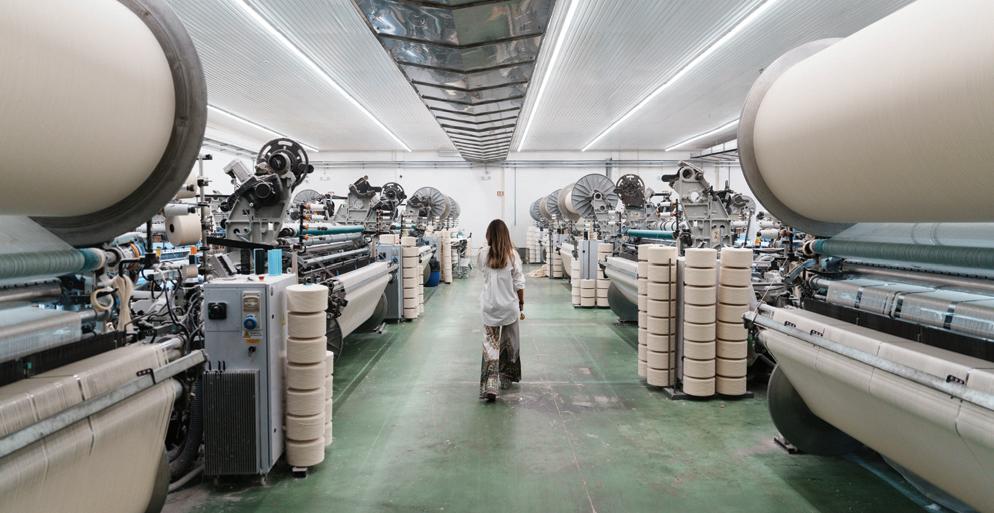
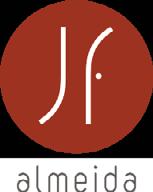

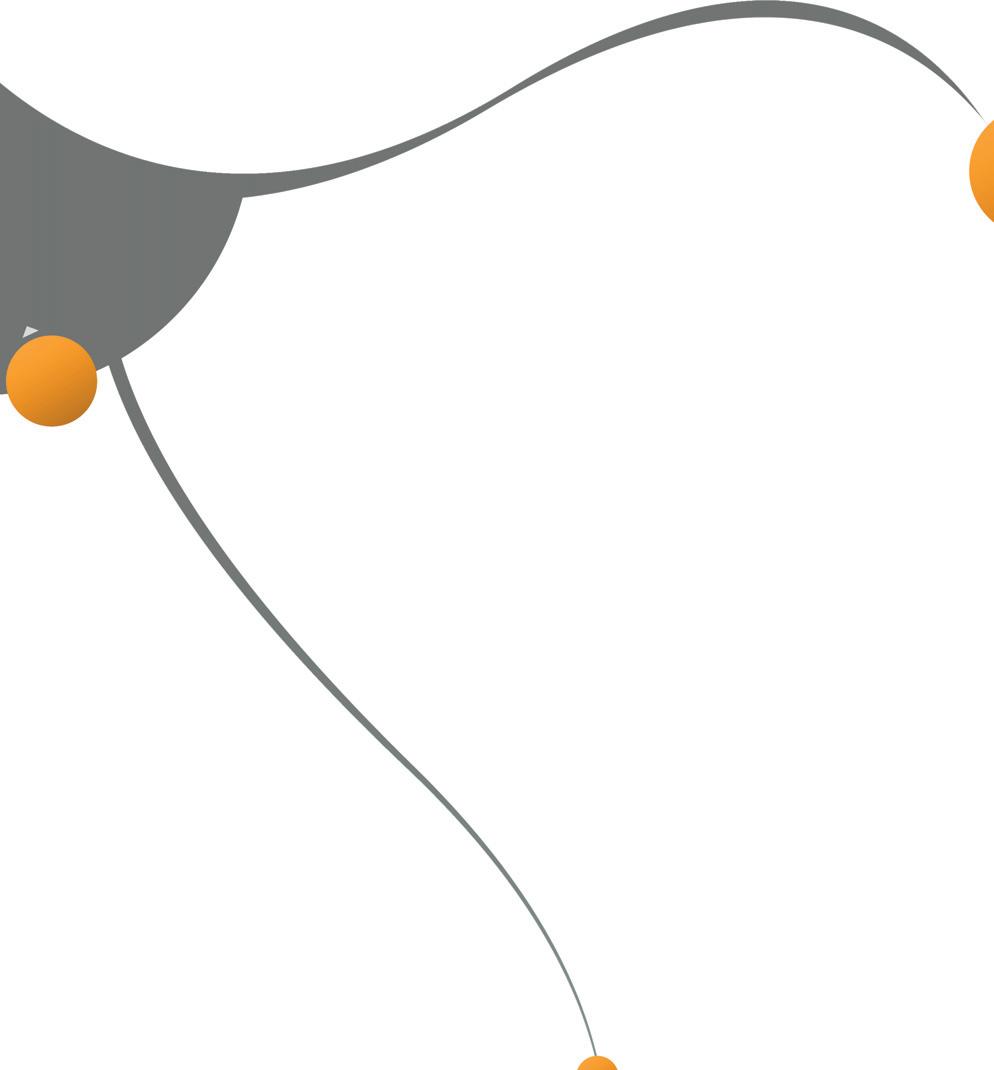
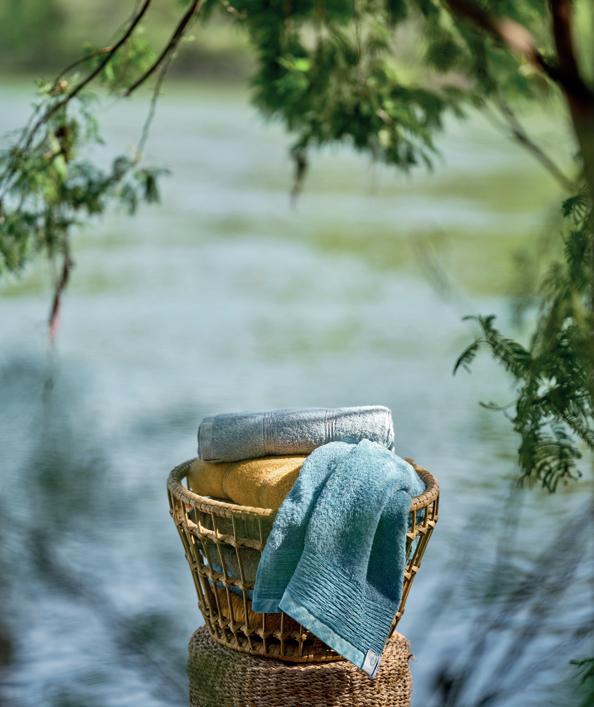
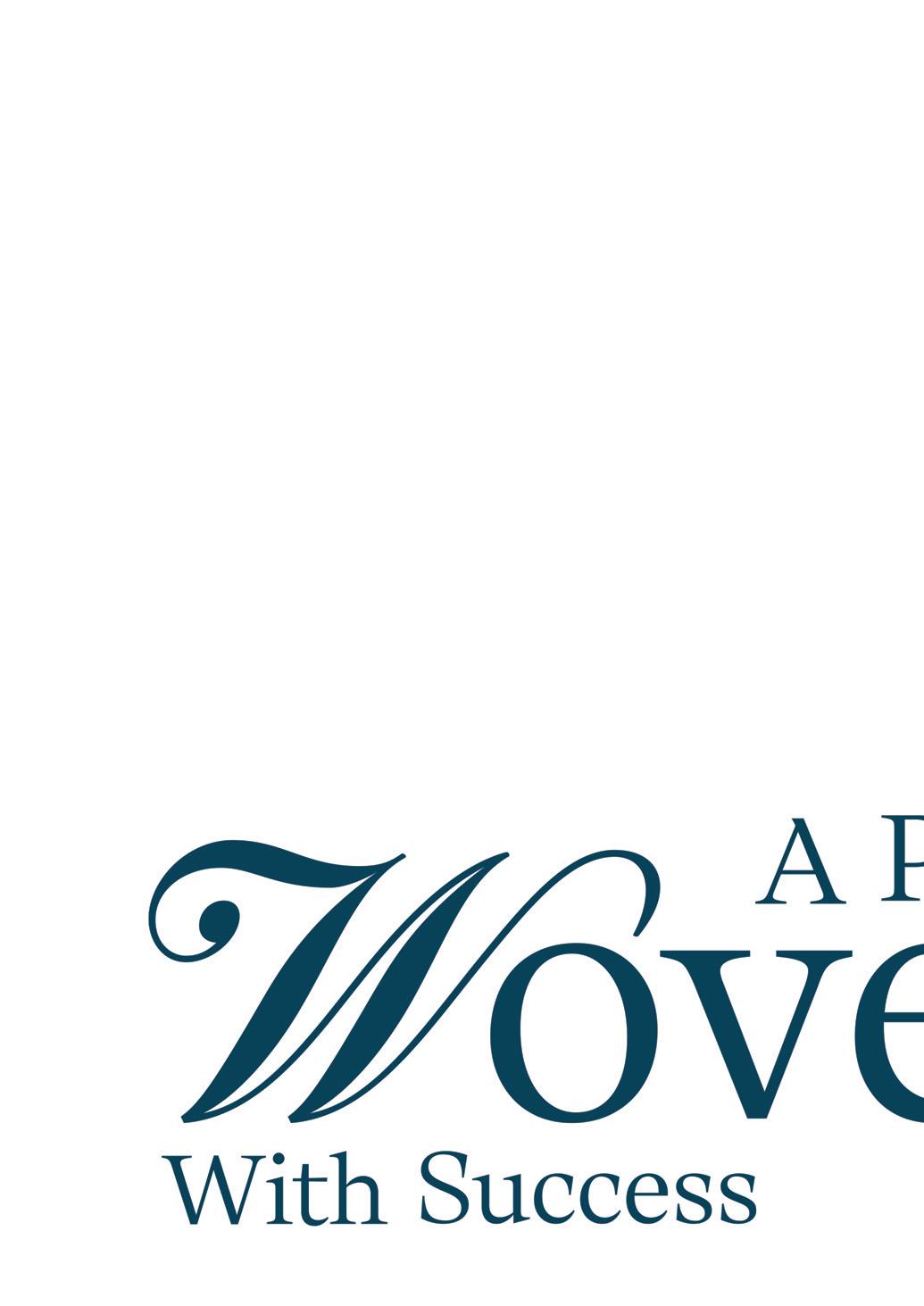
Têxteis J.F. Almeida is a big name in the world of textiles. Over the last 35 years, the manufacturer has developed a strong portfolio of products all while maintaining a commitment to responsible sourcing. Sustainability Manager Mariana Gomes and Raw Material Purchasing & Product Manager Paulo Lopes explained more, during an in-depth interview with Inside Sustainability. Report by Imogen Ward.
