FEATURES
Organics opportunities lost found and future FOGO caddy liners – the verdict is in A chip off the old block
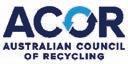
Advanced Energy Recovery Centre is safe for local communities
Organics opportunities lost found and future FOGO caddy liners – the verdict is in A chip off the old block
Advanced Energy Recovery Centre is safe for local communities
George Hatzimanolis, Repurpose It CEO, had a vision to create a resource recovery precinct unlike any other. Five years on and his vision is a reality.
REMONDIS came to Australia in 1982, with 35,000 plastic wheelie bins and a contract with Penrith City Council. Today, we support 24,000 commercial and industrial customers with waste collection, processing, recycling and circular economy solutions, right across Australia. We’ve grown to 1,100 employees across 38 branches from Weipa to Coolaroo, Jandakot to St Marys. We rise to the challenge of complex waste streams and ambitious resource recovery goals and we have the scale and expertise – both local and global – to make a difference. Best of all, we love what we do.
Composting will be the frontrunner in helping Australia reach national landfill diversion rates for organics, according to NuGrow’s Jacob Wilson.
34
George Hatzimanolis, Repurpose It Chief Executive Officer, had a vision to establish a resource recovery precinct unlike any other. Five years on and his vision is a reality.
“LOOKING AT WHAT WE’VE DONE, I’M QUITE PROUD OF THE FACT THAT WE’VE BEEN ABLE TO SUPPORT THE TRANSITION TO A CIRCULAR ECONOMY OF MATERIALS THAT HADN’T BEEN THOUGHT OF BEFORE.”
- George Hatzimanolis, Chief Executive Officer, Repurpose It
Turmec is shoring up its place in Australia’s recycling sector with a commitment to a local workforce. 64
OPPORTUNITIES
NWRIC members take stock of a challenging year and prepare for renewed focus on waste targets. 17
AND FUTURE REMONDIS discusses the key moves to reducing organic waste to landfill in Australia. 20
AORA says composting will lead the way in helping Australia reach landfill diversion rates. 23
Source Separation Systems has a solution for councils to get FOGO caddy liners on a needs basis. 26
Manco has developed a new collection solution specifically for food waste. 29
Compost Revolution delivers organics behaviour change. 32 HEAPS
Radicle Agriculture’s compost technology is generating interest.
Green Care Mulching’s Russell Norton discusses his business, and its partnership with equipment distributor CEA. 36
The team at SOILCO reflects on a big year of growth for the family-led business and what’s on the horizon. 38
Komatsu Forest has stood beside an Australian timber contracting company through three generations.
EMISSIONS
NSW EPA compares the emissions impacts of food waste technologies. 40 MOVING
Enviropacific is improving environmental outcomes for infrastructure projects. 43
Quality and safety are powerful drivers when it comes to choosing waste recycling equipment.
Wastech Engineering has signed a deal to distribute McCloskey waste recycling equipment.
Celebrate all the winners of the 2022 Waste Innovation and Recycling Awards.
Introducing a comprehensive resource tool for anyone involved in waste and recycling. 58
74
Waste Expo Australia Event Director Samantha Martin reflects on a successful event. Regulars 77 LAST WORD
ECO
Veolia releases the findings of an Environmental Impact Statement for its proposed Advanced Energy Recovery Centre. 60
Ecocycle is making inroads with its vision to make Australia cleaner.
Sometimes in life you meet people who have a profound effect on you.
In the past few months, I’ve had the privilege to interview people in the waste, recycling and resource recovery sector who, to paraphrase Jack Nicholson’s quote from the 1997 movie As Good as It Gets, make me want to do better.
At a time when the world appears to be full of wannabe influencers, we have the real deal – people who can affect real change for the environment and strive to do so, not because they want to increase their followers or ‘likes’ on social media, but because they believe there is a better way.
Waste warrior Professor Veena Sahajwalla; Jessica North, Co- Chief Executive Officer of LGI; and George Hatzimanolis, Repurpose It Chief Executive Officer, to name just a few.
George and Repurpose It are synonymous with forward thinking and viewing waste as a resource – seeing opportunity where others see roadblocks.
I spoke with George for this month’s Waste Management Review cover story and got an insight into the company, its founder and where-to from here. Days later, George was named the Leader of the Year at the 2022 Waste Innovation and Recycling Awards.
It’s another feather in the cap for a company which started just five years ago with four people and high ambitions.
But George is not alone. The awards were a chance to recognise the innovation, leadership, and hard work across the entire industry from advanced recycling facilities to multi-lingual education programs and high-impact waste and resource recovery projects.
This year’s awards generated record interest and high calibre nominees, providing judges with a tough choice.
In this edition we feature all the winners from the night. It feels like a fitting way to finish off a year of trials, tribulations and triumphs.
Have a great holiday period and I’ll see you all in the new year.
CHIEF OPERATING OFFICER
Christine Clancy christine.clancy@primecreative.com.au
GROUP MANAGING EDITOR
Sarah Baker sarah.baker@primecreative.com.au
MANAGING EDITOR Mike Wheeler mike.wheeler@primecreative.com.au
EDITOR
Lisa Korycki lisa.korycki@primecreative.com.au
JOURNALIST
Leon Cranswick leon.cranswick@primecreative.com.au
DESIGN PRODUCTION MANAGER
Michelle Weston michelle.weston@primecreative.com.au
ART DIRECTOR Blake Storey blake.storey@primecreative.com.au
DESIGN Louis Romero, Kerry Pert
BRAND MANAGER Chelsea Daniel-Young chelsea.daniel@primecreative.com.au p: +61 425 699 878
CLIENT SUCCESS MANAGER Justine Nardone justine.nardone@primecreative.com.au
HEAD OFFICE
Prime Creative Pty Ltd 379 Docklands Drive Docklands VIC 3008 Australia p: +61 3 9690 8766 f: +61 3 9682 0044 enquiries@primecreative.com.au www.wastemanagementreview.com.au
SUBSCRIPTIONS +61 3 9690 8766 subscriptions@primecreative.com.au Waste Management Review is available by subscription from the publisher. The rights of refusal are reserved by the publisher
All articles submitted for publication become the property of the publisher. The Editor reserves the right to adjust any article to conform with the magazine format.
Waste Management Review is owned by Prime Creative Media and published by John Murphy. All material in Waste Management Review is copyright and no part may be reproduced or copied in any form or by any means (graphic, electronic or mechanical including information and retrieval systems) without written permission of the publisher. The Editor welcomes contributions but reserves the right to accept or reject any material. While every effort has been made to ensure the accuracy of information, Prime Creative Media will not accept responsibility for errors or omissions or for any consequences arising from reliance on information published. The opinions expressed in Waste Management Review are not necessarily the opinions of, or endorsed by the publisher unless otherwise stated.
In an industrial estate in Melbourne’s north, Repurpose It is transforming a concrete jungle of debris into new resources.
The company has built a reputation on thinking outside of the box and finding ways to give new life to waste. It has been linked to some of the biggest building projects in Victoria and recognised for its readiness to meet challenges of the future.
But it’s not until you visit the Cooper Street site that you get a true sense of the scale of what the business is achieving. Spread across 230 ares in Epping, Repurpose It could warrant its own post code.
Within five years, the company has grown from four employees to 200 and cemented its environmental credentials. Along the way there’s been two Premier Sustainability Awards, a Westpac Top 20 Business of Tomorrow award and in October 2022, the company was
recognised as one of Australia and New Zealand’s Most Innovative Companies by Australian Financial Review.
It’s a meteoric rise by many standards. For those who know or work with George Hatzimanolis, Chief Executive Officer of Repurpose It, the acclaim comes as no surprise – he is driven to make a difference.
By his own admission, George has always had high ambitions to establish a resource recovery precinct that would be a reference not only for Victoria, but Australia. But he admits he never envisaged five years ago that the company would grow with such momentum.
“It was the vision from day one to introduce best practice technologies,” he says. “We had a fantastic site at Epping with a large footprint, great buffers and great access. There was an opportunity that we could set up something of scale.
“But if we were going to do it, we had to set it up with the best technology available.”
There’s an often-quoted proverb that timing is everything.
The introduction of Repurpose It to the resource recovery sector coincided with Australia’s recognition that it had a recycling crisis, the introduction of the China National Sword Policy which limited waste imports, and the beginning of Victoria’s Big Build infrastructure boost.
George says that combination gave Repurpose It a strong catalyst to grow the business with scale.
“We knew we timed the venture well but five years in, it’s bigger than we thought we would be at this stage.”
From the outset, Repurpose It aimed to tackle several waste streams including construction and demolition (C&D) waste, and organics. It began in 2017 receiving and processing street
sweepings that were previously destined for landfill.
At the time, C&D, and excavation waste more broadly, had the highest recovery rate of any waste stream. George says he knew that if Repurpose It was going to enter a mature market it needed a point of difference.
“We knew we needed to be innovative and do something nobody had done before,” he says. “Rather than compete on volume and scale we were challenging the more problematic materials and doing it differently.”
In 2018, Victorian Minister for Energy, Environment and Climate Change Lily D’Ambrosio officially opened Australia’s first wash plant at Repurpose It’s Epping site.
George says the CDE wash plant revolutionised the way waste was managed, allowing the company to supply in-demand materials back to the construction industry, while preserving the environment.
CDE has since installed several plants across Australia.
“In many ways we were pioneers for that type of resource recovery of excavation soil more broadly across the nation,” George says. “Looking at what we’ve done, I’m quite proud of the fact that we’ve been able to support
“It’s not just about our capability but the industry more broadly. That’s something that does drive us forward.”
While organics recycling was always an ambition, it took longer to develop.
the transition to a circular economy of materials that hadn’t been thought of before.Organic waste collection tenders are traditionally long-term contracts and Repurpose It had to wait for years for a tender to open.
It was fortuitous that the first tender available was in 2020 for the City of Whittlesea – in the heartland of Repurpose It.
“That was a must-win tender,” George says. “We really wanted to get going in organics and it was important that we cemented our position here in Epping.
“It took a few years, but that Whittlesea tender kicked off our organics journey and we’ve since invested quite a bit in that space.”
That investment includes the 2021 purchase of Bark King, the largest supplier of bark mulch to Victorian landscaping businesses; preparations for the construction of an in vessel composting facility; and the opening
earlier this year of a 3000-square metre decontamination hall for packaged and unpackaged food waste. At full capacity the facility will process up to 200,000 tonnes of food waste annually.
In 2022, the Environment Protection Authority also approved plans for Repurpose It to build an anaerobic digestor that will produce energy from organics. The company is now keen to secure feedstock for the facility.
George’s “pet project” will eventually produce enough biogas to take Repurpose It off the grid.
Looking back, it’s a long way from the early days when George often manned the weighbridge and Anthony van Schaik, Co-Founder and Director, was on the front-end loader.
But the company has always taken the philosophy that you have to be in it to win it. It was that conviction that led to
entry into the Westpac Business Awards in 2018.
George says they were batting above their weight, but only two years into operation Repurpose It was named in the top 20 of 2500 applications in the Business of Tomorrow award.
“That really was recognition that our willingness to invest in Australian first technology and to bring best international practice to the country was going to be well supported,” George says.
“The credibility and being able to build on our brand as a result of that recognition was important to keep the momentum in the early stages.”
The Westpac Awards were followed by two Premier Sustainability awards, a Sustainability Victoria grant, and the Chair’s Award for the Northern Business Achievement Awards.
All have played a role in building Repurpose It’s brand, its relationship with customers, and attracting talent to the business.
As the company’s capabilities have expanded, so too has the expertise of employees. The pay roll now includes specialist engineers, environment teams, data scientists and laboratory technicians.
“Attracting talent is a lot easier now than it was in 2017 with George and a wild idea,” George laughs.
“We’ve been fortunate to find excellent talent in specialist engineers and environment teams through to finance and marketing. We’ve got a broad range of skills in the business now.”
While there has been plenty of success, George points out these ventures didn’t come without stumbling blocks. He says the company didn’t always get it right.
“If you don’t have a huge list of failures, I’m not sure you can call yourself innovative,” he says.
At Repurpose It, innovation doesn’t just happen. It takes discipline. A strong innovation framework is built into the organisation and project teams are encouraged to stay connected
with international developments and best practice.
It’s by giving a range of people exposure to what’s happening globally that the company can look at best practice not only in technology but in market conditions and how to apply them in Australia.
George says Australia has got some momentum building in the resource recovery sector but there is still work to be done. A recent survey commissioned by Repurpose It found that there is a lack of confidence in recycling infrastructure.
“We need to let people know that when they make the effort, at the back end there are facilities like ours and others in the industry that are ensuring material is being recycled,” he says.
“The more we build that confidence, the more uptake we’re going to get to shift toward a circular economy.”
A circular economy was core to Repurpose It’s values long before Australia’s national waste plan was enacted.
George describes the national targets as ambitious, but much needed.
While industry is reacting and building capability to reach the 2030 target of 80 per cent diversion from landfill, George says there are policy and regulatory challenges and not enough momentum to set up a logistics network and collection chain.
For its part, Repurpose It will continue its vision to eliminate waste and pollution through closed loop resource recovery with a renewed focus on value adding to refine its products.
“I think the momentum we’ve got and the brand we’ve got has been fundamental for the success of Repurpose It,” says George. “But it also sets a benchmark for us to maintain.
“We need to continue to think outside the square and bring new technology to Australia. It’s full steam ahead. We’re about to embark on an exciting journey.”
For more information, visit: www.repurposeit.com.au
NATIONAL
RECYCLING
MEMBERS TAKE STOCK OF A CHALLENGING YEAR AND PREPARE FOR RENEWED FOCUS ON THE NATIONAL WASTE TARGETS. RICK RALPH, CHIEF EXECUTIVE OFFICER, EXPLAINS.
The National Waste and Recycling Industry Council (NWRIC) is the principal business council representing international and national business owners of the sector. Our members’ investments include landfills, resource recovery facilities, firming power facilities, all forms of collection services and a comprehensive range of secondary reprocessing/remanufacturing operations.
Council members directly employ more than 16,000 Australians in more than 725 specialty industry-owned assets.
In 2018 the National Waste Policy was adopted, followed closely in 2019 by the National Waste Action Plan.
Ambitious targets and objectives were agreed, and all states and territories are now focused on those deliverables. Unforeseen subsequent challenges such as fire and flood disasters and the COVID-19 pandemic
provided a huge distraction to the waste policy agenda.
As we realign our sights to the policy agenda of the newly elected Federal Government and both Victorian and New South Wales election results, it is prudent we take stock and focus on what is important to all stakeholders, communities, elected representatives and our industry more broadly.
Critically if the policies impacting our industry are to be realised, we must identify and remove the roadblocks and regulatory disconnects that cause us to fall short of the Action Plan targets.
