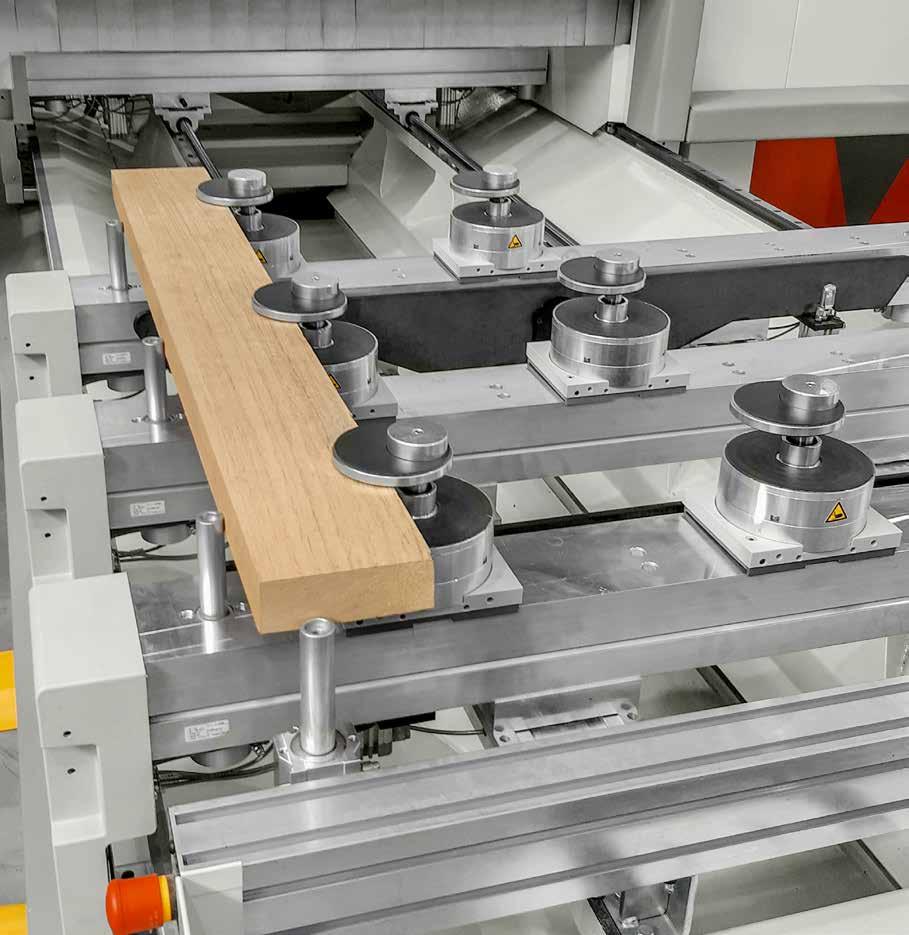
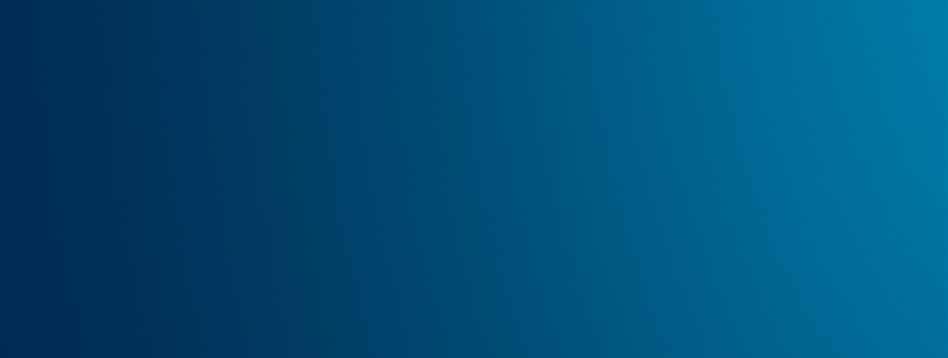

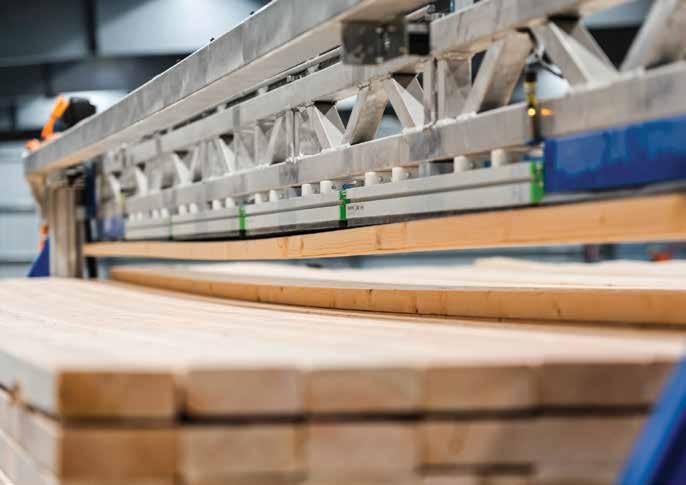
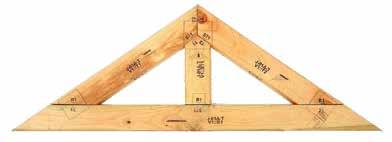


IMPORTED timber prices will increase as, potentially, quality decreases because of the decisions leading to the closure of native timber industry in Western Australia and Victoria, according to a leading Adelaide timber importer.
And Ridgewood Timber’s Jon Eldridge says the next problem is that there aren’t many options.
“When it comes to hardwoods, the ones that stick out are US and Europe,” he said.
“So European oak, American oak and their related species. But that’s going to be very expensive.
“So politicians that have made these calls, they need
to explain to people that if they want to buy a locally made dining table, a locally constructed staircase, the price is now going to go through the roof.”
Ridgewood Timber in Port Adelaide started operations in the mid 80s.
Mr Eldridge said that initially the business revolved around imports.
“Even early 90s it was imports, predominantly from Canada, Southeast Asia, and New Zealand,” he said.
“We still import a small amount out of Southeast Asia. That’s dropped off due to architectural trends and demands, but we still do import products out of Southeast Asia. We do still bring
in western red cedar from Canada and American oak and some products out of New Zealand.”
Mr Eldridge said Canadian and American oak was available, but those regions were under pressure from environmentalists.
“So is it a long term fix? Probably not,” he said.
“Not only that, you’re in the European international wood market. So prices fluctuate, you’ve got foreign exchange fluctuations, which could mean that comparing it to say a Victorian ash select rate board, people could be paying double, if not more, for that same size piece of timber for whatever project.”
Mr Eldridge said the other option was Merbau out of Indonesia, Rosewood out of Papua New Guinea, and various species out of Malaysia.
But the whole world was looking at buying timber from those sources so there was huge demand out of India, Vietnam and China for those species.
Mr Eldridge said that locally architects, builders and retail had over the past 10-15 years moved away from Southeast Asian species purely because of the rhetoric from environmentalists over rainforests and Orangutan habitat.
He said the bottom line for the timber industry following the decisions in WA and Victoria – and potentially
other States - was that jobs will go.
“Not just the jobs at the mills but the supporting businesses - the mechanic in the town, the snack bar, everything.
“Not only that, then the manufacturing jobs such as bespoke furniture manufacturers they’re going to find it harder and harder.
“It’s very short sighted,” he said.
“I think the timber industry will lose out to alternative products such as steel and concrete.
“Composite products is a growing market and we are going to see more and more composite type products filling the gaps.”
Issue 6 – Volume 33
Incorporating Australian and New Zealand Timberman. Established 1977.