ASPortugal’s largest vertical textile company, Têxteis J.F. Almeida (JFA) has set a preceden t for all things spinning, weaving and dyeing. Originally operating as a weaving business, the family-run enterprise continued to grow over the years, expanding both its presence in the market and its capabilities. “When we began operating in 1979, we only had four looms, and now, we are operating with 123,” explained Raw Material Purchasing & Product Manager Paulo Lopes.
“The business has experienced gradual and consistent expansion, reinjecting 10 per cent of its turnover back into the business each year,” added Sustainability Manager Mariana Gomes. “This has really helped with growing the business and upgrading our machines.”
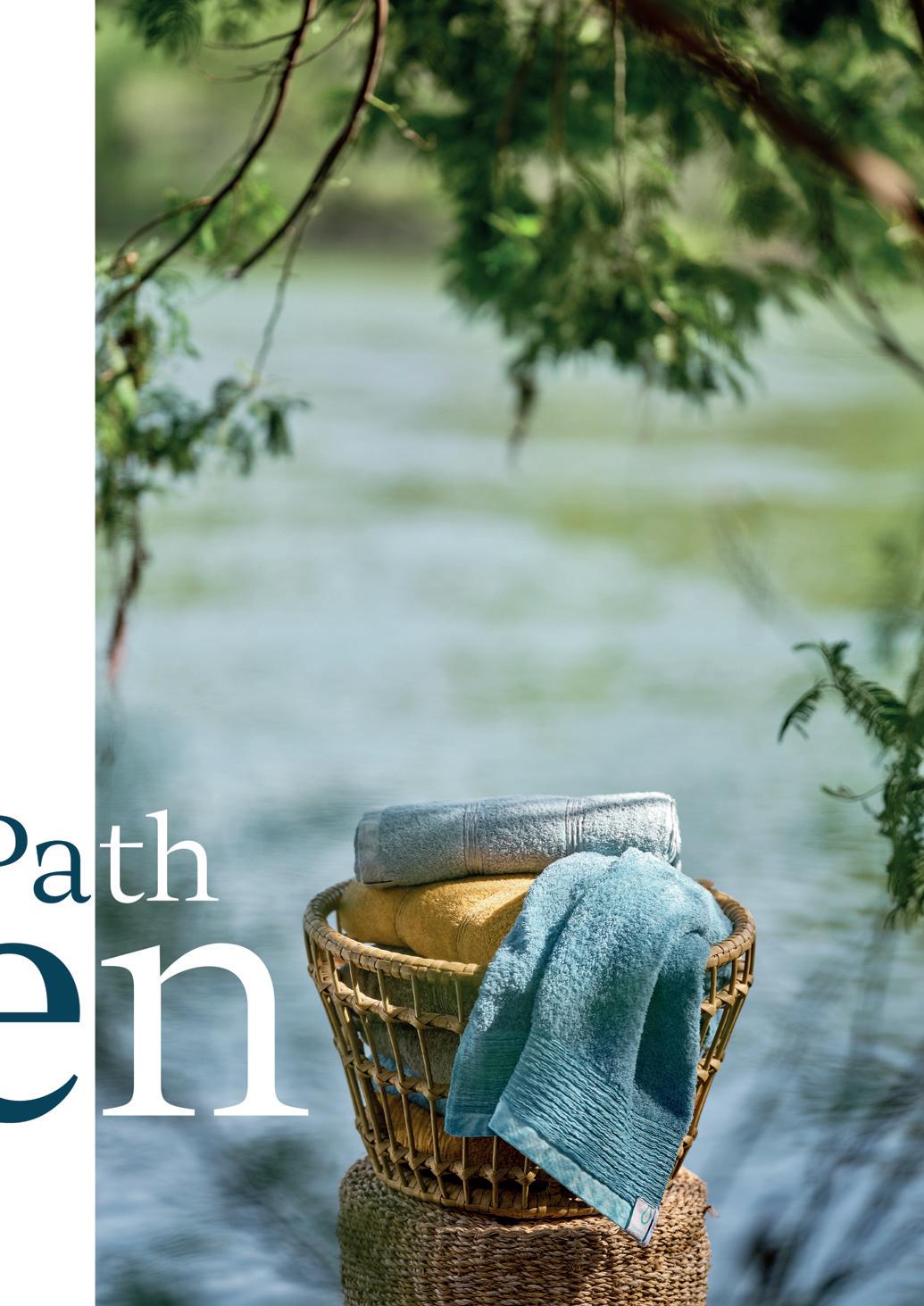
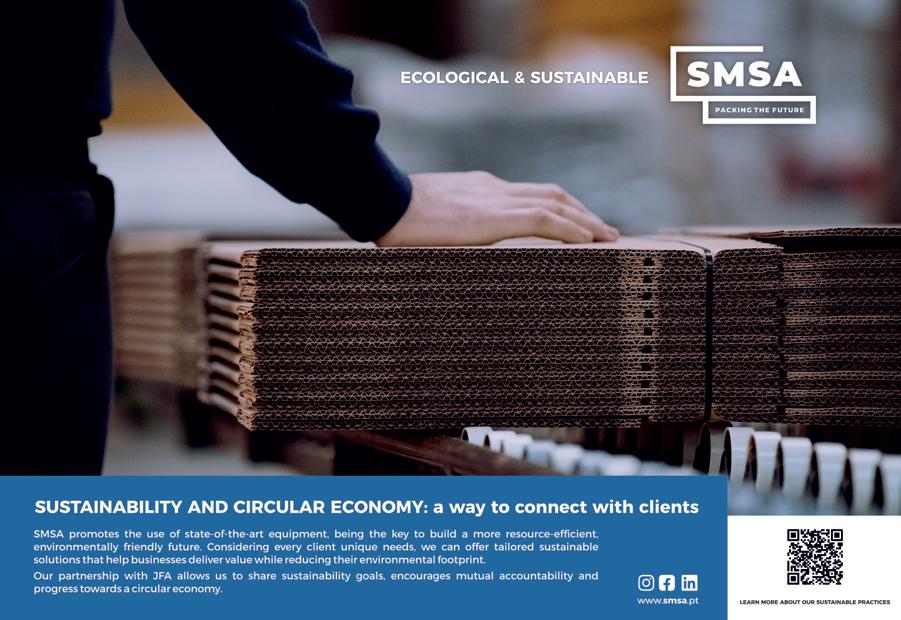
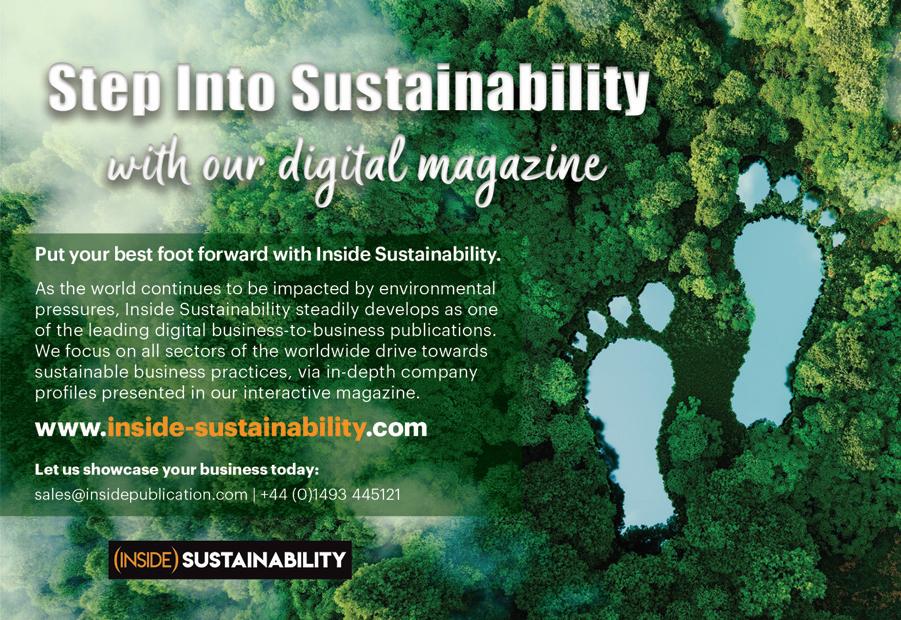
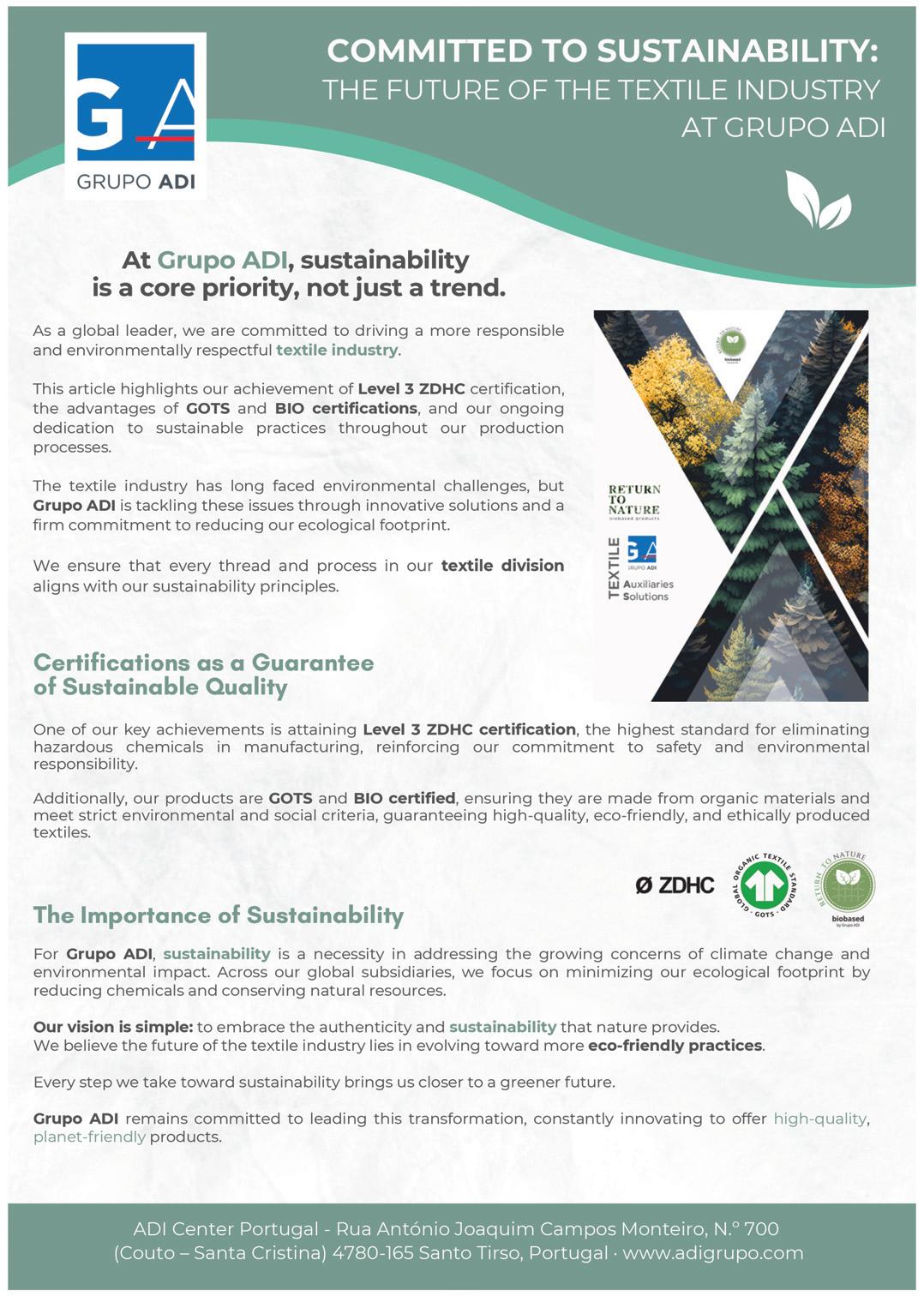
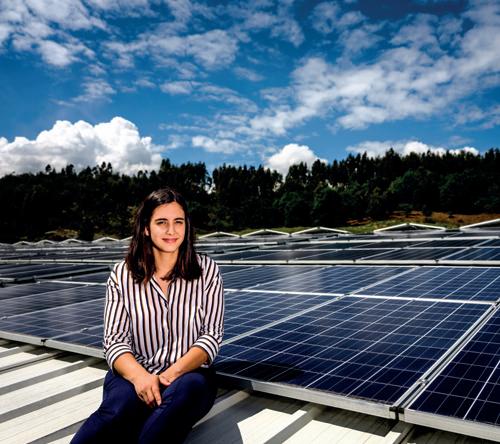
A more diverse offering
During the 2022/2023 period, the company decided to be bold and invest a whopping €35 million into new development. Included in this sum was a brand-new finishing line.
“Having previously focused our attention on terry cloths, the 2022 investment enabled us to advance our focus in the home textiles market,” said Mr Lopes.
