MACPLAS INTERNATIONAL
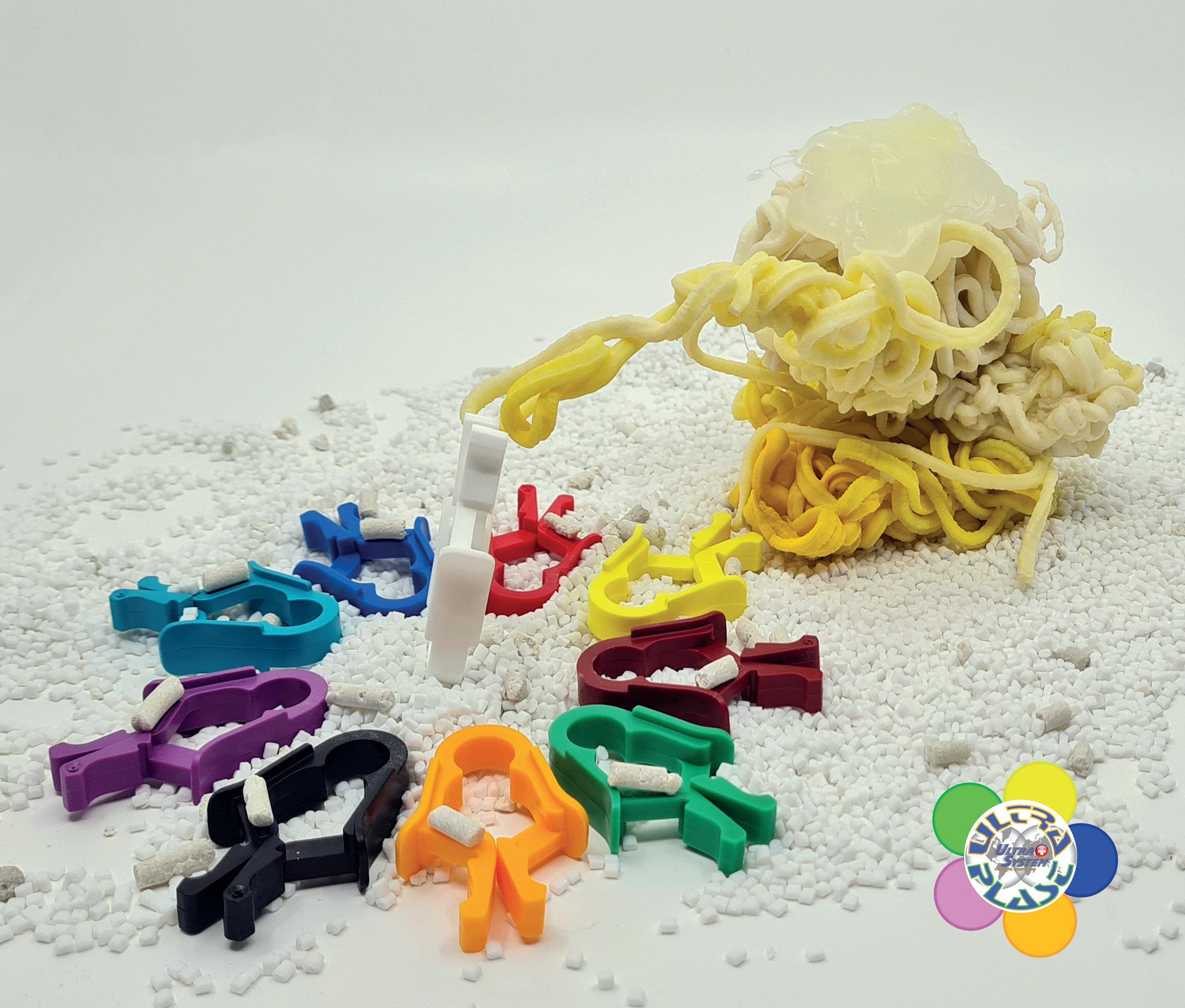
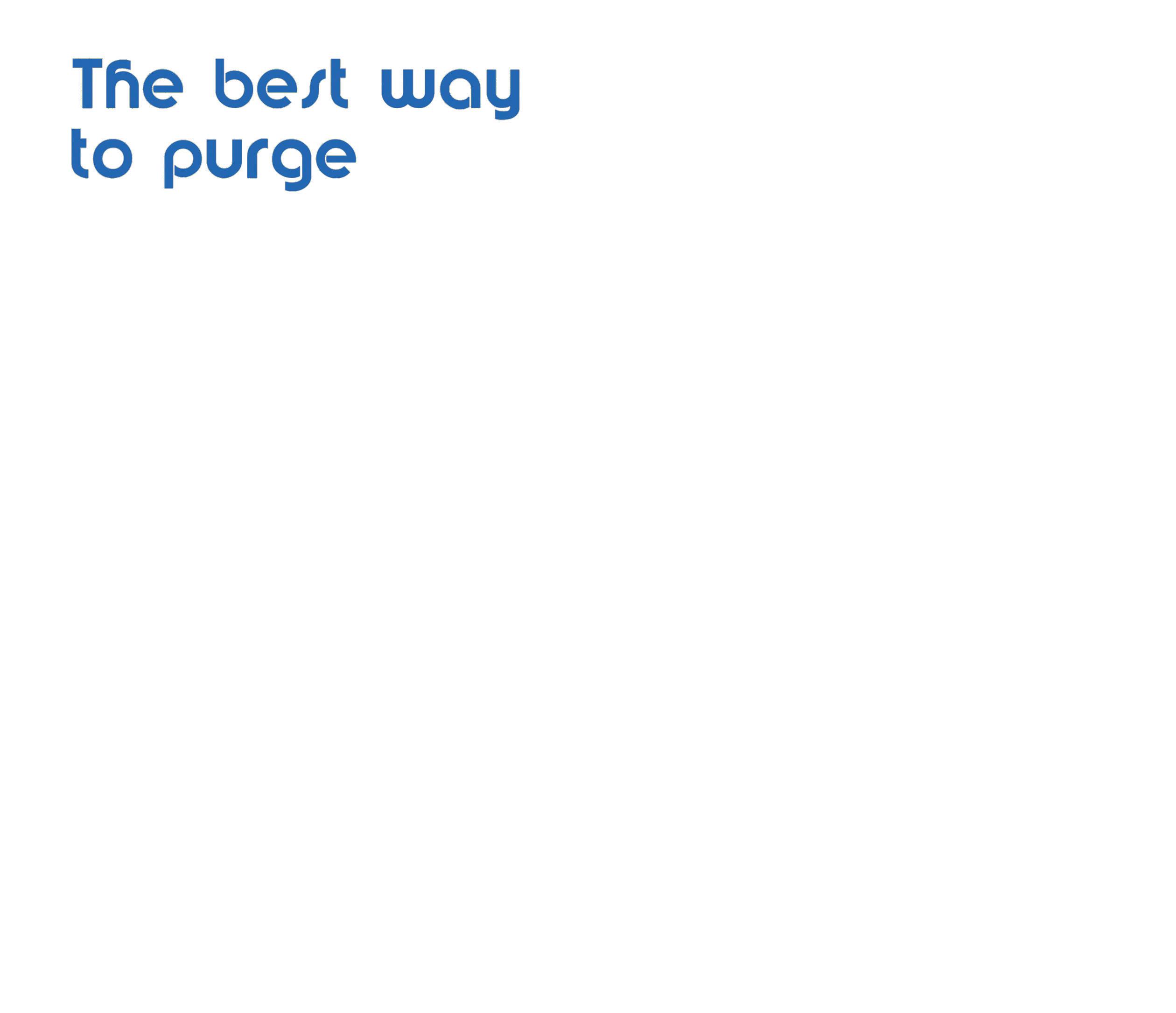
OFF AND CUTTING FOR MICRO-TUBES
The Tecno System micro-extrusion lines for medical tubes are prepared for high speed and tight dimensional tolerances. All our extrusion lines carry the CE marking certifying full compliance with the corresponding EU standards and are explicitly designed, manufactured and adapted according to our customer requirements.
• MONO MULTI-LUMEN
• MONO MULTI-LAYERS
• BUMP TUBING
• STARTING FROM 0.4 mm OD
Ultra System, a well-established company based in Switzerland, has been providing top-notch solutions for colour and material change processes, preventive maintenance, and machine shutdowns for the past 20 years.
The company’s growth is attributed to strategic marketing efforts and field promotions. Its participation in major international trade fairs grants visibility that would otherwise be unattainable. The quality achieved by its technicians and experts in the formulation of Ultra Plast is fundamental to its success. Ultra Plast materials are free from abrasive additives, suitable for injection into hot runners without risk of damage, and require no soaking times. They produce no unpleasant odours or smoke, are quick and efficient, and each material boasts over twenty certifications. This is what clients can expect when working with Ultra System.
The “green” aspect is also of significant importance. The plastics industry is often scrutinised due to ongoing issues with recycling. All Ultra Plast products are recyclable after use, reflecting the company’s commitment to reducing unnecessary waste. With six production sites across the globe, Ultra System maintains a strong presence in major markets. Ultra System participates in the Fakuma exhibition, an important international event for the plastics industry. By showcasing two laboratory machines, the company performs cleaning tests live at their booth and distribute branded coloured plastic cups. This year has been exceptionally busy, with Ultra System participating in 14 shows and expos as an exhibitor. In 2025, the company will attend both well-known markets and those requiring further development, including Arabplast in Dubai, Warsaw Plast Expo in Poland, Plastimagen in Mexico, Plastico do Brasil, Chinaplas in China, K Show in Germany, and others. While organising and attending these fairs requires considerable time and effort, Ultra System recognises the necessity of maintaining close contact with customers. These events also serve as valuable opportunities for agents and distributors, who engage with potential clients daily and promote Ultra Plast products.
Furthermore, this year marks the 20th anniversary of Ultra System, celebrating two decades of research, development, and professionalism that have established Ultra Plast as the premier choice in the industry.
www.ultrasystem.ch
Kirk Winstead appointed president of the US subsidiary
Expanding the team to improve performance
Expansion in North Africa
A new CEO in Sumitomo (SHI) Demag
Illig acquired by a German financial investor
Change at the helm of Borealis
AND ENVIRONMENT
snapshot of the Italian compostable bioplastics supply chain
stock on the sustainability of the PVC value
An eco-compactor donated for Pope Francis
… and the winners of the Plastics Recycling Awards Europe 2024 are…
For the first time two co-chairs at the helm of European bioplastics
Eight packaging solutions based on renewable raw materials
Durable and sustainable packaging for the International Red Cross
The future is a place we have been exploring since 1962.
Lifetime value for pipes
54 Double filtration in plastics recycling: more than a trend
56 To do things well, it takes… head
57 Tailor-made solutions for the extrusion market
58 New range of automatic coilers for large pipes
59 Between novelties and confirmations
61 Focus on new machines and upcoming topics
Innovative Rieber socket in PVC-O pipes
Tamper-evident and sustainable packaging
Insert loading automation for automotive
A reliable cooperation
Production without collapse of PE foam pipes
Improving moulded packaging quality
New sizes for the DUO screen changer
Filtration system for extrusion and recycling
Optimizing lamination of PVC sheets with nonwoven
An infrared testing centre: where all starts
High-performance, low consumption blow moulding
72 Leveraging Artificial intelligence to drive sustainable transition
75 Will the factory of the future be more high-tech and environmentally friendly?
82 Additives to impart antistatic properties to products
86 3D printed wheelchair racing gloves
88 “Made polypropylene”
101 NPE 2024: official data 16 30 42
89 Prize-winning intake manifold
90 Light, heat and chemical stabiliser for agricultural plastics
91 New foamed polymer for athletic footwear
92 Filament identification directly in the plastic for originality check
92 Tackling the end-of-life challenges of durable goods
94 Recycled polymers for food contact
94 Safe and ecological blowing agents
95 Chemical recycling of PMMA in Rho
95 Polycarbonate panels for a kindergarten
96 High stability and prolonged durability of batteries and charging devices
96 Polyamides with recyclate also for food contact
98 A crucial platform for exploring sustainability and innovation in the plastics sector
100 Messe Düsseldorf operative managing director to retire
100 Sold out at K 2025
101 From start-ups to industry giants: unveiling innovation
October 2024
Managing director Mario Maggiani
Editor in chief Luca Mei
Editor
Giampiero Zazzaro
Editorial assistant Alice Polimeno
Sales manager
Roberta Pagan (Italy)
Martina Lerner (Europe)
Administration Debora Mastrangelo
Editorial committee
Massimo Margaglione, Gabriele Caccia, Barbara Ulcelli
Contributors to this issue
Stefania Arioli
Published by Centro Direzionale Milanofiori - Palazzo F/3
20057 Assago (Milano, Italy)
Tel.: +39 02 82283735
Fax: +39 02 57512490
e-mail: macplas@macplas.it www.macplas.it
Registration at the Court of Milan n. 68, 13/02/1976
Registration at the National Press Office n. 4620, 24/05/1994
Layout and prepress Faenza Printing SpA
Printed by Faenza Printing SpA
Postal delivery: IFS Italy
ISSUE PRICE: 8 euro if not sent with mother magazine
The managing direction of the magazine declines any responsibility for possible unreliability of editorial articles and notes coming from various sources
ASSOCIATED TO:
55 AMAPLAST www.amaplast.org 60 AMUT www.amut.it 13 ARBURG www.arburg.com
103 BD PLAST www.bdplast.com
66 BIESSE www.biesse.com Back cover BMB www.bmb-spa.com
4 BREAK MACHINERY www.breakmachinery.com
62 CALDARA PLAST www.caldara.it
63 CAMPETELLA www.campetella.com
53 COMERIO ERCOLE www.comercole.it
47 EUROVITI www.euroviti.com
65 FB BALZANELLI www.fb-balzanelli.it
3 FIMIC www.fimic.it
41 GAMMA MECCANICA www.gamma-meccanica.it
68 GIBITRE www.gibitre.it
46 GIURGOLA STAMPI www.giurgolastampi.com
87 GRAFE www.grafe.com
97 GREENPLAST www.greenplast.org
80 HELIOS QUARTZ www.heliosquartz.com
83 HS-UMFORMTECHNIK www.hs-umformtechnik.de
33 IMG www.imgmacchine.it
85 MAIN TECH www.maintechsrl.com
9 MARIS www.mariscorp.com
51 MAST www.mastsrl.it
49 ME.RO www.mero.it
93 MIXACO www.mixaco.com
29 MORETTO www.moretto.com
69 MOVING www.movingsrl.it
102 PACKAGING SPEAKS GREEN www.packagingspeaksgreen.com
64 PET SOLUTIONS www.petsolutions.it
81 PLASTORE www.plastore.it
5 PRESMA www.presma.it
70 PROFILE DIES www.profiledies.it
37 ROBOLINE SYTRAMA www.sytrama.com
74 SARA www.sarasrl.eu
7 SICA www.sica-italy.com 73 SITRA www.sitramasterbatch.com
2 TECNO SYSTEM www.tecnosystemfe.it
TECNOMATIC www.tecnomaticsrl.net
Cover
TECNOVA www.tecnovarecycling.it
www.ultrasystem.ch
ASSOCIAZIONE NAZIONALE EDITORIA DI SETTORE
INSTITUTIONAL SPONSORS
AMAPLAST
ITALIAN PLASTICS AND RUBBER PROCESSING MACHINERY AND MOULDS MANUFACTURERS’ ASSOCIATION
AIPE
ITALIAN ASSOCIATION OF EXPANDED POLYSTYRENE
ASSOGOMMA
ITALIAN RUBBER, CABLES, WIRES AND SIMILAR MANUFACTURERS’ ASSOCIATION
CIPAD
COUNCIL OF INTERNATIONAL PLASTICS ASSOCIATIONS DIRECTORS
www.zambello.it
www.zeon.eu
SPE ITALIA SOCIETY OF PLASTICS ENGINEERS
UNIONPLAST ASSOCIATION OF ITALIAN PLASTICS PROCESSING COMPANIES
UNIPLAST
ITALIAN
Boost your extrusion! To achieve perfection and continuous improvement, Tecnomatic chooses maximum specialization and concentrates its efforts on the
development of extrusion lines for the production of polyolefin pipes with diameter up to 3.000 mm. Technical knowledge, constant research and great passion
allow Tecnomatic to offer highperformance solutions fulfilling all possible customer requirements since 1977.
GreenPlast 2025, the second edition of this exhibition devoted to the environment, will be held from 27 to 31 May next year at the Rho-Pero exhibition centre of Fiera Milano.
The first time this event was held (3-6 May 2022), it occupied a net exhibition area of approximately 6,000 square metres (the whole of hall 14), accommodating a total of 170 exhibitors (80% Italian and 20% foreign) and 20,000 visitors, coming from 30 countries (in addition, naturally, to those from Italy, Germany, Switzerland, France, Spain, Turkey etc.).
It is important to remember that GreenPlast is held in conjunction with three other important supply chain fairs: Ipack-Ima (for the packaging world), Intralogistica Italia (dealing with logistics, as its name suggests), and Print4All (printing and converting).
Created, almost as a bet, in the midst of the pandemic, GreenPlast was a great success, a result driven in part by the exhibition-conference formula, but also by its highly competitive pricing (exhibitors particularly appreciated the pre-fitted booth format for exhibition areas of up to 48 square metres, a threshold increased to 64 square metres for 2025).
Exhibitors, for their part, want innovative and affordable formulas.
And this is why GreenPlast is not just a trade fair in the traditional sense of the term, but an exhibitionconference. Precisely to enhance the conference part of the event, an agreement has been reached with AMI, a leading company in market researches and event organisation, which will stage a conference lasting over the entire four days (from the afternoon of the first day to the morning of the fourth and final day), obviously dedicated to the environment and examining every aspect of this theme.
The environment has, after all, become a crucially important issue.
During the pandemic, some people deluded themselves that, in view of the widespread use of polymers for the production of face masks, but also, more simply, of disposable plastic packaging that guarantees food (and not only food) safety, plastic would be definitively “back in favour”, and attacks against this material would cease.
Nothing could be further from the truth!
Responsible management of plastic packaging, ecodesign, and the circular economy are all issues on the agenda.
And GreenPlast is the perfect showcase for anyone offering innovation in any related area: materials, products or technology.
This is why GreenPlast 2025 will be an even bigger success than the 2022 edition. We look forward to seeing many of you there, exhibitors and visitors, keen to see all the latest developments, listen to the leading sector experts, and - why not? - work together for a better world.
Further growth for the national association of plastics and rubber machinery, equipment and moulds manufacturers in 2023. The main driving force was exports, which consolidated Italy as the third largest exporter in the sector worldwide. Although less significant than in the previous two years, this is still a reason for satisfaction.
By Stefania Arioli and Luca Mei
On 6 June 2024 Villa Arconati hosted the annual Members Assembly of Amaplast - the national trade association affiliated with Confindustria representing approximately 170 manufacturers of machinery, equipment, and moulds for plastics and rubber.
During his speech, President Massimo
Margaglione made remarks about the performance of the Italian industry of machinery, equipment, and moulds for plastics and rubber. Drawing on data from the association’s research centre, he observed that, despite a challenging global environment, the sector had seen growth of 2.8% in 2023. Although this increase was less pronounced than in the previous two years, it brought the value of production to a record 4.8 billion euros. Exports remain the main driving force with an 11% increase compared to 2022, solidifying Italy’s position as the world’s third-largest exporter, following China and Germany.
Vice Presidents Gabriele Caccia and Barbara Ulcelli recapped the initiatives undertaken by Amaplast over the past year,
with particular emphasis on the Plast 2023 fair. They also provided details regarding upcoming plans, highlighting the preparations for Greenplast 2025 (Milan, 27-30 May 2025, once again as part of The Innovation Alliance).
On the occasion, the association’s leadership was renewed with the election of new members:
- General Council, with the election of Luna Artico (Friul Filiere), Alessandro Balzanelli (FB Balzanelli), Michele Bandera (Bandera), Alessandra Bosco (Inglass), Gianfranco Cattapan (Plastic Systems), Maria Grazia Colombo (BFM), Giovanna Franceschetti (Gefran), Gianni Luoni (Elba), Fabiola Plebani (Mast) for the 2024-2026 term;
- Board of Arbitrators, with the election
of Erica Canaia (Fimic), Carlo Cominelli (Itib Machinery), Andrea Fantozzi (Moss), Valeria Giacomoni (Sica), Aldo Zaffaroni (Zaffaroni) for the 2024-2028 term; - Board of Auditors, with the election of Gianni Cazzulo (chartered accountant), Claudia Cribiù (Crizaf), Roberta Rivi (Rivi Magnetics) for the 2024-2028 term. The assembly endorsed their commitment to the federative project that led to the founding of Confindustria Machinery Federation, for ceramics, wood, plastics and rubber, and packing and packaging. Alongside Amaplast, this federation includes Acimac - Association of Italian Manufactures of Machinery and Equipment for Ceramics - Acimall - Italian Woodworking Technology Association - and Ucima - Italian Packaging Machinery Manufacturers’ Association. The goal is to pool the skills and experiences of each association to expand and further
improve the quality of the services offered to member companies. The newly formed Federation represents over 1,300 companies, with a workforce approaching 70,000 employees, and a total revenue surpassing 19 billion euros.
In closing, Federico Rampini, journalist, author, and columnist of the Italian daily newspaper “Il Corriere della Sera”, delivered a speech outlining the macroeconomic and political trends shaping the global landscape, with a focus on conflicts, upheavals, risks, and opportunities.
According to the analyses conducted by the Mecs-Amaplast research centre, the Italian industry for machinery, equipment, and plastics and rubber moulds closed 2023 with growth of 2.8% despite the challenging global context marked
(Δ% 2023/2022 and % shares of total)
10
in 2023 (Δ% 2023/2022 and % shares of total)
Top 10
2023 (Δ% 2023/2022 and % shares of total)
Top 10
in 2023 (Δ% 2023/2022 and % shares of total)
2014-2023)
Source
+10.4% (97.6 million euros in 2023)
by conflicts, inflationary pressures, and high interest rates. This increase, though more modest compared to that of the preceding two years, propelled production to an unprecedented record of 4.8 billion euros.
Despite economic and commercial uncertainties across various geographical regions, which worsened in the last quarter of the year, the performance of the sector remained positive, driven primarily by exports. Said exports saw a remarkable growth of nearly eleven percentage points compared to 2022. Italian manufacturers of plastic and rubber machinery experienced particularly strong sales in key markets such as the European Union (+9% over 2022), North America (+18%), and Asia (+8%, with the Middle East up by 50% and the Far East down by 1%). Though with smaller shares, South America also registered a 23% increase.
In the top ten export markets for Italian manufacturers, notably positive results have been observed in France, Spain, and Romania, as well as in Mexico and Turkey. Only Poland and India showed declines, despite both having enjoyed very favourable trends in previous periods.
The comparison with Germany and China - Italy’s two main competitors - reveals that their respective exports of machinery for plastics and rubber registered increases of 7.5% and 12.9% compared to 2022. Even when looking at the past decade, Italy’s performance lies somewhere between that of its two primary competitors, totalling an average of 3.5%, compared to Germany’s 2.9% and China’s 9%.
However, it is undeniable that the commercial pressure from China has been steadily intensifying over the past decade across all major geographical regions. At Chinaplast, held from 23 to 26 April, it was all the more evident that Chinese technology is advancing at a quick pace. This serves as an impetus for Italy to leverage its unique ability to develop increasingly innovative, flexible, and
Participants were offered a guided tour of the beautiful Villa Arconati, which provided an attractive setting not only for the private and public part of the event, but also for an aperitif and dinner, which on these occasions are further useful moments for meeting partners and networking but in a more relaxed and convivial atmosphere.
ITALIAN MARKET OF MACHINERY, EQUIPMENT AND MOULDS FOR
naturally performing solutions - also in terms of energy efficiency.
