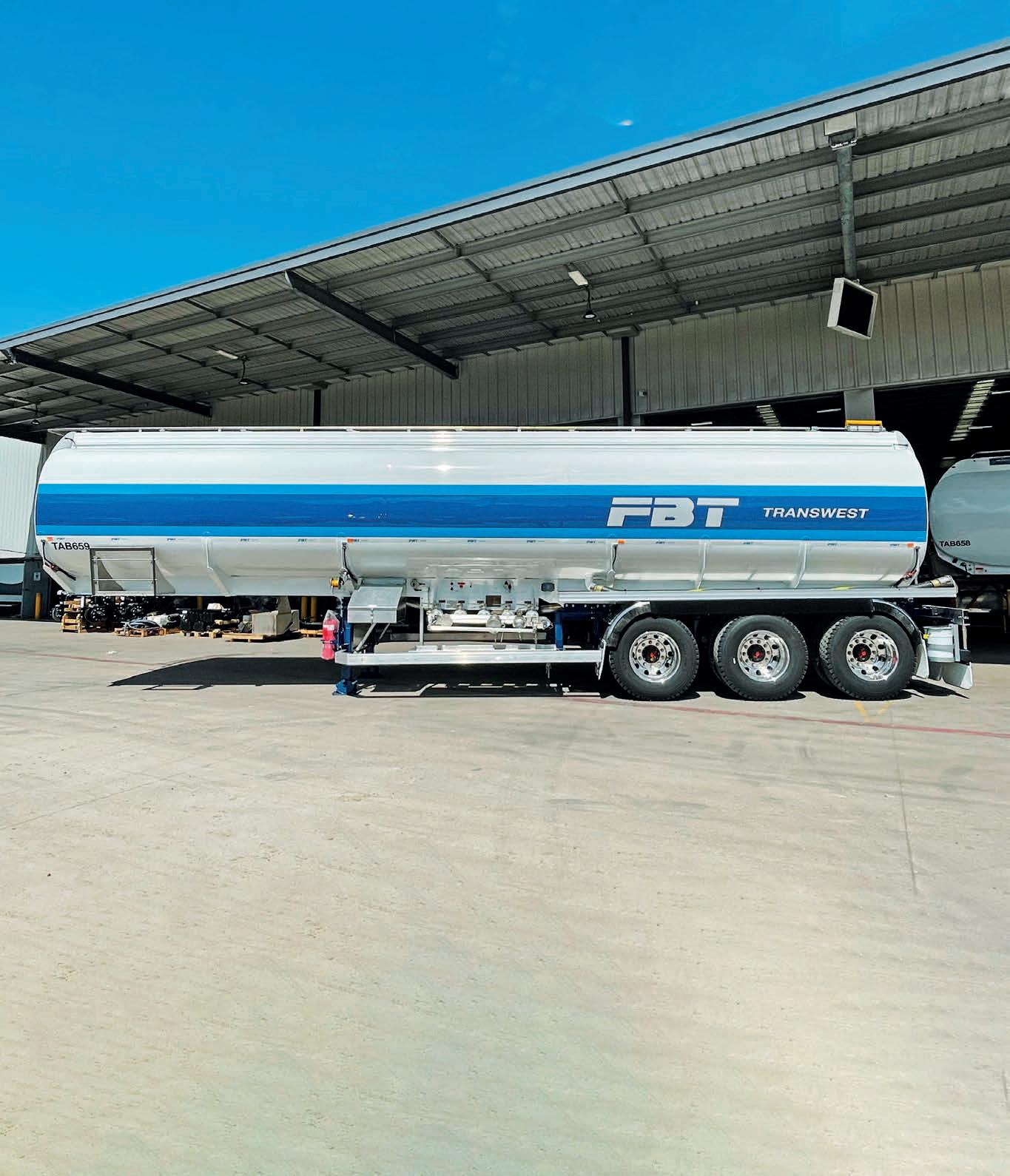
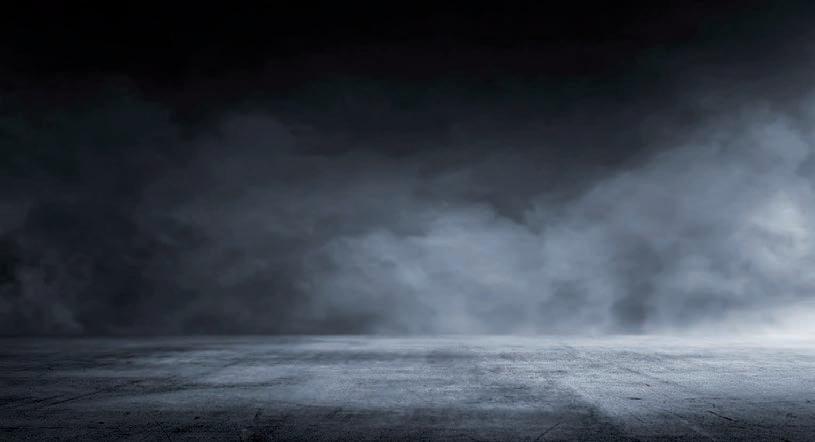
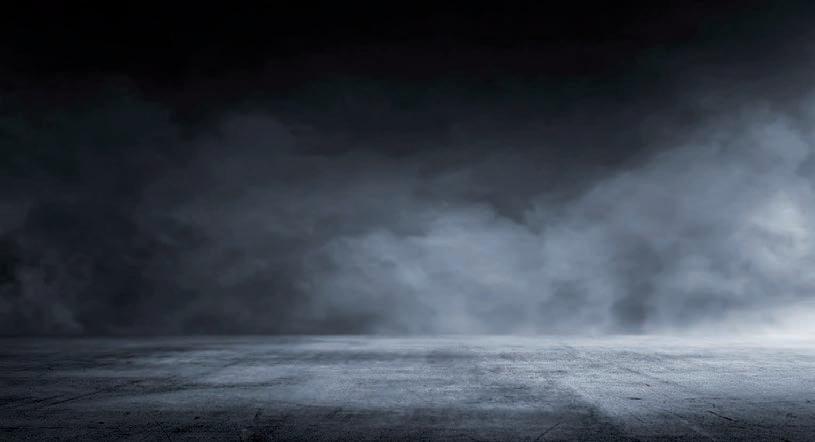
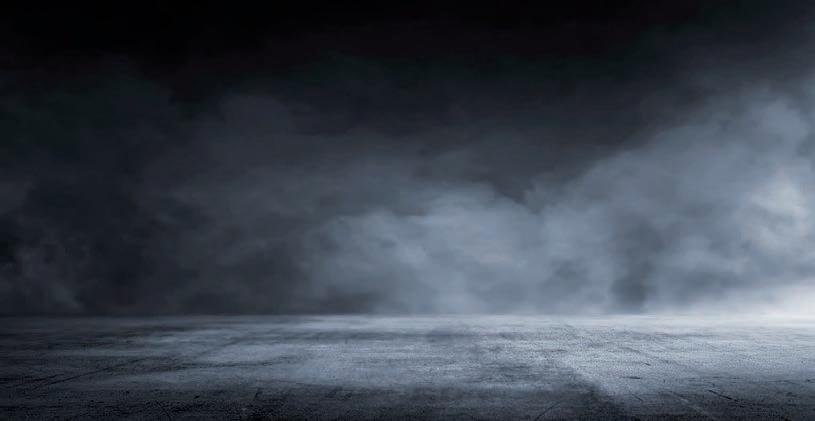
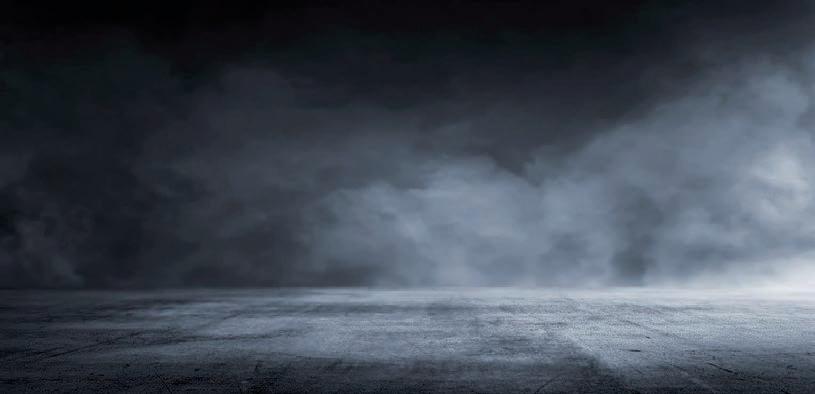
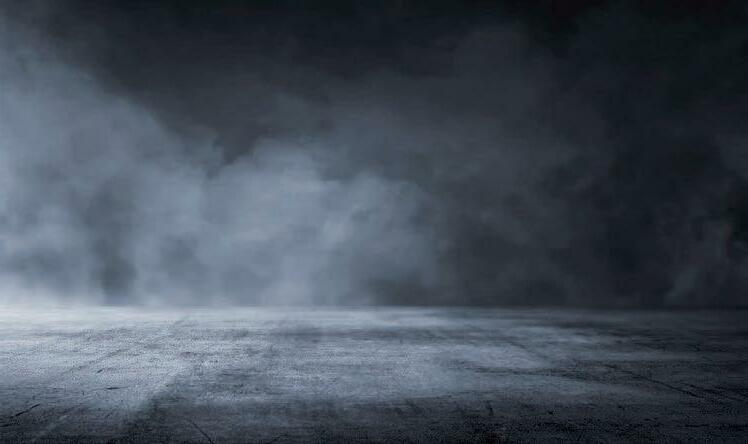
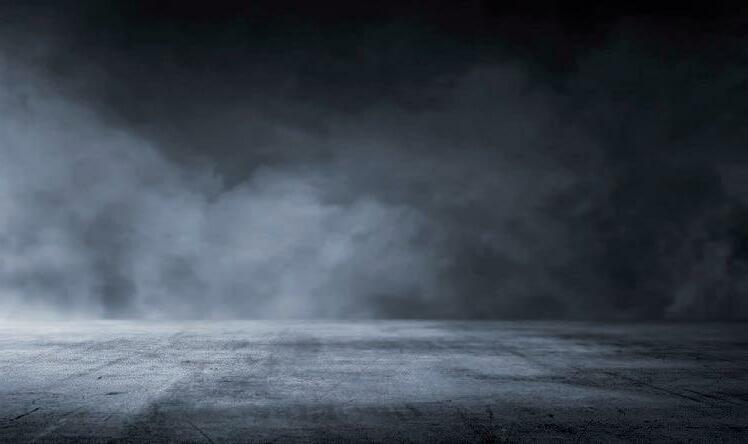
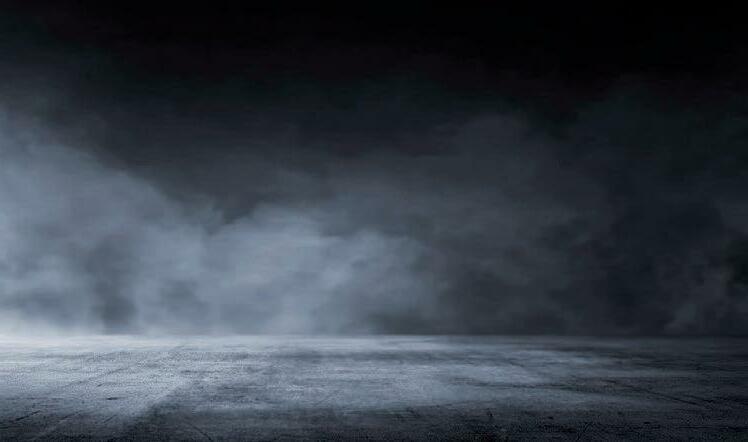
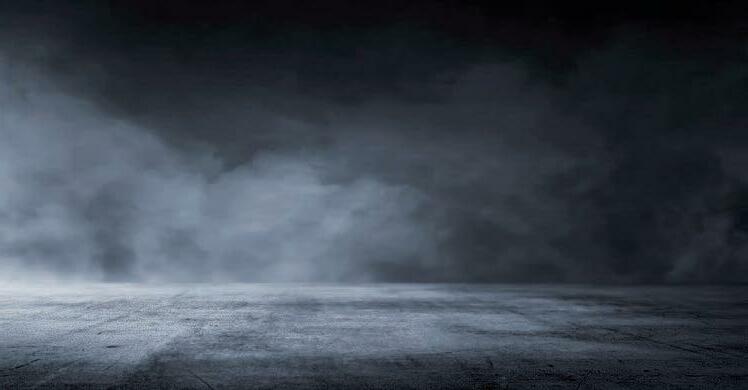
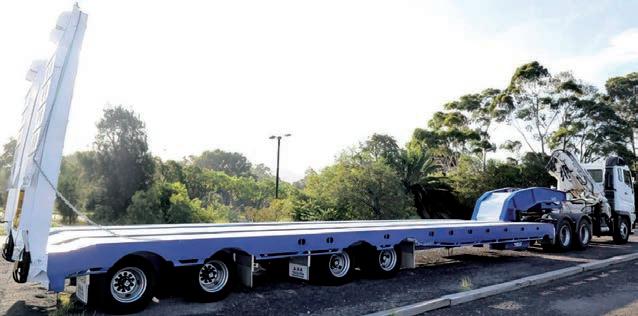
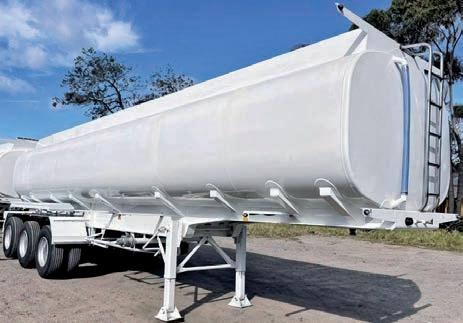
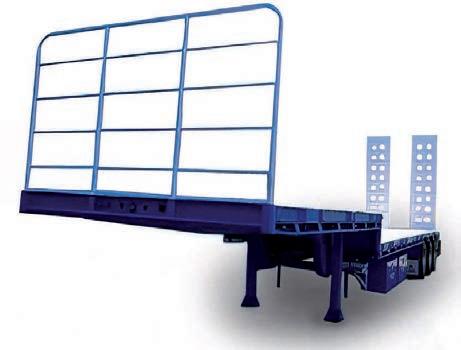
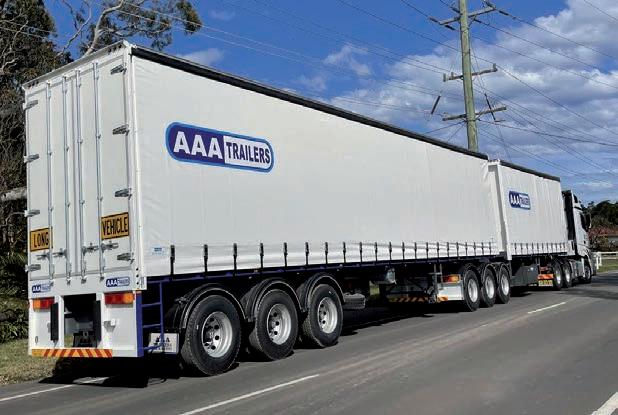
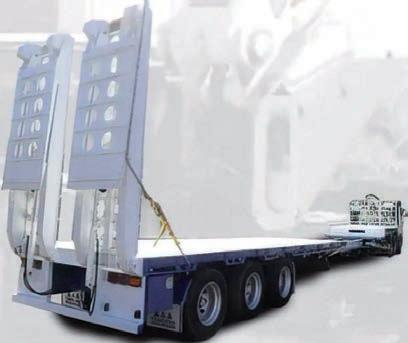


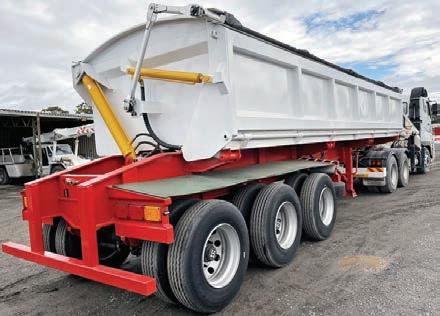
PUBLISHER
John Murphy
john.murphy@primecreative.com.au
Luke Applebee luke.applebee@primecreative.com.au
William Craske william.craske@primecreative.com.au
Peter White peter.white@primecreative.com.au
Anjali Behl anjali.behl@primecreative.com.au
ADVERTISING
Con Zarocostas: 0422 222 822 conzarocostas@primecreative.com.au
Ashley Blachford: 0425 699 819 ashley.blachford@primecreative.com.au
DIRECTOR/DESIGN
Daz Woolley
DIRECTOR
Blake Storey
PRODUCTION MANAGER
Michelle Weston michelle.weston@primecreative.com.au
MANAGER
Justine Nardone justine.nardone@primecreative.com.au
A Tesla manufacturing plant in Australia would be ‘absolutely’ welcome according to Minister for Infrastructure, Transport, Regional Development and Local Government, Catherine King. Her optimism follows the release of a consultation paper for a new national Electric Vehicle (EV) strategy which seeks views on proposed goals, objectives and actions for the National Electric Vehicle Strategy, to ensure Australians can access the best transport technologies and help meet emission reduction targets.
