FEATURES Tyre recyclers call to arms for domestic markets The next generation of WtE The first dual waste collection truck heads Down Under Celebrating women in industry PROUDLY SUPPORTED BY: SEPTEMBER 2022 PMS 380 PMS 376 PMS 355 As REMONDIS celebrates 40 years in Australia, CEO Jochen Behr predicts significant changes for the nation’s recycling Workingindustry. for the future
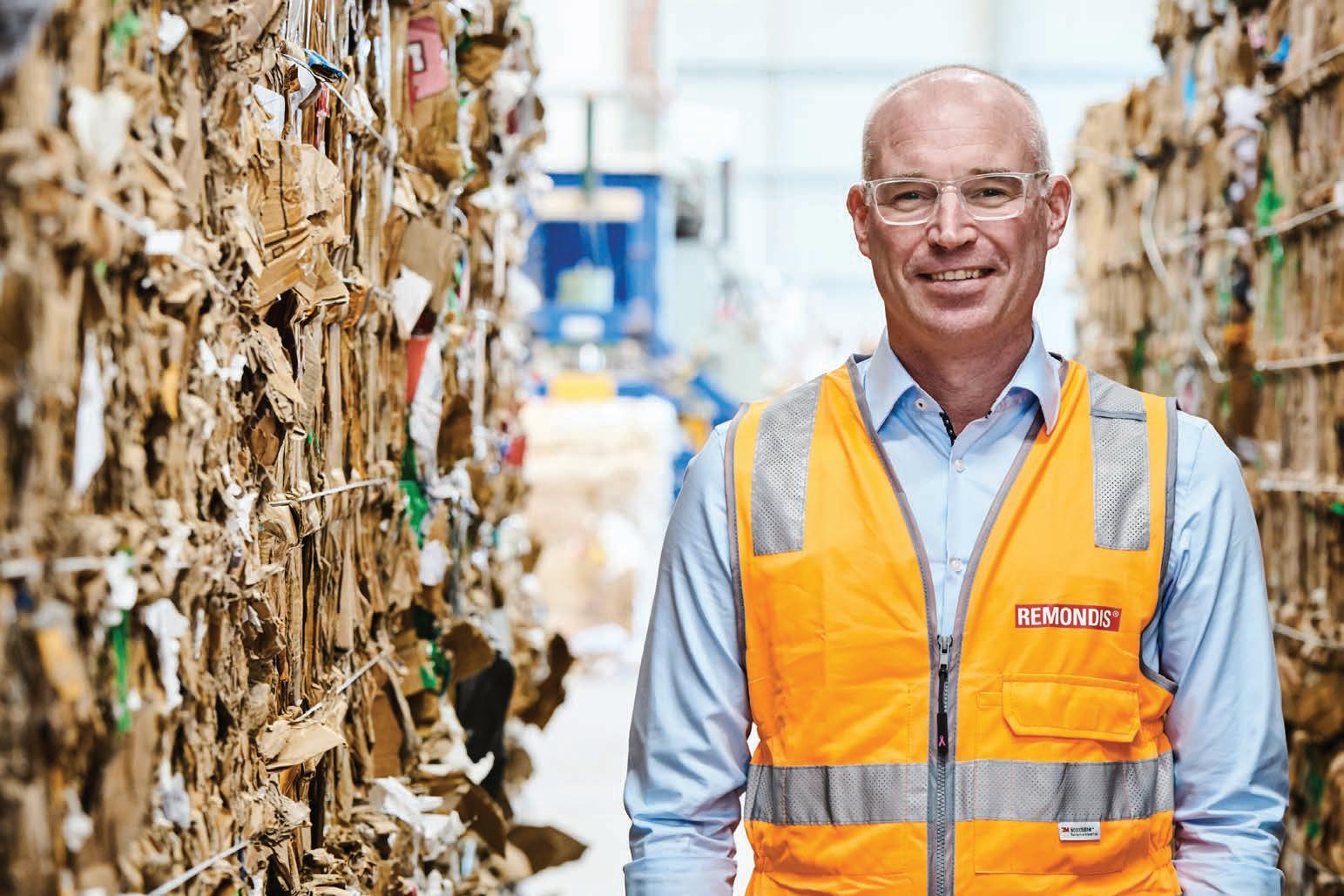

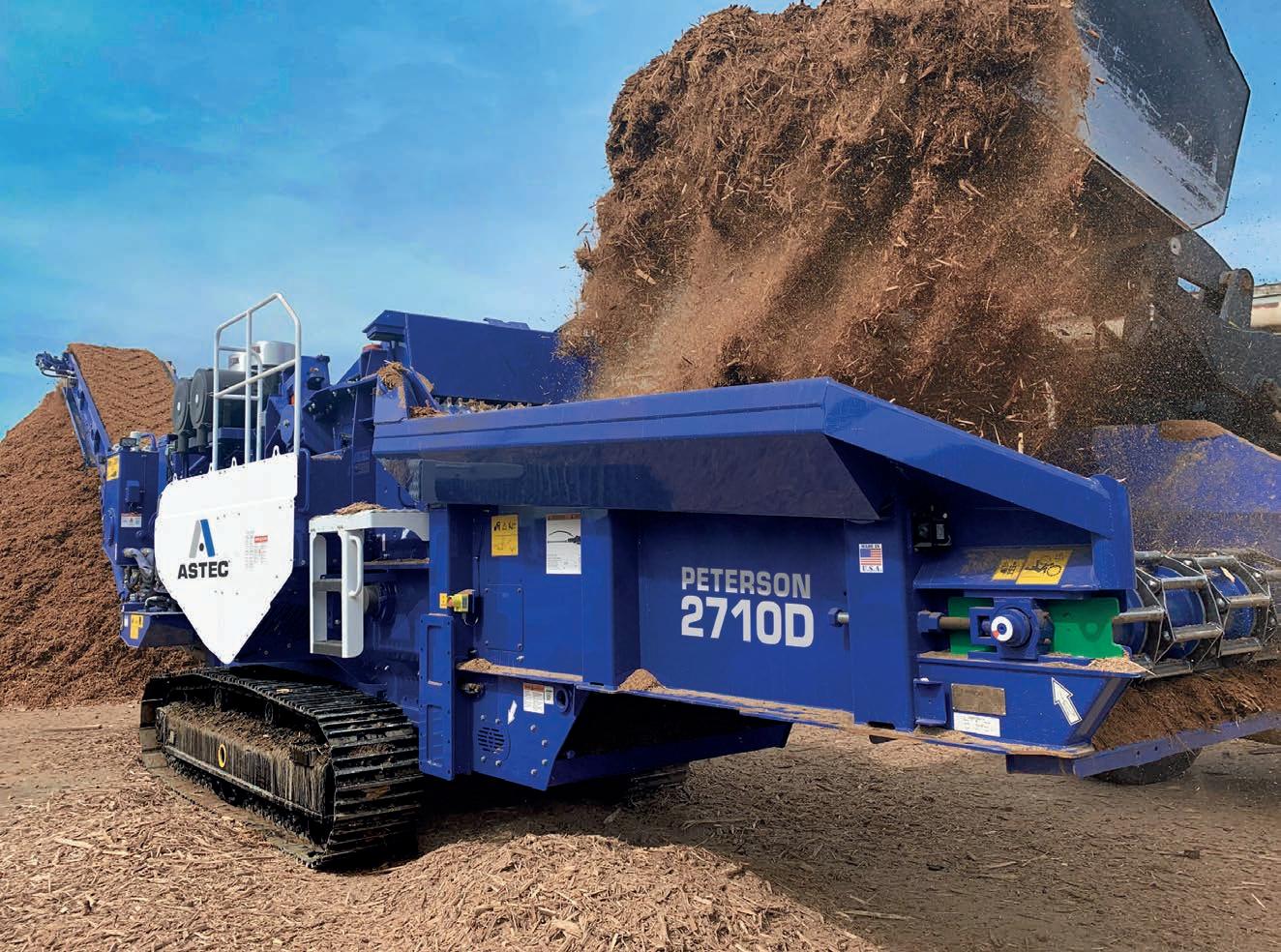

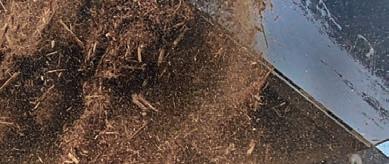


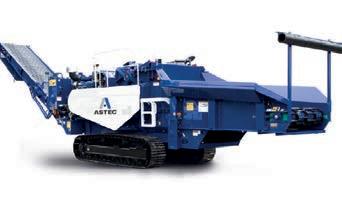

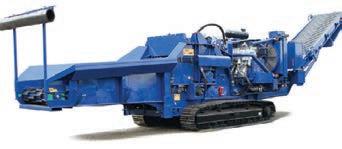
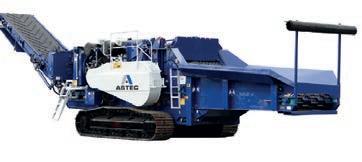
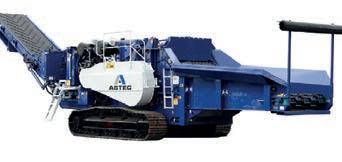
WORKING FOR THE FUTURE REMONDIS leaders reflect on 40 years in Australia as new policies, ambitions and targets accelerate the nation’s recycling industry. this issue WANT TO BECOME ONE OF THE LEADERS IN THE CIRCULAR ECONOMY. WANT TO BE A PARTNER WHO CAN BRING TECHNOLOGY AND IMPROVE THE INFRASTRUCTURE FOR RECYCLING IN AUSTRALIA.”
52
22
EnviroChoice Industries is the right choice for liquid waste disposal and clean-up. 64
Manufacturer JDM Aust is using its on-shore capabilities to help the nation’s tyre recycling industry.
38
WE
IN THE DRIVER’S SEAT Ecocycle is preparing for the days when electric vehicles rule the roads.
54
Clean Energy Group is set to launch an Australian-first project for tyre recycling.
CLEAR WATER REVIVAL A new closed-loop wash line is bringing added benefits to a Geelong plastics recycler. 56
33
25
CHIPPING AWAY A Queensland company is taking tyre recycling to the next level.
DOUBLE DUTY STG Global is bringing the first dual waste collection truck Down Under. 58
GOTTA KEEP IT SEPARATED Eriez provides sorting equipment for effective resource recovery 68 A FUTURESUSTAINABLE A preview of this year ’s Waste Expo Australia. WOMEN IN INDUSTRY WMR chats to two trail-blazing women in waste. CLOSING IN CIRCULARITYON Planet Ark’s Adam Culley discusses the new Circularity conference. Regulars 74 PRODUCT SPOTLIGHT 77 LAST WORD
Hitachi Zosen Inova is designing the next generation of EfW plants.
Central Coast Council maximises efficiency with machine guidance.
POWERHOUSEINDUSTRY
COVER STORY
In
TRIED AND TESTED
“WE
52
50
www.wastemanagementreview.com.au / WMR / 3 15
48
WHERE ARE WE NOW? MRA Consulting Group’s Esther Hughes takes a look at the state of EfW in NSW.
BOLD AMBITIONS Babcock & Wilcox sheds light on an increasing trend to establish EfW plants for specific waste streams.
PUSHING BOUNDARIES
WASTE TRACKER New laws are now in place for tyre recyclers in Victoria. EPA explains.
36
45
NO FOSSIL, NO FUSS Australia could look to Finnish innovation to optimise its EfW future.
ResourceCo CEO Jim Fairweather discusses the need for a domestic market for tyre-derived products.
60
LGI is building its capacity for renewable energy to help meet wider market demand.
A GUIDING HAND
66
MADE TO ORDER Liebherr ’s engineers thrive on providing unique equipment. 62
HOME TRUTHS
70
18
THE HYDROGEN ROAD
29
UP FRONT A look at the state-of-play for the use of tyre-derived crumb rubber in road asphalt in Australia.
CALL TO ARMS Australian Tyre Recyclers Association wants to fire up the use of tyre-derived fuel.
THE RIGHT CHOICE
- Jochen Behr, Chief Executive Officer REMONDIS Australia Features Australia could look to Finnish innovators such as BMH Technology to optimise its energyfrom-waste future in the context of a circular economy. NONOFOSSIL,FUSS
72
41
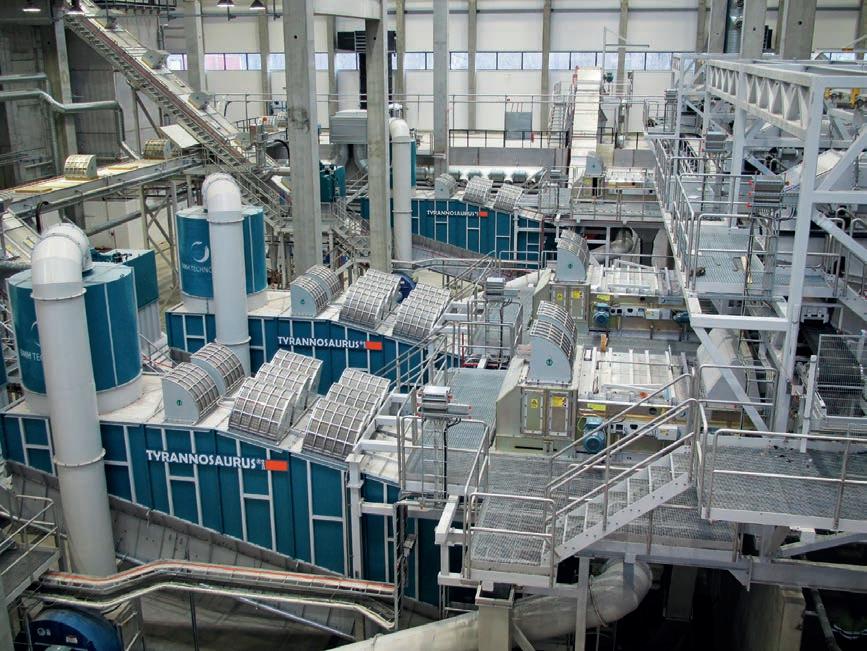
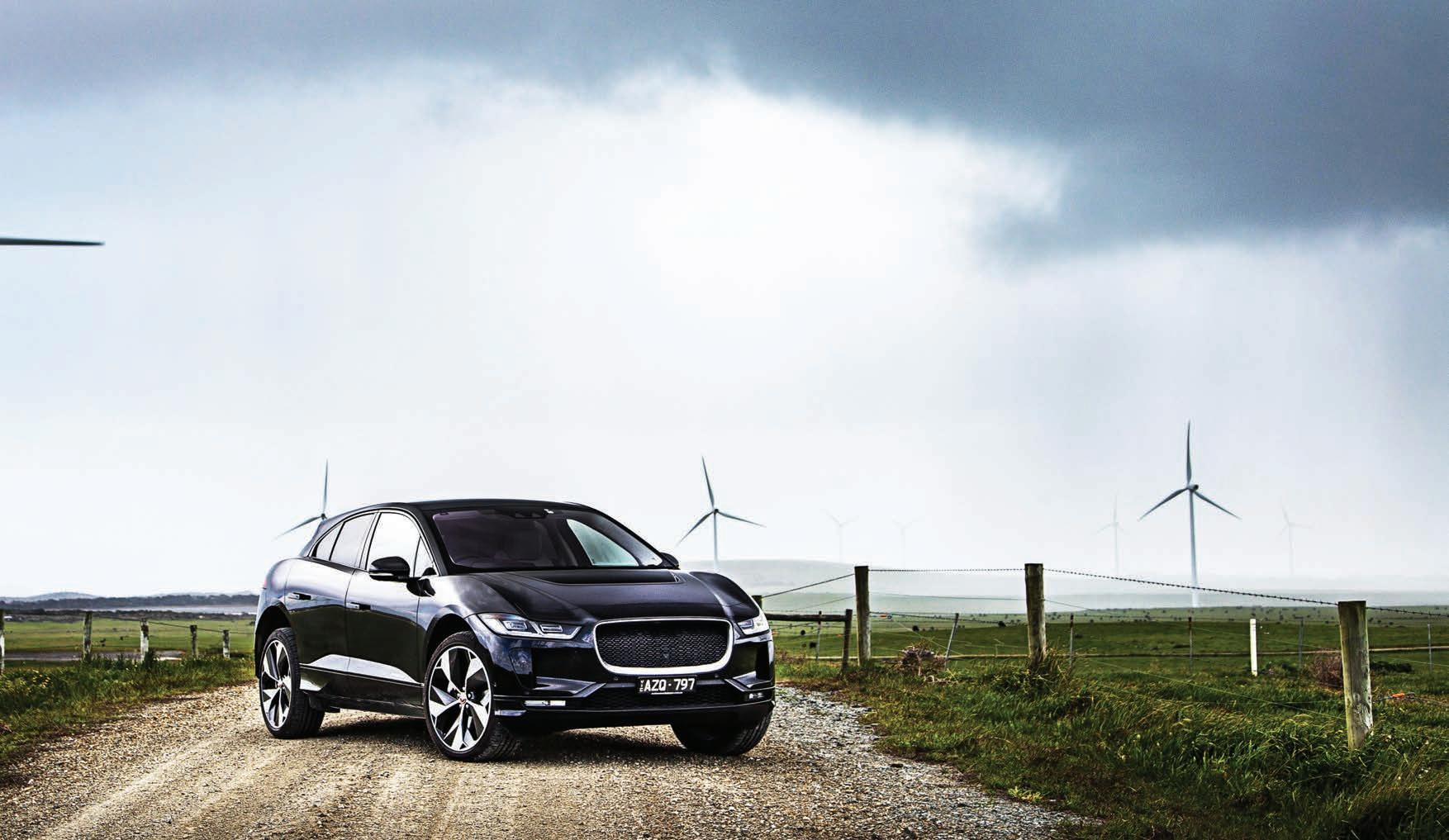


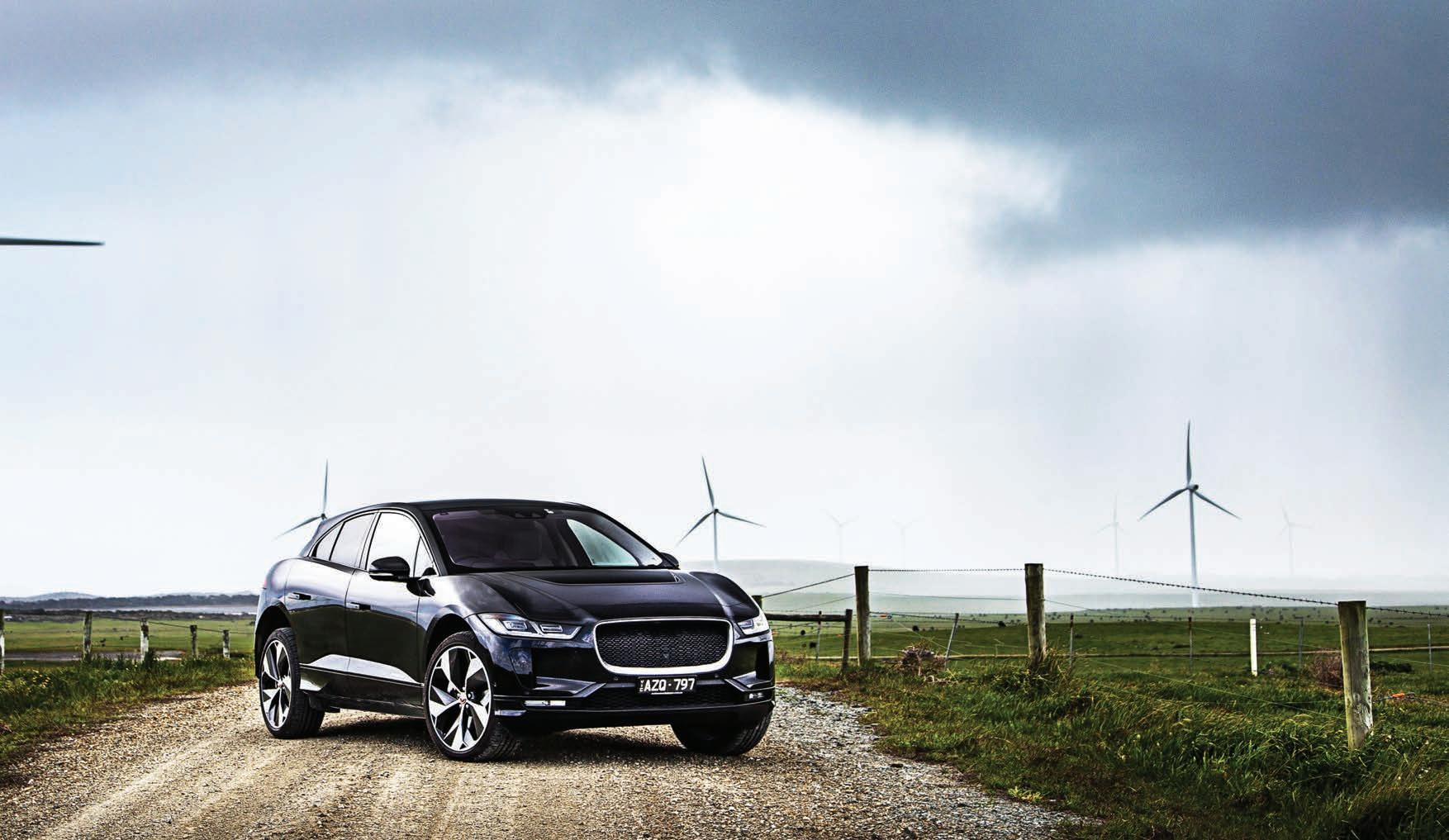
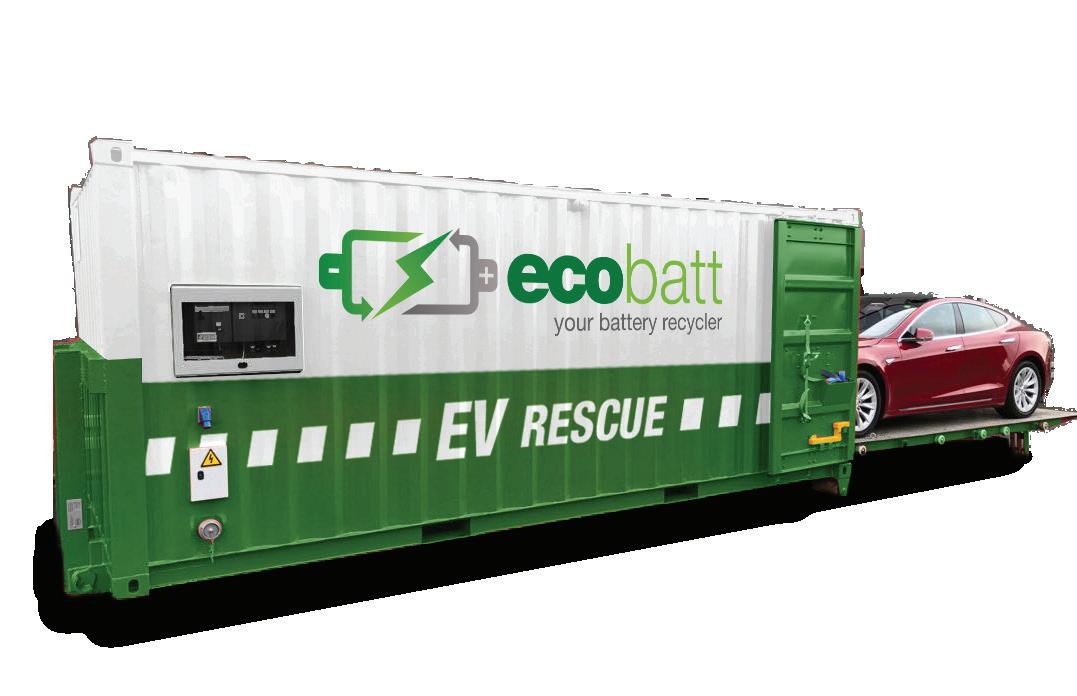
A recent tech talk at RMIT in Melbourne discussed the state of play for the use of tyre-derived crumb rubber in asphalt for roads in Australia, noting that in Victoria, 71 per cent of end-of-life tyres are recovered and processed, but 80 per cent of that material is exported.
FromtoClosehometheEditor
CHIEF OPERATING OFFICER Christine Clancy christine.clancy@primecreative.com.au GROUP MANAGING EDITOR Sarah Baker sarah.baker@primecreative.com.au
Circular economy and resource recovery are no longer phrases used only within the bounds of materials recovery facilities. It’s part of the vernacular in schools, supermarkets, sporting groups and everywhere in between.
Andrew Waite, Director of Sales and Business Development for Babcock & Wilcox, sums it up when he says: “If we’re looking at a circular economy, you have to have the ability to collect and process waste and make the most of it”.
SUBSCRIPTIONS +61 3 9690 subscriptions@primecreative.com.au8766
COPYRIGHT Waste Management Review is owned by Prime Creative Media and published by John Murphy.
And while numerous clean energy companies are tech-ready to introduce energy-from-waste solutions to treat our residual waste, they’re hampered by local support to get on-shore projects off the ground.
The Editor welcomes contributions but reserves the right to accept or reject any material. While every effort has been made to ensure the accuracy of information, Prime Creative Media will not accept responsibility for errors or omissions or for any consequences arising from reliance on information published.
ARTICLES
Prime Creative Pty Ltd 11-15 Buckhurst Street South Melbourne VIC 3205 Australia p: +61 3 9690 8766 f: +61 3 9682 www.wastemanagementreview.com.auenquiries@primecreative.com.au0044
All articles submitted for publication become the property of the publisher. The Editor reserves the right to adjust any article to conform with the magazine format.
DESIGN PRODUCTION MANAGER Michelle Weston michelle.weston@primecreative.com.au ART DIRECTOR Blake Storey blake.storey@primecreative.com.au DESIGN Louis Romero, Kerry Pert BRAND MANAGER Chelsea Daniel-Young chelsea.daniel@primecreative.com.aup:+61425699878
JOURNALIST Leon Cranswick leon.cranswick@primecreative.com.au
HEAD OFFICE
Jim Fairweather, ResourceCo Chief Executive Officer, and Rob Kelman, Executive Officer Australian Tyre Recyclers Association, are strong advocates for domestic markets for tyre-derived products, whether it be crumb rubber or tyre-derived fuel (TDF).
Now then, say industry insiders, is the time to feed an appetite for change.
Lisa Korycki
The opinions expressed in Waste Management Review are not necessarily the opinions of, or endorsed by the publisher unless otherwise stated.
6 / WMR / September 2022
As highlighted in this edition of Waste Management Review, there’s momentum across industries to develop domestic markets to ensure our recycled waste does find new purpose.
Let’s hope Australia seizes these opportunities.
MANAGING EDITOR Mike Wheeler mike.wheeler@primecreative.com.au
CLIENT SUCCESS MANAGER Justine Nardone justine.nardone@primecreative.com.au
Waste Management Review is available by subscription from the publisher. The rights of refusal are reserved by the publisher
There’s no denying there’s been a seismic shift in the way Australians regard The National Waste Policy Action Plan and Council of Australian Governments (COAG) export bans on plastic, paper, glass and tyres have catapulted how we dispose of our waste into the public arena.
All material in Waste Management Review is copyright and no part may be reproduced or copied in any form or by any means (graphic, electronic or mechanical including information and retrieval systems) without written permission of the publisher.
It’s a sentiment echoed by REMONDIS Australia Chief Executive Officer Jochen Behr. As the company celebrates 40 years in Australia, Jochen says that supporting a circular economy by introducing new technology and improved recycling infrastructure is key to maintaining our momentum.
EDITOR Lisa Korycki lisa.korycki@primecreative.com.au
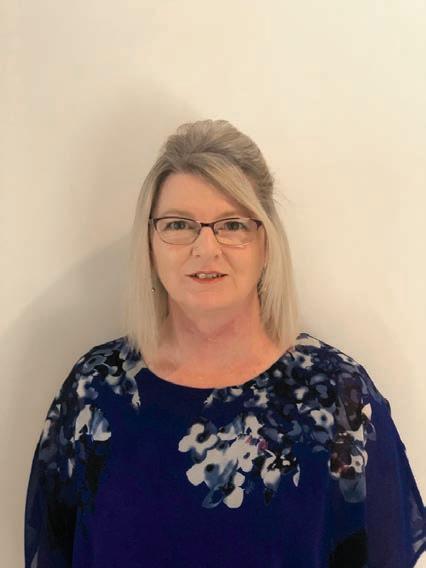
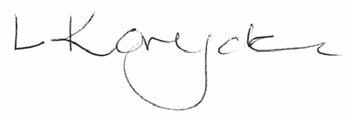
resourceco.com.au TOMORROW’S SOLUTIONS. TODAY • Construction and Demolition Waste • Commercial and Industrial Waste • Tyre Recycling • Energy from Waste • Complete Material Solutions • Circular Economy Carbon Abatement Since 1992, we have repurposed over 60 million tonnes of waste. We are in the business of resource recovery –transforming waste into usable products. Find out what we can do for you.
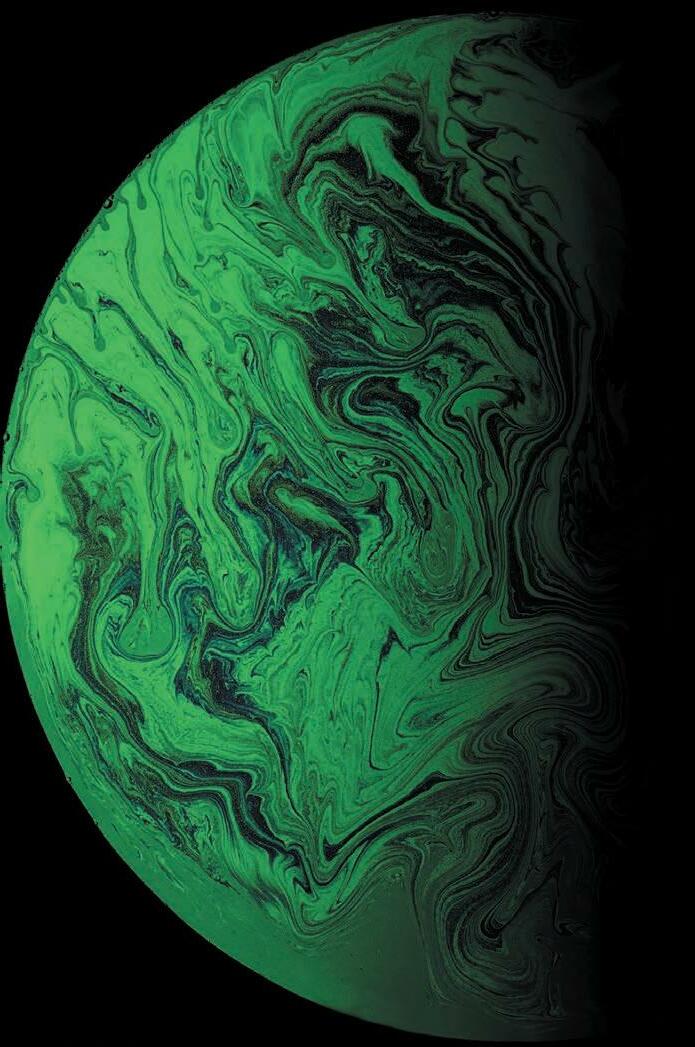
News
“The ban means it is now illegal for companies and organisations in Australia to export any mixed waste plastics. “It is expected to result in even more recyclable materials being sent to landfill every year unless product stewardship and industry-led initiatives like this one are quickly implemented.”
Close the Loop Founder Steve Morriss and Close the Loop CosmeticElsieSpecialistFulton
“This Australian Government, industry, and sector partnership can pave the way for the global cosmetics industry to become much more sustainable. It is a great example of what can be achieved when all stakeholders work together to enable end-of-life products to be efficiently collected, and then recycled or remanufactured into other products – a true circular economy in action,” he“Thesaid.launch of the trial is very timely given the Australian Government’s second round of plastics export bans has just come into effect.
Close the Loop Limited is conducting a trial product stewardship for cosmetics. In conjunction with Myer and with guidance from peak industry body, Accord, the trial will research new ways of recycling cosmetics to reduce the estimated 5000 to 11,500 tonnes of cosmetic packaging that is currently being landfilled in Australia each year. Consumers will be able to take their used cosmetic items from any brand to collection points in 12 participating MyerThestores.trialproject received grant funding from the Australian Government’s National Product Stewardship Investment Fund and will run for an initial eight weeks to mid-September 2022. It will inform the feasibility of any future ongoing product stewardship schemes for cosmetics. Products collected during the program will be sorted into eight categories and processed by Close the Loop to be recycled or remanufactured into newHardproducts.andsoft plastics will be shredded and used in Close the Loop’s TonerPlas, an award-winning asphalt additive which uses waste plastics and toner from old printer cartridges to create roads. The plastics will also be used in the company’s Resin8 concrete additive. Metals will be separated and sent to a metals recycling facility and glass will be crushed for use as a sand replacement in building materials for the construction industry. Materials that cannot be processed will be used to fire a low-carbon emissions cement kiln, ensuring that no products collected will be sent to Joelandfill.Foster, Chief Executive Officer of Close the Loop Group, said cosmetics packaging is traditionally a complex waste stream – often including plastics, glass, metals, foils, rubber, natural fibres, mirrors, foam, paper and residual products.
Close the Loop, Myer to trial product stewardship for cosmetics
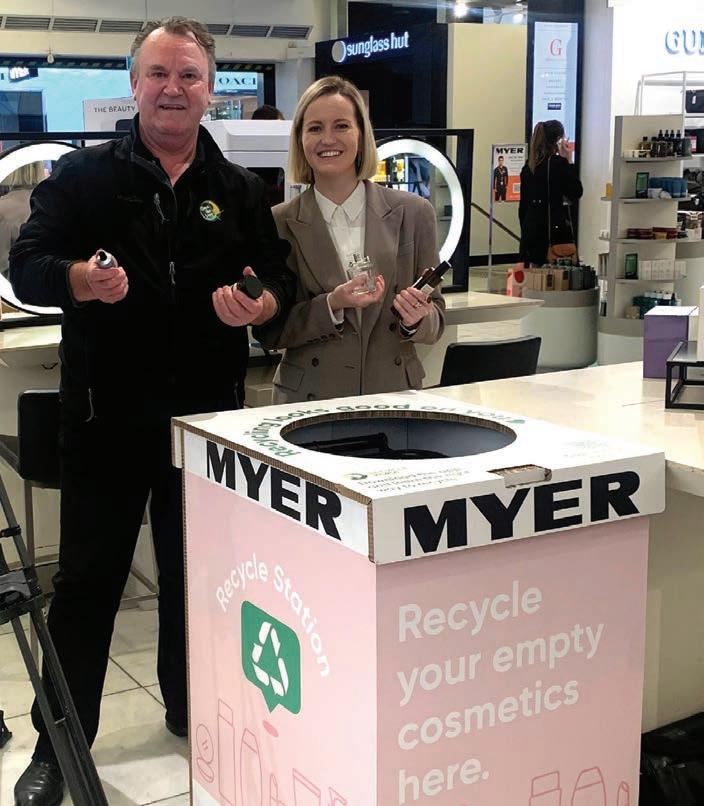
To find out more, call: 03 9706 8066, Email: sales@appliedmachinery.com.au, or visit: www.appliedmachinery.com.au Recycling Technology. Shredders, Raspers, Granulators, Wash Plants, C&D, eWaste Lines, Tyre Plants, Repelletising and more. That’s Applied Thinking.
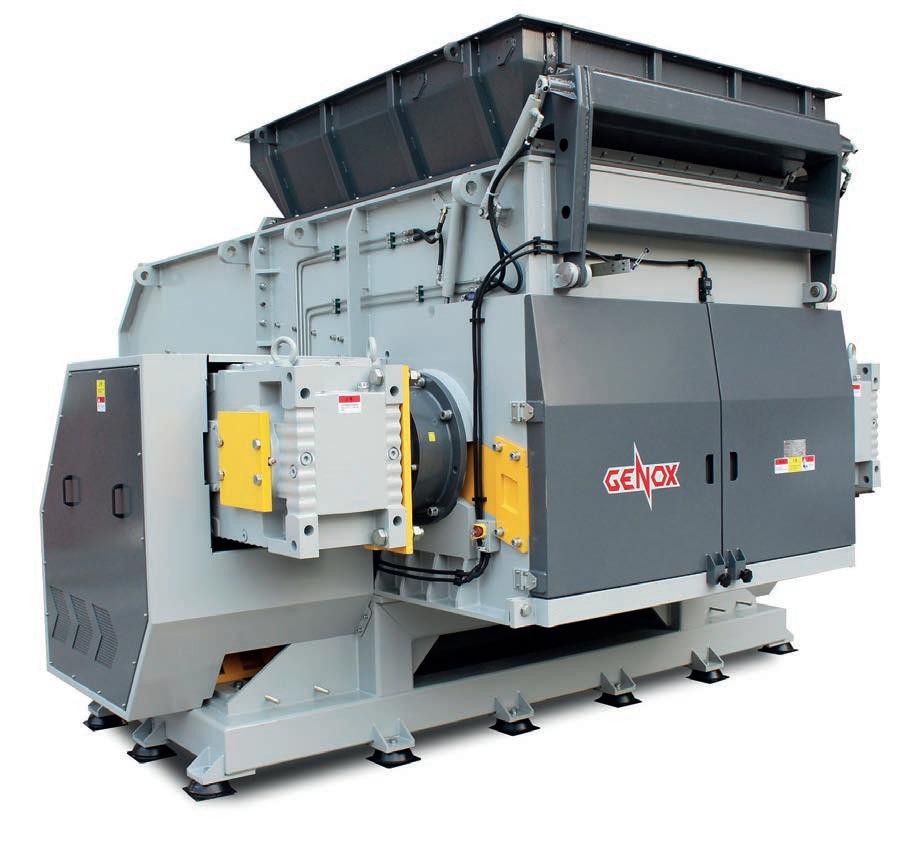
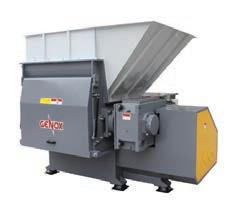
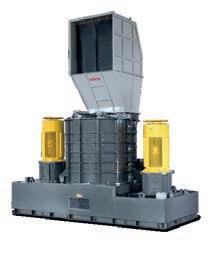
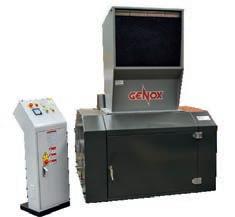
And when identifying the reason why, another 42 per cent pointed to confusion over what is suitable for recycling.
Daniel Baker, Director Corporate Responsibility ALDI Australia said the company was on-track to achieving its plastic packaging targets.
The project is expected to be completed by the end of 2022.
ALDI reveals Aussies want to be better projectAustralia’srecyclersfirstgas-to-gridkicksoff
News 10 / WMR / September 2022 Research commissioned by ALDI Australia confirms a reduction in plastics waste is top of mind for shoppers, with 73 per cent of Australians agreeing supermarkets should work with suppliers to reduce the packaging on products.
To help curb this confusion, as part of ALDI’s plastics and packaging commitments, the Australasian Recycling Label (ARL) logo and recycling instructions will be featured on 100 per cent of ALDI’s exclusive brand products by the end of this year.
Helping customers recycle in their home with best-in-class packaging information is coupled with the supermarket’s own plastic reduction achievements. At the end of 2021, ALDI achieved a plastic packaging reduction of 11 per cent as compared to 2019 –the equivalent to preventing more than 4000 tonnes of plastic from entering the Australian environment.
Resource Recovery
ALDI has also partnered with REDcycle to offer a soft plastics recycling program across all of its stores nationally by the end of 2022. The program will enable shoppers to return soft plastics to its stores to be then re-processed into new packaging materials.
Brooke Donnelly, Australian Packaging Covenant Organisation Chief Executive Officer, welcomes the plan to help put more knowledge in the hands of customers to encourage accurate recycling: “The ARL increases recycling recovery rates and contributes to cleaner recycling streams and it is commendable to see ALDI support its customers to play their part in correctly recycling and disposing of their packaging,” Donnelly said.
Four in five, or 79 per cent, of shoppers said they would correctly sort and dispose of their household waste if given clearer instructions.
An Australian first trial at Sydney Water’s Malabar Wastewater Resource Recovery Plant will use renewable biomethane to support the energy demands of up to 13,000 homes. Kevin Anderson, Minister for Lands and Water, said the works at Sydney Water’s Malabar facility will deliver reliable and cleaner gas and help to reduce the carbon footprint of “Thehouseholds.Wastewater
This hunger for greater recycling action extends into their own homes, with 64 per cent saying it is important that packaging left over from a grocery shop can be Aussies’recycled.recycling prowess is hampered by confusion over how it all works. More than two in five (43 per cent) Australians don’t always recycle packaging from their household waste.
Facility will create about 95,000 gigajoules of biomethane, from organic material in wastewater, to supply gas to about 6300 homes by the end of the year, with the capacity to double production by 2030,” Anderson said. “This five-year pilot will put gas directly into the supply network and will help industries across New South Wales meet their net-zero emissions targets, with the facility able to turn waste material into a new clean energy source.” Paul Plowman, Sydney Water’s General Manager of Asset Lifecycle, said the first of its kind biomethane project is expected to remove 5000 tonnes of carbon emissions each year – the equivalent of almost 2000 cars off the road.
The $16 million project is a joint partnership between the Federal Government’s Australian Renewable Energy Agency (ARENA), that is providing a $5.9 million grant, the NSW Government, Sydney Water and energy infrastructure company, Jemena.
www.TelfordSmith.com.au Washing Plants for Plastics DestructionProductSeparation& Balers for Solid Waste SeparatingElectronicSorting& matterssizewhenFor MaterialsHandlingSystems The SIZE REDUCTION SPECIALISTS with equipment designed for the most extreme and universal applications required in today ’s recycling for plastics, rubber, wood, e -waste to cardboard, paper, & more. GRANULATORS + SHREDDERS + PULVERISERS + HAMMER MILLS + BALER S + SMART BINS + MOR E Want to profit more from your size reduction activities? Contact TELFORD SMITH today!

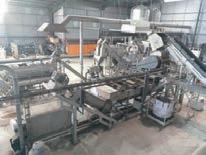



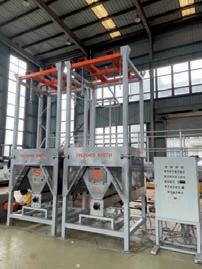
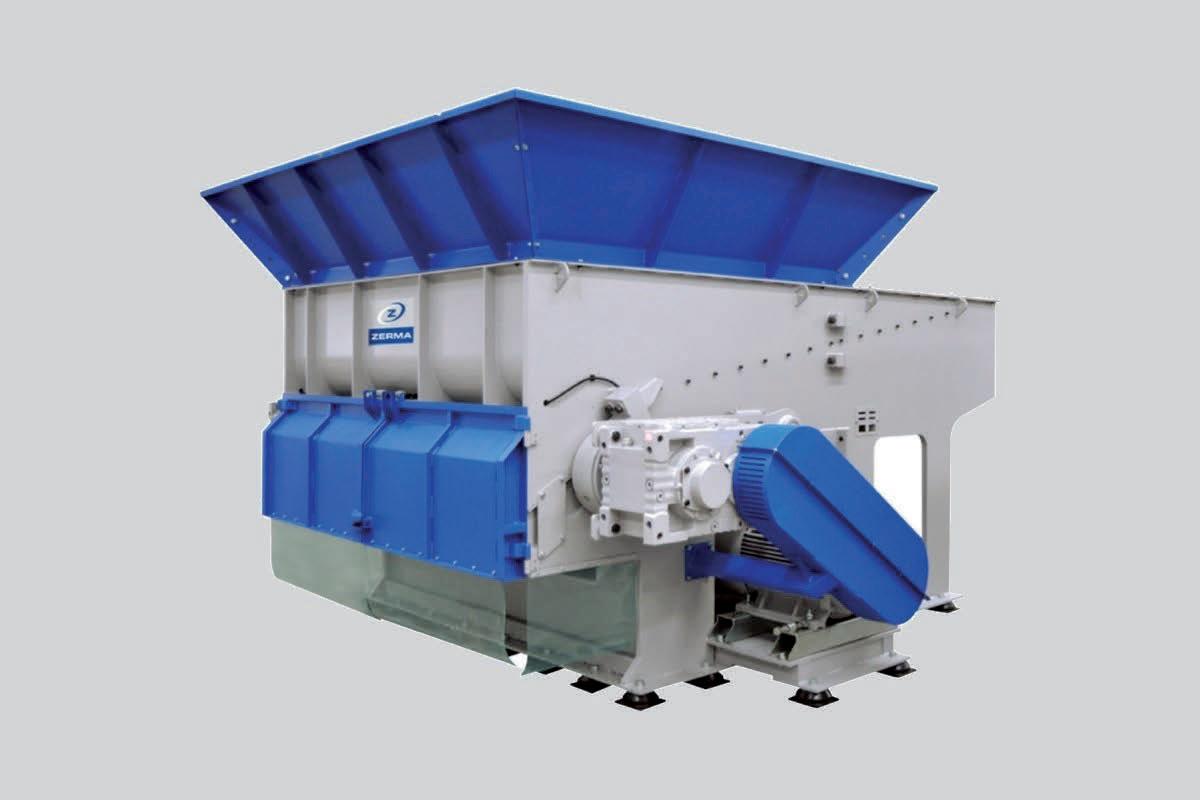
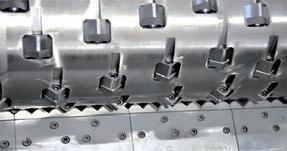
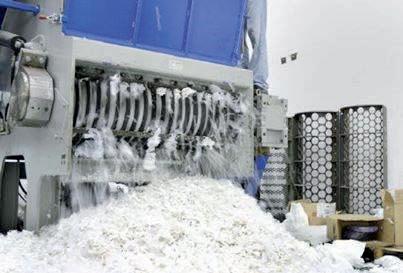
BRONWYN VOYCE IS MAKING IT EASIER FOR SMALL BUSINESSES TO DONATE, NOT DITCH, SURPLUS SINGLE-USE PLASTIC STOCK
“For the recycling and resource recovery sectors this is valuable material. If separated it has an opportunity to go on to a longer life as new products through advanced manufacturing,” Bronwyn says. “I’m passionate about intervening in the burial of valuable, recyclable
I
The great
The Great Plastic Rescue sorts and then secures recycling and remanufacturing partners for the excess stock, ensuring a sustainable second life.
plastic rescue 2022
n 2021 the Great Plastic Rescue saved three million banned single-use plastic items in Queensland, reprocessing 1.94 tonnes of plastics destined for the dump.
The circular economy start-up is upping the ante as New South Wales prepares to introduce the next stage of its single-use plastics, banning straws, stirrers and cutlery, bowls and plates, expanded polystyrene food ware and cups and cotton buds from 1 November 2022.Bronwyn Voyce, Great Plastic Rescue Founder, says while the bans are a vital step toward less plastic pollution – they are tipped to prevent almost 2.7 billion items of plastic litter from entering the environment in NSW during the next 20 years – they present a short-term dilemma of useful plastics ending up in landfill because retailers have been caught short. She says there are wholesalers, distributors, small-to-medium-businesses, schools and community groups that have boxes of single-use plastics in the storeroom that will no longer be usable.
FEATURE NEWS 12 / WMR / September
Queensland’s Great Plastic Rescue Captains Amy Cobb and Bronwyn Voyce.