News 3-8
Technology 10
Timber preservation 12-14
Associations 16-18
FRONT Cover:
A profile being created on an arched work piece using a Casadei Busellato 5-Axis CNC. Story Page 15
PUBLISHER and Chief Executive:
Hartley Higgins
General Manager:
Robyn Haworth
Editor:
Bruce Mitchell
b.mitchell@ryanmediapl.com.au
Adelaide Office (08) 8369 9512
Advertising:
Jon Andryciw
j.andryciw@ryanmediapl.com.au
Adelaide Office (08) 8369 9517
Creative Services:
Tim Coleman
Publication Design:
Tim Coleman
Timber classifieds: j.andryciw@ryanmediapl.com.au
Adelaide Office (08) 8369 9517
Subscriptions: subs@forestsandtimber.com.au
Adelaide Office (08) 8369 9522
Subcription rates
One-year (8 editions) $59.50
Two-years (16 editions) $103.50
Accounts:
Adelaide Office (08) 8369 9514
Postal Address:
630 Regency Road, Broadview South Australia 5083
Phone: (08) 8369 9555
Fax: (08) 8369 9501
Melbourne Office: Suite 2262, 442 Auburn Rd, Hawthorn VIC 3122 Phone: (03) 9810 3262
Find us on Facebook @AustralasianTimber
Website
IFULLY realise Jack Bowen wrote recently criticising the Victorian Government’s decision to cease native forest production in Victoria (Australasian Timber August 2023).
So why do I as an ordinary employee of Bowens, feel compelled to lend my critical voice to this decision?
In doing so, I confess my love for not only the timber products we sell but also for the trees from which these products come from. There is nothing more exhilarating than driving through the Dandenong ranges admiring giant Mountain Ash trees, gun barrel straight, reaching for the sky. Or the magnificent stand of Californian Redwoods near Warburton.
Interestingly, like 65% of our native forests, the trees mentioned above are in national parks and reserves where logging is not permitted.
I also appreciate during a tree’s growth, they absorb carbon dioxide and store this as carbon in the form of wood fibre and release oxygen into the atmosphere, they are essential and support the biodiversity of the earth. I call trees the lungs of the Earth.
However, as our native forests progress through their
JEFF HARVEY BOWEN TIMBER SPECIALISTactive growth stage, perhaps 80 years to 100 years, eucalypts become mature and branches, leaves and bark fall or break off. Consequently results in, this forests becoming carbon neutral, even carbon negative. If a tree dies or part thereof it will release the stored carbon back into the atmosphere; as is the result during bushfires. There are some misguided thoughts that hardwood plantations will replace the void left by this logging ban. I would ask, where are the established plantations and whether the quality produced by a young regrowth plantation tree will produce the renowned quality from older naturally grown Victorian Ash.
I can recall about 20 years ago a renowned timber producer purchased a plantation to produce structural timber and flooring products which resulted in a failed business. They found the trees had too much growth in the branches and not enough in the stems.
Notwithstanding my timber bias, the government’s decision defies logic and facts (below) as to why this decision has been taken.
Accordingly, I thought I should state the following:
• 65% of our native forests are in national parks and reserves, like water catchments, that cannot be logged.
• The timber industry only harvests 0.04% of the forest estate – the equivalent of only 4 trees in every 10,000!!
• For every tree harvested another is required to be planted… by law!!
• Accordingly, how can this not be considered sustainable!!
• Younger regrowth trees absorb more carbon.
• Some regional Victorian communities will be hit with unemployment.
• Plantations will not fill the logging ban void.
• Expensive hardwood imports may be necessary to fill the void.
• Well-managed native forests can actually provide superior biodiversity, fire and climate outcomes.
Another possibility could be the increased use of non-timber products such as steel, aluminium and concrete. These products consume significant amounts of non-renewable fossil fuel energy to produce, releasing greenhouse gases into the atmosphere. Just compare this to our raw timber that comes from trees that grow from the sun and rain. Also, the carbon dioxide that a tree adsorbs is still present in the timber products we sell. My final comment, I have tried to make my comments non-political, but based on the established facts listed above and with that in mind, the Government’s decision to me makes no sense. That said, they should have reviewed and taken a more holistic view of the timber industry based on the facts. It is an industry I have been proud to say I have been part of for over 60 years.
Two things are certain about Victoria. The premier Dan Andrews plays a mean political game, and certain sections of the media in that State will do all it can - indeed everything it can - to bring him down.
The latest was the story that the Andrews government was being accused of plundering timber from Tasmania after announcing the closure of the Victorian industry.
The Herald Sun reported that the Heyfield Mill, 49 per cent owned by the Victorian Government and operated by Australian Sustainable Hardwoods, has been importing logs from across the Bass Strait for several months.
All true. It was reported in 2021 that the private partners of the Heyfield Mill
australasian
were pursuing the purchase of Artec’s Western Junction Sawmill in north Tasmania. Outrage that the Andrews’ government was commercially killing local familyowned mills in Tasmania by offering above market price for timber logs ensued.
Well, it wasn’t actually the Andrews government was it? It was Australian Sustainable Hardwood, or more precisely two of ASH’s most senior directors – managing director Vince Hurley and company secretary Ian Jones and their privatelyowned company.
Mr Hurley told The Australian in 2021 that the pur-
chase of Artec’s mill would be by a company he founded with Mr Jones for that purpose.
The deal would be at arm’s length from ASH, he said.
“Yes, we will sell some timber to ASH but we will also be selling timber to some of the existing Artec customers as well,” he told The Australian.
He said the Victorian Government had nothing to do with management of ASH and no link to Western Junction Sawmill.
It was indeed a clever move by Mr Hurley and Mr Jones. With the end of the native timber industry in Victoria in sight they sorted a way of staying in business.
That’s simply good business sense.
Again, all true. But deep down it’s the hypocrisy that
rankles.
Victorian Nationals Leader Peter Walsh pointed out that while he was not opposed to commerce, it was “hypocritical that the Andrews Government would close the Victorian industry down but be a major shareholder in a business that’s now going to Tasmania to buy timber to bring back to Victoria”.
When asked about the importation of Tasmanian wood to Heyfield a Victorian Government spokesman said: “The Andrews Labor Government is supporting mill workers across the industry, including at Heyfield.”
The hypocrisy of that statement is outrageous.
SALES of new homes across Australia fell by 2.4 per cent in July, continuing to bounce along very low levels, according to the Housing Industry Association’s Senior Economist Tom Devitt.
The HIA New Home Sales report – a monthly survey of the largest volume home builders in the five largest states – is a leading indicator of future detached home construction.
“This month’s decline leaves sales in the three months to July 2023 down by 33.4 per
cent compared to the same period in 2022,” Mr Devitt said.
“Weak new home sales, together with an elevated number of previous sales being cancelled, reinforce the expectation that Australia will see a decade-low level of home building next year. Even a cut to the cash rate now would not produce a recovery in new house commencements until the second half of 2024.
“Underlying demand for housing continues to be supported by population growth,
acute shortages of rental accommodation and strong employment figures.”
Mr Devitt said that meeting the appropriate levels of new housing for Australia’s current and future population would require changes to the other policies that inflate construction costs. These were not only interest rates, but also tax settings, land release and planning reforms, and macro-prudential rules that squeezed out owner-occupiers and investors alike.
“The National Cabinet’s
recent announcement to increase its five-year housing supply target is a welcome step in the right direction,” Mr Devitt said.
“Coordination among all levels of government and the industry will be crucial to achieving this goal.”
Compared to the previous month, sales in July 2023 decreased in most of the large states, led by Queensland (-11.6 per cent) and followed by Western Australia (-9.3 per cent), New South Wales (-1.6 per cent) and Victoria (-0.6
per cent). South Australia was the only state to see an increase (+35.5 per cent). Similarly, sales in the three months to July 2023 decreased compared to the same period in 2022 across most of the large states. This was led by Queensland (-52.3 per cent) and followed by New South Wales (-48.4 per cent), Victoria (-37.2 per cent) and South Australia (-26.0 per cent). Sales in Western Australia on the other hand increased by 17.3 per cent.
Designed and engineered for high accuracy cutting
Two head saw configuration
Digital controllers allow accurate saw wheel positioning
Automatic blade tension is controlled by hydraulic cylinders
Variable feed speed by hydraulic motor drive
Large horsepower Seimens or equivalent saw wheel motors drive the blades allowing for heavy-duty cutting
The conveyor belt is driven by a high performance hydraulic motor
Adjustable feed speed allows flexibility to saw hard and soft wood
Full wheel and blade lubrication
Low maintenance Safety cage.
IT started with a bold idea. It progressed because of an unwavering belief that it could be done. And in June 2021, the newly branded Cusp Building Solutions launched the first certified plantation hardwood CLT in the world.
