Gauging safety
Helping to educate a new generation of maintenance specialists
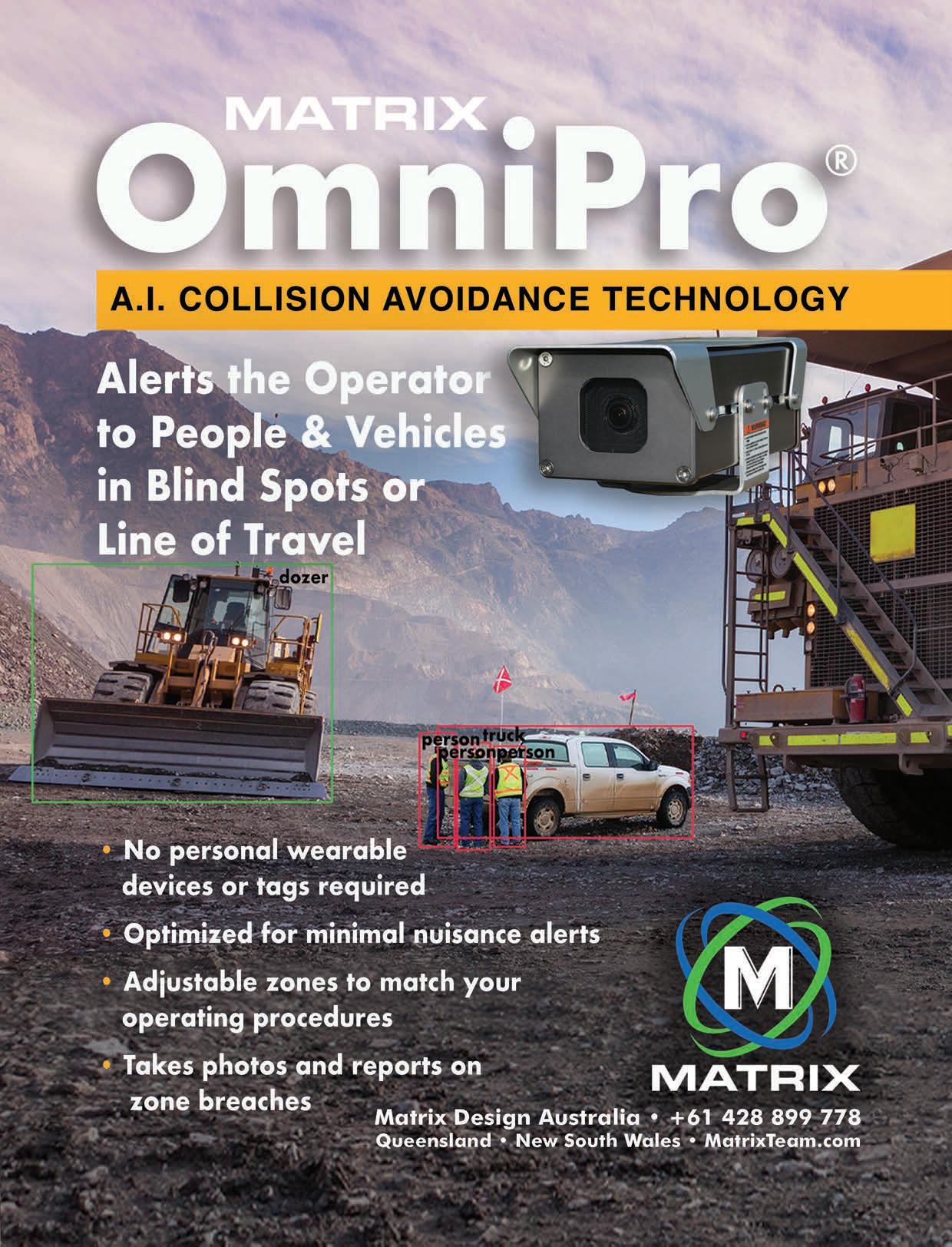
OFFICIAL MEDIA PARTNERS
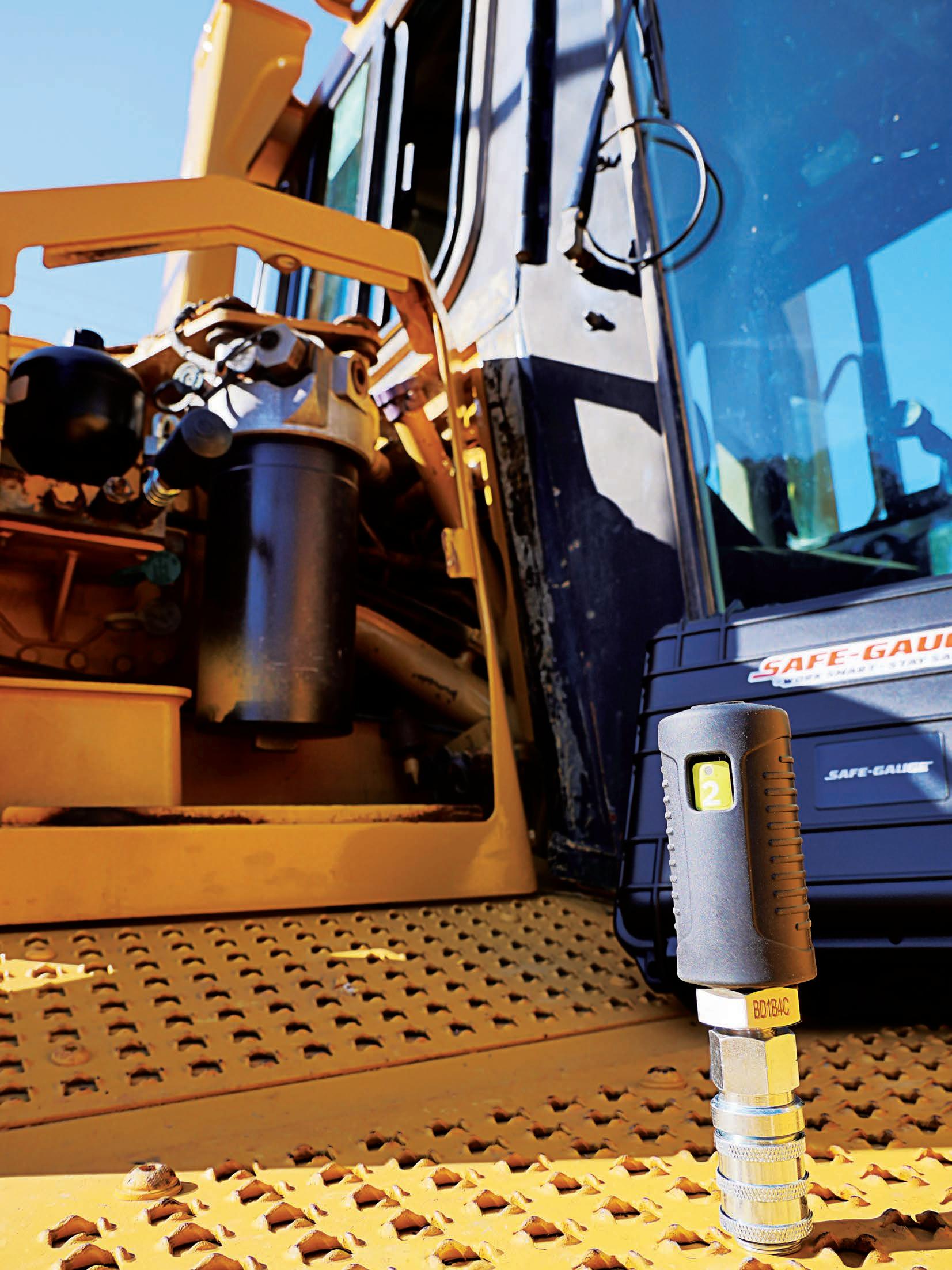
Helping to educate a new generation of maintenance specialists
OFFICIAL MEDIA PARTNERS
Having the highest energy density in the industry, the Scooptram ST18 SG safeguards autonomy and productivity without taking focus from the safety of the operation. It defines safety standards thanks to its ISO ROPS and FOPS certified cabin, speed limiter and best operator visibility in its class. Scooptram ST18 SG ensures that every operation can be carried out in the best way for both people and equipment.
epiroc.com/en-au
COO CHRISTINE CLANCY
MANAGING EDITOR PAUL HAYES
Tel: (03) 9690 8766
Email: paul.hayes@primecreative.com.a
ASSISTANT EDITOR
ASHLEY PERRY
Tel: (03) 9690 8766
Email: ashley.perry@primecreative.com.au
As the world continues opening up to international trade and greater resources production is needed, equipment must advance to keep pace.
It’s for this reason that bulk material handling is such an important factor in today’s mining industry.
Broadly speaking, bulk handling focuses on the design and engineering of handling dry materials. These materials are usually powdery, granular or lumpy in their make-up, and they are usually stored in (for lack of a better word) heaps.
So, not surprisingly, this makes the process a huge part of the mining industry.
Once all of those ores and metals are dug from the ground, they need to be moved from point A to point B – and beyond. Bulk material handling plays is key in keeping the world moving, but there are inherent safety risks.
JOURNALISTS
TIMOTHY BOND
Tel: (03) 9690 8766
Email: tim.bond@primecreative.com.au
OLIVIA THOMSON
Tel: (03) 9690 8766
Email: olivia.thomson@primecreative.com.au
CLIENT SUCCESS MANAGER
JANINE CLEMENTS
Tel: (02) 9439 7227
Email: janine.clements@primecreative.com.au
Thankfully, ever-improving technology is increasingly central in mine safety. Refining the way material is handled is key to improving safety outcomes, ensuring that important commodities are transported to locations where they are needed most.
And that’s why the May–June edition of Safe to Work will showcase some of the latest products, services and innovations in bulk material handling. From belt alignment products to monitoring systems to switchgears to smart washers, we look at some of the best gear to ensure people are safe and mines are productive.
We also examine some of the latest in collision-avoidance gear. Companies are becoming increasingly sophisticated in their use of technology in this area, using things like artificial intelligence, data analytics, global navigation satellite systems, and more.
RESOURCES GROUP LEAD
JONATHAN DUCKETT
Mob: 0498 091 027
Email: jonathan.duckett@primecreative.com.au
DESIGN PRODUCTION MANAGER
Looking more broadly, we get a preview of the Queensland Mining Industry Health and Safety Conference. This year’s theme, ‘Inside looking out’, will see attendees look outside their industry at what measures and initiatives are transferable to the resources sector. Lots of great work is being done in different industries – why shouldn’t the mining sector tap these ideas if it will help keep people safe?
Paul Hayes Managing EditorSUBSCRIPTION RATES
Australia (surface mail)
$140.00 (incl GST)
New Zealand A$148.00
Overseas A$156.00
For subscriptions enquiries please call 03 9690 8766
PRIME CREATIVE MEDIA
379 Docklands Drive Docklands, VIC 3008 Australia www.primecreative.com.au
© Copyright Prime Creative Media, 2016 All rights reserved. No part of the publication may be reproduced
SafeGauge’s commitment to providing cutting-edge live testing solutions has extended to training the next generation of equipment maintenance specialists.
18
The risk of accidental impact is a primary concern for anyone who works in surface mining, and collision avoidance system technology is one of the best ways to mitigate potential accidents.
DYNA Engineering’s approach to meaningful environmental, social and governance practices is underpinned by its sustainable high-density polyethylene conveyor guards.
Mis-tracking conveyor belts can cause unwanted downtime, significant production delays and major safety problems. Martin Engineering is more than capable of solving the issue.
Productivity is important, but safety is a non-negotiable. Flexco strives to ensure workers are protected during repair and maintenance of belt conveyor systems.
Kinder Australia places a premium on supplying the country’s resources industry with efficient, robust and safe conveyor system equipment.
With its strong focus on keeping workers safe, Epiroc understands that digital solutions can help maintain an efficient, safe and sustainable workplace.
KITO Academy is committed to educating customers and end users through product knowledge, safe operation, and preventive maintenance on hoisting equipment.
Nivek Industries’ new Beast of Burden – BOB – heavy-load carriers will further enhance the company’s reputation for tailored safety solutions.
When a recovery sling failed, an unoccupied dozer recently travelled for 230m – in an uncontrolled manner – before coming to a stop on a windrow at a NSW open-cut mine. The safety incident occurred on January 15 at the Maules Creek coal mine located 45km south-east of Narrabri in the Gunnedah basin. No workers were injured. Workers from three different contracting companies undertook the recovery of an inoperable Caterpillar D10T2 dozer that
required it to be conveyed to an inpit maintenance area. A float was initially arranged to relocate the dozer, but it was later identified to be unsuitable for the task and was not used.
The workers completed a job hazard assessment (JHA) that specified towing the dozer to the maintenance area using a Caterpillar 992-wheel loader, with a Caterpillar D11T dozer used as a brake stop.
The JHA also required the axles of the D10 dozer to be removed for free movement of the tracks.
The Capricorn Copper mine will not be fully operational until the first half of 2024 after unprecedented floods in north-west Queensland in March.
The mine, located 120km north of Mount Isa, was inundated with water after record rainfall and flooding across the region.
Capricorn Copper formally suspended operations on March 9. Owner 29 Metals announced in an ASX statement on April 20 that there had been complete loss of major infrastructure, including the facility’s water treatment plant, site workshops and warehouses. 29 Metals said one of its main tenements, the Esperanza South underground mine, had borne the brunt of damage after it was hit by 500 million litres of water. The primary focus of recovery efforts was managing water quality to meet regulatory requirements, dewatering mine sites and rebuilding damaged infrastructure.
When the task was ready to start, the wheel loader was not available, and a decision was made to deviate from the JHA and use the D11 dozer as the tow machine, with a 36-tonne excavator used as a brake stop. Preliminary enquiries indicate the JHA was not reconsidered and the risks from the work task were not reassessed once the wheel loader was no longer to be used as part of the recovery, and the function of the D11 dozer changed. These changes ultimately contributed to the cause of the safety incident.
