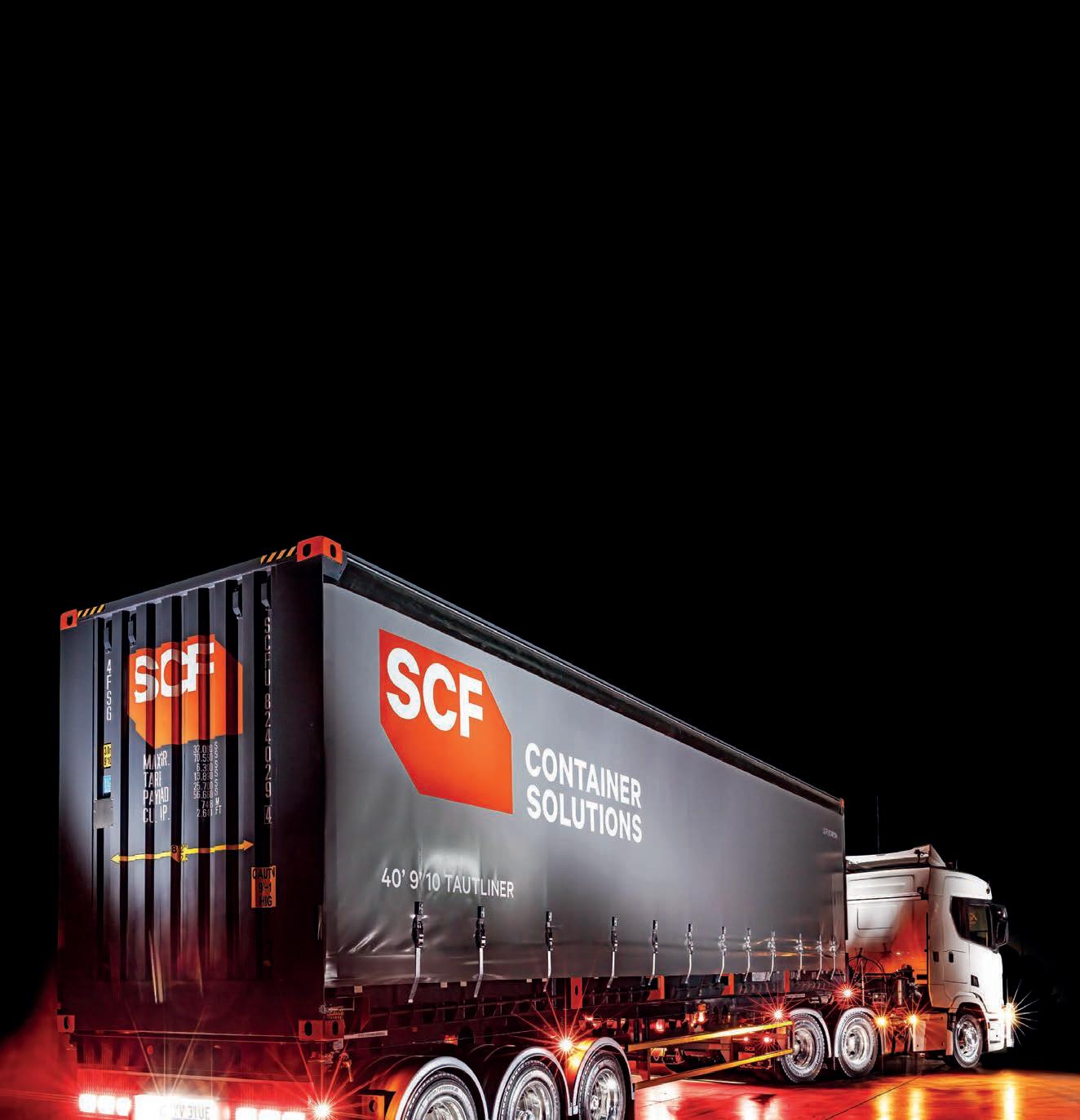
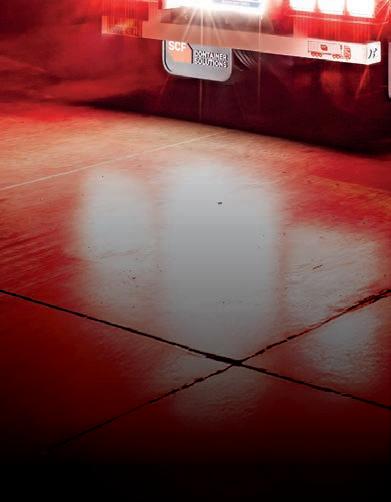

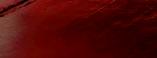

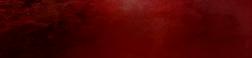



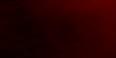

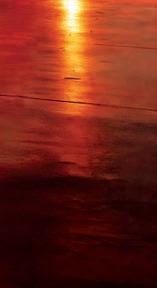



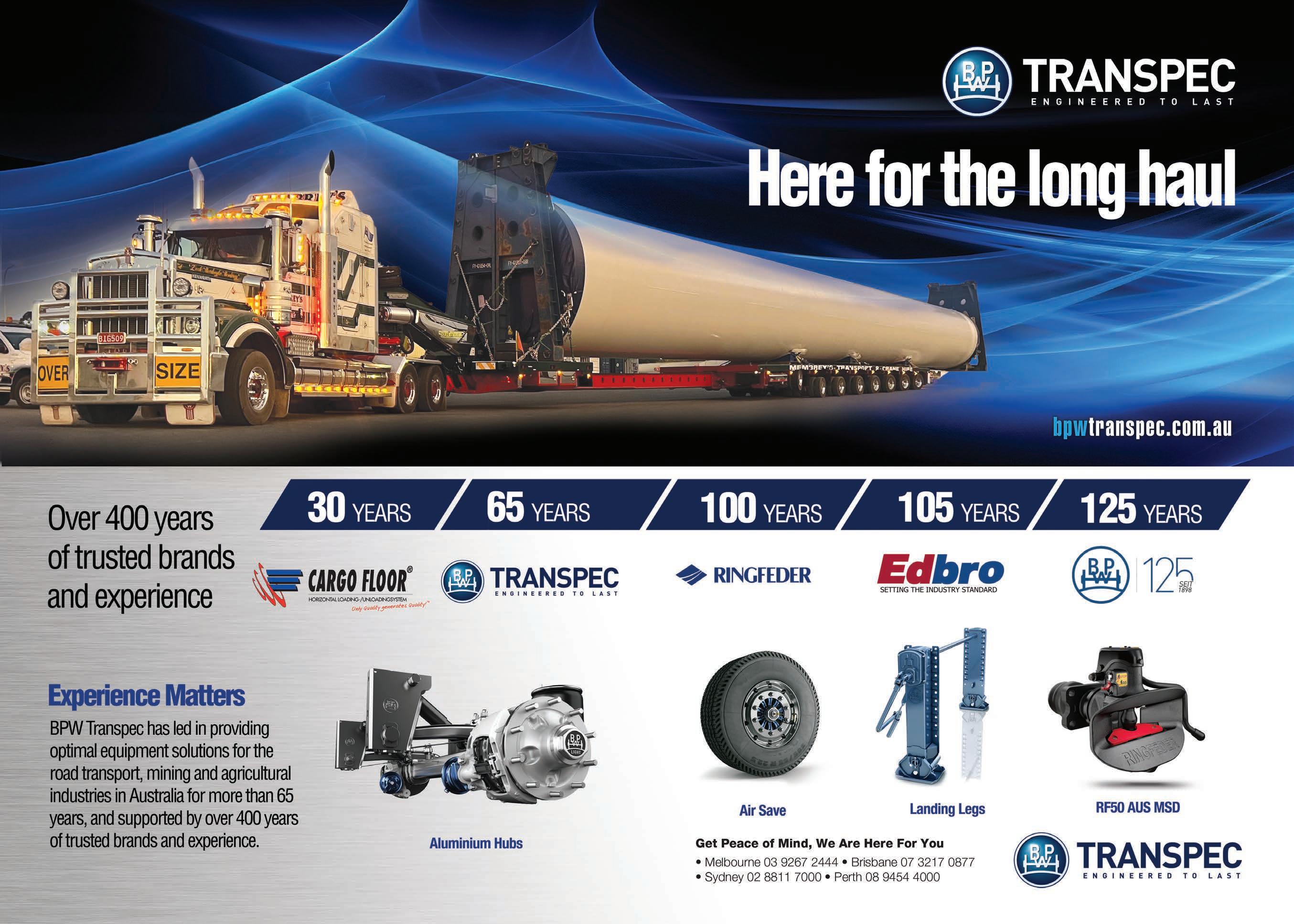
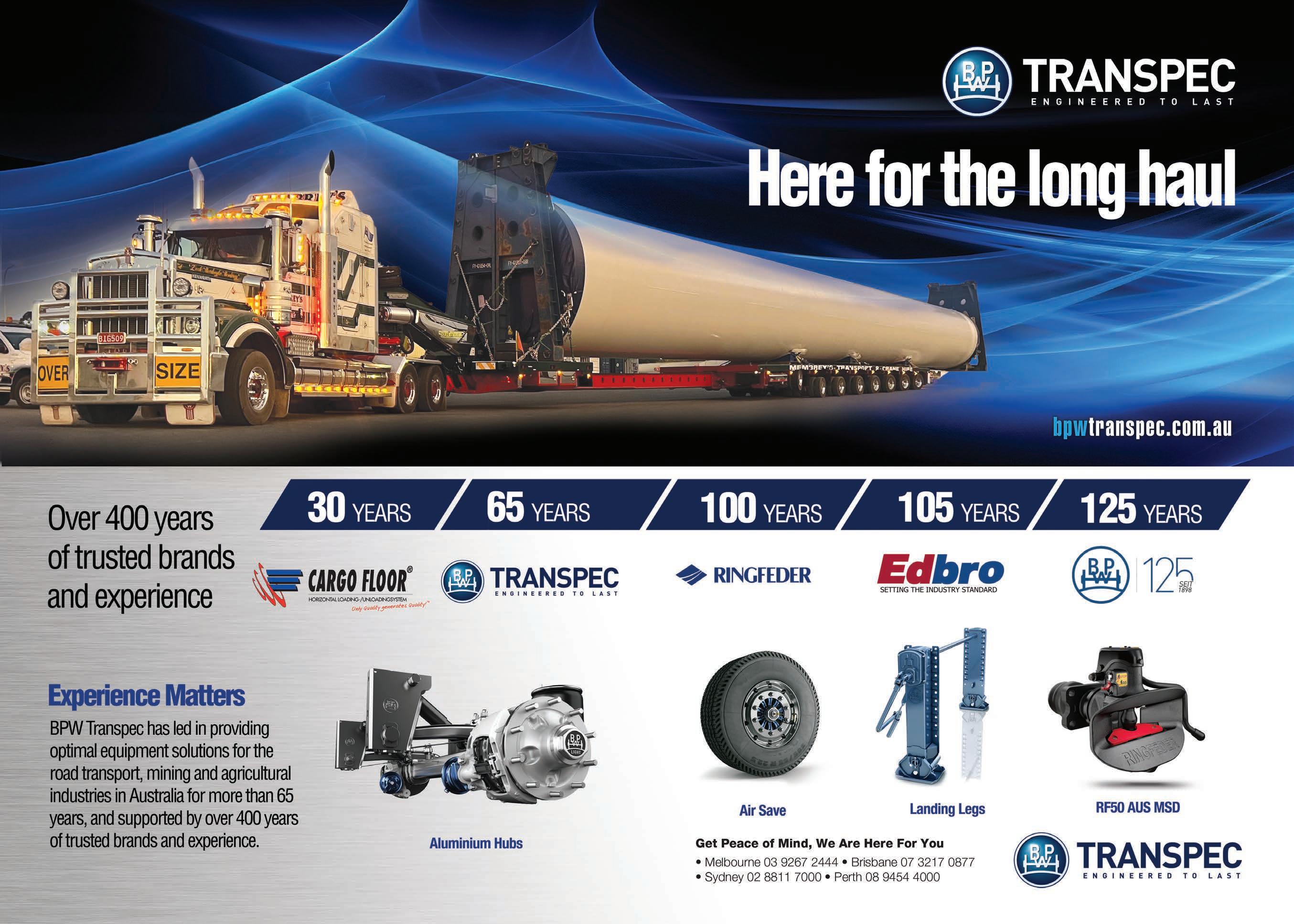
PUBLISHER
John Murphy
john.murphy@primecreative.com.au
MANAGING EDITOR
Luke Applebee luke.applebee@primecreative.com.au
EDITOR
Peter White peter.white@primecreative.com.au
JOURNALIST
Sean Gustini sean.gustini@primecreative.com.au
CONTRIBUTOR
William Craske william.craske@primecreative.com.au
ADVERTISING
Con Zarocostas: 0422 222 822 conzarocostas@primecreative.com.au
Ashley Blachford: 0425 699 819 ashley.blachford@primecreative.com.au
DESIGN
Alejandro Molano
ART DIRECTOR
Blake Storey
CLIENT SUCCESS MANAGER
Salma Kennedy salma.kennedy@primecreative.com.au
HEAD OFFICE
Prime Creative Pty Ltd
379 Docklands Drive Docklands VIC 3008 Australia
SUBSCRIPTIONS
03 9690 8766 subscriptions@primecreative.com.au
Trailer Magazine is available by subscription from the publisher.
Annual rates: AUS $99.00 (inc GST). For overseas subscriptions, airmail postage should be added to the subscription rate. The right of refusal is reserved by the publisher.
ARTICLES
All articles submitted for publication become the property of the publisher. The Editor reserves the right to adjust any article to conform with the magazine format.
COPYRIGHT
Trailer Magazine is owned by Prime Creative and published by John Murphy.
All material in Trailer Magazine is copyright and no part may be reproduced or copied in any form or by any means (graphic, electronic or mechanical including information and retrieval systems) without written permission of the publisher. The Editor welcomes contributions but reserves the right to accept or reject any material.
While every e ort has been made to ensure the accuracy of information Prime Creative will not accept responsibility for errors or omissions or for any consequences arising from reliance on information published. The opinions expressed in Trailer Magazine are not necessarily the opinions of, or endorsed by the publisher unless otherwise stated.
O cially endorsed by the VTA
are closing the year off with a bang, thanks to $28.6 million in funding from the Australian Renewable Energy Agency (ARENA).
In a recent announcement, ARENA revealed that $100 million in funding would be available under its ‘Driving the Nation’ program in three key focus areas as part of its objective of transitioning heavy vehicles to electric ones. Highlighting this decarbonisation commitment, it’s separately providing $19.6 million to Linfox and $9 million to Toll and unlocking more than $124 million worth of investments in electric vehicles and freight decarbonisation.