Electrification is certainly on-trend both domestically and internationally. Just take a look at this edition’s World map feature for a glimpse of the recent IAA Transportation show in Hanover, Germany, and what could be entering our market in the next five or so years.
This push for EVs at government level to replace passenger cars is interesting. King points to some averages to reinforce her message: New passenger vehicles in Australia have around 20 per cent higher emissions than the US, and around 40 per cent higher emissions than in Europe.
For King, it’s about catching up with the rest of the world when it comes to transport emissions. But is it the more sustainable, economical way forward? Other goals mentioned in the paper include making EVs more affordable, expanding EV uptake and choice,
reducing emissions and saving Australians money on fuel.
Tesla Board Chair, Robyn Denholm, noted that Australia is uniquely positioned in the manufacturing market because of its access to minerals that other countries do not have. Denholm went on to say that the supply chains for EVs and lithium-ion storage batteries that are key for renewable energy are being formed now.
Despite our Federal Government’s messaging around private sector and government collaboration on the electrification of vehicles both light and heavy, Denholm does not think these parties need to work together nor does government need to provide business incentives. The reason: Most business people will see the exponential growth that’s going to happen over the next period of time in those minerals.
Meanwhile, Minister for Energy, Chris Bowen, said the economics of electric vehicle manufacturing are very different to traditional internal combustion engines, whether it’s full vehicles or those components of vehicles. He reckons the more we have an electric vehicle market in Australia, the more it will support electric vehicle component and manufacturing. Well, that’s all rather positive. Here’s to decarbonisation.
6 Industry news
The latest news and industry developments.
Economy
A look at the trucking industry’s safety performance and Australia Post’s Net Zero plans.
30 Modern road tankers
See the latest in Australia’s road tanker technology.
36 Moving floor
Keith Walking Floor slats are available in a wide range of profiles and thicknesses.
38 Trailer builder
The Davey Group’s low loader division manufactures quality custom-built heavy haulage equipment.
For the last 15 years Goodride Tyres has been a major player in wheel and tyre distribution.
These are the suppliers that keep Australia’s heavy vehicles operating safer and more productive.
Australian Truck Radio is a one-of-its-kind 24/7 national digital radio station.
52
map
A debrief of IAA Transportation which was recently held in Hanover, Germany.
54
of the month
SCT Logistics has completed a daring replacement program of a dedicated sugarcane fleet.
At this year’s Australian Freight Industry Awards, Rachel Michaud and the Knorr-Bremse team won the Application of Technology Award.
58 What’s on
Upcoming shows and field days.
National courier, Australia Post, has announced the recipients of its 2022 Community Grants in support of mental health.
Grants of up to $10,000 each have been awarded to help fund initiatives across every state and territory, ranging from art therapy, peer support groups and cultural connection programs. Half the successful applicants are in rural and remote locations.
In total, Australia Post is investing more than $500,000 in community-led, local projects that connect individuals and promote improved mental health. It is the third consecutive year the Community Grants program has focussed on connection and mental wellbeing.
Australia Post Executive General Manager Community, Sustainability and Stakeholder Engagement, Tanny Mangos, said the grants enabled local organisations to run programs making a real difference to mental health, and to tailor support to the needs of their community.
“Australia Post recognises the important role that local organisations can play in building resilience and supporting mental wellbeing within their community,” she said.
“These grants help enhance community connections, and we know that when we connect with others, we feel better. We also know that this often results in
improved mental health outcomes, and we want to support the organisations that are helping make this happen.”
The 2022 grant recipients support a range of groups including Aboriginal and Torres Strait Islander communities, LGBTIQ+ communities, Culturally and Linguistically Diverse (CALD) communities, people with a disability or care commitments, and young people.
“The continued impact of the pandemic, financial pressures, isolation and the constant demands of everyday life can all impact on mental wellbeing,” said Mangos. “Mental health is a key area of focus at Australia Post, and we’re pleased to award these grants to support such a diverse range of important projects.”
The announcement of grant recipients continues a focus on mental health during September, with Australia Post also encouraging people to connect using free pre-paid postcards as part of a collaboration with Beyond Blue.
“We aim to make mental health part of everyday conversations and support people to stay well and our postcards initiative and the community grants both play a role in this,” said Mangos.
In other news, Australia Post is actively recruiting for up to 6,000 new team members and is looking to attract a wide range of job hunters, including school leavers and seniors. The recruitment drive
for permanent and casual team members comes ahead of what’s expected to be another huge Cyber sales and Christmas period.
Job hunters with a forklift, truck or motorcycle licence are top of Australia Post’s wish list, with other available roles including sorting and delivering parcels as well as customer service. Currently there are vacancies in every state and territory, with morning, afternoon and evening shifts all available – and for many roles, no previous experience is necessary.
Australia Post Executive General Manager People and Culture, Susan Davies, said the new team members would be joining an incredibly diverse extended workforce of more than 64,000 people from all walks of life, with people from 134 nationalities.
“We know that many businesses are recruiting at the moment, but we see Australia Post standing out from the pack as a truly inclusive workplace,” said Davies.
“We offer certainty around shifts for the coming peak period and competitive salaries for a wide range of roles, many of which need no previous experience.
“We’re proud of the fact that more than 5.6 per cent of our team identify as having a disability, reflecting our commitment to creating an inclusive organisation as the largest Australian employer to be certified as a Disability Confident Recruiter.
“And while there are great seasonal roles that may suit a number of people in the short term, for others it can also open up more permanent career opportunities. We’ve had many fantastic team members who started as casuals stay on with us long after Christmas.”
There are more than 2,500 casual positions available in parcel and mail processing, as well as more than 780 roles for truck drivers and other delivery drivers, more than 300 positions supporting customers with queries and around 200 opportunities for forklift drivers.
Additional ongoing roles include motorcycle, bicycle, walking and EDV (electric delivery vehicle) posties; truck and van drivers, freight and parcel handlers, forklift operators and opportunities in the Post Office network.
The Andrews Labor Government is launching an innovative heavy vehicle monitoring camera trial to clarify existing truck curfews and restrictions for trucks moving through Melbourne’s inner west.
Video analysis technology will be applied to capture heavy vehicle compliance data and detect, identify, categorise and report on different heavy vehicle types using Somerville Road, Yarraville.
The outcomes would help determine the roll-out of the technology on other key routes in the inner west to ensure ongoing safety and amenity for the community.
In collaboration with Maribyrnong City Council, the Department of Transport (DoT) is also installing truck advisory signs to warn truck drivers that A-double and B-double trucks are not permitted on specific sections of Somerville Road.
Minister for Roads and Road Safety, Ben Carroll, said the outcome will make restrictions clearer for everyone.
“Initiatives such as the heavy vehicle monitoring cameras and our guide developed to educate truck drivers about where and when they can travel will improve safety for inner west residents and provide further clarity for industry,” he said.
“We’re working with community, local government and the NHVR to instal
Equipment specialist, JOST Australia, has named a new Managing Director for Australia and New Zealand.
Guy Locke accepted the role, effective 14 September 2022.
Results driven, Locke thrives on building successful teams and individuals. His past truck driving experience and passion for the road transport industry will ensure customers continue to benefit from JOST’s innovative portfolio and service support.
“The opportunity to work with such a pioneering, innovative and market leading business is truly exciting,” said Locke.
additional truck advisory signs on key routes to make restrictions and messaging clearer for everyone.”
Minister for Ports and Freight, Melissa Horne, said the transport challenges in the growing area require an integrated response across government to ensure the safety and amenity of the community.
“This means creating more direct freight connections, shifting more freight to rail, and streamlining access to the port to meet our growing freight task,” she said.
DoT has also developed a simple guide published in six different languages to help
inform truck drivers about where and when they can travel, and to help the industry better plan journeys to port.
These actions will assist DoT to continue to develop a monitoring and compliance response strategy for key inner west routes subject to truck bans when the West Gate Tunnel opens. When open, the West Gate Tunnel will take 9,000 trucks off roads in the inner west and allow for the introduction of 24-hour truck bans on six local roads, including Blackshaws Road, Hudsons Road, Francis Street, Somerville Road, Buckley Street and Moore Street.
Transport and logistics company, Toll Group, has announced a senior executive appointment.
Matthew Warrington is now the President of Toll’s Global Forwarding division.
This business unit provides international freight forwarding solutions across 150 countries with annual revenue of $3.0 billion.
Warrington joined Toll 18 months ago to lead the company’s strategy function where he oversaw the successful divestment of its Australian Express business.
He has more than 30 years of experience in contract logistics and freight forwarding as well as a unique perspective, having worked on both the customer and operator sides across Linfox, BevChain, Visy Group and GrainCorp.
Before joining Toll, Warringron was a Partner and Director at the Boston Consulting Group, leading the Supply Chain practice area for ANZ.
Warrington holds a Bachelor of Engineering (Chemical) and a Master of Business Administration from the University of Melbourne.
“I’m delighted to lead Toll’s global forwarding business and support our customers’ growth in a changing market,” said Warrington.
“I’m excited to lead to the business as we implement new digital solutions and plan to expand into new markets, which will benefit our customers and help deliver our next phase of growth.”
Toll Group Managing Director, Alan Beacham, said: “Matthew brings a wealth of industry expertise and has a proven track record in delivering results in a competitive industry. I am confident that our customers and team members are in good hands as Matthew builds on our growth momentum.”
The National Heavy Vehicle Regulator (NHVR) has released its National Class 3 20m Long 3-axle Truck and 4-axle Dog Trailer Mass and Dimension Notice 2022 (No.1).
The notice will allow operators to use the specified combination on approved networks without having to go through the Performance Based Standards (PBS) approval process.
NHVR CEO, Sal Petroccitto, said the notice will help move mature combinations out of the PBS scheme and into the normal regulatory framework.
“With over 15 years knowledge and experience of hundreds of three-axle truck and four-axle dog combination designs, we are confident we can remove the need for them to go through the PBS assessment process,” he said.
“Rigorous, tried-and-tested templates for these combinations have been developed through the PBS scheme, and the combinations operating under this notice will use these templates and adhere to the same strict safety standards.
“By moving these common, wellunderstood truck and dog trailer combinations out of the PBS scheme, we
can reduce the regulatory and cost burden for industry, as well as allow PBS to focus on new vehicle innovation.”