“Substantial effort has gone into ensuring that we properly understand the full impact of this unprecedented weather event and implement a responsible plan for the safe return to operations,” 29 Metals managing director and chief executive officer Peter Albert said. “Water quality and reducing the additional water brought onto site by this event are the key enablers to recovery.
“The extraordinary work from our team on-site to manage the impact during this extreme event – with no health or safety incidents, no uncontrolled releases of water from on-site water storage facilities and no loss of containment of tailings –is being matched by group-wide efforts to develop and evaluate recovery scenarios.”
A worker was attempting to tack weld a metal thread ring on an oil drum after cleaning it with brake fluid to remove impurities when an incident occurred in SA on March 17. Fumes were still present in the drum and the weld sparked a fireball that engulfed the worker’s head and shoulders as he leaned over the drum.
The man was taken to the Royal Adelaide Hospital burns unit. SafeWork SA was making enquiries into the incident and warned anyone who plans to modify a storage drum to first stop and think.
Storage drums that have been empty for a long time can contain enough residual substance to
explode and/or emit hazardous vapour when exposed to heat. Rinsing drums with water or other cleaning fluids does not guarantee vapours are purged.
SafeWork SA recommends that before conducting any hazardous work, the provision of proper training and supervision to workers needs to take place, ensuring they understand the hazards and risks associated with the task. They should never weld, grind or do any other hot work activity near empty drums, and should not use drums as a welding or work platform. Empty drums should be stored with bungs removed in a well-ventilated place away from other work areas,
BHP is in the early stages of reviewing its policies, processes and behaviours in an effort to prevent racism in the workplace.
The key policies being reviewed include how BHP responds to racism matters, listening to the company’s employees in order to gain a deeper
understanding of racism, and building capability within leadership to ensure it is prepared to recognise racism and to take action against it. The company will form a racial equity working group led by chief commercial officer and executive sponsor for racial equity Vandita Pant.
Pant said one of BHP’s greatest strengths is its diversity and that there is no place for racism.
“A workforce made up of a wide range of people from different backgrounds brings a range of different perspectives, capabilities, and overall benefits that diverse
“We want every person to feel empowered and safe to bring their whole selves to work. This starts with the right attitude, words, and actions
Pant said BHP wants to be a company where its staff members are
though this will not guarantee all residues and vapours have been naturally vented. Also, they should not cut or apply heat to the drums.
“seen, heard, valued, and treated with dignity and respect”. For BHP vice president for health and hygiene Dr Rod Gutierrez, racism is “damaging to one’s mental health” and has a “deep effect on (one’s) psychology”. He believes reviewing the company’s racism policies will facilitate a “psychologically healthy workforce”.
“For this reason, at BHP it is imperative that we work collectively to identify and eliminate racism and enable everyone to thrive and have a sense of belonging,” Gutierrez said.
“We are engaging the whole business and inviting everyone to the dialogue. Together we are imagining a future free of racial discrimination.”
BHP announced the reviews on March 21, the International Day for the Elimination of Racial Discrimination, when communities globally aim to foster a culture of anti-discrimination.
SafeGauge wireless technology removes technicians from the machine footprint during routine maintenance tests; elevating safety and delivering significant productivity gains.
Contact us to learn more.
safegauge.com
A man in his 30s died underground in April after suffering a “medical event” while on night shift at a mine in Western Australia’s northern Goldfields.
WA Police confirmed to the ABC that the man died in the early hours of Tuesday April 11.
The man was working as a contractor at the Sunrise Dam gold mine, 55km south of Laverton. The death was not being treated as suspicious and a report will be prepared for the coroner.
The mine owner, South Africa’s AngloGold Ashanti, briefly suspended operations but has resumed mining after police released the scene.
medical event,” and said that next of kin was still being notified.
A Federal Government senate committee is scrutinising a proposal for a 3300km rail connection between the Pilbara in the west to the Bowen Basin in the east.
The plan is to build a rail line between Newman in Western Australia and Moranbah in Queensland to manufacture steel.
The proposal is for the steel slabs that are produced in multiple mills at either end of the rail connection to be exported by ships at Port Hedland and Abbot Point.
Shane Condon, the founder of Project Iron Boomerang, is in the meat and seafood industries.
Condon established East West Line Parks to build the rail line, and has been working on the project since 2005.
“The world’s biggest seaborne export coking coal fields and iron ore fields are conveniently in one continent, one
country,” Condon said. “We needed to connect those.”
The idea behind Project Iron Boomerang hailed back to Condon’s childhood.
“It’s an old idea that originates from … the Queensland social study books when I was (at school) in the 1950s,” he told the ABC.
Condon believes Project Iron Boomerang is practical rather than ambitious, and it would be expensive.
He said his company was working to shore up investors.
“We are now negotiating letters of intent deed contracts with sovereign fund governments that want to invest,” Condon said.
“It’s $US7 billion for one steel mill, which will have a share in the railway line because they’re taking the initial risk. Each country can have a maximum investment of two steel mills, 20 per cent, which complies (with) the Foreign
Investment Review Board.”
The Rural and Regional Affairs and Transport References Committee is to examine the viability of the project. It has been scrutinising environmental impacts, the employment generated, impacts on local Aboriginal communities, and the resources required to build a rail line of that scale. Australia is the world’s largest exporter of iron ore and metallurgical coal, commodities worth billions of dollars to the country’s economy.
Condon believes exporting steel slabs will bring in even more revenue.
“It’s an incredible opportunity for the future of Australia to value-add,” he said. “By value-adding it we tax that activity.”
The PIB is a transcontinental multiuser rail infrastructure corridor and steel manufacturing complex that seeks to revolutionise global steel manufacturing.
Communities in Western Australia’s north-west region affected by destructive winds and heavy rainfall associated with Tropical Cyclone Ilsa may now access disaster recovery assistance.
The Town of Port Hedland and the shires of East Pilbara and Broome are now eligible for support through the jointly-funded CommonwealthState Disaster Recovery Funding Arrangements (DRFA).
Under these arrangements, emergency assistance may be available to cover temporary living expenses, replacement of essential household goods, housing repairs and personal and financial counselling.
Support for clean-up activities and the restoration of essential public assets that may have sustained damage is also available.
“My thoughts are with those residents in communities in the path of Cyclone Ilsa’s destructive trail,” acting Federal Minister for Emergency Management Andrew Giles said.
Tropical Cyclone Ilsa crossed the WA
coast 120km east north-east of Port Hedland around midnight on Thursday 13 April as a Category 5 system. It brought destructive wind gusts of more than 250km per hour, extended inland after crossing the coast and remained at cyclone intensity further inland as it moved towards the northern interior district of WA.
On the morning of Friday April 14, gusts of up to 195 km per hour affected areas near the system centre to the east of Marble Bar as it tracked inland. Heavy rainfall of between 150mm and 200mm was also recorded as the cyclone tracked inland.
“This financial assistance will be especially helpful in the immediate aftermath of Ilsa as local residents and councils begin the repair and recovery work,” Giles said.
“This cyclone has impacted on many extremely remote communities, and while it may take some time to fully understand the extent of the impact, we have worked quickly and collaboratively to make this assistance available.
“We know communities in rural areas
are more vulnerable to severe weather events, so we are working around the clock to assess the impact and we stand ready to provide help if necessary.”
Acting WA Minister for Emergency Services Sue Ellery said the assistance would provide much-needed support for those who have been affected by Tropical Cyclone Ilsa.
“Our primary focus is to secure people’s lives and livelihoods and I’d like to acknowledge the efforts of all the government agencies and local governments for working around the clock to keep people safe,” Ellery said.
“I would also like to commend members of the community, volunteers and businesses for the outstanding work they did preparing their properties by securing loose items, which prevented further damage.
“We will be working closely with the Commonwealth Government to make sure people impacted by Tropical Cyclone Ilsa have access to assistance available under the jointly funded DRFA.”
The Wisdom 6A cordless LED cap lamp from Perfect Image is a water-resistant, USB-rechargeable unit that has a nickel adjustable bracket and is powered by two Panasonic 3.5-volt lithium-ion batteries.
The lamp is ATEX ia Ma and IECEx Ex ia Ma certified and features both a high (240 lumens) and low (50 lumens) lighting mode. Its rated capacity is 7000 milliampere per hour (maH), and the unit has a high beam distance of 220m and low beam distance of 85m.
The lamp’s run time is 13 hours in high mode and 60 hours in low mode, with a battery lifecycle of 1200 cycles, a charge time of 5.5 hours and a weight of only 169g.
The Wisdom 6A is distributed by Perfect Image, a company that stocks an extensive range of quality products across multiple industry sectors.
• pii.net.au
Hardox 500 Tuf is the latest upgrade in the Hardox range. It delivers high strength, extreme hardness and guaranteed toughness in one
Hardox 500 Tuf combines the best properties from the Hardox 450 and Hardox 500 grades. The result is a wear plate which they company believes has no real competition on the market. It has the toughness necessary to perform as a structural material in heavyduty tipper bodies, containers and buckets. It also works in freezing conditions, as the impact energy values indicate.
High-level wear and dent resistance gives extended service life and the ability to endure heavy impact. Typical working conditions include loading and unloading of heavy and sharp rocks in quarries and mines, handling large and heavy steel scrap, and in demolition when pieces of concrete with rebar are loaded or dropped into tippers. ssab.com/en/brands-and-products/hardox/product-
Designed and engineered for hazardous underground coal mining, the Truflo Pumps’ Explosion Proof Submersible Pump series is now available for immediate delivery.
There are six pumps in the series with applications suited from swilly and general transfer right though to high-flow, high-head multi-purpose big lifting. The pumps have superior performance in class across the board, the company said. Importantly, each pump is officially IECEx certified with SIMTARS accreditation. This certification is proof of compliance to industry safety standards adherence and that mining personnel are protected.
Build quality of each pump is extremely robust for the most challenging of underground environments, with casing pressure tested to guarantee flame paths.
Depending on the configuration, pumps have double mechanical seals, buffering oil chambers, L10 bearings packed with lithium grease. The pumps feature fast change-out of worn impellers (which in some cases can be done underground). • truflopumps.com.au
Since the company’s recent inception, SafeGauge has remained devoted to providing innovative solutions for removing technicians from the line of fire when undertaking live testing on heavy equipment.
The company’s award-winning SafeTest range of smart diagnostic tools, including Pressure Transducers and Dial Indicators, along with its highly intuitive MultiTool, has extended across mining, construction, agriculture, and oil and gas.
SafeGauge recently entered a partnership with TAFE WA at Thornlie, the largest campus of South Metropolitan TAFE, to utilise
the MultiTool during the delivery of training in its specialised Heavy Vehicle Mechanical Training Centre.
“We initially reached out to SafeGauge because we perceived the concept of being able to remotely conduct maintenance tasks on heavy mobile plant machinery, eliminating the live work aspect, as representing a significant improvement on safe work practices within industry,” South Metropolitan TAFE portfolio manager – heavy vehicle mechanical training Jeff Gittos said.
“As one of the largest training providers in Western Australia, providing repair and maintenance, training along with qualifications and conducting testing on heavy mobile plant machinery.”
At the Thornlie campus, Gittos and his colleagues are responsible for teaching the next generation of technicians, at the pre-apprentice and Certificate III apprentice level, who will enter the many sectors within heavy industries.
“These are people who are currently out there working in the industry under the supervision of experienced technicians, many of whom many may not necessarily have been exposed to the types of new technology, such as the smart tools developed by SafeGauge, that are now appearing,” Gittos said.
“So as we train our students in hydraulics, steering, suspension and
TESTING SOLUTIONS HAS EXTENDED TO TRAINING THE NEXT GENERATION OF EQUIPMENT MAINTENANCE SPECIALISTS.South Metropolitan TAFE portfolio manager – heavy vehicle mechanical training Jeff Gittos. Students can become familiar with smart diagnostic tools like the Pressure Transducer.
environment of heavy machinery maintenance for the first time do not have a deep understanding of the inherent dangers associated with the work until they are exposed to them. It rapidly becomes apparent, however, when they are confronted with situations in which they are required to perform tasks from a repair, maintenance or service perspective.
This was a key concern of SafeGauge founder Luke Dawson, when as a heavy plant mechanic he was aware of the regular exposure to severe or even fatal injuries technicians faced when conducting routine pressure testing of hydraulic systems.
This was the catalyst for his development of safer remote testing products to help eliminate live testing
on-site, eventually leading to the creation of SafeGauge.
There are also distinct advantages when utilising SafeGauge’s diagnostic tools in a training environment.
The focus at Thornlie is currently on the students becoming familiar with the use of smart diagnostic tools, and in particular the role and operation of the Pressure Transducer.
“Our students are exposed to a range of mobile machinery throughout their training at the college, including wheel loaders, small excavators, dump trucks, drill rigs and bulldozers, where they experience diagnostic testing,” Gittos said.
“The SafeGauge range of products raises the awareness of maintenance safety and, from a training perspective, holds some distinct advantages.
“With these smart tools, we can therefore demonstrate the testing of the live equipment but without a student or technician within the footprint of the mobile equipment, and this represents a significant safety training enhancement.”
The high level of digital knowledge within today’s generations helps to ensure students are able to
quickly adapt to the digital nature of SafeGauge’s diagnostic tools.
“Our students are becoming much more digitally aware, accustomed to utilising apps on their phones for just about everything. This digital connectivity in their day-to-day lives means their ability to understand the processes and procedures linked to the diagnostic smart tools, and more importantly the intrinsic benefits of the technology, is clear,” Gittos said.
South Metropolitan TAFE contacted SafeGauge at the beginning of this year with a view to purchasing a range of its products, and the company was quick to offer donations to ensure the students would have access to the best equipment.