“The heavy vehicle market has matured significantly over the past year in relation to battery electric vehicles, particularly vehicle availability and infrastructure,” said ARENA CEO, Darren Miller. “However, there are still significant hurdles including upfront costs for operators, challenges with charging technology and infrastructure, as well as the lack of real-world data.”
Linfox’s $19.6 million will go towards 26 battery electric trucks and charging infrastructure across three distribution centres in Queensland, South Australia and Victoria. The trucks are set to be deployed over three years to a range of different customers across metropolitan and regional routes, and they will reportedly look to validate the performance of heavy electric vehicle trucks at scale over longer distances and through multiple duty cycles per day.
Linfox CEO Australia and New Zealand, Mark Mazurek, was pleased to welcome the funding.
“As an early adopter of electric vehicles, Linfox is proud to be partnering with the Federal Government to grow our electric fleet and accelerate efforts to decarbonise the logistics and supply chain in Australia,” he said.
Meanwhile, Toll’s $9 million will support its ‘Project TruckVolt’ which will roll out 28 battery electric trucks and required infrastructure at 10 customer and Tollowned sites across Australia.
Toll Group Managing Director, Alan Beacham, explained that the funds will be critical for the business’ electrification journey.
“The funding from ARENA supports an important part of our broader strategy to optimise the environmental sustainability of our operations, and we’re delighted to be supporting our customers through a shared commitment to decarbonising their supply chains without needing to rely solely on carbon offsets,” he said. “We’re excited at the prospect of expanding electrification across a larger portion of our fleet over time.”
According to Miller, the Linfox and Toll projects will not only contribute to ARENA’s decarbonisation goals but they will also assist the industry in assessing the ‘technical and commercial feasibility’ of electrifying heavy vehicle fleets. Ultimately, he claims they will be “showing” the transport and freight sectors what is possible when decarbonising heavy vehicles.
That being said, it will be interesting to see what will be in store for the trailer fleets of these massive companies over the next year.
December 2024 19
8 Industry news
Business partnerships, people movements, developments that bolster freight productivity and more.
16Economy
The Tasmanian Government is taking the state’s $2 billion advanced manufacturing industry to the next level.
19PBS report
NHVR Chief Engineer, Les Bruzsa, speaks exclusively to Trailer about Performance-Based Standards.
24PBS equipment & engineering
Porthaul’s new PBS Lusty EMS road train has paid o .
26Trailer builder
The trailer manufacturing industry is as strong as ever.
36Tippers
MFT Hughenden has launched a new PBS AB-triple.
38Service & maintenance
An inside look at Bruce Rock Engineering’s capabilities.
40Landing legs
Learn more about Fuwa K Hitch’s and JOST’s extensive landing leg o erings.
44Trailer building materials/components
A showcase of the products and services that keep trailers on the move.
52ALRTA
The ALRTA is sharing an important livestock message.
54Infrastructure spotlight
What you need to know about Australia’s biggest road projects this month.
56World map
IAA Transportation 2024 organisers are declaring this year’s event a rousing success.
58Fleet of the month
MGM Bulk is deploying 20 new PBS ultra quad road trains along with a fleet of new Kenworth C509s.
60What’s on
Upcoming shows and field days.
24
The Victorian Transport Association (VTA) has recognised Cameron Dunn, one of the transport industry’s greatest contributors, with its highest accolade.
At the 2024 VTA President’s Dinner on 15 October, the former VTA President, Vice President and long-time Executive Council member was presented with the WFD Chalmers Award.
The WFD Chalmers Award is presented annually to recognise individuals that have supported and worked with the VTA over many years with dedication, loyalty and commitment to its existence and longevity.
It was instituted by the VTA in memory of Daryl Chalmers, who was a member of the Executive Council for over 40 years.
VTA CEO, Peter Anderson, said Dunn was a very worthy recipient of the Association’s greatest honour.
“Cameron has served on the VTA Executive Committee for over 12 years and has served the industry with distinction for almost 40 years,” he said.
“He served the VTA as President and Vice President, and has provided his time and counsel on several VTA committees.”
Dunn was presented with the award by VTA President, Mike Lean, who succeeded him in 2019.
Having been involved in choosing past winners during his time as President,
Dunn told Trailer he felt extremely proud to receive the award himself.
“I know the prestige of the award and the requirements of choosing someone, so I was absolutely honoured and blown away,” he said.
“I didn’t even expect to be considered, so it was a huge surprise and I was very honoured.”
Dunn has made several contributions to the transport industry through his past and current roles at the VTA, as well as his positions as Deputy Chairman at the National Bulk Tanker Association (NBTA) and Board Member at Chemistry Australia.
He’s also worked in freight and logistics in a variety of roles.
Dunn joined accredited Dangerous Goods and food transporter, FBT Transwest, as Managing Director in 2009 and continues to lead the company in this position to this day.
Prior to this, he held senior roles within the transport and logistics industry in a career that commenced in 1986 at United Tankers.
Having all of these efforts acknowledged through the WFD Chalmers Award, Dunn said, is a true privilege.
“It’s a recognition, so it’s very special,” he said.
“I feel very proud to be on that honour board with the other past winners.”
It’s also something that he’s extremely humble about.
“You do it anyway, it’s part of what you do,” said Dunn.
“My family’s background is in farming, and their ethos were to always to put in more than what you get out.
“I say that to my kids now, and that’s basically what you do in terms of the industry. You put in more than what you get out, and you reap the rewards.”
Dunn reflected on some of his highlights at the VTA, expressing his gratitude for the ability to be involved in its committees – particularly the Finance Committee and his position as Chair – and of course for the opportunity to represent the Association as President.
Now, being on the VTA’s Executive Council and approaching his 40th year in the industry, he said it’s about giving back.
“I wouldn’t have been able to do any of this if I didn’t have a great team and the support of my family,” said Dunn.
“You need a great team behind you, and it’s exciting times with FBT Transwest at the moment.
“We’re growing and getting some really good people on board, and you need that to be able to provide a good service, but also more importantly, a safe service. And that’s what we need as an industry – we need a safer industry.”
Western Australia 5 Freight Road, Kenwick WA, 6107
Tel -(08) 9350 6470
Silk Logistics Holdings has entered into a Scheme Implementation Deed (SID) with DP World Australia for the acquisition of 100 per cent of the issued share capital of Silk by way of a scheme of arrangement.
Under the terms of the scheme, Silk shareholders will receive total cash consideration of $2.14 per share, less any dividends declared or paid prior to shareholders on or before the date of implementation of the scheme.
The scheme consideration values Silk’s equity at approximately $174.5 million and represents:
• a 45.6 per cent premium to the last close of $1.47 on 8 November 2024;
• a 60.6 per cent premium to the 1-month volume weighted average price (VWAP) of $1.33 to 8 November 2024; and
• a 58.4 per cent premium to the three-month VWAP of $1.35 to 8 November 2024.
Silk’s Board of Directors have unanimously recommended that Silk shareholders vote in favour of the scheme, in the absence of a superior proposal and subject to an Independent Expert concluding that it is in the best interests of
the company’s shareholders.
Each Silk Director reportedly intends to vote all of the shares that they hold or control in favour of the scheme, subject to those same qualifications.
“The Board has carefully considered the proposal from DP World Australia and believes it represents compelling value for the company and an attractive outcome for Silk shareholders,” said Silk Logistics Chair, Terry Sinclair.
expertise, Silk will continue to focus on providing the highest quality services to its customers.
“The Board unanimously recommends that Silk shareholders vote in favour of the scheme, subject to the conditions outlined in this announcement.”
Silk Logistics CEO and Managing Director, John Sood, commented on the significance of the announcement made.
“Today is an important and exciting day in the history of Silk,” he said.
“The proposed transaction recognises the significant investment that Silk has made into its national integrated port to door service offering, extensive capabilities and the strong relationships we have built with our dedicated customer base.
“With the benefit of DP World Australia’s infrastructure combined with Silk’s landside
Rio Tinto has announced a new five-year partnership with Channel 7 Telethon to continue supporting the health and wellbeing of children in Western Australia.
Rio Tinto’s new $27.5 million partnership will contribute to important healthcare initiatives as well as provide funding to a range of not-for-profit organisations through the Channel 7 Telethon Trust to help transform the lives of WA children.
“Rio Tinto is delighted to continue its partnership with Channel 7 Telethon, supporting important research and health programs to help improve the wellbeing of children across the state,” said Rio Tinto Iron Ore Chief Executive, Simon Trott.
“Channel 7 Telethon is an iconic Western Australian charity making a meaningful difference to the lives of children and
families, and Rio Tinto and our entire workforce are proud to support this wonderful cause.
“We want a better future for all Western Australians and we’re excited our contribution will support important children’s charities.”
Rio Tinto’s previous partnership provided support for mental health research, type 1 diabetes and Channel 7 Telethon Trust beneficiaries.
Channel 7 Telethon Chairman, Richard Goyder, extended his gratitude to Rio Tino for its contributions.
“We see strong strategic and cultural alignment between Silk and DP World Australia and we look forward to working together to achieve our shared goals.”
DP World CEO and Managing Director, Asia Pacific, Glen Hilton, said DP World Australia is excited about the opportunity to welcome Silk into its portfolio.
“This acquisition aligns with our strategy to deliver complementary logistics solutions for a broad customer base across Oceania,” he said.
“Combining DP World Australia’s terminal operations with Silk’s value add services enhances our capability to deliver enhanced solutions for customers and to create sustainable value for all stakeholders.”
make a lasting difference in the lives of vulnerable children and their families in our communities.
“We are very grateful to Rio Tinto for their generous annual donation of $5.5 million to Telethon,” he said.
“This incredible contribution and support enables Telethon and its beneficiaries to
“Thanks to this commitment, community organisations and charities can provide essential services, educational opportunities, and vital programs that inspire hope and foster resilience.
“Together, Telethon and Rio Tinto are building a better and brighter future for our kids, one that is filled with possibility and promise.”
National Heavy Vehicle Regulator (NHVR) CEO, Sal Petroccitto, has announced his resignation.
Petroccitto will step down as of 24 January 2025 after successfully leading the regulator for more than 10 years.
NHVR Chair, Duncan Gay, expressed his gratitude for Petroccitto – explaining that he is leaving the NHVR in great shape following an unheralded period of achievements in establishing a modern and respected national body.
“On behalf of the NHVR Board, staff and the road transport industry, I want to share my sincere thanks to Sal for his outstanding dedication and passion in championing better outcomes for the safety and livelihood of the heavy vehicle industry and all road users,” he said.
“Sal has worked tirelessly to build industry trust and respect to ensure the modern regulatory approach being implemented by the NHVR will achieve genuine and tangible
national safety and productivity reform.
“His no nonsense and practical approach in saying it as it is was embraced by industry and a critical part of the partnership and trust he built.”
Gay said Petroccitto drove the successful transition of participating state-based regulatory functions to establish the NHVR.
“Under Sal’s leadership, we are now seeing consistent enforcement and education outcomes paving the way for more on-road consistency,” he said.
“This includes leaving a legacy of achieving genuine safety behavioural change and improved culture through the establishment of an inform, educate and enforce approach to compliance.”
Petroccitto informed the NHVR Board of his decision to resign as CEO in October.
He made the announcement to the public in a statement online on 4 November.
“It is difficult to fully express the rewarding journey I have been on both personally and
professionally since commencing as the CEO of the NHVR in May 2014,” he said.
“I knew the challenges that laid ahead and embraced them to prove we could deliver one of the largest national reform programs in this country. I’m so proud to say that we did it.”
“I hope the small part I have played will leave a legacy where industry feels respected and heard and can continue to work openly with the regulator and government to achieve the common goal of keeping our roadsides safe and trucks moving.”
An extensive nationwide recruitment process will commence over the coming weeks to appoint a new CEO to the NHVR.
Border Express has opened its brandnew depot located in Cranbourne West, Victoria.
The new facility replaces Border Express’ existing site in Dandenong as its operational hub for Victoria’s southern and eastern areas.
Boasting a 40-per-cent increase in floorspace and the latest safety technology, the depot is strategically positioned in a major growth corridor – a prime location which not only enhances Border Express’ operational capabilities but also aligns with its commitment to better serving its pickup and receiver base.
The new depot measures in at 20,000 square metres, a substantial increase from the company’s previous 12,000-squaremetre facility.
It features raised docks, a bulk layout tailored to Border Express’ needs, oneway traffic flow, pallet racking and larger staging areas.
These enhancements, Border Express claims, will translate to improved operational flow, reduced congestion and increased productivity.
“This state-of-the-art facility marks a major milestone in our growth journey, enhancing our operational efficiency and capacity in Victoria’s Southeast region,” a Border Express spokesperson said.
leadership roles within the new site.”
Toll Group has opened a new state-ofthe-art healthcare logistics warehouse in Melbourne.
Located within the Tullamarine Airport Business Park, the 10,000-square-metre custom-built distribution centre is a TGA licensed site specifically designed to support life sciences and healthcare logistics as well as the unique requirements of customers – including Toll’s valued strategic partner, CSL.
It boasts operational capabilities such as controlled ambient, cold chain and ultra-low frozen product storage which allow Toll to handle a wide range of sensitive healthcare
The new depot offers ample parking space for 35 doubles, singles, rigids and prime movers, facilitating smooth operations and easy accessibility for Border Express’ fleet.
In addition, it is expected to ensure job security and stability for the next decade.
“With seating for more staff members, our new office space accommodates for more employees than our current setup,” the spokesperson said.
“This expansion not only supports our growing team but also creates opportunities for individuals to step into
The increased floor space will allow Border Express to handle larger volumes, redesign boundaries for more efficient service coverage and enhance linehaul capacity.
Moreover, the new location opens doors for the company to explore automation in sortation processes, adopt sustainable practices such as solar energy utilisation and waste diversion, upgraded security features and improved safety by separating material handling equipment from personnel through raised docks.
“This expansion not only supports our revenue growth objectives but also reflects our commitment to providing reliable and sustainable logistics solutions,” the spokesperson said.
“With 20,000 square metres of space, raised docks, improved traffic flow, and sustainable initiatives like solar energy, we’re ready to take things to the next level.”
products with the utmost precision and care.
Another standout feature of the facility is its strategic location which provides Toll with access to major transportation hubs across Melbourne including the airport, seaport, rail terminals and critical road-freight arterials.
“We were honoured to have some special guests and VIPs join our Toll team including Managing Director, Alan Beacham, Executive Director, Mikiyasu Yuasa, President of Government and Defence, Perry Singh, and General Manager of Healthcare, Michael Lawrence, to officially open the facility and see some of the advanced technology available to
assist government and industry with future healthcare logistics challenges,” Toll said in a statement online.