We must take affirmative action to harmonise current definitions used to describe and report what the sector does. We need effective regulations and environmental standards that are consistent across all borders to ensure the data
industry reports is accurate and aligned to both federal and state agendas. We cannot plan or manage in the future what we cannot measure.
Our industry must have the confidence its investments are secure and that we have the social licence to build and operate facilities that support these key government objectives without fear of sovereign risk or other political interventions.
This is an ongoing business challenge. Importantly we must maintain a robust, dynamic and forward-looking industry that supports communities expectations, including climate change and emissions targets, lowering our environmental footprints, and leaving a better world for future generations.
We want to provide a true benchmark for improved performance that others aspire to follow. We need to build robust and
genuine trust that the Australian waste and secondary resources industry is world’s best, innovative, and underpins the transition to a circular economy environment.
As we say good bye to another year that has presented many business challenges, we need to embrace tough conversations in 2023 that will realise these essential reforms ensuring we can deliver the aspirations set out in the National Waste Action Plan to, achieving its 80 per cent diversion targets and contributing significantly to achieving the nation’s 43 per cent emissions targets by 2030.
The New South Wales EPA recently published the independent review of the Resource Recovery Framework.
Commissioned in 2021 by the EPA and delivered by independent reviewer Dr Cathy Wilkinson of Monash University, the review outlines 22 recommendations to help refine and strengthen the framework.
The recommendations cover four key areas including: improved administration and decision making, the definition of waste and enhancements to the regulatory framework, enabling high quality materials to facilitate circularity, and improving approaches to known and emerging contaminants.
Dr Wilkinson’s recommendations include making processes for resource recovery order and exemptions clearer, seeking the advice or independent technical experts by establishing a panel or panels, investigating pathways for ‘end-of-waste’ outcomes to exclude suitable materials from the waste regulatory framework, and developing a resource recovery innovation pathway to support new and innovative technology and processes.
Tony Khoury from the Waste Contractors and Recyclers Association (WCRA) of NSW stated: “WCRA supports the findings and recommendations that have been made, which, if delivered, would benefit the industry, the NSW EPA and
the community. The review is an important first step in the process towards creating a more effective resource recovery framework that can better support a circular economy.
“It is clear from Dr Wilkinson’s report that reform is needed if NSW is to safely encourage and grow an efficient circular economy.
In his review of the Wilkinson report, Ross Fox, Principal of law firm Fishburn Watson O’Brien, commented “The findings and recommendations reflect what is widely understood in the industry. The regulatory framework put in place in 2008 is showing its age in 2022.”
In relation to the extent of the changes, Fox said the terms of reference stopped short of a wholesale review of the policy and legislative framework for resource recovery.
WRISA Waste and Recycling Industry South Australia (WRISA) has initiated an industry-led project ‘Boosting recycled material use in infrastructure assets’.
The project is a collaboration between the Institute of Public Works Engineering (IPWEA), WRISA and the Local Government Association of South Australia (LGA), with funding from the Green Industries SA Circular Economy Market Development Grant.
The project will build collaborative links, extend knowledge, address barriers and give practitioners confidence to extend their use of recycled materials into infrastructure assets.
Asphalt, concrete, steel, glass, tyres, plastics, PVC and organics will all be included and their potential use in more than 200 assets including roads, buildings, and outdoor furniture will be assessed.
Jacqueline Balston, Director of Sustainability, IPWEA, says the association is excited to be working with project partners to increase the uptake of recycled materials, introduce circular economy processes and reduce waste to the environment.
Jim Fairweather, WRISA President, says the resource recovery industry contributes significantly to the South Australian economy and increasing the uptake of recovered content materials will enable it to grow providing more jobs and beneficial economic activity while delivering a great outcome for the environment.
The recently released Australia’s Local Government 2021 National State of the Assets Report identified that Australian local government controls a $523 billion dollar asset portfolio that is growing at a rate of 6.4 per cent and being consumed at a rate of 1.6 per cent per annum. It is projected that 60 to 70 per cent of the 2050 infrastructure is not yet built.
These two elements combined make it clear that the infrastructure sector has enormous potential to reduce, reuse and recycle waste resources while at the same time reducing the impacts of climate change and demand on water and other raw materials.
WRISA is also undertaking an economic analysis study to better understand the financial contribution currently made by the waste and resource recovery (WARR) industry in SA and the potential for growth under different solid waste levy investment scenarios.
The study has already identified the SA WARR industry as an employer of more than 3700 jobs, and contributing more than $629 million to the state’s economy.
“With the aligned state government and industry objectives to increase resource recovery and circular economy outcomes WRISA is advocating for the state to unlock those solid waste levy funds collected and invest in the waste and resource recovery sector,” says Adam Gray, WRISA Executive Officer. “This WRISA economic analysis shows that the industry has significant potential to create more jobs and deliver innovative sustainability solutions for the benefit of the state,.”
For more information, visit: www.nwric.com.au
When REMONDIS started Australia’s first fully enclosed in-vessel Organic Resource Recovery Facility at Port Macquarie 20 years ago, many locals viewed the project as ambitious, at best.
It turned out to be a milestone in waste management Down Under, proof that there were smarter ways of dealing with organics including garden waste and food scraps, says Jochen Behr, REMONDIS Australia Chief Executive Officer.
These days the facility receives up to 50,000 tonnes of organics annually, including kerbside collection FOGO
waste and garden waste from homes, businesses and municipal precincts. About half is broken down through biological degradation and evaporation during the composting process while the other half is sold to market as compost to improve soil health and fertility.
Less than a per cent of material that can’t be recycled ends up as landfill – a stunning turn-around from the days of all local organics ending up in holes in the ground, Jochen says.
Twenty years ago, few might have
thought that the New South Wales and Commonwealth governments would eventually invest millions of dollars into such organic waste facilities.
Earlier this year REMONDIS’ Lake Macquarie Organics Resource Recovery Facility at Awaba secured two million dollars in funding to future-proof its food and garden waste recycling operation.
Awarded under the Commonwealth’s Food Waste for Healthy Soils Fund and matched dollar-for-dollar by the New South Wales Environmental Trust, the money is to support expansion work that will lift processing capacity to
60,000 tonnes and assure operations for another 20 years.
Despite such successes, REMONDIS is concerned that Australia is lagging when it comes to world’s-best organic waste management.
“These facilities have exceeded themselves in every conceivable way,” Jochen says. “The local governments, homes and businesses in both localities have proven to be keen to divert their organics into the circular economy, and we’re sure that will be the case as we prepare to establish similar facilities in other areas of the country.
“We underestimated demand at Awaba, which reached capacity ahead of time, triggering our need to expand. With that in mind, it’s hard to believe Australia-wide organic waste management is yet to catch on in any way that can be compared to what’s happening in other developed countries.”
REMONDIS has operated organic recycling facilities globally for many decades, with more than 85 facilities developed to date.
Jochen attributed the relatively slow evolution in Australia to start-up cost burdens and concerns about waste supply. He says that to set up organic recycling
centre infrastructure, there needs to be guarantees around input volumes, with contracts in place from councils who are the main waste generators.
“The initial outlay can be costly, so you’ve generally got to be a big player with experience behind you, which REMONDIS has in spades,” Jochen says.
“Then there’s the matter of contractual underpinnings to ensure returns on investment. From our own experience, local government support has been vital. The local councils have given us the contractual certainty and security we need to make the operations work over the long term.”
Australia produces about 14 million tonnes of core organics waste annually, with half still going to landfill.
Australia’s organics recycling rate is about 49 per cent, and there are geographical disparities, for example, the rate is 75 per cent in the Australian Capital Territory and just one per cent in the Northern Territory, according to the Department of Climate Change, Energy, the Environment and Water.
“If Australia is to halve the amount of organic waste sent to landfill by 2030, there’s an onus on everyone from government and industry through to people at home to recognise and embrace organic recycling for what it is – a waste
management no-brainer and gamechanger,” Jochen says.
Alex Hatherly, REMONDIS Australia
Chief Technical Officer, cited organics-tofuel conversion as a significant missing link in Australia’s waste management landscape.
“REMONDIS alone has 20 conversion facilities in Europe that generate biogas and bio methane from organic waste, which can be used for things such as electricity production and truck fuel,” Alex says.
“Despite REMONDIS being willing and able to advance anaerobic digestion options in Australia, the reality is Australia’s regulatory framework isn’t ready to accommodate such technology. That’s because of a lack of clear regulations around digestate and long-term commitments for energy off-take.”
Alex says given that it costs more than $20 million to roll out such a plant, no commercial player would be game to contemplate such expenditure until governments put up anaerobic digestion ‘open for business’ signs.
E
Jan Duebbelde, REMONDIS Australia National Organics Manager, says that even simpler actions could make big differences in terms of Australia’s organic waste management success and overall landfill reduction targets.
“Implementation of a kerbside FOGO collection for every household will be the best chance to achieve ambitious targets,” Jan says. “About 50 per cent of organics are still ending up in red bins because some councils don’t have green bins.”
Another key is avoiding organics contamination by ensuring materials are cleanly separated.
“Education is a part of the solution –every dollar spent reminding people on what goes where, is a dollar well spent.”
For more information, visit: www.remondis-australia.com.au
Composting will be the frontrunner in helping Australia reach national landfill diversion rates for organics, according to Jacob Wilson, Chief Commercial Officer of NuGrow.
Jacob heads up the Queenslandbased company which operates several composting facilities across the state, including a flagship facility in Ipswich. It was established in 2007 to provide Queensland farmers and landscapers with an alternative to chemical-based fertilisers.
The company has developed technologies that reduce the amount of waste going into landfill by converting it into sustainable compost and has contracts to receive food waste, green waste and garden organics from various local government areas.
Jacob says that as the nation looks for ways to remove waste from landfill, organics is the “low-hanging fruit” with 40 to 50 per cent of organic material compostable in the redtop bin.
“One of the things we like about composting is that it’s quite resilient,” Jacob says. “We’re not having to work to a maximum capacity, and it allows for a vast variability in feedstock that we can control.
“It’s an old process but the science around it is developing and it provides significant benefits back to the agriculture industry.
“Food organic and garden organic (FOGO) recycling is one of the easiest ways to reach our emissions and recycling targets in Queensland.”
The Queensland Government has set a target to achieve zero net emissions by 2050 and an interim emissions reductions target of at least 30 per cent below 2005 levels by 2030.
According to the Queensland Organics Strategy 2022-2032 organic waste is one of the main types of waste sent to landfill and makes up about half of what Queenslanders throw away in their rubbish bin each week. When it breaks down in a typical landfill it releases methane, a greenhouse gas with
an estimated global warming potential of between 28 and 36 times that of carbon dioxide.
The report states that key objectives for Queensland by 2030 are to halve the amount of food waste generated; divert 80 per cent of the organic material generated from landfill; and achieve a minimum organic recycling rate of 70 per cent.
However, the Australian Organics Recycling Association (AORA) Australian Organics Recycling Industry Capacity Assessment: 2020–21 identified that Queensland does not currently have the capacity to meet the 70 per cent target.
The Queensland Waste and Resource Recovery Infrastructure Report also found that five of the eight Queensland regions have insufficient, or potentially insufficient, organic waste processing capacity to meet waste and resource recovery infrastructure needs from 2020 to 2050. Strategically located infrastructure and services are needed to increase the state’s capacity to collect and process organic material.
Queensland’s organics strategy requires improved organics management across the state, with councils to determine the most appropriate solutions for their needs by 2023.
Jacob says the opportunity is ripe for regional and south-east Queensland councils to take action.
NuGrow previously undertook a FOGO trial with Ipswich City Council and now has a collection service up and running.
The company is currently conducting a FOGO trial within Rockhampton and is working with several of 19 council areas that will be affected by the reintroduction of the Queensland landfill levy.
Jacob says NuGrow is providing councils with feasibility studies that look at organics processes that could work for them. These studies consider the council’s demographics, geography, waste streams and contaminants and the risk that poses.
“It’s important that councils are engaging with industry and providing
real data in relation to their waste,” he says. “Councils shouldn’t just be looking at the headline tonnage of diversion, it has to be the whole supply chain. The headline numbers don’t necessarily give you the full story.
“The higher the contamination the less chance of reusing that material. If two per cent of a waste collection was contaminated that’s two per cent that had to go to landfill.”
Jacob predicts that as target dates loom there will be an uptake in the rollout of garden organics or food organics recycling across municipalities which will create what he describes as a “whiplash” affect for the supply chain of businesses involved in the waste collection.
“At the moment there is a gap between what the department wants, what local government wants and what the industry wants,” he says. “There needs to be more collaboration.”
Australian Organics Recycling Association National Executive Officer, John McKew, concurs.
NuGrow is providing councils with feasibility studies that look at organics processes.
“NuGrow, as an AORA member, is at the forefront of meeting the challenges of organic recycling in Queensland. The disconnect noted by Jacob between what the department wants, what local government wants and what the industry wants, is a key consideration for AORA as the Australian organics recycling industry’s peak industry body.
“We are all seeking the same outcomes from different perspectives across the value chain, but we must collaborate, communicate and commit in a united way to make it work. Across the country right now, contamination, especially as it relates to FOGO is a major issue.
“AORA, through its members such as NuGrow, is committed to working to achieve the substantial benefits for all of our communities we know await from getting this right. AORA commends the efforts of NuGrow in Queensland for its work in highlighting the issues and its commitment to collaboration”.
For more information, visit: www.aora.org.au
IT’S OFFICIAL, CADDY LINERS ARE ENCOURAGED IN FOOD ORGANIC, GARDEN ORGANIC (FOGO) PROGRAMS WITHIN NEW SOUTH WALES. SOURCE SEPARATION SYSTEMS HAS COME UP WITH A SOLUTION FOR COUNCILS TO GET LINERS INTO THE HANDS OF RESIDENTS ON A NEEDS BASIS.
The New South Wales Environment Protection Authority recently released a statement legislating its position on what can and can’t be placed into food organics, garden organics (FOGO) programs.
The new rules are simple – FOGO programs can include food, garden organics, and liners, either compostable plastic caddy liners (Certified AS 47362006) or fibre-based caddy liners (paper).
Pet poo, food packaging (regardless of certifications), additional biodegradable bags, vacuum cleaner dust and dryer lint are all now banned.
While the speed of the changes has surprised many, the EPA says the ruling has been based on research that shows some of the banned items contain harmful chemicals.
It also states that compostable plastic kitchen caddy liners have been shown to help divert food waste from landfill by enabling easier and cleaner food waste collections for households and businesses.
A recent study by MRA Consulting quantified this benefit, finding councils that supplied liners had on average 30 per cent more FOGO capture than those without.
While the study noted that those councils not supplying liners did so to save costs, modelling showed that the avoided landfill gate fees for the additional food waste captured because liners were provided, resulted in savings well exceeding the cost of providing liners. Essentially, providing liners
improved the overall cost benefits of the program.