“This is a range of products that has been developed by a former maintenance technician who wanted to find a safer way of doing things and to fundamentally eliminate the risks for maintenance personnel across the industry,” Gittos said.
“To those of us who train young people to conduct maintenance on heavy mobile plant machinery SafeGauge, to their credit, has provided a very useful tool.”
According to a recent study by GlobalData, ‘Minesite technology adoption survey’, 49 per cent of mines surveyed expected to implement collision avoidance technology in the next 12 months. While up on the previous year’s 36 per cent, it leaves a significant proportion of mines without potentially life-saving technology.
The International Council of Metals and Minerals (ICMM) hopes to make collision avoidance technology capable of eliminating fatalities available to miners by 2025.
Put simply, collision avoidance acts to stop collisions between workers and
Collision avoidance technology comes in many forms. Some systems exist to identify specific types of hazards on the road, such as rocks or pedestrians, while others provide a broader range of warnings.
Early warning systems like collision avoidance have been around since the late 1950s and were first installed in cars. However, at the time they were considered too costly to manufacture and were more or less abandoned by car manufactures.
It wasn’t until 1990 that the first modern collision avoidance would be patented by William L. Kelley. This device included a microwave pulsed transmitter and receiver for scanning the space around vehicles. Any
Broadly speaking, collision avoidance is made up of radar, lasers or cameras to detect obstacles in the path of a vehicle that may cause a collision or accident.
Fitted in the cab of a vehicle, collision avoidance emits an audible warning if the driver is nearing a hazard and allows the driver to see objects in what would otherwise be a blind spot.
Many companies offer different versions of a collision avoidance, but all exist for one essential reason: to ensure everyone gets home safely.
One company that has developed its own collision avoidance is RockAware, an artificial intelligence (AI)
can effectively impose a second set of eyes on the road.
THE RISK OF ACCIDENTAL IMPACT IS A PRIMARY CONCERN FOR ANYONE WHO WORKS IN SURFACE MINING, AND COLLISION AVOIDANCE SYSTEM TECHNOLOGY IS ONE OF THE BEST WAYS TO MITIGATE POTENTIAL ACCIDENTS.With so many machines at work on a mine site, collision avoidance is vital.
and heard about the issues they were having with tyres,” Decoda executive general manager George Spink said.
Many of Decoda’s customers had expressed their frustration with how quickly tyres wear out and the potential safety hazards – a rock run over by a haul truck can quickly become a dangerous projectile.
“The risk of a fatality during tyre maintenance is 10 times higher than that of non-tyre related vehicle maintenance,” Spink said. “Every customer I’ve spoken to has told me how much they worry about tyre explosions and the risk that comes from them.”
The 2022 death of a mine worker in the Pilbara was a tragic event that brought the need for safety technology like collision avoidance more squarely into the public eye.
On 13 October, a 59-year-old worker sitting in his light vehicle at Capricorn Metals’ Karlawinda gold mine was run over by a haul truck and died at the scene.
the most important thing that comes out of a mine site are the people who go into it every day,” Pilbara district superintendent Kim Massam said at the time.
Mining vehicles are often so large that if another vehicle is struck by one, the operator sometimes doesn’t even notice the collision – unless potentially life-saving technology is installed in the truck to prevent such an occurrence.
Incidents like the one at the Karlawinda gold mine help to illustrate why the technology remains a vital aspect of safety.
In order to limit – and one day eliminate – incidents such as this, the Cat MineStar Detect system was developed to help operator see more objects around them while on the job.
“Mining equipment is large and space is often tight, reducing visibility in critical areas,” WesTrac, which sells the MineStar Detect, said on its website.
“If your space is tight, or you have multiple trucks operating in the same area, collision avoidance systems are one of mining’s most crucial safety systems.
allowing for visual and sensor checks to give your operator peace of mind.”
MineStar Detect also offers fatigue and distraction management by way of its in-cab cameras. The cameras monitor facial expressions and provide alerts when drivers show signs of drowsiness.
“No operation is immune to fatigue and distraction, particularly when tasks are repetitive,” WesTrac said.
Just like on long car journeys, a seconds-long microsleep can be deadly on a mining operation, so catching the first sign of drowsiness is an important step in eliminating accidents.
An integral part of a mine’s safety portfolio, collision avoidance technology goes a long way to ensuring that mining operations can continue safely and smoothly.
Not only does collision avoidance create a better driving experience for the operator, but it also allows productivity to remain at a high, meaning workers can go home with a sense of accomplishment and the knowledge that their safety has been put first.
The Australian resources sector understands it must provide leadership when it comes to sustainably and achieving positive environmental, social and governances (ESG) outcomes.
Key industry stakeholders –including customers, workers, suppliers and regulators – are increasingly expecting mine operators and the wider mining equipment, technology and services (METS) sector to prove their commitment to ESGrelated policies and practices.
According to the ‘Responsible Mining Foundation (RMI) Report 2022’, 94 per cent of mining companies
scored less than 20 per cent on 15 ESG metrics, with many found to be ineffective at tracking and reporting their management.
DYNA Engineering general manager Thomas Greaves told Safe to Work one of the biggest challenges for operators in the mining industry is the ability to implement policies that can effectively manage various forms of pollution, including greenhouse gas emissions.
“As our industry has come to develop a greater understanding of mining’s impact on the planet, environmental management policies and practices must include strategies to mitigate climate risk,” he said.
“By effectively managing greenhouse gas emissions, along with energy and water usage, mining companies, contractors and METS providers will all recognise the benefits, and these will lead to improvements in their ESG performance. Additionally, mining and minerals processing companies may experience operational improvements, and even develop better relationships with their customers, suppliers, employees and local community.”
Greaves said one of the most significant examples of DYNA’s ESG considerations was the recognition and introduction of its high-density polyethylene (HDPE) conveyor guards.
“The guards are made from environmentally sustainable HDPE, which in itself is recycled and recyclable, instead of the traditional high-energy-hungry and environmentally straining steel,” he said.
“The sustainability benefits of our HDPE plastic guards are significant and position us at the forefront of the circular economy, as the panels are infinitely usable.
“We firmly believe that recycled material is the future, and we are determined to see the rest of the industry embrace a greater focus on its use.
“Our mining and mineral processing customers have supported these HDPE conveyor guards enthusiastically, in many cases supporting their own ESG initiatives. They want to use a product made out plastic that can be recycled, that isn’t going to end up in landfill.
“We have also invested heavily over the past couple of years in additional facilities and staff purely to enable us to add more sustainable HDPE products to our range.”
Greaves also pointed to DYNA’s work in certification against International Standards Organisation (ISO) in the categories of quality, environmental and occupational health, and safety management systems.
“These certifications relate to the company’s activities in the design, manufacture, supply, inspection, and maintenance of conveyor systems and guarding, including related services,” he said.
METS companies that can effectively incorporate and communicate their ESG practices can benefit from risk reduction and improved cash flow.
Those that don’t, on the other hand, may soon experience significant
impacts to their businesses, including potential loss of customers and difficulties in attracting and securing employees.
Greaves said there was a connection between a company’s financial performance and its embrace of ESG considerations.
“The respected McKinsey Quarterly Report back in November 2019 showed ESG is linked to cash flow in five important ways,” he said.
“It facilitates top-line growth, reduces costs, minimises regulatory and legal interventions, increases employee productivity and optimises investment and capital expenditures.
“Every business owner and company director is interested in improving cash flow.”
DYNA Engineering will continue to support and implement ESG practices in its own operations.
This is, in part, because METS providers could decide to which prospective customers they would consider supplying their goods and services. This choice could be based on how well a particular customer accepts and applies an adequate level of ESG considerations.
Greaves said this was the reverse of the conventional process, whereby the customer selects its suppliers based on the product, price, availability or after-sale service.
“The reality being if they didn’t favour ‘yours’ they could simply go another supplier,” he said.
“This should not be mistaken as a veiled threat; it’s simply an acknowledgement of what could very easily happen due to the accelerating surge of ESG consideration requirements swelling and gaining momentum globally, especially for businesses operating in the mining and mineral processing sectors.
“In a way, it’s similar to how some of the major superannuation funds are now making ethical considerations as well as financial ones when deciding where to invest members’ money. Or which brand of jogging shoes an athlete might select based on which country they were made in and that government’s policy on underpaying workers already in poverty.
“Companies operating in the mining and mineral processing industries can no longer take a ‘wait and see’ approach with ESG. Not only will it soon become a minimum acceptable expectation of every stakeholder, but understanding and adopting ESG practices can actually provide significant benefits for those companies.
“Fortunately, it’s not too late to get started transforming into a more sustainable and competitive business by truly embracing ESG practices.”
Martin Engineering is more than an equipment supplier – it’s a problemsolver dedicated to ensuring conveyor systems run effectively and efficiently.
Martin’s belt alignment products provide immediate and continuous precision adjustment that ensures conveyor belts remain perfectly tracked and able to withstand the stress caused by wider and thicker belts carrying heavier loads at higher speeds.
The company’s belt tracking products are renowned for preventing edge damage while extending the
life of the belt, reducing material spillage, minimising wear and tear of equipment, and increasing safety.
Martin manufactures trackers that can sense the direction of the belt movement and make the adjustments needed to keep conveyors correctly centred.
“In my experience, most belt tracking problems are related to misalignment,” Martin Engineering Australia application engineer Marcelo Silvestre told Safe to Work.
The Martin Tracker provides immediate and continuous adjustment through the deployment of a patented steering system. The Tracker has four
main sections: steering roll, torque arm, parallel stay and guide rolls.
As the bell contacts the guide rolls the torque arm pivots the steering roll, causing the bell to track to the centre of the conveyor structure.
“The Tracker has been designed to keep the belt in alignment with continuous automatic adjustments,” Silvestre said.
The Tracker works where other belt training devices can fail by significantly reducing edge damage, preventing spillage and extending belt life.
“When loads remain centred, there is less spillage and this leads to productivity gains, substantially
MIS-TRACKING CONVEYOR BELTS CAN CAUSE UNWANTED DOWNTIME, SIGNIFICANT PRODUCTION DELAYS AND MAJOR SAFETY PROBLEMS. MARTIN ENGINEERING IS MORE THAN CAPABLE OF SOLVING THE ISSUE.Martin’s belt alignment products provide immediate and continuous precision adjustment.
lowering costs, as the conveyor doesn’t need to be shut down for manual cleaning to occur,” Silvestre said.
The Tracker is designed to withstand significant mis-tracking forces, especially if the distances of a conveyor systems pulleys are less than ideal.
The Tracker is available in three models, or duty ratings, to match the requirements of each application.
The Tracker is highly capable under typical industrial material handling conditions; the Tracker HD has been developed to withstand the significant stress associated with wider and thicker belts moving at higher speeds and carrying heavier material loads; and the Tracker XHD has been engineered to operate under the most extreme applications.
Martin’s Reversing Tracker features sensing rollers and lever arms located on both sides of the unit. It’s available with stainless steel paddle wheel or air cylinder to activate the sensing rolls on the proper end of the unit.
Martin’s Idler Aligner provides a safe method to manually fine tune selfadjusting idlers. This unit eliminates the need to tie off idlers to the
workers to make manual adjustments safely and conveniently from outside of the stringer.
The Idler Aligner features a hole for the placement of a padlock to restrict access.
Installation of this unit is a one-person job, as it requires no measuring, cutting or heavy lifting. But help is available if it’s needed.
“Martin’s technicians and engineers are available to provide expert advice, as well as detailed assistance on conveyor system products for their customers, and can also respond to other bulk material handling issues,” Silvestre said.
An example of Martin’s engineers solving a belt alignment problem occurred recently at Minera del Norte´s Cemesa iron ore mine in central Mexico, when the operation was experiencing serious tracking problems with the conveyor belt leading from the primary crushing area.
After drifting into constant contact with the frame, longitudinal tears formed on the belt, which reduced the usable width from 36 inches (914mm) to 32 inches (812mm). This caused spillage and lowered the
The company was replacing the 170-foot (52m) belt monthly, at a price of approximately $US140 per metre. Personnel also had to be hired to inspect and report on misalignment, adding further to the expense.
Cemesa invited technicians from Martin to provide a solution.
After a comprehensive technical survey, Martin’s representative proposed installing four Trackers (two above and two below the conveyor belt).
Using the patented parallel steering/training system, the units automatically commenced making continuous adjustments to the belt path, preventing it from drifting.
After the installation of the Tracker units, the mine’s operators reported prolonged belt health, consistent alignment, and no contact with the conveyor frame.
Since loads have remained centred, spillage has been reduced and the company has withdrawn the requirement for extra staff to undertake remedial work.
Cemesa has expressed its deep satisfaction with the outcome of the project and is more than aware of the benefits of implementing Martin’s products and solutions.
It’s clear that a key aspect of Martin expertise is its knowledge of the critical requirements to an evolved conveyor system and anticipating future production requirements.
Catering for maintenance-minded solutions across all aspects of a conveyor system, including the loading zone, can markedly improve safety outcomes and reduce downtime.
For Martin’s technicians, the role of dust, spillage and belt tracking is significant, and that’s why the correct engineering of safer and more productive conveyor systems is at the heart of the company’s customer relationships.
Flexco has long been at the forefront of providing technologically advanced efficiency and safety solutions for conveyor belt systems.
Elevate, a belt cleaner monitoring system, embodies Flexco’s ethos of providing real world solutions for its mining customers.
The sophisticated system enables operations to remotely gather critical data and perform real-time analysis of belt cleaner performance.
“The power of Elevate is that we don’t have to have personnel undertake visual inspections of the cleaners, day-in day-out. We can make
significant time savings by scheduling inspections on a weekly or fortnightly basis,” Flexco Australia western regional manager Jayden Baker told Safe to Work
Preventing unexpected downtime as a result of belt cleaner maintenance is of primary concern for operational productivity and efficiency, but remote monitoring helps to ensure a reduction in manual maintenance inspections, which in turn fundamentally improves team safety.