With sustainability also at the core of Toll’s operations, the facility incorporates various eco-friendly practices and technologies.
The site, for example, gets 100-per-cent of its power from the Melbourne Airport’s independent solar power network.
It also has access to 20,000 litres of sustainable sourced water through its sitespecific irrigation system and smart use of grey water.
In addition, it is the process of securing 5-star Green Star Rating.
Linfox has officially opened its biggest supersite in Laverton, Victoria.
The purpose-built Linfox BevChain beverage distribution centre will support more than 14 major brands and valued customers across the beverage retail sector and Australian beverage manufacturers.
Spanning an impressive 70,000 square
Auswide Transport Solutions has recently opened a new state-of-the-art depot in Direk, South Australia.
Built by industrial design and construct specialists, Sagle Constructions, the facility features brake and suspension testing technology, in ground mechanical service pits, a fully automated truck wash bay, an accredited weigh bridge and modern sleeping quarters.
The 20,000-square-metre site is comprised of a 3,000-square-metre building and 15,000-square-metres of pavements and hardstand, and joins Auswide’s depots and workshops in Brisbane, Sydney, Dubbo, Adelaide and Perth.
The new facility was opened by South Australia Minister for Infrastructure and Transport, Tom Koutsantonis, on 23 October.
Also in attendance were South Australian Road Transport Association board members and President, Sharon Middleton, Western Roads Federation CEO, Cam Dumesny, and senior representatives from the National Heavy Vehicle Regulator.
Auswide Transport Solutions Director,
Amrit Kankar, said the $13 million investment was testament to the company’s ongoing commitment as an industry leader in raising the bar on equipment and driver safety improvements.
“We are committed to continuously improving the safety of our business, and in turn demonstrating leadership to the national industry,” he said.
“As a result, our track record for on-time customer deliveries while maintaining the highest levels of safety speaks for itself.
The final report of an investigation into dynamic loads on couplings fitted to heavy High Productivity Freight Vehicles (HPFV) and Performance-Based Standards (PBS) combinations has been released.
The project, led by ARTSA-i, involved measurement of the coupling forces on quad-trailer 160-tonne road trains during routine daily journeys of hundreds of kilometres in the Northern Territory.
An instrumented dolly was used in different positions on a Direct Haul bulk fuel road train to measure forces at different locations.
The study found that the forces experienced by the couplings were similar, whether the dolly was underneath the second, third or fourth trailers.
This result was contrary to the conventional understanding as reflected in the current Australian Standards. The peak forces were predicted
using the existing formulae in the Australian Standards.
According to ARTSA-i, there was no evidence of a maximum force plateau that could be expected as road trains get longer. Instead, the peak forces appeared to increase in proportion to the overall mass.
The most common occurrence of very high forces was when a vehicle was at very slow speeds or coming to a stop – when braking, shunting, or manoeuvring the long combination vehicle.
The project was funded by the National Heavy Vehicle Regulator’s (NHVR) Heavy Vehicle Safety Initiative (HVSI) and supported by the Australian Government.
ARTSA-i Chair, Dr Peter Hart, commented on the significance of the study.
“The benefits of the study for industry are many as there are huge cost and logistical advantages in using regular coupling sizes
onsite reduces downtime and benefits our customers, but it also gives our drivers time and quarters for best practice rest and recovery.”
In addition to the technical features, the facility includes nine individual sound dampened sleeping quarters with blackout blinds, a modern well-appointed kitchen and shower facilities to allow drivers to manage fatigue and properly rest and recover.
or increasingly heavy combinations,” he said.
“It is hoped that the study findings will enable road train drivers and operators to safely utilise conventional couplings on heavy road train fleets into the future.”
Furthermore, he recognised the project as an international effort by extending his gratitude to all that contributed.
“Engineers from the various coupling manufacturers in Australia and Europe also contributed their knowledge, with Ringfeder/VBG engineering input of immense value given their recent experience with similar coupling integrity testing in Sweden,” he said.
“This project would not have been possible without this coordinated, industry support approach.
“The project has international significance because Australia leads the world with the use of long and heavy multi-combinations.”
Engineered for durability and superior performance, Lucidity Australia's 26281CARK-BVG2 LED marker with a 6-way Moulded Deutsch Connector ensures reliable visibility and easy installation for trailers on the road.
the local manufacturing industry.
The AMAP is focused on building a resilient, diversified and sustainable manufacturing industry which contributes significantly to Tasmania’s economy.
According to the Tasmanian Government, it will foster collaborations between manufacturers, suppliers and service providers to create strong industry clusters that can innovate together.
The 2028 Plan follows the delivery of the state’s four-year AMAP 2024, with all 20 of its actions delivered in full.
Tasmania Premier and Minister for Trade and Major Investment, Jeremy Rockliff, emphasised its importance and how it will benefit the sector.
“Manufacturers employ nearly 20,000 Tasmanians and support 33,000 Tasmanian jobs through the flow-on effects to their supply chains and in their local communities,” he said.
“As part of our 2030 Strong Plan for Tasmania’s Future, we are strengthening manufacturing which is Tasmania’s largest export industry.”
The 2028 Plan is built around three key themes – people, productivity and market success.
Developed through extensive consultation with industry and stakeholders, it has 15 actions designed to support growth and innovation in each of these areas.
The AMAP 2028 is the Tasmanian Government’s third successive action plan for the manufacturing sector.
It follows 141 grants being delivered to Tasmanian manufacturers as part of the AMAP 2024 to support improvement initiatives – with around $10 million in new investments made by 51 businesses that received grants.
“The new Action Plan will build on these highly successful activities to strengthen this industry, support local jobs and keep our economy strong,” Rockliff said.
“With shifting global forces changing the landscape for our manufacturers, the Tasmanian Government recognises the need to support our industry to adapt and continue to thrive.
“We are committed to strengthening our industry and building on the successes to date.”
According to the State Government,
Tasmania’s manufacturing environment has seen extraordinary change since the original plan was released in 2016.
“There are new opportunities with changing technologies and a renewed push to decarbonise the Australian and global economy,” the Government said.
“Our major industrials, large manufacturers and processors hold a key position in the Tasmanian economy as they drive continual improvements, build local supply chains and generate wealth for the state.”
Developed in close consultation with industry and organisations, construction of the AMAP 2028 involved over 90 conversations and a statewide workshop to identify industry needs, concerns and areas where government can assist.
Skel trailers
Evolution side tippers
Road train dollies
Flat tops, drop decks
Deck wideners and extendables
Coldcore
Etnyre
Titan
PBS
National Heavy Vehicle Regulator Chief Engineer, Les Bruzsa, speaks exclusively to Trailer about Performance-Based Standards over the last year and what 2025 will entail.
Les Bruzsa is highly regarded both nationally and internationally for his contributions to the transport engineering industry in the areas of heavy vehicle dynamics, Performance-Based Standards (PBS), computer simulation and heavy vehicle technology. In his current position as Chief Engineer at the National Heavy Vehicle Regulator (NHVR), Les is leading the continuous improvement of heavy vehicle regulations and standards while overseeing a broad variety of engineering and technical activities within the regulation.
Les has been at the forefront of advocating for PBS since the early 2000s, taking a leading role in pushing the boundaries of innovation necessary to make heavy vehicles safer and to manage the increasing freight task.
Trailer: Are there any emerging trends in PBS that you can discuss?
Les Bruzsa: In terms of the current trends, I think there are a few things that we have to mention. What’s interesting is we’ve currently got more than 24,400 PBS-approved combinations in our books. You might not think that it’s a big number, but if you consider the size of the fleets where there is a PBS combination available, that’s roughly around 110,000 combinations – so that would include truck and dogs, prime mover semis, road trains and B-doubles – and PBS combinations would represent more than 20 per cent of that fleet. We’re going to have 25,000 combinations by the end of the year, so it’s not a niche market anymore.
In the last few years there has been
a huge increase in the growth of PBS combination numbers. In 2021 and 2022 we approved around 2,100 to 2,200 PBS combinations. Last year we approved more than 3,800 and as of October this year we have approved more than 4,300 combinations. What this shows is that the industry is turning more towards PBS combinations and that industries are recognising their importance in terms of the benefits they deliver when switched to.
T: Do the NHVR’s statistics reveal anything else particularly interesting?
LB: The crash statistics show that PBS vehicles are the safest in the heavy vehicle fleet. They’re more than 50 per cent safer than ‘prescriptive’ combinations. If you look at Australia’s
PBS fleet by the level, roughly 90 per cent of it is still PBS Level 1 and Level 2 combinations. So, while there was originally an expectation that PBS would lead to more larger combinations, we can see that 90 per cent of Australia’s fleet would be Level 1 and Level 2. And if you look at length, that’s roughly the same. More than 92 per cent of the national PBS fleet would be below 30 metres. Those are the levels where the more popular PBS combinations are.
T: What are your reflections on PBS over the past 12 months?
LB: It’s obvious that PBS access is still probably the biggest issue in the PBS scheme. Over the last couple of years and especially in the last 12 months, Victoria and New South Wales have opened up significant networks for PBS Level 2B vehicles and that resulted in a huge increase in the numbers of the entire PBS Level 2B class. So, I think what was demonstrated was that if we can resolve the access issues the industry will have more confidence, and it will be able to introduce a range of different combinations which have more benefits.
T: What would you say has been the biggest change in PBS in recent times?
LB: The PBS 30-metre A-double is now the new workhorse of the of the Australian heavy vehicle fleet, and we can see that in the increasing numbers. Up until recently, it was mainly the different truck and dog combinations which represented the biggest proportion of the national fleet. In the last couple of years, we’ve also seen that the A-double numbers are going up. So, looking at the numbers in our books, we’ve got around 10,000 truck and dogs, more than 5,000 A-double combinations, around 3,600 prime mover semis and around 3,000 B-doubles. So, Australia’s fleet has changed significantly in the last couple of years and A-doubles are extremely important now.
T: Have there been any noticeable changes with how industry is taking up PBS equipment?
LB: We’ve seen a wider range of new combinations since the introduction of PBS. We’ve currently got more than 110 different PBS combinations on our register which are all different types if you
consider the extra axle configurations as well. We have also seen the introduction of semi-trailers with two axle groups which is a completely new idea for increasing payloads.
PBS has opened up opportunities for the industry to develop specialised, tailored units for its freight task which I think is great. It’s also increased opportunities for different vehicle design features – for example, we now have an increased amount of innovative ideas and designs such as rigid drawbars, steerable axles, different axle configurations and the application of super singles.
T: You mentioned that access for PBS vehicles has been a fairly big issue as of late. Have there been any updates to route access that you would like to discuss?
LB: The interesting thing about our access certainty is that we, the NHVR, can now analyse the performance of the PBS fleets operating in different jurisdictions, even though there are freight tasks which are going through a number of states or jurisdictions.
I mentioned earlier that Victoria and New South Wales have increased their PBS networks significantly, and that’s beneficial in terms of the productivity and safety. So, one thing we will be trying to do in the near future is showing information about the safety and productivity benefits of a PBS fleet to decision makers. We have to deal with more than 530 local governments when we are talking about access, and so if we can demonstrate all these benefits that a PBS fleet can deliver – not just safety but productivity and the environmental advantages – then hopefully the result is that better networks are opened up for the operation of these combinations.
T: PBS 2.0 – do you have any insight that you can share on how it’s progressing?
LB: We are working on a number of things to better the current scheme. One key element of PBS 2.0 is reviewing the standards to check if those PBS levels
are still appropriate with what we currently have. The other question is do we need any new standards? Do we find that some of the standards are not relevant anymore? We have to understand that technology has changed in the last 15 to 20 years. For instance, there is a standard in PBS called ‘Directional Stability Under Braking’. This existing PBS requirement is still calling up the very old braking standards for trailers and trucks in the scheme and currently doesn’t recognise improvements in heavy vehicle technology. So, one of our reforms is to move away from the traditional load proportioning valve system in terms of the braking requirements for PBS vehicles. This standard is planned to be introduced in the very near future. We’re aiming to
update the braking requirements and line it up with the current Australian Design Rules (ADR). PBS vehicles will have to comply with those standards, and that means they will have all the stability systems which are currently not there as a requirement as well. PBS also doesn’t currently consider the benefits of roll stability systems in PBS assessments, so the other important element of this review is how we can modernize the PBS standards and how we can have consideration for technology such as roll stability systems or electronically steered axles. The other focus is about changing the legislative framework around PBS. The NHVR is still very constrained in terms of how we maintain the PBS Standards and Vehicle Assessment Rules.
The legislative process could be slow, so as part of the current review of the Heavy Vehicle National Law (HVNL), we are hoping that that there will be some reforms so that we can have better opportunities or abilities to change the regulatory framework around PBS and make it more adaptive for all the technological changes. So, that’s what our plans in terms of PBS 2.0 are. At the same time, we are doing lots of work in terms of working with road managers and providing them with engineering and technical advice in connection with the performance of PBS vehicles, and I hope that would help with improved PBS access.
T: Is there an update on when PBS 2.0 will arrive?
LB: We hope to have some elements ready early next year. We have already started the consultation process with jurisdictions and we’ve got a number of discussion papers around for consultation. So, we have the Heavy Vehicle Productivity Plan which is mainly about how we can improve productivity in the road transport sector and a document which identifies the current regulatory roadblocks that we want to change in terms of improving the scheme.
T: Congratulations on all of your work and success with PBS. Is there anything else you would like to mention?
LB: They are calling me ‘The Quadfather’ and sometimes ‘The father of PBS’. I care about PBS because I’ve been there from day one in the early 2000s, and for me, it’s just amazing to see how it has grown. It’s a fantastic scheme and it’s very unique. There’s no other country around the world which has such a comprehensive performance-based scheme for the management of vehicles, so what we have achieved here in Australia is amazing. Obviously, there are still issues and difficulties, but I think the scheme is going well and it’s delivering all the things that we expected it to 15 years ago. I was driving back from Toowoomba to Brisbane last week and I counted 28 PBS A-doubles and a large number of other PBS combinations in one hour. I remember how difficult it was to put the first PBS A-double on the road back in 2011, and now they are running everywhere. So for me, that’s, that’s the big achievement – to see these vehicles on the road.
Porthaul has taken its Freighter Group fleet to the next level with the launch of a new Performance-Based Standards Lusty EMS A-double road train which has delivered significant productivity gains for the company.
Porthaul, a carrier of various commodities based in Portland, Victoria, made its first move in the transport industry by opening its doors on 1 November 1990. The business first started off carting bulk agricultural products such as grain, fertiliser and limestone, yet Australia’s ever-increasing demand for goods coupled with the business’ craving for more saw new paths reveal themselves to the business.
“It started with my father, Brian Williamson, who was a subcontractor in those early days,” says Porthaul General Manager, Edward Williamson. “There was another company at the time called Bulkhaul which was going to close its doors, and he went to their customers and asked them if they would support him if he kept going. They said they would, and it’s basically grown from there.”
