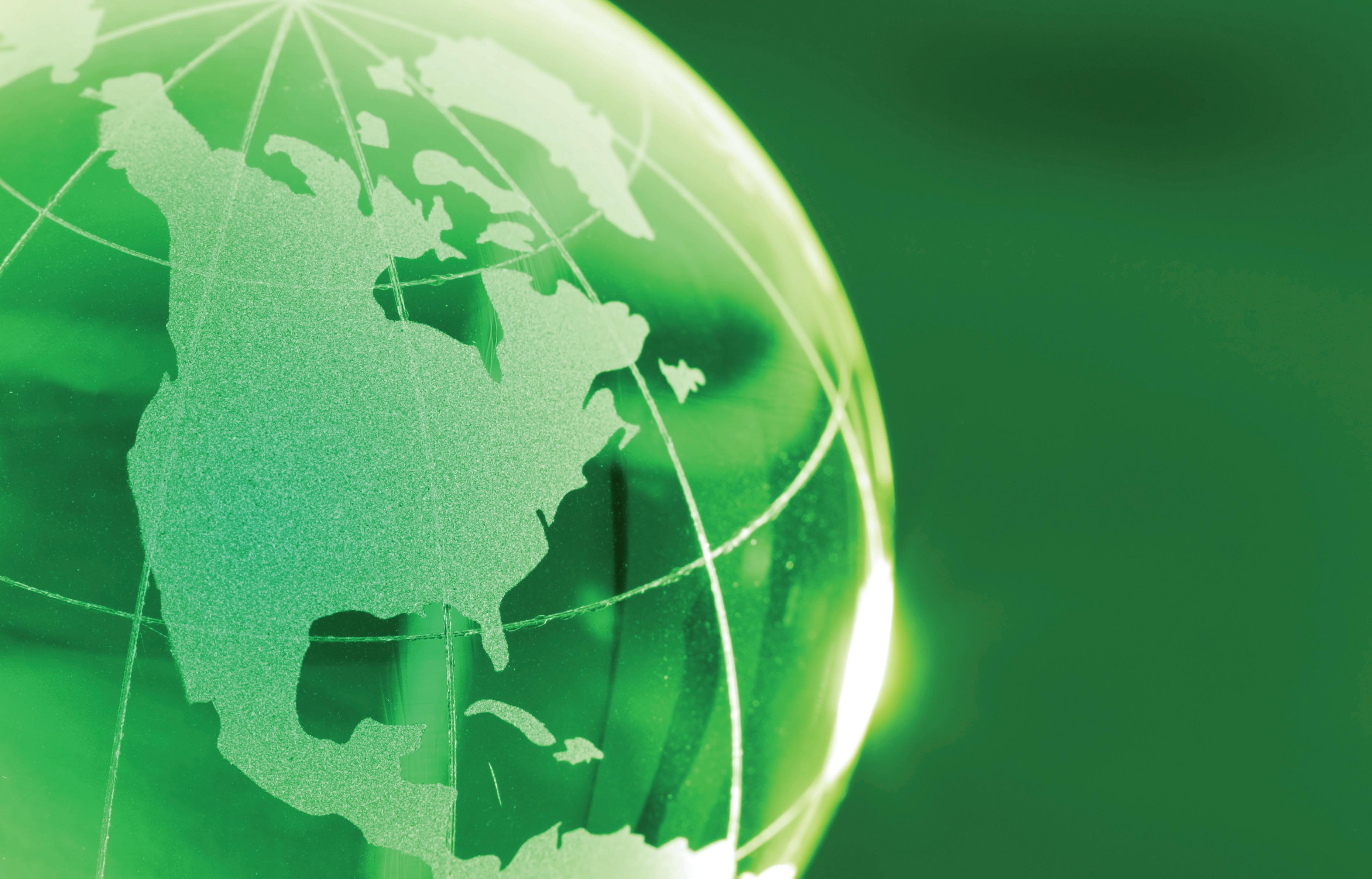
32 minute read
PLASTICA & AMBIENTE
A CURA DI WALTER REGIS E MARILENA DI BRINO
NOTIZIARIO ASSORIMAP
DIRETTIVA SUP
Il recepimento nazionale “dimentica” il riciclo meccanico
In seguito all’approvazione da parte del Consiglio dei Ministri, avvenuta il 5 agosto 2021, è stato inviato alle Camere, per il relativo parere formale, lo “Schema di decreto legislativo recante attuazione della direttiva (UE) 2019/904 del Parlamento europeo e del Consiglio, del 5 giugno 2019, sulla riduzione dell’incidenza di determinati prodotti di plastica sull’ambiente” (cosiddetta Direttiva SUP: Single Use Plastics). Nell’ambito del ciclo di audizioni indetto dalla 10ª Commissione (Industria, commercio, turismo) e dalla 13ª Commissione (Territorio, ambiente, beni ambientali) del Senato della Repubblica, Assorimap è stata convocata lo scorso 20 settembre per illustrare la propria posizione in merito allo schema di recepimento nazionale. All’audizione, svoltasi in modalità di videoconferenza, ha partecipato il vicepresidente dell’associazione, Maurizio Foresti, accompagnato dal segretario Marilena Di Brino. “Assorimap ha evidenziato come la Direttiva europea SUP abbia il merito d’introdurre nell’ordinamento comunitario il contenuto minimo obbligatorio di plastica riciclata (25% al 2025 e 30% al 2030, limitatamente ai contenitori per liquidi alimentari con capacità fino a tre litri). Si tratta, a nostro avviso, di una misura importante a favore del riciclo, che amplierà il mercato per la materia prima seconda (nel caso specifico per il PET riciclato), contribuendo in parte al raggiungimento degli ambiziosi target fissati dal Pacchetto per l’economia circolare”, ha dichiarato Foresti. “Tuttavia, l’utilizzo circolare delle materie plastiche potrebbe essere favorito maggiormente estendendo le previsioni di contenuto minimo obbligatorio di plastica riciclata tracciata post consumo, che Assorimap propone al 50%, anche ai prodotti monouso elencati nella parte B dell’allegato (messi al bando dalla direttiva), qualora non sia possibile l’uso di alternative riutilizzabili”. In effetti, la stessa eccezione prevista per i materiali biodegradabili e compostabili, se estesa anche a prodotti e imballaggi che contengano una percentuale minima di plastica riciclata, avrebbe il merito di perseguire a tutti gli effetti l’obiettivo della circolarità delle materie plastiche, che sappiamo essere il fine della direttiva. A fine vita, infatti, questi stessi prodotti risulterebbero conferibili nella frazione plastica della raccolta differenziata e, pertanto, nuovamente valorizzabili attraverso il recupero di materia, prioritario alle altre forme di recupero secondo la gerarchia comunitaria di trattamento dei rifiuti. “Il governo si è dimenticato del riciclo meccanico della plastica, attività green per eccellenza”, ha affermato il presidente di Assorimap, Walter Regis, in un’intervista al quotidiano La Repubblica dell’11 ottobre scorso. “Nel nostro Paese sono presenti solo 60 imprese per il riciclo meccanico della plastica ma, nonostante il numero così esiguo, possediamo un know-how all’avanguardia nel mondo… Ritengo inconcepibile il fatto che non esista una deroga per i prodotti che contengono percentuali elevate di plastica riciclata”. Le principali proposte di Assorimap, contenute in una memoria scritta e depositata in occasione dell’audizione, sono state accolte dalle Commissioni riunite del Senato e riprese dal parere del 13 ottobre 2021, che non è però vincolante ai fini del recepimento della direttiva. Lo schema di recepimento era stato già inviato, in
via preventiva, alla Commissione UE lo scorso 22 settembre, per un esame che durerà fino al prossimo mese di dicembre.
PNRR: PUBBLICATI I DECRETI RIGUARDANTI I PROGETTI SU RIFIUTI ED ECONOMIA CIRCOLARE

Lo scorso 30 settembre sono stati pubblicati i Decreti MiTE recanti i criteri di selezione per i progetti nell’ambito degli Investimenti 1.1 e 1.2 della Missione 2, Componente 1, del PNRR: il DM 396 del 28/09/2021 (PNRR M2C1 Investimento 1.1) stanzia 1,5 miliardi di euro per la realizzazione di nuovi impianti di gestione rifiuti e per l’ammodernamento di quelli esistenti, mentre il DM 397 del 28/09/2021 (PNRR M2C1 Investimento 1.2) stanzia 600 milioni di euro per la realizzazione di progetti faro d’economia circolare per le filiere industriali strategiche (RAEE, carta e cartone, plastiche, tessili). Entrambi i decreti assegnano il 60% delle risorse al centro-sud Italia. Il DM 396 prevede la selezione di progetti afferenti alle seguenti linee d’intervento: A. 600 milioni di euro complessivi (fino a 1 milione di euro per progetto) per il miglioramento e la meccanizzazione della rete di raccolta differenziata dei rifiuti urbani; B. 450 milioni di euro complessivi (fino a 40 milioni per progetto) per l’ammodernamento/ampliamento d’impianti esistenti e la realizzazione di nuovi impianti di trattamento/riciclo dei rifiuti urbani provenienti dalla raccolta differenziata; C. 450 milioni di euro complessivi (fino a 10 milioni per progetto) per l’ammodernamento/ampliamento e la realizzazione di nuovi impianti di trattamento/riciclo per lo smaltimento di materiali assorbenti ad uso personale, fanghi d’acque reflue, rifiuti di pelletteria e rifiuti tessili. I soggetti destinatari delle risorse sono gli Enti di Governo d’Ambito Territoriale Ottimale (EGATO) o, laddove questi non siano costituiti, i Comuni. Il DM 397 prevede invece la selezione di progetti riguardanti le seguenti linee d’intervento: A. 150 milioni di euro per l’ammodernamento/ ampliamento d’impianti esistenti e la realizzazione di nuovi impianti per il miglioramento di raccolta, logistica e riciclo dei RAEE, comprese pale di turbine eoliche e pannelli fotovoltaici; B. 150 milioni di euro per l’ammodernamento/ampliamento d’impianti esistenti e la realizzazione di nuovi impianti per il miglioramento di raccolta, logistica e riciclo dei rifiuti in carta e cartone; C. 150 milioni di euro per la realizzazione di nuovi impianti per il riciclo dei rifiuti plastici (attraverso riciclo meccanico, chimico, “plastic hub”), compreso il cosiddetto “marine litter”; D. 150 milioni di euro per l’infrastrutturazione della raccolta delle frazioni di prodotti tessili pre e post consumo, l’ammodernamento
dell’impiantistica e la realizzazione di nuovi impianti di riciclo delle frazioni tessili in ottica sistemica (cosiddetti “textile hub”). In questo caso, i destinatari delle risorse sono le imprese. Si evidenzia che, nell’ambito dell’Investimento 1.2, il decreto non stabilisce un massimale erogabile per le proposte, ma rimanda all’art. 56 sexies, comma 7, lettera b), del regolamento UE n. 651/2014 GBER, come modificato dal regolamento 2021/1237, che fissa a 100 milioni di euro “l’importo nominale del finanziamento totale concesso a qualsiasi beneficiario finale per progetto nell’ambito del sostegno del Fondo InvestEU”. Su quest’ultimo decreto, in particolare, Assorimap manifesta insoddisfazione a causa dell’irrisorietà delle risorse: solo 150 milioni di euro per ogni singolo flusso di materiali e nessun massimale previsto per singolo progetto; in particolare, per la sola plastica, nessun finanziamento agli impianti preesistenti. Lo scorso anno, congiuntamente ad Assofermet e Unirima, l’associazione aveva chiesto, sempre nell’ambito del PNRR, risorse per il revamping degli impianti da destinare alle imprese del riciclo meccanico che, producendo materie prime seconde (MPS), già contribuiscono al raggiungimento dei target fissati dall’UE.