Peter Cruwys, Managing Director of Source Separation Systems, says the legislation provides a clear guideline for a best practice and simplified approach to FOGO, which will encourage consistency across the state, and potentially Australia.
Peter has been running FOGO programs nationwide for more than 10 years, often providing the company’s Compost-A-Pak liners. He believes providing liners is key to a successful FOGO program for councils and suggests that the new legislation will only increase the distribution of liners.
“The new rules for FOGO in NSW are exceptionally simple. It’s food and
garden organics only, and then liners,” he says.
“Liners are imperative given the increase in diversion they provide; however they are a key contamination point. That’s not surprising given customer confusion when they face the shelves and shelves of greenwashed hybrid bags in the supermarket sitting alongside those Australian Certified Compostable.
“When councils instead provide their preferred and trusted liners to residents, they can optimise diversion, nearly eliminate contamination, and save money. The key is getting liners into the hands of residents conveniently, particularly on a needs basis outside the annual distribution cycle.”
Peter says that as FOGO is embraced, councils are seeking a convenient way to provide residents with additional liners when they run out. The approach varies from council to council.
Some councils have heavily promoted the distribution of subsequent CompostA-Pak liners through their service centres and libraries. Peter says that some of these programs have had a flow-on effect of increasing library visits, engagement and borrowing.
“Alternatively, COVID-19 really fast-tracked our community’s willingness to engage and order online, and so our innovative new FOGO Ordering Portal is really being embraced,” he says.
Source Separation Systems has been building on its FOGO residential distribution experience and software with a new service to get caddy liners to residents when they need them.
The Source Separation Systems FOGO Ordering Platform is a customisable bolt-on solution that councils can imbed in their website to direct their residents to access additional Compost-A-Pak liners for use throughout the year.
It allows only those residents with predetermined eligibility to access either partially or fully subsidised liners or caddies from a chosen subset of products. The resident can choose to have the products delivered or pick up from listed local council hubs.
The portal is customised for each council, with branding and a unique experience depending on the eligibility, product limitation, subsidy settings and freight options chosen by each council.
Source Separation Systems supports the FOGO Ordering Portal with an in house logistics solution so all warehousing, storage, stock control, labour and program delivery costs are managed, allowing council teams to focus on engaging with their communities.
“The FOGO Ordering Portal technology, administration and logistics support that our team provides really does free up the councils to instead focus on critical community engagement,” Peter says. “The flexibility of the portal is even allowing councils to target community subsets such as multi-unit dwellings (MUDs) with more tailored programs, which is promising.”
Peter says that while MUDs are notoriously difficult to engage, the Portal allows councils to target specific groups and provide them with a convenient way to access FOGO liners and caddies if they opt in.
He says Source Separation Systems is currently working with a Melbourne council to target MUDs less than five storeys. “As with many industries, technology is improving the service experience and Source Separation Systems certainly believes it’s a key component to a successful FOGO program.”
For more information, visit: www.sourceseparationsystems.com.au
Australia’s National Waste Policy has set an ambitious target of introducing food organic garden organic (FOGO) collection services to households and businesses by 2023.
While organics processing has gained attention as the deadline looms, the policy will affect the entire supply chain, including councils and waste collectors.
Waste and recycling industries equipment manufacturer Manco Environmental has developed the Future Organics 12 (FO12), a
lightweight system specifically for food waste collection.
Jaclyn Vanderent, Manco Australia General Manager, says food waste collection vehicles are essential in any populated areas as they’re the most economical way of collection in high density urban environments due to their small footprint and large payload.
While advances in technologies such as hydraulics and electronics have made waste collection trucks more ergonomic and efficient over the years, and various
loading and unloading mechanics have reduced the work required of operators, not all trucks are well adapted to handling all types of waste.
“Municipalities and contractors need to ensure their capital investment in collection vehicles is cost effective and provides efficiency combined with a safe and ergonomic environment,” Jaclyn says.
The Future Organics 12 design is so uniquely geared toward food waste collection that a number of patents have been included. The body consists of two independently sealed compartments for front loading and storage.
Jaclyn says several issues need to be considered when planning a dedicated kerbside food waste collection, including the collection of 27-litre kitchen caddies, reflective of practices around the world. Ergonomic loading of the caddies has been a key component in the body’s design.
“Firstly, the loading hopper should be as low as possible, preferably not more than 800 millimetres from kerb height, and have good capacity, around 300 litres, to reduce dumping frequency into the main body to a minimum,” she says.
“Depending on the season, the food waste product can have a high moisture content of more than 65 per cent, that can lead to issues with obtaining good payload capacity and the possibility of leachate leakage.”
She says the Future Organics 12 addresses these issues.
MANCO HAS DEVELOPED A NEW COLLECTION SOLUTION SPECIFICALLY FOR FOOD WASTE COLLECTION.Offering an 800mm loading height into a 300-litre transfer bin, the Future Organics 12 can accommodate up to 20 caddie discharges before a lift is required. With a live drive hydraulic system, the bin tipping cycle can be completed in under 11 seconds, comparable to the traditional automated side loading arm.
Emptying into the front compartment automatically activates a 45 degree, 400 millimetres shaftless auger that transfers the food waste in under 15 seconds, discharging midway along the top of the body.
Jaclyn says this ensures that payloads can be achieved and, given the live drive hydraulic, the auger cycle can be completed on the run, saving valuable route time. The design also provides a sealed roof enclosure of the food waste, providing odour control along with
deterrents for birds and the like when on the route.
“A key performance metric of waste collection vehicles is the volume of waste they can feasibly store and transport because this increases the number of locations a vehicle can visit before needing to unload,” Jaclyn says.
Jaclyn says some people might question the use of high grade 316 stainless-steel. However, the acidic levels contained in food waste can pose a major problem when using traditional refuse body steels.
The Future Organics system comes standard as a full stainless or mixed stainless and polyethylene body both providing long service life in such a corrosive environment while allowing for a higher payload. The rear roof section opens automatically during the tip cycle, and with no rear tailgate there
is reduced risk of leachate leakage.
Jaclyn says Manco is so confident with this stainless-steel body that it offers an unconditional 10-year guarantee on the fabrication.
The Future Organics 12 has impressed operators during prototype testing with more than 25 already ordered.
Jaclyn says Manco is keen to grow the Australian market to assist councils with the introduction of FOGO services.
Manco currently has two demonstration vehicles operating in Australia with plans for another unit in the first quarter of 2023. Councils looking to implement or audit potential food organics waste streams can register for a free trail.
For more information, visit: www.mancoeng.com.au
SINCE 2010. TODAY THAT INCLUDES SUPPORT FOR FOGO ROLLOUTS TOO. WMR TALKS WITH DAVID GRAVINA, CHIEF COMPOSTING OFFICER, AND FOUNDER, TO LEARN MORE.
According to the 2020 National Waste Report, more than 14 million tonnes of organic waste was generated in Australia in 2019-20 – more than six million tonnes of that was municipal.
As councils across Australia look to develop a circular economy for organics, Compost Revolution now offers a food organics garden organics (FOGO) engagement behaviour change package, as well as its classic HOCO program (Home Organics Community Organics).
David Gravina, Compost Revolution’s Chief Composting Officer and Founder, says that council partners have said they are overwhelmed by their FOGO rollouts, so Compost Revolution launched its newest service ‘FOGO à gogo’ supporting councils with communications as well as caddy supply and logistics.
The new service won’t aim to reinvent the wheel for FOGO rollouts but will instead build on standardised messaging while easing the financial burden and increasing the chances of a program’s success.
“We’re offering tailored communications plans plus print and digital collateral, all informed by our decade of market experience and research in residential organics engagement,” David says.
The ‘FOGO à gogo’ service includes a menu of ready to go print and digital material, along with Compost Revolutions’
signature tutorials – customised with council and community stakeholders where required.
David says everything needed to communicate key messages to reduce confusion, lower contamination and onboard residents at rollout and beyond, is included.
“One way we really stand out is in our ability to clearly communicate FOGO and HOCO in harmony,” he says.
“By offering residents a clear and coherent message councils can achieve universal FOGO outcomes while using opt-in HOCO to drive additional social, environmental and economic results too.”
If you work in waste education at a
council, chances are you’ll know the Compost Revolution. Its award-winning behaviour change program upscales home and community composting via a purpose-built website, with engaging tutorials and delivery of subsidised equipment, along with life-long support for participating residents.
Co-designed with founding councils Randwick, Waverley and Woollahra in 2010, the program has been rolled out to 68 councils nationally to date.
“It’s amazing to think that as of today, 84,026 households have joined us, diverting more than 27,000 tonnes of organics,” says David. “Together we’ve saved councils – and ratepayers – more than $6 million in landfill fees.”
More than 90 per cent of participants are still composting at the end of their first year
of joining the program, with 75 per cent still composting half or more of their food organics themselves up to 12 years on.
“We achieve this by making it easy for people at every step of their journey, and establishing social norms using Community Based Social Marketing (CBSM) techniques,” David says. “Whether HOCO or FOGO, behaviour change isn’t driven by information alone.”
Compost Revolution uses data from before and after participant mobile garbage bin weighs, material type characterisations, and its annual participant survey answered by several thousand people.
“We know why people start composting, what they struggle with and why they love it so much,” says David. “We’re now leveraging these insights for FOGO engagement as well as our classic HOCO program.”
“Compost Revolution is passionate about
organics diversion, and that includes FOGO,” says David. “Today one in four Australian households compost at home, while one in five have access to FOGO, according to the Fight Food Waste CRC (2019) Food Waste Australian Household Attitudes and Behaviours National Benchmarking Study Summary Report
“So HOCO plays a sizeable role already, it’s just not measured as well, outside our program anyway.
“We support FOGO as a catchall solution to keep household organics out of landfill. But we know HOCO delivers a whole lot of environmental, financial and social outcomes that FOGO alone doesn’t.”
HOCO households compost food scraps locally with a compost bin, worm farm or bokashi bin.
The natural next step is to harvest this compost to give their garden, balcony or indoor plants some love. David says the process not only localises resource recovery,
but also, for a large cohort of households, food production.
“We love FOGO, but HOCO has lower entry costs, is 20 per cent cheaper per tonne over time, has less contaminants and doesn’t require transport from plate to material recovery facilities to paddock. It’s simply more circular,” David says.
He says HOCO even engages residents more deeply on a broader sustainability journey.
According to Compost Revolution’s annual survey, in addition to the organic diversion targeted directly by the program, 46 per cent of respondents say they are sorting their co-mingled recycling better since joining the Compost Revolution. More than 60 per cent of respondents say they have reduced the food waste they generate in the first place, while nearly 50 per cent started growing food or increased their food growing activities.
“Getting hands-on increases resource literacy,” says David. “These trends are also seen in Compost Revolution participant bin weighs and characterisations by EC sustainable and Hyder Consulting.”
Another interesting aspect of HOCO is what David calls ‘internalities’.
He says HOCO can open the door to gardening for participants, improving the health, social bonds and food security of their communities. Those gardens provide habitats for local wildlife, while also cooling neighbourhoods, improving the lives of everyone in the community.
“It’s a social, financial and environmental win to have people manage their own waste, but at the end of the day, lots of people are too busy.
“That’s why we believe council organics management best practice is opt-in HOCO atop universal FOGO.”
For more information, visit: www.compostrevolution.com.au/fogo
Positive outcomes from the food organics, garden organics (FOGO) composting trial at Lockyer Valley Regional Council using HEAPS aerated floor technology has generated interest in several sectors including agriculture, mining, and regional governments.
Martin Tower, Manager Director Radicle Agriculture, says the benefits that HEAPS provides through low capital and operational costs, when compared to both turner windrow and in vessel options, are a key point of interest.
The HEAPS system uses aerated floor technology, a series of pipes running underneath the organics pile, to introduce oxygen on a more frequent basis, optimising conditions for decomposition.
The computer-controlled system is connected to a series of sensors which monitor oxygen levels in the pile and automatically introduce air when levels fall below a set parameter. The same technology can be applied to an irrigation system to monitor and automatically adjust moisture levels.
Radicle Agriculture has four operational sites with several more in various stages of planning. Martin says clients have been impressed with the simplicity and low cost of operating the system.
“Many potential clients have been surprised by the relatively small footprint of the system compared with alternatives,” Martin says. “HEAPS generally requires about 20 per cent of the land required for a turned windrow system of similar capacity.”
Martin says he’s often asked how the HEAPS prevents odours from impacting the environment. There are several
elements to this. Firstly, it’s crucial that feedstocks are managed to ensure suitable carbon to nitrogen ratios are maintained. Odours frequently occur when there is excess nitrogen present.
He says it’s fortunate that kerbside collected FOGO provides a suitable mix for the HEAPS.
Secondly, Radicle Agriculture recommends users apply a layer of finished compost to the top of each pile which acts as a biofilter.
Finally, most odours result from the existence of anaerobic conditions within the pile or windrow. Oxygen saturation levels can drop rapidly in an active pile however the HEAPS controller generally introduces air, for about five minutes every hour, to maintain optimal levels.
The challenges of per- and polyfluoroalkyl substances (PFAS), prevalent in food packaging and cooking equipment, are a common concern in FOGO-based systems. Martin says contamination management, starting with client education, has been instrumental in achieving compliant results in the Lockyer Valley trial.
“There is no doubt that the efforts of the Lockyer Valley team towards educating their client base about contamination management has significantly contributed to the successful outcomes,” he says.
“We have learned a great deal from this experience and look forward to working with more councils to implement successful systems.”
Martin says while the Lockyer Valley trial has proven that a basic HEAPS system can adequately manage FOGO
processing, what’s more exciting is that the compost being produced from various waste streams is now reused for rehabilitation, urban amenity, and agricultural use.
He says Radicle Agriculture’s experience working with growers to manage their soil health gives clients an inside into market creation and development for their composts.
“We are seeing a significant increase in demand for alternative fertilisers due to both costs and environmental concerns in the farming community,” Martin says.
“There is also a massive potential for the use of composts as an input to mine-site rehabilitation. Our mining clients are focused on this potential reuse for the organic waste produced by their canteens and within their supply chains.”
The ability of the HEAPS compost controller to automatically record compliance data, including batch temperatures, oxygen saturations and moisture levels every 15 minutes, provides a unique opportunity to reduce the
The material previously managed in these windrows is now processed in the six blocks at the top of the picture.
COMPOST TECHNOLOGY IS GENERATING INTEREST FROM VARIOUS SECTORS KEEN TO TURN THEIR FOGO WASTE INTO A RESOURCE.
compliance record keeping burden. This data can be stored online, along with data from an integrated weather station, to keep thorough life batch data stored in a single location. Martin says that when users add input and out-loading dockets, the lifetime data for each batch is available in a permanent record.
The controller system can also be retrofitted to existing composting systems.
“HEAPS offers remote sites and regional councils with a cost-effective option to establish a circular economy for organics within their own region,” Martin says.