In the time that has followed, Porthaul has evolved even further to specialise in a larger range of freight types such as wood chips, fuel, refrigerated goods, general freight and containers. Yet for the business, one thing still remains the same – and that is its reliance on Freighter Group for its trailer needs.
for all of its trailing needs for over 10 years, and as a result has accumulated over a dozen Performance-Based Standards (PBS) combinations ranging from skels to log trailers and Tautliners.
“We’ve been working with Freighter Group for many years now,” Edward says. “We’ve always had a good relationship with them, and it’s definitely been a relationship that has had many different applications. They have always looked after us and have helped us get the product that we need.”
In its latest trailer delivery from Freighter Group, Porthaul has deployed a new PBS Lusty EMS A-double road train combination which consists of two chassis tippers and a rigid drawbar dolly.
reference design and includes a plethora of features suited to Porthaul’s particular application. Meanwhile, the inclusion of a rigid drawbar dolly further enhances the combination’s on-road performance and stability.
The unit is primarily being used to transport grain to the Port of Portland for export, which sees it travel through the business’ hometown and the Wimmera region to arrive at its final destination. Around this, it also delivers fertiliser to various farmers which occasionally sees it
end up in southern New South Wales.
According to Edward, the Lusty EMS road train has been showing extremely positive signs through its on-road performance.
“Driver reports are all very good,” he says. “The higher productivity and safety of the vehicle is obviously the big contributor to that. It rides well and has a good weight distribution, and the drivers haven’t had any issues with it which is good.”
The Lusty EMS bodies also feature a tapered hoistwell which results in a lower centre of gravity and allows for more cubic capacity if needed. This, as well as the overall design of the model, is what stands out to Edward.
“Having the drop deck allows for that lower centre of gravity and cubic capacity if needed,” he says. “It gives us an opportunity to vary the products that the trailers are able to cart.”
worth it, as the A-double’s deployment has resulted in increased profitability and productivity business-wide.
Freighter Group, Edward says, was chosen once again for this application due to its “proven track record of producing highquality trailers”. For him, the aftersales service experienced following each purchase is the icing on the cake.
“All of our Freighter trailers have been excellent,” he says. “We’ve had our Freighter PBS wood chip road trains for 10 years now, and we haven’t had too many issues at all. They’ve all stood the test of time.”
“Freighter Group has always built a good product, and now that the network is starting to open up in terms of PBS vehicles and road trains it was time that we moved towards the bulk tippers.”
This venture into tippers from Freighter Group, Edward explains, has been well
“It’s definitely much more cost-effective, because we’re increasing the amount of product we can cart with the one prime mover,” he says. “That’s the main aspect of it. The features that come with these trailers are always good, but it’s definitely the higher capacity that has benefitted us most. It’s effectively one-and-a-half trucks on the road.”
This new Lusty EMS PBS road train combination has also been given a massive role in Porthaul’s new business venture.
“We’ve just built a 4,500-square-metre grain storage facility in Portland,” Edward says. “It’s being used to store grain for export down here, so coming into Portland carting the extra capacity with the A-double is definitely an advantage for us because we can do it with less trucks and with bigger weights.
“It’s a significant amount of grain that needs to come down here, so having
the new trailers with that extra capacity definitely takes the pressure off.”
Based on what he’s seen so far, Edward is very confident in the Lusty EMS combination’s ability to lead this operation. And because of that, he believes it’s also likely that similar trailers will follow suit as business ramps up.
“I don’t think we’ll have any issues with the trailers themselves,” he says. “They’re a reliable build and a great product.
“It’s exciting to finally have an A-double tipper in the fleet, and I’m looking forward to increasing them in the future. We’ve had Freighter Group PBS vehicles for over 10 years now, and this is just another one that we’ve relied on them to develop for us and to get us going. It’s certainly delivered.”
Contact Freighter Group
Ph: 03 5339 0300
Web: www.freighter.com.au
SCF is one of Australia’s leading suppliers of tailored intermodal equipment solutions, with its purpose-built containers providing businesses like Woolworths, Australia Post and Total Logistic Solutions with an efficient way to enhance their fleets, increase flexibility and keep freight moving.
SCF first began in 1992, and within two years it was on track to become a dominant force in Australia’s logistics sector. The company’s market share was significantly bolstered by its innovative intermodal container offering which provided the flexibility to transport any freight across the country’s vast network of roads and railways.
Today, SCF’s fleet includes over 16,000 high-quality units across 10 nationwide depots in Australia and New Zealand –meaning availability is always high and the changing needs of industry and customers can be met with ease.
Built upon 30 years of experience, SCF’s intermodal containers are purposedesigned with the specific safety features and functionalities required for road and rail transport. SCF General Manager of
Intermodal Equipment, Nick Schwartz, describes the company’s fleet as durable, hard-wearing, safe and secure.
“Our containers come with many of the same great features as traditional trailers, while also being multimodal for use on road and rail,” he says. “Each unit is two pallets wide and carefully crafted to maximise payload and capacity for Australian freight.”
End-door and side-door options are available along with custom builds and refrigerated containers. SCF’s refrigerated range is kitted out with superior thermal insulation and can maintain temperature with reduced machinery run time – helping keep fuel consumption and expenses down. They also feature diesel TK or Carrier machinery with on-board fuel tanks, allowing them to operate without being connected to truck diesel or power.
One of the most compelling features of intermodal containers is their highly versatile nature. As Nick explains, they can be quickly and easily swapped out for new freight types.
“Conversion from a dry combination to a refrigerated combination takes just minutes,” he says. “The ability to rapidly interchange equipment types allows our customers to quickly adjust to changing freight requirements while using their existing skel fleet.
“This adaptability also enables fleets to expand and contract when required, allowing an increase in deliveries and better fleet utilisation overall. In addition, there are numerous occasions where containers provide a temporary storage solution prior to the actual freight linehaul movement.”
Flexible intermodal solutions, according to Nick, can also unlock multiple new revenue opportunities. He says the ease of conversion means businesses can rapidly adapt to meet changing client needs, freight profiles and seasonal demands.
“Many of our customers with skel fleets naturally experience periods of lower utilisation,” he says. “We have worked with many of these customers to supply transport containers to convert underutilised skels into trailers.
“For example, a company that mainly uses skels for wharf cartage can easily add a curtainsider container to undertake PUD work.”
Additionally, intermodal containers can open the door to entirely new transport modes such as rail. Nick explains that expanding from road-only to road-and-rail applications could lead businesses to new territories, clients and revenue streams.
“We are seeing a growing trend in the market for road and intermodal users to push more freight onto rail due to benefits in cost, geographical reach and ESG,” he says. “A rail offering can complement road operations and allow for new growth opportunities with new and existing customers.”
SCF has helped a huge range of companies bolster their logistical reaches
with intermodal containers. One of these companies is Total Logistic Solutions (TLS).
When TLS sought a container option to pair with nine new Vawdrey A-double skels earlier this year, it reached out to SCF. Drawn to SCF’s durability, flexibility and two-pallet wide specifications, TLS chose its solution of 40’ containers and skels which would operate as dynamic and sturdy long-haul freight trailers.
“We partnered with SCF because we had heard good things about them in the market,” says TLS CEO, Jason McHenry.
“Having the containers two pallets wide has given us the flexibility to transport carpet rolls one way and then palletised freight on return trips from Brisbane to Melbourne.”
For companies with high-volume operations like these, intermodal containers are an ideal solution.
“Our national footprint and high intermodal container availability means that as a business grows so can its operations, and any increased demand can be met efficiently, effectively and consistently,” Nick says.
By enhancing their fleets with intermodal containers and/or skel trailers supplied by SCF, Nick says businesses can ultimately open themselves up to both new customers and new freight across a wider range of transport channels.
“Backed by our 30-year tenure in the industry”, he says, “SCF is well-placed to provide the optimal intermodal solution – helping improve operational flexibility, increase revenue and strengthen the country’s supply chain.”
A 19-metre B-double tanker from Marshall Lethlean Industries Australia has played a big role in Pacific Fuels’ expanding operations. A new combination set to join the fleet next year will further back the company as it takes things to the next level.
Pacific Fuels is a business specialising in food and fuel with several service stations located within Queensland. The business was established in 1997 by founder, Joseph Matoki, who prior to creating it already had a fair taste of the industry.
Before Pacific Fuels, Joseph ran several fuel franchises in Melbourne during the early ‘90s which allowed him to become very familiar with the business.
So, when he decided to go out on his own, he purchased his first service station in Withcott, Queensland, using the knowledge he had gathered to form Pacific Fuels.
“That’s what I knew,” he says. “I used to have franchises, so I started to purchase service stations and do things myself.”
Following that initial decision, opportunities continued to arise and the company continued to flourish.
“When we were discounting, our volume increased and increased,” Joseph says. “We bought some more service stations and purchased some land, and we did it ourselves. The company expanded enough for us to go and purchase our own trucks and it kept growing from there.”
Pacific Fuels now has various sites within the Toowoomba region, with a second location having joined the original one in Withcott and a third being established in Helidon Spa. And, thanks to record growth experienced in recent times, the company is going to expand even further by opening a fourth service station in Toowoomba this month.
“We make records every year over the previous year because we keep investing our money,” Joseph says. “So, we’re increasing volumes by about 20 per cent every year. Now, we’re going to complete a service station in Toowoomba that will increase our volume even further.”
The 200-square-metre convenience store will offer customers in the region fuel and takeaway food, featuring six dispensers and a truck bay with an extra four pumps. This will not only build on the reputation that Pacific Fuels has created for itself, but it will expand the company’s footprint and capabilities further.
“It will increase our volume in selling fuel,” Joseph says. “The more volume we do, the more we can afford to pay. So, that’s what it comes down to for us.
“I think we’ve built a trust everywhere we do business,” he adds. “We’ve got a very good reputation, and I think we’re also very likeable by the companies that we work with because we’re never late in paying our bills, we always make time and we’re never difficult with things.”
A big contributor to the aforementioned growth that Pacific Fuels has experienced over the last year has been a 19-metre B-double tanker from Marshall Lethlean Industries. The unit, deployed in late 2023, has been essential to the company by transporting its fuel from nearby Quantem, Chevron and IOR terminals straight to the Pacific Fuels Toowoomba sites. Constantly travelling six days a week on highways at great speeds, it hasn’t let the company down.
“It’s done great,” says Pacific Fuels Site Manager, Jeremee Matoki. “It has 200,000 kilometres on it and there have been no issues at all. It’s been managing everything really well.”
The trailer combination, Jeremee says, is a pretty stock-standard spec but it’s served the business well. It features lightweight Hendrickson INTRAAX suspension with
HXL7 extended life wheel ends which has given Pacific Fuels comfort in knowing that it has maximised its payload capacity due to the lightweight suspension.
In addition, the company has increased its operation time with the HXL7 wheel ends due to limited maintenance requirements which have reduced servicing downtimes.
“It suits all of our needs,” Jeremee says. “It’s doing a great job of keeping up with the job, and it’s easy to maintain as well.”
According to Jeremee, the main benefit of having this unit is that it means the business can completely rely on itself.
“It’s allowed us to pick up our own fuel,” he says. “We had to use either third-party companies or the terminals itself before, so it lets us play the fuel market on the retail side and save a decent chunk of money as well.”
The B-double is the first Marshall Lethlean unit to join Pacific Fuels’ fleet. Impressive lead times, Jeremee says, were originally what drew him to the OEM. And after seeing just how well the combination has performed, he’s ordered a new 25-metre B-double from Marshall Lethlean.
“The fact that we’ve been running it without a single issue makes us feel pretty good about their product,” he says. “It’s doing a great job with how hard we’re running it.”
The trailer set is expected to arrive early next year and will be spec’d with some additional features to help the business carry out some expanded services.
“We’re looking at getting pumping gear and other things to start doing wholesale work,” Jeremee says. “So, we’ll get a bit more equipment and some extra features
is aiming for it to be the “biggest service station in the Southern Hemisphere”, and for the entire operation to be a success, Jeremee says additional units from Marshall Lethlean will be required.
“I’ll need another set just to supply that one itself, so there will definitely be more sets in the future,” he says. “We’ve got a couple of other new sites coming and we’ll still be wanting to supply our own fuel when those open up, so we’ll likely get another 19-metre set to supply different regions too.”
As Pacific Fuels closes 2024 with a successful Marshall Lethlean B-double and prepares to open 2025 with a brand-new 25m B-double combination, it envisions
to this, Joseph says a lot of the business’ success has resulted from the support of his customers.
“We appreciate every customer,” he says. “Every customer that supports us means we can get more volume and pass on further discounts.
“The more we purchase, the more discounts we can give – and that’s the key. The more support we get from customers, the more we can lower the price for them.”
Contact Marshall Lethlean Industries Australia
Ph: 1300 202 462
Web: www.cimc.com.au
The Drake Group is looking to close 2024 off with a bang, and it’s planning for an even bigger year ahead.
For The Drake Group, 2024 has been nothing short of success. Record trailer deliveries, significant business growth, new market opportunities and various company highlights across the board have all been contributing factors.
As The Drake Group Director, Sam Drake, reflects on the past 12 months, he says 2024 has been one of biggest years ever for the business.
“We’ve been in a super cycle, and it’s been absolutely crazy,” he says. “We haven’t been able to get enough staff to keep up with the demand of the orders coming in, so that’s been a massive factor.
“We’ve grown the Drake Collectibles business which has attracted a lot of interest due to the new models we’ve released this year, and our engineering company, DBE, has also experienced a lot of growth to the point that we’ve acquired more property for it. So, it’s been a big year with heaps of highlights and growth across all of our businesses.”
Headlining the latest developments at The Drake Group is its arrival into the rental market. Following increased demand from companies looking to hire equipment,
The Drake Group has created a trailer fleet rental business which, although in its infancy, is already showing great signs.
“We’ve entered the trailer hire business for low loaders,” Sam says. “We saw an opportunity in the market for medium to long-term rentals and so we decided to get into the rental business.
“Some people can’t justify buying a trailer straight away. They might want to trial one first, or they might have a
specific project where they only need a trailer for 12 months or two years. So, we’ve now got a fleet of about half a dozen trailers which are a mix of used and brand-new 4x4 full wideners, deck wideners and 2x4 and 2x8 dollies, and we’ll be building it up over time.”
Simultaneously, The Drake Group has
opened a major 22,800-square-metre service and repair facility in Richlands, Queensland.
“The service and repair business is huge,” Sam says. “We’ve taken on a new facility which is highlighting aftersales, remanned parts including leg exchange, service and support. We’re trying to grow that full end-to-end service business where we can do basic servicing right through to midlife and full rebuilds.”