The economic benefit is further realised through growth in sustainable product and packaging manufacturing onshore.”Therescue mission began in Queensland in 2021 when the single-use plastics ban came into effect. The free service was driven by a passionate support crew of manufacturing and recycling leaders, Evolve Group and Resitech, who provided space and resources.
Bronwyn says a range of recycling and remanufacturing partners are lined up for the NSW rescue because the end product will depend on the type and volume of polymers rescued.However, the group has been working with a new brand seeking to solve the current pallet and logistics crisis. The LODI pallet, made from recycled plastics, will have a longer life span and higher degree of recyclability.
resources, particularly clean, unused boxed stock.
In Queensland, Resitech turned rescued plastic forks, knives, sporks and spoons into resin used to manufacture BuildTuff’s TuffBlock by Evolve Group. TuffBlocks are made from 100 per cent recycled polypropylene, and are a foundation designed to replace traditional concrete deck footings and steel posts.
“This circular project demonstrates that by diverting sorted, plastic waste, we can increase the volume of quality feedstock for recyclable plastics in Australia, enhancing the viability of the sector in the long-term.
The Great Plastic Rescue is an official NSW Environment Protection Authority sustainability partner and has received some funding to support two NSW rescue rounds.
The first was held in July and August, the second will be from mid-October to mid-November.
Carbon neutral courier service Sendle has also joined the plastic mission, enabling registered rescue businesses to send their first 25 kilograms of parcels for free.
To participate in round two of the voluntary campaign, organisations can register at https://www. greatplasticrescue.co before 15 November 2022. For more information, visit: www.greatplasticrescue.co
BESTSMALL CONSULTANCY MRA’s Planning Team can help you navigate development and licensing approvals –Development Applications Planning Permits Environmental Management Plans AdvisorLicencesy services Contact our award-winning team today to find out what we can do for you Do you need WastewhoEnvironmentalanPlannerunderstandsandResourceRecovery?0285416169
“Single-use plastics are more complex than they look,” she says. “They’re made from different polymers which require different recycling processes.”
info@mraconsulting.com.au
Bronwyn was keen to avoid downcycling of donated stock, which occurs when mixed plastics are recycled into a lower quality polymer or product. She, along with Great Plastic Rescue support crew, spent hours manually sorting every box to maintain the integrity of the polymer and trying to find homes for them.
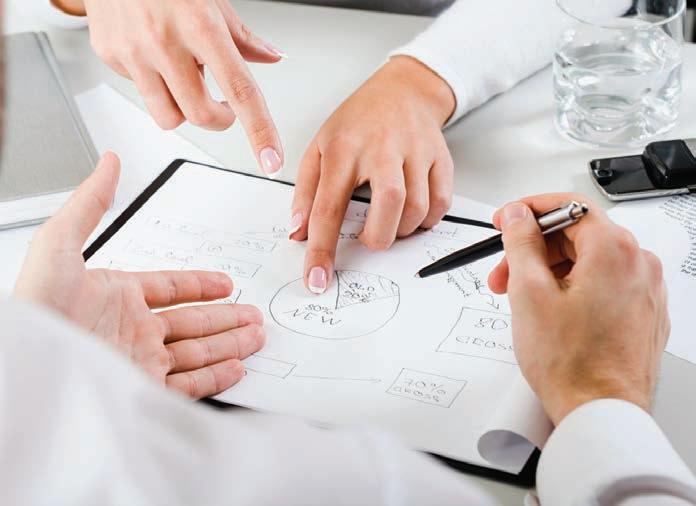
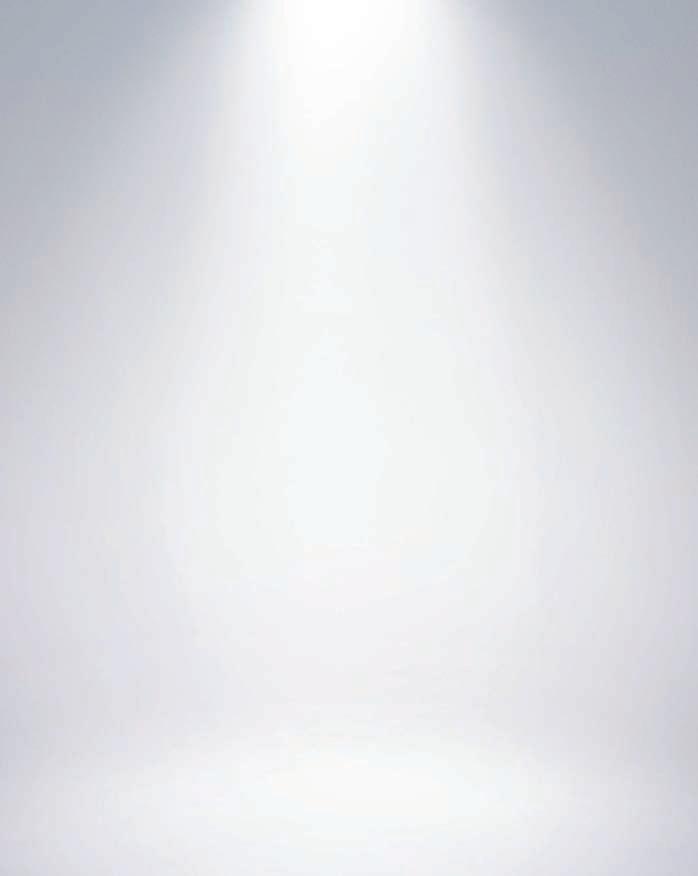
TRUCK DERIMMER
The patented Eagle Punch Cutter II is portable and designed to split Off the Road (OTR) tires into two halves, cutting through the center of the tread.
The Truck Tire Derimmer is a rim crusher that separates the rim from semi-truck tires.
TIRE-RECYCLING EQUIPMENT
The Titan II has the ability to handle and shear through large Off the Road (OTR) and mining tires up to 44 inches.
REDUCE SIZE REDUCE WASTE REDUCE IMPACT
Please contact your Australian dealer: 1300 767 sales@jdmaust.net.aujdmaust.net.au589
OTR DEBEADER
PUNCH CUTTER II
TITAN II
SIDEWALL CUTTER
The ultimate bead puller on the market, the patented Eagle OTR Debeader is designed to pull the bead bundles out of radial Off the Road (OTR) tires.
TRU-CUT This patented tire cutting equipment is designed to slice passenger and semi tires into disposable segments.
The Eagle Sidewall Cutter is designed to remove the side walls of truck and car tires.
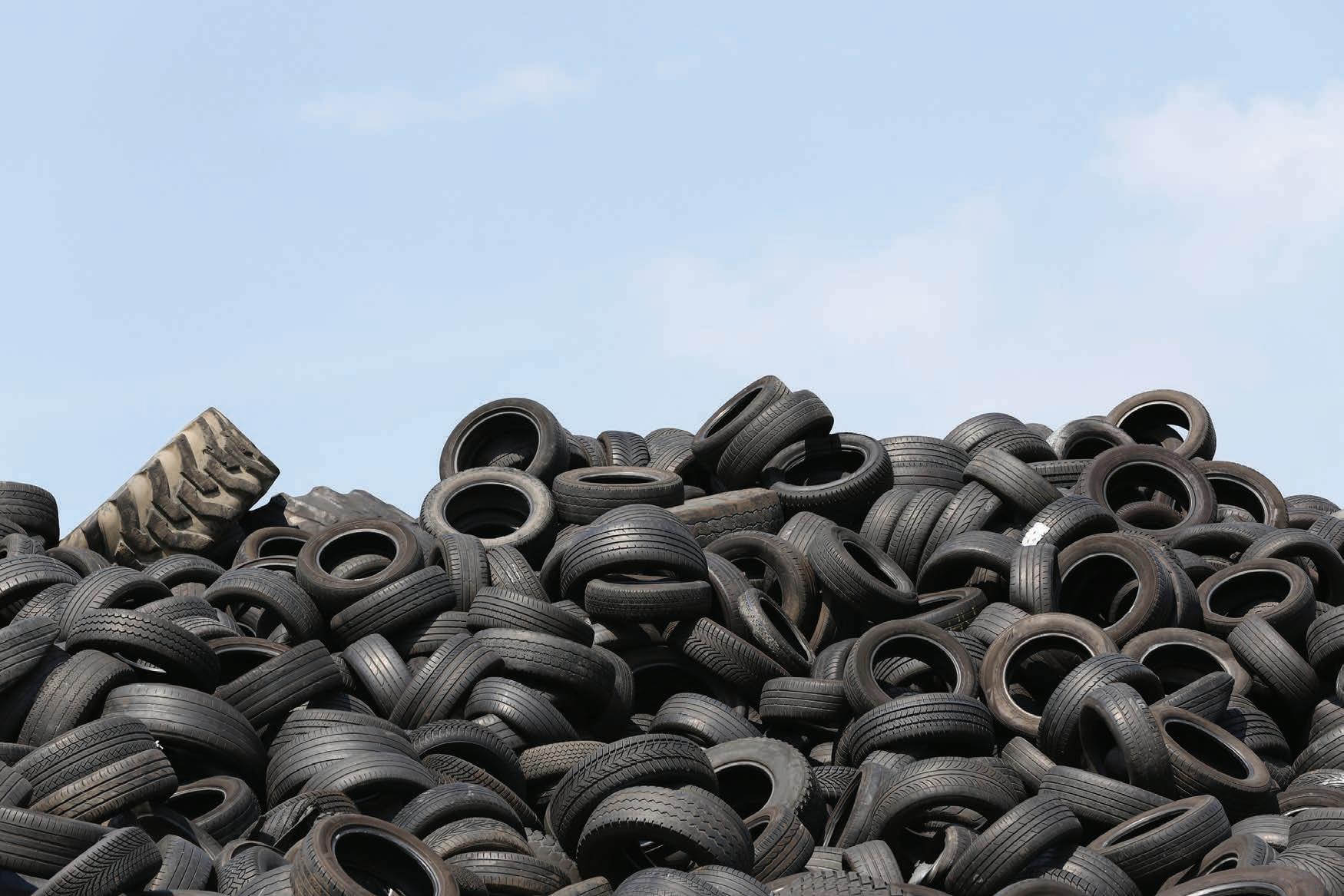
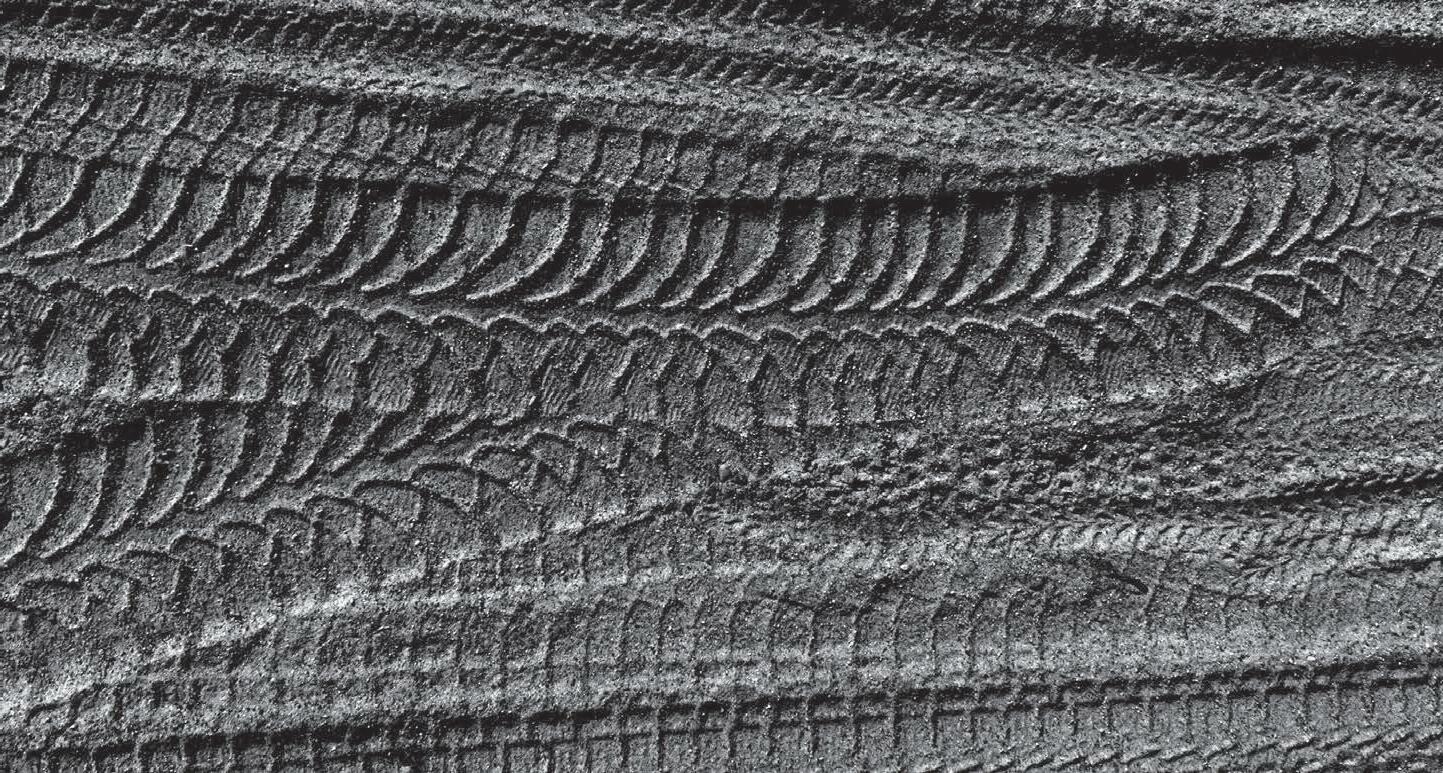
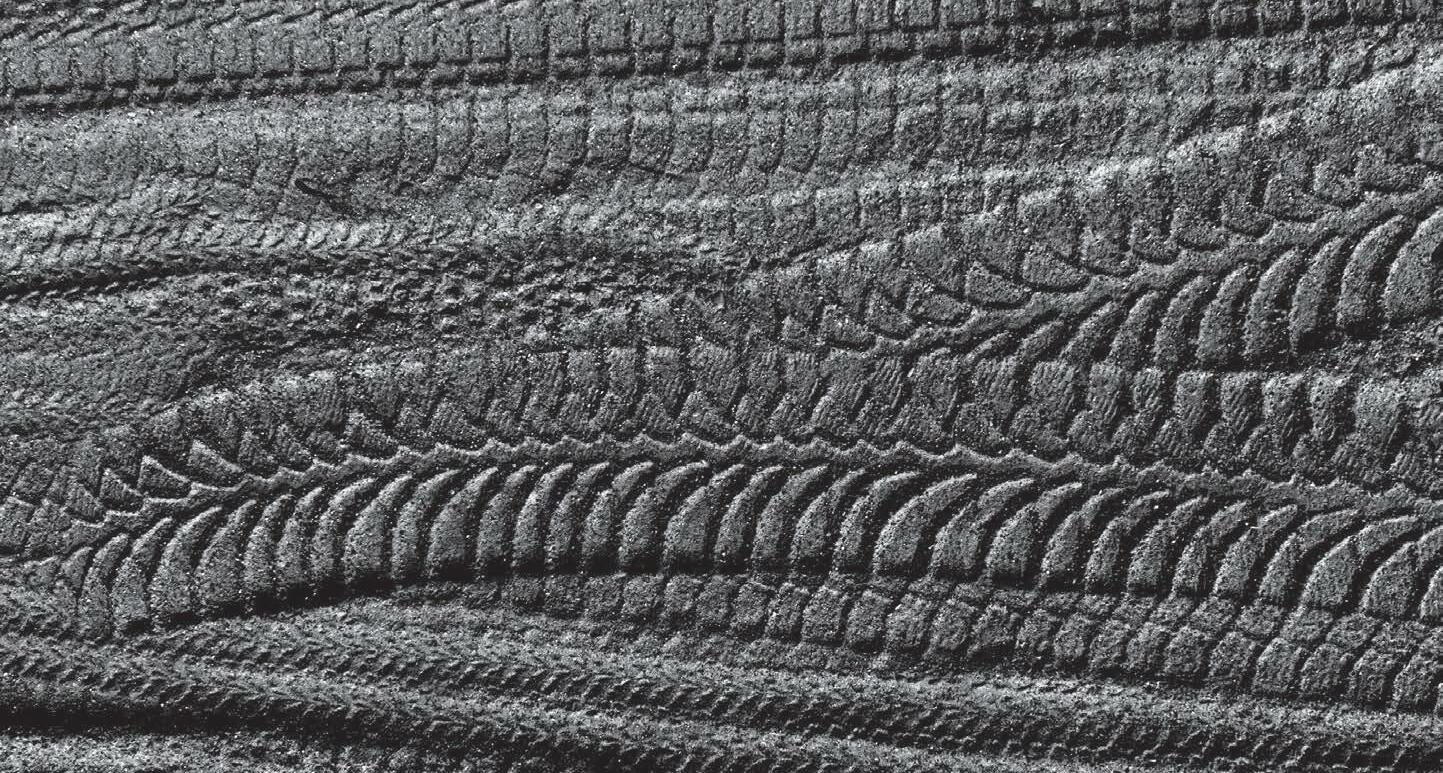

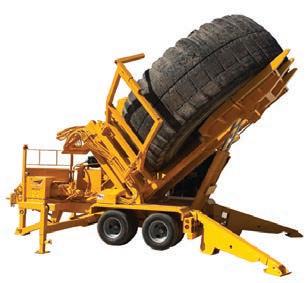
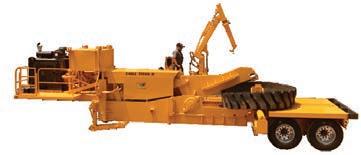
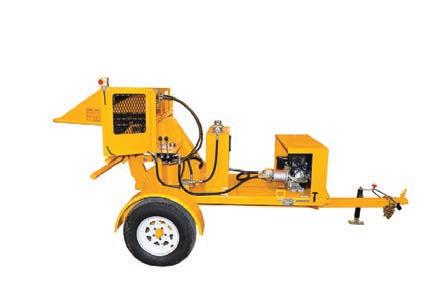


/ WMR / 15 UP FRONT
The road to crumb rubber in
Lina Goodman, TSA Chief Executive Officer, used Victorian data to provide a snapshot of where Australian end-of-life tyres are currently ending up. According to TSA figures, Victoria generates on average an estimated 120,000 tonnes of end-of-life tyres each year. Of that, 71 per cent is recovered and processed for reuse.
The Australian Flexible Pavement Association (AfPA) recently hosted a tech talk at RMIT in Melbourne, outlining the state-of-play of crumb rubber in asphalt mixes in Australia.
“We really need to focus our attention on utilising this recovery rate to our benefit,” Lina said. “It’s being collected, it’s being processed. Now we need the market to be able to consume theOnematerial.”ofthemain challenges for the TSA is fostering increased demand for products containing tyre-derived material, such as crumb rubber.
In Victoria, 71 per cent of end-of-life tyres are recovered and processed, but 80 per cent of that material is exported.
www.wastemanagementreview.com.au
For the uninitiated, asphalt typically comprises the aggregate – a mix of rock, sand, and other granular elements; and the binder – the sticky bitumen that holds it together. The coarseness of the aggregate and the recipe of the mix can be adjusted based on a range of variables, including the location and application of theCrumbroad.
Originally used in sprayed seals, the viability of crumb rubber as a component of asphalt has been an area of increasing interest – from both sustainability and performance perspectives.
CRUMB RUBBER IN AUSTRALIA
Sponsored by Tyre Stewardship Australia (TSA), along with bitumen suppliers Puma Bitumen and Boral Australia, the talk featured speakers involved in tyre recycling, ongoing research, national specifications, and practical trials.
Australiansustainability:roads A
T
he use of crumb rubber from endof-life tyres for Australian roads is nothing new – it has been used in Victoria since 1975.
The catch is, 80 per cent of that material – 85,000 tonnes worth – is exported, meaning just 20 per cent makes it back into the local market.
rubber can be added to asphalt in either ‘dry’ process – crumb rubber particles incorporated as part of the aggregate during the mix, or ‘wet’ –crumb rubber particles added to the binder prior to the mix. Regardless of the process, studies have demonstrated that crumb rubbermodified asphalt can yield roads that are more durable, quieter, and safer.
Lina presented preliminary research by the TSA on the greenhouse gas emissions associated with the use of tyre-derived materials. This included the emissions profile of crumb rubber use in asphalt mixes, and the significant reductions it can offer. RECENT TECH TALK AT RMIT IN MELBOURNE DISCUSSED THE STATE-OF-PLAY FOR THE USE OF TYRE-DERIVED CRUMB RUBBER IN ASPHALT FOR ROADS IN AUSTRALIA.
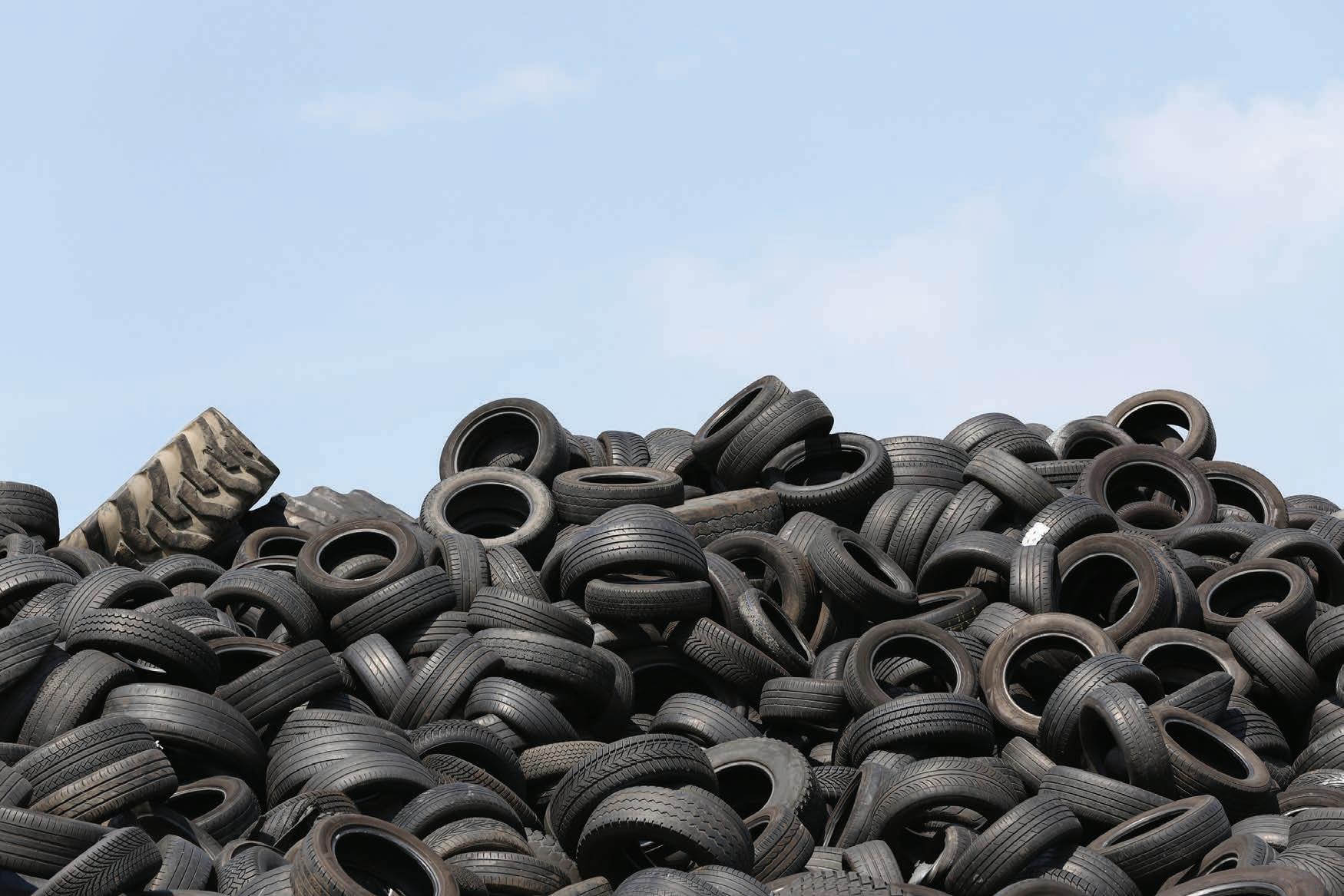
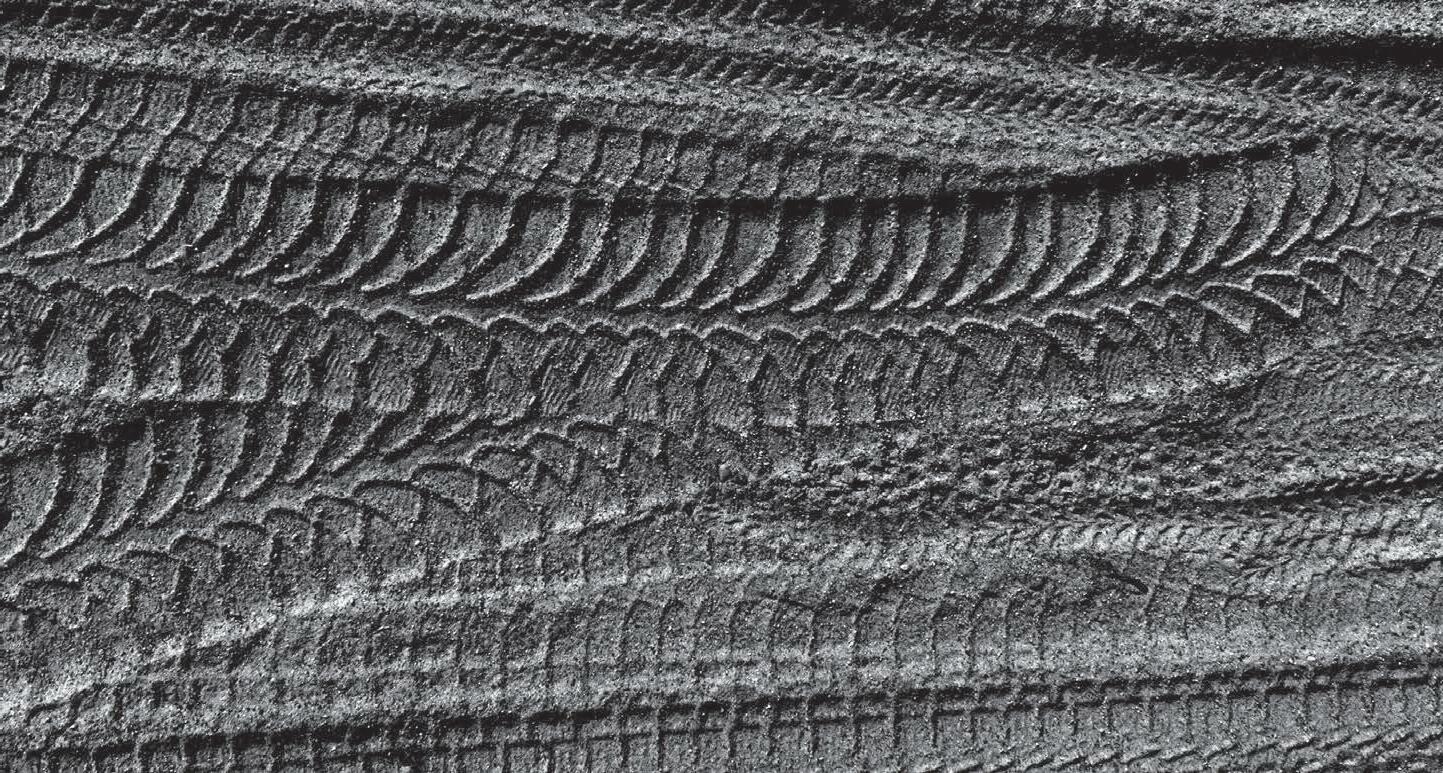
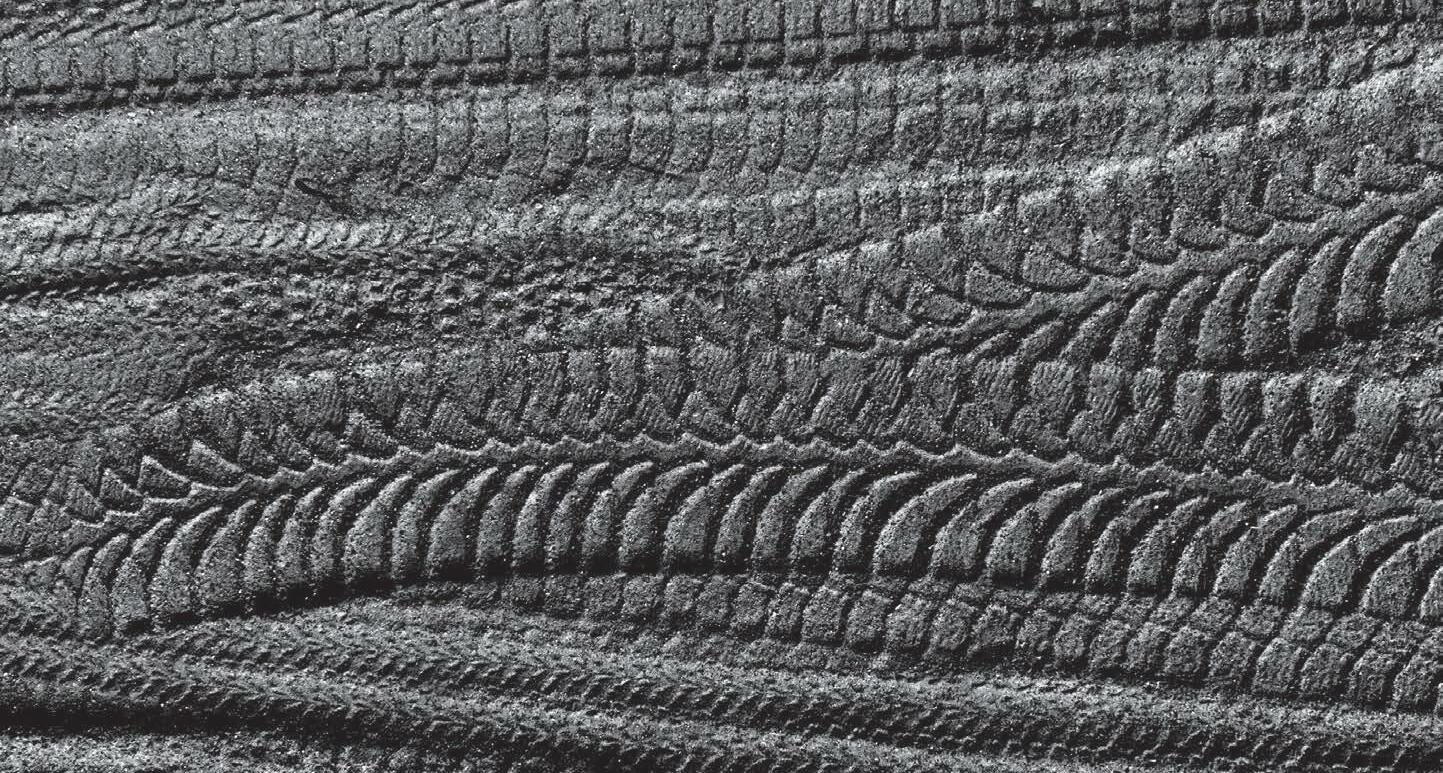
As well as some technical details of the project’s mix design, Carl outlined the overall logistical challenges Boral faced in adapting its plants and fleet for the production and transport of the modified asphalt. Boral also monitored the reduced emissions offered by use of the warm crumb rubber mix – something Carl said was of interest to TMR.
Feedback from the workers on the project was positive, with the product’s significant reduction in fumes improving comfort on the job. John Esnouf, of VicRoads, outlined a crumb rubber asphalt trial on East Boundary Road in East Bentleigh, which ran from March 2020. These trials focused on longterm durability in roads modified with crumb rubber, with test areas featuring experimental and control sections to measure the effectiveness of different processes.
UP FRONT 16 / WMR / September 2022
CRUMB RUBBER IN ACTION
The second, in partnership with the Southern Sydney Regional Organisation of Councils (SSROC) and the TSA, is a multi-council demonstration project testing the performance of various crumb rubber asphalt mixes across various sites. Erik Denneman, Puma Bitumen Global Technical Manager, followed up with an outline of the AfPA crumb rubber asphalt specification, which came about as a collaboration between industry and road agencies.
Carl Topp, Boral Asphalt Technical Manager, summarised the company’s experience with trialling crumb rubber modified asphalt on the Sunshine Coast in Queensland in mid-2021 – a project which used the equivalent of 22,000 passenger tyres. He said that Transport and Main Roads Queensland (TMR), which specified the project, was looking for something with better performance than dense-graded asphalt, and with the benefits of recycled material.
LOCAL AND GLOBAL RESEARCH
Filippo Giustozzi, Associate Professor –Roads, Railways and Airports at RMIT University, said while there has been extensive research into road durability from a traffic wear-and-tear perspective, very little attention has been given to the ageing effects of sun damage on roads.
“This is based on a life-per-life basis,” Lina said. “But we know crumb rubber content in roads does increase the life of the roads. So, if you consider an increased service life, the emissions reductions improve exponentially.” These emissions reductions could amount to 40 and 41 per cent respectively if a three-year service life increase is factored in. Anna D’Angelo, AfPA Executive Director Technology and Leadership, offered a deeper dive into the process of recovering crumb rubber from tyres. AfPA is involved in multiple projects to generate further knowledge around crumb rubber use. These include a national study with AustRoads and the TSA into sourcing crumb rubber from passenger tyres as well as other non-truck tyres, such as those from the mining and agriculture sectors.
The specification is based on international best practice, particularly that used in the United States. One important element of the AfPA specification is the mandated maximum mix temperature to keep emissions and fuming down. “If you use a warm mix, you reduce the temperature,” Erik said. “For every 12 degrees you reduce the temperature, you halve the emissions.”
“We decided we’d give industry a chance to innovate – with freedom from our specifications,” John said. “A real job where a whole lot of different mixtures could be trialled. The design, the production, and the placement were all up to the individual companies.” Testing was conducted throughout the project, including monitoring for emissions, with overall positive results.
Comparing ultraviolet radiation levels across the globe, he noted the relatively high dosage Australia is subjected to, and how that can accelerate the degradation of the nation’s roads. His team’s research involved using RMIT’s UV machines to simulate longterm UV exposure to bitumen samples containing different crumb rubber ratios, revealing its highly beneficial “sunscreen” effect.
AfPA’s tech talk featured speakers covering tyre recycling, asphalt production, crumb rubber research, and more.
Closing out the tech talk, United Kingdom-based Daru Widyatmoko, Technical Director/Pavement Materials Research Team Leader at AECOM, outlined the UK’s experience with crumb rubber in asphalt. In a pre-recorded presentation, Daru said the urgency for pursuing sustainable road paving solutions was crucial, but that a balance must be struck between sustainability and performance.
Early figures indicate that crumb rubber used as 15 per cent of an asphalt binder in a wet process could yield a 10 per cent reduction in emissions compared with traditional polymermodified bitumen mixes. This jumped to 12 per cent when used as 27 per cent of an asphalt binder in a dry process, compared with conventional asphalt.
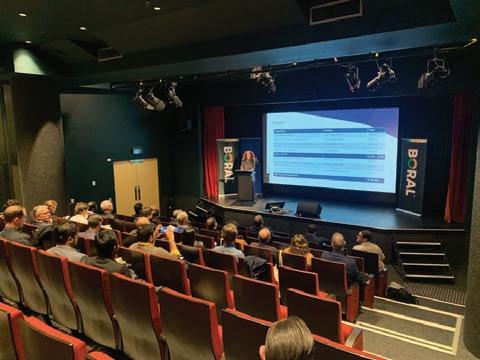

CLEAN ENERGY GROUP P/L 7 BERENDS DRIVE DANDENONG SOUTH VICTORIA 3175 e: warren@cleanenergygroup.com.aum:0466975001p:97683298 CLEAN ENERGY Moving forward with tyre pyrolysis
Clean Energy Group (CEG) has continued to develop tyre recycling with two pyrolysis machines in Dandenong South Victoria. The process separates steel & oil and carbon powder from the tyres. These materials can be used in steel recycling, bunker fuels, power generation and industrial heating kilns. The pyrolysis process has made little progress in Australia, yet most tyres that are exported every year by the local collectors and recyclers go to overseas pyrolysis plants. There is a future for pyrolysis in Australia. Currently, with growing stockpiles of tyres and high export freight costs, pyrolysis is a known and proven recycling process. The other option is generally tyre crumb in asphalt and playground Cleanmarkets.Energy Group will continue to support tyre pyrolysis now and into the future. Together with BXB Technologies, develop Tyre to Hydrogen processing systems making Hydrogen and carburising coke additives for the steel manufacturing industries.

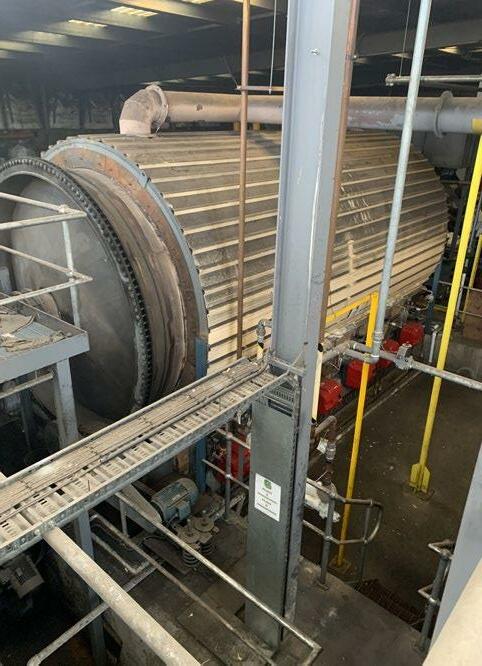
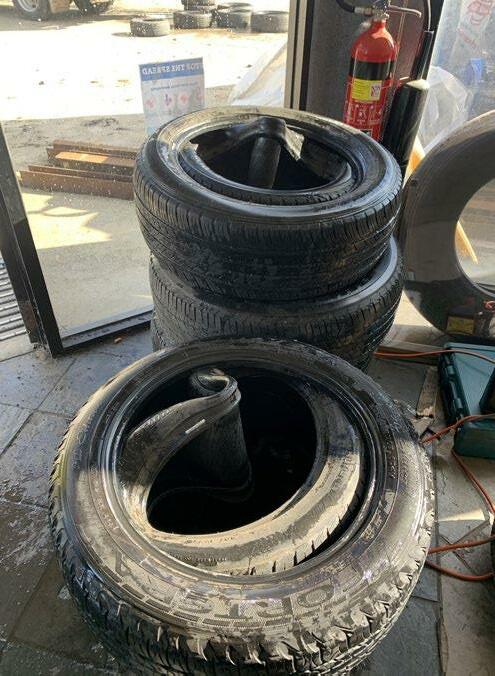
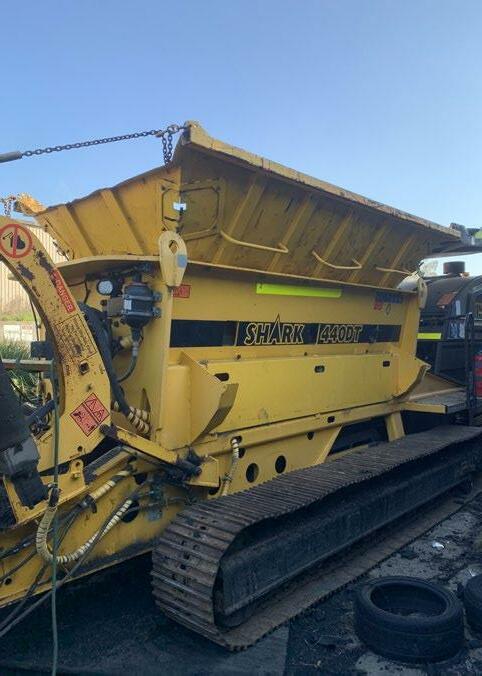
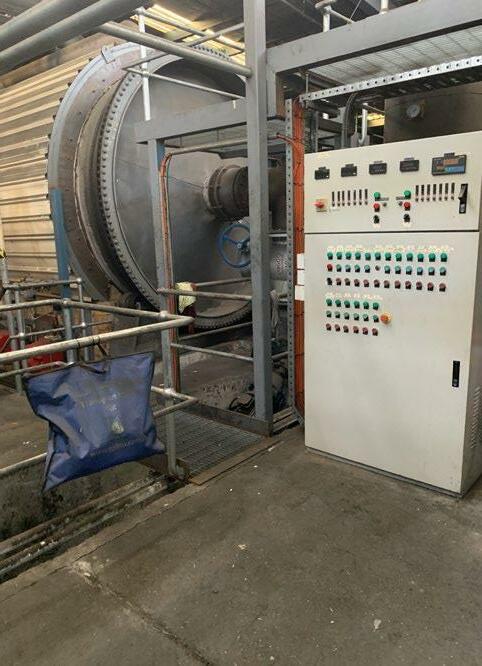
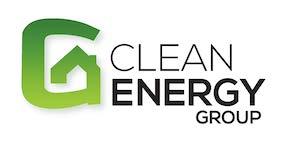
I
18 / WMR / September
Arriving in Australia 1982, then branded Resch.
Working for
t’s a sunny day as Norbert Rethmann pauses outside the Penrith City Council offices in New South Wales for a quick photo with RETHMANN’s then Chief Executive Officer, Dr Hermann Niehues, and Brian King, Mayor of Penrith. He’s relaxed and smiling. It’s 1982 and Norbert, the pioneer of a successful German waste disposal company, has just inked a deal that will transform Australia.
A GLOBAL PLAYER REMONDIS has been an active driver to develop the industry and be one of the major global players in the circular economy market for water, recycling and services solutions. Jochen sees scaling up investments in food organics, container the future 2022
DURING 40 YEARS IN AUSTRALIA REMONDIS HAS DIVERSIFIED TO BE A LEADING WASTE AND RECYCLING COMPANY BUT ITS GOAL HAS REMAINED THE SAME – FOR WASTE TO BE A RESOURCE.
“There’s a big appetite for change,” Jochen says. “There’s a lot of focus by consumers and recycling is stepping into the spotlight.
Fast-forward 40 years, and REMONDIS is the third largest resource recovery company in the world. In Australia, it employs more than 1100 people and operates from more than 35Fromsites. humble beginnings –REMONDIS supplied the first plastic wheelie bins in Australia when it secured the contract for waste collection services of Penrith Council – the company has evolved to play an important role in the nation’s economy. And as the world begins to accept waste as a resource, REMONDIS Australia continues to search for ways to treat it, rather than dispose of it.
Jochen Behr, who took over the role of Chief Executive Officer in April 2022, paints a picture of new policies, ambitions and targets that will accelerate Australia’s recycling sector.
“In the past, many customers were only concerned about whether their bin was empty. There were not many questions about what happens to that“That’swaste.changed and people are more conscious. As a company we have to live up to that expectation. We have to be transparent, and we have to invest in recycling infrastructure.”

Partnering with Paintback since 2020, the company is contracted to handle collections, processing and decanting across Queensland, the Northern Territory and Victoria.
CLOSING THE LOOP Björn Becker, Chairman of REMONDIS Australia and former Chief Executive Officer, is convinced it is the right step at the right time to improve the treatment of waste volumes in Australia. He says it’s a core market for REMONDIS to further develop and achieve better recycling rates and help close the loop to bring recovered materials back to a production process.
deposit scheme innovation and product stewardship, as key for the business in TheAustralia.factthe company is one of a few fully integrated players can only be of benefit. Still family-owned after almost 90 years, REMONDIS has a presence in collection, resource recovery, recycling, and disposal solutions, with a focus on technologies available globally.
While there are a growing number of stewardship schemes and steps in the right direction within Australia, Björn believes government support is needed to make product stewardship mandatory or “Certainly,binding. the best solution is not to generate waste in the first instance,” he says. “But once the waste is there, we need to get the best possible processing and recycling solution we can in order to get secondary raw materials.”
/ WMR / 19
“It has a holistic approach, which we believe is important to address some of those more difficult waste categories,” he says.
The technology is being used in several countries to address landfill diversion targets on food waste and, while previously there wasn’t a market for anaerobic digestion in Australia, changes in the regulatory environment and rising landfill levies are opening “When you look at the Federal Government strategy to halve food waste going to landfill, there will be a big market for these kinds of facilities,” Jochen says.
Jochen says the next step is anaerobic digestion, a process that uses bacteria to break down organic matter to manage waste or to produce fuels.
REMONDIS is a leading player in product stewardship schemes including the Paintback program, Big Bag Recovery and container deposit schemes including the multi-award-winning Containers for Change scheme in Western Australia.
www.wastemanagementreview.com.au
In the Big Bag Recovery scheme alone, there is the potential to collect 60,000 tonnes of polypropylene and low-density polyethylene bulk bags acrossJochenAustralia.saysit’s a way to find solutions for difficult waste streams and to address some regulations within that stream.
Norbert Rethmann, Dr Hermann Niehues and Brian King, Mayor of Penrith. Björn Becker, Chairman, REMONDIS Australia.
REMONDIS was one of the first to introduce in-vessel composting with a facility in Port Macquarie in 2001.
Product stewardship, he believes, is also an important piece in the puzzle, helping to recover clean, quality resources that can be processed back into secondary materials for new products.
“One of our key ambitions is supporting a circular economy,” Jochen says. “In Germany, landfilling was banned almost 20 years ago, which created a need to innovate. We are now proud of being able to draw from thatHeexperience.”seesorganics recycling as one of the biggest opportunities in Australia –from food and garden waste collection and processing through to the potential to create green energy.

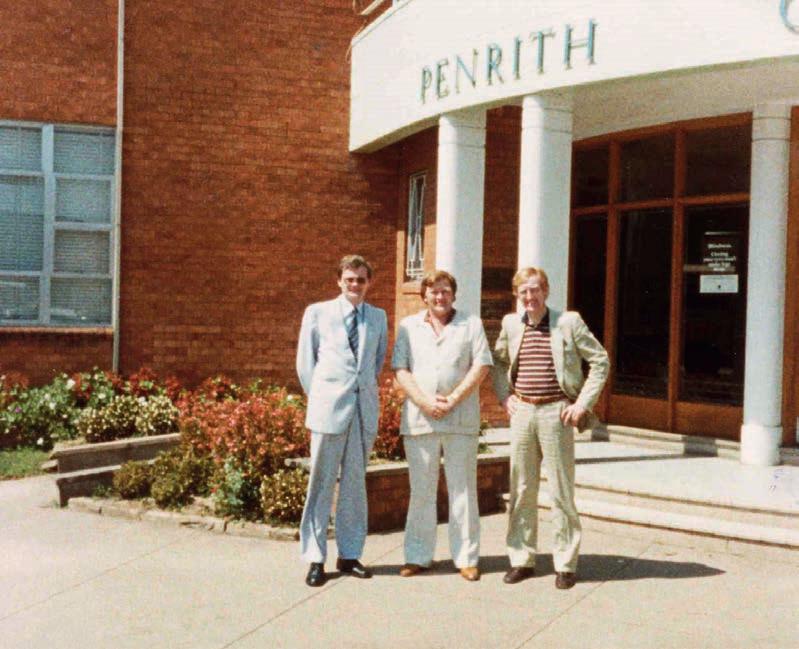
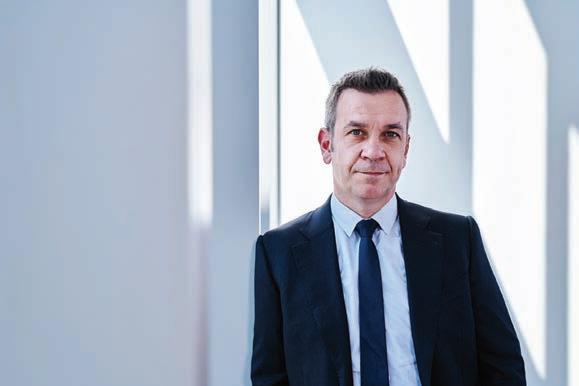
20 / WMR / September 2022 COVER STORY
2006-2007 Australian operations start with the awarding of Penrith City Council’s residential waste collections contract, NSW, which led to the introduction of the first wheelie bin into Australia 1982 Established state-of-theart Organic Resource Recovery Facility (ORRF) in Port Macquarie, NSW 2001
Jochen Behr, Chief Executive Officer REMONDIS Australia.
Germany. Spread across 240 hectares, the park has various recycling facilities to process dozens of different waste streams on the one site, while generating climateneutral energy. It’s a scenario being replicated at REMONDIS’ Tomago Resource Recovery facility in Newcastle. Jochen says Tomago will have multiple sections receiving an array of waste for processing and recycling.
A centrepiece is a Refuse Derived Fuel facility that will process waste into a solid fuel that can be used for energy-making in industrial settings and as a cleaner alternative to the burning of fossil fuels such as coal. “It’s a great opportunity to bring together recycling facilities in one space,” Jochen says. “I do think it’s the future for wastes that complement one another when it comes to licences.” That future also includes energy recovery, AKA energy-from-waste or EfW. REMONDIS operates 16 EfW facilities around the world. In February, it withdrew a project application for a $400 million plant at its Swanbank precinct near Ipswich after being advised by the Queensland Government that the project wouldn’t be approved. Despite the reluctance by some states to introduce EfW, two plants are currently being built in Western Australia. Björn is convinced once those projects are operating, there will be further progress“Energy-from-wastenationally. is a superior solution compared to landfilling waste,” he says. “I predict that in the future we will see a lot of improvement in terms of recycling and a lot of diversion from landfill towards EfW and resource“REMONDISrecovery.plans to be involved and take a leadership role in that development. When we talk about diversion from landfill it’s not just about building energy-from-waste facilities
operationsVictoriaestablishedwithdepot in Footscray 1982 Brisbane
QLD.establisheddepotinRocklea,StartedoperationsinSouthAustralia(Wingfield)andWesternAustralia(OsbornePark)
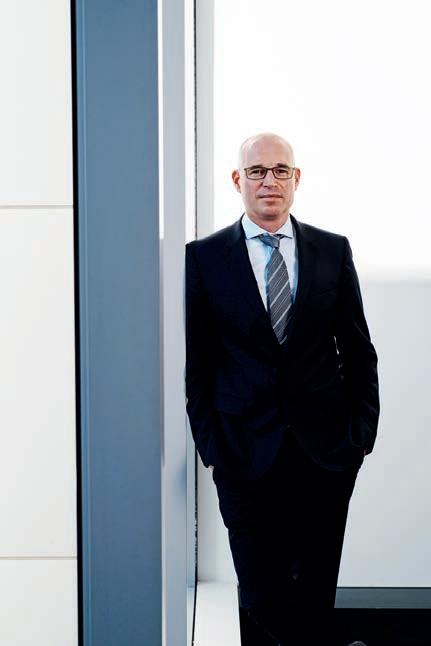
Jochen says there will be other opportunities for energy recovery projects, but it’s important there is social licence. With any change, comes questions and community uncertainty. It’s something the industry has to accept.
to replace these landfill capacities. It’s also about diverting other materials and separating them from each other.”
For more information, www.remondis-australia.com.auvisit:
www.wastemanagementreview.com.au
“There’s been terrific improvement in the past few years, and we see a lot of opportunities to bring new technology to the market. We are quite optimistic.”
Container Deposit Scheme starts in WA with collection logistics and processing by REMONDIS 2020 Jochen Behr appointed CEO of REMONDIS Australia and Björn Becker appointed Chairman Completed acquisition of SUEZ C&I operations in SA, Veolia C&I operations in WA and Veolia transfer station at Seven Hills NSW 2022 Björn Becker joins REMONDIS Australia, initially as Chief Sales Officer (April 2018) then CEO (September 2019) 2018
Established Indigenous Joint Venture with JAI-MEC Rural Contracting to create Red Earth Industrial Services 2021 REMONDIS provides logistics services for WA Containers for Change CDS.
“We have a long-term approach,” he says. “Our mission is working for the future. We want to become one of the leaders in the circular economy. We want to be a partner who can bring technology and improve the infrastructure for recycling in Australia.
Over the years, REMONDIS has implemented more recycling facilities to extend the value chain of services it can offer customers. Björn says the company has a lot more to offer, but government support is needed. He says faster approval processes and regulatory support are needed to accelerate change. “It feels a bit like we’re always seen as an industry causing problems –pollutions, noise, etc. “But we’re here to solve problems,” Björn says. “We’re doing that by recycling materials and enabling the circular economy we’re all striving for.”
/ WMR / 21

Jim says interest in TDF has increased in the past six months, driven by customers keen to decarbonise their operations and the rising price of coal. But he says it’s important as a recycling industry that any investment in TDF in Australia is based on long-term structured agreements rather than a short-term reaction to rising coal costs.
Social licence to consume tyre-derived products and regulator willingness to let that happen will determine the success of Australia’s waste export bans, says Jim Fairweather, Chief Executive Officer of WhileTyrecycle.aban on the export of wholebaled tyres was crucial in changing the way Australia manages its waste,
Jim Fairweather, Chief Executive Officer, Tyrecycle.
“The only way to avoid that pressure is to have the products consumed domestically. It’s important we work as an industry toward that outcome,” Jim“It’ssays.crucial we generate domestic consumption, be that tyre-derivedfuel (TDF) or rubber crumb for use in asphalt, or tile adhesives or sportingTyrecyclefields.”has produced TDF as an alternate fuel for domestic and international use in industrial applications such as cement kilns, electricity generation or industrial process heat. It is estimated that 150,000 tonnes of fuel generated by such a process avoids 174,000 tonnes of carbon emissions compared to brown coal.
“There needs to be a partnership between the producer of the fuel and the consumer,” he says. “Tyrecycle has long-term agreements for processing in the fuel space. They’re critical to making the right products.”
Tyrecycle sells 120,000 tonnes annually of TDF to overseas markets.
“Tyrecycle is working on one domestic opportunity at the moment and the regulator is saying it will take six to eight months for licence approval to take that material,” Jim says. “There’s a role government can play in helping smooth the road.”
FEATURED TOPIC – TYRE RECYCLING 22 / WMR / September 2022
He says low use of tyre derived products in Australia exposes the market to risk factors such as exchange rates and global shipping costs.
WITH COAG WASTE BANS FOR WASTE TYRES NOW IN EFFECT, IT’S TIME TO SHIFT ATTENTION TO CREATING DOMESTIC MARKETS. JIM FAIRWEATHER, CHIEF EXECUTIVE OFFICER TYRECYCLE EXPLAINS.
It’s roads, Jim says, where the government can take a leading role. He says Australia is underdeveloped in its use of crumbed rubber asphalt compared with other countries. What movement there has been, has mainly been propelled by roads“Thecontractors.rubbercrumb domestic market needs to be grown for the success of the waste ban. Governments are the ones that buy roads. When it comes to crumbed rubber, the government has to drive policy and procurement.”
Jim describes the scenario of exporting to Asian operations that have a presence in Australia as “madness”. He says a local market would present opportunities for more high value, oil-based inputs for manufacturing, but it should be industry-driven. Government can play a part in helping the market develop, particularly in the approval process.
Home truths
Jim says it’s time to shift attention to creating a domestic market to encourage industry investment.
Jim applauds the former Federal Government for implementing the waste export bans and introducing them so quickly. However, he says there are concerns that need to be“We’veaddressed.still got unscrupulous operators sending whole-baled tyres off-shore under falsified codes,” he says. “While most freight-forwarding companies are absolutely legitimate and operate to high standards, some in the market are trying to coach

He says the uptake of tyre-derived fuels or products is driven by customers seeking the carbon benefit of using tyre products over fossil fuels, and those looking for circularity and product reuse. Some are starting to considerCollectionboth.customers who chose to manage their waste appropriately play an important role.
Even more pleasing, Jim says, is the establishment of several industry and government committees to look at how the ban is being managed and the challenges industry is facing.
“We absolutely have to make sure that we stop these operators eroding the value proposition of those companies and operations that have invested in infrastructure and plant equipment to make sure that we recycle right.”
He says the global market has added to those challenges. Securing ships and containers is difficult and what is available is expensive on certain routes.
“There is no spare capacity in the global shipping market. That’s what’s causing pricing angst and difficulties around moving our product off-shore,” Jim“Whichsays. reinforces the fact that we need to make sure we’ve got domestic markets being developed.”
For more information, visit: www.tyrecycle.com.au www.wastemanagementreview.com.au
“Without those retailers we wouldn’t have a valued-added tyre recycling industry,” Jim says. “There are still some retailers that aren’t prepared to pay a price for recycling and look the other way when it comes to disposing of their tyres. “It’s a real shame that some social drivers are not being enforced. Most retailers walk the talk but unfortunately others don’t. We need to be braver as an industry in calling those people out.”
Tyrecycle sells 120,000 tonnes annually of TDF to overseas markets.
and train exporters on how to write shipping documents to get around theHeban.”says that before the bans were introduced there were fears and rumour mongering that they would createWhilestockpiling.therewas stockpiling for a short time, Jim says it was because a government portal to apply for an export licence was opened too late. The process was arduous, and many recyclers were without a licence when the bans came into effect on 1 December 2021. He says that generated a natural tension for the department between enforcement and perceived success of the ban. The industry would still like to see more enforcement at a federal customs export level. “There are active regulators in New South Wales and Victoria,” Jim says. “They know that there may be operators out there that haven’t altered their business model. We’re really pleased to see that those operators are being dealt with swiftly by regulators.
/ WMR / 23


A QUEENSLAND COMPANY IS TAKING TYRE RECYCLING TO THE NEXT LEVEL.
David is now aiming to recover up to 80 per cent of the material sourced with the installation of a pyrolysis and distillation plant at Chip Tyre’s six-hectare site in New Chum, Queensland. “Any over-supply of tyres will ultimately be fed through pyrolysis and turned into biofuel,” David says. “We’re doing things a bit different by also adding a distillation plant. We can take dirty pyrolysis oil and refine it into a diesel-like product. “I see it as being one of the solutions to our tyre recycling problem.”About140,000 tonnes of off-theroad tyres are sold into the Australian market each year to industries including mining, agriculture, manufacturing, construction, and aviation, according to Tyre Stewardship Australia. Less than 15 per cent of end-of-life tyres within the sector are recovered as a resource.
Chipping away at
David says while a portion of the biofuel created by Chip Tyre will be used in-house, several mining companies are showing interest in having their tyres turned into oil and supplied back for reuse.
Chip Tyre has worked with TELFORD SMITH and Zerma over the years to develop the tyre shredding process.
www.wastemanagementreview.com.au / WMR / 25 FEATURED TOPIC – TYRE RECYCLING
a national problem
When David Mohr founded Chip Tyre in 1998, he was processing 2000 tonnes of heavy vehicle used tyres a year. He’s now churning through more than that every month.
As demand for rubber has increased over the years, Chip Tyre has evolved with the industry to produce a range of rubber crumb and powder for noise reduction products, playground matting, sports field underlays, tile adhesive and spray-on bitumen.
He says Chip Tyre will start with three batch machines that can process solid forklift tyres and excavator tracks, while maintaining the existing
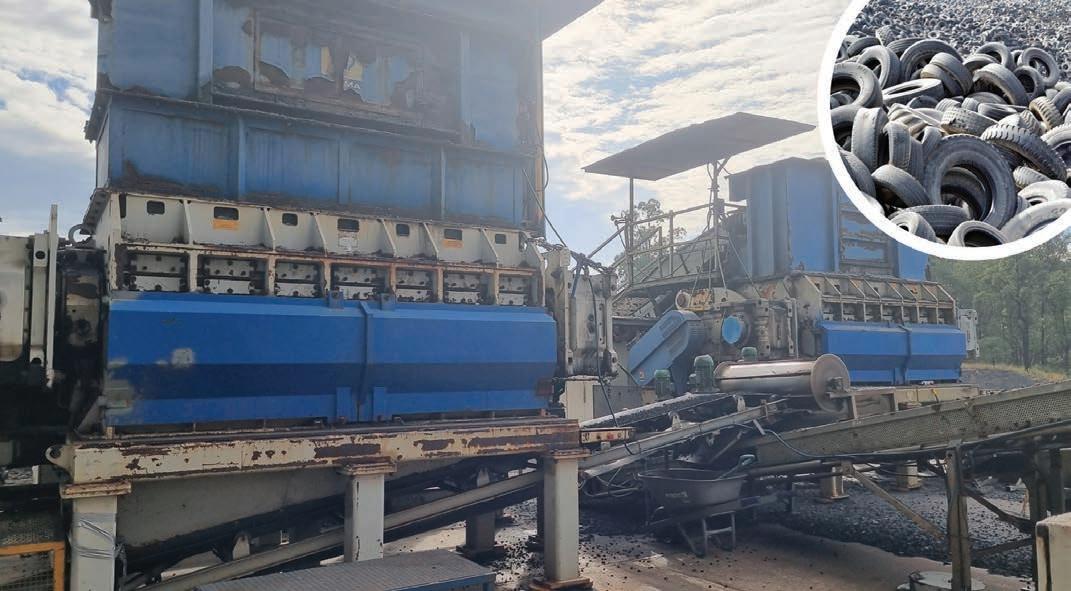