The 2023 financial report for Amaplast member companies is in line with that of the entire sector: the association noted a revenue growth of 2.4% - not as strong as the one registered over the previous two years, but significant still. Additionally, there was a modest increase (1.1%) in the workforce. While core-machinery (primary processing equipment) production has registered a slowdown, the production of auxiliary and downstream equipment, components, and moulds has continued to show a significant increase. As mentioned, the trend among the sector - mirroring that of the industry generally and the capital goods sector - cooled down over the final months of 2023 but more encouraging signs were observed in April and May. Nevertheless, forecasts for the upcoming months are rather cautious: many companies will find it challenging to achieve further growth, and a
period of stabilization and transition is to be expected. Domestic demand, in particular, may remain weak due to uncertainties surrounding the effective implementation of Transizione 5.0 measures.
Concluding the meeting, president Masimo Margaglione expressed his thoughts on the matter: “A justified sense of concern has spread among entrepreneurs of the sector, but I for one am optimistic:
RUBBER (million
not because it is philosophically better to speak of the good rather than the bad, nor because of that corporate mindset that sometimes tells us to conceal negativity, but because, despite our flaws and shortcomings, we never fail to showcase truly exceptional ingenuity thanks to our unparalleled creativity, our vigorous entrepreneurship, and an extremely diverse and dynamic business fabric.”
Last year’s record results will keep values at medium-high levels in the current year, despite expectations of a moderate decline. Exports, for their part, are supporting the domestic market. And we need to act quickly to take advantage of the funds earmarked for Transition 5.0.
In 2023, the Italian capital goods industry saw further growth in turnover, which reached a new record for the sector. Although a moderate decline across almost all economic indicators is expected in 2024, values will remain at medium-high levels. This is what emerged from data collected by the Federmacchine Statistics Group and presented at the federation’s general meeting held on 17 July. Speaking alongside the president of Federmacchine, Bruno Bettelli, was the vice president of Confindustria, Marco Nocivelli.
In 2023, the sector’s total turnover stood at 56.6 billion euros with a 2.1% increase compared to 2022, thus setting a new record.
Exports grew by 5.8% to 37.7 billion euros, exceeding the previous year’s result and reaching a new record as well. On the other hand, deliveries by Italian manufacturers on the domestic market went down in the wake of the decline in domestic consumption at 18.9 billion euros, 4.6% less than in 2022. Demand from the Italian domestic market fell by 4% to 30.4 billion euros. Imports were also affected by the weakness of domestic demand, settling at 11.5 billion euros with a 3% decrease compared to 2022.
Italian operators demonstrated, once again, that they know very well how to preside over the domestic market, as highlighted by the import/consumption figure which stood at 37.9%. The export/turnover ratio grew by almost two percentage points reaching 66.6%.
According to forecasts, 2024 will mark a trend reversal for the Italian capital good market with a modest slowdown, while still remaining at high average levels. In particular, turnover should reach 54.7 billion euros (-3.3% compared to 2023) with domestic consumption decreasing by 8.3% to 27.9 billion euros. Both imports, expected to fall by -2.6% to 11.2 billion euros, and manufacturers’ deliveries, which are expected to settle at 16.7 billion euros (down 11.7% compared to the previous year), will be affected. Exports, on the other hand, will grow further, albeit slightly (+0.9%), exceeding 38 billion euros, a new record for the sector.
*forecasts
Source: Gruppo Statistiche Federmacchine
With reference to the breakdown of sales by geographical area, the share of turnover generated in Italy in 2023 stood at 33.4% while 36.1% came from other European countries. The European market therefore accounts for almost 70% of Italian sales, followed by exports to the Americas (15.6%) and Asia (11.3%).
In 2023, Italian exports grew in all major markets except for China, Turkey and the United Kingdom. The highest growth rates was recorded in Mexico and Poland. The main outlet markets were the United States (5 billion euros, +6.7%), Germany (3.9 billion euros, +4.3%), France (2.6 billion euros, +7.9%), China (1.8 billion euros, -4.4%) and Poland (1.6 billion euros, +15.6%).
“The international market represents the ideal outlet for the members of Federmacchine. This is borne out by the level of exports expressed as a percentage of turnover, which in some periods has been as high as 75%,” said Federmacchine president, Bruno Bettelli. “This is why, also in the course of 2023, the federation has poured a great deal of effort into initiatives aimed at fostering relations with foreign users. In 2022, the Ingenium Report, drawn up by Confindustria and Federmacchine, highlighted a potential 16 billion euros’ worth of unrealised exports, distributed between emerging and already established markets, which could potentially be within our companies’ reach. Taking this as our starting point, we started to think about actions that could support the drive to internationalise the sector, participating in meetings and organising contact opportunities with representatives of the industrial systems of several important countries such as China, Vietnam and Saudi Arabia. But the work certainly does not end here. On the contrary, we have already started working on the second edition of the report, so as to have a more updated picture of the situation. Clearly, though, despite the efforts of companies operating in this sector and the organisations representing them, there is still a need for institutional support for their internationalisation activity, of the kind that could be provided, for example, by ICE Agency, Sace and Simest.”
“Instead, on the Italian domestic market,” Bettelli went on, “just as we supported the introduction and continuation of the Industry/Enterprise provision, and also Transition 4.0 aimed at digitisation, so we immediately embraced the government’s energy saving-focused proposal linked to Transition 5.0. Quite apart from its obvious economic benefits, this measure will certainly act as a driving force for the transition towards green manufacturing. Basically, it can and must be interpreted as
a lever to make companies aware of a new way of operating. This, in turn, will help to increase the competitiveness of Italian manufacturing in our sector and in all those sectors that use last-generation machinery. However, the measure needs to be up and running as soon as possible, alongside Transition 4.0. We are losing precious time that we risk not being able to recover, given that the dedicated resources are linked to the National Recovery and Resilience Plan, and in particular to the Repower EU Fund which, under the reporting rules, stipulates that 5.0 machinery can benefit from the expected relief only if it is installed and interconnected by 31 December 2025. The very short time between the availability of the resource and the deadline set for delivery and interconnection of the machinery is creating difficulties for Italian manufacturers, who, being specialised in customised products, operate with production times of about 6-8 months. There is a risk that the current delay will end up favouring, above all, imports - which notoriously come from Asia - to the detriment of our products or in any case of European-made products.”
“This is why we at Confindustria,” the president ended, “are appealing to the authorities to take action as soon as possible, with a view to extending until 2026 the possibility of using the funds earmarked for this measure. We are aware of the constraints linked to the use of these 6.3 billion euros allocated by Europe, but we also know that there are countries whose industrial systems are really not in great shape right now. We therefore feel that we are not the only ones that could benefit from a review geared at introducing some flexibility in the implementation of the measure, and avoiding funds having to be returned to Brussels because there wasn’t the time, technically, to spend them. However, our authorities need to coordinate with their European counterparts as soon as possible, to see how much room for manoeuvre there actually is.”
Automation Systems, a company indirectly owned by the Investindustrial fund and managed independently, signed an agreement for the acquisition of 58.35% of the share capital of Piovan from Pentafin through the purchase of 31,275,541 ordinary shares at a total price of approximately 438 million euros.
Under the terms of the agreement, the closure of the transaction is conditional on the obtainment, within nine months, of the authorisations required by the competent antitrust agencies, as well as the authorisations necessary for foreign investments. The latter should be granted by October 15 and the transaction closed in the following weeks. The agreement also provides that, after the closure, Pentafin will purchase a 25% stake in Automation Systems.
Once this transaction is closed, Automation Systems will be required to promote a public purchase offer on the remaining shares of Piovan at a price of 14 euros each, with the aim of delisting the company from Euronext Star Milan. In addition, Nicola Piovan will keep his role as executive chairman of the board of directors while Filippo Zuppichin will be confirmed as CEO of Piovan.
At the same time, Automation Systems also signed an agreement for the acquisition of an additional 6.47% of Piovan’s share capital from 7-Industries Holding through the purchase of 3,467,698 ordinary shares at a total price of 49 million euros. This transaction is subject to the closure of the above-mentioned transactions between Automation Systems and Pentafin.
“I am very proud of the growth path undertaken and the results achieved by the Piovan Group from its establishment to today. Over the last few years, the Piovan Group has been able to strongly consolidate its position as one of the main global players in the development and fabrication of automation systems for production processes. Today a new chapter opens for the future of the Piovan Group and
Nicola Piovan, pictured, and Filippo Zuppichin will continue to serve as executive chairman of the board and managing director of Piovan, respectively.
its collaborators that will be written together with Investindustrial, an international partner with a strong entrepreneurial spirit whose vision, values and attention to sustainability I fully share. In a constantly evolving market, Investindustrial’s skills and resources will be key in continuing and accelerating the growth path for the benefit of all stakeholders,” commented Nicola Piovan.
Investindustrial is a European group of independently managed investment, holding and advisory companies with €15 billion of raised fund capital. It provides industrial solutions and capital to European mid-market companies and its mission is to actively
contribute to the development of the enterprises in which it invests, creating growth opportunities and offering global solutions based on a pan-European entrepreneurial vision. Characterized by a strong vocation towards sustainability, Investindustrial boasts a history of over thirty years of partnerships with entrepreneurs and companies in Europe. Certain companies in the Investindustrial group are authorised and subject to the regulatory supervision of FCA in the UK and CSSF in Luxembourg. Investindustrial’s investment companies operate independently of each other as well as of the investment funds within the group.
Despite the adverse conditions on the international markets, the German plastics and rubber machinery industry closed 2023 with a price-adjusted increase in turnover of 13 per cent. In nominal terms, the increase even amounted to 22 per cent. “This growth is pleasing and demonstrates that companies have been able to bring in many orders in recent years, which have now been successively filled. However, in the meantime, the signs have changed significantly worldwide. Most companies have worked through their order backlog and are currently facing up to the issue of underutilisation,” explains Ulrich Reifenhäuser, Chairman of the VDMA Plastics and Rubber Machinery Association. In addition to the wars in Ukraine and the Middle East, high energy costs, inflation and high interest rates in particular are weighing on machine manufacturers, resulting in uncertainty and higher overheads, and therefore, lower investment on the part of plastics processors.
Although some of the general economic conditions, such as energy costs and inflation, have returned to normal, the downward trend in new orders has not yet been halted. “After we already had to cope with a priceadjusted decline of 13 per cent in 2022, we recorded another 22 per cent fewer orders on the books last year, after adjusting for price changes. As a result, many companies were forced to take countermeasures by introducing reduced working hours,” warns Thorsten Kühmann, Managing Director of the Plastics and Rubber Machinery Association.
On the sales side, the current year remains challenging, due to a lack of new orders. Moving forward, when the uncertainty on the markets slowly subsides from summer onwards, and interest rates stabilise at a more tolerable level, investment in new machines will once again pick up, and the sales trend for this year will either see a sideways movement or slight drop, depending on how quickly new orders are received.
Mechanical engineering is a cyclical
business. However, the current economic downturn in the plastics and rubber machinery industry is more than just a cyclical dip. “We cannot and must not play down the economic weakness resulting from the current situation. What we can do, however, is to focus on our strengths, utilise our innovative power, and use new solutions to solve current market issues in a surprising and precise manner,” Reifenhäuser states with convinction.
European mechanical engineering companies provide the technology and digital solutions needed to tackle today’s major challenges: more circular economy and recycling, climate protection through lower CO 2 emissions, and machines and systems tailored to global customer requirements; that is where there are considerable opportunities. The new trade association board therefore fully supports the key themes of K 2025: “The Power of Plastics! Green - SmartResponsible”.
The trade association includes more than 200 companies as members that cover over 90% of the industry’s
production in Germany, and representing a turnover of 7 billion euros in core machine manufacturing and 10 billion euros including peripheral technology. According to estimates, every fourth plastics machine manufactured worldwide comes from Germany in terms of value, and the export quota of the country is 70%.
At its recent general meeting, the company representatives of the trade association elected the new Board of the Plastics and Rubber Machinery Association for 2024 to 2027. Ulrich Reifenhäuser remains Chairman of the Board, that also includes: Gerhard Böhm, Arburg; Jörg Bremer, KraussMaffei Group; Stefan Engleder, Engel Austria; Sandra Füllsack, Motan Holding; Manfred Hackl, Erema Group; Thomas Holzer, Troester; Henning Stieglitz, Battenfeld-Cincinnati Germany; Markus Vollmer, Kampf Schneid- und Wickeltechnik; Axel von Wiedersperg, Brückner Group (Deputy Chairman); Sascha Witt, Windmöller & Hölscher; Rainer Zimmermann, AZO.
At its Annual General Meeting, members of the British Plastic Federation’s council re-elected existing president
Nigel Flowers for a further year and elected a new vice president: Chief Executive of Rehau UK and Ireland and Scandinavia, Martin Hitchin.
Commenting on the appointment, BPF
Director General Philip Law stated: “We are very pleased to have Martin Hitchin as the new vice president of the British
Plastics Federation. His nomination is very well deserved. Martin has had a very distinguished career and is a highly valued member of the BPF Council. I am sure that he will be an excellent vice president, helping the BPF to continue to provide value to its members and promote the varied interests of our industry.”
Director of Sumitomo (SHI) Demag UK and BPF President Nigel Flowers stated: “I happily welcome Martin Hitchin as vice president. His experience in several areas of plastic processing will be invaluable. Martin has a background in working with windows, pipes, automotive and also recyclers, so really offers a wealth of knowledge we can all benefit from.”
Newly-elected BPF Vice President Martin Hitchin added: “It is an honour to be voted in as vice president of the BPF. I have been involved with the trade association for many years, and am aware of the wide variety of
work it does to champion our industry. The work of the BPF Council helps to shape the approach and priorities of the organisation. I look forward to my new role and am keen to support the existing ambitions of the current president, Nigel Flowers.”
Martin Hitchin gained a degree in Combined Engineering at Coventry University before going on to do post graduate training in China, followed by an MSc at North London University in Polymer Science and Engineering. He has since worked in the manufacturing and construction sector for 35 years.
Martin started working with Reah in 1988 as an Applications Engineer. After numerous promotions he was made CEO at Rehau in 2007, where he has overseen steady evolution of the company and positive growth.
Martin is also the vice Chair of New Model Institute for Technology and Engineering (NMITE), a start-up engineering university in Hereford.
Ilham Kadri, CEO of Syensqo, has been elected Cefic President, succeeding Martin Brudermüller. Ilham Kadri is one of Europe’s most prominent and well-known business leaders.
She holds a degree in chemical engineering from L’École des Hauts Polymères in Strasbourg, and a PhD in macromolecular physicochemistry from Strasbourg’s Louis Pasteur University. Kadri served as Cefic’s Vice President before becoming the President and holds several key positions in business associations around the world.
Ilham Kadri is a world citizen with Moroccan-French roots and professional experience across four continents. During her 30-year career, she has held various positions at leading companies. Her responsibilities have included research and development, strategy, business and digital in industries spanning automotive, aerospace, oil & gas, mining, water desalination,
construction, consumer goods, food service, hospitality and healthcare. Ilham Kadri actively speaks out for the role of science, innovation, sustainability, inclusion and diversity, mentoring and promoting female leadership in science, technology, engineering and mathematics.
Ilham Kadri, along with outgoing President Martin Brudermueller, played a key role in the recent European Industrial Summit, hosting key government officials such as European Commission President Ursula von der Leyen, Belgian Prime Minister Alexander de Croo and former Italian Prime Minister Enrico Letta. In these months, Brussels is being seen a series of Antwerp Dialogues, further exploring the key requests in the Antwerp Declaration.
Ilham Kadri, CEO of Syensqo, spinoff of Solvay, was appointed to lead Cefic, the European Council of Chemical Industry Federations.
The Italian manufacturer Previero is achieving certification for gender equality in the company. The process confirms Previero’s commitment to promoting an inclusive and diverse working environment, in accordance with the UNI PDR 125/2022 standard.
To achieve this, an in-depth analysis of the company’s policies was carried out in the areas identified as relevant to an inclusive and gender-balanced organisation: culture and strategy, social processes, opportunities for growth and inclusion of women in the company, gender pay equity and protection of parenthood and work-life balance.
“Achieving this certification recognises
agreement
our commitment to creating an inclusive organisation where every individual has the opportunity to grow and contribute equally to the company’s success”, Flavio Previero, President of Previero, said.
“Gender equality in the company is not just a matter of regulation, but to us a strategic investment which will generate tangible benefits, such as greater growth in innovation and the ability to attract and retain talent”.
With regard to gender equality, a sensitive issue in corporate life, Previero has embarked on a virtuous path which includes the adoption of impartial methods for the selection and remuneration of female and male
workers, an aspect that is evidenced by the increasing presence of women in technological development and research positions, as well as in clerical positions.
For Previero, gender equality is an investment capable of generating multiple benefits.
Gefran entered into an agreement with the current CEO, Marcello Perini, including the commitment to keep the manager at the helm of Gefran in the role of CEO until the approval of the 2028 financial statements. Perini agreed to continue to contribute to the leadership of the company at least until the agreed date. The decision to confirm Marcello Perini as CEO of the group rewards the work done in recent years by the manager: under his leadership Gefran went on a path of continuous growth that allowed the company to achieve a record turnover of 134.4 million euros in 2022. Moreover, during the recent years, the company successfully overcame very complex issues, such as challenges related to
the pandemic crisis and the supply chain discontinuities, as well as it was satisfactorily concluded the sale of the drives business to the WEG Group.
The agreement reached will therefore enable the company to consolidate the leadership and progress achieved so far, with the goal of continuing to grow in the coming years, and to seize the new opportunities that, although in a continuous changing context, the market will offer. The manager’s confirmation at the helm of the Group will ensure continuity for the many development initiatives that the company is conducting about innovation and internationalization.
Through the agreement we signed, together with the parent holding
company, we confirm both the trust we place in our CEO for the future development of the Group and the wisdom of the intuition we had when he was entrusted with the leadership of the company in 2020,” said Giovanna and Maria Chiara Franceschetti, respectively Chairwoman of Fingefran and of Gefran. “The results we have achieved together with Mr. Perini in recent years are very satisfactory, and we believe that ensuring stability and continuity at the helm of our organization ensures consistency of strategy and execution. This is a fundamental condition for realizing the ambitious growth projects we have planned, and for which Marcello’s contribution will be, as in the past, very important.”
With extensive experience in the plastics industry, Kirk Winstead is the new President of Tria America. “I am excited to join Tria America, a company I have long admired for its commitment to customers, quality and innovation,” said the new President. “The ownership and strong values that Tria upholds are commendable and perfectly aligned with my professional principles. I look forward to contributing to the continued success and growth of Tria America and working with such a talented team.”
Winstead’s career spans nearly forty years in the plastics processing equipment industry, twenty-seven of which have been spent in size reduction. He has made significant contributions in a variety of corporate roles, most recently as CEO of Piovan North America and previously as CEO of Ipeg Group and CEO of Rapid Granulator Group. His in-depth knowledge of the industry and his many years of experience will be instrumental in leading Tria America.
“We are delighted to welcome Kirk to the Tria family,” said Stefano Venturelli, Managing Director of Tria Group. “His
extensive experience and proven track record in the industry make him the ideal leader to take our US subsidiary into the future. We are confident that his leadership will bring new perspectives and further drive innovation to enhance our ability to serve our customers and strengthen our market position”.
Union strengthened its asset of human resources with two experienced
professionals in the extrusion sector: Massimo Gomis and Simone Coccoletti. With many years of experience in OEM companies in the plastics processing sector, both in the technical and service fields, both professionals have consolidated technical and commercial relationships with major companies in the world of extrusion in Europe. Massimo Gomis took on the role of Southern European Markets Manager and Senior Innovation Manager to support Union and Tecom’s key
Tria America is one of the leading local providers of state-of-the-art waste reduction solutions for the plastics industry. With Winstead at the helm, the company looks forward to continuing to deliver high quality products and services while expanding its presence in North America.
customers in the domestic market, while Simone Coccoletti took on the role of Global Head of the Commissioning & After Sales Customer Care team to support customers in maintaining plant OEE and ensuring correct start-up of lines. Motivation, concreteness, experience and entrepreneurial spirit of Massimo Gomis and Simone Coccoletti, together with their ability to develop turnkey projects, will allow Union to strengthen its position as a company specialising in flathead extrusion technology.
Machinery manufacturer Windmöller & Hölscher marked a significant milestone on the last days, with the groundbreaking of a major expansion at its North American headquarters in Lincoln, Rhode Island. “Our investment in this expansion reflects our commitment to enhancing service capabilities and ensuring we meet our customers’ needs more swiftly and efficiently than ever before. By doubling our warehouse capacity and making space for our growing team, we are dedicated to strengthening our support and fostering further growth in North America”, Andrew Wheeler, President of Windmöller & Hölscher in North America, stated.
The first phase of the project will expand the warehouse by more than 1,000 sqm and the office building by more than 500 sqm with completion anticipated within twelve months. The second phase is the complete renovation of the existing 800 sqm of office space, slated to take six months. The entire project is expected to be completed by winter 2025. In line with Windmöller & Hölscher commitment to sustainability, photovoltaic panels are being installed to generate nearly all the building’s electricity, including powering the HVAC (Heating, Ventilation, Air Conditioning) system for the office space. Additionally, electric vehicle charging stations will be installed.
Sumitomo (SHI) Demag announced the next phase of the company’s succession plan following the retirement of incumbent CEO Gerd Liebig, who has led the Group for nine years. Effective 1 September 2024, Christian Maget assumed the role of CEO. Drawing upon his deep internal knowledge of the business, Christian Maget was the natural choice for overseeing the internal operational aspects of the group’s strategic direction. He will continue to assume management responsibility for human resources and IT. Christian Maget joined the company in 2013. Expressing his deepest appreciation for Gerd Liebig’s inspiring commitment to Sumitomo (SHI) Demag during his tenure, Christian Maget will lead the team in highlighting some of the extraordinary achievements that will pave the way for the next years. “What the Group has accomplished steering through some of the most challenging economic circumstances is testament to Gerd Liebig’s work ethic, drive and integrity. From expanding our global sector capabilities, to becoming the world leader for all-electric machines and competing in the digital world, his ability to continuously innovate cannot be underplayed. Mr. Liebig has been
instrumental in expanding our service offerings as well as driving forward the development of more sustainable, automated manufacturing solutions.”
At the same time, Anatol Sattel assumed the new role of Chief Sales Officer (CSO). Overseeing the frontline external presence with customers, business partners, subsidiaries and representatives, the 46-year-old is also aiming to strengthen cooperation with Japan. Anatol Sattel, who joined the company in September 2017, took over as Director of Business Development Medical in April 2019 and laid the foundations for the successful accomplishments of the medical technology team. The management and strengthening of international sales as well as global customer service led by Andreas Holzer also falls within Sattel’s core responsibilities. This means that he will also oversee the industry-specific business development teams, comprising packaging, medical, automotive, electronics and consumer.
“It has always been important for our customers to have access to marketleading innovations. However, one of the best ways for them to improve performance and productivity is through collaboration. This is what the plastics
industry does exceptionally well. Customers want to experience these synergies and have the certainty that everything is available from one single source”, said Anatol Sattel. to experience these synergies and have the certainty that everything is available from one single source”, says Anatol Sattel.
The management team is completed by Takaaki Kaneko, whose position as COO remains unchanged, and the technology director Martin Pütz, who reports into Maget from September.
Illig, the German specialist for thermoforming and packaging systems, successfully completed the equity capitalization and restructuring process initiated at the end of 2023 with the entry of the German
financial investor Orlando Capital. The experienced German investor, focusing on medium-sized companies in complex situations, acquired the entire product portfolio and continue the business in all sales regions worldwide. All tangible assets and the entire business operations of the engineering company has been transferred to the new company. The continuation of the Illig brand and the existing product portfolio of thermoforming and packaging systems in all sales regions is therefore assured. In addition to the acquisition, the investor will use significant cash resources to position Illig as a market leader in the long term. The acquisition has been funded exclusively with equity capital and aims to achieve a very high equity ratio.
With the entry of a financially strong investor, Illig will once again invest more in the development of new technologies and innovations. At the same time, the company will focus even more strongly on international growth and the further development of strategically important product areas and markets.
The Supervisory Board of Borealis announced Stefan Doboczky as the new CEO of Borealis, effective since 1 July.
The new CEO career started in 1992, culminating in executive board and CEO positions at listed chemicals companies internationally. He held a position on the OMV Supervisory Board since 2019, from which he stepped down due to his new role at Borealis. Stefan Doboczky holds a PhD in Chemistry from the Technical University Vienna and an MBA from IMD Lausanne.