The new facility replaces a shed at The Drake Group’s Queensland headquarters which the business quickly outgrew this year.
“We identified it as a growth business,” Sam says. “We moved into the new shed last month. It has overhead cranes, wash bays, service pits, reman component bays and great access especially for our clients with larger trailers.
“Our spare parts, collectibles, storage, service and repairs are going to move all under the one roof over there, and then we’re going to centralise our trailer building warehousing at the existing site.”
Around this, The Drake Group has been working hard to improve its existing services. It has introduced a lot of lean practices into its business to streamline operations, enhance quality and become as efficient as possible.
“Trying to be as lean as we can has been a big focus,” Sam says. “With rising material and labour costs, you’ve got to find every single bit of efficiency you can.”
upgrades and a new ‘stock’ spec program introduced for Drake quad full wideners and quad deck wideners, this reduced lead delivery times on specific models by 60 per cent and improved efficiency across the board.
More than eight months down the track, Sam says the benefits are still showing, both from an OEM and a customer perspective.
“It’s been going really well,” he says. “We’re trying to become as efficient as we can as well as streamlining our manufacturing processes as best as we can.
“The stock program has been helping with that by getting people into trailers quicker – if you were to order a customised trailer it could take two years, whereas if you order a stock trailer you can get it in around one year. So, it’s been a good thing.”
As part of the program, customers can opt for a stock spec full widener or deck widener that are fitted with The Drake Group’s most popular components.
“The spec that we came up with is based on the most common specs that we sell,” Sam says. “The market has been pretty accepting of it. People have been happy to forego their exact specification requirements because they can get into a trailer quicker. For example, someone might have a specific axle brand that they use or a wheel size that they generally go for, but if the trailer’s there and they can get it quicker, they’re happy to compromise and take what they can get.”
to rein in its lead times as of late.
“Lead times are getting much better,” he says. “You can get into a rows of four trailer within 12 months and a rows of eight trailer within 18 months now. That’s massive – it’s basically half of what it was.”
Looking ahead, The Drake Group is gearing up for an even bigger year in 2025. Growing its service and repair business even further will be a main priority, as well as a series of other plans in place such as the relaunch of an O’Phee flat top trailer as ‘The Queenslander’ which will take place at the 2025 Brisbane Truck Show in May.
But for now, it’s focused on closing the year out with the finish it deserves.
“We’re finishing the year strong, there’s no doubt about that,” Sam says. “We’ve got plenty of builds to complete. We’ve got a full orderbook for 18 months to two years, but in terms of this year’s production output, we’ve got committed deliveries happening. And there’s still plenty of interest in the market.
“I think the customers are a little bit happier that they can get equipment quicker now, whereas before they had to wait a lot longer. That’s been a real benefit to us and the customers, which is something we will continue to strive towards.”
This builds on one of the company’s initiatives earlier this year which saw it completely restructure its Queensland factory. With multiple equipment Contact
The stock program, Sam says, has also played a part in The Drake Group’s ability
QLD 4076
Ph: 07 3271 5888
Web: www.thedrakegroup.com.au
Krueger’s noteworthy 2024 experience has yet again solidified the company’s reputation as a premium trailer manufacturer in Australia’s transport industry.
If Krueger could describe 2024 in one word, it would be ‘remarkable’. In its 46-year journey, the trailer builder has experienced various highlights with highs and lows forming the company into the giant it’s become today. Yet, the last year has been filled with numerous key moments which have added to the business’ history even further.
“It’s been an exceptional year for the company in so many ways,” says Krueger CEO, Kevin Dennis. “We have achieved so many milestones along the way and we are now laying the foundations for continued growth across all of our products and brands. So, the future looks very bright.”
In the last 12 months, business for Krueger has been just as expected. The company kicked the year off with the largest single order in its entire existence, which of course was the one which saw over 250 semi-trailers delivered to Linfox
in collaboration with Schmitz Cargobull Germany.
“The order had been in planning since mid-2023, but to see it all come together was a feat,” says Krueger National Sales Director, Grant Krueger. “Through our relationship with Linfox, we have always been tested to deliver for them. As they continue to grow as one of Australia’s biggest freight logistics companies, they lean on us to deliver and trust us to do so.”
The overall outcome of this order, Grant says, showed that Krueger possesses an incredible ability to continue to think outside the box in delivering for its customers. At the same time, it demonstrated that the relationships Krueger has with its supplier network, business partners and processes is stronger than ever.
“A lot of this comes from the work we put in to understand our clients’ needs,” he says. “On the surface, it’s building
or acquiring trailers to help them move freight, but the work our engineering team does behind the scenes to understand where pain points such as asset integrity are is where Krueger really flexes its muscles.
“Dad built the business based on these factors, and his history in this industry shows it. Today, we still hold the same ideals and values in building the best product that will stand the test of time in the industry.”
On the back of the Linfox task, Krueger has experienced continued growth across the various brands within its business.
Grant explains that its manufacturing group has continued to advance utilising its investments in advanced technology, while its retail businesses have performed “well despite challenges in the labour markets”.
“With a continued focus on high-level support to our customers, our national
parts and service departments are firmly engaged in keeping customers on the road and with lower total costs of ownership,” he says. “Our RENU brand, previously known as the refurbishment part of our service business, has been very busy delivering high-quality remanufactured trailers back to their owners as well – providing second and third lives to Krueger trailers and other brands.”
In terms of product developments and innovations, Krueger’s manufacturing and sales departments have been extensively working on the new K-Van range of dry vans. As they continue to make strides with the product’s development, customer feedback, Kevin says, has been critical in helping Krueger understand how it can make the K-Van even better.
“We initially sold some our of dry vans to Diamond Brothers, and their feedback on how those assets performed has meant that we now have a product that we are happy with and understand,” he says. “Similarly, we have now launched our freezer box product, KoolBox. We’ve had customers wanting the combination of a Krueger build chassis with the Schmitz Cargobull box for many years, and we are now in a position of offer it as a Kruegerbranded product.
“KoolBox does incorporate Schmitz Cargobull’s FERROPLAST technology,
but there are options available that give customers a range of choices in what could be the best freezer asset in the industry.”
The biggest change to Krueger’s operations in 2024 has been its investments in advanced technology such as a state-of-the-art fibre laser cutting machine. Now 12 months into this journey of technological progression, Kevin says the company is starting to see the major advantages of the equipment and what it can truly do for both Krueger and its customers.
“Its value has been outstanding,” he says. “We’ve seen benefits across the whole business. We’re now cutting more steel with less waste than ever before, and in terms of what it means for our manufacturing arm, it gives us faster and more access to the parts required. We are outsourcing less and reducing costs, and as we continue to push the machine to do more we are buying more.”
It’s this same innovation that was recognised at the Victorian Transport Association’s 2024 Australian Freight Industry Awards (AFIAs) in September where it was nominated for the Application of Technology Award. Although the laser cutter didn’t take the win home, Kevin says it was a major honour for the technology to even make it in the running.
“It was great to be recognised for the
money and workmanship that we have invested into this technology,” he says. “It was the only laser cutter of its kind in the country at the time of its arrival, and that meant we needed to do a lot of work with our supplier and the programming to make it perform right for us.
“I believe the work that we’ve done in this space is now benefitting the industry, and I’m very proud to say that.”
This year has been the biggest one for Krueger in terms of nominations and awards. With the various achievements made, Krueger Creative Lead – Marketing, James Tamanika, says the company has showed that it’s still as strong as ever.
“As well as the nomination for the Application of Technology Award at the AFIAs, we were also a finalist in the Victorian Manufacturing Hall of Fame for the Leader in Transport and Rail Award,” he says. “It was such an honour, and although we didn’t win anything, we were being recognised for our business practices and quality.”
Headlining Krueger’s 2024 achievements was the introduction of its founder, John Krueger, into the Victorian Manufacturing Hall of Fame Honour Roll. For Krueger, James says this one took the cake.
“With 46 years of Krueger and many other years as a truck driver in the industry, this award is a massive
recognition to John’s legacy in the transport and manufacturing industry,” he says. “We could not be happier with this recognition.”
The accolade, presented on 9 October, recognised John’s outstanding service and contributions to the industry through his decades-long commitment to advancing Australian manufacturing.
Since creating Krueger in 1976, John has been at the forefront of building semitrailers from the business’ operations based in Melbourne’s western suburbs.
And during that time, Krueger has become a respected name in the industry known for its innovative designs, high-quality products and unwavering dedication to customer service.
The Honour Roll itself celebrates individuals who have made a lasting impact on Victoria’s manufacturing industry across all industries, and it’s fair to say that John has done just that with constant contributions to the transport industry’s evolution well as his ongoing support for local manufacturing and community engagement. But for him, the award was totally unexpected.
“It was a highlight, that’s for sure,” he says. “I never set out to become an award winner or for Krueger to even be a major manufacturer like it is today. I built this business for my family, and I guess I had some good ideas and good ways of making things too.
“I’ve had a great group of people around me over this 46-year journey to help me
achieve what we have today. The business has been through its ups and downs but we are still here, and we always will be.”
Following this recognition, John is planning to release a book about himself and Krueger – another trophy for the business to add to the shelf once it’s released.
“I have been working on a book of memoirs for a few years now,” he says. “It’s a collection of stories and thoughts over my past from growing up and building the business, as well as some notes on my passions, family and some of the values and lessons that I have learnt along the way.
“I don’t think it’ll be a best seller but rather something for my friends and family to read and reflect on.”
For Krueger, another big reward of 2024 has been a $250,000 technology grant from Business Victoria.
“Earlier this year, we began discussions with the Victorian Government around our business and how we are looking towards the future,” Kevin says. “Following these discussions, we had visits from over five different State Government members which led to us to being awarded the grant.”
The funding arrived as part of the Victorian Government’s Made in Victoria – Manufacturing Growth Programme which helps small and mediumsized manufacturers introduce new technologies, expand their operations, improve productivity and enhance
sovereign manufacturing.
For Krueger, it will see major developments kick off in the new year.
“We can’t say much, but what it means for the business is future progression,” Kevin says. “We are looking towards technology, new processes and new job employment as part of a huge project which will be launched in 2025.
“Around this, we had a visit from Professor the Honourable Professor Margaret Gardner AC who is the 30th Governor of Victoria. She met with us to go through the project as it stands and the plans over the next six to 12 months.
“This whole arrangement means a lot to Krueger, so we want to thank the Honourable Natalie Hutchins MP and the Honourable Sarah Connolly MP for their time and support with the grant.”
Amid all of the success experienced during 2024, Krueger has been focused on giving back to the community. The company, as James explains, has spent this year getting back in touch with the local community and industry bodies as a way to pay it forward.
“Doing this not only grounds the company but also boosts our brand inside the local community which a lot of our staff belong to,” he says. “With participation in charity golf days and attending women in business lunches and industry catch-ups, Krueger has had a face to talk to in attendance.”
In addition to this, Krueger, in recent times, has had two major community engagements affect the company in a very positive way.
farming communities of Australia in need,” James says. “We partnered with him at the end of 2023 to help maintain his trailer so that every chance he had to volunteer, it would be good to go.
“Mark is a great example of true human nature, and given he drives an old Krueger combination we wanted to make sure he would be ready to go to work when needed.”
the supervision of the nurses and staff. However, after leaving the hospital, John set up a donation drive to raise money for the men and women of Ambulance Victoria and The Royal Melbourne Hospital. To date, Krueger has raised over $70,000 for this cause with donations from John, his staff and the company’s valued customers and suppliers.
great achievement, and we’re still raising donations.”
Looking ahead, Krueger has a lot planned for 2025 and the years to follow. And while the family behind the company can’t say too much about what’s going to happen, the next few years, too, are set to be remarkable.
Contact
MFT Hughenden has added another Performance-Based Standards AB-triple tipper combination to its expanding collection of high productivity Moore Trailers units.
The story of MFT Hughenden began in 2007. Headquartered in North Queensland, the business was established by identical twin brothers, Peter and Robert Mills, who both set out to start transporting cows and cotton seed throughout Australia. Together, they saw everything grow from there.
In the time that has passed, AB-triples, road trains and B-doubles from Moore Trailers have been essential in the fleet’s freight tasks around the country, with the trailer manufacturer being the fleet’s sole supplier.
MFT Hughenden has now accumulated 10 AB-triple sets from the OEM which are all identical to each other. They’ve been spec’d directly to the fleet’s needs, with underneath hook-up and double return lines, 60A road train plugs and air fittings, Hendrickson axles and suspension, custom-made tarps, submarine doors for easier access and improved safety and much more.
“We’ve been buying between two and three new A-double or AB-triple sets from Moore Trailers every year since 2021,”
Robert says. “The sturdy Moore trailers suit our business. We do a lot of rough work in North Queensland and in the bush and we can also deliver to the Port of Brisbane or the Port of Newcastle with the same trailers.”
MFT Hughenden’s latest addition to the fleet is a Performance-Based Standards (PBS) AB-triple road train of drop deck chassis tippers which are built exactly like the others within the business. With a Gross Combination Mass (GCM) of 114.5 tonnes, it provides the Mills brothers with a 74-tonne payload to operate under Higher Mass Limits (HML) for up to 250,000 kilometres per year.
“It suits our application in every way,” Robert says. “We’ve been buying A-double sets with a 23-foot slideback that can be removed. If you put the slideback into that combination, you’re under 36.5 metres with a six-two wheelbase truck that can go anywhere.
“I only own Moore trailers, so everything in my fleet is interchangeable, compliant and legal for an A-double or AB-triple.”
MFT Hughenden’s new AB-triple is the
culmination of years of collaboration with Moore Trailers, a company which Robert says has been extremely accommodating to his requirements by making improvements in each and every build.
“For the new one, we’ve put a drop pin in the front of the A trailer so that it can be hooked up to a quad combination,” he says. “Our A trailers also have a return line in them so that the rear A trailer can be slid back.”
This versatility, Robert says, is why he only runs Moore trailers and will continue to do so.
“The Moore Trailers brand and the ‘MFT’ name are pretty much stuck together,” he says. “We have a very good working relationship with Moore because they can get very precise on what a client wants. My trailers would not be as good as they are without Scott Gollan and Corey Ruhle.”
Contact Moore Trailers
Ph: 07 4693 1088
Web: www.mooretrailers.com.au
Bruce Rock Engineering operates four sites across Western Australia, with three of them offering service and repair assistance in addition to quality road transport equipment. The company’s Forrestfield site is a key location in this manufacturing and servicing process.
Founded in 1980 by Mike and Gay Verhoogt, Bruce Rock Engineering (BRE) first operated out of a 300-squaremetre workshop with a single employee in the country town of Bruce Rock in Western Australia.
At that time, the company’s grand vision of becoming a leader of Australia’s road transport industry was larger than its humble production capabilities, but the Verhoogts trusted the process and the company grew massively.
