, there hasn’t been consistent advice to help shift workers sleep, and that has meant a lot of them
were trying to adapt standard advice to their non-standard sleep or wake patterns,” lead study author and PhD candidate at CQUniversity Alexandra Shriane said.
Another study from Edith Cowan University found that FIFO shift workers accumulate ‘sleep debt’ over the course of their time working onsite before they then return home.
Shepherd emphasised the need to help operators make data-driven decisions about the structure of FIFO travel and accommodation.
“Until now there has been no national FIFO experience benchmark,” she said. “We launched ‘FIFO Insider’ to bring all FIFO workers to the table so they can play an active role in improving their experience in villages.
“Our ‘FIFO Insider’ reporting provides insight into the factors that drive staff attrition and how to stem the talent drain through datadriven investments.”
“We want to redefine what it means to be a FIFO worker by creating a home-away-from-home and a genuine community environment for our people.”
The pods feature queen-size beds, in-room washer–dryers, big-screen televisions with a video call function, kitchenettes, and an outdoor veranda with electric barbecues.
So what are operators doing with that kind of data?
Mineral Resources (MinRes) has been on a mission to improve the mental and physical wellbeing of its FIFO workers with the construction of 750 resort-style ‘pods’ at its Onslow iron project in the Pilbara.
Designed to be suitable for singles or couples, the pods feature rooms three times the size of traditional FIFO accommodation.
“We want to redefine what it means to be a FIFO worker by creating a home-away-from-home and a genuine community environment for our people,” MinRes chief people and shared services officer Bronwyn Grieve said.
“To do that, we must have highquality, comfortable and secure accommodation. That’s exactly what these pods will deliver. They are a game-changer.”
The accommodation is decked out with a range of amenities MinRes said is aimed at improving the quality of workers’ downtime and creating a complete lifestyle experience.
On-site amenities boast an Olympic-size swimming pool, bistro, lounge, indoor fitness centre, recreation building and sports courts.
MinRes general manager infrastructure Tim Clements said the Onslow Iron accommodation sets a new industry standard.
“Everything is a first from a construction point of view and the rooms are just one part of it,” he said.
“The amenities are designed to improve the quality of peoples’ downtime and create a complete lifestyle experience.”
But MinRes isn’t stopping there. The miner also recently launched the first direct flight from Brisbane to two of its mine sites in the Pilbara.
Miners would previously have to make round-about trips to get to MinRes’ Ken’s Bore and Wodinga mine sites in WA. But the direct weekly flights shave hours or even days from the time east-coast workers had to spend away from their families, while significantly reducing the cost of travel.
“Direct interstate flights make it faster, easier and cheaper for our
people and contractors to travel to and from MinRes sites,” MinRes general manager people facilities Bethanie Ibrahim said.
“For many of our workforce who live in Queensland or elsewhere on the east coast, these services will reduce their travel time by one full day.”
Ken’s Bore airport became operational last year as part of MinRes’ plan to shake up the traditional FIFO experience.
“These direct services will reduce fatigue and ensure our people have more time to spend at home with family and friends,” MinRes executive general manager people Andrea Chapman said.
“It’s part of our commitment to redefine the FIFO experience, which also includes the construction of resort-style accommodation and an industry-leading food offering.”
MinRes is also building 10 fourbedroom homes in Onslow to attract more families to relocate to the town and become a part of the community.
With companies like MinRes setting the trend of people-first travel and accommodation, FIFO workers can look forward to a safer future spent sleeping in style.
You don’t have to be afraid of heights to understand the risks of working a long way about the ground.
In a 2020 study, Safe Work Australia revealed that 122 workers lost their lives due to falls from height between 2015–19 – that’s 13 per cent of all workplace fatalities in that period.
While the mining industry is only marginally represented in these figures thanks to its rigorous safety standards, accidents can still occur.
An earlier study revealed that falls from height caused the second most fatalities in the mining industry between 2007–12. Five workers lost their lives during that timeframe, with two falling
down a shaft, one falling from a building or walkway, one falling from a ladder, and one falling from a truck.
The same study found that falls, trips and slips accounted for 22 per cent of serious workers’ compensation claims.
Falls can happen on mobile equipment, fixed structures, and even in underground mines. The risks are many, but luckily there is no shortage of helpful resources from regulators and safety experts to help keep workers safe when working at heights.
Working at height in underground a publication from Western Australia’s Department of Mines and Petroleum (DMP), is one such resource, laying out the most common risks that workers might encounter on
Some of those mine-site risks are
When working near openings, it is essential to first consider whether the work or travel in question can be done elsewhere, thereby eliminating the risk
However, in some situations work inextricably involves moving around openings, such as a bulldozer operator preparing a stockpile over a valve.
In one such case, which occurred on a Queensland coal mine in 2023, a bulldozer was stockpiling coal over a closed valve which, when opened, would allow coal to be pushed into a void and onto a conveyor system below.