From a resource traditionally used for woodchips, Cusp now creates a range of mass timber elements for the built environment. Cusp is now set to relocate to a larger manufacturing facility to enable an immediate increase in production of 100 per cent, with further increases planned for the medium and long term.
“Having proven our capability and established market demand, Cusp Building Solutions is now ready to scale,” said founder Ron Goldschlager.
“Up until now, Cusp has been a start-up. The start-up phase was hampered in no small part by the global pandemic. Still, we are excited to begin the commercialisation process of significantly increasing our manufacturing capacity,” he said.
In the start-up phase, Cusp has exceeded expectations, proving its R&D capability with a series of both world and national firsts, including:
The first certified plantation hardwood Cross Laminated Timber (CLT) in the world.
The strongest CLT in the world.
The only CLT certified by the Engineered Wood Products Association of Australasia (EWPAA) in Australasia.
The first and only 120-minute Fire Certification
The world’s thinnest CLT
The largest Glue Laminated Timber (GLT) beam capacity in Australia
The only curved GLT manufacturer in Australia.
The company will now strategically invest in people, machinery, and facilities to meet market demand and price expectations and has invited expressions of interest from investors who want to partner with Cusp to accelerate growth.
Bold ideas have become the norm at Cusp, and the current construction of Launceston’s $30 million, 28-metrehigh timber building which will house Tasmanian health insurer St Lukes Health in
Launceston is a case in point.
Encompassing 500m2 of Cusp CLT, it also aims to be the first building to have a zero-carbon footprint, showing what’s possible in the built industry when it comes to the adoption of mass timber.
The CLT posts and beams were originally slated to come from Austria because Cusp could not supply them at that time.
But Cusp General Manager Michael Lee had a think.
“After we looked at it we realised that we had missed out on how that would have a whole heap of work,” he said.
“We just didn’t have a press so management decided to go ahead and purchase press so we could make those beams.
“We got a press designed and made in China to our specifications
“So we have the capability now, which is a great story,” he said.
Mr Lee said Cusp’s biggest challenge at present was continuity of supply out of the Tasmanian plantation resource.
“We’ve got no guarantees. There seems to be a bit consternation about who’s getting what and we need that to settle down,” he said.
“We really need one of the big players to put in a sawmill so they can push sawn board upstream.”
Cusp has two ways it sources timber.
“We opportunity buy which has been great and companies like Brittons, McKays and Neville Smith really supported us. Porters as well to an extent when they can,” Mr Lee said.
“But they’ve got a sporadic supply of plantation as well.
“There needs to be some firmer process from Sustain-
market or looking at other products.
“If one of those big guys actually jumped in and then work with all of us pushing timber upstream Tasmania would be in a great position.”
products both in board and in mass timber out of this Grandis.”
able Timbers Tasmania on what’s going where and how much the real volumes are. But I think the real key to drive this to where we want to get to - and we want to get to 1000 cubic meters of mass timber a month - I need a major company to defray the risk of just putting chips into the
While Eucalyptus Nitens is the plantation timber that Cusp was founded on, the company also produces products from other plantation sources, including Grandis, a eucalypt from Urofor in Uruguay, and Spruce, a plantation-grown European softwood.
“We’re getting Grandis from South America, from Uruguay specifically, which is a different product for a different market,” Mr Lee said.
“We make a few appearance beans out of it for the market but we’re developing a new range of appearance
Cusp now plans to double production by late 2024 and expects to be manufacturing four times its current monthly throughput with further increases planned beyond that time.
To facilitate the expansion, Cusp is working towards relocation to a larger facility at Deep Creek in Tasmania. The facility is designed for both GLT and CLT production volumes. It is anticipated that this will be the new home of Cusp for the medium term.
“We are hoping to be firing up at Deep Creek by the end of September or early October,” Mr Lee said.
“And we’ll by that stage, we will have nearly doubled our workforce.”
AFTER a successful campaign in 2022, FWPA’s The Ultimate Renewable 2023 campaign went live across Australia on August 20.
The imagery in the new television commercial and campaign challenges the current consumer perceptions of forestry, showing harvested and then replanted trees to reinforce The Ultimate Renewable positioning.
The new campaign was launched across free to air television, streaming video, out of home, radio, and social media, and is once again presented by popular ambassador Adam Dovile, builder and television presenter.
While last year’s message focussed primarily on wood as a building material, the new campaign extends the communication from seedlings to final product and promotes the transgenerational benefits of wood.
Accompanied by videos and images of forestry and children in wood-rich environments, the messaging conveys that by growing and using more certified wood we
can tackle climate change for future generations.
“This is an opportunity to reshape consumer perceptions of the industry,” said Sarah Downey, Head of Marketing and Communications at Forest & Wood Products Australia (FWPA).
“People are naturally saddened when they see images of a newly harvested forest
area, but what they don’t think about is the climatechange-tackling carbon stored in the wood that’s been removed from the atmosphere by growing trees and the replanting of the trees for future generations.
“Sustainably sourced wood is an important renewable building material, and we should be supporting and
celebrating the renewable aspects of its production and use.”
The 2023 campaign is expected to achieve great results after the previous campaign resulted in one quarter of Australians recalling seeing at least one of The Ultimate Renewable messages.
The 2023 media buy will see the commercial run through-
out top-rating programs such as The Block, Seven and Nine news and both AFL and NRL matches, including their finals series via video on demand.
A wide range of free-to-access campaign materials will be available in The Ultimate Renewable Digital Toolkit, on the new website – theultimaterenewable.com.au
The highly successful Timber Offsite Construction Conference and Exhibition (TOC) scheduled for September 11-12 at Crown Promenade Melbourne has now finalised the extensive speaker line up.
Now in its 24th year, conference host Andrew Dunn confirmed the speaker sessions program is aimed directly at design professionals looking at the design and construction of timber buildings. The primary focus is on commercial-ready applications of timber technology.
Speakers will cover a diverse range of topics such as why to consider timber, how to select appropriate timber systems, avoiding common problems, and innovative construction methods.
The high level program includes Andrew Ball from oWoW presenting on the use of post and plate (pointsupported) high-rise timber buildings he is developing in California, and Anders Carlsson from Derome, Sweden, who is talking on how he can build the superstructure of a six-storey timber framed building in three days.
oWOW is an exciting new firm undertaking cutting-edge timber con-
struction in California. It is a vertically integrated company whose mission is to build homes that people love at affordable prices. They have an in-house Development, Design, Construction and Property Management team with a vision for a sustainable building product that is repeatable, highly sustainable and provides affordable luxury housing to the middle income.
MONDAY 11 SEPTEMBER 2023
8.00 am Delegate Registration
9.00am The sustainable future for timber buildings
11:00am Design Process for 8-Storey Building
12.30pm Lunch Break
1.30pm Building Design Challenges & Solutions
3:30pm Latest and greatest timber developments
5.00pm Delegate Hospitality
TUESDAY 12 SEPTEMBER 2023
8.00 am Delegate Registration
9.00am Global Developments & Trends
10:30am Construction Process for 8-Storey Building
12.30pm Lunch Break
1.30pm Iconic Buildings – Case Studies
4:00pm Future Concept Buildings and Cities
5.00pm Resilient Timber Homes Design Competition Awards
Their construction system of choice is a point support (post and flat plate) timber construction system. A timber point support system is a system that uses mass timber floor panels supported on columns only. The columns are spaced along the mass timber panel edge at 3.0 m centres, removing the need for beams. The system was first used on the Brock Commons, an 18-storey student accommodation building in Canada. It was exceptionally fast to build, and this feature is being repeated in this project.
oWoW is currently building 18 storeys of mass timber over a one-level concrete podium in Oakland, California. Called 1510 Webster, it is 57 m tall and includes 222 residential rental units, 900 m2 of offices, and 270 m2 of ground-level retail/commercial space. Of the residential rental units, 35 are designated as affordable for households earning 80% of the Area Median Income.
oWow claims that their previous projects are 25% faster than a standard concrete building of similar size. They further claim to save 20% on cold shell costs and an even better 31% on total savings.
The 1510 Webster building will become the second tallest mass timber building in the USA. The tallest mass timber building in the country and the world is the recently completed Ascent Building in Milwaukee. However, they will be challenging this record with their next project, 1523 Harrison St, at 25 storeys.