Armed with a mission to support world-class road transport solutions while collaborating with customers on
design and manufacturing – in addition to strong company values that have been consistently upheld to this day – BRE has crossed state boundaries and accrued a larger team along the way.
True to its customer-oriented approach, the company’s service and repair capabilities have been just as integral to the brand identity as its trailer manufacturing. Today, with operations helmed by the next generation of Verhoogts, BRE manages four facilities in WA and has extended its offerings to the east coast with representation based in Victoria. Additionally, this presence
is bolstered by its sister companies, Transbeam Industries and Bruce Rock Tyres. Each of BRE’s main facilities have a specialised focus, with Geraldton and Port Hedland sites specifically providing dedicated service and repair capabilities and its Forrestfield site serving as a onestop shop for all customer needs according to BRE Forrestfield Service Manager, Tony Smith.
“Everything is done in-house,” he says. “We can service and complete repairs, including refurbishment projects and accident damage to pretty much any trailer brand, parts dependent. We specialise in
our own product lines, with our services ranging from basic servicing all the way up to major accident repairs for trailers or units that have received substantial damage.
“We assess, quote and submit directly to insurance companies, taking the stress from the customer. Then, we complete the repairs all under one roof – everything from the mechanical and fabrication aspects of the repairs to the final blasting, painting and finishing.”
The consolidation of these tasks to one site is a massive benefit to BRE’s service and repair capabilities. To host all these tasks, the Forrestfield site (which opened on 27 October 2023) consists of two buildings. One is dedicated to steel processing and chassis fabrication, while the other hosts a combination of repair, maintenance and refurbishment services, respectively.
The whole facility boasts an area of 18,000 square metres on a 40,000-square-metre block of land and cuts out the presence of any middlemen during all aspects of production. According to BRE Managing Director, Damion Verhoogt, this helps the company to strengthen its position in the trailer manufacturing market.
“It underpins our ability to keep up with our market growth and continue to service our current and new customers,” he says. “It gets us back under one site in the metro area.
“We never had a blast and paint facility in Perth, so we were relying on third party contractors to do any of that stuff in Perth for us which was problematic from a cost, timing, logistics and management front. So, bringing that in-house is a big bonus.”
The manufacturing, service and repair capabilities present at BRE’s Forrestfield facility that can also be found at other sites in Geraldton and Port Hedland further strengthen the company’s outreach and service opportunities for customers.
Tony says that BRE’s ability to service and repair a large scope of trailer brands wasn’t a conscious business choice as much as a natural progression of the company’s skillset.
“We’ve always been focused on providing a solid aftersales service to our brand-loyal customers that are looking to have their product serviced, repaired and fixed,” he says. “From there, we just expanded into servicing other brands of trailers and doing other repairs.
“Initially, we were there to support our customers and their new products with that aftersales service, but now we’re at a stage where we can provide that same service and more to other trailer manufacturers and brands.”
While effectively servicing demand
through its various multi-purpose facilities, BRE has more plans in store for these sites. According to Tony, the next focus is restructuring the facilities’ service and repair operating hours and adopting a shift system to provide further capability and flexibility for customers.
“From a service and repairs point of view, a number of other sites are currently working shift systems,” he says. “Some of them are working 24 hours. The vision for service and repairs is that we hope to move to a 12-hour, seven-day-a-week operation, wish the goal to offer a 24-hour service in the near future.”
The full capacity of BRE’s Forrestfield site is a testament to the company’s major growth. While its footprint has expanded, the company remains grounded in its humble beginnings – always striving to serve the demand of its loyal customer base.
With multiple facilities equipped to meet demand and deliver comprehensive services, BRE ensures that all customers’ needs are met seamlessly in one place.
Contact
Bruce Rock Engineering
15 Swan Street, WA 6418
Ph: 08 9061 1253
Web: www.brucerockengineering.com.au
A key component of Fuwa K Hitch’s trailer equipment offering are its landing legs which come in many reliable forms to accommodate different customer needs.
Fuwa K Hitch’s servicing of the local transport industry has undergone substantial development since K Hitch’s founding in 1989. Over time, K Hitch’s manufacturing capability has grown, along with the company itself which redefined entirely when merging with Chinese manufacturer, FUWA, in 2001.
According to Fuwa K Hitch State Manager, Ryan Ussher, this association grew the business’ product range massively.
“When FUWA came into the business, the whole product range fully expanded,” he says. “Now, Fuwa K Hitch is pretty much a one-stop shop, with axles, suspensions, landing legs – the whole package.”
Fuwa K Hitch’s commitment to quality and price-setting is exemplified through its reliable and substantial product range, and its landing legs are no exception. The company offers an extensive range of landing leg types meticulously produced to various specifications according to the many customer preferences that Fuwa K Hitch is capable of satisfying.
“Our product offering aims to cover whatever the customer’s requirements are,” Ryan says. “The same thing can be said for our landing legs which cover the range of what people need.”
Fuwa K Hitch provides trailer manufacturers with six series of trailer landing legs in addition to three different stroke lengths and two options of landing leg feet. Two particular landing leg models, the KH32P and KH25, are heavy-duty lifters which specialise in lifting larger loads with internal-geared or external-geared designs respectively. Both of these models are capable of holding a static load of 80 tonnes and lifting 28 tonnes.
Meanwhile, the company’s KH227 landing leg has been specifically designed for high-speed movements, featuring a speed low of 1mm per turn and a speed high of 24.60mm per turn. The KH227’s main lift screw has been
encased, grease filled and sealed to require low maintenance while providing quick turning speeds.
On the other hand, Fuwa K Hitch’s ‘eLEG’ is an electrically powered landing leg which has been manufactured with the aim of automating the trailer
lifting process to minimise occupational health and safety hazards. The eLEG’s manufacturing has also ensured low maintenance and an extended service life.
A sealed maintenance-free geared drive, electric motor and battery allows
KH32P landing leg.
for the eLEG’s remote operation independent from the towing vehicle. The model also comes with a charger to maintain its battery condition.
Other key landing leg models in the Fuwa K Hitch lineup include the KH275 and the KH32E, which, like its
KH25 landing leg.
siblings, have proven their worth in onroad applications.
According to Ryan, this allencompassing landing leg range is used by countless customers of different sizes across the country. Like Fuwa K Hitch’s other products, he says that the high
demand for them is a combination of their reliability and attractive pricing.
“We have a lot of manufacturers and fleets who use our leg sets as standard for their trailers,” he says. “These days we are a very well-known company. We’ve been around for many years, and I think over these years we have proven our products to be strong
“We offer a very good landing leg at a very keen price. Our prices are a very
manufacturing efforts have placed the company among Australia’s leading suppliers for trailer manufacturing, utilising an international supply of material to create high-quality products like the company’s ample line of landing legs and other items.
Contact
Fuwa K Hitch
Ph: 03 9369 0000
Web: www.khitch.com.au
For Minus 1’s leading refrigerated transport operations, JOST’s landing legs and overall manufacturing capabilities serve as essential components which are delivered through the fleet’s trailer manufacturer, Vawdrey.
Minus 1’s eventual nationwide operation was first established in Victoria in 1989.
Founded by Dominic Barba, the cold chain logistics transporter initially handled the storage and movement of chickens across the state, developing a strong reputation for its efficient and reliable service.
The company formed a healthy customer base, warranting the establishment of linehaul operations in 1996, and the business has been skyrocketing ever since.
This momentum continues to carry Minus 1 into the 2020s, to a medley of positive changes. In 2023, Dominic’s son, Billy, assumed the role of CEO and Managing Director and has since worked tirelessly to consolidate Minus 1’s locations in Australia for a new era of company operations.
“I think the largest change since I’ve taken over has been our push to give the team the infrastructure it needs in all states around the country,” he says. “That’s something we haven’t had prior, and it seems to be really paving the way for us at the moment.”
This push for infrastructure has been massive, building upon the presence of Minus 1 depots in Brisbane and Adelaide with the scheduled opening of a new Sydney site in September 2025. These
operational sites are being supported and connected by a fleet of over 430 vehicles active on the road at any given time, comprising a series of semitrailers, rigids, prime movers and other transport equipment.
Minus 1’s indispensable fleet is the product of the company’s crucial partnerships with an array of industry manufacturers. Of these many partnerships, the company’s collaborations with manufacturing dynamos Vawdrey and JOST have underpinned much of its fleet strength for many years.
In addition to Minus 1’s own application of JOST components in its workshops, JOST’s special-made landing legs are integral components of Vawdrey’s A-double and B-triple Iceliner refrigerated trailer builds for Minus 1’s fleet.
“We’ve been using JOST equipment since the operation started,” Billy says. “We’ve always used their products in some capacity. We use JOST’s turntables on all of our prime movers and their landing legs and kingpins on all of our trailers.
“JOST has cemented themselves as our equipment supplier for landing legs.”
Part of JOST’s Modul series, these landing legs are implemented by
Vawdrey to hold up the reefer boxes on Minus 1’s trailers and play a vital role in supporting the fleet’s refrigeration transport capabilities. Billy, along with Minus 1’s seasoned workshop team, hold great admiration for the JOST landing legs due to their top quality and reliable performance.
“JOST provides an immense amount of strength and longevity with their products,” he says. “The Modul leg is a strong product, and a product that we have confidence in.”
JOST’s Modul series of landing legs are very durable products with high-speed internal gearboxes to assist drivers in lowering landing gear efficiently. They are manufactured in Germany and arrive in Australia with outstanding corrosion protection, a premium surface treatment through powder coating and longlasting resistance against environmental influences – making them ideal for Australia’s harsh operating conditions.
“To us, it’s a product that essentially doesn’t need replacing,” Billy says.
“Strength and reliability are the qualities that reflect our view on the JOST landing leg.”
This sentiment is greatly echoed by
Vawdrey itself which frequently uses JOST’s landing legs and other products for its builds. The two OEMs have fostered a mutually beneficial business relationship for 30 years which, according to Vawdrey General Manager, Alastair Lang, is built on a shared approach to manufacturing.
“JOST is a brand that is widely known throughout the transport industry,” he says. “We at Vawdrey don’t settle for second best in terms of the brands we partner with. JOST is tried, it’s trusted and it’s a brand that is recognised across the sector.
“The JOST Modul landing leg series, with its sealed no-maintenance drive mechanism and easy to use high/low drive, is the preferred landing leg fitment on Vawdrey trailers.”
According to Alastair, Vawdrey has fitted over 13,000 sets of JOST landing legs in the last decade – clearly illustrating not only the reliability of the product but the strength of the relationship between the two manufacturers.
Additionally, JOST’s diligence extends beyond its landing leg offering, according to both Minus 1 and Vawdrey. The component manufacturer offers extremely purposeful aftersales service, ensuring that those who have adopted JOST products are successful in implementing them to their desired effect.
Minus 1’s own workshop has greatly benefitted from this aftersales service, as according to Billy, JOST has established set training sessions with them on a regular basis.
“JOST provides an immense amount of aftersales support that comes in the way of training our workshop teams,” he says. “They provide installation and maintenance training as well as new product training, and that’s something that we’ve collaborated really well on.”
Minus 1’s country-wide presence as a dominant refrigerated transport solutions provider is the result of the company’s ambitious commitment to expansion. Its fleet, supporting the business’ large delivery network, has been crafted by quality manufacturers with quality parts.
JOST’s landing legs, a staple among Vawdrey trailer builds, are no exception, enabling Minus 1’s smooth and cool transport all over Australia.
Contact
www.jostaustralia.com.au
“JOST has cemented themselves as our equipment supplier for landing legs.”
Dulux has announced the relaunch of its popular FleetShield product range, offering a newly enhanced and consolidated painting, coating and finishing experience for customers like Krueger which rely on it.
Dulux Automotive Coatings has played the important role of offering paint coating and finishing services into the passenger, commercial vehicle and light industrial markets for more than 50 years – providing them with a combination of protection against harsh conditions on the road, repeated exposure to elements, wear and tear from frequent loading and unloading and recognisability with its variety of striking colour options.
investing heavily in a more efficient and clearer exhibition of these options to customers in a way that clearly distinguishes each product’s applications and capabilities in the world of painting, finishing, coating and protection.
FleetShield is the primary focus of a relaunch which aims to provide a better user experience with the addition of a new packaging design for the product.
of time transforming and enhancing our packaging so we can provide our customers with a superior user experience.”
Under Japanese-based parent company, Nippon Paint, and part of DuluxGroup, Dulux Automotive Coatings’ services extend beyond refinishing to many sales support services. Operating with a strong presence in both Australia and New Zealand, the company has established a plethora of sub-brands which provide commercial vehicle drivers, fleet managers and other road transportadjacent positions with unique paint and protection solutions.
Dulux Automotive Coatings is now
According to Dulux Powder, Industrial and Automotive Marketing Manager, Steve Barnard, this redesign reflects Dulux’s commitment to providing top quality products and solutions for its customers.
“The streamlined range and new packaging design not only reflects our dedication to providing exceptional products, but it also makes it easier for our customers to choose and use the right FleetShield solution for their specific automotive coating needs,” he says. “We spent a significant amount
FleetShield itself offers excellent durability, damage resistance and versatility as a commercial vehicle topcoat. The new packaging displays an updated Dulux Automotive Coatings logo and surrounding branding, reinforcing the company’s commitment to delivering trusted quality automotive coating solutions.
FleetShield is an essential component for a wide range of commercial vehicle providers. Krueger, for example, has enjoyed a decade-long relationship with Dulux Automotive Coatings, and in this period has received consistent service from it.
According to Krueger Supervisor –Purchasing, Daniel Hunt, Dulux has always been striving to stay ahead of the market through the refinement of its products.
“The only constant is change in our business and in Dulux’s business, so they’ve always got something on the go that is being improved,” he says. “They are always on the hunt for the next thing that will make the paint, finish, quality and overall experience better.”
Krueger was first introduced to Dulux through one of its own customers, but the partnership quickly proved successful due to the mutual values that both companies held.
“At Krueger, we have a commitment to excellence as a business, and we look for that in partners as well,” Daniel says. “We always want the best price but not at the expense of quality, service and product development.
“With Dulux, we experience the best of all of that. We keep our product in excellent condition thanks to FleetShield.”
Krueger mainly utilises FleetShield on its trailer chassis which require protective coats against harsh road conditions during transport journeys. By implementing FleetShield, Daniel says that these chassis look clean and attractive in the eyes of customers despite the dirty work that they’re involved in.
“Our premium trailers travel hundreds of thousands of kilometres per year, and in doing that, they experience a lot of work in a variety of conditions,” he says. “A lot of the paint on the chassis is close to the road, so the chassis really does need a
good coat to transform it from something that looks like a basic steel structure to something that’s beautiful and ready for the customer.