Although the mine site employed physical indicator poles to mark the boundaries of the void, this was only a partial reference. In addition, the indicator poles were not always visible
to the operator due to the shape and size of the stockpile.
Without visually confirming the location of the valve (as was required by the site’s standard operating procedure) the operator commenced work, reversing over the true location of the valve and falling into the void.
Fortunately, the operator was recovered by the emergency response team without injury.
GPS units were not fitted to the dozer, as is standard at some sites, and other GPS units on the mine were not programmed with valve feeder locations.
After an investigation, Resources Safety and Health Queensland found that geofencing and visual confirmation of the valve might have avoided the incident.
Stopes are another common height hazard on mine sites. Once ore is mined from a stope tunnel, they are typically backfilled. However, voids can occur within this backfilling, which
can give way in the event of ground movement or heavy equipment passing over the stope area.
Such an event occurred at a Queensland coal mine in February 2023. Two miners tragically lost their lives mine when a stope void collapsed beneath the weight of their vehicle, causing the ground to give way and the pair to fall 15m.
Though workers should always follow procedures, keeping people safe near openings like open valves and stopes depends largely on mine planners.
According to the WA DMP, a competent person conducting risk assessments concerning work near openings should have due regard to factors such as ground stability, visibility of openings, adequacy of lighting, suitable barriers, proximity of operations, structural soundness of backfilled stopes, trip hazards from displaced rock or materials, and other potential hazards.
Ladders are a primary means of access to some working areas in many underground mines. In some cases, however, these ladders are years old and have begun to deteriorate.
The difficulties of working in ladderways can also be exacerbated by potential deficiencies in ventilation, visibility, manoeuvring space and ground conditions.
To mitigate the risks, the DMP said sites should:
• use properly considered, designed and installed means of safely moving equipment through the ladderway (rope pulley systems, slinging, etc)
• wear a full body harness attached to an approved fall-arrest system that is hooked up to a suitable anchorage point
• train workers and assess them as competent in the use of fall arrest equipment.
To safely ascend or descend a ladderway, workers should:
• keep both hands free for climbing and face the ladder
• maintain three points of contact when moving
• securely sling loads on the back and shoulders
• hoist heavy or bulky loads rather than carrying them.
Equipment such as scissor lifts, work baskets and purpose-designed platforms provide access to difficult-toreach areas, usually at height.
The DMP said that most fall incidents involving mobile platforms occur when workers are not correctly connected to an anchorage point, when there is a sudden movement of equipment (being struck by a vehicle), when the platform is located on an uneven surface, and when workers are inadequately trained.
When it comes to mitigating these risks, the DMP suggest:
• using scissor lifts that are appropriate for their environment, including purpose-built lifts for underground mines
• f itting the mobile work platform with suitable anchorage points for harnesses
• protecting controls from accidental activation
• f itting the equipment with the means to safely lower the basket in an emergency or a powersupply failure
• using pre-start checks of the equipment and working environment
• limiting the transport, tramming and number of workers in the basket
• not allowing workers to stand on basket rails to gain extra height
• providing an effective means of communication between a worker in the basket and the operator
• training and instructing workers operating the platform in safe operating procedures for the particular brand and type of equipment, as well as the safe use of fall-arrest equipment and emergency rescue procedures.
Any time plant, including mobile equipment, requires a worker to climb a ladderway or staircase to gain access, it introduces the risk of a fall from height.
Poor lighting, slippery surfaces, insufficient railing, quality of ventilation, unstable ground and collisions with other equipment are just a few of the risks that could result in a fall.
Many of these risks can be eliminated by applying design standards and safety criteria to plant at the purchasing stage. A few good features to look out for are suitable
access and egress (ladderways, steps, handrails), suitable anchorage points, and common service points accessible from ground level.
An example of this is Liebherr’s gargantuan R9800, one of the largest excavators in the world. To counterbalance the height risks, it features enlarged walkways with handrails and non-slip perforated steps, as well as a generous amount of lighting to help keep workers safe.
Plant and equipment can also be retrofitted with height safety features like better lighting and handrails.
Companies like Bend-Tech manufacture specialty handrails for mining vehicles. Not only is this approach more economical than looking for an entirely new vehicle with updated safety features, but in some instances these safety experts can actually improve aspects of the original equipment manufacturer design, such as Bend-
Tech’s vibration-resistant handrails which reduces cracking.
Although many areas in the mining industry involve work from
heights, there is thankfully a wealth of knowledge, technologies and safety practices available to help minimise the risks.
Enhance your mining operations with Flomax solutions. Our advanced fuel nozzles and non-pressure fuelling systems are engineered for maximum efficiency and safety, reducing spill risks and ensuring easy fuel transfer. Our products guarantee a safer, cleaner, and more efficient fuel management process. Our strength comes from high-quality distribution partners who manage installation, service, technical support & training nationwide.