WEBINAR SUI CERTIFICATI DEL RICICLO
Il 13 ottobre 2021 si è svolto, su piattaforma digitale, l’evento intitolato “Certificati del riciclo: l’anello mancante”, promosso da Laboratorio REF con il coinvolgimento, a mo’ di tavola rotonda, di importanti rappresentanze del mondo del recupero e del riciclo: A2A, Arera, Assofermet, Assorimap, Conai, Coripet, Fise, Hera, Unirima, Utilitalia. Per l’occasione, Laboratorio REF ha presentato il position paper “Certificati del riciclo: il secondo pilastro della responsabilità estesa”. Lo studio illustra i possibili meccanismi di quelli che potrebbero divenire strumenti economici finanziari similari ai certificati bianchi già previsti per l’efficienza
Il vicepresidente di Assorimap, Maurizio Foresti, durante l’audizione al Senato della Repubblica
energetica e la riduzione delle emissioni di CO2: tale fattispecie si porrebbe invece l’obiettivo di massimizzare il recupero di materia, premiando le imprese del riciclo e caricando gli oneri economici su soggetti produttori più o meno virtuosi. In effetti, i nuovi target ambiziosi e sfidanti per il riciclo dei rifiuti d’imballaggio impongono un ripensamento dei modelli di responsabilità estesa del produttore. I Certificati del riciclo potrebbero costituire parte della risposta, in grado di assicurare l’equilibrio economico delle attività di riciclo, esposte alle fluttuazioni della domanda e dei prezzi delle MPS. Si tratterebbe, pertanto, di affiancare al sostegno per le raccolte differenziate anche uno strumento di mercato dedicato al riciclo. Il presidente di Assorimap, Walter Regis, è intervenuto alla tavola rotonda apprezzando il position paper presentato da Laboratorio REF ed evidenziando come si allinei agli obiettivi UE (Pacchetto economia circolare, Direttiva SUP e plastic tax europea), al fine di stabilizzare il mercato e, quindi, il comparto delle imprese del riciclo, che devono essere messe in condizione di realizzare numeri decisamente più importanti rispetto agli attuali. Assorimap ha inoltre condiviso i seguenti punti: • obiettivo di perseguire l’equilibrio economico finanziario per il mercato del riciclo; • promozione della raccolta differenziata finalizzata al riciclo e alla produzione di MPS; • necessità di approfondire gli elementi necessari alla costruzione del meccanismo dei prezzi dei Certificati del riciclo: il costo del riciclo degli imballaggi (con, in evidenza, la voce “approvvigionamento dei materiali”); il prezzo delle MPS; la distanza dagli obiettivi di riciclo per specifica frazione.
ASSORIMAP - Associazione nazionale riciclatori e rigeneratori di materie plastiche Via Tagliamento, 25 - 00198 Roma Tel.: +39 06 83772547 E-mail: info@assorimap.it www.assorimap.it

POLIMERI DI ORIGINE BIOLOGICA
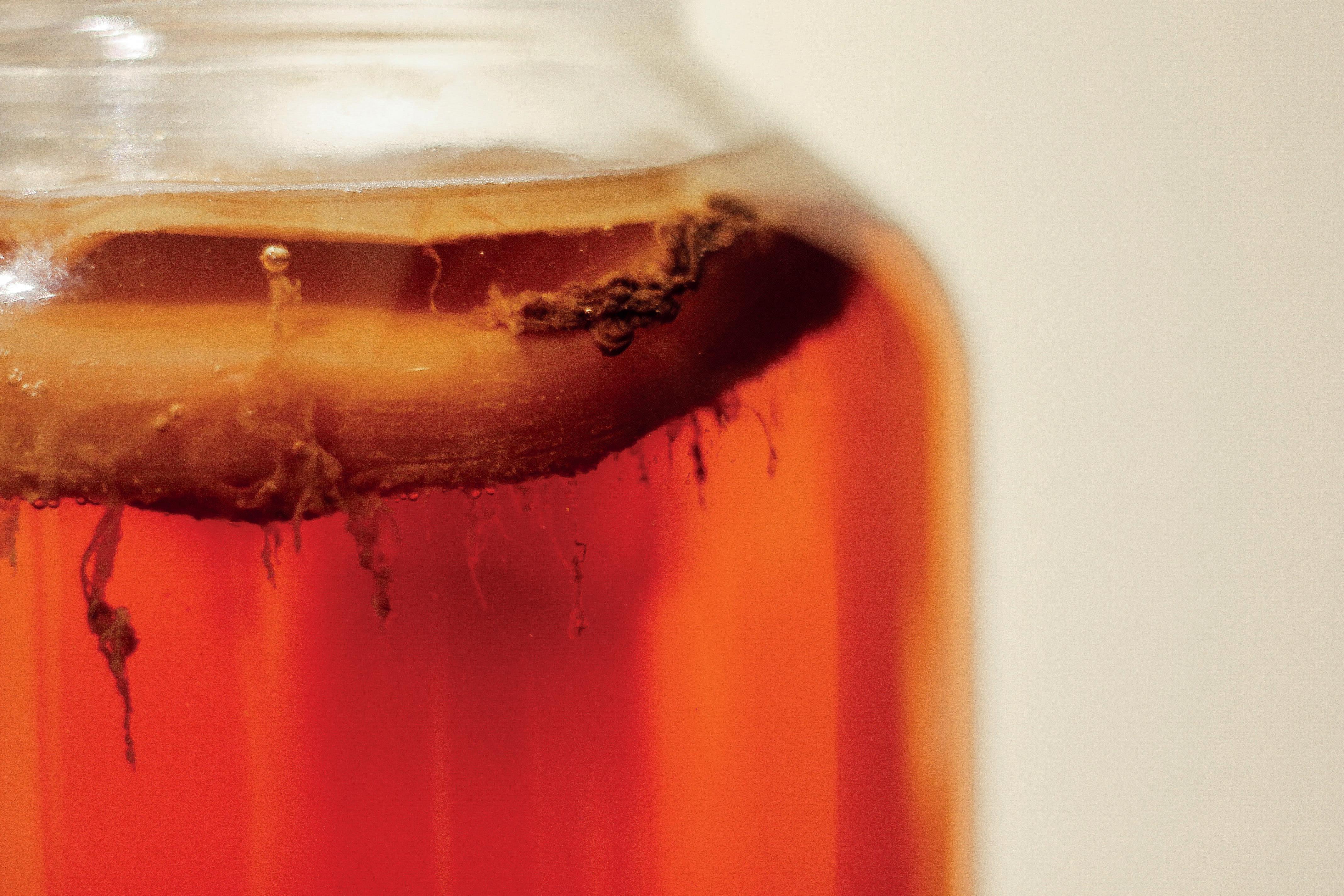
CELLULOSA ALLA RISCOSSA
GRAZIE ALLA SUA BIODEGRADABILITÀ E ALLE OTTIME PROPRIETÀ FISICHE E MECCANICHE, LA CELLULOSA D’ORIGINE VEGETALE ATTRAE SEMPRE DI PIÙ L’ATTENZIONE DEL MONDO DEL PACKAGING. E LA CELLULOSA BATTERICA SEMBREREBBE ANCHE MEGLIO…