Elevate creates critical insights into belt cleaner performance, including proper tip and blade engagement and tension, locations of installed cleaners
across an operation, blade wear, and abnormal event notification.
“A belt cleaner is one of the most important components on a conveyor system,” Baker said.
“A correctly configured belt cleaner means you’ve got effective belt hygiene which ensures you don’t get carry back.
“Alternatively, if the belt cleaner isn’t performing properly, then excessive carry back will lead to material building up on walkways and on the conveyor structure, creating a range of safety concerns from trip hazards – as ant hills develop – to catastrophic damage where the
unchecked material build-up has fallen onto vehicles and equipment located beneath a conveyor system.”
The autonomous gathering of this information ensures the overall safety of personnel is significantly enhanced and alleviates the requirement for plant operators to gather data, providing them with the freedom to focus teams on other critical areas.
“Significant clean-up costs are associated with poor belt maintenance, as the manual handling required to remove built-up material remains a difficult and time-consuming process,” Baker said.
Flexco enhances its belt cleaner solutions with its Universal Lightweight Pole, which is a pole cleaner designed to be up to 60 per cent lighter than equivalent steel poles.
“The Flexco Universal Lightweight Pole is made from aluminium and can be used with a safety mandrel which enables access to slide the lightweight pole out of the head chute,” Baker said.
When Flexco started the development of this product six years ago, it set itself the challenge to make a 1800mm pole weighing less than 20kg to increase the safety of workers on site. This was achieved in 2019, when the company launched the 19.4kg pole to market.
A belt cleaner complete with a Universal Lightweight Pole is more than 40 per cent lighter than an equivalent belt cleaner with a standard steel pole.
“Because it’s manufactured out of aluminium,” Baker said.
“From a manual handling point of view, where a standard cleaner fit for 1800mm belt width weighs approximately 70kg, this cleaner is less than 40kg.
“It’s fundamentally safer for workers to lift on-site, while still providing the strength and rigidity needed for highperforming belt cleaners.”
suit a wide variety of Flexco primary and secondary belt cleaners, making ordering and stock piling easy for emergency shutdowns. Among the key features and benefits of the lightweight cleaner is its universal mounting plate that allows users to have one type of pole per belt width on-site, as well as the fact it has been developed and manufactured for the extreme conditions of Australian mining.
The two most common approaches to belt maintenance are reactive and proactive.
Reactive maintenance focuses on a beltline issue that needs to be fixed because it has already caused downtime or imminently threatens to do so. Proactive maintenance involves assessing the situation and taking action before a problem occurs.
While reactive maintenance is sometimes an unavoidable reality, proactive maintenance is much preferred and contributes significantly to safety, not to mention the operation’s bottom line.
Flexco believes that the most efficient and effective operations embrace a philosophy of proactive maintenance.
“This approach requires operations to have a comprehensive, up-tothe-minute view of the health and performance of all equipment,” Baker
said. “For belt cleaners, Flexco Elevate provides this view”.
Prior to Elevate, labour was monopolised performing manual inspections. This meant valuable time was spent walking the conveyor lines to examine belts and, perhaps most concerningly, worker safety was potentially compromised as they squeezed into confined spaces to inspect equipment.
“Allowing operations to better evaluate belt conveyor health anytime, anywhere without dispatching a crew to the physical belt location is a significant advancement in how operations are run,” Baker said.
Many operations are embracing technology solutions in safety protocols because they can proactively contribute to best practices while increasing operational efficiencies.
The combination of Flexco Elevate and the Universal Lightweight Pole is at the forefront of this shift, allowing operations to remotely gather critical data before dispatching a crew and reducing the risk of manual handling injuries when maintenance is required.
The benefits of the Universal Lightweight Pole and Elevate technology demonstrate Flexco’s desire to continually position itself as a leader in providing sophisticated customer solutions that increase safety.
Safety and electrical conveyor technology, including belt alignment and pull-wire switches, is usually required to operate under a wide range of harsh operational environments.
As a leading independent supplier of conveyor products around the world, Kinder Australia supplies new and robust conveyer system switchgears to the resources sector. The ZS 92 S / KST switchgear series, manufactured in Germany by Steute, is a prime example of equipment that has been especially developed for extreme conditions.
The series is available in two tough, corrosion-proof and shockproof material options: aluminium diecast enclosures and thermoset plastic enclosures.
This makes them suitable for multiple applications, including surface mining operations, quarries and sand pits, as well as in the heavy manufacturing industry.
“The emergency pull-wire and belt alignment switch Extreme series have been tested according to Australian standards and satisfy all operational requirements,” Kinder Australia
The new mechanics embedded in the ZS 92 S / KST series facilitate a wire length of up to 2x100m and can significantly reduced release forces and paths when actuating the emergency stop function.
Installation accessories specific to each pull-wire switch are available in the form of compensation springs, tensioners and wire clamps. Visual indication of a tripped switch is made easier with the choice of LED lamp switch versions.
Safely mounting the pull-wire switches is critical to have them operate according to stipulated standards and, as such, back and base mounting of the switchgear is possible. Wire breakage detection is an important feature of the ZS 92 S / KST to help ensure a conveyor is stopped immediately in the event a pull-wire breaks.
Kinder’s ZS 80 KST Extreme pullwire switch has also been developed for severe operating conditions. This unit represents a robust switchgear solution designed to guarantee a reliable emergency stop function, along with wire-break monitoring. The ZS 80 KST series facilitates a wire length of up to 75m while maintaining a maximum pull force of 70N required to actuate the emergency stop function.
Another key product in Kinder’s safety and electrical conveyor technology range is the ZS 92 SR / KST Extreme series belt alignment switch.
This switch is designed to closely monitor conveyor belt alignment, ensuring uneven loads or some other adverse process is not causing belt misalignment.
A new feature of the belt alignment switch ZS 92 SR / KST Extreme series
is the use of staggered contacts with individually adjustable switching points. The switching points for advanced warning and switching off can be individually set within a range of 5–35°, which is made possible via a simple unlocking, shifting and latching of the switching inserts. The switch first generates a warning and stops the belt at further actuation.
“These pre-warning contacts reduce the downtime of the conveyor system; however, the operator still has the ability to react to events before the belt
Belt and machinery damage due to a continually mis-tracking belt is averted with the application of such a belt alignment switch.
Similar to the ZS 92 S / KST Extreme series, the Steute belt alignment Extreme series are resistant to severe temperatures, retain a high enclosure protection rating of IP 66 and IP 67, and are available in a tough, corrosion-resistant aluminium diecast or thermoset enclosure to resist harsh operating environments.
Options for the switches include a belt alignment lever that is adjustable in 12° steps using a selflocking mechanism, plus an indicator lamp on a toothed shaft P or a continuously adjustable belt alignment lever using a clamp mechanism. It is also available with an indicator lamp L.
Kinder also supplies the K-MotorShield, which the company describes as a simple, safe and durable product that protects electric motors against dust, debris and water ingress.
The K-MotorShield is designed to ensure adequate covering of motors to prevent an acceleration in the wear of bearings, brushes and windings, therefore lowering maintenance-related costs and
The consequences of failing to adequately protect mine workers are severe. Incidents involving conveyors, while infrequent, can be catastrophic. Unguarded moving parts and pinch points pose a severe danger, and incidents such as slips, trips and falls can become fatal.
Failing to provide safe working conditions can also result in fines. It is not enough to install policies for ‘best practice’; physical barriers to the conveyer must be put in place.
Guarding is an essential element in protecting personnel around moving machinery and conveyors; however, guarding has traditionally been heavy and cumbersome to remove.
Some guards provide a suitable barrier from but create a new manualhandling hazard when removed for inspection or maintenance. This guarding is not compliant with newer Australian standards, which may not be compliant with existing standards.
To comply with AS4024.3610:2015, guarding must:
• provide a protective physical barrier which removes the foreseeable risk of personal injury by accidental contact or approach
• be identifiable as guarding, primarily through safety colours
• not allow any body parts to fit through the guarding apertures and reach the hazard
• allow visual inspection without the ability to make contact with the hazard physically
• not impede the operation of the plant
and easily replaced when the work is finished
• not create a new manual handling hazard, such as overly large and heavy panels
• be secured in position so they cannot be removed without the use of tools unless an interlocking device is provided to stop the conveyor when the guard is removed automatically.
ESS’ EZI-GUARD system has been engineered to meet the guard design requirements of AS 4024.3610:2015 Safety of Machinery – Conveyors and ISO 14120-2015 Safety of Machinery.
The modular guarding system that ensures compliance by utilising lightweight panels (aluminium, powder-coated), mild steel (galvanised), stainless steel, or highdensity polyethylene (HDPE) plastic. This eliminates additional hazards by that come from being overly heavy or
Material options for panels allow for EZI-GUARD to be used in various environments, with the stainless steel and HDPE plastic suitable for corrosive applications. Its design is flexible enough to also be used for applications like free-standing barriers, workshop machinery, and anywhere with potential to fall from heights.
EZI-GUARD is also customisable. Where the conveyors require a nonstandard height or specific items need to be secured, ESS can manufacture panels that fit specific requirements.
While EZI-GUARD is an off-the-shelf solution, ESS also provides bespoke services, providing designs and quotations for specific requirements.
ESS maintains stores and service crews for most Australian mining centres and can deploy personnel to a site for installations, servicing, inspections and troubleshooting for EZI-GUARD systems.
WHILE SAFE PRACTICE IS ESSENTIAL ACROSS A MINE SITE, CONVEYORS CAN BE ESPECIALLY DANGEROUS – ESPECIALLY WHEN UNGUARDED.The modular EZI-GUARD system can be customised to meet specific requirements.
On average, Big TED can help to get your digestor pots reinstalled and back in action one whole day sooner. That’s an estimated $960,000 saved in down time every couple of months, not to mention freeing up the maintainers for further tasks a day sooner.
When the Exxon Valdez oil tanker bound for California struck a reef off the pristine coast of Alaska in March 1989, spilling millions of gallons of crude oil into the ocean, it was the was the largest oil spill to occur on US waters at the time.
That disaster was surpassed in 2010 when the Deep Water Horizon explosion led to a major oil spill in the Gulf of Mexico.
These events were catastrophic, but share something unique: for both spills, living microorganisms were used to naturally degrade the toxic waste and reduce the severity of the spill.
The concept of bioremediation refers to the use of existing, or deliberately
introduced, microorganisms that actively break down unwanted pollutants within a particular environment.
After the Exxon Valdez and Deep Water Horizon oil spills, this process was put to the test across a large, open space. Scale that down to the size of a worksite sink, and you’ve got CRC Industries’ industrial parts-washing system – the SmartWasher.
For workers on mine sites, being able to quickly remove oil and grease from machinery parts and tools is important to keep operations moving.
The industry has traditionally relied on harsh chemical solvents to do the job properly, but such products pose myriad risks to people and the environment.
The SmartWasher cuts through contaminants just as effectively, but uses a solution that is non-toxic, nonflammable and PH-neutral.
“Australia has some of the biggest mining sites in the world and most will utilise both an automatic washer and a manual parts washer – similar to how you would have both a dishwasher and a sink in your kitchen at home,” CRC Industries global program director Steve Colson said. “The SmartWasher is like the sink for when you need to clean something quickly or something small like tools and componentry.”
As parts are washed, the oil contaminants enter the CRC OzzyJuice liquid, starting the emulsification process.
At the bottom of the sink, the OzzyMat releases microbes into the solution, which eat the emulsified oil, converting it into harmless water and carbon dioxide. This self-cleaning cycle keeps the fluid clean and ready to use over multiple cycles, and the mobile system can be moved to wherever it’s needed most on-site.
“There are different variations of the OzzyJuice cleaning fluid, but the SWX1 has been developed specifically for Australia’s heavy mining industry,” Colson said.
“It rapidly emulsifies and creates a better cleaning experience for the technician and is just as aggressive as a harmful solvent cleaner on grease and oil.
“The SmartWasher has become a truly global product, and we are supplying it across the Asia-Pacific, Europe, the Middle East, and different parts of Europe.
“In Australia, we’re looking at rollouts of up to 100 machines at a time, because industrial sites are doing away altogether with solvent parts washing.”
According to Colson, CRC’s range of bio-cleaners is backed by decades of research and development. And due to growing interest in the reduction of carbon emissions and pollution, the mining industry is catching up to the idea of water-based and eco-friendly products.
“Every major company now has sustainability development goals, and those targets are extremely important when it comes to attracting investors,” Colson said.
“We are putting out a very simple and easy-to-implement solution that doesn’t generate toxic waste, is safer for users and the environment, and has a much lower carbon footprint. It ticks every box and does the job properly.”
Because the SmartWasher mitigates the need for toxic waste haulage, and is an incredibly scalable and mobile solution, it can reduce a company’s carbon footprint at multiple stages of the production chain.
Conversely, the resource-intensive waste cycle of chemical solvents adds costs and liability risks to any operation and is dependent on fossil fuels.
The unit itself is robust and features modern cleaning components built to last. It is easy to use and maintain, which makes the day-to-day life of miners more straightforward.
This is important to the SmartWasher’s design, as Colson’s team, working alongside Motion Australia, offers above and beyond the industry baseline for effective cleaning solutions.
“When it comes to sustainability goals, the onus is not only on consumers to make greener choices,” Colson said.
“We work within supply networks like Motion Australia to help the transition towards greater product availability and awareness in the market concerning the pathway forward for less harmful lubrication and cleaning products.”
DYNA Engineering has developed a “chamfered mesh pattern”, designed to reduce washdown splash back and increase visibility through the guard panels.
This design feature is a major “point of difference” compared to standard HDPE mesh and will improve inspection and cleaning operations.