Operators are still able operate these truck and dog combinations under the existing PBS arrangements if preferred, or they can opt to use the new notice arrangements.
“The change does not affect the current access available to PBS operators of three-axle truck and four-axle dog combinations,” Petroccitto said.
Heavy Vehicle Industry Australia (HVIA) Chief Executive, Todd Hacking, said the reform reflects the maturation of the PBS scheme.
“This move allows the scheme to get back to focusing on the next iteration of innovative vehicles, further enhancing productivity and safety,” he said.
“Firstly, it will increase the level of productivity within the truck and dog fleet, while simultaneously removing the burden for both industry and the NHVR during the PBS assessment process of these combinations.”
Eligible vehicles under the notice will operate on Level One (up to mass 50.5 tonne) and Level Two (up to mass 57.5 tonne) networks.
Transport and logistics company, Linfox, has celebrated the 10th anniversary of a facility in Victoria.
More than 230 Linfox team members reportedly gathered to celebrate the 10th birthday of the Linfox Coles Truganina site.
The company said it is its biggest warehouse at 85,000-square-metres, picking goods for Coles stores across Victoria and interstate.
The celebration included all team members at site, together with the Coles management team.
The new Liquip 450 Series Swing Hatch has been designed and tested in line with the recently released Australian Standard AS2809:2020.
SH450 Series Swing Hatch offers a
for
Australia’s stringent
while
Liquip’s Swing Hatch gives you
of
knowing that
a
Fifteen Heavy Vehicle Safety Initiative (HVSI) projects will be receiving crucial funding from the Australian Government.
$3.5 million will be invested into the projects through Round Seven of the HVSI program to improve heavy vehicle safety.
The Government has also committed a further $1.7 million to the National Heavy Vehicle Regulator (NHVR) to fund targeted projects which aim to improve heavy
The National Heavy Vehicle Regulator (NHVR) has announced the opening of its new headquarters located in Parramatta, New South Wales.
Minister for Regional Transport and Roads, Sam Farraway, opened the new office last Friday as part of the transition of state-based heavy vehicle services to the NHVR.
“Over the last six months, the NSW Government and Transport for New South Wales have been working closely with the NHVR to make the transition as smooth as possible while ensuring the heavy vehicle industry continues to operate safely and productively,” he said.
“On 1 August, we saw the transition of roadside heavy vehicle inspections, investigations and prosecutions and
vehicle safety, taking total commitment for HVSI projects in 2022-23 to $5.6 million.
Assistant Minister for Infrastructure and Transport Senator, Carol Brown, said the Government is taking several measures to fund the industry’s safety.
“The Australian Government is also investing in further driver training, including a road hazard program that helps new drivers navigate driving in
different conditions, managing fatigue and the importance of conducting daily safety checks to ensure a heavy vehicle is roadworthy,” she said.
“Another project is a web-based calculator that can be used across multiple different heavy vehicle combinations, to instantly identify the risk of a heavy vehicle rolling over.”
NHVR CEO, Sal Petroccitto, said greater road safety outcomes can be achieved through collaboration with government, industry and the community.
“There are some exciting grassroots projects included in Round Seven that can create meaningful change across a local, regional and national level,” he said.
“We’re supporting those who have strong, implementable ideas to deliver safer drivers, safer vehicles and safer road use for all Australians.”
The Australian Government has invested in 132 HVSI projects over six years to progress a safer, more productive heavy vehicle industry.
These heavy vehicle projects are created for the industry, by the industry, to make the workplace safer.
administration services to the NHVR, and I’m pleased to officially open the new Parramatta headquarters.
“Nationally consistent compliance is essential for the safety and productivity of heavy vehicle operators, and I look forward to continuing to work with the NHVR to keep NSW roads safe and our economy growing.”
NHVR Chair, Duncan Gay, said the transition would reduce the impact of state borders on the movement of freight across Australia.
“With staff now based in NSW, we can continue to work towards a national approach to heavy vehicle safety and compliance and improve consistency for operators,” he said.
“The transition is part of an ongoing
journey towards becoming a single national regulator, and I’d particularly like to thank the heavy vehicle industry across NSW for their time and feedback throughout the process.
“While drivers will see a new logo on our vehicles and uniforms, they will continue to receive the same services and support, and will need to meet the same safety requirements as they have in the past.”
The 310 NHVR staff will include 270 Safety and Compliance Officers who will continue to deliver services from more than 200 existing Heavy Vehicle Inspection Stations, safety stations and onroad enforcement sites across NSW.
NSW is now the fifth state or territory where the NHVR is directly delivering heavy vehicle regulatory services.
Viva Energy Group Limited has announced that it will be acquiring Coles Express, creating the largest fuel and convenience network in Australia under a single retail operator.
The acquisition is expected to complete in the first half of 2023 and will see the Shell brand continue to be retained.
Viva Energy CEO, Scott Wyatt, said the process will accelerate the company’s strategy to transition into a fully integrated fuel and convenience retailer while maintaining its position in the fast growing convenience segment.
“This is an exciting step for Viva Energy that will enable us to further extend our network, invest in new and innovative convenience offers across our stores, and enhance our loyalty and digital programs to simplify the way our customers transact with us,” he said.
“By bringing our two businesses together we will be better placed to make the investments and innovations which will be necessary to deliver more value to our customers and drive our future success.”
According to Wyatt, Viva Energy’s relationship with Coles spans almost 20 years, and he is delighted to continue it through this major step.
“Our nationwide network of more than 700 stores is ideally placed to meet these evolving needs and we are excited about the opportunity to expand and grow our fuel and convenience business with the acquisition of Coles Express,” he said.
“While the Coles Express brand will eventually be replaced, customers will be able to continue to redeem their Coles Shopper Dockets and earn Flybuys points, and in time we plan to broaden the range of loyalty and digital offers to provide even more value to our customers.”
JOST Australia has donated a JOST JSK37 Sensor Coupling fifth wheel to non-profit industry initiative, TRANSAFE WA, and its iNSTRUCKTA! Safety Truck project.
iNSTRUCKTA! is the name of TRANSAFE WA’s custom truck and semi-trailer combination in development, which is spec’d to deliver innovative educational road safety programs.
The project was made possible with the support of the Federal Government’s Heavy Vehicle Safety Initiative (HVSI), WA’s Road Safety Commission and other industry partners.
TRANSAFE WA Executive Officer, Rob Sharpe, told Trailer that JOST Australia is one of the initiative’s safety partners who have kindly donated products for the project.
“The Sensor Coupling was chosen as it offers a safety solution when coupling the trailer and it also permanently monitors the connection status,” he said.
“The connection sensor, king pin sensor and coupling height sensors are monitored by the remote dash display or can be optioned up for truck specific dash display integration.
“Our JOST JSK 37 Sensor Coupling fifth wheel has been fitted with Lubetronic technology for the king pin and has a greaseless plate, so it ticks all the boxes for us and is a great example of a safer practice.”
The iNSTRUCKTA! Safety Truck will compromise of five main activities: Participants will be encouraged to climb up into the cabin to get a first-hand experience of where a truck driver sits
and to see what the driver can and can’t see.
Participants will be encouraged to enter the trailer where they can sit in one of 10 truck seats, being immersed in a virtual reality experience via wireless VR headsets. The experience will highlight situations such as overtaking, turning trucks, blind spots and cutting in.
Participants will be encouraged to use the wall-mounted touch screens to guide them through an interactive quiz/ learning experience.
Participants will also get to view various road safety videos that will be shown on the full rear wall of the trailer’s interior.
Lastly, participants will be encouraged to pledge to do their part in reducing the road toll via another couple of wall mounted touch screens.
Sharpe explained that the safety truck is mostly about teaching current and future road users on how to safely interact with heavy vehicles while also exposing each participant to trucks and the transport industry.
“iNSTRUCKTA! will be out there to encourage our current and future drivers to consider entering the Road Transport Industry as a career,” he said.
“This secondary benefit will help to alleviate the growing road transport freight task to which the number of trucks on the road is set to treble by 2050.”
The trailer build is nearing completion and is expected to be ready to hit the road before the end of 2022.
Emissions standard, Euro 6, will be phased in over 12 months from 1 November 2024 for new trucks and buses according to the Federal Government.
By introducing tighter noxious emissions standards it is the Federal Government’s aim to save lives, prevent toxic air pollution and provide environmental and economic benefits for communities.
The Australian Government’s Bureau of Infrastructure and Transport Research Economics estimates introducing Euro VI will save the Australian community $6.4 billion over 25 years from fewer premature deaths and chronic illnesses.
Australian based truck manufacturers and importers have been calling for the introduction of Euro VI standards for years.
These standards are already in place in the European Union and United Kingdom, and equivalent standards also apply in
most developed countries, including the United States and Japan. China and India have also recently adopted equivalent standards.
Introducing Euro VI will mean manufacturers must add the advanced safety and fuel-saving technologies to Australian models that other countries already have. This will help improve safety outcomes, and contribute to our emissions reduction targets.
The National Heavy Vehicle Regulator and National Transport Commission are working with state and territory governments to make changes to ensure operators purchasing cleaner and safer trucks maintain productivity when the new standards become mandatory.
Further improvements to fuel quality could help support introduction of tighter standards for light vehicles, known as Euro 6d. The Government is considering
how best to improve fuel quality and enable all new light vehicles sold in Australia to meet Euro 6d standards.
“Australia has been lagging in our vehicle noxious emissions standards for years now, and this move will help bring our vehicle market into the 21st century – and into line with overseas vehicle markets,” said Infrastructure, Transport, Regional Development and Local Government Minister, Catherine King. Climate Change and Energy Minister, Chris Bowen, said: “The Albanese Government has hit the ground running in cleaning up transport pollution and reducing it’s health burden, first by reducing the amount of sulphur in our petrol and now introducing tighter noxious emissions standards for new trucks and buses.
“We’re making transport emissions cleaner and greener.”
Holmwood Highgate is a 3rd generation family owned & operated business located in both Queensland and Victoria. We specialise in bulk liquid transport solutions, with a tailor made feel and personal touch experience for our customers nationwide.
Quality is in our DNA, with our history as a company spanning 7 decades and hundreds upon hundreds of happy owners using a Holmwood Highgate tanker on the daily. We understand reliability and dependability is everything for a logistics company, thus we ensure every product we make is manufactured with reliability as a key focus to keep our tankers on the road for longer than our competition.
We specialise in multiple facets of transport, including Fuel, Bitumen, Ammonium Nitrate, Mining, Waste Oil, and more. Our capability in recent years has also seen an expansion into specialised applications such as Aviation refuellers and Military grade transport modules.
Holmwood Highgate has also expanded our capability to include the importation and distribution of LPG and Dry Bulk tankers. These new options add to our current repertoire and help us cater to more businesses needs than ever before.
Queensland 20-26 Burchill Street, Loganholme, QLD, 4129
Find out more at: www.holmwoodhighgate.com.au +61 7 3440 9000 +61 3 9936 0360
Victoria 425 Fitzgerald Road, Derrimut, VIC, 3026
The Queensland Trucking Association (QTA) honoured several distinguished guests and gave thanks to their efforts at the 2022 Queensland Road Freight Industry Awards.
Gathering at the Royal International Convention Centre in Brisbane, more than 400 guests were invited to reconnect with colleagues and friends while seeing some of the peers being acknowledged for their achievements within the last year.
Keynote speaker of the evening, Dr Craig Challen SC OAM, spoke of his challenging experiences as a decorated diver and cave explorer, touching on his ordeal that led him to rescuing the Thai soccer team in 2018.
QTA CEO, Gary Mahon, applauded Dr Challen’s bravery and courage in sharing his experiences.
He said the ‘orthodox thinking’ Dr Challen mentioned in his speech is what the trucking industry in Australia needs.
Alongside Dr Challen, several honourable government representatives were in attendance, including Minister for Agriculture and Emergency Management, Senator, Murray Watt, and Shadow Minister for Northern Australia and Resources, Senator Susan McDonald.
To congratulate the efforts of Queensland truck drivers, several awards were presented throughout the gala.
With a career in the transport industry spanning over 65 years, Jim Hurley has been known as one of the most committed members of the trucking community. His fourth-generation family business has become one of the largest truck dealerships groups in Australia, and Jim has been the figurehead of making Brown and Hurley what it is today. His achievements earned him the 2022 Industry Excellence Award at the gala, congratulating his dedication and commitment to his work and the community around him.
More awards followed over the night, including the 2022 Trucking Woman of the Year, Professional Driver of the Year, Daimler Emerging Leader of the Year and 2022 Young Achiever of the Year, bringing about dual award winners.
Melira Lister was gracious enough to accept the honour of Trucking Woman of the Year, finding a great passion in the industry, particularly in heavy lifting and oversize overmass freight tasks.
Working on major multimillion dollar infrastructure and renewable energy projects, her skills in negotiation, advocacy and problem solving have been put to use, leading to successful results for her clients. As a strong advocate for women in the transport community, Lister recognises the lack of female representation within the industry. Her peers can endorse her ambitious work ethic and passion for challenging tasks, ones that have led her
Achiever of the Year award were congratulated for their extreme dedication and motivation to their work, recognising their contribution at a young age. Dean Ryan of Clayton’s Towing began his career in the industry at 18 years old and has since proved an excellent work ethic and passion for the job. Similarly valued by his employer and colleagues, Hugh Paton of Sizer and Coggil has put his hard work into various roles in the trucking industry. A dual apprenticeship post high school and opening up his own business soon after has given him the skills and opportunities that landed him his current role of Operations Manager.
Frasers Livestock Transport was awarded for training and skilling excellence.