DI STEFANO BERTACCHI*
Quando si parla di argomenti scientifici il contesto è spesso fondamentale, in quanto alcuni termini, nonostante mantengano lo stesso significato generale, possono essere intesi in maniera diversa a seconda dell’ascoltatore. La parola “polimeri” ne è un esempio: le persone del settore della gomma e della plastica associano questo termine primariamente a molecole di sintesi petrolchimica, costituite da monomeri che si ripetono, come appunto la maggior parte delle gomme e delle plastiche, dal poliisoprene al polistirene. Chi lavora invece nell’ambito delle scienze della vita tende a collegare la parola “polimeri” a una serie di macromolecole biologiche, costituite anche in questo caso da unità monomeriche, come le proteine, il DNA e i polisaccaridi. Le bioplastiche sono il campo in cui questi due mondi si intersecano, in quanto si tratta di materiali derivanti da origine rinnovabile o biodegradabili/compostabili, oppure con entrambe le caratteristiche. In questo senso, la bioplastica può derivare dalla trasformazione di materiale organico in un polimero plastico, come nel caso della sintesi di bioPET a partire da amido di mais, oppure dall’uso diretto del polimero naturale, come nel caso del MaterBi (marchio registrato di Novamont), costituito per la maggior parte proprio da amido di mais. Questo discorso non dovrebbe suonare strano, perché in realtà un polimero biologico è già stato coinvolto nell’origine di alcune materie plastiche sviluppate a livello industriale: la cellulosa è stata infatti la base per la sintesi della celluloide, una delle primissime plastiche di origine semisintetica immesse sul mercato. La cui porta è stata così “sfondata”, portando all’esplosione di varietà diverse di materiali plastici, ora primariamente di origine completamente sintetica. Alla luce dell’impatto ambientale del settore petrolchimico e della sua progressiva riduzione attuata da politiche nazionali e internazionali, siamo oggi testimoni di un ritorno alle origini. Un trend che interessa anche il settore dei combustibili, in quanto la prima auto sviluppata da Ford era alimentata ad alcol e ora, dopo il dominio incontrastato delle risorse fossili durato un secolo, stiamo tornando a usare etanolo e altri biocarbu-
Pellicola cinematografica in celluloide
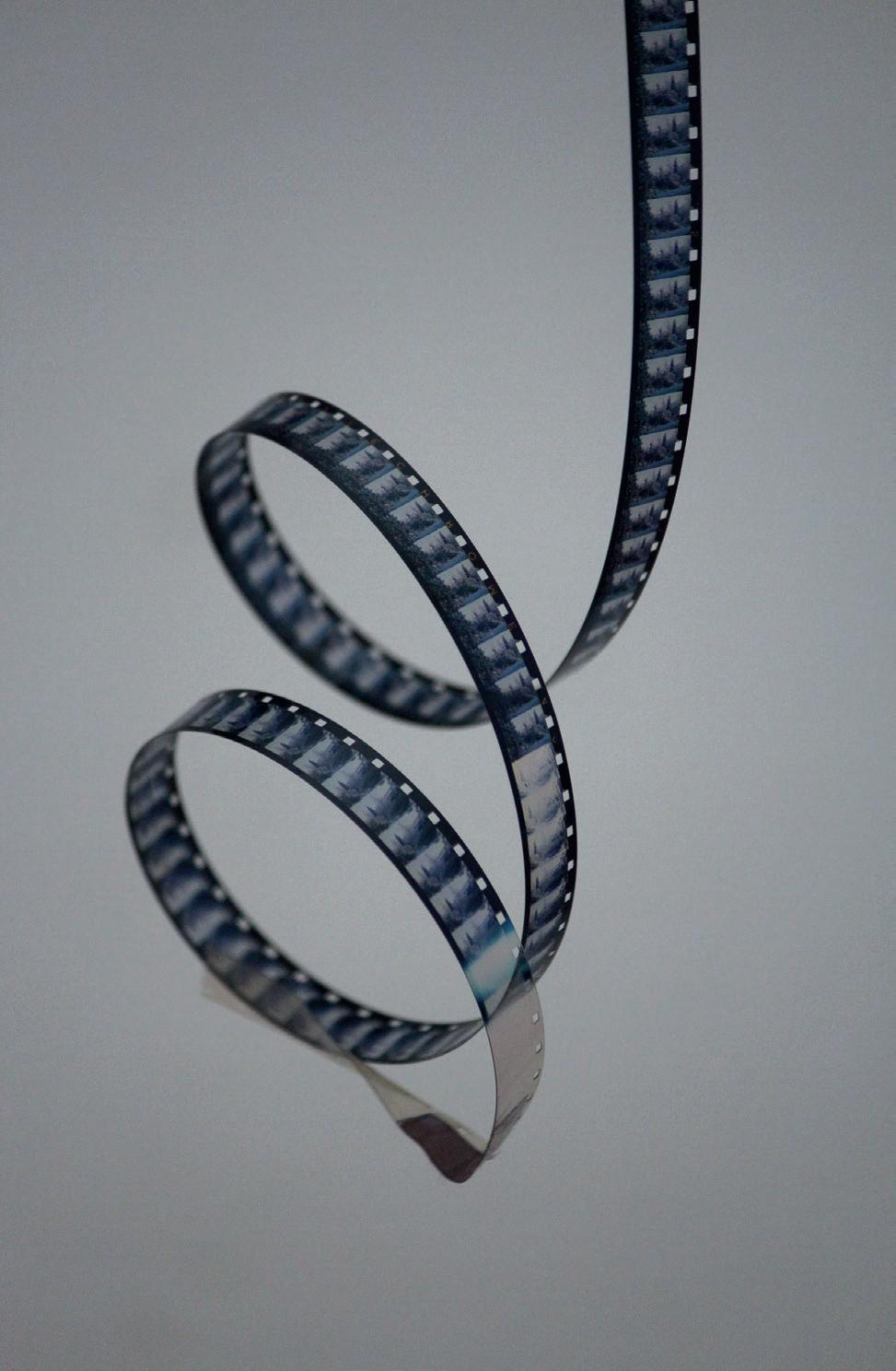
Denise Jans / Unsplash.com
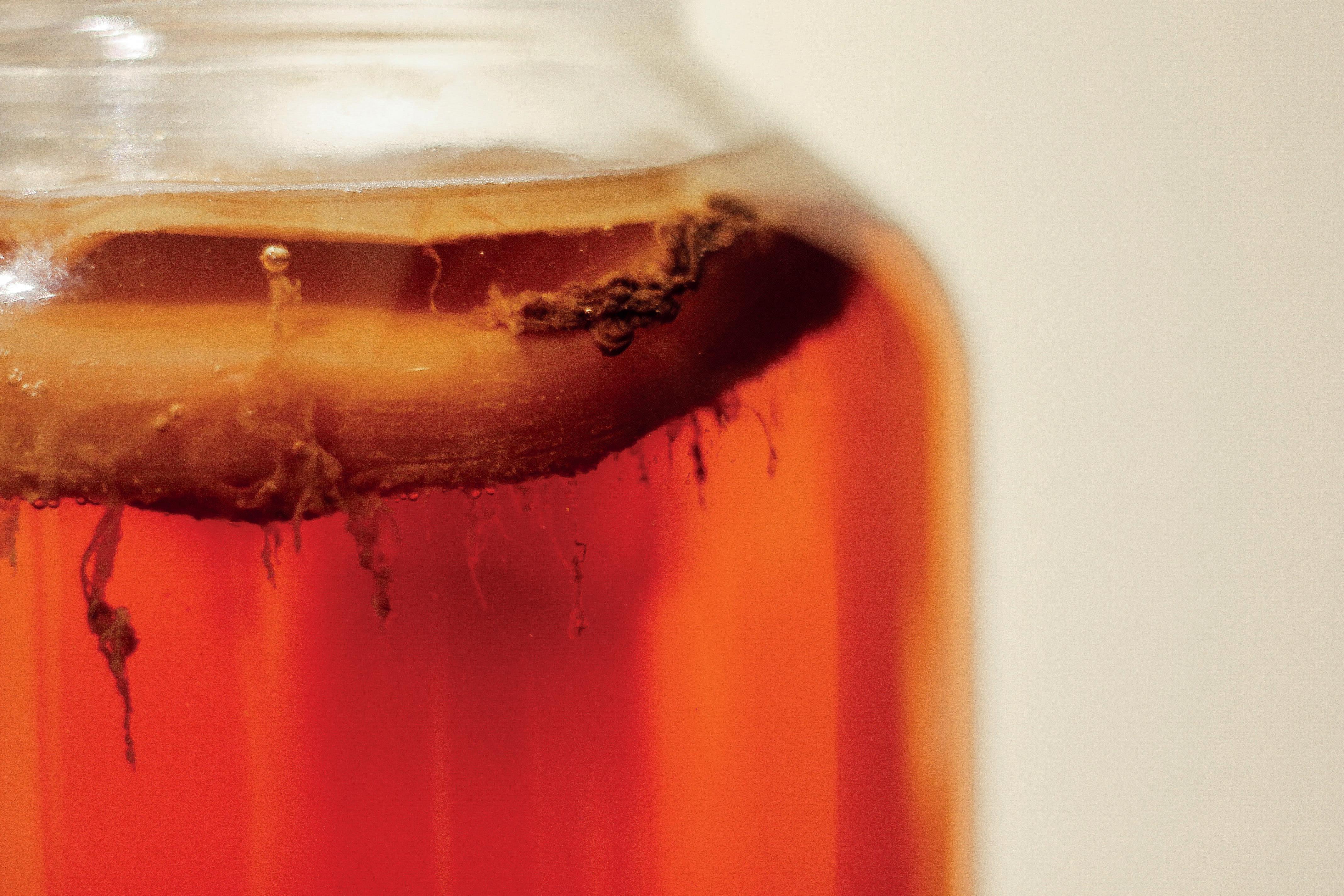
ranti per quello stesso scopo. Similmente la cellulosa, per la sua relativa abbondanza e per la semplicità di modificazione chimica, sta tornando in auge per espanderne le applicazioni. Attenzione però all’origine, perché il rischio è che tale tendenza possa portare a un ulteriore disboscamento: per questo motivo si possono mettere in gioco altre fonti di cellulosa, come gli scarti di vari settori industriali, o addirittura i microrganismi.