Wfirst realised the potential of low-frequency transmission technology to send a radio signal through the strata of an underground mine, he
one-way communication with miners underground and was commercialised by MST in 1989, is called the personal emergency device (PED). It’s still available today, with all the bells and
cost-effective safety system in underground mining and put the MST name on the map. Since the technology’s inception, MST has developed an extensive range of hardware and software solutions to revolutionise safety and operational success in underground mining.
Recognition of the company’s expertise came in July 2022 when MST was acquired by Komatsu as its underground mining technology specialist. MST became the second arm of Komatsu’s mining technology business, sitting alongside Modular Mining, which is well known for surface mining productivity solutions.
The ability to effectively communicate in an underground mine is as critical to safety as it is challenging to implement. MST’s AXON suite of products provides underground mines with the necessary infrastructure to enable instant and reliable
communication among people, assets and control rooms.
MST offers a range of specific voice and data communication systems and devices depending on a site’s requirements. These include Wi-Fibased communications, radio, and leaky feeder systems.
This high bandwidth connectivity is provided through MST’s fibreoptic cables and Ethernet copper cables, and wirelessly through Wi-Fi APs and mesh.
Much more than a communications hardware provider, MST has also leaned heavily into the software space.
“Our enterprise software platform for underground mining is called HELIX,” MST product manager for HELIX Ramodh Rangasamy said.
“The foundation of HELIX shows real-time personnel and asset-tracking using Wi-Fi tags. HELIX collects and visualises live data from MST’s voice, tracking and networking systems, helping personnel on the ground and in command centres keep track of everything in the mine as it happens.
“Tracking is done using our wireless network infrastructure, eliminating the need for any additional dedicated tracking infrastructure.”
HELIX helps to create a much safer mining environment, affording vehicle operators awareness of potentially dangerous situations when working in proximity to workers and other assets.
In its base form, HELIX also provides network monitoring and the ability to send messages to mine phone users on the network, and can run reports on the movement of people and assets.
“HELIX comes with other modular software features such as equipment condition-monitoring, sensormonitoring for strata, environment and vehicles [Internet of Things], automation for things such as traffic management, water pumps, ventilation fans, and more,” Rangasamy said.
“HELIX offers our customers a flexible solution portfolio. We’re proud to be able to offer our mining industry customers everything to operate their site safely and optimise their production.”
As Modular Mining’s underground counterpart, the two companies are able to share technologies, which has resulted in some impressive developments.
First developed by Modular Mining and now perfected for underground mining by MST, HELIX Dispatch is the latest module to be released to the market.
“HELIX Dispatch is a fleetmanagement solution that fundamentally helps underground mines maximise their material extraction,” MST product manager for HELIX Dispatch Nick Rebeiro said.
“We accomplish this by automating production tracking, which eliminates the need for operators to manually write down their load data, which saves a lot of time.
“One of the other foundational pieces of Dispatch is equipmentand status-tracking, which allows command centres to monitor the status of vehicles in real-time.”
The data provided by HELIX Dispatch allows a mine to see any
PED has become a well known, cost-effective safety system in underground mining and put the MST name on the map. Since the technology’s inception, MST has developed an extensive range of hardware and software solutions to revolutionise safety and operational success in underground mining.
inefficiencies occurring during operation, which the site can then take steps to address.
“No matter how good our networks are, you can’t create a system that relies on perfect coverage,” Rebeiro said.
“HELIX Dispatch was designed to work offline, meaning it can run all of the logistics on-board and then re-synchronise once the network connection is re-established.”
On the safety side of things, HELIX Dispatch has digitised and enhanced existing processes such as pre-start checks.
“Traditionally, an operator fills out a physical form checking the state of a machine’s core components. With Dispatch, that process now takes place digitally through the machine’s dashboard,” Rebeiro said.
“An operator is required to fill it out when they log in. That form is then sent to the dispatcher, who can check the state of the components and make a decision on whether that machine is safe to operate.
“An operator may not always know which components are critical, so by digitising the checklist we hope to prevent equipment operation in unsafe condition.”
HELIX Dispatch is the latest in MST’s long line of solutions to underground mining operations. And now as a part of Komatsu, MST’s story is starting an exciting new chapter.
THE PNG INDUSTRIAL & MINING RESOURCES EXHIBITION AND CONFERENCE WILL DEBUT UNDER NEW OWNERSHIP IN 2024. SAFE TO WORK TAKES A LOOK AT WHAT ATTENDEES CAN EXPECT.
The mining industry is one of the main pillars of economic growth in Papua New Guinea.
In particular, the country has a storied gold and copper mining history harking back to the early 1900s, but as the resources industry evolved, so too did the types of commodities mined in the Pacific nation.