Daniela Vlad, Chairwoman of the Supervisory Board of Borealis and EVP Chemicals of OMV, stated: “Stefan Doboczky brings a wealth of experience with an impressive leadership track record in the chemicals industry spanning over 30 years. I am delighted to welcome him to Borealis with his indepth knowledge of our industry and his strong commitment to further elevating
Borealis’ market leadership through its proven innovation and technological capabilities. OMV and ADNOC - both companies represented in the Borealis Supervisory Board - are supportive of this appointment. I look forward to working with Stefan Doboczky in his new role, as he takes the helm of a worldclass company which is one of OMV Group’s pivotal driver for future growth.”
Stefan Doboczky declared: “I would like to thank the Supervisory Board of Borealis for the trust and look forward to further advancing Borealis’ development in the evolving chemicals sector. As a global leader in the area of polymers, Borealis is uniquely positioned in this market with its focus on innovation, sustainability and outstanding circular economy solutions. I look forward to exploring new strategic advancements with my new colleagues at Borealis and delivering sustained growth while
tapping into new market opportunities internationally. I am looking forward to getting to know the Borealis community of customers and suppliers, but most of all its employees.”
Perfect polymer drying
Guaranteed by the combination of 100% Zeolite molecular sieves and advanced engineering technology for zero-defect production.
Drying time is reduced on average by at least 38% thanks to the OTX internal geometry.
Other benefits:
Hyper Flow turbocompressors, developed by Moretto, ensure high performance and low energy consumption. High energy efficiency
User friendly
Homogeneous material flow Discover more on X COMB
Only two parameters need to be set: material type and throughput.
• Smallest footprint, whether installed on IMM or trolley.
• Touch view interface, simple and intuitive.
• Shockproof Spyro finishing, a distinctive and robust design.
As an important resource for Italy, the compostable bioplastics industry should be supported and protected against any illegal behaviours, dumping practices and misinformation. According to Assobioplastiche-Biorepack-Italian Composting and Biogas Association (Consorzio Italiano Compostatori), without rapid and effective regulatory measures it will be very hard to safeguard a sector which represents a European excellence in achieving the EU’s environmental goals.
Illegal activities that are still too widespread, dangerous dumping practices, a drop in consumption, price hikes, the steady spread of “pseudo-reusable” tableware, the growing presence of non-compostable materials in organic waste, and a serious state of misinformation. There are many factors to take into consideration in order to understand the figures describing the situation of the compostable bioplastics industry and the separate collection of organic waste in Italy.
After a decade of almost steady growth - which saw a 300% increase in volumes and over 200% in turnover, number of employees and enterprises - 2023 brought the first real setback.
This situation is analysed in the “X rapporto sulla filiera italiana delle bioplastiche compostabili (10th report on the Italian compostable bioplastics industry)” presented during the first Italian forum on compostable bioplastics organised by Biorepack, Assobioplastiche and the Italian Composting and Biogas Association (CIC) in Rome on 12 June 2024.
Though not alarming, these figures should not be downplayed, given the strategic value that, year after year, the bioplastics industry has demonstrated both for its propensity to invest in research and development, and for the ability to build and multiply synergies with other sectors starting from agriculture and, not least, for the undoubted environmental benefits that it guarantees. In short, a valuable sector to be protected, which
in two decades has become a highly interconnected economic system capable of combining research with agriculture and industry, the world of consumers and retail with that of recycling and the production of compost and biogas. A sector that Italy is called upon to protect if it does not want to lose its leadership in circular bio-economy.
The report, drawn up by the research company Plastic Consult, shows that the turnover generated by this industry, after the record-breaking results of 2022 (1.16 billion euros) fell to 828 million (-29.1%) in 2023, following the sharp decrease in the prices of raw materials, semi-finished and finished goods. The total volumes of manufactured goods produced also went down, amounting to 120,900 tons (-5.5% on 2022), a situation similar to that recorded in the conventional virgin thermoplastics market (-6%). Among the main application segments, in 2023 the greatest difficulties were encountered by single-use products (-20%), crushed between the unfair competition of the so-called “pseudo reusables” and the imports of compostable products from the Far East. On the other hand, the trend was positive for products related to the collection of organic waste and agricultural films.
During the first Italian forum dedicated to bioplastics, it emerged that without rapid and effective regulatory measures, it will be very difficult to safeguard a sector that today represents excellence at European level and guarantees the possibility of achieving the EU’s environmental goals.
In 2023, however, the number of enterprises reached 288, divided into base and intermediate chemicals producers (5), pellet producers and distributors (20), primary processors (198), secondary processors (65). The number of dedicated employees – i.e. directly dealing with products entering the compostable bioplastics value chain – was substantially stable compared to 2022 (2,980 or -0.8%).
As far as the organic recycling of compostable bioplastics is concerned, the figures remain positive. In 2023, the net volume was in fact 56.9% of the total amount released for consumption (44,338 tons compared to 77,900 tons placed on the market). A figure that is confirmed to be higher than the recycling targets set for 2025 (50%) and 2030 (55%). At the same time, the number of municipalities affiliated with the Biorepack consortium is growing: today they are over 4,600 (58.5% of the total) representing more than 43.6 million inhabitants (i.e. 74.1% of Italy’s population, a figure up almost 10 percentage points compared to 2022). The affiliated municipalities received payments equal to 9.4 million euros in total (in line with the previous year) to cover the costs of collection, transport and treatment of compostable bioplastic packaging disposed of together with household organic waste.
No less relevant are the figures relating to processing operations: the 155 composting, anaerobic digestion and integrated system plants across the various Italian regions processed just over 5 million tons of urban organic waste in 2022. Their contribution to compost production amounted to 1.44 million tons. The environmental figures are also significant: in fact, as highlighted by the Italian National Committee for Biosafety, Biotechnology and Life Sciences of the Presidency of the Council of Ministers, every ton of organic waste that is processed through composting instead of being disposed of in landfills, avoids the emission of 1.4 tons of CO2eq thanks to the benefits associated with the use of compost in agricultural land.
Apart from the macroeconomic situation, characterised by weak growth and high interest rates with significantly depressive effects on final consumption, operators in the value chain are worried about several aspects that are well known to insiders but nevertheless continue to be underestimated by lawmakers.
In particular, illegal behaviours are still too widespread, endangering the legal value chain and causing an enormous environmental fallout. Above all – despite a law introduced more than ten years ago in Italy – the segment of bioplastic shoppers and bags for fruit and vegetables is affected by the distribution of take-away bags made of non-compostable materials defying any legal requirements and carrying false and misleading environmental claims that deceit consumers.
“At the same time,” commented Luca Bianconi, president of
Assobioplastiche, “the import of low-cost shopping bags of dubious quality from the Far East is steadily increasing, likely with the support from the governments of that region. All this represents a dumping practice that is no longer sustainable, on which our authorities must shed full light because it damages the economic sustainability of national production. Italy must equip itself with all the necessary tools to safeguard its industrial excellence.”
Then there are the so-called “pseudo reusables”, which are to be found increasingly on the shelves of markets and supermarkets. Plates, glasses, cutlery made of traditional plastic that are prohibited under single-use regulations, but which continue to be marketed simply because they are one-sidedly declared as “reusable.” All this is made possible by a loophole in the Italian law: despite the fact that the European Delegation Law 20192020 (52/2021) provided that specific technical parameters should be identified in order to define a product as reusable, the Italian Legislative Decree 196/2021 did not indicate them, activating a vicious circle with extremely worrying consequences: proliferation of environmental declarations on prod-
In particular, illegal behaviours are still too widespread, endangering the legal value chain and entailing an enormous environmental fallout. Among the most affected products are bio-shoppers and fruit and vegetable bags.
Assobioplastiche, Biorepack and the Italian Composting and Biogas Association have organised the first Italian forum on compostable bioplastics as an opportunity to take stock of the current situation, together with industry insiders, in favour of a growing sector that needs timely and effective regulatory measures. The Italian industry
ucts bordering on greenwashing, disincentive for companies to carry out production conversions, brake on the development of circular bio-economy, risk of frustrating environmental and plastic reduction targets, possible misuse of public resources with the paradox that tax credits and incentives could end up financing companies not converting to the production of real reusables. Added to this is a worrying increase in misleading information, which, based on prejudicial and absolutely anti-scientific positions, end up spreading fake news about compostable materials, creating doubts among people and affecting the quality of separate collection.
“All these elements represent an incredible obstacle to the growth of the organic recycling capacity of compostable materials and affect the performance of Italian compost production,” commented Marco Versari, president of Biorepack, recalling how every kilogram of non-compostable materials (mainly traditional plastics, glass and metals) mixed with organic waste and that must be then separated before recycling operations, also subtracts 1.65 kg of compostable matrices.
“This phenomenon,” added Versari, “reduces the growth margins of companies and causes economic and management problems for municipalities. That is why we expect urgent action to be taken by the Government and by local authorities.
THE POLYMER VALUE CHAIN - 2023 DATA
Source: Plastic Consult for Assobioplastiche
At the European level, our country must act as a spokesperson so that the promotion of organic and compostable waste become a cornerstone of the ecological policies of the next European legislature.”
The link between the use of compostable materials and the correct separate collection of organic waste to be converted into compost should not be underestimated: the possibility of winning the most important Italian and European environmental challenges depends on it. “Producing compost from compostable waste means recovering a fraction of household waste that represents 40% of the total,” explained Lella Miccolis, President of CIC. “This typical product of the circular bio-economy helps restore fertility to farmland by reducing the use of chemical fertilisers. In this way, waste sent to landfills is drastically reduced, the production of additional CO2 is avoided and the carbon storage capacity of agricultural land is preserved. At European level, the compulsory collection of organic waste and compostable materials can provide significant opportunities for growth. Enhancing and supporting the production of compost is consistent with the targets of soil protection that the EU itself has set itself in recent years with its ‘Mission Soil’ initiative and with the directive approved by the European Parliament.”
The VinylPlus Sustainability Forum 2024, the main international event on PVC sustainability held in Cologne, focused on the theme “Together Towards Higher Ambitions”. From 22 countries, 190 delegates representing the national government and the federal states of Germany, the academia, designers, architects, recyclers and the European PVC value chain, met in the German city to take stock of the situation in the PVC industry, in particular its contribution to sustainability and the industrial transition. VinylPlus Sustainability Forum 2024
The twelfth VinylPlus forum on sustainability (VinylPlus Sustainability Forum 2024), held in Cologne, Germany, highlighted how important it is for both lawmakers and the industry to share common goals in terms of innovation, industrial transition and competitiveness, in order to step up and accelerate a positive change at the European Union and global level. Focusing on the theme “Together Towards Higher Ambitions”, the event was attended by over 190 delegates from 22 countries representing the German government, academia, designers, architects, recyclers and the PVC value chain.
“Together Towards Higher Ambitions” expresses the awareness of the need to work together to achieve common goals. This awareness is increasingly widespread and shared among operators in the PVC value chain, EU Member States, European institutions, academia, the different industrial sectors and stakeholders, and initiatives such as the future EU Industrial Development Strategy - which calls for a deep systemic transformation geared to resilience, while enabling and accelerating the transition towards more sustainable goals in Europe and at a global level - strengthen the industry’s programmes aimed to sustainability.
“The theme of your forum contains two very important elements: sharing and ambition,” said Mona Neubaur, Deputy Premier and Minister for Economic Affairs, Industry, Climate Action and Energy of the State of North Rhine-Westphalia. “The challenges that society and the economy are facing should be tackled together. Solutions must be supported by everyone and dialogue on the right way forward is essential. The current industrial transition is a task that we must accept and shape together, and we must keep ambitions high because high standards are needed to maintain competitiveness.”
“We need to achieve a fundamental transformation of the economy: climate action, circular economy and social justice
should be at the heart of our economic activities,” urged Svenja Schulze, the German Federal Minister for Economic Cooperation and Development. “We need sectoral initiatives like VinylPlus. Your commitment to a sustainable material, more recycling and less waste is very important. I would like to encourage all of you to systematically continue your efforts in the work you are doing.”
Presenting the “Progress Report 2024” Karl-Martin Schellerer, VinylPlus Chairman, pointed out that 2023 was a very demanding year for the PVC industry, which continued to face unprecedented regulatory and macro-economic challenges that also had repercussions on PVC recycling and the demand for recyclates. During 2023, despite a significant drop in demand for PVC, 737,645 tonnes of PVC waste were recycled by VinylPlus members, down from the previous year. However, at the same time, the share of recycled pre-consumer waste and post-consumer waste has remained stable.
“VinylPlus aims to remain a leader in the circular economy, continuing to push recycling and ensure the safe and sustainable use of recyclates,” said Karl-Martin Schellerer. “Recovinyl played a leading role in the establishment of PolyREC and its RecoTrace common data collection system, which has now become a model for many other industries. I would also like to highlight our commitment to carbon neutrality and to reducing the environmental footprint, as well as to researching and supporting innovative recycling technologies. In addition, the VinylPlus Product Label is now recognised at European level and several VinylPlus partners have been committed to obtaining the VinylPlus Suppliers Certifications.”
In the first session “Towards Meeting EU and Global Ambitions” Charlotte Röber, Managing Director of VinylPlus, said that “a frank dialogue like this shows how important it is to continue to draw inspiration from different experiences and incorporate different perspectives and points of view. For over 20 years, VinylPlus has been at the forefront of sustainability and circular economy. But for this purpose it is essential to work together, as a single value chain certainly, but also in close contact with lawmakers, other industrial sectors and academic partners. At the European level, we have recently demonstrated our commitment through the important and active contribution to ECHA’s “Investigation report on PVC and PVC additives”. Globally, we are actively participating in discussions on how to eliminate plastic pollution around the world through policies based on solid scientific foundations in cooperation with other regional PVC and plastics associations.” Research and innovation are key elements in VinylPlus’ efforts towards its circularity goals. The second session focused on the potential for future PVC recycling and how to fill any gaps in existing data to improve the accuracy of predictions. State-
Coils and mandrels (0.2%)
Floor covering Other B&C applications
Packaging (0.2%)
of-the-art developments for the recycling of large volumes of non-mechanically recyclable PVC waste using advanced technologies for chlorine recovery, pyrolysis and gasification, depolymerisation and chemical dechlorination were also presented.
In the third session, an analysis was proposed on how the PVC industry can progress further towards carbon neutrality and the minimisation of its environmental footprint. In this regard, sustainability experts presented examples of concrete initiatives aimed at achieving ambitious decarbonisation targets and transforming waste into quality resources. The event ended with the award ceremony for the VinylPlus sustainability certifications of companies that obtained the VinylPlus Product Label and the VinylPlus Supplier Certificates in 2023.
“Today’s discussions have confirmed the vitality of our industry and our willingness to continue to contribute to the sustainable transformation of the economy in Europe and around the world. Innovation and collaboration remain the keys to achieving VinylPlus’ 2030 goals. We are ready to continue working collaboratively, transparently and constructively with regulators, in line with our science and evidence based approach. To carry out this work effectively, the industry needs to level the playing field, which is why we are calling for a comprehensive action plan to make competitiveness a strategic priority in Europe,” said Karl-Martin Schellerer on closing the forum.
Traffic management
Horticultural and stable equipment
From European Environment Agency
According to a European Environment Agency (EEA) briefing recently published, plastics production and consumption patterns across Europe remain unsustainable and need to be made more circular to reduce waste, pollution, climate change and other negative impacts on the environment. The briefing also highlights the introduction of a new monitoring tool where people, policy makers and others can check progress on plastics circularity in Europe.
The European Environment Agency proposes a new monitoring tool to examine the progress of plastic circularity in Europe. The monitoring tool, which is one of the thematic modules of the broader Circularity Metrics Lab, looks at progress made on the circularity of plastics across Europe. It provides detailed insights into the circularity of plastics, with technical information for policymakers, stake-
holders and the public. The module will be updated annually with the latest data and new data streams as they emerge.
The EEA’s Circularity Metrics Lab encompasses a wide array of metrics on the transition to a circular economy. This initiative addresses the unsustainable patterns of plastics production and consumption, which contribute significantly to waste, pollution, climate change and other environmental impacts.
Together with the new monitoring tool, the new EEA briefing “The role of plastics in Europe’s circular economy”, in which it is included, indicates that the consumption of plastics is projected to rise both in Europe and globally. The briefing compiles data from diverse sources to assess the current state of plastics production and consumption, and its environmental and climatic repercussions. It also explores strategies for transitioning Europe towards a circular economy for plastics. The thematic module on plastics supports the EU’s contribution to international efforts to curb plastic pollution. The United Nations Interngovernmental Negotiating Committee (INC) is crafting an international, legally binding agreement to elim-
The circularity of plastics in Europe is increasing, although this is happening slowly, but some signs of progress and growth are encouraging.
plastic circularity monitoring tool proposed by the European Environment Agency is aimed at all stakeholders, from political and institutional decision-makers to the public, also to eliminate any possible knowledge gaps that may hinder it.
inate plastic pollution, including marine pollution. A critical component of these discussions is the establishment of robust monitoring mechanisms to support and track the commitments that may be finally agreed in that international process.
The EEA’s European Topic Centre on Circular Economy and Resource Use has produced a supporting report highlighting knowledge gaps and suggests improvements on data collection and monitoring efforts. Currently, most data on plastics production and consumption originate from industry, suggesting a need for greater involvement from public authorities.
Key insights from the plastics monitoring tool highlight that plastic consumption in Europe is high and it is expected to grow in line with projected increases in global plastics production.
The consumption and production of plastics negatively affect the environment and contribute to climate change. More marine litter is washing up on Europe’s beaches, high levels of microplastics are entering the environment, and future growth in
the automation market for
plastic consumption means greenhouse gas (GHG) emissions from the value chain are likely to increase as a result.
The circularity of plastics material is increasing at a slow pace. Nevertheless, there are encouraging trends: mechanical recycling capacity is increasing, EU exports of plastics waste are decreasing, bioplastics production capacity is growing slowly, as is the use of recycled plastics.
In conclusion, developing a circular economy is critical to making plastics more sustainable and is a central aim of the EU in its plastic strategy and recent legislation related to plastics and is part of the negotiations of the UN treaty to end plastic pollution.
Even the Vatican is embracing sustainability: ahead of the 2025 Jubilee, Corepla has donated a RecoPet eco-compactor to Pope Francis, which has been installed in one of the most frequented areas by tourists and worshippers. The aim is to prevent plastic waste from dispersing into the environment and to raise awareness among citizens and visitors about recycling.
During the presentation, Pope Francis highlighted the connection between science and spirituality. “Science allows us to extend our horizons much further and to feel more deeply the mystery that surrounds and inhabits us,” the Pope remarked. “Humility is fundamental to Christian life. Indeed, humble derives from humus, or earth. Contemplating a starry sky is enough to regain the right perspective.”
Nearly nine years after the publication of Laudato Si’, the encyclical in which Pope Francis called for a renewed commitment to sustainability and a new approach to our Common Home, Corepla has continued to champion a debate on the relationship between progress, the environment,
and social responsibility. The organisation has also focused on sustainability and the future of plastic packaging, emphasising the importance of communication in countering false narratives surrounding this material.
“Corepla’s commitment to sustainability and innovation stems from the need to protect our Common Home. Young people demand change from us and constantly express concern about climate crisis issues and an uncertain future. Against eco-anxiety, we have a powerful tool: information,” said Giovanni Cassuti, President of Corepla. “For over 25 years, Corepla has been dedicated to activities aimed at the younger generation. Through our school projects and local initiatives, we have engaged over half a million students. Building on these results, we aim to strengthen our educational offerings, recognising the increasing importance of providing answers and seeking solutions together.”
Plastics Recycling Awards Europe 2024
Announced on 20 June at the Plastics Recycling Show Europe in Amsterdam, the Plastics Recycling Awards Europe 2024 represent examples of the best advances in the circular use of plastics and their recycling technologies. For the first time in the seven-year history of the awards, the jury has nominated two ambassadors for plastics recycling, in addition to the winners of the products and innovations of the year. The prestigious Plastic Recycling Ambassador of the Year category gives special recognition to individuals who have made an outstanding contribution to plastic recycling in Europe. This year, the jury honoured the achievements of Erica Canaia, CEO of Fimic and co-founder of AreyouR, a project aimed at raising public awareness and the importance of plastic recycling, and Vicente Olmos Jorge, CEO and founder of Sintac Recycling.
The winner in the Automotive, Electrical and Electronic Product of the Year category was Electrolux’s 900 Series Air Purifier, which the judges praised for its high percentage of post-consumer recycled content in a multi-functional product. In the Building & Construction Product of the Year category, the winner was Fluidra’s Skinner RPS, a component of a swimming pool filtration system that must have a long service life. The judges were impressed by the high percentage of recycled content used in the product and its recyclability at the end of its life. The award in the Household & Leisure Product of the Year category went to Bywyd’s Blue Finn multi-functional, stackable chair with a seat and back made from 85% recycled Bluewrap polymer and featuring high impact resistance. Beiersdorf and Morssinkhof Plastics Heerenveen won the Plastic Packaging Product of the Year award for the Nivea solar creation bottle.
Multi-Color Corporation’s NextCycle IML won the Product
Technology Innovation of the Year award for maximising the value of recycled polypropylene and striking a balance between shelf appeal and the recyclability of PP monomaterial packaging. Finally, in the Recycling Machinery Innovation of the Year category, the winner was DischargePro Technology from Powerfil (Erema Group), a new generation of melt filters for the extrusion process.
All eight winners received a trophy with a 100% recycled ABS base made from car dashboards and a multi-coloured top cut using laser technology from recycled HDPE caps from beach clean-ups.
A new office opens in Brussels, new team and institutional identity to advance EuBP’s transformation initiated
European Bioplastics (EuBP), the association representing the interests of the bioplastics industry in Europe, has elected a new Board during its General Assembly on 4 June. For the next two years, the EuBP leadership team will be headed by Co-Chairs Mariagiovanna Vetere (Natureworks) and Franz Kraus (Novamont), and supported by the
new Vice-Chair, Afsaneh Nabifar (Basf). Andy Sweetman (Futamura), Frédéric Van Gansberghe (Futerro), Myriam Moeyersons (Ingevity), Robert Mack (Kimberly-Clark), Jack McKeivor (TotalEnergies Corbion) and Erwin Lepoudre (Kaneka) are also members of the new Board, with the latter serving as the treasurer. This is the first time in EuBP’s history that a board elects two Co-Chairs to lead the association. Mariagiovanna Vetere and Franz Kraus were already chairing EuBP together in the last months.
“I have been involved in the Board of EuBP for eleven years. My passion and dedication for this industry has increased continuously, and now, more than ever before, we witness a shift in mindset. The bioeconomy is finally being part of conversations at the highest political level, and EuBP is willing to drive the growth of the
European project coordinated by Novamont kicked-off
bioplastics sector in Europe. I am thrilled to be re-elected as Co-Chair of EuBP, where I hope to continue to inspire and lead the change”, said Mariagiovanna Vetere (first from the right in the photo), Co-Chair of EuBP.
“This year is a year of tremendous change. Externally, the stage for a more resilient and sustainable Europe will be set by a new Parliament to be elected this weekend and a new Commission to start its mandate before the year is over. Internally, we will continue on the transformative journey which we had started last year, with a new office opened in Brussels, a new team and a new corporate identity. We are at a crossroads, and I am delighted to help guide the association in these exciting times that hold both challenges and opportunities”, said Franz Kraus (second from the right in the photo), Co-Chair of European Bioplastics.
Kick-off to the European research project “Terrific”NexT genERation circulaR bIo-based Flagship packagIng: a catalyst for the green transition.
Early June, at the Novamont Headquarters and Research Center in Novara, the kick-off meeting was held for the European flagship project “Terrific” - NexT genERation circulaR bIobased Flagship packagIng: a catalyst for the green transition - one of the four flagship projects funded in 2024 by the CBE-JU (Circular Bio-based Europe Joint Undertaking), the public-private
partnership between the European Union and the Bio-based Industries Consortium (BIC), which supports the development of the European bio-based industry. This initiative is funded with more than 16 million euros.