IN DIFESA DEL CIBO

Il settore alimentare è tra quelli più coinvolti nell’impiego di packaging derivante dalla cellulosa, in quanto permette una buona implementazione dei materiali bioplastici, meglio ancora se compostabili. In tal senso, invogliare il consumatore ad associare il cibo a un packaging più sostenibile è un target molto più semplice da centrare rispetto ad altri contesti in cui l’impatto degli imballaggi risulta meno evidente. A questo va aggiunto il fatto che la cellulosa è un polimero che si tende già ad associare alla carta, che di per sé rappresenta un’alternativa alla plastica in alcuni contesti. Non si tratta inoltre di un materiale dal nome complicato, o mai sentito, e che per questo necessiterebbe di complesse manovre comunicative, come nel caso di bioplastiche quali il poli-acido lattico (PLA) e i poliidrossialcanoati (PHA). La cellulosa è poi un materiale a basso costo e che fa registrare una grande domanda da parte del mercato globale, in particolare dall’industria alimentare e tessile. Una vasta quantità di rifiuti agricoli, tra cui quelli derivanti da frutta, verdura, steli di cotone e residui forestali, dovrebbe per questo essere avviata sempre di più al riciclo, in modo da recuperare la preziosa cellulosa. Nonostante presentino hanno alcune limitazioni, come un’elevata capacità d’assorbimento dell’acqua e una scarsa adesione interfacciale, la cellulosa e la nanocellulosa (compresi i loro derivati) stanno guadagnando sempre maggiore attenzione nell’industria degli imballaggi alimentari grazie a caratteristiche uniche, alla biodegradabilità e alle eccezionali proprietà fisiche e meccaniche. Questi materiali, soprattutto in miscela con altri compositi, possono raggiungere una buona resistenza termica e fornire protezione dai raggi ultravioletti, oltre a veicolare agenti antiossidanti e antibatterici, utili per aumentare la “shelf life” degli alimenti. Con la crescente applicazione delle tecnologie di stampa 3D, la cellulosa e i suoi derivati offrono anche la possibilità di creare forme innovative, aumentandone l’appeal sul mercato. La cellulosa biocomposita, come la nanocellulosa, ha poi numerose applicazioni industriali, compreso un ampio uso negli imballaggi a base di carta. A tutto ciò va infine aggiunta la possibilità di ottenere molti devirati della cellulosa, inclusi esteri o eteri, che ne espandono le applicazioni.
CELLULOSA & CO.
Numerose tipologie di cellulosa possono essere ottenute a partire dal polimero naturale, mediante classica sintesi chimica, che potrebbe però avere un certo impatto sull’ambiente a causa dell’uso di solventi, acidi e basi. Per fortuna, l’avvento della cosiddetta chimica verde può aiutare a migliorare la sostenibilità di questi processi. L’acetato di cellulosa può essere considerato uno dei primi polimeri immessi sul mercato, sintetizzato mediante l’uso combinato di anidride acetica, acido solforico e acido acetico. Il prodotto risultante è in realtà il triacetato di cellulosa, poi idrolizzabile a diacetato di cellulosa e quindi ad acetato di cellulosa, per soddisfare diverse applicazioni. Nel campo dei biomateriali, l’acetato di cellulosa viene utilizzato come membrana per usi biomedici (adsorbimento, separazione, biosensing, rigenerazione tissutale, somministrazione di farmaci o catalisi). Il solfato di cellulosa, invece, può essere ottenuto mediante procedure di solfatazione; ha proprietà antibatteriche ed è solubile in acqua ad alte concentrazioni. Il processo di sintesi consiste in una progressiva dissoluzione della cellulosa in N,N-dimetilformammide, combinata con una miscela di agenti solfatanti e acetilanti (per esempio, acido clorosolforico/anidride acetica), seguita dalla scissione dei gruppi acetilici durante la precipitazione. La nitrocellulosa, comunemente nota come fulmicotone, è usata come elemento importante nella polvere da sparo perché ha una propensione a rompersi in modo esplosivo. Questa molecola viene prodotta mediante nitrazione della cellulosa derivante dalla polpa di legno o da cascami di cotone, tramite agenti nitrati forti, come l’acido nitrico. Le applicazioni della nitrocellulosa dipendono fortemente dalla percentuale di azoto: se compresa tra 12,6% e 13,3%, è classificata come esplosivo, mentre se inferiore al 12,6% ha un’ottima biocompatibilità e stabilità fisico-chimica ed è considerata idonea per applicazioni biomedicali. Questa proprietà la rende adatta anche per applicazioni in emodialisi e biosensori. La carbossimetilcellulosa (CMC) è invece un etere ottenuto mediante dissoluzione della cellulosa in un solvente acquoso di idrossido di sodio, seguita dalla reazione della cellulosa alcalina con acido monocloroacetico. Numerose fonti di cellulosa, inclusi residui di legno, fanghi di cartiera, cascami di cotone e foglie di mais, sono state descritte per la sintesi di CMC. Grazie alle sue proprietà, questo materiale trova impieghi in settori in cui vengono utilizzati gli idrogel e, in particolare, in quello medicale1 . La nanocellulosa viene estratta dalla parete cellulare delle piante e, in virtù delle sue dimensioni “nano”, possiede caratteristiche speciali, come un’elevata area superficiale, rigidità e resistenza. Inoltre, nella struttura sono presenti
Canapa e cotone (in foto) sono costituiti da cellulosa fibrosa
23 Ranurte / Unsplash.com
numerosi gruppi ossidrilici, accessibili per ulteriori modifiche. La nanocellulosa è considerata un materiale biodegradabile, in quanto derivante dalla cellulosa pura, e presenta un peso ridotto, una resistenza eccezionale e una bassa densità. Sono noti tre diversi tipi di nanocellulosa, che possiedono una composizione chimica simile, ma una morfologia diversa: la nanocellulosa fibrillata (NFC), i nanocristalli di cellulosa (CNC) e la nanocellulosa batterica (BNC). A proposito di batteri, questi ultimi possono essere sorprendenti alleati del settore della cellulosa: contrariamente a quanto si possa pensare, la sintesi di questa molecola non è affatto esclusiva delle piante.

I BATTERI E LA CELLULOSA PURA
Si è parlato finora di cellulosa senza davvero sottolinearne la provenienza. Forse perché nella mente di ciascuno di noi è già ovvio che si tratta di una fibra vegetale, con cui produrre la carta o al massimo la viscosa. In ogni caso, il mondo della cellulosa parrebbe dominato dalle piante. Ma così non è, poiché anche alcuni batteri sono capaci di sintetizzare questo polisaccaride e, proprio per questo, stanno diventando sempre più interessanti come alternativa alle piante stesse. In realtà, i batteri produttori di cellulosa non sono per niente una scoperta recente, in quanto già protagonisti di alcuni processi alimentari, come quello per ottenere il kombucha: tè fermentato originario della Cina2. In questo caso, la trasformazione avviene grazie all’uso di un disco gelatinoso chiamato SCOBY, acronimo che sta per “consorzio simbiontico di batteri e lieviti”. E proprio di questo si tratta, ovvero di un mix di specie microbiche diverse tra loro, che vivono e lavorano insieme per farci bere il kombucha. Che sia chiaro, non lo fanno tanto per farci un favore, ma essenzialmente perché li obblighiamo a fermentare il tè zuccherato, dopo esse-

Cellulosa batterica - Scoby asciutto
@emmasicher 2017 re stati selezionati nel tempo dagli umani per questo scopo. La struttura stessa dello Scoby (un disco dall’aspetto “flaccido”) è collegata direttamente alla cellulosa che viene prodotta da alcune delle specie batteriche presenti. Il produttore di cellulosa più noto nel mondo microbico è Acetobacter xylinus, chiamato anche Gluconacetobacter xylinus, ma successivamente riclassificato come Komagataeibacter xylinus: la seconda parte del nome ci ricorda il legno (xylon in greco), con un chiaro riferimento alla cellulosa. Questo batterio è parte della vasta e diversificata popolazione microbica nello Scoby, la quale rende più complessa la comprensione della cinetica di fermentazione e della produzione di cellulosa insieme a vari altri metaboliti (sottoprodotti) presenti nel brodo di fermentazione. La cellulosa batterica viene prodotta consumando tutto l’ossigeno nel liquido, ma allo stesso tempo riporta in superficie galleggiando i microrganismi stessi, che possono nuovamente trovare ossigeno nell’aria e produrre ulteriori strati. In questo modo la cellulosa batterica s’inspessisce e il biofilm (ovvero lo strato di microrganismi) si arricchisce, fino a quando l’ossigeno non è più accessibile e il processo s’interrompe. I batteri rimangono quindi in uno stato dormiente sia nel biofilm che nel brodo liquido, che può essere attivato utilizzando altro tè zuccherato, oppure sfruttato come inoculo per una successiva fermentazione.