Now, vast quantities of gold, copper, silver, nickel, and oil and gas can be found in Papua New Guinea, making the country a prolific mining centre.
The PNG Industrial & Mining Resources Exhibition and Conference (PNG Expo) will celebrate everything the country’s resources industry has to offer when it opens its doors in Port Moresby this year.
Held from July 3–4, the PNG Expo now sits under the Prime Creative Media banner. The event will bring together the industrial, mining and resources industries into a single location to create a marketplace where business is done.
The two-day exhibition will feature over 100 displays of equipment and stands, while the conference will showcase experts from across
the mining and resources sector presenting on challenges and opportunities for the local industry.
“We have received really positive feedback from the industry so far,” show director Lauren Chartres said. “We’re excited to see this event moving to a new phase of development and bringing additional value to the Papua New Guinea resources sector.”
Leaders in delivering productivity solutions will be exhibiting at the event to present their innovative technology, showcasing how they can benefit the Papua New Guinea mining industry.
“We know productivity and efficiency is a huge driver of future success in Papua New Guinea,” Chartres said. “We can’t wait to see the solutions that are available being demonstrated at the event in July.”
Experts from the mining and resources sector will be attending the conference, presenting on crucial topics for the local industry. The event is an opportunity to hear from landowners, as well as government, mining, energy, petroleum and infrastructure representatives on topics of productivity, safety, sustainability, and innovation in technology.
Sustainability will be a particular focus at the PNG Expo, as the conference aims to help pave the way for businesses committed to driving positive change.
“The PNG Expo will be the platform to engage and drive transformative changes towards a sustainable future,” Chartres said.
“Our mission is to equip the industry with the right tools.”
Prime Creative Media chief executive officer John Murphy travelled to Papua New Guinea in October 2023 to meet with government delegates and the heads of top mining companies in the country to chat about the event and to launch the official publication of the conference, PNG Mining
“It was great to connect with industry leaders and officials to launch PNG Mining,” he said. “We had great feedback from these meetings and are looking forward to working closely together in the future.
“This publication and event will be a champion for the entire Papua New Guinea resources sector, so it was important that we meet with professionals and decision-makers from across the local industry.”
CSE Uniserve provides current limiting protectors designed for the End-user to deliver safety and comprehensive peace of mind on mine sites.
Site personnel safety
Capital expenditure savings
Protection of renewable systems
Network life protection
Low maintenance solution
Avoid unnecessary system upgrades
Protection of under-rated equipment
With the development of renewable energy and complex site generation creating expanded electrical infrastructure, the protection from catastrophic damage and downtime, and safety of personnel is essential.
A current limiting protector (CLiP) is a proven, retrofit solution that’s helping the mining industry navigate an evolving energy landscape.
Experience real value with CSE Uniserve’s local integration and lifetime support. For more information, visit cse-uniserve.com.
When the AusIMM International Mine Health and Safety Conference kicks off from April 15–17, it will get underway with a line-up of industry-leading keynote speakers, panel discussions and a suite of technical presentations.
One speaker keen to take the stage is Edith Cowan University MARS Centre director Tim Bentley. And he’s got a message for the industry.
“We all need to play our role in creating healthy workplaces with a culture of safety and respect into the future,” Bentley told Safe to Work “My hope is that there is as much collaboration as possible in developing solutions to pave a way ahead for the Australian mining industry.”
The AusIMM International Mine Health and Safety Conference (formally known as MineSafe) serves
in mine health and safety. Bentley’s address will focus specifically on how the work of the Edith Cowan University Mental Awareness, Respect and Safety (MARS) Centre is tackling mental health, bolstering positive culture, and preparing workers for the future of mining.
The MARS Centre’s mission is to revolutionise mine safety through educating workers and future leaders, as well as driving research into fostering a culture of safety and respect in the mining sector.
“Mining is a great industry, and we want to foster an environment based on healthy, sustainable work where people from all backgrounds can grow and thrive,” Bentley said.
“If we can help contribute to that by helping to lift work health and safety capabilities in the sector, and helping people tackle
the industry’s future will look so much brighter.”
Bentley spent his early career on the front lines of some of the UK and New Zealand’s toughest industries. He saw first-hand the need for strong physical and psychosocial health and safety advocacy to protect workers.
“It’s important to look across the board woke system and see how different factors interact to produce negative outcomes that we sometimes see in the workplace,” he said.
“Conversations around mental health and issues facing people from diverse backgrounds looking to enter the industry need to be at the fore.”
The MARS Centre partners with Edith Cowan to provide current and incoming mining professionals with focused development through training and courses. It’s all part of what Bentley said is MARS’ mission to create solutions with a systems-
“We want to do research with the industry, not on the industry,” he said. “This is an opportunity for the industry to develop leaders fully equipped to rise to the future of mining
Bentley hopes the AusIMM International Mine Health and Safety Conference will again prove to be a platform primed to equip attendees with the resources they need to take
“I’m really thrilled with the interest we’ve had from the industry in what we’re trying to do, and a willingness to engage with our mission,” he said.
