
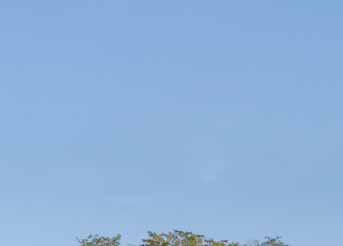
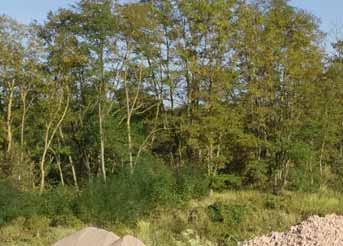
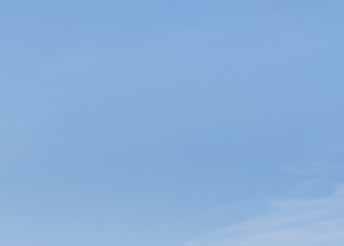
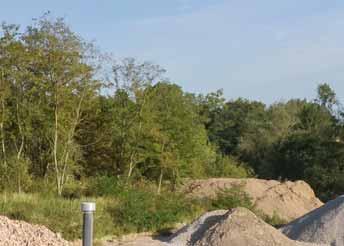
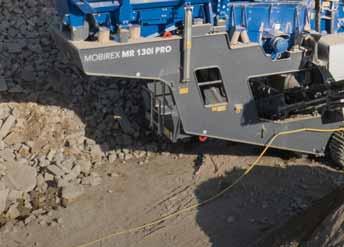
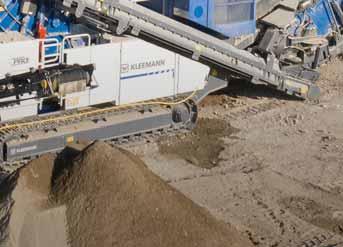

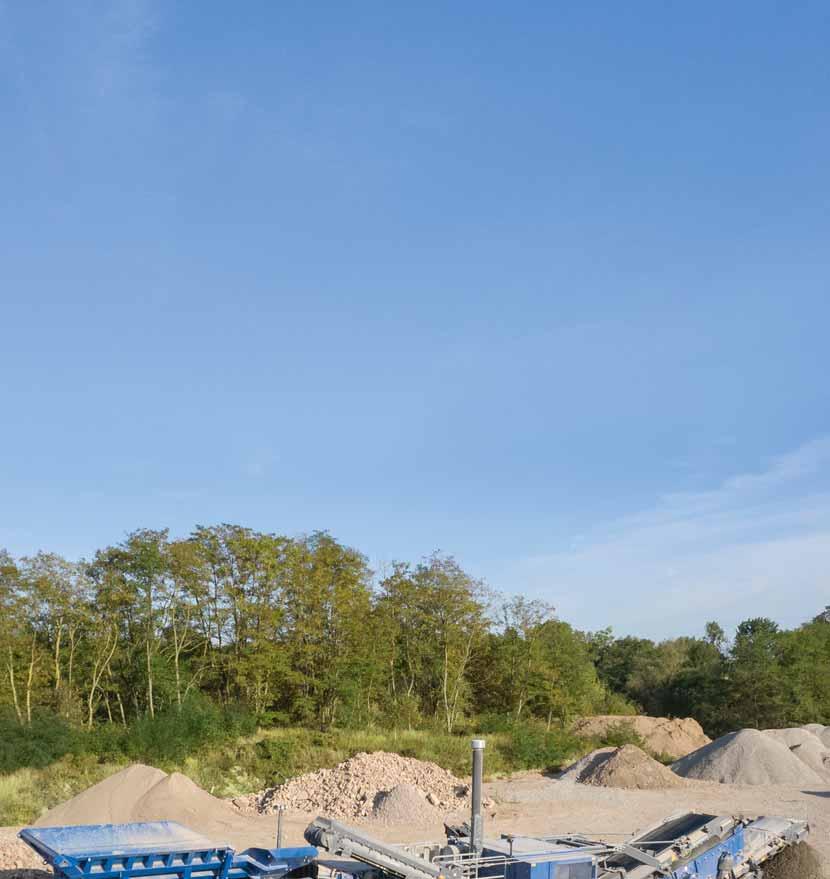
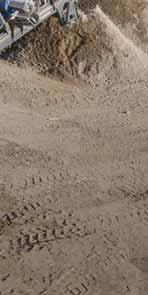
INNOVATION
Page 2: Sustainability and Muscle-Power
PASSION
Page 3: The Ideal Solution for the Quarry
Pages 4–5: Full Power with Electric Drive
NEWS
Pages 6–7 From the Smart Job with Surface Miners
MOBIREX MR 130(i) PRO IMPACT CRUSHER
INNOVATION
Page 2: Sustainability and Muscle-Power
PASSION
Page 3: The Ideal Solution for the Quarry
Pages 4–5: Full Power with Electric Drive
NEWS
Pages 6–7 From the Smart Job with Surface Miners
MOBIREX MR 130(i) PRO IMPACT CRUSHER
The MOBIREX MR 130i PRO mobile impact crusher is the latest representative of the PRO line from Kleemann. Thanks -
ronmental standards as a primary and secondary crusher in natural stone and recycling applications.