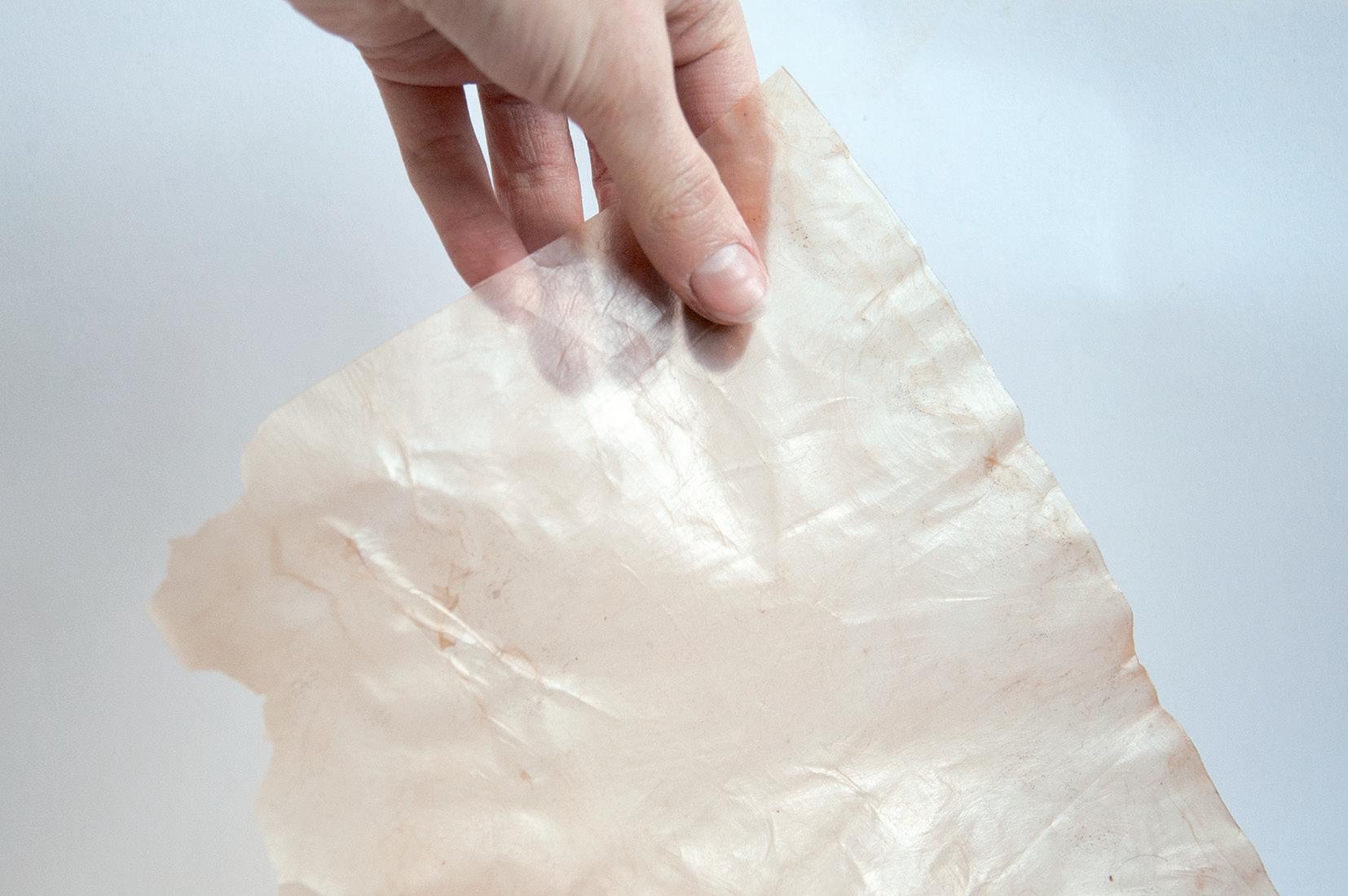
PIANTE O BATTERI?
La cellulosa batterica può essere confrontata con quella vegetale: le loro formule molecolari sono molto simili, ma vi sono differenze nelle proprietà fisiche e chimiche. La cellulosa vegetale è ramificata ed è legata ad altri polimeri come emicellulosa e lignina (tipici della lignocellulosa), assenti invece in quella batterica. Quest’ultima, infatti, non è ramificata ed è costituita esclusivamente da cellulosa. Quindi, paradossalmente, la cellulosa batterica è più pura rispetto a quella vegetale, che si accompagna a polimeri di cui occorre poi liberarsi. Inoltre, la purificazione della cellulosa vegetale richiede un trattamento chimico con un certo impatto ambientale, a differenza di quella batterica, più facilmente recuperabile. Non è quindi un caso che questo materiale abbia attirato l’attenzione del mondo della plastica, ma anche del biodesign, alla luce della versatilità della cellulosa batterica, che apre scenari interessanti soprattutto nell’ambito del packaging edibile3 . Per ottenere la cellulosa batterica non è per forza necessario utilizzare tè mescolato con lo zucchero, come per il kombucha, in quanto anche altri substrati possono essere usati per la fermentazione degli scarti di frutta e verdura, o persino fondi di caffè. Lo zucchero extra non sarebbe poi necessario, poiché già naturalmente presente negli scarti organici, come nella lignocellulosa di cui sopra. Anche i sottoprodotti dell’industria della fermentazione possono fornire “dolci assist” ai microrganismi produttori di cellulosa, in quanto fornitori di zuccheri a basso costo, che altrimenti sarebbe necessario smaltire. In conclusione, è quindi possibile affermare ancora una volta che la microbiologia e le biotecnologie possono essere d’aiuto per sviluppare vie alternative all’interno del mondo delle bioplastiche, in questo caso fornendoci cellulosa pura in cambio di scarti alimentari, con la quale costruire una vasta gamma di materiali dalle proprietà uniche.
Cellulosa batterica - Scoby in soluzione acquosa
@emmasicher 2017
Megumi Nachev / Unsplash.com
Scoby per il Kombucha: tè fermentato originario della Cina
*Biotecnologo industriale e ricercatore presso l’Università degli Studi di Milano Bicocca; scrittore e divulgatore scientifico
1Liu Y. et al. “A review of cellulose and its derivatives in biopolymer-based for food packaging application”. Trends in Food Science & Technology (2021). 2Laavanya D., et al. “Current challenges, applications and future perspectives of Scoby cellulose of Kombucha fermentation”. Journal of Cleaner Production (2021): 126454. 3Cohen N., Sicher E., and Ugur Yavuz S. “Designing with microbial cellulose to feed new biological cycles”. International Journal of Food Design 4.2 (2020): 155-171.
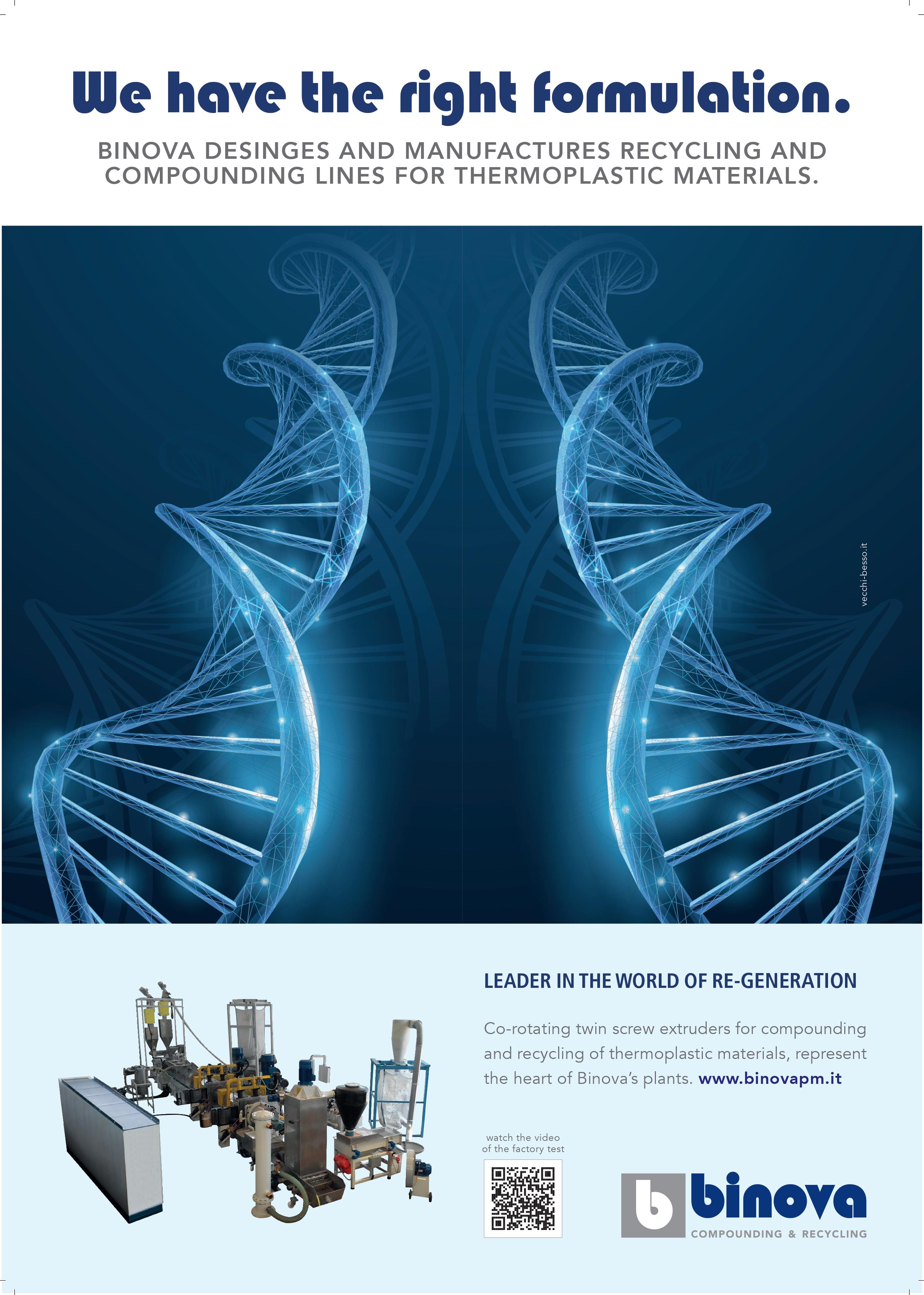
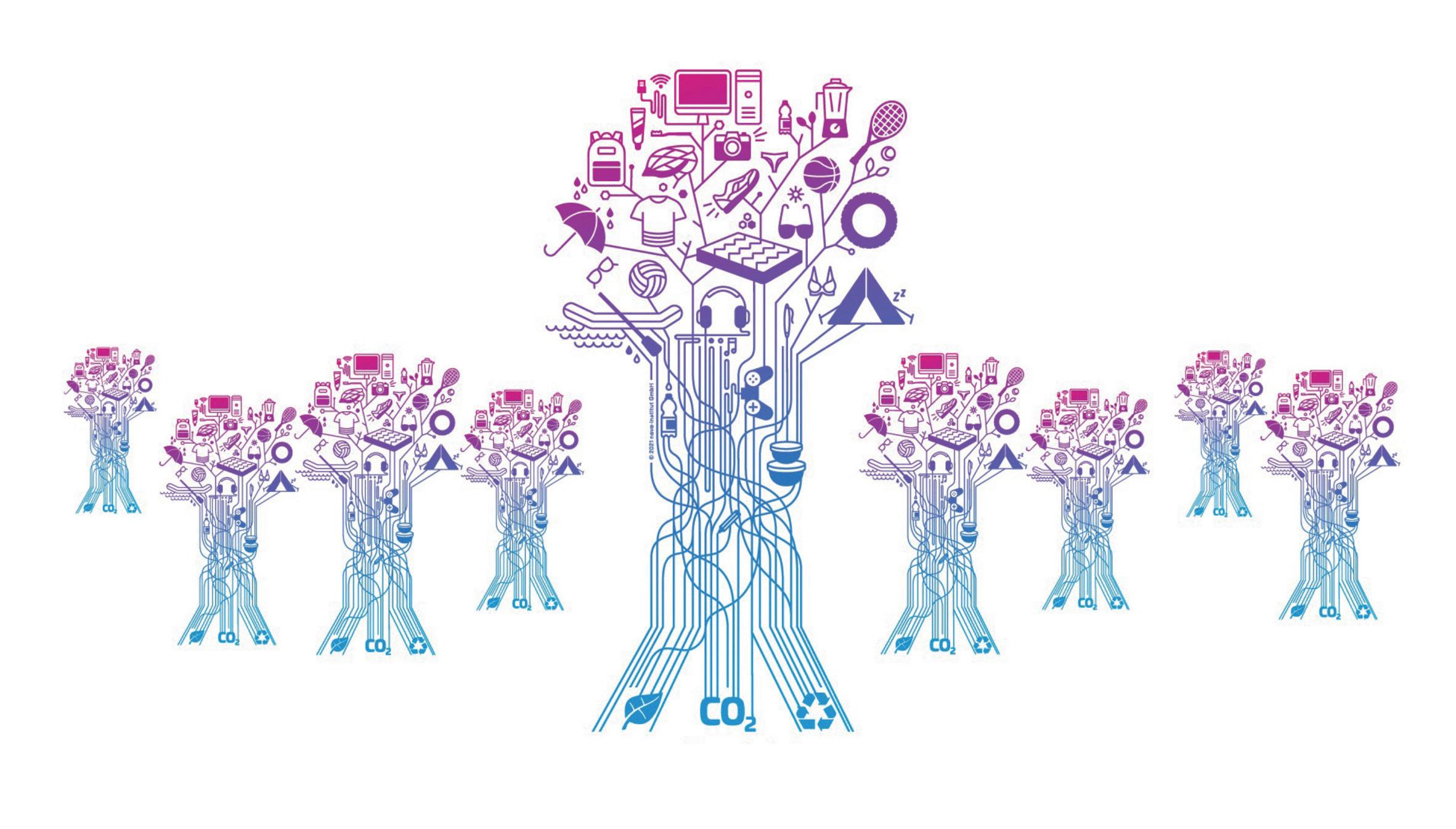
UN ANNO DI RCI LA RENEWABLE CARBON INITIATIVE CELEBRA IL SUO PRIMO ANNIVERSARIO...
...E LO FA GUARDANDO INDIETRO A UN PRIMO ANNO RICCO DI SUCCESSI (CON UN NUMERO TRIPLICATO DI ASSOCIATI) E PRESENTANDO OBIETTIVI CHIARI E CONCRETI PER IL SECONDO ANNO
Fondata il 20 settembre 2020, la Renewable Carbon Initiative (RCI) celebra quest’autunno il suo primo anniversario. Il bilancio del primo anno d’attività è impressionante: partendo da 11 soci fondatori, il numero delle imprese e delle istituzioni associate è salito a 30 nel giro di 12 mesi, a cui si sono aggiunti 6 partner e oltre 200 sostenitori. La chiave del successo di quest’associazione risiede nel fatto che sia la politica sia l’industria si stanno concentrando sempre di più sul tema del carbonio rinnovabile all’interno di sostanze chimiche e materiali. Le modifiche legislative riguardanti il Green Deal europeo prevedono che le imprese più grandi debbano dichiarare le proprie emissioni di gas a effetto serra (GHG), nonché l’impronta ambientale dei loro prodotti. In tale contesto, le emissioni indirette e le fonti di carbonio dei materiali svolgeranno un