“We have seen real positive attitudes from good people in these organisations that really want to make a difference. I’m really optimistic about
WOMEN IN INDUSTRY NOMINATIONS ARE NOW OPEN. Now is your chance to nominate an industry leader who you believe is advocating for positive change and deserves to be recognised.
PROUDLY PRESENTED BY
The Women in Industry Awards recognise outstanding women leaders from across Australia’s industrials sector.
For as long as miners have been digging things out of the earth, they have battled with dust.
Unfortunately, inhaling certain kinds of dust can lead to pneumoconioses, a group of lung diseases. For coal miners, this has long been called black lung disease. And while diagnoses continue in Australia, its causes and effects have been understood for decades, with relevant regulation evolving in turn.
A name familiar to most in the resources industry, silicosis is another in the pneumoconiosis family. It is a debilitating lung disease caused by the inhalation of respirable crystalline silica.
This silica is found in stone, concrete, sand, mortar and other staples of the resources industry.
“[Silica] is the dust that is generated from these materials that has the potential to cause harm when it is breathed in,” Safe Work Australia said in a guide for working with silicosis.
“Very small particles of silica dust cannot be seen under normal lighting or with the naked eye and stay airborne for long periods of time.
“When airborne, workers can inhale the small silica dust particles deep into their lungs where they can lead to a range of respiratory diseases.”
When inhaled, these particles manifest as fibrotic scarring in the lungs. People with the lung disease report debilitating issues such as shortness of breath, weakness, chest pains, and the need for supplemental oxygen and mobility aids. Silicosis can be fatal, and there is no known treatment to reverse the disease.
According to the Australian Government’s National Dust Disease Taskforce’s ‘Final report to the minister for health and aged care’, it is estimated up to 600,000 Australian
workers are potentially being exposed to silica dust each year across a wide range of industries. But unlike black lung disease, silicosis only recently started becoming more regulated.
High-quality respiratory protective equipment (RPE) is something that sites can implement today to help prevent silicosis.
When it comes to safety, personal protective equipment (PPE) supplier
Safety Mate believes that only the best is good enough.
Safety Mate’s answer to the problem of silicosis is the Skytec 3030V disposable P2 respirator, which is ideal for mining industry conditions.
“Wrong or ill-fitting PPE means that silica dust can harm your workers,” Safe Work Australia said.
“As silica dust particles are very small, workers should use a tight-fitting respirator with an effective face seal.”
Just as important as the tech contained in the filter is the fit of the mask and, according to Safety Mate, the 3030V is the only disposable mask in the Australian market with a full foam face seal, ensuring excellent fit. The product will also be introduced in a smaller size (3030V-S) to ensure
every face shape and size is catered for and fully protected.
offer an outstanding level of protection demonstrated when conducting face
fit testing,” Safety Mate managing director Clint Tee told Safe to Work. “Having a lightweight outer shell also means the mask maintains excellent shape during use, boasting extreme comfort and wearability for prolonged periods of time.”
Safety Mate also offers the Skytec Primus P2 respirator, a comfortable, low-profile, three-panel disposable respirator.
Primus respirators allow wearers to talk comfortably without compromising face seal and fit. With low breathing resistance and an adjustable nose bridge, the Primus is designed to be wearable for long periods of time.
Safety Mate offers free on-site trials for its respirators, helping workers in the heavy industries stay protected from silicosis. They can also facilitate face fit testing.
From July 1 2024, Australia will become the first country in the world to ban engineered stone bench tops due to contained silica. And while this is a significant step, there are numerous other sources of silica which still threaten workers in the heavy industries.
Increased regulation over silica exposure in the workplace is inevitable, but it may take years for these engineered controls to roll in. That’s why it’s critical for site managers to take the initiative with the health and safety of their workforce.
INNOVATION MEETS MINING
With our world-leading AXXIS electronic detonator systems and new facilities in WA and Queensland, we’re setting new standards in: SAFETY EFFICIENCY SUSTAINABILITY
EPIROC’S TITAN COLLISION-AVOIDANCE SYSTEM IS A GIANT IN SIMPLIFIED SITE SAFETY.
Modern mines are rife with obstacles. From the uncertain depths of an underground operations to the maze-like sprawl of an open pit, caution is key.
Collision-avoidance systems (CAS) are an essential tool in an operator’s kit for the protection of miners and multi-million-dollar assets.
Operators need equipment they can trust; it’s that simple. And Epiroc’s Titan CAS is even simpler.
“Titan is a robust and versatile solution designed to enhance safety in mining operations,” Epiroc global director product management Hans Wahlquist told Safe to Work.
“Developed and refined over 10 years in harsh South African mining
conditions, it offers a comprehensive range of sensor technologies that allow operators to effectively manage proximity risks between vehicles and pedestrians across both underground and surface mining environments.”