To end a night of recognition, two companies were acknowledged for their endeavours and contribution to industry within the last year. Frasers Livestock Transport has an extensive knowledge of cattle behaviour and handling technique and have since identified a gap in training principles for drivers. To combat this gap, a new curriculum was created to promote safer work practices and to improve animal welfare. In its success, it has reached three locations across Queensland, with over 150 trainees and earned the 2022 Training and Skilling Excellence Award at the gala.
With an outstanding driving record and hardworking attitude, Kathryn Mobbs became the first ever female QTA Professional Driver of the Year. Admired by her clients and colleagues within her 25-year employment at the Easter Group, Kathryn provides them with reassurance of safety and organisation with her extensive mechanical and technical knowledge.
Like Mobbs, Canea Mersky was recognised for her constant motivation and engagement in her career as a young person in the industry. As a Customer Service Manager at South East Queensland Hauliers, the 2022 Daimler Emerging Leader of the Year recognition was awarded for her formidable efforts within the last year.
Dual winners of the 2022 Young
The Innovation and Safety Award is a top priority of the trucking industry, and Jarratt Transport Solutions has implemented a low-cost and fundamental tool to prevent injury and promote safety. Sitting on top of trailers to assist climbing on and off the truck, the handle always maintains three points of contact and can be easily stored away when not in use. All Jarratt trailers now include this new feature, hoping it reduces the risk of injury and disaster.
QTA President, Paul Kahert, commended the winners from the evening.
“Our members recognised tonight are outstanding and the QTA is proud to have them as representatives of the Association,” he said.
“On behalf of the QTA Board of Directors, I offer congratulations to all who have been honoured tonight, all are very worthy winners.”
With construction near complete, the New South Wales Government has confirmed that the WestConnex M4-M5 Link project will be renamed as extensions of the M4 and M8 motorways upon operation.
The 7.5 kilometre underground tunnels will connect the two motorways, providing a seamless link between Haberfield and St Peters – while cutting travel times by up to 40 minutes between Western Sydney and Sydney Kingsford Smith Airport.
The new link is expected to open in early 2023 and will connect to the Rozelle
Interchange at the end of 2023, marking the completion of Australia’s largest road infrastructure project.
Minister for Metropolitan Roads, Natalie Ward, said the operational names aligned with the NSW motorways’ numbering system, making it easier for motorists travelling across the broader network.
“We are in the final stages of one of the most significant road infrastructure projects ever undertaken in Australia,” she said.
“Naming the tunnels the M4 and M8
Brisbane crane truck company, CNC Cartage Transport Solutions, has taken ownership of BSA Transport.
The deal includes procurement of staff and multiple mobile assets.
It was officially completed in September after an independent evaluation.
Preliminary discussions regarding the acquisition first commenced in July.
As part of the arrangement, CNC Cartage will receive an undisclosed quantity of commercial vehicles from BSA’s fleet in addition to several trailers.
A challenging environment for purchasing new trucks and finding staff to pilot them were key factors for CNC Cartage Director Chad Brown.
Brown said adding the trucks to boost his fleet capacity was vital given CNC Cartage’s current workload and contracts.
“Without those trucks there’s definitely a shortfall in the market for all of the customers BSA Transport was servicing,” he said.
“It was decided that we needed to service those guys somehow. We’ve
motorways will help motorists join the dots on the new and improved network when the tunnels open next year.
“Once complete, the tunnels will significantly improve connections between west and southwest Sydney, reducing travel times into the city for Western Sydney residents.”
The project will also include future links to the Western Harbour Tunnel, Sydney Gateway and the M6 to improve freight routes and better connect communities across the cities.
come to the point that we’re servicing most of the customers BSA had originally before the sale.”
A dedicated crane truck business primarily servicing southeast Queensland, BSA Transport has maintained a client base consisting of, but not limited to, steel frame and roofing manufacturers since its inception in 2004.
BSA Transport have traditionally turned over their crane trucks every 10 to 11 years with around 750,000km on the odometer.
Safety improvements have been planned for the Strzelecki Highway between Morwell and Mirboo North, to make the key freight route safer for heavy vehicle drivers and motorists.
Victoria Minister for Roads and Road Safety, Ben Carroll, said a $8.2 million investment will deliver a package of works to build a northbound overtaking lane on the highway near Creamery Road.
The upgrades will benefit freight operators travelling on the highway connecting to the South Gippsland and Latrobe regions, ensuring goods can get where they need to go.
“We know how important the Strezlecki Highway is as a link for local communities and also freight operators transporting goods – that is why this upgrade is going to be a boon for all road users, enhancing safety and making travel more reliable,” said Member for Eastern Victoria, Harriet Shing.
The project will also deliver flexible safety barriers along the centreline and left-hand side to boost safety for all road users, and is part of a $226.7 million investment in high-priority road and intersection upgrade projects at locations across Victoria, including the Bass Highway in Kilcunda.
Pre-construction activities are expected to commence in early 2023, with construction to be completed within three years.
The National Heavy Vehicle Regulator (NHVR) will be introducing changes to the Performance Based Standards (PBS) scheme Vehicle Approval (VA) document.
This development aims to reduce administrative burden for industry and provide a better customer experience.
NHVR CEO, Sal Petroccitto, said the changes would remove some of the unnecessary complexity in getting a PBS vehicle approved, meaning we can get safer, smarter, more productive vehicles on our roads sooner.
“The PBS scheme allows heavy vehicle operators to use innovative and optimised vehicle designs – allowing freight to be moved in a safe way with fewer truck movements,” said Petroccitto said.
“As the sector continues to address the challenges associated with Covid, including driver shortages and the growing freight task, it is critical we improve accessibility to these safer and more productive heavy vehicles.
“The new changes will simplify and accelerate the approval of PBS combinations by removing the transfer of PBS vehicle applications when a vehicle is sold and removing duplication, which will reduce the size of a vehicle application by 30 per cent.
“These changes are just the latest improvements in a suite of initiatives
we will be delivering over the next year to reform and modernise the PBS scheme.”
The changes will to PBS VAs will be introduced from 14 November 2022, following industry stakeholder consultation earlier this year.
The first change includes removing the operator’s name from the PBS VA. This means that the VA will become an authorisation to the vehicles listed on the VA, regardless of who owns or operates them, eliminating the need for a VA transfer when vehicles are sold.
Also, subcontractors will be able to use the VA without having to transfer it into their name. All existing VAs will be unaffected, although operators with an existing VA will be able to request the NHVR to remove their name from their VA document should they wish.
Access permits will also be unaffected by these changes.
In the second change, the NHVR will be replacing the specification tables with a simpler table.
Specification tables contain key vehicle parameters, including dimensions, components and Vehicle Identification Numbers (VINs). The new table will only contain key vehicle information, such as VINs, vehicle make and model. This will eliminate duplicated information and reduce the workload for PBS certifiers.
The New South Wales Government has announced the completion of construction on City Road, which involved two intersection upgrades.
The project was funded through $13.5 million from the Hunter Pinch Points Program, which involved extending right turn lanes, building new left turn lanes, adding an extra right turn lane out of Kahibah Road and widening sections of the road to improve traffic flows.
Minister for Regional Roads, Sam Farraway, said the intersection upgrades will bring a series of benefits to road users and the transport industry.
“City Road is a vital transport, tourist and freight route which is used by about 6,000 vehicles per hour at this location, including 150 heavy vehicles,” he said.
“The upgraded intersections are now open to traffic, and we can now complete work on a new crossing connecting to a new ramp and existing footpath across Northcott Drive.”
Farraway said the work has improved safety at the location while providing a boost to the local economy by supporting 75 new jobs during the construction period.
A report has found that a lack of gender diversity in the workforce and leadership is undermining net zero carbon targets in transport.
A study by the International Transport Forum, supported by Fédération Internationale de l’Automobile (FIA) Foundation, examined linkages between gender equality, transport and climate change to better understand the development of policies that can achiever both gender equality and decarbonising transport goals by 2050.
The report identified that a consistent approach to incorporating a gender dimension into decarbonising transport policies and improving the gender balance in the workforce would have a significant impact.
It sets out four groups of guiding principles, which include capacity building, knowledge management and communication; gender balance, participation and women’s leadership; implementation; monitoring and reporting.
Specific actions accompany each principle for countries and companies to improve gender equality and decarbonising transport measures simultaneously.
ITF Secretary-General, Young Tae Kim,
said the report brings a pragmatic understanding of how the industry has improved gender equality.
“We cannot address climate change without decarbonising transport and we cannot make our mobility sustainable without addressing the gender imbalance in how we design and use transport,” he said.
“Under my instruction, we analyse all our work at ITF to ensure the most inclusive approach and result possible.
“It is my great hope that this will become the norm worldwide. We are all in this together; we all stand to benefit.”
FIA Foundation Deputy Director, Sheila Watson, said the organisation was privileged to support the report.
“The FIA Foundation is delighted to support this exciting new research with the International Transport Forum to consider the extent to which the vital process of transport decarbonisation and gender are interlinked,” she said.
“This report highlights the clear message that unless there is meaningful gender representation throughout the transport sector, in employment, planning systems, and disaggregated data, then our transport systems will fail us all.”
To prepare Victoria for any biosecurity risk from Emergency Animal Disease (EAD), the state government is delivering a $23 million package for rapid outbreak response measures.
Funding will reportedly go towards the recruitment of biosecurity experts to undertake key planning, field-based operational roles and provide training to a workforce from across government and industry in the event of an outbreak.
It will also provide tailored industry engagement to build on industries’ ability to manage biosecurity risks and contribute to a response.
The state government will also purchase automated diagnostic equipment that will fast-track foot-and-mouth disease sample testing, enhanced data management systems and essential tools such as livestock scanners and sensors at livestock accumulation points.
Funding will be provided to the Environment Protection Authority (EPA) and the Department of Environment, Land, Water and Planning (DELWP) to support a response and to reduce environmental risks associated with a possible outbreak.
This work will build on Agriculture
Victoria’s nation-leading biosecurity efforts such as the mandatory electronic National Livestock Identification System (NLIS) for sheep and goats that supports rapid traceability, which is critical in a livestock biosecurity response.
“This funding is extremely valuable to ensure we are best prepared to respond to an emergency animal outbreak and reduce potential environmental risks,” said
Minister for the Environment and Climate Action, Lily D’Ambrosio.
This $23 million package builds on the $10 million investment made in August for portable sample testing, mobile incident centres, IT system upgrades, specialist training materials, and the preparedness work of the Emergency Animal Disease Taskforce, which was established by the state government earlier this year.
A senior executive with more than 35 years of experience in ports, logistics, rail haulage, renewables, agriculture and resources has joined the Qube Board.
Lindsay Ward has been appointed the role of Director at Qube, effective 4 October 2022.
He is currently a Non-Executive Director of Whitehaven Coal and was previously a Non-Executive Director of ASX listed Metro Mining, Quantum Bulk Liquid Storage, Global Renewables and Waterloo Wind Farm.
Ward has worked in senior executive roles including CEO, Managing Director
and General Manager with companies including Palisade Investment Partners, Asciano, Toll Holdings and BHP.
“Lindsay brings both extensive business leadership and wide industry experience to the Qube board, together with a proven track record in delivering high standards of safety, environmental, governance and financial performance,” said Qube Chairman, Allan Davies.
Ward holds a Bachelor of Applied Science (Geology) and a Graduate Diploma in Business Management. He is also a Fellow of the Australian Institute of Company Directors.
Transport and logistics company, Toll Global Express, which recently rebranded to Team Global Express (TGE), has refinanced $250 million of debt with the Commonwealth Bank of Australia (CBA).
The funding will reportedly underpin TGE’s business transformation and provide additional liquidity to support further investment into the business and fund its growth plans.
The company aims to be the most sustainable national logistics solutions partner, as demands for national deliveries continue to accelerate and the business leans into the changing demands of consumers, e-commerce trends and emissions reductions targets.
Christine Holgate – TGE CEO – told Nine Entertainment Company the announcement is reflective of the strong momentum of the TGE business since it was acquired by equity firm, Allegro Funds, a year ago.
“In our first year we have achieved 16 per cent revenue growth, invested in the
business, and improved our profitability,” said Holgate.
“We have more work to do, but our results combined with our new agreement with CBA, underpin a stronger future for our group.
“I want to thank the Commonwealth Bank team, particularly Andrew Hinchliff (CBA’s Group Executive, Institutional Banking and Markets) for working with the Global Express Team to make this agreement possible.
“As we continue to simplify, transform and grow the Team Global Express business, we are pleased with our progress achieved by putting the focus back on our people and customers.”
Hinchliff said TGE’s momentum and strategic direction position it well to meet strong demand for sustainable solutions across Australia’s transport system.
“We’re pleased to support TGE’s continued transformation through the provision of this loan facility, which demonstrates CBA’s structuring
Heavy vehicle information specialist, ARTSA-i Data, has reported steady performance across the sector in its September quarter report.
The June quarter posted a steady performance with new registrations for the quarter mirroring those for the previous quarter according to ARTSA-i Data analytics Executive Director, Rob Perkins.
“This is a little unusual in that history tells us that new registrations rise throughout the quarters of the calendar year and generally finish on a high with the December quarter.
“To have a flat September (Q3) quarter is unusual but perhaps reflective of the supply chain struggles with meeting demand.
“There is plenty of anecdotal evidence that demand is very strong, but this demand is not translating into record sales due to a shortage of both equipment and skilled labour.
Prime movers: The positive trend is reported to continue even with a slowing in Q3 registrations by 2.8 per cent compared to the previous quarter although annual growth is still recording 8.4 per cent to end September 2022. The trend line shows growth of some 20 per cent compared with data from four years ago.
Like prime movers, trailers have had a small negative quarter compared to Q2 with -0.8 per cent however the annual growth is 4.1 per cent to ends September 2022. Trailer growth over the last four years has been a cumulative 35 per cent which is almost double that for prime mover growth.