ruolo molto più decisivo. RCI è impegnata attivamente nello sviluppo di soluzioni per la transizione delle imprese dal carbonio fossile a quello rinnovabile; un passaggio attuabile su tre livelli, attraverso l’impiego di materie prime a base biologica, risorse a base di CO2 e materiali riciclati. In futuro, la rendicontazione di GHG dovrà includere anche le cosiddette emissioni Scope 3, cioè quelle indirette rilasciate lungo la filiera produttiva e di approvvigionamento dell’azienda, dove sono le materie prime utilizzate a contribuire in larga misura all’impronta di carbonio. È qui che la fonte di carbonio di sostanze chimiche e plastiche entra in gioco come fattore cruciale nella determinazione dell’impronta. Senza una transizione dalle materie prime fossili a quelle rinnovabili, gli obiettivi stabiliti dall’Accordo di Parigi (e quindi un futuro sostenibile) saranno praticamente impossibili da raggiungere. Al fine di discutere, promuovere e attuare il cambiamento, 30 aziende innovative hanno già unito le proprie forze in RCI per sostenere la transizione al carbonio rinnovabile, considerando gli interventi che si renderanno necessari a livello sia tecnologico sia economico e aiutando a delineare un quadro politico conforme. Per il secondo anno, l’associazione prevede poi di concentrarsi su un’idea chiara e completa delle condizioni quadro previste a livello politico in Europa e nel mondo. Sarebbe infatti necessario integrare sistematicamente il tema del carbonio rinnovabile nelle nuove direttive politiche, cosa che finora non è stata ancora realizzata in modo efficace. In realtà, la politica si sta focalizzando sulla strategia di decarbonizzazione del settore energetico,

Per sensibilizzare il grande pubblico e i più giovani, Nora e il suo FlyPhone illustrano il concetto di carbonio rinnovabile in modo semplice e attrattivo
Fonte: nova-Institute
un compito erculeo e che riveste un ruolo centrale. Tuttavia, tale strategia non è applicabile al mondo della chimica e dei materiali, dal momento che il carbonio rappresenta in genere una risorsa essenziale, di cui non si può fare a meno. Anzi, entro il 2050 si prevede una domanda di carbonio più che raddoppiata in questo settore. Al fine di soddisfare tale domanda in maniera sostenibile, è necessario abbandonare al più presto il carbonio fossile (e quindi i prodotti petrolchimici), cercando di soddisfare completamente la domanda attraverso l’utilizzo di biomasse, CO2, materie prime alternative e materiale riciclato. Solo così si potrà fare meno affidamento in futuro sulla rimozione di enormi quantitativi di CO2 dall’aria. RCI invita tutte le parti interessate a entrare a far parte di una rete unica di pionieri dei prodotti chimici e dei materiali rinnovabili, ad apportare idee innovative e a dare ulteriore slancio alla strategia basata sul carbonio rinnovabile. Nelle prossime settimane vedrà la luce anche la nuova piattaforma “Renewable Carbon Community (RCC)”, destinata a facilitare la comunicazione e l’interazione in rete tra le aziende associate.
STUDIO DELLE INIZIATIVE POLITICHE
Nel frattempo, sono già iniziate diverse attività di cui potranno beneficiare anche i futuri membri della Renewable Carbon Initiative. La prima e più importante riguarda l’avvio di un’analisi ad ampio raggio delle attuali politiche nell’Unione Europea e, successivamente, anche di quelle in America e in Asia. Le questioni principali da esaminare sono quelle inerenti: la nuova legge sul clima e il “Fit for 55-Package” per le sostanze chimiche e i materiali; il regolamento Reach e le restrizioni sulle microplastiche; la “Sustainable Products Initiative” e le prossime restrizioni per i Green Claims. “Economia circolare”, “inquinamento zero” e “finanziamento sostenibile” sono le parole chiave del futuro panorama europeo, che nei prossimi anni potrebbero trovare un’applicazione molto più concreta nell’ambito della chimica e dei materiali. Al gruppo di lavoro “Politica” possono partecipare tutti i membri di RCI.