The Terrific project, coordinated by Novamont, aims to demonstrate and develop eight innovative solutions for the packaging sector, using renewable raw materials in a circular perspective.
One of the objectives is to use subproducts from agro-industrial value chains to produce compostable and recyclable biopolyesters and biomaterials with over 95% renewable content. The multidisciplinary consortium is made up of 19 European partners, including four SMEs, from Italy, Spain, Belgium, Switzerland, Sweden, Germany, Portugal, Luxembourg and the Czech Republic.
The kick-off meeting provided an opportunity for the consortium members to present and discuss the project activities and to outline future actions. In addition, the partners were able to learn more about Novamont’s circular bioeconomy model by visiting the laboratories of the Research and Development Centre at the Novara site.
“Bio-based biodegradable materials are an important tool for developing smart solutions within the circular bioeconomy approach. This project will provide a practical demonstration of the full innovative potential of these versatile materials in the packaging sector, combining a range of technologies, connecting various sectors and promoting diversified solutions in different areas,” said Catia Bastioli, Managing Director of Novamont.
Aimplas develops multi-layer bags
Aimplas, a technology and consultancy centre specialising in the plastics industry based in Spain, has pioneered the development of over 2,000 sustainable and durable multi-layer bags. These bags, made from recycled materials and enhanced with additives to slow their degradation, are designed to contain flour, dried beans, and blankets distributed by the International Red Cross.
This initiative is part of a project funded by Innovation Norway, the Norwegian Business and Industry Innovation and Development Facility, and managed by the International Committee of the Red Cross (ICRC), the United Nations High Commissioner for Refugees (UNHCR), and the United Nations World Food Programme (WFP). The project aims to explore alternatives to traditional
polypropylene bags used for packaging food and relief items.
Aimplas has played a pivotal role in the project by designing a multi-layer structure for over 1,500 sacks intended for transporting wheat flour and dry beans. These sacks are engineered to withstand extreme environmental conditions and delay degradation. Additionally, Aimplas has developed a second coating, also incorporating recycled materials, which has been used to produce another 500 sacks for blankets.
Rafia Industrial, a division of the Spanish Armando Álvarez Group, has contributed by manufacturing raffia bags, an essential material in the textile industry, on an industrial scale.
The newly designed humanitarian aid bags will be tested across three selected
supply chains in varying and challenging environments. The bags developed by Aimplas will be deployed in Cameroon, India, and Turkey. The project also includes contributions from Aust, a Bangladeshi university whose textile engineering department is developing a jute bag with a biopolymer coating, and Giotto & SUPSI, a consortium consisting of a consulting firm and a Swiss university. This consortium will focus on developing a material based on natural fibres and will conduct life cycle assessments of polypropylene bags and their alternatives to evaluate practical performance in the field.
IMG expands sales network
Increase the share of export turnover to 30% in three years. This is the aim of the internationalisation strategy started by IMG, supported through products that are well recognised in Italy and abroad.
Manufacturer of injection and compression moulding machines for elastomers and thermosets, IMG is opening up to new markets, a process of internationalisation launched in 2021 in which the company strongly believes. The Italian market today represents 80% for IMG, the foreign market 20%, and the goal is to increase foreign turnover to 30% within three years. “The attitude towards opening up to foreign markets, in addition to the domestic market, which is still very important, is taking place gradually”, explains Managing Director Barbara Ulcelli. “‘The quality of our machines is now recognised internationally, and we believe that the added value of new international collaborations is beneficial for both parties, for us and for those who choose us”.
Germany is the first country in which IMG has entered and in which it intends to establish itself with increasing authority. Germany has great potential and, after Italy, is IMG’s second market. “An ambitious start, with quality, innovation and sustainability as key factors, concepts that are well established at IMG”, Barbara Ulcelli continues. “Germany boasts a long-standing manufacturing tradition: we wanted to start from here to prove our quality”. IMG will face this challenge with the characteristics that have made it one of the protagonists of Italy’s “Rubber Valley”, that is, the Sebino district known worldwide for the production of rubber articles, which includes part of the provinces of Bergamo and Brescia (Italy).
It was exactly in Germany, in 2022 at the K trade fair in Düsseldorf, that IMG presented the REM 300, the world’s first full electric rubber machine, which is already one of the winners of the Lombardy Region’s “Tech Fast” tender. A highly innovative product, both in terms of performance and approach to sustainability. On German soil IMG is represented by the Rolf Schlicht agency, which is supported by collaborations with representatives in five other European and overseas countries. The first, in order of arrival, concerns Great Britain and Ireland, where IMG is present through the Mapra Technik agency. The British marketplace is particularly interesting because the
A view of IMG’s production departments at the Capriano del Colle site (Brescia, Italy).
rubber industry in the United Kingdom is more characterised by companies that specialise in the moulding of this material, producing small volumes and batches of many different types, from O-ring seals to hydraulic seals to shoe soles. Rubber parts are produced for demanding industries with very high-quality standards, such as the automotive, oil, gas and aerospace industries. The main application is in the automotive sector, consisting of well-known car manufacturers, but also Formula 1 racing teams and engine manufacturers. The production value of rubber products in the United Kingdom is estimated at over 4 billion euros and the sector provides employment for over 20,000 people.
In addition to Germany and Great Britain, IMG is also targeting Eastern Europe, in particular Poland, the Czech Republic, Hungary, Slovakia and Slovenia, where it also operates through Subter Plus, while on the other side it is active in the Iberian Peninsula through Ruy la Cerda & C. in Portugal and with Protecnic 1967, its longstanding partner agency, in Spain. The latter country also represents a market with good potential for IMG: according to the estimates of the Consorcio Nacional de Industriales del Caucho, the Iberian elastomer processing sector consists of around 300 companies with 22,000 employees, of which 12,400 work in the tyre segment and 9,600 in the technical articles segment.
Furthermore, IMG is active in South Korea with the Sol Mon Korea agency and is also present in China, in the Zhenhai district in the east of the country, where it has a warehouse for storing spare parts for customers in the East, which is functional in order to be closer, and as a result faster, in sending spare parts. “These partnerships allow us greater proximity and are a guarantee of constant support for foreign customers. They allow us to understand and intercept customer needs in order to better meet the demands of very different markets, which have equally peculiar characteristics”, emphasises Barbara Ulcelli. The focus on the customer has always been essential for IMG, according to which the supply of machines never ends with the sale but continues with an accurate and always active after-sales service. Support is also provided through remote assistance: this is possible thanks to the technological component of IMG presses, which can also be remotely controlled via web with continuous diagnosis and monitoring. By means of remote assistance, indeed, it is possible to connect with IMG’s control room, a service that is particularly appreciated by foreign customers, which, in fact, eliminates the physical distance. From this location, the IMG specialist technicians offer online support and dedicated advice to solve problems quickly. Spare parts management is also guaranteed globally, to avoid any unpleasant production downtime situations.
In order to provide all agents with the knowledge they need to be able to get the best out of IMG products, the company creates dedicated webinars in English, through which it provides a proper training course to provide all the skills on technological evolution and on the portfolio. A range consisting not only of horizontal and vertical presses for injection and compression moulding of elastomers and thermosets, but also of special machines to increase productivity or reduce cycle times, and customisable robotic islands built ad hoc for the specific needs of individual customers. Added to these, the new full-electric machine offers outstanding economy and efficiency.
After attending DKT in Nuremberg (1-4 July 2024) with a stand, IMG has already confirmed its participation as an exhibitor at the K 2025 trade fair in Düsseldorf. Not only that: IMG is looking at the American market and participated in the International Elastomer Conference IEC (10-12 September 2024) in Pittsburgh, Pennsylvania. The location is not at all coincidental, bordering the rubber valley of the Mid-West in the USA. For the company, this was the first time in the United States, further proof of its openness to foreign countries.
One of the most important manufacturers worldwide of complete extrusion lines, especially when it comes to co-rotating twin-screw extrusion lines, for the compounding and the granulation of recyclable and non-recyclable plastics materials: this is Maris today.
Experience and research. These are the basis of the extruders proposed by Maris to such an application. Let’s take a look at how this happens and has been developed.
Today Maris is one of the most important manufacturers worldwide of complete extrusion lines, especially when it comes to co-rotating twin-screw extrusion lines, for the compounding and the granulation of recyclable and non-recyclable plastics materials. Its constat commitment to research and the extensive experience gained over the years have strengthened its leading market role and position in the compounding field. When it comes to high quality mixing of plastics and rubber, nowadays Maris extruders have affirmed themselves as a standard.
questions about machines, and related processes, for producing adhesives.
Let’s start with the strengths of co-rotating twin-screw extruders in adhesive production: what are they and why?
Starting from these premises, we have asked to the technicians at the Maris Technological Center some
“There are three different advantages: the first one is that Maris extruders are modular and run in a continuous process. This type of work improves the reproducibility of the product features, granting a constant quality of the adhesive produced; the second one concerns the screws geometry: thanks to the self-cleaning shape of each screw element, it is possible to process different formulations (different viscosities, different colours), without excessive consumption of materials. Last but not least, the residence time inside the extruder is very short and therefore, the risk of thermal degradation is dramatically reduced, compared to the batch process”.
“While in the past the adhesives were mainly produced with discontinuous systems (batch), now the co-rotating twinscrew extruders are being used more and more. It should be kept in mind that the discontinuous systems involve a num-
ber of complications and critical issues in terms of both the product quality and the safety at the workplace. A couple of examples can be useful: the Hot Melt Pressure Sensitive Adhesive (HMPSA) and the Solvent-Based Adhesives production. The firsts are materials which need high temperatures to be processed. An organic substance left in such thermal conditions and in an open container, produces oxo- and thermal-degradation phenomena, resulting in molecular weight variations inside the same stock of material. In this case, using a co-rotating twin-screw extruder to produce HMPSA improves the quality of final product. As far as the seconds, the greater advantages result in terms of safety. In fact, the co-rotating twin-screw extruder collects the solvent in a closed system, reducing the solvent released into the workplace and into the atmosphere. The result is less pollution and reduced costs of solvent recovering. Finally, it should not be forgotten that a batch system requires numerous manual operations, as well as cleaning and reproducibility difficulties”.
The example of SolventBased Adhesives is interesting and certainly deserves further investigation. How is this process carried out using Maris extruders?
“We have developed and patented two different processes. The first one, based on a single-step machine, is certainly an out-of-the-ordinary system. This extruder has a L/D of 100, compared to the average length of the extruders, which is normally between 40 and 52. The further development of this system is a two-steps machine, resulting in higher production flexibility and production capacity. Both processes have been tuned together with a long-time customer. In their plant, we have installed two lines for the production of Solvent-Based Adhesives, replacing the outdated batch systems.
From the quality point of view, the adhesives produced are comparable with those produced with the batch system, with the further advantage that all types of natural rubbers can be processed with a reduced quantity of solvent (with positive effects on environment and workplace safety, as well as costs saving). Furthermore, the system is fully automated: from the mill, which reduces the natural rubber to a size suitable for the extruder feeding, up to the coating machine”.
The natural rubber has different properties depending on its geographical origin and the characteristics may be related to seasonal factors: how is it possible to keep constant the final product properties?
“The key point is to keep the viscosity constant. This can be done by means of an on-line rheometer, which continuously monitors such property. In this way, the control system automatically adjusts the process parameters, such as the solvent
distribution and the screw speed. Therefore, the quality of the material entering the coating machine is always constant”.
This suggests that the operator intervention is minimal.
“Exactly. Of course, the simultaneous presence on the line of different machinery working together requires suitable attention levels and monitoring. However, the effort of the operator is quite reduced”.
Earlier we talked about “flexibility”. How do co-rotating twin-screw extruders allow for greater flexibility?
“For example, during the two-steps production process of Solvent-Based Adhesive, the first extruder processes the solid components of the recipe, with just little quantity of solvent. In the second extruder, the quantity of solvent required is added by the final recipe. The shear-stress conditions of the material inside the two extruders are quite different, allowing better flexibility operations in terms of materials choice and output.
For the HMPSA, the flexibility of our extruder concerns the resin feeding: the total amount of resin can be injected in different sections of the barrel. Thanks to this solution, the number of workable recipes can be increased using a single production line”.
Which are the new trends in adhesives production?
“The interest for the so-called “total solid adhesives” is increasingly growing. These adhesives are based on natural rubber
without solvent. This type of adhesive can be produced with our machines, too, and we have already tested some recipes with our customers”.
How does Maris Technological Center support the companies for developing new projects? Is it possible to carry out some tests?
“Maris Technological Center is at complete disposal to carry out process trials using our customers’ materials. We are ready to support each type of project thanks to four lines, complete with the necessary equipment. The first step for the organization of the trials is to identify, together with the customers, the most interesting formulations. At this point, as soon as the samples quantity to be produced has been defined, we will prepare the correct line configuration for the tests. The customer is involved during each step and can be present. It is therefore an experience of absolute and constructive sharing of information and data, which leads to professional growth for both parties involved in the project; in this way, success is guaranteed”.
“While in the past the adhesives were mainly produced with discontinuous systems (batch), now the co-rotating twinscrew extruders are being used more and more”, explain the technicians of the Maris Technological Center.
The circular container moulded at the Enelkon booth through a full electric 2800kN eKW28Pi/1300 machine.
BMB at Fakuma 2024
As usual the German trade fair on the shore of Costanza Lake represents an unmissable appointment for BMB. This year the company of Brescia has focused its attention in particular on energy saving solutions, without penalizing the productivity necessary in packaging world.
At the moment at BMB there is a lot of pending projects and Fakuma is only the anticipation of other substantial novelties that the R&D department of the company is working on for 2025. It is of course working on existing hybrid and electric presses, but not only that. For BMB, Fakuma means once again fast thin-wall moulding with the HP Hybrid machine, but with the new servo-motor driven pump solution that reduces overall consumption significantly.
The application at BMB booth includes an eKW35HP/2200 hybrid machine with Muller mould and automation. The turnkey system involves the production of around 3,000 containers per hour, labelled with IML technology, controlled by a high-definition camera system and then automatically boxed with a collaborative robot.
The HP series machine features a toggle 3,500-kN clamping unit, driven by two direct motors and satellite roller screws to guarantee maximum opening and closing speed, in the absence of belts and gearboxes, to the advantage of great reliability over time and silence. The thrust in the centre of the moving platen and the exclusive design by BMB guarantee a perfect parallelism between plates, required for any type of moulding, but fundamental in the processing of thin-walled products.
The 2200 HP Hybrid Injection model is compact and powerful to guarantee injection speeds even even beyond 1,500
mm/s. A torque motor directly coupled to the plasticising screw, with a dedicated profile to enhance injection capacity (g/s), echoes the BMB philosophy used for the clamping unit, i.e. direct coupling with the screw, absence of belts and gearboxes to favour high performance, reliability and high plasticisation level with barrier screw and L/D 27 ratio. Hydraulic injection under accumulator is the beating heart of this machine, which, with only 60-mm screw diameter, is capable of injecting 3,700 cm3/s and reaching injection speeds of over 1,500 mm/s, indispensable features of a packaging-focused machine. The solution of the classic three-phase asynchronous motor is abandoned in favour of the new servo-motor to drive the gear pump; this novelty allows considerable energy savings compared to the standard hybrid machine, which is also improved compared the solution with an inverter on the motor pump. The “servo-pump” solution allows considerable energy saving advantages, especially in the production of technical articles, where the moulding cycle is much longer, and permits the pump to be completely switched off after charging the accumulator battery. The double servo-valve, necessary for achieving high injection speeds, also offers more accurate management of the moulding parameters, resulting in high constantly production.
All mechanical machining for BMB press is carried out within the company plants and the production of raw steels comes exclusively from the Brescia foundries. These choices, as well as the production being concentrated solely in the Brescia site, are a great guarantee of the traditional reliability and quality of the product. The production standards are very high and able to meet the most refined requirements, from the point of view
both of Muller automation, with side entry robot, a vision system and packaging in boxes of the moulded products, and the decorative point of view, with the MCC label equipped with the “HollyGrail 2.0” system, capable of guide the product after use automatically through the supply chain for proper recycling.
BMB partner Enelkon presents at its fair booth a packaging application with a 4-cavity mould for a 195 ml circular container weighing 10 g. Here too, the hourly output of over 3,600 pieces per hour, labelled and controlled by vision systems, is highlighted. The machine on display is a Full Electric 2800-kN eKW28Pi/1300, which stands out for its precision, speed and,
above all, low energy consumption. The choice of an electric press stems from the fact that the product container, although very thin walled (approximately 0.4 mm), has a very low height and therefore the injection speed of 450 mm/s is sufficient for correct filling. This application is perhaps the best example of the relationship between productivity and energy consumption, thanks both to the machine all-electric drives and the high-speed handling of the moulded product, guaranteed by Enelkon in the extraction time, IML and quality control activities with single rejection in the event of an anomaly. It is also important to emphasise the reduced footprint of the system, thanks mainly to Enelkon automation system, which optimised the space with experience and great capacity.
The container (into the oval) produced at BMB booth by means the eKW35HP/2200 hybrid machine equipped with Muller mould and automation and using a 100% recycled material from Borealis, in line with the EU regulations, and the use of virgin material, as resulted from moulding tests recently carried out.
One of Tecno System fields of specialisation is that of lines for the extrusion of different types of medical tubing destined for various applications. A sector that requires high standards of precision and quality that do not allow for technological compromises.
One of the leading companies in the design and development of complete extrusion lines, Tecno System finds in the manufacture of lines for the production of medical tubes one of its crucial activities. The company’s constant commitment to quality control and stringent standards on internal and external processes ensure that its products fully comply with relevant national and international regulations.
One of the strong point and flagships offered by Tecno System is the medical micro-tubes extrusion lines. These lines can generate mono-lumen, multi-lumens (up to 18 lumens), mono-layer and multi-layer (up to 5 layers) tubes. The tubes can have an outer diameter ranging from 0.40 mm up to 14 mm and can be made from many thermoplastic material. Micro-extruded semi-finished products are widely used in a variety of biomedical sectors,
including those cardiovascular, epiduroscopy, neurology, gynaecology, urology, and more.
In the extrusion of bump tubing, which is a tube that changes in diameter along its length, the end of the tubing closest to the person operating the device (known as the proximal end) is larger, while the end further away (the distal end) is smaller. This kind of tubing, sometimes called taper tubing or draw-down tubing, can have different diameters not only at each end but also along its entire length. Usually, the smaller end is inserted into the body, while the larger end connects to the medical device.
Manufacturers can make bump tubing from various materials and in different configurations. They can customize the length of the transition zones between diameters and the overall sizes to fit specific needs.
Flexibility and precision of these tubes make them an ideal choice for medical applications that require reliable performance and compliance with the highest quality and safety standards offered by Tecno System.
Another field of application for Tecno System extruders is the production of PVC catheters. The line is usually equipped with a extruder TM 60-25 with 15-inch touch panel and a medical extrusion head HD 2-12. Downstream there are a cooling unit R 50/5,5, a belt haul-off unit TT800, and an appropriate diameter gauge system (ODAC 14 x/y/j) that ensures the accuracy of the entire tube before being rolled up by a semi-automatic double winding station TS2600 equipped with an electronic roller system. Alternative configurations are available, for example with a hauloff unit or choosing from several options like frosty kits, wall thickness monitoring systems, and many others.
As key feature the Tecno System lines are perfectly suitable also
for spiral smoothbore medical tubes with rigid or semi-rigid spirals and for combining different polymers. These lines are powered by two extruders (TM45-25 and TM60-25 series) with a 15inch digital touchscreen and a 1.2316 steel medical extrusion die-head ensures high quality standards for this type of thermoplastic tubing extrusion, while a spindle trolley CM 50 series can be easily handled by operators to move and set up dies with diameters ranging from 12 to 50 mm.
A perfect internal calibration through the spindle, in the downstream units, is guaranteed by calibrating systems located in a special stainless steel water tank with a closed-loop water circuit to prevent any type of contamination. Water can be maintained constantly cool by a dedicated chiller that can be installed as an option alongside the line, and a dedicated tube drying system allowing for the automatic drying of the pipes from the water in excess after the cooling processes.
All lines are totally customizable to meet customers’ needs. Potential options about the line configuration consist in, for
example, the possibility to implement double hopper loaders, different screws for different thermoplastic materials, as well as maximum levels of customization for what concerns the unloading bench.
In addition, each Tecno System’s extrusion line can be suited to the Industry 4.0 standards with an appropriate OPC-UA communication protocol to increase exponentially the potential opportunities through digitization of the processes: real-time information, remote control of the line and hyperconnectivity between machines are some examples among the practical implications of this approach.
By opting for Tecno System’s solutions, the processors will be supported in each stage to simplify as much as possible the investment project. Every product, indeed, is completely designed, manufactured and tested within the production plant located in Consandolo (Ferrara, Italy), enabling the company to directly supervise every single phase in the supply chain, thus ensuring the best qualitative standards for the final product and the possibility for the processor to rely on a unique referent for any type of issue.
Recycling according to PET Solutions
The production of food-grade regranulated material, in this case rPET, requires state-of-theart technology to ensure performance and high final quality. An inseparable combination. Here is the technology proposal developed by PET Solutions for this purpose.
The state-of-the-art PET plant designed by PET Solutions ensures the production of food-grade PET regranulate through a process that begins with washed post-consumer bottle flakes, which are subjected to a meticulously organized series of treatments and ultimately resulting in the production of exceptionally high-quality PET regranulate.
The main PET Solutions process components are big bag emptying unit, vibrating sieve and dedusting system, flakes transportation and waste management from sorters, product storage units, gravimetric dosing system for recipe preparation, and crystallization and dehumidification system as for the first stage; crystallinity increase system, deacetylation system, cooling system, and finished product storage in big bags or silos as for the second stage.
The recycling process starts with the management of PET flakes, which are introduced into the system via a big bag emptying unit or silos. This step is crucial as it ensures a steady and uniform feed of material into the processing line, preventing disruptions and maintaining the efficiency of the subsequent stages. There are different solutions available like: a shaking system for those who want to recover the bag, and a cutting tool to empty the bag without the operator’s assistance.
Once the flakes are loaded, they are directed through a series of advanced sorters. These sorters employ cutting-edge optical and mechanical technologies to meticulously separate the flakes based on size, color, and material composition. This stage is essential for removing any residual contaminants, such as non-PET materials, metals, or colored flakes, with an accuracy of over 99.6%, ensuring that the resulting material is of the highest possible quality. There are various dedusting systems and storage options depending on the quality of incoming flakes.
Following the sorting process, the cleaned and sorted flakes are transferred (via thrust loading group or vacuum system) to storage silos (various types of silos are available, such as aluminum, flexible, and steel). These silos serve as temporary holding areas (to facilitate continuous processing without the need for 24/7 operator supervision), allowing the material to stabilize before entering the next phase of processing. The silos can hold up to 300 metric tons of PET flakes, facilitating a continuous and controlled flow of material into the downstream processes.
The next crucial step involves the crystallization process. Here, the flakes undergo thermal treatment in a crystallizer, where crystallinity is increased by up to 30-35%. The crystallization process is carefully controlled to increase the crystallinity, which
is a critical parameter for ensuring the mechanical properties and quality of the regranulate. This stage also helps in reducing the moisture content of the material to below 50-100 parts per million (ppm), which is vital for preventing degradation during the subsequent processing stages. After crystallization, the material is fed into a reactor, where it undergoes further treatment. In the reactor, the PET is subjected to a solid-state polycondensation (SSP) process, which can increase the IV value to as high as 0.85-0.9 dl/g. The reactor is designed to maintain precise temperature and pressure conditions, optimizing the polymer chains and improving the overall material properties. Finally, the treated PET is extruded into granules, which are then cooled and cut into uniform regranulate pellets. These pellets represent the final product, which is now ready for reuse in the production of new PET products, including food and beverage containers. The entire process is continuously monitored, with inline material supervisors ensuring that the intrinsic viscosity and other quality parameters meet the stringent requirements for food-grade materials. The product is finally stored in Big Bags or Silos equipped with weighing systems (for constant
monitoring of material usage) and labeling of the final product. Depending on the reactor used, the material at the end of the line may not meet the required standards for crystallinity and acetaldehyde levels. This is where Pet Solutions truly stands out. With advanced technology, Pet Solutions can take the hot, amorphous material at the end of the line and, through a dedicated crystallization and deacetylation process, achieve remarkable results: crystallinity levels of 35% and acetaldehyde levels of less than 1 ppm.