Washdown Mesh
• Up to 50% additional spray-through for washdown.
Increased Visibility
• Up to 25% additional viewing angle and see-through visability.
Epiroc encourages a holistic approach to creating digital solutions for health, safety and sustainability in the mining and construction industries.
“With our digital solutions, you can work with mixed fleets, existing equipment, and existing partners to increase to increase health and safety for mine operations mine health, reduce risk and support compliance,” the company said.
Epiroc provides products and services in several key areas as it looks to achieve key areas to support the safest operation a mine could be.
Perhaps one of the most relevant areas beside of health and safety is environmental, social and governance (ESG) regulations and sustainable practices.
Epiroc subsidiary MineRP, which Epiroc acquired in May 2021, said mining companies are often stuck somewhere between making genuine but groundless ESG promises, and creating ambiguous ESG reports after the fact.
By genuinely practising ESG commitments on mine sites, companies are able to demonstrate a higher level of care and consideration to stakeholders in terms of how they have strategised, planned, operated and reported on a project’s progress.
Epiroc, for its part, recognises the renewable energy path the industry is taking and recommends changing to battery-electric vehicles, among other things, to reduce a carbon footprint and emissions.
Utilising batteries and renewables will allow companies to reform their supply chains by choosing to work with environmentally-friendly suppliers, an example of how a company can practise governance and engage closely with stakeholders.
Practising governance in such a way can lead to mining establishments saving time where it is vital, especially in emergencies.
Epiroc’s Mobilaris Emergency Support portfolio consists of digital solutions to help emergency crew and key personnel deliver guidance in case of an emergency situation in clearing out a site while abiding by company procedures.
“In an emergency that requires evacuation, time is of the essence, so relevant evacuation personnel must have the best tools and processes to ensure staff members are evacuated as quickly as possible, while ensuring safety is not compromised,” Epiroc said.
Epiroc’s Mobilaris Emergency Support application features emergency messaging through various channels so relevant personnel can acknowledge the communication has been received. The company said having the system in place shortens evacuation time by 25–50 per cent.
“People who have received the evacuation information are monitored and individual attention is prioritised based on who needs attention first,” Epiroc said.
WITH ITS STRONG FOCUS ON KEEPING WORKERS SAFE, EPIROC UNDERSTANDS THAT DIGITAL SOLUTIONS CAN HELP MAINTAIN AN EFFICIENT, SAFE AND SUSTAINABLE WORKPLACE.Mobilaris helps workers to receive messages navigate situations while underground. Image: Epiroc
Evacuation personnel can customise checklists and an evacuation analysis can be made by using the history viewer.
The control person can choose which assets to search for, view and follow in real-time, which can be utilised to learn traffic patterns and to investigate evacuation events and accidents.
“Onboard, our underground navigation and traffic awareness solution, and our mobile application, Pocket mine, allow operators to navigate to the three closest refuge chambers and by knowing the traffic around you, the solutions contribute to a safer workplace,” Epiroc said.
Real-time data is also utilised in Epiroc’s three-dimensional Mobilaris Situational Awareness map, which encourages transparency for control room workers.
Epiroc said site workers having awareness of their surroundings is the first step towards a safer and more productive mining operation.
The Mobilaris Situational Awareness digital solution enables the real-time tracking of people, mobile and fixed assets and vehicles while the status of various operations is monitored within the mine. Information
can be searched and a report can be instantly created.
Epiroc has a desire to bring the power of automation to the mine. This is where the Mobilaris Event Automation tool enters the scene. A versatile tool with an easy-to-understand interface, Mobilaris Event Automation can create event triggers based on data produced by Mobilaris or third-party systems.
“The Mobilaris Event Automation system has customised Mobilaris nodes based on inputs such as emergency messages,” Epiroc said.
“Event triggers can highlight asset events in the Mobilaris Situational Awareness map or be pushed to a third-party system.
“Simple dashboards can be built directly in the Mobilaris Event Automation platform, or reports can be emailed at pre-defined intervals, while automation workflows can be created to save time, money and increase safety.
“For example, Mobilaris Event Automation can trigger automatic ramp announcements for vehicles going down and send a message if the maximum amount of people in an area is met or if someone’s tag battery is low.”
Mobilaris Event Automation can also be used to calculate the amount of air needed for ventilation on-demand, count cycle times and volumes for trucks, and notify third-party systems if an emergency evacuation is initiated.
Through its digital safety solutions, Epiroc achieves its three key values, where the original equipment manufacturer (OEM) is striving for industry innovation, places an emphasis on collaboration, and is committed to putting safety first.
Epiroc’s digital solutions are built not to be mutually exclusive but to complement each other and thirdparty solutions, and any business that implements them has the opportunity to progressively improve its practices, regulatory compliance, and ESG performance.
Alongside premium product quality, KITO PWB is offering a comprehensive training program through Kito Academy, which consists of Product Academy, Safety Orientation Session, and Repair Demonstration Clinic.
The Product Academy has been developed to provide the company’s distributors, particularly its sales and marketing employees, with a greater understanding of the features and benefits of KITO hoists by allowing participants the ability to see, hear
and touch the products up close, and to compare them against some of the other products in the market.
Topics in the Product Academy include a product overview, hoist applications, unique features of the hoists, and users’ benefits and values.
“As a global leader of lifting equipment industry, we believe we have a significant responsibility to offer the safest quality products in the market, and complete after-care service to ensure safe and productive operations for our customers,” KITO’s Satoshi Ito told Safe to Work
Studies indicate that an unsafe act and an unsafe condition are the leading causes of accidents in the workplace. A large percentage of accidents can therefore be prevented by implementing simple measures, and KITO is dedicated to educating customers on these actions with Safety Orientation Session.
Other than safe handling of lifting equipment, topics such as the use of safety features and practical methods for troubleshooting major hoist problems are covered.
“Experienced operators consider themselves to be hoist specialists and this approach can lead to overconfidence and negligence when it comes to safety. Therefore, this kind of safety awareness activity is important.” Ito said.
Ito teaches operators the importance of a pre-operational inspection and ensures they are conducted correctly for compliance with AS 2550.1-2011 – Safe Use of Cranes, Hoists and Winches.
“It is vitally important to confirm the hoist is in good condition before use; however, it is also very important to understand how the hoist operates
Without this understanding, it is impossible to detect abnormal conditions such as abnormal sounds, abnormal hand pull force, and so on.”
Hoist operators, operations managers, safety officers and technicians are all encouraged to participate in the Safety Orientation Session.
The Repair Demonstration Clinic is a key aspect of the KITO Academy, with the correct repair and maintenance placing an emphasis on providing service technicians, mechanics and operators with the skills and knowledge to inspect, repair and test lever hoists and manual chain hoists.
This hands-on session is a combination of theoretical and interactive training modules that teach the basics of maintenance and repair. The program covers directives and standards such as inspection classification, required maintenance work, and preoperational checks.
Participants will also learn about equipment technology, including disassembling the hoists into individual
to know KITO’s manual hoists down to the smallest detail.
“The Repair Demonstration Clinic helps to provide maintenance staff with the necessary preventive maintenance and troubleshooting skills they need to ensure any unforeseen or sudden breakdowns can be quickly resolved,” Ito said.
At the end of the program, KITO said participants will be confident in their ability to carry out maintenance and repairs according to a manufacturer’s specifications, ensuring that manual hoists remain in top working condition.
Certification is provided for all attendees on successful completion of the Repair Demonstration Clinic.
“KITO Academy participants start to understand what quality and safety mean at KITO and can then fully appreciate why KITO has a superior level of safety and performance,” Ito said.
KITO PWB’s KITO Academy offers a comprehensive and valuable resource for anyone looking to gain the skills and knowledge in the world
KITO Academy offers plenty of hands-on opportunities. Participants can get to know KITO’s manual hoists down to the smallest detail.Hatch achieves its client goals by bringing together diverse teams with a focus on innovation in order to achieve safe and sustainable outcomes.
The company is passionately committed to the pursuit of a better world through positive change.
With more than 65 years of experience, Hatch is a leading global services firm specialising in mining and metals, energy, infrastructure and digital technologies. The company draws on more than 9000 specialist employees in 150 countries, and has offices in Melbourne, Sydney, Brisbane, Perth, Adelaide, Wollongong and Newcastle.
Complexity and disruption within the resources sector are growing. Mines are not only getting deeper, but they are in increasingly inaccessible locations and require more complicated operations.
All of this means the safety stakes are heightened and the sector needs to continually transform to be able to provide reliable and sustainable resources that are required to achieve global decarbonisation and electrification imperatives.
Hatch is at the forefront of technology and project delivery within the mining industry, supporting clients from business case development through to execution and ongoing operational support.
Hatch has expertise to develop market strategies, manage and optimise production, develop new technologies, and design and deliver complex mining
projects. The company is relentless in the pursuit of positive change, and at the core of this is building and nurturing long-term relationships to help clients solve their toughest challenges.
Safe to Work sat down with Hatch’s Luke Stone and Andrew Catto to discuss how these solutions are delivering outcomes for their clients.
According to Stone, Hatch bulk materials handling regional engineering lead, the company’s capacity to leverage a range of diverse technologies and engineering capabilities helps clients with planning and decision making.
“For instance, we can undertake discrete event modelling to test various operational scenarios across a mine processing plant, or engage in concept planning via discrete element flow modelling to test the capacity of bulk systems prior to implementation,” he said.
The role of advanced technology in the form of dynamic simulation, 3D modelling and virtual reality is also
critical to operational planning and the design of safe systems. Hatch provides the digital environments where critical insights and planning can be validated and incorporated within their design.
“Within the design environment, the use of 3D modelling is commonplace; however, we’re now experiencing that next phase of virtual engagement,” Catto, Hatch senior bulk materials handling engineer, said.
“We have the ability to place operators in a simulated environment many years prior to a facility being constructed, so they can familiarise themselves with their future workspace, whilst influencing the design to promote and increase safe operations.
“In these virtual environments you can build a significant amount of safety detail which would have been unintentionally excluded in traditional design and planning methods, resulting in an increased expenditure and the risk of poor safety outcomes.”
Hatch employs a range of digital solutions for mining clients, taking a
multi-disciplinary approach that helps to provide efficiency and productivity gains, while also incorporating key safety dimensions.
“In relation to bulk material handling, our digital teams are closely aligned with the process mechanical and digital engineering teams to understand flow sheet requirements and maximise throughput,” Catto said.
“Our digital solutions ensure large systems – designed to move materials and products – don’t jeopardise operational efficiency and personnel safety.
“Hatch has developed digital twins for many clients – in essence, a digital version of a client’s operational facility – which has the capacity to monitor real-time behaviours whilst allowing for the completion of virtual tests or scenarios on equipment and systems
to improve a range of operational and safety processes.”
Hatch can help its mining clients by deploying strategic innovation to drive shareholder value and emphasising sustainability and growth via a focus on simplification. This includes the ability to create a detailed transformation roadmap featuring tactile point solutions extending to enterprise-level pivoting with a view to present, near future and longer-term solutions.
It can also develop a digital mining platform with transparency, from initial data collection to advanced analytics, with the ability to improve operational decision making and forward planning.
By producing infrastructure that incorporates leading designs and construction processes, as well as ensuring the efficient operation of large systems such as hoisting, bulk-material
handling and logistics, Hatch helps clients deliver on operational goals.
“Hatch’s focus is to create positive change in the world by partnering with our clients to tackle their toughest challenges,” Catto said. “Whether it’s leveraging digital tools or pen and paper, we’re engaged in innovation, looking for the next thing with an entrepreneurial mindset to implement the most effective solution.”
Hatch is a member of Austmine and values its relationship with the leading not-for-profit industry association for the mining equipment, technology and services (METS) sector.
“Austmine is vital to the industry,” Stone said. “Its ability to create a collaborative platform for organisations like Hatch to share its knowledge and experiences, especially in face-to-face interactions, is extremely valuable.”
POTENTIAL SAFETY HAZARDS AT A MINE SITE CAN BE MITIGATED BY STATE-OF-THE-ART PERSONAL PROTECTIVE EQUIPMENT. THANKFULLY, HONEYWELL CAN PROVIDE JUST THAT.
The potential for falling or flying objects, chemical spills, airborne particles and radiation have always been staple safety
But as technology advances and safety hazards become better understood, companies like Honeywell are actively working toward ensuring operations become as safe as they can be.
Since personal protective equipment (PPE) is often worn on top of other clothing, it’s important to choose lightweight and breathable gear to increase comfort. High-performance synthetic materials absorb sweat and allow quicker drying.
The Honeywell Miller AirCore Harness is a lightweight full-body harness designed with breathable, open-core padding technology that provides optimal airflow while reducing heat and moisture build-up to keep workers cooler and drier.
Hard hats go hand-in-hand with face shields, as many of the hazards at a mine site can put pretty much everything above the neck in danger. Whenever there is a potential for injury to the head from falling objects, collision impact, debris and shock, among other hazards, Honeywell’s line of hard hats is designed to provide safety and comfort.
Available in a variety of styles, colours and materials, Honeywell hard hats are lightweight and available in ventilated options, as well as lighter colours to reflect sunlight, keeping the wearer cooler and more comfortable.
The Honeywell SEETHRU hard hat range is UV400-rated for outdoor use in order to protect against the risk of harmful UV exposure.
Eye protection is required for a wide range of tasks and may involve masks or goggles for chemical burns or polarised safety sunglasses for glare.
Standard lenses may fog up when working in hot, humid environments. The Honeywell Duramaxx goggles feature an anti-fog lens coating that prevents fog build-up and helps to improve vision.
The mining industry has a high incidence of noise-induced hearing loss. A study published in the Journal of Occupational and Environmental Hygiene estimated that 90 per cent of miners experience some degree of hearing impairment by the age of 50.