“Many councils are considering options to freight FOGO significant distances for processing. In many cases, the diesel used in this process will be greater than the greenhouse gas emissions saved from landfill diversion.
“HEAPS may offer a regional based solution, create regional jobs and benefit their communities through the use of composted product. As Lockyer Valley has demonstrated, it is possible for a virtuous circle to be created where
regional communities can benefit directly from their efforts in source separation and contamination management.”
For more information, visit: www.radicleag.com.au
With a solution from ELDAN, your recycling will be versatile and customized to your needs.
The modular design enables you to expand or upgrade your plant as the market changes.
From chip production to granulate, from granulate to powder.
You also get a guaranteed capacity and output purity.
For more information please contact: Area sales manager Carsten Nielsen at cn@eldan-recycling.com or visit www.eldan-recycling.com
This chart shows how rapidly the oxygen saturation levels drop in an active pile and the response of the HEAPS controller to maintain optimal levels. This generally occurs for about five minutes every hour.Led by rapidly evolving technology, processes, and community expectations, the waste management game is often in flux. But, in some corners of the industry, there are fundamental services that will always be in demand –the shredding, processing, and recycling of green waste is one of these.
Green Care Mulching specialises in grinding services, primarily for green and timber waste, but is well equipped to handle anything from plastic waste to tyres.
The family-owned company is based in Geelong, Victoria, where it processes green and timber waste into mulch and compost for businesses, government departments, and the general public.
“We process an enormous quantity of timber and green waste, which we resize, decontaminate, and manufacture into different-sized products,” says Russell Norton, Green Care Mulching Managing Director.
The business has developed a customer base across a range of markets, including poultry and dairy farms, landscaping businesses, and bioenergy producers.
“We also provide material grinding services on-site around Victoria and interstate,” Russell says. “We’ve even been involved in cyclone clean-ups, including one that went through the Yarra and Macedon Ranges in June 2021.
“That project resulted in four of our grinders processing debris for months. The project generated more than 300,000 cubic metres of mulch, which we resized down to 50 millimetres.”
The origins of the business date back to 1988, when Russell began his professional life as an arborist. He began exploring the shredding and processing side of the tree business in 2008, which led him down the path to the world of compost.
Green Care Mulching in its current form began in 2015. It was at this point the business purchased its first Komptech Crambo shredder – the start of what would develop into a positive working relationship with CEA, which distributes and supports JCB, Komptech, and a range of other brands in Australia.
Today, with a staff of 50, Green Care Mulching operates a large fleet of machinery, including 10 JCB machines – excavators, telehandlers, and loaders; four Komptech shredders; and two Komptech screeners. As well as the value and reliability these machines offer his
business, Russell says being able to rely on a single point of contact for support is a big reason he continues to deal with CEA for such a large portion of the company’s fleet.
“We take the same approach with our trucks, passenger vehicles and prime movers too,” he says. “We’ve found brands that work for us, and we continue to build those relationships.
“Having confidence in a brand develops a mutual trust. That gives us the confidence that we’ll be supported when something happens – and my contacts at CEA are always available on the phone when I need assistance.”
With global supply chain issues continuing to cause delays in securing spare parts, Russell says the company’s in-house workshop now carries more spare parts for its machines than ever before.
“We’re quite fortunate to be in the financial position where we can order multiples of any spare parts we need,” he says. “But we’re comfortable knowing CEA can provide a quick turnover for parts if it comes to that.”
Russell says Green Care Mulching’s relationship with CEA has developed to the point where he’s happy to demonstrate his Komptech or JCB machines for those considering purchasing one for themselves.
“These days, people will do a lot of their machine research on YouTube,” he says. “And when people in our region find out that we’re running them, they’ll often come to us for our opinion, or to help decide whether they want to hire or purchase.
“I’m more than happy to act as a spokesman for CEA’s brands, and our journey with them – though we won’t pull any punches. We’ll let people know what works, any issues we might have, and what we do to overcome any of those issues.”
Russell says when dealing with equipment sales on the scale he does, it’s inevitable that you’ll come across salespeople overpromising and under delivering.
“Over the years, I’ve had hundreds of thousands of dollars’ worth of equipment from some suppliers that I’ve just never heard from again.
“You won’t get that with CEA. I don’t think we would be in the position we’re in
today without the support of partners like them. We’re in a very fortunate position.”
Russell says the communication he and his business has with CEA is a two-way street.
“They often have questions for us about how we’re using their equipment, what material we’re using it for, our throughput rates,” he says. “And they’re able to share that information with prospective customers of theirs.”
Russell says CEA is always willing to let Green Care Mulching trial products, including prototypes, to ensure they know what they’re getting before a purchase.
“We’re currently trialling a 50-millimetre screen with our Crambo shredder, and we’re getting good results from it,” he says. “It’s helpful for CEA to see how contractors might use these products.
“Businesses like ours are an important part of these manufacturers’ research and development. We’re able to tell them what works and what doesn’t.
“What’s great about Komptech and JCB machinery, is that more works than doesn’t.”
Russell is excited for Green Care Mulching to embrace new, more sustainable solutions such as electric and hydrogen –technologies that JCB, for instance, has been developing in recent years.
“It’s an exciting time to be in this business,” he says. “I’m looking forward to turning off the diesel and running with alternative fuel sources as it becomes more commercially available.
“Four of my children are involved in the business, and that next generation is going to be able to use that new technology to help take the business to levels I never dreamed of.”
For more information, visit: www.greencaremulching.com.au
Managing Director Russell Norton (front) and the Green Care Mulching team.SOILCO has come a long way since 1974, when the Emery family first purchased a truck and started selling soil from its dairy property in the Shoalhaven region of New South Wales.
Led by a desire to reduce the reliance on natural resources and improve its products, the business has steadily climbed the organics ladder from quarrying soil to the development of state-of-the-art composting facilities that supply quality assured soil health products.
The company now specialises in the design, construction, and operation of advanced organics recycling facilities, but also offers end-to-end solutions from food waste collection through to product manufacture and distribution.
In December 2021, private equity firm I Squared Capital (ISQ) came on board as a majority shareholder in SOILCO – a move that opened up a world of opportunity for the company, according to Roslyn Florie-George, Executive General Manager – Business Growth and Sustainability.
“ISQ’s knowledge of international sustainability infrastructure, the carbon economy and renewable energy markets, coupled with a full appreciation and
understanding of our business were all important factors in the decision for SOILCO,” Roslyn says.
“They see the growth potential for organics recycling in Australia. They’re very supportive of our management team and of our growth strategy – which is why they chose us, and SOILCO chose them. After a year of working together, it is clear we both made the right choice.”
Key to the partnership was ISQ’s alignment with the family values and ambition from which SOILCO was built – and a willingness to help it maintain its identity as an Australian business that is locally led by experts in the field.
Critically, second-generation SOILCO family members Charlie and Mark Emery are still at the forefront of the business, continuing as Managing Director and Sales and Service Manager respectively. Both remain shareholders and have more than 40 years of combined experience at SOILCO.
Over the past year, SOILCO has focused considerable attention on strengthening and broadening its infrastructure network along Australia’s east coast.
“Since ISQ came on board, we’ve secured a greenfield site in Western Sydney,” Roslyn
says. “Our infrastructure team, led by Lance Jeffery, Executive General Manager – Infrastructure Delivery, is working hard to progress the EIS for the facility, and we have selected our technology partners to help us make it a reality.
“We’ve also secured two sites in southeast Queensland: a 190-hectare regional site at Bromelton, and a six-hectare site at Pinkenba near Brisbane Airport, in preparation for Queensland’s transition to FOGO.”
These will add to SOILCO’s existing operational New South Wales facilities, including at Nowra and Kembla Grange in the state’s south-east, and at Tweed in the north-east.
The Tweed facility began operating in August 2021, and is the first functional piece of a new South-East Queensland and Northern Rivers network that will include Bromelton and Pinkenba.
“Despite the challenges of extreme weather events and the pandemic, the Tweed facility was delivered on time and has been operating exceptionally well,” Roslyn says. “
It’s a small in-vessel site with a 25,000-tonne capacity license that currently processes FOGO from the Tweed and Ballina communities.”
SOILCO is now preparing to commission additional infrastructure on site to increase the range of endproducts produced at the facility. Roslyn says the team has been working with local farmers to understand their requirements and further develop SOILCO’s existing range of compost products.
“The Tweed facility works well as an independent site, but the addition of Bromelton will give us more service options and further flexibility to adapt our products to meet the soil improvement needs of the region,” she says.
“As with our New South Wales network, we see value in having multiple facilities close together in Queensland and the Northern Rivers to complement each other.”
Another key development in 2022 was the construction and commissioning of four in-vessel composting tunnels at Kembla Grange, increasing the site’s processing capacity by 40,000 tonnesper-annum. This will enable SOILCO to produce FOGO compost on site, saving on both emissions and transport costs.
As critical as this infrastructure expansion is for SOILCO, it doesn’t mean much without the people to bring it all to life.
Roslyn says ISQ’s investment, combined with the Emery family’s vision and values, has enabled SOILCO to expand its workforce with key people across the company – from laboratory personnel, through to quality control and safety
experts, and senior management. “We’ve been able to diversify and strengthen the SOILCO team, and be very targeted in doing so,” she says. “Charlie has worked hard to find the right people for the roles – and we’re almost there, which is very exciting.
“This has set us up well for the next three years as we build our new facilities and expand our network. And ISQ has been very supportive of the process – they’re very much about resourcing appropriately and setting the business up to succeed.”
One such addition to SOILCO’s team is Duncan Le Good, who came on board in October as Executive General Manager – Product Sales and Innovation. Duncan brought with him more than a decade of experience in the organics processing industry, including roles with major resource recovery companies, as well as serving as a Director at the Australian Organics Recycling Association (AORA).
Duncan stresses that while expanding the reach of SOILCO’s operation is of vital importance, the quality of the company’s product will always be the primary focus.
“The word ‘quality’ gets used a lot, but it can mean a whole lot of different things,” Duncan says. “Part of my role is to understand what we produce at our facilities, and where it can go in the market – it’s very much about product that’s fit for purpose.”
“Local feedstocks and technology requirements all differ for each site,” Roslyn adds. “It’s not a one-size-fits-all approach. We like to work very closely
with our customers to make sure the design of our operations is right for the area, and that the products are right for those markets.”
Duncan says what’s produced from smaller footprint in-vessel facilities such as Tweed, and what’s produced at larger area composting facilities such as Nowra are very different, and it’s important to know how each can be used, and for what.
“You’ve got to be very mindful about the product you’re manufacturing,” Duncan says. “You have to know exactly what it is, the parameters of it, and then structure everything you do around that quality product. That strategy goes all the way up in the business – from us to the Emery family, to ISQ – and it’s been working really well.
“What makes up our main markets now may not be our main markets in the future, and we want to be prepared for that. ISQ understands our vision, and is prepared to listen and look for other opportunities as the market changes.”
This is indicative of the fundamental trust and understanding at the core of SOILCO and ISQ’s working relationship –one Roslyn says has the growing SOILCO team excited about the future.
“We’ve come a long way over the past year,” she says. “Now, we’re excited by the opportunity to develop critical infrastructure to divert more organics from landfill, regenerate more soil, and help transition to a net-zero economy.”
For more information, visit: www.soilco.com.au
Protein farming, using insect larvae to convert food waste into stockfeed, could significantly reduce net greenhouse gas emissions, according to research by the New South Wales Environment Protection Authority (NSW EPA).
The research, which compared landfilling to the emissions profiles of four options for managing household food organic and garden organic (FOGO) waste, found protein farming could result in minus 2520 kilograms of carbon dioxide equivalent emissions for every tonne of food waste, if the harvested protein is used as a substitute for other protein sources.
Modelling shows that recovering biogas energy from off-site anaerobic
digestion systems can also result in a net reduction in emissions, while food waste to landfill generates the most emissions compared to other management options considered.
Emissions from collection and transport of food waste off-site are a minor component of net emissions, according to the findings.
Amanda Kane, Organics Manager NSW EPA, says the research highlights the important contribution the organics industry plays in helping Australia reach its emissions target.
In September 2022 the Commonwealth Government’s Climate Change Bills were passed, locking in a national emissions reduction target of 43 per cent and net zero emissions by 2050.
Increasing Australia’s organic waste recycling rate from 49 per cent to 80 per cent by 2030 is also a key target of the National Waste Policy. In New South Wales, the government is requiring food and garden collection for all households and select businesses by 2030 and that large food waste generating businesses to source separate food waste by 2025.
“While greenhouse gas emissions are just one of many factors in choosing a suitable food waste management option, the research can help councils, businesses and communities quantify the benefits of processes available,” Amanda says.
The research also looked at the emissions profile of composting, dehydration and bio-dehydration.
It is part of a multi-pronged approach, including grants programs and resources, that the NSW EPA is delivering to ensure relevant information is available as the state edges closer to the mandate deadlines.
The latest stream of funding, a total pool of $46 million for Go FOGO grants, aims to support NSW councils deliver new weekly food only (FO) or FOGO services to their communities.
Two grant rounds are planned each year for four years, with the successful recipients of round one expected to be announced in early 2023.
The Go FOGO grants build on the funding provided under the Waste Less Recycle More Organics Collections grants program running since 2013.
With some elements of the program wrapping up in June 2022, NSW EPA has developed a one-stop
resource for end-use customers of compost called Cool Compost. Cool Compost brings together in one place the expertise of grant recipients under the market development program, to
share everything learned by them across five target markets – graziers, vegetable growers, councils, landscapers/urban planners, and government agencies.
Amanda describes Cool Compost as a living resource that will continue to be built upon.
“Industry perspectives, videos and podcasts showcasing the benefits of compost are now live on the NSW Circular Ag platform,” she says.
“It’s really useful in terms of sharing with customers information that’s been supported by the regulator and is delivered in an accessible, positive format.”
With a focus on accessible information, NSW EPA also delivered a series of masterclasses throughout October and November, featuring Australian and international speakers
sharing their experiences on delivering FOGO.
Recordings of all sessions are available on the EPA website.
“It was a highly successful series and highlights the appetite for relevant, reliable information,” Amanda says.
“Food and garden waste continue to be the largest waste stream going into the red lid bin and landfill. There’s a whole range of elements to consider within the organics space and not a great deal of awareness about them.
“NSW EPA has done a huge amount of work to address this by pulling together a range of information and resources.”
For more information, visit: www.epa.nsw.gov.au
Victoria’s West Gate Tunnel Project will move 9000 trucks off local roads in Melbourne’s west when it’s completed.
While new twin tunnels, elevated roads and river crossings are taking shape, giving motorists a visual barometer of the project’s progression, behind the scenes, specialist environmental service Enviropacific is moving mountains. In the past two years, Enviropacific has moved and
processed more than 35,000 tonnes of material for the project, including per- and poly-fluoroalkyl (PFAS) contaminated soil.