“Non c’è nulla di più potente di un’idea giusta al momento giusto. Non posso spiegare in altro modo il successo di RCI. Le emissioni di gas serra stanno diventando sempre più visibili e rilevanti. Quindi, l’industria necessita di una strategia che dia una chiara direzione di manovra per raggiungere la sostenibilità il prima possibile. Il momento è arrivato e nuove aziende si stanno unendo ogni mese alla Renewable Carbon Initiative”, così Michael Carus, CEO di nova-Institute, ha commentato il rapido successo di RCI La Renewable Carbon Initiative supporta il Green Deal europeo, ma mira a un’estensione al settore dei materiali attraverso una strategia globale basata sul carbonio rinnovabile
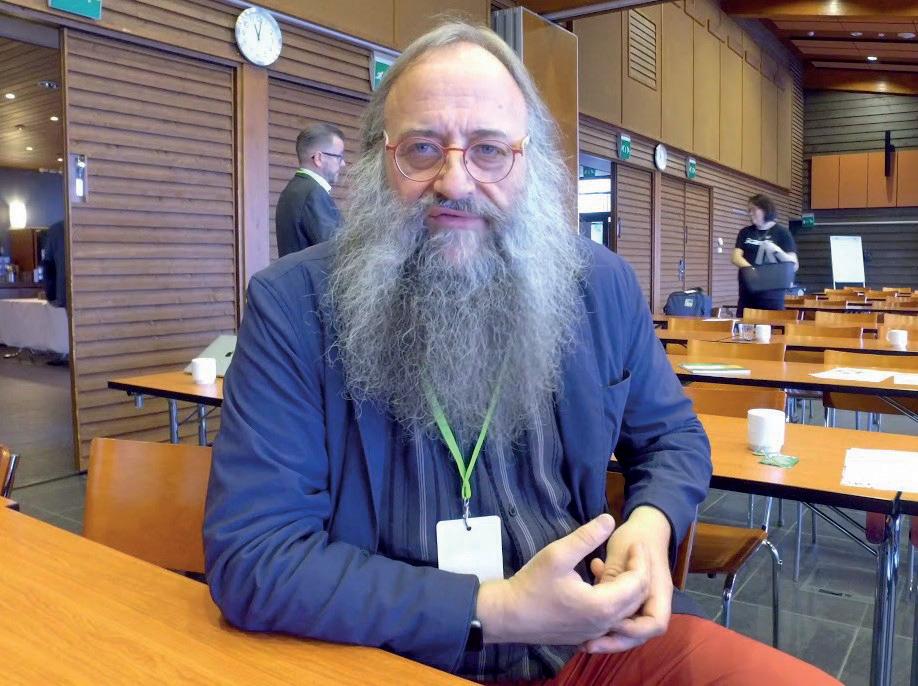

RIUTILIZZABILE? SÌ, ASSOLUTAMENTE!
La RCI sostiene il divieto d’utilizzo degli articoli in plastica monouso (entrato in vigore a luglio nell’UE con l’ormai nota direttiva SUP) per applicazioni quali: posate, piatti o cannucce, ma anche salviette umidificate e bastoncini nettaorecchie. Il cambio di sistema, dal monouso al riutilizzabile, riduce infatti lo spreco di risorse e il flusso di plastica nell’ambiente e consente d’iniziare ad abbandonare le risorse fossili. “Il carbonio fossile, dal quale si produce oggi il 99% delle materie plastiche, è la causa principale dei cambiamenti climatici dovuti all’uomo, in quanto genera emissioni addizionali di CO2 nell’atmosfera. Quindi, se adesso s’intende introdurre nuovi sistemi riutilizzabili, sostenibili e orientati al futuro per gli imballaggi e il catering, questi non dovranno più basarsi sul petrolio greggio. Specialmente oggi, dato che quasi tutta la plastica e molti altri materiali possono essere ottenuti anche da biomassa, sfruttamento diretto della CO2 (da gas di scarico industriali o prelevata direttamente dall’atmosfera) e riciclo”, ha dichiarato Michael Carus, fondatore della Renewable Carbon Initiative e CEO di nova-Institute. Le aziende che hanno aderito alla RCI sono già in grado di offrire molte soluzioni in questa direzione, che andrebbero sostenute. Per esempio, piatti, posate e contenitori riutilizzabili del catering possono essere già prodotti a partire da polietilene ottenuto dalle biomasse, dalla CO2 o dal riciclo, e non più derivato dal petrolio. Più concretamente, la società finlandese Neste sta già producendo PE dalla canna da zucchero e dall’olio di cucina usato, mentre la statunitense LanzaTech sfrutta i gas di scarico delle acciaierie per lo stesso scopo. Numerose aziende offrono poi PE riciclato di alta qualità. Anche i poliesteri potranno presto essere ottenuti da fonti rinnovabili: dal 2023 l’azienda finlandese UPM produrrà MEG (materia prima per PET e PEF) dal legname, presso la sua nuova bioraffineria in Germania, mentre l’olandese Cosun Beet Company ha l’ambizione di trasformare le barbabietole da zucchero in MEG. È poi già noto che alcuni polimeri ad alte prestazioni di Covestro e DuPont Biomaterials possano essere prodotti anche da biomassa e CO2, almeno in una certa percentuale. Inoltre, l’azienda israeliana TripleW offre numerose soluzioni a partire da plastica derivata dai rifiuti organici. Laddove non sia possibile riutilizzare gli articoli a fine vita, come nel caso delle salviette umide, queste ultime possono essere prodotte al 100% in modo biologico, senza comprometterne la qualità. Questo è dimostrato, tra gli altri, dal produttore austriaco Lenzing e dal tedesco Beiersdorf, che utilizzano solo fibre vegetali per le loro salviette detergenti.
UN FUMETTO, UN GLOSSARIO E VARI VIDEO PER SPIEGARE IL CARBONIO RINNOVABILE
Col fine di sensibilizzare il pubblico in merito al concetto di carbonio rinnovabile, ancorandolo al discorso politico, la Renewable Carbon Initiative sta dando vita a molteplici attività. Tale concetto, per esempio, è illustrato brillantemente, per mezzo di un’avvincente narrazione illustrata, nel fumetto “Nora and her FlyPhone on Renewable Carbon”. Ulteriori approfondimenti sono forniti dai video pubblicati sul canale YouTube di RCI, in cui aziende come BioBTX (riciclo di sostanze chimiche), Stahl (prodotti chimici speciali) e nova-Institute forniscono informazioni sulle strategie dei soci. Per chi volesse saperne di più, sul sito www.renewable-carbon-initiative.com è disponibile anche un glossario con i termini principali legati al concetto di carbonio rinnovabile.
NEWS
Accelerazione del settore per rispettare gli obiettivi UE Cresce il riciclo di film flessibile, nonostante la pandemia

In Europa, nel 2020, il settore del riciclo di film flessibili in materiale plastico ha registrato un incremento di quasi il 10% in termini di capacità installata, evidenziando una crescita solida nonostante la pandemia da Covid-19 che, peraltro, ha provocato gravi problemi nella gestione dei rifiuti. Le stime più recenti di Plastics Recyclers Europe (PRE) indicano che la capacità di riciclo dei film in PE è salita a 2,7 milioni di tonnellate grazie all’avvio di 30 nuovi impianti, per un totale complessivo di 218 unità. Con una domanda di oltre 9 milioni di tonnellate, LDPE ed LLDPE rappresentano la seconda frazione in termini di volumi nel mercato UE e offrono quindi un importante potenziale di riciclo. Oggi il 17% del film flessibile in rPE trova già sbocco nelle applicazioni “film-tofilm” per imballaggi non alimentari ed edilizia (i maggiori mercati per questi materiali), ma le previsioni indicano che entro il 2030 i film a base di PE potrebbero contenere complessivamente fino al 38% di materiale riciclato. “Una volta ritenuto un materiale difficile da riciclare, il polietilene flessibile post consumo ha dato vita a un modello di riciclo di successo. I rapidi sviluppi tecnologici in raccolta, selezione e riciclo consentono oggi processi di trasformazione film-to-film. Il riciclo meccanico a circuito chiuso rappresenta il futuro, ponendo l’Europa all’avanguardia della circolarità in questo particolare campo”, ha dichiarato Ton Emans, presidente di Plastics Recyclers Europe e del Gruppo di lavoro PRE LDPE. “Questo non significa che non vi siano nuove sfide da affrontare. I principali ostacoli nell’individuazione di nuove applicazioni di fascia alta sono rappresentati dai prodotti multistrato e multimateriale, che attualmente non sono in linea con i principi del Design for Recycling”. Ciò nonostante, il riciclo della plastica flessibile è destinato ad accelerare sull’onda delle attuali tendenze positive. In primo luogo, grazie all’implementazione dei sistemi di raccolta in tutti gli Stati membri, al fine di centrare gli obiettivi UE di riciclo. In secondo luogo, le migliori tecnologie di selezione, combinate con i risultati dei sistemi EPR e dei centri di selezione, generano flussi monomateriale diminuendo gradualmente la frazione poliolefinica mista. Infine, anche la domanda di PE flessibile riciclato di alta qualità è destinata ad aumentare grazie all’impegno assunto dagli operatori della filiera per migliorare la riciclabilità dei materiali, o per incorporare plastica di riciclo nei loro prodotti. Per consolidare queste tendenze positive, tuttavia, gli operatori del settore dovranno guardare a soluzioni a lungo termine, piuttosto che a veloci e temporanei “rimedi”. Ad esempio, il processo Qua-
Erema
“I processi che propongono di destinare solamente il 20% del film di riciclo alle applicazioni film-to-film e il restante 80% allo stampaggio a iniezione sono un passo indietro per il nostro settore, in quanto non sono allineati con i principi dell’economia circolare. Inoltre, non diventeranno mai un business case redditizio”, ha dichiarato il presidente di PRE, Ton Emans
lity Recycling sviluppato da Ceflex non è in linea con l’obiettivo di rendere completamente circolari i flussi post consumo di imballaggi flessibili. Al contrario, potrebbe ostacolare la diffusione di processi già consolidati e ben funzionanti, portando al contempo a un punto morto gli sforzi per rendere gli imballaggi in plastica flessibile completamente riciclabili. L’implementazione di questa “nuova soluzione” potrebbe generare ulteriori flussi di poliolefine miste da destinare solamente a un mercato dello stampaggio a iniezione già saturo, che non è più in grado di assorbire le notevoli quantità di materiali riciclati originate dai rifiuti di plastica flessibile.