Zerma are some of the most economical and efficient machines for tyre shredding.
crumbing operations. “The reactors that we start with will keep our landfill requirement down and then when we have continuous oil production there will be cost savings as well,” he says. “We can really churn out some good numbers as far as oil recovery goes. By using smaller material with less steel, we expect to get a yield of about 46 per cent.” Chip Tyre is assured of consistent material thanks to a long-standing relationship with TELFORD SMITH and the range of machinery and equipment they supply. David has multiple Zerma GSH-700/1000 heavy-duty granulators and Zerma ZTTS-2000 Hybrid tyre shredders among the machinery supplied by TELFORD SMITH. He has worked closely with TELFORD SMITH and Zerma over the years to design the tyre shredder, making them what they are today. “I wanted to use an original two-metre machine as a hybrid granulator with a redesigned motor and configuration,” David says. “I talked to TELFORD SMITH about the design, sent drawings back and forth and they had a machine made for me and one for a trade show in Guangzhou. At the trade show some customers from Korea saw the new design and ordered two before I market for its end-product, from 100 millimetres down to rubber crumb as fine as 0.71 millimetres, the machinery needs to be accurate and tough. David says tyres can be “brutal” on steel, and the machines can be running up to 16 hours a day, four days a week. He says such a large capital investment also needs quality service and spare parts, something TELFORD SMITH never falls short on. “The granulators have been running now for 15-16 years, a few spare parts wouldn’t hurt them,” he jokes. “We’ve built a good working relationship with TELFORD SMITH. They’ve been with us the whole journey. They’re the type of company that your success is their success.” and understood the importance of “Ifmaintenance.youdon’tmaintain your equipment in tyre recycling it simply falls apart,” he says. “Cost of maintenance and spares in tyre recycling is probably 10 times higher than plastics processing and Zerma has one of the most economical machines to run on the market.” He says a lot of people inquire about and try to get into tyre recycling but fail because they buy cheap equipment. He says for a complete A-Z plant, customers need to spend more than $2.5 million just on the equipment.
FEATURED TOPIC – TYRE RECYCLING 26 / WMR / September 2022
“We often get the help call when a customer buys cheap machines and they don’t work,” he says. “Unfortunately, there is nothing we can do to make this equipment process tyres, they just need to start again.“It’s heartbreaking explaining that to someone. It really drives home why we are so strict about what we sell and being sure customers get what they need – not cheap solutions or what they think will do the job.”
TELFORD SMITH machinery stands up to the rigours of tyre recycling.
For more information, www.telfordsmith.com.auvisit:
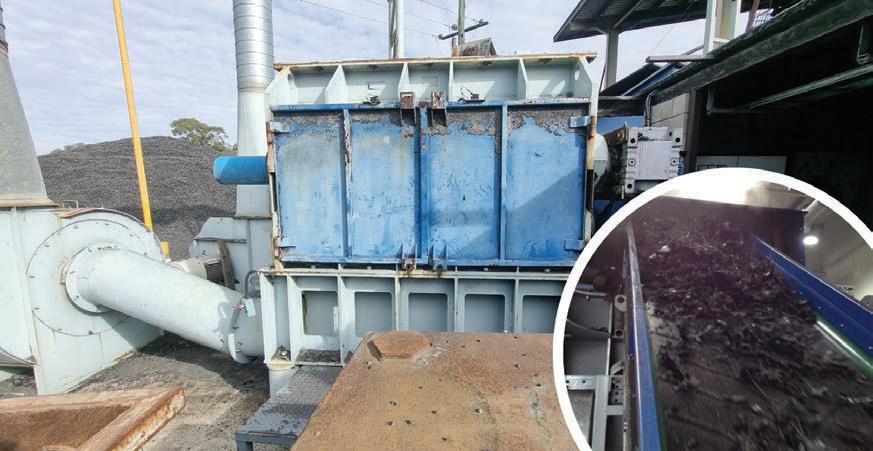
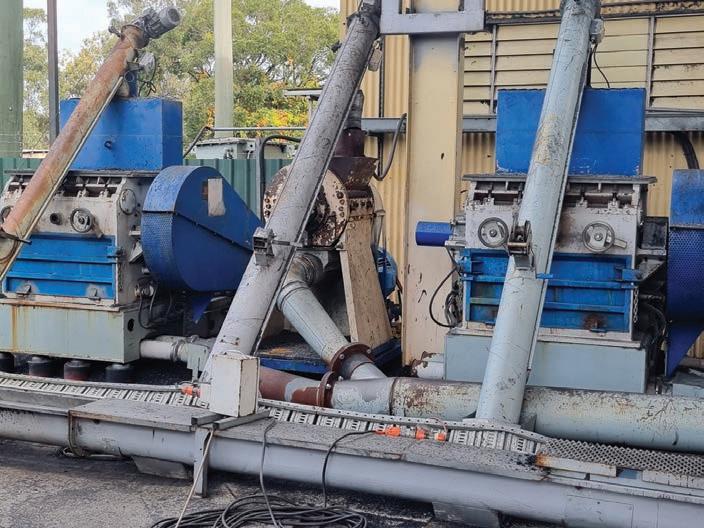
T 13 73 73 // remondis-australia.com.au
40 years in Australia REMONDIS came to Australia in 1982, with 35,000 plastic wheelie bins and a contract with Penrith City Council. Today, we support 24,000 commercial and industrial customers with waste collection, processing, recycling and circular economy solutions, right across Australia. We’ve grown to 1,100 employees across 38 branches from Weipa to Coolaroo, Jandakot to St Marys. We rise to the challenge of complex waste streams and ambitious resource recovery goals and we have the scale and expertise – both local and global – to make a difference. Best of all, we love what we do.
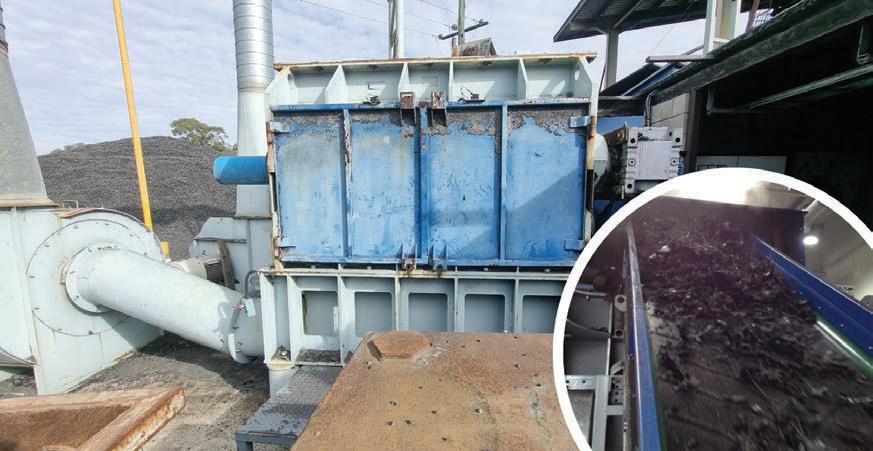
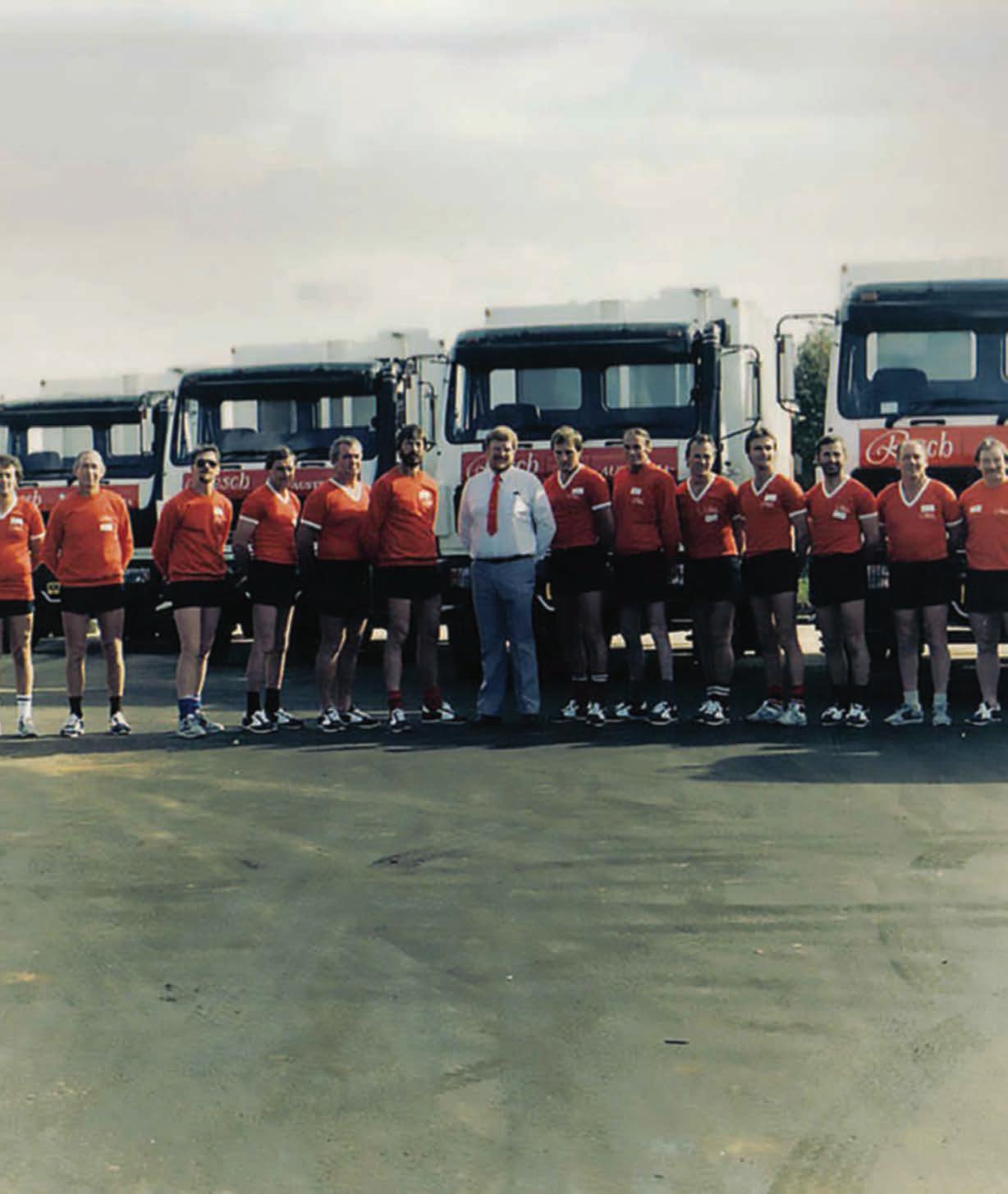
Our solutions are based on efficient and environmentally sound in-house technology, and cover the entire life cycle of an Energy-from-Waste facility. Our proven technologies have been part of more than 700 plants world wide. As a global leader in energy from waste we are proud to be able to say: We deliver. Check our references.
Waste is our Energy www.hz-inova.com London, Oslo and Dublin Rely on Our Energy-from-Waste Technology. So Does Perth. Oslo, Norway Dublin, IrelandLondon, United Kingdom Rockingham, Australia
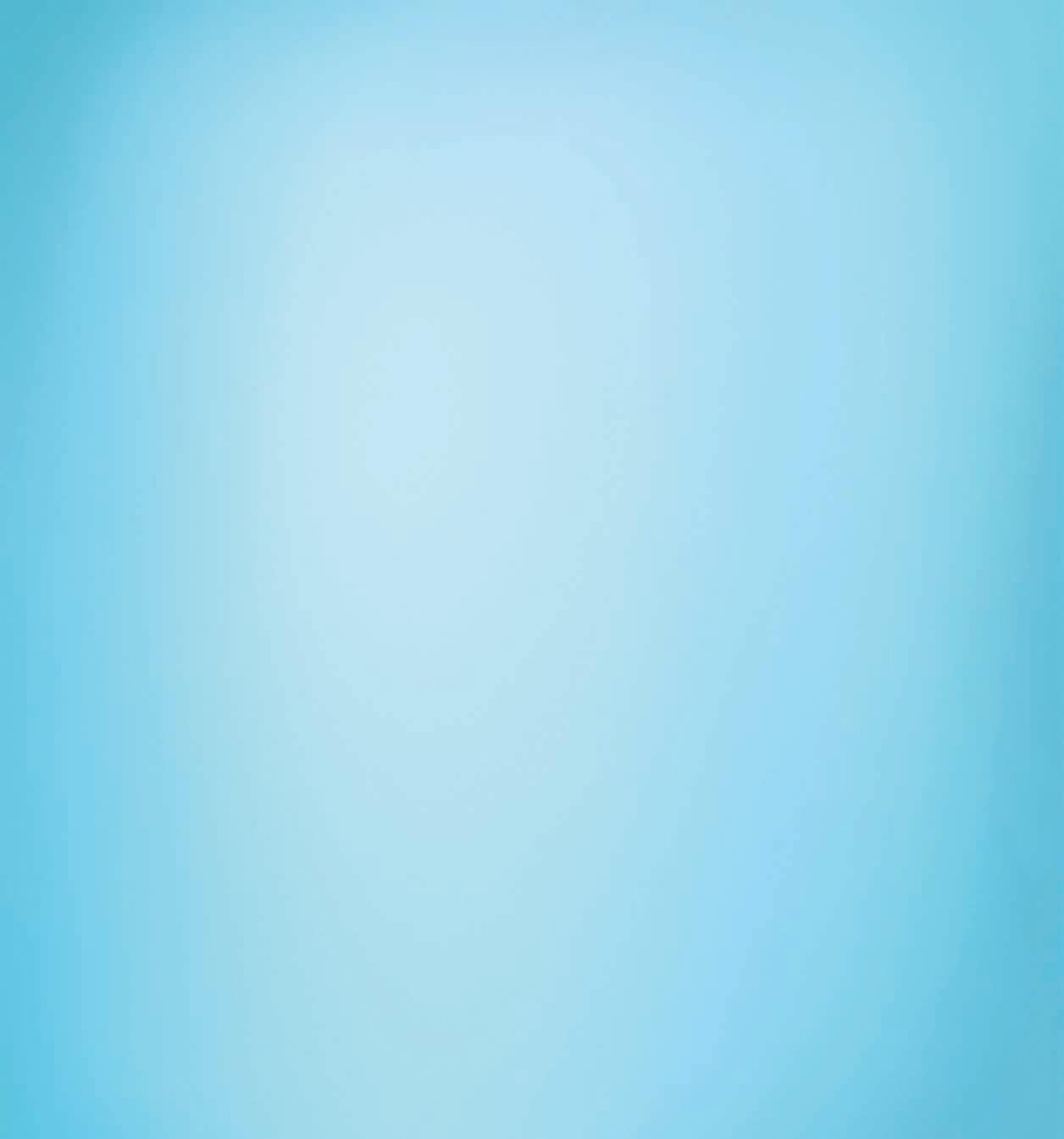
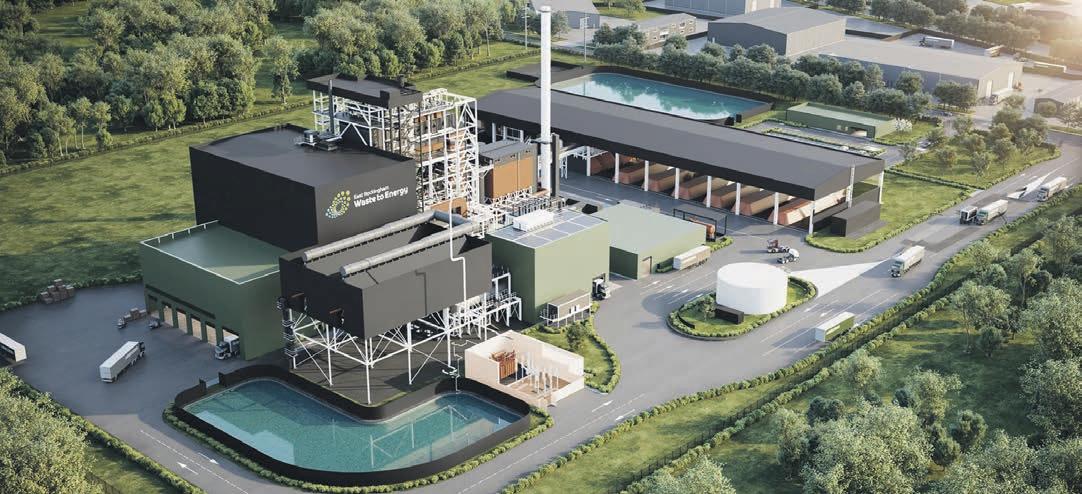

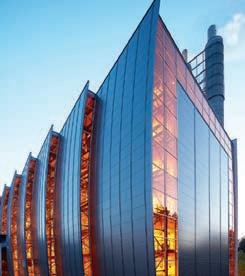
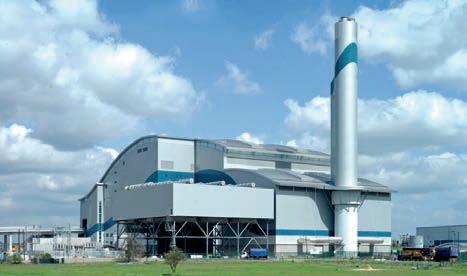
www.wastemanagementreview.com.au / WMR / 29
ATRA was established to represent sustainable used tyre collection and recycling in Australia. Its members recycle more than 20 million used tyres a year, or about 400,000 tyres a week.Used tyres processed by ATRA members are recycled for reuse as rubber crumb for sports fields and other soft fall surfacing, in bitumen and asphalt, for civil works and as TDF replacing coal in industrial facilities in Japan and South Korea. Rob says TDF is a global commodity. About half of all tyres in America are used domestically as TDF for paper mills and cement kilns. In Europe, companies are paying up to 80 euros a tonne for CO2, which is a big driver for using TDF and other alternate fuels. He says a recent visit to a Portuguese cement kiln demonstrated what’s possible for energy intensive industries through the use of alternate fuels. Like much of the global cement industry, Portugal’s Secil Outao cement plant on the outskirts of Lisbon, has and is working to meet the climate change challenges. Consumer, government and customer demands for lowered greenhouse gas emissions are resulting in innovations across the sector. Shifting from fossil fuels to the use of alternate fuels offers significant CO2 reduction opportunities.
The Secil Outao plant uses a 50/50 mix of PET coke and alternate fuels including TDF, Solid Recovered Fuels (shredder flock and other postconsumer and commercial materials including imported SRF pellets from the UK) and biomass, including toFEATUREDarmsTOPIC–TYRERECYCLING Australia exports 130,000 tonnes of tyre-derived-fuel a year.
Call
ATRA has commissioned a report into the global use of TDF and how learnings can be applied nationally. Rob says it’s particularly relevant to Australia’s five operating cement kilns. “There is a wake-up call around the need to mitigate greenhouse gas emissions and carbon dioxide,” he“Newsays. national greenhouse and energy reports show that using TDF can save 30-40 per cent of emissions compared with using coal – that’s a big carbon dioxide reduction. “Cement kilns in Australia are huge energy consumers and CO2 emitters. They can’t reduce their energy consumption, but they can reduce their emissions and TDF is a prime way to do that. “It’s about communicating the value of the material to the industrial sector. It’s a viable fuel, we want to see it used here in Australia.”
USE OF TYRE-DERIVED FUEL IN AUSTRALIA IS ON A SLOW BURN BUT THE AUSTRALIAN TYRE RECYCLERS ASSOCIATION IS EAGER TO FIRE THINGS UP.
While TDF is recognised worldwide as an alternative fuel because of its high calorific value, Rob says Australia’s industrial sector is failing to capitalise on an abundant supply right on its doorstep – exporting 130,000 tonnes of TDF a year.
Australia needs to increase the domestic market for tyre-derived-fuel (TDF), according to Rob Kelman, Executive Officer, Australian Tyre Recyclers Association (ATRA).
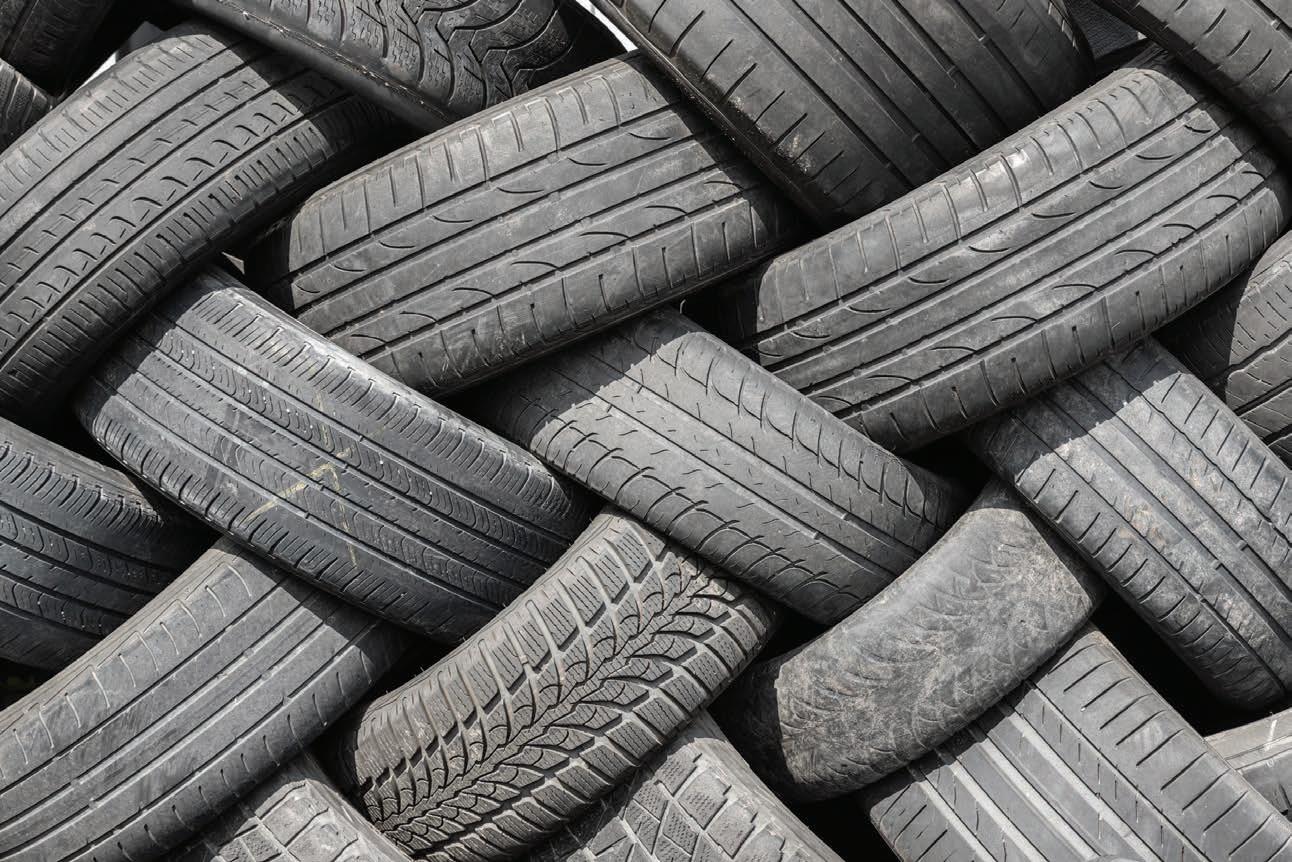
FEATURED TOPIC – TYRE RECYCLING 30 / WMR / September 2022 residues from Portugal’s olive industry. The plant is now undergoing a $26 million upgrade to further use alternate fuels, capture and use production heat for its processes and other energy efficiency upgrades. New Zealand’s Golden Bay cement kiln has recently converted to use TDF for about 50 per cent of its fuel demands. Accounts from the plant suggest it’s a successful program resulting in CO2 savings and tyre radials used for about 15 per cent of the TDF incorporated into the clinker.
The ban has resulted in increased capital investment in the industry, much of it toward shredding of tyres.
Australia is in the early phase of what’s possible, but Rob is encouraged that there are some conversations and a trial use of TDF taking place. One of the biggest hurdles to overcome is a lack of understanding and dispelling the perception that fuel from tyres is a less desirable outcome.
“Part of the export ban agenda was for Australia to use our resources domestically and not impose our waste on other countries,” Rob says.
The Secil Outao plant uses a 50/50 mix of PET coke and alternate fuels including TDF, Solid Recovered Fuels and biomass.
“We’re now seeing large volumes of tyres being shredded and sent to landfill because there’s so many of them, and they’re going to keep“Wecoming.haveto do something. Using them for fuel is not a bad outcome.”
Rob says a tyre has similar properties to coal and is a viable alternative for a kiln.
TDF is a clean-burning fuel and burns hot, which is ideal for the cement industry. It’s also consumed and incorporated into the endproduct, resulting in less residual ash.
While there is a growing market for crumb rubber, it’s not large enough to recycle the 56 million tyres at end of use every year. “Tyres are unique because they’re difficult to recycle and there’s so few applications for them,” Rob says.
While Australia has traditionally been recalcitrant in considering alternative fuel because of access to cheap coal and the lack of a real price on carbon, Rob says it’s time to rethink TDF on the back of an export ban of whole-baled tyres, which came into effect on 1 December 2021.
Cement production offers a unique option for TDF as all input materials are co-processed.
“A critical part of the narrative is, what’s our next step? To get TDF used here will be a good outcome for many in the industry.” For more information, visit: www.atra.asn.au
Portugal’s Secil Outao cement plant.
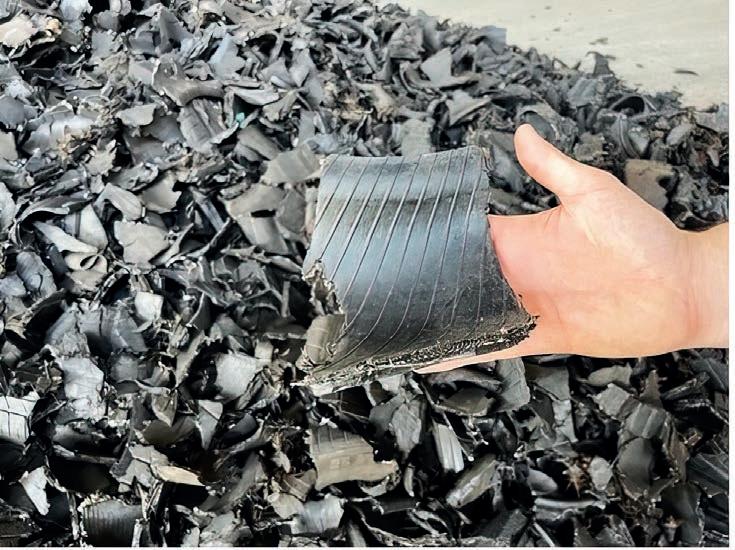

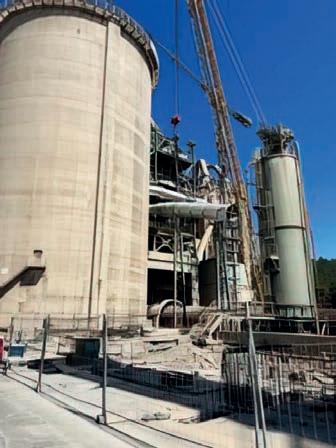
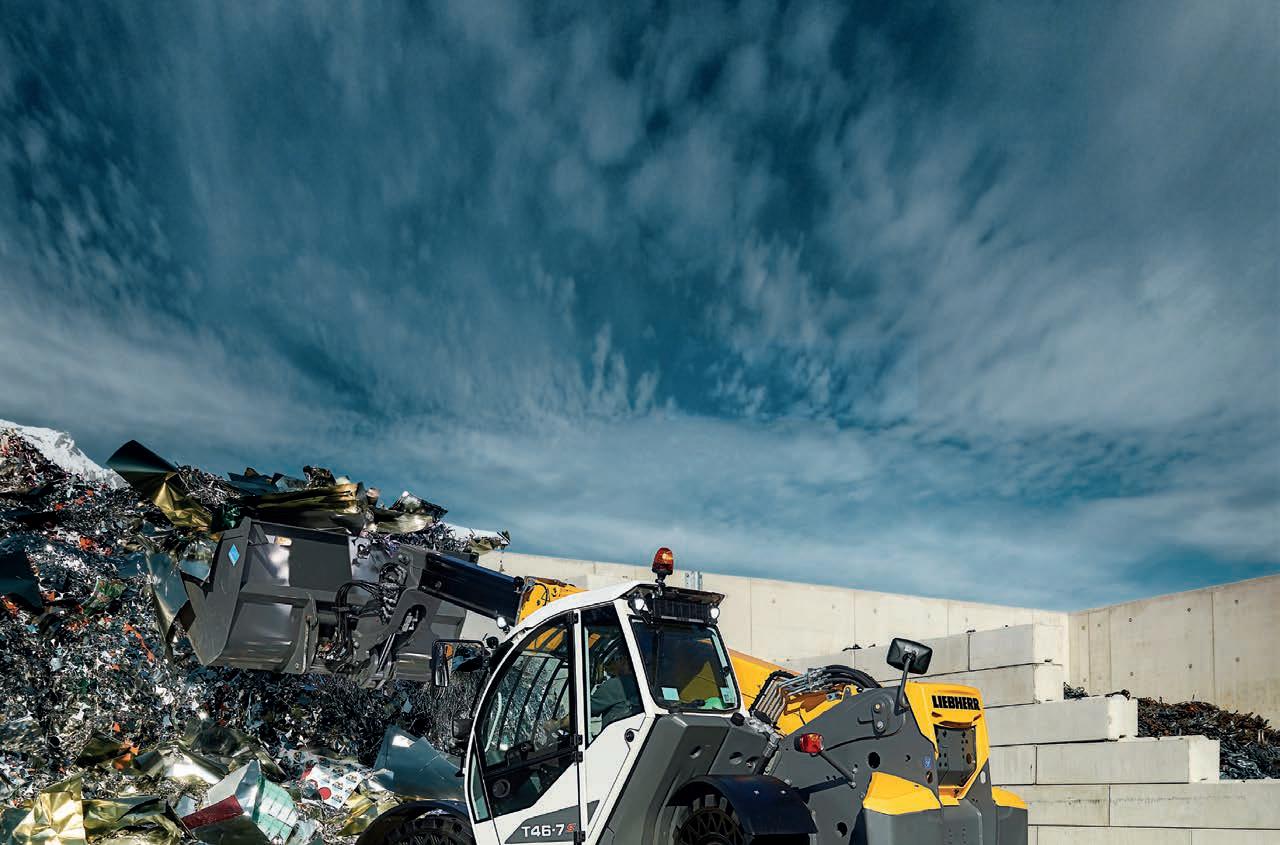
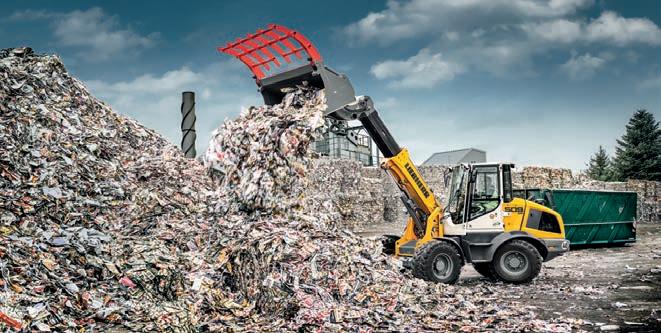
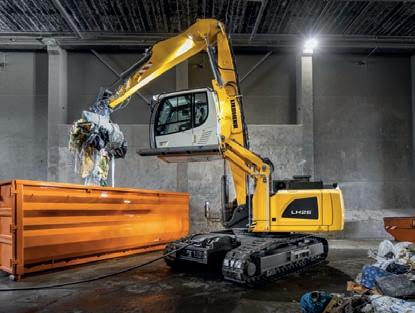
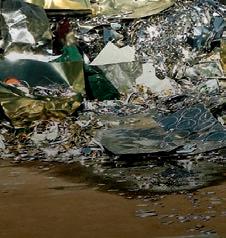
We’ve got it covered www.liebherr.com Material handling equipment Liebherr-Australia Pty Ltd • em-sales.las@liebherr.com • www.facebook.com/LiebherrConstruction www.linkedin.com/company/liebherranz • www.liebherr.com.au Visit us at 24 – 25 August 2022 ICC Sydney Darling Harbour Stand: D42
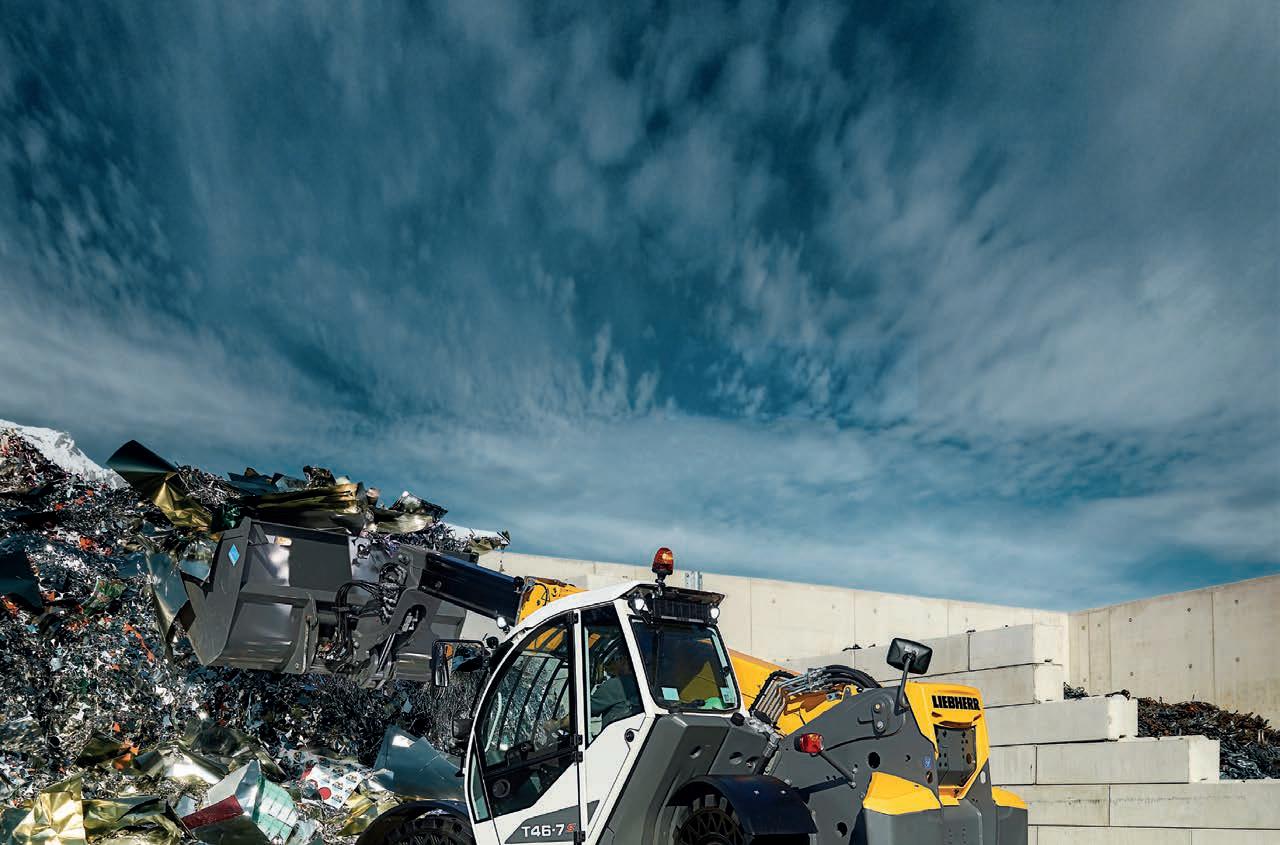
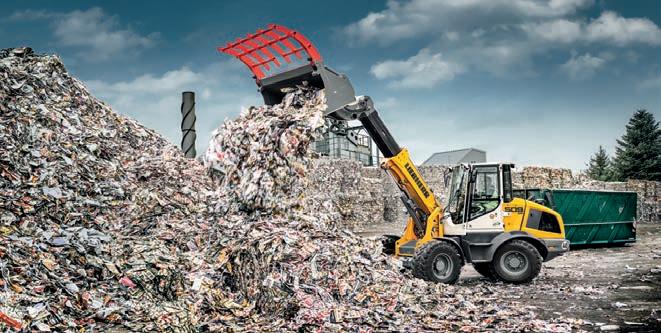
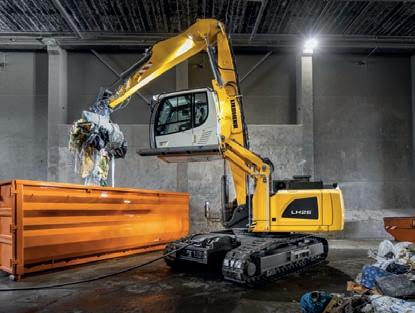
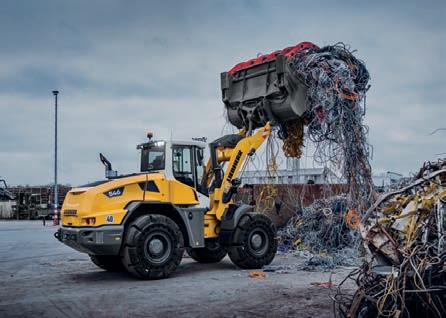
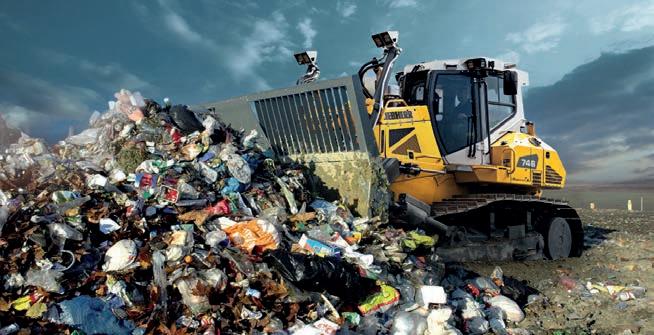
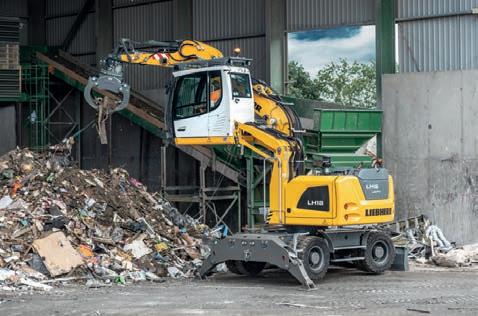
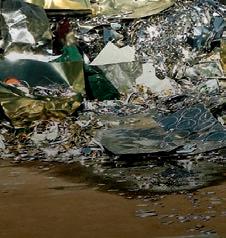
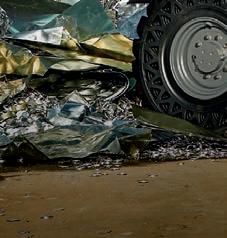
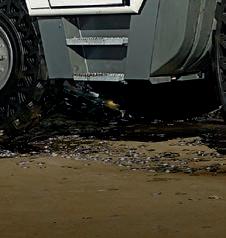
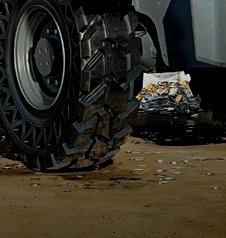
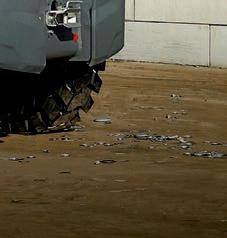
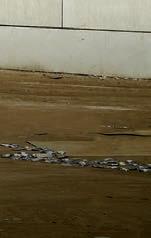
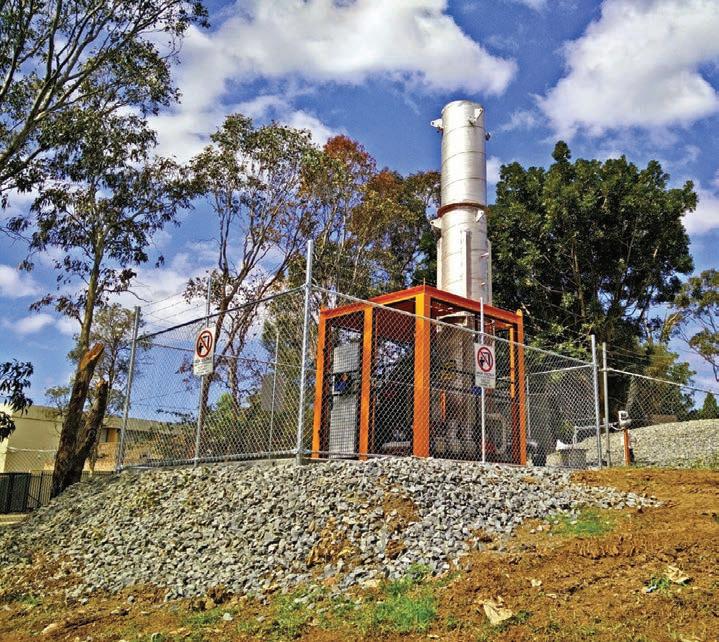
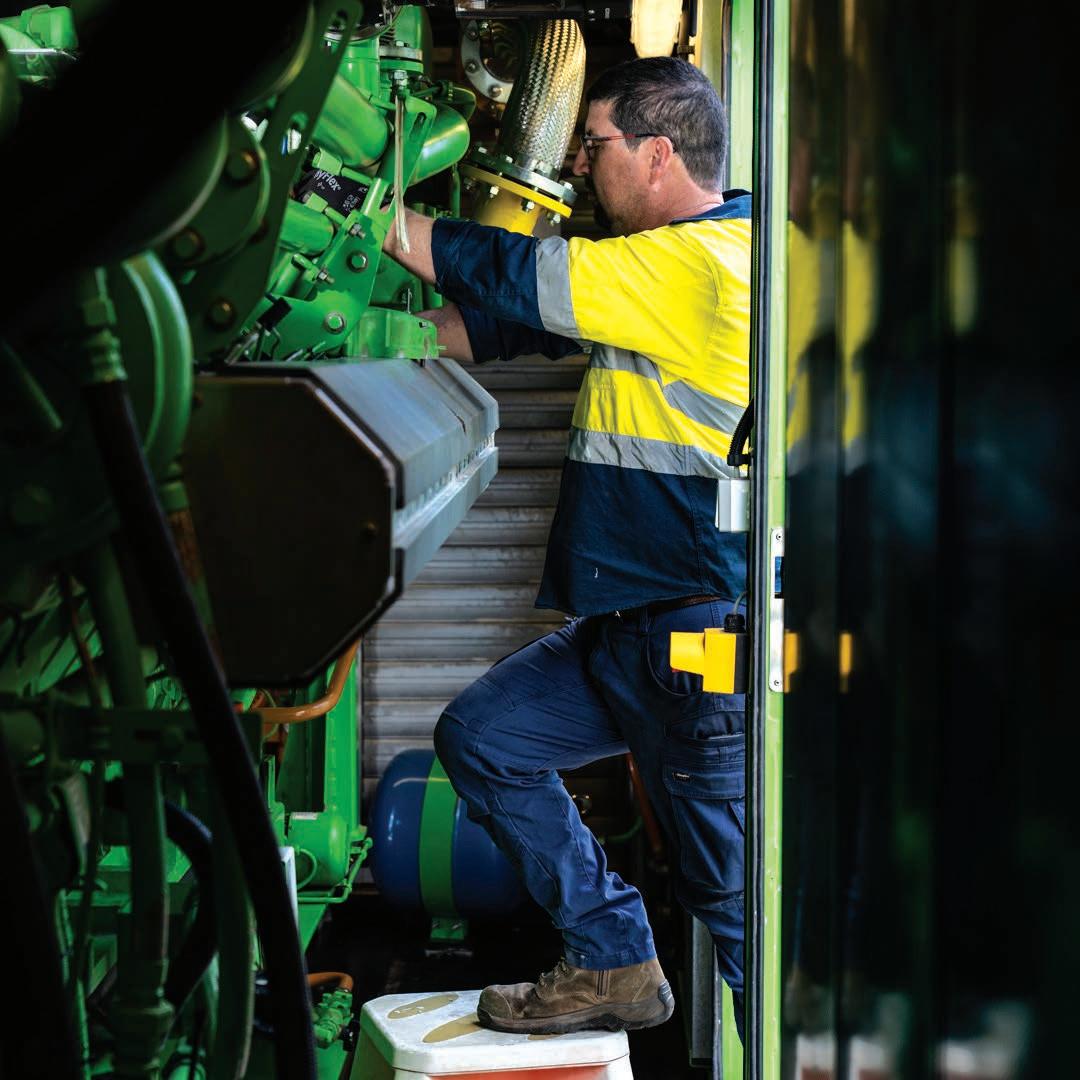

The company prides itself on being an Australian manufacturer, providing cost-effective solutions including shredders, sorting technology, screens, grinders and compactors. It has also sought out internationally recognised manufacturers of machinery to www.wastemanagementreview.com.au
JDM Aust prides itself on machines built to process off-the-road tyres.
xport bans, increased demand for equipment and a global shipping crisis has created a perfect storm for Australian tyreJDMrecyclers.Austis helping weather the storm by increasing the manufacturing capacity of its Queensland facilities.
“We own and operate manufacturing facilities in Queensland so we’ve tried to produce as much as we can locally, for our piece of mind and that of ourJDMcustomers.”Austwas founded in 2004 after identifying a need for recycling and material handling equipment for the waste, mining, and quarry industries.
RECYCLING EQUIPMENT MANUFACTURER JDM AUST IS USING ITS ON-SHORE CAPABILITIES TO HELP THE NATION’S RECYCLING INDUSTRY.
E
Lucas says. “The lead time for some of our partner suppliers from overseas has blown out to more than 12 months. No business can survive without cash flow for 12 months.
/ WMR / 33 FEATURED TOPIC – TYRE RECYCLING
Tried and tested
Lucas Stewart, Group General Manager, JDM Aust says in-house mechanical engineers have spent the past year working on designs for various machines that will cater to the market. He says the shift is an opportunity to help shore up local companies, reduce wait time for equipment and promote Australian“Gettingmade.supplies and certain components from anywhere in the world is difficult at the moment,”
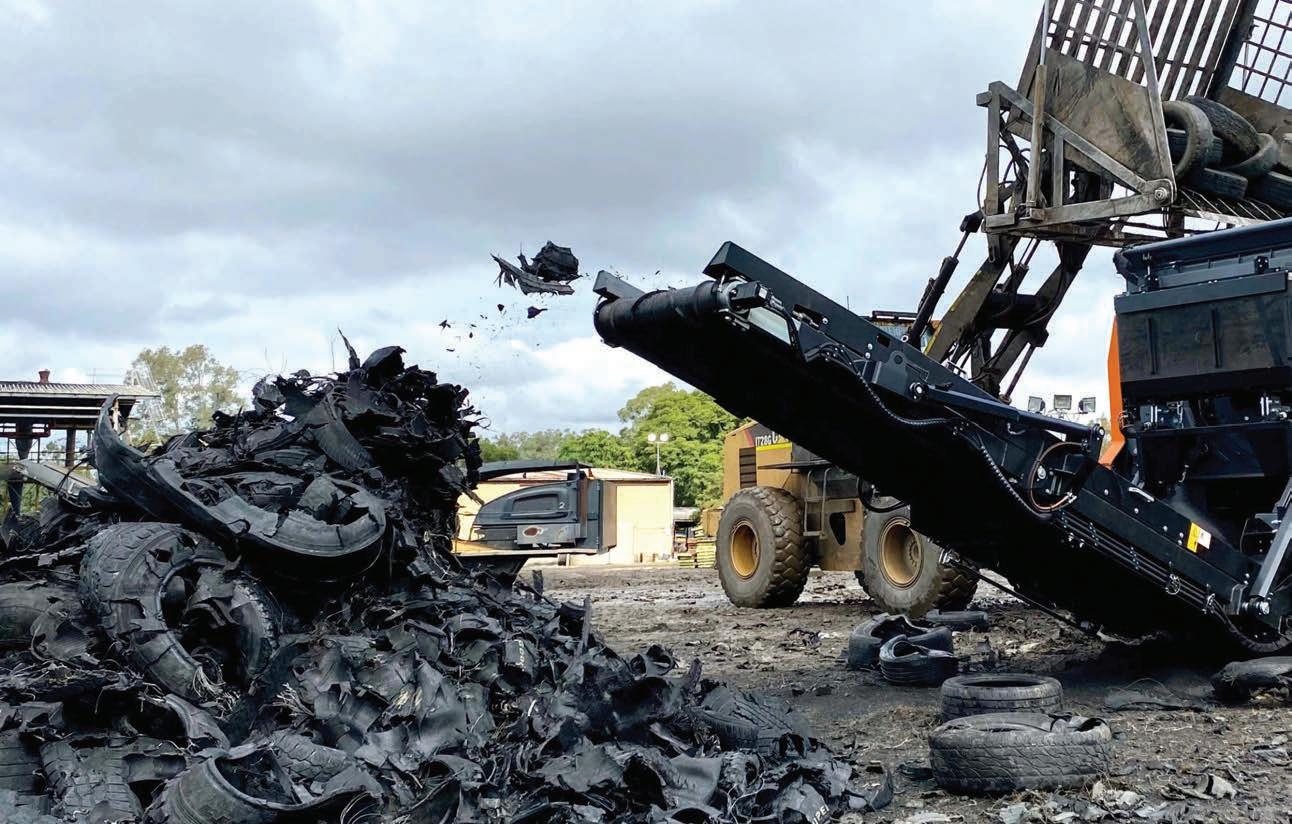
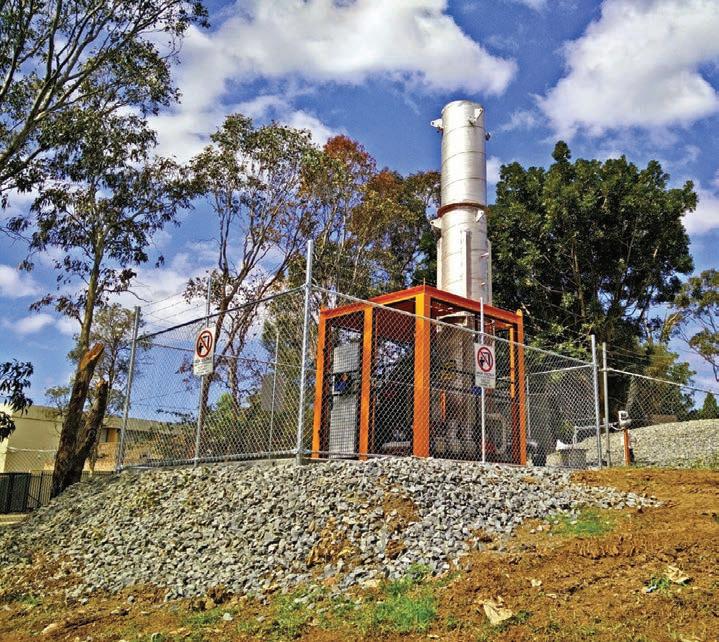
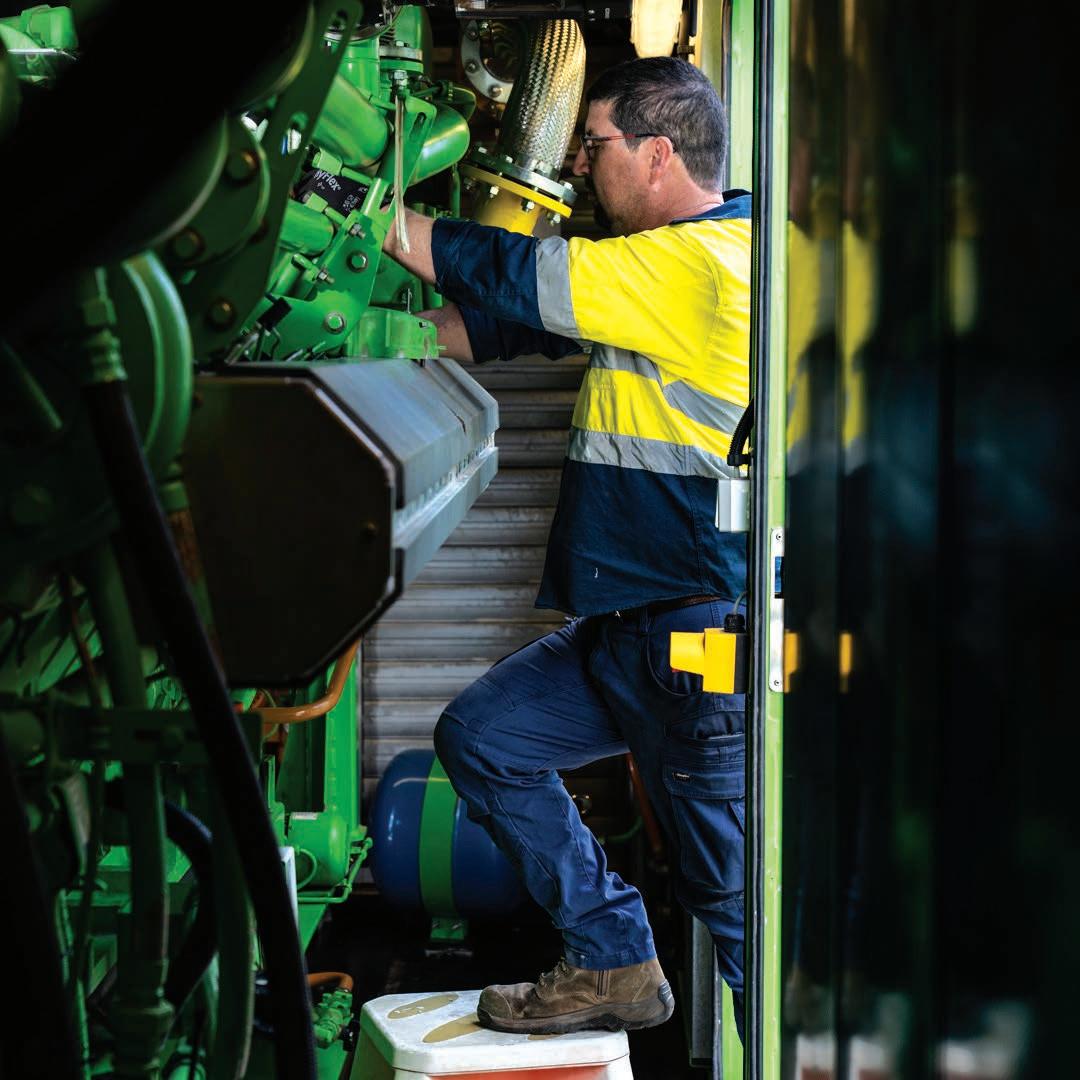

Lucas says JDM Aust identified tyre recycling as a growing market several years ago and began research and development into the equipment that would be required. Part of that research included learning from overseas“Europeanmarkets.tyre recycling is a lot further advanced than ours,” he says.
FEATURED TOPIC – TYRE RECYCLING 34 / WMR / September 2022
JDM Aust’s offerings have grown over the years to cover all aspects of the tyre recycling process. Side wall cutters have been in demand since an export ban on whole-baled tyres was introduced in 2021. The side wall of a tyre contains embedded cords that give the tyre its strength. They’re generally cut away to allow the remainder of the tyre to be shredded for recycling.
complement its range and expertise and is the Australian agent for principal suppliers of recycling and materials handling equipment manufactured in Germany, Austria, the Netherlands and the USA.
JDM Aust has a network of agents and contractors Australia-wide.
“With Australia being so resource heavy, there’s a need to be able to process larger mining tyres.”
“Processing of tyres requires an extreme amount of energy. Machinery has to be beefed up to be able to handleWhilethem.”reduced wait time is an obvious advantage, local producing equipment has other benefits. JDM Aust provides full back-up services such as technical support, spare parts and servicing carried out by a network of agents and contractors Australia-wide. For more information, visit: www.jdmaust.net.au
The Eagle International side wall can cut through a truck tyre within 11 seconds; seven seconds for a car tyre. The cutter is available as a portable or stationary piece of “Ifequipment.youcancut away the side wall you can flatten the tyres and bale them,” Lucas says. “About 50 per cent of transport costs for a tyre is air. “By cutting the side wall you can start to reduce your free volume in a truck or landfill because the tyres are compressed into smaller bits.”
JDM Aust partnered with long-time American tyre processing company Eagle International about five years ago. Apart from Eagle International’s global reputation, it has a proven process for recycling large off-the-road (OTR)“Beingtyres.able to process OTR tyres made them stand out,” Lucas says.
Lucas describes the current tyre recycling market as “positive andWhiledesperate”.alotof recyclers are changing their operations to work within new guidelines, a global shortage on shipping containers and supply chain issues is “There’schallenging.alotofdesperation to have a solution and have it now,” Lucas says. “But these things obviously takeHelpingtime.”provide a short turnaround is one of the reasons JDM Aust has expanded its capabilities for manufacturing recycling equipment. A JDM Aust product is generally available within threeLucasmonths.saysJDM Aust has adapted some of its machine designs to be able to process materials more“There’sefficiently.alot involved in making sure machines are capable of shredding and processing tyres,” he says.