Dino Adikaram, SOLVE Manager Enviropacific, says the company has supported the resource recovery of a growing number of infrastructure and remediation projects since commissioning its SOLVE thermal plant in 2018 and a non-destructive digging (NDD) plant in February 2022.
“We’ve been supporting the West Gate Tunnel Project since 2020 but with the new NDD plant we can treat waste streams that we weren’t previously able to accept,” Dino says.
“The feedback we’re getting from infrastructure projects within Melbourne, such as the West Gate Tunnel project, the North-East Link and various Level Crossing Removal projects is that our processes are extremely compliant and safe.
“Customers know that when material comes to us, we can guarantee it’s going to be treated. From a sustainability and resource recovery point of view, they’re also doing their part for the environment.”
Enviropacific comprises three core services: remediation, water treatment and hazardous waste management.
When the company opened SOLVE, it’s contaminated soil and waste cleanup facility in Victoria, it revolutionised hazardous waste clean-up. SOLVE uses specialist thermal technology to treat contaminated soil, diverting it from landfill.
Thermal desorption separates contaminants from soil by heating it in a chamber and vaporising the moisture and organic contaminants. A vacuum or gas system takes the vaporised water and contaminants into an off-gas treatment system which converts them to carbon dioxide and water.
The facility treats more than 20 kinds of contaminated soils, wastes and liquids and has the capability to remediate Category A and B contaminant streams, including PFAS, scheduled and other prescribed industrial waste. All treated material is stored for sampling, validation, and waste categorisation. It can then be returned to where it was excavated from, reused, or safely disposed into landfill if required.
In February 2022, a drill mud plant to wash the sludge from NDD projects and recover materials to be reused was built as an addition to the SOLVE facility.
The plant can process up to 30 tonnes of NDD mud an hour, sorting it into oversized rocks and gravels, segregating naturally occurring sands and pulling out silts and clays, each becoming products that can be reused rather than be sent to landfill.
What materials can’t be recovered during the cleaning process are diverted to the onsite thermal plant.
The goal is 100 per cent resource recovery.
tonne
Dino says the NDD plant is meeting all expectations.
Since February, about 25,000 tonne of materials that would otherwise have been sent to landfill has been recovered at the plant.
While recovering valuable resources, the plant is also unearthing some details about Melbourne’s geology.
“No two loads are the same,” Dino says. “We’re getting the material we suspected but the percentage of rock, sand, clay and water that makes up a drill mud load changes depending on the soil type and where it’s from. Some areas are clay, some are more sandy or loamy.
“There are things we’re learning as we become involved in more projects.”
Dino says Enviropacific continues to search for innovative technology to grow the business. It’s one of the reasons he made the switch from the
oil and gas industry to the independent environmental company about five years ago.
He says the company is well known in the remediation space. It is one of the largest PFAS treatment companies in Australia and while NDD has been used by other companies for about 10 years, the resultant product was predominantly landfilled.
“The key for Enviropacific is to divert as much hazardous waste from landfill as possible and to support large infrastructure projects that will benefit from sustainable disposal options,” Dino says.
“Interlinked with that is a policy to promote the reuse of materials and the circular economy.
“We’re committed to providing a better, more sustainable solution for waste owners.”
For more information, visit: www.enviropacific.com.au
Welcome to Waste Management Review’s Waste and Recycling Equipment and Machinery Showcase, compiled to be an easy reference point for anyone searching for waste and recycling equipment and machinery.
Australia’s waste and recycling industry has undergone rapid transformation in the past 12 months and as more export bans are introduced and national targets for increased recycling loom, there is a growing demand for solutions to remove or repurpose our waste.
Equipment and machinery specialists are keeping abreast of development and technological advances worldwide and are often the gateway to new solutions, from single pieces of equipment to complete builds.
The Recycling Equipment and Machinery Showcase aims to be a one-stop shop to connect industry with equipment and machinery providers for specific waste streams across Australia.
Whether it’s kerbside collection equipment, materials handlers or specialised recycling machinery, there’s a wide network of experts and
manufacturers available to put you on the right path.
While the team at WMR has done its best to include all the companies in the waste and recycling equipment and machinery sector, it takes no responsibility for omissions.
The data has been collected through a variety of measures including mailouts, website survey collection points, and emails to comprehensive databases, as well as organically from companies themselves.
This collection of data will be published online at a future date.
Tutt Bryant Equipment is the Equipment Sales & After-Sales Support (Parts & Service) division of Tutt Bryant Group. Tutt Bryant Equipment exclusively represents a number of industry leading global brands in Australia.
Our industry specific range of equipment includes Sumitomo and Yanmar excavators, Bomag heavy and light compaction equipment, Metso:Outotec mobile crushing and screen equipment, M&J Recycling shredding equipment, Gehl wheeled and tracked skid steer loaders, Venieri and Yanmar wheel loaders, Weiler motor graders, Okada hydraulic hammers and demolition equipment, diesel generator series from AJ Power and used equipment. We also offer a range of cranes from leading international manufacturers such as Kato, HSC Cranes and SANY. To ensure the longevity of your equipment, we also offer Berco undercarriage and Combi Wear Parts (ground engaging tools).
Tutt Bryant Equipment is also proud to welcome 600 Cranes Australasia into our family, adding to our impressive portfolio of quality construction equipment, parts and services. 600 Cranes is the national distributor of Fassi knuckle boom truck loading and marine cranes, Marrel hooklifts, Jekko mini crawler cranes and Idrobenne grapples and clamshell buckets for cranes.
Tutt Bryant Equipment’s core capability in the waste industry revolves around its supply and support of a broad range of products from which customers have come to expect reliability. Highly regarded industry leading brands like M&J Shredders, Metso Crushers & Screens and Bomag compactors, just to name a few, for part of our stable.
These machines come from powerhouse European manufacturers with decades of product refinement in their design and engineering. Coupled with the Tutt Bryant national footprint, vast parts holding, trained and dedicated service teams located throughout the country, you have a winning combination.
Many of Tutt Bryant’s OEMs have chosen to remain their partners for many years and as the largest multi-franchised supplier in Australia, we can supply and support almost all of the equipment you may require at your waste facility, including excavators and loaders.
Since becoming the local M&J Recycling distributor, Tutt Bryant has provided three M&J 4000-8 shredders to Cleanaway and one to BMI Group and SBI Group. These private waste companies have seen the value in shredding to reduce air voids at their
landfill sites to extend landfill life.
• AJ Power Diesel Generators
• Bomag Heavy and Light Compaction Equipment
• Combi Wear Parts
• Berco Undercarriage
• Metso: Outotec Crushing & Screening Equipment
• M&J Mobile Shredding Equipment
• Yanmar and Sumitomo Excavators
• KATO, HSC and SANY Cranes
• Okada Hydraulic Hammers and attachments
• Weiler Motor Graders
• Yanmar and Venieri Wheel Loaders
• Gehl Wheeled and Tracked Skid Steer Loaders
Contact details
P 1300 658 888
E equipment@tuttbryant.com.au
W www.tuttbryant.com.au
Komptech CEA is the Australasian distributor of Komptech machinery and systems for the treatment and processing of solid waste and organics waste materials for recovery and recycling. Our product range includes more than 30 different types of both mobile and stationary machines that cover all key processes in modern waste processing including:
• Single-shaft and dual-shaft industrial shredders
• Compost windrow turners for commercial operations
• Star screen and trommel screen machines
• Material separation equipment including windsifters, ballistic separators and stone contaminant separators
• Stationary recycling
With a specialised product portfolio
that includes more than 30 different types of machines covering all key processes in modern waste handling, a consultative guiding approach to solution development for customers, and full service after- sales support and parts, Komptech CEA has become a leading supplier to the recycling and waste processing industry. Providing customer value is our focus as we strive to be the industry’s technological leader through continual innovation. Komptech CEA is dedicated to working with you to help you solve your waste problems and identify opportunities with comprehensive, detailed solutions driven by worldclass technology.
• Diamond Z
• Screenpod
• Trackstack
• Rowan
• Komptech
Contact details
Melbourne
Adelaide
Key
Turmec designs, manufactures, installs and commissions bespoke recycling plants.
Established in 1972, Turmec is a leading international provider of materials handling and recovery solutions to the waste processing sector. It specialises in the end-to-end design and build of complex waste separation and processing systems which are critical for large-scale, efficient waste processing and recycling plants.
Turmec serves some of the largest waste management companies globally including Biffa, Suez and Powerday in the UK, Thorntons Recycling in Ireland, and Rino Recycling and Bingo Industries in Australia. The business employs 90 people operating from a 66,000 sq. ft manufacturing facility at Rathcairn within the Irish-speaking Gaeltacht area of County Meath.
Turmec is ISO 45001-accredited, along with several other industry accreditations across quality, environment and health and safety, which reflects its ongoing and
consistent commitment to providing its clients with the best service and support.
Turmec plants process the primary material mixes of Construction & Demolition (C&D), Commercial & Industrial (C&I), Municipal Solid Waste (MSW), and Dry Mixed Recyclables (DMR) to produce high-quality recyclates. These include aggregate (in various size classifications), ferrous and non-ferrous metals, wood (split between natural and manufactured), plastic (bottles, film, mixed rigids), fibre, RDF, SRF, PEF and fines (organic and inert).
Turmec also provides secondary recyclates processing and has experience producing colour-sorted cullet from mixed glass bottles, rubber recycling, composting, fines washing, and fuel pellet production.
Turmec offers spares packages and service level agreements to cover the pre- and post-
warranty expiry dates to support plant uptime objectives.
MOST RECENT PROJECT: Rino, Brisbane - a $44m million contract to design, build and install a state-of-theart construction waste processing plant for Rino Recycling at its Pinkenba facility near Brisbane.
The new plant will be one of the largest C&D waste recovery sites in the world, designed to achieve market-leading landfill diversion and recovery rates of up to 99 per cent and with a processing capacity of 475 tonnes per hour.
Recovered C&D materials will be recycled by Rino Recycling into a range of high-quality sand, fill, road base and aggregate materials which will be utilised in new construction projects. PEF will be produced from the non-inert fraction.
Contact details
Turmec P +353 46 9432243
W www.turmec.com
Wastech is a leading design, engineering and manufacturing company that services the waste management and resource recovery sectors throughout Australia and New Zealand.
Known for technology-enabled solutions, we solve our customers problems through engineering innovation and are driven by the goal of sustainability. We work with customers to treat their waste in the best interests of both the environment and their businesses. Wastech has more than 29 years’ experience supplying state-of-the-art waste and recycling equipment to commercial and government clients.
Wastech is a solution driven business covering cardboard, plastic and polystyrene to e-waste and general waste. We are leaders in major project concept design, manufacturing and installation (eg material recovery facilities, transfer station systems), with the expertise to seamlessly deliver an end-to-end facility solution. We provide leading Australian made equipment (eg compactors, chute systems and other engineered solutions) and distribute globally leading brands such as Bramidan balers and McCloskey shredding and screening equipment.
From concept to completion, we deliver to the unique needs of our customers enabling better outcomes and cost savings while promoting a sustainable future.
• Balers (vertical and horizontal), compactors and round baling systems
• Fire suppression systems
• Crushing and screening equipment
• Material recovery facilities
• Transfer stations and transfer trailers
• De-packaging systems
• Commercial waste chute systems
• Bins, lifters and washers
• Waste equipment service and maintenance
• Flexible equipment rental solutions
• Bramidan – cardboard and plastic vertical balers
• CPG and MSS – material recycling equipment
• Neue Herbod – plastic processing equipment
• Atritor Turbo Separator – de-packaging and separation equipment
• Flexus –baling and wrapping system
• Pilot Crushtec – crushing and screening equipment and systems
• McCloskey Environmental – shredders, screeners, trommels, stackers
• Fire Rover – fire detection and suppression system
We are an Australian design, engineering and manufacturing company that services the waste management and resource recovery sectors across Australia and New Zealand. We invest heavily in research and development, best-practice design and sourcing globally innovative technology and materials.
We offer service and support for our entire range of equipment and major waste management facilities, including mobile breakdown services nationally,
repair centres in multiple Australian cities and 24/7 support. We have a dedicated engineering team for complex machinery repairs.
We are specialists in complex project delivery – end-to-end design, project management, procurement, installation of material recovery facilities, transfer stations and waste management facilities. Our engineering team develops customised solutions for small, medium and large projects.
We have a quality-led, lean manufacturing operation at our Hallam facility producing a variety of fabricated equipment and engineered solutions. Our commitment to sustainability includes power sourced from our own 85kw solar array enabling customer savings while helping the environment.
• Suez Bibra Lake MRF WA – fibre line optical sorter upgrade
• K-Trans WA – 65m quad Axle
Transfer trailers
• Top Soil Organics – Turbo Separator de-packaging solution
Contact details
Wastech Engineering
33 Wedgewood Road, Hallam VIC 3803 Australia Website: www.wastech.com.au Email: info@wastech.com.au
Sales & General Enquiries – 1800 814 923
TELFORD SMITH earned its name from the company founder, Cecil Telford-Smith who started the business back in 1923 based in South Melbourne, Australia.
Since then, Telford Smith has earned a reputation for the highest quality design and manufacture of machinery which remains at the heart of the business, almost 100 years later.
The company remains the largest manufacturer of machinery for the plastics industry within Australia with many decades of experience in plastics processing and recycling equipment.
Telford Smith’s major focus is on specialised applications including:
• Wash plants for plastic waste
• Size reduction equipment for plastic, rubber (tyres), timber waste
• Plastics moulding machinery
• Plastics ancillary and automation equipment for efficient processes
• Balers, waste compactors and smart bins
• Extrusion applications
The company has an experienced team in Australia supported by a well-equipped manufacturing and engineering facility in China.
Telford Smith has a wealth of experience in manufacturing and outsourcing in China and controls all aspects of the company’s manufacturing with educated and accomplished engineers.
The company’s electrical engineers have high skill levels in designing electrical control panels and PLC programming.
Telford Smith’s mandate is to progress for the next 100 years and beyond, continuing to keep up with the latest technology, maintaining the highest integrity with customers, and not losing sight of its traditional “old fashioned values” of service and quality.
• FILTON rotary unions and mechanical seals
• FORREC shredding systems
• GREEN CREATIVE high-
performance depackaging machines
• GALA underwater pelletising systems
• TEDERIC injection moulding machines
• LIAD blenders, feeders, weighing and control systems
• ORWAK balers, waste compactors and smart bins
• RUNI screw compactors for dewatering various materials
• SESOTEC separation and sorting technology
• SHINI plastics ancillar y and automation equipment
• TELFORD SMITH extrusion equipment and complete wash plants
• UNITEK extrusion crossheads
• XALOY bimetallic extrusion barrels
• ZERMA granulators, shredders and recycling systems
Contact details
N Telford Smith
A 250 Hammond Road, Dandenong 3175
Victoria Australia
P (03) 8792 9777
W www.TelfordSmith.com.au
Komatsu Forest is one of the world’s largest manufacturers of forest machines. We are represented on six world continents by a network of dealers and our own sales companies.