Other presenters are advising on fire safety issues, including an update on
the EuroCode 2025 fire section and a research program of compartment fire tests in Canada. Presentations also include discussion on emerging technology in mass timber and digital tools to optimise timber construction.
Rounding out the conference program are two iconic building case studies, Murdoch University Boola Katitjin building in Perth, and Hines T3 Collingwood 15-storey timber building in Melbourne.
One-third of the TOC conference’s outstanding speakers are international, from USA, Canada, New Zealand, Sweden and Estonia. Dunn emphasises that the program and speakers are the most impressive of all previous TOC conferences.
Mr Dunn said TOC 2023 anticipates an even larger turnout, attracting industry leaders and professionals eager to explore the potential of timber building construction, both from Australia and overseas.
OUR series of case studies draws on past winners and short-listed projects in the timber veneer category of the Australian Timber Design Awards. This issue we look at an Australia Post office fitout in Melbourne by Geyer Design.
The project used a range of Australian hardwoods, including sugar gum and spotted gum, combined with the darker tones of European walnut veneer.
Native to South Australia, sugar gum has been trialled as a plantation species in Gippsland. It was chosen by Geyer Design for its golden tan
colour and attractive grain. Its hardness and durability were important features for high traffic areas and stairs. Recycled spotted gum was used for planter boxes and cladding to benches.
Darker coloured European walnut contrasted with the sugar gum and spotted gum. The FSC certified walnut was used for ceiling panelling and table tops. In the reception area walnut panels were installed on the diagonal in an ashlar pattern (see image). Walnut panels were also la-
Made
ser-cut in a motif referencing the edges of stamps to create a screened element for privacy areas.
Timber veneer was combined with solid timber to create an overall theme of the Australian metro and suburban environment. Darker colours evoked a feeling of the traditional Melbourne CBD, while the detailing of tables, and a pergola-like portico, aimed for an outdoor terrace quality.
Walnut is one of the many exotic species that are avail-
able in the form of veneer but would be difficult to source, or prohibitively expensive, in the form of solid timber.
Detailed information on the specification of timber veneers, including panel terminology, methods of assembling and matching, substrates, finishes and more. can be found on the Timber Veneer Association’s website at timberveneer.asn. au. Current projects are also featured on the Association’s Facebook page.
ECI Software Solutions, a global provider of cloud-based business management software and services, has announced the launch of Spruce eCommerce, an innovative ecommerce solution purpose-built for the unique needs of timber, building material supply, and hardware businesses.
“Spruce eCommerce is an exciting product because it allows users to build a sleek, professional storefront website and customer portal without needing any expertise in coding or web development,”
John Maiuri, division president, LBMH, ECI Software Solutions, said.
“For consumers and tradespeople, this means unlocking the ability to shop online for delivery or in-store pickup, browse products, create accounts, build self-service quotes, pay invoices and more.
Designed as an all-in-one ecommerce solution and backed by ECI’s website design and digital marketing team, Spruce eCommerce features built-in marketing tools such as abandoned carts, content pages, blog tool, drag and drop layouts, rewards and loyalty programs, badges, banners, customer segmentation, reports and Google Analytics.
“Not only does Spruce eCommerce have the features and functionality we need to succeed, but having only one provider for both our core business system and webstore greatly simplifies operations,” Brent Burrows II, a Spruce eCommerce user, said.
“ECI sees the big picture and understands our longterm growth goals. We’ve been operating in the ecommerce world for about 3.5 years now, and this is the first time I’ve felt excited about the future and our ability to evolve with a system that easily scales as we grow.”
Spruce eCommerce also includes a Spruce-proprietary Product Information Management (PIM) system and pre-built taxonomy for implementing the software faster, seamlessly adding products to the ecommerce storefront and housing content customers need to make informed buying decisions.
MANY of the things we buy are classified with star ratings, from fridges to even our most expensive investments – like our homes.
A home’s energy star rating is judged using tools like The Nationwide House Energy Rating Scheme (NatHERS) alongside the mandatory energy efficiency requirements set out in the National Construction Code (NCC).
NatHERs uses software based on scientific research by the CSIRO. It analyses house plans to identify how much energy will be needed for heating and cooling to determine a home’s energy star rating. The more stars a home has, the more can potentially be saved on energy bills, the higher the home’s potential resale value, and of course by reducing energy needs there’s a benefit to the environment (Dept. Industry, Science and Resources, 2017).
Builders use NatHERs to show new homes or renovations meet minimum energy requirements. In 2022 the NCC updated requirements, and now states all new home building shells must have a minimum energy efficiency of 7-stars.
This is a big deal, as in 2019 research from RMIT revealed that 80% of new housing in Australia was only built to the minimum standard (at the time 6-stars), and less than 1.5% were built to the
optimal environmental and economic performance of 7.5-stars (RMIT, 2019). This is where timber framing comes in.
In timber framed homes actual energy performance is often higher than when using other materials. Many builders have reported that by using timber framing, they have been able to achieve home energy star ratings
above 7.5-stars. Additionally, market leaders and many informed homeowners are already reportedly aiming for homes that are 8-stars and above (Sustainability Victoria, 2023).
Studies by the CSIRO and Forest & Wood Products Australia (FWPA) both found that when assessing building materials for thermal bridging, timber framing conducts heat at a much lower rate, and that steel frames required greater insulation to perform on par (FWPA, 2021).
Thermal bridges give heat an easy pathway to escape, reducing the effectiveness of insulation and a building’s energy star rating. In an airtight and insulated home, thermal bridges can account for heat loss of 20- 30%. This
directly impacts star ratings generated by NatHERS (Carbon Futures, 2022).
While thermal bridging occurs in both timber and steel frames, timber framing conducts heat at a much lower rate, adding resistance to heat loss from a home.
The CSIRO found that thermal bridging can decrease a building’s energy rating by:
– Up to 0.4 stars for a timber framed home
– Up to 0.9 stars for metal framed designs with a thermal barrier
– Up to 1.2 stars for metal framed designs without thermal barriers.
When comparing building materials and planning for higher energy star ratings for our homes, it’s clear timber framing is the natural choice.
ITI Australia, a leading timber and building products distributer, has positioned itself as an industry trailblazer by prioritizing sustainability.
Since its establishment in 1987 in Five Dock, NSW, Independent Timber Importers (ITI) has been on a mission to redefine the timber industry wholesale/distribution landscape.
ITI has worked closely with industry suppliers, customers and associations to promote the strength, beauty and environmental benefits of using timber.
At the same time ITI redefined the role of the wholesaler with its distribution and service models.
With its large investments in distribution centres, product development, people and service standards in early 2002 ITI dropped the name Independent Timber Importers and replaced this with ITI and introduced the new logo with the “Innovative Timber Ideas” phrase which more accurately describes the attitude of the company.
Today ITI consists of nine distribution sites across Australia with 130,000m2 of undercover storage, a state of the art remanufacturing, treating and priming plant in Chile, an office in Indonesia, two distribution locations in New Zealand and growing sales in the USA.
True to its name, the success of ITI lies in its commitment to innovation in both service and product development. This commitment has led to the development of premier brands such as Design Pine and EziTrim Plus, the distribution of market-leading products such as KlevaKlip, Weathertex and Modwood.
Responsible Wood
Manager Matt de Jongh and Sydney Branch Manager James Bailie recently caught up at the ITI facility in Sydney and shed light on ITI Australia’s commitment to responsible practices and its collaboration with Responsible Wood.
Through their dedication to responsible forestry and innovative timber solutions, ITI Australia continues to lead the way towards a more sustainable future.
“ITI Australia’s unwavering commitment to sustainability is truly commendable,” Mr de Jongh said.
“Their integration of responsible practices and innovative technologies sets an inspiring example for the entire industry.”
Mr de Jongh said Responsible Wood certification ensured that the timber used by ITI Australia is sourced from responsibly managed forests, safeguarding biodiversity and supporting local communities.
He said that this dedication to responsible resource management was crucial for a sustainable supply chain.
“At ITI Australia, we believe in promoting sustainable practices throughout our operations,” Mr Bailie said.
“Our collaboration with Responsible Wood enables us to provide our customers with timber products that are sourced responsibly.