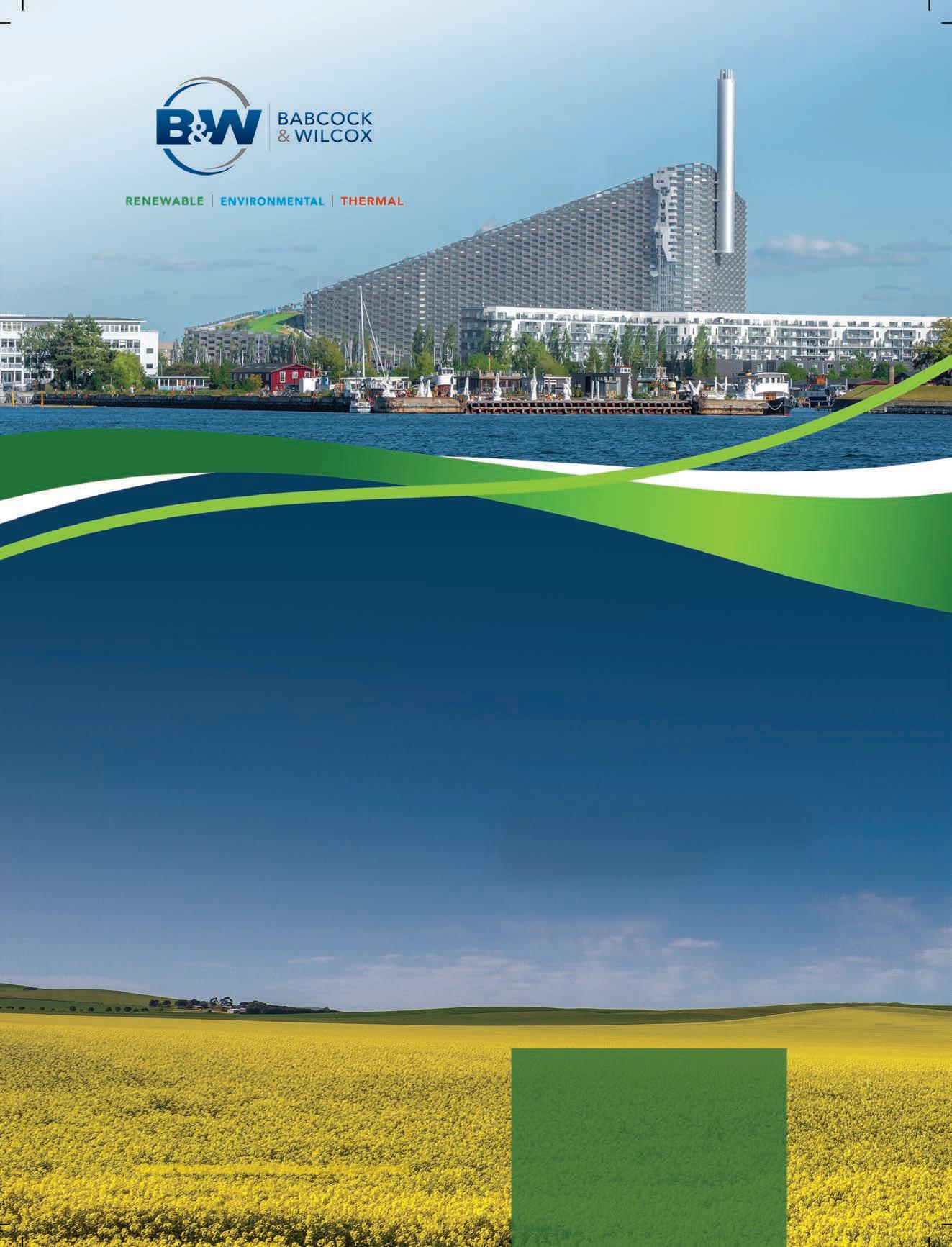
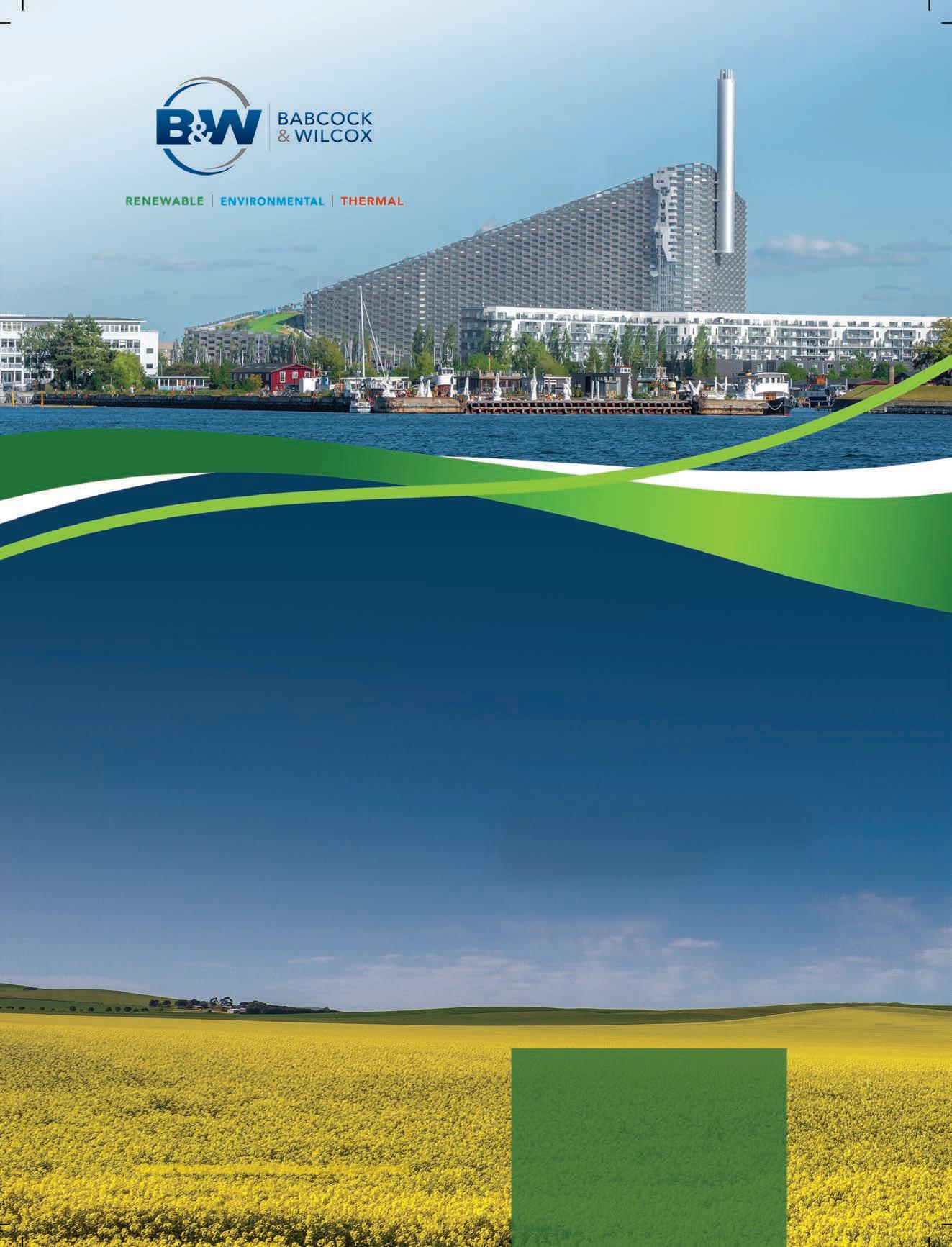

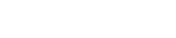

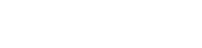



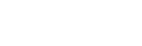

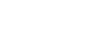
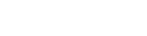

WASTE TRACKER Waste Tracker is a secure online system that captures the volume and category of waste, its source, transport arrangements, and reuse, recycling or lawful disposal of the waste. It is free to use and accessible via mobile app or EPA’sMarkwebsite.saysusing Waste Tracker is also mandatory for those producing, transporting or receiving reportable priority waste such as waste“Usingtyres.Waste Tracker is a legal requirement,” he says. “It also provides waste producers and handlers with confidence that their activities are not harming our environment and that they comply with the EP “InspectionsAct.occur every day across Victoria, so ensure you’re meeting your obligations.” For more information, visit www.epa.vic.gov.au right track Waste tyres are a special category of reportable priority waste.
TRACKING WASTE TYRES IS NOW MANDATORY IN VICTORIA. MARK ROSSITER, EXECUTIVE DIRECTOR, ENVIRONMENT PROTECTION AUTHORITY VICTORIA, EXPLAINS.
Be on the Victoria produces up to 113,400 tonnes of waste tyres each year and it is important they’re managed safely. Waste tyres are now considered reportable priority waste under Victorian Law and special provisions within the Environment Protection Act 2017 (EP Act) apply when storing, moving, or further processing them.
FEATURED TOPIC – TYRE RECYCLING 36 / WMR / September 2022
On 12 February 2022, Environment Protection Authority Victoria (EPA) laid charges against a Balwyn North company over stockpiles of waste“Stockpiledtyres. tyres can create an unacceptable fire risk,” says Mark Rossiter Executive Director. “EPA and the Victorian community have a no-tolerance approach to businesses that allow that to happen and we have been actively inspecting. Most businesses will already be doing the right thing and EPA will take action where necessary to ensure proper regulation of the waste tyreWasteindustry.”tyresare a special category of reportable priority waste that require movements to be tracked using EPA’s Waste Tracker system. Mark says that Waste Tracker helps all businesses and individuals handling waste tyres to meet their obligations under legislation and get waste tyres to a lawful place.
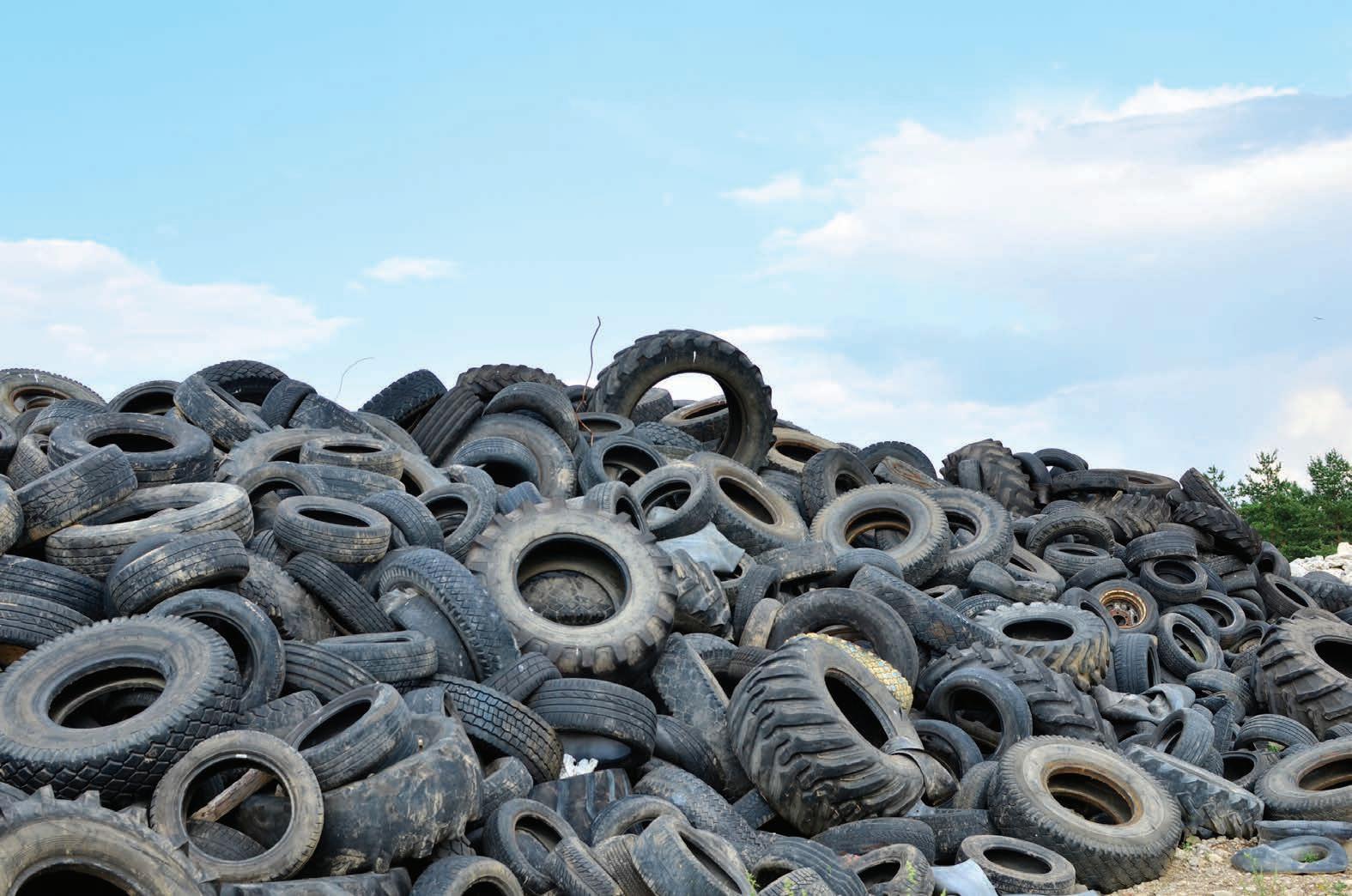
www.wastemanagementreview.com.au / WMR / 37
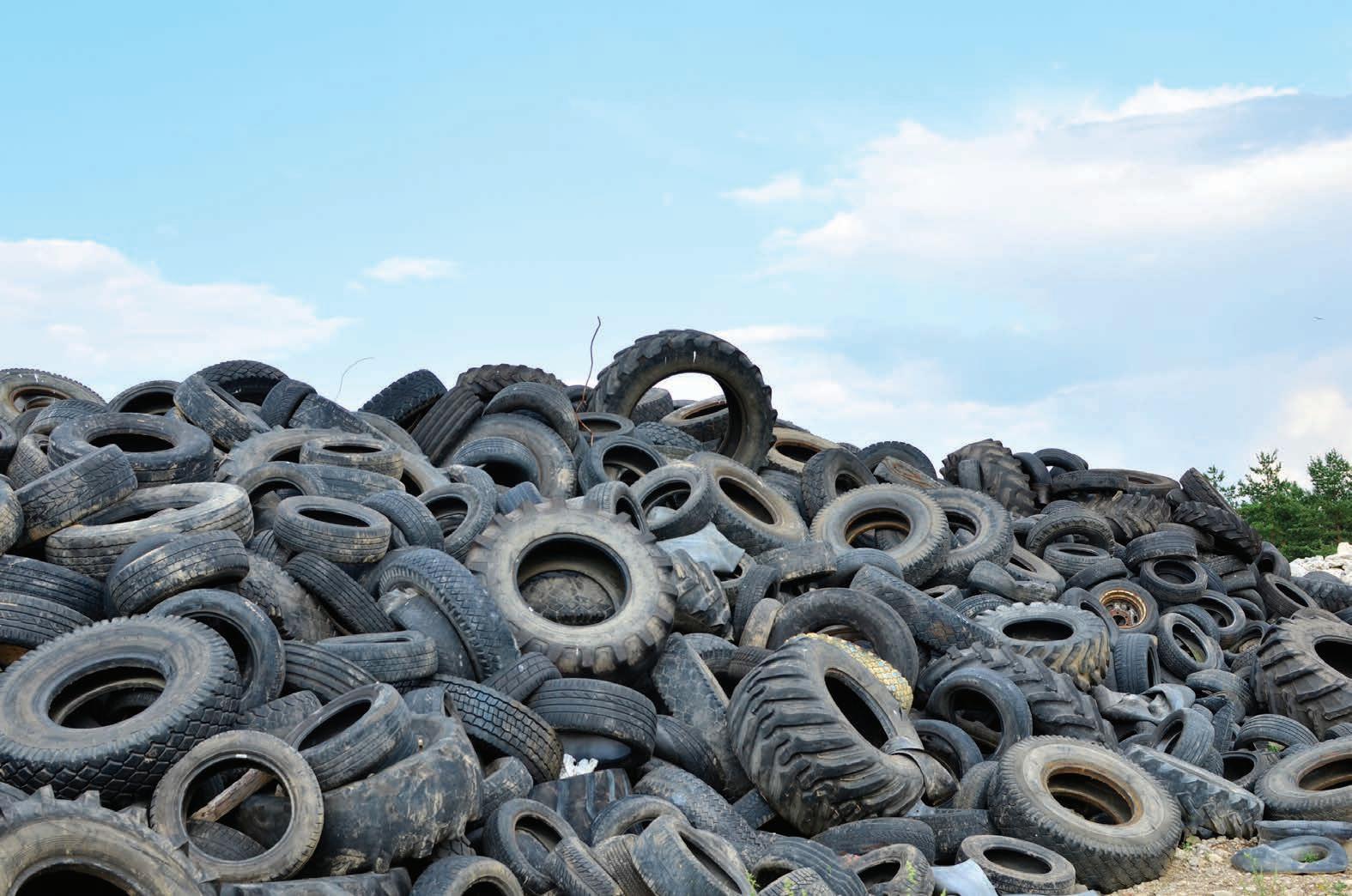
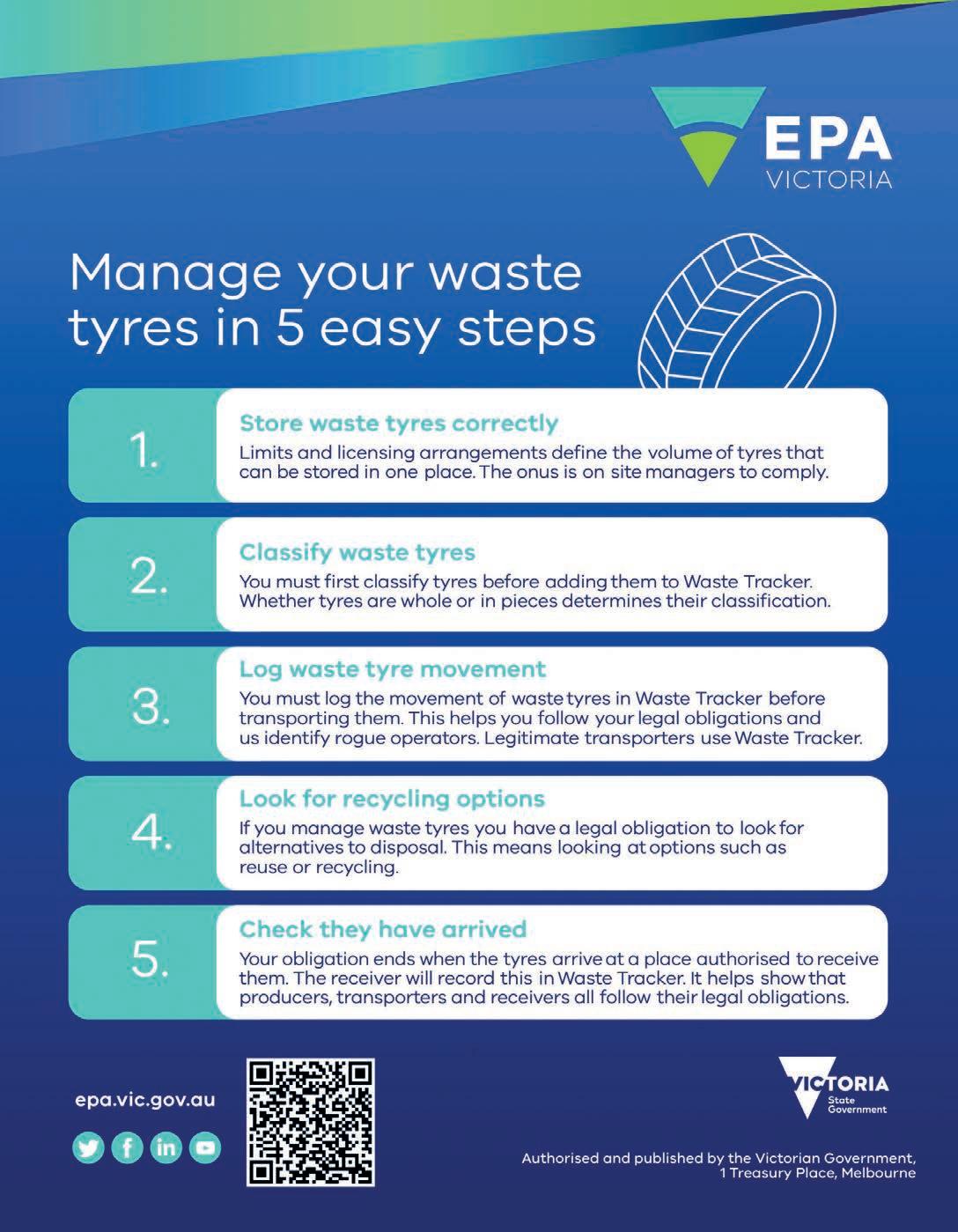
FEATURED TOPIC – TYRE RECYCLING 38 / WMR / September
Warren Tibbitts, Operations Manager, says the company is adding to the pyrolysis process by teaming up with Bruno Angelico of BXB Technologies to launch its Tyres-toHydrogen (T2H) project in 2023.
Clean Energy Group installed two pyrolysis plants in 2015.
The joint venture is just one project Clean Energy Group is undertaking to help meet the current demands forInrecycling.2021,the company purchased large mobile shredder units that can be dispatched to enable on-site tyre clean-ups in rural and council areas and to clear stockpiles.
CLEAN ENERGY GROUP IS SET TO LAUNCH AN AUSTRALIAN-FIRST PROJECT FOR TYRE RECYCLING.
The new joint venture company, T2H, will be the only tyre recycler in Australia to use the patented BXB catalyst which reduces rubber to hydrogen and coke. The coke is used as a carburiser in the steelmaking industry. The hydrogen is generated in the T2H system and can be used as fuel for a hydrogen-over-diesel generator to make on-site and grid zerocarbon electricity. The T2H team believes the introduction of the T2H process will make major inroads into recycling the thousands of end-of-life tyres in WarrenAustralia.says the process has unlimited potential in its ability to turn the whole tyre into a recycled commodity.
The CEG pyrolysis plant site at Dandenong South, Victoria, can collect, mobile shred, compress, debead and turn tyres into oil. In September 2022, T2H is set to launch on-site compactor machines developed to save tyre retailers time, space, and money. The tyre retailers can obtain a machine that suits the volume of tyres they turn over. “The time and labour required to collect tyres from a retail location is a very big issue in the industry,” Warren says. “We’ve developed machinery that will help make the process moreWarrenstreamlined.”saysthere are several issues facing retailers in relation to tyre collection, including recently published requirements for tyre storage in Victoria by The Tyre Stewardship Australia and Environment Protection Authority that stipulate any on-site tyre storage more than five cubic metres is considered reportable waste.
hydrogen road 2022
Taking the Clean Energy Group has always strived to do things differently and stand out from the rest. Now it’s developing an end-to-end solution for tyre recycling in TheAustralia.Dandenong South company installed two pyrolysis machines in 2015 to convert tyres into an oil and carbon char product.
“In a normal pyrolysis process a tyre will split to 40 per cent oil, 40 per cent char. T2H will be able to process the tyre more efficiently using less energy, without any emissions, and process much higher volumes,” heThere’ssays. a ready-made market for the coke and hydrogen export markets are easy to find.
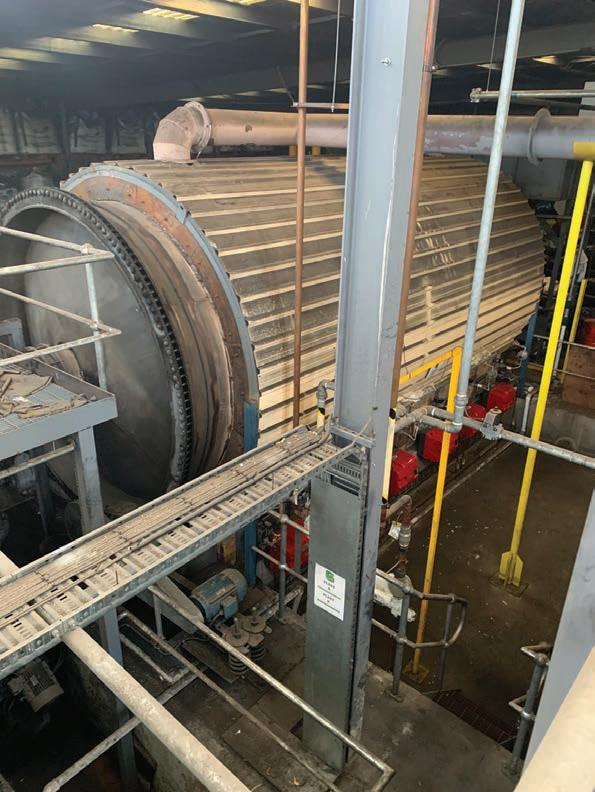
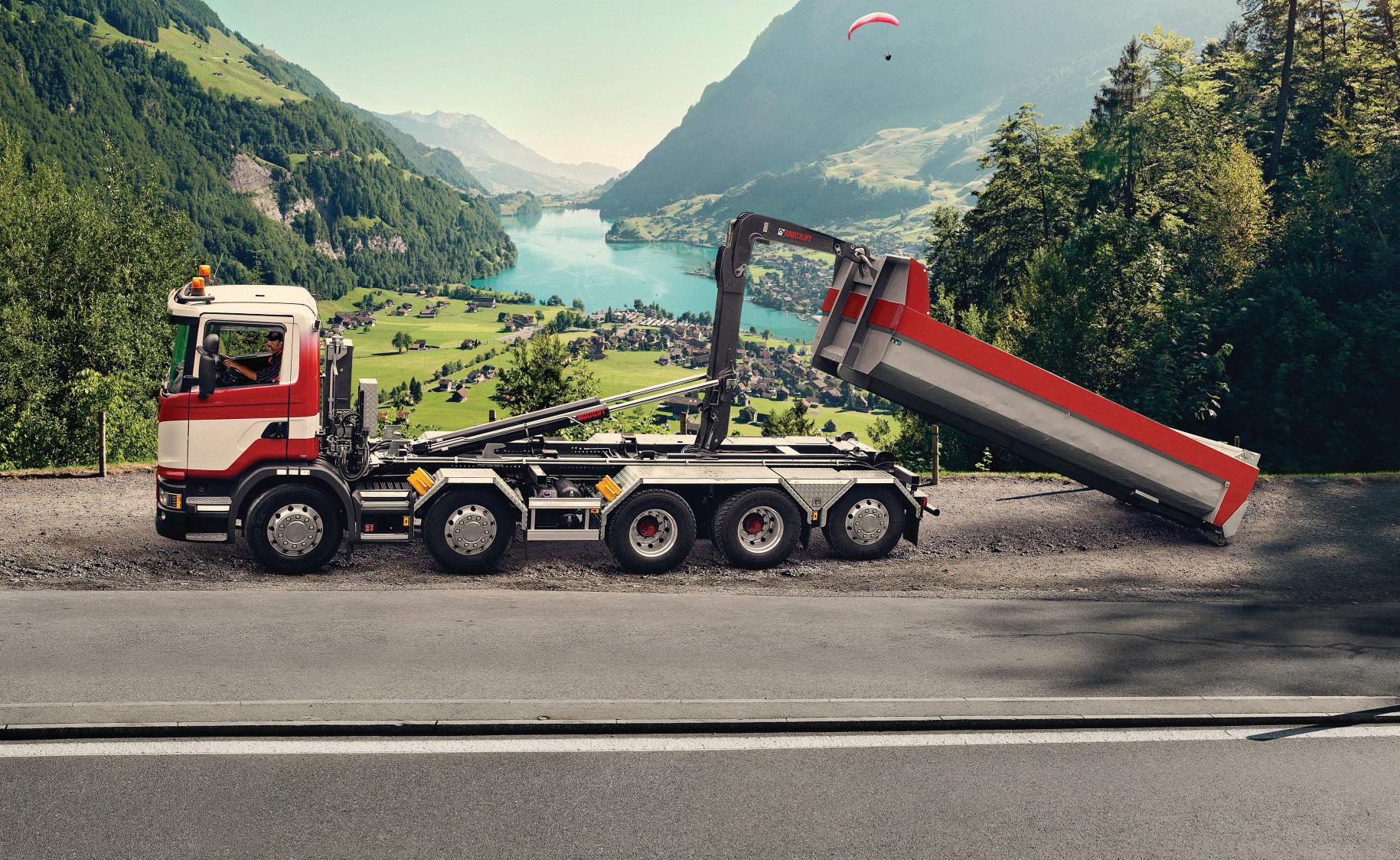
Most retailers stack used tyres at the back of their premises in a loose lace pattern. However, about 50 per cent of each tyre is “space” which can fill with water when stacked outside posing a health and environmental hazard for staff.
Tyre collectors unpack the stack, carry and load tyres onto a truck then reverse the process at the depot. Until now, it’s been time-consuming and expensive in terms of labour, transport and fuel costs. Warren says the new system approach of compacting, storing and loading means the overall collection productivity will improve by about 70 per“Atcent.the end of the day it’s a win win.” For more information, visit: www.bxbtech.com.au
MULTILIFT Ultima is engineered with radical innovations that give greater control, safety and productivity for all loading jobs. Ready for immediate fitment from August 2022. SPECIFICATIONS | Capacity 21t | G Length 5900 | BW1070 | HH1450-1570 | HWPL | HLOS | HFBL (08) 9271 8000 | info@watm.com.au | watm.com.au MULTILIFT ULTIMA 21Z.59 V19 The CEG pyrolysis plant site can collect, shred, compress, debead and turn tyres into oil.
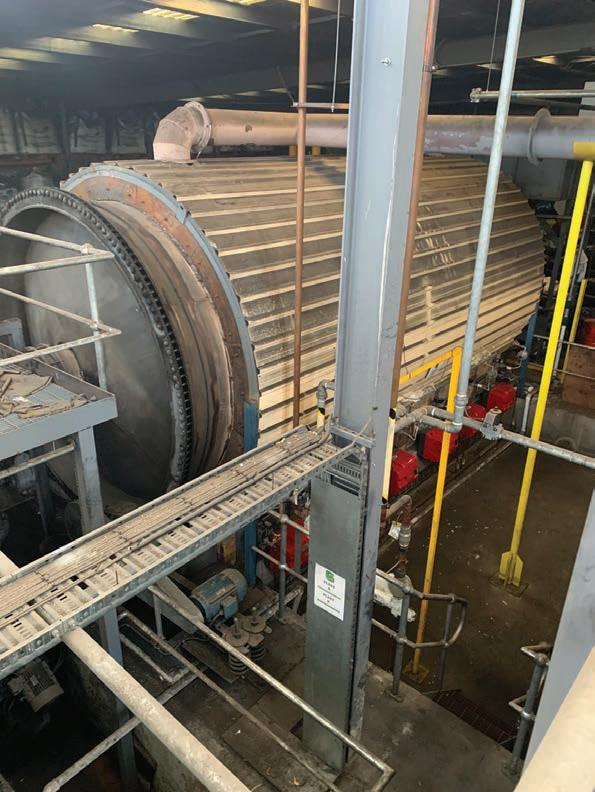
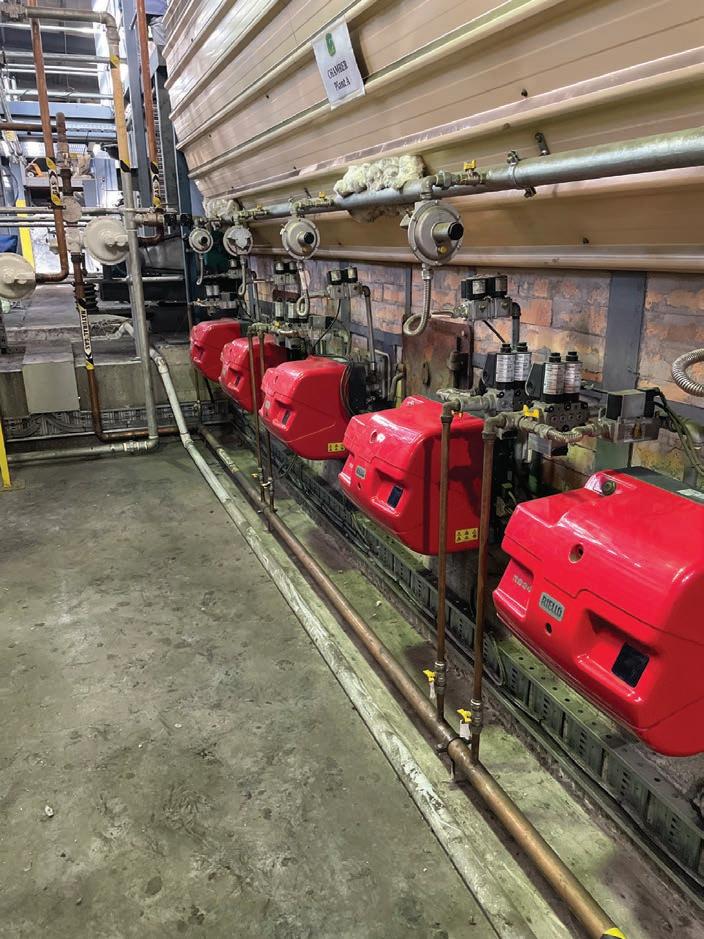
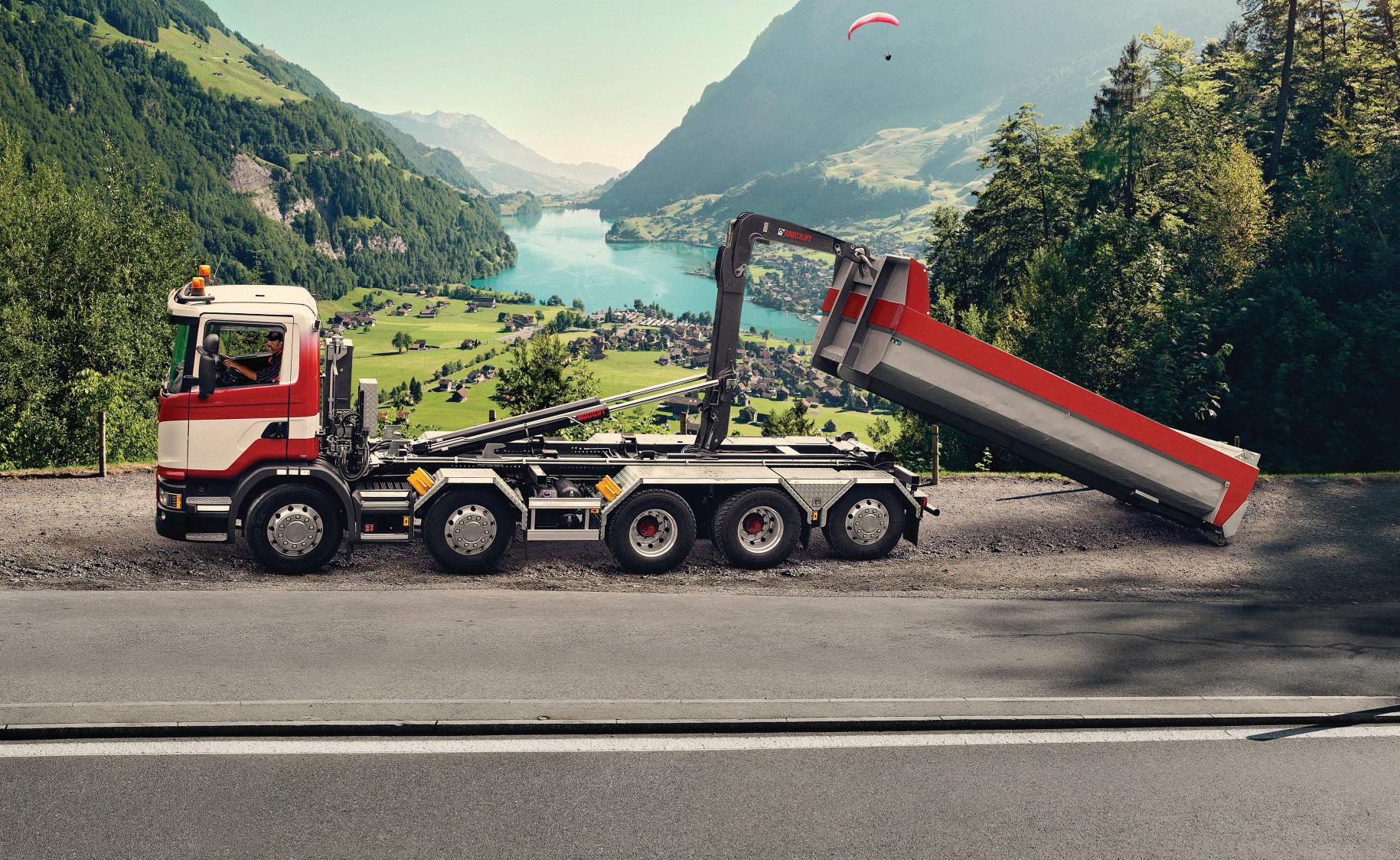

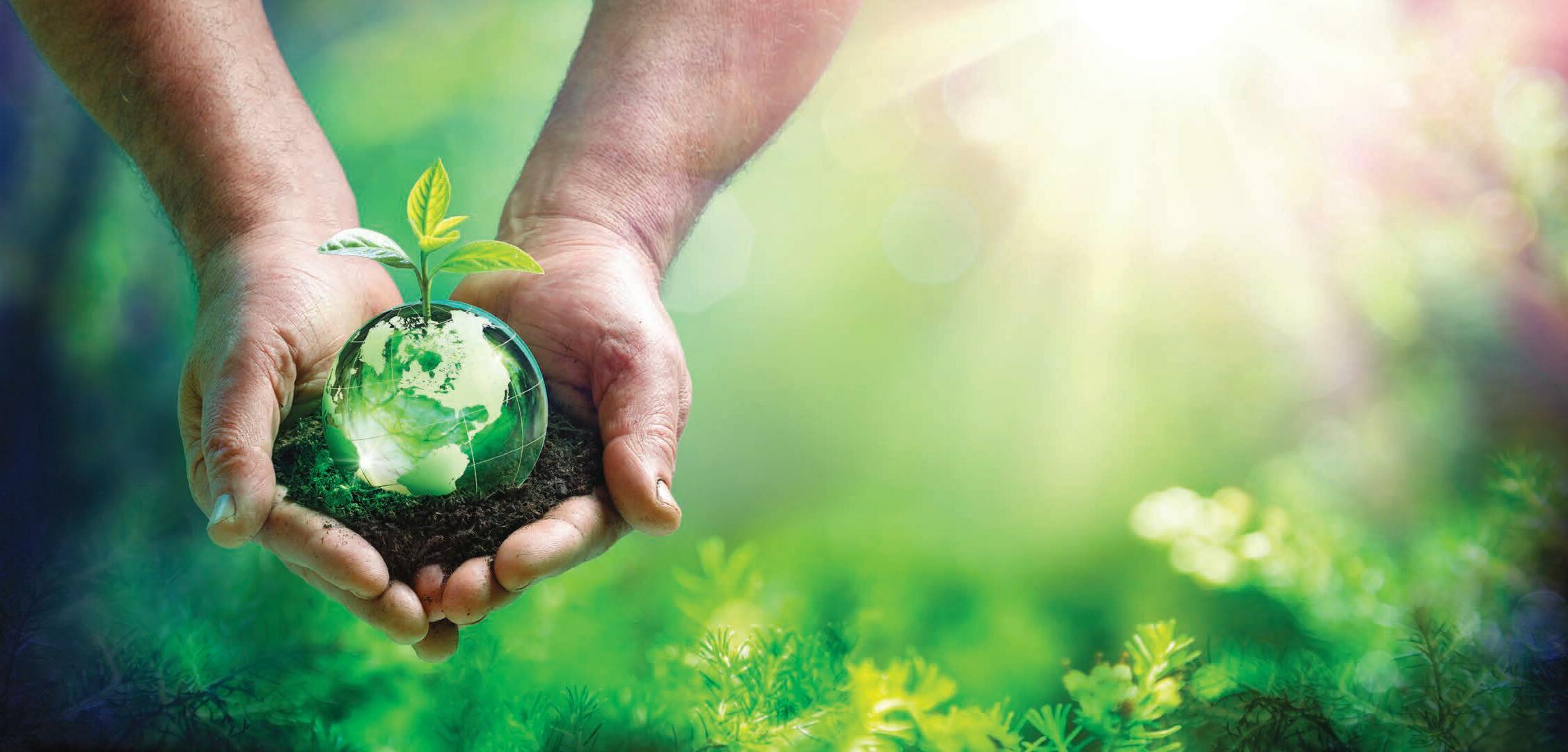
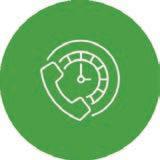
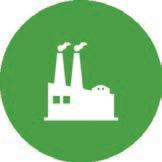

The design engineers at Hitachi Zosen Inova (HZI) have taken on this challenge head-on.
“By contrast, the new dry discharge system used in Horgen maximises the recovery of materials sent for recycling with recovery efficiencies more than doubling for the non-ferrous metal fine fraction. These materials are recovered there were two combustion lines. Now, one line is generating the same power export in the form of electricity and heat for district heating from 60 per cent of the waste previously required.
Amal says the plant upgrade included improvements and automation of the combustion system. Because of the lower excess air in the combustion process, the amount of flue gas is reduced and heat is recovered more efficiently. This also means lower NOx production and utilityConstantconsumption.analysisof the flue gas, fire position on the moving grate via video analysis, bed height measurements, 3D laser scans at the feed hopper and the complete automation of the feed waste crane allow for steadier combustion and steam production.
The moving grate consists of four optimised and individually driven zones that facilitate the different www.wastemanagementreview.com.au
Lifting an air-cooled condenser module in place at the Dubai EfW under construction.
“Most plants feed the slag (incinerator bottom ash) into a water-filled wet extractor for cooling. However, this changes chemical compositions, particularly in the fine fraction of materials, making it difficult to extract valuable nonferrous metals such as aluminium, zinc, copper, and gold contained in the bottom ash,” Amal says.
Amal says that as one of the first EfW plants in the world with dry bottom ash discharge technology, KVA Horgen is a pioneer when it comes to futureoriented material recycling.
Amal Jugdeo, Senior Engineer at HZI Australia says HZI continues to search for smarter ways to combine new and complementary technologies.
“We are improving existing technologies to meet and exceed the challenges of tighter emissions requirements, maximising waste recycling and reducing carbon emissions,” Amal says. the KVA Horgen plant in Switzerland.
/ WMR / 41 FEATURED TOPIC – ENERGY FROM WASTE
Tat Energy from Waste (EfW) facilities and, in particular, thermal treatment plants in recent years. Improving waste recycling rates in line with the principles of the circular economy and driving up air quality are top priorities for many countries around the world.
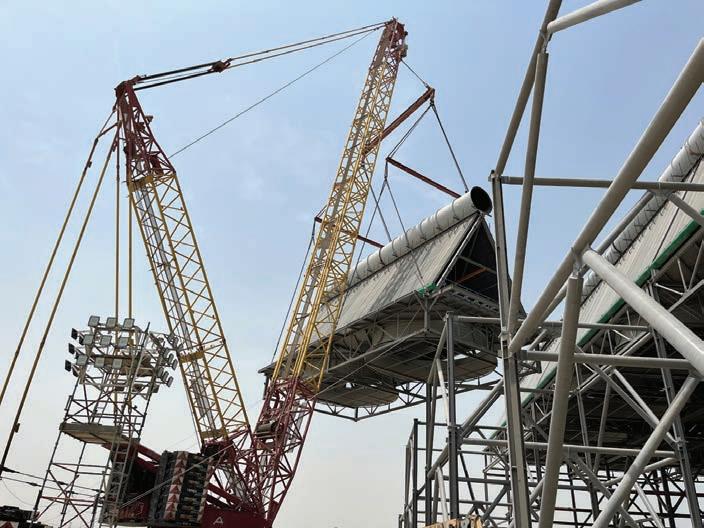
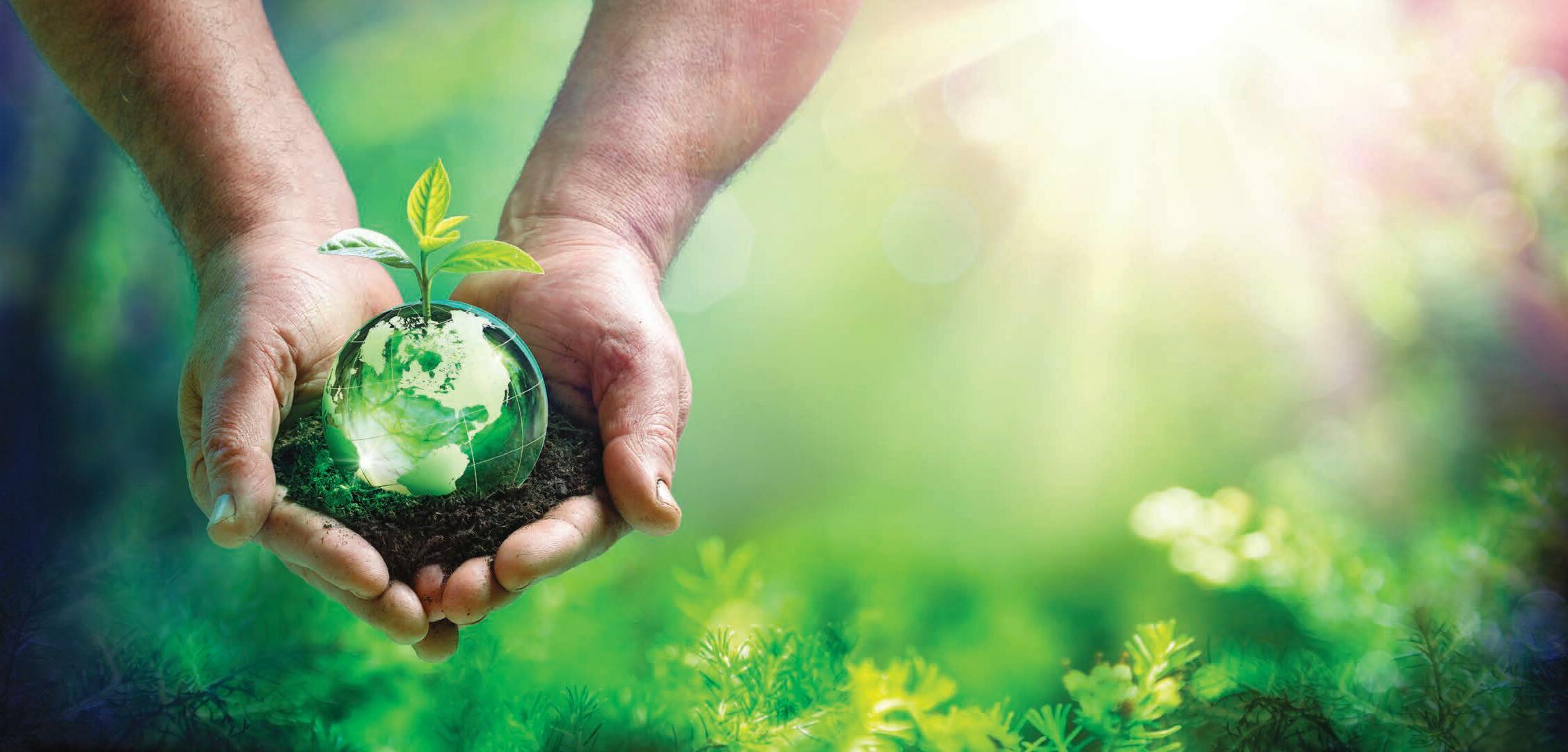
Another example of pushing the technology boundaries can be found at the world’s largest EfW plant under construction in Dubai. Once completed in 2024, it will process up to 45 per cent of Dubai’s current municipal waste, converting 1.9 million tonnes of residual waste a year into electricity for about 120,000 households.
EfW plants require substantial capital outlay. Any improvement in the capital cost per tonne of waste processed has a material impact on the business case for such a facility. The Dubai project and HZI’s Newhurst Energy Recovery Facility in the UK (with the latter set to enter commercial operations in 2023) will be the largest single-line boiler designs in the world (124.6 MWth and 126.3MWth respectively). HZI engineers conducted fluid dynamic modelling prior to commercialising these ultra large boilers and they continue to push the boundaries by designing even larger single-line facilities. Amal says that such designs offer up to a 20 per cent discount on an equivalent two-line design and therefore result in a discount on the gate fee for such facilities.
INCREASING EFFICIENCY
CARBON CAPTURE Australia has committed itself to reducing greenhouse gas (GHG) emissions by 43 per cent below 2005 levels by 2030. “The waste management sector in Australia contributes just under three per cent to Australia’s overall GHG emissions,” Amal says. “EfW technology already presents a quick win by reducing net GHG emissions compared to residual waste disposal via conventional landfills. “Although landfill gas capture reduces GHG emissions compared to landfill sites without gas capture, studies highlight that the net impact of fugitive methane emissions as ‘carbon dioxide equivalent’ from such landfills far exceed the GHG emissions that residual waste treatment in an EfW would bring.”
“With a net energy efficiency of more than 30 per cent, Dubai’s future waste incineration plant will rank among the very best in the world,” says Amal.
To improve the EfW footprint even further, HZI has partnered with technology providers to capture the carbon dioxide (CO2) contained in EfW flue gases. One such process involves the reaction of the CO2 with calcium to form mineral calcium carbonate – a stable, non-toxic, valuable component that has many uses, including as a raw material in the construction industry, fertiliser, as well as a mineral filler in the paper, paint, and plastics industries. The capture rates can enable EfW plants to become carbon sinks. The system is also geographically independent and does not require storing carbon dioxide in a gaseous state underground, nor additional pipelines for“Suchtransportation.technologies will enable us to reduce CO2 emissions from EfW plants to zero or even negative, further embedding our technology within the circular economy,” Amal says. “The technology exists to produce hydrogen from the electricity produced at the facility. By combining this with recovered CO2 in a processed called methanation, methane is produced that could be injected into the domestic gasDrnetwork.”MarcStammbach, HZI’s Managing Director for the Australian HZI subsidiary, says that with hundreds of EfW plants as reference throughout the world, EfW technology has proven itself to be an environmentally safe and reliable solution for the disposal of residual waste. “As demand grows to improve overall material recovery and re-use, together with a drive to increase energy efficiency and reduce greenhouse gas emissions in a cost-effective package, HZI has stepped up to the challenge and is ready to offer the next generation of EfW plants,” says Marc. For more information, visit: www.hz-inova.com
FEATURED TOPIC – ENERGY FROM WASTE 42 / WMR / September 2022
The East Rockingham EfW under construction.
The location in the Dubai desert brings with it a number of challenges such as ambient temperatures that allow limited air-cooling of the steam. The plant design included provision for a larger air-cooled condenser (ACC). Another potential issue is desert sand clogging up the surface of the ACC and preventing air flow. To counteract this, the ACC has to be cleaned more often and thoroughly than it does in other plants in cooler climates. Amal says that despite this unusual environment for an EfW plant, the Dubai project will achieve world-leading energy efficiency.
phases of the combustion process (i.e., drying, ignition, gasification and combustion of volatiles – where the excess oxygen is essentially zero and charAmalburn-out).saysthat these combustion system enhancements have also been applied by HZI to the 330,000 tonnes per year EfW plant under construction in East Rockingham, Western Australia, which is scheduled for start-up in 2023.
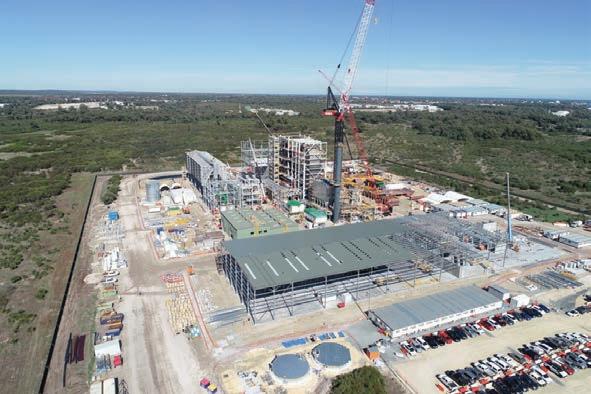
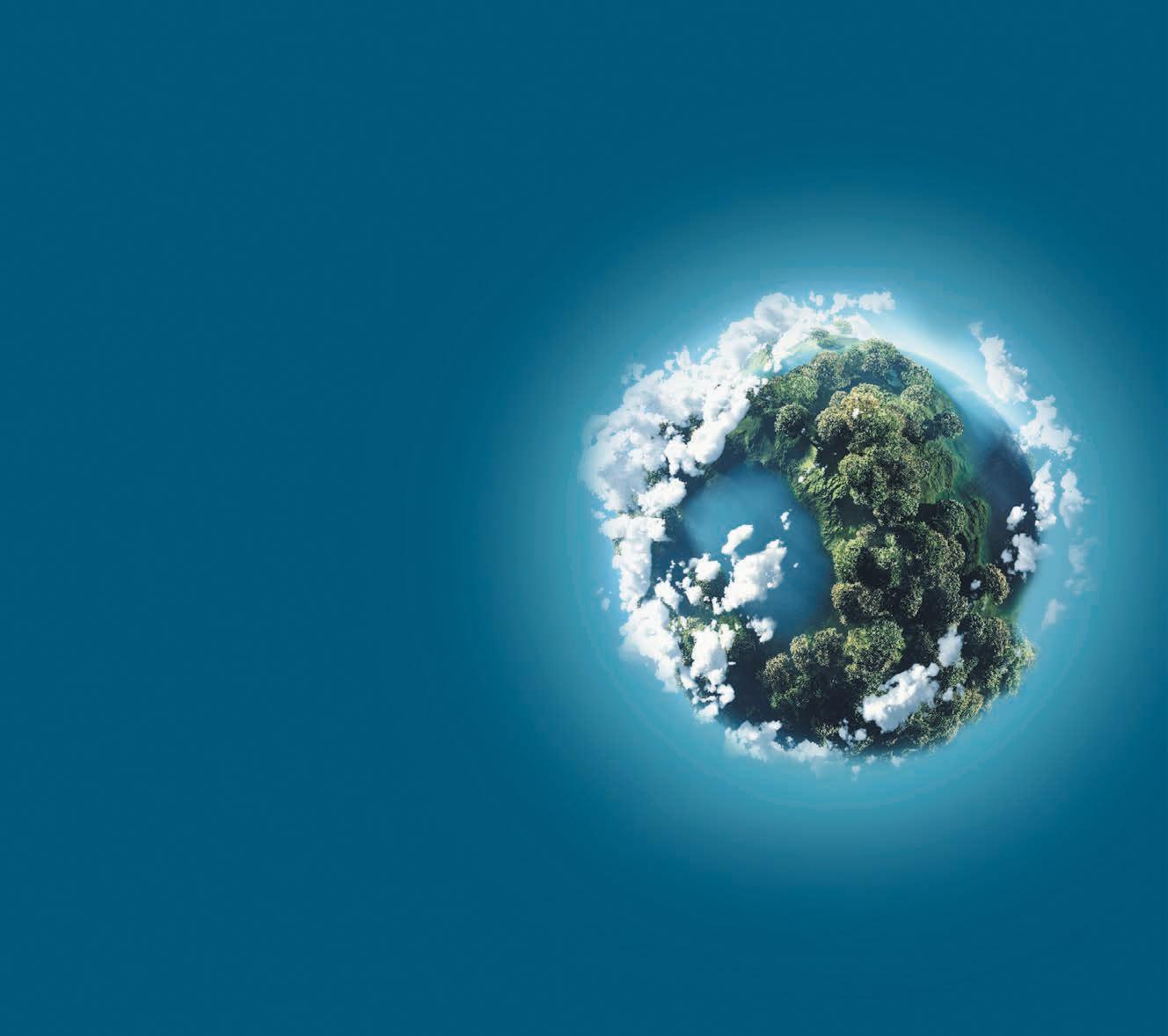
TOMORROW’S SOLUTIONS. TODAY
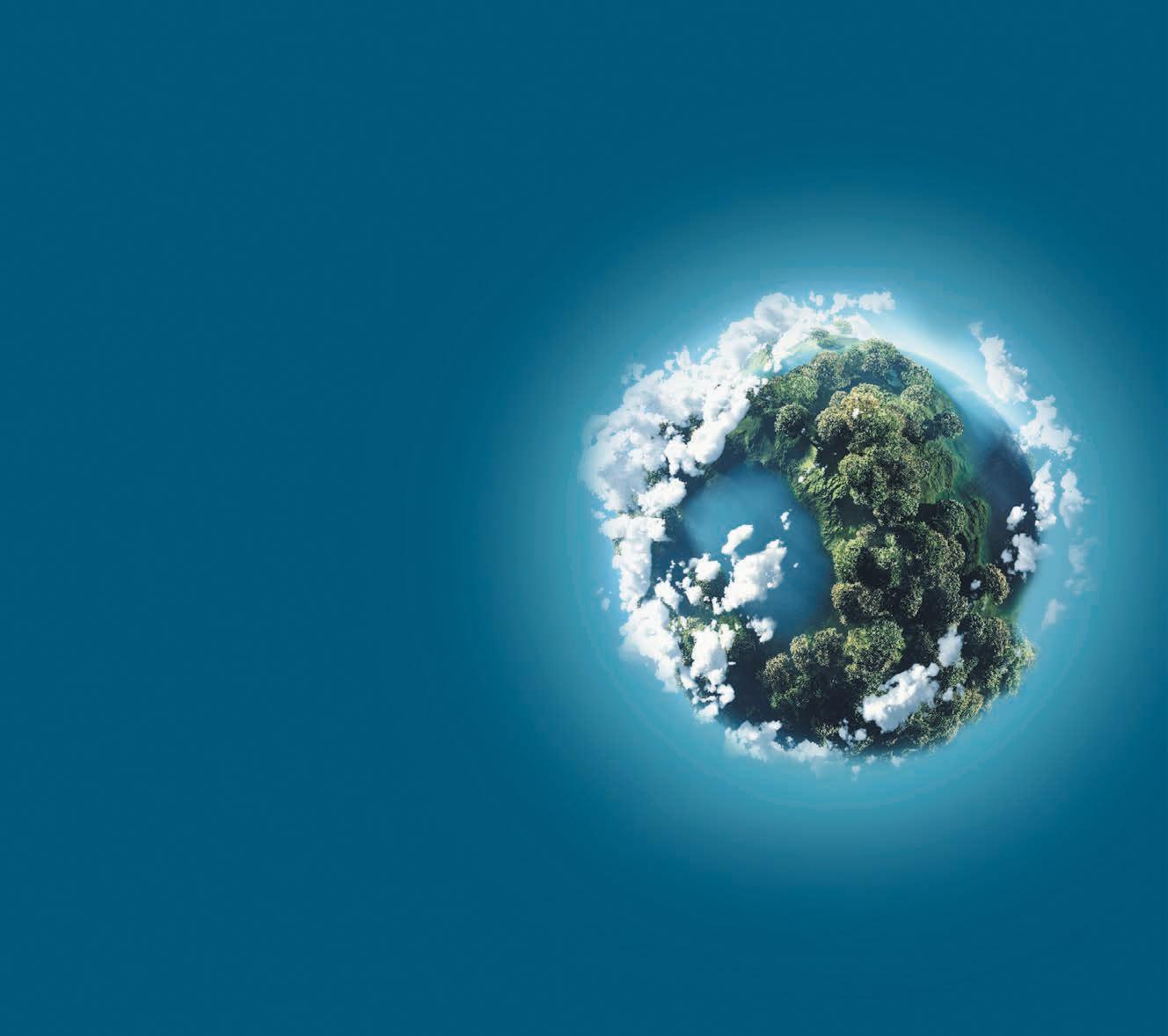
www.wasteawards.com.au WASTE INNOVATION&RECYCLING AWARDS STAND OUT AS AN INDUSTRY LEADER NOMINATIONS NOW OPEN HELD IN CONJUNCTION WITH Sponsors