Komatsu Forest is one of the world’s largest manufacturers of forest machines. We are represented on six world continents by a network of dealers and our own sales companies.
Komatsu Forest’s head office is in Umeå, Sweden, and we have two manufacturing units, in Sweden and the USA. Our own sales companies are located in Sweden, Norway, Finland, Germany, Austria, France, United Kingdom, Russia, USA, Australia and Brazil, and our network of dealers represent us on all other important forestry markets.
Komatsu Forest’s head office is in Umeå, Sweden, and we have two manufacturing units, in Sweden and the USA. Our own sales companies are located in Sweden, Norway, Finland, Germany, Austria, France, United Kingdom, Russia, USA, Australia and Brazil, and our network of dealers represent us on all other important forestry markets.
Our extensive service organisation takes care of the machines, ensuring that they perform their best throughout their service lives. We have workshops throughout the world, service vehicles for quick assistance, in-house machine and methodology instructors to help maximise productivity, and support functions for everything related to our machines and services.
increase productivity while simplifying the working day for you as a machine owner.
We combine all our services under our Customer Care concept. This is our promise that you will enjoy the benefits of Komatsu Forest’s investments in research, development, servicing, support, logistics and innovative services. These combined resources are at the very heart of Komatsu Forest’s offer.
choosing Komatsu, peace of mind and accessibility can become a natural part of your working day.
Our extensive service organisation takes care of the machines, ensuring that they perform their best throughout their service lives. We have workshops throughout the world, service vehicles for quick assistance, in-house machine and methodology instructors to help maximise productivity, and support functions for everything related to our machines and services.
• Komatsu
• Peterson
We offer products and services that increase productivity while simplifying the working day for you as a machine owner.
We offer products and services that
We combine all our services under our Customer Care concept. This is our promise that you will enjoy the benefits of Komatsu Forest’s investments in research, development, servicing, support, logistics and innovative services. These combined resources are at the very heart of Komatsu Forest’s offer.
Our goal is to make your working day as safe, problem-free and profitable as possible, no matter where in the world you operate. Let us show you that by
Our goal is to make your working day as safe, problem-free and profitable as possible, no matter where in the world you operate. Let us show you that by choosing Komatsu, peace of mind and accessibility can become a natural part of your working day.
Brands
• TimberPro
• Komatsu
• Peterson
• TimberPro
Our world-wide network of highly trained service professionals is ready for you.
Core Capabilities:
We know how important it is to be close to service and maintenance when help is needed. Therefore, we have a market-wide network of highly trained service professionals that know your Komatsu, Peterson and TimberPro machine in every detail. They are, in turn, in constant contact with the Komatsu Forest head office so your voice or needs are never more than a call away from our collective expertise. Furthermore, we are constantly developing new services that will help you in your everyday work.
We offer:
• Workshops and field services throughout Australia and New Zealand
close to service and maintenance help is needed. Therefore, market-wide network of service professionals that Komatsu, Peterson & Timberpro in every detail. They are, constant contact with the Forest head office so your are never more than a call our collective expertise. are constantly developing that will help you in your
• Qualified personnel with expert knowledge of Komatsu and affiliated machines
• Field Service that enables us to remain close to you and your machine
We offer:
• Workshops and field throughout Australia
• Support and maintenance throughout your machine’s service life
Our world-wide network of highly trained service professionals is ready for you. We know how important it is to be
• Maintenance agreements with fixed maintenance prices and other benefits. Contact details
AUSTRALIA
• Well qualified personnel knowledge of Komatsu machines
• Field Service that enables remain close to you
Komatsu Forest Pty Ltd 4/11 Ave of Americas Newington, NSW 2127 T +61 2 9647 3600 E info.au@komatsuforest.com
NEW ZEALAND
Komatsu Forest Pty Ltd 15C Hyland Cres Rotorua, New Zealand
M John Kosar + 64 274 865 844
M Paul Roche + 64 21 350 747
Applied Machinery is one of Australia’s largest suppliers of quality recycling machinery. Over 30 years industry experience enables us to deliver turnkey solutions for all manner of recycling applications across Australia. We don’t just sell machinery; we have specialist service engineers who install the machinery and, most crucially, train our customers and their staff to use it efficiently and safely.
• Shredders and granulators
• Plastic washing, tyre, and e-waste recycling plants
•
• Genox
•
Applied Machinery has the capability to service the smallest single machine requirement through to the largest of multi-site, staged installations and complete recycling line, turnkey projects. We supply some of Australia’s largest recycling organisations. A wide range of shredders and granulators are always in stock for quick delivery.
D & M Waste Management, Perth Complete plant installed to recycle waste plastic pipes. The waste pipes are shredded, granulated, washed, dried and pelletised to produce clean dry pellets. These are then fed into a plastic pipe extrusion line that produces a range of corrugated pipes for stormwater drainage applications.
Contact details
55-61 Nissan Drive Dandenong VIC 3175 P 03 9706 8066
Peter Koueik: Sales Manager – Recycling Division
E sales@appliedmachinery.com.au
W www.appliedmachinery.com.au
Veolia has released the findings of the Environmental Impact Statement (EIS) for its proposed Advanced Energy Recovery Centre (ARC) at its existing Woodlawn Eco Precinct.
Kathryn Whitfield, Project Director for Veolia’s ARC, says independently verified assessments, undertaken over a period of more than 12 months, confirm the proposed project is safe for local people, farming, and the environment.
She says key findings confirm that the predicted air quality levels are safely below limits set by the New South Wales Environment Protection Authority (EPA); the ARC meets all regulations for human health, water quality and food production; and water concentrations within rainwater tanks are well within safe drinking water guidelines.
The EIS also found that the introduction of the ARC project will not change local soil conditions, and farms with organic farming status would not be affected, instead, 96 per cent of the waste diverted from landfill will be recovered or recycled.
The proposed facility amounts to a more than $600 million capital investment in regional New South Wales, with a further $2 billion in the lifetime maintenance and operations of the project.
Kathryn says the economic assessment showed this would create a more than $250 million financial boost to local suppliers and increases in household incomes.
In addition, the economic assessment confirmed the project would further
boost the region with 300 direct project jobs during construction, and a further 40 roles during operation. An estimated additional 383 indirect jobs will be created through spending with local suppliers.
“The economic and environmental benefits of the ARC are indicative of proven technology, which has been operating in developed countries for decades,” Kathryn says.
“The studies followed a rigorous assessment process to simulate realworld impacts, using actual operating data. This was then applied to local conditions to show it will be safe for people, farming and the environment.
“The studies demonstrate that energyfrom-waste technology can be safely built and operated in Woodlawn, with many benefits, whether they be to help prevent climate change, or to boost the local economy.”
The ARC will divert 380,000 tonnes of non-recyclable waste from landfill
every year and turn it to energy, using power production technology. The solution will generate enough electricity to power 40,000 homes per year, as well as recycle and recover 20 per cent of the waste outputs that would otherwise be lost to landfill.
Aligning with the state government’s recovery, environmental protection and decarbonisation targets, Kathryn says the project is set to propel New South Wales into a new era of sustainability.
“The NSW Government has established bold emission reduction and recovery targets, designed to halt global warming, and bring about environmental improvements,” she says.
“Energy-from-Waste plays a role in this transition, and the government’s stance on its safe application aligns with our project objectives. The NSW Government has set the world’s strictest regulations for energy-from-waste technology, and we now have the evidence to show how we’ll comply.”
The project has been on public exhibition and the community can formally submit their views on the proposal to the NSW Department of Planning and Environment (DPE).
“We are holding a series of events right around the region to showcase the details of the studies,”
“Now is the time for people to hear the facts from qualified and independent experts, and to have their say by making a submission.”
“Energy-from-waste technology is recognised by the Federal and NSW Governments as more sustainable than landfilling. It works by drying
controlled setting, where all gasses are treated and cleaned, then uses the heat produced to boil water into steam to drive a turbine, which generates electricity.
“This is a significant step in reducing reliance on fossil fuels and is cleaner than gas and coal fuel alternatives, particularly given that landfill gas emissions are avoided.”
Veolia operates more than 65 energy recovery facilities (ERF) globally and will operate and maintain Australia’s first two energy recovery facilities in Perth.
The ARC will be classified as a State Significant Development and, if approved, the project will take up to three years to commission.
For more information, visit:
Veolia’s ARC
Doug Rowe can draw on the experiences and learnings from a long line of overseas colleagues and recycling experts, but the Director of Ecocycle and Recycal has his sights set firmly on the future.
The experienced recycling specialist has spent years investing in research and development and new technology to keep the company that one step ahead.
The hard yards put in by Doug and the team over the past few years gave rise to new facilities, programs, and public recognition. The company, with a footprint in each state, is well placed to handle the growing e-waste recycling challenges that lie ahead.
Doug says he’s keen to build on the momentum moving forward.
“We’re looking to invest in other stateof-the art facilities to ensure we have the very best of technology for the years ahead,” he says.
“We also now have room to grow and employee the staff needed for the expansion we are experiencing.”
In August, Ecocycle said goodbye to the portable offices it had called home for two years and moved into purpose-built “green” headquarters in Campbellfield.
The two-storey building is a showcase of green technology and reflects the company’s ethos of recycle, reduce and reuse as it reinforces its resource recovery credentials.
To that end, Ecocycle is a partner of B-cycle, an industry-led product stewardship scheme run by the Battery Stewardship Council. Launched in January 2022, the scheme sets out to create a circular economy for batteries
to ensure they don’t end up in landfill. Within the first six months, more than 900,000 kilograms of batteries were collected for recycling, with more than 3200 drop-off points established across eight states and territories, according to the B-cycle positive change report.
EcoBatt, the battery collection, sorting and processing side of the Ecocycle group, rolled out battery collection points in major supermarkets across Australia, including regional and remote areas.
“This means all of the Australian population has a local solution only a few minutes from their homes and businesses to recycle all of their old batteries,” Doug says.
“As a business that’s committed to servicing industry and protecting the
environment, Ecocycle is proud to be part of the B-cycle initiative.
“It enables us to reduce our ecosystem’s exposure to toxic chemicals by diverting batteries from landfill, while recovering finite resources to ensure the future of Australia’s energy security.”
Ecocycle was also included in the National Television and Computer Recycling Scheme (NTCRS) from 1 July 2022.
Doug says the inclusion is recognition of Ecocycle’s work in recycling flat panel displays.
Recycling flat panel displays has always posed a problem for e-waste recyclers because of the mercury in cold cathode fluorescent lamps (CCFL), the light source for LCD screens.
Ecocycle introduced Flat Panel Display (FPD) processing technology involving Artificial Intelligence and robotics.
“It’s time to start looking at e-waste as a source of valuable materials, rather than harmful toxic waste that is pushed around until it ends up in landfills,” Doug says. “Advanced robotic recycling technologies allow us to move away from the take-make-waste linear model to a circular economy.
“We have lots to learn as far as the NTCRS goes, but the services we can offer will be unique, and tailored to suit the needs of our clients.
“Staff will be trained and placed into this team to ensure we are covering the needs around Australia.”
In another move to cover the needs of Australia, Ecocycle added EcoPlastics
convert hard and soft plastics into plastic pellets which can be reused to make new products.
Doug says this addition to the group will also require a new team to sell the materials and develop new products to take to market.
“It’s a nice mix how we’ve vertically integrated everything into the business,” Doug says.
“We’ve created a place where people want to come and be part of that recycling story.
“We’ve put in so much investment and so much work. The years ahead will be positive ones for our group as we build a team of passionate, likeminded people committed to making a difference.”
For more information, visit:
Over the years the world has advanced toward a circular economy making the ecosystem more restorative and regenerative by design and practice.
Australia is a growing market for resource recovery solutions as momentum builds towards this circular economy.
“Turmec, as specialists in recycling solutions, offers bespoke systems that enable our Australian customers to efficiently recover highquality material from waste,” says Gavin Dunne, Associate Director of Recycling Sales for Turmec.
Already with a foothold in Australia, the recycling plant manufacturer is making a commitment to have a ‘feet on the ground’ presence in every state.
Gavin sees similarities in Australia to how things used to be in Europe.
“The reduction of landfills is a priority for government and industry and the repurposing of waste is a key component in the way forward,” he says. “Turmec has experience on both fronts with our involvement in this marketplace over the past 10 years.”
An exclusive agency agreement with Environmental Group Limited (EGL) has been a key move to expand Turmec’s presence in Australia.
“With EGL, we’re setting up aftersales support in Australia. We’ll have a spare parts hub and fully trained local technicians,” Gavin says. “We’ll have a trained workforce on the ground which will allow us to cater for after-sales support with a breakdown service, setting up service level agreements post installation completion and even carry out the day-to-day servicing of the facilities.
“From speaking with our clients, it is very difficult for them to find their own service technicians. Our service will be able to give that support.”
Turmec already has a solid reputation within Australia. While the nation is
IRISH COMPANY TURMEC IS SHORING UP ITS PLACE IN AUSTRALIA’S RECYCLING SECTOR WITH A COMMITMENT TO A LOCAL WORKFORCE.not the company’s biggest market in terms of the number of projects, it comes out on top for scale of projects.
There are five Turmec systems operating in Australia, each processing a combined tonnage of 700tph of mixed wastes. Among them is the major mixed-waste recycling facility for Bingo Industries at Eastern Creek Ecology Park in Western Sydney.
“Turmec is proud to be a key and supportive partner in Bingo’s journey to increase the amount of waste diverted from landfill,” Gavin says.
In August this year, Turmec was awarded a $44 million contract to design and install what is believed to be the world’s largest construction waste processing facility, for Rino Recycling at Pinkenba, Brisbane.
The facility has been designed to achieve materials recovery and landfill diversion rates of up to 99 per cent and will be capable of processing up to 475 tonnes per hour to produce a full range of construction materials.
Putting infrastructure in place that allows the separation of waste as it comes in so that facilities can either sell the output as a product or, send it off as a recyclate for someone else to recycle, is now the key focus thanks to policy makers and government entities who have introduced levies and capital grants to encourage the diversion of waste to landfills.
Australia is catching up fast but there is still work to be done says Gavin.
Australia is about 10 years behind Europe where very little goes to landfill. Any residual waste left over after the primary materials recovery process is used for waste to energy or is shredded down to solid recoverable fuel, known as process-engineered fuel (PEF), in Australia
Gavin predicts that in the next five years, as regulations change, there will be a move toward PEF preparation in Australia.
“We design our facilities to remove as much of the recoverable material as economically possible – initially targeting all the inert fractions and the heavy fractions,” he says. “The next step is refining the residual lighter material to meet the specifications of the PEF, which is outlet dependent.”