Con un accordo sottoscritto lo scorso 16 settembre, la società Versalis (ENI) ha acquisito in esclusiva la tecnologia e gli impianti di Ecoplastic, azienda italiana del gruppo De Berg, attivo nella filiera di recupero, riciclo e trasformazione dei polimeri stirenici. L’accordo garantisce a Versalis il know-how sviluppato da Ecoplastic e, in sinergia con le proprie competenze tecnologiche, le consente di accelerare gli sviluppi nel campo del riciclo meccanico avanzato, di ampliare la propria gamma Revive di polimeri riciclati e di consolidare la leadership europea nei polimeri stirenici da riciclo. Versalis acquisisce tecnologie e impianti da Ecoplastic Un nuovo polo per il riciclo meccanico a Porto Marghera
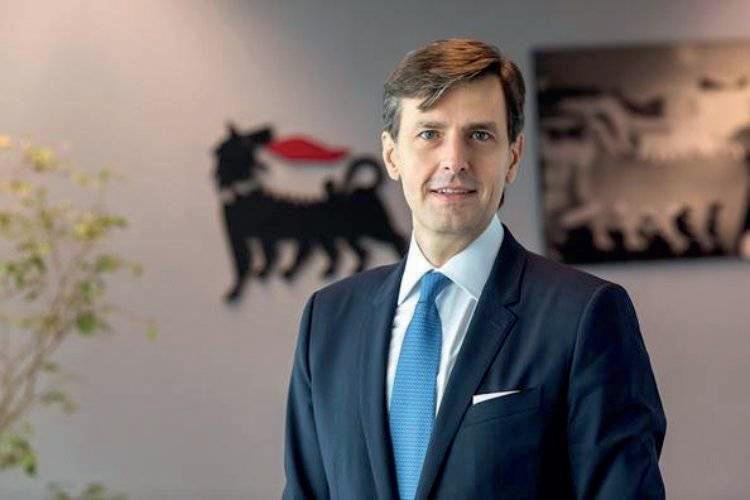
Dal canto suo, Ecoplastic ha infatti sviluppato un processo di produzione di polimeri stirenici, polistirene espanso e compatto con contenuto di riciclato fino al 100%, proveniente da rifiuti in polistirene espanso selezionati dai settori industriali e dal commercio. I nuovi prodotti saranno destinati a settori applicativi per i quali i requisiti di
“Il riciclo delle materie plastiche è una delle leve fondamentali per accelerare la trasformazione di Versalis attraverso modelli circolari e s’inserisce nell’ambito della più ampia strategia di ENI per la transizione energetica, di cui l’economia circolare è uno dei pilastri”, ha dichiarato Adriano Alfani, amministratore delegato Versalis sostenibilità e circolarità sono essenziali, come il packaging e l’edilizia, in linea con il quadro normativo di riferimento. L’accordo con il gruppo De Berg costituisce un passo concreto per l’avvio della prima fase di realizzazione di un polo per il riciclo meccanico avanzato nell’ambito del progetto di trasformazione del sito di Porto Marghera, che dal prossimo anno vedrà l’installazione degli impianti acquisiti da Ecoplastic per la produzione di polimeri stirenici ottenuti totalmente da materiale riciclato già selezionato e pretrattato. La capacità complessiva, in questa prima fase, sarà di circa 20 mila tonnellate all’anno.
CAC per gli imballaggi in plastica Dal 2022 contributo ambientale Conai più basso

Il CdA di Conai ha ribadito la volontà di proseguire il percorso di analisi per rafforzare ulteriormente la diversificazione contributiva, in particolare per legare in misura più rilevante i valori del CAC di ogni fascia agli effettivi costi
Il consiglio d’amministrazione di Conai ha deliberato un’ulteriore riduzione del contributo ambientale (CAC) per quasi tutti gli imballaggi in plastica, in carta e in cartone, a partire dal primo gennaio 2022. La riduzione si aggiunge a quelle già decise nel corso del 2021 per i contributi relativi agli imballaggi a base cellulosica, in acciaio, in alluminio, in plastica e in vetro. La decisione è legata essenzialmente alle quotazioni delle materie prime cellulosiche e plastiche, i cui valori di mercato continuano a mantenersi a livelli molto alti. Anche in questa occasione il sistema conferma la sua tempestività d’intervento nel contemperare le esigenze economiche con quelle tipicamente ambientali in contesti sia positivi, come quello attuale, sia negativi, come nel recente passato. Una tendenza a cui Conai intende ispirarsi anche in futuro. La conferma dell’andamento positivo nei valori delle materie prime seconde ha permesso anche al consorzio Corepla di migliorare i ricavi dalle vendite all’asta delle frazioni valorizzabili, in particolare per gli imballaggi della fascia B1, che comprende bottiglie, flaconi e altri contenitori rigidi in PET o in HDPE. Questa situazione ha consentito di ridurre il CAC per quasi tutti gli imballaggi in plastica e in particolare per quelli che hanno portato al miglioramento dei risultati economici. Per la fascia A1 (imballaggi rigidi e flessibili, con una filiera industriale di selezione e riciclo efficace e consolidata, in prevalenza gestiti in circuiti di commercio e industria) il contributo si ridurrà da 150 a 104 euro/t. Il contributo della fascia B1 (imballaggi con una filiera industriale di selezione e riciclo efficace e consolidata, in prevalenza da circuito domestico) si ridurrà da 208 a 149 euro/t. La fascia B2 (altri imballaggi selezionabili/riciclabili da circuito domestico e/o commercio e industria) passerà da 560 a 520 euro/t. La riduzione del CAC interesserà anche la fascia C (imballaggi con attività sperimentali di selezione/ riciclo in corso o non selezionabili/riciclabili con le tecnologie attuali) e passerà da 660 a 642 euro/t. Per quanto riguarda, invece, gli imballaggi compresi nella fascia A2 (imballaggi flessibili con una filiera industriale di selezione e riciclo efficace e consolidata, in prevalenza da circuito commercio e industria, ma significativamente presenti in raccolta differenziata urbana), si conferma il continuo incremento dei volumi presenti nella raccolta differenziata urbana, con costi crescenti per la gestione consortile. Fino al 30 giugno 2022 il contributo di questa fascia resterà invariato, pari a 150 euro/t, mentre dal primo luglio aumenterà a 168 euro/t, coerentemente con i maggiori costi d’avvio a riciclo.
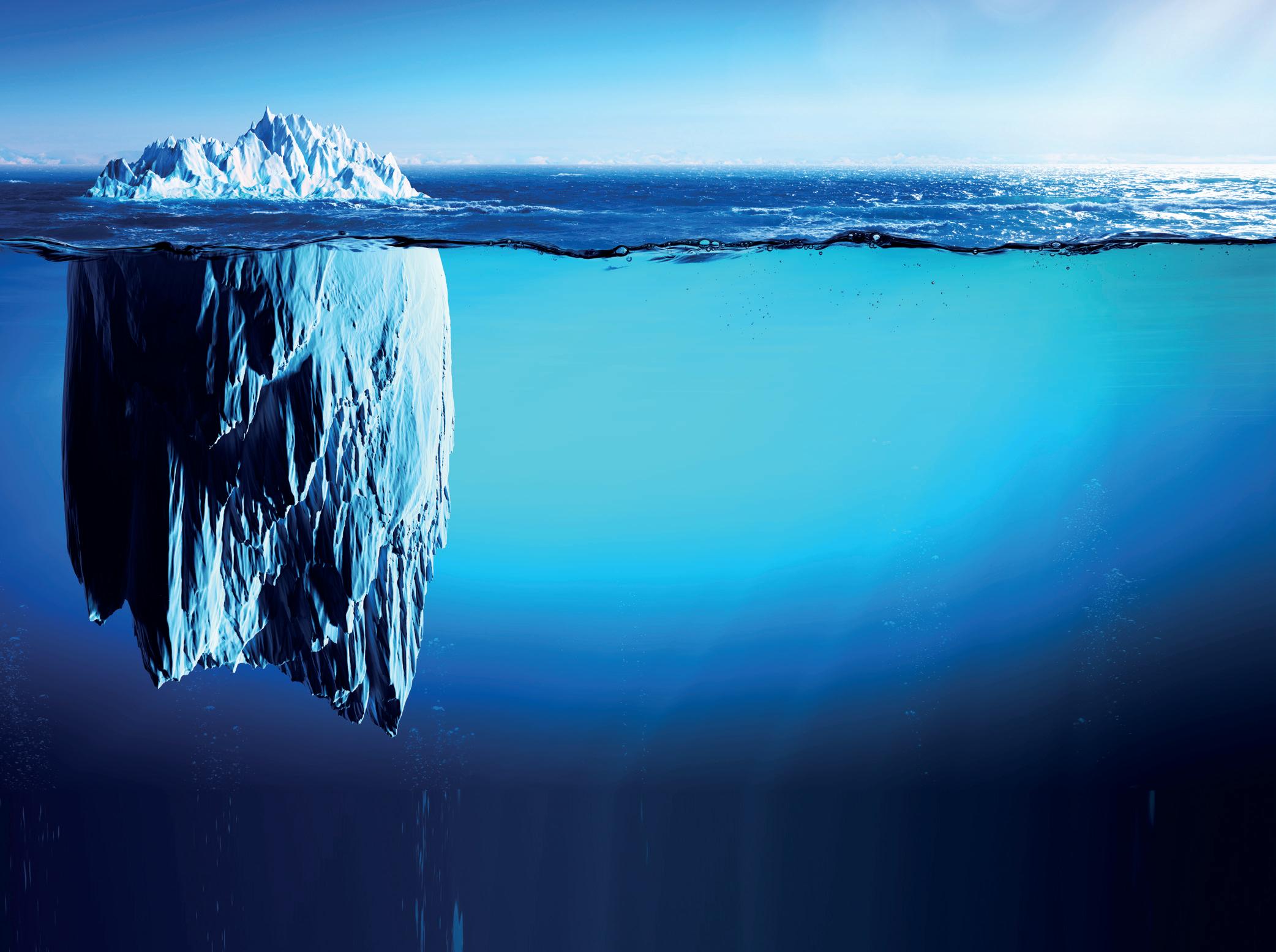
