
3 minute read
Unlocking SA’s Development and Economic Potential
variables to improve drilling efficiency through the most efficient use of compressed air, ultimately dramatically reducing fuel costs. What sets these two compressors apart is their advanced Pace and DrillAir AirXpert technologies, which are simple to use and place drill operators firmly in control. Pace (Pressure-Assisted through Cognitive Electronics) is a dynamic optimisation feature, which allows the user to tap into the compressor’s electric engine to control pressure and flow. Being able to match flow and pressure to their application requirements now eliminates the need to have two separate machines.
Performance management system
Advertisement
DrillAir AirXpert furthermore offers up to 30% improved drilling speeds. This performance management system includes software (Dynamic Flow Boost, Dynamic Control and XPR), as well as a LED hardware controller (Xc4003), electronically controlled inlet valve and a variable minimum pressure valve. The Dynamic Flow Boost provides up to 4m³ a minute additional flow when flashing and during drill stem refills. In addition, it gives 10% more flow at lower working pressure for large diameter drilling. The key benefits include quicker flushing, faster drill stem refill, and a shorter time to complete drilling. “Atlas Copco’s XPR (Extended Pressure Range) extends the working pressure range while setting it as low as 21 bar. In addition, the FuelXpert
system ensures fuel efficiency and partial load with an additional fuel filter for better engine protection,” he explains. “The combination of DrillAir AirXpert technology, the Atlas Copco screw element and the Cummins Stage III engine provides high efficiency for a wide range of pressure and flow settings,” Craig adds.
Simple maintenance
With its 500-hour service intervals, the compressors offer customers trouble-free service, quick and simple maintenance and low operational costs. The machines’ centralised drain and air filtration systems facilitate easy servicing; while the design of the new oil separator system reduces maintenance time by over an hour.
A dedicated service door allows for convenient oil level observation and oil filling. A three-layer coating on the body of the machine offers an extended life of corrosion-free service, further contributing to lower operational costs. “Our new compressors have been chosen for their robustness, and the fact that they are therefore wellsuited for use in remote and harsh environments, where support is sometimes hard to access,” Craig concludes. Rand-Air, Tel: (011) 345-0700 Email: info@randair.com, www.randair.co.za
SKF Power
Transmission
Power transmission products are a vital link between moving parts in equipment and consequently play a key role in overall bearing performance. We have developed our own range of power transmission products to help optimise overall machine performance. Well matched to given bearing applications, SKF power transmission products are designed to give engineers a wide design choice according to performance and cost considerations. The SKF power transmission product range includes: Belts, Pulleys, Chains, Sprockets, Couplings, Bushings and Hubs, and Smart Tools. All products are available through our local Authorised Distributor network and backed by our international logistic centres.
Your BBBEE Level 1 Partner
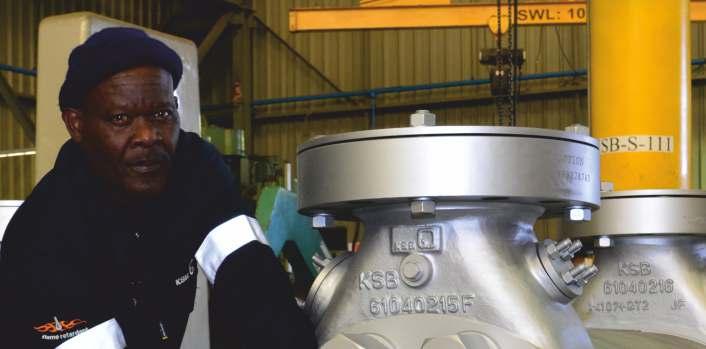
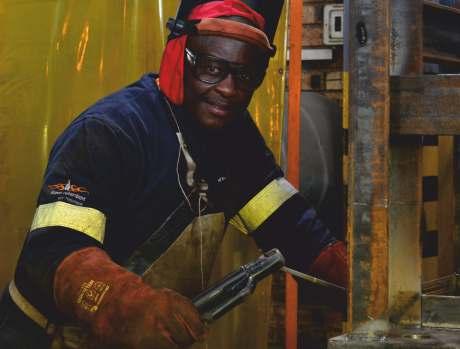
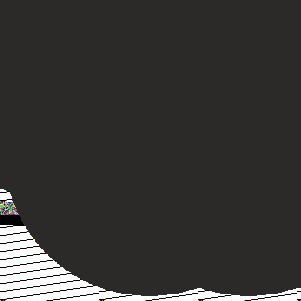
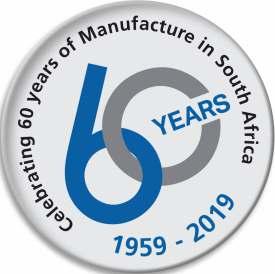
KSB Pumps and Valves, operating out of Activia Park, Germiston, is part of the KSB group, one of the world’s largest manufacturers of industrial pumps, valves and related systems. With a company history that dates back to 1871 in Germany, the KSB Group is one of the most experienced pump manufacturers worldwide.
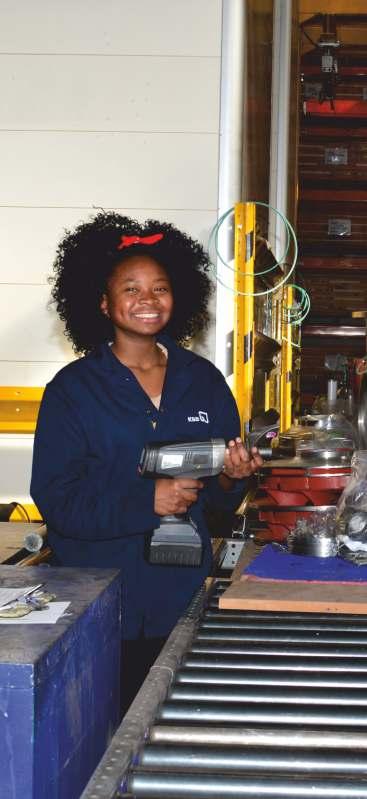
Since 1959, KSB Pumps and Valves South Africa has brought the groups extensive expertise and portfolio of world class products to the Local Irrigation, Water Transfer and Treatment, Water Supply and Sewage, General Industry, Chemical and Petrochemical Industry, Mining and Construction markets.
Setting the Standards for 60 years.
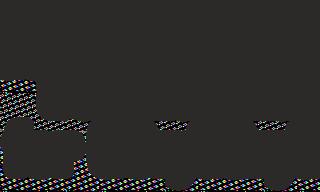
We are one of the largest KSB manufacturing entities outside of Germany and France, and proudly hold the KSB MBK quality certificate. This certificate is issued to KSB manufacturing sites within the group which are accredited to produce the KSB range of world products for distribution worldwide. This noteworthy accolade underscores the quality processes within our facilities and is a testament to our local manufacturing capabilities.
This combined with the group's unparalleled expertise makes KSB Pumps and Valves a leading pump and valve manufacturer in the local South African market.