The new finishing line, which is dedicated to bed sheets, linens and fabrics, introduced Envigorate to the market (a finish that adds negative ions to materials for a more positive night’s sleep). The resultant finish can help improve relaxation and reduce tiredness amongst users.
“Of course, we are still stable in the terry towels market, but this line has provided us with an exciting new market to explore,” added Ms Gomes.
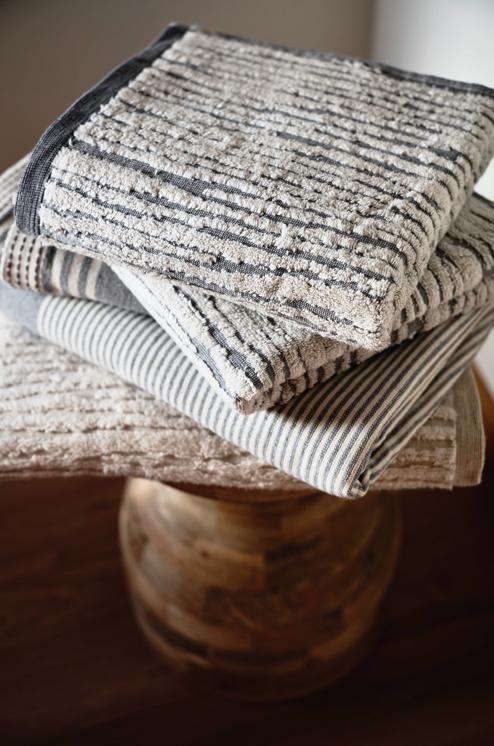
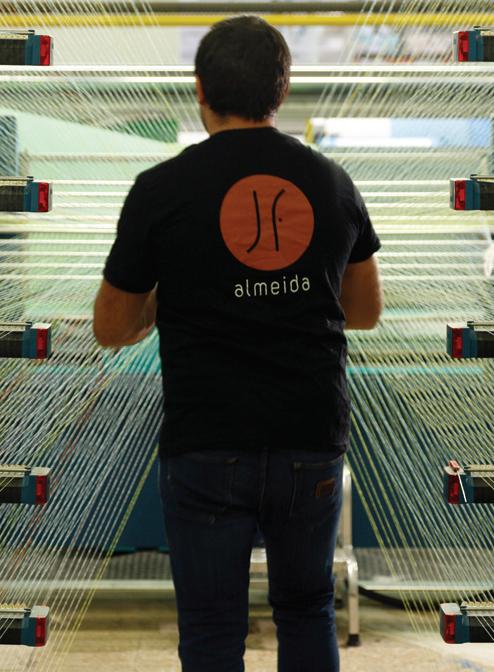
Over €6 million of the 2022 overhaul were also dedicated to key sustainability initiatives designed to advance the company’s energy efficiency and its decarbonisation efforts.