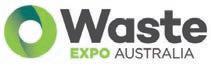
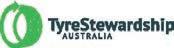


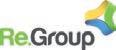
AN INCREASING DEMAND FOR ENERGY-FROM-WASTE SOLUTIONS FOR INDUSTRIAL WASTE IS DRIVING INNOVATION. ANDREW WAITE, DIRECTOR OF SALES AND BUSINESS DEVELOPMENT FOR BABCOCK & WILCOX, EXPLAINS.
Andrew says B&W, a US-based clean energy and environmental technologies company with regional offices in Australia, has developed methods to use this type of waste to produce energy while at the same time isolating the carbon dioxide in a concentrated stream that will provide a more cost effective way for it to be used as feed stock for other value adding processes or“Municipalsequestration.and industrial waste are considered renewable energy sources, and the captured carbon dioxide would be considered biogenic carbon dioxide, as opposed to carbon dioxide captured from burning fossil fuels,” he“Wesays.can use this source of CO2 to produce higher value products such as methanol and fertilisers and perhaps even take it up to the next level in sustainable aviation fuels.
www.wastemanagementreview.com.au
Bold ambitions
Andrew says similar facilities have been operating in Europe and the United Kingdom for years. In the UK several hubs are now taking the process further and creating hubs for carbon dioxide sequestration into old oil and gas reservoirs. “Once Australia has a price on carbon dioxide emissions there will be a greater incentive to trap it and do something with it so that it doesn’t escape into the atmosphere,” Andrew says. The technology is ready and available now.
Andrew says Energy-from-Waste (EfW) providers are looking to establish facilities that can process up to 200,000 tonnes of waste per annum, because they can be cost effective when provided with a consistent feedstock from localSeveralcompanies.facilities are being proposed for existing or new industrial estates in Victoria, as well as one in Queensland. “Commercial and industrial companies have waste to dispose of,” Andrew says. “It’s a cost to them to transport and dispose of in a regulated industrial landfill, particularly if it’s food or building waste. “If you’re just filling up landfill, you should start thinking, what are you doing next? It makes sense to take it to an EfW facility rather than pay a landfill or hardfill site to park it.”
Andrew Waite, Director of Sales and Business Development for Babcock & Wilcox (B&W) says there’s an increasing trend to establish waste-to-energy plants that can use specific waste streams, particularly for commercial and industrial waste. These types of waste typically offer a higher calorific value than municipal solid waste because the waste stream is more consistent, which means less processing costs. Long-term, these plants can be designed to incorporate carbon capture and potentially provide another revenue stream.
“Landfill is a low-cost solution today, but in future we’re going to have to be a bit smarter.”
/ WMR / 45 FEATURED TOPIC – ENERGY FROM WASTE
The Palm Beach Renewable Energy Center No.2, in West Palm Beach, Florida.
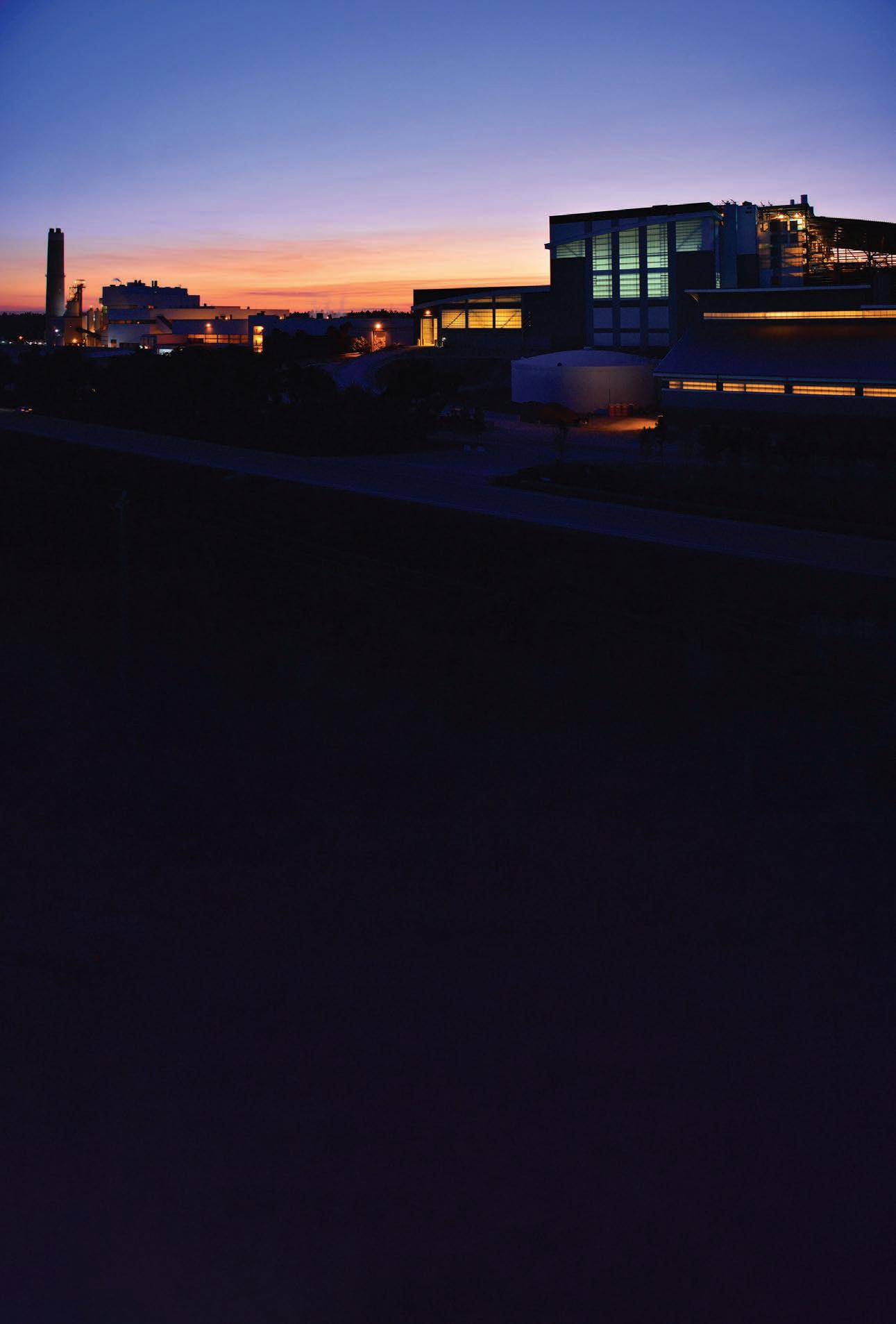
The Palm Beach Renewable Energy Center No.2 in West Palm Beach is a key fixture in the community, providing clean, sustainable, renewable energy for residents.
The Amager Bakke Copenhill plant in Copenhagen, Denmark. Babcock & Wilcox provided the waste-to-energy, steam generation and environmental technologies for the plant.
“Having these types of plants give you options because you can do something with what you’re collecting. Initially you can avoid emissions and have an alternative to landfills, but ultimately capturing CO2 is a way to carbon negative emissions.
“If we’re looking at a circular economy you have to have the ability to collect and process waste and make the most of it.”
Andrew says the technology is ready to go, it just takes someone to stand up and say, “let’s do it.” He says one of the challenges of EfW is overcoming the NIMBY (not in my back yard) aspect. That, he says, comes down to education and asking the community to question whether they want to put waste in a hole in the ground forever. “The better way to deal with all of that waste is to put it through a wasteto-energy facility,” he says. “You don’t have the methane emissions created by decomposing waste in a landfill, and you know when you put waste into an incineration process you will destroy all of the methane.
“There’s no reason why we can’t achieve minimal waste while delivering economic and environmental benefits.” Economics, Andrew says, is a key driver for smaller, localised waste processing facilities in industrial areas. For the EfW operators it is a smart way to recover waste streams with minimal processing. For industry, it’s having to pay to transport and landfill waste versus the alternative of turning waste into energy where they can save some money from it. “The company can get rid of their waste in a better way, there are no emissions and it’s in line with good environmental, social and governance outcomes,” Andrew says. “The driver for development of EfW facilities needs to be social, from the community. For business, it has to be an alternative that still makes sense economically.”
“It is important to note that we should never look at an EfW facility purely as an electricity generating device” he says. “It should be viewed as a waste disposal device first and foremost because we want to get rid of our waste and manage emissions.”
Two EfW plants are presently being established in Western Australia. Once commissioned, they will process the municipal solid waste for the entire Perth area. Andrew says there is scope for similar-style plants strategically placed to service Melbourne, Sydney andHe’sBrisbane.hopeful once the WA plants are operational the community will see that energy from waste is complementary to recycling and is cost-effective and economically sound.
For more information, visit: www.babcock.com FROM WASTE
46 / WMR / September 2022 FEATURED TOPIC – ENERGY
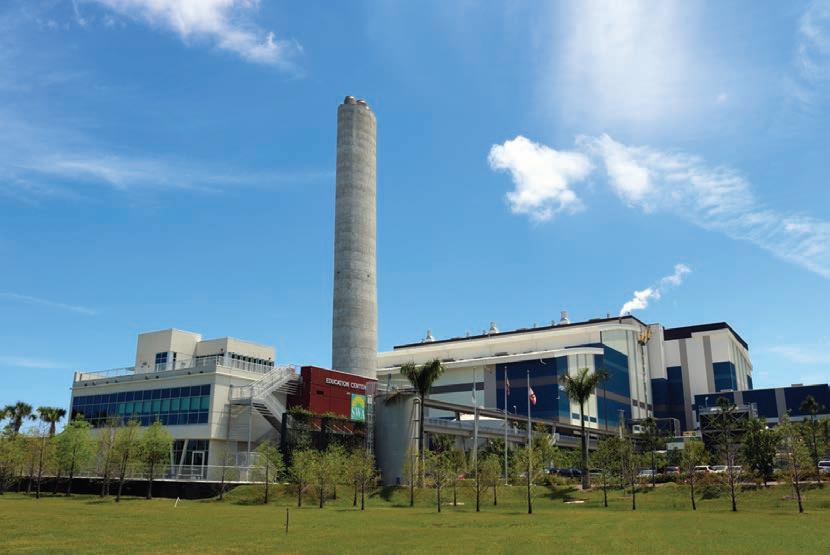
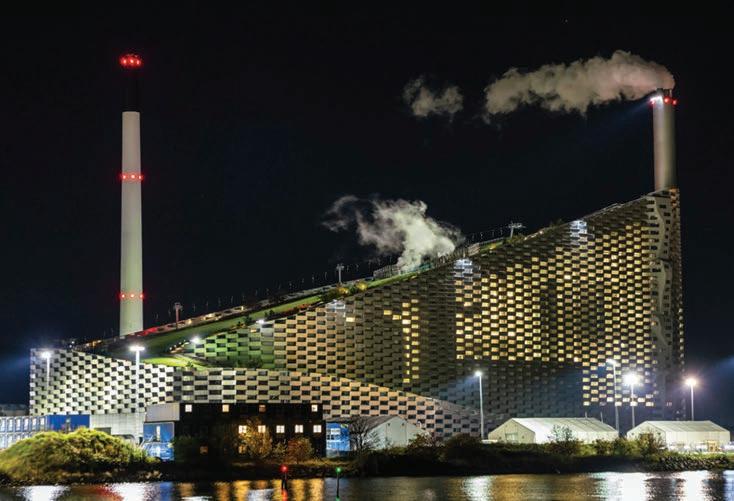
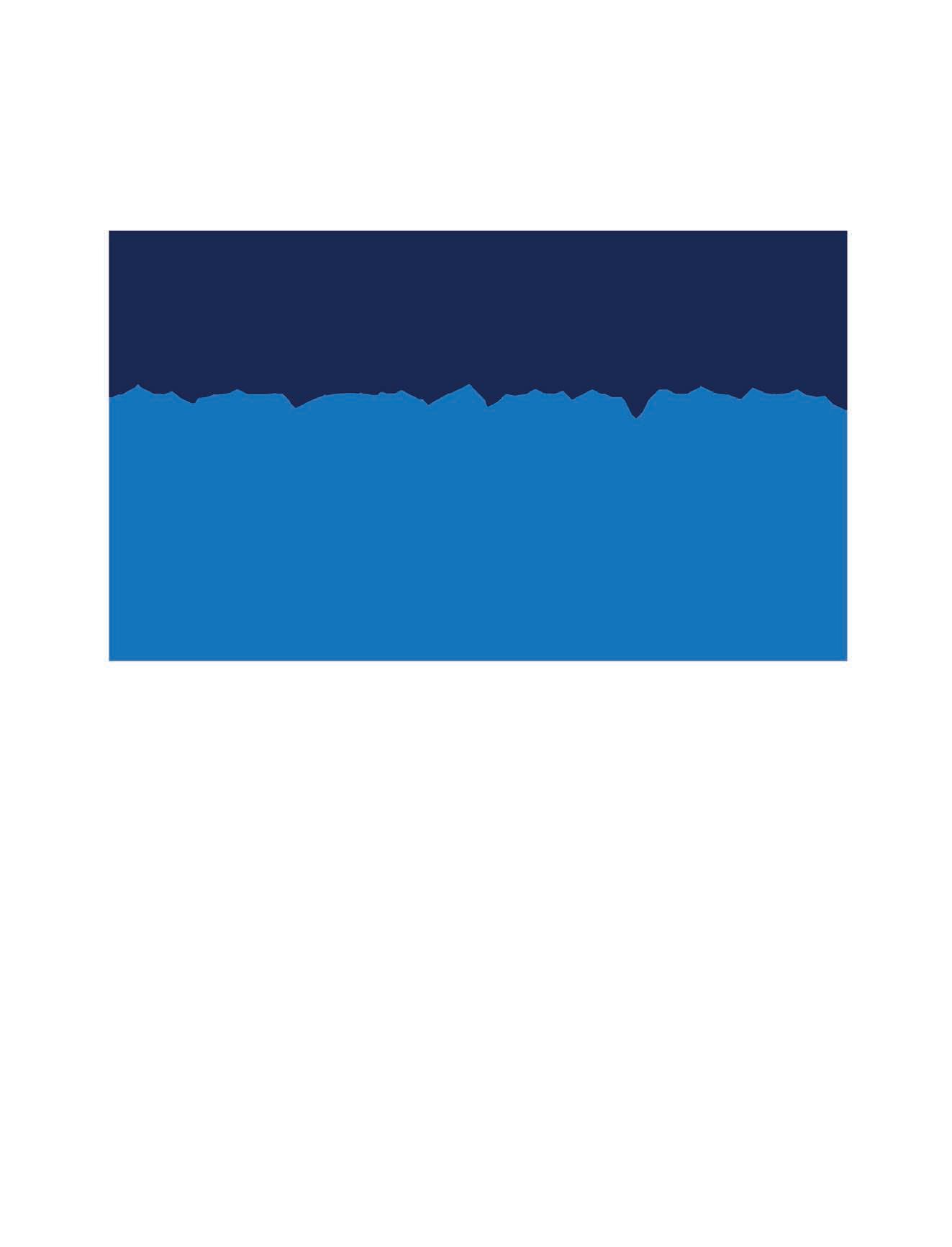
TOPIC – ENERGY FROM WASTE
The significance of the first EfW facilities to be approved in Australia should not be underestimated.
The Plan is focused on strategic planning that provides for economic and job opportunities in regional areas. Synergies with existing or planned infrastructure, including rail or road transport, are encouraged.
ESTHER HUGHES, PRINCIPAL ENVIRONMENTAL PLANNER, MRA CONSULTING GROUP, TAKES A LOOK AT THE STATE OF ENERGY FROM WASTE.
Following on from the Infrastructure Plan, on 8 July 2022 the NSW Protection of the Environment Operations (General) Amendment (Thermal Energy from Waste) Regulation 2022 came into effect. It’s
EfW in NSW –Where are we now?
An article on the MRA blog dated July 2014 is a summary of the Energy from Waste (EfW) Symposium held the same year in Lorne, Victoria, which featured a panel representing all the states and territories except Northern Territory and the ACT.
The conversation is familiar to this decade – landfill avoidance, thermal efficiencies, waste hierarchy, cannibalising recycling, bringing the community along, the effect of the landfill levy, and Energy from Waste policies. So, what has changed? Well, lots and notOnmuch.thepolicy front, there are five major states and territories that have published standalone EfW policies, placing conditions around many of the main issues that were discussed eight years ago. The ACT has declared that it is a no-go zone for thermal EfW facilities. Victoria has placed a cap on EfWOnthroughput.theground, and the first in Australia employing modern technology, two large-scale thermal EfW facilities have been approved in Western Australia, followed by five in Victoria. The significance of these facilities to spearhead the modern alternative to landfills should not be underestimated. An Australian-based facility provides relevant data for other potential development and may help to alleviate fears about the EfW industry. Hopefully, our next holiday to WA will include a tour of Kwinana.
One might wonder what New South Wales, the most populous state with the highest waste levy, has achieved in the way of progress toward its first energy from waste facility.
In September 2021, the NSW government issued the Energy from Waste Infrastructure Plan 2021, in which it identifies three principles that would guide future energy from waste infrastructure investment. They are: to improve certainty to communities and industry around acceptable locations and facilities; to commit to caution where there are areas of high population and exceedances to air quality standards, and to maximise efficiencies in infrastructure, waste management, innovation and energy recovery.
48 / WMR / September 2022 FEATURED
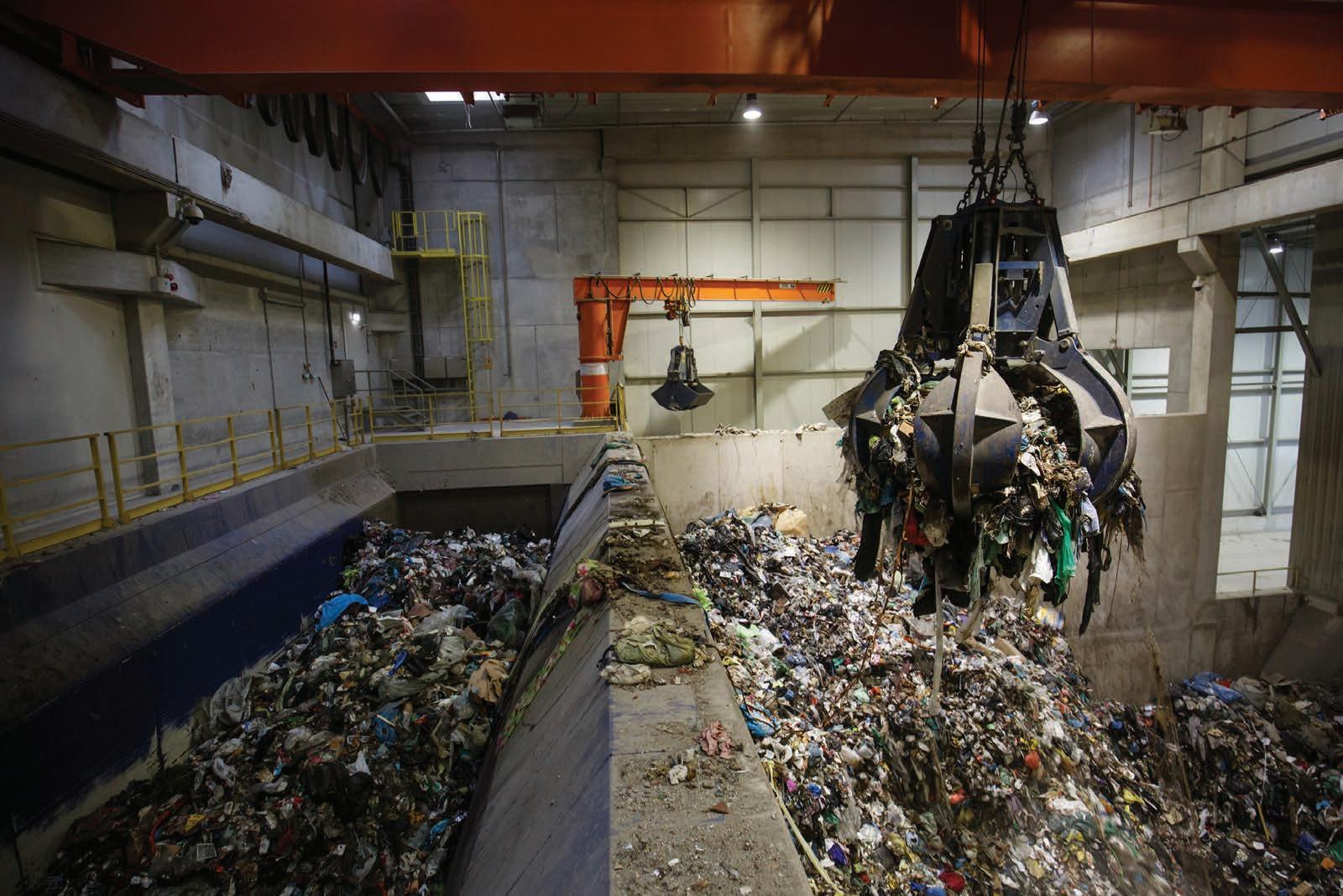
a bit of a mouthful, but the intent of the amendment is to enforce a blanket prohibition on the thermal treatment of waste (energy from waste) in NSW except under certain circumstances. There are three exceptions. The activity or work may be carried out at certain precincts or premises, the activity may be an established and operating activity at the premises immediately before the prohibition comes into force, and the activity may be carried out to replace a less environmentally sound fuel in certain circumstances.
2. The facility had to be running, or was approved to run, before the amendment occurred.
4. At least 90 per cent of the energy recovered from wastederived-fuels will be used for industrial or manufacturing processes in a given year. By way of definition, the legislation captures the recovery of electrical energy, mechanical energy, heat and fuel production. It is applicable to any licensable activity, which is a 200 tonnes per annum waste throughput limit for energy recovery.
While Parkes is the first key precinct to move ahead, with streamlined development pathways for waste infrastructure to support the strategic plan and provide industrial ecology synergies, other opportunities face regulatory barriers to their development.
On a positive note, within the parameters of the Energy from Waste Policy, the Energy from Waste Infrastructure Plan and the Amended PoEO (General) Regulation, NSW is set to move forward to the considered approval of their first EfW facility for thermal treatment of waste, with regional areas benefiting from job opportunities and increased investment. For more information, info@mraconsulting.com.aucontact: www.wastemanagementreview.com.au
The stand-out impact of the infrastructure plan and the regulation is that there are only four precinct locations to establish new EfW facilities. Other opportunities are extremely limited, with five applications in NSW already being axed as a result. Within precinct planning, however, there is generous support for waste and resource recovery infrastructure investment.
The Regional Jobs Precincts is an extension of the SAP program which also aims to assist fast-track approvals, growth and investment in regional NSW. The Regional Jobs Precinct program is less developed than Parkes, but it is likely to follow a similar approvals system with specialist studies already commissioned.
3. At least 90 per cent of the replaced fuel was used for industrial or manufacturing processes at the premises in the year before the amendment occurred.
/ WMR / 49 Five Australian states and territories have published standalone EfW policies.
A Special Activation Precinct (SAP) is a dedicated area in a regional location become a thriving business hub. SAPs use fast-track planning, investment in infrastructure, government-led studies and development/business concierge.
A high level of regulatory control arises from the NSW Energy from Waste Infrastructure Plan and associated legislation.
The precincts that are not prohibited from energy from waste include the Parkes Activation Precinct, the Richmond Valley Regional Jobs Precinct, the Southern Goulburn Mulwaree Precinct and the West Lithgow Precinct. There is provision for other precinct(s) that are yet to be gazetted, potentially at a former mine site or former electricity generation site.
Parkes is the first of six SAPs to be developed, and has particular opportunities aligned with the east-west rail line and the Inland Rail project. The Regional Growth and Development Corporation is responsible for the delivery of the Parkes SAP, facilitating fast-track approvals for many activities, including thermal electricity generating works and waste management facilities.
1. The replaced fuel has to be less environmentally sound.
An EfW facility is also not prohibited if it is an established and operating facility prior to the changes to the regulation. Hence the sites in NSW that currently thermally treat waste – in Berrima and Tumut – are not impacted by theThereregulation.arefour criteria to be eligible to establish an EfW facility that
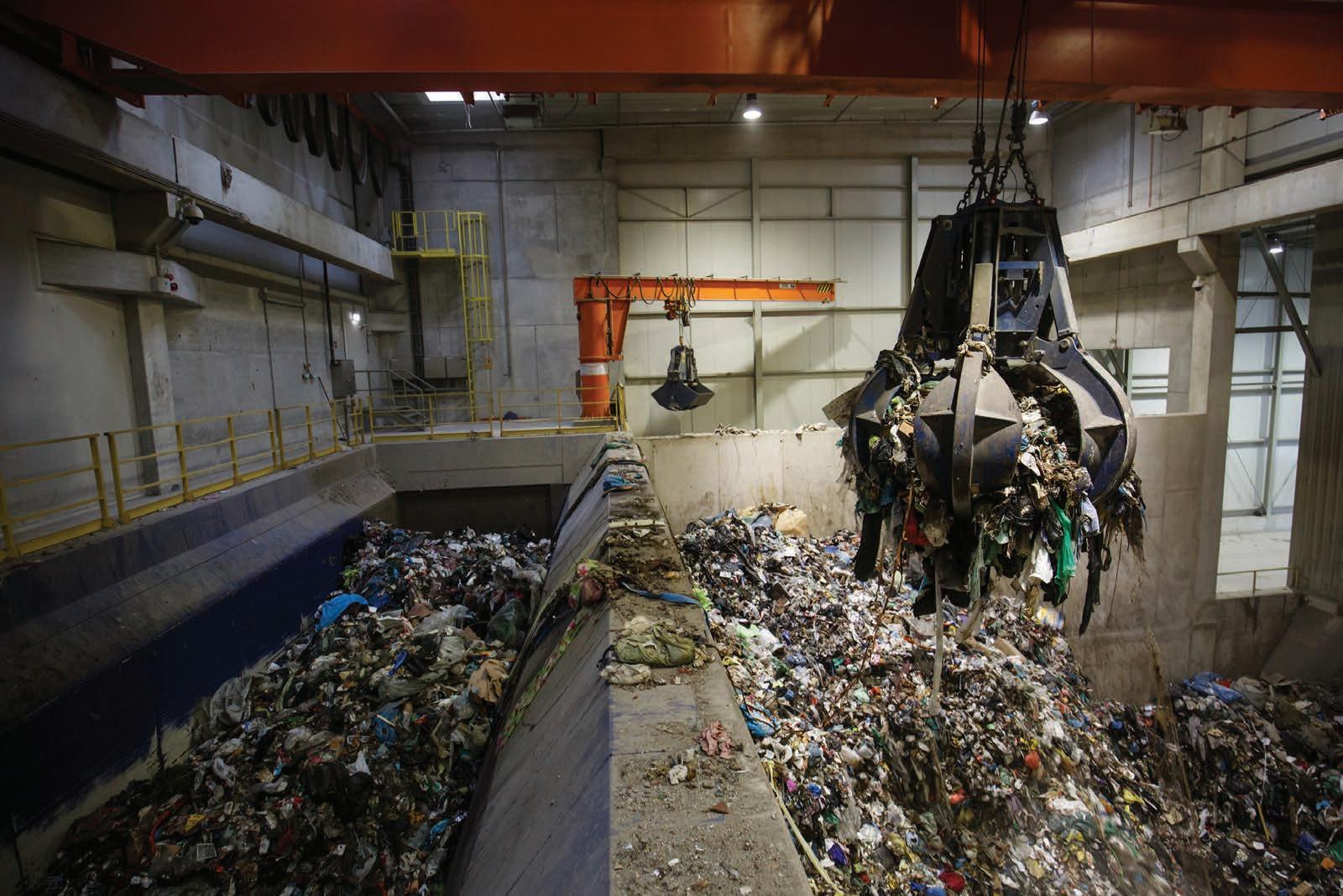
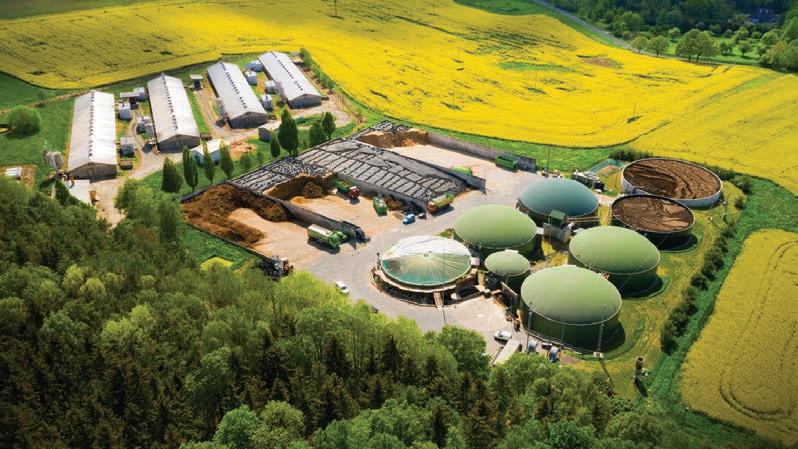
Industry powerhouse
One of the sites where LGI is planning to add batteries is the Mugga Lane biogas to renewable power project, on the largest landfill in theSinceACT.commencing operations on site in 2020, LGI has built a
LGI plans to add batteries to the Mugga Lane biogas to renewable power project.
LGI IS BUILDING ITS CAPACITY FOR RENEWABLE ENERGY TO HELP MEET GROWING DEMAND FOR DISPATCHABLE POWER.
LGIway?’”(formerly Landfill Gas Industries) has been offering a viable alternative, mostly to regional It captures biogas from landfill to generate electricity, while still abating carbon. The power stations produce dispatchable renewable electricity, create carbon credits and help councils reduce their greenhouse gas emissions. For councils without biogas extraction systems on their landfills, typically 7080 per cent of their carbon footprint can be from their landfill.
FEATURED TOPIC – ENERGY FROM WASTE 50 / WMR / September 2022
Australia’s eastern states this winter, when coal shortages and maintenance of ageing power assets meant there was insufficient supply to meet high demand, highlighted the volatility of the market, says Jarryd Doran, Chief Operations Officer at ItLGI.also gave rise to discussions around the need for more viable, alternative power sources to enter the“Timesmarket.are changing. The community is becoming more aware of problems with traditional energy supplies,” Jarryd says. “As a community we’re asking, ‘are we happy to leave ourselves exposed in that
T
“LGI’s modular design enables us to build a power station within three months from when construction commences on site. In fact, the longest part of developing a power station is securing the grid connection,” Jarryd says.
The company has built about 40 biogas systems with biogas flaring and power generation on landfills in its 13-year history. It is now adding grid scale battery storage across its generation portfolio to provide even more dispatchable renewable energy
LGI power stations can already respond in minutes and batteries can respond in seconds to help the electricity grid remain stable to keep the lights on. opportunity between large-scale renewables and rooftop solar for generation projects connected to the distribution network where the demand is. These projects can be funded by the private sector to complement government investment and be connected quickly.
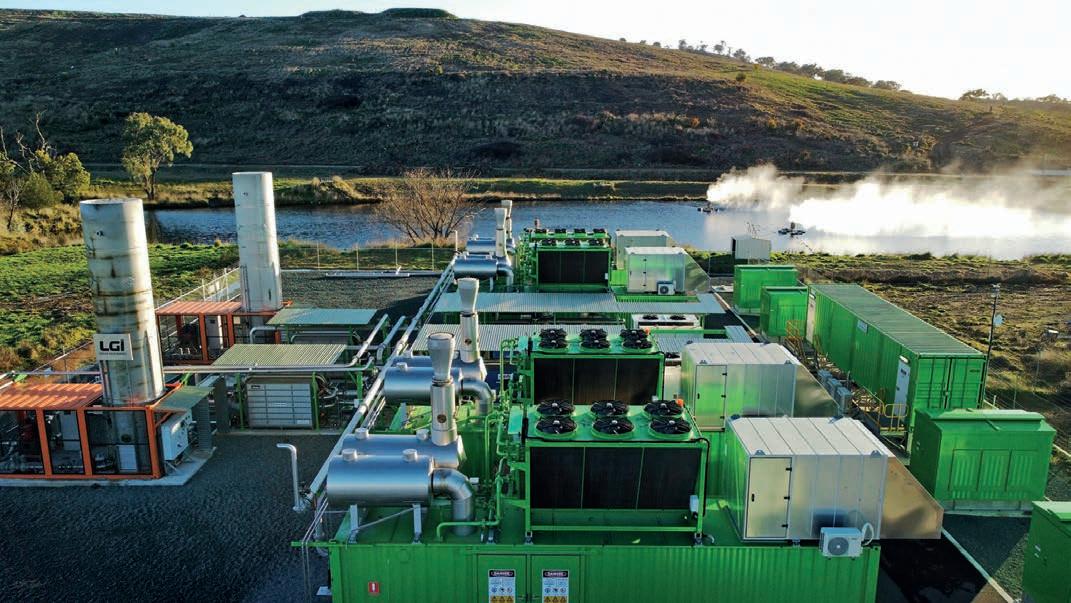
Smaller landfills across Australia have previously been considered sub scale or have been subject to an out-of-sight, out-of-mind mentality.
“If we don’t extract the gas, it will ultimately find a way out,” he says. “Methane is 28 times more harmful to the environment than carbon dioxide. By capturing and combusting it to produce energy we reduce its impact on the environment and put it to good“We’reuse. not pro landfill, but we’re here to help ensure the sector is managing the legacy associated with existing landfills by doing something positive with the gas. With the seven power generation facilities we already have operating, we are producing 87,500MWh annually. That’s more than enough electricity to power about 15,000 local homes for a year.
capture, carbon abatement and electricity production. The station can produce four megawatts of power every hour. Jarryd says adding extra gas engines and battery power could take it up to 20 megawatts of capacity.
Historically, there was also no financial driver to manage the waste gas differently. But all landfills can emit biogas, which is ~50 per cent methane that impacts the environment and the community, unless properly managed.
“We can offer councils a range of benefits from the biogas we manage on their tip. This can include carbon abatement, contributing to best practice landfill operations and even supplying them long-term renewable energy with a firm predictable price. For more information, visit: www.lgi.com.au Jarryd Doran, Chief Operations Officer, LGI.
At Toowoomba, in Queensland, LGI is designing and building its latest power station which is due for completion this year. The council’s emissions profile will change, and its wastewater treatment facility will be powered with renewable energy made entirely from the biogas produced by theJarrydtip. says the Toowoomba station is a good example of what LGI does –help waste operators to better manage landfill sites and unlock the value of gas that’s recovered. “We commenced with a biogas extraction system with a flare in 2020 to abate carbon and improve local air quality and very soon we’ll be supplying council with renewable energy,” he says.
“The Canberra electricity network will receive predictable energy at the time of day when it’s most needed,” hePlanningsays. and design of the Mugga Lane power station expansion is well advanced in anticipation of the site having six megawatts installed in 2023 and further enhanced with batteries in the following year.
If a landfill is closed today and no longer used for rubbish it can still produce gas for more than 20 years. Jarryd says that one of the first power stations installed by LGI, at a landfill in Brisbane that was closed in 1998, is still producing enough gas to consistently generate power.
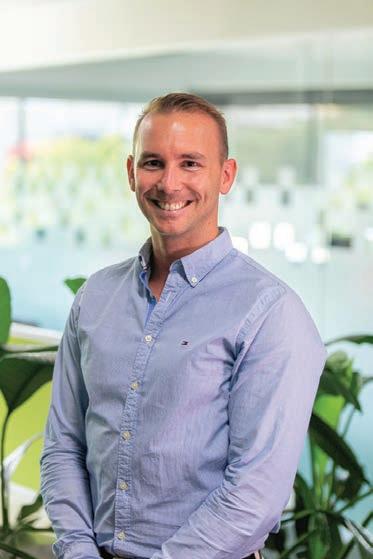
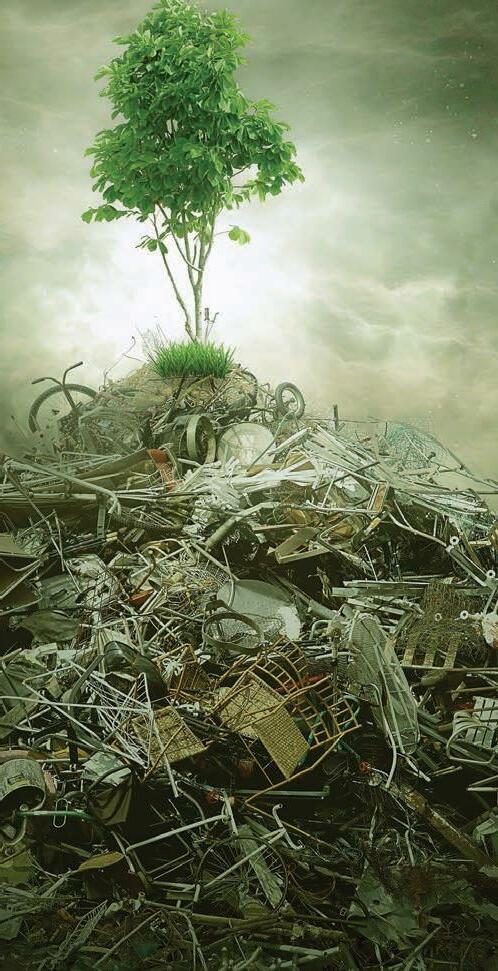
No fossil, For more than 40 years, Finnish technology companies have been at the forefront of developing and refining energy-from-waste solutions.
Finland, 70 per cent of which is covered by forest, is a country boasting no natural fossil fuel resources of its own. Historically, this has meant a heavy reliance on trade to meet its high demand for power, as well as a susceptibility to global economic trends.
In the 1990s, Finnish technology companies started pioneering processes to tap into other waste streams otherwise destined for landfill, processing them for solid recovered fuel (SRF) and refuse-derived-fuel (RDF).
AUSTRALIA COULD LOOK TO FINNISH INNOVATION TO OPTIMISE ITS ENERGYFROM-WASTE FUTURE IN THE CONTEXT OF A CIRCULAR ECONOMY. MINNA VILKUNA, BMH TECHNOLOGY’S AUSTRALIAN AGENT, EXPLAINS.
Minna Vilkuna, the BMH Technology agent for Australia and New Zealand, has more than 20 years’ experience in the waste industry, including 10 years overseeing BMH’s operations in China. She says smart energy-from-waste solutions can play a key role in the circular economy, as has been the case in her home country.
Over time, this has led to significant investment in alternative power solutions, with companies initially developing methods to harness an abundance of solid biomass waste from forestry for energy production.
“Finland has a long tradition when it comes to energy efficiency and resource recovery, because circumstances have dictated that we have had to. And it’s great that the rest of the world is now interested in what we’ve developed.”
PROVEN TECHNOLOGY
A SOLUTION FOR ANY STREAM BMH Technology’s flagship product is its TYRANNOSAURUS® process, a customisable end-to-end waste sorting, refining, and processing plant for energy-from-waste production.
no fuss 52 / WMR / September 2022 FEATURED TOPIC – ENERGY FROM
“In 2016, Finland was the first country in the world to create a national circular economy road map, one that was formally adopted by the Finnish Government,” Minna says. “As a small country, we are highly dependent on export, and a big part of that is technology. We have put a lot of money into innovation, because we have had to do so to survive.
BMH Technology is one such company with a proven track record in all aspects of the energy-from-waste process. It is now one of the biggest material handling system suppliers in the world, serving customers in 22 countries on five continents.
The system specialises in the pretreatment of waste streams, shredding, sorting and removing recyclable material, including valuable metals, prior to combustion. This ensures a more consistent quality of fuel, and offers higher power production from the same amount of waste. This means reduced emissions compared to energy-from-waste technologies without pre-treatment.ThisSRF/RDF fuel is then suitable, for example, for circulating fluidised bed (CFB) combustion boilers. These versatile co-combustion power plants don’t rely entirely on SRF/RDF, which gives them an edge over traditional moving grate incineration energy-fromwaste technology, as they can make use WASTE Lahti Energy’s power plant in Lahti, Finland uses a Tyrannosaurus SRF fuel-handling process including receiving, screening, a silo storage system, and a feeding conveyor.
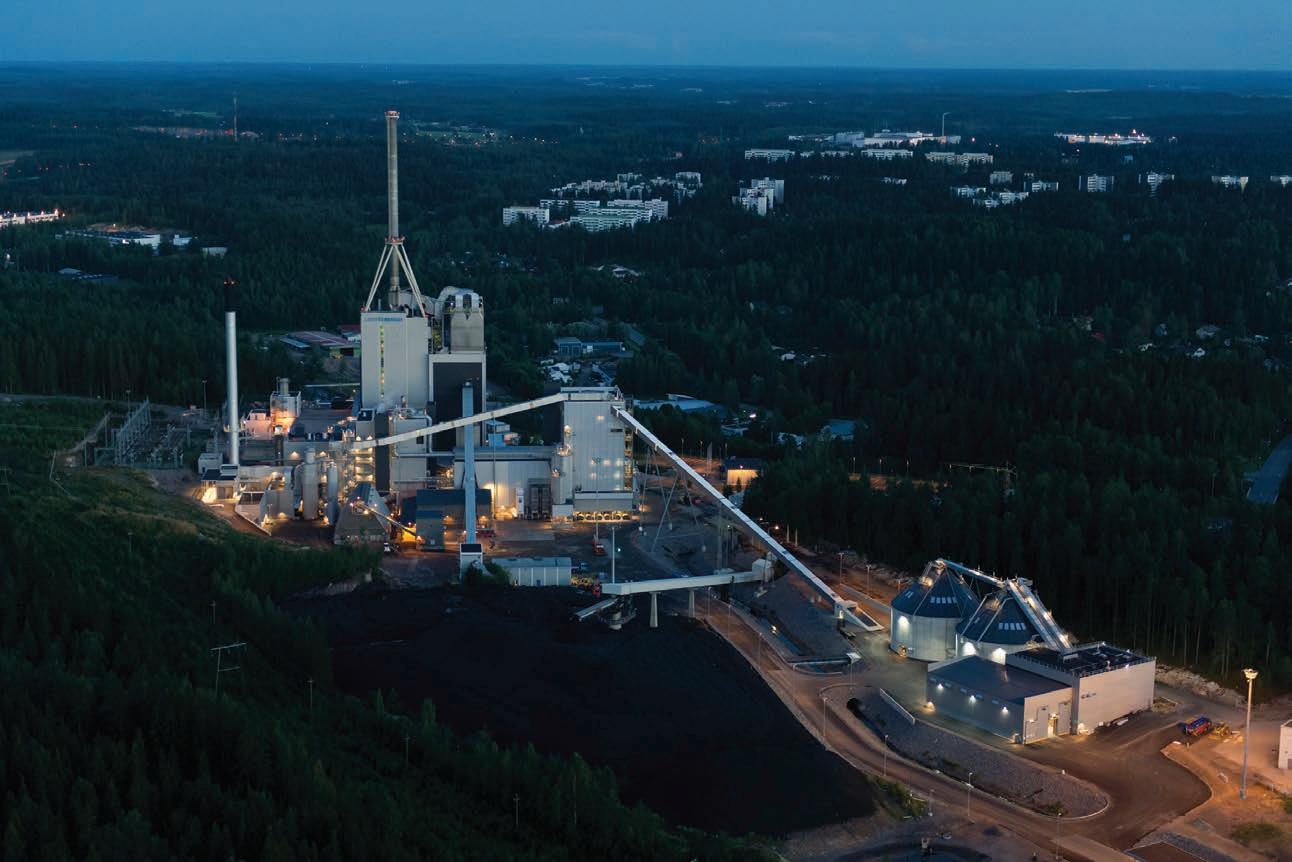
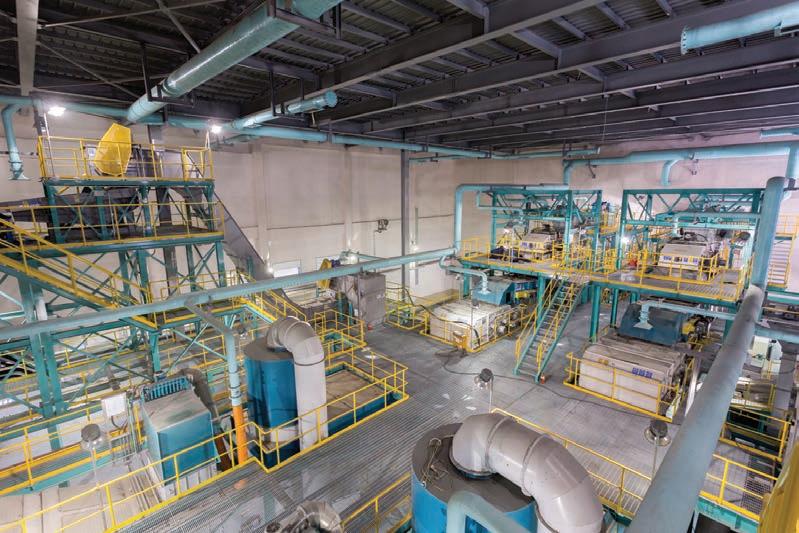
Whatever the combination of Tyrannosaurus machines, Minna says BMH Technology provides assurances that the system is always working at its“Youbest. may have one manufacturer’s feeder going into another manufacturer’s shredder into another’s magnet, and so-on,” she says. “Then if there’s a problem in the system, the customer doesn’t know who to call.
Let’s say this company wants to pivot into gasification, waste-to-chemicals, waste-to-jet fuel, waste-to-hydrogen or combustible pellets – the existing system for waste pre-treatment is already there, and it will still be required for future technologies as well. “Within a circular economy context, as the waste streams change, what is required now and what will be required in the future will change. Our technology is designed such that it can adapt to serve those needs without having to make big new investments. You can just make relatively small changes or add modules to the same processing line to incorporate new technology.”
One criticism that has been levelled at investment in energy-from-waste in Australia is that it is, at best, technology that relies on a finite and irregular supply of feedstock or, at worst, an approach that threatens to undermine progress in resource recovery and landfillMinnadiversion.explains that the modular Tyrannosaurus system is dynamic and flexible enough to counter this –especially when coupled with multifuel co-combustion CFB power plant technology. The ease with which its modular elements can be switched and replaced means a treatment plant can adapt to changes in feedstock and desired outputs with relative ease, thereby allowing for a high degree of “Forfuture-proofing.example,if there is a company that operates a power plant or a cement kiln, and they have installed a Tyrannosaurus system for making fuel.
In BMH Technology’s case, because we take responsibility for our whole process, they would just have to call one“Ournumber.lines also feature remote E&A service access, so, if necessary, our engineers can take control of the line, assess, and fix the problem remotely.”
/ WMR / 53
A Tyrannosaurus waste processing line produces RDF for POSCO Engineering & Construction’s fluidised bed boiler EfW power plant in Gwangju, South Korea.
In Australia, BMH Technology has a repeat customer in Visy Pulp & Paper, which has recently ordered a Tyrannosaurus 7703 Shredder, a Tyrannosaurus Feeder, and a Tyrannosaurus Rotating Screw Reclaimer for its paper mill at Gibson Island in Queensland. Minna says a similar Tyrannosaurus set-up has been used by one of Visy’s Melbourne sites for several years. Visy Gibson Island once had to send its mill rejects to landfill, but with the Tyrannosaurus system, the plant will be able to process it into RDF and feed it into their boiler, generating steam and electricity for the paper mill.
“It’s well proven technology,” she says. “It has been used for decades around the world, and has a reputation for high reliability and assured service.”
For more information, visit: www.bmh.fi www.wastemanagementreview.com.au
“Or, you could just add BMH’s Tyrannosaurus Rotating Screw Reclaimer silo system, which has been very popular around the world.”
of alternative feedstocks in the future as available landfill waste diminishes. Minna says one of the strengths of the Tyrannosaurus system is that it is modular and can be tailored to suit any of the varying waste streams around the“Weworld.operate in many countries, including in Asia and southern Europe, where waste streams are really demanding,” she says. “For example, in China, mixed municipal solid waste is very wet. There’s almost anything in there, but our system can handle it all. “Australian waste streams are very similar to those in Northern or Central Europe, where our technology has a proven track record. I think BMH’s solutions suit Australia very well.”
SCALABLE SOLUTIONS Minna says the company can also provide Tyrannosaurus configurations on any scale, depending on the needs of the“It’scustomer.notonly complete SRF lines,” she says. “For example, we can deliver a standalone shredder platform, which consists of a feeder, a shredder, and a discharge conveyor for moving the material further into the process.
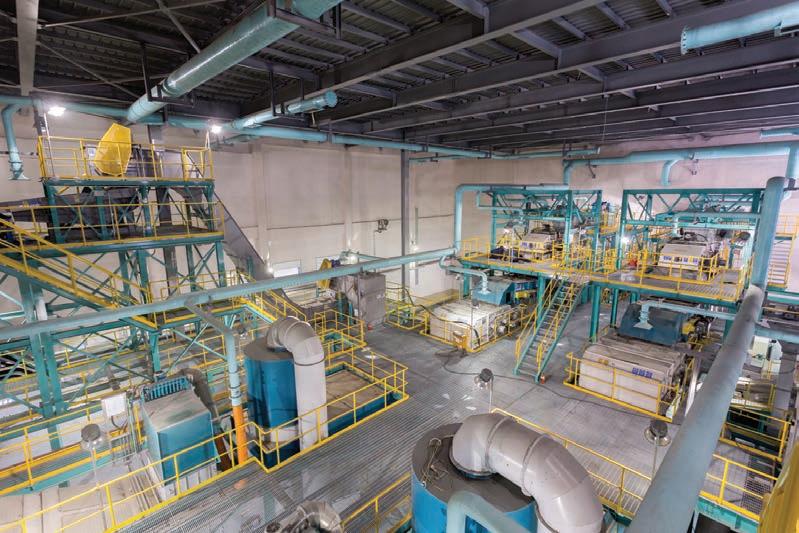
GT Recycling has achieved increased efficiences, a cleaner product and lower water consumption with the new plant.
“The plant has exceeded our expectations,” he says. “It’s significantly improved our process in several areas including will meet the company’s needs going forward.”
T Recycling Business Advisor
GT Recycling was first introduced to Aerofloat technology at a recycling and waste trade exhibition in Melbourne. Doug says Aerofloat got to know the company’s needs IN TREATMENT 2022
54 / WMR / September
Doug McLean knew that an upgraded water treatment system would help increase the company’s capacity. The flow-on effect the system has had on product quality is a welcome addition.
WASTE MANAGEMENT
A NEW CLOSED-LOOP WASH LINE IS BRINGING ADDED BENEFITS TO A GEELONG PLASTICS RECYCLER.
“We wanted the latest technology that would be reliable and meet our internal and Environment Protection Authority compliance standards,” Doug says. “But we also wanted a water quality that was suitable to be used again in our washing process rather than be disposed of as trade waste.”
ACTION – WASTEWATER
Clear water revival G
GT Recycling is a family-owned recycling company with more than 40 years’ experience in recycling passed through three generations. It processes a range of polyolefin hard and soft plastics including wheelie bins, garden pots, milk crates and PE poly pipe. Doug says the company plans to double its current capacity by the end of 2022, with a focus on recycling a range of flexible plastics affected by the export ban, which came into effect on 1 July this year. Part of the expansion was to increase the plant’s washing capacity, accommodate increased throughput capacity to allow for future growth, improved water quality and reliability.
Doug says that since the Aerofloat system (containing an AeroMBBR and AeroWAVE) was installed at the Geelong, Victoria plant, the end-product of both the flake and extruded plastic has improved.
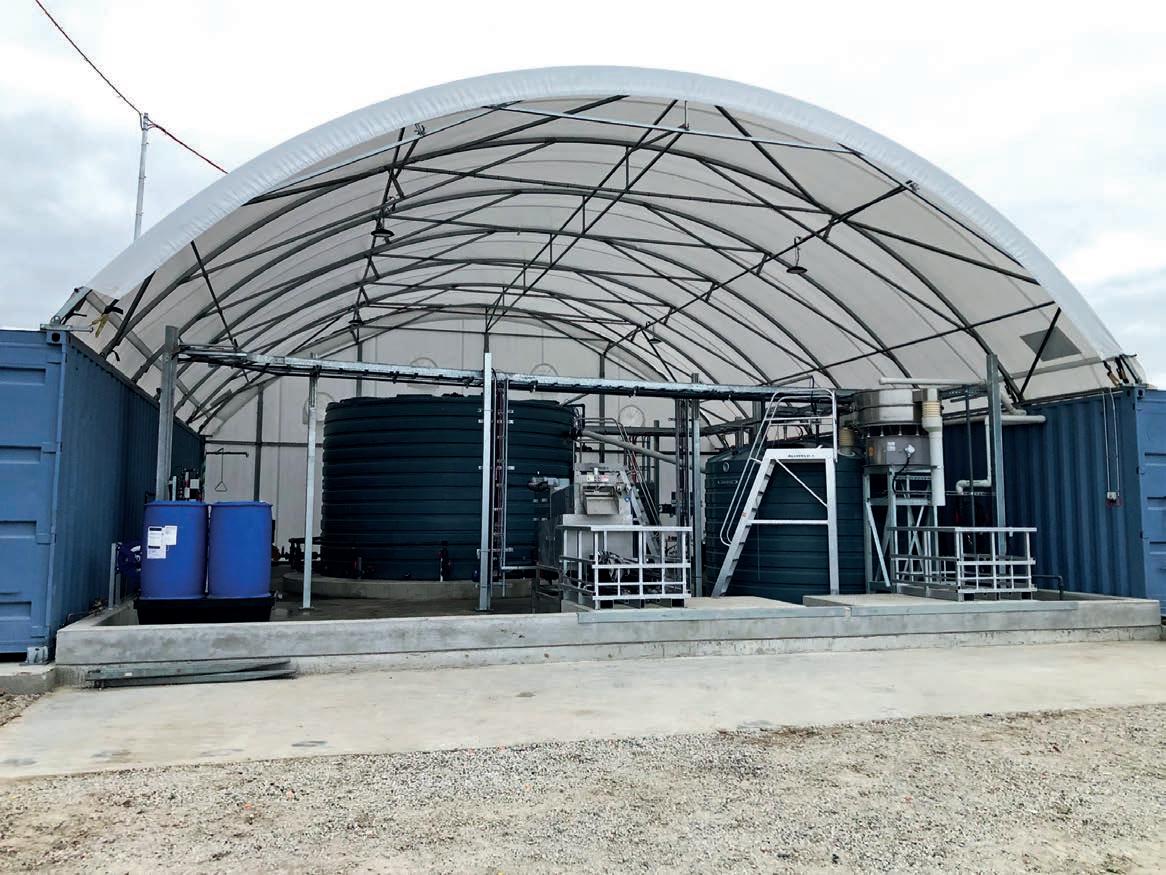
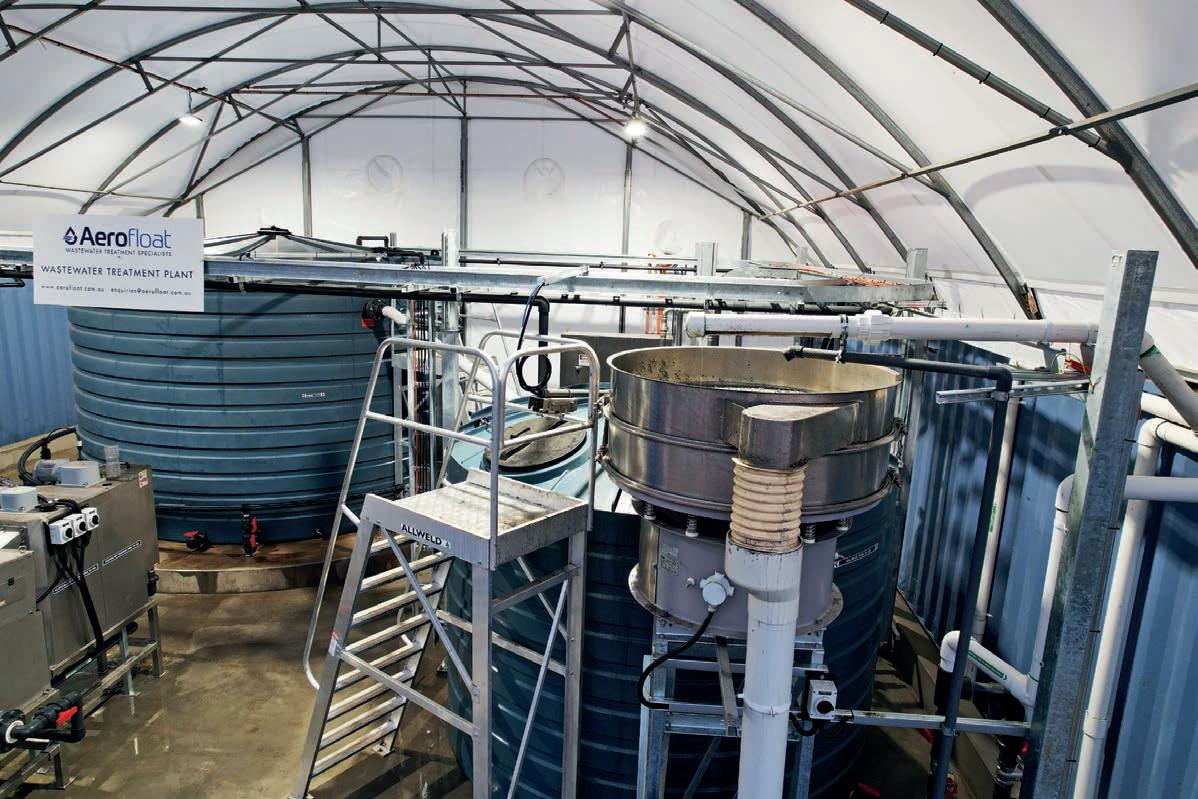
“That’s what wastewater engineering is, selecting the right product for the right application. As a business, we’re always looking to improve technology.”
technical and maintenance support.
Michael says that because cleaner water is being used all the time, there is less pressure on the extruders and “It targets a very specific need where the water quality only has to reach a certain level,” he says. “It’s quite good at handling the sludge.
A biological step has been added to scrub soluble contaminants from the water and ensure it remains odourless.
For more information, visit: www.aerofloat.com.au www.wastemanagementreview.com.au
“That’s important as we continue to strive for GeneralMichaelimprovement.”Anderson,AerofloatManager–Engineering
The GT Recycling wash plant is a closed loop. Water used is treated and then sent back to the wash line.
Michael says there is some water loss due to evaporation and part of the drying process, but far less than the previous system, which would often have to be fully drained and refilled.
and selling plastic and now they’ve got a better product to sell.
GT Recycling’s new wastewater treatment system will allow for future growth.
“Commissioning and changeover to the new system was seamless,” he says. “The project was on time and on budget.”
GT Recycling’s wastewater treatment system was prefabricated in Sydney and then built on site. The system is capable of treating double the current load. Doug praises the professionalism and knowledge of Michael and the Aerofloat team.
“Aerofloat listened, advised and designed a plant that completely met our current and future needs,” Doug“We’resays.getting lower water consumption because of the recyclability of the treated water and improved efficiencies with the wash plant and the subsequent extrusion process due to a cleaner product.
“They’re already noticing the colour of their finished product has improved. Their saleable commodity has improved; that’s something they didn’t“That’sexpect.what we sell.”
Aerofloat engineers offered advice on several suitable placement options for the plant and the final design and layout was completed in line with GT Recycling’s requirements. The plant was installed and commissioned during a three-week period in May 2022.
/ WMR / 55
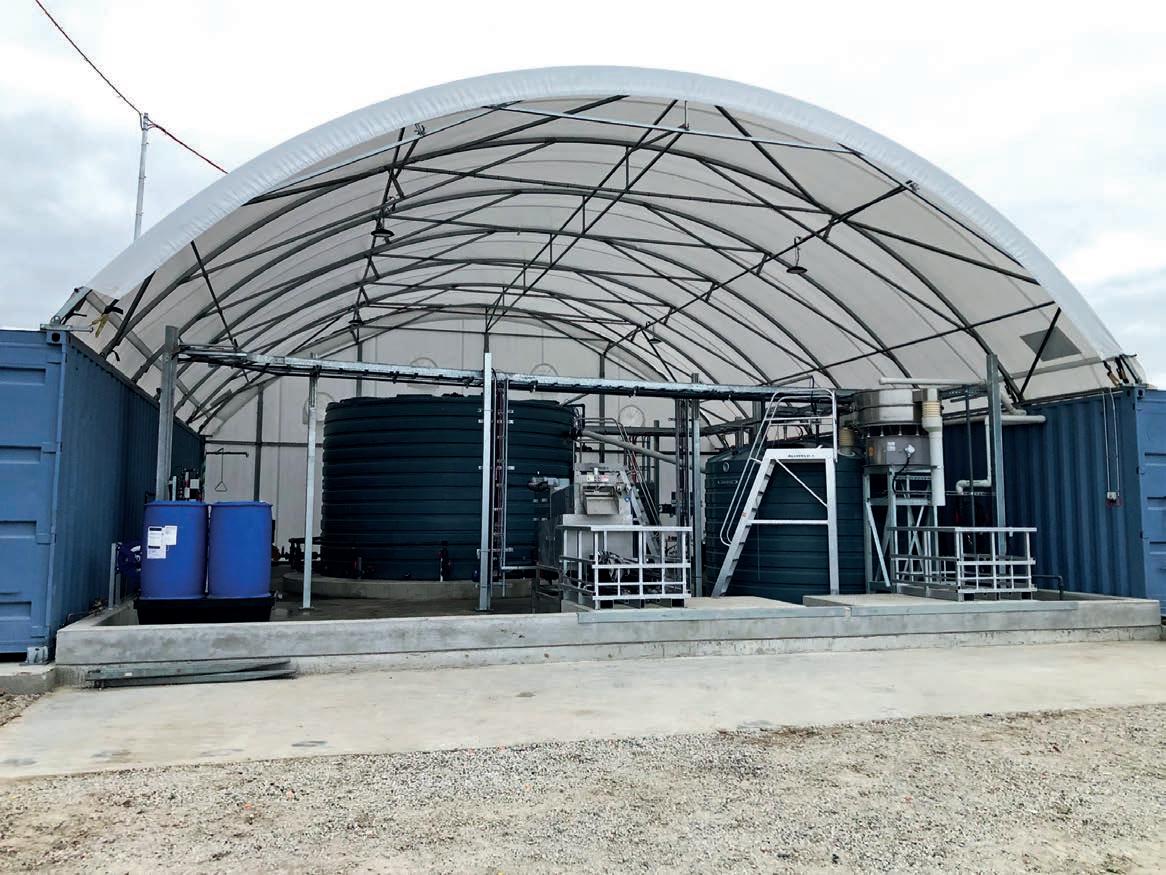
STG Global recently signed a five-year agreement with Iowa-based New Way Trucks, the largest private manufacturer of refuse equipment in North America, to be the exclusive distributor of New Way products in the Asia-Pacific region. Under the terms of the agreement, STG Global will distribute and produce New Way waste collection trucks from its Melbourne base, including the ROTO PAC, Viper, Diamondback and Mamba.RossYendle,
The ROTO PAC can manage both organics refuse collection and municipal solid waste.
STG GLOBAL IS BRINGING THE FIRST DUAL WASTE COLLECTION TRUCK DOWN UNDER.
STG Global Managing Director says the ROTO PAC is the world’s first waste collection truck that can manage both organics refuse collection and municipal solid waste, eliminating the need for local councils to maintain separate truck fleets. The truck’s self-cleaning auger can displace municipal waste, recyclables, and organic waste three times faster than traditional pack-panel designed trucks and is available in fully and semi-automated modes. The ROTO PAC is also securely sealed, ensuring no bin juice leaks or nasty smells are left behind.
ruck body specialist STG Global is bringing an Australian-first to the waste management market after inking a deal with a major United States company to supply its dual organic and solid waste processing trucks to the Australian market.
Ross says the ROTO PAC’s auger efficiently compacts organic materials, such as grass clipping and food waste, and will automatically reverse if there is a Thejam.more than 1000 kilograms of auger torque makes quick work of compaction and self-cleaning, eliminating downtime to clean out behind the packer RAM. The automated arm has a 3.6 metre reach
Ross says the ROTO PAC design is a huge step forward for local authorities seeking to eliminate waste going to landfill and introduce Food Organics Garden Organics (FOGO) collections in line with the National Waste Policy Action“ThePlan.advent of multi-purpose trucks is massive for the local waste management industry because of the efficiencies able to be achieved,” he says.“More and more local councils are looking at collecting organic waste, so the ROTO PAC is ideal, and the bonus is they won’t have to buy separate trucks because it does it all.”
Pulling
MANAGEMENT IN ACTION – TRANSPORTATION AND COLLECTION 56 / WMR / September 2022
WASTE
T
double duty