“By utilizing timber certified by Responsible Wood, we support responsible forestry practices and contribute to the overall health of our environment. Additionally, the certification guarantees that our customers can trust the sustainability and quality of the timber products they receive from ITI Australia.”
ITI Australia’s history is marked by its continuous efforts to redefine the timber industry wholesale/distribution landscape. With a deep commitment to innovation, the company has invested in distribution centres, product development, and service standards.
“Since our establishment in 1987, we have strived to promote the strength, versatility and environmental benefits of timber. We have built innovative brands such as Design Pine, Flamefixx and EziTrim Plus, while also partnering with industryleading products like Weathertex, Easycraft and Modwood,” Mr Bailie said.
ITI Australia stands out as a trusted partner for responsible timber solutions. With the Responsible Wood certification, customers can have confidence in the environmentally conscious practices followed by ITI Australia.
“By choosing ITI Australia, customers are making a conscious choice to
support responsible resource management and contribute to a more sustainable future,” Mr de Jongh said.
ITI Australia’s commitment to sustainability, coupled with its collaboration with Responsible Wood, has
positioned the company as an industry leader in providing innovative and responsible timber solutions. It is evident that ITI Australia is dedicated to responsible forestry practices, supporting local communities, and preserving biodiversity.
The family owned 138-yearold Hyne Timber company is continuing to call for government support to direct Australian nsaw logs destined for China to its mill in Tumbarumba.
Chief Executive Officer Jon Kleinschmidt said employees and the community were increasingly concerned about the mill’s future following last summer’s devastating bushfires, which decimated 40 per cent of Hyne’s local log supply.
Following discussions with private growers in Victoria and South Australia, Hyne Timber has confirmed at least 441,000 cubic metres of sustainably grown, plantation pine can be made available to the mill over the next three years.
THE CONFEDERATION of Timber Industries (CTI) has announced the reconstitution of the Timber Industries All Party Parliamentary Group (APPG), following the general election.
The Timber Industries APPG will help promote timber as the most sustainable and renewable building material and develop initiatives and economic measures to grow the whole UK Timber Industry supply chain. The Confederation of Timber Industries will assist Parliamentarians in their work by acting as the group’s secretariat and providing relevant information and logistic support.
RESEARCHERS AT the University of Melbourne are reporting the success of a remote monitoring device that can accurately measure decay and insect infestations in construction timber over vast distances – and could save Australia’s building and electrical distribution industries, millions of dollars.
The wireless device, which will eventually fit into the palm of a hand, can be attached to timber beams, joists or power poles, where it monitors at predetermined intervals their structural integrity, moisture content, and – through an ingenious ‘listening device’ – the movement of termites and other wood-boring insects.
LEWIS (‘Lew’) Fisher started working for his father, William Fisher, in the 1960’s at the family’s hardware and plumbing business based in Korumburra, South Gippsland, Victoria.
William Fisher had started the business in the 1930’s as a bricklayer and built up the business to operate on three sites (retail shop and two yards). The business included timber preservation, plumbing and building supplies.
After William passed away in 1974, Lew got out of the hardware/plumbing business and focused on timber preservation with a pressure wood treatment plant, carting timber from Crawford’s Mill in East Gippsland to Korumburra.
In 1979, Lew Fisher opened a timber preservation business called Fishers (Latrobe Valley) Pty Ltd at 30 Swan Rd Morwell, providing Copper Chrome Arsenic (‘CCA’) treatment.
The CCA Treatment was mainly fence posts (round poles) using a pressure treatment process. Lew increasingly operated from Morwell, while his wife, Elaine Fisher, kept the Korumburra treatment business operating.
In 1998 the timber preservation side of the business was incorporated as a separate entity called Fishers Timber Preservation Pty Ltd which specialised in custom treatment of hardwood and softwood timber for wholesalers and mills.
Fishers (Latrobe Valley) Pty Ltd continued to manufacture and supply timber pallets. The two business today
operate from adjoining sites in Morwell.
Lew’s daughter Catherine Fisher manages both businesses on a daily operational basis.
Lew was always very passionate about wood treatment and interested in new technology and processes.
Lew was heavily involved in the TPAA (Timber Preservers Association of Australia) and the Melbourne branch of the Hoo Hoo Club (The Fraternal Order of the Forest Products Industry) for many years.
Fishers changed over from LOSP (light organic solvent preservatives) to water-based Tru-Core by KOP-Coat around 12 years ago. Fisher’s were the first in Australia to use this technology.
Tru-Core Wood For Life by Kop-Coat is the most advanced wood treating technology in the world – capable of penetrating normally regarded hard to treat species.
The water-based treatment is a U.S. invention and achieves glue-line penetration of plywood and manufactured products (eg. glulam beams, lvl).
Fisher’s timber treatment does not contain volatile organic compounds (VOC) and is a low uptake process which does not damage engineered timbers, for example LVL, glulam and plywood.
The pressure impregnated treatment is a safe waterbased treatment that goes above and beyond the Australian Standards.
H2 and H3 treatments penetrate both sapwood and heartwood fibres, providing superior protection to your timber.
By treating timber, you are making it resistant to forces of nature such as rot and decay—as well as protecting it from termite or borer attack.
FISHER’S TIMBER TREATMENT IS AVAILABLE IN:
H2 red –to minimise the risk of an attack by insects and termites.
• inside above-ground applications.
• typical uses are framing, flooring and any other dry situations.
H3 –to make timber resistant to termites & borers, fungal decay and rot.
• Outside, above-ground
• Used in weatherboards, fascia, pergola posts, window joinery, framing and decking.
AFTER 33 years, Davids Timber remains focused on providing its customers with quality treated timber products and a high level of customer service.
Davids Timber, based in Dandenong South, are wholesalers supplying merchants, fencing suppliers, landscape and garden yards, and rural stores.
The company’s core range of products includes fencing, landscaping, structural, decking and rounds preservative treated with either CCA H3 & H4, Micropro H3 & H4 and LOSP H3.The company also carry a full range of Cypress Pine posts. No other business in Victoria has the ability to offer such a range of products, treatments and services.
The company history dates back to 1990 when Davids Timber started trading in Frankston Dandenong Road, Dandenong, supplying trade
and retail customers with fencing timbers.
In the early 1990’s, David and Maurice Efron made the decision that treated pine was to become the future of the industry and built their first treatment plant in 1994, and have continued to develop and expand the business since then.
Today the company operates from its substantial site located at 29 Princes Highway Dandenong South. Davids Timber has continued to invest on this site where all processing including kiln drying and preservative treatment takes place.
The most recent upgrade being the installation of a larger Mahild kiln which allows Davids timber to offer a custom service for kiln dried softwoods and hardwoods, as well as offering custom treatment service.
The company has also recently invested in solar panels, water tanks to col-
lect roof water, as well as increasing their hard stand area.
Other recent improvements include online delivery tracking for our customers, improving overall customer service and on time delivery performance.
Maurice Efron, as Managing Director, remains very active
in the business and is backed by a strong executive team including General Manager ,David Caroselli, Operations Manager, Terry Chinnock, Sales Manager ,Tim Lovell and Finance Manager ,Rosie Garbett.
Maurice believes one of the key reasons a business succeeds is by having a great
culture and team. “We have a wonderful mixture of experienced and younger people who are all focused on delivering a high level of customer service and supplying quality timber products,” he said. “We never rest on our laurels and are always aiming to continuously improve.”
SINCE 1929, nestled in the verdant heart of New Zealand’s Eastern Bay of Plenty, Tunnicliffe Timber’s story has unfurled, borne of resilience, innovation, and a deep respect for the land.
Today, standing at the forefront of advanced timber technology, Tunnicliffe continues to craft the future of sustainable construction, its roots reaching back almost a century.
The Tunnicliffe narrative traces back to humble beginnings as a native sawmilling operation, an endeavour as enduring as the timber it transformed. As the decades unfurled, Tunnicliffe weathered a pivotal merger, a name change, and the Kawerau pulp mill surge of the mid-20th century. The latter, in particular, propelled Tunnicliffe into a vortex of growth and innovation.
1997 marked a shift, as the original Tunnicliffe family name was reinstated. This nostalgic reversion offered an opportunity for introspection, a chance to honour a
rich heritage whilst charting a trail into new territories.