Unlike prime movers and trailers, rigids did increase new registrations over the previous quarter with a modest 2.5 per cent growth. Annually they are growing at 1.8 per cent which is below both prime mover and trailer growth. In the last four years the trend line in growth
capability and supply chains expertise,” he said.
“We look forward to continuing to work closely with Christine and the TGE management team as they further invest in the business, and in a range of exciting new sustainability initiatives. Supporting Australia’s transition to a brighter, more sustainable future is a strategic priority for CBA, and it aligns well with the goals of TGE.”
Samuel Anketell commented on the announcement via LinkedIn: “As a truck driver with [TGE] and only a small cog in the machine, I’m extremely proud to be part of this machine and having Christine Holgate at the wheel makes me really hopeful of a prosperous future. Excellent work Team.”
Allegro Funds Managing Director, Adrian Loader, added: “Thanks Avin Luther and the whole CBA team for your trust and support. Well done to Nick Stratford and Uri Gordon for leading the transaction for Toll Global Express.”
has been around 5.0 per cent in total which is well down compared to prime movers and trailers which have had 20 per cent and 35 per cent growth respectively.
The heavy sector of rigids often tows dog trailers. These have displayed a downward trend in new registrations over the last four years with flat new registrations particularly over the last three years.
ARTSA-i Data analytics can supply a range of custom heavy vehicle reports that provide considerable detail by manufacturer, but can also be analysed by state, by year and other variables such as registration category, VIN, postcode, age and more.
ARTSA-I Data also offers an interactive Tableau driven analytics package that allows users to build their own data reports – the graphs above are taken from that online system.
National Transport Insurance (NTI) recently released the 2022 Major Accident Report from its National Truck Accident Research Centre (NTARC) and has analysed trends since 2005.
It found while there’s been a 55 per cent increase in the number of trucks on the road and a 51 per cent rise in road freight volumes, the rate of serious truck accidents has not followed this trend.
Report author since 2019, Adam Gibson, said the data shows a combination of tighter government regulation and industry investment in safety, technology, professional development and leadership has improved road safety.
“We saw, for example, fatigue-related crashes fall by a massive 50 per cent the year after driving hours reforms and standardised logbooks were introduced,” said Gibson.
“They dropped from a high of 27.3 per cent in 2008 to a low of 8.0 per cent in 2020.”
The other key improvement was in crashes caused by inappropriate speed for the conditions.
“In 2009, inappropriate speed was the cause of almost one third of crashes (31.8 per cent) but encouragingly, that dropped to a record low of 12.5 per cent last year,” said Gibson.
“That’s likely related to Chain of Responsibility laws coupled with new
safety technologies, including electronic braking systems (EBS) and electronic stability control (ESC).”
Gibson said outside of these positive trends, what remains as opportunities for improvement are Driver Error, Inappropriate Speed and Fatigue.
“Our data helps address what we need to change in drivers’ working environments to better support them and to deliver safer outcomes,” he added.
NTI Chief Sustainability Officer, Chris Hogarty said the industry and its supporting bodies have been transformative through working together and shifting to a safer and more sustainable way of operating.
“The Australian transport and logistics industry has made considerable progress nearing the last two decades,” he said.
We are committed to sustaining the momentum and creating safer conditions for all road users,” continued Hogarty.
National Heavy Vehicle Regulator Acting Chief Regulatory Policy and Standards Officer Ray Hassall said while the safety improvements show industry’s effort in prioritising safety in the workplace and on the road – there is still more work to do.
“Tragically safety risks such as driver distraction, speed, inappropriate vehicle positioning and following distances continue to cause crashes resulting in
serious injuries and fatalities on our roads,” he said.
“In the lead up to the busiest season on our roads, I urge everyone to do their part and remember to rest, never speed, and always give heavy vehicles space, to keep you safe.”
The Australian Government has committed to invest $65 million per year into the Heavy Vehicle Safety and Productivity Program. The Heavy Vehicle Safety and Productivity Program funds projects to widen and upgrade freight routes as well as upgrading and building new truck stops.
“The annual report from NTI is an important measure of truck related incidents on our roads,” said Assistant Minister for Infrastructure and Transport, Carol Brown.
“Within the next 10 years, Australia’s freight task is expected to increase by 80 per cent. With more trucks on our roads than ever before, the Australian Government is investing in road safety through infrastructure and dedicated programs for transport workers.
“I am proud to be delivering the Rest Area Program which will work with truck drivers and industry experts to build and upgrade rest areas across freight routes across the country.
“As a government, we know that quality rest is essential for safe trucking.”
A review of almost two decades of truck accident data has revealed a vast improvement in the trucking industry’s safety performance. Meanwhile, national courier, Australia Post, is playing its part to achieve Net Zero.Australia Post will be undertaking a comprehensive range of initiatives to reduce Scopes 1, 2 and 3 emissions.
Australia Post boasts Australia’s largest fleet of electric delivery vehicles and the Roadmap outlines a range of targets to deliver a sustainable future that benefits all Australians, including: Targeting net zero carbon emissions by 2050; reducing emissions by 15 per cent by 2025 (FY19 baseline); sourcing 100 per cent renewable energy by 2025; 100 per cent ‘fully sustainable’ packaging range aligned to the 2025 National Packaging Targets by 2025; decreasing waste to landfill by 20 per cent (FY2019 baseline) by 2025; and spending $100 million with social enterprise and Indigenous suppliers by 2025.
The Roadmap outlines a science-based approach that aligns with the aims of the UN Paris Agreement and includes a 2025 emissions reduction target validated by the
Officer and Managing Director, Paul Graham, said the Roadmap will build on the strong results Australia Post has already achieved in reducing the carbon intensity of operations.
“I am incredibly proud of our sustainability credentials. Over the past few years, we have seen unprecedented growth in our parcels business because of the pandemic,” he said.
“Although, as our revenue has climbed, our carbon intensity has dropped. In fact, the carbon emissions per parcel associated with sending the average domestic parcel via Parcel Post halved between FY2018 and FY2021.
“That’s a great start but we still have a long way to go, and I am delighted to announce Australia Post will target Net Zero by 2050 as part of our 2025 Sustainability Roadmap launched today. This plan will guide Australia Post in the next phase of our sustainability journey as
3 combined reduced by 21 per cent. In particular, in FY2022 Australia Post revenue grew by 8.5 per cent while carbon intensity for Scopes 1, 2 and 3 combined reduced by 4 per cent.
• Between FY2018 and FY2021 the carbon intensity for Scopes 1, 2 and 3 combined per parcel associated with sending the average: Domestic parcel via Parcel Post reduced by 51 per cent; domestic parcel via Express Post reduced by 35 per cent; and international parcel reduced by 16 per cent.
• Australia Post has increased its fleet of electric delivery vehicles to 4,635, making it the largest electric delivery vehicle fleet in Australia.
• Australia Post’s fleet of electric delivery vehicles covers more than 28 million kilometres each year – that’s more than twice the distance of Earth’s circumference every delivery day.
The Reserve Bank of Australia (RBA) released a statement on monetary policy decision in September. The RBA Board decided to increase the cash rate target by 50 basis points to 2.35 per cent. It also increased the interest rate on Exchange Settlement balances by 50 basis points to 2.25 per cent.
The Board reported it is committed to returning inflation to the 2–3 per cent range over time. It is seeking to do this while keeping the economy on an even keel. The path to achieving this balance is a narrow one and clouded in uncertainty, according to RBA, not least because of global developments. The outlook for global economic growth has deteriorated due to pressures on real incomes from high inflation, the tightening of monetary policy in most countries, Russia’s invasion of Ukraine, and the Covid containment measures and other policy challenges in China.
Inflation in Australia is the highest it has been since the early 1990s and is expected to increase further over the months ahead. Global factors explain much of the increase in inflation, but domestic factors are also playing a role. There are widespread upward pressures on prices from strong demand, a tight labour market and capacity constraints in some sectors of the economy.
Inflation is expected to peak later this year and then decline back towards the 2–3 per cent range. The expected moderation in inflation reflects the ongoing resolution of global supply-side problems, recent declines in some commodity prices and the impact of rising interest rates. Medium-term inflation expectations remain well anchored, and it is important that this remains the case. The Bank’s central forecast is for CPI inflation to be around 7¾ per cent over 2022, a little above 4.0 per cent over 2023 and around 3 per cent over 2024.
The Australian economy is continuing to grow solidly and national income is being boosted by a record level of the terms of trade. The labour market is very tight and many firms are having difficulty hiring workers. The unemployment rate declined further in July to 3.4 per cent, the lowest rate in almost 50 years. Job vacancies and job ads are both at very high levels, suggesting a further decline in the unemployment rate over the months ahead. Beyond that, some increase in the unemployment rate is expected as economic growth slows.
Wages growth has picked up from the low rates of recent years and there are some pockets where labour costs are increasing briskly. Given the tight labour market and the upstream price pressures, the Board will continue to pay close attention to both the evolution of labour costs and the price-setting behaviour of firms in the period ahead.
An important source of uncertainty continues to be the behaviour of household spending. Higher inflation and higher interest rates are putting pressure on household budgets, with the full effects of higher interest rates yet to be felt in mortgage payments. Consumer confidence has also fallen and housing prices are declining in most markets after the earlier large increases. Working in the other direction, people are finding jobs, gaining more hours of work and receiving higher wages. Many households have also built up large financial buffers and the saving rate remains higher than it was before the pandemic. The Board will be paying close attention to how these various factors balance out as it assesses the appropriate setting of monetary policy. A further increase in interest rates is expected to help bring inflation back to target and create a more sustainable balance of demand and supply in the Australian economy. Price stability is a prerequisite for a strong economy and a sustained period of full employment. The Board expects to increase interest rates further over the months ahead, but it is not on a pre-set path. The size and timing of future interest rate increases will be guided by the incoming data and the Board’s assessment of the outlook for inflation and the labour market. The Board is committed to doing what is necessary to ensure that inflation in Australia returns to target over time.
The first of Air & Gas’s (AGI) revolutionary builds is two 8x8 rigid Dangerous Goods (DG) chemical tankers for Santos’ natural gas operations; it now delivers chemicals to gas wells as part of the company’s daily operations.
The tankers feature a stainless-steel, three-compartment storage vessel able to carry three different products. The first compartment has a capacity of 2,100 litres and carries a product called Biocide which falls under Class 8 DGs. The second carries 3,200 litres of a Class 9 DG, a corrosion inhibitor, and the last 6,300-litre compartment holds a non-hazardous material which is a foamer product. Along with the split compartments, the tanker has a hydraulic air compressor, pumping system and delivery hose reels – rated to carry DGs of Class 6.1, 8 and 9.
AGI Manufacturing Group Manufacturer, Michael Fowler, explains that the duo tankers replaced a different piece of equipment that was being used to do the
job, which, according to Santos, could have been performing better.
“Aesthetically it wasn’t very appealing, and it wasn’t purpose-built for their operations,” he says – adding that Santos needed equipment specifically designed
for their operations as “things probably weren’t built quite robust enough for their work conditions.”
So, the idea was to create a fresh start for
Air & Gas Industries is at the top of the chain for custom, specialised transport equipment for dangerous goods and other applications as seen in two recent deliveries.equipment was needed, he and the team at Air & Gas were able to create a more purpose-built design thought through from start to finish, which now provides more reliability for Santos’s day-to-day operations in remote areas.
“It’s been in operation for a year or so now and they’re happy with the overall product,” he says. “They’ve been using it regularly, so it has been reliable for them. They’re really happy with how everything is integrated and how it’s all nice and easy to use, and it’s been a big improvement over what they had previously.”
AGI’s second project included building five vacuum tanker units for Contract Resources, which were purpose-built to collect Class 3 flammable liquids from refineries when cleaning out waste oil and fuel from refinery tanks. They are also able to carry other DGs as well, compared to the fleet’s previous restricted vehicle only being able to transport flammable liquids.
“We’re currently building another two as well,” Michael says. “These tankers have the ability to carry oxidising substances, toxic substances and corrosive substances
and allowed them to open up to new business opportunities.”
The unit itself is an 8,500-litre vacuum waste tank which also features a tipping system and a fully opening rear door, allowing for easy unloading of dry goods that aren’t in a liquid form.
AGI’s customer wanted something with a very high flow rate that was also safe for use with DGs. The end result – a HV2004000 liquid ring vacuum pump with a flow rate of 3,900 cubic metres per hour.
custom equipment and we take a lot of pride in the quality that we build with,” he says. “Our other niche is building something that’s suitable for DG use which isn’t widely done necessarily, either.”
Contact
Air & Gas Industries Ph: 07 3271 5899 Web: www.airgas.com.au Email: sales@airgas.com.au
With a strong commitment to quality and safety, FBT Transwest is an
goods and food transporter based in Melbourne.
services around the world since 1972.
FBT Transwest (FBT) has built up a strong client base through its services to most leading manufacturers and importers of chemicals, agricultural, plastics, edible oils and waste stream products.
FBT is represented by several transport industry bodies and holds a series of certifications and licences which demonstrate its value for care and safety, including an ISO 9001 accreditation, Chemistry Australia Carrier Accreditation, Major Hazards Facility (Victoria) and much more.
The history of Holmwood dates back to 1950 when AMA (Adams, Mellish, Anderson) was formed and was tasked to refurbish an ex-war tanker constructed of aluminium. Welding of light alloys was unheard of locally at the time, so AMA imported the first aluminium welding equipment and technology into Australia. By 1956 AMA was constructing its own aluminium tanker designs, with several
of them being the largest petrol carrying tankers in the country. In 1963, Sid Mellish formed Holmwood Enterprises which saw his son, Colin Mellish, take over and continue to lead the path in Queensland to this day.