Turmec can also retrofit facilities to cater for changing waste streams and recycling demands.
The company is currently retrofitting a UK paper sorting plant so it can process plastic film. It also commissioned a plant in 2021, which saw a traditional comingled MRF, transform into a PRF (plastics recycling facility) that is now processing mixed plastics, glass, and metals.
“We’re talking to several big players within the Australian market, whether it be for upgrades or new facilities, and looking at incorporating plastics recycling,” Gavin says.
“We try to future-proof a facility by designing plants to be developed in phases. Recycling plastics is one area where there is going to be a lot of investment in Australia.”
Where Turmec sets itself apart is the level of automation and in the choice of technology employed.
“We evaluate and look at all the technologies in the marketplace, therefore, offering the most up-todate solution to our clients that will optimise the economic return in terms of the various targeted recyclate streams being separated,” Gavin says.
“Many existing plants still require a lot of manual labour and it’s getting more expensive and difficult for waste companies to fill these low skill positions.
“With Turmec systems, the machinery does 90 per cent of the work with manned positions performing final quality checks to remove contaminants.”
For more information, visit: www.turmec.com
Volatility from China, due to Chinese government bans on Australia’s exports, and the COVID-19 pandemic contributed to fluctuations in the wood chipping industry over the past few years.
Despite this variability, domestic demand increased, and the upward trend is forecast to continue for the local market, according to an Ibis World Industry report.
It’s a rise that Phil Dohnt, Owner/ Manager of LV Dohnt & Co, Pty Ltd hopes will continue. With more than 40 years’ experience within the industry, Phil has seen the effects of the many ups and downs, including the closure of some companies, and he’s hopeful there’s some security in sight.
“There has been some instability,” he says. “There’s not the relationship between the growers and the contractors there once was. However, it’s a privilege to work in the renewable timber sector and it’s important we all work at improving relationships and as a team.”
While not immune to industry volatility – LV Dohnt & Co was forced to reduce operations during the height of COVID-19 – the company knows a thing or two about enduring relationships. It has partnered with Komatsu Forest for forestry equipment for decades.
LV Dohnt purchased the first Petersen 5000 Flail/Chipper combination in Australia in 1999 and over the years the company has purchased 15 units. Today Phil has eight in operation and is waiting
on delivery of another two in the coming months. In addition, he has two Petersen 4300B drum chippers in operation.
“When Petersen was able to offer bigger horsepower in one engine, in the 1990s, it convinced us to purchase the first 5000 Fail /Chipper and we’ve been with them ever since,” Phil says.
“The thing that rates them highly for us is the overall specification and the product support.”
LV Dohnt & Co Pty Ltd was founded in 1932 in Bundaleer, north of Adelaide, by Phil’s grandfather. The company shifted to Penola in 1939 with a contract to supply timber for a local sawmill and provided wood to build ammunition boxes in the Second World War.
Phil started with the Woods and Forest Department at Nangwarry Sawmill before joining the family business in 1985. He
has overseen its transformation from hand fallers through to one of the largest infield chipping contractors in Australia with more than 140 employees.
This year LV Dohnt & Co Pty Ltd is celebrating its 90th year and through 30 years of succession planning has managed to reduce shareholdings back to one, third generation family. Phil believes this is an important step to stop dilution of ownership and set it up to be bigger and highly focused to achieve 100 years of timber harvesting in 2032.
The company currently has six infield chipping operations in South Australia and five in Western Australia, producing between 90,000 to 120,000 tonnes per chipper, per year.
The timber is processed and chipped in forest, requiring equipment that is robust, manoeuvrable, and highly productive.
Brenton Yon, National Sales Manager Komatsu Forest, says the Peterson 5000H processes whole trees in one continuous operation. It has a proven track record in the industry for high productive capacity and reliable, export quality chip.
Equipped with a large feed throat, the 5000H can accept up to a 56-centimetre (23 inch) tree or multiple small stems.
“It can be configured with a three or four pocket disc, with several optional sheave sizes to make precisely the chip you need,” Brenton says. “The standard threepocket disc produces chips from 16 to 32 millimetres long.
“Chipping production from 90 to 120 tonnes per hour can be
achieved depending on chip size and wood characteristics.”
He says upper and lower chain flails strip bark and limbs from the stems, while replaceable UHMW wear liners protect the flail housing sidewalls.
Ergonomic joystick controls provide precise control of the two-section knuckleboom log loader. End loading or top loading spouts are also available.
Phil says LV Dohnt & Co aims for less than half of one per cent of a load to contain green weight bark, placing more importance on the flail chain. A low standard chain will affect chip quality and increase chipper knife costs.
He says that over the years, the company has collaborated with Petersen and Komatsu Forest to improve the chippers.
“In conjunction with Mal Windrim (local Peterson Product Specialist) we were the first to start looking at increasing from a three-pocket disc to a four to improve productivity,” Phil says.
“We looked at how the machine worked and got a good understanding of it. The ability to go from two to three flails improved the debarking aspect which then helped with throughput.
“Over the years we’ve had a good relationship. Both parties have worked together to try and improve the product.”
Spread across what is referred to as the green triangle of South Australia, Western
Victoria and part of Western Australia, LV Dohnt & Co covers a wide geographical area. The availability of service and parts is vital.
Brenton says Komatsu Forest takes its after sales responsibilities seriously and engineering, sales, manufacturing, and dealer personnel work together to ensure the right support is delivered when it’s needed.
“Every wasted minute impacts the bottom line,” he says. “Producers must be able to rely on service to keep their operations profitable.
“We ensure our equipment operates effectively and efficiently throughout its life because our reputation depends on our customer’s satisfaction.”
The company also offers hands-on or online training so that customers grasp the key aspects of maintenance and operation of machinery.
Phil says it’s that service that makes Komatsu Forest stand out.
“At times they’ve flown parts in from America to get the machine back up and running,” he says.
“The availability of service after hours is also a big plus. If something goes wrong and you need that back-up, you need it. It’s that simple.”
For more information, visit: www.komatsuforest.com.au
QUALITY AND SAFETY ARE POWERFUL DRIVERS WHEN IT COMES TO CHOOSING WASTE RECYCLING EQUIPMENT. WMR SPEAKS WITH STEFAN TODOROSKI, GENERAL MANAGER OF WEST TIP WASTE MANAGEMENT, ABOUT HIS PREFERENCE FOR HIAB.
Safety and quality are paramount when you’re running a waste disposal service.
Which is why Stefan Todoroski, General Manager of West Tip Waste Management in Western Australia, made the switch to HIAB Multilift hooklifts and skiploaders.
“We’ve been using HIAB equipment exclusively for two to three years,” Stefan says. “We wanted something reliable that would stand the test of time and importantly, have the back-up and support.
“HIAB is synonymous with quality, in my opinion.”
West Tip Waste Management is a family-owned business operating in the wider Perth area.
With a recycling facility that achieves more than 80 per cent recovery of incoming waste, the company is predominantly moving construction and demolition and commercial and industrial waste.
It runs a fleet of skip trucks, hook
trucks compactor trucks and bulk semis for one-off services or a regular wasteremoval solution.
Stefan says the company bought its first HIAB Multilift hooklift from WATM Crane Sales and Service for a job where safety was particularly important.
Hooklifts are mounted on trucks to enable haulers to change out flatbeds, dumpster bodies, and similar containers.
Traditional pneumatic hooklift safety latches are usually switched on manually by the truck driver. The HIAB Multilift lock is naturally on. The driver presses a button to turn the latch off, once the button is released the latch automatically re-engages.
“It doesn’t happen often but sometimes a hooklift can fall out of the mouth of the hook and bins drop,” Stefan says.
“We do a lot of work in public areas. We had a specific job where we were working around a lot of pedestrian traffic. We couldn’t risk dropping a bin with people around. The HIAB alleviates
having to rely on a driver to ensure the lift is locked. I believe it’s the safest hook on the market.
“It’s my favourite hooklift so far. We’ve got another one on order and we’ll keep using them going forward.”
Stephen Molloy, WATM Sales Executive, says HIAB offers a range of hooklifts including some developed for specific applications within construction, waste and recycling. Each is tailored to meet a user need – from basic to high performance, and from low to high capacity.
Other safety features include digital HiVision technology that combines external cameras and sensors with in-cabin viewing technology and controls, and obstacle detection software that minimises the risk of injury to personnel or damage to equipment.
Stephen says the Multilift skiploaders are also built to perform. The Futura range, as the name implies, is the next generation and includes advancements such as EvoLight construction for a higher payload; a SwanNeck that increases reach; FlexControl; SkipTop that covers any load automatically and quickly and; SafetyPlus which boosts safety for both operator and surroundings.
“We pride ourselves on bringing the very latest technology to the waste industry, thus increasing safety and increasing efficiency,” Stephen says.
Stefan has added a Multilift Futura 12 and Multilift Futura 18 skiploader to the fleet and is impressed by the EvoLight construction.
“They’re a very good design,” he says.
“Instead of being thick heavy steel everywhere, they’ve been engineered to have a strong frame where it’s needed and lighter structural steel everywhere else.
“The lighter unit helps with the payload on the truck. If a driver can get an extra tonne on the truck, that might be an extra bin on a run or about 20-30 per cent productivity on a job. That’s great for us.”
Stefan says the company tried the skiploader for about six months before committing and hasn’t looked back. Apart from the extra payload, he says other benefits include a two-speed operation that makes the skiploaders efficient and easy to use.
“The drivers use them every day and they love them,” he says.
While durability and reliability of the product is important to WATM, another key aspect of the company’s service is the after sales support. Anthony Lazenby, WATM Managing Director, says WATM has spare parts valued at more than $3.5 million in stock and a support team available seven days a week, 24-hours a day right across Western Australia.
“We understand the nature of the waste industry and that downtime costs money,” he says. “We also understand the tyranny of distance and work toward solving a problem as efficiently as possible. We believe we are the only company in this space to have the capability to send technicians anywhere in Western Australia overnight if need be.
“All our technicians are experienced in resolving issues. We understand you need to have the right person, the spare part and the capability to fix a problem. They’re not mutually exclusive.”
It’s an affirmation that Stefan backs up.
“WATM support us well,” he says.
“They keep spare parts and there’s good turnaround times for any breakdowns or issues.
“Same day servicing in this market wasn’t heard of, until now.”
For more information, visit: www.watm.com.au
WASTECH ENGINEERING HAS SIGNED A DEAL TO DISTRIBUTE MCCLOSKEY WASTE RECYCLING EQUIPMENT. NEIL BONE, WASTECH MANAGING DIRECTOR, TELLS WMR WHAT THE PARTNERSHIP WILL BRING TO THE LOCAL MARKET.
McCloskey has been designing and building a line of equipment including crushers, trommels, screeners and a stacker range for more than 35 years.
It has established a reputation for reliability in construction and demolition, topsoil and many other large industrial screening applications.
Now the trusted brand is branching into the waste and recycling industry, with the establishment of McCloskey Environmental, and
is teaming up with an Australian engineering mainstay.
Wastech Engineering has a strong presence in Australia and New Zealand’s waste management and resource recovery sectors, with more than 30 years’ experience devising ways to treat waste in the best way for the environment.
Neil Bone, Wastech Managing Director, says it was this experience that led McCloskey to approach them to take on the Australian agency.
“This new range of McCloskey equipment is targeted towards a different sector than their crushing equipment,” Neil says. “McCloskey wanted a partner that was well established in the waste and recycling sector and that had an established sales, service and support network. Wastech was an ideal choice for them, and their products are a natural extension of our existing range, customer base and solutions.”
Wastech has a long history of supplying waste and recycling
equipment to a diverse range of businesses and governments.
Neil says that when launching the range of new products, McCloskey wanted to hit the ground running so has coupled its proven drive systems and tracked running gear with tried and tested, heavy duty shredding tables from Rentec and Tana.
He says having an established presence in the shredding and processing industry in this way provided McCloskey with a head start. These supply partnerships also provide a cost-effective outcome
for customers when selecting their next machine.
“Using the existing structural and drive components of their established mobile plant and coupling this with the Rentec and Tana range of shredder tables gives McCloskey global credibility in the shredder industry,” Neil says.
“Their products are reliable and competitively priced, which is vital when entering a new market place.”
There are numerous McCloskey crushing and screening plants around the country, but the new Environmental range was only established in 2021 and is expected to arrive in Australia in early 2023.
Neil says compost processing is a large and growing industry within Australia and will be a key market for McCloskey shredders, trommels and screens.
“As landfills run out of capacity and waste-to-energy becomes established in Australia, there will be a big push to sort, shred and screen all types of waste so as to divert as much as possible from landfill and recycle as much as possible while supplying valuable fuel for emerging waste-to-
energy plants,” he says. “Other waste streams will include tyre and mattress shredding, forestry reprocessing, landfill reclamation and size reduction to maximise transport efficiencies.”
McCloskey equipment can be installed as a complete process line, to replace existing equipment for greater efficiency or be an end-of-life replacement.
Wastech has established a national service and support network during the company’s three decades in business. Spare parts for the new range will be held in a central distribution warehouse with most parts available the next day.
Neil says McCloskey is committed to a sustainable future and is constantly looking for new opportunities in equipment design to solve the challenges of maximising diversion from landfill.
He looks forward to a partnership that continues to be on the cutting edge of innovation.
For more information, visit: www.wastech.com.au
Innovation, hard work and leadership are core elements of the waste and recycling sectors and the 2022 Waste Innovation and Recycling Awards were a perfect opportunity to salute the companies and people who have made a difference.
Held in conjunction with Waste Expo Australia, the awards recognise the best in waste and resource recovery from across the country.
Repurpose It Chief Executive Officer George Hatzimanolis collected the Leader of the Year award, while the Repurpose It Operations Team won the award for Operational Excellence.
MRA Consulting Group was awarded both the Small Consultancy Award, and WARR Workplace of the Year. Additionally, General Manager and Principal Consultant Katherine Dodd was recognised as Young Professional of the Year.
OUTSTANDING
Recognising new infrastructure projects that commenced operating in 2021 or 2022.
Winner: Southern Materials Recovery Facility, Re.Group & SRWRA
The Southern Materials Recovery Facility is South Australia’s largest and most advanced recycling facility with a capacity to process more than 70,000 tonnes per annum.
The first large-scale Australian MRF designed with COAG export bans in mind, the facility deploys advanced screening and optical sorting technologies as well as robotic quality control to meet high
standards of recycling purity and maximise recovery rates.
The facility was developed through an innovative joint venture between Re.Group and the Southern Region Waste Resource Authority, which is a joint subsidiary of the City of Onkaparingka, City of Marion and City of Holdfast Bay.
Collecting the award on the night, company representatives described the facility as a model for the future, with private and public sector working together for outstanding results for the community.