The dawn of a new era arrived in 2018, under the stewardship of Mark and Elizabeth Andrew.
Their innovative vision, geared towards sustainable timber treatment, earned support from the Provincial Growth Fund (PGF) via the Kānoa – Regional Economic Development & Investment Unit, enabling Tunnicliffe to embrace cutting-edge thermal modification technology.
Tunnicliffe’s long-standing relationship with thermally modified timber can be traced back to 2003/2004. Back then, the company became the proud owner of New Zealand’s first-ever thermal modification kiln, an open system. This early adoption armed the company with unrivalled local expertise in the realm of thermally modified timber.
Their mastery over this open system granted Tunnicliffe deep insights into its
strengths and shortcomings. Recognising a need for progression, the company charted a course towards a more resource-efficient closed system. This move not only amplified efficiency but accelerated processes, encompassing every imaginable feature, save for a cup holder.
The creation of Tunnicliffe TMT+H3.2 involves a twostep process, each contributing uniquely to the final product’s characteristics. The journey begins with the application of Thermal Modification Technology (TMT) in a carefully controlled closed system. This pivotal step enhances the dimensional stability of the timber, improves its thermal insulation properties, and ramps up its resistance to decay, rot, and woodboring insects.
Contrary to the open system variant, the closed TMT system retains a fraction of the timber’s moisture content. This residual moisture is integral to the next stage
of the process, catalysing an exothermic reaction and establishing the ideal conditions for interaction with the MCA treatment.
Subsequently, the timber undergoes a Light Organic Solvent Preservative (LOSP) application of Micronised Copper Azole (MCA), a cutting-edge preservative employing copper and an organic co-biocide, azole. This pressure-impregnated solution adds an additional layer of durability and resilience to the thermally modified timber, providing robust resistance against fungal decay and insect attack.
THE RESULT: PERFORMANCE & AESTHETIC EXCELLENCE
Tunnicliffe TMT+H3.2 represents a composite greater than the sum of its parts. It combines the stability and thermal insulation of TMT with the resilience and decay resistance of MCA, arming a readily available softwood with the superior attributes of high-end hardwoods.
Moreover, Tunnicliffe TMT+H3.2 is a visual delight,
UK insurance company Aviva has underlined its sustainability commitments by expanding its underwriting appetite to include engineered timber in commercial developments.
This follows a successful pilot, which saw the UK’s largest insurer working with a handful of developers on sustainable building projects.
In the UK alone, the built environment contributes 40% of
carbon emissions. By working with contractors who want to build more sustainably, Aviva aims to help the construction and real estate sectors reduce their carbon footprint.
Although a growing number of developers are seeking to build more sustainable buildings for commercial use, insurer appetite for these risks has not kept pace. By putting significant underwriting capacity towards these projects,
Aviva is demonstrating that risk management can support the UK as it moves to become climate-ready.
Aviva is one of the first UK insurers to commit dedicated underwriting resource for the development of more sustainable buildings.
Working with contractors, brokers and owners from the design stage, the insurer is helping to ensure the resilience and repairability of
buildings by using leading risk management strategies to safeguard them from water damage and fire.
Putting risk management at the centre of the design process can help to remove or mitigate these risks, while enabling a competitive and sustainable approach to insurance pricing.
“There are a growing number of developers looking to build more sustainably, both
exhibiting a captivating colour palette of Gold, Orange, and Caramel tones. This aesthetic transformation offers architects, homeowners, and tradespeople a high-performing, environmentally friendly, and aesthetically pleasing alternative to imported hardwoods for exterior design applications.
THE KEY: THE CLOSED SYSTEM TMT
The closed TMT system plays an essential role in the success of Tunnicliffe TMT+H3.2. It ensures a uniform distribution and enhanced penetration of the MCA preservative, significantly contributing to the timber’s overall performance and unique visual appeal.
In essence, TMT+H3.2 presents the industry with a sustainable alternative to imported hardwoods and exotic timbers. It elevates local, renewable Radiata Pine to unmatched levels, making it a preferred choice for ecoconscious builders, architects, and specifiers.
by using sustainable materials like engineered timber, and by adopting modern methods of construction,” Adam Winslow, CEO, UK & Ireland General Insurance, Aviva, said.
“Aviva wants to embrace both: widening our underwriting appetite to insure commercial buildings using engineered timber, and using our risk management expertise to minimise associated risks."
THE Stirling Group has become the authorised Australia and New Zealand distributors of Casadei Busellato woodworking machinery.
The Italian manufacturer’s product line includes 5-axis CNCs, wide belt sanders, spindle moulders, thicknessers, surfacers and sliding table saws, and more.
The Stirling Group’s Craig Honeyman says the distributorship represents yet another way the Group can service customers’ needs with high-quality machinery.
“We’re making a strong foray into the furniture and joinery industry,” he says. “We originally brought on Bacci, another incredible Italian machinery manufacturer, as a starting point, and we’ve had our eyes on a couple of other suppliers. Casadei Busellato fulfils the complete range for us.”
Aside from the company’s longstanding reputation for excellence, another compelling feature of Casadei Busellato is that it offers versatility along the spectrum of business size and output. As such, The Stirling Group can support customers utilising very simple manual operations through to industry-leading technology-driven machines.
“With Casadei Busellato on board, we can service businesses from sole traders through to high-volume manufacturers,” Craig explains. “We can cater for anyone going into CNC for the first time, right up to quite intricate 5-axis CNC work. And we can supply traditional machinery as well as the high-end automated equipment.”
Leon Botes, Group Product development Manager for The Stirling Group says the Casadei Busellato offering opens up a wide array of options for customers.
Six models of wide belt sanders are on offer, starting with the Libra 10, catering for small artisan shops right up to the Libra 65X for large factories requiring high production rates.
Leon says the Libra 45 model will be an excellent addition to most factories, equipped with technologies that are usually only available on larger machines, which makes it a very versatile machine for small to medium size factories.
“A unique feature we are really excited about,” Leon says, “is their Sanding Belt/Feed Mat Optimising System. This feature shows the operator the optimal position to place the workpiece to optimise the sanding belt and feed mat wear by means of coloured LEDs.”
Casadei Busellato offers three ranges, starting with the basic range with manual adjusting through to the top
range offering NC adjusting and electronic programming, ensuring quick and precise setups.
The F235 Spindle Moulder will be a welcome option for small to large factories, equipped with NC adjustment for the spindle and fence positioning and the option to add an HSK spindle for quick tool changes.
“We’re particularly thrilled with the heavy-duty independent tenon table for the spindle moulder. It provides the ability to process large tenons with a cutter diameter of up to 300mm.”
There are two models in pod and rail CNCs, starting with the Jet Elite, available in 3- or 4-axis, with a set working area of 3115mm x 1320mm. The Jet Master T is available in 3-, 4-, and 5-axis, with a maximum working area of up to 5515mm x 1620mm.
Leon says the Jet Master T–XL will be a particularly attractive solution for door and staircase manufacturers, offering a 5515mm long X-axis, ideal for machining long frames and stringers.
“We know our customers will be excited by the IMCs (Interchangeable Modular Cups), supporting the whole range of vacuum pods and clamps and offering the flexibility to use the bestsuited support for any application.”
On the CNC side, Panel Tools (The Stirling Group’s CNC tooling business) will be supplying the tooling package to go with the Casadei Busellato machines. Panel Tools specialises in supplying CNC tools and producing custom tools for the flat panel and solid timber manufacturing industries. Its co-founder and co-director, Fraser Killen, says there is an obvious synergy in the partnership.
“We see Panel Tools as being another jewel in the crown for The Stirling Group’s Casadei Busellato distributorship,” he says. “Even the most elite machinery in the world can only be as good as the tooling used with it. We are already known by our customers to go the extra mile to help. Not only is our tooling of the highest quality, but we also provide custom tooling options to suit specific purposes.”
Leon says that bringing together The Stirling Group, Casadei Busellato, and Panel Tools creates a powerful supply line for customers in the furniture and joinery industry.
“Having them all under the one umbrella is fantastic,” he says. “When we talk about supplying mul-
tiple machines to the same customer, all from the same brand, it makes it easier to interlink the equipment. Also, when customers set up a brand new factory, if we can accommodate that with the same brand of machinery throughout, it streamlines everything.”