The Honeywell VeriShield 100 Series Passive Earmuffs feature wider earcup openings to accommodate larger ears or hearing aids, in addition to a lightweight cushioned headband and memory foam ear cushions for enhanced comfort.
To help protect against dust and chemicals, Honeywell engineers a
on safety performance, including airpurifying respirators, full facepieces, half-masks, and disposable respirators.
Made from 100 per cent medicalgrade silicone, the Honeywell North 7700 Series is the company’s lightest silicone half-mask. Its wide sealing area provides exceptional fit and comfort.
Impact-resistant gloves are ideal for use in mining environments. If gloves aren’t comfortable or hinder workers’ ability to do their jobs, it’s likely they won’t want to wear them.
With this in mind, Honeywell
These gloves offer enhanced impact protection and energy absorption on the back of the hand, without compromising dexterity and comfort. The inner layer is also quick drying to provide the wearer with optimal comfort conditions.
Safety boots for mining need to be tough and rugged. Waterproof protection is key for underground drilling environments, while ensuring comfort is crucial for workers who have to endure long shifts.
Oliver Footwear has quickly become a preferred safety footwear choice for mining and drilling crews. The Oliver AT 55-332Z all-terrain water-resistant nubuck leather steel-toe safety boot packs a punch with heavyweight protection, featuring a lightweight 300°C heatresistant rubber outsole, Kevlar thread on critical wear seams for maximum abrasion and chemical resistance, and water-resistant leather lining to absorb moisture and order, and more.
With the multitude of hazards present on a mining site, having PPE solutions to protect workers is critical. Honeywell can be a guide to creating a safer working environment.
Complexity is a key characteristic of surface mining. Success is dependent on maintaining efficient and productive operations, as well as ensuring personnel are not subjected to unnecessary hazards.
Matrix Design Group offers effective solutions to these potential safety issues.
Headquartered in the US, with offices in Queensland and New South Wales, the company provides its mining customers with sophisticated safety solutions, including the award-winning OmniPro artificial intelligence (AI) collision avoidance system (CAS).
“Since 2006, Matrix has been engaged in providing sophisticated safety solutions for the mining industry, both above and below ground, and we continue to develop integrated and cutting-edge safety systems in tandem with our customers and partners,” Matrix vice president of international operations Wes Chitwood told Safe to Work
“Matrix is at the forefront of incorporating the latest safety innovations, including AI and realworld data analytics, into our next generation of products with the aim of enhancing mine safety – without sacrificing productivity – while reducing machine downtime.
“We formed Matrix Design Australia in March 2022 to service and support the Australian and New Zealand markets with our industryleading AI CAS technologies, which we continue to innovate according to the strong feedback we receive from our customers.”
OmniPro is a powerful CAS solution that, with the use of a single or multiple cameras, effectively implements visual AI technology to immediately detect personnel or objects moving in the projected travel path of mobile equipment. The system alerts the operator to their presence without requiring personal wearable devices or tags.
“The OmniPro system is fully customisable – we actually teach the camera what it sees – and it can be fitted to various types of mobile equipment within specific mine environments,” Matrix Design Group Australia and New Zealand general manager Pieter De Klerk told Safe to Work
“Its sophisticated vision technology can simultaneously identify a variety of mobile machinery and objects
associated with mine sites and industrial workspaces.”
“The client can select the detection options that best match their operating environment, whether it be a worker, a truck, a car, a forklift, a stop or pedestrian sign, along with any other notable object within the site.”
The system has many key features specifically designed for open-space mining and industrial environments, including its ability to be configured as a single or multiple camera system with the capacity to achieve a 360° field of view. The operator has access to an in-cab screen that can be configured to provide vision for multiple zones around their mobile equipment.
“When the OmniPro solution is deployed on mobile equipment within a mine site or industrial zone, all workers can do away with the requirement to
carry personal locators or tags, and this also applies to mobile equipment and other mine site machinery. No tags are required,” De Klerk said.
“In busy environments, and really anytime there is activity, OmniPro can act as another set of eyes for the equipment operator.”
Importantly, OmniPro is a plug-and-play design, which helps to ensure easy installation.
The OmniPro reporting system supplies breach notification and incident reporting, which includes full-data capture and analysis, the ability to calculate average daily breaches per machine and trending breaches over time, access to an event graph with images time-stamped for alert, and warning zone breaches.
The system also has the ability to filter breaches by zone type, sort by type of event (eg person, sign, car, etc), and provide SMS or text message alerts in the case of a safety event.
The key benefits of the OmniPro reporting system include its ability to precisely track safety and performance, clearly identify accident risk areas, and identify the most hazardous safety times in hours and days to provide near-miss reporting, with the identification of location via the time-stamping of images.
In development and ready for release in late 2023 is a new powerful application, the OmniPro Cloud reporting system, which provides 24–7 access to additional software tools via a fully integrated dashboard offering real-time data metrics and analytics for mobile equipment using the OmniPro AI CAS.
These types of features and advantages were front and centre when Matrix won the US National Institute for Occupational Health and Safety’s Mine Safety and Health Technology Innovation Award for its OmniPro system in 2020.
Matrix has entered the established mining markets of Australia and New Zealand in a big way with two powerful safety products that have already been deployed in both above- and below-ground mining operations.
In addition to OmniPro AI CAS for surface mining and industrial environments, the company’s IntelliZone is an award-winning proximity detection system (PDS) designed for use in underground mining.
Together, these solutions have proven themselves as technologically advanced safety systems that work under the extreme mining environments of Australia and New Zealand.
Moving parts and pinch points pose a serious danger to people who work around machinery. While most machinery guards eliminate incidents around moving parts, it is often heavy and cumbersome enough to become a manual handling hazard.
The patented ESS EZI-GUARD system comprises of a range of versatile, easy-to-install brackets, lightweight panels and standard structural tubing which forms an ‘off the shelf’ system that can be adapted to almost any application.
The EZI-GUARD System has been developed to exceed the guard design requirements of AS4024.3610:2015.
The patented ESS EZI-GUARD is;
• Quick and easy to retrofit
• Easy to remove for maintenance
• Modular ‘off the shelf’ design
• Corrosion Resistant
• Strong but lightweight panels
• Easily handled
• Available in a variety of materials
• Available in barricade form
• Coloured Safety Yellow or black as standard
Speedshield Technologies, an Australian-owned-andoperated business, has provided safety, control and telematic solutions to sectors such as aviation, automotive, industrial and mining for over 25 years.
The company’s latest development involves building a safety system to enhance vehicle and pedestrian separation in the workplace.
The Artificial Intelligence Vision Assist, known as AiVA, is a vision-based system designed to detect pedestrians using advanced machine vision and artificial intelligence (AI).
Given the latest Safe Work Australia statistics show that 38 per cent of all workplace fatalities in 2021 were due to a vehicle collision, this type of technology is especially vital on a mine site.
AiVA was built with the intention of increasing operator situational awareness by automatically detecting and advising when pedestrians approach the heavy machinery to which the system is attached.
The system does not require pedestrians to carry any type of beacon or wear any specific types of clothing to be detected, taking the onus off the person and allowing its operation in mixed-use environments where members of the public may be located.
Speedshield Technologies chief executive officer Nathan McKenzie spoke to Safe to Work about the
AiVA system’s development. He said Speedshield’s engineers considered previous knowledge of industrial equipment and telemetry solutions when working to create a software that can best detect pedestrians.
“We decided to use what we knew about industrial equipment and the environments they operate in through our work with telematics and control systems and put that into an idea for building a piece of hardware that we can then build software over the top of which could detect pedestrians,” McKenzie said.
“Our artificial intelligence detection model is capable of detecting any utility,
but we wanted to really focus on being a pedestrian-detection system and to be very good at it, and for it to be reliable in cluttered, complex environments.”
So how does the AiVA system work?
It consists of a network with four or more rugged weatherproof cameras and a single operator remote. The cameras are installed and trained on specific segments of vehicles that correspond to a matching segment on the remote.
Speedshield manufactures these cameras and has built in the ability to network them together.
“(Operators) can have multiple cameras and create 360° coverage,” McKenzie said.
“In some cases, we have five and six cameras attached, depending on the size and complexity of the equipment. We’ve got very large forklifts, cranes and loaders, machinery that can have more than four cameras because they are so big and may have particular blind spots.
“We decided to build a system that can network together and cover a whole vehicle, improving detection performance to the point where (AiVA would) always pick people up.”
The operator remote provides a radar-like aerial view of the entire vehicle’s surroundings, showing pedestrian locations clearly to the operator. The remote also includes an operator acknowledgement button and a weather-proof speaker to provide loud and effective voice prompts to alert machine operators and nearby pedestrians of any proximity breaches.
McKenzie said AiVA’s design team didn’t want a screen with multiple cameras playing footage at the same time, which he believes can divert attention.
“We didn’t want to further distract the operator,” he said.
“We thought the only reason you have a screen is so the operator can interpret what’s in the frame. Instead, we’re doing that with the artificial intelligence.”
The operator remote incorporates a colour-code system that detects different ranges within which a pedestrian is near the machinery. AiVA can detect pedestrians at ranges of 8m and beyond.
The operator remote features three levels of pedestrian detection displayed via LED lights.
The first is a yellow LED in the outer ring of the segmented display, which flashes when pedestrians are at distance greater than, for example, 5m.
The second level is a red LED in the outer ring of the segmented display, and it shows when pedestrians are within
5m of the vehicle but no closer than, for example, 3m.
The final level is another red LED within the inner ring of the segmented display, which will appear when pedestrians are within 3m of the machinery. A voice prompt will also notify those within 3m
“There is verbal feedback. It isn’t just another buzzer,” McKenzie said.
The data collected by the AiVA system can sync to an optional cloud-based storage platform, which automatically collects the information, details operational policy breaches, and records near misses across a fleet.
“We’re looking at the pedestrian interaction, and its date, time and position, and then an event is generated by the entry into that inner zone (on the operator remote),” McKenzie said.
“When (AiVA) talks, that’s an event. That event is then distilled further, such as you may have several people in the event, there might be more than one threat, and the time in which (pedestrians) remain in that area, and the closest point they came to the equipment. These can be really good differentiators.
“We don’t just get a picture, because a static picture tells us nothing. When you get multiple video angles, you get to see why somebody came into the area; it might have been to get out of the way of something else. You get real context around what has happened.”
AiVA saves data locally, and video snippets of problematic events are automatically captured and can be used for organisational analytics, training and continuous improvement.
McKenzie emphasised that systems and collision avoidance such as AiVA are not just for large companies; they should exist within a broader safety structure.
While having these innovative features and technologies is all well and good for collision avoidance and pedestrian separation, Speedshield Technologies stresses that installing and utilising the AiVA system should not be the only form of collision avoidance any site or operation has.
“It should rather act as a complement to the normal required vigilance of the operator,” the company said. “(It) was not designed as a replacement of good vehicle operation, such as keeping a continuous lookout, and driving slowly and to the conditions.”
THE LATEST VERSION OF HEXAGON’S MINEPROTECT COLLISION AVOIDANCE SYSTEM PROMISES NEW FEATURES TO FURTHER PROTECT MINERS FROM POSSIBLE ACCIDENTS.
GlobalData’s 2022 mine-site survey revealed that 58 per cent of Australian mines had made at least a moderate investment in collision avoidance.
If a company is yet to invest in collision avoidance technology or systems, or would like to improve on existing technology in which it has already invested, they could benefit from looking at Hexagon’s MineProtect Collision Avoidance System (CAS).
CAS is a featured system under Hexagon’s Mining division, which has the intention to connect mines to technology that organises and delivers real-time data to help operators reduce costs and improve a site’s safety, decision-making and productivity.
The system is currently being utilised in more than 40,000 vehicles worldwide and has a range of features that make it stand out among other collision avoidance technology.
CAS has a 360° operator awareness for any speed or travel conditions through non-intrusive cabin display units, which improves operator vision, eliminates blind spots, and heightens situational awareness within 500m.
Global manager of MineProtect Safety Solutions in Hexagon’s Mining division Josh Savit told Safe to Work that the latest CAS model is more dynamic than previous iterations.
“The current CAS-10 system, specifically with our QD 1400 display, really offers the ability to know what your traffic awareness is, and then know what your most imminent risk is,” Savit said.
“It’s really about risk and it’s about decision-making,” Savit said.
CAS includes a global navigation satellite system (GNSS) unit, which calculates the vehicle’s speed and path of movement, improving vision and heightening situational awareness to avoid collision.
It also incorporates a built-in safety zone feature, where real-life traffic alerts come through to the operator so other vehicles, their locations and possible directions can be seen, which helps predict potential collisions ahead of time.
Having this data readily available allows operators to make informed decisions and to improve safety in the area. CAS is also easy to install and quick to configure.
The standard system hardware consists of a display, the main unit, a combined antenna which contains the GNSS, real-time radio antennas, and WiFi for real-time tracking and reporting.
The latest incarnation of CAS utilises many new technologies, according to Savit.
“From a sensor point of view, but also from the ability to provide operators with a sense of understanding and comprehension, CAS moves functionality from being a tool which is there to alert
by adding on the data to inform and positively impact the decision-making process,” he said.
Savit said all site incidents, particularly when they are metal-to-metal, are devastating to an operation from a personnel and an operational point of view, thus the need to invest in the right safety technology.
“Collision avoidance is a critical path,” he said. “It’s also a very attainable path that allows operations to make adjustments that have low impact to the operation and to utilise it for high impact results.”
Savit described CAS technology as iterative and the gateway to vehicle intervention.
“If you look at what we have in our passenger cars today, we drive cars with (CAS-like technology) in them,”
“They are giving us that traffic awareness, whether it be the lights or the indicators in our mirrors telling us that there are people in our blind spots, all the way up to active alarms that are beeping at us if we get too close backing up or pulling forward.”