The Titan CAS is a one-stop shop designed to be used on all mining machines and across all systems. It does the hard work of detecting collisions while also acting as the central interface, coordinating and sending out information when miners need it most.
“The Titan CAS provides realtime alerts, advice and intervention for dangerous proximity situations straight from the control room to the cockpit, empowering operators to make informed decisions and take
appropriate action to avoid collisions,” Wahlquist said.
“Special proximity tags are also available for pedestrians, further enhancing overall safety by alerting them whenever a proximity situation occurs.”
Titan monitors vehicle-to-vehicle (V2V), vehicle-to-pedestrian (V2P), and vehicle-to-equipment (V2E) proximity risks across an entire mining operation, whether underground or on the surface.
“Epiroc’s Titan CAS automatically takes control of the machine to slow down and stop it if the operator is unable to do so, providing an unparalleled level of safety,” Wahlquist said.
“It also offers a variety of available technologies, including low frequency, time-of-flight, global positioning system [GPS], and artificial intelligence [AI] cameras, allowing for customisation
and optimisation to suit each operation’s specific risk requirements.”
Underground miners have to contend with tighter spaces and less time to act when obstacles arise, while surface mining can be just a fraught with stray personnel and more vehicles reaching higher speeds.
Wahlquist said there are two fundamental capabilities in place for most digitalisation solutions: communication and positioning.
“In surface mining, positioning can often be solved by using available technology like GPS, while communication is quite straightforward, using modern mobile phone [LTE] technology,” he said. “V2V, V2P and V2E might need various technologies to perform well.
“In underground mining, positioning is much trickier to solve and sometimes needs a variety of technologies to enable the right accuracy for specific uses. Most common in today’s underground mines are Wi-Fi or Wi-Fi and Bluetooth. Communication in underground mines is made predominately by Wi-Fi or LTE.
“By enabling usage of multitechnology, multi-vendor solutions for both communication and positioning, we can optimise a solution based on the customer needs.”
While collision avoidance is the last stand between a miner and disaster, it’s an essential technology on any modern mine site. But it’s not a silver bullet.
Epiroc has taken the next step in a holistic approach to site safety.
The company’s Mobilaris Onboard solution allows Titan to maintain a lookout for immediate danger while it does the heavy lifting of site-wide traffic management.
Mobilaris provides navigation in an underground mine even without any network coverage, as well as early warnings for any incoming vehicles within 600m.
Wahlquist said the solution doesn’t replace common sense but is a vital tool that even allows users who have never set foot on site before to navigate with ease.
“Imagine two trucks driving quite fast – say, 30kph – towards each other near a tight corner. A CAS solution will not solve that situation,” he said. “Even if you had CAS level nine, which is an automatic brake, it would probably not avoid metal-to-metal at such speeds.
“Now imagine a vehicle with only Mobilaris Onboard. That will warn you about incoming collisions far in advance, giving you time to decide if you want to proceed driving or find the best parking bay quickly, but it won’t warn you for a pedestrian walking close to your vehicle.
“That’s why we combine the two state-of-the-art solutions and create the best of both worlds.”
Wahlquist said the effect on safety and productivity is huge.
“The early warnings for incoming traffic makes driving safer and increases productivity, as it leads to better traffic flows with fewer unplanned stops or congestions. Some mines have measured this and seen a huge improvement in haulage tonnes,” he said.
“For the driver, the work environment gets much less stressed and it leads to much less chatter on the radio.”
Epiroc’s digital division is growing rapidly as technologies continue to develop. The company has made a number of recent acquisitions like the Titan CAS and Mobilaris that have the potential to create similar synergies on sites across Australia.
It’s that kind of innovation that puts mines in the path of success.
MillSafe Solutions are compatible with AG, SAG and ball mills.
Agrinding mill is a critical asset to a mining operation. Capable of breaking down ore, these incredibly powerful machines are built from equally robust materials.
It’s precisely this combination that makes them hazardous for workers during maintenance.
One of the most hazardous aspects of mill maintenance is the relining process, as it involves workers accessing the interior of the grinding mill, which is classified as a confined space.
The grinding mill needs to be isolated and safe for people to enter the confined space. The worn liners are removed and the mill shell is manually cleaned in preparation for
new liner installation. New steel liners are then installed, and these can weigh up to five tonnes each.
Traditionally, steel liners are bolted in manually from inside the mill, a process that involves workers operating near heavy machinery and suspended loads for hours at a time.
Relining a mill chamber usually can take up to 100 hours to complete.
“During a reline the mill requires good lighting and ventilation to create a safe working environment. Furthermore, the use of heavy equipment during the relining process contributes to a highly hazardous area of work for the reline crew,” Bradken principal product manager Craig Faulkner told Safe to Work
Bradken’s values focus on protecting personnel. The company’s ‘Arrive safe, Leave safe’ philosophy helped to fuel the development of the MillSafe solution.