Craig is keen to point out that the Casadei Busellato distributorship means The Stirling Group can also look after the manufacturer’s existing customers in Australia and New Zealand.
“Honestly, Casadei Busellato machines are built to last and offer many years of reliable service,” he says. “In terms of support, maintenance, and servicing, we’re here for all Australian and New Zealand Casadei Busellato users. If they have questions, we’ll have answers. If they need special tooling, we’ll have that too. I can’t emphasise enough how powerful this relationship is. We look forward to introducing the Casadei Busellato excellence to customers all over the two countries.”
FTMA Australia recognises that if we are learning anything as an industry it is that we are not just individual businesses operating as silos, but we are connected in our goals, projects, assets, and our difficulties.
The purpose of researching and collecting data can bring us many insights into what we are all facing, as well as help us plan strategically, as individuals and as a collaborative, for the future.
FTMA have funded this research to directly benefit our members, and it is important to recognise that the FATSO report is a commercial product of FTMA Australia and our research partner, IndustryEdge.
We have decided to share the Executive Summary from the first edition of the Frame & Truss Sector Overview and Outlook produced by FTMA Australia. The full report is only available to FTMA Members as this project is costing the Association considerable funds.
Quarterly editions of the FATSO will be produced for members. Each edition involves a reasonably large number of interviews conducted over a short period of time. The interviews are confidential, only the interviewer from IndustryEdge and the person being interviewed know what was discussed.
In fact, the only other person who knows who is being interviewed each edition is me.
Once interviews are conducted, the industry ‘pulse’ is linked up and analysed with the data that is available to understand what is happening in the supply chain, for fabricators, their customers and suppliers, and to consider what might happen next.
Overall, the objective is to provide the sector and its entire supply chain with the best information about what is most likely to happen next.
For too long our industry has operated in a disjointed and fractured manner. The last few years have shown us that the real threats to our business lie outside that of healthy competition.
As a sector made up of approximately 280 plants, we are a metaphorical school of fish. All primarily focused on our own survival but unconsciously reliant on being part of something much larger. We respond to each other’s reactions to mar-
KERSTEN GENTLE Executive Officer FTMA Australiaket conditions and fight to get to the front of a collective group that is ultimately navigating blindly.
The FATSO reports look to give fabricators a source of information and opinion unavailable anywhere else. Collectively we can strengthen our industry, build for the future, and re-establish what our sector is valued for, “A bespoke, designed, engineered, manufactured product that is both sustainable and critical for the country’s economy and social obligations“.
FTMA is appreciative of our fabricator and supplier members who have participated in these interviews, providing their insights into our sector, which makes this report unique.
We also thank our members for respecting that this is a commercial product of FTMA Australia and our research partner, IndustryEdge, and thank them for not sharing outside of our membership.
Finally, without the support of our valued partners, we would not be in a position to produce this research, and we thank our partners, who are listed at the back of the document, for their outstanding support.
We hope you enjoy the executive and just a word, the full report is worth every cent of your membership, as this is data, which has never been available to our industry before, and will definitely help members and suppliers plan for the future.
Second half of 2023 could be toughest ever as slowdowns, high input prices and cancellations take their toll.
As this first edition of FTMA’s Frame and Truss Sector Overview and Outlook (FATSO for short) comes out, there is deepening industry concern about cancellation of projects in the pipeline of housing work.
Industry feedback does not quite include a consensus, but there is a strong view that the second half of 2023 will become increasingly tough.
For builders, fixed price contracts see them trying to exit unprofitable work, but for fab-
ricators and others who have made commitments based on preorders, these are worrying times.
There has long been concern about the ‘profitless boom’ and now it seems, we’re seeing the results of a lengthy period when there was plenty of work, but much of it was unprofitable, due to higher input prices. Little wonder there are quite a few builders struggling to make it through the current situation.
Inventories throughout the supply chain are higher than desired. There may not currently be an industry measure of inventory, but there are plenty of stories and no one interviewed for this first FATSO is having any trouble getting materials at the moment. Labour is another matter.
The market situation compounds the concerns of fabricators and the timber supply chain that the next few months and the early part of 2024 could be more than a little difficult.
As with most of these events and issues, the devil may be in the detail and that includes timing. Anyone who can pick the bottom and top of any market consistently is destined for greatness. It does seem very difficult right now to call the market.
In that context, new house sales and approvals may already have bottomed, if we look at the latest data. For a country with insufficient housing and looking to migration to solve major labour shortages, its vital to get more dwellings built, as early as possible.
Most interviewees talked up the role of Government in supporting the housing sector, and there are some looking for action on the new National Housing Accord as a means of getting the sector moving again.
In the absence of that, most consider the sector will be overcapacity, especially when steel’s new capacity is factored into the total market.
The next FATSO report will be released for members in the first week of October. The interviewees have all been locked in, and Tim will be doing a special focus on the South Australian market for this edition.
If anyone has any queries about the Frame and Truss Sector Outlook, please give me a call on 0418 226 242.
FTMA is recognised as the trusted representative body and unified voice for all timber frame and truss manufacturers in Australia, whilst strengthening the connection with the broad supply chain.
FTMA thanks our dedicated partners and encourages you to support those who support your industry
For a full list of the conditions of membership and a downloadable application form visit: ftmanews.com
have
AN effective performance management process (PMP) can help in managing employee underperformance and may assist in successfully defending legal claims made by underperforming employees.
A PMP is a formal process which can be undertaken when an employee is not at or up to reasonably expected and required standards. A PMP is not a process which is undertaken to address behavioural or conduct issues, the PMP is limited to the performance of an employee – an assessment of how well the employee is undertaking the job they are employed to do.
A PMP will usually be appropriate in circumstances where informal attempts to resolve underperformance have not been successful.
Best practice steps
Address underperformance concerns promptly and with careful consideration. If employers fail to undertake a PMP in a considered, sensitive, and prompt manner, the culture and productivity of the workplace can be compromised. When undertaking a PMP, the following ‘best practice’ approach may reduce exposure to legal risks.
Employers should commence this process by documenting examples of performance-related deficiencies that are causing issues. Identify when problematic instances take place and the frequency. It is helpful to document specific instances that illustrate the underperformance, including the date and time of the incident where possible. For example, information such as business statistics, customer feedback and examples of the employee’s work can be collected.
Consider how serious the underperformance is and how long the problem has existed. Analyse the gap between what is expected or required of the employee and what they are delivering. Once the employer has assessed and analysed the nature of the problem, they should organise a perfor-
MARIE-CLAIRE MCKIERNAN NATIONAL MEMBERSHIP MANAGERmance review meeting with the employee. The employee should be advised in writing of the reason for the meeting in advance and with reasonable notice so they are able to prepare or seek independent legal advice. Consider providing copies of relevant documents to the employee before the meeting. Employees should be permitted to bring a support person of their choice to the performance review meeting. This may be a co-worker, family member, friend, or union representative.
The performance review meeting should take place in a private, comfortable and nonthreatening environment. The meeting should not be overheard by any other employees. The meeting should take place during reasonable hours, such as during rostered hours of work, and the employee’s attendance should be considered paid time.
During the meeting, employers should outline the underperformance concerns, explain their expectations of the role and invite the employee to provide a response, explanation and/or solution.
Relevant discussion points may include the following, depending on the circumstances of the issues:
• A clear description of the problem and reference to specific examples
• Outline of how the conduct is impacting the business, the employee’s work or colleagues
• Explanation of reasonable outcomes to be achieved from the meeting and setting expectations of a reasonable timeframe which improvement is required (this could range from 1 to 3 months depending on the performance
concerns with regular follow ups or progress meetings in between)
• Outlining potential consequences if the requirement improvement is not achieved within the specified timeframe, which may include disciplinary action or further performance management.
After discussing the issues in accordance with the previous step, a reasonable attempt should be made to reach a mutually acceptable agreement. Generally, employees are more likely to improve their performance if they feel they have contributed to the process.
If an agreement cannot be reached, the employer should notify the employee of their decision regarding the outcome of the discussion.