The information collected and interpreted by CAS can then utilised in Hexagon’s Power of One platform, which is the company’s set of holistic solutions.
The platform connects all processes of a mine from the pit to the plant by joining all sensors and software with an intelligent monitoring system that can be accessed from the field to the cloud. This can then be used to make informed decisions and increase productivity and safety.
Savit said using CAS is about a
“It can be the main tool for over speeding and from harsh braking,” Savit said. “These are all maintenance pieces, but they’re also productivity pieces.
“It’s not just about avoiding metalto-metal incidents or other incidents that can potentially stop the vehicle that potentially cost money when you’re not moving.
“It’s also reducing wear parts, greenhouse emissions and fuel because a more stable and driven vehicle is a more productive vehicle, but it’s also a more efficient vehicle.”
CAS isn’t just about reducing actual site incidents and collisions, Savit said, but also about reducing near misses.
“This creates a much more dynamic (operator) mind and operation, which will also be more productive,” Savit said.
“Because anything flowing steady is
When Nivek Industries was founded in 2011, it was on the back of the creation of its highly capable, self-propelled, tracked elevated device (TED), a machine designed to mitigate the dangers to personnel when removing and replacing heavy mobile plant components. The functional design of the TED belly-plate jack helps make the difficult, dangerous, time-consuming task of undertaking heavy component replacement or repair a thing of the past.
“TED has been adopted by the mining industry and is in use across various types of mine-site settings, and has also found its way into use in the rail and civil construction sectors,” Nivek general manager Derrick Cant told Safe to Work
dozers, graders and haul trucks, or any other type of mining or earthmoving machinery involving hoists, slings and chains, TED can effectively and efficiently remove personnel from the crush zone of suspended loads.
“TED has been designed for the safe removal of heavy machinery components and achieves this by removing the suspended load hazard and efficiently transferring the manual handling element onto the unit,”
Designed by a fitter for fitters, TED, along with the larger and more powerful Big TED, is now widely sought after throughout the mining industry.
to provide tailor-made solutions for mining and heavy industry clients, remaining committed to manufacturing innovative products that make workplaces safer and more efficient.
“A good deal of our success is that we listen to the feedback of our mining clients and take into account their specific requirements,” Cant said.
This has led Nivek to up the ante with the development of a new range of low-profile heavy-load carriers named the Beast of Burden (BOB).
“With strong client interest from across the mining industry in a custom-made carrier, we have been working hard to provide an off-theshelf solution,” Cant said.
“In doing so, we aim to further enhance our strong reputation as a company that can provide effective
the TED is an easily adaptable piece of safety equipment that has recently evolved into a larger and more powerful unit.
The aptly named Big TED has an expanded capacity to move substantially heavier loads, with the ability to shift weights of up to 3000kg while maintaining its relatively low profile.
TED and Big TED significantly impact mine site safety by ensuring the physical stress often experienced by technicians and other maintenance personnel is alleviated, while at the same time reducing downtime and increasing productivity gains.
The units work tirelessly under the most extreme environmental and operational conditions.
The drive system on the Big TED comprises two independent 3.5kW infinite control electric drive motors, controlled by a proportional joystick on the remote-control unit, which is highly responsive and
Both motors produce enough torque to ensure heavy loads can be carried across various types of terrain, and the 24VDC 448Ah rechargeable
battery system provides at least two hours of continuous operation.
Additional features of Big TED include remote-controlled side shift, powered turntable and AUX (auxiliary port) functionality to enable the utilisation of smart attachments.
The machine also has built-in load cells to measure the load and tilt sensor to ensure it is operating within design parameters.
For Nivek, safety in the workplace is paramount, especially when maintenance and repair technicians are working around heavy machine components.
The old methods of removing components, such as belly plates, can often led to catastrophic outcomes when a safety incident occurred.
Today, these hazardous practices are being eliminated by the employment of Nivek’s TED, Big TED and, in the not-too-distant future, BOB.
“We remain committed to developing innovative and safe products for mining and heavy industry that enhance workplace safety, efficiency and productivity,” Cant said.
BOB designs for a while now and are starting to get close to finalising a design and building a prototype,” Cant said.
“In essence, they are going to be low-profile, remote-controlled tracked carriers designed to travel longer distances than the TED range.
“Like the TED range, the table will have mounting points and auxiliary power allowing customers to adapt their BOB with smart attachments to suit their requirements.”
With several key design features, including remote-control operation, all-terrain capability and a low profile,
Makita is a trusted mining industry partner and its XGT (Next Generation Technology) system, featuring a range of innovative, powerful and robust battery-powered tools and equipment, performs under the harshest of workplace conditions.
At the heart of this vision is the role of safety, which aligns with Makita’s core philosophy of ‘listen, act and deliver’.
Makita believes the best products are made through a process of listening to the people who rely on them and acting on their feedback to deliver innovation and safety improvements.
A key safety aspect of the XGT product range is the ability to eliminate the many trip, entanglement and shock hazards associated with corded tools.
“Makita’s vision is a workspace future that is 100 per cent free from the physical and environmental hazards associated with air hoses, power leads and petrol power products,”
Makita Australia industrial business development manager Andrew Shaw told Safe to WorkThe XGT range has benefited from this ethos. The product line features in-built software that provides real-time digital communication between the battery and the tool, ensuring optimum and safe charging performance.
Makita’s approach to incorporating practical and effective safety features is also found in the GA013GZ 125mm angle grinder, a rugged tool capable of performing under extreme conditions.
Featuring active feedback-sensing technology (AFT), the tool maintains the ability to predict imminent kickback, with immediate cut-off whenever there’s a sudden drop in wheel speed, while the electric brake rapidly slows wheel rotation upon release of the trigger.
The GA013GZ also features an antirestart function, preventing the tool from unexpectedly starting if the battery is inserted while the trigger is depressed, and its two-stage safety paddle switch prevents the tool from being locked on over an extended period.
Makita’s TW001GZ 0.75-inch drive
the user has enhanced control during operation. This is especially relevant to the removal of fasteners; auto reverse stop prevents uncontrolled removal of the fastener that otherwise could result in it becoming a harmful projectile.
The TW001GZ also features four-speed selection that reduces unnecessary reactive force on the operator, while rubber joint suppression limits vibration to operator, as well as to the battery and the battery terminals, preventing flog out.
Another key aspect of Makita’s XGT system is the ability to record operations
can then be used to help identify and improve a range of operational and safety use.
“The smart technology embedded in the XGT system offers the ability for operators to collect a significant amount of valuable data, which can assist with improvements in how users operate the tools as well as influence safety protocols and training,” Shaw said.
“This adaptor also has the ability to provide advanced assetmanagement, including the incorporation of pin codes to prevent unauthorised use, or to restrict operation within specified time parameters.”
In addition to using tools with key safety features, substituting a tool such as a cold cutting saw in place of an angle grinder – a more traditional option – may provide a safer and more efficient solution.
Makita’s 40v CS0026 cold cutting saw can cut steel up to 12mm thick (with appropriate blade) and significantly reduces sparks, while collecting the swath in a metal chip collector. Added features such as AFT, protecting against kickback, and an electric brake make this option a safe alternative in certain cutting applications.
A recent example of Makita providing solutions that ensure work processes are safer and more efficient occurred when a client had an application requiring a 0.75inch high torque wrench to be operated for the adjustment of hard skirt plates.
The client managed about 20 hard skirt plates per shift, but after changing to a Makita XGT 40v 0.5-inch wrench, the power was sufficient to complete the same task, yet the weight dropped by half (6.5kg to 3.2kg), and the client was able to complete 40 skirt plates per shift.
This represented a 100 per cent increase in output, and when asked what the biggest contributing factor was, the client said it was due to less fatigue on the body, enabling her to work continuously.
ion batteries to strict standards. These batteries are engineered with internal electronic circuitry to monitor conditions when in use with Makita tools, equipment and chargers.
The in-built safety systems are designed to prevent over-charging, over-discharging and over-heating when charged on genuine lithium ioncharges.
According to the company, by using non-Makita or generic batteries that have been altered, the sophisticated electronic communication system between the battery and charger, as well as between the battery and the tool or equipment, may be compromised and lead to the possibility of thermal runaway.
Thermal runaway occurs when heat generated within a battery exceeds the amount of heat that is dissipated to its surroundings. The rise in temperature in a single battery will begin to affect other batteries in proximity, and the pattern will continue, thus the term “runaway”.
If left uncorrected, internal temperature will continue to increase, causing battery overheating and the
damage to equipment, and possibly personal injury.
Genuine Makita batteries are designed to prevent this type of event. The batteries are easily identifiable as they are black in colour, have the Makita trademark logo with lithium-Ion identification on both sides, and have the Makita trademark logo on the bottom of the battery.
Makita only approves the use of genuine parts and accessories with its tools and equipment.
“Fit-for-purpose tooling with the required safety features represents a key aspect of Makita’s overall solution,” Shaw said.
“How the power tools and equipment are managed within a business setting – for example, a mining operation – is also critical.
“In this respect, Makita offers a national industrial business development team which is able to provide a comprehensive equipment management program that, when combined with the tooling solution, provides a comprehensive approach to Makita’s overall support to the mining industry.”
WITH OVER A MILLION PEOPLE WEARING ITS MATERIALS, TENCATE PROTECTIVE FABRICS CREATES SAFETY CLOTHING THAT WILL LAST A LIFETIME.
Founded back in 1704, TenCate Protective Fabrics has been creating and supplying protective gear to generations of professionals in sectors such as emergency response, military, light and heavy industry, energy, and oil and gas, to name a few.
Originating in the Netherlands, the company expanded its global business before acquiring Southern Mills in 2004 and moving its headquarters to Atlanta, Georgia, in the US, to service its global markets in North America, Europe, the Middle East, and Australia.
TenCate is now one of Australia’s leading providers of protective fabrics for clothing that aims to bring out the best in professionals.
Safe to Work spoke to Mark Grundy, TenCate APAC sales and end Use market manager for Australia and New Zealand, about the company’s flameresistant fabrics, the line for which TenCate is arguably best known.
“We have three market segments of our business,” Grundy said. “We have a military segment, an emergency response segment, which covers firefighting ensembles that are flameresistant.
“You also have an industrial segment, covering people that work at petrochemical plants, oil and gas, and electrical utilities. It’s electrical protection from arc flash that can influence mining as well, because they can be dealing with not only oil and gas, but liquid natural gas, and they can have power transformers on-site.
“It’s not only protection in an industrial sense, from flames that come from combustible materials, but it can also be from what’s considered to be arc flash, where you have a high voltage that arcs across switchgear. It can create really high temperatures over a short period of time, which these garments can protect the user from.”
The first step in TenCate creating flame-resistant is sourcing the correct fibres, which is the unspun material that makes up yarn. Blending the right fibre types together with the correct ratios creates yarns that are weaved together to create the raw flame-resistant fabric that is dyed and shipped to garment makers for the clothing to be produced.
TenCate believes the most essential protective properties of a garment are defined by the fabric used to create it, which is why the company works
throughout the entire value chain to give its customers the expert advice they need to make confident choices.
TenCate’s customers include those who actively work with the fabric, such as the garment manufacturers, as well as distributors, industrial laundries, and end users. Manufacturers are those who buy TenCate’s fabric and turn it into garments for various industries. The distributors supply what kind of gear the end user – those who will be wearing the protective clothing – is looking for.
When it comes to getting things clean, TenCate encourages the use of industrial laundries, as professional washing maximises the durability of the garment, ensures it is correctly cleaned, and the fabrics are designed with industrial laundering in mind to their colour, comfort and inherent flame-resistant properties for the life of the garment, well beyond normal yearly clothing supply
The supply chain process of the fabrics can unfold in various ways, Grundy said, depending on the country in question.
“In parts of Asia, what you’ll tend to find is the end user will talk directly with
a garment maker, someone that actually assembles the garments,” he said.
“Whereas in Australia, we tend to we have a mixture of methods, but predominantly in an industrial sense you will talk with various distribution companies who stock brand garments that are warehoused in Australia but are made offshore.”
And according to Grundy, TenCate’s flame-resistant clothing is exactly that.
Grundy believes Australia is a very safety-oriented country, as evidenced by the fact it is standard for many workers to wear high-visibility clothing and utilise UPF ratings.
“(Australia is) very educated and has got a long history of safety in our markets for developing and adopting standards relative to our specific environmental conditions,” he said.
TenCate is not just committed
sustainable fabric utilising Lyocell fibres blended with flame-resistant fibres.
“Lyocell, sometimes called Tencel, is derived from sustainable eucalypt wood, which uses far less water than cotton. It can keep the wearer cool and give the fabric softness, while the blended flame-resistant fibres stop the fabric from burning.
“You can reduce the water and carbon dioxide used to create your
Today’s mission-critical communications rely on dedicated land mobile radio (LMR) networks to provide a high grade of service for availability, reliability and security.
This is vital to supporting public safety, emergency response and critical infrastructure, where there is a significant risk to the individual, the environment, and any members of the public.
Many of these networks are based on the TETRA (terrestrial trunked radio) standard, providing narrowband voice and data services to its users, with a high standard of service and exacting requirements for availability, reliability and security.
Mission-critical users have traditionally relied on voice services, but they are evolving their operations to encompass more data services and applications, many of which can be carried over TETRA.
There is, however, an increasing need for data services such as video, access to online tools or databases, and the ability to upload or download large data items.
These tasks need a much higher bandwidth than narrowband systems can deliver, and require broadband data services, such as LTE (long-term evolution), to satisfy this demand.
But these new platforms don’t yet offer equivalent performance, with many standards yet to be confirmed. The technology lacks mission-critical voice such as priority or group calls, direct mode operation and end-to-end
encryption. There are also concerns over coverage.
To address these needs, and to support organisations transitioning to future LTE solutions, Sepura has a hybrid device that supports TETRA for mission-critical voice and LTE for access to data.