Among the advantages of the system described above can be listed the fact that the turnkey system covers all stages of the transformation process, from flakes to granules, as well as providing the most modern dehumidification systems for rPET. Secondly, the design and integration of the entire system with sorter and rPET producers. Thirdly, the supervision system and product traceability. And finally, last but not least, the treatment of the post-reactor material to achieve crystallinity levels of 35% and acetaldehyde levels of less than 1 ppm.
In the face of growing environmental concerns and regulatory pressures, the plastics industry is undergoing a significant transformation. According to Fimic, central to this change is the adoption of more advanced recycling technologies, particularly double filtration systems. As the demand for high-quality recycled plastics intensifies, double filtration is emerging as a critical process that ensures the purity and consistency of recycled materials, making them suitable for a wider range of applications. The global plastic waste crisis has reached alarming levels, with millions of tons of plastic waste generated annually. Much of this waste ends up in landfills or the environment, where it can take centuries to decompose. Recycling offers a solution, but traditional recycling processes often struggle to produce materials of sufficient quality for reuse in high-value applications. Contaminants such as dirt, oils, and non-plastic ma-
From Fimic a solution for a growing environmental problem
The Italian manufacturer of filtration systems reflects on a growing environmental concern that also affects the plastics industry. Illustrating the current situation and proposing its technological solution.
terials can compromise the integrity of recycled plastics, limiting their use and market value.
The increasing demand for high-quality recycled plastics, driven by both consumer preferences and regulatory mandates, is leading to broader adoption of double filtration systems in recycling facilities. Companies across the plastics value chain are investing in advanced recycling technologies to enhance the quality of their output and to stay competitive in a rapidly evolving market.
For example, in Europe, where stringent regulations like the EU Single-Use Plastics Directive are driving the need for more sustainable plastic solutions, double filtration is becoming a standard practice in many recycling plants. In the United States, similar trends are emerging as states and municipalities enact laws aimed at reducing plastic waste and increasing recycling rates.
In response to these challenges, the in-
dustry is increasingly turning to double filtration techniques. This process involves passing plastic materials through two successive filtration stages during recycling, significantly improving the purity and quality of the end product.
This second filtration stage employs a finer filter, or an additional specialized filtration system designed to remove even smaller particles and contaminants that may have passed through the first filter. The result is a much purer, higher-quality recycled plastic that can meet the stringent requirements of various industries, including automotive, packaging, and consumer goods.
Despite its advantages, double filtration is not without challenges. The process requires significant investment in equipment and technology, which can be a barrier for smaller recycling operations.
Additionally, the increased complexity of the recycling process can lead to higher operational costs.
However, Fimic has a proven double filtration technology that allows to process heavily contaminated plastic waste streams, with only one machine and two filtration steps: ERA melt filter (in the opening picture).
This new Fimic technology allows to process heavily contaminated plastic waste streams, with only one machine and two filtration steps, by using a much cheaper filtering screen to filter out the coarser (and usually the most dangerous) impurities to then proceed to a fin-
Evolution of RAS, ERA is the new generation of melt filters. It allows processing higher contamination levels and guarantees a consistent reduction in consumption thanks to the double filter, designed for all materials which require two filtration steps. This results in a significant cut in costs, and an excellent, topquality end product.
er filtration screen (i.e. the most expensive one).
Fimic melt filter ERA represents a significant advancement in plastics recycling technology, offering a solution to some of the industry’s most pressing challenges. With its automatic operation, self-cleaning system, and ability to handle high contamination levels, the ERA melt filter is setting new standards for efficiency, quality, and versatility in the recycling process. As the demand for high-quality recycled plastics continues to grow, the ERA is poised to play a crucial role in the industry’s efforts to achieve sustainability and reduce plastic waste.
Fimic CEO, Erica Canaia (in the picture), was recently awarded the title of Plastics Recycling Ambassador 2024, an accolade bestowed during the Plastics Recycling Awards Europe 2024, the awards ceremony of which took place at the Plastics Recycling Show Europe held in Amsterdam on 19 and 20 June. Erica Canaia received the prestigious award of Ambassador of Plastics Recycling 2024 for her contribution and self-sacrifice in promoting plastic recycling in Europe. The title was also awarded ex equo to Vicente Olmos Jorge, CEO and founder, Sintac Recycling. This is the first time in the history of the award that two ambassadors for plastics recycling have been nominated, recognising the importance of both the outstanding personalities awarded the title and underlining the growing awareness of this practice not only among professionals but also among the general public.
ITALY IS MORE THAN FOOD... WE ARE LEADERS IN PLASTICS AND RUBBER TECHNOLOGY
Microtube production calls, Tecnomatic answers
In the era of rapid technological advancement, where connectivity is king, the demand for high-speed internet has never been greater. With this surge in demand comes the need for robust and efficient infrastructure to support it. Enter microduct pipes for optical fibre, a groundbreaking solution that is revolutionizing the telecommunications industry.
Micro-duct pipes are small, flexible conduits designed to house optical fibres, protecting them from environmental factors while facilitating easy installation and maintenance. Their compact size and flexibility make them ideal for various applications, from urban environments to rural areas, and even within buildings.
One of the key players in this burgeoning market is Tecnomatic, a company at the forefront of innovation in extrusion technology. Tecnomatic groundbreaking lines, specifically engineered for micro-duct pipe production, have set new standards in terms of speed, efficiency, and quality.
At the heart of Tecnomatic innovation lies its die-head, meticulously designed to achieve unprecedented production speeds. Capable of reaching up to 400 metres per minute for diameters of 7/3.5 mm and up to 200 metres per minute for diameters of 14/10 mm, this die-head stands as a milestone in micro-duct pipe manufacturing.
The secret behind Tecnomatic remarkable speed and precision lies in its innovative geometries, precise line adjustments, and profound understanding of the production process. By optimizing these factors, Tecnomatic has been able to push the boundaries of what was once thought possible, achieving production speeds that were previously unimaginable.
One of the most remarkable achievements of Tecnomatic diehead is its ability to maintain impeccable sizing results even at such high speeds. With minimal tolerance and ovality, the micro-duct pipes produced are of the highest quality, meeting
the stringent standards of the telecommunications industry. Moreover, Tecnomatic die-head is engineered for efficiency and flexibility, allowing for fast skin and colour changes with the adoption of special valves and multiple extruders. This feature not only enhances productivity but also enables manufacturers to meet the diverse needs of their customers with ease.
The implications of Tecnomatic innovative die-head extend far beyond the realm of micro-duct pipe production. By enabling faster, more efficient manufacturing processes, it paves the way for accelerated deployment of fibre optic networks worldwide. This, in turn, translates to improved connectivity, economic growth, and quality of life for millions of people around the globe.
As the demand for high-speed internet continues to rise, so too does the importance of robust and efficient infrastructure. With Tecnomatic groundbreaking die-head leading the way, the future of fibre optic connectivity has never looked brighter.
Partnership is the key element and the sine qua non at the base of each project undertaken by Campetella. Besides offering a wide range of standard automation solutions to choose from, the company uses them as a modular and configurable starting point to develop extrusion solutions, tailor-made for and with their customers to meet their most varied production needs. The company aims to establish a solid cooperation with its customers, based on the importance of sharing the mutual know-how to create the most suitable solution to the customer’s specific production process.
Campetella Robotic Center boasts decades of experience in the design and production of coilers for the extrusion of flexible pipes. Their proposition is wide and aimed at increasing the productivity of those who benefit from it by optimizing their processes, always keeping a keen eye on the operators’ safety.
Campetella takes care for their customers and listens to them to be sure to meet their expectations while offering integrated and innovative solutions.
Their coilers are featured by: performance, user-friendliness, flexibility, sturdiness, reliability, and construction quality. Their machines are designed for either rapid manual or automatic setting of the reel format in such a way as to allow maximum configurability and flexibility depending on the specific production needs. Furthermore, the binders have been mechanically redesigned, to avoid wear, as well as optimised with brushless servomotors to increase programmability and get maximum control, while reducing the binding cycle time and avoiding any potential damage to the reel.
The peculiar configuration of the Campetella’s coiling platforms is aimed at optimising the customers’ plant layout by reducing the footprint on the ground and by giving them the possibility to choose between the lateral or the rear exit of the reels, depending on the space available.
A great added value is definitely given by the end-of-line customisation. Thanks to the synergy between the coiler and the robot in charge of palletising and / or handling the finished coil, Campetella provides its customers with a complete package that exceeds the mere wrapping process, ranging from extrusion to final packaging for a turnkey solution aimed at optimising not only the entire process, but also the customer’s investment.
The global, digital and interconnected assistance network ensures a widespread presence and constant operation, always and everywhere, thus guaranteeing prompt and targeted intervention, besides including a wide training program.
The Campetella team’s commitment and dedication comes not only from their being passionate about their work, but also from believing that the customers’ success is their own success, resulting not only from their experience and professionalism in the design and implementation of the right automation, but also from an effective, efficient and timely after-sales assistance.
From the initial consultation to the after-sales assistance, Campetella Robotic Center ensures constant presence and support, transforming itself from a mere supplier to a true partner.
FB
Balzanelli strengthens its technology
Among the pipe manufacturing companies, it has been growing the demand for coils of large PE pipes sizes such as 75 up to 160 mm, most commonly, and in some cases, also up to 250 mm.
The reason for this growing demand comes from two aspects: simplification and reduction of piping installation times.
Installation is eased if starts from a coil rather than many sections of pipes to be welded together using fittings. The time required for the installation of many sections of pipe is much higher as it involves laying the pipe, positioning the fittings and their welding, all depending on the number of sections to be connected.
The longer is the piping disposed from a coil, less fittings are involved. In that case not only time is reduced (and costs) but lower are the chances of leaking.
FB Balzanelli has been designing and producing up-to-date coilers, suitable for the most common dimensions of PE pipes from 75 to 160 mm but even up to 250 mm.
While developing the new series, particularly the Excellence TR3515PE coilers, many innovative features were integrated to make the equipment either more automated and safer to operate.
The design of a versatile machine concept, allow many configurations of the coiler and it can be easily mirrored during the assembling, when needed by the customer layout. This means one single head coiler of the kind can be, easily, configured to work as left to right or right to left direction.
The coilers can be upgraded in steps and, the following, are the three main features: automatic width adjustment and
semi-automatic coil ejection; round pipe system, features one haul-off on board that reduces the ovalization of the pipe yet optimizes the coiling process; automatic strapping systems with one or two strapping heads increases the performance of the coiler making the machine safer to operate.
That technology was developed from the experience made on the Excellence Series automatic coilers, adding functions necessary to obtain compact dimensions, while respecting the residual ovality values of the pipes.
In the strapping heads designed and built by FB Balzanelli: the strapping is performed automatically on small or large coils without any adjustment; given the size of the coil, it must be done safely by the machine itself without operator intervention; safer and faster strapping allows to reduce the packing time; if necessary, the strapping time can be reduced adding a second strapping head; even with one strapping head intermediate strappings are possible (after the number of turns or layers chosen); with a double strapping head, the intermediate strappings are carried out quicker, the amount of pipe on the floor is reduced to the minimum and, it is immediately recovered.
Summing up, the distinctive elements of this Excellence TR3515PE coiler for large PE pipes are: increased effectiveness while producing the coils by integrating the Round Pipe System = reduction, where possible, of the coils ID dimensions in favour of transport and installation; increased efficiency and safety integrating one or two strapping heads = intermediate and final strapping are performed safely and quickly.
Moretto at Fakuma 2024
Constantly focused on energy efficiency, that today finds in automation and digitalisation further drivers of development, Moretto presents its entire product range increasingly oriented towards this objective at Fakuma 2024. Displayed for the first time, the new Hyper Cut “hungry mouth”, multiblade, low-speed granulator with variable trim, is a machine with 15 moving blades suitable for grinding workpieces, rejects, purges and blown bodies. Motor power is discharged onto one mobile blade and three standard fixed blades, for a hyper-productive granulator with an extraordinary reduction in consumption.
At the trade fair, the Padua-based company also offers solutions dedicated to dehumidification, dosing and process automation for plastics processing. The drying solutions on display include the OTX (Original Thermal eXchanger) hopper, the compact fully electric X Comb dryer, and the Moisture Meter analyzer for measuring in real time the residual moisture content of plastic granules, eliminating the need for offline sampling.
The range of automation for dosing includes the recently upgraded DGM Gravix batch gravimetric dosing unit, complemented by the DGM Gravix 20 model, specifically developed for micro-dosing. Furthermore, in exhibition also the exclusive automatic manifold Dolphin for materialmachine allocation in plastics conveying plants, while Silcontrol system is presented for controlling the loading of plastic granules into the storage silos.
All the solutions can be perfectly integrated with Mowis, a supervision and management system entirely developed inhouse by Moretto. It allows connectivity between machines, processes, departments, plants and factories. A demo version
EXTRUSION TECHNOLOGIES
RECYCLING TECHNOLOGIES
STRETCH FILM LINES
Your trustworthy partner for Extrusion and Recycling custom-engineered solutions.
Arburg is attending Fakuma 2024 with a total of 18 exhibits, including partner stands, and the arburgSolutionworld highlights compelling upcoming topics for customers.
The German premiere of the electric Allrounder 720 E Golden Electric in a new design is another highlight, together with groundbreaking trends in plastics processing that are set to be presented by the company from Lossburg. Arburg is also getting involved in the “Mould your future” initiative.
In the arburgSolutionworld, in particular, Arburg offers comprehensive advice on topics that are on everyone’s mind, as well as future-proof digital products and services. The interactive exhibition area is once again the focus of attention. Trade visitors get specific answers to questions on compelling topics such as productivity increases, efficiency, sustainability, the lack of skilled workers and subsidies.
Arburg is debuting its latest machine to the general public in Germany at Fakuma 2024: the electric Allrounder 720 E Golden Electric with a clamping force of 2,800 kN. Its main advantages in a nutshell? A slim design with a price to match. The new machine is set apart by its electric precision, process stability and its extremely slimline installation area, offering high component quality with low investment costs and short delivery times.
As above mentioned, with a total of 18 exhibits, Arburg is demonstrating its extraordinarily broad range for the efficient
German premiers at Fakuma 2024: thanks to its new design and standardised equipment, the new Allrounder 720 E Golden Electric machine has an extremely slimline installation area and a price to match.
production of plastic parts. Visitors are able to see, for example, multi-component and paper injection moulding, recyclate and LSR processing, robotic systems, complex turnkey solutions and additive manufacturing.
Last but not least, under the motto “Mould your dreams, mould your future”, Arburg is participating in the new Career Friday, initiated by the organiser Schall and the trade fair committees, and is extending this campaign to Saturday as well. The campaign is aimed at school pupils, students and jobseekers.
At Fakuma 2024, they gain an insight into the diverse career opportunities offered by the plastics sector.
Sica, a manufacturer of plastic pipe processing machinery, has developed an innovative Rieber belling process, specific for PVC-O pipes (oriented molecule PVC pipes). At the same operating pressure, these pipes require a wall thickness of about 35-40% less than those in PVC-U and allow the construction of water supply pipes up to 25 bar of operating pressure. Because of these and other advantages, PVC-O piping systems are becoming increasingly popular.
Like PVC-U pipes, the PVC-O pipes are joined in a socket. The socket, including the gasket seat, is made in an extrusion line with a special belling machine.
In PVC-U pipes, Anger type socket are used, i.e. with removable and replaceable gaskets, as well as Rieber
type sockets that have a gasket already integrated in the belling phase and not removable during the assembly of the pipeline. The Rieber system is popular because during installation the possibility of accidental displacement of the gasket is reduced and the risks of external water dispersion are lower.
The realization of the socket in PVC-O pipe requires different procedures than the conventional ones for PVC-U pipes. Up to now, these specific procedures have proved to be industrially applicable only for forming Anger-type sockets.
The absence of the Rieber socket joint in the PVC-O piping sector has excluded its application where the Rieber socket is considered decisive for the operating conditions for laying the pipelines.
The innovative and exclusive Sica Rieber belling process for PVC-O pipes changes the scenario and makes the Rieber system possible on belling machines used in bioriented pipe production plants. In fact, the belling machines are able to process both pipes produced and oriented continuously in the extrusion line, but also pipes oriented off-line in a tank. The Rieber Sica belling system is functional in PVC-O pipes that comply with all the following technical standards: European EN 17176; American ANSI/AWWA C909 and ASTM F1483; Australian AS/NZS 4441; Canadian CAN/ CSA-B137; International ISO 16422. It is significant that, as with the wellestablished Sica Starbell belling machines used for making Anger sockets, the innovative Sica procedure is applied to pipes up to the maximum molecular orientation required by the standards, including class 500 established by ISO 16422; a standard that, among all those indicated, imposes the most stringent requirements for resistance to hydrostatic pressure in PVC-O piping systems.
The Sica belling machines that implement the Rieber belling process are available in three models based on the dimensions range of the machinable pipe.
Giurgola
Giurgola Stampi has recently developed a revolutionary new mould for the food sector, with a particular focus on spice packaging. The primary objective of the project was to create a multi-pour cap with guaranteed tamper evidence for both lids. This goal was achieved thanks to our well-established expertise in flip-top cap moulds and their implementation.
Developing new and advantageous solutions for a cap often involves designing and developing a new production system, technologically distinct from those previously designed and manufactured.
Specifically, this project required finding a stable and efficient solution to seal both lids of the cap during the moulding cycle; this way, the plastic parts would be ejected from the mould closed and ready for assembly on the container. The conventional technical solutions the company have studied and patented so far for flip-top moulds were not applicable to this project. Given this, the design team developed a mechanism for rotating the cavities themselves, ensuring that the pins and undercuts for closure were perfectly aligned and
Our goal was to design a cap that avoided complex and composite closures, ensuring significant benefits. Firstly, it was necessary to offer the same ease of use as the caps already on the market while guaranteeing absolute tamper evidence. To achieve this, Giurgola employed a unique approach to tamper-evident features, leading to a true innovation in the plastic component. Once both lids are closed, what was initially a hinge now serves as the tamper-evident feature, and vice versa.
As previously mentioned, this innovative solution was made possible by the unique closure system with rotating mould cavities, allowing the cap to be produced in a single phase using just one mould and one moulding machine. This single-phase production process makes the operation efficient and reduces energy consumption. The result is a production system with minimal ecological impact.
This solution demonstrates Giurgola Stampi’s commitment to continuous innovation and sustainability. Giurgola Stampi’s approach to research and development embodies
idea must be translated into technical production solutions, taking into account their impact on the market and the environment. With over 40 years of experience, Giurgola Stampi continues to create products that not only meet market requirements, but also promote sustainable and cutting-
Stampi has developed a mould for the food sector to create a multi-pour cap with guaranteed tamper evidence for both lids.
Sytrama cartesian robot
Automation can foster production efficiencies, leads to faster cycle times, quality improvements and, most importantly, can generate new business opportunities. Sytrama has been chosen by one of its Italian customers, based in the Motor Valley, to project and realise a new turnkey plant that consists in insert loading and palletizing the final products.
“Quality is our striking feature, that allows us to stand out from our competitors. Our tailored made plants generate value and, most importantly, customers cut human errors off, increasing efficiency” said Domenico Ghilardi, CEO of Sytrama. The goal was to automate the production of rotors useful for motor applications in the automotive world.
The complete system has been developed and put in place with a Sytrama certesian robot S10-L model, coupled with two anthropomorphic robots. The mould had 4 cavities and total cycle time was around 25 seconds. The project has been done on a 160ton IMM. The inserts are fed by racks, manually put by the operator onto a conveyor belt. The first 6-axes robot collects the four inserts, one by one, checks the correct orientation by using a DVT camera, and then places them onto
a four positions jig. The camera check allows to avoid any orientation mistake made by operator during the rack filling operation.
After this insert preparation cycle phase, the Sytrama S10-L robot grabs the four inserts and moves towards the IMM.
Once the mould is opened, the S10-L moves in, picks-up the overmoulded products and then places the four metal inserts into the mould recesses for the next cycle.
Once the metal inserts are loaded, the S10-L puts the overmoulded parts on a
second jig. Here, the second 6-axes robot collects the injected parts one by one and place them onto the empty racks placed on the same conveyor belt. All the automated cell is completed with floor mounted guarding. The entire cell is then certified by Sytrama, complying with the CE safety standards.
The new system resulted more reliable in every single operation, reducing human errors, scrap parts and allowing a higher production standard, which was the main request for a such high-end customer.
The 6-axes robot collects the four inserts and checks the correct orientation by using a DVT camera.
Amut’s commitment to the continuous improvement of its technology rewards the company which sees an increasing number of loyal customers in all the sectors in which it operates.
The guaranteed performance and automation, which allows constant and continuous quality control of the final product, are widely appreciated. Amut’s custom-designed lines meet the most stringent project specifications, in full compliance with major international standards. Customers choose Amut for reliability and often confirm their trust in the company’s systems by entrusting new projects.
The company’s position as a preferred partner has once again been confirmed by Proxima Coopbox, the plant of Coopbox belonging to Happy Group, specialising in the production of technical plastic films.
As a consequence of the above salient points, Coopbox required Amut to supply two PET food-grade foil extrusion lines: one in 2023 and the second in 2024, for Proxima, its plant in Ferrandina, in the province of Matera, southern Italy.”
These state-of-the-art food grade quality lines, 1200 kg/h capacity each, provide high quality foil suitable for sustainable containers, ensuring food preservation.
The line is capable of producing widths up to 1500mm and thicknesses up to 1,2 mm.
Each line is equipped with the well proven and reliable single screw extruders, core technology of Amut range of production, automatic die, horizontal calender roll equipped with PE film lamination device, silicon spreading machine, automatic winder and operator friendly control panel.
Food grade is reached by the suitable reactor supplied by another specialized manufacturer.
Amut was proud to once again support Happy Group in the delivery of a new plants designed by the interdisciplinary design and engineering experts in extrusion technology. The customengineered solutions were conceived by Amut technical team to meet the thermoforming requirements for the production of plastic food trays. The first high-performance line is in operation to the utmost satisfaction of the customer, producing around the clock 24 hour/ day while the second one will be commissioned within this year. Amut is constantly striving to generate value for customers by focusing on the design and execution of cutting-edge projects.
Happy Group has confirmed its
confidence in the Amut “Made in Italy” extrusion technology, for their expansion project.
Over the years Amut has proven to be a trusted leader in providing diversified extrusion technology with a wide track record worldwide. The company is deeply committed in generating value for customers, focusing on cuttingedge project design and execution for its plants, as testified by the recent accomplishments of Proxima.
The Amut wide range of technologically advanced solutions for foils and sheets, suitable for a vast array of thermoplastic materials, includes extrusion lines with nominal widths from 400 to 4,000 mm and thicknesses from 150 microns for foils or sheets up to a few centimetres, as well as multi-cellular panels.
After several years of experience in the extrusion of expanded thermoplastic resins by direct gassing Sara has developed the new extrusion line “Rs40” for the production of PE foam pipes. The extrusion system is by direct injection of a gas, which acts as an expanding agent in the basic resin (polyethylene).
The particular difficulty in preventing collapse during the expansion, when polyethylene tubing is extruded with considerable thickness (10÷30 mm.), is overcome thanks to improvements of the Sara technology, which guarantee the low density of the product, as well as a continuous and reliable operation
of the lines.
The screws and the barrel of the extruder have been designed to obtain a high mixing effect of the components.
The Rs 40 line is complete with every accessory and is based on a corotating twin screw extruder, having a production rate of 30 ÷ 50 kg/h.
new extrusion line “Rs40” for the production of PE foam pipes.
Founded in 1992 and located in the heartland of industrialized Lombardy in northern Italy, Euroviti is a leading company in the production of injection and extrusion plasticizing screws and barrels. The company has had consistent growth and expansion since its foundation and never lost its focus: offer a complete service, not only by producing mechanical parts, but also by assisting customers in choosing the best materials and providing them with
tailored plasticizing unit designs. One of its latest examples in a groundbreaking project involved a Japanese injection moulding machine from a leading international market player. The team embarked on a mission to enhance moulded packaging quality. By focusing exclusively on redesigning the screw, rather than replacing the plasticizing unit as competitors or the OEM were suggesting, Euroviti managed to offer a more efficient and costeffective solution.