ERIEZ WORKS TOWARDS A SUSTAINABLE FUTURE ERIEZ METAL RECLAMATION IN POWER GENERATION Convert Waste to Energy ERIEZ_ Waste2EnergyAd_WMR9_22.qxp_Layout 1 8/15/22 7:12 PM Page 1
enhance your
Front-end
separation
Ross says he reached out to New Way after researching truck designs that would be more efficient for organics collection in Australia. “The Australian organics market is really coming into its own,” he says. “But I realised we didn’t really have a truck that was right for the materials.
“New Way will bring Australia to the forefront of the collection industry with a breadth of products not seen here.” A 2021 report MarketsandMarketsby predicted the international waste management market would grow to $753 billion by 2026, with the biggest growth coming from the Asia-Pacific region.
and can manage up to 226 kilograms at maximum extension.
Ross says STG Global, which last year opened its new 2000-square-metre manufacturing facility in Dandenong South, was growing strongly, hitting a key manufacturing target of 250 water, waste and commercial trucks in the 2022 financial year and is expecting to build 300-350 trucks in the 2023 financial year. “This partnership is set to accelerate our growth by expanding and opening up the Australian market to innovative technologies pioneered by New Way,” he“Theresays. is nothing else like the ROTO PAC on the market so we’re anticipating strong demand, both locally and in the Asia-Pacific region. “STG Global is very proud of the New Way partnership and the confidence shown in us by the company.”STGGlobal will first display the new trucks at the Waste Expo Australia in Melbourne from 26-27 October.
Eriez products separate ferrous and non-ferrous metals from waste.
613 8401 7400 Harvest
Don’t burn or dispose valuable commodities. Establish an efficient recycling system you can rely on and reduce waste going to landfill.
Mike McLaughlin, McLaughlin Family Companies President said New Way was proud to partner with another family-owned equipment manufacturer with decades of experience. “STG Global introducing our rugged, world-class equipment to Australia and Southeast Asia will meet the unique needs of an ever-evolving global solid waste market,” he says. For more information, visit: www.stgglobal.net lucrative by-products from your Waste to Energy process. feedstock or bottom ash recovery, Eriez state-of-the-art equipment will help you create an extra revenue stream to bottom line.
New Way Trucks is the cornerstone brand of Iowa-based McLaughlin Family Companies. Its equipment currently operates in all 50 states in the United States and its distributor network extends to Canada, Puerto Rico, Mexico, South America and the Middle East.
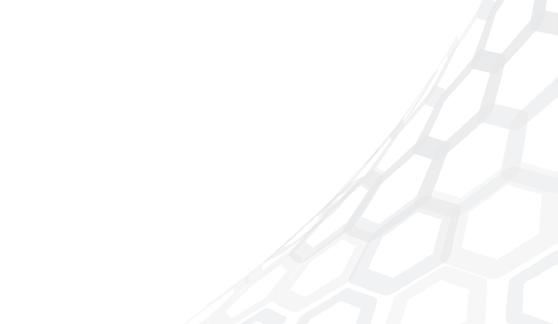
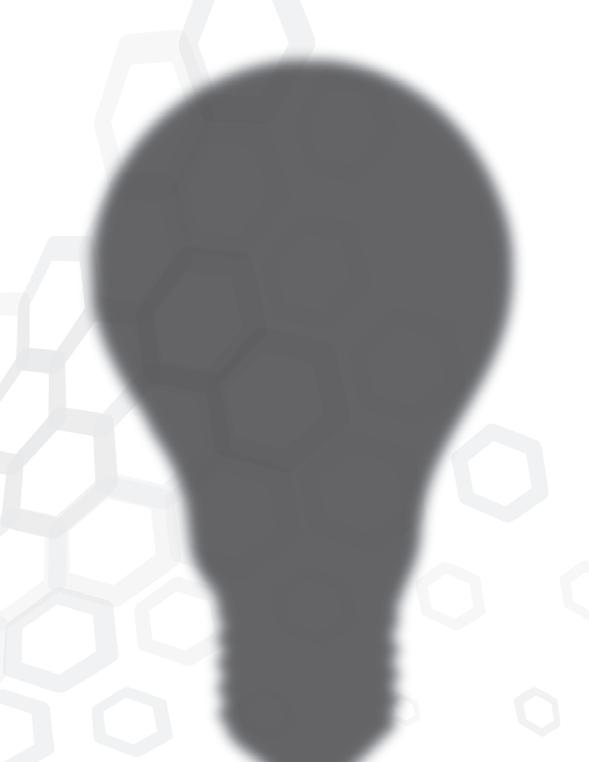



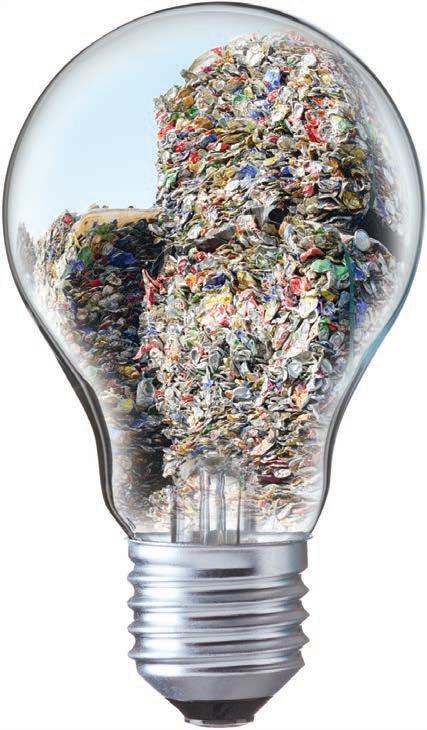
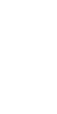
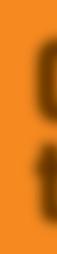
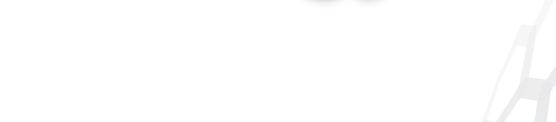
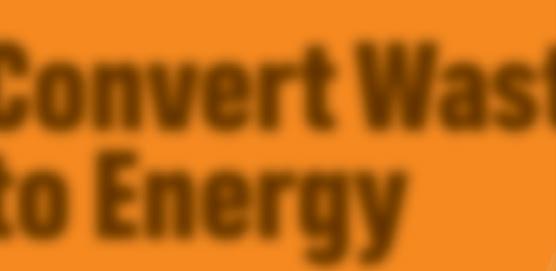
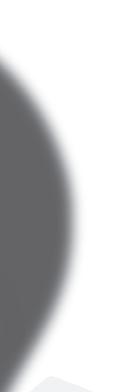
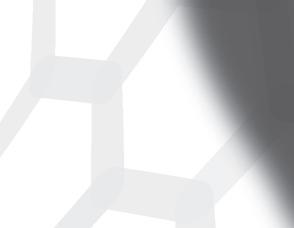
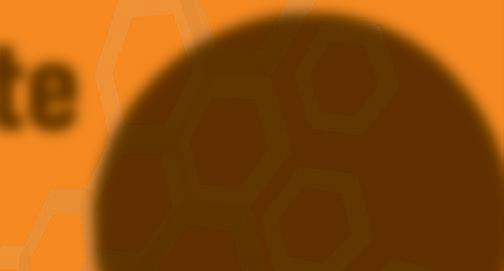

WASTE MANAGEMENT IN ACTION – BATTERY RECYCLING 58 / WMR / September 2022
ECOCYCLE IS PREPARING FOR THE DAYS WHEN ELECTRIC VEHICLES RULE THE ROADS.
Andrew launched the ACT Government’s 2022-2030 Zero Emissions Vehicles (ZEV) Strategy, in July, setting out an ambitious plan to phase out vehicles with light internal combustion engines by 2035. The plan ensures the ACT network can keep up with the increased demand for electric vehicles – at the time of the launch there were more than 2000 EV cars registered in theMostterritory.private vehicle manufacturers have plans to deliver more EVs over Doug Rowe, Director of Ecocycle and Recycal, has seen the rapid transition to electric vehicles overseas and is on the front foot to ensure Australia has the capacity for a circular economy for the batteries that power them. “EV batteries are here already in smaller numbers,” Doug says. “And while it is some way before we see these EV batteries coming in for endof-life recycling, the numbers will be growing each year.” Doug says there will be some EV batteries that are damaged, some that fail, are faulty and need replacing, and many that will have a second life after their useful period as an EV battery. electric vehicle service. Doug’s drawing on techniques from his past to ensure the batteries stay in circulation. “EV batteries are so new. Five years ago, if one failed it was just replaced,” Doug says. “But now we can pull it apart, replace the damaged cell with a new one and the battery is back to full life again. For others, you might not be able to use it in a car again, but they can have a useful second life in power storage.” The damaged or faulty cells will be recycled, and the metals recovered for furtherDougrefining.saysrecycling EV batteries will be a growing part of the business, but he doesn’t expect to see any viable
In the driver’s seat Zero emissions vehicles are the way of the future, according to Andrew Barr, Chief Minister for the Australian Capital Territory.
Ecocycle has invested heavily in the latest technologies for all battery recycling.
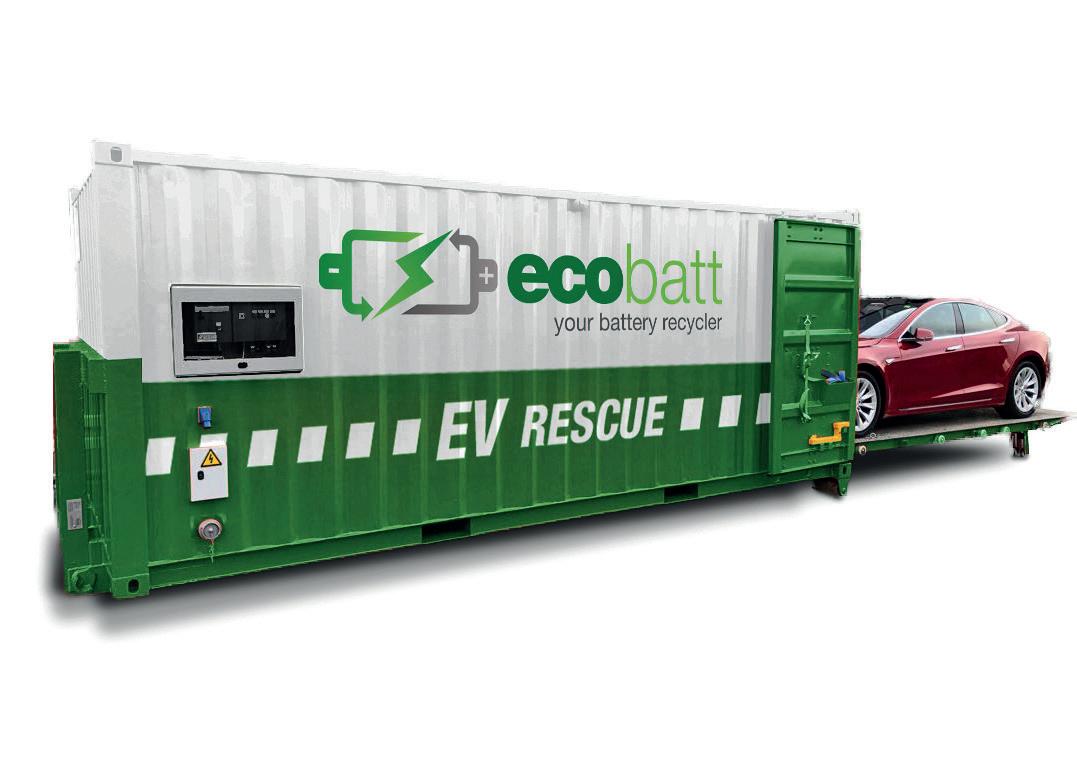
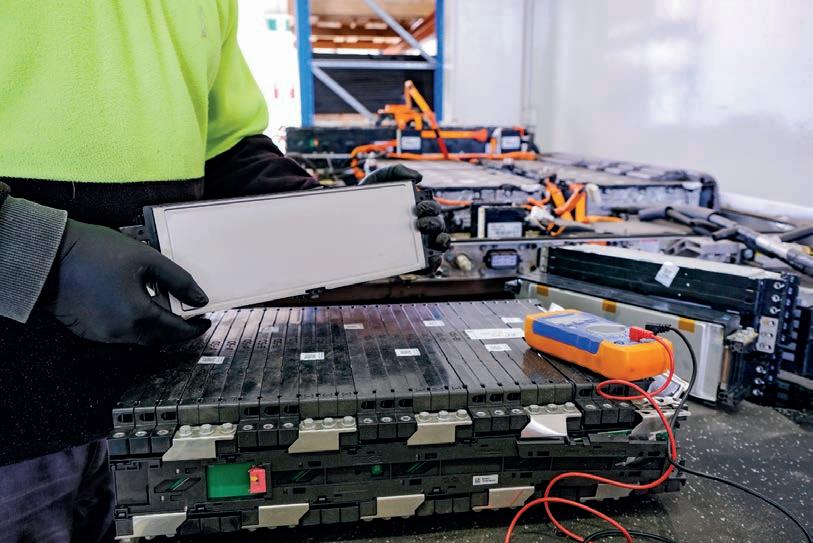
“The range of places they could work in are vast,” Doug says. “Where we can, we’ll aim to repair or refurbish any damaged or faulty EV batteries, then look to areas for re-use when that life cycle comes around. At the end of the recycling chain, we and the smaller storage batteries now being installed as part of household solar“Thesystems.industry is moving quickly,” he says. “There’s new technologies, new chemistries, and a much better understanding of what needs to have given us the room to carry out this work. Overhead lifting equipment is currently being installed to allow a more automated, smooth and freeflowingSafetyworkplace.”isafocusat Ecocycle. Doug has invested in specialised containers and a range of options for transporting batteries including trucks and vans with Fire Pro aerosol suppression that are recognised by the Environment Protection Authority. All drivers are registered to handle dangerous goods. “Battery collection and recycling can all be done right, safely and successfully,” Doug says. “But we all need to work together to ensure things are handled correctly. If we do that, we can reduce the risks and manage the challenges in a professional and responsible manner.”
For more information, visit: www.ecobatt.net www.wastemanagementreview.com.au Ecocycle will repair and refurbish newly failed EV batteries for reuse in electric vehicles. Damaged or faulty cells will be recycled and the metals recovered.
/ WMR / 59
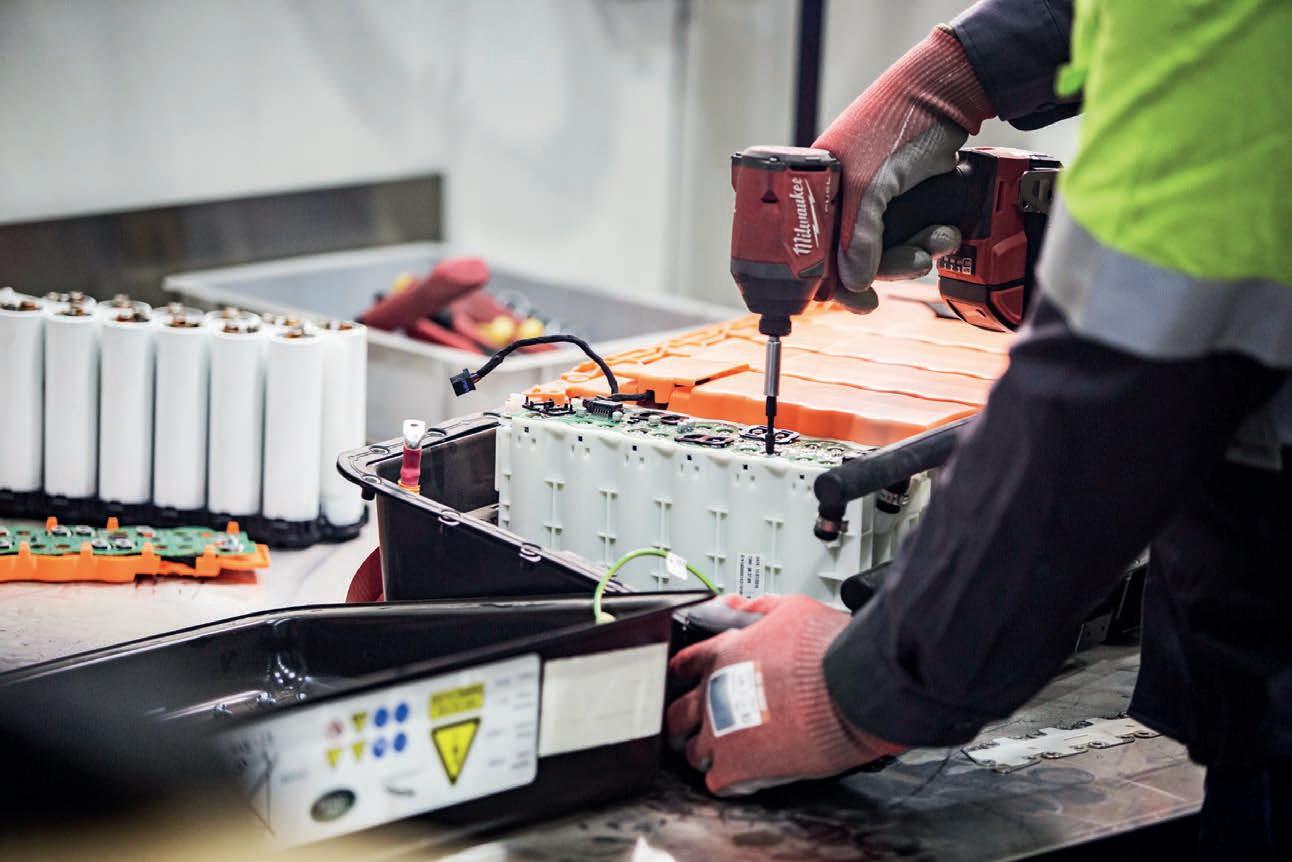
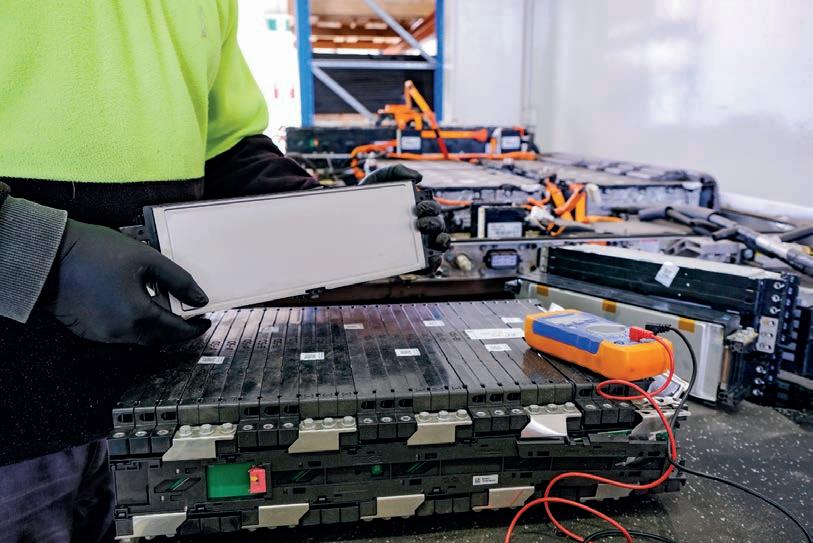
A heavy-duty lifting winch was installed to complete general lifting tasks and Liebherr’s TR 25 Compact Tiltrotator was fitted to assist in the handling of stop logs. The stop log lifter attachment was engineered locally to complement the machine.
MATERIAL HANDLERS 60 / WMR / September 2022
The LH 22 C Industry material handler was purpose-built.
Several weeks after delivery and the LH 22 C Industry is being put to order
ACTION
Robbie Bonner, SA Water Coordinator for locks four, five and six, says there is no such thing as an off-theshelf machine for the work the LH 22 C Industry was built to carry out.
WASTE IN –
MANAGEMENT
T
he waste sector has changed over the past few years with many companies turning their focus to specialised operations. Machine manufacturers have had to adapt with the changing sector, developing machine and equipment options that can handle a variety of Cameronapplications.Tanner, Liebherr Area Sales Manager for South Australia and the Northern Territory, says there are many challenges working in the waste industry, but Liebherr is well-placed to meet“Thethem.new generation of Liebherr material handlers are adept to a wide range of tasks, from feeding a crusher, loading and unloading trucks and containers, sorting materials waste products and stockpiling materials of any kind,” he says.
“Our engineers enjoy designing custom projects because they have to come up with something unique.”
Cameron says one of the main requirements was the need to counterbalance the machine so that it had a high lift capacity, of about five tonnes, while being under 26 tonnes in weight.
Robbie says his team worked with Liebherr through the entire process, ensuring the design was based on operator requirements and input.
He says Liebherr’s engineers in Germany delivered exactly what was specified. “Liebherr has previously designed another purpose-built machine for us so they’d already proven they can build something that’s fit for purpose.”
One of Liebherr’s most recent custom projects was a material handler for SA Water, South Australia’s provider of water and sewerage services for about 1.6 million people.
Liebherr and SA Water worked in collaboration to design and manufacture a purpose-built material handler, the LH 22 C Industry, to carry out river operations on the Goolwa Barrage.
LIEBHERR’S ENGINEERS THRIVE ON THE CHALLENGE OF PROVIDING MACHINES AND EQUIPMENT FOR ANY APPLICATION. Made
The machine consists of a Liebherr LH 22 upper carriage with a fixed cab rise, 5.3-metre angled boom and a 3.05-metre stick. The rail undercarriage was manufactured to fit on the unique 3.3-metre rail tracks.
“Because Liebherr manufactures a majority of parts in-house, machines can be tailor-made for customer requirements.
“It was a very custom project,” Cameron says. “Everything on that machine was unique to the application. Quite a bit of engineering went into it.”

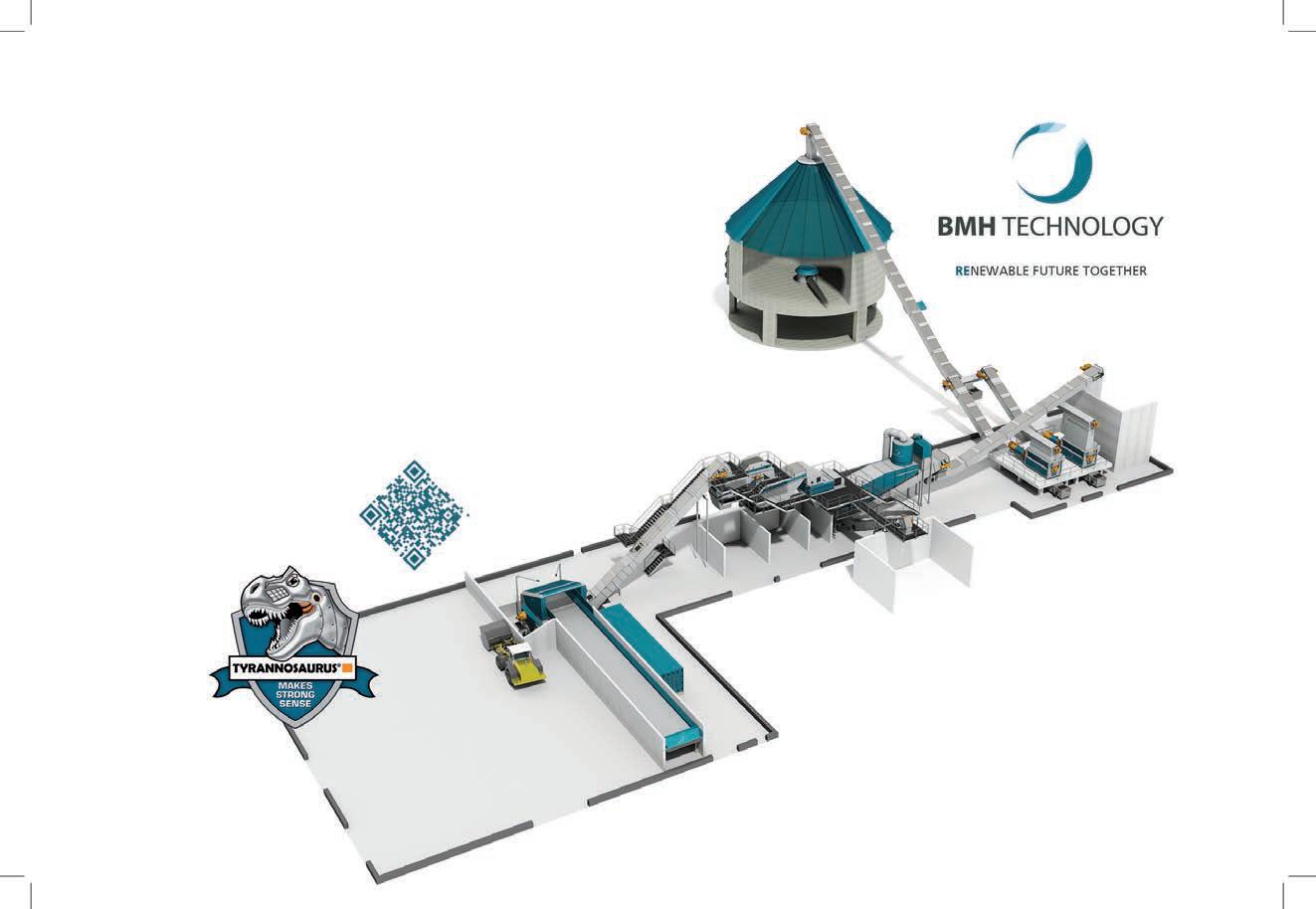
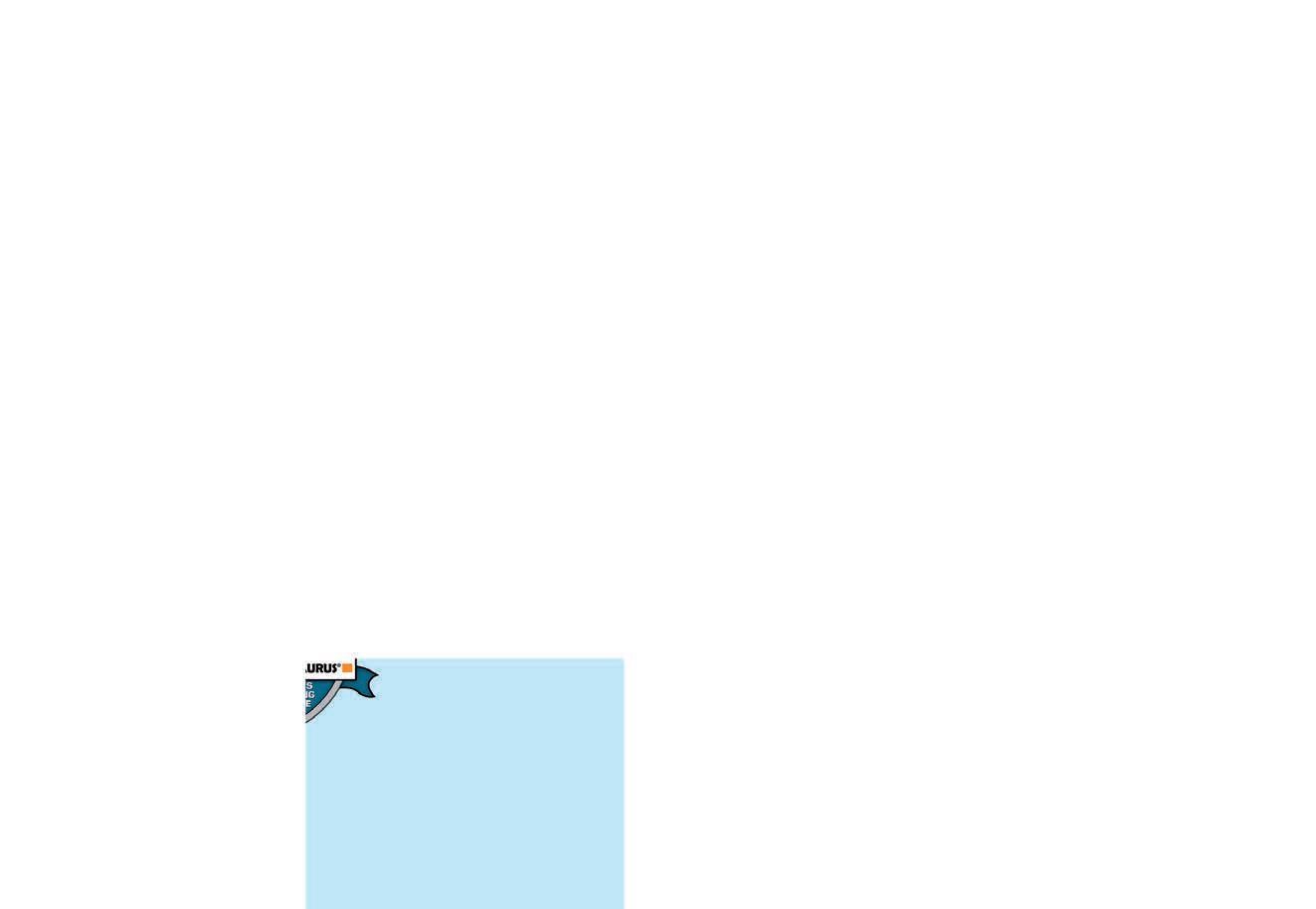
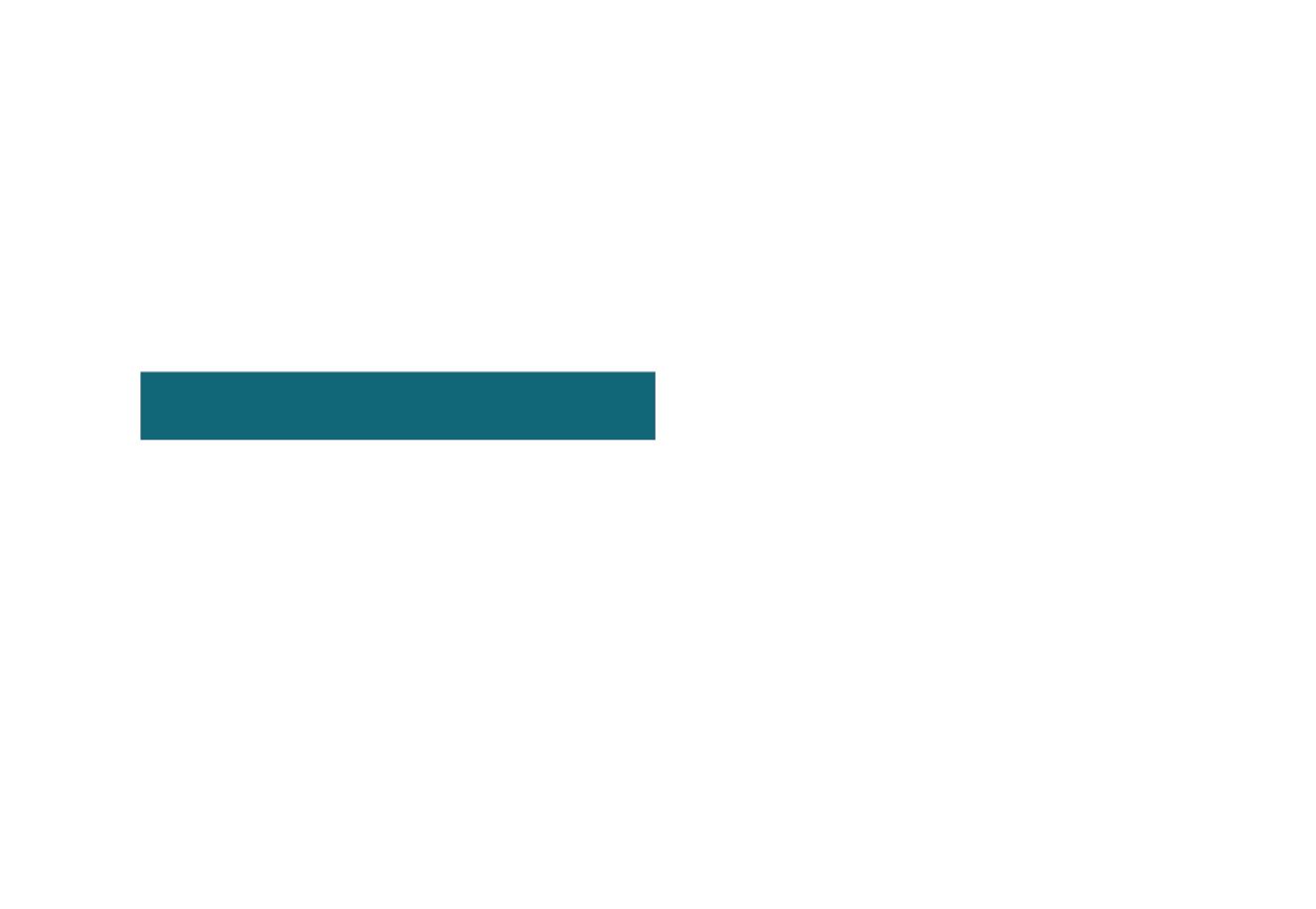
The Liebherr LH 22 C Industry.
Liebherr material handlers have high load capacities and long reach thanks to optimised kinematic properties and robust construction, allowing for greater handling performance. A quick coupling system and wide range of attachments, made by Liebherr, ensure they can be used for a variety of applications.
through its paces. Robbie says Liebherr staff have been on hand to ensure a smooth“Theirtransition.teamofpeople were on site to make sure everything went according to plan,” he says. “The machine has gone through all the testing very well with our focus on making sure it meets our requirements for safety, operation and capability. Liebherr has achieved what we asked Cameronfor.”says
The latest engine technology with intelligent machine control means the machines are fuel efficient – on average, a Liebherr LH 22 C Industry requires 9.03 litres per operating hour. Optimal engine output and high pump flow allow for fast work cycles, while cleverly designed maintenance access points guarantee minimum machine downtime. Air filters with dust extraction, reversible fans or coarse matrix radiators, have been developed for machines that are required to work in areas heavily contaminated withUndercarriagedust. options are available including one with a dozer blade to further increase machine versatility. For more information, visit: www.liebherr.com.au