“The application of the FleetShield paint does exactly that – it transforms the steel chassis into something of beauty that the customer is ready to say yes to.”
The relaunch of FleetShield serves as the latest display of Dulux’s dedication to the improvement and enhancement of its product range to meet the evolving needs of customers, both new and old.
Contact
Dulux Automotive Coatings
Ph: 0448 558 361
Web: www.duluxautomotive.com
Thanks to Carrier Transicold’s highly efficient refrigeration units, Duotank is able to keep the beer it transports during long and dry journeys meticulously cold and fresh.
For 12 years, Duotank has been transporting tank beer to venues all across Australia – serving as an essential connecting link between breweries and venues for one of the country’s most popular options when it comes to alcoholic beverages.
As a global brand hailing from Europe, Duotank itself has developed and installed beer tank and shipment systems around the world since 1985, defining its manufacturing with a key focus on quality, craftsmanship and co-operation at every possible turn.
The brand entered the Australian market in 2012 and has grown exponentially since. It now operates across Victoria, New South Wales, Queensland and Australian Capital Territory delivering beer to around 250 venues for Carlton & United Breweries.
According to Duotank Australasia
Director, Nick Philp, this deal requires the constant movement of beer to a varying number of venues which overall has increased since the beginning of Duotank’s deliveries.
“Based on some recent numbers, we’ve delivered around 22 million litres since the beginning,” he says. “We have 12 trucks on the road as of today to move this amount, with another three in build.”
The temperature of beer during its transport from brewery to pub is pivotal. Duotank has honed its craft in keeping unpasteurised beer under pressure and cold during transit, which according to Nick is essential in maintaining beer to the standards that the brewer intended.
Duotank has developed propriety bag-in tank technology protecting the liquid from oxygen ingress while maintaining the correct carbonation level that is set by the brewery. From there, the liquid is kept at
serving temperature with a near fleet-wide reliance on Carrier Transicold’s Supra 850 refrigeration units.
“The Carrier 850s on our trucks keep the beer at four degrees Celsius during transport,” Nick says. “We pump cold beer up from the brewery into our trucks’ insulated tanks, transport it and then dose it into cold tanks at designated venues all at the same temperature. The Carrier units ensure that the beer never goes above serving temperature.”
With Carrier’s refrigeration systems maintaining perfect serving temperature, Duotank’s beer delivery systems and cold venue tanks use compressed air to dispense beer from tank to tap, mitigating over or under carbonation while reducing the amount of manual handling involved.
“A lot of the venues we supply have 500-litre tanks,” Nick says. “Once those tanks are full and opened, the venue
“Everything we do to keep the beer cold is Carrier-based. The company is integral to our cold-chain logistics operations.”
doesn’t have to touch them. There’s no carbon dioxide needed to dispense the beer.”
The partnership between Duotank and Carrier has been long and fruitful since it began. When Duotank initially entered the Australian market, Nick approached Carrier based on both the recommendations he had been given within the industry as well as his desire to limit the amount of equipment suppliers Duotank would have deal with.
Over the years, Nick has never looked back. He cites Carrier’s reliable and diligent work as the main contributor to the partnership’s enduring success.
“Everything we do to keep the beer cold is Carrier-based,” he says. “The company is integral to our cold-chain logistics. Carrier is a key supplier.”
Sharing similar values of quality
and craftsmanship, Carrier provides Duotank with frequent fridge servicing and maintenance on the 850 units, guaranteeing effective temperature control for each transport journey. This collaboration also extends to ideas of environmentally conscious operations and sustainability, an increasingly important issue in the logistics sector that both companies are aware of.
On its own, Duotank has started its transition towards electric vehicles in Australia as part of an overall pledge to reduce carbon emissions.
“We’re oriented towards any form of environmental benefit that we can bring to both the industry and the world around us,” Nick says.
Duotank’s devotion to environmental sustainability is being greatly assisted by Carrier’s new Supra HE 9 fridge unit
which is the latest piece of equipment from the OEM to join the fleet.
The system is built for greater functionality while reducing diesel and overall power usage from the host truck both during transport and when on standby. And to Nick, it’s a privilege to be able to utilise it. He views it as a symbol of the companies’ compatible visions and continued ability to operate sustainably.
“We at Duotank are so thankful to Carrier for giving us the opportunity to be one of the early adopters of using this new model,” he says. “We also appreciate Carrier’s like-mindedness in and around sustainability and innovation in its field.”
The partnership with Carrier has enabled temperature sensitive unpasteurised beer to be transported across Australia in Duotank’s network, combining quality, safety, precision and sustainability to successfully move millions of litres right from the start.
Della Bosca Transport’s latest pocket road train incorporates an effective BPW Transpec setup that the fleet has become accustomed to due to its easy maintenance and high reliability.
Della Bosca Transport, established in 2012, is a proud family-owned and operated rural transport company based in the town of Westonia in Western Australia. The business specialises in a range of transport operations catered to the agricultural and mining sectors, particularly with bulk commodities, oversized buildings, oversized machinery and bulk stemming, and it also carts grain, hay, dirt and other agricultural goods of the sorts.
Prior to entering the transport industry, the family behind Della Bosca Transport had been running a farm in the local region. This gave Director, Tim Della Bosca, an introduction to the heavy vehicle industry with prior experience ahead of his decision to begin transporting.
“We’ve always had trucks”, he explains, “but we wanted to step out and do our
own work while also finding some other work to pay for itself. So, we bought our first truck and trailer combination.
“Since then, we’ve done a lot of different things. We’ve just carted accommodation buildings for some mining companies, but our main work is trailers in agriculture.”
For these operations, Della Bosca Transport had previously relied on two sets of end tippers to carry out its tasks. Although a brand-new delivery of aluminium end tippers from Boomerang Engineering – set up as a 27.5m pocket road train and spec’d with BPW Transpec TS2 disc brakes, ECO Plus 3 hubs, AL2 suspension with airbags and a Transpec Electronic Braking System (EBS) has made the job much easier.
“That’s a combination we’ve got with BPW Transpec now, and it’s been very good,” Tim says. “We haven’t had any issues whatsoever.”
This setup is also one that has already proven its worth through various applications in the fleet. For over five years these BPW Transpec products have performed effortlessly on Tim’s different trailer combinations, and they’ve been no different on the new pocket road train.
As Tim explains, the fleet transports a significant amount of dirt in and out of mines, and as a result, has been able to gauge just how effective and durable the BPW Transpec products are in different conditions.
“They’ve all been really good,” he says. “The suspension and axles haven’t faulted at all. I haven’t had any suspension issues with the bags, and the discs work really well. So, I haven’t had any problems whatsoever.”
In terms of on-road performance, Tim has been very happy with the way the pocket road train handles. This, in part,
is due to the BPW Transpec AL2 air suspension fitted.
“I find that the trailers all tow very well,” he says. “They’re sitting behind Kenworth T909s and they handle flawlessly.”
According to Tim, the ECO Plus hubs and disc brakes have been standout features of the new unit.
“I love the ECO Plus,” he says. “The trailers are running 22-inch discs and their braking ability is really good too. We’ve had a great run out of the BPW gear.”
For Tim, specifying BPW Transpec on new trailer builds is a no-brainer. He’s found the products to never let him down over thousands of kilometres, and when it comes to maintaining them, he says they’re just as impressive.
“I spec them specifically,” he says. “I’m really familiar with the products now, and they perform well for me. So, I’m happy to stay with them and will continue to do so.
“The reason why is because of their easy maintenance. In terms of the ECO Plus hubs specifically, they’re just so simple. They’re very easy to check in
terms of bearing tensions and being able to do them up so they click.
“That’s the main reason why we go with BPW. The price never really came into the picture because of the easy maintenance.”
Overall, Tim has been able to receive a complete package in his dealings with BPW Transpec. He says he gets a product that he can rely on, at a reasonable price that’s justified by its extremely high quality and an aftersales service that is secondto-none.
“The service I get in Perth is great,” he says. “Aaron Moore has always been there for me, especially through the EBS system. He’s always been easy to get a hold of, and that’s probably another reason why I stay with BPW Transpec – because I’m able to get parts and have him there as a support network.
“I bought my first set of axles and suspensions from BPW in 2019, and I would stick with them for anything that I purchase going forward.”
Contact
BPW Transpec
Ph: 03 9267 2444
Web: www.bpwtranspec.com.au
It has been a stellar year for Lucidity Australia, with new business opportunities and many new products providing substantial growth.
Lucidity Australia’s success goes a long way back. Founded in 1999 as Phaser Industries by Mathew Jenkins, the company was a customer of internationalbased Lucidity and enjoyed a fruitful partnership based in providing lighting and wiring solutions to the Australian market, until Phaser was acquired by the latter in 2013.
Since then, the two have been unified as Lucidity Australia, continuing to prosper as a leading lighting and wiring solutions provider for some of the country’s largest trailer manufacturers and transport companies.
Two thousand twenty-four is merely the latest in a string of successful years which according to Mathew (now Lucidity Australia’s President) saw big change across every aspect of the company. This year’s success comes as no surprise to him, with the powerhouse that is Lucidity reaping the benefits of 25 years of hard work and solid customerfocused business.
The last year saw some big movements in business for Lucidity, and Mathew says it will be known in history as a year that saw a little bit of everything.
“This year has been outstanding,”
he says. “We’ve had a very good year from a sales perspective. Growth and opportunities have all come about after putting ourselves on the frontline.
“There have been a number of new clients this year and we have experienced excellent organic growth.
“The take-up of new products has been fabulous. It’s been a really solid year for us all around.”
This immense success is the product of a simple mantra embraced by a strong community. Lucidity’s 46 staff members have all worked diligently to develop specialised lighting solution products that
are aligned with the company’s established consumer base. According to Mathew, this strategy of knowing the market, combined with essential teamwork, has been Lucidity’s key approach to achieving strong performance.
“We don’t try and do everything, we just do what we can really well,” he says. “The whole team comes together to do this Our success is a combination of everybody –everyone gets in and does their bit.”
This strategy’s payoff was clearly demonstrated through the company’s new 26281CAARK-BV2 LED Marker Lamp which was released earlier this year. This product is the latest in Lucidity’s 26281 series and is the company’s most popular OEM trailer lamp. This iteration has been designed to offer new and improved lighting solutions, focusing on delivering functionality and safety to trailer and transport manufacturers.
The 26281CAARK-BV2 has been Australian Design Rules (ADR) approved and is constructed to feature a side marker with a built-in side-turn indicator function. The lamp is also part of the renowned Lucidity Link series of innovative lighting and wiring equipment which allows users to easily install multiple of them to a given vehicle.
Safety is another focal point of the marker lamp’s value proposition. The product’s lighting capability ultimately reduces the number of lamps needed on a trailer or transport vehicle and is very easy for drivers or fleet owners to install by themselves.
According to Mathew, the combination
of functionality and convenience in the marker lamp’s design is a testament to Lucidity’s fundamental design principes.
“This lamp goes back to our philosophy of ‘no splicing or splice joints on trailers’, because you can actually use each little 26281CAARK-BV2 lamp as a junction box,” he says. “It’s very easy to install.”
Despite some challenges with the product’s development, Lucidity’s design philosophy triumphed.
“There were some challenges but overcoming them was just a matter of letting the optical engineers do their work,” Mathew says. “It’s all about using the team you have to come through on the promises you’ve made.”
The company’s design philosophy, which is present among all other Lucidity Link products, has been crucial for Lucidity’s success. According to Mathew, the industry’s extremely warm reception to the new marker lamp has seen the product make an ‘undeniable ripple’ within the market.
“The whole Lucidity Link philosophy works brilliantly for our customers,” he says. “We have won new customers this year as their clients are asking for them.
“It’s a no-brainer – our lamps create the simplest and most repetable installations and the repair process is unmatched. This product range has been a gamechanger for everyone.”
The trailblazing success enjoyed by the 26281CAARK-BV2 LED marker lamp has been no surprise for anyone at Lucidity, as the company’s entire upward momentum in 2024 has been scrupulously planned and
executed to a tee. In an industry contingent on frequent technological innovation, one misstep or undelivered promise in product capability could cost a company its brand power in the eyes of customers. This, Mathew says, is a factor Lucidity keeps a close eye on.
“We very carefully plan our budgets and we also anticipate new clients as well as organic growth with existing clients,” he says. “This planning is essential because the industry doesn’t jump – it moves with technology, and it moves cautiously.
“You need to make sure that the product you are introducing to the market does what you say it will do, otherwise it won’t have an impact on people.”
Sticking the landing in 2024, the Lucidity Link series is slated to return in 2025 by seeking to further innovate the lighting and wiring solutions market.
“In terms of the Lucidity Link range, we’ve got a lot more coming,” Mathew says. “We’ve got a few surprises coming next year which will be really cool. There is certainly more in store.”
Following a successful 2024, Lucidity remains a leading force for lighting and wiring solutions in the market. Coming off a victory lap and with more to roll out, it seems that for Lucidity, 2025 is looking bright.
Contact
Lucidity Australia
37 Paraweena Drive
Truganina VIC 3029
Web: www.lucidityaustralia.com.au
Ph: 03 9219 4074
While it’s often challenging to prevent effluent escaping from livestock trailers, it’s important to minimise load loss on roads as it could potentially affect road safety, public amenity and risk Australia’s biosecurity. This is a key message the Australian Livestock and Rural Transporters Association is sharing.
The Australian Livestock and Rural Transporters Association (ALRTA) has been working to improve the management of livestock effluent during road transport for many years. Its focus is on driver safety, animal welfare, biosecurity and compliance with the Heavy Vehicle National Law (HVNL) and environmental safeguards across Australia.
The ALRTA is a peak body for rural and regional transport companies which provides first and last mile access to the supply chain for Australia’s agricultural industries. According to the association, its members recognise that managing livestock effluent at every stage of a heavy vehicle transport journey, from preparing livestock for transit to unloading livestock at the destination, requires a cooperative approach across all responsible parties.
The ALRTA therefore claims that the problem for livestock transporters has historically been that off-road parties in the livestock supply chain have denied any accountability. In this space, the association has focused its efforts on better access to a network of truck wash and effluent disposal facilities as well as working with parties in the livestock supply chain to develop a Code of Practice for managing effluent.
Following consultation with stakeholders in the livestock and transport industries and with the assistance of National Heavy Vehicle Regulator (NHVR) Codes Advisors, the Effluent Code – ‘Managing effluent in the livestock supply chain’ was registered in 2022.
According to ALRTA Chair of the Driver and Animal Welfare Sub-Committee, Graeme Hoare, the process of consulting with supply chain parties and transporters to develop the Effluent Code represented a significant and positive opportunity for collaboration.