From the beginning, Holmwood has grown to become a national force and a much-respected name in the bulk liquid
Holmwood’s operations date back to 1950 when the family formed AMA (Adams, Mellish Anderson) and received a job to refurbish an ex-war tanker constructed of aluminium. Welding of light alloys was unheard of locally at the time, so AMA imported the first aluminium welding equipment and technology into Australia.
transport industry, with a reputation for the most reliable equipment.
FBT Managing Director, Cameron Dunn, began his journey with the company in 2009 and he explains that Holmwood was already established as its key supplier.
“Holmwood Highgate is a key supplier to us in terms of aluminium tankers,” he says. “They have the same value set as us and our terms of quality and safety match, which makes them a good fit for our business. They work well – quality is what we’re about. It’s not about the cheapest, it’s about the quality.”
Cameron’s most recent order with Holmwood included two new aluminium tankers and ended with a positive result, like every other order.
“We’ve ordered two tankers with them and have experienced no issues whatsoever,” he says. “It was a very smooth process and I’m very happy with the outcome. Holmwood is always
manufactured by Holmwood Highgate, it
end
very responsive and their designs work well with us, as far as customising the equipment for us and how we build it. Together we’ll select the suspension and the lids, valving and pipework – we have them custom made for our design, which obviously has a key aspect to safety in there.”
Along with being responsive and reliable, Cameron explains that Holmwood is also into innovation and welcomes any suggestions from FBT. He often suggests cutting-edge innovations and they will look at how they can be incorporated into the design of their equipment.
“Our business is very user-focussed,” he says. “We have operators operating these tankers, so we need to put ourselves in their shoes and we need them to be able to be innovative while thinking of the operator using the tanker, and Holmwood accommodates those discussions that we have with them very well.
“For us it’s not just the sale but the after sale as well.
“When we look at purchasing equipment it’s the complete package. Sales is one part of it, but the aftersales and the relationship after that is just as important to us. In Holmwood’s case, if something’s not right or goes wrong we can pick up the phone and we will get a response straight away, and that’s what we value as a business.
“A saying I always go by is, ‘Good business is a safe business, safe businesses are sustainable businesses.’”
Contact Holmwood Highgate VIC Ph: 03 9936 0360 QLD Ph: 07 3440 9000 Web: www.holmwoodhighgate.com.au
tanker servicing and truck retrofitting.
AJL’s stock of fuel-specific parts reflects the stringent maintenance requirements of the bulk fuel transport industry and accompanying environmental protection requirements. Together with their local knowledge and expertise, and the support of the Liquip nation-wide sales support network AJL employs a holistic approach to equipment maintenance.
AJL brings a broad mix of expertise to servicing equipment from the wheels up by providing general maintenance, fleet
Based in Tasmania with branches in Victoria, AJL Heavy Equipment is a key service provider to the road transport, terminal, stevedoring, mining, marine, forestry and earthmoving industries. By partnering with Liquip International in Tasmania, AJL is able to provide maintenance service and technical support to the fuel transport industry.
management, application engineering, maintenance planning, budgeting and general engineering. To keep up with customer requirements, AJL’s skilled technicians work around the clock both on and off site to suit customer operations.
AJL’s mission statement reflects its commitment to first-class infrastructure, with construction of its state-of-the-art 3,500-square-metre maintenance facility in Burnie which was completed in 2015.
AJL’s Burnie Workshop Supervisor, Michael Shires, says one of the things he likes most about AJL is that every day presents a new opportunity.
“With such a big, diverse business, you’re always bound to come across something new,” he says. “The Dangerous Goods (DG)
work is a big part of our daily workload, along with keeping on top of the servicing and repairs of major fleets. We strive to offer our customer the best service and the end result of keeping the vehicles moving and the customers happy is the most rewarding part for me.”
In 2021, a similar 3,500-square-metre facility in Truganina was added to the 2,000-square-metre and 1,500-squaremetre sites on Webb Dock and Appleton Dock, Melbourne. Increasing workloads sees AJL’s second Tasmanian site at Devonport also undergoing major upgrades.
In addition to traditional workshop functions, Burnie’s facility includes a designated DG bay which is segregated from the main workshop to enable the company to complete a variety of services on any configuration of hazardous DG vehicles including: Degassing of road tankers and self-bunded storage tanks, welding and general repairs, gas free certificates,
Safe Load passes, 30 Month inspections, return to work and general hydro testing, hose testing and certification, transport equipment fit ups and meter and level gauging calibrations. To support their fuel related operations AJL have dedicated an onsite equipment store for technicians to use so all necessary equipment is always on hand.
The DG bay contains a second level platform, with a drawbridge incorporating a safety harness at the rear, to enable safe
access to all compartments from the tanker hatches. Both levels have their own hot water pressure washers as well as truck wash and degreaser on tap.
Onsite AJL also have a three bay boilermaker workshop for welding repairs, modification and fabrication, ten service bays with two oil gantries for general maintenance and repairs, a service pit and roller brake tester.
“We’ve invested heavily in the fuel service industry with infrastructure, spare parts, ongoing staff training and compliance,” says AJL General Manager, Phil Duthoit. “We work closely with Liquip International and other fuel system manufacturers to provide the best solutions to our customers. We have dedicated personnel for fuel system servicing and repairs and see it as an integral part of our business.”
AJL is a certified Safe Load Program (SLP) and fuel tanker hydro testing facility. SLP and the associated Pass-2-Load Scheme apply to all tankers loading fuel products and gantries at facilities operated by major oil companies. It ensures all fuel hoses and equipment are tested and maintained at sixmonth intervals to ensure compliance with relevant Australian standards and codes and SLP standard reference documents. This ensures the safest possible entry, loading and exit at fuel storage facilities.
AJL’s technicians undergo stringent training and are well versed in DG compliance and its strict guidelines. As a part of their quality assurance process, supervisors must check and sign off on all servicing and repairs. These records can be provided to customers as needed. This ensures equipment is 100 per cent fit for work and is safe and compliant.
AJL’s commitment to the bulk tanker industry is recognised and appreciated by major Tasmanian fuel hauliers who choose AJL to inspect and service their vehicles, including Lowes Petroleum, Bennett’s Petroleum, Bonney Energy and Tas Petroleum. AJL has recently been acknowledged by Tas Petroleum for this commitment and dedication.
Tas Petroleum Maintenance Manager, Glen Doherty, thanks AJL for its quality service.
“We would like to take the opportunity to thank AJL for their prompt & excellent level of service provided to maintain our fleet of tankers,” he says. “It’s extremely convenient to get our DG inspections done
in Devonport as our trucks load out of the Shell terminal every day. We always find it easy to communicate with Paul & Brett at East Devonport regarding bookings and pick up times. We look forward to continuing the relationship with AJL’s Burnie workshop as well.”
Contact Liquip 148 Newton Road Wetherill Park, Sydney NSW 2164 Ph: 02 9725 9000 Web: www.liquip.com
ANo one wants a ‘one trick pony’ when it comes to choosing a trailer. Purchasing a trailer that can efficiently haul a variety of loads – from bulk to baled products – can double your profitability by backhauling.
Trailers with moving floors offer several advantages to operators over tipping trailers, including the ability to efficiently unload a wide range of products at nearly any location. The hydraulically driven unloading system features a series of floor slats that ‘walk’ material out the rear of the trailer. Trailers unload horizontally without the need to raise the trailer and eliminating the risk of tipping over or hitting overhead hazards with the tilted trailer bed.
Horizontal unloading not only prevents the trailer from toppling like a tipping trailer, but it also offers much needed flexibility in unloading locations. Trailers
can discharge inside buildings, under trees and near utility cables.
According to Zyggy Reinoga of KEITH Walking Floor Australia, horizontal unloading also provides operators with flexibility in the loads they haul.
“Operators don’t make money on an empty trailer. With a Walking Floor trailer, you can load out bulk material like cattle feed or compost one way and bring back baled hay or palletised goods for the return trip,” he says.
Increasing fuel costs make maximising the most of trailers even more important these days.
“If you aren’t being paid for the ride back home, you’ve missed out on half the earning potential of your trailer,” Zyggy says.
For operators who need proper clean out
before hauling the next load, KEITH offers its CleenSweep tarp system as an optional accessory to its Walking Floor unloader. Used in conjunction with the Walking Floor system, the CleenSweep tarp sweeps out the residual material as the trailer unloads. It eliminates brooms and manual tarps, reducing the risk associated with drivers entering the trailer.
“Keeping personnel out of the back of the trailer is always preferable,” Zyggy says. “The risk of being buried by material, falls and knee and back injuries are all increased when drivers are getting in and out of the trailers.”
The tarp is attached to a winch system, where it extends down the inside of the trailer. The load rests on the bottom of the tarp and as the Walking Floor system unloads the trailer, the weight of the
material pulls the tarp along the floor cleaning it as it goes. Once the unloading is complete, the CleenSweep tarp is retracted with the push of a button.
Based on the product and situation, Walking Floor technology can offer various material handling solutions.
As a result, KEITH Walking Floor has a long relationship with the transportation industry, with some operators using Walking Floor trailers since the early 1980s. “We are very familiar with the challenges faced by transport professionals and design our products not only for durability, but dependability as well,” Zyggy says.
The slats from KEITH Walking Floor are available in a wide range of profiles and thicknesses to address different applications and unloading needs. Whether
you are transporting high moisture loads that require leakproof and leak resistant options, or abrasive materials such as asphalt, sand, scrap, glass or fly ash, or need backhauling options for bulk materials, pallets or bales, or simply need standard or high-impact flooring for top loading
Contact Keith Walking Floor Web: www.keithwalkingfloor.com Ph: 0404 041 833
If you aren’t being paid for the ride back home, you’ve missed out on half the earning potential of your trailer
“
”applications, KEITH Walking Floor has the right solution.
Rhino Trailers and Low Loaders has a long-standing reputation for producing a diverse range of quality trailers and low loaders. Part of The Davey Group, Rhino Trailers and Low Loaders is an Australianowned and operated business based in Toowoomba, Queensland. Its trailers are renowned for their superior strength, reinforcing the company’s motto ‘strength in design’.
Over the years Rhino has built many special-purpose transport equipment for specific tasks, in particular for the livestock, bulk transport and heavy haulage industries.
Rhino’s extensive tipper range includes high-tensile, light-weight steel and aluminium trailers, including hybrid models. These are available in high-volume single,
B-double, road-train and PerformanceBased Standards (PBS) configurations. Its drop-bed bulk tubs, made in alloy and high-tensile light-weight steel, work well with light weight / high volume products. Its range of Rhino (formally Lusty) low loaders covers deck wideners and full wideners on rows of four tyres as well as widening rows of eight low loaders with the accompanying rows of four and rows of eight dollies.
Rhino also manufactures two rows of four, and three rows of four, roadtrain dollies for tipper combinations, skel trailers and stock crate road-train combinations as well as two rows of four and three rows of four tag trailers for plant and equipment. It also has a wide range of stock crates designed and developed for the tough Australian conditions.
To further bolster its quality benchmark two years ago the Group committed to developing and implementing an Integrated Management System (IMS) to achieve certification in: ISO 9001:2015 Quality Management Systems; ISO 45001:2018 Safety Management Systems; and ISO 14001:2015 Environmental Management Systems.
A solid quality management system behind the doors means customers can count on improved standards and controls, performance, reliability and overall quality of the products.
The Rhino team ensures complete customer satisfaction by following a steadfast quality policy that includes accurately capturing customer specifications; implementing, maintaining and continually improving a third-
The Davey Group’s low loader division manufactures quality custom-built heavy haulage transport equipment tailored for the Australian market.party certified ISO 9001:2015 Quality Management System; conducting in process and final quality and test inspections, and adhering to all applicable statutory or regulatory requirements and internal processes.
With a history dating back over 30 years, and the combined knowledge and expertise of businesses like Lusty Low Loader and AFM-O’Phee Trailers that have been purchased and consolidated into the Rhino brand by the parent company, the Rhino range has gone from strength to strength.
Its 40,000-square-metre factory at Toowoomba is a one-stop outlet for all trailer requirements, featuring a comprehensive offering under one roof, including a protective coatings facility, as well as facilities for servicing, modifications and refurbishments.
The team includes over 100 highly skilled tradespeople and design engineers, who ensure that the quality of the trailers is always at the forefront and never compromised. Aside from its IMS commitment, the technicians have always
been striving for continual improvement, reviewing existing designs and manufacturing methods to allow existing and new customers find the right match for their business depending on their evolving needs and growth.
The Rhino team is also focused on reducing lead times through improved manufacturing processes.
The capabilities of The Davey Group are not limited road transport, with its divisions offering standard engineered products, and design and construct capabilities servicing the mining, oil and gas, agriculture and forestry sectors.
The company specialises in the delivery of complete turnkey solutions including large, complex industrial equipment, storage solutions, bulk materials handling, processing plants, structural steel buildings and supporting plant infrastructure.
Its Toowoomba site also features a modern 1,500-square-metre abrasive blasting and protective coatings facility that has a 23m x 6.2m x 6.2m environmentally friendly abrasive blast
chamber capable of using all types of material for surface preparation.
The 13m wide x 42m long booth is suitable for all large equipment and machinery with industrial finishes and a 24m long heated spray booth to offer greater flexibility in applying quality coatings to commercial and industrial machinery and equipment to exact Australian Standards and International specifications.
The Davey Group’s Managing Director, Tony Davey, is particularly proud of this capability and noted that the protective coating division will underwrite delivery commitments on finished products –something the division has successfully been doing since it was established.
As a result, this state-of-the-art facility is where Rhino gets its trailers painted, bringing two business divisions of The Davey Group together to deliver products that are unbeatable in quality, design and construction.