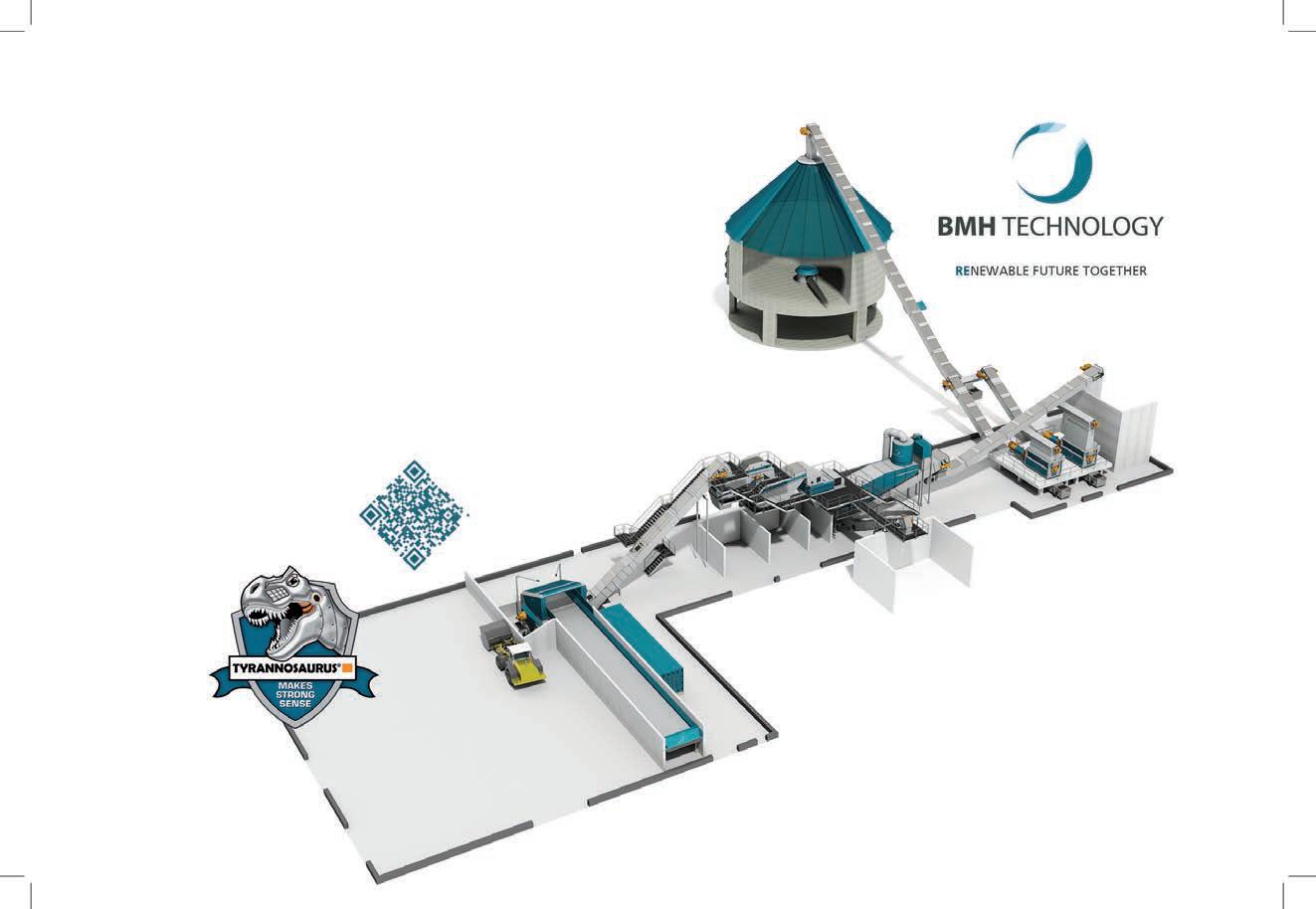
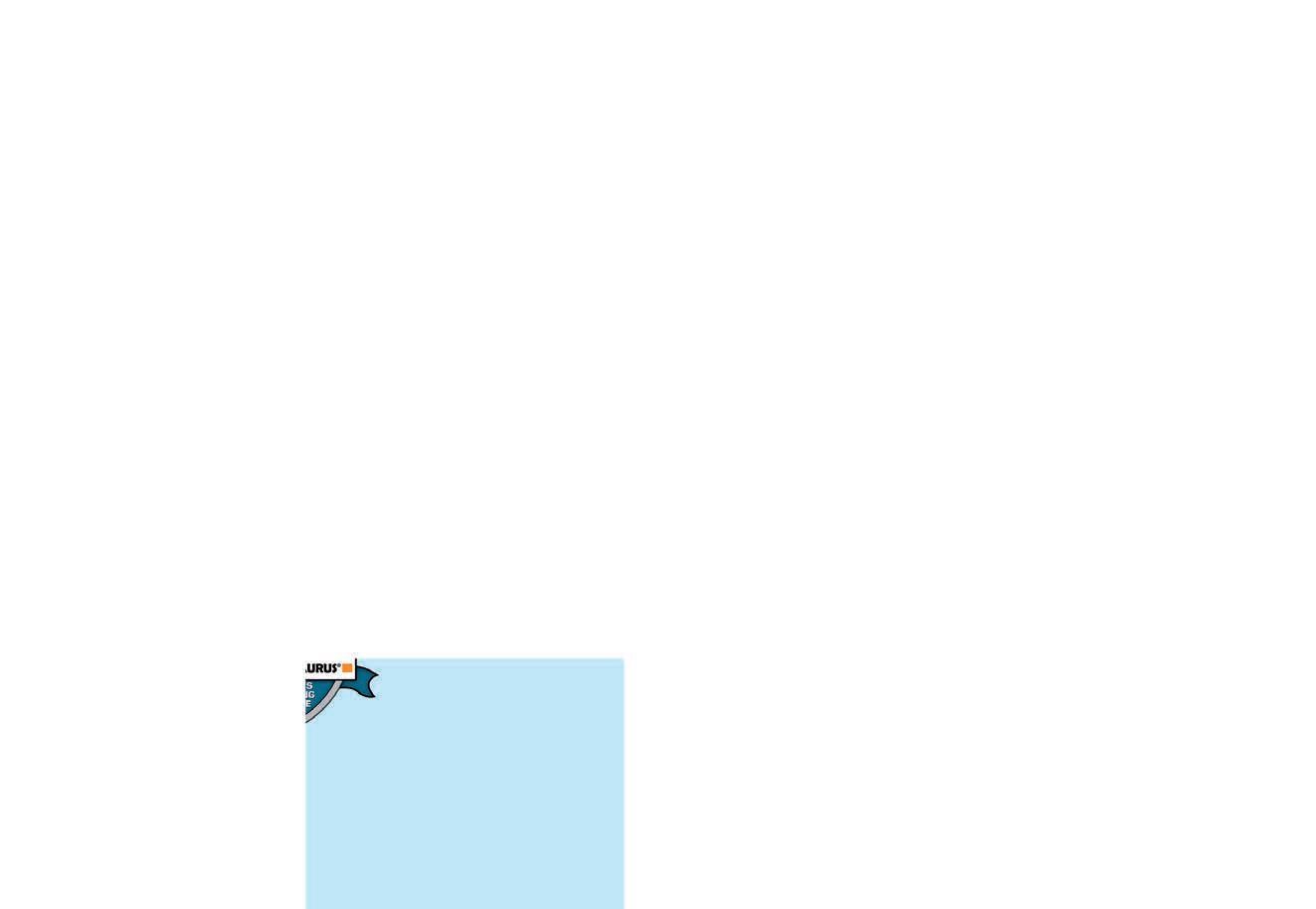
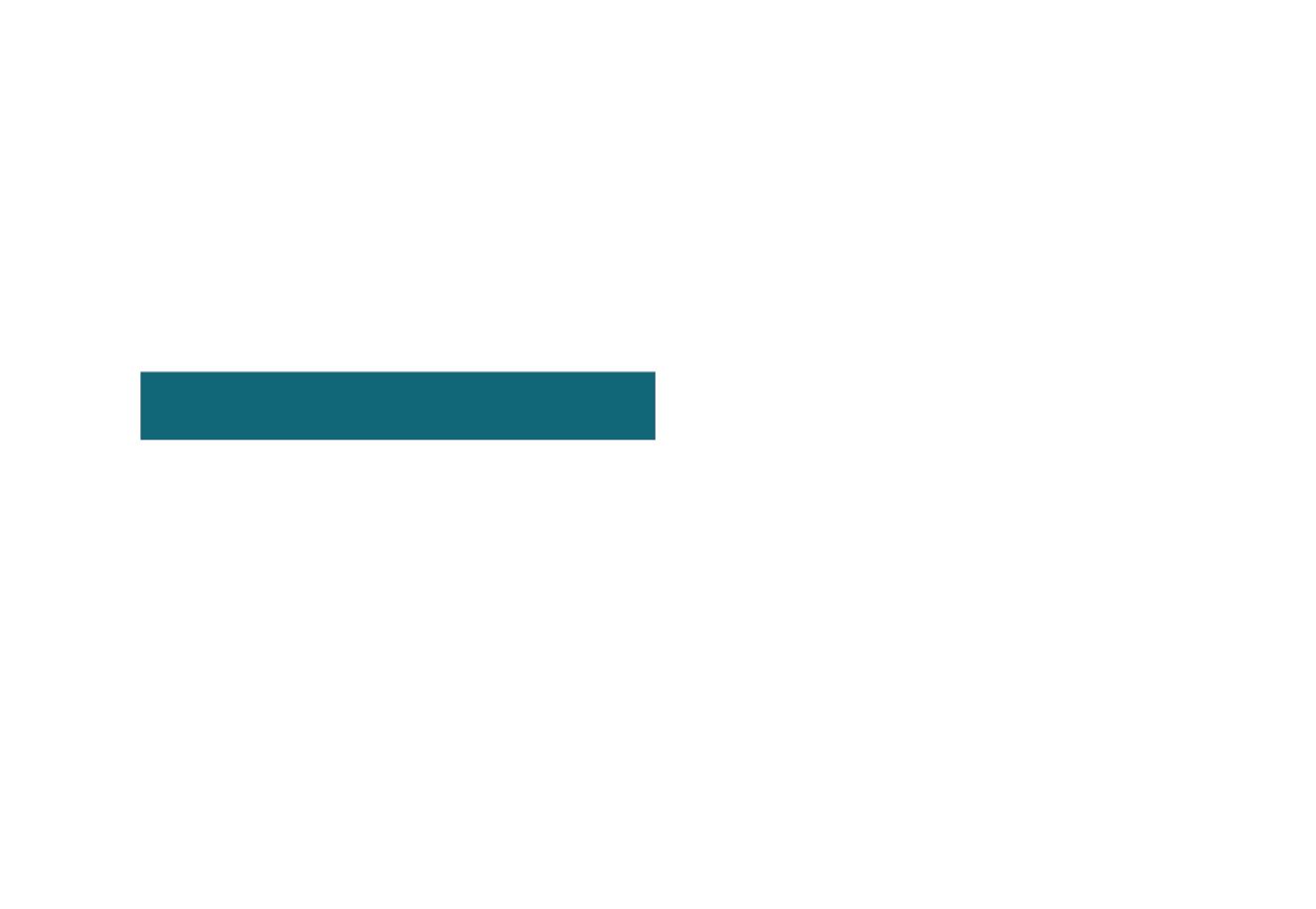
EnviroChoice Industries has specialised equipment for a range of industrial services.
W
WHEN IT COMES TO LIQUID WASTE DISPOSAL AND CLEAN-UP, ENVIROCHOICE INDUSTRIES IS THE RIGHT CHOICE
The right choice
General Manager of EnviroChoice Industries has always used the guiding principles of safety and minimising environmental impact since starting the company 15 years ago. What began as a pressure cleaning business has evolved to offer a wide range of industrial services including non-destructive digging (NDD), dry vac truck services, pressure clean and capture and road asset maintenance services. With a wide range of skilled hand the ECI team can provide custom solutions for their client’s specific needs.
The ECI team takes particular pride in delivering every job above expectations, which involves not only completing the job, but managing the waste in accordance to strict Environment Protection Authority regulations. This provides comfort to the clients knowing their project, reputation and environment are in 2022
WASTE MANAGEMENT IN ACTION – LIQUID WASTE 62 / WMR / September
hen an emergency liquid waste spill cleanup is required, a quick response time with environmentally responsible handling and disposal of waste can be the difference between a disruption and a disaster. Whether it’s an immediate on site emergency response after a liquid waste spill or providing road asset maintenance, the core focus for EnviroChoice Industries (ECI) is to protect the environment.
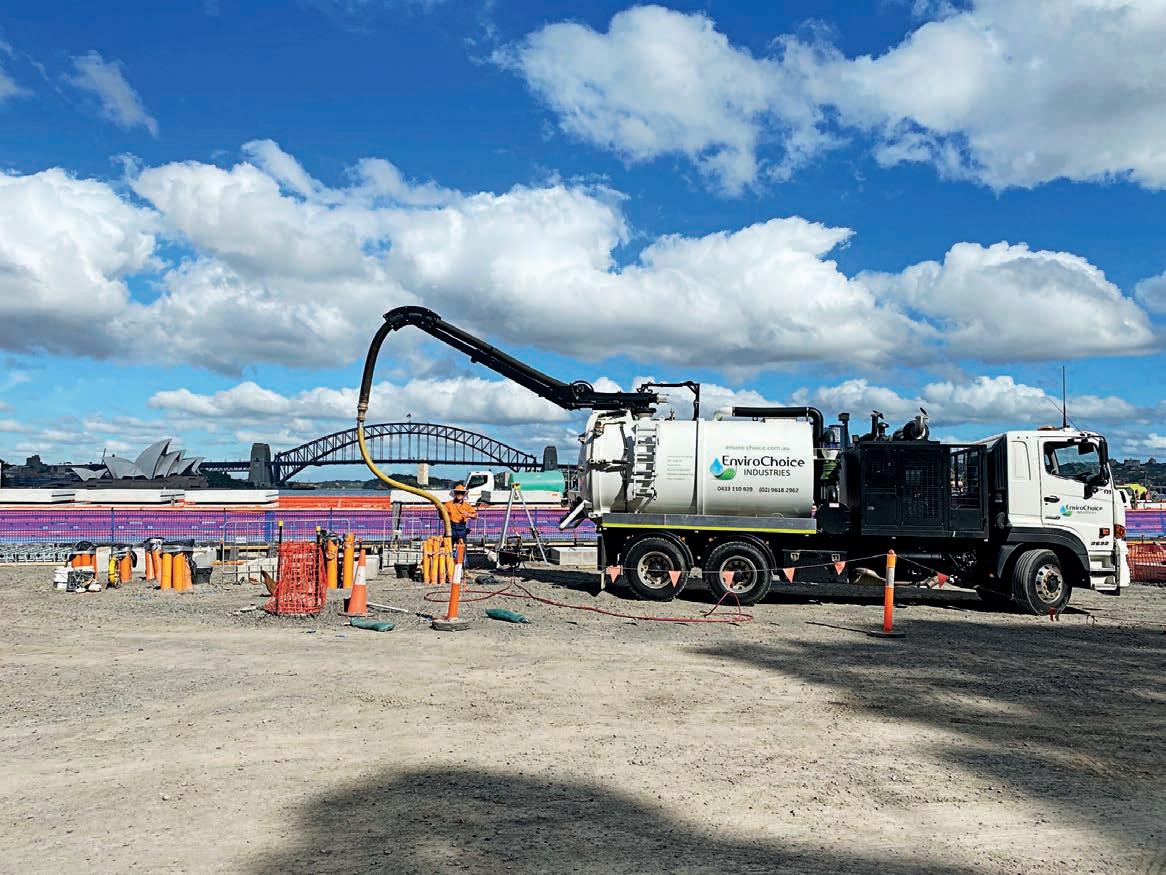
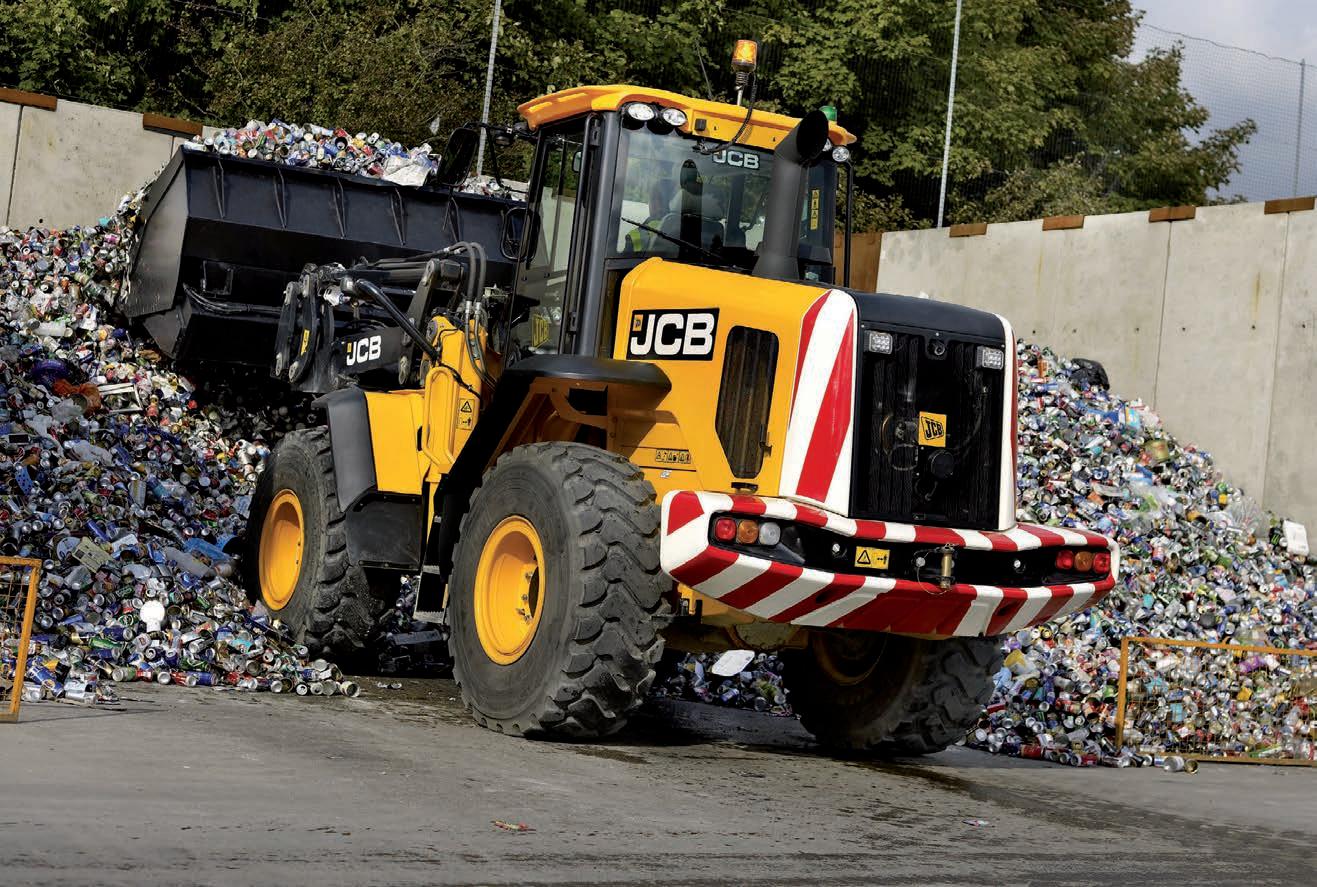
For more information, www.enviro-choice.com.auvisit:
The
JCB range of wheel loaders are built to be strong, reliable and provide comfort for long days in the cab. Designed for ultimate productivity, and offering superb performance the JCB wheel loader range features best-in-class comfort, visibility, safety ergonomics and superior serviceability plus a whole lot more.
RELIABLEPROVEN PRODUCTIVEAND
JCB WHEEL LOADERS 1300 522 232 jcbcea.com.au
The merger between EnviroChoice and Cleanway Group in August 2021 is delivering a broad range of waste solutions for customers across a diverse spectrum of industries. Cleanway Group has managed and disposed of industrial waste since 1996, offering a variety of services including tailored waste management, chemical and hazardous waste disposal, contaminated soil disposal and a 24/7 emergency spill responseMarcusservice.saysthe merger creates further learning opportunities and career pathways for the team at EnviroChoice Industries, leveraging the expertise and systems in place at Cleanway Group. “We pride ourselves on delivering quality outcomes, safely and efficiently, while providing value to customers,” he says. “This, combined with a workforce that is happy and engaged, has been our formula for growth. By continuing this, creating better systems and opportunities for our staff, we intend to continue this growth into the future.”
Most of the tasks undertaken involve managing the waste produced from non-destructive digging through to graffiti removal and industrial clean-up. It is a core responsibility to get the waste to the appropriate facility for treatment or re-use. “It’s all part of managing waste properly,” Marcus says. “Businesses are now more aware of their responsibilities and doing thingsWhileproperly.”technology in the industry hasn’t changed much over the years, the variety of applications for high pressure water and vacuums has, according to Marcus. NDD is used to safely dig around underground utilities such as gas connections, electricity and fibre optics. Highpressure water breaks up the dirt, which is vacuumed into a truck.
A spill clean-up team offers a quick and environmentally responsible response for handling and disposal ofEvenwaste.the company’s road asset jobs have a recovery aspect to them. When tunnels are washed to remove diesel dust and pollution, the water used is taken to an appropriate processing facility for separation. “We’re not just digging or cleaning, we’re recovering,” Marcus says.
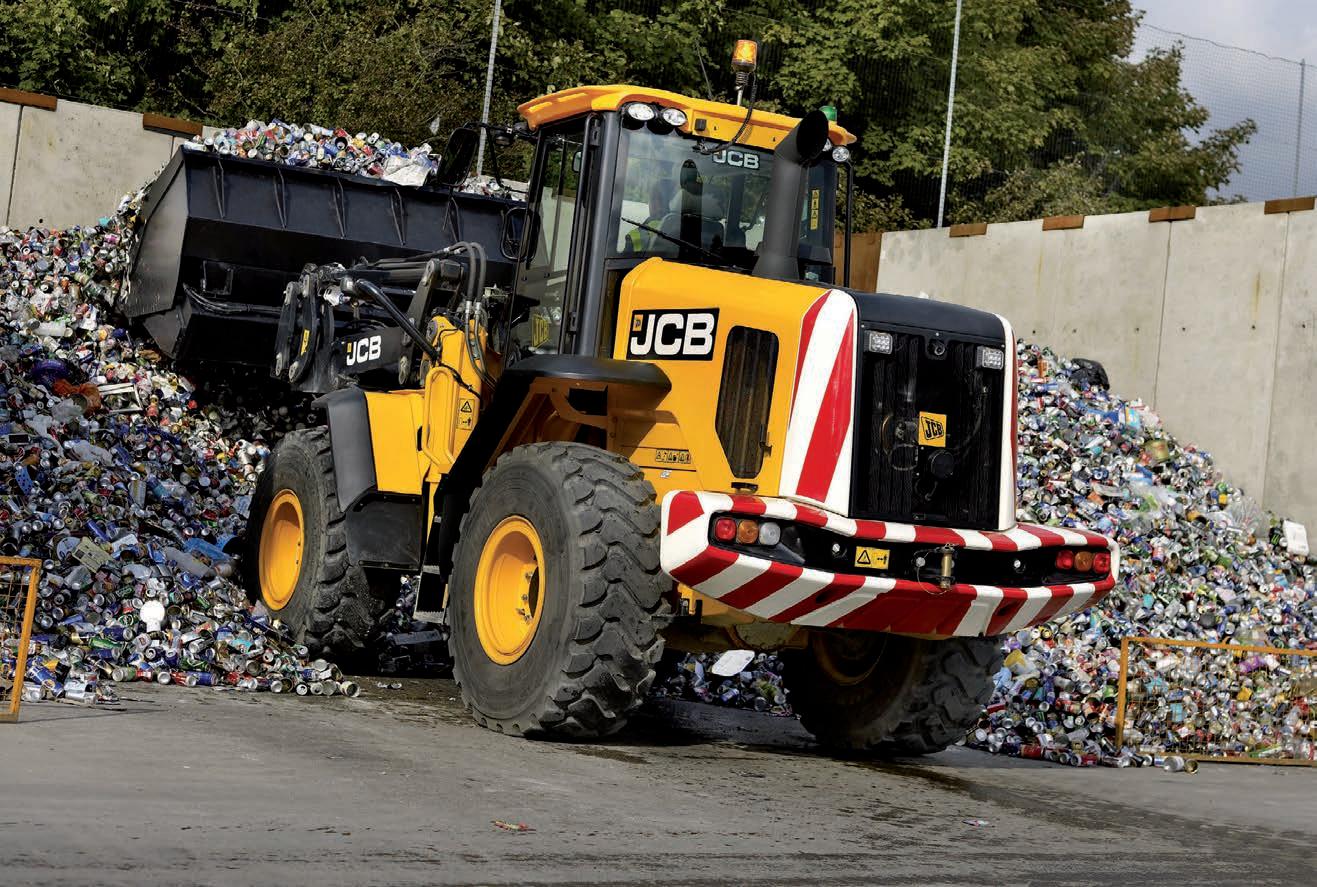

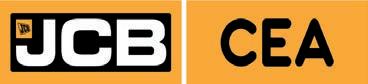
“The Buttonderry compactor is due for replacement soon so we will be updating that machine this financial year,” Andrew says.
Central Coast Council’s compactors are fitted with machine guidance systems.
Operating two of the largest waste facilities in the region requires the team to be continually focused on maximising“Procuringefficiency.gradecontrol technology was seen as an integral step to increasing efficiency and successfully delivering on our business plans,” Andrew says.
A guiding hand
“We went to market with our criteria of performance requirements for a new landfill compactor incorporating a machine guidance system and the
WASTE MANAGEMENT IN ACTION – MACHINE GUIDANCE
Andrew Pearce is the Unit Manager for Waste and Resource Recovery at the council, responsible for all active and closed waste facilities as well as waste collections
As New South Wales’ second largest council by population, Central Coast Council supports some 333,000 residents with more than 14.5 million domestic, commercial, and public waste collections per annum. The council operates two active waste management facilities that include both landfill and resource recovery activities at Woy Woy, south of Gosford and Buttonderry, between Gosford and Newcastle.
“We have a multi-disciplinary workforce and rotate our staff to operate different plant, including traxcavators, material handlers, loaders, excavators, and the compactors,” he says. “It adds some variety to their work, which they enjoy.”
“Combined,services.thefacilities receive approximately 450,000 tonnes of waste and resources per year, of which approximately 230,000 tonnes goes to landfill,” Andrew says. “This makes both sites regionally significant given the amount of waste they process.
The council installed machine guidance in conjunction with the procurement of new compactors: first in Buttonderry in 2016 and more recently at the Woy Woy site in 2020.
CENTRAL COAST COUNCIL IS MAXIMISING EFFICIENCY AT TWO WASTE MANAGEMENT FACILITIES WITH THE HELP OF MACHINE GUIDANCE SYSTEMS ON ITS LANDFILL COMPACTORS.
64 / WMR / September 2022
In choosing the right system to meet council’s requirements, he says that the solution was recommended through the Tana distributor, GCM.
The domestic waste collection trucks alone travel the distance equivalent to two round trips to the moon and back eachBothyear.”waste facilities have a Tana 52-tonne compactor fitted with Carlson Landfill Grade machine guidance, supplied by Australian distributor PositionAndrewPartners.saysthat there are 12 operators trained in the use of the machine guidance system.
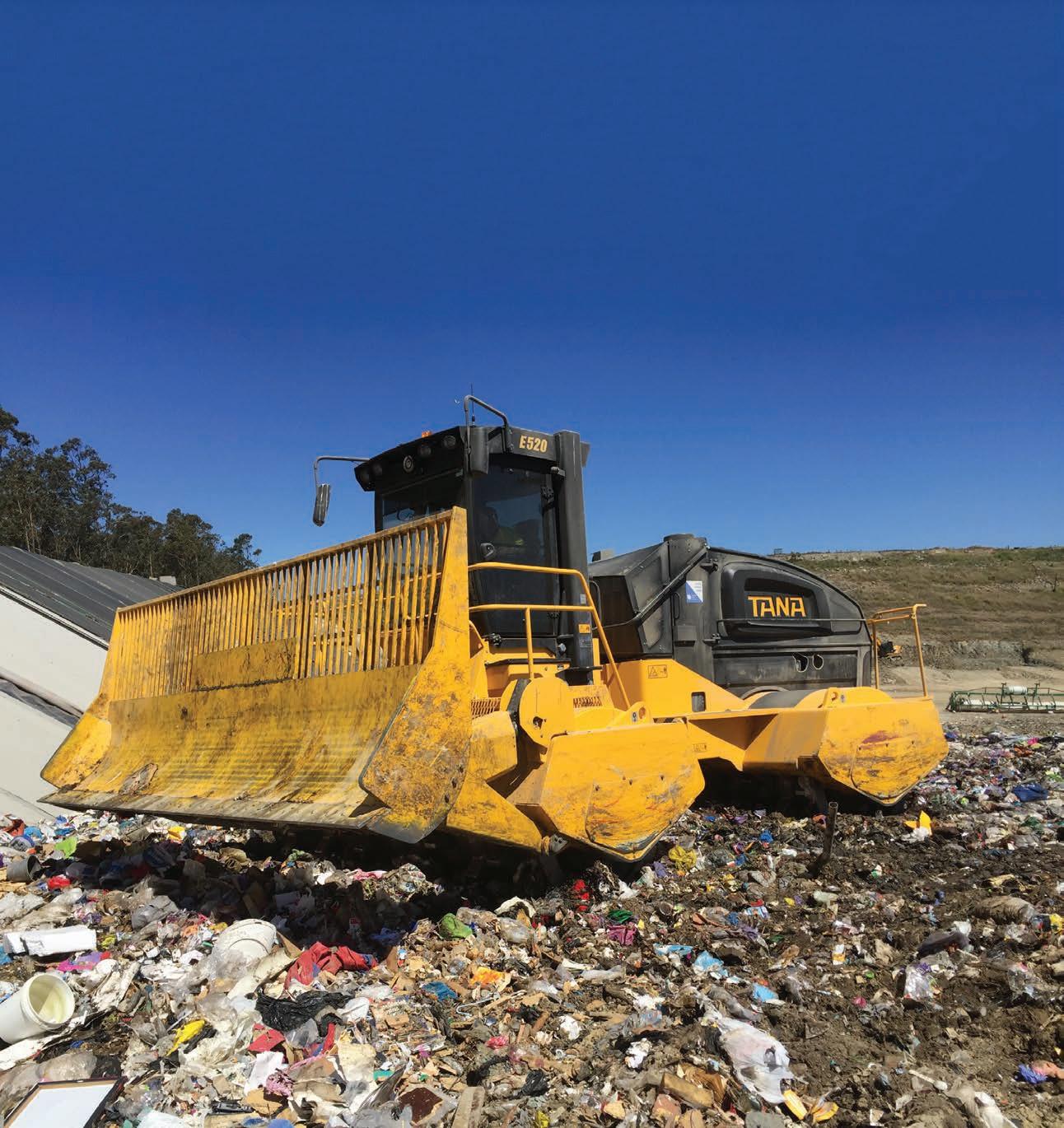
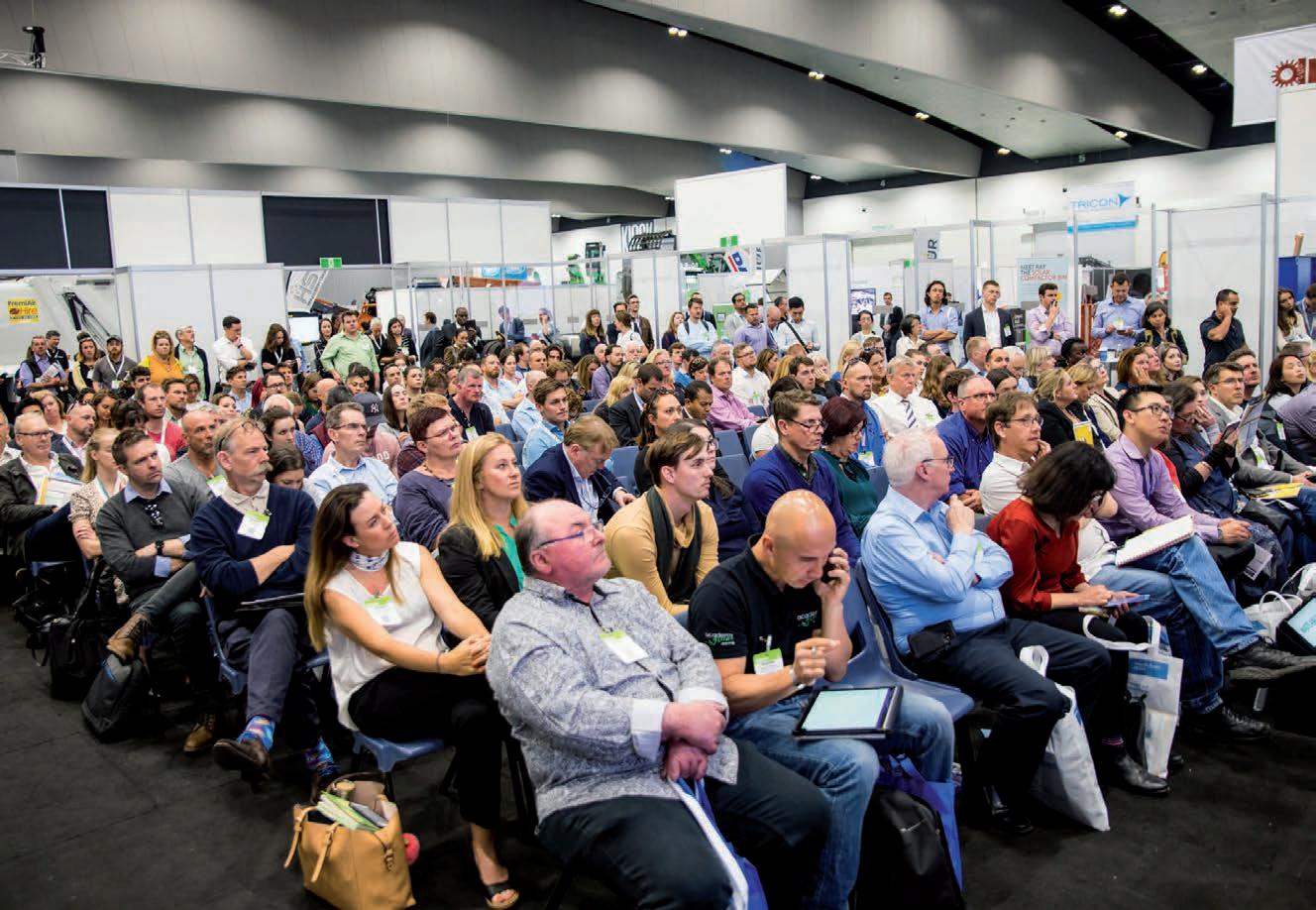
The grade control system also records and assists the operator’s work, helping to prevent overfill and accurately record the placement of material, as well as optimising efficiency in the use of the machines to reap the environmental and economic benefits of reduced fuel consumption. Andrew says these benefits assist the council in meeting legislative requirements, including a minimum compaction rate of 85 per cent, or 850 kilograms per cubic metre. “From a management perspective, the technology certainly assists us in improving efficiency and productivity,” he“Importantly,says. our landfill spaces are finite, so we have a responsibility to use that space as effectively as possible. The Carlson system from Position Partners helps us pack as much material as we can into every cubic metre.”
For more information, www.positionpartners.com.auvisit:
The grade control systems help boost efficiency and productivity. Registration is Now Open Face-to-face with over 6,200+ focused buyers Waste Expo Australia 2019 at a glance 6,200+* *Attendees CAB audited figure 100+ Local Internationaland Brands 60+ ExpertsIndustry 4+ StagesConference 26-27 October 2022 MCEC, wasteexpoaustralia.com.auMelbourne #WasteExpoAU ExpoFree-to-attend&Conference
Carlson solution best met those criteria, being specifically designed for landfill,” heAndrewsays. says a range of key benefits have been realised since implementing the grade control system. These include enabling the workforce to optimise the use of airspace; saving time through pre-set design levels; increasing time, cost, and safety benefits by eliminating the need for surveyors to be on site as often; and eliminating rework by entering design plans for landfill cells on the on-board system, enabling operators to continuously apply the design from start to finish. It has also allowed for continuous monitoring and control of density and gradient of landfill compaction and final form of landscaping; and assists operators in avoiding critical zones, such as gas wells and hazardous material placement areas.
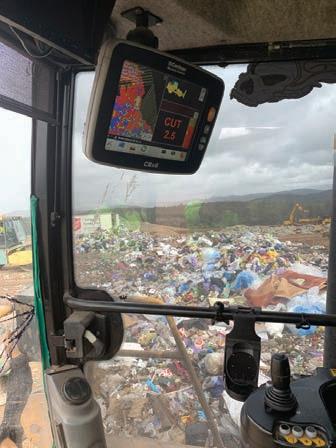
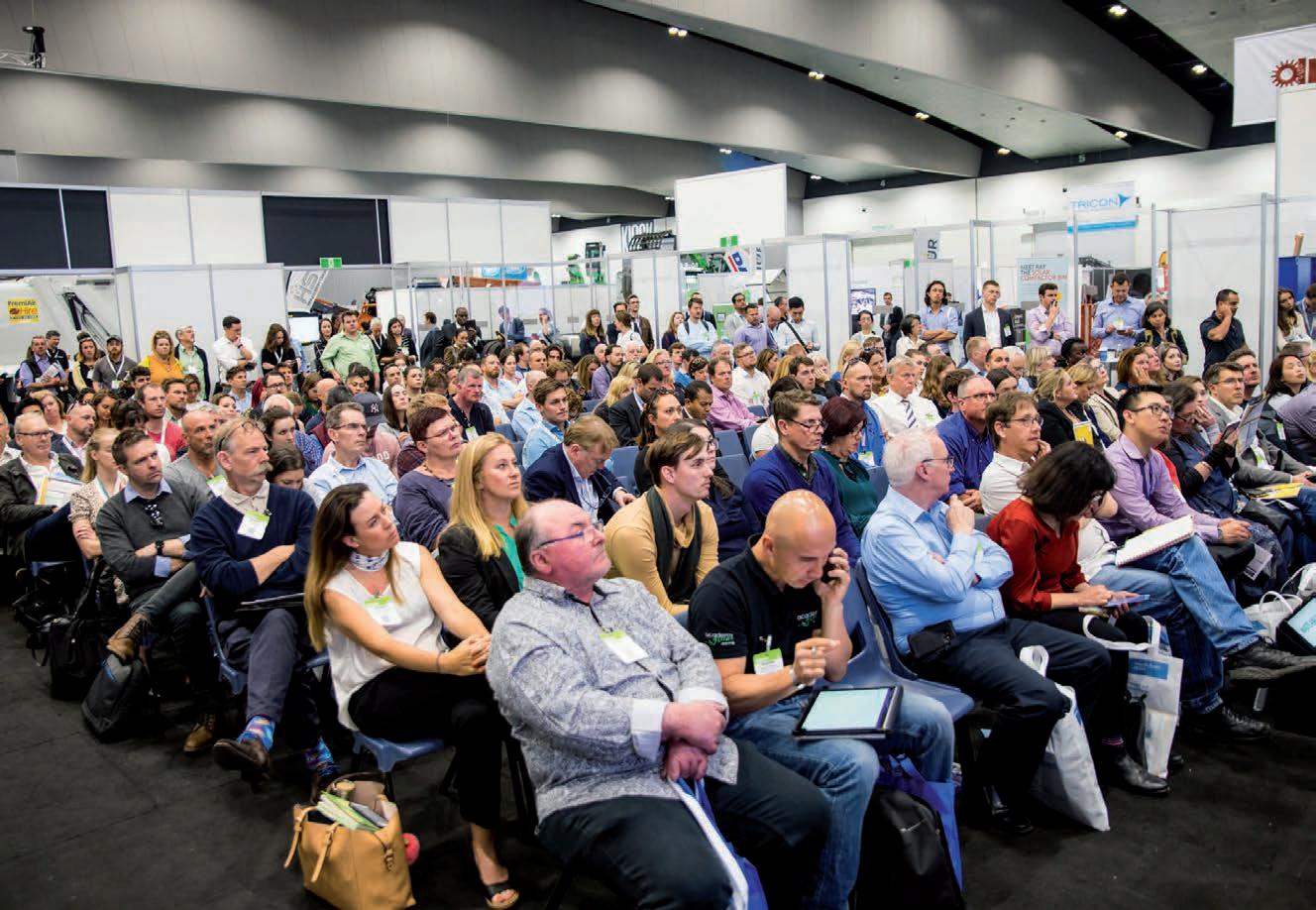
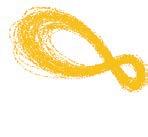
“Often, a piece of equipment is pigeonholed into one particular industry,” he says. “But recycling as an industry is so broad, and it covers a wide range of product streams. How you combat contamination in those product streams is where we comeEriezin.”offers a range of ferrous and nonferrous separation equipment for materials recovery facilities (MRF) and municipal solid waste (MSW) facilities, including dynamic drum separators, suspended magnets, and eddy current separators.
“They’re also widely used in the scrap metal industry as a revenue generator.”
WASTE MANAGEMENT IN ACTION – MAGNETIC SEPARATION 66 / WMR / September 2022
In an MRF context, he says, capturing aluminium cans, ringpulls and bottle-caps makes for a valuable revenue stream, but it’s also key to avoiding issues in downstream equipment.
For circular solutions to be financially viable, manufacturers of recycled products rely on supplies of feedstock that are of a consistently highSortingstandard.and separating metal from waste streams is also critical in the growing waste-to-energy and tyre recycling industries, where the recovery of fine metal contaminants is of economic and environmental importance.
Jonathan Schulberg, head of Resource Recovery and Recycling Business Development at Eriez Australia, says the company provides sorting and processing solutions for a wide range of industries – but recycling is where things get interesting.
The Eriez Dynamic Pulley Separator removes trapped steel and weak magnetic fines from waste streams.
You’ve
JONATHAN SCHULBERG OF ERIEZ AUSTRALIA DISCUSSES HOW THE COMPANY’S SORTING EQUIPMENT CAN MAKE RESOURCE RECOVERY MORE EFFECTIVE AND ECONOMICAL. gotta
Jonathan says Eriez’s eddy current separators are among the company’s best-selling equipment, largely because they play a role in almost every aspect of “You’llrecycling.see them in MRF plants to remove aluminium and the like from product lines such as paper, plastic and cardboard,” he says.
GETTING THE VALUE OUT
As the demand for recycled and recyclable products surges across the globe, so too does the need for uncontaminated streams of recycled material.
“If you have paper or cardboard going to a baling machine, having a piece of aluminium in that creates contamination, which lessens the value of that product. But it can cause damage to keep it separated
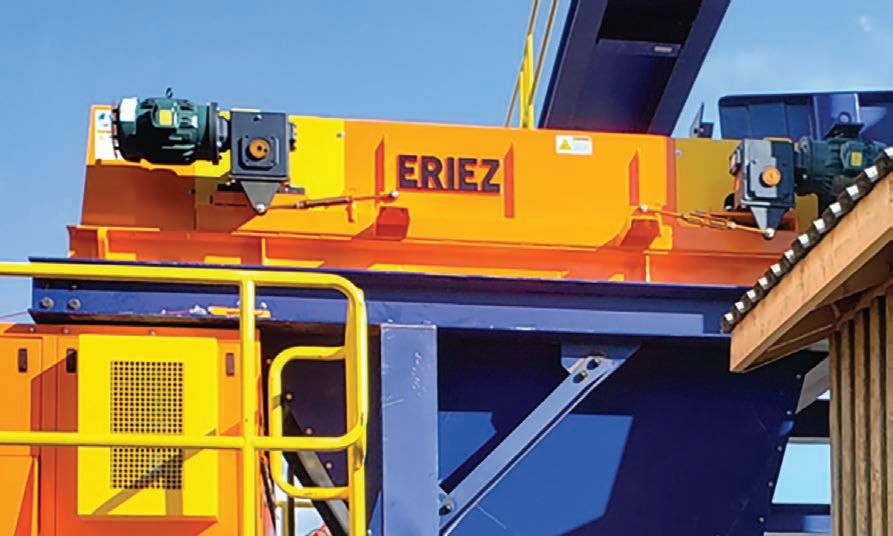
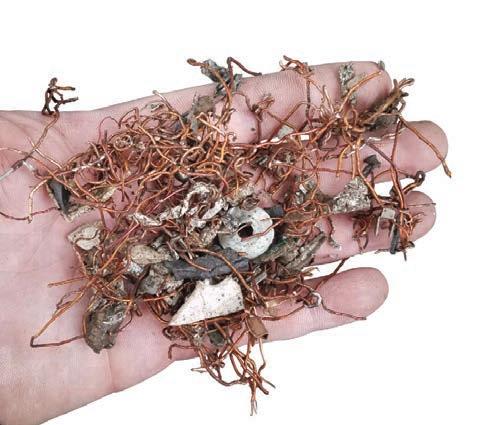
/ WMR / 67
that equipment as well, which is even more“Thatcostly.aluminium, as soon as it’s recovered, is instantly sellable. That makes an eddy current separator very easy to quantify from a dollars and cents point of view, and it’s also very easy to prove its reliability and feasibility in a process.”
“There’s been a positive response from the industry too, especially in the scrap metal space. In part, I think, because there’s been very little in the way of major product development in ferrous separation for some time.”
Recovered non-ferrous micro fines processed through the Eriez MKIII UHF Eddy Current Separator.
“Having a product like this, that can agitate and work that material free and remove it from the product stream, is very advantageous.
This is an element of Eriez’s service that the company takes seriously –regardless of what they’re supplying and to which industry. Whenever Eriez is in talks with a prospective customer, the company always prefers to arrange a site visit to ensure the product will fit the“Topurpose.trulyunderstand what you’re working with, you’ve got to be on-site,” Jonathan says. “Then you can get a real sense of how a plant operates, the pitfalls in the process. These things can be quite difficult to explain in an email or with photos. “It also builds better communication between yourself and the customer. When you’re explaining how the product is going to work, you’re both visualising the same thing. “It’s a must-have for any product that we sell, and that’s why we’ve never sold any of our products online. Because if you don’t develop that understanding, nine times out of ten, someone’s going to buy the wrong thing.”
SUPPLYING THE FUTURE Jonathan says that with how fast Australia’s recycling and resource recovery streams are changing, trying to think years or even decades into the future is standard practice for the“Theindustry.waste streams that many Australian plants are seeing now are completely different to what they were seeing a decade ago, both in terms of volume and how they’re separated,” he says. “There’s no point in supplying something that fixes the problem you have right now if it’s going to be obsolete in five years. There’s a lot of forward-thinking that goes into the supply of equipment.” For more information, visit: www.eriez.com.au www.wastemanagementreview.com.au
DYNAMIC INNOVATION Eriez has recently introduced the Dynamic Pulley Separator, a high-strength ferrous separator designed to remove trapped steel and weak magnetic fines from recycled materials. Placed before an eddy current separator in a recycling line, the Dynamic Pulley Separator helps improve metal separation and recovery in downstream equipment, while reducing wear or damage on those“It’smachines.designed for reprocessing very fine ferrous metals, which otherwise generally get missed in applications such as bottom ash processing in waste-to-energy production,” Jonathan says. “It’s also great for businesses in the scrap metal industry, where they’re wanting to extract every piece of valuable metal from their waste streams – material that is otherwise put on a truck and goes to landfill. That is literally throwing money into theExistingground.”equipment for capturing ferrous metals, such as suspended magnets and drum magnets, work to a point, Jonathan says. But technological limitations mean some of the smaller stuff will always get“Thethrough.smaller material often gets embedded into what’s around it, whether it’s dirt, plastic, foam or rubber. It’s very hard to remove because it’s of a lesser density than the thing it’s stuck in,” he says.
Jonathan sees potential for the Dynamic Pulley Separator in Australia’s tyre recycling industry, where he says minimising contamination in recovered material can be a “Therechallenge.arealotof fantastic companies repurposing tyres for playground surfaces, road bases and other construction applications but there are issues in being able to maintain purity in the material and removing that ferrous metal contamination. That’s where we canJonathanassist.” says the Dynamic Pulley Separator’s unobtrusive footprint –they are available in one-metre and 1.5-metre conveyor set-ups – means it can easily be incorporated into any existing treatment plant.
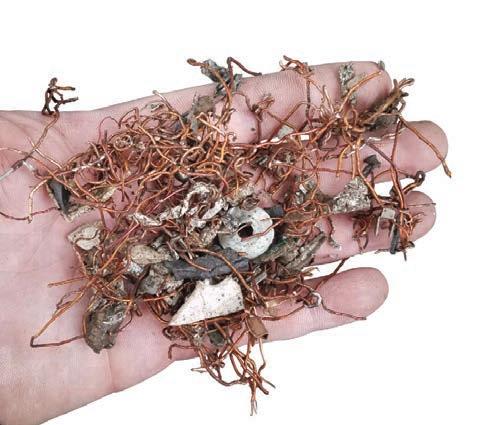
waste to recovery
It’s one of the largest gatherings of waste management and resource recovery professionals in the country, ready to share ways in which Australia can transform how materials are used, ensure effective recovery, and reduce waste sent to landfills. Creating a sustainable future requires a joint effort that encompasses business, government, and the community. In the lead-up to the 2022 expo in Melbourne on October 26-27, Waste Management Review asked several members of the advisory board their views on how Australia can create a functional roadmap to circularity. How can we transform the waste economy, or rather how can we move away from waste and create a waste as a resource-led future? Kate Ringvall, Technical Director Circular Economy from GHD has worked for governments at all levels, across large corporations and universities implementing and integrating sustainability principles. She says it is crucial to ensure that economic activity and the consumption of finite resources be separated. She suggests that “greater harmonisation is needed and an understanding of the components of waste, what can be recycled and what can’t, to have an effective move away from a linear model”. However keeping natural resources in circulation, especially from a local government perspective is no easyBinitafeat.Shrestha, Senior Waste Management Specialist from the City of Port Phillip, stresses the importance of “educating the community as crucial to creating behaviour change”. She says that with a growing population, it is important to get community buy-in. In 2020, Binita led the award-winning Glass Recycling Trial, which introduced a kerbside and communal glass recycling service across the Port Phillip municipality.
A move to a resource-led future requires the marrying of legislation, all tiers of government and industry to come together on a zerowasteOneapproach.waytoget all of stakeholder buy-in is through driving home the economic value of investing in a circular model, and its impact on the creation of new business andMichelleopportunities.Mandl-Keating, from TOMRA Cleanaway says that “innovation is key”.
W
During a 20-year career in waste, resource recovery, and sustainability, Michelle has held a variety of roles within state and local government and private industry. She says that a lot of innovation is currently happening to push Australian industry into a more circular model.
Transition from
If a sustainable future is the end goal, will a move to circularity and a move away from waste to resource, through innovation and collaboration, be the best step forward to achieving it?
EVENTS 68 / WMR / September 2022
WASTE EXPO 2022 BRINGS TOGETHER INDUSTRY, BUSINESS AND GOVERNMENT LEADERS TO SHARE THEIR VIEWS ON CREATING A SUSTAINABLE FUTURE.
Benita Shrestha, Waste Management Specialist, City of Port Phillip.
aste Expo Australia provides a platform to advancing best practices in waste management and making a positive difference to the environment and community.
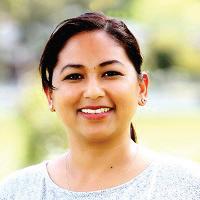
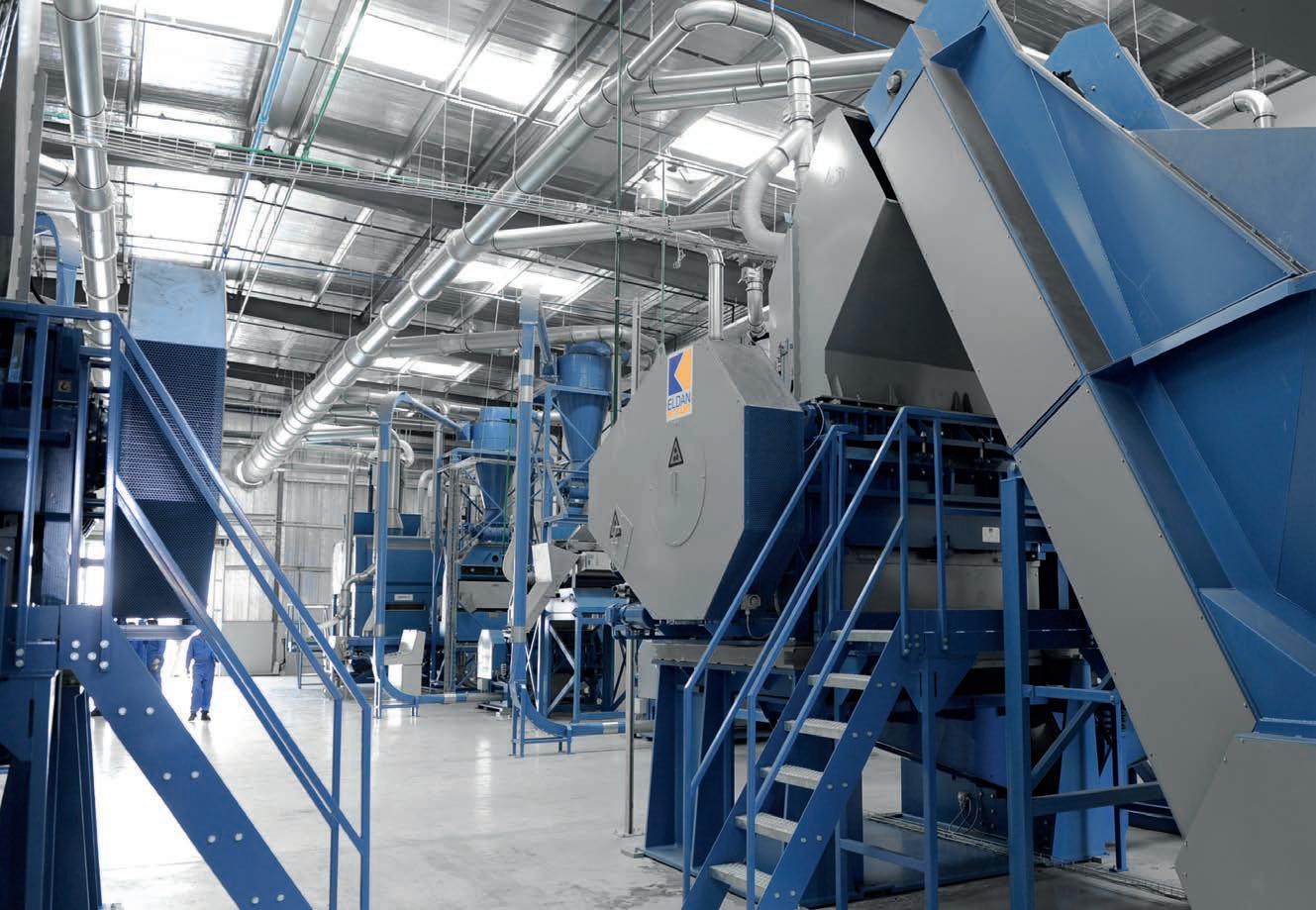
TYRE SOLUTIONSRECYCLINGTURNKEY BOOTH: B-100 Come and meet us at our stand to discuss your recycling requirements WWW.ELDAN-RECYC LING.COM With a solution from ELDAN, your recycling will be versatile and customized to your Theneeds.modular design enables you to expand or upgrade your plant as the market Fromchanges.chip production to granulate, from granulate to powder. You also get a guaranteed capacity and output purity. Meet
October 2022.
Technical Director Circular Economy from
Michelle Mandl-Keating, TOMRA Cleanaway.
Ben Morgan, GM Vic Operations from Bingo Industries says there shouldn’t be an end game. Continuous innovation is the driver for Bingo Industries, and Ben believes this should be the approach for the whole sector to ensure the move to a more circular consumption model is not only achieved but sustained. You can hear more about the transition from waste to recovery, as well as the latest updates in waste legislation and innovation at the Waste Expo Australia from 26 – 27 Anyone interested in exhibiting at the event can email Sherri Pearson, Waste Account Manager sherri.pearson@rxglobal.comat Carsten Nielsen 26-27 Kate Ringvall, GHD.
at Waste EXPO Australia
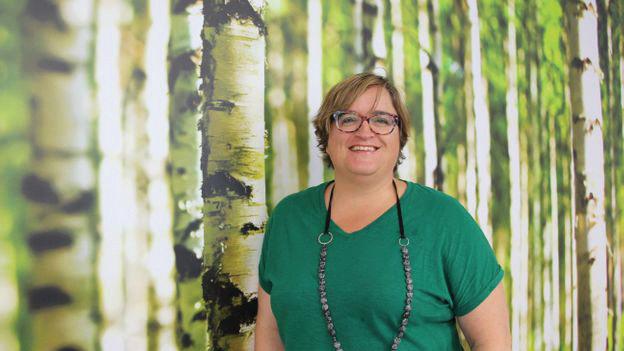
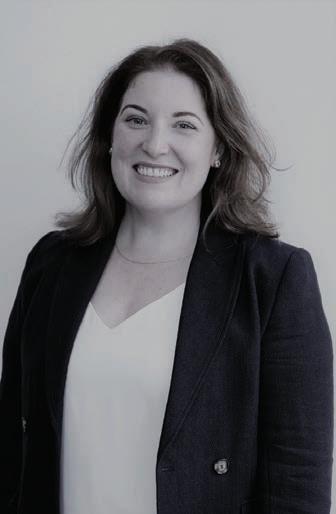
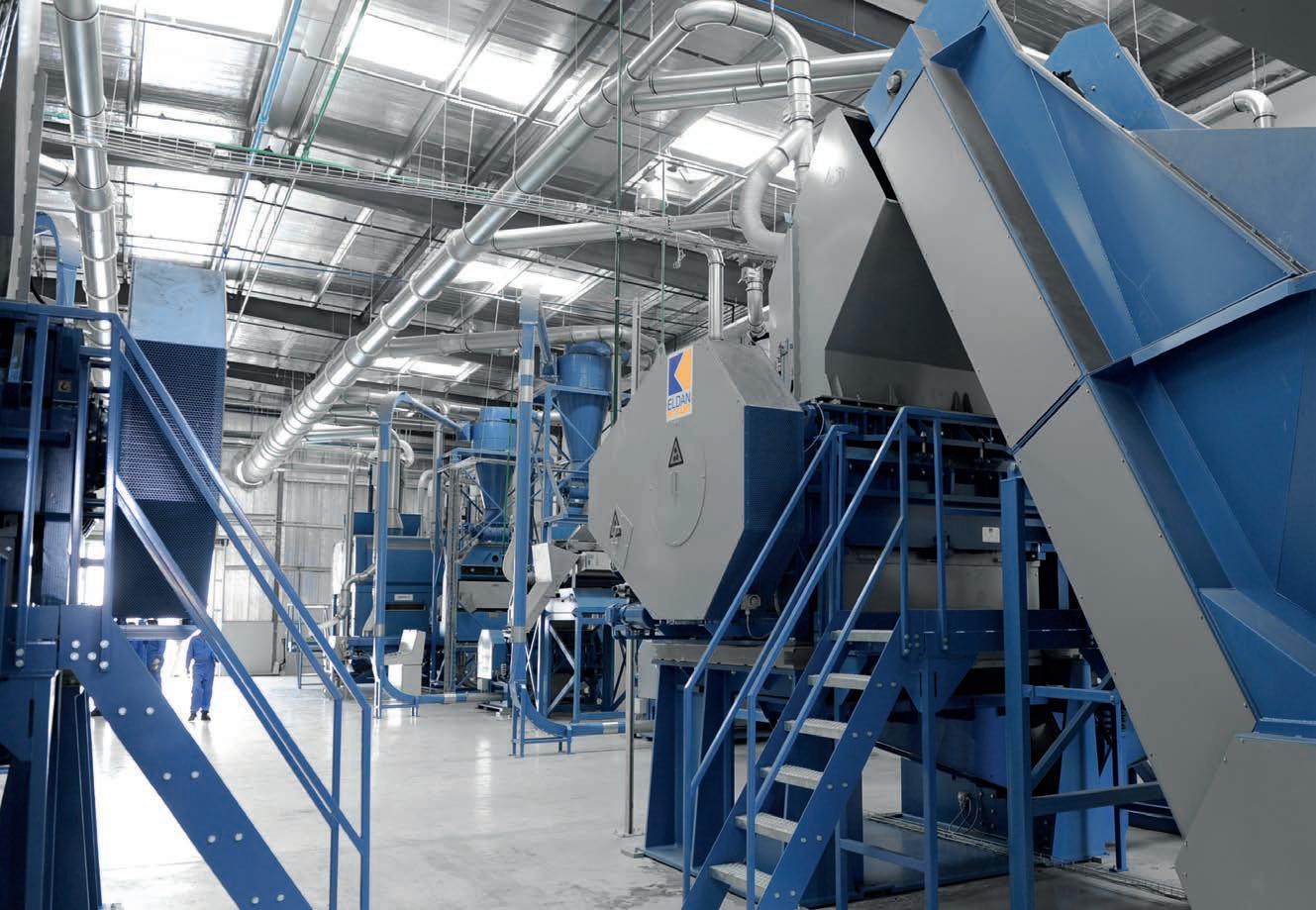
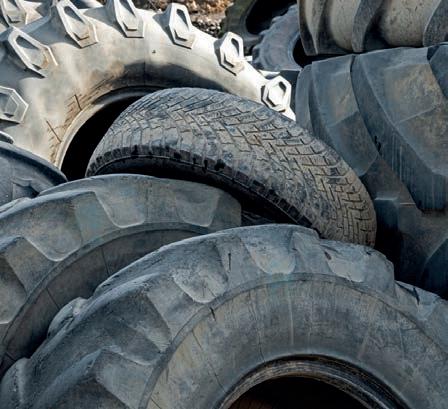
The awards aim to recognise and raise the profile of the exceptional women who have achieved success through leadership, innovation, and commitment to their sector.
This year, two trail-blazing women from the waste sector are finalists in their respective categories: Sage Hahn and Rebecca Healy. Sage Hahn, Bio Gro Sage Hahn, Victorian State Manager at Bio Gro, a family-owned business that has been involved in organics recycling for more than 45 years, is a finalist in the Business Development Success of the Year“I’mcategory.extremely passionate about the organics industry,” she says. “The way that Bio Gro operates – thinking of and using organics as a resource, rather than seeing it as waste – is really important to Sageme.”has been with Bio Gro for 10 years, starting in operations as a weighbridge operator and progressing through various roles in the company. She is now a key part of the Executive Leadership Team and the current Chairperson of the Victorian branch of the Australian Organics Recycling Association (AORA). “I’ve had some really good mentors at Bio Gro, and I’ve learned something from each of them,” Sage says. “Because it’s a smaller family-owned business, you can always talk to the owners, which is important. It allows you to be flexible and agile as a business as well, and I think that’s been a part of ourLeighsuccess.”Barry, Bio Gro Chief Operating Officer, says Sage’s enthusiasm and initiative has been invaluable to the“Overbusiness.the past three years in particular, Sage’s passion for organics recycling has been instrumental in significantly growing this division of the business,” he says.
The awards recognise women who have achieved success in their sectors.
WASTE MANAGEMENT REVIEW CHATS TO TWO OF THE 2022 WOMEN IN INDUSTRY AWARDS FINALISTS FROM THE WASTE AND RESOURCE RECOVERY SECTOR.
he Women in Industry Awards celebrate the achievements of Australian women across a range of traditionally male-dominated industries such as mining, transport, manufacturing, engineering, logistics, infrastructure, and waste management.
The women of T
Following her promotion in June 2020 from Victorian Sales Manager to Victorian State Manager, Sage began exploring options for increasing the volume of organics received at Bio Gro. She identified three main steams of opportunity for new business, including additional metropolitan council kerbside waste collection, commercial green waste from landscapers, and commercial timber waste from construction andSagedemolition.reachedout to each of these sectors, establishing connections and boosting visibility for the business and its capabilities. By the end of the 2020-21 resource recovery
EVENTS 70 / WMR / September 2022
The 2021 awards produced two winners from the waste management and resource recovery sector: Lacey Webb, Founder and Director, Resource Hub, took out the Business Development Success of the Year award; and Larissa Rose, Director Consultant, GG Enviro, was awarded Mentor of the Year.
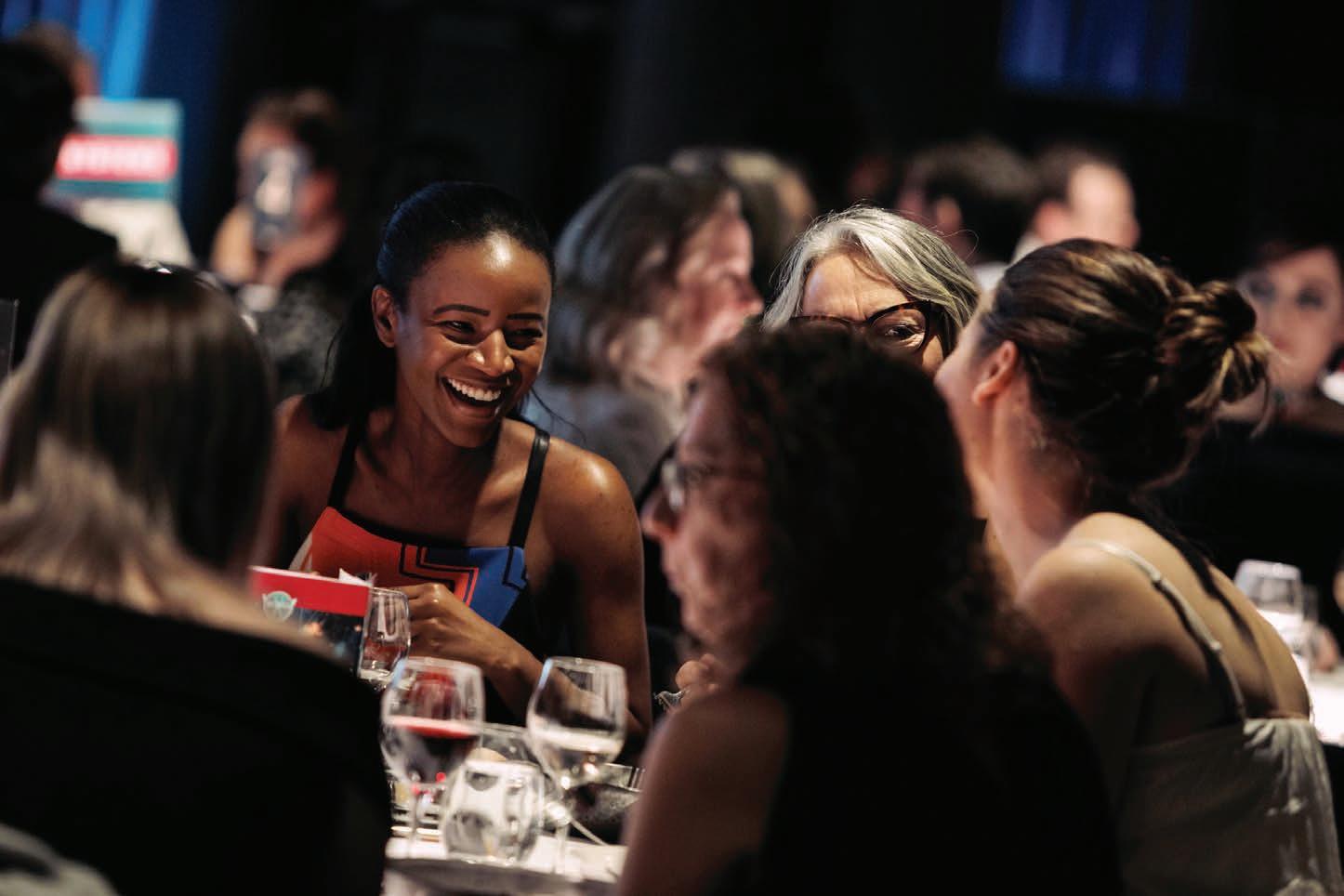
By July 2022, Bio Gro’s Dandenong South facility had processed 112,000 tonnes of product, an 85 per cent increase over the previous year. Sage also spearheaded an operation to deal with the logistical challenges presented by this growth, seeking a material handling solution to enable Bio Gro’s continued growth. This resulted in the implementation of a new multimillion-dollar organics processing line in Dandenong South, improving capacity, productivity, and safety. For any woman considering a career in the waste industry, Sage has some powerful advice: “Listen and learn to the people around you, but don’t be afraid to have a voice,” she says. “You might be surprised how much you know. People do value different perspectives and different ideas, so don’t be silent – just put your case forward.”
Sage Hahn, Bio Gro Victorian State Manager.
Rebecca Healy, Boxhead Plastics Founder and CEO.
“I think anybody can give it a go if you have a passion,” Rebecca says. “I had no prior qualifications, no prior training or history in the industry. With the help of some good support and education, I just gave it a crack.”
/ WMR / 71
financial year, the business registered a 50 per cent increase in the volume of product taken in. Going into the 2021-22 financial year, Sage was confident she could bring in additional volumes of material through metropolitan council contracts.
In the years before Boxhead Plastics was born, Rebecca studied part-time to become a polymer technician while working a full-time administration job in the power industry. She left that career after 15 years to commit full-time to a dream of positive environmental change, combining her leadership, customer relations, and administrative skills with her newly obtained qualification as an injection mouldWithoperator.theBoxhead Plastics operation now off the ground, she is continuing her studies, working towards a Diploma of Sustainable Practices.
Boxhead Plastics is expanding its product range to include coasters and dog ball throwers, both also manufactured from recovered car bumpers. Meanwhile, Rebecca continues to develop relationships with local smash repairers to provide feedstock and divert more waste from landfill. Rebecca credits the support of the people around her as a big part of her success so far. TAFE NSW Lidcombe, which helped her to develop the original Naiteev Golf Tee idea, also played a key“Irole.was the only woman in my TAFE class, but I found everybody really supportive,” Rebecca says. “I wasn’t singled out at all, I was asked the same questions as everybody else in the class, I was asked to lift what everybody else was asked to lift. “If I could say anything to anybody, it’s that being a woman in industry is not as much of a barrier as it was once perceived to be. I think just give it a go –you might be surprised.” For more information, www.womeninindustry.com.auvisit: www.wastemanagementreview.com.au
“Golf courses are often criticised for their negative impact on their surroundings, from high water usage to pollution caused by fertilisers and the loss of natural habitats,” Rebecca says. “The Naiteev Golf Tee offers the golf industry a way to offset some of its environmental impact.”
Rebecca is the Founder and Chief Executive Officer of Boxhead Plastics, a not-for-profit social enterprise targeting the diversion of landfill-bound plastic waste from the automotive industry. From her early experiments in 2017 recycling plastic bottles into filament for 3D printers, Rebecca has steadily grown Boxhead Plastics into a unique remanufacturing operation. In that time, Boxhead Plastics has pioneered a process that repurposes polypropylene car bumpers into durable, high-performance products. Boxhead Plastics launched its first product, the Naiteev Golf Tee, in 2021. Since then, the manufacturer has sold more than 30,000 of them to local and international customers.
Rebecca Healy, Boxhead Plastics Rebecca Healy is a finalist in the Excellence in Manufacturing category.
“These sorts of contracts can take a long time to establish,” Leigh says. “We were thinking we wouldn’t get an outcome until 2023-24. But Sage was adamant we could bring this in earlier and devoted a lot of her time to it.”
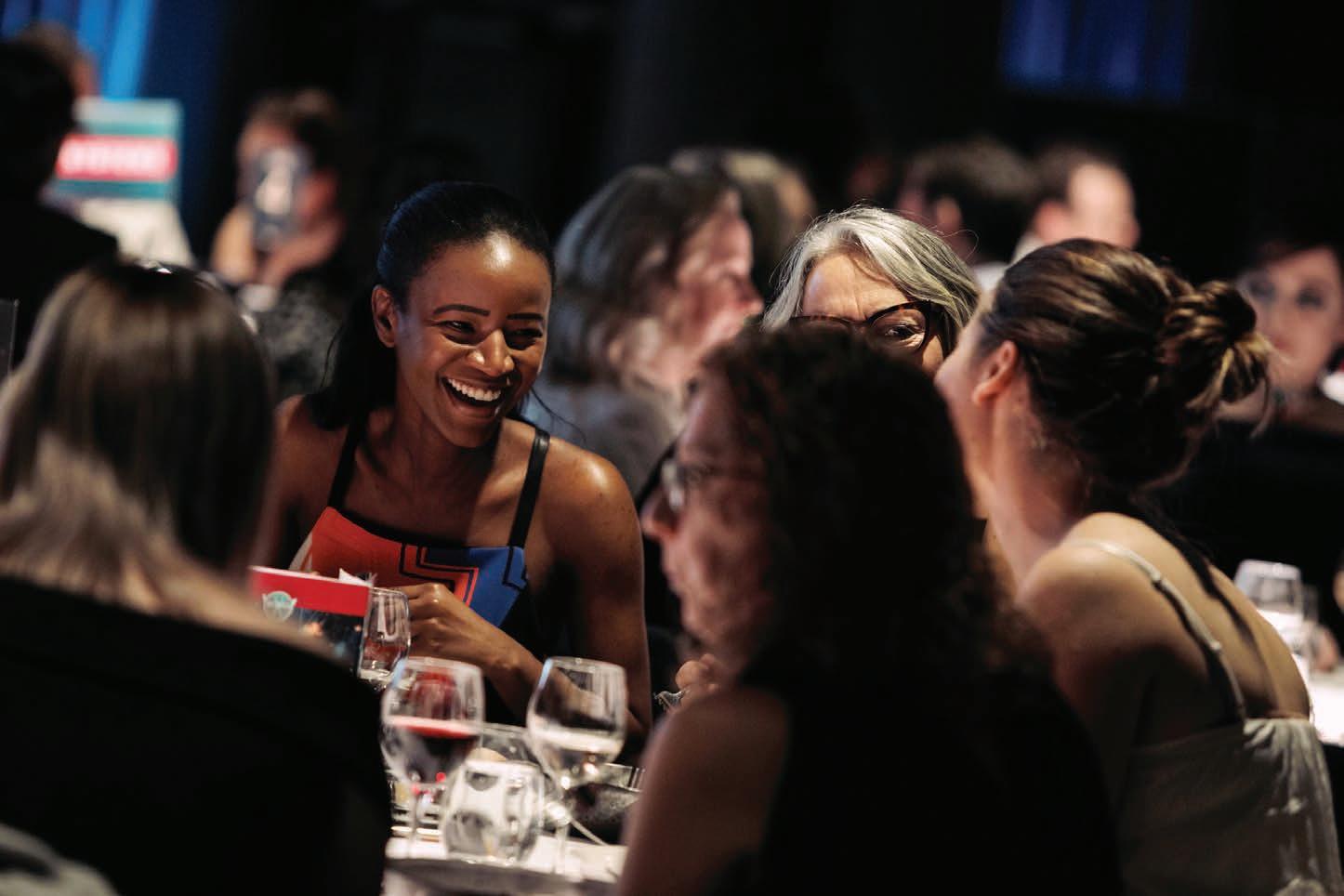
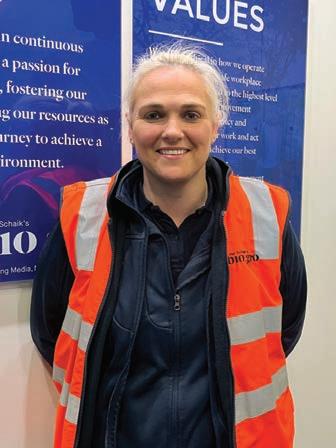
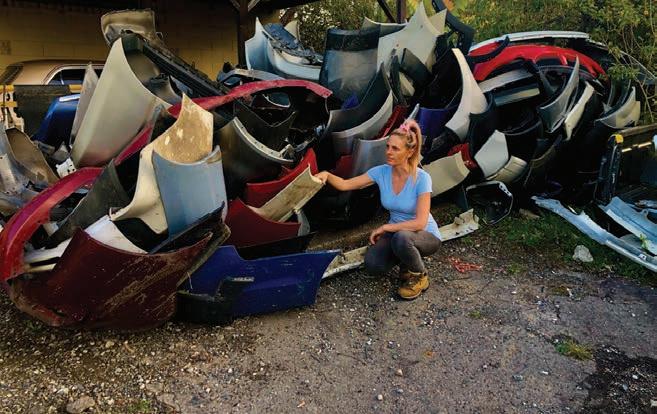
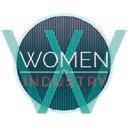
PLANET ARK’S ADAM CULLEY DISCUSSES THE NEW CIRCULARITY CONFERENCE, RUNNING FROM 24-25 NOVEMBER 2022 AT HILTON SYDNEY. In November 2020, Planet Ark established the Australian Circular Economy Hub (ACE Hub) to help encourage and facilitate the country’s transition to a circular economy. Its primary aim: to act as a central platform for all circular economy discussion, education, inspiration, collaboration, and action.
“We found that 88 per cent of the more than 500 CEOs and directors interviewed, agreed that the circular economy was important to the future of their business. While 34 per cent identified the concept as extremely important, very few could identify what the correct definition of a circular economy was.”
“You can’t become a circular business on your own,” he says. “You need all the different parts of the value chain to come together to share information and collaborate for mutual benefit.
“At Planet Ark, we very deliberately changed our language away from ‘waste’ to ‘resource’, because everything is a resource that can be used. “Traditionally we look downstream at the waste we create, whereas with Circularity, we’ll be looking at the full system. We’ll look at how to design waste out, create regenerative models.
72 / WMR / September 2022 EVENTS
“We’ve done research over the past couple of years on circularity in Australian business – sort of taking the temperature of how the circular economy is perceived.
Circularity will feature conference sessions, an exhibition, and a range of networking opportunities.
Adam says addressing this knowledge gap is a big part of what the ACE Hub is all about, and Circularity is a great circularity
“Our working groups are looking to address the fundamentals such as how to measure circularity, what’s the procurement around the circular economy, how do we finance it, and so-on.”Adam says figuring out these details necessitates commitment from business leaders who are determined to make sustainable change a priority.
on
“We’ve looked to, and learned from, our European partners, such as the Holland Circular Hotspot or To this end, the ACE Hub is introducing its first conference, Circularity, which will run from 24-25 November at the Hilton Sydney – one of the City of Sydney’s Sustainable Destination Partners. The event will feature conference sessions, an exhibition, and a range of networking opportunities, including a gala and an awards dinner. “This is a conference for anyone in industry, any kind of practitioner or academic, and anyone in government, to come and participate, network, and look for circular solutions,” Adam says. He says Circularity will attract guests and delegates from around Australia and the Asia-Pacific region. “We have a really fantastic list of speakers, including representation at all levels of government,” he says. “We’ll also have some really senior business Circularity will distinguish itself from for another kind of system,” he says.
Closing in
Adam Culley, Head of Partnerships at Planet Ark, says the ACE Hub exists to bring together and connect businesses and thought leaders around this common topic.
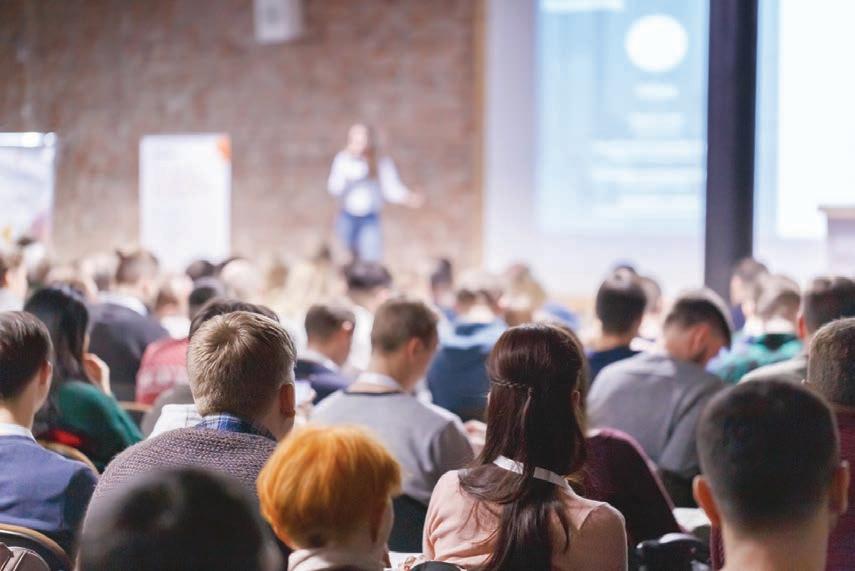
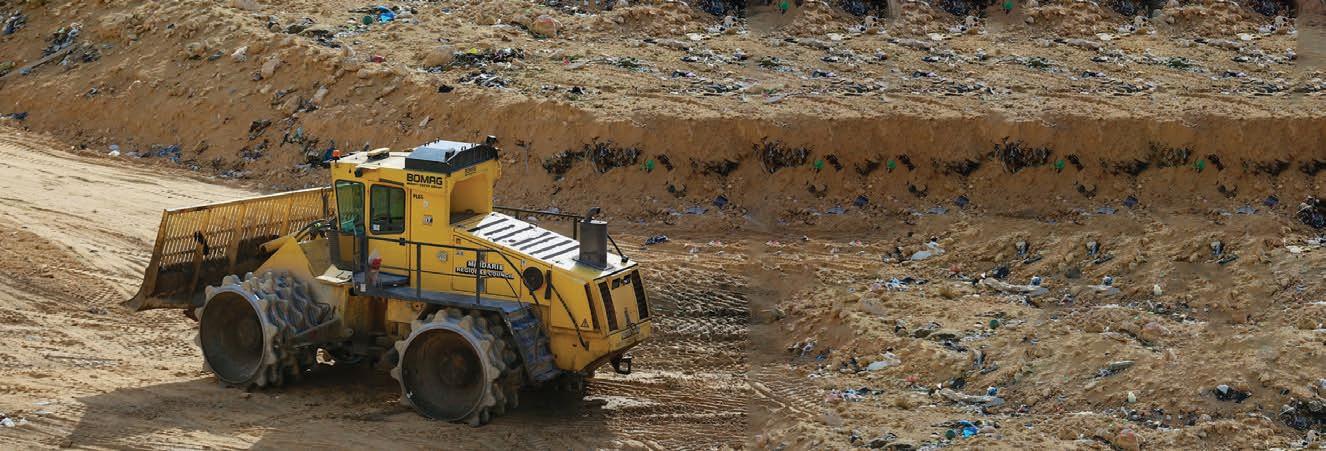
Optimise compaction and increase productivity with Carlson machine guidance. Backed by industry expertise & nationwide support at Position
way to start building that level of education in Australia. “You can’t ever undervalue the importance of getting people together, having them sit together, network and learn from each other,” he says.
It is Adam’s hope that businesses will learn that embracing circularity can also build resilience and new opportunity for them in the long term. “Suddenly, they’ll see that what has previously been considered waste can be reused, resold, or circled back into their own operations to help decouple themselves from at-risk parts of their supply chains. Especially with international supply chains being threatened by COVID-19, I think there will be a lot more looking to local solutions powered by renewable resources.”
Partnerships, Planet Ark.
As to why now is the right time for a conference like Circularity – as well as the ACE Hub it represents – Adam says we have reached what he describes as an inflection point in human history. “You only need to look outside your window to see it,” he says. “In Europe, everyone’s experiencing record climatic conditions. It’s 40 degrees in the United Kingdom and there are bushfires outside of London. It’s evidence that there is a huge change and that is intrinsically linked to how we manage our relationship with the environment, particularly how we use our resources.
“We’ve got this amazing melting pot right now of knowledge, the evidence outside our windows, youth momentum and climate protests, as well as businesses and governments starting to understand and commit.
Head
1300 867 266 • positionpartners.com.auWANT TO MANAGE YOUR SITE MORE EFFECTIVELY? Adam
“There’s a huge amount of momentum. And, for the first time in history, we have the technology to be able to solve this problem. We just need to do it. That’s the focus of Circularity: bringing people together to work on theseLimitedsolutions.”earlybird tickets are available today for $1200 + GST. Early bird pricing is available until 30 September or until sold out. For more information, www.circularitylive.com.auvisit: Partners. Culley, of
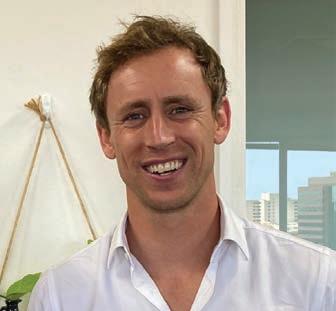
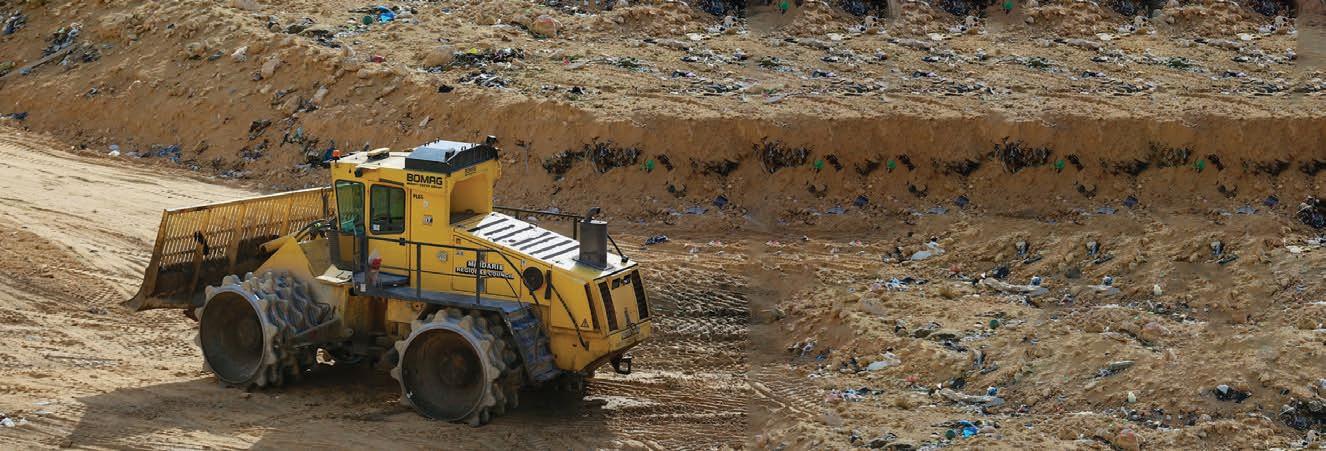
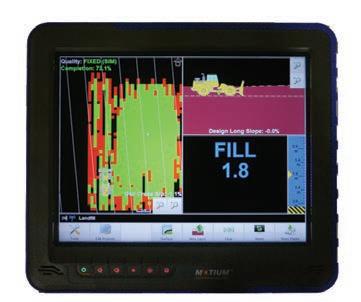
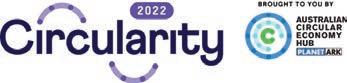
Thewww.watm.com.auMULTILIFTFutura.
SMITH can offer turnkey solutions incorporating electronic materials sorting and separating, metal detection, dewatering and compacting, extrusion and pelletising lines, as well as materials handling, conveying and bagging systems and complete wash plants for plastics.
A member of the Hiab family, the MULTILIFT Futura is a combination of good looks, street smarts and forwardLeadingthinking.theway in skip-handling, the MULTILIFT Futura features a list of design innovations, many you can see and many more behind the scenes. All ensuring durability, performance, and safe, easy, fast operation.
ZERMA granulators are designed for the most extreme and universal applications required for today’s recycling facilities including size reduction of plastics, rubber, wood andZERMAe-waste.shredders have been developed as rugged machines suitable for heavy duty applications including size reduction of materials such as plastic lumps, purgings, large hollow parts, film, fibre, and paper down to a size of less thanTELFORD25mm.
TELFORD SMITH, GRANULATORS AND SHREDDERS
shredders.andgranulatorsZERMA PRODUCT SPOTLIGHT 74 / WMR / September 2022
FUTURA’s radio remote means the driver can operate the skiploader around the vehicle and see what’s happening The SwanNeck 1.4-metre telescopic arm has been designed to give the driver more flexibility and increased reach over fences and obstacles The EvoLight construction means the skiploader is made of lightweight, but tough, steel. This provides 300-500 kilograms extra payload, meaning users can haul more while saving fuel. Available in three models 8,12 and 18T there’s one to suit every business.
SafetyPlus features include hydraulic side stops, container locks and lashing points, which work together to keep the skip securely in place. External alert buzzers warn people around the skiploader that it is in operation.
WATM CRANE SALES AND SERVICES, MULTILIFT FUTURAContact-WATM
Contact – Telford Smith P 03 8792 9777 W www.TelfordSmith.com.au
Crane Sales and Services P 08 9271 8000 W
The in-built SkipTop system, an optional extra, covers loads automatically and quickly to prevent anything flying out of the FlexControl,container.which also contributes to user safety, allows the customer to choose what control they have for operating the skiploader. Options include outside, in-cab, radio remote controls, or a combination.
A dynamic on-board weighing system also contributes to operational safety. It weighs the container during the loading movement, helping prevent overloading and its risks to road-users.
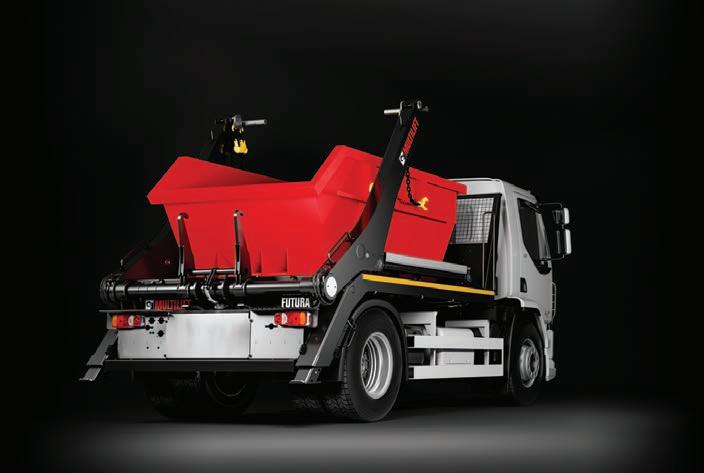
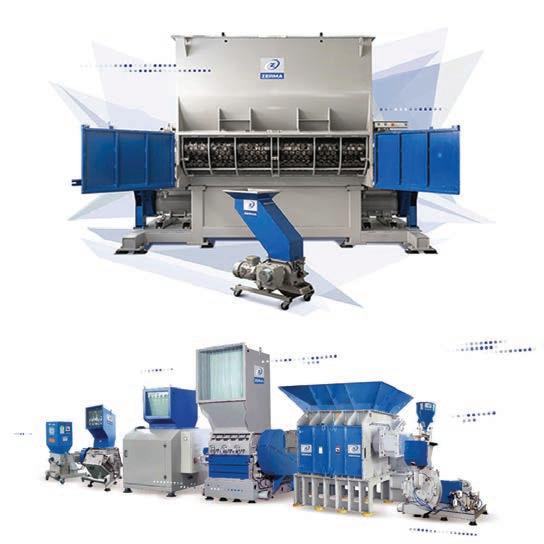
Load Once. Loadrite. Optimise every truckload by loading right the first time with Loadrite scales. Loadrite scales eliminate double handling of material, help you avoid overload fines and reduce haulage costs by moving more material each shift. The L3180 offers more precise weighing in a range of conditions including adjusting for rough terrain, operator technique and machine movement.scales offer more precise weighing. The Komptech Terminator is the ideal machine when it comes to volume reduction shredding of various waste streams. As a low-speed, high torque single-shaft shredder, the Terminator can be used on many types of waste applications, including tyres and mattresses, thanks to its drum and counter comb system. This system allows the machine to handle a range of tasks with ease as the The Komptech product range stands for quality and reliability using high quality components, the Terminator is built to handle the toughest conditions. Contact - Komptech CEA P 1300 788 757 W www.komptechcea.com.au The Komptech Terminator.
www.wastemanagementreview.com.au / WMR / 75 PRODUCT SPOTLIGHT
LOADRITE L3180 SMARTSCALE FOR WHEEL LOADERS Contact
Loadrite New Zealand P 0800 493 444 E info@loadritescales.co.nz W www.loadritescales.co.nz Contact
SmartTech Australia P 1800 655 860 W www.smarttechaustralia.com.au Loadrite
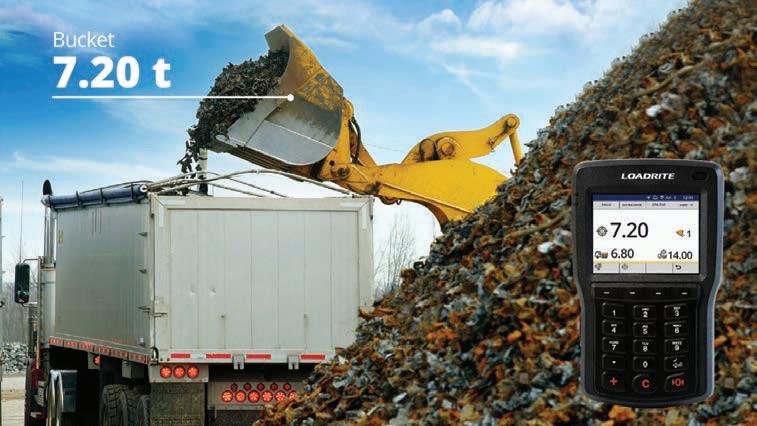
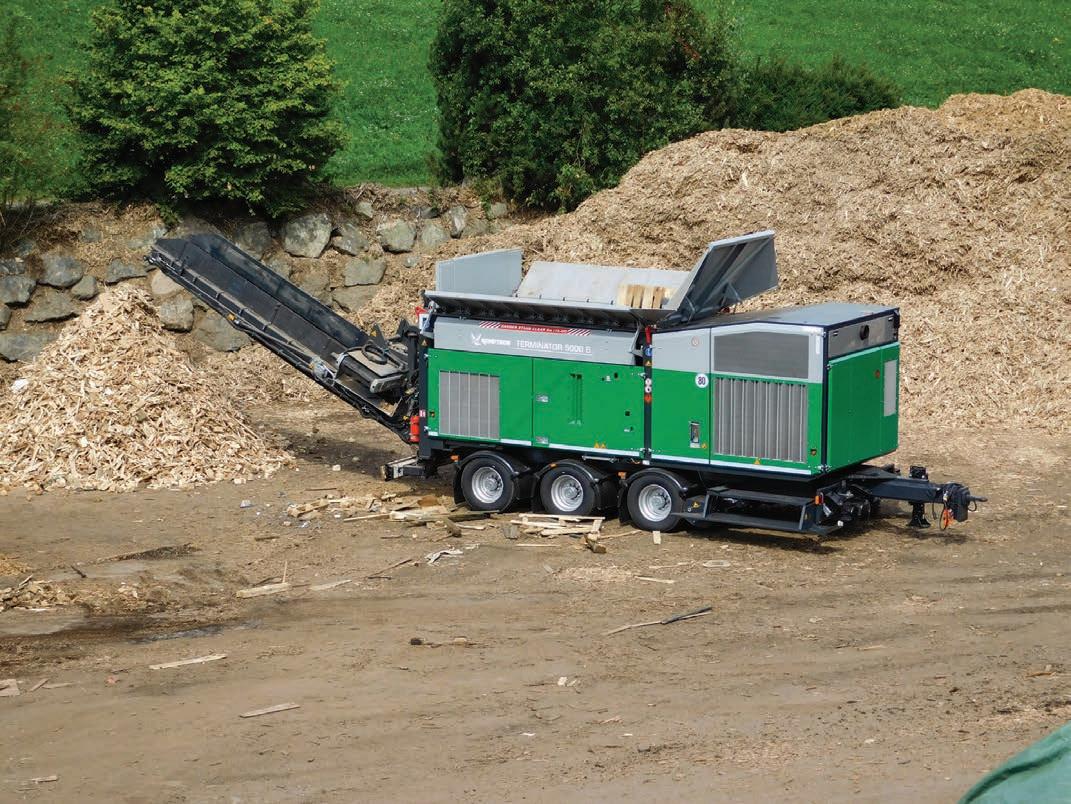
No matter what sector of construction you’re in, you’ll leave CONEXPO-CON/AGG with new ideas, new relationships, and new opportunities to grow your business, and your place within the industry. This isn’t just North America’s largest construction trade show, it’s taking construction to the next level. LEARN MORE AT CONEXPOCONAGG.COM 250,000sqm of exhibits / 130,000 attendees / 1,800 exhibitors / 150 education sessions TAKING CONSTRUCTION TO THE NEXT LEVEL.2020AttendeeMissy Scherber, T. Scherber Demolition & Excavating MARCH 14-18 / 2023 / LAS VEGAS / NEVADA
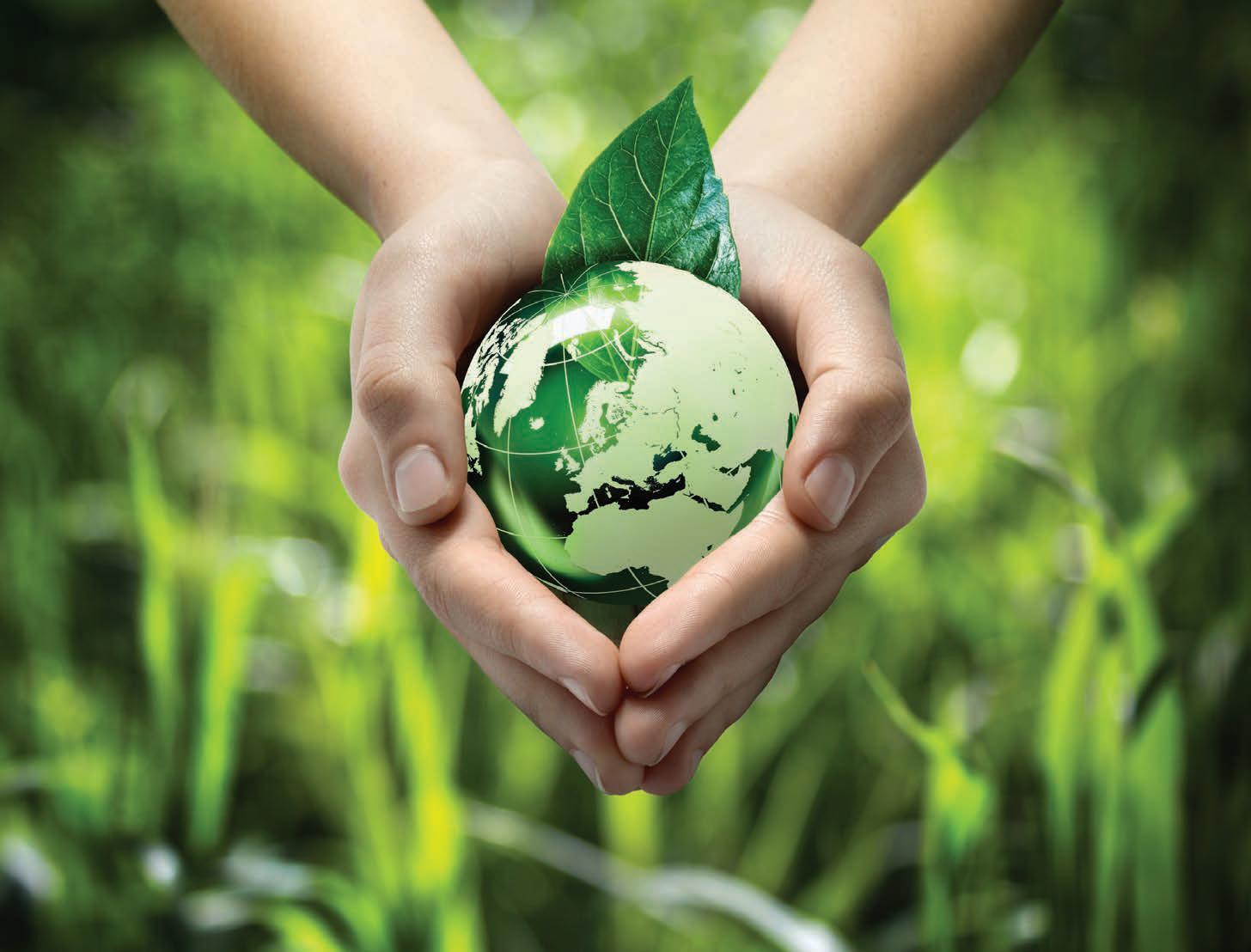