“The Effluent Code provides recommended best practice advice for identified livestock transport activities from trip planning and preparing livestock to managing effluent in transit and at the destination,” he says. “When a Chain of Responsibility breach occurs, the procedures outlined in the Code can be used in court as evidence of what is considered ‘reasonably practicable’.”
Following publication of the Effluent Code, the ALRTA mounted an awareness campaign which was funded by the NHVR’s Heavy Vehicle Safety Initiative (HVSI) and supported by the Australian Government. Delivering presentations to transporters, saleyards managers and livestock producer groups – together with a targeted ‘Mind your pees and poos’ print and social media campaign – has seen a steady flow of traffic to access the Effluent Code from ALRTA and NHVR websites.
This year, the ALRTA also contributed to the development of the NHVR’s Livestock Regulatory Advice which provides useful information for transporters and offroad parties about their CoR obligations concerning livestock transport generally, and it had significant input to MLA’s Transport Hub content. Hosted by Meat and Livestock Australia (MLA), the Transport Hub is a one stop shop for best practice information about transporting livestock safely and humanely to ensure the profitability and sustainability of the livestock industry.
Meanwhile, with the benefit of HVSI funding the ALRTA has supported the construction of ‘drop and go’ effluent disposal facilities at saleyards in Horsham, Victoria, and Mount Gambier, South Australia.
“Our members are keen to see a
network of similar facilities constructed along livestock freight routes like the very effective network of roadside effluent disposal facilities in New Zealand,” Graeme says. “ALRTA members continue their efforts to share the load of responsible livestock effluent management across the supply chain to help to improve animal welfare outcomes, mitigate biosecurity threats, contribute towards sustainability, support hardworking livestock transporters and make the roads safer for all road users.”
Contact
Australian Livestock and Rural Transporters
Association
Ph: 02 6247 5434
Web: www.alrta.org.au
What you need to know about Australia’s biggest road projects this month
Queensland’s $1.2B Gympie Bypass officially opens
The Australian and Queensland Governments have announced the completion of the new Gympie Bypass, a long-awaited project which began 15 years ago.
The new Gympie Bypass is a significant improvement for transport operators, with heavy vehicles no longer needing to travel through Gympie, Queensland.
In addition to reducing travel times, the $1.2 billion bypass improves road safety and flood immunity.
The project has constructed a new 26-kilometre, four-lane divided highway between the existing Bruce Highway interchange at Woondum, just south of Gympie, and Curra.
It includes three new interchanges – at Flood Road, Gympie Connection Road and Curra.
There are also 42 new bridges at 23 locations.
The project’s completion is expected to lead to a positive impact of fewer heavy vehicles, with freight efficiency also to be improved.
“This stretch of highway will improve safety, flood resilience and capacity for motorists as well as meet the transport needs of the Gympie and Sunshine Coast communities well into the future,” said Minister for Infrastructure, Transport, Regional Development and Local Government, Catherine King.
“We know how important continued investment in major infrastructure upgrades is, and that’s why in this year’s Federal Budget we allocated a further $467 million towards several projects along the Bruce Highway like the Gympie Bypass to ensure they get delivered for Queenslanders.”
The Gympie Bypass is the final section of a 62-kilometre Bruce Highway program of works between Cooroy and Curra, totalling $2.5 billion.
Construction of the overall Cooroy to Curra program began in September 2009.
Blue Water Shipping has secured a large infrastructure logistics contract for the North East Link Project, one of Australia’s largest road projects which is valued at $15.8 billion.
The North East Link Project will connect key growth areas in Melbourne, improve transport connections and enhance local infrastructure.
After more than a year of dedicated planning and collaboration, Blue Water has been selected to provide a comprehensive range of logistics services.
This includes warehouse management services, warehouse management systems and transportation from the warehouse to the project site.
Blue Water State Manager Victoria/ Tasmania, Rebecca Peat, said this win underlines Blue Water’s solutionsbased approach and builds on expertise gained from other major Australian infrastructure projects.
“Securing the logistics contract for the North East Link project is a testament to our commitment to providing bespoke solutions to meet the unique requirements of major infrastructure projects,” she said.
“We look forward to contributing to such a transformational project.”
The North East Link Project is being delivered by the Spark Consortium, a group of world-leading contractors and operators including WeBuild, GS Engineering and Construction, and CPB Contractors.
The construction started in 2022 and is expected to be completed by 2028.
“Blue Water is looking forward to beginning its involvement in this contract,” the company said in a statement.
“The lessons learned and successes achieved in previous endeavours have positioned Blue Water as the ideal partner to deliver reliable and efficient logistics for this major project.”
According to Blue Water, the win underlines its solutions-based approach and builds on expertise gained from other major Australian infrastructure projects.
South Australia’s Porter Street, Liverpool Street and Railway Place intersection upgrade is expected to improve heavy vehicle movements while boosting safety for all road users.
The $4.5 million upgrade will include the installation of traffic signals at the intersection and pedestrian actuated crossings on all approaches, as well as new line marking and signage throughout the project area.
Funded by the Australian and South Australian Governments as part of the Heavy Vehicle Safety and Productivity Program, the upgrade was proposed to the Port Lincoln community through information sessions and online surveys earlier this year.
During this engagement, a total of 77 online survey responses were received with 70 per cent of them supporting the design.
According to the State Government, heavy vehicle movements and light sequencing were key focuses for the community, and the project scope has been further developed in response to this feedback.
The upgrade’s final design will be shared with the local community over the coming months, with construction expected to commence by mid-2025.
The planned works follow the recent completion of four other intersection upgrades in Port Lincoln, including:
• Flinders Highway/Light Street and Lincoln Highway/Hallett Place
• New West Road/Lewis Street and Hallett Place
• Hallett Place/Liverpool Street and Adelaide Place
• Liverpool Street and Mortlock Terrace/ Bligh Street.
These works form part of a $51.3 million commitment, funded by the Australian and South Australian Governments to deliver Eyre Peninsula road upgrades.
MaxiTRANS has changed its name to Freighter Group.
The new Freighter Group stands for something more powerful than ever before. It stands for being ready.
Ready to push boundaries, deliver excellence and to help you go further. Be part of a new era in transport.
freighter.com.au
With records broken, tough issues broached and an industry looking positively to the future, IAA Transportation 2024 organisers are declaring this year’s event a rousing success.
IAA Transportation 2024 in Hanover, Germany, brought together manufacturers, industry stakeholders and business leaders from around the world to discuss the latest clean-energy solutions for the transportation industry.
The number of attendees jumped to 145,000, about 10 per cent more than the last event in 2022. The conference also set a new record for the number of test drives – 6,300, a 15 per cent increase over 2022.
Visitors took emission-free commercial vehicles out on the event grounds and on public roads. Manufacturers offered test drives in 60 vehicles.
“Here at IAA Transportation, the industry shows that we have already developed and are producing products for climateneutral mobility,” said President of the German Association of the Automotive Industry, Hildegard Müller, in her opening speech. “Now it’s about getting these production-ready vehicles on the road.”
Presenters speaking during the event made it clear that policymakers must develop and implement a concrete action plan focusing on infrastructure.
“The biggest obstacle to a swift, successful and widespread adoption of climate-neutral drives is the necessary
infrastructure – especially in terms of charging stations and forward-thinking grid expansion, as well as hydrogen refuelling stations,” Müller said.
She added that equipment manufacturers have already created climate-neutral and digital solutions to address many of the industry’s various challenges.
“Freight forwarders want to convert, want change and then face reality,” Müller said. “The local grid operator often reports several years of waiting time to provide the necessary capacities.
“It’s clear and evident that something is going wrong here and decisive countermeasures are urgently needed.”
Throughout the event, component and vehicle manufacturers displayed their latest offerings.
Volker Wissing, Germany’s Federal Minister for Digital and Transport, said IAA Transportation “provides a prominent stage for the latest technologies and developments in the commercial vehicle industry” and is a “great showcase for the innovative power of the transport sector and related industries”.
Going forward, Müller said all relevant stakeholders must now be held accountable, with a clear road map,
regular monitoring and opportunities for adjustments.
The next IAA Transportation will take place on 15-20 September 2026.
This year’s event delivered everything it promised with its final statistics speaking for themselves.
• 1,700 exhibitors from 41 countries, a 21 per cent increase
• 72 per cent international participation
• 145 premieres presented
• 145,000 visitors
• 1,400 journalists from 52 countries
• 80 press conferences
• 45 per cent of trade visitors were international with the Netherlands, China and Sweden the most represented
• 50 per cent of trade visitors held executive positions
• 50 per cent of trade visitors planned to invest within the next twelve months
MGM Bulk is set to deploy 20 new Bruce Rock Engineering Performance-Based Standards ultra quad road trains along with a fleet of new Kenworth C509s.
The identity behind MGM Bulk was first established in the 1950s when founder, Mario Giacci, started a small business with his family which was known as Giacci Bros at the time. From there the ‘MGM Group’ name was formed in 2004, and its bulk division, MGM Bulk, was later added to the mix in 2014.
This was when MGM Bulk first approached Bruce Rock Engineering (BRE) in hopes of building a fleet of tipper trailers, and 10 years down the track, it’s accumulated 76 sets of them. These include a series of super and ultra quads rated for high productivity capabilities under Performance-Based Standards (PBS).
The fleet’s latest delivery from BRE is a 60m PBS ultra quad road train made up of a three-axle lead tippers with three-axle dollies and three four-axle tippers behind. It’s part of an order of 20 in the same spec. With a Gross Combination Mass (GCM) of 210 tonnes and a 150-tonne payload, it features BPW Transpec axles, aluminium hubs and mechanical spring suspension, along with SSAB Hardox HiAce material
on the bodies which resists corrosion and provides better wear.
“The new combination has been very good,” says MGM Bulk Fleet Manager, Allan Thomas. “It’s a very similar spec to what we already have – we’ve been running these trailers since 2018, and we have worked together with BRE over that time to improve different things such as the material of the bodies.”
MGM Bulk’s partnership with BRE began through its purchase of some secondhand units when the business first set out, and from there it saw countless new combinations follow suit. BRE’s innovations, attention to detail and extreme durability, Allan says, is what drew the fleet to it.
“They were one of the first ones to develop the super quad and ultra quad combinations,” he says. “They’re really strong trailers with very light tare weights, and that’s ultimately what got our attention. We’ve also been able to refine things with them over the last 10 years which adds to the benefits.”
The latest ultra quad arrived with a new Kenworth C509 prime mover and has
been dedicated to carting iron ore in the northern regions of Western Australia through the Pilbara and Port Hedland. This freight task sees the combination undergo some pretty harsh operating conditions, but with the power and reliability of the 600hp Cummins X15 engine together with the durability of the BRE tipper bodies, it’s been performing effortlessly.
“It’s been doing really well,” Allan says. “We’re getting great life out of the X15s, and we’ve been really happy with them.”
Like its partnership with BRE, MGM Bulk has been collaborating with Kenworth for a number of deliveries over the last 10 years. This has seen the fleet collect over 200 prime movers from the OEM including C509s, T909s, K200s, K220s and T410s.
The latest Kenworth C509 and BRE ultra quad combination are set to be joined by more units of their sorts next year which will assist the fleet in its tasks of transporting more than 16 million tonnes annually across five strategic locations.
B-DOUBLE DROP DECK CURTAINSIDER
• Full mezz deck
• Hanging gates, toolboxes & provision for tow coupling
• Locally supplied curtains
B-DOUBLE FLAT DECK CURTAINSIDER
• Rear doors
• Gates, toolboxes & provision for tow coupling
• Locally supplied curtains
45’ Drop Deck with BiFold Ramp
• 12V Power Pack
• 3 Way Twist locks
• Machinery tie-down points in floor
40’ DROP DECK SKELETAL TRAILER
• 3 way twist locks
• Dangerous goods rated
• Container tilt airbag fitted
13.7-21.5m Extendable Flat Top
• 3 Way Twist locks
• Pneumatic warning flags
• Provision for tow coupling
40’ 3 WAY SKELETAL
• Standar & lightweight designs
• Side loader pads
• Provision for tow coupling
• CIMC has a long term commitment to Australia by investing in infrastructure to provide high quality products, support and service.
• Local production capacity for Semi-Trailers and Tankers with CNC cutter, welding machines and start-of-the-art heated paint shop.
• Comprehensive parts store stocking genuine CIMC parts, along with additional OEM sourced items.
• Dedicated service & repairs workshop.
• Total site area 51,000 sqm, with a 13,000 sqm workshop.
Melbourne
CIMC TRAILERS 1300 202 462 20 Whitfield Blvd, Cranbourne
Brisbane CIMC TRAILERS 0423 795 649 68 Tile Street, Wacol
Perth
GTE 08 9352 4000 159 McDowell Street, Kewdale Sydney
GROUP 02 9355 3400
Pencil in some information on dates and venues of various truck shows, field days and road transport industry conferences both locally and internationally.
January
Victoria
Geelong Classic Truck and Machinery Show 11–12 January
Geelong, VIC Visit: www.classictruckandmachinery.com.au
Queensland
LRTAQ Annual Conference
13-14 February
Gold Coast, QLD Visit: www.lrtaq.com.au/annual-conference
EvokeAG
18-19 February
Brisbane, QLD Visit: www.evokeag.com
Wimmera Machinery Field Days 4-6 March
Horsham, VIC Visit: www.wimmerafielddays.com.au
South Australia
South East Field Days 21-22 March
Lucindale, SA Visit: www.sefd.com.au
2025 National Rural Carriers Convention 4-5 April
Canberra, ACT Visit: www.lbrca.org.au/lbrca-events
New South Wales
Tocal Field Days 2-4 May
Paterson, NSW Visit: www.tocalfielddays.com
Queensland
Brisbane Truck Show 15-18 May
Brisbane, QLD Visit: www.brisbanetruckshow.com.au
National Diesel Dirt and Turf Expo 16-18 May
Sydney, NSW Visit: www.dieseldirtandturf.com.au
France
Solutrans 18-22 November
Lyon, France Visit: www.solutrans.fr
...IT’S NOT IN HERE! ...IT’S NOT IN HERE!
INTRODUCiNG THE KRUEGER KOOLBOX ENGiNEERED FOR THE DEMANDS OF FOOD DiSTRiBUTiON. THE KOOLBOX OFFERS REAR-END LOADiNG AND AN EXPANSiVE RANGE OF CUSTOMiSABLE OPTiONS, ALLOWiNG OPERATORS TO TAiLOR THE TRAiLER TO YOUR FLEETS SPECiFiC NEEDS.
At the heart of the Koolbox’s superiority is its market-leading FERROPLAST® thermal technology. Built on Krueger’s renowned rolling body chassis. Built tough to survive the needs of the australian transport industry.
The KoolBox comes equipped with Krueger’s renowned MarkV RFS suspension system.
The advanced doubledecker system offers enhanced flexibility and maximises the usable space within the KoolBox.