Contact Rhino Trailers and Low Loaders Ph: 1300 4 RHINO Web: www.rhinotrailers.com.au
Silk Logistics Holdings has been working on increasing productivity to and from the wharf precinct by adding additional Higher Productivity Freight Vehicles (HPFVs) to its Victoria-based fleet in recent years. Silk’s Port Logistics operation in Victoria is made up of two businesses, Silk Contract Logistics and Rocke Brothers. It currently has 15 HPFV sets across the two businesses and it recently took delivery of three additional sets of HPFVs from CIMC to allow more operational flexibility and an increased capacity to deal with its growing customer requirements.
“We have 298 company-owned trailers of various brands in the Victorian fleet. The business also rents in excess of 200 trailers
each day from Rentco,” says Chris Pearce, Operations and Maintenance Manager of Silk Contract Logistics. Chris is responsible for maintaining the Victoria-based fleet of both Silk Contract Logistics and Rocke Brothers, purchasing new equipment, Victorian port logistics depot maintenance, supplier relationships and supporting operations. “Our fleet choice is driven by our customers’ work requirements. It predominantly features 40’ skels but also includes retractable trailers, specialised equipment including 20’ and 40’ tippers, side loaders, extendable drop deck trailers for over height transport, 20’ skels, Super Bs and A-doubles.”
Silk’s new 30m A-double trailers from
CIMC will be carting 20’ and 40’ import and export containers, between the wharf precinct in Melbourne and our strategically located depots in the southeast and western suburbs. The trailers have been fitted with purpose-built light weight Fuwa K-Hitch KIS Integrated axle and air suspension system with ConMet Alloy wheel ends. They feature three-way twist locks with side loader pads, and the dollies come with dolly-lock provision. The trailers and dollies have undergone a fully automated KTL surface treatment with powder coating finish. All CIMC skel trailers have dangerous goods wiring and raise/ lower valves as a standard.
“The new A-double equipment was
purchased with versatility and higher payloads in mind,” Chris says. “Other features include provision for dual kingpin locations, provision for ring feeders to be added to tag trailers, and Right Weigh digital on-board mass scales.
“One of our internal goals is to have a minimum number of vehicles on public roads to achieve our workload and CIMC are helping us with our journey to achieve this.”
The company’s relationship with CIMC dates back a decade across both the Rocke Brothers’ and Silk Contract Logistics’ fleets. Over the years, the two businesses have purchased several A-doubles, B-doubles and 40’ skels custom-built for container cartage. “The majority of the units we have
“One of the key drivers to purchase CIMC equipment is the value for money they offer. The equipment is very reliable and the strength of the relationship is built around the company’s willingness to assist at all times. The CIMC trailers we have in the current fleet have always proven to be reliable and fit for task, hence we have returned to purchase more over the years. There is no doubt these new A-double sets will be reliable and provide us with the flexibility and productivity they were purchased for.
“CIMC has been a pleasure to deal with and we look forward to maintaining this relationship into the future. Dealing with Sven and James has been easy, the
Goodride is an Australian-owned business with extensive industry knowledge across multiple tyre categories and applications.
Goodride tyres are manufactured by ZC Rubber – one of the largest factories in China and one of the top 10 manufacturers in the world.
ZC Rubber is equipped with the latest technology and testing facilities and by being at the forefront of the tyre industry, the Goodride brand has come to represent
safety, value for money and remarkable performance.
Goodride Tyres has experienced significant growth during recent years, which CEO, Joe Limina, explains led to relocating several of its warehouse facilities.
“Over the last two years we have relocated our warehouses in Brisbane and Townsville,” he says.
“Most recently we have recently moved our Melbourne warehouse from Huntingdale
Many of Goodride Tyres’ customers have partnered with the company for many years due to its wheel and tyre assembly with JOST. The products are respected in the market and is an option that continues to be requested on trailer combinations.
for the OEM trailer market, Goodride Tyres continues to keep the ball rolling in the ever-growing transport industry.
across to Truganina to a new purpose-built facility, which will help us better service our customers. Having this new facility allows us to hold more inventory to ensure that we can fulfil our customers’ needs on time, every time.
“Moving from a 3,000-squaremetre warehouse to a purpose built 5,000-square-metre warehouse also delivered many efficiencies on how we handle inventory and service our customers.
“Being positioned in the western freight hub means our transport partners are more accessible to us, to ensure we deliver on our delivery promise.”
Along with its variety of options Goodride also provides a solution to the OEM trailer market, by partnering with JOST Australia to deliver wheel and tyre packages to trailer manufacturers.
“We partner with JOST to supply OEM trailer manufacturers with a bolt on solution,” he says. “We also sell JOST wheels to our retail dealer network to fulfil any replacement requirements. We established a relationship with JOST around six years ago to provide an endto-end solution for trailer manufacturers that require a tyre and wheel assembly. It’s
on to their trailers. If the trailer is designed with a PBS requirement, we can provide a suitable option for that as well.”
Goodride and JOST share similar values in providing quality products at a reasonable price, and the tyre distributor prides itself on providing great service to meet customer expectations.
Goodride’s decision to partnering with JOST is clearly favoured by its customers,
the quality of the product along with the service that comes with it is what stands out when lined up next to the other options.
Contact JOST Australia Ph: 1800 811 487 Web: www.jostaustralia.com.au
Goodride Tyres Ph: 1300 918 221 Web: www.goodridetyresaustralia.com.au
Smart Truck Solutions (STS) is the distributor of Australia’s first wireless smart on-board mass (OBM) management solution – the Right Weigh load scales.
Leading on-board truck scales and weigh gauges expert, Right Weigh, teamed up with compliance telematics provider V-DAQ to offer a smart On-Board Mass (OBM) system suited for Australian transport and logistics needs. The Type B approved air suspension gauge provides a connected on-board weighing system that offers productivity and compliance benefits.
One of the key considerations for all transport and logistics operators is how to maximise payload capacity and make the most of their vehicle’s cargo space while remaining compliant with weight distribution and load restraint regulations.
Right Weigh load scales are on-point to address those exact concerns. The in-dash and exterior digital scales readout screens with digital displays are designed to be compatible with most truck and trailer airsuspension axle configurations, which is
crucial for observing Gross Vehicle Mass (GVM).
By combining Right Weigh’s trusted weigh gauges with V-DAQ’s smart telematics the solution offers operators an easy and reliable way to monitor weight by axle group and more via the Right Weigh mobile app, which is available on iOS and Android devices.
“Users can view on-ground weight of their truck and trailer either from the gauge on the unit or anywhere within Bluetooth range,” says Leigh Noske, owner of Smart Truck Solutions. “They can also share that information with fleet operators via email – promoting a safer and more productive way to monitor and maintain legal payload limits.”
The smart OBM solution features a new driver app (currently available for Android) that allows operators to easily view and record real-time weights from within the cab. It’s flexible, easy to use, and enables location and mass tracking. It offers extreme accuracy with payload weight checks – right down into small 10kg
increments, which is a big advantage over analogue air gauges.
A testament to its popularity and proven benefits is the number of operators across Australia who are using the solution to boost productivity, and improve safety and compliance.
Apart from the accuracy, affordability and user friendliness of the OBM solution, the teams at Smart Truck Solutions ensure excellent customer service and in case of there is ever a problem with the gauge, they make sure the problem is resolved promptly and there is no time loss for the customer.
The Right Weigh load scales offer telematics for compliance with permits and/or notices. Smart Truck Solutions is in the process of getting connected with most telematics companies for Smart OBM compliance.
The Smart OBM solution is flexible, easy to use, and allows location and mass tracking. It provides the convenience of higher mass, greater access, lower risk, tag and go in 30 seconds. The simple,
The on-board digital scales from commercial vehicle equipment supplier, Smart Truck Solutions, feature Bluetooth integration and mobile app capability for maximum operational efficiency.plug-and-play road access solution allows fleet operators to seamlessly manage their data, quickly comply with new regulatory measures, and access value-added
opportunities that increase profitability and efficiency.
“The 201 Series is one of the most versatile exterior on-board digital scale
systems from Right Weigh,” Leigh says. “It is available with a dual air input that can be used to monitor a single axle group with two height control valves or it can be used to monitor two separate axle groups on the same vehicle.”
The additional features of Right Weigh’s 201 Series exterior digital load scales, including PIN code protection and an overweight warning feature, make the OBM system ideal for maintaining legal weights efficiently and safely. Used in conjunction with the free mobile phone App, Right Weigh’s load scales provide real-time data on payload weight for drivers and fleet operators without leaving the cab.
Contact Right Weigh Web: www.rightweigh.com.au
Maintaining the strength and durability of the trailer from its initial concept to the final product that can withstand even the roughest Australian road conditions is at the heart of The Drake Group’s operations. Manufacturing trailers for a wide range of applications requires not just the best team of technicians but also the best materials available. This is where SSAB comes in.
Backed by a global network of mining and manufacturing operations, SSAB is one of the most trusted names in the steelmaking market. Like The Drake Group, SSAB prides itself on delivering products that represent strength and durability.
“SSAB products are of extremely high quality and reliable material,” says Khali Lake, Group General Manager of The Drake Group. “These properties are consistent and the material is great to work with from a cutting, bending and welding perspective.”
SSAB is a global steel supplier in advanced high-strength steels (AHSS), quenched and tempered steels (Q&T), in addition to steels for the construction industry and strip, plate and tubular products. The Drake Group primarily uses Hardox® 450 wear plate and Strenx® 700, with some speciality products in its applications.
Hardox® wear plate, a popular choice with The Drake Group’s customers, is known for its surface hardness and overall strength. It is particularly suited to earthmoving applications. “Customers carrying earthmoving equipment with steel tracks, demolition equipment like compactors or anything with a metal track that needs to go up and down the ramps often request Hardox®, as these kinds of equipment can be quite damaging to the trailer,” Khali says.
The other major SSAB-supplied brand used by The Drake Group, Strenx® performance steel, is ideal for heavy duty
The Drake Group’s range of high-performance heavy haulage trailers for the mining and transport industries have the backing of SSAB -supplied steel.applications where weight is as much a key consideration as structural strength. The Drake Group relies on Strenx® performance steel to make the trailers frames, decks and structural elements. As a result, SSAB is one of Drake’s top suppliers.
“SSAB delivers on reliability that comes from supplying high-quality materials,” Khali says. “Their service and technical support is excellent and the reliability we get from mill-to-door has always been exceptional.”
As the Group GM, Khali oversees the day-to-day operations of the entire Group of companies and in conjunction with the Directors, provides strategic and structural direction for growth and ongoing performance.
The Drake Group is a diversified
engineering, manufacturing and supply group that has been in operation for over 60 years. The Group consists of four main manufacturing units – Drake Trailers, O’Phee Trailers, Drake Collectibles, and Dalzell and Bagley Engineering. It employs over 350 people, and has purpose-built facilities in Wacol and Archerfield in Queensland, with a support office in Perth in Western Australia.
“We pride ourselves on designing and manufacturing high-quality trailers and components that are standard and bespoke for the Australian market,” Khali says. “We have large spare parts, and service and repairs businesses that cater to the national market. In addition to this, we have agency agreements to manufacture the Swinglift and Boxloader
container side loaders from France. We also have agency agreements to distribute the Cometto range out of Italy and Sunseeker Motor Yachts out of the UK.”
In the past decade, there has been a steady increase in the amount of SSABsupplied steel used within the Drake, O’Phee, Boxloader, Swinglift and Dalzell and Bagley range of products. Apart from ensuring that its products are always delivered exactly to specification in terms of the size and thickness, the SSAB team is committed to providing the best technical support in the market.
Email: australia@ssab.com Web: www.ssab.com
Generally, Transport Certification Australia (TCA) grants approval for On-Board Mass (OBM) systems which are independently tested against its OBM System Functional and Technical Specification. The OBM supplier meets the required technical specification as published by TCA which gives them categories A, B or C. Category
a Smart OBM or IAP-M program and Category A is not sufficient for Category B functions.
E-Max Managing Director, Phillip Carthew, explains that for the OBM system to be used in a Smart OBM or IAP-M program it must be able to be integrated with the telematics provider.
OBM provider may have met the technical requirements for Category B approval for the scale but then cannot connect to an approved Smart OBM telematics provider yet,” he says. “The risk here is that there is no way knowing whether they will ever get a working connection or how far down the track that might be. So, it is
Those already operating and working within the National Telematics Framework most likely understand the requirements for smart On-Board Mass systems and IAP-M. However, E-Max Australia explains that for those who aren’t involved and are interested in taking advantage of such programs, there is much information to understand on the technical side.
telematics provider the OBM system has inter-connectivity with.”
Air-Weigh, one of E-Max’s leading products, currently has connectivity with every approved telematics provider approved for Smart OBM and IAP-M. Phillip says he and his team truly believe that they have created the most streamline and easiest-integrated OBM system possible.
“We have developed over the years a system that I believe to be one of the most user-friendly systems for use in both small and large fleet applications,” he says.
“A focus of our development was to produce a system that, once setup, requires little or no additional pairing of truck to trailers like many of our competitors. Once installed into a fleet and set up properly, it requires no ongoing pairing of trailer scales or truck scales when they are swapped between prime movers within a fleet.
“We call this a hot swap function. Essentially it is seamless – the user has to hook up trailers as normal then and the system will automatically do the rest. By using this hot swap function and the FSK technology, we remove the time wasting for the driver of having to find and pair trailers within the system while eliminating the frustration of pairing into nearby trailers that are not actual trailers behind the prime mover. Key on and go, is the best solution
of any size fleet, big or small.”
Air-Weigh integrates with all approved telematics providers within the National Telematics Framework, and integration with all of these providers is also a seamless process. Once connected, the Air-Weigh system processes mass information within a secured network between the telematics device and the OBM system.