The issue arose with transparent pieces produced using a sandwichtype mould and an original plasticizing unit equipped with a barrier screw for processing polypropylene (PP). Due to contractual obligations, a 1.5% clarifying additive was added to ensure the excellent transparency of a globally recognized sweet box cover. However, the moulded pieces exhibited whitish streaks and veins, making the product unacceptable and compromising the
• Customized automation and robotics systems
• Handle fitting/form and fitting machine for buckets
look of the packaging.
The Challenge was to eliminate whitish streaks and veins to ensure product quality in transparent pieces and the optional goal was to improve cycle time.
After a thorough analysis of the original screw design and plasticizing cycle time, the company’s team implemented a comprehensive design overhaul. They have modified the shearing gates of the barrier, adjusted the pitches, and added a mixing area. These changes made possible the creation of a customized HPB-mixing design tailored to address the client’s specific issues. Resulting in the elimination of product non-compliance due to streaks, ensuring that the moulded pieces met the required quality standards reaching enhanced transparency levels with a visually appealing and flawless product. The business even reached a 30% reduction in feeding time and 9-11% improvement in total cycle time.
• Palletizing systems
• Assembly and control systems
Break Machinery expands the range
The Padua-based company Break Machinery has recently developed a new filtering machine, with a screw discharge system capable of bringing numerous advantages to the line into which it is integrated, whether new or existing, and for which three patents have been granted. Break DUO is designed for the filtration of various types of plastics. It enables the processing of materials with high percentages of impurities and can handle different types of contamination. It guarantees high process stability and helps extend the life of consumables.
Furthermore, the presence of two filters allows for a large filtering surface area and increases the productivity of the entire line, working up to 12,000 kg/h. In order to meet the different market demands, Break has created variants of the DUO, which is now available in four sizes: 1400, 1750, 2800, and 3500.
As for the scraping operating mode, the melted plastic material is conveyed into the chamber and passes through two opposing filters. Between filters is a scraper disc, equipped with blades, which rotates to remove the contamination deposited on the filters by channelling it into the scraper disc itself. The centre of the scraper disc is in communication with a screw that ejects the contamination. The melted plastic material filtered from filters rejoins the exit channel to pass on to the next process.
Break Machinery has developed a new solution that has a dual function: keep the size of the system components small to facilitate filter replacement, while increasing the filter surface area; ensure process stability and continuity.
DUO 5600 and 7000 Twin allow outputs of up to 10,000 and 12,000 kg/h respectively. Duo Twin consist of two Duo screen changers of the same size (2800 or 3500) operating in parallel. When it becomes necessary to change the filter in the first machine, the flow of that branch of the line is interrupted, and production remains active only on the other branch, connected to the second filter changer. In this way, production is not interrupted, and the filter can be changed, without having to stop the line. The same process is then carried out for changing the filter in the second machine.
The measurement of mechanical properties is crucial to ensure that your products conform to technical specifications.
Gibitre′s programmable Tensile Tester, with 20 kN capacity and double-column design, is ideal for these measurements. The instrument, equipped with ISO 17025 - accredited Calibration and SQL database Software with more than 100 pre-installed test methods for plastics and rubber, can be configured with strain gauges, clamps and load cells suitable for your products, and can be equipped with thickness gauge and a environmental chamber for testing between -40 and +250°C.
An advanced solution from BD Plast
Filtration systems are a crucial component of extrusion, re-manufacturing, and recycling lines of polymeric materials. BD Plast supplies a complete range of products to extrusion plant manufacturers and plastics processors composed by manual, hydraulic, continuous flow, and continuous flow self-cleaning screen changers, static filters, extrusion components (adapters, elbows, pipes, static mixers, diverter valves, strand dies), and accessories (hydraulic power units, undercarriage supports, elastomers). Thanks to its wide products range, the company technology can supply specific solutions capable of processing any kind of polymer while maximizing production and reducing at minimum material waste. Thirty-eight years of innovation, development of
to various changes in the production context.
The patented self-cleaning continuous flow screen changer, CleanChanger, is currently at the top of BD Plast range of products. The main strength of this product is conducting the self-cleaning cycle at particularly low back pressure. Additionally, this is continuous flow equipment, which means that, unlike other types of screen changers, the filtering elements can be replaced without halting the extrusion line. This eliminates the time loss and material waste typically associated with stopping and restarting the line. On CleanChanger the replacement of the screens takes place with the automatic ejection of the breaker plates, allowing easy replacement of the filtering elements and further timesaving. Key features like low back pressure, automatic plate ejection, and reduced purge times enable 400 self-cleaning
Material: PE blend
Pipe diameters: 12/16/20/22 mm.
Line speed: 250 mt./1 min.
Pitch: 10 cm. min.
Pipe thickness: from 0.15 up to 0.4 mm.
Extruder type: Diam. 65 mm.
Water output: From1 up to 2 Lt./h CV=3%
Drilling machine: Mechanical or laser, on request
Marking system: Inkjet or laser
Coiler: Automatic
Coextrusion: On request
The need to produce high-quality materials, increase process speed and productivity, and ensure plant flexibility has led to technical evolution in the manufacturing process of high-precision calenders for PVC. For a long time, Comerio Ercole has provided turnkey 5-roll calendering units based on a sophisticated hydraulic nip adjustment system, Hydrogap. This unit controls the position of each movable roll of the calender to ensure perfect control of the product gauge. In the latest supply, commissioned in June 2024 at a major European customer site, Comerio Ercole developed a device named Hydronip that allows the operator to switch from position control to force control. This optimizes the lamination of PVC sheets with a nonwoven substrate, allowing the selection of the best conditions for highquality products.
The scope of supply includes a stripper and stretching unit consisting of many small diameters rolls with high thermal exchange efficiency. All rolls are thermoregulated and driven, located at short distances from each
other and from the calender roll, which is made of forged steel and chrome plated. This arrangement accurately controls product conditions, such as temperature variations and the consistency of stretching between the calender and wind-up stand. This offers outstanding advantages regarding sheet flatness and very limited transversal shrinkage. Furthermore, productivity can be improved with lower energy consumption. To ensure efficient heat exchange, the stripper and stretching rolls are made with peripheral drillings. The stripper and stretching unit, designed and manufactured by Comerio Ercole, offers many advantages in installation, operation, and ease of maintenance. Compared to the traditional configuration near the calender in a fixed position, the unit is composed of a sliding wagon on which all the drive devices, sliding, and temperature fluid media connections are fitted.
The calender frames must support large stresses caused by the material being processed between the rolls
85 years of history for Helios Quartz
and are subject to deformation under load. Frame deformation related to the separation forces between the rolls can cause errors in product thickness. These frames are manufactured using steel with a high elasticity modulus. The steel sheet fabricated construction system with proper stiffening ribs, together with the heat treatment provided, ensures maximum rigidity and the absence of distortions and vibrations. This construction solution allows the side frames to act only as support elements without interfering with the adjustment devices. All mechanical components are simply fixed to the frames. Besides the easy adjustment and optimization of all mechanical components in effective process conditions, maintenance management is also very simple.
Helios Quartz has gone a long way from the family-own company in the 1940s and it is now an international group of companies with two production plants - the historical one in Italy (Helios Italquartz) and the new facility in Switzerland (Helios Quartz Group) - and its own commercial branches in the USA, South America, China and Hong Kong. In the last few years, Helios Quartz has invested in a cutting-edge infrared testing centre in the production plant in Cambiago, Milan, Italy, where customers can personally come and perform tests on several types of plastic materials and for different applications like stretching, thermoforming, embossing, lamination and deburring, just to mention a few. It is possible to test both material
samples and roll-to-roll films with four types of infrared wavelength (short wave, medium wave, fast medium wave, fast medium wave medium), in order to find the right one for the specific process and material. With the test results the company team can design customized solutions, its infrared modules, already cabled and ready to be mounted on the line of customers. The company can also supply the matching electrical cabinet with control software. The tests at the infrared centre are a key part of the collaboration the company builds with its partners: it can determine crucial data such as needed process time and distance between heaters and product, and at the same time customers can see first-hand the product they are going to
buy and use. The result is a turnkey solution, ready to be integrated in the customer production process, with the confidence to avoid mistakes and engineering flaws.
Testing both material samples and roll-to-roll films with four types of infrared wavelength allows finding the right one for the specific process and material.
for the US market, and
The HE480D extrusionblow moulding machine, displayed by Meccanoplastica at NPE, is fully electric and features a double station (EBM), making it ideal for HDPE, PE, and PP hollow blow moulding.
Back after six years, the NPE 2024 show held in Orlando, Florida, from 6 to 10 May marked an important milestone for Meccanoplastica, a reliable manufacturer of blow moulding machines based on the outskirts of Florence, that was able to strengthen relationships on the one hand, and start new contacts and projects with customers in a “challenging” key region
such as North America on the other. The Tuscan company brought to Orlando two high-tech blow moulding machine models: the HE480D and the MIPET 4-P.
The HE480D is an full-electric twostation extrusion blow moulding machine (EBM), the ideal technology for producing HDPE, PE and PP hollow bodies up to 5 litre capacity. The machine features a carriage stroke of 480 mm and a clamping force of up to 12-16 tons. The HE480D is a “userfriendly”, high-performance and efficient machine. In addition, thanks to a device similar to the KERS used in Formula One, the machine recovers energy from the braking system, increasing overall efficiency.
The MIPET 4-P, on the other hand, is a full-electric stretch blow moulding machine (SBM) equipped with a 4-cavity mould, ideal for the production of PET bottles up to 2-2.5 litres from
New Omap launches New OmAPP
Artificial Intelligence algorithms integrated into the New OmAPP application, through the Nebula cloud system, enable the management of machine parameters by optimizing their consumption. The objective is to make the transformation more sustainable.
preforms. This solution ensures low energy consumption and incorporates an optimised mould heating system.
The MIPET 4-P features a new, more compact layout and a new highperformance “green” oven that speeds up preform preparation, increasing production performance. The machine is also equipped with a pressure control system operating inside the finished piece, so that any defective bottles are automatically rejected. The MIPET 4-P machine is extremely efficient and allows high energy savings.
After the American fair, Meccanoplastica also took part in Plastpol, Kielce, Poland, from 21 to 24 May, exhibiting the JET754 full-electric 4-station injection blow moulding machine (IBM). This machine features a mould-injection clamping force of 65 tons and a mould-blow mould clamping force of 10 tons with an injection speed of 65 mm/sec.
How can Artificial Intelligence support sustainability practices? The answer is the Nebes project, developed by New Omap and promoted by Smact Competence Center through the Iriss
public call, which aims to provide a response and a solution thanks to intelligent software that monitors the energy impact of industrial machinery.
In fact, the goal of the project’s development over the next 18 months is to offer solutions in two specific areas: cybersecurity and sustainability, making it possible to increase energy efficiency in enterprises. The technology behind the project integrates various AI algorithms into a single application, New OmApp, which controls all the operating parameters of the machines through a cloud system called Nebula, optimising energy consumption.
More specifically, New OmAPP is a mobile application that enables the user to retrieve information on New Omap products, receive customised notifications and interact remotely with the Nebula cloud system. In addition,
thanks to this app, the user can receive support for auxiliary systems quickly and efficiently at any time. The app enables access, directly and without credentials, to the New Omap website and browsing by product sector, by product category or by system application.
By entering the Business reserved area with the credentials provided by New Omap, the user can also download the documentation on his systems, use the dashboard to receive information on promotions and access the Nebula cloud system, which was created to remotely directly control and manage New Omap machines from a smartphone. Through the app it is possible to view the machines connected and check their operating status, access their control panel and control the main functions as well as view the list of parameters in order to control their performance.
In modern life, plastics have also become indispensable in shaping a truly sustainable future. That is why Covestro provides polymers that help many key sectors achieve circularity and climate neutrality, and is constantly developing new ideas to make production more sustainable. Sucheta Govil gave an overview of the company’s recent activities to meet the needs of an ever-changing market with numerous challenges.
By Giampiero Zazzaro
Covestro, established in 2015 from the chemicals and plastics division of the Bayer Group, has emerged as a pivotal entity in the production of polymers across a diverse array of sectors, including transportation, construction, sports and leisure, cosmetics, healthcare, the electrical and electronics industry, and chemicals. The Group also maintains a robust presence in Italy, encompassing a comprehensive network of sales, production, and research and development, alongside a Colour and Design Centre (CDC). Founded in 2002 and integrated within a global network of other colour centres, the CDC serves as a locus of significant developments and an incubator for novel design trends utilising coloured polymers.
In the financial year 2022, the Group generated a turnover of 18 billion euros, with 50 production sites worldwide and 18,000 employees. Covestro is structured into two principal divisions: Performance Materials and Solutions & Specialties, which collectively encompass seven business units including commodity polycarbonates, urethane components and base chemicals, engineering polymers, coatings and adhesives, custom urethanes, thermoplastic polyurethanes, speciality films, and elastomers.
Sucheta Govil, Director of the seven business units, provided our editorial team with an elucidation of the innovations, perspectives, and strategies envisaged for 2024, offering insights into pertinent topics such as artificial intelligence, recycling, and circularity.
Sucheta Govil is Chief Commercial Officer (CCO), responsible for central marketing, innovation management and commercial services and member of the Covestro Board of Directors.
Estoli, a manufacturer specialising in bathroom furnishings, has created a shower tray that makes the most of Arfinio’s natural anti-slip properties. It can weigh up to 50% less than a similar product made from traditional materials, optimising logistics and transport resources.
The polymers produced by Covestro are also used in the cosmetics industry. An example of this is a makeup palette featuring a range of colours.
What innovations have characterised your activities in 2024, both in terms of materials and applications?
“We have seen a growing change in our industry. There is a rising demand for sustainable products by our customers. Covestro will keep the innovation pipeline fueled to stay ahead of this development. Therefore, we will extend the principle of mass balancing to our acrylic polymer product range, that is products suitable for industrial wood and architectural coatings. Moreover, we will expand the range of our low monomer content isocyanate products to further improve the safety of use of the products. In Turin we are starting substantial sales of a new B3 metal panel system created in 2023. And we are proceeding with promoting our full range of mass balancing products in MDI, TDI and PET.
Another product we are very excited about is Arfinio®: this revolutionary material is the result of a new technology that combines high-performance liquid polymers and unique minerals with reaction-based injection moulding. It is a lightweight and durable solid surface material that allows complex projects to be completed quickly and easily in a single operation and can be easily repaired and recycled.
Arfinio® combines the advantages of aliphatic polyurethane chemistry with those of reaction injection moulding and solid surfaces: a combination that was considered unfeasible for decades, but is now a reality thanks to Covestro and its partner Arcesso Dynamics.
We will venture into new areas. There is a high sales potential in the design market for our products. The Milan Design Week 2023 has been proof of that. We witness a rising demand for materials that allow creative solutions to be aesthetic, func-
tional and sustainable at the same time, creating added value for their customers. Together with designers and CMF (Color, Material, Finish) professionals, we are also developing scalable design solutions with a focus on circularity and higher volume production. Worldwide, we operate six Color & Design Centers close to our customers”.
“What are your principal global markets, both with respect to applications and geographical regions? In this context, how did the year 2023 conclude, and what are the projections for 2024?”
“We were very happy after the first quarter in 2023 when we realized that our results for this year will be better than expected. With this optimism we navigated through the still difficult market environment and started into 2024.
Also, for Italy, as far as the outlook for 2024 is concerned, we are cautiously optimistic. When inflation goes down, we expect to see a potential increase in demand.
Our Italian customers export to a broad range of markets in the EU, the Americas and Asia. Their export range covers different applications such as wood and metal coatings, or varnishes for can and architectural sectors. In the business segments Performance Materials, Tailored Urethanes and Engineering Plastics, applications such as soft furniture or metal panel and appliances our exports are mainly in Europe of North Africa”.
There are numerous ongoing crises in the world today: geopolitical tensions, the Ukrainian-Russian and IsraeliPalestinian conflicts, and the continued
high costs and scarcity of raw materials and industrial components, to name but a few. How are these issues impacting your business, and what strategies are you implementing to mitigate these challenges?
“The ever more obvious consequences of global crises like climate change and increasing geopolitical uncertainties are shaking companies awake: how can the business be crisis-proofed? Resilient and more diversified supply chains can make the difference. Exporting businesses are particularly dependent on stable supply chains and reliable foreign trade conditions. Therefore, companies need to future-proof their supply chains, make them more diversified, sustainable and more resilient to disruptions, and thus secure sales, growth and jobs. With a clever balance of global and regional supply networks that pays off in several respects: dependence on individual companies is reduced and unforeseen failures in one place can be more easily compensated for elsewhere. The success of this strategy depends largely on digitalisation. This is why Covestro is consistently investing in the expansion of a digital infrastructure that ensures a seamless flow of data along the entire supply chain. Supply chain analyses optimise planning, procurement, production and sales and ensure greater transparency along the entire value chain.
We are aware though, that our market is highly volatile and strained by factors like rising costs and shortages of raw materials. As in other industries, energy costs are one of our biggest concerns. At the same time, energy costs also affect our customers, they also seek ways to make their production more cost-effective and differentiated. That is something where we can support our customers with our innovative products. Despite the challenges our industry faces, we are ambitious to grow the business in Italy and worldwide through by introducing innovative products in line with the market trends, especially with regard to the rising demand for more sustainable chemical products”.
One of the hot topics at the moment is artificial intelligence: how does it affect your production and products?
“The development of artificial intelligence is as disruptive as the development of the internet and the smartphone combined. At Covestro, we see AI as a long-term opportunity to pave the way for a fully circular economy.
Covestro has been using AI for years, particularly in production, research & development and finance. At the same time, we are preparing the broad use of Generative AI across the entire workforce in the form of a personal virtual assistant. Common GenAI systems (e.g. ChatGPT, BingChat, Midjourney) are already being used by employees. One example can be found
in our plant in Dormagen, Germany: by using artificial intelligence, we were able to reduce the variance in polyester production and thus shorten the time required. In this way, we were able to increase production capacity by 5%. Also, Covestro is working on a personal virtual assistant for all employees that works on the basis of generative AI. The assistant provides support based on both internal and external data, making day-to-day work easier. Employees can also independently feed the assistant with new knowledge without any technical expertise”.
Alongside other leading global companies, you recently established the Global Impact Coalition, which unites CEOs and managers from the worldwide chemical industry. Could you elaborate on the objectives of this initiative and the role you will play in it?
“Transforming the chemical industry and moving from a fossil-based production to more sustainable alternatives is a challenge. At Covestro, we are at the forefront of this change. With the Global Impact Coalition, we will boost our ambition to achieve net-zero emissions by 2050. I am more than confident that together we will really make a difference. The alliance is led by CEOs of seven international chemical companies, including Covestro. Launched by the World Economic Forum, the Coalition will start a series of lighthouse projects to develop low-carbon production technologies and promote innovative ways of recycling plastics.
Transformation can only be successful when people work together. At Covestro, we trust in the strength of cooperation and
The Colourful Garden art installation showcases the range of colours, textures, varying levels of transparency and gloss of Covestro’s PCR polycarbonates, highlighting their exceptional design flexibility.
partnerships. And I am proud to say that the network of our Coalition is growing. It already includes over 70 managers from the chemical industry. And we are also strengthening our collaboration with a wide range of suppliers, partners in the value chain, political decision-makers and financial institutions”.
Polycarbonate has long been a core product for your company, dating back to the Bayer days. How are you currently faring in this sector, especially regarding the production of recyclable product families and the mechanical and chemical recycling of the material?
“In line with our vision to become fully circular we offer customers climate-neutral polycarbonates and polyurethane raw materials, but also develop innovative recycling technologies and engage in the reuse of recycled post-consumer plastics. We are actively promoting products with recycled content, and this is seen quite positively in the market.
A successful product example is Makrolon® RE: with this material we proved that plastic can be circular, recyclable and durable. The renewable polycarbonate is made with raw materials derived from organic waste rather than fossil fuels. Makrolon supports our sustainability goals and offers enormous creative possibilities in terms of colour, shape and decoration, enabling the creation of mono-material or modular, reusable and durable objects and projects.
Our new polycarbonate grades are carbon-neutral from cradle to factory gate. We achieve this by multiple factors: we use renewable electricity for production processes and have introduced raw materials derived from mass-balanced biowaste and residual materials. The plastics offer equally good quality
as their fossil-based counterparts and can be seamlessly integrated into customers’ existing production processes without compromising on quality.
Another example are thermoplastic polyurethanes (TPUs) that are used in a variety of applications, from electronic devices to sporting goods. We aim to make these products more circular and are working with partners in the value chain to achieve this. The current range includes partially bio-based raw materials, mass-balanced as well as recycled TPUs.
Another field our experts have been busy in is the area of recycling. Enzymatic recycling is becoming more and more interesting for us as it complements chemical recycling methods like chemolysis and smart pyrolysis. Enzymatic recycling allows us to break down plastics into individual chemical building blocks known as monomers. They can then be reassembled into long molecular chains - the polymers - and be processed into new plastics. This is particularly interesting for polyurethanes (PU) and other thermoset products, as these are usually not mechanically recyclable. The aim of chemical recycling processes is to produce recycled plastics in new product quality and significantly reduce the environmental footprint compared to conventional fossil-based production.
Covestro continues to invest in biotechnological processes. At our competence centre in Leverkusen, we included a special research unit for enzyme catalysis, NEnzy. In cooperation with RWTH Aachen University, our researchers are working on leveraging the potential of biotechnology for plastics recycling”.
What are your offerings in the realm of fully or partially bio-based solutions? For instance, you were among the pioneers in using carbon dioxide as a ‘renewable’
resource. What steps are you taking to produce raw materials from renewable sources?
“The demand for greater sustainability is growing. Urbanization, for example, calls for new approaches to constructing energy-efficient houses or modernizing existing buildings. Large quantities of MDI (methylene diphenyl diisocyanate), an indispensable material for the production of polyurethane (PU) foams, among other things, are used as a raw material worldwide. Covestro has now added climate-neutral MDI to its product range.
Covestro is currently conducting research in two areas in particular: the production of chemicals from plant-based raw materials and chemical as well as enzymatic recycling. We invest in a range of projects to produce alternative raw materials with a lower carbon footprint. These include the production of bio-based raw materials and the use of our own recycling technologies.
Bio-based raw materials will play an important bridging role until waste-based raw materials are available on a large scale from 2030 onwards. We are paving the way for sustainable growth in the field of white biotechnology, also known as industrial biotechnology. Enzymes and microorganisms can be used to produce more sustainable chemical products from renewable raw materials.
We add more and more products based on biotechnology to our product portfolio. For example, bio aniline: for the first time, Covestro has succeeded in using a special microorganism to obtain the carbon required to produce the basic chemical aniline entirely from plant-based raw materials. With a production capacity of more than one million tons, Covestro is one of the leading manufacturers of aniline, which is a basis for MDI, a component of rigid polyurethane foam, which is used, for example, in building insulation or the insulation of refrigerators. Next steps towards the development of production in an industrial scale are to be seen in the near future.
Biotechnology can also play a role in the production of hexamethylenediamine (HMDA), an important precursor for our coating and adhesive raw materials. Together with the Californian biotech company Genomatica, Covestro has succeeded for the first time in using biotechnology to produce HMDA from plants instead of fossil raw materials. A pilot plant has already produced significant quantities of the bio-based alternative. Our aim is to further boost the circular economy and reduce the use of raw materials. We want to reshape the market for alternative, non-fossil materials together with other partners and companies. For us, alternative raw materials already include biomass, waste products, carbon dioxide and hydrogen; we can utilise these for our purposes thanks to pioneering technologies and collaborations.
Mass balancing is a key factor in reaching our goal to better utilize alternative raw materials for our products such as biobased or recycled materials. With this approach we can quickly and economically increase the proportion of sustainable raw material alternatives instead of fossil raw materials. This means that we rely on a sensible mix of, for example, bio-based materials that are processed in existing plants together with fossil components. The bio-based proportion is then allocated to the individual products according to the ISCC Plus certification scheme. Many Covestro production sites around the world are now ISCC Plus-certified. We will continue to expand our range of mass-balanced products in order to offer our customers sustainable solutions.