According to Bradken, “the end-to-end mill lining system aims to deliver state-of-the art, cuttingedge technology that seamlessly integrates while providing uncompromising safety measures during the relining process”.
Bradken’s suite of MillSafe solutions has been designed to reduce risk and remove workers from the inside of grinding mills during relining, making it a safer process.
The suite is comprised of the following products: MillSafe Bolting system, MillSafe Backing, MillSafe
Bolting system, liners can now be bolted on from outside of the mill.
“By installing the bolts from outside, there is no need for maintenance personnel to be in the vicinity of the reline machine during liner placement and positioning of the bolt holes, making it a much safer practice,” Faulkner said.
The internal mill shell is typically lined with a 6mm rubber sheet to protect the mill shell and create a consistent seating area for the steel liners. Personnel normally need to manually clean the mill shell and repair damaged rubber sections, which can require spending hours scraping off the worn-down rubber and replacing it, but with Bradken’s MillSafe Backing that’s no longer the case.
“MillSafe Backing is an integral coating on the fit face of our liners, reducing the need for personnel to access the mill to repair the rubber sheeting” Faulkner said. “In addition, MillSafe Backing wraps around the side
of the liners to eliminate the need for rubber filler strips, removing another process where personnel have to enter the mill.”
Bradken’s MillSafe Combined Corner Liners are cast as part of the liner, eliminating loose corner liners and the risk posed by traditional products. This also has the benefit of reducing overall liner mass.
Finally, Bradken’s MillSafe Liner Location Stripes provide visual guidance to position the liners and deliver a safer and more efficient liner install.
Faulkner noted that the MillSafe suite really came into its own two years ago, when one of Bradken’s customers was looking to fully automate the relining process for a grinding mill.
“By installing the bolts from outside, there is no need for maintenance personnel to be in the vicinity of the reline machine during liner placement and positioning of the bolt holes, making it a much safer practice.”
Safety incidents have been recorded during relining where the unsecured loose corner liners have fallen in close proximity to the reline crew and, in some cases, resulting in injury.
Bradken analysed the benefit of the MillSafe Combined Corner Liners on a 40-foot SAG mill.
This resulted in the reduction of 60 liners required, saving an estimated 12 hours in relining time. It also supported an increase in mill availability, which improved the operation’s profitability.
“This aligned with our vision and the opportunity to improve mine site safety standards and reline efficiency across the global mining industry,” Faulkner said.
“Miners are always looking for opportunities to reduce risk to their personnel, and the MillSafe suite of products presents that opportunity.
“Bradken continues to look for opportunities to partner with our customers to deliver sustainable solutions that optimise safety and performance.”
Australia’s transition towards electrifying the energy grid has been hard and fast, and that ethos is well underway in the mining industry with the development of renewable energy, duel energy outcomes, and complex site generation.
These developments expand electrical infrastructure and increase electrical outcomes, requiring a proven solution to enhance protection and safety.
In an evolving energy landscape, it’s common for mine site electrical infrastructure to become outdated and no longer fit for purpose, with higher fault levels than potentially dated systems can safely manage.
“Electrical infrastructure, both in terms of power and capacity, has expanded dramatically,” Martin Zuiderwijk, major projects lead at CSE Uniserve, a leading supplier of electrical equipment, engineering and support solutions, told Safe to Work.
“And because high-voltage [HV] equipment typically has a 20-year
lifespan, it’s easy for it to become outdated, bringing challenges to remain operationally safe and within design limits over its life.
“By changing your infrastructure, or adding renewables or additional supply, it’s possible that your equipment and therefore your personnel are no longer completely protected from high or extremely high electrical fault events.”
If an incident such as a fault occurs on underrated HV equipment, results can include arc flashes and switchgear destruction, which can be devastating to production, potentially extending supply outages and risking the safety of personnel.
So how can miners manage this changing electrical hazard landscape?
A complete overhaul of a site’s electrical infrastructure is one option, although perhaps not an appealing one. In addition to being extremely costly, an overhaul would significantly disrupt production until works are finished.
Another option is for an operation to gradually implement new
electrical infrastructure, introducing a second circuit into the site. This option also has issues, including long-time risk exposure.
CSE Uniserve’s current-limiting protector (CLiP), however, has emerged as a proven solution, providing comprehensive peace of mind.
Ideal for HV or low-voltage networks and downstream electrical devices, the best way to think of a CLiP, according to Zuiderwijk, is an upstream, automatic, high-speed electrical insurance, preventing damage and losses over a 20-year service life.
Developed by G&W Electric and supplied by CSE Uniserve’s local specialists, CLiPs are a cost-effective retrofit solution that are helping the mining industry navigate an evolving energy landscape.