The SCU3 dual-mode solution is the most recent addition Sepura, a leader in mission-critical solutions with over three million TETRA devices sold around the world.
“We are seeing across the world a shift to users investigating and testing the opportunities presented by LTE, which has been talked about for some time but is now moving toward reality,” Ronan Rafferty, country manager for Sepura in Australia, said.
“Sepura has spent a lot of time with users around the world, understanding their needs and challenges to ensure their solution answers these needs. LTE solutions can answer mission-critical users’ operational needs by providing access to critical data in the field.”
The SCU3 dual-mode device has been designed for use in vehicles and/or fixed office locations and supports TETRA for missioncritical voice and data through 4G/5G or Wi-Fi connectivity.
Built on an Android operating system, the device provides compatibility with a wide range of applications designed to run on existing smartphones and tablets. Organisations can enable tools such as mapping, database query, connection to third-party devices, location reporting, and more.
Sepura has a proven history of providing mission-critical devices to users around the world, in a variety of harsh environments. The SCU3 is the latest evolution of this journey – a fitfor-purpose unit designed for exactly the type of use in which Sepura has decades of experience.
In combination with the Sepura accessory hub, the SCU3 can be connected to a wide range of Sepura and third-party accessories. This provides flexibility for vehicle and fixed installations, including a vehicle control unit that gives the user complete control, with ergonomic buttons designed to enable safe, errorfree use in vehicles that may be moving at speed.
The option to re-use existing Sepura accessories means total cost of ownership is minimised and training requirements are significantly lowered.
Mission-critical users are always looking for ways to extend their capability, and the Sepura hybrid solution is designed to allows them to do exactly that. It adds broadband data to support users’ operations, while they benefit from the proven quality, coverage and robustness of TETRA voice communications.
The Queensland Mining Industry Health and Safety Conference (QMIHSC) has been promoting health and safety in the state’s mining industry for more than 30 years. The annual event provides people throughout the sector with opportunities to exchange information, form connections and foster proactive health and safety management techniques.
And this year’s QMIHSC committee promises the best of the best.
“The committee is looking to bring to the stage interesting and varied keynotes relevant to the breadth of organisational delegates in attendance, and to address changing dynamics in health, wellbeing and safety, and current and future matters impacting our industry,” chair Larnie Mackay said in a welcome letter.
Mackay spoke to Safe to Work about how the conference holds tremendous importance within an industry as potentially high-risk as mining.
“We work with a lot of big equipment. We work in an environment that is underground, as well as surface. Some areas are quite remote,” Mackay said.
“There’s a lot of associated risks operating the mines themselves, as well as personal factors such as fatigue, working away from family, etcetera.
“So the health and safety of everybody who is on a mine site, or supporting a mine site, is absolutely critical.”
This is the 34th year in which the QMIHSC has been held, and the central theme for 2023 is ‘inside looking out’.
Mackay said the theme is designed to examine health and safety practices that have worked in other industries and see what is transferable to the resources sector.
“For many years, we’ve looked at what we, as an industry, can do to improve health safety,” Mackay said. “We’ve looked at innovation and technology to be able to improve upon our own.
“But I think we also need to look at programs, systems and initiatives that are considered best practice in other industries that can be adapted to the mining industry.”
The QMIHSC originated in Townsville when a couple of hundred delegates from the resources industry were having a conversation surrounding health and safety, and how it needs to come to the forefront of the sector.
THIS YEAR’S QUEENSLAND MINING INDUSTRY HEALTH AND SAFETY CONFERENCE IS LOOKING OUTSIDE ITS OWN INDUSTRY TO SEE WHAT PROGRAMS, SYSTEMS AND INITIATIVES ARE TRANSFERABLE TO THE RESOURCES SECTOR.The conference will provide opportunities to exchange information and form connections.
“Then over the years, through the support of industry and seeing the value that comes out of the conference from keynotes, from innovation, presentations, health awards, what our suppliers bring to the exhibition hall, it actually grew to the point that it was too big for Townsville, so we had to move it to the Gold Coast,” Mackay said.
“Now it’s further grown to a point were every year we continue to be elated by the phenomenal interest and support from industry, including exhibitors.
“Last year was the first year we had international interest and international attendees at the conference.”
Within the resources sphere, high reliability organisation (HRO) theory is becoming more prevalent.
HRO is when a company or
HRO theory suggests organisations that achieve health and safety objectives do so by understanding sensitivity to operations, recognising the complexity of some practices, viewing failure as a chance to grow, welcoming safety insights from staff, and practicing resilience across the board.
“To be confident in HRO is absolutely where the sector needs to go,” Mackay said.
“We need to find an industry that has implemented HRO, and (in which) it works well. We don’t need to take off on that journey completely by ourselves and then fall at the same hurdles that other industries have already fallen and learnt from.
“Let’s see the outcomes, take those learnings and adapt for our industry, ensuring we implement a robust and positive way forward.”
the conference, I’ve taken it back and I’m putting it into my workplace’,” Mackay said.
The committee has also proactively grown the conference in terms of its diversity and inclusion across speakers and topics.
“There is going to be a vast array of keynote speakers this year – from within and outside the industry,” Mackay said.
The event has already seen great success even before it has been held, with all exhibitors and various other conference offerings selling out.
“The mining iiIndustry is great at looking inside and outside for innovation inspiration,” Mackay said.
“Through the Innovation Awards we will be providing a platform for selected innovators to present to the industry what is going on in this space.
“There is the Health Hub showcasing various industry support services that are available for people who want to know a little bit more as to what they can do for themselves as well as others.”
The QMIHSC has changed the look of the exhibition hall this year to ensure more, and different, exhibitors are available for the industry.
Mackay describes the legacy of the QMIHSC as bringing multiple elements of the resources sector together.
“It’s across unions, regulators, operators, coal and hard rock, quarries, surface, underground,” she said.
“Everybody gets to attend, everyone has the opportunity to have their say, and all feedback received goes into the next conference.”
THE AUSTRALIAN GOLD INDUSTRY IS HOME TO GENUINE ENTRY-LEVEL ROLES FOR SCHOOL-LEAVERS AND THOSE WITHOUT MINING QUALIFICATIONS WHO ARE WILLING TO LEARN ON THE JOB.
Since the early 1850s, the gold industry has deeply shaped Australia society, generating $25.8 billion in revenue during the 2021–22 financial year. And there are lots of people – and jobs – behind all of that prosperity.
Ongoing strength in gold exploration and production leads to career opportunities across a range of roles, many not immediately associated with gold mining, such as environmental and health professionals, accountants and the various other types of positions required to support mining operations.
Agnico Eagle’s Fosterville Gold Mine is the largest gold producer in Victoria, having extracted over 3.9 million ounces since the commencement of the current operation in 2005.
With over 800 people employed at the mine, the majority of whom are local to the area, Fosterville strongly believes in engaging with, and contributing to, the local community.
The company’s ethos of social responsibility extends towards its commitment to providing straightforward access and opportunities for jobseekers, whether they by entry-level roles or those requiring more formal qualifications, through a range of programs and pathways.
“We have a number of pathways available for employment in our operation, and we are working hard to increase awareness of those pathways through community and industry interaction, including multiple school mine site visits across the year and supporting tertiary and secondary careers events where we can explain the various types of careers and employment opportunities that are available,” Agnico Eagle’s human resources manager Nikki Hartrey told Safe to Work.
Having spent a decade in education before finding her place in the resources industry more than 15 years ago, Hartrey knows first-hand
how transferable skills can be applied to roles in mining.
With a strong advocate for regional opportunities coupled with a passion for developing career pathways and development opportunities, Hartrey understands that the longevity of the gold industry is closely linked to its ability to build awareness and grow skills in the rural and regional communities within which mining takes place.
“For example, over the past 24 months we have really focused on developing and extending our vacation student program at Fosterville, with the aim of engaging more students earlier on and in nontraditional disciplines, then providing them exposure to our mining operations,” Hartrey said.
“Additionally, opportunities for people with existing trade qualifications are significant, as their skills are often transferable and we are able to provide industry exposure to the unique types of plant, equipment
and technological advancements beyond what they may have experienced outside of a mine setting.
“At Fosterville we are committed to providing entry-level employment opportunities for local people who have transferable skills, especially in our processing and underground operations, where we conduct significant training for new arrivals to ensure they gain the appropriate levels of operational and technical competency and are fully aware of workplace health and safety.”
As the industry becomes smarter through the acceleration of automation and technological innovation, there’s an increased presence and complexity of data and intelligent systems to support it. This gives Fosterville the ability to offer exposure to almost every type of technological discipline.
“We appreciate that for some people working underground or behind a desk is not for them, but there’s such a big variety of other
challenging roles in the industry that they might not be considering if they don’t know they exist.” Hartrey said.
“Our approach has been to highlight career opportunities and pathways that might not be obvious to those who are new to the industry, which encompass many professional disciplines from engineering, geology, metallurgy, environmental science, communications, and data science, as well as the opportunity to work alongside a fascinating collection of professionals.
“Traditionally, we have been good at creating apprenticeship pathways for school-leavers, which we continue to do. We have also been working collaboratively with our Victorian industry colleagues and partners to develop a Certification III resources course to increase entrylevel pathway to employment in the broader mining industry.”
Many other members of the Gold Industry Group offer a variety of apprenticeships, traineeships and
graduate programs designed to provide recent graduates and entrylevel jobseekers the opportunities to explore what the sector has to offer, while at the same time developing the appropriate skills to develop their careers.
The Gold Industry Group proudly promotes the National Gold Education Program within Australian primary and secondary schools. The program is designed to change perceptions and encourage future generations to consider a career in resources.
“Agnico Eagle and Fosterville Gold Mine are focused on our people and our values, on trust, equality, accountability, respect and family,” Hartrey said.
“These are guiding principles and our senior leaders at Agnico Eagle believe in these principles –it’s about people at the centre.
“We’re a big company, and we produce gold but to do that we need to attract and develop really good people.”
EVENT SUBMISSIONS CAN BE EMAILED TO EDITOR@SAFETOWORK.COM.AU
The Mineral Resource Estimation Conference 2023 will attract resource geologists to demonstrate Australasian excellence on resource estimation. The conference aims to showcase best practice, case studies and research on resource estimation and required software applications. Facilitating open exchange of information, the conference will feature interactive sessions, panel discussions and keynote presentations alongside case studies and peer-reviewed papers. Sessions will showcase advancements and examples in QA/QC and sampling, 3D geological and estimation domain modelling, geostatistical analysis, estimation, validation, and risk analysis and reporting.
• ausimm.com/conferences-and-events/ mineral-resource-estimation
Inaugurated in 1958, the World Mining Congress is the leading international forum for the global mining and resources sectors.
The World Mining Congress 2023 (WMC) is a unique opportunity for international representatives of the world’s leading resource economies to meet, find new partners, discuss current challenges and share the latest research, technology and best practice. WMC events have set the scene for international agreements and high-level discussions that have influenced mining practices and the resource industry for decades.
Join senior mining industry owners, investors, national and international government representatives, researchers, educators, regulators, suppliers and operators from
around the world in Brisbane for this genuine opportunity to demonstrate real leadership and presence on a world stage.
• wmc2023.org
The 2023 Mine Waste and Tailings Conference welcomes delegates from across to globe to explore all aspects of lifecycle waste rock and tailings management, from site selection and design to post-closure care, and addresses current and future challenges affecting mining systems re-engineering.
Co-hosted by AusIMM and the University of Queensland, the conference will feature industry-leading keynote presentations, thought-provoking panel discussions, interactive Q&As, a suite of insightful technical presentations, and exhibitors showcasing the latest innovations.
• ausimm.com/conferences-and-events/minewaste-and-tailings
AusIMM and the University of Queensland’s Sustainable Minerals’ Centre for Mined Land Rehabilitation are welcoming attendees back to the highly successful Life of Mine Conference 2023. The conference welcomed a record number of attendees from over 15 countries in 2021 and is set to bring a wider global audience in 2023. Join professionals, researchers, government, and academia from a diverse range of sectors as the program explores the full lifecycle of a mine, from exploration to rehabilitation.
Delivered in-person and online, this technical conference addresses current and future challenges affecting the mining value
chain and will present leading examples of sustainability in mining.
• ausimm.com/conferences-and-events/minewaste-and-tailings
The Mechanical Engineering Safety Seminar is returning in 2023.
The NSW Resource Regulator is proud to be hosting the 31st annual event and is seeking experienced and enthusiastic presenters. The in-person seminar will be held at the Hyatt Regency, Sydney, with no online broadcast available.
This is an opportunity to share experience, insight and lessons with mechanical engineers from across NSW mining.
• resourcesregulator.nsw.gov.au/newsarticles/call-for-speakers-mess-2023
The Australian Mining Prospect Awards are a great opportunity to recognise people and companies in the mining sector. Nominations are now open, with awards in categories such as Indigenous and Community Engagement, Mine Project Success of the Year, Outstanding Mine Performance, Sustainability Project of the Year, Discovery of the Year, and more.
Some 2022 award winners included Kestrel Coal for Australian Mine of the Year, Roy Hill for Mine Project Success of the Year, and Flexco Australia for Excellence in IIoT Application. The awards return to Brisbane in appreciation of the vibrancy of the state’s mining industry.
• prospectawards.com.au
Safe Work Australia ranks mining as one of the most dangerous industrial sectors to work in, with an average of nine deaths per year.*
From falls, noise hazards, to hand and foot injuries, it can be challenging to know what type of PPE to wear on the job.
Honeywell’s best in class range of PPE is specifically designed with the hazards of the mining industry in mind, to provide the highest level of safety – even in the toughest conditions.
For more information call 1300 139 166, or visit www.sps.honeywell.com
SCAN TO LEARN MORE ABOUT SAFETY IN THE MINING INDUSTRY