“It is a native integration with the telematics provider and there is no requirement for a third-party device such as a smart phone or tablet,” Phillip says. “Some other systems require the aggregation of information on a thirdparty device, which then passes off the information to the telematics provider. I see some challenges here – when a driver is required to use his own phone to be a link between the OBM devices and telematics device there is a potential of privacy breaches of the data and also the unwanted collection of data through a device that does not belong to the transport company.”
When it comes to E-Max’s Air-Weigh product, Phillip explains that complete data security is one of its top priorities.
“Air-Weigh data is encrypted across the OBM network on the truck,” he says. “The system contains its own 128-bit security and electronic PIN, so there is
no requirement to seal up the calibration process or any protective box. It can be an inconvenience at a calibration interval to remove the seal before calibration and replace it with a new one after the calibration is complete, not to mention the ongoing cost of the seal. Also, a physical seal does not stop tampering and you must have seals on hand to complete a calibration to be compliant with the regulators.”
Security of the system like all other features is seamless. According to Phillip, once setup it doesn’t to be addressed again unless there is a requirement to change PIN numbers.
“We have served this market here in Australia for over two decades,” he says. “Our product comes with an industry leading three-year-warranty with national coverage. We are grateful and feel privileged to be involved in the Australian transport industry, they are some of the greatest people on earth. We look forward to continuing to serve this great sector of industry.”
Since the regulations and standards for Australian commercial radio became more relaxed in the 1990s, the Australian broadcasting industry has seen consolidation of many commercial radio networks.
In the recent years there has been a consistent shift in focus from niche markets to even more specific market subsets such as a station dedicated to young home owners or other small community radio stations.
Australian trucking is a big mobile community looking for industry-specific news and information. At the same time, the drivers are looking for a radio station they can lock on and leave on while they are in their cabs, listening to the information and entertainment that relates to their own work activities as well as their
sometimes unique lifestyles.
Aussie veteran radio broadcaster, Simon Smith, recognised the need for a broadcasting connection to trucking community, and also the responsibilities which come with it, and went on to deliver an industry-focussed digital radio station dedicated to long-haul truckies –Australian Truck Radio.
“They’re a huge mobile community and they are looking for their own station, and now we have to technology and resources to provide that nationally 24/7.
“The mobile phone is today’s radio transmitter and receiver,” says Simon, Founder and Manager of Australian Truck Radio.
Simon has a long history with Australian radio, and as the Program Director of Radio 2WG Wagga he was involved with the
original team who created the successful ‘truckers radio’ format out of southern New South Wales during the late 1980’s, mostly on the midnight to dawn shift. It became hugely popular and an unexpected bonus that was observed when the original show had been on air for some time was an anecdotal reduction in fatigue-related accidents involving heavy vehicles in the areas where the broadcasts were being received.
However, the trucking landscape has changed in the past few decades, and so has the technology.
The internet and modern technologies have made the pathway to a listenerfocused broadcaster like the Australian Truck Radio ideally positioned for the captive niche market of Australian trucking. Simon and his team understand that
the future of Australian Broadcasting is digital. They also know that truckies enjoy listening to something on the road and with mobile technology it means that their favourite radio station will never go out of frequency at any time of the day.
All you need to do is simply visit: www.australiantruckradio.com.au
“The mobile phone is today’s radio transmitter,” Simon says.
“You can download the app straight onto your mobile plus you can of course listen online from our Australian Truck Radio website.
“The trucking industry has changed. It’s mostly dual carriageway between capital cities such as Melbourne, Sydney and Brisbane. In the past, drivers would pull up at a roadhouse and sit around and have a meal together, but now with the
dual carriageways, that opportunity for camaraderie is no longer there. We want a provide a radio station that’s like a truckies’ campfire where they can sit around and talk and listen.”
Australian Truck Radio, dubbed the ‘voice of Australian trucking’, is also available in a handy podcast format fortnightly and distributed across its social media network.
“If you’ve got a radio station and you’re trying to be everything to everybody it’s not going to work,” Simon says. “We provide something that people want with a music-driven format, and in between the songs we can have a bit of a laugh and a bit of variety including regular on-air conversations with industry people.”
Of course, being a radio station there is plenty of music, with trucking classics every hour and bopping tunes anywhere
Bruce Springsteen.
It will also regularly host Aussie singing stars such as rock legend Jimmy Barnes and many Australian country music stars like the ‘Boy from the Bush’, Lee Kernaghan. The legendary country singer, who shot his concert-cum-road trip documentary earlier this year travelling through the outback on his beloved ’79 series Toyota Landcruiser, is sure to have lots of tunes to entertain truckies travelling across cities and towns.
“It’s a jukebox for truckies that goes everywhere you do,” Simon says.
“The trucking industry is the biggest niche market in Australian radio and this huge mobile community deserves to have their own 24/7 radio station – now they do.”
Simon Smith.For the first time, the event organisers of IAA transformed their bi-annual exhibition concept to embrace the entire transport and logistics spectrum. Such a decision seemed highly appropriate as the 2020 edition which specifically focused on trucks, trailers and componentry was cancelled due to Covid-19. Four years between events is an incredibly long time. The anticipation for IAA Transportation this year was, without exaggeration, highly anticipated as a platform to exchange ideas, promote innovation but more importantly reconnect with customers, colleagues and friends. Never underestimate the power of direct faceto-face engagement because the simple act of shaking hands and saying hello to one another was for many a key takeaway from the show. The Global Trailer team, for instance, met with many industry partners but were also introduced to new contacts
and businesses from around the world. Again, there is no adequate substitute for networking in person.
This year, there were a total of 1,402 exhibitors from 42 countries and 230 national and international speakers. That’s an impressive turnout.
“Following on from IAA Mobility, we have successfully developed and reinvented IAA Transportation,” said VDA President, Hildegard Müller. “We are now exhibiting the entire logistics spectrum, ranging from trucks to cargo bikes and delivery vans to parcel drones. This courage has paid off as the tremendous response from exhibitors and visitors showed that our new approach was the right way to go. Transport and logistics are the lifelines of our society and economy. The new IAA Transportation concept has provided answers to the many challenges that the industry is now facing throughout the world. It became clear in
Hanover that our industry is delivering what is needed for a sustainable future.”
This is true. The pandemic really did highlight how important the supply chain is and how vital it is to move critical freight to where it is needed most. What made IAA Transportation particularly significant this year was how front and centre supply chain issues are and that there are remarkable solutions that can be actioned immediately. Some concepts that were theory or very early in their development four years ago, like the electric axle, are now being widely adopted.
The event organisers were ecstatic to report that IAA Transportation 2022 has consolidated its position as the world’s largest platform for the transport and logistics industry – about two thirds of the exhibitors were international companies with visitors coming from 72 countries.
While electrification, sustainability and digitalisation were prominent themes of this year’s IAA Transportation event in Hanover, Germany, we are finally seeing practical solutions not only emerge but finally integrate into real-world applications.
At the start of each harvest a dedicated fleet of 31 trucks, embossed in the SCT insignia, roars to life. Since 2005, SCT Logistics has serviced the Sunshine Sugar account, ferrying its commercial vehicles between farm sites and the nearby mills.
The trucks work 24 hours a day, seven days a week. A pick-up or delivery might only entail trips of a few kilometres, at the most a 150 km round trip, but the work is relentless. Farmers, tip harvested sugarcane into bins parked on cane pads or marshalling areas amongst the cane fields. The bins, which can carry up to 28-tonnes at a time, are retrieved by the trucks and delivered to the mill. A rear door on the bin opens, from which its contents are tipped from a purposebuilt trailer into a hopper at the mill for processing. The emptied bin is then taken back to the farm.
Driving is not dissimilar to shuttle work between distribution centres, but the payload requirement and apparatus of
discharging it makes it a very different and intricate application, unique to not only this part of the world, but to the industry.
Up until 2019, SCT Logistics had been using Kenworths for the operation. That all changed two years ago when it introduced 16 new Euro 6 Mercedes-Benz Actros 2646LS trucks as part of a comprehensive fleet replacement program involving seven purpose-built quad axle skel trailers — the first of its kind approved under Performance-Based Standards (PBS).
The operation is perhaps even more payload sensitive given the sugarcane market varies season to season. Maximising every dollar is crucial as the volume of next year’s crop is always unknown. Therefore, any improvements to payload capacity on each vehicle is regarded as significant.
SCT Logistics National Fleet Manager Michael Sommers says payload advantages were a driving force behind the decision to update the fleet.
“We worked out that we could get a better payload with the cabover Mercedes-Benz Actros, even though it is a heavier truck,” he says. “But with the axle and the wheel configuration, it actually gave us a better load profile. So, in the end we’ve managed to have a heavier prime mover but get an extra half-tonne payload.”
With an ageing Kenworth fleet needing to be replaced, SCT Logistics, who already had an existing alliance with Daimler Truck across other areas of its business, opted to try something new. Introducing a quadaxle trailer on the Mercedes-Benz Actros allowed SCT Logistics to increase its load capacity to 50.5-tonnes across each unit, with 27 tonnes assigned to the trailer, all the while maintaining a total vehicle length of under 19 metres.
It’s not viable, however, to go any longer, according to Michael, when taking into consideration the singularity of the combination and bins. It would throw out axle weights.
PoweredAt this year’s Australian Freight Industry Awards, Rachel Michaud and the Knorr-Bremse team won the Application of Technology Award for their iMass On-board weighing system. Graduating from Monash University in 2010 with a Bachelor of Mechanical Engineering with Honours, Rachel has made many significant impacts on the transport industry during her successful career.
Before her graduation, Rachel spent some time at Monash’s Formula SAE Team, where she led it through several global and local competitions. This is where Rachel found her love for all things vehicles and moving, which she explains then opened doors for other opportunities.
Made possible by Smedley’s Engineers, Industry Innovators is a series dedicated to honouring the individuals who are transforming the commercial road transport industry.
“I was quite fortunate to be team leader there and we competed at SilverStone, coming third in the world and first in Australia as well,” she says. “From that team I got a job offer to work for Thales in Bendigo. I worked for them for two years on the Bushmaster and on survivability project upgrades, which was very exciting. I got to redesign the seating frame, which meant that when soldiers were in a mine blast in a Bushmaster, they would no longer suffer severe damage to their legs, and they could basically walk away from those incidents.”
Following Rachel’s work with Bushmaster Protected Mobility Vehicles, she applied for a position at Knorr-Bremse, where she
worked as an Applications Engineer on the electronic safety systems for trucks and trailers and then transitioning into a Technical Account Manager and projects role.
During Rachel’s time at Knorr-Bremse, she has been heavily involved with the company’s iMass product, which is its OnBoard Mass (OBM) offering produced for truck and trailer. According to her, it’s the first certified OBM system globally to tap into the ISO connection between the truck and trailer for Electronic Braking System (EBS) modules, and it’s the one that won the team the big award.
“We’ve just recently won an award for iMass at the Australian Freight Industry Awards,” Rachel says. “It’s also a global first for us as we’re the first company in the world to use the mass measurement from the trailer EBS and have it certified. We think it’s the future of onboard weighing technology.
“It was a pretty big deal as this is the first product that we’ve locally designed, developed and released in Australia,” she says. “It’s been five years in the making, it’s had its ups and downs and I think the whole team was just astonished to finally release it and then to win an award. It’s really brought our entire team here together.”
While being a female in the transport industry may provide some challenges to some, Rachel says that she is currently in a very supportive environment that has allowed her to further catapult in her aspirations and projects.
“I’m in a very supportive environment here, being a female in the industry,” she says. “In the earlier days it was a little bit daunting being in a male-dominated profession, but Knorr-Bremse has proven to be a diverse and inclusive employer and really supportive of all its people. I’ve never been treated any differently and I have been given all the same opportunities as anyone. I’m just very lucky to be in such a great industry.”
In the earlier days it was a little bit daunting being in a male-dominated profession, but KnorrBremse has proven to be a diverse and inclusive employer
“ ”
“As someone who grew up around the trucking industry here in Australia, and is still close to it, I love what I do both here in Australia and overseas with the industry. I know just how important it is for truckies to have a voice in this huge mobile community that carries the nation 24/7. What Australian Truck Radio is building is a really great thing for the trucking industry. I very much look forward to contributing and supporting what they do at Australian Truck Radio, which I reckon will make a real difference to hardworking Aussie Truckies.”
Pencil in some information on dates and venues of various truck shows, field days and road transport industry conferences both locally and internationally.
Got
Queensland
Brisbane Convoy For Kids 5 November Redcliffe Showgrounds, QLD Visit: brisbaneconvoyforkids.com.au
Sao Paulo Expo 7-11 November Brazil Visit: www.fenatran.com.br
Convoy For Kids Goulburn 19 November Goulburn, NSW Visit: www.convoyforkidsgoulburn.com.au
Dane Ballinger Memorial Truck Show 19 November Bathurst, NSW Visit: www.bathursttruckshow.com.au
Illawarra Convoy 20 November Illawarra, NSW Visit: www.illawarraconvoy.com.au
Castlemaine Rotary Truck Show 26-27 November Castlemaine, VIC Visit: www.castlemainetruckshow.com
Geelong Classic Truck and Machinery Show 14-15 January Geelong, VIC Visit: www.classictruckandmachinery.com.au
South East Field Days 17-18 March
Lucindale, SA Visit: www.sefd.com.au
Wimmera Machinery Field Days 7-8 March Horsham, VIC Visit: www.wimmerafielddays.com.au
Tocal Field Days 5-7 May Paterson, NSW Visit: www.tocalfielddays.com
Brisbane Truck Show 18-21 May
Brisbane, QLD Visit: www.brisbanetruckshow.com.au