In the long run, we want to offer all of our products in a climate-neutral version. For our CQ solutions, we utilise alternative raw materials and energy sources as well as unique, newly developed technologies. CQ stands for “Circular Intelligence”, a smarter approach to more sustainable materials and technologies”.
Is achieving decarbonisation and zero emissions a realistic goal? Where do we currently stand on this journey?
“Thanks to successfully implemented operational excellence in all our major production sites, Covestro has cut specific emissions by 54% already in 2021, compared to base year 2005. For the next years we plan with realistic milestones that guide us to a lower carbon footprint. By 2035, we want to be operationally climate-neutral in terms of emissions from our own production, that is Scope 1 emissions, and of emissions from purchased energy sources, Scope 2. For Scope 3 emissions, the targets will be announced soon. We know that we can only be successful if we involve our partners, customers and suppliers from the outset”.
WELDING OF PLASTIC PARTS Heating of prepreg composite materials
LAMINATING Shrinking of plastic foil
STRETCHING OF PLASTIC FILMS IR HEATING FOR PET PREFORMS
Thermoforming of plastic parts Deburring of stamped part EMBOSSING PROCESS DRYING OF PLASTIC PELLETS
Crystallization and drying of PET, PPS, PLA Curing of paints on plastic
Softening process Forming process Bending process Vulcanization processed in rubber industry
Drawing of plastic tubes SEALING PROCESS GLUING PROCESS
www.heliosquartz.com
Helios Quartz Group SA
Via Roncaglia 20 6883 Novazzano - Switzerland
Tel. +41 (0) 919233555/6 Fax +41 (0) 919233557
swiss@heliosquartz.com
Helios Italquartz S.r.l. Via delle Industrie 103/A 20040 Cambiago - Milano - Italy
Tel. +39 02 95 34 93 18 Fax +39 02 95 34 50 85 italy@heliosquartz.com
The Italian company Sitra develops a wide range of masterbatch and additives for several applications in the plastics processing. The following is a specific product for imparting antistatic properties to various artefacts, making them more efficient and safer.
Awide range of masterbatch for satisfying the most applications and capable of providing maximum coverage and the best colorimetric yield in the various technological processes used by processors are produced by Sitra. Masterbatch are concentrates of pigments dispersed on a thermoplastic polymer support (polyethylene, polypropylene, polystyrene) obtained by mixing and at the same time plasticing resin and pigments in an extrusion plant, and the mixture is the cooled and finally granulated. Those produced by Sitra are white, black, and coloured of the highest quality and used for the colouring of thermoplastic articles made on a polymer support intended for various application sectors, such as monofilament, fibres, films, sheets and tubes extrusion, injection moulding and blow moulding. Given the widespread use of thermoplastic articles in the daily life, in addition to the colour of the thermoplastic article, over time the need has arisen to improve and enhance their properties of mechanical, thermal, UV etc. resistance. Therefore, to provide specific functions to the final article, concentrates
of additives are produced on a polymeric support such as anti-UV, antistatic, flame retardants, anti-blocking, process aid.
Sitra highlights the antistatic masterbatch that give such properties to thermoplastic products, capable of inducing an electrostatic effect during the use of the final product, due to the formation of the thin layer of humidity on the surface of the polymer, which to a certain extent can be conductive. Thermoplastic polymers are generally poor current conductors. Tacking advantage of this high insulating power they are used to cover electrical cables, screwdrivers etc. However, in some cases, this characteristic causes problems related to the accumulation of electrical charges, which can occur during transformation, storage on use. The electrostatic charges present on the final product can be head to the accumulation of dust, attraction explosive substances, etc. To reduce the electrostatic effect, additives applied externally or incorporated into the product are used. These additives
are surfactants called antistatic which have the characteristic of being incompatible with the polymer and migration to the surface. The hydrophilic part, present in the additive, captures atmospheric humidity, creating a thin layer of water on the surface of the product. It is the layer of water that makes the artifact conductive. It should be kept in mind that migration to the surface is rather slow, and the evaluation of electrical conductivity must be carried out by the final transformer. Furthermore, relative atmospheric humidity has a notable influence, in particular conditions, in winter and in closed places, it drops below 30%, a polymer with antistatic additives still appears insulating. The electrostatic charge increases a million times when moving from an environment with a relative humidity of 80% to one with 30%.
Antistatic masterbatch are used in various applications, such as:
- packaging: bags, films, and containers, in which the presence of the antistatic prevents the accumulation of dust and facilitates the handling of materials;
- electronic components: in the electronics sector, the addition of antistatic protects sensitive components, such as electronic boards, integrated circuits and semiconductor devices;
- materials for the automotive industry: in interior coatings and car components, the addition of antistatic improves the resistance to the accumulation of electrostatic charges.
From Sitra range, PE 00211 AS is a dispersion of organic additives in polyethylene free from fillers, waxes, or other lubricants. It is an antistatic masterbatch recommended for all transformations of polyolefin polymers with Cast technology. The additive contained in the masterbatch has excellent thermal stability and used in the suggested conditions does not affect the welding and printing of the final product. However, it is good practice to carry out approval tests before industrial use. The additive masterbatch does not interfere with the optical characteristics of the film. The formulation is non-toxic.
Used for the creation of an LDPE film obtained with cast technology, with a thickness of 40 micron; from the tests for the evaluation of the surface resistivity in conditions of 20 °C and 50 % HRH it gave results of 1016 ohm and 1011 ohm for grades LDPE blank and LDPE + 3% MB respectively.
Masterbatch will find more space in the world of applications, thanks to continuous and constant research into the various and constant research into the various implementations and “customizations” to best satisfy demands and evolutions of the market. The sectors that require increasingly high-performance products are the most diverse and represent an open challenge for companies that operate in the present while investing in the creation of future realities.
stainless steel pipe bends and aluminium couplings suitable for vacuum and pressure conveyors
stainless steel pipe bends in all common pipe dimensions from 38.0 x 1.5 mm till 204.0 x 2.0 mm; radii: 75, 250, 300, 500, 800, 1.000, 1.200 and 1.500 mm (AISI 304)
highly wear-resistant pipe bends: glass pipe bends and HVA NIRO® stainless steel pipe bends
HS Umformtechnik GmbH
D-97947 Grünsfeld Germany
Phone +49 (0) 93 46 / 92 99-0 kontakt@hs-umformtechnik.de www.hs-umformtechnik.de - immediately, from stock -
FAKUMA Hall B3 – booth 3309
ZEONEX®/ZEONOR® Cyclo Olefin Polymers (COP) are used in many applications worldwide. We know that the development partnership with our customers provides important stimulus and generates the required power to find appropriate solutions. In this way, ZEON helps their customers to continue offering competitive products to the market now and in the future.
WWW.ZEON.EU
WWW.ZEONEX.COM
CRP USA cooperates with paralympic athlete Tatyana McFadden
CRP USA, a 3D printing service company, has partnered with eight-time paralympic gold medalist Tatyana McFadden to create groundbreaking 3D printed wheelchair racing gloves using the Selective Laser Sintering process and Windform XT 2.0 composite material. This collaboration addresses significant manufacturing challenges and sets a new standard for elite athletic gear.
WTatyana McFadden (also in the opening picture) in training; the new gloves weigh about 100 g, making them 50% lighter than conventional ones.
heelchair racing demands exceptional performance from athletes due to the high friction generated by constant hand-wheel contact. Traditional gloves often fail to meet the standards required by athletes like Tatyana McFadden, an 8-time paralympic gold medalist. Before adopting CRP USA (a company that is part, together with the Italian CRP Technology and the Emirati CRP Gulf, of the CRP Group, specialising in 3D printing services) solution, Tatyana used standard mould kits for her gloves, finding the quality inadequate. Conventional methods struggled to produce gloves that could withstand the intense stress of wheelchair racing while maintaining precision and comfort.
“My first wheelchair racing gloves were called “harness gloves”. They were shaped like thumbs and made of heavy-duty fabric with rubber padding. Their softness made me feel the impact every time I hit the hand ring. By the 2008 Paralympic Games, my team and I began making hard gloves. We would take plastic beads, melt them in a pot of boiling water, and then mould the plastic to my hands. This process took days to perfect. Sometimes we would have to start over and throw the whole plastic glove back in the water. Once perfected, I did not let the gloves out of my sight because they would melt if left in the car or in the heat for too long. Over time, the plastic would wear down, so we made the gloves thick, but they were heavy”, Tatyana McFadden told. Even these gloves were not up to Tatyana’s needs for the highest sporting level.
In 2015, a significant change occurred when Tatyana had the opportunity to experiment with 3D-printed gloves. In 2016, Tatyana connected with CRP USA to continue developing 3D printing racing gloves, aiming for them to be “stronger and more durable” compared to what they were using in 2015. “After a friend of
mine told me about CRP USA,” Tatyana added, “I reached out to them and shared my story. I was so excited when I met everyone in person. They are an incredible partner and have really helped me so much. Not just in their innovation but the confidence they gave me since I do not have to worry about the performance of my racing gloves.” Tatyana explained that the CRP USA team helped bring her vision for the current gloves to life, making the vision a reality.
Strength and durability were undoubtedly important characteristics that Tatyana required from CRP USA to compete at her best, but they were not the only ones. Lightness, stiffness, resistance to wear and tear, and resistance to weather were other important features Tatyana wanted for her new gloves. “When I met with the CRP USA team,” she specified, “we also talked about heat, rubber, weather effects, and straps for the gloves so they can stay in my hands better. When competing outside, we face various weather conditions, and I want to be ready for anything. My gloves have cracked in the past. My strokes produce a lot of force when I hit the hand ring, and my previous gloves lasted less than a year. I also wanted a better way to add rubber to the hand rings. The CRP USA team listened to my needs and managed to satisfy them in the best possible way.”
Before the construction of the parts, discussions with customers are essential to understand their needs in order to satisfy them as best as possible. After several meetings with Tatyana, the CRP USA team opted for Laser Sintering technology and Windform XT 2.0 as the manufacturing material. This solution was selected as the best one to address Tatyana’s everyday challenges. In this specific case, the rubber used in the 3D printed gloves is a standard off-the-shelf item. The CRP USA team trims it to size and bonds it to the gloves using a structural adhesive. This operation demonstrates the compatibility of Windform XT 2.0 with various components, ensuring seamless bonding without any issues.
“Throughout her career, Tatyana found that the quality and detail of her gloves were just not up to the high standard she needed. That’s when the Windform range of composites for 3D printing, created by our Italian partner CRP Technology, came into play. At CRP USA, we have tried several different Windform materials for her, with the gold standard becoming Windform XT 2.0”, Nathan Baker, Senior Project Coordinator at CRP USA, explained.
Windform XT 2.0 is known for its superior mechanical properties.
These properties ensured the gloves could withstand the constant, high-friction environment of wheelchair racing without deterioration. This durability significantly extended the lifespan of the gloves compared to traditional materials. Additionally, the flexibility and shock-absorbing properties of Windform XT 2.0 ensured maximum comfort, allowing Tatyana to focus solely on her performance without discomfort or distraction. CRP USA hollowed the parts out and inserted an internal structuring. This allowed a reduction in the weight of the gloves while maintaining strength, integrity, and improving durability. This was a sig-
nificant contribution to Tatyana’s agility and speed during races. The weight reduction was indeed substantial, with the resulting 3D printed gloves in Windform XT 2.0 weighing approximately 100 grams, a 50% reduction from traditional gloves. Once completed, the 3D printed wheelchair racing gloves in Windform XT 2.0 underwent testing for weight and durability, and the results were excellent.
Tatyana was very satisfied with the outcome. “I remember using the gloves in Windform XT 2.0 for the very first time on the track and on the road,” she said. “I was so impressed by how light and durable they were. My hands felt so light, it felt like I wasn’t holding onto anything. When I first put my hands into the glove, it was so smooth. They had also built in two holes where I could strap on the gloves to my hands instead of using additional clips.” CRP USA and Tatyana continue to collaborate to enhance the 3D printed wheelchair racing gloves, focusing on improving grip and comfort, especially when competing in the rain. This ongoing partnership ensures that Tatyana always has access to the latest advancements in additive manufacturing technology, allowing her to maintain her competitive edge.
The original page in Giulio Natta’s work diary with the date 11 March 1954 bears the scientist’s note “Fatto il polipropilene” (“Made polypropylene”): mankind’s daily life had changed forever.
11 March 1954 was a Thursday and Giulio Natta’s diary entry for that day read “Fatto il polipropilene” (Made polypropylene). That was indeed the day that saw the birth of polypropylene, which therefore celebrates seventy years exactly this year. A landmark birthday for a material that, from Italy, would go on to become widespread throughout the world, and more less directly affect the daily lives of everyone.
The first formulation was created in the laboratories of the Department of Chemistry, Materials and Chemical Engineering of the Polytechnic University of Milan, now named after the scientist. Back then, polypropylene was a by-product of catalytic cracking, and the discovery was significant not so much for the polymerisation of polypropylene, which was nevertheless fundamental, but for the fact that it made it possible to control the spatial structure of the polymer, making it ordered and regular. Natta himself termed “isotactic” the resulting polypropylene, precisely to differentiate it from the amorphous, aka atactic, type. In fact, the ordered chemical structure of isotactic polymer gives it the high crystallinity that in turn determines the remarkable mechanical properties that have led to its widespread use in countless applications. According to the most recent estimates, almost 100 million tons per year are produced worldwide, corresponding to over 10 kg per person, with a total value of around 150 billion dollars, i.e., 0.15% of the global GDP.
Giulio Natta was born on 26 February 1903 in Porto Maurizio (Imperia). After graduating from the Cristoforo Colombo classical high school in Genoa at just 16 years of age, he remained in Genoa to do a two-year preparatory engineering course. In 1921, he embarked on a degree course in industrial engineering at the Polytechnic University of Milan and the following year became an internal student at the Polytechnic’s Institute of General and Inorganic Chemistry. At just 21, he graduated in chemical engineering under Giuseppe Bruni, immediately becoming his assistant, and from 1925 to 1933 he was head of analytical chemistry at the Polytechnic. At the same time, from 1929 to 1933, he was also in charge of physical chemistry at the Faculty of Science of the University
of Milan, a period in which he rose to prominence for some of his research in crystallography and inorganic industrial chemistry.
From the early 1950s, Natta began to focus, within the field of macromolecular chemistry, on questions concerning the stereochemistry of polymers and macromolecules in general. As a result, he learned of the polymerisation of ethylene and the dimerisation of alpha-olefins in the presence of aluminiumalkyl compounds, processes that were being carried out in that period by the German chemist Karl Ziegler using organometallic catalysts, or “Ziegler catalysts”. Natta realised that these catalytic (metallorganic) polymerisation processes could potentially be used to obtain very linear, low polymers starting from monomers such as ethylene, whose linear structure he compared with the branched one typical of high polymers. When Ziegler went on to produce high-density linear polyethylene by means of the same polymerisation procedures used for ethylene but with other catalysts, Natta had the idea of applying this method not just to ethylene but also to polypropylene and other higher alpha olefins, using some variants of the Ziegler-type catalysts. Thus, on 11 March 1954, he managed to obtain isotactic polypropylene, a new organic compound with a highly ordered crystalline structure, which gave rise to stereospecific (or stereoregular) polymers that boasted excellent chemical and mechanical properties, and were later patented under trade names like Moplen, Meraklon and Mopeflan.
In recognition of their invention of new catalysts for stereospecific polymerisation, later dubbed Ziegler-Natta catalysers, Natta and Ziegler were jointly awarded the Nobel Prize for Chemistry in 1963. The subsequent global industrial production of isotactic polypropylene, the most appreciated of the polypropylenes, was based on the patents (known as the “Natta-Montecatini patents”) that Natta, starting in the mid-1950s, went on to file in co-ownership with the Montecatini company. These patents were the fundamental inspiration for all the other production methodologies subsequently developed independently by other companies.
An air intake manifold made of 100% Renycle, the RadiciGroup brand identifying engineering polymers obtained from recycled polyammide: this application was recognized with the prestigious award in the Power Train category by the Society of Plastics Engineers (SPE) at the 22nd SPE Automotive Awards.
The air intake manifold is a high technology application typical of the automotive sector, where glass-fibre reinforced nylon has, over the years, almost completely replaced metals. RadiciGroup supplies both PA6-FV and PA66-FV polymers for various engines of motor vehicles worldwide. In this particular case, however, the challenge was to use a 100% mechanically recycled polyamide, the result of a careful process involving the selection, cleaning and control of raw materials to ensure very high-quality consistency.
This component, which was designed and manufactured by Marelli, must meet stringent performance requirements: high burst pressure, pressure pulsation and prolonged vibration tests subjected to thermal cycles, thermal shocks etc. Particular attention was paid to NVH (Noise Vibration Harshness) analysis with the aim of ensuring, among other things, acoustic performance in line with the other materials used today.
In developing the recycled material Renycle, RadiciGroup not only worked to optimize the performance, keeping in mind the specific requirements of the air intake manifold application (mechanical and thermal performance, etc.), but also sought to maximize the environmental benefits. Indeed, a more than 70% reduction in CO2 emissions, measured
according to the Life Cycle Assessment (LCA) methodology, was achieved compared to the equivalent fossil source material.
The jury evaluated about fifty projects, many of which were aimed at making cars and motorbikes more sustainable. As a matter of fact, sustainability is a priority at RadiciGroup, which has long focused on offering products made from recycled or renewable source raw materials, as well as on developing a Group strategy based on environmental, social and governance (ESG) principles. RadiciGroup’s commitment to numerous environmental and social issues is ever-growing.
“It is a great satisfaction for us to be recognized by the Society of Plastics Engineers,” pointed out Erico Spini, Global Marketing Director of RadiciGroup High Performance Polymers. “This award valorizes the work and commitment we put in every day to give shape to truly innovative and valuable projects. Moreover, it recognizes our teamwork with Marelli, our long-standing customer, that we have achieved by focusing on quality, reliability and durability. These principles, or better yet our tangible results, are the basis of our global offering, which decisively raises the bar in the development of winning solutions from the viewpoint of sustainability. To sum up, we hope this application can give impetus to new initiatives fostering sustainable mobility.”
The intake manifold made of 100% recycled polyamide is the application developed by RadiciGroup for Marelli that has won an award from the Society of Plastics Engineers (SPE).
Basf launches Tinuvin NOR 211 AR to support film producers and converters globally in navigating the challenging landscape of plasticulture - the use of plastic materials in agricultural applications. This new high-performance heat and light stabilizer protects and prolongs the lifespan of agricultural plastics that require resistance to high levels of inorganic chemicals like sulfur and chlorine. Tinuvin NOR 211 AR offers an effective value-in-use solution for agricultural plastics exposed to intense UV radiation, thermal stress, and inorganic chemicals commonly used in crop management and disinfection.
The advancements in plasticulture, heavily influenced by polyethylene grades, have led to a growing trend in downgauging and a greater emphasis on the use of plastic materials. Downgauging involves reducing the thickness of plastic films while maintaining their performance, made possible by incorporating new polymer grades to enhance the mechanical properties of PE materials. At the same time, converters are investing in new equipment to increase the number of layers in their films thereby improving performance and durability. This transition to thinner and more durable films is crucial for the sustainability of agricultural plastics as it helps to reduce plastic waste, enhances production efficiency and facilitates practices like recycling and upcycling.
Tinuvin NOR 211 AR is a unique stabilization system that can be used in plasticulture, even in intensive horticulture, regardless of the application region’s severity of UV radiation,
heat, and chemicals that are present. This new product solution is the best option when downgauging is required, especially in the presence of high levels of sulfur and chlorine. With the increasing use of inorganic chemicals in agriculture due to the adoption of “Integrated Pest Management” and “Organic Farming” practices, the need for effective stabilization of agricultural films is crucial. “Tinuvin NOR 211 AR additive solution addresses a broad variety of challenges for agricultural plastics, including sustainability requirements, increased chemical exposure, longer use durations and downgauging trends,” said Bettina Sobotka, Head of Global Marketing and Development for Plastic Additives at Basf.
“Basf’s NOR HALS solutions improve stabilization by moving beyond solutions based on secondary and methylated HALS. Through collaboration with agricultural plastic producers as well as farmers, we facilitate the exchange of knowledge and expertise, creating solutions that will ultimately lead to improved crop yield.”
Company commitment to innovation and sustainability is reflected in the expansion of its NOR platform. Tinuvin NOR 211 AR, part of the Valeras portfolio, utilizes renewable electricity in production and optimizes product form to reduce energy consumption and emissions. It also improves material dosing precision, minimizes dust exposure, and promotes water and aquatic organism protection, leading to a safer, more efficient, and environmentally friendly workflow.
Celanese introduces biobased Hytrel TPC
The global specialty materials and chemical Celanese has introduced new biobased Hytrel TPC RS40F2, which, when foamed, is ideal for athletic footwear applications. Incorporating a minimum of 20% segregated bio-content, Hytrel TPC RS40F2 foamed using a physical supercritical fluid (SCF) foaming process helps support the sustainable development objectives of athletic footwear brand owners and manufacturers. The bio-content is verifiable via the C14 method.
Pristine white foamed biobased Hytrel TPC RS40F2 is wellsuited to the midsole components of athletic footwear as it delivers lightweighting opportunities while elevating energy return performance with excellent rebound and resilience associated with other Hytrel TPC grades. Hytrel TPC is widely used in different industries due to its advantages in lightweighting, heat insulation, sound absorption, shock resistance, moisture resistance and corrosion resistance. Hytrel TPC RS40F2 can be colored to meet design needs while maintaining material properties.
“This new biobased grade is part of our expanding Hytrel TPC ECO-B portfolio,” said Peter Wing, Celanese Global Marketing Manager of Consumer Products. “It offers numerous benefits for athletic footwear brand owners and manufacturers that align not only with their sustainability ambitions but also their aspirations for elevating shoe performance. We are very excited about how we can enable athletic footwear designers to redefine the category, as well as the contributions this new foamed polymer can make across the value chain.”
Physical SCF foaming, which is leading a process technology transformation, results in a unique cell structure with elevated properties and good skin compatibility. The process itself offers environmental benefits as there are no corrosive foaming agent residues to impair mechanical properties. Additionally, it generates low odor/emissions and exhibits no toxicity.
The traditional use of materials for insoles and midsoles has typically relied on chemical foaming agents that can generate volatile organic compounds (VOCs), which react with sunlight to form ground-level smog. This is an environmental concern.
Celanese is collaborating with Xingxun Enterprise, an innovative processor, to produce world-class foamed polymer applications. Experts from both companies have worked together to successfully develop the processing of Hytrel TPC RS40F2 shoe soles using physical SCF foaming technology. This new foaming polymer enables Xingxun to deliver a lower carbon footprint solution to athletic footwear brand owners. Additional benefits offered include drop-in performance with fossil-based foamable grade where no further evaluation is needed, and availability of ISCC+ certified bio-mass balanced Hytrel TPC materials for customers’ selection.
“Celanese proprietary technology allows the bio-content of many of our ECO-B materials to be tailored, and we look forward to working with customers on their specific athletic footwear applications,” said Wing.
A masterbatch for the identification of materials in industrial 3D printing has been developed by the Grafe Group. “This allows the authenticity of licensed materials to be reliably and unmistakably determined in the filament that is processed in this additive manufacturing process”, explains Lars Schulze, Head of Color Development and Material Sciences. He sees prostheses in medical technology, systemrelevant machine or automotive parts that have to withstand warranty, or recourse claims as areas of application. Other sectors such as furniture, electronics or consumer goods could also be of interest for the originality check.
“In the future, more products and spare parts will come from 3D printers. If you imagine that spare parts for licensed products are printed from inferior and untested material, recourse claims or warranty claims would be forfeited and, in the worst case, property damage or personal injury would occur“, reports Schulze. This is where Grafe’s idea comes in: “We incorporate a marker into the filament that can be used to check
whether the correct material has been used. It is permanent in the component and cannot be removed. The marker offers perfect protection against counterfeiting and proof of originality.”