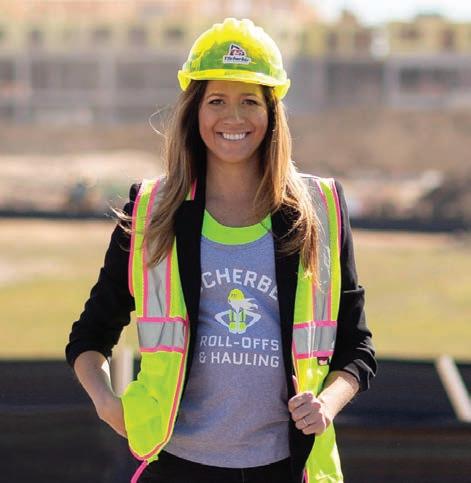
The roadmap has been a long time coming and is the result of the determination of Peter Olah, former AORA National Executive Officer, to bring together a document that is built on facts and figures but offers a tangible pathway for the industry.
/ WMR / 77
Roadmap to 2031
THE AUSTRALIAN ORGANICS RECYCLING INDUSTRY’S VISION 2031
Vision 2031 offers a tangible pathway for the recyclingorganicsindustry.
PROVIDES A SNAPSHOT OF THE INDUSTRY AND THE ROAD AHEAD TO MEET GOVERNMENT ORGANIC RECYCLING TARGETS. JOHN MCKEW, AORA
Laying the baseline for the roadmap is the AORA Economic Contribution Report, launched in March 2020 and using data from 2018-19 when Australia’s overall organic recycling rate was 51.5 per cent. South Australia is currently achieving the highest organics material recycling rate at 78.9 per cent (equivalent to 722 kilograms per person per year), followed by the Australian Capital Territory, New South Wales, Victoria, Queensland, Tasmania, Western Australia, and the Northern Territory. The industry provides 4845 jobs, pays more than $366 million in wages and salaries, and has a collective turnover of more than $2 billion. In 2018-19, Australia produced 14.6 million tonnes of organic waste, of which 5.6 million tonnes went to landfill, 7.5 million tonnes were recycled, and 1.5 million tonnes recovered as energy. Of the 7.5 million tonnes of organic material recycled, food organics accounted for seven per cent, garden organics 42 per cent, www.wastemanagementreview.com.au
LAST WORD
NATIONAL EXECUTIVE OFFICER, EXPLAINS.
Launched at the 2022 Australian Organics and Recycling Association (AORA) conference by Peter Wadewitz OAM, AORA Chairperson, the roadmap is a comprehensive analysis of the industry now, how it is developing to meet government targets for organic recycling rates and the benefits that will be derived by the Australian economy, environment, public and industry if the targets can be met. At its core, Vision 2031 asks two questions: How do we get to 80 per cent recycling of organics by 2026 and 95 per cent by 2031; and how do we remove the obstacles to growth?
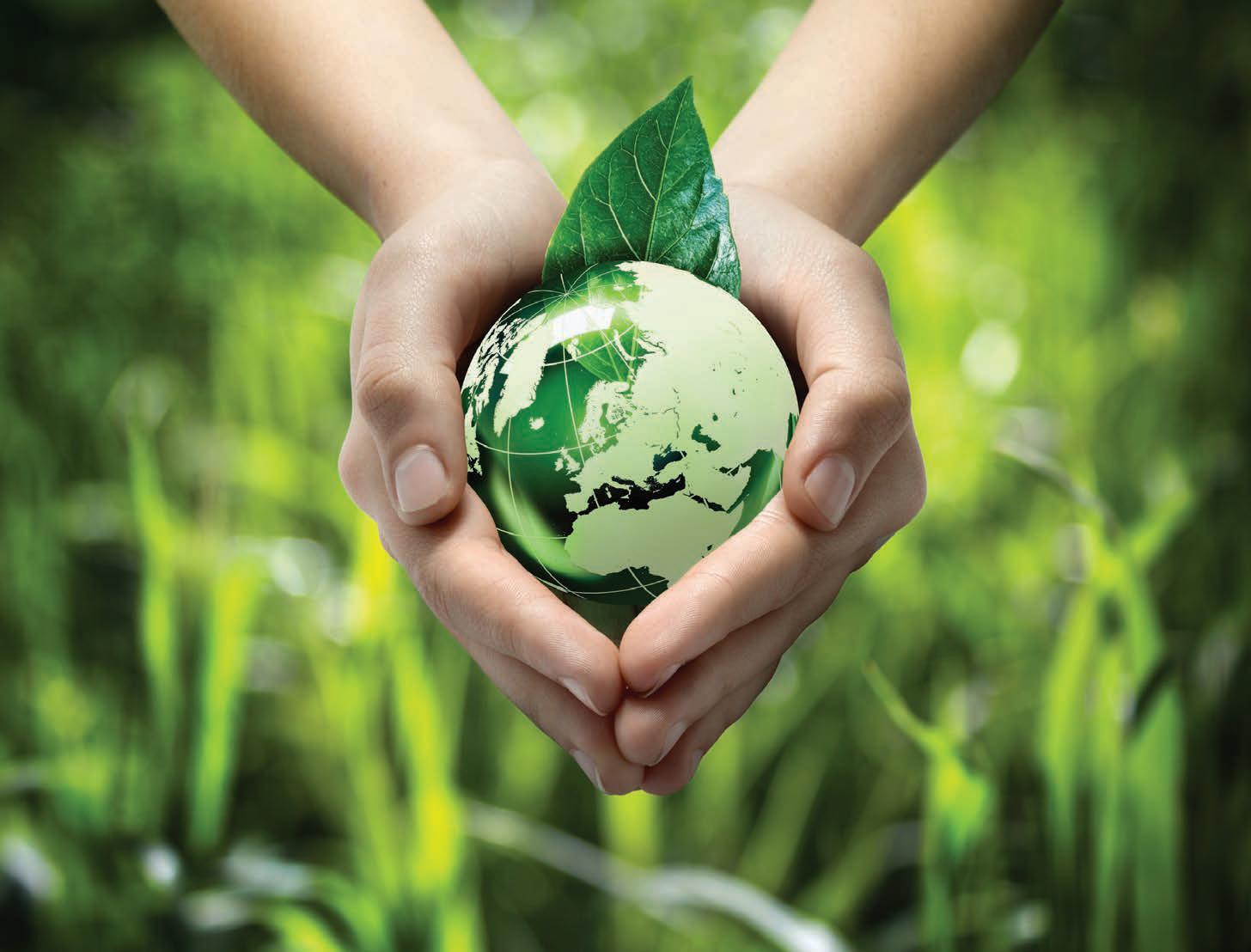

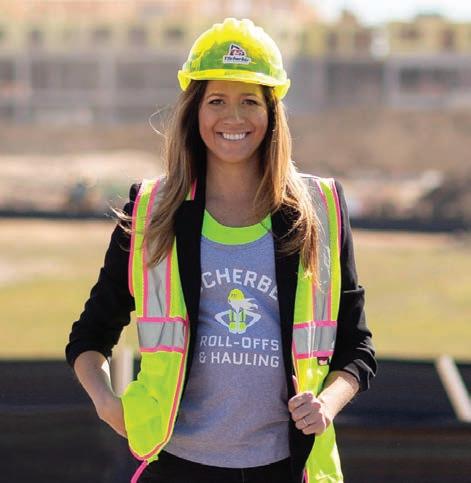
The roadmap is broken down into seven key sections: context, starting point, possible future, inputs, industry, and outputs, culminating in the roadmap itself. The roadmap highlights the importance of all three levels of government working together with the industry. It doesn’t seek to reinvent the wheel but looks at the key objectives of the National Waste Policy, of which 11 of the 14 are central to the future of organics recycling. The risk to the industry is not an off-shore decision, such as China’s National Sword policy, or export bans, the risk is siloed decisionmaking within the different arms of Governmentsgovernment. are a key player in moving finished product to end users. Put simply, governments and the industry must work together to do better. Vision 2031 is a roadmap to doAORA,so. on behalf of the Australian organics recycling industry, commits to achieving an 80 per cent organics recycling rate nationally and in each jurisdiction by 2026, and 95 per cent by 2031 at the latest.
The two major end use markets are urban amenity (52.5) and intensive agriculture (26.2). The industry’s environmental contributions are just as impressive as its economic contributions.
LAST WORD 78 / WMR / September 2022 Output products of the organics industry include composted soil conditioners, soil and soil blends, composted mulches and pasteurised mulches.
Greenhouse gas savings from organics recycling tops 3.8 million tonnes of carbon dioxide (CO2) annually, equivalent to planting 5.7 million trees or taking 876,663 cars off the road. If all states and territories achieved an 80 per cent recycling rate for organic material, the industry would generate 2682 extra jobs paying $203 million in wages and salaries, an extra $1.7 billion in sales, an additional $1.6 billion in supply chain opportunity and $401 million in industry direct value toward the Australian economy. If the economics of this were not compelling on their own, the environmental considerations are equally persuasive – an additional 2,102,377 tonnes of greenhouse gas emissions would be saved, equivalent to 3,144,006 trees planted or 486,021 cars taken off the road each year. That is without the considerable benefits to improving soil quality, water retention, drought mitigation, and the positive impacts on soil salinity and soil compaction as a result of the application of the industry’s products.
Vision 2031 is available to download at www.aora.org.au
The industry’s major output products include composted soil conditioners (40.1 per cent), soil and soil blends (33.7), composted mulches (11.2) and pasteurised mulches (10.7).
timber 14 per cent, other organics 19 per cent and biosolids also at 19 per cent (rounded percentages).
To realise the potential economic and environmental benefits, the report clearly notes two conditions have to be met: The right policy settings from governments, and industry capacity to take up the opportunities. Neither of these conditions areAORAinevitable.isalready well established and dedicated to working with all levels of Australian government to secure consistent and appropriate policy settlings for organics recycling. It is why AORA delivered its second industry study, the second supporting document to Vision 2031, addressing industry capacity. Vision 2031 is neither an academic study nor a technical analysis of organic recycling in Australia. It has been designed and written to capture the practical knowledge and common sense of the Australian Organics Recycling Industry and to show a clear and achievable path to its significant growth and opportunities.
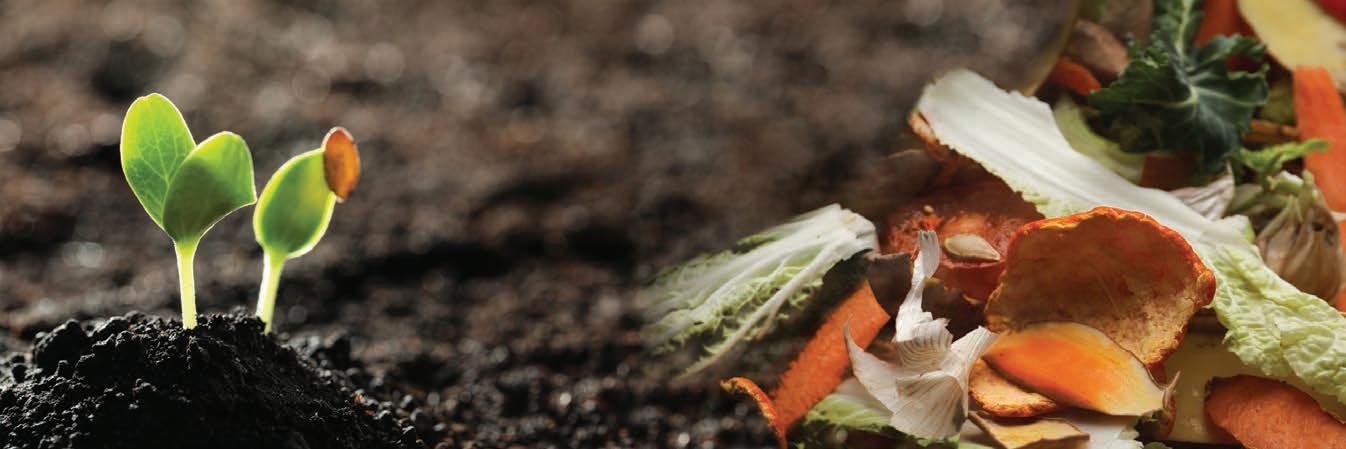
STG WASTE TRUCKS INDUSTRY LEADING TECHNOLOGY www.stgglobal.net marketing@stgglobal.net1300 998 784 - Australia-wide service support and parts - Optional locked in-service packages - Guaranteed buy backs CONTACT US TO BOOK A DEMO INTERFACEIPAD ALL IN ONE SINGLE DISPLAY SSAB MANUFACTURED,SWEDISH AWARD-WINNING STEEL AUSTRALIAN SUPPLIER OF WORLD-CLASSCOMPONENTSHYDRAULIC
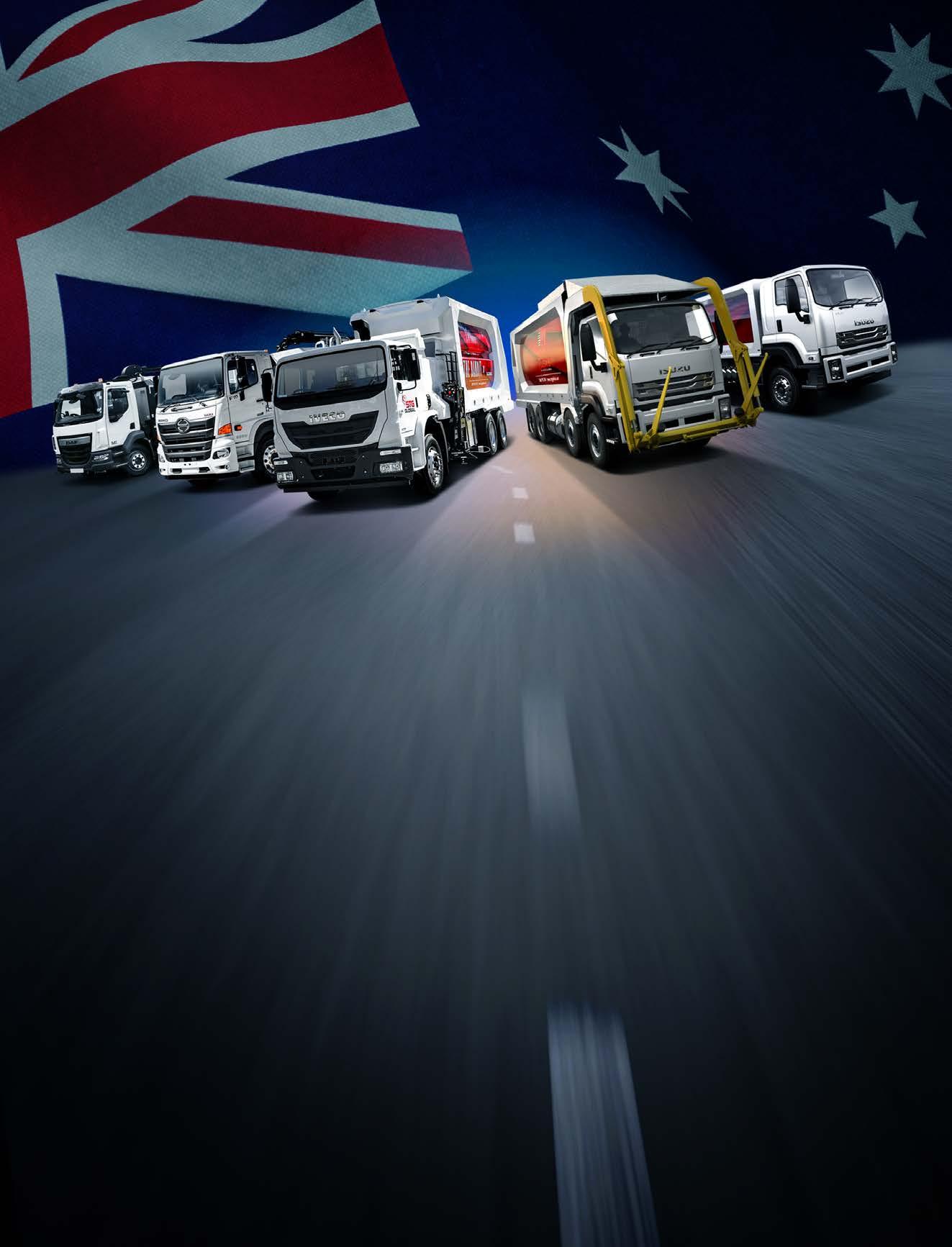

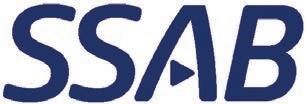
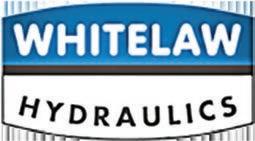
Komptech CEA
is a leading supplier of machinery and systems for the treatment of solid waste through mechanical and mechanical biological treatments, as well as the treatment of biomass as a renewable energy source. Komptech CEA is proud to provide innovative solutions for handling waste and biomass. Komptech CEA’s extensive range of products cover all key processing steps in modern waste handling. At Komptech CEA the focus is always on innovative technology and solutions ensuring maximum benefit to the customer. Like to know more? why not speak to one of our team today? TERMINATOR Where Function Meets Technology A slow-running, single-shaft shredder suited to all types of CRAMBOwaste. Less Fuel, More Power Ideal for shredding all types of wood and green cuttings. MULTI STAR Screening with a Star Makes waste wood and biomass processing highly efficient. TOPTURN X The Ideal Combination of Performance and Design With a sturdy frame, powerful hydraulics and large drum, the Topturn X is ready to handle any work situation. NEMUS Robust and Reliable Combining the practice-proven virtues of its predecessors with new solutions for even greater AXTORperformance. Shredding and Chipping Made Easy One of the most versatile machines around for processing wood and green cuttings. SHREDDERS TROMMEL SCREENS STAR SCREENS WINDROW TURNERS
DELIVERING1300komptechcea.com.au788757A GREENER FUTURE
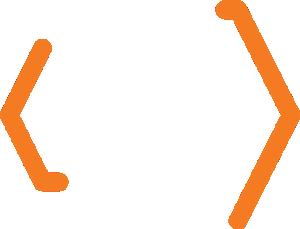
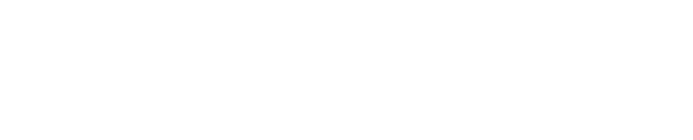
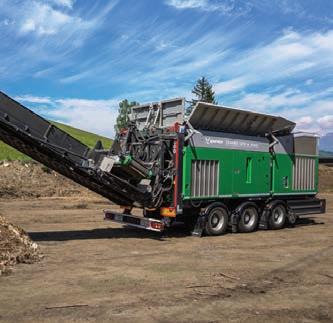

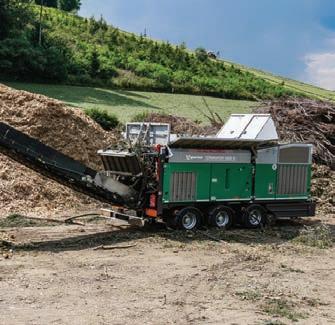
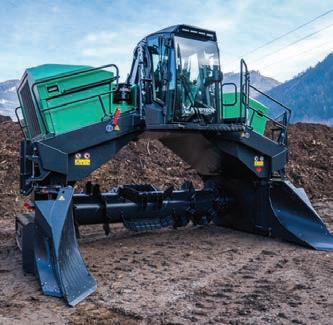
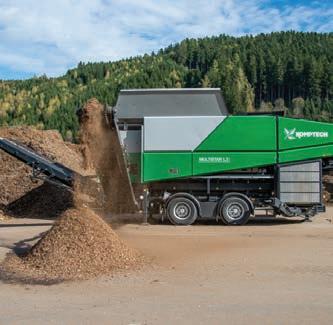
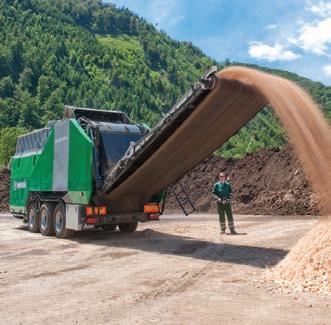