“Many sites have a mix of old and
moment re-configuration of the supply can expose downstream circuits and equipment to the full supply capacity, potentially causing an extreme highenergy incident.
“This is a time where we see a CLiP at its best and providing safety to personnel; when the situation on-site changes the electrical infrastructure configuration, you now have overcurrent insurance.”
excessive financial investment,” Zuiderwijk said.
By tripping in the event of extreme high-energy events, CLiPs are preserving significant equipment investment, minimising product loss and saving lives. The unique technology also helps electrical infrastructure reach its lifespan without early replacement.
“CLiPs allow sites to retain older infrastructures at a safe level without
Once set up, CLiPs can protect a switch yard for up to 20 years. In the event of a trip, CLiPs have a selfcontained fuse element that mine sites can easily replace.
“A mine’s existing HV personnel can change the fuse element, so the reset time is driven by the needs and the expertise of the end user rather than requiring a third party,” Zuiderwijk said.
With an ingress protection rating of IP66, CLiPs are built to handle Australian mine sites.
“Switch yards are exposed to high temperatures and dust, but the CLiP takes those conditions head on,” Zuiderwijk said.
“It’s designed to be treated the same way as any other piece of HV equipment found in a switch yard.”
As technology evolves and mine sites continue to electrify, it’s more important than ever for site operators to ensure they are protected against electrical faults. Despite the complexities of a changing environment, CSE Uniserve’s CLiP solutions present a straightforward path to electrical safety and maintaining production forecasts.
EVENT SUBMISSIONS CAN BE EMAILED TO EDITOR@SAFETOWORK.COM.AU
A new-look International Mine Health and Safety Conference is coming to Perth in April 2024.
AusIMM’s biennial conference (formally known as MineSafe) will be a gathering of industry professionals, researchers, policy-makers, and stakeholders from across the world.
The conference will serve as a platform to discuss the latest developments, best practices and innovative solutions in the field of mine health and safety. It will feature industry-leading keynote speakers, thought-provoking panel discussions, interactive Q&As and a suite of technical presentations with the objective of promoting a safe and healthy work environment across all mining operations.
• ausimm.com/conferences-and-events/ mine-health-and-safety
A quadrennial conference that has been around for over 40 years, Molten 2024 will be held in Brisbane from June 17–19.
What sets this conference apart is its scientific focus and support of the transition to sustainable technologies. The majority of metals undergo some form of high-temperature processing, whether in production, refining or recycling. It is the aim of this conference to make a positive contribution to the exchange and dissemination of knowledge on this important class of processing systems, and thereby enhance the rate of progress to more sustainable industrial processing systems.
• ausimm.com/conferences-and-events/ molten-conferences-2024
The Women in Industry awards are an opportunity to celebrate the success of women who work in the mining industry. The awards night, to be held in Sydney on June 20, features multiple categories that showcase exceptional examples of industry advocacy, mentorship and broad sector excellence.
The awards recognise outstanding women from across a range of industrials sectors; for example, those who work in mining, transport, manufacturing, engineering, logistics, bulk handling, waste management, rail and construction and infrastructure – all sectors that are traditionally male-dominated. This is an opportunity to recognise the women who are driving change in industry, breaking down barriers and creating new possibilities for the next generation.
• womeninindustry.com.au
The Queensland Mining & Engineering Exhibition (QME) connects leading suppliers and technical experts with those seeking better efficiency, better productivity and increased optimisation for their business and site.
QME will feature over 250 suppliers and beyond the exhibition floor will host a free-to-attend seminar series that will give people the opportunity to hear from industry professionals on the current needs of the industry. With live demonstrations and topical presentations, QME will be the ultimate destination for the Queensland mining industry.
QME is a key place for the industry to come together to be inspired, innovate and connect over three days. In one of the world’s most dynamic industries, QME has
maintained its relevance and importance within the mining sector.
• queenslandminingexpo.com.au
The 2024 PNG Industrial & Mining Resources Exhibition will showcase over 100 local, national and international manufacturers and suppliers with the latest innovations in the supply of services and equipment for the industrial, mining and oil and gas sectors. The two-day exhibition is a place to connect and network with industry decision-makers across a broad industry reach, including senior management, procurement, government personnel, engineers, contractors and trade technicians.
With support from key stakeholders in government, associations and industry, PNG2024 is a premier meeting place and a forum for establishing high-quality customer contacts and conducting business.
• pngexpo.com
The International Mining and Resources Conference (IMARC) is where people from across the industry come together to deliver ideas and inspiration.
Learn from more than 500 mining leaders and resource experts in seven concurrent conferences with a program covering the entire value chain. Attend one of the many networking events or catch up with industry colleagues on an exhibition show floor featuring more than 470 leading companies. There will be practically endless opportunities to network, brainstorm and share knowledge over the three days at the ICC Sydney.
• imarcglobal.com