Wherever high output and outstanding versatility are required, the MR 130i PRO is in its element. With a processing capacity of up to 600 tons of material per hour, it
range. The high output is enabled by the combination of a crusher unit with a-
tric power demands of the impact crush-
E-DRIVE concept. Thanks to an external power supply option, the plant can be operated with zero local emissions. This guarantees a low energy consumption -
ment is considerably reduced by water spraying at relevant points.
gles and a variety of blow bar options with an optionally available 8.4 square meter double-deck post screening unit. This enables the production of two clas-product quality.
The intuitive SPECTIVE operating concept makes the everyday work of its users easier and simultaneously enables high productivity. In addition to a large touchscreen panel and two SPECTIVE wireless remote control units – one for the convenient control of all relevant functions of automatic mode from the excavator –-
work site digitalization of the MOBIREX MR 130i PRO.
LEGAL INFORMATION
THE ROCK
The WIRTGEN GROUP’s Magazine for Materials Processing
Publisher
WIRTGEN GROUP, Branch of John Deere GmbH & Co. KG, Reinhard-Wirtgen-Strasse 2, 53578 Windhagen, Germany
E-mail: magazine@wirtgen-group.com, www.wirtgen-group.com
Mannheim District Court, HRA 704371, VAT ID No.: DE 283 504 884
General Partner
John Deere GmbH, limited liability company based in Luxembourg, Commercial Registry No. R.C.S Luxembourg B 161281
General Managers
Dr. Volker Knickel, Markwart von Pentz, Dr. Thomas Peuntner, Alejandro Sayago
Editorial Team
Wirtgen Group Corporate Communications
Production
muehlhausmoers corporate communications gmbh
The outstanding product quality delivered by the MOBIREX MR 130i PRO is guaranteed by the combination of a robust crushing unit with two impact tog-
red the MOBIREX MR 130i PRO is uaranteed by the combination a roust unit wit h two impact tog -
The MR 130i PRO can be operated with zero local emissions and thus guarantees a low power consumption per ton of
Discover more online
With its double-deck post screening unit, the MR 130i screening and outstanding product quality with just one single plant – without the need for an additional
The new impact crusher has been hard at work – and showing its particular strengths – in a quarry in western Germany since August 2022.
The Kalkwerke Oetelshofen quarry in Wuppertal has been a source for the limestone re-
naces of the iron and steel industry for many years. Since August 2022, quarry operator AMIRO GmbH now relies on a combination plant in which the screening unit is connected directly to the crusher. The perfect solution for this challenge is the new Kleemann MOBIREX MR 130i PRO impact crusher, which is now demonstrating its numerous advantages
screening and outstanding product quality. And all of this with just a single plant and no additional screening system. An
consumption, as only one machine, which is also characterized by low fuel consumption values, needs to be fueled.
At AMIRO GmbH, the long-standing collaboration based on mutual trust played an important role in the decision to invest in the Kleemann plant. In the words of CEO Dirk Frorath, after his visit to the Kleemann factory in Göppingen, where he was able to take a close and critical look at the impact crusher, "The massive running gear with its heavy-duty frame construction, the ladders and platforms for easy access to all components, and the solidly-built double-deck post screening unit all made a per-
concept. The plant operators in the quarry are already familiar with the concept from their work with other MR 130 EVO2 plants. "Time and again we receive very positive feedback from the users," reports Christoph Obalski, sales and marketing specialist at Kleemann, "the plant operators have no problems at all with the system. Once you're familiar with how SPECTIVE works, you can operate all Kleemann crushing plants intuitively.
Emil Steidle GmbH & Co. KG from Sigmaringen is breaking new ground Kleemann.
As a part of its diverse portfolio, Emil Steidle GmbH & Co. KG, founded 200 years ago, has also been extracting and processing quartz sand for over 50 years. After preliminary processing, the company directly markets some of the material produced, for instance for the construction of sports facilities, while the greater
of glass or building materials such as plaster or adhesives. The screening plants.