As an exclusive development partner, Grafe relies on the security pigments from Tailorlux. The company also supplies the matching Tailor-Scan 4 hand-held measuring device, which can be used to check the authenticity of the plastic used directly from the filament to the component. Certification laboratories can also check the material. The test electronics to be used can also be integrated directly into an existing 3D printing system.
Schulze refers to the significant basic idea with which the safety principle can be consistently applied if the filament is tested directly in the printing unit. “In this way, the safety marking in the filament can be checked in the printer via a sensor when the spool is inserted. Printing can only begin once it is certain that the material is correct”, he adds.
“Our solution is fully developed and works”, says Schulze.
“So far, the marker has mainly been used in PLA and PETG (glycol), but it can also be used in PA and PC. There is no influence on the color. Thanks to a wide selection of markers, almost any plastic can be equipped”, he assures.
LyondellBasell invests in a new closed-loop recycling centre
LyondellBasell is investing in a new closed-loop preparation centre in Lich, Germany, for transforming plastic waste into high-quality feedstock for high-performance materials, supporting the circular economy and contributing to industry sustainability goals. The closed-loop preparation center
supports the LyondellBasell integrated hub strategy, bringing together existing assets with new advanced sorting and recycling capabilities to create operational scale, reduce cost and capture value from plastic waste. This new centre marks a significant leap in waste processing capabilities for durable goods, such as automotive and white good appliance parts.
The requirements for recycling durable goods once they’ve reached their end-of-life are complex. The materials need to be stripped of any paint, metal and other additives to get to a plastic suitable for a high-quality feedstock.
The recycling centre employs mechanical recycling to transform end-of-life automotive and appliance plastics, such as bumpers and trim, into high-quality recycled materials. These recycled materials will be incorporated into the LyondellBasell CirculenRecover product range, offering more sustainable solutions based on recycled content for demanding applications in the automotive and white goods sectors, including structural parts, interior components, and visible applications. The Lich recycling center is expected to reach commercial scale in the fourth quarter of 2024. This investment aligns with the company’s ambitious goal to produce and market at least 2 million metric tons of recycled and renewable-based polymers annually by 2030.
Following the collaboration between Versalis, Eni’s chemical company, and Forever Plast, Italy’s leading company in post-consumer plastic recycling, comes Refence, an innovative range of recycled polymers for food contact packaging. The range is already available in the market for polystyrene applications such as yogurt pots, trays for meat and fish, and other types of rigid and expanded packaging. These new products will expand the Versalis Revive portfolio of mechanically recycled materials, redefining their application limits and enabling direct contact with food. Refence has been produced due to Newer technology, which is developed in Versalis’ research laboratories in Mantua and industrialised at Forever Plast’s facilities in Lograto (Brescia, Italy) under a co-development agreement between Versalis and Forever Plast. Newer enables the purification of recycled polymers in compliance with EU Regulation 1616/2022 on recycling. The technology has also obtained the Non-Objection Letter (NOL) from the US Food and Drug Administration (FDA).
“Circularity is a fundamental strategic lever. For this reason, we are committed to developing complementary recycling processes to enhance the value of endof-life plastics and integrate ourselves into the Italian national collection chain. We are completing works on our first advanced mechanical recycling hub at Porto Marghera for post-consumer plastics, in particular styrenic polymers. Our collaboration with Forever Plast aims to reach application sectors, such as food packaging, where sustainability
and quality requirements are essential, thus strengthening our European leadership in mechanical recycling”, Adriano Alfani, CEO of Versalis, said.
“We are very pleased with the result achieved, especially as there was no recycling chain for polystyrene from separate waste collection at a European level until a few years ago. The collaboration with Versalis has allowed us to reach this extraordinary milestone”, Piersandro Arrighini, CEO of Forever Plast, added.
The global leader in essential chemistry Solvay recently inaugurated its groundbreaking Alve-One production unit in Rosignano, Livorno, Italy. This marks a new milestone with the launch of a significant European production facility for Alve-One, a chemical blowing agent eco-designed to transform the thermoplastic foaming industry. Solvay’s Alve-One unit aims to address the growing demand for safer and more sustainable blowing agents in various consumer and industrial uses, globally. These include automotive, footwear, building and construction, and consumer goods, aiming to reduce carbon footprints in foamed endproducts while enhancing overall health and safety standards to protect both people and the environment. AlveOne solutions have received official recognition as a sustainable alternative for foamed thermoplastics from various organizations. These include the International Chemical Secretariat (ChemSec), the Solar Impulse Foundation, which acknowledged it
as an Efficient Solution, Inovyn, which honored it with an Innovation Award and France Chimie, which awarded it with the Pierre Potier Prize.
“The inauguration of our Alve-One production unit in Rosignano reflects Solvay’s dedication to delivering innovative and sustainable solutions that directly benefit our customers and society,” commented Etienne Galan, President of the Soda Ash & Derivatives business at Solvay. “This facility equips us to effectively address our customers’ evolving needs, while also fostering a positive environmental footprint. It marks a pivotal advancement in our mission to lead transformative change across multiple industries, guaranteeing our customers access to top-tier solutions that meet their highest expectations.”
Trinseo starts pilot plant on the outskirts of Milan
A pilot plant for the depolymerisation of polymethyl methacrylate (PMMA) was started by Trinseo in Rho (Milan). The pilot facility represents a significant step forward in the company’s commitment to sustainability, as the next-generation recycling technology helps advance a circular infrastructure for acrylic solutions and is aligned with Trinseo’s 2030 sustainable product portfolio goals. Depolymerization is a chemical recycling process that returns acrylic solutions to the constituent monomer, methyl methacrylate (MMA). Complementary to other recycling technologies, depolymerization helps close the loop for acrylic recycling with several advantages over traditional processes. By utilizing this technology, acrylic solutions can be recycled - including PMMA sheets, which previously could not be mechanically recycled. Additionally, returning the material to its monomer form allows additives and contaminants
to be removed from pre- and postconsumer acrylic products. This enables more PMMA to be recycled.
The recycled MMA (rMMA) generated by Trinseo’s depolymerization facility is utilized in the company’s Altuglas and Plexiglas R-Life product portfolios.
Through this new facility, Trinseo can produce rMMA that is comparable to virgin raw materials. This enables use in high-demand applications, such as vehicle taillights or caravan windows that require high optical quality.
“We are thrilled about the opening of our depolymerization facility, which will help advance our goal to support a circular economy,” said Francesca Reverberi, Senior Vice President of Engineered Materials and Chief Sustainability Officer at Trinseo. “Our company remains committed to our sustainability goals, including investing in new recycling technologies that can support our customers in reaching their sustainability
goals as well.”
“This is a critical milestone in our sustainability journey,” said Han Hendriks, Chief Technology Officer at Trinseo. “Depolymerization expands our recycled feedstock capabilities, which in turn, will help us innovate new solutions. With this new capability, we can build a more robust recycled acrylics portfolio to better meet the evolving needs of our customers.”
Bright rooms for carefree play. With the construction of a new public kindergarten, the Polish municipality of Bobrowniki near Katowice in Poland has created a modern environment for its youngest community members. This award-winning building is a showcase for the successful combination of polycarbonate with other - equally unusual - materials for facades. The click panel system from Exolon Group creates bright rooms that keep energy consumption to a minimum.
The construction of the new kindergarten was commissioned by the municipality of Bobrowniki and was the municipality’s largest investment to date - at approximately 24 million euros. The result was a kindergarten with an outdoor area measuring a total of 950 square metres that meets the latest requirements in early childhood education. The one-storey building and outdoor facilities are completely barrierfree. The building envelope is covered with a flat roof. The facades were
finished using polycarbonate, textured plaster, laminate and aluminium cladding. One key aspect of the project involved selecting quality building materials. They had to be aesthetically pleasing, energy-efficient and sustainable. For the double-shell facade, the builders opted for system profiles from the Exolon Group: the Exolon Panel 9P with a thickness of 40 millimetres. The Exolon Panel 40 9P is a polycarbonate panel system featuring a tongue and groove joint. The 9-fold tunnel structure, which has a low Ug value, significantly improves thermal insulation and helps to reduce energy consumption. At the same time, it minimises the building’s CO2 emissions and therefore its environmental footprint. The “Clear Frost” colour gives the facade a friendly aesthetic that blends seamlessly into the environment and matches the educational environment of a kindergarten well. This project not only created a modern kindergarten, but contributed to the
community’s quality of life in the long term. For this, the construction company was awarded the “Grand Silesian Construction Award 2023”.
Thermally conductive TPEs meet the increasing requirements for quality and quantity of batteries.
Kraiburg TPE has launched Thermally Conductive TPEs for batteries and charging system used in e-mobility, which meet the increasing requirements in terms of quantity and quality to a large extent. Along with the requirements for a
power density as high as possible with the same installation space size and minimal charging times, durability is one of the quality factors that determine purchases. In this context, an intelligently designed thermal management system, which ensures that high temperatures generated in the battery during the charging process are dissipated quickly and continuously to the outside, is an essential prerequisite for the optimization of durability, because the battery loses its quality when exposed to high heat. Kraiburg TPE has recently invested more in the development of distinctly thermally conductive materials to guarantee batteries the longest possible service life. Compared to liquid or paste-like thermal conductors, these new TPEs provide the advantage of significantly higher functional and spatial stability when assembling the module. Another advantage of the newly
Syensqo has introduced a range of new circular Omnix Echo HPPA solutions with high massbalanced PCR/PIR content for household appliances and other consumer goods, helping brand owners and manufacturers to reduce the carbon footprint of their sustainable product innovations.
developed Thermally Conductive TPEs is their special touch quality. Features particularly worth emphasizing are the high-quality, evenly “dry” surface and the absence of PVC or silicones. The heat difference between the ambient and body temperature is usually sufficient to produce a cooling effect on the skin when the user comes into contact with the material.
Kraiburg TPE has collaborated with Lehvoss Group, a partner company, to determine the overall performance of the new TPEs in different applications. The newly developed TPEs were combined with thermal conductive and adhesion-optimized polyamide compounds from Lehvos to determine the adhesion properties of different material combinations. The results confirm the suitability of the new materials particularly for applications in multicomponent composites to a high degree.
Syensqo has introduced five new high performance Echo grades as part of the company’s growing Omnix Echo portfolio of circular polymers. With a mass-balanced allocated recycled content between 33% and 98% from post-consumer and/or postindustrial sources, including fibres, the new sustainable products offer a considerably reduced product carbon
footprint potential. These products maintain the same mechanical performance and superior flowability as PA 6 and PA 66 all-virgin base materials. The Omnix 1000 Echo series, with up to 98% mass-balanced allocated recycled content, providing up to 56% product carbon footprint reduction, is ideal for drop-in replacement of conventional polyamide resins. The Omnix FC 6000 Echo HPPA series (food-contact approved) exceeds the performance of PA virgin incumbents and includes the industry’s first food-contact approved HPPA compound with recycled content (33%, achieving a 34% lower product carbon footprint). The Omnix 6000 Echo HPPA series (non-food-contact) delivers a superior balance of higher performance and lower product carbon footprint than engineered polyamides
PA 6 or PA 66 base materials, with up to 83% mass-balanced allocated recycled content and 45% lower product carbon footprint. The new Omnix Echo series are primarily targeted at household appliances and consumer goods, such as drip and single-serve coffee makers, food processors and slow cookers, ovens and air fryers, kitchen robot chassis and kitchen utensils as well as razor brackets.
“As brand owners and manufacturers are seeking to minimize the carbon footprint of their products, our Omnix Echo series now offer a range of attractive, Echo solutions engineered to enable outstanding sustainability with no compromises on processability, dimensional stability, stiffness, impact strength or surface aspect,” said Ricardo Calumby, Global Marketing Manager Sustainability at Syensqo.
GreenPlast 2025 (27-30 May 2025, Fiera Milano, Rho Pero, Milan - Italy) will be an excellent opportunity for professionals in sustainability and energy efficiency to gather and discuss the latest advancements.
Preparations are in full swing for GreenPlast 2025, the highly anticipated international conference-exhibition dedicated to advancing materials, technologies, and processes in the plastics and rubber industries.
Scheduled to take place from 27 to 30 May 2025 at the Fiera Milano in Rho Pero, Milan, Italy, GreenPlast promises to be a pivotal gathering with a pronounced focus on environmental sustainability and energy efficiency.
GreenPlast was conceived as a strategic response to the postponement of Plast 2021 due to the Covid-19 pandemic. The initiative aimed to fill the void left by the delay, creating a fresh platform for addressing urgent issues impacting the plastics and rubber sectors. These include production and product sustainability, eco-design, recycling, and the circular economy. The event also seeks to combat “greenwashing” by promoting robust and credible environmental policies.
The event’s innovative format, blending conference and exhibition elements with competitive pricing, has heightened its appeal. The success of the inaugural 2022 edition, which garnered enthusiastic feedback and widespread consensus from participants, affirmed its value and set the stage for its return in 2025. GreenPlast is anticipated to be the second instalment in what is expected to become a long-standing series, reflecting current market trends and trade fair demands.
Transitioning to a circular model is vital for preserving the benefits of plastics, which are deeply integrated into daily life. Projections suggest that the European plastics sector could achieve up to 78% circularity by 2050, driven by effective policies and technological advancements. Understanding the dynamics of the plastics supply chain is crucial, as these factors increasingly influence industry practices and environmental strategies. In this regard, GreenPlast is establishing itself as a key event in promoting the circular economy for plastics. The collaborative efforts across the supply chain are crucial for advancing this transition, aiming to reduce emissions and enhance the sustainable use of plastics, an essential material in various sectors. The compound annual growth rate (CAGR) for recycled materials underscores robust growth and significant potential across multiple industries. In the current climate, issues such as decarbonisation, the circular economy, recycling, reuse, and the impact of micro- and nanoplastics have become critical. These topics are frequently highlighted in the media and are shaping public opinion. For professionals in the plastics industry, it is vital to stay informed about market trends, technological advancements, and innovations in materials and processes. GreenPlast is set to be at the
forefront of these developments, providing a crucial platform for industry progress.
Since its debut in 2022, GreenPlast has distinguished itself as Italy’s premier exhibition and conference focused on sustainability and energy efficiency within the plastics and rubber industries. Organised by Amaplast, the Italian association of machinery and moulds manufacturers, through its operational arm Promaplast, the event benefits from the extensive experience and expertise of the team behind the Plast exhibition. GreenPlast offers a unique forum for addressing key industry challenges and driving forward sustainable practices.
The inaugural event featured 170 exhibitors, with a notable 80% from Italy and 20% from international participants. Spanning 6,000 square metres, the exhibition attracted over 20,000 visitors from 55 countries, reflecting the high level of interest and commitment to sustainable practices within the industry.
GreenPlast 2025 will once again be a key component of The Innovation Alliance, a collaborative initiative that includes Ipack-Ima, Print4All, and Intralogistica Italia. These events will be held concurrently at the Fiera Milano facility in Rho Pero, allowing visitors comprehensive access to all halls. This integrated approach is designed to foster extensive networking opportunities and provide a complete overview of the industry. By bringing together sectors such as plastics and rubber, packaging and packing, printing and converting, and logistics, The Innovation Alliance aims to highlight the interconnected nature of these industries and drive innovation across the board.
A notable highlight of GreenPlast 2025 is its strategic collaboration with AMI, a leading consultancy in the plastics sector. This partnership ensures a conference programme rich in detailed sessions and high-quality technical content, addressing the industry’s most pressing challenges with an innovative approach. The conference will spotlight sustainability from both national and international perspectives, examining the measures, objectives, and targets introduced by the European Union since 2018. These regulations aim to boost the use of recycled plastics, improve waste separation, and reduce single-use materials, steering member states towards a tangible ecological transition. GreenPlast 2025 will feature a comprehensive programme, including roundtables and technical presentations curated by internationally renowned experts selected by AMI and Promaplast. The event’s second edition is poised to further solidify its reputation with exclusive, high-calibre content, catering to an audience increasingly committed to environmental issues.
GreenPlast, organised by Amaplast and managed by Promaplast, benefits from the expertise of the Plast exhibition team.
GreenPlast 2025 will once more be a vital part of The Innovation Alliance, a collaborative effort featuring IpackIma, Print4All, and Intralogistica Italia. These events will take place simultaneously at the Fiera Milano venue in Rho Pero, providing visitors with full access to all the exhibition halls.
Marius Berlemann succeeds Erhard Wienkamp
In his 30 years at Messe Düsseldorf, Erhard Wienkamp has made a significant contribution to the company’s current level of internationality and to the size of its leading global trade shows K, interpack and ProWein. On 31 July, he retired as Messe Düsseldorf’s operative managing director. His successor is Marius Berlemann, who started in his new position on 1 August.
Erhard Wienkamp has worked in various functions at Messe Düsseldorf
since 1993. After holding positions in the foreign trade department of the Federation of German Wholesale and Foreign Trade in Bonn and the GermanArgentinean Chamber of Industry and Commerce in Buenos Aires, he took over the project management of the Papro, K and interpack trade shows at the beginning of his trade show career. Since 2002, the economics graduate has been responsible for Messe Düsseldorf’s international trade show business as divisional manager and authorized signatory. In this role, he was also responsible for partner and guest events, official participations such as the joint exhibition booths of the Federal Republic of Germany and the State of North Rhine-Westphalia, special events, and the management of Messe Düsseldorf’s international shows. Erhard Wienkamp succeeded Hans Werner Reinhard as operative managing director in January 2020. In this role, he was responsible for the plastics and rubber portfolio with the leading global trade show K and nine
“The Power of Plastics!
Green - SmartResponsible” is the slogan under which the next edition of K Düsseldorf will take place.
K 2025 will follow on from an extremely successful event in 2022. After the official registration deadline in late May one thing is certain: all renowned companies in the international plastics and rubber industry will take part in this their leading trade fair held in October next year.
Demand for stand space is high and all 18 halls of Düsseldorf Exhibition Centre and the outdoor premises will be fully occupied again. To Erhard Wienkamp,
Past Managing Director at Messe Düsseldorf, the great interest shown by the industry as a whole confirms the outstanding position of K Düsseldorf: “K 2025 will provide the complete overview of a plastics industry undergoing transformation and again have a plethora of impressive innovations in store. We know that many of our exhibitors are already preparing their product innovations and presentations at full speed. Düsseldorf will once again provide forward-looking impetus for the entire plastics and rubber industry.” More than 3,000 exhibitors will participate in K 2025 from 8 to 15 October and introduce the global expert audience to their ranges in the areas of: raw materials, auxiliaries; semi-finished products, technical components and reinforced plastic parts; machinery and
trade shows abroad.
“Erhard Wienkamp didn’t wait for the world to come to Düsseldorf, he went out into the world and carried the reputation of Messe Düsseldorf and the entire city to other countries and continents. His work has shaped the company like no one else’s”, Wolfram N. Diener, President and CEO of Messe Düsseldorf, emphasized.
Having worked at Messe Düsseldorf for 13 years, the 38-year-old Marius Berlemann most recently served as General Manager of Messe Düsseldorf Shanghai and Managing Director of Messe Düsseldorf China.
“It’s been an honour to be part of such a dynamic and dedicated team, one that has always strived to set the highest standards in the trade show industry.
I’m confident that my successor, with his extensive experience and commitment, will continue to propel Messe Düsseldorf forward. I wish him and the entire team nothing but success for the future”, Erhard Wienkamp declared.
equipment for the plastics and rubber industry. Especially well represented again will be the suppliers from Germany, Italy, Turkey, Austria, Switzerland and the USA while the number of producers from China, India and Taiwan has increased yet again.
“The Power of Plastics! Green - Smart - Responsible” reads the slogan of K 2025, which is complemented by three core messages “Shaping the Circular Economy”, “Embracing Digitalisation” and “Caring about People”. This places the focus on the three most relevant fields of action for the sector: circular economy, digitalisation and people. The latter involves corporate social responsibility just as much as future career perspectives for young professionals in the plastics and rubber sectors.
Nuremberg will host SPS - Smart Production Solutions 2024 from 1214 November, an event focused on advancements in smart production technologies. This premier automation trade fair promises an immersive experience, showcasing groundbreaking products and solutions across a sprawling 130,000 square metres. With around 1,300 companies exhibiting across 16 halls, SPS 2024 marks its 33rd edition as a crucial platform for diving deep into the world of automation, fostering idea exchange, and engaging with industry experts.
For Italian businesses, SPS has long been a significant event, offering a valuable opportunity to present new products and stay abreast of sector developments. The 2023 event saw 1,337 Italian visitors and 77 exhibiting companies, solidifying Italy’s position as one of the top three nations consistently participating in SPS. These statistics
underscore the fair’s importance for the Italian market and its progressive manufacturing landscape.
Attendees can explore four dedicated forums situated in halls 1, 3, 6, and 8, where they’ll find a wealth of information on emerging trends and innovations. The Technology Stage, hosted in hall 3 by the VDMA and ZVEI associations, will address pivotal themes for 2024, including digital transformation, industrial communication, security and protection, data rooms, smart and data-driven models for control and visualisation, sensor innovations, drives, sustainability, and the role of artificial intelligence in automation.
Returning for another year, the “Automation meets IT” collective stand in hall 6 will feature around 24 exhibitors. This section provides a comprehensive overview of IT integration in automation and offers expert consultation on topics such as IT management for production,
At mid-July, NPE 2024, held in Orlando, Florida, from 6 to 10 May, announced its final registration and paid exhibit space results data, totaling 51,396 registrants and more than 102,000 square metres respectively. NPE 2024 saw a recordbreaking number of international attendees, first-time attendees and paid exhibit space. Additional numbers include: 15,156 international registrants from 133 countries, establishing NPE 2024 as the most global show in the event’s history; 36,123 domestic registrants, 70% of the total; 20,378 firsttime attendees, a nearly 9% increase over NPE 2018.
With the outstanding number of NPE 2024 international registrations, the results also revealed a significant growth in attendance across different regions, including: 4,438 Latin American registrants, 29.3% of international registration and a 9.9% increase of Latin American registrations compared to NPE
cloud and edge-based solutions, production security measures, IoT, artificial intelligence, and open-source technologies. To offer a sneak peek of this year’s highlights, SPS will host a pre-fair event on 24 October 2024 via the digital platform “SPS on air”. This virtual event will feature 10-minute presentations from companies unveiling their latest products and providing detailed insights into what attendees can expect at the fair. Access to this preview will be straightforward with a free fair login.
12-14 November,
highlight innovation and industry collaboration, setting the stage for the future of automation.
2018; significant registration increases were seen from countries including Brazil, Colombia and Guatemala; 2,801 European registrants, 18.5% of international registration and a 23% increase of European registrations over NPE 2018 with the largest registration increase from Italy.
“This growing presence of European and Latin Americans registrants is indicative of the respective countries’ impact on the plastics industry,” said Perc Pineda, Plastics Industry Association Chief Economist. “As the US is the second largest importer of plastics machinery,
accounting for 12% of global imports, European countries make up six of the top ten countries supplying the US in 2023, totaling 1.6 billion dollars. Similarly, over the past five years, US exports of plastics machinery to Latin America have also grown by 6.5% annually, supporting the region’s expanding plastics industry.”
As for the exhibition area of over 102,000 square metres, it grew by some 980 square metres compared to NPE 2018, in comparison to which the number of exhibitors also increased (by 10.3 per cent), which turned out to be 2,202.
DID YOU KNOW THAT MANY COMPONENTS OF A SCOOTER CAN BE MADE WITH RECYCLED PLASTIC?
From the selection of mixed heterogeneous plastics, coming from the separate collection, counter shield, platform, plate holder, under seat compartment, mudguard and side are made.
A perfect combination to get the circular economy in motion!
BMB Full Electric, machine for high productivity and respect for the environment.
HIGH TECHNOLOGY AT THE SERVICE OF THE ENVIRONMENT In a world where energy saving and waste elimination become a necessity for everyone, BMB offers you the Full Electric Series.
Machines characterized by water-cooled, direct drives plasticizing screws with innovative profiles that allow homogeneously moulding with new vegetable resins, recycled in flakes and other innovative composites.
The BMB Full Electric machine is the answer to the new standards with which the production departments must face today.