“Due to JFA’s size, we are obliged to report our sustainability data for the 2025 financial year,” explained Ms Gomes. “The 2022 investment was valuable in helping kickstart some of our targets for this report. For example, we hope to reduce our Scope 1 and 2 emissions by 50 per cent in 2025, compared to our 2021 baseline.
“We also intend to reduce our water consumption from 74 litres per kilo to 50 litres per kilo.”
“It is important to note that before 2020 we were using around 120 litres per kilo of water, so we have already come a long way,” added Mr Lopes.
Following all these amazing investments, it is no wonder that JFA achieved a turnover of €58 million for the 2023 period.
Today, the company operates with six units, where it provides services relating to spinning, weaving, dyeing and logistics. JFA is capable of producing 1,000 tonnes of yarn per month, its weaving unit has a capacity of 700 tonnes per month and it is also home to the largest dyeing unit in Europe. And thanks to its logistics unit that opened in 2016, JFA can also store 4,400 pallets of finished products.
An important project
In line with its continued commitment to greener operations, JFA signed up to the tExtended project in 2022. Aimed at finding solutions to textile waste, the tExtended project is a 48-month long
initiative that involves the collaboration efforts of 20 different companies.
Fewer than 1% of textile waste is currently being recycled worldwide and JFA was determined to do something about it.

“We understand that this is a feat we could not accomplish on our own,” said Ms Gomes. “That is why we are participating in several national and international projects to help advance the progress. The tExtended project is a great example of that, as we are working with partners from all over Europe to try and make a difference.”
JFA already has ample experience in addressing the concern on waste, having developed a new product that utilises the raw material waste from its own internal processes. The environmentally friendly product, 360JFA Recycled Yarn, entered the market in 2018.
“Through this process, we are able to reuse almost 100 per cent of our internal waste and manufacture a product with the same characteristics and quality as a similar option manufactured with only raw cotton,” revealed Ms Gomes.
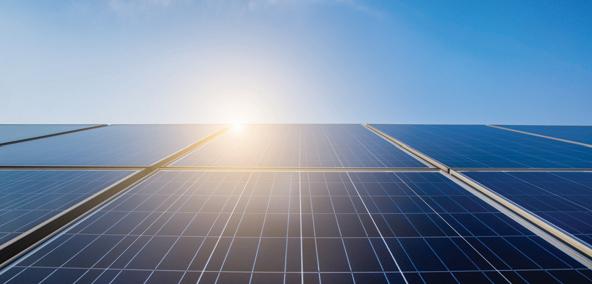
A team effort
JFA is proud to offer its customers a highly flexible approach to manufacturing, and its vertical business structure is one of the reasons it can do so.
“We don’t need to outsource our manufacturing processes, and that gives us full control of the entire process,” explained Ms Gomes. “This enables us to provide our customers with complete flexibility. We also benefit from a wide range of machines dedicated to different quantities. Whether a client wants 50kg of product or 50,000kg, we can make it happen.”
Of course, the company’s loyal and hardworking supply chain is still a crucial part of the process. JFA relies on several companies for the supply of fibres, yarns and chemicals.
“Most of our chemical suppliers are not just suppliers, they are partners,” said Ms Gomes. “If we need to make improvements to a process, they will collaborate with us and find a solution that works.
“We also rely on a lot of smaller suppliers who help cover extra capacity, when our
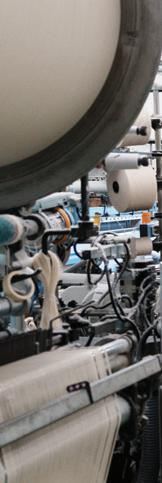
processes can’t cover the demand for delivery. These are all local companies who are extremely important to our success.”
JFA is also actively working with its supply chain to calculate its baseline Scope 3 emissions. In time, the company i ntends to collaborate to improve this rate.
“Even though we haven’t broadcast it, we have been actively working to improve our sustainability since 2016,” explained Ms Gomes. “We were actually one of the first textile companies to have a full-time Sustainability Manager. JFA has the experience; it has the results, and the next steps will be to put those results into writing for the world to see.”
“We also have plans to increase our work in natural fibres, while developing new collections with sustainability and a circular economy in mind,” added Mr Lopes.