Eventually, the company decided to invest in a which has now been in operation since March 2023. On the one
hand, it has a very wide, large screening surface that can deliver a very high output. On the other hand, Kleemann provides an option for purely-electric operation of the plant – a future-oriented drive system that works on site without CO2 emissions – which assurance of quality. To guarantee the power supply on site, the company built a transformer station that accompanies the plant, which is moved 2–3 times a year. “All things considered, we regard this as an investment in the future,” says Achim Haßdenteufel, Division Manager at Steidle. “As far as the subject of energy is concerned, we have always been a forward-looking company. In the medium-to-long term view, we intend to generate our electric power with a photovoltaic system here on our systems and self-generated electricity.”
so this must equally apply to the plant. After all, there are many properties, we need to perfectly match the screen medium, screen pitch, the speed, and many other factors," says Michell Blasczyk. Here is where the technically mature and well-thoughtout details of the MSC 702i EVO come into play. Several factors in the collaboration with Kleemann impressed the Swabian com-
pany. "It was simply very professional how the Kleemann team made sure we had the right settings and optimized the screen pitch or the choice of screen media. The delivery was also fast. You can just sense the presence of committed, experienced employees who know exactly what they are doing." explains Achim Haßdenteufel. "The output of the plant is impressive,” adds Walter Kieper, Operations Manager at Steidle, “everything can be operated very conveniently by remote control. Although it was totally new to employees previously used to controlling plants with hydraulic levers, they very soon managed to get to grips with the digital display. It all has a logically structured and intuitive layout." What also impressed was the fact that the John Deere engine and the plant are produced by members of the same company group, which guarantees smooth and seamless collaboration.
ration tool for rapid determination of theurator. It saves time, provides safety and with the lowest possible wear and fuel consumption in the hands of both inexperienced and experienced plant users.
The applications for crushing plants are diverse. The parameters required depend on the feed material and the desired end result, and it takes time and plant operator’s day-to-day work much the SPECTIVE touch display.
For automatic optimization of the crushing process between crushing plants, and to achieve maximum utilization of the plant train, Kleemann plants are simply linked with one another by smart line coupling. There is now a wireless line coupling option as an alternative to safety-relevant cable coupling. Wireless line coupling is easier to handle and considerably reduces the plant operator’s daily workload.
Genuine wear linings from Kleemann extend the service life of
nents. Crushing and screening plants are always subject to high forces and, in many cases, particularly high wear – above all in certain areas, or on components that are in direct physical contact with the material to be processed. This wear results from pressure, impacts and friction.
In Bad Fredeburg, in the Sauerland region of Germany, two Hamm H 25i VC compactors with special crusher drums were used to crush and simultaneously compact slate for the construction of an up to 15-meter-high embankment for a new bypass. The use of the VC compactors enabled the contractor to streamline the construction process, removing the need for a separate stone crusher and eliminating a major part of the material transport required. This speeded up the process and simultaneously reduced the overall costs. "As soon as I saw the rock, I had a feeling that the Hamm compactor would be perfect for crushing this material," said Michael Tillmann, Construction Manager from lead contractor Straßen- und Tiefbau GmbH. The slabby rock in question was Fredeburg slate, also known as schisty graywacke. Originally, the materials was to have been broken up to a maximum particle size of 200 mm at source by several jaw crushers, then loaded onto trucks by excavators and transported to the embankment construction site. Dozers would then have distributed the broken material to allow compactors to compact it layer-by-layer.
A trial soon showed that the Hamm VC compactors delivered the right crushing pattern for this application. Site inspectors
the degree of compaction achieved in the layers making up the embankment. As Michael Tillman explains, "After a few days, it was clear that we were working much faster than when using crushers, mainly because of us working layer-by-layer.” “By decoupling the process steps, we were able to handle around 4,500 cubic meters of material per day. That’s almost twice as
cantly fewer machines were required, the costs for crushing and compaction were able to be reduced by around 50 percent. At the same time, the CO2 the entire construction site.
The Wirtgen Surface Miner 280 SMi is being used for the selective mining of limestone in northern Estonia. The big advantage? The material is broken down to the required size during cutting, so that it can be used directly without the need for additional crushing and screening. Thanks to the Wirtgen Surface Miner’s leveling technology, the oil shale can be cleanly separated from the limestone layers, which ensures that the materials are extracted in exceptionally high quality and purity. In addition to the selective mining of materials, precise leveling also enables optimum regulation of the water balance at the mine. The Surface Miner 280 SMi creates surfaces with
the drainage of water from the working area.
The central-drum concept of the 280 SMi is the ideal solution, deposits. Wear-resistant toolholder systems and picks mean fewer idle times, and the hard-rock cutting drum unit provides maximum durability in hard rock layers. In addition, a variety of automatic functions contribute to operator comfort, reduce the risk of fatigue and assist in the achievement of high productivity. And that in a region that presents the enormous challenges of temperatures reaching into the double digits below zero and around 100 days of snow per year.
KLEEMANN ORIGINAL TRON BLOW BARS
POWERFUL,
parts.wirtgen-group.com