Recognising councils that have rolled out programs/initiatives that have measurable success in engaging and communicating with the community, resulting in positive outcomes for the industry.
Winner: City of Wanneroo
The ‘WasteSorted – Talking My Language’ educational toolkit developed by the City of Wanneroo, in partnership with the Waste Authority WA, aims to help overcome language and literacy barriers to communicate the importance of responsible waste disposal to the city’s culturally and linguistically diverse (CaLD) community.
Since April 2021 the city has empowered more than 50 community leaders and teachers to reach more than 900 participants and the contamination level of the city’s recycling has been reduced.
recycling contamination, increase use of FOGO and diversion of food waste from the general waste bin, and divert glass from the comingled recycling bin.
Recognising projects that have delivered cost-effective and high-impact success in their targeted fields.
Winner: Four Bin System (Let’s get sorted) Macedon Ranges Shire Council There’s nothing like a crisis to make people jump forward, according to a Macedon Ranges Shire Council spokesperson.
The comingled and glass recycling changes within Victoria signalled a crisis for many councils. Macedon Ranges Shire Council was on the front foot and supported the four-bin household recycling service with a new campaign to reduce
As a result of the campaign, the shire’s landfill diversion rate increased from 34 per cent to 76 per cent.
OUTSTANDING WARR PROJECT: METRO Recognising projects that have delivered cost-effective and high-impact success in their targeted fields.
Winner: Mordialloc Freeway Project, McConnell Dowell Decmil Joint Venture with Major Road Project Victoria The Mordialloc Freeway Project in Victoria
comprises a nine-kilometre freeway link including several grade-separated interchanges, bridges over wetlands and Mordialloc Creek, and a parallel shared user path along the alignment.
The project has become an example of implementing Victoria’s new Recycled First Strategy through sustainable procurement, collaborating with the supply chain to source sustainable materials that saved more than 300,000 tonnes of materials from landfill and more than 4000 tonnes of greenhouse gas emissions.
A project spokesperson said it was through “great vision, dedication and hard work” that the company continues to kick goals in this space.
There was a big focus on waste diversion for the Mordialloc Freeway and it had a big impact despite a shakey start when 42 cubic metres of asbestos contaminated soil was discovered. The soil was remediated and reused on site rather than taken to landfill.
Construction waste landfill diversion for the project was 97 per cent. Other circular economy outcomes included 6000 tonnes of concrete, 115 tonnes of brick and more than 1000 tonnes of asphalt recycled and returned to the project in road base.
The project also included a world first recycled plastic noise wall, made with hard to recycle soft plastics, equivalent to the waste from about 30,000 households.
Covers consultancies with less than 50 people on the staff. These companies are involved in an array of projects within the waste arena involving innovations, ideas and new technologies. As well as being voted on by clients, voters were asked to cite a project that was worked on by the consultancy and whether the outcome was set out in the original scope.
Winner: MRA Consulting Group
Covers consultancies with less than 50 people on the staff.
Winner: GHD
Collecting the award on the night GHD’s Bettina Zimmermann said they were proud and humble to be recognised.
“All of our clients are trying to achieve better, more sustainable ways of waste management and, moving forward, having as much waste avoidance as possible.
“We look forward to continuing to work in waste management.”
Recognising excellence or teams that have achieved demonstrable improvements in efficiency, best practice OHS, and impeccable records.
Winner: Repurpose It Operations Team Repurpose It operations team is described as the heartbeat of the organisation.
From delivering daily business activities, including making high-quality repurposed materials, to delivering major capital programs and ensuring operations are optimised.
The team has a focus on driving a zeroharm culture and strives for operational excellence, adding business value socially, environmentally, and commercially.
A range of diverse backgrounds and operational knowledge has been credited with the team’s success.
management and resource recovery. She found her passion for the industry while at university conducting a research project on behalf of Broadcast Australia looking at how to manage e-waste during the analogue to digital switch.
Shortly following university, Katherine began working at URS-AECOM where she developed her industry knowledge working with clients to support the advancement of the resource recovery industry, and a passion for leadership and mentoring.
Katherine joined MRA in 2020 as General Manager and a Principal Consultant. Accepting the award Katherine reflected on a great career and said she appreciative of the opportunity at MRA to help grow the company and train other young people within the industry.
Recognising individuals aged 35 years or younger who have impressed with their contribution and impact to their organisation and excellence inservice.
Winner: Katherine Dodd, MRA Consulting Group
Katherine has more than 12 years’ experience specialising in waste
Recognising individuals or companies that have implemented process and practices that have successfully closed the loop, creating a demonstrative circular economy.
Winner: Recycled glass construction products, Orca Civil Products
Orca Civil has developed patented technology that takes all types of glass waste destined for landfill to produce recycled glass polymer concrete as the core material for building products. Value-added
products include recycled glass pavers, modular bike lane separators and tramway separators rolled out across Australian roads which translated to about 150,000 glass bottles diverted from landfill.
A company spokesperson described the recycled glass products as a passion project that had taken years of hard work but had been a “wonderful trip”.
Recognising any private, not-for-profit or government organisation that has proven to achieve high levels of workplace engagement.
After more than a decade in the road maintenance industry, George founded Repurpose It in 2017 with a mission to transition Australia to a circular economy.
Recognising women in the industry who have driven change and continue to do so.
Winner: Rebecca Healy, Boxhead Plastics
Rebecca Healey is the founder of Boxhead Plastics, a non-profit social enterprise that locally collects, recycles, and remanufactures scrap plastic car bumper bars.
After 15 years of public service, Rebecca retrained as a Polymer Technician and pioneered a process that repurposes low grade plastic waste car bumper bars into products such as golf tees and coasters.
The award was collected on the night by Maree Noble, Treasurer of Boxhead Plastics, who said it was Rebecca’s dedication and commitment that had made the project a success. She also paid tribute to the endless hours put into the organisation by volunteers and the committee.
Winner: MRA Consulting Group. MRA is one of Australia’s leading environmental consultancy firms specialising in all aspects of waste and recycling. The team includes experts in waste, resource recovery and technology, climate change, carbon and sustainable development. Its vision of the future is one that is environmentally sustainable and economically rational.
Collecting the award, Principal Consultant Katherine Dodd said it was “one for the team”.
“It’s such a great organisation to be part of, with like-minded individuals who are just as passionate about resource recovery and moving waste up the chain,” she said.
“Thank you to the great people we get to work with. Consulting can be stressful, our organisation is a different part of consulting and a great place to work.”
Recognising leaders who hold senior positions who have shaped their business’ success, delivered financial growth, significantly and positively impacted the business’ culture and championed the industry widely.
Winner: George Hatzimanolis, Repurpose It
Under his leadership, Repurpose It is disrupting the industry with innovative technology that turns ‘untreatable waste’ into usable products.
George said the award recognition was amazing, but so too was the fact he was nominated by the “fantastic team” he leads.
Reflecting on his journey, George described the waste and recycling industry about 10 years ago as relatively small.
“I started attending waste and recycling conferences because I was looking for a resource opportunity. I wanted to find things to differentiate and reduce our reliance on extractive resources,” he said.
“Coming into the industry with that lens is something I’ve employed from day one.”
From 26-27 October, the Melbourne Convention and Exhibition Centre was abuzz with enthusiasm for all things waste, resource recovery, and circular economy.
For the first time since 2019, Waste Expo Australia made its long-awaited in-person return to the rainy city, which lived up to its reputation, though not enough to thin the crowds.
With a conference program featuring more than 90 speakers, and a show floor packed with exhibitors from every corner of the waste industry, attendees were not starved for options.
Samantha Martin, Waste Expo Australia Event Director, said attendees were excited to be back face-to-face, catching up with peers and industry leaders, and able to see and touch products again.
“Let’s be honest – waste is not sexy,” she says. “But when you get all these passionate people together in a room, the excitement that generates is quite contagious.
“It’s one thing I love about trade events – something you really can’t replicate by reading an article or talking to somebody online. You need that enthusiasm and energy that comes directly from somebody’s voice and the sparkle in their eye.”
Samantha says in-person events also allow for chance meetings when exploring the show floor – and when that happens, discussion is often much more free-flowing than when communicating digitally.
“The feedback from the exhibitors is that there’s been a great deal of interest, and a lot of deals being done on the floor too, which is always exciting.”
CHANGE FROM THE TOP Waste Expo Australia’s Waste Summit offered sessions split across four dedicated streams: local government; construction and demolition, and commercial and industrial waste; circular economy and waste innovation; and energy from waste.
Samantha says there was an appetite for policy discussion, which was clear from the response to the opening talks on day one which included an address from Recycling Victoria’s newly appointed head, Tony Circelli.
“The big take away is that the next challenge for the industry is moving towards a cohesive federal roadmap,”
OCTOBER FOR THE FIRST TIME IN THREE YEARS. EVENT DIRECTOR SAMANTHA MARTIN REFLECTS ON A SUCCESSFUL EVENT.she says. “The waste industry is going to be imperative to decarbonisation and hitting the nation’s emissions targets, so I think we’re going to have to have a federal consensus on a few things. Once we get there, we’ll see some rapid shifts.”
Samantha says keeping Waste Expo Australia free-to-attend presents opportunities for smaller industry players that may not otherwise have access to the resources on offer.
“We pride ourselves on not charging for our content,” she says. “Which means you can come in from anywhere in the industry, and hear from leaders and experts that might otherwise carry a significant price tag.”
This is reinforced by the expo’s co-location with the All-Energy Australia Exhibition and Conference, where the overlap with the waste sector is increasing, as topics such as energy from-waste continue to grow interest.
Samantha sees opportunities to build on this overlap in the future: “I think we can look to better integrate the two in the future, and perhaps be a bit more targeted about how they’re combined – those are challenges I’m looking forward to.
“The energy-from-waste stream was very well attended, and I heard a lot of
feedback that people would like to see more of it in the main theatres.
“That’s quite different to what we heard back in 2019, and that’s always part of the challenge for us – figuring out how to evolve and grow the streams for our audience.”
This requires the Waste Expo team to keep fingers on the pulse of industry trends throughout the year.
“We can’t do that without industry support,” Samantha says. “We have great relationships across the sector, from government to waste processors to supply chain and it’s important to keep those relationships strong.
“We rely on the insight from people in the sector to help understand the current challenges, and what we can do to address those at the event.”
Looking forward, Samantha says the waste and resource recovery industry has a lot of work to do, but much to be excited about.
“One thing that excites me about the waste sector right now is it’s becoming increasingly collaborative,” she says.
“Everyone’s realising they can’t do it alone – they need to share ideas, best practice, or how they’ve tackled and overcome certain issues.
“Because without that industry collaboration, we’re not going to hit all these waste and emissions targets.”
By providing a vital platform for this collaboration, Samantha wants to see Waste Expo Australia continue to help facilitate the industry’s momentum.
“We’ve got a really great foundation to keep growing this event,” she says. “Going forward, I’m really excited for Waste Expo to continue being a staple on the resource recovery calendar.”
For more information, visit: www.wasteexpoaustralia.com.au
Many years ago, when I first started in the waste industry, I was told that it would get under my skin, fast forward to 2022, and they were right.
As we count down to Christmas, and turkeys start disappearing on mass from farms, it’s a good time to reflect on 2022. And what a huge year it has been in Victoria (sorry interstate readers).
The number of opportunities within the industry is almost limitless. Innovation and investments are happening across the state on both a large and small scale. All we need to do is find some people to staff them.... and maybe some regulatory reform to help speed things along.
As Victorians shed their COVID-19 work from home attire and were thrust back into the sunshine of 2022, the waste industry was fatigued. Chronic workforce shortages, surging fuel and energy prices and new environmental regulations and tracking requirements added fuel to the fire. But the trucks kept
rolling, the bins kept being collected and resources continued to be recovered or repurposed – behind it all was an unseen supply chain of drivers and operational teams that continued to juggle collections and processing.
Despite these challenges, the industry continued to grow, and innovative recycling and processing plants continue to be established.
The introduction of the Circular Economy Act solidified the need for more innovation and infrastructure, it also provided some guidance to help create and drive these initiatives.
Let’s not omit the introduction of a new regulator with the establishment of Recycling Victoria. While it’s early days, so far so good.
The introduction of the four bin system (or five if you live in one particular municipality) and bin content standards is widely viewed as a step forward. Consistent educational messaging across the state will
go a long way to reducing contamination and will allow MRFs and other recyclers to hone in on particular waste streams. In years to come the system can be reviewed and further streams added.
Victoria is jumping on the Container Deposit Scheme bandwagon, with legislation passing through Parliament earlier this year and commencement of the
BRETT LEMIN, EXECUTIVE OFFICER OF THE VICTORIAN WASTE MANAGEMENT ASSOCIATION, REFLECTS ON THE INDUSTRY HIGHS AND LOWS THROUGHOUT 2022.scheme set for 2023. The CDS has proven to be a success in other jurisdictions while reducing litter and helping community groups to fund their projects.
The past year hasn’t all been rainbows and sunshine though;
Emerging contaminants such as PFAS and compostable products containing PFAS are having an impact on the waste industry and communities. We need more research, education and awareness into this contaminant and its effects. As more innovative ways of treating PFAScontaminated waste come to the market it is important for the rules and regulations to keep up with the scientific data and technology within this space.
Delays with EPA permission, licencing and permits in 2022 have left many organisations frustrated and wanting answers. A huge amount of investment dollars is held up while businesses wait for applications to be approved. Delays are spanning into the months, and while reputable companies are on the sidelines awaiting their approvals, illegal activities increase in the background, further damaging the reputation of our industry.
The fallout from COVID-19, waste export bans and the building crisis has led to an increase in illegal dumping with many councils having to pick up the bill.
Brett Lemin , Executive Officer of The Victorian Waste Management AssociationVictoria’s Waste Crimes Directorate was disbanded in 2021 to assist with the budget repair after the COVID blowout of 2020-21 only two years after it was established. With the industry expanding at such a rate, we need it now more than ever.
Education and awareness continue to be areas where, as a society, we are falling short. More focus needs to be put on producers and manufacturers regarding the downstream issues their products are creating. It is also welcoming to see that the Australian Competition and Consumer Commission (ACCC) is starting to target greenwashing across multiple industries.
With so much change in the industry, the environment in which we operate and the society we live in, the need for active
associations has never been higher than right now. I would urge all readers to reach out to their relevant associations and get involved in the discussions.
Changes are happening at a rapid rate and an association is one of the best ways to get involved and talk with knowledgeable waste professionals, stay informed on what is happening within the industry from a government and industry level, and let’s not forget, the opportunity to connect with peers. It’s important to be involved in the conversations and help create a better industry for all.
I hope you all have a happy and safe holiday period and spare a thought for those that continue to work through to ensure our circular economy continues to roll along.
The waste industry continues to grow with investment across the board.“The number of opportunities within the industry is almost limitless. Innovation and investments are hapenning across the state on both a large and small scale.”