“We all know that the textile industry is one of the worst when it comes to the environment,” said Ms Gomes, in conclusion, “but things are changing, and I am so excited that the work JFA does is helping to create a cleaner, greener industry.” n
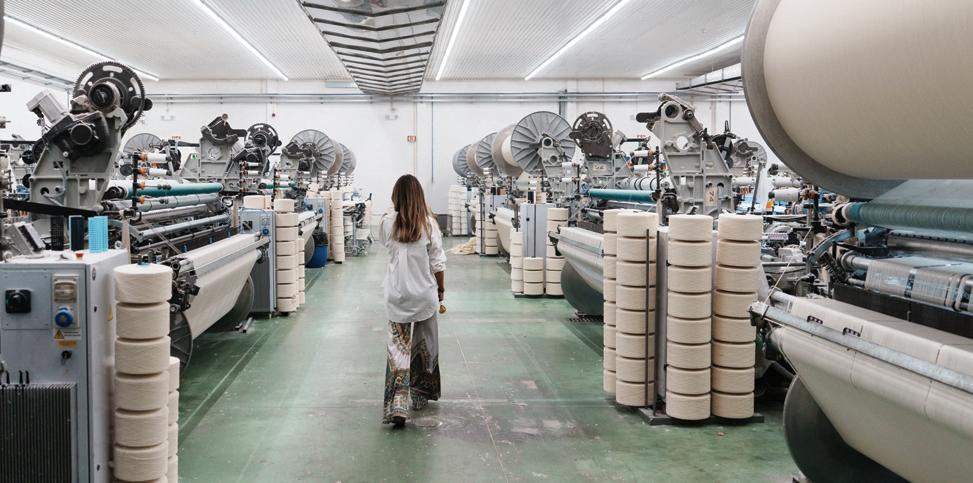
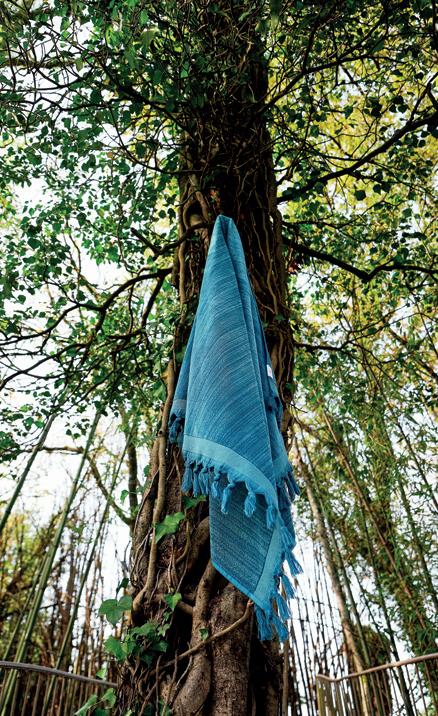
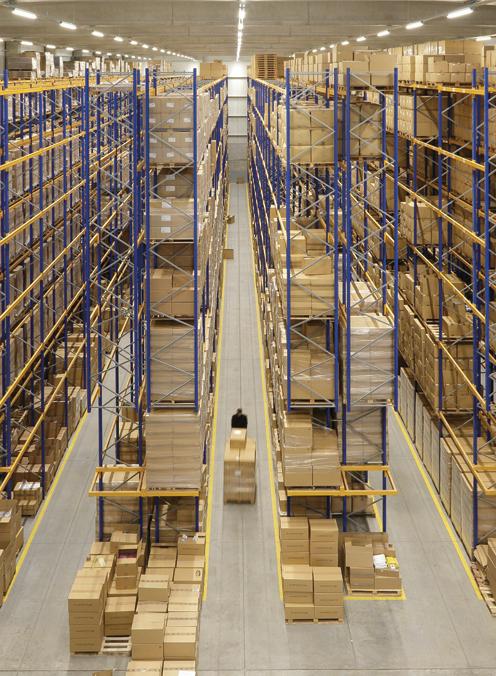
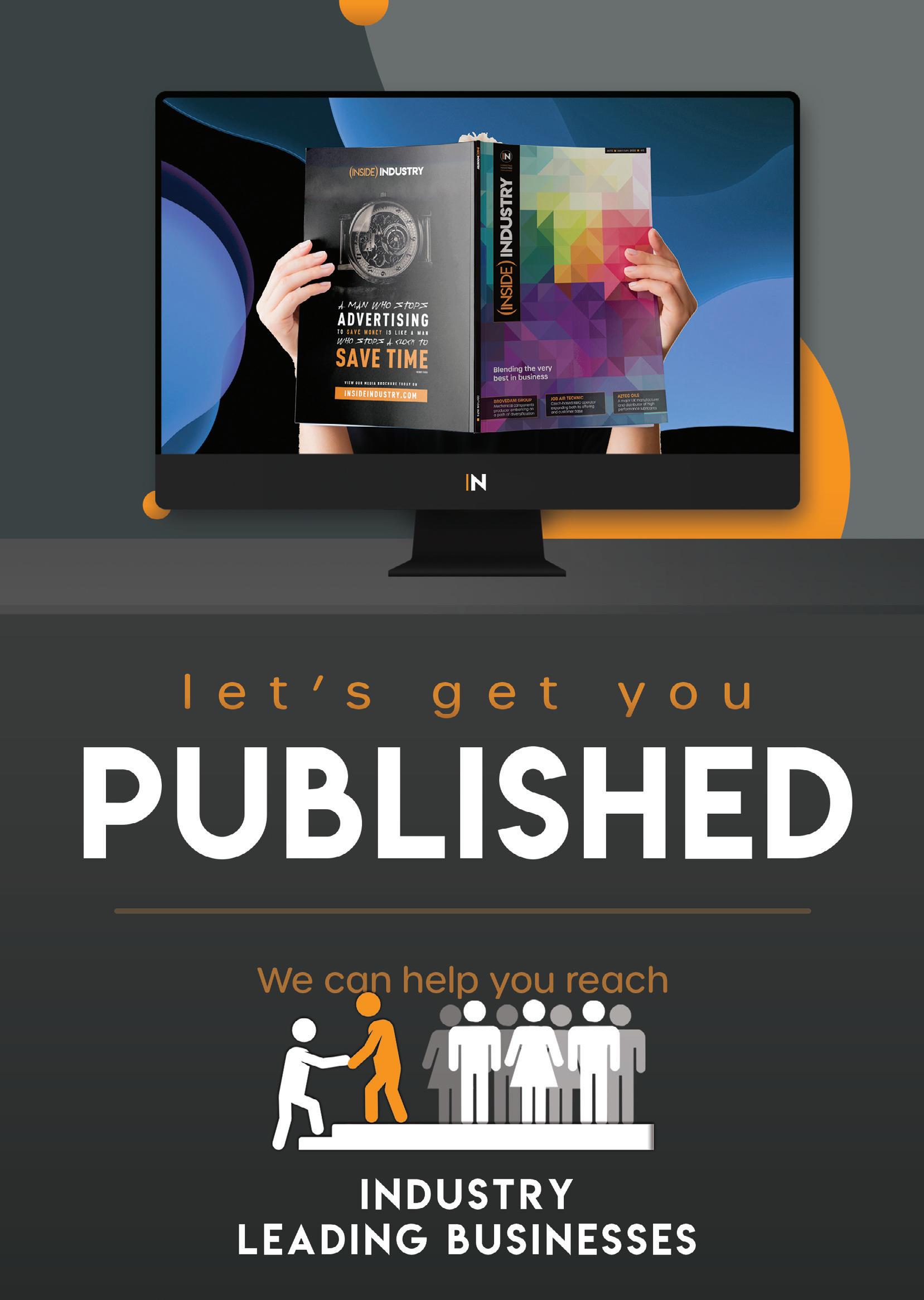
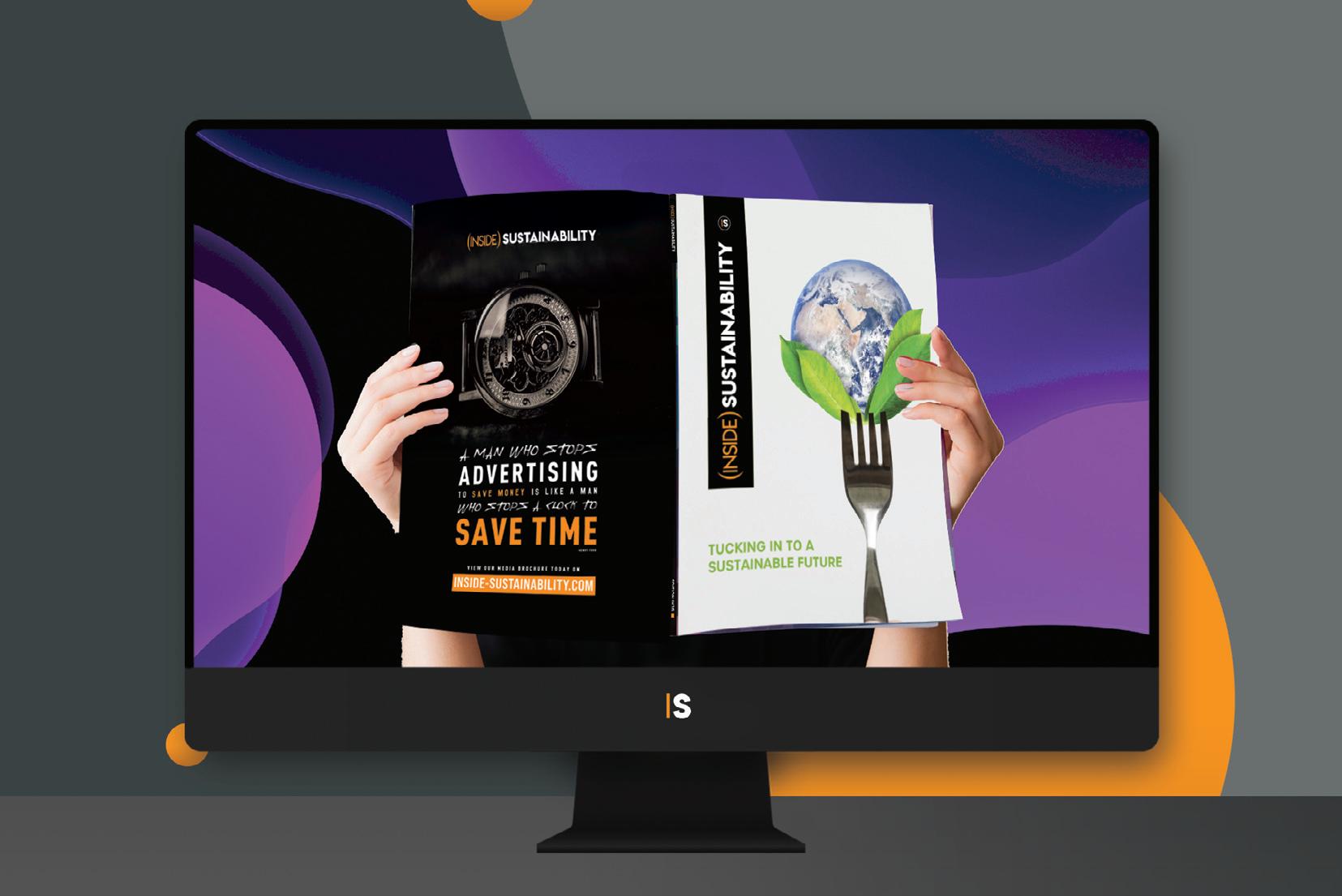