The agreement or outcome notification should be recorded in a performance improvement plan. This is a document that outlines what the underperformance concerns are, the expected standard of performance, available support or resources, the timeframes which an improvement must occur and to what degree and a summary of potential outcomes if performance does not improve.
5 MONITOR, REVIEW AND IF NECESSARY CONSIDER NEXT STEPS
Often, more than one performance review meeting
may be necessary to resolve an issue. Regular follow up and progress meetings can be helpful for the employee and employer.
If performance does improve to a satisfactory level, this should be acknowledged by the employer along with a notification that the PMP has concluded.
If the employee has failed to improve their performance, disciplinary action may need to be considered. Before any decision is made to commence a disciplinary process,
a careful assessment of legal risks should be undertaken and professional legal advice regarding next steps is strongly recommended.
The above article is provided for general information purposes only. Nothing in this article should be construed as legal advice and you should consider seeking professional legal advice which is tailored to your specific circumstances.
If you would like to learn more about the benefits of MGA TMA membership, please contact us on (03) 9824 4111 to discuss.
TTIA conducted half day briefing sessions nationwide for employers across the entire timber products supply chain in the months of July and August.
The essential briefings took place to equip the industry with the knowledge and resources to deal with the introduction of the Albanese Government’s Fair Work Legislation Amendment (Secure Jobs, Better Pay) Act introduced in December 2022 and its implementation over the course of 2023.
The industrial/workplace changes are probably the most dramatic in the past 20 years and impact on enterprise bargaining, flexible working arrangements, job advertisements, pay secrecy clauses, fixed term contracts, sexual harassment obligations and small claims proceedings. We also covered new requirements regarding reducing psychosocial risks at work, as well as recent decisions that affect annual leave closedowns and public holiday rostering.
One of the most controversial topics covered was the introduction of multi-employer bargaining with agreements covering multiple employers. Under this new regime, employers can be forced to bargain for agreements that cover multiple employers as the Fair Work Commission (FWC) can make supported bargaining authorisations and single-interest employer authorisations. For a granting of an authorisation, the FWC only need consider whether the employers have clearly identifiable common interests in terms of their location, nature of their enterprise and the terms and conditions in those enterprises. Employers need to discuss their options with TTIA regarding the best strategy for their business circumstances. These changes took effect on 6 June 2023.
The new laws have expanded the scope for employees to request flexible working arrangements and give the FWC the power to resolve disputes through conciliation and arbitration.
The new requirements focus on employers undertaking genuine attempts to reach agreement with an employee, in an attempt to accommodate their situation. An employer may be hit with penalties if they fail to follow the new process or refuse a flexible work request without good reason. These new requirements take effect from 7 June 2023. Employers should consult TTIA when refusing requests to ensure due compliance has been followed.
The new legislation increases the cap that can be awarded through small claims proceedings from 20K to 100K. The court is now able to award filing fees as costs to successful small claims applicants, which overturns the previous understanding that parties cannot usually recover costs on matters arising under the Fair Work Act.
The change commenced on 1 July 2023. It reinforces the government’s message on its crackdown on payroll compliance and is consistent with this government’s use of emotive language like ‘wage theft’.
In a similar move by the government aimed at ensuring wage compliance, as of 7 December 2022 pay secrecy clauses in employment contracts have no effect. Put simply, employees should not be restrained from discussing their pay with their fellow workers.
In truth, I have come across almost zero pay secrecy clauses in the timber industry and most Members will tell you that employees are not backward in discussing their rates of pay with their fellow workers. There may be some employers with this type of clause for senior staff, so businesses need to just ensure it is deleted.
The new laws make it unlawful to advertise a pay rate which is less than the minimum rate of pay, including the minimum rate of pay under an award or enterprise agreement. Employers with harvesting operations in particular should be aware that when hiring pieceworkers, they will need to specify a rate of pay relating to the role, for instance the tonnage rate.
The reality is many employers don’t specify a rate of pay when advertising and it is discussed in an interview depending on the employee’s skills and experience, so this aspect should be manageable for most businesses.
If your business uses fixed term contracts, you should contact TTIA about their suitability and necessity. Rather than employees being on rolling contracts of six months or a year, a business will only be able to offer a maximum of two consecutive contracts in that limited span of two years unless an exemption applies. Ultimately, it’s the government’s preference that such employees be made full time and it is an attempt to limit the use of such contracts.
If you employ staff on back-to-back contracts, you should contact us for advice. It should also be noted that employers will be required to provide a Fixed Term Contract Information Statement issued by the Fair Work Ombudsmen to all employees entering a fixed term contract.
The FWC may now settle sexual harassment disputes through conciliation or arbitration. From 6 March 2023 the FWC will have the capacity to give an opinion that sexual harassment has occurred, make compensation orders, orders to pay lost wages, or orders to redress loss or damage. The FWC may issue a stop sexual harassment order as one way of dealing with such a dispute.
In a move that places a vicarious liability on the business and puts it directly in the firing line where an employee harasses another person contravening the provisions in the FW Act, the employer will be taken to have also done
that act unless the business can prove that it took all reasonable steps to prevent the employee from doing it in the first place.
The Respect at Work Act, which complements the Secure Jobs Act provisions, introduces a positive duty for employers to take reasonable steps as far as possible to prevent conduct that includes sexual harassment and conduct that subjects a person to a hostile workplace environment on the grounds of sex or acts of victimisation if a complaint is made in relation to such conduct.
Clearly employers need to have an updated sexual harassment policy in place and conduct a risk assessment of areas where problems may exist. Policies and procedures need to be reviewed regularly and employees should participate in regular training as to what is acceptable workplace behaviour. TTIA can support industry in this process and welcome any company who needs support to contact us.
At the industry sessions TTIA emphasised the point that WHS laws now clearly define health to include mental health.
The basic approach is the same for other types of hazards including identifying the risks, assessment and control of them and elimination of the risks where possible.
Employers are expected to eliminate work overload and bullying at the workplace which are two of the leading factors resulting in more claims for psychosocial injuries as well as pushing up the cost of workers compensation claims and insurance.
Employee consultation is essential to understand the mental health issues at the workplace and to ensure measures put in place are relevant and effective.
TTIA can assist businesses in the timber products industry with a policy and tips to manage this emerging area of management responsibility.
I’m pleased to say the support from the entire industry was huge and the briefings a great success.
Without doubt a major take from the industry wide briefings was the genuine desire by all participants to comes
to terms and manage these challenges. The fact that venues were extremely well attended in all States was proof of that. We took the decision, despite webinars being more commonly used since COVID, that these issues were far too important not to have face to face meetings and let industry ask questions on the detail in managing these significant obligations.
As a result of this Labor government legislation, I have no doubt every business will be spending more time on IR/ HR issues than ever before. If you’re not a member of TTIA, now is definitely the time to join up. We are non-profit with a Board elected by the Members and the more businesses join, the stronger our voice can be to government, as well as offering you key protection as a business.
If you belong to another Association that purports to provide HR/IR/WHS that is not a registered industrial organisation under the Fair Work Act and engages outside consultants without a legal background in IR, my best advice to you is, don’t risk it.
It is absolutely critical at this point that the timber products industry supports TTIA as its very own long established Industrial Association (since 1927) whose sole purpose is to provide legal assistance on IR/HR/WHS and not splinter or fracture the industry with unnecessary and damaging duplication.
The IR challenges will likely increase in the near future with the Albanese government looking to further restrict the use of casual employees, labour hire arrangements and the use of independent contractors. TTIA will run our industry briefings again next year and if you were unable to attend the recent round, contact us and we will organise an on-site briefing in your region or at your business.
Finally, if any business needs assistance with drafting or updating your policies or employment agreements in relation to the changes in this legislation, or advice on managing all or parts of the new laws, contact the TTIA’s IR/ Legal Unit on (02) 9264 0011 or email ttia@ttia.asn.au, as we are here to support you as a valuable industry resource.
The Stirling Group are excited to announce Stirling Machinery as the new authorised Australia and New Zealand distributors of Casadei Busellato woodworking machinery.
Carrying a wide range of Italian made machinery including 5-Axis CNC’s, wide belt sanders, spindle moulders, thicknessers, surfacers and sliding table saws. Ideal for solid timber processors and joineries.
Speak to us today to discover how the Stirling Group can help your business.